我国硬质合金可转位刀片技术要求
硬质合金可转位车刀设计
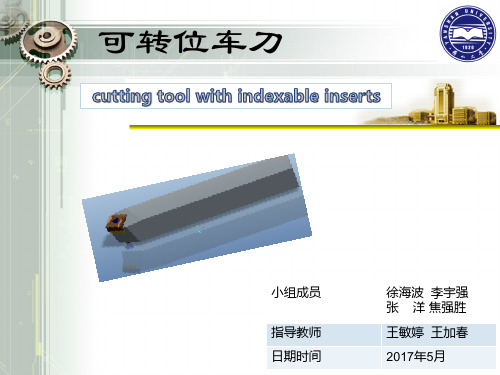
度。
可转位车刀设计
(4)刀片内切圈直径d或长度L。
Sa
asp sinkrco210选择L=12.7mm
(5)刀片厚度 根据《刀具课程设计指导书》表2-13
选择S=4.76mm
(6)刀片断削槽形式和尺寸, A型断屑槽根据《刀具课
程设计指导书》表2-45
可转位车刀设计
综上选刀片SNUM120408ER-A3,其具体尺寸为
基本尺寸 极限偏 S
孔d1
差
D=L=12.7 U±0.13 4.76± 5.16±0.08
0.13
刀尖圆弧 m 半径 0.8±0.10 2.301±0.20
车刀刀杆的截面型式有圆形截面,正方形截面和和矩形截 面。车刀刀杆截面尺寸的选取应根据机床中心高,刀夹形式 及切削截面尺寸等几方面因素。
可转位车刀设计
我们机床是选用机床为CA6140型号。
产品型号 床身回转直径 主轴中心至床身平面导轨距离 主轴中心线至刀具支承距离 刀杆截面尺寸 刀架上回转直径
CA6140A 400mm 200mm 26mm 20mm×20mm 210mm
数控加工工艺设计
1 毛坯尺寸确定 尺寸长125mm、宽25mm、高25mm
2工艺路线确定 (1)加工毛坯至截面尺寸为20*20 (2)加工主后刀面 (3)加工副后刀面 (4)铣槽
数控编程及加工
1数控程序编制 毛坯加工程序(将25*25毛坯切至20*20) 主后刀面加工程序 副后刀面加工程序 刀槽加工程序
(4)根据表2-48,钢材粗车,λs =0°~ -6°
初步选择车刀合理角度
γ0 =14° α0 = 9° kr’=10° λs =-4°
硬质合金可转位车刀设计
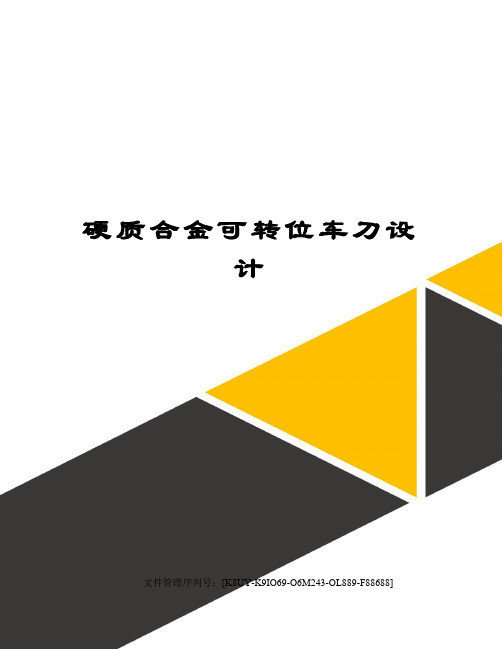
硬质合金可转位车刀设计文件管理序列号:[K8UY-K9IO69-O6M243-OL889-F88688]七、硬质合金可转位车刀设计[原始条件]加工推动架工序1中车¢50端面,工件材料HT200,铸件。
表面粗糙度要求达到Ra6.3,需采用粗车完成其端面车削,总余量为3 mm,使用机床为CA6140普通车床。
试设计一把硬质合金可转位车刀。
设计步骤为:(1)选择刀片夹固结构。
考虑到加工在CA6140普通车床上进行,且属于连续切削,由《切削手册》表4-22典型刀片夹固结构简图和特点,采用偏心式刀片夹固结构。
(2)选择刀片材料(硬质合金牌号)。
由原始条件给定:被加工工件材料为HT200,连续切削,完成粗车工序,按照硬质合金的选用原则,选取刀片材料(硬质合金牌号)为YT15。
(3)选择车刀合理角度。
根据刀具合理几何参数的选择原则,并考虑到可转位车刀几何角度的形成特点,选取如下四个主要角度:①前角γo= 15°;②后角?o= 5°;③主偏角k r = 90°;④刃倾角λs= -6°。
后角?o的实际数值以及副后角??o和副偏角k?rg在计算刀槽角度时,经校验后确定。
(4)选择切削用量。
根据切削用量的选择原则,查表确定切削用量。
粗车时:切削深度ap=3mm,进给量f=0.5mm/r,切削速度v=122m/min ;(5)选择刀片型号和尺寸:①选择刀片有无中心固定孔。
由于刀片夹具结构已选定为偏心式,因此应选用中心有固定孔的刀片。
②选择刀片形状。
按选定的主偏角k r = 90°,根据《切削手册》表4-20刀片形状的选择原则,选用正三角形刀片。
③选择刀片精度等级。
由《切削手册》表4-17刀片精度等级的选择原则,选用U级。
④选择刀片内切圆直径d(或刀片边长L)。
根据已确定的ap=3mm,k r = 90°和λs= 0°,将a p、k r和λs代入《金属切削刀具课程设计指导书》公式(2.5),可求出刀刃的实际参加工作长度Lse为L se =srpkaλcossin=︒-︒6cos90sin3=3.0mm则所选用的刀片边长L应为L>1.5 Lse=1.5×3.016=4.50mm因为是正三角形刀片,L=√3d d=2.60mm⑤选择刀片厚度s。
可转位车刀

45°可转位车刀设计一、设计背景硬质合金刀片是标准化、系列化生产的,其几何形状均事先磨出。
而车刀的前后角是靠刀片在刀杆槽中安装后得到的,刀片可以转动,当一条切削刃用钝后可以迅速转位将相邻的新刀刃换成主切削刃继续工作,直到全部刀刃用钝后才取下刀片报废回收,再换上新的刀片继续工作。
因此可转位式车刀完全避免了焊接式和机械夹固式车刀因焊接和重磨带来的缺陷,无须磨刀换刀,切削性能稳定,生产效率和质量均大大提高,是当前我国重点推广应用的刀具之一二、原始数据工件材料:40Cr Ra3.2机床:C620 CA6140v=80~120m/min,a p=0.2~8mm,f=0.5~2mm/r其他数据:c三、刀片材料的选择由给定的原始材料:被加工工件材料为40Cr,连续切削完成粗车工序,按照硬质合金选用原则,选取刀片材料(硬质合金牌号)为YT5。
四、刀片夹固结构的选择考虑到加工在CA6140普通机床上进行,且属于连续切削,参照《刀具课程设计指导书》表2.1典型刀片加固结构简图和特点,采用偏心式刀片夹固结构。
五、 刀具合理几何参数的选择根据刀具几何参数的选用原则,并考虑到可转位车刀的几何角度形成特点,选取如下四个主要角度:①前角°07.5ϒ=②后角°07.5α= ③主偏角°r 45K = ④刃倾角°5s λ=-。
后角的实际数值以及副后角和副角在计算刀槽角度时经校验后确定。
六、 切削用量的选择根据切削用量的选择原则,查表确定切削用量。
粗车时切削深度p a =3mm ,进给量f=0.5mm/r,切削速度v=80m/min.七、 刀片形状和尺寸的选择① 选择刀片有无中心固定孔。
由于刀片加固结构已选定为偏心式,因此应选用有中心固定孔的刀片。
② 选择刀片形状。
按选定主偏角45°,参照本章2.4节的表2.3刀片形状的选用原则,选用正方形刀片(这样既可以提高刀尖强度,又增加了散热面积,使刀具寿命有所提高,还可以减小已加工表面的残余面积,使表面粗糙度数值减小)。
数控刀具国家标准

国内数控机床刀具标准及选择国内数控机床刀具标准1.国家标准GB10944-89《自动换刀机床用7:24圆锥工具柄部40、45和50号圆锥柄》这个国家标准规定的柄部,在型式与尺寸上与国际标准ISO7388/1完全相同。
详见图7.3-1和7.3-1。
与ISO7388/1相比,增加了一些必要的技术要求,标注了表面粗糙度及形位公差,以保证刀柄的制造质量,满足自动加工中刀具的重复换刀精度要求。
它主要应用于镗铣类加工中心机床的各种刀柄。
2.国家标准所规定的拉钉,《自动换刀机床用7:24圆锥工具柄部40、45和50号圆锥柄用拉钉》这个国家标准所规定的拉钉,在型式与尺寸上与ISO7388/Ⅱ相同。
可与前述标准GB10944-89中所规定的柄部配合使用。
3.日本标准JIS B6339-1986《加工中心机床用工具柄部及拉钉》这个标准只适用于日本进口的加工中心机床及过去几年我国的部分机床厂与日本合作设计和生产的加工中心机床。
它是在日本机床工业协会标准MAS403-1982的基础上制订出来的,在日本得到广泛的应用。
我国1985年以后设计的加工中心机床已改用新的国家标准GB10994和GB10945。
4.国家标准GB3837-83《机床工具7:24圆锥联结》这种锥柄主要用于手动换刀数控机床及重型镗铣床等。
二.整体式工具系统标准JB/GQ5010-1983《TSG工具系统型式与尺寸》TSG工具系统中的刀柄,其代号(按1990年国家标准报批稿)由四部分(JT-45-Q32-120)组成,各部分的含义如下:JT-表示工具柄型代码。
45-对圆锥柄表示锥度规格。
Q32-表示工具的规格。
120-表示刀柄的工作长度。
它所表示的工具为:自动换刀机床用7:24圆锥工具柄(GB10944),锥柄为45号,前部为弹簧夹,最大夹持直径32mm,刀柄工作长度(锥柄大端直径φ57.15mm处到弹簧夹头前端面的距离)为120mm。
表1 工具柄部型式代号代号工具柄部型式JT 自动换刀机床用7:24圆锥工具柄 GB 10944-89BT 自动换刀机床用7:24圆锥BT型工具柄 JIS B6339ST 手动换刀机床用7:24圆锥工具柄 GB 3837.3-83MT 带扁尾莫氏圆锥工具柄 GB 1443-85MW 无扁尾莫氏圆锥工具柄 GB 1443-85ZB 直柄工具柄 GB 6131-85表2 工具的用途代号及规格参数用途代号用途规格参数表示的内容J 装直柄接杆工具装接杆也直径—刀柄工作长度Q 弹簧夹头最大夹持直径—刀柄工作长度XP 装削平型直柄工具装刀孔直径—刀柄工作长度Z 装莫氏短锥钻夹头莫氏短锥号—刀柄工作长度ZJ 装莫氏锥度钻夹头贾氏锥柄号—刀柄工作长度M 装带扁尾莫氏圆锥柄工具莫氏锥柄号—刀柄工作长度MW 装无扁尾莫氏圆锥柄工具莫氏锥柄号—刀柄工作长度MD 装短莫氏圆锥柄工具莫氏锥柄号—刀柄工作长度JF 装浮动绞刀绞刀块宽度—刀柄工作长度G 攻丝夹头最大攻丝规格—刀柄工作长度TQW 倾斜型微调镗刀最小镗孔直径—刀柄工作长TS 双刃镗刀最小镗刀直径—刀柄工作长度TZC 直角型粗镗刀最小镗孔直径—刀柄工作长度TQC 倾斜型粗镗刀最小镗孔直径—刀柄工作长度TF 复合镗刀小孔直径/大孔直径—孔工作长度TK 可调镗刀头装刀孔直径—刀柄工作长度XS 装三面刃铣刀刀具内孔直径—刀柄工作长度XL 装套式立铣刀刀具内孔直径—刀柄工作长度XMA 装A类面铣刀刀具内孔直径—刀柄工作长度XMB 装B类面铣刀刀具内孔直径—刀柄工作长度XMC 装C类面铣刀刀具内孔直径—刀柄工作长度KJ 装扩孔钻和铰刀1:30圆锥大端直径—刀柄工作长度数控刀具国家标准概述:1、可转位刀具的基本概念可转位刀具是将预先加工好并带有若干个切削刃的多边形刀片,用机械夹固的方法夹紧在刀体上的一种刀具。
《带圆孔的硬质合金可转位刀片》标准编制说明
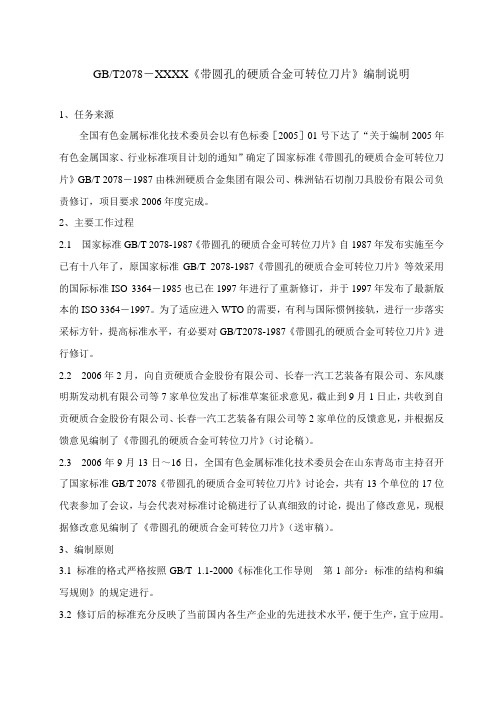
GB/T2078-XXXX《带圆孔的硬质合金可转位刀片》编制说明1、任务来源全国有色金属标准化技术委员会以有色标委[2005]01号下达了“关于编制2005年有色金属国家、行业标准项目计划的通知”确定了国家标准《带圆孔的硬质合金可转位刀片》GB/T 2078-1987由株洲硬质合金集团有限公司、株洲钻石切削刀具股份有限公司负责修订,项目要求2006年度完成。
2、主要工作过程2.1 国家标准GB/T 2078-1987《带圆孔的硬质合金可转位刀片》自1987年发布实施至今已有十八年了,原国家标准GB/T 2078-1987《带圆孔的硬质合金可转位刀片》等效采用的国际标准ISO 3364-1985也已在1997年进行了重新修订,并于1997年发布了最新版本的ISO 3364-1997。
为了适应进入WTO的需要,有利与国际惯例接轨,进行一步落实采标方针,提高标准水平,有必要对GB/T2078-1987《带圆孔的硬质合金可转位刀片》进行修订。
2.2 2006年2月,向自贡硬质合金股份有限公司、长春一汽工艺装备有限公司、东风康明斯发动机有限公司等7家单位发出了标准草案征求意见,截止到9月1日止,共收到自贡硬质合金股份有限公司、长春一汽工艺装备有限公司等2家单位的反馈意见,并根据反馈意见编制了《带圆孔的硬质合金可转位刀片》(讨论稿)。
2.3 2006年9月13日~16日,全国有色金属标准化技术委员会在山东青岛市主持召开了国家标准GB/T 2078《带圆孔的硬质合金可转位刀片》讨论会,共有13个单位的17位代表参加了会议,与会代表对标准讨论稿进行了认真细致的讨论,提出了修改意见,现根据修改意见编制了《带圆孔的硬质合金可转位刀片》(送审稿)。
3、编制原则3.1 标准的格式严格按照GB/T 1.1-2000《标准化工作导则第1部分:标准的结构和编写规则》的规定进行。
3.2 修订后的标准充分反映了当前国内各生产企业的先进技术水平,便于生产,宜于应用。
《切削刀具用可转位刀片型号表示规则》标准编制说明
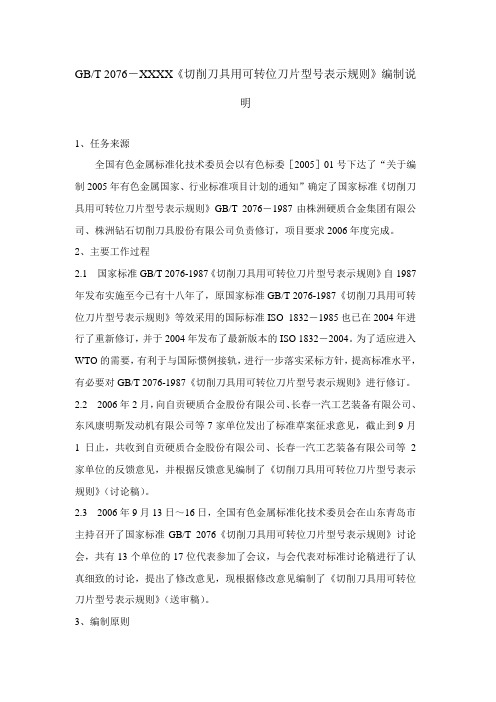
3.1标准的格式严格按照GB/T1.1-2000《标准化工作导则 第1部分:标准的结构和编写规则》的规定进行。
3.2修订后的标准充分反映了当前国内各生产企业的先进技术水平,便于生产,宜于应用。
3.3采用国际先进标准,有利于与国际先进行水平接轨,对国内生产企业及相关行业的技术进步将产生积极的推动作用。
解释:
结合b)的修改,更符合我国可转位刀片实情。
d)表5中增加了3种V型刀片的规格:12.7mm、15.875mm、19.05mm。
解释:
更符合我国可转位刀片实情。
e)表10中双倒棱刀刃的代号由“K”改为“Q”。
解释:
更符合我国可转位刀片实情。
株洲硬质合金集团有限公司、株洲钻石切削刀具股份有限公司
2006-09-21
4.6对圆形刀片的刀尖转角形状或刀尖圆角半径代号的规定由原国家标准中规定用“00”改为新国标中“MO”。
4.7在原国标基础上增加了两种刀处切削刃截面形状的代号规定。
4.8删去了表示刀片断屑槽形式和宽度的代号的规定。
5、本标准修改采用ISO 1832:2004,根据ISO 1832:2004重新起草,并纳入了ISO 1832 Technical Corrigendum 1-2005《切削刀具用可转位刀片.名称与代号.技术勘误1》。
2.32006年9月13日~16日,全国有色金属标准化技术委员会在山东青岛市主持召开了国家标准GB/T 2076《切削刀具用可转位刀片型号表示规则》讨论会,共有13个单位的17位代表参加了会议,与会代表对标准讨论稿进行了认真细致的讨论,提出了修改意见,现根据修改意见编制了《切削刀具用可转位刀片型号表示规则》(送审稿)。
4、主要修订内容
4.1适用范围增加,原国家标准仅适用于硬质合金和陶瓷可转位刀片,修订后的国家标准不仅适用于硬质合金和陶瓷可转位刀片,还适用于镶有立方氮化硼及聚晶金刚石的刀片。
硬质合金可转位刀片技术要求.

硬质合金可转位刀片技术要求1带圆孔的、无孔和沉孔硬质合金可转位刀片的技术要求⑴、刀片后面平直度,向内凹不大于0.05mm,向外凸不大于0.03mm。
⑵、刀片基面平直度,带圆孔的和无孔刀片只允许向内凹,其值不大于0.05mm;沉孔刀片只允许向内凹,其值不大于0.03mm。
⑶、刀片表面不得有对使用有害的缺陷,刃口部分不得有掉边掉角;非工作部位掉边掉角不大于0.3mm。
⑷、刀片的主要性能及组织结构应符合YB849-75《硬质合金牌号》或相关标准的规定。
⑸、刀片断面组织应均匀一致,不得有对使用有害的缺陷。
⑹、凡新开发的或引进的新材料应高于YB849-75标准,符合企业推荐值。
2硬质合金可转位铣刀片的技术要求⑴、可转位铣刀片表面粗糙度应符合下表要求:允许偏差等级前面及后面(Ra) 修光刃后面(Ra)A 0.4 0.4C 0.8 0.8K 1.6 0.8E 1.6 0.8⑵、铣刀片常用精度等级A、C、E、K的d、m和s的允差,见下表。
d d的允许偏差 m的允许偏差 s的允许偏差偏差等级偏差等级偏差等级A、C、E K A C、K E A、C、E、K6.35 ±0.025 ±0.05 ±0.005 ±0.013 ±0.025 ±0.0259.525 ±0.0512.70 ±0.0815.875 ±0.1019.05 ±0.10⑶、刀片基面平直度,只允许向内凹,A级不大于0.005mm;C级不大于0.01mm;K级和E级不大于0.02mm。
⑷、刀片表面不得有对使用有害的缺陷,刃口部分不得有掉边掉角;非工作部位掉边掉角不大于0.3mm。
⑸、刀片的主要性能及组织结构应符合YB849-75《硬质合金牌号》或相关标准的规定。
⑹、刀片断面组织应均匀一致,不得有对使用有害的缺陷。
3硬质合金可转位刀片其他共性技术要术⑴、凡进行表面化学涂层(CVD)的刀片,包括车刀片、铣刀片或其他硬质合金刀片,涂层前刀片刃口皆须进行倒圆处理,刃口圆弧半径γε≤5μm。
硬质合金刀片制造工艺与设备要点

硬质合金刀片制造工艺与设备要点首先,硬质合金片的制备是其中的关键步骤之一、硬质合金是通过将金属钴和金属碳化物(如钨碳化物)烧结得到的材料,具有高硬度和抗腐蚀性。
在制备其硬质合金片时,需要先将金属钴和金属碳化物按一定比例混合,然后通过粉末冶金工艺进行颗粒状压制,最后进行高温烧结。
接下来,刀片基体的制造也是不可忽视的一环。
传统的刀片基体通常采用高速钢或合金钢材料,而现代一些高级硬质合金刀片则采用了更先进的陶瓷基体。
对于高速钢或合金钢刀片基体的制造,通常采用锻造、精密锻造或铸造工艺。
陶瓷基体则需要通过陶瓷粉末冶金或热等静压工艺进行制造。
接下来是硬质合金片与刀片基体的焊接。
通常采用硬质合金与刀片基体预制焊料,通过高温和压力进行焊接,以保证焊接强度和连接性。
常用的焊接工艺有等离子弧焊、电子束焊、激光焊等。
焊接完毕后,还需要进行后续热处理,以减轻焊接产生的应力。
最后一道工序是对硬质合金刀片进行研磨和配置。
这一步骤将刀片进行尺寸研磨、刃部磨削和其他加工,以满足具体的加工需求。
研磨工艺和设备通常根据硬质合金刀片的具体形状、尺寸和要求进行选择,常见的研磨设备有平面磨床、外圆磨床、数控磨床等。
总的来说,硬质合金刀片的制造工艺涉及到硬质合金片制备、刀片基体制造、硬质合金片与刀片基体的焊接以及刀片的研磨和配置等多个步骤。
这些工艺需要借助不同的设备和工具,如粉末冶金设备、锻造设备、焊接设备、研磨设备等。
只有通过精细的工艺和适当的设备选择,才能制造出具有高质量和性能的硬质合金刀片,满足不同行业的需求。
刀具刃口强化技巧的最新长大[高效]
![刀具刃口强化技巧的最新长大[高效]](https://img.taocdn.com/s3/m/1c45c606cd7931b765ce0508763231126edb7702.png)
刀具刃口强化技术的最新发展一、刀具刃口强化的重要性刀具刃口强化是刀片生产中不可缺少的重要工序,可以大大提高刀具性能和使用寿命。
经普通砂轮或金刚石砂轮刃磨后的刀具刃口,存在程度不同的微观缺口(即微小崩刃与锯口)。
前者可用肉眼和普通放大镜观察到,后者用100倍(带0.010mm刻线)显微镜能够观察到,其微观缺口一般在0.01-0.05mm,严重者高达0.1mm以上。
在切削过程中刀具刃口微观缺口极易扩展,加快刀具磨损和损坏。
现代高速切削加工和自动化机床对刀具性能和稳定性提出了更高的要求,特别是涂层刀具在涂层前必须经过刀口的钝化处理,才能保证涂层的牢固性和使用寿命。
从国外引进数控机床和生产线所用刀具,其刃口已全部钝化处理。
有众多的信息表明,刀具刃口钝化可有效延长刀具寿命200%或更多,大大降低刀具成本,给用户带来巨大的经济效益。
刀具的最早钝化工具是皮子、石头等,如到理发馆刮脸,理发员在皮子上鐾刀,使刀刃更加锋利耐用。
再比如在农村,几乎每家每户都有磨刀石。
而在机械加工方面所用的刀具,我们的前辈也有很多丰富的刀刃强化经验。
比如在粗加工时,一把新刃磨好的刀具鐾刀可以减少初级磨损阶段磨损值,在正常磨损阶段后期鐾刀,仍可再延长正常磨损阶段,一般刀具寿命提高0.5倍以上。
精加工使用铰刀时,未经鐾刀其内孔表面有时达不到图纸要求,精心鐾刀后表面粗糙度可稳定Ra1.6-0.8µm,同时刀具寿命可提高1倍左右。
精刨机床导轨,采用负前角宽刃压光刀,其前后刀面必须经过平板精心研磨,提高了表面质量才能保证刃口锋利平直,导轨加工表面粗糙度可稳定达到Ra0.8µm以下。
但是传统的刃口技术存在很大安全问题,比如某厂加工大炮筒内孔来复线使用的拉槽刀,由于被加工材料韧性和强度高,刀具磨损快,甚至切屑被卡住造成事故,所以必须专门安排有经验的老工人鐾刀,才能完成这项关键性加工。
印刷机墙板精孔加工,采用浮动镗刀,有进给的走刀痕迹,经研制带有放大镜的鐾刀工具后,刃口锋利平直。
刀具标准

数控刀具国家标准一.可转位刀具刀片型号编制标准1.可转位车刀型号表示规则GB/T5343.1,它等效采用ISO5680-1989。
它适用于可转位外圆车刀、端面车刀、防形车刀及拼装复合刀具的模块刀头的型号编制。
其型号也是由按规定顺序排列的一组字母和数字代号所组成。
2.可转位带孔铣刀型号表示规则它是在ISO7406-1986的基础上制订的。
它适用于可转位面铣刀、三面刃(槽)铣刀、套式立铣刀及圆柱形铣刀型号的编制。
其型号由11个号位组成(面铣刀只有10个号位,没有第11个号位)。
前1~4号位表明刀体的特征。
波折号后边的号位表示刀片装夹方式和刀片特征。
3.可转位带柄铣刀型号表示规则它是在国际标准ISO7848-1986的基础上制订的。
它的型号也由11个号位组成。
其中有5个号位表示刀体的特征,两个号位表示柄部的特征,另外4个号位则表示刀片的装夹方法及其切削刃长度的特征。
4.可转位刀片型号表示规则GB2076-87,等效ISO1832-85,国内外硬质合金厂生产的切削用可转位刀片(包括车刀片和铣刀片)的型号都符合这个标准。
它是由给定意义的字母和数字代号,按一定顺序排列的十个号位组成。
其中第8和第9个号位分别表示切削刃截面形状和刀片切削方向,只有在需要的情况下才予标出。
二.可转位刀片标准1.GB2079-87(代替GB2079-80)无孔的硬质合金可转位刀片:此标准等采用国际标准ISO0883-1995。
标准中规定了TNUN、TNGN、TPUN、TPGN、SNUN、SNGN、SPUN、SPGN、TPUR、TPMR、SPUR、SPMR共12种类型刀片的系列尺寸。
2.GB2077-87(代替GB2077-80)硬质合金可转位刀片圆角半径:此标准等效采用国际标准ISO3286-1976。
标准规定刀尖圆角半径rε的尺寸系列为0.2、0.4、0.8、1.6、2.0、2.4、3.2mm。
3.GB2078-78(代替GB2078-80)带圆孔的硬质合金可转位刀片:此标准等效采用国际标准ISO3364-1985。
硬质合金可转位车刀设计

七、硬质合金可转位车刀设计[原始条件]加工推动架工序1中车¢50端面,工件材料HT200,铸件。
表面粗糙度要求达到Ra6.3,需采用粗车完成其端面车削,总余量为3 mm,使用机床为CA6140普通车床。
试设计一把硬质合金可转位车刀。
设计步骤为:(1)选择刀片夹固结构。
考虑到加工在CA6140普通车床上进行,且属于连续切削,由《切削手册》表4-22典型刀片夹固结构简图和特点,采用偏心式刀片夹固结构。
(2)选择刀片材料(硬质合金牌号)。
由原始条件给定:被加工工件材料为HT200,连续切削,完成粗车工序,按照硬质合金的选用原则,选取刀片材料(硬质合金牌号)为YT15。
(3)选择车刀合理角度。
根据刀具合理几何参数的选择原则,并考虑到可转位车刀几何角度的形成特点,选取如下四个主要角度:①前角γo=15°;②后角?o= 5°;③主偏角k r = 90°;④刃倾角λs= -6°。
后角?o的实际数值以及副后角??o和副偏角k?rg在计算刀槽角度时,经校验后确定。
(4)选择切削用量。
根据切削用量的选择原则,查表确定切削用量。
粗车时:切削深度a p=3mm,进给量f=0.5mm/r,切削速度v= 122m/min ;(5)选择刀片型号和尺寸:①选择刀片有无中心固定孔。
由于刀片夹具结构已选定为偏心式,因此应选用中心有固定孔的刀片。
②选择刀片形状。
按选定的主偏角k r = 90°,根据《切削手册》表4-20刀片形状的选择原则,选用正三角形刀片。
③选择刀片精度等级。
由《切削手册》表4-17刀片精度等级的选择原则,选用U级。
④选择刀片内切圆直径d(或刀片边长L)。
根据已确定的a p=3mm,k r = 90°和λs= 0°,将a p、k r和λs代入《金属切削刀具课程设计指导书》公式(2.5),可求出刀刃的实际参加工作长度L se为L se =s r pk a λcos sin =︒-︒6cos 90sin 3=3.0mm 则所选用的刀片边长L 应为L >1.5 L se =1.5×3.016=4.50mm因为是正三角形刀片,L=√3d d=2.60mm⑤选择刀片厚度s 。
可转位车刀设计说明书

目 录要求 (1)一、选择刀片夹固结构 (1)二、选择刀片结构材料 (1)三、刀具合理几何参数的选择和切削用量的选择 (1)3.1刀具合理集合参数的选择 (1)3.2切削用量的选择 (1)四、可转位车刀刀片型号和基本参数 (1)4.1选择刀片有无中心孔 (1)4.2选择刀片形状 (2)4.3选择刀片的精度等级 (2)4.4选择刀片内切圆直径d(或刀片边长L) (2)4.5选择刀片厚度 (2)4.6选择刀尖圆弧半径εr (2)4.7选择刀片断屑槽型式和尺寸 (2)五、选择硬质合金刀垫型号和尺寸 (2)六、计算刀槽角度 (3)七、计算铣制刀槽时所需的角度 (4)7.1计算刀槽最大副前角gg γ及其方位角gg τ (4)7.2计算刀槽切深剖面前角pg γ和进给剖面前角fg γ (4)八、选择刀杆材料和尺寸 (4)8.1选择刀杆材料 (4)8.2选择刀杆尺寸 (4)九、选取偏心销机器相关尺寸 (4)9.1选择偏心销材料 (4)9.2选择偏心销直径c d 和偏心量 (5)9.3计算偏心销转轴孔中心在刀槽前刀面上的位置 (5)十、绘制车刀工作图 (5)要求工件材料黄铜H62、GPa b /σ0.34、D60±0.1mm 、L180mm 、热处理状态正火处理一.选择刀片夹固结构工件的直径D 为70mm ,工件长度L=180mm 。
因此可以在普通机床CA6140上加工。
表面粗糙度要求1.6μm ,为精加工,但由于可转为车刀刃倾角s λ通常取负值,切屑流向已加工表面从而划伤工件,因此只能达到半精加工。
二.选择刀片结构材料由原始给定条件:被加工工件材料为黄铜H62,冷拔处理,选取刀片材料为YT15。
三.刀具合理几何参数的选择和切削用量的选择3.1刀具合理集合参数的选择根据《机械制造技术基础》刀具合理几何参数的选择,四个角度做如下的 择:a.前角0γ:根据《刀具课程设计指导书》图2.5,工件材料为黄铜H62(冷拔),半精车,因此前角可选0γ=15°;b.后角0∂:根据《刀具课程设计指导书》图2.5,工件材料为黄铜H62(冷拔),半精车,因此后角可选0∂=5°;c.主偏角γκ:主偏角γκ=75°;d.刃倾角s λ:为获得大于0°的后角0∂及大于0°的副刃后角'0∂,刃倾角s λ=-6°;e.后角0∂:后角0∂的实际数值及副刃后角'0∂和副偏角'γκ在计算刀槽角度时经校验确定。
可转位刀片的转位精度

可转位刀片的转位精度对于可转位硬质合金刀片来说,高精度转位通常只在中等精度加工时才需要,这听上去似乎有些矛盾。
(本文中,转位精度定义为将刀片换到一新的切削刃后测得的精度。
)产生这种矛盾的原因很简单,因为刀片之外有很多因素影响加工精度,所以精确转位对极严格公差的加工是无甚意义的。
也就是说,假如加工公差非常紧,以致每次对片转位后都必须作调整的话,则使用普通刀片更为合算。
另一方面,假如加工公差非常宽,刀片精度对其影响不大,则使用精密刀片就不值得。
只有一个例外,即把工件粗加工至下公差尺寸时(由于下面工序的需要),须采用精密刀片,以免切出尺寸过小而造成报废。
影响可转位精度的因素有许多,包括直接与刀片有关和与刀片无关的因素。
一、刀杆的磨损或损坏刀杆的问题很容易使刀片失去精度。
假如刀片槽因磨损而变大或产生任何形式的变形,则转位后的刀片位置会有较大的差别。
二、刀杆的式样不同的刀杆其主偏角也不同,这也能影响转位精度。
图1中刀杆A为90°主偏角,与刀杆D相比,转位精度易受刀片误差的影响。
当然这种差别是很小的,但与其他误差累积起来也会变得很可观。
图1三、刀槽角刀杆上的刀片槽也有其公差范围。
三角形刀片的刀槽角通常为60°-1°,而正方形刀片则为90°-1°,这个公差范围已被证明对于限制刀片的走动是最恰当的。
从对转位精度的影响来看,刀槽角小一度比大一度要好,可参见图2。
左图的刀槽角为+1°,刀片会以其后刀尖为转轴而走动,便得切削刀尖产生大于-1°刀槽角时的移动(右图)。
后者的刀片只在其后端摆动,移动只围绕靠近中心的一点进行,切削刀尖则很少转动。
当主偏角变大时(由于刀杆式样不一),因刀片槽内的转动而产生的影响也将变大。
‘ 四、热膨胀钢质刀杆和硬质含金刀片均会受热膨胀,典型牌号的平直碳化钨其线膨胀系数为2.66× 10-6in/in°F(注:1°F=0.556K )。
切削刀具用可转位刀片 型号表示规则-编制说明

国家标准《切削刀具用可转位刀片型号表示规则》编制说明(征求意见稿)一、工作简况1.1 任务来源根据国标委发【2019】11号文件任务要求,国家标准GB/T 2076—2007《切削刀具用可转位刀片型号表示规则》由株洲硬质合金集团有限公司负责起草修订,计划编号为:20190756-T-610,要求2020年度完成“三稿三审”程序,提交报批稿。
1.2 起草单位情况及主要工作过程1.2.1 起草单位情况作为主要承担单位,株洲硬质合金集团有限公司(以下简称“株硬集团”)是国家“一五”期间建设的重点工程之一,现为中国五矿旗下国有独资公司,是目前国内最大的硬质合金生产、科研、经营和出口基地,是中国钨业及硬质合金行业的龙头企业,是世界上规模最大的硬质合金企业。
公司注册资本21.23亿元,总资产56.48亿元,负债率48.8%,近6年利润合计61248万元,银行信用等级A-,职工人数6500余人,研发人员765人,目前下设5家控股子公司、7个产品专业事业部、2个生产厂。
拥有硬质合金国家重点实验室、国家级技术中心、分析测试中心、博士后科研工作站等国家级创新平台。
被国家经贸委列入300家扶优扶强企业和520家国家重点企业,被湖南省认定为“十大标志性工程”企业。
株硬集团是高新技术企业,在国家技术创新示范企业中全国排名第一,满分通过复核。
2017年11月被国家工信部公示为“硬质合金产品制造业单项冠军示范企业”。
株硬集团通过了ISO9001:2000质量认证和GB/T24001-ISO14001环境体系认证。
拥有一批专业的质量检验与管理人员。
同时,公司拥有较强的技术创新能力。
拥有国家级技术中心、分析测试中心和具有国际先进水平的研发中心,同时组织实施了钨钼、钽铌和硬质合金老系统等10多项技术改造,多项生产技术达到或接近当代世界先进水平。
技术创新投入达到销售收入的4%,新产品对销售收入的贡献率达到25%以上。
株硬集团拥有健全的营销网络。
硬质合金可转位车刀设计及数控技术三级项目报告PPT课件

将ap、kr和λs代入《金属切削刀具课程设计指导资料》公式(2-1),可求出刀刃的实际
参加工作长度Lse为
Lse =
=8.33mm
则所选用的刀片边长L应为L>1.5 Lse=1.5×8.33=12.5mm 因为是正方形刀片,L=d =12.5mm
2023/10/4
5
⑤选择刀片厚度s。根据已选定的ap=8mm、f=0.5mm/r,根据刀片厚度的诺模图求得 刀片厚度s≥6.3mm。
( 2-16 )
tanλsg = tanγog sinεrg + tanλsg cosεrg
( 2-17)
将γog = -6°、sg =-6°、εrg =εr =90.63° 代入式(2-16)、(2-17 )中,得
tanγog = - tan(-6°)cos90.63°+ tan(-6°)sin90.63°= -0.106
选择刀杆长度尺寸。参照《金属切削刀具课程设计指导 资料》第二章四、2、2节刀杆长度尺寸选择原则,选取的刀 杆长度为125mm。
2023/10/4
15
(10)选择偏心销及其相关尺寸。 ①选择偏心销材料。偏心销材料选用45号钢,热处理硬度为HRC40。 ②选择偏心销直径dc和偏心量e。偏心销直径由《金属切削刀具课程设计指导资料》 式(2-4)求出,即
所以o =5.99°,可以满足切削要求。
2023/1刀0/4槽副后角og ≈o ,故og =5.99°,取og =6°。
11
综合上述计算结果,可以归纳出: 车刀的几何角度
γo= 14°,o = 5.94° ,kr =75°,kr = 14.37° ,s= -6°,o =5.99°
刀槽的几何角度
γog= -6°,αog= 6° ,krg =75°,krg = 14.5°,sg= -6°,og =6°
硬质合金可转位车刀设计方案

螺纹成形车刀设计1.初始条件设计螺纹车刀,加工 M10 的外螺纹,加工材料为 45 钢,机夹形式为楔销(块)式,刀片有后角。
假定刀具完成粗车、半精车两道工序,所用车床为 CA6140 普通车床。
2.题目分析(1)加工外螺纹,说明在此之前已经完成直径为 10mm 的圆柱面加工;(2)所加工的普通螺纹由 GB/T 196-81 知其属于极少用的第三系列公称直径,其螺距 P=1mm,中径 d2=9.350mm,小径 d1=8.917mm。
3.刀片选择随着对螺纹车刀研究的积累,现在已经有公司生产专门针对螺纹车刀刀具的硬质合金刀片,虽然没有形成标准,但是每个公司已经有自己的生产标准。
但是选用此类刀片的话,刀槽不需要特殊设计,只需与基面平行即可。
为了体现螺纹刀具刀槽的设计,故本题选用通用刀片。
(1)选择刀片夹固结构由于已知条件知,刀片夹固结构为楔销(块)式。
(2)选择刀片材料(硬质合金牌号)由原始条件给定:被加工工件材料为 45 钢,连续切削,完成粗车、半精车两道工序。
按照硬质合金的选用原则,选取刀片材料(硬质合金牌号)为 YT15。
(3)选择车刀合理角度。
根据刀具合理几何参数你的选用原则,并考虑到可转位车刀几何角度的形成特点,选取如下五个主要要角度:①刀尖角εr=60°;②纵向前角γ0=0° (同左侧刃前角γ1=0°,右侧刃前角γ2=0°);③左侧刃后角α1=3°~5°,右侧刃后角α2=3°~5°;④刃倾角λ=0°(左右两侧刃);⑤左侧刃偏角κr=60°。
后角的实际数值,以及刃倾角,前角在计算刀槽角度时,经校验后确定。
说明:①由于螺纹车刀(此处设计的为平体车刀)可归属于成型车刀,切削普通螺纹时其刀尖角须与螺纹牙型角相等,为60°;②取前角γ0=0°是为了减少加工螺纹的理论误差,考虑到牙型精度。
硬质合金可转位刀具技术讲座:第二讲 可转位刀具切削部分的材料

硬质合金可转位刀具技术讲座:第二讲可转位刀具切削部分
的材料
张翰潮
【期刊名称】《机械工人:冷加工》
【年(卷),期】1992(000)004
【摘要】最初研制可转位刀具结构,其目的是要解决硬质合金在焊接、刃磨时带来的缺陷。
但是,当这种形式的刀具出现以后,人们发现它的性能比设想的更好,固此,可转位刀具的材材,也就不再限于硬质合金了。
刀具陶瓷、立方氮化?以及金刚石等材料,均可制成可转位刀具。
硬质合金表面涂层刀片,更需要采用可转位的刀具结构,才能充分显示出它的优越性。
目前连高速钢也被制成可转位刀片形式用于生产。
【总页数】7页(P47-53)
【作者】张翰潮
【作者单位】无
【正文语种】中文
【中图分类】TG711
【相关文献】
1.硬质合金可转位刀具技术讲座:第九讲硬质合金... [J], 张翰潮
2.硬质合金可转位刀具技术讲座:第六讲硬质合金... [J], 张翰潮
3.硬质合金可转位刀具技术讲座:第十讲自动化生产中的可转位刀具 [J], 张翰潮
4.硬质合金可转位刀具技术讲座——第七讲硬质合金可转位铣刀 [J], 张翰潮
5.硬质合金可转位刀具技术讲座第三讲硬质合金可转位刀片 [J], 张翰潮
因版权原因,仅展示原文概要,查看原文内容请购买。
数控刀具国家标准

国内数控机床刀具标准及选择国内数控机床刀具标准1.国家标准GB10944-89《自动换刀机床用7:24圆锥工具柄部40、45和50号圆锥柄》这个国家标准规定的柄部,在型式与尺寸上与国际标准ISO7388/1完全相同。
详见图7.3-1和7.3-1。
与ISO7388/1相比,增加了一些必要的技术要求,标注了表面粗糙度及形位公差,以保证刀柄的制造质量,满足自动加工中刀具的重复换刀精度要求。
它主要应用于镗铣类加工中心机床的各种刀柄。
2.国家标准所规定的拉钉,《自动换刀机床用7:24圆锥工具柄部40、45和50号圆锥柄用拉钉》这个国家标准所规定的拉钉,在型式与尺寸上与ISO7388/Ⅱ相同。
可与前述标准GB10944-89中所规定的柄部配合使用。
3.日本标准JIS B6339-1986《加工中心机床用工具柄部及拉钉》这个标准只适用于日本进口的加工中心机床及过去几年我国的部分机床厂与日本合作设计和生产的加工中心机床。
它是在日本机床工业协会标准MAS403-1982的基础上制订出来的,在日本得到广泛的应用。
我国1985年以后设计的加工中心机床已改用新的国家标准GB10994和GB10945。
4.国家标准GB3837-83《机床工具7:24圆锥联结》这种锥柄主要用于手动换刀数控机床及重型镗铣床等。
二.整体式工具系统标准JB/GQ5010-1983《TSG工具系统型式与尺寸》TSG工具系统中的刀柄,其代号(按1990年国家标准报批稿)由四部分(JT-45-Q32-120)组成,各部分的含义如下:JT-表示工具柄型代码。
45-对圆锥柄表示锥度规格。
Q32-表示工具的规格。
120-表示刀柄的工作长度。
它所表示的工具为:自动换刀机床用7:24圆锥工具柄(GB10944),锥柄为45号,前部为弹簧夹,最大夹持直径32mm,刀柄工作长度(锥柄大端直径φ57.15mm处到弹簧夹头前端面的距离)为120mm。
表1 工具柄部型式代号代号工具柄部型式JT 自动换刀机床用7:24圆锥工具柄 GB 10944-89BT 自动换刀机床用7:24圆锥BT型工具柄 JIS B6339ST 手动换刀机床用7:24圆锥工具柄 GB 3837.3-83MT 带扁尾莫氏圆锥工具柄 GB 1443-85MW 无扁尾莫氏圆锥工具柄 GB 1443-85ZB 直柄工具柄 GB 6131-85表2 工具的用途代号及规格参数用途代号用途规格参数表示的内容J 装直柄接杆工具装接杆也直径—刀柄工作长度Q 弹簧夹头最大夹持直径—刀柄工作长度XP 装削平型直柄工具装刀孔直径—刀柄工作长度Z 装莫氏短锥钻夹头莫氏短锥号—刀柄工作长度ZJ 装莫氏锥度钻夹头贾氏锥柄号—刀柄工作长度M 装带扁尾莫氏圆锥柄工具莫氏锥柄号—刀柄工作长度MW 装无扁尾莫氏圆锥柄工具莫氏锥柄号—刀柄工作长度MD 装短莫氏圆锥柄工具莫氏锥柄号—刀柄工作长度JF 装浮动绞刀绞刀块宽度—刀柄工作长度G 攻丝夹头最大攻丝规格—刀柄工作长度TQW 倾斜型微调镗刀最小镗孔直径—刀柄工作长TS 双刃镗刀最小镗刀直径—刀柄工作长度TZC 直角型粗镗刀最小镗孔直径—刀柄工作长度TQC 倾斜型粗镗刀最小镗孔直径—刀柄工作长度TF 复合镗刀小孔直径/大孔直径—孔工作长度TK 可调镗刀头装刀孔直径—刀柄工作长度XS 装三面刃铣刀刀具内孔直径—刀柄工作长度XL 装套式立铣刀刀具内孔直径—刀柄工作长度XMA 装A类面铣刀刀具内孔直径—刀柄工作长度XMB 装B类面铣刀刀具内孔直径—刀柄工作长度XMC 装C类面铣刀刀具内孔直径—刀柄工作长度KJ 装扩孔钻和铰刀1:30圆锥大端直径—刀柄工作长度数控刀具国家标准概述:1、可转位刀具的基本概念可转位刀具是将预先加工好并带有若干个切削刃的多边形刀片,用机械夹固的方法夹紧在刀体上的一种刀具。
- 1、下载文档前请自行甄别文档内容的完整性,平台不提供额外的编辑、内容补充、找答案等附加服务。
- 2、"仅部分预览"的文档,不可在线预览部分如存在完整性等问题,可反馈申请退款(可完整预览的文档不适用该条件!)。
- 3、如文档侵犯您的权益,请联系客服反馈,我们会尽快为您处理(人工客服工作时间:9:00-18:30)。
3、刀片基面平直度,只允许向内凹,A级不大于0.005mm;C级不大于0.01mm;K级和E级不大于0.02mm。
4、刀片表面不得有对使用有害的缺陷,刃口部分不得有掉边掉角;非工作部位掉边掉角不大于0.3mm。
5、刀片的主要性能及组织结构应符合YB849-75《硬质合金牌号》或相关标准的规定。
6、刀片断面组织应均匀一致,不得有对使用有害的缺陷。
3硬质合金可转位刀片其他共性技术要术
1、凡进行表面化学涂层(CVD)的刀片,包括车刀片、铣刀片或其他硬质合金刀片,涂层前刀片刃口皆须进行倒圆处理,刃口圆弧半径γε≤5μm。
2、可转位刀片未标注后角允差的,皆为允许偏差为±1°;此外,刀尖圆弧半径γε≤1.0mm,允许偏差为±0.1mm,γεr>1.0~2.0mm,允许偏差为±0.15mm。
3、可转位刀片产品,在每个刀片上应刻、蚀有可识别特征的标志,特征如:材料类别或涂层代码。