旋转机械不对中故障特征提取及诊断方法研究
旋转机械的状态监测及故障诊断

同步振动:工作频率=激振频率。 强迫振动:对线性系统,在周期激振下的稳态响应 一般采用滚动轴承
2)系统分类——以临界转速分类
⑵ 柔性转子系统--工作转速在一阶临界转速以上的 系统
判别依据:一般工作频率>100Hz的机械系统属于柔性转 子系统。
1 旋转机械的状态特征参数与测试
4)旋转机械的转速检测
齿式轮盘测速 转速测量一般是在轴的测量圆周上设置多个凹槽
或凸键标己或者在轴上安装一个齿轮盘使每转产生多 个脉冲。
1 旋转机械的状态特征参数与测试
5)轴向位移检测
测量转子的轴 向位移时,测量面 应该与轴是一个整 体,这个测量面以 探头中心线为中心。
1 旋转机械的状态特征参数与测试
6)轴心轨迹测试
轴心轨迹非常直观地显示了转子在轴承中的旋转 和振动情况,是故障诊断中常用的非常重要的特征信 息。
1 旋转机械的状态特征参数与测试
正向进动(轴转向与轴心轨迹 转向一致)----例如:转子不 平衡、不对中、油膜失稳产生 的亚同步涡动、内摩擦激发的 涡动等均为正向进动。绝大多 数为正向进动。
振动特点:振动频率(自激振动)<工作频率,并与一阶 横向自振频率有关。
自激振动:振动过程中,由于系统内部不断有能量输入而 产生的共振现象,在设备诊断中又称为亚同步振动。
一般采用滑动轴承。
两种系统振动特点比较
激振原因
频率与工作 频率的关系
强迫振动(刚性系统)
由于外部激振力 或激振位移引起的
振动频率与工作频率同步
1 旋转机械的状态特征参数与测试
3)旋转机械振动相位检测
旋转机械常见故障诊断分析案例

第5章旋转机械常见故障诊断分析案例积累典型设备诊断案例在设备监测诊断工作中具有重要作用。
首先它为设备诊断理论提供支撑。
常见的设备故障有成熟的理论基础,一个成功的案例通常是诊断理论在现场正确应用和诊断人员长期实践的结果。
典型诊断案例具有强大的说服力,一次成功而关键的诊断足可以改变某些人根深蒂固的传统观念,对现场推广设备诊断技术具有重要意义。
其次它为理论研究提供素材。
在医学上,由典型的特例研究发现病理或重大理论的案例很多。
设备故障的情形多种多样,现场疑难杂症还比较多,有许多故障很难用现有理论解释,只能作为诊断经验看待,这种经验有没有通用参考价值,需要在理论上进行说明。
另外,有许多案例无法在试验室模拟,而它们在不同的现场又常常出现,因此典型案例为同行提供了宝贵经验和经过证实的分析方法。
诊断人员可以参考相似案例的解决方案解决新的问题,提供快速的决策维护支持,并为基于案例的推理方法提供数据基础。
典型案例分析的重要性还表现在它是监测诊断人员快速成长的捷径。
目前实用的振动诊断方法、技术和诊断仪器已经相当完善,而许多企业在诊断技术推广应用方面存在困难除了思想观念方面的原因外,更主要的原因是缺乏专业人才。
研究案例的一般做法是,从新安装设备或刚检修好的设备开始,可以选择重点或典型设备进行监测,根据不同设备制定不同的监测方案和监控参数,定期测试设备的振动,包括各种幅值、振动波形和频谱等。
如果设备出现劣化迹象或异常,要缩短监测周期,倍加留心振动波形和频谱的变化,注意新出现的谱线及其幅值的变化,在检修之前做出故障原因的判断。
设备检修时要到现场,了解第一手资料,全程跟踪设备拆检情况,掌握设备参数(如轴承型号,必要时测量有关尺寸、齿轮齿数、叶片数、密封结构、联轴器和滑动轴承形式等),做好检修记录(有时需要拍照记录),比较自己的判断对在哪里,错在哪里,进行完善的技术总结。
几个过程下来,水平自然有很大提高。
总之,添置几件诊断仪器是很容易的事,诊断成果和效益的产生不是一朝一夕的事,需要柞大量艰苦、细致的工作,长期积累设备的状态数据,对此应有应清醒地认识。
5 旋转机械常见故障特征
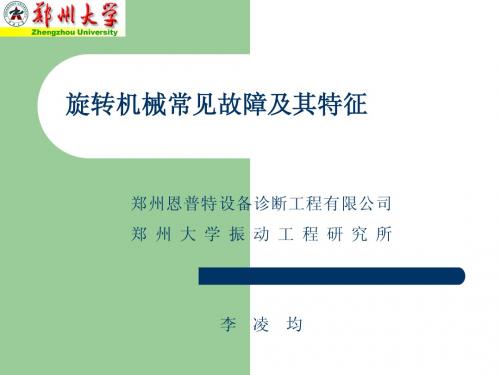
特征频 常伴 振动稳 振动 相位 轴心 时域 率 频率 定性 方向 特征 轨迹 波形 1× 简谐 稳定 径向 稳定 椭圆 波形
转子不平衡振动敏感参数
1 振动 随转 速变 化 明显 2 振动 随负 荷变 化 不明 显 3 振动 随油 温变 化 不变 4 振动 随流 量变 化 不变 5 振动 随压 力变 化 不变 6 其它 识别 方法 低速 时趋 于零
转子不平衡产生的原因
转子不平衡产生的原因
转子不平衡类型
力不平衡
力偶不平衡
转子不平衡类型
动不平衡
悬臂转子不平衡
转子不平衡动力学特性
x = Acos(Ωt +θ )
me λ2 A= • M (1− λ2 )2 + 4ζ 2 λ2
2ζλ tanθ = 1− λ2
转子不平衡振动特征
1 2 3 4 5 6 7
转子不对中故障形式
轴线平行不对中
角度不对中
综合不对中
转子不对中故障轴心轨迹
∆α
∆y Z
∆α / 2
Z
∆L
(b)
Z
∆y
∆L
(a)
∆L
(c)
轴线平行不对中
角度不对中
综合不对中
转子不对中故障特征
1)齿式联轴器不对中故障的特征频率为轴转 角频率的2 角频率的2倍。 由不对中故障产生的对转子的激振力幅, 2)由不对中故障产生的对转子的激振力幅, 随转速的升高而加大,因此, 随转速的升高而加大,因此,高速旋转机 械应更加注重转子的对中要求。 械应更加注重转子的对中要求。 激励力幅与不对中量成正比, 3)激励力幅与不对中量成正比,随不对中量 的增加,激励力幅呈线性加大。 的增加,激励力幅呈线性加大。
旋转机械故障基本机理与诊断技术

图 陀螺力矩的影响
这一力矩与成正比,相当于弹性力矩。在正进动 (0< </2)的情况下,它使转轴的变形减小, 因而提高了转轴的弹性刚度,即提高了转子的临界 角速度。在反进动( /2 < <)的情况下, 这力矩使转轴的变形增大,从而降低了转轴的刚度, 即降低了转子的临界角速度。故陀螺力矩对转于临 界转速的影响是正进动时,它提高了临界转速;反 进动时,它降低了临界转速。
量信息的基础上,基于机器的故障机理,从中提取 故障特征,进行周密的分析。例如,对于汽轮机、 压缩机等流体旋转机械的异常振动和噪声,其振动 信号从幅值域、频率域和时间域为诊断机器故障提 供了重要的信息,然而它只是机器故障信息的一部 分;而流体机械的负荷变化,以及介质的温度、压 力和流量等,对机器的运行状态有重要的影响,往 往是造成机器发生异常振动和运行失稳的重要因素。
(c)当= n时,A,是共振情况,实际上由于 存在阻尼,振幅A不是无穷大而是较大的有限值, 转轴的振动仍然非常剧烈,以致有可能断裂。 n 称为转轴的“临界角速度”;与其对应的每分钟的 转数则称为“临界转速”,以nc表示 ,即
因
故
研究不平衡响应时如果考虑外阻力的作用, 则复变量式变为
其特解为
Z=|A |ej(t+)
一、概述
旋转机械的种类繁多,有发电机、汽轮机、 离心式压缩机、水泵、通风机以及电动机等,这 类机械的主要功能都是由旋转动作完成的,统称 为机器。旋转机械故障是指机器的功能失常,即 其动态性能劣化,不符合技术要求。例如,机器 运行失稳,机器发生异常振动和噪声,机器的工 作转速、输出功率发生变化,以及介质的温度、 压力、流量异常等。机器发生故障的原因不同, 所产生的信息也不一样,根据机器特有的信息, 可以对机器故障进行诊断。但是,机器发生故障 的原因往往不是单一的因素,特别是对于机械系 统中的旋转机械故障,往往是多种故障因素的耦 合结果,所以对旋转机械进行故障诊断,必须进 行全面的综合分析研究。
《2024年旋转机械故障诊断与预测方法及其应用研究》范文
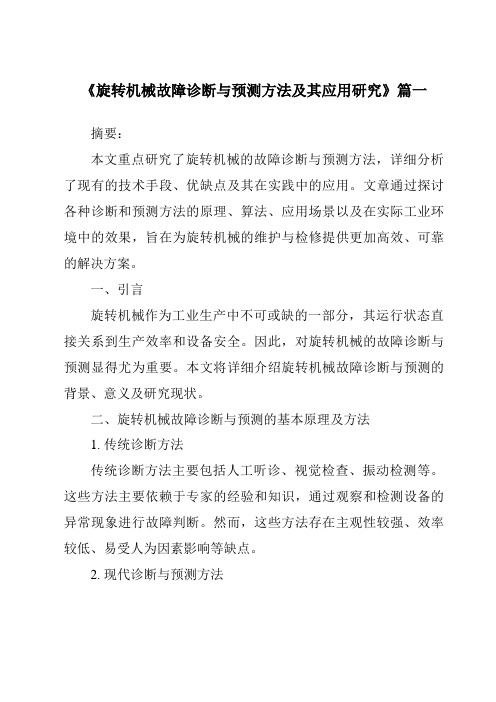
《旋转机械故障诊断与预测方法及其应用研究》篇一摘要:本文重点研究了旋转机械的故障诊断与预测方法,详细分析了现有的技术手段、优缺点及其在实践中的应用。
文章通过探讨各种诊断和预测方法的原理、算法、应用场景以及在实际工业环境中的效果,旨在为旋转机械的维护与检修提供更加高效、可靠的解决方案。
一、引言旋转机械作为工业生产中不可或缺的一部分,其运行状态直接关系到生产效率和设备安全。
因此,对旋转机械的故障诊断与预测显得尤为重要。
本文将详细介绍旋转机械故障诊断与预测的背景、意义及研究现状。
二、旋转机械故障诊断与预测的基本原理及方法1. 传统诊断方法传统诊断方法主要包括人工听诊、视觉检查、振动检测等。
这些方法主要依赖于专家的经验和知识,通过观察和检测设备的异常现象进行故障判断。
然而,这些方法存在主观性较强、效率较低、易受人为因素影响等缺点。
2. 现代诊断与预测方法(1)基于信号处理的诊断方法:通过采集设备的振动、声音等信号,利用信号处理技术对信号进行分析和处理,提取出故障特征,从而判断设备的运行状态。
(2)基于人工智能的诊断与预测方法:包括神经网络、支持向量机、深度学习等。
这些方法能够通过对大量数据进行学习和分析,建立设备的故障模型和预测模型,实现设备的智能诊断和预测。
三、各种诊断与预测方法的优缺点分析1. 传统诊断方法的优点在于简单易行,对于经验丰富的专家来说,能够快速定位故障。
然而,其缺点也较为明显,如主观性较强、效率较低、易受人为因素影响等。
2. 现代诊断与预测方法的优点在于能够处理大量数据,提高诊断和预测的准确性,同时减少人为因素的干扰。
然而,这些方法也存在计算复杂、对数据质量要求较高等问题。
四、旋转机械故障诊断与预测方法的应用研究1. 在制造业的应用:通过采用智能诊断和预测技术,实现对生产线上旋转机械设备的实时监测和故障预警,提高生产效率和设备运行安全性。
2. 在能源领域的应用:在风力发电、水力发电等能源领域,通过采用振动检测和信号处理技术,实现对风力发电机组、水轮机等设备的故障诊断和预测,保障能源供应的稳定性和安全性。
大型旋转机械不对中故障研究及分析
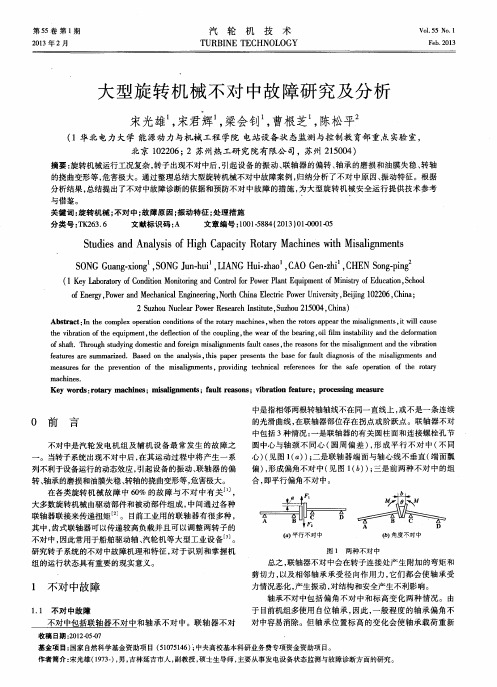
S t u d i e s a n d A n a l y s i s o f H i g h C a p a c i t y R o t a r y Ma c h i n e S w i t h Mi s a l i g n me n t s
第5 5卷 第 1 期
2 0 1 3年 2月
汽
轮
机
技
术
V0 1 . 5 5 No . 1 F e b . 2 01 3
TURBI NE TECHN0L 0GY
大型旋转机械不对 中故 障研究及 分析
宋光雄 , 宋君辉 , 梁会钊 , 曹根 芝 , 陈松平
( 1华北 电力大学 能源动力与机械工程 学院 电站设备状态监测与控制教育部重点实验 室, 北京 1 0 2 2 0 6 ; 2苏州热 工研 究 院有 限公 司 ,苏 州 2 1 5 0 0 4 )
( 1 K e y L a b o r a t o r y o f C o n d i t i o n M o n i t o i r n g a n d C o n t r o l f o r P o w e r P l a n t E q u i p m e n t o f M i n i s t y r o f E d u c a t i o n , S c h o o l
S O N G G u a n g . x i o n g , S O N G J u n — h u i , L I A N G Hu i — z h a o , C A O G e n - z h i , C H E N S o n g - p i n g
基于振动信号分析的旋转机械故障诊断方法研究

VS
故障诊断结果
根据实验结果,可以发现不同故障类型对 应的振动信号特征各不相同。例如,轴承 故障时在频域上会出现以转速频率为基频 的振动分量,而轴不平衡故障时则会出现 以二倍转速频率为基频的振动分量。通过 对比分析,可以准确地对旋转机械的故障 类型进行诊断。
05
基于振动信号分析的旋转机械故障诊断方
深入研究不同故障类型和程度下振动信号的特征 ,提高故障诊断的准确性和可靠性。
研究多传感器融合技术,实现对旋转机械全方位 、多角度的监测和诊断。
结合深度学习、机器学习等先进技术,建立更加 智能、自适应的故障诊断模型。
将基于振动信号分析的故障诊断方法应用于工业 现场,验证其在实际生产中的可行性和效果。
THANK YOU.
的准确性和稳定性。 • 故障特征提取难度高:振动信号复杂多变,需要专业的知识和经验才能准确提取故障特征,对诊断人员的
技能要求较高。 • 故障诊断自动化程度低:目前基于振动信号分析的故障诊断方法主要依赖人工经验进行故障识别和判断,
自动化程度较低。
基于振动信号分析的旋转机械故障诊断方法改进方向
加强信号处理和特征提取技术的研究
02
研究现状和发展趋势
研究现状
振动信号采集与分析
基于振动信号分析的故障诊断方法,首先要对设备进行振动信号的采集,然后通过频谱分 析、时域分析等技术手段对信号进行分析。
特征提取与模式识别
通过对振动信号的分析,提取设备的特征,并利用这些特征进行模式识别,以判断设备是 否出现故障。
故障诊断算法
基于振动信号分析的故障诊断方法需要借助各种算法,如支持向量机(SVM)、神经网络 等,以实现对设备故障的准确诊断。
法优缺点及改进方向
基于振动信号分析的旋转机械故障诊断方法优缺点
《2024年旋转机械故障诊断与预测方法及其应用研究》范文

《旋转机械故障诊断与预测方法及其应用研究》篇一一、引言旋转机械作为工业生产中不可或缺的重要设备,其稳定运行对生产效率和产品质量具有重大影响。
然而,由于操作环境复杂、维护不当或设备老化等因素,旋转机械常会出现各种故障。
这些故障如不及时发现和处理,可能会对生产造成巨大损失。
因此,对旋转机械的故障诊断与预测显得尤为重要。
本文将重点研究旋转机械的故障诊断与预测方法,以及其在工程实践中的应用。
二、旋转机械故障诊断与预测方法(一)基于信号处理的诊断与预测方法1. 信号采集:通过传感器技术,实时采集旋转机械的振动、声音、温度等信号。
2. 信号处理:利用信号处理技术,如频谱分析、小波变换等,对采集的信号进行预处理和特征提取。
3. 故障诊断与预测:根据处理后的信号特征,结合专家系统或模式识别技术,实现故障的诊断与预测。
(二)基于机器学习的诊断与预测方法1. 数据预处理:对历史故障数据进行清洗、标注和整理,构建故障数据集。
2. 模型训练:采用机器学习算法,如支持向量机、神经网络等,对故障数据集进行训练,建立故障诊断与预测模型。
3. 模型应用:将训练好的模型应用于实际场景中,实现旋转机械的故障诊断与预测。
(三)基于深度学习的诊断与预测方法深度学习通过模拟人脑神经网络的工作方式,可以自动提取数据的深层特征。
在旋转机械的故障诊断与预测中,深度学习模型可以更好地处理复杂、非线性的故障数据。
常见的深度学习模型包括卷积神经网络、循环神经网络等。
三、旋转机械故障诊断与预测方法的应用研究(一)在设备维护中的应用通过实时监测和诊断旋转机械的故障,可以及时发现潜在的问题并采取相应的维护措施,从而避免设备停机或损坏。
这不仅可以提高设备的运行效率,还可以延长设备的使用寿命。
(二)在生产管理中的应用通过对旋转机械的故障进行预测和预警,可以提前制定生产计划和调整生产安排,避免因设备故障而导致的生产延误和资源浪费。
这有助于提高生产效率和产品质量。
基于深度学习的旋转机械故障诊断方法研究共3篇

基于深度学习的旋转机械故障诊断方法研究共3篇基于深度学习的旋转机械故障诊断方法研究1近年来,随着工业化进程的不断加速,机械设备的运转质量直接影响到企业的生产效率和质量。
然而,机械设备在长时间运转中,由于材料的疲劳、外界干扰等因素作用下,容易出现故障。
因此,研究机械设备故障诊断方法显得尤为重要。
随着人工智能技术的不断发展,深度学习作为其中的一种重要方法,已经被广泛应用于机械故障诊断中。
本文基于深度学习的旋转机械故障诊断方法进行研究。
首先,本文对旋转机械的工作过程和常见的故障模式进行了介绍。
旋转机械是指在运转过程中,产生旋转运动的机械装置。
其主要工作原理是将动力源输入到旋转轴上,通过传递动能到旋转的零部件上,从而实现机械的工作。
旋转机械常见的故障模式包括轴承故障、齿轮故障、不平衡、间隙、磨损等。
接着,本文详细阐述了深度学习在旋转机械故障诊断中的应用。
深度学习是一种基于神经网络的机器学习技术,其主要优势在于能够处理高维度和非线性的大规模数据,适用于机械故障数据的分析和识别。
深度学习在机械故障诊断中的主要流程包括特征提取、模型训练和故障分类。
其中,特征提取是指对机械故障数据进行处理,提取出对诊断故障有重要意义的特征。
模型训练是指将提取出的特征输入到深度学习模型中进行训练,从而得到具有较高分类能力的模型。
故障分类是指将待诊断的故障数据输入到训练好的深度学习模型中,通过模型进行分类识别。
最后,本文在实验室的旋转机械故障诊断数据集上进行了实验。
通过比较不同深度学习模型的性能,并结合实验结果,得出了基于深度学习的旋转机械故障诊断方法的优点和局限性。
优点在于深度学习能够自动学习特征,对机械故障数据进行高效处理,具有高准确率和快速性。
局限性在于需要大量的样本数据进行训练,且对于小样本数据处理能力较弱。
综上所述,本文基于深度学习的旋转机械故障诊断方法研究,对旋转机械的工作原理和常见故障进行了介绍,详细阐述了深度学习在旋转机械故障诊断中的应用,并通过实验验证了该方法的有效性。
旋转机械故障诊断
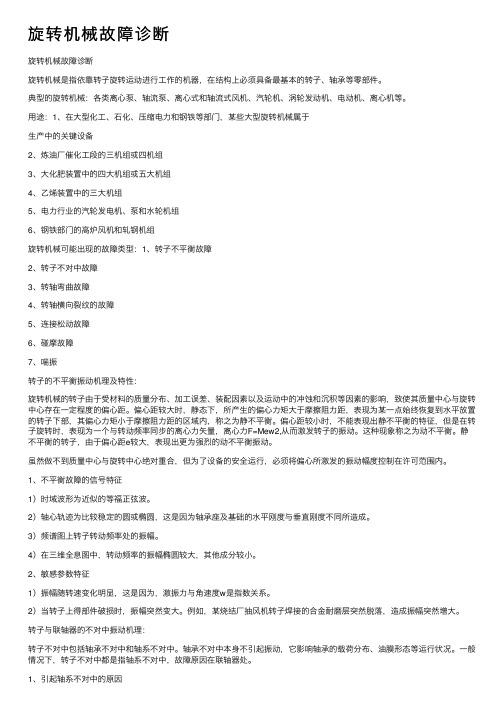
旋转机械故障诊断旋转机械故障诊断旋转机械是指依靠转⼦旋转运动进⾏⼯作的机器,在结构上必须具备最基本的转⼦、轴承等零部件。
典型的旋转机械:各类离⼼泵、轴流泵、离⼼式和轴流式风机、汽轮机、涡轮发动机、电动机、离⼼机等。
⽤途:1、在⼤型化⼯、⽯化、压缩电⼒和钢铁等部门,某些⼤型旋转机械属于⽣产中的关键设备2、炼油⼚催化⼯段的三机组或四机组3、⼤化肥装置中的四⼤机组或五⼤机组4、⼄烯装置中的三⼤机组5、电⼒⾏业的汽轮发电机、泵和⽔轮机组6、钢铁部门的⾼炉风机和轧钢机组旋转机械可能出现的故障类型:1、转⼦不平衡故障2、转⼦不对中故障3、转轴弯曲故障4、转轴横向裂纹的故障5、连接松动故障6、碰摩故障7、喘振转⼦的不平衡振动机理及特性:旋转机械的转⼦由于受材料的质量分布、加⼯误差、装配因素以及运动中的冲蚀和沉积等因素的影响,致使其质量中⼼与旋转中⼼存在⼀定程度的偏⼼距。
偏⼼距较⼤时,静态下,所产⽣的偏⼼⼒矩⼤于摩擦阻⼒距,表现为某⼀点始终恢复到⽔平放置的转⼦下部,其偏⼼⼒矩⼩于摩擦阻⼒距的区域内,称之为静不平衡。
偏⼼距较⼩时,不能表现出静不平衡的特征,但是在转⼦旋转时,表现为⼀个与转动频率同步的离⼼⼒⽮量,离⼼⼒F=Mew2,从⽽激发转⼦的振动。
这种现象称之为动不平衡。
静不平衡的转⼦,由于偏⼼距e较⼤,表现出更为强烈的动不平衡振动。
虽然做不到质量中⼼与旋转中⼼绝对重合,但为了设备的安全运⾏,必须将偏⼼所激发的振动幅度控制在许可范围内。
1、不平衡故障的信号特征1)时域波形为近似的等福正弦波。
2)轴⼼轨迹为⽐较稳定的圆或椭圆,这是因为轴承座及基础的⽔平刚度与垂直刚度不同所造成。
3)频谱图上转⼦转动频率处的振幅。
4)在三维全息图中,转动频率的振幅椭圆较⼤,其他成分较⼩。
2、敏感参数特征1)振幅随转速变化明显,这是因为,激振⼒与⾓速度w是指数关系。
2)当转⼦上得部件破损时,振幅突然变⼤。
例如,某烧结⼚抽风机转⼦焊接的合⾦耐磨层突然脱落,造成振幅突然增⼤。
旋转机械故障诊断设计

齿轮故障表现为齿面磨损、断齿和齿合不良等。诊断方法包括声音检测、振动分析和润滑油检查等, 以确定齿轮的损伤程度和类型。
案例三:转子不平衡故障诊断
总结词
转子不平衡是旋转机械中常见的故障之 一,可能导致设备振动增大和轴承损伤 。
VS
详细描述
转子不平衡表现为设备振动增大,特别是 在低速时。诊断方法包括振动分析和频谱 分析等,以确定转子的不平衡程度和位置 。
旋转机械故障诊断设计
汇报人: 日期:
目录
• 旋转机械故障诊断概述 • 旋转机械故障诊断方法 • 旋转机械故障诊断系统设计 • 旋转机械故障诊断案例分析 • 旋转机械故障预防与维护策略 • 未来展望与研究方向
01
旋转机械故障诊断概述
旋转机械的定义与重要性
旋转机械定义
旋转机械是指通过旋转运动来完 成工作任务的机械设备,如电机 、泵、风机、压缩机等。
详细描述
逻辑分析诊断法是利用人工智能和专家系统等技术,建立旋转机械的故障诊断模型。该 模型可以根据机器的历史数据、运行状态以及专家经验等信息,进行逻辑推理和判断, 以确定故障的原因和位置。逻辑分析诊断法具有较高的智能化程度和准确性,是未来旋
转机械故障诊断的重要发展方向之一。
03
旋转机械故障诊断系统设计
数据记录与分析
记录设备的运行数据和故障信息, 对数据进行深入分析,找出故障原 因和规律,为预防性维护提供依据 。
快速响应与处理
建立快速响应机制,一旦发生故障 ,立即组织人员进行检查和维修, 缩短停机时间,减少损失。
06
未来展望与研究方向
人工智能与机器学习在旋转机械故障诊断中的应用
深度学习
利用深度学习算法对大量数据进行学习,自动提取故障特征,提 高故障诊断准确率。
旋转机械故障诊断与预测方法及其应用研究

旋转机械故障诊断与预测方法及其应用研究旋转机械在工业生产中起着至关重要的作用,然而在运行过程中会出现各种各样的故障,给生产和运营带来了很大的困扰。
旋转机械故障诊断与预测方法的研究对于提高机械设备的可靠性、减少故障停机时间以及降低维护成本具有重要意义。
本文将从故障诊断与预测方法的研究、应用案例以及发展趋势等方面展开讨论。
1. 传统的故障诊断方法传统的故障诊断方法主要依靠经验、观察以及简单的检测手段,例如听声音、观察振动等。
这些方法往往无法及时准确地发现故障,容易导致机械设备在故障状态下继续运行,增加了后续维修的难度和成本。
2. 基于振动信号分析的故障诊断方法随着科学技术的不断进步,基于振动信号分析的故障诊断方法逐渐成为了研究的热点。
这种方法通过对机械设备振动信号的采集和分析,识别出其中蕴藏的故障信息,进而实现故障的早期诊断和预测。
3. 基于机器学习的故障预测方法机器学习技术的发展为旋转机械故障预测提供了新的思路和方法。
通过对机器设备运行数据的采集和分析,建立机器学习模型,可以实现对机械设备未来故障发生的预测,提前制定维护计划,降低维护成本。
2. 工业泵的故障预测工业泵是工业生产中常见的旋转机械设备,其故障会严重影响生产效率。
利用基于机器学习的故障预测方法,可以通过监测泵的运行数据,建立泵的健康模型,实现对泵故障的提前预测,避免因突发故障而导致的生产中断。
三、旋转机械故障诊断与预测方法的发展趋势1. 多传感器融合技术将多种传感器融合在一起,可以获得更加全面和准确的机械设备运行数据,为故障的诊断与预测提供更可靠的依据。
2. 数据驱动的故障诊断技术利用大数据分析和人工智能技术,可以挖掘出数据中潜藏的故障特征,实现对机械设备故障的更加精准的诊断与预测。
3. 在线监测与远程诊断利用互联网和物联网技术,可以实现对机械设备的在线监测和远程诊断,为故障的及时发现和处理提供便利。
旋转机械故障诊断与预测方法的研究与应用将对工业生产的安全和稳定起着至关重要的作用。
旋转机械故障机理及诊断讲稿

相频响应曲线
当ζ=0时,当z<1,则ψ=0;当z>1,则ψ=π ;当z=1,则共振点前后相位角发生突然变化 当ζ很小时,在z<<1,即转子运行在低频范围 内,ψ≈0,即表示位移与激振力的相位相同 ;在z>>1,ψ≈π,在高频范围内,即表示位 移与激振力的相位相反 当ζ很大时,相位角ψ随z增加而增大。当z=1 (即共振)时,相位角ψ=π/2,与阻尼大小 无关,这是共振时的一个共同特征
当ω=p时,即z=1 B= e/2ζ,ψ=π/2回转半径 即为转轴的横向位移最大值B= e/2ζ 子临界转速的影响 弹性支承对转子临界转速的影响 组合转子对临界转速的影响
转子不平衡的故障机理及诊断
转子不平衡的分类
静不平衡 动不平衡 一般不平衡
转子临界转速及其影响因素
当ω<p时,ψ<π/2,在ω<<p,z≈0即转子运行 在低频范围内 ψ≈0,即表示位移与激振力的相 位相同,这时转子的重点和高点同相位
当ω>p时,ψ>π/2,在ω>>p ,z→∞,即转子 运行在高速范围内 ψ≈π,即表示位移与激振 力的相位相反,这时转子的振动很小,自动对心.
第一阶(和第二阶、第三阶……)共振频率是否 降低(轴裂纹使系统刚度下降,故共振频率也 有所降低)
共振峰的开裂(与裂纹有关的轴的不对称性导 致了两个横向振型的差别)
轴振动变化
3-2-1
p2=k/m;2n=r/m
..
.
x+2nx+ px2x=eω2 cosωt
.y.+2ny. + py2y=eω2 sinωt
旋转机械故障诊断与预测方法及其应用研究

旋转机械故障诊断与预测方法及其应用研究
旋转机械是现代工业生产中常用的一种类型的机械设备,其具有结构简单、工作效率高等特点。
然而,在实际使用过程中,旋转机械故障率较高,且故障可能对生产造成重大影响。
为了防止机械故障的发生,提高设备的可靠性和使用寿命,需要对旋转机械进行故障诊断与预测。
1. 振动分析法:通过振动传感器采集旋转机械的振动数据,借助计算机分析振动信号的频率、幅值等参数,识别故障类型和故障位置。
常用于诊断轴承故障、不平衡、松动等问题。
2. 信号处理法:通过采集旋转机械的电信号(如电流、电压)进行分析,利用计算机进行信号处理,获得电信号的各个参数(如频率、幅值、相位等),从而判断机械是否存在故障。
常用于诊断电机故障、电缆连接故障等。
3. 温度分析法:通过测量旋转机械各个部位的温度变化情况,分析温度变化的规律和机理,诊断机械是否存在故障。
常用于诊断电机绕组、轴承局部加热等问题。
在实际应用中,多种分析方法可以结合使用,以更全面地诊断和预测旋转机械故障。
例如,振动分析法和温度分析法可以结合使用,对轴承故障进行诊断;信号处理法和声学分析法可以结合使用,对电机故障进行诊断。
旋转机械故障诊断与预测方法在工业生产中得到广泛应用。
通过对机械故障进行及时诊断和预测,可以减少设备的停机时间,提高设备的可靠性和安全性,降低生产成本,增强竞争力。
《2024年旋转机械故障诊断与预测方法及其应用研究》范文

《旋转机械故障诊断与预测方法及其应用研究》篇一一、引言旋转机械广泛应用于各种工业领域,如风力发电、航空航天、交通运输等。
然而,由于长时间运行和复杂的工作环境,旋转机械经常会出现各种故障,如轴承磨损、齿轮断裂等。
这些故障不仅影响设备的正常运行,还可能导致严重的安全事故。
因此,对旋转机械进行故障诊断与预测显得尤为重要。
本文将介绍旋转机械故障诊断与预测的方法及其应用研究。
二、旋转机械故障诊断与预测方法1. 基于振动信号分析的方法振动信号分析是旋转机械故障诊断与预测的常用方法。
通过传感器采集设备的振动信号,对信号进行时域、频域和时频域分析,可以提取出设备运行状态的特征信息。
当特征信息超过设定的阈值时,即可判断设备存在故障。
此外,还可以通过对比历史数据,预测设备未来可能出现的故障。
2. 基于声音信号分析的方法声音信号分析是另一种有效的故障诊断与预测方法。
通过采集设备的声波信号,对信号进行频谱分析和声强分析,可以判断设备的运行状态和故障类型。
该方法具有非接触式、实时性强的优点,适用于对复杂工作环境下的设备进行故障诊断。
3. 基于数据驱动的智能诊断方法随着人工智能技术的发展,基于数据驱动的智能诊断方法在旋转机械故障诊断与预测中得到了广泛应用。
该方法通过收集设备的运行数据,利用机器学习、深度学习等算法对数据进行训练和建模,实现对设备运行状态的监测和故障预测。
该方法具有准确度高、适应性强、可扩展性强的优点。
三、旋转机械故障诊断与预测方法的应用研究1. 在风力发电领域的应用风力发电是旋转机械的重要应用领域之一。
通过采用振动信号分析和声音信号分析等方法,可以对风力发电机组的齿轮箱、轴承等关键部件进行实时监测和故障诊断。
同时,采用基于数据驱动的智能诊断方法,可以实现对风力发电机组运行状态的预测和优化,提高设备的可靠性和效率。
2. 在航空航天领域的应用航空航天领域对设备的可靠性和安全性要求极高。
采用基于振动信号分析和声音信号分析等方法,可以对航空发动机、螺旋桨等旋转机械进行实时监测和故障诊断。
旋转机械故障诊断与预测方法及其应用研究

旋转机械故障诊断与预测方法及其应用研究1. 引言1.1 研究背景旋转机械是工业生产中常见的设备,其故障可能会导致生产中断和安全隐患。
旋转机械故障诊断与预测方法的研究备受关注。
目前,随着传感技术、数据分析和人工智能的发展,针对旋转机械故障诊断与预测方法的研究取得了不少进展。
旋转机械故障诊断方法的研究包括基于振动、声音、温度等传感数据的分析,通过识别故障特征来实现快速准确的故障诊断。
预测方法则是通过数据建模和算法分析,预测旋转机械未来的运行状态,提前采取维护措施,避免故障发生。
在实际应用案例分析中,研究人员通过实验验证了不同的故障诊断与预测方法在旋转机械上的有效性和实用性。
技术优势的讨论则涉及不同方法的优缺点比较和适用范围。
未来的发展方向包括不断优化算法和模型,提高故障诊断和预测的准确性和可靠性,推动旋转机械故障管理技术的进一步发展和应用。
1.2 研究意义旋转机械故障诊断与预测方法及其应用研究的研究意义在于提高旋转机械设备的运行可靠性和安全性,减少设备故障对生产造成的影响,提高生产效率和降低维护成本。
通过研究旋转机械故障诊断和预测方法,可以实现对设备运行状态的实时监测和评估,及时发现故障隐患,提前采取维修措施,避免设备停机损失。
通过建立预测模型和算法,可以对设备未来的运行状态进行预测,有针对性地制定维护计划,延长设备寿命,降低维护成本。
旋转机械在现代工业生产中扮演着重要的角色,涉及到诸如风力发电机组、涡轮机、离心泵等关键设备。
这些设备的故障通常会导致生产中断,造成巨大经济损失,并可能带来安全隐患。
研究旋转机械故障诊断和预测方法对于提升工业生产的稳定性和可靠性具有重要意义。
通过不断完善故障诊断和预测技术,可以不断提高设备运行的效率和安全性,推动工业生产向更高水平发展。
1.3 研究目的研究目的是为了探讨旋转机械故障诊断与预测方法及其应用的相关问题,通过系统性的研究和实践,对旋转机械故障诊断与预测方法进行深入理解和探讨,为相关领域的研究和实践提供理论支持和技术指导。
- 1、下载文档前请自行甄别文档内容的完整性,平台不提供额外的编辑、内容补充、找答案等附加服务。
- 2、"仅部分预览"的文档,不可在线预览部分如存在完整性等问题,可反馈申请退款(可完整预览的文档不适用该条件!)。
- 3、如文档侵犯您的权益,请联系客服反馈,我们会尽快为您处理(人工客服工作时间:9:00-18:30)。
收稿日期:1998-12-05 旋转机械不对中故障特征提取及诊断方法研究张新江 焦映厚 张玉国 杨东波(哈尔滨工业大学动力工程系) (哈尔滨汽轮机有限责任公司)【摘要】对旋转机械转子系统不对中故障的征兆机理进行了分析,得出在不对中条件下,旋转机械产生二倍频振动这一典型征兆的原因,在转子实验台上对该类故障进行转子系统实验测试,并对原始信号进行频谱特征提取,使该类故障征兆得以验证。
用实验测得的振动数据特征归一化处理后作为神经网络的输入变元,以实现对该类故障的准确分离和正确诊断。
关键词:旋转机械 不对中 振动实验 故障诊断 神经网络0 前 言随着科学技术的发展,现代大型旋转机械的结构越来越复杂,自动化程度也在不断提高。
但由于许多无法避免的因素影响,有时设备会出现各种故障,降低其使用功能,甚至造成灾难性事故。
因此,及时准确地对故障做出诊断,对于提高设备的可靠性、安全性及有效性,以期把故障损失降到最低水平,具有重大现实意义。
在各类旋转机械故障中,不对中是最为常见的故障之一,旋转机械故障中60%的故障与不对中有关,转子系统出现不对中后,在其运动过程中将产生一系列的不利于设备运行的动态效应。
引起设备的振动、联轴器的偏转、轴承的磨损和油膜失稳、轴的挠曲变形等[1]。
因此,研究发动机转子系统不对中故障的征兆机理和特征,对于掌握系统的运行状态具有重要的现实意义。
目前,对转子系统中该类问题的研究很多[2,3],而且在诊断方法上也有很大发展[4]。
本文针对旋转机械的具体特点,对其转子系统不对中故障的征兆机理进行了分析,得出径向振动二倍频特征为该类故障的典型特征。
同时,为验证该结论,在转子实验台上对该类故障进行转子系统实验测试,并对原始信号进行频谱特征提取,使该类故障征兆得以验证。
用实验测得的振动数据归一化特征值作为神经网络故障诊断系统的输入变元,以实现对该类故障的诊断。
1 机理分析1.1 转子系统平行不对中当转子系统轴线之间存在径向位移Δy时,则联轴器的中心是沿着以径向位移Δy为直径的圆作圆周运动[5],如图1所示。
设A 为主动转子的轴心投影,B 为从动转子的轴心投影,K 为联轴器的中心,那么A K 为联轴器与主动轴的连线,B K 为联轴器与从动轴的连线,A K 垂直B K ,如图2所示。
设AB 长为D ,K 点坐标为K (x ,y ),取θ为自变量,图1 平行不对中第41卷第2期汽 轮 机 技 术V ol.41N o.21999年4月T URBI NE TECH NO LOGYApr.1999图2 联轴器运动分析则有x =D sin θcos θ=12D sin (2θ)y =12D -D cos θcos θ=12D (1-cos2θ)(1) 对θ求导,得 d x =D cos (2θ)d θ d y =D sin (2θ)d θ K 点的线速度为v k =d x d t2+d y d t2=Dd θd t(2) 由于联轴器平面运动的角速度(d θΠd t )等于转轴的角速度,即d θΠd t =ω,所以K 点绕圆周中心运动的角速度为ωk =2v k ΠD =2ω(3) 由(3)式可知,K 点的转动为转子转动角速度的两倍,因此当转子高速运转时,就会产生很大的离心力,激励转子产生径向振动,其振动频率为转子工频的两倍。
1.2 转子系统偏角不对中图3 偏角不对中当转子轴线之间存在偏角位移时,如图(3)所示,从动转子与主动转子的角速度是不同的。
当主动转子轴线与从动转子轴线位置存在径向偏角α时,若主动转子回转角度为φ1时,从动转子转角为φ2,则由几何关系可得:tg φ1=tg φ2cosα(4)将上式对时间微分,并注意d φ1d t =ω1及d φ2d t=ω2得 i =ω2ω1=sec 2φ1sec 2φ2cos α=sec 2φ1cos α(1+tg 2φ2)cos 2α=sec 2φ1cos αcos 2α+tg 2φ1=cos αcos 2αcos 2φ1+sin 2φ1=cos α1-sin 2αcos 2φ1(5)设A =4cos α3+cos2α,B =1-cos2α3+cos2α,代入(5)式得:ω2ω1=A1+B cos2φ1(6) 把式(6)由二项式定理展开成级数有 ω2ω1=C 0-C 2cos2φ1+C 4cos4φ1-C 6cos6φ1+ (7)其中C 0、C 2、C 4、C 6…都是与A 和B ,亦即与夹角α有关的系数。
(7)式充分反映了该类不对中的二倍转频振动特性。
1.3 平行偏角不对中实际旋转机械各转子联轴器处既有平行不对中又有偏角不对中,即为两种情况的综合,因而转子发生径向振动的频谱机理是两者的综合结果,其径向振动频率为转子工频的两倍。
2 实验测试转子试验台及测量系统简图如图4所示,将两半联轴器错开1mm 并将3号轴承垫高0.5mm ,用以模拟不对中故障,当转速达到3000r Πmin 时进行数据采集,然后对实验数据进行频谱和功率谱分析,其中一组结果如图5所示。
由理论分析和图5的实验结果表明,由501第2期张新江等:旋转机械不对中故障特征提取及诊断方法研究 图4 实验装置及测量系统1—轴承1;2—轴承2;3—轴承3;4—轴承4;5—电动机;6—皮带传动装置;7—轮盘;8—联轴器;9—传感器;10—A ΠD 转换器;11—放大器;12—计算机图5 频谱特性图于不对中位移及偏角的存在,使转子在高速运转时就会有一个两倍频的附加径向力作用于轴承上,从而激励转子产生振动频率为工频二倍的径向振动。
3 诊 断3.1 归一化本文采用频率作为阈值,提取最大幅值作为特征值。
为了保证神经网络诊断系统的稳定性必须对提取的特征值归一化,根据网络的特点应将每个特征值归一化到[-1,+1]区间。
为了满足这一条件,本文采用改进的升半柯西函数作为归一化函数,如公式(8)所示。
μ(y )=k (y -a )|y -a |1+k (y -a )2(8)其中k 值的大小取决于某一变量的阈值,当y 等于阈值时μ(y )=0.5,以此确定k 值。
用此归一化后的特征值训练神经网络,可使神经网络易于收敛。
3.2 神经网络的选取本文采用神经网络故障诊断系统对该类故障进行诊断,网络选为3层B P 网络,输入层节点数为5,输出层节点数为3,为保证网络的普化能力和特殊化能力,中间层节点数选为16,节点函数为sigm oid 函数:F (s )=11+e-s(9)当其导数为:F ′(s )=F (s )[1-F (s )]=y (1-y )(10) 当输入向量x 时,隐蔽层节点h 的输入加权和为:s h =∑iw ihx i(11) 相应节点输出为:y h =F∑iw ihx i(12) 输出层节点j 的输入加权和为:s j =∑hw hjy h =∑hw hjF∑iw ihx i(13) 相应节点输出为:y j =F (s j )=F∑hw hjF∑iw ihx i(14) 将节点的门限值用一连接的加权等效θ=w 0h ・w 0j 。
这些连接是由各连接点连到具有固定值-1的偏值节点。
这些加权也是可调的,同其它权值一样参与调节过程。
这里601 汽 轮 机 技 术第41卷我们采用熟知的误差函数:E (w )=12∑j(T j -y i )2(15)即:E (w )=12∑jT j-F∑hw hj F∑iw ih x i2(16)其中,T j 为节点j 的目标输出值。
由于转移函数是连续可微的,显然(16)式是每个加权的连续可微函数。
为了使误差函数最小,用梯度下降法求的最优化的权值该权值总是从输出层开始修正,然后修正前层权值。
根据梯度下降法,由隐蔽层到输出层的加权调节量为:Δw hj =-η5E5w hj =η(T j -y j )F ′(s j )y h =ηδj y h (17)其中δj 定义为输出节点的误差信号:δj =F ′(s j )(T j -y j )(18)令Δj =T j -y j同样,由输入到隐层的加权修正量为: Δw ih =-η5E 5w ih =-η5E 5y h ・5y h5w ih=η∑j(Tj-y j )F ′(s j )w hj F ′(s h )x i =η∑j δjw hjF ′(s h)x i=ηδhx i(19)其中δh =F ′(s h)∑jw hj δj,令Δh=∑jw hjδj。
一般说来,BP 训练算法对于任意层的加权修正量的一般形式为:Δw pq =ηδ0y in(20)y in 代表输入端点的实际输出,δ0表示输出端点的误差,δ0具体的含义由具体的层决定。
对输出层由(18)式确定,对隐蔽层具有(19)的形式。
输出层Δj =T j -y j 可直接算得,于是误差值δj 得到。
对前一隐层没有直接给出目标值,不能计算Δh ,而是利用输出层的δj 计算,即:Δh =∑jw hjδj(21)然后求得δh 。
如果前面还有隐层,用δh 再按式(20)的方法计算Δl 和δl ,依次类推,一直将δ输出误差一层一层地算到第一隐层为止。
各层的δ求得后,各层的加权调节量也就可以按(21)式求得了。
3.3 诊断表1为该类故障的训练样本和测试样本的特征值,表2为诊断结果。
表1训练样本和测试样本故障样本编 号0.5f 0.5~1f 1f 1~2f 2f >2f 训练样本 0.10430.48540.44320.30640.98320.1367测试样本10.23430.35560.44430.13690.96550.229020.47150.01980.22670.44290.88650.3357 表2诊 断 结 果编 号迭代次数置 信 度18000.843680000.982728000.821380000.94224 结 论通过对转子系统不对中故障的征兆机理分析,得出该类故障径向振动出现二倍频这一显著特征,并通过实验测试加以验证,用测得的振动数据归一化后训练神经网络故障诊断系统,以便于对该类故障的正确分离和准确诊断。
参考文献1 夏松波,张新江.旋转机械不对中故障研究综述.振动、测试与诊断,1998,18(3):157~1612 陆 钟.转子不对中故障的机理.全国首届转子动力学学术会议论文集,1986,321~3273 韩 捷.齿式联结不对中转子的故障物理特性研究,振动工程学报,1996,9(3),297~3014 黄文虎,夏松波.设备诊断原理、技术及应用,科学出版社,19965 张瑞林等.不对中、不平衡频谱分析.化工机械,1983,5:1~9701第2期张新江等:旋转机械不对中故障特征提取及诊断方法研究。