降低抽提系统溶剂损失的措施探讨
降低溶剂消耗量的方法
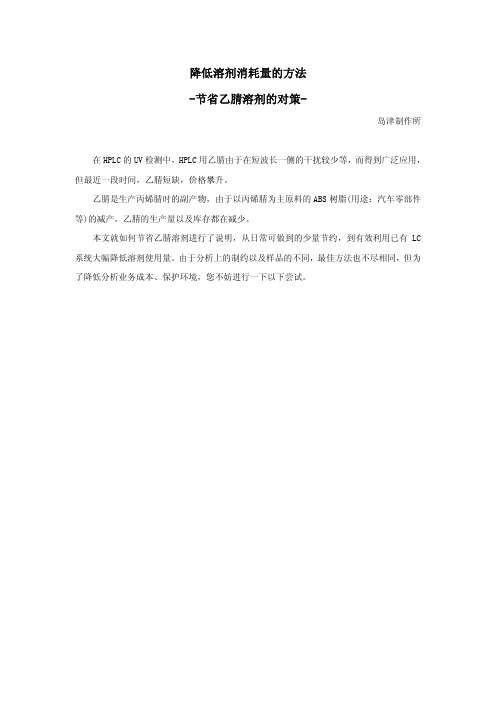
降低溶剂消耗量的方法-节省乙腈溶剂的对策-岛津制作所在HPLC的UV检测中,HPLC用乙腈由于在短波长一侧的干扰较少等,而得到广泛应用,但最近一段时间,乙腈短缺,价格攀升。
乙腈是生产丙烯腈时的副产物,由于以丙烯腈为主原料的ABS树脂(用途:汽车零部件等)的减产,乙腈的生产量以及库存都在减少。
本文就如何节省乙腈溶剂进行了说明,从日常可做到的少量节约,到有效利用已有LC 系统大幅降低溶剂使用量。
由于分析上的制约以及样品的不同,最佳方法也不尽相同,但为了降低分析业务成本、保护环境,您不妨进行一下以下尝试。
1日常可做到的节约 (3)1-1) 将色谱柱清洗溶剂变更为甲醇1-2) 降低调整、分析结束后停机时消耗的溶剂量1-3) 在等度洗脱条件下进行流动相2液混合 (已有梯度洗脱系统时)2使用已有LC系统时的方法 (5)2-1) 流动相从乙腈变更为甲醇2-2) 使用高性能短色谱柱3变更已有LC系统的配置 (9)3-1) 色谱柱内径的尺寸减小(半微量化)・・分离得以保留不变,降低流动相流量 3-2) 快速化 ・・使用分离性能出色的小尺寸色谱柱,缩短分析时间3-3) 溶剂再循环・・未检测到峰时,将从检测器出口排出的洗脱液返回到流动相储液瓶中,以节约溶剂4介绍省溶剂实施方案 (18)・・将已有LC系统升级为省溶剂型LC系统1日常可做到的节约首先,完善乙腈的库存管理,最为重要的是在流动相储液瓶上记载使用者的姓名、流动相组成/配制日期(避免因内容不明而废弃流动相)。
并且,重新审视日常的分析业务,通过实行以下措施,可以减少溶剂的浪费。
(1)将色谱柱清洗溶剂变更为甲醇(2)降低在分析前的调整以及分析结束后停机时消耗的溶剂量(3)在等度洗脱条件下进行流动相2液混合 (已有梯度洗脱系统时)1-1) 将色谱柱清洗溶剂变更为甲醇您是否因为分析流动相使用的是乙腈,所以在色谱柱清洗中也在使用着乙腈呢?为了将用于分析的乙腈变更为甲醇,需要考虑分离模式的变化,但在多数的场合下,可以使用甲醇进行清洗。
降低浸出油厂溶剂消耗的措施

降低浸出油厂溶剂消耗的措施
1减少溶剂消耗的方法
溶剂浸出油厂是一种很耗费溶剂的工艺过程,溶剂消耗非常大,需要控制在最低限度上。
那么,要想降低溶剂消耗,应该采取哪些措施?
1.1改进工艺
改进浸出油厂的生产工艺,减少溶剂流量,是减少溶剂消耗的最有效的方法。
通过改进提取条件,降低液体固比,增强液体推动力,提高液体吸收能力,采用低温、低流速的方格提取,以及通过改进系统水的分离质量,可以有效地减少溶剂消耗。
1.2改善设备操作
设备操作对溶剂消耗有直接影响。
应根据设备构造,合理调整设备运行参数,如溶液压力、流速和温度等,将溶剂利用率提高到最高。
同时,应增强对设备操作的培训,保证操作人员对设备参数的控制,以降低溶剂消耗。
1.3采用先进技术
采用先进的技术,以节省溶剂消耗,比如表面活性剂的应用,人工智能技术,分子筛技术,多层激浆气流选择技术等。
这些新技术的应用将有助于节约投入的投入资源流,减少溶剂的消耗量。
总的来说,要想有效降低溶剂消耗,应综合考虑改进工艺、改善设备操作以及采用先进技术等多方面因素,这样才能够取得良好的降低溶剂消耗的效果。
优化溶剂油系统工艺,增效降耗

优化溶剂油系统工艺,增效降耗溶剂油系统是一种常见的工业生产系统,主要用于溶剂回收和再利用。
在实际工程应用中,优化溶剂油系统工艺可以显著提高生产效率,并降低能耗,降低生产成本。
本文将从以下几个方面探讨如何优化溶剂油系统工艺,增效降耗。
一、优化溶剂回收系统溶剂回收系统是溶剂油系统的核心部分,对其进行优化可以有效提高溶剂的回收率,降低能耗。
要合理设计溶剂油系统的结构,包括溶剂存储罐、回收设备、循环管道等,确保系统稳定运行。
优化溶剂回收过程中的操作参数,比如温度、压力、流量等,以提高溶剂回收率,减少溶剂损失。
可采用先进的溶剂回收设备和技术,如膜分离、蒸馏、浓缩等,以提高回收效率、降低能耗。
二、改善溶剂油系统的热能利用溶剂油系统往往需要大量的热能来完成溶剂回收和再利用过程。
改善热能利用是提高系统效率的关键。
一方面,要采用高效的热能回收技术,如余热利用装置、热交换器等,将系统中产生的热量充分利用,减少对外能源的依赖。
可优化热能利用方案,选择合适的加热方式和供热温度,以实现最佳的能量利用效果,降低系统能耗。
三、优化溶剂回收过程中的操作控制在溶剂回收过程中,操作控制是关键因素之一。
优化操作控制可以提高系统运行效率,降低能耗。
要对系统进行智能化改造,引入先进的自动控制系统和设备,实现对溶剂回收过程的精准控制。
需加强对操作人员的培训和管理,提高其对系统运行状态的监控和调控能力,以减少人为误操作对系统性能的影响。
四、加强对溶剂油系统的维护和管理溶剂油系统的正常运行和效率提高离不开对系统的维护和管理。
加强对系统的维护管理,可及时发现和排除系统故障,保障系统稳定运行。
要建立系统的日常巡检和定期维护制度,以延长设备的使用寿命,减少故障率。
还需加强对原材料和产品质量的监控和管理,确保溶剂油系统生产的产品符合质量要求。
以上几点是优化溶剂油系统工艺、增效降耗的一些方法和措施。
通过合理设计和结构优化、加强热能利用、优化操作控制和加强维护管理,可以提高系统的生产效率,降低系统的能耗,从而达到增效降耗的目的。
分析浸出车间降低溶剂损耗的方法
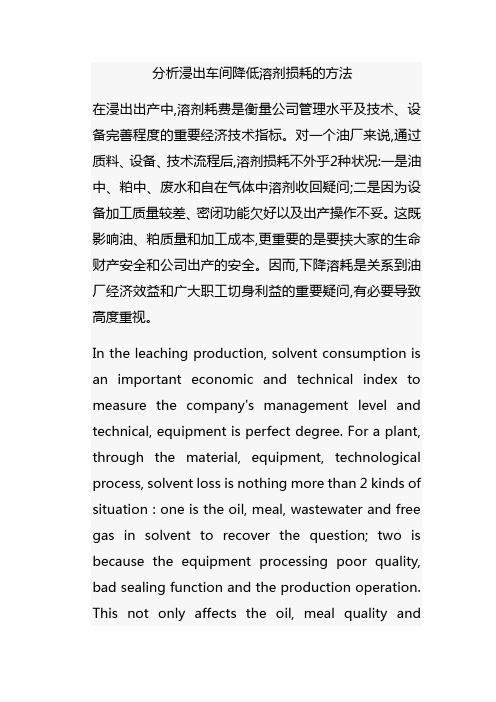
分析浸出车间降低溶剂损耗的方法在浸出出产中,溶剂耗费是衡量公司管理水平及技术、设备完善程度的重要经济技术指标。
对一个油厂来说,通过质料、设备、技术流程后,溶剂损耗不外乎2种状况:一是油中、粕中、废水和自在气体中溶剂收回疑问;二是因为设备加工质量较差、密闭功能欠好以及出产操作不妥。
这既影响油、粕质量和加工成本,更重要的是要挟大家的生命财产安全和公司出产的安全。
因而,下降溶耗是关系到油厂经济效益和广大职工切身利益的重要疑问,有必要导致高度重视。
In the leaching production, solvent consumption is an important economic and technical index to measure the company's management level and technical, equipment is perfect degree. For a plant, through the material, equipment, technological process, solvent loss is nothing more than 2 kinds of situation : one is the oil, meal, wastewater and free gas in solvent to recover the question; two is because the equipment processing poor quality, bad sealing function and the production operation. This not only affects the oil, meal quality andprocessing costs, more important is to everyone's life and property safety and production safety. Thus, reduced solvent consumption is an important question related to the oil refinery economic benefits and the immediate interests of the workers, it is necessary to attach great importance to.1下降毛油中的溶剂含量The 1 decline in the solvent content in crude oil1.1进步混合油浓度,把握好溶剂比1.1 progress of mixed oil concentration, a good grasp of the solvent ratio要合理挑选恰当的溶剂比,溶剂比大,对下降粕中的残油有必定效果,但所收到的混合油浓度太低,会给收回体系添加负荷,易形成毛油中含溶。
优化操作降低芳烃抽提装置溶剂损失

化 工一厂4 0 万吨/ 年芳烃抽 提三套 装置于2 0 1 2 年9 月投产 , 采 用北京金 伟晖 工程 技术有 限公司的苯 抽提专有 工艺 技术 进行 单苯抽提 生产技术 , 使用 的溶剂 为环 丁砜 。 表 1环丁 砜物 化性 质表
项 目 密度 .
30
彦 法 ^ s T M B
科 学 论 坛
啊
I
优化 操 作 降 低 芳烃 抽 提 装 置 溶 剂 损 失
鲁 鹏
( 大庆 石化 公 司化 工一 厂芳 烃联 合车 间 黑 龙江 大庆 1 6 3 7 1 4 )・ . [ 摘 要】 本 文简要 叙述 了4 0 万 吨/ 年芳烃 抽提 装置 的溶 剂环 丁砜 在生 产实 际 中损失 的原 因 , 并对 一些 问题 提 出 了相 应措 施 。 [ 关键 词] 溶剂 、 损失、 原因。 中图分 类号 : T E 6 2 4 . 5 文 献标识码 : A 文章编 号 : 1 0 0 9 — 9 1 4 X( 2 0 1 4 ) 1 8 —0 0 9 5 一O l
参数
∞§
2
水洗 比
抽 油 中; 帮甜 台量
(阼m ,
{" h C h ≤ ) ) )
戢 需- 慢 9 定, 但 规
中含有 的溶剂环丁砜 , 由于未水洗的抽余油在冷却时 , 其 中的—半溶剂 回从溶液 中 分 离出来并于抽余油 中所含有的少量苯形成第二富溶剂相 , 为 了加强洗涤效果 , 减 少在未水洗 的抽 余油中形成的精细分散 的溶剂的稳定悬浮液 , 将 从抽余油水洗 塔 底采 出的一 部分含溶 剂较多的水液用泵升压 后与抽余油在冷却 器前进行混合 , 加 强抽余 油水洗 效果 , 以便更 好地 回收抽余油 中含有 的溶 剂环丁砜 , 建立 水循环 。 同 样, 从抽 余油水洗塔顶采 出的—部分 水洗过的抽余油用泵升压 后直接打入抽余 油 水洗塔底 , 加强抽余油水洗 效果 , 便更好地 回收抽余 油 中含有 的溶剂环 丁砜 , 建 立 油循环 。 本 装置的抽余油水洗塔共有七块塔板 , 由抽提塔顶抽 出的抽余油从第 七 块板进 入抽 余油 水洗塔 , 从 回收塔来的水洗水从抽余 油水洗 塔顶进入油水逆相 接 触。 由于设计和操作上均存在一定 的问题 , 水洗后 的抽余油 中 剂环 丁砜 的量
溶脱剂耗分析及应对措施

溶脱剂耗分析及应对措施郭 伟(长庆石化公司 陕西咸阳 712000)摘 要:随着生产的进行,溶脱装置出现了溶剂(混合C4)损耗偏大的问题,其表现为V-2205液位下降过快,班组收溶剂频次多,单次收溶剂量偏大。
我们针对以上问题对工艺参数、设备运转情况等进行了分析,找出影响溶剂损耗的原因。
关键词:溶剂损耗 V-2205至V-2207泄压线 溶剂密封 汽提蒸汽1 前言1.1 工艺原理(1)溶剂抽提沉降的工艺原理溶剂脱沥青是重油深度加工的一种有效途径,他可以生产更多的脱沥青油(DAO)供给催化裂化装置[1]。
本装置是以丁烷(混合C4)为溶剂,以减压渣油为原料,在一定的温度和压力下,利用溶剂对原料中的饱和烃和芳烃有较大的溶解性而对胶质和沥青质几乎不溶的特性,达到脱沥青油和沥青分离的目的,得到脱沥青油和脱油沥青。
(2)溶剂的超临界回收的工艺原理溶剂对脱沥青油的溶解性能随温度的升高而减小,当溶剂达到溶剂临界状态时,则溶解度最小。
利用溶剂的这种特性,使脱沥青油溶液达到溶液的临界状态,则溶液中的脱沥青油就将从中解析出来,从而达到脱沥青油和溶剂分离的目的[2]。
压力和温度在高于溶剂临界状态下操作:即所谓超临界溶剂回收,则能使油和溶剂的分离效果更好,由于在超临界状态下,溶剂在升温通过临界温度并发生相变时,没有显著的相变热,所以超临界回收与普通蒸发、汽提相比是非常节能的工艺,节能效果更佳,本装置即采用超临界溶剂回收。
(3)溶剂的汽提回收的工艺原理溶剂的汽提回收也是蒸发回收的一种形式,根据道尔顿分压定律,即混合气体的总压等于其组成气体各分压之和。
在总压一定情况下,向汽提塔内吹入蒸汽,提高水蒸汽分压,则溶剂分压变小,根据减压蒸馏原理,在一定温度、压力下,降低油气分压则可降低溶剂的沸点,使溶剂在极低的分压下进一步汽化,从而就可以将沥青或脱沥青油中的微量溶剂从中分离出去,达到充分回收溶剂的目的[3]。
2 问题描述2.1 溶剂使用过程中剂耗明显增大催化原料预处理装置采用混合C4作为溶剂生产脱沥青油和半沥青质,在生产过程中会产生一定比例的剂耗,按照设计要求,催化原料预处理装置的溶剂剂耗应当控制在2.5kg/t以内。
苯抽提装置运行中的问题及优化改造

苯抽提装置运行中的问题及优化改造在苯抽提装置的运行过程中,可能会出现一些问题,并且需要进行优化改造。
以下是一些可能存在的问题以及相应的优化改造方案。
苯抽提过程中可能存在操作条件的不稳定性问题。
苯和溶剂的流量变化、压力波动等因素可能导致抽提效果的波动。
为了解决这个问题,可以采取以下优化改造措施:1)安装流量、压力等仪表,实时监测和调整操作条件,确保其稳定性;2)优化控制系统,采用先进的控制策略,对操作条件进行精确调节。
苯抽提过程中可能存在能耗较高的问题。
传统的蒸馏塔结构可能存在物料和热量的大量损失。
为了降低能耗,可以进行以下优化改造:1)采用高效传质填料和装置结构,提高传质效率;2)优化冷却和加热系统,充分利用废热,降低能耗。
苯抽提过程中还可能存在环境污染问题。
在溶剂回收过程中可能会产生废水、废气等污染物。
为了减少环境污染,可以进行以下优化改造:1)安装废水处理设备,对废水进行处理;2)优化废气处理系统,降低废气中有害物质的排放。
苯抽提装置还可能存在设备磨损和结垢问题。
由于物料流动的摩擦和冲击,设备内壁可能会产生磨损和结垢,影响抽提效果。
为了解决这个问题,可以采取以下优化改造措施:1)选用耐磨材料制作设备内壁,提高其耐磨性;2)定期清洗设备,防止结垢问题的产生;3)加强设备维护和检修,及时更换磨损部件。
苯抽提装置的操作过程可能缺乏自动化控制和监测手段。
为了提高装置的智能化水平,可以进行以下优化改造:1)引入先进的自动控制系统,实现对抽提过程的自动化控制;2)利用物联网技术,建立装置的远程监控系统,实时监测和分析装置运行情况,提高生产效率和安全性。
苯抽提装置的运行中可能会出现一些问题,通过优化改造可以提高装置的稳定性、降低能耗、减少环境污染、延长设备寿命,进一步提高生产效率和产品质量。
关于芳烃抽提溶剂环丁砜保护问题的探讨

筛板塔
0. 10~ 0. 17 0. 7~ 120~ 140 0. 7~ 0. 8
0. 04~ 0. 05 1. 4
抽提 汽提 非芳水洗馏
溶剂再生
筛板或转盘塔 0. 02~ 0. 04
0. 4~ 0. 6
70~ 90 0. 3~ 0. 5
项目
U dex Sulfo lane
芳烃回收率 /%
苯> 99. 5 苯> 99. 9
Sulfolane 法是美国 U OP 公司与荷兰 Shell 公 司共同开发的一种以环丁砜为溶剂的芳烃抽提工 艺, 由于环丁砜溶剂使用性能的多种优越性, 加上 其建设投资及操作费用均比较低, 已成为当今世
界上应用最广泛的一种芳烃抽提工艺, 尤其是新 建装置大都采用此工艺。
2 环丁砜溶剂的特点
对抽提过程来说, 溶剂的选择十分重要, 而溶 剂最主要的指标是溶剂对芳烃的溶解能力和选择 性, 以及溶剂本身的化学稳定性、热稳定性、密度 和粘度等。
( 3) 每次开停工过程中, 都要注意管线、设备 的密封保护, 防止空气介入。如有必要, 用 N 2 或 蒸汽先行置换。 3. 1. 3 氯离子
氯离子极易与环丁砜发生化学反应, 使其变 成酸性物质, 并在高温下与烯烃生成聚合物, 使系 统中的 pH 值迅速下降。氯离子的 来源, 通常是 由再沸器、冷却器、原料中带水及系统补充的循环 水带入, 为防止氯离子对环丁砜的影响要注意以
表 2 主要芳烃抽提工艺产耗比较表
芳烃回收率 芳烃回收率
/%
/%
每吨芳烃消耗 冷却水/m 3
每吨芳烃消耗 电/ ( kW h)
甲苯> 98 二甲苯> 95
41~ 100
24~ 36
芳烃抽提装置问题分析及优化措施

芳烃抽提装置问题分析及优化措施摘要:芳烃抽油机设备泄漏的原因很多,采用定期分析方法受到各种实际经验的影响,因此在后续作业中稳定性仍然不足。
为了进一步提高芳烃开采设备的运行效率和效益,降低随后的维护成本和压力,有必要解决芳烃开采设备频繁泄漏的问题。
下文讨论了芳烃开采设备在实际生产中经常泄漏的情况分析。
关键词:芳烃抽提;精馏;换热网络;优化引言芳烃抽运装置用于从翻新或裂解汽油中回收轻质芳烃(苯、甲苯、二甲苯)。
中国石油60万t/a芳烃抽油机采用GT-BTX技术,以氢裂解汽油为原料,由脱甲塔C≥9组分去除三联苯。
该设备自2009年投入使用以来运作良好,但近年来,由于升降塔拆卸后材料组太重,造成托莱多的产量和质量问题。
为解决这一问题,建议将脱氧塔中的C≥9部件更换为C≥8部件,并以联苯萃取说明取代三联苯萃取说明。
本文采用美国stellenbosch公司VMGSim过程模拟软件的advanced dpeng-Robinson物理方程进行脱硅塔的过程模拟,分析了将组分C≥9改为组分C≥8和三氧化苯改为两种苯二氮杂卓的可能性,以实现1芳烃抽提装置泵送系统的主要目的是从富含芳烃的C6~C8馏分中回收芳烃。
混合芳烃(C6~C8部分)进入泵塔,与循环塔底贫化溶剂的反向流动相接触,用于液液泵。
撤离塔顶部的大部分抽油机液(非芳烃)直接送入撤离塔进口,稀释进料中的芳烃,提高抽运效果;抽油机另一部分冷却后送至抽油机。
塔底富溶剂换成回收塔底贫溶剂,送到汽提塔顶部。
脱衣舞厅被蒸汽加热。
含有非芳烃和部分芳烃的汽提塔顶部蒸汽经冷凝冷却后进入汽提塔顶部罐壳分离;轻非芳烃和轻芳烃加压后进入泵塔,水被送至汽提塔顶部;塔底液体送入溶剂回收塔,将芳香烃与再生溶剂分离。
回收塔顶部的蒸汽经冷凝后进入回收塔返库,分离冷凝水和混合芳烃,然后加热回收塔底部的蒸汽;一部分混合芳烃返回回回收塔顶部,另一部分作为合格材料送往混合芳烃中间罐。
回流罐内的水送至分散液洗涤塔冲洗水;汽提塔增压器冷却塔底部的贫化溶剂后,一部分去汽提塔取溶剂,另一部分在富、贫溶剂热交换器热交换后用作汽提塔的溶剂。
浸出车间降低溶剂损耗的几种方法

浸出车间降低溶剂损耗的几种方法摘要介绍浸出车间降低溶剂损耗的方法,包括降低毛油中的溶剂含量、降低粕中的溶剂含量、降低废水中溶剂含量、降低尾气中带走的溶剂、减少设备滴漏,以为浸出车间降低溶剂损耗提供参考。
关键词溶剂损耗;溶剂回收;降低溶耗;浸出车间在浸出生产中,溶剂消耗是衡量企业管理水平及工艺、设备完善程度的重要经济技术指标。
对一个油厂来说,经过原料、设备、工艺流程后,溶剂损耗不外乎2种情况:一是油中、粕中、废水和自由气体中溶剂回收问题;二是由于设备加工质量较差、密闭性能不好以及生产操作不当。
这既影响油、粕质量和加工成本,更重要的是威胁人们的生命财产安全和企业生产的安全。
因此,降低溶耗是关系到油厂经济效益和广大职工切身利益的重要问题,必须引起高度重视。
1降低毛油中的溶剂含量1.1提高混合油浓度,掌握好溶剂比要合理选择适当的溶剂比,溶剂比大,对降低粕中的残油有一定作用,但所收到的混合油浓度太低,会给回收系统增加负荷,易造成毛油中含溶。
一般以原料含油为基础,混合油浓度在此基础上增加5%~10%。
在保证粕中残油及混合油浓度提高的情况下,实际生产中溶剂用量一般为0.6∶1(喷淋式浸出)。
喷淋方式采用溶剂或混合油与料胚逆流的方式,即刚进浸出器的物料用较低浓度的混合油喷淋,这样能得到较浓的混合油。
油厂常用的平转式浸出器浸出时溶剂比为0.8~1.1∶1,也采用逆流的方式。
1.2掌握好蒸发中的主要蒸发要素常压的蒸发温度,1#蒸发器在75~80 ∶,间接蒸汽压力0.2~0.3 mpa;2#蒸发器在95~115 ∶,间接蒸汽压力0.3~0.4 mpa;汽提塔在125 ∶左右,间接蒸汽压力0.4 mpa,直接蒸汽压力0.05 mpa。
直接蒸汽含水多和用量大,会造成汽提塔液泛,毛油中的溶剂含量超标;可加汽水分离器或者把直接蒸汽加热成过热直接蒸汽提高蒸汽质量,减少汽提塔液泛。
蒸发量一定要均匀,不可忽大忽小,否则会造成1#、2#蒸发器液泛和汽提塔脱溶不干净,致使毛油残溶不稳定,甚至超标,直接蒸汽的用量是混合油量的0.3~1.4倍。
浸出油厂降低溶剂消耗的措施
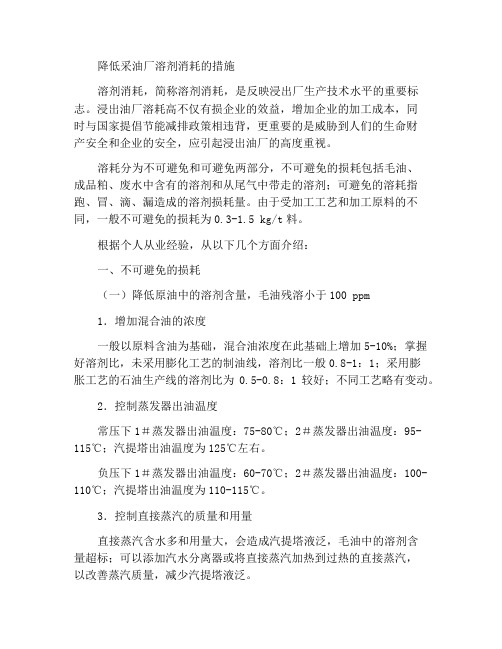
降低采油厂溶剂消耗的措施溶剂消耗,简称溶剂消耗,是反映浸出厂生产技术水平的重要标志。
浸出油厂溶耗高不仅有损企业的效益,增加企业的加工成本,同时与国家提倡节能减排政策相违背,更重要的是威胁到人们的生命财产安全和企业的安全,应引起浸出油厂的高度重视。
溶耗分为不可避免和可避免两部分,不可避免的损耗包括毛油、成品粕、废水中含有的溶剂和从尾气中带走的溶剂;可避免的溶耗指跑、冒、滴、漏造成的溶剂损耗量。
由于受加工工艺和加工原料的不同,一般不可避免的损耗为0.3-1.5 kg/t料。
根据个人从业经验,从以下几个方面介绍:一、不可避免的损耗(一)降低原油中的溶剂含量,毛油残溶小于100 ppm1.增加混合油的浓度一般以原料含油为基础,混合油浓度在此基础上增加5-10%;掌握好溶剂比,未采用膨化工艺的制油线,溶剂比一般0.8-1:1;采用膨胀工艺的石油生产线的溶剂比为0.5-0.8:1较好;不同工艺略有变动。
2.控制蒸发器出油温度常压下1#蒸发器出油温度:75-80℃;2#蒸发器出油温度:95-115℃;汽提塔出油温度为125℃左右。
负压下1#蒸发器出油温度:60-70℃;2#蒸发器出油温度:100-110℃;汽提塔出油温度为110-115℃。
3.控制直接蒸汽的质量和用量直接蒸汽含水多和用量大,会造成汽提塔液泛,毛油中的溶剂含量超标;可以添加汽水分离器或将直接蒸汽加热到过热的直接蒸汽,以改善蒸汽质量,减少汽提塔液泛。
4.蒸发量一定要均匀,不可忽大忽小,否则会造成1#、2#蒸发器溢流和汽提塔脱溶不干净,致使毛油残溶不稳定,甚至超标。
5.对混合油进行沉淀或过滤,去除有机和无机杂质,减少蒸发系统结垢和液泛。
(二)减少膳食中的溶剂含量,成品粕残溶含量小于700 ppm1.清选出来的土杂全部接出,由于土杂透气性差,土壤中的溶剂不易蒸发,会残留在豆粕中;不仅会造成粕残溶超标,同时也影响粕残油。
2.控制好胚片厚度0.3-0.4mm较合适,太薄溶剂渗透效果差,湿粕含溶剂量大;太厚粕中的溶剂不宜蒸脱出来;坚决杜绝跑生现象,润盛豆粕中溶剂含量严重超标。
丁二烯装置乙腈溶剂损失原因分析及优化措施

丁二烯装置乙腈溶剂损失原因分析及优化措施摘要:该装置采用含水乙酰作为萃取剂,乙烯分离出四氧化碳作为原料,经过2个萃取步骤和2个常规精制步骤后,丁烷、丁烷和重组组分最终从原料中产生聚合物产物丁二烯,乙烯溶液经循环处理后去除。
随着设备运行周期的增加,溶剂中的杂质逐渐增多,原来的无色透明液体变成粉红色。
对循环乙烯溶剂的全部成分的分析表明,污染物的总质量包括乙醇,丙酮,异丙醇,未明确的数量等。
接近3%。
基于此,分析了丁二烯装置乙酰化溶剂损失的原因及优化措施,供参考。
关键词:丁二烯;乙腈;溶剂损失;水解;优化引言随着石油工业的发展,用于分解石油原料的高温原料越来越重,分解温度也相应提高,而用于分解四段碳(简称分解四段碳)的乙烯组合物也越来越多。
一般来说,二氧化碳中丁二烯的含量约为50%(Wt),以及丁烷,丁烷,含有少量碳III和碳V。
由于碳4分解中组分的相对挥发性非常接近于丁烷,其中一些也与丁烷形成环氧化,因此很难用传统的精炼方法将它们分开。
目前工业上采用萃取精炼和常规精炼相结合的方法生产高纯度丁二烯,以满足合成橡胶工业的要求,并按不同的萃取剂分为乙酰法、二甲基甲酰胺法和N-甲基丙烯酸甲酯法。
1装置简介丁二烯装置的生产采用乙酰化法,以乙二烯为溶剂,先通过萃取精炼,然后通过常规精炼,从乙烯分解装置中提取出的碳中提纯丁二烯组分。
在碳四组分中,除丁二烯外,还有丁烷、丁二烯、丁二烯等种类的碳氢化合物,这些组分具有相同的沸点,并且还可以形成环氧化,当溶剂添加到分离系统中时,组分之间的相对波动差异增加。
采用两步精炼萃取法,先将轻组分作为多余的IV-1碳产品去除,然后再去除重组碳氢化合物,以获得较高的纯度。
然后,使用常规的两步精炼方法,首先去除重组分锡丁烯,碳等。
然后去除甲基乙酰和水的痕迹,最终得到符合国家标准的丁二烯产品。
2乙腈溶剂损失原因2.1 循环溶剂中的高污染物纯乙烯溶剂是一种无色透明液体,随着丁二烯装置的运行,溶剂中的杂质会积聚,溶剂逐渐变成浅黄色、红褐色甚至不透明。
(DMF法)丁二烯抽提装置降低溶剂精制塔塔顶损失措施

自 19 9 2年投 产 开车 至今 , 已接 近 2 0年 。 为适 应 高 负荷 下生 产 的需要 ,开工 初期 针对 溶 剂 系统进 行 了改造 , 0 2 5年 5月 丁二烯 装 置检 修期 间 ,对第 二 0 汽 提塔 ( 1 6 C 0 )进行 扩 能改造 。塔 盘更 新 为高效 导
结 合 本 装 置 工 艺 技 术 特点 , 过 局 部 改 造 和 优 化 操 作 调 整 ,降 低 了 塔 顶 D 通 MF损 失 。 关 键 词: D MF法 丁 二 烯 装 置 ;溶 剂 精 制塔 ;溶 剂 ;二 甲基 甲酰 胺
文 献标 识 码 : A 文 章编 号 : 17 — 4 0 ( 0 ) 3 0 8 — 3 6 1 0 6 2 1 0 — 2 9 0 1 中 图分 类 号 : T 2 . Q2 1 23 2
图 1 溶 剂 系 统 流 程
Fi . o har o v nts s e g 1Fl w c tofs l e y t m
图 1 我装 置溶 剂 系统 的流 程 。 是
12 溶剂 精制 塔损 失现 状 .
由于 以前 只对 塔 底 的 精 制 溶 剂 控 制 在 3 0x 0
第4 0卷 第 3期 21 0 1年 3月
当
代
化
工
C n e o a yC e ia n u t y o t mp r r h m c lI d s r
V 14 . N . o.0 O3 M r h. 0 a c 2 11
( DMF法 )丁 二 烯 抽 提 装 置 降低 溶 剂 精 制塔 塔 顶 损 失措 施
董 毓 华 ,邓 有 恒 ,刘 新 元 ,杨 鲁 明
浸出车间降低溶剂消耗的途径与措施

浸出车间降低溶剂消耗的途径与措施摘要:溶剂消耗是浸出生产中的一项重要综合性经济技术指标。
本文从分析溶剂消耗的定义入手,系统地提出了降低溶剂消耗的途径,并对当前不被人们广泛认识的提高设备处理量、减少废水和废气排放量等可十分有效地降低溶剂消耗的途径进行了论述,并提出了具体的实施办法。
关键词:溶剂消耗;途径;措施溶剂消耗是浸出生产中的一项重要综合性经济技术指标。
之所以说是综合性经济技术指标,是因为它不仅与操作人员的操作水平有关,同时还有工艺情况、设备状态及管理水平等众多影响因素;之所以说是重要经济技术指标,是因为它不仅关系到生产的经济效益,同时也直接关系到安全生产。
为此,各生产厂家都十分重视降低生产过程中的溶剂消耗,在实践过程中取得不少经验,广大技术人员也从各个角度对此进行了较为深入的研究。
本文试图从分析溶剂消耗的定义本身着手,阐述降低浸出车间溶剂消耗的途径,并提出一些的措施,以此求教于各位同行。
一、降低浸出车间溶剂消耗途径的分析浸出车间溶剂消耗的定义可表述为:浸出生产中每处理一吨入浸料所损失溶剂的重量,其计算公式为:从上述定义及计算公式我们不难看出,溶剂消耗指标不是一个绝对的量,而是两个量之间的比值,要使该比值减小,即要降低溶剂消耗,有两个基本的途径:一是减小分子——降低溶剂损失的绝对量,二是加大分母——提高入浸料的数量。
要降低溶剂损失的绝对量,其实质是减少跑出浸出系统溶剂的量。
溶剂脱离浸出系统总的途径有两类:一类是因密封不严,溶剂以液态和气态的方式直接泄漏,即常说的跑、冒、滴、漏。
另一类是离开浸出系统的物料带出的溶剂,有粕、浸出毛油、废气和废水(渣)四种物料带出的溶剂,这方面溶剂损失的量又取决于物料中残留溶剂的浓度和物料的数量这两个因素,减少排出物料中残留溶剂的浓度和减少排出物料的数量都可降低溶剂损失,前一因素被人们广泛认识,研究得也比较深入,后一个因素则似乎被人们所遗忘,但其作为一个降低溶剂消耗的途径是显而易见的,当然,这一途径主要是指减少废气和废水的数量。
浸出车间降低溶剂损耗的几种方法
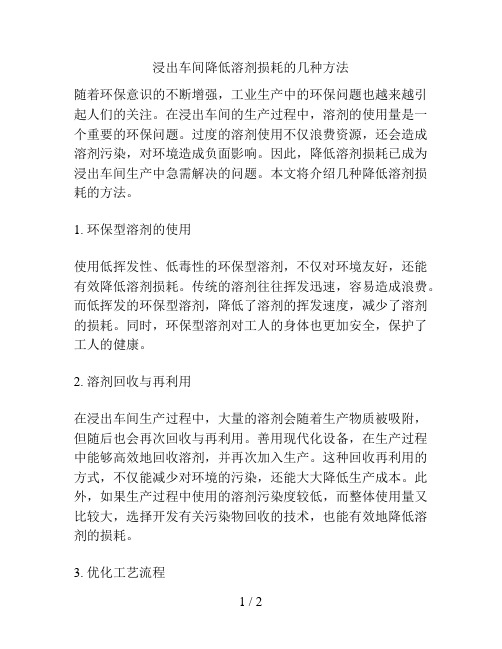
浸出车间降低溶剂损耗的几种方法随着环保意识的不断增强,工业生产中的环保问题也越来越引起人们的关注。
在浸出车间的生产过程中,溶剂的使用量是一个重要的环保问题。
过度的溶剂使用不仅浪费资源,还会造成溶剂污染,对环境造成负面影响。
因此,降低溶剂损耗已成为浸出车间生产中急需解决的问题。
本文将介绍几种降低溶剂损耗的方法。
1. 环保型溶剂的使用使用低挥发性、低毒性的环保型溶剂,不仅对环境友好,还能有效降低溶剂损耗。
传统的溶剂往往挥发迅速,容易造成浪费。
而低挥发的环保型溶剂,降低了溶剂的挥发速度,减少了溶剂的损耗。
同时,环保型溶剂对工人的身体也更加安全,保护了工人的健康。
2. 溶剂回收与再利用在浸出车间生产过程中,大量的溶剂会随着生产物质被吸附,但随后也会再次回收与再利用。
善用现代化设备,在生产过程中能够高效地回收溶剂,并再次加入生产。
这种回收再利用的方式,不仅能减少对环境的污染,还能大大降低生产成本。
此外,如果生产过程中使用的溶剂污染度较低,而整体使用量又比较大,选择开发有关污染物回收的技术,也能有效地降低溶剂的损耗。
3. 优化工艺流程优化工艺流程,缩短浸泡时间,完善物料滤布及处理设备等,也是降低溶剂损耗的有效方法。
在浸出过程中,较长的浸泡时间会使物料所吸附的溶剂增多,从而造成溶剂的浪费。
在操作过程中,适当地缩短浸泡时间,提高物料的滤布质量,或者根据实际的工艺要求,进行合适的调整,都能够有效地降低溶剂的损耗。
总之,降低溶剂损耗是浸出车间生产中需要解决的一项重要问题。
选择环保型溶剂、进行溶剂回收与再利用、优化工艺流程等方法,都可以有效地降低溶剂损耗。
同时,也能够提高生产效率,降低生产成本,更好地适应现代化生产的要求。
NMP法丁二烯生产装置降低溶剂损失的措施
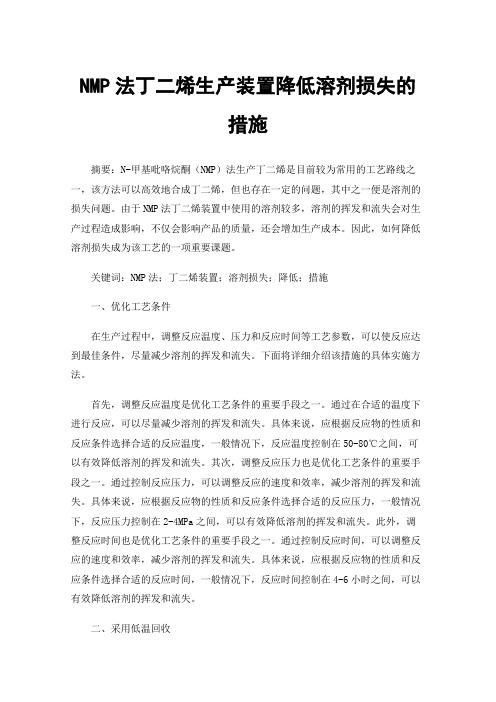
NMP法丁二烯生产装置降低溶剂损失的措施摘要:N-甲基吡咯烷酮(NMP)法生产丁二烯是目前较为常用的工艺路线之一,该方法可以高效地合成丁二烯,但也存在一定的问题,其中之一便是溶剂的损失问题。
由于NMP法丁二烯装置中使用的溶剂较多,溶剂的挥发和流失会对生产过程造成影响,不仅会影响产品的质量,还会增加生产成本。
因此,如何降低溶剂损失成为该工艺的一项重要课题。
关键词:NMP法;丁二烯装置;溶剂损失;降低;措施一、优化工艺条件在生产过程中,调整反应温度、压力和反应时间等工艺参数,可以使反应达到最佳条件,尽量减少溶剂的挥发和流失。
下面将详细介绍该措施的具体实施方法。
首先,调整反应温度是优化工艺条件的重要手段之一。
通过在合适的温度下进行反应,可以尽量减少溶剂的挥发和流失。
具体来说,应根据反应物的性质和反应条件选择合适的反应温度,一般情况下,反应温度控制在50-80℃之间,可以有效降低溶剂的挥发和流失。
其次,调整反应压力也是优化工艺条件的重要手段之一。
通过控制反应压力,可以调整反应的速度和效率,减少溶剂的挥发和流失。
具体来说,应根据反应物的性质和反应条件选择合适的反应压力,一般情况下,反应压力控制在2-4MPa之间,可以有效降低溶剂的挥发和流失。
此外,调整反应时间也是优化工艺条件的重要手段之一。
通过控制反应时间,可以调整反应的速度和效率,减少溶剂的挥发和流失。
具体来说,应根据反应物的性质和反应条件选择合适的反应时间,一般情况下,反应时间控制在4-6小时之间,可以有效降低溶剂的挥发和流失。
二、采用低温回收首先,采用低温回收技术需要在反应结束后立即进行。
具体来说,可以将反应混合物放入低温回收器中,然后通过降低回收器的温度使溶剂凝结,并将溶剂收集回收。
在此过程中,应尽量避免将溶剂带入下一步反应中,以确保产品的纯度和质量。
其次,低温回收的过程需要精确控制温度和压力。
具体来说,应在适宜的温度和压力下进行蒸馏分离,以充分利用冷凝器和蒸馏塔等设备的功能,将溶剂分离出来。
湿法脱硫装置减少溶剂损耗的措施

湿法脱硫装置减少溶剂损耗的措施摘要:公司的焦化干气经湿法脱硫后部分直接作为燃料气使用,大部分再经干法脱硫处理后进入转化炉生成合成气,经PSA提纯后制取氢气。
湿法脱硫的设计和操作要点是提高脱硫效果、减少溶剂损耗和降低设备腐蚀。
文章结合实际操作经验,浅谈如何减少溶剂损耗、降低生产成本。
关键词:干气、脱硫、溶剂、损耗1.前言在含硫原油的二次加工过程中,原油中硫化物的大部分都转化为硫化氢,存在于炼厂气中。
以这样的含硫气体做为石油化工生产的原料或燃料,会引起设备和管线的腐蚀,使催化剂中毒,危害人体健康,污染大气。
因此炼厂气和液态烃需要经过脱硫单元去除其中的硫化氢,再作为石化原料或燃料。
气体脱硫方法可分为两大类,一是干法脱硫,主要用于需要较高脱硫率的场合;二为湿法脱硫,即化学吸收法,炼厂干气和液化石油气脱硫基本都采用这种方法,其中应用最普遍的是醇胺法脱硫。
近年来,国外醇胺法脱硫的主要发展方向是节能降耗,开发了高选择性的新溶剂,显著降低了溶液循环量和蒸汽消耗量,并开发了一系列不同用途、不同要求的新溶剂。
1981年美国首次成功进行MDEA(N-甲基二乙醇胺)选择性脱除H2S的工业实验,国内于1986年完成MDEA溶液压力下选择脱硫工艺的工业化,90年代开始在炼厂气脱硫装置上应用。
由于炼厂目前大都采用全厂集中再生的模式,干气和液化气脱硫采用同一种溶剂,因此往往是在MDEA溶剂中加入少量助剂,如阻泡剂、缓蚀剂、抗氧化剂和活化剂等,以进一步改善MDEA溶剂的性能。
与国外相比,我国在溶剂系列化、质量和稳定性等方面仍有一定差距,还需科研、设计、生产单位等密切配合,研制和开发成本低、综合性能好的系列脱硫溶剂。
2.装置介绍公司加氢制氢装置设计制氢能力为20000Nm3/h,1988年12月建成,1989年投料试车。
制氢装置以焦化干气或轻油为原料,用烃类-水蒸汽转化法制取氢气。
1993年实现焦化干气制氢工艺,后于1995年进行改造,转化炉-302/1生产甲醇装置的原料气。
- 1、下载文档前请自行甄别文档内容的完整性,平台不提供额外的编辑、内容补充、找答案等附加服务。
- 2、"仅部分预览"的文档,不可在线预览部分如存在完整性等问题,可反馈申请退款(可完整预览的文档不适用该条件!)。
- 3、如文档侵犯您的权益,请联系客服反馈,我们会尽快为您处理(人工客服工作时间:9:00-18:30)。
R E F I N I N G A N D C H E M I C A L I 提 系统溶剂损失的措施探讨
陈 勇
( 大庆石化公 司炼油厂 , 黑龙江 大庆 1 6 3 7 1 1 )
某石化公司炼油厂 的催化重整装置 1 9 6 5 年建 成投 产 ,
2 采取 措 施 2 . 1 减 压 塔 再 生 系统
四乙二醇 醚属于甘醇类溶剂 , 对芳烃具 有较高 的选择 性和溶解 能力 , 与芳 烃易分离 ; 毒性和对设备 的腐蚀性 低 ,
便 于操 作 和 设 备 的选 用 。 四 乙二 醇醚 的分解 温 度 高 达
2 3 7℃, 热稳 定性 好 , 但在 实际运行过程 中仍会 出现 老化 变
大 。整个 减压 系统也 时常 因水 压波 动导致再 生 中断 。在
1 . 1溶剂再生 系统 溶剂 在高温下和 系统 中存 在的活性 氧接 触 , 逐 渐老化
运行 中, 只能通 过提 高溶 剂再 生温 度来 弥补 真 空度 的不
足, 同时也加速了溶剂老化 速率 。 通过联系厂家对水 环泵进行改造 , 提高 了系统的真空 度至 1 0 0 k P a , 再 生温 度也 由之前 的2 0 0 降至 1 8 5℃, 不仅
2 . 2 控 稳汽 提 塔 底 温 度
根据四 乙二醇醚 的再生工艺要求 , 溶剂再 生塔 的控制
参数见表 1 。 表 1 溶 剂 再 生 减 压 塔 控 制 参数
优化操 作之前气 体塔底 的温度在 1 2 5 ~ 1 3 2 o C 波动 , 热
载体 的流量 在 7 0 ~ 1 0 0 t / h 波动 。流 量的大幅波动加速 了溶
8 0 t / h , 并将换 热器芯子 更换为 白钢材质 , 固定 了管束和折
流板 。通 过 2 0 1 0年和 2 0 1 2 年的2 次检修 发现该 问题得 到
了根 本解 决 。
在生产 中由于真 空度 达不到要求导致溶 剂再生不 畅 ,
中部溶剂 落至底 部 , 导致再 生溶剂 蒸发 空间不足 , 无 法进 行 溶剂再 生 , 装置 被迫排 渣 。溶剂 再生 中断后 , 操作 人员 只能 通过 提高 再生 温度 强制 溶 剂再 生 , 导 致大 量溶 剂分 解, 也 是溶剂耗损 的原 因。减压塔顶温度 高会造成部分溶
抽提 塔的界位 控制 不稳定 , 会 造成抽 余油 量波 动 , 不
仅会 影响抽 提效果 , 而且会使 抽余油携 带溶剂 量增 大 , 增 加水 洗塔 、 沉 降塔 的负荷 , 如果调 整不及 时就会 造成抽余 油 中含溶剂 量增加 , 影 响装置 溶剂消 耗。在冬 季生 产时 , 抽余油带溶剂还会造成管线冻凝 的事故 。
通 过真空 泵进行 改造 , 提 高 了减 压系统 的真 空度 , 增 加 了减压 塔 的溶 剂再生量 , 降低 了系统排渣 次数 ; 对 抽提 系统操作参数进行 了优化 , 降低 了溶剂在 汽提塔底加热器
质、 分 解现象 , 不 仅影 响抽 提效果 , 还 会堵塞 管道和设 备 ,
一
方 面造成抽提系统剂耗 上升 , 另一方面缩短装置 的运 转
该装 置 的真空泵 为水环 真空泵 , 由于使 用年 限较长 ,
周期 。
1原 因分 析
减 压 系统 的 真空 度 只能 达到 9 5 k P a , 而且 受水 压 影 响较
变质生成 大分子 有机 酸物质 , 对运 行设备造 成腐蚀 , 还 会 在流速低 的部位 以及高 温部位积 聚 , 堵塞 管线和设 备 , 影
响装置 长周期运 行 。因此需要 不断 的对系统 溶剂进行 再 生, 保持溶剂的抽提性能。
提高了溶剂再 生量 , 也大幅降低 了溶 剂老化速率 。
剂 老化速率 , 溶 剂在换 热器 的壳 程结 焦 , 降低 了换热 器的 换热 效果 , 加 速 了设备 腐蚀 , 迫 使操作上 进一 步提高 热载 体流量 , 形成 恶性循环 。 温度 的大 幅波动 使富溶 剂 的流量在换 热器 的壳 程形 成 强大 的湍流 , 引起 换热器 管束 的振 动 , 增加 管束 与折流 板 的摩擦 , 最终导致管束泄漏 。 通过 优化热载体 系统的操作参数 , 稳定热 载体系统压
3 结束 语
剂随真空泵排出 , 是 由于减压塔中部回流量过低造成 的。
1 . 2 汽提 塔底 温度控 制不稳定 汽提塔 底温度控 制在 1 3 0℃左 右 , 所用 的热源为热 载 体, 人 口温 度一 般在 2 3 0℃, 接 近 四乙二醇醚 的分 解温 度 2 3 7℃, 如果 塔底温度控制不稳定 , 热载体流量 波动较大就
对抽提系统操作参数进行了优化降低了溶剂在汽提塔底加热器2015年第4期炼油与化工refiningandchemicalindustry67废气回收装置催化燃烧反应器操作工艺分析李楠侯丙南刘庆鹏大庆石化公司化工三厂黑龙江大庆163714某石化公司顺丁橡胶装置的废气来自于新区以及老区顺丁橡胶生产装置
炼 油 与 化 工
力, 将汽提塔底温度平稳控制 在 1 2 9℃, 热载体流量在控制
老化变质 的溶剂积聚在减 压塔 底 , 随之运行时 间逐 渐
增大, 溶剂 的粘 度也 随之上 升 , 最 后根 据机泵运行 情况 对 减压塔 进行排渣 。每次排 渣量为 5 t 左右 。排 渣过程也 是 溶剂耗损 的主要部分 , 经过化验 分析在装置排 除的老化溶 剂 中含 有约 8 0 %的溶剂 , 因此减少装 置排渣次数可 以极大 的降低装置溶剂耗损 。
工艺采用 半再生 固定 床技 术 , 现装置规模 为 3 0 0 k t / a , 其 中 抽提部分 处理能力为 1 0 0 k t / a , 采用北京石科 院技术 , 抽提
溶 剂 为 四乙 二 醇 醚 。
容易造成溶剂在换热器的管程 内分解结焦 , 堵塞管束 。
1 . 3抽提塔、 水洗塔 、 沉 降塔 界 位 不 稳
2 . 3控制抽提塔 、 水洗塔、 沉降塔界位
通过 D C S 系统 P I D参数整合 项 目的实施 , 对 抽提 系统
各参数进 行优化 , 取 得了 良好 的效果 , 仪表 自控 率 , 装 置平
稳率 升高 , 抽提 塔 、 水洗塔 、 沉降塔 界位控制 平稳 , 减少 了 抽余油 中溶剂含量 。