saej131v003
SAEJ(标准参考)翻译

SAEJ(标准参考)翻译1 范围该SAE标准涵盖了应⽤于汽车球墨铸铁铸件和相关的⾏业的铸铁试件的⾦相组织和最低机械性能要求。
铸件需详细说明是铸态或热处理状态。
如果铸件需热处理,需获得客户的批准。
本附录提供了在化学成分,显微组织和⼒学性能,铸造性能等⽅⾯⾯信息以及为特定条件服务的其他信息。
在此标准的SI单位是磅2.2参考⽂献2.1 相关出版物The following publications form a part of the specification to the extent specified herein. Unless otherwise indicated, the latest revision of SAE publications shall apply2.1.1 ASTM 国际出版物Available from ASTM INTERNA TIONAL, 100 Barr Harbor Drive, West Conshohocken, PA 19428-2959ASTM E10 –-Standard Test Method for Brinell Hardness of Metallic MaterialsASTM E23—Standard Test Methods for Notched Bar Impact Testing of Metallic Materials ASTM E111—Standard Test Method for Young's Modulus, Tangent Modulus and Chord Modulus ASTM A247—Standard Test Method for Evaluation the Microstructure of Graphite in Iron CastingsASTM A536—Standard Specification for Ductile Iron CastingsSTP-455—Gray, Ductile, and Malleable Iron Castings Current Capabilities (out-of-print)2.1.2其他出版物Metals Handbook, V ol. 1, 2, and 5, 8th Edition, American Society for Metals, Metals Park, OH Gray and Ductile Iron Castings Handbook, Gray and Ductile Iron Founder Society, Cleveland, OH H. D. Angus, Physical Engineering Properties of Cast Iron, British Cast Iron Research Association, Birmingham, England3.3 牌号机械性能和冶⾦描述如表1所⽰。
SAEJ1711V001混合动力汽车经济性和排放测试标准

Recommended Practice for Measuring the Exhaust Emissions and Fuel Economy of Hybrid-Electric Vehicles
Foreword—Recent advances in electric powertrain components and computer controls have prompted a renewed effort to develop practical hybrid-electric vehicles (HEVs). HEVs combine powertrain elements of conventional vehicles and electric vehicles (EVs) and hold the promise of substantially reduced fuel consumption and exhaust emissions. One obstacle to the development of commercial HEVs has been the absence of a broadly applicable and widely accepted procedure for measuring HEV exhaust emissions and fuel economy. The Light Duty Vehicle Performance and Economy Measurement Standards Committee of the Society of Automotive Engineers (SAE) established a task force in the Fall of 1992 to develop a recommended practice for uniform testing of HEVs. This HEV task force followed a similar SAE effort to develop a recommended practice for testing of EVs, which resulted in the publication of SAE J1634. The SAE HEV Task Force has included a broad spectrum of representatives from vehicle manufacturers, national laboratories, and other interested parties. Membership has changed significantly over the years, so that the present version represents the combined input from a larger number of experts than the current roster would indicate. In addition, representatives from the U.S. Environmental Protection Agency and the California Air Resources Board have participated informally in ongoing discussions with the HEV Task Force. Their input has been valuable and, hopefully, will increase the usefulness of this document as a technical basis for certification protocols. Initial work by the SAE HEV Task Force involved agreeing on the objectives of the document and performing an analytical evaluation of three previous proposals for HEV testing. This was followed by an effort to build on the best elements of each proposal and develop a consensus SAE proposal. That proposal has evolved significantly since then, benefiting from analysis and discussions of all the major issues surrounding HEV testing. In addition, once a fairly complete draft was available, the test procedure was tested at a General Motors chassis dynamometer facility using three HEVs built for the SAE HEV Challenge student competition. More recent versions have been evaluated by a team from the National Renewable Energy Laboratory using a hybrid vehicle simulation program. The sustained efforts of all participant organizations and individuals in the complex task are greatly appreciated. This document should be viewed as a starting point for standardizing HEV testing. The task force members realize that both the technology and the methodology for testing HEVs are in their infancy. It is most likely that lessons learned in the process of testing HEVs and changes in HEV and testing technology in the coming years will require this document to be refined considerably from its present form.
SAEJ20V003

SAE Technical Standards Board Rules provide that: “This report is published by SAE to advance the state of technical and engineering sciences. The use of this report is entirely voluntary, and its applicability and suitability for any particular use, including any patent infringement arising therefrom, is the sole responsibility of the user.”SAE reviews each technical report at least every five years at which time it may be reaffirmed, revised, or cancelled. SAE invites your written comments and suggestions.TO PLACE A DOCUMENT ORDER; (724) 776-4970 FAX: (724) 776-0790SAE WEB ADDRESS Copyright 2000 Society of Automotive Engineers, Inc.and servicing2.1.4A UTOMO TIVE I NDUSTRY P UB LICATION—Available from AIAG, 26200 Lasher Road, Suite 200, Southfield, MI48034-7100.QS 9000—Quality System Requirements2.2Related Publications—The following publications are provided for information purposes only and are not arequired part of this document.2.2.1SAE P UBLICATIO NS—Available from SAE, 400 Commonwealth Drive, Warrendale, PA 15096-0001.SAE J20-1—Coolant Hose (Supplement to SAE J20 for Government Use Replacing Part of MS51230)SAE J20-2—Coolant Hose—Normal Service Type Convoluted, Wire Support Hose(Supplement to SAE J20 for Government Use Replacing Part of MS51008)3.Definitions of Hose Types3.1SAE 20R1—Heavy-duty type for service in heavy-duty application. This type is available in two wallthicknesses as indicated in 6.3.3.2SAE 20R2—Flexible heavy-duty wire embedded type for the same service as SAE 20R1.3.3SAE 20R3—Heater hose for normal service.3.4SAE 20R4—Radiator hose for normal service.3.5SAE 20R5—Convoluted wire supported type for normal service.3.6Hose Special Designators for SAE 20RXY—X Refers to the hose type. Y designators may be used forhoses with special features. Multiple Y designators may be used if needed.3.6.1HT—This High Temperature designation is for any hose type, SAE 20R1 to SAE 20R5, which is required tooperate in an environment above 125 °C. (See Section 11.)3.6.2EC—This Electrochemical designation is for any hose type SAE 20R1 to SAE 20R5 which is required tohave electrochemical resistance as defined by SAE J1684. (See Section 12.)3.6.3LT—This Low Temperature designation is for any hose type SAE 20R1 to SAE 20R5 which is required tooperate in an environment down to –55 °C. (See Section 13.)3.7Hose Classes—Compounds based on different synthetic rubber grades are specified and designated (see 5.2for test methods):Class A—high-temperature resistantClass B—high oil resistantClass C—medium oil resistantClass D-1—low oil resistant, improved serviceClass D-2—low oil resistant, standard serviceClass D-3—low oil resistant, high-temperature resistant, premium serviceClass E—low oil resistant, fiber elastomer compositePhysical characteristics for each hose class are shown in Table 1.3.8Marking—The outer cover will be printed with the designation SAE 20RXY (the X being the hose type and Y any special designator(s) such as “LT”), class, size of the inside diameter in millimeters, hose manufacturer’s code marking, and any other identification as agreed upon between user and manufacturer/supplier. It is recommended that this marking shall appear on the outer cover of the hose at intervals not greater than 380mm.3.8.1S MALL ID O R S HORT H OSE —If there is insufficient space on the hose for the required marking due to size or configuration, the marking shall be agreed upon by the customer and the manufacturer/supplier.4.Dimensional Requirements—Geometric Dimensioning and Tolerancing requirements are outlined in SAE J2370. The following requirements are minimal standards:4.1Tube and Cover Thickness—Minimum thickness shall be 1.6 mm for the tube and 0.8 mm for the cover.NOTE—This requirement does not apply for hoses without distinctive tube and cover construction.TABLE 1—COOLANT SYSTEM HOSE ELASTOMERIC MATERIAL, PHYSICAL PROPERTIESSAE Designation Typical Elastomer Class A Silicone Class B NBR Class C CR Class D–1EPDM Class D–2EPDM Class D–3EPDM Class E EPDM/Fiber Typical Temperature Range, °C –55 to 175–40 to 100–40 to 100–40 to 125–40 to 125–40 to 150–40 to 125Original PropertiesDurometer, points Shore A 55 to 7555 to 7555 to 7555 to 7555 to 7555 to 7565 to 85 Tensile, min, MPa 5.58.57.07.0 5.07.0 5.0 Elongation, min, %200250200300150300100Oven Aging Conditions and Change Limits, Hours/°C 70/17570/10070/10070/12570/125168/15070/125 Durometer, points Shore A +10+15+20+15+15+15+15 Tensile, max %–15–15–20–20–20–35–20 Elongation, max, %–40–50–50–50–50–65–50Oil Immersion Change Limits ASTM No. 3 Oil or IRM 903 (IRM 903 is being phased in to replace ASTM No. 3) Hours/°C 70/10070/10070/100———— Volume, max, %0 to +45–5 to +25+80———— Tensile, max, %–40–20–50————Coolant Immersion (Tube only)Change Limits Hours/at Boiling Point 707070707016870 Volume, %0 to +400 to +200 to +20–5 to +20–5 to +20–5 to +20–5 to +20 Durometer, points Shore A –10 to +10–10 to +10–10 to +10–10 to +10–10 to +10–10 to +10–10 to +10Tensile, max, %–30–20–20–20–20–20–20 Elongation, max, %–25–40–40–50–25–25–25Compression Set °C 125100100125125125125 70 h, max, %40507575857585Cold Flexibility (°C)(1)1.LT designator extends the low temperature flexibility to –55 °C.–55–40–40–40–40–40–404.2Length Tolerancea.Straight Hose—Unless otherwise specified by the customer or manufacturer, Commercial Tolerances will be used. See Table 2.b.Curved Hose—The tolerances on arm lengths, measured from end to intersection of nearest centerline, shall be as shown in Table 3.4.3General Layout Tolerances, Curved Hose—Dimensions locating bend intersections and centerline radii are to establish the theoretical design centerline of the hose. Actual outside contour of hose must be held within a total range of 9.6 mm of all planes with respect to theoretical outside contour of hose. For hose check, hose ends should first be placed in theoretical design position before checking (hose may have to be flexed to correct for any distortion caused by handling or during shipment). SAE arm length tolerances shall apply.Tolerances apply to all arm and body lengths in addition to contour tolerances. Dimensions covering more than one arm or body length are reference only and have no tolerances. The wall thickness within bends of a curved hose may differ from the wall thickness of the straight by no more than 33%.When an alignment mark is required for assembly operations, the basic identifier in Figure 1 is recommended:FIGURE 1—ALIGNMENT MARKLocation of the alignment mark and/or additional information shall be determined by the customer and the manufacturer.4.4Enlarged Ends—When the ID of one end of the hose is enlarged, normally the ID of the enlarged end should not exceed the ID of the rest of the hose by more than 33%. Enlarged ends should be considered arm lengths for tolerance purposes. The wall thickness normally changes with enlarged ends.TABLE 2—LENGTH TOLERANCELength mm Precision TolerancemmCommercial Tolerancemm0–300±3.2+9.7–3.2>300±1%+3%–1%TABLE 3—TOLERANCE ON ARM LENGTHArm Lengthmm Precision TolerancemmCommercial Tolerancemm0–300.0±4.0±6.4300.1–610.0±4.8±7.2610.1–910.0±6.4±9.7910.1–1220.0±9.7±11.21220.1–1830.0±12.7±15.9over 1830±1%±2%4.5End Squareness—All points on the hose end surface must lie within a tolerance zone consisting of twoparallel planes perpendicular to the hose axis. The tolerance zone is determined by Table 4.TABLE 4—END SQUARENESSHose ID Precision Tolerance Commercial Tolerance25.4 mm and larger10% of ID15% of IDsmaller than 25.4 mm 2.54 mm 3.75 mm4.6Finish and Roundness on Connections—Users of coolant hose should take every precaution to obtainconnections as smooth and round as practical. (Reference SAE J1231)4.7Clamps—Refer to SAE J1508 for available clamp types.5.Physical Test Requirements and Procedures5.1Finished Product5.1.1A DHES IO N—When applicable, use test procedure ASTM D 413. The minimum requirement is 1400 N/mbetween all elastomer or elastomer-coated plies.5.1.2C OLD F LEX IB ILITY—The following procedure shall be used:For hose 25.4 mm ID and smaller, specimen shall consist of a complete hose of length sufficient to perform bend test described as follows: the hose shall be placed in a cold box for 5 h at the temperature specified in Table 1. The hose shall then be flexed in the cold chamber through 180 degrees from the centerline to a diameter of ten times the maximum outside diameter of the hose within 4 s. The hose shall not fracture and shall not show any cracks or breaks in the tube or cover.For hose larger than 25.4 mm ID, specimens are to be 25.4 mm long sections of the complete hose. The specimen and test fixture shall be placed in a cold box for 5 h at the temperature specified in Table 1. The specimen is then compressed to 50% of its original inside diameter between parallel plates within 4 s. The specimen shall not crack or break. The testing fixture shall be in the cold box during the entire test.NOTE—For LT hose, refer to Section 13 for specific cold flexibility requirements.5.1.3O ZONE T EST AND R EQ UIREMENTS—The following test and requirements apply:When applicable, use test procedure ASTM D 1149.For hose 25.4 mm ID and smaller, a specimen of hose of sufficient length shall be bent around a mandrel with an outside diameter equal to eight times the specified OD of the sample. The two ends shall be tied at their crossing with enameled copper or aluminum wire. After mounting, the specimen shall be allowed to rest in an ozone-free atmosphere for 24 h at standard laboratory test temperature. The mounted specimen shall be placed in a test chamber containing ozone at a partial pressure of 50 mPa ± 5 mPa at a temperature of 40°C ± 1 °C.After 100 h of exposure, the specimen shall be removed and allowed to cool to standard laboratory test temperature and then be inspected visually under 7X magnification. The sample must not show any cracks except for the area immediately adjacent to the wire, which shall be ignored.For hose larger than 25.4 mm ID, prepare a specimen by cutting a strip of the whole hose 12.7 mm x 100mm and tie specimen (cover out) around a 12.7 mm diameter mandrel. Condition in the same manner as specified previously for the whole hose and apply the same conditions and requirements. This test applies to the cover only and cracks in the exposed tube or cut edges of the cover shall be ignored.5.1.4K INK T EST —This test applies to SAE 20R3 hose only. (Not recommended for formed hoses.)5.1.4.1Test Procedure—Condition specimen length of hose at standard laboratory test temperature for at least 2h. Measure the minimum OD at the approximate center of the specimen length. When a sufficient length of hose is available, it is permissible and suggested that a length in excess of the specimen length be used in an effort to minimize the handling variable and overbending. Insert one end of the hose into one hole of the specified test fixture, carefully bend the hose (in direction of natural curvature) and insert the other hose end into the second test fixture hole. Do not overbend or bend hose with sharp motion to prevent excessive kinking or collapse. Within 30 s, measure the minimum diameter at the point of greatest collapse.5.1.4.2Test Fixture—Shall consist of 25.4 mm thick flat plate drilled with holes not to exceed the hose OD by more than 1.6 mm and separated by the specified center distances.5.1.4.3Test Requirements—See Table 5.5.1.5V ACUUM C O LLA PSE T EST —When practical, the entire hose shall be tested as specified in Tables 6A and 6B.The minimum outside diameter shall decrease by no more than 20% during application of vacuum for 15 s and not to exceed 30 s.5.1.6B URST —This test shall be performed on a straight length of hose in accordance with ASTM D 380 to meet the requirement in Tables 6A and 6B.For curved 20R3 and 20R4 hose, the same reference applies, except that the test shall be performed on the individual curved hose with one end free and unrestrained and the rate of application of pressure shall be not less than 2.0 MPa nor more than 7.0 MPa/min. The aged burst requirement (11.2.2) will apply to all HT hoses.5.1.7P RESSURE V IBRATIO N AND T E MP ERATURE OR P RE SSURE AND T EMPE RATURE T EST —This test shall be used when agreed upon between customer and manufacturer/supplier, using SAE J1610 as the referenced test method. If required, test limits can be modified if agreed upon by the customer and manufacturer/supplier.TABLE 5—KINK TEST REQUIREMENTS FOR SAE 20R3 HOSENominal Hose ID mmSpecimen LengthmmCenter DistancemmCollapse of Hose Allowed, %15 and larger 24 x ID 10 x ID 25smaller than 1524 x ID8 x ID25TABLE 6A—BURST AND VACUUM VALUES(20R1 AND 20R2)NominalSizemm20R1Heavy-DutyStandard WallMinBurstMPa20R1Heavy-DutyStandard WallMinVacuumkPa20R1Heavy-DutyHeavy WallMinBurstMPa20R1Heavy-DutyHeavy WallMinVacuum,kPa20R2WireInsertedMinBurstMPa20R2WireInsertedMinVacuumkPa10 3.2933.813 2.9333.816 2.5927.019 2.2427.022 2.2423.625 2.0623.6 2.0684.429 2.0620.332 1.9016.9 3.4533.8 1.9084.435 1.9013.538 1.7210.1 3.1033.8 1.7284.441 1.72 6.844 1.55 3.4 2.7616.9 1.5584.451 1.38 2.4110.1 1.3884.457 1.21 2.41 3.4 1.2184.460 1.2164 1.03 2.06 1.0384.4700.86 1.720.8684.4 760.60 1.720.6984.4 83890.52 1.380.5284.4 1020.34 1.030.3484.4 NOTE—For hose sizes between sizes listed, use the values for the next larger size.5.2Physical Properties are to be Obtained from Specimens Removed from Hose—See ASTMD380 for pro-cedure.NOTE—For 20R5 hoses, test specimens are to be taken from the cuffs.5.2.1D UROMETER H ARDNESS —Hardness shall be measured with a Shore A Durometer according to ASTM D 2240.5.2.2T ENSILE S TRENGTH AND E LONGATION —Test according to ASTM D 412.5.2.3O VE N A GING —Shall conform to ASTM D 573.TABLE 6B—BURST AND VACUUM VALUES(20R3, 20R4, AND 20R5)Nominal Size mm 20R3Heater Min Burst MPa 20R3Heater Min Vacuum kPa 20R4Radiator Min Burst MPa20R4Radiator Min Vacuum kPa20R5Wire SupportedMin Burst MPa20R5Wire SupportedMin Vacuum kPa5 1.7233.86 1.7233.87 1.7233.8 8 1.7233.89 1.7233.8 10 1.7233.8 1.24 13 1.7233.8 1.17 16 1.7227.0 1.10 19 1.3823.6 1.03 22 25 1.2120.30.970.97 29 32 1.2116.90.900.90 35 380.830.83 41 440.760.76 510.690.69 570.620.62 60 640.550.55700.48 760.41 830.34 890.27102NOTE—For hose sizes between sizes listed, use the values for the next larger size.5.2.4C OOLANT I MMERS ION—Volume change, tensile, elongation, and durometer changes shall be observed afterimmersion in the following mixture maintained at the boiling point under a water-cooled reflux condenser.Maintain the fluid level during the test by adding distilled water as needed.a.1/2 by volume, distilled waterb.1/2 by volume, ethylene glycol-based coolant agreed to between supplier and customerMeasurements of tensile, elongation, durometer, and volume change shall be made in accordance with appropriate ASTM methods.5.2.5O IL I MME RSIO N—Shall conform to ASTM D 471.5.2.6C OMPRESSION S E T—Test to be performed per ASTM D 395, Method B. For cover specimens, ply to 8.9 mm± 1 mm, not to exceed 7 plies where applicable. For tube specimens, ply to 12.7 mm ± 1 mm, not to exceed7 plies. When unable to meet the required thickness, use standard ASTM slabs cured at similar cureconditions as the hose.NOTE—SAE J1638 may be considered as an alternate test method with criteria to be agreed upon between customer and manufacturer.6.SAE 20R1 Heavy-Duty Type6.1Scope—This type of hose is primarily for heavy-duty service of which the diesel-locomotive application is atypical example. The hose is intended to withstand the effects of higher pressure systems. When desired, hose with one class of material in the tube and another in the cover may be obtained. In such cases, the physical properties specified for respective parts shall apply.6.2Reinforcement—The reinforcement may consist of multiple plies of woven or cord fabric, or ply or plies ofbraided, knit, or spiraled yarn and shall be such that the hose meets the minimum burst and vacuum requirements as given in Table 6A.6.3Dimensions—The ID Tolerance is ±0.8 mm for sizes smaller than 51 mm and ±1.6 mm for sizes 51 mm andlarger. The Wall Thickness Range for Standard Wall Thickness hose is 4.3 to 5.6 mm. The Wall Thickness Range for Heavy Wall Thickness Hose is 5.8 to 7.1 mm. These dimensions shall be measured at a section not including a lap.7.SAE 20R2 Heavy-Duty Wire Embedded Type7.1Scope—This is similar to SAE 20R1 hose except that it utilizes wire helix or helices built into the wall of thehose. The hose is intended to withstand high vacuum and/or some forced curvature.7.2Reinforcement—The reinforcement is typically multiple plies of woven or cord fabric or ply or plies of braidedor knot yarn and wire helix or helices such that the hose will meet the minimum vacuum and burst requirements as given in Table 6A.7.3Dimensions—The ID Tolerance is ±0.8 mm for sizes smaller than 51 mm and ±1.6 mm for sizes 51 mm andlarger. The Wall Thickness Range at hose ends exclusive of wire gauge is 4.3 to 6.4 mm.8.SAE 20R3 Heater Hose8.1Scope—This type of hose is used in connecting heater systems and other components in the coolantcirculating systems of ground vehicles.8.2Reinforcement—The reinforcement typically consists of one or more plies of woven, braided, knit, or spiraled yarn, or class E material, and shall be such that the hose will meet the minimum burst and vacuum requirements in Table 6B.8.3Dimensions and Tolerances—Target dimensions and tolerances are shown in Table 7. Measurement method must be agreed upon by manufacturer and customer. Since expanded ends may cause wall thickness to change, ODs and tolerances for the expanded ends must also be agreed upon by the manufacturer and customer. Tolerances and dimensions other than those listed as follows must be agreed upon by manufacturer and customer. The values in Table 7 are standard wall dimensions and commercial tolerances.If thin-wall dimensions or precision tolerances are required, refer to SAE J2387.9.SAE 20R4 Radiator Hose Normal Service Type9.1Scope—This is a hose for coolant circulating systems of automotive type engines, commonly known as radiator hose. When resistance to vacuum collapse is a requirement, an inserted wire helix may be specified if desired.9.2Reinforcement—The reinforcement typically consists of one or more plies of woven, braided, knit, or spiraled yarn, or Class E material, and shall be such that the hose will meet the minimum burst and vacuum requirements in Table 6B.9.3Dimensions—Target dimensions and tolerances are shown in 9.3.1. Measurement method must be agreed upon by manufacturer and customer. Since expanded ends may cause wall thickness to change, ODs and tolerances for the expanded ends must also be agreed upon by the manufacturer and customer. Tolerances and dimensions other than those listed as follows must be agreed upon by the manufacturer and customer.Since the wall thickness may change due to bends near the end of hoses, the wall thickness reported will be the average of 4 readings taken 90 degrees apart. The values in 9.3.1 are standard wall dimensions and commercial tolerances. If thin-wall dimensions or precision tolerances are required, refer to SAE J2387.9.3.1D IME NSIO NS AND T OLERANCES —The ID tolerance is ±0.8 mm for hose sizes smaller than 70 mm and ±1.6mm for hose sizes 70 mm and larger. The wall thickness and tolerance is 4.95 mm ± 0.65 mm (4.3 to 5.6mm) for hose sizes smaller than 50.8 mm and 5.35 mm ± 1.05 mm (4.3 to 6.4 mm) for hose sizes 50.8mm and larger.TABLE 7—STANDARD DIMENSIONS AND COMMERCIAL TOLERANCES FOR SAE 20R3ID mm IDTolerance,mmTarget OD (1)mm1. The target OD should be measured over a plug gauge equal to the specified maximum ID.OD Tolerance mm Reference Wall mmMaximum Wall ThicknessVariation mm5.0 to <9.0±0.8Maximum ID Plus 7 mm ±0.8 3.5 1.09.0 to <25.4±0.8Maximum ID Plus 8 mm±0.8 4.0 1.025.4±0.834.0±1.2 4.3 1.0>25.4±0.8Maximum ID Plus 9.9 mm±1.64.951.010.SAE 20R5 Normal Service Type Convoluted, Wire Supported Hose10.1Scope—This is a wire reinforced hose for coolant circulating systems of automotive type engines, commonlyknown as universal type hose. This hose consists of a convoluted section with plain ends. The hose shall contain a wire helix or helices in the convoluted section.10.2Reinforcement—The reinforcement is typically a ply or plies of woven or cord fabric, braided, knot, or spiraledyarn. The hose must meet the minimum burst requirements listed in Table 6B.10.3Dimensions—The ID Tolerance is +0.8 to –1.6 mm. The Wall Thickness Range is 3.6 to 4.8 mm.11.High-Temperature Service Hose HT11.1Scope—Any hose type SAE 20R1 to SAE 20R5 which is required to be operated in an environment above125°C. The letters HT will be used to designate this new requirement, for example, SAE 20R1 HT Class A standard wall.11.2Requirements11.2.1T UBE AND C OVER—The tube and cover compounds must be Class A or Class D-3.11.2.2A GED B URST—The reinforcement yarn or fabric must be such that the hose passes the minimum burstrequirements given on the appropriate table after aging 168 h at 150 °C in a hot air oven.12.Electrochemical Resistant Hose EC12.1Scope—Any hose type SAE 20R1 to SAE 20R5 which is required to have electrochemical resistance. Theletters EC will be used to designate this requirement, for example SAE 20R1 EC.12.2Requirement—Hoses shall be tested in accordance with SAE J1684. Test method 1 shall be utilized todetermine the electrochemical resistance of the hose assembly.13.Low-Temperature Service Hose LT13.1Scope—Any hose type SAE 20R1 to SAE 20R5 and any hose class which is required to be operated in anenvironment down to –55 °C. The letters LT will be used to designate this requirement, for example, SAE 20R1LT Class A standard wall.13.2Requirements—Test frequency is a minimum of annually, per QS 9000.13.2.1R ESISTA NCE TO V IBRATION—This applies to SAE 20R2 wire embedded hoses only. The requirements of5.1.7 shall apply, using SAE J1610, Test Procedure #1, as the recommended practice.13.2.2P ROOF P RESSURE—This test shall be performed on a straight length of hose in accordance with ASTM D 380with the pressure being equal to 50% of the Burst Pressure requirement in Tables 6A and 6B. For curved 20R3 and 20R4 hose, the same reference applies, except that the test shall be performed on the individual curved hose with one end free and unrestrained and the rate of application of pressure shall be not less than2.0 MPa/min nor more than 7.0 MPa/min.13.2.3C OLD F LEX IB ILITY—The test temperature shall be –55 °C. Test per 5.1.2.13.3Qualification Tests13.3.1R EQUIREMENTS FOR Q UALIFICATION—Qualification is required for all hoses to the Low-Temperature ServiceHose requirement. Qualification will consist of initial qualification testing and inspection. Each manufacturer will be responsible for meeting the requirements for qualification.13.3.2Q UALIFICATION T ESTS—For qualification tests, one 8 m length of bulk hose or 10 hoses or assemblies of eachsize to be qualified shall be tested. In order to qualify under this document, hose and hose assemblies must meet the requirements of SAE J20, type and class as specified, and the following tests: visual inspection, cold flexibility at –55 °C, proof pressure as specified in 13.3.3 and resistance to vibration (for wire embedded hoses only.)13.3.3Q UALIFICATION R ETESTS AND R EJECTION—Any hose or assembly that fails in one or more tests shall beresampled and retested. Twice the number of specimens shall be selected from the lot in question for any retests, and failure of any of the retested samples shall be cause for rejection.13.4Qualification Frequency—Testing on the LT-type family of hose shall be performed to show that the hosemeets the requirements of the Low-Temperature hose at least every two years or if the formulation is changed, or for major design or process changes. Data that supports the manufacturer meeting the requirements shall be maintained and be made available to any present or prospective customer. Data may be obtained from performance of other program testing requirements, such as QS 9000 or ISO 9001, as long as it is the same design as the Low-Temperature hose described herein.14.Notes14.1Marginal Indicia—The change bar (l) located in the left margin is for the convenience of the user in locatingareas where technical revisions have been made to the previous issue of the report. An (R) symbol to the left of the document title indicates a complete revision of the report.PREPARED BY THE SAE COOLANT HOSE COMMITTEERationale—The format and verbiage have been modified to better incorporate the revisions that have been made over the past several years, such as, the LT special designator, the references to the SAE J20-1 and J20-2 publications, and the PVT paragraph.Relationship of SAE Standard to ISO Standard—Not applicable.Application—This SAE Standard covers reinforced and flexible hoses intended for use in water and ethylene glycol-based engine-coolant system applications.Reference SectionSAE J20-1—Coolant Hose (Supplement to SAE J20 for Government Use Replacing Part of MS51230) SAE J20-2—Coolant Hose—Normal Service Type Convoluted, Wire Support Hose(Supplement to SAE J20 for Government Use Replacing Part of MS51008)SAE J1231—Formed Tube Ends for Hose Connections and Hose FittingsSAE J1508—Hose Clamp SpecificationSAEJ1610—Test Method for Evaluating the Sealing Capability of Hose Connections with a PVT Test FacilitySAE J1616—Recommended Practice for Compressed Natural Gas Vehicle FuelSAE J1638—Compression Set of Hoses or Solid DiscsSAEJ1684—Test Method for Evaluating the Electrochemical Resistance of Coolant System Hoses and MaterialsSAE J2370—Geometric Dimensions and Tolerancing for Curved HoseSAE J2387—Dimensions and Tolerances for Coolant System HosesASTM D 380—Methods of Testing Rubber HoseASTM D 395—Test Methods for Rubber Property Compression SetASTM D 412—Test Method for Rubber Properties in TensionASTM D 413—Test Methods for Rubber Property Adhesion to Flexible SubstrateASTM D 471—Test Method for Rubber Property Effect of LiquidsASTM D 573—Test Method for Rubber Deterioration in an Air OvenASTMD1149—Test Method for Rubber Deterioration Surface Ozone Cracking in a Chamber (FlatSpecimens)ASTM D 2240—Test Method for Rubber Property Durometer HardnessDeveloped by the SAE Coolant Hose Committee。
SAE认证

SAE认证(美国机动车工程师学会)美国机动车工程师学会(SAE)的认证:规定了市场上销售的汽车配件(SAE认证)的标准.至于包铅和包塑,是生产工艺,只有通过这道工艺才能保证管子的表面光滑。
目前一般工厂都是采用包铅的,因为包塑的工艺并不是很成熟。
附:SAE标准目录编号名称修订日期字数(千字)页数备注SAE J1019高温输油软管、发动机润滑油软管、以及软管总成试验及程序1990-06-122.665SAE J1037挡风玻璃喷洗器软管2001-082.935SAE J1183弹性材料及部件的疲劳试验推荐指南1998-0211.317SAE J1273液压软管总成推荐操作规程2001-038.6SAE J1288液压制动软管总成的包装、贮存和贮存期1999-042.394SAE J1401公路车辆——采用非石油基液压液体的液压软管总成1999-0912.7SAE J1403真空制动软管1989-073.38SAE J1405液压软管总成可选脉冲试验程序1990-06-182.87SAE J1406液压制动软管在机动车辆上的应用2002-043.816SAE J1527船用燃油软管1993-02-055.6SAE J1570液压盘式制动活塞橡胶防尘套1991-09-303.976SAE J1661CFC-12(R-12)汽车空调系统至HFC-134a(R -134a)改型程序1998-115.268SAE J1662致冷剂改型对于空调系统材料的兼容性1998-113.46SAE J1873传输所含水分试验程序——液压制动软管总成2000-102.474SAE J188动力转向回流软管——高膨胀型1998-013.266SAE J189动力转向回流软管——低压1998-013.29SAE J190动力转向压力软管——钢丝编织型1998-052.985SAE J191动力转向压力软管——低膨胀型1998-053.076SAE J20冷却剂系统软管2002-017.6713SAE J2050高温动力转向压力软管2001-043.46SAE J2064R134a制冷剂汽车空调软管1999-067.3911SAE J30燃料及油软管1998-0635.83SAE J343SAE 100R系列液压软管及软管总成试验及试验程序2001-074.79SAE J51致冷剂12汽车空调系统软管1998-085.698SAE J51附表1.052SAE J517液压软管2001-0435.7通用规范合计25185.22172SAE标准简介SAE各汽车协议和标准的简介1905年初,美国汽车工程师学会(SAE)认识到必须标准化。
SAE J标准目录中文
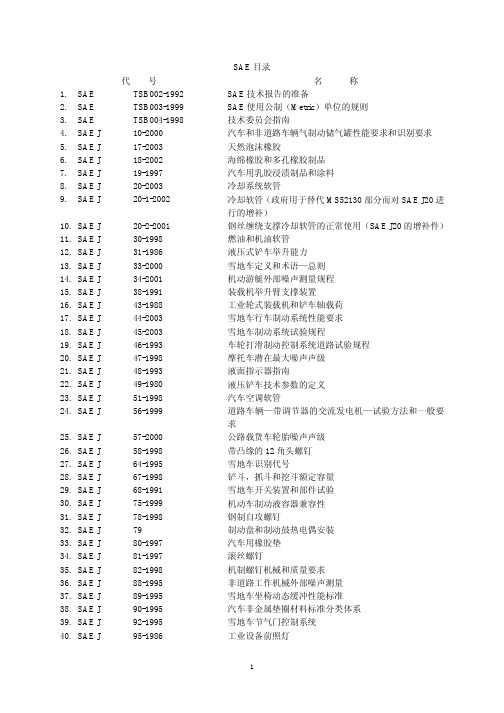
技术委员会指南
汽车和非道路车辆气制动储气罐性能要求和识别要求
天然泡沫橡胶
海绵橡胶和多孔橡胶制品
汽车用乳胶浸渍制品和涂料
冷却系统软管
冷却软管(政府用于替代 MS52130 部分而对 SAE J20 进
行的增补)
钢丝缠绕支撑冷却软管的正常使用(SAE J20 的增补件)
燃油和机油软管
液压式铲车举升能力
雪地车定义和术语—总则
机动游艇外部噪声测量规程
装载机举升臂支撑装置
工业轮式装载机和铲车轴载荷
雪地车行车制动系统性能要求
雪地车制动系统试验规程
车轮打滑制动控制系统道路试验规程
摩托车潜在最大噪声声级
液面指示器指南
液压铲车技术参数的定义
汽车空调软管
道路车辆—带调节器的交流发电机—试验方法和一般要
求
公路载货车轮胎噪声声级
带凸缘的 12 角头螺钉
135-1993 138 139-1999 140-1995 141-1995 153-1987 156-2000 159-2002 160-2001 163-2001 164-1997 167-2002 169-1985 174-1998 174M-1998 175-2003 176-1994 179-2001
名
称
建筑和工业机械充电系统
机动车辆基准标志和三维参考系
发动机油性能和发动机维修分类(除节能方面外)
噪声数据获得系统的检定
非道路机械的接近系统
载货车识别号码
高体积膨胀型动力转向压力软管
低压动力转向回油软管
钢丝编织动力转向压力软管
低体积膨胀型动力转向压力软管
雪地车外部噪声等级
球节及球座总成试验规程
SAE_J标准目录中文
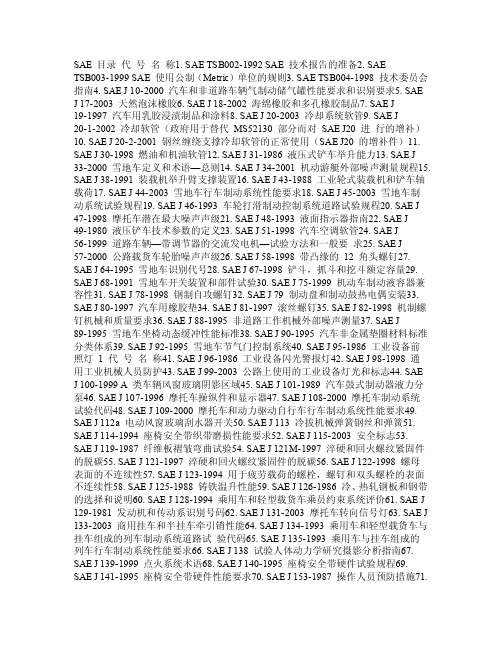
SAE 目录代号名称1. SAE TSB002-1992 SAE 技术报告的准备2. SAETSB003-1999 SAE 使用公制(Metric)单位的规则3. SAE TSB004-1998 技术委员会指南4. SAE J 10-2000 汽车和非道路车辆气制动储气罐性能要求和识别要求5. SAE J 17-2003 天然泡沫橡胶6. SAE J 18-2002 海绵橡胶和多孔橡胶制品7. SAE J19-1997 汽车用乳胶浸渍制品和涂料8. SAE J 20-2003 冷却系统软管9. SAE J20-1-2002 冷却软管(政府用于替代MS52130 部分而对SAE J20 进行的增补)10. SAE J 20-2-2001 钢丝缠绕支撑冷却软管的正常使用(SAE J20 的增补件)11. SAE J 30-1998 燃油和机油软管12. SAE J 31-1986 液压式铲车举升能力13. SAE J33-2000 雪地车定义和术语—总则14. SAE J 34-2001 机动游艇外部噪声测量规程15. SAE J 38-1991 装载机举升臂支撑装置16. SAE J 43-1988 工业轮式装载机和铲车轴载荷17. SAE J 44-2003 雪地车行车制动系统性能要求18. SAE J 45-2003 雪地车制动系统试验规程19. SAE J 46-1993 车轮打滑制动控制系统道路试验规程20. SAE J 47-1998 摩托车潜在最大噪声声级21. SAE J 48-1993 液面指示器指南22. SAE J49-1980 液压铲车技术参数的定义23. SAE J 51-1998 汽车空调软管24. SAE J56-1999 道路车辆—带调节器的交流发电机—试验方法和一般要求25. SAE J57-2000 公路载货车轮胎噪声声级26. SAE J 58-1998 带凸缘的12 角头螺钉27. SAE J 64-1995 雪地车识别代号28. SAE J 67-1998 铲斗,抓斗和挖斗额定容量29. SAE J 68-1991 雪地车开关装置和部件试验30. SAE J 75-1999 机动车制动液容器兼容性31. SAE J 78-1998 钢制自攻螺钉32. SAE J 79 制动盘和制动鼓热电偶安装33. SAE J 80-1997 汽车用橡胶垫34. SAE J 81-1997 滚丝螺钉35. SAE J 82-1998 机制螺钉机械和质量要求36. SAE J 88-1995 非道路工作机械外部噪声测量37. SAE J89-1995 雪地车坐椅动态缓冲性能标准38. SAE J 90-1995 汽车非金属垫圈材料标准分类体系39. SAE J 92-1995 雪地车节气门控制系统40. SAE J 95-1986 工业设备前照灯 1 代号名称41. SAE J 96-1986 工业设备闪光警报灯42. SAE J 98-1998 通用工业机械人员防护43. SAE J 99-2003 公路上使用的工业设备灯光和标志44. SAE J 100-1999 A 类车辆风窗玻璃阴影区域45. SAE J 101-1989 汽车鼓式制动器液力分泵46. SAE J 107-1996 摩托车操纵件和显示器47. SAE J 108-2000 摩托车制动系统试验代码48. SAE J 109-2000 摩托车和动力驱动自行车行车制动系统性能要求49. SAE J 112a 电动风窗玻璃刮水器开关50. SAE J 113 冷拔机械弹簧钢丝和弹簧51. SAE J 114-1994 座椅安全带织带磨损性能要求52. SAE J 115-2003 安全标志53. SAE J 119-1987 纤维板褶皱弯曲试验54. SAE J 121M-1997 淬硬和回火螺纹紧固件的脱碳55. SAE J 121-1997 淬硬和回火螺纹紧固件的脱碳56. SAE J 122-1998 螺母表面的不连续性57. SAE J 123-1994 用于疲劳载荷的螺栓,螺钉和双头螺栓的表面不连续性58. SAE J 125-1988 铸铁温升性能59. SAE J 126-1986 冷、热轧钢板和钢带的选择和说明60. SAE J 128-1994 乘用车和轻型载货车乘员约束系统评价61. SAE J 129-1981 发动机和传动系识别号码62. SAE J 131-2003 摩托车转向信号灯63. SAE J 133-2003 商用挂车和半挂车牵引销性能64. SAE J 134-1993 乘用车和轻型载货车与挂车组成的列车制动系统道路试验代码65. SAE J 135-1993 乘用车与挂车组成的列车行车制动系统性能要求66. SAE J 138 试验人体动力学研究摄影分析指南67. SAE J 139-1999 点火系统术语68. SAE J 140-1995 座椅安全带硬件试验规程69. SAE J 141-1995 座椅安全带硬件性能要求70. SAE J 153-1987 操作人员预防措施71.SAE J 156-2000 保险丝72. SAE J 159-2002 额定容量系统73. SAE J 160-2001 摩擦材料在暴露在温度升高的环境中时尺寸的稳定性74. SAE J 163-2001 低压电线和电缆终端接头及铰接夹75. SAE J 164-1997 散热器盖和加水口颈76. SAE J 167-2002农用拖拉机顶部防护—试验规程和性能要求77. SAE J 169-1985 非道路车辆操作人员空间内空调系统的设计指南78. SAE J 174-1998 英制钢螺纹紧固件力矩-应力试验规程79. SAE J 174M-1998 公制钢螺纹紧固件力矩-应力试验规程80. SAE J 175-2003 道路车辆车轮冲击试验规程81. SAE J 176-1994 非道路自驱动工作机械快速加油设备82. SAE J 179-2001 载货车盘式车轮和可拆卸轮辋—表识 2 代号名称83. SAE J 180-2002 建筑和工业机械充电系统84. SAE J 182-1997 机动车辆基准标志和三维参考系85. SAE J 183-2002 发动机油性能和发动机维修分类(除节能方面外)86. SAE J 184-1998 噪声数据获得系统的检定87. SAE J 185-2003 非道路机械的接近系统88. SAE J 187 载货车识别号码89. SAE J 188-2003 高体积膨胀型动力转向压力软管90. SAE J 189-1998 低压动力转向回油软管91. SAE J 190-1998 钢丝编织动力转向压力软管92. SAE J 191-2003 低体积膨胀型动力转向压力软管93. SAE J 192-2003 雪地车外部噪声等级94. SAE J 193-1996 球节及球座总成试验规程95. SAE J 195-1988机动车辆自动车速控制器96. SAE J 198-2003 载货车、大客车及多用途车风窗玻璃刮水系统97. SAE J 200-2001 橡胶材料分类体系98. SAE J 201-1997 乘用车和轻型载货车在用制动器性能试验规程99. SAE J 207-1985 汽车金属装饰件和结构件的镀铬和镍100.101. SAE J 211-1-2003 冲击试验用仪器—第 1 部分—电子仪器102. SAE J 211-2-2001 冲击试验用仪器—第2 部分—摄影仪器103. SAE J 212-1998 乘用车制动系统测功机试验规程104. SAE J 213-1997 摩托车分类105.106. SAE J216-1999 乘用车玻璃—电路107. SAE J 217-1994 不锈钢17-7PH 弹簧钢丝和弹簧108. SAE J 218-1981 乘用车识别术语109. SAE J 220-1998 起重机起重臂限位装置110. SAE J 222-2000 驻车灯(前位置灯)111. SAE J 224-1980 碰撞变形分类112. SAE J 225-2003 商用车制动系统扭矩平衡试验代码113. SAE J 226-1995 发动机预热器114. SAE J 228-1995 空气流量参考标准115. SAE J 229-1993 乘用车行车制动器结构总成试验规程116. SAE J 230-1994 不锈钢,SAE 30302,弹簧钢丝和弹簧117. SAE J 232-1994 工业旋转割草机118. SAE J 234 电动风窗玻璃清洗器开关119. SAE J 235 电动鼓风机电机开关120. SAE J 238-1998 螺母和锥形弹簧垫圈总成121. SAE J 240-2002 汽车蓄电池寿命试验122. SAE J 243 汽车密封胶,粘结剂和缓冲胶剂的试验方法123. SAE J 244-1992 柴油机进气或排气流量测量124. SAE J 246-2000 球面和凸缘管接头125. SAE J 247-1987 测量车内噪声脉冲的仪器3 代号名称126. SAE J 249-1988 机械制动灯开关127. SAE J 250 合成树脂塑料密封胶—不干型128. SAE J 253-1989 前照灯开关129. SAE J 254-1993 废气排放测量用仪器和测量技术130. SAE J 257-1997 商用车制动器额定功率要求131. SAE J 259 点火开关132. SAE J 264-1998 视野术语133. SAE J 265-2002 柴油机燃油喷嘴总成—8,9,10 和11 型134. SAE J 266-1996 乘用车和轻型载货车稳态方向控制试验规程135. SAE J267-1999 车轮/轮辋—载货车—性能要求和试验规程136. SAE J 268-1989 摩托车后视镜137. SAE J 272-1981 车辆识别号码体系138. SAE J 273-1981 乘用车识别号码体系139. SAE J 274-1989 悬架弹簧额定承载能力140. SAE J 276-2002 铰接式装载机和拖拉机转向锁141. SAE J 277-1995 雪地车电气系统设计电压的维持142. SAE J278-1995 雪地车制动灯143. SAE J 279-1995 雪地车尾灯(后位置灯)144. SAE J 280-1984 雪地车前照灯145. SAE J 283-1999 带三点式挂接装置的农用拖拉机液压举升能力试验规程146. SAE J 284-2002 农用、建筑和工业装备安全警报信号147. SAE J 285-1999 汽油分配泵喷嘴148. SAE J 286-1996 SAE 第2 号离合器摩擦试验机械指南149. SAE J 287-1988 驾驶员手控制区域150. SAE J 288-2002 雪地车燃油箱151. SAE J 291-1980 制动液温度的确定152. SAE J 292-1995 雪地车及车灯、反射装置和相关装备153. SAE J 293-1995 车辆坡道驻车性能要求154. SAE J 294-1993 GVWR 大于4 500 公斤(10 000 lb)车辆的行车制动器总成试验规程155. SAE J 297-2002 工业装备操作人员控制件156. SAE J 299-1993 制动距离试验规程157. SAE J 300-1999 发动机机油黏度分级158. SAE J 301-1999 新的或已修订技术报告的有效日期159. SAE J 304-1999 发动机机油试验160. SAE J 306-1998 汽车齿轮润滑剂黏度分级161. SAE J 308-1996 轴和手动变速器润滑剂162. SAE J 310-2000 汽车润滑脂163. SAE J 311-2000 乘用车自动变速器液164. SAE J 312-2001 车用汽油165. SAE J 313-1998 柴油166. SAE J 314-2002 毛毡—羊毛和部分羊毛167. SAE J 315-1985 纤维板试验规程4 代号名称168. SAE J 318-2003 汽车气制动管接头169. SAE J 321-1999 推土机牵引机械操作人员防护轮罩170. SAE J 322-1996 非金属装饰材料—确定抗硫化氢腐蚀性的试验方法171. SAE J 323-1998 确定柔性塑料材料冷裂性的试验方法172. SAE J 326-1986 液压反铲挖掘机术语173. SAE J328-1994 乘用车及轻型载货车车轮性能要求和试验规程174. SAE J 331-2000 摩托车噪声声级175. SAE J 332-2002 测量乘用车和轻型载货车轮胎一致性的试验机械176. SAE J 335-1995 多位小型发动机排气系统点火抑制177. SAE J 336-2001 载货车驾驶室内部噪声声级178. SAE J 339-1994 座椅安全带织带磨损试验规程179. SAE J 342-1991 大型发动机火花防止器试验规程180. SAE J 343-2001 SAE 100R 系列液压软管和软管总成试验和试验规程181. SAE J 345a 干或湿路面乘用车轮胎最大和抱死时车轮制动力182. SAE J 347-2002 7 型(9.5 mm)柴油机燃油喷嘴总成183. SAE J 348-1990 车轮三角垫木184. SAE J 349-1991 黑色金属杆,棒,管和丝的表面缺陷检查185. SAE J 350-1991 中型发动机火花防止器试验规程186. SAE J 356-1999 可以抑制焊瘤的弯曲,双层扩口和卷边正火低碳钢187. SAE J 357-1999 发动机油的物理和化学特性188. SAE J 358-1991 非破坏性试验189. SAE J 359-1991 红外线试验190. SAE J 360-2001 载货车和大客车坡道驻车性能试验规程191. SAE J 361-1996汽车内饰件和外饰件视觉评价规程192. SAE J 363-1994 滤清器座的安装193. SAE J 365-1994 装饰材料抗擦伤性试验方法194. SAE J 366-2001 重型载货车和大客车外部噪声声级195.196. SAE J 369-2003 车辆内部聚合物材料燃烧特性—试验方法197. SAE J 370-1998 建筑和工业机械用螺栓和内六角螺钉尺寸198. SAE J 371-1993 非道路自驱动工作机械的放油、注油和油位螺塞199. SAE J 373-1993 单片和双片弹簧加载式离合器壳内尺寸200. SAE J 374-2002 车顶抗压试验规程201. SAE J 375-1994 负荷半径式悬臂角指示系统202. SAE J 376-1985 起重机举升负载指示装置203. SAE J 377-2001 车辆通行声音信号装置204. SAE J 378-1988 船用发动机布线205. SAE J 379-1996 制动衬片高氏硬度206. SAE J 380-2002 摩擦材料比重207. SAE J381-2000 载货车,大客车和多用途车风窗玻璃除雾系统试验规程和性能要求208. SAE J 383-1995 机动车辆座椅安全带固定点设计建议209. SAE J 384-1994 机动车辆座椅安全带固定点试验规程5 代号名称210. SAE J 385-1995 机动车辆座椅安全带固定点性能要求211. SAE J 386-1997 非道路工作机械操作人员约束系统212. SAE J 387-1995 机动车辆灯光术语213. SAE J 390-1999 双向尺寸214. SAE J391-1981 颗粒物尺寸定义215.216. SAE J 393-2001 商用车辆车轮,轮毂,轮辋术语217. SAE J 397-1995 防护结构试验室评价—偏转极限值218. SAE J 398-1995 乘用车,多用途车和轻型载货车燃油箱加注口条件219. SAE J 399-1985 阳极化处理的铝制汽车部件220. SAE J 400-2002 表面覆层的耐剥落试验221. SAE J 401-2000 钢的选择和使用222. SAE J 402-1997 锻制钢和轧制钢的SAE 编号系统223. SAE J403-2001 SAE 碳素钢的化学成分224. SAE J 404-2000 SAE 合金钢的化学成分225. SAE J 405-1998 SAE 锻制不锈钢的化学成分226. SAE J 406-1998 钢的可淬性确定方法227. SAE J 409-1995 产品分析—热处理或铸钢化学成分分析的容许变差228. SAE J 411-1997 碳素钢和合金钢229. SAE J 412-1995 钢的热处理和一般特性230. SAE J 413-2002 热处理可锻钢的机械性能231. SAE J 415-1995 热处理术语定义232. SAE J 417-1983 硬度试验和硬度值换算233. SAE J 419-1983 脱碳的测量方法234. SAE J 420-1991 磁粉检查235. SAE J 422-1983 用显微镜确定钢所含物质的方法236. SAE J 423-1998 硬化层深度测量方法237. SAE J 425-1991 用涡电流法进行电磁试验238. SAE J 426-1991 液体渗透剂试验方法239. SAE J 427-1991 渗透辐射检查240. SAE J 428-1991 超声波检查241. SAE J 429-1999 外螺纹紧固件机械性能和材料要求242. SAE J 430-1998 非螺纹紧固件碳素钢实心铆钉机械性能和材料要求243. SAE J 431-2000 汽车灰铸铁件244. SAE J 434-1986 汽车可锻(球墨)铸铁件245. SAE J 435-2002 汽车铸钢件246. SAE J 437a 工具和模具钢的选用和热处理247. SAE J438b 工具和模具钢248. SAE J 439a 硬质合金刀具249. SAE J 441-1993 切割钢丝喷丸250. SAE J 442-2001 喷丸处理用试验带,支架和钢带251. SAE J 443-2003 使用标准喷丸试验带的规程252. SAE J 444-1993 喷丸处理和喷砂清洗用铸丸和铸粒的规格 6 代号名称253. SAE J 445-1996 金属喷丸和喷粒的机械性能试验254. SAE J 447-1995 机动车辆车身及底盘部件的防腐255. SAE J 448a 表面质地256. SAE J449a 表面质地的控制257. SAE J 450-2002 屈服强度和屈服点术语的使用258. SAE J 451-1989 铝合金—基本原理259. SAE J 452-2003 SAE 铸铝合金的一般信息—化学组成,机械和物理性能260. SAE J 454-1991 锻制铝合金的一半数据261. SAE J 457-1991 SAE 锻制铝合金的化学组成,机械性能限值和尺寸公差262. SAE J459-1991 轴承和轴瓦合金263. SAE J 460-1991 轴承和轴瓦合金—SAE 轴承和轴瓦的化学组成264. SAE J 461-2002 锻铜和铸铜合金265. SAE J 462-1981 锻铜合金266. SAE J 463-2002 锻铜和铜合金267. SAE J 464-1989 镁合金268. SAE J 465-1989 铸镁合金269. SAE J 466-1989 锻镁合金270. SAE J 467b 特殊用途合金(超级合金)271. SAE J 468-1988 锌合金锭和压铸件锌合金的成分272. SAE J 469-1989 锌模铸合金273. SAE J 470c 锻镍和与镍有关的合金274. SAE J 471d 粉末冶金黑色金属部件275. SAE J 473a 焊锡276. SAE J 474-1985 电镀及抛光277. SAE J 476a 干密封式管螺纹278. SAE J 482-1998 高六角头螺母279. SAE J 483-1998 槽顶(暗,盖帽式)螺母280. SAE J 485-1998 安装开口销用螺栓和螺钉杆上的孔及螺母的槽281. SAE J 490-1996 球节282. SAE J 491-1987 转向球头销和球座总成283. SAE J 492 铆钉和铆接284. SAE J 493 杆端销和U 形夹285. SAE J 494 带槽销286. SAE J 495 圆柱销(实心)287. SAE J 496 弹性圆柱销288. SAE J 497 非淬火接地柱销289. SAE J 499a 装配用零件软拉孔直齿内花键290. SAE J 501 轴端291. SAE J 502 半圆键292. SAE J 503 半圆键槽和键沟2.。
SAE标准目录

SAE标准目录编辑整理:尊敬的读者朋友们:这里是精品文档编辑中心,本文档内容是由我和我的同事精心编辑整理后发布的,发布之前我们对文中内容进行仔细校对,但是难免会有疏漏的地方,但是任然希望(SAE标准目录)的内容能够给您的工作和学习带来便利。
同时也真诚的希望收到您的建议和反馈,这将是我们进步的源泉,前进的动力。
本文可编辑可修改,如果觉得对您有帮助请收藏以便随时查阅,最后祝您生活愉快业绩进步,以下为SAE标准目录的全部内容。
ETA-UTP001 Revision 0(SAE J1263)[P19].pdf ETA-UTP001-Effective March 23,2001 Implementation of SAE J1263—1996.pdf NASA-SAE—88-1448 LDV Surveys Over Fighter Model at Moderate High Angles of Attack[P27].pdf SAE—Automotive Chassis Engineering Principles (SECOND EDITION)[P454].pdf SAE- Automotive Chassis—Engineering Principles [SECOND EDITION][P456]。
pdf SAE- Automotive Physical Layer SAE—J1708 DS36277。
pdf SAE- Structural Steel Designer's Handbook (Brockenbrough & Merritt)(3Rd Edition)[P1201].pdf SAE—174M-MAY1998 TORQUE—TENSION TEST PROCEDURESTEEL THREADED FASTENERS,METRIC SERIES。
pdf SAE-2006 Formula SAE—Chassis Design(Queen's University)[P18].pdf SAE—720709—1972 Design&Development of a High horsepower torque sensing variable speed drive。
AESJ003 Instrumentation – Basic Design Criteria沙特阿美仪表规范
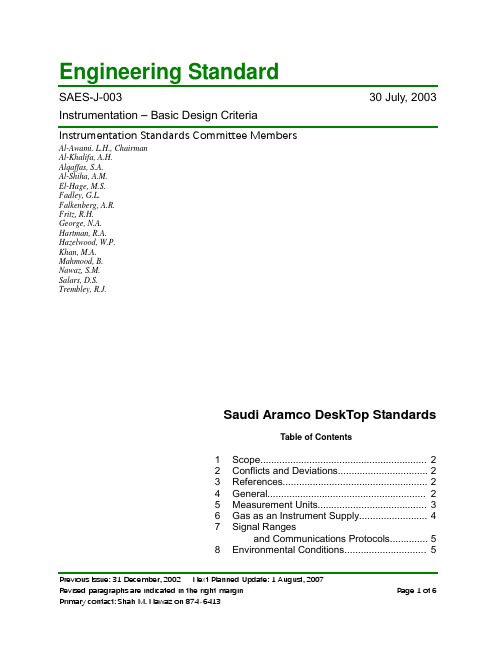
Engineering StandardSAES-J-003 30 July, 2003 Instrumentation – Basic Design CriteriaInstrumentation Standards Committee MembersAl-Awami. L.H., ChairmanAl-Khalifa, A.H.Alqaffas, S.A.Al-Shiha, A.M.El-Hage, M.S.Fadley, G.L.Falkenberg, A.R.Fritz, R.H.George, N.A.Hartman, R.A.Hazelwood, W.P.Khan, M.A.Mahmood, B.Nawaz, S.M.Salars, D.S.Trembley, R.J.Saudi Aramco DeskTop StandardsTable of Contents1 Scope (2)2 Conflicts and Deviations (2)3 References (2)4 General (2)5 Measurement Units (3)6 Gas as an Instrument Supply (4)7 Signal Rangesand Communications Protocols (5)8 Environmental Conditions (5)Previous Issue: 31 December, 2002 Next Planned Update: 1 August, 2007Next Planned Update: 1 August, 2007 Instrumentation – Basic Design Criteria 1 ScopeThis Engineering Standard covers the basic requirements for the selection, design, and application of process instrumentation and control systems.2 Conflicts and Deviations2.1 Any conflicts between this standard and other Saudi Aramco Engineering Standards (SAESs),Saudi Aramco Materials System Specifications (SAMSSs), Industry Standards, codes, forms,and Saudi Aramco Standard Drawings (SASDs) shall be resolved by the Manager, Process &Control Systems Department of Saudi Aramco, Dhahran.2.2 Direct all requests to deviate from this specification in writing to the Company or BuyerRepresentative, who shall follow internal company procedure SAEP-302 and forward suchrequests to the Manager, Process & Control Systems Department of Saudi Aramco, Dhahran.3 ReferencesThe selection of material and equipment, and the design, construction, maintenance, and repair of equipment and facilities covered by this standard shall comply with the latest edition of the references below, unless otherwise noted.Saudi Aramco Engineering ProceduresSAEP-103 Metric Units of Weights and MeasuresSAEP-302 Instructions for Obtaining a Waiver of a Mandatory SaudiAramco Engineering RequirementSaudi Aramco Engineering StandardsSAES-A-105 Noise ControlSAES-A-112 Meteorological and Seismic Design DataSAES-J-700 Control ValvesSAES-J-904 F OUNDATION™ Fieldbus (FF) Systems4 GeneralAll continuous measurement electronic field instruments, and control valve positioners, shall be smart.The design requirements for each type of instrument are covered by the individual standards and specifications.The design and selection of process control and instrumentation systems should include consideration of the following:- Application suitability- ReliabilityNext Planned Update: 1 August, 2007 Instrumentation – Basic Design Criteria- Quality- Accuracy- Repeatability- Life cycle cost- Previous acceptance as a stock item (i.e., savings on spares)- Availability of spares beyond the end of the production run of the respective item- Compatibility with existing equipment (i.e., a Plant Expansion)- Flexibility of use- Compatibility with the environment (climatic and electrical classification)- Ease of maintenance (reduction of down-time)- Ease of operation (confidence and familiarity of the operator)Commentary Note:The priority of the above aspects will depend on the application and equipment underconsideration.5 Measurement UnitsAll new facilities shall be designed for operation in English units with the following exception.Operating Departments which have historically utilized operating units other than English units shall determine whether these units or English units will be used for new facilities under their jurisdiction.Upgrades or modifications to existing facilities shall retain existing operating units unless otherwise specified in project documentation.Next Planned Update: 1 August, 2007 Instrumentation – Basic Design CriteriaNotes: 1. SI Units shall conform to SAEP-103, Metric Units of Weight & Measures.2.Flowrate given in units per day is based on operating day, e.g., BPOD. This is to be differentiated from flow rate percalendar day, e.g., BPCD, which is used for plant design, and takes into account the operating factor (less than unity) of the plant. Thus, BPCD = BPOD * (operating factor).3.Saudi Aramco-defined standard conditions for process flow measurement are as follows:Standard conditions for custody metering are as follows:Next Planned Update: 1 August, 2007 Instrumentation – Basic Design Criteria 6 Gas as an Instrument SupplySour gas shall not be used in lieu of instrument air. Gas with less than 10 ppm H2O, 10 ppm CO2 and5 ppm H2S may be used with prior written approval by the Supervisor, Instrumentation Unit, ProcessInstrumentation Division, Process & Control Systems Department.7 Signal Ranges and Communications Protocols(when used between their controllers and their respective field devices). In the context oflimited to, the above signal types.for plant control. F OUNDATIONpursuant to requirements specified in SAES-J-904.Process Instrumentation Division, Process & Control Systems Department8 Environmental Conditions8.1 TemperatureInstruments and control systems shall operate continuously under the following ambient airtemperatures without any degradation of the manufacturer's guaranteed performance:Notes:1) "Sheltered" refers to permanent, ventilated enclosures or buildings, or permanently fixed sunshadeswith a top and three sides.2) For instruments which dissipate internal heat and are installed in custom engineered enclosures (e.g.,enclosures not included in the original manufacturer's temperature certification), an additional 15°C shallbe added to the above maximum temperatures. An example, for "indoor air conditioned" installation, theequipment must perform at 35 + 15 = 50°C. Similarly, for the "outdoor unsheltered" case, the equipmentshall be designed for a maximum operating temperature of 65 + 15 = 80°C.3) For the outdoor installations only, the designer can take credit for forced or passive cooling to eliminate orreduce the 15°C heat rise. For example, if vortex coolers are used, the heat removal capacity of thecoolers may be subtracted from the generated heat. No more than 15°C reduction in temperature will begiven as credit. The designer shall substantiate his claim by providing the support data and calculations.8.2 ContaminantsInstallations shall be designed for operation in an environment with contaminant levels asdefined in the Ambient Air Quality Section of SAES-A-112.Next Planned Update: 1 August, 2007 Instrumentation – Basic Design Criteria8.3 HumidityIndoor humidity design basis shall be 20% to 80% relative humidity.Outdoor design basis shall be 5% to 95% relative humidity (non-condensing).8.4 NoiseInstruments that generate noise shall be selected so that the effect on the environment islimited in accordance with SAES-A-105.Control valve installations shall meet the noise requirements specified inSAES-J-700.8.5 Offshore and Nearshore EnvironmentEquipment which is not enclosed or hermetically sealed, but is situated offshore or nearshore,shall be protected against corrosion and operational failure due to wind-borne sea water sprayand the accumulation of wetted salt (NaCl). Nearshore is defined as any outdoor, onshorelocation within one kilometer from the shoreline of the Arabian Gulf; all of the Ras TanuraRefinery and Terminal; and within three kilometers from the shoreline of the Red Sea.Revision Summary30 July, 2003 Revised the "Next Planned Update". Reaffirmed the contents of the document, and reissuedwith minor/editorial revision.。
saej1459v003_多楔带和带轮
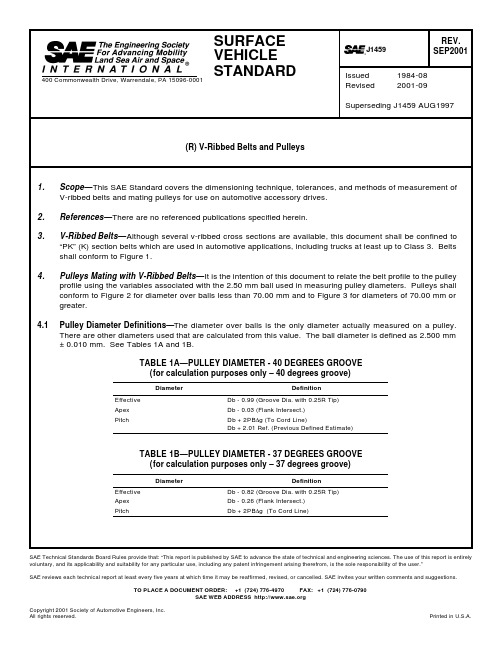
SAE Technical Standards Board Rules provide that: “This report is published by SAE to advance the state of technical and engineering sciences. The use of this report is entirely voluntary, and its applicability and suitability for any particular use, including any patent infringement arising therefrom, is the sole responsibility of the user.”SAE reviews each technical report at least every five years at which time it may be reaffirmed, revised, or cancelled. SAE invites your written comments and suggestions.TO PLACE A DOCUMENT ORDER: +1 (724) 776-4970 FAX: +1 (724) 776-0790SAE WEB ADDRESS Copyright 2001 Society of Automotive Engineers, Inc.FIGURE 1—BELT DIMENSIONING TEMPLATEFIGURE 2—PULLEY DIMENSIONING TEMPLATE (6) GROOVE SHOWN (TYPICAL)FIGURE 3—PULLEY DIMENSIONING TEMPLATE (6) GROOVE SHOWN (TYPICAL)5.Measurement Method—Since the templates in Figures 1 to 3 have profile of a line callouts, it is necessary tocapture the entire profile digitally and compare it to the drawing dimensions. This requires a digital profilometer and eliminates the optical comparator as acceptable for metrology. Because of the inherent speed of these devices, the frequency of audit may have to be reduced, depending on the process used in production. If verification of ongoing quality requires more frequent measurement, the audit with the profilometer is still required, while the supplier can use traditional methods to measure additional belts to satisfy an internal process control characteristic, if they feel the need.6.Belt Dimension Determination—The shape of the belt profile changes with bending, either as profiled backbent, if it is not molded, or between manufacture and measurement. The intent of the document is to achievea precise mating of the belt as bent around a grooved pulley. The 37 degree pulley standard deals with thedistortion of the belt around small diameter pulleys. For larger pulleys, the 40 degree belt rib angle is to be defined on a 127 mm pulley as measured in an arch with a dental compound casting, or equivalent. The detail drawing is to show the rib dimensions as measured in production with the digital profilometer (usually flat).These dimensions may be different from those measured in the arch. Once the relationship between the arch and the production measurements due to the rubber distortion is established, the arch dimensions shall not be measured on an ongoing basis, but rather the detail drawing dimensions representing the flat profilometer method.7.Metrological Issues—In order to facilitate the execution of the programs for digital profilometers to measureboth belts and pulleys, it is permissible to calculate the points defined on the flanks of the belt ribs or pulley grooves. This can be done from the line defined by points along the rib/groove flank line between the tangent points of the tip and root radii. Gage R&R improves with increasing distance between the points selected.Precise methodology can be mutually agreed upon between supplier and OEM.8.V-Ribbed Belt Size—Belt size is designated by a standard series of alphanumeric characters. Beltsmeasured on a metric length system are designated by the number of ribs followed by the belt cross-sectional size (“PK” or “PL”) and the effective length in millimeters. For example, 6PK1370 signifies a 6-rib “PK” section belt, with an effective length of 1370 mm.9.Measurement of V-Ribbed Belts—The length of a V-ribbed belt is determined by use of a measuring fixturecomprised of two pulleys of equal diameter, a method of applying force, and a means of measuring the center distance between the two pulleys. One of the two pulleys is fixed in position while the other is movable along a graduated scale. Both pulleys are allowed to rotate. The fixture is shown schematically in Figure 4. Grooves of master inspection pulleys shall be machined to dimension tolerances shown in Table 2, treated to resist wear, and checked periodically for wear and damage.FIGURE 4—DIAGRAM OF A FIXTURE FOR MEASURING V-RIBBED BELTS9.1Length—To measure the length, the belt is placed on the measuring fixture at the total measuring force shownin Table 2, and rotated around the pulleys at least two revolutions to seat the belt properly in the pulley grooves and to divide the total force equally between the two strands of the belt. The midpoint of the center distance travel of the movable pulley defines the center distance and will be measured through a minimum of one revolution of the belt after the two seating revolutions. The belt effective length is equal to two times the center distance plus the pulley effective circumference. Standard belt center distance tolerances are shown in Table3. For center distance tolerances less than standard, the belt manufacturer should be consulted.10.Other Dimensional Notes—Standard lengths up to and including 2000 mm are to be in 10 mm increments.Standard lengths over 2000 mm up to and including 4000 mm are to be in 25 mm increments.NOTE 1—The sides of the groove are to be 3.2 µm A.A. maximum.NOTE 2—Radial and axial run-out is not to exceed 0.25 mm full indicator movement (FIM). Run-out in the twodirections is measured separately with a ball mounted under spring pressure to follow the groove asthe pulley is rotated.NOTE 3—The diameters over the ball gauges are not to vary from groove to groove more than 0.25 mm forany one belt groove set in a pulley.NOTE 4—Centerline of groove is to be 90.0 degrees ± 0.5 degrees with pulley axis.11.Notes11.1Marginal Indicia—The change bar (I) located in the left margin is for the convenience of the user in locatingareas where technical revisions have been made to the previous issue of the report. An (R) symbol to the left of the document titles indicates a complete revision of the report.PREPARED BY THE SAE BELT DRIVE SYSTEMS COMMITTEETABLE 2—MEASURING CONDITIONS—MILLIMETERSCrossSectionSizeEffective Diameter (reference)Effective Circumference (reference)d B Ball or Rod Diameter ±0.010Diameter Over Ball or Rods ±0.10Total Measuring Force Per Rib (N)PK 95.49300 2.500 96.48100TABLE 3—STANDARD BELT CENTER DISTANCETOLERANCES (1)—MILLIMETERS1.These tolerances are for reference only, and depend on manu-facturing process as well as cost. Supplier and OEM agree-ment must be reached on each application.Belt LengthTolerance on Center Distance 0 – 1200± –4.0Over 1200 – 2000± –5.0Over 2000 – 2500± –6.0Over 2500 – 3000± –7.0Rationale—This document has been revised to update pulley dimensioning to GD&T and to create a compatible belt template.Relationship of SAE Standard to ISO Standard—Not applicable.Application—This SAE Standard covers dimensioning technique, tolerances, and methods of measurement of V-ribbed belts and mating pulleys for use on automotive accessory drives.Reference Section—There are no referenced publications specified herein.Developed by the SAE Belt Drive Systems Committee。
SAEJ1204v001
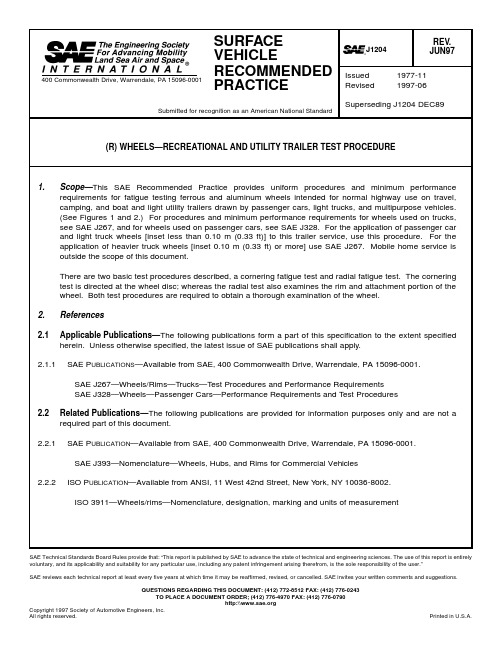
SAE Technical Standards Board Rules provide that: “This report is published by SAE to advance the state of technical and engineering sciences. The use of this report is entirely voluntary, and its applicability and suitability for any particular use, including any patent infringement arising therefrom, is the sole responsibility of the user.”SAE reviews each technical report at least every five years at which time it may be reaffirmed, revised, or cancelled. SAE invites your written comments and suggestions.QUESTIONS REGARDING THIS DOCUMENT: (412) 772-8512 FAX: (412) 776-0243TO PLACE A DOCUMENT ORDER; (412) 776-4970 FAX: (412) 776-0790http:\\Copyright 1997 Society of Automotive Engineers, Inc.FIGURE 1—NOMENCLATURE FOR DROP CENTER WHEELFIGURE 2—NOMENCLATURE FOR DIVIDED WHEEL3.Test Procedures3.1Wheels for Test—Use only fully processed new wheels that are representative of production parts intended for the vehicle and ready for road use. Separate wheels are to be used for each test.3.2Dynamic Cornering Fatigue3.2.1E QUIPMENT —The test machine shall be one with a means to impart a constant rotating bending moment of the wheel.3.2.2P ROCEDURE —The rim shall be clamped securely to the test device. A rigid load arm shaft with a test adaptor shall be attached to the mounting surface of the wheel, using studs and nuts representative of those specified for the wheel.These wheel nuts shall be tightened to the torque limits specified in Table 1 for the stud size and the type of nut. The mating surface of the test adaptor and wheel shall be free of build-up of paint, dirt, wear, or foreign matter. The final clamped position of the wheel without load shall not exceed an eccentricity of 0.25 mm (0.010 in) total indicator reading normal to the shaft axis at the point of loading. The application of the test load will be parallel to a plane through the center of the rim as shown in Figure 3. The loading system should maintain the bending moment within ±3%.TABLE 1—MOUNTING NUT TORQUES (1) FOR LABORATORY WHEEL/TESTS1.Nut torque values may be checked and reset during the course of a wheel test inorder to compensate for the "wearing in" of mating surfaces of nuts and bolt holes. This shall be done at 1000 cycles and it may be done again at 5000 cycles.Application Thread Size Torque (dry)N·m Torque (dry)lbf·ft Disc Wheels7/16 – 20115 ± 7 85 ± 512 x 1.5 mm 115 ± 7 85 ± 51/2 – 20115 ± 7 85 ± 514 x 1.5 mm 158 ± 7115 ± 59/16 – 18158 ± 7115 ± 55/8 – 18178 ± 7130 ± 5FIGURE 3—ROTARY TEST3.2.3B ENDING M OMENT —Bending moment is determined by Equation 1:(Eq. 1)where:M = Bending moment N·m (lbf·ft)W =The maximum static wheel load as specified by vehicle manufacturer and/or wheel manufacturer;N (lbf)R =Static loaded radius of the largest tire to be used on the wheel as specified by the vehicle and/or wheelmanufacturer; m (ft)µ=Coefficient of friction between the tire and the road; use µ - 0.7d =The inset or outset of the wheel m (ft). Use positive sign for inset and negative sign for outset.S =Load Factor (see Table 2)TABLE 2—TEST FACTORS AND MINIMUM CYCLE REQUIREMENTS FOR WHEELSIN NORMAL HIGHWAY SERVICE—DYNAMIC CORNERING FATIGUEWheel Type (Material)“S”Minimum Cycles Ferrous All1.4518 000Cold Formed Aluminum 1.5550 0005000 Series’Aluminum Cast and Forged1.7550 000With 3% or less magnesium content.M W R µd +()S=The test load is determined from Equation 2:(Eq. 2)where:F = Test load; N (lbf)D = Moment arm; m (ft)M = Bending moment N·m (lbf·ft)3.2.4Minimum Cycle Requirement = See Table 2.3.2.5T EST T ERMINATION D EFINITIONS —The wheel under test must complete the minimum number of test cycles (see Table 2) prior to test termination. The test shall be terminated when the operating deflection exceeds the initial deflection at point of load application by 20%. Broken studs or other parts of the test fixture do not require test determination but may result in damage to the wheel and test invalidation.3.3Dynamic Radial Fatigue Test3.3.1E QUIPMENT —The test machine shall be one with a driven rotatable drum, which presents a smooth surface wider than the loaded test tire section width. The suggested diameter of the drum is 1707.6 m (67.23 in)which is 187.5 rev/km (300 rev/mile). The test wheel and tire must provide loading normal to the surface of the drum and in line radially with the center of the test wheel and the drum. The axes of the test wheel and the drum must be parallel. Equipment must hold test load to within ±3%.3.3.2P ROCEDURE —Tires selected for this test shall be representative of the maximum size and type approved by the trailer or the wheel manufacturer for the wheel under test. The test adaptor, studs, and nuts shall be representative of those specified for the wheel. The wheel nuts shall be torqued to the torque limits specified in Table 1 for stud size and type of nut used. Test inflation pressures shall be selected in accordance with Table 3.3.3.3R ADIAL L OAD D ETERMINATION —The radial load is determined by Equation 3:(Eq. 3)where:F r = Radial load; N (lbf)W = The maximum static wheel load as specified by the wheel or trailer manufacturer; N (lbf)K = Load factor = See Table 4TABLE 3—TEST INFLATION PRESSURESUsage Tire Pressure kPa Usage Tire Pressure psi Test Pressure ±20 kPa kPaTest Pressure±3 psi psiUp to 280Up to 40450 65280 – 41041 – 60550 80420 – 55061 – 80690100560 – 69081 – 100900130F MD---- (see Figure 3)=F r WK=3.3.4Minimum Cycle Requirement = See Table4.3.3.5T EST T ERMINATION D EFINITION —T EST C RITERIA —The wheel under test must complete the minimum number of test cycles (see Table 4) prior to test termination. The test shall be terminated by loss of inflation pressure through a fatigue crack or the inability of the wheel to sustain the test load. Failure of the test tire or other parts of the test fixture do not require test termination, but may result in damage to the wheel and test invalidation.PREPARED BY THE SAE WHEEL STANDARDS COMMITTEETABLE 4—TEST FACTORS AND MINIMUM CYCLE REQUIREMENTS FOR WHEELSIN NORMAL HIGHWAY SERVICE—DYNAMIC RADIAL FATIGUEWheel Type (Material)“K”Minimum Cycles Ferrous All 2.0400 000Aluminum All2.25600 000Rationale—Not applicable.Relationship of SAE Standard to ISO Standard—Not applicable.Application—This SAE Recommended Practice provides uniform procedures and minimum performance requirements for fatigue testing ferrous and aluminum wheels intended for normal highway use on travel, camping, and boat and light utility trailers drawn by passenger cars, light trucks, and multipurpose vehicles. For procedures and minimum performance requirements for wheels used on trucks, see SAE J267, and for wheels used on passenger cars, see SAE J328. For the application of passenger car and light truck wheels [inset less than 0.10 m (0.33 ft)] to this trailer service, use this procedure. For the application of heavier truck wheels [inset less than 0.10 m (0.33 ft)] to this trailer service, use this procedure. For the application of heavier truck wheels [inset 0.10 m (0.33 ft) or more] use SAE J267.Mobile home service is outside the scope of this document.There are two basic test procedures described, a cornering fatigue test and radial fatigue test. The cornering test is directed at the wheel disc; whereas the radial test also examines the rim and attachment portion of the wheel. Both test procedures are required to obtain a thorough examination of the wheel.Reference SectionSAE J267—Wheels/Rims—Trucks—Test Procedures and Performance RequirementsSAE J328—Wheels—Passenger Cars—Performance Requirements and Test ProceduresSAE J393—Nomenclature—Wheels, Hubs, and Rims for Commercial VehiclesISO 3911—Wheels/rims—Nomenclature, designation, marking and units of measurementDeveloped by the SAE Wheel Standards Committee。
SAEJ30燃料及油软管
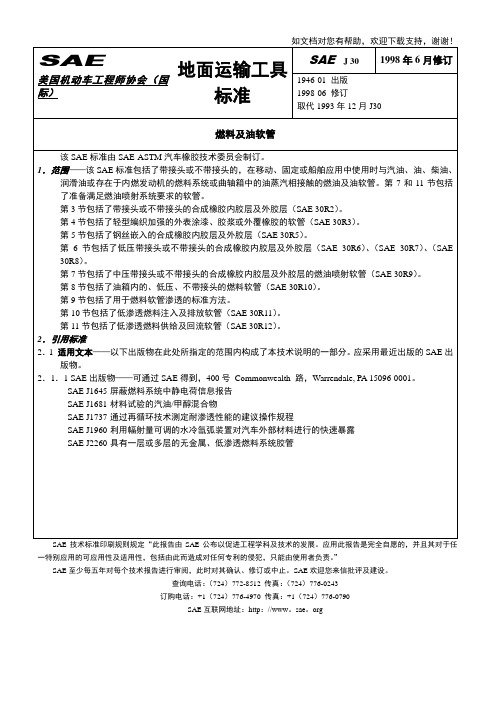
3.4.1合格鉴定试验——为进行合格鉴定试验,每种规格应提供一条7.6m(25英尺)长的未配管接头的软管或10条总成用作合格鉴定。为根据此标准进行鉴定,软管及软管总成必须满足以下试验要求:(a)长度变化,(b)爆破,(c)真空塌陷,(d)低温屈挠,(e)拉伸强度及伸长率,内胶层和外胶层,(f)耐热空气性能,(g)耐燃油性能,(h)耐油性能,(i)耐臭氧性能,以及(j)粘合。
28.58
1.062
1.125
26.97
28.58
1.062
1.125
22.23
7/8
22.23±0.79
0.875±0.031
30.18
31.75
1.188
1.250
25.40
1
25.40±0.79
1.000±0.031
32.54
34.93
1.281
1.375
32.54
34.93
1.281
1.375
第7节包括了中压带接头或不带接头的合成橡胶内胶层及外胶层的燃油喷射软管(SAE 30R9)。
第8节包括了油箱内的、低压、不带接头的燃料软管(SAE 30R10)。
第9节包括了用于燃料软管渗透的标准方法。
第10节包括了低渗透燃料注入及排放软管(SAE 30R11)。
第11节包括了低渗透燃料供给及回流软管(SAE 30R12)。
ASTM D 117-盐浴(Fog)试验方法
ASTM D 257-绝缘材料的DC电阻或导电能力
ASTM D 380-橡胶软管试验方法
ASTM D 412-橡胶拉伸特性试验方法
ASTM D 413-橡胶柔性衬层粘合特性试验方法
ASTM D 471-橡胶特性受流体影响的试验方法
saej211-1v003

J211-1IssuedRevised 2007-07(R) Instrumentation for Impact Test—Part 1—Electronic InstrumentationRATIONALERevisions to SAE J211 are a continuing process and are considered at each five year review. Changes were made as part of an ongoing effort of harmonization with ISO 6487 and include additional definitions, tightening of the filter corridors, procedures for verifying system performance, changes and additions to CFC recommendations, specification of transducer equivalency, and changes to data format recommendations.1. SCOPEThis recommended practice outlines a series of performance recommendations, which concern the whole data channel. These recommendations are not subject to any variation and all of them shall be adhered to by any agency conducting tests to this practice. However, the method of demonstrating compliance with the recommendations is flexible and can be adapted to suit the needs of the particular equipment the agency is using.It is not intended that each recommendation be taken in a literal sense, as necessitating a single test to demonstrate that the recommendation is met. Rather, it is intended that any agency proposing to conduct tests to this practice shall be able to demonstrate that if such a single test could be and were carried out, then their equipment would meet the recommendations. This demonstration shall be undertaken on the basis of reasonable deductions from evidence in their possession, such as the results of partial tests.In some systems it may be necessary to divide the whole channel into subsystems, for calibration and checking purposes. The recommendations have been written only for the whole channel, as this is the sole route by which subsystem performances affect the quality of the output. If it is difficult to measure the whole channel performance, which is usually the case, the test agency may treat the channel as two or more convenient subsystems. The whole channel performance could then be demonstrated on the basis of subsystem results, together with a rationale for combining the subsystem results together.Part 1 of this recommended practice covers electronic instrumentation and Part 2 covers photographic instrumentation. PART 1 - ELECTRONIC INSTRUMENTATION1.1 PurposeThe purpose of this SAE Recommended practice is to provide guidelines and recommendations for the techniques of measurement used in impact tests. The aim is to achieve uniformity in instrumentation practice and in reporting test results. Use of this recommended practice will provide a basis for meaningful comparisons of test results from different sources.__________________________________________________________________________________________________________________________________________ SAE Technical Standards Board Rules provide that: “This report is published by SAE to advance the state of technical and engineering sciences. The use of this report is entirely voluntary, and its applicability and suitability for any particular use, including any patent infringement arising therefrom, is the sole responsibility of the user.”SAE reviews each technical report at least every five years at which time it may be reaffirmed, revised, or cancelled. SAE invites your written comments and suggestions. Copyright © 2007 SAE InternationalAll rights reserved. No part of this publication may be reproduced, stored in a retrieval system or transmitted, in any form or by any means, electronic, mechanical, photocopying, recording, or otherwise, without the prior written permission of SAE.TO PLACE A DOCUMENT ORDER: Tel: 877-606-7323 (inside USA and Canada)Tel: 724-776-4970 (outside USA)Fax: 724-776-0790Email: CustomerService@SAE WEB ADDRESS: h ttp://1.2 Field of ApplicationThe instrumentation as defined in this recommended practice applies in particular to impact tests for road vehicles, including tests of their sub-assemblies, and occupant surrogates.2. REFERENCES2.1 Applicable PublicationsThe following publications form a part of this specification to the extent specified herein. Unless otherwise indicated, the latest version of SAE publications shall apply.Publications2.1.1 SAEAvailable from SAE, 400 Commonwealth Drive, Warrendale, PA 15096-0001, Tel: 877-606-7323 (inside USA and Canada) or 724-776-4970 (outside USA), .SAE J670 Vehicle Dynamics TerminologySAE J1727 Injury Calculations GuidelinesSAE J1733 Sign Convention for Vehicle Crash TestingSAE J2570 Performance Specifications for Anthropomorphic Test Device TransducersSAE Paper 930100 An Evaluation of Various Viscous Criterion Computational AlgorithmsPublication2.1.2 NHTSAAvailable from Department of Transportation, The Office of Crashworthiness Research, 408 7th Street SW, Washington, DC 20590.NHTSA Version 5 Test Reference Guide: Volume 1 – Vehicle Tests, Volume 2 – Biomechanics, Volume 3 – Components, and Volume 4 – Signal Waveform Generator3. DEFINITIONSThe definitions in paragraphs 3.5 to 3.14 apply to the whole data channel, as defined in paragraph 3.1.3.1 Data ChannelAll of the instrumentation from and including a single transducer (or multiple transducers whose outputs are combined in some specified way) up to and including any analysis procedures that may alter the frequency content or the amplitude content or the timing of data. It also includes all cabling and interconnections.3.2 TransducerThe first device in a data channel, used to convert a physical quantity to be measured into a second quantity (such as an electrical voltage) which can be processed by the remainder of the channel. For transducer equivalency, see Appendix B.3.3 Full ScaleThe maximum usable linear range of a data channel. For ATD transducers, see SAE J2570.3.4 Data Channel Full ScaleThat value of a data channel determined by the component of the channel with the lowest full scale level. This is expressed in terms of the measured variable (input). For example, F.S. = 50 G, 1000 N, 1 m/s, etc.3.5 Channel Amplitude Class, CACThe designation for a data channel that meets certain amplitude characteristics as specified by this recommended practice. The CAC number is numerically equal to the upper limit of the measurement range (that is, equivalent to the data channel full scale).3.6 Characteristic Frequencies, F H, F L, F NThese frequencies are defined in Figures 1 and 2.3.7 Channel Frequency Class, CFCThe channel frequency class is designated by a number indicating that the channel frequency response lies within limits specified by Figure 1 for CFCs of 1000 and 600, and by Figure 2 for CFCs of 60 and 180.NOTE: Figure 1 has not changed in reference to J211 March 1995 except to specify nodal points instead of slopes. This number and the value of the frequency F H in hertz are numerically equal.3.8 Calibration ValueThe value measured and read during the calibration of a data channel (see paragraph 4.6).3.9 Sensitivity CoefficientThe slope of the straight line representing the best fit to the calibration values determined by the method of least squares within the channel amplitude class.3.10 Calibration Factor of a Data ChannelThe arithmetic mean of the sensitivity coefficients evaluated over frequencies which are evenly spaced on a logarithmic scale between F L and F H/2.5.3.11 Linearity ErrorThe ratio, in percent, of the maximum difference between the calibration value and the corresponding value read on the straight line defined in paragraph 3.9 at the upper limit of the channel amplitude class (data channel full scale).3.12 SensitivityThe ratio of the output signal (in equivalent physical units) to the input signal (physical excitation), when an excitation is applied to the transducer. (Example: 10.24 mV/G/V for a strain gage accelerometer.) For ATD transducers, see SAE J2570.3.13 Phase Delay TimeThe phase delay time of a data channel is equal to the phase delay (in radians) of a sinusoidal signal, divided by the angular frequency of that signal (in radians per second).3.14 EnvironmentThe aggregate, at a given moment, of all external conditions and influences to which the data channel is subjected.3.15 Transverse Sensitivity (of a rectilinear transducer)The sensitivity to excitation in a nominal direction perpendicular to its sensitive axis.NOTE: The transverse sensitivity is usually a function of the nominal direction of the axis chosen. For ATD transducers, see SAE J2570.3.16 Transverse Sensitivity Ratio (of a rectilinear transducer)The ratio of the transverse sensitivity to its sensitivity along its sensitive axis.3.17 FFT (Fast Fourier Transform)A mathematical function used to convert data from the time domain to the frequency domain (FFT filter, a filter which operates in the frequency domain).3.18 ATDAnthropomorphic Test Device (Crash Test Dummy).4. DATA CHANNEL PERFORMANCE REQUIREMENTS4.1 Linearity ErrorThe absolute value of the linearity error of a data channel at any frequency in the CFC, shall be less than or equal to 2.5% of the value of the CAC, through the whole measurement range. In general a sufficient number of measurements shall be carried out in order to ensure the linearity in the range of interest, that is, between F L and F H.FIGURE 1 - DATA CHANNEL DYNAMIC ACCURACY, CLASS 600 AND 1000FIGURE 2 - DATA CHANNEL DYNAMIC ACCURACY, CLASS 60 AND 1804.2 Amplitude Against FrequencyThe frequency response of a data channel shall lie within the limiting curves given in Figure 1 for CFCs of 1000 or 600. For CFCs of 180 or 60 the frequency response of a data channel shall lie within the limiting curves given in Figure 2. The 0 dB line is defined by the calibration factor. Note: The Figure 2 envelopes have been derived to center the frequency responses of the March 1995 J211 Appendix C CFC 60 and 180 filters in the corridors.4.3 Phase Delay TimeThe phase delay time between the input and the output of a data channel shall be determined, and shall not vary more than 1/(10*F H) seconds between 0.03*F H and F H. This includes the transducer, that is, the input is the excitation to the transducer.4.4 TimeBase4.4.1 TimeA time base shall give at least 1/100 second resolution with an error of less than 1/10000 second.4.4.2 Relative Time DelayThe relative time delay between the signals of two or more data channels regardless of their frequency class, must not exceed 1 millisecond. Two or more data channels of which the signals are combined shall have the same frequency class and shall not have a relative time delay greater than 1/(10*F H) seconds. This requirement applies to analog signals as well as digital signals.4.5 Transducer Transverse Sensitivity RatioThe transverse sensitivity ratio of all transducers shall be less than 5% in any direction. For ATD transducers, see SAE J2570.4.6 CalibrationValues in this section apply to reference equipment or "standards" against which a data channel is "calibrated", that is, itsperformance is determined.4.6.1 GeneralA data channel shall be calibrated at least once a year against reference equipment traceable to known standards. The methods used to carry out a comparison with reference equipment shall not introduce an error greater than 1% of the CAC. The use of the reference equipment is limited to the range of frequencies for which they have been calibrated. Subsystems of a data channel may be evaluated individually and the results factored into the accuracy of the total data channel. This can be accomplished for example by an electrical signal of known amplitude simulating the output signal of the transducer which allows a check to be made on the gain of the data channel, except the transducer.4.6.2 Accuracy of Reference Equipment for CalibrationThe accuracy of the reference equipment shall be certified or endorsed by an approved metrology service (for example, traceable to the National Institute of Standards and Technology).4.6.2.1 StaticCalibration4.6.2.1.1 AccelerationsThe error shall be less than 1.5% of the channel amplitude class.4.6.2.1.2 ForcesThe error shall be less than 1% of the channel amplitude class.4.6.2.1.3 DisplacementsThe error shall be less than 1% of the channel amplitude class.Calibration4.6.2.2 Dynamic4.6.2.2.1 AccelerationsThe error in the reference accelerations expressed as a percentage of the channel amplitude class shall be less than 1.5% below 400 Hz, less than 2% between 400 and 900 Hz, and less than 2.5% between 900 Hz and the maximum frequency at which the reference acceleration is utilized (see paragraph 4.6.4).4.6.2.2.2 Forces,Moments, and DisplacementsSee SAE J2570 for load cell specifications titled “Free Air Resonance” for force and moment info.4.6.2.3 TimeThe error in the reference time shall be less than 1/(10 * sample rate).4.6.3 SensitivityCoefficient and Linearity ErrorThe sensitivity coefficient and the linearity error shall be determined by measuring the output signal of the data channel against a known input signal, for various values of this signal. (The input signal is referenced to well known physical data, which is, a load or acceleration, but not voltage.)The calibration of the data channel shall cover the whole range of the amplitude class. (This is between F L and F H/2.5.)For bi-directional channels, both the positive and negative values shall be evaluated. If the calibration equipment cannot produce the required input, due to excessively high values of the quantity to be measured, calibrations shall be carried out within the limits of these calibration standards and these limits shall be recorded in the report.A total data channel shall be calibrated at a frequency or at a spectrum of frequencies with its significant values comprised between F L and F H/2.5.4.6.4 Calibration of the Frequency ResponseThe response curves of phase and amplitude against frequency for the data channel shall be determined by measuring the output signals of the data channel in terms of phase and amplitude against a known input signal, for various values of this signal varying between F L and 10 times the CFC or 3000 Hz whichever is the lower value.4.7 Environmental EffectsThe presence of any environmental effects shall be checked (that is, electric or magnetic flux, electrostatic discharge, cable velocity, etc.). This can be done for instance by recording the output of spare channels equipped with dummy transducers. If such an output signal is greater than 2% of the expected data peak value, corrective action shall be taken, for instance re-allocation or replacement of cables.5. DATA CHANNEL SELECTIONThe selection of a frequency response class is dependent upon many considerations, some of which may be unique to a particular test. The ultimate usage of the data and good engineering judgment will determine what portions of the frequency spectrum are significant or useful. The various classes of frequency response in Figures 1 and 2 are intended to permit appropriate choices for different engineering requirements.It is important to note that valid comparisons using different frequency response classes may be difficult to make. It is useful to establish specific frequency response classes when comparing test results from different sources. The frequency response classes in Table 1 are recommended for that purpose. These recommendations reflect current practices and equipment. However, it is recognized that other considerations (for example, biomechanics) may impose special instrumentation requirements.The channel class recommendations for a particular application shall not be considered to imply that all the frequencies passed by that channel are significant for the application. In several cases, such as occupant head accelerations, headform accelerations, and femur force, the recommendation may be higher than necessary, but current biomechanical knowledge will not permit a closer specification. All data are to be gathered at CFC 1000 or higher, for any purpose.TABLE 1 - FREQUENCY RESPONSE CLASSESTypical Test Measurements Channel Frequency Class (CFC)Vehicle structural accelerations for use in:Total vehicle comparison 60(1)Collision simulation input 60Component analysis 600Integration for velocity or displacement 180Barrier face force 60Belt restraint system loads 60Anthropomorphic Test DeviceHead accelerations (linear and angular) 1000eck Forces 1000(2,3,7)Moments 600(2,3)Arm Forces 600(5)Moments 600(5)Accelerations 600(5)ThoraxSpine accelerations 180Rib accelerations 1000(2)Sternum accelerations 1000(2)Deflections 600(2,4)LumbarForces 600(6)Moments 600(6)PelvisAccelerations 1000(2)Forces 600(6)Moments 600(6)Femur/Knee/Tibia/AnkleAccelerations 1000Forces 600Moments 600(2)Displacements 180(2)Sled acceleration 60Steering column loads 600Headform acceleration 10001. When overall acceleration of the frame or body in a given direction is desired and a higher frequencyresponse class is used, readability of the data may be improved by averaging outputs of two or moretransducers at different locations.2. UMTRI-86-32 and ISO/TC22/SC12/WG3 N194.3. These classifications are needed to calculate head impact forces based on neck forces and headaccelerations when using an ATD.4. SAE paper 930100.5. SAE paper 2002-01-0806 or ISO/TC22/SC12/WG6 N557.6. Reference Appendix B.7. When Force channels are multiplied by a moment arm, a CFC 600 filter shall be used.6. MOUNTING OF TRANSDUCERSMechanical resonance associated with transducer mounting shall not distort readout data.Transducers shall be mounted on dummies using a support specially provided for this purpose. In cases where properties of non-mechanical test subjects preclude rigid transducer mounting, an analytical or experimental evaluation of mounting effects on the data shall be provided.Acceleration transducers, in particular, shall be mounted in such a way that the initial angle of the actual measurement axis to the corresponding axis of the reference axis system is not greater than 5 degrees unless analytical or experimental assessment of the effect of the mounting on the collected data is made. When multi-axial accelerations at a point are to be measured, each acceleration transducer axis shall pass within 10 mm of that point, and the center of seismic mass of each accelerometer shall be within 30 mm of that point.7. SIGN CONVENTIONIn order to compare test results obtained from different crash test facilities, standardized coordinate systems need to be defined for crash test dummies, vehicle structures and laboratory fixtures. In addition, recorded polarities for various transducer outputs need to be defined relative to positive directions of the appropriate coordinate systems. This section describes the standardized sign convention.7.1 Right-Handed Coordinate SystemTo assure consistent vector directions of moments and angular velocities and accelerations produced by vector multiplications all coordinate systems used in vehicle testing will be "right-handed".Right-handed coordinate system consists of an ordered set of three mutually perpendicular axes (x, y, z) which have a common origin and whose positive directions point in the same directions as the ordered set of the thumb, forefinger and middle finger of the right hand when positioned as shown in Figure 3. Note that one can choose the positive x-axis to point in the direction of either the thumb, forefinger or middle finger as shown in the orientations 1, 2, and 3 of Figure 3. However, once this decision is made then the positive directions of the y- and z-axes must be as indicated by corresponding orientation shown in Figure 3.FIGURE 3 - THE THREE POSSIBLE ORIENTATIONS OF A RIGHT-HANDED COORDINATE SYSTEM RELATIVE TO THE THUMB, FOREFINGER AND MIDDLE FINGER OF THE RIGHT HANDPositive angular motion and moment directions are determined by the right-handed screw rule. If a positive axis is grasped with the right hand with the thumb extended in the positive direction as shown in Figure 4, then the curl of the fingers indicate the positive direction for angular motions and moments.FIGURE 4 - RIGHT-HANDED SCREW RULEA simple method to determine if a (x, y, z) coordinate system is right-handed is to rotate the system 90 degrees about the z-axis using the right-handed screw rule. If the positive x-axis rotates to the position previously occupied by the positive y-axis, then the system is right handed.7.2 Vehicle and Laboratory Coordinate SystemsFor vehicle and laboratory coordinate systems, positive z-axis will be directed downward, positive x-axis will be directed forward relative to the vehicle and positive y-axis will be directed away from the vehicle's left to its right (see SAE J670 – Vehicle Dynamics Terminology). For structures within the vehicle that have a principle axis of motion such as the steering wheel and column, the vehicle coordinate system may be rotated about the y-axis such that the positive x-axis is directed along the column axis.7.3 Dummy Coordinate SystemsCoordinate systems can be affixed to any point on the dummy. To determine the orientation of the coordinate axes, the dummy will always be considered as standing erect. For this posture, the positive y-axis will be directed from the dummy's left to its right side, the positive z-axis will be directed downward from head to toe, and the positive x-axis will be directed forward. In anatomical terminology, the positive x-axis is directed from the posterior to the anterior (P-A), the positive y-axis is directed form the left to right (L-R), and the positive z-axis is directed from superior to inferior (S-I). Figure 5 shows examples of this standardized orientation for coordinate systems attached to a few body points. Note that as the dummy is articulated to sit in a vehicle or if the dummy is articulated for a test, the coordinate systems rotate with their respective dummy parts.7.4 Polarities of Acceleration, Velocity, and DisplacementPositive recorded outputs for these transducers are to be consistent with the positive axes of the coordinate system defined for the specific dummy or vehicle point being measured. For example, a blow to the back of the dummy's head produces an acceleration in the forward direction (+x) which shall be recorded as a positive acceleration. A blow to the top of the head produces a +z acceleration. A blow to the left side of the head produces a +y acceleration.For displacements, the coordinate systems of interest must be defined. For example, frontal chest compression is the distance that the sternum moves relative to the thoracic spine. In this case, the coordinate system is fixed to the thoracic spine. When the sternum moves closer to the spine, its displacement is rearward relative to the spine which is in the negative x-direction. Hence, the polarity for frontal chest compression is negative. For lateral chest compression, a blow to the left side of the chest produces a positive displacement of the impacted ribs relative to the thoracic spine. However, a blow to the right side of the chest produces a negative rib displacement. The rearward displacement of the tibia relative to the femur that is measured by the knee shear transducer is in the negative x-direction. The polarity for this motion shall be negative.FIGURE 5 - ORIENTATIONS OF STANDARDIZED DUMMY COORDINATE SYSTEMSFOR STANDING AND SEATED POSTURES7.5 Polarities of Measured External LoadsFor load cells that measure loads applied directly to the dummy or vehicle structure, their recorded output polarities shall be consistent with the direction of the applied external load referenced to the standardized coordinate system at the point of the load application. For example, load cells that measure shoulder belt loading of the clavicle are designed to measure Fx and Fz applied to the clavicle. Positive directions for these applied forces would be forward (+x) and downward (+z) relative to the dummy, respectively. For the BIOSID, a lateral inward load applied to the crest of the left ilium would be positive (+y), while a lateral inward load applied to the crest of the right ilium would be negative (-y).7.6 Polarities of Measured Internal LoadsDefining recorded output polarities for load cells that measure loads internal to the dummy requires a standardized dummy sectioning scheme and a definition of what sectioned dummy part is to be loaded in the positive direction since internal loads occur in pairs of equal magnitudes but opposite directions. The standardized sectioning scheme is illustrated by the free-body diagram of a cube shown in Figure 6. It is assumed that the load cell of interest is contained within the cube and responds to loads applied to the surfaces of the cube. Load cell outputs shall be recorded with positive polarities when normal loads, shear loads, torques or moments are applied in the positive direction, as defined by the standardized coordinate system, to the right, front, and/or bottom surfaces of the cube. These loads are represented by solid arrows. For static equilibrium, equal magnitude but opposite (negative) direction loads must be applied to the left, back and/or top surfaces of the cube as indicated by the dashed arrows. For example, upper and lower neck, lumbar spine, and upper and lower tibia load cells shall have positive recorded outputs when the dummy is sectioned below the load cell in question and positive loads are applied to the bottom surface of the load cell in question. Free-body diagrams showing the load systems that produce the required recorded polarities for specific dummy load cells are given in the appropriate dummy users manual and in SAE Information Report J1733 - Sign Convention for Vehicle Crash Testing.DUMMY PART CONTAINING THE LOAD CELL OF INTEREST (ILLUSTRATEDAS A CUBE) FOR POSITIVE RECORDED POLARITIESNotes for Figure 4:1. Principle axes of load cell are aligned parallel to respective axes of local dummy coordinate system.2. Bold arrows of normal forces (F), shear forces (S), and moments (M) are shown in positive directions. These Positiveloads are applied to front, right, and bottom surfaces of the cube. Dotted arrows indicate direction of loads applied to the back, left and top surfaces for static equilibrium.7.7 Dummy Manipulations for Checking Polarities of Measured LoadsTable 2 contains descriptions of dummy manipulations and the corresponding polarities for recorded outputs for some of the more common load cells used in dummies. Manipulations for checking polarities of load cells not listed in Table 2 may be found in the users manual for the specific dummy being used or SAE Information Report J1733 - Sign Conventionfor Vehicle Crash Testing.TABLE 2 - DUMMY MANIPULATIONS FOR CHECKING RECORDEDLOAD CELL POLARITY RELATIVE TO SIGN CONVENTIONLoad Cell Measure DummyManipulations Polarity Upper Fx Head rearward, chest forward +And Fy Head leftward, chest rightward +Lower Fz Head upward, chest downward +Neck Mx Left ear toward left shoulder +Loads My Chin toward sternum +Mz Chin toward left shoulder+Left shoulder Fx Left shoulder forward, chest rearward +Loads Fy Left shoulder rightward, chest leftward +(BioSID) Fz Left shoulder downward, chest upward +Right shoulder Fx Right shoulder forward, chest rearward +Loads Fy Right shoulder rightward, chest leftward +(BioSID) Fz Right shoulder downward, chest upward +Clavicle Fx Shoulder forward, chest rearward +Loads Fz Shoulder downward, chest upward +Rib force Upper AndLower Lumbar Spine FxFxFyFzMxMyMzCompressionChest rearward, Pelvis forwardChest leftward, pelvis rightwardChest upward, pelvis downwardLeft shoulder toward left hipSternum toward front of legsRight shoulder forward, left shoulder rearward(-)++++++Sacrum load(BioSID)Fy Left H-point pad leftward, chest rightward +Left iliac load(BioSID)Fy Left iliac rightward, chest leftward +Right iliac load(BioSID)Fy Right iliac rightward, chest leftward +Pubic load(side impact)Fy Right H-point pad leftward, left pad rightward (-)Crotch belt Loads FxFzPubic rearward, pelvis forwardPubic upward, chest downward(-)(-)Iliac lap belt Loads FxMyUpper iliac spine rearward, chest forwardUpper iliac spine rearward, chest forward(-)+。
- 1、下载文档前请自行甄别文档内容的完整性,平台不提供额外的编辑、内容补充、找答案等附加服务。
- 2、"仅部分预览"的文档,不可在线预览部分如存在完整性等问题,可反馈申请退款(可完整预览的文档不适用该条件!)。
- 3、如文档侵犯您的权益,请联系客服反馈,我们会尽快为您处理(人工客服工作时间:9:00-18:30)。
SAE Technical Standards Board Rules provide that: “This report is published by SAE to advance the state of technical and engineering sciences. The use of this report is entirely voluntary, and its applicability and suitability for any particular use, including any patent infringement arising therefrom, is the sole responsibility of the user.”SAE reviews each technical report at least every five years at which time it may be reaffirmed, revised, or cancelled. SAE invites your written comments and suggestions.Copyright © 2003 SAE InternationalAll rights reserved. No part of this publication may be reproduced, stored in a retrieval system or transmitted, in any form or by any means, electronic, mechanical, photocopying,recording, or otherwise, without the prior written permission of SAE.TO PLACE A DOCUMENT ORDER:Tel: 877-606-7323 (inside USA and Canada)Tel: 724-776-4970 (outside USA)Fax: 724-776-0790Email: custsvc@J1Motorcycle Turn Signal Lamps1.Scope—This SAE Standard provides design parameters and general requirements for motorcycle turn signal lamps. It does not apply to mopeds.2.References2.1Applicable Publications—The following publications form a part of the specification to the extent specified herein. Unless otherwise indicated, the latest revision of SAE publications shall apply.2.1.1SAE P UBLICATIONS —Available from SAE, 400 Commonwealth Drive, Warrendale, PA 15096-0001.SAE J213—Motorcycle Classification SAE J567—Lamp Bulb Retention SystemSAE J575—Tests Methods and Equipment for Lighting Devices and Components for Use on VehiclesLess than 2032 mm in Overall WidthSAE J576—Plastic Materials for Use in O ptical Parts Such as Lenses and Reflectors of Motor VehicleLighting DevicesSAE J578—Color Specification3.Definition3.1Motorcycle Turn Signal Lamps—The signaling elements of a turn signal system which indicate the intent to change direction by giving a flashing light on the side toward which the turn will be made.4.General Requirements—The effective projected illuminated area measured on a plane at right angles to the axis of a lamp shall not be less than 22 cm 2 (3-1/2 in 2).4.1The following sections from SAE J575 are a part of this document:4.1.1S ECTION 3.1—Vibration T est 4.1.2S ECTION 3.2—Moisture T est 4.1.3S ECTION 3.3—Dust Exposure Test 4.1.4S ECTION 3.4—Corrosion Test4.1.5S ECTION 3.5—Warpage Test on Devices with Plastic Components 4.1.6S ECTION 3.6—Photometry Test4.1.6.1See Table 1 for Motorcycle Class including C, D + H and T able 2 for Class including A,B,E,+L.4.1.6.2All intensity measurements shall be made with the filament of the signal lamp at least 3 m (10 ft) from the photometer screen. The H-V axis shall be taken as parallel to the longitudinal axis of the vehicle.TABLE 1—MINIMUM INTENSITY REQUIREMENTS (cd) CLASS C,D+H MOTORCYCLES (1)(2)1.Specifications in T ables 1 and 2 are based on laboratories using accurate, rated bulbs during testing.mps designed for use in both 6 V and 12 V systems shall be tested with 12 V bulbs. Lamps designedto operate on the vehicle through a resistor or equivalent shall be photometered with the listed design volt-age of the design source applied across the combination of resistance and filament.Test Points (degrees)Front Signal YellowRear SignalRedRear Signal Yellow10 U and D 10 L and R V 133038820 5 U and D20 L and R 10 L and R 5 L and R V 13 38638831015208254055 H20 L and R 10 L and R 5 L and R V1850100100513252513336865Maximum Rear Lamp Only——300750TABLE 2—MINIMUM INTENSITY REQUIREMENTS (cd) CLASS A,B,E+L AND C MOTORCYCLES (1)(2)1.Specifications in T ables 1 and 2 are based on laboratories using accurate, rated bulbs during testing.mps designed for use in both 6 V and 12 V systems shall be tested with 12 V bulbs. Lamps designed to operate on the vehicle through a resistor or equivalent shall be photome-tered with the listed design voltage of the design source applied across the combination of resistance and filament.Test Points (degrees)Red Yellow 10 U and D 10 L and R38 V 7155 U and D20 L and R 3810 L and R 820 5 L and R 1330 V1845 H20 L and R 41010 L and R 1028 5 L and R 2060 V2060Maximum Rear Lamp Only3007505.Color Test—The color of the light emitted from turn signal lamps shall be red or yellow to the rear and yellowto the front of the vehicle. See SAE J578.6.Plastic Materials—Any plastic materials used in optical parts shall comply with requirements set forth in SAEJ576.7.Installation Requirements—The following requirements apply to the device as used on the vehicle and arenot a part of the laboratory requirements and test procedures.7.1The filament center of each signal lamp on the front shall be symmetrically spaced a minimum of 200 mm (8 in)from the centerline of the vehicle and 100 mm (4 in) from the inside diameter of the retaining ring of the headlamp unit providing the lower beam. On the rear, the symmetrical spacing shall be a minimum of 110 mm (4-1/2 in) from the centerline of the vehicle to the filament axis of the signal lamp. A minimum edge to edge separation of 100 mm (4 in) when a single tail/stop lamp is mounted on the verical centerline and the turn signal lamps are red.7.1.1Visibility of the front turn signal to the front and the rear turn signal to the rear shall not be obstructed by anypart of the vehicle throughout the test angles for the lamps, if such obstruction causes the lamp to fail to meet minimum photometric visibility requirements.7.1.2The signals from each lamp shall be visible through a horizontal angle of 45 degrees outboard. To beconsidered visible, the lamp must project a minimum unobstructed illuminated area of 12.5 cm2 (2 in2), measured at all angles throughout the 45 degrees requirement.7.2Turn Signal Pilot Indicator—There shall be either a light or sound signal to give the operator a clear andunmistakable indication that the turn signal system is functioning correctly. The illuminated indicator shall consist of one or more lights flashing at the same frequency as the signal lamps, and shall be plainly visible to operators of all heights when seated in normal position in the operator's seat, while driving in bright sunlight.If a sound signal is used, it shall be audible to the operator when the motorcycle is operating at 55 km/h (35mph) or less. The signal shall cycle on and off at the same frequency as the signal lamps. Failure of one or more turn signal lamps to operate shall be indicated by a continuous tone or by failure of the signal to sound.PREPARED BY THE SAE MOTORCYCLE TECHNICAL COMMITTEEAPPENDIX AA.1As a matter of information, attention is called to SAE J567 for requirements and gages to be used in socketdesign.A.2All motorcycle class designations are those given in SAE J213.Rationale—J131 has been reaffirmed to comply with the SAE 5-Y ear Review policy.Relationship of SAE Standard to ISO Standard—Not applicable.Application—This SAE Standard provides design parameters and general requirements for motorcycle turn signal lamps. It does not apply to mopeds.Reference SectionSAE J213—Motorcycle ClassificationSAE J567—Lamp Bulb Retention SystemSAE J575—Tests Methods and Equipment for Lighting Devices and Components for Use on Vehicles Less than 2032 mm in Overall WidthSAE J576—Plastic Materials for Use in O ptical Parts Such as Lenses and Reflectors of Motor Vehicle Lighting DevicesSAE J578—Color SpecificationDeveloped by the SAE Motorcycle Technical Committee。