数控机床加工精度高的误解
数控机床加工精度的影响因素及提高方法

数控机床加工精度的影响因素及提高方法数控机床加工精度是指机床在进行加工过程中所能达到的准确度和稳定性。
影响机床加工精度的因素非常多,下面将对影响因素和提高方法进行一些阐述。
1. 机床自身的优劣:机床的设计、制造和装配技术对加工精度有直接影响。
优质的机床在设计和制造过程中会注重减小传动误差、提高定位精度和重复定位精度等。
2. 机床的刚性和稳定性:机床的刚性和稳定性对加工精度起着决定性的作用。
刚性不足会导致机床在加工过程中出现振动和变形,从而影响加工精度。
3. 传动装置的精度和可靠性:传动装置的传动误差、反向间隙等都会影响加工精度。
传动装置的精度和可靠性越高,加工精度也越高。
4. 控制系统的精度:数控机床的控制系统对加工精度有直接影响。
控制系统的精度主要包括伺服系统的控制精度、编码器的精度以及数控系统的实时性等。
5. 刀具和夹具的精度:刀具和夹具的精度直接影响加工质量。
刀具和夹具的选择和安装都需要考虑其精度和稳定性。
1. 选用优质的机床:选择优质的机床是提高加工精度的基础。
优质的机床具有高精度、高刚性和高稳定性,能够更好地满足加工要求。
2. 优化加工工艺:通过优化加工工艺,合理设置切削参数和进给速度等,可以减小加工误差,提高加工精度。
4. 优化编程和加工过程:合理优化数控程序和加工过程,减小加工误差。
尽量避免急停和急转等情况,保证加工过程的平稳性和稳定性。
5. 定期进行机床维护和保养:定期进行机床的维护和保养,保证机床的正常运行和精度稳定性。
包括清洁、润滑和紧固等工作。
数控机床加工精度的提高需要从机床自身的优劣、刚性和稳定性、传动装置的精度和可靠性、控制系统的精度以及刀具和夹具的精度等方面进行综合考虑。
通过优化加工工艺、合理选择刀具和夹具、加强编程和加工过程的管理以及定期进行机床维护和保养等措施,可以有效提高数控机床的加工精度。
数控机床加工误差原因及对策分析

数控机床加工误差原因及对策分析数控机床是当今制造业的主要设备之一。
数控机床生产效率高,运行速度快,加工精度高,成品质量好,成本相对较低。
但是,在实际生产过程中,经常会出现加工误差,影响生产效率和成品质量。
因此,分析数控机床加工误差原因并寻找对策是很必要的。
本文将探讨数控机床加工误差的原因,以及如何通过改进措施来减少误差的发生。
一、误差的种类数控机床加工误差通常包括以下几种:1.轨迹误差。
轨迹误差是指数控机床加工时导致实际加工轨迹与期望轨迹之间的误差。
2.定位误差。
定位误差是指数控机床在加工中出现的位置偏差。
定位误差可能由机床本身、工件、刀具等方面的原因引起。
3.回转误差。
回转误差是指数控机床在进行旋转加工时出现的偏差。
回转误差通常由转台本身、传动系统和工件等原因引起。
4.表面误差。
表面误差是指数控机床加工表面的粗糙度、平整度、垂直度和平行度等参数上的误差。
二、误差产生的原因1.机床本身的精度。
数控机床的精度与质量直接相关,是影响加工质量的最重要因素。
如果机床本身的精度不高,则会直接导致加工误差的发生。
2.工具刃磨质量。
如果刀具的刃磨质量不好,切屑排出不畅等问题,也容易引起加工误差。
3.刀具稳定性。
刀具的稳定性是指在加工过程中刀具的稳定性,如果刀具不稳定,则极易引起加工误差的发生。
4.机床几何精度调整。
机床几何精度调整直接影响加工误差发生的概率,如果机床几何精度调整不当,则会引起加工误差的出现。
5.机床零部件磨损。
随着机床的使用,部件常会出现磨损,进而影响加工精度。
三、解决方案1.提高加工前的加工过程控制。
在加工前加强对加工过程的控制,可通过模具设计等预处理阶段减少误差出现的可能性。
2.注意刀具选择。
选择质量高的刀具,并保持刀具在加工过程中的稳定性。
3.指导及培训操作人员。
操作人员要具备相应的知识和技能,遵循正确的加工流程,熟练使用数控机床,能够及时发现和解决数控机床加工过程中的问题。
4.定期机床保养。
数控加工产生误差的根源及解决方案

数控加工产生误差的根源及解决方案数控加工是利用数控技术通过控制机床和刀具相对运动的方式,对工件进行加工的一种工艺。
虽然数控加工相对手工加工来说具有高精度、高效率、高一致性等优点,但是由于一些原因还是会在实际应用中产生一些误差,下面我们对数控加工误差的根源及解决方案进行详细介绍。
一、误差产生的根源1.机床本身问题机床是数控加工的基础,如果机床本身精度不高,则会直接影响到加工的精度。
例如机床的重复定位精度、圆度等问题都会导致数控加工中的误差。
2.编程和操作问题编程和操作的问题也是数控加工中产生误差的重要原因。
编写的程序是否符合实际加工的要求、操作人员能否正确的操作数控设备、调整数控设备的参数等都会影响加工的精度。
3.工件材料和加工工艺工件的材料和加工工艺也是数控加工中产生误差的原因之一。
因为不同的材料及加工工艺的选用,需要有不同的加工参数设置,否则加工出来的零件尺寸不稳定,而且不同的材料具有不同的热膨胀系数,会使得加工出来的工件产生偏差。
二、误差的解决方案1.提高机床精度如何提高机床精度呢?首先我们要选用性能稳定、精度高的数控机床。
同时,在加工过程中要注意定期检查机床的重复定位精度、圆形度等指标,及时进行维护和保养。
2.优化编程和操作流程软件程序的编写和操作过程是决定加工精度的重要环节之一,因此编写程序时要结合实际加工要求,同时要对操作流程进行规范化和标准化,让操作流程尽量简单,便于操作人员进行操作。
3.优化材料和加工工艺合理选用材料及加工工艺,是提高精度的重要环节之一,因此选择合适的加工工艺的同时,要注意材料的热膨胀系数等性质,以此来保证加工出来的工件符合设计要求。
总之,数控加工误差的根源较多,但只要我们能够从机器、人员和程序三个方面入手,针对性的进行优化,加工精度是能够得到不断提高的。
数控机床的加工精度误差分析与校正方法
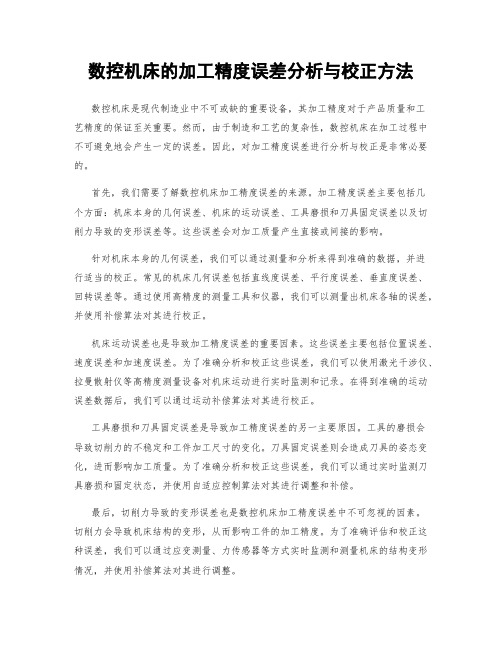
数控机床的加工精度误差分析与校正方法数控机床是现代制造业中不可或缺的重要设备,其加工精度对于产品质量和工艺精度的保证至关重要。
然而,由于制造和工艺的复杂性,数控机床在加工过程中不可避免地会产生一定的误差。
因此,对加工精度误差进行分析与校正是非常必要的。
首先,我们需要了解数控机床加工精度误差的来源。
加工精度误差主要包括几个方面:机床本身的几何误差、机床的运动误差、工具磨损和刀具固定误差以及切削力导致的变形误差等。
这些误差会对加工质量产生直接或间接的影响。
针对机床本身的几何误差,我们可以通过测量和分析来得到准确的数据,并进行适当的校正。
常见的机床几何误差包括直线度误差、平行度误差、垂直度误差、回转误差等。
通过使用高精度的测量工具和仪器,我们可以测量出机床各轴的误差,并使用补偿算法对其进行校正。
机床运动误差也是导致加工精度误差的重要因素。
这些误差主要包括位置误差、速度误差和加速度误差。
为了准确分析和校正这些误差,我们可以使用激光干涉仪、拉曼散射仪等高精度测量设备对机床运动进行实时监测和记录。
在得到准确的运动误差数据后,我们可以通过运动补偿算法对其进行校正。
工具磨损和刀具固定误差是导致加工精度误差的另一主要原因。
工具的磨损会导致切削力的不稳定和工件加工尺寸的变化。
刀具固定误差则会造成刀具的姿态变化,进而影响加工质量。
为了准确分析和校正这些误差,我们可以通过实时监测刀具磨损和固定状态,并使用自适应控制算法对其进行调整和补偿。
最后,切削力导致的变形误差也是数控机床加工精度误差中不可忽视的因素。
切削力会导致机床结构的变形,从而影响工件的加工精度。
为了准确评估和校正这种误差,我们可以通过应变测量、力传感器等方式实时监测和测量机床的结构变形情况,并使用补偿算法对其进行调整。
总结来说,数控机床的加工精度误差分析与校正是确保产品质量和工艺精度的关键步骤。
在这个过程中,我们需要准确地识别和分析加工精度误差的来源,并采取相应的校正措施。
数控机床加工精度的影响因素及提高方法
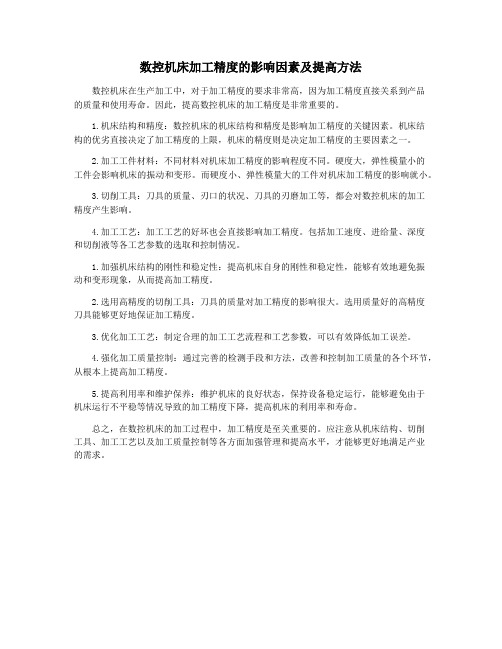
数控机床加工精度的影响因素及提高方法数控机床在生产加工中,对于加工精度的要求非常高,因为加工精度直接关系到产品的质量和使用寿命。
因此,提高数控机床的加工精度是非常重要的。
1.机床结构和精度:数控机床的机床结构和精度是影响加工精度的关键因素。
机床结构的优劣直接决定了加工精度的上限,机床的精度则是决定加工精度的主要因素之一。
2.加工工件材料:不同材料对机床加工精度的影响程度不同。
硬度大,弹性模量小的工件会影响机床的振动和变形。
而硬度小、弹性模量大的工件对机床加工精度的影响就小。
3.切削工具:刀具的质量、刃口的状况、刀具的刃磨加工等,都会对数控机床的加工精度产生影响。
4.加工工艺:加工工艺的好坏也会直接影响加工精度。
包括加工速度、进给量、深度和切削液等各工艺参数的选取和控制情况。
1.加强机床结构的刚性和稳定性:提高机床自身的刚性和稳定性,能够有效地避免振动和变形现象,从而提高加工精度。
2.选用高精度的切削工具:刀具的质量对加工精度的影响很大。
选用质量好的高精度刀具能够更好地保证加工精度。
3.优化加工工艺:制定合理的加工工艺流程和工艺参数,可以有效降低加工误差。
4.强化加工质量控制:通过完善的检测手段和方法,改善和控制加工质量的各个环节,从根本上提高加工精度。
5.提高利用率和维护保养:维护机床的良好状态,保持设备稳定运行,能够避免由于机床运行不平稳等情况导致的加工精度下降,提高机床的利用率和寿命。
总之,在数控机床的加工过程中,加工精度是至关重要的。
应注意从机床结构、切削工具、加工工艺以及加工质量控制等各方面加强管理和提高水平,才能够更好地满足产业的需求。
数控加工产生误差的根源及解决方案

数控加工产生误差的根源及解决方案数控加工是一种高精度的金属加工方法,利用计算机控制的精密设备进行金属材料的切削和加工。
但是即使使用数控加工,仍然会产生一定的误差。
这些误差的产生主要与数控系统、机床、刀具以及加工环境等因素有关。
为了解决这些误差,需要从源头控制、精度校准、工艺优化等方面入手。
下面详细介绍数控加工产生误差的根源及解决方案。
一、数控系统引起的误差:1. 数控系统内部误差:数控系统内部误差是指控制器和伺服系统的误差。
在日常使用中,数控系统会出现一些误差,主要是由于控制器的精度、伺服系统的响应速度、传感器的精度等方面引起的。
解决这些误差的方法主要有:及时进行维护和保养,更新升级数控系统软件,提高系统的稳定性和精度。
2. 机床误差:机床误差是指机床本身的精度和稳定性问题,如机床导轨磨损、轴承松动等。
解决机床误差的方法主要有:定期进行机床维护,及时更换磨损的机床部件,提高机床的整体刚性和精度。
二、加工误差的根源及解决方案:1. 刀具误差:刀具的质量和磨损程度直接影响加工精度。
刀具的质量差、磨损过度等都会导致加工误差的产生。
解决刀具误差的方法主要有:选用质量好的刀具,定期检查和更换磨损的刀具,确保刀具与工件的匹配度。
2. 加工工艺误差:加工工艺参数的不合理设置也会导致加工误差的产生。
例如,进给速度、切削速度、切削深度等参数的选择不当会引起加工误差。
解决加工工艺误差的方法主要有:制定科学合理的加工工艺参数,根据具体情况调整切削速度和进给速度,并设定合理的切削深度。
3. 加工环境误差:加工环境的温度和湿度等因素也会对加工误差产生一定的影响。
例如,温度过高会导致机床热变形,湿度过大会导致机床表面生锈,都会影响加工的精度。
解决加工环境误差的方法主要有:合理调节加工环境的温度和湿度,保持机床的干燥和清洁,定期进行维护和检查。
综上所述,数控加工误差的产生主要与数控系统、机床、刀具以及加工环境等因素有关。
为了解决这些误差,需要从源头控制、精度校准、工艺优化等方面入手。
普通机床和数控机床的差别

一、数控机床与普通机床的区别数控机床对零件的加工过程,是严格按照加工程序所规定的参数及动作执行的。
它是一种高效能自动或半自动机床,与普通机床相比,具有以下明显特点:1、适合于复杂异形零件的加工数控机床可以完成普通机床难以完成或根本不能加工的复杂零件的加工,因此在宇航、造船、模具等加工业中得到广泛应用。
2、加工精度高3、加工稳定可靠实现计算机控制,排除人为误差,零件的加工一致性好,质量稳定可靠。
4、高柔性加工对象改变时,一般只需要更改数控程序,体现出很好的适应性,可大大节省生产准备时间。
在数控机床的基础上,可以组成具有更高柔性的自动化制造系统—FMS。
5、高生产率数控机床本身的精度高、刚性大,可选择有利的加工用量,生产率高,一般为普通机床的3~5 倍,对某些复杂零件的加工,生产效率可以提高十几倍甚至几十倍。
6、劳动条件好机床自动化程度高,操作人员劳动强度大大降低,工作环境较好.7、有利于管理现代化采用数控机床有利于向计算机控制与管理生产方面发展,为实现生产过程自动化创造了条件。
8、投资大,使用费用高9、生产准备工作复杂由于整个加工过程采用程序控制,数控加工的前期准备工作较为复杂,包含工艺确定、程序编制等.10、维修困难数控机床是典型的机电一体化产品,技术含量高,对维修人员的技术要求很高。
二、数控机床的适用范围由于数控机床的上述特点,适用于数控加工的零件有:1、批量小而又多次重复生产的零件;2、几何形状复杂的零件;3、贵重零件加工;4、需要全部检验的零件;5、试制件。
对以上零件采用数控加工,才能最大限度地发挥出数控加工的优势.数控机床——是数字控制机床(Computer numerical control machine tools)的简称,是一种装有程序控制系统的自动化机床。
数控机床与普通机床的主要区别在于:数控机床带有数控系统(程序控制系统),可以通过编制程序来实现自动化加工。
而普通机床没有该特性.其他方面的区别及容易引起的误解:1.通常数控机床加工过程不需要人为去操作,定好原点及编制好数控程序即可。
数控机床加工精度的影响因素及提高方法

数控机床加工精度的影响因素及提高方法数控机床加工精度是衡量机床性能和加工质量的重要指标之一。
机床加工精度的高低直接影响到加工零件的尺寸精度和表面质量。
正确理解数控机床加工精度的影响因素及提高方法,可以有效提高机床加工精度,满足不同的加工要求。
一、影响因素1. 机床本身的精度:机床加工精度的高低取决于机床本身精度的高低。
包括机床的机械结构精度、控制系统精度以及加工刀具等。
2. 工件加工材料的性质:工件的材料的硬度、韧性、温度等都会影响加工时的切削力、振动、温度变化等,从而影响机床加工精度。
3. 切削工艺参数:如切削速度、进给量、切削深度和切削方向等,都会对零件的尺寸和形状精度产生影响。
4. 加工环境:加工环境的湿度、温度、气压等也会对机床加工精度产生影响。
特别是在高温、潮湿的环境中长时间工作,会导致机床部件热膨胀和受潮,进而影响机床加工精度。
二、提高方法1. 优化机床结构:通过提高机床的机械结构精度,例如采用高刚性材料,优化结构设计,优化装配工艺等,以提高机床加工精度和稳定性。
2. 提高控制系统精度:控制系统是数控机床的重要组成部分。
通过对机床控制系统进行优化,提高控制精度、数据传输速率和控制方式等。
例如采用高精度伺服电机、编码器、传感器等辅助检测设备,提高机床的动态响应能力和精度。
3. 优化加工工艺:根据工件材料的特性,优化加工刀具的选型、切削工艺参数等,以确保加工过程中的稳定性和精度。
4. 控制加工环境:通过控制加工环境的温度、湿度、气压等条件,提高机床加工精度和稳定性。
综上所述,数控机床加工精度的影响因素和提高方法是相互关联的。
只有综合考虑机床结构、控制系统、加工工艺和加工环境等各个方面因素,才能最大限度的提高机床加工精度和稳定性,从而满足不同的加工要求。
数控加工工艺中的误差分析
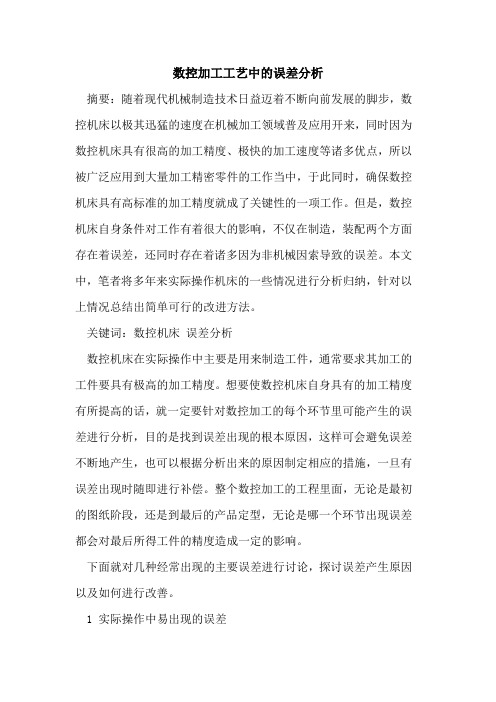
数控加工工艺中的误差分析摘要:随着现代机械制造技术日益迈着不断向前发展的脚步,数控机床以极其迅猛的速度在机械加工领域普及应用开来,同时因为数控机床具有很高的加工精度、极快的加工速度等诸多优点,所以被广泛应用到大量加工精密零件的工作当中,于此同时,确保数控机床具有高标准的加工精度就成了关键性的一项工作。
但是,数控机床自身条件对工作有着很大的影响,不仅在制造,装配两个方面存在着误差,还同时存在着诸多因为非机械因索导致的误差。
本文中,笔者将多年来实际操作机床的一些情况进行分析归纳,针对以上情况总结出简单可行的改进方法。
关键词:数控机床误差分析数控机床在实际操作中主要是用来制造工件,通常要求其加工的工件要具有极高的加工精度。
想要使数控机床自身具有的加工精度有所提高的话,就一定要针对数控加工的每个环节里可能产生的误差进行分析,目的是找到误差出现的根本原因,这样可会避免误差不断地产生,也可以根据分析出来的原因制定相应的措施,一旦有误差出现时随即进行补偿。
整个数控加工的工程里面,无论是最初的图纸阶段,还是到最后的产品定型,无论是哪一个环节出现误差都会对最后所得工件的精度造成一定的影响。
下面就对几种经常出现的主要误差进行讨论,探讨误差产生原因以及如何进行改善。
1 实际操作中易出现的误差1.1 编程误差。
这一点误差主要是由数控编程软件的过程中产生,属于一种插补误差,在使用数控机床来对零件进行加工时,由于数控装置之间具有互不相同的插补功能,所以与零件轮廓互相逼近的时候,都是选择直线的方式来进行,有的时候则是用圆弧。
直线或圆弧在马上临近零件轮廓曲线的时候,逼近曲线和现实中轮廓原来的曲线之间会产生一个最大差值,这就是通常所说的插补误差,在对零件加工精度起到影响的因素里面,这是非常重要的一个原因。
1.2 刀尖圆弧误差。
在对内孔进行切割的过程里,当操作进行到外圆时,刀尖圆弧通常不会对尺寸、形状产生影响,但是对锥面或圆弧进行加工的时候,刀尖圆弧就会对其产生影响,一般来说会导致出现过切或少切的情况。
解析数控车床加工精度的影响因素及提高措施
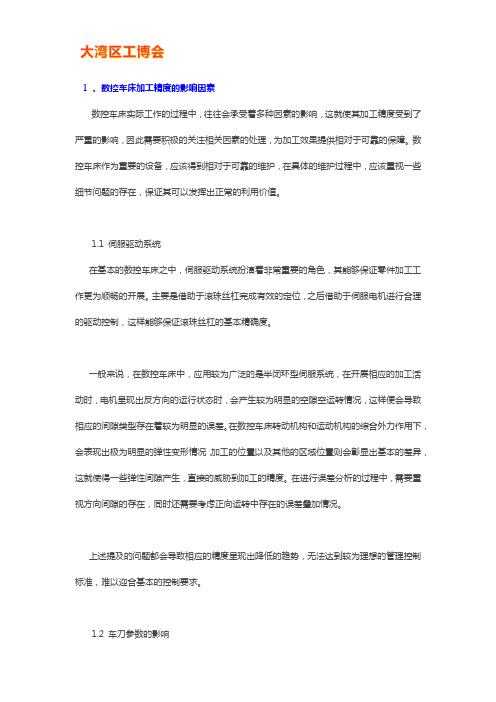
1 、数控车床加工精度的影响因素数控车床实际工作的过程中,往往会承受着多种因素的影响,这就使其加工精度受到了严重的影响,因此需要积极的关注相关因素的处理,为加工效果提供相对于可靠的保障。
数控车床作为重要的设备,应该得到相对于可靠的维护,在具体的维护过程中,应该重视一些细节问题的存在,保证其可以发挥出正常的利用价值。
1.1 伺服驱动系统在基本的数控车床之中,伺服驱动系统扮演着非常重要的角色,其能够保证零件加工工作更为顺畅的开展。
主要是借助于滚珠丝杠完成有效的定位,之后借助于伺服电机进行合理的驱动控制,这样能够保证滚珠丝杠的基本精确度。
一般来说,在数控车床中,应用较为广泛的是半闭环型伺服系统,在开展相应的加工活动时,电机呈现出反方向的运行状态时,会产生较为明显的空隙空运转情况,这样便会导致相应的间隙类型存在着较为明显的误差。
在数控车床转动机构和运动机构的综合外力作用下,会表现出极为明显的弹性变形情况,加工的位置以及其他的区域位置则会彰显出基本的差异,这就使得一些弹性间隙产生,直接的威胁到加工的精度。
在进行误差分析的过程中,需要重视方向间隙的存在,同时还需要考虑正向运转中存在的误差叠加情况。
上述提及的问题都会导致相应的精度呈现出降低的趋势,无法达到较为理想的管理控制标准,难以迎合基本的控制要求。
1.2 车刀参数的影响通常来讲,在数控车床的加工实践中,往往是借助于编程控制的基本手段落实车刀的调整,保证可以更加顺畅的开展零部件的切削工作,由此让其基本的形状符合相应的要求。
在车削加工的基本环节之中,车刀一般会反映出主偏角以及刀尖圆弧半径的基本数值,在对棒料进行适当的加工时,轴向的尺寸还是很容易产生一些误差问题,面对这样的情况应该做出合理的分析,判断这类误差和主偏角往往是呈现出一种反比的关系,当不断地增加相应的主偏角之后,相应的误差可以适当的降低,但是对比于刀尖圆弧半径来看,两者之间还是存在着正比的关联。
如果在具体加工的过程中车刀的参数发生了较为显著的变化,会使得相应的精度受到较为直接的影响。
数控机床加工中的瑕疵分析与解决方法

数控机床加工中的瑕疵分析与解决方法随着科技的不断进步和发展,数控机床作为一种先进的加工设备,在各个行业中得到了广泛的应用。
然而,在数控机床加工过程中,瑕疵问题不可避免地出现。
本文将对数控机床加工中常见的瑕疵进行分析,并提供解决方法,以帮助读者更好地应对这些问题。
一、瑕疵分析1. 加工精度不高:数控机床的加工精度是影响产品质量的重要因素。
加工精度不高可能导致尺寸偏差、表面粗糙度不达标等问题。
2. 加工失真:加工失真主要是指加工过程中由于热变形、应力集中等原因导致加工形状与设计要求不符合。
3. 加工热损伤:由于数控机床加工过程中涉及高速切削、高温摩擦等因素,可能会导致零件表面出现热损伤,如烧伤、氧化等。
4. 加工表面质量不佳:数控机床加工表面质量是考验产品外观质量的重要指标,表面存在凹凸不平、毛刺、划痕等问题,会影响产品的档次和使用寿命。
二、解决方法1. 提高加工精度:首先应对数控机床进行维护保养,保证设备的正常工作状态。
其次,选择合适的刀具和切削参数,并按照加工标准进行程序的编写和调试,以确保加工精度的达标。
2. 预防加工失真:加工失真问题主要与材料的热变形和应力有关。
因此,在选择材料时要根据产品的要求选择合适的材料,避免出现热变形和应力集中的情况。
另外,在加工过程中,要控制加工温度,避免过高的温度对材料的影响。
3. 预防加工热损伤:数控机床在加工时会产生大量热量,主要集中在刀具和工件之间的切削区域。
为了预防加工热损伤,可以采用切削液冷却的方法,及时将热量带走,保持切削区域的温度在适宜范围内。
4. 改善加工表面质量:为了改善加工表面质量,可以采用一些方法,如切削参数的调整、切削工艺的优化、使用合适的刀具和刀具涂层等。
此外,还可以采用表面处理技术,如砂光、抛光、氮化等,来改善加工表面质量。
总结:数控机床加工中的瑕疵是无法避免的,但通过合理的分析和解决方法,可以有效地减少瑕疵的发生率,提高产品质量。
在实际应用中,需要根据具体情况选择相应的措施,并进行合理的调试和优化。
数控机床加工精度调整方法及误差原因

加工精度主要用于生产产品程度,加工精度与加工误差都是评价加工表面几何参数的术语。
加工精度用公差等级衡量,等级值越小,其精度越高;加工误差用数值表示,数值越大,其误差越大。
加工精度高,就是加工误差小,反之亦然。
公差等级从IT01,IT0,IT1,IT2,IT3至IT18一共有20个,其中IT01表示的话该零件加工精度最高的,IT18表示的话该零件加工精度是最低的,一般上IT7、IT8是加工精度中等级别。
任何加工方法所得到的实际参数都不会绝对准确,从零件的功能看,只要加工误差在零件图要求的公差范围内,就认为保证了加工精度。
机器的质量取决于零件的加工质量和机器的装配质量,零件加工质量包含零件加工精度和表面质量两大部分。
机械加工精度是指零件加工后的实际几何参数(尺寸、形状和位置)与理想几何参数相符合的程度。
它们之间的差异称为加工误差。
加工误差的大小反映了加工精度的高低。
误差越大加工精度越低,误差越小加工精度越高。
一、加工精度的调整方法1、减小机床误差(1)提高主轴部件的制造精度1)应提高轴承的回转精度:①选用高精度的滚动轴承;②采用高精度的多油锲动压轴承;③采用高精度的静压轴承。
2)应提高与轴承相配件的精度:①提高箱体支撑孔、主轴轴颈的加工精度;②提高与轴承相配合表面的加工精度;③测量及调节相应件的径向跳动范围,使误差补偿或相抵消。
(2)对滚动轴承适当预紧①可消除间隙;②增加轴承刚度;③均化滚动体误差。
(3)使主轴回转精度不反映到工件上。
2、对工艺系统进行调整(1)试切法调整通过试切—测量尺寸—调整刀具的吃刀量—走刀切削—再试切,如此反复直至达到所需尺寸。
此法生产效率低,主要用于单件小批生产。
(2)调整法通过预先调整好机床、夹具、工件和刀具的相对位置获得所需尺寸。
此法生产率高,主要用于大批大量生产。
3、减小刀具磨损在刀具尺寸磨损达到急剧磨损阶段前就必须重新磨刀。
4、减少传动链传动误差(1)传动件数少,传动链短,传动精度高;(2)采用降速传动,是保证传动精度的重要原则,且越接近末端的传动副,其传动比应越小;(3)末端件精度应高于其他传动件。
CNC机床加工中的加工误差分析与校正
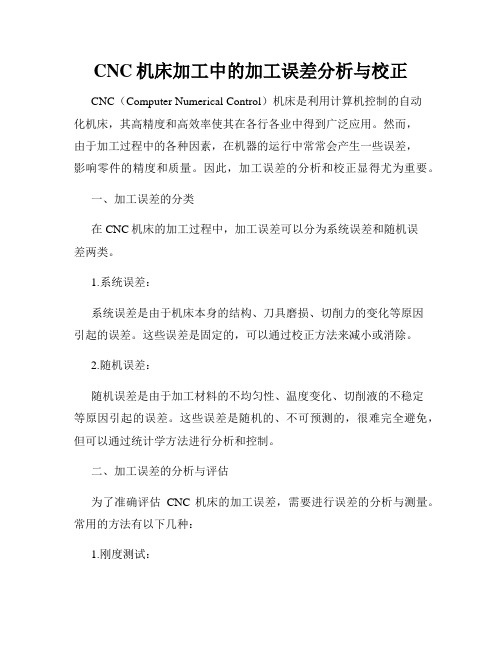
CNC机床加工中的加工误差分析与校正CNC(Computer Numerical Control)机床是利用计算机控制的自动化机床,其高精度和高效率使其在各行各业中得到广泛应用。
然而,由于加工过程中的各种因素,在机器的运行中常常会产生一些误差,影响零件的精度和质量。
因此,加工误差的分析和校正显得尤为重要。
一、加工误差的分类在CNC机床的加工过程中,加工误差可以分为系统误差和随机误差两类。
1.系统误差:系统误差是由于机床本身的结构、刀具磨损、切削力的变化等原因引起的误差。
这些误差是固定的,可以通过校正方法来减小或消除。
2.随机误差:随机误差是由于加工材料的不均匀性、温度变化、切削液的不稳定等原因引起的误差。
这些误差是随机的、不可预测的,很难完全避免,但可以通过统计学方法进行分析和控制。
二、加工误差的分析与评估为了准确评估CNC机床的加工误差,需要进行误差的分析与测量。
常用的方法有以下几种:1.刚度测试:通过在不同刀具载荷下测量机床的变形量,来评估机床的刚度,从而得到系统误差的信息。
2.几何误差测量:利用测量仪器如测角仪、千分尺等,测量机床各个部分的几何误差,如直线度、平行度等,以确定系统误差的来源。
3.工件测量:通过测量机床加工出的工件的尺寸和形状,与理论值进行对比,确定系统误差的大小和分布。
三、加工误差的校正方法根据加工误差的分析结果,可以采取以下一些校正方法来提高CNC 机床的加工精度:1.几何误差补偿:通过调整机床的机械结构,如滚珠丝杠的间隙、导轨的松紧程度等,来减小或消除系统误差。
2.温度补偿:由于温度的变化会导致机床零件的热膨胀,从而引起误差。
采用温度传感器和控制系统,可以根据实时温度变化来进行补偿。
3.刀具磨损监测与自动补偿:由于刀具的磨损会影响加工精度,因此可以通过监测刀具磨损情况,并及时进行自动补偿,以保证工件的精度。
4.工艺参数优化:通过调整切削速度、进给量等工艺参数,来减小误差的影响,以提高加工的精度。
数控车床加工精度的影响因素与提高策略
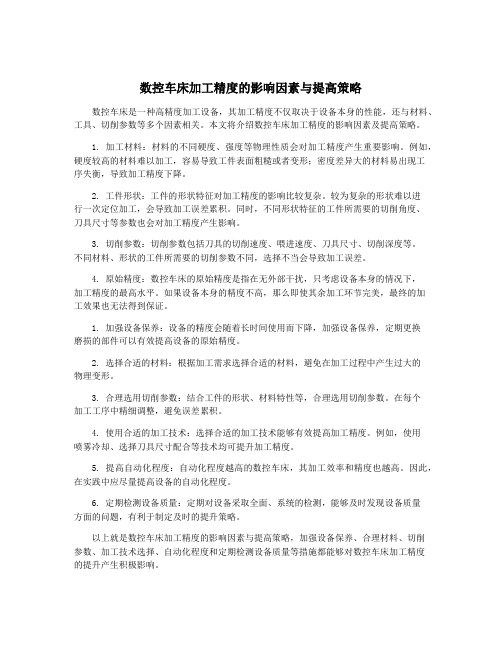
数控车床加工精度的影响因素与提高策略数控车床是一种高精度加工设备,其加工精度不仅取决于设备本身的性能,还与材料、工具、切削参数等多个因素相关。
本文将介绍数控车床加工精度的影响因素及提高策略。
1. 加工材料:材料的不同硬度、强度等物理性质会对加工精度产生重要影响。
例如,硬度较高的材料难以加工,容易导致工件表面粗糙或者变形;密度差异大的材料易出现工序失衡,导致加工精度下降。
2. 工件形状:工件的形状特征对加工精度的影响比较复杂。
较为复杂的形状难以进行一次定位加工,会导致加工误差累积。
同时,不同形状特征的工件所需要的切削角度、刀具尺寸等参数也会对加工精度产生影响。
3. 切削参数:切削参数包括刀具的切削速度、喂进速度、刀具尺寸、切削深度等。
不同材料、形状的工件所需要的切削参数不同,选择不当会导致加工误差。
4. 原始精度:数控车床的原始精度是指在无外部干扰,只考虑设备本身的情况下,加工精度的最高水平。
如果设备本身的精度不高,那么即使其余加工环节完美,最终的加工效果也无法得到保证。
1. 加强设备保养:设备的精度会随着长时间使用而下降,加强设备保养,定期更换磨损的部件可以有效提高设备的原始精度。
2. 选择合适的材料:根据加工需求选择合适的材料,避免在加工过程中产生过大的物理变形。
3. 合理选用切削参数:结合工件的形状、材料特性等,合理选用切削参数。
在每个加工工序中精细调整,避免误差累积。
4. 使用合适的加工技术:选择合适的加工技术能够有效提高加工精度。
例如,使用喷雾冷却、选择刀具尺寸配合等技术均可提升加工精度。
5. 提高自动化程度:自动化程度越高的数控车床,其加工效率和精度也越高。
因此,在实践中应尽量提高设备的自动化程度。
6. 定期检测设备质量:定期对设备采取全面、系统的检测,能够及时发现设备质量方面的问题,有利于制定及时的提升策略。
以上就是数控车床加工精度的影响因素与提高策略,加强设备保养、合理材料、切削参数、加工技术选择、自动化程度和定期检测设备质量等措施都能够对数控车床加工精度的提升产生积极影响。
普通机床和数控机床的差别

一、数控机床与普通机床的区别数控机床对零件的加工过程,是严格按照加工程序所规定的参数及动作执行的。
它是一种高效能自动或半自动机床,与普通机床相比,具有以下明显特点:1、适合于复杂异形零件的加工数控机床可以完成普通机床难以完成或根本不能加工的复杂零件的加工,因此在宇航、造船、模具等加工业中得到广泛应用。
2、加工精度高3、加工稳定可靠实现计算机控制,排除人为误差,零件的加工一致性好,质量稳定可靠。
4、高柔性加工对象改变时,一般只需要更改数控程序,体现出很好的适应性,可大大节省生产准备时间。
在数控机床的基础上,可以组成具有更高柔性的自动化制造系统—FMS。
5、高生产率数控机床本身的精度高、刚性大,可选择有利的加工用量,生产率高,一般为普通机床的3~5倍,对某些复杂零件的加工,生产效率可以提高十几倍甚至几十倍。
6、劳动条件好机床自动化程度高,操作人员劳动强度大大降低,工作环境较好。
7、有利于管理现代化采用数控机床有利于向计算机控制与管理生产方面发展,为实现生产过程自动化创造了条件。
8、投资大,使用费用高9、生产准备工作复杂由于整个加工过程采用程序控制,数控加工的前期准备工作较为复杂,包含工艺确定、程序编制等。
10、维修困难数控机床是典型的机电一体化产品,技术含量高,对维修人员的技术要求很高。
二、数控机床的适用范围由于数控机床的上述特点,适用于数控加工的零件有:1、批量小而又多次重复生产的零件;2、几何形状复杂的零件;3、贵重零件加工;4、需要全部检验的零件;5、试制件。
对以上零件采用数控加工,才能最大限度地发挥出数控加工的优势。
数控机床——是数字控制机床(Computer numerical control machine tools)的简称,是一种装有程序控制系统的自动化机床。
数控机床与普通机床的主要区别在于:数控机床带有数控系统(程序控制系统),可以通过编制程序来实现自动化加工。
而普通机床没有该特性。
数控机床加工过程中的常见问题及解决方法
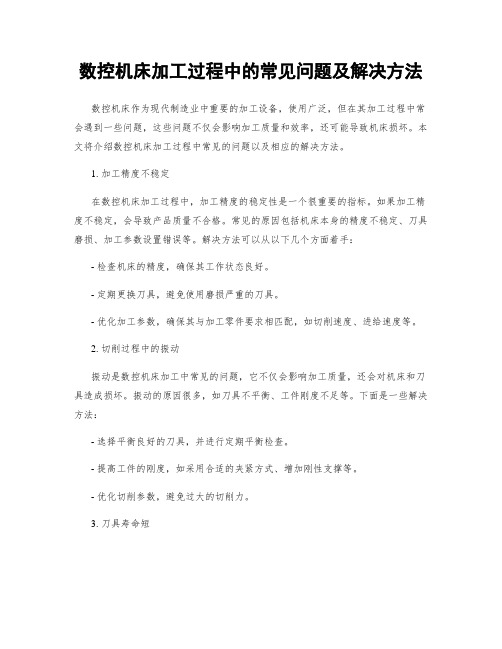
数控机床加工过程中的常见问题及解决方法数控机床作为现代制造业中重要的加工设备,使用广泛,但在其加工过程中常会遇到一些问题,这些问题不仅会影响加工质量和效率,还可能导致机床损坏。
本文将介绍数控机床加工过程中常见的问题以及相应的解决方法。
1. 加工精度不稳定在数控机床加工过程中,加工精度的稳定性是一个很重要的指标。
如果加工精度不稳定,会导致产品质量不合格。
常见的原因包括机床本身的精度不稳定、刀具磨损、加工参数设置错误等。
解决方法可以从以下几个方面着手:- 检查机床的精度,确保其工作状态良好。
- 定期更换刀具,避免使用磨损严重的刀具。
- 优化加工参数,确保其与加工零件要求相匹配,如切削速度、进给速度等。
2. 切削过程中的振动振动是数控机床加工中常见的问题,它不仅会影响加工质量,还会对机床和刀具造成损坏。
振动的原因很多,如刀具不平衡、工件刚度不足等。
下面是一些解决方法:- 选择平衡良好的刀具,并进行定期平衡检查。
- 提高工件的刚度,如采用合适的夹紧方式、增加刚性支撑等。
- 优化切削参数,避免过大的切削力。
3. 刀具寿命短刀具寿命的长短直接影响到加工效率和成本。
在数控机床加工过程中,刀具寿命过短的原因主要包括切削温度过高、刀具材料选择不合理等。
以下是一些解决方法:- 使用合适的刀具材料,以满足具体的加工要求。
- 控制切削温度,如采用切削液进行冷却、降低切削速度等。
- 利用先进的刀具涂层技术,提高刀具耐磨性。
4. 数控编程错误数控编程是数控机床加工的核心,但在编程过程中常会出现一些错误,如坐标定位错误、刀具路径错误等。
这些错误会导致加工不准确,甚至会损坏工件和机床。
以下是一些建议:- 给程序编写提供足够的时间,避免匆忙操作。
- 使用先进的CAD/CAM系统进行程序编写,以减少编程错误的发生。
- 进行严格的程序验证和模拟,以保证加工的准确性。
5. 加工材料选择不当数控机床可以加工多种材料,但不同材料的加工特性有所不同,如果选择不当会导致加工问题。
数控机床操作中的误差分析与修正

数控机床操作中的误差分析与修正数控机床是当今工业生产过程中必不可少的一种高精度加工设备,它通过电子控制系统实现了对工件的精确加工。
然而,由于各种因素的影响,数控机床在实际操作中存在着一定的误差。
为了保证产品质量,提高加工效率,操作人员需要对误差进行分析,并及时进行修正。
本文将对数控机床操作中的误差进行分析,并提供修正的方法。
误差来源分析数控机床操作中的误差来源主要包括机床自身误差、刀具误差、工件装夹误差和运动控制误差等。
首先是机床自身误差。
机床自身的几何精度、运动传动系统、定位系统等方面存在一定误差,例如导轨的平行度、直线度、回转度等。
这些误差会直接影响到加工的精度和稳定性。
刀具误差是指刀具在使用过程中由于磨损而产生的误差。
刀具磨损会导致切削力的变化,从而影响到加工质量。
此外,刀具的安装和夹持也会引起误差。
工件装夹误差是指在夹持工件时产生的装夹偏差。
工件装夹不稳定会导致工件在加工过程中产生振动和位移,进而影响到加工质量。
运动控制误差包括机床伺服系统的误差和数控系统的误差。
伺服系统的误差主要来自于位置反馈误差、传动误差和非线性误差等。
数控系统的误差主要包括插补误差、指令误差和输出误差等。
误差修正方法对于数控机床操作中的误差,我们可以采取以下几种修正方法:首先是机床自身误差的修正。
在使用数控机床之前,可以通过校正设备对机床进行定期检测和校准,以确保机床的几何精度和运动传动系统的精度。
此外,在加工过程中也可以通过优化切削参数来减小机床自身误差对加工质量的影响。
其次是刀具误差的修正。
刀具的磨损是一个不可避免的过程,为了减小刀具磨损对加工质量的影响,操作人员可以根据加工情况定期更换刀具,并确保刀具的正确安装和夹持。
对于工件装夹误差,操作人员需要在夹持工件时严格按照操作规程进行操作,确保工件的稳定夹持。
如有条件,可以使用更加稳定可靠的夹具,以减小装夹误差对加工质量的影响。
运动控制误差的修正需要依靠数控系统和伺服系统的调试。
浅析数控车床的加工精度

浅析数控车床的加工精度摘要:数控车床作为一种重要的加工设备,其加工精度直接影响到工件的质量和精度要求。
本文通过对数控车床的加工精度进行浅析,探讨了影响加工精度的因素,并提出了提高加工精度的方法与措施。
旨在为数控车床的加工精度提升提供一定的理论支持和实践指导。
关键词:数控车床;加工精度随着制造业的发展,数控车床作为一种高效、精确的加工设备,被广泛应用于各个领域。
而加工精度作为衡量数控车床性能的重要指标,对于满足工件的精度要求具有关键意义。
一、数控车床的加工精度概述数控车床加工精度是指在数控车床上进行加工过程中,工件达到的尺寸、形状和位置的精确程度。
它是衡量数控车床加工质量的重要指标之一。
随着工业技术的不断发展,数控车床在各个领域得到了广泛应用,而加工精度的提高也成为了人们关注的焦点。
首先,尺寸精度是数控车床加工中的一个重要方面。
在工件加工过程中,尺寸精度的高低直接影响着工件能否符合设计要求。
要提高尺寸精度,可以通过控制切削量、刀具和刀具夹持方式、工件夹紧方式等来实现。
只有确保这些因素的合理选择和控制,才能保证工件加工后的尺寸与设计要求之间的偏差尽可能小。
其次,形状精度也是数控车床加工中不可忽视的一点。
在实际应用中,工件的形状往往要求具备一定的几何精度,例如平面度、圆度、圆柱度等。
为了提高形状精度,可以采取优化工艺参数、选择合适的刀具和夹具、控制加工温度等措施。
通过这些方式,能够有效减小工件加工后形状与设计要求之间的偏差,确保工件的几何形状达到精确的要求。
此外,位置精度也是影响数控车床加工精度的重要因素之一。
位置精度主要指工件上各个特定点之间的相对位置精度,例如平行度、垂直度、同轴度等。
要提高位置精度,可以通过优化工艺参数、提高机床刚性、加强夹紧与定位等来实现。
只有确保工件在加工过程中的稳定性和精度,才能保证位置精度的提升。
最后,表面粗糙度也是数控车床加工精度的重要方面之一。
工件表面的光洁程度对于某些特定工件的功能和装配要求有着重要影响。
CNC机床加工中的加工精度与重复性
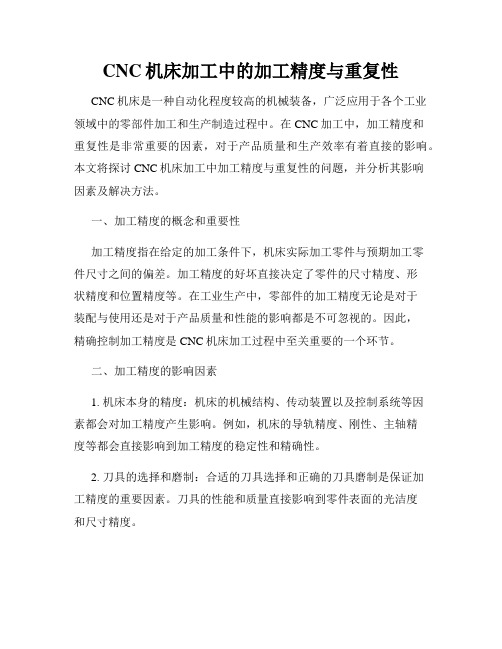
CNC机床加工中的加工精度与重复性CNC机床是一种自动化程度较高的机械装备,广泛应用于各个工业领域中的零部件加工和生产制造过程中。
在CNC加工中,加工精度和重复性是非常重要的因素,对于产品质量和生产效率有着直接的影响。
本文将探讨CNC机床加工中加工精度与重复性的问题,并分析其影响因素及解决方法。
一、加工精度的概念和重要性加工精度指在给定的加工条件下,机床实际加工零件与预期加工零件尺寸之间的偏差。
加工精度的好坏直接决定了零件的尺寸精度、形状精度和位置精度等。
在工业生产中,零部件的加工精度无论是对于装配与使用还是对于产品质量和性能的影响都是不可忽视的。
因此,精确控制加工精度是CNC机床加工过程中至关重要的一个环节。
二、加工精度的影响因素1. 机床本身的精度:机床的机械结构、传动装置以及控制系统等因素都会对加工精度产生影响。
例如,机床的导轨精度、刚性、主轴精度等都会直接影响到加工精度的稳定性和精确性。
2. 刀具的选择和磨制:合适的刀具选择和正确的刀具磨制是保证加工精度的重要因素。
刀具的性能和质量直接影响到零件表面的光洁度和尺寸精度。
3. 工艺参数的设定:在CNC机床加工中,包括进给速度、主轴转速、切削进给量等工艺参数的设定会对加工精度产生重要影响。
合理的工艺参数设置可以减小误差和提高加工精度。
三、重复性的概念和要求重复性是指在一定加工条件下进行连续多次加工时,加工零件的尺寸精度能否保持在一定范围内的能力。
在大批量生产中,重复性是保证产品一致性和稳定性的关键因素。
重复性的要求在不同行业和不同产品之间会存在一定的差异,但是对于CNC加工来说,重复性的要求通常较高。
四、解决加工精度与重复性问题的方法1. 选用高精度的机床设备:选择机床时,要考虑机床的精度等级、刚性和稳定性等因素,并确保其适应加工产品的要求。
2. 保证刀具的质量和准确度:定期检查和维护刀具,保持其锋利度和精度,以确保切削能力的稳定性和一致性。
- 1、下载文档前请自行甄别文档内容的完整性,平台不提供额外的编辑、内容补充、找答案等附加服务。
- 2、"仅部分预览"的文档,不可在线预览部分如存在完整性等问题,可反馈申请退款(可完整预览的文档不适用该条件!)。
- 3、如文档侵犯您的权益,请联系客服反馈,我们会尽快为您处理(人工客服工作时间:9:00-18:30)。
数控机床加工精度高的误解
从事CNC机床设计也有一段时候了,发觉不少机械从业人员甚至专业工程技术人员对数控机床的加工精度存在不小的误解,在生产中常能听到这个是用某某数控机床加工出来的,精度如何如何,其实是不科学的,作为专业的技术人员,在下觉得有必要说明下数控的精度是不是真的如传说中那样神忽其神,还是另有隐情。
首先,我们要搞清楚何谓精度。
通常机械加工上的精度指的主要是四点:1、尺寸公差 2、形状度公差 3、位置度公差 4、表面光洁度(至于其他最大实体尺寸之流其实是近年才出现的概念,可参考本科教材,这些概念,在公差的教学中是提到的,而且他举例时花键的标注是用到这些概念的;但你参看《机械设计课程设计》以及《机械实用设计手册》他在花键的标注中没有使用到这些概念,可见其实他是可用可不用的锦上添花型概念。
新手可能觉得奇怪,怎么可能呢?实际上机械中有很多概念都可以互换的,比如说平行度公差,也可以说成两个面同时对和他们垂直的面有处置度公差。
)
回到精度问题上,既然现在搞清楚精度的概念,下个问题就是数控机床是否这些精度做的好呢。
首先,要搞清楚数控机床的特点。
数控机床,其实就是把数控系统(NC)装在机床上,所以叫CNC。
我国很多好机床数控化改装的就是把普通机床装上数控装置和饲服系统就改装成功了(当然做的考究点的会加滚珠丝杆,提高下主轴轴承精度啊,但根据偶的经验其实机械部分的精度提高对整床加工精度提高影响不多,因为刀具的影响,这个以后再说)。
那么加数控装置和饲服系统提高了什么精度呢?位置度公差!!!对其他公差等级的提高有帮助吗?我研究下来的结果是没有!!!!
这就是我要阐述的第一个观点,那就是CNC机床的核心(也就是人们最神化的)数控装置和饲服系统提高的就是机床加工的位置度公差(其实整个数控机床比普通机床提高的主要也是这个,以后会说到)。
因为你想想数字控制提高的是什么,是刀具或则工作台在进给是走的准确度,位置走的准了位置度公差也就提高了。
但他能提高其他公差吗?不可能,你位置走准了就能提高表面光洁度吗?没门啊,光洁度是什么保证的,一是刀具,二是机床刚性好,震动下,你装了数控装置和饲服系统能改善他们啊,不能啊,无论数控车床还是镗铣床甚至加工中心是不可能做到磨床的表面光洁度的。
而形状度公差也一样啊,所谓形状度公差就是他这个平面做的平不平,圆做的圆不圆,那时靠工作台的位置准保证的了的吗,不可能啊,他归根结底靠的是你表面做得光洁啊,你想表面不光,平面怎么可能平呢。
至于尺寸公差,那更是没关系拉,高精度的尺寸公差其实就是靠机床机械部分的精度保证的,与电气上的控制(在高精度加工时)没有关系,所以你看一般介绍数控机床的加工精度是0.01mm,也就是统称的1丝,要知道这个公差你仪表车床也能做到,磨床更是随便搞搞啊。
也许有人要质疑,说数控机床主轴部件和主轴支承旋转精度高,刚性好,进给传动采用滚珠丝杆,且通过加预紧力消除方向间隙,所以机械部分精度高。
那在下可以告诉你,一、机械部分精度的提高与电器无关,换而言之任何机床这样做都能提
高精度何必非数控不可。
二、其实这些对机床的光洁度以及形状度公差影响不大,因为精加工,关键是金属切削,而切削的最后一环在于刀具,磨床之所以精度高就在于砂轮和刀具存在本质上的区别,这个区别所造成的质量差异绝不是你提高下传动链精度所能够改观的,就好比再厉害在强壮的老虎能吃的了象吗?不可能,他也是老虎,最多老虎中厉害点,不可能变成象的;也就是说,你数控的车床、镗床甚至加工中心之流是都不可能做出磨床的品质,如光洁度、形状度等等。
说了这么多,恐怕有人要说在下反对先进生产了。
不是的,在下写本文是希望各位能了解到什么是数控机床最适宜加工的零件,其实最典型的就是类似变速箱箱体这样有多个孔的孔系类零件,而其中各个孔之间都存在位置度公差关系的零件,而箱体无论是孔还是安装基准面其实它的表面光洁度以及圆度平面度公差要求都不是很高,一般的精铣精镗都可做到,这样就可以发挥数控机床加工位置度公差高的特点,而且由于编程后不需改变,加工效率也很高。
反之,某些工件,加工曲线很简单,表面光洁度的要求较高(0.8要上磨床),又没有特殊位置度要求的(如减速箱的轴),就根本没必要上数车,那才叫劳命伤财,得不偿失呢.
工艺是一件复杂而严肃的事情,是科学的事,可是现在不少工艺员知识不多,还不负责任,动则数控机床、加工中心,是的,这些先进的设备是使现在的加工变得方便了许多,许多传统机械中的技术如样板等由于这些技术的出现已不需要了;但事情都有双向性,若一味强调简单而依赖数控,势必造成零件生产成本的高涨,要知道数控的设备价格是很贵的,远超普通设备;数控加工人员的学历一般是专科以上,人力成本也是高的;数控机床的功率及主轴转速远高于普通机床,机床运行的成本也是惊人的。
所以我的意见是,我们生产中做工艺要尽量避免设备使用的成本提高,在同样条件下一定应该选取成本小的加工方法,因为企业是赢利为目的的,那些叫嚣不计成本的是自欺欺人的书呆子看法,是不切实际的。
所以切不可把数控当万宝全书,动则加工中心,这样对企业的发展、产品的成熟、市场的推广都是不利的,数控应该实实在在成为生产过程中的一把尖刀(好钢用在刀刃上),而不应该像不少公司那样成了工艺偷懒的代名词或抬高身价的名片,那才是机械业从业者的悲哀。