可转位车刀的设计方案
硬质合金可转位车刀设计
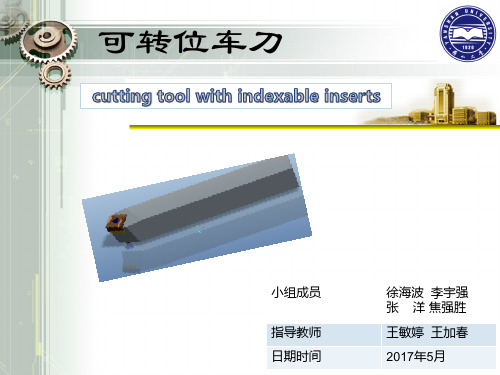
度。
可转位车刀设计
(4)刀片内切圈直径d或长度L。
Sa
asp sinkrco210选择L=12.7mm
(5)刀片厚度 根据《刀具课程设计指导书》表2-13
选择S=4.76mm
(6)刀片断削槽形式和尺寸, A型断屑槽根据《刀具课
程设计指导书》表2-45
可转位车刀设计
综上选刀片SNUM120408ER-A3,其具体尺寸为
基本尺寸 极限偏 S
孔d1
差
D=L=12.7 U±0.13 4.76± 5.16±0.08
0.13
刀尖圆弧 m 半径 0.8±0.10 2.301±0.20
车刀刀杆的截面型式有圆形截面,正方形截面和和矩形截 面。车刀刀杆截面尺寸的选取应根据机床中心高,刀夹形式 及切削截面尺寸等几方面因素。
可转位车刀设计
我们机床是选用机床为CA6140型号。
产品型号 床身回转直径 主轴中心至床身平面导轨距离 主轴中心线至刀具支承距离 刀杆截面尺寸 刀架上回转直径
CA6140A 400mm 200mm 26mm 20mm×20mm 210mm
数控加工工艺设计
1 毛坯尺寸确定 尺寸长125mm、宽25mm、高25mm
2工艺路线确定 (1)加工毛坯至截面尺寸为20*20 (2)加工主后刀面 (3)加工副后刀面 (4)铣槽
数控编程及加工
1数控程序编制 毛坯加工程序(将25*25毛坯切至20*20) 主后刀面加工程序 副后刀面加工程序 刀槽加工程序
(4)根据表2-48,钢材粗车,λs =0°~ -6°
初步选择车刀合理角度
γ0 =14° α0 = 9° kr’=10° λs =-4°
硬质合金可转位车刀设计
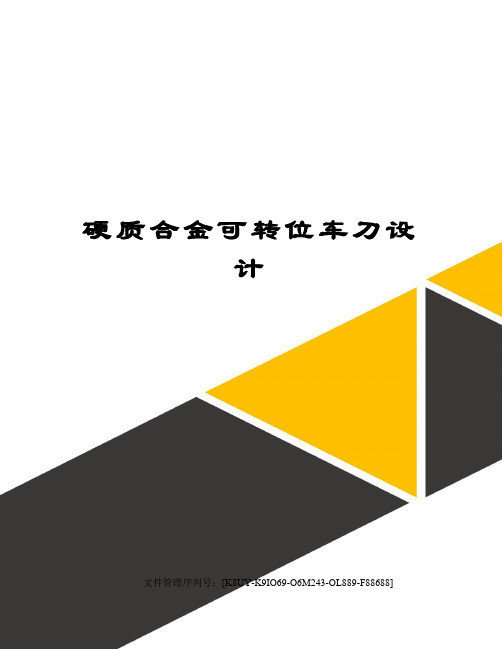
硬质合金可转位车刀设计文件管理序列号:[K8UY-K9IO69-O6M243-OL889-F88688]七、硬质合金可转位车刀设计[原始条件]加工推动架工序1中车¢50端面,工件材料HT200,铸件。
表面粗糙度要求达到Ra6.3,需采用粗车完成其端面车削,总余量为3 mm,使用机床为CA6140普通车床。
试设计一把硬质合金可转位车刀。
设计步骤为:(1)选择刀片夹固结构。
考虑到加工在CA6140普通车床上进行,且属于连续切削,由《切削手册》表4-22典型刀片夹固结构简图和特点,采用偏心式刀片夹固结构。
(2)选择刀片材料(硬质合金牌号)。
由原始条件给定:被加工工件材料为HT200,连续切削,完成粗车工序,按照硬质合金的选用原则,选取刀片材料(硬质合金牌号)为YT15。
(3)选择车刀合理角度。
根据刀具合理几何参数的选择原则,并考虑到可转位车刀几何角度的形成特点,选取如下四个主要角度:①前角γo= 15°;②后角?o= 5°;③主偏角k r = 90°;④刃倾角λs= -6°。
后角?o的实际数值以及副后角??o和副偏角k?rg在计算刀槽角度时,经校验后确定。
(4)选择切削用量。
根据切削用量的选择原则,查表确定切削用量。
粗车时:切削深度ap=3mm,进给量f=0.5mm/r,切削速度v=122m/min ;(5)选择刀片型号和尺寸:①选择刀片有无中心固定孔。
由于刀片夹具结构已选定为偏心式,因此应选用中心有固定孔的刀片。
②选择刀片形状。
按选定的主偏角k r = 90°,根据《切削手册》表4-20刀片形状的选择原则,选用正三角形刀片。
③选择刀片精度等级。
由《切削手册》表4-17刀片精度等级的选择原则,选用U级。
④选择刀片内切圆直径d(或刀片边长L)。
根据已确定的ap=3mm,k r = 90°和λs= 0°,将a p、k r和λs代入《金属切削刀具课程设计指导书》公式(2.5),可求出刀刃的实际参加工作长度Lse为L se =srpkaλcossin=︒-︒6cos90sin3=3.0mm则所选用的刀片边长L应为L>1.5 Lse=1.5×3.016=4.50mm因为是正三角形刀片,L=√3d d=2.60mm⑤选择刀片厚度s。
可转位车刀

45°可转位车刀设计一、设计背景硬质合金刀片是标准化、系列化生产的,其几何形状均事先磨出。
而车刀的前后角是靠刀片在刀杆槽中安装后得到的,刀片可以转动,当一条切削刃用钝后可以迅速转位将相邻的新刀刃换成主切削刃继续工作,直到全部刀刃用钝后才取下刀片报废回收,再换上新的刀片继续工作。
因此可转位式车刀完全避免了焊接式和机械夹固式车刀因焊接和重磨带来的缺陷,无须磨刀换刀,切削性能稳定,生产效率和质量均大大提高,是当前我国重点推广应用的刀具之一二、原始数据工件材料:40Cr Ra3.2机床:C620 CA6140v=80~120m/min,a p=0.2~8mm,f=0.5~2mm/r其他数据:c三、刀片材料的选择由给定的原始材料:被加工工件材料为40Cr,连续切削完成粗车工序,按照硬质合金选用原则,选取刀片材料(硬质合金牌号)为YT5。
四、刀片夹固结构的选择考虑到加工在CA6140普通机床上进行,且属于连续切削,参照《刀具课程设计指导书》表2.1典型刀片加固结构简图和特点,采用偏心式刀片夹固结构。
五、 刀具合理几何参数的选择根据刀具几何参数的选用原则,并考虑到可转位车刀的几何角度形成特点,选取如下四个主要角度:①前角°07.5ϒ=②后角°07.5α= ③主偏角°r 45K = ④刃倾角°5s λ=-。
后角的实际数值以及副后角和副角在计算刀槽角度时经校验后确定。
六、 切削用量的选择根据切削用量的选择原则,查表确定切削用量。
粗车时切削深度p a =3mm ,进给量f=0.5mm/r,切削速度v=80m/min.七、 刀片形状和尺寸的选择① 选择刀片有无中心固定孔。
由于刀片加固结构已选定为偏心式,因此应选用有中心固定孔的刀片。
② 选择刀片形状。
按选定主偏角45°,参照本章2.4节的表2.3刀片形状的选用原则,选用正方形刀片(这样既可以提高刀尖强度,又增加了散热面积,使刀具寿命有所提高,还可以减小已加工表面的残余面积,使表面粗糙度数值减小)。
可转位车刀的设计方案-推荐下载
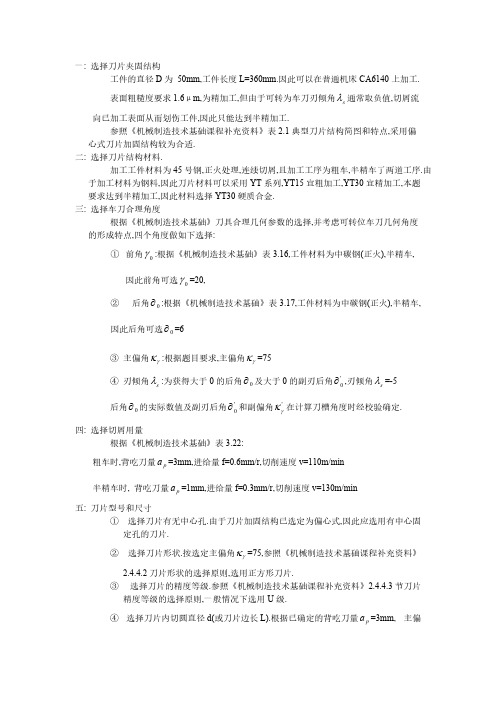
d 1 =7.6mm.材料为高速钢 YG8 七: 计算刀槽角度
可转为车刀几何角度,刀片几何角度,刀槽几何角度之间的关系: 刀槽角度的计算:
因此后角可选 0 =6
③ 主偏角 :根据题目要求,主偏角 =75
④
刃倾角
后角 0
s
:为获得大于
的实际数值及副刃后角
0
四: 选择切屑用量 根据《机械制造技术基础》表 3.22:
粗车时,背吃刀量 a p =3mm,进给量 f=0.6mm/r,切削速度 v=110m/min
的后角
一: 选择刀片夹固结构 工件的直径 D 为 50mm,工件长度 L=360mm.因此可以在普通机床 CA6140 上加工.
表面粗糙度要求 1.6μm,为精加工,但由于可转为车刀刃倾角 s 通常取负值,切屑流
向已加工表面从而划伤工件,因此只能达到半精加工. 参照《机械制造技术基础课程补充资料》表 2.1 典型刀片结构简图和特点,采用偏
切削时 r =1.2mm
⑦ 选择刀片断屑槽型式和尺寸.参照《机械制造技术基础课程补充资料》2.4.4.4 节中刀片断屑槽类型和尺寸的选择原则,根据已知的已知条件,选择 A 型断屑槽.
综上 7 方面的选择结果,根据《机械制造技术基础课程补充资料》表 2.10 确定选用 的刀片型号为 SNUM150612-A4.
接近
而刀杆后角 a og ≈a 0 =6
⑤ 刀槽副偏角
k
' rg
=k
' r
硬质合金可转位车刀设计(待修改)【可编辑】
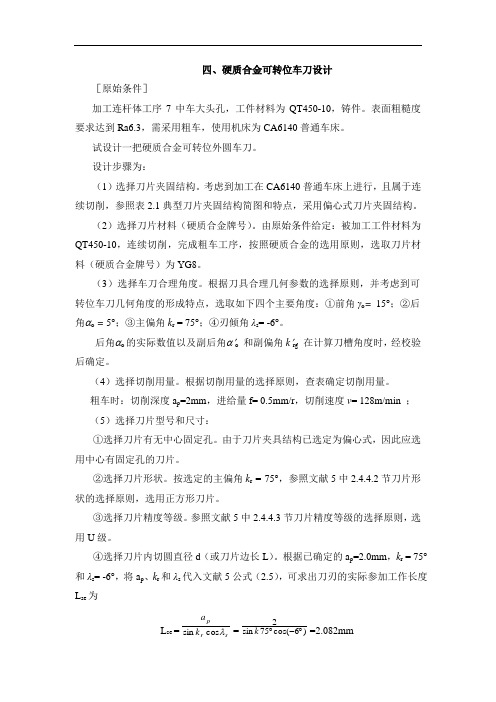
四、硬质合金可转位车刀设计[原始条件]加工连杆体工序7中车大头孔,工件材料为QT450-10,铸件。
表面粗糙度要求达到Ra6.3,需采用粗车,使用机床为CA6140普通车床。
试设计一把硬质合金可转位外圆车刀。
设计步骤为:(1)选择刀片夹固结构。
考虑到加工在CA6140普通车床上进行,且属于连续切削,参照表2.1典型刀片夹固结构简图和特点,采用偏心式刀片夹固结构。
(2)选择刀片材料(硬质合金牌号)。
由原始条件给定:被加工工件材料为QT450-10,连续切削,完成粗车工序,按照硬质合金的选用原则,选取刀片材料(硬质合金牌号)为YG8。
(3)选择车刀合理角度。
根据刀具合理几何参数的选择原则,并考虑到可转位车刀几何角度的形成特点,选取如下四个主要角度:①前角γo = 15°;②后角αo = 5°;③主偏角k r = 75°;④刃倾角λs = -6°。
后角αo 的实际数值以及副后角α'o 和副偏角k 'rg 在计算刀槽角度时,经校验后确定。
(4)选择切削用量。
根据切削用量的选择原则,查表确定切削用量。
粗车时:切削深度a p =2mm ,进给量f= 0.5mm/r ,切削速度v = 128m/min ;(5)选择刀片型号和尺寸:①选择刀片有无中心固定孔。
由于刀片夹具结构已选定为偏心式,因此应选用中心有固定孔的刀片。
②选择刀片形状。
按选定的主偏角k r = 75°,参照文献5中2.4.4.2节刀片形状的选择原则,选用正方形刀片。
③选择刀片精度等级。
参照文献5中2.4.4.3节刀片精度等级的选择原则,选用U 级。
④选择刀片内切圆直径d (或刀片边长L )。
根据已确定的a p =2.0mm ,k r = 75°和λs = -6°,将a p 、k r 和λs 代入文献5公式(2.5),可求出刀刃的实际参加工作长度L se 为L se =s r pk a λcos sin =)6cos(75sin 2︒-︒k =2.082mm则所选用的刀片边长L 应为L >1.5 L se =1.5×2.082=3.123mm因为是正方形刀片,所以 L=d >3.123mm⑤选择刀片厚度s 。
可转位车刀的设计方案

一、车刀的结构机夹可转位车刀是将可转位硬质合金刀片用机械的方法夹持在刀杆上形成的车刀,一般由刀片、刀垫、夹紧元件和刀体组成(见图1)。
图1 机夹可转位车刀组成根据夹紧结构的不同可分为以下几种形式。
·偏心式(见图2)偏心式夹紧结构利用螺钉上端的一个偏心心轴将刀片夹紧在刀杆上,该结构依靠偏心夹紧,螺钉自锁,结构简单,操作方便,但不能双边定位。
当偏心量过小时,要求刀片制造的精度高,若偏心量过大时,在切削力冲击作用下刀片易松动,因此偏心式夹紧结构适于连续平稳切削的场合。
图2 偏心式夹紧结构组成·杠杆式(见图3)杠杆式夹紧结构应用杠杆原理对刀片进行夹紧。
当旋动螺钉时,通过杠杆产生夹紧力,从而将刀片定位在刀槽侧面上,旋出螺钉时,刀片松开,半圆筒形弹簧片可保持刀垫位置不动。
该结构特点是定位精度高、夹固牢靠、受力合理、适用方便,但工艺性较差。
图3 杠杆式夹紧结构组成·楔块式(见图4)刀片内孔定位在刀片槽的销轴上,带有斜面的压块由压紧螺钉下压时,楔块一面靠紧刀杆上的凸台,另一面将刀片推往刀片中间孔的圆柱销上压紧刀片。
该结构的特点是操作简单方便,但定位精度较低,且夹紧力与切削力相反。
图4 楔块式夹紧结构不论采用何种夹紧方式,刀片在夹紧时必须满足以下条件:①刀片装夹定位要符合切削力的定位夹紧原理,即切削力的合力必须作用在刀片支承面周界内。
②刀片周边尺寸定位需满足三点定位原理。
③切削力与装夹力的合力在定位基面(刀片与刀体)上所产生的摩擦力必须大于切削振动等引起的使刀片脱离定位基面的交变力。
夹紧力的作用原理如表1所示。
可转位车刀片的形状有三角形、正方形、棱形、五边形、六边形和圆形等,是由硬质合金厂压模成形,使刀片具有供切削时选用的几何参数(不需刃磨);同时,刀片具有3个以上供转位用的切削刃,当一个切削刃磨损后,松开夹紧机构,将刀片转位到另一切削刃,即可进行切削,当所有切削刃都磨损后再取下,换上新的同类型的刀片。
可转位车刀设计样本

可转位车刀设计样本H a r b i n I n s t i t u t e o f T e c h n o l o g y设计说明书一、选择刀片夹固结构工件的直径D为142mm,工件长度L=100mm.因此可以在普通机床CA6140上加工.表面粗糙度要求 1.6μm,为精加工,但由于可转为车刀刃倾角通常取负值,切屑s流向已加工表面从而划伤工件,因此只能达到半精加工.参照《机械制造技术基础课程补充资料》表2.1典型刀片结构简图和特点,采用偏心式刀片加固结构较为合适.二、选择刀片结构材料加工工件材料为HT200,正火处理,连续切屑,且加工工序为粗车,半精车了两道工序.由于加工材料为铸铁料,因此刀片材料可以采用YG系列,YG8宜粗加工,YG3宜精加工,本题第三步要求达到半精加工,因此材料选择YG3硬质合金.三、选择车刀合理角度根据《机械制造技术基础》刀具合理几何参数的选择,并考虑可转位车刀几何角度的形成特点,四个角度做如下选择:①前角γ:根据《机械制造技术基础》表3.16,工件材料为中碳钢(正火),半精车,因此前角可选γ=10°,②后角∂:根据《机械制造技术基础》表3.17,工件材料为铸造材料,精车,因此后角可选∂=7°③主偏角κ:根据《机械制造技术基础》表γ3.16,主偏角γκ=75°④刃倾角λ:为获得大于0的后角0∂s及大于0的副刃后角'∂,刃倾角sλ=-5后角∂的实际数值及副刃后角'0∂和副偏角'κ在计算刀槽角度时经校验确定.γ四、选择切屑用量根据《机械制造技术基础》表3.22:精车时, 背吃刀量pa =1mm,进给量f=0.3mm/r,切削速度v=130m/min 。
五、刀片型号和尺寸① 选择刀片有无中心孔.由于刀片加固结构已选定为偏心式,因此应选用有中心固定孔的刀片.② 选择刀片形状.按选定主偏角γκ=75,参照《机械制造技术基础课程补充资料》2.4.4.2刀片形状的选择原则,选用正方形刀片.③ 选择刀片的精度等级.参照《机械制造技术基础课程补充资料》2.4.4.3节刀片精度等级的选择原则,一般情况下选用U 级.④ 选择刀片内切圆直径d(或刀片边长L).根据已确定的背吃刀量pa =3mm,主偏角γκ=75,刃倾角sλ=-5,将pa ,γκ,sλ代入下式可得刀刃的实际参加工作长L se为L se=scos sin λκγρ∂=cos(-5)75sin 3=3.118mm令刀片的刃口长度(即便长)L>1.5 L se=4.677mm,保证切削工作顺利进行.⑤选择刀片厚度.根据已选择的背吃刀量a=3mm,进给量f=0.6mm/r及p《机械制造技术基础课程补充资料》选择刀片厚度的诺莫图图2.3,求得刀片厚度S≥4.8mm.⑥选择刀尖圆弧半径r.根据已选择的ε背吃刀量a=3mm,进给量pf=0.6mm/r及《机械制造技术基础课程补充资料》选择刀尖圆角半径的诺莫图 2.4,求得连续切削时r=1.2mmε⑦选择刀片断屑槽型式和尺寸.参照《机械制造技术基础课程补充资料》2.4.4.4节中刀片断屑槽类型和尺寸的选择原则,根据已知的已知条件,选择A型断屑槽.综上7方面的选择结果,根据《机械制造技术基础课程补充资料》表2.10确定选用的刀片型号为SNUM150612-A4.=6.35mm;L=d=14.88mm;s=6.35mm;d1m=2.79mm; εr=1.2mm刀片刀尖角ε=90;刀片刃倾角sbλ=0;断b屑槽宽W取法前角bnγ=25n=4mm;六、选择硬质合金刀垫型号和尺寸硬质合金刀垫形状和尺寸的选择,取决于刀片加固结构及刀片的型号和尺寸,选择与刀片形状相同的刀垫,正方形,中间有圆孔.根据《机械制造技术基础课程补充资料》表2.18选择型号为S15B型刀垫.尺寸为:长度L=14.88mm,厚度s=4.76mm中心孔直径=7.6mm.材料为高速钢YG8d1七、计算刀槽角度可转为车刀几何角度,刀片几何角度,刀槽几何角度之间的关系:刀槽角度的计算:①刀杆主偏角krgk=γκ=75rg② 刀槽刃倾角sgλsgλ=sλ=-5③ 刀槽前角ogr 将0γ=20,bnγ=25, sλ=-5代入下式tanogγ=snb s bnλγγλγγcos tan tan 1cos /tan tan 0+-=-0.089则ogγ=-5.089,取ogγ=-5④ 验算车刀后角a 0.车刀后角a 0的验算公式为:tan a 0=sog nb s og nb aa λγλγcos tan tan 1)cos tan (tan +-当nba =0时,则上式成为: tan a 0=-sogλγ2cos tan将ogγ=-5, sλ=-5代入上式得a 0=5.05前面所选后角a 0=6,与验算值有差距,故车刀后角a 0应选a 0=5才能与验算角度接近 而刀杆后角a og≈a 0=5⑤ 刀槽副偏角 k 'rg=k 'r=180-γκ=rεk rg=γκ,rg ε=rε因此k 'rg=180-γκ-rε车刀刀尖角rε的计算公式为cos rε=[cos rbεs og s ogλγλλsin tan )(tan 12-+]cos s λ当rbε=90时,上式变为cos rε= -sogλγsin tancos sλ将ogγ=-5, s λ=-5代入上式得rε=90.4故k 'rg≈k 'r=180-75-90.4=14.6取k 'rg=14.6⑥ 验算车刀副后角a '0车刀副后角的验算公式为: tan a '0=''''''cos tan tan 1cos tan tan sgognbogog nb aa λγλγ+-当a nb=0时, tan a '0= -'2'cos tan sgogλγ而tan 'ogγ=osγtan sin rg ε+tan'sg λsin rg εtan 'ogλ=osγtan sin rg ε+tan'sg λsin rg ε将osλ=-5,sgλ=sλ=-5,rgε=rε=90.4代入上式tan'ogγ=tan(-5)sin90.4+tan(-5)sin90.4 =>'ogγ=-4.97 tan 'ogλ=)5tan(-sin90.4+tan (-5)sin90.4=>'og λ=-4.97再将'og γ=-4.97'og λ=-4.97代入得 tan a '0= -)97.4(cos )97.4tan(2-- =>a '0=4.93可以满足切削要求刀槽副后角a 'og≈a '0,故a 'og=4.93,取a 'og=5综上述计算结果,可以归纳出: 车刀的几何角度:γ=20,∂=6,γκ=75, k 'r=14.6,sλ=-5, a '0=4.93刀槽的几何角度:ogγ=-5 , a og=5,k rg=75 , k 'rg =14.6,sgλ=-5, a 'og=5八、计算铣制刀槽时所需的角度① 计算刀槽最大副前角ggγ及其方位角ggτ将ogγ=-5 ,sgλ=sλ=-5代入下式得:tan gg γ=-sgog λγ22tan tan + =>ggγ=-7.05将ogγ=-5 ,sgλ=sλ=-5代入下式得:tan ggτ=sgogλλtan tan => ggτ=45② 计算刀槽切深剖面前角pgγ和进给剖面前角fgγ将ogγ=-5 ,sgλ=-5, k rg =75代入下式tan pgγ=osγtan sin rgε+tan'sg λsin rg ε =>pgγ=-6.12tan fgγ=os γtan sin rgε+tan'sg λsin rg ε =>fgγ=-3.54九、选择刀杆材料和尺寸① 选择刀杆材料:为保证刀杆强度,增加刀杆使用寿命,刀杆材料一般可用中碳钢,采用45号钢,热处理硬度为HRC38-45,发黑处理② 选择刀杆尺寸:⑴选择刀杆截面尺寸.车床中心高度为220mm,根据《机械制造技术基础课程补充资料》表 2.37,选取截面尺寸为:20×25(mm 2)由于切削深度及进给量太小,故强度足够 ⑵选择刀杆长度尺寸:参照《机械制造技术基础课程补充资料》2.5.1.3刀杆长度选择原则,选取刀杆长度为160mm.十、选取偏心销机器相关尺寸① 选择偏心销材料:偏心销材料选用40Cr,热处理硬度为HRC40~45,发黑处理.② 选择偏心销直径d c和偏心量偏心销直径可用下式: d c=d 1-(0.2~0.4mm)故可取d c=6mm偏心量e 可用: e=mm d c2)10~7(1=0.3~0.428mm则e 可取0.4mm为使刀具夹固可靠,可选用自锁性能较好的螺钉偏心销,并取螺钉偏心销转轴半径d 2=M6③计算偏心销转轴孔中心在刀槽前刀面上的位置,根据前面已选好的各尺寸d 1=6mm, d=15.875mmd c=6mm, e=0.4mm取β=30,代入下式m=30sin 75.02875.15+=8.31mm n=30cos 75.02875.15-=8.59mm十一、绘制车刀结构简图偏心式75硬质合金可转位外圆车刀如下图参考文献[1] 李旦,韩荣第,巩亚东,陈明君.机械制造技术基础.哈尔滨工业大学出版社.2009.2[2] 王娜君.机械制造技术基础课程补充材料.2010.3[3] 袁长良.机械制造工艺装备设计手册.中国计量出版社;1992.1[4] 陆剑中,孙家宁.金属切削原理与刀具.机械工业出版社;2005.3。
可转位车刀几何角度的设计、加工及检测
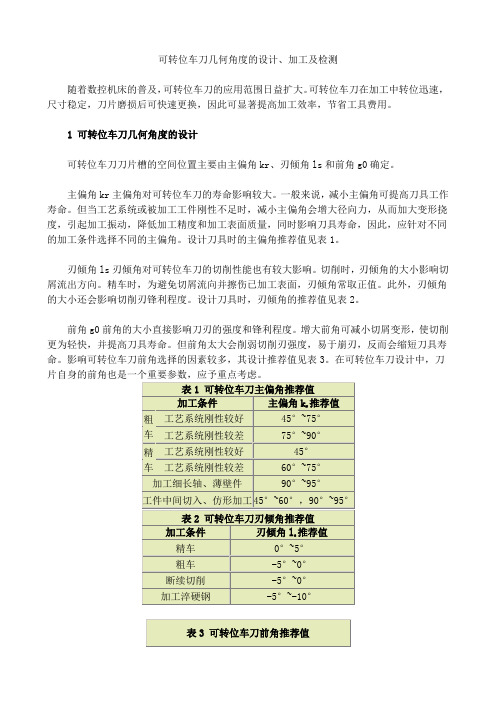
可转位车刀几何角度的设计、加工及检测随着数控机床的普及,可转位车刀的应用范围日益扩大。
可转位车刀在加工中转位迅速,尺寸稳定,刀片磨损后可快速更换,因此可显著提高加工效率,节省工具费用。
1 可转位车刀几何角度的设计可转位车刀刀片槽的空间位置主要由主偏角kr、刃倾角ls和前角g0确定。
主偏角kr主偏角对可转位车刀的寿命影响较大。
一般来说,减小主偏角可提高刀具工作寿命。
但当工艺系统或被加工工件刚性不足时,减小主偏角会增大径向力,从而加大变形挠度,引起加工振动,降低加工精度和加工表面质量,同时影响刀具寿命,因此,应针对不同的加工条件选择不同的主偏角。
设计刀具时的主偏角推荐值见表1。
刃倾角ls刃倾角对可转位车刀的切削性能也有较大影响。
切削时,刃倾角的大小影响切屑流出方向。
精车时,为避免切屑流向并擦伤已加工表面,刃倾角常取正值。
此外,刃倾角的大小还会影响切削刃锋利程度。
设计刀具时,刃倾角的推荐值见表2。
前角g0前角的大小直接影响刀刃的强度和锋利程度。
增大前角可减小切屑变形,使切削更为轻快,并提高刀具寿命。
但前角太大会削弱切削刃强度,易于崩刃,反而会缩短刀具寿命。
影响可转位车刀前角选择的因素较多,其设计推荐值见表3。
在可转位车刀设计中,刀片自身的前角也是一个重要参数,应予重点考虑。
后角后角主要用于减小切削过程中后刀面与过渡表面之间的摩擦。
设计可转位车刀时,需要对后角与前角进行综合考虑,选定刀片后角后,再根据刀片槽前角确定刀片槽后角。
可转位车刀后角的设计推荐值见表4。
造型设计及图纸标注可转位车刀切削参数的图纸标注如图1所示。
用AutoCAD2000的实体功能设计可转位车刀时,首先根据加工条件选择刀片,然后减去刀片本身的前角和后角,即可确定设计可转位车刀所需全部参数。
进行实体造型设计时,不能完全按照所需刃倾角和前角来旋转刀片,而应将其换算为法向前角,换算公式为tangn=tang0cosls (1)实体造型时刀片旋转的顺序应为:主偏角→刃倾角→法向前角。
可转位车刀的选择及设计

可转位车刀的选择及设计1.在工程应用中的优点与缺点可转位车刀就是机夹式刀具,有刀片,刀排锁紧装置组成,车削时遇刀具磨损了,只要松开锁紧转一个角度紧固就能继续使用了,比焊接式普通刀具方便,可转位车刀:价格较高,形状是标准的,如果工件有临时变化那又要重新买了,因为这不能重磨。
由于不需要磨刀所以工人上手比较快,适合于大批量高精度的数控加工。
避免了硬质合金钎焊时容易产生裂纹的缺陷;可转位刀片适合用气相沉积法在硬质合金刀片表面沉积薄层更硬的材料(碳化钛氮化钛和氧化铝),以提高切削性能;换刀时间较短;由于可转位刀片是标准化和集中生产的,刀片几何参数一致性强,切屑控制稳定。
因此可转位刀具得到广泛应用,如各种车刀、镗刀、铣刀、外表面拉刀、大直径深孔钻和套料钻等2.主要应用领域可转位式刀具取代了焊接刀具,并且,应用,显示了它的优越性。
但是,推广速度仍然比较缓慢。
当然,原因是多方面的,其中,刀杆结构与刀片的精化(重磨)问题,在部份企业不易解决,是影响推广的因素之一。
3.刀片材料,选型中注意的几类问题多数可转位刀具的刀片采用硬质合金,也有采用陶瓷、多晶立方氮化硼或多晶金刚石车外圆的刀片:选用原则主要是根据加工工艺的具体情况决定。
一般要选通用性较高的及在同一刀片上切削刃数较多刀片。
粗车时选较大尺寸,精、半精车时选较小尺寸。
S形:四个刃口,刃口较短(指同等内切圆直径),刀尖强度较高,主要用于75°、45°车刀,在内孔刀中用于加工通孔。
T形:三个刃口,刃口较长,刀尖强度低,在普通车床上使用时常采用带副偏角的刀片以提高刀尖强度。
主要用于90°车刀。
在内孔车刀中主要用于加工盲孔、台阶孔。
C形:有两种刀尖角。
100°刀尖角的两个刀尖强度高,一般做成75°车刀,用来粗车外圆、端面,80°刀尖角的两个刃口强度较高,用它不用换刀即可加工端面或圆柱面,在内孔车刀中一般用于加工台阶孔。
硬质合金可转位车刀设计(待修改)
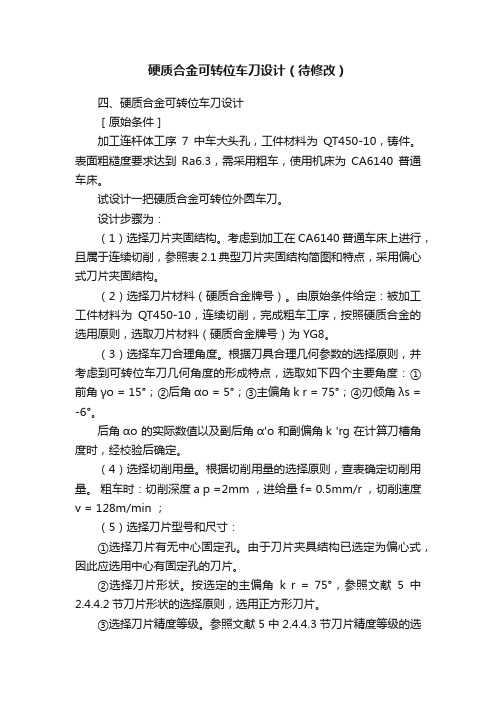
硬质合金可转位车刀设计(待修改)四、硬质合金可转位车刀设计[原始条件]加工连杆体工序7中车大头孔,工件材料为QT450-10,铸件。
表面粗糙度要求达到Ra6.3,需采用粗车,使用机床为CA6140普通车床。
试设计一把硬质合金可转位外圆车刀。
设计步骤为:(1)选择刀片夹固结构。
考虑到加工在CA6140普通车床上进行,且属于连续切削,参照表2.1典型刀片夹固结构简图和特点,采用偏心式刀片夹固结构。
(2)选择刀片材料(硬质合金牌号)。
由原始条件给定:被加工工件材料为QT450-10,连续切削,完成粗车工序,按照硬质合金的选用原则,选取刀片材料(硬质合金牌号)为YG8。
(3)选择车刀合理角度。
根据刀具合理几何参数的选择原则,并考虑到可转位车刀几何角度的形成特点,选取如下四个主要角度:①前角γo = 15°;②后角αo = 5°;③主偏角k r = 75°;④刃倾角λs = -6°。
后角αo 的实际数值以及副后角α'o 和副偏角k 'rg 在计算刀槽角度时,经校验后确定。
(4)选择切削用量。
根据切削用量的选择原则,查表确定切削用量。
粗车时:切削深度a p =2mm ,进给量f= 0.5mm/r ,切削速度v = 128m/min ;(5)选择刀片型号和尺寸:①选择刀片有无中心固定孔。
由于刀片夹具结构已选定为偏心式,因此应选用中心有固定孔的刀片。
②选择刀片形状。
按选定的主偏角k r = 75°,参照文献5中2.4.4.2节刀片形状的选择原则,选用正方形刀片。
③选择刀片精度等级。
参照文献5中2.4.4.3节刀片精度等级的选择原则,选用U 级。
④选择刀片内切圆直径d (或刀片边长L )。
根据已确定的a p =2.0mm ,k r = 75°和λs = -6°,将a p 、k r 和λs 代入文献5公式(2.5),可求出刀刃的实际参加工作长度L se 为L se =s r pk a λcos sin =)6cos(75sin 2?-?k =2.082mm则所选用的刀片边长L 应为L >1.5 L se =1.5×2.082=3.123mm因为是正方形刀片,所以 L=d >3.123mm⑤选择刀片厚度s 。
硬质合金可转位车刀设计方案

螺纹成形车刀设计1.初始条件设计螺纹车刀,加工 M10 的外螺纹,加工材料为 45 钢,机夹形式为楔销(块)式,刀片有后角。
假定刀具完成粗车、半精车两道工序,所用车床为 CA6140 普通车床。
2.题目分析(1)加工外螺纹,说明在此之前已经完成直径为 10mm 的圆柱面加工;(2)所加工的普通螺纹由 GB/T 196-81 知其属于极少用的第三系列公称直径,其螺距 P=1mm,中径 d2=9.350mm,小径 d1=8.917mm。
3.刀片选择随着对螺纹车刀研究的积累,现在已经有公司生产专门针对螺纹车刀刀具的硬质合金刀片,虽然没有形成标准,但是每个公司已经有自己的生产标准。
但是选用此类刀片的话,刀槽不需要特殊设计,只需与基面平行即可。
为了体现螺纹刀具刀槽的设计,故本题选用通用刀片。
(1)选择刀片夹固结构由于已知条件知,刀片夹固结构为楔销(块)式。
(2)选择刀片材料(硬质合金牌号)由原始条件给定:被加工工件材料为 45 钢,连续切削,完成粗车、半精车两道工序。
按照硬质合金的选用原则,选取刀片材料(硬质合金牌号)为 YT15。
(3)选择车刀合理角度。
根据刀具合理几何参数你的选用原则,并考虑到可转位车刀几何角度的形成特点,选取如下五个主要要角度:①刀尖角εr=60°;②纵向前角γ0=0° (同左侧刃前角γ1=0°,右侧刃前角γ2=0°);③左侧刃后角α1=3°~5°,右侧刃后角α2=3°~5°;④刃倾角λ=0°(左右两侧刃);⑤左侧刃偏角κr=60°。
后角的实际数值,以及刃倾角,前角在计算刀槽角度时,经校验后确定。
说明:①由于螺纹车刀(此处设计的为平体车刀)可归属于成型车刀,切削普通螺纹时其刀尖角须与螺纹牙型角相等,为60°;②取前角γ0=0°是为了减少加工螺纹的理论误差,考虑到牙型精度。
可转为车刀

已知:工件材料Y12,使用机床CA6140,加工后dm=18,Ra3.2,需粗、半精车完成,加工余量自定,设计装D刀片930偏头外圆车刀一.试设计一把硬质合金可转位外圆车刀。
设计步骤为:1 .选择刀片夹固结构考虑到加工是在CA6140 普通车床上进行,属于连续切削,参照表1 一1典型刀片夹固结构简图和特点,采用偏心式刀片夹固结构。
2 .选择刀片材料(硬质合金牌号)由原始条件给定:被加工工件材料为Y12易切削结构钢,连续切削,完成粗车、精车两道工序,按照硬质合金的选用原则,选取刀片材料(硬质合金牌号)为YT14 。
3 .选择车刀合理角度根据刀具合理几何参数的选择原则,并考虑到可转位车刀:几何角度的形成特点,选取如下四个主要角度.( l )前角=150, ( 2 )后角=50 ,( 3 )主偏角=930;( 4 )刃倾角=-50,后角0 的实际数值以及副后角和副偏角在计算刀槽角度时,经校验后确定。
4.选择切削用量根据切削用量的选择原则,查表确定切削用量为:粗车时:切削深度p a = 3mm ,进给量f=0 . 4m m /r ,切削速度v= 110m /min 精车时:ap = 0.5 mm ,f = 0. 3mm / r ,v=150m/min 。
5.选择刀片型号和尺寸: ( 1 )选择刀片有无中心固定孔由于刀片夹固结构已选定为偏心式,因此应选用有中心固定孔的刀片。
( 2 )选择刀片形状按选定的主偏角= 93° ,选用55°菱形车刀。
( 3 )选择刀片精度等级 选用U 级.( 4 )选择刀片内切圆直径d (或刀片边长L )根据已选定的p a 、κr 、λs ,可求出刀刃的实际参加工作长度seL02.3)5cos(93sin 3cos sin =︒-︒==s r p se k a L λL>1.5Lse=4.53 因为是菱形 ,L=d>4.53( 5 ) 选择刀片厚度S :根据p a ,f ,利用诺模图,得S ≥2.5 ( 6 ) 选择刀尖圆弧半径r ε:根据p a ,f ,利用诺模图,得连续切削r ε=0.4( 7 ) 选择刀片断屑槽型式和尺寸 无断屑槽确定刀片型号:DNUM150608-V2,尺寸为L=16.5,d=12.70,S=6.53,d1=5.16,m=6.477, r ε=0.8刀片参数:刀尖角εb=55°,刃倾角λn s =-5°,法后角αsn=0度°,法前角γn s =20° 6. 确定刀垫型号和尺寸硬质合金刀垫型号和尺寸的选择,取决于刀片夹固结构的需要及刀片的型号和尺寸:适合于偏心式夹固结构的需要,并与刀片型号为DNUM150608-V2 相对应的硬质合金刀垫的型号为:D15TB ,其具体尺寸为.L=14.282 ,d=11.70,S =3.18, r ε=0.4;D=8;C=1.57. 计算刀槽角度可转位车刀几何角度、刀片几何角度和刀槽几何角度之间的关系: ( 1 )刀杆主偏角︒==93r rz K K ( 2 )刀槽刃倾角︒-==5s sg λλ( 3 )刀槽前角oc γ, 刀槽底面可看作前刀面,则刀槽前刀角oc γ的计算公式为:so nb s nb og λγαλγαγcos tan tan 1)cos tan (tan tan 0+-=将o γ=15°,nb γ=20°,s λ=-5°代入式得: ︒-=074.5og γ 取og γ=-5°( 4 )验算车刀后角0α车刀后角0α的验算公式是:sog nb s og nb λγαλγααcos tan tan 1)cos tan (tan tan 0+-=将︒=0nb α,︒-=︒-=55s og λγ,代入公式得: ︒=→=96.4087.0tan 00αα 与所选后角相近,可以满足切削要求。
可转位车刀S刀片75°直头外圆车刀
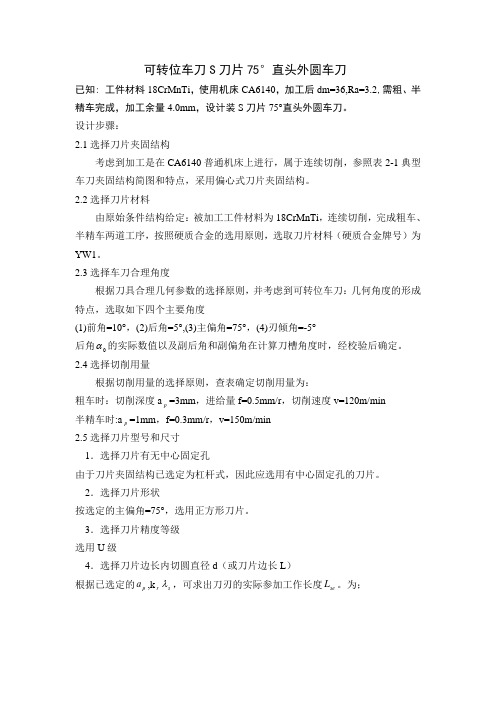
可转位车刀S 刀片75°直头外圆车刀已知: 工件材料18CrMnTi ,使用机床CA6140,加工后dm=36,Ra=3.2,需粗、半精车完成,加工余量4.0mm ,设计装S 刀片75°直头外圆车刀。
设计步骤:2.1选择刀片夹固结构考虑到加工是在CA6140普通机床上进行,属于连续切削,参照表2-1典型车刀夹固结构简图和特点,采用偏心式刀片夹固结构。
2.2选择刀片材料由原始条件结构给定:被加工工件材料为18CrMnTi ,连续切削,完成粗车、半精车两道工序,按照硬质合金的选用原则,选取刀片材料(硬质合金牌号)为YW1。
2.3选择车刀合理角度根据刀具合理几何参数的选择原则,并考虑到可转位车刀:几何角度的形成特点,选取如下四个主要角度(1)前角=10°,(2)后角=5°,(3)主偏角=75°,(4)刃倾角=-5°后角0α的实际数值以及副后角和副偏角在计算刀槽角度时,经校验后确定。
2.4选择切削用量根据切削用量的选择原则,查表确定切削用量为:粗车时:切削深度a p =3mm ,进给量f=0.5mm/r ,切削速度v=120m/min 半精车时:a p =1mm ,f=0.3mm/r ,v=150m/min 2.5选择刀片型号和尺寸 1.选择刀片有无中心固定孔由于刀片夹固结构已选定为杠杆式,因此应选用有中心固定孔的刀片。
2.选择刀片形状按选定的主偏角=75°,选用正方形刀片。
3.选择刀片精度等级 选用U 级4.选择刀片边长内切圆直径d (或刀片边长L )根据已选定的p a ,k r s λ,可求出刀刃的实际参加工作长度se L 。
为;L se =sr pk a λcos sin =)5cos(75sin 3o o -=3.123mmL>1.5L se =4.685mm因为是正方形,L=d>4.685 5.选择刀片厚度S根据a p ,f ,利用诺模图,得S ≥4.86.选择刀尖圆半径r ε:根据a p ,f, 利用诺模图,得连续切削r ε=1.2 7.选择刀片切屑槽型式和尺寸根据条件,选择A 型。
可转位车刀的选择及设计

可转位车刀的选择及设计1.在工程应用中的优点与缺点可转位车刀就是机夹式刀具,有刀片,刀排锁紧装置组成,车削时遇刀具磨损了,只要松开锁紧转一个角度紧固就能继续使用了,比焊接式普通刀具方便,可转位车刀:价格较高,形状是标准的,如果工件有临时变化那又要重新买了,因为这不能重磨。
由于不需要磨刀所以工人上手比较快,适合于大批量高精度的数控加工。
避免了硬质合金钎焊时容易产生裂纹的缺陷;可转位刀片适合用气相沉积法在硬质合金刀片表面沉积薄层更硬的材料(碳化钛氮化钛和氧化铝),以提高切削性能;换刀时间较短;由于可转位刀片是标准化和集中生产的,刀片几何参数一致性强,切屑控制稳定。
因此可转位刀具得到广泛应用,如各种车刀、镗刀、铣刀、外表面拉刀、大直径深孔钻和套料钻等2.主要应用领域可转位式刀具取代了焊接刀具,并且 ,应用 ,显示了它的优越性。
但是,推广速度仍然比较缓慢。
当然 ,原因是多方面的,其中,刀杆结构与刀片的精化(重磨)问题,在部份企业不易解决,是影响推广的因素之一。
3.刀片材料,选型中注意的几类问题多数可转位刀具的刀片采用硬质合金,也有采用陶瓷、多晶立方氮化硼或多晶金刚石车外圆的刀片:选用原则主要是根据加工工艺的具体情况决定。
一般要选通用性较高的及在同一刀片上切削刃数较多刀片。
粗车时选较大尺寸,精、半精车时选较小尺寸。
S 形:四个刃口,刃口较短(指同等内切圆直径),刀尖强度较高,主要用于75°、45°车刀,在内孔刀中用于加工通孔。
T形:三个刃口,刃口较长,刀尖强度低,在普通车床上使用时常采用带副偏角的刀片以提高刀尖强度。
主要用于90°车刀。
在内孔车刀中主要用于加工盲孔、台阶孔。
C形:有两种刀尖角。
100°刀尖角的两个刀尖强度高,一般做成75°车刀,用来粗车外圆、端面,80°刀尖角的两个刃口强度较高,用它不用换刀即可加工端面或圆柱面,在内孔车刀中一般用于加工台阶孔。
- 1、下载文档前请自行甄别文档内容的完整性,平台不提供额外的编辑、内容补充、找答案等附加服务。
- 2、"仅部分预览"的文档,不可在线预览部分如存在完整性等问题,可反馈申请退款(可完整预览的文档不适用该条件!)。
- 3、如文档侵犯您的权益,请联系客服反馈,我们会尽快为您处理(人工客服工作时间:9:00-18:30)。
一: 选择刀片夹固结构工件的直径D 为 50mm,工件长度L=360mm.因此可以在普通机床CA6140上加工.表面粗糙度要求1.6μm,为精加工,但由于可转为车刀刃倾角s λ通常取负值,切屑流向已加工表面从而划伤工件,因此只能达到半精加工.参照《机械制造技术基础课程补充资料》表2.1典型刀片结构简图和特点,采用偏心式刀片加固结构较为合适.二: 选择刀片结构材料.加工工件材料为45号钢,正火处理,连续切屑,且加工工序为粗车,半精车了两道工序.由于加工材料为钢料,因此刀片材料可以采用YT 系列,YT15宜粗加工,YT30宜精加工,本题要求达到半精加工,因此材料选择YT30硬质合金.三: 选择车刀合理角度根据《机械制造技术基础》刀具合理几何参数的选择,并考虑可转位车刀几何角度的形成特点,四个角度做如下选择:① 前角0γ:根据《机械制造技术基础》表3.16,工件材料为中碳钢(正火),半精车,因此前角可选0γ=20,② 后角0∂:根据《机械制造技术基础》表3.17,工件材料为中碳钢(正火),半精车,因此后角可选0∂=6③ 主偏角γκ:根据题目要求,主偏角γκ=75④ 刃倾角s λ:为获得大于0的后角0∂及大于0的副刃后角'0∂,刃倾角s λ=-5后角0∂的实际数值及副刃后角'0∂和副偏角'γκ在计算刀槽角度时经校验确定.四: 选择切屑用量根据《机械制造技术基础》表3.22:粗车时,背吃刀量p a =3mm,进给量f=0.6mm/r,切削速度v=110m/min半精车时, 背吃刀量p a =1mm,进给量f=0.3mm/r,切削速度v=130m/min五: 刀片型号和尺寸① 选择刀片有无中心孔.由于刀片加固结构已选定为偏心式,因此应选用有中心固定孔的刀片.② 选择刀片形状.按选定主偏角γκ=75,参照《机械制造技术基础课程补充资料》2.4.4.2刀片形状的选择原则,选用正方形刀片.③ 选择刀片的精度等级.参照《机械制造技术基础课程补充资料》2.4.4.3节刀片精度等级的选择原则,一般情况下选用U 级.④ 选择刀片内切圆直径d(或刀片边长L).根据已确定的背吃刀量p a =3mm, 主偏角γκ=75,刃倾角s λ=-5,将p a ,γκ,s λ代入下式可得刀刃的实际参加工作长L se 为L se =s cos sin λκγρ∂=cos(-5)75sin 3=3.118mm 令刀片的刃口长度(即便长)L>1.5 L se =4.677mm,保证切削工作顺利进行.⑤ 选择刀片厚度.根据已选择的背吃刀量p a =3mm,进给量f=0.6mm/r 及《机械制造技术基础课程补充资料》选择刀片厚度的诺莫图图 2.3,求得刀片厚度S ≥4.8mm.⑥ 选择刀尖圆弧半径εr .根据已选择的背吃刀量p a =3mm,进给量f=0.6mm/r 及《机械制造技术基础课程补充资料》选择刀尖圆角半径的诺莫图 2.4,求得连续切削时εr =1.2mm⑦ 选择刀片断屑槽型式和尺寸.参照《机械制造技术基础课程补充资料》2.4.4.4节中刀片断屑槽类型和尺寸的选择原则,根据已知的已知条件,选择A 型断屑槽.综上7方面的选择结果,根据《机械制造技术基础课程补充资料》表2.10确定选用的刀片型号为SNUM150612-A4.L=d=14.88mm;s=6.35mm;d 1=6.35mm;m=2.79mm; εr =1.2mm刀片刀尖角b ε=90;刀片刃倾角sb λ=0;断屑槽宽W n =4mm;取法前角bn γ=25六: 选择硬质合金刀垫型号和尺寸硬质合金刀垫形状和尺寸的选择,取决于刀片加固结构及刀片的型号和尺寸,选择与刀片形状相同的刀垫,正方形,中间有圆孔.根据《机械制造技术基础课程补充资料》表2.18选择型号为S15B 型刀垫.尺寸为:长度L=14.88mm,厚度s=4.76mm 中心孔直径d 1=7.6mm.材料为高速钢YG8七: 计算刀槽角度可转为车刀几何角度,刀片几何角度,刀槽几何角度之间的关系:刀槽角度的计算:① 刀杆主偏角rg krg k =γκ=75② 刀槽刃倾角sg λsg λ=s λ=-5③ 刀槽前角og r将0γ=20, bn γ=25, s λ=-5代入下式tan og γ=snb s bn λγγλγγcos tan tan 1cos /tan tan 00+-=-0.089 则og γ=-5.089,取og γ=-5④ 验算车刀后角a 0.车刀后角a 0的验算公式为:tan a 0=s og nb s og nb a a λγλγcos tan tan 1)cos tan (tan +-当nb a =0时,则上式成为:tan a 0=-s og λγ2cos tan将og γ=-5, s λ=-5代入上式得a 0=5.05前面所选后角a 0=6,与验算值有差距,故车刀后角a 0应选a 0=5才能与验算角度接近而刀杆后角a og ≈a 0=5⑤ 刀槽副偏角k 'rg =k 'r =180-γκ=r εk rg =γκ,rg ε=r ε因此k 'rg =180-γκ-r ε车刀刀尖角r ε的计算公式为cos r ε=[cos rb εs og s og λγλλsin tan )(tan 12-+]cos s λ当rb ε=90时,上式变为cos r ε= -s og λγsin tan cos s λ将og γ=-5, s λ=-5代入上式得r ε=90.4故k 'rg ≈k 'r =180-75-90.4=14.6取k 'rg =14.6⑥ 验算车刀副后角a '0车刀副后角的验算公式为:tan a '0=''''''cos tan tan 1cos tan tan sg og nb ogog nb a a λγλγ+- 当a nb =0时, tan a '0= -'2'cos tan sg og λγ而tan 'og γ=os γtan sin rg ε+tan 'sg λsin rg εtan 'og λ=os γtan sin rg ε+tan 'sg λsin rg ε将os λ=-5, sg λ=s λ=-5,rg ε=r ε=90.4代入上式tan 'og γ=tan(-5)sin90.4+tan (-5)sin90.4 =>'og γ=-4.97 tan 'og λ=)5tan(-sin90.4+tan (-5)sin90.4 =>'og λ=-4.97 再将'og γ=-4.97 'og λ=-4.97代入得tan a '0= -)97.4(cos )97.4tan(2-- => a '0=4.93可以满足切削要求刀槽副后角a 'og ≈a '0,故a 'og =4.93,取a 'og =5综上述计算结果,可以归纳出:车刀的几何角度: 0γ=20, 0∂=6, γκ=75, k 'r =14.6,s λ=-5, a '0=4.93 刀槽的几何角度: og γ=-5 , a og =5, k rg =75 , k 'rg =14.6, sg λ=-5, a 'og =5八: 计算铣制刀槽时所需的角度① 计算刀槽最大副前角gg γ及其方位角gg τ将og γ=-5 , sg λ=s λ=-5代入下式得:tan gg γ=-sg og λγ22tan tan + => gg γ=-7.05将og γ=-5 , sg λ=s λ=-5代入下式得:tan gg τ=sg ogλλtan tan => gg τ=45② 计算刀槽切深剖面前角pg γ和进给剖面前角fgγ将og γ=-5 , sg λ=-5, k rg =75代入下式tan pg γ=os γtan sin rg ε+tan'sg λsin rg ε => pg γ=-6.12 tan fg γ=os γtan sin rg ε+tan'sg λsin rg ε => fg γ=-3.54 九: 选择刀杆材料和尺寸① 选择刀杆材料:为保证刀杆强度,增加刀杆使用寿命,刀杆材料一般可用中碳钢,采用45号钢,热处理硬度为HRC38-45,发黑处理② 选择刀杆尺寸:⑴选择刀杆截面尺寸.车床中心高度为220mm,根据《机械制造技术基础课程补充资料》表2.37,选取截面尺寸为:20×25(mm 2)由于切削深度及进给量太小,故强度足够⑵选择刀杆长度尺寸:参照《机械制造技术基础课程补充资料》2.5.1.3刀杆长度选择原则,选取刀杆长度为160mm.十: 选取偏心销机器相关尺寸.① 选择偏心销材料:偏心销材料选用40Cr,热处理硬度为HRC40~45,发黑处理.② 选择偏心销直径d c 和偏心量偏心销直径可用下式: d c =d 1-(0.2~0.4mm)故可取d c =6mm偏心量e 可用: e=mm d c 2)10~7(1=0.3~0.428mm 则e 可取0.4mm为使刀具夹固可靠,可选用自锁性能较好的螺钉偏心销,并取螺钉偏心销转轴半径d 2=M6③计算偏心销转轴孔中心在刀槽前刀面上的位置,根据前面已选好的各尺寸d 1=6mm, d=15.875mmd c =6mm, e=0.4mm取β=30,代入下式m=30sin 75.02875.15+=8.31mm n=30cos 75.02875.15-=8.59mm 十一: 绘制车刀工作图偏心式75硬质合金可转位外圆车刀如下图。