RX114012中文资料
1140使用说明书

6.
6
先输入密码,进入定值区,按“▼”搜索出某个定值的汉语拼音提示符,按一下“◄►”则显示该定值大小,再按一下“◄►”则进入修改状态,修改方法与输入密码方法相同,修改后按“▼”确认,此时显示为do,表示装置正在存储定值,存储完毕后,显示good.
6.2
出厂前已调好,在检修或调试遇到问题时可用到此项
请参照设计图纸,看37-44端子哪些端子有开关量输入,并用定点显示查看.
21
ih.on/ih.of
高压侧零序过流投入/退出
22
il.on/il.of
低压侧零序过流投入/退出
23
dy.on/dy.of
低电压保护投入/退出
24
fs.on/fs.of
低压侧零序过流反时限投入/低压侧零序过流定时限投入
25
gyon/gyof
过电压投入/退出
26
27
28
29
30
31
5.2.4
数码管显示码
3
ji0
零序电流回路
6
注意:
1.此处所有定值均为随意设定,有正式定值请按正式定值输入。请参考保护原理,保护出口见原理图.
19
抗干扰
共模干扰:2.5KV/1MHZ/2S
差模差模:1.0KV/1MHZ/2S
RX324012资料

R i g h t s t o c h a n g e d a t a /d e s i g n r e s e r v e dE d i t i o n : 03/2004Features•1C/O or 1N/O or 2 C/O contacts •DC- or AC-coil•4kV /8mm coil-contact•Reinforced insulation (protection class II)•Height 15.7mm•transparent cover optionalApplicationsDomestic appliances, heating control, emergency lightingZVApproval in processContact dataConfiguration 1 C/O or 1 N/O2 C/OType of contact single contactRated current12 A 16A 8ARated voltage /max.breaking voltage AC 250Vac / 440VacMaximum breaking capacity AC 3000VA 4000VA 2000VAContact materialAgNi 90/10Coil dataNominal voltage DC coil 5...110Vdc AC coil 24...230Vac Nominal coil power DC coil 500mW AC coil0.75VA Operate category2Coil versions, DC-coil Coil Nominal Pull-in Release Maximum Coil Coil code voltage voltage voltage voltage resistancecurrent Vdc Vdc Vdc Vdc cmA 0055 3.50.59.850+5%100.0 0066 4.20.611.868+5%87.7 012128.4 1.223.5274+5%43.8 0242416.8 2.447.01095+5%21.9 0484833.6 4.894.14380+5%11.0 0606042.0 6.0117.66845+5%8.8 11011077.011.0215.623010+5% 4.8All figures are given for coil without preenergization, at ambient temperature +20°COther coil voltages on requestR i g h t s t o c h a n g e d a t a /d e s i g n r e s e r v e dE d i t i o n : 03/2004InsulationDielectric strengthcoil-contacts4000V rms open contact circuit1000V rmsClearance /creepage 8/8mm Voltage rating 250V Pollution degree3Overvoltage categoryIIIInsulation dimensionscoil-contacts reinforced insulation contact-contactbasic / functional insulationacross open contactsmicro-disconnectionTracking resistance of relay baseCTI 250Coil versions, AC-coil code voltage voltage voltage voltage resistancecurrent Vac Vac Vac Vac cmA 5242418.0 3.636.0350+10%31.6 61511586.317.3172.58100+15% 6.6 730230172.534.5345.032500+15% 3.2All figures are given for coil without preenergization, at ambient temperature +20°COther dataFlammability class according to UL 94standard / transparent cover V-0 / HBCoil insulation system according to UL 1446Class F Min. ambient temperature -40 °C DC-coil 85 °C 1)/ 2.5 mm 70 °C / 2.5 mm AC-coil 70 °C / 2.5 mm 70 °C / 5 mmDC-coil >5x106operations AC-coil >1x106operationsMax. switching rate at rated-/minimum load 6min -1/600 min -1Operate-/release time DC-coil typ. 7/2ms Bounce time N/O contact/N/C contact typ. 1/3ms Vibration resistance N/O 20 g, 10...150Hz Shock resistance (destruction)100g Category of protection (IEC 61810)RT II - flux proof 2)Relay weight 13g Packaging unit 500pcs. 1)version with transparent cover: 70°C 2)RT III (wash tight) on requestE d i t i o n : 03/2004PCB layout / terminal assignment1 pole 12AS0163-BGS0163-BH1 pole 16AS0163-BE S0163-BFR i g h t s t o c h a n g e d a t a /d e s i g n r e s e r v e dS0163-BJ2 pole 8 ADimensionsDimensions in mmS0272-AAView on solder pins Dimensions in mm*) With the recommended PCB hole sizes a grid pattern from 2.5mm to 2.54mm can be used.R i g h t s t o c h a n g e d a t a /d e s i g n r e s e r v e dE d i t i o n : 03/2004。
SF1140B;中文规格书,Datasheet资料

Notes:1.Unless noted otherwise, all specifications apply over the operating temperature range with filter soldered to the specified demo nstration board with impedance matching to 50 Ω and measured with 50 Ω network analyzer.2.Unless noted otherwise, all frequency specifications are referenced to the nominal center frequency, fc.3.The design, manufacturing process, and specifications of this filter are subject to change.4.Either Port 1 or Port 2 may be used for either input or output in the design. However, impedances and impedance matching may va ry between Port 1 and Port 2, so that the filter must always be installed in one direction per the circuit design. and international patents may apply.6.©Copyright 1999, RF Monolithics Inc.7.Electrical CharacteristicsCharacteristicSym Notes MinTyp Max Units Nominal Center Frequency f C175.000MHz PassbandInsertion Loss at fc IL11.013.0dB 1dB Passband BW 11, 2±2.1±2.7MHz Fast Amplitude Ripple over fc ±2.1 MHz 1.0dB P-P Group Delay Variation over fc ±2.1 MHz GDV40200ns P-P Rejection fc-15 to fc-7.15 and fc+15 to fc+65 MHz1, 2, 34043dBfc+7.15 to fc+15 MHz36Operating Temperature Range T A 1-40+85°CDifferential Input and Output Impedance 250 ohmsCase Style6SMP-03 7 x 5 mm Nominal FootprintLid Symbolization (YY=year, WW=week, S=shift) See note 4RFM SF1140B YYWWS•Designed for SDARS IF Receiver •Low Insertion Loss• 5.0 X 7.0 mm Surface-Mount Case •Differential Input and Output•Complies with Directive 2002/95/EC (RoHS)Absolute Maximum RatingsRatingValue Units Maximum Incident Power in Passband +10dBm Max. DC voltage between any 2 terminals 30VDC Storage Temperature Range -40 to +85°CMax Soldering Profile265°C for 10 s 75.00 MHzSAW FilterSF1140B Connection TerminalsPort 1 Hot10Port 1 Ground Return 1Port 2 Hot5Port 2 Ground Return 6Case GroundAll OthersElectrical ConnectionsPbTape and Reel Specifications“B “Nominal Size Quantity Per ReelInchesmillimeters7178500133302000USER DIRECTION OF FEEDCOMPONENT ORIENTATION and DIMENSIONSCarrier Tape DimensionsTolerance Ao 5.5 mm ± 0.1mm Bo 7.5 mm ± 0.1mm Ko 2.0 mm ± 0.1mm Pitch 8.0 mm ± 0.1mm W16.0 mm± 0.2mmPIN #110-Terminal Ceramic Surface-Mount Case7 x 5 mm Nominal FootprintSMP-03 CaseRecommended PCB FootprintCHCase Dimensions Dimensionmm Inches Min Nom Max Min Nom Max A 6.807.007.200.2680.2760.283B 4.80 5.00 5.200.1890.1970.205C 1.65 2.000.0650.079D .470.60.730.0190.0240.029E 2.41 2.54 2.670.0950.1000.105H 0.87 1.0 1.130.0340.0390.044J 4.87 5.00 5.130.1920.1970.202K 2.87 3.00 3.130.1130.1180.123P1.141.271.400.0450.0500.055MaterialsSolder Pad Termination Au plating 30 - 60 uInches (76.2-152 uM) over 80-200 uInches (203-508 uM) Ni.Lid Fe-Ni-Co Alloy Electroless Nickel Plate (8-11% Phosphorus) 100-200 uInches Thick Body Al 2O 3 CeramicPb FreeElectrical ConnectionsConnectionTerminalsPort 1Input or Return 10Return or Input 1Port 2Output or Return 5Return or Output 6GroundAll others Single Ended Operation Return is ground Differential OperationReturn is hot分销商库存信息: RFMSF1140B。
AX-12完整中文资料

Main Specifications主要规格精度°操作角度300 ° 或转动电压7V 〜 10V(推荐电压:)最大电流900mA工作温度-5 〜 85 ℃℃控制信号数字信号协议类型半双工异步串行通信( 8位, 1位停止位,无奇偶校验)物理连接多降式TTL电平(总线型)ID 最多254个ID(编号0 〜 253 )比特率7343bps 〜 1 Mbps反馈类型位置,温度,负载,输入电压等Connection to UART 连接到UARTTo control the Dynamixel actuators, the main controller needs to convert its UART signals to the half duplex type. The recommended circuit diagram for this is shown below.为了控制Dynamixel舵机,主控制器需要转换UART信号为半双工类型。
建议电路图所示。
The power is supplied to the Dynamixel actuator from the main controller through Pin 1 and Pin 2 of the Molex3P connector. (The circuit shown above is presented only to explain the use of half duplex UART. The CM-5 controller already has the above circuitry built in, thus the Dynamixel actuators can be directly connected to it)Dynamixel的电源供应器是从主控制器通过Molex3P连接器的PIN1引脚和PIN2引脚。
4组合开关1140V说明书(1)
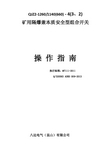
QJZ2-1260/1140(660) - 4(3、2) 矿用隔爆兼本质安全型组合开关操作指南执行标准:MT111-2011Q/320583 ADBD 009-2013八达电气(昆山)有限公司感谢您使用八达电气的产品。
本操作指南是根据用户几年来反馈的建议,针对使用该产品的一线操作人员编写的,力求简单、精炼,希望能带给您方便。
一、电气结构 1.1 进线有三组接线柱R1、S1、T1;R2、S2、T2如图1所示,供1140V(660V)进线使用。
注意:若使用不同的移动变电站的多路电源给开关供电,须拆开进线的并联母排;若使用同一移变的多路电源给开关供电,需计算各路电源的短路阻抗、联接组别、电压比等是否满足并联条件,如果满足,须确保并联的多路电源各相的相序一致。
1.2 出线1.2.1 驱动功率单元选用630A 、400A 和250A 三种,若该回路为630A ,前面的空心圆用红色记号标识。
1.2.2 出线腔有动力线和控制线。
动力线出线采用两种方式:电缆连接器式和压盘式。
电缆连接器式出线布局,如图1所示图1 电缆连接器式出线布局压盘式出线布局,如图2所示VP W U出线接线示意图R1R2S1S2标记接触器容量T1T2400A 250A 630A1#回路VP W U400A 250A630A2#回路V P W U400A 250A 630A3#回路V P W U400A 250A 630A4#回路图2 压盘式出线布局1.2.3控制线自上而下有X1、X2两组控制线接线端子排,其定义如图3所示。
X1自上而下依次为4路的起、停控制、双速自锁线端子。
X2自上而下依次为485通讯、4路的反馈无源接点、风电闭锁、瓦斯闭锁、远方急停端子。
X1 X2图3控制线端子排定义1.3 主控腔开关所有主回路和控制保护元件均装在主控腔内。
1.3.1真空隔离换相开关GHZ1、GHZ2安装在开关右侧,其作用是确保供电电源正向—分断—反向三个位置的出线接线示意图T1T2S1S2标记接触器容量R1R2U1250A 1#回路V1400A W1630AU2250A2#回路V2400AW2630AU3250A3#回路V3400AW3630AU4250A4#回路V4400AW4630A无载转换,特殊情况下可带负荷分断;1.3.2由真空接触器、中间继电器等元件组成的驱动功率单元,安装在开关主控腔的支架上,用于控制普通电动机或双速电动机;1.3.3 控制变压器T1,为驱动功率单元的接触器、继电器、数据采集处理器等提供电源;1.3.4 限流熔断器FU11、FU12、……等,做为PLC短路故障的后备保护;1.3.5 阻容保护TBP1、TBP2、……等,用于吸收过电压;1.3.6 AC3300V/127/4KVA变压器及照明信号综合保护。
1240W中文资料

Document Number: 63053For any questions, contact: foil@1240Vishay Foil ResistorsBulk Metal ® Foil Technology Precision TrimmingPotentiometers, 1/4 Inch Square, RJ26 Style, Designed to Meet or Exceed the Requirements of MIL-PRF-39035, Char. HFEATURES•Temperature coefficient of resistance (TCR): ± 10 ppm/°C. (- 55 °C to + 150 °C ref. at + 25 °C);through the wiper 3); ± 25 ppm/°C (see table 2 for low values)•Load life stability: 0.1 % typical ΔR, 1.0 % maximum ΔR under full rated power at + 85 °C for 10000 h •Settability: 0.05 % typical; 0.1 % maximum•Setting stability: 0.1 % typical; 0.5 % maximum, ΔSS •Power rating: 0.25 W at + 85 °C •Resistance range: 5 Ω to 10 k ΩNote:* See Figure 1, next pageTABLE 1 - MODEL SELECTION *MODELTERMINATION STYLE AVERAGE WEIGHT (g)POWER RATING at + 85 °C AMBIENTNO. OF TURNS1240W-edge mount, top adjust0.40.25 W21 ± 2X-edge mount, side adjust P-horizontal mount, side adjustTABLE 2 -1240 (RJ26) SERIESELECTRICAL SPECIFICATIONSTemperature Coefficient of Resistance (TCR) 50 Ω to 10K End-to-end 2)± 10 ppm/°C maximum (- 55 °C to + 150 °C,+ 25 °C ref.)Temperature Coefficient of Resistance 5, 10 and 20 ΩThrough the wiper 3)± 20 ppm/°C ± 25 ppm/°CStabilityLoad life at 10000 h0.1 % typical ΔR 1.0 % maximum ΔR(under full rated power of 0.25 W at + 85 °C)Power Rating 4)0.25 W at + 85 °C Settability 0.05 % typical;0.1 % maximum Setting Stability 0.1 % typical;0.5 % maximum Contact Resistance Variation - CRV (noise)5) 3 Ω typical; 10 Ω maximum Hop-off0.25 % typical;1.0 % maximum High-Frequency Operation Rise time Inductance Capacitance1.0 ns without ringing 0.08 µH typical 0.5 pF typical Operating Temperature Range- 55 °C to + 150 °CTABLE 3 - VALUES VS. TOLERANCESSTANDARD RESISTANCE VALUES(in Ω)STANDARD TOLERANCE5, 10± 10 %20, 50, 100, 200, 500, 1K, 2K, 5K, 10K± 5 %TABLE 4 - MECHANICAL SPECIFICATIONSAdjustment Turns 21 ± 2Mechanical Stops Wiper idles - no discontinuity InternalTerminations All welded - no fluxCase Material1240X - diallyl-phthalate: green (DAP)1240W - diallyl-phthalate: green (DAP)1240P - thermoplastic: blackShaft Torque 3 oz. in. maximum Backlash0.005 % typical1240Vishay Foil ResistorsBulk Metal ® Foil Technology Precision Trimming Potentiometers, 1/4 Inch Square, RJ26 Style, Designed to Meet or Exceed the Requirements of MIL-PRF-39035, Char. H For any questions, contact: foil@Document Number: 63053Document Number: 63053For any questions, contact: foil@1240Bulk Metal ® Foil Technology Precision Trimming Potentiometers, 1/4 Inch Square, RJ26 Style, Designed to Meet or Exceed the Requirements of MIL-PRF-39035, Char. HVishay Foil Resistors Notes:1.Maximum is 1.0 % A.Q.L. standard for all specifications except TCR. (For TCR information, see notes 2 and 3.)2.Maximum TCR applies to the 3 σ (sigma) limit or 99.73 % of a production lot. (Measured end-to-end with wiper off the element.)3.Measurements of TCR through the wiper are influenced more by setting stability and the percentage of the total resistance in use (at the wiper) than by fundamental resistance change due to temperature alone. The parameter shown in Table 2 is a 2 s distribution typifying the behavior of the device when used with 40% or more of the total resistance in use.4.Derated linearly for full power at + 85 °C to zero (0) W at +150°C.See Figure 2 on previous page.5.Independent of resistance value. 3 W maximum available on special request.6.All ΔR’s are measured to the tolerance specified + 0.01 Ω.7.Whichever is greater.Special Available Options:Special markingBurn-in and screening operations.VISHAY TRIMMERS ARE INSPECTED100 % for:•Short-time overload(6.25 x rated power for 5 s on; and for 30 s off - 3 cycles)•Immersion•Resistance tolerance check •End resistance •Visual-mechanical•Dynamic tests for continuity, CRV By sample for:•TCR •DWVTABLE 5 - COMPARISONMIL-PRF-39035/3 CHARACTERISTIC H 6)MODEL 1240 MAXIMUM TEST GROUP I ConditioningContact resistance variation - CRV (noise)Immersion± 1.0 %± 3.0 % or 3 Ω7)No continuous stream of bubbles± 0.5 %3 Ω typical, 10 Ω maximum No continuous stream of bubbles TEST GROUP I aVisual and mechanicalActual effective electrical travel End resistanceDielectric withstanding voltage - DWV (atmospheric and barometric pressure)Insulation resistance Shaft torque Thermal shock Setting stability No failures 10 to 25 turns 2 % or 2 Ω7)Per MIL-STD-202, methods 301 and 105≥ 1000 M Ω3 oz. in. maximum± 1.0 %± 1.0 %No failures 21 ± 2 turns2 Ω for values ≤ 1 k Ω;5 Ω for values ≥ 2 k Ω;Per MIL-STD-202, methods 301 and 105> 1000 M Ω3 oz. in. maximum± 0.5 %± 0.5 %TEST GROUP II SolderabilityPer MIL-STD-202, method 208Per MIL-STD-202, method 208TEST GROUP IIIResistance temperature characteristic - TCR Moisture resistanceContact resistance variation - CRV (noise)± 0.005 % (± 50 ppm/°C)± 1.0 %3.0 % or 3 Ω7)± 0.001 % (± 10 ppm/°C)± 0.5 %3 Ω typical, 10 Ω maximum TEST GROUP IV Settability ShockSetting stability VibrationSetting stabilityContact resistance variation - CRV (noise)Salt spray± 1.0 %± 1.0 %± 1.0 %± 1.0 %± 1.0 %3.0 % or 3 Ω7)No corrosion ± 0.1 %± 0.5 %± 0.5 %± 0.5 %± 0.5 %3 Ω typical, 10 Ω maximumNo corrosion TEST GROUP V Solder heatLow-temperature operation Setting stabilityLow-temperature storage High-temperature exposure Setting stabilityContact resistance variation - CRV (noise)Integrity of shaft± 1.0 %± 1.0 %± 2.0 %± 1.0 %± 3.0 %± 2.0 %3 % or 3 Ω7)No loosening or breakage± 0.1 %± 0.5 %± 0.5 %± 0.5 %± 0.5 %± 0.5 %3 Ω typical, 10 Ω maximum No loosening or breakage TEST GROUP VIRotational life (200 cycles)Contact resistance variation - CRV (noise)T erminal strength ± 2.0 %3 % or 3 Ω7)2 lbs.± 2.0 %3 Ω typical, 10 Ω maximum2 lbs.TEST GROUP VIILife (2000 h) at + 85 °C Life (10000 h) at + 85 °C ± 3.0 %± 5.0 %± 0.1 % typical, ± 1.0 % maximum ± 0.1 % typical, ± 1.0 % maximumTEST GROUP VIII Solvent resistance No failuresNo failures1240Vishay Foil ResistorsBulk Metal ® Foil Technology Precision Trimming Potentiometers, 1/4 Inch Square, RJ26 Style, Designed to Meet or Exceed the Requirements of MIL-PRF-39035, Char. H For any questions, contact: foil@Document Number: 63053Note* Application engineering release: for non-standard requests, please contact application engineering.TABLE 6 - GLOBAL PART NUMBER INFORMATIONNEW GLOBAL PART NUMBER:Y4053500R000J0L (preferred part number format)DENOTES PRECISIONVALUE AER*YR = ΩK = k Ω0 = standard part, gold termination 1 - 999 = customPRODUCT CODE TOLERANCE PACKAGING 4053 = 1240W 5053 = 1240X 0053 = 1240PJ = ± 5 %K = ± 10 %L = bulk packFOR EXAMPLE: ABOVE GLOBAL ORDER Y4053 500R000 J 0 L:TYPE: 1240W VALUE: 500.0 ΩABSOLUTE TOLERANCE: ± 5.0 %AER: standard part, gold termination PACKAGING: bulk packHISTORICAL PART NUMBER:1240W 500R00J B (will continue to be used)1240W 500R00J B MODEL RESISTANCE VALUE TOLERANCE PACKAGING 1240W 1240X 1240P500R00 = 500.0 ΩJ = ± 5 %K = ± 10 %B = bulk pack05350R 00Y 4J 00LDisclaimer Legal Disclaimer NoticeVishayAll product specifications and data are subject to change without notice.Vishay Intertechnology, Inc., its affiliates, agents, and employees, and all persons acting on its or their behalf (collectively, “Vishay”), disclaim any and all liability for any errors, inaccuracies or incompleteness contained herein or in any other disclosure relating to any product.Vishay disclaims any and all liability arising out of the use or application of any product described herein or of any information provided herein to the maximum extent permitted by law. The product specifications do not expand or otherwise modify Vishay’s terms and conditions of purchase, including but not limited to the warranty expressed therein, which apply to these products.No license, express or implied, by estoppel or otherwise, to any intellectual property rights is granted by this document or by any conduct of Vishay.The products shown herein are not designed for use in medical, life-saving, or life-sustaining applications unless otherwise expressly indicated. Customers using or selling Vishay products not expressly indicated for use in such applications do so entirely at their own risk and agree to fully indemnify Vishay for any damages arising or resulting from such use or sale. Please contact authorized Vishay personnel to obtain written terms and conditions regarding products designed for such applications.Product names and markings noted herein may be trademarks of their respective owners.元器件交易网Document Number: 。
RPC1240中文资料

400
600
800
1000
1200
Input Resistance [k ]
Input Resistance [k ]
Input Resistance [k ]
©2002 CRYDOM CORP, Specifications subject to change without notice.
INPUT SPECIFICATIONS ➀ Resistor, Variable [Ohms] ➃
GENERAL NOTES
150K (1W) 150K (1W) 150K (1W)
1M (1/2W) 1M (1/2W) 1M (1/2W) 1M (1/2W) 1M (1/2W) 1M (1/2W)
1.48
25 80 600 250 1.6
1.02
40 90 600 625 1.6
.63
25 80 1200 250 1.6
1.02
40 90 1200 625 1.6
.63
Max. On-State Voltage Drop @ Rated Current [Vpk] 1.6 Thermal Resistance Junction to Case [RθJC] Maximum I2 t for Fusing, (8.3 msec.) [A2sec] 1.48
6-32 TERMINAL (2 PLACES)
.78 (19.8) .87 (22.1)
CURRENT DERATING CURVES
15A
15
2˚C/W Power Dissipation 4˚C/W
25A
30 112
Base Plate Temp [˚C] Power Dissipation 1˚C/W Base Plate Temp [˚C]
众诚1140组合说明书
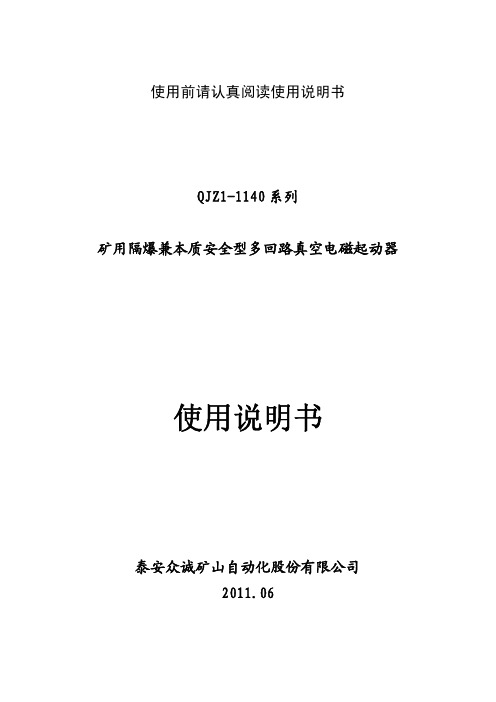
目录
第一章 概述 .......................................................................................................... 1 1.1 主要用途及适用范围 ............................................................................. 1 1.2 正常使用环境要求 ................................................................................. 1 1.3 产品规格及外形尺寸 ............................................................................. 1 1.4 产品型号及意义 ..................................................................................... 2 1.5 工作条件 ................................................................................................. 2 1.6 执行标准 ................................................................................................. 3 1.7 隔爆形式 ................................................................................................. 3
派顿1140rc用户手册.pdf说明书

USER MANUALSALES OFFICE (301) 975-1000TECHNICAL SUPPORT (301) 975-1007Part #07M1140RC Doc #018031U,Rev. DRevised 1/22/08An ISO-9001Certified Company1.0 WARRANTY INFORMATIONPatton Electronics warrants all Model 1140RC components to be free from defects, and will—at our option—repair or replace the product should it fail within one year from the first date of shipment.This warranty is limited to defects in workmanship or materials, and does not cover customer damage, abuse or unauthorized modification. If this product fails or does not perform as warranted, your sole recourse shall be repair or replacement as described above. Under no condition shall Patton Electronics be liable for any damages incurred by the use of this product. These damages include, but are not limited to, the following: lost profits, lost savings and incidental or consequential damages arising from the use of or inability to use this product. Patton Electronics specifically disclaims all other warranties, expressed or implied, and the installation or use of this product shall be deemed an acceptance of these terms by the user.1.1 RADIO AND TV INTERFERENCEThe Model 1140RC generates and uses radio frequency energy, and if not installed and used properly—that is, in strict accordance with the manufacturer's instructions—may cause interference to radio and television reception. The Model 1140RC has been tested and found to comply with the limits for a Class A computing device in accordance with the specifications in Subpart J of Part 15 of FCC rules, which are designed to provide reasonable protection from such interference in a commercial installation. However, there is no guarantee that interference will not occur in a particular installation. If the Model1140RC does cause interference to radio or television reception, which can be determined by turning the power off or removing the card, the user is encouraged to try to correct the interference by one or more of the following measures: moving the computing equipment away from the receiver, re-orienting the receiving antenna and/or plugging the receiving equipment into a different AC outlet (such that the computing equipment and receiver are on different branches). In the event the user detects intermittent or continuous product malfunction due to nearby high power transmitting radio frequency equipment, the user is strongly advised to take the following steps: use only data cables with an external outer shield bonded to a metal or metalized connector; and, configure the rear card as shown in section 3.2 of this manual.1.2CE NOTICEThe CE symbol on your Patton Electronics equipment indicates that it is in compliance with the Electromagnetic Compatibility (EMC) directive and the Low Voltage Directive (LVD) of the Union European (EU). A Certificate of Compliance is available by contacting Technical Support.1All warranty and nonwarranty repairs must be returned freight prepaid and insured to Patton Electronics. All returns must have a Return Materials Authorization number on the outside of the shipping container. This number may be obtained from Patton Electronics Technical Support: (301) 975-1007; ; or,******************.NOTE: Packages received without an RMA number will not be accepted.Patton Electronics' technical staff is also available to answer any questions that might arise concerning the installation or use of your Model 1140RC. Technical Service hours: 8AM to 5PM EST, Monday through Friday.22.0 GENERAL INFORMATIONThank you for your purchase of this Patton Electronics product. This product has been thoroughly inspected and tested and is warranted for One Year parts and labor. If any questions or problems arise during installation or use of this product, please do not hesitate to contact Patton Electronics Technical Support at(301) 975-1007,***********************.2.1 FEATURES• Supports async or sync communication over dual optical fibers • RS-232 Data rates to 57.6 Kbps• Distances to 2 miles•V.54 and V.52 Diagnostics• Mounts in Patton’s 16-Card Rack Chassis• Compatible with the Patton Model 1140 self-powered modem• Immune to RFI/EMI noise, ground loops and transient surges• Easily accessible configuration jumpers & switches• Bi-level LED status indicators• Works with switchable 120V or 240V rack mount power supply • SMA or ST connectors available (HD-26 female RS-232 port) on rear Interface card2.2 DESCRIPTIONThe Patton Model 1140RC fiber optic rack card modem is the rack mountable counterpart to Patton’s Model 1140 self-powered, fiber optic modem. Communicating full or half duplex over dual optical fibers, the Model 1140RC supports data rates to 57.6 Kbps and distances to 2 miles. Both V.54 and V.52 diagnostics are built into the unit. Like all fiber optic modems, the Model 1140RC is inherently immune to RFI/EMI noise, ground loops and transient surges. The carrier may be switch selected as either “Continuously On” or “Controlled by RTS”. Five pairs of bi-level LED indicators monitor TD, RD, RTS, CD, test and error. A single LED monitors power.The Model 1140RC is designed to mount in Patton’s 2U high 19”rack chassis. This 16-card chassis has a switchable 120/240 volt power supply and mounts cards in a mid-plane architecture: The front “brains” half-card can be plugged into different rear “interface” cards. The Model 1140RC is available with a choice of two interface cards: one with SMA connectors, and one with ST connectors. Both cards are equipped with an HD-26 female connector for the RS-232 interface.3The power supply on/off switch is located on the front panel. When plugged in and switched on, a red front panel LED will glow. Since the Model 1000R16 is a “hot swappable” rack, it is not necessary for any cards to be installed before switching on the power supply. The power supply may be switched off at any time without harming the installed cards.NOTE: Please refer to the Model 1000RP Series User Manual AC and DC Rack Mount Power Supplie s for fuse and power cardreplacement information.4.2 INSTALLING THE MODEL 1140RC INTO THE CHASSISThe Model 1140RC is comprised of a front card and a rear card. The two cards meet inside the rack chassis and plug into each other via mating 50 pin card edge connectors. Use the following steps as a guideline for installing each Model 1140RC into the Model 1000R16 rack chassis:1.Slide the rear card into the back of the chassis along the metalrails.2.Secure the rear card using the metal screws provided.3.Slide the front card into the front of the chassis. It should meet therear card when it’s almost all the way into the chassis.4.Push the front card gently into the card-edge receptacle of the rearcard. It should “click” into place.5.Secure the front card using the thumb screws.NOTE:Since the Model 1000R16 chassis allows “hot swapping”of cards, it is not necessary to power down the rack when youinstall or remove a Model 1140RC.5.0 OPERATIONOnce you have configured each Model 1140RC and connected the cables, you are ready to operate the units. This section describes the LED status monitors and power-up procedure.5.1 LED STATUS MONITORSThe Model 1140RC features ten front panel status LEDs that indicate the condition of the modem and communication link:•The green “PWR” LED glows when power is applied to the modem card through its mid-plane chassis connection.•The green “TD” and “RD” indicators blink to show positive state data activity. The Red “TD” and “RD” indicators blink to shownegative state data activity. Solid red indicates an idle state.•The green “RTS” and “CD” indicators glow solid to show the control signal is on. The red “RTS” and “CD” indicators glow solid to show the control signal is off. When the 1140RC is connected to a DTE, RTS will glow green for an incoming signal on RS-232 pin 4. CD will glow green for an incoming signal from the line, and anoutgoing signal on RS-232 pin 8.•The “Test” LED glows when either the Local Analog Loopback (LAL) or Remote Digital Loopback (RDL) V.54 test mode isinitiated. The “Error” LED blinks when an error is detected by the V.52 diagnostics.5.2 POWER-UPThere is no power switch on the Model 1140RC: Power is automatically applied to the 1140RC when its card-edge connector makes contact with the chassis’ mid-plane socket, or when the chassis’power supply is turned on. Note: The 1140RC is a “hot swappable”card—it will not be damaged by plugging it in or removing it while the rack is powered up.When the local and remote units are both powered up, and are passing data normally, the following LED conditions will exist:• PWR = green• TD & RD = flashing red and green• RTS & CD = green• Test = off• Error = offThe Model 1140RC offers two V.54 test modes and two V.52 test modes to evaluate the condition of the modems and the communication link. Both sets of tests can be activated physically from the front panel. The V.54 test can also be activated from the RS-232 interface. Note: V.54 and V.52 test modes on the Model 1140RC are available for point-to-point applications only.5.3.1 LOCAL ANALOG LOOPBACK (LAL)The Local Analog Loopback (LAL) test checks the operation of the local Model 1140RC, and is performed separately on each unit.Any data sent to the local Model 1140RC in this test mode will be echoed (returned) back to the user device. For example, characters typed on the keyboard of a terminal will appear on the terminal screen. To perform a LAL test, follow these steps:1.Activate LAL. This may be done in one of two ways: First, bymoving the upper front panel toggle switch RIGHT to “Analog”.Second, by raising pin 18 on the RS-232 interface (note: besure DIP switch S2-8 is off). Once LAL is activated, the Model1140RC transmit output is connected to its own receiver. The“Test” LED should be lit.2.Verify that the data terminal equipment is operating properlyand can be used for a test.3.Locate the lower of the two toggle switches on the front panelof the Model 1140RC and move it to the right. This willactivate the V.52 BER test mode and inject a “511” test patterninto the local loop. If any errors are present in the loop, thered “Error” LED will blink sporadically.4.If the BER test indicates no errors are present, move the V.52toggle switch to the left, thus activating the “511/E” test withperiodic errors. If the test is working properly, the red “Error”LED will light. A successful “511/E” test will confirm that theloop is in place, and that the Model 1140RC’s built-in “511”generator and detector are working properly.5.If the BER test indicates that errors are present, check to seethat the RS-232 cable connecting the DTE to the Model1140RC is wired straight through, and is plugged in properly.Also, ensure that the Model 1140RC is configured properly.Then re-check your DTE equipment. If you still have errors,call Patton Technical Support at (301) 975-1007.The Remote Digital Loopback (RDL) test checks the performance of both the local and remote Model 1140RCs, and the communication link between them. Any characters sent to the remote 1140RC in this test mode will be returned back to the originating device. For example, characters typed on the keyboard of the local terminal will appear on the local terminal screen after having been passed to the remote Model 1140RC and looped back. To perform an RDL test, follow these steps:1.Activate RDL. This may be done in two ways: First, bymoving the upper front panel toggle switch LEFT to “Remote”.Second, by raising pin 21 on the RS-232 interface. (Note: besure DIP switch S2-8 is off).2.Verify that the DTE equipment on the local end is operatingproperly and can be used for a test.3. Locate the lower of the two toggle switches on the front panelof the 1140RC and move it to the right. This will activate theV.52 BER test mode and inject a “511” test pattern into theremote loop. If any errors are present in the loop, the red“Error” LED will blink sporadically.4.If the BER test indicates no errors are present, move the V.52toggle switch to the left, thus activating the “511/E” test withperiodic errors. If the test is working properly, the red “Error”LED will light. A successful “511/E” test will confirm that theloop is in place, and that the Model 1140RC’s built-in “511”generator and detector are working properly.5.If the remote BER test indicates that errors are present, andthe local analog loopback/BER tests showed that both Model1140RCs were functioning properly, this suggests a problemwith the twisted pair communication line connecting the twomodems. A common problem is improper crossing of thepairs. Also, verify that the modular connections are pinnedproperly, and the twisted pair line has continuity. If you stillhave errors, call Technical Support at (301) 975-1007.5.3.3 USING THE V.52 BER TEST INDEPENDENTLYThe Model 1140RC's V.52 BER test can be used independent of the V.54 loopback tests. This requires two operators: one to initiate and monitor the test at both the local and the remote Model 1140RC. To use the V.52 BER test by itself, both operators should simultaneouslyfollow these steps:of the Model 1140RC and move it to the right. This willactivate the V.52 BER test mode and transmit a “511” testpattern to the other unit. If any errors are present, thereceiving modem’s red “Error” LED will blink sporadically.Note: For this independent test to function, the “511” switch on both Model 1140RCs must be turned on.2.If the test indicates no errors are present, move the V.52toggle switch to the left, thus activating the “511/E” test withperiodic errors present. If the test is working properly, thereceiving modem’s red “Error” LED will blink regularly. Asuccessful “511/E” test will confirm that the link is in place, and that the Model 1140RC’s built-in “511” generator and detectorare working properly.APPENDIX ASPECIFICATIONSTransmission Line: Dual optical cableTransmission Mode: Asynchronous, half or full duplex, point-to-point Interfaces:EIA RS-232, CCITT V.24Data Rates: 0 - 57.6 KbpsDistance: 2 miles over continuous fiberRTS/CTS Delay: Switch-selectable: No delay, 7.0 mS, 53 mS Receiver Sensitivity: -45 dBmCoupled Power Output: -30 to -36 dBmOptic Wavelength: 850 nmLED Indicators: Power, TD, RD, RTS, CD, Test Mode, Error Connectors: HD-26 female on RS-232 side; ST or SMA connectors on fiber sidePower Supply: 120/240V (switchable) on rack chassis Temperature Range: 0-60°C (32-140°F)Altitude: 0-15,000 feetHumidity: Up to 95% non-condensingWeight: 2 oz.Dimensions: 0.95”W x 3.1”H x 5.4”LAPPENDIX DBLOCK DIAGRAMCopyright ©Patton Electronics CompanyAll Rights ReservedMODEL1140RC BLOCKD IAGRAM21Dear Valued Customer,Thank you for purchasing Patton Electronics products! We do appreciate your business. I trust that you find this user manual helpful.We manufacture one of the widest selections of data communications products in the world including CSU/DSU's, network termination units, powered and self-powered short range modems, fiber optic modems, interface converters, baluns, electronic data switches, data-line surge protectors, multiplexers, transceivers, hubs, print servers and much more. We produce these products at our Gaithersburg, MD, USA, facility, and cancustom manufacture products for your unique needs.We would like to hear from you. Please contact us in any of the following ways to tell us how you like this product and how we can meet your product needs today and in the future.Web: Sales E-mail: ****************Support E-mail: ******************Phone - Sales (301) 975-1000Phone - Support (301) 975-1007Fax: (301) 869-9293Mail: Patton Electronics Company7622 Rickenbacker DriveGaithersburg, MD 20879 USAWe are committed to a quality product at a quality price. Patton Electronics is ISO 9001 certified. We meet and exceed the highest standards in the industry (CE, UL, etc.).It is our business to serve you. If you are not satisfied with any aspect of this product or the service provided from Patton Electronics or its distributors, please let us know.Thank you.Burton A.PattonVice PresidentP.S. Please tell us where you purchased this product._________________________________________________________ __________________________________________________________________________________________________________________ _________________________________________________________ _________________________________________________________ _________________________________________________________ _________________________________________________________。
罗克韦尔自动化 Trusted TMR 处理器接口适配器 T8120, T8121, T8122,

ICSTT-RM239J-EN-P (PD-T812X) Trusted Trusted TMR Processor Interface Adapter(T8120, T8121, T8122, T8123)Product OverviewThis document provides general information for the Trusted® Processor Interface Adapter T812X. The Adapter provides easy access to the communications ports of the Trusted Triple Modular Redundant (TMR) Processor (T8110B & T8111) in the Controller Chassis for the Distributed Control System (DCS) and other links. The unit is also used to enable a number of extended facilities available on the Trusted TMR Processor including facilities for the reception of IRIG-B time synchronisation signals, enabling the use of Dual (‘enhanced’) Peer to Peer and enabling the Trusted System to become MODBUS Master.Features:•Allows easy access for external systems to communicate with a Trusted TMR Processor.•Easy installation (connects directly to the rear of the Controller Chassis).•Two RS422/485 configurable 2 or 4 wire connections.•One RS422/485 2 wire connection.•Fault/fail connections for Active and Standby Processors.•Processor diagnostics connection.•PSU shutdown monitor connections.•Option for connecting IRIG-B122 and IRIG-B002 time synchronisation signals.•Option to enable MODBUS Master on the Trusted Communications Interface.Trusted ICSTT-RM239J-EN-P (PD-T812X)Page intentionally left blankPREFACEIn no event will Rockwell Automation be responsible or liable for indirect or consequential damages resulting from the use or application of this equipment. The examples given in this manual are included solely for illustrative purposes. Because of the many variables and requirements related to any particular installation, Rockwell Automation does not assume responsibility or reliability for actual use based on the examples and diagrams.No patent liability is assumed by Rockwell Automation, with respect to use of information, circuits, equipment, or software described in this manual.Allen-Bradley, LISTEN. THINK. SOLVE., Rockwell Automation, TechConnect, and Trusted are trademarks of Rockwell Automation, Inc.All trademarks are acknowledged.DISCLAIMERIt is not intended that the information in this publication covers every possible detail about the construction, operation, or maintenance of a control system installation. You should also refer to your own local (or supplied) system safety manual, installation and operator/maintenance manuals. REVISION AND UPDATING POLICYThis document is based on information available at the time of its publication. The document contents are subject to change from time to time. The latest versions of the manuals are available at the Rockwell Automation Literature Library under "Product Information" information "Critical Process Control & Safety Systems".TRUSTED RELEASEThis technical manual was updated for Trusted Release 4.0.LATEST PRODUCT INFORMATIONFor the latest information about this product review the Product Notifications and Technical Notes issued by technical support. Product Notifications and product support are available at the Rockwell Automation Support Centre atAt the Search Knowledgebase tab select the option "By Product" then scroll down and select the Trusted product.Some of the Answer ID’s in the Knowledge Base require a TechConnect℠ Support Contract. For more information about TechConnect Support Contract Access Level and Features, click on the following link:https:///app/answers/detail/a_id/898272This will get you to the login page where you must enter your login details.IMPORTANT A login is required to access the link. If you do not have an account then you can create one using the "Sign Up" link at the top right of the web page.DOCUMENTATION FEEDBACKYour comments will help us serve your documentation needs better. If you have any suggestions on how to improve this document, complete the How Are We Doing? format /idc/groups/literature/documents/du/ra-du002_-en-e.pdf.SCOPEThis manual specifies the maintenance requirements and describes the procedures to assist troubleshooting and maintenance of a Trusted system. WHO SHOULD USE THIS MANUALThis manual is for plant maintenance personnel who are experienced in the operation and maintenance of electronic equipment and are trained to work with safety systems. SYMBOLSIn this manual we will use these notices to tell you about safety considerations.SHOCK HAZARD: Identifies an electrical shock hazard. If a warning label is fitted, it can be on or inside the equipment.WARNING: Identifies information about practices or circumstances that can cause an explosion in a hazardous environment, which can cause injury or death, property damage or economic loss.ATTENTION: Identifies information about practices or circumstances that can cause injury or death.CAUTION: Identifies information about practices or circumstances that can cause property damage or economic loss.BURN HAZARD: Identifies where a surface can reach dangerous temperatures. If a warning label is fitted, it can be on or inside the equipment.This symbol identifies items which must be thought about and put in place when designing and assembling a Trusted controller for use in a Safety Instrumented Function (SIF). It appears extensively in the Trusted Safety Manual.IMPORTANT Identifies information that is critical for successful application and understanding of the product.NOTE Provides key information about the product or service.TIP Tips give helpful information about using or setting up the equipment.WARNINGS AND CAUTIONSWARNING: EXPLOSION RISKDo not connect or disconnect equipment while the circuit is live or unless the area is known to be free of ignitable concentrations or equivalentAVERTISSEMENT - RISQUE D’EXPLOSIONNe pas connecter ou déconnecter l’équipement alors qu’il est sous tension, sauf si l’environnement est exempt de concentrations inflammables ou équivalenteMAINTENANCEMaintenance must be carried out only by qualified personnel. Failure to follow these instructions may result in personal injury.CAUTION: RADIO FREQUENCY INTERFERENCEMost electronic equipment is influenced by Radio Frequency Interference. Caution should be exercised with regard to the use of portable communications equipment around such equipment. Signs should be posted in the vicinity of the equipment cautioning against the use of portable communications equipment.CAUTION:The module PCBs contains static sensitive components. Static handling precautions must be observed. DO NOT touch exposed connector pins or attempt to dismantle a module.ISSUE RECORDIssue Date Comments6 Sep 05 Format7 Aug 06 Dual Peer to Peer8 Sep 07 Port purposes9 Sep 14 Fault/Fail connector identity10 Sep 15 Rebranded and reformatted with standardisation of the RelativeHumidity Range and Operating Temperature specifications11 Apr 16 Updated to incorporate IEEE standards and correct typographical errors12 Oct 19 Updated Figure 2 Adapter LayoutUpdated Table 2 Connector SK1 PinoutUpdated Section 1.2 Fault/Fail ConnectorsRemoved Diagnostic Connector (J4) informationSplit J5 into two connectors, J5 and J13Updated Table 7 Mating ConnectorsAdded Table 8 Single Point ConnectionAdded Table 9 Multi-drop ConnectionUpdated Section 3.2 IRIG-B PortsUpdated Specifications tablePage intentionally left blankTrusted TMR Processor Interface Adapter Table of Contents Table of Contents1.Description (3)1.1. Processor Interface Connector (SK1) (5)1.2. Fault/Fail Connectors (J2 and J3) (J17 and J15) (6)1.3. PSU Shutdown Monitor Connector (J6) (6)1.4. Serial Port 1 (Diagnostic) Connectors (J7 and J12) (6)1.5. Serial Ports 2 and 3 Connectors (J8 to J11) (7)1.6. IRIG B Connectors (J5 and J13) (7)1.7. Mating Connectors (8)2.Installation (9)3.Input Configuration (11)3.1. Serial Ports (11)3.2. IRIG-B Ports (12)4.Available Operations (13)5.Specifications (15)Table of Contents Trusted TMR Processor Interface AdapterPage intentionally left blankTrusted TMR Processor Interface Adapter 1. Description 1.DescriptionFigure 1 Photo T812XThe Trusted Processor Interface Adapter T812x is designed to be connected directly to the rear of a Trusted TMR Processor position in a Trusted Controller Chassis T8100. The Adapter provides a communications connection interface between the Trusted TMR Processor and remote systems. The Adapter also provides the option of connecting IRIG-B time synchronisation signals to the Processor. Connection between the Adapter and the Trusted TMR Processor is via two 48-way DIN41612 E-type connectors (SK1), one each for connection to the Active and Standby Processors.1. Description Trusted TMR Processor Interface Adapter Figure 2 shows the physical layout of serial port, diagnostics and IRIG-B connectors on the Adapter printed circuit board (PCB).Figure 2 Adapter LayoutThe Adapter comprises a PCB on which the communications ports, IRIG-B connectors and both SK1 sockets (connectors to the Active/Standby Trusted TMR Processors) are mounted. The Adapter is contained within a metal enclosure and is designed to be clipped onto the appropriate connector at the rear of the Controller Chassis. Release buttons are provided to enable the Adapter to be disconnected.The communication ports available at the Adapter are RS422/RS485 2 wire on Port 1, and RS422/RS485 2 or 4 wire on Ports 2 and 3.An earth point is provided on the PCB so that the Chassis earth of the Processor will be connected to the shell of the Adapter and module rack earth. It is an important safety and Electrostatic Discharge (ESD) requirement that the equipotential bonding is connected and maintained.Trusted TMR Processor Interface Adapter 1. Description 1.1.Processor Interface Connector (SK1)SK1 is a 48-way DIN41612, E-type connector.PinCONNECTOR SK1 PINOUTA C E2 Fault Relay (NC) DIAG_RTN (NC) Failed Relay (NC)4 Fault Relay(Common) DIAG_IN_1 (NC) Failed Relay(Common)6 Fault Relay (NO) 0 V Port 1 Failed Relay (NO)8 N.C. Serial Port 1 B N.C.10 5 V_D Serial Port 1 A IRIG B122+12 DATA_OUT 0 V Port 2 IRIG B122-14 ENABLE Serial Port 2 B TX Reserved16 DATA_IN Serial Port 2 A TX Reserved18 CLK Serial Port 2 B RX/TX IRIG-B002-20 0 V Serial Port 2 A RX/TX IRIG-B002+22 Chassis GND 0 V Port 3 Chassis GND24 Chassis GND Serial Port 3 B TX Chassis GND26 Chassis GND Serial Port 3 A TX Chassis GND28 24 V PSU 1 LVWarningSerial Port 3 B RX/TX 24 V PSU 1 Shutdown30 24 V PSU 2 LVWarningSerial Port 3 A RX/TX 24 V PSU 2 Shutdown 32 24 V Return 24 V Return 24 V ReturnTable 1 Connector SK1 Pinout1. Description Trusted TMR Processor Interface Adapter1.2.Fault/Fail Connectors (J2 and J3) (J17 and J15)J2, J3, J15 and J17 are Phoenix contact 2.5 mm pitch connectors.J2 / J3Pin Service1. FAULT_n_NC2. FAULT_n_COM3. FAULT_n_NOJ17 / J15Pin Service1.FAIL_n_NC2. FAIL_n_COM3. FAIL_n_NOTable 2 Fault/Fail ConnectorsNote: n=1 for connectors J2 and J17, n=2 for connectors J3 and J15 providing fault and fail connections for the Active and Standby Processors respectively. FAULT NC relay contacts open on any system fault which sets the Processor System Healthy LED flashing red. FAIL NC relay contacts open on Processor shutdown.1.3.PSU Shutdown Monitor Connector (J6)J6 is Phoenix contact 2.5 mm pitch connector. These two system inputs are made available to the application on the Processor’s complex I/O equipment definition. The inputs expect volt-free contacts to the RTN pin.Pin Service1 24 V_PSU1_SHUTDOWN2 24 V_PSU2_SHUTDOWN3 24 V_RTNTable 3 PSU S/D Monitor Connection1.4.Serial Port 1 (Diagnostic) Connectors (J7 and J12)J7 and J12 are Phoenix 2.5 mm pitch connectors.Trusted TMR Processor Interface Adapter 1. DescriptionPin Service1 0 V2 SERIAL_1_B3 SERIAL_1_ATable 4 Serial Port 1 Diagnostic Connectors1.5.Serial Ports 2 and 3 Connectors (J8 to J11)These are Phoenix 2.5 mm pitch connectors.Pin Service1 0 V2 SERIAL_TX_B3 SERIAL_TX_A4 SERIAL_RX/TX_B5 SERIAL_RX/TX_ATable 5 Serial Ports 2 and 3 Connectors1.6.IRIG B Connectors (J5 and J13)J5 and J13 Phoenix 2.5 mm pitch connectors.J5Pin Service1 IRIG-B122+2 IRIG-B122-J13Pin Service1 IRIG-B002-2 IRIG-B002+1. Description Trusted TMR Processor Interface AdapterTable 6 IRIG-B Connectors1.7.Mating ConnectorsThe following table lists the connectors required to mate with the Trusted Processor Interface Adapter.Connector Phoenix Contact Part No ICS Part No No of WaysJ5, J13 18 81 32 5 3JX073 2J2, J3, J6,J7,J12, J15, J17 18 81 33 8 3JX075 3J8,J9,J10,J11 18 81 35 4 3JX076 5Table 7 Mating ConnectorsTrusted TMR Processor Interface Adapter 2. Installation 2.InstallationFigure 3 Correct Installation PositionThe Adapter should be fitted on the rear of the chassis behind the Processor slots, as shown above. The two connectors should fit into the third and sixth slots from the right, where the Processor connectors will fit. In the correct position, two empty slots will be visible on the right. Insert the Adapter into position about 5 mm lower than its final position, and ensure it is slotted in on both sides. Raise the Adapter upwards until the retaining clips click into place.2. Installation Trusted TMR Processor Interface AdapterPage intentionally left blankTrusted TMR Processor Interface Adapter 3. Input Configuration 3.Input Configuration3.1.Serial PortsThe serial ports connectors are arranged so that multi-drop RS422/485 connections can be easily configured. J7, J8 and J10 together with LK1, LK2 and LK3 form the basic terminations for ports 1, 2 and 3 respectively.Port No. Serial In TerminationPort 1 J7 Fit LK1Port 2 J8 Fit LK2Port 3 J10 Fit LK3Table 8 Single Point ConnectionPort No. Serial In Serial OutPort 1 J7 J12Port 2 J8 J9Port 3 J10 J11Table 9 Multi-drop ConnectionFor a single point connection the termination would be made to the relevant connector and its corresponding link would be fitted. For a multi-drop connection the ‘incoming’ connections would be made to the connections listed above and the ‘outgoing’ to J12, J9 or J11 for ports 1 to 3 respectively. This time however, the link will be removed as only the last connection on a multi-drop chain should be terminated.The provision of the two connectors for each serial port will enable quicker configuration of serial cabling as there is now no need to terminate two cables onto the same connector. The links LK1 to LK3 provide the serial ports with an easy way to add 120 Ω AC termination onto the receivers extremely close to the receiving devices.The 4 wire serial ports 2 and 3 have connectors that are pin compatible with those used on the Trusted Communications Interface Termination Unit (T8153).Serial connections should use screened twisted pair cable with the A-B signals connected as a pair. The screen should be connected to chassis ground at one end only. Some equipment may require a common 0 V connection. In order to operate correctly, the 0 V on the connector should be connected to 0 V on the other equipment to facilitate this.3. Input Configuration Trusted TMR Processor Interface Adapter Note: RS485 bus biasing is implemented differently in the T8111 compared to legacy T8110. For more information and technical support, refer to the Rockwell Automation Support Centre:Further information on serial port configuration can be found in the standards listed below: •EIA/TIA-422-B•EIA-485•CCITT V.113.2.IRIG-B PortsThe IRIG-B002 input is a pulse width modulated signal at 100bits/s and uses RS422 voltage levels. Connection to this port should be by twisted pair cable. A 120 Ω termination (R13) is provided on the module. The termination resistance connects to the circuit by fitting LK4. For multi-drop configurations, remove LK4 from all but the last interface adapter.The IRIG-B122 input is a 1 kHz amplitude modulated signal where the modulating signal has the same format as IRIG-B002. The peak amplitude (mark) of the input signal is nominally 1 V to 6 V into 600 Ω. The Trusted TMR Processor is able to receive signals in the range 0.25 V PK-PK to 10 V PK-PK. IRIG-B122 is normally provide via co-axial cable although any suitable medium would be acceptable.Further information on IRIG configuration can be found in the standards listed below: •Range Commanders Council IRIG STANDARD 200-98•IEEE Std 1344-1995 Annex F.2Trusted TMR Processor Interface Adapter 4. Available Operations 4.Available OperationsThe following table lists the variants of the Trusted Processor Adapter Unit and the Trusted TMR Processor options that can be made available by using them. All the variants below will enable the use of Dual (‘enhanced’) Peer to Peer with other Trusted Systems, using the dxpnc40 I/O definition and its associated data transfer I/O definitions.Variant Options EnabledT8120 None.Basic module with terminations for serial ports and ancillary connections.T8121 IRIG-B.Enables decode of IRIG-B002 or IRIG-B122 time synchronisation signals by theTrusted TMR Processor.T8122 MODBUS Master.Enables the Trusted System to operate as MODBUS Master.See Note.T8123 IRIG-B and MODBUS Master.Enables IRIG-B time signal decode and MODBUS Master operation.Table 10 Available OptionsNote: The Trusted Communications Interface (T815X) is also required for MODBUS Master operation. The serial ports on the Trusted TMR Processor can only be used for MODBUS Slave operation.4. Available Operations Trusted TMR Processor Interface AdapterPage intentionally left blankTrusted TMR Processor Interface Adapter 5.Specifications 5.SpecificationsPower Supply Powered from Trusted TMR ProcessorPower Dissipation 0.1 WIsolationBetween; Rear Serial Ports, IRIG Ports, Relay Ports and Chassis 50 V Reinforced (continuous) (1) 250 V Basic (fault) (2)[Type tested at 2436 Vdc for 60 s]Fusing None PortsPort 1 Ports 2 and 3 IRIG B RS422/485RS422/485IRIG-B122 and IRIG-B002 on a single connectorOperating Temperature 0 °C to +60 °C (+32 °F to +140 °F)Storage Temperature -25 °C to +70 °C (-13 °F to +158 °F)Relative Humidity – Operating and Storage 10 % – 95 %, non-condensingEnvironmental Specifications Refer to Trusted 8000 - Series B: InternationalSafety & Environmental Approvals, publicationICSTT-TD003DimensionsHeight: 138 mm (5.43 in)Width: 120 mm (4.72 in)Depth: 108 mm (4.25 in)Weight 877 g (1.93 lb)Note 1) 50 Vrms Secondary circuit derived from Mains, OVC II up to 300V.Note 2) 250 Vrms Mains circuit, OVC II up to 300V. Exposure to voltages at these levels shall be temporally constrained consistent with the system MTTR.。
EM-1240 硬件用户手册说明书
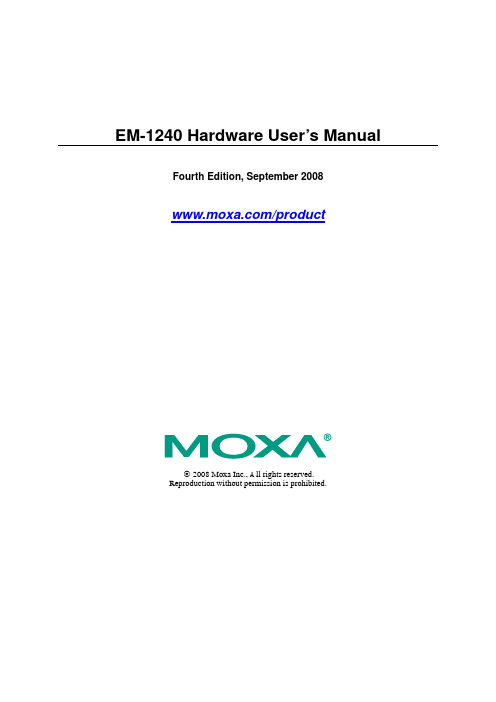
EM-1240 Hardware User’s Manual Fourth Edition, September 2008/product© 2008 Moxa Inc., A ll rights reserved.Reproduction without permission is prohibited.EM-1240 Hardware User’s ManualThe software described in this manual is furnished under a license agreement and may be used only inaccordance with the terms of that agreement.Copyright NoticeCopyright © 2008 Moxa Inc.All rights reserved.Reproduction without permission is prohibited.TrademarksMOXA is a registered trademark of Moxa Inc.All other trademarks or registered marks in this manual belong to their respective manufacturers.DisclaimerInformation in this document is subject to change without notice and does not represent a commitment on the part of Moxa.Moxa provides this document “as is,” without warranty of any kind, either expressed or implied, including, but not limited to, its particular purpose. Moxa reserves the right to make improvements and/or changes to this manual, or to the products and/or the programs described in this manual, at any time.Information provided in this manual is intended to be accurate and reliable. However, Moxa assumes no responsibility for its use, or for any infringements on the rights of third parties that may result from its use.This product might include unintentional technical or typographical errors. Changes are periodically made to the information herein to correct such errors, and these changes are incorporated into new editions of the publication.Technical Support Contact Information/supportMoxa Americas:Toll-free: 1-888-669-2872 Tel: +1-714-528-6777 Fax: +1-714-528-6778 Moxa China (Shanghai office): Toll-free: 800-820-5036 Tel: +86-21-5258-9955 Fax: +86-10-6872-3958Moxa Europe:Tel: +49-89-3 70 03 99-0 Fax: +49-89-3 70 03 99-99 Moxa Asia-Pacific:Tel: +886-2-8919-1230 Fax: +886-2-8919-1231Table of ContentsChapter 1Introduction..................................................................................................1-1 Overview..................................................................................................................................1-2Package Checklist....................................................................................................................1-2Product Features......................................................................................................................1-2EM-1240 Hardware Specifications..........................................................................................1-3EM-1240 Hardware Block Diagram........................................................................................1-4Appearance..............................................................................................................................1-4Dimensions..............................................................................................................................1-6 Chapter 2EM-1240 Functionality.................................................................................2-1 EM-1240 Embedded Module Functions..................................................................................2-2RS-232/422/485 Serial Ports....................................................................................................2-2Console Port.............................................................................................................................2-2LAN Ports................................................................................................................................2-2SD Signals...............................................................................................................................2-2GPIO........................................................................................................................................2-2Pin Assignments.......................................................................................................................2-3Definition of SD Signals..........................................................................................................2-6Mechanical Specifications of Pin Header Dimensions............................................................2-6 Chapter 3EM-1240-DK Functionality...........................................................................3-1 EM-1240-DK Function............................................................................................................3-2Combining EM-1240-DK with the Embedded Module...........................................................3-2LED Indicators.........................................................................................................................3-2Wiring Requirements...............................................................................................................3-3Connecting the Power..............................................................................................................3-3Grounding the EM-1240 Development Kit..............................................................................3-3Serial Ports and Pin Assignments.............................................................................................3-4Console Ports and Pin Assignments.........................................................................................3-5LAN Ports and Pin Assignments..............................................................................................3-5SD Socket................................................................................................................................3-5GPIO........................................................................................................................................3-6Mechanical Specifications of Console and Serial Ports Pin Headers.......................................3-6Reset Button.............................................................................................................................3-61Introduction Thank you for purchasing the Moxa EM-1240 Embedded Module. The product’s features include4 software-selectable RS-232/422/485 serial ports, two 10/100 Mbps Ethernet ports, and SD signals for external SD socket connection based on the Moxa ARM9 32-bit 192 MHz communication processor. These features make the EM-1240 ideal for the core module of an industrial embedded system design.The EM-1240 Development Kit, which is designed for system and software program development at the system evaluation stage, is also available. The kit combines the EM-1240 and EM-1240-DK, which is the carrier board used to evaluate the EM-1240. The EM-1240’s pre-installedready-to-run μClinux Kernel 2.6 makes it easy to develop programs for any application.In this manual, we introduce the hardware features and functions of the EM-1240 Embedded Module and the EM-1240 Development Kit. After a brief introduction of the hardware features,the manual focuses on installation and hardware configuration with device interfaces.The following topics are covered in this chapter:OverviewPackage ChecklistProduct FeaturesEM-1240 Hardware SpecificationsEM-1240 Hardware Block DiagramAppearanceDimensionsOverviewThe EM-1240 Embedded Module is designed for system integration and software development inindustrial data applications. The module features 4 software-selectable RS-232/422/485 serialports, two 10/100 Mbps Ethernet ports, and an SD function based on the Moxa ART ARM9 32-bit192 MHz communication processor. In addition, you may order the EM-1240 Development Kit.The kit includes an EM-1240 embedded module, an EM-1240-DK carrier board, and the itemsneeded for setting up a basic layout. The kit is makes it easy for users to evaluate the functionalityof the EM-1240. You can develop and integrate specific systems on the module in advance tomake the EM-1240 Embedded Module completely compatible with industrial systems andapplications.The pre-installed open Linux operating system makes the EM-1240 suitable for developing thecontrol programs used on a standard PC. The software you develop for your own applications canbe stored in the onboard Flash memory. The EM-1240 lets you build an application that has apowerful serial communication capability, but which is still small in size. The EM-1240 is suitedfor control systems that use a distributed, embedded architecture, such as those systems used formanufacturing automation, intelligent transportation systems, medical management, and dataacquisition and control.Package ChecklistThe EM-1240 package includes the EM-1240 embedded module only. The EM-1240 DevelopmentKit is available for evaluation purposes. The EM-1240 Development Kit package contains thefollowing items:y 1 EM-1240 Embedded Moduley 1 EM-1240-DK, the carrier board of the EM-1240 Development Kity Quick Installation Guidey Document & Software CDy Cross-over Ethernet cabley Universal Power Adaptery Warranty StatementNOTE: Notify your sales representative if any of the above items is missing or damaged. Product FeaturesThe EM-1240 Embedded Module has the following features:y Moxa ART ARM9 32-bit 192 MHz communication processory16 MB RAM and 8 MB Flash ROM onboardy 4 software-selectable RS-232/422/485 serial portsy Dual 10/100 Mbps Ethernet portsy RS-232 serial console port (supports full signal and PPP)y Ready-to-run μClinux Kernel 2.6.9 communication platformy SD signals supported for external Secure Digital (SD) socket connectiony10 GPIO reserved for system integration (to enable GPIO, SD must be disabled)1-2EM-1240 Hardware SpecificationsModel EM-1240 Embedded ModuleCPU Moxa ART ARM9 32-bit 192 MHz processorRAM 16 MBFlash 8 MBLAN Auto-sensing 10/100 Mbps ×2 Built-in 1.5 KV magnetic isolationFour serial ports that support RS-232/422/485 signalsRS-232 signals: TxD, RxD, DTR, DSR, RTS, CTS, DCD, GNDRS-422 signals: TxD+, TxD-, RxD+, RxD-, GND4 wire RS-485 signals: TxD+, TxD-, RxD+, RxD-, GND2 wire RS-485 signals: Data+, Data-, GNDSerial Protection: 15 KV ESD for all signalsData bits: 5,6,7,8Stop bits: 1,1.5,2Parity: None, even, odd, space, markFlow Control: RTC/CTS, XON/XOFFSerial PortsSpeed: 50 bps to 921.6 Kbps, support Any BaudrateSerial Console RS-232 ×1, full signals, supports PPPStorage Expansion SD signals for external Secure Digital (SD) socket connectionGPIO GPIO ×10 (to enable GPIO, SD must be disabled.)Real-time Clock YesWatchdog Timer YesBuzzer Signals Buzzer signals reserved for external buzzer connectionLED Signals Reserve signals for the following LED connections: System: Ready×1LAN: 10M/Link ×2, 100M/Link ×2Serial: TxD ×4, RxD ×4Reset Signal Reserve signal for external “Reset to Default” button connection Power Input Accept external 5 VDC through pin headerDimensions (W ×L) 90 ×80 mmOperating Temperature -10 to 60°C (14 to 141°F), 5 to 95%RHStorage Temperature -20 to 80°C (-4 to 176°F), 5 to 95%RHModule Interface Two 2 ×28 pin-headers; pitch: 1.27 ×1.27 (mm)1-3EM-1240 Hardware Block DiagramRS-232/422/485AppearanceEM-1240 Development Kit: EM-1240 Embedded Module + EM-1240-DK, carrierboard of EM-1240 Development Kit1-4EM-1240 Embedded ModuleTop View Bottom ViewEM-1240 Development Kit1-5DimensionsEM-1240 Embedded Module1-6EM-1240-DK, Carrier board of EM-1240 Development Kit1-72EM-1240 Functionality In this chapter, we explain the basic features of the EM-1240 Embedded Module. The followingtopics are covered:EM-1240 Embedded Module FunctionsRS-232/422/485 Serial PortsConsole PortLAN PortsSD SignalsGPIOPin AssignmentsDefinition of SD SignalsMechanical Specifications of Pin Header DimensionsEM-1240 Embedded Module FunctionsThe EM-1240 Embedded Module is designed to be integrated directly into the user’s system andapplication. The module has four software-selectable RS-232/422/485 serial ports, dual 10/100Mbps LAN ports, 1 RS-232 console port, and GPIO/SD signals. In addition, the EM-1240 uses theMoxa ART ARM9 32-bit 192 MHz communication processor, which ensures excellentperformance for data transmission.The pre-installed μClinux Kernel 2.6.9 makes it easy for users to develop programs for a variety ofapplications. The EM-1240 is an ideal solution for manufacturing automation, intelligenttransportation monitoring, and remote device control.RS-232/422/485 Serial PortsThe EM-1240 Embedded Module has 4 software-selectable RS-232/422/485 serial ports. Pinassignment diagrams are shown in a later section. The ports can be configured by software. Pleaserefer to Software User’s Manual for details.Console PortThe EM-1240 Embedded Module has 1 console port for onsite configuration. However, it can alsobe used as a serial port with standard RS-232 interface and PPP function support. Refer to theSoftware User’s Manual for details.LAN PortsThe EM-1240 Embedded Module has 2 10/100 Mbps LAN ports that can be used to set up aredundant Ethernet network for non-stop operation, and the on-board transformer provides 1.5 KVisolation protection.SD SignalsThe EM-1240 Embedded Module provides SD signals for storage expansion. Designers can usethese signals to create an SD socket. Note that you can use a Secure Digital (SD) memory cardcompliant with the SD 1.0 standard to provide up to 1GB of additional memory space. However,the SD signals share the same mechanical layout with GPIO. When you enable the SD signals, theGPIO function will be disabled, and vice versa.GPIOThe EM-1240 Embedded Module provides 10 software-selectable GPIOs. Note that users canchoose to enable either the SD Signals or the GPIO function, but not both. When you enable theGPIO function, the SD Signals will be disabled.2-2Pin AssignmentsThere are two 56-pin pin headers on the EM-1240 embedded module. To use the EM-1240Embedded Module to develop your own independent system, refer to the following tables for thepin assignments of jumpers JP3 and JP4.JP4JP3222-3Signals JP3 Pin No. Signals2 Eth0_RxDjn-Eth0_TxD_out- 14 Eth0_RxD_in+Eth0_TxD_out+ 36 Eth0_LED_10MEth0_LED_100M 58 Eth1_TxD_out-Eth1_RxDjn- 7Eth1_TxD_out+ Eth1_RxDjn+ 91012 Eth1_LED_10MEth1_LED_100M 11GPIO0 (I/O) 13 14 SW_ResetGPIO2 (I/O) 15 16 GPIO1 (I/O)GPIO4 (I/O) 17 18 GPIO3 (I/O)GPIO6 (I/O) 19 20 GPIO5 (I/O)GPIO8 (I/O) 21 22 GPIO7 (I/O)Buzzer (Beeper) 23 24 GPIO9 (I/O)LED_Ready (SW_RDY) 25 26 HW Reset (nReset) BLCM_DO (I/O) 27 28 BLCM_D1 (I/O)BLCM_D2 (I/O) 29 30 BLCM_D3 (I/O)BLCM_D4 (I/O) 31 32 BLCM_D5 (I/O)BLCM_D6 (I/O) 33 34 BLCM_D7 (I/O)D/I (LCM) (O) 35 36 R/W (LCM) (O)E (LCM) (O) 37 38 BL (LCM) (O)CL (LCM) (O) 39 40 RST (LCM) (O)CS1 (LCM) (O) 41 42 CS2 (LCM) (O)44 GNDGND 43KEY_OUT0 (KEYPAD) 45 46 KEY_OUT1 (KEYPAD)KEY_OUT2 (KEYPAD) 47 48 KEY_OUT3 (KEYPAD)KEY_OUT4 (KEYPAD) 49 50 KEY_OUT5 (KEYPAD)KEY_I N0 (KEYPAD) 51 52 KEY_I N1 (KEYPAD)KEY_I N2 (KEYPAD) 53 54 KEY_I N3 (KEYPAD)56 GNDGND 552-4Signals JP4 Pin No. SignalsGND 12 GND VCC (5V)34 VCC (5V)VCC (5V) 5 6 VCC (5V)GND 78 GNDGND 910RS-232:TxD0RS-422: RXD0+RS-485: Data0+RS-232: RxD0 RS-422: TXD0+ RS-485: X 11 12 RS-232:CTS0RS-422: XRS-485: XRS-232: RTS0 RS-422: XRS-485: X 13 14 RS-232:DSR0RS-422: XRS-485: XRS-232: DTR0 RS-422: RXD0- RS-485: Data0- 15 16 RS-232:DCD0RS-422: TXD0-RS-485: XRS-232: RxD1 RS-422: TXD1+ RS-485: X 17 18 RS-232:TxD1RS-422: RXD1+RS-485: Data1+RS-232: CTS1 RS-422: XRS-485: X 19 20 RS-232:RTS1RS-422: XRS-485: XRS-232: DSR1 RS-422: XRS-485: X 21 22 RS-232:DTR1RS-422: RXD1-RS-485: Data1-RS-232: DCD1 RS-422: TXD1- RS-485: X 23 24 RS-232:RTS2RS-422: XRS-485: XRS-232: RxD2 RS-422: TXD2+ RS-485: X 25 26 RS-232:TxD2RS-422: RXD2+RS-485: Data2+RS-232: DCD2 RS-422: TXD2- RS-485: X 27 28 RS-232:DSR2RS-422: XRS-485: XRS-232: DTR2 RS-422: RXD2- RS-485: Data2- 29 30 RS-232:CTS2RS-422: XRS-485: XRS-232: RxD3 RS-422: TXD3+ RS-485: X 31 32 RS-232:RTS3RS-422: XRS-485: XRS-232: DCD3 RS-422: TXD3- RS-485: X 33 34 RS-232:TxD3RS-422: RXD3+RS-485: Data3+RS-232: DSR3 RS-422: XRS-485: X 35 36 RS-232:DTR3RS-422: RXD3-RS-485: Data3-RS-232: CTS3 RS-422: XRS-485: X 37 38 TxD_Console(RS-232)RxD_Console (RS-232) 39 40 CTS_Console (RS-232) RTS_Console (RS-232) 41 42 DSR_Console (RS-232)2-5DTR_Console (RS-232) 43 44 DCD_Console (RS-232)46 GNDGND 45Serial LED_Tx0 47 48 Serial LED_Rx0Serial LED_Tx1 49 50 Serial LED_Rx1Serial LED_Tx2 51 52 Serial LED_Rx2Serial LED_Tx3 53 54 Serial LED_Rx3GND 5556 GND Definition of SD SignalsThe following table gives the definition of the SD signals. Note that the signal pins from the JP3pin header share the same pin as the GPIO.Signal Name Direction GPIO DescriptionSD_CLK Output GPIO 7 Clock signal to SD/MMCSD_CMD Bidirectional GPIO 2 Bidirectional line for command and responseSD_DAT<3:0> Bidirectional GPIO<6:3> Bidirectional line for read and write dataCarddetect1SD_CD Input GPIOprotect0 WriteSD_WP Input GPIOMechanical Specifications of Pin Header DimensionsRefer to the following figures for the mechanical specifications of the Pin Header dimensions ofthe EM-1240 Embedded Module. The figures define the mechanical specifications of jumpers JP3and JP4 on the EM-1240.2-63EM-1240-DK Functionality This chapter includes information about the EM-1240-DK (carrier board of the EM-1240Development Kit).This chapter covers the following topics:EM-1240-DK FunctionCombining EM-1240-DK with the Embedded ModuleLED IndicatorsWiring RequirementsConnecting the PowerGrounding the EM-1240 Development KitSerial Ports and Pin AssignmentsConsole Ports and Pin AssignmentsLAN Ports and Pin AssignmentsSD SocketGPIOMechanical Specifications of Console and Serial Ports Pin HeadersReset ButtonEM-1240-DK FunctionThe EM-1240 Development Kit is a well-designed PCB board with complete layout. The kit helpsusers evaluate, develop, and integrate the EM-1240 Embedded Module into their systems andapplications. Simply combine the EM-1240 Embedded Module with the Development Kit to startporting the relevant software, and create a solution for the applications you wish to implement.Refer to the following picture for the basic layout of the EM-1240-DK.Combining EM-1240-DK with the Embedded ModuleInsert the EM-1240 Embedded Module vertically onto the EM-1240-DK. Note that the Pin marked“JP4” on the Embedded Module must be matched with the Pin marked “JP6” on the EM-1240-DK;and the Pin marked “JP3” on the Embedded Module must be matched with the Pin marked “JP4”on the EM-1240-DK. Be careful when installing the board to avoid damaging the pins.LED IndicatorsThe following table explains the function of the LED indicators located on EM-1240-DK.LED Name LED Color LED FunctionPower Green Power is on.Ready Green Power is on and system functions normally.P1-P4 (Tx)Green Serial port 1-4 is transmitting data.Off Serial port 1-4 is not transmitting data.P1-P4 (Rx)Yellow Serial port 1-4 is receiving data.Off Serial port 1-4 is not receiving data.3-2Wiring RequirementsThis section describes how to connect the EM-1240 Development Kit to serial devices.You should heed the following common safety precautions before proceeding with the installationof any electronic device:y Use separate paths to route wiring for power and devices. If power wiring and device wiring paths must cross, make sure the wires are perpendicular at the intersection point.NOTE: Do not run signal or communication wiring and power wiring in the same wire conduit.To avoid interference, wires with different signal characteristics should be routed separately.y Use the type of signal transmitted through a wire to determine which wires should be kept separate. The rule of thumb is that wiring that shares similar electrical characteristics can bebundled together.y Keep input wiring and output wiring separate.y It is advisable to label the wiring to all devices in the system.Be sure to disconnect the power cord before installing and/or wiring your EM-1240 DevelopmentKit.Connecting the PowerYou may use either a power jack or 3-pin terminal block for connecting the power. The powerinput range of the EM-1240-DK is from 12 to 48 VDC. Note that you may only use one powerinput source at the same time. DO NOT connect the power to both the power jack and terminalblock simultaneously. You may use the power on-off switch to turn on and turn off the power tothe Development Kit. If the power is properly supplied, the “Power” LED will light upimmediately and the “Ready” LED will glow a solid green after a 25 to 30 second delay. Grounding the EM-1240 Development KitGrounding and wire routing help limit the effects of noise due to electromagnetic interference(EMI). Run the ground wire from the ground screw to the grounding surface prior to connectingdevices.3-3Serial Ports and Pin AssignmentsThe EM-1240 Development Kit has 4 software-selectable serial ports. If you would like to connectto a serial device, use male DB9 connectors. They can be configured for RS-232/422/485 bysoftware. Refer to the Software User’s Manual for details. Furthermore, you may also use serialport pin headers to extend the serial port with other devices using a homemade cable. Simplyconnect one end of the cable to serial port pin header and the other end of the cable to other device.Pay attention to the cable length for the various serial communication standards. Refer to the following figure for pinouts and pin assignments of the DB9 connector and pin header.J1/J3/J4/J6 Serial Ports 1-4Male DB9 Port Pin HeaderJ1/J3/J4/J6Pin RS-232RS-422 4-wire RS-485 2-wire RS-485 1 DCD TxDA(-)TxDA(-)--- 2 RxD TxDB(+)TxDB(+)--- 3 TxD RxDB(+)RxDB(+)DataB(+) 4 DTR RxDA(-)RxDA(-)DataA(-) 5 GND GND GND GND 6 DSR --- --- --- 7 RTS --- --- --- 8 CTS --- --- ---3-4Consol r of the serial console port to extend the serial port to other devices. Thepinout onsole port ar tandard serial port that was mentioned inthe pre s Male DB9 PortJ5 Console Port e Ports and Pin AssignmentsThe serial console port on the EM-1240-DK is an RS-232 port with full modem signal. It isdesigned for serial console terminals, which can be used for local configuration. PPP is alsosupported to make it easy to set up a modem connection for long distance data transmission. Youmay use the Pin heade s of this RS-232 c viou section.e the same as the sLAN Po the Ethernetcable to ent Kit LAN port ther end of the cable to the Ethernet network.The LA p e pin RJ45ector e following figures for the pinouts.8-pin RJ45rts and Pin AssignmentsThe EM-1240 Development Kit has two 10/100 Mbps LAN ports. Connect one end of the Developm N orts us 8-and the o h c n ons. See tPin Signal 1 ETx+ 2 E Tx-3 E Rx+4 --- 5 --- 6 E Rx-7 ---8 ---SD Soc t if you want to remove it. Note that the SD will not work if you enable the GPIOnction. Refer to the section about the EM-1240’s SD function to see a table that describes the SDard interface.ketThe EM-1240 Development Kit provides an internal SD socket for storage expansion. It allowsusers to plug in a Secure Digital (SD) memory card compliant with the SD 1.0 standard for up to 1GB of additional memory space. Plug the SD card into the socket directly and remember to pressthe SD card firs fu c3-53-6GPIOGPIO Signal Pin Header JP7ls function. Use theGPIO pin header for connecting with devices. See thefollowing figure for GPIO pinouts. The EM-1240 Development Kit has 10 GPIOs. You may configure digital input channels and digital outputchannels by software. Note that the GPIO function will not work if you enable the SD signaMechanical Specifications of Console and Serial Ports Pin Header Refer to the following figure for the specifications of console and serial ports of the EM-1240-DK.sReset Balwaysuse the software reboot command />reboot to protect the integrity of data being transmitted orprocessed. The Reset button is not designed to hard reboot the EM-1240 Development Kit.uttonPress the Reset button on the EM-1240-DK continuously for at least 5 seconds to load the factorydefault configuration. After the factory default configuration has been loaded, the system willreboot automatically. We recommend that you only use this function if the software is not working properly and you want to load factory default settings. To reset an embedded Linux system,。
1140说明书_20101215

ZJT系列矿用隔爆兼本质安全型变频调速装置使用说明书山西华鑫电气有限公司1序言感谢您选用山西华鑫电气有限公司的ZJT系列矿用隔爆兼本质安全型变频调速装置。
本产品是山西华鑫电气有限公司自主开发、生产的可靠性高、性能优异的变频器,采用高品质的元器件、优质材料并结合高新数字集成控制技术制造而成。
本手册提供用户安装配线、参数设定、故障诊断和故障排除、日常维护相关事宜,为确保能正确操作此系列变频器,发挥其优越性能,请在装机之前,详细阅读本使用手册,将本手册交于该机器的使用者,并请妥善保存。
本公司对客户提供全方位的技术支持。
如对于本变频器的使用存在疑难或有特殊要求,请与就近的办事处、客户服务中心或者经销商联系,也可直接与公司本部联系,我们将竭诚为您服务。
本公司一直致力于产品的不断改进和完善,故本系列变频器的相应资料(操作手册、宣传资料等)如有变动,恕不另行通知。
开箱检查注意事项开箱时,请认真确认以下内容:1.产品是否有破损,零部件是否有损坏、脱落等现象,主体是否有碰伤现象;2.本机铭牌所标注的额定值是否与您的订货要求一致;3.本公司在产品的制造及包装出厂方面,已严格检验,但若发现有某种遗漏,请速与本公司或供应商联系,我们将在第一时间为您解决。
山西华鑫电气有限公司地址:山西省阳泉市李家庄华鑫工业园邮编:0450082 安全注意事项为了确保您的人身和设备安全,在使用本装置之前,请务必仔细阅读本章内容,并在以后的搬运、安装、运行、调试与检修过程中遵照执行。
1. 安全标识定义本符号提示如果不按要求操作,可能导致死亡、重伤或严重的财产损失。
本符号提示如果不按要求操作,可能使身体受伤或设备损坏。
本符号说明操作时需注意的事项。
本符号提示一些有用的信息。
2. 安装注意事项 危险!请将本装置安装在金属等不可燃物体上,以免火灾的发生。
请将易燃物远离本装置,否则有发生火灾的危险。
严禁私自拆装、改装本装置,否则后果自负。
必须由具有专业资格的技术人员进行配线作业,以免触电危险。
RTE24012中文资料

RTD14005 RTD14012 RTD14024
RTD34012 RTD34024 RT424012
RT424024 RT444012 RT444024
RTE24005 RTE24012 RTE24024
RTE44012 RTE44024
Outline Dimensions
.62 (15.7)
1.14 (29)
.051 DIA. (1.30)
.276
.400
(7.0)
(10.16)
.800 (20.32)
.800 (20.32)
.051 DIA. (1.30)
.300 (7.62)
.051 DIA. (1.30)
Contact Data
Arrangements: 1 Form A (SPST-NO) Wiring Diagram Code 1, 3. 2 Form A (DPST-NO) Wiring Diagram Code 5. 1 Form C (SPDT) Wiring Diagram Code 1, 3. 2 Form C (DPDT) Wiring Diagram Code 5.
Material: Silver-nickel 90/10. Minimum Load: 12V/100mA. Expected Mechanical Life: 10 million operations. Initial Contact Resistance: 100 milliohms max @ 1A 12VDC.
018 = 18VDC 048 = 48VDC 024 = 24VDC
4
012
Stock Items
RT114012 RT114024 RT134012
1140V多回路组合开关说明书(光纤通讯)-12

3038
宽(mm) 870
870
高(mm) 1067
1067
>组合开关快插式外形尺寸见下表:
尺寸 规格 4 组合
6 组合
长(mm) 2640
2900
8 组合 3320 870 1067
8 0 1377
10 组合 3320 870 1377
11 组合 3320 870 1377
7
器, 主控腔内前门按装智能保护器模块等,主控腔右侧装有 GHK-800/1140 真空隔离换向开关或 GHK-400/1140 隔离换向开关,和用于控制回路用的 GHK-200/1140 或 LW5-40/1140 隔离开关。
>组合开关压盘式外形尺寸见下表:
尺寸 规格 4 组合
6 组合
长(mm) 2700
6
(1)过载保护特性
项目
过电流/整定电流
动作时间
起始状态
1
1.05
2h 不动作
冷态
2
1.2
<20min
热态
3
1.5
<3min
热态
4
6
(2)断相保护特性
8~16S
冷态
项目
过电流/整定电流
任意两相
第三相
动作时间
起始状态
1
1.0
0.9
不动作
冷态
2
1.15
(3)漏电闭锁保护特性
0
<20min
热态
主回路额定工作电压(V) 1140 660
Q J Z 1 – □ / 1140(660)– □
回路数
额定工作电压
总额定电流
设计序号
真空
隔爆兼本安
摩卡电子V2401 2402系列独立计算机商品介绍说明书

The V2401/2402 Series embedded computers are based on the Intel Atom N270 x86 processor, and feature 4 RS-232/422/485 serial ports, 8 RS-232 serial ports, dual Gigabit LAN ports, 6 USB 2.0 hosts, and a CompactFlash socket. The V2401 computer provides VGA, DVI, and LVDS outputs, and the V2402 computer provides both VGA and DVI outputs, making them particularly well-suited for industrial applications such as SCADA and factory automation.The V2401 and V2402 come with 4 RS-232/422/485 serial ports, and the V2401 has an additional 8 RS-232 ports, making them ideal for connecting a wide range of serial devices, and the dual 10/100/1000 Mbps Ethernet ports offer a reliable solution for network redundancy, Front View promising continuous operation for data communication and management. As an added convenience, the V2401/2402 computers have 4 DIs, and 4 DOs for connecting digital input/output devices. In addition, the CompactFlash and USB sockets provide the V2401/2402 computers with the reliability needed for industrial applications that require data buffering and storage expansion.Pre-installed with Linux, Windows CE 6.0, or Windows Embedded Standard 2009, the V2401/2402 Series provides programmers with a friendly environment for developing sophisticated, bug-free application software at a low cost.In addition, the V2402 series also offers -40 to 70°C wide temperature models for harsh environments.V2401/2402 SeriesOverviewAppearancePower/Storage 10/100/1000 Mbps(V2401)Rear ViewHardware SpecificationsComputerCPU: Intel Atom N270 1.6 GHz processorOS (pre-installed): Linux, Windows CE 6.0 or Windows Embedded Standard 2009System Chipset: Intel 945GSE + ICH7-MBIOS: 8 Mbit Flash BIOS, SPI type, ACPI function supportedFSB: 400/533 MHzSystem Memory: 2 GB capacity, 1 GB pre-installed: 1 x 2 GBDDR2-533 200 pin SO-DIMM SDRAM slotUSB: USB 2.0 compliant hosts x 6, type A connector, supports system boot upStorageBuilt-in: 2 GB onboard industrial DOM to store OSStorage Expansion: CompactFlash socket for CF card expansion, supporting CF Type-I/II socket with DMA modeHDD Support: 1 SATA-II connector for HDD expansionOther PeripheralsKB/MS: 1 PS/2 interface supporting standard PS/2 keyboard and mouse through Y-type cableAudio: HD audio, with line-in and line-out interfaceDisplayGraphics Controller: Intel Gen 2.5 Integrated Graphics Engine, 250 MHz core render clock and 200 MHz core display clock at 1.05-V core voltage VGA Interface: DB15 female connectorLVDS Interface: Onboard HIROSE DF13-40DP-1.25 V connector (V2401 only)DVI Interface: DVI-connector (chrontel CH7307 SDVO to DVI transmitter)Ethernet InterfaceLAN: 2 auto-sensing 10/100/1000 Mbps ports (RJ45)Serial InterfaceSerial Standards:• V2401/2402: 4 RS-232/422/485 ports*, software selectable (DB9 male connector)• V2401 only: 8 RS-232 ports (68-pin VHDC connector)*COM1’s pin 9 signal can be set by jumper as N/C (default), +5 V, or +12 V ESD Protection: 4 kV for all signalsSerial Communication ParametersData Bits: 5, 6, 7, 8Stop Bits: 1, 1.5, 2Parity: None, Even, Odd, Space, MarkFlow Control: RTS/CTS, XON/XOFF, ADDC® (automatic data direction control) for RS-485Baudrate: 50 bps to 921.6 kbps (non-standard baudrates supported; see user’s manual for details)Serial LEDs RS-232/422/485RS-232 Serial Port x 8 DI x 4Software SpecificationsSerial SignalsRS-232: TxD, RxD, DTR, DSR, RTS, CTS, DCD, GND RS-422: TxD+, TxD-, RxD+, RxD-, GND RS-485-4w: TxD+, TxD-, RxD+, RxD-, GND RS-485-2w: Data+, Data-, GNDDigital InputInput Channels: 4, source type Input Voltage: 0 to 30 VDC at 25 Hz Digital Input Levels for Dry Contacts: • Logic level 0: Close to GND • Logic level 1: OpenDigital Input Levels for Wet Contacts: • Logic level 0: +3 V max.• Logic level 1: +10 V to +30 V (Source to DI)Isolation: 3 kV opticalDigital OutputOutput Channels: 4, sink typeOutput Current: Max. 200 mA per channelOn-state Voltage: 24 VDC nominal, open collector to 30 VDC Connector Type: 10-pin screw terminal block (4 DI points, 4 DO points, DI Source, GND)Isolation: 3 kV optical isolationLEDsSystem: Power, StorageLAN: 100M/Link x 2, 1000M/Link x 2 (on connector)Switches and ButtonsPower Switch: on/off (front panel)Reset Button: For warm reboot (rear panel)Physical CharacteristicsHousing: Aluminum Weight:• V2401: 2.1 kg • V2402: 2 kg Dimensions:Without ears: 250 x 57 x 152 mm (9.84 x 2.24 x 5.98 in)With ears: 275 x 63 x 152 mm (10.83 x 2.48 x 5.98 in)Mounting: DIN rail, wall, VESAEnvironmental LimitsOperating Temperature:• Standard models: -10 to 60°C (14 to 140°F) • Wide temp. models : -40 to 70°C (-40 to 158°F)Storage Temperature: -40 to 85°C (-40 to 185°F)Ambient Relative Humidity: 5 to 95% (non-condensing)Anti-vibration: 5 g rms @ IEC-68-2-34, random wave, 5-500 Hz, 1 hr/axisAnti-shock: 50 g @ IEC-68-2-27, half sine wave, 11 msPower RequirementsInput Voltage: 9 to 36 VDC (3-pin terminal block for V+, V-, SG)Power Consumption: 26 W (without LVDS output) 2.9 A @ 9 VDC 1.08 A @ 24 VDC 720 mA @ 36 VDCStandards and CertificationsSafety: UL 508, UL 60950-1, CSA C22.2 No. 60950-1-07, EN 60950-1, CCC (GB9254, GB17625.1)EMC: EN 55022 Class A, EN 61000-3-2 Class D, EN 61000-3-3, EN 55024, FCC Part 15 Subpart B Class A Wheeled Vehicles: e-Mark (e4)Green Product: RoHS, CRoHS, WEEEReliabilityAutomatic Reboot Trigger: Built-in WDT (watchdog timer) supporting 1-255 level time interval system reset, software programmable MTBF (mean time between failures): V2401: 238,762 hrs V2402: 228,172 hrsWarrantyWarranty Period: 3 yearsDetails: See /warrantyLinuxOS: Linux 2.6.26, Debian Lenny 5.0File System: EXT2Internet Protocol Suite: TCP, UDP, IPv4, SNMPv1/v2c/v3, ICMP, ARP, HTTP, CHAP, PAP, SSH 1.0/2.0, SSL, DHCP, NTP, NFS, Telnet, FTP, TFTP, PPP, PPPoEInternet Security: OpenVPN, iptables firewallWeb Server (Apache): Allows you to create and manage web sites; supports PHP and XMLTerminal Server (SSH): Provides secure encrypted communications between two un-trusted hosts over an insecure networkDial-up Networking: PPP Daemon for Linux that allows Unix machines to connect to the Internet through dialup lines, using the PPP protocol, as a PPP server or client. Works with ‘chat’, ‘dip’, and ‘diald’, among (many) others. Supports IP, TCP, UDP, and (for Linux) IPX (Novell).File Server: Enables remote clients to access files and other resources over the networkWatchdog: Features a hardware function to trigger system reset in a user specified time interval (Moxa API provided)Application Development Software:• Moxa API Library (Watchdog timer, Moxa serial I/O control, Moxa DI/DO API)• GNU C/C++ compiler • GNU C library • PerlWindows XP EmbeddedOS: Windows Embedded Standard 2009 SP3File System: NTFSInternet Protocol Suite: DHCP, DNS, FTP, HTTP, SNTP, NTP, Telnet, SMTP, SNMPv2, TCP, UDP, IPv4, ICMP, IGMP, IPsec, TAPI, ICS, PPP, CHAP, EAP, PPPoE, PPTP, NetBIOSWeb Server (IIS): Allows users to create and manage websitesSilverlight 2.0: A free runtime that powers rich application experiences and delivers high quality, interactive video across multiple platforms and browsers, using the .NET frameworkRemote Registry Service: Enables remote users to modify registry settings on this computerRemote Desktop: The Terminal Server Remote Desktop component provides remote access for the desktop of a computer running Terminal ServicesWatchdog: Features a hardware function to trigger system reset in a user specified time interval (Moxa API provided)Enhanced Writer Filter: Redirect disk write operations to volatile (RAM) or non-volatile (disk) storageFile Based Write Filter: The File Based Write Filter (FBWF) component redirects all write requests directed at protected volumes to the overlay cache, which records and displays the changes while preserving the protected status of the target volume.Application Development Software: • Moxa API Library• Microsoft .Net Framework 3.5 with SP1• Active Directory Service Interface (ADSI) Core • Active Template Library (ATL), 2.0 • Common Control Libraries • Common File Dialogs• Direct3D, DirectPlay, DirectShow, and Direct show filtersOrdering InformationAvailable ModelsV2401-CE: x86 ready-to-run embedded computer with Intel Atom N270, VGA, LVDS, DVI, Audio, 2 LANs, 12 serial ports, 4 DIs, 4 DOs, 6 USB 2.0 ports, CF, WinCE 6.0V2401-XPE: x86 ready-to-run embedded computer with Intel Atom N270, VGA, LVDS, DVI, Audio, 2 LANs, 12 serial ports, 4 DIs, 4 DOs, 6 USB 2.0 ports, CF, Windows Embedded Standard 2009V2401-LX: x86 ready-to-run embedded computer with Intel Atom N270, VGA, LVDS, DVI, Audio, 2 LANs, 12 serial ports, 4 DIs, 4 DOs, 6 USB 2.0 ports, CF, Linux 2.6V2402-CE: x86 ready-to-run embedded computer with Intel Atom N270, VGA, DVI, Audio, 2 LANs, 4 serial ports, 4 DIs, 4 DOs, 6 USB 2.0 ports, CF, WinCE 6.0V2402-XPE: x86 ready-to-run embedded computer with Intel Atom N270, VGA, DVI, Audio, 2 LANs, 4 serial ports, 4 DIs, 4 DOs, 6 USB 2.0 ports, CF, Windows Embedded Standard 2009, -10 to 60°C operating temperatureV2402-LX: x86 ready-to-run embedded computer with Intel Atom N270, VGA, DVI, Audio, 2 LANs, 4 serial ports, 4 DIs, 4 DOs, 6 USB 2.0 ports, CF, Linux 2.6, -10 to 60°C operating temperatureV2402-T-XPE: x86 ready-to-run embedded computer with Intel Atom N270, VGA, DVI, Audio, 2 LANs, 4 serial ports, 4 DIs, 4 DOs, 6 USB 2.0 ports, CF, Windows Embedded Standard 2009, -40 to 70°C operating temperatureV2402-T-LX: x86 ready-to-run embedded computer with Intel Atom N270, VGA, DVI, Audio, 2 LANs, 4 serial ports, 4 DIs, 4 DOs, 6 USB 2.0 ports, CF,Linux 2.6, -40 to 70°C operating temperatureOptional Accessories (can be purchased separately) CBL-M68M9x8-100: 8-port RS-232 cable with VHDC connector PWR-24250-DT-S1: Power adaptorPWC-C7US-2B-183: Power cord with 2-pin connector, USA plug PWC-C7EU-2B-183: Power cord with 2-pin connector, Euro plug PWC-C7UK-2B-183: Power cord with 2-pin connector, British plug PWC-C7AU-2B-183: Power cord with 2-pin connector, Australia plug PWC-C7CN-2B-183: Power cord with 2-pin connector, China plug FK-75125-01: Hard disk installation package (for SSD)DK-DC50131-01: DIN-Rail mounting kit Package Checklist• V2401 or V2402 embedded computer • Terminal block to power jack converter • PS2 to KB/MS Y-type cable• Wall mounting kit• Documentation and software CD or DVD • Quick installation guide (printed)• Warranty card• Mapi32 Libraries• Message Queuing (MSMQ) Core• Microsoft Visual C++ Run Time Libraries• Power Management dynamic-link library• RPC• Windows API, Script Engines, and WMIWindows Embedded CE 6.0OS: Windows Embedded CE 6.0 R3File System: FAT (for on-board flash)Internet Protocol Suite: TCP, UDP, IPv4, SNMPv2, ICMP, IGMP, ARP, HTTP, CHAP, PAP, SSL, DHCP, SNTP, SMTP, Telnet, FTP, PPPWeb Server (WinCE IIS): Supports ASP, ISAPI Secure Socket Layer (SSL 2/3) and Transport Layer Security (TLS/SSL 3.1) publickey-based protocols, and Web Administration ISAPI ExtensionsDial-up Networking: Supports RAS client API and PPP, Extensible Authentication Protocol (EAP), and RAS scriptingFile Server: Enables remote clients to access files and other resources over the networkWatchdog: Features a hardware function to trigger system reset in a user specified time interval. (Moxa API provided)Application Development Software:• Moxa WinCE 6.0 SDK• Moxa API Library• C Libraries and Run-times• Component Services (COM and DCOM)• Microsoft® .NET Compact Framework 2.0• XML, including DOM, XQL, XPATH, XSLT, SAX, SAX2• SOAP Toolkit Client• Winsock 2.2。
MAX1241中文资料datasheet

MAX1240 / MAX1241 采用 8 引脚封装的低 功耗、12 位模数转换器转换器(ADC)。 MAX1240 采 用 + 2.7V 至 + 3.6V 的 电 源 供 电,MAX1241 采用单电源供电范围是+ 2.7V 至+ 5.25V。这两款设备都具有 7.5μs 的功 能 逐次逼近 ADC,快速跟踪/保持(1.5μs), 片上时钟和高速 3 线串行接口。 在 73ksps 的 最 大 采 样 速 度 下 , 功 耗 仅 为 37mW(VDD = 3V)。2μA 关断模式以较 慢的吞吐率来降低功耗。 MAX1240 具 有 内 部 2.5V 参 考 电 压 , 而 MAX1241 需要外部参考电 压。MAX1241 接受从 0V 到VREF 和参考信号输入范围包括 正电源轨。外部的时钟从 3 线接口访问数据, 它直接连接到标准微控制器的 I/O 港口。该 接口与 SPI™,QSPI™和 MICROWIRE™兼容。 该接卓越的交流特性和极低的功耗,易于使 用和小封装尺寸,使这些转换器成为远程传 感器和数据采集应用的理想之选,或者是要 求降低功耗和对空间有要求的电路的最好 选择。MAX1240/MAX1241 采用 8 引脚 PDIP 和 SO 封装。
兑换率
转换时间 跟踪/保持采集时 间 转换时间 吞吐率 光圈抖动
tCONV
t ACQ
t APR
fSCLK=2.1MHz 图8
5.5
7.5
us
1.5
us
73
ksps
30
ns
<50
ps
模拟输入
输入电压范围 输入电容
0
VREF V
16
pF
电源要求
QJZ2-2000(1140)说明书(接线箱式,带综保,带127V电源式)改详解

QJZ2-2000/1140(660)系列矿用隔爆型兼本质安全型组合开关使用说明书八达电气有限公司QJZ2-2000/1140(660)系列矿用隔爆兼本质安全型组合开关使用说明书1、概述1.1用途及适用范围QJZ2-2000/1140(660)系列矿用隔爆兼本质安全型组合开关(以下简称组合开关)适用于含有爆炸性危险气体和煤尘的矿井中,在交流50Hz、额定电压1140V(660)的线路中,对三相鼠笼型异步电动机的起动、停止进行控制和保护,并可在停止时改变相序。
1.2 型号及意义1.2.1组合开关的型号及其代号含义如下:Q J Z 2—主回路数额定电压(V)总电流(A),按用户需要组合各回路电流真空式隔爆兼本质安全型起动器1.2.2防爆形式和防爆标志防爆形式: 矿用隔爆兼本质安全型防爆标志: Exd(ib)I1.3 使用环境条件1.3.1海拔不超过2000m;1.3.2运行环境温度为-5℃~+40℃;1.3.3周围空气相对湿度不大于95%(+25℃时);1.3.4在有煤尘和爆炸性气体混合物的矿井中;1.3.5与垂直面的安装倾斜度不超过15°;11.3.6在无显著振动和冲击的地方;1.3.7在无破坏绝缘的气体和蒸汽的环境中;1.3.8无滴水的地方;1.3.9污染等级:3级;1.3.10安装类别:Ⅲ类。
1.4用途与特点1.4.1组合开关从4路直到12路组合共用一套PLC控制器和数据采集处理器,使得控制、保护、显示设置相对简单化。
1.4.2主回路的真空接触器、电流互感器、阻容保护装置及二次回路的电流变送器、中间继电器等保护元件,均装在设有滚轮的抽屉小车上,主回路和二次回路都为接插式,方便用户检修与更换。
1.4.3各主回路装设的限流熔断器FU与PLC,对各主回路短路故障进行双重保护,增加了对短路保护的可靠性。
1.4.4组合开关的电缆引入方式,可选用进出线腔压盘式连接,也可选用主回路及控制回路电缆连接器方式连接。
井间电磁成像测井技术

2021年4月14日5
P. 14
4、井间电磁成像测井技术 前期研究工作回顾
电阻率对孔隙度、饱和度变化反映灵敏
Resistivity (ohm-m)
Velocity (m/s)
100
10 5
Resistivity (ohm-m)
上Pertama层与下Pertama层蒸汽驱波及范围视图 ,高采收
率主要取决对蒸汽驱替的垂向和区域波及范围的了解
2021年4月14日5
P. 31
2021年4月14日5 Faja油田参数井的测井资料解释图
P. 32
蒸汽辅助重油泄油概念
2021年4月14日5
P. 33
5、三次大型的井间电磁成像试验
从而大大提高油藏研究的精度和有效性 • 是提高测井横向探测能力的重大突破
把测井发现油气藏和描述油气藏特性的能力,提高到 一个新的高度
2021年4月14日5
P. 6
• 由于具有重大的技术意义和实用价值, 美国能源部把井间电磁成像,特别是金 属套管井间电磁成像技术,列为“面向 21世纪的石油科技战略发展规划”的重 点技术研究项目
井间电磁成像 测井技术的应用研究
进一步 提高测井技术的 横向探测能力
2021年4月14日5
P. 2
• 精细分析“井”及其周围地层的地质特性 测井技术的固有优势
• 横向探测能力不足
测井技术的传统弱势
这两方面的特点就规定了测井技术发展的两个基
本方向
2021年4月5
P. 3
技术目标
• 井间电磁成像测井是当代地球物理应用技术发展的重 要前沿,也是一项极具挑战性的重大研究课题
- 1、下载文档前请自行甄别文档内容的完整性,平台不提供额外的编辑、内容补充、找答案等附加服务。
- 2、"仅部分预览"的文档,不可在线预览部分如存在完整性等问题,可反馈申请退款(可完整预览的文档不适用该条件!)。
- 3、如文档侵犯您的权益,请联系客服反馈,我们会尽快为您处理(人工客服工作时间:9:00-18:30)。
V REG.-Nr. A651, Z E214025Contact data
Contact configuration 1 CO or 1 NO Contact set single contact Type of interruption micro disconnection Rated current 12A 16A Rated voltage / max.switching voltage AC 240/400VAC Maximum breaking capacity AC 3000VA 4000VA Limiting making capacity, max 4 s, duty factor 10%25A Contact material AgNi 90/106AC coil > 1 x 106cycles
Rated frequency of operation with / without load 6 / 600 min -1Contact ratings Type Load Cycles
RX112A, 250VAC, DC coil, NO contact, 85°C, EN61810-11x105RX112A, 250VAC, AC coil, NO contact, 70°C, EN61810-11x105RX316A, 250VAC, NO contact, 70°C, DF 50%, EN61810-15x104RX316A, 250VAC, NO contact, 85°C, DF 10%, UL508
5x104
Coil data
Rated coil voltage range DC coil
5...110VDC AC coil
24...230VAC Coil power DC coil
520mW AC coil
typ 0,75VA
Operative range
2Coil insulation system according UL1446
class F
Coil versions,DC-coil code voltage voltage voltage resistance power
VDC VDC VDC Ohm mW
0055 3.50.550+10%5000066 4.20.668+10%529012128.4 1.2274+10%5260242416.8 2.41095+10%5260484833.6 4.84380+10%5260606042.0 6.06845+10%52611011077.011.023010+10%526All figures are given for coil without preenergization, at ambient temperature +23°C
S0271-A
Coil versions,AC-coil 50Hz
Coil Rated Operate Release Coil Rated coil code voltage voltage voltage resistance power
50Hz50Hz50Hz VAC VAC VAC Ohm VA 5242418.0 3.6350+10%0.76 61511586.317.38100+15%0.76 730230172.534.532500+15%0.74 All figures are given for coil without preenergization, at ambient temperature +23°C Insulation
rms
open contact circuit1000V rms
Clearance/creepage coil-contact circuit W8 / 8mm
Material group of insulation parts W IIIa
Tracking index of relay base PTI 250 V
Insulation to IEC 60664-1
Type of insulation coil-contact circuit reinforced
open contact circuit functional
Rated insulation voltage250 V
Pollution degree12A version33
16A version32 Rated voltage system 240V400V
Overvoltage category III
Other data
RoHS - Directive 2002/95/EC compliant as per product date code 0413 Flammability class according to UL94 V-0 1)
2
AC coil-40...+70°C
Operate- / release time DC coil typ 7 / 2ms
Bounce time DC coil, NO / NC contact typ 1 / 3ms
Vibration resistance (function) NO / NC contact20 / 4g, 10 ... 150 Hz
Shock resistance (destruction) 100 g
Category of protection RTII - flux proof
Mounting standard version (white cover)pcb or on socket transparent version pcb
Mounting distance 2,5 mm 3)
Resistance to soldering heat flux-proof version270 °C / 10 s
Relay weight14 g
Packaging unit500 pcs
1) Version with transparent cover: V-2
2) Version with transparent cover: -40...+70°C
3) Version with transparent cover: 5 mm
Accessories
For standard version (white cover), details see datasheet accessories RT
PCB layout / terminal assignment
Bottom view on solder pins
Dimensions
12A, pinning 3.5
mm
16A, pinning 5
mm
S0163-BE
S0163-BG S0163-BH S0163-BF
*)With the recommended PCB hole sizes a grid pattern from 2.5mm to 2.54mm can be used.。