液压系统漏油的原因及其预防
浅析液压系统产生漏油的原因及处理措施

浅析液压系统产生漏油的原因及处理措施重庆泰山电缆有限公司液压系统漏油的原因是非常复杂的,主要是由于振动、腐蚀、压差、温度、装配不良等原因造成的。
液压系统漏油,还与液压元件的生产制造、管路的连接安装、系统的设计、使用及维护等多方面因素有关。
液压系统可能漏油的地方很多,有接头、接合面、密封面以及壳体(包括焊缝)等。
液压元件本身也可能由于各种原因有漏油现象。
人们通常是以提高几何精度、降低表面粗糙度和加强密封的方法来解决漏油问题。
解决液压元件与液压系统泄漏的方法主要有“堵”、“导”、“防”,与“用”四种途径。
这些方法过去多年以来起到了很好作用,近年来随着科技不断进步,解决泄漏的方法也有所改进。
“导”的办法主要是内导法,如挡油板,泄漏管等,使泄漏油液流回油箱,对外观也无影响。
下面举例说明具体情况:一、元件接合面间漏油如何解决?元件接合面间漏油,主要由以下原因造成的:1)安装面加工粗糙不符合要求。
由于对某些液压件底平面粗糙度、平面度重视不够,标准要求不高,致使液压件出厂后往往底平面还留有粗加工痕迹与严重磕碰痕迹,出现符号字头打后没有修平等现象。
有时还会遇到底平面O型圈沟槽直径过大,同一底面上沟槽深浅不一致、大部分过深、沟槽底平面粗糙度低,有明显凸楞等情况。
解决办法是底平面重新精磨,对O型圈沟槽进行补充加工,严格控制深度尺寸,使沟槽底的粗糙度达到Ra3.2μm。
2)装配不良引起的漏油。
在装配时有污物或棉线形成毛线管渗透而引起的漏油。
或者是油道内铁屑等污物没清除干净而造成堵塞引起外部漏油。
二、液压缸漏油如何解决?液压缸漏油,大致可分为密封结构的内泄漏和外泄漏以及因液压缸缸体破损而引起的漏油。
对于液压缸来说,其活塞杆表面经常与各种杂质接触。
特别是对于那些在恶劣条件下的液压设备来说,活塞杆表面经常粘附粉尘、泥土、盐雾等等,受到石块等硬性物质打击的机会也相当多。
此外,从使用过程来看,在液压缸最大外伸时受外力作用的可能性也很大,因此,防止液压缸漏油是一个非常难解决的问题。
液压油箱漏油最简单处理方法

液压油箱漏油最简单处理方法液压油箱漏油是一个常见但严重的问题,如果不及时处理,可能会导致液压系统失效,甚至对整个机械设备造成损害。
下面将详细介绍液压油箱漏油的最简单处理方法,旨在帮助读者快速、有效地解决这一问题。
首先,当发现液压油箱漏油时,应立即停机检查。
这一步骤至关重要,因为只有在停机状态下,才能准确判断漏油的位置和原因。
在检查过程中,要注意观察油箱外部是否有明显的油迹或油滴,同时检查油箱的密封件、接头和管路是否有损坏或松动。
确定了漏油的位置后,接下来就可以进行简单的处理了。
如果是密封件老化或损坏导致的漏油,可以更换新的密封件。
在更换密封件时,要确保选用与原件相同型号和规格的密封件,并按照正确的安装方法进行安装。
同时,要注意清洁密封件和安装面,确保无杂质和油污,以免影响密封效果。
如果是接头松动导致的漏油,可以使用合适的工具紧固接头。
在紧固过程中,要注意力度适中,避免过紧或过松。
过紧可能导致接头损坏,过松则可能导致漏油问题无法根本解决。
如果漏油问题是由于管路损坏导致的,可以考虑修复或更换管路。
对于较小的管路损坏,可以使用专业的修复剂进行修复;对于较大的损坏或老化严重的管路,则需要更换新的管路。
在更换管路时,要确保选用与原件相同型号和规格的管路,并按照正确的安装方法进行安装。
在处理液压油箱漏油问题时,还需要注意以下几点:首先,要确保操作环境干燥、清洁,避免杂质和油污进入液压系统;其次,在处理过程中要轻拿轻放,避免对液压系统和机械设备造成额外的损坏;最后,在处理完漏油问题后,要仔细检查液压系统的工作状态,确保一切正常后再进行试机。
总之,液压油箱漏油问题的处理并不复杂,关键是要找准漏油的位置和原因,并采取相应的措施进行修复。
通过以上的简单处理方法,相信读者能够迅速解决液压油箱漏油问题,确保液压系统的正常运行和机械设备的稳定工作。
同时,也建议读者在日常使用中加强对液压系统的维护和保养,定期检查和更换密封件、接头和管路等易损件,以预防漏油问题的发生。
液压系统漏油故障的分析与排除

液压系统漏油故障的分析与排除作者:王孟来源:《城市建设理论研究》2013年第23期【摘要】当今社会,液压传动与其他形式的传动方式相比存在着许多优点,因此广泛地应用在筑路机械中。
但其中液压系统漏油的原因及排除是值得关注的。
【关键词】液压系统;故障分析;排除中图分类号:S951.3 文献标识码:A 文章编号:前言液压系统漏油有内漏和外漏,一旦出现漏油就必须停机维修,为此,本人着重分析漏油故障及排除。
二、液压系统漏油原因分析液压系统漏油分为内漏和外漏,通常所说的漏油主要是指系统外部漏油。
液压系统漏油的原因很多,从方案设计到每个工艺过程(铸造、焊接、机加工及装配),从密封件质量到维修管理等都会造成漏油。
漏油原因主要有以下几个方面。
1、加工或操作不当而造成漏油(一)、零件密封槽加工不当造成漏油。
密封槽过深或过浅,相对运动件的密封接触面椭圆度、锥度超差等,使O型密封圈安装后很难得到均匀准确的压缩量。
这种情况在低压时可能不明显,甚至不漏,但在高压时就比较严重。
(二)、固定螺孔深度不合适造成漏油。
平面密封的固定螺钉孔的深度有两种情况:一种是孔够深但螺纹长度不够;另一种是孔浅而螺纹过短,不论哪种情况,都是螺纹长度不够。
若用原来设计的螺钉来连接,就显得长了。
表面看起来已经拧紧,而实际两个平面并未贴紧,密封不严,产生漏油。
高压时,甚至会把密封圈挤坏。
(三)、平面密封加工不当造成漏油。
平面密封中,若在同一平面上装有多个O型密封圈,其尺寸可能不同,其安装槽又有止口型和凹槽型两种。
除前述原因造成漏油外,还有端面上的压力不够、压缩量不均匀、止口尺寸较小、O型圈在工作时易脱出、结合面不平行、平面和螺孔不垂直、结合面的光洁度太差、凹槽边缘太薄、受力后产生卷边现象等都是产生漏油的根源。
另外,在平面密封中,除阀体平面和螺孔不垂直,接头体两个密封面不平行会产生漏油外,阀体或接头体的密封面上受砸伤、划伤等缺陷,也会引起漏油。
(四)、密封面粗糙造成漏油。
液压系统泄漏的原因及控制途径
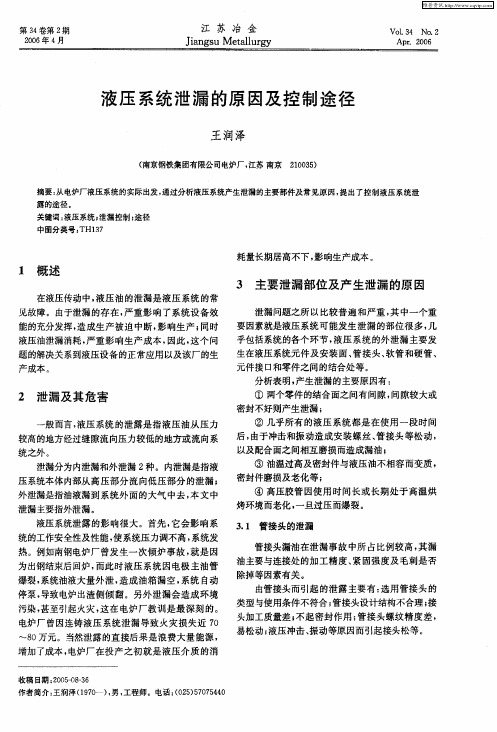
泄漏问题之所 以比较普遍和严重, 中一个重 其 要因素就是液压系统 可能发生泄漏的部位很多, 几 乎包括系统的各个环节 , 液压系统 的外泄漏主要发 生在液压系统元件及安装面 、 管接头 、 软管和硬管、
元件接 口和零件之间的结合处等。
分析表明, 产生泄漏的主要原因有 : ① 两个零件 的结合面之间有间隙, 间隙较大或 密封不好则产生泄漏 ; ② 几乎所有 的液压 系统都是在使用一段时间 后, 由于冲击和振动造成安装螺丝 、 管接头等松动 ,
2 泄漏及 其危害
一
般 而言 , 压 系统 的泄 露 是指 液 压 油 从 压 力 液
电炉厂 曾因连铸 液压 系统泄漏导致火灾损失近 7 O
~
8 万元 。当然泄露的直接后果是浪费大量能源 , O
易松动; 液压冲击 、 振动等原因而引起接头松等。
增加了成本 , 电炉厂在投产之初就是 液压介质的消
收 稿 日期 :0 50 -6 20 -83
作者简介 : 王润泽 (9 O )男 , 1 7一 , 工程师 。电话 :0 5 5 0 5 4 ( 2 ) 77 4 0
家生产 ; 其次, 安装过程中弯 曲度不能过大 , 环境温
密封沟槽尺寸不对 , 密封机构尺寸要求不严格;
结合面光洁度不够 ; 表面加工粗糙 ; 安装时螺杆紧固 力不均匀或使用一段时间后 因振动螺杆松动 ; 密封 面碰伤划伤等。
3 4 管 线漏油 .
度确实很高时应考虑改用硬管或选用高压金属波纹 管 。南钢电炉厂 出钢 口及连铸拉矫机处采用 了耐高
压系统本体内部从高压部分流向低压部分的泄漏 ;
外泄漏是指油液漏到系统外面的大气 中去 , 本文中
液压缸泄漏分析及预防

山东农机化液压缸泄漏分析及预防液压缸是液压系统中的主要执行元件。
目前常规液压缸的工作压力可达32MPa,甚至可达70MPa。
随着农用机械向大型、高压化发展,液压缸的防漏与治漏越来越受到重视。
据有关资料统计,在工程机械所有故障中,液压缸漏油故障约占30%。
液压缸漏油会严重影响设备的平稳性、可靠性和使用寿命。
准确地分析泄漏产生的原因,可以帮助我们及时排除液压系统的泄漏故障。
在液压系统中,液压元件各零件之间如有相对的运动,就必须有一定的配合间隙。
压力油就会由配合间隙从高压区流向低压区,产生泄漏。
泄漏可使液压系统的功能下降,严重的会导致液压系统失效。
在实际中,泄漏是无法避免的,完全达到“零泄漏”是不可能的。
我们只有设法尽量减小液压系统的泄漏量,以提高液压系统的功效。
一、液压缸泄漏的原因及预防措施液压缸泄漏的因素是多方面的,譬如:密封件的质量、液压元件的机加质量、结构设计的合理性、颗粒的污染及装配的影响、液压缸的工作温度等,这些因素都可使液压缸发生泄漏。
1.正确选用和装配密封件。
密封件选用不当,会造成液压油的泄漏。
密封件的质量差,那么其耐压能力就低,使用寿命短,同时密封性能差,密封件使用不久就会产生泄漏。
密封件装配不当,也会导致泄漏的发生。
正确地安装密封件,是预防漏油的重要措施之一。
安装O形圈时,不要将其拉到永久变形的位置,也不要边滚动边套装,否则可能因密封圈扭曲而造成漏油。
安装Y形和V形密封圈时,要注意安装方向,避免因装反而漏油。
对Y形密封圈而言,其唇边应对着有压力的油腔;此外,对Y形密封圈还要注意区分是轴用还是孔用,不要装错。
V形密封圈由形状不同的支承环、密封环和压环组成,当压环压紧密封环时,支承环可使密封环产生变形而起密封作用,安装时应将密封环开口面向压力油腔;调整压环时,应以不漏油为限,不可压得过紧,以防密封阻力过大。
密封装置如与滑动表面配合,装配时应涂以适量的液压油。
拆卸后的O形密封圈和防尘圈应全部更新。
A320系列飞机液压系统渗漏检查与预防

A320系列飞机液压系统渗漏检查与预防液压系统油液渗漏问题一直是困扰机务维修工作的难题,维护中存在很多困难,是影响航班正常性的重要因素之一。
如何做好油液的预防检查和控制措施就是我们各个飞机保障部门所力求解决的一大课题。
本文结合空客关于液压渗漏的SIL,分析了航线常见渗漏模式,与大家分享交流。
一、A320系列飞机液压系统的特点:在A320系列这样的现代民用客机上,尽管与电气、电子系统相比,液压系统的科技含量不高,但由于其自身具备体积功率比小,技术成熟,工作可靠性高等一系列优点,使得液压系统仍然广泛使用在各系统甚至是一些关键系统中,为它们提供动力源。
涉及液压系统的章节有:24章(应急发电);27章(飞控);29章(液压);32章(起落架);52章(货舱门);78章(反推)。
如下图所示同时液压系统部件(动力部件、控制部件、执行部件、辅助部件,接头及管路)分布范围广,包括有:3个起落架及起落架轮舱、液压/勤务舱、货舱地板及侧板下、后附件舱、各飞行操纵面内部、发动机短舱吊架。
这么大的分布范围导致部件和管路数量很多,管路纵横密布,检查起来十分困难。
二、液压系统渗漏形式和特点:由于液压系统是以液体作为工作媒介,所以自诞生之日起一直伴随着一个突出问题,就是“油液渗漏”。
随着飞机设计、制造水平的提高,现代民用航空器的液压油渗漏问题有所改善,但却无法根治。
对于A320系列飞机来说,渗漏形式可分为以下两大类:1、部件本体渗漏:包括有壳体裂纹,结合面渗漏,作动部件渗漏等,部件封圈损伤;2、管路渗漏:包括有硬管管壁损伤,软管断丝,接头力矩不当,接头损伤,底座封圈损伤等;下图是几种常见的渗漏点:部件自身封严性能下降和接头封圈失效在部件渗漏中占了绝大部分比重。
通常情况下部件渗漏多为渐变过程,渗漏程度逐渐恶化,如果在渗漏前期及时发现并予以处理,就可以阻断严重渗漏的发生。
管接头漏油一般是由接头松动或损伤所致,前期也能发现并做预防处理。
常见漏油原因与处理方法

常见漏油原因与治漏通常将漏油划分为渗油、滴油和流油三种形态。
一般规定,静结合面部位,每半个小时滴一滴油为渗油;动结合面部位,每六分钟滴一滴油为渗油。
无论是动结合面还是静结合面,每二至三分钟滴一滴油时,就认为是在滴油;每分钟滴五滴油时,就认为是在流油。
在排除设备漏油故障中,使设备达到治漏目的的一般要求是,设备外部静结合面处不得有渗油现象,动结合面处允许有轻微渗油,但不允许流到地面上;设备内部允许有些渗油,但不得渗入电气箱和传动带上,不得滴落到地面,并能引回到润滑油箱内。
一、设备漏油的常见原因1,由设计不合理引起的漏油(1)没有合理的回油通路,使回油不畅造成设备漏油。
例如,轴承处回油不畅,就容易在轴承盖处出现积油,或者形成一定压力,使轴承盖处出現漏油现象。
有的设备回油孔位置不对,容易发生被污物堵塞,回油不畅出現漏油的现象,有的设备回油槽容量过小,容易造成回油从回油槽溢出的现象。
有的设备在工作台旋转时,容易将油甩出,而又没有设计适用的回收装置,就会造成润滑油漏到地面的现象。
(2)密封件与使用条件不相适应,造成设备漏油现象。
在机械设备中最常用的密封件是O型橡胶密封圈,选用时必须根据设备的使用条件和工作状态进行选择。
在用油润滑条件下,当密封压力小于2,9MPa时,可选用低硬度耐油橡胶O型密封圈。
当密封压力达到2.9〜4.9MPa时,应选用中硬度耐油橡胶O型密封圈。
当密封压力达到4.9〜7.8MPa时,应选用高硬度耐油橡胶O型密封圈。
若用油润滑选择了普通橡胶O型密封圈;或者虽然选用了耐油橡胶O型密封圈,但应用压力范围低于设备密封压力,就会造成设备漏油故障。
(3)该密封的没有设计密封,或者密封尺寸不当,与密封件相配的结构不合理造成设备出现漏油现象。
例如箱体上的螺钉孔设计成通孔,又没有密封措施;箱体盖处没有设计密封垫;转轴与箱体孔的配合间隙过大;密封圈与轴配合的过盈量不合要求;密封槽设计不合理等情况都可能使设备中的润滑油从没有实现密封的环节中漏出。
液压油箱喷油的原因及防止措施
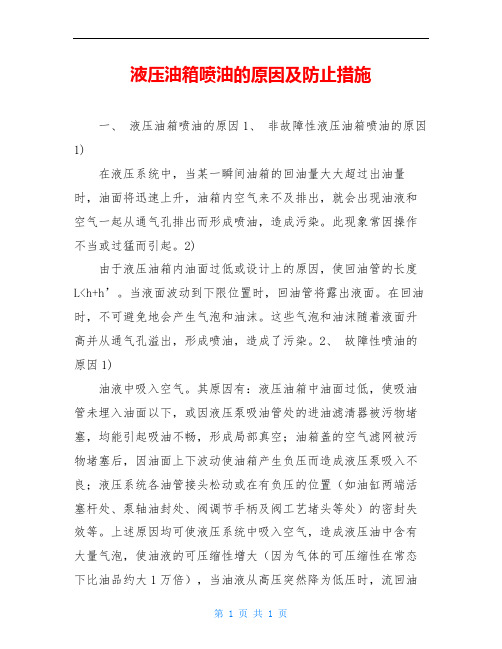
液压油箱喷油的原因及防止措施一、液压油箱喷油的原因1、非故障性液压油箱喷油的原因1)在液压系统中,当某一瞬间油箱的回油量大大超过出油量时,油面将迅速上升,油箱内空气来不及排出,就会出现油液和空气一起从通气孔排出而形成喷油,造成污染。
此现象常因操作不当或过猛而引起。
2)由于液压油箱内油面过低或设计上的原因,使回油管的长度L<h+h’。
当液面波动到下限位置时,回油管将露出液面。
在回油时,不可避免地会产生气泡和油沫。
这些气泡和油沫随着液面升高并从通气孔溢出,形成喷油,造成了污染。
2、故障性喷油的原因1)油液中吸入空气。
其原因有:液压油箱中油面过低,使吸油管未埋入油面以下,或因液压泵吸油管处的进油滤清器被污物堵塞,均能引起吸油不畅,形成局部真空;油箱盖的空气滤网被污物堵塞后,因油面上下波动使油箱产生负压而造成液压泵吸入不良;液压系统各油管接头松动或在有负压的位置(如油缸两端活塞杆处、泵轴油封处、阀调节手柄及阀工艺堵头等处)的密封失效等。
上述原因均可使液压系统中吸入空气,造成液压油中含有大量气泡,使油液的可压缩性增大(因为气体的可压缩性在常态下比油品约大1万倍),当油液从高压突然降为低压时,流回油箱油液中的气泡在油箱内将急剧膨胀,使油箱内压力高于大气压力,导致油液混同空气一起从通气孔排出,即出现喷油。
此类喷油如果不及时排除,液压系统中将会产生气穴现象,使油泵产生噪声,并增大液压泵的吸入阻力,使排油量降低;液压泵、马达和阀等的金属表面被腐蚀;液压动力元件、随动阀等动作不灵及促使液压油变质恶化等。
2)液压系统工作液压泵的轴端因油封损坏而与变矩器-变速箱系统的变速泵串油,致使变速箱内的液力传动油参与液压系统循环,并不断地被送到液压油箱内,使液压油箱内油面不断升高而溢出,形成喷油。
如果不及时排除,会使变矩器-变速箱系统缺油,影响变矩器-变速箱系统的正常运转。
液压油因混有液力传动油而发生添加剂之间相互化学反应,造成油液混浊,降低使用效果,增加气泡,影响液压系统的正常运转。
液压系统常见漏油故障治理

液压系统常见漏油故障治理作者:张洪喜来源:《职业·下旬》2013年第01期摘要:液压传动是利用密封容积的变化来传递运动,通过液体内部的压力传递动力的传动方式。
液压系统在工作过程中由于有压力存在,工作介质的泄漏会严重影响系统的正常工作。
本文阐述常见的液压系统漏油原因和治理方法。
关键词:液压元件液压系统漏油故障治理一、液压系统常见漏油故障及诊断方法1.液压元件与安装板接合面间漏油各种液压元件与安装板接合面间常有漏油的问题,主要原因是阀体平面和安装板平面的加工不符合要求,表面直线度差,表面粗糙不符合要求,或加工面有碰伤,或在装配时平面上有污物引起配合不良等。
2.O形密封圈磨损漏油O形密封圈必须具有耐油,耐高温,耐压和耐磨损性能。
密封圈的沟槽尺寸为正公差。
这样就使密封圈在受压状态下被过分撑大而使截面变小,容易漏油。
阀体O形圈处漏油先要从检查阀块的加工入手,检查表面粗糙度加工精度是否合格,然后检查O形圈压缩量是否符合要求,检查O形圈的耐高温性能,必要时采用进口密封件。
这里关键是要找到问题的原因,才能对症下药。
3.卡套式管接头、紧固螺母和接头螺纹配合不当漏油此原因是管壁破裂,螺纹上有毛刺,在拧紧时将螺纹挤坏,螺纹牙形不标准,不能保证良好贴合。
另外,管接头和油塞一般都是锥管螺纹连接,贴合性差,也易发生漏油现象。
4.电磁换向阀漏油电磁换向阀漏油主要是电磁铁推杆和阀体的接触面及油塞螺纹处漏油,推杆与挡圈孔的配合间隙过大,致使推杆推动阀芯时,因导向不良而倾斜,油容易从杆与阀体的接触面渗漏出来。
阀体的油塞螺纹漏油是因密封填料不良引起的。
5.调速阀、节流阀漏油调速阀、节流阀漏油,主要是调节手柄、压盖螺纹、油塞螺纹接合面等处漏油。
调节手柄处漏油主要是由于调节杆上的O形密封圈不耐油产生破损,或者沟槽底径尺寸太小,以致起不到密封作用。
压盖螺纹处漏油也是因为O形密封圈沟槽位置不对。
6.箱体或其他机械部件漏油对于箱体或其他机械部件,可先把要检查部位的外表面用棉纱擦干净,再进行观察,看从什么部位出现渗漏现象,并测量其渗漏程度;肉眼不易观察时,可先将部件擦干净,然后将怀疑是由于裂纹、疏松引起漏油的部位涂上煤油,过一段时间再将煤油擦净,并敷上白粉,用小锤连续敲击,渗在金属裂缝中的煤油就会透过白粉显出裂纹、疏松的轮廓。
液压马达油封漏油的原因

液压马达油封漏油的原因液压马达是液压传动系统中的重要组成部分,常用于工业生产中的机械设备中。
然而,由于液压马达油封漏油的问题,导致其正常运行受到影响。
本文将分析液压马达油封漏油的原因,并提出相应的解决方法。
一、液压马达油封漏油的原因1.油封老化或损坏:油封作为液压马达的关键部件之一,其主要功能是防止液压油从马达内部泄漏到外部环境。
然而,由于长时间使用或外部因素的影响,油封会出现老化、磨损或破裂等情况,导致液压马达发生油封漏油现象。
2.密封面不平整:液压马达中的密封面是确保油封密封性能的重要因素之一。
如果密封面存在磨损、凹凸不平或划痕等情况,将导致油封无法密封,从而发生漏油现象。
3.液压马达过载:过载是液压马达油封漏油的常见原因之一。
当液压马达承受超过其额定负载的工作压力时,会导致液压油通过油封的缝隙泄漏到外部环境。
4.液压油污染:液压系统中的液压油质量直接影响液压马达的正常运行。
如果液压油中存在杂质、水分或气泡等污染物,会对油封产生不良影响,导致油封漏油问题的发生。
5.安装不当:液压马达的安装过程中,如果操作不当或存在安装误差,可能会导致油封与密封面之间的间隙不合适,从而引发油封漏油现象。
二、液压马达油封漏油的解决方法1.更换油封:当液压马达发生油封漏油问题时,首先需要检查油封的状况。
如果发现油封老化、磨损或破裂等情况,应及时更换新的油封。
2.修复密封面:对于存在密封面不平整的情况,可以采取研磨、修复或更换的方式来解决。
确保密封面的平整度和光洁度,以提高油封的密封性能。
3.控制负载:合理控制液压马达的负载,避免超过其额定工作压力。
可以通过调整液压系统的参数或增加负载保护装置来实现。
4.保持液压油清洁:定期检查和更换液压油,避免液压油受到污染。
使用过滤器和除水器等设备来保持液压油的清洁度,提高液压马达的工作效率和寿命。
5.正确安装:在安装液压马达时,注意正确调整油封与密封面之间的间隙,确保其密封性能正常。
车辆液压系统漏油原因分析及防漏措施

施 ,会 因振 动加 大而加 速泄 漏发 生。⑧ 装 配 不 当引 起。 系统装 配粗糙 , 如配合 不 当、 污染 物进 入 、 件碰 元
撞损伤 等 而造成 泄漏 。 ( 作维 护不 当引起 。 操 系统超
压使用 、 未按 规定 对 系统适 时检 查及 处理 、 元件 寿命 到期 而未及 时更换 ,以及 恶 劣工况 条件和使 用 环境
冲 击和振 动 引起 。 液压 系统 的冲 击主要产 生于 变压 、
变速 、 向的过 程 中 , 时管路 内流动 的液压 油 因急 换 此
速 换 向和 阀 口突然 关 闭而 瞬 间形 成很 高 的压 力 , 使 连接 件 、接头 与法 兰松动或 密封 圈挤入 间隙而损坏 等, 造成 泄 漏 。另 外 , 作装 置若 缺 乏减 振 、 工 隔振 措
等, 密封件就会有变形、 划伤 , 使其 密封性能下降。 ④ 情况 需要使 用代 用油 时 ,应 力求其 性 能与原牌 号性 铸件 和焊接 件 缺 陷引起 。壳体 的泄漏 主要 是 由于铸 能相近 。 同牌 号 的液 压油 不 能混合使 用 。 不 ( 防止 固 件和 焊接件 有缺 陷,在 液压 系统 的压 力脉 动或冲 击 体 杂质 混入 液压 系统 。 意正确 安装液压 油 滤清器 。 注 振 动的作用 下 , 陷逐 渐扩 大 , 成泄 漏。( 液污 并定期 清洁 或更换 。 用合 适 的防尘 密封 件 , 免尘 缺 造 油 选 避 染 引起。 首先是 气体 污染 引起 。 液压 油 中可溶解 一定 埃 等污 物进入 。液压 元件 安装前 , 应检 查 、 清理 干净 量 的空气 , 空气在 油液 中形 成气泡 , 在工 作过 程 中压 其 表 面和 内部 的杂 质。 加油 和维修保 养 时 , 做好过 滤 力急 剧变化 , 会使 气泡 在高压 侧产 生高 温 , 在低 压 侧 和 防护 , 确保 油液 的清洁 。 ( 防止 空气和水 入侵液 压 发 生爆裂 。 气泡爆 裂使 液 压油 高速 冲 向元 件表 面 , 加 系统 。维修和 换 油后 , 要按 规定排 除系统 中 的空气。 速 表 面 的磨 损 , 引起泄 漏 ; 次是颗 粒污 染 引起 。液 保 证油 箱 中的油位 .不 能让 液压 油泵 的吸 油管 口露 其 压 油缸 作 为 一 些工 程 机 械 液 压 系统 的主 要 执 行 元 出油面 , 吸油 管路 必须 密封 良好 。 防止 液压 泵吸入 空 件. 由于工作 过程 中活 塞杆裸 露在 外 . 接 - 直 9环境 接 气。 禁加注 含水 量大 的液压 油。 严 ( 定期检 查油液 质 触, 虽然在 导 向套 上装 有 防尘 圈及 密封件 。 也难 免 量 。 但 深褐 色 、 白色 、 异味 的液压 油是变质 油 , 能 乳 有 不
浅谈液压设备漏油的分析和治理

浅谈液压设备漏油的分析和治理液压设备漏油问题常常会导致设备的故障和影响设备的正常运行,不仅影响了生产效率和质量,还会造成环境污染和能源浪费。
因此,对液压设备漏油问题的分析和治理具有很重要的意义。
本文将从具体的实践出发,对液压设备漏油的分析和治理进行探讨。
一、漏油情况分析液压设备漏油的原因主要有以下几方面:1.密封失效在液压设备中,密封件的失效是导致漏油的主要原因之一。
密封件在工作时会受到外界环境、压力和温度等多种因素的影响,导致密封层磨损,失去密封性能。
常见的密封件包括O型圈、油封、活塞杆密封件等。
如果密封件老化或磨损过度,会导致油液泄漏。
2.管路连接松动液压设备中的管路连接件因长期使用、受到外力影响或安装不当等原因,可能使管路连接松动,导致漏油。
出现这种情况时,需要及时进行检查和紧固。
3.液压元件损坏液压设备中的液压混合器、液压缸、液压泵、油罐等液压元件经过长时间的工作,可能会出现磨损、腐蚀、变形等问题,导致漏油。
4.操作不当在液压设备的操作过程中,如果操作不当,比如疏通、清洗管路,使用外力对液压元件进行强制操作等,都可能导致元件破裂、损坏和漏油。
二、治理方法1.加强维护保养对液压设备进行经常性的检查和维护,及时更换老化或损坏的密封件和管路连接件,并进行紧固;定期清洗管路和换油,保证油液清洁,减少泵、阀等易受腐蚀的部件因油液中杂质或水分引起的故障;对液压系统进行分析和评估,根据实际情况进行升级和改造,增强液压设备的可靠性和稳定性。
2.选择合适的液压元件选用质量好、性能稳定的液压元件,避免选用低价格、不合格的元件,是减少液压设备漏油问题的重要手段。
3.合理的操作方式在操作液压设备时,要注意操作规范,杜绝操作不当的行为;对液压设备进行适当的保护,减小外力对设备的影响,防止因操作不当造成的设备损坏和漏油问题。
4.采取最优化处理措施采取科学的处理措施,对漏油问题进行彻底的处理。
对于漏油问题严重的液压设备,可以采取更换液压元件、改造液压管路等更加全面的措施进行处理。
浅析船舶机械液压系统漏油原因及解决措施
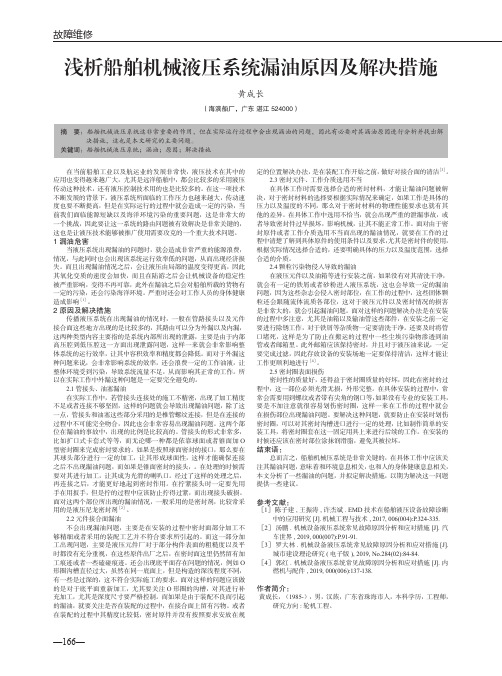
—166—故障维修在当前船舶工业以及航运业的发展非常快,液压技术在其中的应用也变得越来越广大,尤其是远洋船舶中,都会比较多的采用液压传动这种技术,还有液压控制技术用的也是比较多的。
在这一项技术不断发展的背景下,液压系统所面临的工作压力也越来越大,传动速度也要不断提高,但是在实际运行的过程中就会造成一定的污染,当前我们面临能源短缺以及海洋环境污染的重要问题,这是非常大的一个挑战,因此要让这一系统的路由问题被有效解决是非常关键的,这也是让液压技术能够被推广使用需要攻克的一个重大技术问题。
1 漏油危害当液压系统出现漏油的问题时,就会造成非常严重的能源浪费,情况,与此同时也会出现该系统运行效率低的问题,从而出现经济损失。
而且出现漏油情况之后,会让液压由局部的温度变得更高,因此其氧化变质的速度会加快,而且在陆游之后会让机械设备的稳定性被严重影响,变得不再可靠,此外在漏油之后会对船舶所载的货物有一定的污染,还会污染海洋环境。
严重时还会对工作人员的身体健康造成影响[1]。
2 原因及解决措施传播液压系统在出现漏油的情况时,一般在管路接头以及元件接合面这些地方出现的是比较多的,其路由可以分为外漏以及内漏,这两种类型内容主要指的是系统内部所出现的泄露,主要是由于内部高压腔到低压腔这一方面出现泄露问题,这样一来就会非常影响整体系统的运行效率,让其中容积效率和精度都会降低。
而对于外漏这种问题来说,会非常影响系统的效率,还会浪费一定的工作油液,让整体环境受到污染,导致系统流量不足,从而影响其正常的工作。
所以在实际工作中外漏这种问题是一定要完全避免的。
2.1管接头、油塞漏油在实际工作中,若管接头连接处的施工不精密,出现了加工精度不足或者连接不够坚固,这样的问题就会导致出现漏油问题,除了这一点,管接头和油塞这些部分采用的是椎管螺纹连接,但是在连接的过程中不可能完全吻合,因此也会非常容易出现漏油问题。
这两个部位在漏油的事故中,出现的比例是比较高的。
某大型液压设备渗漏油原因分析及解决措施

某大型液压设备渗漏油原因分析及解决措施某型液压设备各项作业功能是由液压系统完成的,而液压系统的各类故障中,渗漏有时比较普遍。
液压系统的渗漏会造成液压系统容积效率下降和液压能的损失,液压系统的总效率降低或者达不到要求的工作压力。
甚至使液压系统不能正常的工作。
而且损失的液压能转化成为热能,使液压油温度升高,影响设备的工作精度和性能。
外漏的液压油会污染环境。
如何解决该液压系统的渗漏油一直是该液压设备亟待解决的问题。
一、液压系统的渗漏的原因分析(一)接头处渗漏油液压设备系统的各液压元件之間均油管路通过接头来完成整个系统的连通,接头的连接出成为最容易出现渗漏油的地方。
1.安装不当引起渗漏油。
该液压设备金属管路的连接多采用球头连接,球头密封靠内、外的圆锥度气密封作用,球头连接一般不会渗漏油,出现渗漏多是球头发生了磨损,原因是管路安装时方向不正或受力过大造成咬死,造成管接头磨损。
2.加工超差引起渗漏油。
管路和阀体一般采取端面密封,阀门与管接头间靠O型密封圈密封,这种密封性很好,又问上升到70℃左右,压力达到30MPa左右也不会漏油。
当安放密封圈槽的深度加工太大,端面与密封圈压缩率太小,当油温上升到50℃左右就会漏油;当安放密封圈槽的深度较小会把O型密封圈压缩变形,加快磨损或扭曲破坏,同样导致漏油。
3.冲击和振动引起渗漏油。
该设备的工作环境较为恶劣,冲击和振动频繁,容易引起接头松动,造成渗漏油。
尤其是与液压泵连接的金属管路接头,因冲击和振动大,出现渗漏油甚至管接头磨损的情况比较频繁。
(二)管路渗漏油1.管路弯曲不良。
管路安装时应按规定的弯曲半径,否则产生不同的弯曲内应力,在液压油的作用下逐渐产生渗漏。
硬管路弯曲半径过小,导致管外侧管壁变薄,内侧管壁存在皱纹,使管弯曲处内应力很大,强度大大减弱,在强振动或高压冲击时,管路易产生横向裂纹而漏油;若弯曲处出现较大的椭圆度,当管内的油压脉动时,会产生纵向裂纹而漏油。
2.管路疲劳破坏或老化。
浅析液压系统泄漏故障排除及控制措施

浅析液压系统泄漏故障排除及控制措施摘要:液压系统的泄漏严重影响着机械设备工作的安全性和可靠性,不仅造成油液浪费、环境污染、还会增加机械设备的停工时间,降低作业率、直接增加生产成本,对产品造成污损,因此,我们应及时排除液压系统的泄漏故障并采取行之有效的控制措施来防漏治漏,以安全可靠地使用液压传动系统设备。
本文针对此浅析液压系统泄漏的原因、排除方法以及防漏与治漏的主要措施,对于推广液压传动系统的应用,优化液压系统的设计,指导维修人员排除故障、维护液压设备有着积极意义。
关键词液压系统泄漏故障排除防漏措施液压传动系统具有体积小、重量轻、传递功率大、运行平稳、可实现无级调速等优点,近年来得到广泛应用。
但由于液压油的可压缩性和泄漏造成液压传动不能保证严格的传动比,也因为流体流动的阻力损失和泄漏较大,导致液压系统效率低,由此可见液压系统的泄漏直接制约着液压系统推广应用。
液压系统泄露治理是一项系统性工程,涵盖了液压系统设计,元件的选型,制造,安装,冲洗,调试及运行各个环节。
本文就针对此浅析液压系统泄漏故障的排除及防漏、治漏的措施,对于推广液压传动系统的应用,优化液压系统的设计,指导维修人员排除故障、维护液压设备有着积极意义。
正文液压系统油液的泄漏是指油液在液压元件、附件(含管道)组成的封闭容腔内,由于压差的存在,液压油从高压侧通过缝隙流向低压侧而不做功的过程。
泄漏可分为外泄漏和内泄漏。
外泄漏主要是指液压油从系统漏到环境中,如管路、阀件连接出现松动、密封破损等造成的泄露,致使油液由系统外泄至周围环境。
内泄漏是指因液压元件内高低压力差的存在以及密封件失效,使液压油在系统内部从高压腔流向低压腔,但液压油仍在系统内循环,尽管对环境不造成影响,但内泄严重时可造成液压传动效率低,不能完成指定动作。
一、液压系统常见泄漏故障的排除方法:1.齿轮液压泵内漏的处理方法:1.1液压泵齿轮与泵壳的配合径向间隙超过规定极限偏差。
处理方法是:更换泵壳或采用镶套法修复,保证液压泵齿轮齿顶与壳体配合间隙在正常范围之内(正常间隙为0.13~0.16mm)。
怎样处理液压系统的泄露问题

怎样处理液压系统的泄露问题液压系统的泄漏会造成液压量减少且不能建立正常压力,从而导致系统不能正常工作。
液压系统的泄露主要有两种情况:外漏和内漏。
本文主要介绍液压系统泄漏的两种主要泄漏故障的排除方法以及防漏与治漏的主要措施。
一.液压系统泄漏的两种主要泄漏故障的排除方法A、液压系统内漏故障的排除内漏主要是液压系统内部的液压泵、液压缸、分配器等产生泄漏造成的。
内漏的故障不易被发现,有时还需借助仪器进行检测和调整,才能排除。
归纳起来主要在以下几个方面:1、齿轮液压泵相关部位严重磨损或装配错误(1)液压泵齿轮与泵壳的配合间隙超过规定极限。
处理方法是:更换泵壳或采用镶套法修复,保证液压泵齿轮齿顶与壳体配合间隙在规定范围之内。
(2)齿轮轴套与齿轮端面过度磨损,使卸压密封圈预压缩量不足而失去密封作用,导致液压泵高压腔与低压腔串通,内漏严重。
处理方法是:在后轴套下面加补偿垫片(补偿垫片厚度一般不宜超过2mm),保证密封圈安放的压缩量。
(3)拆装液压泵时,在2个轴套(螺旋油沟的轴套)结合面处,将导向钢丝装错方向。
处理方法是:保证导向钢丝能同时将2个轴套按被动齿轮旋转方向偏转一个角度,使2个轴套平面贴合紧密。
(4)在拆装液压泵时,隔压密封圈老化损坏,卸压片密封胶圈被装错。
处理方法是:若隔压密封圈老化,应更换新件:卸压片密封胶圈应装在吸液腔(口)一侧(低压腔),并保证有一定的预紧压力。
如装在压液腔一侧,密封胶圈会很快损坏,造成高压腔与低压腔相通,使液压泵丧失工作能力。
2、液压缸密封圈老化和损坏活塞杆锁紧螺母松动(1)液压缸活塞上的密封圈、活塞杆与活塞接合处的密封挡圈、定位阀密封圈损坏。
处理方法是:更换密封圈和密封挡圈。
但要注意,选用的密封圈表面应光滑;无皱纹、无裂缝、无气孔、无擦伤等。
(2)活塞杆锁紧螺母松动。
处理方法是:拧紧活塞杆锁紧螺母。
(3)缸筒失圆严重时,可能导致液压缸上下腔的液压油相通。
处理方法:若失圆不太严重,可采取更换加大活塞密封圈的办法来恢复其密封性;若圆度、圆柱度误差超过0.05mm时,则应对缸筒进行珩磨加工,更换加大活塞,来恢复正常配合间隙。
工程机械液压系统泄漏分析及预防措施

工程机械液压系统泄漏分析及预防措施摘要:随着工程机械的普及,对其液压控制技术提出了更高的要求。
但是,在工程机械中,液压系统的泄露问题一直是一个无法回避的问题。
早期的密封元件失效往往不易被检测到,一旦发生失效,不但会影响生产效率,还会对环境造成污染,甚至会导致人员的死亡。
所以,对施工机械液压系统发生泄漏的原因进行分析,并提出有效的解决措施就显得非常重要。
关键词:工程机械;液压系统;泄漏;预防措施1工程液压系统泄漏的定义及分类在不同的工程机械设备中,由于缺乏加工工艺和装配工艺,设备表面之间存在着移动,会产生磨损缝隙。
当润滑油通过配合间隙时,润滑油从间隙中溢出,此现象称为泄漏。
在施工机械中液压传动系统中,在互相移动的密封元件和静止元件的密封元件之间存在着较大的泄露。
相互运动密封处泄漏,主要指的是油缸活塞杆部位、多路阀阀杆等部位。
固定装置密封处泄漏指的是液压阀组、各管接头的连接处泄露。
此外,还可以从油液的泄漏方向上来进行分类,它可以被分为两种方向,一种是外泄漏,另一种是内泄漏。
内泄露是因为系统中有压差,导致密封松脱时,液压油会油压高的一侧泄露向油压低的一侧。
2工程机械液压系统泄漏位置及原因分析2.1液压胶管处泄漏液压软管泄漏包括橡胶软管部分长期磨损引起的泄漏和软管接头处的泄漏。
橡胶管接头的泄漏主要发生在橡胶管接头与橡胶管扣压接头的接合面附近,以及橡胶管接头和直接头的装配和密封位置。
软管泄漏的主要原因是:软管接头尺寸不合格;橡胶软管未压到位;液压冲击或机械振动引起的接头松动;橡胶软管的方向不合理;橡胶软管总成拧紧力矩不当;与橡胶软管连接的直接头密封面尺寸不合格;软管压力等级选择不当。
2.2设计不合理常见的泄露问题,其中一个重要的因素是密封元件的选型不合理或元件的不完善。
密封元件是防止泄露的关键部件,其构造的优劣将直接影响到其使用效果及使用寿命,若所构造的密封元件无法达到最根本的密封要求,则会导致在实际使用中无法实现有效的密封,从而造成液压系统泄露。
液压系统漏油原因分析及控制措施

液压系统漏油原因分析及控制措施【摘要】液压系统的漏油仍是当前液压设备存在的普遍性问题, 由于密封不良, 外界污染物侵入, 导致恶性循环, 液压元件出现磨损、乃至失效,这使液压系统的效率显著降低。
本文对液压系统漏油的类型、危害及其原因进行了分析,并提出了控制液压系统泄漏的措施,以此进一步提高液压系统的可靠性和工作质量。
关键词:液压系统; 漏油; 原因; 控制措施;1 液压系统漏油的类型、危害液压系统中的液压油是在液压元件、辅件组合的封闭容腔内暂存或流动的, 循环的液压油理应限定于规定的容腔内, 但由于压力、间隙等因素的影响, 有部分液压油超过容腔边界流出, 这种现象称为漏油。
1.1 漏油的类型漏油分为内泄漏和外泄漏。
内泄漏是指液压元(辅)件的高压腔流向低压腔的泄漏。
外泄漏是指液压元件或管路中流向外部的泄漏。
1.2漏油的危害漏油如果得不到控制, 将会造成:(1) 系统发热;(2) 系统压力调不高;(3) 元件容积效率低;(4) 执行机构速度不稳定;(5) 控制失灵;(6) 油液浪费;(7) 污染环境;(8) 引起火灾。
2漏油的原因液压传动在实际中漏油情况复杂,产生漏油的原因较多,有设计、制造方面的问题, 也有设备维护、保养等方面的问题。
但液压系统中漏油问题的大多数原因是密封失效。
2.1管路接头漏油液压系统漏油发生在管路接头处最为多见。
其根本原因是接头密封不良, 封油压力低于液压油峰值压力, 此时将管接头拆洗并重新拧紧即可解决。
2.2橡胶密封圈破损漏油(1) 密封面之间的间隙过大。
在有相对运动的密封面之间, 都留有一定的间隙。
工作中, 橡胶密封圈在液压油压力的作用下, 有一部分被挤入间隙。
当工作压力一定时, 密封面之间的间隙扩大, 橡胶密封圈被挤入的部分就增加, 所承受的剪力也就增大, 也就越容易被撕裂。
(2) 工作压力过大和油压脉动的影响。
如果工作压力过大, 将使橡胶密封圈挤入间隙部分增多, 从而加剧了对橡胶圈的磨削和切割作用。
液压站常见漏油原因
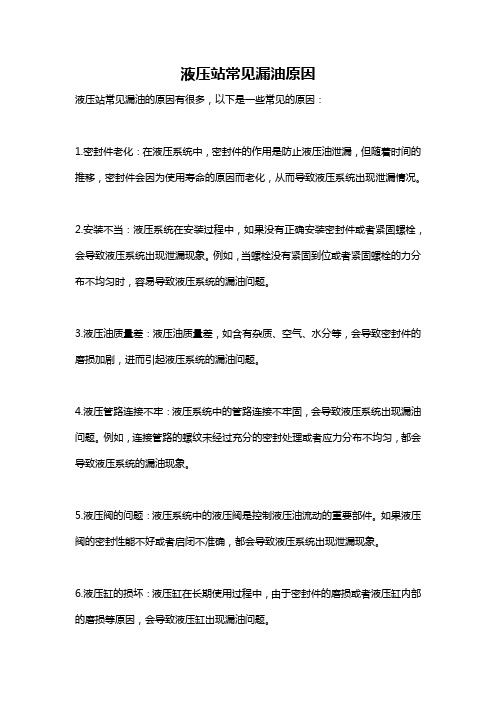
液压站常见漏油原因液压站常见漏油的原因有很多,以下是一些常见的原因:1.密封件老化:在液压系统中,密封件的作用是防止液压油泄漏,但随着时间的推移,密封件会因为使用寿命的原因而老化,从而导致液压系统出现泄漏情况。
2.安装不当:液压系统在安装过程中,如果没有正确安装密封件或者紧固螺栓,会导致液压系统出现泄漏现象。
例如,当螺栓没有紧固到位或者紧固螺栓的力分布不均匀时,容易导致液压系统的漏油问题。
3.液压油质量差:液压油质量差,如含有杂质、空气、水分等,会导致密封件的磨损加剧,进而引起液压系统的漏油问题。
4.液压管路连接不牢:液压系统中的管路连接不牢固,会导致液压系统出现漏油问题。
例如,连接管路的螺纹未经过充分的密封处理或者应力分布不均匀,都会导致液压系统的漏油现象。
5.液压阀的问题:液压系统中的液压阀是控制液压油流动的重要部件。
如果液压阀的密封性能不好或者启闭不准确,都会导致液压系统出现泄漏现象。
6.液压缸的损坏:液压缸在长期使用过程中,由于密封件的磨损或者液压缸内部的磨损等原因,会导致液压缸出现漏油问题。
7.液压泵的问题:液压系统中的液压泵是提供液压系统所需的能量的设备,如果液压泵的密封性能不好或者叶轮磨损严重,都会导致液压系统出现泄漏现象。
8.操作不当:如果操作人员在使用液压设备时不按照操作规程进行操作,例如操作阀门不当、过度压力使用、过度开关频繁等,都会导致液压系统出现漏油问题。
9.温度变化:液压系统在运行过程中存在温度变化的情况,特别是在高温环境下,液压系统的密封件容易受到影响而导致漏油问题的发生。
对于液压站常见的漏油问题,可以通过以下方法来解决:1.定期维护保养:定期检查液压系统的密封件、管路连接、液压阀和液压缸等部件的状态,及时更换老化的密封件以及修复磨损或损坏的部件,确保液压系统的正常工作。
2.正确安装:在安装液压系统时,要确保密封件和管路连接的正确安装,并且按照规范进行紧固,避免因为安装不当导致液压系统的泄漏问题。
液压系统漏油原因
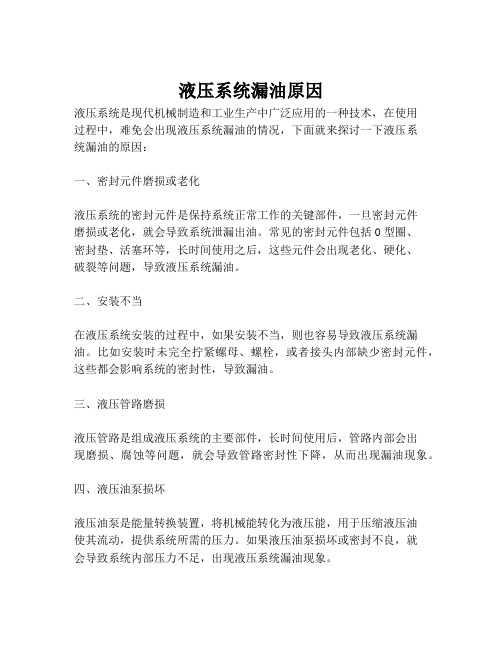
液压系统漏油原因
液压系统是现代机械制造和工业生产中广泛应用的一种技术,在使用
过程中,难免会出现液压系统漏油的情况,下面就来探讨一下液压系
统漏油的原因:
一、密封元件磨损或老化
液压系统的密封元件是保持系统正常工作的关键部件,一旦密封元件
磨损或老化,就会导致系统泄漏出油。
常见的密封元件包括O型圈、
密封垫、活塞环等,长时间使用之后,这些元件会出现老化、硬化、
破裂等问题,导致液压系统漏油。
二、安装不当
在液压系统安装的过程中,如果安装不当,则也容易导致液压系统漏油。
比如安装时未完全拧紧螺母、螺栓,或者接头内部缺少密封元件,这些都会影响系统的密封性,导致漏油。
三、液压管路磨损
液压管路是组成液压系统的主要部件,长时间使用后,管路内部会出
现磨损、腐蚀等问题,就会导致管路密封性下降,从而出现漏油现象。
四、液压油泵损坏
液压油泵是能量转换装置,将机械能转化为液压能,用于压缩液压油
使其流动,提供系统所需的压力。
如果液压油泵损坏或密封不良,就
会导致系统内部压力不足,出现液压系统漏油现象。
五、操作不当
使用液压系统时,如果操作不当,则也会导致系统漏油。
比如过度使
用或过度压力会导致密封元件失效、管路损坏,从而出现漏油现象。
综上所述,液压系统漏油的原因有很多,需要在日常使用中高度关注,及时进行维护和更换故障件,以确保液压系统的正常运行。
- 1、下载文档前请自行甄别文档内容的完整性,平台不提供额外的编辑、内容补充、找答案等附加服务。
- 2、"仅部分预览"的文档,不可在线预览部分如存在完整性等问题,可反馈申请退款(可完整预览的文档不适用该条件!)。
- 3、如文档侵犯您的权益,请联系客服反馈,我们会尽快为您处理(人工客服工作时间:9:00-18:30)。
液压系统漏油的原因及其预防
根据液压李工分享由于加工不良而造成液压系统漏油的原因及其预防
①密封槽过深或过浅、相对运动件的密封接触面椭圆度、锥度超差等,使0型密封圈安装后很难得到均匀准确的压缩量
例如:在圆柱面上,轴和孔的环形槽都易车深或挖浅使0型圈的压缩量不够(或根本无压缩量),以致产生漏油。
这种情况在低压时可能不明显,甚至不漏,但在高压时就比较严重。
例如:平面密封时,若0型密封槽太浅,将造成安装时槽卡不住0型圈,容易脱出,甚至还可能把密封圈挤到结合面之间。
短时间可能不漏,但时间长了,挤在结合面间的那部分橡胶就要被高压油挤出去,产生漏油。
②平面密封的固定螺孔深度不合适。
若用原来设计的螺钉来连接,就显得长了,表面看起来已经拧紧,而实际两个平面并未贴紧,密封不严,产生漏油。
高压时,甚至会把密封圈挤坏。
③平面密封部分的定位误差引起漏油:
泵(阀)体四个螺孔位置与法兰盘上四个通孔位置,由于加工产生误差,1和2的轴线不重合,产生一个偏心e,致使阀体孔一边落在0型密封圈平均直径的外边,,结果产生间隙,造成漏油。
④在同一平面内装有多个0型密封圈,其尺寸可能不同,其安装槽又有止口型和凹槽型两种:
除前述原因造成漏油外,还有端面上的压力不够,压缩量不均匀、止口尺寸较小、0型圈在工作时易脱出,结合面不平行。
平面和螺孔不垂直、结合面的光洁度太差。
凹槽边缘太薄,受力后产生卷边现象等都是漏油的根源(尤其在高压工况下)
⑤使用组合密封垫的地方,若孔(包括螺孔)的倒角加工太大就会产生漏油。
⑥密封面粗糙造成泄漏:
如果密封面加工粗糙,则管接头旋紧时,就会划伤密封圈表面。
严重时,会使组合密封圈的挂胶尖部软掉,使密封失效产生泄漏,所以有的工厂采用经过软化处理的紫铜垫(硬度HB=32~45),代替组合密封圈,但一般只能用一次:如拆卸后再用,密封效果大大降低。