制作汽车刹车片的高分子材料解析
刹车片原材料的组成

刹车片原材料的组成基材是刹车片的主体,它需要具有足够的强度和稳定性来承受来自刹车系统的力量和热量。
常见的刹车片基材材料包括钢、铸铁和铝。
这些材料具有良好的热传导性和机械强度,能够抵抗刹车系统产生的高温和高压。
衬片是安装在基材上的一层材料,可以提供增强刹车片性能的特殊功能。
衬片通常由金属材料制成,如钢、铜合金或铝合金。
这些金属材料具有良好的热传导性,能够迅速将刹车系统产生的热量导入基材,保持刹车片的稳定性。
摩擦材料是刹车片的关键组成部分,它能够和刹车盘产生摩擦力,将车辆的动能转化为热能,从而实现刹车的效果。
常见的刹车片摩擦材料有无机纤维(如石棉和陶瓷纤维)和有机材料(如橡胶和树脂)。
无机摩擦材料具有较高的摩擦系数和耐磨性,而有机摩擦材料则更加柔软,有助于提高刹车片的舒适性和制动性能。
粘结剂是将基材、衬片和摩擦材料粘结在一起的关键材料。
常见的粘结剂有无机粘结剂(如硬脂酸锌和硅酮)和有机粘结剂(如热塑性树脂和热固性树脂)。
粘结剂具有良好的粘结性能和热稳定性,能够确保刹车片在高温和高压的工作环境中保持稳定。
除了基材、衬片、摩擦材料和粘结剂,刹车片的制造过程中还需要考虑其他因素,如添加剂、填料和润滑剂。
添加剂能够改变刹车片的性能特点,如提高耐磨性、降低噪音和减小摩擦系数。
填料可以增加刹车片的密度和强度,提高制动效果。
润滑剂能够减少刹车片与刹车盘之间的摩擦,降低磨损和噪音。
总之,刹车片原材料的组成是多种多样的,各种材料的选择和组合取决于刹车系统的要求、制造工艺和性能需求,以确保刹车片在各种工作条件下都能稳定可靠地工作。
刹车片材料
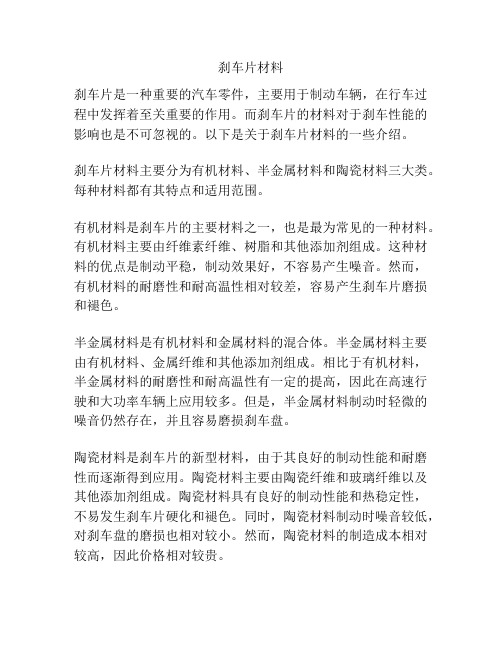
刹车片材料刹车片是一种重要的汽车零件,主要用于制动车辆,在行车过程中发挥着至关重要的作用。
而刹车片的材料对于刹车性能的影响也是不可忽视的。
以下是关于刹车片材料的一些介绍。
刹车片材料主要分为有机材料、半金属材料和陶瓷材料三大类。
每种材料都有其特点和适用范围。
有机材料是刹车片的主要材料之一,也是最为常见的一种材料。
有机材料主要由纤维素纤维、树脂和其他添加剂组成。
这种材料的优点是制动平稳,制动效果好,不容易产生噪音。
然而,有机材料的耐磨性和耐高温性相对较差,容易产生刹车片磨损和褪色。
半金属材料是有机材料和金属材料的混合体。
半金属材料主要由有机材料、金属纤维和其他添加剂组成。
相比于有机材料,半金属材料的耐磨性和耐高温性有一定的提高,因此在高速行驶和大功率车辆上应用较多。
但是,半金属材料制动时轻微的噪音仍然存在,并且容易磨损刹车盘。
陶瓷材料是刹车片的新型材料,由于其良好的制动性能和耐磨性而逐渐得到应用。
陶瓷材料主要由陶瓷纤维和玻璃纤维以及其他添加剂组成。
陶瓷材料具有良好的制动性能和热稳定性,不易发生刹车片硬化和褪色。
同时,陶瓷材料制动时噪音较低,对刹车盘的磨损也相对较小。
然而,陶瓷材料的制造成本相对较高,因此价格相对较贵。
除了以上几种主要的刹车片材料外,还有一些其他材料也被应用在刹车片上。
比如钢铁材料,它具有良好的耐磨性和制动性能,但制动时容易产生噪音。
还有碳材料,碳材料具有优异的制动性能和热稳定性,但价格昂贵。
钛合金材料具有良好的制动性能和耐高温性,但制造成本高。
综上所述,刹车片的材料对于刹车性能有着重要的影响。
不同的材料具有自己的特点和适用范围,需要根据车辆的具体情况选择适合的刹车片材料。
在选择刹车片材料时,不仅需要考虑制动性能,还需要考虑耐磨性、耐高温性、噪音等因素,以提高刹车片的使用寿命和性能。
汽车工程中的制动系统刹车片材料研究
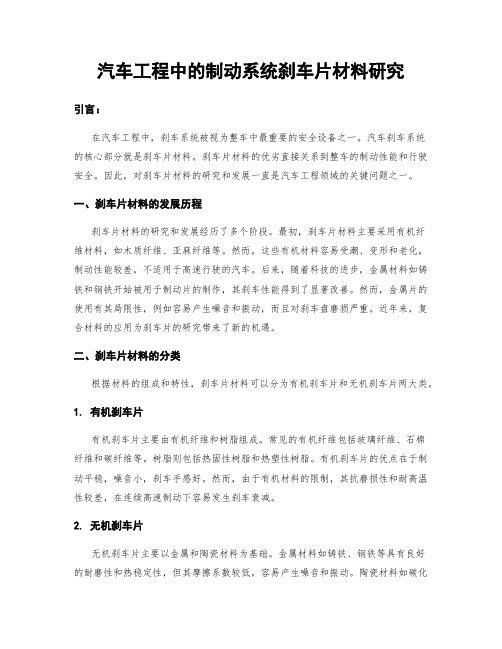
汽车工程中的制动系统刹车片材料研究引言:在汽车工程中,刹车系统被视为整车中最重要的安全设备之一。
汽车刹车系统的核心部分就是刹车片材料。
刹车片材料的优劣直接关系到整车的制动性能和行驶安全。
因此,对刹车片材料的研究和发展一直是汽车工程领域的关键问题之一。
一、刹车片材料的发展历程刹车片材料的研究和发展经历了多个阶段。
最初,刹车片材料主要采用有机纤维材料,如木质纤维、亚麻纤维等。
然而,这些有机材料容易受潮、变形和老化,制动性能较差,不适用于高速行驶的汽车。
后来,随着科技的进步,金属材料如铸铁和钢铁开始被用于制动片的制作,其刹车性能得到了显著改善。
然而,金属片的使用有其局限性,例如容易产生噪音和振动,而且对刹车盘磨损严重。
近年来,复合材料的应用为刹车片的研究带来了新的机遇。
二、刹车片材料的分类根据材料的组成和特性,刹车片材料可以分为有机刹车片和无机刹车片两大类。
1. 有机刹车片有机刹车片主要由有机纤维和树脂组成。
常见的有机纤维包括玻璃纤维、石棉纤维和碳纤维等。
树脂则包括热固性树脂和热塑性树脂。
有机刹车片的优点在于制动平稳,噪音小,刹车手感好。
然而,由于有机材料的限制,其抗磨损性和耐高温性较差,在连续高速制动下容易发生刹车衰减。
2. 无机刹车片无机刹车片主要以金属和陶瓷材料为基础。
金属材料如铸铁、钢铁等具有良好的耐磨性和热稳定性,但其摩擦系数较低,容易产生噪音和振动。
陶瓷材料如碳化硅和氧化铝等具有较高的摩擦系数和耐磨性,但对刹车盘的磨损较大。
目前,无机刹车片正处于不断改进和探索的阶段,以追求更好的性能和更低的噪音。
三、刹车片材料的研究方向随着汽车工程的发展和用户需求的变化,刹车片材料的研究方向也在不断扩展。
1. 绿色环保随着全球环保意识的提高,对于刹车片材料的环境影响和可持续性逐渐受到关注。
研究人员正致力于开发更环保的刹车片材料,例如使用可再生材料和无毒无害的树脂。
2. 抗高温性高速行驶中刹车片温度会急剧升高,因此刹车片材料的抗高温性至关重要。
芳纶陶瓷刹车片配方成分-概念解析以及定义

芳纶陶瓷刹车片配方成分-概述说明以及解释1.引言1.1 概述:芳纶陶瓷刹车片是一种新型的高性能刹车材料,具有耐磨损、耐高温、稳定制动性能等优点,因此在汽车、摩托车等汽车制动系统中得到广泛应用。
刹车片的配方成分直接影响其性能和品质,因此对刹车片的配方成分进行深入研究和优化具有重要意义。
本文将对芳纶陶瓷刹车片的配方成分进行深入解析,探讨其作用及优化配方的方法,以期为刹车片制造工艺的改进和刹车性能的提升提供参考。
1.2 文章结构文章结构部分的内容可以包括对整篇文章的主要结构进行介绍,说明每个部分的内容和重点。
例如:文章结构部分可以介绍整篇文章的主要结构,包括引言、正文和结论部分。
引言部分用于引出文章的主题和目的,介绍了芳纶陶瓷刹车片配方成分的重要性和研究意义。
正文部分将重点介绍芳纶陶瓷刹车片的特点、刹车片配方成分的作用以及优化配方的方法。
结论部分将总结全文的内容,展望芳纶陶瓷刹车片配方成分在未来的应用前景,并提出进一步研究的展望。
通过对文章结构的介绍,读者可以清晰地了解到整篇文章的内容梗概,有助于他们更好地理解和阅读全文。
1.3 目的本文旨在深入探讨芳纶陶瓷刹车片配方成分的作用及优化配方的方法,从而更好地了解该类产品的特点和应用前景。
通过本文的阐述,读者可以全面了解芳纶陶瓷刹车片配方成分在刹车片制造中的重要性,以及如何通过优化配方来提高产品性能和品质。
同时,也希望通过对未来发展前景的展望,为相关行业的研究和应用提供一定的参考和指导。
2.正文2.1 芳纶陶瓷刹车片的特点芳纶陶瓷刹车片是一种高性能的刹车片,主要由芳纶纤维和陶瓷材料组成。
其特点主要包括以下几点:1. 高温性能优异:芳纶纤维和陶瓷材料具有良好的高温稳定性,能够在高速行驶和紧急制动情况下保持稳定的刹车性能,不易发生刹车衰减现象。
2. 耐磨性强:由于芳纶纤维和陶瓷材料均具有优秀的耐磨性能,芳纶陶瓷刹车片在长期使用过程中具有较长的使用寿命,不易产生刹车片磨损过快的问题。
刹车片材料

刹车片材料汽车制动部件的工作原理相信大家都清楚了,当踩下刹车踏板时,刹车总泵会在刹车油路中建立压力。
压力经由刹车油传送到卡钳上的活塞,活塞受压后推动刹车片夹紧刹车盘或刹车鼓,使得刹车片与刹车盘发生摩擦,以降低车轮的转速让车辆停下。
那么刹车片材料有哪些呢?半金属摩擦材料因此而得名。
是最早取代石棉而发展起来的一种无石棉材料。
其特点:耐热性好,单位面积吸收功率高,导热系数大,能适用于汽车在高速、重负荷运行时的制动工况要求。
但其存在制动噪音大、边角脆裂等缺点。
(b)NAO摩擦材料。
从广义上是指非石棉-非钢纤维型摩擦材料,但现盘式片也含有少量的钢纤维。
NAO摩擦材料中的基材料在大多数情况下为两种或两种(c)粉末冶金摩擦材料。
又称烧结摩擦材料,系将铁基、铜基粉状物料经混合、压型,并在在高温下烧结而成。
适用于较高温度下的制动与传动工况条件。
如:飞机、载重汽车、重型工程机械的制动与传动。
优点:使用寿命长;缺点:制品价格高,制动噪音大,重而脆性大,对偶磨损大。
(d)碳纤维摩擦材料。
系用碳纤维为增强材料制成的一类摩擦材料。
碳纤维具有高模量、导热好、耐热等特点。
碳纤维摩擦材料是各种类型摩擦材料中性能最好的一种。
碳纤维摩擦片的单位面积吸收功率高及比重轻,特别适合生产飞机刹车片,国外有些高档轿车的刹车片也使用。
因其价格昂贵,故其应用范围受到限制,产量较少。
在碳纤维摩擦材料组分中,除了碳纤维外,还使用石墨,碳的化合物。
组分中的有机粘结剂也要经过碳化处理,故碳纤维摩擦材料也称为碳——碳摩擦材料或碳基摩擦材料。
关于刹车片材料的知识。
超高分子量聚合物制备工艺的分子量与形态控制
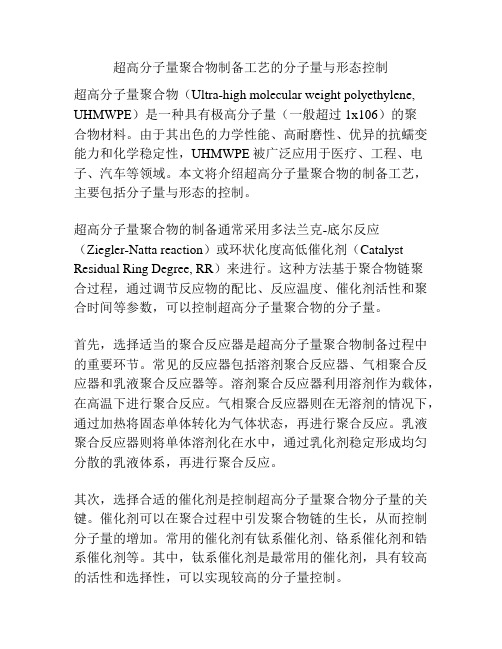
超高分子量聚合物制备工艺的分子量与形态控制超高分子量聚合物(Ultra-high molecular weight polyethylene, UHMWPE)是一种具有极高分子量(一般超过1x106)的聚合物材料。
由于其出色的力学性能、高耐磨性、优异的抗蠕变能力和化学稳定性,UHMWPE被广泛应用于医疗、工程、电子、汽车等领域。
本文将介绍超高分子量聚合物的制备工艺,主要包括分子量与形态的控制。
超高分子量聚合物的制备通常采用多法兰克-底尔反应(Ziegler-Natta reaction)或环状化度高低催化剂(Catalyst Residual Ring Degree, RR)来进行。
这种方法基于聚合物链聚合过程,通过调节反应物的配比、反应温度、催化剂活性和聚合时间等参数,可以控制超高分子量聚合物的分子量。
首先,选择适当的聚合反应器是超高分子量聚合物制备过程中的重要环节。
常见的反应器包括溶剂聚合反应器、气相聚合反应器和乳液聚合反应器等。
溶剂聚合反应器利用溶剂作为载体,在高温下进行聚合反应。
气相聚合反应器则在无溶剂的情况下,通过加热将固态单体转化为气体状态,再进行聚合反应。
乳液聚合反应器则将单体溶剂化在水中,通过乳化剂稳定形成均匀分散的乳液体系,再进行聚合反应。
其次,选择合适的催化剂是控制超高分子量聚合物分子量的关键。
催化剂可以在聚合过程中引发聚合物链的生长,从而控制分子量的增加。
常用的催化剂有钛系催化剂、铬系催化剂和锆系催化剂等。
其中,钛系催化剂是最常用的催化剂,具有较高的活性和选择性,可以实现较高的分子量控制。
调节反应条件也是影响超高分子量聚合物分子量的重要因素。
反应温度通常在聚合反应器的摄氏175度至225度之间。
较高的反应温度可以促进活性位点的形成和超高分子量聚合物链的生长。
同时,控制聚合时间也是控制分子量的重要手段。
延长聚合时间可以增加分子量,但过长的聚合时间会导致聚合物分子量分布变宽,降低聚合物的力学性能。
刹车摩擦材料

刹车摩擦材料刹车摩擦材料是指用于制动系统的摩擦材料,它直接影响着汽车的刹车性能和安全性。
目前,常见的刹车摩擦材料主要包括有机材料、无机材料和半金属材料。
在选择刹车摩擦材料时,需要考虑摩擦性能、耐磨性能、热稳定性、环保性以及成本等因素。
有机材料是指以有机高分子材料为基础的刹车摩擦材料,主要包括有机树脂、纤维和填料等。
有机材料具有摩擦性能好、制动时噪音小、对刹车盘磨损小等优点,但耐热性和耐磨性相对较差。
因此,有机材料通常用于小型车辆和低速车辆的制动系统中。
无机材料是指以无机非金属材料为主要成分的刹车摩擦材料,主要包括氧化物、硼化物、碳化物等。
无机材料具有耐热性和耐磨性好的特点,适用于高速、高负荷的制动系统,如卡车、赛车等。
半金属材料是指以金属粉末为基础,添加少量有机树脂和无机材料的刹车摩擦材料。
半金属材料综合了有机材料和无机材料的优点,具有良好的摩擦性能、耐磨性能和耐热性能,适用于大多数中高档车辆的制动系统。
除了以上几种常见的刹车摩擦材料外,还有一些新型材料在研发和应用中,如陶瓷复合材料、碳纤维复合材料等。
这些新型材料具有高温稳定性好、耐磨性能好、重量轻等优点,但成本较高。
在选择刹车摩擦材料时,需要根据车辆类型、使用环境、制动性能要求等因素进行综合考虑。
同时,还需要注意刹车摩擦材料的更换周期,及时更换磨损严重的刹车摩擦材料,以确保车辆的刹车性能和安全性。
总的来说,刹车摩擦材料是制动系统中至关重要的一部分,选择合适的刹车摩擦材料对于车辆的刹车性能和安全性具有重要影响。
随着科技的发展和材料的不断创新,相信未来会有更多更优秀的刹车摩擦材料出现,为汽车制动系统的性能提升提供更多可能。
干货360°无死角了解“刹车材料”!

干货360°无死角了解“刹车材料”!【材料+】说:刹车片(或刹车盘)在刹车系统中,是最关键的安全零件,对刹车效果的好坏都起着决定性作用,好的刹车片(或刹车盘)是人和车(飞机)的保护神。
今天,小编360°无死角的为大家揭开刹车材料的神秘面纱,让你对它不再陌生!01刹车片的起源1897 年,HerbertFrood 发明了第一块刹车片( 使用棉线作为增强纤维),并用于马车和早期的汽车,从此,世界著名的Ferodo 公司成立了。
随后在1909 年,该公司发明了世界上第一个固化石棉基刹车片;1968年,发明世界上第一个半金属基刹车片,此后,摩擦材料开始向无石棉化发展。
国内外开始研究各种石棉的替代纤维如钢纤维、玻璃纤维、芳纶纤维、碳纤维等在摩擦材料上的应用。
02刹车片的分类刹车材料的分类方法主要有两种。
一种是以使用机构来划分。
如汽车刹车材料、火车刹车材料和航空刹车材料等。
该分类法简单且易理解;一种是根据材料材质类型来划分。
这种分类方法较为科学。
现代制动用刹车材料主要包括以下3大类:树脂基刹车材料(石棉刹车材料、无石棉刹车材料、纸基刹车材料)、粉末冶金刹车材料、碳/碳复合刹车材料和陶瓷基刹车材料。
汽车刹车材料汽车刹车材料种类按制造材料不同。
可分为石棉片、半金属片或低金属片、NAO( 无石棉有机物)片、碳碳片和陶瓷片等。
石棉片从最初开始石棉就已经被用作刹车片的加固材料,由于石棉纤维具有高强度和耐高温的特性,因此可以满足刹车片及离合器盘和衬垫的要求。
这种纤维具有较强的抗张能力,甚至可以同高级钢材相匹配,且可以承受316℃的高温。
更重要的是石棉相对廉价,它是从闪石矿石中提炼出来的,而此种矿石在很多国家已被大量发现。
石棉摩擦材料主要以石棉纤维即水合硅酸镁(3MgO·2SiO2·2H2O)作为增强纤维。
经添加调节摩擦性能的填料。
再用粘结剂在热压模内压制成型而得到的一种有机基复合材料。
刹车片中丁腈橡胶的应用
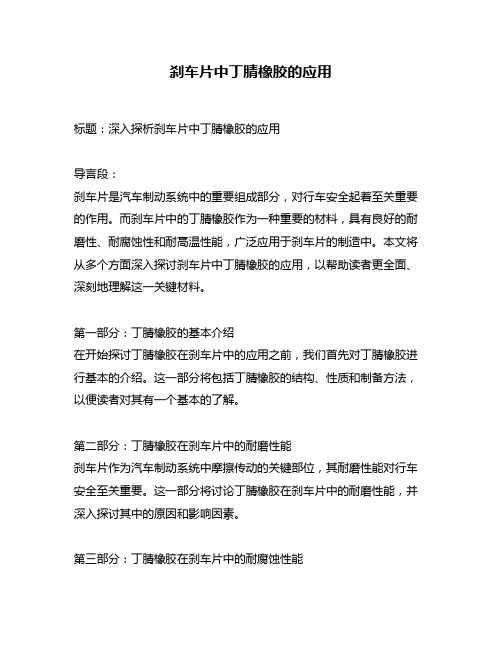
刹车片中丁腈橡胶的应用标题:深入探析刹车片中丁腈橡胶的应用导言段:刹车片是汽车制动系统中的重要组成部分,对行车安全起着至关重要的作用。
而刹车片中的丁腈橡胶作为一种重要的材料,具有良好的耐磨性、耐腐蚀性和耐高温性能,广泛应用于刹车片的制造中。
本文将从多个方面深入探讨刹车片中丁腈橡胶的应用,以帮助读者更全面、深刻地理解这一关键材料。
第一部分:丁腈橡胶的基本介绍在开始探讨丁腈橡胶在刹车片中的应用之前,我们首先对丁腈橡胶进行基本的介绍。
这一部分将包括丁腈橡胶的结构、性质和制备方法,以便读者对其有一个基本的了解。
第二部分:丁腈橡胶在刹车片中的耐磨性能刹车片作为汽车制动系统中摩擦传动的关键部位,其耐磨性能对行车安全至关重要。
这一部分将讨论丁腈橡胶在刹车片中的耐磨性能,并深入探讨其中的原因和影响因素。
第三部分:丁腈橡胶在刹车片中的耐腐蚀性能除了良好的耐磨性能,刹车片还需要具有较好的耐腐蚀性能,以应对长期使用中的各种腐蚀介质。
本部分将详细研究丁腈橡胶在刹车片中的耐腐蚀性能,并分析其相关因素和应对措施。
第四部分:丁腈橡胶在刹车片中的耐高温性能高温环境是刹车片在实际使用中常常面临的挑战,因此,刹车片中的材料需要具有良好的耐高温性能。
这一部分将评估丁腈橡胶在刹车片中的耐高温性能,并分析其影响因素以及相应的解决方法。
总结段:通过对刹车片中丁腈橡胶的应用的深入探讨,我们可以得出结论:丁腈橡胶作为一种具有优异性能的材料,为刹车片的制造提供了重要的保障。
其耐磨性能、耐腐蚀性能和耐高温性能使得刹车片具有更长寿命、更稳定的制动性能,提高了行车安全性。
然而,我们也要认识到丁腈橡胶在刹车片制造中的一些应用问题和改进空间。
在未来的发展中,我们可以进一步研究优化丁腈橡胶的性能,以满足不断变化的市场需求。
观点和理解:在我看来,丁腈橡胶在刹车片制造中的应用是一种非常重要且有前景的技术。
通过研究和优化丁腈橡胶的性能,我们可以进一步提高刹车片的质量和性能,为汽车行业的可持续发展做出贡献。
酚醛树脂摩擦材料

酚醛树脂摩擦材料说到“酚醛树脂摩擦材料”,乍一听这名字,可能很多人都觉得有点晦涩难懂,甚至觉得是不是又是什么高大上的科技东西。
其实啊,它就在咱们生活中默默地发挥着重要作用。
酚醛树脂摩擦材料这个东西,简直可以说是汽车、机械等很多设备“背后的英雄”。
你要是觉得它太专业,那我就带你慢慢走进这个神秘的小世界,保证你听了之后,一定会对它刮目相看,甚至可能会产生点“小崇拜”呢。
先来说说什么是酚醛树脂。
简单说,它是一种由酚类化合物和醛类化合物经过一系列化学反应后合成的高分子材料。
听起来是不是有点绕?其实呢,这玩意儿可比你想的耐用得多。
它耐高温,耐腐蚀,强度高,简直就是个“万金油”,用途广泛。
从家庭小电器到工业设备,都能看到它的身影。
尤其是在摩擦材料领域,它简直就是一位超级明星。
讲到摩擦材料,大家脑海里是不是立马浮现出刹车片、离合器片那些常常和摩擦打交道的零件?对啦,就是这些东西,它们天天在高温高压的环境下“拼搏”,不出问题才怪呢。
而酚醛树脂摩擦材料就是这些“拼命三郎”们的得力助手。
它的好处在于,能有效减少摩擦过程中的磨损,确保这些零件的稳定性,延长使用寿命。
这么一说,是不是有点像车主换刹车片一样,虽然不常去注意,但换了之后就会发现车子刹车更平稳,反应更灵敏了?你想啊,汽车的刹车片在开车的时候那是相当辛苦的,不停地与车轮摩擦,冒着火花还得保持足够的稳定性,不让车子失控。
想象一下,如果刹车片的材料不够好,那摩擦一多,就会过热、变形,甚至完全失去功能,岂不是“酿大祸”?可是有了酚醛树脂摩擦材料的加持,整个过程就像有了一副坚固的“护甲”,耐高温又耐磨损,大大降低了刹车系统故障的几率。
那么为什么偏偏是酚醛树脂摩擦材料呢?原因其实很简单,酚醛树脂摩擦材料耐高温,特别适合在汽车刹车片、离合器片这种需要高温高压的环境下使用。
它不容易被磨损,能长期保持良好的摩擦性能。
更重要的是,酚醛树脂摩擦材料还可以有效降低噪音和振动,开车的时候大家可能并不觉得,但你要是用过那种劣质刹车片,绝对能感受到噪音那是“山响得很”啊。
丁腈橡胶在刹车片中的应用
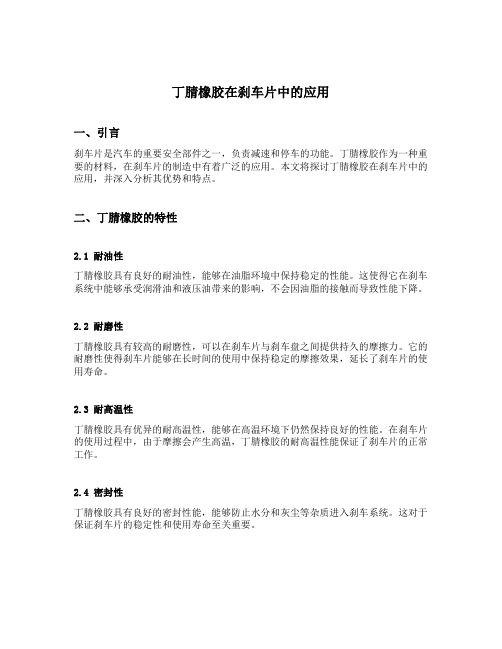
丁腈橡胶在刹车片中的应用一、引言刹车片是汽车的重要安全部件之一,负责减速和停车的功能。
丁腈橡胶作为一种重要的材料,在刹车片的制造中有着广泛的应用。
本文将探讨丁腈橡胶在刹车片中的应用,并深入分析其优势和特点。
二、丁腈橡胶的特性2.1 耐油性丁腈橡胶具有良好的耐油性,能够在油脂环境中保持稳定的性能。
这使得它在刹车系统中能够承受润滑油和液压油带来的影响,不会因油脂的接触而导致性能下降。
2.2 耐磨性丁腈橡胶具有较高的耐磨性,可以在刹车片与刹车盘之间提供持久的摩擦力。
它的耐磨性使得刹车片能够在长时间的使用中保持稳定的摩擦效果,延长了刹车片的使用寿命。
2.3 耐高温性丁腈橡胶具有优异的耐高温性,能够在高温环境下仍然保持良好的性能。
在刹车片的使用过程中,由于摩擦会产生高温,丁腈橡胶的耐高温性能保证了刹车片的正常工作。
2.4 密封性丁腈橡胶具有良好的密封性能,能够防止水分和灰尘等杂质进入刹车系统。
这对于保证刹车片的稳定性和使用寿命至关重要。
三、丁腈橡胶在刹车片中的应用3.1 刹车片衬片丁腈橡胶常用作刹车片衬片的材料,在刹车片与刹车盘之间起到缓冲和密封的作用。
其耐磨性和耐高温性能使得刹车片能够在摩擦过程中保持稳定的摩擦力,增加刹车效果和使用寿命。
3.2 制动液密封圈丁腈橡胶材料也广泛用于制动液密封圈的制造。
制动液密封圈位于刹车系统中,起到密封刹车液的作用。
丁腈橡胶的耐油性和密封性能使得制动液能够有效地封闭在系统内,保证整个刹车系统的正常运作。
3.3 减震垫丁腈橡胶还可用于制造刹车片减震垫,减缓刹车时的冲击和振动。
这种减震垫在刹车过程中能够提供更平稳的刹车效果,使驾驶者感受更舒适,同时也减少了刹车系统的磨损。
3.4 其他应用除了以上几种常见的应用,丁腈橡胶还可以用于制造刹车片的其他部件,如刹车片的支撑结构和辅助材料等。
这些部件对于提高整个刹车系统的性能和可靠性起到重要作用。
四、丁腈橡胶刹车片的优势和挑战4.1 优势•良好的耐油性使得刹车片能够在润滑油和液压油的环境中正常工作。
刹车片新材料摩擦磨损机理实验解析

刹车片新材料摩擦磨损机理实验解析刹车片是汽车安全行驶过程中至关重要的部件之一。
为了提高刹车片的性能和耐久性,制造商们一直在寻求新的材料和制造技术。
其中,研究刹车片新材料的摩擦磨损机理是非常重要的一环,它可以帮助我们更好地了解刹车片在使用过程中的摩擦磨损特性,并为新材料的研发提供指导。
摩擦磨损是指两个物体相对运动时表面之间的相互作用所导致的材料剥离、磨损和变形现象。
在刹车片的使用中,摩擦磨损机理主要包括热磨损、表面摩擦、车轮截面磨损等。
首先,热磨损是刹车片磨损的主要机理之一。
当刹车片与刹车盘之间的接触摩擦产生高温时,刹车片表面的材料会发生相变和加热,形成热软化层。
这种热软化层的存在会使刹车片表面的摩擦系数降低,增加刹车片和刹车盘的接触面积,从而增加了磨损。
此外,刹车片磨损生成的高温还会导致刹车片内部材料的结构改变,进一步加剧磨损。
其次,表面摩擦是刹车片磨损的另一个重要机理。
刹车片与刹车盘之间的高速接触会产生大量的摩擦热,使刹车片表面的温度升高。
随着温度升高,刹车片表面的材料会剥离、氧化和软化,从而导致表面磨损。
除了温度的影响,表面粗糙度、材料硬度、润滑剂的使用等也会影响刹车片的表面摩擦特性。
最后,车轮截面磨损也是刹车片磨损的一个重要机理。
车轮截面磨损指的是刹车片表面与车轮之间的相互作用磨损。
当刹车片与车轮之间的接触面积增大时,摩擦力也会相应增加,从而导致刹车片的磨损。
车轮截面磨损的程度取决于刹车片和车轮的材料特性、接触面积和接触压力等因素。
针对以上磨损机理,科学家们已经采取了一系列的实验手段来进一步研究和解析刹车片的摩擦磨损特性。
其中,摩擦副试验是一个常用的手段之一。
在这样的实验中,科学家们通过模拟刹车片与刹车盘之间的接触摩擦过程,对刹车片表面的摩擦磨损进行定量分析。
实验数据的收集和分析可以帮助科学家们了解不同材料在不同条件下的磨损特性,为刹车片的研发提供指导。
除了摩擦副试验,还有一些其他的实验手段也被应用于刹车片新材料的摩擦磨损机理研究中。
简析刹车片配方——摩擦材料

简析刹车片配方——摩擦材料今天简单聊一聊刹车片的摩擦材料。
市场上的配方体系种类繁多,但万变不离其宗,就像武侠小说说的一样,拳出少林,剑归华山,功夫无非是“快准直狠”,李小龙先生在这四个方面发挥到极致。
跑题了,书归正传。
概括的说摩擦材料是一种高分子三元复合材料,是物理与化学复合体。
它是由高分子粘结剂(树脂与橡胶)、增强纤维和摩擦性能调节剂三大类组成及其它配合剂构成,经一系列生产加工而制成的制品。
摩擦材料的特点是具有良好的摩擦系数和耐磨损性能,同时具有一定的耐热性和机械强度,能满足车辆或机械的传动与制动的性能要求。
一、摩擦材料分类1. 按工作功能分为传动与制动两大类摩擦材料。
如传动作用的离合器片,系通过离合器总成中离合器摩擦面片的贴合与分离将发动机产生的动力传递到驱动轮上,使车辆开始行走。
制动作用的刹车片(分为盘式与鼓式刹车片),系通过车辆制动机构将刹车片紧贴在制动盘(鼓)上,使行走中的车辆减速或停下来。
2. 按产品形状分可分为刹车片(盘式片、鼓式片)、刹车带、闸瓦、离合器片、异性摩擦片。
盘式片呈平面状,鼓式片呈弧形。
闸瓦(火车闸瓦、石油钻机)为弧形产品,但比普通弧形刹车片要厚的多,25~30mm范围。
刹车带常用于农机和工程机械上,属软质摩擦材料。
离合器片一般为圆环形状制品。
异性摩擦片多用于各种工程机械方面,如摩擦压力机,电葫芦等。
3. 按产品材质分:主要根据增强纤维分类,可分为石棉摩擦材料、金属摩擦材料、碳陶摩擦材料。
二、摩擦材料的组成摩擦材料属于高分子三元复合材料,它包括三部分:以高分子化合物为粘结剂;以无机或有机纤维为增强组分;以填料为摩擦性能调节剂或配合剂。
1. 有机粘结剂摩擦材料所用的有机粘结剂为酚醛类树脂和合成橡胶,而以酚醛类树脂为主。
它们的特点和作用是当处于一定加热温度下时先呈软化而后进入粘流态,产生流动并均匀分布在材料中形成材料的基体,最后通过树脂固化作用的橡胶硫化作用,把纤维和填料粘结在一起,形成质地致密的有相当强度及能满足摩擦材料使用性能要求的摩擦片制品。
刹车片材料基本知识、摩擦材料和发展方向要点
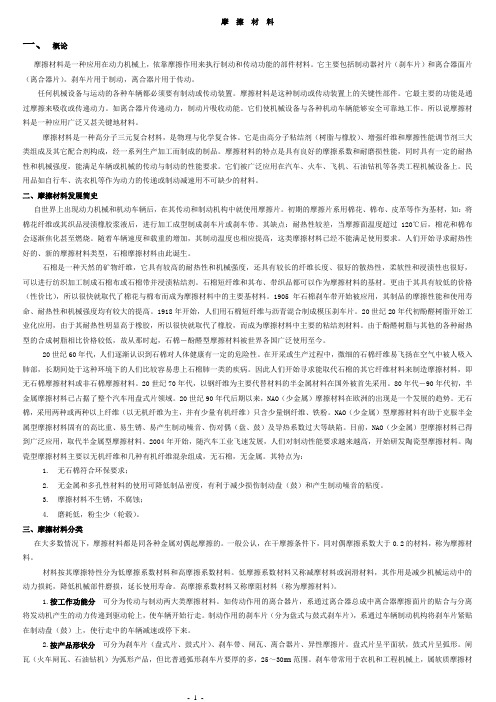
摩擦材料一、概论摩擦材料是一种应用在动力机械上,依靠摩擦作用来执行制动和传动功能的部件材料。
它主要包括制动器衬片(刹车片)和离合器面片(离合器片)。
刹车片用于制动,离合器片用于传动。
任何机械设备与运动的各种车辆都必须要有制动或传动装置。
摩擦材料是这种制动或传动装置上的关键性部件。
它最主要的功能是通过摩擦来吸收或传递动力。
如离合器片传递动力,制动片吸收动能。
它们使机械设备与各种机动车辆能够安全可靠地工作。
所以说摩擦材料是一种应用广泛又甚关键地材料。
摩擦材料是一种高分子三元复合材料,是物理与化学复合体。
它是由高分子粘结剂(树脂与橡胶)、增强纤维和摩擦性能调节剂三大类组成及其它配合剂构成,经一系列生产加工而制成的制品。
摩擦材料的特点是具有良好的摩擦系数和耐磨损性能,同时具有一定的耐热性和机械强度,能满足车辆或机械的传动与制动的性能要求。
它们被广泛应用在汽车、火车、飞机、石油钻机等各类工程机械设备上。
民用品如自行车、洗衣机等作为动力的传递或制动减速用不可缺少的材料。
二、摩擦材料发展简史自世界上出现动力机械和机动车辆后,在其传动和制动机构中就使用摩擦片。
初期的摩擦片系用棉花、棉布、皮革等作为基材,如:将棉花纤维或其织品浸渍橡胶浆液后,进行加工成型制成刹车片或刹车带。
其缺点:耐热性较差,当摩擦面温度超过120℃后,棉花和棉布会逐渐焦化甚至燃烧。
随着车辆速度和载重的增加,其制动温度也相应提高,这类摩擦材料已经不能满足使用要求。
人们开始寻求耐热性好的、新的摩擦材料类型,石棉摩擦材料由此诞生。
石棉是一种天然的矿物纤维,它具有较高的耐热性和机械强度,还具有较长的纤维长度、很好的散热性,柔软性和浸渍性也很好,可以进行纺织加工制成石棉布或石棉带并浸渍粘结剂。
石棉短纤维和其布、带织品都可以作为摩擦材料的基材。
更由于其具有较低的价格(性价比),所以很快就取代了棉花与棉布而成为摩擦材料中的主要基材料。
1905年石棉刹车带开始被应用,其制品的摩擦性能和使用寿命、耐热性和机械强度均有较大的提高。
关于汽车刹车片的研究

关于汽车刹车片的研究汽车刹车片研究引言:刹车片是汽车制动系统的重要组成部分,负责实现车辆的停止和减速功能。
随着汽车工业的不断发展,对刹车片的研究也越来越深入。
本文将对汽车刹车片的材料、结构和研究进展进行详细介绍。
一、刹车片的材料:刹车片的材料一般分为有机刹车片、石棉刹车片和陶瓷刹车片。
1.有机刹车片:有机刹车片的主要材料是有机纤维和树脂材料。
这种刹车片具有制动力平稳、噪音小、使用寿命长等优点,但其制动效果较差,在高速行驶或长时间制动时易发生褪色和变形。
2.石棉刹车片:石棉刹车片的主要材料是石棉纤维和树脂。
这种刹车片使用广泛,具有制动效果好、耐磨损、散热性能好等特点。
但由于石棉是致癌物质,在安全和环保方面存在问题,逐渐被淘汰。
3.陶瓷刹车片:陶瓷刹车片的主要材料是碳化硅和陶瓷颗粒。
这种刹车片具有制动效果好、散热性能优秀、使用寿命长等优点。
但其成本高昂,制造工艺复杂,对制动系统的要求较高,因此应用范围有限。
二、刹车片的结构:1.面层:刹车片的面层是直接与刹车盘接触的部分,其材料通常为摩擦材料,用于产生摩擦力实现制动效果。
面层通常由有机或无机材料构成,其选择需综合考虑刹车性能、使用寿命和经济性。
2.支撑层:支撑层是刹车片的骨架,能够承受摩擦力和温度变化。
支撑层的材料通常为钢板或铝合金,具有较高的强度和刚度,以保持刹车片的稳定性和可靠性。
3.背面涂层:背面涂层能够增加刹车片与刹车钳之间的粘接力,并减少噪音和振动。
背面涂层通常由沥青、树脂等材料构成。
三、刹车片的研究进展:1.材料研究:目前,研究人员正在不断开发新型的刹车片材料,旨在提高刹车性能和使用寿命。
例如,利用纳米材料、纳米涂层和纳米复合材料可以提高刹车片的摩擦系数和磨损性能。
2.结构研究:研究人员对刹车片的结构进行优化,以提高刹车片的热稳定性和耐疲劳性能。
例如,通过改变刹车片的面层组成和支撑层的结构,可以提高刹车片的耐高温性能和稳定性。
3.制造工艺研究:研究人员致力于改进刹车片的制造工艺,以提高生产效率和降低成本。
汽车刹车片是如何制造出来的,一起工厂来探密

汽车刹车⽚是如何制造出来的,⼀起⼯⼚来探密这⼀期的⽂章我们⼀起来看看汽车刹车⽚是如何制造出来的,出⼚之前它都要经过哪些测试环节,让我们对刹车⽚有⼀个清晰的认识。
⼯程师⾸先需要3D建模,建模后刹车卡钳和刹车⽚所有的精准数据都会来⾃这个模型,然后进⼊冲压过程。
进⼊⼯⼚以后,我们可以看到这⾥停放了⼤量的钢材。
你可以看到这些钢材都是⼀卷⼀卷的,每⼀卷钢材重达3-5吨。
这些钢材都是制造刹车⽚⽀撑板的材质。
这些钢材放置在⾃然的空⽓中,钢材会跟空⽓⾥的氧⽓进⾏化学反应,钢材表⾯会产⽣锈蚀,这就是上图右侧的Black Steel。
左侧的这两块钢板是经过特殊处理的,它们都热轧以后进⾏了酸洗⼯艺,然后表⾯进⾏了上油处理,所以你看左右钢板的颜⾊和光泽都明显不同。
这⼀部分经过处理的钢材才是我们制造刹车⽚的材料。
⼯⼈将处理好的钢材放⼊压机⾥,这⾥你可以看到这⼀卷⼀卷的钢材都是这样卷好成型的。
制造汽车的钢板也都是这样⼀卷⼀卷的钢板,然后送⼊压机成型。
⼀卷⼀卷的钢材是盘绕的,所以打开以后它是弯曲的,弯曲的钢材不能进⾏冲压。
这个时候需要把这些弯曲的钢材送⼊机器压平,这样才能进⼊冲压环节。
压平的钢材进⼊到压机进⾏冲压环节,压机将施加800吨的压⼒以冲压出单个刹车⽚⽀撑板。
这就是加⼯完的刹车⽚⽀撑板,师傅会对其进⾏抽检,如果发现不合格的产品,师傅会中断压机的⼯作,避免这批产品都不符合要求。
对于不合格的产品会丢⼊另⼀个垃圾桶,这些师傅都是经过专业训练的,他们可以⾁眼塞选这些产品。
这就是压制完成型的⽀撑板。
⼀些⼩的制造⼚商他们没有这样⼤型的设备,他们会采取其它的⼯艺,制造出来的产品跟这些就存在明显的区别,所以很多⼈⼀眼就可以看出配件是原⼚还是副⼚的,这道⼯序⾄关重要。
初选以后的这些背板,然后会送⼊质量控制实验室,技术⼈员⽤这些⾼端的检测仪器对背板的⼤⼩和质量进⾏检测,合格后才会送⼊下⼀个环节。
合格后的产品会标注上序列号,这个序列号就是它的⾝份证,出现问题可以追溯到是那⼀批钢材。
- 1、下载文档前请自行甄别文档内容的完整性,平台不提供额外的编辑、内容补充、找答案等附加服务。
- 2、"仅部分预览"的文档,不可在线预览部分如存在完整性等问题,可反馈申请退款(可完整预览的文档不适用该条件!)。
- 3、如文档侵犯您的权益,请联系客服反馈,我们会尽快为您处理(人工客服工作时间:9:00-18:30)。
摩擦材料主要用于车辆和动力机械制动与传动,正从单一材 料向复合材料发展,其质量的好坏直接影响机器的可靠性和操 作人员的生命安全。随着科学技术的发展,人们对交通运输工 具和动力机械的速度、负荷和安全性要求越来越高。高速列车、 重载货车、轿车、赛车、摩托车等重载、高速行驶、制动频繁 的民用运载工具, 以及使用环境恶劣的装甲车、坦克、直升机等, 都对响应快、摩擦因数足够高而稳定、抗热衰减性能良好、质 量轻、寿命长和环境适应性强的高性能摩擦材料提出了迫切的 需求。20世纪90年代中期,C/C2SiC复合材料开始应用于摩擦 领域, 成为最新一代高性能制动材料而引起研究者的广泛关注和 重视,德、日等工业发达国家正逐步展开理论和应用研究。 C/C2SiC陶瓷制动材料具有密度低、耐磨性好、摩擦因数高、 制动平稳、抗腐蚀、抗氧化、耐高温、环境适应性强和寿命长 等优点,C/C2SiC陶瓷材料必将在高速高能载交通工具和工程 机械的摩擦机构上得到广泛应用,并且成本合理,所以该材料 在机械制动等领域有良好的应用前景。
C/C复合材料,即炭纤维增强炭基体复合材料。 自从1958年问世以来,由于其具有比重小(约为铁的 1/5)、强度高(抗拉强度>2GP)、热膨胀系数小、 耐高温等优点,在军工、航空、航天等方面取得了长 足的发展。其在民用领域方面的应用也日益扩大,很 多民用飞机(如波音系列:Boeing747、Boeing757 等,空客系列:A330、A340等)和高档赛车(Ferrari F2005、Renault R25、Toyota TF105等)已开始装备 C/C刹车副。目前国内中南大学、西北工业大学、中 科院金属所、航天集团第四院43所、621所等几家单位 的研究在国内居于领先水平。中南大学以博云新材料 股份有限公司为依托,C/C刹车副已全面实现产业化、 国产化[13-15]。由于C/C复合材料采用化学气相沉积 (CVD),液相浸渍炭化的生产工艺,生产周期较长, 因此成本较高,价格昂贵(一副C/C刹车盘价格高达 上万元),这也制约了其在更广阔领域特别是汽车领 域的应用。
刹车片的材料——摩擦材料?
1粉末冶金摩擦材料 2新型混杂纤维摩擦材料 3新型陶瓷基摩擦材料 4C/C复合材料
★摩擦材料是一种以摩擦为主要功能、 兼有结构性能要求的复合材料。汽车 用摩擦材料主要是用于制造制动摩擦 片和离合器片。这些摩擦材料主要采 用石棉基摩擦材料,随着对环保和安 全的要求越来越高,逐渐出现了半金 属型摩擦材料、复合纤维摩擦材料、 陶瓷纤维摩擦材料。
的界面上形成转移膜,摩擦曲线波动幅度比单一炭纤
维增强的试样普遍要小,即加入了芳纶浆粕改善了摩
擦系数的平稳性,证明了混杂的优异效应。中国专利
利用一种价格极为低廉的叶蜡作为填料,采用硅酸铝
纤维、钢纤维混杂增强制得一种新型混杂纤维摩擦材
料。通过实验磨损率小、制动效果好,具有很大的市场竞争优
★由于摩擦材料在汽车上主要用于制造 制动系和传动系的零件,要求有足够 高的而且稳定的摩擦系数和较好的耐 磨性
粉末冶金摩擦材料又称烧结金属摩擦材料, 是以金属及其合金为基体,添加摩擦组元和 润滑组元,通过压制成型,然后在高温中烧 结而成。采用粉末冶金技术生产摩擦材料时, 不但在性能上有突出的优点,特别是在组分 的设计上极具灵活性。法国、瑞典、加拿大 等国的高速列车均使用这种闸瓦,且取得不 错的效果。但其对对偶的磨损偏大,成本与 有机摩擦材料相比偏高,尚有待进一步改进
势
由于无石棉有机制动材料存在耐热性问题,半金属摩擦材料又 存在密度较大、攻击对偶、产生噪音等不足。陶瓷摩擦材料具有密 度适中、耐高温、耐腐蚀、价格适宜等优点,已被广泛的应用于制 动领域。一般来说,陶瓷基摩擦材料中陶瓷的体积分数至少占到 45%以上,有的甚至达到80%~90%。常用的性能优良的陶瓷有: SiC、B4C、Si3N4、Al2O3、AlN等。目前在国外,添加陶瓷纤维 作为增强材料,利用改性树脂和橡胶为粘合剂,以多种人工合成的 有机和无机材料作为摩擦性能调节剂制成的一种非金属摩擦材料, 也叫做陶瓷基摩擦材料。其特点是:1无噪音。陶瓷配方不但很好 的消除了行车制动噪音,而且通过对静摩擦系数和动摩擦系数的平 衡,解决了半金属和少金属配方很难克服的低频噪音。2无落灰, 抗腐蚀能力强。陶瓷配方中没有金属成分的加入,很好的解决了金 属纤维锈蚀的问题。对油酸不敏感,且其具有优异的摩擦粉尘性能, 一般行车一千公里以内不会有明显的轮毂落灰现象。3使用寿命长。 陶瓷摩擦材料采用大量的有机和无机材料,材料之间有良好的亲和 性能,并在制动过程中可以形成较好的摩擦膜和转移层,具有很好 的润滑效果,大大提高了材料的使用寿命,与半金属相比,其使用 寿命可提高1.5倍以上。4绿色环保,制动舒适。陶瓷材料优异的理 化性能以及不含重金属的配方,使制动材料具有噪音低、粉尘少的 特点,且对环境无污染,完全符合日益提高的环保要求。
C/ C2SiC 复合材料制备工艺技术的关键是:1纤 维损伤尽量少; 2 纤维/ 基体(F/M)界面形成适当 的结合强度;3)克服基体致密化的“瓶颈效应”; 4 低的制备成本。目前制备C/ C2SiC 复合材料的 工艺主要有热压烧结法( Heat press2sinter ,HPS) 、先驱体转化法(Liquid polymer infilt ration ,LPI)、化学气相浸渗法(Chemical vapor infilt ra2tion , CVI)和反应熔体浸渗法(Reactive melt infil2t ration,RMI),但真正能实现制备异型 C/C2SiC摩擦材料的只有LPI 法、CVI 法、RMI 法及其组合的方法。
目前世界上已极少采用单一纤维作为制动材料的
增强纤维,混杂纤维增强是摩擦材料的发展方向。所
谓新型混杂纤维摩擦材料是指采用两种或两种以上的
纤维增强同一种树脂基体的摩擦复合材料。采用混杂
技术时,一般都采用性能和价格互补的两种纤维。郭
洪涛研究认为炭纤维与芳纶浆粕的混杂表现出很好的
摩擦学性能,芳纶纤维在材料摩擦过程中容易在对偶