软件数控S型加减速在高精高速加工中的快速应用方法
数控机床的高速高精技术应用探析

数控机床的高速高精技术应用探析随着工业自动化水平的不断提高,数控机床已经成为现代制造业中不可或缺的一部分。
它具有高效、精密、灵活等特点,能够满足迅速变化的市场需求。
而在数控机床的发展过程中,高速高精技术更是成为了制造业的发展趋势。
本文将就数控机床的高速高精技术应用进行探析。
一、高速高精技术的定义高速高精技术是指在数控机床加工中,通过提高加工速度和加工精度,使得产品能够更快速、更精准地完成加工工艺。
高速高精技术的应用主要包括加工速度的提升、加工精度的提高以及加工过程的稳定性。
高速高精技术的主要目的是提高加工效率,减少加工时间,提高产品质量,降低生产成本。
随着市场竞争的加剧,制造业对于产品的质量和交货周期有了更高的要求,因此高速高精技术的应用已成为了现代数控机床的发展方向。
1. 加工速度的提升高速加工是数控机床在近年来的一个重要发展方向。
在传统加工中,加工速度受到刀具和工件材料的限制,在高速加工中,加工速度大大提高,使得加工效率得到明显提升。
在高速加工中,需要考虑的因素较多,包括刀具选择、切削参数的设计、加工路径的优化等。
还需要考虑机床的动态性能、稳定性能、热变形和冷却系统等因素,以保证加工质量和加工稳定性。
3. 加工过程的稳定性高速高精加工是一个复杂的加工过程,在加工过程中需要考虑切削力、切削热、加工动态、刀具槽铣、表面粗糙度、切削死角、切削扭矩等因素的影响,以保证加工的稳定性和可靠性。
针对高速高精加工的特点,需要合理设计加工工艺和切削参数,采用适当的刀具和刀具槽铣技术,提高机床的刚性和稳定性,优化冷却系统和润滑系统,避免机床的共振和振动,以保证加工过程的稳定性和可靠性。
三、数控机床高速高精技术的发展趋势随着尖端刀具材料和涂层技术的不断发展,以及高速铣削技术和高效切削技术的应用,数控机床的加工速度和精度将会进一步提升。
高速高精加工技术将成为未来数控机床的主要发展方向。
2. 智能化和柔性化的加工系统随着人工智能技术和柔性制造技术的不断发展,未来的数控机床将更加智能化和柔性化,能够实现自动化生产、智能化监控和自适应加工。
数控机床的高速高精技术应用探析

数控机床的高速高精技术应用探析随着科技的不断发展,数控机床在制造业中的应用越来越广泛。
特别是在高速高精加工领域,数控机床的应用已经成为现代制造业的重要组成部分。
本文将就数控机床在高速高精技术应用方面进行探析,分析其在制造业中的重要性和未来的发展趋势。
一、高速高精加工技术的意义高速高精加工技术是现代制造业中的重要技术,它能够实现对工件的高效加工和高精度加工。
在工业制造过程中,要求对工件进行高速高精加工已经成为制造业发展的趋势。
高速高精加工技术的应用不仅能够提高生产效率,降低生产成本,还可以大大提高产品的质量和稳定性。
研究高速高精加工技术的应用在制造业中具有重要意义。
数控机床在高速高精加工技术中的应用可以实现对工件的高效加工。
利用数控机床,可以实现对工件的高速加工,大大提高了生产效率。
而且数控机床的加工精度高,加工质量稳定,可以保证加工后的工件具有高精度和高质量。
三、数控机床在高速高精加工技术中的发展趋势数控机床在高速高精加工技术中的发展将会更加智能化。
随着人工智能、大数据和云计算技术的发展,数控机床将可以实现更智能的加工过程控制,提高生产效率和加工质量。
四、结语从以上分析可以看出,数控机床在高速高精加工技术中的应用已经成为制造业中不可或缺的重要工具。
随着科技的不断发展,数控机床在高速高精加工技术中的发展将会更加智能化、精密化和高效化。
未来,数控机床的应用将会在制造业中发挥越来越重要的作用,推动制造业向着高速高精发展。
我们应该不断加大对数控机床在高速高精加工技术中的研究和应用,为现代制造业的发展注入新的动力。
s曲线加减速算法研究

s曲线加减速算法研究S形曲线加减速算法在机械和工程领域被广泛应用,尤其在机器人、数控机床等领域,它可以有效地提高机器的运行效率和精度。
以下是S形曲线加减速算法的原理和应用。
一、S形曲线加减速算法的原理S形曲线加减速算法是一种特殊的加减速控制算法,其速度曲线呈现一个类似于英文字母“S”的形状。
该算法基于加速度匀速变化的原理,通过将加速过程分为多个阶段,使得加速过程更加平滑,避免了传统加减速过程中的冲击和振动,提高了机器的运行精度和稳定性。
S形曲线加减速算法通常分为7个阶段:加加速段(T1)、匀加速段(T2)、减加速段(T3)、匀速段(T4)、加减速段(T5)、匀减速段(T6)和减减速度段(T7)。
在不同的阶段,加速度和速度的变化情况也不同。
通过合理地控制各阶段的时长和速度变化,可以使得机器的运行轨迹更加精确和平稳。
二、S形曲线加减速算法的应用S形曲线加减速算法在许多领域都有广泛的应用,例如在机器人领域中,该算法可以用于控制机器人的运动轨迹和速度变化,提高机器人的运行精度和稳定性。
此外,在数控机床领域中,该算法也可以用于控制机床的运动轨迹和速度变化,提高加工精度和效率。
在应用S形曲线加减速算法时,需要考虑到机器的负载和运动轨迹等因素。
针对不同的应用场景和机器参数,需要对算法进行相应的调整和优化,以确保机器能够安全、稳定地运行。
三、结论S形曲线加减速算法是一种先进的加减速控制算法,它可以有效地提高机器的运行效率和精度。
通过将加速过程分为多个阶段,使得加速过程更加平滑,避免了传统加减速过程中的冲击和振动,提高了机器的运行精度和稳定性。
在未来的研究中,可以进一步探索S形曲线加减速算法的优化方法和应用范围,为机器人的运动控制和数控机床等领域提供更加精准、稳定的控制方案。
一种简化计算的s型加减速nurbs插补算法

一种简化计算的s型加减速nurbs插补算法一种简化计算的S型加减速NURBS插补算法NURBS曲线插补算法是现代数控系统中的重要算法之一,用于控制加工设备完成高精度的加工任务。
其中,S型加减速是常用的运动控制方式之一,能够保证机床在开始加工、过程中和结束加工时都具有很好的平稳性。
本文将介绍一种简化计算的S型加减速NURBS插补算法,以提高机床的控制精度和加工效率。
一、S型加减速运动控制原理S型加减速是一种基于速度的控制方法,其核心原理是根据速度变化规律来控制机床的运动。
具体来说,S型加减速运动分为加速段、匀速段和减速段三个阶段。
在加速阶段,机床匀加速运动,使速度随时间线性增加,到达一定速度后,进入匀速阶段,使速度恒定不变。
在减速阶段,速度随时间线性减小,直到机床停止。
该方法可以避免机床突然加速或停止时产生的惯性冲击,从而保证了机床的运动平稳。
二、NURBS插补算法NURBS插补算法是一种基于贝塞尔曲线的算法,通过多个曲线段的拼接来实现曲线的绘制。
其优点是可以绘制复杂的曲线形状,并且对于曲线的控制点位置和权重系数都具有很好的控制性。
三、S型加减速NURBS插补算法该算法核心思想是在NURBS曲线上进行S型加减速运动控制,以实现更加平稳的加工运动。
具体来说,该算法的步骤如下:1. 将NURBS曲线按照一定间隔进行采样,得到离散点序列。
2. 对离散点序列进行处理,获取三个阶段的状态点:起始点、加速段末点、减速段起点、最终点。
3. 对加速段末点和减速段起点进行插值,获取中间匀速段起点和末点。
4. 根据三个状态点之间的距离和时间进行速度和加速度控制计算。
5. 根据速度和加速度计算出每个采样点的位置坐标,使用NURBS 插值得到平滑的曲线。
6. 基于机床的动力学模型,通过PID算法进行控制,实现机床的运动。
该算法的优点在于简化了S型加减速的计算过程,同时保持了曲线的平滑性,提高了机床的运动精度。
三菱最新系统的高精度控制说明

CONFIDENTIAL
SSS控制
13
©2015 Mitsubishi Electric Corporation
SSS控制
CONFIDENTIAL
SSS(Super Smooth Surface)控制
◆ 美观:加工面无伤痕 ◆ 快速:加工时间短 ◆ 简单:参数调整容易
SSS控制OFF
SSS控制ON
SSS控制
CONFIDENTIAL
SSS控制的想法
以前控制(SSS控制OFF)
SSS控制
前提
・程序绝对正确
・程序包含误差及其他不定性因 素
对策
・严密控制,使其通过程序指定 ・形状类似则速度样式也类似
的形状
・针对误差的低通性
速度控制 ・至细节(局部)严密控制轨迹 ・参考全局形状,考虑伺服系延
方法
・基于形状信息(角度、曲率) 迟,通过模拟预测移动时的加速
SSS控制
依赖加工程序品质,加工面品质低下
相邻路径的指令形状不同 →相邻路径速度不同 →加工面发生伤痕
CONFIDENTIAL
以前的 高精度控制的
问题点
路径A
路径B
微小段差
路径C
:指令的微小线段
:指令点
速度
時間
速度
減速
加工面上 发生伤痕
速度
時間
時間
16
©2015 Mitsubishi Electric Corporation
11
©2015 Mitsubishi Electric Corporation
5.前馈控制
没有前馈
速度
延迟
实际的 电机速度
高精度控制
NCの指令値
S曲线加减速控制方法研究
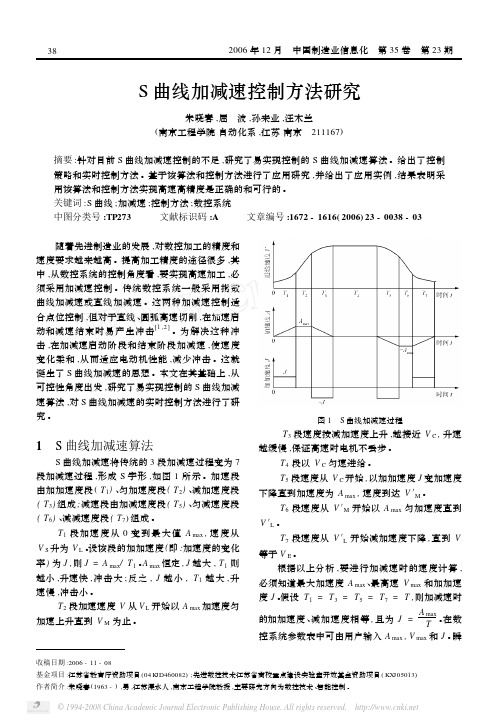
∫ 所以 S =
i
V id t
0
=
V S ·t
+
1 6
Jt3
即:
Vi
=
VS +
1 2
Jt2
∫ S =
t
V id t
0
=
V S ·t
+
1 6
Jt3
其中 : t ∈ (0 , T1) ; V i ∈ ( V S , V L) , V L = V S +
1 2Biblioteka JT2 1
。
b. 匀加速度段 ( T2 段) 。
1 S 曲线加减速算法
S 曲线加减速将传统的 3 段加减速过程变为 7 段加减速过程 ,形成 S 字形 ,如图 1 所示 。加速段 由加加速度段 ( T1) 、匀加速度段 ( T2) 、减加速度段 ( T3) 组成 ;减速段由加减速度段 ( T5) 、匀减速度段 ( T6) 、减减速度段 ( T7) 组成 。
© 1994-2008 China Academic Journal Electronic Publishing House. All rights reserved.
·智能控制技术· 朱晓春 屈 波 孙来业 等 S 曲线加减速控制方法研究
39
时速度等由数控系统自动计算 。
减速区曲线与加速区曲线类似 ,不同之处在于 数据采样插补用小线段拟合圆弧时的剩余量要均 匀处理 ,否则 ,会影响加工速度 。该圆弧的 S 加减 速曲线如图 2 所示 。
3 应用实例
以数据采样插补的圆弧加工控制为例 ,介绍实 现 S 曲线加减速控制的过程 。数据采样插补以弦 代替弧 ,会产生弓高误差 ,为保证加工精度 ,要根据 圆弧半径和加工精度 ,限制最大进给速度 。
高速加工数控系统的加减速控制研究

这是一篇高速加工数控系统开发方面的理论性较强的文章。
众所周知,加减速控制是CNC系统中插补器的一项十分重要的控制功能,它对加工精度和系统性能都有着十分重要的影响。
特别是在高速加工中,加减速就显得尤为重要。
文中,作者在分别分析了数控系统中直线形、三角函数形、指数形、S形、直线加抛物线形加减速控制曲线的基础上,对这几种控制方法各自的优缺点及适用场合进行了比较,并着重讨论了S曲线加减速算法。
加减速控制是数控系统插补器的重要组成部分,是数控系统开发的关键技术之一。
数控加工的目标是实现高精度、高效率的加工,因此,一方面要求数控机床反应快,各坐标运动部件能在极短的时间内达到给定的速度,并能在高速运行中快速准确地停止在预定位置,缩短准备时间;另一方面要求加工过程运动平稳,冲击小。
因此,如何保证在机床运动平稳的前提下,实现以过渡过程时间最短为目标的最优加减速控制规律,使机床具有满足高速加工要求的加减速特性,是研究中的一个关键问题。
一、加减速控制方式在CNC装置中,为了保证机床在起动或停止时不产生冲击、失步、超程或振荡,必须对进给电机的脉冲频率或电压进行加减速控制,即在机床加速起动时,保证加在伺服电机上的脉冲频率或电压逐渐增加,而当机床减速停止时,保证加在伺服电机上的脉冲频率或电压逐渐减小。
根据加减速控制在控制系统中的位置,加减速有前加减速和后加减速之分。
前加减速中加减速控制放在插补器的前面,后加减速中加减速控制放在插补器的后面,如图1所示。
图1 前加减速与后加减速前加减速的控制对象是指令进给速度V,它是在插补前计算出进给速度V′,然后根据进给速度进行插补,得到各坐标轴的进给量△X、△Y,最后转换为进给脉冲或电压驱动电机。
这种方法能够得到准确地加工轮廓曲线,但需要预测减速点,运算量较大。
后加减速的控制算法放在插补器之后,它的控制量是各运动轴的速度分量。
它不需要预测减速点,而是在插补输出为零时开始减速,并通过一定的时间延迟逐渐靠近程序段的终点。
数控系统的加减速控制及在高速加工中的应用

数控系统的加减速控制及在高速加工中的应用数控系统的加减速控制及在高速加工中的应用引言数控系统是现代制造业中的重要装备之一,其性能的优劣直接影响着加工效率和产品质量。
在数控系统中,加减速控制是其核心功能之一,尤其在高速加工中更为重要。
本文将重点讨论数控系统的加减速控制原理和在高速加工中的应用。
一、数控系统的加减速控制原理加减速控制是数控系统中的一项基本功能,其核心原理是控制伺服系统的加速度和减速度。
在进行加减速控制之前,需要先对系统进行参数设定,以确保系统能够按照预期的速度进行加减速。
1. 加速段控制在加速段控制中,主要是通过调整系统的加速度来控制加速过程的平稳性。
在数控系统中,通常使用S曲线进行加速。
S曲线的特点是开始和结束时加速度较小,中间时加速度较大,使得整个加速过程更加平滑。
2. 减速段控制在减速段控制中,主要是通过调整系统的减速度来控制减速过程的平稳性。
同样,数控系统中也使用S曲线进行减速。
减速段的加速度也是开始和结束时较小,中间时较大。
3. 加减速过程中的速度控制在加减速过程中,需要根据设定的加速度和减速度,通过数学计算来调整系统的速度。
通常使用速度闭环控制方法,通过与编码器反馈的速度值进行比较,根据误差进行调整,以实现精确的速度控制。
二、数控系统在高速加工中的应用高速加工是现代制造业中的重要工艺之一,其特点是加工速度快、效率高,可以大大提高生产效率。
数控系统作为高速加工的核心部分,发挥着重要的作用。
1. 高速切削加工高速切削加工是高速加工中的一种常见工艺,它通过提高切削速度和加工进给速度,实现对材料的高效率切削。
在高速切削加工中,数控系统的加减速控制能够确保机床在高速运动中的平稳性和精度,从而保证产品的质量和精度。
2. 快速换刀在高速加工中,快速换刀是提高生产效率的关键。
数控系统的加减速控制技术可以实现快速、精确的换刀动作,大大减少换刀时间,提高切削时间比例,从而提高生产效率。
3. 高速进给高速进给是高速加工的另一个重要工艺,它可以通过提高机床的进给速度,实现对工件的高速加工。
数控机床的高速高精技术应用探析

数控机床的高速高精技术应用探析数控机床作为现代制造业中的重要核心装备,对于提高生产效率、降低制造成本、提高产品质量和创新能力等方面具有重要作用。
而高速高精加工技术则是数控机床的重要发展方向,其应用范围广泛,可用于金属、非金属、复合材料、硬质材料等各种材料的加工。
下面从几个方面探析数控机床的高速高精技术应用。
首先,数控机床的高速高精加工技术可以提高生产效率。
高速加工是指在保证加工质量和精度的前提下,通过提高切削速度、切削进给量等参数,使工件的加工时间减少,从而提高生产效率。
而数控机床的高速加工技术可以实现对零件的快速加工,使得机械加工效率得以提高,生产周期缩短,加工成本降低。
其次,数控机床的高速高精加工技术可以提高加工精度。
高精度加工是指在一定公差范围内,确保工件能够满足要求的精度和表面光洁度,达到高精度、高质量的工艺水平。
而数控机床的高精度加工技术可以通过提高数控机床的加工精度和控制精度来实现,使加工精度提高到数百分之一毫米以下,提高了机械加工制造的精度和质量。
再次,数控机床的高速高精加工技术可以提高产品质量。
产品质量是企业的生命线,是企业竞争的一个重要因素。
而数控机床的高速高精加工技术可以提高产品的精度、表面光洁度、尺寸精度等方面,提高产品的质量水平,减少了工件的加工误差和缺陷,从而提高了产品的可靠性和使用寿命。
最后,数控机床的高速高精加工技术可以提高企业的创新能力。
高速高精加工技术能够有效地实现对复杂零件的加工和制造,提高企业的技术水平和竞争力。
同时,还可以促进新材料的开发和应用,拓宽企业的经济效益和发展空间。
数控机床的高速高精技术应用探析

数控机床的高速高精技术应用探析数控机床是近年来发展迅速的一种高端装备,随着工业4.0的深入推进,数字化、智能化、高速化和高精度成为了数控机床发展的重要趋势。
高速高精的技术应用不仅提高了机床加工的效率和精度,也极大地推动了制造业的升级和转型。
本文将就数控机床的高速高精技术应用进行探析,分析其发展趋势和应用前景。
一、高速高精技术的发展现状近年来,随着数控机床的发展,高速高精的技术应用越来越成为行业的热点。
在高速加工方面,数控机床的主轴转速不断提高,采用了更加刚性的机床结构和更高性能的主轴驱动系统,加工速度和加工效率得到了大幅提升。
在高精度加工方面,数控机床采用了更加精密的传感器和控制系统,实现了对加工精度的更精准控制,使得零件的尺寸和表面质量得到了极大提高。
高速高精技术的应用也成为了不同行业的共同需求。
在航空航天、汽车制造、模具制造、光学仪器等高端制造领域,对于零件加工精度和表面质量的要求越来越高,而高速高精加工技术恰恰能够满足这一需求,因此得到了广泛的应用。
1. 高速加工特点高速加工技术通过提高切削速度和进给速度,缩短加工周期,提高生产效率。
在数控车床、数控铣床和数控磨床等设备上,高速加工技术广泛应用,能够实现对不同材料的高速加工,包括金属、塑料、陶瓷等。
高精度加工技术通过提高机床的定位精度、运动精度和重复定位精度,有效保证了零件的加工精度、表面质量和尺寸稳定性。
对于微小零件、精密零件和高要求的零件加工,高精度加工技术尤为重要。
3. 技术融合特点高速高精加工技术不仅仅是单一技术的应用,还包括了多种技术的融合。
比如高速铣削技术中,常常结合了高速切削、高速进给、高速刀具和高速主轴等多种技术,使得加工效率和加工质量得到了提升。
1. 高速高精机床的更高性能随着先进材料和先进加工技术的不断突破,高速高精机床的性能将会得到更大的提升,包括主轴转速、进给速度、定位精度和重复定位精度等方面。
随着人工智能、大数据和云计算等技术的快速发展,高速高精机床将会走向智能化方向,实现自动化生产和智能化管理,提高生产效率和降低成本。
数控技术在加工过程中的高效应用策略分享

数控技术在加工过程中的高效应用策略分享随着科技的不断进步,数控技术在制造业中的应用越来越广泛。
数控技术以其高精度、高效率和高稳定性的特点,成为现代工业生产中不可或缺的一部分。
本文将分享数控技术在加工过程中的高效应用策略,希望能对读者有所启发。
首先,合理的加工路径规划是提高数控加工效率的重要策略之一。
在进行数控加工之前,我们需要根据产品的形状、尺寸和材料等因素,合理规划加工路径。
通过优化路径规划,可以最大程度地减少刀具行程,降低加工时间。
同时,合理的路径规划还可以减少切削力和切削温度,提高刀具寿命,降低生产成本。
其次,选择合适的刀具和切削参数也是提高数控加工效率的重要策略。
不同的材料和加工方式需要选择不同的刀具和切削参数。
合适的刀具和切削参数可以提高加工质量,减少切削力和切削温度,降低刀具磨损,延长刀具寿命。
此外,合适的刀具和切削参数还可以提高加工速度,缩短加工周期,提高生产效率。
再次,合理利用数控编程技术可以提高数控加工效率。
数控编程是数控加工的核心环节,编程的质量直接影响到加工效率和加工精度。
合理利用数控编程技术,可以通过编写高效的加工程序,减少加工时间和切削量。
同时,合理利用数控编程技术还可以实现多道工序的自动化加工,提高生产效率和产品质量。
此外,合理利用数控机床的功能和特点也是提高加工效率的重要策略。
数控机床具有多种功能和特点,如自动换刀、自动测量、自动校正等。
合理利用这些功能和特点,可以实现加工过程的自动化和智能化,提高生产效率和产品质量。
例如,利用自动换刀功能可以实现多种刀具的自动切换,减少人工干预,提高加工效率。
最后,加强数控技术的培训和人才引进也是提高数控加工效率的重要策略。
数控技术的应用需要专业的操作和维护人员,他们需要熟悉数控机床的操作和维护知识,熟练掌握数控编程技术。
通过加强数控技术的培训和人才引进,可以提高操作人员的技术水平,提高数控加工效率和产品质量。
综上所述,数控技术在加工过程中的高效应用策略包括合理的加工路径规划、选择合适的刀具和切削参数、合理利用数控编程技术、合理利用数控机床的功能和特点,以及加强数控技术的培训和人才引进。
小线段S型加减速方式高速衔接算法

小线段S型加减速方式高速衔接算法叶百胜;张立强【摘要】针对连续小线段拐角处衔接速度受夹角影响,导致过渡速度低且易引起机床振动等问题,研究了利用圆弧光滑连续小线段建立多周期匀速衔接数学模型,提出通过转接的几何约束和运动约束以及转接参数的计算,来实现多周期匀速衔接高速插补的方法.同时采用离散S型加减速规划实现加工速度和加速度的连续.通过仿真验证了该方法的有效性和实用性.该方法在满足加工精度的前提下,使数控机床的柔性提高,降低了机床的振动.【期刊名称】《轻工机械》【年(卷),期】2016(034)003【总页数】5页(P34-38)【关键词】数控机床;连续小线段插补;多周期衔接;S型加减速规划【作者】叶百胜;张立强【作者单位】上海工程技术大学机械工程学院,上海201620;上海工程技术大学机械工程学院,上海201620【正文语种】中文【中图分类】O241.5;TP391[研究·设计]连续小线段插补是数控机床加工的主要手段,若以各段小线段为单位直接进行加减速会造成伺服电机的频繁加减速,导致加工工件表面质量下降而且耗时较多。
因此在保证加工精度的前提下,提高连续微小线段加工速度是中高档数控系统中关键的问题。
同时使用传统的梯形加减速方式规划,存在加速度不连续的问题,易造成机床的振动,从而影响机床加工的质量。
传统的连续小线段插补方法(每小线段的首末端速度降为零)存在加工效率极低,不适用于高效的加工场合的不足,因此,为提高连续小线段的拐角通过速度,文献[1]采用小线段拐角处等速率过渡插补方法,该方法虽然改善了小线段速度连续插补控制,但是在假设连续小线段之间的夹角很小的情况且拐角过渡速度也较小的情况下,其拐角误差控制才可行。
而实际情况是连续小线段之间的夹角未必都很小,小线段之间较大夹角出现也是有可能的,因此实际使用中有一定的限制。
文献[2]采用拐角圆弧过渡方式时加工速度有所提高,但存在圆弧转接误差和圆弧插补时产生的弓高误差,两者配置关系比较复杂。
数控系统S曲线加减速规划研究

数控系统S曲线加减速规划研究作者:王剡来源:《内燃机与配件》2020年第15期摘要:在当前数控加工中为防止机床在启停时存在振荡或冲击问题,需要进一步提高加工精度、效率,进而提出了数控系统s曲线加减速规划法,能够结合轨迹段特点,归纳规划中存在的s曲线加减速方式,并结合不同的方式,采用迭代法或解析法给出具体数学模型和仿真分析结果。
关键词:数控系统;S曲线;加减速;规划0 ;引言本研究中基于前行研究的基础上,提出经过改进之后的S型曲线加减速算法,能够利用S 型曲线对称性,初、末速度不同特点,对算法进行简化,能够快速对不同阶段运行时间进行准确计算。
1 ;S型曲线加减速算法分析在处于加减速过程中,指数型加减速算法和直线型加减速算法存在加速度突变问题,从一定程度上来看,这种局限性会导致轨迹规划生成速度曲线平滑度不好,如果由轨迹生成器形成的进给驱动加速指令不平滑,最终会使滚珠丝杠中的力矩以及施加于直线电动机驱动上的作用力会包含高频分量,进而会将激励进给驱动结构动态响应,引发不良震动。
为获得平滑速度以及加速度曲线图,可以使用S型曲线加减速算法,也就是有限加加速度的轨迹生成算法。
从S 型曲线加减速的原理上来看,这种S型曲线加减速算法也被称为是由系统在处于加减速过程中的速度曲线为S型得来的,S型曲线加减速控制是指在处于加减速过程中使加速度导数为常数,通过对该导数值的控制进而能够减小对机械系统产生的冲击。
除此之外,可通过加速度以及加速度导数这两个参数进行设定,进而实现柔性加减速控制,使其能够适应不同机床类型。
在数控系统中尤其对于存在较大区域变化的位置需要减速,为使速度处于平衡状态下,结合减速度需要将其降低到最低点速度以及这两点之间的位移,同时还需要考虑系统最大加速度,以规划S曲线不同阶段运行时间,获得最短的规划时间,提高系统处理能力。
首先从加减速原理上来看,在加工过程中S型曲线加减速中加速度导数是常数,可通过加减导数防止加减速中存在加速度突变问题,减少数控加工时由于加速度变化而导致整个系统出现较大的振动。
《高速高精加工轨迹间速度平滑方法的研究与应用》

《高速高精加工轨迹间速度平滑方法的研究与应用》一、引言随着现代制造业的快速发展,高速高精加工技术已成为制造业的核心竞争力。
然而,在高速加工过程中,由于加速度和减速度的突变,往往会导致加工轨迹间出现速度不平滑的问题,进而影响加工精度和表面质量。
因此,研究高速高精加工轨迹间速度平滑方法具有重要的实际意义。
本文将首先探讨高速高精加工中速度不平滑问题的原因及影响,随后详细介绍几种常用的速度平滑方法,并对其应用进行深入分析。
二、速度不平滑问题的原因及影响1. 原因分析:(1)加工参数设置不当:包括进给速度、加速度等参数设置不合理,导致加工过程中速度变化剧烈。
(2)轨迹规划不合理:加工轨迹的规划未能充分考虑速度的连续性和平滑性。
(3)机床动态性能限制:机床的动态性能限制了加工速度的变化范围和速度的平滑性。
2. 影响:(1)降低加工精度:速度的不平滑会导致加工过程中的振动和变形,从而降低加工精度。
(2)影响表面质量:速度变化大,容易在工件表面产生刀痕、毛刺等缺陷,影响工件表面质量。
(3)降低机床使用寿命:频繁的加速度和减速度会加剧机床的磨损,缩短机床的使用寿命。
三、常见的高速高精加工轨迹间速度平滑方法1. 梯形加速度规划法:该方法通过合理设置进给速度和加速度,使加工过程中的速度变化呈梯形,从而实现速度的平滑过渡。
2. S型曲线速度规划法:该方法通过引入S型曲线,使加工过程中的速度变化更加平滑,有效减少加速度和减速度的突变。
3. 基于预测控制的速度平滑方法:该方法通过预测加工过程中的速度变化,实时调整进给速度和加速度,实现速度的动态平滑。
4. 智能优化算法:利用智能优化算法对加工轨迹进行优化,使速度变化更加平滑,同时考虑加工效率、工件表面质量等多方面因素。
四、应用分析1. 梯形加速度规划法的应用:该方法适用于对加工精度和表面质量要求较高的场合,如精密模具、汽车零部件等的加工。
通过合理设置进给速度和加速度,可以实现加工轨迹间速度的平滑过渡,提高加工精度和表面质量。
- 1、下载文档前请自行甄别文档内容的完整性,平台不提供额外的编辑、内容补充、找答案等附加服务。
- 2、"仅部分预览"的文档,不可在线预览部分如存在完整性等问题,可反馈申请退款(可完整预览的文档不适用该条件!)。
- 3、如文档侵犯您的权益,请联系客服反馈,我们会尽快为您处理(人工客服工作时间:9:00-18:30)。
软件数控S型加减速在高精高速加工中的快速应用方法摘要在高速数控加工过程中,为避免机床在启动或停止时出现冲击、超调或振荡等现象,并提高加工效率和精度,提出S 曲线加减速规划方法,根据轨迹段的特征,归纳出规划中可能出现的8 种S 曲线加减速方式。
针对每种方式,采用解析式或者迭代法的方法,给出了详细的数学描述,并进行仿真求解。
关键词:高速加工;速度规划;S 曲线加减速;数控系统CTP Mechanical Structure DesignStudent:zhengqiaolu Advisor: Dr. zhougangSchool of Mechanical and Automotive EngineeringZhejiang University of Science and TechnologyAbstractIn high speed machining process, in order to avoid machine in starting or stopping attack, overshoot or oscillation phenomenon, and improve the processing efficiency and accuracy, put forward S curve acceleration and deceleration control method, according to the trajectory segment characteristics, summed up the planning may arise in8S curve acceleration and deceleration mode. In every way, adopts the analytic type or iteration method, gives a detailed mathematical description, and carries on the simulation solutionKeywords:high - speed machining ;feedrate cont rol ;S curve acceleration and deceleration ;numeri2 cal cont rol目录第一章绪论1.1研究背景中国数控技术和产业经过40多年的发展,核心的数控控制器技术经历了5代的发展,其中目前最热门的,当属具有柔性制造能力的第5代控制技术。
加减速时是数控系统插补器的重要组成部分,是数控系统开发的关键技术之一,也是柔性制造的重要技术组成环节。
在高精高速数控加工过程中,如何在运行中快速准确地停止在预定位置,缩短准备时间,并实现加工过程运动平稳,冲击小。
本论文就此方面展开研究,采用S型加减速方式,着重研究其在高精高速中的快速应用方法,缩短数控系统开发的周期,提高系统开放性。
目前数控系统的加减速种类较多,直线型和指数型是传统的加减速方式,实现相对简单,如图1所示,直线型加减速的时间节点简单,只需加速、减速和匀速3个阶段各个点的位置容易把握,实现也比较简单。
指数型加减速能够对速度和加速度进行光顺,运动过程相对平滑。
1.2国内外情况由于对加工精度和效率要求的不断提高,前瞻技术广泛应用于数控系统中并且在近几年中发展迅速.前瞻的主要功能是根据所加工曲线的特征信息和数控机床的动力学特性生成平滑的进给速度曲线,以减少机床的震动提高加工精度,提高生产效率.总体上来说,前瞻技术可以分成为两个步骤:1)根据所加工曲线的特征信息和机床特性计算获得进给速度限制曲线;2)根据一定的加减速算法对进给速度曲线进行重新规划.一般来说,在数控系统中应用比较广泛的加减速算法包括:梯形加减速,指数加减速,S形加减速.梯形加减速和指数加减速具有公式简单,计算量小的优点,一般用于经济型数控系统.但是在这两种加减速方案中加速度会产生突变,会产生震动影响加工质量.S形加减速算法不但计算量适中而且加速度曲线连续,加工质量高,广泛用于高档数控系统.而S形加减速算法也有自己的缺点:1.由于S形加减速算法的表达式是分段表达式,方程的形式难以确定;2.可能产生无理方程或高次方程,难以在微处理器中求解.国内外有一些研究人员已经提出了一些方法来解决这些问题.目前存在的问题1.3研究的意义(一)利用S型加减速曲线进行速度控制,弓高误差、加速度为主要因素,利用时间顺延法,实现了在线实时自适应的加减速控制。
(二)利用插补前加减速控制的位置精确定位,预测减速点,使得加工过程具有位置精度高、无冲击、自适应等优点。
(三)利用快速简化S型加减速在速度曲线中的应用,使得在经济型的数控系统中实现较高的柔性。
1.4 研究的基本内容与拟解决的主要问题通过对课题的分析研究,查找其相关方面的资料,并对其进行深入分析与研究。
先对其进行系统规划,在高速数控加工过程中 ,为避免机床在启动或停止时出现冲击、超调或振荡等现象 ,并提高加工效率和精度 ,提出针对 S 曲线的加减速规划方法 ,根据轨迹段的特征 , 给出了详细的数学描述 ,并进行减速点预判、前瞻减速等应用算法,最后给出具体的应用。
本次设计拟解决下列主要研究内容:1.分析S型曲线的特点,进行7个阶段的规划,寻找减速点,给出对应的数学描述方程。
2.利用减速点的计算,进行合理的数字化分解,并对减速点进行前移或者局部补偿。
3.对上述的方法,进行数控编程,应用于数控控制器的研发中,对结果进行验证,给出对比数据。
1.5 本章小结本章主要介绍了本次毕业设计课题的背景、研究意义、国内外研究现状及本论文的研究内容。
第二章数控系统S 曲线加减速规划2.1S 曲线加减速图1 所示为S 曲线加减速全过程中的位置、速度、加速度以及加加速度曲线。
加速过程包含加加速段、匀加速段及减加速段;减速过程包含加减速段、匀减速段及减减速段;加速和减速之间通过匀速运动衔接,整个过程分为7 段。
7 段中加加速度j 、加速度a、速度v 以及位移s 的方程如下:式中, a max 为机床允许的最大加速度; j max 为机床允许的最大加加速度; v s 为起点速度。
事实上, S 曲线加减速可能不完整包含上述7段。
根据给定的起点速度v s 、指令速度v、终点速度v e 以及待插补曲线的位移s , S 曲线可能不含匀速段、匀加速段或匀减速段。
因此, 规划后的S 曲线可能出现8 种情况,如图2 所示。
(a) 包含匀速段、匀加速段、 (b) 不含匀速段,包含匀加速匀减速段的速度曲线段、匀减速段的速度曲线(c) 包含匀速段、匀加速段, (d) 包含匀加速段,不含匀不含匀减速段的速度曲线速段及匀减速段的速度曲线(e) 包含匀速段、匀减速段, (f) 包含匀减速段,不含匀速不含匀加速段的速度曲线段及匀加速段的速度曲线(g) 包含匀速段,不含匀加速 (h) 不含匀速段、匀加速段及匀减速段的速度曲线段及匀减速段的速度曲线在规划中,首先根据v s 、v e 、v 规划S 曲线加减速的加速段及减速段, 之后通过比较加减速段的总位移s′与待插补位移s 的关系确定是否含有匀速段。
如不含匀速段,则求解整个规划过程中所能达到的实际最大速度v′, 并以此重新规划加速段及减速段。
2.2S 曲线变速段规划S 曲线加速段是否含有匀加速段, 可由给定的起点速度v s 、指令速度v 、机床允许的最大加速度a max 以及最大加加速度j max 确定。
由S曲线特性可知,加加速段和减加速段对称。
且在加速过程中,应尽量满足加速度a可达到a max 。
所以,匀加速段存在的条件是给定的v 和v s 之差不小于a2max / j max 。
若,则加速过程中存在匀加速段,加速过程中三段时间t1 、t2 和t3 分别为若则加速过程中无匀加速段,加速过程中三段时间分别为加速过程中达到的实际最大加速度为将得到的t1 、t2 、t3 代入式(4) ,若t2 = 0 ,则用a′max 代替a max ,求出加速段位移,记为s Acc 。
按相同思路可规划出减速段中加减速段、匀减速段和减减速段各自的时间t5 、t6 、t7 。
将得到的t5 、t6 、t7 代入式(4) ,求出减速段位移,记为s Dec 。
比较s Acc 与s Dec 之和与待插补位移s的关系可确定S 曲线加减速规划中是否含有匀速段。
2.2S 曲线加减速含有匀速段若s Acc + s Dec < s ,则S曲线加减速规划中含有匀速段,匀速段时间为若s Acc + s Dec ≥s ,则S曲线加减速规划中不含匀速段,即t4 = 0 。
若s Acc + s Dec > s ,则加速过程中实际能达到的最大速度v max 小于给定的v ,需重新确定。
下面说明v max 的求解过程。
2. 3 S 曲线加减速不含匀速段首先假设实际最大速度为即取v s 和v e 中较大值,以此求出v′max 。
以v e 较大为例求出v′max 。
因v e > v s ,所以加速段包含加加速段、匀加速段以及减加速段,整个规划过程分为5段。
求出v′max 后,将加减速过程总位移s′max 与待插补位移s 比较。
若s′max = s ,则求出的v′max 即为规划出来的实际最大速度,即v max = v′max 。
若s′max < s ,则实际最大速度为式中, a max 为机床允许的最大加速度; j max 为机床允许的最大加加速度; s 为待插补轨迹位移。
若s′max > s ,则S 曲线加减速规划中匀加速度段和匀减速段不同时存在, 需重新求解v max 。
此时,假设实际最大速度为即选取v s 和v e 中较小值,以此求出v″max 。
以v s 较小为例求出v″max 。
因v e > v s ,所以减速段只有加减速段和减减速段, 整个规划过程分为4 段。
求出v″max 后,将加减速过程总位移s″max 与待插补位移s比较。
若s″max = s ,则求出的v″max 即为规划出来的实际最大速度,即v max = v″max 。
若s″max < s ,则S 曲线加减速规划中只有匀加速段(若v s < v e ) 或者匀减速段(若v e < v s ) ,需重新求解v max 。
若s″max > s ,则S 曲线加减速规划中不含匀加速段及匀减速段,需重新求解v max 。
对s″max < s 及s″max > s 这两种情况,可通过二分法迭代求解v max 。
由于在某个确定的速度v max下,加减速过程的总位移s max 是v max 的单调增函数,因此迭代一定次数可最终求出v max 。