高炉炉料落点的确定
高炉工艺装料制度
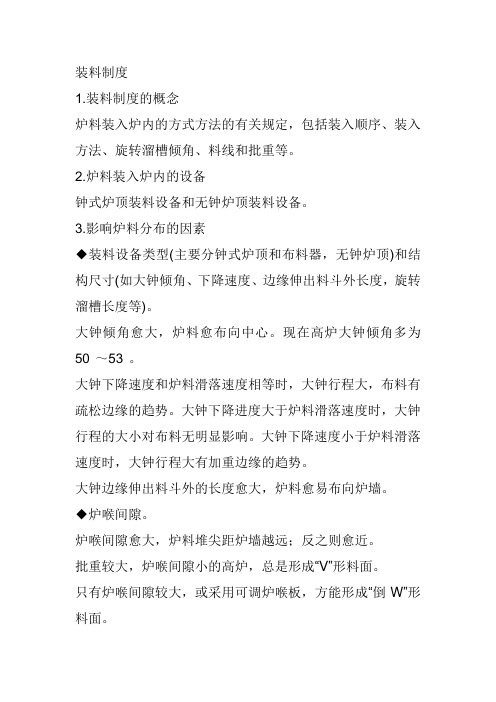
装料制度1.装料制度的概念炉料装入炉内的方式方法的有关规定,包括装入顺序、装入方法、旋转溜槽倾角、料线和批重等。
2.炉料装入炉内的设备钟式炉顶装料设备和无钟炉顶装料设备。
3.影响炉料分布的因素◆装料设备类型(主要分钟式炉顶和布料器,无钟炉顶)和结构尺寸(如大钟倾角、下降速度、边缘伸出料斗外长度,旋转溜槽长度等)。
大钟倾角愈大,炉料愈布向中心。
现在高炉大钟倾角多为50°~53°。
大钟下降速度和炉料滑落速度相等时,大钟行程大,布料有疏松边缘的趋势。
大钟下降进度大于炉料滑落速度时,大钟行程的大小对布料无明显影响。
大钟下降速度小于炉料滑落速度时,大钟行程大有加重边缘的趋势。
大钟边缘伸出料斗外的长度愈大,炉料愈易布向炉墙。
◆炉喉间隙。
炉喉间隙愈大,炉料堆尖距炉墙越远;反之则愈近。
批重较大,炉喉间隙小的高炉,总是形成“V”形料面。
只有炉喉间隙较大,或采用可调炉喉板,方能形成“倒W”形料面。
◆炉料自身特性(粒度、堆角、堆密度、形状等)。
◆旋转溜槽倾角、转速、旋转角。
◆活动炉喉位置。
◆料线高度。
◆炉料装入顺序。
◆批重。
◆煤气流速。
4.钟式炉顶布料的特征◆矿石对焦炭的推挤作用。
矿石落入炉内时,对其下的焦炭层产生推挤作用,使焦炭产生径向迁移。
矿石落点附近的焦炭层厚度减薄,矿石层自身厚度则增厚;但炉喉中心区焦炭层却增厚,矿石层厚度随之减薄。
大型高炉炉喉直径大,推向中心的焦炭阻挡矿石布向中心的现象更为严重,以致中心出现无矿区。
◆不同装入顺序对气流分布的影响。
炉料落入炉内,从堆尖两侧按一定角度形成斜面。
堆尖位置与料线、批重、炉料粒度、密度和堆角以及煤气速度有关。
先装入矿石加重边缘,先加入焦炭则发展边缘。
5.无料钟布料无料钟布料特征◆焦炭平台:高炉通过旋转溜槽进行多环布料,易形成一个焦炭平台,即料面由平台和漏斗组成,通过平台形式调整中心焦炭和矿石量。
平台小,漏斗深,料面不稳定。
平台大,漏斗浅,中心气流受抑制。
高炉基本操作制度

基本操作制度高炉冶炼过程是许多矛盾的集合体,矛盾贯穿于高炉冶炼的始终,因此需要高炉操作人员发挥主观能动性,保持高度的责任感,及时地发现问题、分析问题,抓住主要矛盾,以实事求是的态度,勤观察、勤检查、勤分析、勤调剂,正确掌握和运用装料制度,造渣制度、送风制度及炉缸热制度的关系,确保高炉顺行,以求得高产、优产、低耗的生产效果。
第一节送风制度合理的送风制度,是高炉工作正常的基础,是高炉顺行和炉温稳定的必要条件,作为高炉操作制度的核心,它决定着煤气流的初始分布和炉缸工作状态是否正常。
(1)、正常使用风口直径在φ105~120mm,长度240~320mm,斜度5~80。
(2)适宜的鼓风动能范围为4200~4800kgm/s。
(3)风量调剂A、在炉况顺行焦比适中及保证焦炭质量的前提下,应保持合适而稳定的冶炼强度。
B、在全压差允许条件下,坚持全风作业,尽量避免长期慢风作业。
C、日常操作上减风可迅速减到需要水平(但注意风口不灌渣),而加风速度则按高炉进程和风压情况逐步进行。
(4)风温调剂A、提高风温是增加高炉热量,降低焦比的主要途径之一,所以风温使用应稳定在最高水平。
B、减风温可一次减到需要水平。
C、增加风温应缓慢进行,提高风温每次一般不超过50℃,两次间隔不得少于30分钟。
(5)风压调济A、正常使用风压在190~200Kpa;B、若遇塌料现象可一次性减风30~40Kpa;C、在恢复过程中风压随炉况走势酌情处理;第二节装料制度(1)、正常炉料入炉次序np↓nk↓,防止灰石落在边缘,而洗炉时应把洗炉剂加在边缘;(2)、料尺零点规定在炉喉钢砖上沿;(3)、工长应经常或定期观察料车在炉顶的倾角;(4)、料线由两根链式探尺测明,两尺偏差在250mm以上时,应按指示最小的探尺上料,并采取纠正偏料的措施;(5)、因设备故障或其它原因发生亏料线,并估计在20分钟内不能正常上料时,高压操作转常压,同时控制炉顶温度,若布袋除尘器发生报警时,打开炉顶放散阀,切断煤气,以防布袋烧坏,炉顶温度禁止超过500℃;(6)、禁止低料线作业(料线低于规定料线0.5米为低料线);(7)、装料次顺:对于无钟布料可以通过改变矿石和焦炭的布料角度对边缘和中心进行控制,流槽可在13~53°范围内布料,在13°时可进行中心加焦;(8)、缩小料批可加重边缘,反之加得中心;(9)、禁止长期使用剧烈发展边缘的操作制度;(10)、赶料线过程中,应适当控制风量(100~200米3/分),要根据料线的深浅程度和赶料速度,适当加补料线焦。
高炉操作03炉况的判断与调节

高炉操作第3章 炉况的判断与调节保持高炉高产、优质、低耗和炉况顺行,从操作方面看主要是选择好各种操作制度与搞好日常调剂。
怎样正确地判断各种操作制度是否合理和正确地进行日常调剂,熟练地掌握综合判断高炉行程的方法与调剂规律,是一项非常重要的工作。
一般观察炉况的内容是:炉况的动向与波动幅度。
这两者相比,首先要掌握变化的方向,使调剂不发生方向性的差错。
其次,要掌握波动的幅度,有了量的概念,调剂才能既对症下药又恰如其分。
3.1 直接观测法3.1.1 看风口风口是唯一可以直接看到炉内局部冶炼现象的窗口,可以随时观察,比看铁、看渣所显示的炉况波动也早。
(1)炉缸温度。
炉热时风口明亮、无大块和生料下降;炉凉时风口发暗,炉料少降与大块多,甚至出现风口前涌渣、挂渣现象。
还要注意边缘发展时风口明亮但炉温不高。
(2)下料速度。
(3)循环区大小。
(4)炉缸圆周工作均匀性,其中包括各个风口的温度均匀性,煤气分布均匀性,下料状态均匀性。
(5)风口冷却器漏水情况。
3.1.2 看铁水每次出铁,必须观看铁水变化,其内容主要看以下几方面:(1)看炉温;铁水明亮,炉温适中,铁水暗红,炉温低。
(2)看[Si]含量,也是看炉温。
(3)看铁水[S]含量,铁水是否要炉外脱硫或是否符合要求,一般在炉前可以判断出来。
3.1.3 看炉渣从炉渣的流动状态与断口颜色可以判明炉缸热度、渣碱度及渣中FeO、MnO 等的含量。
(1)炉热时,渣流动性好、光亮耀眼,从炉子流出时表面冒出火苗、水渣白色。
(2)炉凉时,渣流动性差、颜色发红,从炉内流出来时无火苗而有小火星、水渣变黑。
(3)炉渣成分不同时其颜色不同,断面状态不同。
(4)液态炉渣时,酸性渣可拉丝,碱性渣成滴状滴下,因此前者叫长涪后者叫短渣。
固态炉渣时,玻璃渣为酸性渣;石头渣为碱性渣。
3.2 间接观测法随着科学技术的发展,高炉监测内容越来越多,精度越来越高,已成为观察判断炉况的主要手段。
监测高炉生产的主要仪表,按测量对象可分为以下几类:压力计类:有热风压力计、炉顶煤气压力计、炉身静压力计、压差计等。
第六章 炉料下降的条件

第六章炉料下降的条件一、炉料下降的条件1、炉料下降的前提条件是:在炉内不断存在使其下降的自由空间。
2、形成自由空间的原因有:(1)焦炭在风口前燃烧,变成气体离开高炉,为炉料下降提供35-40%的自由空间。
(2)焦炭在下降过程中被氧化,使体积缩小,提供15%的空间。
(3)炉料在下降过程中,小块不断充填于大块之间,同时,随温度升高炉料熔化,使其体积缩小。
(4)定期排放渣铁,可使炉缸内经常保持一定的空间,使上部炉料得以下降。
结论:风口前焦炭的燃烧和炉料熔化引起体积的缩减对炉料下降有决定影响。
原因:①它所产生的自由空间体积大;②没有焦炭的燃烧过程的进行,其它因素则无法发挥作用。
二、炉料下降的力学分析1、促使炉料下降的因素:重力2、阻碍炉料下降的因素:①炉墙的摩擦力;②炉料之间的相对摩擦;③煤气流对炉料支撑力。
3、促使炉料下降的因素与阻碍炉料下降的因素的关系:用下式表示:炉料下降的有效重量:W效=W料-P墙-P料A、影响W效的因素:①炉身角越小或炉腹角越大,则炉墙对炉料的摩擦力越小,炉料的和效重量就越大。
②料柱增高,炉料的有效重量增加。
③增加风口数量,减少炉墙与炉料的摩擦力,增大料柱有效重量。
④炉料平均堆比重越大,料柱的有效重量也越大。
B、影响△P的因素:①原料的粒度:若粒度大,则△P减小。
②原料粒度的均匀性:原料粒度的均匀性与料层的空隙率有直接关系。
空隙率越小,则△P越大。
B、影响△P因素①原料的粒度:若粒度大,则△P减小。
②原料粒度的均匀性:原料粒度的均匀与料层的空隙率有直接关系。
空隙率越小,则△P越大。
③风量:增大时,煤气流速大,△P也随之增大。
④煤气比重和粘度:两者降低,均使△P下降,煤气中H2量增加,可使煤气比重和粘度降低。
⑤炉温和煤气平均压力:炉温升高,△P增大。
煤气平均压力升高,△P减小。
三、高炉内炉料的运动了解炉料运动的方法:采用探尺和风口观察的上、下部结合的方法了解。
(一)探尺1、探尺工作过程:(1)装入炉内的料下降到料线,探尺自动提升到零位。
高炉降料面总结

2#高炉停炉操作总结一、停炉方案的确定2#高炉于2017年5月1日19:15分降料面停炉。
为确保停炉工作的安全、顺利以及停炉工艺的先进,对停炉方案制定了以下原则。
1、采用空料线打水法;2、空料线期间常压不回收煤气;3、根据安装特殊长探尺;结合煤气成份变化及累计风量分析法判断料面高度。
二、停炉准备工作1、停炉前1天,高炉有计划空仓,保证炉况顺行;2、停炉前1天开始适度发展边缘气流,冲刷炉墙,使渣皮脱落,保持全风作业,保证停炉后炉墙干净,炉缸活跃。
3、停炉前1天生铁[Si]控制水平由0.30-0.50%提高到0.40-0.60%,炉渣碱度由校核1.20降低至1.17±0.02;4、停炉前1天,对高炉冷却设备进行全面检查,严禁向炉内漏水。
5、停炉前2天,制做出一套(4根)打水管,并试验合格;要求水压>1.2Mpa,水量>80t/h(每根打水管水量20t/h)。
6、停炉预休风前5小时7:00改焦比630kg一级焦比例增加到50%,15:00改焦比633kg矿批28t,炉料配比为67%烧结+33%球团,预休风前加盖面焦30吨(15:21休风);7、停炉前预休风(实际5月1日15:21-19:15);7.1 休风后料线控制在7m左右(实际约7.8m);7.2 安装打水装置以及流量计(四个方位安装高压水管及电调控制实现远程控制);7.3 从炉顶东南上升管接煤气取样管并引至风口平台。
三、停炉降料线操作1、预休风复风后开始正式降料面;2. 降料面期间料线和风量之间关系确定吨焦风耗的确定根据对前3天对2#高炉的耗风量进行统计,计算统计吨焦耗风量为2850m3。
考虑随料线的下降,煤气利用和风量的利用率下降的影响,吨焦风耗取2900m3。
(根据计算预休风后炉内共计湿焦319t,焦水取6%则干焦300t,料线将至风口共需耗风710000m3)3、严格控制煤气含H2和O2,要求H2<6%,O2<2%,当炉顶温度300℃时,O2小于1.8%。
铁水[Si]偏差管理规定
![铁水[Si]偏差管理规定](https://img.taocdn.com/s3/m/ff818bcbd5bbfd0a7956734a.png)
铁水[Si]偏差管理规定为控制高炉炉温平稳,保持炉缸热量及初始气流、渣皮稳定,减少烧风口套几率,特对值班工长操作技能、责任心加强管理,并作以下要求:一、高炉[Si]偏差控制标准:1、2#、3#炉[Si]偏差不大于0.14。
2、1#、4#、5#、6#炉[Si]偏差不大于0.13。
3、7#炉[Si]偏差不大于0.11。
4、[Si]偏差计算公式为=STDEVP(罐数1:罐数x);以罐数炉温监控数字为准。
二、管理及考核要求:1、[Si]偏差控制考核管理以工段为单位、高炉生产运行12小时为计点,对高炉值班工长操作炉温进行管控。
2、白班或夜班(8:00-20:00或20:00-8:00)[Si]偏差超出上述范围,请工段自行安排培训人(炉长或副炉长)对本工段高炉值班正副工长进行培训,工段自定培训地点,并且在9:30或21:30分左右到调度室签字等台账,内调做好培训台账记录管理。
3、培训结束后,各工段培训人及[Si]偏差操作超标的正、副工长不到调度室做好台账或视为无台账的,处罚工段长、责任高炉炉长各100元/次。
生产科工艺组刘工安排核实!4、[Si]偏差操作超标工段未自觉执行培训要求,处罚工段长300元/次;生产科工艺组刘工安排核实!5、[Si]偏差控制超标一次处罚炉长20元,[Si]偏差控制合格一次奖励炉长40元。
6、高炉[Si]偏差控制全月合格率达到以上80%奖励高炉值班室1500元,连带奖励工段长300元。
7、因调度原因等非高炉自身因素造成的休慢风或计划休风致高炉炉温波动大,工段2-3个工作日内可提出书面申请报生产科工艺组刘工处,经核实,[Si]偏差超标不纳入处罚而控制合格可奖励,但培训工作依然要做。
OA申请流程:高炉——工段——生产科:刘喜华、陶善胜。
三、解释权在厂部,自本月15日试行。
生产技术科2012年12月10日。
高炉内地炉料运动 Microsoft Word 文档
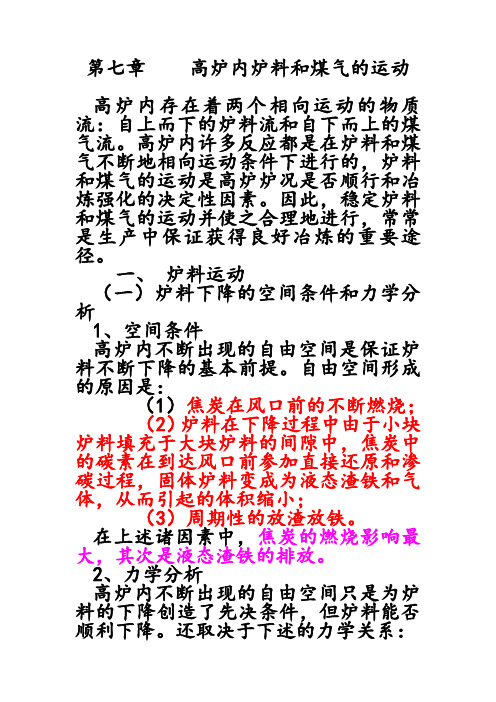
第七章高炉内炉料和煤气的运动高炉内存在着两个相向运动的物质流:自上而下的炉料流和自下而上的煤气流。
高炉内许多反应都是在炉料和煤气不断地相向运动条件下进行的,炉料和煤气的运动是高炉炉况是否顺行和冶炼强化的决定性因素。
因此,稳定炉料和煤气的运动并使之合理地进行,常常是生产中保证获得良好冶炼的重要途径。
一、炉料运动(一)炉料下降的空间条件和力学分析1、空间条件高炉内不断出现的自由空间是保证炉料不断下降的基本前提。
自由空间形成的原因是:(1)焦炭在风口前的不断燃烧;(2)炉料在下降过程中由于小块炉料填充于大块炉料的间隙中,焦炭中的碳素在到达风口前参加直接还原和渗碳过程,固体炉料变成为液态渣铁和气体,从而引起的体积缩小;(3)周期性的放渣放铁。
在上述诸因素中,焦炭的燃烧影响最大,其次是液态渣铁的排放。
2、力学分析高炉内不断出现的自由空间只是为炉料的下降创造了先决条件,但炉料能否顺利下降。
还取决于下述的力学关系:P=P料-P c-P k-P气= P料-P摩-P气(7-1)式中P——使炉料下降的力;P料——炉料的重量;P c——炉料与炉墙之间的摩擦力;P k——炉料与炉料之间的摩擦力;P摩——炉料下降时受到的总的摩擦力;P气——煤气对炉料的阻力(浮力)。
很显然,只有当P>0时炉料才能下降;P愈大,则愈有利于炉料顺利下降;当P 接近或等于零时,则炉料产生难行或悬料。
须要指出的是,要使炉料顺利下降(也称为炉料顺利),不仅要求整个料柱的P 大于零,而且还要求各个不同高度截面上和同一截面不同位置上的P大于零。
显然,某处的P=0时,则某处的炉料是悬料。
因此,炉料不顺行的现象,不仅可能在高炉上部或下部出现,也可能在某一截面上的某一区域出现。
为了讨论问题方便起见,引入料住有效重量这一概念。
料柱的重量克服了摩擦阻力后所剩下的重量,称为料柱的有效重量,即P有效=P料-P摩(7-2)就整个料柱而言,料柱本身的重量由于受到摩擦阻力的反作用,并没有全部作用在风口平面或炉底上,真正起作用的只是料柱的有效重量。
高炉基本操作制度

基本操作制度高炉冶炼过程是许多矛盾的集合体,矛盾贯穿于高炉冶炼的始终,因此需要高炉操作人员发挥主观能动性,保持高度的责任感,及时地发现问题、分析问题,抓住主要矛盾,以实事求是的态度,勤观察、勤检查、勤分析、勤调剂,正确掌握和运用装料制度,造渣制度、送风制度及炉缸热制度的关系,确保高炉顺行,以求得高产、优产、低耗的生产效果。
第一节送风制度合理的送风制度,是高炉工作正常的基础,是高炉顺行和炉温稳定的必要条件,作为高炉操作制度的核心,它决定着煤气流的初始分布和炉缸工作状态是否正常。
(1)、正常使用风口直径在φ105~120mm,长度240~320mm,斜度5~80。
(2)适宜的鼓风动能范围为4200~4800kgm/s。
(3)风量调剂A、在炉况顺行焦比适中及保证焦炭质量的前提下,应保持合适而稳定的冶炼强度。
B、在全压差允许条件下,坚持全风作业,尽量避免长期慢风作业。
C、日常操作上减风可迅速减到需要水平(但注意风口不灌渣),而加风速度则按高炉进程和风压情况逐步进行。
(4)风温调剂A、提高风温是增加高炉热量,降低焦比的主要途径之一,所以风温使用应稳定在最高水平。
B、减风温可一次减到需要水平。
C、增加风温应缓慢进行,提高风温每次一般不超过50℃,两次间隔不得少于30分钟。
(5)风压调济A、正常使用风压在190~200Kpa;B、若遇塌料现象可一次性减风30~40Kpa;C、在恢复过程中风压随炉况走势酌情处理;第二节装料制度(1)、正常炉料入炉次序np↓nk↓,防止灰石落在边缘,而洗炉时应把洗炉剂加在边缘;(2)、料尺零点规定在炉喉钢砖上沿;(3)、工长应经常或定期观察料车在炉顶的倾角;(4)、料线由两根链式探尺测明,两尺偏差在250mm 以上时,应按指示最小的探尺上料,并采取纠正偏料的措施;(5)、因设备故障或其它原因发生亏料线,并估计在20分钟内不能正常上料时,高压操作转常压,同时控制炉顶温度,若布袋除尘器发生报警时,打开炉顶放散阀,切断煤气,以防布袋烧坏,炉顶温度禁止超过500℃;(6)、禁止低料线作业(料线低于规定料线0.5米为低料线);(7)、装料次顺:对于无钟布料可以通过改变矿石和焦炭的布料角度对边缘和中心进行控制,流槽可在13~53°范围内布料,在13°时可进行中心加焦;(8)、缩小料批可加重边缘,反之加得中心;(9)、禁止长期使用剧烈发展边缘的操作制度;(10)、赶料线过程中,应适当控制风量(100~200米3/分),要根据料线的深浅程度和赶料速度,适当加补料线焦。
高炉内的基本知识

高炉内的基本知识1、高炉内的分区按照炉料在高炉内的状态可分为五个区域,依次为:(1)、块状带:固体料软熔前所分布的区域。
(2)、软熔带:炉料从开始软化到熔化所占的区域。
软熔带通常有倒V型、V 型、可型三种,该区域为间接还原区。
(3)、滴落带:渣、铁全部熔化滴落,穿过焦炭层下到炉缸的区域,是高温物理化学反应的主要区域。
(4)、风口带风口前燃料燃烧的区域,是高炉热能和气体还原剂的发源地,也是初始煤气流分布的起点。
(5)、渣铁贮存区是形成最终渣、铁的区域。
2、炉内还原过程高炉内铁氧化物的还原可分为三类:用气体CO还原,生成产物CO2,称间接还原;用固体碳还原,生成产物CO,称直接还原;一部分氢在低温代替CO还原,另部分氢在高温代替碳进行直接还原,统称氢的还原。
根据温度不同,高炉内还原过程划分三个区,低于800°C的块状带是间接还原区;800°C〜1100°C是间接还原和直接还原共存区;高于1100C的是直接还原区。
高炉内的主要化学反应为:(1)、用CO还原高于570C时:3 FeO+CO=2 Fe O +CO2 3 3 4 2Fe3O4+CO=3FeO+CO2低于570C时:3 FeO +CO=2 Fe O + CO2 3 3 4 2Fe3O4+4CO=3Fe+4 CO2(2)、用固体碳还原高于570C时:3 Fe O +C=2 Fe O +CO2 3 3 4FeO+C=3FeO+CO3 4FeO+C=Fe+CO低于570°C时由于FeO不能稳定存在,进行下列反应:FeO+4C=3Fe+4CO 3 4FeO+C=Fe+CO(3)、用H2还原高于570C时:3 FeO+ H =2 Fe O + HO2 3 2 3 4 2Fe3O4+ H2=3FeO+ H2OFeO+ H2=Fe+ H2O小于570C时:3 FeO+ H=2 Fe O + HO23 2 34 2Fe3O4+4 H2=3Fe+4 H2O3、高炉对原燃料质量的要求(1)、对原燃料的整体要求精料是高炉操作稳定顺行的必要条件,精料的内容可概括为:高品位、强度、冶金性能指标等都高。
炉料的运动

(6)炉料的堆积密度
炉料的堆积密度越大,Q有效越大。炉料堆密度提高,对顺行有利。
四、课堂检测
1、炉料下降的必要条件是( 产生空间 ) 2、炉料下降的充分条件是( Q有效>∆P ) 3、炉腹角增大,炉身角减小,炉料的有效质量(增加) 4、温度升高,煤气阻力( 加大 ) 5、风口数目( 增加 ),有利于提高炉料的有效质量
(3)炉料的运动状态
炉料在运动的状态下,有效质量系数比静止的大 。
(4)造渣制度
因为炉渣尤其是初成渣和中间渣,是一种黏稠的液体,它会增加炉墙 与炉料之间及炉料相互之间的摩擦力。因此成渣带位置越高、成渣带越厚、 炉渣的物理性质越差和渣量越大时,则P墙摩和P料摩越大,而Q有效越小。
(5)风口数目
风口数目的增加,扩大了燃烧带炉料的活动区域,减小了P墙摩和P料 摩,所以有利于提高Q有效。
作业
• 试述高炉炼铁过程中,如何为炉料 的正常下降创造条件?
授课人: 青龙职教中心 张翔宇
知识回顾
• 的条件 二、影响炉料有效质量(Q有效) 的因素 重点:影响炉料有效质量(Q有效) 的因素 难点:炉料下降的条件
一、炉料的下降条件
1、炉料下降的基本条件
炉料下降的基本(必要)条件是 在高炉内不断存在着的促使炉料下降 的自由空间。
2、炉料下降的充分条件
P=(P炉料- P墙摩- P料摩) - ∆P =Q有效-∆P
二、影响炉料有效质量(Q有效)的因素
(1)高炉设计参数(炉 腹角和炉身角)
炉腹角增大,炉身角减小,炉料和炉墙 间摩擦力减小,炉料的有效质量增大,有利 于炉料顺行。
(2)料柱的高度
一般情况下,当料柱逐渐增高时,料柱的有效质量系数是不断降 低的。所以矮胖型高炉有利于顺行,尤其适合大中型高炉。
《高炉炼铁技术》项目10任务10.4影响煤气分布的因素

冶金工程系
张丰红制作
14
(2)炉喉直径及高度
采用钟式布料设备的高炉,如果每批料的矿石量不 变,随炉喉直径增大,到达炉中心的矿石量相应减少, 中心通过的煤气量增多。
冶金工程系
张丰红制作
15
(3)大钟和炉喉间隙
大钟和炉喉间隙过大那么堆尖远离炉墙,大块料大量 滚向边缘,会造成边缘气流过分开展;假设间隙太小,那 么堆尖紧靠炉墙,使边缘负荷加重,中心过分开展。一般 大中型高炉此间隙在900~1000毫米。
[学习任务]
• 1.炉料的物理性质、装料制度、送风制度等对炉料分布 和煤气流分布的影响。
• 2.炉料在炉候径向分布的影响因素、自然堆角、实际堆 角的概念;
• 3.装料制度、送风制度的概念和内容,调节方法; • 4.上部调节、下部调剂的概念和上、下部调剂在实际生
产中的应用。
冶金工程系
张丰红制作
1
在高炉内的实际测定发现,各种物料在炉内的实际堆角为炉料下 落高度,炉喉大小及其自身物理性质所决定,并符合如下关系:
冶金工程系
张丰红制作
13
3.炉型及其他因素
(1)炉型 炉身角小,炉腹角大和高径比(H/D)小的所谓“矮胖
高炉〞上,边缘气流比较开展,容易提高冶炼强度。但如 果炉身角过小,边缘气流过于开展,对煤气能量利用和炉 身砖衬保护不利;如果炉腹角过大,风口前高温火焰容易 将炉腹砖衬烧坏:如高径比太小,因炉身太矮影响了炉料 的预热复原,使焦比升高。
由图10—4看出,缩小批重(如B),那么矿 石(堆角大)靠近边缘,加重了边缘;扩大批重那 么中心矿石分布增多,开展边缘。
冶金工程系
张丰红制作
12
因此,要加重边缘,可缩小批重;要抑制中 心,开展边缘,可加大料批(如A)。在一定的冶 炼条件下,有一个适宜矿石批重;原料较好的高 炉,可维持较重的批重。一般条件下,矿石批重 可控制在炉喉料面厚为半米左右为适宜。
高炉炉料落点的确定

堆密度(2 k / 3 , 55 m )则计算结果分别为 188 g . m, 1 181 . m。通过比较看出, 1 不考虑颗粒受曳力作用所 计算的布料半径存在很大偏差 , 而如果在计算曳力 则结果也相差很大, 且这些偏 d , =一F s v v/ t d p () 时选择密度值不正确, 1 初速及煤气流速等参数的影响 y dyd=一F v v/t p () 差受颗粒下落距离、 2 很大; 因而, 在计算料流轨迹时应正确选择颗粒的表 dx F ( ) p g l z+( p gp () v d= D /t v一v : - ) 3 观密度。如密度选择正确 , 计算曳力时是以分速度 F =1 AR 8 e } 的平方 求 颗 粒所 受 的 曳力 分 量 , 计算 结 果 为 则 洲2 2 4 R d} 一 v 18 1 可见偏差也相当大, . m, 3 且此公式与曳力的定 拌 义有误。从结果看出, 此计算值比理想状态要远, 而 式中 一F V D x s 方向单位质量的曳力, /g N k; 实际比理想的布料半径要近。所以, 计算料流轨迹 一F v 方向单位质量的曳力, /g p , , y N k; 时正确考虑曳力影响是相 当重要的。
D 忍
F (: v) D 一 z V — z 方向单位质量的曳力, /g N k; 9 阻力系数, 一- 对于不规则颗粒 } =f ( e0}( 为颗粒的形状因子) R ,)} '0 ; v, ,二 sv v一一颗粒在 x y z y , , 方向上的分速度,
- 1、下载文档前请自行甄别文档内容的完整性,平台不提供额外的编辑、内容补充、找答案等附加服务。
- 2、"仅部分预览"的文档,不可在线预览部分如存在完整性等问题,可反馈申请退款(可完整预览的文档不适用该条件!)。
- 3、如文档侵犯您的权益,请联系客服反馈,我们会尽快为您处理(人工客服工作时间:9:00-18:30)。
对炉料的阻力 ; ②颗粒阻力系数取球形颗粒在流体 的系数大小, 这比实际复杂体误差较大; ③密度选择 不当, 对于材料 的密度一般分为 : 密度 ( 绝对密实状 态)表观密度( 、 考虑颗粒 自身孔隙率) 和堆密度( 考 虑炉料料层的空隙度) 三者依次减小, , 在研究颗粒 下落中应选用表观密度, 而不是在布料 中通常所说 的料层堆积密度; ④在计算曳力分量时, 认为与其对 应的速度分量的平方成正比( ; v )这不符合矢 F =C 2 , 量的平行四边形法则, 也与曳力的定义不符。曳力 的大小与煤气相对颗粒的流速平方成正 比, 由于总 曳力与总相对速度存在二次方 的关 系 , 因而不能简 单地通过速度分量求分曳力。 本文通过对空区下落时颗粒 的受力分析 , 计算
已知焦炭颗粒粒径范围[为 00 ^01 m, C 6 . -. 烧 1 2 0 从上式可见, 决定曳力的主要因素是 F 值, p 结矿为 005 . m, 团矿为 005 8 D F . - 00 球 0 0 5 . 一00 0 . 1 =0 为不考虑曳力的理想状态。如炉料颗粒在运动 m, 相应颗粒的布料半径见图 2 。在 3 种炉料平均布 中R 保持不变, F 为常数, 。 则 o 而初速度分别为 v , 料半径分别为 188 182 184 } o . , 1 , 2 m。可见 , 1 . . 在煤 v , ,v , , } 对式()()() 0 O 1,2,3积分可求得 v, z而 气流速为零时, } v, v, y 焦炭的平均落点比烧结矿要远, 且二
2 X ah a n d eGru C L dX ah a 50 , bi C i ) . n u I a Sel p t , un u 0 10 Hee, n u r n t o o o 7 ha
A s atR d l r ui o bre idtr i d te io o prc l d g i cag g l t - bt c, i d tb t n udn e m n b h psi f tl a i d r g ri i ba fr r a a i i o f s s e e y o t n a ie n u n h n n s u n
度要小 , 比堆积密度要大得多。 而
2 计算与分析
以焦炭颗粒为例比较计算 : ①正确考虑曳力作 用; ②不考虑曳力作用 ; ③选用炉料堆密度 ; 曳力 ④ 公式使用不当等情况的布料半径。从图 1 可见 , 如 不考虑煤气曳力作用 , 计算 布料半径为 1 86 . mo 2
1 模型
本模型研究了炉料颗粒在空区中的运动状况。
sae I pbse ppr, r a sm pol s h ng cn te g c o gs cos g i- hp. ulhd e te r o e b m sc a; l t g da f e a, oi te n i a s h e e r e u s e e i h r o f h n h m r poe dni ad n ie vn y da fr fr u , te e ne w e cl li ad cc i rpr sy ui r l at te g c om l s h d f ec bten c ao n pate e t n s g e l h r o e a o i r r f e a u t n r i s l g. tippr te i gai , yny gs g c ae s ee. ad i , m te ai l a e I hs e, ga rv y boac ad da fr r cni r I dio te hm ta r n a h r n t u n a r o e o d d n t n h a c m dl ee pd te vmet etr o a t li f e e o p t . cri t cag g i oe idvl e ad m e n t j oy prc n zn icm ue A od g hri rd s o n h o r c a f a ie r o s e d c n o n a -
堆密度(2 k / 3 , 55 m )则计算结果分别为 188 g . m, 1 181 . m。通过比较看出, 1 不考虑颗粒受曳力作用所 计算的布料半径存在很大偏差 , 而如果在计算曳力 则结果也相差很大, 且这些偏 d , =一F s v v/ t d p () 时选择密度值不正确, 1 初速及煤气流速等参数的影响 y dyd=一F v v/t p () 差受颗粒下落距离、 2 很大; 因而, 在计算料流轨迹时应正确选择颗粒的表 dx F ( ) p g l z+( p gp () v d= D /t v一v : - ) 3 观密度。如密度选择正确 , 计算曳力时是以分速度 F =1 AR 8 e } 的平方 求 颗 粒所 受 的 曳力 分 量 , 计算 结 果 为 则 洲2 2 4 R d} 一 v 18 1 可见偏差也相当大, . m, 3 且此公式与曳力的定 拌 义有误。从结果看出, 此计算值比理想状态要远, 而 式中 一F V D x s 方向单位质量的曳力, /g N k; 实际比理想的布料半径要近。所以, 计算料流轨迹 一F v 方向单位质量的曳力, /g p , , y N k; 时正确考虑曳力影响是相 当重要的。
UO i i' X- n b Z n, C N S usn, WE Z ii g G HU igt l Qn-a i HE G -e` h I -a 2 hjn
(. i ri o Si c ad cnl y i g Bi g 08 ,h a 1 U v s y c ne T ho g B j ,ei 1 03C i ; n e t f e n e o ei n j 0 n n
第 1 卷第 9 6 期
20 06年 9 月
中 国冶金 C ia tl ry hn Me l g au
Vo. , . l1 No 9 6
Sp 2 0 e . 0 6
高炉炉料落点的确定
朱清天’ 程树森‘ 魏 志江“ 郭喜斌“ , , ,
(. 1北京科技大学冶金与生态工程学院, 北京 108 ; 003 2宣化钢铁集团有限责任公司第二炼铁厂, . 河北 宣化 050) 710
作者简介: 朱清天(91) 男, 18-, 硕士生;
Em i b ekl ao. . - a : ry ll u @yhocm c; o n
修订日期:06 52 20- -4 0
万方数据ห้องสมุดไป่ตู้
第 9期
朱清天等 : 高炉炉料落点的确定
了实际煤气流下炉料的料流轨迹, 为准确预测炉内 料面形状 以及径 向矿焦 比分布奠定 了基础 , 而为 从 实现合理煤气分布提供 了可能。
摘 要: 在实际装料时, 不同密度、 粒径及形状系数的颗粒在料面上的落点也各不相同。目前, 文献在计算料流轨
迹时存在忽略煤气曳力、 密度选择不当或曳力公式使用有误等问题 , 与实际计算常有很大偏差。为此, 针对 目前
料流轨迹计算存在的问题, 准确考虑了颗粒在空区下落中所受重力、 浮力及煤气曳力的作用, 建立数学模型计算 炉料颗粒在空区下落的运动轨迹。通过对不同炉料在其粒径范围内的布料半径变化及煤气对其曳力大小的讨
da f c iipr n w e cm un te dn j t y ah v g ot abre d tbtn r o e m ot t n pt g bre t e o f ci i te i l dn r uo. g s a h o r i h u r cr o a r e n h p m u ii i s K y rsb s frae ca i ; g c; dn j tr; d g i e w d: t nc; r n da fr b re t e oy l i p n o l u a hgg r oe u r c a a n ot n
论, 正确考虑料流轨迹计算时煤气曳力的影响, 为准确实现合理布料奠定基础。 关键词 : 高炉; 装料; 曳力 ; 料流轨迹 ; 落点 中图分类号: F 4 T5 文献标识码 : A 文章编号:0695 (060-040 10-3620)902-3
E tbi m n o L n ig it B re i Bls Fu n c s lh et adn P n o udn n a t r a e a s f o f
炉料颗粒以一定初速度 v , v , s v , 进人空区, o x y o o 在空
中受 自身重力和煤气的曳力、 浮力作用下作抛物运 动。曳力大小随颗粒与煤气相对速率 的变化而变 化, 方向与相对速度相反。在直角坐标系下( ( z轴竖 直向下)则各方向的加速度可表示为: ,
计算考虑曳力时, 分别选用表观密度(9 k/ 3与 90 m ) g
nc. pate te dn pit o prc s e t sme cue te df rn dni , e d ae I rci , l i ons at l a n te n c h a g n f ie r o h a b as o hi ieet s y s a e f r f e t i n z
高炉装料制度对煤气流的分布起着决定性的作 用。在装料过程中, 除炉料本身性质外, 对煤气分布 影响最大的操作是炉料的径向分布, 即炉料堆尖所 在位置 , 它直接决定了料面的形状变化。高炉料流 落点实测表明, 焦炭与矿石的落点存在很大差异, 即 使是相同的炉料颗粒, 因其粒径不 同则料流宽度也 有相当大的区别[ 颗粒在理想状态中下落的落点 C i 7 基本相同。在实际装料 中, 颗粒在空区下降时除受 自身重力作用外, 还承受煤气曳力和浮力的作用。 这些阻力随颗粒的密度、 粒径和形状等的不 同而变 化, 其落点也将发生很大偏差。 目前 , 许多文献计算的高炉料流轨迹大都与实 际有很大偏差。存在的问题主要有[ 1①忽略煤气 [ 2 . 3