Portable Gas Monitors
有限空间作业气体检测流程

有限空间作业气体检测流程英文回答:Gas detection in confined spaces is a critical safety measure to protect workers from potential hazards. The process of gas detection in a limited space involves several key steps to ensure a safe working environment.The first step in the gas detection process is to conduct a thorough assessment of the confined space. This includes identifying potential sources of gas emissions, understanding the nature of the work being performed, and evaluating the ventilation and air circulation within the space.Once the assessment is complete, the next step is to select the appropriate gas detection equipment. This may include portable gas monitors, fixed gas detection systems, or personal gas detectors, depending on the specific requirements of the confined space.After the equipment is selected, it is essential to calibrate and test the gas detection devices to ensuretheir accuracy and reliability. Regular maintenance and calibration of the equipment are critical to ensuring thatit functions properly when needed.With the gas detection equipment in place, the nextstep is to establish a monitoring plan for the confined space. This may involve continuous monitoring with fixedgas detection systems, periodic spot checks with portable gas monitors, or a combination of both, depending on the nature of the work and the potential gas hazards present.In addition to monitoring, it is crucial to establish clear procedures for responding to gas alarms or detections. This includes defining evacuation protocols, notifying appropriate personnel, and taking corrective actions to address the source of the gas emissions.Finally, it is essential to document the gas detection process, including the results of monitoring and anyactions taken in response to gas detections. This documentation serves as a record of the safety measures taken and provides valuable information for future risk assessments and safety planning.中文回答:有限空间作业气体检测是保护工人免受潜在危险的关键安全措施。
Gasboard-3100P系列便携式红外煤气分析仪使用说明书

GASBOARD-3100P S ERIESP ORTABLE I NFRARED C OAL G AS A NALYZER U SER M ANUALNo.Ver.2012.3Wuhan Cubic Optoelectronics Co.,LtdI ForewordThanks for using Portable infrared coal gas analyzer Gasboard-3100P series1.Pls reading and using the operation manual carefully,to install,operate and repair the instrumentafter understanding the content completely.There would be happen to human injury or analyzer damage if your operation unqualified.2.Never remove the configuration and spare parts of the instrument unless approving by company.Our company will be derelict of duty due to the user make bold to remove the configuration and spare parts mistakenly.3.The specification and guide content of this analyzer may be change due to the technology improveof the product.Pls forgive us shall not give out an inform previous.4.This operation manual have to give the practice user to save,and put the user can refer to it at anymoment.。
ppbRAE 3000 + 可燃有机化学品气体监测仪手持数据记录仪说明书

The compact ppbRAE 3000 + is a comprehensive VOC gas monitor and datalogger for hazardous environments. The ppbRAE 3000 + is one ofthe most advanced handheld VOC monitors available for parts-per-billion detection. This third-generation patented PID device monitors VOCsusing a photoionization detector with a 9.8 eV, 10.6 eV UV-discharge lamp.The built-in wireless modem allowsreal-time data connectivity with the command center located up to twomiles/3 km away (with optional RAELink3 portable modem) from the detector.Proven PID Technology •3-second response time •Extended range from 1 ppb to 10,000 ppm with highly acute linearity •Humidity compensation with integral humidity and temperature sensors •Reflex PID Technology TM Integrated •Highly connectivity capability through multiple wireless module options• Integrated Correction Factors list of 220 compounds—more than any other PID •Includes flashlight for dark conditions •Large graphic display presents gas type,Correction Factor and concentration Durable •Easy access to battery, lamp and sensor in seconds without tools •Rugged housing withstands use in harsh environments •IP-67 waterproof design for easy cleaning and decontamination•Oil & Gas •HazMat•Industrial Safety •Civil Defense•Environmental & Indoor Air QualityF E AT U R E S & B E NE F I T SA PPL IC AT IO N SWorkers can easily measure VOCs and wirelessly transmit readings up to 2 miles/3 km away.•Accurate VOC measurement in all operating conditions •Easy access to lamp and sensor in seconds without tools •Patented sensor and lamp autocleaning reduces maintenance•Monitors real-time readings and location of people •Low Cost of Ownership: 3-year 10.6 eV lamp Warranty •BLE module and dedicated APP for enhanced datalogging functionppbRAE 3000 +Portable Handheld VOC MonitorMONITOR ONLY INCLUDES:• ppbRAE 3000 + Monitor• Wireless communication module built in, as specified• Charging/download adapter • Organic vapor zeroing kit • Tedlar® bag for calibration • Flex-I-Probe™• External filter• Rubber boot with straps • Alkaline battery adapter • Lamp-cleaning and tool kit • Soft leather caseMONITOR WITH ACCESSORIES KIT:• Hard transport case with pre-cut foam padding • Charging/download cradle• 5 Porous metal filters and O-rings • Gas outlet port adapter and tubing OPTIONAL CALIBRATION KIT ADDS:• 10 ppm isobutylene calibration gas, 34L • Calibration regulator and flow controller OPTIONAL GUARANTEEDCOST-OF-OWNERSHIP PROGRAM:• 4-year repair and replacement warranty • Annual maintenance service1Contact RAE Systems for country-specific wireless approvals and certificates. Specifications are subject to change.For more information Europe, Middle East, AfricaLife Safety Distribution GmbHTel: 00800 333 222 44 (Freephone number)Tel: +41 44 943 4380 (Alternative number)Middle East Tel: +971 4 450 5800 (Fixed Gas Detection) **************************AmericasHoneywell Analytics Distribution Inc.Tel: +1 847 955 8200Toll free: +1 800 538 0363***********************Honeywell RAE Systems Phone: +1 408 952 8200Toll Free: +1 888 723 4800Asia PacificHoneywell Analytics Asia Pacific Tel: +82 (0) 2 6909 0300India Tel: +91 124 4752700China Tel: +86 10 5885 8788-3000 **************************Technical ServicesEMEA:**********************US:***************************AP:***************************Datasheet_ppbRAE 3000_+_DS-1018-_EN ©2018 Honeywell International Inc.。
GasAlertMicro 5 系列便携式气体检测仪器说明书
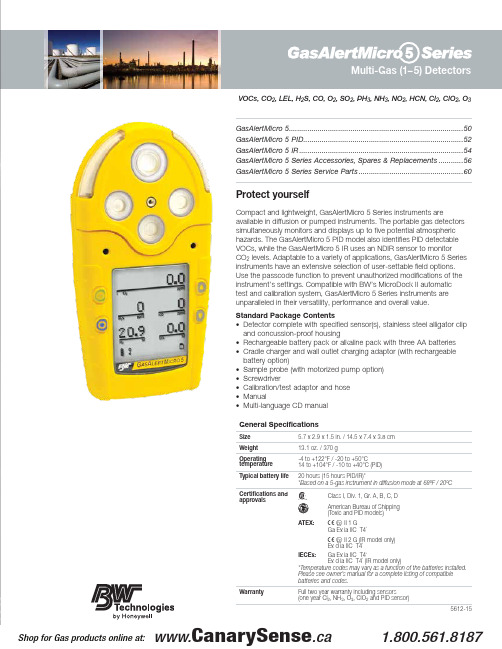
VOCs, CO 2, LEL, H 2S, CO, O 2, SO 2, PH 3, NH 3, NO 2, HCN, Cl 2, ClO 2, O 3Protect yourselfCompact and lightweight, GasAlertMicro 5 Series instruments areavailable in diffusion or pumped instruments. The portable gas detectors simultaneously monitors and displays up to five potential atmospheric hazards. The GasAlertMicro 5 PID model also identifies PID detectable VOCs, while the GasAlertMicro 5 IR uses an NDIR sensor to monitorCO 2 levels. Adaptable to a variety of applications, GasAlertMicro 5 Series instruments have an extensive selection of user-settable field options. Use the passcode function to prevent unauthorized modifications of the instrument’s settings. Compatible with BW’s MicroDock II automatic test and calibration system, GasAlertMicro 5 Series instruments are unparalleled in their versatility, performance and overall value.Standard Package Contents• D etector complete with specified sensor(s), stainless steel alligator clip and concussion-proof housing• Rechargeable battery pack or alkaline pack with three AA batteries • Cradle charger and wall outlet charging adaptor (with rechargeable battery option)• Sample probe (with motorized pump option)• Screwdriver• Calibration/test adaptor and hose • Manual• Multi-language CD manual General SpecificationsSize 5.7 x 2.9 x 1.5 in. / 14.5 x 7.4 x 3.8 cm Weight 13.1 oz. / 370 gOperating temperature -4 to +122°F / -20 to +50°C14 to +104°F / -10 to +40°C (PID)Typical battery life 20 hours (15 hours PID/IR)**Based on a 5-gas instrument in diffusion mode at 68ºF / 20ºCCertifications and approvalsClass I, Div. 1, Gr. A, B, C, D American Bureau of Shipping (Toxic and PID models)ATEX: X g II 1 G Ga Ex ia IIC T4*X g II 2 G (IR model only)Ex d ia IIC T4*IECEx: Ga Ex ia IIC T4* Ex d ia IIC T4* (IR model only)*Temperature codes may vary as a function of the batteries installed. Please see owner’s manual for a complete listing of compatible batteries and codes.WarrantyFull two year warranty including sensors (one year Cl 2, NH 3, O 3, ClO 2 and PID sensor)5612-15GasAlertMicro 5.....................................................................................50GasAlertMicro 5 PID ..............................................................................52GasAlertMicro 5 IR ................................................................................54GasAlertMicro 5 Series Accessories, Spares & Replacements ............56GasAlertMicro 5 Series Service Parts (60)GasAlertMicro 5 DetectorOrder NumberGasAlertMicro 5 Region CodesNote: Listed above are commonly ordered instrument configurations. To create a custom GasAlertMicro 5 detector, use the configurator table on the next page or contact BW Technologies for a copy of the electronic order number configurator.GasAlertMicro 5Pump versionGasAlertMicro 5Diffusion versionOrder Number ConfiguratorOrder number:For example, the order number for a GasAlertMicro 5 configured for O 2, %LEL, Cl 2, H 2S and CO and equipped with a rechargeable battery pack and cradle charger, motorized sampling pump, yellow housing and North American powerconnectivity would be M5-XWCY-R-P-D-Y-N-00.*Note: Some gases (e.g. SO 2 and NH 3) cannot be combined in the same GasAlertMicro 5 configuration. Please checkwith Customer Service for specific availability.†Note: HCN can only be ordered in the Toxic 1 location when the Duo-Tox (CO/H 2S) sensor is ordered in theToxic 2 location. In all other configurations, HCN must be ordered in the Toxic 2 location.Note: Listed above are commonly ordered instrument configurations. To create a custom GasAlertMicro 5 PID detector, use the configurator table on the next page or contact BW Technologies for a copy of the electronic order number configurator.GasAlertMicro 5 PIDPump versionGasAlertMicro 5 PIDDiffusion versionOrder Number ConfiguratorOrder number:For example, the order number for a GasAlertMicro 5 PID configured for O 2, %LEL, VOCs, H 2S and CO and equipped with a rechargeable battery pack and cradle charger, motorized sampling pump, yellow housing and North Americanpower connectivity would be M5PID-XWQY-R-P-D-Y-N-00.*Note: Some gases cannot be combined in the same GasAlertMicro 5 configuration. Please check with CustomerService for specific availability.GasAlertMicro 5 IR DetectorOrder NumberGasAlertMicro 5 IR Region CodesNote: Listed above are commonly ordered instrument configurations. To create a custom GasAlertMicro 5 IR detector, use the configurator table on the next page or contact BW Technologies for a copy of the electronic order number configurator.Gas LegendGasAlertMicro 5 IRPump versionGasAlertMicro 5 IRDiffusion versionOrder number:For example, the order number for a GasAlertMicro 5 IR configured for O 2, %LEL, CO 2, H 2S and CO and equipped with a rechargeable battery pack and cradle charger, motorized sampling pump, yellow housing and North American powerconnectivity would be M5IR-XWBY-R-P-D-Y-N-00.*Note: Some gases cannot be combined in the same GasAlertMicro 5 configuration. Please check with CustomerService for specific availability.Order Number ConfiguratorDeluxe Confined Space KitM5-CK-DLConcussion-Proof BootGA-BM5-2For GasAlertMicro 5 Seriespumped unitsCarrying HolsterGA-HM5Fits securely on belt Confined Space Kits Order Number Carrying & Protective Accessories Order NumberConcussion-Proof BootGA-BM5-1For GasAlertMicro 5 Seriesdiffusion unitsSampling & Testing Equipment Order NumberNote: For complete list of Sampling & Testing Equipment, see the Sampling Equipment section.ReplacementTest Cap and HoseM5-TC-1Pump ModuleM5-PUMPReplacementDiffusion CoverM5-DC-1Manual Aspirator PumpGA-AS02For remote sampling; complete withprobe, hose and aspirator pumpAuxiliary Pump Filter withHose ConnectorM5-QCONN-K1Auxiliary Pump FilterM5-AF-K2 / M5-AF-K2-100Kit of 5 or 100, for legacyGeneration 1 pump modules onlyAuxiliary Pump FilterM5-AF-K3 / M5-AF-K3-100Kit of 5 or 100, for Generation 2pump modulesPower Accessories Order Number *Note: Battery packs and chargers should be used with the new version GasAlertMicro 5 Series gas detectors (red circuit boards).MicroDock IIOrder Number Cradle ChargerM5-C01Cradle charger for rechargeable battery packs(can charge battery pack with or without detector attached)Vehicle Adaptor 12 V dcGA-V-CHRG4Vehicle adaptor cable for use with cradle charger (M5-C01)Cradle Charger Kit with BatteryM5-C01-BAT08 / M5-C01-BAT08BComplete with charger and rechargeable battery packAlkaline Battery PackM5-BAT0501/M5-BAT0501B M5-BAT0502/M5-BAT0502BRechargeable Battery PackM5-BAT08/M5-BAT08B5062-26-NCL-EN59PID Cleaning KitM5PID-CLN-K1For PID sensorsReplacement Electrode StackM5PID-ES-1For PID sensorsReplacement 10.6 eV PID LampRL-PID10.6For PID sensorsReplacement Sensor Screens Order Number Replacement SensorsOrder Number Note: All sensors come with a 2 year warranty unless marked with an asterisk (*), denoting 1 year warranty.†Advisory: Detectors are equipped on a standard basis with SR-W04 combustible sensors. This sensor includes a heavy duty silicone filter that make it ideal for use in environments that have known sources of silicone or vapors containing silicon. The SR-W04 silicone filter equipped sensor should not be used when monitoring diesel, kerosene, jet fuel or other heavy hydrocarbon vapors with flashpoint temperatures above 38°C (100°F).Replacement IR SensorSR-B04Replacement PID SensorSR-Q07www.CanarySense .ca Shop for Gas products online at:1.800.561.8187605062-26-NCL-EN Note: Please refer to the instrument’s documentation (shipped with the product or available at ) for complete instructions on common service procedures. Improper servicing or maintenance may affect warranty eligibility. Honeywell assumes no liability for damages resulting from improper servicing or maintenance.www.CanarySense.caShop for Gas products online at: 1.800.561.81875062-26-NCL-EN61Note: Please refer to the instrument’s documentation (shipped with the product or available at ) for complete instructions on common service procedures. Improper servicing or maintenance may affect warranty eligibility. Honeywell assumes no liability for damages resulting from improper servicing or maintenance.LegendService PartsOrder Number How to Replace a Sensor1. With detector OFF , use No. 1 Phillips screwdriver to remove2 screws (G) from back enclosure (F) on either side of the belt clip 2. Lift diffusion cover (A) or pump module straight up3. Remove sensor (O-R) by pulling straight up from PCB (E)4. Insert new sensor (O-R) into PCB (E)5. Replace diffusion cover (A) or pump module6. Replace 2 screws (G) in back enclosure (F) andhand-tighten until firmHow to Replace the Sensor Screen1. With detector OFF , use No. 1 Phillips screwdriver to remove2 screws (G) from back enclosure (F) on either side of the belt clip 2. Lift diffusion cover (A) or pump module straight up3. Remove sensor screen (B) by pulling it straight up fromdiffusion cover (A) or pump module4. Insert sensor screen (B) into diffusion cover (A) orpump module5. Replace diffusion cover (A) or pump module6. Replace 2 screws (G) in back enclosure (F) andhand-tighten until firmwww.CanarySense .ca Shop for Gas products online at:1.800.561.8187。
ANSI ISA-92.00.02-2013、安装、操作和维护有毒气体检测仪器说明书

AMERICAN NATIONAL STANDARD ANSI/ISA-92.00.02-2013 Installation, Operation, and Maintenance of Toxic Gas-Detection Instruments Approved 30 September 2013ANSI/ISA-92.00.02-2013, Installation, Operation, and Maintenance of Toxic Gas-Detection InstrumentsISBN: 978-0-876640-45-6Copyright © 2013by the International Society of Automation. All rights reserved. Not for resale. Printed in the United States of America. No part of this publication may be reproduced, stored in a retrieval system, or transmitted in any form or by any means (electronic mechanical, photocopying, recording, or otherwise), without the prior written permission of the Publisher.ISA67 Alexander DriveP.O. Box 12277Research Triangle Park, North Carolina 27709- 3 - ANSI/ISA-92.00.02-2013PrefaceThis preface, as well as all footnotes and annexes, is included for information purposes and is not part of ISA-92.00.02-2013.This document has been prepared as part of the service of ISA toward a goal of uniformity in the field of instrumentation. To be of real value, this document should not be static but should be subject to periodic review. Toward this end, the Society welcomes all comments and criticisms and asks that they be addressed to the Secretary, Standards and Practices Board; ISA; 67 Alexander Drive; P. O. Box 12277; Research Triangle Park, NC 27709; Telephone (919) 549-8411;Fax(919)549-8288;E-mail:*****************.The ISA Standards and Practices Department is aware of the growing need for attention to the metric system of units in general, and the International System of Units (SI) in particular, in the preparation of instrumentation standards. The Department is further aware of the benefits to USA users of ISA standards of incorporating suitable references to the SI (and the metric system) in their business and professional dealings with other countries. Toward this end, this Department will endeavor to introduce SI-acceptable metric units in all new and revised standards, recommended practices, and technical reports to the greatest extent possible. IEEE/ASTM SI 10, American National Standard for Metric Practice, and future revisions, will be the reference guide for definitions, symbols, abbreviations, and conversion factors.It is the policy of ISA to encourage and welcome the participation of all concerned individuals and interests in the development of ISA standards, recommended practices, and technical reports. Participation in the ISA standards-making process by an individual in no way constitutes endorsement by the employer of that individual, of ISA, or of any of the standards, recommended practices, and technical reports that ISA develops.CAUTION — ISA DOES NOT TAKE ANY POSITION WITH RESPECT TO THE EXISTENCEOR VALIDITY OF ANY PATENT RIGHTS ASSERTED IN CONNECTION WITH THIS DOCUMENT, AND ISA DISCLAIMS LIABILITY FOR THE INFRINGEMENT OF ANY PATENT RESULTING FROM THE USE OF THIS DOCUMENT. USERS ARE ADVISED THAT DETERMINATION OF THE VALIDITY OF ANY PATENT RIGHTS, AND THE RISK OF INFRINGEMENT OF SUCH RIGHTS, IS ENTIRELY THEIR OWN RESPONSIBILITY. PURSUANT TO ISA’S PATENT POLICY, ONE OR MORE PATENT HOLDERS OR PATENT APPLICANTS MAY HAVE DISCLOSED PATENTS THAT COULD BE INFRINGED BY USEOF THIS DOCUMENT AND EXECUTED A LETTER OF ASSURANCE COMMITTING TO THE GRANTING OF A LICENSE ON A WORLDWIDE, NON-DISCRIMINATORY BASIS, WITH A FAIR AND REASONABLE ROYALTY RATE AND FAIR AND REASONABLE TERMS AND CONDITIONS. FOR MORE INFORMATION ON SUCH DISCLOSURES AND LETTERS OF ASSURANCE, CONTACT ISA OR VISIT /STANDARDSPATENTS.OTHER PATENTS OR PATENT CLAIMS MAY EXIST FOR WHICH A DISCLOSURE OR LETTER OF ASSURANCE HAS NOT BEEN RECEIVED. ISA IS NOT RESPONSIBLE FOR IDENTIFYING PATENTS OR PATENT APPLICATIONS FOR WHICH A LICENSE MAY BE REQUIRED, FOR CONDUCTING INQUIRIES INTO THE LEGAL VALIDITY OR SCOPE OF PATENTS, OR DETERMINING WHETHER ANY LICENSING TERMS OR CONDITIONS PROVIDED IN CONNECTION WITH SUBMISSION OF A LETTER OF ASSURANCE, IF ANY, OR IN ANY LICENSING AGREEMENTS ARE REASONABLE OR NON-DISCRIMINATORY. ISA REQUESTS THAT ANYONE REVIEWING THIS DOCUMENT WHO IS AWARE OF ANY PATENTS THAT MAY IMPACT IMPLEMENTATION OF THE DOCUMENT NOTIFY THE ISA STANDARDS AND PRACTICES DEPARTMENT OF THE PATENT AND ITS OWNER. ADDITIONALLY, THE USE OF THIS DOCUMENT MAY INVOLVE HAZARDOUS MATERIALS,ANSI/ISA-92.00.02-2013 - 4 -OPERATIONS OR EQUIPMENT. THE DOCUMENT CANNOT ANTICIPATE ALL POSSIBLE APPLICATIONS OR ADDRESS ALL POSSIBLE SAFETY ISSUES ASSOCIATED WITH USE IN HAZARDOUS CONDITIONS. THE USER OF THIS DOCUMENT MUST EXERCISE SOUND PROFESSIONAL JUDGMENT CONCERNING ITS USE AND APPLICABILITY UNDER THE USER’S PARTICULAR CIRCUMSTANCES. THE USER MUST ALSO CONSIDER THE APPLICABILITY OF ANY GOVERNMENTAL REGULATORY LIMITATIONS AND ESTABLISHED SAFETY AND HEALTH PRACTICES BEFORE IMPLEMENTING THIS DOCUMENT.The following people served as members of ISA Subcommittee ISA92.NAME COMPANYJ. Miller, Chair Detector Electronics CorporationR. Seitz, Vice Chair Artech EngineeringM. Coppler, Managing Director Det Norske Veritas Certification Inc.S. Baliga General MonitorsW. Bennett Mine Safety Appliances Co.T. Crawford Intertek Testing ServicesG. Garcha GE EnergyR. Goins Lyondell BasellK. Hedrick MSHA Approval & Certification CenterS. Henney FM ApprovalsC. Lucarino SenscientR. Masi Detcon Inc.D. Mills Underwriters Laboratories Inc.L. Owen Dooley Tackaberry Inc.A. Skinner GMI Gas Measurement Instruments LLCJ. Stratman Honeywell Analytics Inc.J. Thomason Omni Industrial Systems Inc.A. Vial Shell Exploration & Production Co.D. Wechsler American Chemistry CouncilThis standard was approved for publication by the ISA Standards and Practices Board on____________________.NAME COMPANYE. Cosman, Vice President The Dow Chemical CompanyD. Bartusiak ExxonMobil Chemical Co.P. Brett Honeywell Inc.J. Campbell ConsultantM. Coppler Det Norske Veritas Certification Inc.B. Dumortier Schneider ElectricD. Dunn Aramco Services Co.J. Federlein Federlein & Assoc. Inc.J. Gilsinn Kenexis ConsultingE. Icayan AtkinsJ. Jamison Spectra Energy Ltd.K. P. Lindner Endress + Hauser Process Solutions AGV. Maggioli Feltronics Corp.T. McAvinew Instrumentation and Control Engineering, LLC V. Mezzano Fluor CorporationC. Monchinski Automated Control Concepts Inc.R. Reimer Rockwell AutomationS. Russell Valero Energy Corp.- 5 - ANSI/ISA-92.00.02-2013 N. Sands DuPontH. Sasajima Azbil Corp.T. Schnaare Rosemount Inc.J. Tatera Tatera & Associates Inc.I. Verhappen Industrial Automation Networks Inc.W. Weidman WCW ConsultingJ. Weiss Applied Control Solutions LLCM. Wilkins Yokogawa IA Global Marketing (USMK)D. Zetterberg Chevron Energy Technology Co.This page intentionally left blank.- 7 - ANSI/ISA-92.00.02-2013Contents1Scope (11)2References (12)3Terms and definitions (12)4Basic information on the properties, behavior, and detection of gases and vapors (16)4.1Detecting gases and vapors – General (17)4.2Some common properties of gases and vapors (18)4.3The differences between detecting gases and vapors (19)4.4Oxygen deficiency (23)5Measuring principles (25)5.1General (25)5.2Selection criteria (26)5.3Miscellaneous factors affecting selection of equipment (30)6Behavior of gas releases (30)6.1Nature of a release (30)6.2Buildings and enclosures (33)6.3Unventilated buildings and enclosures (33)6.4Ventilated buildings and enclosures (34)6.5Natural ventilation (34)7Design and installation of fixed gas detection systems (35)7.1Basic considerations for the installation of fixed systems (35)7.2Location of detection points (36)7.3Access for calibration and maintenance (40)7.4Additional considerations for sample lines (40)7.5Summary of considerations for the location of sensors or sampling points (41)7.6Installation of sensors (42)7.7Integrity and safety of fixed systems (42)7.8Timing of installation during construction operations (44)7.9Commissioning (44)7.10Operating instructions, plans and records (45)8Use of portable and transportable toxic gas detection equipment (46)8.1General (46)8.2Initial and periodic check procedures for portable and transportableinstrumentation (47)8.3Guidance on the use of portable and transportable equipment (50)9Training of operational personnel (52)9.1General (52)9.2General training – Basic limitations and safety (53)9.3Operator training (54)9.4Maintenance training (54)10Maintenance, routine procedures and general administrative control (55)ANSI/ISA-92.00.02-2013 - 8 -10.1General (55)10.2Operational checks (56)10.3Maintenance (58)10.4Sensors (59)10.5Flow systems (60)10.6Readout devices (60)10.7Alarms (61)10.8Workshop calibration test and equipment (61)Annex A − Applicability & acceptance criteria (normative) (65)Annex B − Environmental parameters (informative) (67)Annex C − Instrument maintenance record for toxic gas detectors (typical) (informative) (71)INTRODUCTIONToxic gas detection equipment may be used whenever there is the possibility of a hazard to life or property caused by the accumulation of a toxic gas-air mixture. Such equipment can provide a means of reducing the hazard by detecting the presence of a toxic gas and issuing suitable audible or visual warnings. Gas detectors may also be used to initiate precautionary steps (for example plant shutdown, evacuation, and operation of fire extinguishing procedures).Equipment may be used to monitor a gas atmosphere below the applicable level, (PEL, REL, TWA, STEL or IDLH), limit in circumstances where accumulation of toxic gas may result in a concentration of the gas/air mixture to potential risks to life and health. Performance requirements for gas detecting equipment for such purposes are set out in ANSI/ISA-92.00.01 and ISA-92.00.04. However performance capability alone cannot ensure that the use of such equipment will properly safeguard life or property where toxic gases may be present. The level of safety obtained depends heavily upon correct selection, installation, calibration and periodic maintenance of the equipment, combined with knowledge of the limitations of the detection technique required. This cannot be achieved without responsible informed management.Portable equipment covered by the AN SI/ISA-92.00.01 and ISA-92.00.04 commonly have additional detectors for combustible gases and also for oxygen deficiency. Users are cautioned that even mild oxygen deficiency may be due to toxic concentrations of some other gas or vapor, which may not be detectable or adequately detected by the equipment in use. This concept must not be relied upon for detection of a non-monitored toxic gas because 0.1% oxygen reduction can mean 1,000 ppm or greater of the unknown toxic gas, which usually exceeds most toxic gas safety limits. All toxic gases suspected should be monitored by the proper equipment.Minimum requirements for the instruction manual of any particular toxic gas detection equipment are specified in ANSI/ISA-92.00.01 and ISA-92.00.04. These standards provide some necessary background knowledge on the points mentioned above.This standard has been specifically written to cover all the functions necessary from the need for gas detection all the way through ongoing maintenance of a successful gas detection operation. Different clauses are appropriate for different tasks within this range of operations. Each clause has been written as stand-alone as far as practicable. This means that some information is repeated in different clauses but with a different emphasis.The following table gives a broad suggestion as to the most relevant clauses to the typical tasks to be performed.ANSI/ISA-92.00.02-2013 - 10 -Table 1 – Functional applicabilityThis standard makes recommendations how to establish maintenance and calibration intervals. In certain countries there are general or industry-specific regulations that are mandatory and those shall be followed as a minimum requirement.- 11 - ANSI/ISA-92.00.02-20131 ScopeThis standard gives guidance on, and recommended practice for, the selection, installation, use and maintenance of electrically operated equipment intended for use in industrial and commercial safety applications for the detection and measurement of toxic gases complying with the requirements of ANSI/ISA-92.00.01 and ISA-92.00.04.This standard is a compilation of practical knowledge to assist the user, and applies to equipment, instruments and systems that indicate the presence of a toxic mixture of gasor vapor with air by using an electrical signal from a gas sensor to produce a meter reading, to activate a visual or audible pre-set alarm or other device, or any combination of these.Such equipment may be used as a means of reducing the risk whenever there is the possibility of a risk to life or health specifically due to the accumulation of a toxic gas-air mixture, by providing such warnings. It may also be used to initiate specific safety precautions (e.g. plant shutdown, evacuation, ventilation).This can be applied to all new permanent installations and, where reasonably practicable,to existing permanent installations. It is also applicable to temporary installations, whethernew or existing.Similarly it is applicable to the safe use of portable or transportable equipment, irrespective of the age or complexity of such equipment. Since much modern equipment ofthis type also includes other types of gas detection, some additional guidance is given for these topics.NOTE Equipment intended for use in hazardous(classified) areas should be Listed or Labeled for use withinthe intended area. For fixed equipment, installation should be in accordance with the National Electrical Code,ANSI/NFPA 70.For the purposes of this standard, except where specifically stated otherwise, toxic gases shall include toxic vapors.For the purposes of this standard, equipment includesa) fixed equipment;b) transportable equipment, andc) portable equipment.This standard is not intended to cover, but may provide useful information, for the following:a) equipment of laboratory or scientific type intended only for analysis or measurementpurposes;b) equipment intended for underground mining applications (group I equipment);c) equipment intended only for process control applications;d) equipment intended for applications in explosives processing and manufacture;。
微型气体探测器5: GasAlertMicro 5说明书
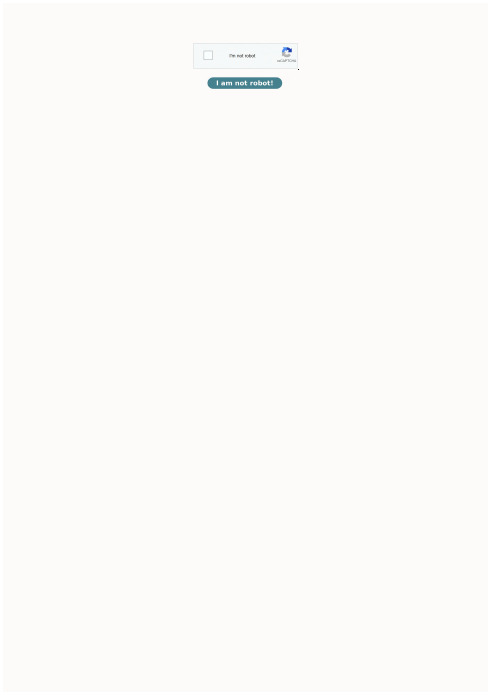
Multilingual support in English, French, German, Spanish and Portuguese. Large LCD display with user-selectable backlight. Four alert levels: low, high, TWA and STEL stealth modes. prehensive self-test confirms sensor, battery and circuit integrity, plus audible/visual alarms when activated.Protection where you need it.Features and benefits. Monitoring of volatile organic compounds (VOC), H2S, CO, O2, SO2, PH3, CI2, NH3, NO2, HCN, CIO2, O3 and flammable substances.
工业科学 维斯特 m x4 多气体监测器 产品手册说明书

1Multi-gas Monitor产品手册设 置操 作 维 护部件号:版本复合式气体检测报警器珠海司福斯特科技有限w w w .sa f e d t e c h .c o m气体/火焰检测专家!Ventis ™ MX4 产品手册目录版权声明 (3)警告及注意事项 (3)常规 ......................................................................................................................................................................... 3 人员 ........................................................................................................................................................................ 3 危险情况、毒物和污染物 ........................................................................................................................................ 3 一般用法.................................................................................................................................................................. 3 监管机构发布的使用条件与警告 .............................................................................................................................. 4 建议做法 .. (4)VENTIS MX4™ 资源 (6)VENTIS MX4 功能 (6)仪器拆箱 (7)箱内部件.................................................................................................................................................................. 7 反馈问题 .. (7)监测仪概述 (8)特点与功能 .............................................................................................................................................................. 8 显示屏幕.................................................................................................................................................................. 9 警报 .. (11)监测仪设置 ................................................................................................................................................................... 13 电池特性和监测仪兼容性 ...................................................................................................................................... 13 充电锂离子电池盒 (14)说明................................................................................................................................................................ 14 开机和关机 ............................................................................................................................................................ 16 配置 .. (17)介绍................................................................................................................................................................ 17 说明................................................................................................................................................................ 17 配置过程 .. (18)监测仪使用和维护 (25)调零、标定和通气测试 (25)程序................................................................................................................................................................ 25 建议................................................................................................................................................................ 25 一般信息. (26)说明 ............................................................................................................................................................... 26 现场空气采样建议做法 ......................................................................................................................................... 33 清洁 ...................................................................................................................................................................... 33 维护 .. (33)电池盒 ............................................................................................................................................................ 33 监测仪转换 ..................................................................................................................................................... 37 传感器、传感器防水膜、LCD 和振动电机更换 .............................................................................................. 39 泵模块 ............................................................................................................................................................ 42 Ventis MX4 分解图 .. (43)产品、规格与认证 (46)Ventis MX4 配件与部件 ......................................................................................................................................... 46 监测仪规格 ............................................................................................................................................................ 48 作业条件................................................................................................................................................................ 48 储存条件................................................................................................................................................................ 49 传感器规格 ............................................................................................................................................................ 49 有毒气体传感器 交叉灵敏度表 .............................................................................................................................. 49 可燃性气体的LEL 及LEL 相关系数 ...................................................................................................................... 50 认证 .. (51)质保 .............................................................................................................................................................................. 53 责任限定. (53)英思科公司全球办事处 .............................................................................................................................................. 封底珠海司福斯特科技有限w w w .sa f e d t e c h .c o m气体/火焰检测专家!Ventis™ MX4 产品手册►版权声明Ventis MX4™ 和Ventis™ 是英思科公司的商标。
《INNOVA 移动气体监测器》产品说明书

Portable Gas MonitorsFor one, two, three or four gasesInnova™(Standard Multi Gas)Innova FV™(Fuel Vapor)Innova LS™(Land Surveyor)Innova SV™(Soil Vapor)Innova XT™(Transformer)Specifications subject to change without notice (Aug 99)Distributed ByTel 1800 999 902Fax 1800 999 903GasTech Australia Pty LtdWangara Western Australia 606524 Baretta Rd.au®housing Thermo GasTech’s Innova Series of portable gas monitors are designed to protect workers from hazardous gases in confined spaces and other industrial work sites. The Innova features a powerful built-in pump, rugged electronics for the harshest conditions, simple operation, quick calibration, and robust sensors for long life. The Innova Series Portable Gas Monitors are available in several different gas combinations.I NNOVA™Portable Gas Monitors for one, two,three or four gasesSensors:Combustibles: Catalytic compensatedElectrochemical: Cl 2, CO, HCN, H 2S, NH 3, NO, NO 2, O 2, PH 3, SO 2Methane (Innova LS): Thermal Conductivity Sampling Methods:Sample-draw, internal pump Response Time:90% in 30 seconds90% in 50 seconds (HCN)90% in 60 seconds (NH 3)Accuracy:LEL: ±5% of reading O 2: ±5% Vol.Repeatability:LEL: ±2% of reading O 2: ±0.2% Vol.Operating Temperature:-4°F to 113°F (-20°C to 45°C)Humidity Range:0 to 95% RH, non-condensing Alarms:• user defined, programmable alarm levels • latching or self-resetting modes• low battery, low flow, or sensor failure• two levels of alarm with audible & visual indication to warn of unsafe gas levels LCD Display:• real-time gas concentrations• date & time • battery capacity • alarm set points Power Sources:Four “D” alkaline or NiCd batteries Battery Life:Alkaline: 24 hrs at 68˚F (20˚C)NiCd: 12 hrs at 68˚F (20˚C)Dimensions:10 in. (254 mm) L x 6 in. (152 mm) H x 5 in. (127 mm) W Weight:Approximately 5 lbs. (2.25 kg)Casing Materials:High impact, chemical, and RF resistant Xenoy ®(polycarbonate-polyester) plastic Splash Resistance:Water-resistant, gasketed housing Approvals:CSA Certified Intrinsically Safe to U.S. and Canadian Standards, Hazardous Locations Class I, Groups A, B, C & D LCIE Certified, EEX ia d IIC T4 Hazardous Locations Warranty:One year (materials and workmanship)S PECIFICATIONSppm, Cl 2, CO, HCN, H 2S, NH 3, NO, NO 2, PH 3, SO 2: ±5% of reading ppm, Cl 2, CO, HCN, H 2S, NH 3, NO, NO 2, PH 3, SO 2: ±10% of reading • backlight on demand •TWA, STEL, minimum & maximum readingsInnova LSInnova ™– One, Two, Three, or Four GasesThis multi-gas internal pump monitor is ideal for pre-testing confined spaces in refineries, wastewater treatment plants, fire departments, offshore oil wells,fish processing plants, utilities, tanneries, etc. This unit can be configured to monitor up to four gases in several combinations, including the detection of hydrocarbons in the % Vol., LEL or ppm range, oxygen content, and a choice of one or two toxics: Ammonia (NH 3), Carbon Monoxide (CO), Chlorine (Cl 2),Hydrogen Cyanide (HCN), Hydrogen Sulfide (H 2S), Nitrogen Dioxide (NO 2),Nitric Oxide (NO), Phosphine (PH 3), or Sulfur Dioxide (SO 2).•Monitors hydrocarbons in LEL or PPM ranges as a standard•Microprocessor electronics and convenient top-mounted switches make operation and calibration simple •Easy replacement of batteries and sensorsInnova FV ™ – Fuel VaporInnova FV is designed to measure combustible fuel vapors in aircraft wing tanks and fuel storage areas. This instrument monitors for oxygen content and hydrocarbons in either percent LEL or PPM.•Extra sensitive PPM combustible range (0-1000 ppm) in 10 ppm increments•Humidity resistant, combustible sensor is not affected by changes in relative humidity (RH)•Calibrated with hexane to represent fuel vaporsInnova LS ™– Land SurveyorThe Innova LS is designed to test for methane and other gases in landfills,vaults, trenches, bar holes, vents, and other applications. This multi-gas monitor detects methane in the ppm, % LEL, and % Vol. ranges, oxygen, and one toxic gas (either carbon monoxide or hydrogen sulfide).•Monitoring of methane in two optional range sets• Autorange adjusts to the correct range as methane concentrations increase, allowing hands-free operation.Innova SV ™– Soil VaporThe INNOVA SV is designed for applications such as soil remediation and bar-hole monitoring. Designed to detect total hydrocarbons (including methane) in percent LEL or PPM, and includes unique operation mode selection for non-methane hydrocarbons.• Dual mode operation can distinguish between methane or natural gas and other volatile combustibles.• Extra sensitive PPM combustible range (0 - 1000 ppm) in 10 ppm increments• Humidity resistant combustible sensor is not affected by changes in the relative humidity (RH)Innova XT ™– TransformerInnova XT tests for the presence of combustible gases in the inert headspace of power transformers. It offers significant time and cost savings over the traditional dissolved gas analysis. The test is simple, as results are given in real-time. One instrument is able to test many transformers. This unit can monitor hydrocarbons in percent LEL or PPM, as well as oxygen content.•Extra sensitive detection in PPM or LEL is standard •Significant cost savings over dissolved gas analysis (DGA)•All necessary accessories (dilution fitting, probe, and two tedlar bags) come standard with each unitF VL SS VX TR ANGE OF G ASES D ETECTED Array *Specify range at time of order(Note: Specify up to two toxic gas sensors on the Standard INNOVA monitor)Thermo GasTech Innova model name designationsInnova ST Standard MonitorInnova FV Fuel Vapor MonitorInnova LS Land Surveyor MonitorInnova SV Soil Vapor MonitorInnova XT Transformer MonitorFloat Probe 82-507130" probe with dust filter80-0187-04Specifications subject to change without notice (Aug 99)Wangara Western Australia 6065.au。
Gas detector说明书

CertificateN": B AM|ZBN006/05
>(
Herebyit is certifiedby the BAMCertificatioBn odythatthe
Portablegas detector Model:,,GasAlertMicro"
Types : ,,GAM|C-X(y)-(DL2-|wRi)t"h H2S& COsensor
and GAMIC-BAT2-03
Accessories: BatterychargerModelGAMlC-CO1-K-EUandGAMlC-C03-K-EU
TestreportBAMll-1332t2OOo4f Augusst th2, OO5
Thetestreporct omprise5s1 pagesand30annexews ith847pages.
E x a m i n a t i do on c u m e n t s :
1. QuickReferencGe uideGasAlertMicDro55541(4Englishin) theversionof 2004,20pages
2. GasAlertMicArToEXApprovaLlabelwitdhrawinNg o.GMlA-2o5f1April25th, 2005,GasAlertMicBroAMCertificatioSntickeGr MIA-328of Septembe8rth,2005 andBAMCalGasLabewl ithdrawingNo.FXUA09C of April2nd,2004,3pages
ofthemanufactureBrW TechnologieLs td.
BW气体检测仪认证证书GasAlert-XT_Approval(ABS)

中国区经销商:深圳市深国安电子科技有限公司 http://www.singoan.comDate Issued:12/MAY/2003Certificate Number:VA-348169-X11/MAR/2005Valid as of: Array Certificate of Type Approval(RQS)This is to certify that BW Technologieshas met the requirements of ABS Product Type Approval forGas DetectorsModel Name(s):GASALERT EXTREME SERIES:GAXT-H(H2S),GAXT-S(SO2), GAXT-D(NO2),GAXT-E(ETO),GAXT-N(NO),GAXT-M(CO),GAXT-C(CI2), GAXT-A(NH3),GAXT-V(CIO2),GAXT-X(O2),GAXT-Z(HCN),GAXT-P(PH3),GAXT-G(O3).Presented to:BW Technologies2840-2nd Avenue S.E.CalgaryAlberta T2A7X9CanadaIntended Service:Single gas detector,intrinsically safe for use in Class1,Division1Groups A,B,Cand D.Description:Portable,disposable battery operated,single gas detector,intrinsically safe for usein Class1,Division1Groups A,B,C and D toxic gas and oxygen depletionmonitors with audible and visual alarms.Ratings:Operating Temperature:H2S,SO2&HCN:-40deg.C to+50deg.C(-40deg.F to+122deg.F)CO:-30deg.C to+50deg.C(-22deg.F to+122deg.F)OtherGases:-20deg.C to+50deg.C(-4deg.F to+122deg.F)Operating Humidity:CO,H2S,SO2,CI2,HCN,NO2,NH3,PH3,ETO,NO,O3:15%to90%CI2:10%to95%CIO2:15%to95%O2:0%to99%Operating Voltage:One3.6V Lithiumbattery,replaceable IECEx:Ex ia IIC T4;Rugged,IP-66/67highly water-resistantdesign For detail specification see attached"pdf"fileService Restrictions:Unit Certification is not required for this product.Comments:To be used in accordance with user manual D5561/4,iEPR:117000.Notes/Documentation:Term of Validity:This product/model is covered under Product Design Assessment(PDA)Certificate#05-HS486614-PDA,dated28/Feb/2005.This PDA Certificate expires Feb of2010.It will remain valid for the5years from date of issue or until the Rules orspecifications used in the assessment are revised(whichever occurs first).ABS Rules:2005Steel Vessel Rules1-1-4/7.7National Standards:UL20040910-E131021dated10September2004.Certificate for use in Class1,Division1Group A,B,C&D ANSI UL913.International Standards:IECEX Certificate of Conformity#IECEx UL04.0003dated21December2004.IEC60079-0and IEC60079-11.EEX Ia IICCE0539Ex II1G DEMCO04ATEX0336363IECEX.EC-Type Examination Certificate#DEMKO04ATEX0336363dated28December2004Government Authority:Date Issued:12/MAY/2003Certificate Number:VA-348169-XValid as of:11/MAR/2005 EUMED:Others:Manager,ABS Programs ABS has used due diligence in the preparation of this certificate and it represents the information on the product in the ABS Records as of the date and time the certificate was printed.Type Approval requires Drawing Assessment,Prototype Testing and assessment of the manufacturer's quality assurance and quality control arrangements.Limited circumstances may allow only Prototype Testing to satisfy Type Approval.The approvals of Drawings and Products remain valid as long as the ABS Rule,to which they were assessed,remains valid.ABS cautions manufacturers to review and maintain compliance with all other specifications to which the product may have been assessed.Further, unless it is specifically indicated in the description of the product;Type Approval does not necessarily waive witnessed inspection or survey procedures(where otherwise required)for products to be used in a vessel,MODU or facility intended to be ABS classed or that is presently in class with ABS.Questions regarding the validity of ABS Rules or the need for supplemental testing or inspection of such products should,in all cases,be addressed to ABS.。
受限空间作业气体检测要求

受限空间作业气体检测要求Working in confined spaces presents unique challenges, especially when it comes to gas detection requirements. The need to monitor and detect potentially harmful gases in these environments is crucial for ensuring the safety and well-being of workers. In this essay, we will explore the various aspects of gas detection in confined spaces, including the importance of monitoring, the types of gases that may be present, the potential risks involved, the technology and equipment used for detection, the regulations and standards that govern gas detection in confined spaces, and the best practices for ensuring a safe working environment.Gas detection in confined spaces is of utmost importance due to the potential presence of hazardous gases that can pose serious risks to workers. These gases can be colorless, odorless, and tasteless, making them virtually undetectable without the use of specialized equipment. Some of the most common gases found in confined spaces includecarbon monoxide, hydrogen sulfide, methane, and various volatile organic compounds. Exposure to these gases canlead to asphyxiation, poisoning, and even death, making it essential to have effective gas detection measures in place.The risks associated with gas exposure in confined spaces are significant, and the consequences can be severe. Workers may experience symptoms such as dizziness, nausea, headaches, and respiratory problems when exposed to high levels of gases. In extreme cases, gas exposure can lead to loss of consciousness, coma, and even death. Additionally, the lack of proper gas detection and monitoring can resultin catastrophic accidents, including explosions and fires, further emphasizing the critical need for effective gas detection in confined spaces.To address the challenges of gas detection in confined spaces, various technologies and equipment are utilized to monitor and detect the presence of hazardous gases.Portable gas detectors, fixed gas monitoring systems, and personal gas monitors are commonly used to continuously monitor the air quality in confined spaces. These devicesare equipped with sensors that can detect a wide range of gases and provide real-time data on gas concentrations, allowing for immediate action to be taken in the event of a gas leak or buildup.In addition to the technology and equipment used for gas detection, there are also specific regulations and standards that govern the monitoring and detection of gases in confined spaces. For example, the Occupational Safety and Health Administration (OSHA) in the United States has established regulations such as 29 CFR 1910.146, which outlines the requirements for permit-required confined spaces and the necessary measures for gas detection and monitoring. Compliance with these regulations is essential for ensuring the safety and well-being of workers in confined spaces.In order to maintain a safe working environment in confined spaces, it is crucial to follow best practices for gas detection and monitoring. This includes conducting thorough risk assessments to identify potential hazards, implementing effective ventilation systems to control thebuildup of gases, providing proper training for workers on gas detection equipment and procedures, and establishing clear communication protocols for responding to gas-related emergencies. By adhering to these best practices, employers can create a safer and healthier work environment for their employees.In conclusion, gas detection in confined spaces is a critical aspect of ensuring the safety and well-being of workers. The potential presence of hazardous gases, the associated risks, the technology and equipment used for detection, the regulations and standards that govern gas detection, and the best practices for maintaining a safe working environment all highlight the importance of effective gas detection measures in confined spaces. By prioritizing gas detection and monitoring, employers can mitigate the risks associated with confined space work and protect the health and safety of their employees.。
多道气体监测仪 MultiRAE 技术指南说明书

HORIBA PG-250辅助连续排放监测仪说明书

Portable Gas AnalyzerPG-250A single portable analyzer capable of measuring five components with the same methods used by permanent CEMS.A single analyzer capable of measuring five componentsThe HORI BA PG-250 is a highly reliable and versatile gas analyzer for compliance testing of NOx, SO 2, CO, CO 2, and O 2, housed in a single lightweight and fully portable case. Unlike other portable gas analyzers that rely upon electro-chemical sensors, the HORI BA PG-250 utilizes the same measurement principles as a permanently installed CEMS. These include NDIR (pneumatic) for CO and SO 2; NDIR (pyrosensor) for CO 2; Chemillumine-scence (cross flow modulation) for NOx; and Galvanic Cell for O 2 measurements.More importantly, the HOR I BA PG-250 meets or exceeds the regulatory requirements established by agencies such as the EPA in the U.S. for portable or backup continuous emission monitoring systems.Compact and lightweightThe PG-250 is capable of intermittent or continuous measurement of five compo- nents simultaneously. The compact and lightweight case, with a built-in carrying handle, is as easy to transport as a suitcase. Thus, the PG-250 is ideal for moving between several stacks at a single plant or for carrying across the country to measure clusters of stack emissions at multiple locations.Built-in sampling unitThe HORIBA PG-250 consists of a sample probe, drain separator and gas analyzer. The built-in sampling system consists of a filter, an acid mist catcher, a sampling pump, an electronic cooler for removal of water vapor, a solenoid valve for auto-draining, an NOx to NO converter and a scrubber to remove internally generated ozone from the instrument exhaust.Simple to operate, easy to readA major feature of the PG-250 is its ease of operation and large, easy-to-read front panel displays. Screens can be selected from a menu or appropriate screens and messages will appear automatically during operation.Calibration screenOthers screens and messages are:Parameter setting: To set O 2 concentration to be used to correct the measured values for NOx and SO 2 and to set the measurement arranging time. (10 or 30 s)Battery drained: Memory back up battery needs to be replaced.Purge: In process, completed Drain dischargingDisplay : Reset the number of operating days.Optional electronic coolerTo measure sample gases that contain greater than 20 by volume concentra-tions of water vapor, such as those encountered during continuous monitoring of internal gas turbins, boilers, waste incinerators incineration, etc., an optional sample gas pre-conditioning unit, called an "electronic cooler," is available. This accessory is recommended when the instrument will be sampling stack gases continuously for longer than eight hours.(Max. 3 days)Measurement screen"WARM-UP" screenConcentrations for five components, along with the sample flow rates, are indicated simultane-ously on the LCD. Raw measurements are auto-matically adjusted for oxygen concentration.ndicates the analyzers range, and zero and span calibration infor-mation for all compo-nents with calibration commands.Indicates that the power has recently been turned on. When ready, "MEASUREMENT" is displayed.(Forced mea-surement is possible in the WARM-UP mode.)ProbeBoilers GasturbinesElectricutilitiesIncineratorsRefineries()HORIBA continues contributing to the preservation of the global environment through analysis and measuring technology.Bulletin:HRE-2849GPrinted in Japan ZK-TH(SK)33●The contents of this catalog are subject to change without prior notice, and without any subsequent liability to this company.●The color of the actual products may differ from the color pictured in this catalog due to printing limitations.●It is strictly forbidden to copy the content of this catalog in part or in full.●All brand names, product names and service names in this catalog are trademarks or registered trademarks of their respective companies. e-mail:**************.jp●HORIBA, Ltd.Head OfficeMiyanohigashi, Kisshoin Minami-ku, Kyoto, Japan Phone: 81 (75) 313-8123Fax: 81 (75) 321-5725Tokyo Sales Office 1-7-8 Higashi-KandaChiyoda-ku, Tokyo, Japan Phone: 81 (3) 3861-8231Fax: 81 (3) 3861-8259●HORIBA KOREA L t d .112-6 Sogong-DongChoong-ku, Seoul, Korea Phone: 82 (2) 753-7911Fax: 82 (2) 756-4972●HORIBA INSTRUMENTS I NCORPORATED Irvine Facility17671 Armstrong Avenue Irvine, CA 92614, U.S.A.Phone: 1 (949) 250-4811Fax: 1 (949) 250-0924Leichlingen FacilityJulius-kronenberg Strasse D-42799 Leichlingen GermanyPhone: 49 (2175) 8978-0Fax: 49 (2175) 8978-50●HORIBA INSTRUMENTS LIMITED Kyoto CloseSummerhouse RoadMoulton Park, Northampton NN3 6FL, U.K.Phone: 44 (1604) 542500Fax: 44 (1604) 542699●HORIBA INSTRUMENTS Pte. L TD.10 Ubi Crescent#05-11/12, Ubi Techpark Singapore 408564Phone: 65 6745-8300Fax: 65 6745-8155●HORIBA EUROPE GmbH Head Office Hans-Mess-Str.6D-61440 Oberursel/Ts.GermanyPhone: 49 (6172) 1396-0 Fax: 49 (6172) 137385●HORIBA GmbH Kaplanstrasse 5A-3430 Tulln, AustriaPhone: 43 (2272) 65225Fax: 43 (2272) 65230HORIBA CZECHIAOrganizachi slozka Praha Petrohradska 13CZ-101 00 Praha 10, Czech RepublicPhone: 420 (2) 717-464-80Fax: 420 (2) 717-470-64●HORIBA TRADING (SHANGHAI) CO., Ltd.Shanghai OfficeRoom 1701, United Plaza,1468 Nanjing Rd. West,Shanghai, 200040, ChinaPhone: 21-6289-6060Fax: 21-6289-5553Beijing Office Room 1801, Capital Tower Beijing, Tower 1 No.6Jia, Jianguomenwai Ave., Chaoyang District, Beijing, 100022 China Phone: 10-8567-9966Fax: 10-8567-9066●HORIBA FRANCE12, Avenue des Tropiques 91955 LES ULIS FrancePhone: 33 (1) 69-29-96-23Fax: 33 (1) 69-29-95-77●HORIBA India Private Limited Delhi Office 1212A, Hemkunt Tower, 98 Nehru Place,New Delhi - 110019 INDIA Phone: +91 11-4669-5001/5002 Pune Office 502, Purushottam Plaza,Baner Road, Baner, Pune - 411045 INDIAPhone: +91 20-2729-1121。
Honeywell Vertex Gas Monitoring System用户手册说明书

MUL TI-POINT TOXIC GAS2 | | Honeywell Vertex™ Gas Monitoring SystemVertex™ – the highly sensitive and reliable multi-point low-level toxic gas monitoring system backed by physical evidence of an actual gas release.VERTEX OFFERS A GAS MONITORING SOLUTION THAT ADAPTS TO YOUR CHANGING GAS DETECTION NEEDSAccuracyThe Vertex provides various benefits, including improved accuracy and safetythrough well-defined visual staining even at low concentrations detection enabled by Honeywell’s flow-through closed-loop optical system. This feature enhances the system’s ability to detect toxic gases, leading to a more efficient, safer operation and helps to minimize downtime.Enhanced safety and operational efficiencyThe Vertex’s full suite of redundancy features advanced communications that mitigate the risk of system failure, such as • Dual power supply • Dual hard drives • Dual pumpsSupport continuous operation even in the event of system continuity issues, promoting enhanced safety and improved operational efficiency.Reduced total cost of ownershipVertex provides a reduced total cost of ownership through automatic flow adjustments, which reduces the time required for servicing and maintenance. Advanced diagnostics include 100+ instrument and maintenance faults to advise the user of the system’s operational stateACCURATE, CONTINUOUS MUL TI-POINT DETECTION OF TOXIC GASES AT A HIGH LEVEL OF RELIABILITYVertex™ offers powerful,built-in system redundancyas standard equipment toeffectively safeguard againstdowntime.Honeywell Vertex™ Gas Monitoring System | | 34 | | Honeywell Vertex™ Gas Monitoring SystemAs the pioneer of Chemcassette® gas analyzers, we engineered the Vertex to deliver an increased level of reliability.A CLEARL Y VISIBLE STAIN FOR LOW-LEVEL DETECTION YOU CAN COUNT ONWith Honeywell Chemcassette technology, the density of the stain on the tape is proportional to the concentration of the gas, so visibility of the stain is critical. That’s why Honeywell Vertex tape-based systems, generates a clear, easy-to-view stain that matches the severity of the gas release. With this precision, the opticalscanners in Vertex can measure the stain accurately and trigger the right alarm.ReliableVertex offers powerful, built-in system redundancy as standard equipment to effectively safeguard against downtime.• Back-up pump and internalpower module• Chemcassette technology provides physical evidence of a gas event• System data backup. If main data acquisition PC fails, analyzerscontinue to monitor, log data andalarm• Drip-resistant cap for systemprotection from overhead leaks• Automated leak test with lineintegrity optionFlexibleStart your Vertex system with as littleas eight points. Vertex expands as your monitoring needs change, offering up to 72 points of continuous gas detection. Place sampling points up to 400 feet (120 meters) from the system. There is a choice of universal analyzer modules and/or pyrolyzer analyzers.Easy to use• Touchscreen for easy access to data • Software updates via CD-ROM or network to all system components • Configuration profile editing and dataretrieval are all achievable withouttaking unit offline• Radio frequency identificationtag (RFID) ensures Chemcassetteare installed into appropriatelyprogrammed analyzer, eliminatinghuman error• Online help systemSecurity• Multiple levels of password protection• Reconfigure security setup withouttaking unit offlineReduced total cost of ownership• Vertex’s smaller footprint and greaterdensity of points reduces your costper point• Eight points per analyzer lowersChemcassette costs• Maximized 72-point systems providelow cost per point as compared toother continuous monitors• One system monitors up to nine gasfamilies and more than 40 gases• You can split your sample into morethan one analyzerEasy to maintain• Vertex uses cost-effective XPChemcassettes providing up to fourmonths of continuous monitoring• Simplified replacement ofChemcassettes and automated opticsverification• No dynamic calibration required• Easy access to analyzers, pumps,power supplies and touchscreen fromfront panel• Onscreen interactiveelectronic manualAdvanced communications• Built-in configurable PLCs withoptional 176 relay contacts• Standard OPC interface for easyintegration into your existing factoryautomation system or HMI• Optional Ethernet/CIP, DeviceNet™,Profibus®, Profinet®, Modbus/TCP orControlNet™ outputs available• Optional ChemCam camera permitsviewing of stain, locally or remotely,for proof of the gas event. Image iselectronically saved for future retrieval.• Optional remote control/viewingsoftware enables total visualization ofthe monitor screens at a remote PCOperating system• Windows® 10 IoT Enterprise to improveIT securityFEATURES AND BENEFITSHoneywell Vertex™ Gas Monitoring System | | 5DESIGNED FOR THE TOXIC GASES IN YOUR OPERATIONSHoneywell Vertex can be tailored to meet the requirements of your facility. With up to nine Chemcassette gas analyzers, each with eight points of detection, the system monitors virtually every gas used in semiconductor fabs — down to parts per billion (ppb). These gases include:• Chemcam Camera• Line Filters• TubingDESIGNED FOR THE TOXIC GASES INYOUROPERATIONSNew calibrations are continuously developed.6 | | Honeywell Vertex™ Gas Monitoring SystemHoneywell Vertex™ Gas Monitoring System | | 7RELIABILITY AND DURABLE SUPPORTHoneywell is a major gas detection provider with a division focused exclusively on semiconductor manufacturing and other high tech industries such as solar material, flat panel displays and more. That means we know your business — and how you need to protect it.At Honeywell, we understand the value of your production. That’s why we engineered the Honeywell Vertex for an enhanced standard of accuracy and reliability, so you can feel confident that your toxic gas management system is helping to keep your people safe and your operations running.Every day, Honeywell gas detection technologies protect people and billions of dollars in assets at semiconductor fabs, research labs and other high tech facilities throughout the world. And since we are the original manufacturer of the Vertexproduct lines we sell, we know how to support it. Honeywell has a worldwide network of service engineers who are knowledgeable and passionate about gas detection.Honeywell Vertex is part of a comprehensive ecosystem of gas-detection products and services for your operations, including fixed systems, portable and transportable gas detectors, controllers, software, systems integration and more. So when you demand enhanced safety standards and deep knowledge of industrial technologyand applications, Honeywell is here for you.WORLD LEADER IN GAS DETECTIONHoneywell Analytics offers you more than 30 years’ experience in developing patented Chemcassette® tape technology. Vertex™ Multi-Point Toxic Gas Monitoring System complements electrochemical cell, catalytic bead and infrared monitors.24 HOUR SERVICEHoneywell’s global team oftechnical service professionals is at your service 24 hours a day, 7 days a week in more than 60 countries.For more informationHoneywell Sensing and Safety Technologies830 East Arapaho Road Richardson, TX 75081 Contact usUS & CanadaTel. 302 613 4491***************************HGAS_Vertex™_BRO_US-EN_0323©2023 Honeywell International Inc.Profibus and Profinet are trademarks or registered trademarks of Profinet International (PI).DeviceNet and ControlNet are trademarks or registered trademarks of ODVA, Inc.Windows is a trademark or registered trademark of Microsoft Corporation in the United States and other countries.Vertex and Chemcassette are trademarks or registered trademarks of Honeywell International Inc.。
得捷电子 Intellidox端口重组模块及可启用包说明书

What’s in the BoxIntellidox Docking ModuleEach Intellidox Docking Module package contains one Intellidox module with a factory-installed nest for the ConneX1 portable gas detector. The power adapter, power cord, calibration gas tubing, exhaust tubing, and user manual are packaged sepa-rately as the Intellidox Enabler Kit. One Enabler Kit is required for each stand-alone Intellidox module.If the Intellidox module is damaged or if parts are missing, con-tact BW T echnologies or an authorized distributor immediately.Intellidox Enabler KitOne Intellidox Enabler Kit is required for each stand-alone Intel-lidox module. Each Enabler Kit contains:1. Power supply and AC power cord appropriate to shippingdestination;2. Ethernet cable;3. Calibration gas and purge gas tubing, cut to 1 meter(3.3 feet);4. Quick connect fittings;5. Exhaust tubing, cut to 4.57 meters (15 feet);6. Inlet (purge) filter assembly;7. Intellidox end plate;8. CD containing the Intellidox Operator’s Manual in PDFformat; and9. CD containing FleetManager II version 3.0.0 software orhigher.If Enabler Kit parts are damaged or missing, or if additionalEnabler Kits are required, contact BW T echnologies or an autho-rized distributor immediately.A b o u t t h i s P u b l i c a t i o nT h i s p u b l i c a t i o n i s a q u i c k -s t a r t r e f e r e n c e g u i d e t o a s s e m b l i n g t h e I n t e l l i d o x D o c k i n g M o d u l e , a n d p r e p a r i n g i t f o r fi r s t u s e . E n s u r e t h a t y o u a r e f a m i l i a r w i t h t h e u s e o f p e r s o n a l g a s d e t e c -t i o n d e v i c e s a n d a c c e s s o r i e s , a n d t a k e a p p r o p r i a t e a c t i o n i n t h ee v e n t of a n a l a r m c o n d i t i o n .F o r a d d i t i o n a l i n f o r m a t i o n r e g a r d i n g I n t e l l i d o x i n s t a l l a t i o n , c o n fi g u r a t i o n , o p e r a t i o n a n d m a i n t e n a n c e , r e f e r t o t h e I n t e l l i d o xO p e r a t o r M a n u a l o r v i s i t w w w .g a s m o n i t o r s .c o m .A b o u t t h e I n t e l l i d o x D o c k i n g M o d u l eT h e I n t e l l i d o x D o c k i n g M o d u l e (‘I n t e l l i d o x ’ o r ‘I n t e l l i d o x m o d u l e ’) i s a n a u t o m a t i c b u m p t e s t a n d c a l i b r a t i o n d o c k i n g s t a t i o n f o r u s e w i t h C o n n e X 1 p o r t a b l e g a s d e t e c t o r s m a n u f a c t u r e d b y B W T e c h n o l o g i e s . T h e I n t e l l i d o x a u t o m a t i c a l l y p e r f o r m s e s s e n t i a l p r o c e d u r e s i n c l u d i n g s e n s o r i d e n t i fi c a t i o n , b u m p t e s t s , c a l i b r a -t i o n s , a l a r m t e s t s a n d d a t a t r a n s f e r s . I t a l s o r e t a i n s a c u m u l a t i v e r e c o r d o f d e t e c t o r d a t a l o g s t h a t a r e t r a n s f e r r e d t o i t s o n b o a r dm e m o r y .T h e I n t e l l i d o x c a n b e u s e d o n a t a b l e t o p o r o t h e r fl a t s u r f a c e . A b u i l t -i n r e t r a c t a b l e s t a n d c a n b e d e p l o y e d t o h o l d t h e I n t e l l i d o x u p r i g h t a t a n a n g l e t h a t i s s u i t a b l e f o r r o u t i n e u s e . I n t e l l i d o x m o d u l e s c a n a l s o b e m o u n t e d o n a w a l l o r o t h e r fl a t s u r f a c e . F o ra d d i t i o n a l i n f o r m a t i o n , r e f e r t o t h e O p e r a t o r M a n u a l.T h i s I n t e l l i d o x m o d e l i s i n t e n d e d f o r u s e a s a s t a n d -a l o n e d o c k -i n g m o d u l e o n l y . D o n o t c o n n e c t t w o o r m o r e I n t e l l i d o x m o d u l e st o g e t h e r .I n t e n d e d U s eU n l e s s o t h e r w i s e s p e c i fi e d a t t i m e o f p u r c h a s e , I n t e l l i d o x m o d -u l e s s h i p p e d f r o m B W T e c h n o l o g i e s :• A r e f a c t o r y c o n fi g u r e d f o r u s e w i t h C o n n e X 1 p o r t a b l e g a s d e t e c t o r s c o n t a i n i n g H 2S s e n s o r s w i t h s t a n d a r d c a l i b r a t i o ng a s s e t t i n g s .• C o n t a i n a m u l t i -g a s e x p a n s i o n m o d u l e .• O p e r a t e a s s t a n d -a l o n e b u m p t e s t a n d c a l i b r a t i o n s t a t i o n s .• M a y b e c o n n e c t e d t o a n e t w o r k v i a E t h e r n e t c a b l e f o r e n h a n c e d a c c e s s t o a n d c o n t r o l o f a d m i n i s t r a t i v e a n dm a i n t e n a n c e t a s k s .• A r e c o m p a t i b l e w i t h F l e e t M a n a g e r I I v e r s i o n 3.0.0 s o f t w a r eo r h i g h e r .I f t h e I n t e l l i d o x m o d u l e o r a n y o f i t s p a r t s a r e d a m a g e d o r m i s s i n g , c o n t a c t B W T e c h n o l o g i e s o r a n a u t h o r i z e d d i s t r i b u t o ri m m e d i a t e l y .N o r m a l O p e r a t i n g C o n d i t i o n sT h e I n t e l l i d o x i s d e s i g n e d t o b e s a f e u n d e r t h e f o l l o w i n g c o n d i -t i o n s :• I n d o o r u s e o n l y• N o r m a l a t m o s p h e r e (20.9% O 2) t h a t i s f r e e o f h a z a r d o u sg a s• T e m p e r a t u r e r a n g e o f +10°C t o +35°C• R e l a t i v e h u m i d i t y o f 0% t o 50%I f t h e i n t e n d e d o p e r a t i n g e n v i r o n m e n t d o e s n o t m a t c h t h e s e c r i -t e r i a , B W T e c h n o l o g i e s r e c o m m e n d s t h a t y o u c o n s u l t a q u a l i fi e d p r o f e s s i o n a l s p e c i a l i s t p r i o r t o i n s t a l l i n g a n d u s i n g a n y I n t e l l i d o xm o d u l e s .T h i s e q u i p m e n t u s e s p o t e n t i a l l y h a r m f u l g a s f o r c a l i b r a t i o n s . T h e I n t e l l i d o x m u s t b e a t t a c h e d t o a v e n t i n g s y s t e m o r b e u s e d i n aw e l l -v e n t i l a t e d a r e a .Copyright, Notices, TrademarksWhile this information is presented in good faith and believed to be accurate, BW Technologies disclaims the implied warranties of merchantability and fitness for a particular purpose and makes no express warranties except as may be stated in its written agree-ment with and for its customers.In no event is BW T echnologies liable to anyone for any indirect, special or consequential damages. The information and specifica-tions in this document are subject to change without notice.Intellidox, ConneX1, and FleetManager II are trademarks of BW Technologies. Other brand or product names are trademarks of their respective owners.Symbol DefinitionsThis manual uses the following signal words, as defined by ANSI Z535.4-1998:Important Safety Information: Read First1. To ensure personal safety, read Safety Information andWarnings before using the Intellidox.2. Use the Intellidox only as specified by the manufacturer.Failure to do so may impair protection provided by the Intellidox.3. The safety and security of any system or networkincorporating the Intellidox and its accessory components is the responsibility of the assembler of the system.4. Follow all required National Electric Codes (NEC) and safetystandards.Prepare for First UseT o ensure that the Intellidox module is ready for safe opera-tion, you must attach the endplate, attach the purge inlet filter assembly, and connect the exhaust tubing before you connect power or attach a gas cylinder.Attach the EndplateEach Intellidox Enabler Kit contains one endplate. T o prevent gas leaks, the end plate must be attached and locked with the lock latch arm before connecting power supply or connecting gas cylinders. The end plate must remain securely latched at all times during operation. If the end plate is detached during operation, disconnect power and replace the end plate immedi-ately.1. Unhook and lift latch arm.2. Attach end plate.3. Lower and lock latch arm.Connect the Purge Inlet Filter AssemblyEach Intellidox Enabler Kit contains one purge inlet filter as-sembly. Unless otherwise specified, the purge inlet is configured to use ambient air in a fresh air environment with a normal atmosphere of 20.9% O 2 that is free of hazardous gas . Ensure that the purge inlet filter assembly is attached before using the Intellidox module. Y ou may attach an extension tubing to the filter assembly to draw ambient air from an adjacent fresh air environment.D o c k i n g M o d u l e50104991-166 || Q R G -E N -F M S U _B 2 E n g l i s h ©2016 B W T e c h n o l o g i e s . Al l r i g h t s r e s e r v e d .2840 2 A v e . S E C a l g a r y , A l b e r t a C a n a d a T 2A 7X 9C a n a d a : 1-800-663-4164U S A : 1-888-749-8878E u r o p e : +44 (0) 1295 700300O t h e r r e g i o n s : 1-403-248-9226F a x : 1-403-273-3708W e b : w w w .h o n e y w e l l a n a l y t i c s .c o mQ u i c k R e f e r e n c eG u i d eBW TECHNOLOGIES BY HONEYWELL 50104991-166 || QRG-EN-FMSU_B2 INTELLIDOX DOCKING MODULE QUICK REFERENCE GUIDEB W T EC H N O L O G I E S B Y H O N E Y W E L L W W W .H O N E Y W E L L A N A L Y T I C S .C O M I N T E L L I D O X D O C K I N G M O D U L E Q U I C K R E F E R E N C E G U I D EI n t e l l i d o x2. If AutoDownload Datalog is set usingFleetManager II software, detector datalogs are automatically transferred to Intellidox.Bump Test PassWhen the bump test is successful, LCD screen background changes to green and Bump test passed message is displayed. Alarm responseand sensor response test items are checked.Press to return to Intellidox user menu.Bump Test FailWhen the bump test fails, LCD screen back-ground changes to red and Bump test failed message is displayed. Failed alarm response and/or sensor response test items are markedwith .If the AutoCal on Failed Bump is set using Fleet-Manager II software, calibration automatically begins.CalibrationCalibration is a two-step procedure that deter-mines the measurement scale for the detector’s response to gas. In the first step, a baseline reading is taken in a clean, uncontaminated environment. In the second step, the sensors are exposed to known concentrations of gas. The detector uses the baseline and known gas concentrations to determine the measurement scale.Calibration Guidelines1. Calibrate only in a normal environment thatis 20.9% O 2 and free of hazardous gas. Do not operate the docking module in a hazardous area. Failure to adhere to this guideline can result in possible personal injury and/or property damage.2. Use only premium grade calibrationgases and cylinders that are approved by BW Technologies, and supplied by BW Technologies or an authorized distributor. The calibration gases mustmeet the accuracy of the detector. For more information, refer to the Operator Manual.3. Do not use a gas cylinder beyond itsexpiration date.4. All calibration cylinders must be usedwith a demand flow regulator and must meet these maximum inlet pressurespecifications: disposable cylinders: 000 psig/70 bar, refillable cylinders: 03000 psig/207 bar5. Do not calibrate the detector duringcharging or immediately after charging is complete.6. Calibrate the sensor if ambient gasreadings vary during startup.7. Calibrate a new sensor before use. Allowthe sensor to stabilize before starting calibration.8. Used sensor: wait 60 seconds 9. New sensor: wait 5 minutes10. When calibrating the same gas detectormultiple times, wait 10 minutes between calibrations to allow the sensor to stabilize.11. If a certified calibration is required,contact BW Technologies or an authorized distributor.Calibrate a DetectorIf AutoCal on Overdue Sensors is set using FleetManager II software and sensors are over-due, then calibration starts automatically once Intellidox recognizes the detector.1. Insert a detector.2. Use and to move to Calibrate mydetector on the Intellidox user menu.3. Press to select Calibrate my detector.The LCD screen background changes to yellow and the calibration progress screen is displayed.4. Calibration begins. Progress screens aredisplayed while the tests are performed.5. If AutoDownload Datalog is set usingFleetManager II software, detector datalogs are automatically transferred to Intellidox.Calibration PassWhen the calibration is successful, LCD screen background changes to green and Calibration passed is displayed. Alarm response and sensor response test items are checked. Press to return to Intellidox user menu.Calibration FailWhen the calibration fails, LCD screen back-ground changes to red and Calibration failed is displayed. Failed alarm response and/or sensor response test items are marked with .1. Ensure that the filter assembly is freeof obstructions and defects.2. Connect the filter assembly to thepurge inlet.3. If necessary, attach an extensiontubing to the filter assembly to draw ambient air from an adjacent fresh air environment.Connect the Exhaust TubingEach Intellidox Enabler Kit includes one exhaust tubing that is 4.57 meters (15 feet) long.1. Inspect the exhaust tubing to ensurethat it is free of obstructions and defects.2. Connect the exhaust tubing to theexhaust outlet.3. Ensure that the exhaust tubing is notconnected to a negative pressure system, or obstructed in any way.Connect the PowerEach Intellidox Enabler Kit contains one power supply and AC power cord. Use only the power supply provided in the Enabler Kit to connect the Intellidox Docking Module to an appropriate electrical power outlet. When the power is connected, the Intellidoxactivates and a self-test is performed.1. Connect the AC power cord to thepower supply2. Connect the power supply to theIntellidox power port.3. Plug the AC power cord into a suitable wall outlet.4. When the power is connected, theIntellidox LCD activates and a self-testis performed.To prevent the corruption or loss of data and/or software and/or firmware, do not deactivate the equipment while performing datalog transfers, bump tests, calibrations or other operations.Charge a DetectorUse the Intellidox to charge detectors fitted with rechargeable batteries. For more infor-mation on battery maintenance, refer to the detector manual.1. Charge only in a normal environmentthat is 20.9% O 2 and free of hazardous gas. Do not operate the docking module in a hazardous area. Failure to adhere to this guideline can result in possible personal injury and/or property damage.2. Deactivate the detector.3. Insert the detector into the Intellidoxmodule.4. Battery charging begins immediately.Battery charging is disabled during bump test and calibration procedures.Once tests and other routines are com-pleted, you may leave the detector in the module for charging. If the detector isactivated, the module will deactivate it after 10 minutes of inactivity. When charging is complete, remove the detector. Do not store the detector in the module.Prepare for Bump Tests and CalibrationsThe Intellidox module is factory-configured for use with ConneX1 portable gas detec-tors containing H 2S sensors. Gas inlets are configured at the factory. Inlet con-figurations cannot be altered. The Intel-lidox Enabler Kit includes quick connect fittings and calibration tubing cut to the minimum recommended length of 1 meter (39 inches). Use only tubing that is between 1 meter (39 inches) and 10 meters (33 feet) in length when you connect gas cylinders to an Intellidox module.Connect Calibration Gas1. Connect a demand flow regulator to the calibration gas cylinder.2. Use the quick connect fittings and calibration gas tubing to connect the calibration gas cylinder to the gas.Bump Test Bump test is a procedure that confirms a detector’s ability to respond to target gasesby exposing the detector to gas concentra-tions that exceed its alarm setpoints.If AutoBump on Insertion is set using FleetManager II software, then bump test starts automatically when Intellidox recog-nizes the detector. If AutoCal on OverdueSensors is enabled and if a calibration is also due, then no bump test is performed. Instead, calibration starts automatically when the detector is recognized.1. Insert a detector.2. Press and on the keypad tomove to Bump test my detector on theIntellidox user menu.3. Press to select Bump Test. TheLCD screen background changes to yellow and the bump test progress screen is displayed.1. The bump test begins. T estsequence progress screens are displayed while the tests are per-formed.Touchpad and buttonsActionMove right Move left Move up Move down Select menu item Save changesClose menu itemReturn to previous screen Cancel changesLCD BacklightBacklight StatusIdlePrompt for user action Activity in progress Activity successful WarningActivity Failed50104991-166 || QRG-EN-FMSU_B2 INTELLIDOX DOCKING MODULE QUICK REFERENCE GUIDE。
RDQJ-1 固定式可燃气体监测报警装置

Combustible Gas Detection SystemRDQJ-1固定式可燃气体监测报警装置信号输出RS485:报警状态%LEL主报警:3010%LEL预报警(报警设定值可调)故障报警电源主电源AC220V/AC 110V :副电源DC24V 功耗:10W 量程范围0~100%LEL或1~100%V/V :测量精度±5%LE :L报警形式:声光报警检测对象空气中的可燃性气体;:Power:10W Accuracy:5%LEL ±Measuring range:0100%LEL,1100%V/V ~~Alarm type:audio-visual alarmSignal output RS485:Voltage:Main AC220V AC 110V/Back up DC24VAlarm state:30%LEL(main alarm)10%LEL(pre-alarm,adjustable)failure alarmSample object:Combustible gas in air;便携式气体探测器是可连续检测可燃气体浓度或有毒性气体的浓度的便携式检测设备。
当探测器检测到待测气体的浓度达到或超过预置报警值时,探测器立即发出声光报警。
适用于防爆场所、有毒气体泄漏抢险、地下管道、石油、化工、冶金或矿井等场所,能有效保证工作人员的生命安全不受侵害,生产设备不受损失。
Portable Gas Detector便携式气体探测器The device is used to continuously detect the concentration of combustiblegas or toxic gas concentrations by person.When the concentration is reach orexceed the alarm limit,thedevice immediately issued an audio-visual alarm.It issuible for explostion-proof field,Toxic gas leak emergency,mine industry orothers to effectively protect the staff and production equipment fromdamagement.本装置由可燃气体检测变送器和报警控制箱两部分组成,当装置运行时,由可燃气体监测探头将监视区域内空气中可燃气体浓度,转换为DC4-20mA标准信号,传送到设在控制箱内的RDYB计算机控制单元,并由显示单元对各监测点的可燃气体浓度进行实时显示;当可燃气体浓度超过设定的预报警值或极限报警值时,由报警控制单元发出相应的声、光报警信号,并指明发出报警信号的部位。
RAE Systems Gas监测器用户说明书

An explosion-proof device is designed so that if a flammable mixture inside the device ignites, the flame will not get outside of the device to ignite a flammable mixture outside of it. An example of an explosionproof device is a catalytic-bead Wheatstone bridge LEL sensor used to measure flammable gases by gas monitor manufacturers worldwide. Essentially a tiny electric stove, a LEL sensor uses a sintered metal flame arrestor to prevent any flame that might start on the hot sensing bead from getting outside of the sensor itself.
Testing at 21% oxygen is consistent throughout industry and among different approval agencies. It does not mean that the device is not intrinsically safe at 21.1% oxygen. Agencies only certify instruments as intrinsically safe for normal atmospheric oxygen concentrations. Flammability characteristics can change as oxygen concentrations change. Reduced oxygen levels decrease the risk of flammability, and enriched oxygen concentrations can increase the risk.
RAE Systems 亨利光 Cavimeter 糖炭化合物检测方法指南说明书

Certain professions have higher risk of exposure due to constant contact with automobile fumes these being truck drivers, police, and conductors of urban buses. Although the base risk is the same as other people these types of professions have repeated daily exposure throughout their careers. The actual risk by measurement of the atmospheric readings of the European Counsel and the National Board of Health and Welfare is on the order of 10mcg/m3 of atmosphere or less, this being overall a low risk (INRS).
• Petroleum refining (Oil refineries) • Coke and Coal manufacturing • Rubber tire manufacturing • Storage sites (tank farms) • Transportation services (ships, tanker trucks) • Laboratories • Chemical manufacturing
• Lubricants
• Rubbers
• Detergents
• Drugs
- 1、下载文档前请自行甄别文档内容的完整性,平台不提供额外的编辑、内容补充、找答案等附加服务。
- 2、"仅部分预览"的文档,不可在线预览部分如存在完整性等问题,可反馈申请退款(可完整预览的文档不适用该条件!)。
- 3、如文档侵犯您的权益,请联系客服反馈,我们会尽快为您处理(人工客服工作时间:9:00-18:30)。
Best Practices for Use of Portable Gas Monitors in Confined SpacesIn the confined work spaces found in chemical plants, paper mills, refineries, underground mines and utility passageways, the air may be contaminated with toxic or combustible gases or suffer from a lack of oxygen. Regulations call for the monitoring of these environments.TOP ARTICLESIn the confined work spaces found in chemical plants, paper mills, refineries, underground mines and utility passageways, the air may be contaminated with toxic or combustible gases or suffer from a lack of oxygen. Regulations call for the monitoring of these environments.Every day, workers who are just doing their jobs can come into contact with airborne contaminants that are harmful or even fatal. This especially is true of workers who must enter confined spaces to perform job tasks.Draeger SafetyTo protect workers, employers are required by law to have a way to monitor the air before entry and during the entire time employees occupy the confined space. Employers must ensure a safe and healthy worksite to maintain production and to protect their workers.Each person entering the confined space should be equipped with a portable gas monitor worn where it can be checked easily and frequently. It’s a must-have, life-saving tool that can be used in a wide range of industrial settings.GAS MONITOR DESIGNPortable gas monitoring systems may be designed for a single substance, or can be fitted with multiple sensors. Some measure up to six gases and include piercing audible and attention-getting 360-degree visual alarms.An alternative or adjunct to personal monitors is a transportable area monitor. Look for one with area monitoring via diffusion or with a sampling pump, wireless communications capabilities and a waterproof housing with continuous operation of around 60 hours. More run time helps increase productivity by minimizing new checks of the atmosphere for each shift change or when the space may be unattended. A multiple sensor design often is driven by OSHA requirements, which specify confined space monitoring by following this detection sequence: oxygen, combustible gases and any potential toxic contaminants (see 29 CFR 1910.146(c)(5)(ii)(C)).Portable gas monitors are lightweight with dimensions similar to a mobile phone for ease of use. They run on either rechargeable or replaceable batteries.SENSORS ARE THE HEART OF A GAS MONITORAs you might imagine, the sensor is the most important component inside a gas monitor. When facing an unknown gas hazard, you need a sensor that provides dependable detection of combustible atmospheres. It quickly should respond to explosive gases and have a high level of sensitivity to combustible organic vapors in a confined space. The monitor you choose should include sensors for:➤ O2 – To check the oxygen level for deficiency or enrichment.➤ Combustible gas – To test for levels of flammable or explosive gases.➤ Toxic gas levels – Typical confined space monitors have hydrogen sulfide (H2S) and carbon monoxide (CO) sensors; additional toxic sensors may be used based on the application.Gas monitors also provide an alarm at the appropriate real-time concentration, short-term exposure limit (STEL) or time-weighted average (TWA) for the monitored substance.Electronic gas monitors with four or five different sensors (multi-gas monitors) may be sufficient for many confined space applications. Some situations may require monitoring capabilities for additional substances. As a general rule, each type of sensor is best suited for certain substance categoriesElectrochemical (EC) oxygen sensors measure the volume of oxygen in air over the range of 0-25 percent. They can provide a relatively accurate alarm point at a volume of 19.5 percent to protect workers from reduced oxygen levels. EC toxic gas sensors can detect, monitor and accurately measure CO, H2S, SO2, Cl2 and many other toxic gases at parts per million (ppm) levels, making them suitable for monitoring STELs and TWAs specified by OSHA and other agencies.Catalytic (CAT) oxidation sensors for combustible gases can detect a wide range of substances and can be calibrated to measure combustible gas concentrations in the range of 0-100 percent of the lower explosive limit (LEL). While not specific to any one gas or vapor, they are sensitive to several different ones within the same general group of substances.Infrared (IR) combustible gas sensors are not subject to poisoning, do not require oxygen to operate and, like CAT sensors, can measure a wide range of combustible gases and vapors over the range of 0-100 percent LEL. They cannot measure some inorganic combustibles like hydrogen, and although more expensive up front, last much longer.Photo ionization detector (PID) sensors are used to detect low concentrations of volatile organic compounds in the air, such as fuels like gasoline and diesel, and to measure solvents such as acetone, xylene, etc. Because of their ppm sensitivity, they can be used for STEL and TWA measurement applications. Their detection capabilities are not specific to any one compound, and their relative responses to different compounds can vary widely.Other sensor characteristics to consider based on your workplace needs include:➤ Monitor design that allows gas intake from both the top and front of the monitor.➤ The contaminant concentration measurement range, minimum detection limit and resolution.➤ Environmental conditions during use (range of temperature, pressure and relative humidity).➤ Sensor replacement procedures (on site versus manufacturer replacement).➤ Warranty period.ELECTRONIC CIRCUITRYIntrinsic safety is a key feature of the electronic circuitry in a gas monitor. This means the available electrical and thermal energy in the gas monitor always is low enough that ignition of the hazardous atmosphere cannot occur. Among other things, electrical sparks are not produced and even under fault conditions, the temperature of a component cannot reach a level that could cause autoignition of a combustible atmosphere.To sell a gas monitor as an intrinsically safe device, the manufacturer must have it tested and certified by one or more independent testing labs.Hazardous areas are separated by classes, divisions and groups to define the level of safety required for equipment in these locations. The most common intrinsic safety approval ratings on portable gas monitors are Class I; Division 1; Groups A, B, C and D; and Temperature Rating T4.Make sure that when choosing a gas detector that might be used in a work environment where explosive, combustible or flammable vapors are present, the detector design has been tested and verified to be intrinsically safe by a recognized testing lab (UL, etc.). This verification assures users that the detector will not cause an explosion or combustion when used in such locations, even if something goes wrong in the electronic circuitry of the detector.USER INTERFACEAn external feature of a gas monitor’s internal electronics is the user interface. Some considerations in selecting a gas monitor that is user friendly include:➤ Is its operation intuitively obvious?➤ Are controls easy to understand?➤ Is it easily operated by a user fitted with gloves and equipment?➤ Are there adequate security features to prevent tampering?➤ Is the display large enough to be easily read?➤ Besides warning properties, are there functions that support documentation and reporting, such as built-in data logging?A bright, flashing LED lamp is an excellent visual alarm, and a loud multi-tone horn sound is a good audible alarm. A strong vibrating alarm the user can feel also might be necessary in case of loud background noises or if the monitor is not attached to the user where it easily can be seen. Alarm thresholds should be able to be individually adjusted to comply with company policy or other standards.Once an alarm is detected, a large, easy-to-read digital display is necessary to verify the concentration of a dangerous gas. In case of low light conditions, the display should be adequately backlit.Detector tubes help determine the sensors required.A signal output interface facilitates the downloading of gas concentrations from a built-in data logger or event recorder. Various interface types are available, including those that use a USB cable to transfer data to a PC, and infrared interfaces that perform a similar function.Some gas monitors have the ability to store thousands of events and gas concentrations over many hours of sampling. Other significant events you might want to have recorded can include switching the gas monitor on or off, gas and battery alarms, error codes, configuration changes, fresh air calibrations and bump tests conducted.In addition, various software packages are available for PCs and Mac computers to store and manipulate data and generate reports.Typically, a thermoplastic polymer is used for the gas monitor housing. Other features related to the housing to consider when evaluating a portable gas monitor are:➤ Size and weight;➤ Portability accessories;➤ Protection from radio frequency interference;➤ Protection from dust and water ingress;➤ Chemical resistance; and➤ Resistance to physical shock damage.An IP65 or IP67 rating may be needed for adequate protection from dust, rain and water spray. In harsh environments, a polymer housing may be rubber coated or a rubber boot may be added for greater protection from aggressive chemicals and temperature extremes.MAINTENANCEAs part of good operating practices, gas monitors should be bump tested every day before use. A bump test is defined as a qualitative function check where a challenge gas is passed over the sensor(s) at a concentration and exposure time sufficient to activate all alarm indicators to present at least their lower alarm setting.Note that a bump test is not required to provide a measure of calibration accuracy. Additional considerations in bump testing include checking the manufacturer’s expiration date on the bump station gas cylinder, and documenting proper instrument calibration and other functions.Detector tubes can be valuable tools in determining the type of sensor that should be used in a gas monitor, as well as in checking a confined space before entry. A detector tube is a hermetically sealed glass tube containing an inert carrier material mixed with one or more reagents that undergo a colorimetric reaction when specific contaminants are drawn into the tube. The length of the color change in the tube, or the intensity of color change as compared to a standard, indicates the amount of contaminant present.OBSERVE PROPER SAMPLING PROCEDURESNormally, a sampling hose and probe are attached to the gas monitor to allow the air inside a confined space to be sampled. The air sample is brought into the gas monitor by a sample pump. Some gas monitors have a built-in pump and some have an external pump. This could be either a manual pump or one that is battery-powered with automatic volume control.Follow the manufacturer’s recommendations and all rules and regulations published by the employer, which should be consistent with guidelines published by OSHA, NIOSH, OHSB (Canada) the American Conference of Governmental Industrial Hygienists and other recognized authorities. When the atmosphere in the confined space has reached the immediately dangerous to life and health level, do not enter without a properly fitted self-contained breathing apparatus and take other appropriate precautions.Checking the air in a confined space for oxygen, combustibles and toxics before entry is essential in protecting a worker’s health and safety. Consider including portable gas monitors as part of your organization’s confined space safety management plan。