用PLC实现分段液位的控制
封闭式液位控制系统的PLC分段PID控制方法

S (+ ) 3 2 :输 入 滤波 常数O ; L S (+ ) 3 3 :比例增 益 ;
S (+ ) 3 4 :积 分 时 间 T I;
图 3 通 用 PD控 制 程 序 I
增 益 越 大 ,系 统调 节 时 间越 短 ,但 系统稳 定 性
致 ,如 果 不一 致 ,则 需要 进 行 液位 显 示 校 正 ,可 采用 线 性 变换 的方 式 进行 转 换 校 正 。例 如 :如果 测 量 值 的范 围是 2 O一10 2 ,对 应 的 液 位 显 示 刻 度 为 :0~2 0 m,则 需要 通 过 线 性 变 换 将 2 2m 0~10 2 映射 成 0 2 ,可采用 如下 方法 。 ~2 0 设 测 量 值 为 自变 量 ,液 位 显 示 值 为 因 变 量 ,
由于 该 封 闭式 液 位 控 制 系 统 的特 殊 性 ,采 用
上述 的P 控制方法 ,无论怎样设置参数 ,系统性 I 能都不理想 ,要么超调量过大 ,要 么控制时间过
长 。 如果 采 用 分段 PD控 制 ,当 偏 差较 大 时 ,将 I 比例 作 用 和 积 分作 用 增 强 , 当偏 差 较 小 时 ,将 比
系统性 能 ,达 到调 节 时间短 且无超 调性 能 。
2 P C的 PD指 令 L I
以三 菱 F X系 列 P C为 例 ,P C的 PD指 令 L L I 】
如图2 所示 。
I X 0 06
⑧
⑧
⑨
①
l
0 '0 O 5 卜[ PI D2 I3 D6 O D1 0 H _ D
od roe sr ooesot n hr ajsn me h emett nPDcnrl to ail. codn egpbt ente re nue vrh o adsot dut gt ,tesg nao I otomeh di f s e A crigt t a ew e t n i i i se b oh h
用PLC实现多种液体自动混合控制
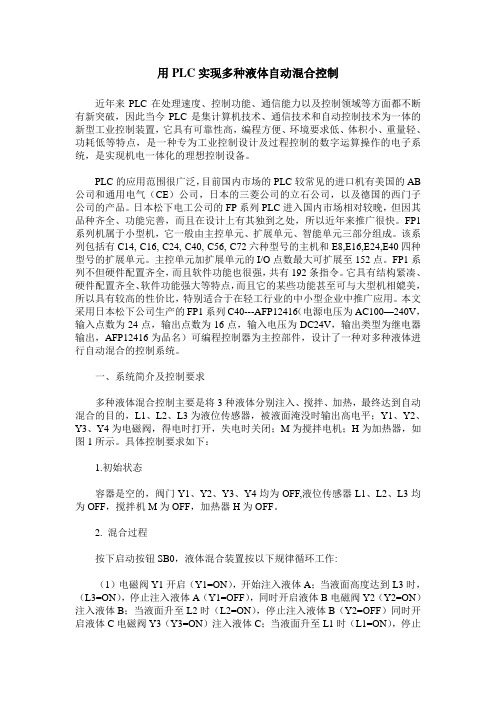
用PLC实现多种液体自动混合控制近年来PLC在处理速度、控制功能、通信能力以及控制领域等方面都不断有新突破,因此当今PLC是集计算机技术、通信技术和自动控制技术为一体的新型工业控制装置,它具有可靠性高,编程方便、环境要求低、体积小、重量轻、功耗低等特点,是一种专为工业控制设计及过程控制的数字运算操作的电子系统,是实现机电一体化的理想控制设备。
PLC的应用范围很广泛,目前国内市场的PLC较常见的进口机有美国的AB 公司和通用电气(CE)公司,日本的三菱公司的立石公司,以及德国的西门子公司的产品。
日本松下电工公司的FP系列PLC进入国内市场相对较晚,但因其品种齐全、功能完善,而且在设计上有其独到之处,所以近年来推广很快。
FP1系列机属于小型机,它一般由主控单元、扩展单元、智能单元三部分组成。
该系列包括有C14, C16, C24, C40, C56, C72六种型号的主机和E8,E16,E24,E40四种型号的扩展单元。
主控单元加扩展单元的I/O点数最大可扩展至152点。
FP1系列不但硬件配置齐全,而且软件功能也很强,共有192条指令。
它具有结构紧凑、硬件配置齐全、软件功能强大等特点,而且它的某些功能甚至可与大型机相媲美,所以具有较高的性价比,特别适合于在轻工行业的中小型企业中推广应用。
本文采用日本松下公司生产的FP1系列C40---AFP12416(电源电压为AC100—240V,输入点数为24点,输出点数为16点,输入电压为DC24V,输出类型为继电器输出,AFP12416为品名)可编程控制器为主控部件,设计了一种对多种液体进行自动混合的控制系统。
一、系统简介及控制要求多种液体混合控制主要是将3种液体分别注入、搅拌、加热,最终达到自动混合的目的,L1、L2、L3为液位传感器,被液面淹没时输出高电平;Y1、Y2、Y3、Y4为电磁阀,得电时打开,失电时关闭;M为搅拌电机;H为加热器,如图1所示。
具体控制要求如下:1.初始状态容器是空的,阀门Y1、Y2、Y3、Y4均为OFF,液位传感器L1、L2、L3均为OFF,搅拌机M为OFF,加热器H为OFF。
基于PLC的变频器液位控制设计

结 构框 图 , 然后 在根据 工艺要 求 , 绘制 出各功 能单 元的详细功 能框 图。 4 3编 写程序 . 编写 程序就 是 根据设 计 出的 框 图逐 条地
编写控制 程序 , 这是整个 程序设计 工作的核心
部分 。 4 4 程 序测试和 调试 . 程序 测试和调试 不 同 , 软件测试 的 目的是 尽 可能 多地 发现软件 中的错误 , 软件调 试的任 务是 进一 步 诊 断和 改正 软 件 中的错 误 。 4 5 编 写程序说 明书 . 程序说 明书是对 程序的综 合说 明 , 是整个 程 序 设 计 工 作 的总 结 。 图 1 系统设计流 程 图。 是
维普资讯
2Q Q: Q!
Sc en a Tech ogY i ce nd nol Consu tng I i Her d al
工 业 技 术
基于 P C的变频器 液位控制设计 L
张 斌 ( 哈工ห้องสมุดไป่ตู้ 电子仪器 厂 )
摘 要: 随着 电力电子技术以及工业 自动控制技术的发展 , 得交流变频调 速系统在工业 电机 拖动领域得 到了广泛应用 。另外 , 使 由于 P C L 的功能 强大、容 易使 用、高可靠性 , 常常被用 来作为现场数据 的采集 和设 备的控制 。 本设计就是利 用变频 器和 PL C实现水 池水位的控
的选 用高性 能的 P C, 全能够 胜任 此功 能 。 L 完 系统 控制结构 如 图 l 示。 所 P C采集 传感 器 、监 控 电机及变 频器等 L 有关 的各类对象 的信息 。本 系统 中, 电机采 对 用一 台变 频 器来进 行频 率 的调节 控制 。采用 P C输 出 的模拟量 信号作 为变频 器的控 制端 L 输 入 信号 , 而 控制 电机 转 速大 小 , 从 并且 向 P LC反馈 自身 的工 作状 态信号 , 当发生 故障 时, 能够 向 P C 出报警信号 。由于变 频调速 L 发 是通 过改 变 电动机 定子 供 电频率 以改 变 同步 转速来 实现 的 , 故在调 速过 程 中从 高速到 低速 都可 以保 持 有 限的 转 差功 率 , 此具 有 高效 因 率 、宽范 围、高精 度的调速 性 能。
分段液位的PLC控制

② 采用 主控指令 ,通过X1 旋钮 实现手动/ 2 自动两
种 功 能 的 选 择 , 当X1旋 钮 闭合 时 , 自动 指 示 灯 亮 ,系 2 统 执 行 主 控 内程 序 , 完 成 自动 监 控 ; 当x1 旋 钮 打 开 2 时 ,手 动 指 示灯 亮 ,系 统 执 行 分 支 外 程 序 ,通 过 X1 、 0 X1旋 钮 实 现 手动 启 泵 、停 泵 。 2
P C内部 器件 说 明 L
最低 液位 指 示灯 Y 0 较低 液位 指 示灯 Y 1 较高 液位 指示 灯 Y 2 最 高痕 位 指示灯 y 3 电子 音响 Y q 手动指 示 灯 Y 5 自动 指 示灯 Y 6 料 泵 Y 7
最低液 位标 志 M O 较低液位标志 M 1 较高 液位标 志 M 2 最高液 位标 志 M3
5 8
JNY应 。 用 TL技 E。 术 cG H
分 段 液位 的P C 制 L控
李 丽 霞 ( 南 化 工职 业技 术 学 院 湖 南 株 洲 湖 4 0 4) 1 0 2
摘 要 :本 文主要 介 绍如 何使 用P C实现 多段 液位 的设 定 、显 示 、报 警和 液 位 的 自动 控 制 。 L 关 键 词 : P C;液位 ;监 控 L
32接 线 图 (图1) .
格 比 ,选择 可靠性高 ,功 能相 当 ,负载 能力合适 ,经 济实惠的P C L 。本文介绍 以四段液位控制对象为例 ,据
4系统软 件设计 .
41 制程 序 思路 流。L 。GY 技 术应 用
l 5 9
最 位 低 较 位 氍 较 位 高 最 位 高
基于PLC的液位控制系统设计_图文

课程设计说明书名称2010年 6月7日至 2010年6月11日共 1 周院系班级姓名学号系主任教研室主任指导教师目录绪论 . (2)第1章液位控制系统总体方案设计 . (3)1.1单回路控制系统 (3)1.2水箱液位的串级控制系统 (4)第2章过程控制装置概述 . (6)2.1系统简介 (6)2.2系统装置 (7)2.3 S7-300PLC 控制柜的组成 . (8)第3章硬件组态设计 . (10)3.1PLC 的选择 (10)3.2组态硬件 (11)第4章软件组态设计 . (12)4.1 实现WINCC 与S 7-300的软件通讯 (12)4.2 程序设计 (15)第5章调试过程及结果分析 . (20)5.1单容液位控制系统调试结果及分析 (20)5.2双容串级液位控制系统调试结果及分析 (23)第6章课程设计总结 . (26)参考文献: . (27)绪论课程设计是检验我们本学期学习的情况的一项综合测试,它要求我们把所学的知识全部适用,融会贯通的一项训练,是对我们能力的一项综合评定,它要求我们充分发掘自身的潜力,开拓思路设计出合理适用的自动控制系统。
课程设计也是教学过程中的一个重要环节,通过设计可以巩固各课程理论知识,培养独立分析和解决实际工程技术问题的能力,同时对工业的有关方针、技术规程有一定的了解,在计算绘图、编号、设计说明书等方面得到训练,为以后工作奠定基础。
工业生产过程控制是现代工业自动化的一个重要领域。
它是控制理论、生产工艺、计算机技术和仪器仪表等知识相结合的一门综合性应用学科,理论性、综合性和实践性都很强。
随着人们物质生活水平的提高以及市场竞争的日益激烈,产品的质量和功能也向更高的档次发展,制造产品的工艺过程变得越来越复杂,为满足优质、高产、低消耗,以及安全生产、保护环境等要求,做为工业自动化重要分支的过程控制的任务也愈来愈繁重。
在控制方式上经历了从人工控制到自动控制两个发展时期。
在自动控制时期内,过程控制系统又经历了三个发展阶段, 它们是:分散控制阶段, 集中控制阶段和集散控制阶段。
基于PLC技术的液位控制系统设计
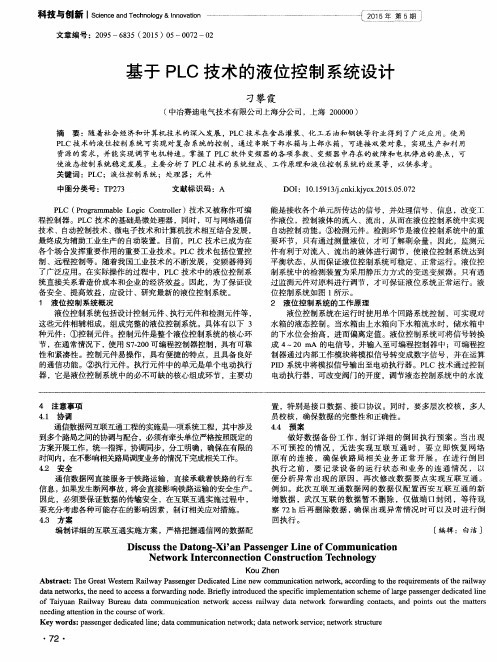
置 ,特别是接 口数 据 、接 口协议 。同时 ,要多层 次校核 ,多人 员校核 ,确保数据 的完整性和正确性 。 4 . 4 预 案 做好 数据备 份 工作 ,制订 详 细 的倒 回执行 预 案 。当出 现 不 可 预控 的情 况 ,无法 实 现 互联 互 通 时 ,要 立 即恢 复 网 络 原 有 的 连接 ,确 保 铁路 局 相 关 业务 正 常 开展 。在 进 行 倒 回 执 行 之 前 ,要 记 录设 备 的运 行 状态 和 业 务 的 连通 情 况 ,以 便 分 析异 常 出现 的原 因 ,再 次修 改数据 要点 实现 互联互 通 。 例 如 。此 次互联 互通 数据 网 的数 据仅 配置 西安互 联互 通 的新 增 数据 ,武汉 互联 的数据 暂不删 除 ,仅做 端 口封 闭 ,等待 观 察7 2 h后再 删 除数 据 , 确保 出现异 常情况 时可 以及 时进行 倒
关 键 词 :P L C;液 位 控 制 系统 ; 处理 器 ;元 件
中图分类号 :T P 2 7 3
文献标识码 :A
D OI :1 0 . 1 5 9 1 3  ̄ . c n k i . k j y c x . 2 0 1 5 . 0 5 . 0 7 2
P L C( P r o g r a mma b l e L o g i c C o n t r o l l e r ) 技术又被称作可编 程控制器 。P L C技术 的基础是微处理器 ,同时 ,可与 网络通信 技术 、自动控制技术 、微电子技术和计算 机技术相互结合 发展 , 最终成为辅助工业生产 的自动装置 。目前 ,P L C技术 已成为在 各个场合发挥重要作用 的重要工业技术 。P L C技术包括位置控 制 、远程控制等 。随着我国工业技术的不断发展 ,变频器得 到 了广泛应用 。在实际操作 的过程 中,P L C技术 中的液位控制 系 统直接关 系着造 价成 本和企业的经济效益 。因此 ,为 了保证设 备安全 、提 高效益 ,应设计 、研究最新 的液位控制系统 。 1 液位控制 系统概况 液位控制系统包括设计控制元件 、 执行元件和检测元件等 , 这些元件相 辅相成 ,组成完整的液位控制系统 。具体有 以下 3 种元件 :① 控制元件。控制元件是整个液位控制系统 的核 心环 节 ,在通常情况下 ,使用 s 7 . 2 0 0 可 编程控制器控制 , 具 有可 靠 性 和紧凑性。控制元件易操作 ,具有便捷 的特 点 ,且具 备 良好 的通信 功能。②执行元件 。执行元件 中的单元是单个 电动执行 器 ,它是液位控制系统 中的必不可缺 的核 心组成环 节 ,主要功
基于PLC的液位控制系统研究毕业设计(论文)

毕业设计论文基于PLC的液位控制系统研究摘要本文设计了一种基于PLC的储罐液位控制系统。
它以一台S7-200系列的CPU224和一个模拟量扩展模块EM235进行液位检测和电动阀门开度调节。
系统主要实现的功能是恒液位PID控制和高低限报警。
本文的主要研究内容:控制系统方案的选择,系统硬件配置,PID算法介绍,系统建模及仿真和PLC编程实现。
本设计用PLC编程实现对储罐液位的控制,具有接线简单、编程容易,易于修改、维护方便等优点。
关键字:储罐;液位控制;仿真;PLCAbstractThis article is designed based on PLC, tank level control system. It takes a series s7-200 CPU224 and an analog quantities of EM235 expansion module to level detection and electric valve opening regulation.System main function is to achieve constant low level PID control and limiting alarm.The main contents of this paper: the choice of the control system plan, system hardware configuration, PID algorithm introduced, system modeling and simulation, and PLC programming. PLC programming with the design of the tank level control have the advantage of simple wiring, easy programming, easy to modify, easy maintenance and so on.Key word: tank ; level ;control ;simulation ;plc目录摘要 (I)ABSTRACT ........................................................... I I 1 绪论. (1)1.1盐酸储罐恒液位控制任务 (1)1.2本文研究的意义 (2)1.3本文研究的主要内容 (2)2 控制系统方案设计 (3)2.1储罐液位控制的发展及现状 (3)2.2系统功能分析 (3)2.3系统方案设计 (4)3 系统硬件配置 (5)3.1电动控制阀的选择 (5)3.1.1 控制阀的选择原则 (5)3.1.2 ZAJP 精小型电动单座调节阀性能和技术参数介绍 (10)3.2液位测量变送仪表的选择 (13)3.2.1 液位仪表的现状及发展趋势 (13)3.2.2 差压变送器的测量原理 (13)3.2.3 差压式液位变送器的选型原则 (14)3.2.4 DP系列LT型智能液位变送器产品介绍 (15)3.3PLC机型选择 (16)3.3.1 PLC历史及发展现状 (16)3.3.2 PLC机型的选择 (18)3.3.3 S7-200系列CPU224和EM235介绍 (20)4 PID算法原理及指令介绍 (21)4.1PID算法介绍 (22)4.2PID回路指令 (24)5 系统建模及仿真 (28)5.1系统建模 (28)5.2系统仿真 (30)5.2,1 MATLAB语言中Simulink交互式仿真环境简介 (30)5.2.2 系统仿真 (31)第6章系统编程实现 (33)6.1硬件设计 (33)6.1.1 绘制控制接线示意图 (33)6,1.2 I/O资源分配 (33)6.2软件设计 (34)6.2.1 STEP 7 Micro/Win V4.0 SP6编程软件介绍 (34)6.2.2 恒液位PID控制系统的PLC控制流程 (35)6.2.3 编写控制程序 (36)6.2.4 程序清单 (39)结束语 (40)参考文献 (41)致谢 (42)1 绪论1.1 盐酸储罐恒液位控制任务如图1.1所示为某化工厂稀盐酸储罐,该罐为钢衬聚四氟乙烯储罐,罐体高6米,容量为50立方米,重500千克。
基于PLC的液位控制系统设计

毕业设计开题报告1. PID 简述简述 过程控制通常是指石油、化工、冶金、轻工、纺织、制药、建材等工业生产过程中的自动控制程中的自动控制,它是自动化技术的一个极其重要的方面。
本次毕业设计是基于PLC 的液位控制系统的设计,它的控制对象是水箱的液位,是过程控制中经常遇到热工参数。
本人在这次设计中主要负责控制策略——PID 算法的确定,就在次将PID 算法作个简要的介绍。
算法作个简要的介绍。
在生产过程自动控制的发展历程中在生产过程自动控制的发展历程中,PID ,PID 控制是历史最久、生命力最强的基本控制方式。
它简单实用制方式。
它简单实用,,易于实现易于实现,,适用范围广适用范围广,,鲁棒性好鲁棒性好,,在现今的工业过程中获得了广泛的应用广泛的应用..据统计据统计,,目前工业控制器中约有90%90%仍是仍是PID 控制器。
PID 控制器的设计及其参数整定一直是控制领域所关注的问题。
其设计和整定方法得到国内外广泛研究, 著名的如Ziegler-Nichols 法、基于内模控制的方法及基于误差的积分的优化方法。
基于误差的积分准则由于能较好地反映闭环系统的性能以及易于计算的原因基于误差的积分准则由于能较好地反映闭环系统的性能以及易于计算的原因,,在PID 优化设计中被广泛采用。
(1)在工业生产过程控制中,模拟量的模拟量的 PID (比例、比例、积分、积分、微分)调节是常见的一种控制方式,这是由于这是由于PID 调节不需要求出控制系统的数学模型,至今为止,很难求出许多控制对象准确的数学模型,对于这一类系统,使用使用PID 控制可以取得比较令人满意的效果,同时同时PID 调节器又具有典型的结构,可以根据被控对象的具体情况,采用各种PID 的变种,有较强的灵活性和适用性。
在模拟量的控制中,经常用到经常用到PID 运算来执行来执行PID 回路的功能,PID 回路指令使这一任务的编程和实现变得非常容易。
如果一个果一个 PID 回路的输出回路的输出M ( t)是时间的函数,则可以看作是比例项、积分项和微分项三部分之和(2),即:,即:dt de K M edt K e K t M C tc C *+++*=⎰00)( 式中式中 e ——偏差;——偏差;T i ——积分常数;——积分常数;T d ——微分常数;——微分常数;K c ——放大倍数(比例系数)——放大倍数(比例系数)M 0——偏差为零时的控制值,有积分环节存在,此项也可不加——偏差为零时的控制值,有积分环节存在,此项也可不加以上各量都是连续量,第一项为比例项,最后一项为微分项,中间两项为积分项。
PLC液位控制程序

1.控制要求控制系统可以根据生产的需要将液位分为多段来设定,并分段显示,当液位为最低限时自动启动料泵加液,液位到达设定值时发出声光报警,并停泵;操作人员可通过确认按钮解除音响报警信号,闪烁灯光转平光;系统具有手动/自动两种控制方式,并设有试验功能。
2.PLC选型目前在国内市场上有从美国、德国、日本等国引进的多种系列PLC,国内也有许多厂家组装、开发数十种PLC,故PLC系列标准不一,功能参差不齐,价格悬殊。
在此情况下,PLC的选择应着重考虑PLC的性能价格比,选择可靠性高,功能相当,负载能力合适,经济实惠的PLC。
本文介绍以四段液位控制对象为例,据对多种因素的分析比较及监控系统输入、输出点数的要求,选用日本立石(OMRON)公司C20P型PLC。
3.系统硬件配置为实现液位的手动/自动控制,需要输入口12点,输出口8点,选用C20P 20点I/O单元的PLC,输入光电隔离,输出继电器隔离,负载能力强;液位检测采用干簧管传感器,手动/自动转换、运行/试验转换和液位设定采用双位旋钮,手动启泵、停泵和确认、试验采用常开按钮;输出选用电子音响报警器和24V直流指示灯、继电器。
参见图一系统硬件配置图。
图一系统硬件配置图为节省输入口数量,节省投资,本系统运行/试验功能的转换采用了对I/O模块接线的优化,使PLC输入模块中1个输入节点起到2个输入节点的作用,完成PLC工作在两种方式下的I/O功能。
参见图二I/O模块接线的优化。
图二I/O模块接线的优化来4.系统软件设计4.1 控制程序流程图图三系统流程图4.2 编程说明①本系统为液位的双位控制系统。
液位可分四段设定和显示,在最低液位时自动启泵,当液位到达设定值时自动停泵。
②采用IL/ILC分支指令,通过0008旋钮实现手动/自动两种功能的选择,当0008旋钮闭合时,自动指示灯亮,系统执行IL/ILC分支内程序,完成自动监控;当0008旋钮打开时,手动指示灯亮,系统执行分支外程序,通过0010、0011旋钮实现手动启泵、停泵。
基于PLC与组态王的液位控制系统设计与实现

控制对其参数整定,并利用组态王软件构建组态环境进行调试 结果表明,采用 P I E ) 控制算法实现对液位的控制,系统运
行平稳 ,超调量为 1 1 %,调节时 间大概为 3 mi n ,能够基本 满足液位控制要求。
关键字:P L C;液位控制;组态;P I D控 制 中图分类号:T P 2 7 3 文献标识码 :A 文章编号:1 6 7 3 - 2 2 1 9( 2 0 1 3 )0 8 - 0 0 2 4 - 0 4
参数 ,阀门的进水量 Q1 为控制变量 。如果 QI = Q2时,系统处于平衡 状态 ,此时的液位为 给定值 h ,假定某一时刻 ,阀门 1
突然开大
,导致 Q 1 进 水量变大 ,平衡 被打破则会 引起
—
h 液位开始变化 。于是有 :
( 2 - 1 )
d A h ( △ Q l 一 △ Q 2 ) : — A
0 引 言
液位是过程控制系统中非常普遍 的被控对象 ,液位控制涉及工控领域广泛 ,同时液位控制具有非线性及滞后性等特点 ,
常规控制方法往往难以满足控制要求 ,因此液位控制系统 的可业 生产
控制环境下 , P L C的高可靠性及稳定性得到广泛应用 , 组态软件能够完成对现场数据 的采集、实时 曲 线 和历史曲线的 显示 、 在线修改控制参数及报表输 出等功能 而被 广泛应用。本文介绍 的液位控制系统结合 P L C技 术和组态 王软件实现液位控制 , 对控制过程进行实 时整定及在线监控 ,具有控 制灵 活方便 、显示直观及控制效果好等优点 。
调节阀选用气体打开式,如果液位大于给定,则 P L C输出信号减小使阀门开度减小 ,液位降低,反之则升高。系统 自动运
行调节使液位高度维持到工艺要求 范围内【 j J 。
基于PLC的液位控制系统设计

2024年7月16日
11
基于PLC的液位控制系统设计
液位控制系统的硬件组成
计算机液位控制系统电路图如图所示。在本控制系统中、用计算机实现控 制算法, PLC控制系统带有A/D模块SM331和D/A模块SM332。电动调节阀作为 执行机构。
控制系统硬件电路连接图
2024年7月16日
12
基于PLC的液位控制系统设计
液位变送器 : 采用液位变送器 BP800采用工业用的扩散硅压力变送器, 含不绣钢隔离膜片,同时采用信号隔离技术,对传感器温度漂移跟随补 偿 。压力传感器用来对上水箱和下水箱的液位进行检测,变送器为二 线制,故工作时需串接24VDC电源 。
电动调节阀 : 采用智能型电动调节阀,用来进行控制回路流量的调节。。 电动调节阀号为: QSVP-16K。具有精度高、技术先进、体积小、重量轻、 推动力大、功能强、控制单元与电动执行机构一体化、可靠性高、操作 方便等优点,控制信号为4—20mADC或1—5VDC,输出4—2OmADC的阀位信 号,使用和校正非常方便。
2
基于PLC的液位控制系统设计
建立数学模型
被控对象的数学模型 :
将Q1作为被控过程的输入变量,h为其输出变量,则该被控过程的数学模型 就是h与Q1之间的数学表达式。根据动态物料平衡关系有:
2024年7月16日
3
基于PLC的液位控制系统设计
表示为增量形式:
式中: ΔQ1,ΔQ2,Δh分别为偏离某一平衡状态的增量;A为水箱截 面积。
基于PLC的液位控制系统设计
本文设计的主要目的是控制下水箱的液位。使下水箱的 液位在某一比较小的范围变化。
研究对象是双容水箱的串级系统。 液位控制系统的组成:
控制器 电动调节阀 上水箱、下水箱 液位变送器等 电动调节阀用于调节上水箱的进水量大小,液位变送器 用于检测上水箱和下水箱的液位。控制器的输出量用于控制 调节阀的开度。
基于PLC的变频器液位控制设计

基于PLC的变频器液位控制设计随着电力电子技术以及工业自动控制技术的开展,使得交流变频调速系统在工业电机拖动领域得到了广泛应用。
另外,由于PLC的功能强大、容易使用、高可靠性,常常被用来作为现场数据的采集和设备的控制。
本设计就是利用变频器和PLC实现水池水位的控制。
变频器技术是一门综合性的技术,它建立在控制技术、电子电力技术、微电子技术和计算机技术的根底上。
它与传统的交流拖动系统相比,利用变频器对交流电动机进展调速控制,有许多优点,如节电、容易实现对现有电动机的调速控制、可以实现大*围内的高效连续调速控制、实现速度的准确控制。
容易实现电动机的正反转切换,可以进展高额度的起停运转,可以进展电气制动,可以对电动机进展高速驱动。
完善的保护功能:变频器保护功能很强,在运行过程中能随时检测到各种故障,并显示故障类别(如电网瞬时电压降低,电网缺相,直流过电压,功率模块过热,电机短路等),并立即封锁输出电压。
这种“自我保护〞的功能,不仅保护了变频器,还保护了电机不易损坏。
PLC特点:第一,可靠性高、抗干扰能力强,平均故障时间为几十万小时。
而且PLC采用了许多硬件和软件抗干扰措施。
第二,编程简单、使用方便目前大多数PLC采用继电器控制形式的梯形图编程方式,很容易被操作人员承受。
一些PLC还根据具体问题设计了如步进梯形指令等,进一步简化了编程。
第三,设计安装容易,维护工作量少。
第四,适用于恶劣的工业环境,采用封装的方式,适合于各种震动、腐蚀、有毒气体等的应用场合。
第五,与外部设备连接方便,采用统一接线方式的可拆装的活动端子排,提供不同的端子功能适合于多种电气规格。
第六,功能完善、通用性强、体积小、能耗低、性能价格比高。
在应用PLC系统设计时,应遵循以下的根本原则,才能保证系统工作的稳定。
〔1〕最大限度地满足被控对象的控制要求;〔2〕系统构造力求简单;〔3〕系统工作要稳定、可靠;〔4〕控制系统能方便的进展功能扩展、升级;〔5〕人机界面友好。
基于PLC的液位控制
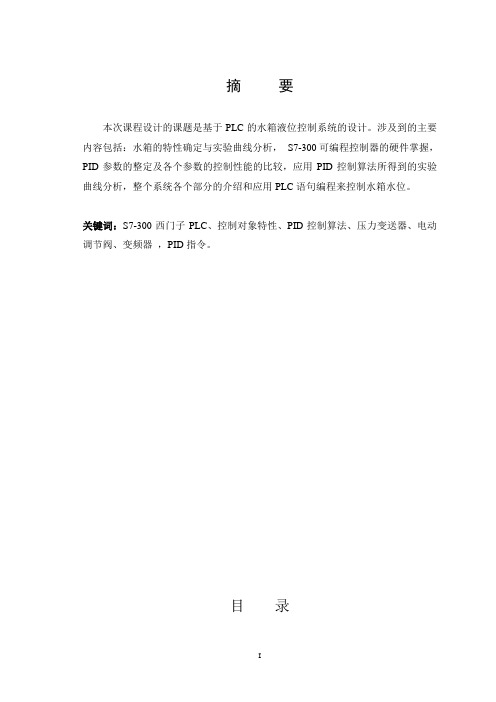
摘要本次课程设计的课题是基于PLC的水箱液位控制系统的设计。
涉及到的主要内容包括:水箱的特性确定与实验曲线分析,S7-300可编程控制器的硬件掌握,PID参数的整定及各个参数的控制性能的比较,应用PID控制算法所得到的实验曲线分析,整个系统各个部分的介绍和应用PLC语句编程来控制水箱水位。
关键词:S7-300西门子PLC、控制对象特性、PID控制算法、压力变送器、电动调节阀、变频器,PID指令。
目录摘要 (I)第1章引言 (1)1.1 实验目的 (1)1.2 实验原理 (1)1.3 设计方案的确定 (2)第2章系统硬件介绍 (2)2.1 西门子PLC控制系统简介 (2)2.3模拟量输入模块 (3)2.4模拟量输出模块 (3)2.5 电源模块 (4)第三章系统硬件控制设计 (5)3.1 系统设计 (5)3.2 硬件设计 (6)3.2.1 检测单元 (6)3.2.2 执行单元 (7)第四章软件设计 (8)4.1 FC105 介绍: (8)4.2 FC 106 介绍: (8)4.3 FB41 介绍 (9)4.4 软件控制流程图: (10)第五章程序实现 (10)5.1 step 7 软件编程: (10)5.2程序调试与结果 (15)5.3 过程中出现的问题与解决办法 (15)第6章实验心得与体会 (19)附录:程序清单 (20)参考文献 (24)第1章引言1.1 实验目的1熟悉可编程序控制器的工作原理、主要参数、硬件结构、模块特性、安装配置及指令系统、程序设计、调试方法。
2、熟悉S7-300模拟量模块的工作原理,掌握硬件安装接线的方法及软件的设置及编程。
3、掌握模拟量模/数、数/模转换的原理,输入输出编程方法及STEP7开发环境的使用。
4 掌握过程控制的中pid的调节方法,实现液位的自由控制。
1.2 实验原理本次实验采用PLC 控制,将液位控制在设定高度,根据上水箱液位信号输出给PLC ,PLC根据P I D 参数进行PID 运算,输出信号给变频器,然后由变频器控制水泵供水系统的进水流量,从而达到控制液位的恒定的目的。
基于PLC的液位控制系统设计设计

基于PLC的液位控制系统设计设计一、设计背景:液位控制系统是工业自动化领域中常见的一种工艺控制系统,用于控制容器内液体的液位。
液位控制系统在化工、冶金、电力、制药等行业中广泛应用,对于保证生产过程中液位的稳定和控制具有重要意义。
基于PLC的液位控制系统可以实现对液位的精确控制和自动化操作,提高生产效率和产品质量。
二、设计原理:三、系统组成:1.传感器:用于检测容器内液体的液位变化,并将液位信号转换为电信号,传输给PLC;2.信号处理模块:对传感器传输过来的信号进行调理和处理,将处理后的信号传输给PLC;3.PLC:作为控制核心,接收信号处理模块传输过来的信号,并根据事先设定的控制策略进行逻辑控制;4.执行机构:根据PLC控制信号对容器内液体进行加输或排泄操作,以控制液位的变化;5.人机界面:通过触摸屏或键盘等控制输入设备,实时监控和调整液位控制系统的参数,以及实施手动控制。
四、设计步骤:1.确定液位控制系统的控制目标和要求:根据具体的应用场景,确定液位的目标值、控制精度、稳定性要求等;2.选择合适的传感器:根据液体的性质和工业环境,选择适合的液位传感器,如浮子式液位传感器、压力式液位传感器等;3.确定信号处理模块:根据传感器输出的信号特点,确定合适的信号处理模块,对传感器信号进行调理和处理,以适应PLC输入信号的要求;4.PLC逻辑控制程序设计:根据液位控制系统的控制目标和要求,设计PLC的逻辑控制程序,包括液位目标设定、控制策略、输出控制信号等;5.确定执行机构:根据液体的加输或排泄要求,选择适当的执行机构,如电动阀门、气动阀门等;6.进行系统的连接和调试:将传感器、信号处理模块、PLC、执行机构按照设计要求进行连接,并进行系统的调试和测试,确保系统的功能正常;7.人机界面设计和实施:根据液位控制系统的需要,设计合适的人机界面,以实现参数设置、控制操作、故障诊断等功能。
五、优势与应用:1.精度高:PLC控制系统可以实现对液位的精确控制,提高控制精度和稳定性;2.自动化程度高:PLC可以根据设定的控制策略进行自动化控制操作,减少人工操作,提高生产效率;3.可靠性强:PLC控制系统具有较强的抗干扰能力,能够稳定运行,并且具有自动故障诊断功能,便于维护和排除故障;4.灵活性好:PLC控制系统可以根据实际需求进行灵活配置和调整,适应不同的液位控制要求。
基于PLC的液位控制系统毕业设计论文

基于PLC的液位控制系统毕业设计论文目录1. 内容概述 (2)1.1 研究背景 (3)1.2 研究目的 (4)1.3 研究意义 (4)1.4 国内外研究现状 (5)1.5 论文结构 (6)2. PLC控制系统基础 (7)3. 液位控制系统需求分析 (9)3.1 系统概述 (10)3.2 系统功能需求 (11)3.3 系统性能指标 (12)3.4 系统设计约束 (14)4. 液位控制系统硬件设计 (15)4.1 硬件组成及连接方式 (17)4.2 传感器选型及安装方式 (18)4.3 执行器选型及安装方式 (20)4.4 PLC选型及安装方式 (22)4.5 电气接线及调试 (24)5. 液位控制系统软件设计 (24)5.1 软件架构设计 (26)5.2 控制算法设计 (28)5.3 PLC程序编写 (29)5.4 仿真与调试 (31)6. 系统集成与测试 (33)6.1 系统集成方案设计 (34)6.2 系统测试与验证 (36)6.3 结果分析与讨论 (37)7. 结论与展望 (38)7.1 研究成果总结 (39)7.2 进一步研究方向建议 (40)1. 内容概述本毕业设计论文旨在深入研究和探讨基于可编程逻辑控制器(PLC)的液位控制系统设计与实现。
通过系统化的设计流程,结合理论分析与实际应用,全面阐述PLC在液位控制中的关键作用及其优化策略。
随着工业自动化技术的不断发展,液位控制作为工业生产过程中的重要环节,其精确性和稳定性对于保障产品质量和生产效率具有至关重要的作用。
PLC作为一种高效、可靠的工业控制设备,在液位控制领域得到了广泛应用。
本研究将围绕基于PLC的液位控制系统展开深入研究。
PLC具有强大的数据处理能力,能够实时监控液位变化,并根据预设的控制算法输出相应的控制信号。
PLC的可靠性高、抗干扰能力强,能够在恶劣的工业环境下稳定运行。
PLC还具有易于扩展和维护的特点,便于用户根据实际需求进行系统升级和改造。
毕业设计-基于PLC的液位控制系统设计
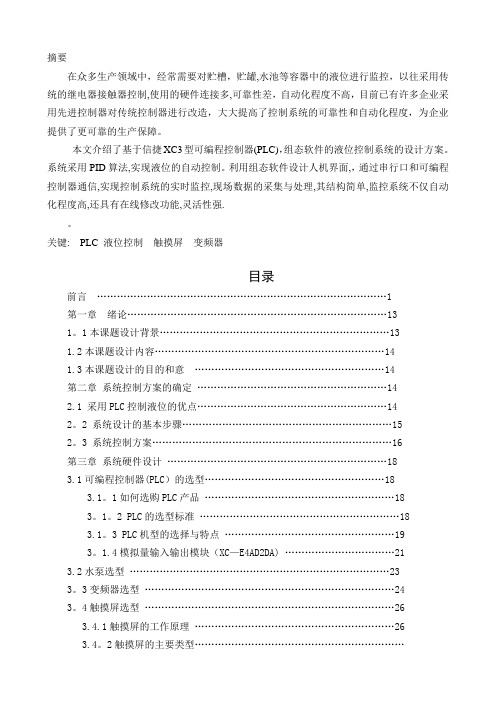
摘要在众多生产领域中,经常需要对贮槽,贮罐,水池等容器中的液位进行监控,以往采用传统的继电器接触器控制,使用的硬件连接多,可靠性差,自动化程度不高,目前已有许多企业采用先进控制器对传统控制器进行改造,大大提高了控制系统的可靠性和自动化程度,为企业提供了更可靠的生产保障。
本文介绍了基于信捷XC3型可编程控制器(PLC),组态软件的液位控制系统的设计方案。
系统采用PID算法,实现液位的自动控制。
利用组态软件设计人机界面,,通过串行口和可编程控制器通信,实现控制系统的实时监控,现场数据的采集与处理,其结构简单,监控系统不仅自动化程度高,还具有在线修改功能,灵活性强.。
关键: PLC 液位控制触摸屏变频器目录前言 (1)第一章绪论 (13)1。
1本课题设计背景 (13)1.2本课题设计内容 (14)1.3本课题设计的目的和意 (14)第二章系统控制方案的确定 (14)2.1 采用PLC控制液位的优点 (14)2。
2 系统设计的基本步骤 (15)2。
3 系统控制方案 (16)第三章系统硬件设计 (18)3.1可编程控制器(PLC)的选型 (18)3.1。
1如何选购PLC产品 (18)3。
1。
2 PLC的选型标准 (18)3.1。
3 PLC机型的选择与特点 (19)3。
1.4模拟量输入输出模块(XC—E4AD2DA) (21)3.2水泵选型 (23)3。
3变频器选型 (24)3。
4触摸屏选型 (26)3.4.1触摸屏的工作原理 (26)3.4。
2触摸屏的主要类型………………………………………………………3.4.3触摸屏的选择 (27)3.5硬件接线图 (28)第四章系统软件设计 (28)4。
1程序设计编程基本原则与注意问题 (28)4。
1。
1 程序设计(梯形图)编程基本原则 (28)4.1。
2 程序设计注意问题 (28)4.2所用编程软件特点及界面操作 (29)4。
2。
1编程软件特点 (29)4。
2。
2信捷XCPPro编程软件操作 (29)4.3变频器参数设定 (31)4.4触摸屏程序 (32)4。
基于PLC的液位控制系统毕业设计论文

基于PLC的液位控制系统毕业设计论文随着工业自动化水平的不断提高,液位控制系统在工业领域中得到了
广泛的应用。
液位控制系统是通过感知到液体的高度来实现对液位的控制,常用于储罐、水塔等场所,以确保液位在安全范围内。
本篇毕业设计论文将基于PLC(可编程逻辑控制器)设计一个液位控
制系统。
PLC是一种专门用于工和生产过程中的自动化控制的计算机控制
系统。
本设计将通过PLC来实现对液位的检测和控制,并结合开关、传感
器和执行器等设备实现自动液位控制。
在设计过程中,首先需要对液位控制系统的硬件架构进行规划。
本设
计将使用PLC作为控制核心,并结合液位传感器、执行器和HMI(人机界面)等设备来完成整个系统。
同时,需要对传感器和执行器的选型进行讨论,并确定合适的设备参数。
其次,将进行软件编程工作。
通过PLC的编程软件,将液位传感器与PLC进行连接,并设置液位控制的逻辑程序。
根据液位高度的变化,PLC
将实时采集并处理液位信号,然后通过输出信号控制执行器,实现液位的
自动控制。
同时,将设计一个简单直观的人机界面,能够实时显示液位的
变化情况,方便操作和监控。
最后,需要进行液位控制系统的测试和验证。
通过模拟液位的变化情况,测试液位控制系统的响应速度和准确性。
根据测试结果,进行相应的
调整和改进,使其达到设计要求。
综上所述,本设计将通过PLC实现液位控制系统的设计和开发,并通
过对硬件和软件的完善,使其具备良好的稳定性、响应速度和准确性。
该
设计具有一定的实用价值,可在工业领域中得到广泛的应用。
基于PLC的变频器液位控制设计

基于PLC的变频器液位控制设计在工业控制领域中,液位控制是一个常见的任务。
液位控制的主要目标是维持容器中的液体的稳定液位。
在过去,这通常是通过使用传统的电气组件和传感器来实现的。
然而,近年来,随着PLC(可编程逻辑控制器)技术的发展以及变频器的普及,基于PLC的变频器液位控制设计变得越来越受欢迎。
本文将介绍基于PLC的变频器液位控制设计的步骤和原理。
步骤1:硬件配置要实现基于PLC的变频器液位控制设计,需要一个PLC控制器、一个变频器、一个电动阀门和一个液位传感器。
首先,将PLC控制器连接到计算机上,并使用PLC编程软件进行配置。
然后,将变频器连接到PLC控制器,并将电动阀门和液位传感器分别连接到变频器。
步骤2:软件编程使用PLC编程软件创建一个新的程序,并编写逻辑代码来控制液位。
在程序中,可以定义变量来存储液位传感器的数据,以及设置变频器的输出频率。
通过使用逻辑代码,可以实现液位控制的逻辑。
步骤3:传感器校准在操作之前,需要对液位传感器进行校准。
校准液位传感器是确保液位测量精确性的重要步骤。
可以使用已知液位的参考容器来进行校准,并使用PLC编程软件来调整传感器的输出。
步骤4:参数设置通过PLC编程软件,可以设置变频器的参数。
这些参数包括变频器的输出频率范围、启动和停止时间、加减速度等。
根据液位变化的速度和容器的大小,可以根据实际需求进行参数设置。
步骤5:控制逻辑通过PLC编程软件,可以编写逻辑代码来实现液位控制的功能。
根据液位传感器的数据和设定的控制逻辑,PLC可以控制变频器的输出频率来调整电动阀门的开闭程度,从而实现液位的控制。
原理基于PLC的变频器液位控制设计基于反馈控制原理。
液位传感器通过感知容器的液位,并将液位数据传输给PLC。
PLC根据液位传感器的数据和预设的控制算法来控制变频器的输出频率。
变频器会根据PLC发出的指令来调整电动阀门的开闭程度,从而实现液位的控制。
如果液位低于预设值,PLC将增加变频器的输出频率,使电动阀门打开。
基于PLC的液位自动控制系统

Abstract:
Automatic control systems of liquids height with PLC has obtained good effect in RE extraction production.
Key Words:
PLC; liquids height; automat ic control systems
摘
要:
基于 PLC 的液位自动控制系 统 , 在稀土萃取生产中取得了较好的效果。
关 键 词: 中图分类号 :
PLC; 液位 ; 自动控制系统 TP273 文献标识码:
C
Automatic Control Systems of Liquids Height with PLC
TAO Mei xiong
( Jiangx i Golden Century New Materials Co. , Ltd. , Jiangxi Nanchang 330013, China)
熄灭, 如此周而复始, 实现了高位贮液桶的液位自动 控制。利用 PLC 的通讯功能, 通过 RS - 232 或 RS - 422 等接口与上位计算 机联网, 可以监视 PLC 的 运行情况并可随时统计出各种溶液的累积消耗量。
பைடு நூலகம்
5
结束语
该自动控制系统经一年多正常运行, 性能稳定, 减轻了操作人员的劳动强度 , 提高了生产效率。
表1输入输出i0分配表输入继电器输出继电器料液上限kf0常闭料液下限kf1常开洗酸上限kf2常闭洗酸下限kf3常开反酸上限kf4常闭反酸下限kf5常开氨水上限kf6常闭氨水下限kf7常开有机上限kf8常闭有机下限kf9常开料液手动关泵sb0常闭料液手动开泵sb1常开洗酸手动关泵sb2常闭洗酸手动开泵sb3常开反酸手动关泵sb4常闭反酸手动开泵sb5常开氨水手动关泵sb6常闭氨水手动开泵sb7常开有机手动关泵sb8常闭有机手动开泵sb9常开0000料液泵k0洗酸泵k1反酸泵k2氨水泵k3有机泵k4料液下限报警led0绿料液上限报警led1红洗酸下限报警led2绿洗酸上限报警led3红反酸下限报警led4绿反酸上限报警led5红氨水下限报警led6绿氨水上限报警led7红有机下限报警led8绿有机上限报警led9红0500000105010002050200030503000405040005050500060506000705070008050800090509001005100011060000120601001306020014060300150100010101020103图1液位传感器结构示意图4系统的软件设计利用c系列机丰富的基本指令系统编程
PLC在液位控制中的应用

PLC在液位控制中的应用PLC(可编程逻辑控制器)是一种常用于自动化控制系统中的电子设备,广泛应用于各个领域,包括液位控制。
液位控制是一种重要的工业过程控制技术,用于监测和控制液体或气体在容器中的水平。
在本文中,将探讨PLC在液位控制中的应用,以及它的优势和限制。
一、PLC在液位控制中的原理PLC的核心是中央处理器(CPU),它负责接收和处理来自不同传感器的信号,并根据预先编程的逻辑指令执行相应的控制操作。
在液位控制中,PLC通常与传感器、执行器(如电动阀门或泵)和人机界面(HMI)等设备连接,并通过输入/输出(I/O)模块进行数据交换。
液位传感器常用的类型包括浮球传感器、电容传感器和超声波传感器等。
它们通过测量液体表面与容器底部的距离来确定液位的高低。
当液位达到特定的阈值时,传感器会向PLC发送信号。
PLC接收到传感器的信号后,会根据预设的控制逻辑进行判断和操作。
例如,当液位过高时,PLC可以通过执行器控制泵的启停,以调整液位至设定值。
当液位过低时,PLC可以控制泵的启动以增加液位。
使用HMI界面,操作员可以监测和调整液位控制过程。
二、PLC在液位控制中的优势1. 灵活性和可编程性:PLC的灵活性使其能够适应不同的液位控制需求。
通过简单地修改PLC的编程代码,可以实现不同的控制策略,例如时间控制、比例控制和序列控制等。
这种可编程性使得PLC对于不同规模和复杂度的液位控制系统都具有适应性。
2. 可靠性和稳定性:PLC采用了工业级的硬件和软件设计,具有高可靠性和稳定性。
它们可以在恶劣环境条件下工作,并能够承受噪声、干扰和电磁辐射等不良因素的影响。
此外,PLC还具有自诊断和故障排除功能,可以及时检测和修复故障,提高系统的可靠性。
3. 扩展性和互连性:PLC系统可以轻松地与其他设备和系统进行集成,实现实时数据传输和通信。
这意味着PLC可以实现与SCADA(监控与数据采集)系统、远程控制系统和企业资源计划(ERP)系统等的无缝集成,从而提高液位控制系统的整体效率和管理能力。
- 1、下载文档前请自行甄别文档内容的完整性,平台不提供额外的编辑、内容补充、找答案等附加服务。
- 2、"仅部分预览"的文档,不可在线预览部分如存在完整性等问题,可反馈申请退款(可完整预览的文档不适用该条件!)。
- 3、如文档侵犯您的权益,请联系客服反馈,我们会尽快为您处理(人工客服工作时间:9:00-18:30)。
用PLC实现分段液位的控制
PLC在社会生产中应用广泛,其技术也在不断的进步,并且在各个领域所涉及到的内容都存在着很大的空间,以下这篇PLC的专业论文主要是阐释了如何使用PLC实现多段液位的设定、显示、报警和液位的自动控制。
The Application of PLC in Control by Multiplex Liquid Level
金彦平
(常州工程职业技术学院常州 213004)
摘要:本文主要介绍如何使用PLC实现多段液位的设定、显示、报警和液位的自动控制。
关键词: PLC 液位监控
在众多生产领域中,经常需要对贮槽、贮罐、水池等容器中的液位进行监控,以往常采用传统的继电器接触控制,使用硬连接电器多,可靠性差,自动化程度不高,目前已有许多企业采用先进控制器对传统接触控制进行改造,大大提高了控制系统的可靠性和自控程度,为企业提供了更可靠的生产保障。
本文在此介绍一种采用可编程控制器(PLC)对液位进行监控的一种方法,其电路结构简单,投资少(可利用原有设施改造),监控系统不仅自动化程度高,还具有在线修改功能,灵活性强,适用于多段液位监控场合。
1.控制要求
控制系统可以根据生产的需要将液位分为多段来设定,并分段显示,当液位为最低限时自动启动料泵加液,液位到达设定值时发出声光报警,并停泵;操作人员可通过确认按钮解除音响报警信号,闪烁灯光转平光;系统具有手动/自动两种控制方式,并设有试验功能。
2.PLC选型
目前在国内市场上有从美国、德国、日本等国引进的多种系列PLC,国内也有许多厂家组装、开发数十种PLC,故PLC系列标准不一,功能参差不齐,价格悬殊。
在此情况下,PLC的选择应着重考虑PLC的性能价格比,选择可靠性高,功能相当,负载能力合适,经济实惠的PLC。
本文介绍以四段液位控制对象为例,据对多种因素的分析比较及监控系统输入、输出点数的要求,选用日本立石(OMRON)公司C20P型PLC。
3.系统硬件配置
为实现液位的手动/自动控制,需要输入口12点,输出口8点,选用C20P 20点I/O单元的PLC,输入光电隔离,输出继电器隔离,负载能力强;液位检测采用干簧管传感器,手动/自动转换、运行/试验转换和液位设定采用双位旋钮,手动启泵、停泵和确认、试验采用常开按钮;输出选用电子音响报警器和24V直流指示灯、继电器。
参见图一系统硬件配置图。
图一系统硬件配置图
为节省输入口数量,节省投资,本系统运行/试验功能的转换采用了对I/O 模块接线的优化,使PLC输入模块中1个输入节点起到2个输入节点的作用,完成PLC工作在两种方式下的I/O功能。
参见图二I/O模块接线的优化。
图二 I/O模块接线的优化
系统正常运行时,运行/试验转换旋钮S接通1-3接点,各试验按钮不起作用,液位信号由各干簧管传感器传输给PLC;系统处于试验状态时,S接通1-2接点,各传感器输入信号不起作用,此时可用各试验按钮模拟各段液位信号传输
给PLC。
两种控制方式下的两个信号共用一个输入节点,成倍提高I/O端口的利用率,节省I/O点数。
4.系统软件设计
4.1 控制程序流程图
图三系统流程图
4.2 编程说明
= 1 \* GB3 ①本系统为液位的双位控制系统。
液位可分四段设定和显示,在最低液位时自动启泵,当液位到达设定值时自动停泵。
= 2 \* GB3 ②采用IL/ILC分支指令,通过0008旋钮实现手动/自动两种功能的选择,当0008旋钮闭合时,自动指示灯亮,系统执行IL/ILC分支内程序,完成自动监控;当0008旋钮打开时,手动指示灯亮,系统执行分支外程序,通过0010、0011旋钮实现手动启泵、停泵。
= 3 \* GB3 ③液位由0004~0007旋钮分最低、较低、较高、最高四段设定,系统设置由低到高的优先权,即当多个设定旋钮同时闭合时,低液位设定优先。
= 4 \* GB3 ④采用干簧管检测液位时,当液位到达检测点时其触点闭合,指示灯点亮;液位离开检测点时其触点打开,为保证相应测量段指示灯不立即熄灭及不受液位波动的影响,每段指示灯的控制均采用KEEP保持指令,只有当液位上升或下降到相邻段时指示灯才熄灭。
= 5 \* GB3 ⑤当液位到达检测点时,液位指示灯闪烁,灯光闪烁因子采用内部闪烁内标1902,以1S为周期闪烁;若液位到达设定值时,自动停泵,并设置电子音响报警,报警声设计为响3S停2S,循环30S后自停,或在30S内按0009确认按钮停音响,指示灯传平光。
电子音响报警和泵的启停同样考虑液位的波动影响,设计时采用KEEP保持指令和DIFU微分指令联合使用。
= 6 \* GB3 ⑥首次开车时,液位低于或高于最低液位时,需先手动启泵,再切换成自动运行;或先进入试验方式,按最低液位试验按钮启动料泵,再进入自动运行方式。
4.3 PLC梯形图
图四 PLC梯形图
参考文献:1.OMRON可编程序控制器操作手册
2.扬唯实.用PLC实现水位监控.自动化仪表.2001(3)。