StudiesonFactorsInfluencingHydrodynamicCharacteris
超高压辅助酶解法改性汉麻分离蛋白及其理化性质的研究

刘容旭,李春雨,王语聪,等. 超高压辅助酶解法改性汉麻分离蛋白及其理化性质的研究[J]. 食品工业科技,2023,44(19):99−107.doi: 10.13386/j.issn1002-0306.2023010016LIU Rongxu, LI Chunyu, WANG Yucong, et al. Study on the Modification and Physicochemical Properties of Hemp Protein Isolate by Ultra-High Pressure Assisted Enzymatic Hydrolysis[J]. Science and Technology of Food Industry, 2023, 44(19): 99−107. (in Chinese with English abstract). doi: 10.13386/j.issn1002-0306.2023010016· 研究与探讨 ·超高压辅助酶解法改性汉麻分离蛋白及其理化性质的研究刘容旭1,李春雨2,王语聪2,谢智鑫2,谢宜桐2,李双鹏2,刘丹怡1, *,韩建春2,*(1.黑龙江省绿色食品科学研究院,黑龙江哈尔滨 150028;2.东北农业大学 食品学院,黑龙江哈尔滨 150030)摘 要:本研究以汉麻分离蛋白(Hemp Protein Isolate ,HPI )为原料,通过超高压辅助酶解反应对HPI 进行改性,以溶解度和水解度为判定指标筛选酶解改性反应最佳条件,并探究超高压辅助酶解反应对酶解产物溶解性、起泡性、乳化性、持水性、持油性的影响。
结果表明,HPI 酶解反应最适条件为:加酶量(复合蛋白酶)5000 U/g 、酶解改性pH8.0、酶解改性温度55 ℃、酶解改性时间50 min 。
以HPI 为对照,当压力为200 MPa 时,酶解产物的溶解度、起泡性、乳化性、持油性最高,压力为100 MPa 时,泡沫稳定性最好,酶解后的乳化稳定性存在不同程度的下降,压力为0.1 MPa 时其持水性达到最大值。
当表面活性剂遇到大环分子
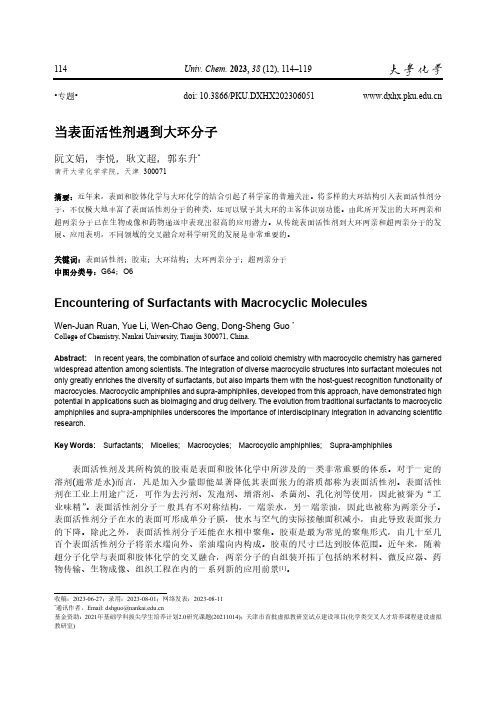
114Univ. Chem. 2023, 38 (12), 114–119收稿:2023-06-27;录用:2023-08-01;网络发表:2023-08-11*通讯作者,Email:*****************.cn基金资助:2021年基础学科拔尖学生培养计划2.0研究课题(20211014);天津市首批虚拟教研室试点建设项目(化学类交叉人才培养课程建设虚拟教研室)•专题• doi: 10.3866/PKU.DXHX202306051 当表面活性剂遇到大环分子阮文娟,李悦,耿文超,郭东升*南开大学化学学院,天津 300071摘要:近年来,表面和胶体化学与大环化学的结合引起了科学家的普遍关注。
将多样的大环结构引入表面活性剂分子,不仅极大地丰富了表面活性剂分子的种类,还可以赋予其大环的主客体识别功能。
由此所开发出的大环两亲和超两亲分子已在生物成像和药物递送中表现出很高的应用潜力。
从传统表面活性剂到大环两亲和超两亲分子的发展、应用表明,不同领域的交叉融合对科学研究的发展是非常重要的。
关键词:表面活性剂;胶束;大环结构;大环两亲分子;超两亲分子中图分类号:G64;O6Encountering of Surfactants with Macrocyclic MoleculesWen-Juan Ruan, Yue Li, Wen-Chao Geng, Dong-Sheng Guo *College of Chemistry, Nankai University, Tianjin 300071, China.Abstract: In recent years, the combination of surface and colloid chemistry with macrocyclic chemistry has garnered widespread attention among scientists. The integration of diverse macrocyclic structures into surfactant molecules not only greatly enriches the diversity of surfactants, but also imparts them with the host-guest recognition functionality of macrocycles. Macrocyclic amphiphiles and supra-amphiphiles, developed from this approach, have demonstrated high potential in applications such as bioimaging and drug delivery. The evolution from traditional surfactants to macrocyclic amphiphiles and supra-amphiphiles underscores the importance of interdisciplinary integration in advancing scientific research.Key Words: Surfactants; Micelles; Macrocycles; Macrocyclic amphiphiles; Supra-amphiphiles表面活性剂及其所构筑的胶束是表面和胶体化学中所涉及的一类非常重要的体系。
水凝胶 英语作文
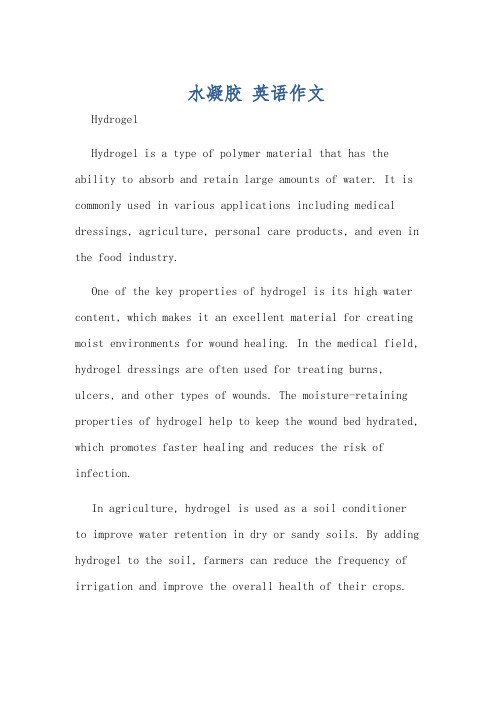
水凝胶英语作文HydrogelHydrogel is a type of polymer material that has the ability to absorb and retain large amounts of water. It is commonly used in various applications including medical dressings, agriculture, personal care products, and even in the food industry.One of the key properties of hydrogel is its high water content, which makes it an excellent material for creating moist environments for wound healing. In the medical field, hydrogel dressings are often used for treating burns, ulcers, and other types of wounds. The moisture-retaining properties of hydrogel help to keep the wound bed hydrated, which promotes faster healing and reduces the risk of infection.In agriculture, hydrogel is used as a soil conditionerto improve water retention in dry or sandy soils. By adding hydrogel to the soil, farmers can reduce the frequency of irrigation and improve the overall health of their crops.This is particularly beneficial in regions with limited water resources or in areas that are prone to drought.In personal care products, hydrogel is commonly found in products such as contact lenses, facial masks, and moisturizing creams. Its ability to retain water makes it an ideal ingredient for products designed to hydrate and nourish the skin.In the food industry, hydrogel is used as a thickening agent and stabilizer in various food products. It can be found in a wide range of items including sauces, dressings, and bakery items. Its ability to absorb and retain water makes it useful for creating desired textures and improving the shelf life of food products.Overall, hydrogel is a versatile and useful material with a wide range of applications. Its unique properties make it an important component in various industries, contributing to advancements in healthcare, agriculture, personal care, and food technology.水凝胶水凝胶是一种聚合物材料,具有吸收和保持大量水分的能力。
对水的研究英文作文

对水的研究英文作文Water is essential for life. It covers most of the Earth's surface and makes up a large percentage of our bodies. Without water, we would not be able to survive.Water is a fascinating substance. It can exist in three states: solid, liquid, and gas. This ability to change form is what makes water so unique and versatile.Researchers study water for many reasons. They want to understand its properties, how it interacts with other substances, and how it moves through the environment. By studying water, scientists can learn more about the world around us.One interesting area of water research is its role in climate change. Water plays a crucial role in regulating the Earth's temperature and weather patterns. Scientists are studying how changes in water distribution and temperature are affecting our planet.Water research also extends to the oceans. Researchers study the chemistry of seawater, the creatures that live in it, and the impact of human activities on marine ecosystems. Understanding the oceans is crucial for protecting marinelife and preserving the health of our planet.Overall, water research is a diverse and important field. Scientists are constantly learning new things about this essential substance and its role in the world. By studying water, we can better understand our environmentand work towards a more sustainable future.。
预氧化技术

3 Introduction
• ClO2 oxidation prior to chlorination can reduce the levels of THM and total organic halogen (TOX) formation (Lykins and Griese,1986; Linder et al., 2006 ).
(1) the changes of NOM properties with ClO2 pretreatment.
(2) the formation of regulated and emerging DBPs from ClO2 preoxidation and in combination with chlorination or chloramination.
第33页,共33页。
• 与浊度不同,滤后水高锰酸盐指数自运行开始后一直保持稳定,说 明生物过滤对水中易氧化有机物的去除相关性不大;滤后水UV254 变化很小,说明难生物降解(shēnɡ wù jiànɡ jiě)有机物很难在生物 过滤中被去除; O3 —生物过滤对DOC 的去除率稍高。O3 和PPC 预氧化后SUVA 相对于空白试验分别降低和升高(见表1) ,而 O3 —生物过滤出水SUVA 升高较明显(见表2) ,说明O3 预氧化更 有助于生物过滤对可生物降解(shēnɡ wù jiànɡ jiě)有机物的去除。
transformed large aromatic and long aliphatic chain organic structures to small
and hydrophilic organics.
第33页,共33页。
Conclusion
有机水凝胶 电阻为600的英文文献

有机水凝胶电阻为600的英文文献English:There are several English-language articles available on the topic of organic hydrogels with a resistance of 600. These articles explore various aspects of organic hydrogels, including their synthesis, properties, applications, and electrical conductivity. One such article titled "Synthesis and Characterization of Organic Hydrogels with Tunable Electrical Properties" investigates the synthesis of organic hydrogels with controllable electrical conductivity, where the resistance values around 600 ohms are within the scope of the study. The article discusses the fabrication process, the characterization techniques employed to analyze the electrical properties, and potential applications of these hydrogels in fields such as sensors, actuators, and biomedical devices. Another relevant study, "Electroconductive Organic Hydrogels for Bioelectronics: Mechanisms, Materials, and Applications," delves into the mechanisms underlying the electrical conductivity of organic hydrogels and the materials used to enhance their conductivity. While the specific resistance value of 600 ohms may not be explicitly mentioned in all articles, these studies provide valuable insights intothe fabrication and utilization of organic hydrogels with electrical properties suitable for various applications.中文翻译:关于有机水凝胶电阻为600的英文文献有多篇可供参考。
纳米压痕 纯铁 氢 硬度 位错

Recent developments in the study of hydrogen embrittlement:Hydrogeneffect on dislocation nucleationAfrooz Barnoush *,Horst VehoffSaarland University,Department of Materials Science,Bldg.D22,P.O.Box 151150,D-66041Saarbruecken,GermanyReceived 11March 2010;received in revised form 30May 2010;accepted 30May 2010Available online 2July 2010AbstractIn this paper,the intrinsic complexities of the experimental examination of hydrogen embrittlement are discussed.On the basis of these complexities,an experimental approach,in situ electrochemical nanoindentation,is proposed and performed on different materials.This technique is capable of registering the onset of plasticity in extremely small volumes,namely perfect crystals in hydrogen-free and charged conditions.It is shown that hydrogen reduces the required stress for the onset of plasticity,i.e.homogeneous dislocation nucle-ation by reduction in the shear modulus,dislocation line energy and stacking fault energy.The change in the shear modulus can be related to reduction in crystal cohesion whereas the reduction in dislocation line energy and stacking fault energy are explained by the defactant concept,i.e.reduction in the defect formation energy in the presence of hydrogen.Thus,neither hydrogen-enhanced dec-ohesion nor hydrogen-enhanced plasticity,but the reduction in the cohesion and defect formation energy are responsible for hydrogen embrittlement.Ó2010Acta Materialia Inc.Published by Elsevier Ltd.All rights reserved.Keywords:Hydrogen embrittlement;Nanoindentation;Yield phenomena;Electrochemistry;Dislocation nucleation1.IntroductionHydrogen embrittlement is a severe environmental type of failure that affects almost all metals and alloys.With advancing technology,the use of high-strength structural materials for lightweight construction and energy conser-vation becomes a necessity.In spite of the success of mate-rials scientists in developing alloys with outstanding combinations of high tensile strength and high fracture toughness,hydrogen embrittlement still has a widespread effect that severely degrades the fracture resistance of these alloys.On the other hand,with the depletion of fossil fuels,mankind is searching for other sources of energy.Hydro-gen is believed to be a possible future energy source and it is very possible that a “hydrogen economy ”will be real-ized within the next 50years.In such a scenario,large-scale production,storage,transportation and use of hydrogenwill become necessary.However,the problems in materials caused by hydrogen embrittlement,reported as early as 1875by Johnson [1],could limit the progress of such an economy.Since Johnson first reported on hydrogen embrittlement,various strong views on the mechanisms of hydrogen embrittlement have been vigorously discussed and thoroughly reviewed in the literature [2–4].Because of the technological importance of hydrogen embrittlement,many people have explored the nature,causes and control of hydrogen-related degradation of metals [5–7].This has resulted in an enormous number of sometimes controver-sial findings and/or interpretations.Moreover,frequently an ad hoc approach,focusing on urgent technical problems at hand,is adopted which raises the question of how this isolated case or interpretation really reflects on any basic,general concepts.It thus seems apparent that the findings gathered so far cannot be accounted for by a single domi-nant mechanism.As an example,Fig.1shows the results of conventional hydrogen embrittlement testing of 34different grades of1359-6454/$36.00Ó2010Acta Materialia Inc.Published by Elsevier Ltd.All rights reserved.doi:10.1016/j.actamat.2010.05.057*Corresponding author.E-mail address:a.barnoush@matsci.uni-sb.de (A.Barnoush)./locate/actamatActa Materialia 58(2010)5274–5285steel within465test runs[8].The embrittlement index shown in Fig.1is the reduction in the fracture area in hydrogen-charged vs.hydrogen-free conditions during uni-axial tensile tests.The scatter observed within the results shown in Fig.1demonstrates the need for a new experi-mental approach to the investigation of hydrogen embrit-tlement.It is necessary tofind the source of this scatter in conventional hydrogen embrittlement testing methods. In this paper we will briefly review the different experimen-tal approaches used to study hydrogen embrittlement with a special focus on in situ local examination methods of hydrogen–dislocation interactions due to the conclusive role of dislocations in fracture and hydrogen embrittlement aspect is the wide range of intrinsic/extrinsic variables con-cerning the material itself.The experimental approach for examination of hydrogen embrittlement is based on the elimination of diverse factors within these three aspects. For example,let us consider uniaxial straining of a single crystal sample combined with controlled hydrogen charg-ing on the surface.The uniaxial stressfield simplifies the stress condition,i.e.the mechanical aspect of hydrogen embrittlement,in the e of a single crystal and con-trolled hydrogen charging condition reduces the complexi-ties due to the material and environmental aspects of hydrogen embrittlement in the test.Unfortunately,due to the large difference in the scale of these aspects controlling the process of hydrogen embrittlement,this experimental methodology is not very successful.The uniaxial stressfield of the above-mentioned example is not uniform,unlike the scale of hydrogen interacting with defects like dislocations and vacancies.This problem becomes more complicated as the microstructure becomes more complex with the intro-duction of grain boundaries,pores,second phases,etc. On the other hand,surface hydrogen charging of macro-scopic samples results in a concentration gradient,which again can override the microscopic process of hydrogen embrittlement.Additionally,microstructural features like dislocations,grain boundaries and interfaces can interact with hydrogen diffusion by providing faster diffusion routes or acting as traps for hydrogen.Superimpose upon this theFig. 1.The hydrogen embrittlement index measured by conventionalmechanical testing for34different grades of steel within465test runsFig.2.Global description of hydrogen embrittlement interaction aspects.Materialia58(2010)5274–52855275grain boundary fracture,enhanced shear or enhanced localized microvoid formation,or all of the above.One possible solution to these problems,arising from the experimental methodology used for studying hydrogen embrittlement,is the local examination of the hydrogen effect.This entails reducing the scale of the testing method down to the microstructural level such that all three con-trolling aspects of hydrogen embrittlement(Fig.2)can be defined within the test.Few attempts of this kind of approach have been done previously.Vehoffand Neumann [9]developed a method for studying crack propagation in a controlled environment under controlled plastic strain con-ditions.This method was used to study the hydrogen effect on crack growth mechanisms in Fe–2.6%Si[10]and Ni [11].In their experiments they controlled:(i)environmental aspects by using an ultrahigh-vacuum chamber and con-trolling the partial pressure of hydrogen;(2)mechanical aspects by controlling plastic strain and confining the stress to a smallfield ahead of the crack;and(iii)material aspects by selection of specifically oriented single crystals and focusing on the fracture process zone(Fig.3).Through these perfectly defined experimental conditions they were able to propose a model based on hydrogen-enhanced dec-ohesion(HEDE)and hydrogen trapping in front of a crack tip in the fracture process zone[10,11].Another intelligent experimental approach for small-scale observation of hydrogen effects on mechanical prop-erties was use of in situ straining tests in an environmental transmission electron microscope(TEM)developed by Birnbaum and Sofronis[12].With this technique it was possible for thefirst time to directly observe the effect of hydrogen on dislocations.Unfortunately,there are some uncertainties within the experimental conditions of this technique which must be mentioned here:(i)The electron beam dissociates hydrogen molecules to produce atomic hydrogen.Bond et al.[13]determined that the fugacity of the dissociated hydrogen was between30and750MPa. (ii)Since mode III(shear off)is usually easier in thinfilms, crack growth experiments under a defined mode I loading are very difficult to realize and therefore interpretation of the crack growth results become very difficult.(iii)Field of view is limited to the transparent region of the sample.By the introduction of micro-and nanoscale mechanical testing methods,like instrumented nanoindentation(NI) and nanoindenting atomic force microscopy(NI-AFM),a new era in mechanical testing of extremely small volumes started[14].Gerberich et al.[15]was thefirst one who men-tioned the potential application of micromechanical tests for the examination of hydrogen embrittlement.Since then, several researchers have used the NI technique to probe the effects of hydrogen on mechanical properties[16–20].The main advantage of the NI technique is its capability to resolve the dislocation nucleation in samples with low dis-location density[21,22].Additionally,analytical solutions for stress underneath the tip prior to dislocation nucleation within the elastic deformation are available,so the mechan-ical aspects of the experiments can be defined.The volume probed during the test is extremely small and can be char-acterized by means of different techniques,like electron backscatter diffraction(EBSD)and electron channeling contrast[23],and therefore,material aspects can be resolved.The referenced studies[16–20]used ex situ hydro-gen charging techniques which resulted in uncertaintiesFig.3.Hydrogen effect on the crack tip opening angle in:(a)vacuum and(b)hydrogen atmosphere.Sharpness of the crack tip in stressed Fe–3wt.%single crystal increases progressively with increasing hydrogen pressure[10].Table1Summary of the high-resolution testing methods used for local examination of hydrogen embrittlement. Experimental approach Different aspects of the hydrogen embrittlementMechanical Environmental MaterialIn situ crackpropagation test Defined and analyticallycan be treatedDefined Defined in the case of macroscopic single crystals withspecific orientation,very hard to apply on complexmicrostructuresIn situenvironmentalTEM tests Undefined Undefined due to dissociation of Hmolecules by electron beam(low pressure,very high fugacity)Defined with very high-resolution but only within thefield of viewNanoindentation on ex situ chargedsamples Before pop-in is definedand can analytically betreatedUndefined,due to out gassing andconcentration gradientPerfect defect-free crystalIn situ ECnanoindentation Before pop-in is definedand can analytically betreatedDefined Perfect defect-free crystalMaterialia58(2010)5274–5285within the hydrogen concentration especially near the sur-face of the sample where the mechanical testing was carried out.We solved this problem by performing in situ ECNI tests while the surface hydrogen concentration was kept constant by setting the surface electrochemical potential inside the proper electrolyte[24–26].Table1summarizes the local high-resolution techniques for examination of hydrogen embrittlement.A comparison of these methods shows the advantage of ECNI in provid-ing the required conditions to perform a defined experi-ment in accordance with different aspects of hydrogen embrittlement.In this paper,we report the results of ECNI tests on different metals with different hydrogen embrittle-ment susceptibilities.It will be shown that ECNI is capable of quantitatively resolving the sensitivity to hydrogen embrittlement.3.Experimental3.1.MaterialsThe materials used in this study and the electropolishing parameters and electrochemical hydrogen charging condi-tions for each are summarized in Tables2and3.The sin-gle-crystal specimens were cut by spark erosion from large single crystals with a misalignment of less than2°controlled by EBSD.The polycrystalline specimens were cut from samples with large grains a few millimeters in diameter which act like a single crystal during NI when all tests are performed in the same rge grains or single crystals eliminate the scatter in the data due to orien-tation differences.The samples were mechanically polished down to0.25l m.Afterwards,samples were annealed at 80%of the melting temperature in a vacuum greater than 10À6mbar for24h and cooled in the furnace in order to minimize the lattice defect density.Immediately before indentation the samples were electropolished according to the parameters given in Table2to have a well-defined reproducible surface condition.Special attention was paid to surface preparation since,as mentioned before,a defect-free and low-roughness surface is necessary in order to observe the dislocation nucleation during NI.When examined with an AFM,the sample surface had an root-mean-square roughness of less than1nm,and asperities or steps appeared infrequently on the surface.3.2.InstrumentationThe experiments were performed with a Hysitron Tribo-ScopeÒin conjunction with a Digital Instruments Nano-scope IIÒand a Hysitron TriboIndenterÒ.The indenter, designed especially for tests in liquid,had a Berkovich or conical diamond tip(see Table3).For the NI-AFM system, a three-electrode electrochemical setup with a platinum counter electrode and an Ag/AgCl reference electrode was developed,as shown schematically in Fig.4.Consequently, all the electrochemical potentials in this work are reported against an Ag/AgCl reference electrode.A Bank Elektronik TG97potentiostat was used to control the electrochemical potentials,and the electrochemical data were recorded on a PC using an AD–DA interface.The cell was made from Tef-lon e,and made tofit into the nanoindenter sample holder. Nanoindentation tests were made inside this electrochemi-cal cell while the sample was covered with approximately 2mm of electrolyte.The whole system was put into a cham-ber containing a protective atmosphere of nitrogen and helium in order to eliminate the oxygen effect in the electro-chemical reaction.The solution was injected from outside the chamber through a polyethylene tube connected to a MicroFil e pipette.There are additional concerns that arise when indenting in a liquid environment due to the capillary and buoyancyTable2Summary of the samples studied and their electropolishing conditions.Material Purity Microstructure Electropolishing conditionSolution Potential(V)Temperature(°C)Time(s) Copper Zone refined(111)H3PO4/ethanol202030 Aluminum99.991mm grains HClO4/ethanol40030Fe–3wt.%Si See Table41mm grains H2SO4/CH3OH121060FeAl(40at.%Al)Zone refined(100)H2SO4/CH3OH351090 Nickel Zone refined(111)H2SO4/CH3OH301560 Table3Summary of the electrochemical hydrogen charging and discharging(passivation)conditions.Material Test solution pH H-charging potential Passivation potential Indenter tip Copper Borate buffer9À1000mV250mV Berkovich Aluminum Borate buffer9À1250mV OCP Berkovich Aluminum0.05M Na2SO46OCP250mV Berkovich Fe–3wt.%Si Borate buffer9À1000mV n.a.Berkovich FeAl0.05M Na2SO46À1100mV100mV Conical Nickel0.05M Na2SO46À1000mV500mV BerkovichA.Barnoush,H.Vehoff/Acta Materialia58(2010)5274–52855277forces acting on the tip.To overcome this,the surface is first engaged with a higher set point of contact force.The tip is then moved a few nanometres away from the surface and the forces on the tip balance while it rests above the surface.After this procedure the surface can be easily engaged as usual.Another important concern during the in situ ECNI test is cleanliness.Therefore,all electrolytes were prepared from analytical grade compounds and dou-ble-distilled water.Prior to the tests,the electrochemical cell was cleaned in piranha acid to remove most organic matter and to make it hydrophilic and water compatible.The tip and its shaft were also cleaned carefully before each test in a mixture of ethanol and isopropanol and then in double-distilled water.A clean tip shaft reduces the capil-lary forces acting on it and reduces the probability of dis-engagement of the tip during surface imaging inside the solution.A low impurity content in the electrolyte inhibitsthe deposition of these impurities during electrochemical polarization of the surface.The electrolyte pH and compo-sition should also be selected very carefully to inhibit any possible corrosion and surface roughening.Hence,these parameters are selected for each sample individually.4.Results 4.1.CopperCopper is known for its very low hydrogen solubility and diffusivity.DeWulf and Bard [27]showed that without hydrogen recombination poisons (e.g.As 2O 3)no detectable hydrogen concentration develops in copper.This makes the copper a proper calibration material for in situ ECNI tests,where no effect of cathodic charging should be observed.Typical load–displacement (L –D )curves under cathodic and anodic potentials are given in Fig.5.4.2.AluminumAluminum is a reactive metal protected by a thin stable oxide layer with semi-conductive properties.At potentials cathodic to the open circuit potential (OCP)of Al,cathodic hydrogen evolution due to the reduction of hydrogen ions and water occurs simultaneously with anodic oxidation and dissolution processes [28].This makes the electrochem-ical hydrogen charging of Al without damaging the surface difficult.Therefore,an alternative method controlling the pH of the solution was developed and used for hydrogen charging of Al [29].It is well known that oxide-covered metals immersed in aqueous solutions terminate in an out-ermost layer of hydroxyl groups due to their interaction with water molecules [30].In aqueous solutions,the surface hydroxyl groups will remain undissociated if the pH of theTable 4Analysis of the Fe–3wt.%Si alloy used in this study in.C Si Mn P S Cr Ni Mo Cu Al Ti Nb V B Zr Ce 0.0032.3830.2020.0130.0120.0330.0480.0150.0200.3650.0050.0200.0020.00080.0050.009Fig.4.Schematic drawing of the experimental setup.10020030040050001020304050607080Depth (nm)01002003004005006000102030405060708090Depth (nm)Fig.5.Typical L –D curves of copper under:cathodic and (b)anodic polarization.Materialia 58(2010)5274–5285aqueous solution is the same as the isoelectric point (IEP)of the oxide.If the pH is less than the IEP,the surface will acquire a positive charge.MOH ðsurf ÞþH þðaq Þ!MOH þ2ðsurf Þð1ÞIf the pH is greater than the IEP,the surface will acquire a negative charge MOH ðsurf ÞþOH Àðaq Þ!MO Àðsurf ÞþH 2Oð2ÞThe air-formed oxide film on Al has the IEP value of9.5[31].According to the Eqs.(1)and (2),the pH can greatly affect the hydrogen absorption during immersion of the sample in electrolyte under OCP.Hence,the tests on Al were performed in two different solutions (Table 3).Typical L –D curves of the aluminum sample at different pH levels and electrochemical polarizations are given in Fig.6.4.3.Fe–3wt.%SiThe Fe–3wt.%Si alloy is a single-phase body-centered cubic crystal.The electrochemical behavior of this metal is quite similar to that of pure iron and has a very low aqueous corrosion resistance in solutions with low pH.Therefore,in situ ECNI tests were performed in a pH 9borate buffer solution.This electrolyte is preferred because of the possibility of both controlled cathodic removal of prior oxide films and highly efficient anodic passivation.However,during the in situ ECNI experiments,due to the limited volume of the electrochemical cell and the use of Ag/AgCl reference electrodes,contamination of electro-lyte with Cl Àions resulted in the breakdown of the passive layer.All attempts for producing a stable passive layer failed and resulted in a corroded surface that was not suit-able for NI experiments.Therefore,in the case of the Fe–3wt.%Si sample,the NI results under cathodic potential are compared with the results in air.Fig.7a shows typical load displacement curves during NI of the Fe–3wt.%Si sample in air.The same sample was indented in the same grain under a cathodic potential of À1000mV.This resulted in the load displacement curves shown in Fig.7b.4.4.FeAl intermetallicThe commercial importance of iron aluminides for high temperature structural applications has been well estab-lished [32].Iron aluminides contain two of the most widely available metals,namely Fe and Al.They offer low mate-rial costs,conservation of strategic materials and lower density than stainless steels,with excellent oxidation and sulfidation resistance.In spite of all these inherent advanta-ges,the binary iron aluminides suffer from hydrogen embrittlement.A conical indenter with a cone angle of 90°was used to perform the indentations on FeAl intermetallic alloy with 40at.%Al.The resulting L –D curves in different conditions are given in Fig.8.4.5.NickelThe freshly electropolished nickel has a thin (0.6–0.8nm)film of NiO which can be reduced by cathodic polarization in Na 2SO 4solution with a pH lower than 8[33].Anodic polarization of nickel in the same solution produces a new passive layer,which is a 0.9–1.2nm film of NiO.This film cannot be reduced in a neutral solution.This fact was used during in situ ECNI experiments to exclude surface effects from the effects of hydrogen [34].D curves of aluminum in:(a)pH6solution (OCP light-colored/anodic dark-colored)and (b)pH9solution (cathodic light-colored/OCP 05001000150020002500255075100Depth (nm)o a d (µN )H-chargedH-freeHertzian fitL –D curves of Fe–3wt.%Si in:(a)air and (b)hydrogen-charged condition.Typical load displacement curves obtained in different con-dition are shown in Fig.9.5.DiscussionThe L –D curves of Figs.5–9all show three stages:elastic loading,an excursion in depth (pop-in)at the onset of plas-ticity and continued elastoplastic loading.The initial elastic portion of the loading curves can be fitted with the Hertz-ian elastic responseP ¼43E r ffiffiffiffiffiffiffiffiRh 3p ð3Þwhere P is the applied load,h is the indentation depth,R is the radius of the tip curvature and E r is the reduced mod-ulus,given by 1E r ¼1Àm 21E 1þ1Àm 22E 2ð4ÞHere E is the elastic modulus of the material,m is the Poisson’s ratio,and the subscripts 1and 2refer to the tip and the sample respectively.The initial elastic loading begins as soon as the tip contacts the material surface and continues until dislocation nucleation or motion occurs.Typical dislocation densities in an annealed metal are in the range 106–108cm À2,with dislocations spaced between 1and 10l m apart.A typical indentation test in the elastic regime probes a lateral region of at most a couple of hun-dred nanometers to the point where the pop-in is noted.This suggests the volume of material sampled by the inden-tation test at this depth is smaller than the average disloca-tion spacing,so that an indentation placed randomly on the surface would have a significant probability of sampling a region that contains no pre-existing dislocations.Experi-mental studies [35,36]have been conducted and all lend credibility to the assumption that,for a well-annealed and electropolished sample,the indenter tip can initially contact a volume of material small enough to be dislocation free.The absence of dislocations means the material continues to load elastically until the shear stress under the tip reaches a value near the theoretical shear strength of the material,well above that necessary to activate an existing dislocation source.At this point dislocations are homogeneously nucle-ated,followed by subsequent glide and multiplication events.Homogeneous dislocation nucleation (HDN)should occur when the stress beneath the indenter tip approaches the theoretical shear strength of the material.The term HDN is used here to indicate that dislocations are nucleated from otherwise dislocation-free material.For an indentation test,the applied shear stress that nucle-ates a dislocation can be assumed to be the maximum shear stress beneath the indenter during purely elastic loading.According to continuum mechanics,the maximum shear stress is acting on a point 0.48times the contact radius,a ,below the sample puter simulations have also shown that dislocations nucleate at this point [37].The posi-tion of this maximum shear stress z s (max)and its value s max is givenbyFig.8.Typical L –D curves of FeAl in:(a)hydrogen-free and (b)hydrogen-charged conditions.0501001502002503000102030405060Depth (nm)Depth (nm)a10020030040050001020304050607080ba d (µN )a d (µN )Pop-inFig.9.L –D curves for nickel in:(a)hydrogen-charged and (b)hydrogen-free conditions.z sðmaxÞ¼0:48Áa¼0:483PR4E r13ð5Þs max¼0:316E2rp3RP13ð6ÞTable5summarizes the effect of hydrogen charging on the mean value of pop-in load s max and its position below the surface of all studied samples.For comparison,the the-oretical strength(s th%l/20)according to Frenkel’s model is also given in the Table5.5.1.Hydrogen effect on HDNThe above results clearly indicate that the pop-in load in the hydrogen-charged condition is lower than in the hydrogen-free condition.This change cannot be attributed to the surface topography since it has been imaged and revealed no surface roughening[24,25].Fig.10,as an example,shows the surface topography of the FeAl sam-ple inside the electrolyte.Therefore,the reduction in the pop-in load clearly shows the hydrogen effect on HDN. This is in good agreement with molecular dynamic simu-lations performed by Wen et al.[37].Their results,like other experimental NI results on hydrogen-charged mate-rials[18–20],used hydrogen-enhanced plasticity(HELP) to explain the reduction in the pop-in load.However, the analytical description of the HELP mechanism is based on reduction of elastic interactions by solute hydro-gen between dislocations and elastic centers which act as barriers,such as nearby dislocations and solute pinning points[12].As mentioned before,during NI,the probed volume of the material is so small that it can be assumed to be a perfect crystal without any defects.Therefore,elas-tic shielding of the dislocations by trapped hydrogen atoms is not capable of explaining the observed enhanced plasticity.In adsorption-induced dislocation emission (AIDE)[2,38]the formation energy of dislocations at the crack tip is reduced by hydrogen being absorbed on the crack surfaces.As opposed to HELP,it is the external hydrogen on the crack surface and not the internal hydro-gen in the bulk that enhances the dislocation nucleation in AIDE.Therefore,neither HELP(in the original formula-tion[12])nor AIDE is capable of explaining the hydro-gen-induced reduction in the pop-in load during NI.According to the classic dislocation theory,the free energy required for HDN during NI is determined by the line energy of the newly formed loop c dis and the work for extending the dislocation loop s b per loop area.Here s is the maximum shear stress under the indenter induced by the external load and b is the Burgers vector of the dis-location.If the dislocation forms as a partial,the stacking fault energy(SFE)c also contributes to the required energy for HDN.Then the formation energy of a circular loop of radius r isD G¼2p r cdisþp r2cÀp r2b sð7ÞThe elastic self-energy for a full circular dislocation loop of radius r in an infinite elastic solid is given byc dis¼2Àt1Àtl b2r4ln4rqÀ2ð8ÞFig.11shows the plots of D G as a function of loop radius calculated for the observed mean values of s max in the hydrogen-charged and hydrogen-free conditions.The material constants used are given in Tables5and6.The free-energy curves for HDN pass through a maximumTable5Summary of the mean pop-in load for the H-charged and H-free conditions and comparison between theoretical strength,l/20and measured shear stress at the onset of the pop-in.3topography of FeAl sample under:(a)cathodic and(b)anodic potential where no surface rougheningA.Barnoush,H.Vehoff/Acta Materialia58(2010)5274–52855281。
制氢技术的生命周期评价研究进展
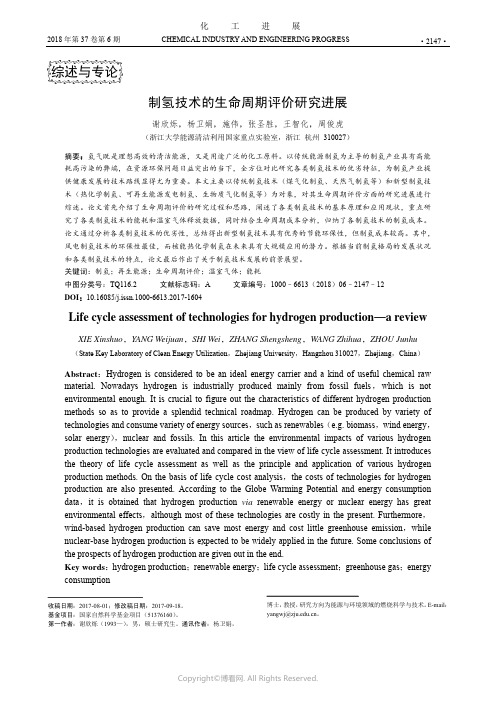
2018年第37卷第6期 CHEMICAL INDUSTRY AND ENGINEERING PROGRESS·2147·化 工 进展制氢技术的生命周期评价研究进展谢欣烁,杨卫娟,施伟,张圣胜,王智化,周俊虎(浙江大学能源清洁利用国家重点实验室,浙江 杭州 310027)摘要:氢气既是理想高效的清洁能源,又是用途广泛的化工原料。
以传统能源制氢为主导的制氢产业具有高能耗高污染的弊端,在资源环保问题日益突出的当下,全方位对比研究各类制氢技术的优劣特征,为制氢产业提供健康发展的技术路线显得尤为重要。
本文主要以传统制氢技术(煤气化制氢、天然气制氢等)和新型制氢技术(热化学制氢、可再生能源发电制氢、生物质气化制氢等)为对象,对其生命周期评价方面的研究进展进行综述。
论文首先介绍了生命周期评价的研究过程和思路,阐述了各类制氢技术的基本原理和应用现状,重点研究了各类制氢技术的能耗和温室气体释放数据,同时结合生命周期成本分析,归纳了各制氢技术的制氢成本。
论文通过分析各类制氢技术的优劣性,总结得出新型制氢技术具有优秀的节能环保性,但制氢成本较高。
其中,风电制氢技术的环保性最佳,而核能热化学制氢在未来具有大规模应用的潜力。
根据当前制氢格局的发展状况和各类制氢技术的特点,论文最后作出了关于制氢技术发展的前景展望。
关键词:制氢;再生能源;生命周期评价;温室气体;能耗中图分类号:TQ116.2 文献标志码:A 文章编号:1000–6613(2018)06–2147–12 DOI :10.16085/j.issn.1000-6613.2017-1604Life cycle assessment of technologies for hydrogen production —a reviewXIE Xinshuo ,YANG Weijuan ,SHI Wei ,ZHANG Shengsheng ,WANG Zhihua ,ZHOU Junhu(State Key Laboratory of Clean Energy Utilization ,Zhejiang University ,Hangzhou 310027,Zhejiang ,China )Abstract :Hydrogen is considered to be an ideal energy carrier and a kind of useful chemical rawmaterial. Nowadays hydrogen is industrially produced mainly from fossil fuels ,which is not environmental enough. It is crucial to figure out the characteristics of different hydrogen production methods so as to provide a splendid technical roadmap. Hydrogen can be produced by variety of technologies and consume variety of energy sources ,such as renewables (e.g. biomass ,wind energy ,solar energy ),nuclear and fossils. In this article the environmental impacts of various hydrogen production technologies are evaluated and compared in the view of life cycle assessment. It introduces the theory of life cycle assessment as well as the principle and application of various hydrogen production methods. On the basis of life cycle cost analysis ,the costs of technologies for hydrogen production are also presented. According to the Globe Warming Potential and energy consumption data ,it is obtained that hydrogen production via renewable energy or nuclear energy has great environmental effects ,although most of these technologies are costly in the present. Furthermore ,wind-based hydrogen production can save most energy and cost little greenhouse emission ,while nuclear-base hydrogen production is expected to be widely applied in the future. Some conclusions of the prospects of hydrogen production are given out in the end.Key words :hydrogen production ;renewable energy ;life cycle assessment ;greenhouse gas ;energy consumption博士,教授,研究方向为能源与环境领域的燃烧科学与技术。
- 1、下载文档前请自行甄别文档内容的完整性,平台不提供额外的编辑、内容补充、找答案等附加服务。
- 2、"仅部分预览"的文档,不可在线预览部分如存在完整性等问题,可反馈申请退款(可完整预览的文档不适用该条件!)。
- 3、如文档侵犯您的权益,请联系客服反馈,我们会尽快为您处理(人工客服工作时间:9:00-18:30)。
J. Ocean Univ. China(Oceanic and Coastal Sea Research)https:///10.1007/s11802-019-3706-zISSN 1672-5182, 2019 18 (1): 193-202/xbywb/E-mail:xbywb@Studies on Factors Influencing Hydrodynamic Characteristicsof Plates Used in Artificial ReefsTANG Yanli1), YANG Wenzhao1), SUN Liyuan2), ZHAO Fenfang1), *, LONG Xiangyu1),and WANG Gang1)1) College of Fishery, Ocean University of China, Qingdao 266003, China2) Shandong Hydrobios Resources Conservation and Management Center, Yantai 264003, China(Received October 25, 2017; revised January 29, 2018; accepted September 20, 2018)© Ocean University of China, Science Press and Springer-Verlag GmbH Germany 2019Abstract As a simplified model of artificial reefs, a series of plate models punched with square or circular openings are de-signed to investigate the effects of openings on the hydrodynamic characteristics of artificial reefs. The models are grouped by various opening numbers and opening-area ratios. They are physically tested in a water flume or used in the numerical simulation to obtain the drag force in the uniform flow with different speeds. The simulation results are found in good agreement with the experimental measurements. By the non-dimensional analysis, the drag coefficient specified to each model is achieved and the effects of openings are examined. It is found that the key factor affecting the drag coefficient is the open-area ratio. Generally, the drag coefficient is a linear function of the open area ratio with a minus slope. The empirical formulae for the square and circular openings respectively are deduced by means of the multiple regression analysis based on the measured and numerical data. They will be good references for the design of new artificial reefs. As a result of numerical simulation, the vorticity contours and pres-sure distribution are also presented in this work to better understand the hydrodynamic characteristics of different models.Key words artificial reefs; drag coefficient; hydrodynamic characteristics; model experiment1 IntroductionArtificial reefs are man-made structures placed in the natural water area, either in the bays or along the coastal line, to restore and optimize the ecological environment. It has been reported that the artificial reefs can affect the bay’s natural cleaning capacity to improve the water quality (Antsulevich, 1994). The artificial reefs play a role of protecting coastal environment for nursery, micro- habitat and food supply against the illegal otter trawling, which increase the biodiversity and biomass of benthos and fishes, and provide facilities for ecotourism as well (Relini et al., 2007). The main function of artificial reefs is to disturb the flow field and form upwelling or com-plex wake regions, which can promote the circulation of the water column (Kim et al., 2014; Jiang et al., 2016). Once the reef is installed to the sea bottom, it is sub-jected to the action of waves and sea current, namely, the hydrodynamic force. As an obstacle fixed in the water flow, the term of drag force is borrowed to designate this force here. The reef will be displaced when the drag force outweighs the maximum static friction between the reef and the seabed. Meanwhile, when the overturning * Corresponding author. Tel: 0086-532-82032511E-mail: zhaoff@ moment of drag force acting on the reef is larger than the restoring moment caused by the weight of the reef body, the reef will be turned over. In both cases, it might de-crease the desired ecological effect of reefs or reduce their service life. Therefore, it is important to consider the structure stability of artificial reefs. However, most of the researches on the artificial reefs have been focused on their effects on the ecological environment. In order to ensure the stability of artificial reefs, it is necessary to investigate the surrounding flow field and the hydrody-namic forces acting on the reefs (Liu et al., 2011; Liu et al., 2014).There are mainly three methods to study the flow field around the artificial reefs to obtain the hydrodynamic forces, i.e., field investigation, experiments in flume or wind tunnel, and numerical simulation. The first method, i.e., field investigations, is very costly both in money and time due to the complexity of sea environment. Thanks to the development in modern computational mechanics and computer technology, satisfactory accuracy can be achieved by numerical calculation with reasonable efforts (Woo et al., 2014). The model tests in flumes or wind tunnel give the direct and intuitive results. Carrying out both physical experiments and numerical calculation can ob-tain reliable results (Ross et al., 2004; Nisugi et al., 2004; Su et al., 2008; Cui et al., 2009; Liu and Su, 2013; Taka-hashi et al., 2015; Mellibovsky et al., 2015; Xu et al.,TANG et al . / J . Ocean Univ . China (Oceanic and Coastal Sea Research ) 2019 18: 193-202194 2017).The artificial reefs are usually made of block bodies, opened with several holes to stimulate flows. Their hy-drodynamic characteristics are mainly determined by their shapes including the opening rate of those holes. In the flume experiments of porous cubic reefs, a concept of open area ratio is proposed by Kageyama and his col-leagues (1981). It is defined as the ratio between the pro-jected area of the opening part, i .e ., the holes, and the full projection area of the reef surface.10/A A γ=, (1)where γ is the open area ratio (or briefly opening ratio); A 1 is the projected area of openings, and A 0 is the total projected area of the reef. As pointed out by Kageyamaet al. (1981), this parameter plays an important role to theflow around the artificial reefs.In order to investigate how the hydrodynamic charac-teristics of artificial reef are affected by its opening area, including the shape of reef holes, their numbers and openarea ratio, a series of model tests are performed in thepresent work. The models are square plates punched withsquare or circular holes. The models are grouped accord-ing to their opening modes. In one group, the reefs havethe same number of holes but with various opening ratios. In the other group, the reefs have various numbers ofholes while with the same opening ratio. These modelsare tested in a water flume at different flow speeds tomeasure the drag force acting on the model. Meanwhile,numerical simulation is made with the same reef modeland at the same flow speed. The results of these two ap-proaches are compared to check the accuracy. Based onboth the experimental and numerical results, the rela-tionship between the hydrodynamic characteristics of artificial reefs and their various opening shapes are de-tected.2 Experiments in the FlumeThe experiment is carried out in the hydrodynamic flume of Tokyo University of Marine Science and Tech-nology. The main scale of water flume is 22.00 m (length) × 8.35 m (width) × 3.05 m (height). The flow speed can be adjusted from 0.10 to 2.0 m s −1 with an accuracy of 2%. The testing model is fixed in the middle part of the flume experimental section, where an observation window is installed with a scale of 9.00 m (length) × 2.20 m (width) × 1.60 m (water depth).To avoid the complexity of reef shapes and focus on the effects of reef openings, the models used in the pre-sent work are square-shaped plates made of acrylic mate-rial. They take the same size, i .e ., with a side length a = 0.2 m and a thickness of t = 0.005 m. The plates are punched with square or circular holes neatly. The dimen-sions of all the models are listed in Table 1. The opening area of a models is given by A 1 = nL 2 for square openings and A 1 = n πR 2 for circular openings, where n is the num-ber of openings, L is the side length of square openings,and R is the radius of circular openings as shown in Table 1. According to the definition made in Eq. (1), the open-ing ratio of the models is calculated as γ = nL 2 /a 2 in the case of square openings or γ = n πR 2/a 2 for those with cir-cular openings.The models are divided into three groups. In the first two groups, the opening ratio varies between 0.1 and 0.6 but the number of openings is kept unchanged, one open-ing for the first group and four for the second one. In the third group, the opening ratio is kept to γ = 0.3 but the number of openings varies.Table 1 The dimensions of all 30 models usedin the experimentOpening shape Circle Square Number of holes n Opening ratio γRadius R (m) Side length L (m)0.1 0.0357 0.0632 0.2 0.0505 0.0894 0.3 0.0618 0.1095 0.4 0.0714 0.12650.5 0.0798 0.141410.6 0.0874 0.15490.1 0.0178 0.0316 0.2 0.0252 0.0447 0.3 0.0309 0.0548 0.4 0.0357 0.0632 0.5 0.0399 0.0707 40.6 0.0437 0.0775 2 0.3 0.0437 0.0775 6 0.3 0.0252 0.0447 8 0.3 0.0219 0.0387Fig.1 The sketch of the circulative hydrodynamic flume and the arrangement of model testing devices.In the experiments, the water depth is set to 1.60m. The tests are conducted in the middle part of the flume experimental section. The model is fixed to a strut which is connected to the rotating table of the flume frame through a load cell (see Fig.1). The center of the model is located at a depth of 1.25 m beneath the water surface. By adjusting the rotating frame of the flume, the model is fixed to a position that its plate face is perpendicular to the incoming flow. The speed of testing flow is set from V = 0.1 m s −1 to 1.0 m s −1 at a step of 0.1 m s −1. The flow speed is very slow so that the effect of free surface is considered to be negligible. The force in the direction of the flow, i .e ., the drag force F x is measured by the load cell during the tests. The drag force acting on the strut is measured at each flow speed in advance of the modelTANG et al . / J . Ocean Univ . China (Oceanic and Coastal Sea Research ) 2019 18: 193-202195installation, which will be subtracted from the former measurement for model tests. The interference of the strut is thus corrected.3 Numerical SimulationThe numerical simulation is performed by means of the software CFX in the present work. The software CFX is developed under the assumptions that the fluid is an in-compressible and Newtonian viscous fluid. The flow has reached at a steady state. Based on these hypotheses, the governing equations, i .e ., the continuity equation and the Reynolds-averaged Navier–Stokes equation in the three- dimensional Cartesian coordinate system, are expressed as follows:()0i iu t x ρρ∂∂+=∂∂, (2) ''()()()()i i i j i j j i j j ju p u u u u u t x x x x x μ∂∂∂∂∂∂+=-++-∂∂∂∂∂∂,(3)where u i and u j represent the average velocity (i = 1, 2, 3 represent components x , y , and z in the Cartesian coordi-nate system), p is the static pressure, ρ is the density of the fluid, μ is the dynamic viscosity of the fluid, u i ' and u j ' represent the fluctuating velocity, and ''i j u u - are the Reynolds stresses.The standard k-ε turbulence model is accepted in the present numerical analysis, which is described by the following equations (Liu et al ., 2013; Li et al ., 2017):()()()i t k i jk j ku k k G t x x x ρμρμρεσ⎡⎤∂∂∂∂+=++-⎢⎥∂∂∂∂⎢⎥⎣⎦, (4)(i t i j j u t x x x ερεμρεεμσ⎡⎤∂()∂()∂∂+=++⎢⎥∂∂∂∂⎢⎥⎣⎦ 21k C G C kkεεεερ2-. (5)Here, G k represents the generation of turbulence ki-netic energy owing to the mean velocity gradients; C μ, C 1ε, and C 2ε are constants; and σk and σε are the turbulent Prandtl numbers for k and ε, respectively. These parame-ters were calculated as follows:()j i ik t j i j u u u G x x x μ∂∂∂=+∂∂∂, 2,0.09t k C C μμμρε= =,121.44, 1.92, 1.0, 1.3.C C εεκεσσ= = = =In the above equations, the summation convention hasbeen adopted, i.e., any term in the equation that containsthe same index twice should be summed over that index. In this simulation, the element-based finite volume method (EbFVM) (Profito et al ., 2015; Kim et al ., 2016) in the CFX was used to discretize the governing equa-tions. High resolution advection scheme, which is robust in the solving advection term, was used in this research. A coupled solver, which solved the hydrodynamic equa-tions as a single system, was adopted in the procedure of obtaining the numerical solutions of discretized govern-ing equations. For steady-state problems, the time-step was to guide the approximate solutions in a physically based manner to a steady-state solution. This reduced the number of iterations required for convergence to a steady state (ANSYS-Inc, 2013). Furthermore, the solution was assumed convergent, whereas all residuals including the continuity, velocities (x , y , z components), pressure, tur-bulent energy and dissipation rate fell below 10−4, and a maximum of 1000 time steps in the steady state simula-tions was used to ensure the final results were stable and converged.The boundary conditions are the same as those used in the verification tests when studying the effect of spacing on the flow field. Fig.2 shows the boundary conditions. It is assumed a boundary condition of trivial pressure gra-dient at the downstream surface. The boundary at both sides and the bottom of the fluid domain are rigid sta-tionary no-slip walls. Since the effect of free surface is neglected in the flume tests, it is assumed a free stream over there in the numerical simulation. The center of the model is set at the same depth as in the flume tests. In the numerical simulation, the upstream is a uniform flow of constant speed.Fig.2 The computational domain and boundary condi-tions used in the numerical simulation (L is reef length, Wis reef width, and H is reef height).The computational domain can be narrowed properly in order to reduce computation, and the dimension of the computational domain is set according to the size of the reef monomer (Cui et al ., 2011; Zheng et al ., 2015). The length of computational domain is 601 times of the thick- ness of the reef (3.005 m). The width is 10 times of the reef width (2 m). The height is 10 times of the reef height (2 m). The reef models are located at the center of the computational domain. The grid system is shown in Fig.3, the total number of nodes and elements were approxi-mately 4.50×105 and 2.49×106 in each case after meshing respectively.TANG et al . / J . Ocean Univ . China (Oceanic and Coastal Sea Research ) 2019 18: 193-202196Fig.3 Grid system in computational domain.In order to verify the accuracy of the numerical simu-lation, the models with different opening numbers (n ) and an open area ratio 0.3 are taken as examples to be evaluated, and the results are compared to the experiment measurements (see Table 2).Table 2 The comparison between experimental results andsimulated values of C d (γ = 0.3)Drag coefficient C d nOpening shape Experimental results Simulated values Relativedifference2 Square 0.982 0.981 0.10% 2 Circular 0.977 1.013 3.68%4 Square 0.989 1.029 4.04% 4 Circular 1.008 1.020 1.19% 8 Square 0.997 0.921 7.62% 8 Circular0.9730.9572.36%Then, a group of twelve models with nine opening holes (see Table 3) are used in the numerical simulation. The open area ratio varies from 0.1 to 0.6 as those used inthe experiments. The calculated results are sump up to the empirical formula to further extend the experimental re-sults.Table 3 The parameters of all twelve models in thenumerical simulationOpening shape Circle Square n γR (m) L (m) 0.1 0.0119 0.02110.2 0.0168 0.0298 0.3 0.0206 0.03659 0.4 0.0238 0.04220.5 0.0266 0.04710.6 0.0291 0.05164 Results and Discussion The drag force measured from model tests are plottedin Fig.4 against the flow speed. In the legend of Fig.4, regardless to the opening shape, it can be observed that the drag force increases with the decrease of opening ratio at the same flow speed when the opening number is kept unchanged (see Figs.4(a)–(d)). However, if the open- ing ratio is fixed, the change of opening number will not make significant change in the drag force (see Figs.4(e, f)). The drag force of panels with no openings in all cases are completely larger than the others. Generally, the drag force is roughly a quadratic function of the flow speed. To express the results in dimensionless expressions, the drag coefficient and the Reynolds number are adopted in the present work. The drag coefficient is defined as:22/(0.5)d x C F V a ρ=, (6)while the Reynolds number is given by/Re V a v =⋅, (7)here, V is flow speed (unit is m s −1); v is the kinematicviscosity of the water (m 2 s −1); a (m) is the characteristic length, namely the side length of the plate models.Expressed as the drag coefficient, the experimental data are presented together with the Reynolds number inFig.5. The conventions used in the legend of Fig.4 are also applied here and the plots in Fig.5 are arranged in a similar way as those in Fig.4.Similar to the results in Fig.4, the drag coefficient de-creases as the opening ratio increases for the same open-ing number (Figs.5(a)–(e)), when the Reynolds number isgreater than 0.8×105. In the same region of Reynolds number, the influence of opening number is not obvious for fixed opening ratio (see Figs.5(e) and (f)). Further-more, when the Reynolds number exceeds 0.8×105, the drag coefficient for a certain model remains basically unchanged even though the Reynolds number increases. It is said that the automatic model region has been reached. An average value of the drag coefficients in the automatic model region are evaluated by the SOLVER function built in the Excel and this value is referred asthe drag coefficient specifying to that model later on.To examine the relative importance of the three factors, i.e ., the opening-area ratio, opening shape and opening numbers, to the drag coefficient C d , the correlation ana- lysis for three-factor variances is made by means of a program written in R language by calculating the F valueTANG et al . / J . Ocean Univ . China (Oceanic and Coastal Sea Research ) 2019 18: 193-202197that can judge the difference. The results are shown in Ta-ble 4. It can be concluded that the influence of the opening- area ratio on the drag coefficient is dominant (P < 0.001) while the opening shape and opening numbers have rela-tively less influence on the drag coefficient (P < 0.05).Table 4 The results of correlation analysis amongthree factorsF valuePr (>F ) Correlation analysisOpening shape 5.429 < 0.05 P < 0.05Open area ratio 115.799 < 0.001 P < 0.001 Opening numbers5.754 < 0.05P < 0.05To examine the effects of opening shapes, the drag co-efficient C d for the models of group 1 (or group 2), i.e .,with one (or four) opening(s), is plotted in Fig.6(a) (or Fig.6(b)) verse the opening ratio. Meanwhile, results in Fig.6(c) is the drag coefficients for a group of models with nine openings, as a result of numerical simulation. It can be seen that the influence of opening shape is not so significant especially when the opening number is in-creased. Generally, the drag coefficient C d decreases as the opening ratio increases for fixed opening number. A regression analysis is made to the above data to obtainempirical formulae for models with the same opening number and opening shape. The results are presented in Table 5 together with the coefficient of determination R 2, which is an indicator to show the fitness of the regression equation to the used data. It can be observed that the drag coefficient C d is basically a linear function of the opening ratio γ.To compare the drag coefficient C d for models with different opening numbers, the results are reorganized so that they are presented in the same illustration for the models with the same opening shape in Fig.7(a) for square opening and (b) for circular opening. It can be observed from the diagram in Fig.7 that the drag coefficient C d for models with nine openings is obviously greater than the other ones. In addition, the opening number has more significant influence on the drag coefficient than the opening shape.To obtain a more general empirical formula for the drag coefficient C d as a function of both the parameters, i.e ., the opening-area ratio γ and the number of openings n , a multiple regression analysis is made based on the experiment and numerical data. The results are given by the following two equations.Fig.4 The drag force measured from flume tests as a function of flow velocity. (a) one square opening; (b) one circular opening; (c) four square openings; (d) four circular openings. The opening ratio is fixed at γ = 0.3 with varying opening number in (e) for square openings and (f) for circular openings. S means square and C means circle, which both indi-cate the shape of openings. Panel represents the model with no openings.TANG et al. / J. Ocean Univ. China (Oceanic and Coastal Sea Research) 2019 18: 193-202198Fig.5 The drag coefficient vs. Reynolds number of experimental data: (a) one square opening; (b) one circular opening;(c) four square openings; (d) four circular openings. The opening ratio is fixed at γ=0.3 with varying opening numbers in (e) for square openings and (f) for circular openings. S means square and C means circle, which both indicate theshape of openings. Panel represents the model with no openings.Fig.6 The relationship between the opening shape and drag coefficient C d for models with (a) one opening; (b) four openings; (c) nine openings (results of numerical calculation).TANG et al . / J . Ocean Univ . China (Oceanic and Coastal Sea Research ) 2019 18: 193-202199Table 5 Regression equations of the drag coefficient Cd as a function of the opening ratio γ formodels with the same opening shape and numberSquare openingsCircle openingsOpening numberRegression equationR 2Regression equationR 21 C d = −1.0062γ + 1.2467 0.99669 C d = −1.2416γ + 1.3136 0.99832 4 C d = −1.0725γ + 1.2889 0.98579 C d = −1.0267γ + 1.2666 0.95379 9 C d = −0.9007γ + 1.2759 0.95098 C d = −0.9350γ + 1.2875 0.88409Note: R denotes the coefficient of determination.Fig.7 The relationship between opening numbers and drag coefficient C d for models having (a) square openings (b) circular openings.For square openings (with R 2 = 0.975):1.260.0070 1.05d C n γ=+-. (8)For circular openings (with R 2 = 0.932):1.280.0068 1.14d C n γ=+-. (9)It can be observed from the regression equations that the coefficient of the opening ratio is much greater than the coefficient of the opening number. Comparing Eqs.(8) and (9), the difference between the corresponding coefficients is not so significant. Therefore, the opening- area ratio plays an important role to influence the drag coefficient C d among these three factors. The drag coef- ficient is generally linearly decreases as the opening ratio increases. The confidence interval of the regression equa-tion is 95%, it can be observed that the regression equa-tions have a significant regression effect at the sig- nifi-cance level of α =0.05.Fig.8 The vorticity contours along the center cross-section of the fluid domain for 4 models with opening ratio γ = 0.3. (a) S1-0.3, one square opening; (b) C1-0.3, one circular opening; (c) S4-0.3, 4 square openings; (d) C4-0.3, four circu-lar openings.TANG et al . / J . Ocean Univ . China (Oceanic and Coastal Sea Research ) 2019 18: 193-202200 The numerical simulation is also performed in the pre-sent work. As a validation of the numerical results, the models with four openings, square or circle, and the opening ratio 0.3 are taken as examples to be calculated by the software CFX. The results of numerical calcula-tion are compared with the data measured in the flume tests and the comparison is shown in Table 2. The rela-tive error is less than 8%.Then, a group of twelve models with nine openings and various opening ratios (Table 3) is used in the nu-merical simulation to further extend the experimental results. The calculated drag coefficient for these models are demonstrated in Fig.6(c) as a supplement of meas-ured data.For a better understand of the mechanism how the opening mode affects the hydrodynamic characteristics of artificial reefs, the fluid field around the plate models is numerically simulated by means of ANSYS CFX. The models used in the simulation have one or four square (or circular) opening(s) with opening ratio γ = 0.3. The in-coming flow speed is set to V = 1.0 m s −1 in the numerical simulations.The simulated flow field is illustrated in the diagrams of velocity vectors (Fig.8). It can be observed that there exists an eddy wake behind the model. Compared to the flow behind one-opening model, the vortexes in the wake of four-opening model are greater and the flow becomes more unstable. It might cause a bigger pressure differ-ence between the front and back surfaces of the modeland lead to a larger value in drag coefficient. On the other hand, disturbed flow field around the artificial reefs is just the purpose of their construction to improve the surrounding environment and attract more fishes. So it would be a trade-off between their functions and stability in the design stage of the artificial reefs. The wake vol-ume size of different simulated models was compared (Fig.9). The wake volume has a negative correlation with the open area ratio, and the volume reaches the maximum when the open area ratio is 0.1. In the actual production, we need to increase the wake volume and reduce the drag coefficient at the same time. The panel with 4 openings (γ = 0.3) is the ideal design on account of its stable hydro-dynamic performance and larger wake volume.Fig.9 The relationship between wake volume and open area ratio.Fig.10 The diagrams of pressure distribution on the front surface of 4 models with opening ratio γ = 0.3. (a) S1-0.3, one square opening; (b) C1-0.3, one circular opening; (c) S4-0.3, 4 square openings; (d) C4-0.3, four circular openings.The pressure distribution is evaluated in the simulation as well. As an example, the pressure distribution on thefront surface of four models is demonstrated in Fig.10. It has a tendency that the pressure is more likely to concen-TANG et al . / J . Ocean Univ . China (Oceanic and Coastal Sea Research ) 2019 18: 193-202201trate to the area near the openings of the model especially at the sharp corners of openings. The model with less opening number has a smaller drag coefficient under the same opening ratio due to fewer sharp corners. Taking the models with square openings as an example, the length of the boundary line for 4 openings is two times of that for a single opening. We can find the drag force of plate with 4 openings is bigger than that with 1 single opening when the flow velocity is 1 m s −1 (Fig.4). The reason might be the length of the boundary is in propor- tion to the frictional force, and the drag force increases with longer boundary line. It can be concluded that the drag coefficient may be determined by both the number of sharp corners and the length of the boundary line.5 ConclusionsIn the present work, a series of models are designed to investigate the effects of openings to the hydrodynamic characteristics of the artificial reefs. To simplify the problem, the models are basically two-dimensional and square-shaped plates punched with various numbers of square or circular openings. Various opening ratios are obtained by adjusting the size of openings. Both flume experiments and numerical simulations are carried out with these models in a uniform flow. The drag forces acting on the models are measured in the tests or evalu-ated in the simulation.It is observed that the drag force is generally a quad-ratic function of the flow speed. Expressed in dimen-sionless terms, it is found that the automatic model re-gion has been reached as the Reynolds number exceeds 0.8×105. The drag coefficient is approximately a constant regardless of the change of Reynolds number in that re-gion. Then the average value is obtained by the regres-sion analysis, which is referred as the drag coefficient C d specifying to that model.The dependence of this drag coefficient C d on the opening modes, i.e ., the opening shape, opening number and opening ratio, is investigated. It can be observed that the drag coefficient C d is mostly affected by the opening ratio especially in the case of circular openings. It de-creases linearly as the opening ratio increases. Increasing opening number may increase the value of drag coeffi-cient C d , but the contribution is much less than the open-ing ratio. Comparing the coefficients in these two equa-tions, it can be observed that the opening shape will not give much difference to the drag coefficient C d , particu-larly as the opening number increases. The empirical formulae offer a reference for the stability evaluation in the design stage. For the practical application in the fish-ing engineering, more complicated models including the three dimensional effects should be investigated in the future work. At the same time, the problems emerged in the actual production should be noticed. The effects of sessile organisms attached on the artificial reefs should be considered, considering the sessile organisms can in-crease the surface friction to influence the drag force and the fluid field around the reefs.The numerical simulation is made in the present work. The numerical results are in good agreement with the measured data, and the accuracy of numerical calculation is acceptable. In addition, the numerical simulation pro-vides pictures of the fluid field and the pressure distribu-tion to make a better understand of the hydrodynamic characteristics of artificial reefs. It will be a useful and powerful method in the development of new type of arti-ficial reefs.AcknowledgementsThe study is supported by Shandong Provincial Oceanic and Fishery Department (Ecological Simulation Test of the Offshore Area in Shandong Peninsula) and the Pri-mary Research and Development Program of Shandong Province (Nos. 2016CYJS04A01 and 2017CXGC0107).ReferencesANSYS-Inc, 2013. ANSYS Fluent Theory Guide, Release 15.0. Antsulevich, A. E., 1994. Artificial reefs project for improve- ment of water quality and environmental enhancement of Neva Bay (St. Petersburg County region). Bulletin of Marine Science , 55 (2-3): 1189-1192.Cui, Y ., Guan, C. T., Wan, R., Li, J., and Huang, B., 2009. Re- search and numerical simulation on features of flow field around artificial reefs. Journal of System Simulation , 21 (23): 7393-7396, DOI: 10.16182/ ki.joss.2009.23.007 (in Chinese with English abstract)Cui, Y ., Guan, C. T., Wan, R., Li, J., and Huang, B., 2011. Nu- merical simulation on influence of disposal space on effects of flow field around artificial reefs. Transactions of Oceanology and Limnology , 22 (2): 59-65 (in Chinese with English ab- stract).Jiang, Z. Y ., Liang, Z. L., Zhu, L. X., and Liu, Y ., 2016. Nu- merical simulation of effect of guide plate on flow field of artificial reef. Ocean Engineering , 116: 236-241, DOI: 10. 1016/ j.oceaneng. 2016.03.005.Kageyama, Y ., Osaka, H., Yamada, H., Hasegawa, H., and Naka- kura, Y ., 1981. Water tunnel visualization around the per- forated cube: 1st report, flow visualization in a center plane. Memoirs of the Faculty of Engineering Yamaguchi University , 31: 351-359 (in Japanese).Kim, D., Woo, J., Yoon, H. S., and Na, W. B., 2014. Wake lengths and structural responses of Korean general artificial reefs. Ocean Engineering , 92: 83-91, DOI: 10.1016/j.oceaneng. 2014.09.040.Kim, D., Woo, J., Yoon, H. S., and Na, W. B., 2016. Efficiency, tranquillity and stability indices to evaluate performance in the artificial reef wake region. Ocean Engineering , 122: 253-261, DOI: 10.1016/j.oceaneng.2016.06.030.Li, J., Zheng, Y . X., Gong, P. H., and Guan, C. T., 2017. Nu- merical simulation and PIV experimental study of the effect of fl ow fields around tube artificial reefs. Ocean Engineering , 134: 96-104, DOI: 10.1016/j.oceaneng.2017.02.016.Liu, J., Huang, H. L., Chen, S., Wu, Y ., Li, L. Z., and Rao, X., 2014. Model test of the hydrodynamic characteristics of two vertical cambered V type otter boards. Chinese Journal of Hydrodynamics , 29 (2): 183-188, DOI: 10.3969/j.issn1000- 4874.2014.02.007 (in Chinese with English abstract).Liu, J., Xu, L. X., Zhang, S., and Huang, H. L., 2011. Research。