加工余量和切削参数表
数控切削参数表

碳素结构钢的力学性能(GB700-88)注:A、B、C为质量等级,D级为优质级。
铣削加工常用切削速度经验值(m/min)铣削时的切削速度铣削加工每齿进给量推荐值 (mm/z)数控铣削每齿进给量经验值H13~H7孔加工方式余量(孔长度小于5倍直径)注:当孔径≤30mm、直径余量≤4mm和孔径>30~80mm、直径余量≤6mm时,采用一次扩孔或一次镗孔。
H7与H8级精度孔加工方式及余量(在实体材料上加工) (mm)注:在铸铁上加工直径为30mm与32mm的孔可用Ф28与Ф30钻头钻一次。
按H7与H8级精度加工已预先铸出或热冲出的孔 (mm)注:1.如果铸出的孔有很大的加工余量时,则第一次粗镗可分为两次或多次; 2.如果只进行一次半精镗,由其加工余量为表中“半精镗”和“粗铰或二次半精镗”加工余量之和。
平面精铣、磨削加工方式余量(mm)注:1. 精铣时,最后一次行程前留的雨量应该≥0.5mm。
2. 热处理零件磨削的加工余量系将表中值乘以1.2。
高速钢钻头加工钢件的切削用量高速钢钻头加工铝件的切削用量高速钢钻头扩孔、钻孔的切削用量 (mm/r)高速钢铰刀铰孔的切削用量攻螺纹切削速度 (m/min)钻孔的进给量镗孔切削用量硬质合金端面铣刀的铣削用量不锈钢的铣削用量不锈钢的铣削用量硬质合金车刀粗车外圆及端面的进给量注:1、加工断续表面及有冲击的工件时,表内进给量应乘系数K=0.75~0.85;2、在无外皮加工时,表内进给量应乘第数K=1.1;3、加工耐热钢及其合金时,进给量不大于1mm/r;4、加工淬硬钢时,进给量应减小。
当钢的硬度为44~56HRC时,乘系数K=0.8;当钢的硬度为57~62HRC时,乘系数K=0.5。
5、可转位刀片的允许最大进给量不应超过其刀尖圆弧半径数值的80%。
硬质合金外圆车刀半精车的进给量(参考值) mm/r注:rε=0.5mm,用于12×12以下刀杆,rε=1mm,用于30×30以下刀杆,rε=2mm,用于30×45及以上刀杆。
加工余量参数表

附录三加工余量参数表表 1 粗车、半精车外圆的加工余量(单位:mm)注:加工带凸台的零件时,其加工余量要根据零件的全长和最大直径来确定。
表 2 精车外圆的加工余量(单位:mm)1.舍五入)。
这时的粗车外圆的公差等级为14 级。
2. 决定加工余量用轴的长度计算与装夹方式有关。
3. 粗车外圆的公差带相当于h12~h13。
注:1. 在单件或小批生产时,本表的余量值应乘上系数,并化成一位小数,如×=,采用(四舍五入)。
2. 决定加工余量用轴的长度计算与装夹方式有关。
3. 磨前加工公差相当于h11。
表 4 精车端面的加工余量(单位:mm)1. d2. 表中的公差系指尺寸L 的公差。
表 5 磨端面的加工余量(单位:mm)注: 1. 加工有台阶的轴时,每台阶的加工余量应根据该台阶的d 及零件的全长分别选用。
2. 表中的公差系指尺寸L 的公差。
加工孔直径钻用车刀 扩孔钻粗铰精铰的直径第一次第二次镗以后3- - - - 3H7 4- - - - 4H7 5-- - - 5H7 6- - --6H7 8-- -8H7 10- --10H712--12H7 13- -13H7 14--14H715- -15H7 16--16H718- -18H7 20-20H7 22-22H724-24H7 25-25H726-26H7 28-28H7302830H7 3232H7 3535H73838H7 4040H74242H7 4545H74848H7 5050H760 3060H7 70 3070H780 3080H790 30-90H7 100 30-100H7120 30-120H7 140 30-140H716030-160H7 180 30-180H7注: 1. 在铸铁上加工直径到 15mm 的孔时,不用扩孔钻扩孔。
2. 在铸铁上加工直径为 30 到 32mm 的孔时,仅用直径为 28 与 30mm 的钻头钻一次。
孔加工的切削参数表格(精)
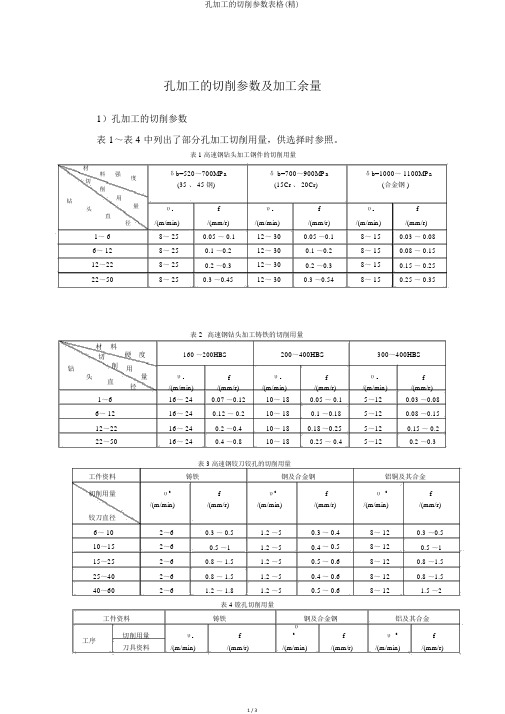
孔加工的切削参数及加工余量1)孔加工的切削参数表 1~表 4 中列出了部分孔加工切削用量,供选择时参照。
表 1 高速钢钻头加工钢件的切削用量材料强δb=520~700MPa δ b=700~900MPa δb=1000~ 1100MPa 切度(35 、 45 钢) (15Cr 、 20Cr) (合金钢 )削钻用量 f f f头υc υ c υc 直径/(m/min) /(mm/r) /(m/min) /(mm/r) /(m/min) /(mm/r) 1~ 6 8~ 25 0.05 ~ 0.1 12~ 30 0.05 ~0.1 8~ 15 0.03 ~ 0.08 6~ 12 8~ 25 0.1 ~0.2 12~ 30 0.1 ~0.2 8~ 15 0.08 ~ 0.15 12~22 8~ 25 0.2 ~0.3 12~ 30 0.2 ~0.3 8~ 15 0.15 ~ 0.25 22~50 8~ 25 0.3 ~0.45 12~ 30 0.3 ~0.54 8~ 15 0.25 ~ 0.35表 2 高速钢钻头加工铸铁的切削用量材料硬度160 ~200HBS 200~400HBS 300~400HBS 切钻削用量υ c f υ c f υ c f 头直径/(m/min) /(mm/r) /(m/min) /(mm/r) /(m/min) /(mm/r) 1~6 16~ 24 0.07 ~0.12 10~ 18 0.05 ~ 0.1 5~12 0.03 ~0.08 6~ 12 16~ 24 0.12 ~ 0.2 10~ 18 0.1 ~0.18 5~12 0.08 ~0.15 12~22 16~ 24 0.2 ~0.4 10~ 18 0.18 ~0.25 5~12 0.15 ~ 0.2 22~50 16~ 24 0.4 ~0.8 10~ 18 0.25 ~ 0.4 5~12 0.2 ~0.3表 3 高速钢铰刀铰孔的切削用量工件资料铸铁钢及合金钢铝铜及其合金切削用量υc f υc f υ c f /(m/min) /(mm/r) /(m/min) /(mm/r) /(m/min) /(mm/r) 铰刀直径6~ 10 2~6 0.3 ~ 0.5 1.2 ~5 0.3 ~ 0.4 8~ 12 0.3 ~0.5 10~15 2~6 0.5 ~1 1.2 ~5 0.4 ~ 0.5 8~ 12 0.5 ~1 15~25 2~6 0.8 ~ 1.5 1.2 ~5 0.5 ~ 0.6 8~ 12 0.8 ~1.5 25~40 2~6 0.8 ~ 1.5 1.2 ~5 0.4 ~ 0.6 8~ 12 0.8 ~1.5 40~60 2~6 1.2 ~ 1.8 1.2 ~5 0.5 ~ 0.6 8~ 12 1.5 ~2表 4 镗孔切削用量工件资料铸铁钢及合金钢铝及其合金工序切削用量υc fυc f υ c f刀具资料/(m/min) /(mm/r) /(m/min) /(mm/r) /(m/min) /(mm/r)高速钢20~2515~300.35 ~0.7100~ 150 0.5 ~ 1.5粗加工35~50 0.4 ~0.45100~ 250 合金 50~70高速钢20~35 15~50 0.15 ~0.45100~ 2000.2 ~ 0.5半精加工50~70 0.15 ~ 0.45 合金 95~135高速钢70~90D1 级<0.08 0.02 ~0.15150~ 4000.06 ~ 0.1精加工100~135合金D 级 0.12 ~0.152)孔加工的加工余量表 5 中列出在实体资料上的孔加工方式及加工余量,供选择时参照。
刀具切削用量表

S(转速)=线速度×1000/(直径×3.14) F(进给量)=刃数×每刃切削量×转速 每刃切削量 粗加工 精加工
0.05 ~ 0.10 0.04 ~ 0.05
ቤተ መጻሕፍቲ ባይዱ
例:20MM硬质合金4刃铣刀精铣45#钢,线速度取60。每刃切0.05。则转速=60×1000/( 给量=4×0.05×955=191。
以上是比较笼统的概括,适用于大多数铣刀、钻头、镗刀(不包括绞刀)加工工艺的计算 还要针对不同实际情况做出调整。如:工件形状、余量大小、冷却条件、刀具磨损等。 每刃切削量参数的选择:如果太小小于0.02,那不是在切削,是在磨刀,如果太大大于 削,是在撞击。所以并非转速越高,进给量越小越好切削,刀具必须处在一个合理的运动状态下 质、稳定的切削。
应该会提供一份刀具针对各种材 7~8折的。
刀具加工中,对刀具寿命影响最大的是线速度,刀具商提供刀具的同时,应该会提供一份刀具针对各种 料的线速度表,但刀具供应商的参数是在理想状态下得到的,在实际加工中,得打个7~8
铸铁 15~20 60 30
(20×3.14)=955,进
加工工艺的计算。在实际加工中 。
如果太大大于0.2,那也不是切 一个合理的运动状态下,才是均
加工余量和切削参数表
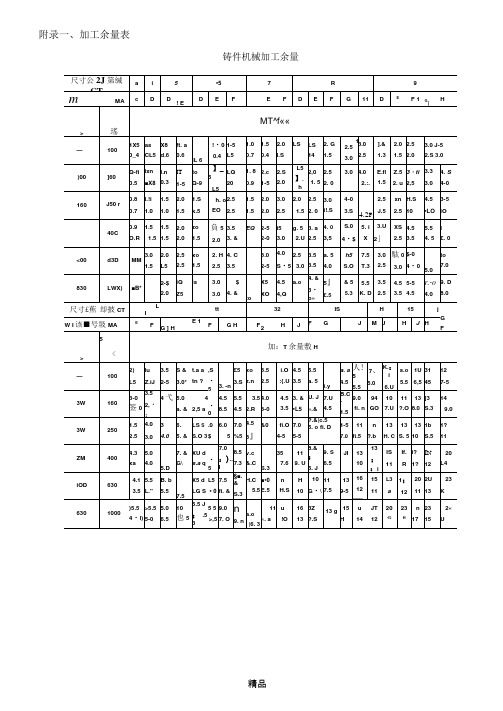
附录一、加工余量表铸件机械加工余量表磨孔余量ft 4-29平面租刨后精诜的加工余■/mm/mm表脣30铳平面的加工余・寬度冬200 寬度>200〜400 宽直M200 «« >200-400加工表面不同长度下的加工余・*8-31 ■平面的加工余・/mm魚处理后«8-33绩面的加工余■/mm« 879各种加工方法所能达到的表面粗糙度/pm 加工方法&值1 加工方法R•值车削外圆10 〜80 圜柱优刀半精车 2. 5 〜10 2. 5 〜20 精车1・25〜10 精饶0. 63〜5.细车0・16〜1・25 细饶0. 32〜1. 25 车削端面-一 - .................粗丰5〜20 aft 2. 5—20 半精车 2. 5〜10 0. 32 〜5 精车】・25〜10 细饶0.167 25 细车“0. 327 25 髙速饶IW车削割槽和切斷粗铳手炉“・・0. 63〜2・5 一次行程10〜20 0. 16~0・ 63 二次行程 2.5-10 刨削僮孔5〜20 粗僅5〜20 精刨1・25〜10 半箱桃2・5〜10 细刨(光»mi)0・16〜1・25 梢铿0・63〜5 槽的表面 2. 5 〜10 细蚀(金刚键床贰孔〉0・16〜1・25 插削 2. 5〜20钻孔 1.25 〜20 拉削扩孔精拉0. 32-2. 5 粗扩(有毛面)5〜20 细拉0. 08〜0・ 32 梢扩 1.25-10 推削储孔•倒角1・25〜5 精推0.16〜1・ 25 较孔细推0. 02〜0・ 63 • 一次较孔嫖纹加工钢2・5〜10 |用板牙、丝傩•自动张开式板牙头0. 63~5附录二、切削***、/ » 8-50碘质合蚩及髙連解车刀粗车外■和■面时的进给■注,1. 1JUT斷续表面及肓冲击时.表内的进给■应象票数K・0・75〜0.85.2. 加工酚热制及其合金不采用大于1.0mm/r的进给*.3. 加工淬缺钢时.我内进给it应桑系数K・0・8 (当材料硬度为44〜56HHC)或K-0. 5《当竇度为57〜62HRC时).表8・52切断及切槽的进给■注,1 •在直径大于60mm 的实心村料上切断时•当切刀接近峯件轴线0・5倍半径时・表中进给量应减小40% 〜50%.2.加工淬理钢时.表内进给量应橄小30% (当现度小于50HRC 时)或50% (当硬度大于50HRC 时).» 8-55切断和切槽时的切削用■/ft 8-57外圓切削速度參考袁,1・6090min.2.车孔切削速度要比车外圆时低10%〜20%.衰8・69高連•祸钻头钻孔时的进给■估头直径几/mm钢 %/MPa铸铁、铜、铝合金硬度<800800〜1000>1000<200HBS>200HBS进给 就//mm •◎0. 05 〜0・ 0§ . 0. 04 〜0・ 05 - 0. 03〜0・04・ 0. 09 〜0・ 11 0. 05—0. 07 >2〜4 0. 08-0.10 0. 06—0. 08 0. 04 〜0・ 06 0. 18 〜0・ 22 •0.11-0.13 >4〜6 0・14〜0・10 0・10〜0・12 0. 08 〜0・ 10 0. 27 〜0・ 33 0. 18-0. 22 >6〜8 0. 18 〜0・ 22 0・13〜0・15 0. 11-0. 13 0. 36〜0・ 44 0. 22 〜0・ 26 >8 〜10 0. 22 〜0・ 28 0.17-0.21 0. 13 〜0・ 17 0. 47〜0・ 57 0. 28 〜0・ 34 >10 〜13 0. 25 〜0・ 31 0.19-0. 23 0. 15 〜0. 19 0. 52〜0・ 64 0・3】〜0・39 >13~160・31〜0・37 0. 22 〜0・ 28 0・】8〜0・22 0.61-0. 75 0. 37 〜0・ 45 >】6〜200. 35〜0・ 43 0. 26 〜0・ 32 0.21-0. 25 0. 70〜0・ 86 0. 43〜0・ 53 >20 〜250. 39〜0.47 0. 29〜0・ 35 0. 23 〜0・ 29 0. 78-0. 96 0. 47〜0・ 57 >25 〜30 0・45〜0・55 0. 32〜0・ 40 0. 27 〜0・ 33 0. 9〜1・1 0. 54〜0・ 66 >30 〜600. 60〜0・ 700. 40〜0・ 500. 30〜0・ 401・0〜1・20. 70 〜0・ 80tt钻头直径必/mm工艺婴 求分类InIn进给 最 //mm •严0. 22*0. 280.8r 0・ 22 0.】8〜0. 22 Q. 13-0.17 >8~12 0. 20〜0・ 36 0. 22 〜0・ 28 0. 25 〜30 0.18〜0・ 22 >12 〜160. 25〜0・ 40 0. 25 〜0・ 30 0・ 28 〜0. 24 0. 20〜0・ 25 1>16 〜20 0. 40〜0・ 48 0. 27〜0・ 33 0. 32〜0・ 28 0・23〜0・28、 >20 〜24 0. 45~0・ 55 0. 33〜0・ 38 0. 38〜0. 43 0. 27〜0・ 32 >24 〜26 0. 50〜0・ 60 0. 37〜0・ 41 0・ 40〜0. 46 0. 32~0・ 28 >20 〜300. 55 〜0・ 650. 40〜0・ 500. 45 〜0. 500. 36〜0・ 44>200HBS復质合金YG8钻头鮎灰铸铁时的进给■/m-1丧8・99各种常用工件材料的饶剤琼度推荐范BI如有侵权请联系告知删除,感谢你们的配合!。
刀具切削参数表7
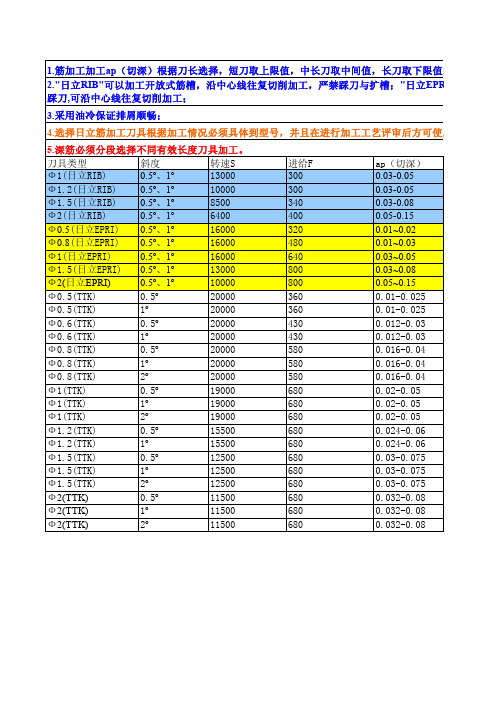
流道加工参数
序号 1 2 3 4 5 6 工艺 普通机床加工参数 刀具规格 加工方式 转速(S)进给率(F)Aa 粗加工 3200 600 0.08 Ф3R1.5 精加工 3200 200 0.08 粗加工 3200 800 0.08 Ф4R2 精加工 3200 300 0.08 粗加工 2600 1000 0.1 Ф6R3 精加工 2600 400 0.1 粗加工 2200 1000 0.1 Ф8R4 精加工 2200 500 0.1 粗加工 1800 1000 0.15 Ф10R5 精加工 1800 600 0.1 粗加工 1800 1000 0.15 1800 600 0.1 Ф12R6 精加工 备注 合金刀具 合金刀具 合金刀具 合金刀具 合金刀具 合金刀具 刀具规格 加工方式 粗加工 Ф3R1.5 精加工 粗加工 Ф4R2 精加工 粗加工 Ф6R3 精加工 粗加工 Ф8R4 精加工 粗加工 Ф10R5 精加工 粗加工 Ф12R6 精加工
1、粗加工 底部留0.1余量 2、精加工 光刀,光两遍 3、全部单向加工 4、加工时选用新刀具,刀具悬伸长度尽量缩短,冷却时选用切削液冷却。
高速机床加工参数 转速(S)进给率(F)Aa 备注 12000 800 0.08 12000 200 0.08 合金刀具 10000 1000 0.08 10000 300 0.08 合金刀具 13000 3000 0.1 10000 400 0.1 10000 2000 0.1 8000 500 0.1 9500 2000 0.15 5000 600 0.1 6850 2200 0.15 5000 600 0.1
采用插铣加工效率优于等高铣,(一般深度大于60以上采用插铣方式)加工时全部采用单向走刀方式 高于最高面5mm(见下表) 横向间距 (锁紧面) 精加工 1.2 1.2 0.8 0.8 0.6 横向间距 (型腔) 精加工 0.8 0.8 0.5 0.5 0.4
孔加工的切削参数表格(精)

孔加工的切削参数及加工余量
1)孔加工的切削参数
表1~表4中列出了部分孔加工切削用量,供选择时参考。
表1 高速钢钻头加工钢件的切削用量
表2 高速钢钻头加工铸铁的切削用量
表3 高速钢铰刀铰孔的切削用量
表4 镗孔切削用量
2)孔加工的加工余量
表5中列出在实体材料上的孔加工方式及加工余量,供选择时参考。
表5 在实体材料上的孔加工方式及加工余量
4.攻螺纹的加工工艺
1)底孔直径的确定
攻螺纹之前要先打底孔,底孔直径的确定方法如下:对钢和塑性大的材料
D孔=D-P
对铸铁和塑性小的材料
D孔=D-(1.05~1.1)P
式中:D孔—螺纹底孔直径,mm;
D─螺纹大径,mm;
P─螺距,mm。
2)盲孔螺纹底孔深度
盲孔螺纹底孔深度的计算方法如下:
盲孔螺纹底孔深度=螺纹孔深度+0.7d
式中:d─钻头的直径,mm。
刀具切削参数表

对长度与直径比(l/d)超过5倍的刀具在加工中应降低转速与进给率,并减少吃
倍数(l/d) 参数比例 转数S 进给率F Ar(切深)
1-5倍 100% 100% 100%
6倍 70% 70% 70%
7倍 60% 60% 60%
8-10倍 50%↓ 50%↓ 50%↓
6.球刀加工时应根据工件不同要求进行参数选择,参阅《模具加工工艺规范》
0.1
外观型腔面平坦部位尽可能避免采用球刀光刀,避开零切削区。方法:采用圆鼻刀或球 加工方式优选 机床选用最底限 电蚀及数控工艺选用 筋加工方式 等高铣 II级精度 优先电蚀 优先数控 II级精度 优先电蚀 优先数控
7.刀具夹持部分最小长度与刀具直径比例原则:
序号 1 2 3 4 刀具直径 Φ 20-Φ 32 Φ 10-Φ 20 Φ 5-Φ 10 Φ 3-Φ 5
切削线速度 主轴转速 进给速度 金属去除率 端铣飞刀计算 N=Vc*1000/(p*Dc) rpm Vf=fz*N*Zn mm/min Q=ap*ae*Vf/1000 CM3
Vc=p*Dc*N/1000 m/min(切削线速度可参考刀具商
端铣飞刀计算
Dc刀具切削位置直径 ap轴向切削深度(可参考刀具商推荐值) ae 径向切削深度(可参考刀具商推荐值) Fz每齿进给量(可参考刀具商推荐值) Zn刀具齿数 以32日立飞刀为例计算
*895*.4=716
*1342* .2=536.8 *N *Zn mm/min
De*N/1000 m/min
*1000/(p*De) rpm
√ap(Dc2-ap) N*Zn mm/min
Dc*N/1000 m/min (可参考刀具商推荐值)
1000/(p*Dc) rpm
常用机械加工工艺参数表

第 1 页,共 4 页
2946821407.xlsx
用硬质合金精镗孔(铸铁)的切削用量
加工直径
切削用量
(毫米)
V(米/分)
So(毫米/转)
0~999
70~90
0.12~0.15
主偏角 30 45 60 75 90
PxPy 修正系数
KPx2
KPz2 r
0.63 1 1.14 1.2 1.28 1.05 1 0.96 0.94 1.12
KPz3 0.95 0.98 1 1
用硬质合金半精镗孔(钢)的切削用量
加工直径
切削用量
(毫米)
V(米/分)
So(毫米/转)
0~999
90~135
0.15~0.45
主偏角 30 45 60 75 90
PxPy 修正系数
KPx2
KPz2 r
0.63 1 1.14 1.2 1.28 1.05 1 0.96 0.94 1.12
<30 30~130
>130
精镗孔常用工序间余量 在直径上的工序间余量 (毫米) 0.2~0.25 0.25~0.40
0.35~0.5
攻螺纹(钢件)切削速度V(米/分)
加工螺纹直
螺距 t (毫米)
径(毫米) 0.5 0.75 1 1.25 1.5 2 3
3~6
67 8
8~10
7 8 9 9 10
12~16 8 9 10 10 11 11
用硬质合金铰刀铰孔(铸铁)的切削用量
加工直径
切削用量
(毫米) V(米/分)
So(毫米/转)
6~10
8~10
0.30~0.50
10~15
刀具切削参数表

B12R6 B12R6 B12R6 B12R6
高速涂层 高速涂层 高速涂层 高速涂层 高速涂层 高速涂层 高速涂层 高速涂层 高速涂层 高速涂层 高速涂层 高速涂层 高速涂层 高速涂层 高速涂层 高速涂层 高速涂层 高速涂层 高速涂层 高速涂层 高速涂层 高速涂层 高速涂层 高速涂层 高速涂层 高速涂层 高速涂层 高速涂层 高速涂层 高速涂层
3000 6850
0.28 0.28
B10R5 B10R5 B10R5 B10R5 B8R4 B8R4 B8R4 B8R4 B6R3 B6R3 B6R3 B6R3 B4R2 B4R2 B4R2 B4R2 B3R1.5 B3R1.5 B3R1.5 B3R1.5 B2R1 B2R1 B2R1 B2R1 B1R0.5 B1R0.5
aa(mm) ar(mm)
F(mm/min) S(转/min)
0.3 1 2200 6850 0.5 2 3000 9500 0.5 1.6 3000 10000 0.3 1.2 3000 13000 0.2 0.8 2000 15000 0.2 0.5 2000 16500 0.15 0.42 2000 13000 \ \
\ \ \ \
\ \ \ \
\ \ \ \
\ \ \ \ \ \
加工工艺要求 外观型腔面 非外观型腔面 分型面 锁紧面 半精加工 半精加工余量 避空面
A级 0.002 (I) 0.002 0.003 0.003 0.01
B级
C级
D级
E级 0.005 0.008 (III) 0.008 (III) 0.008 0.02
F级
0.005(镜面 0.002 (I)) 0.005 0.005 0.005 0.015 0.015
加工余量参数表
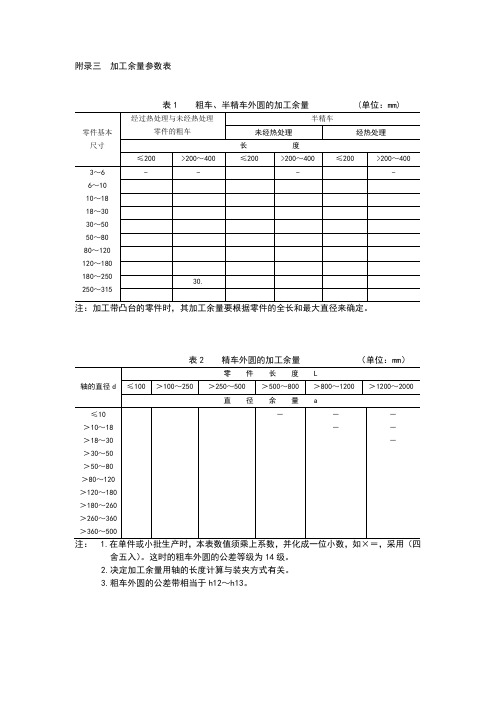
附录三加工余量参数表表1 粗车、半精车外圆的加工余量 (单位:mm)注: 1.在单件或小批生产时,本表数值须乘上系数,并化成一位小数,如×=,采用(四舍五入)。
这时的粗车外圆的公差等级为14级。
2.决定加工余量用轴的长度计算与装夹方式有关。
3.粗车外圆的公差带相当于h12~h13。
表3 磨削外圆的加工余量 (单位:mm)舍五入)。
2.决定加工余量用轴的长度计算与装夹方式有关。
3.磨前加工公差相当于h11。
注:1.加工有台阶的轴时,每台阶的加工余量应根据该台阶的d及零件的全长分别选用。
2.表中的公差系指尺寸L的公差。
表5 磨端面的加工余量 (单位:mm)注:1.加工有台阶的轴时,每台阶的加工余量应根据该台阶的d及零件的全长分别选用。
2.表中的公差系指尺寸L的公差。
2.在铸铁上加工直径为30到32mm的孔时,仅用直径为28与30mm的钻头钻一次。
3.用磨削作为孔的最后加工方法时,精镗以后的直径根据表1-23查得。
4.用金刚石细镗作为孔的最后加工方法时,精镗以后的直径根据表1-24查得。
5.如仅用一次铰孔,则铰孔的加工余量为本表中粗铰与精铰的加工余量总和。
2.在铸铁上加工直径为30、32mm的孔时,仅用直径为28、30mm的钻头钻一次。
3.用磨削作为孔的最后加工方法时,精镗以后的直径根据表1-23查得。
4.用金刚石细镗作为孔的最后加工方法时,精镗以后的直径根据表1-24查得。
5.如仅用一次铰孔,则铰孔的加工余量为本表中粗铰与精铰的加工余量总和。
注:1.当加工在热处理极易变形的、薄的轴套及其他零件时,应将表中的加工余量数值乘以。
2.如被加工孔在以后必须作为基准孔时,其公差应按7级公差来制定。
3.在单件、小批生产时,本表的数值应乘以,并化成一位小数。
例如×=,采用(四舍五入)。
表9 平面加工余量 (单位:mm)注:1.如几个零件同时加工时,长度及宽度为装置在一起的各零件长度或宽度及各零件间的间隙之总和。
切削参数表

FSaeapFSaeapFSae ap FSaeapF S ae apD12330043507.50.23600600070.25330092000.10.180070000.080.05 D83300650050.183600800050.25350095000.10.180085000.080.05 D633008500 3.50.1335009000 3.50.23200110000.070.0780085000.060.05 D432001200020.0830001200020.153000120000.050.0570090000.050.05 D33000125001.50.062600120000.0350.03570095000.030.05D2D1.5D1D12R0.53800500070.223800630070.3300085000.220.22850800070.06320085000.250.3 D8R0.53800720040.23800800040.25350095000.20.2850850050.06320095000.250.3 D6R0.53500850030.133200950030.253300110000.20.2850850030.063000100000.20.22 D4R0.532001200020.0830001200020.23000120000.150.157********.063000130000.170.17 R6250055000.350.3300072000.350.3285085000.220.22300085000.350.35 R4300075000.350.25300085000.350.3285090000.220.223000100000.320.32 R3300095000.30.22800100000.30.253000110000.180.183000120000.270.27 R23000120000.250.182800120000.220.183000120000.180.182600130000.230.23 R1.52200130000.150.122800135000.150.152500135000.170.17 26ER0.8300016500.20.228501800160.1300018000.30.3 21ER2 21ER0.8300018000.20.188501800100.1300018000.30.3 17ER0.8 16BR8320050000.250.25350050000.380.38CNC 钢料 切削参数表(高速机)Vc =150-300 Fz =0.15Vc =160-280 Fz =0.13Vc =50-350 Fz =0.09底面/侧面精加工Vc =260 Fz =0.03Vc =200-260 Fz =0.13PL面仿形精加工刀具开粗半精加工仿形精加工 1 当刀具长度在直径的5倍以内下列参数适用.切记!刀具长度不可大过直径的9倍2 当刀具长度在直径的5倍以上时需将F/S值下调10%;Ae/Ap减小30%4 工件锐角处需做过渡圆角;钢料为R2、铜料为R1 石墨为R0.6n=主轴转数(公式套用)3 工件在精加工之前需保证余量均匀;不可让刀具产生过大的切削负荷 代码诠释:D =刀具直径 R =刀角半径F =进给速率 S =主轴转数Vc =线性切削速度 (m/min) Fz =每齿切削量(mm/tooth)Ae =径向进给量 (mm) Ap =轴向进给量(mm)加工参数的注意事项:Dv n c ⨯⨯=π1000FSaeapFSaeapFSaeapFSaeapF S ae apD12320043507.50.23200600070.25300060000.10.180060000.080.05 D83000600050.173200600050.25300060000.10.175060000.080.05 D6280060003.50.132006000 3.50.2300060000.070.0775060000.060.05 D43000600020.152********.050.0570060000.050.05 D326006000 1.50.08220060000.0350.0357*******.030.05 D12R0.53500600070.23200600070.3300060000.20.22800600070.06300060000.250.28 D8R0.53800600040.173200600040.3300060000.20.2800600050.06300060000.250.28 D6R0.52800600030.130********.25300060000.20.2800600030.06280060000.20.22 D4R0.52600600020.152********.150.15700600020.05250060000.150.18 R6250060000.350.3320060000.30.3300060000.220.22300060000.350.35 R4300060000.350.25320060000.30.3300060000.220.22300060000.320.32 R3280060000.30.2300060000.250.25280060000.180.183********.280.28 R2220060000.220.15265060000.150.152********.150.152********.220.22 R1.5200060000.120.1180060000.150.15200060000.180.18R1 30ER53500160016.50.4535001600160.4 26ER0.835001650150.435001650150.35300016500.20.228501800160.1300018000.250.25 21ER235001800130.4535001800130.4CNC 钢料 切削参数表(低速机)开粗半精加工仿形精加工制表:刘亚超 2009-06-15审核:加工参数的注意事项:2 当刀具长度在直径的5倍以上时需将F/S值下调10%;Ae/Ap减小30%3 工件在精加工之前需保证余量均匀;不可让刀具产生过大的切削负荷底面/侧面精加工PL面仿形精加工Vc =130-160 Fz =0.22Vc =110-200 Fz =0.15Vc =80-200 Fz =0.1Vc =150-200 Fz =0.035Vc =160-200 Fz =0.13刀具n=主轴转数(公式套用)4 工件锐角处需做过渡圆角;钢料为R2、铜料为R1 石墨为R0.6代码诠释:D =刀具直径 R =刀角半径F =进给速率 S =主轴转数Vc =线性切削速度 (m/min) Fz =每齿切削量(mm/tooth)Ae =径向进给量 (mm) Ap =轴向进给量(mm)1 当刀具长度在直径的5倍以内下列参数适用.切记!刀具长度不可大过直径的9倍Dv n c ⨯⨯=π100017ER0.83200185090.43500185090.35300018500.20.28501850100.1300018000.250.25 16BR8300050000.250.25350050000.350.35 12BR6300055000.220.22350055000.350.35FSaeapFSaeapFSaeapFSaeapFSaeapD124500750060.454000750060.35320080000.120.1285070000.10.1 D84500900040.454000900040.35350092000.120.1285085000.10.1 D64000950030.34000950030.33500110000.10.185088000.10.12000115000.050.1 D435001100020.2535001100020.253200120000.10.180090000.10.11500130000.050.1 D3300012500 1.50.2300012500 1.50.153000130000.080.0870*******.050.081500130000.050.08 D228001300010.1530001300010.132500145000.050.0565*******.050.0812********.050.06 D1.52300135000.50.122200135000.50.12000150000.050.05600125000.050.0510********.030.05 D11800150000.050.05850150000.030.03D12R0.54500800060.454000800060.4320080000.150.258507500 6.50.1 D8R0.54500900040.454000900040.4350095000.150.228508500 4.50.1 D6R0.54000950030.34000950030.33500110000.10.228509000 3.50.1 D4R0.535001100020.335001100020.33000120000.10.28009000 2.50.1 D3R0.5280012500 1.50.2300012500 1.50.253000125000.080.15700100001.50.08R4450085000.70.4400085000.50.4350085000.220.22 R3400092000.50.4400092000.40.43500100000.220.22Vc =160-200 Fz =0.1Vc =110-300 Fz =0.2Vc =110-300 Fz =0.15Vc =150-320 Fz =0.1半精加工仿形精加工底面/侧面精加工细小工件/骨位精加工CNC 铜料电极 切削参数表刀具开粗Vc =150-200 Fz =0.05制表:刘亚超 2009-06-15审核:n=主轴转数(公式套用)4 工件锐角处需做过渡圆角;钢料为R2、铜料为R1 石墨为R0.6Ae =径向进给量 (mm) Ap =轴向进给量(mm)加工参数的注意事项:1 当刀具长度在直径的5倍以内下列参数适用.切记!刀具长度不可大过直径的9倍2 当刀具长度在直径的5倍以上时需将F/S值下调10%;Ae/Ap减小30%3 工件在精加工之前需保证余量均匀;不可让刀具产生过大的切削负荷 代码诠释:D =刀具直径 R =刀角半径F =进给速率 S =主轴转数Vc =线性切削速度 (m/min) Fz =每齿切削量(mm/tooth)Dv n c ⨯⨯=π1000R1.53000130000.30.23200130000.250.23000130000.170.171800120000.10.1 R12500150000.10.11300135000.080.08 R0.51350150000.050.05850150000.050.05FSaeapFSaeapFSaeapFSaeapFSaeapD12500070006 1.54500700060.6350070000.150.285055000.150.12 D640009000314500900030.5350095000.120.1585070000.120.12130088000.060.1 D436001100020.5535001100020.353500120000.10.1580085000.10.11200100000.060.1 D3320012000 1.50.35320012000 1.50.33000130000.10.12700100000.10.11000120000.060.06 D226001300010.230001300010.252800140000.080.1650120000.080.0810********.050.05 D11800160000.050.05850150000.030.03D6R0.540009500314500950030.5350095000.120.158507000 3.50.12 D4R0.535001100020.5540001100020.353500120000.10.158008500 2.50.1 D3R0.5320012000 1.50.35300012000 1.50.253000125000.10.12700100001.50.1R4450085000.80.8450085000.80.6350085000.20.2 R3400092000.50.6420092000.50.43500100000.20.2 R2350095000.450.3400095000.40.353500120000.150.151********.080.08 R1.53000125000.350.253200125000.30.23000130000.150.151600120000.080.08 R12500150000.10.11300135000.050.05 R0.51350160000.050.05850150000.050.05底面/侧面精加工细小工件/骨位精加工Vc =110-300 Fz =0.25Vc =110-300 Fz =0.2Vc =150-300 Fz =0.15Vc =150-200 Fz =0.15Vc =160-200 Fz =0.1刀具开粗半精加工仿形精加工制表:刘亚超 2009-06-15审核:CNC 石墨电极 切削参数表4 工件锐角处需做过渡圆角;钢料为R2、铜料为R1 石墨为R0.6Ae =径向进给量 (mm) Ap =轴向进给量(mm)加工参数的注意事项:1 当刀具长度在直径的5倍以内下列参数适用.切记!刀具长度不可大过直径的9倍2 当刀具长度在直径的5倍以上时需将F/S值下调10%;Ae/Ap减小30%3 工件在精加工之前需保证余量均匀;不可让刀具产生过大的切削负荷 代码诠释:D =刀具直径 R =刀角半径F =进给速率 S =主轴转数Vc =线性切削速度 (m/min) Fz =每齿切削量(mm/tooth)n=主轴转数(公式套用)Dv n c ⨯⨯=π1000制表:刘亚超 2009-06-15审核:。
刀具基本切削参数表
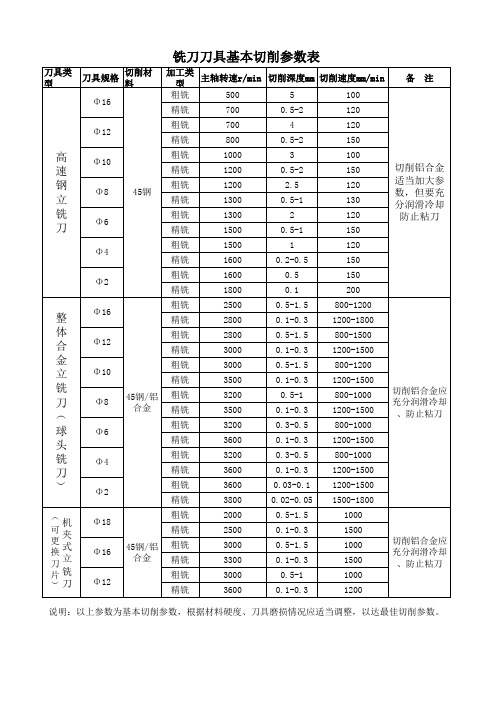
120
防止粘刀
精铣
1500
0.5-1
150
粗铣
1500
1
120
精铣
1600
0.2-0.5
150
粗铣
1600
0.5
150
精铣
1800
0.1
200
粗铣
2500
0.5-1.5
800-1200
精铣
2800
0.1-0.3
1200-1800
粗铣
2800
0.5-1.5
800-1500
精铣
3000
0.1-0.3
1200-1500
说明:以上参数为基本切削参数,根据材料硬度、刀具磨损情况应适当调整,以达最佳切削参数。
刀具类 型
高 速 钢 立 铣 刀
整 体 合 金 立 铣 刀 (
球 头 铣 刀 )
(机
可 更 换 刀
夹 式 立
片铣
)刀
刀具规格
切削材 料
Φ16
Φ12
Φ10
Φ8
45钢
Φ6
Φ4
Φ2
Φ16
Φ12
Φ10
Φ8
45钢/铝 合金
Φ6
Φ4
Φ2
Φ18
Φ16
45钢/铝 合金
Φ12
铣刀刀具基本切削参数表
加工类 型
主轴转速r/min
1500 1000 1500 1000
切削铝合金应 充分润滑冷却 、防止粘刀
精铣
3600
0.1-0.3
1200
说明:以上参数为基本切削参数,根据材料硬度、刀具磨损情况应适当调整,以达最佳切削参数。
铣刀刀具基本切削参数表
加工余量
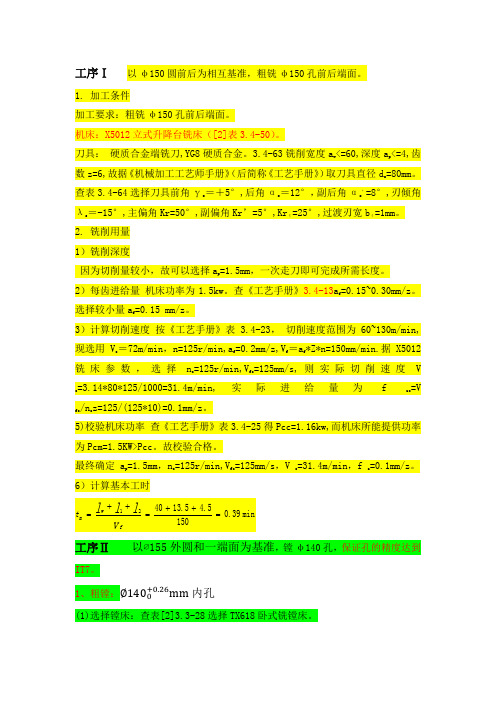
1) 铣削深度 查[2]表3.4-43因为切削量较小,故可以选择ap=0.5mm,一次走刀即可完成所需长度。
2) 每齿进给量 机床功率为1.5kw。查[2]表3.4-13af=0.15~0.30mm/z。由于是对称铣,选较小量af=0.15mm/z。
查《工艺手册》表30-25,寿命T=180min
由表3.2-3得:kMv=1.0,klv=1.0,故V'表=13.5 m/min×1.0×1.0=13.5 m/min.
查Z5040机床说明书,取n=245r/min.实际切削速度为
由表[2]3.2-5得:
kMT=kMF=0.94,故F=6460*0.94=6072N,
T=58*0.94=54.5 N·m
工序Ⅶ: 和∅155一端面为基准,钻圆柱面上两小孔,2X ,保证两孔间距离为32±0.1mm。
1.选择钻床查表[2]3.2-57选Z512-A立式钻床。
加工刀具为:钻孔—ø7.2mm直柄小麻花钻。
2.确定钻削用量
(1)确定进给量
查[2]表3.2-10得:取f=0.4mm/r, 根据表3.2-8,按钻头强度所允许的进给量f'>1.22mm/r, 由于机床进给机构允许的轴向力Fmax=15690N(由机床说明书查出)。
2. 铣削用量
1)铣削深度
因为切削量较小,故可以选择ap=1.5mm,一次走刀即可完成所需长度。
2)每齿进给量 机床功率为1.5kw。查《工艺手册》3.4-13af=0.15~0.30mm/z。选择较小量af=0.15mm/z。
3)计算切削速度 按《工艺手册》表3.4-23,切削速度范围为60~130m/min,现选用Vc=72m/min,n=125r/min,af=0.2mm/z,Vf=af*Z*n=150mm/min.据X5012铣床参数,选择nc=125r/min,Vfc=125mm/s,则实际切削速度Vc=3.14*80*125/1000=31.4m/min,实际进给量为fzc=Vfc/ncz=125/(125*10)=0.1mm/z。
常用加工的切削参数参考表

工件磨削表面面直径D
mm
加工材料
非淬火钢及铸铁
淬火钢及耐热钢
V(m/min)
N(r/min)
V(m/min)
N(r/min)
30
18-35
191-382
22-35
243-382
50
20-40
127-254
25-40
159-254
80
25-50
100-200
30-50
120-200
常用加工的切削参数参考表
1、常用硬质合金或涂层硬质合金切削不同材料时的切削用量推荐值见下表
刀具材料
工件材料
粗加工
精加工
切削速度(m/min
进给量(mm/r)
背吃刀量mm
切削速度(m/min
进给量(mm/r)
背吃刀量mm
硬质合金或涂层硬质合金
碳钢
220
0.2
3
260
0.l
0.4
低合金刚
180
0.2
3
220
公制螺纹:t<1 dz=d-t
t>1 dz=d-(1.04-1.06)t
其中:t――螺距离d――螺纹公制直径dz――攻丝前钻头直径
7、铰孔余量见表
孔直径(mm)
<5
5-20
21-32
33-50
51-70
铰削余量(mm)
0.1-0.2
0.15-0.25
0.20-0.3
0.25-0.35
0.25-0.35
0.4
13
0.45
13
0.5
13
3-8
走刀量
切削速度
0.12
加工中心切削参数表

加工中心切削参数表CNC加工切削刀具参数⑴一般大小的钢料开粗时尽量选用Φ30R5,较大型的钢料尽量选用Φ63R6;⑶铜公2D外形光刀,高度50mm以下选用M12刀具;高度在50-70mm 之间,选用M16刀具;高度在70-85mm之间,选用M20;高度在85-120mm 之间,选用M25;超过120mm以上用Φ25R0.8、Φ32R0.8飞刀把加工;⑷较平坦的曲面或较高的外形曲面尽量选用Φ20R4、Φ25R5、Φ40R6作为光刀刀具;5. 钢料开粗时,Z下刀量0.5-0.7mm。
铜料开粗时Z下刀量1.0-1.5mm(内部开粗1.0mm,基准边开粗1.5mm)6. 平行式精铣时,ma×imum stepover按“精加工平行式最佳等高参数表”来设定。
精铣前余留量尽量留小点,钢料0.10—0.2mm。
铜料0.2--0.5mm。
不要使用R刀精锣面积大的平面8. 快速下刀至3mm高度使用F速下刀(相对加工深度)正常下刀F 速一律300mm/m,有螺旋下刀和外部进刀的Z下刀F速一律是900 mm/ m,有踩刀地方的Z下刀F速一律150mm/m,内部快速移动F 速一律是6500mm/m(必须走G01)。
9. 使用Φ63R6、Φ40R6、Φ30R5飞刀开粗时,余量留单边0.8mm,不能出现踩刀现象,不能使用Φ63R6加工范围较小的内型框。
挖槽开完粗后,要使用同一把刀具,将较大的平面再加工,保证底部留0.2mm余量,方便下一把刀具可以直接精加工工件底部。
10. 精铣前必须先用较小直径的刀将角位的余量粗清角,无法清角的地方,必须做曲面挡住,避免精铣时角位余量过多导致刀具损坏2、在二次开组选用参考刀具易造成过切或撞刀" R; _, b2 g q0 ^& f解决方法﹕在选用参考刀具时我们应当设置参考的刀具S" w+ N: m$ h) g! 比实际上一把刀具的直径大2~~3MM 牛鼻刀9 @( k* |/ z# q0 L/ S的话也要比之前的R角设置大点。