脱硫工艺参数
脱硫系统主要技术指标

13.773
空塔流速
m/s
<3.5
烟气塔内停留时间
s
>6
喷淋层数
层
4
设计Ca/S
mol/mol
≤1.05
石灰用量
t/h
设计石膏含水率
%
设计石膏产量(湿渣,含湿<10%)
t/h
十二、供货清单
12.1 设备清单
系
统
序
号
名 称
规 格 参 数
单
位
数
量
生 产 厂 家
备 注
烟
气
系
统
1
原烟道
规格:6000×3200δ=6mm 材质:Q235
个
3
辽阳三峰
79
密度计
个
1
辽阳三峰
80
液位计
范围:0-10米,输出:4-20 mA
个
5
辽阳三峰
81
料位计
阻尼式料位计
个
1
辽阳三峰
82
PH计
范围:0-14,精度:≤±1FS
个
2
辽阳三峰
83
就地压力表
范围:0-1.0 MPa
套
1
辽阳三峰
84
压力变送器
范围:0-0.5 MPa,输出:4-20 mA
个
3
辽阳三峰
85
压差变送器
范围:0-0.5 MPa,输出:4-20 mA
个
1
辽阳三峰
86
其他仪表
套
1
辽阳三峰
12.2 土建清单
系统
序号
名 称
说 明
单
位
数
量
着重解析半干法烟气脱硫技术工艺及技术参数
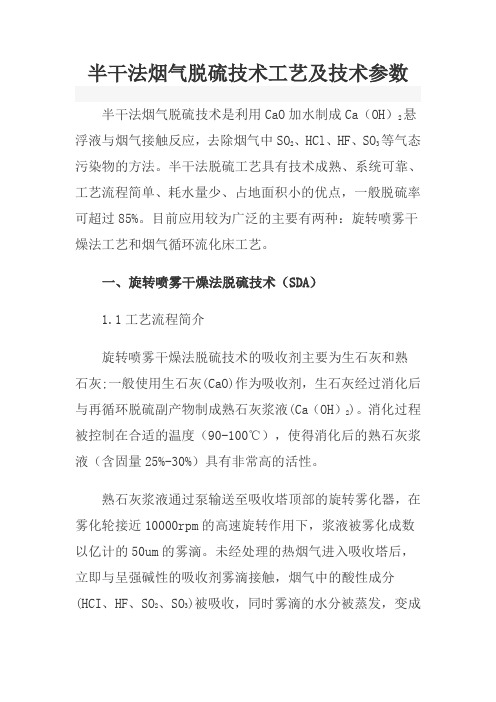
半干法烟气脱硫技术工艺及技术参数半干法烟气脱硫技术是利用CaO加水制成Ca(OH)2悬浮液与烟气接触反应,去除烟气中SO2、HCl、HF、SO3等气态污染物的方法。
半干法脱硫工艺具有技术成熟、系统可靠、工艺流程简单、耗水量少、占地面积小的优点,一般脱硫率可超过85%。
目前应用较为广泛的主要有两种:旋转喷雾干燥法工艺和烟气循环流化床工艺。
一、旋转喷雾干燥法脱硫技术(SDA)1.1工艺流程简介旋转喷雾干燥法脱硫技术的吸收剂主要为生石灰和熟石灰;一般使用生石灰(CaO)作为吸收剂,生石灰经过消化后与再循环脱硫副产物制成熟石灰浆液(Ca(OH)2)。
消化过程被控制在合适的温度(90-100℃),使得消化后的熟石灰浆液(含固量25%-30%)具有非常高的活性。
熟石灰浆液通过泵输送至吸收塔顶部的旋转雾化器,在雾化轮接近10000rpm的高速旋转作用下,浆液被雾化成数以亿计的50um的雾滴。
未经处理的热烟气进入吸收塔后,立即与呈强碱性的吸收剂雾滴接触,烟气中的酸性成分(HCI、HF、SO2、SO3)被吸收,同时雾滴的水分被蒸发,变成干燥的脱硫产物。
这些干燥的产物有少量直接从吸收塔底部排出,大部分随烟气进人吸收塔后的除尘器内被收集,再通过机械或气力方式输送,处理后的洁净烟气通过烟囱排放。
根据实际情况,SDA系统还可以采用部分脱硫产物再循环制浆以提高吸收剂的利用率。
烟气在喷雾干燥吸收塔中的停留时间一般为10-12S,吸收塔内飞灰和脱硫灰大部分通过除尘器收集,只有5%-10%的干燥固体物从吸收塔底部排出。
1.2影响脱硫效率的主要因素1.2.1雾滴粒径雾滴粒径越小,传质面积也越大,但粒径过细,干燥速度也越快,气液反应就变成了气固反应,脱硫效率反而会降低。
有关研究表明,雾化粒径在50um时脱硫率较高。
1.2.2接触时间在旋转喷雾干燥法脱硫技术中,以烟气在脱硫塔中的停留时间来衡量烟气与脱硫剂的接触时间,停留时间主要取决于液滴的蒸发干燥时间,一般为10-12S,降低脱硫塔的空塔流速,延长停留时间,有利于提供脱硫率。
石灰脱硫设计方案
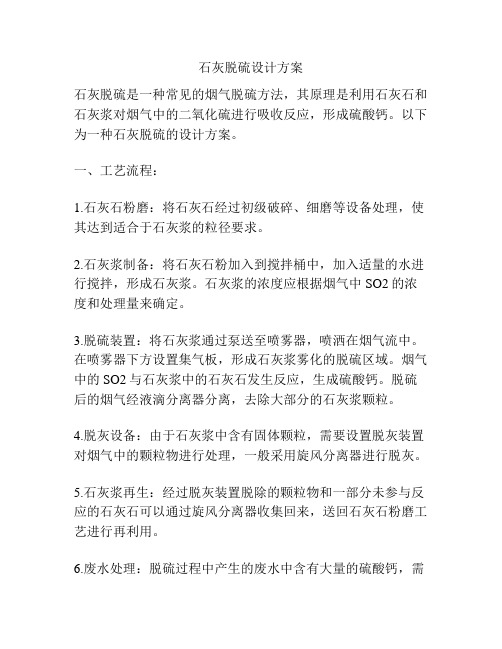
石灰脱硫设计方案石灰脱硫是一种常见的烟气脱硫方法,其原理是利用石灰石和石灰浆对烟气中的二氧化硫进行吸收反应,形成硫酸钙。
以下为一种石灰脱硫的设计方案。
一、工艺流程:1.石灰石粉磨:将石灰石经过初级破碎、细磨等设备处理,使其达到适合于石灰浆的粒径要求。
2.石灰浆制备:将石灰石粉加入到搅拌桶中,加入适量的水进行搅拌,形成石灰浆。
石灰浆的浓度应根据烟气中SO2的浓度和处理量来确定。
3.脱硫装置:将石灰浆通过泵送至喷雾器,喷洒在烟气流中。
在喷雾器下方设置集气板,形成石灰浆雾化的脱硫区域。
烟气中的SO2与石灰浆中的石灰石发生反应,生成硫酸钙。
脱硫后的烟气经液滴分离器分离,去除大部分的石灰浆颗粒。
4.脱灰设备:由于石灰浆中含有固体颗粒,需要设置脱灰装置对烟气中的颗粒物进行处理,一般采用旋风分离器进行脱灰。
5.石灰浆再生:经过脱灰装置脱除的颗粒物和一部分未参与反应的石灰石可以通过旋风分离器收集回来,送回石灰石粉磨工艺进行再利用。
6.废水处理:脱硫过程中产生的废水中含有大量的硫酸钙,需要进行处理。
一般采用沉淀池沉淀、浓缩、过滤等方法,使得其中的石灰浆固体颗粒沉淀,废水中的SO2浓度降低后排放。
二、设备选型:1.石灰浆制备设备:包括搅拌桶、加水装置、泵等。
2.喷雾器:根据处理量和SO2浓度选择合适的喷雾器,一般采用旋喷雾器和喷淋塔。
3.液滴分离器:常用的液滴分离器有旋风分离器、湿式静电除尘器等。
4.脱灰设备:旋风分离器可用于脱除石灰浆中的颗粒物。
5.废水处理设备:包括沉淀池、浓缩系统、过滤设备等。
三、控制参数:1.石灰浆浓度:根据烟气中SO2的浓度和处理量来确定。
2.喷雾器喷雾量:根据烟气中SO2的浓度和处理量来确定。
3.脱灰效率:根据废气排放标准来确定。
4.废水处理效率:根据废水排放标准来确定。
石灰脱硫是一种成熟可靠的烟气脱硫方法,可以有效降低烟气中的二氧化硫含量,减少对环境的污染。
在设计方案中,需要合理选用设备,控制参数,确保脱硫效果和废水处理效果达到排放标准。
石灰石湿法脱硫浆液密度控制范围

石灰石湿法脱硫工艺是一种常用的烟气脱硫方法,其脱硫效率高、操作稳定、设备耐腐蚀等特点使其成为工业上广泛应用的脱硫技术之一。
在石灰石湿法脱硫中,脱硫浆液密度是一个重要的操作参数,对保证脱硫效率、减少能耗、延长设备寿命具有重要作用。
本篇文章将围绕石灰石湿法脱硫浆液密度控制范围展开详细的讨论。
一、脱硫工艺概述石灰石湿法脱硫是将石灰石石灰化后与烟气中的二氧化硫进行化学反应,生成硫酸钙或碳酸钙,并将其分离出烟气,从而达到脱硫的目的。
其脱硫过程可以分为石灰石石灰化、吸收反应、浆液处理等几个步骤。
在整个脱硫过程中,脱硫浆液密度是一个需要被精确控制的操作参数。
二、脱硫浆液密度的作用1. 影响脱硫效率:脱硫反应的进行需要一定的时间和一定的条件,而脱硫浆液的密度会影响反应的进行速率,进而影响脱硫效率。
2. 影响设备运行稳定性:脱硫塔内的浆液密度过高或过低都会影响设备的运行稳定性,甚至导致设备堵塞或浆液泵的运行不稳定。
3. 影响原料消耗:脱硫时消耗的原料主要是石灰石,而脱硫浆液密度的不合适会导致原料的浪费,增加脱硫成本。
三、脱硫浆液密度的控制范围1. 过高的浆液密度:当脱硫浆液密度过高时,会导致吸收塔内的浆液循环困难,甚至发生黏结与结垢,影响脱硫效率。
应控制脱硫浆液的密度不得高于1.35g/cm³。
2. 过低的浆液密度:脱硫浆液密度过低将导致溶液中的固体物质质量分数下降,反应物含量下降,降低脱硫效果,还将影响设备的正常运行。
脱硫浆液密度不应低于1.15g/cm³。
四、脱硫浆液密度控制的方法1. 控制石灰石浆液比例:通过调节石灰石与水的比例,来控制脱硫浆液的密度。
一般来说,增加水量可以降低密度,而增加石灰石的用量可以提高密度。
2. 合理控制搅拌时间:在制备脱硫浆液过程中,通过合理的搅拌时间可以保证悬浮在水中的石灰石颗粒均匀分散,从而影响脱硫浆液的密度。
3. 控制配料温度:在配料时控制水温和石灰石温度,可以影响脱硫浆液的密度。
石灰石膏法脱硫工艺参数设计

吸收塔系统
吸收系统组成: SO2吸收系统、浆液循环系统、石 膏氧化系统、除雾器
• 烟气中的SO2被吸收浆液洗涤并与浆液中 的CaCO3发生反应,反应生成的亚硫酸钙 在吸收塔底部的循环浆池内被氧化风机鼓 入的空气强制氧化,最终生成石膏,石膏 由石膏浆排出泵排出,送入石膏处理系统 脱水。烟气从吸收塔出来后,经过二级除 雾器,以除去脱硫后烟气夹带的细小液滴 ,使烟气在含雾量低于100mg/ Nm 3下排 出。
工艺技术参数设计
湿式石灰石—石膏法烟气脱硫工艺
• (1)石灰石制浆系统; • (2)烟气系统; • (3)吸收塔系统; • (4)石膏脱水系统; • (5)脱硫废水处理系统 • (6)浆液排放及收集系统; • (7)工艺水系统; • (8)电气及仪表控制系统。
工艺流程图
工艺流程图
石灰石制浆系统
吸收塔系统
• 四、除雾器 当带有液滴的烟气进入除雾器通道时,由于流线的偏折 在惯性力的作用下实现气液分离,部分液滴撞击在除雾 器叶片上被捕集下来。
除雾器的组成: 由除雾器本体及冲洗系统(有单面冲洗和 双 面冲洗两种形式)组成。 除雾器本体由除雾器叶片、卡具、夹具、支架等按一定 结构组装而成。除雾器冲洗系统主要由冲洗喷嘴、除雾 器冲洗泵、管路、阀门、压力仪表及电气控制部分组成 。其作用是定期冲洗由除雾器叶片捕集的液滴、粉尘, 保持叶片表面清洁,防止叶片结垢和堵塞,维持系统正 常运行。
排水坑: 容积 V = 90 m3 长×宽×高 = 6m×6m×2.5m
排水坑泵: 设计流量Q = 40m3/h 扬程H = 20m 为单流单级离心液下泵,一用一备
事故浆液储存池:容积 V = 1290.4 m3 长×宽×高 = 16m×16m×5.1m
脱硫工艺及其计算公式全解析
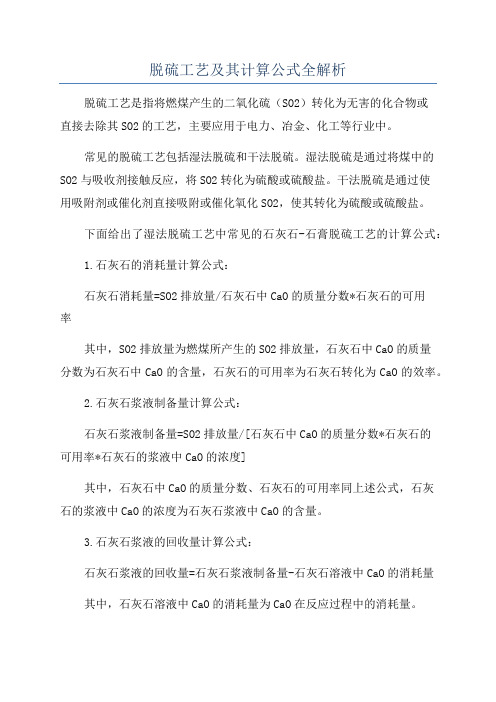
脱硫工艺及其计算公式全解析脱硫工艺是指将燃煤产生的二氧化硫(SO2)转化为无害的化合物或直接去除其SO2的工艺,主要应用于电力、冶金、化工等行业中。
常见的脱硫工艺包括湿法脱硫和干法脱硫。
湿法脱硫是通过将煤中的SO2与吸收剂接触反应,将SO2转化为硫酸或硫酸盐。
干法脱硫是通过使用吸附剂或催化剂直接吸附或催化氧化SO2,使其转化为硫酸或硫酸盐。
下面给出了湿法脱硫工艺中常见的石灰石-石膏脱硫工艺的计算公式:1.石灰石的消耗量计算公式:石灰石消耗量=SO2排放量/石灰石中CaO的质量分数*石灰石的可用率其中,SO2排放量为燃煤所产生的SO2排放量,石灰石中CaO的质量分数为石灰石中CaO的含量,石灰石的可用率为石灰石转化为CaO的效率。
2.石灰石浆液制备量计算公式:石灰石浆液制备量=SO2排放量/[石灰石中CaO的质量分数*石灰石的可用率*石灰石的浆液中CaO的浓度]其中,石灰石中CaO的质量分数、石灰石的可用率同上述公式,石灰石的浆液中CaO的浓度为石灰石浆液中CaO的含量。
3.石灰石浆液的回收量计算公式:石灰石浆液的回收量=石灰石浆液制备量-石灰石溶液中CaO的消耗量其中,石灰石溶液中CaO的消耗量为CaO在反应过程中的消耗量。
4.石膏产量计算公式:石膏产量=SO2排放量/[石膏中CaSO4的质量分数*石膏中CaSO4的可用率]其中,石膏中CaSO4的质量分数为石膏中CaSO4的含量,石膏中CaSO4的可用率为石膏转化为CaSO4的效率。
需要注意的是,以上公式中的各项参数需要实际运行的数据进行计算,并且不同的脱硫工艺可能存在不同的计算公式。
此外,脱硫工艺还涉及到反应温度、压力、吸收剂浓度等因素的影响,这些因素也需要考虑在内。
因此,在实际应用中,需要结合具体情况和工艺要求进行合理计算和调整。
半干法烟气脱硫技术工艺及技术参数
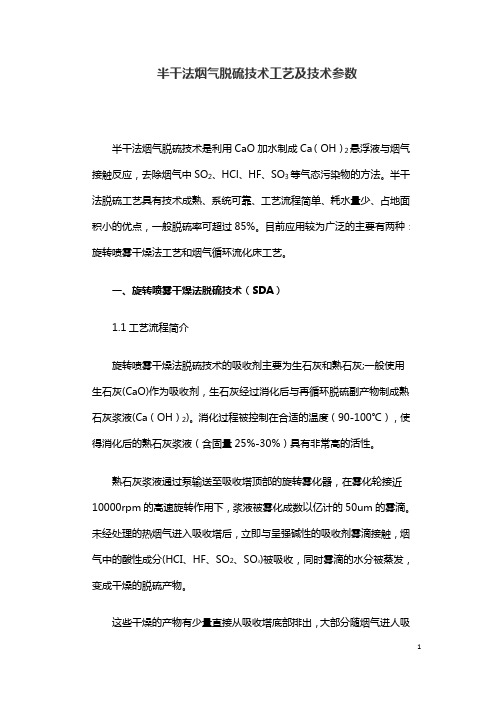
半干法烟气脱硫技术工艺及技术参数半干法烟气脱硫技术是利用CaO加水制成Ca(OH)2悬浮液与烟气接触反应,去除烟气中SO2、HCl、HF、SO3等气态污染物的方法。
半干法脱硫工艺具有技术成熟、系统可靠、工艺流程简单、耗水量少、占地面积小的优点,一般脱硫率可超过85%。
目前应用较为广泛的主要有两种:旋转喷雾干燥法工艺和烟气循环流化床工艺。
一、旋转喷雾干燥法脱硫技术(SDA)1.1工艺流程简介旋转喷雾干燥法脱硫技术的吸收剂主要为生石灰和熟石灰;一般使用生石灰(CaO)作为吸收剂,生石灰经过消化后与再循环脱硫副产物制成熟石灰浆液(Ca(OH)2)。
消化过程被控制在合适的温度(90-100℃),使得消化后的熟石灰浆液(含固量25%-30%)具有非常高的活性。
熟石灰浆液通过泵输送至吸收塔顶部的旋转雾化器,在雾化轮接近10000rpm的高速旋转作用下,浆液被雾化成数以亿计的50um的雾滴。
未经处理的热烟气进入吸收塔后,立即与呈强碱性的吸收剂雾滴接触,烟气中的酸性成分(HCI、HF、SO2、SO3)被吸收,同时雾滴的水分被蒸发,变成干燥的脱硫产物。
这些干燥的产物有少量直接从吸收塔底部排出,大部分随烟气进人吸收塔后的除尘器内被收集,再通过机械或气力方式输送,处理后的洁净烟气通过烟囱排放。
根据实际情况,SDA系统还可以采用部分脱硫产物再循环制浆以提高吸收剂的利用率。
烟气在喷雾干燥吸收塔中的停留时间一般为10-12S,吸收塔内飞灰和脱硫灰大部分通过除尘器收集,只有5%-10%的干燥固体物从吸收塔底部排出。
1.2影响脱硫效率的主要因素1.2.1雾滴粒径雾滴粒径越小,传质面积也越大,但粒径过细,干燥速度也越快,气液反应就变成了气固反应,脱硫效率反而会降低。
有关研究表明,雾化粒径在50um时脱硫率较高。
1.2.2接触时间在旋转喷雾干燥法脱硫技术中,以烟气在脱硫塔中的停留时间来衡量烟气与脱硫剂的接触时间,停留时间主要取决于液滴的蒸发干燥时间,一般为10-12S,降低脱硫塔的空塔流速,延长停留时间,有利于提供脱硫率。
脱硫工艺流程说明

脱硫工艺流程说明湿法脱硫工艺流程主要包括石灰石-石膏法和碱性洗涤液法两种方式。
1. 石灰石-石膏法:将石灰石(CaCO3)加入到反应塔中与燃烧产生的SO2发生反应,生成石膏(CaSO4)和二氧化碳(CO2)。
石膏随后被分离出来用于再利用或处理。
2. 碱性洗涤液法:用碱性洗涤液(如氢氧化钠、氨水等)与燃烧产生的SO2进行反应,生成相应的盐类,然后通过沉淀或其他方式分离出来。
干法脱硫工艺流程主要包括石灰石喷雾干法脱硫和双碱法两种方式。
1. 石灰石喷雾干法脱硫:将粉状石灰石喷射到燃烧产生的SO2气流中,通过干法吸收,然后分离出SO2和粉尘。
2. 双碱法:使用两种碱性吸收剂,通常是碳酸氢钠和氢氧化钙,通过干法反应吸收SO2,然后分离出生成的产物。
脱硫工艺流程中需要考虑的参数包括燃料类型、SO2排放浓度、处理效率、再生利用和处理废料等。
不同的工艺流程适用于不同的工业设备和排放标准,因此在选择和设计脱硫工艺时需要综合考虑各种因素。
对于脱硫工艺流程,还有一些其他重要的细节和注意事项需要考虑。
首先,脱硫工艺需要根据具体的工业设备和生产流程进行选择和设计。
比如在煤电厂中,石灰石-石膏法常被用于处理燃煤产生的二氧化硫。
而在工业炉窑中,干法脱硫工艺更为常见。
各种工艺都需要根据具体情况进行优化设计,以提高脱硫效率、减少能耗和减少对环境的影响。
其次,脱硫工艺需要考虑处理后的副产品处理问题。
例如,石膏、除尘灰等副产品需要经过处理后才能达到国家排放标准,或者进行再利用。
对副产品的有效利用不仅可以减少环境污染,还可以降低生产成本。
此外,脱硫工艺的运行参数也需要严格控制。
这包括脱硫剂的投加量、反应温度、气体流速以及脱硫设备的清洁维护等。
通过对这些参数的严格控制,能够确保脱硫工艺的高效运行,减少设备的停机维护,提高设备的使用寿命。
在脱硫工艺的选择中,也需要考虑对能源的消耗。
比如干法脱硫通常需要更多的能源用于干燥和加热过程,而湿法脱硫则需要更多的水资源。
湿法脱硫工艺计算书

120
96606 161426.83 128011.5 -122203.48
90.5 71451
标态 无冷凝水
第 2 页,共 7 页
项目名称
烟台
日
审核
期
烟气脱硫工程设计
日
专 业 工艺
设计阶段
投标
计算书
校核
期日
计算
期
版次
序
项
目 代号 单位
计算公式或依据
计算结果 取 值
备注
2 氧化空气量 二氧化硫的含量 烟气中二氧化硫量
G'
烟气中的含水量
wv'
水蒸汽质量流量
W'
冷凝水的量
CW
℃ Nm3/h Nm3/h m3/h
Nm3/h kg/h kg/h
℃ Pa kg/h Nm3/h kg/h
T'=T+3.5 Q2=Q1 Q2'=Q1' Q2''=Q2*(P0/P2)*(273+T')/273
158.5 80000 71560 123044
101325
71867
71867
第 6 页,共 7 页
日
项目名称
烟台
审核
期
烟气脱硫工程设计
日
设计阶段
投标
计算书
校核
期日
计算
期
序
项
目 代号 单位
计算公式或依据
计算结果 取 值
标态,湿态(Nm3/h)
80000
80000
#REF!
#REF!
运行工况(m3/h,湿)
含水量(%) SO2浓度(mg/Nm3)
脱硫脱硝工艺参数
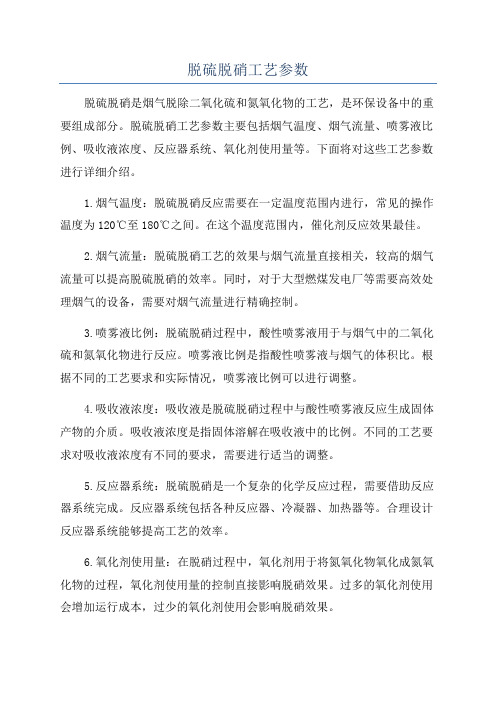
脱硫脱硝工艺参数脱硫脱硝是烟气脱除二氧化硫和氮氧化物的工艺,是环保设备中的重要组成部分。
脱硫脱硝工艺参数主要包括烟气温度、烟气流量、喷雾液比例、吸收液浓度、反应器系统、氧化剂使用量等。
下面将对这些工艺参数进行详细介绍。
1.烟气温度:脱硫脱硝反应需要在一定温度范围内进行,常见的操作温度为120℃至180℃之间。
在这个温度范围内,催化剂反应效果最佳。
2.烟气流量:脱硫脱硝工艺的效果与烟气流量直接相关,较高的烟气流量可以提高脱硫脱硝的效率。
同时,对于大型燃煤发电厂等需要高效处理烟气的设备,需要对烟气流量进行精确控制。
3.喷雾液比例:脱硫脱硝过程中,酸性喷雾液用于与烟气中的二氧化硫和氮氧化物进行反应。
喷雾液比例是指酸性喷雾液与烟气的体积比。
根据不同的工艺要求和实际情况,喷雾液比例可以进行调整。
4.吸收液浓度:吸收液是脱硫脱硝过程中与酸性喷雾液反应生成固体产物的介质。
吸收液浓度是指固体溶解在吸收液中的比例。
不同的工艺要求对吸收液浓度有不同的要求,需要进行适当的调整。
5.反应器系统:脱硫脱硝是一个复杂的化学反应过程,需要借助反应器系统完成。
反应器系统包括各种反应器、冷凝器、加热器等。
合理设计反应器系统能够提高工艺的效率。
6.氧化剂使用量:在脱硝过程中,氧化剂用于将氮氧化物氧化成氮氧化物的过程,氧化剂使用量的控制直接影响脱硝效果。
过多的氧化剂使用会增加运行成本,过少的氧化剂使用会影响脱硝效果。
总之,脱硫脱硝工艺参数的选择和控制对于脱硫脱硝效果至关重要。
科学合理的工艺参数调整能够提高工艺的效率,降低污染物排放。
不同的工艺参数需要根据具体的工艺要求和实际情况进行调整,以达到理想的脱硫脱硝效果。
常见脱硫工艺、设备及参数

常见脱硫工艺、设备及参数一.脱硫方法分类脱硫是减少化石燃料(主要指煤)生成的SO2排放到大气中的所有技术手段的通称,常见脱硫方法按照燃烧过程可以分为三类:⑴燃烧前清洁技术:煤炭洗选、煤气化、液化和水煤浆技术;⑵燃烧中清洁技术:循环流化床燃烧、煤气联合循环发电、型煤;⑶燃烧后清洁技术:烟气脱硫技术。
在上述方法中,烟气脱硫技术是目前世界上唯一大规模商业化应用的脱硫方式,世界各国研究开发和商业应用的烟气脱硫技术已达200种之上。
烟气脱硫技术按照反应物的状态可以分为:⑴湿法烟气脱硫;⑵干法烟气脱硫。
湿法烟气脱硫技术主要有石灰石/石灰洗涤法,双碱法、韦尔曼洛德法、氧化镁法和氨法。
据国际能源机构煤炭研究组织调查表明,湿式脱硫占世界安装烟气脱硫的机组总容量的85%,美、德、日等发达国家更达到90%以上。
湿发烟气脱硫技术特点主要有:①脱硫效率高,适用于各种煤种;②脱硫剂利用率高;③占用场地大,一次性投资大;④反应物显液态,需进行水处理;⑤设备易腐蚀,结垢及堵塞。
可以看出,在资金和场地许可的情况下,采用湿法烟气脱硫是较稳妥的方法。
干式烟气脱硫技术主要有喷雾干燥法、炉内喷钙法和循环流化床排烟脱硫法。
其特点主要有:①投资费用较低;②脱硫产物呈干态,并与飞灰相混;③无需装设除雾器及烟气再热器;④设备不易腐蚀,不易发生结垢及堵塞;⑤吸收剂利用率相对较低,不适用于高硫煤(含硫量>2%)脱硫;⑥飞灰与脱硫产物相混可能影响综合利用;⑦对干燥过程控制要求很高。
干式烟气脱硫技术适用于硫含量低于2%,场地及资金受限制的情况,通常老厂改造适用此方式。
目前循环流化床排烟脱硫法(CFB)在国内电厂的应用较广,仅次于石灰石湿法的应用,已投入使用的最大机组为20万KW,且效果不理想。
二.石灰石-石膏湿式脱硫装置构成该法原则上可分为下列结构单元:⑴浆液系统。
由粉仓、磨机、漩流分离站、浆液箱组成。
⑵吸收系统。
由洗涤循环系统、除雾器、氧化系统组成。
石灰石石灰法湿法烟气脱硫技术

化学成分,如氯化物。在酸性环境中,它们对金属(包括 不锈钢)的腐蚀性相当强。目前广泛应用的吸收塔材料是 合金C-276,其价格是常规不锈钢的15倍,为延长设备的 使用寿命,溶液中氯离子的浓度不能太高。为保证氯离子 不发生浓缩,有效地方法是在脱硫系统中根据物料平衡排 出适量的废水,以清水补充。
1.反应原理
用石灰石或者石灰浆液吸收烟气中的SO2,首先生成亚 硫酸钙:
石灰石:CaCO3+ SO2+0.5H2O→CaSO3•0.5H2O+CO↑ 石灰:CaO+ SO2+0.5H2O→CaSO3•0.5H2O
然后亚硫酸钙再被氧化为硫酸钙。
石灰石石灰法湿法烟气脱硫反应机 理比较表格
石灰石系统和石灰系统的主要区别
②结要原因,特别是硫酸钙结构坚硬、 板结,一旦结垢难以去除,影响到所有与脱硫液接触的阀 门、水泵、控制仪器和管道等。硫酸钙结垢的原因是SO42和Ca2+的离子积在局部达到过饱和。为此,在吸收塔中要 保持亚硫酸盐的氧化率在20%以下。亚硫酸盐的氧化需要 在脱硫液循环池中完成,可通过鼓氧或空气等方式进行, 形成的硫酸钙发生沉淀。从循环池返回吸收塔的脱硫液中, 还因为含有足量的硫酸钙晶体,起到了晶种的作用,因此 在后续的吸收过程中,可防止固体直接沉积在吸收塔设备
③除雾器堵塞:在吸收塔中,雾化喷嘴并不能产生尺 寸完全均一的雾滴,雾滴的大小存在尺寸分布。较小的雾 滴会被气流所夹带,如果不进行除雾,雾滴将进入烟道, 造成烟道腐蚀和堵塞。除雾器必须保持清洁,目前使用的 除雾器有多种形式(如折流板型等),通常用高速喷嘴每 小时数次喷清水进行冲洗。
④脱硫剂的利用率:脱硫产物亚硫酸盐和硫酸盐可沉 积在脱硫剂颗粒表面,从而堵塞了这些颗粒的溶解通道。 这会造成石灰石或石灰脱硫剂来不及溶解和反应就随产物 排除,增加了脱硫剂和脱硫产物的处理费用。因此脱硫液 再循环池中的停留时间一般要达到5~10min。实际的停留 时间设计与石灰石的反应性能有关,反应性能越差,为使 之完全溶解,要求它在池内的停留时间越长。
石灰石石膏湿法脱硫工艺
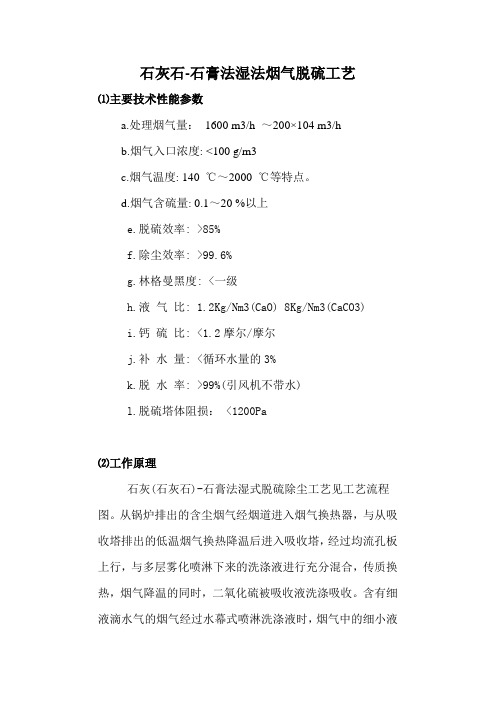
石灰石-石膏法湿法烟气脱硫工艺⑴主要技术性能参数a.处理烟气量:1600 m3/h ~200×104 m3/hb.烟气入口浓度: <100 g/m3c.烟气温度: 140 ℃~2000 ℃等特点。
d.烟气含硫量: 0.1~20 %以上e.脱硫效率: >85%f.除尘效率: >99.6%g.林格曼黑度: <一级h.液气比: 1.2Kg/Nm3(CaO) 8Kg/Nm3(CaCO3)i.钙硫比: <1.2摩尔/摩尔j.补水量: <循环水量的3%k.脱水率: >99%(引风机不带水)l.脱硫塔体阻损: <1200Pa⑵工作原理石灰(石灰石)-石膏法湿式脱硫除尘工艺见工艺流程图。
从锅炉排出的含尘烟气经烟道进入烟气换热器,与从吸收塔排出的低温烟气换热降温后进入吸收塔,经过均流孔板上行,与多层雾化喷淋下来的洗涤液进行充分混合,传质换热,烟气降温的同时,二氧化硫被吸收液洗涤吸收。
含有细液滴水气的烟气经过水幕式喷淋洗涤液时,烟气中的细小液滴被较大液滴吸收分离,再经过上部多层脱水除雾装置进一步除雾后经管道排出吸收塔外,进入烟气换热器,与进口高温烟气换热升温后经引风机进入烟囱高空排放。
洗涤液吸收烟气中的二氧化硫后落入吸收塔下部的氧化池,二氧化硫与石灰反应生成亚硫酸钙,被均布在池底的氧化装置送入的空气进一步氧化成稳定的硫酸钙。
氧化池中部分混合溶液被抽吸送入一级水力旋流器,经旋流浓缩后送入真空带式压滤机,进一步滤出水分,制成工业石膏(CaSO4·2H2O)。
氧化池中低PH值的混合液部分被送入洗涤吸收塔底池,与新投入的脱硫液充分混合,经水泵输送到喷淋层,吸收烟气中的二氧化硫,进行下一个循环。
一级水力旋流器的上清液和真空带式压滤机的下清液均进入循环池,部分被送入二级水力旋流器,部分被送入脱硫液制备搅拌罐。
二级水力旋流器少部分上清液外排。
脱硫剂(石灰或石灰石粉剂)由汽车送入脱硫剂贮仓中,使用时由计量装置通过螺旋混料机送入脱硫剂熟化装置中,按比例制成一定浓度的石灰乳液,自流进入脱硫剂贮液箱中。
湿法脱硫工艺计算书

8 水平衡
项目名称
烟台
设计阶段
投标
代号 单位
日
审核
期
烟气脱硫工程设计
日
计算书
校核
期日
计算
期
计算公式或依据
计算结果 取 值
w3
kg/h
w4
kg/h
w3=wv2*ρ水蒸气,ρ水蒸汽取0.793 w4=w3-W
9242.91 3434.91
DSW DSM
Qr
kg/h mol/h kJ/h
DSM=DSW*1000/64 按SO2计算生成石膏的反应热为339KJ/mol
9 其它
需升温的水量
w12 Kg/h
w12=w6+w7+w11
#REF!
水温升高
△T
℃
△T=Qs*2/3/(c3*w12),c3查表给定
#REF!
热损失约为余热的1/3
三 石灰石用量 1 吸收剂有效成分 2 石灰石粉用量 3 石灰石浆用量
ECa WCa w13
w% Kg/h Kg/h
ECa=Ca WCa=DSW*100/64*(Ca/s)/*100/ECa
80000 76000 155
0.6 0.03 2500 5.5 10.55 96
2 1 1.285 95 1.638 1.03 4 2.5 12 3.5
二 烟温和水平衡计算 1 原烟气(风机前)
专 业 工艺 版次
备注 11%O2 11%O2 收到基 干态 干态
设计值
标态 MET取3.5~5.3
第 1 页,共 7 页
CW=W-W'
120
96606 161426.83 128011.5 -122203.48
常见脱硫工艺设备及参数

常见脱硫工艺设备及参数1. 引言脱硫工艺是指通过使用特定设备和方法,从燃煤、燃气等排放物中去除硫化物。
脱硫过程对于环境保护和空气质量改善具有重要意义。
本文将介绍一些常见的脱硫工艺设备及其参数。
2. 石灰石石膏法脱硫工艺石灰石石膏法是一种常见的湿法脱硫工艺。
该工艺通过将石灰石与脱硫废气中的二氧化硫发生反应,生成石膏并吸收二氧化硫,从而达到脱硫的效果。
以下是该工艺所使用的一些设备及其参数:2.1 石灰石浆液制备设备石灰石浆液制备设备用于将石灰石与水混合,形成石灰石浆液,供脱硫系统使用。
常见的石灰石浆液制备设备有石灰石浆液撞击式制备设备和石灰石浆液循环式制备设备。
2.1.1 石灰石浆液撞击式制备设备•石灰石浆液撞击式制备设备是一种简单易行的设备。
•设备参数:–石灰石浆液配制浓度:10% - 20%–撞击角度:30° - 45°–撞击速度:10 m/s - 20 m/s2.1.2 石灰石浆液循环式制备设备•石灰石浆液循环式制备设备通过循环使用石灰石浆液,提高制备效率。
•设备参数:–石灰石浆液循环比例:1:2 - 1:4–循环次数:2 - 4次2.2 石灰石浆液喷淋设备石灰石浆液喷淋设备用于将石灰石浆液均匀喷洒在脱硫系统的吸收塔中,与废气进行接触和反应。
•设备参数:–喷淋液气比:1.5 - 2.5 L/m³–喷淋液滴径:150 μm - 300 μm–喷淋液流速:10 - 15 m/s2.3 脱硫塔脱硫塔是石灰石石膏法脱硫工艺的核心设备,用于吸收废气中的二氧化硫。
•设备参数:–塔高:10 m - 30 m–底部喷淋液分布类型:层状分布或喷淋罩分布–底部喷淋液喷射速度:5 m/s - 10 m/s–气液比:1.5 - 2.5 L/m³–塔内液相浓度:10% - 20%2.4 石膏脱水脱液设备石膏脱水脱液设备用于将脱硫废水中的石膏进行脱水处理。
•设备参数:–过滤压力:0.5 MPa - 1.5 MPa–过滤速度:10 m/h - 20 m/h–滤饼含水率:20% - 30%3. 活性炭吸附法脱硫工艺活性炭吸附法脱硫工艺是一种常见的干法脱硫工艺,通过将二氧化硫与活性炭表面的吸附剂相互作用,将其中的硫化物吸附起来。
常见脱硫工艺设备及参数

常见脱硫工艺设备及参数1. 概述脱硫是指通过一系列的工艺和设备将煤炭、石油和天然气中的二氧化硫(SO2)去除的过程。
脱硫工艺设备主要包括湿法脱硫、半干法脱硫和干法脱硫等,每种工艺都有其适用的场合和特点。
本文将介绍常见的脱硫工艺设备及其相关参数。
2. 湿法脱硫工艺设备湿法脱硫是指通过溶液中的化学反应将SO2转化成硫酸钙(CaSO4)或二硫化钙(CaS)来实现脱硫的过程。
常用的湿法脱硫工艺设备包括石灰石/石膏石浆液脱硫法、海水脱硫法和氧化钙脱硫法。
2.1 石灰石/石膏石浆液脱硫法该工艺主要由炉脱、浆液制备和海水脱硫三个环节组成。
•炉脱:煤炭气化过程中产生的SO2被石灰石吸收转化成石膏。
•浆液制备:由软化水与石膏石混合生成浆液,浆液中含有高浓度的石膏。
•海水脱硫:将SO2气体通过注入含有浓度适当的石膏的海水中实现脱硫。
2.2 海水脱硫法海水脱硫法是一种较为简单和环保的湿法脱硫工艺,原理是将SO2与海水中的碱性成分发生反应,生成硫酸盐。
该工艺设备的参数:•海水注入速率:20 - 50L/h•SO2吸收塔高度:10 - 15m•海水浓度:3% - 5%2.3 氧化钙脱硫法氧化钙脱硫法是通过将SO2气体与氧化钙(CaO)发生反应,生成硫酸钙固体来实现脱硫。
该工艺设备的主要参数包括氧化钙的使用率和反应温度。
•氧化钙使用率:95% - 99%•反应温度:1000 - 1100℃3. 半干法脱硫工艺设备半干法脱硫是湿法脱硫和干法脱硫的结合,主要是将煤炭燃烧过程中产生的SO2通过喷雾液滴与脱硫石灰反应来实现脱硫。
常用的半干法脱硫工艺设备有喷射式脱硫和旋流塔脱硫。
3.1 喷射式脱硫喷射式脱硫是通过将石灰浆液或石灰石/石膏石浆液喷射到燃烧器内部,与燃烧产生的SO2发生反应来实现脱硫。
该工艺设备的参数:•进浆比:2 - 6L/kg•脱硫效率:90% - 95%3.2 旋流塔脱硫旋流塔脱硫是通过在脱硫塔内部区域产生旋流,将喷射的石灰浆液或石灰石/石膏石浆液与SO2接触来实现脱硫。
脱硫脱硝工艺参数
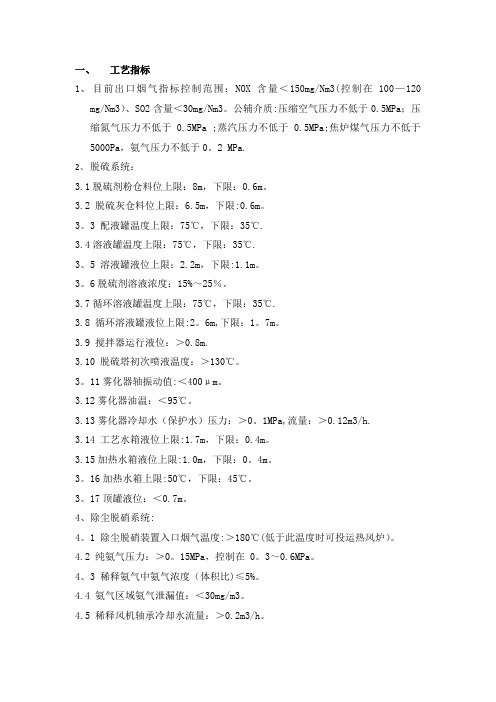
一、工艺指标1、目前出口烟气指标控制范围:NOX含量<150mg/Nm3(控制在100—120mg/Nm3)、SO2含量<30mg/Nm3。
公辅介质:压缩空气压力不低于0.5MPa;压缩氮气压力不低于0.5MPa ;蒸汽压力不低于0.5MPa;焦炉煤气压力不低于5000Pa,氨气压力不低于0。
2 MPa.2、脱硫系统:3.1脱硫剂粉仓料位上限:8m,下限:0.6m。
3.2 脱硫灰仓料位上限:6.5m,下限:0.6m。
3。
3 配液罐温度上限:75℃,下限:35℃.3.4溶液罐温度上限:75℃,下限:35℃.3。
5 溶液罐液位上限:2.2m,下限:1.1m。
3。
6脱硫剂溶液浓度:15%~25%。
3.7循环溶液罐温度上限:75℃,下限:35℃.3.8 循环溶液罐液位上限:2。
6m,下限:1。
7m。
3.9 搅拌器运行液位:>0.8m.3.10 脱硫塔初次喷液温度:>130℃。
3。
11雾化器轴振动值:<400μm。
3.12雾化器油温:<95℃。
3.13雾化器冷却水(保护水)压力:>0。
1MPa,流量:>0.12m3/h.3.14 工艺水箱液位上限:1.7m,下限:0.4m。
3.15加热水箱液位上限:1.0m,下限:0。
4m。
3。
16加热水箱上限:50℃,下限:45℃。
3。
17顶罐液位:<0.7m。
4、除尘脱硝系统:4。
1 除尘脱硝装置入口烟气温度:>180℃(低于此温度时可投运热风炉)。
4.2 纯氨气压力:>0。
15MPa,控制在 0。
3~0.6MPa。
4。
3 稀释氨气中氨气浓度(体积比)≤5%。
4.4 氨气区域氨气泄漏值:<30mg/m3。
4.5 稀释风机轴承冷却水流量:>0.2m3/h。
4。
6 催化剂层温度下限:180℃,(控制 200±3℃)。
4.7出口烟气氨逃逸:<3mg/Nm3。
4。
8压缩空气:耗量 5m3/min,压力 0.3~0.6MPa。
4.9热风炉温度控制在680±20℃4.10方信立华公司催化剂起活适用烟气温度为 240~280℃,起活时间不低于48h;思博盈公司催化剂起活适用烟气温度为180~280℃,起活时间不低于24h;.5、引风机系统:引风机冷却水流量计水流量>3t/h;引风机轴承振幅<6.3mm/s;引风机轴承温度<70℃;电机轴承温度<90℃;电机定子温度<140℃。
- 1、下载文档前请自行甄别文档内容的完整性,平台不提供额外的编辑、内容补充、找答案等附加服务。
- 2、"仅部分预览"的文档,不可在线预览部分如存在完整性等问题,可反馈申请退款(可完整预览的文档不适用该条件!)。
- 3、如文档侵犯您的权益,请联系客服反馈,我们会尽快为您处理(人工客服工作时间:9:00-18:30)。
1×200MW 石灰石/石膏湿法脱硫工艺参数设计
一. 课程设计的目的
通过课题设计进一步巩固本课程所学的内容,培养学生运用所学理论知识进行湿法烟气脱硫设计的初步能力,使所学的知识系统化。
通过本次设计,应了解设计的内容、方法及步骤,使学生具有调研技术资料,自行确定设计方案,进行设计计算,并绘制设备结构图、编写设计说明书的能力。
二.课程设计课题的内容与要求
(1)根据给定的设计任务及操作条件,查阅相关资料,确定自选参数,进行工艺参数的计算;
(2)根据设计指导书及相关资料,计算系统工艺参数及主要设备设备尺寸;
(3)编写设计说明书;
(4)对设计结果进行分析。
1.已知参数:
(1)校核煤质:
%64=ar C ,%5=ar H ,%6.6=ar O ,%1=ar N ,%4.0=ar S ,%8=ar W ,%16=ar A ,%15=ar V
(2)环境温度:-1℃
(3)除尘器出口排烟温度:135℃
(4)烟气密度(标准状态):1.34)/(3m kg
(5)空气过剩系数:3.1=α
(6)排烟中飞灰占煤中不可燃组分的比例:16%
(7)烟气在锅炉出口前阻力:800Pa
(8)当地大气压力:97.86kPa
(9)空气含水(标准状态下):0.01293)/(3m kg
(10)基准氧含量:6%
(11)按锅炉大气污染物排放标准(GB13271-2011)中二类区标准执行
烟尘浓度排放标准(标准状态下):30)/(3m mg
二氧化硫排放标准(标准状态下):200)
/(3m mg
2.设计内容:
(1)燃煤锅炉排烟量及烟尘和二氧化硫的浓度计算。
(2)采用石灰石石膏湿法烟气脱硫。
(3)计算石灰石消耗量,石膏产量,并进行水平衡的计算。
(4)选择合适的液气比和空塔气速计算吸收塔塔径塔高并对喷淋系统,除雾器,浆液箱,石膏脱水系统进行计算。
(5)风机及电机的选择设计:根据脱硫系统所处理的烟气量,烟气温度,系统总阻力等计算选择风机种类,型号及电动机的种类,型号和功率。
(6)编写设计说明书:设计说明书按设计程序编写,包括方案的确定,设计计算,设备选择和有关设计的简图等内容。
课程设计说明书包括封面,目录,前言,正文,小结及参考文献等部分,文字应简明通顺,内容正确完整,书写工整,装订成册。
(7)图纸要求:脱硫系统图一张(A3)。
系统图应按比例绘制,标出设备管件编号,并附明细表。
前言
我国的能源构成以煤炭为主,其消费量占一次能源总消费量的70%左右,这种局面在今后相当长的时间内不会改变。
火电厂以煤作为主要燃料进行发电,煤
直接燃烧开释出大量SO
2,造成大气环境污染,且随着装机容量的递增,SO
2
的排
放量也在不断增加,加大火电厂SO
2的控制力度就显得非常紧迫和必要。
SO
2
的控
制途径有三个:燃烧前脱硫、燃烧中脱硫、燃烧后脱硫即烟气脱硫(FGD),目前
烟气脱硫被以为是控制SO
2
最行之有效的途径。
目前国内外的烟气脱硫方法种类繁多,主要分为干法(或半干法)和湿法两大类。
湿法脱硫工艺绝大多数采用碱性浆液或溶液作为吸收剂,技术比较成熟,是目前使用最广泛的脱硫技术,根据吸收剂种类的不同又可分为石灰石/石膏法(钙法)、氨法、海水法等。
其中钙法因其成熟的工艺技术,在世界脱硫市场上占有的份额超过80%。
截至2011年底,我国脱硫装机超过6亿千瓦,其中85%以上为湿法烟气脱硫,多存系统稳定性差,脱硫效率波动较大等问题。
火电厂大气污染物排放标准
GB13223-2011将执行200mg/m3的SO
2
排放浓度限值,且新建脱硫装置将不允许设置旁路,对脱硫装置性能与可靠性要求极高。
工艺介绍
本课程设计采用的工艺为石灰石-石膏湿法全烟气脱硫工艺,吸收塔采用单回路喷淋塔工艺,含有氧化空气管道的浆池布置在吸收塔底部,氧化空气空压机(1用1备)安装独立风机房内,用以向吸收塔浆池提供足够的氧气和/或空气,以便亚硫酸钙进一步氧化成硫酸钙,形成石膏。
塔内上部烟气区设置四层喷淋。
4台吸收塔离心式循环浆泵(3运1备)每个泵对应于各自的一层喷淋层。
塔内喷淋层采用FRP管,浆液循环管道采用法兰联结的碳钢衬胶管。
喷嘴采用耐磨性能极佳的进口产品。
吸收塔循环泵将净化浆液输送到喷嘴,通过喷嘴将浆液细密地喷淋到烟气区。
从锅炉来的100%原烟气
中所含的SO
2
通过石灰石浆液的吸收在吸收塔内进行脱硫反应,生成的亚硫酸钙悬浮颗粒通过强制氧化在吸收塔浆池中生成石膏颗粒。
其他同样有害的物质如飞
灰、SO
3
、HCI和HF大部分含量也得到去除。
吸收塔内置两级除雾器,烟气在含液滴量低于100mg/Nm3(干态)。
除雾器的冲洗由程序控制,冲洗方式为脉冲式。
石膏浆液通过石膏排出泵(1用1备)从吸收塔浆液池抽出,输送至至石膏浆液缓冲箱,经过石膏旋流站一级脱水后的底流石膏浆液其含水率约为50%左右,直接送至真空皮带过滤机进行过滤脱水。
溢流含3~5%的细小固体微粒在重力作用下流入滤液箱,最终返回到吸收塔。
旋流器的溢流被输送到废水旋流站进一步分离处理。
石膏被脱水后含水量降到10%以下。
在第二级脱水系统中还对石膏滤饼进行冲洗以去除氯化物,保证成品石膏中氯化物含量低于100ppm,以保证生成石膏板或用作生产水泥填加料(掺合物)优质原料(石膏处理系统共用)。
图1 石灰石/石膏湿法烟气脱硫工艺流程
三.脱硫系统各部分设计计算
1.热值与燃料量的计算
热值计算
%64=ar C ,%5=ar H ,%6.6=ar O ,%1=ar N ,%4.0=ar S ,%8=ar W ,%16=ar A ,%15=ar V
换算成干燥无灰基的元素含量
%2.84=daf C ,%6.6=daf H ,%7.8=daf O ,%5.0=daf S )(1091030339,daf daf daf daf net daf S O H C Q --+=
=34.4)/(kg MJ
换算成低位收到基发热量 100
76,,⨯=net daf net ar Q Q =25.8)/(kg MJ
全厂效率为38%,含硫量为0.4%
燃烧计算: m u el coal H P ⋅⋅=
η600.3 m )/(4.7325800
38.0600.3200h t coal =⋅⋅= 2.标准状况下理论空气量
)7.07.056.5867.1(76.4Y Y Y Y a
O S H C Q -++=' ='a
Q 6.80)/(3kg m 3.标准状况下理论烟气量(空气含湿量为12.933/m g )
Y a Y Y Y Y s
N Q Q W H S C Q 8.079.0016.024.12.11)375.0(867.1+'+++++='。