某金矿在焙烧_氰化浸出时银的物理化学行为
我矿难处理金精矿焙烧氰化浸出试验

我矿难处理金精矿各处理方案对比分析历年来我矿通过外委和自已多次对难选冶金精矿进行焙烧氰化实验,目的是为了探索我矿难处理金精矿焙烧法预处理技术的可行性。
下面就历次实验情况介绍如下。
一、北京有色冶金设计研究总院所做的小型试验试验原料为选矿富集得到的高硫金精矿,化学分析结果如下(此试验为1999年完成):表1 主要化学组成(Au、Ag单位为g/t,其余为%)方案1 固硫、固砷焙烧氰化试验通过添加生石灰熟石灰添加剂,在焙烧过程中,使二氧化硫与砷固定,既保证金的浸出,又达到环保要求。
实验结果见表3 表3 固砷焙烧预处理及氰化试验固砷焙烧氰化的实验分析:通过加入固砷剂焙烧,砷的固定率约为95%,而金的浸出率在80~~85%之间。
由于精矿含砷、硫高,加入石灰量大,反应生成的砷酸钙造成的二次包裹,明显地降低了金的浸出率。
试验结果表明该方案不理想。
方案2 二段焙烧氰化试验:一段焙烧在低温、中性或弱还原性气氛下,使砷以三氧化二砷的形式挥发;二段在高温氧化性气氛下焙烧,使硫化物充分氧化。
保证金的浸出。
实验结果见表4表4 二段焙烧焙砂粒度与金浸出率的关系二段法焙烧氰化实验分析:随着焙砂粒度变细,金的浸出率逐渐提高。
一段的温度为500至550摄氏度,时间为60至90分钟,中性或弱氧化气氛下进行;二段的温度为700摄氏度,时间为120分钟,氧化气氛下进行。
金的浸出率大于92%。
其中砷的脱除率为80%左右,硫的脱除率可达96%,硫化物氧化比较彻底。
方案3 一段焙烧在一定温度下进行氧化焙烧,部分砷挥发,部分砷残留于焙砂中。
实验结果见表5表5 一段焙烧焙砂粒度与金浸出率的关系一段焙烧氰化实验焙浇温度为700摄氏度,时间为180分钟,金的浸出率约为95%,氧化渣含金5g/t左右。
其中砷的脱除率接近70%,硫的脱除率大于98%。
金的浸出率随焙砂的细度的增加有所提高。
对含砷硫化物难处理金矿,多倾向于两段焙烧,以利于砷的脱除,但这并不是绝对的。
含碳金精矿焙烧与金矿石混合氰化浸出的生产实践

要资源 。针对我矿开采生产的含碳 ( 石墨 ) 型金矿石 , 由于此矿石中含碳( 石墨) 或其它形态 的碳物质 , 若不 经过处理直接氰化浸 出, 在氰化浸 出的过程中 , 这种 含碳( 石墨 ) 物质对金氰络合物具有相当强 的吸附活
性, 一部分金转入溶液的氰化过程中 , 另一部分金却
31 磨 矿细 度对 氰化 浸 出的影 响 .
C 一+H0 =O 一 N 2 H +H Nt C
水解所生成 的 H N部分从溶液 中挥发 出来 , C 造
.
成氰化钠的损失 , 而且还会使厂房内的空气受到有毒 磨矿细度越细越有利于氰化浸出 , 但是过磨就会 气体污染。 当向溶液 中加入石灰后 , 溶液呈碱性 , 使反 增大磨机 的能耗 ,同时也把大量的矿物杂质裸露 出 应 向左 , 也就抑制氰化钠的水解 。 其次 , 氧化钙能和部 来, 也会增大氰化钠的消耗 ; 其次 , 焙烧生产出来的焙 分贱金属生成不溶物, 降低 了氰化钠 的消耗。 第三, 氧 砂, 疏松多孔易磨 , 在浓密机浓缩的过程 中, 粒度太细 化钙在 浓 密机浓 缩矿 浆 时还起 着凝 聚剂 的作用 , 而促 会影响矿粒 的沉 降速度 , 矿浆浓度不易控制 , 操作不 进矿 粒 的沉降 。 当, 浓密机就会“ 跑浑” , 影响浸出作业 ; 三 , 第 一定要 3 矿浆浓度 ( . 5 液固比) 对氰化浸 出的影响 控制好金矿石在分级机的溢流细度 , 在与焙砂混合进 矿浆浓度 ( 液固 比) 是浸 出工艺 中的一个重要参 入再磨机时 , 以缩短矿粒在再磨机中的磨矿时间。 数, 如果矿浆浓度波动较大 , 它会间接导致浸出工艺 32 金精 矿焙 烧质 量对 氰化 浸 出的影 响 . 的不稳定而影响浸出率 。矿浆浓度太浓 , 金的氰化浸 金精矿焙烧质量 的好坏决定 了含碳物质焙烧程 出的速度降低, 且往往难 以正常操作 ; 矿浆浓度太稀, 度。一般来说 , 金精矿焙烧质量好 , 焙砂颜色呈红褐 矿浆的体积会增 大, 的氰化浸出的时间不够 , 降 金 会 色 , 明金精矿含碳物质极少 , 说 有利于氰化浸 出; 金精 低浸 出率 , 且氰化钠 的消耗量也会增大 。 矿焙烧 的不好 , 焙砂颜色呈暗红色 , 且略有点发灰黑 36 含 碳 金精 矿 焙 烧量 与金 矿石 处 理 量 的 比例 对 氰 . 色, 说明金精矿含碳物质烧的不透 , 夹杂着碳 , 不利于 化 浸 出的影 响 氰化浸出。 在氰化浸出的过程中, 在脱气槽处 , 可通过 在氰化钠浓度稳定 的情况下 , 控制好含碳金精矿 观察矿浆的颜色来判断。这就取决于金精矿焙烧时, 焙烧量与金矿石处理量的比例 , 也是很关键 的。含碳 定要控 制好 沸腾 炉 的温度 。 金精矿的比例小 ,进人到生产系统中的金属量少 , 有 33 氰化钠浓度对氰化浸出的影响 。 . 利于浸出, 但是劳动生产效率低 , 且造成氰化钠 的浪 在氧化钙浓度保持稳定 的情况下 , 氰化钠浓度过 费; 含碳金精矿 的比例大 , 进人到生产系统中的金属 低, 只有少量的金溶解 , 其氰化浸出率较低 , 随着氰化 量增大, 氰化浸出的时间不够 , 造成金的损失。其次 , 钠浓度的不断升高 , 其浸 出率也在不断升高 , 当氰 但 掌握金矿石 和焙砂的品位变化 , 来调整金矿石的处理 化钠浓度超过某一个范围时 , 其浸出率上升幅度变化 量 。我厂的氰化浸出车间是一个 日 处理矿石 10 生 0 t 不大 , 再不断地提高氰化钠浓度 , 势必造成氰化钠的 产线 , 根据生产实践 , 在和金矿石混合氰化浸 出时, 将 浪费 , 这也增大了生产成本 。 最佳的氰化钠浓度范围 , 含碳金精矿 日焙烧量控制在 2 ~ 8 以内。 0 2t 要根据金矿石和焙砂的矿物组成和含量 , 以及氰化浸 37 控制焙烧收尘系统的放矿量对氰化浸 出的影响 - 出的生产工艺流程和生产工艺结构来确定。 含碳金精矿在焙烧 的过程中, 一部分较粗的焙砂 34 氧化钙浓度对氰化浸出的影响 . 从沸腾炉的放渣 口直接进入搅拌桶 , 另一部分较细的 首先 , 由于金精矿经过焙烧后 , 焙砂 中含有少量
金矿浮选-焙烧-浸出-置换试验研究方案

金矿浮选-焙烧-浸出-置换试验研究方案2009-3-11 11:57:09 中国选矿技术网浏览366 次收藏我来说两句黑龙江乌拉嘎黄金矿业有限责任公司(简称乌拉嘎金矿)选矿厂处理能力为1450t/d,选矿工艺流程为浮选-金精矿氰化-锌粉置换。
随着矿区内东坑矿石供矿量的减少,西坑矿石出矿量的增大,入选矿石性质发生了很大变化,致使浮选回收率、金精矿浸出率逐渐降低。
对西坑矿石进行系统的选矿试验研究,目的是寻求适于该矿石性质的选矿工艺流程,合理利用矿产资源,提高金的总回收率及企业的经济效益。
一、矿石性质西坑矿石为石英黄铁矿型、碳酸盐黄铁矿型和玉髓质石英黄铁矿型。
矿石中有价元素为金,品位为2.86g/t。
主要金属矿物以白铁矿、黄铁矿为主;非金属矿物以石英、长石为主,含一定量的高岭土、云母等黏土矿物。
矿石中金属硫化物嵌布粒度较细,0.037mm以下占64.14%。
白铁矿与黄铁矿关系密切,是金的主要载体矿物。
原矿多元素分析结果见表1,金的粒度测量结果见表2。
*ω(Au),ω(Ag)/10-6金矿物的赋存状态以粒间金为主,占48.42%,裂隙金占1.82%,剩余为包裹金。
其中,脉石包裹金占29.51%,硫化物包裹金占20.25%。
硫化物包裹的金均为次显微金,机械磨矿无法使之解离或裸露。
脉石包裹金也不易完全单体解离。
二、选矿试验(一)浮选工艺流程对比试验验证现场生产工艺原矿浮选-金精矿氰化试验流程及条件见图1,浮选综合条件试验流程见图2,浮选工艺流程对比试验结果见表3。
图1 乌拉嘎金矿现场选矿工艺流程图2 乌拉嘎金矿西坑矿石浮选试验工艺流程磨矿细度-0.074mm占75%,对一次粗选、一次精选、二次扫选浮选生产工艺流程进行的验证试验,获得金精矿产率8.69%、金品位24.87g/t、金浮选回收率75.45%的技术指标,金精矿氰化浸出率71.09%,金的选矿总回收率仅为53.64%,其技术指标与生产指标基本相符。
采用一次粗选、二次精选、三次扫选浮选-中矿氰化工艺流程,金精矿的产率明显降低,品位大幅度提高,金的总回收率提高了4.93%。
含砷金精矿的焙烧和氰化浸出试验及焙砂和浸渣的矿物学研究
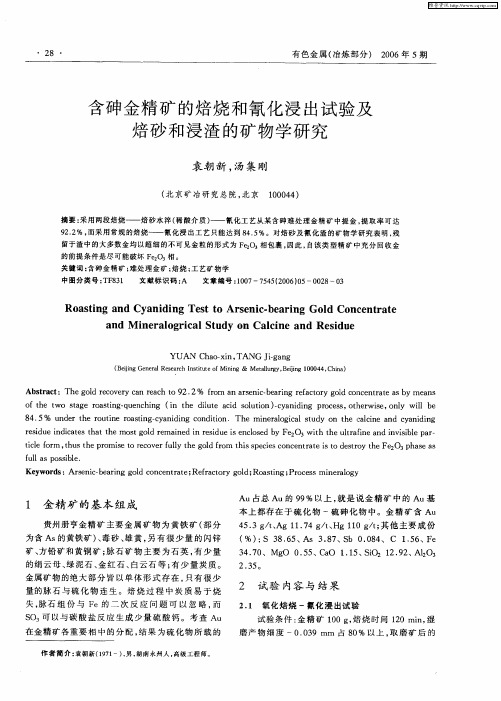
Ab ta t s r c :Th o d r c v r a e c o 9 2% fo a r e i— e rn ea t r o d c n e ta e a y me n eg l e o e y c n r a h t 2. r m n a s n c b a i g r f c o y g l o c n r t sb a s
维普资讯
・
2 ・ 8
有色 金 属 ( 冶炼 部 分) 2 0 0 6年 5期
含砷金精矿 的焙烧 和氰化浸 出试 验及 焙 砂 和 浸 渣 的矿 物学 研 究
袁朝新 , 集刚 汤
( 京矿 冶 研究 总院 ,类 号 : 8 1 TF 3 文献标识码 : A 文 章 编 号 :0 7 5 5 2 0 )5 0 8—0 10 —7 4 (0 6 0 —0 2 3
Ro s i nd Cy ni i s o Ar e c be r ng Go d Co c nt a e a tng a a d ng Te t t s ni — a i l n e r t a d M i e a o r c lS u y o l i e a d Re i u n n r l g i a t d n Ca c n n s d e
( ) S 3 .5 A . 7 S .8 、 C .6 e % : 8 6 、 s 38 、 b 00 4 1 5 、F 3 . 0 Mg . 5 a .5 So 2 9 、 1 47 、 O 0 5 、C o 1 1 、 i 2 1 .2 A 2 03
o h w tg osigq e c ig (n te dlt ai slt n 一y ndn rcs, tewi , ny wi b fte t o sae rat —u n hn i h i e c oui )ca iig po es oh r s o l n u d o e l e l
提高金、银、铜回收率的焙烧—氰化试验研究

试 验 发现 , 金精 矿 中加 人一 定 量 的碳 酸 钠进 在 行焙烧 , 可大 大地提 高 A 、 、 u的 回收率 , 其是 u c 尤 银的 回收 率可 提 高 3 % 以 上 。经 焙烧 后 的 焙 砂呈 0
号 . 60 t 2 4 0
维普资讯
第2 3卷
20 年 02
第 5期 9 .5 , 的 浸 出 率 为 3 .6 铜 的 浸 出 率 为 72 % 银 09 %,
金精矿
7 .5 15 %。这与 目前 国内 外 常 规 焙 烧一 氰 化 浸 出工 艺的指标 相 一致。
搅拌均 匀 , 以保 证 焙烧完全 。 焙烧渣 冷 却 后 , 用 2 硫 酸 浸 铜 , 取 温 度 采 % 浸 g% , 0 时间 2 , 拌 , 时 铜 以硫 酸 铜 进 人 溶 液 , h搅 此 过 滤 , 将浸渣 洗 至 中性 。 并 将浸 渣烘 干后 , 以下 氰化 条 件在 电动 搅 拌浸 按 出槽 内进行 氰化 浸 出。氰 化 钠浓 度 1% , 固质 量 5 o液 比 2 1p l ( : ,H O 用碳酸 钠调 节 ) 浸 出时 间 3 h , 6。 将氰 化浸 渣经 过滤 、 洗涤 、 烘干 、 取样 , 后送 交 然 分 析室 测 定 A 、 c u A u含 量 , 别计 算 金 、 、 的 分 银 铜
低, 为此, 采用焙烧一氰化法综台回收金 、 、 银 铜c 3 试 验 方 法
将金精 矿烘 干 后 , 按一 定质量 比加入碳 酸钠 , 搅 匀后 , 于瓷舟 上 , 人 马弗 炉 内 , 置 放 以低温 逐 渐 升 至
高 温进行 焙烧 , 烧 时半 开炉 门 自然通 人 空气 , 分 焙 充
广西某金矿石氰化浸出试验研究

该 工 艺具
1 材 料 与 方 法
1 1 试 验 原 料 .
有 工 艺成 熟 、操 作 简 单 且 氰 化 废 水 的处 理 易 达 到 排 放 标 准 等 特点 。对 于 易 处 理 金 矿 石 , 可 首 选 氰 化 法 进 行 提 金
;
试 验 用 的金 矿 石 取 自广 西 平 南 金 矿 山
,
.
垂
05 . 1 15 . 2 25
.
收 稿 日期 :2 0 - 1 - 0 09 1 9
誓 冶 学 硕( 4 , 从 , 南 广 院 …究 主 壮 ) 差研 生 要 事 宁 蒜 1- 9. 广 人 大 用 究 金 耋 士 8 )女(族物 西 喜 , 西 学 研
验 结 果 见 图 1 。
O 0
,
因 此 该 矿
。
采用批次法进行 浸出试验 ,主要考察 了磨 矿细度
氰 用 量 、矿浆 浓 度 、浸 出时 间 和 焙 烧 预 处 理 等 对 金 浸 出
、
蠢- 蓁 . ●
9 o
J
8 8 9 9 0 5 0 5 10 0
,
效果 体 的影 响 。利 用 搅 拌 浸 出 试 验 机 进 行 金 的 氰 化 浸 出 矗
中 图分 类 号 :T 0 ・ 1 F 8 3 2 文 献标 识 码 :A 文章 编 号
: l l一 85 O ( 。l 67 5 2 O) O 3一 。 4一 。2 03
0 引 言
氰 化 浸 出 工艺 是 提 金 工 业 普 遍 采 用 的 方 法
,
可 浸 性 ,为 该 矿 石 的开 发 利 用 提 供 技术 依 据
。
磨矿粒度对金 浸 出率影 响较 大
云南某氧化金矿石氰化浸出渣对金和银氰络合物的吸附

卜 等 金 属 氰 络 合 物 , 金 在
氰 络合物 沉积 之 前 就 发 生 了沉 积 , 助 于稳 定 溶 液 有
中的金氰 络合 物 , 制 劫金 现 象 。 在 自由氰 根 离子 抑
不 足 的浸 出条件 下 , 铁矿 也 强 烈 地 产 生 “ 金 ” 黄 劫 现 象 。C rs l 研 究 发现 , hymui s 由于 吸 附 的 可逆 性 , 附 吸 在黄 铁矿 上 的金 易 于 回收 , 过 Hasn和 B c ma 不 ue uk n
收 稿 日期 :0 5 1 7 2 0 —0 —2 基 金 项 目 : 南 省 中青 年 学 术 技 术 带 头 人 后 备 人 才 资 助 项 目 云
(0 3c4 2 0 r1 )
1 矿 石 性 质
试验 所 用 的含 金氧 化矿 石 由云南 某 资源 公 司提
作 者 简 介 : 琦 (90 , 。 南南 阳市人 . 土 。 要从 事难 崔毅 18 一)女 河 博 主
28 . %和 1 5 . %。结 果 显 示 , 黄铁 矿 精 矿 弱 劫 金 , 浮
物全 部 消耗完 , 铜 矿 将 与 活性 炭 竞 争 并 吸 附掉 矿 黄
浆 中 的大部 分金 , 而 A ( N) 一 F ( N)4 z 然 g C 2 , e C 6一, n ( N) 一 C ( N) C 4 和 uC
.
选给料温和劫金。纽芒特黄金公司应用硫代硫酸盐
技术 从低 品位 和 难 处 理 硫 化 物 劫金 矿 石 中提 取 金 , 取得 了很 好 的 试 验 指 标 。 P ipA.cmi 等 采 用 hl Sh t i z 硫代硫 酸 盐浸 出经 高 压 处 理 后 的炭 质 矿样 , 管 原 不
高砷难处理金精矿焙烧——氰化浸出工艺研究

了以下变化: 1 砷黄铁矿 、 () 黄铁矿等载金矿物中的
硫和砷在焙烧过程 中升华 , 形成布满微孔的磁铁矿
和赤铁矿颗粒 , 有利于金与氰 化物接触 。( ) 2 在焙
烧过程中, 亚微细金粒聚结在一起 , 出大的金表 暴露
面积。( ) 3 有机炭 等劫金物质被烧 掉 , 消除了它们
的劫金效应 。( ) 和砷 升华后 , 4硫 不会在金粒表 面
高砷难 处理 金精 矿焙 烧一 氰 化 浸 出工 艺 研 究
伍赠玲
( 金矿 业集 团股份 有 限公司矿 冶设计 研 究院 ,福建 紫 上杭 34 0 ) 6 20
摘 妻: 对甘肃某高砷 高硫难 处理金精 矿进行 了氧化焙烧预处理一氰化浸 出试 验研 究 , 取得 了砷 、 脱除率分别 硫 达 9 .3 、9 8 % , 的浸 出率达 8 . 3 的较好技术指标 , 为有效利用高砷微 细浸 染型金矿 资源提供参考。 26% 9 .1 金 52% 可 关键词 : 金精矿 ; 焙烧 ; 化浸出 氰 中图分类号 :F 0 . ; F 3 文献标识码 : 文章编号 : 0 - 3 (0 6 0 -0 60 T 83 2 T 8 1 A 1 06 2 2 0 )6 1 - 0 5 0 3
() 1 () 2
As
T S
SO2 i
O3 F 2 e O3
C u
7. O 6 1. 2 4 .8 2 2 1 .6 O 04 2 7 9 2 O. l 2 1 . 4
在氧气不足和 40C 5 o 左右 的条件下 , 砷黄铁矿 中的砷以硫化物或氧化物的形式转入到气相中:
的结构构造 , 使其疏松多孔 。难处理金矿焙烧时, 随 着温度、 气氛 、 矿物组合 的不 同, 可能 发生下列化学
金精矿的焙烧条件对金、银提取的影响研究
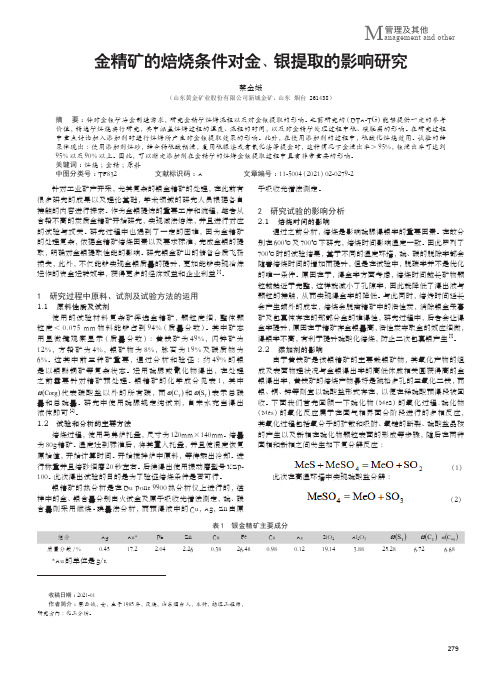
参考文献
[1] 王瑞祥,刘茶香,杨裕东,袁远亮,周杰,王艳阳,徐志峰 . 复杂金矿物氧化 焙烧 - 硫酸浸出 - 氰化法回收金银模拟计算 [J]. 有色金属(冶炼部分),2020 (07):69-75.
[2] 曹攀,张霜华,郑雅杰 . 难冶金精矿烟尘中铁砷碳的脱除对氰化浸金的影响 [J]. 中国有色金属学报,2020,30(05):1142-1152.
( 3) 逸出 SO3 和外部 MeO 反应,产生二次硫酸盐 MeSO4。
只有满足硫酸化焙烧条件。
( 4)
( 5) 二次硫酸盐(MeSO :)才能稳定地存在,而式(3)也只有在 较高的温度 so2 和 o。浓度(分压)下且有催化剂(如 FezOs)存在 的条件下,才能有足够的反应速度,而在黄铁矿的串联的 4 个氧 化步骤 :
1 研究过程中原料、试剂及试验方法的运用 1.1 原料性质及试剂
使 用 的 试 验 材 料 复 杂 矿 浮 选 金 精 矿,颗 粒 度 细,整 体 颗 粒 度 < 0.075 mm 物 料 能 够 占 到 94%( 质 量 分 数 )。其 中 矿 态 用 显 微 镜 观 察 显 示( 质 量 分 数 ):黄 铁 矿 为 49%,闪 锌 矿 为 12%,方 铅 矿 为 4%,银 矿 物 为 8%,脉 石 为 19% 及 碳 质 物 为 6%。这 其 中 前 三 种 矿 重 要,通 过 分 析 和 验 证 :约 49% 的 银 是 以 银 黝 铜 矿 等 复 杂 状 态。运 用 硫 脲 或 氰 化 物 浸 出,在 处 理 之 前 需 要 针 对 精 矿 预 处 理。银 精 矿 的 化 学 成 分 见 表 1,其 中
某含金银硫精矿焙烧—氰化浸出试验研究

表 1 硫精矿化学成分分析结果
成分 w/% 成分 w/%
S 47.10
As 0.48
Aua 2.46
Cu 0.09
Agb 40.60
Fe 44.45
C 0.59 SiO2 4.51
F 0.086 MgO 0.25
Pb 0.12 CaO 0.24
Zn 0.031
aw(Au)/(g·t-1),bw(Ag)/(g·t-1)。
3∶1,氰化钠用量 4kg/t,搅拌速度 1380r/min。试验 结果见表 2。
表 2 硫精矿直接氰浸出试验结果
序号 1 2 3
平均
金浸出率 /% 39.12 39.46 38.99 39.19
银浸出率 /% 19.21 20.02 20.78 20.00
收稿日期:2017-12-24;修回日期:2018-03-15 作者简介:尹常文(1991—),男,云南腾冲人,助理工程师,从事有色金属及稀贵金属选矿工作;云南省大理州鹤庆县北衙村,鹤庆北衙矿业有限公
高,在焙烧温度 600℃,焙烧时间 3h,石灰调 pH值至 11,搅拌速度 1380r/min,磨矿细度 -0.043mm
占 92.48%,氰化钠用量 3kg/t,矿浆液固比 3∶1,浸出时间 36h的最佳条件下,金浸出率可达
81.41%,银浸出率 46.77%,较直接氰化浸出分别提高 42.22百分点和 26.77百分点。
焙烧—氰化浸出试验流程见图 1。
图 1 焙烧—氰化浸出试验流程
2.2.2 焙烧条件试验
在高温焙烧环境中,硫精矿能与氧气反应生成三
氧化二铁和二氧化硫气体,其中焙烧温度和焙烧时间
是影响反应进程的 2个重要因素。
2.2.2.1 焙烧温度
焙烧-酸浸-氰化法从复杂金精矿中回收金银铜

焙烧-酸浸-氰化法从复杂金精矿中回收金银铜吴在玖【摘要】采用焙烧-酸浸-氰化工艺综合回收复杂金精矿中的金、银、铜.结果表明,焙烧温度、焙烧时间、焙烧添加剂种类和用量对金、银、铜浸出率影响显著.实验确定了较优工艺条件为:焙烧添加剂NaOH用量为6%,温度630℃,焙烧时间3 h,硫酸浓度1 mol/L,酸浸液固体积质量比5∶1,酸浸温度50℃,酸浸4 h,氰化纳浓度3‰,氰化浸出液固体积质量比5∶1,常温氰化72 h.在上述条件下,金、银、铜浸出率分别达到93.53%、75.37%、94.23%.%Gold, silver and copper were extracted from complex gold concentrate by roasting-acidic leaching-cyanidation process. The experimental results show that the roasting temperature, time, additive and its dosage have great influenceon the leaching of gold, silver and copper. The optimal conditions were further determined as follows: NaOH dosage of 6 %(ω), roasting temperature of 630 °C, roasting time of 3 h, sulfuric acid concentration of 1 mol/L, liquid to solid rat io of 5∶1 in acidic leach, leaching temperature of 50 °C, leaching time of 4 h, sodium cyanide concentration of 3 ‰, liquid to solid ratio of 5∶1 in cyanidation, room temperature and cyanidation timeof 72 h. Under above-mentioned conditions, the leaching rate of gold, silver and copper achieved at 93.53%, 75.37%and 94.23%respectively.【期刊名称】《有色金属科学与工程》【年(卷),期】2013(000)002【总页数】5页(P25-29)【关键词】复杂金精矿;添加剂;焙烧;酸浸;氰化浸出【作者】吴在玖【作者单位】【正文语种】中文【中图分类】TF803.2随着黄金价格的高涨,世界黄金产量不断增长,能够直接氰化利用的金矿资源日益匮乏,复杂金精矿成为黄金冶炼行业的重要原料[1-2],目前复杂金精矿预处理主要有:热压氧化、生物氧化、焙烧氧化3种基本工艺.生物氧化法[3],投资小、能耗低、环保优,但适应性差,菌种对矿物成分依赖性高;热压氧化法[4-5],环境友好、氧化充分、反应周期短、金回收率高,但对设备要求高,安全系数低,生产规模有限;焙烧氧化法[6],是一种传统的预处理方法,工艺成熟,对矿物性质适应性强,尤其是处理含碳、含硫、含铜复杂金精矿优势明显.国内外学者对复杂金精矿氧化焙烧预处理工艺进行了广泛研究[7-15],取得了丰硕的成果,但复杂金精矿中银的氰化浸出率仍然偏低.某黄金冶炼厂采用氧化焙烧-酸浸分铜-氰化工艺处理复杂金精矿,银氰化浸出率偏低(≤45%),本试验在该厂现有工艺基础上,研究了添加剂种类和用量、焙烧温度、焙烧时间等因素对金、银、铜浸出率的影响,取得了良好的结果.1 试验原料与方法1.1 试验原料实验原料为国内某黄金冶炼厂复杂金精矿,平均粒度≤74μm占80.88%,矿物化学成分如表1所示,化学物相分析如表2所示.金主要以黄铁矿包裹形式存在,占金总量的88.62%,另有少量金以自然金和硅酸盐包裹金;银主要以自然银、硫化银和硅酸盐中银等形式存在,分别占银总量的26.64%、22.67%、47.58%;铜主要以氧化铜和硫化铜形式存在,分别占铜总量的4.27%和93.71%.试验所用主要试剂浓硫酸、NaCN、NaCO3、NaOH、Na2SO4、Na2SO3、CaO 和 Na2S 均为分析纯,蒸馏水自制.1.2 试验方法1.2.1 氧化焙烧每次称取复杂金精矿100 g,装入不锈钢盆内,根据试验要求加入相应种类和数量的添加剂,加入蒸馏水搅匀,在电炉上蒸干,待马弗炉达到预定实验温度后,置于马弗炉中焙烧,焙烧结束后,将焙砂从马弗炉中取出置于空气中冷却.表1 试样化学成分分析/%?表2 试样化学物相分析/%注:“/”表示未统计该数据.?1.2.2 酸浸分铜冷却后的焙砂用MZ100型震动磨矿机磨矿30 s,然后装入1000 mL烧杯中,按照液固体积质量比(指溶液每毫升液体中所含固体质量的克数,下同)5∶1加入1 moL/L的稀硫酸溶液,用DF-1型水浴锅控制浸出温度50℃,机械搅拌浸出4 h,酸浸完成后用2YI-30型号真空泵过滤分离,浸出渣用100 mL与浸出剂同浓度的稀硫酸溶液洗涤,洗渣在电热鼓风干燥箱中干燥.1.2.3 氰化浸出先用碳酸钠调整矿浆pH值为9.5~10.5,再按照液固体积质量比5∶1,加入氰化钠至浓度为3‰,用空气泵供氧,磁粒子搅拌,常温浸出时间72 h.氰化浸出结束后,用3‰氰化钠溶液洗涤抽滤,滤渣干燥称重送样分析,金、银、铜的浸出率以渣中金、银、铜含量计算.1.3 试验原理1.3.1 氧化焙烧原理复杂金精矿预处理采用一段焙烧氧化法.随着焙烧氧化的进行[16],金精矿中的硫化物被氧化,破坏了对金、银的包裹形态,使金、银暴露充分,然后通过酸浸除去有害杂质金属,氰化提金、银.金精矿在焙烧过程中,黄铁矿、闪锌矿、黄铜矿比较容易分解,而方铅矿比较难分解.在 300~500℃时,氧化焙烧反应有:如图1所示,焙烧温度>600℃时,铜硫化矿开始氧化分解,铜硫化物被氧化为氧化物或硫酸盐,闪锌矿和部分方铅矿也开始分解,反应式如下:1.3.2 加入添加剂焙烧原理添加剂的加入,一方面是作为复杂金精矿氧化焙烧的膨松剂,使复杂金精矿在焙烧过程中有良好的透气性,利于焙烧氧化.另一方面与复杂金精矿中的SiO2等成分反应,生成硅酸钠盐2NaO·SiO2等物质,抑制了硅等成分与铜、金、银等有价金属化合物之间的作用,减少了不利于浸出回收物质的产生.本试验采用的添加剂有 Na2CO3、NaOH、 Na2SO4、Na2SO3、CaO 和 Na2S,焙烧反应如下:2 实验结果与分析2.1 添加剂的遴选分别选取 Na2CO3、NaOH、Na2SO4、Na2SO3、Na2S、CaO作为添加剂,添加剂用量为复杂金精矿质量的6%,焙烧温度650℃,焙烧时间3 h,然后进行酸浸分铜-氰化浸出,考察添加剂种类对金、银、铜浸出率的影响,结果见表3.表3 添加剂对浸出率的影响?由表3可知,未加入添加剂时,金、银的浸出率很低,尤其是银的浸出率仅有16.23%.加入添加剂后,金、银浸出率均有提高,而铜的浸出率表现不一.以NaOH作为添加剂时,金、银、铜的浸出率均为最高,分别达到91.58%、72.26%和95.7%,而所用添加剂中NaOH碱性最强,说明金、银、铜的浸出率与添加剂碱性强弱呈正相关.因此后续试验选用NaOH作为焙烧添加剂.2.2 焙烧温度对金、银、铜浸出率的影响在100 g复杂金精矿,NaOH用量6%,焙烧时间3 h条件下,焙烧温度分别控制在550℃、600℃、610℃、620℃、630℃、640℃、650℃、700℃,考察焙烧温度对金、银、铜浸出率的影响,结果如图2所示.由图2可以看出,氧化焙烧温度低于600℃或高于650℃时,复杂金精矿中金、银、铜的浸出率均不理想,温度太低,复杂金精矿中的硫脱除率低,不利于氰化浸出提金、银工序.温度过高,硫脱除率高,但复杂金精矿易出现烧结现象,造成金、银、铜的二次包裹,不利于金、银、铜的浸出.当焙烧温度区间为600~650℃时,金、银、铜的浸出率只有小幅度的波动,当焙烧温度为630℃时,金、银、铜浸出率分别为93.53%、71.37%、94.42%,焙烧效果好.综合比较,氧化焙烧温度控制在630±5℃.2.3 焙烧时间对金、银、铜浸出率的影响NaOH用量 6%,焙烧温度630℃,控制不同的焙烧时间,考察焙烧时间对金、银、铜浸出率的影响.结果如图3所示.图3可知,焙烧时间对于复杂金精矿金、银的浸出率影响非常显著.在焙烧时间较短时(≤2 h),金、银的浸出率均较低,然后随着焙烧时间的延长,金、银的浸出率快速提高,金、银的浸出率在焙烧时间为3 h时达到最高.焙烧时间对铜的浸出率影响不大,在试验条件下均保持在90%以上,在焙烧时间为4 h时,铜浸出率达到最高为94.80%.焙烧时间超过4 h后,金、银的浸出率急剧下降.采用焙烧预处理的目的在于,使复杂金精矿中的FeS2转变为Fe2O3等铁氧化物,破坏其对金、银等的包裹,同时使铜的硫化物转变为氧化物、硫酸盐等易浸出的物相,从而提高其浸出率,硫化物氧化反应十分容易发生,在本试验条件下可以在3 h之内完成,继续延长焙烧时间,对硫化矿的氧化率没有帮助,反而导致铁酸盐、硅酸盐等物质的生成,对金、银、铜等有价成分形成新的包裹,降低了金、银的浸出率.由此可知焙烧时间并非越长越好,综合考虑,选择氧化焙烧时间为3 h更加适宜. 2.4 添加剂用量对金、银、铜浸出率的影响在焙烧温度630℃,焙烧时间3 h条件下,考察添加剂用量对金、银、铜浸出率的影响,试验结果如图4所示.图4表明,随着NaOH用量的增大,复杂金精矿中金、银、铜的浸出率逐渐提高,然后趋于稳定.在NaOH用量达到2%以后,金、铜的浸出率升高的速度趋于平缓.银浸出率对于NaOH加入量相对敏感,在NaOH用量未达到4%以前,浸出率随NaOH用量的增大快速升高,而后基本维持不变.由于金的价格比银和铜高很多,因此选择NaOH加入量为6%为宜.3 结论(1)研究表明,用一段氧化焙烧法预处理复杂金精矿时,焙烧温度,焙烧时间,添加剂的种类和用量,对于焙烧效果的影响非常显著,平衡这4个因素的关系,对于提高金、银、铜的浸出率至关重要.(2)选用NaOH作为焙烧添加剂可以有效提高金、银、铜的浸出率,在NaOH用量6%、焙烧温度630℃、焙烧时间3 h,50℃酸浸4 h,硫酸浓度1 mol/L,酸浸液固体积质量比5∶1,常温氰化72 h,氰化纳浓度3‰,氰化浸出液固体积质量比5∶1条件下,金、银、铜浸出率分别为93.53%、75.37%、94.23%.其中银浸出率相对该黄金冶炼厂原工艺提高了近25%,同时铜和金的浸出率也较优. (3)复杂金精矿综合回收过程中银的浸出率始终较低,其原因有待后续进一步探讨.参考文献:[1]吴荣庆,张燕如,张安宁.我国黄金矿产资源特点及循环经济发展现状与趋势[J].中国金属通报,2008(13):32-34.[2]康增奎.我国难处理金矿资源的开发的现状与问题的研究[J].资源与产业,2009,11(6):60-63.[3]崔永霞,沈艳.难处理金矿石提炼技术研究进展[J].黄金科学技术,2007,15(3):53-57.[4]杨洪英,佟琳琳,殷书岩.湖南某难处理金矿的加压预氧化——氰化浸金试验研究[J].东北大学报:自然科学版,2007,28(9):1305-1308.[5]王瑞祥,刘建华,夏李斌.从高酸浸出钴渣中回收金银的实验研究[J].黄金,2007,28(5):32-35.[6]薛光,任文生.我国金精矿焙烧——氰化浸出工艺的发展[J].中国有色金属,2007,6(3):44-50.[7]崔日成,杨洪英,张谷平,等.毒砂型高砷金精矿的细菌氧化[J].化工学报,2008,59(12):3090-3094.[8]薛光,李峰,焦国华,等.加压氧化——氰化浸出法提取金银的研究[J].贵金属,2003,6(3):19-21.[9]Whitlock J A.Biooxidation of refractory gold ores(the Gobiotics process)[J].Biomining:Theory,Microbes and Industrial Process,1988,11(6):118-125.[10]Fraser K S,Walton R H,Wells A J.Processing of refractory goldore[J].Minerals engineering,1991(4):1029-1041.[11]张福元,张玉华.氰渣综合利用提取金银的试验研究[J].稀有金属材料与工程,2007(s3):335-3381.[12]袁朝新,汤集刚.含砷金精矿的焙烧和氰化浸出试验及焙砂和浸渣的矿物学研究[J].有色金属:冶炼部分,2006(5):28-301.[13]薛光.加氢氧化钠提高焙烧-氰化法银浸出率的试验研究[J].有色冶炼,2002(5):19-21.[14]刘汉钊.难处理金矿石难浸的原因及预处理方法[J].黄金,1997(9):44-48.[15]Deschenes G,Xia C,Fulton M,et al.Evaluation of leaching parameters fora refractory gold ore containing aurostibite and antimony minerals:Part I-Central zone[J].Minerals Engineering,2009,22(9/10):799-808.[16]薛光,任文生,薛元昕.金银湿法冶金及分析测试方法[M].北京:科学出版社,2009.。
含砷金精矿焙烧-氰化浸取金、银的试验方案

含砷金精矿焙烧-氰化浸取金、银的试验方案2010-1-21 17:39:55 中国选矿技术网浏览136 次收藏我来说两句在金精矿焙烧-氰化工艺中,砷是影响金、银氰化浸出率的主要因素。
为此,在焙烧-氰化浸取金、银工艺中对砷的含量要求比较严格,通常控制金精矿中砷的含量在0.1%以下,随着砷含量的增加,金、银的氰化浸出率逐渐降低。
笔者曾对提高含砷金精矿焙烧-氰化浸取工艺金、银、铜回收率进行了研究。
本文在此基础上研究了在焙烧金精矿中加入硫酸钠,借以提高含砷金精矿焙烧-氰化浸出工艺中金、银浸出率。
试验结果表明,对砷质量分数为0.45%金精矿,在焙烧时加入矿样量4%~5%的硫酸钠,可使金、银的氰化浸出率比原工艺方法分别提高5.0%和40%以上。
这不但充分利用了国家资源、拓宽了原料来源,而且提高了企业的经济效益和社会效益,具有推广价值。
一、矿样性质本试验采用的矿样由某黄金矿山提供。
矿物成分主要为黄铁矿、砷黄铁矿、黄铜矿、方铅矿、闪锌矿等硫化矿物,金、银则以细微粒状态被硫化物包裹。
经分析测定,矿样的主要化学成分见表1。
表1 矿样的化学成分/%*(Au)、(Ag)/10-6从表1可见,矿样中除含有较高的Au、Ag外,Cu、Pb、As、S的含量均比较高。
该矿样属于含砷、铜难处理金精矿类型。
采用现行的焙烧-氰化浸出工艺,难以取得较高的金、银氰化浸出率。
二、直接氰化浸出试验采用直接氰化浸出工艺对该矿样进行试验。
试验浸出条件:NaCN质量分数0.5%,液固比2:1,浸出液pH>11(石灰调节),浸出时间为42h。
浸出试验结果见表2。
表2 直接氰化浸出试验从表2可见,在常规条件下进行氰化浸出,金、银的氰化浸出率很低,尤其银的氰化浸出率更低,仅有7.2%。
主要原因是铜、砷的含量较高,影响了金、银的氰化浸出,另外,大量硫化物的存在,对细微粒的金、银包裹,使金、银的氰化浸出反应难以进行。
三、焙烧-氰化浸出试验采用焙烧-氰化浸出工艺对该矿样进行浸出试验。
新疆某难选金矿浮选-焙烧-氰化选矿工艺的试验研究
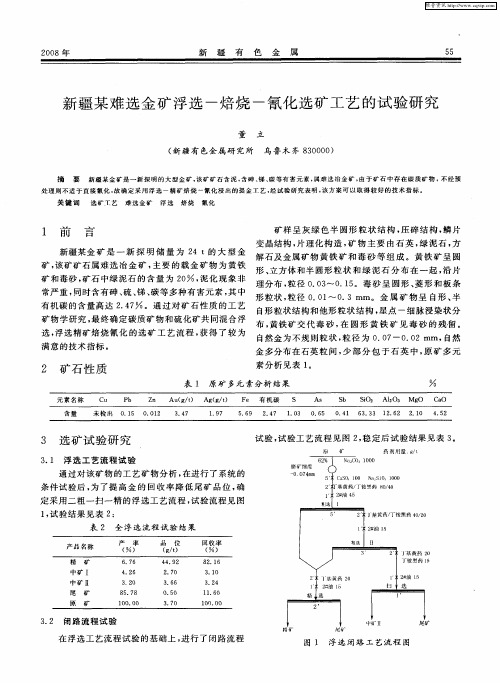
定 采用 二粗一 扫一 精 的浮选 工艺 流程 , 验流程 见 图 试
1 试验 结果 见表 2 , :
表 2 全 浮 选 流 程 试 验 结 果
3 2 闭 路 流 程 试 验 .
在 浮 选 工 艺 流 程 试 验 的 基 础 上 , 行 了 闭 路 流 程 进
图 1 浮 选 闭 路 工 艺 流 程 图
素分析 见表 1 。
2 矿 石 性 质
表 1 原矿 多元 素分析 结果
%
3 选 矿试 验 研 究
3 1 浮 选 工 艺 流 程 试 验 .
试验 , 试验 工艺 流程 见图 2 稳 定 后试 验 结果见 表 3 , 。
原 矿 药 剂 用量 : / gt
通 过对 该矿 物 的工 艺 矿物分 析 , 在进行 了系统 的 条件试 验后 , 了提 高金 的 回收 率 降低 尾 矿 品位 , 为 确
解离 , 且呈 低价 氧化物 挥发脱 除 , 使包裹 金充分 表露 , 便 于氰 化 浸取 , 其焙烧 效果 的好坏 将直 接影 响精矿浸
出率 , 表 4 见 。
试 验 室采 用 马 弗 炉 焙 烧 , 一 段 焙 烧 温 度 5 0 第 5
℃ , 烧 时间 9 n 第 二 段 焙 烧 温 度 6 0℃ , 烧 焙 0mi , 5 焙 时 间 9 i , 烧指标 见表 5 0r n 焙 a 。
处 理 则 不 适 于 直 接 氰化 . 确 定 采 用 浮 选 一 精 矿 焙 烧 ~ 氰化 浸 m的 提 金 工 艺 , 试 验研 究 表 明 , 方 案 可 以 取 得 较 好 的 技 术 指 标 。 故 经 该
关键 词 选矿T艺
难选金矿
浮选
焙烧
氰化
山东某金矿氰化浸出过程中影响因素的研究

浓 度 测 定 结 果
预 处 理 时 间 / c h N 浓度 / mg.L
一
-
孑 雀 石 、 铜 矿 等存 在 , 矿 物 量 占 1 3 ; L 斑 其 .7
有 害元 素 铅 主要 呈 方 铅矿 产 出 , 量 为铅 矾 ; 少
有 害 元 素 锌 主要 呈 闪锌 矿 状 态存 在 , 有 个 亦 别 的 氧化 成 了菱锌 矿 。
Ci l
2 ̄
Fe +
O .OO O. 26 3. 51 O. 96 1 43 .
2
zn2 +
O .O6 8 O.3 6 O .O2 2 O .O1 7 O. O96
1. 3 4.1 4.1
O .12 1 .2 07 13 8 8. 12 O 9. 17 2 5.
擀 惜
选褂
山东 某 金 矿 氰 化 浸 出 过 程 中影 响 因素 的研 究
捧 锵
谷 晋 川 1 , 亚川 , 允 湘 ,刘 2 张ห้องสมุดไป่ตู้
( . 川 大 学 化 工 学 院 , 川 成 都 1四 四 606) 1 0 5
(. 2 中国地 质 科 学 院成 都 矿产 综 合 利用 研 究所 , 四川 成 都 6 0 4 ) 1 0 1
复杂金精矿焙烧-氰化浸取金银的研究与生产实践

砷的含量 , 高铜矿尽力提高 S的含量, 在生产实践中
也得 到了证 实 。
2 结果 与讨论
收稿 日期  ̄0 9—0 20 9—1 5
3 焙烧 一 氰化浸取金银 的技术改进
作者简介 : 王洪凯( 9 8 )男 , 16 一 , 本科学历 , 工程师, 从事贵金属冶金工作 。
第 3期
对 生产 调试 期 含铜不 同的酸 浸渣 进行 金银 浸 出 试 验 , 验 结果 见表 2, 试 可见 酸浸 渣含 铜达 到 0 5g t . /
除 影 响 , 高 A 、 g的浸 出率 。 提 uA
生 产 中对 酸浸 渣 洗 涤 工 艺进 行 了改 造 , 由二 段
以上时 , 的 浸 出 率下 降 明 显 , 化 钠 消 耗 成 倍 增 银 氰
表 1 。
表 1 生产投入原料成份表 ( ) %
金精矿含砷( 0 2 %) . 82 金浸 出率( 9 . %) 银浸出率( ) % O6 .
9 3 7.
金精矿含碳 ( %) 0 3 0 5 0 7 0 9 11 15 2 0 . . . . . . .
12 .
本实验考察了金精矿中铜 、 碳和砷等元素对 硫、 氰化过程的影响 , 并依据实验结果改进了实 际生产 时金精 矿焙烧 一氰化 浸取 工艺 , 取得 了较好效 果 。
综合 表 2一表 5实验 数 据 , 以得 出 : 炉 物料 可 入
含硫越高 , 硫酸化氛 围越好 , 铜的浸出率越高, 金银 的浸出率也越高 。碳的含量不应超过 1 , j % 特别 是有机碳的含量 , 含量越低铜的浸 出率越高 。有机
表 2 酸浸渣含铜对 金银浸 出率的影响
U 日 吾 U 某公 司 10 td全 泥 氰 化 工 艺 流 程 , 化 尾 渣 0 / 氰
沸腾焙烧烟灰浸出金、银、铜的研究

2 0 1 4年 第 3 期
有色金属 ( 冶炼部分) ( h t t p : / / y s y 1 . b g r i mm. c n )
・ 2 5 ・
d o i :1 0 . 3 9 6 9 / j . i s s n . 1 0 0 7 — 7 5 4 5 . 2 0 1 4 . 0 3 . 0 0 8
沸 腾 焙 烧 烟 灰 浸 出金 、 银、 铜 的研 究
曾斌 , 赖子球 , 王瑞祥 , 余 攀
( 1 .江西理 工 大 学 冶 金 与化 学工程 学 院 , 江 西赣 州 3 4 1 0 0 0 ;
2 .紫金矿 业 集 团股份 有 限公 司 , 福 建上 杭 3 6 4 2 1 4 )
St u dy o n Le a c hi ng o f Go l d - - S i l v e r - Co p pe r f r o m Fl u i di z e d - - b e d Ro a s t i ng As h
ZEN G Bi n ,LA I Zi — q i u ,W A N G Ru i — x i a n g ,Y U Pa n
金矿石预处理工艺之焙烧氧化工艺_概述说明以及解释

金矿石预处理工艺之焙烧氧化工艺概述说明以及解释1. 引言1.1 概述在金矿石的预处理过程中,焙烧氧化工艺被广泛应用。
这种工艺通过加热金矿石样品,在高温下使其发生氧化反应,从而改善金矿的浸出性能和提高提取率。
本文旨在介绍焙烧氧化工艺的概念、原理及其在金矿预处理中的应用情况。
1.2 文章结构文章分为五个主要部分。
首先是引言,其中包括概述、文章结构和目的三个小节。
接下来是对焙烧氧化工艺的概念和原理进行阐述,包括定义、目标和原理以及氧化反应的机制与影响因素。
然后,我们将介绍焙烧氧化在金矿石预处理中的应用场景,分别讨论其在提高金浸出率、去除硫化物和解离难处理金属元素方面的应用。
接着,我们将探讨焙烧氧化工艺参数对金矿浸出过程的影响,并提供相应的优化策略。
最后,在结论部分总结焙烧氧化工艺,并展望未来该技术的发展方向。
1.3 目的本文旨在深入了解焙烧氧化工艺,从概念到原理,从应用场景到参数影响分析,全面解释其在金矿石预处理中的重要作用。
作者希望读者能通过本文了解焙烧氧化工艺的优势和限制,并获得对其未来发展的展望。
同时,本文也旨在为金矿石预处理相关行业提供参考和指导,以帮助他们提高产能和效益。
这是“1. 引言”部分内容的详细清晰撰写,请参考使用。
2. 焙烧氧化工艺的概念和原理2.1 焙烧氧化工艺的定义焙烧氧化工艺是金矿石预处理中的一种重要方法,通过将金矿石在高温下进行氧化反应,使得其中的物质发生结构或成分上的变化。
这种方法可以改善金矿石的性质和可浸出性,为后续金提取过程提供更好的条件。
2.2 焙烧氧化工艺的目标和原理焙烧氧化工艺的主要目标是促使金矿中难以被溶解或提取的有益金属元素转变为易溶解或提取的形式。
其原理基于气体和固体之间的作用力平衡及物质转移原理。
在焙烧过程中,高温下某些金属元素会与基质发生反应,形成能被有效溶解、提取或分离出来的物质。
例如,对于含硫金铜矿,焙烧过程中硫元素可能被转化为二氧化硫(SO2),从而使得含硫物质得到去除;同时,焙烧还会导致产生一些物理和化学结构的改变,如晶体的尺寸变大、结构松散等。
金精矿焙烧-氰化-精炼过程污染物识别与处理回收技术
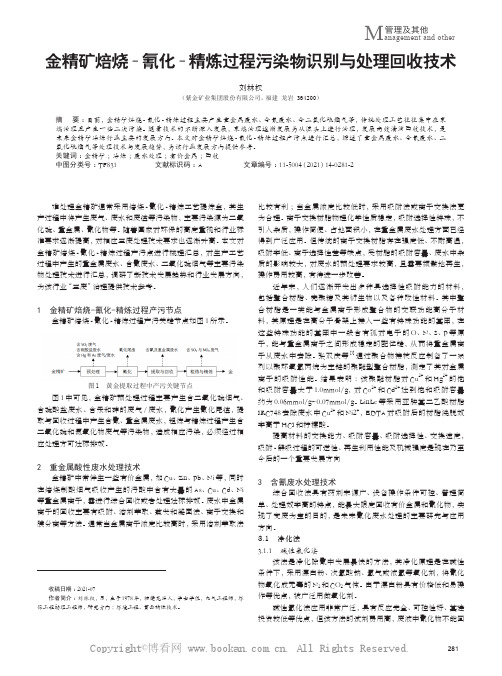
281管理及其他M anagement and other金精矿焙烧-氰化-精炼过程污染物识别与处理回收技术刘林权(紫金矿业集团股份有限公司,福建 龙岩 364200)摘 要:目前,金精矿焙烧-氰化-精炼过程主要产生重金属废水、含氰废水、含二氧化硫烟气等,传统处理工艺往往集中在末端治理且产生一些二次污染。
随着技术的不断深入发展,末端治理逐渐发展为从源头上进行治理,发展高效清洁回收技术,是未来金精矿冶炼行业主要的发展方向。
本文对金精矿焙烧-氰化-精炼过程产污点进行汇总,综述了重金属废水、含氰废水、二氧化硫烟气等处理技术与发展趋势,为该行业发展方向提供参考。
关键词:金精矿;冶炼;废水处理;有价金属;回收中图分类号:TF831 文献标识码:A 文章编号:11-5004(2021)14-0281-2收稿日期:2021-07作者简介:刘林权,男,生于1978年,福建龙岩人,学士学位,电气工程师,环保工程助理工程师,研究方向:环境工程、黄金精炼技术。
难处理金精矿通常采用焙烧-氰化-精炼工艺提炼金,其生产过程中将产生废气、废水和废渣等污染物,主要污染源为二氧化硫、重金属、氰化物等。
随着国家对环保的高度重视和行业标准要求逐渐提高,对相应三废处理技术要求也逐渐升高。
本文对金精矿焙烧-氰化-精炼过程产污点进行梳理汇总,对生产工艺过程中产生的重金属废水、含氰废水、二氧化硫烟气等主要污染物处理技术进行汇总,调研了新技术发展趋势和行业发展方向,为该行业“三废”治理提供技术参考。
1 金精矿焙烧-氰化-精炼过程产污节点金精矿焙烧-氰化-精炼过程产污关键节点如图1所示。
图1 黄金提取过程中产污关键节点图1中可见,金精矿预处理过程主要产生含二氧化硫烟气、含硫酸盐废水、含汞和砷的废气/废水,氰化产生氰化尾渣,提取与回收过程中产生含氰、重金属废水,粗炼与精炼过程产生含二氧化硫和氮氧化物废气等污染物,造成相应污染,必须经过相应处理方可达标排放。
采用循环流态化焙烧—氰化浸出工艺处理难处理金矿原矿的工业实践

采用循环流态化焙烧—氰化浸出工艺处理难处理金矿原矿的
工业实践
孙留根;刘朋;赵磊;杨玮姣
【期刊名称】《中国资源综合利用》
【年(卷),期】2018(036)011
【摘要】为了高效利用含Au 3~8 g/t、S 1.0%~1.2%的复杂金矿原矿资源,本研究自主研发了循环流态化焙烧—氰化浸出工艺.工业实践表明,Au的回收率可达80%,节省浮选工段和脱硫工段;相较于传统的焙烧—细磨—氰化浸出工艺,金的回收率提高20%.采用循环流态化焙烧—氰化浸出工艺处理低硫低品位复杂金矿,运行成本较低,经济效益好,可为我国西部、西南部地区复杂难处理金矿原矿的开发利用提供借鉴.
【总页数】3页(P23-25)
【作者】孙留根;刘朋;赵磊;杨玮姣
【作者单位】北京矿冶科技集团有限公司,北京 100160;招金矿业股份有限公司,山东招远 265400;北京矿冶科技集团有限公司,北京 100160;北京矿冶科技集团有限公司,北京 100160
【正文语种】中文
【中图分类】TD953
【相关文献】
1.原矿焙烧-焙砂氰化工艺处理鹿峰金矿矿石研究与实践 [J], 雷军
2.高硫铝土矿循环流态化焙烧脱硫半工业试验 [J], 赵磊;孙留根;李相良
3.含砷含碳难处理金矿原矿的生物预处理—氰化提金试验 [J], 董博文
4.循环流态化焙烧-加压浸出从极难浸石煤中提取钒 [J], 冯雅丽;蔡震雷;李浩然;汪平;刘欣伟;杨志超
5.循环流态化固硫固砷焙烧金矿的试验及应用实践 [J], 李云;刘洪晓;张立征;靳冉功;王云
因版权原因,仅展示原文概要,查看原文内容请购买。
- 1、下载文档前请自行甄别文档内容的完整性,平台不提供额外的编辑、内容补充、找答案等附加服务。
- 2、"仅部分预览"的文档,不可在线预览部分如存在完整性等问题,可反馈申请退款(可完整预览的文档不适用该条件!)。
- 3、如文档侵犯您的权益,请联系客服反馈,我们会尽快为您处理(人工客服工作时间:9:00-18:30)。
硫化物、金银碲化物的分解反应及单质
银与硫的化合反应过程中, 均放出大量的热,
这种反应生成热, 可使局部温度升高到能使
其中的单质金银互化成银金合金 (照片 4)。
在硫银化合物生成球粒而产生局部高温
的同时, 碲的氧化物呈气态挥发形成了局部
的缺氧环境。此时, 球粒外缘与硫化铁矿物接
触, 可有如下反应生成:
上述工艺流程对于提金而言已达到较为 满意的指标。但对于银而言, 它在上述焙砂浸 渣中品位为 74. 10g t, 浸出率为 19. 31% , 银 的总回收率仅为 8. 27%。为了查明在上述流 程中制约银有效回收的原因, 研究了银的工 艺矿物学变化规律, 找到了银的总回收率低 的原因, 为今后综合利用该金矿中共生的银 奠定了深入研究的基础。
现。球粒直径为 0. 058~ 0. 081mm。其外缘可 具磁铁矿环边者。 在球粒中, 分布有多种相 态: 固相呈不同成分、不同形态及不同粒度的 乳滴状物、粒状物及包裹前二者的基底形式
析其含银量高于基底硫化银。 与上述球粒颇 有些不同的是, 具有六条含 Fe、A u 的硫化银 张裂纹 (照片 3)。 其环边能谱分析见图 1。
2 原矿中银的赋存状态
矿石中银元素主要呈银的独立矿物碲金 银矿、碲银矿等存在, 并且分布于金矿物如自 然金、针碲银金矿中, 其化学成分电子探针分 析结果见表 2。
金银碲化物及自然金以粒间、裂隙及包 裹体状态产出。 金银碲化物以前二种产出形 式为主, 与碲铅矿、自然金、碲金矿、方铅矿、 黄铜矿及自然铅等矿物呈连生镶嵌关系主要 产出于石英粒间、裂隙中, 少数分布于黄铁 矿、方铅矿裂隙中并呈包裹体状产出于此二 者矿物中。
Au 81. 52 0. 47 1. 04 5. 44
Fe 0. 17 0. 57 0. 74 0. 18
Pb 0. 00 85. 95 9. 87 0. 00
10# - 3- 4 10# - 3- 6
乳滴状银金合金 基底硫化银
30. 06 66. 29 84. 16 1. 85
1. 55 0. 41
浸渣中绝大部分的银呈烧结态的球粒出
化, 具有二颗含金量不同的乳滴状银金合金 及乳滴状硫化铅。 此球粒具有磁铁矿的被膜 状环边, 环边由磁铁矿颗粒排列较为紧密的 磁铁矿组成, 其颗粒之间具有 1~ 10Λm 的缝 隙, 环宽约 8Λm。
球粒 10# —6 的电镜分析结果表明, 贱 金属硫化物除了 PbS 外, 尚有 FeS2, 密集分 布的小乳滴为硫化银颗粒, 经能谱半定量分
摘要: 应用电子探针及扫描电镜, 对某金矿氰化浸渣中的银球粒进行了成分和形貌研究, 在此 基础上探讨了银球粒的形成机理, 解释了该类型矿石中的银在焙烧—氰化浸出时大部分不被浸出 而进入氰化浸渣的原因。
关键词: 金矿; 银; 金银碲化物; 银球粒; 硫化银 中图分类号: P578. 1+ 1 文献标识码: A 文章编号: 100026532 (2002) 0420020205
为 0. 203g t。 然而浸渣中银品位却高达 74. 10g t, 故其他形式的银品位= 74. 10- 0. 203 = 73. 897g t, 占总银含量的 99. 73%。
事实上, 浸渣中的金并不都呈自然金状 态存在, 除了未溶解完全的自然金外, 尚有银 金合金、银的硫化物等合成物存在, 故上述计 算应为合理。
碲银矿 0. 10 68. 67
0. 07 30. 87 0. 00
对烧结球粒进行了扫描电镜形貌照相分 析。
球 粒 10# —5 的 背 散 射 电 子 像 上 可 见 (照片 1) , 球粒内部共存在有四个固态物相: 粒状银金合金、乳滴状银铅合金、乳滴状铅银 合金及基底硫化银。 其固相成分电子探针分 析结果见表 3。
物的连生体或载体矿物碲铅矿、方铅矿及黄
铁矿、黄铜矿等矿物中的部分元素。
在焙烧时, 碲金矿进行下述反应:
A u2T e+ O 2→2A u+ T eO 2
(1)
由于金具有高的电离势和电子亲和力,
故呈微粒自然元素状态而被氰化液溶解。
金银碲化物在焙烧时有如下反应: A g3A uT e+ O 2→3A g+ A u+ T eO 2 (2)
第4期
刘敏: 某金矿在焙烧—氰化浸出时银的物理化学行为
·21·
表 2 贵金属矿物电子探针分析结果 %
项 目 A u A g Fe Cu T e B i
自然金 89. 55 8. 73
0. 32 0. 00 2. 51
自然金 99. 98 0. 00 0. 17
0. 34
碲金矿 40. 06 1. 20
收稿日期: 2001209207; 修订日期: 2001210208 作者简介: 刘敏 (1963- ) , 女, 工程师, 硕士研究生, 主要从事工艺矿物学研究工作。
© 1994-2006 China Academic Journal Electronic Publishing House. All rights reserved.
大颗粒白色者为银金合金, 小颗粒乳滴状白 色者为银铅合金, 乳滴状灰色者为铅银合金, 基 底灰色者为硫化银。
以 自 然 金 形 式 存 在 ( 矿 物 金 银 含 量: A u90% ±,A g10% ±) , 则浸渣中的银品位应
球粒 10# - 3 的电镜分析结果表明 (照 片 2) , 其内部固态物相成分较前者略有变
解, 故金回收率较高;
2. 按 (2)~ (4) 式, 焙烧时矿石中的碲挥
发;
3. 按 (2)~ (4) 和 (6)~ (8) 式, 焙烧时矿
石中的银游离出来并与硫铁矿分解出的硫结
合成硫化银;
照片 4 10# —4 背散射电子像 1000×
4. 按 (9) 式在硫化银球粒外缘形成了相
浅灰色粒状、蠕虫状者为银金合金, 灰色乳 滴状者及基底均为硫化银。
当多磁铁矿环边, 使大部分被环边包裹的硫 化银无法被氰化浸出, 从而解释了该金矿共
A gA uT e4+ 4O 2→A g+ A u+ 4T eO 2 (3)
A g2T e+ O 2→2A g+ T eO 2
(4)
同时, 重浮精矿中黄铁矿的焙烧反应为:
4F eS2+ 11O 2→2F e2O 3+ 8SO 2↑ (5)
1 前 言
四川省某金矿为低硫化物蚀变岩型及石
英脉型金矿, 经化学多项分析 (见表 1) , 矿石 中除有价元素金外, 还伴生有银, 其他元素无 工业利用价值。
表 1 矿石化学成分多项分析结果 %
A u3 A g3 SiO 2 T Fe A l2O 3 M gO CaO N a2O K2O S
Cu Pb Zn A s
C
Te
7. 06 12. 50 65. 42 3. 79 5. 65 1. 87 4. 45 1. 88 1. 93 1. 35 0. 0063 0. 015 0. 019 < 0. 001 1. 14 0. 0037
3 单位为 g t。
对该矿矿石采用重选—浮选—焙烧—氰 化浸出—锌粉置换—金泥熔炼工艺流程, 可 获得含金 82. 60%、含银 12. 90% 的金银合质 金, 金的总回收率为 83. 31% , 技术指标较 好。
0. 13 57. 25 0. 45
针碲银44 63. 67 0. 70
碲金银矿 28. 25 38. 11 0. 49
33. 15
碲金银矿 26. 95 39. 29 0. 11 0. 27 32. 04 0. 04
碲银矿 1. 48 53. 23 0. 35 0. 00 44. 72 0. 18
球粒 10# —4 相态表现为三种, 较前三
出现; 气相则为圆形气孔的存在所体现。
个球粒而言, 此球粒保留了粒状银金合金处
© 1994-2006 China Academic Journal Electronic Publishing House. All rights reserved.
·22·
10# - 5 10# - 3 10# - 6 10# - 4
矿产综合利用
2002 年
表 3 焙砂浸渣中球粒固态物相电子探针分析结果 %
项 目
10# - 5- 1 10# - 5- 2 10# - 5- 3 10# - 5- 4
粒状银金合金 乳滴状银铅合金 乳滴状铅银合金
基底硫化银
Ag 18. 31 7. 76 84. 76 80. 66
3F eS2+ 8O 2→F e3O 4+ 6SO 2↑
(9)
故在球粒外缘形成了磁铁矿的环边。 但
是, 并非所有的球粒外缘都有条件形成。
少量的单质银与单质铅在高温下形成银
铅合金及铅银合金。
5 从焙砂浸渣中回收银的可能 性探讨
从上述分析可将该金矿焙烧时其中的
金、银发生的变化机理归纳为:
1. 按 (1) 式金游离出来、被氰化物溶液溶
由于球粒基底硫化银中含有微量的碲, 并且球粒阳离子主成分为银、金和铅, 因此可 以判定形成球粒的物质成分来源于矿物碲金 银矿、碲银矿等金银碲化物, 并聚集了上述矿
照片 3 10# —6 背散射电子像 1000×
圆孔周边稍大浅灰色者为硫化铅, 浅灰色蠕 虫状、乳滴状者为硫化银, 中部深灰色者为硫化 铁, 环边深灰色者为磁铁矿, 基底硫化银。
为主的硫化物, 在马弗炉中对其进行焙烧, 意
味着矿样经历着硫化气氛下的氧化过程。 在
照片 1 10# —5 背散射电子像 1000×
650℃温 度 下 焙 烧 1h, 金 的 氰 化 浸 出 率 为 97% , 银的氰化浸出率仅达 19. 31%。 浸渣中仍有 2. 03g t 的金, 假设其全是