工艺参数对注塑成型质量影响的粗糙集分析
注塑成型工艺参数及其影响

注塑成型工艺参数及其影响11209040112 黄卓摘要:塑料材料在生活中所占比例越来越高,而对于其质量的要求也越来越高,注塑成型作为重要的生产手段,对技术的提高也越来越迫切,而注塑成型制品的影响因素较多,但注塑成型加工工艺条件是重要的影响因素之一,下面将会介绍个个工艺参数对于制品性能的影响。
关键词:注塑成型工艺参数一、注塑成型概念传统的模具设计和工艺参数设置主要依赖于设计者的经验和技巧,模具设计的合理性只有靠反复的试模和修模,工艺参数的设置也只能靠反复的试模来进行修改,缺乏科学依据,生产周期长,成本高,质量也难以保证。
而对成型过程进行模拟,在模具制造之前就可发现设计中的问题,使模具设计和工艺参数设置建立在科学的分析基础之上,可缩短生产周期,提高制品质量。
随着对制品质量要求的提高,对成型过程进行预测己经成为设计不可缺少的环节。
因此,建立注塑成型过程熔体在模腔中流动和传热的数学模型,并采用数值仿真方法实现成型过程的模拟具有重要的意义。
由于成型过程的工艺参数直接决定了熔体在模腔中的流动状态,对制品质量有着最直接最深远的影响,因此找到制品成型的最优工艺条件,对成型过程进行工艺控制,是提高塑料制品质量的有效途径。
这是因为,成型过程中,精密的成型机械、合理的模具设计和优良的材料性能只有在合理的成型工艺设置下刁`能体现出来另一方面,成型机械、模具设计和材料性能的缺陷有时可通过合适的成型工艺设置来弥补。
由此可见,注塑成型工艺对制品质量有着至关重要的作用二、注塑工艺条件及其影响1、注塑压力注射压力指的是在注射过程中螺杆顶部或柱塞对于塑料熔体所加载的压力。
它的作用是对于使熔料混合和塑化,螺杆(或柱塞)必须提供克服固体粒子和熔料在料筒和喷嘴中的流动阻力。
使得塑料熔体以一定的速度来充满型腔,在型腔充满熔体后注射压力起到压实的作用。
从而使得塑件致密,并对熔料因冷却而产生的收缩进行补料,从而使塑件保持精确的形状,获得所需要的性能。
工艺参数对pvc塑料成品质量的影响

工艺参数对pvc塑料成品质量的影响摘要:考察含不同配方以及工艺参数对PVc配混料的成品质量的影响,通过实验的方式完成对PVC塑料成品的分析,关键词:PVC塑料工艺参数成品质量对策1、实验部分1.1主要原料硬脂酸钙,马来西亚佳利安公司;碳酸钙,广西桂林长安零星化工材料有限公司;聚氯乙烯树脂,中国海洋石油总公司;稳定剂,自行配置;钛白粉,澳洲美礼联公司,696型;石蜡,广东佛山南海化工厂,56型。
1.2主要仪器手提式高速粉碎机,转速为24000r/min,RETSCH公司;转矩流变仪,长春市智能仪器设备有限公司;高速混合机,GRH-5Z,转速为1400到2800r/min,由张家港亚通机械有限公司。
1.3试样制备实验配方见(表一),首先是基料的配置,将除石蜡和硬脂酸钙之外的原料首先加入到高速混合机中搅拌5分钟;再取定量的基料,分别按表一中的几种比例方法加入石蜡和硬脂酸钙,然后将配方倒入手提式高速中药粉碎机中搅拌1分钟,均匀的配成千混料,接下来就是将定量干混料加入到转矩流变仪中进行实验。
2、PVC塑料成品质量的结果讨论2.1PVC树脂颗粒的层次结构与加工过程的凝胶化由于PVC在其他的单体中不能溶解,在聚合本体与聚合悬浮时,当转化率在2%左右的时侯,PVC从其单体中开始沉淀,将会产生一个直径为1μm左右的初级粒子,粒子会发生凝聚变法,产生一个直径3—10μm左右的凝聚体初级粒子。
另外在聚合悬浮开始时所生产的PVC粒子被吸引到直径在30-100μm范围的悬浮液面界面上,然而形成一层皮层环绕液滴,这些液滴将会聚合成直径为100-200μm左右的树脂颗粒,所以,聚合悬浮的树脂颗粒就具有由0.5-5μm的皮层所包裹,直径在3-10μm左右的粒子凝聚体所形成的层次结构如表二所示:PVc的初级粒子存在微区结构,其主要体现是表现出无定形,然而也含有5%-10%的微晶,其主要原因是由于有大约50%的间规立链段在PVC中,由于这些规立构链段,一部分形成了微晶,处于微区结构中心,尺寸在0.01μm左右,由带状分子联接。
工艺参数对注塑制品质量的影响研究

收稿日期:2003-04-28;修订日期:2003-06-20 基金项目:国家“863”计划资助项目(2002AA336120) 作者简介:王利霞(1969-),女,河南省长垣县人,郑州大学副教授,博士研究生,主要从事高聚物成型模拟、工艺优化及制品质量控制方面的研究1 文章编号:1671-6833(2003)03-0062-05工艺参数对注塑制品质量的影响研究王利霞,王 蓓,申长雨(郑州大学橡塑模具国家工程研究中心,河南郑州450002)摘 要:注塑成型工艺过程极其复杂且其对制品质量有重要的影响,获得优化的工艺参数是改善制品质量的关键.C AE 技术可辅助优化工艺,但目前的应用是在计算机上的反复试错,依赖于设计者的经验,费时、费力且难以获得最优的工艺.将C AE 及T aguchi DOE 技术结合,可在较少的分析次数下自动获得优化工艺,从而改善了制品质量.收缩和沉降斑是衡量注塑制品质量的两个重要指标,文中基于一个工业产品,采用L9(34)正交矩阵进行实验,研究工艺参数对注塑制品内最大沉降斑和体收缩率变化的影响,获得优化工艺参数使体收缩率变化和沉降斑指数达到最小,分析结果表明了该方法的有效性1关键词:注塑成型;工艺优化;DOE;体收缩率;沉降斑中图分类号:T Q 320166 文献标识码:A0 引言注塑成型是重要的塑料制品成型方式,适于大批量生产形状复杂、尺寸要求精确的塑料制品.在成型过程中,材料开始要经历温度和压力增加、严重的剪切变形,随后在模具型腔中温度和压力急剧下降,使得制品固化,同时未来得及松弛的残余应力和取向及其他一些制品性能保留了下来,决定了制品的质量.因此,注塑成型制品的质量受到许多因素的影响.这些因素有:与模具设计和冷却管道设计有关的几何参数,材料性能参数包括聚合物材料的流变性能、热力学性能、物理性能、机械性能及在充填、保压和冷却过程中的工艺参数等.随着热塑性塑料在生产中的应用越来越广泛,获得合适的工艺条件越来越显得迫切.在制品和模具设计中已经广泛采用数值模拟辅助设计[1],而在工艺设置和调节方面,还没有类似的方法辅助工艺工程师.上个世纪90年代,基于知识的专家系统可帮助提供工艺设计的智能建议和智能决策[2].然而,因为其自身的定性和定量推理的不完整性,仅仅靠基于知识的专家系统还难以给出优化解.近年来,研究者们采用多种方法对工艺优化进行了研究[3,4],如传统优化技术、遗传算法、神经网络等,这些方法理论性太强,工厂的技术人员很难理解,使得其在实际中的应用存在一定的困难.注射成型的非线性、多变量特性,使得其工艺的设置非常困难.而传统的试错方法虽然可以改善制品质量,却费时费力耗资.C AE 技术的出现,使得注塑成型工艺的计算机模拟能帮助工艺工程师迎接这一挑战,可通过对成型过程的模拟,及早发现不合理的工艺设置,修改参数并最终获得无明显缺陷的注塑制品.而C AE 技术与DOE 技术的结合,可方便实现工艺的自动优化.本文结合C AE 技术和DOE 技术研究工艺参数对制品质量的影响并优化工艺参数.1 数值模拟与实验设计结合的工艺优化理论 C AE 技术可用来确定合适的工艺参数,这对于大型、复杂和尺寸要求精确的制品显得尤为重要.应用C AE 技术优化工艺参数时,甚至还可以没有制品和模具原型,可节省大量的时间和资金.但目前的应用也仅限于应用C AE 分析代替反复试模,这只能使工艺调节到无明显制品缺陷的工艺,而不能达到最优工艺,而且对于大型复杂的制2003年 9月第24卷 第3期郑州大学学报(工学版)Journal of Zhengzhou University (Engineering Science )Sep 1 2003V ol 124 N o 13品,由于工艺模型及几何模型的复杂性,C AE分析时间较长,限制了其在工艺优化方面的应用.因此,合理设计实验,有效利用C AE分析,以较少的分析次数获得足够的实验信息,并实现工艺参数的自动优化具有重要的意义.111 注塑成型充填/后充填过程的数值模拟在塑料制品生产中,塑料、模具和加工设备三者密切相关,塑料加工不单纯是物理过程,而是控制制品的结构和性能的中心环节.近年来,随着计算机辅助工程(C AE)技术的发展,该技术在塑料加工行业的应用也越来越广泛.对加工过程进行数值模拟,可研究加工条件的变化规律,预测制品的结构和性能,选择制品和模具设计以及工艺条件的最佳方案,对塑料在加工过程中的流动、传热以及在力场和温度场的作用下所出现的物理变化及化学变化得以深刻的了解,使加工成型从一门实用技术变为一门应用科学.在注塑成型过程中,由于模腔的复杂性及聚合物熔体流变性质的复杂性,再加上移动边界的存在,问题的求解存在着很大的困难.但由于注塑件通常都是薄壁件,通过引入Hele-Shaw近似并给出适当的简化,得到最终的控制方程组压力方程是二维的,而温度场控制方程仍然保持三维.本文基于非牛顿流体在非等温下的广义Hele -Shaw流动的控制方程,建立注塑成型充填/后充填过程统一的数学模型.在注塑成型充填/后充填阶段,熔体在模具中流动的控制方程可表示为[1]:ρt +x(ρv x)+y(ρv y)=0(1)px-z(ηv xz)=0(2)py-z(ηv yz)=0(3) ρC p(T)Tt +v xTx+v yTy=z (k(T)Tz)+ηγ・2(4)式中:P为压力;T为温度;ρ为密度;C p(T)是比热;k(T)是聚合物熔体的热传导率;η为剪切粘度;γ・为剪切速率;x,y为中面的坐标;z是型腔厚度方向的坐标;S是流通率1在充填和后充填阶段,聚合物在模腔中的流动行为强烈地依赖于熔体的流变、物理及热性能,这里剪切粘度采用cross-W LF[1]粘度模型,p-v -T方程采用双域T ait经验方程[1],k(T)和C p(T)均为温度的函数[1].基于上述控制方程,结合适当的边界条件,采用混合有限元/有限差分/控制体积法实现充填/后充填一体化模拟.通过充填/后充填模拟,我们可对成型过程中熔体的流动行为、各种场(温度、压力、速度、密度等等)的分布及变化得以深刻的了解,并可预测制品的性能.采用数值模拟代替真实实验具有以下优势:①方便改变输入参数值的范围.在真实实验中,一些极端值会受到实际条件的限制.②独立变量的任意水平组合都是可能的.③计算机模拟实验结果的重复性较高.④许多情况下,模拟实验的时间及花费要求较少.⑤可预测实际实验难以测量的一些质量性能指标.112 T aguchi实验设计(DOE)技术多因子实验布置技术最早由英国R1A1Fisher 提出,这种方法称为因子实验设计.全因子实验要包含所有因子的所有可能组合,在真实的工业实验中一般包含大量的实验因子,这将导致实验数目巨大.为了降低实验数目,只需由所有可能组合中挑选一小部分因子组合进行实验并可获得充分的实验信息,T aguchi实验设计技术即是这样一种实验设计技术.T aguchi实验基于一定的规则设计正交实验矩阵,确保以最小数目的实验获得全因子实验中影响性能参数的全部信息.正交矩阵方法的关键在于每个实验的设计变量水平组合的挑选.T aguchi实验设计技术传统的应用是设置各个影响因子的水平组合进行真实的实验并研究实验结果.然而,有许多情况真实实验难以进行且有些质量指标很难测量,随着数值模拟技术在工业中的应用,可用数值方法模拟真实实验.本文利用注塑成型充填/后充填的数值模拟代替真实实验进行模拟实验预测成型过程及制品性能.注塑制品质量受到很多因素的影响,而且这些变量的变化范围很广,这些因素对制品质量的影响研究即使采用C AE模拟工作量也非常大.因此,如在实际实验中一样,采用DOE技术设计实验以减少实验次数而获得足够的信息[5~8].这里采用T AG UCHI DOE技术设计实验,并通过一系列数值实验研究各个工艺参数对制品质量的影响而得到优化解,数值模拟与DOE结合进行工艺优化的具体思路如图1所示.应用正交矩阵是一种有效的方法同时研究多个工艺参数的影响.在T aguchi DOE技术中,一旦36第3期 王利霞等 工艺参数对注塑制品质量的影响研究 参数和水平确定,从许多参考书中即可查到对应的正交矩阵布置.注意在实验中,所选参数必须是相互独立的且在操作窗口内是连续的,否则将导致错误结论[7].图1 数值模拟与DOE 结合的注塑工艺优化实施思路Fig 11 F low ch art of the process optimization for plastic injection molding using CAE/DOE combination method 上述工艺优化过程可方便地在计算机上自动实现,避免了人工干预带来的误差.2 实验和结果本文选用一个工业产品作为研究算例(图2),材料为PP ,实验参数及参数水平设置见表1.基于4参数3水平的正交矩阵见表2.对于注塑制品,沉降斑[6~8]和收缩[5,7]是制品质量的两个重要指标,沉降斑严重影响制品的表面质量,而收缩及收缩不均匀会使得制品产生翘曲,严重影响制品的尺寸和形状,因此本文选用制品内的最大沉降斑深度及体收缩率变化(最大和最小体收缩率的差值)作为质量指标,用C AE 分析代替真实实验,数值实验结果见表2.图2 几何模型Fig 12 Model geometry表1 因子和水平设置T ab 11 F actors and levels 参数水平1水平2水平3熔体温度A /℃215230245模具温度B /℃455055充填时间C /s 116210214保压时间D /s8101012表2 实验正交矩阵及实验结果T ab 12 Experiments array and the results实验号A B C D沉降斑深度/%体收缩率变化/%111110143166501393760212220124122601529573313330127005801639262421230143274501747449522310169046901380614623120137610201339869731320146357001574878832130135512901553461933211103817601283321K 1101314316014426600138763201720103K 1201499772014289410157071501360299K 1301618958015614450147469901352644R101304642011325040118308301367459K 2101520865015720290142903001352565K 2201489311014878830152011401481440K 2301470553014208170153158501646724R 201050312011512120110255501294159 说明:K q i 是在某个工艺参数第i 个水平下的第q 个质量指标的平均值;R q 代表某个工艺参数影响下第q 个质量指标的极差;i =1,2,3代表三个水平;q =1,2分别代表沉降斑和体收缩率.46 郑州大学学报(工学版) 2003年3 结果分析和讨论对实验结果进行分析.参数对沉降斑深度和体收缩率的影响见图3.基于变量分析(ANOVA ),计算各个变量的主效应,预测优化的工艺组合并对优化结果进行预测.图3 各个因子对质量指标的影响Fig 13 I nfluence of factors on sinkm arks and volumetic shrink age311 工艺参数对沉降斑的影响图3(a )给出各因子对沉降斑的影响,图中的数字表示各个因子的值的变化.由图3(a ),对于材料PP ,在所研究的工艺范围内,可得出以下结论:①熔体温度对沉降斑的影响最强,熔体温度越高,沉降斑深度越大.②模具温度升高导致沉降斑深度增大.③注射时间越长,相应的注射速率越低,导致沉降斑深度增大.④在浇口凝固前保压时间越长则沉降斑深度越小.312 工艺参数对体收缩率变化的影响由图3(b )可得出如下结论,对于材料PP ,在所研究的工艺范围内:①保压时间对体收缩率变化影响最大,保压时间越长体收缩率变化越大.②模具温度对体收缩率的影响也较强,模具温度越高,体收缩率变化越低.③熔体温度和充填时间对体收缩率的影响较弱.313工艺参数优化由图3,可以得到引起最小制品质量缺陷的工艺组合如下:基于最小化沉降斑深度,优化的工艺组合为:A 1B 2C 1D 3(即A =215℃,B =50℃,C =116s ,D =12s );而基于最小化体收缩率变化,优化工艺组合为:A 3B 3C 1D 1(即A =245℃,B =55℃,C =116s ,D =8s ).可以看到,预测的优化工艺组合没有包含在正交矩阵中的主实验中,需要对预测结果进行验证.采用数值实验验证优化工艺,在优化工艺组合A 1B 2C 1D 3下,沉降斑深度为01241208,其值小于所有主实验的值;在优化工艺组合A 3B 3C 1D 1下,体收缩率变化为01136725,小于所有主实验中的结果.因此,应用优化因子水平可以改善注塑成型制品的质量,同时也表明所选因子之间的影响关系较弱.如果想同时对多个质量指标进行优化,可根据各个质量指标的重要性和各个工艺参数对质量指标的影响程度进行综合评判,得出使得制品总体质量最优的工艺组合.4 结论(1)T aguchi DOE 是一种有效的方法研究工艺参数对注塑成型制品的影响,象在真实实验中一样,应用该技术可用较少的数值实验获得足够的信息.采用C AE 可方便地进行数值实验,较真实实验节省大量时间和费用.C AE 与实验设计技术结合,可方便地实现注塑成型工艺的自动优化.(2)本研究中,对于材料PP ,在所研究的工艺范围内,降低熔体温度,降低模具温度,缩短注射时间及延长保压时间可减小沉降斑深度.(3)本研究中,对于材料PP ,在所研究的工艺范围内,升高熔体温度、升高模具温度、缩短注射时间、缩短保压时间可使体收缩率变化减小,即体收缩率均匀,从而减小制品产生翘曲的可能性.参考文献:[1] CHI ANG H H ,HIE BER C A ,W ANG K K 1A unifiedsimulation of the filling and post -filling stages in injection m olding,part I :formulation [J ]1P olymer Engineering and Science ,1991,31(2):116~1391[2] KI M S ,S UH N ,K nowledge -based synthesis system forinjection m olding [J ]1R obotics and C omputer Integrated Manu facturing ,1987,3(2):181~1861[3] CH OI G H ,LEE KD ,CH ANGN 1Optimization of pro 2cess parameters of injection m olding with neural netw ork application in a process simulation environment [J ]1An 2nals of the CIRP ,1994,43(1):449~4521[4] YE Hua ,W U Y inghui ,W ANG K K 1An optimizationscheme for part quality in injection m olding [A ]1M D -V ol 79,C AE and Intelligent Processing of P olymetric Ma 2terials ,AS ME 1997[C]119971139~149156第3期 王利霞等 工艺参数对注塑制品质量的影响研究 [5] CH ANG T ao C1Shrinkage behavior and optimization of in2jection m olded parts studied by taguchi method[J]1P oly2 mer Engineering and Science,2001,41(5):703~7101 [6] LI U Shih Jung,CH ANG Jer Haur,Application of thetaguchi method to optimize the surface quality of gas assist injection m olded composites[J]1Journal of Rein forcedPlastics and C omposites,2000,19(17):1352~13621 [7] OTT O Vtinen,PE NTTI Jrvel,KY STI Valta,et al1The ef2fect of processing parameters on the quality of injection m oulded parts by using the taguchi parameter design method[J]1Plastics,Rubber and C omposites Processing and Applications,1994,21(4):21~2171[8] LI U Shih Jung1E ffects of processing parameters on forma2tion of sinkmarks on injection m oulded parts[J]1Plastics,Rubber and C omposites,2001,30(4):170~174I nfluence of Processing P arameter on Q uality of PlasticI njection Molded P artsW ANGLi-xia,W ANG Bei,SHE N Chang-yu(National Engineering Research C enter for Advanced P olymer Processing T echn ology,Z heng zh ou University,Z heng zh ou450002,China)Abstract:The process com plexity of plastic injection m olding makes it difficult to set up desired processing condi2 tions and the quality of an injection-m olded part is affected by these process factors,s o how to get the optimum process conditions is key to im proving the part quality1C AE can aid process engineer to optimize the process condi2 tions,but this method is only the trial-and-error on the com puter1It als o depends on the experience of the oper2 ator and only the reas onable not the best process parameters can be obtained1In this paper,C AE and T aguchi DOE (design of experiment)technique are combined to optimize the process conditions and to im prove the part quality automatically by using smaller number of experiments1Sink mark and shrinkage are tw o im portant quality indexes of injection-m olded part1In this paper,An L9(34)orthog onal array is conducted to investigate the significance of each factors on the sink mark indexes and v olumetric shrinkage variation,and optimum process conditions are g ot to minimize the selected quality indexes based on an industry part1The results prove the validity of the method1K ey w ords:injection m olding;process optimization;DOE;v olumetric shrinkage;sink mark;66 郑州大学学报(工学版) 2003年。
塑料注塑成型中的材料选择与工艺参数调整案例分析
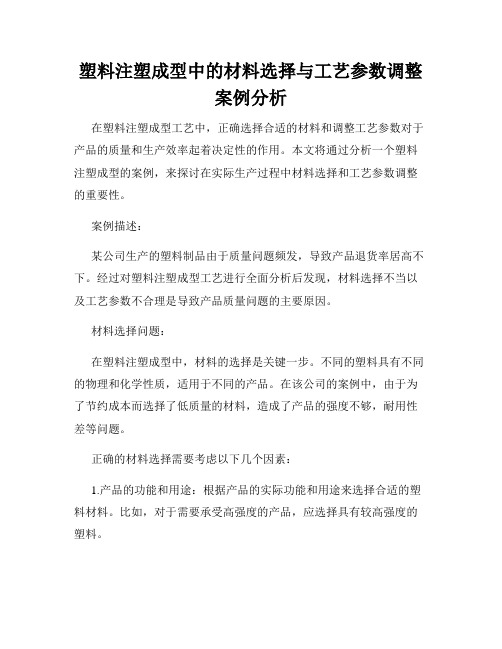
塑料注塑成型中的材料选择与工艺参数调整案例分析在塑料注塑成型工艺中,正确选择合适的材料和调整工艺参数对于产品的质量和生产效率起着决定性的作用。
本文将通过分析一个塑料注塑成型的案例,来探讨在实际生产过程中材料选择和工艺参数调整的重要性。
案例描述:某公司生产的塑料制品由于质量问题频发,导致产品退货率居高不下。
经过对塑料注塑成型工艺进行全面分析后发现,材料选择不当以及工艺参数不合理是导致产品质量问题的主要原因。
材料选择问题:在塑料注塑成型中,材料的选择是关键一步。
不同的塑料具有不同的物理和化学性质,适用于不同的产品。
在该公司的案例中,由于为了节约成本而选择了低质量的材料,造成了产品的强度不够,耐用性差等问题。
正确的材料选择需要考虑以下几个因素:1.产品的功能和用途:根据产品的实际功能和用途来选择合适的塑料材料。
比如,对于需要承受高强度的产品,应选择具有较高强度的塑料。
2.环境要求:考虑产品使用环境的温度、湿度、化学物质等因素,选择能够适应这些环境的材料。
3.加工性能:考虑材料的流动性、熔融温度、收缩率等因素,选择适合注塑成型的材料。
工艺参数调整问题:除了材料选择外,工艺参数的调整也是确保产品质量的重要环节。
在该公司的案例中,由于没有正确调整工艺参数,产品出现了缺陷,如翘曲、短射、气泡等。
正确的工艺参数调整需要考虑以下几个因素:1.注射速度:注射速度过快容易造成气泡和短射,而注射速度过慢则会导致产品外观不光滑。
应根据材料的熔融特性调整注射速度。
2.熔融温度:熔融温度过高容易导致产品变形,过低则会引起短射。
应根据材料的熔融温度范围来调整熔融温度。
3.模具温度:模具温度的过高或过低都会影响产品的尺寸精度和表面质量。
应根据材料的熔融温度和产品的要求来调整模具温度。
通过对该案例的分析,该公司采取了以下措施来解决产品质量问题:1.改善材料选择:重新评估产品的功能和使用环境,选择符合要求的高质量塑料材料,确保产品的性能。
工艺参数对注塑制品质量的影响相关分析

36技术应用与研究一、1.工艺参数对注塑制品质量的影响方面分析据有关调查显示,我国大多数注塑制品的生产过程中都会由于工艺参数的设定以及应用等存在不同的制品生产效果,并由此对注塑制品自身的质量产生直接性影响。
对于工艺参数对注塑制品质量的相关性影响分析,需要从实际的影响内容、工艺参数变化以及原因等多个角度入手,进而为提高注塑制品的质量措施研究奠定基础。
下面展开详细的论述。
1.影响内容一般而言,在工艺参数的设定过程中,对于注塑制品质量的影响主要集中在尺寸设定、表面缺陷以及翘曲变形等三方面。
具体地,在尺寸设定上的影响是通过分析不同的工艺参数设定差异对于实际的注塑制品中收缩率的大小分析,进而直接对于注塑制品的尺寸等质量内容产生决定性影响。
在翘曲变形的影响上则是由于注塑制品中注塑工艺的应用会使得其在成型时由于浇注和冷却系统的功能而使得注塑制品出现翘曲变形。
最后,在对于表面缺陷等质量问题的影响是直接由于工艺参数对于实际注塑成型的过程存在的关键性影响而导致注塑制品表现出现一系列的缺陷。
2.影响原因调查显示,在经过工艺参数的设定之后,注塑制品的质量主要是受到制品结构、胜场模具、原材料、注塑工艺、工艺参数以及扰动等多种因素的影响。
其中,工艺参数的存在是极容易导致注塑制品质量出现问题的。
具体的影响原因上见表1。
表1 工艺参数对注塑制品质量的影响原因分析质量问题阶段原因制品尺寸注塑工艺参数设定影响制品收缩率、效果保压压力与时间、模具与熔体温度、注射压力的不同设定差异翘曲变形注塑工艺参数设定影响成型过程表面缺陷注塑工艺参数设定影响物料成型状态 通过对上表的分析可以发现:保压压力、保压时间、模具温度、熔体温度、注射压力等五种工艺参数的设定是直接影响到注塑制品质量的关键性因素,需要在具体的生产过程中从注塑制品的成型、物料监督到收缩等加强检测分析。
二、工艺参数对注塑制品质量改进的实践分析上面已经对工艺参数对注塑制品质量的相关影响等进行了初步的分析和实际情况介绍,可以发现:目前我国存在的注塑制品的质量问题大多集中在尺寸、翘曲变形以及表现缺陷等三个角度,并通过不同阶段的生产过程而造成最终的质量问题。
影响塑胶成型的主要工艺参数
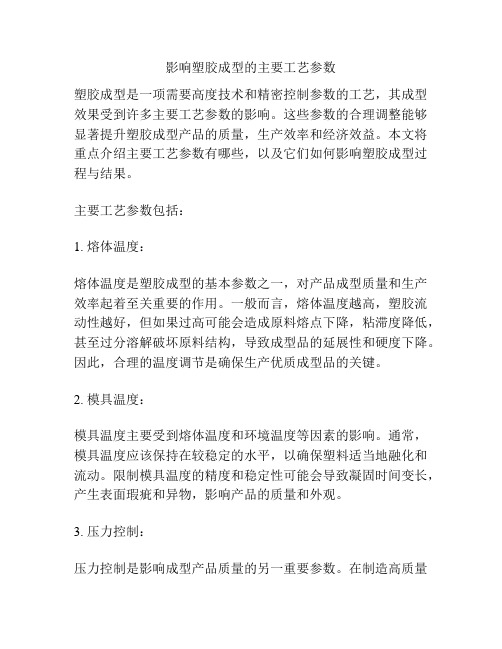
影响塑胶成型的主要工艺参数塑胶成型是一项需要高度技术和精密控制参数的工艺,其成型效果受到许多主要工艺参数的影响。
这些参数的合理调整能够显著提升塑胶成型产品的质量,生产效率和经济效益。
本文将重点介绍主要工艺参数有哪些,以及它们如何影响塑胶成型过程与结果。
主要工艺参数包括:1. 熔体温度:熔体温度是塑胶成型的基本参数之一,对产品成型质量和生产效率起着至关重要的作用。
一般而言,熔体温度越高,塑胶流动性越好,但如果过高可能会造成原料熔点下降,粘滞度降低,甚至过分溶解破坏原料结构,导致成型品的延展性和硬度下降。
因此,合理的温度调节是确保生产优质成型品的关键。
2. 模具温度:模具温度主要受到熔体温度和环境温度等因素的影响。
通常,模具温度应该保持在较稳定的水平,以确保塑料适当地融化和流动。
限制模具温度的精度和稳定性可能会导致凝固时间变长,产生表面瑕疵和异物,影响产品的质量和外观。
3. 压力控制:压力控制是影响成型产品质量的另一重要参数。
在制造高质量的塑料部件的过程中,要保证合适的压力,以确保塑料适当定位并填充全部空间。
压力过大会导致产品变形、沉降和缩放,而过小则会影响填充时间和产品外观质量等问题。
4. 塑胶流量速度和时间:塑料流量速度和时间也是成型过程的关键参数因素之一。
如果速度过高,可能会产生熔态的塑料物料,导致产生空隙和变形、熔料的正常填充和降低表面质量等缺陷,而速度过慢则会导致产品脆性等问题。
5. 锁模力:锁模力是实现整个成型过程的一个关键参数。
如果锁模力不足,会导致在填充时模具会发生形变,产生喷漏或剪切破裂痕迹等问题。
相反,过高的锁模力也可能导致模具损坏,降低模具的使用寿命等问题。
综合来看,合理的工艺参数调节和控制,不仅仅可以提高生产效率,更重要的是可以生产出高质量的成型品,为塑胶成型行业的未来增添更多的发展潜力和机会。
除上述主要工艺参数外,还有一些其他的参数也会影响到塑胶成型的生产效果和产量,例如:6. 压力传感器与控制系统:在塑胶成型过程中,主要通过压力传感器和控制系统来控制和监视各个节点的压力变化。
FDM工艺参数对成型制品表面粗糙度影响的研究_邬宗鹏
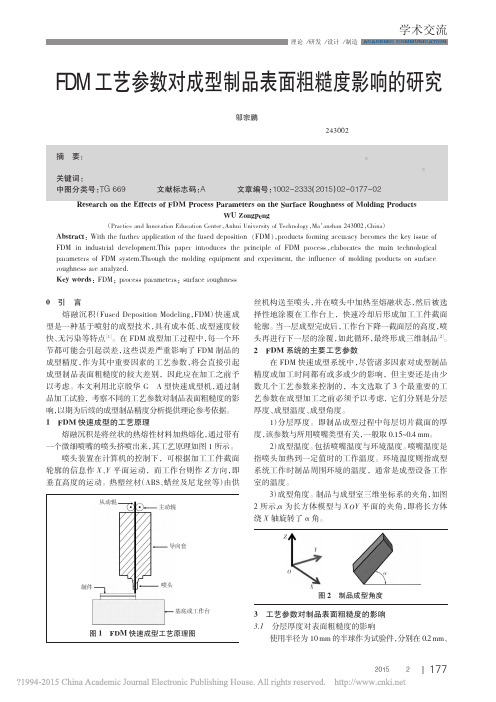
制件
喷头
基底或工作台
图 1 FDM 快速成型工艺原理图
O
α
X
图 2 制品成型角度
3 工艺参数对制品表面粗糙度的影响 3.1 分层厚度对表面粗糙度的影响
使用半径为 10 mm 的半球作为试验件,分别在 0.2 mm、
机械工程师 2015 年第 2 期 177
学术交流
ACADEMIC COMMUNICATION 理论 / 研发 / 设计 / 制造
试验件对象,经过加工后不同长方体试件表面粗糙度间 的比较,得出喷嘴温度合理范围,如图 5 所示。
从图 5 中可知,成型的喷嘴合理温度范围区域是
!!!!!!!!!! 作者简介:邬宗鹏(1980—),男,助理实验师,工程硕士研究生,研究
方向为工程实践教学及快速成型技术。
收稿日期:2014-10-21
178 机械工程师 2015 年第 2 期
0引言 熔融沉积(Fused Deposition Modeling,FDM)快速成
型是一种基于喷射的成型技术,具有成本低、成型速度较 快、无污染等特点[1]。在 FDM 成型加工过程中,每一个环 节都可能会引起误差,这些误差严重影响了 FDM 制品的 成型精度,作为其中重要因素的工艺参数,将会直接引起 成型制品表面粗糙度的较大差别,因此应在加工之前予 以考虑。本文利用北京殷华 GⅡA 型快速成型机,通过制 品加工试验,考察不同的工艺参数对制品表面粗糙度的影 响,以期为后续的成型制品精度分析提供理论参考依据。 1 FDM 快速成型的工艺原理
2)成型温度。包括喷嘴温度与环境温度。喷嘴温度是 指喷头加热到一定值时的工作温度。环境温度则指成型 系统工作时制品周围环境的温度,通常是成型设备工作 室的温度。
工艺参数对注塑制品变形影响的研究

( 海 交 通 大 学 塑 性成 形 工程 系 ,上 海 上 203 ) 0 0 0
摘
要 :注塑制品的 变形影响产品的最终形状和尺寸精度 。通过模拟注塑成型过程 ,并结
合 田口实验 设 计法 ,研 究 了工 艺参 数 与注 塑制 品 翘 曲 变形 的 关 系,得 到 了优 化 的工 艺参数 。
su id. Th pi l r c si gp r me e sae o tie t de eo tma o e sn a a tr r b an d. Ba e n ti . t eef cso od p s do h h fe t f m l
t pr ue e t prt e i ef ni e n h l n t e n e et n r d cs dut r e e t ,m l e e u ,  ̄ co t d od g m o df co a i us fr e. m ar t m ar i m a i i l i e s e h
材料为P ,具体牌号为H nm P t c e i P o a e oh m . r
Ke rs net nmodn ;wapg ;n meia muain aa tco t zt n ywod :i ci lig j o rae u rcli lt ;prmer pi ai s o i mi o
0 引言
注塑制品的变形影响产品的最终形状和尺寸 精度。产品变形的根本原因是收缩不均匀 ,而影
收稿 日期 :20- -8 051 1 0 作者简介 : 连昌伟 ( 9 2 ),男 ,硕士研究生 。 18 ̄
数的范围,然后对各个参数选取不同水平得 出实
验 方案 的安 排 ,对 每个 方案 进行 模拟 得到 最后 的 变 形量 ,通 过 结果 的分 析得 到工最优的工艺参数组合 。
常用塑料工艺参数、常见注塑制品的缺陷及原因分析

1,料温过低 2,料温太高或停留 时间太长 3,保压时间太长 4,脱模剂过多
焦 点
1,不同料混入 2,混入油污或异物
1,浇口太小 1,料筒内有焦料 2,排气不良 2,喷嘴不干净 3,型腔复杂,阻料 混合慢 4,型腔光洁度差
1,料温过高 2,注射压力太高 3,注射速度太快 4,停机时间过长 5,脱模剂不干净
1,料温过高 2,注射压力太高 3,注射速度过快 4,塑化不均 5,脱模剂过多
1,含水分而未干燥 2,润滑剂过量
厚薄不均
脱 模 困 难
1,无脱模斜度 2,光洁度不够 3,顶出方式不当 4,配合精度不当 5,进,排气不良 6,模板变形
1,顶出力不够 顶程不够
2, 1,注射压力太高 2,保压时间太长 3,注射量太多 4,模具温度太高
原材料
1,牌号品种有变动 2,颗粒大小不均 3,含挥发物质
制品设计
壁太厚
注 塑 不 满
尺 寸 不 稳 定
溢 边
1,锁模力不足 2,模板闭合未紧 3,锁模油路中途卸荷 4,模板不平行,拉杆 与套磨损严重
1,塑化温度过高 2,注射时间过长 3,加料量太多 4,注射压力过高 5,模温太高 6,模板间有杂料 1,加料量不足 2,注塑时间过短 3,保压时间过短 4,料温过高 5,模温太高 6,冷却时间太短 1,料温过低 2,模温过低 3,注塑速度太慢 4,脱模剂过多
流 痕
1,浇口太小 2,浇口数量少 3,流道、浇口粗糙 4,型面光洁度差 5,冷料穴太小
1,温控系统失灵 2,油泵压力下降 3,“小马拉大车”塑 化能力不足
1,料温太低,未完 1,含挥发物太多 全塑化 2,流动性太差 2,注塑速度过低 3,混入杂料。 3,注射压力太小 4,保压压力不够 5,模具温度太低 6,注塑量不足
注塑工艺注塑成型缺陷分析及不良解决对策

注塑成型技术培训资料一、如何解决注塑产品存在的品质缺陷1、注塑产品存在的品质缺陷:塑料制品的成型加工过程中,由于加工设备不一,成型性能各异,原料品种繁多,加之设备的运行状态,模具的型腔结构、物料的流变性筹多种因素错综变化的影响,得塑料的内在及外观质量经常会出现各种各样的成型缺陷。
常见的外观缺陷有:缩水、飞边、黑点、流纹、熔接线、亮纹、缺胶、气泡、料花等。
2、如何解决缩水•缩水产生的原因制件在模具中冷却时,由于制件的胶厚不一致而导致塑胶收缩不均匀而引起的凹痕。
解决缩水的原理是:在制件冷却过程中,熔胶不断补充制件收缩引起的空缺。
因此在正常情况下要保证熔胶补充的通道不受阻和足够的补充压力。
•在注塑工艺上的解决办法:(1)注塑条件问题:①注射量不足;②提高注射压力;③增加注射时间;④增加保压压力或时间;⑤提高注射速度;⑥增加注射周期;⑦操作原因造成的注射周期反常。
(2)温度问题:①物料太热造成过量收缩;②物料太冷造成充料压实不足;③模温太高造成模壁处物料不能很快固化;④模温太低造成充模不足;⑤模子有局部过热点;⑥改变冷却方案。
(3)模具问题:①增大浇口;②增大分流道;③增大主流道;④增大喷嘴孔;⑤改进模子排气;⑥平衡充模速率;⑦避免充模料流中断;⑧浇口进料安排在制品厚壁部位;⑨如果有可能,减少制品壁厚差异;⑩模子造成的注射周期反常。
(4)设备问题:①增大注压机的塑化容量;②使注射周期正常;(5)冷却条件问题:①部件在模内冷却过长,避免由外往里收缩,缩短模子冷却时间;②将制件在热水中冷却。
3、如何解决飞边•产生飞边的原因:产品溢边往往由于模子的缺陷造成,其他原因有:注射力大于锁模力、物料温度太高、排气不足、加料过量、模子上沾有异物等。
•如何判断产生飞边的原因:在一般情况下,采用短射的办法。
即在注塑压力速度较低、不用保压的情况下注塑出制件90%的样板,检查样板是否出现飞边,如果出现,则是模具没有配好或注塑机的锁模压力不足,如果没有出现,则是由于注塑条件变化而引起的飞边,比如:保压太大、注射速度太快等。
有关工艺参数对注塑件成型质量产生的影响探究

3 、 温 度参 数 熔 体气温 主要 由喷 嘴和 机筒两 部位 的气温 所决定 , 注射 气温 的增 熔体气 温的增 高, 可降 低注塑件 的内应 力、 伸拉 的循 环链 条中, 因材料 自身的特性 以及相对 繁琐的加 工条件, 使材 料的 加 可增强熔体 流动性 。 成型历经相对较 长的状态 变化, 如固体的运送 、 熔融 、 熔体运输 、 压实、 强度等物理 力学性 能, 而使与流线 方向相互垂直 的冲击强度有所增强 , 熔 体气温的 增 高可增强制 品的综 合 牢固、 纤维取 向等。 注塑件的成型不单使 材料拥有 了 _ 一 定 的尺寸及形态 , 并可 使制品后 收缩 性能 得以下 降 。 使充模 状况得 到一定 的改观 。 当熔体气温 达到注 塑件气温 的上限 更使材 料 的性 能及组 织结 构有 了根 本性的 更新 。 成 型加 工工艺 的终极 性 能,
前沿部 位的前进速率, 确保熔体 的前沿速率在充填时均等化。 本文通过 分 面 的取向性 , 使熔体 出现 弹性湍流 的现象 , 造成注塑件 的外 表的纹 裂或 实践 表明 , 注 射速率 偏离正常值均 会降低冲 击的强度 , 假 若注 射 析注塑件成型的影响因素以及各 类工艺参数, 经由构建合 乎实际需要 的数 飞 边 。
会 因气体 数量 的增加使 注塑件出现 空洞甚至色泽 变化等 现象 , 降低 目标便 是产生较 高品质和高使用价 值的 注塑制品 , 然而, 假若 工艺参数 时, 存在彼 此 之 间的制约 和影 响关 联, 仅凭 操作 经验是 很难 获得最 优质的 制品品质 ; 气温较 高所产生的 降解 作用, 还 会削弱注 塑件 的强度 , 降低 加 工工艺办法 的。 所 以说, 怎样将当代前沿 的优化设 计方案贯穿于聚合 其使用价值 。 物 的成 型加工之 中, 已是当下成型加工所面 临的重大课题 。
注塑工艺参数对塑料产品成型的影响
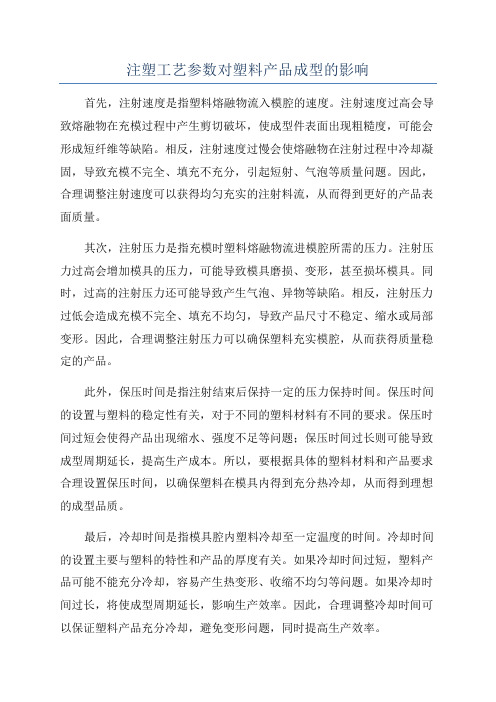
注塑工艺参数对塑料产品成型的影响首先,注射速度是指塑料熔融物流入模腔的速度。
注射速度过高会导致熔融物在充模过程中产生剪切破坏,使成型件表面出现粗糙度,可能会形成短纤维等缺陷。
相反,注射速度过慢会使熔融物在注射过程中冷却凝固,导致充模不完全、填充不充分,引起短射、气泡等质量问题。
因此,合理调整注射速度可以获得均匀充实的注射料流,从而得到更好的产品表面质量。
其次,注射压力是指充模时塑料熔融物流进模腔所需的压力。
注射压力过高会增加模具的压力,可能导致模具磨损、变形,甚至损坏模具。
同时,过高的注射压力还可能导致产生气泡、异物等缺陷。
相反,注射压力过低会造成充模不完全、填充不均匀,导致产品尺寸不稳定、缩水或局部变形。
因此,合理调整注射压力可以确保塑料充实模腔,从而获得质量稳定的产品。
此外,保压时间是指注射结束后保持一定的压力保持时间。
保压时间的设置与塑料的稳定性有关,对于不同的塑料材料有不同的要求。
保压时间过短会使得产品出现缩水、强度不足等问题;保压时间过长则可能导致成型周期延长,提高生产成本。
所以,要根据具体的塑料材料和产品要求合理设置保压时间,以确保塑料在模具内得到充分热冷却,从而得到理想的成型品质。
最后,冷却时间是指模具腔内塑料冷却至一定温度的时间。
冷却时间的设置主要与塑料的特性和产品的厚度有关。
如果冷却时间过短,塑料产品可能不能充分冷却,容易产生热变形、收缩不均匀等问题。
如果冷却时间过长,将使成型周期延长,影响生产效率。
因此,合理调整冷却时间可以保证塑料产品充分冷却,避免变形问题,同时提高生产效率。
总之,注塑工艺参数的设置对于塑料产品的成型质量和性能有着重要的影响。
通过合理调整注射速度、注射压力、保压时间和冷却时间等参数,可以获得质量稳定、表面质量良好的塑料产品。
因此,在注塑生产过程中,应根据具体的塑料材料特性和产品要求,选择合适的工艺参数,以提高注塑成型的质量和效率。
成型工艺参数对材料表面质量的影响研究
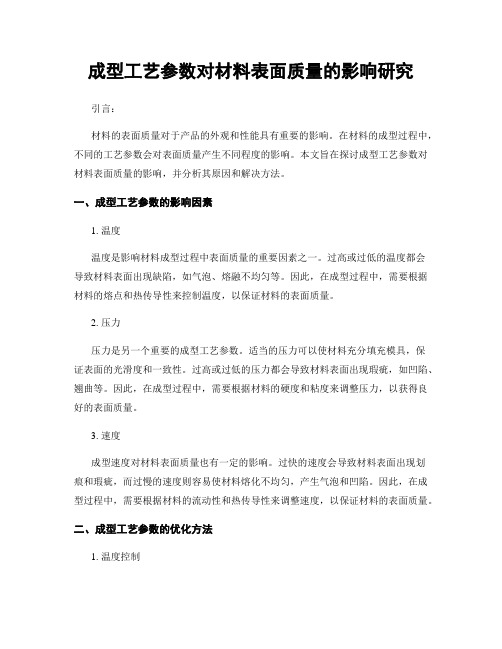
成型工艺参数对材料表面质量的影响研究引言:材料的表面质量对于产品的外观和性能具有重要的影响。
在材料的成型过程中,不同的工艺参数会对表面质量产生不同程度的影响。
本文旨在探讨成型工艺参数对材料表面质量的影响,并分析其原因和解决方法。
一、成型工艺参数的影响因素1. 温度温度是影响材料成型过程中表面质量的重要因素之一。
过高或过低的温度都会导致材料表面出现缺陷,如气泡、熔融不均匀等。
因此,在成型过程中,需要根据材料的熔点和热传导性来控制温度,以保证材料的表面质量。
2. 压力压力是另一个重要的成型工艺参数。
适当的压力可以使材料充分填充模具,保证表面的光滑度和一致性。
过高或过低的压力都会导致材料表面出现瑕疵,如凹陷、翘曲等。
因此,在成型过程中,需要根据材料的硬度和粘度来调整压力,以获得良好的表面质量。
3. 速度成型速度对材料表面质量也有一定的影响。
过快的速度会导致材料表面出现划痕和瑕疵,而过慢的速度则容易使材料熔化不均匀,产生气泡和凹陷。
因此,在成型过程中,需要根据材料的流动性和热传导性来调整速度,以保证材料的表面质量。
二、成型工艺参数的优化方法1. 温度控制通过控制加热器的温度和冷却器的温度,可以实现对材料温度的精确控制。
此外,还可以采用预热和后冷却的方式,使材料在成型过程中温度变化更加均匀,从而提高表面质量。
2. 压力控制通过调整液压系统的压力和流量,可以实现对成型过程中压力的精确控制。
此外,还可以采用多级压力和快速压力释放的方式,使材料在填充模具过程中压力分布更加均匀,从而提高表面质量。
3. 速度控制通过调整液压系统的流量和速度,可以实现对成型过程中速度的精确控制。
此外,还可以采用加速和减速的方式,使材料在填充模具和冷却过程中速度变化更加平稳,从而提高表面质量。
三、成型工艺参数的实验研究为了验证成型工艺参数对材料表面质量的影响,进行了一系列实验研究。
选取了不同的温度、压力和速度参数,并通过显微镜和表面粗糙度仪等测试设备对材料的表面质量进行了评估。
SMC模压成型工艺参数对成型质量的影响
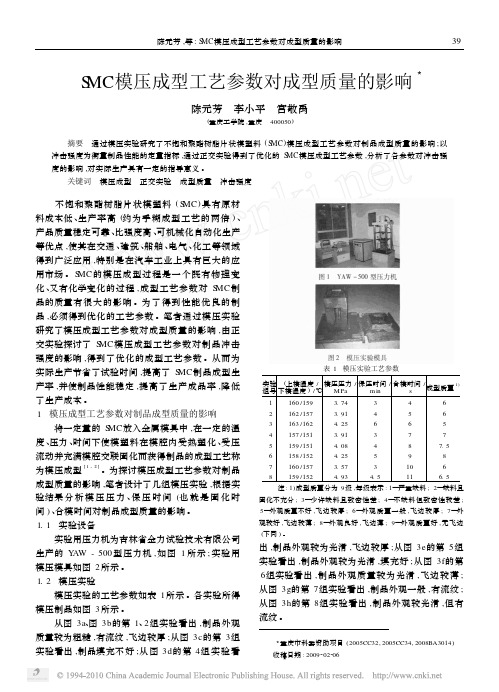
表 1 模压实验工艺参数
实验 (上模温度 / 模压压力 组号 下模温度 ) / ℃ MPa
/
保压时间 m in
/
合模时间 s
/成型质量 1)
1 160 /159
3. 74
3
4
6
2 162 /157
3. 91
4
5
6
3 163 /162
4. 25
6
6
5
4 157 /151
3. 91
3
7
7
5 159 /151
不饱和聚酯树脂 SMC模压成型过程中 ,影响制 品成型质量及性能的因素主要是模压温度 、保压时 间 、合模时间 。因此 ,在设计正交表时 ,以这几个参 数为影响因素 ,于是模压成型工艺实验的正交表为 L9 ( 34 ) 。
陈元芳 ,等 : SMC模压成型工艺参数对成型质量的影响
41
2. 2 冲击强度的正交实验 冲击实验参照 GB / T 1451 - 1983; 冲击实验机
观较好 ,飞边较薄 ; 8—外观良好 ,飞边薄 ; 9—外观质量好 ,无飞边
(下同 ) 。
出 ,制品外观较为光滑 ,飞边较厚 ;从图 3e的第 5组
实验看出 ,制品外观较为光滑 ,填充好 ;从图 3f的第
6组实验看出 ,制品外观质量较为光滑 ,飞边较薄 ;
从图 3g的第 7组实验看出 ,制品外观一般 ,有流纹 ;
陈元芳 ,等 : SMC模压成型工艺参数对成型质量的影响
39
SMC模压成型工艺参数对成型质量的影响 3
陈元芳 李小平 宫敬禹
(重庆工学院 ,重庆 400050)
摘要 通过模压实验研究了不饱和聚酯树脂片状模塑料 ( SMC)模压成型工艺参数对制品成型质量的影响 ;以 冲击强度为衡量制品性能的定量指标 ,通过正交实验得到了优化的 SMC模压成型工艺参数 ,分析了各参数对冲击强 度的影响 ,对实际生产具有一定的指导意义 。
用正交法分析注塑工艺参数对制品质量的影响

XI H o g me , LI E n - i AO a — i g Xi o p n
( c o l f e h nc l n ie r g Gu n x i v ri ,Na n n 3 0 4 C ia S h o c a ia E gn ei , a g i oM n Un e s y t n ig 5 0 0 , h n )
Hale Waihona Puke ijci lig x ei n s r d nt e lsi i et nmodn c iea cr igt h r net n modn .E p r o me t e a ma eo h a t jci ligmahn codn t e — p cn o o o
p o ie s fl eee c o u l y cn rlo rd csa d rg lt n o ne t n p o esp rme rvd su eu frn efrq ai o to fp o u t n e uai fijci r cs aa — r t o o
Ab ta t Th r c s a a ee sh v ie tifu n eo h e f r a c n u l yo ia a t sr c : ep o e sp rm tr a edr c l e c n t ep ro m n ea d q ai ffn l rsi n t p n
用 正 交 法 分 析 注 塑 工 艺 参 数 对 制 品质 量 的影 响
谢 红梅 , 廖 小平
( 广西大学 机械工程 学院, 西 南宁 广 500) 3 0 4
塑料成型工艺参数对产品质量的影响实验心得

塑料成型工艺参数对产品质量的影响实验心得
1. 温度:温度是塑料成型的重要参数,对产品的物理性能、表面质量以及尺寸稳定性都有影响。
如果温度过高,可能导致材料熔化不均匀,产生气泡或烧焦的现象;如果温度过低,则可能导致成型件不完整或收缩不足。
因此,合适的温度范围对于保证产品质量非常重要。
2. 压力:压力是保证塑料充填和充实的重要参数。
适当的压力可以确保塑料在模具中充填均匀,并充实到预定的位置,避免产生缩孔和其他缺陷。
不同的成型工艺有不同的压力要求,需要进行适当的调整。
3. 时间:成型时间直接影响到产品形状的准确性和尺寸的稳定性。
过长或过短的时间都可能导致产品质量不稳定、尺寸变化或翘曲等问题。
因此,需要根据具体材料和产品要求来调整成型时间。
4. 冷却系统:冷却是保证产品质量的关键环节。
合理的冷却系统可以确保成型件在模具中完全固化和收缩,避免变形和内应力的产生。
因此,冷却时间和温度的控制非常重要。
总的来说,塑料成型工艺参数的调整对产品质量有重要影响。
合理调整温度、压力、时间和冷却系统,可以确保产品的物理性能、表面质量和尺寸稳定性。
在实际操作中,还需要结合具体的材料和产品要求,进行综合考虑和优化调整。
注塑成型工艺参数对制品质量影响的实验研究

郑州大学硕士学位论文注塑成型工艺参数对制品质量影响的实验研究姓名:***申请学位级别:硕士专业:材料加工工程指导教师:申长雨;王利霞20060425郑州大学工学硕十学位论文图1.4简化的注塑成型设备示意图Figl-4s妇plmedInjecdonMoldingMachine1.4注塑成型质量控制发展趋势注塑成型技术已经是一项比较成熟的技术,但是随着注塑制品在家电、汽车等高科技领域的应用,对制品的质量、性能及产品更新换代提出了更高的要求。
高质量高精度高灵敏度的严格要求成为阻止塑料制品快速进入这些高尖领域的限制和束缚。
注塑成型是一个多变量的过程,在注塑成型过程中,影响制品质量的因素可以分为四类:机器参数、材料参数、工艺参数和扰动。
其中机器参数同注望成型机直接相关用以表征机器的机械特征,它包括:料筒温度、喷嘴温度、液压系统背压、螺杆旋转速度、模具温度及注塑机和模具的几何特征等。
材料参数为注塑材料的一些典型特征,一般由材料供应商提供,包括材料的流变性能、热物理性能(包括密度、分子组成、分子量、比热和热传导率等等)。
工艺参数反映了成型过程中材料的状态,受机器参数、材料参数的影响,注塑成型过程中的典型工艺参数有:熔体温度、熔体压力及它们在型腔中的分布、熔体注射速率、模具内的热流分布等等。
当然,这些参数虽然被划分在不同的范围内,但是相互之间有着密切关系,互相产生影响。
机器参数、材料参数决定了工艺参数。
对工艺参数的要求,直接影响到机器参数、材料参数的选取,从而确定出相应的注塑机和对应材料。
由于复杂的动态工艺及材料特性,使得注塑技术难以预测及控制制件的质量。
因此,如何提高注塑制品质量和性能成为该领域的重要研究课题。
注塑成型l31是复杂的多变量、非线性且具有周期性的非稳态过程。
成型过程中聚合物在型腔中的状态如压力、温度、形态等直接决定了制品的质量,因此如何实现机器设置参数和熔体状态参数之间的闭环控制成为注塑成型技术的研究热4第三章工艺参数对制品质量的交互影响分析因子之间存在交互作用15“。
注塑成型工艺参数对注塑件缩痕影响的研究

注塑成型工艺参数对注塑件缩痕影响的研究摘要:利用Moldflow软件的最佳浇口位置分析功能确定出最佳浇口位置。
研究了注塑成型工艺参数对注塑件缩痕的影响,对不同的工艺参数进行了分析,确定出用于注塑成型的较合适的工艺参数。
研究结果表明:熔体温度、模具温度的降低以及注射时间的增加都能够有效的减小缩痕。
关键词:机械;工艺参数;Moldflow;缩痕0 引言随着市场经济的快速发展,消费者的需求趋于个性化,市场环境瞬息万变。
消费者对于产品的要求越来越高,而对产品需求的变化也越来越快。
对于注塑成型产品而言,其外观形状与表面质量直接决定了该产品能否为消费者所接受。
因此,需要产品的设计人员设计出符合消费者需求的产品,而对产品的制造人员而言,则需要提高产品的质量,以满足消费者的要求。
此外,瞬息万变的市场环境要求企业缩短产品的开发周期[1-3]。
注塑成型产品是利用模具来进行生产的,因此模具的质量与开发周期直接决定了该产品能否成功的占据市场[4]。
目前,企业模具的设计主要依靠个人经验,设计的质量不高。
设计过程中手工作业太多,设计的效率低,设计的时间周期太长,留给制造调试的时间太短。
设计过程中缺乏先进的技术手段,对产品、模具进行分析、模拟,模具制造后试模的合格率低,需要反复修改、调试,延长了开发周期,增加了开发成本。
这些问题已经成为制约企业发展的瓶颈[5-7]。
在模具初步设计完成之后,可以利用CAE软件进行注塑成型分析,来发现设计中存在的缺陷,保证模具设计的合理性,提高模具的一次试模成功率,降低企业的生产成本[8]。
本文主要就注塑成型工艺参数对缩痕产生的影响这一问题进行研究。
1 实例分析本文以相机面壳为例进行分析,要求确定出最佳浇口位置,并确定出较为合理的工艺参数。
因此,需要利用Moldflow软件进行注塑模拟流动分析。
本文用三维实体造型软件Proe/E软件完成相机面壳的三维实体造型,具体几何模型如图1所示。
图2 是利用Moldflow软件划分的有限元网格。
粗糙集理论在注射成型中的应用

r utn ndt ec i ul h ta 如P由n i j eci ,a h do edi o e a r O i n u s nr st e 心地 山 o l r l a etc d em d e t r xr t g n u i ss e a e . 丁er u so t t a l i t ul o 而etnm l ,t cm 】 on bt a t h e 1 hw h i ny n i st s a n az g 1 at f ci o d eq i y o g n e i h o P xc tui e i 理f o r l cr s a e 如P i y sl cnb s l db ui 功昭hst 屺 吓 a U c a a m r c c dc o-ai rl f i e r g e 廿 。 n 犯 l r n o e oi ei nnk退 ue d ee d n s e i s I l s c e otnd a nb b i . ae Kyw 八 : uls ;妇 tnm k ; o i q l ; t bt x utn dc o ue e o如 r g e 永c o l o l t o i g n i m d u i aru e ci ; i nr ln a t g y i e do e a i l
中 发现隐 知 揭示潜在的 含的 识, 规律。 世纪印年 0 2 代以来, 关于粗糙集理论及其应用的研究逐渐成为
- 1、下载文档前请自行甄别文档内容的完整性,平台不提供额外的编辑、内容补充、找答案等附加服务。
- 2、"仅部分预览"的文档,不可在线预览部分如存在完整性等问题,可反馈申请退款(可完整预览的文档不适用该条件!)。
- 3、如文档侵犯您的权益,请联系客服反馈,我们会尽快为您处理(人工客服工作时间:9:00-18:30)。
从众 多 的 因素 中 找 出 关 键 因素 以及 不 同 因 素 间 的关 系 ,采取 有效 的对 策 和措施来 提 高塑料 制 品的质 量是
一
确定 ( ne a t) 信 息 的新 型 数 学 工 具 - 。粗 糙 集 U cr i y tn l J
理论 不 需要关 于数据 的任何初 始 或 附加信 息 ,能直接 对 不完 整 、不精确 数据 进行 分析 处理 ,发 现数 据之 间 NA L , P SnCS I NDUS TRY
第 3 5卷 第 2期
20 07年 2月
工 艺 参数 对 注 塑 成 型质 量 影 响 的粗 糙 集分 析
高 晓康 一 -,齐从 谦 ,施 雨辰 ,张 今渡
3 Sh l f rnpr& C m ui tn , h ga M r m n e i , hnh 0 3 ,C i ) . o aso c oT t o m n aos Sah i ai eU vrt Saga 2 15 h a ci n t i i sy i 0 n
Ab ta t h f c fpoesn aa tm n teisf ce tfl g po lmsi h rcs fijcin sr c :T ee eto rc sigp rmee o h n uf in ii rbe nte po eso et i ln n o
K y od : og e T er;D c i al;R d co ; dn u i ;D c i ue ew rs R uhSt o h y eio T e eut n Md igQ at sn b i l y eio R l sn s
粗 糙 集 理 论 是 一 种 处 理 含 糊 ( au ns)和 不 V g ees
modn s a ay e y u ig r u h s tt e r Th k y fcos fe t g t e q ai f modn r ee td li gwa n lz d b sn g e h oy. o e e a tr a ci h u t o l ig we e d tce n l y t r u h ati ue r d ci n a d v l e rd cin,a d t e d cso ue mp ra tt o t lte modn e ut r h o g trb t e u to n au e u to n h e iin r ls i o t o c nr li g rs ls wee n o h t u b an d.T e c s ・ ay i e ut h we hsn w ig o i t o o l mp v h bl y o a l da n ・ h s o ti e h a e a l ss rs l s o d t i e d a n ssmeh d c u d i r et ea ii ffu t ig o n s o t ss e u e da n si i d b s f li n ie rn rcie. i ,r d c ig otc t me a e u eu n e gn e g p a tc n i
力 ,减 少 了 诊 断 时 间 ,具 有 实 际 工 程 应 用 价 值 。
关 键 词 :粗 糙 集 理 论 ;决 策 表 ;约 简 ;成 型 质 量 ;决 策 规 则
中 图分 类 号 :T 3 0 6 Q 2 .6 2 文 献 标 识码 :A 文 章 编 号 :1 0 —5 7 (0 7 2 0 2 0 5 7 0 2 0 )o — O 6—0 3
Ro g e a y i fEfe t o o e sng Pa a e e u h S tAn l ss o l c f Pr c s i r m t r f
o n e t n M odn ai n Ijci lig Qu l y o t
GAO a . a g ' Xio k n  ̄
2.S h o fMe h n c la d Au o t n E g. S a g a n ttt pid T c noo y,S a g a 0 2 c o lo c a a n tmai n , h n h iI s ue o Ap le e h lg i o i f h n h i2 0 33, Chn i a;
(. I 同济 大 学 机 械 工 程 学 院 ,上 海 209 ; . 海 应 用 技 术 学 院机 械 与 自动 化 工 程 学 院 ,上海 203 ; 002 2 上 023
3 上海 海 事 大 学 交 通 运 输 学 院 ,上 海 2 0 3 ) . 0 15
摘 要 :用粗 糙 集 理 论 ,分 析 了 注 塑 成 型 过 程 中工 艺 参 数 对 成 型 不 足 问题 的 影 响 。 通 过 属 性 约 简 和 值 约 简 ,找 出影 响成 型 质 量 的 关键 因 素 ,从 而 得 到 判 断 成 型 结 果 的 决 策 规 则 。实 例 分 析 表 明 ,这 种 新 的诊 断 方 法 提 高 了故 障 诊 断 能
,
Q ogqa S I uc e3 Z A G J .u ICn .i , H . n , H N i d 2 n Y h n
( . c ol f e hn a E g , o g nvr t, h n h i 0 0 2 C i ; 1 Sh o o ca i l n . T nj U e i S a g a 2 0 9 , h a M c i i sy n