SAE AMS2475G-2009
热电偶标准 SAE AMS 2750D(chinese)09-5-6

航空航天材料规范SAE AMS 2750D1. 范围:该规范描述了对热处理设备的温度要求。
包括温度传感器、仪器、热处理设备、系统精确度测试和温度均匀性测试。
这些对确保零件或原材料按照适用规范进行热处理,是必要的。
除非材质或过程规范特别规定,否则该规范不适用于加热或中间热处理,。
该规范适用于实验炉,参见第3.6节。
2. 适用文件:以下文件从订单发布之日起生效,并构成了该规范的一部分。
除非对使用的文件版本有专门的规定,否则供应商要使用最新版本的文件。
当参考文件取消,而且没有文件替代时,使用最新发行的那版文件。
ASTM文件可以从ASTM, 100 Barr Harbor Drive, 邮箱C700,West Conshohocken,PA19428-2959或获得。
ASTME 207,ASTM E 220,ASTM E 230,ASTM E 608,ASTM E 1129,ASTM MNL 7,ASTM MNL 12。
3. 技术要求温度传感器:温度传感器必须符合表1要求和如下要求。
一些例外情况在下文中有提到。
温度应该用此规范中规定的热电偶来测量,或用其他的精度相同或更高的热电偶或温度传感器来测。
热电偶用裸线或涂装线或MIMS线(矿物绝缘,金属铠装的)制成。
没有特殊说明的话,要求适用于所有温度传感器材料。
此规范中的“传感器”即指“温度传感器”。
从传感器首次校准或后来校准所得到的修正系数可以用来提高温度的精确度,且在此规范要求下要被使用。
校准:传感器应该有合格证明,注明校准数据的来源、理论测试温度,实际测试温度读数、校准方法和每个可追溯到NIST或其他认可的国家标准的校准温度的修正系数。
校准方法应符合ASTM E 220,ASTM E 207或其他国家标准的要求。
从毫伏到度或从度到毫伏的转化,应该遵守ASTM E 230或其他国家标准。
温度传感器必须在使用的温度范围内校准。
所有热电偶的校准点间隔不能超过250 o F(140 o C) ,不包括那些按照ASTM MNL 12或其他国家标准要求,在固定点上校准的热电偶。
SAE AMS-QQ-A-200-8-1997
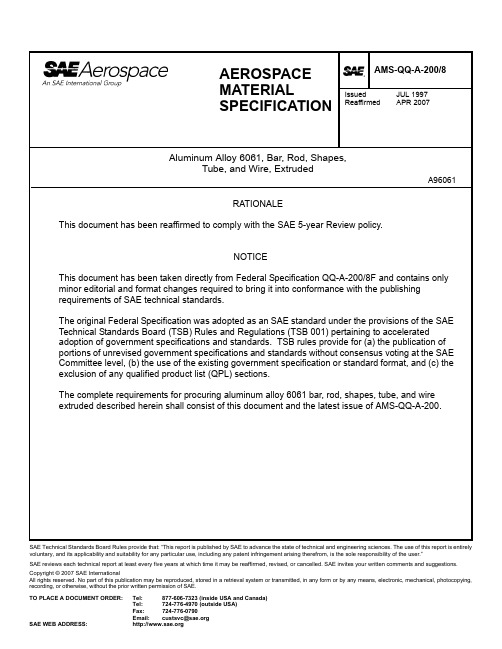
SAE Technical Standards Board Rules provide that: “This report is published by SAE to advance the state of technical and engineering sciences. The use of this report is entirely voluntary, and its applicability and suitability for any particular use, including any patent infringement arising therefrom, is the sole responsibility of the user.”SAE reviews each technical report at least every five years at which time it may be reaffirmed, revised, or cancelled. SAE invites your written comments and suggestions.Copyright © 2007 SAE InternationalAll rights reserved. No part of this publication may be reproduced, stored in a retrieval system or transmitted, in any form or by any means, electronic, mechanical, photocopying,recording, or otherwise, without the prior written permission of SAE.TO PLACE A DOCUMENT ORDER:Tel: 877-606-7323 (inside USA and Canada)Tel: 724-776-4970 (outside USA)Aluminum Alloy 6061, Bar, Rod, Shapes,Tube, and Wire, ExtrudedA96061RATIONALEThis document has been reaffirmed to comply with the SAE 5-year Review policy.NOTICEThis document has been taken directly from Federal Specification QQ-A-200/8F and contains only minor editorial and format changes required to bring it into conformance with the publishing requirements of SAE technical standards.The original Federal Specification was adopted as an SAE standard under the provisions of the SAE Technical Standards Board (TSB) Rules and Regulations (TSB 001) pertaining to accelerated adoption of government specifications and standards. TSB rules provide for (a) the publication of portions of unrevised government specifications and standards without consensus voting at the SAE Committee level, (b) the use of the existing government specification or standard format, and (c) the exclusion of any qualified product list (QPL) sections.The complete requirements for procuring aluminum alloy 6061 bar, rod, shapes, tube, and wire extruded described herein shall consist of this document and the latest issue of AMS-QQ-A-200.AEROSPACE MATERIALSPECIFICATIONAMS-QQ-A-200/8Issued JUL 1997 ReaffirmedAPR 20071.SCOPE AND CLASSIFICATION:1.1Scope:This specification covers the specific requirements for aluminum alloy 6061 bar, rod, shapes, tube, and wire produced by extrusion.1.2Classification:1.2.1Tempers: Bar, rod, shapes, tube, and wire are classified in the following tempers as specified (See6.2): O,T1, T4, T42, T4510, T4511, T51, T6, T62, T6510, or T6511. Definitions of tempers arespecified in AMS-QQ-A-200.1.2.2Tubing: Tubing shall be additionally classified as follows:Type DescriptionI-Tubing extruded from hollow billets using die and mandrel (SeeAMS-QQ-A-200).II-Tubing extruded from solid billets using a porthole or spiderdie or similar tooling (See AMS-QQ-A-200).2.APPLICABLE DOCUMENTS:See AMS-QQ-A-200.3.REQUIREMENTS:3.1Chemical Composition:The chemical composition shall conform to the requirements specified in Table I.TABLE I. Chemical Composition 1/ElementPercent Minimum MaximumMagnesium0.8 1.2 Silicon0.400.8 Copper0.150.40 Iron--0.7 Chromium0.040.35 Zinc--0.25 Titanium--0.15 Manganese--0.15 Other Elements, each--0.05 Other Elements, total 2/--0.15 Aluminum Remainder1/Analysis shall routinely be made only for the elements specifically mentioned in Table I. If, however, the presence of other elements isindicated or suspected in amounts greater than the specified limits, further analysis shall bemade to determine that these elements are not present in excess of the limits specified.2/The sum of those "Others" metallic elements0.010 percent or more each, expressed to thesecond decimal before determining the sum.3.2Mechanical Properties:3.2.1Mechanical Properties of Material as Supplied: The mechanical properties in the direction of extrusion shall conform to requirements specified in Table II.3.2.2Mechanical Properties After Heat Treatment: In addition to conforming to requirements of 3.2.1, materials identified in the following paragraphs shall, after having been heat-treated to other tempers also identified therein, have properties in the extrusion direction conforming to those specified in Table II, as applicable.3.2.2.1Material in the O Temper: Material in the O temper, without the subsequent imposition of cold work or forming operations, shall, after proper solution heat treatment and natural aging, develop the properties specified in Table II for the T42 temper.3.2.2.2Material in the T1, T4, T42, T4510 and T4511 Tempers: Material in the T1, T4, T42, T4510, and T4511 tempers shall be age-hardenable artificially to the properties specified for T51, T6, T62, T6510, and T6511 tempers, respectively. Such capability shall be demonstrated when specified (See 6.2).TABLE II. Mechanical PropertiesTemper Thickness, (bar and shapes); di-ameter, (rod and wire); wall thickness (tube)Inches TensileStrengthMinimum ksi Yield Strength at 0.2 percent Offset or at extension indicatedElongation in2 inches or 4times D 1/, 4/Minimum percent Minimum ksi Extension under load inch perinch O All2/2/0.003616T1Up thru 0.62526.014.00.003416T4, T4510,All 26.016.00.003616and T4511T42 3/All26.012.00.003216T51Up thru 0.62535.030.00.0050 8T6, T62 3/,Up thru 0.24938.035.00.0055 8T6510 and 0.250 and over38.035.00.005510T65111/D represents specimen diameter.2/No minimum; maximum tensile and yield strengths are 22.0 ksi and 16.0 ksi, respectively.3/Material in the T42 or T62 temper is not available from material producers.4/See AMS-QQ-A-200 for elongation requirement exceptions.3.3Heat Treatment:Unless otherwise specified in the contract or purchase order for T4, T4510, T4511, T6, T6510, and T6511 material, the producer may use an alternative heat treating procedure in lieu of a furnace heat treatment covered by MIL-H-6088, provided the material conforms to all other requirements of this specification when sampled and tested in accordance with 4.2. The alternative heat treatment shall be performed on the whole of a piece, never on a part only, and shall be performed on the whole of a piece, never a part only, and shall be performed in a manner that will produce the utmost uniformity (See 6.2).3.4Marking:In addition to marking required by AMS-QQ-A-200, material in the T51, T6, T6510, and T6511tempers and, when specified (See 6.2), material in the T1, T4, T4510, and T4511 tempers, shall also be identified by inspection lot number, marked in at least one location on each piece.4.QUALITY ASSURANCE PROVISIONS:See AMS-QQ-A-200 and the following:4.1Heat Treatment:4.1.1Aging Treatment Before Testing: Test specimens selected from material in the T1, T4, T42, T4510,and T4511 tempers may be tested within 4 days following solution heat treatment. In the event of test failures caused by insufficient aging, retests shall be performed using material aged for 4 days or longer. Test specimens shall be prepared from the same coupons or location in the lot or lots from which the previously tested specimens were taken.4.2Additional Sampling and Testing of Material Heat-Treated by Methods Not Covered by MIL-H-6088: 4.2.1Alloy Heat-Treated to the T6, T6510, or T6511 Tempers: When material in the T6, T6510, or T6511tempers has not been heat-treated by a method covered by MIL-H-6088, internal quality controls shall be applied to establish that product so-treated meets all requirements of this detailspecification and AMS-QQ-A-200. Compliance with the requirements of Table II may bedetermined by hardness tests followed by tension tests performed on samples from the two softest extrusions in the inspection lot. The method of hardness testing shall be left to the discretion of the producer.4.2.2Alloy Heat-Treated to the T4, T4510, or T4511 Tempers: When material in the T4, T4510, or T4511temper has not been solution heat-treated by a method covered by MIL-H-6088, internal quality controls shall be applied to establish that product so-treated meets all requirements of this detail specification and AMS-QQ-A-200. In addition, specimens taken from extrusions in these tempers shall be artificially aged to determine conformance to 3.2.2.2, as applicable, and be hardness-tested and tension-tested in accordance with 4.2.1. Any specimen blank selected for an age-hardenability determination shall be removed from the softest extrusion in the lot undergoinginspection.4.3Number of Tests After Heat Treatment:From material in each temper of those specified for heat treatment capability demonstrations in 3.2.2 and the purchase documents (See 6.2), an additional number of specimens equal to that required by AMS-QQ-A-200 shall be taken and tested after heat treatment to each temper specified to determine conformance to 3.2.2.5.PREPARATION FOR DELIVERY:See AMS-QQ-A-200.6.NOTES:6.1Intended Use:This alloy is intended for use where good strength and workability are required. The T4510 and T6510 tempers are intended primarily to provide material with low residual stresses and consequent minimum distortion during machining. The T4511 and T6511 tempers are straightened T4510 and T6510 material, respectively, and may have unknown residual stresses and may or may not distort during machining.6.2Mechanical Properties After Solution Heat Treatment:Material in the T1, T4511, T51, T6, T6510, and T6511 tempers may not meet the requirements of Table II for T42 temper after re-solution heat treatment because of a tendency for grain growth.6.3Properties After Heat Treatment:Mechanical properties and corrosion properties, where applicable, are certified for the temper of material supplied. The producer’s capability demonstration is not evidence that user-treated material conforms to property requirements of a given temper. Frequently, user-heat-treated material may develop a lower level of properties, especially if any cold, warm, or hot work is introduced, prior to solution heat treatment. The user should be held responsible for demonstration that his processing will yield properties meeting requirements.--` , , , , ` ` ` ` ` ` , ` ` , ` , , , , ` , , , ` ` , ` , , -` -` , , ` , , ` , ` , , ` ---6.4Ordering Data:Purchasers should select the preferred options permitted herein and include the followinginformation in procurement documents:Title, number, and date of this specification.Form, quantity, and temper required (See 1.2.1).Dimensions required.Requirements for sizes not specifically covered (See AMS-QQ-A-200).When lot number marking for material in the T1, T4, T4510, or T4511 temper is required (See 3.4).Which, if any, heat treatment capabilities shall be demonstrated where such demonstrations arepurchaser’s options (See 3.2.2.2).Whether heat treatments not covered by MIL-H-6088 are disallowed (See 3.3).Special end use requirements.Selection of applicable levels of preservation and packing, whether Level A, Level B, or commercial (See AMS-QQ-A-200).Whether Type I tubing is required (See 1.2.2); (where no type is specified, Type I should be applied).6.5Product produced and marked to the requirements of AMS-QQ-A-200/8 also meets the requirementsof QQ-A-200/8F. Product produced and marked to the requirements of QQ-A-200/8F also meets the requirements of AMS-QQ-A-200/8.6.6The properties listed in 3.2.1 are exactly the same as QQ-A-200/8, Revision F. These propertieshave not been substantiated in accordance with the Manual for Preparation of AerospaceSpecifications.PREPARED UNDER THE JURISDICTION OF AMS COMMITTEE "D"。
SAE AMS 2460-2007 镀铬

SAE Technical Standards Board Rules provide that: “This report is published by SAE to advance the state of technical and engineering sciences. The use of this report is entirely voluntary, and its applicability and suitability for any particular use, including any patent infringement arising therefrom, is the sole responsibility of the user.”SAE reviews each technical report at least every five years at which time it may be reaffirmed, revised, or cancelled. SAE invites your written comments and suggestions. Copyright © 2007 SAE InternationalAll rights reserved. No part of this publication may be reproduced, stored in a retrieval system or transmitted, in any form or by any means, electronic, mechanical, photocopying, recording, or otherwise, without the prior written permission of SAE.TO PLACE A DOCUMENT ORDER:Tel: 877-606-7323 (inside USA and Canada)Tel: 724-776-4970 (outside USA) AMS 2460 AEROSPACE MATERIALSPECIFICATIONIssued JUL 2007Plating, ChromiumRATIONALE AMS 2460 is a new specification to cover chromium plating, intended to replace AMS-QQ-C-320 (QQ-C-320).NOTICEORDERING INFORMATION: The following information shall be provided to the plating processor by the purchaser:1) Purchase Orders shall specify not less than the following:• AMS 2460 • Part number and quantity of pieces to be plated • Class of plating. See 1.4.1. • For Class 1 plating, type of surface luster. See 1.4.2 and 3.5.1.2. • Plating thickness. See 3.4.1.2 and 3.4.1.3. • Underplating, if different from 3.3.2 • Basis metal to be plated •Tensile strength or hardness of the basis metal • Pre-plate stress relief (time and temperature) if different from 3.2.1, or instructions that pre-plate stress relief has already been performed prior to submitting parts to the plating processor, or statement that pre-plate stress relief is not required• Plating coverage; special features, geometry or processing present on parts that requires special attention by the plating processor• Hydrogen embrittlement relief to be performed by the plating processor (parameters or requirements document), if different from 3.3.4• Peening requirements, if peening is required to be performed by the plating processor. See 3.1 and 8.4.1. • If tests for hardness, porosity, or hydrogen embrittlement are required for lot acceptance. See 4.2.1. • If adhesion is to be evaluated by grinding. See 3.4.2.1. and responsibility (plating processor or part fabricator) to perform this evaluation.2) Parts manufacturing operations such as heat treating, forming, joining, and media finishing can affect the condition of the substrate for plating, or if performed after plating, could adversely affect the plated part. The sequencing of these types of operations should be specified by the cognizant engineering organization or purchaser and is not controlled by this specification, except as noted herein. Requirements for peening (3.1.1), basis metal quality (3.1.2), and preplating stress relief (3.2.1) require special coordination with the plating processor.1. SCOPE1.1 PurposeThis specification covers the requirements for electrodeposited chromium plating.1.2 ApplicationThis plating has been used typically as a decorative finish, to improve corrosion resistance, to increase wear resistance, to extend tool and die life, to maintain accuracy of gauges, and to recondition worn or undersized parts, but usage is not limited to such applications. While this document is primarily intended to address electrodeposition on steels, the process has been performed on aluminum, heat resistant alloys, high nickel alloys, super alloys, and other metals. The requirements of this specification are equivalent to AMS-QQ-320 but generally more stringent than AMS 2406. Thin Dense Chrome plating should be specified by reference to AMS 2438.1.2.1 RestrictionApplication of chromium plating to steel parts having a hardness of 48 HRC (ultimate tensile strength of 238 ksi [1641 MPa]) or higher shall not be performed unless authorized by the design documentation of the cognizant engineering organization. See 4.4.1.2 and 8.4.2. Application of chromium plating for repair of steel parts having a hardness of 48 HRC(ultimate tensile strength of 238 ksi (1641 Mpa) or higher requires a special design evaluation and shall not be performed unless specific approval has been received from the cognizant engineering organizationMaterials1.3 Safety-HazardousWhile the materials, methods, applications and processes described or referenced in this specification may involve the use of hazardous materials, this specification does not address the hazards which may be involved in such use. It is the responsibility of the user to ensure familiarity with the safe and proper use of any hazardous materials, to take precautionary measures to ensure the health and safety of all personnel involved.1.4 Classification1.4.1 ClassesElectrodeposited chromium plating shall be one of the following classes.Class 1 - Corrosion protective plating. See 8.4.3.Class 2 - Engineering plating. See 8.4.4.1.4.2 AppearanceClass 1 plating shall have one of the following types of lusters, as specified.Type I - Bright finishType II - Satin finish.2. APPLICABLE DOCUMENTSThe issue of the following documents in effect on the date of the purchase order forms a part of this specification to the extent specified herein. The supplier may work to a subsequent revision of a document unless a specific document issue is specified. The supplier may also work to a prior revision of a document when directed by the cognizant engineering authority. When the referenced document has been cancelled and no superseding document has been specified, the last published issue of that document shall apply.2.1 SAEPublicationsAvailable from SAE International, 400 Commonwealth Drive, Warrendale, PA 15096-0001, Tel: 877-606-7323 (inside USA and Canada) or 724-776-4970 (outside USA), .AMS 2403 Nickel Plating, General PurposeAMS 2406 Plating, Chromium, Hard DepositAMS 2438 Plating, Chromium, Thin, Hard, Dense DepositAMS 2759/9 Hydrogen Embrittlement Relief (Baking) of Steel PartsAMS 2759/11 Stress Relief of Steel PartsAMS 2750 PyrometryAMS-QQ-C-320 Chromium Plating, ElectrodepositedAMS-QQ-N-290 Nickel Plating (Electrodeposited)Publications2.2 ASTMAvailable from ASTM International, 100 Barr Harbor Drive, P.O. Box C700, West Conshohocken, PA 19428-2959, Tel: 610-832-9585, .ASTM B 253 Standard Guide for Preparation of Aluminum Alloys for ElectroplatingASTM B 487 Measurement of Metal and Oxide Coating Thickness by Microscopic Examination of a Cross SectionASTM B 499 Measurement of Coating Thick nesses by the magnetic Method: Nonmagnetic Coatings on Magnetic Base MetalsASTM B 504 Measuring the Thickness of Metallic Coatings by the Coulometric MethodASTM B 556 Thin Chromium Coatings by the Spot Test, Guideline for Measurement ofASTM B 567 Method for Measurement of Coating Thickness by Beta Backscatter MethodASTM B 568 Measurement of Coating Thickness by X-Ray SpectrometryASTM B 571 Qualitative Adhesion of Metallic CoatingsASTM B 748 Measurement of Thickness of Metallic Coatings by Measurement of Cross Section with a Scanning Electron MicroscopeASTM B 764 Simultaneous Thickness and Electrochemical Potential Determination of Individual Layers on the Multilayer Nickel Deposit (STEP Test)ASTM E 384 Test Method for Microhardness of MaterialsASTM F 519 Mechanical Hydrogen Embrittlement Testing of Plating Processes and Service Environments2.3 Aerospace Industries Association PublicationsAvailable from Aerospace Industries Association, 1000 Wilson Boulevard, Suite 1700, Arlington, VA 22209-3928, Tel: 703-358-1000, .NASM1312-12 Fastener Test Methods, Thickness of Metallic Coatings3. TECHNICAL REQUIREMENTS3.1 The requirements for peening (3.1.1) and basis metal quality (3.1.2) are established by the cognizant engineeringorganization and, unless otherwise specified, are the responsibility of the part fabricator.3.1.1 PeeningWhen specified, parts shall be peened prior to plating. Unless otherwise specified, such peening shall be accomplished on all surfaces for which the plating is required and on all immediately adjacent surfaces that contain notches, fillets or other abrupt changes of section size. See 8.4.1. Peening shall be performed by or on behalf of the part fabricator, unless specifically delegated to the plating processor.3.1.2 Basis Metal QualityThe basis metal (parts) shall be submitted to the plating processor free from visible defects such as blemishes, prior pitting from corrosion, nicks, scratches, burrs or other geometrical or base metal defects that could be detrimental to the appearance or performance of the plating. The plating processor shall perform such cleaning and plating procedures as necessary to yield a deposit that conforms to the specified requirements.3.2 Preparation3.2.1 Stress Relief TreatmentUnless otherwise specified, steel parts 34 HRC (ultimate tensile strength 152 ksi [1048 MPa]) and higher that have been ground, machined, cold formed, or cold straightened after heat treatment shall be stress relieved by the plating processor. Stress relief shall conform to the requirements of AMS 2759/11. Depending on the metallurgical condition of the parts at time of plating (i.e., alloy, hardness, prior heat treatment - carburized, induction hardened, etc.), the cognizant engineering authority may elect to prescribe different stress relief requirements. Stress relief shall be preceded by cleaning to remove surface contamination; acid cleaning shall not be used. See 8.4.2.3.3.2.2 CleaningThe plating shall be applied over a surface free from water breaks. The cleaning procedure shall not produce pitting, intergranular attack, or hydrogen embrittlement of the basis metal and shall preserve dimensional requirements. See 8.4.2.3.2.3 Electrical Contact PointsFor parts which are to be plated all over, locations shall be acceptable to purchaser. For parts which are not to be plated all over, locations shall be in areas on which plating is not required.3.2.4 Aluminum alloys shall be zincate treated in accordance with ASTM B 253 or other method acceptable to purchaserprior to plating.3.3 Procedure3.3.1 Parts shall be plated by electrodeposition of chromium plating onto a properly prepared surface.3.3.2 UnderplatingUnless otherwise specified (8.6), the following apply:3.3.2.1 Class 1 plating shall be applied over an intermediate plating of nickel in accordance with AMS 2403 or AMS-QQ-N-290 on steel, zinc, and copper alloys.3.3.2.2 Class 2 plating shall be deposited directly on the basis metal without a preliminary plating of another metal,except parts made from maraging steel, or corrosion resistant steel, or aluminum alloy may receive a preliminary deposit of nickel or other suitable metal to a thickness not greater than 0.0002 inch (5 μm).3.3.2.3 Underplate shall not be substituted for any portion of the specified chromium plate thickness.3.3.3 Plating re-start procedures, if used, shall be approved by the cognizant engineering organization. See4.4.3.3.3.4 Hydrogen Embrittlement Relief (Baking)Hydrogen embrittlement relief baking applies only to steel alloys unless otherwise specified by the cognizant engineering authority. At the option of the processor, hydrogen embrittlement relief baking may be performed on other families of alloys. If performed on other alloy families, all hydrogen embrittlement relief baking operations shall be documented. Hydrogen embrittlement relief baking shall be in accordance with AMS 2759/9, except as shown in Table 1. Depending on the metallurgical condition of the parts at time of plating (i.e., alloy, hardness, prior heat treatment - carburized, induction hardened, etc.), the cognizant engineering authority may elect to prescribe hydrogen embrittlement relief baking temperatures and times different from those shown in Table 1.TABLE 1 - HYDROGEN EMBRITTLEMENT RELIEF (BAKING) REQUIREMENTS (1)Ultimate Tensile Strength Inch/Pound Units Ultimate Tensile StrengthSI Units HardnessTime in Hours at375 o F (191 o C)160 ksi to 182 ksi, excl. 1103 MPa to 1255 MPa, excl. 36 to 39 HRC 3182 ksi to 221 ksi, excl. 1255 MPa to 1518 MPa, excl. 40 to 45 HRC 8221 ksi, and higher 1518 MPa, and higher 46 HRC and higher 23(1) NOTE: All times shown are minimum times. For high strength steels 40 HRC (ultimate tensile strength182 ksi [1255 MPa]) and higher, it may be beneficial, and the processor is permitted, to extend the bakingtime to 23 hours to ensure complete relief from hydrogen embrittlement.3.4 PropertiesThe plating shall conform to the following requirements:3.4.1 ThicknessThickness shall be as specified on the drawing, determined in accordance with any of the following methods as applicable: ASTM B 487, ASTM B 499, ASTM B 504, ASTM B 556, ASTM B 567, ASTM B 568, ASTM B 748, ASTM B 764 or by other method acceptable to the purchaser. NASM1312-12 may be used for thickness measurement of plated fasteners. ASTM B 556 (spot test) may be used for Class 1 plating, when a destructive procedure is applicable.3.4.1.1 All surfaces of the part, except those which cannot be touched by a sphere 0.75 inch (19 mm) in diameter, shallbe plated to the specified thickness. Unless otherwise specified, surfaces such as holes, recesses, threads and other areas where a controlled deposit cannot be obtained under normal plating conditions, may be under the specified limit provided they show visual plating coverage. The plate shall be substantially uniform in thickness on significant surfaces except that build-up at exterior corners or edges shall be permitted provided finished drawing dimensions are met.3.4.1.2 Class1Unless otherwise specified, the minimum thickness of Class 1 chromium plating shall be 0.00001 inch (0.25 μm).3.4.1.3 Class2The thickness of Class 2 plating shall be as specified by the purchaser. If the as-plated thickness is not specified, the minimum thickness shall be 0.002 inches (51 μm) plus any grinding or finishing allowance such that the minimum thickness of the finished part is 0.002 inches (51 μm).3.4.2 AdhesionThe plating and any underplate shall be tightly adherent to the substrate as determined in accordance with ASTM B 571, knife-chisel or bend test with no mandrel. When examined at a magnification of approximately 4X, neither the chromium plating nor any electrodeposited underplate(s) shall show separation from the basis metal or from each other. The formation of cracks in the plating or the basis metal which do not result in flaking, peeling, or blistering of the plating shall not be cause for rejection.3.4.2.1 Class2When specified, Class 2 plating may be evaluated by grinding as an alternative to the bend test or knife-chisel test. The plating shall withstand the grinding operations with no evidence of delamination of plated layers or separation from the basis metal.3.4.3 Hardness (Class 2 Only)When tested in accordance with ASTM E 384 using a Vickers indentor and 100 gram load, the minimum hardness of a cross section Class 2 plating shall be 600 Vickers Hardness Number (HVN) if the plating is finished to a semi-bright or matte luster. If the plating is finished to a bright pebbly bright lusters, the minimum hardness shall be 850 HVN. Alternative hardness requirement or test method shall be as specified by the cognizant engineering organization.3.4.4 Porosity (Class 2 Only)Class 2 plating shall be as free from porosity as possible as defined in 3.4.4.1. Although not capable of providing sacrificial corrosion protection as with some other metallic plating systems, the Class 2 plating shall be porosity free to the extent that it protects the basis metal from corrosion due to pits, pores, or cracking. Criteria for evaluating this characteristic shall be as shown in 3.4.4.1 and 3.4.4.2.3.4.4.1 Class 2 plating, when subjected to the test specified in 3.4.4.2, shall show no more than 15 isolated blue spotsor pits, none larger than 0.03 inch (0.8 mm) in diameter, in a total of 150 square inches (967 cm2) of test area. In addition no more that five isolated spots or pits are permitted, none larger than 0.03 inch (0.8 mm) in any 30 square inches (193 cm2) of test area. Isolated linear indications are acceptable. Linear cracking or crazing indications occurring over 5% or more the surface area are not acceptable. Panel edges, identification markings, and electrical contact locations are exempt from these requirements.3.4.4.2 Potassium Ferricyanide (Ferroxyl) Porosity TestPlated low alloy steel parts or low steel specimens shall be evaluated. See 4.3.3.2. Note: Panels subjected to distortion or flexing during processing can exhibit cracking or crazing type indications, so care should be exercised to prevent such false indications. All specimen surfaces shall be cleaned to remove any oil or grease. Contamination removal shall be accomplished with a solvent acceptable to the purchaser. A sheet of filter paper or other suitable adsorbent paper, saturated in the ferroxyl solution shall be applied for 10 minutes to the flat surface of the specimen or the article. Complete contact of the filter paper with the chrome plated test specimen shall be ensured using strokes with a soft bristle brush. Filter paper shall be kept saturated during the duration of the 10 minute test. Pits, pores, or cracking of the chrome are revealed by dark blue spots or lines. For a permanent record, the filter paper may be dried. The approximate solution composition shall be as follows:Potassium ferricyanide (K3Fe(CN)6) 1 gmSodium Chloride (NaCl) 10 gmWater (distilled or deionized) to make 1 literEmbrittlement3.4.5 HydrogenThe plating process shall not cause hydrogen embrittlement in steel parts determined in accordance with 4.3.3.3 or alternative acceptable to the cognizant engineering organization. Control of and testing for hydrogen embrittlement shall include all aspects of the process including stripping, surface preparation, reagent or electro cleaning, electrodeposition of the chromium onto the basis steel using acceptable bath chemistries, and the subsequent hydrogen embrittlement relief (baking) operation. Care should be exercised to control all aspects of the chromium plating process. See 8.4.2 and 4.6.1.1.3.5 Quality3.5.1 Plating, as received by purchaser, shall be smooth, continuous, adherent, free from delamination within theplating, uniform in appearance, fine grained, and shall be free from blisters, nodules, excessive pits, and other imperfections detrimental to usage of the plate. Slight staining or discoloration is permissible. The plating shall show no indication of contamination or improper processing such as excessively powdered or darkened plating, excessive edge build up, or other defects.3.5.1.1 Boundaries of Class 2 plating between plated and unplated area shall be free from beads, nodules, jaggededges or other irregularities.3.5.1.2 LusterClass 1, Type I plate shall be fully bright in appearance. Class 1, Type II plate shall be a satin finish in appearance. Unless otherwise specified either a fully bright or a dull matte finish shall be acceptable for Class 2 plate. See 8.6.4. QUALITY ASSURANCE PROVISIONS4.1 Responsibility for InspectionThe processor shall supply all samples for processor’s tests and shall be responsible for the performance of all required tests. When parts or special specimens are to be tested, the parts or special test specimens shall be provided by the purchaser. Purchaser reserves the right to sample and perform any testing deemed necessary to ensure that processing conforms to specified requirements.4.2 Classification of TestsTests4.2.1 AcceptanceThickness (3.4.1), adhesion (3.4.2), and quality (3.5) are acceptance tests and shall be performed on parts or samples representing parts from each lot. When specified by the purchaser, hardness of Class 2 plating (3.4.3), porosity of Class 2 plating (3.4.4), and hydrogen embrittlement (3.4.5) are also acceptance tests.Tests4.2.2 PeriodicPeriodic (Production Control) are tests performed on a regular monthly basis and are intended to control the quality of the production process. Thickness (3.4.1), adhesion (3.4.2), hardness of Class 2 plating (3.4.3), porosity of Class 2 plating (3.4.4), and tests of cleaning and plating solutions are periodic tests and shall be performed at least monthly on each plating bath. Hydrogen embrittlement (3.4.5) is a periodic test and shall be performed at least once each month on each plating bath in which steel parts 36 HRC (ultimate tensile strength 161 ksi [1110 MPa]) and higher are plated.4.2.2.1 Process Control RecordsThe supplier shall maintain a record of each processing bath, showing all additions of chemicals or treatments to the bath, the results of all tests and chemical analysis performed, and the quantity of parts plated during operation. These records shall be maintained and made available for review for not less than one year after completion of the contract or purchase order.4.2.2.2 Interruption of ProductionIf continuous month to month production ceases for a particular plating bath, the processor is not required to continue periodic production control testing (4.2.2.1). However, all property verification tests of section 3.4 shall be performed on the idled plating bath prior to processing of production parts.4.2.3 PreproductionTestsAll property verification tests of section 3.4 are preproduction tests and shall be performed prior to production and when the purchaser deems confirmatory testing is required.4.2.3.1 Steel parts 40 HRC (ultimate tensile strength 182 ksi [1255 MPa]) and higher shall not be plated until approvalhas been received from the purchaser concerning acceptance of hydrogen embrittlement test results. See 4.4 and 8.4.2.4.3 SamplingSampling for testing shall be not less than the following; a lot shall be all parts of the same part number processed in a continuous operation to the same thickness range, in the same set of solutions, in not longer than 24 consecutive hours, and presented for processor’s inspection at one time. Adhesion verified by grinding on parts, thickness, and quality are classified as non-destructive tests. Adhesion verified by knife-chisel or bend test, hardness, porosity, and hydrogen embrittlement render actual parts not useable after testing and are classified as destructive tests.4.3.1 NondestructiveTestsSamples shall be randomly selected from all parts in the lot. The minimum number of parts tested shall be as indicated in Table 2.TABLE 2 - SAMPLING FOR NONDESTRUCTIVE ACCEPTANCE TESTSNumber of Parts in the Lot Number of Parts to be Tested15 or less 7 (1)16 to 40 1041 to 110 15111 to 300 25301 to 500 35501 and over 50(1) If the number of parts in the lot is less than 7, then all parts shallbe tested.4.3.2 DestructiveTestsSample quantities shall be as shown in Table 3.TABLE 3 - SAMPLING FOR PERIODIC DESTRUCTIVE TESTSTest Class ofCoatingNumber ofSamples tobe TestedRequirementParagraphSpecimenParagraphTest MethodParagraphThickness 1 & 2 4 3.4.1 4.3.3.1 3.4.1Adhesion 1 & 2 4 3.4.2 4.3.3.1 3.4.2Hardness 2 4 3.4.3 4.3.3.1 3.4.3Porosity 2 5 3.4.4 4.3.3.2 3.4.4.1HydrogenEmbrittlement1 &2 4 3.4.5 4.3.3.3 4.3.3.34.3.3 SampleConfigurationSeparate test specimens may be used under the following circumstances: When plated parts are of a configuration, size, quantity or value as to not be readily adaptable to a specified tests, when nondestructive testing is not practical on actual parts, or when it is not economically acceptable to perform destructive tests on actual parts. When used, separate test specimens shall be made of the same generic class of alloy as the parts as defined in 8.7, distributed within the lot of parts to be cleaned, plated and post treated with the actual parts.4.3.3.1 Separate test specimens for thickness, adhesion, and hardness tests shall be approximately 1 x 4 x 0.040inches (25 x 100 x 1 mm).4.3.3.2 Separate test specimens for porosity test shall be low alloy steel and approximately 3 x 10 x 0.040 inches (75 x250 x 1 mm).4.3.3.3 Hydrogen Embrittlement TestTest shall be in accordance with the requirements of ASTM F 519 Type 1a.1 using round notched specimens, unless a different specimen is specified by the purchaser, stressed in tension under constant load. For test purposes, the plating thickness shall be a minimum of 0.002 inch (51 μm) measured on the smooth section of the test specimen, but with visual plating at the root of the notch. The test samples shall be exposed to all steps of the documented plating process including surface preparation (reagent, electro-cleaning or abrasive blasting as applicable), underplate, electrodeposition of the chromium onto the basis metal, and the prescribed baking schedule per Table 1 and AMS 2759/9.4.3.3.4 Periodic and Preproduction Test Specimens for Thickness, Adhesion, Hardness, and PorosityWhen Class 2 plating is performed, separate test specimens shall be chromium plated onto bare steel to a nominal thickness of 0.002 inch (51 μm).4.4 Approval4.4.1 The process and control factors or a preproduction part, or both, whichever is specified, shall be approved by thecognizant engineering organization before production parts are processed.4.4.1.1 When specified, records of process control and all pre-production control test results shall be approved by thecognizant engineering organization before production parts are processed.4.4.2 If the processor makes a significant change to any material, process, or control factor from that which was usedfor process approval, all preproduction tests shall be performed and the results submitted to the purchaser for process reapproval unless the change is approved by the cognizant engineering organization. A significant change is one which, in the judgment of the cognizant engineering organization, could affect the properties or performance of the parts.4.4.3 Control factors shall include, but not limited to the following:Stress relief performed by plating processor (temperature and time)Surface preparation and cleaning methodsPlating material trade name and manufacturerPlating bath composition and composition control limitsPlating bath temperature limits and controlsPlating interruption and restart procedures, when applicableStripping procedure, when applicableRack locationsCurrent density (amps per part or amps per total surface area of the parts plated at one time in each tank)Hydrogen embrittlement relief (bake) temperature and time, when applicablePeriodic test plan for process solutions and records. See 4.2.2, 8.5, and 4.2.2.1.4.5 ReportsThe processor shall furnish with each shipment a report stating that the parts have been processed and tested in accordance with the specified requirements and that they conform to the acceptance test requirements. This report shall include the purchase order number, AMS 2460, the part number, lot identification, and quantity.4.6 Resampling and Retesting4.6.1 If any acceptance test for quality or thickness, and when specified, adhesion, hardness, or porosity fails to meetspecified test requirements, the parts in that lot may be stripped, pretreated, plated and post treated as defined herein and retested. Alternatively, all parts in the lot may be inspected for the non-conforming attribute, and the non-conforming parts may be stripped, pretreated, plated, and post treated as defined herein and then retested.When specified for acceptance testing, if hydrogen embrittlement fails to meet test requirements, retesting in accordance with the procedures of ASTM F 519 is permitted4.6.1.1 When stripping is performed, the method shall be acceptable to the purchaser and shall not roughen, pit, orembrittle the basis metal or adversely affect part dimensions. When parts have been stripped and replated, the reprocessing shall be documented and the purchaser shall be informed.4.6.2 If any periodic test fails to meet specified requirements, the process is nonconforming. No additional parts shall beplated until the process is corrected and new specimens are plated and tested. Results of all tests shall be recorded and, when requested, reported. Purchasers shall be notified of all parts coated since the last acceptable periodic test.5. PREPARATION FOR DELIVERY5.1 Plated parts shall be handled and packaged in such as manner as will ensure that the required physicalcharacteristics and properties of the plating are preserved.5.2 Packages of plated parts shall be prepared for shipment in accordance with commercial practice and in compliancewith applicable rules and regulations pertaining to the handling, packaging and transportation of the plated parts to ensure carrier acceptance and safe delivery.6. ACKNOWLEDGEMENTThe processor shall mention this specification number and its revision letter in all quotations and when acknowledging purchase orders.7. REJECTIONSParts on which plating does not conform to this specification or to modifications authorized by purchaser will be subject to rejection.8. NOTES8.1 A change bar (|) located in the left margin is for the convenience of the user in locating areas where technicalrevisions, not editorial changes, have been made to the previous issue of a specification. An (R) symbol to the left of the document title indicates a complete revision of the specification, including technical revision. Change bars and (R) are not used in original publications, nor in specifications that contain editorial changes only.8.2 This plating process alters the product dimensions. Compliance with dimensional tolerances affected by the platingprocess requires communications of manufacturing planning information between the part fabricator and the plating processor. The cognizant engineering organization should specify the stage at which the plating thickness and the product dimensions (e.g., threads, features) apply such as before plating, as-plated, or after metal removal operations that are to follow plating.8.3 The purchaser is expected to provide the processor with a properly dimensioned part that allows for the change indimensions expected from this process. The purchaser should also provide any special instructions that may need to be observed concerning plating thickness or plated part dimensions.8.4 The information in this section is provided for guidance, but does not alter the requirements of this specification.。
SAE-AMS-QQ-A-200-11-1997-R2007.pdf
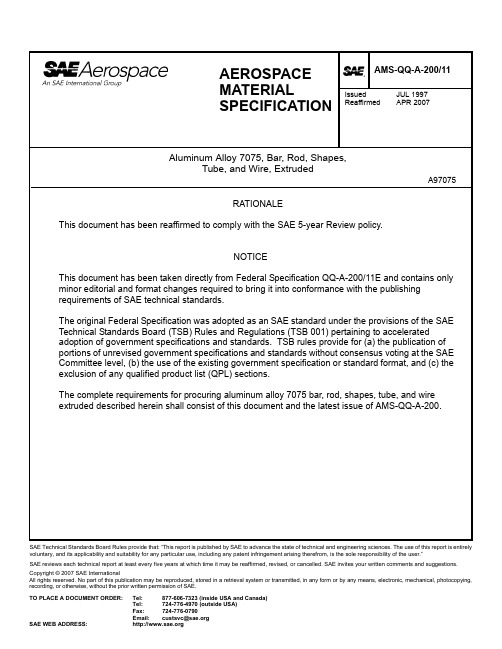
SAE Technical Standards Board Rules provide that: “This report is published by SAE to advance the state of technical and engineering sciences. The use of this report is entirely voluntary, and its applicability and suitability for any particular use, including any patent infringement arising therefrom, is the sole responsibility of the user.”SAE reviews each technical report at least every five years at which time it may be reaffirmed, revised, or cancelled. SAE invites your written comments and suggestions.Copyright © 2007 SAE InternationalAll rights reserved. No part of this publication may be reproduced, stored in a retrieval system or transmitted, in any form or by any means, electronic, mechanical, photocopying,recording, or otherwise, without the prior written permission of SAE.TO PLACE A DOCUMENT ORDER:Tel: 877-606-7323 (inside USA and Canada)Tel: 724-776-4970 (outside USA)Aluminum Alloy 7075, Bar, Rod, Shapes,Tube, and Wire, ExtrudedA97075RATIONALEThis document has been reaffirmed to comply with the SAE 5-year Review policy.NOTICEThis document has been taken directly from Federal Specification QQ-A-200/11E and contains only minor editorial and format changes required to bring it into conformance with the publishing requirements of SAE technical standards.The original Federal Specification was adopted as an SAE standard under the provisions of the SAE Technical Standards Board (TSB) Rules and Regulations (TSB 001) pertaining to accelerated adoption of government specifications and standards. TSB rules provide for (a) the publication of portions of unrevised government specifications and standards without consensus voting at the SAE Committee level, (b) the use of the existing government specification or standard format, and (c) the exclusion of any qualified product list (QPL) sections.The complete requirements for procuring aluminum alloy 7075 bar, rod, shapes, tube, and wire extruded described herein shall consist of this document and the latest issue of AMS-QQ-A-200.AEROSPACE MATERIALSPECIFICATIONAMS-QQ-A-200/11Issued JUL 1997 ReaffirmedAPR 20071.SCOPE AND CLASSIFICATION:1.1Scope:This specification covers the specific requirements for aluminum alloy 7075 bar, rod, shapes, tube, and wire produced by extrusion.1.2Classification:1.2.1Tempers: Bar, rod, shapes, tube, and wire are classified in the following tempers as specified(See6.2): O,T6, T62, T6510, T6511, T73, T73510, or T73511. Definitions of tempers arespecified in AMS-QQ-A-200.1.2.2Tubing: Tubing shall be additionally classified as follows:Type DescriptionI-Tubing extruded from hollow billets using die and mandrel (SeeAMS-QQ-A-200).II-Tubing extruded from solid billets using a porthole or spiderdie or similar tooling (See AMS-QQ-A-200) 1/.1/ Type II tubing is not commonly available from the producers.2.APPLICABLE DOCUMENTS:See AMS-QQ-A-200.3.REQUIREMENTS: 3.1Chemical Composition:The chemical composition shall conform to the requirements specified in Table I.3.2Mechanical Properties:3.2.1Mechanical Properties of Material as Supplied: Mechanical properties of as-supplied material shall, in the longitudinal (extrusion) direction, conform to property requirements specified in Table II, except as exempted in AMS-QQ-A-200.TABLE I. Chemical Composition 1/ElementPercentMinimum Maximum Zinc5.16.1Magnesium 2.1 2.9Copper 1.2 2.0Chromium 0.180.28Iron --0.50Silicon--0.40Manganese --0.30Titanium--0.20Other Elements, each --0.05Other Elements, total 2/--0.15AluminumRemainder1/Analysis shall routinely be made only for the elements specifically mentioned in Table I. If, however, thepresence of other elements is indicated or suspected in amounts greater than the specified limits, furtheranalysis shall be made to determine that these elements are not present in excess of specified limits.2/The sum of those "Others" metallic elements 0.010percent or more each, expressed to the second decimal before determining the sum.3.2.2Mechanical Properties After Heat Treatment: In addition to conforming to the requirements of3.2.1, materials identified in the following paragraphs shall, after having been heat-treated to other tempers also identified therein, have properties in the longitudinal (extrusion) direction conforming to those specified in Table II, as applicable.TABLE II. Mechanical PropertiesTemperThickness, (bar and shapes); diameter,(rod and wire); wall thickness, (tube)InchesArea Square Inches TensileStrengthMinimum ksi Yield Strength at 0.2 percent Offset or at extension indicatedElongation in2 inches or 4times D 1/Minimum percent Minimum ksi Extension under load inch perinch O AllAll 2/2/--10T6, T62 3/, Up to 0.249, incl All 78.070.00.0088 7T6510 and 0.250to 0.499, incl All 81.073.00.0090 7T6511 4/0.500to 2.999, inclAll 81.072.00.0090 73.000to 4.499, incl Up thru 2081.071.00.0088 73.000to 4.499, incl Over 20 thru 3278.070.00.0088 64.500to 5.000, incl Up thru 3278.068.00.0086 6T73,0.062to 0.249, incl Up thru 2068.058.00.0076 7T73510,0.250to 1.499, incl Up thru 2570.061.00.0079 8T73511 4/ 1.500to 2.999, incl Up thru 2569.059.00.0077 83.000to 4.499, incl Up thru 2068.057.00.0075 73.000to 4.499, inclOver 20 thru 3265.055.00.007371/D represents specimen diameter.2/No minimum required. Maximum tensile and yield strengths shall be 40.0 ksi and 24.0 ksi, respectively.3/Material in the T62 temper is not available from material producers.4/For stress-relieved tempers, the characteristics and properties, other than those specified, may differ somewhat from the corresponding characteristics and properties of the material in the basic temper.3.2.2.1Material in the O Temper: Material in the O temper, without the subsequent imposition of cold work or forming operations, shall, after proper solution heat treatment and artificial aging,develop the properties specified in Table II for the T62 temper. Material in the O temper, without the subsequent imposition of cold work or forming operations, shall be capable of being solution heat-treated and overaged (stabilized) to the properties specified for the T73 temper. Such capability shall be demonstrated when specified (See 6.2).3.2.2.2Material in the T6, T6510, T6511, T73, T73510, and T73511 Tempers: Material in the T6, T6510, T6511, T73, T73510, and T73511 tempers, without the subsequent imposition of cold work or forming operations, shall be capable of being solution heat-treated and artificially aged or overaged, as applicable, to the properties specified for the T62 and T73 tempers. Such capability shall be demonstrated when specified (See 6.2).3.3Internal Defects:When specified (See 6.2), bar, rod, tube, and shapes shall be ultrasonically inspected (SeeAMS-QQ-A-200). Acceptance limits shall be as specified in Table III. The technique for inspection of tube shall be as agreed upon by the procuring activity and the contractor (See 6.2).3.4Resistance to Stress-Corrosion Cracking:Material supplied in the T73, T73510, and T73511 tempers shall exhibit no evidence of stress-corrosion cracking when subjected to the test specified in 4.2. Sampling frequency shall be in accordance with AMS-QQ-A-200.TABLE III. Ultrasonic Discontinuity Acceptance Limits 1/Thickness, (bar and shapes); diameter(rod); wall thickness, (tube);inches 2/Maximum weightper piece poundsMaximum width to thicknessratio 3/Discontinuityclass 4/0.500 to 1.49960010 to 1B 1.500 and over60010 to 1A1/Discontinuities in excess of those listed in Table III may be allowed subject to approval of the procuring activity, if it is established that they will be removed by machining or that they are in noncritical areas.2/The thickness of any element of a shape shall be deemed to be the smallest dimension of that element, and the discontinuity class applicable to that particular thickness shall apply to that element of the shape.3/Not applicable to rod and tube.4/Discontinuity class limits are defined in MIL-STD-2154.3.4.1Lot Acceptance Criteria for Stress-Corrosion Cracking: Resistance to stress-corrosion cracking foreach inspection lot of 7075-T73, T73510, and T73511 material shall be established by testing the previously selected tensile test specimens to the following criteria:Determine electrical conductivity and tensile properties.If the conductivity is below 38.0 percent International Annealed Copper Standard (IACS), thematerial is considered unsatisfactory and must be reprocessed, regardless of property level.If the conductivity is 40.0 percent IACS or higher and tensile properties meet the minimum values specified herein, the material is considered to be satisfactory.If conductivity is 38.0 through 39.9 percent IACS, if tensile properties meet the minimum limitsspecified herein, and if the yield strength does not exceed the specified minimum by more than11.9 ksi, the material is considered to be satisfactory.If conductivity is 38.0 through 39.9 percent IACS and the yield strength exceeds the specifiedminimum value by 12.0 ksi or more, the material is considered suspect.When material is considered suspect, it may either be given additional second step aging or be reprocessed.3.5Marking:In addition to the marking required by AMS-QQ-A-200, material in the T6, T6510, T6511, T73,T73510, and T73511 tempers shall be identified by an inspection lot number marked in at least one location on each piece.4.QUALITY ASSURANCE PROVISIONS:See AMS-QQ-A-200 and the following:4.1Mechanical Tests After Heat Treatment:4.1.1Material in the O Temper: From material in the O temper, an additional number of specimens,equal to that required by AMS-QQ-A-200, shall be taken and tested after solution heat treatment and artificial aging to determine compliance with 3.2.2.1 relative to the T62 temper. Whenspecified (See 6.2), from material in the O temper, a number of specimens, equal to that required by AMS-QQ-A-200, shall be taken and tested after solution heat treatment and over-aging todetermine compliance with 3.2.2.1 relative to the T73 temper.4.1.2Material in Tempers Other Than O: When specified (See 6.2), from material in a temper other thanthe O temper, an additional number of specimens, equal to that required by AMS-QQ-A-200, shall be taken and tested after the appropriate solution heat treatment and aging treatment to determine compliance with 3.2.2.2.4.2Stress-Corrosion Cracking Test:Specimens shall be selected from 7075-T73, -T73510, and -T73511 material, 0.750 inch and greater in thickness, in a manner which will permit application of the specified tensile stress in the short-transverse direction with respect to grain flow. Specimens shall be stressed in tension in the short-transverse direction and held at constant strain. The stress level shall be 75 percent of the specified longitudinal yield strength. The specimens shall be subjected to the stress-corrosion test specified in AMS-QQ-A-200, the exposure duration to be 20 days. It is the responsibility of the contractor that test results be recorded, identified as to inspection lot, and maintained.4.3Electrical Conductivity Testing:Conductivity measurements shall be made prior to tensile testing on samples selected from the extruded 7075-T73, -T73510, and -T73511 material, to determine compliance with 3.4.1. For all material in the thickness range of 0.500 through 1.500 inches, conductivity measurements shall be made at the approximate center of the section thickness on a plane parallel to the longitudinalcenterline of the extrusion. For material over 1.500 inches in thickness, the conductivity shall be measured on the test coupon surface which is closest to the center of the extrusion thickness and ona plane parallel to the extrusion surface. For extruded sections of non-constant cross-sectionaldimensions, conductivity measurements shall be made at the center of the section possessing the greatest cross-sectional thickness. For material 0.101 through 0.499 inch in thickness, theconductivity shall be determined on the subsurface after removal of approximately 10 percent of the thickness from one surface. For material up through 0.100 inch in thickness, the conductivity shall be measured on the surface of the tensile test specimen. For curved surfaces, the conductivity shall be measured on a machined flat spot; however, for small sizes of tubes, a cut-out portion may be flattened and the conductivity determined on the surface.5.PREPARATION FOR DELIVERY:See AMS-QQ-A-200.6.NOTES:6.1Intended Use:This alloy is intended for use where high strength is required, and where good resistance to general corrosion is not important. The T6510 and T73510 tempers are intended primarily to provideextruded material with low residual stresses and consequent minimum distortion during machining.The T6511 and T73511 tempers are straightened T6510 and T73510 material respectively and may have unknown residual stresses and may or may not distort during machining. The T73, T73510, and T73511 tempers provide resistance to stress corrosion.6.2Properties After Heat Treatment:Mechanical properties and corrosion properties, where applicable, are certified for the temper of material supplied. The producer’s capability demonstration is not evidence that user-treated material conforms to property requirements of a given temper. Frequently, user-heat-treated material may develop a lower level of properties, especially if any cold, warm, or hot work is introduced prior to solution heat treatment. The user should be held responsible for demonstrating that his processing will yield properties meeting requirements.6.3Ordering Data:Purchasers should select the preferred options permitted herein and include the followinginformation in procurement documents:Title, number, and date of this specification.Form, quantity, and temper required (See 1.2.1).Dimensions required.Requirements for sizes not specifically covered (See AMS-QQ-A-200).Special end use requirements.Which, if any, demonstrations of heat treatability are to be performed where such demonstrations are optional (See 3.2.2.1 and 3.2.2.2).Whether ultrasonic inspection of material is required (See 3.3). Method of inspection of tubing,where applicable. Requirements for sizes, maximum weights, and discontinuityclasses not coveredin Table III.Selection of applicable levels of preservation, packaging, and packing (See AMS-QQ-A-200).6.4Product produced and marked to the requirements of AMS-QQ-A-200/11 also meets therequirements of QQ-A-200/11E. Product produced and marked to the requirements ofQQ-A-200/11E also meets the requirements of AMS-QQ-A-200/11.6.5The properties listed in 3.2.1 are exactly the same as QQ-A-200/11, Revision E. These propertieshave not been substantiated in accordance with the AMS Manual for Preparation of Aerospace Specifications.PREPARED UNDER THE JURISDICTION OF AMS COMMITTEE "D"。
SAE AMS 2417G-2004 镀锌-镍合金

SAE Technical Standards Board Rules provide that: “This report is published by SAE to advance the state of technical and engineering sciences. The use of this report is entirely voluntary, and its applicability and suitability for any particular use, including any patent infringement arising therefrom, is the sole responsibility of the user.”SAE reviews each technical report at least every five years at which time it may be reaffirmed, revised, or cancelled. SAE invites your written comments and suggestions. Copyright © 2004 SAE InternationalAll rights reserved. No part of this publication may be reproduced, stored in a retrieval system or transmitted, in any form or by any means, electronic, mechanical, photocopying, recording, or otherwise, without the prior written permission of SAE.TO PLACE A DOCUMENT ORDER: Tel: 877-606-7323 (inside USA and Canada)Tel: 724-776-4970 (outside USA)2.APPLICABLE DOCUMENTS:The issue of the following documents in effect on the date of the purchase order forms a part of this specification to the extent specified herein. The supplier may work to a subsequent revision ofa document unless a specific document issue is specified. When the referenced document hasbeen canceled and no superseding document has been specified, the last published issue of that document shall apply.2.1SAE Publications:Available from SAE, 400 Commonwealth Drive, Warrendale, PA 15096-0001 or .AMS 2759/9 Hydrogen Embrittlement Relief (Baking) of Steel Parts2.2ASTM Publications:Available from ASTM, 100 Barr Harbor Drive, P.O. Box C700, West Conshohocken, PA19428-2959 or .ASTM B 117 Practice for Operating Salt Spray (Fog) ApparatusASTM B 253 Guide for Preparation of Aluminum Alloys for ElectroplatingASTM B 487 Test Method for Measurement of Metal and Oxide Coating Thicknessesby Microscopical Examination of a CrossSectionASTM B 499 Test Method for Measurement of Coating Thicknesses by the MagneticMethod: Nonmagnetic Coatings on Magnetic Basis Metals ASTM B 504 Test Method for Measurement of Thickness of Metallic Coatings by theCoulometric MethodASTM B 568 Test Method for Measurement of Coating Thickness by X-RaySpectrometryASTM B 571 Test Methods for Adhesion of Metallic CoatingsASTM E 376 Practice for Measuring Coating Thickness by Magnetic-Field or Eddy-Current (Electromagnetic) Examination MethodsASTM F 519 Test Method for Mechanical Hydrogen Embrittlement Evaluation ofPlating Processes and Service Environments3.TECHNICAL REQUIREMENTS:3.1Preparation:3.1.1Steel parts having a hardness of 40 HRC or higher and which have been straightened,formed, or ground after heat treatment shall be suitably stress relieved before cleaning andplating. Temperatures to which parts are heated shall be such that maximum stress relief isobtained without reducing hardness of parts below drawing limits, but, unless otherwisespecified, not less than 275 °F ± 10 (135 °C ± 6) for not less than five hours for parts 55 HRC or greater, or 375 °F ± 25 (191 °C ± 14) for not less than four hours for other parts.3.1.2Parts shall have clean surfaces free of water break prior to immersion in the plating solution.3.1.3Electrical contact between the parts and power source shall be made to prevent chemical orimmersion deposition, electrical arcing, and overheating. If parts are to be plated all over,contact points shall be located where specified or where agreed upon by purchaser andprocessor. If parts are not required to be plated all over, contact points shall be located onareas on which plating is not required or is optional.3.1.4Prior to deposition of the zinc-nickel alloy, parts may be given an electrodeposited nickelstrike, or may be dry or wet abrasive blasted. Mechanical finishing, if employed, shall becompleted prior to application of a nickel strike, when used, and shall be accomplished in amanner that will not affect the appearance or quality of the finished part.3.2Procedure:3.2.1The zinc-nickel alloy plate shall be electrodeposited from a suitable electrolyte. Stress-reducing agents shall not be used unless approved by purchaser.3.2.1.1Aluminum alloys may be zincate treated in accordance with ASTM B 253 before plating.3.2.1.2Parts which specify Type 2 plating shall be given a supplementary chromate conversioncoating, which will meet the requirements of 3.4.4.2. Any post thermal treatment shall bedone prior to application of the chromate conversion treatment. Steel parts requiring a postthermal treatment as in 3.3 may require reactivation prior to application of the conversioncoating.3.2.1.3Parts which specify Type 3 plating shall, after hydrogen embrittlement relief baking, be givena supplementary zinc phosphate conversion coating, which meets the requirements of3.4.4.3. Steel parts requiring post thermal treatment as in 3.3 may require reactivation priorto application of the conversion coating.3.3Hydrogen Embrittlement Relief:Treatment of steel parts shall be in accordance with AMS 2759/9.3.4Properties:Zinc-nickel alloy plate shall conform to the following requirements. (Composition and thickness for Types 2 and 3 apply prior to conversion coating).3.4.1Composition: The zinc-nickel alloy plate shall contain 6 to 20% nickel and the balanceessentially zinc, determined by a method acceptable to purchaser.3.4.2Thickness: Shall be as follows, determined on representative parts or test panels inaccordance with ASTM B 487, ASTM B 499, ASTM B 504, ASTM B 568, ASTM E 376, orother method acceptable to purchaser (See 8.3).3.4.2.1Nickel Strike: When applied, shall be 0.0001 inch (2.5 µm) maximum.3.4.2.2Zinc-Nickel Alloy Plate:3.4.2.2.1Parts Without External Threads (other than washers): Shall have total plate thickness of0.0003 to 0.0007 inch (8 to 18 µm).3.4.2.2.2Washers and Parts With External Threads: Shall have total plate thickness of 0.0002 to0.0004 inch (5 to 10 µm).3.4.2.2.3Except for external threads, thickness shall be considered only where surfaces of partscan be touched by a sphere 0.75 inch (19 mm) in diameter. No requirements areestablished for minimum plating thickness on surfaces of holes, recesses, internalthreads, contact areas of parts plated all over, and other areas where a controlled depositcannot be obtained under normal plating conditions, but such areas shall not be maskedto prevent plating.3.4.3Adhesion: Shall meet the requirements of ASTM B 571 for zinc plating.3.4.4Corrosion Resistance:3.4.4.1Type 1 plated parts or representative specimens, plated to a thickness of 0.0004 to 0.0007inch (10 to 18 µm) shall show no visual evidence of red corrosion on the basis metal incontrolled thickness areas, determined by exposure for 500 hours to salt spray corrosiontest conducted in accordance with ASTM B 117 (See 4.3.1.3).3.4.4.2Type 2 plated parts or representative specimens, plated to a thickness of 0.0004 to 0.0007inch (10 to 18 µm) shall show no visual evidence of white corrosion product after 96 hoursand no evidence of red corrosion on the basis metal in controlled thickness areas after 500 hours, determined by exposure to salt spray corrosion testing in accordance with ASTM B117. (See 4.3.1.3).3.4.4.3Type 3 plated parts or representative specimens, which have received a supplementaryType 3 phosphate conversion coating shall be uniform in texture, evenly deposited, andmedium gray to black in color. The coating shall not show smut, powder, or white stains.Corrosion test not required; visual requirement only.3.4.5Hydrogen Embrittlement: The plating process shall not cause hydrogen embrittlement in steelparts, after baking, determined in accordance with ASTM F 519 (See 4.3.1.4).3.5Quality:Plating, as received by purchaser, shall be smooth, continuous, adherent to the basis metal, and visually free from porosity, blisters, nodules, pits, and other imperfections detrimental to performance of the plating. Slight staining or discoloration is permissible. There shall be no evidence of double plating or spotting-in.4.QUALITY ASSURANCE PROVISIONS:4.1Responsibility for Inspection:The processor shall supply all samples for processor’s tests and shall be responsible for the performance of all required tests. Parts, if required for tests, shall be supplied by purchaser.Purchaser reserves the right to sample and to perform any confirmatory tests deemednecessary to ensure that processing conforms to the specified requirements.4.2Classification of Tests:4.2.1Acceptance Tests: Thickness (3.4.2), adhesion (3.4.3), and quality (3.5) are acceptance testsand shall be performed to represent each lot.4.2.2Periodic Tests: Composition (3.4.1), corrosion resistance (3.4.4.2) (white corrosion productonly), hydrogen embrittlement (3.4.5), and tests of preparatory and plating solutions (See 8.7) to ensure that the deposited metal will conform to specified requirements are periodic testsand shall be performed at a frequency selected by the processor unless frequency of testing is specified by purchaser, except corrosion resistance (3.4.4.2), which shall be conducted not less than monthly.4.2.3Preproduction Tests: All technical requirements are preproduction tests and shall beperformed prior to or on the initial shipment of plated parts to a purchaser, when a change in material and/or processing requires reapproval by the cognizant engineering organization(See 4.4.2), and when purchaser deems confirmatory testing to be required.4.3Sampling and Testing:Shall be not less than the following: A lot shall be all parts of the same material and part number or similar part configuration, plated to the same range of plate thickness using the samesolutions, plated in a single, continuous plating cycle, not to exceed 16 hours, and presented for processor’s inspection at one time.4.3.1Sample Configuration:4.3.1.1Nondestructive testing shall be performed wherever practical and authorized herein. Exceptas noted, actual parts shall be selected as samples for tests.4.3.1.2Thickness and Adhesion: Separate test panels of the same generic class of alloy and heattreat condition as the parts, distributed throughout the lot, cleaned, plated, and post treatedwith the parts represented shall be used when plated parts are of such configuration or sizeas to be not readily adaptable to the specified tests, when nondestructive testing is notpractical on actual parts, or it is not economically acceptable to perform destructive tests onactual parts.4.4.3Control Factors: Shall include, but not be limited to the following:Surface preparation including strike, if usedPlating bath composition and composition control limitsType of supplementary coating, if usedThermal pretreatment times and temperaturesThermal post treatment times and temperaturesMethod of testing plating thicknessMethod of adhesion testingPeriodic test plan.4.5Reports:The processor of plated parts shall furnish with each shipment a report stating that the parts have been processed and tested in accordance with the specified requirements and that they conform to acceptance test requirements. This report shall include the purchase order number, lot number, AMS 2417G, part number, and quantity.4.6Resampling and Retesting:4.6.1If the results of any acceptance test fails to meet the specified requirements, the partsrepresented may be stripped by a method acceptable to the purchaser that does not roughen, pit, or adversely affect part dimensions, pretreated, coated, supplementary treated, ifspecified, as defined herein, and tested. Alternatively, all parts in the lot may be inspected for the nonconforming attribute, and the nonconforming parts may be stripped by a methodacceptable to purchaser that does not roughen, pit, or adversely affect part dimensions and treated as above.4.6.2If the results of any periodic test fails to meet the specified requirements, the process isnonconforming. No additional part shall be coated until the process is corrected and newspecimens are coated and tested. Results of all tests shall be recorded, and, when requested, reported. Purchaser shall be notified of all parts coated since the last acceptable test.5.PREPARATION FOR DELIVERY:5.1Plated parts shall be handled and packaged to ensure that the required physical characteristicsand properties of the plate are preserved.5.2Packages of plated parts shall be prepared for shipment in accordance with commercialpractice and in compliance with applicable rules and regulations pertaining to the handling,packaging, and transportation of the parts to ensure carrier acceptance and safe delivery.6.ACKNOWLEDGMENT:A processor shall mention this specification number and its revision letter in all quotations andwhen acknowledging purchase orders.7.REJECTIONS:Parts on which plating does not conform to this specification, or to modifications authorized by purchaser, will be subjected to rejection.8.NOTES:8.1 A change bar (|) located in the left margin is for the convenience of the user in locating areaswhere technical revisions, not editorial changes, have been made to the previous issue of this specification. An (R) symbol to the left of the document title indicates a complete revision of the specification, including technical revisions. Change bars and (R) are not used in originalpublications, nor in specifications that contain editorial changes only.8.2Terms used in AMS are clarified in ARP1917.8.3Dimensions in inch/pound units and the Fahrenheit temperatures are primary; dimensions in SIunits and Celsius temperatures are shown as the approximate equivalents of the primary units and are presented only for information.8.4Purchase documents should specify not less than the following:AMS 2417GPlating typePlate thickness desired, if different from 3.4.2.2Quantity of parts to be plated.8.5Part manufacturing operations such as heat treatment, forming, machining, joining, and mediafinishing, can affect the condition of the substrate for plating, or if performed after plating, could adversely affect the plating. The sequencing of these operations should be specified by thecognizant engineering organization and is not controlled by this specification.8.6The parts manufacturer should ensure that surfaces of metal parts supplied to the processorare free from blemishes, pits, tool marks, and other irregularities that will affect the quality of the finished parts. Defects and variations in appearance that arise from surface conditions of the substrate, such as porosity, scratches, or inclusions, that persist in the finished plate despite observance of industry accepted plating practices would not be considered as cause forrejection.8.7An acid dip may be used for surface activation or neutralization of residual alkaline cleaners.However, the immersion time should be minimized to preclude pitting.8.8ARP4992, Periodic Test Plan for Process Solutions, may be used to satisfy the requirements forcontrol of processing solutions (See 4.4.3).8.9Because zinc will plate more rapidly in high current density areas such as sharp corners andedges, Zn-Ni deposits having composition at the low end of the 6 to 20% nickel range may drop below the 6% nickel minimum in these high current density areas.8.10When Zn-Ni is used as an alternate for cadmium plating on threaded fasteners, use cautionsince Zn-Ni produces less preload for a given torque than cadmium plate.8.11This specification permits either alkaline or acid Zn-Ni plating; however, the acid processescurrently provide superior corrosion resistance and reduced tendency for hydrogenembrittlement than the alkaline processes.8.12Plating meeting the requirements of this specification has been classified under FederalStandardization Area Symbol “MFFP”.8.13Key Words:Electrodeposited, corrosion resistancePREPARED UNDER THE JURISDICTION OF AMS COMMITTEE “B”。
SAE标准目录

ETA-UTP001 Revision 0(SAE J1263)[P19].pdfETA-UTP001-Effective March 23,2001 Implementation of SAE J1263-1996.pdfNASA-SAE-88-1448 LDV Surveys Over Fighter Model at Moderate High Angles of Attack[P27].pdf SAE- Automotive Chassis Engineering Principles (SECOND EDITION)[P454].pdfSAE- Automotive Chassis-Engineering Principles [SECOND EDITION][P456].pdfSAE- Automotive Physical Layer SAE-J1708 DS36277.pdfSAE- Structural Steel Designer's Handbook (Brockenbrough & Merritt)(3Rd Edition)[P1201].pdf SAE-174M-MAY1998 TORQUE-TENSION TEST PROCEDURESTEEL THREADED FASTENERS,METRIC SERIES.pdfSAE-2006 Formula SAE-Chassis Design(Queen's University)[P18].pdfSAE-720709-1972 Design&Development of a High horsepower torque sensing variable speed drive.pdfSAE-AIR1228-2001 Standard Impulse Machine Equipment&Operation[P6].pdfSAE-AIR1377A-2004 Fire Test Equipment for Flexible Hose&Tube Assemblies[P22].pdfSAE-AIR3260-2006 Identification of Standard Utility Parts - Bolts&Nuts[P4].pdfSAE-AIR4002-1994 8000 psi Hydraulic Systems Experience&Test Results.pdfSAE-AIR4069A-1998 Sealing of Integral Fuel Tanks [P94].pdfSAE-AIR4069A-1998 Sealing of Integral Fuel Tanks[P95].pdfSAE-AIR4176-1995(R2005) Cost Versus Benefits of Engine Monitoring Systems.pdfSAE-AIR5120-2006 Engine Monitoring System Reliability&Validity[P27].pdfSAE-AIR797E-2001 Hose Characteristics&Selection Chart[P15].pdfSAE-AMS1376B-1992 R1998 Remover,Epoxy Paint Acid-Type,Thickened.pdfSAE-AMS1379A-1996 COMPOUND,ALKALINE RUST REMOVER Aircraft Turbine Engine Components[P7].pdfSAE-AMS1380A-1992 SCALE CONDITIONER,ALKALINE Aircraft Turbine Engine Components[P6].pdfSAE-AMS1382A-1991 OXIDE REMOVER COMPOUND,ACIDIC Aircraft Turbine Engine Components[P6].pdfSAE-AMS1383A-1999 Oxide Conditioner,Alkaline Permanganate Aircraft Turbine Engine Components.pdfSAE-AMS1384A-1991 ACID,INHIBITED PHOSPHORIC Aircraft Turbine Engine Components Room Temperature Application[P6].pdfSAE-AMS1385A-2004 Compound,Hot Carbon&Paint Remover Aircraft Turbine Engine Components.pdfSAE-AMS1386A-2004 Compound,Silicone Rubber Remover Aircraft Turbine Engine Components Room Temperature Application.pdfSAE-AMS1387A-2004 Remover,Anti-Galling Compound Aircraft Turbine Engine Components Room Temperature Application.pdfSAE-AMS1424G-2006 (R) Deicing_Anti-Icing Fluid,Aircraft SAE-Type I.pdfSAE-AMS1424H-2007 Deicing_Anti-Icing Fluid,Aircraft,SAE-Type I[P15].pdfSAE-AMS1426C-1993 FLUID,DEICINGANTI-ICING,RUNWAYS&TAXIWAYS Glycol Base.pdf SAE-AMS1428E-2006 Fluid,Aircraft DeicingAnti-Icing,Non-Newtonian (Pseudoplastic),SAE-Types II,III,&IV.pdfSAE-AMS1431B-1998 Compound,Solid Runway&Taxiway Deicing_Anti-Icing.pdfSAE-AMS1435A-1999 Fluid,Generic,Deicing_Anti-Icing Runways&Taxiways.pdfSAE-AMS1453-2004 Disinfectant Cleaner for Aircraft Interior General Purpose Liquid .pdfSAE-AMS1476B-2004 Deodorant,Aircraft Toilet.pdfSAE-AMS1526B-2000 Cleaner for Aircraft Exterior Surfaces Water-Miscible,Pressure-Spraying Type.pdfSAE-AMS1534B-2004 Cleaner,Aircraft Glass Window.pdfSAE-AMS1535C-2002 Cleaner,Transparent Plastic.pdfSAE-AMS1537B-2001 Cleaner,Alkaline Hot-Tank Type.pdfSAE-AMS1538A-1996 DEOXIDER,ACIDIC,FOR MAGNESIUM ALLOYS.pdfSAE-AMS1547-1996 Cleaner,Anodic,Electrolytic,Alkaline For Steel,Tank Type .pdfSAE-AMS1595A-1998 Qualification of Aircraft,Missile&Aerospace Fusion Welders.pdfSAE-AMS1625B-1989 DESMUTTER,ALUMINUM,POWDERED.pdfSAE-AMS1626B-1989 DESMUTTER,ALUMINUM Liquid.pdfSAE-AMS1631C-2005 Cleaner,Carpet Water Extraction Type.pdfSAE-AMS1640B-1988 CORROSION REMOVING COMPOUND For Aircraft Surfaces.pdfSAE-AMS2154-2005 Inspection,Ultrasonic,Wrought Metals,Process For.pdfSAE-AMS2154-2005 Inspection,Ultrasonic,Wrought Metals,Process For[P41].pdfSAE-AMS2175-2003 Castings,Classification&Inspection of.pdfSAE-AMS2241P-2005 Tolerances,Corrosion&Heat-Resistant Steel,Iron Alloy,Titanium,&Titanium Alloy Bars&Wire.pdfSAE-AMS2242F-2006 Tolerances Corrosion&Heat Resistant Steel,Iron Alloy,Titanium,&Titanium Alloy Sheet,Strip,&Plate.pdfSAE-AMS2243H-2006 Tolerances Corrosion&Heat-Resistant Steel Tubing.pdfSAE-AMS2244C-2003 Tolerances (R) Titanium&Titanium Alloy Tubing.pdfSAE-AMS2249F-2005 Chemical Check Analysis Limits Titanium&Titanium Alloys.pdfSAE-AMS2249F-2005 Chemical Check Analysis Limits Titanium&Titanium Alloys[1].pdfSAE-AMS2251G-1998 Tolerances Low-Alloy Steel Bars.pdfSAE-AMS2251H-2006 Tolerances Low-Alloy Steel Bars.pdfSAE-AMS2252D-2006 Tolerances Low-Alloy Steel Sheet,Strip,&Plate.pdfSAE-AMS2269F-2006 Chemical Check Analysis Limits Nickel,Nickel Alloys,and Cobalt Alloys.pdf SAE-AMS2372D 碳钢和低合金钢取样规范[中文版].pdfSAE-AMS2372D-JAN2002 Quality Assurance Sampling&Testing Carbon&Low-Alloy Steel Forgings[P6].pdfSAE-AMS2375D-2007 Control of Forgings Requiring First Article Approval [P6].pdfSAE-AMS2406L-2007 Plating,Chromium Hard Deposit [p7].pdfSAE-AMS2411F-2007 Plating,Silver for High Temperature Applications [P8].pdfSAE-AMS2412H-2007 Plating,Silver Copper Strike,Low Bake[P7].pdfSAE-AMS2417G-2004 Plating,Zinc-Nickel Alloy.pdfSAE-AMS2422E-2007 Plating,Gold[P9].pdfSAE-AMS2435G-2007 Coating,Tungsten Carbide-Cobalt Coating,Detonation Process [P8].pdfSAE-AMS2448-2004 Application of Tungsten Carbide Coatings on Ultra High Strength Steels High Velocity Oxygen Fuel Process[P13].pdfSAE-AMS2448-2004 Application of Tungsten Carbide Coatings on Ultra High Strength Steels High Velocity Oxygen Fuel Process.pdfSAE-AMS2469G-2004 Hard Anodic Coating Treatment of Aluminum&Aluminum Alloys Processing&Performance Requirements.[P8].pdfSAE-AMS2470M-2007 Anodic Treatment of Aluminum Alloys Chromic Acid Process[P8].pdfSAE-AMS2482C-2006 Hard Coating Treatment of Aluminum Alloys Teflon-Impregnated or Codeposited.pdfSAE-AMS2482C-2006 Hard Coating Treatment of Aluminum Alloys Teflon-Impregnated or Codeposited[P7].pdfSAE-AMS2546-2004 Reaffirmed 2010-05 Laser Peening.pdfSAE-AMS2633C-2007 Ultrasonic Inspection Centrifugally-Cast,Corrosion-Resistant Steel Tubular Cylinders[P13].pdfSAE-AMS2643D-2007 Structural Examination of Titanium Alloys Chemical Etch Inspection Procedure [P5].pdfSAE-AMS2647C-2009 Fluorescent Penetrant Inspection Aircraft&Engine Component Maintenance.pdfSAE-AMS2649C-2008 Etch Inspection of High Strength Steel Parts.pdfSAE-AMS2753B-1991 Liquid Salt Bath Ferritic Nitrocarburizing Non-Cyanide Bath[P8].pdfSAE-AMS2757-B-2004 气体氮碳共渗.pdfSAE-AMS2759_11-2005 Stress Relief of Steel Parts[P5].pdfSAE-AMS2759_2C-2000 低合金钢零件的热处理最小拉伸强度大于等于220KSI[中文版][P13].pdfSAE-AMS2759_3C-2000 沉淀硬化不锈钢和马氏体时效钢的热处理[中文版][P16].pdfSAE-AMS2759_3D-2005 Heat Treatment Precipitation-Hardening Corrosion-Resistant&Maraging Steel Parts[P16].pdfSAE-AMS2759_3D-2005 Heat Treatment Precipitation-Hardening Corrosion-Resistant&Maraging Steel Parts[P16][1].pdfSAE-AMS2759-11-1992 Ion Nitriding.pdfSAE-AMS2759-11-2005 Stress Relief of Steel Parts.pdfSAE-AMS27591-12A-2007 Gaseous Nitrocarburizing,Automatically Controlled by Potentials.pdf SAE-AMS2759-12A 2007 Gaseous Nitrocarburizing,Automatically Controlled by Potentials.pdfSAE-AMS2759-1C-2000 最低抗拉强度低于220 ksi (1517 MPa)低合金碳钢零件的热处理.pdf SAE-AMS2759-2C-2000 Heat Treatment of Low-Alloy Steel Parts Minimum Tensile Strength 220 ksi (1 51 7 MPa)&Higher.pdfSAE-AMS2759-2C-2000 中文版低合金钢零件的热处理最小拉伸强度大于等于220KSI(1517MPa).pdfSAE-AMS2759-3C-2000 中文版沉淀硬化不锈钢和马氏体时效钢的热处理.pdfSAE-AMS2759-3D-2005 Heat Treatment Precipitation-Hardening Corrosion-Resistant&Maraging Steel Parts.pdfSAE-AMS2759-4B-2001 Heat Treatment Austenitic Corrosion-Resistant Steel Parts.pdfSAE-AMS2759-5D-2004 Heat Treatment Martensitic Corrosion-Resistant Steel Parts.pdfSAE-AMS2759-6A-2002 Gas Nitriding&Heat Treatment of Low-Alloy Steel Parts.pdfSAE-AMS2759-7A-2006 Carburizing&Heat Treatment of Carburizing Grade Steel Parts.pdfSAE-AMS2759-9_8-1992 Ion Nitriding [P12].pdfSAE-AMS2759C-2000 Heat Treatment of Steel Parts General Requirements[P15].pdfSAE-AMS2770H-2006 Heat Treatment of Wrought Aluminum Alloy Parts.pdfSAE-AMS2771C-2004 Heat Treatment of Aluminum Alloy Castings.pdfSAE-AMS2772C-2002 Heat Treatment of Aluminum Alloy Raw Materials.pdfSAE-AMS2772E-2008 Heat Treatment of Aluminum Alloy Raw Materials.pdfSAE-AMS2809-1986 R2002 Identification Titanium&Titanium Alloy Wrought Products.pdfSAE-AMS2809-2002 Identification Titanium&Titanium Alloy Wrought Products.pdfSAE-AMS2814F-2001 优质焊丝包的包装和标识.pdfSAE-AMS2814F-2001 优质焊丝包的包装和标识[P8].pdfSAE-AMS3021D-2007 Fluid,Reference for Testing Di-Ester (Polyol) Resistant Material [P4].pdfSAE-AMS3302G-1990 Silicone Rubber,General Purpose,50 Durometer.pdfSAE-AMS3650C-1991 Rods,Sheets,&Molded Shapes,Polychlorotrifluoroethylene (PCTFE),Unplasticized.pdfSAE-AMS3901C-1998 Organic Fiber (Para-Aramid),Yarn&Roving,High Modulus[P13].pdfSAE-AMS4045J-2007 Aluminum Alloy Sheet&Plate 5.6Zn-2.5Mg-1.6Cu-0.23Cr 7075 (-T6 Sheet,-T651 Plate)[P5].pdfSAE-AMS4100D-2007 Aluminum Alloy,Alclad,Sheet 5.7Zn-2.2Mg-1.6Cu-0.22Cr (Alclad 7475-T761)[P6].pdfSAE-AMS4108F-2003 Aluminum Alloy,Hand Forgings 6.2Zn-2.3Cu-2.2Mg-0.12Zr (7050-T7452)Solution Heat Treated,Compression Stress-Relieved,and Overaged.pdfSAE-AMS4111D-2007 Aluminum Alloy Forgings 7.7Zn-2.5Mg-1.5Cu-0.16Cr (7049-T73)[P8].pdf SAE-AMS4143D-2001 Aluminum Alloy Forgings&Rolled or Forged Rings 6.3Cu-0.30Mn-0.18Zr-0.10V-0.06Ti (2219-T6) Solution&Precipitation Heat Treated.pdfSAE-AMS4147D-2007 Aluminum Alloy Forgings 5.6Zn-2.5Mg-1.6Cu-0.23Cr(7075-T7352) Solution Heat Treated,Stress Relieved by Compression,&Overaged[P7].pdfSAE-AMS4150L-2003(R2008) Aluminum Alloy,Extrusions&Rings 1.0Mg-0.60Si-0.28Cu-0.20Cr-(6061-T6) Solution&Precipitation Heat Treated.pdfSAE-AMS4152M-2007 Aluminum Alloy,Extrusions 4.4Cu 1.5Mg 0.60Mn Solution Heat Treated[P5].pdfSAE-AMS4157D-2007 Aluminum Alloy Extrusions 7.7Zn-2.4Mg-1.6Cu-0.16Cr (7049-T73511)[P5].pdfSAE-AMS4162D-2003 Aluminum Alloy,Extrusions 6.3Cu - 0.30Mn - 0.18Zr - 0.10V - 0.06Ti (2219-T8511) Solution Treated,Stress Relief Stretched,Straightened,&Precipitation Heat Treated.pdf SAE-AMS4169K-2003 Aluminum Alloy,Extrusions 5.6Zn - 2.5Mg - 1.6Cu - 0.23Cr (7075-T6511)&Precipitation Heat Treated.pdfSAE-AMS4173E-2003 Aluminum Alloy,Extrusions 1.0Mg - 0.60Si - 0.30Cu - 0.20Cr (6061-T6511) Solution Heat Treated Stress.pdfSAE-AMS4206A-2006 Aluminum Alloy,Plate (7055-T7751) 8.0Zn - 2.3Cu - 2.0Mg - 0.16Zr Solution Heat Treated,Stress Relieved,&Overaged.pdfSAE-AMS4218H-2001 Aluminum Alloy Castings 7.0Si 0.35Mg (A356.0-T6P) (Formerly T61P Temper) Solution&Precipitation Heat Treated.pdfSAE-AMS4270B-2007 Aluminum Alloy,Alclad Flat Sheet 4.1Cu-1.4Mg-0.45Mn (Alclad 2424-T3) [P7].pdfSAE-AMS4279B-2006 Aluminum Alloy,Alclad Sheet 4.4Cu 1.5Mg 0.60Mn (2024-T4 Flat Sheet) Solution Heat Treated,High Formability.pdfSAE-AMS4324-2002(R2007) 固溶热处理的、消除应力的和过老化的(7055-T74511)含8.0Zn-2.3Cu-2.0Mg-0.16Zr挤压的铝合金杆材、棒材和型材.pdfSAE-AMS4329A-2006 Aluminum Alloy,Plate (7085-T7651) 7.5Zn - 1.6Cu - 1.5Mg - 0.12Zr Solution Heat Treated,Stress-Relieved,&Ove[P6].pdfSAE-AMS4337A-2006 Aluminum Alloy,Extruded Profiles (7055-T77511) 8.0Zn 2.3Cu 2.0Mg 0.16Zr Solution Heat Treated,Stress Relieved,&Overaged.pdfSAE-AMS4342E-2007 Aluminum Alloy,Extrusions 6.2Zn 2.3Cu 2.2Mg 0.12Zr (7050-T74511) Solution Heat Treated,Stress Relieved,Straightened,&Overaged.pdfSAE-AMS4484K-2007 Magnesium Alloy Castings,Permanent Mold 9.0Al-2.0Zn (AZ92A-T6) [P7].pdfSAE-AMS4500J-2007 Copper,Sheet,Strip,and Plate Soft Annealed [P4].pdfSAE-AMS4640-2005 ALUMINUM BRONZE BARS. RODS. SHAPES. TUBES.&FORGINGS 81.5 CU- 10.A1 - 4.8NI - 3.0FE DRAWN&STRESS RELIEVED (HR50) OR TEMPER ANNEALED (TQ50[P8 OCR].pdfSAE-AMS4775H-2005 Nickel Alloy,Brazing Filler Metal 73Ni - 0.75C - 4.5Si - 14Cr - 3.1B - 4.5Fe 1790 to 1970 °F (977 to 1077 °C) Solidus-Liquidus Range.pdfSAE-AMS4805E-2007 Bearings,Sintered Metal Powder 89Cu-10Sn Oil Impregnated [P6].pdfSAE-AMS4900M-2006 AEROSPACE MATERIAL SPECIFICA TION Titanium Sheet,Strip,&Plate Commercially Pure Annealed,55 ksi (379 MPa) [P6].pdfSAE-AMS4911K-2007 Titanium Alloy,Sheet,Strip,and Plate 6AI-4V Annealed [P7].pdfSAE-AMS4911L-2007 Titanium Alloy,Sheet,Strip,and Plate 6AI-4V Annealed [P7].pdfSAE-AMS4918L-2006 Titanium Alloy,Sheet,Strip,&Plate6AI - 6V - 2Sn Annealed[P7].pdfSAE-AMS4921K-2006 [P8].pdfSAE-AMS4921L-2007 Titanium Bars,Wire,Forgings,and Rings Commercially Pure 70 ksi (483 MPa) Yield Strength [P7].pdfSAE-AMS4928Q-2001 Titanium Alloy Bars,Wire,Forgings,Rings,&Drawn Shapes.pdfSAE-AMS4928R-2007 Titanium Alloy Bars,Wire,Forgings,Rings,&Drawn Shapes 6Al - 4V Annealed.pdfSAE-AMS4931B-2002 含6Al-4V超低填隙的、二次退火的、断裂韧度的钛合金棒材、锻件和环件.pdfSAE-AMS4931C-2007 Titanium Alloy bars,Forgings&Rings 6Al-4V Extra low interstitial(ELI) Duplex.pdfSAE-AMS4933D-2008 Titanium Alloy Extrusions and Flash Welded Rings 8Al-1Mo-1V Solution Heat Treated and Stabilized[P8].pdfSAE-AMS4942E-2006 Titanium Tubing,Seamless Annealed,40.0 ksi (275 MPa) Yield Strength.pdf SAE-AMS4943H-2008 Titanium Alloy.Hydraulic. Seamless Tubing 3.0Al-2.5V Annealed.pdfSAE-AMS4944G-2006 Titanium Alloy Tubing,Seamless,Hydraulic 3.0Al - 2.5V Cold Worked,Stress Relieved.pdfSAE-AMS4958C-2008 Titanium Alloy Bars and Rods 3Al-8V-6Cr-4Mo-4Zr Consumable Electrode Melted Solution Heat Treated and Centerless Ground[P6].pdfSAE-AMS4965J-2007 Titanium Alloy,Bars,Wire,Forgings,and Rings 6.0AI-4.0V Solution Heat Treated&Aged [P8].pdfSAE-AMS4971G-2007 Titanium Alloy,Bars,Wire,Forgings,and Rings 6Al-6V-2Sn Annealed,Heat Treatable[P8].pdfSAE-AMS4975J-2007 Titanium Alloy,Bars,Wire,andRings6.0Al-2.0Sn-4.0Zr-2.0Mo-0.08SiSolution&Precipitation Heat Treated[P7].pdfSAE-AMS4982D-2007 Titanium Alloy Wire 44.5 Cb [P6].pdfSAE-AMS5010K-2006 Steel Bars Free Machining Cold Drawn (SAE-1212 or SAE-1215) UNS G12120[P4].pdfSAE-AMS5046C-2007 Carbon Steel,Sheet,Strip,and Plate (SAE-1020&1025) Annealed[P5].pdfSAE-AMS5047F-2007 Steel,Sheet&Strip 0.08-0.13C,Aluminum Killed (SAE-1010) Deep Forming Grade [P4].pdfSAE-AMS5085G-2008 Steel Sheet. Strip.&Plate 0.47-0.55C (SAE-1050) Annealed.pdfSAE-AMS5349D-2007 Steel,Corrosion-Resistant,Investment Castings 13Cr Free Machining; Hardened&Tempered[P11].pdfSAE-AMS5352E-2007 Steel,Corrosion-Resistant,Investment Castings 17Cr-0.55Mo (0.95-1.20C) Annealed[P9].pdfSAE-AMS5353D-2007 Steel,Corrosion-Resistant,Investment Castings 16Cr-1.8Ni-0.08N ASCast [P10].pdfSAE-AMS5355H-2001 steel,corrosion resistant,investment casting[P14 OCR].pdfSAE-AMS5383E-2007 Nickel Alloy,Corrosion&Heat-Resistant,Investment Castings 52.5Ni-19Cr-3.0Mo-5.1Cb(Nb)-0.90Ti-0.60Al-18Fe[P11].pdfSAE-AMS5385G-1999 铸造状态的含62Co-27Cr-2.8Ni-5.5Mo耐腐蚀和耐热的钴合金熔模铸件.pdfSAE-AMS5398F-2006 Steel,Corrosion Resistant,Sand&Centrifugal Castings 16Cr 4.1Ni 0.22(Cb + Ta) 2.8Cu Solution Heat Treated[P9].pdfSAE-AMS5512L-2007 Steel,Corrosion&Heat-Resistant,Sheet,Strip,and Plate 18Cr-10.5Ni-0.80Cb (SAE-30347)Solution Heat Treated[P5].pdfSAE-AMS5516P-2007 Steel,Corrosion-Resistant,Sheet,Strip,and Plate 18Cr-9.0Ni (SAE-30302)Solution Heat Treated[P5].pdfSAE-AMS5542N-2007 Nickel Alloy,Corrosion&Heat-Resistant,Sheet,Strip,and Plate72Ni-15.5Cr-0.95Cb(Nb)-2.5Ti-0.70Al-7.0Fe[p6].pdfSAE-AMS5548P-2007 Steel,Corrosion&Heat-Resistant,Sheet&Strip 16.5Cr-4.5Ni-2.9Mo-0.10N 1850 to 1975 °F (1010 to 1079 °C) Annealed[P6].pdfSAE-AMS5561G-2007 Steel,Corrosion&Heat-Resistant,Welded&Drawn or Seamless&Drawn Tubing 9.0Mn-20Cr-6.5Ni-0.28N High-Pressure Hydraulic[P8].pdfSAE-AMS5569A-2001 Steel,Corrosion&Heat Resistant,Seamless&Welded Hydraulic Tubing 19Cr-9.5Ni-0.03C max Cold Drawn,1∕8 Hard Temper.pdfSAE-AMS5575N-2007 Steel,Corrosion&Heat-Resistant,Welded Tubing 18Cr-10.5Ni-0.70Cb(Nb) (SAE-30347)Solution Heat Treated[P6].pdfSAE-AMS5581D-2001 Nickel Alloy,Corrosion&Heat Resistant,Seamless or Welded Tubing 62Ni-21.5Cr-9.0Mo-3.7Cb Annealed.pdfSAE-AMS5589E-2007 Nickel Alloy,Corrosion&Heat-Resistant,Seamless Tubing 52.5Ni-19Cr-3.0Mo-5.1Cb (Nb)-0.90Ti-0.50Al-18Fe[P6].pdfSAE-AMS5596K-2007 Nickel Alloy,Corrosion&Heat-Resistant,Sheet,Strip,Foil&Plate 52.5Ni-19Cr-3.0Mo-5.1Cb (Nb)-0.90Ti-0.50Al-18Fe[P8].pdfSAE-AMS5599G-2007 Nickel Alloy,Corrosion&Heat-Resistant,Sheet,Strip,and Plate 62Ni-21.5Cr-9.0Mo-3.7 Cb (Nb)[P5].pdfSAE-AMS5612J-2007 Steel,Corrosion&Heat-Resistant,Bars,Wire,Forgings,Tubing,and Rings 12CrFerrite Controlled,Annealed[P7].pdfSAE-AMS5629E-2002 真空感应加真空自耗预热处理沉淀硬化型耐蚀13Cr-8.0Ni-2.2Mo-1.1Al钢棒、丝、锻件、环和模锻件.pdfSAE-AMS5630G-2000 Steel,Corrosion Resistant,Bars,Wire,and Forgings 17Cr-0.52Mo (0.95-1.20C) (SAE-51440C).pdfSAE-AMS5639H-2002(R2007) 管口连接用备份密封圈的六角螺母[P7].pdfSAE-AMS5643Q-2003 Steel,Corrosion-Resistant,Bars,Wire,Forgings,Tubing,and Rings 16Cr-4.0Ni-0.30Cb-4.0Cu Solution Heat Treated,Precipitation Hardenable.pdfSAE-AMS5659K-1998 Steel,Corrosion Resistant,Bars,Wire,Forgings,Rings,&Extrusions 15Cr - 4.5Ni - 0.30Cb - 3.5Cu Consumable Electrode Melted Solution Heat Treated,Precipitation Hardenable.pdf SAE-AMS5659L-2004 Steel,Corrosion-Resistant,Bars,Wire,Forgings,Rings,&Extrusions[P10].pdf SAE-AMS5662M-2004 镍基高温合金[P17].pdfSAE-AMS5668J-2007 Nickel Alloy,Corrosion&Heat-Resistant,Bars,Forgings,and Rings 72Ni-15.5Cr-7.0Fe-2.5Ti-1.0Cb (Nb)-0.70Al[P7].pdfSAE-AMS5678F-2002(R2007) Steel,Corrosion Resistant,Wire 17Cr-7.1Ni-1.1Al Cold Drawn,Precipitation-Hardenable-UNS S17700.pdfSAE-AMS5688L-2007 Steel,Corrosion Resistant,Wire 18Cr 9.0Ni (SAE-30302) Spring Temper.pdf SAE-AMS5698G-2003(R2007) Nickel Alloy,Corrosion&Heat-Resistant,Wire 72Ni-15.5Cr-0.95Cb-2.5Ti-0.70Al-7.0Fe No.1 Temper,Precipitation Hardenable-UNS N07750.pdf SAE-AMS5699G-2003(R2007) Nickel Alloy,Corrosion&Heat-Resistant,Wire 72Ni 15.5Cr 0.95Cb 2.5Ti 0.70Al 7.0Fe Spring Temper,Precipitation Hardenable.pdfSAE-AMS5713J-2007 Nickel Alloy,Corrosion&Heat-Resistant,Bars,Forgings,&Rings 53Ni - 19Cr - 11Co - 9.8Mo - 3.2Ti - 1.6Al - 0.006B Vacuum Melted,Solution&Precipitation Heat Treated.pdfSAE-AMS5713J-2007 Nickel Alloy,Corrosion&Heat-Resistant,Bars,Forgings,and Rings 53Ni-19Cr-11Co-9.8Mo-3.2Ti-1.6Al-0.006B[P7].pdfSAE-AMS5732J-2006 Steel,Corrosion&Heat-Resistant,Bars,Wire,Forgings,Tubing,and Rings 15Cr-25.5Ni-1.2Mo-2.1Ti-0.006B-0.30V Consumable Electrode Melted 1800 °F (982 °C) Solution&P.pdfSAE-AMS5759-2004 Cobalt Alloy,Corrosion&Heat-Resistant,Bars,Forgings,&Rings 52Co- 20Cr- 10Ni- 15W Solution Heat Treated.pdfSAE-AMS5772D-2004(R2009) Cobalt Alloy,Corrosion&Heat-Resistant,Bars,Forgings&Rings 40Co 22Cr 22Ni 14.5W 0.07La,Solution Heat Treated.pdfSAE-AMS5786E-2002 Nickel Alloy,corrosion&heat-resistant,welding wire 62.5Ni-5.0Cr-24.5Mo-5.5Fe.pdfSAE-AMS5796D-2000 Cobalt Alloy,Corrosion&Heat Resistant,Welding Wire 52Co-20Cr-10Ni-15W.pdfSAE-AMS5830C-2007 Nickel-Iron Alloy,Corrosion&Heat-Resistant,Welding Wire 12.5Cr-42.5Ni-6.0Mo-2.7Ti-0.015B-35Fe.pdfSAE-AMS5830C-2007 Nickel-Iron Alloy,Corrosion&Heat-Resistant,Welding Wire 12.5Cr-42.5Ni-6.0Mo-2.7Ti-0.015B-35Fe[P6].pdfSAE-AMS5857B-2007 Steel,Corrosion-Resistant,Bars&Wire 19Cr-10Ni (SAE-30304)High Yield Strength Solution Heat Treated&Cold Worked[P4].pdfSAE-AMS5869C-2008 Nickel Alloy.Corrosion&Heat-Resistant.Sheet.Strip.and Plate 62Ni-21.5Cr-9.0Mo-3.7Cb Solution Heat Treated.pdfSAE-AMS6257D-2007 Steel Bars,Forgings,and Tubing 1.6Si-0.82Cr-1.8Ni-0.40Mo-0.08V (0.40-0.44C)[P9].pdfSAE-AMS6260P-2007 Steel,Bars,Forgings,and Tubing 1.2Cr-3.2Ni-0.12Mo (0.07-0.13C) (SAE-9310)[P6].pdfSAE-AMS6267G-2007 Steel Bars,Forgings,and Tubing 1.2Cr-3.25Ni-0.12Mo (0.07-0.13C) (SAE-9310)[p6].pdfSAE-AMS6345B-2007 Steel,Sheet,Strip,and Plate 0.95Cr-0.20Mo (0.28-0.33C) (SAE-4130)[p7].pdf SAE-AMS6354F-2007 Steel,Sheet,Strip,and Plate 0.75Si-0.62Cr-0.20Mo-0.10Zr (0.10-0.17C)[P5].pdf SAE-AMS6359H-2007 Steel,Sheet,Strip,and Plate 0.80Cr-1.8Ni-0.25Mo (0.38-0.43C) (SAE-4340)[p6].pdfSAE-AMS6409C-2007 Steel,Bars,Forgings,and Tubing 0.80Cr-1.8Ni-0.25Mo (0.38-0.43C) (SAE-4340)[p8].pdfSAE-AMS6414K-2007 Steel,Bars,Forgings,and Tubing 0.80Cr-1.8Ni-0.25Mo (0.38-0.43C) (SAE-4340)[p9].pdfSAE-AMS6415S-2007 Steel,Bars,Forgings,and Tubing 0.80Cr-1.8Ni-0.25Mo (0.38-0.43C) (SAE-4340)[P8].pdfSAE-AMS6417F-2006 Steel,Bars,Forgings,and Tubing 1.6Si-0.82Cr-1.8Ni-0.40Mo-0.08V (0.38-0.43C)Consumable Electrode Vacuum Remelted.pdfSAE-AMS6440P-2007 Steel,Bars,Forgings,and Tubing 1.45Cr (0.93-1.05C) (SAE-52100) For Bearing Applications[p7].pdfSAE-AMS6454D-2007 Steel,Sheet,Strip,and Plate 1.8Ni-0.80Cr-0.25Mo (0.38-0.43C) (SAE-4340)Vacuum Consumable Electrode Remelted[p7].pdfSAE-AMS6501D-2007 Steel,Maraging,Welding Wire 18Ni-8.0Co-4.9Mo-0.40Ti-0.10Al Vacuum Induction Melted,Environment Controlled Packaging[p6].pdfSAE-AMS753-1998 Corrosion-Resistant Steel Parts Sampling,Inspection&Testing for Surface Passivation[P11].pdfSAE-AMS7721C-2007 Lead Alloy Sheet&Extrusions 93Pb-6.5Sb-0.50Sn ASFabricated[p5].pdfSAE-AMS7731C-2007 Gold Wire&Ribbon 99.97Au Annealed[p6].pdfSAE-AMS7881-2007 Tungsten Carbide-Cobalt Powder Agglomerated&Sintered[p5].pdfSAE-AMS7881-2007 Tungsten Carbide--Cobalt Powder Agglomerated&Sintered[P5].pdfSAE-AMS7882A-2007 Tungsten Carbide-Cobalt Chrome Powder Agglomerated&Sintered[p5].pdf SAE-AMS7882A-2007 Tungsten Carbide--Cobalt Chrome Powder Agglomerated&Sintered[P5].pdf SAE-AMS-A-22771A-2007 Aluminum Alloy Forgings,Heat Treated[p25].pdfSAE-AMS-C-5541A-2003 Chemical Conversion Coatings on Aluminum&Aluminum Alloys.pdfSAE-AMS-F-7190A-2007 Forging,Steel,For Aircraft_Aerospace Equipment&Special Ordnance Applications[p11].pdfSAE-AMS-H-6875-1998(R2006) Heat Treatment of Steel Raw Materials [P29].pdfSAE-AMS-I-23011A-2007 Iron-Nickel Alloys for Sealing to Glasses&Ceramic[P22].pdfSAE-AMS-M-7866A-2007 Molybdenum Disulfide,Technical,Lubrication Grade[p11].pdfSAE-AMS-QQ-A-200-13B-2007 Aluminum Alloy 7178,Bar,Rod,Shapes,Tube,and Wire,Extruded[p8].pdfSAE-AMS-QQ-A-200-14A-2007 Aluminum Alloy,Bar,Rod,Shapes,and Wire,Extruded,7178-T76 Improved Exfoliation Resistance[p8].pdfSAE-AMS-QQ-A-200-5A-2007 Aluminum Alloy 5086,Bar,Rod,Shapes,Tube,andWire,Extruded[p7].pdfSAE-AMS-QQ-A-200-7B-2007 Aluminum Alloy 5456,Bar,Rod,Shapes,Tube,and Wire,Extruded[p6].pdfSAE-AMS-QQ-A-200-9-1997 Aluminum Alloy 6063,Bar,Rod,Shapes,Tube,&Wire,Extruded.pdfSAE-AMS-QQ-A-250-10A-2007 Aluminum Alloy 5454,Plate&Sheet.pdfSAE-AMS-QQ-A-250-11A-2007 Aluminum Alloy 6061,Plate&Sheet.pdfSAE-AMS-QQ-A-250-12-2007 Aluminum Alloy 7075,Plate&Sheet.pdfSAE-AMS-QQ-A-250-13-2007 Aluminum Alloy Alclad 7075,Plate&Sheet.pdfSAE-AMS-QQ-A-250-14A-2007 Aluminum Alloy 7178,Plate&Sheet [p7].pdfSAE-AMS-QQ-A-250-15B-2007 Aluminum Alloy Alclad 7178,Plate&Sheet[p8].pdfSAE-AMS-QQ-A-250-21B-2007 Aluminum Alloy,7178-T76,Plate&Sheet Improved Exfoliation Resistant[p7].pdfSAE-AMS-QQ-A-250-22B-2007 Aluminum Alloy,7178-T76,Alclad Plate&Sheet,Improved Exfoliation Resistant[p10].pdfSAE-AMS-QQ-A-250-28B-2007 Aluminum Alloy,7011 Alclad 7178 Plate&Sheet[p14].pdfSAE-AMS-QQ-A-250-4A-2007 Aluminum Alloy 2024,Plate&Sheet..pdfSAE-AMS-QQ-A-250-5A-2007 Aluminum Alloy Alclad 2024,Plate&Sheet.pdfSAE-AMS-QQ-A-250-8A-1998 Aluminum Alloy 5052,Plate&Sheet.pdfSAE-AMS-QQ-A-250-9A-2006 Aluminum Alloy 5456,Plate&Sheet.pdfSAE-AMS-QQ-A-250A-2004 Aluminum&Aluminum Alloy,Plate&Sheet General Specification for.pdf SAE-AMS-QQ-A-367A-2007 Aluminum Alloy Forgings[p29].pdfSAE-AMS-S-13165 Issued NOV1997 Shot Peening of Metal Parts[P27].pdfSAE-AMS-W-6858A-2000 Welding,Resistance Spot&Seam[P46].pdfSAE-ARP1232B-2001 Gland Design,Elastomeric O-Ring Seals,Static Radial..pdfSAE-ARP1420B-2002 Gas Turbine Engine Inlet Flow Distortion Guidelines.pdfSAE-ARP1420B-2002 Gas Turbine Engine Inlet Flow Distortion Guidelines[P24].pdfSAE-ARP1755B-2000 Effect of Cleaning Agents on Aircraft Engine Materials Stock Loss Test Method.PDFSAE-ARP1962A-1995 TRAINING&APPROVAL OF HEAT-TREA TING PERSONNEL.PDFSAE-ARP4191-2003 C Gas Turbine Engine Performance Presentation[P9].pdfSAE-ARP4191C-2003 Gas Turbine Engine Performance PresentationDigital Computer Programs Using FORTRAN 77.pdfSAE-ARP4191C-2003Gas Turbine Engine Performance Presentation [P9].pdfSAE-ARP4754-1996 ConsiderationsHighly-Integrated or Complex Aircraft Systems[P101].pdfSAE-ARP5316B-2002 Storage of Elastomer Seals&Seal Assemblies Which Include an Elastomer Element Prior to Hardware Assembly.pdfSAE-ARP5580-2001 非机动车用的故障模式和效果分析的推荐实施规范.pdfSAE-ARP598C-2003 Aerospace Microscopic Sizing&Counting of Particulate Contamination for Fluid Power Systems[P16].pdfSAE-AS122026A THRU AS122075A-2007 WASHER-LOCK,SPRING,CADMI[p3].pdfSAE-AS123601 THRU AS123750B-2007 RIVET,SOLID,100 FLUSH HEA[p3].pdfSAE-AS1241-1997 Fire Resistant Phosphate Ester Hydraulic Fluid for Aircraft.pdfSAE-AS14101-1998 低速自调心自润滑关节轴承.pdfSAE-AS14153B-2007 CIRCUIT BREAKER-AIRCRAFT,TRIP-FREE,[P3].pdfSAE-AS14154B-2007 Circuit Breaker-Aircraft,Trip-Free,Push-P[P3].pdfSAE-AS15001B-2007 FITTING,LUBRICATION,HYDRAULIC,SURFACE CHEC[P3].pdfSAE-AS15002B-2007 FITTING,LUBRICATION,HYDRAULIC,SURFACE CHEC[P3].pdfSAE-AS15003B-2007 FITTING,LUBRICATION,HYDRAULIC,SURFACE CHEC[P3].pdfSAE-AS15005B-2007 FITTING,LUBRICATION,HYDRAULIC,THROA T OR SU[P3].pdfSAE-AS15006B-2007 FITTING,LUBRICATION,HYDRAULIC,LEAKPROOF,1_8 PIPE THREADS[P3].pdfSAE-AS155001 THRU AS155300A-2007 STUD,STEPPED,2 DIA ENGAGEME[p3].pdfSAE-AS155301 THRU AS155600A-2007 STUD,STEPPED,2 DIA ENGAGEME[p3].pdfSAE-AS155901 THRU AS156200A-2007 STUD,STEPPED,2 DIA ENGAGEMENT,CADMIUM PLATED,STEEL UNS G87400,[p2].pdfSAE-AS158901 THRU AS159200A-2007 STUD,STEPPED,NECKED,1.5 DIA ENGAGEMENT,CADMIUM PLATED,STEEL[P3].pdfSAE-AS162501 THRU AS162800A-2007 STUD,STEPPED,DRILLED,NECKED,2 DIA ENGAGEMENT,CADMIUM PLATED,STEEL[p3].pdfSAE-AS17108A-2008 (R) bearing,ball,annular,primarily for aircraft generators&motor-generators,wide cartridge,type ii.pdfSAE-AS22759-10-2000 wire,electrical,fluoropolymer-insulated,extruded tfe,nickel-coated copper conductor,1000 volt.pdfSAE-AS22759-86B-2007 wire,electrical,polytetrafluoroethylene polyimide insulated,normal weight,silver coated,copper conductor,200 °c,600 volts.pdfSAE-AS22759-87B-2007 wire,electrical,polytetrafluoroethylene-polyimide insulated,normal weight,nickel coated,copper conductor,260 °c,600 volts.pdfSAE-AS22759-89B-2007 Wire,Electrical,Polytetrafluoroethylene-Polyimide Insulated,Normal Weight,Silver Coated,High Strength or Ultra High Strength Copper Alloy,200-mDC,600 V olts.pdf SAE-AS23190-1-1999(R2006) Straps,Clamps,&Mounting Hardware,Plastic for Cable Harness Tying&Support Clamp,Loop,Nylon,Adjustable,Wire Support[P5].pdfSAE-AS23190-1998 Straps,Clamps,&Mounting Hardware,Plastic&Metal for Cable Harness Tying&Support-FSC 5975[P42].pdfSAE-AS23190-2-1998(R2003) Straps,Clamps,Plastic&Metal,&Mounting Hardware,Plastic for Cable Harness Tying&Support Clamp,Loop,Metal[P9].pdfSAE-AS23190-3-2008 Straps,Clamps,&Mounting Hardware,Plastic&Metal for Cable Harness Tying&Support Strap,Tie down[P3].pdfSAE-AS25244-2007 CIRCUIT BREAKER,TRIP-FREE,PUSH-PULL,5 THRU [P6].pdfSAE-AS25361A-2007 CIRCUIT BREAKER -AIRCRAFT,TRIP-FREE,PUSH-PULL,50 THRU 100 AMP,TYPE I,[P3].pdfSAE-AS3086A-2007 STUD-STRAIGHT,KEY LOCKED,CADMIUM PLA TED,S[p2].pdfSAE-AS3087A-2007 STUD-STRAIGHT,KEY LOCKED,CADMIUM PLA TED,S[P3].pdfSAE-AS3088A-2007 STUD,STRAIGHT,KEY LOCKED,CADMIUM PLA TED,ST[P3].pdfSAE-AS3089A-2007 STUD,STRAIGHT,KEY LOCKED,CADMIUM PLA TED,ST[P3].pdfSAE-AS33514A-2007 Fitting End,Standard Dimensions for Flareles[P3].pdfSAE-AS33515A-2007 FITTING END,STANDARD DIMENSIONS FOR BULKHEAD[P3].pdfSAE-AS39029-19A-2007 CONTACTS,ELECTRICAL CONNECTOR,PIN,CRIMP[P5].pdfSAE-AS39029-21A-2007 CONTACTS,ELECTRICAL CONNECTOR,SOCKET,CR[P5].pdf。
SAE J2380-2009 Vibration Testing of Electric Vehicle Batteries

__________________________________________________________________________________________________________________________________________ SAE Technical Standards Board Rules provide that: “This report is published by SAE to advance the state of technical and engineering sciences. The use of this report is entirely voluntary, and its applicability and suitability for any particular use, including any patent infringement arising therefrom, is the sole responsibility of the user.” SAE reviews each technical report at least every five years at which time it may be reaffirmed, revised, or cancelled. SAE invites your written comments and suggestions. Copyright © 2009 SAE InternationalAll rights reserved. No part of this publication may be reproduced, stored in a retrieval system or transmitted, in any form or by any means, electronic, mechanical, photocopying, recording, or otherwise, without the prior written permission of SAE.TO PLACE A DOCUMENT ORDER:Tel: 877-606-7323 (inside USA and Canada)Tel: 724-776-4970 (outside USA)SURFACE VEHICLE RECOMMENDEDPRACTICE J2380 MAR2009 Issued 1998-01 Revised 2009-03Superseding J2380 JAN1998Vibration Testing of Electric Vehicle BatteriesRATIONALESAE J2380 provides a test procedure for characterizing the effect of long-term, road-induced vibration and shock on the performance and service life of electric vehicle batteries. For mature, production-ready batteries, the intent of the procedure is to qualify the vibration durability of the battery. The vibration spectrum has been synthesized from rough-road measurements is the late 1990s.Vibration and shock tests are relevant to the new fleet of electric or hybrid electric vehicles that are being developed with advanced battery technology.FOREWORDThis document provides a test procedure for characterizing the effect of long-term, road-induced vibration and shock on the performance and service life of electric vehicle batteries. For mature, production-ready batteries, the intent of the procedure is to qualify the vibration durability of the battery. Either swept sine wave vibration or random vibration is typically used for the performance of such testing. However, swept sine wave testing is considered somewhat more representative and is addressed in this document, which is generally based on a corresponding test for electric vehicle batteries developed by the U.S. Advanced Battery Consortium.The vibration tests defined in this procedure are based on rough-road measurements at locations likely to be appropriate for mounting of traction batteries in EVs. The data were analyzed to determine an appropriate cumulative number of occurrences of shock pulses at various given G-levels over the life of the vehicle. The vibration envelopes shown in Figure 1 of this procedure correspond to approximately 100 000 miles of usage at the 90th percentile. The vibration spectra contained in this procedure have been designed to approximate this cumulative exposure envelope. For testing efficiency, a time-compressed vibration regime is specified to allow completion of the test procedure in a minimum of 13.6 h and a maximum of 92.6 h of testing, depending on the type of shaker table available and the choice of acceleration levels.FIGURE 1 - CUMULATIVE VIBRATION ENVELOPESTABLE OF CONTENTS1.SCOPE (3)2.REFERENCES (3)2.1Applicable Publications (3)2.1.1SAE Publications (3)2.2Related Publication (3)2.2.1USABC Publication (3)3.DEFINITIONS (3)4.TECHNICAL REQUIREMENTS (3)4.1Prerequisites (3)4.2Test Equipment (4)4.3Determination of Test Conditions and Test Termination Criteria (4)4.4Test Procedure (4)4.5Testing Precautions (6)4.6Data Acquisition and Reporting (6)5.NOTES (7)5.1Marginal Indicia (7)FIGURE 1 CUMULATIVE VIBRATION ENVELOPES (2)FIGURE 2 VIBRATION SPECTRA FOR RANDOM VIBRATION TEST (5)TABLE 1 VIBRATION SCHEDULE FOR RANDOM VIBRATION TEST (5)1. SCOPEThis SAE Recommended Practice describes the vibration durability testing of a single battery (test unit) consisting of either an electric vehicle battery module or an electric vehicle battery pack. For statistical purposes, multiple samples would normally be subjected to such testing. Additionally, some test units may be subjected to life cycle testing (either after or during vibration testing) to determine the effects of vibration on battery life. Such life testing is not described in this procedure; SAE J2288 may be used for this purpose as applicable.2. REFERENCES2.1 Applicable PublicationsThe following publications form a part of this specification to the extent specified herein. Unless otherwise specified, the latest issue of SAE publications shall apply.Publications2.1.1 SAEAvailable from SAE International, 400 Commonwealth Drive, Warrendale, PA 15096-0001, Tel: 877-606-7323 (inside USA and Canada) or 724-776-4970 (outside USA), .SAE J1715 Hybrid Electric Vehicle (HEV) and Electric Vehicle (EV) TerminologySAE J1798 Recommended Practice for Performance Rating of Electric Vehicle Battery ModulesSAE J2288 Life Cycle Testing of Electric Vehicle Battery ModulesSAE J2464 Electric Vehicle Battery Abuse Testing2.2 Related PublicationThe following publication is provided for information purposes only and is not a required part of this document.Publication2.2.1 USABCAvailable from National Technical Information Service, 5285 Port Royal Road, Springfield, VA 22161, Tel: 703-605-6000, .USABC Electric Vehicle Battery Test Procedures Manual, Revision 2, January 1996. Obtainable by mail order as Report No. DOE/ID-10479, Rev. 2.3. DEFINITIONSExcept as specifically noted in this section, the definitions of SAE J1715 shall apply to this document.4. TECHNICAL REQUIREMENTS4.1 PrerequisitesA battery test plan or other test requirements document is normally required for testing using this procedure. The test plan specifies the appropriate test conditions for the Reference Performance Tests (see 4.4.1) and certain vibration frequencies to be used, along with testing precautions and any special handling/testing instructions specified for the battery by the manufacturer and/or the test sponsor. Note that SAE J2464 also describes shock tests (25 g acceleration, half sine wave form with duration of 15 msec).Performance of certain Reference Performance Tests specified in SAE J1798 is normally required before and after the conduct of vibration testing. For completeness, these are itemized within the procedure steps in 4.4.Unless otherwise specified in a test plan document, the test unit shall be tested early in its life (i.e., prior to the performance of any life cycle testing.)4.2 Test Equipment4.2.1 EquipmentPerformance of this procedure requires a one- to three-axis table capable of producing accelerations up to 1.9 G over the vibration spectra detailed in Figure 2, extending from 10 to approximately 200 Hz. If the unit to be tested can only be vibrated while in a particular physical orientation, a multi-axis table will be required. Additionally, the time required to perform the test can be significantly reduced if the longitudinal and lateral axis vibration (or all three axes) can be performed concurrently.4.2.2 FixturesTest fixtures are required to properly secure the test unit to the shaker table. The exact nature of these fixtures depends on the type of table used, the test unit itself, and any restrictions on physical orientation of the test unit.4.2.3 InstrumentationSpecial instrumentation hookups capable of withstanding the vibration are required so that important battery conditions can be monitored during testing. (See 4.5.)4.3 Determination of Test Conditions and Test Termination Criteria4.3.1 Electrical Test ConditionsAre determined according to the procedures in SAE J1798 which are specified in 4.4.1.4.3.2 VibrationFrequenciesVibration test conditions are as specified in the procedure steps in 4.4.Termination4.3.3 TestVibration testing shall be suspended or terminated if any observed component degradation produces conditions which are abnormal or outside the operating ranges of the battery as specified by the manufacturer. Conditions to be monitored are defined in 4.5.Procedure4.4 Test4.4.1 Perform a sequence of Reference Performance Tests consisting of a C/3 Constant Current discharge, a DynamicCapacity Test discharge to 100% of rated capacity, and a Peak Power discharge, as defined in SAE J1798.4.4.2 Charge the battery fully using the manufacturer's recommended charge method.4.4.3 For each of the vertical, longitudinal, and lateral axes of the battery, select either the normal or alternativeG-levels from Table 1 and program the shaker table appropriately. This choice will determine the vibration time required for each axis, also in accordance with Table 1. (The vibration spectra, shown in Figure 2, are expressed in G2/Hz, so they can be scaled for either set of G-levels.)TABLE 1 - VIBRATION SCHEDULE FOR RANDOM VIBRATION TESTTEST CONDITIONS VIBRATIONSPECTRUMTESTCONDITIONSSOC(%)NORMALTESTAccel(g rms)NORMALTESTTime(h)NORMALTESTCumulTime, hALTERNATIVETESTAccel(g rms)ALTERNATIVETESTTime(h)ALTERNATIVETESTCumulTime, hVertical Axis Vibration:Vertical 1 spectrum 100 1.9 0.15 0.15 1.9 0.15 0.15 Vertical 1 spectrum 100 0.75 5.25 5.4 0.95 3.5 3.65 Vertical 2 spectrum 100 1.9 0.15 5.55 1.9 0.15 3.8 Vertical 2 spectrum 100 0.75 5.25 10.8 0.95 3.5 7.3 Vertical 3 spectrum 20 1.9 0.15 10.95 1.9 0.15 7.45 Vertical 3 spectrum 20 0.75 5.25 16.2 0.95 3.5 10.95Longitudinal Axis Vibration:Longitudinal spectrum 60 1.5 0.09 16.29 1.5 0.09 11.04 Longitudinal spectrum 60 0.4 19.0 35.29 0.75 6.7 17.74 Longitudinal spectrum 60 1.5 0.09 35.38 1.5 0.09 17.83 Longitudinal spectrum 60 0.4 19.0 54.38 0.75 6.7 24.53Lateral Axis Vibration:Longitudinal spectrum 60 1.5 0.09 54.47(1) 1.5 0.09 24.62(1) Longitudinal spectrum 60 0.4 19.0 73.47(1) 0.75 6.7 31.32(1) Longitudinal spectrum 60 1.5 0.09 73.56(1) 1.5 0.09 31.41(1) Longitudinal spectrum 60 0.4 19.0 92.56(1) 0.75 6.7 38.11(1)1. These cumulative times apply only if all three axes are done separately.FIGURE 2 - VIBRATION SPECTRA FOR RANDOM VIBRATION TEST4.4.4 Mount the test unit so that it will be subjected to vibration along the appropriate axes, based on the manufacturer'srecommended physical orientation. This procedure permits the required vibration to be performed in one, two, or all three axial directions simultaneously depending on the capabilities of the shaker table used (but see 4.4.5 for other considerations.)4.4.5 Perform the programmed vibration for the required times, while battery depth-of-discharge is varied from 0% (fullcharge) to 80% (minimal charge) over the course of the vibration testing of a given battery. Two approaches are permitted to accomplish this:a. If a one- or two-axis vibration table is used, approximately two-thirds of the vertical axis testing should be done at fullcharge, followed by the longitudinal and lateral vibration at 40% DOD, and then the remaining vertical axis vibration at 80% DOD.b. If a three-axis table is used to perform all vibration regimes simultaneously, the total testing period can be divided intothree intervals of roughly equal length. The first interval should be performed with the battery fully charged, the second interval with the battery at 40% DOD, and the third interval at 80% DOD.4.4.6 Between each pair of the three intervals of vibration specified in 4.4.5, the battery should be discharged at a C/3constant current rate for 40% of the rated capacity of the battery. Following the third vibration interval, the battery should be fully recharged.4.4.7 Repeat the Reference Performance Tests using SAE J1798. This sequence includes a C/3 Constant Currentdischarge, a Dynamic Capacity Test discharge to 100% of rated capacity, and a Peak Power discharge.4.5 Testing PrecautionsDuring the application of the vibration regimes, the test unit shall be instrumented to determine the presence of any of the following conditions:a. Loss of electrical isolation between the battery positive connection and the battery case and/or test equipment ground.The degree of isolation shall be verified regularly, e.g., daily, during any period of vibration testing to be 0.5 MΩ or greater (1.0 mA or less leakage at 500V DC).b. Abnormal battery voltages indicating the presence of open- or short-circuit conditions.c. Unexpected resonance conditions within the battery, indicating failure of mechanical tie-down components.d. Abnormal temperature conditions indicating possible damage to battery cells or thermal management systemcomponents.Detection of any of the conditions listed in (a) through (d) shall cause testing to be suspended until the condition has been evaluated and a determination has been made that either it is safe to proceed or the testing should be terminated.4.6 Data Acquisition and Reporting4.6.1 Data to be acquired during the Reference Performance Tests of 4.4.1 or 4.4.7 shall be as required for the normalconduct of those tests. Data from these measurements (other than summary results) need not be retained if no anomalous behavior is observed during testing.4.6.2 A report shall be prepared detailing the actual vibration regimes applied, a compilation and interpretation of alldata acquired, and any results of detailed component failure analyses. Also, the pre- and post-vibration electrical performance data that confirms the adequacy of the battery design to withstand the vibration environments shall be summarized.5. NOTES5.1 Marginal IndiciaA change bar (l) located in the left margin is for the convenience of the user in locating areas where technical revisions, not editorial changes, have been made to the previous issue of this document. An (R) symbol to the left of the document title indicates a complete revision of the document, including technical revisions. Change bars and (R) are not used in original publications, nor in documents that contain editorial changes only.PREPARED BY THE SAE ELECTRIC VEHICLE SAFETY COMMITTEE。
SAE AMS-2750E 高温测定法(中英文对照版)介绍

A EROSPACEMA TERIA L SPECIFICATION 航空航天材料规范A MS2750REV. E发行1980-04修订2012-07替代 AMS2750D(R)高温测定法5 年一次的更新,复查并重审了该规范以提高其使用量,技术革新导致了使用的变化。
变化范围较大并且没有做标记。
目录1. SCOPE范围 (3)2. APPLICABLE DOCUMENTS引用文件 (3)2.1 ASTM PublicationsASTM 出版物 (3)2.2 Definitions定义 (4)3. TECHNICAL REQUIREMENTS技术要求 (12)3.1 Temperature Sensors温度传感器 (12)3.2 Instrumentation (See Tables 3, 4, and 5)仪表(见表3, 4, 和表5) (17)3.3 Thermal Processing Equipment热处理设备 (25)3.4 System Accuracy Tests (SATs)系统精度测试(SATs) (29)3.5 Furnace Temperature Uniformity Surveys (TUS)炉温均匀性测试(TUS) (36)3.6 Laboratory Furnaces实验室炉子 (52)3.7 Records记录 (52)3.8 Rounding取舍 (52)4. QUALITY ASSURANCE PROVISIONS质量保证条款 (52)4.1 Responsibility for Inspection检验职责 (52)5. PREPARATION FOR DELIVERY交货准备 (70)6. ACKNOWLEDGEMENT接收 (70)7. REJECTIONS8. NOTES注释 (70)FIGURE 1 REUSE AND RECALIBRATION OF TEST AND LOAD SENSORS (20)图1 负载传感器的再使用和重新校检 (21)FIGURE 2 FURNACE CLASS UNIFORMITY RANGES图2 不同等级炉子的炉温均匀性范围 (26)FIGURE 3 INSTRUMENTATION TYPE REQUIREMENTS图3 仪表类型要求 (27)FIGURE 4 MINIMUM SENSORS REQUIRED PER ZONE图4 每个区域最少传感器支数 (28)FIGURE 5 ALLOWABLE COMBINATIONS OF RESIDENT SAT SENSOR WITH SENSOR BEING TESTED FOR TEMPERATURES OVER 500 °F (260 °C)图5 固定的SAT传感器与在500℉(260℃)以上温度测试的传感器的允许组合 (31)FIGURE 6 SAT CALCULATION EXAMPLES图6 系统精度测试(SAT)计算的实例 (33)TABLE 1 SENSORS AND SENSOR CALIBRATION表1 传感器和传感器校检 (54)TABLE 2 THERMOCOUPLES AND EXTENSION WIRE表2 热电偶和补偿导线 (56)TABLE 3 INSTRUMENTS AND INSTRUMENT CALIBRATION表3 使用仪器及校准 (57)TABLE 4 RESOLUTION REQUIREMENTS FOR CHART RECORDERS表4 炉子记录图表的确定要求 (60)TABLE 5 PROCESS RECORDER PRINT AND CHART SPEEDS表5 记录器打印图表及速度 (61)TABLE 6 PARTS FURNACE CLASS, INSTRUMENT TYPE, AND SAT INTERVAL (62)表6 零件加热炉等级、仪表类型和SAT校验周期 (63)TABLE 7 RAW MATERIAL FURNACE CLASS, INSTRUMENT TYPE, AND SAT INTERVAL (64)表7 原材料加热炉等级、仪表类型和SAT校验周期 (65)TABLE 8 PARTS FURNACE CLASS, INSTRUMENT TYPE, AND TUS INTERVAL表8 零件加热炉等级、仪表类型和TUS校验周期 (66)TABLE 9 RAW MATERIAL FURNACE CLASS, INSTRUMENT TYPE, AND TUS INTERVAL表9 原材料加热炉等级、仪表类型和TUS校验周期 (67)TABLE 10 PERMITTED CALIBRATION/TEST INTERVAL EXTENSION表10 校验或试验间隔延长的容许值 (68)TABLE 11 NUMBER OF TUS SENSORS REQUIRED表11 TUS传感器数量要求 (69)附录A:E版与D版变更内容说明 (71)1.SCOPE范围1.1This specification covers pyrometric requirements for thermal processing equipment used for heat treatment. Itcovers temperature sensors, instrumentation, thermal processing equipment, system accuracy tests, and temperature uniformity surveys. These are necessary to ensure that parts or raw materials are heat treated in accordance with the applicable specification(s).本规范涵盖了热处理过程中用到的热处理设备的高温测量要求,包括温度传感器,仪器仪表,热处理设备,系统精度测试和温度均匀性测量。
AMS_2471E

SAE Technical Standards Board Rules provide that: “This report is published by SAE to advance the state of technical and engineering sciences. The use of this report is entirely voluntary, and its applicability and suitability for any particular use, including any patent infringement arising therefrom, is the sole responsibility of the user.”SAE reviews each technical report at least every five years at which time it may be reaffirmed, revised, or cancelled. SAE invites your written comments and suggestions. Copyright 2003 SAE InternationalAll rights reserved. No part of this publication may be reproduced, stored in a retrieval system or transmitted, in any form or by any means, electronic, mechanical, photocopying, recording, or otherwise, without the prior written permission of SAE.TO PLACE A DOCUMENT ORDER:Tel: 877-606-7323 (inside USA and Canada)Tel: 724-776-4970 (outside USA) Issued AUG 1958 Revised AUG 2003 Superseding AMS 2471E2.1 SAE Publications:Available from SAE, 400 Commonwealth Drive, Warrendale, PA 15096-0001 or .AMS 2472 A nodic Treatment of Aluminum Alloys, Sulfuric Acid Process, Dyed Coating AMS 2473 C hemical Treatment for Aluminum Alloys, General Purpose CoatingAMS 4037 A luminum Alloy, Sheet and Plate, 4.4Cu - 1.5Mg - 0.60Mn, (2024; -73 FlatSheet, -T351 Plate), Solution Heat Treated2.2 ASTM Publications:Available from ASTM, 100 Barr Harbor Drive, West Conshohocken, PA 19428-2959 or.ASTM B 117 Operating Salt Spray (Fog) Testing ApparatusASTM B 137 M easurement of Mass of Coating on Anodically Coated Aluminum3. TECHNICAL REQUIREMENTS:3.1 Solutions:3.1.1 Electrolyte: Shall be an aqueous solution of sulfuric acid of suitable concentration maintainedwithin ±2 °F (±1 °C) of the temperature approved in 4.4.2.3.1.1.1 The nominal concentration of the electrolyte should be 15 to 20% by weight. Thetemperature should be selected from within the range 64 to 75 °F (18 to 24 °C).3.1.2 Sealer: Unless otherwise permitted, the sealer shall be an aqueous solution of sodiumdichromate or potassium dichromate (See 8.2.9).3.2 Procedure:3.2.1 Cleaning and Deoxidation: Parts shall have clean surfaces, free from water break, prior toimmersion in the anodizing bath. Etching to achieve metal removal is required for castsurfaces.3.2.1.1 Cleaning materials or products used for surface preparation containing iron, such as steelwool, iron oxide rouge, or steel wire, which may become embedded in the metal andaccelerate subsequent corrosion, are prohibited.3.2.2 Tight electrical contact shall be maintained during the anodic treatment to prevent contactarcing (burning) of parts, but small irregularities of coating at points of electrical contact are acceptable.3.2.3 Coating: The cleaned parts shall be made the anode(s) in the electrolyte contained in achemical-resistant tank which may also serve as the cathode. The processing shall beadjusted to obtain the required weight and quality of the coatings. The anodizing current shall be maintained within ±2 amperes per square foot (±21.5 A/m2) of the nominal value.Alternatively, the anodizing current shall be ramped up over a five minute or other preselected period to the desired final voltage and maintained until the anodic coating reaches the desired thickness. After anodizing, parts shall be rinsed in clean water at ambient temperature.3.2.4 Sealing: Parts shall be immersed in the sealant solution for a suitable time (See 8.2.9), thenrinsed. The rinse shall be thorough, but slight staining resulting from the sealant solution isacceptable. Rinsing is not required if deionized water is used for sealing.3.2.5 Masking: Areas where anodizing is prohibited shall be masked.3.3 Properties:Coated parts shall conform to the following requirements:3.3.1 Coating Weight: The sealed coating weight (See4.3.2.1), determined in accordance withASTM B 137, shall be not less than 600 mg/square foot (6.5 g/m2).3.3.1.1 If small parts, such as rivets or machine screws, are anodized in bulk in a container, thespecified coating weight shall apply to not less than 75% of the parts treated together,determined by random sampling, but in no case shall any part show uncoated areas.3.3.2 Corrosion Resistance: Panels (See4.3.2.2) shall meet the following requirements, determinedafter exposure for not less than 336 hours to salt spray corrosion test in accordance withASTM B 117, except that significant surface shall be inclined six degrees from vertical. Areas within 1/16 inch (1.6 mm) of identification markings or of an edge, or at electrode contactmarks, shall not be included.Fifteen scattered spots or pits, none larger than 1/32 inch (0.8 mm) diameter, on a total of 150 square inches (968 cm2) of test area from five or more test pieces.Five scattered spots or pits, none larger than 1/32 inch (0.8 mm) diameter, on any 30 square inches (194 cm2) of test area from one or more test pieces.3.4 Touch Up:Parts on which the anodic coating has been scratched or damaged superficially may be coated using AMS 2473 or another method acceptable to the cognizant engineering organization.Touch-up, unless otherwise specified, shall not exceed 0.5 inch (13 mm) in its longestdimension, except that scratches that are essentially one dimensional (less than 0.03 inches(0.8 mm) wide) may be reworked. The total reworked area shall not exceed 5% of the totalsurface area.3.5 Quality:Anodic coating, as received by purchaser, shall be continuous, smooth, adherent, and uniform in appearance, and shall be free from powdery areas, loose films, discontinuities such asbreaks or scratches (except at contact points), or other damage or imperfections detrimental to usage of the coating.4. QUALITY ASSURANCE PROVISIONS:4.1 Responsibility for Inspection:The coating processor shall supply all samples for processor’s tests and shall be responsible for the performance of all required tests. Parts, if required for tests, shall be supplied by purchaser.Processor may utilize his own or any other inspection facilities or services acceptable topurchaser. Purchaser reserves the right to sample and to perform any confirmatory testingdeemed necessary to ensure that processing conforms to specified requirements.4.2 Classification of Tests:4.2.1 Acceptance Tests: Quality (3.5) is an acceptance test and shall be performed on each lot.4.2.2 Periodic Tests: Coating weight (3.3.1), corrosion resistance (3.3.2), and tests of cleaning andprocessing solutions (See 8.3) to ensure that the anodic coating will conform to specifiedrequirements are periodic tests and shall be performed at a frequency selected by theprocessor unless frequency of testing is specified by purchaser.4.2.3 Preproduction Tests: All technical requirements are preproduction tests and shall beperformed prior to or on the initial shipment of processed parts to a purchaser, when a change in material and/ or processing requires approval by the cognizant engineering organization(See 4.4.2), and when purchaser deems confirmatory testing to be required.4.3 Sampling and Testing:Shall be not less than the following; a lot shall be all parts of the same part number, processed in a continuous series of operations (3.2.4 to 3.2.5, inclusive), in not longer than 24 consecutive hours, and presented for processor’s inspection at one time.4.3.1 For Acceptance Tests: Shall be as shown in Table 1.4.5 Reports:The processor of coated parts shall furnish with each shipment a report stating that the parts have been processed and tested in accordance with specified requirements and that theyconform to the acceptance test requirements. This report shall include the purchase ordernumber, lot number, AMS 2471F, part number, and quantity.4.6 Resampling and Retesting:4.6.1 If any lot acceptance test fails to meet specified requirements, parts in that lot may be strippedby a method acceptable to purchaser which does not roughen, pit or embrittle the basis metal or adversely affect part dimensions, pretreated, coated, post-treated as defined herein andtested. Alternatively, all parts in the lot may be inspected for the nonconforming attribute, and the nonconforming parts may be stripped by a method acceptable to purchaser that does not pit, roughen, embrittle the basis metal, or adversely affect part dimensions, pretreated,recoated, post- treated as defined herein, and tested. After any stripping and recoating, parts shall meet the dimensional requirements of the drawing.4.6.2 If results of any periodic test fail to meet specified test requirements, the process isnonconforming. No additional parts shall be plated until the process is corrected and newspecimens are coated and tested. Results of all tests shall be recorded and, when requested, reported. Purchaser shall be notified of all parts coated since the last acceptable test.5. PREPARATION FOR DELIVERY:5.1 Coated parts shall be handled and packaged to ensure that the required physical characteristicsand properties of the coating are preserved.5.2 Packages of coated parts shall be prepared for shipment in accordance with commercialpractice and in compliance with applicable rules and regulations pertaining to the handling,packaging, and transportation of the coated parts to ensure carrier acceptance and safedelivery.6. ACKNOWLEDGMENT:A processor shall mention this specification number and its revision letter in all quotations andwhen acknowledging purchase orders.7. REJECTIONS:Parts on which the coating does not conform to this specification, or to modifications authorized by purchaser, will be subject to rejection.8. NOTES:8.1 A change bar (|) located in the left margin is for the convenience of the user in locating areaswhere technical revisions, not editorial changes, have been made to the previous issue of a specification. An (R) symbol to the left of the document title indicates a complete revision of the specification, including technical revision. Change bars and (R) are not used in originalpublications, nor in specifications that contain editorial changes only.8.2 Precautions:8.2.1 Preparation: All fabrication-type operations, such as forming, shot peening, brazing, welding,perforating, machining, and heat treatment, shall be completed before parts are anodized. 8.2.2 Surfaces to be painted should be handled with care after anodizing to prevent rupture of thefilm and contamination by dirt or oil. Painting, if required, should be performed as soon after treatment as practicable.8.2.3 Aluminum parts which contain inserts of other metals should be masked before anodizing toseal off the non-aluminum material.8.2.4 Hooks or racks, except those made from titanium, should have the anodic film removed fromthe contact areas prior to reuse.8.2.5 Holes, whether tapped or not, 0.25 inch (6.4 mm) in diameter or greater, with an L/D ratio ofthree or less, should anodize. In the case of small holes, coating thickness may vary from no film to a full normal coating.8.2.6 Anodic coatings will affect dimensions. Special attention should be given to external andinternal threads. The pitch diameter of external threads may increase two to four times the coating thickness.8.2.7 Although the exact thickness of sulfuric acid anodic coatings will depend on the processingparameters, the normal range is 0.0002 to 0.0006 inch (5 to 15 µm). This, with the growth, which is one-third to one-half the coating thickness, and inherent brittleness of the coating,should be considered for possible cause of damage during interference fit of assemblies.8.2.8 Surface finish of the machined part prior to anodizing should be better than the surface finishrequirement of the anodized area. Any polishing or honing of the coating will be harmful.8.2.9 Dichromate concentration should be 4.5 to 6% by weight. The pH should be within the range5.5 to6.5, and may be adjusted by the addition of chromic acid to lower the pH or sodiumhydroxide to raise the pH. The temperature should be within the range 190 to 212 °F(88 to 100 °C).8.2.10 Sealing Time: Should be not less than 20 minutes.8.3 ARP4992, Periodic Test Plan for Processing Solutions, is recommended to satisfy control ofprocessing solutions.8.4 Dimensions in inch/pound units and the Fahrenheit temperatures are primary; dimensions in SIunits and the Celsius temperatures are shown as the approximate equivalents of the primary units and are presented only for information.8.5 Purchase documents should specify not less than the following:AMS 2471FPart number of parts to be coatedQuantity of parts to be coated.8.6 Key Words:Corrosion resistance, adherence, organic finishes, paintPREPARED UNDER THE JURISDICTION OF AMS COMMITTEE “B”。
sae ams 3095a标准
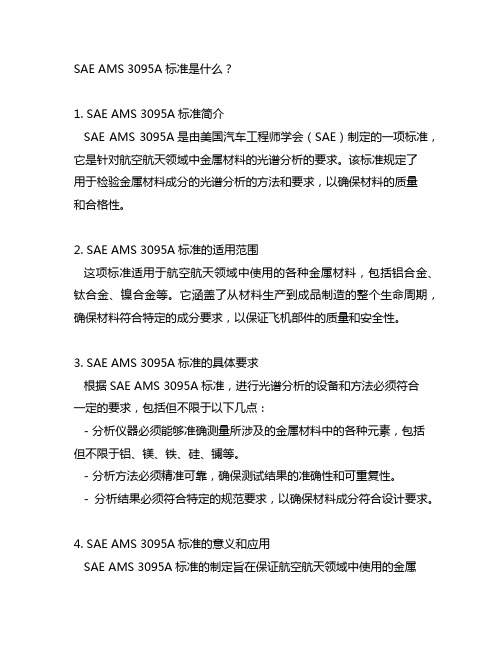
SAE AMS 3095A标准是什么?1. SAE AMS 3095A标准简介SAE AMS 3095A是由美国汽车工程师学会(SAE)制定的一项标准,它是针对航空航天领域中金属材料的光谱分析的要求。
该标准规定了用于检验金属材料成分的光谱分析的方法和要求,以确保材料的质量和合格性。
2. SAE AMS 3095A标准的适用范围这项标准适用于航空航天领域中使用的各种金属材料,包括铝合金、钛合金、镍合金等。
它涵盖了从材料生产到成品制造的整个生命周期,确保材料符合特定的成分要求,以保证飞机部件的质量和安全性。
3. SAE AMS 3095A标准的具体要求根据SAE AMS 3095A标准,进行光谱分析的设备和方法必须符合一定的要求,包括但不限于以下几点:- 分析仪器必须能够准确测量所涉及的金属材料中的各种元素,包括但不限于铝、镁、铁、硅、镧等。
- 分析方法必须精准可靠,确保测试结果的准确性和可重复性。
- 分析结果必须符合特定的规范要求,以确保材料成分符合设计要求。
4. SAE AMS 3095A标准的意义和应用SAE AMS 3095A标准的制定旨在保证航空航天领域中使用的金属材料的质量和可靠性。
通过严格的光谱分析要求,可以有效地避免杂质和成分偏差对材料性能的影响,保证飞机部件在高强度、高温、高压等复杂环境下的安全可靠运行。
SAE AMS 3095A标准也为材料生产厂家、航空航天制造商以及相关监管部门提供了一致的技术规范和标准化要求,有利于提高产业整体的质量水平和竞争力。
5. SAE AMS 3095A标准的更新和发展随着航空航天领域的发展和技术的进步,金属材料的要求也在不断提高。
SAE AMS 3095A标准也将不断进行更新和完善,以适应新材料、新工艺和新需求的发展。
通过持续改进和更新,SAE AMS 3095A 标准将为航空航天材料分析提供更加可靠和先进的技术支持。
结论SAE AMS 3095A标准作为航空航天领域中材料分析的重要标准,对于保证材料质量、促进产业发展具有重要意义。
SAE AMS 2411G-2008

SAE Technical Standards Board Rules provide that: “This report is published by SAE to advance the state of technical and engineering sciences. The use of this report is entirely voluntary, and its applicability and suitability for any particular use, including any patent infringement arising therefrom, is the sole responsibility of the user.”SAE reviews each technical report at least every five years at which time it may be reaffirmed, revised, or cancelled. SAE invites your written comments and suggestions. Copyright © 2008 SAE InternationalAll rights reserved. No part of this publication may be reproduced, stored in a retrieval system or transmitted, in any form or by any means, electronic, mechanical, photocopying, recording, or otherwise, without the prior written permission of SAE. TO PLACE A DOCUMENT ORDER: Tel: 877-606-7323 (inside USA and Canada) Tel: 724-776-4970 (outside USA) Fax: 724-776-0790Email: CustomerService@ SAE WEB ADDRESS:h ttp://AMS2411GAEROSPACE MATERIALSPECIFICATIONIssued 1966-09 Revised 2008-02 Superseding AMS2411FPlating, Silverfor High Temperature ApplicationsRATIONALEThis revision was issued to prohibit use of certain additives (3.2.1) and to ensure costly composition tests are not performed too frequently (4.2.2).NOTICEORDERING INFORMATION: The following information shall be provided to the plating processor by the purchaser. 1. Purchase order shall specify not less than the following:• AMS2411G • Plating thickness desired (see 3.4.1) • Basis metal to be plated• Tensile strength or hardness of the basis metal• Preplate stress relief to be performed by plating processor (time and temperature) if different from 3.1.1•Special features, geometry or processing present on parts that requires special attention by the plating processor• Hydrogen embrittlement relief to be performed by plating processor (parameters or reference document) ifdifferent from 3.3.1 • Minimum thickness on internal surfaces, if required (see 3.4.1.3) •Quantity of pieces to be plated2. Parts manufacturing operations such as heat treating, forming, joining and media finishing can affect the condition ofthe substrate for plating, or if performed after plating, could adversely affect the plated part. The sequencing of these types of operations should be specified by the cognizant engineering organization or purchaser and is not controlled by this specification.1. SCOPE 1.1 PurposeThis specification covers the requirements for silver deposited on metal parts with a nickel strike between the basis metal and the silver deposit. 1.2 ApplicationThis process has been used typically to prevent galling or seizing of surfaces of parts, such as fasteners, made of low-alloy steel, corrosion and heat resistant steel, and nickel alloys for use up to 1400 °F (760 °C). 1.3 Safety-Hazardous MaterialsWhile the materials, methods, applications, and processes described or referenced in this specification may involve the use of hazardous materials, this specification does not address the hazards which may be involved in such use. It is the sole responsibility of the user to ensure familiarity with the safe and proper use of any hazardous materials and to take necessary precautionary measures to ensure the health and safety of all personnel involved. 2. APPLICABLE DOCUMENTSThe issue of the following documents in effect on the date of the purchase order forms a part of this specification to the extent specified herein. The supplier may work to a subsequent revision of a document unless a specific document issue is specified. When the referenced document has been cancelled and no superseding document has been specified, the last published issue of that document shall apply. 2.1 SAE PublicationsAvailable from SAE International, 400 Commonwealth Drive, Warrendale, PA 15096-0001, Tel: 877-606-7323 (inside USA and Canada) or 724-776-4970 (outside USA), . AMS2759/9 Hydrogen Embrittlement Relief (Baking) of Steel PartsAMS5616Steel, Corrosion and Heat-Resistant, Bars, Wire, Forgings, Tubing and Rings, 13Cr - 2.0Ni - 3.0W, AnnealedAMS5640 Steel, Corrosion-Resistant, Bars, Wire, and Forgings, 18Cr - 9.0Ni, Free Machining AMS5643 Steel, Corrosion-Resistant, Bars, Wire, Forgings, Tubing, and Rings, 16Cr - 4.0Ni - 0.30Cb -4.0Cu, Solution Heat Treated, Precipitation HardenableAMS5709 Nickel Alloy, Corrosion and Heat-Resistant, Bars and Forgings, 58Ni - 19.5Cr - 13.5Co - 4.3Mo -3.0Ti - 1.4AI - 0.05Zr - 0.006B, Consumable Electrode or Vacuum Induction Melted, 1975 °F (1079 °C) Solution, Stabilization, and Precipitation Heat TreatedAMS5732 Steel, Corrosion and Heat-Resistant, Bars, Wire, Forgings, Tubing, and Rings, 15Cr - 25.5Ni -1.2Mo -2.1Ti - 0.006B - 0.30V, Consumable Electrode Melted, 1800 °F (982 °C) Solution and Precipitation Heat TreatedAMS6304 Low-Alloy Steel, Heat-Resistant, Bars, Forgings, and Tubing, 0.95Cr - 0.55Mo - 0.30V (0.40 -0.50C)AS2390 C hemical Process Test Specimen Material--`,```````,`,,,,`,,``,,,``````-`-`,,`,,`,`,,`---2.2 ASTM PublicationsAvailable from ASTM International, 100 Barr Harbor Drive, P.O. Box C700, West Conshohocken, PA 19428-2959, Tel: 610-832-9585, .ASTM B 487 Measurement of Metal and Oxide Coating Thicknesses by Microscopical Examination of a Cross SectionASTM B 499 Measurement of Coating Thicknesses by the Magnetic Method: Nonmagnetic Coatings on Magnetic Basis MetalsASTM B 504 Measurement of the Thickness of Metallic Coatings by the Coulometric MethodASTM B 567 Measurement of Coating Thickness by the Beta Backscatter MethodASTM B 568 Measurement of Coating Thickness by X-Ray SpectrometryASTM B 571 Qualitative Adhesion Testing of Metallic CoatingsASTM E 376 Measuring Coating Thickness by Magnetic-Field or Eddy-Current (Electromagnetic) Examination MethodsASTM F 519 Mechanical Hydrogen Embrittlement Evaluation of Plating/Coating Processes and Service Environments2.3 ANSI PublicationsAvailable from American National Standards Institute, 25 West 43rd Street, New York, NY 10036, Tel: 212-642-4900, .ASME B46.1 Surface Texture3. TECHNICAL REQUIREMENTS3.1 Preparation3.1.1 Steel parts having a hardness of 40 HRC or higher and which have been ground, machined, or cold straightenedafter heat treatment shall be cleaned to remove surface contamination and stress relieved before preparation for plating. Temperatures to which parts are heated shall be such that maximum stress relief is obtained without reducing hardness of parts below drawing limits, but, unless otherwise specified, not less than 275 °F (135 °C) for not less than 5 hours for parts having hardness of 55 HRC or higher or not less than 375 °F (191 °C) for not less than 4 hours for other parts.3.1.2 Nickel strike plating shall be applied over a clean and active surface that will result in a deposit that meet theadhesion and quality requirements of this specification. The pretreatment process shall not produce pitting or intergranular attack of the basis metal and shall preserve dimensional requirements.3.1.3 Surface roughness of surfaces to be plated, other than that of nuts, shall be 80 microinches (2 µm) Ra orsmoother determined in accordance with ASME B46.1.3.1.4 Except for barrel plating, electrical contact points shall be as follows. For parts which are to be plated all over,locations shall be acceptable to the cognizant engineering organization. For parts which are not to be plated all over, locations shall be in areas on which plating is not required or other location acceptable to the cognizant engineering organization.3.2 Procedure3.2.1 Parts shall be plated using a three-step process: nickel strike, silver strike, and silver plate. The nickel strike shall0.0005 inch (13 µm) maximum. The use of organic base grain refining and brightener additives shall beprohibited in both the silver strike and silver plate solutions.3.2.1.1 When approved by the cognizant engineering organization, an alternative to nickel strike is permitted.3.2.2 Double plating and spotting in are prohibited.3.3 Post Treatment3.3.1 Hydrogen embrittlement relief treatment of steel parts shall be in accordance with AMS2759/9.3.4 PropertiesPlated parts shall conform to the following requirements:3.4.1 Thickness of the deposit shall be as specified on the drawing, determined in accordance with any of the followingmethods as applicable: ASTM B 487, ASTM B 499, ASTM B 504, ASTM B 567, ASTM B 568, ASTM E 376, or other method acceptable to the cognizant engineering organization (See 8.6).3.4.1.1 Nickel strike shall not exceed 0.0005 inch (13 µm).3.4.1.2 Where silver flash is specified, plate thickness shall be approximately 0.0001 inch (2.5 µm).3.4.1.3 All surfaces of the part, except those which cannot be touched by a sphere 0.75 inch (19 mm) in diameter, shallbe plated to the specified thickness. Unless otherwise specified, surfaces such as holes, recesses, threads and other areas where a controlled deposit cannot be obtained under normal plating conditions, may be under the specified limit provided they show visual plating coverage.3.4.2 Composition of the deposit shall be not less than 99.9% silver determined by a method acceptable to thecognizant engineering organization.3.4.3 AdhesionThe deposit shall firmly adhere to the basis metal.3.4.3.1 Parts or test panels to be adhesion tested shall be heated in an air atmosphere to the following applicabletemperature, held at heat within ±15 °F (±8 °C) for not less than 2 hours, and cooled in still air.WARNING: T he following are destructive tests and parts so tested are not acceptable for shipment.3.4.3.1.1 Parts or test panels made of low-alloy steels, such as AMS6304, and martensitic or precipitation-hardenable --`,```````,`,,,,`,,``,,,``````-`-`,,`,,`,`,,`---corrosion resistant steels, such as AMS5616 or AMS5643, shall be heated at 900 °F (482 °C).3.4.3.1.2 Parts or test panels made of austenitic corrosion-resistant steels, such as AMS5640, and precipitation-hardenable, corrosion and heat resistant steels, such as AMS5732, shall be heated at 1200 °F (648 °C).3.4.3.1.3 Parts or test panels made of precipitation-hardenable, corrosion and heat resistant nickel alloys, such asAMS5709, shall be heated at 1400 °F (760 °C).3.4.3.1.4 Parts or test panels made of materials of a type not listed in 3.4.3.1.1 through 3.4.3.1.3 shall be heated at thetemperature specified on the drawing or as directed by the cognizant engineering organization.3.4.3.2 After heating as in 3.4.3.1, parts or test panels shall be examined at 10X magnification. Parts shall be free ofblisters and of indications of poor bond such as flaking and lifting of the plating. Small blisters are acceptable provided the parts meet the adherence requirements of 3.4.3.3. Blisters 0.015 inch (0.38 mm) and larger in diameter, measured under 10X magnification are not acceptable.3.4.3.3 After visual examination as in 3.4.3.2, parts or test panels, shall be shear or chisel-tested in accordance withASTM B 571. There shall be no signs of peeling of the plating from the underlying metal except where the chiseling or whittling action cuts through blisters permitted by 3.4.3.2. If parts show lifting and/or peeling, or both, of the plating except where the cutting is through blisters, all parts of the lot represented shall be rejected unless there is indication of shearing or cutting effect on the plating adjacent to the area from which blisters have been removed.3.4.4 HydrogenEmbrittlementThe plating process shall not cause hydrogen embrittlement in steel parts, determined in accordance with 4.3.3.2.3.5 Quality3.5.1 Plating, as received by purchaser, shall be smooth, continuous, adherent to basis metal, uniform in appearanceand visually free from pin holes, blisters, nodules, pits, and other imperfections detrimental to usage of the parts.Slight staining or discoloration is permissible. There shall be no evidence of electrical arcing or local overheating.3.5.2 Silver plate which is to be machined shall be free from excessive modulation or treeing at edges. Finished partsshall be free from visible pits excessive porosity, and other imperfections detrimental to fabrication or to performance of parts.3.5.3 Abrasion of plating on corners and edges of threaded fasteners is acceptable but plate shall be continuous onthreads. Marking of the cone section of self-locking nuts, produced in offsetting the locking beams or other deformation, is acceptable.4. QUALITY ASSURANCE PROVISIONS4.1 Responsibility for InspectionThe processor shall supply all samples for processor's tests and shall be responsible for the performance of all required tests. When parts are required for tests, such parts shall be supplied by purchaser. The cognizant engineering organization reserves the right to sample and to perform any confirmatory testing deemed necessary to ensure that processing conforms to specified requirements.4.2 Classification of Tests4.2.1 AcceptanceTestsThickness (3.4.1), adhesion (3.4.3), and quality (3.5) are acceptance tests and shall be performed on parts, or samples representing parts when permitted, from each lot.4.2.2 PeriodicTestsComposition (3.4.2) is a periodic test and shall be performed at least once in each calendar quarter that parts are processed. Tests of cleaning and plating solutions are periodic tests and shall be performed at a frequency established by the processor unless frequency of testing is specified by the cognizant engineering organization (See 4.4.3 and 8.4). Hydrogen embrittlement (3.4.4) is a periodic test and shall be performed in accordance with 4.3.3.2 at least once each month that steel parts 36 HRC and over are processed unless frequency of testing is specified by the cognizant engineering organization.4.2.3 PreproductionTestsAll property verification tests (section 3.4) are preproduction tests and shall be performed prior to production and when the cognizant engineering organization deems confirmatory testing to be required. --` , ` ` ` ` ` ` ` , ` , , , , ` , , ` ` , , , ` ` ` ` ` ` -` -` , , ` , , ` , ` , , ` ---4.3 Sampling for testing shall be not less than the following; a lot shall be all parts of the same part number plated tothe same range of plate thicknesses in the same set of solutions in each consecutive 24 hours of operation, and presented for processor's inspection at one time.4.3.1 AcceptanceTestsTest samples shall be randomly selected from all parts in the lot. The minimum number of samples shall be as shown in Table 1.TABLE 1 - SAMPLING FOR ACCEPTANCE TESTSNumber ofParts in Lot Quality Thickness and AdhesionUp to 7 All All or 3*8 to 15 7 416 to 40 10 441 to 110 15 5111 to 300 25 6301 to 500 35 7501 to 700 50 8701 to 1200 75 10Over 1200 125 15*Whichever is less4.3.2 P eriodic TestsSample quantities shall be selected at the discretion of the processor, unless otherwise specified.4.3.3 SampleConfiguration4.3.3.1 Separate test specimens may be used any under one of the following circumstances: The plated parts are ofsuch configuration or size as to be not readily adaptable to the specified tests, nondestructive testing is not practical on actual parts, or it is not economically acceptable to perform destructive tests on actual parts. When used, separate test specimens shall be made of the same generic class of alloy as the parts, distributed within the lot, cleaned, plated and post treated with the parts represented. For adhesion tests, such specimens shall be panels fabricated from a material generically similar to the parts being plated approximately 0.032 x 1 x 4 inch (1 x 25 x 102 mm) and for thickness tests shall be panels of annealed, low carbon steel approximately0.032 x 1 x 4 inches (1 x 25 x 102 mm). Adhesion acceptance test specimens shall be made of the samegeneric class of alloy as the parts, established in accordance with AS2390, distributed within the lot, cleaned, plated, and post treated with the parts.4.3.3.2 Hydrogen Embrittlement Relief TestThis test shall be in accordance with the requirements of ASTM F 519 Type 1a.1 using round notched specimens, unless a different specimen is specified by the cognizant engineering organization, stressed in tension under constant load. For test purposes, the plating thickness shall be 0.002 inch ± 0.0002 (51 µm ± 5) or plated to a thickness not less than twice the maximum thickness to which the plate is to be qualified, whichever is less. Thickness shall be measured on the smooth, unnotched sections of the specimens but with visual plating in the root of the notch.4.4 Approval4.4.1 The process and control factors or a preproduction part, or both, whichever is specified, shall be approved by thecognizant engineering organization before production parts are supplied.4.4.2 If the processor makes a significant change to any material, process, or control factor from that which was usedfor process approval, all preproduction tests shall be performed and the results submitted to the cognizant engineering organization for process reapproval unless the change is approved by the cognizant engineering organization. A significant change is one which, in the judgment of the cognizant engineering organization, could affect the properties or performance of the parts.4.4.3 Control factors shall include, but not be limited to, the followingSurface preparation and cleaning methodPlating bath composition and composition control limitsPlating bath temperature limits and controlsThermal post treatment times and temperaturesMethod for determining plating thicknessRack locationsStripping procedure, when applicableCurrent density (amps per part or amps per total surface area of the parts plated at one time in each tank)Periodic test plan (See 8.4).4.5 ReportsThe processor of plated parts shall furnish with each shipment a report stating that the parts have been processed and tested in accordance with the specified requirements and that they conform to the acceptance test requirements. This report shall include the purchase order number, AMS2411G, part number, lot identification and quantity.4.6 Resampling and Retesting4.6.1 If any acceptance test fails to meet specified test requirements, the parts in that lot may be stripped, pretreated,plated, and post treated as defined herein and retested. Alternatively, all parts in the lot may be inspected for the nonconforming attribute, and the nonconforming parts may be stripped, pretreated, plated, post treated as defined herein, and retested. After stripping and replating, parts shall meet the dimensions on the drawing.4.6.1.1 When stripping is performed, the method shall be acceptable to the cognizant engineering organization andshall not roughen, pit, or embrittle the basis metal or adversely affect part dimensions. When parts have been stripped and replated, the cognizant engineering organization shall be informed unless directed otherwise. --`,```````,`,,,,`,,``,,,``````-`-`,,`,,`,`,,`---4.6.2 If any periodic test fails to meet specified test requirements, the process is nonconforming. No additional partsshall be plated until the process is corrected and new specimens are plated and tested. Results of all tests shall be recorded and, when requested, reported. The cognizant engineering organization shall be notified of all parts plated since the last acceptable test.5. PREPARATION FOR DELIVERY5.1 Plated parts shall be handled and packaged in such a manner as will ensure that the required physicalcharacteristics and properties of the plate are preserved.5.2 Packages of parts shall be prepared for shipment in accordance with commercial practice and in compliance withapplicable rules and regulations pertaining to the handling, packaging, and transportation of the parts to ensure carrier acceptance and safe delivery.6. ACKNOWLEDGMENTThe processor shall mention this specification number and its revision letter in all quotations and when acknowledging purchase orders.7. REJECTIONSParts on which plating does not conform to this specification, or to modifications authorized by the cognizant engineering organization, will be subject to rejection.8. NOTES8.1 A change bar (|) located in the left margin is for the convenience of the user in locating areas where technicalrevisions, not editorial changes, have been made to the previous issue of this document. An (R) symbol to the left of the document title indicates a complete revision of the document, including technical revisions. Change bars and (R) are not used in original publications, nor in documents that contain editorial changes only.8.2 Part manufacturing operations, such as heat treatment, forming, joining, and media finishing, can affect thecondition of the substrate for plating, or, if performed after plating, could adversely affect the plate. The sequencing of these operations should be specified by the cognizant engineering organization and is not controlled by this specification.8.3 The parts manufacturer should ensure that the surfaces of the metal parts supplied to the plater are free fromblemishes, pits, tool marks, and other irregularities that will affect the quality of the finished parts. Defects and variations in appearance that arise from surface conditions of the substrate, such as porosity, scratches, or inclusions, that persist in the finish plate despite the observance of accepted industry practices shall not be cause for rejection.8.4 ARP4992, Periodic Test Plan for Process Solutions, is recommended to satisfy the requirements for the control ofprocessing solutions.8.5 An acid dip may be used for surface activation or neutralization of residual alkaline cleaner. However, theimmersion time should be minimized to preclude pitting.8.6 When machining of plated metal is required, deposit thickness must be sufficient to allow specified dimensions tobe met.8.7 Terms used in AMS are clarified in ARP1917. ASTM B 374 “Terminology Relating to Electroplating” should beutilized as a reference and referee document when areas of design definition or technical interpretation arise.8.7.1 Plating is intended to be deposited in an uninterrupted process except as may be required by the operator formaking thickness measurements. After the plate has dried, resumption of plating can result in detectable visual discontinuities or weak interlaminar adhesion that may not be readily apparent. Such resumption of plating is known as ‘double plating’ and localized addition of plate is known as ‘spotting-in.’8.8 Dimensions and properties in inch/pound units and the Fahrenheit temperatures are primary; dimensions andproperties in SI units and the Celsius temperatures are shown as the approximate equivalents of the primary units and are presented only for information.PREPARED BY AMS COMMITTEE "B"--`,```````,`,,,,`,,``,,,``````-`-`,,`,,`主营业务范围:ASTM、NAS、NASM、MIL、ISO、EN、DIN等技术标准翻译;技术资料翻译。
- 1、下载文档前请自行甄别文档内容的完整性,平台不提供额外的编辑、内容补充、找答案等附加服务。
- 2、"仅部分预览"的文档,不可在线预览部分如存在完整性等问题,可反馈申请退款(可完整预览的文档不适用该条件!)。
- 3、如文档侵犯您的权益,请联系客服反馈,我们会尽快为您处理(人工客服工作时间:9:00-18:30)。
__________________________________________________________________________________________________________________________________________ SAE Technical Standards Board Rules provide that: “This report is published by SAE to advance the state of technical and engineering sciences. The use of this report is entirely voluntary, and its applicability and suitability for any particular use, including any patent infringement arising therefrom, is the sole responsibility of the user.”SAE reviews each technical report at least every five years at which time it may be reaffirmed, revised, or cancelled. SAE invites your written comments and suggestions. Copyright © 2009 SAE InternationalAll rights reserved. No part of this publication may be reproduced, stored in a retrieval system or transmitted, in any form or by any means, electronic, mechanical,photocopying, recording, or otherwise, without the prior written permission of SAE.TO PLACE A DOCUMENT ORDER: Tel: 877-606-7323 (inside USA and Canada)Tel: +1 724-776-4970 (outside USA)Fax: 724-776-0790Email: CustomerService@SAE WEB ADDRESS: h ttp://AMS2475Issued 1940-03 Reaffirmed 2006-04RATIONALEAMS2475G results from a Five Year Review and update of this specification.1. SCOPE1.1 PurposeThis specification establishes the requirements for chromate conversion coatings on magnesium alloys.1.2 ApplicationThis process has been used typically to improve corrosion resistance and adherence of organic finishes but usage is not limited to such applications. The dichromate treatment may not be suitable for alloys with high manganese content. The chrome pickle treatment has been used as touch-up for previously dichromate-treated surfaces and for improving corrosion protection temporarily, but usages are not limited to such applications.1.3 Safety - Hazardous MaterialsWhile the materials, methods, applications, and processes described or referenced in this specification may involve the use of hazardous materials, this specification does not address the hazards that may be involved in such use. It is the sole responsibility of the user to ensure familiarity with the safe and proper use of any hazardous materials and to take necessary precautionary measures to ensure the health and safety of all personnel involved.2. APPLICABLE DOCUMENTSThe issue of the following documents in effect on the date of the purchase order forms a part of this specification to the extent specified herein. The supplier may work to a subsequent revision of a document unless a specific document issue is specified. When the referenced document has been canceled and no superseding document has been specified, the last published issue of that document shall apply.2.1 SAE PublicationsAvailable from SAE International, 400 Commonwealth Drive, Warrendale, PA 15096-0001, Tel: 877-606-7323 (inside USA and Canada) or 724-776-4970 (outside USA), .AMS-M-3171 Magnesium Alloy, Processes for Pretreatment and Prevention of Corrosion on3. TECHNICAL REQUIREMENTS3.1 Solutions3.1.1 Acid Pretreatment and Preparation3.1.1.1 Hydrofluoric acid solution shall be an aqueous solution containing 15 to 20% by weight of 48% hydrofluoric acid(HF). The hydrofluoric acid solution shall be operated at room temperature.3.1.1.1.1 When handling hydrofluoric acid, great care should be taken to avoid contact with the skin; rubber gloves,face shield, and protective clothing should be worn by operators.3.1.1.2 Acid pickle solution (3.2.2):TABLE 1 - Acid Pickle Solution**Ingredients Quantity for CastSurfaces*Quantity for Otherthan Cast Surfaces*Sulfuric acid (H2SO4, sp gr 1.84) 2.5 fl oz (63 mL) noneNitric acid (HNO3, sp gr 1.42) 10.25 fl oz (260 mL) noneChromic acid none 1.5 lbs (680 g)Water to make 1 gallon (3.8 L) 1 gallon (3.8 L)*Quantities are approximate** Ambient temperature operation required3.1.2 Sodium dichromate solution shall be an aqueous solution containing 10 to 15% of sodium dichromate(Na2Cr207•2H20) and 0.25% of either magnesium fluoride (MgF2) or calcium fluoride (CaF2) by weight. The solution shall be maintained saturated with magnesium or calcium fluoride by the continuous immersion of a cloth bag, or equivalent, containing the compound. The sodium dichromate solution shall be operated at not lower than 200 °F (93 °C) and preferably at its boiling point.3.1.3 Chrome pickle solution shall be as shown in Table 2.TABLE 2 - Chrome Pickle Solution**Ingredients Quantity for WroughtSurfacesQuantity for Cast Surfaces*Sodium dichromate (Na2Cr2O7•2H2O) 1.5 pounds (680 g) 1.5 pounds (680 g)Nitric acid (HNO3, sp gr 1.42) 1.5 pints (610 mL) 1 to 1.5 pints (450 to 610 mL)Water to make 1 gallon (3.8 L) 1 gallon (3.8 L)NaHF2, KHF2, or NH4HF2None 2 oz (51 g)Quantities are approximate* As defined in AMS-M-3171 Type I.** A proprietary solution, acceptable to the cognizant engineering organization, applied inaccordance with manufacturer’s instructions, may be used.3.2 Preparation3.2.1 The coating shall be applied to a surface free from water breaks, dirt, mill marking, heat scale, and discoloration.The cleaning procedure shall not produce pitting or intergranular attack of the basis metal and shall preserve dimensional requirements.3.2.2 AcidPickle--```,,`,,``,,`,,,,,`,,```,,,,,,3.2.2.1 Castings with oxidized surfaces may be immersed in acid pickle solution in accordance with Table 1 forapproximately ten seconds rinsed thoroughly in cold, flowing water, dipped in hot water, and dried rapidly.3.2.2.2 Parts, other than castings, with oxidized surfaces may be immersed in acid pickle solution in accordance withTable 1, rinsed thoroughly in ambient, flowing water, dipped in hot water at 190 to 212 °F (88 to 100 °C) and dried rapidly.3.3 Procedure3.3.1 Dichromate Treatment3.3.1.1 Prior to dichromate treatment, cleaned parts shall be immersed in the 3.1.1.1 hydrofluoric acid solution for notless than five minutes, or pickled by an alternative procedure approved by the cognizant engineering organization and rinsed thoroughly in ambient, flowing water.3.3.1.2 The wet parts shall be immersed in the 3.1.2 sodium dichromate solution for not less than 30 minutes,thoroughly rinsed in ambient, flowing water, dipped in hot water, and dried rapidly with a clean, dry air blast.3.3.2 Chrome pickle treatment shall be applied by local application to previously dichromate-treated surfaces whererequired application of an organic finish or where surfaces have been marred or to other surfaces when specified by the cognizant engineering organization.3.3.2.1 The surfaces to be treated shall be contacted continuously with freshly-prepared (Table 2) chrome picklesolution by flowing, brushing, or swabbing, or parts shall be immersed in the solution at room temperature.Exposure time to the solution shall be as long as practicable provided dimensional requirements are preserved.Normal exposure time is 30 to 120 seconds. Parts shall then be rinsed thoroughly with clean, flowing water and dried with a clean, dry air blast.3.3.3 Surfaces shall be handled after treatment carefully to prevent rupture of the film and contamination by dirt or oil.Organic finishing shall occur as soon after treatment as practicable.3.4 QualitySurfaces of coated parts, as received by purchaser, shall be substantially uniform in color, texture, and appearance. There shall be no bare or definite light-colored areas, powdery areas, and darkening of the corners and edges. --```,,`,,``,,`,,,,,`,,```,,,,,,-`-`,,`,,`,`,,`---3.4.1 Color of properly applied dichromate coatings may vary, depending on the alloy composition, condition of thesolution, and length of time of treatment. On most alloys, color ranges from dark brown to black; however, some process/alloy combinations may produce different colors, including dark neutral gray and colder tone grays containing slight amounts of blue or green.4. QUALITY ASSURANCE PROVISIONS4.1 Responsibility for InspectionThe processor shall supply all samples for processor’s tests and shall be responsible for the performance of all required tests. The cognizant engineering organization reserves the right to sample and to perform any confirmatory testing deemed necessary to ensure that processing conforms to specified requirements.4.2 Classification of Tests4.2.1 Acceptance TestsQuality (3.4) is an acceptance test and shall be performed on all parts in each lot.4.2.2 Periodic TestsTests of cleaning and processing solutions are periodic tests and shall be performed at a frequency established by the processor unless frequency of testing is specified by the cognizant engineering organization. See 8.5.4.2.3 Preproduction TestsQuality (3.4) is a preproduction test and shall be performed prior to or on the initial shipment of coated parts to a purchaser and when the cognizant engineering organization requires confirmatory testing.4.3 Sampling for testing shall be every part in the lot. A lot shall be all parts of the same part number processed in acontinuous series of operations in the same solutions and presented for processor’s inspection at one time.4.4 Approval4.4.1 The process and control procedures, a preproduction sample, or both, whichever is specified by the cognizantengineering organization, shall be approved by the cognizant engineering organization before production parts are supplied.--```,,`,,``,,`,,,,,`,,```,,,,,,-`-`,,`,,`,`,,`---4.4.2 If the processor makes a significant change to any material, process, or control procedure from that which wasused for process approval, preproduction testing (4.2.3) shall be performed and the results submitted to the cognizant engineering organization for process reapproval unless the change is approved by the cognizant engineering organization. A significant change is one that, in the judgment of the cognizant engineering organization, could affect the properties or performance of the parts.4.4.3 Control factors shall include, but not be limited to, the following:Surface preparation and cleaning methodsCoating material trade name and manufacturerCoating bath composition and composition control limitsCoating bath temperature limits and controlsPeriodic test plan for cleaning and processing solutions. See 8.5.4.5 ReportsThe processor of coated parts shall furnish with each shipment a report stating that the parts have been processed and tested in accordance with specified requirements and that they conform to the acceptance test requirements. This report shall include the purchase order number, lot number, AMS2475G, part number, and quantity.5. PREPARATION FOR DELIVERY5.1 Coated parts shall be handled and packaged to ensure that the required physical characteristics and properties ofthe coating are preserved.5.2 Packages of coated parts shall be prepared for shipment in accordance with commercial practice and incompliance with applicable rules and regulations pertaining to the handling, packaging, and transportation of the coated parts to ensure carrier acceptance and safe delivery.6. ACKNOWLEDGMENTProcessor shall mention this specification number and its revision letter in all quotations and when acknowledging purchase orders.7. REJECTIONSParts on which the coating does not conform to this specification, or to modifications authorized by the cognizant engineering organization, will be subject to rejection.8. NOTES8.1 A change bar (I) located in the left margin is for the convenience of the user in locating areas where technicalrevisions, not editorial changes, have been made to the previous issue of this document. An (R) symbol to the left of the document title indicates a complete revision of the document, including technical revisions. Change bars and (R) are not used in original publications, nor in documents that contain editorial changes only.8.2 Part manufacturing operations, such as heat treatment, forming, joining, and media finishing, can affect thecondition of the substrate, or, if performed after coating, could adversely affect the coating. The sequencing of operations should be specified by the cognizant engineering organization and is not controlled by this specification.8.3 The part manufacturer should ensure that the surfaces of the metal parts supplied to the processor are free fromblemishes, pits, tool marks, and other irregularities that will affect the quality of the finished parts. Defects and variations in appearance that arise from surface conditions of the substrate such as porosity, scratches, or inclusions, that persist in the coating despite the observance of accepted industry practices should not be cause for rejection.--```,,`,,``,,`,,,,,`,,```,,,,,,-`-`,,`,,`,`,,`---8.4 Terms used in AMS are clarified in ARP1917.8.5 ARP4992, Periodic Test Plan for Process Solutions, is recommended to satisfy control of processing solutions.8.6 Dimensions and properties in inch/pound units and the Fahrenheit temperatures are primary; dimensions andproperties in SI units and the Celsius temperatures are shown as the approximate equivalents of the primary units and are presented only for information.8.7 Purchase documents should specify not less than the following:AMS2475GPart number and quantity of parts to be coatedType of treatment desired when dichromate treatment is not authorized: specify “chrome pickle treatment only”.PREPARED BY AMS COMMITTEE “B”。