Header for SPIE use Advanced Lifting-Based Motion-Threading (MTh) Technique for the 3D Wave
GigaSPEED XL 3071E-B ETL Verified Category 6 U UTP
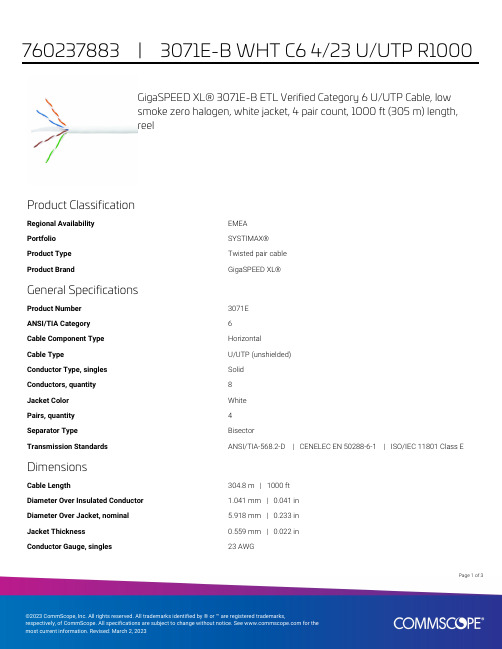
GigaSPEED XL® 3071E-B ETL Verified Category 6 U/UTP Cable, lowsmoke zero halogen, white jacket, 4 pair count, 1000 ft (305 m) length,reelProduct ClassificationRegional Availability EMEAPortfolio SYSTIMAX®Product Type Twisted pair cableProduct Brand GigaSPEED XL®General SpecificationsProduct Number3071EANSI/TIA Category6Cable Component Type HorizontalCable Type U/UTP (unshielded)Conductor Type, singles SolidConductors, quantity8Jacket Color WhitePairs, quantity4Separator Type BisectorTransmission Standards ANSI/TIA-568.2-D | CENELEC EN 50288-6-1 | ISO/IEC 11801 Class E DimensionsCable Length304.8 m | 1000 ftDiameter Over Insulated Conductor 1.041 mm | 0.041 inDiameter Over Jacket, nominal 5.918 mm | 0.233 inJacket Thickness0.559 mm | 0.022 inConductor Gauge, singles23 AWG13Page ofCross Section DrawingElectrical Specificationsdc Resistance Unbalance, maximum 5 %dc Resistance, maximum7.61 ohms/100 m | 2.32 ohms/100 ftDielectric Strength, minimum2500 VdcMutual Capacitance at Frequency 5.6 nF/100 m @ 1 kHzNominal Velocity of Propagation (NVP)70 %Operating Frequency, maximum300 MHzOperating Voltage, maximum80 VRemote Powering Fully complies with the recommendations set forth by IEEE 802.3bt (Type4) for the safe delivery of power over LAN cable when installed accordingto ISO/IEC 14763-2, CENELEC EN 50174-1, CENELEC EN 50174-2 or TIATSB-184-ASegregation Class cMaterial SpecificationsConductor Material Bare copperInsulation Material PolyolefinJacket Material Low Smoke Zero Halogen (LSZH)Separator Material PolyolefinPage of23Mechanical SpecificationsPulling Tension, maximum11.34 kg | 25 lbEnvironmental SpecificationsInstallation temperature0 °C to +60 °C (+32 °F to +140 °F)Operating Temperature-20 °C to +60 °C (-4 °F to +140 °F)Acid Gas Test Method EN 50267-2-3EN50575 CPR Cable EuroClass Fire Performance B2caEN50575 CPR Cable EuroClass Smoke Rating s1aEN50575 CPR Cable EuroClass Droplets Rating d0EN50575 CPR Cable EuroClass Acidity Rating a1Environmental Space Low Smoke Zero Halogen (LSZH)Smoke Test Method IEC 61034-2Packaging and WeightsCable weight38.097 kg/km | 25.6 lb/kftPackaging Type ReelRegulatory Compliance/CertificationsAgency ClassificationCENELEC EN 50575 compliant, Declaration of Performance (DoP) availableCHINA-ROHS Below maximum concentration valueISO 9001:2015Designed, manufactured and/or distributed under this quality management system REACH-SVHC Compliant as per SVHC revision on /ProductCompliance ROHSCompliantPage of33。
BD FACSAria Quick Guide

BD FACSAria Quick GuideBefore Turning On The Instrument1.Open the sheath tank and check the Sheath level, fill the tank with 1X Sheath Fluidusing the Leinco 10X Preservative Free Clear Sort Sheath Fluid, DO NOT USE THE LEINCO 10X CLEAR FLOW SHEATH FLUID.2.Disconnect the pressure line from the ethanol tank and connect it to the top of thesheath tank. Disconnect the sheath line from the short yellow line with in-line filter on the ethanol tank. Connect the sheath line to the short blue line with in-line filter on the top of the sheath tank.3.Disconnect the waste tank and empty the tank in the sink. Reconnect the waste lineand waste level probe into the fluidics cart.4.Turn the instrument on by pressing the large green button. Do not turn off/on anyof the laser main button/dials.Starting up1.Open DIVA and log in with your own user name and password. Watch the bottomright of the cytometer window for ‘Instrument connected’ status at the bottom of the Cytometer window. If the computer cannot connect to the cytometer, do a hard reboot of both the instrument and computer making sure that the computer isturned on first. Once the instrument has connected, select ‘Use CS T Settings’ from the CST mismatch window.Note: Selecting ‘Use CST Settings’ will revert pressure value to that of theselected configuration. Go to Cytometer > View Configurations to change.2.Perform the Fluidic Startup under the ‘Cytometer’ menu as prescribed by thesoftware.3.After the Fluidic Startup has been performed make sure to check that the voltage isoff and open the sort chamber and wipe everything (walls, waste trough, charge plates) with kimwipes to decrease chance of arcing errors.4.Put the desired nozzle tip in place. Place the nozzle tip in position with the o-ringfacing up, close the locking lever to hold it in place. Choose the correct configuration in Cytometer>Configurations if necessary. Choose the correct sort setup in FACSDiva software (sort => sort setup => 70/100 micron) according to the selected nozzle tip from the sort menu if not done automatically.5. Turn the stream on by clicking on the stream button (red X) at the top of the Breakoff Window, the stream button should show as a green checkmark once the stream is turned on.6.Make sure stream is straight in the Break Off window. Adjust the position of thewaste stream to the centre of the waste aspirator by rotating the sort block (use hex tool to release the adjustment screw on left and right of the sort chamber). If time allows, wait 30 minutes for the stream to completely stabilize.7.Close sorting chamber door and make sure screw is tight.8. Close the hood and ensure it snaps into place. This will allow the laser interlock todisengage and allow laser light to pass through the flow cell.Setting up the break off point1. . Make sure that the stream appears in the Break off Window.a. No stream, dripping or spraying: remove nozzle tip. Sonicate the nozzle,wipe out the flow cell and sort chamber.b. Unsteady stream: shut off the stream, turn it on again. If problem persist, remove the nozzle tip, sonicate, and put it back on again.c. Stream obscured by grey area: sheath fluid in front of droplet camera. Turn off the stream, remove the nozzle tip and the key, dry everything out, andclean the chamber with kimwipe.12. Monitor the droplet formation3. The leftmost figure above shows fast converging droplets wherein the satellitesattach to the top of their droplet. Fast converging droplets are required to use the 70um tip and are preferred for the 100um tip. Slow converging droplets, shown in the rightmost figure, are never preferred but can be used for the 100um tip. If you observe slow converging droplets while using the 70um, remove and sonicate the tipas slow converging droplets can never be used with the 70um tip.Drop 1Gap Satellite droplets70um tip85/100/135um tip Gap (wide band): distance between theunbroken stream and the first unattacheddropletDrop1 (thin band): position of the firstunattached droplet70/85um tip: satellites attach to the dropleton top, the gap is located at between theabove satellite droplet and the followingdroplet.85/100/130um tip: Satellites attach thedroplet below, gap is located just on top of thelast attach droplet and its following satellitedroplet4.If possible, the prearranged DIVA settings for Amplitude, Frequency, Drop 1 and Gapshould be used with Sweet Spot Monitoring to guarantee a stable stream.5.An ideal stream will:a.Be vertical and symmetrical with no slant or severe skew on droplets.b.Have fewer than 6 satellite droplets.c.Display fast-converging droplets on the 70um or 100um tip.d.Stabilize with Sweet Spot on. Note that Amplitude and Frequency are lockedwhen Sweet Spot is on.6.If the prearranged settings do not yield an ideal stream, begin with adjustingFrequency. Frequency should be ~85-96kHz for the 70um and ~35-48kHz for the 100um. Use the highest value in that range that yields good droplet formation with a low Amplitude value.7.Adjust Amplitude (usually between 10-50) so there are at least 1-2 drops above andbelow the break off point. Sweet Spot Monitoring tends to increase amplitude over time, so starting with a lower value is best.8.Set the gap target which yields the most distinct and cleanest side streams. Typically,this is set to ~6. You can test different gap settings by adjusting amplitude.9.Set the Drop 1 target based on the actual value displayed to the right. This serves asa target for the Sweet Spot Monitoring, but also tracks drift over the course of theexperiment. If Drop 1 drifts +/- 10 from the original value, redo drop delay.10.Activate Sweet Spot Monitoring. This will track drift in the Gap and Drop 1measurements and automatically adjust Amplitude to compensate and return the stream to your target values. It will also pause sorting if there is significant deviation from the target Gap and Drop 1 until it is able to return the stream to normal. This will not pause acquisition, so it’s best to stop acquisition manually in the event of major stream instability.Optimizing the sort stream1.Get the brightest/sharpest image of the waste and side streams by adjusting thesilver screw next to the sorting chamber.2.In a test sort, set the two inner side streams a deflection of ~40 and the outerstreams to ~70. Then select the 2nd drop value in the stream window. Adjust 2nd drop so there is the least amount of fanning and the streams are distinct and clean.3.Bring all side streams except the inner left back to zero, as you will need this fordrop delay.Drop Delay1.Open the Drop Delay experiment.2.Retrieve the DDCP-70-2 beads and mix well. Dilute 1 drop in about 1mL of DIH2O. To run Auto Delay the beads must acquire at 1,000-3,000 events/sec forthe 70um and 600-1,500 events/sec for the 100um so further dilution may beneeded.3.In the browser window, open the Sort Layout (should sort ‘Not P1’ to the innerleft). Load and acquire the DDCP beads.4.Turn on the Plate Voltage, Test Sort and the Optical Filter icon (which allows youto look at the beads in the waste and side stream).5.At this time, a tight and bright spot should be in the right square (0%/100%).6.Change the inner left deflection value so that the Test Sort side stream is centredin the left window of the Optical Filter. You will have to turn the Optical FilterOn/Off to adjust the position, as they aren’t be ads in the side stream during Test Sort.7.Click on Sort (cancel the opening of the drawer) and select the Sort Precision:Initial. You should now see beads in the left Optical Filter window.8.Click Auto Delay: This process uses an algorithm to determine the best DropDelay setting. It may take a few minutes as the software must run through arange of possible values. Once completed it will display a histogram of thesevalues and automatically select the Drop Delay setting best suited for yourstream.9.Turn off the Optical Filter, the Plate Voltage, and unload the DDCP beads.Sort1.To set deflection values for the side streams, turn on Plate Voltage and Test Sort.ing either the built-in software (Aria Fusion) or the paper guide (AriaII andAriaIIIu), set the side stream deflections according to your collection vessels.3.Alternatively, you can load empty collection tubes and open the Waste Drawer.Then adjust deflection until the side streams are going into the collection tubes. During Sorting1.During a sort:a.In the sort window, Precision should be set to Ultimate.b.Maximum threshold rate is 20,000 evt/s for the 70um and 15,000 evt/sfor the 100um. Higher threshold rates will cause lower efficiency(efficiency = [sorted events]/[aborted events + sorted events]) and viceversa.2.In 3-way or 4-way sorts, separate the most common and rarest populations byplacing rare populations on the periphery and common population in the center.This will prevent cross contamination.3.Clogs: During a full clog, the stream will become so unstable Sweet Spot turnsoff, the Waste Drawer will close over the collection tubes, and the stream itselfwill turn off. Partial clogs might not trigger a stop and could lead to the wastestream flowing into a collection tube. In this event hit the Emergency Stop (bigred button) to stop the stream. After a clog you will have to clean the sortchamber, remove the nozzle, and sonicate it.4.If the software freezes, first minimize and maximize the DIVA software window,if this doesn’t work push the Emergency Stop button.Sort in plates1.Place the ACDU adapter under the sort chamber.2.Select a custom device with the correct number of wells from the bottom of theDevice dropdown menu in the upper left corner of the Sort Layout.3.Align the far-left stream so it will fall vertically as much as possible. (Usually ~18)4.Calibrate>Custom Device. This will default to the custom device selected in theSort Layout.5.Go to Home. Align stream so it falls in the middle of A1 using the arrows andsquirt button in the middle of the Home device screen. Set Home.6.Go to Farthest. Align stream so it falls in the middle of H12 using the arrows andsquirt button in the middle of the Home device screen. Set Farthest.7.Apply>Close8.It is usually useful to do a test sort to make sure the sort arm is well calibrated:sort 100 beads or unstained cells in each corner of the plate or randomly assignwells to be sorted all over the plate to test accuracy.Cleaning and Shut Down (NEVER USE CONTRAD)1.After the experiment, run bleach 10% for 5 minutes at flow rate of 11.2.If you are the last user of the day, you must shutdown the instrument.3.Select Fluidics Shutdown in the Instrument menu: as indicated, take out thenozzle tip (there are no closed loop flow nozzles, ignore this step). Disconnectthe tubes from the Sheath tank and plug them on the EtOH tank and put a tubeof 1.5% Citronox in the sample loader. Follow the software instructions.4.After the shutdown is complete, turn off the software and turn off theinstrument.。
Manual Addendum for VMX-B Configured Soft Start Pa

Manual Addendum for VMX-B Configured Soft Start PackagesFor use with wiring diagram # 93-3880 Rev B (CB/FS), or 93-3881 Rev B (MLO), and VMX2 user manual. Introduction: The VMX-B is a configured enclosed soft start, available as a Combination (with C/B or Fused disconnect) package, or as an MLO (Main Lug Only) package, intended for use in Industrial, Commercial, Agricultural, or Infrastructure applications.Line Voltage:By default units are set-up for 460VAC line power, but can be adjusted to operate on 230VAC or208VAC at the reduced HP rating. To adjust the operating voltage simply move wire #1L2B from the 480V (H4) terminal to the 230V (H3) or 208V (H2) terminal.Power Connections:Line Power input is connected directly to the bottom terminals of the Circuit Breaker, or line terminals on MLO (Main Lug Only) units, and the motor is connected to the lugs at the bottom of the VMX2 soft start.Remote Start / Stop Control connections:The VMX-B is set up for 2 or 3 wire remote control using dry contacts rated at 120VAC (0.1Amp).Remote Two Wire Control:Connect a dry (voltage free) maintained contact closure between terminals 1 and 3 of the customerterminal strip as shown here.123456789RUNCustomer Terminals TBC on TCB3000 PCBRemote Three Wire Control:For standard 3-wire control, connect dry (voltage free) contacts for the Stop / Start buttons as shown below of the customer terminal strip. Connect the normally closed “STOP” pushbutton across terminals 1 & 2, and the normally open “START” pushbutton across terminal s 2 & 3 of the customer terminal strip. Note: the unit can be operated in the “Local” position without any external control.123456789STOPCustomer Terminals TBC on TCB3000 PCBSee page 3.TCB3000 Terminal Control BoardSee page 3.TCB3000 Terminal Control BoardRun Status Output ContactsThe VMX-B unit offers 2 Form-C (N.O and N.C.) “RUN” contacts located on the custom er terminal strip, terminals 4 (NC), 5 (NO), 6 (Common), and terminals 7 (NC), 8 (NO) 9 (Common). These contacts reflect a successful RUN command in “SOFT” or “X -LINE” mode, and should be used for any required “Run / Running” status outputs.VMX2 Auxiliary Contacts(TB2 of Soft Starter)NOTE: YELLOWOVERLOAD DIAL MUST BE SET IN ACCORDANCE WITH THE MOTOR “FULL LOAD AMPS” PER MOTOR NAME PLATE DATAThere are 3 programmable Aux contacts available on TB2 of the VMX2 soft start (2 form-C and 1 form-A). The function of these contacts are labeled on the wiring diagrams, but can be changed in the VMX2 programming. Note however, that the contacts may not function properly when operating in the X-LINE mode. (see description below).X-LINE Operation:VMX-B packages are supplied with a SOFT/X-LINE selector switch, located on the TCB3000 PCB that allows the operator to select Full Voltage operation of the motor via the bypass contactor for emergency operation when the soft start may be inoperable.When operated in the X-LINE mode fullstart/stop control is maintained, and the “Run Status Output Contacts” will func tion correctly.During X-LINE operation, the motor will be protected by the external Bi-Metal overload relay which must be set according to the motor FLA and the Current transformer ratio of the unit.Important:Motor FLA and Service Factor must be entered prior to a start attempt see next section on how to set Motor FLA and Service Factor parameters.123456789Customer Terminals TBC on TCB3000 PCB Run StatusOutput ContactsSee page 3. TCB3000 Terminal Control BoardTCB3000 Terminal BoardGreen LED-Control Power ON-E-Stop Not Active-Fuse OKGreen LEDMotor RunningYellow LEDX-Line Mode Enabled(D.O.L. Start)Red LEDFault(Unit Tripped requiresReset Command)Red LEDExternal O/L Tripped(Reset O/L Manuallyby pressing greenbutton on overloadrelay).Programming InstructionsThis document is intended for use with Models: VMX-B Soft Start PackagesMotor FLA and Service Factor must be entered prior to start attemptFor complete parameter list see pages 6-7 of this documentFnRead0000F0010009 000000090179End F001Default Display Function #1Set value of ones digit (flashing) Cursor Position Shift Use up arrow to scroll to F002 and repeat process ReadEntering Motor FLA & SFOperation and TroubleshootingKeypad Operation Display Mode (Default)Fault Mode*NOTES:“PLd” can be caused by a Grounded delta power system. If one input leg me asures ZERO volts to ground, reduce the setting of F051 to “0054” for operation on a “Grounded Delta”.“SS d ” can be caused by operating without a motor connected, ensure the motor is firmly connected.“LcA, Lcc, or Lcd ” indicates that the Surge absorber is damaged; see NOTE 1 on wiring diagram.VMX-B Door Mounted OperatorsIlluminated E-Stop Pushbutton:∙Removes control power from all circuits and VMX2 soft start.∙Push to activate, twist and pull to release.∙Button Lights when E-stop is pressed.Start/Stop Pushbutton and Run Light Assembly:∙Provides Start/Stop control in "Local" mode.∙Provides "Motor Running" indication in all operating modes.Local/Off/Remote Selector:∙Local" selects door mounted Start/Stop control.∙Remote" selects Start/Stop control from customer supplied signals at terminals 1-3 on TBC.∙Off' Turns motor off.Power ON Light:∙Indicates presence of 120VAC control power, derived from main (L1 & L2) line voltages.Fault Light/Reset Pushbutton:∙When lit, indicates that the unit has tripped, and requires "Reset".∙In "Soft" (normal) mode, the "trip" will be displayed on the VMX2 keypad (inside), and will reset upon activation of the reset pushbutton.∙In "X-Iine" mode, the light indicates that the X-line overload inside the panel is tripped, and must be reset manually by pressing the (green) reset key on the overload itself. Then the unit can be reset, using the pushbutton on the door.Note: If the green reset key on the X-line overload is turned to the "A" (auto) position, the O/L relay will reset itself after the required cooldown, after that the unit can be reset by pushing the reset pushbutton without opening the enclosure door.Wiring Diagram # 93-398011REV-02 100418Wiring Diagram # 93-3981。
BVF kobe 使用说明书

user manualNecessary tools Scope of delivery1.0 HUN-ENG (23.11.2021.)OverviewAssembly2. FOR YOUR SAFETY 2.1 Intended useThe device is intended exclusively for non-commercial operation as a heating device for smallrooms. This product is not intended for commercial use. Generally acknowledged accident preven-tion regulations and enclosed safety instructions must be observed. Only perform work described in these instructions for use. Any other use is improper. The manufacturer will not assume respon-sibility for damage resulting from such use.2.2 General safety instructions• To operate this device safely, the user must have read and understood these instructions for use before using the device for the first time.• Observe all safety instructions! Failure to do so may cause harm to you and others.• Retain all instructions for use, and safety instructions for future reference.• If you sell or pass the device on, you must also hand over these operating instructions.• The device must only be used when it functions properly. If the product or part of the product is defective, it must be taken out of operation and disposed of correctly.• Never use the device in a room where there is a danger of explosion or in the vicinity of flam -mable liquids or gases.• Always ensure that a device which has been switched off cannot be restarted unintentionally.• Do not use devices with an on/off switch that does not function correctly.• Keep children away from the device! Keep the device out of the way of children and other unauthorised persons.• Do not overload the device. Do not use the device for purposes for which it is not intended.• Exercise caution and only work when in good condition: If you are tired, ill, if you have ingest-ed alcohol, medication or illegal drugs, do not use the device, as you are not in a condition to use it safely.• Ensure that children are not able to play with the device.•Always comply with all applicable domestic and international safety, health, and working regulations.2.2 Electrical safety• The device may only be connected to a socket that is correctly installed and grounded.• The fuse must be a residual current circuitbreaker with a measured residual current of no more than 30 mA.• Make sure that the power supply corresponds with the connection specifications of the device before it is connected.• The tool may only be used within the specified limitations for voltage and power (see type plate).• Do not touch the mains plug with wet hands! Always pull out the mains plug at the plug and not by the cable.• Do not bend, crush, pull or drive over the power cable, protect from sharp edges, oil and heat.• Do not lift the device using the cable or use the cable for purposes other than intended.• Check the plug and cable before each use.• If the power cable is damaged immediately disconnect the plug. Never use the device if the power cable is damaged.•If the device is not in use make sure the plug is pulled out.1. TECHNICAL DATAType: BVF kobeNumber of heating rods: 16Nominal voltage: ~230V; 50HzNominal output: 500W IP rating: IP24Dimensions: 540 x 43 x 960 mm• Make sure that the device is switched off before plugging in the mains cable.• Make sure that the device is switched off before unplugging it.• Disconnect the power supply before transporting the device.•If the power connection cable of this device is damaged, it must be replaced by the manufac-turer or the manufacturer’s customer service department or a similarly qualified person in order to prevent risks.2.3 Device-specific safety instructions• To operate this product safely, the user must have read and understood these instructions for use before using the product for the first time.• Always keep the operating instructions within reach.• If you sell or pass on the device, you must also pass on these operating instructions.• When working on walls, ceiling or floors, pay attention to any installed cables as well as gas and water lines.• The surroundings must be free of highly-flammable or explosive materials.• The device may not be operated outdoors.• The device may never be operated without supervision.• Never subject the device to water or other liquids.• The product heats up during operation. Risk of injury!• The device may not be covered. There is danger of fire.• Do not use the heater in conjunction with a timer or any other switch capable of automatic activation, as this creates a fire hazard.• The heater must not be positioned beneath a wall socket.• Do not use adapters or extension cords.•This appliance can be used by children aged from 8 years and above and by persons with reduced physical, sensory or mental capabilities or lack of experience and knowledge if they have been given supervision or instruction concerning use of the appliance in a safe way and if they understand the hazards involved. Children shall not play with the appliance. Cleaning and user maintenance shall not be made by children without supervision.• Children of less than 3 years should be kept away unless continuously supervised.•Children aged from 3 years and less than 8 years shall only switch on/off the appliance pro -vided that it has been placed or installed in its intended normal operating position and they have been given supervision or instruction concerning use of the appliance in a safe way and understand the hazards involved. Children aged from 3 years and less than 8 years shall not plug in, regulate and clean the appliance or perform user maintenance.• CAUTION! Some parts of this product can become very hot and cause burns. Particular atten-tion has to be given where children and vulnerable people are present.•Symbols appearing on your device may not be removed or covered. Signs on the device that are no longer legible must be replaced immediately.3. ASSEMBLYSee from page 4.3.1 Safety distancesDANGER OF ELECTRIC SHOCK!The product is suitable for operation in Zone 3. (P. 4 item 1.)DANGER OF ELECTRIC SHOCK!Before drilling the holds, make sure that there are no electrical or other lines in the wall.DANGER! RISK OF INJURY!The device may not be mounted directly below a wall outlet. Danger of cable fires!ENG•WARNING:•shower.••3.2 Wall mountingDANGER! RISK TO LIFE!When drilling, ensure that sufficient space is left between the hole and the power lines located in the vicinity. There is a high risk of fire or a life-threatening electrical shock.NOTICE! Property damage When drilling, ensure that sufficient space is left between the hole and the water lines located in the vicinity. There is a risk of water damage.• Before installing the heater, mark the positions you wish to use for the wall brackets on the wall.•Using a suitable drill, drill the holes in the wall.3.3 Optimum position of the bracket•Affix the wall brackets and the heater in accordance with the following diagram.4. OPERATIONCheck the safe condition of the device!DANGER! Risk of injury!The device must only be put into operation if no faultsare found during the check-up. If any part ofthe device is defective, it must be replaced before the next use.• Check whether there are any visible defects.•Check whether the switch is on 0 before you insert the plug into the outlet.4.1 Electrical connection•Connect mains cable to outlet.DANGER! Risk of injury!The device may not be mounted directly below a wall outlet. Danger of cable fires!5.2 Mode selectTurn on the device with the button.Press button to select the modes in this sequence:Comfort mode - Setting the temperature in the daytime,available temperature range 7°C - 30°C. Default temperature is 19°C.Economy mode - Setting the temperature in the night, available temperature range 7° - 30°C. The Max temperature shall not exceed the comfortable temperature. Default temperature is 15°C.Press or to set the temperature, press to increase the temperature.Defrost mode - Setting the temperature at 7°C, the unit will turn on at below 7°C and it will turn off at above 7°C.Program mode - For energy saving and convenience, this mode allows the heater to be operated automatically according to a heating program consisting of a time-programmed change of comfort and economy periods. Inactive function - Don’t use.Temperature decrease buttonTemperature increase buttonClock DayHeating onOpen window detection Heating scheduleChild lock on Anti-scald onComfort mode Economy mode5.3 Set time, date and schedule5.3.1 Set time and dateTo enter program mode, press mode button until hour set 00 flashes.Press and to set hour. If no operation for 30s, it will jump to minute setting.Short press mode button until minute 00 flashes, then press and to adjust. If no operation for 30s, it will jump to week setting.Short press mode button untill week 1 flashes, then press and to choose weekday. 1 = Mon, 2 = Tue, 3 = Wed, 4 = Thu, 5 = Fri, 6=Sat, 7 = Sun.After setting, short press mode button and jump to P mode. If no operation for 30s, it will jump to P mode setting. (See section 5.3.2 for details.)5.3.2 Set program scheduleAfter set time and date (5.3.1) available to assign default program modes to weekday.Short press and to choose mode (P1–P7 see at 5.3.3).Assign P mode for Monday to Sunday (1-7), then press model button returning to Program mode.If you want to edit the default P1-P7 program schedule see the steps at 5.3.4.5.3.3 Default program schedulesThe temperature of the comfort period is the last setting you made earlier in (Comfort) mode, the same is true for the temperature set in (Economy) mode. • P1: Comfort mode 6:00–22:00• P2: Comfort mode 19:00–6:00• P3: Comfort mode 6:00–9:00 | 16:00–22:00• P4: Comfort mode 6:00–9:00 | 12:00–14:00 | 16:00–22:00 • P5: Economy mode 0:00–24:00• P6: Comfort mode 0:00–24:00•P7: Comfort mode 16:00–22:00Between comfort periods the heater operates in economy mode (except for modes P5 and P6).5.5 Internal setting and descriptionPress 5s in power off state, enter into internal setting, then short press to switch mode, press and to set.Temperature compensation setting ( F0 ) – Open window detection ( F1 ) – Anti-scald ( F2 ).0 presents off in power off state.5.5.1 Temperature compensation setting F0Temperature compensation setting when temperature is not correct.Press when in power off state into the temperature compensation setting, the range is from 5 °C to -5 °C, short press to exit current setting.5.5.2 Open window detection F10 means open window detection is off. In heating state, when environment temperature drops 2°C within 5 mins, indicating the window is open, Open window detection is start. The unit stops heating for 65 / 90mins, then enter into previous mode. If environment temperature drops 2°C, within 5 mins again, Open window detection starts again and heating stops for 65 / 90mins again. Run in this cycle.Press to start Open window detection, end user ca re-start heating timing set, choose from 0, 65, 90 mins; after setting, short press to switch to other modes.Press set 0 to stop open window detection.5.5.3 Anti-scald F2Press to rise temperature and press to reduce product temperature, choose from 0, 40, 45, 50, 55, 60 °C; after set, short press to switch to other modes.Press set 0 to stop anti-scald.After set, short press to exit internal setting.5.3.4 Edit default program scheduleTo do this, follow the program mode setting (5.3.2), then press mode button until 1 changes to 00 .Press and to revise P1 mode (Press to run (Comfort) mode and press to run (Economy) mode). The hours of the day and their settings are shown at the bottom of the screen. Current operating position flashes, the Comfort mode is indicated full and the Economy mode is indicated empty.After choosing the mode you need then press model button to exit.Press mode button can revise other modes.5.4 Child lockTo avoid misoperation,end user can set child lock to lock current mode.Press and at same time until Child lock icon lights on, current mode is locked; except end user press on / off button , other operations are invalid.If dismiss child lock, press and at same time until Child lock icon lights off.5.5.4 Power failure memory functionIf into power failure suddenly,the working state is lock at the moment of power failure; when into power on, it automatically restore previous mode, except timing mode need to be reset, other modes saved.5.5.5 Restore factory settingThe system will start to restore the factory setting automatically and enter into the power off states when press the 10s. Then press and the temperature is 19°C in Comfort mode, the temper-ature is 15 °C in the Economy mode. The time Current time Present day is Monday Timing mode. Example 6:00-22:00 Current operating position: flashes Icon Description 16 is [0000], week is [1], [P1–P7] is the default setting, all the timing contents are restored to the factory settings.6. CLEANINGDANGER! RISK OF INJURY!Before all work on the device, always disconnect the mains plug.1. Switch off the device and let it cool off completely.2. Pull out the plug.3. Wipe the device with a slightly damp cloth. Never use detergents or solvents for cleaning.This can cause irreparable damage to the product. The plastic parts can be eaten away by chemicals.7. FAULTS AND REMEDIAL MEASURESDANGER! RISK OF INJURY!Improperly performed repairs can lead to the device not functioning safely. This endan-gers yourself and your environment.Malfunctions are often caused by minor faults. You can easily remedy most of these yourself. Please consult the following table before contacting the vendor. You will save yourself a lot of trouble and possibly money too.If you can’t fix the fault yourself, contact your nearest vendor. Please be aware that any improper repairs will also invalidate the warranty and additional costs may be incurred.Fault/malfunction Cause Remedial measureDevice does not heatIs the device switched off?Switch on the device or set thedesired heat level.Is the temperature regulator settoo low?Set the temperature regulatorhigher.No mains voltage?Check cables, plugs, outlets andfuse.The temperatureindicate ErThe temperature is exceed55 °C Wait for the device to cool.The temperature sensor is in shortcircuit state Contact your product dealer.Batteries and rechargeable batteries, electrical or electronic devices must not be disposed of with household waste. They may contain substances that are harmful to the environment and human health.The packaging consists of cardboard and correspondingly marked plastics that can be recycled.Make these materials available for recycling.。
Molex PicoBlade 微型头部连接器数据手册说明书

New SMT header vacuum caps (7 to 15 circuit) and Gold Plated versions have been added to Molex’s PicoBlade Wire-to-Board Connector, a best seller with two header options, affording superior reliability and durability across a wide variety of applications and industries.FEATURES AND ADVANTAGESPicoBlade Connector SystemCompact and small 1.25mm pitch W-to-W/W-to-B connectors Provides space savingsSMT and through-hole options for right-angle headers Offers design flexibilityOptional vacuumcaps for SMT headers (2 to 15 circuits)Allows high-volume placement using industry-standard pickTwo-point contact design Assures a reliable electrical connection under low- current, low-voltage and high-vibration conditionsGold Plated versionsOffers superiorreliability and durability in harsh environmental conditionsW-to-B and W-to-W solutionswith through-hole and SMT headers in straight and right-angle orientations Offers design flexibilityFriction lockProvides secure mating retention PicoBlade Gold Plated Terminal and HeaderPicoBladeMARKETS AND APPLICATIONSAutomotiveIn-vehicle comfort and infotainment Body control modules ShiftersSteering wheelsInstrument clusters Combination switchesConsumer Smart TVs Set top boxes Air conditioners White goodsGaming machines Laser/Inkjet printers Computer screensAutomotiveAir Conditioners Smart TVDronePicoBlade 1.25mmconnectors with Straight andRight-Angle HeadersIndustrial Smart meters Security systems DronesElectric test equipment Data Communications ServersHealthcare Hearing aidsMedical monitorsREFERENCE INFORMATION Packaging: Reel (Terminal)Embossed (SMT Header Assembly)Tray (Through Hole Header Assembly)Bag (Receptacle Housing)Designed In: MillimetersRoHS: YesPHYSICALHousing:Receptacle − PBT (51021)Header − PA66 (53047/53048 /through hole), PA46 (53261/53398 /SMT)Contact: Phosphor, Bronze for crimp terminal, through hole header and SMT header Plating:Contact Area — Gold plated in flash for crimpterminal, through hole header and SMTheaders— Tin plated for crimp terminal, through holeheader and SMT headerUnderplating — Nickel for gold plated crimpterminals, headers and Tin plated53261/53398SMT headersOperating Temperatures:-40 to +105˚C (53398/53261)-40 to +85˚C (53047/53048)MECHANICALCrimp Terminal Insertion Force (max.): 4.9NCrimp Terminal Retention to Housing (min.): 4.9NMating Force(1st): 19.6N (2 Circuit W to B)24.5N (2 Circuit W to W)Unmating Force (1st): 2.8N (2 Circuit)Durability: 30 CyclesELECTRICALVoltage (max.): 125VCurrent (max.): 2.5A at 2 Circuit/26 AWGContact Resistance (max.): 20 MilliohmsDielectric Withstanding Voltage: 250V ACInsulation Resistance (min.): 100 MegaohmsSPECIFICATIONS(1) Values are for REFERENCE ONL Y.(2) Current deratings are based on not exceeding 30°C temperature rise.(3) T emperature Rise is measured in barrel area of crimp terminal.(4) PCB trace design can greatly affect temperature rise results.(5) Data is for all circuits powered.ORDERING INFORMATION*Please contact Molex for available color in circuit size/product/picoblade.htmlMolex is a registered trademark of Molex, LLC in the United States of America and may be registered in other countries; all other trademarks listed herein belong to their respective owners. Order No. 987651-3691 Rev. 6 APN/0k/GF/2022.10 ©2022 Molex。
卡林技术公司产品说明书

UL Recognized UL Standard 1077Component Recognition Program as Protectors,Supplementary (Guide QVNU2,File E75596)UL Standard 508Switches,Industrial Control (Guide NRNT2,File E148683)CSA CertifiedComponent Supplementary Protector under Class 3215 30,FIle 047848 0 000CSA Standard C22.2 No. 235VDE CertifiedEN60934,VDE 0642 under File No.10537Agency CertificationsNotes for T able A:1DC and 1Ø 277 Volt ratings are 1 or 2 poles breaking. 3Ø Ratings are 3 poles breaking.2 Requires branch circuit backup with a UL LISTED Type K5 or RK5 fuse rated 15A minimum and no more than 4 times full load amps not to exceed 150A for 250 Volt rating and 125A for 277and 480 Volt ratings.3 UL Recognition and CSA Certification at 480 Volts refers to 3 and 4 pole versions, used only in a 3Ø wye connected circuit or 2 pole versions connected with 2 poles breaking 1Ø and backedup with series fusing per note 2.Table A:Lists UL Recognized and CSA and VDE Certified configurations and performance capabilities as a Component Supplementary Protector.ElectricalCURRENT RA TINGCIRCUITMAX FULL LOAD WITH WITHOUT (Inc) WITH (Icn) WITHOUTCONFIGURA TIONRA TINGFREQUENCYPHASEAMPSBACKUP FUSEBACKUP FUSEBACKUP FUSEBACKUP FUSE65DC ---0.02 - 50 ---500050001500125/25050/60 1 and 30.02 - 50 ---3000 --- ---25050/60 1 and 30.02 - 505000 ---5000150027750/6010.02 - 505000 --- --- ---480 Y 50/60 1 and 30.02 - 305000---------65DC ---0.02 - 5025050/60 1 and 30.02 - 5027750/6010.02 - 50480 Y50/6030.02 - 30480 Y 50/6010.02 - 30SWITCH ONL Y UL / CSAVDED-SERIES TABLE A: COMPONENT SUPPLEMENTARY PROTECTORVOLT AGEINTERRUPTING CAPACITY (AMPS)SERIESDesigned for snap-on-back panel rail mounting on either a 35mm x 7.5mm, or a 35mm x 15mm Symmetrical Din Rail,allowing rapid and simple mounting and removal of the breaker.It features recessed, wire-ready, touch-proof, shock-resistant ter-minals, suitable for automatic screwdriver assembly, as well as "Dead Front" construction characteristics.Available with a Visi-Rocker two-color actuator, which can be specified to indicate either the ON or the TRIPPED/OFF mode,or solid color rocker or handle type actuators. All actuator types fit in the same industry standard panel cutouts.0.02 - 50 amps, up to 480 VAC or 65 VDC, 1 - 4 poles (Handle),1 - 3 poles (Rocker), with a choice of time delays.Number of PolesRocker Type: 1-3; Handle Type: 1-4 Internal Circuit Config. Switch Only and Series Trip with cur-rent or voltage trip coils.WeighApproximately 128 grams/pole (Approximately 4.57 ounces/pole)Standard Colors Housing - Black; Actuator - See Ordering Scheme.MountingMounts on a standard 35mmSymmetrical DIN Rail (35 x 7.5 or 35x 15mm per DIN EN5002).MechanicalElectricalPhysicalEndurance10,000 ON-OFF operations @ 6 per minute; with rated Current and Voltage.Trip FreeAll D-Series Circuit Breakers will trip on overload,even when actuator is forcibly held in the ON position.Trip IndicationThe operating actuator moves posi-tively to the OFF position when an overload causes the breaker to trip.Designed and tested in accordance with requirements of specifi-cation MIL-PRF-55629 & MIL-STD-202 as follows:Shock Withstands 100 Gs,6ms,sawtoothwhile carrying rated current per Method 213,Test Condition "I".Instantaneous and ultra-short curves tested @ 90% of rated current.Vibration Withstands 0.060" excursion from10-55 Hz,and 10 Gs 55-500 Hz,at rated current per Method 204C,Test Condition A. Instantaneous and ultra-short curves tested at 90% of rated current.Moisture Resistance Method 106D,i.e.,ten 24-hourcycles @ + 25°C to +65°C,80-98%RH.Salt Spray Method 101,Condition A (90-95%RH @ 5% NaCl Solution,96 hrs).Thermal Shock Method 107D,Condition A (Fivecycles @ -55°C to +25°C to +85°C to +25°C).Operating Temperature -40°C to +85°CEnvironmental020 0.0200250.0250300.0300500.050075 0.0750800.0800850.0852100.1002150.1502200.2002250.2502300.3002350.3502400.4002450.450250 0.5002550.5502600.6002650.6502700.7002750.7502800.8002850.850410 1.000512 1.250413 1.300414 1.400415 1.500517 1.750420 2.000522 2.250425 2.500527 2.750430 3.000532 3.250435 3.500436 3.600440 4.000445 4.500547 4.750450 5.000455 5.500460 6.000465 6.5004707.0005727.2504757.5004808.0004858.5004909.0004959.500610 10.00071010.50061111.00071111.50061212.00071212.50061313.00061414.000615 15.00061616.00061717.00061818.00061919.00062020.00062121.00062222.000623 23.00062424.00062525.00062626.00062727.00062828.00062929.00063030.00063232.00063535.00064040.00064545.00065050.000A06 6 DC, 5 DC A1212 DC, 10 DC A1818 DC, 15 DC A2424 DC, 20 DC A3232 DC, 25 DC A4848 DC, 40 DC A6565 DC, 55 DC J06 6 AC, 5 AC J1212 AC, 10 AC J1818 AC, 15 ACJ2424 AC, 20 AC J4848 AC, 40 AC K20120 AC, 65 AC L40240 AC, 130 AC10Agency Approval8Actuator Color8 ACTUATOR COLOR & LEGEND Actuator orVisi-Color Marking: Marking Color: Single Color Visi-Rocker Color:I-O ON-OFF Dual Rocker/Handle (Actuator Black)8White A B 1Black White Black C D 2White n/a Red F G 3White Red Green H J 4White Green Blue K L 5White Blue Y ellow M N 6Black Y ellow Gray P Q 7Black Gray OrangeRS8Black Orange10 AGENCY APPROVAL C UL Recognized & CSA Certified D VDE Certified, UL Recognized & CSA Certified9 MOUNTING/VOLTAGEMOUNTING STYLE VOLTAGE Threaded Insert 16-32 x 0.195 inches< 300C 96-32 X 0.195 inches ≥300 2ISO M3 x 5mm< 300D 9ISO M3 x 5mm ≥3007 TERMINAL1#10 Screw & Pressure Plate for Direct Wire Connection 2#10 Screw without Pressure Plate3 POLES 1One2Two 3Three4Four5 FREQUENCY & DELA Y 03DC 50/60Hz, Switch Only 105DC Instantaneous 11DC Ultra Short 12DC Short 14DC Medium 16DC Long20550/60Hz Instantaneous 2150/60Hz Ultra Short 2250/60Hz Short 2450/60Hz Medium2650/60Hz Long32DC, 50/60Hz Short 34DC, 50/60Hz Medium 36DC, 50/60Hz Long42650/60Hz Short, Hi-Inrush 44650/60Hz Medium, Hi-Inrush 46650/60Hz Long, Hi-Inrush 527DC, Short,Hi-Inrush 547DC,Medium, Hi-Inrush 567DC, Long, Hi-Inrush4 CIRCUITA0 Switch Only (No Coil) 4B0Series Trip (Current)C0Series Trip (Voltage)1 SERIES D6Current Rating4Circuit3Poles2Actuator9Mounting/Voltage7Terminal5Frequency & Delay1SeriesNotes:1 Handle breakers available up to four poles. Rocker breakers available up to three poles.2Actuator Code:A: Multi-pole units factory assembled with common handle tie.B: Handle location as viewed from front of breaker:2 pole - left pole3 pole - center pole4 pole - two handles at center poles3Multipole rocker breakers have one rocker per breaker, as viewed from the front of thepanel. Two pole - left pole. Three pole - center pole 4≤30A, select Current Rating code 630. 31-50A, select Current Rating code 650.5Voltage coil only available with delay codes 10 & 20.6Available to 50A max with circuit code BO only.7Available to 50A (UL/CSA), 30A (VDE) with circuit code BO only.8Color shown is visi and legend with remainder of rocker black.9≥300V: Three pole breaker 3Ø or 2 pole breaker 1Ø, UL/CSA limited to 30 FLA max.10VDE Approval requires Dual (I-O, ON-OFF) or I-O markings6 CURRENT RATING (AMPERES)OR VOLTAGE COIL (VOLTS, MIN. TRIP RATING)5P0LE 3P0LE 2P0LE 1SERIES TRIP (2 TERM'S.)LINELINEROCKER ACTUATOR INDICATE "ON"HANDLE ACTUATORSWITCH ONL Y (2 TERM'S.)#10-32 SCREW AND PRESSURE PLA TE PER TERMINAL"MULTI-POLE IDENTIFICATION SCHEMENotes:1All dimensions are in inches [millimeters].2T olerance ±.015 [.38] unless otherwise specified.3-POLE(DF3) 3-POLE(DC3)REMOVALASSEMBL YNotes:1All dimensions are in inches [millimeters].2T olerance ±.015 [.38] unless otherwise specified.3Dimensions apply to all variations shown. Notice that circuit breaker line and load termi-nal orientation on indicate OFF is opposite of indicate ON.4For pole orientation with horizontal legend, rotate front view clockwise 90°.Notes:1All dimensions are in inches [millimeters].2T olerance ±.010 [.25] unless otherwise specified.。
Fluke 885 FC FCX-6 Digital Multimeter 说明书
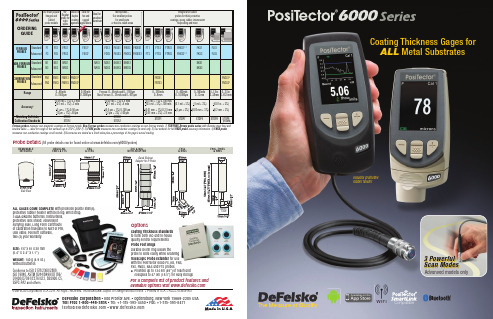
carrying case, Long Form Certificate of Calibration traceable to NIST or PTB,USB cable, PosiSoft Software, two (2)year warranty.SIZE:137 x 61 x 28 mm (5.4" x 2.4" x 1.1")WEIGHT:140 g (4.9 oz.)without batteriesConforms to ISO 2178/2360/2808, ISO 19840, ASTM B244/B499/D1186/D1400/D7091/E376/G12, BS3900-C5, SSPC-PA2 and othersWiFiProbe Details (All probe details can be found online at /p6000/probes )OptionsCoating Thickness Standards to fulfill both ISO and in-house quality control requirements Probe Foot RingsDurable Delrin ring allows the probe to slide easily while scanning Telescopic Probe Extender for use with the PosiTector 6000 FS, NS, FNS, FXS, FNDS, NAS and FTS probes.n Provides up to 124 cm (49”) of reach and collapses to 47 cm (18.5”) for easy storageFerrous probes measure non-magnetic coatings on ferrous metals. Non-Ferrous probes measure non-conductive coatings on non-ferrous metals. 1) FXS/FHXS Xtreme probe series with Alumina wear face and braided cable — ideal for rough or hot surfaces up to 250˚ C (500˚ F). 2)FHXS probe measures non-conductive coatings on steel only. 3)See website for full FNDS probe accuracy information. 4)FNGS probe measures non-conductive coatings on all metals. 5)Accuracies are stated as a fixed value plus a percentage of the gage’s actual reading.©DeFelsko Corporation USA 2019. All Rights Reserved. Technical Data subject to change without notice. • Printed in USA • P6000.v.LW/W1901For a complete list of product features and available options visit CompatibleCoating Thickness Gages for ALL Metal SubstratesDeFelsko Corporation •800 Proctor Ave.•Ogdensburg, New York 13669-2205 USA Toll Free 1-800-448-3835•Tel: +1-315-393-4450•Fax: +1-315-393-8471*********************•Includes protective rubber holsteror hard-to-reach areas FS1FRS1FXS11F0S1F90S1F90ES1FTRS1FHXS11, 2N EW 3 Powerful Scan ModesAdvanced models onlyPosiSoft .netA web-based application offering secure centralized management of readings. Includes customizable, templated PDF Report Generator. Access your PosiSoft Powerful desktop software for downloading, viewing, printing and storing measurement data.Includes customizable, templated PDF Report Generator. No internet connection required.in Memory ModeThick Probes series for thick protectivecoatings: epoxy, rubber, fireproofing and more Xtreme Probes with Alumina wear faces and braided cables for hot/rough surfaces Duplex Probe measures individual layer thicknesses of zinc and paint in a duplex coating systemProbes available for a variety of applicationsRemovable Probes can be detached and replaced with any one of our wide variety of probesCabled Probe StyleAll Regular Cabled Probes are suitable for underwater useand probe styles(see back page ordering guide)Integral Probe StyleRegular45˚0˚90˚Thickflash drives, cameras, or digital audio players. No software to install or internet connection required.Award Winning Compatibility!l Coating Thickness l Surface Profilel Environmental Conditions l Shore Hardness l Salt ContaminationlUltrasonic Wall Thickness™。
DLRO 10和DLRO 10X数字微纳吸力计说明书

DLRO 10 and DLRO 10X Digital MicrohmmeterDESCRIPTIONDLRO 10 and DLRO 10X set the standards for low resistance measurement. DLRO 10 and DLRO 10X are fully automatic instruments, selecting the most suitable test current up to 10 A d.c. to measure resistance from 0.1 µΩ to 2000 Ω, on one of seven ranges.For users who desire more control over the measurement process, DLRO 10X uses a menu system controlled by a two-axis paddle to allow the user to manually select the maximum test current.DLRO 10X also adds real time download of results and on board storage for later download to a PC.Both instruments are built into a strong, lightweight case that is equally at home in the field or in the laboratory. Light enough to be worn around the neck, they are small enough to be taken into areas that were previously too small to access.DLRO 10 uses a large, bright 4 1/2 -digit LED display while DLRO 10X has a large, backlit LCD display. Normally, measurements are made with forward and reverse currents to cancel the effects of any standing voltages across the test sample.The average value is then displayed within 3 seconds, to a basic accuracy of 0.2%. DLRO 10X displays both forward and reverse measurements as well as the average of the two.DLRO 10X allows the user to set high and low pass limits, thereby enabling simple go-no-go testing.At the end of a test DLRO10X will store the test results, as well as any notes relevant to the test.To assist operator safety and ease of use, both instruments are supplied complete with a pair of duplex handspikes with 1.2 m (4 ft) leads. One of the probes is fitted with LED’s, which duplicate indicators on the instrument display indicating that all four contacts have been made, the presence of a high voltage across the load, and the presence of current flow while a load is discharging. A full range of test leads is available with probes, clamps and Kelvin clips. The instruments are supplied as standard with a Nickel Metal Hydride (NiMH) battery pack. The battery packs are inter- changeable so that an exhausted battery may be recharged using the external charger supplied while testing continues using a spare pack. Although full charging will take 4 hours, a fast charge mode allows the battery to be 90% charged within 2 1/2 hours from a 12 volt battery or from a standard 120/230 V AC supply via the supplied charger. The battery pack contains its own battery state indicator, which allows the charge-state to be monitored, even without being connected to the instrument.In addition an optional mains / line power supply, the DLRO10LPU is available. This enables the instruments to be directly powered from 90V to 264V, 50/60Hz ideal for repetitive testing applications such as manufacturing production line use.”DLRO 10X is fitted with RS232 communications that will allow results to be downloaded in real time or stored for later retrieval. Up to 700 sets of results may be stored within DLRO 10X complete with notes containing up to 200 characters which may be added using the on board keypad. These results can also be downloaded to a PC.n Auto current reversal cancels standing emfsn Protected to 600 Vn Automatically detects continuity in potential and current connectionsn Multiple operating modes including fully automaticn Alpha-numeric keypad for entering test notes (DLRO 10X)n User selectable high and low limits (DLRO 10X)n Printer output and memory (DLRO 10X)DLRO 10 AND DLRO10XDigital Microhmmeter 1981DLRO 10 AND DLRO 10XDigital MicrohmmeterMEASUREMENT MODES:A variety of measurement modes are available. Since the introductionof V2.0 firmware, Normal, Auto, Continuous and Inductive mode areavailable on both the DLRO 10 and the DLRO 10X.DLRO 10 will display the average of the measurements achievedusing forward and reverse current, while DLRO 10X displays bothindividual measurements and the average.Normal mode initiates a test by pressing the Test button on theinstrument front panel after connecting the test leads. Continuityof all four connections is checked, forward and reverse currentsare applied.Auto mode allows forward and reverse current measurements tobe made and the average displayed simply by making contact withall four probes. This mode is ideal when working with the suppliedhandspikes. Each time the probes are removed and reconnected tothe load another test will be performed without the need to pressthe test button on the instrument.Continuous mode allows repeated measurements to be madeon the same sample. Simply connect the test leads and press thetest button. The measurement is updated every 3 seconds until thecircuit is broken.Inductive mode is intended for use when measuring inductiveloads. When measuring inductive loads it is necessary to wait forthe voltage to stabilise. This means that the measurement couldtake a few seconds or several minutes. The test leads are firmlyconnected to the item to be measured and the Test button ispressed. The instrument will pass a current through the sampleand wait for the voltage to stabilise. If possible the current willbe increased. This procedure will be repeated until the voltagedetected falls into the range 15 mV to 200 mV. The instrument willthen continue to take readings, which will gradually decrease to thetrue value as the voltage stabilises further. The operator decideswhen the result is stable and presses the test button to terminatethe test. Measurement is made with forward current only.Unidirectional mode, on DLRO 10X only, applies a current in onedirection only. This does not enable any standing emfs to be negatedbut speeds up the measurement process. Test starts automaticallywhen probes are connected.APPLICATIONSThe needs for accurate low resistance measurement are wellknown and very diverse. They range through Goods Receivinginspection of components to ground bonding and welded joints.Typical applications include, but are not limited to, making d.c.resistance measurements of:n Switch and contact breaker resistancen Busbar and cable jointsn Aircraft frame bonds and static control circuitsn Integrity of welded jointsn Inter-cell connections on battery systems up to 600 V peakn Quality control of resistive componentsn Transformer and motor winding resistancen Rail and pipe bondsn Metal alloys, welds and fuse resistancen Graphite electrodes and other compositesn Wire and cable resistancen Transmitter aerial and lightning conductor bondingFEATURES AND BENEFITSn Small, lightweight and portable - can be used in tight places,reduces the need for extra long leads and two person operation.n Four terminal resistance method shows the true resistance of theitem under test.n Bright LED (DLRO 10) and LCD (DLRO 10X) displays are easilyvisible under all lighting conditions and reduce human error.n Automatically applies forward and reverse currents which cancelout any standing voltages across the sample under test.n Checks for undue noise during measurement, reducing thepossibility of recording the incorrect result.n Automatically detects continuity in P and C circuits, preventingerroneously high reading to be taken due to high resistance con-tact.n Battery module has a battery condition indicator allowing the userto check the state of spare batteries without connecting to theinstrument.n RS232 connector on the DLRO 10X allows downloading of resultsin real time or stored for later retrieval.DLRO 10 AND DLRO 10XDigital Microhmmeter Full Scale1.9999 mΩ19.999 mΩ199.99 mΩ1.9999 Ω19.999 Ω199.99 Ω1999.9 ΩResolution0.1 µΩ1 µΩ10 µΩ100 µΩ1 mΩ10 mΩ100 mΩAccuracy*±0.2% ±0.2µΩ±0.2% ±2 µΩ±0.2% ±20 µΩ±0.2% ±0.2 mΩ±0.2% ±2 mΩ±0.2% ±20 mΩ±0.2% ±0.2 ΩResistive20 mV20 mV20 mV20 mV20 mV20 mV200 mVInductiven/a20 mV200 mV200 mV200 mV200 mV200 mVResistive10 A1 A100 mA10 mA1 mA100 µA100 µAInductiven/a1 A1 A100 mA10 mA1 mA100 µAResistance ranges Test currentDLRO 10DLRO 10XMeasurement: Mode:Manual, Auto, Continuous, Inductive Manual, Auto, Continuous, Inductive,UndirectionalControl:Fully Automatic Fully Automatic/ManualSpeed:<3s for forward & reverse current and to display averageDisplay: Measurement: 4 1/2 digit seven segment LEDRange and Safety:LED indication Large backlit LCDTest Method: Single cycle reversing d.c. ratiometric measurement -average result display.Test Current: Accuracy:±10%Stability:<10 ppm per secondMaximum Lead Resistance:100 mΩ total for 10 A operation irrespective of batterycondition.Voltmeter input impedance:> 200 kΩHum rejection:Less than 1% ±20 digits additional error with 100 mV peak 50/60 Hz. on the potential leads.Warning will show if hum or noise exceeds this level.Data:Transfer:Real Time or from storage via RS232Storage:700 testsMemo Field:Up to 200 characters per test via integralalphanumeric keypadBattery: Capacity:7 Ah NiMH rechargeableLife:Typically 1000 x 10 A tests before rechargeRecharge:Via external 90 V - 260 V 50/60 Hz charger or from 12 to 15 V dc supplyCharging Rate: Standard: 2.5 hours to 90% capacity, 4 hrs for full chargeTemperature:Operation:+5 ºC to +45 ºC (41 ºF to 113 ºF) at full specification-10 ºC to +50 ºC (14 ºF to 122 ºF) at reduced accuracyStorageCo-efficient:-30 ºC to +70 ºC (-22 ºF to 158 ºF)Slow charging:<0.01% per ºC over range 5 ºC to 40 ºC (<0.006% per ºF from 4 1ºF to 104 ºF)Humidity (max):+10 ºC to +45 ºC (50 ºF to 113 ºF)Altitude (max):90% RH @ 40 ºC (104 ºF) non-condensingSafety:2000 m (6562 ft) to full safety specificationsEMC:In accordance with IEC61010-1 600 V Category III - only when DH6 leads are used.In accordance with IEC61326-1Dimensions:220 x 100 x 237 mm (8.6 x 4 x 9.5 in)Weight: 2.6 kg (5 3/4 lb.) including battery module* The accuracy stated assumes forward and reverse measurements.Inductive mode or undirectional mode will introduce an undefined error if an external EMF is present.Full scale voltsDLRO 10 AND DLRO 10XUKArchcliffe Road Dover CT17 9EN England T +44 (0) 1304 502101F +44 (0) 1304 207342******************UNITED STATES 4271 Bronze WayDallas TX 75237-1019 USA T 800 723 2861 (USA only)T +1 214 333 3201F +1 214 331 7399******************OTHER TECHNICAL SALES OFFICESValley Forge USA, College Station USA, Sydney AUSTRALIA, Täby SWEDEN, Ontario CANADA, Trappes FRANCE, Oberursel GERMANY, Aargau SWITZERLAND, Kingdom of BAHRAIN, Mumbai INDIA, Johannesburg SOUTH AFRICA, Chonburi THAILAND, Malaga SPAINRegistered to ISO 9001:2008 Cert. no. Q 09250 Registered to ISO 14001-2004 Cert. no. EMS 61597DLR10_DLRO10X_DS_en_Megger is a registered trademarkOPTIONAL MAINS / LINE POWER SUPPLY UNITThe DLRO10 and DLRO10X may also be powered from an optional mains / line power supply unit the DLRO10LPU. This unit is simply fitted to the instrument in place of the standard battery pack.When in use a red LED is illuminated when theinstrument is powered from a mains / line power supplyThe DLRO10X is seen here fitted with the optional DLRO10LPUIdeal for repetitive testing applications such as manufacturing production line use。
Glider Flying Handbook说明书

Glider Flying Handbook2013U.S. Department of TransportationFEDERAL AVIATION ADMINISTRATIONFlight Standards Servicei iPrefaceThe Glider Flying Handbook is designed as a technical manual for applicants who are preparing for glider category rating and for currently certificated glider pilots who wish to improve their knowledge. Certificated flight instructors will find this handbook a valuable training aid, since detailed coverage of aeronautical decision-making, components and systems, aerodynamics, flight instruments, performance limitations, ground operations, flight maneuvers, traffic patterns, emergencies, soaring weather, soaring techniques, and cross-country flight is included. Topics such as radio navigation and communication, use of flight information publications, and regulations are available in other Federal Aviation Administration (FAA) publications.The discussion and explanations reflect the most commonly used practices and principles. Occasionally, the word “must” or similar language is used where the desired action is deemed critical. The use of such language is not intended to add to, interpret, or relieve a duty imposed by Title 14 of the Code of Federal Regulations (14 CFR). Persons working towards a glider rating are advised to review the references from the applicable practical test standards (FAA-G-8082-4, Sport Pilot and Flight Instructor with a Sport Pilot Rating Knowledge Test Guide, FAA-G-8082-5, Commercial Pilot Knowledge Test Guide, and FAA-G-8082-17, Recreational Pilot and Private Pilot Knowledge Test Guide). Resources for study include FAA-H-8083-25, Pilot’s Handbook of Aeronautical Knowledge, FAA-H-8083-2, Risk Management Handbook, and Advisory Circular (AC) 00-6, Aviation Weather For Pilots and Flight Operations Personnel, AC 00-45, Aviation Weather Services, as these documents contain basic material not duplicated herein. All beginning applicants should refer to FAA-H-8083-25, Pilot’s Handbook of Aeronautical Knowledge, for study and basic library reference.It is essential for persons using this handbook to become familiar with and apply the pertinent parts of 14 CFR and the Aeronautical Information Manual (AIM). The AIM is available online at . The current Flight Standards Service airman training and testing material and learning statements for all airman certificates and ratings can be obtained from .This handbook supersedes FAA-H-8083-13, Glider Flying Handbook, dated 2003. Always select the latest edition of any publication and check the website for errata pages and listing of changes to FAA educational publications developed by the FAA’s Airman Testing Standards Branch, AFS-630.This handbook is available for download, in PDF format, from .This handbook is published by the United States Department of Transportation, Federal Aviation Administration, Airman Testing Standards Branch, AFS-630, P.O. Box 25082, Oklahoma City, OK 73125.Comments regarding this publication should be sent, in email form, to the following address:********************************************John M. AllenDirector, Flight Standards Serviceiiii vAcknowledgmentsThe Glider Flying Handbook was produced by the Federal Aviation Administration (FAA) with the assistance of Safety Research Corporation of America (SRCA). The FAA wishes to acknowledge the following contributors: Sue Telford of Telford Fishing & Hunting Services for images used in Chapter 1JerryZieba () for images used in Chapter 2Tim Mara () for images used in Chapters 2 and 12Uli Kremer of Alexander Schleicher GmbH & Co for images used in Chapter 2Richard Lancaster () for images and content used in Chapter 3Dave Nadler of Nadler & Associates for images used in Chapter 6Dave McConeghey for images used in Chapter 6John Brandon (www.raa.asn.au) for images and content used in Chapter 7Patrick Panzera () for images used in Chapter 8Jeff Haby (www.theweatherprediction) for images used in Chapter 8National Soaring Museum () for content used in Chapter 9Bill Elliot () for images used in Chapter 12.Tiffany Fidler for images used in Chapter 12.Additional appreciation is extended to the Soaring Society of America, Inc. (), the Soaring Safety Foundation, and Mr. Brad Temeyer and Mr. Bill Martin from the National Oceanic and Atmospheric Administration (NOAA) for their technical support and input.vv iPreface (iii)Acknowledgments (v)Table of Contents (vii)Chapter 1Gliders and Sailplanes ........................................1-1 Introduction....................................................................1-1 Gliders—The Early Years ..............................................1-2 Glider or Sailplane? .......................................................1-3 Glider Pilot Schools ......................................................1-4 14 CFR Part 141 Pilot Schools ...................................1-5 14 CFR Part 61 Instruction ........................................1-5 Glider Certificate Eligibility Requirements ...................1-5 Common Glider Concepts ..............................................1-6 Terminology...............................................................1-6 Converting Metric Distance to Feet ...........................1-6 Chapter 2Components and Systems .................................2-1 Introduction....................................................................2-1 Glider Design .................................................................2-2 The Fuselage ..................................................................2-4 Wings and Components .............................................2-4 Lift/Drag Devices ...........................................................2-5 Empennage .....................................................................2-6 Towhook Devices .......................................................2-7 Powerplant .....................................................................2-7 Self-Launching Gliders .............................................2-7 Sustainer Engines .......................................................2-8 Landing Gear .................................................................2-8 Wheel Brakes .............................................................2-8 Chapter 3Aerodynamics of Flight .......................................3-1 Introduction....................................................................3-1 Forces of Flight..............................................................3-2 Newton’s Third Law of Motion .................................3-2 Lift ..............................................................................3-2The Effects of Drag on a Glider .....................................3-3 Parasite Drag ..............................................................3-3 Form Drag ...............................................................3-3 Skin Friction Drag ..................................................3-3 Interference Drag ....................................................3-5 Total Drag...................................................................3-6 Wing Planform ...........................................................3-6 Elliptical Wing ........................................................3-6 Rectangular Wing ...................................................3-7 Tapered Wing .........................................................3-7 Swept-Forward Wing ..............................................3-7 Washout ..................................................................3-7 Glide Ratio .................................................................3-8 Aspect Ratio ............................................................3-9 Weight ........................................................................3-9 Thrust .........................................................................3-9 Three Axes of Rotation ..................................................3-9 Stability ........................................................................3-10 Flutter .......................................................................3-11 Lateral Stability ........................................................3-12 Turning Flight ..............................................................3-13 Load Factors .................................................................3-13 Radius of Turn ..........................................................3-14 Turn Coordination ....................................................3-15 Slips ..........................................................................3-15 Forward Slip .........................................................3-16 Sideslip .................................................................3-17 Spins .........................................................................3-17 Ground Effect ...............................................................3-19 Chapter 4Flight Instruments ...............................................4-1 Introduction....................................................................4-1 Pitot-Static Instruments ..................................................4-2 Impact and Static Pressure Lines................................4-2 Airspeed Indicator ......................................................4-2 The Effects of Altitude on the AirspeedIndicator..................................................................4-3 Types of Airspeed ...................................................4-3Table of ContentsviiAirspeed Indicator Markings ......................................4-5 Other Airspeed Limitations ........................................4-6 Altimeter .....................................................................4-6 Principles of Operation ...........................................4-6 Effect of Nonstandard Pressure andTemperature............................................................4-7 Setting the Altimeter (Kollsman Window) .............4-9 Types of Altitude ......................................................4-10 Variometer................................................................4-11 Total Energy System .............................................4-14 Netto .....................................................................4-14 Electronic Flight Computers ....................................4-15 Magnetic Compass .......................................................4-16 Yaw String ................................................................4-16 Inclinometer..............................................................4-16 Gyroscopic Instruments ...............................................4-17 G-Meter ........................................................................4-17 FLARM Collision Avoidance System .........................4-18 Chapter 5Glider Performance .............................................5-1 Introduction....................................................................5-1 Factors Affecting Performance ......................................5-2 High and Low Density Altitude Conditions ...........5-2 Atmospheric Pressure .............................................5-2 Altitude ...................................................................5-3 Temperature............................................................5-3 Wind ...........................................................................5-3 Weight ........................................................................5-5 Rate of Climb .................................................................5-7 Flight Manuals and Placards ..........................................5-8 Placards ......................................................................5-8 Performance Information ...........................................5-8 Glider Polars ...............................................................5-8 Weight and Balance Information .............................5-10 Limitations ...............................................................5-10 Weight and Balance .....................................................5-12 Center of Gravity ......................................................5-12 Problems Associated With CG Forward ofForward Limit .......................................................5-12 Problems Associated With CG Aft of Aft Limit ..5-13 Sample Weight and Balance Problems ....................5-13 Ballast ..........................................................................5-14 Chapter 6Preflight and Ground Operations .......................6-1 Introduction....................................................................6-1 Assembly and Storage Techniques ................................6-2 Trailering....................................................................6-3 Tiedown and Securing ................................................6-4Water Ballast ..............................................................6-4 Ground Handling........................................................6-4 Launch Equipment Inspection ....................................6-5 Glider Preflight Inspection .........................................6-6 Prelaunch Checklist ....................................................6-7 Glider Care .....................................................................6-7 Preventive Maintenance .............................................6-8 Chapter 7Launch and Recovery Procedures and Flight Maneuvers ............................................................7-1 Introduction....................................................................7-1 Aerotow Takeoff Procedures .........................................7-2 Signals ........................................................................7-2 Prelaunch Signals ....................................................7-2 Inflight Signals ........................................................7-3 Takeoff Procedures and Techniques ..........................7-3 Normal Assisted Takeoff............................................7-4 Unassisted Takeoff.....................................................7-5 Crosswind Takeoff .....................................................7-5 Assisted ...................................................................7-5 Unassisted...............................................................7-6 Aerotow Climb-Out ....................................................7-6 Aerotow Release.........................................................7-8 Slack Line ...................................................................7-9 Boxing the Wake ......................................................7-10 Ground Launch Takeoff Procedures ............................7-11 CG Hooks .................................................................7-11 Signals ......................................................................7-11 Prelaunch Signals (Winch/Automobile) ...............7-11 Inflight Signals ......................................................7-12 Tow Speeds ..............................................................7-12 Automobile Launch ..................................................7-14 Crosswind Takeoff and Climb .................................7-14 Normal Into-the-Wind Launch .................................7-15 Climb-Out and Release Procedures ..........................7-16 Self-Launch Takeoff Procedures ..............................7-17 Preparation and Engine Start ....................................7-17 Taxiing .....................................................................7-18 Pretakeoff Check ......................................................7-18 Normal Takeoff ........................................................7-19 Crosswind Takeoff ...................................................7-19 Climb-Out and Shutdown Procedures ......................7-19 Landing .....................................................................7-21 Gliderport/Airport Traffic Patterns and Operations .....7-22 Normal Approach and Landing ................................7-22 Crosswind Landing ..................................................7-25 Slips ..........................................................................7-25 Downwind Landing ..................................................7-27 After Landing and Securing .....................................7-27viiiPerformance Maneuvers ..............................................7-27 Straight Glides ..........................................................7-27 Turns.........................................................................7-28 Roll-In ...................................................................7-29 Roll-Out ................................................................7-30 Steep Turns ...........................................................7-31 Maneuvering at Minimum Controllable Airspeed ...7-31 Stall Recognition and Recovery ...............................7-32 Secondary Stalls ....................................................7-34 Accelerated Stalls .................................................7-34 Crossed-Control Stalls ..........................................7-35 Operating Airspeeds .....................................................7-36 Minimum Sink Airspeed ..........................................7-36 Best Glide Airspeed..................................................7-37 Speed to Fly ..............................................................7-37 Chapter 8Abnormal and Emergency Procedures .............8-1 Introduction....................................................................8-1 Porpoising ......................................................................8-2 Pilot-Induced Oscillations (PIOs) ..............................8-2 PIOs During Launch ...................................................8-2 Factors Influencing PIOs ........................................8-2 Improper Elevator Trim Setting ..............................8-3 Improper Wing Flaps Setting ..................................8-3 Pilot-Induced Roll Oscillations During Launch .........8-3 Pilot-Induced Yaw Oscillations During Launch ........8-4 Gust-Induced Oscillations ..............................................8-5 Vertical Gusts During High-Speed Cruise .................8-5 Pilot-Induced Pitch Oscillations During Landing ......8-6 Glider-Induced Oscillations ...........................................8-6 Pitch Influence of the Glider Towhook Position ........8-6 Self-Launching Glider Oscillations During Powered Flight ...........................................................8-7 Nosewheel Glider Oscillations During Launchesand Landings ..............................................................8-7 Tailwheel/Tailskid Equipped Glider Oscillations During Launches and Landings ..................................8-8 Aerotow Abnormal and Emergency Procedures ............8-8 Abnormal Procedures .................................................8-8 Towing Failures........................................................8-10 Tow Failure With Runway To Land and Stop ......8-11 Tow Failure Without Runway To Land BelowReturning Altitude ................................................8-11 Tow Failure Above Return to Runway Altitude ...8-11 Tow Failure Above 800' AGL ..............................8-12 Tow Failure Above Traffic Pattern Altitude .........8-13 Slack Line .................................................................8-13 Ground Launch Abnormal and Emergency Procedures ....................................................................8-14 Abnormal Procedures ...............................................8-14 Emergency Procedures .............................................8-14 Self-Launch Takeoff Emergency Procedures ..............8-15 Emergency Procedures .............................................8-15 Spiral Dives ..................................................................8-15 Spins .............................................................................8-15 Entry Phase ...............................................................8-17 Incipient Phase .........................................................8-17 Developed Phase ......................................................8-17 Recovery Phase ........................................................8-17 Off-Field Landing Procedures .....................................8-18 Afterlanding Off Field .............................................8-20 Off-Field Landing Without Injury ........................8-20 Off-Field Landing With Injury .............................8-20 System and Equipment Malfunctions ..........................8-20 Flight Instrument Malfunctions ................................8-20 Airspeed Indicator Malfunctions ..........................8-21 Altimeter Malfunctions .........................................8-21 Variometer Malfunctions ......................................8-21 Compass Malfunctions .........................................8-21 Glider Canopy Malfunctions ....................................8-21 Broken Glider Canopy ..........................................8-22 Frosted Glider Canopy ..........................................8-22 Water Ballast Malfunctions ......................................8-22 Retractable Landing Gear Malfunctions ..................8-22 Primary Flight Control Systems ...............................8-22 Elevator Malfunctions ..........................................8-22 Aileron Malfunctions ............................................8-23 Rudder Malfunctions ............................................8-24 Secondary Flight Controls Systems .........................8-24 Elevator Trim Malfunctions .................................8-24 Spoiler/Dive Brake Malfunctions .........................8-24 Miscellaneous Flight System Malfunctions .................8-25 Towhook Malfunctions ............................................8-25 Oxygen System Malfunctions ..................................8-25 Drogue Chute Malfunctions .....................................8-25 Self-Launching Gliders ................................................8-26 Self-Launching/Sustainer Glider Engine Failure During Takeoff or Climb ..........................................8-26 Inability to Restart a Self-Launching/SustainerGlider Engine While Airborne .................................8-27 Self-Launching Glider Propeller Malfunctions ........8-27 Self-Launching Glider Electrical System Malfunctions .............................................................8-27 In-flight Fire .............................................................8-28 Emergency Equipment and Survival Gear ...................8-28 Survival Gear Checklists ..........................................8-28 Food and Water ........................................................8-28ixClothing ....................................................................8-28 Communication ........................................................8-29 Navigation Equipment ..............................................8-29 Medical Equipment ..................................................8-29 Stowage ....................................................................8-30 Parachute ..................................................................8-30 Oxygen System Malfunctions ..................................8-30 Accident Prevention .....................................................8-30 Chapter 9Soaring Weather ..................................................9-1 Introduction....................................................................9-1 The Atmosphere .............................................................9-2 Composition ...............................................................9-2 Properties ....................................................................9-2 Temperature............................................................9-2 Density ....................................................................9-2 Pressure ...................................................................9-2 Standard Atmosphere .................................................9-3 Layers of the Atmosphere ..........................................9-4 Scale of Weather Events ................................................9-4 Thermal Soaring Weather ..............................................9-6 Thermal Shape and Structure .....................................9-6 Atmospheric Stability .................................................9-7 Air Masses Conducive to Thermal Soaring ...................9-9 Cloud Streets ..............................................................9-9 Thermal Waves...........................................................9-9 Thunderstorms..........................................................9-10 Lifted Index ..........................................................9-12 K-Index .................................................................9-12 Weather for Slope Soaring .......................................9-14 Mechanism for Wave Formation ..............................9-16 Lift Due to Convergence ..........................................9-19 Obtaining Weather Information ...................................9-21 Preflight Weather Briefing........................................9-21 Weather-ReIated Information ..................................9-21 Interpreting Weather Charts, Reports, andForecasts ......................................................................9-23 Graphic Weather Charts ...........................................9-23 Winds and Temperatures Aloft Forecast ..............9-23 Composite Moisture Stability Chart .....................9-24 Chapter 10Soaring Techniques ..........................................10-1 Introduction..................................................................10-1 Thermal Soaring ...........................................................10-2 Locating Thermals ....................................................10-2 Cumulus Clouds ...................................................10-2 Other Indicators of Thermals ................................10-3 Wind .....................................................................10-4 The Big Picture .....................................................10-5Entering a Thermal ..............................................10-5 Inside a Thermal.......................................................10-6 Bank Angle ...........................................................10-6 Speed .....................................................................10-6 Centering ...............................................................10-7 Collision Avoidance ................................................10-9 Exiting a Thermal .....................................................10-9 Atypical Thermals ..................................................10-10 Ridge/Slope Soaring ..................................................10-10 Traps ......................................................................10-10 Procedures for Safe Flying .....................................10-12 Bowls and Spurs .....................................................10-13 Slope Lift ................................................................10-13 Obstructions ...........................................................10-14 Tips and Techniques ...............................................10-15 Wave Soaring .............................................................10-16 Preflight Preparation ...............................................10-17 Getting Into the Wave ............................................10-18 Flying in the Wave .................................................10-20 Soaring Convergence Zones ...................................10-23 Combined Sources of Updrafts ..............................10-24 Chapter 11Cross-Country Soaring .....................................11-1 Introduction..................................................................11-1 Flight Preparation and Planning ...................................11-2 Personal and Special Equipment ..................................11-3 Navigation ....................................................................11-5 Using the Plotter .......................................................11-5 A Sample Cross-Country Flight ...............................11-5 Navigation Using GPS .............................................11-8 Cross-Country Techniques ...........................................11-9 Soaring Faster and Farther .........................................11-11 Height Bands ..........................................................11-11 Tips and Techniques ...............................................11-12 Special Situations .......................................................11-14 Course Deviations ..................................................11-14 Lost Procedures ......................................................11-14 Cross-Country Flight in a Self-Launching Glider .....11-15 High-Performance Glider Operations and Considerations ............................................................11-16 Glider Complexity ..................................................11-16 Water Ballast ..........................................................11-17 Cross-Country Flight Using Other Lift Sources ........11-17 Chapter 12Towing ................................................................12-1 Introduction..................................................................12-1 Equipment Inspections and Operational Checks .........12-2 Tow Hook ................................................................12-2 Schweizer Tow Hook ...........................................12-2x。
Telemecanique 产品系列说明书

A complete range ofinnovative and moresimple to use sensorsBenefit from Telemecanique’s major innovation:A worldwide detection first for improving productivity:b product selection simplifiedb product availability simplifiedb installation and setting-up simplifiedb maintenance simplifiedb detection simplified using a single supplier.Improved simplicity for improved productivity. Osi conceptImprove performance bymaking your selection andassembly lesscomplicated andmore intelligent.Improve serviceexpertise with anefficient product lineoffering simplifiedselection and improvedselling potential.Reduce maintenancetime with products thatare simpler andunequalled in flexibility.“Universal” series: Multi-purpose products providing multiple functions. Osi concept products are included in this series.“Optimum” series:Designed foressential andrepetitive functions.“Application” series:Offers functionsspecifically forspecialist needs, thusproviding the idealsolution for your morecomplex applications.Select the sensor according to your specific requirements> A single product that automatically adapts to all conditions> A single product that automatically adapts to all installation environ-ments> Availability of more than 5,000 interchange-able configurations within 24 hours> A user-friendly product at last; easy to parameter prior to installation and to modify during operation> A single product that automatically learns both its detection mode and detection zone> Simple parametering of many differentresolutions on the same product1/11Contentsb Osiris ™ Photo-electric sensors .......................1/2 to 1/11Detection without contact of objects whatever their shape or material> Detection from a few millimeters to several tens of meters> 3D adjustable fixing accessories> Specific products for particular applicationsb Osiprox ™ Inductive proximity sensors ......1/12 to 1/22Detection without contact of metal objects> Sensor / object distance - 60 mm> Generic cylindrical and flat form products > Specific products for particular applicationsb Osiprox Capacitive proximity sensors ....................1/23b Osiprox Ultrasonic sensors ............................1/24 to 1/33Detection without contact of any object of any material> Detection from a few millimeters up to 8 meters > Extra large range to ensure finding the right product > Specific products for particular applicationsb Osiswitch ™ Limit switches ..........................1/34 to 1/39Detection by contact of rigid objects> Positive opening operation of electrical contacts > Object speed - 1.5 m/s> Specific products for particular applicationsb Nautilus Sensors for pressure control .......1/40 to 1/41Detection by contact with fluid> Electronic pressure and vacuum switches > Analog pressure sensors> Electromechanical pressure and vacuum switches1/2For other versions, please consult with your local Schneider Electric/Square D sales office: visit 1/3For other versions, please consult with your local Schneider Electric/Square D sales office: visit 1/7For other versions, please consult with your local Schneider Electric/Square D sales office: visit 1L = 20 m M4 / M2.6 (1)M4 / L = 90 mm M6M4 / M6M6 / L = 90 mm M4 / M2.6M4 / L = 90 mm es u f f i D ma eb -u r h T 250 to 900(3)200 or 1500(1)1807060601518Ø 1Ø 1Ø 1Ø 1Ø 1+16 Ø 0.265Ø 1Ø 0.5 + 4 Ø 0.23Ø 0.5Ø 2.2Ø 2.2Ø 2.2Ø 2.2 x 2Ø 2.2 x 2Ø 2.2 x 2Ø 1 x 2Ø 1 x 2- 25 to + 60- 25 to + 60 - 25 to + 60- 25 to + 60- 25 to + 60- 25 to + 60- 25 to + 60- 25 to + 60XUFZ920XUFN12301XUFN12311XUFN05321XUFN05323XUFN05331XUFN02323XUFN01331(2)M4 x 0.7M4 x 0.7M6 x 0.75M6 x 0.75 / M4 x 0.7M6 x 0.75M4 x 0.7M4 x 0.7Long distance fibers Flexible fibers for t n e m e v o m l a c o r p i c e r s r e b i f e c n a t s i d g n o L sn e l l a r g e t n i h t i w M3 / M2.6 (1)M3 / L = 90 mm M8 / L = 20 mm M4 / M2.6M3 / L = 15 mm M6 / L = 15 mm M6 / L = 17 mm es u f f i D ma eb -u r h T 50 or 1000 (1)55596810052031 Ø5.1 Ø562.0 Ø5.0 Ø1 Ø5.0 Ø5.0 ØØ 1Ø 1Ø 2.2Ø 1 x 2Ø 1 x 2Ø 2.2 x 2Ø 2.2 x 2- 25 to + 60- 25 to + 60- 25 to + 60- 25 to + 60- 25 to + 60- 25 to + 60- 25 to + 60XUFN35301XUFN35311XUFN2L01L2XUFN01321XUFN04331XUFN5P01L2XUFN5S01L2M3 x 0.5M3 x 0.5M8 x 1.25M4 x 0.7M3 x 0.5M6 x 0.75M6 x 0.75Long distance fibers Flexible fibers Teflon fibers M4 / M2.6 (1)M4 / M2.6 (1)Ø 5 / L = 20 mm4C R U X r o s n e s r o l o c l l u f r o f d e s u c o f e s u f f iD ma eb -u r h T 300 or 2000(1)100 or 750(1)302010001Ø 1.5Ø 1Ø 1Transmitter Ø 1Receiver Ø 1.5Transmitter Ø 1.5Receiver Ø 1.5Transmitter and Receiver Ø 1.52 x 2.2 Ø2 x 2.2 Ø2 x 2.2 Ø2.2 Ø2.2 Ø2.2 Ø55 + o t 01 -55 + o t 01 -55 + o t 01 -06 + o t 52 -06 + o t 52 -06 + o t 52 -2L 30L 5N F U X 2L 20L 5N F U X 2L 10L 5N F U X 2L 10T 2N F U X 2L 10S 2N F U X 2L 10P 2N F U X M2.6 x 0.45 / M4 x 0.7M2.6 x 0.45 / M4 x 0.7by clip (included)2 elongated holes Ø 3.2 x 6.7 for M3 screws / fixing centers = 9.8 mmPlastic fiber optic light guides (length 2 m)Osiris1/8For other versions, please consult with your local Schneider Electric/Square D sales office: visit 1Optical frames for detection of passage of objectsXURZ01distanceFor other versions, please consult with your local Schneider Electric/ Square D sales office: visit a t s i dgn i s ne s l an i moN)5(wo l ebe l bagn i l dnahs l a i r e t aseries processingAnalog output1/9ForksNO/NC programmablePB100 In-line accessorypushbutton for teachingwindow limits (for Virtu TMVirtu Analog1/28For other versions, please consult with your local Schneider Electric/Square D sales office: visit 1(continued)Model Number*Accessories for SM602 Seriesh t g n e L e p y t n o i t c e n n o C °09ht g n e L e p y t n o i t c e n n o C t h g i a r t S XSCD101YM12 connector2 m XSCD111YM12 connector2 mAdditional cable lengths are available(*) All possible sensor configurations are not listed hereCharacteristicsHousing Style/Material 18 mm ULTEM ®Stainless Steel Flat-profile ULTEM ®18 mm ULTEM ®Stainless Steel Flat-profile ULTEM ®r o t c e n n o C e l b a C m3e p y T n o i t c e n n o C Supply Voltage CD V 42-21CD V 42-21RangeWindow178 mm 1.6 mmNO SM600A-701-00SM600A-701-00S SM600A-701-00FP SM650A-701-00SM650A-701-00S SM650A-701-00FP NCSM600A-701-10SM600A-701-10SSM600A-701-10FPSM650A-701-10SM650A-701-10SSM650A-701-10FP13 mmNO SM600A-708-00SM600A-708-00S SM600A-708-00FP SM650A-708-00SM650A-708-00S SM650A-708-00FP NCSM600A-708-10SM600A-708-10SSM600A-708-10FPSM650A-708-10SM650A-708-10SSM650A-708-10FP9 mmNO SM600A-712-00SM600A-712-00S SM600A-712-00FP SM650A-712-00SM650A-712-00S SM650A-712-00FP NCSM600A-712-10SM600A-712-10SSM600A-712-10FPSM650A-712-10SM650A-712-10SSM650A-712-10FP25 mmNO SM600A-716-00SM600A-716-00S SM600A-716-00FP SM650A-716-00SM650A-716-00S SM650A-716-00FP NCSM600A-716-10SM600A-716-10SSM600A-716-10FPSM650A-716-10SM650A-716-10SSM650A-716-10FP51 mmNO SM600A-732-00SM600A-732-00S SM600A-732-00FP SM650A-732-00SM650A-732-00S SM650A-732-00FP NCSM600A-732-10SM600A-732-10SSM600A-732-10FPSM650A-732-10SM650A-732-10SSM650A-732-10FP77 mmNO SM600A-748-00SM600A-748-00S SM600A-748-00FP SM650A-748-00SM650A-748-00S SM650A-748-00FP NCSM600A-748-10SM600A-748-10SSM600A-748-10FPSM650A-748-10SM650A-748-10SSM650A-748-10FP127 mmNO SM600A-780-00SM600A-780-00S SM600A-780-00FP SM650A-780-00SM650A-780-00S SM650A-780-00FP NCSM600A-780-10SM600A-780-10SSM600A-780-10FPSM650A-780-10SM650A-780-10SSM650A-780-10FPSM600 Series Ultrasonic Sensors18 mm & Flat-profile (continued)1/29For other versions, please consult with your local Schneider Electric/Square D sales office: visit 1(*) All possible sensor configurations are not listed hereSM602 Dual-levelSM600 SeriesFor other versions, please consult with your local Schneider Electric/1Osiswitch ™Limit switchesUniversal, complete switchesP ositive opening operation1OsiswitchFor other versions, please consult with your local Schneider Electric/1Osiswitch Limit switchesFor customized assembly of miniature1ver Sprwith plastic tipCat whiskerglass fiberrod leverL = 125 mmMetalspringle verL = 2 m4-pinand compact switchesOsiswitchFor other versions, please consult with your local Schneider Electric/1Osiswitch Limit swtichesClassic - XCKJ, complete switches1Complete switch Body/contact Head Le verwith reinforced with metal with thermoplastic with steel with steel roller with steelsteel roller end plunger roller le ver plunger,roller lever plunger,end plunger ball bear ingend plunger 1 direct. or actuation 1 direct.of actuation end plungerlever (2)Catalog number ZCKE09ZCKY71ZCKY61(1) Adjustable throughout 360° in 5° steps, or in 45° steps by reversing the le ver mounting.(2) Adjustable throughout 360° in 5° steps, or in 90° steps by reversing the notched washer.Customized assembly of Classic XCKJswitchesOperating heads, complete or for customer assemblyOsiswitchFor other versions, please consult with your local Schneider Electric/1/41For other versions, please consult with your local Schneider Electric/Square D sales office: visit 1NautilusSensors for pressure controlElectronic sensors XMLF。
诺基亚智能手机使用指南说明书
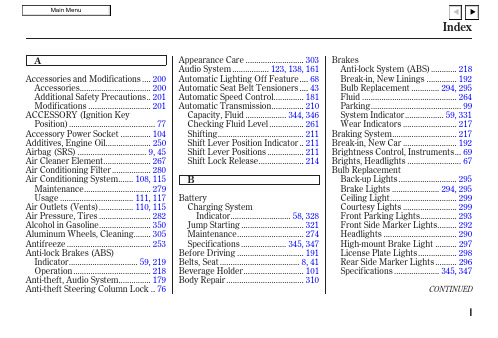
C
Capacities Chart .................... 344, 346 Carbon Monoxide Hazard .............. 52 Carrying Cargo .............................. 202 Cassette Player
Charging System Indicator .... 58, 328 Checklist, Before Driving............. 206 Child Safety ...................................... 20 Child Seats........................................ 25
Before Driving ............................... 191 Belts, Seat ..................................... 8, 41 Beverage Holder............................ 101 Body Repair .................................... 310
Maintenance............................... 279 Usage .................................. 111, 117 Air Outlets (Vents)................ 110, 115 Air Pressure, Tires ........................ 282 Alcohol in Gasoline........................ 350 Aluminum Wheels, Cleaning........ 305 Antifreeze ....................................... 253 Anti-lock Brakes (ABS) Indicator................................ 59, 219 Operation .................................... 218 Anti-theft, Audio System............... 179 Anti-theft Steering Column Lock .. 76
Futaba SBS-01RO RPM传感器说明书
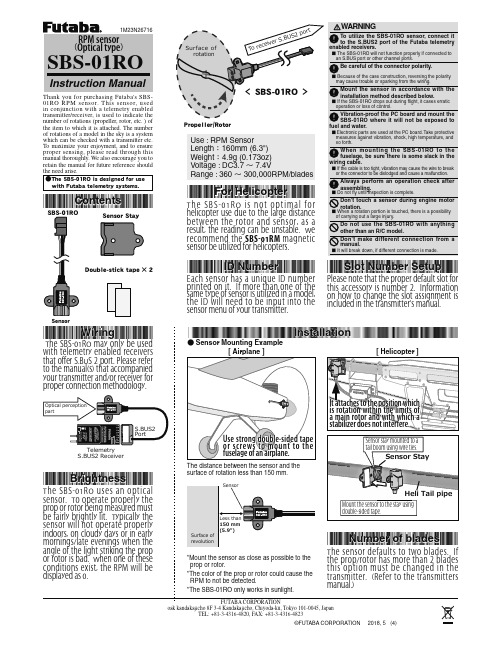
ID Number
&BDI TFOTPS IBT B VOJRVF *% OVNCFS QSJOUFE PO JU *G NPSF UIBO POF PG UIF TBNFUZQFPGTFOTPSJTVUJMJ[FEJOBNPEFM UIF *% XJMM OFFE UP CF JOQVU JOUP UIF TFOTPSNFOVPGZPVSUSBOTNJUUFS
Slot Number Setup
1MFBTFOPUFUIBUUIFQSPQFSEFGBVMUTMPUGPS UIJT BDDFTTPSZ JT OVNCFS *OGPSNBUJPO PO IPX UP DIBOHF UIF TMPU BTTJHONFOU JT JODMVEFEJOUIFUSBOTNJUUFSTNBOVBM
UIBUBDDPNQBOJFE ZPVSUSBOTNJUUFSBOEPSSFDFJWFSGPS QSPQFSDPOOFDUJPONFUIPEPMPHZ
6XUIDFH RI URWDWLRQ
7RUHFHLYHU6%86SRUW
ʻ 4#430 ʼ
1SPQFMMFS3PUPS
Do not use the SBS-01RO with anything other than an R/C model.
Don't make different connection from a manual. ˙ It will break down, if different connection is made.
Always perform an operation check after assembling. ˙ Do not fly until inspection is complete.
Parker Hannifin 公司 Engineered Polymer Systems 部门 B
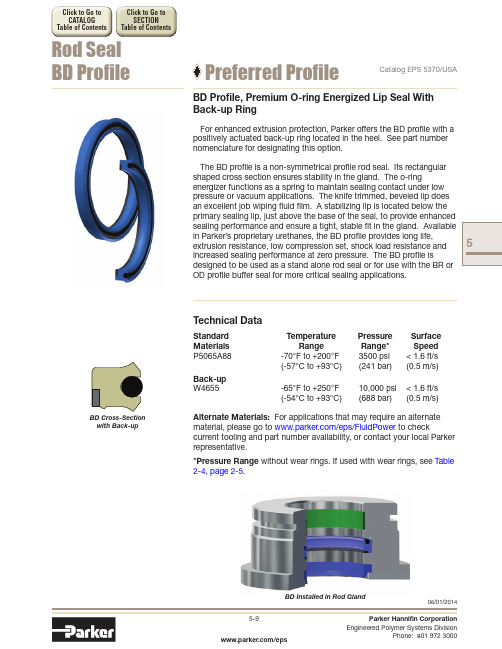
5Click to Go to SECTIONTable of ContentsClick to Go to Table of Contents BD Profile, Premium O-ring Energized Lip Seal With Back-up RingFor enhanced extrusion protection, Parker offers the BD profile with a positively actuated back-up ring located in the heel. See part number nomenclature for designating this option.The BD profile is a non-symmetrical profile rod seal. Its rectangular shaped cross section ensures stability in the gland. The o-ringenergizer functions as a spring to maintain sealing contact under low pressure or vacuum applications. The knife trimmed, beveled lip does an excellent job wiping fluid film. A stabilizing lip is located below the primary sealing lip, just above the base of the seal, to provide enhanced sealing performance and ensure a tight, stable fit in the gland. Available in Parker’s proprietary urethanes, the BD profile provides long life, extrusion resistance, low compression set, shock load resistance and increased sealing performance at zero pressure. The BD profile isdesigned to be used as a stand alone rod seal or for use with the BR or OD profile buffer seal for more critical sealing applications.Catalog EPS 5370/USARod SealBD Profile Preferred ProfileBD Cross-Sectionwith Back-upTechnical DataStandard Temperature Pressure Surface Materials Range Range* Speed P5065A88 -70°F to +200°F 3500 psi < 1.6 ft/s (-57°C to +93°C) (241 bar) (0.5 m/s)Back-up W4655-65°F to +250°F10,000 psi < 1.6 ft/s (-54°C to +93°C)(688 bar) (0.5 m/s)Alternate Materials: For applications that may require an alternate material, please go to /eps/FluidPower to checkcurrent tooling and part number availability, or contact your local Parker representative.*Pressure Range without wear rings. If used with wear rings, see Table 2-4, page 2-5.5Gland Dimensions — BD ProfilePart Number Nomenclature — BD Profile (5065, with Back-up)Table 5-5. BD Profile4-Digit Material Code Example:Example: .375 x 1000 = 375Table 5-6. BD Profile — Rod Gland Calculation*If used with wear rings, refer to wear ring throat diameter, see Section 9. For custom groove calculations, see Appendix C .Above table reflects recommended cross-sections for rod diameters shown. Alternate cross-sections and additional sizes may be considered. Consult /eps/FluidPower for additional cross-sections and sizes, hardware specifications, and part number availability. Contact your Parker representative for assistance.Please refer to Engineering Section 2, page 2-8 for surface finish and additional hardware considerations.5Click to Go to CATALOG Table of ContentsAbove table reflects recommended cross-sections for rod diameters shown. Alternate cross-sections and additional sizes may be considered. Consult /eps/FluidPower for additional cross-sections and sizes, hardware specifications, and part number availability. Contact your Parker representative for assistance.Table 5-7. BD Profile — Rod Gland Dimensions , ·Parker Standard SizesTable 5-7. BD Profile — Rod Gland Dimensions, ·Parker Standard Sizes (cont'd)5。
USAMADE INPCI-GPIB高性能IEEE-488.2接口和驱动软件说明书
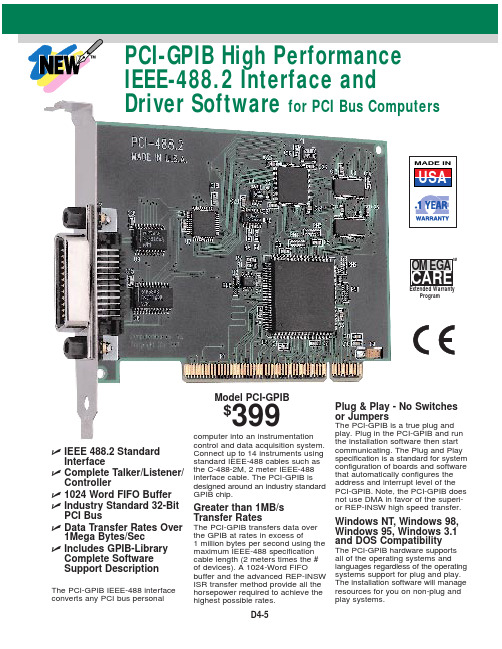
for PCI Bus ComputersߜIEEE 488.2 StandardInterfaceߜComplete Talker/Listener/Controllerߜ1024 Word FIFO BufferߜIndustry Standard 32-BitPCI BusߜData Transfer Rates Over1Mega Bytes/SecߜIncludes GPIB-LibraryComplete SoftwareSupport DescriptionThe PCI-GPIB IEEE-488 interfaceconverts any PCI bus personalcomputer into an instrumentationcontrol and data acquisition system.Connect up to 14 instruments usingstandard IEEE-488 cables such asthe C-488-2M, 2 meter IEEE-488interface cable. The PCI-GPIB isdesigned around an industry standardGPIB chip.Greater than 1MB/sTransfer RatesThe PCI-GPIB transfers data overthe GPIB at rates in excess of1 million bytes per second using themaximum IEEE-488 specificationcable length (2 meters times the #of devices). A 1024-Word FIFObuffer and the advanced REP-INSWISR transfer method provide all thehorsepower required to achieve thehighest possible rates.Plug & Play - No Switchesor JumpersThe PCI-GPIB is a true plug andplay. Plug in the PCI-GPIB and runthe installation software then startcommunicating. The Plug and Playspecification is a standard for systemconfiguration of boards and softwarethat automatically configures theaddress and interrupt level of thePCI-GPIB. Note, the PCI-GPIB doesnot use DMA in favor of the superi-or REP-INSW high speed transfer.Windows NT, Windows 98,Windows 95, Windows 3.1and DOS CompatibilityThe PCI-GPIB hardware supportsall of the operating systems andlanguages regardless of the operatingsystems support for plug and play.The installation software will manageresources for you on non-plug andplay systems.ProgramModel PCI-GPIB$399D4-5D4-6D4SpecificationsThe PCI-GPIB is compatible with IEEE-488.1 and IEEE-488.2 specifications.Transfer Rate: >1Mbyte/secPower: 5 VDC @ 375 mA typical Dimensions: 5.26 X 3.8´´I/O Connector:IEEE-488 Standard 24 pinOperating Temp. & Humidity:0 to 60°C @ 10 to 90%Storage Temp. & Humidity:-40 to 100°C @ 5 to 90%GPIB LibraryThe GPIB Library includes complete Windows Language programming support. You receive installation software and complete DOS,Windows 3.x, Windows 95, Windows 98 and Windows NT language drivers.The GPIB Library for Windows is a Dynamic Link Library (DLL). It can be used with most Windowsprogramming languages including Microsoft Visual C++ and C, Visual Basic, Borland C/C++, Watcom C and Pascal.The GPIB Library is modeled after the National Instruments Library. As of the time of this writing, the Library is syntactically and functionally identical with the NI-488.2 library. This means that a program written for the NI-488.2library may be recompiled for the GPIB Library and will compile, run and function without error in exactly the manner it did when compiled and run with the National Instruments software.IEEE-488.2 (GPIB)CompatibilityThe PCI-GPIB adheres toANSI/IEEE Standard 488-1978.Often referred to as the IEEE-488.2bus or HPIB (Hewlett-Packard Interface Bus), the GPIB (General Purpose Interface Bus) is a standard for instrumentation communication and control forinstruments from manufacturers the world over. The GPIB provides handshaking and interfacecommunications over an 8 bit data bus employing 5 control and 3handshake signals.IEEE-488 ConnectionConnecting GPIB devices together is straightforward. Since the signal lines are connected in parallel, a direct pin-to-pin wiring cable is used. GPIB, or IEEE-488, uses a standardized connector, whichadditionally simplifies interconnecting different instruments.The optional C-488-2M cable is a standard 2 meter IEEE-488 cable. It can be used to connect any of OMEGA’s IEEE-488 devices to other IEEE-488 instruments. Since each connector has two parallel GPIB connections, a user caneasily attach other GPIB devices to either end for expansion.Ordering Example: PCI-GPIB card, C-488-2M cable and OMEGACARE SM 1-year extended warranty for PCI-GPIB (adds 1 year to standard 3-year warranty) $399 + 59 + 30 = $488CANADA www.omega.ca Laval(Quebec) 1-800-TC-OMEGA UNITED KINGDOM www. Manchester, England0800-488-488GERMANY www.omega.deDeckenpfronn, Germany************FRANCE www.omega.frGuyancourt, France088-466-342BENELUX www.omega.nl Amstelveen, NL 0800-099-33-44UNITED STATES 1-800-TC-OMEGA Stamford, CT.CZECH REPUBLIC www.omegaeng.cz Karviná, Czech Republic596-311-899TemperatureCalibrators, Connectors, General Test and MeasurementInstruments, Glass Bulb Thermometers, Handheld Instruments for Temperature Measurement, Ice Point References,Indicating Labels, Crayons, Cements and Lacquers, Infrared Temperature Measurement Instruments, Recorders Relative Humidity Measurement Instruments, RTD Probes, Elements and Assemblies, Temperature & Process Meters, Timers and Counters, Temperature and Process Controllers and Power Switching Devices, Thermistor Elements, Probes andAssemblies,Thermocouples Thermowells and Head and Well Assemblies, Transmitters, WirePressure, Strain and ForceDisplacement Transducers, Dynamic Measurement Force Sensors, Instrumentation for Pressure and Strain Measurements, Load Cells, Pressure Gauges, PressureReference Section, Pressure Switches, Pressure Transducers, Proximity Transducers, Regulators,Strain Gages, Torque Transducers, ValvespH and ConductivityConductivity Instrumentation, Dissolved OxygenInstrumentation, Environmental Instrumentation, pH Electrodes and Instruments, Water and Soil Analysis InstrumentationHeatersBand Heaters, Cartridge Heaters, Circulation Heaters, Comfort Heaters, Controllers, Meters and SwitchingDevices, Flexible Heaters, General Test and Measurement Instruments, Heater Hook-up Wire, Heating Cable Systems, Immersion Heaters, Process Air and Duct, Heaters, Radiant Heaters, Strip Heaters, Tubular HeatersFlow and LevelAir Velocity Indicators, Doppler Flowmeters, LevelMeasurement, Magnetic Flowmeters, Mass Flowmeters,Pitot Tubes, Pumps, Rotameters, Turbine and Paddle Wheel Flowmeters, Ultrasonic Flowmeters, Valves, Variable Area Flowmeters, Vortex Shedding FlowmetersData AcquisitionAuto-Dialers and Alarm Monitoring Systems, Communication Products and Converters, Data Acquisition and Analysis Software, Data LoggersPlug-in Cards, Signal Conditioners, USB, RS232, RS485 and Parallel Port Data Acquisition Systems, Wireless Transmitters and Receivers。
DFM-B 引导驱动模块说明书

Guided drive module DFM-BFlexible & dynamic!High load capacityAdjustable end positionPneumatic cushioning121.1.PSIProduct Short InformationDFM-BMaximum speed v max.= 1.5 m/s.Pneumatic end position cushion-ing or integrated shock absorbers facilitate almost 100 % greater speed and an endposition accura-cy of less than 0.05 mm.Precision stroke adjustmentin retracted and advanced position with two bearings per guide rod for better guiding accuracy and operating behaviour without the need for expensive in-house con-structions.DFM & DFM-BCompact dimensionsHigh-precision guidance and excellent absorption of torque loads and lateral forces.Sturdy designWith drive and guide unit in one housing, with either plain bearing guide or ball-bearing guide plus a wide variety of mounting options.Alternative air connections For greater flexibility together with standardised proximity sensors of type SM..-8.Incredible load capacities, excellent guidance and all in a modular format – that’s the DFM-B. Reliable, flexible and resilient – even with high torque loading.DFM-B with shock absorber for even heavier loads and higher speedsDFM-B as long-stroke variant up to 400 mmOther variants•Heat-resistant design •X strokes•Customer-specific variants in stainless steel or ascylinder/valve combinationsDFM-B with adjustable end position: •Retracted •Advanced•Retracted and advancedDFM-B with pneumatic:end-position cushioning for heavy loads and high speedsFesto AG &Co.KGRuiter Strasse 82D-73734 EsslingenInternet Tel. ++49 (0)711 347-0 Fax ++49 (0)711 347-2144E-mail service_international@160206S u b j e c t t o c h a n g eGuided drive module DFM-B*Tested representatively and certified for the products ADVU, DGPL and DNC.Overview of series, variants and functionsFFMVariantsCushioning•Pneumatic cushioning •Flexible cushioning•Shock absorber at both endsPosition sensing•Contactless sensing of the piston position using SM..-8 standard proximity sensors •Sensing option on both sides thanks to double slotGuide•Plain bearing guide •Ball-bearing guide。
迪电子Micro MATE-N-LOK 3 mm 连接器系统说明说明书
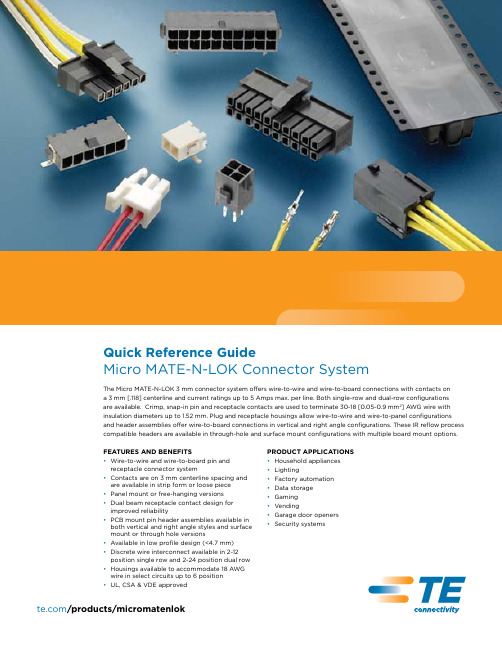
Pin
(mm2)
Range
Strip Form Loose Piece
Tin
Plating 15µ Gold
30µ Gold
Application Tooling*
Hand Tool
26-30 0.12-0.05
.035-.060 0.89-1.52
x
794607
794611
PN-1
1-PN-1
1-PN-2
x
Packing Type
Tray
Tape & Reel
x
x
x
x
x
x
x
x
x
x
x
x
x
x
x
x
x
x
x
x
x
x
x
x
x
x
x
x
x
x
x
x
x
x
x
x
x
x
x
x
x
x
Mating Half
x-1445022-x x-1445022-x x-1445022-x x-1445022-x x-1445022-x x-1445022-x x-1445022-x x-1445022-x x-1445022-x x-1445022-x x-1445022-x x-1445022-x x-1445022-x x-1445022-x x-1445022-x x-1445022-x x-1445022-x x-1445022-x x-1445022-x x-1445022-x x-1445022-x x-1445022-x x-1445022-x x-1445022-x x-1445022-x x-1445022-x x-1445022-x
疑似汽车品牌 Windshield Header 商品说明书

®Quadratec ®WindshieldHeader ChannelPARTS LIST:A. Windshield Header w/Brackets Installed - Qty 1B. Windshield Header Knobs - Qty 2C. Windshield Header Plates - Qty 2REQUIRED TOOLS:Safety GlassesLoss of vehicle control involves risk of death or serious injury,particularly to parts of your body not restrained within vehicle.This product is intended for weather protection only and should Not be relied upon to contain occupants in the event of an accident or to protect from either ground contact or falling objects.To reduce risk of accident or injury:•ALWAYS WEAR SEATBELTS•Always keep head, arms & body parts within vehicle.•Fully secure or stow the fabric top before driving according to instructions. Never try to adjust the fabric top while driving.Do not use if damaged or worn.•Read and follow all instructions & warnings accompanyingthis product, in your vehicle owner’s manual and Off Road Driving Supplement.RISK OF EYE INJURY. Safety glasses should be worn at all times while installing or maintaining this product.For ’07-’18 Wrangler JK Vehicles: #11122.0100ABFront EdgeCPut on safety glasses. With the wind-shield header removed from the vehicle,install the front edge of the header into the pocket sewn on your Bimini Top orBimini Top Plus. Pull the fabric over the header and snap all (8) snaps as shown. (FIG 1)®Before You Begin Installation:Congratulations on your purchase of the Quadratec Windshield Header Channel.This high quality product is designed to work with several brief top options for fair weather driving.When unpacking, check to make sure all parts are included. If any part ismissing or broken, please call Quadratec Customer Service at 800-745-6037 as soon as possible.a hazardous situation which, if not avoided, could result in death or serious injury. You CAN be KILLED or SERIOUSLY HUR T if you don’t follow instructions.a hazardous situation which, if not avoided, could result in minor or moderate injury. You CAN be moderately HURT and also may suffer property damage if you don’t follow instructions.Careful attention is required to this instruction or operation but doesgenerally not relate to personal injury. Damage to your Quadratec ®product or other property may result if you don’t follow instructions.Important Safety Information:Your Quadratec ®Windshield Header is intended to be used with otherQuadratec Products to increase the fair weather enjoyment of your off-road ca-pable vehicle. Before installation, please take a moment to review the followingsafety information and installation in-structions. Important safety information is generally preceded by one of three signal words indicating the relative risk of injury.The signal words mean:Figure 1Center the Bimini Top and Header Channel on the vehicle’s windshield frame, above the footman loops. Position the Header Plate under the Footman Loop. Install the Header knob through the Header Plate and Footman loop and thread it into the header bracket. (FIG 2)Repeat on the opposite side of the vehi-cle. Once both knobs are secure, you can continue installation of the Bimini or Bimini plus onto your vehicle. (FIG 3) See the installation instructions suppliedwith your top for those steps.Fig 2Fig 3MAKE SURE THE WINDSHIELD HEADER AND INSTALLATION BOLTS AREFULLY SECURED AND TIGHTENED. FAILURE TO FULLY TIGHTEN THEBOLTS MAY CAUSE THE HEADER TO COME OFF WHILE DRIVING.Your windshield header channel canused with several Quadratec products,such as the Bimini Top and/or thefull length Bimini Top Plus for theultimate in sunny weather driving!BIMINI TOP BIMINI PLUS Header BracketHeaderPlateHeaderKnobCompleted installationon vehicle.FootmanLoop®®Quadratec ® Exclusive Three Year Limited WarrantyYour Quadratec ®branded accessories are covered by the following Limited Warranty provided exclusively by Quadratec, Inc., 1028Saunders Lane, West Chester PA 19380.This Limited Warranty is the only warranty made in connection with your purchase.Quadratec neither assumes nor authorizes any vendor, retailer or other person or entity to as-sume for it any other obligation or liability in connection with this product orLimited War-ranty . This Limited Warranty does not apply and is not cumulative to any accessory or part distributed by Quadratec for which the Manu-facturer provides a separate written warranty. What is Covered:Subject to the terms, exclu-sions and limitations herein and with respect only to Quadratec branded accessories first sold in the United States, Quadratec warrants to the initial retail purchaser only that yourQuadratec accessory shall be free of defects in material and workmanship: for a period of three (3) years from date of retail purchase.This Limited Warranty is not assignable and shall terminate upon sale of the vehicle upon which the Quadratec accessory is installed or other transfer third persons.All other warranties are hereby disclaimed, ex-cept to the extent prohibited by applicable law in which case any implied warranty of mer-chantability or fitness for a particular purpose on this product is limited to 3 year from date of initial retail sale. Quadratec reserves the rights to: (a.) require invoice or other proof your ac-cessory is within the terms of this Limited Warranty as a condition of warranty service and, (b.) make future revisions to this product and Limited Warranty without prior notice or obligation to upgrade your product.What is Not Covered:Your Quadratec Limited Warranty does not cover products or parts Quadratec determines to have been damaged by or subjected to:(a.) installation damage, alteration, modifica-tion, combination with other parts, failure to maintain or improper repair or service, (b.) nor-mal wear & tear, cosmetic damage or damage from moisture or water immersion, (c.) Acts of God, accidents, misuse, negligence, inadequate mounting or impact with vehicle(s), obstacles or other aspects of the environment, (d.) theft,vandalism or other intentional damage.Remedy Limited to Repair/Replacement:The exclusive remedy provided hereunder shall,upon Quadratec inspection and at Q uadratec’s option, be either repair or replacement of prod-uct or parts (new or refurbished) covered under this Limited Warranty.Customers requesting warranty consideration should first contact Quadratec to obtain a RGA number(610-701-3336). All labor, removal, shipping and installation costs are customer’s responsibility.Other Limitations - Exclusion of Damages -Your Rights Under State Law:In consideration of the purchase price paid, nei-ther Quadratec nor any independent Quadratec distributor/licensee are responsible for any time loss, rental costs, or for any incidental, conse-quential, punitive or other damages you may have or incur in connection with any part or product purchased. Your exclusive remedy hereunder for covered parts is repair/replace-ment as described above.This Limited Warranty gives you specific rights.You may also have other rights that vary from state to state. For example, some states do not allow limitations of how long an implied war-ranty lasts and /or do not allow the exclusion or limitation of incidental or consequential damages, so the limitations and exclusions herein may not apply to you.©Quadratec, Inc. 2017. All Rights Reserved.9.22.17 A4 Version Part #12999.3088。
BEXO HMPE slings for heavy lift projects说明书
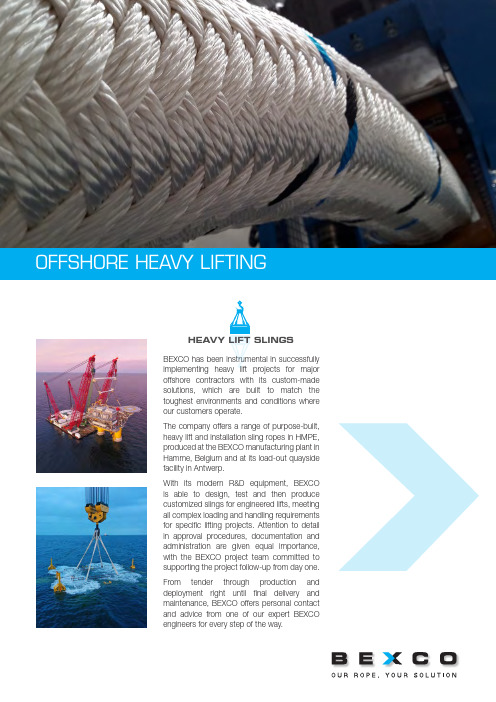
BEXCO has been instrumental in successfully implementing heavy lift projects for major offshore contractors with its custom-made solutions, which are built to match the toughest environments and conditions where our customers operate.The company offers a range of purpose-built, heavy lift and installation sling ropes in HMPE, produced at the BEXCO manufacturing plant in Hamme, Belgium and at its load-out quayside facility in Antwerp.With its modern R&D equipment, BEXCO is able to design, test and then produce customized slings for engineered lifts, meeting all complex loading and handling requirements for specific lifting projects. Attention to detail in approval procedures, documentation and administration are given equal importance, with the BEXCO project team committed to supporting the project follow-up from day one. From tender through production and deployment right until final delivery and maintenance, BEXCO offers personal contactand advice from one of our expert BEXCO engineers for every step of the way.OFFSHORE HEAVY LIFTINGSmulders is an international steel construction company with offices in Belgium, the Netherlands, Poland and the United Kingdom. Smulders specializes in metal constructions for the oil and gas industry and wind energy sector.Smulders uses BEXCO’s FLEXOR slings for the lifting of windmill components in their factory in Hoboken, Belgium.Bert De Vos, Smulders Purchasing Manager “BEXCO’s soft slings are, for the same break strengths, considerably thinner and lighter in comparison with the slings we used in the past, making them so much easier to handle. We choose our slings in function of the capacity of our cranes. The BEXCO’s slings are flexible in usage and can be used on different equipment, which means we can work with a minimum amount of slings for a maximum array of applications.Before the use of the FLEXOR round slings we used PES-soft slings. By changing to FLEXOR, we were able to decrease the hook-up team from 4 to 1 person only. Also we noted a remarkable difference in lifespan thanks to the use of the DURA-1200 sleeve.”ALE is one of the biggest international heavy transportation and lifting contractors, with a global network of operating centres and a large fleet of heavy cranes, specialist transport and installation equipment.For one of their projects off the Nigerian coast, ALE counted on BEXCO’s Ultraline Dyneema@SK78 grommet slings to do the job. Jelle Schepens, Senior Project Manager at ALE “BEXCO’s Ultraline slings had all the advantages we were lookingfor. The reduced weight offers a safer working environment for our people and equipment. The sub-rope system used in these slings is ingenious and reduces any operational risks. The Ultraline slings have a protective and breathing cover, which is a unique asset.We were very satisfied about BEXCO’s communication and project management. Although faced with a very tight time frame, BEXCO was able to deliver all slings inclusive all testing before the project deadline.We had the feeling that BEXCO was one of our partners, not just a supplier.”The general manager of the end user added “I would like to congratulate your company to have been from the beginning transparent with us and for achieving to get the slings delivered on time. I really appreciated your professionalism.”FLEXOR FOR SMULDERS SLINGS FOR ALE HEAVY LIFTDelivered to Smulders• FLEXOR round slings• Lengths between 20 and 53 feet• Breaking loads up to 2,204,000 lbsDelivered to ALE• Ultraline Dyneema SK78 grommet slings• Lengths 8 x 26 feet and 4 x 56 feet• Breaking loads of 9,500,000 lbsPRODUCTS FOR HEAVY LIFTING & INSTALLATIONBEXCO offers various types of lifting and installation arrangements using ropes manufactured with H igh-Modulus Polyethylene (H MPE). With the same strength but weighing 8 to 10 times less than traditional wire ropes, H MPE ropes are more flexible and much easier to handle; HMPE also has a much better fatigue life compared to wire, whilst retaining similar elastic elongation properties.BEXCO’s range of offshore heavy lifting rope has served several onshore and offshore applications, including• Offshore Oil & Gas lifting and installation projects (topsides, modules, substations, flares, modules)• Subsea installation (suction piles, pipelines, anchors, support structures, manifolds) • Foundations for offshore renewable projects (jackets,monopoles, turbines, blades)• Offshore decommissioning & salvageBEXCO supplies the world’s leading engineering contractorswith heavy lift slings to serve at offshore installations locatedin some of the most challenging marine environments on theplanet.BEXCO manufactures its HMPE rope using Dyneema®SK78,having been awarded diamond partnership status with its fibresupplier Royal DSM NV of Holland.• Light and easy handling• Fast rigging installation• Increased lift capacity• Soft contact surfaces• Torque free• Safe operations during use• No abrasion• Maintenance free• Not affected by fresh or salt water• Reduced risk of injuries• No fish hooksDyneema is a registered trademarkof Royal DSM N.V.PRODUCT OVERVIEWStrength(F)Strength(F)Diameter (Inch)Diameter (Inch)HMPE (Dyneema®)Polyester Steel Wire NylonWhen ordering, BEXCO collects detailed operational information so we canoffer, design and deliver exactly the right solution for your needs.ADVANTAGES AND BENEFITS®SK78 COREFLEXOR round slings are tested on various pin diameters to determine bending efficiency on different pin diameters.BEXCO’s precision manufacturing methods ensure production with tight length tolerances of identical batches of FLEXOR Slings.The core is made of Dyneema ® SK78 fibers which gives the sling an unrivaled lightweight in combination with its strength and flexibility.Double protection sleeve with heavy duty velcro closing for easy inspection and repair.Eyes can be lashed together forming a false eye.Strong and sturdy label fastened to sling.BEXCO’s DURA cover made with HMPE, especially designed incollaboration with local weaver. The DURA sleeve is tested intensively and shows a cut and abrasion resistance X10 compared with other round slings.SlingDouble protected eye which retains its shape and resists any flattening whilst operating in harsh conditions, allowing the use of smaller hardware; compared to traditional round slings, the width of the eyes when in use is 30 to 40% smaller.FLEXOR roundslingsEye widthEye width +30%Traditional round slingsFLEXORCONSTRUCTIONFLEXOR is a round sling using a three-strand core. This construction allows a combination of short lengths with high strengths, ensuring ease in handling. FLEXOR is designed for a long lifecycle and flexible usage.The core is made with Dyneema ® SK78 fibres and is protected by a double cover.The outer cover is standard made of a BEXCO DURA-1200 sleeve. This custom-made sleeve offers maximum protection against cuts, punctures, snags and abrasion as well as UV exposure. The strength will be only affected after the covers have been worn through and the cores start to abrade. The eyes are designed to retain their shape during precision lifts and will resist any natural flattening whilst operating in harsh offshore conditions, allowing the use of smaller hardware.FEATURES• Construction: Load bearing cores in Dyneema ® SK78covered with a DURA sleeve made of HMPE • Torque neutral• Specific density: 0.975kg/m3 (floating)• Melting point: 145°C • Abrasion resistance: excellent • Elastic elongation at WLL: +/- 1%• UV Resistance: excellent • Chemical resistance: excellent • Water absorption: 0%• Colour of rope: standard white with blue eyes; other colours on request APPLICATIONS• Heavy lift sling, pennant, A&R recovery, forerunner, pull-in rope,...SECTORS• Onshore and offshore Oil and gas installation • Subsea installation • Offshore renewable• Decommisioning and salvageULTRALINE DYNEEMA SK78®CONSTRUCTIONBEXCO’s precision-engineered Ultraline sling with Dyneema ® SK78 is a so-called parallel core construction. This construction consists of two parts, namely the core elements and the cover (see illustration). It is stronger than conventional steel wire rope, yet the corresponding weight is 8 to 10 times lower.The core elements are three-strand subropes that are oriented parallel to the longitudinal axis of the rope. The cover is a braid (standard consisting of polyester), which provides dimensional stability to the rope structure and protects the cores from external damage. The three-strand core design is used because of the good stretch characteristics and excellent splice strength efficiency exhibited by this type of core design.The braided cover is treated with a marine finish to further enhance the life of the cover under abrasion loads. The cover braid itself does not contribute to the strength of the rope.Remarks:• Sling strengths are for spliced ropes• Single leg sling strengths are for D/d ratio in the eyes >2. See p14 for strength for lower D/d ratios• Grommet sling strengths are for D/d ratio >3. See p14 for strengths for lower FEATURES• Construction: load bearing cores made with Dyneema ®SK78, overbraided with a polyester jacket • Torque neutral• Specific density: depending on rope size, 0.975kg/m3 for the Dyneema ® SK78 core and 1,380kg/m3 for the PES jacket • Melting point: 145°C • Abrasion resistance: excellent • Elastic elongation at WLL: +/-1%• UV Resistance: excellent • Chemical resistance: excellent • Water absorption: 0%• Colour: standard white; other colours on requestAPPLICATIONS• heavy lift sling, pennant, A&R recovery, forerunner, pull-in rope,...SECTORS• Onshore and offshore Oil and gas installation • Subsea installation • Offshore renewable• Decommisioning and salvageSUPERIOR WITH DYNEEMA SK78®FEATURES• Construction: 8- or 12-strand braided rope made withDyneema ® SK78• Torque neutral• Specific density: 0.975kg/m3 (floating)• Melting point: 145°C • Abrasion resistance: excellent • Elastic elongation at WLL: +/- 1%• UV Resistance: excellent • Chemical resistance: excellent • Water absorption: 0%• Colour: standard white Remarks:• Sling strengths are for spliced ropes• Single leg sling strengths are for D/d ratio in the eyes >2. See p14 for strength for lower D/d ratios• Grommet sling strengths are for D/d ratio >2,5. See p14APPLICATIONS• Heavy lift sling, pennant, A&R recovery, forerunner, deepwater lowering line, pull-in rope,...SECTORS• Onshore and offshore Oil and gas installation • Subsea installation • Offshore renewable• Decommisioning and salvage8-s t r a n dCONSTRUCTIONand operation is important.and anti-clockwise strands making the rope torque ing a specialized coating procedure that limits the abrasion and thus significantly extends the lifecycle of the ropes. Other coatings can be applied to suit specific applications.The rope can also be overbraided with a protective jacket or covered with protection sleevesROPE SLING CONFIGURATIONSBEXCO rope slings are available in single and endless configurations.Single leg slingsSingle leg slings are made from a single rope with an eye splice at both ends.• Maximum fiber efficiency• High bending efficiency in eyes (D/d)Disadvantages• Heavier and bigger eyes • Minimum length limitedEndless rope slings or grommetsThe endless rope slings, also known as grommets, are configured splicing both ends of the rope into each other. The splice can be positioned in the center or out of the center. Both grommet legs can be lashed together forming ‘false eyes’.Advantages• Shorter lengths possible • Narrower bearing pointDisadvantages• Lower bending efficiency in the eyes (D/d)• Lower fiber efficiency The choice of sling configuration is depended on the rigging arrangement. Each lift calls for a sling designed for that unique operation. BEXCO can assists in selecting the best solution for a specific project.WLLLengths and elongationBEXCO rope slings are standard supplied with a length tolerance of +/- 0.5%. It is possible to achieve tighter tolerances for e.g. a matched set of slings. These tolerances depend on sling length and configuration. Please contact BEXCO for length tolerances on specific slings.It is import to note that new rope slings will experience an initial elongation when the slings are put under load. This is called bedding-in elongation or constructional elongation. Part of this elongation is recoverable. H owever after a long period of usage, the elongation will no longer be recoverable and the slings will not return to their original length.The below graph highlights the differences between initial bedding-in (constructional) elongation and elastic elongation.ACCESSORIESRope and Eye ProtectionPolyester or HMPE jacketThe Ultraline sling is standard overbraided with a polyester jacket. Also the Superior line can be overbraided with a jacket. The polyester jacket is very durable with excellent abrasion and cut resistance and is non-floating. Rope slings can also be overbraided with an HMPE jacket for superior abrasion and cut resistance making them 100% floating.Deltaweb clothingAs a standard offering, the eyes of BEXCO’s rope slings are protected with a Deltaweb heavy-duty clothing. The clothing is highly abrasion- resistant and remains flexible under working conditions. DURA coverThe eyes can be equipped with a cloth made of HMPE yarns for superior abrasion resistance. These cloths can be applied by sewing or with a removable sleeve applied around the rope with a heavy-duty Velcro tape.CoatingA polyurethane elastomer coating can be applied to a rope. Heavy-duty steel thimblesEyes may also be protected with heavy-duty galvanized steel thimbles. The high-strength thimble protects the rope and maintains the proper bending radius when it is connected to mating hardware.Filter ClothDepending on the installation procedure there may be a potential risk that the rope is dropped on the seabed. Although this in itself has no impact on the rope, it is possible that seabed particles may diffuse into the rope. These particles will have a deteriorating effect on the strength of the rope during its usage life due to their abrasive nature. To avoid this, filter material can be inserted between the cover and the core. The filter stops particles of 5 μm or larger.Handling pointROV Handling points (or clump weight connection points etc.) can be attached to the eyes and the body.Pulling eyesChinese fingers can be installed on the rope for a higher pulling force.BEXCO’s R&D facility performs comprehensive testing of all of its synthetic rope constructions in different configurations. These include break load testing, stiffness and fatigue testing, influence of twist and small D/d ratios. The test facility can be used for proof loading and length verification of slings up to 25m in accordance with various industry standards. FEATURES• 82ft testbed• 16.5ft stroke• 500Tf + 80Tf cylinder• Break testing• Stiffness testing• Creep testing• Fatigue testing• Water spraying• Extensometer systemSERVICESBEXCO has in-house, highly-trained technicians to serve our clients’ needs.• Installation support on site• Inspection on site• Repairs• Our inspectors are trained and hold the required certifications and permits to go offshore.BEXCO H eavy-Lift slings with Dyneema® SK78 are manufactured to the highest standards of quality. BEXCO’s manufacturing facilities are ISO 9001: 2015 certified for the research and development and production of Marine, Offshore and Industrial Ropes in synthetic high performance fibers. All of BEXCO’s production, operational and administrative processes are regularly audited by the world’s leading classification societies including Lloyds Register, DNV GL, Bureau Veritas as the majority of its main offshore synthetic rope solutions serve the world’s leading oil and gas majors. Comprehensive certification packages are put together for each sling including description, drawings, certificates, handling and installation manual.A strong and sturdy identification label is fastened securely to the rope. It typically contains the following data:• Purchase order number• Rope reference number• Rope minimum break strength• Rope diameter• Rope length• Class certification numberCONTACTBEXCO nvIndustriepark Zwaarveld 259220 HammeBelgiumTel: +32 52 499 370E-mail:*****************For more information on our products:www.bexco.beREFERENCESSaipem, Heerema Marine Contracting, Allseas, Geosea, Ale Heavy Lift, Seaway Heavy lifting, Smulders, Bluewater, Jan de Nul, Technip, Subsea 7 Dries HoefkensKey Account ManagerOffshore Lifting and Installation******************Joe McCoyDirector of Sales US***************。
John Deere 600FD-Flexible Draper Active Header Hei

Copyright © 2014 Deere & Company. All Rights Reserved. THIS MATERIAL IS THE PROPERTY OF DEERE & COMPANY. ALL USE AND OR REPRODUCTION NOT SPECIFICALLY AUTHORIZED BY DEERE & COMPANY IS PROHIBITED.All information, illustrations, and specifications in this manual are based on the latest information available at the time of publication. The right is reserved to make changes at any time without notice.HXE77366 (03SEP14)600FD-Flexible Draper Platforms are compatible with John Deere 70 Series STS and John DeereS-Series Combines.• Refer to inside fold out portion of this guide for basic setup andTroubleshooting.• Refer to outside fold out portion of this guide for CalibrationProcedures and a Sensor Voltage Map.IMPORTANT: This guide is to assist operators with correct setup and operation of 600FD Flexible Draper Platform.Always refer to your Operator’s manual for questions.600FD-Flexible DraperActive Header Height Control (AHHC)Quick Reference GuideS-Series LC1 AddressController Address DisplayDescriptionLC121_ _ n n n X X X (A) Left-Hand Auxiliary Height Sensor Voltage (cc #9826)LC121_ _ X X X n n n (B) Left-Hand Main Height Sensor Voltage (cc #9816)LC122_ _ n n n X X X (C) Center Auxiliary Header Height Sensor Voltage (cc #9803)LC122_ _ X X X n n n(D) Center Main Header Height Sensor 1 Voltage630FD/645FD (cc #9817)LC122_ _ _ _ _ n n n (E) Center Main Header Height Sensor 1 Voltage 635FD/640FD (cc #9817)LC123_ _ n n n X X X (F) Center Main Header Height Sensor 2 Voltage 630FD/645FD (cc #9804)LC123_ _ X X X n n n (G) Center Main Header Height Sensor 2 Voltage 70 Series LC1 AddressController Address DisplayDescriptionLC131_ _ _ _ _ n n n (A) Left-Hand Auxiliary Height Sensor Voltage (cc #9826)LC128_ _ _ _ _ n n n (B) Left-Hand Main Height Sensor Voltage (cc #9816)LC132_ _ _ _ _ n n n (C) Center Auxiliary Header Height Sensor Voltage (cc #9803)LC129_ _ _ _ _ n n n(D) Center Main Header Height Sensor 1 Voltage630FD/645FD (cc #9817)LC129_ _ _ _ _ n n n (E) Center Main Header Height Sensor 1 Voltage 635FD/640FD (cc #9817)LC133_ _ _ _ _ n n n (F) Center Main Header Height Sensor 2 Voltage 630FD/645FD (cc #9804)LC133_ _ _ _ _ n n n(G) Center Main Header Height Sensor 2 Voltage 600FD Sensor Voltage MapAdjustments (cont)Hydraulic Feeder House Fore/Aft Tilt AdjustNOTE: Only works if equipped with hydraulic feeder house fore/aft tilt.Hydraulic feeder house fore/aft tilt adjust allows operator to increase or decrease angle of feeder house tilt frame.1. Touch plus (+) or minus (-) symbol or rotate selection dial to adjust angle of feeder house tilt frame.• Increase tilts feeder house tilt frame angle forward.• Decrease tilts feeder house tilt frame angle rearward.2. Display shows operator adjustment settings.Side Belt Speed Reduction SwitchNOTE: Only works on draper platforms.Slowing side draper belts speed enhances feeding performance when crop is harvested on one side of platform, due to irregular shaped fields.Side belt speed reduction switch allows speed of draper belt to automatically slow to a factory setpoint speed.1. Press side belt speed reduction switch.2. Slow speed mode engaged will appear on display and draper belt speed automatically slows to factory setpoint speed.3. Pressing belt speed reduction switch again or attempting to make manual belt speed adjustments while in slow speed mode automatically returns belt speed to original speed set by JABHDEF G CIAHHC Mode OptionsFor Flex Draper, there are two unique Active Header Height Sensing (AHHS) modes:On-ground (“flex mode”) – soybeans, lentils, chickpeasOff-ground (“rigid mode”), auxiliary attachment – wheat, barley, oats, canolaFloat arm brackets may be reinstalled for operating in off-ground mode after the feeder house speed calibration and header When using off-ground mode with the ground-engaging sensor arms unpinned ensure grease has been added to sensor arm pivot shaft and that sensor arm rotates freely. Also, ensure storage pin is placed in correct location on float arm, and not left on sensor arm:Recommended Header Modes to EnableMulti-function lever buttons 2 and 3 will Off-Ground Un-pin AHHC sensor arms Float arm lock-out brackets may remain installed Set HydraFlex pressureto maximum setting to lock cutterbar On-Ground 600FD – S Series or 70 Series Ensure all software is up-to-date Remove float arm lock-out brackets Combine screens for header calibration or refer to Calibrations and Settings section ofOperator’s ManualYes No Pin-up all off-ground AHHC sensor arms Verify all three auxiliary sensors are reading above 0.9 VDC while pinned up (see reverse)See Troubleshooting, Lock-out bracket – REMOVEFloat arm stop bolt – DO NOT REMOVESelect the automatic header modes to be enabled:AUTOCombine - Header Setup AHCAUTO。
- 1、下载文档前请自行甄别文档内容的完整性,平台不提供额外的编辑、内容补充、找答案等附加服务。
- 2、"仅部分预览"的文档,不可在线预览部分如存在完整性等问题,可反馈申请退款(可完整预览的文档不适用该条件!)。
- 3、如文档侵犯您的权益,请联系客服反馈,我们会尽快为您处理(人工客服工作时间:9:00-18:30)。
1. INTRODUCTION
Wavelet transform is an effective method for image and video representation. It can efficiently pack the energy of the image/video and facilitate the latter entropy coding. An additional advantage of wavelet transform is its nice scalability. Studies have been focused on how to efficiently exploit the correlations among frames for wavelet-based video coding. Directly applying the wavelet transform to the predicted residues is usually referred as the MC + 2D wavelet coding [2][3]. Such schemes have been extensively investigated in the past decade. Since the wavelet transform is not good at representing the residual image, it does not show the desired promising efficiency. Another aspect of wavelet video coding is to directly apply wavelet transform in all three directions, i.e., the temporal, horizontal and vertical directions, where the correlations among frames are exploited by the temporal wavelet transform instead of motion compensation. With the inherent scalable property, the 3D wavelet video coding can readily achieve quality, temporal and spatial scalabilities simultaneously, which is a very desirable feature in the video streaming and storage applications [1]. However, due to the existing motion among frames, the pixels located at the same position in different frames may be out of alignment so that the efficiency of the
Header for SPIE use
direct temporal wavelet transform is limited. Some early works have been done to incorporate motion information into the 3D wavelet coding. Taubman and Zakhor used a global displacement model to align different frames before the 3D wavelet transform [4]. Wang et al. [5] proposed to register and warp all frames into a common coordinate system and then apply a shape-adaptive 3D wavelet transform to the warped video. Considering the limitations of the global motion model, Ohm proposed to use the block matching technique similar as that in the traditional video coding schemes and meanwhile specially process the covered/uncovered, connected/unconnected regions [6]. In the above mentioned approaches, either the perfect reconstruction can not be achieved, or the motion accuracy is not sufficient. Even after the motion alignment, the compression efficiency is still not satisfactory. Recently, MPEG is actively investigating and developing the inter-frame wavelet coding technologies. MCEZBC proposed by Chen et al has become prominent because of the excellent performance [8]. In MC-EZBC, each pair of frames is first motion estimated with hierarchical block structure, and then decomposed into a high-band frame and a low-band frame by the motion-aligned lifting-based Haar filter. Further temporal decomposition is performed on each pair of low-band frames with the similar process. MC-EZBC efficiently solves the problems in the fractional-pel motion aligned temporal transform. The performance of MC-EZBC is comparable to that of the JVT standard [9]. However, as a short support wavelet filter, Haar filter may not fully exploit the long-period correlations across video frames. To utilize the long-period correlation along the motion trajectory, Xu et al proposed the motion-threading (MTh) approach [7]. Along with the MB-based estimated motion vectors, pixels are formed into many nonoverlapped motion threads. Multi-layer shape-adaptive wavelet transform is applied to each motion thread. The temporally transformed frames are further decomposed horizontally and vertically within each frame. The entire decomposed coefficients are coded with the embedded entropy coding to organize a scalable bit-stream. Motion-threading technique provides a flexible structure in utilizing the correlation among frames. For simple motion sequences, MTh can achieve a good performance. The limitation of the MTh scheme is the nonoverlapping restriction which intends to ensure the perfect wavelet reconstruction upon motion threads. For some complex motion sequence, many threads which involve many-to-one pixel mapping have to be artificially truncated under this restriction. The wavelet reconstruction error on these thread boundaries considerably decrease the coding efficiency [15]. This paper proposes an advanced motion-threading technique to improve the coding efficiency of the 3D wavelet coding. We first extend the original motion-threading technique with the lifting wavelet structure [10]. Even if many-to-one mapping arises, all the motion threads can still be filtered without being terminated. This can greatly reduce the boundary effects. Furthermore, fractional-pixel motion estimation and alignment, such as half-pixel and quarter-pixel, can be easily applied in the extended scheme with perfect wavelet reconstruction. To reduce the motion cost, this paper also investigates the correlation of motion vectors among adjacent frames. An R-D optimized criterion is designed to select a proper MB mode, considering the motion correlations during motion estimation and motion vector coding. Results show that the proposed advanced MTh scheme improves the coding efficiency up to 1.5~5.5dB generally, and achieves a competitive performance to the state-of-the-art JVT standard [9]. The paper is organized as follows. Section 2 introduces the basic structure of the original motion threading technique. In section 3, an advanced lifting-based motion-threading 3D wavelet coding scheme is proposed. Fractional pixel motion alignment and multi-layer motion threading are discussed in detail. An R-D optimized scheme is designed to consider both the mismatching problem and the motion cost reduction. Experimental results are given in section 4. Finally, we conclude this paper in Section 5.