质量成本分析案例(DOC 10页)
质量成本案例
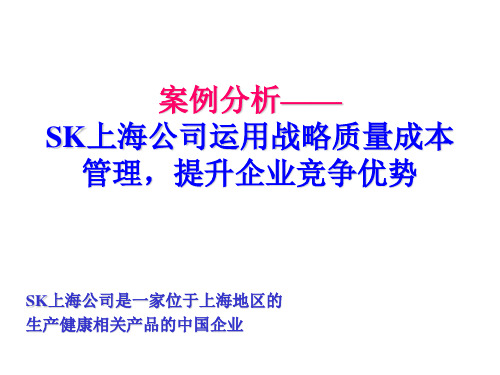
鉴定成本包括: 鉴定成本包括: 测试和检查成本。 检测设备和仪器。 质量审计。 实验室验收检测。 现场评估和测试。 信息费。
(3)内部失败成本
内部失败成本是由于商品在送达顾客之前通过鉴定发 现其质量低劣而发生的成本。这些成本是不增值的并且是 现其质量低劣而发生的成本。 完全不必要的。 完全不必要的。
¥202,300 ¥29,200 ¥14,400 ¥245,900 ¥12,800 ¥3,120 ¥27,000 ¥22,500 ¥180,000 ¥2,220 ¥11,000 ¥2,240 ¥36,000 ¥296,880 0.80% 0.66%
¥301,100 ¥48,600 ¥18,000 ¥367,700 ¥18,920 ¥5,070 ¥48,900 ¥55,800 ¥226,000 ¥4,380 ¥18,900 ¥40,050 ¥51,800 ¥469,820 0.84% 0.66%
3、帕累托图
帕累托图是促成质量问题的各种因素按照发生的频率 由高到低排列的直方图。 由高到低排列的直方图。
图表6-12 质量问题帕累托直方图19X9
累积
次 数 80
60 40 20
0
(1) (2) (3) (4) (5)(6)
质量问题 因素:(1)鸡蛋大小 (2)搅拌速度 (3)溶液
(4)搅拌时间 (5)巧克力质量 (6)不正确冷冻
第一年至第二年 第二年至第三年
上述研究数据说明,SK上海公司通过引入TQM和以稳定 产品质量为特征的战略质量成本控制,取得满意的结果: 客户抱怨减少 公司核心竞争力上升 产品美誉度上升 市场份额占有率提升
一、质量与战略成本管理
质量改进
降低退货率
降低制造成本
提高顾客认知价值
产品质量成本案例蒙牛

产品质量成本案例蒙牛蒙牛集团倡导“没有质量,一切都是负数的理念”。
开始之初,蒙牛对员工进行系统地企业文化培训,并在整个蒙牛发展过程中不断强调完善质量体系的重要性,使得生产出高质量乳制品的观念深入人心。
公司在质量管理上创造性地采取了两项举措,被概括为“一净一稠”。
着眼“净”,在国内第一个建起了“运奶车桑拿浴车间”。
奶罐车从奶源基地每向工厂送完一次奶,都要在高压喷淋设备下进行酸、碱、蒸汽及开水清洗,上上下下,里里外外,杜绝了残留陈奶污染新奶,最大程度地保持了草原牛奶的原汁原味。
二是着眼“稠”,添加了“闪蒸”工艺,在百分之百原奶的基础上再剔除掉一定比例的水分,从而牛奶闻更香饮更浓。
蒙牛具体的质量控制和检验体系如下:在原奶环节,蒙牛会进行滋气味品尝、近20项理化指标和40多项安全指标检测,检测不合格的牛奶,蒙牛全部予以拒收。
生产线上的每一包牛奶都都要经过9道工序、36个监控点、105项指标检测,只要有一项检测项目不合格,整批产品都不允许上市。
产品几乎全部达到或超过国际标准,蒙牛工厂工厂通过了GMP(优质生产规范)、HACC%害分析与关键点控制)等五大体系认证,建立的产品追溯体系也可以保障每一个产品都能追溯到相关责任人。
蒙牛的企业愿景就是要做质量最好、最专业、蒙牛的质量管理系统。
这个系统由三个职能部门组成:质量安全管理中心、营运质量管理中心和奶源质量管理中心,并以此为基础,建立了端到端全产业链质量管理体系,包括种植、养殖、初级加工、原辅料、运输、生产、出库、储运、消费者九大环节,并为这九大环节制定了详尽的管理标准,蒙牛的质量管理已经延伸到奶站,实现了奶站巡检、原奶、原辅料、车间原奶、半成品、成品、市场、环境样全线质量检测,加强了全链条食品安全控制能力。
蒙牛的质量管理控制体系建立了专门的质量管理系统。
蒙牛的质量管理系统覆盖了涉及的所有生产事业部,覆盖了27个检验出,数十个实验室,每年检验各类样品500多万个,严格控制监管了产品的生产品质。
成本核算制度案例分析经典
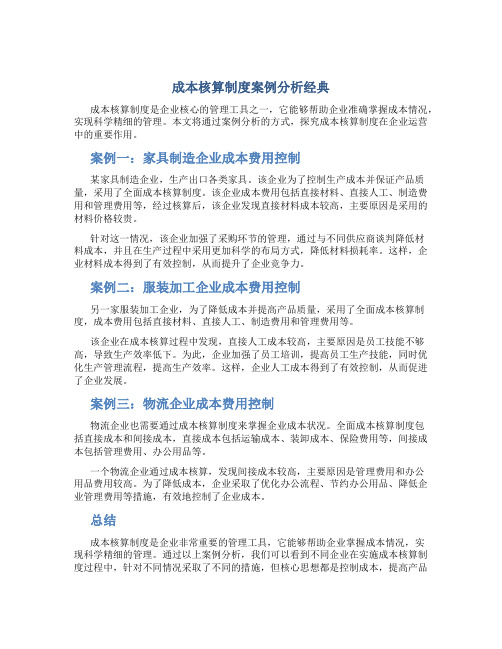
成本核算制度案例分析经典成本核算制度是企业核心的管理工具之一,它能够帮助企业准确掌握成本情况,实现科学精细的管理。
本文将通过案例分析的方式,探究成本核算制度在企业运营中的重要作用。
案例一:家具制造企业成本费用控制某家具制造企业,生产出口各类家具。
该企业为了控制生产成本并保证产品质量,采用了全面成本核算制度。
该企业成本费用包括直接材料、直接人工、制造费用和管理费用等,经过核算后,该企业发现直接材料成本较高,主要原因是采用的材料价格较贵。
针对这一情况,该企业加强了采购环节的管理,通过与不同供应商谈判降低材料成本,并且在生产过程中采用更加科学的布局方式,降低材料损耗率。
这样,企业材料成本得到了有效控制,从而提升了企业竞争力。
案例二:服装加工企业成本费用控制另一家服装加工企业,为了降低成本并提高产品质量,采用了全面成本核算制度,成本费用包括直接材料、直接人工、制造费用和管理费用等。
该企业在成本核算过程中发现,直接人工成本较高,主要原因是员工技能不够高,导致生产效率低下。
为此,企业加强了员工培训,提高员工生产技能,同时优化生产管理流程,提高生产效率。
这样,企业人工成本得到了有效控制,从而促进了企业发展。
案例三:物流企业成本费用控制物流企业也需要通过成本核算制度来掌握企业成本状况。
全面成本核算制度包括直接成本和间接成本,直接成本包括运输成本、装卸成本、保险费用等,间接成本包括管理费用、办公用品等。
一个物流企业通过成本核算,发现间接成本较高,主要原因是管理费用和办公用品费用较高。
为了降低成本,企业采取了优化办公流程、节约办公用品、降低企业管理费用等措施,有效地控制了企业成本。
总结成本核算制度是企业非常重要的管理工具,它能够帮助企业掌握成本情况,实现科学精细的管理。
通过以上案例分析,我们可以看到不同企业在实施成本核算制度过程中,针对不同情况采取了不同的措施,但核心思想都是控制成本,提高产品质量,提升企业竞争力。
某企业质量成本报告

某企业质量成本报告质量成本是由于产品未能达到质量标准而发生的成本(包括机会成本),或者由于可能或存在的质量问题发生的成本。
从产品的生命周期可以将质量成本分为:预防成本、评价成本、内部失败成本、外部失败成本。
本案例是根据这一概念对某电气配件工厂质量成本分析后做出的质量报告,其中原始数据略有改动。
1.背景概述该工厂是厦门某合资低压电气公司配套供货商,XX年前后随着供货量增加,销售额增加,利润却无明显增加,而产品退货量大幅上升,并因质量问题给需方造成过重大损失,受到严重警告。
厂方意识到是质量管理出现问题,狠抓产品检验,增加售后服务人员,结果虽然退货明显减少,废品率却居高不下。
考虑到供需双方合作基础很好,企业求助需方帮助解决难题。
经过调研,需方为该厂制定了一套质量管理方案。
从XX年按该方案实施后,效果不错。
下面将XX、XX 和XX年实行质量管理方案前后的质量成本情况分析如下。
2.质量成本原始数据根据该厂生产特点,其质量成本包括:检测设备折旧、生产工艺、测试用料、产品检测、产品退货、统计过程控制、成品检验、返工成本、废品处理、废料成本、质量退换、成品维护和系统开发。
质量成本原始数据如下表:质量成本原始数据表项目金额(元)XXXXXX生产工艺53,00079,00086,000统计控制72,00076,000废料成本88,000127,00098,000成品维护442,000138,000 69,000检测设备折旧19,00031,00029,000返工成本148,000 218,000 178,000废品处理52,00074,00059,000系统开发66,000 112,000 121,000测试用料3,8005,8006,000产品检测68,000118,000129,000质量退换62,000176,0005,200成品检验86,000148,000168,000产品退货334,00079,00038,000合计1,421,8001,377,8001,062,2003.质量成本报告根据质量成本的概念将原始数据分类形成质量报告如质量成本报告项目金额(元)百分比(%) 金额(元)百分比(%) 金额(元)百分比(%) XXXXXX预防成本: 系统开发66,000 112,000 121,000生产工艺53,00079,00086,000统计控制72,00076,000小计119,000 263,000 283,000评价成本: 检测设备折旧19,00031,00029,000成品检验86,000 148,000 168,000产品检测68,000 118,000 129,000测试用料3,8005,8006,000小计176,800302,800332,000内部失败成本: 废品处理52,00074,00059,000废料成本88,000127,00098,000返工成本148,000218,000178,000小计288,000419,000335,000外部失败成本: 产品退货334,00079,00038,000产品维护442,000138,00069,000质量退换62,000176,0005,200小计838,000393,000112,200质量总成本1,421,8001,377,8001,062,200假定销售额: 10,000,000(元)4.成本分析上表说明,实行质量管理方案之前的XX年,质量总成本达到年度销售额的 %,通过质量管理到XX年已下降到 %。
成本控制有问题的案例及分析

成本控制有问题的案例及分析案例一:美的的成本控制中国制造企业有90%的时间花费在物流上,物流仓储成本占据了总销售成本的30%到40%,供应链上物流的速度以及成本更是令中国企业苦恼的老大难问题。
美的针对供应链的库存问题,利用信息化技术手段,一方面从原材料的库存管理做起,追求零库存标准;另一方面针对销售商,以建立合理库存为目标,从供应链的两段实施挤压,加速了资金、物资的周转,实现了供应链的整合成本优势。
零库存梦想美的虽多年名列空调产业的“三甲”之位,但是不无一朝城门失守之忧。
自2000年来,在降低市场费用、裁员、压低采购价格等方面,美的频繁变招,其路数始终围绕着成本与效率。
在广东地区已经悄悄为终端经销商安装进销存软件,即实现“供应商管理库存”(以下简称VMI)和“管理经销商库存”中的一个步骤。
对于美的来说,其较为稳定的供应商共有300多家,其零配件(出口、内销产品)加起来一共有3万多种。
从2002年中期,利用信息系统,美的集团在全国范围内实现了产销信息的共享。
有了信息平台做保障,美的原有的100多个仓库精简为8个区域仓,在8小时可以运到的地方,全靠配送。
这样一来美的集团流通环节的成本降低了15%到20%。
运输距离长(运货时间3到5天的)的外地供应商,一般都会在美的的仓库里租赁一个片区(仓库所有权归美的),并把其零配件放到片区里面储备。
在美的需要用到这些零配件的时候,它就会通知供应商,然后再进行资金划拨、取货等工作。
这时,零配件的产权,才由供应商转移到美的手上,而在此之前,所有的库存成本都由供应商承担。
此外,美的在ERP(企业资源管理)基础上与供应商建立了直接的交货平台。
供应商在自己的办公地点,通过互联页(WEB)的方式就可登录到美的公司的页面上,看到美的的订单内容;品种、型号、数量和交货时间等等,然后由供应商确认信息,这样一张采购订单就已经合法化了。
实施VMI后,供应商不需要像以前一样疲于应付美的的订单,而只需做一些适当的库存即可。
质量成本分析案例(DOC 10页)
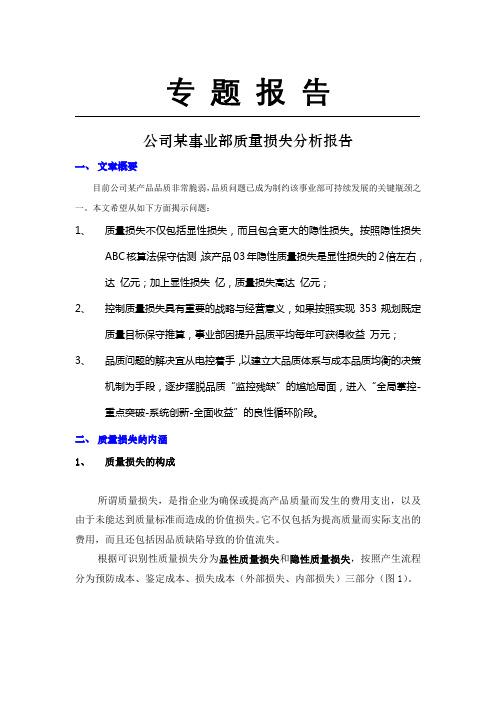
专 题 报 告公司某事业部质量损失分析报告一、 文章概要目前公司某产品品质非常脆弱,品质问题已成为制约该事业部可持续发展的关键瓶颈之一。
本文希望从如下方面揭示问题:1、 质量损失不仅包括显性损失,而且包含更大的隐性损失。
按照隐性损失ABC 核算法保守估测,该产品03年隐性质量损失是显性损失的2倍左右,达 亿元;加上显性损失 亿,质量损失高达 亿元;2、 控制质量损失具有重要的战略与经营意义,如果按照实现353规划既定质量目标保守推算,事业部因提升品质平均每年可获得收益 万元;3、 品质问题的解决宜从电控着手,以建立大品质体系与成本品质均衡的决策机制为手段,逐步摆脱品质“监控残缺”的尴尬局面,进入“全局掌控-重点突破-系统创新-全面收益”的良性循环阶段。
二、 质量损失的内涵 1、 质量损失的构成所谓质量损失,是指企业为确保或提高产品质量而发生的费用支出,以及由于未能达到质量标准而造成的价值损失。
它不仅包括为提高质量而实际支出的费用,而且还包括因品质缺陷导致的价值流失。
根据可识别性质量损失分为显性质量损失和隐性质量损失,按照产生流程分为预防成本、鉴定成本、损失成本(外部损失、内部损失)三部分(图1)。
图1:质量损失构成客户流失 价格流失 供方成本转嫁生产率流失2、隐性质量损失的内涵由产品品质不良导致的价值链机会成本损失是隐性质量成本的本源,包括:顾客流失——老顾客流失和新顾客流失:老顾客流失——顾客因维修体验而在二次选购时放弃选择原品牌,导致企业损失原可获得的收益。
据麦肯锡对中国该产品市场的研究,未来几年老顾客比例呈迅速增长趋势,将由02年的%上升至08年的%。
新顾客流失——经口碑传播而建立某品牌不良品质形象的潜在选购者,当其中部分人作现实购买时放弃选择该品牌,导致该企业损失原可获得的收益。
科特勒曾指出,家电消费品是顾客购买决策受参照群体1影响最大的产品之一,一个有过维修体验的顾客会将痛苦体验传播给4—8个人。
质量与成本案例分析(doc 9页)
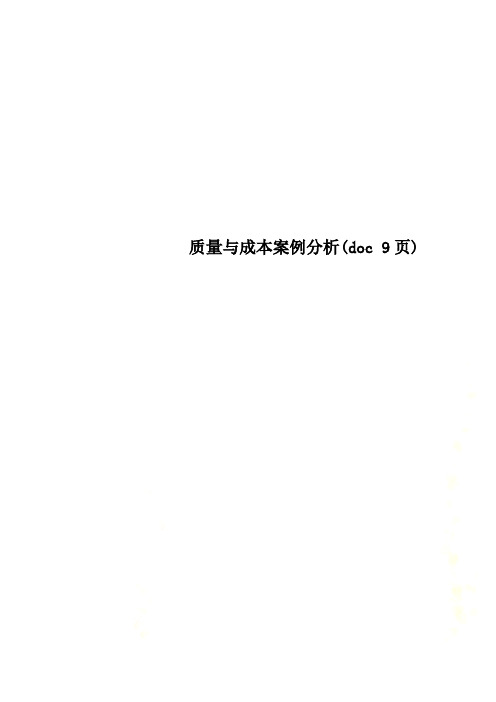
质量与成本案例分析(doc 9页)案例:质量与成本一、案例场景某行业省公司(A单位)信息应用系统工程项目(A项目)通过招标方式选择承建单位,希赛信息技术有限公司(CSAI)以1800万元的标底获得A项目工程合同。
A项目包含1000万元设备采购安装和800万元软件开发费用。
其中设备采购安装预计有150万元利润,CSAI渴望通过A项目的建设能够获得600万元纯利润。
为了能够最大限度地获取利润空间,CSAI在组建项目小组,制定工程费用预算的时候,尽力压缩工程费用预算。
CSAI安排刘工担任A项目的项目经理,刘工在对项目进行工作分解的基础上,制订了工程实施资源计划,编制了项目实施预算经费。
根据刘工的预算,项目实施经费预算(人员工资、差旅费、会议费、行政管理费等)为220万元,其中人员工资占了很大比例,为150万元,CSAI领导在审核经费预算的时候,认为人员工资所占份额太大,CSAI要求刘工将人员工资预算减少为120万元,并列入对刘工的绩效考核指标。
由于人员工资预算的减少,刘工面临两种选择,要么将招聘软件工程师的能力等级降低,要么减少项目组成员数量。
刘工在权衡利弊后认为,项目组员工工资高,容易引起公司其他部门的忌妒,工作不好开展,于是,刘工只能采取降低项目组成员工资的方法。
为此刘工所组建的项目小组有8人没有达到刘工预期的技术资质等级。
A项目经过18个月(延期3个月)的建设周期,项目建设完成并交付用户使用。
CSAI也如愿以偿地获得了预期的利润,项目实施经费190万元,预提项目维护经费60万元(两年免费维护),商务费用50万元,超期3月赔偿A 单位15万元,CSAI认为实现的利润635万元,已经达到了计划的目标。
项目验收交付使用后,CSAI为项目维护配备2位工程师,每位工程师工资加管理成本共计10万元/人年,其他辅助设备购置10万元/年。
但是,A项目的运行维护并不像CSAI想像的那样好,由于A项目定制软件的质量存在很多隐患、缺陷,如软件代码质量差,导致系统运行效率低;技术文件缺乏或文件与实际情况不相符,或技术文件纵向及横向对相应内容的描述不一致;这些问题使得A项目的维护工作难以高质量地开展,经常给A单位的业务开展带来不良的影响。
质量成本案例
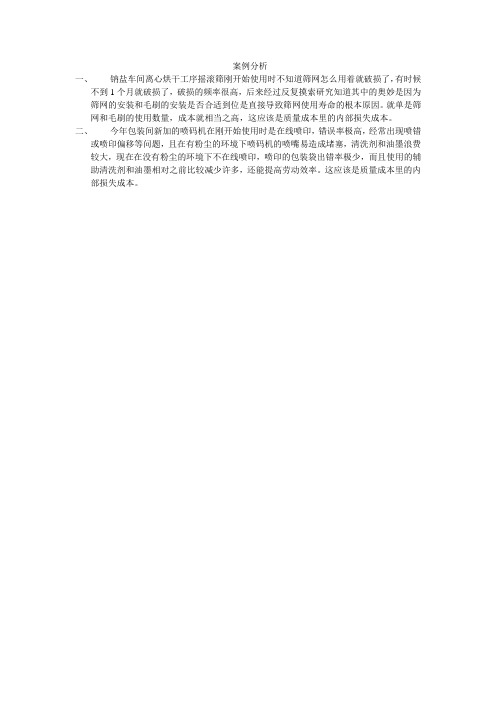
案例分析
一、钠盐车间离心烘干工序摇滚筛刚开始使用时不知道筛网怎么用着就破损了,有时候
不到1个月就破损了,破损的频率很高,后来经过反复摸索研究知道其中的奥妙是因为筛网的安装和毛刷的安装是否合适到位是直接导致筛网使用寿命的根本原因。
就单是筛网和毛刷的使用数量,成本就相当之高,这应该是质量成本里的内部损失成本。
二、今年包装间新加的喷码机在刚开始使用时是在线喷印,错误率极高,经常出现喷错
或喷印偏移等问题,且在有粉尘的环境下喷码机的喷嘴易造成堵塞,清洗剂和油墨浪费较大,现在在没有粉尘的环境下不在线喷印,喷印的包装袋出错率极少,而且使用的辅助清洗剂和油墨相对之前比较减少许多,还能提高劳动效率。
这应该是质量成本里的内部损失成本。
质量成本分析案例(DOC 10页)复习过程

质量成本分析案例(D O C10页)专题报告公司某事业部质量损失分析报告一、文章概要目前公司某产品品质非常脆弱,品质问题已成为制约该事业部可持续发展的关键瓶颈之一。
本文希望从如下方面揭示问题:1、质量损失不仅包括显性损失,而且包含更大的隐性损失。
按照隐性损失ABC核算法保守估测,该产品03年隐性质量损失是显性损失的2倍左右,达亿元;加上显性损失亿,质量损失高达亿元;2、控制质量损失具有重要的战略与经营意义,如果按照实现353规划既定质量目标保守推算,事业部因提升品质平均每年可获得收益万元;3、品质问题的解决宜从电控着手,以建立大品质体系与成本品质均衡的决策机制为手段,逐步摆脱品质“监控残缺”的尴尬局面,进入“全局掌控-重点突破-系统创新-全面收益”的良性循环阶段。
二、质量损失的内涵1、质量损失的构成所谓质量损失,是指企业为确保或提高产品质量而发生的费用支出,以及由于未能达到质量标准而造成的价值损失。
它不仅包括为提高质量而实际支出的费用,而且还包括因品质缺陷导致的价值流失。
根据可识别性质量损失分为显性质量损失和隐性质量损失,按照产生流程分为预防成本、鉴定成本、损失成本(外部损失、内部损失)三部分(图1)。
图1:质量损失构成2、隐性质量损失的内涵由产品品质不良导致的价值链机会成本损失是隐性质量成本的本源,包括:顾客流失——老顾客流失和新顾客流失:老顾客流失——顾客因维修体验而在二次选购时放弃选择原品牌,导致企业损失原可获得的收益。
据麦肯锡对中国该产品市场的研究,未来几年老顾客比例呈迅速增长趋势,将由02年的%上升至08年的%。
新顾客流失——经口碑传播而建立某品牌不良品质形象的潜在选购者,当其中部分人作现实购买时放弃选择该品牌,导致该企业损失原可获得的收益。
科特勒曾指出,家电消费品是顾客购买决策受参照群体1影响最大的产品之一,一个有过维修体验的顾客会将痛苦体验传播给4—8个人。
1有过同类产品使用体验的同事、亲人、朋友。
质量成本分析案例8页word文档
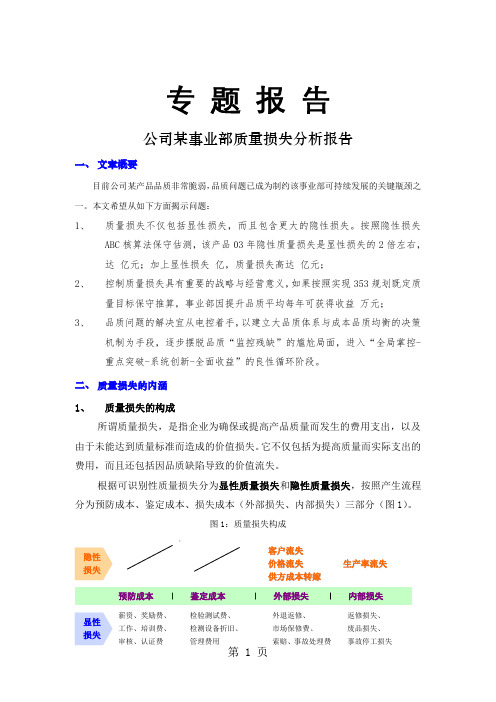
专题报告公司某事业部质量损失分析报告一、文章概要目前公司某产品品质非常脆弱,品质问题已成为制约该事业部可持续发展的关键瓶颈之一。
本文希望从如下方面揭示问题:1、质量损失不仅包括显性损失,而且包含更大的隐性损失。
按照隐性损失ABC核算法保守估测,该产品03年隐性质量损失是显性损失的2倍左右,达亿元;加上显性损失亿,质量损失高达亿元;2、控制质量损失具有重要的战略与经营意义,如果按照实现353规划既定质量目标保守推算,事业部因提升品质平均每年可获得收益万元;3、品质问题的解决宜从电控着手,以建立大品质体系与成本品质均衡的决策机制为手段,逐步摆脱品质“监控残缺”的尴尬局面,进入“全局掌控-重点突破-系统创新-全面收益”的良性循环阶段。
二、质量损失的内涵1、质量损失的构成所谓质量损失,是指企业为确保或提高产品质量而发生的费用支出,以及由于未能达到质量标准而造成的价值损失。
它不仅包括为提高质量而实际支出的费用,而且还包括因品质缺陷导致的价值流失。
根据可识别性质量损失分为显性质量损失和隐性质量损失,按照产生流程分为预防成本、鉴定成本、损失成本(外部损失、内部损失)三部分(图1)。
图1:质量损失构成2、隐性质量损失的内涵由产品品质不良导致的价值链机会成本损失是隐性质量成本的本源,包括:顾客流失——老顾客流失和新顾客流失:老顾客流失——顾客因维修体验而在二次选购时放弃选择原品牌,导致企业损失原可获得的收益。
据麦肯锡对中国该产品市场的研究,未来几年老顾客比例呈迅速增长趋势,将由02年的%上升至08年的%。
新顾客流失——经口碑传播而建立某品牌不良品质形象的潜在选购者,当其中部分人作现实购买时放弃选择该品牌,导致该企业损失原可获得的收益。
科特勒曾指出,家电消费品是顾客购买决策受参照群体1影响最大的产品之一,一个有过维修体验的顾客会将痛苦体验传播给4—8个人。
价格损失——中低价位的该产品,与主要竞争对手相比,产品品质差异因素带来的售价差异平均超过10%2。
质量成本分析报告(模板)

质量成本分析报告
从质量成本构成比例情况分析,预防成本比较高,主要是公司进行国军标认证费用和培训费用等共投入5万,公司领导重视预防成本的投入,这为公司质量体系的建立和产品质量控制打下了良好的基础,从总体质量成本的投入及废品损失情况看,质量成本构成比例较好,满足质量成本的运作要求。
二、质量成本占生产成本的比例
2017年1月至2017年9月公司的生产成本为40万,质量成本为13万元,质量成本占生产成本的32.5%,其中鉴定成本占19%,预防成本占38.5%,目前看质量成本是以预防成本和鉴定成本为主体,但内部故障成本也较高,主要是返工返修的零件较多,在生产过程中没有发生较大的质量问题,为用户提供的产品没有出现因质量问题造成批次性返修、退货现象,也没有出现过顾客投诉现象。
三、总结
根据质量成本统计、分析情况,公司应加强工序过程的控制,适当增加工序控制的费用,做好数控程序编制和确认审批工作,以提高生产过程的能力,减少废品及返工、返修现象,提高成品的合格率,为用户提供满足要求的产品,把不良品控制在生产过程中,减少浪费,提高公司的经济效益。
办公室
年月日
质量成本统计表
年月日
制表:审核:批准:。
成本分析案例
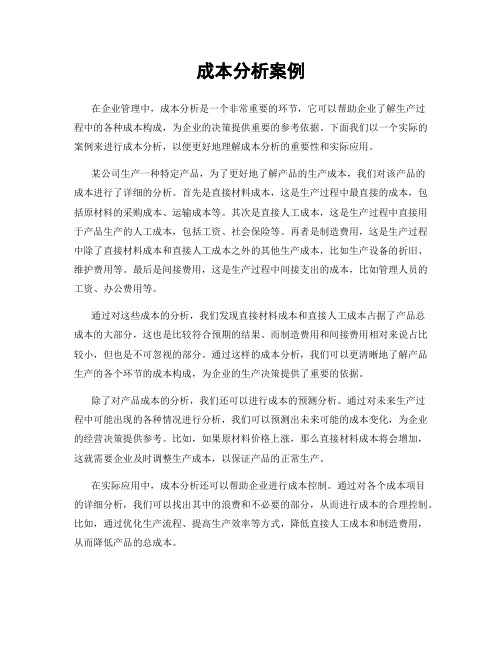
成本分析案例在企业管理中,成本分析是一个非常重要的环节,它可以帮助企业了解生产过程中的各种成本构成,为企业的决策提供重要的参考依据。
下面我们以一个实际的案例来进行成本分析,以便更好地理解成本分析的重要性和实际应用。
某公司生产一种特定产品,为了更好地了解产品的生产成本,我们对该产品的成本进行了详细的分析。
首先是直接材料成本,这是生产过程中最直接的成本,包括原材料的采购成本、运输成本等。
其次是直接人工成本,这是生产过程中直接用于产品生产的人工成本,包括工资、社会保险等。
再者是制造费用,这是生产过程中除了直接材料成本和直接人工成本之外的其他生产成本,比如生产设备的折旧、维护费用等。
最后是间接费用,这是生产过程中间接支出的成本,比如管理人员的工资、办公费用等。
通过对这些成本的分析,我们发现直接材料成本和直接人工成本占据了产品总成本的大部分,这也是比较符合预期的结果。
而制造费用和间接费用相对来说占比较小,但也是不可忽视的部分。
通过这样的成本分析,我们可以更清晰地了解产品生产的各个环节的成本构成,为企业的生产决策提供了重要的依据。
除了对产品成本的分析,我们还可以进行成本的预测分析。
通过对未来生产过程中可能出现的各种情况进行分析,我们可以预测出未来可能的成本变化,为企业的经营决策提供参考。
比如,如果原材料价格上涨,那么直接材料成本将会增加,这就需要企业及时调整生产成本,以保证产品的正常生产。
在实际应用中,成本分析还可以帮助企业进行成本控制。
通过对各个成本项目的详细分析,我们可以找出其中的浪费和不必要的部分,从而进行成本的合理控制。
比如,通过优化生产流程、提高生产效率等方式,降低直接人工成本和制造费用,从而降低产品的总成本。
总的来说,成本分析在企业管理中起着非常重要的作用。
通过对产品成本的分析、预测和控制,可以帮助企业更好地了解自身的经营状况,为企业的决策提供重要的参考依据。
因此,在企业管理中,成本分析是一个不可或缺的环节,也是企业持续发展的重要保障。
质量成本案例
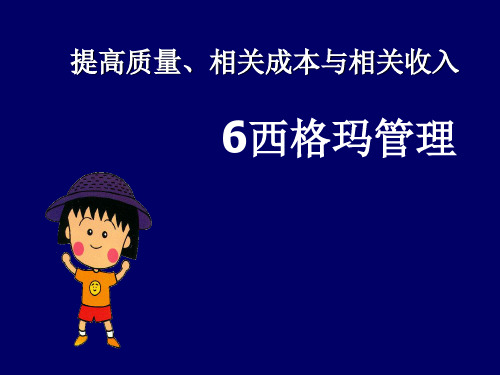
最终售价 $1250 减: 每卷制造总成本 $930 每卷毛利 $320
废品损失:
印花部门每生产出一单位不合格的布料, 成本为$930。 织布部门每生产出一单位不合格的产品, 其成本用期望货币价值来计算:
期望货币价值:
以概率为权数对各种可能 事件的货币价值的加权平 均。
结果1的货币价值*概率 + 结果2的货币价值*概率+…… =整个方案的期望货币价值
财务
顾客
远景与战略
内部经营过程
学习与增长
员工培训
通用电气金融服务集团 改进前:销售人员不能直截了当地回答客户 的问题,需要做大量查询工作。 用“6σ‖的数量采集规则进行改进。随时记 录顾客的问题,统计不能立刻作答的问题, 并进一步分析什么样的问题销售人员没有准 备,无法回答,以确定需要接受什么样的培 训。此外,还可以确定什么样的人适合这项 工作。
采用该方法能为公司带来125000美元的收益
6σ 管理法——废品率的控制
采用统计流程控制(Statistical Process Control)和控制图——确定问题 回归分析——基本原因分析和结果预测 实验设计——最优化方法分析以及结果的有效性 错误检查——缺陷的预防和流程的改进
提高瓶颈资源的生产效率
织布部门生产一单位灰布的成本:$785 机会成本:
合格品灰布期望增加的收益 =销售毛利*概率 =320*0.9 + 0*0.1= 288 织布部门的损失=织布的成本+机会成本(期望货币价值) =785+288=1073
毛利率=毛利/销售收入 =(收入– 变动成本–固定成本)/销售收入 =(1250*8550 –600*8550 –
成本会计案例分析(质量管理)
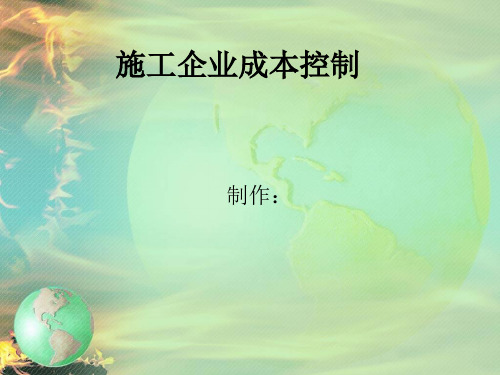
人工费控制
• 工人的工作班内消耗的工作时间分为必须消耗的 时间和损失时间。必须消耗的时间包括有效的工 作时间、休息时间和不可避免的中断时间的消耗。 损失时间包括多余和偶然工作、停工、违背劳动 纪律所引起的工时损失。我把损失时间的控制放 到人工费节约的重点上来,从技术因素和组织因 素两个方面来进行控制。要提高生产工人的技术 水平和班组的组织管理水平,合理进行劳动组织, 减少和避免无效劳动,提高劳动生产率,避免出 现我方自身责任的赶工现象出现。
方案二:每次采购量=600000/5=120000块
采购和存储费合计费用:
=Q/2×P×A+S/Q×C=120000/2×0.43×3%+600000/120000*1100
=6274元
方案三:每次采购量=600000/2=300000块
采购和存储费合计费用:
=Q/2×P×A+S/Q×C=300000/2×0.41×3%+600000/300000*1200=4245元
案例工程主要的材料是钢材2900吨压型钢板12000m2混凝土4050m3三类经过测算其金额占总材料金额的90以上我和材料采购人员以及工程经济类专家对以上三类大宗材料进行了采购竞争性谈判在我公司供应商名册中择优选取了四家供应商又在名册以外选择了两家单位在保质保量的前提下经过了四轮的谈判择优选择了两家单位做为该工程的供应商钢材每吨供应价下降62元压型钢板每m2下降8元混凝土每m3下降15元该部分材料采购就节约了290062120008405015336550元有效的降低了施工成本
6.70
5.54 4.57
7.84 6.49 5.12
2007年
2008年
三五三质量规划目标
• 首先质量成本管理应 纳入总会计师的职责 范围
质量成本分析
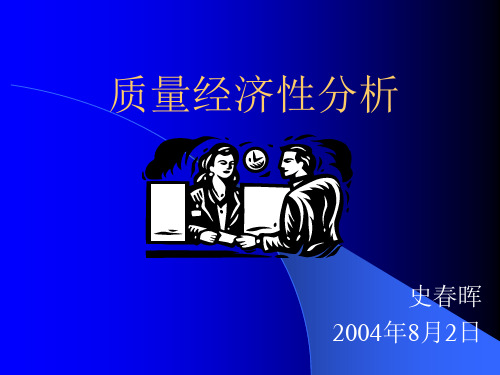
会计核算方法和统计核算方法
经济核算的方法主要是会计核算方法和统计核 算方法。
会计核算方法是采用货币形式,通过记帐、 算帐、报帐等手段,连续系统地反映和监督经 济活动的全过程。
统计核算是采用货币、实物量和工时等多种计 量单位,运用各种调查统计方法,收集和整理 在经济活动过程中能够反映经济现象特征和规 律的数据资料。
伴随着质量概念的不断演变,从符合性发展到 追求顾客满意,质量经济性也越来越重要,逐 渐成为质量管理中的一个重要的课题
质量经济性管理
通过加强质量管理,来提高组织经济效益 的两个方面:
增加收入(销售额)、利润和市场份额。 降低经营所需的资源或成本,减少资源
的投入。 见下图《质量经济性管理指南》
提高组织经济效益
比,用α表示,即:
质量损失变化量 α= 质量投入变化量
α反映了每一元质量投入所减少的质量损失。
质量与经济
质量管理是以质量为中心,努力开发和提供顾 客满意的产品和服务。质量管理的趋势正从 “消除不满意”向“追求满意”方向发展。现 代质量的含义是“满足需要和期望”,即质量 要求(涉及固有质量特性和其价值总和的要求) 满足顾客(含相关方)明确或隐含的需要或期 望
隐含质量成本(implicit quality cost)是指没有 达到满意的质量所减少的收入。
显见质量成本既可以采用会计核算,也可以 采用统计核算,而隐含质量成本只能进行统 计核算。
质量成本的核算方法
目前我国常用的质量成本核算方法有三种:
1.质量成本全部用统计核算 2.显见成本采用会计核算,但不纳入成本核算
控制区域 预防成本≈10 损失成本≈50
预防措施得力 工序控制严格
质量成本控制案例之欧阳语创编
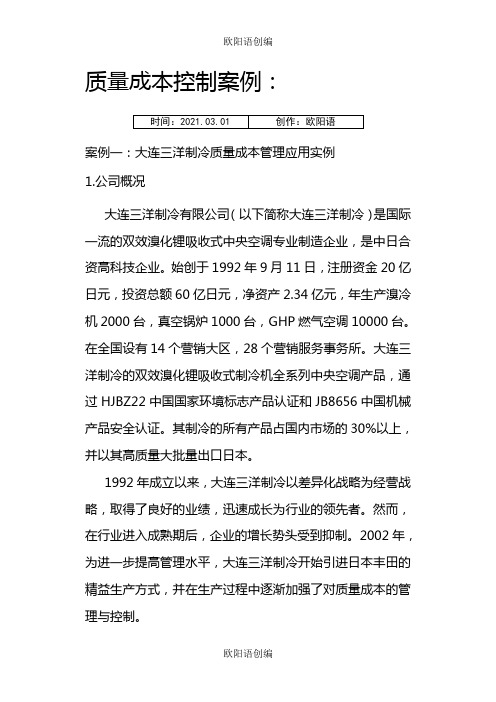
质量成本控制案例:案例一:大连三洋制冷质量成本管理应用实例1.公司概况大连三洋制冷有限公司(以下简称大连三洋制冷)是国际一流的双效溴化锂吸收式中央空调专业制造企业,是中日合资高科技企业。
始创于1992年9月11日,注册资金20亿日元,投资总额60亿日元,净资产2.34亿元,年生产溴冷机2000台,真空锅炉1000台,GHP燃气空调10000台。
在全国设有14个营销大区,28个营销服务事务所。
大连三洋制冷的双效溴化锂吸收式制冷机全系列中央空调产品,通过HJBZ22中国国家环境标志产品认证和JB8656中国机械产品安全认证。
其制冷的所有产品占国内市场的30%以上,并以其高质量大批量出口日本。
1992年成立以来,大连三洋制冷以差异化战略为经营战略,取得了良好的业绩,迅速成长为行业的领先者。
然而,在行业进入成熟期后,企业的增长势头受到抑制。
2002年,为进一步提高管理水平,大连三洋制冷开始引进日本丰田的精益生产方式,并在生产过程中逐渐加强了对质量成本的管理与控制。
2.案例分析2.1质量成本构成简介质量成本是指企业将产品质量保持在规定的质量水平上所需的总费用,它是企业生产总成本的组成部分。
一般认为,质量成本的各项费用是由运行质量成本和外部质量保证成本两部分构成,而运行质量成本又包括预防成本、鉴定成本(两项之和统称为可控成本)、内部损失成本和外部损失成本(两项之和统称为损失成本或结果成本)等。
但质量成本不是产品的制造成本,而是保证产品质量的成本。
按照产生流程质量成本可以分为预防成本、鉴定成本和损失成本(外部损失、内部损失)三部分。
1.预防成本是指为了防止劣质产品或服务而开展的所有活动的成本。
例如进行新产品评审、质量教育和培训、质量改进班组会议、质量策划、供方能力调查和质量部门员工的工资等可以由成本发生部门把成本汇总后提交给公司的财务部门,由财务部按照质量成本的管理要求重新进行科目分配。
2.鉴定成本是指为了确保产品或服务符合质量标准和性能要求而开展的测量、评估或审核成本。
质量成本分析
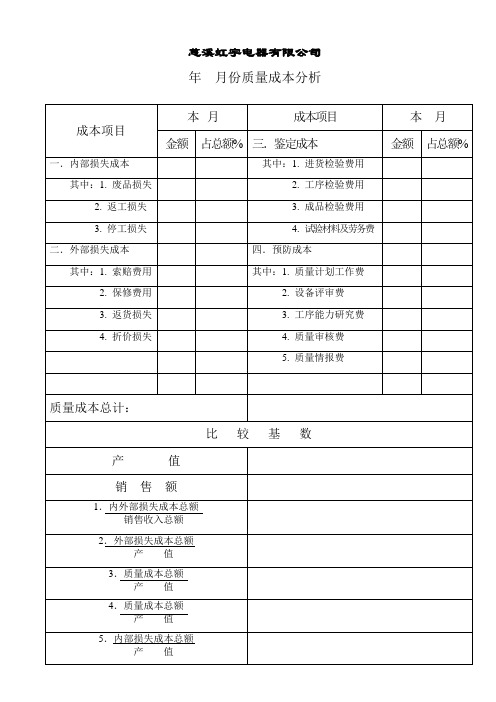
2.设备评审费
3.返货损失
3.工序能力研究费
4.折价损失Βιβλιοθήκη 4.质量审核费5.质量情报费
质量成本总计:
比较基数
产值
销售额
1.内外部损失成本总额
销售收入总额
2.外部损失成本总额
产值
3.质量成本总额
产值
4.质量成本总额
产值
5.内部损失成本总额
产值
慈溪虹宇电器有限公司
年月份质量成本分析
成本项目
本月
成本项目
本月
金额
占总额%
三.鉴定成本
金额
占总额%
一.内部损失成本
其中:1.进货检验费用
其中:1.废品损失
2.工序检验费用
2.返工损失
3.成品检验费用
3.停工损失
4.试验材料及劳务费
二.外部损失成本
四.预防成本
其中:1.索赔费用
其中:1.质量计划工作费
- 1、下载文档前请自行甄别文档内容的完整性,平台不提供额外的编辑、内容补充、找答案等附加服务。
- 2、"仅部分预览"的文档,不可在线预览部分如存在完整性等问题,可反馈申请退款(可完整预览的文档不适用该条件!)。
- 3、如文档侵犯您的权益,请联系客服反馈,我们会尽快为您处理(人工客服工作时间:9:00-18:30)。
专 题 报 告公司某事业部质量损失分析报告一、 文章概要目前公司某产品品质非常脆弱,品质问题已成为制约该事业部可持续发展的关键瓶颈之一。
本文希望从如下方面揭示问题:1、 质量损失不仅包括显性损失,而且包含更大的隐性损失。
按照隐性损失ABC 核算法保守估测,该产品03年隐性质量损失是显性损失的2倍左右,达 亿元;加上显性损失 亿,质量损失高达 亿元;2、 控制质量损失具有重要的战略与经营意义,如果按照实现353规划既定质量目标保守推算,事业部因提升品质平均每年可获得收益 万元;3、 品质问题的解决宜从电控着手,以建立大品质体系与成本品质均衡的决策机制为手段,逐步摆脱品质“监控残缺”的尴尬局面,进入“全局掌控-重点突破-系统创新-全面收益”的良性循环阶段。
二、 质量损失的内涵 1、质量损失的构成所谓质量损失,是指企业为确保或提高产品质量而发生的费用支出,以及由于未能达到质量标准而造成的价值损失。
它不仅包括为提高质量而实际支出的费用,而且还包括因品质缺陷导致的价值流失。
根据可识别性质量损失分为显性质量损失和隐性质量损失,按照产生流程分为预防成本、鉴定成本、损失成本(外部损失、内部损失)三部分(图1)。
图1:质量损失构成客户流失 价格流失 供方成本转嫁生产率流失2、隐性质量损失的内涵由产品品质不良导致的价值链机会成本损失是隐性质量成本的本源,包括:顾客流失——老顾客流失和新顾客流失:老顾客流失——顾客因维修体验而在二次选购时放弃选择原品牌,导致企业损失原可获得的收益。
据麦肯锡对中国该产品市场的研究,未来几年老顾客比例呈迅速增长趋势,将由02年的%上升至08年的%。
新顾客流失——经口碑传播而建立某品牌不良品质形象的潜在选购者,当其中部分人作现实购买时放弃选择该品牌,导致该企业损失原可获得的收益。
科特勒曾指出,家电消费品是顾客购买决策受参照群体1影响最大的产品之一,一个有过维修体验的顾客会将痛苦体验传播给4—8个人。
价格损失——中低价位的该产品,与主要竞争对手相比,产品品质差异因素带来的售价差异平均超过10%2。
生产率流失——将投入到不良品返修的劳动力和设备资源转化为生产合格品可获得的收益。
事实上,同等条件下返修生产往往低于正常生产效率,目前下属某工厂按照正常生产工时的2.5倍来核算返修工时。
供方成本转嫁——从系统性、长远性来看,供方的部分质量成本损失必然会通过后期成交价格、供货质量、议价能力变化等方式,以及采购方供应商转换成本,转嫁给购买者。
这部分转嫁的质量成本,主要体现为筛选不合格退货物料价值、物料在线下线导致的生产率流失。
三、该产品质量损失测算1、显性质量损失呈迅速攀升趋势——2002年,事业本部显性质量损失已达到万元3,比上年净增多万元。
平均单台质量成本元,其中质量损失达到元/台,见图2。
1有过同类产品使用体验的同事、亲人、朋友。
2内部访谈一致认为,产品品质是影响价格差异的关键因素之一,其影响力至少超过50%。
谨慎起见,本文取10%。
3据品质统括部2002年度质量分析报告分析,2000年、2001年质量成本数据存在严重低估失真。
外部损失是攀升过快的主要表现——外部损失呈现出较快的攀升速度,02年占到了显性质量损失的70%。
02年显性质量损失构成如图3。
2、隐性质量损失隐性损失是显性质量成本的2倍以上——根据隐性质量成本估算模型与估量公式(详见附件1)计算可知,03销售年度隐性质量损失合计达亿元,是显性质量成本的2倍以上,其中顾客流失所占比例最大。
按质量成本的来源分,隐性内部损失亿元,隐性外部损失亿元。
(见图4)。
(已删除)相对于品质的“冰山理论”(显性:隐性=1:9)而言,我们对该产品质量隐性损失的以上估算是非常保守的!综合以上分析,我们不难得到如下结论:① 03销售年度该事业部内销总体质量损失4高达 亿元(其中:显性损失为 亿元,隐性损失 亿元),占当年内销销售收入的 %以上。
由此可见,该产品品质收益弹性较大,即通过提高品质降低总体质量损失而增加经营效益的潜力巨大。
在竞争环境极度恶劣,该事业部探索规模与利润平衡增长的盈利模式背景下,提高品质以增加事业部总体收益具有更加重要的现实经营意义与长远战略意义;② 居高不下的市场维修率与质量损失,不仅使公司在与竞争对手的相持中失去经营效益的比较优势,而且导致对顾客满意度、品牌、信誉等企业无形价值的损伤与蚕食。
在空调行业策略转折点即将来临,无形资源竞争逐渐占据主导地位的形势下,公司的品质脆弱性会严重削弱公司可持续发展能力。
为此,必须下决心改变主打产品的品质现状。
四、 提升品质水平(降低质量损失)的经营与战略意义 ㈠ 经营意义1、市场维修率与质量损失相关关系回归分析一般说来,市场维修率与质量损失两个要素之间具有如下正相关关系: c =f(r o )=Ar o +B ,c ——质量损失,r o ——年度市场维修率,A 、B ——相关系数。
4因未作销售年度显性质量成本统计,实际测算03销售年度总质量成本时使用了02财年的数据。
因财年统计区间早于销售年度统计区间半年,实际数据前者会小于后者,故本文测算是谨慎和可信的。
——1个顾客的不满会传给2人,2人传给4人,4人传给16人,…。
——显性特征与隐性特征具有1:9的关系。
隐藏在海面以下的隐性损失(潜——发生1件报废品(1个顾客投诉),意味着29件同样品质问题存在(29冰山理论 海因里奇法则 2级数效应1:9 1:29:300 2n,n=1,2,3,…对01~03年度美的空调市场维修率、质量损失数据的归纳分析(详见附件2),剔除销售价格变化因素影响(折合到03年),该产品年度市场维修率与加权单台质量损失的相关关系为:c =281r o +71,具体回归关系图如下:表中圆点表示事业本部01~03年实际经营所处的品质与质量损失发生点。
说明:质量损失因多变、复杂的经营背景不同而有所不同,由于市场竞争结构、客户结构的不断演变,必然引起以上相关关系系数值的漂移,目前有限的样本数(3个年度数据)所回归的逻辑关系只能揭示变化规律,具体数据则不完全精确。
2、2004-2008年该事业部质量损失预测品质统括部三五三质量规划提出的市场维修率控制目标如表1,到三五三战略阶段的最后一年,市场维修率将下降为 %,总降幅 %。
但与行业品质水准对比,这个指标仍然不及国际大品牌等企业目前品质水平(东芝市场维修率 %),也仅比03年国内竞争对手的品质水平强一点5。
因此树立更为积极、更富有挑战性的质量目标十分必要。
表1:2004—2008年质量规划目标5据内部访谈:主要竞争对手当年市场维修率仅为该事业部 %以下,年度市场维修率与当年市场维修率具有同幅趋同特性,故推测其年度维修率应为该事业部的 %。
图8: 01~03冷年空调市场维修率与质量成本关系50100150200ro=3%ro=9%ro=15%ro=21%市场维修率ro单台质量成本(元)根据以上质量规划目标中的具体数据及回归方程c=281ro+71,可得到2004-2008年该事业部质量损失曲线如下:由上图可见,降低质量损失将为企业带来巨大的节支收益,其增加幅度随着经营规模的扩大而不断扩大。
在三五三战略实施阶段,该产品质量水平如实现品质统括部规划的质量目标,相比参考状态,累计可节约质量损失4.4亿元,平均每年为8800万元;而更积极的质量目标状态将节支达7.8亿元,平均每年1.56亿元。
㈡战略意义1、三大品牌品质战略与实践对比2、源自质量的竞争优劣势比较××:质量损失低于竞争对手一半——市场维修率的差异反应了质量成本的差异。
××市场维修率目前是公司的 ,借鉴公司品质与质量损失回归关系曲线可以推断,××具有低于主要竞争对手一半左右的质量损失控制能力,已形成其核心竞争优势并赢得了较好的消费者口碑;××:质量损失与公司相当——依靠产品工业设计、售后服务来粉饰品牌形象与口碑以维持产品的高价位。
公司:质量损失较高,售后服务没有特色,处于品质竞争的劣势——任何一个行业前三强的国际性品牌,都不是三流的品质能力所能支撑的。
目前我们的品质能力仅处于业界中下游水平,三五三战略需要将其提升到一个适合的水准,至少必须接近乃至超越××、××等国际二流质量水平,而目前差距还相当明显。
公司必须从自身质量损失形成的源头进行检讨梳理,明确战略方向与具体策略并迅速行动。
五、质量损失产生的根源剖析 1、零部件质量问题2002年家用内销维修率前10名的零部件如下图:这里指当年销售产品当年发生的市场维修比率,预测值来自品质统括部市场稽查的经验判断。
图4: 02年维修率前十名零部件结构示意图室内电控主板,9.91%室内开关显示板(柜), 6.88%从上图可以看出:①电子件品质控制能力非常薄弱——近几年,电子件(电控部件、电子元器件)零部件始终占维修总量40%~60%,其中室内电控主板、遥控器等一直处在维修率最前列。
2002年内新进入维修前10名的4类零部件中有3类即是电子件。
管温传感器更是一路攀升,到今年9月不仅一举占据维修排行榜榜首,而且创下了单件零件超过总维修量10%的不良记录。
这充分表明了电子件品质控制能力是提升品质水平的关键瓶颈。
建议事业部对电子件采取“品质优先,兼顾成本”的长期制造开发战略;②关键零部件质量控制能力呈现维持甚至弱化迹象——一方面,一些长期性品质问题尚未得到有效扭转。
例如,自2000年以来室内电控主板、室内连接管等六类零部件始终位于维修率前10名之列;另一方面,以往免检的关键零部件维修率也在迅速上升,如压缩机已跃居维修率前10名,返修率高达2.83%。
2、质量管理问题检讨①品质问题未引起各单位的实质性重视——主要表现为“认识上不到位、思想上不关心、行动上不重视”。
部分单位的主要领导人没有从系统与全局的高度上认识到现阶段公司产品品质提升对降低整体成本、提高总体经营效益的事实,片面将品质与成本、市场反应速度对立起来,总是按照“非此即彼”的简单逻辑处理品质与成本的关系。
在竞争环境恶劣的情况下,往往从部门本位与短期利益出发,采取简单的“竭泽而渔”的方式追求成本最小化而牺牲品质;②品质决策与监控体系“残缺不全”,系统的“大品质体系”远未形成——在降成本的惯性压力下,影响品质的关键环节(如技术开发、供应链招标、工艺技术改进等)进行相关决策时,几乎听不到品质的声音,因此,成本品质的均衡决策与监控机制在关键环节缺失,造成品质工作的“缘木求鱼”;③责任缺位——事业部究竟谁对居高不下的品质损失负责?应该考核谁?如何考核?这些问题尚未落到实处;④涉及品质提升的某些关键问题(如电控)迟迟不能突破,影响了整体品质水平提升——电控开发与制造技术停留在凭感觉摸索的“手工作坊”时代,对行业技术规律与同行的对比分析认识不深,提不出创造性的改革突破方案;⑤事业部品质管理部门“长于技术、疏于管理”——对某些危及品质的严重现象(如产品开发设计的“删、减、换、省”)既缺乏约束机制与评价结论,也缺乏有效的管控制止手段。