浅析铝合金铸锭均匀化退火表面起泡原因
铝板带生产中气泡和黑麻点缺陷的成因及其预防措施

铝板带生产中“气泡”和“黑麻点”缺陷的成因及其预防措施在我国众多的中小型铝板带生产厂仍在广泛地采用铝熔化、精炼→水平连铸、锯切→加热、热轧→粗、中、精轧→退火的工艺。
这是由于水平连铸法具有连续作业、锭长不限、生产效率较高、操作方便以及设备与基建投资较小等优点。
然而,笔者在有关现场深入考察发现:这些厂在生产过程中热轧坯料的表面“气泡”与成品表面的“黑麻点”、“起皮”等缺陷都与水平连铸方法有关。
为此,围绕“气泡”、“黑麻点”形成原因进行分析讨论,并在预防措施方面提出自己一些看法。
1 热轧坯料表面“气泡”成因及其预防经现场了解,出现“气泡”大体规律为:偶尔成批出现在热轧后的坯料表面;“气泡”呈“鼓包”形式;数量不多,大小不一;常出现在坯料的一个大面上。
经观察分析确认:其根本原因是由于中间包上所安装的结晶器结构不合理,它不利于铝熔体结晶凝固时析出的气体的排出,使之滞留于锭坯上侧近表面处所致。
铝熔体易于吸收氢气,且随温度与状态的变化,平衡吸氢量变化很大:高温一次电解铝液,在950 ℃时的平衡吸氢量为2. 9 mL/ 100gAl ,750 ℃为1. 5 mL/100gAl ,660 ℃熔点的液态铝中平衡吸氢量为0. 69mL/ 100gAl ,而在此温度结晶后的固态铝则为0. 036mL/ 100gAl ,即二者相差近20 倍[2 ] 。
由此说明,连铸时在结晶凝固界面附近的铝熔体中会出现氢气的“浓化”,其分压增高,足以成核形成“气泡”。
而此时,由于受石棉挡板xianzhi,“气泡”无法通过中间包中熔体而逸出,只能滞留在锭坯上表面的次表层,使热轧后在气体膨胀压力作用下形成“气泡”。
在现场生产中对此常采用小刀挑破方法试图消除其后续影响,岂不知此举可能形成制品表面的“起皮”、“黑斑”等缺陷。
1. 3 预防措施首先是加强精炼除气效果,使铝熔体在结晶器内即使氢气“浓化”也达不到形成“气泡”的程度。
这点对于直接使用高温电解铝液作原料的情况尤其重要。
铝合金热处理基本形式
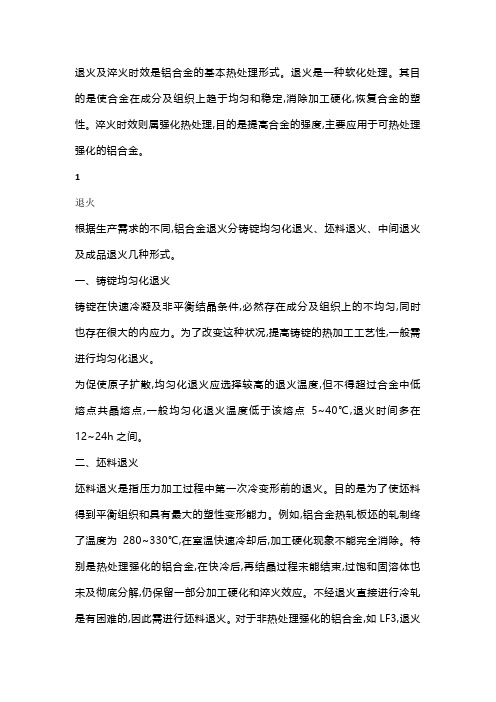
退火及淬火时效是铝合金的基本热处理形式。
退火是一种软化处理。
其目的是使合金在成分及组织上趋于均匀和稳定,消除加工硬化,恢复合金的塑性。
淬火时效则属强化热处理,目的是提高合金的强度,主要应用于可热处理强化的铝合金。
1退火根据生产需求的不同,铝合金退火分铸锭均匀化退火、坯料退火、中间退火及成品退火几种形式。
一、铸锭均匀化退火铸锭在快速冷凝及非平衡结晶条件,必然存在成分及组织上的不均匀,同时也存在很大的内应力。
为了改变这种状况,提高铸锭的热加工工艺性,一般需进行均匀化退火。
为促使原子扩散,均匀化退火应选择较高的退火温度,但不得超过合金中低熔点共晶熔点,一般均匀化退火温度低于该熔点5~40℃,退火时间多在12~24h之间。
二、坯料退火坯料退火是指压力加工过程中第一次冷变形前的退火。
目的是为了使坯料得到平衡组织和具有最大的塑性变形能力。
例如,铝合金热轧板坯的轧制终了温度为280~330℃,在室温快速冷却后,加工硬化现象不能完全消除。
特别是热处理强化的铝合金,在快冷后,再结晶过程未能结束,过饱和固溶体也未及彻底分解,仍保留一部分加工硬化和淬火效应。
不经退火直接进行冷轧是有困难的,因此需进行坯料退火。
对于非热处理强化的铝合金,如LF3,退火温度为370~470℃,保温1.5~2.5H后空冷,用于冷拉伸管加工的坯料、退火温度应适当高一些,可选上限温度。
对于可热处理强化的铝合金,如LY11及LY12,坯料退火温度为390~450℃,保温1~3H,随后在炉中以不大于30℃/h的速度冷却到270℃以下再出炉空冷。
三、中间退火中间退火是指冷变形工序之间的退火,其目的是为了消除加工硬化,以利于继续冷加工变形。
一般来说,经过坯料退火后的材料,在承受45~85%的冷变形后,如不进行中间退火而继续冷加工将会发生困难。
中间退火的工艺制度基本上与坯料退火相同。
根据对冷变形程度的要求,中间退火可分为完全退火(总变形量ε≈60~70%),简单退火(ε≤50%)和轻微退火(ε≈30~40%)三种。
铸锭热处理的分类和目的

1.铸锭热处理的分类
铝合金铸锭热处理有两种形式,一种是均匀化处理,另一种是退火处理。
按处理温度高低,铸锭均匀化分为普通均匀化和高温均匀化两种。
普通均匀化在超过铝中主要合金化组元溶解度曲线并低于合金共晶温度及非平衡固相线的温度进行;高温均匀化在高于非平衡固相线温度(即非平衡共晶熔化温度)而低于合金的平衡固相线温度进行(见图2—10—1)。
由图2—10—1可见,合金I和III可以进行普通均匀化,因为合金l和III在凝固时不形成熔化温度低于平衡固相线温度的组成物;而合金Ⅱ既可进行普通均匀化,也可进行高温均匀化。
铸锭退火是在足以消除内应力的温度300~350℃时进行的。
对于大多数热处理可强化的铝合金而言,这个温度区间相应于固溶体稳定性最小的区间。
2.铸锭均匀化和退火的目的
铸锭均匀化的目的是消除或减少晶内偏析,提高材料热变形和冷变形的能力;改善半制品、特别是较厚较粗的半制品的力学性能;同时还可以消除铸锭在凝固时产生的内应力,也就是使铸态合金具有较大的化学均一性和组织均一性。
铸锭退火的目的是消除铸锭中的内应力和软化铸锭在结晶及随后冷却过程中发生的完全或局部液态淬火现象。
2A14铝合金棒材表面气泡的分析

!"#$%&’& () *+,)#-. /+00$. () !!%# !$+1’"’+1 !$$(% 234,+5.5 6(5&
/(0, 123456783
(7(,48.#&4 9’:84 !$$(% ;(< , 945< , =#,0’" >?@@A@, ;8’"#) !0&4,#-4:+72 98:;<62 =8==>2 ?; !(%# <>8@A3A8@ <>>?B :?C9 A9 D72 @<A3 :2<9?3 D7<D :298>D9 A3 D72 E<9D2C F:?C86DG (66?:CA34 D? F:?5 C86A34 :2<>ADB, D72 D72 98:;<62 =8==>2 <:2 2H<@A32CG +72 6<8929 ?; 98:;<62 =8==>2 <:2 <3<>B92CG +72 F:2I2<DAI29 <:2 :292<:672CG B.% C(,5&:!(%# <>8@A3A8@ <>>?B :?C; 98:;<62 =8==>2; 2H2D:89A?3; J82367
图! 棒材上夹杂气泡的内表面组织照片
用。这样可大大减少通透性气泡。
"
$0%
生产工艺对表面气泡的影响
熔铸工艺的影响 合金熔体精炼时, 通惰性气体时间长一些, 减少
氢原子的固溶, 避免产生气体通透性气泡。铸锭的 高、 低倍组织要符合标准要求。 $0# 挤压工艺对棒材表面气泡的影响 挤压工艺对夹杂气泡没有明显影响, 只要挤压 设备干净就不会产生夹杂气泡; 当挤压温度过高时 会产生挤压分层气泡; 镦粗挤压会产生气体渗透气
均匀化退火对6056铝合金组织与性能的影响

均匀化退火对6056铝合金组织与性能的影响宁波科诺铝业有限责任公司,董培纯邱建平李博摘要:采用热分析技术、扫描电子显微镜、拉伸试验研究均匀化退火处理对于6056铝合金微观组织和力学性能的影响。
结果表明:6056铝合金铸态组织存在严重的枝晶偏析及明显的非平衡共晶组织,经过540℃×12 h 均匀化退火处理后,枝晶偏析和非平衡共晶组织明显消除,其强度降低、塑性大幅度提高。
关键词:均匀化退火;微观组织;力学性能The effect of homogenizing annealing on microstructureand properties of 6056 aluminum alloy(Ningbo KENO Aluminum Co.,Ltd,Ningbo 315033,China)Abstract:The influence of homogenizing annealing on microstructure and properties of 6056 aluminum alloy is investigated by heat analysis technology,scan electrical microscope and tensile test. The results show that severe dendritic-segregation and unequilibrium phases exist in its as-cast structure,After 540℃×12h homogenizing annealing treatment,dendrite segregation and unequilibrium eutectic phases eliminate . The strength decrease and the ductility increase obviously.Keywords:Homogenization annealing;Microstructure;Mechanical properties引言6056铝合金是广泛应用于汽车和航空领域的一种Al-Mg-Si-Cu合金,其强度比6061铝合金高15%,可焊性、耐腐蚀性能和切削加工性能均优于7075和2024铝合金[1,2]。
铝合金铸锭主要缺陷特征、形成原因及防止、补救方法

铝合金铸锭主要缺陷特征、形成原因及防止、补救方法1、化学成份不合格▲缺陷特征及发现方法最终分析结果主要合金元素或杂质含量超标●形成原因1、配料中宜烧损元素取值不合适或计算有误;2、中间合金不符合标准;3、清炉、洗炉不彻底残留有上炉的铝合金及杂质;4、不同合金料相混;5、加镁后停留时间过长,并且无覆盖剂保护、使合金液氧化烧损严重;6、没有彻底搅拌,成分不均匀,导致取样不能反应出真实情况;7、炉前分析不正确。
★防止办法及补救措施1、在配料中,易烧损元素取技术标准上限或经验烧损值的上限,并经过仔细校对,;2、选用符合标准的成分分析值准确的中间合金配料;3、转炉前彻底清炉、洗炉,清洗浇包及工具;4、检查和鉴定炉前分析仪表是否有故障,如有故障,应送有关计量部门或出产厂家或其他维修站修复鉴定;5、严禁加镁后停留时间超过十分钟,并用保护性覆盖剂;6、按分析化验取样技术要求规定取样,取样前要充分搅拌合金液;7、严禁使用混装的废料和不明成份的炉料。
2、气孔▲缺陷特征及发现方法铸锭表面或内部出现的大或小的孔洞,形状比较规则;有分散的和比较集中的两类;在对铸锭作外观检查或机械加工后可发现。
●形成原因1、炉料带水气,使熔炉内水蒸气浓度增加;2、熔炉大、中修后未烘干或烘干不透;3、合金液没有覆盖保护或过热;4、熔炉、浇包工具等未烘干;5、浇注时合金液流动不连续平稳、产生涡流,卷入了气体;6、合金液精去气不充分;7、煤、煤气及油中的含水量超标。
★防止办法及补救措施1、严禁把带有水气的炉料装入炉中,装炉前要在400度左右温度下烘烤2H;2、严格按工艺对大修、中修后的炉子进行烘烤;3、熔化前按工艺要求对熔炉、浇注工具、熔剂等进行烘烧,然后才可使用;4、选用合适的精炼方法和效果好的精炼剂充分精炼合金液,精炼后加覆盖剂保护。
如果精炼后静置时间超过6H,则要进行二次精炼方可浇注或使用;5、控制浇注时液流连续均匀地浇注,未注完锭模不要中断;6、使用含水量符合要求的煤或煤气、油等燃料熔化合金液。
铸件油漆起泡原因
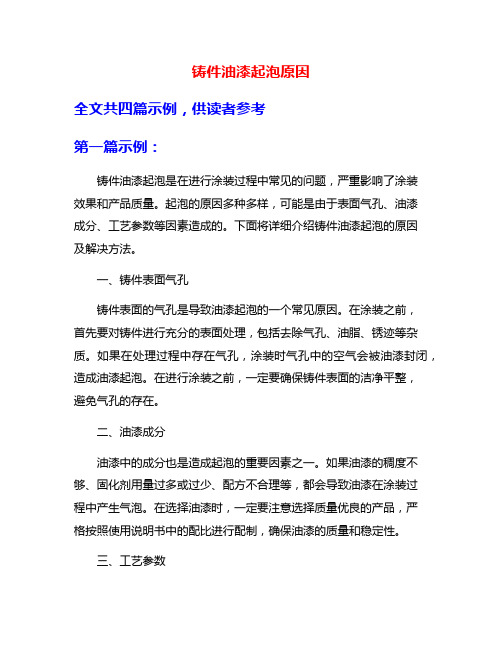
铸件油漆起泡原因全文共四篇示例,供读者参考第一篇示例:铸件油漆起泡是在进行涂装过程中常见的问题,严重影响了涂装效果和产品质量。
起泡的原因多种多样,可能是由于表面气孔、油漆成分、工艺参数等因素造成的。
下面将详细介绍铸件油漆起泡的原因及解决方法。
一、铸件表面气孔铸件表面的气孔是导致油漆起泡的一个常见原因。
在涂装之前,首先要对铸件进行充分的表面处理,包括去除气孔、油脂、锈迹等杂质。
如果在处理过程中存在气孔,涂装时气孔中的空气会被油漆封闭,造成油漆起泡。
在进行涂装之前,一定要确保铸件表面的洁净平整,避免气孔的存在。
二、油漆成分油漆中的成分也是造成起泡的重要因素之一。
如果油漆的稠度不够、固化剂用量过多或过少、配方不合理等,都会导致油漆在涂装过程中产生气泡。
在选择油漆时,一定要注意选择质量优良的产品,严格按照使用说明书中的配比进行配制,确保油漆的质量和稳定性。
三、工艺参数除了铸件表面和油漆成分的因素外,工艺参数也会影响油漆的起泡情况。
涂装时的温度、湿度、喷涂压力等参数都会影响油漆的涂布效果。
如果工艺参数设置不当,容易导致油漆起泡。
在进行涂装前,必须确定好工艺参数,确保涂装过程中的稳定性和质量。
四、解决方法针对铸件油漆起泡的问题,可以采取以下几种解决方法:1. 增加涂装前的表面处理工艺,如喷砂、打磨等,确保铸件表面光滑洁净,减少气孔的存在。
2. 选择合适的油漆产品,避免因油漆成分问题导致起泡。
3. 严格控制工艺参数,确保涂装过程中的稳定性和质量。
4. 多次实验和调整,找出问题根源并进行改进。
5. 及时清理涂装设备和喷嘴,确保涂装设备干净,减少油漆起泡的可能性。
铸件油漆起泡是一个常见的涂装问题,需要我们在生产过程中严格控制各项因素,以确保产品质量和涂装效果。
通过合理的工艺控制、选择优质的油漆产品和严格的质量管理,可以有效减少铸件油漆起泡的发生,提高产品的涂装质量和外观效果。
希望以上内容能够为相关行业提供一些参考和帮助。
5083铝合金铸锭均匀化处理对铸锭和板材组织与性能的影响_吴欣凤

收稿日期:2007-04-29 第一作者简介:吴欣凤(1962-),女,黑龙江哈尔滨人,高级工程师。
5083铝合金铸锭均匀化处理对铸锭和板材组织与性能的影响吴欣凤(东北轻合金有限责任公司,黑龙江哈尔滨150060)摘要:系统研究了5083合金铸锭均匀化处理和不均匀化热处理对铸锭、成品板材组织和性能的影响。
通过高温瞬时试验、剥落腐蚀试验、扫描电镜及力学性能试验,对经均匀化和不经均匀化的5083铝合金铸锭的轧制制品进行对比分析。
关键词:5083铝合金;铸锭;均匀化处理;板材中图分类号:TG146.21;TG156 文献标识码:A 文章编号:1007-7235(2007)08-0048-06Effects of 5083aluminium alloy ingot homogenizing on properties and structures of ingot and platesWU Xin -feng(Northeast Light Alloy Co .,Ltd .,Harbin 150060,C hina )A bstract :The effects of 5083alu minium alloy ingot homogenizing and non -homogenizing on properties and structures of ingot and plates are researched .The rolling products by homogenizing ingot and non -homogenizing ingot are analysed and compared through high temperature property tests ,corrosion tests ,SE M analysis and machine property tests .Key words :5083aluminium alloy ;in got ;homogenizing ;plate 5083是Al -Mg 系铝合金,具有中等强度、良好的耐腐蚀性能和加工成形性能,被广泛用于交通运输、化工等领域。
2024铝合金的均匀化热处理研究

图3 2024铝合金的DSC曲线
2.3均匀化态合金的组织 图4(a)、(b)、(c)、(d)、(e)所示为合金在不
同均匀化温度下进行均匀化处理的金相组织。可 以看出,随均匀化温度的升高,合金组织中的非 平衡低熔点共晶相逐渐溶解,晶界上的残留相由 连续分布转变为不连续分布。经495℃均匀化处理 24h后,合金中的枝晶网络变稀,非溶相和枝晶偏 析基本消除;当均匀化温度进一步升高到505c|C时, 发生轻微过烧;合金经515℃均匀化后,出现晶界 复熔物或三角晶界,合金处于较严重过烧状态。 因此,考虑到T业生产中的各种影响因素(大尺寸 铸锭和炉温波动等),在满足合金性能要求的前提 下,建议合金均匀化温度为490~495。C。
1 实验材料及方法
实验用材料为东北轻合金有限责任公司提供的 2024铝合金铸锭,其主要化学成分(质量分数/%)为 Cu 3.8-4.9,Mg 1.2-1.8,Mn 0.3—0.9,A1余量。铸 锭尺寸为85mmx300mmx200mm。利用线切割将铸 锭切割成15mmxl5mmxlomm(长×宽×高)的小块 试样。小块试样分别在465℃、4800C、495℃、 505℃、515℃下进行均匀化处理,处理时间为24 h。在选定的最佳均匀化温度下分别处理12 h、24 h、48 h和72 h。均匀化处理所用设备为程序控温 SX-4—50箱式电阻炉,温度误差±2℃。采用 POLYVER—MET显微镜观测金相组织,金相试样采 用KeHem试剂腐蚀;Sirion200场发射扫描电镜观 察铸锭枝晶组织、定性观测枝晶网络溶解程度和 残留相的大小、数量和分布特征。采用日本理学G, lnaX 2500X射线衍射仪分析合金中第二相。第二相 组成分析采用Sirion200扫描电镜上配套的EDX设备
共晶相,Cu,Mg和Mn元素在晶内及晶界分布不均匀;经过均匀化处理后,合金组织中的非平衡相逐渐溶解,各组元分布趋
铝合金压铸件气泡产生的原因

铝合金压铸件气泡产生的原因
铝合金压铸件气泡产生的原因有以下几点:
1. 金属液在压射室充满度过低,易产生卷气,初压射速度过高。
2. 模具浇注系统不合理,排气不良。
3. 熔炼温度过高,含气量高,溶液未除气。
4. 模具温度过高,流模时间不够。
金属凝固时间不足,强度不够过早开模,受压气体膨胀起来。
5. 脱模剂、注射头油用量过多。
6. 喷涂后吹气时间过短,模具表面未吹干。
7. 挤压筒、挤压垫磨损超差或尺寸配合不当,两个垫片的直径差超过允许值。
8. 挤压筒和挤压垫太脏,沾有油污、水分、石墨等。
9. 润滑油中含有水。
10. 铸锭表面铲槽太多,过深;或铸锭表面有气孔、砂眼、组织疏松、油污、铸锭氢含量高等。
11. 更换合金时未清理干净。
12. 挤压简化温度和挤压铸锭温度过高。
13. 铸锭尺寸超过允许负偏差。
14. 铸锭过长,填充太快,铸锭温度不均,导致非鼓形填充。
因此,气缸内排气不完全,或操作不当,排气过程未执行。
15. 模孔设计不合理,或切残科不当,分流孔和导流孔中的残科被部分带出,挤压时空隙中的气体进入表面。
为消除气泡,需要严格操作,正确剪切残科和完全排气。
同时,也可以咨询专业人士获取帮助。
铝合金针孔铸造缺陷及原因
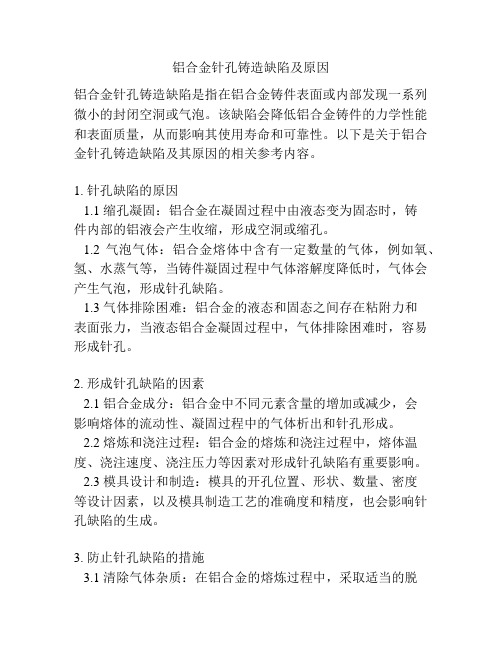
铝合金针孔铸造缺陷及原因铝合金针孔铸造缺陷是指在铝合金铸件表面或内部发现一系列微小的封闭空洞或气泡。
该缺陷会降低铝合金铸件的力学性能和表面质量,从而影响其使用寿命和可靠性。
以下是关于铝合金针孔铸造缺陷及其原因的相关参考内容。
1. 针孔缺陷的原因1.1 缩孔凝固:铝合金在凝固过程中由液态变为固态时,铸件内部的铝液会产生收缩,形成空洞或缩孔。
1.2 气泡气体:铝合金熔体中含有一定数量的气体,例如氧、氢、水蒸气等,当铸件凝固过程中气体溶解度降低时,气体会产生气泡,形成针孔缺陷。
1.3 气体排除困难:铝合金的液态和固态之间存在粘附力和表面张力,当液态铝合金凝固过程中,气体排除困难时,容易形成针孔。
2. 形成针孔缺陷的因素2.1 铝合金成分:铝合金中不同元素含量的增加或减少,会影响熔体的流动性、凝固过程中的气体析出和针孔形成。
2.2 熔炼和浇注过程:铝合金的熔炼和浇注过程中,熔体温度、浇注速度、浇注压力等因素对形成针孔缺陷有重要影响。
2.3 模具设计和制造:模具的开孔位置、形状、数量、密度等设计因素,以及模具制造工艺的准确度和精度,也会影响针孔缺陷的生成。
3. 防止针孔缺陷的措施3.1 清除气体杂质:在铝合金的熔炼过程中,采取适当的脱气措施,例如加入适量的气体剂、气体除湿剂等,有效清除熔体中的气体杂质。
3.2 合理浇注系统:设计合理的浇注系统,包括满足熔体流动条件和减少氧化的浇注温度和速度,以降低针孔缺陷的产生。
3.3 模具设计和制造:合理设计模具的结构和通气孔,控制铸件冷却速度,采用合适的冷却介质。
同时,提高模具制造工艺的准确度和精度,确保模具的质量。
3.4 进行热处理:热处理可以减少造成针孔缺陷的组织缺陷,并提高铸件的力学性能和致密性。
3.5 检测和质量控制:采用合适的无损检测方法,如X射线检测、超声波检测等,对铝合金铸件进行检测,及时发现和修复针孔缺陷。
同时,实施严格的质量控制措施,确保铝合金铸件的质量。
27295591_铝合金模板气泡成因及控制研究

创新152022年第7期0 引言现阶段,铝合金模板应用越来越广,铝合金模板以其高效、绿色、环保、成型效果好等优势被建筑业青睐,尤其是其良好的观感更是得到了业内认可。
组合铝合金模板体系是一种新型的模板体系,在经济、安全、环保、效率等方面比传统模板体系有很大优势,迅速占领市场。
铝合金模板体系的应用从设计到出厂以及现场的施工,从根本上颠覆了传统的施工模式。
铝合金模板厂内的预拼装可以最大限度地避免设计、生产中出现的问题。
在铝合金模板产业发展过程中,其设计体系、生产方式、仓储管理均在使用中进行了不同程度的优化和改善,使其在应用过程中增加了标准件的比例,降低了非标件及异形件的比例,增加模板周转利用次数。
但在使用过程中铝合金模板在施工过程中仍存在麻面、气孔等通病。
本文依托建筑科技公司铝合金模板工程服务项目,针对铝模板在施工中常见气泡成因进行分析总结,供类似项目参考。
1 铝模板气泡主要成因及控制措施混凝土气泡成因主要包括金属模板问题、表面处理问题、施工工艺问题、混凝土自身问题、设计问题五类,针对铝模板特点,结合公司工程服务中遇到的问题分类进行总结分析:1.1 金属模板问题木模板内部水汽可通过木模板排出一部分,相对于木模板,铝模板封闭构造,透气优势不够,浇筑混凝土过程中气泡排出困难。
一些项目选用铝合金模板,在深化设计阶段出现排气孔设置考虑不充分或未设置排气孔现象,现场打孔漏打均会造成墙体气泡产生,混凝土表面形成大量气孔如图1。
图1 未设置排气孔导致气泡产生一些模板本身表面光滑程度不好,表面粗糙,加上模板在现场长时间使用不注重过程维护,导致模板表面光滑度较低,增加了气泡吸附模板的可能性。
控制措施:(1)铝模供应单位在深化设计阶段,需及时与总包单位沟通,考虑窗洞部位、钢筋密集部位排气孔设置,依据现场实施情况调整排气孔数量。
(2)在振捣过程中,快插慢拔,混凝土振捣密实前提下,尽可能把内部气泡排出混凝土体外,避免“漏振”[1]。
五大要素,解决铝压铸件产生气孔问题!

五大要素,解决铝压铸件产生气孔问题!来源:网络欢迎阅读本篇文章~在铝合金压铸厂上班的人都会遇到很多技术问题,比如铸件有缺陷、浇注流道设计、铸件产生气泡等等,那么这些问题究竟是怎么产生的呢?今天小编为大家整理了一份常见铝压铸件产生气孔可能原因专辑,希望对压铸人日常工作有所帮助!一、人为因素1. 脱模剂是否喷得太多?因脱模剂发气重大,用量过多时,浇注前未燃尽,使挥发气体被包在铸件表层。
所以在同一条件下某些工人操作时会产生较多的气孔的原因之一。
选用发气量小的脱模剂,用量薄而均匀,燃净后合模。
2. 未经常清理溢流槽和排气道?3. 开模是否过早?是否对模具进行了预热?各部位是否慢慢均匀升温。
使型腔、型芯表面温度为150C~200C。
4. 刚开始模温低时生产的产品有无隔离?5. 如果无预热装置时是否使用铝合金料浸速推入型腔预热或用其它方法加热?6. 是否取干净的铝液,有无将氧化层注入压室?7. 倒料时,是否将汤勺靠近压室注入口,避免飞波、氧化或卷入空气降温等?8. 金属液一倒入压室,是否即进行压射?温度有无降低了?9. 冷却与开模,是否根据不同的产品选择开模时间?10. 有无因怕铝液飞出 ( 飞水),不敢采用正常压铸压力?更不敢尝试适当增加比压。
11. 操作员有无严格遵守压铸工艺?12. 有无采用定量浇注?如何确定浇注量?二、设备和模具以及工装因素设备、模具、工装因素主要是涉及模具质量、设备性能。
1. 压铸模具设计是否合理,会否导致有气孔?压铸模具方面的原因:①流口位置的选择和导流形状是否不当,导致金属液进入型腔产生正面撞击和产生旋涡。
(降低压射速度,避免涡流包气)②浇道形状有无设计不良?③内浇口速度有无太高,产生消流?④排气是否不畅?⑤模具型腔位置是否太深?⑥机械加工余量是否太大?穿透了表面致密层,露出皮下气孔?压铸件的机械切削加工余量应取得小一些,一般在0.5mm 左右,既可减轻铸件重量、减少切削加工量以降低成本,又可避免皮下气孔露出。
2014铝合金挤压棒材表面气泡分析

0前言2014铝合金是典型的可热处理强化的硬铝合金,其挤压棒材具有较高的强度,广泛应用于航空、航天等领域。
我公司挤压的2014铝合金棒材,在立式淬火炉淬火后表面出现大量的直径为1~5mm 的气泡,且气泡尾端大而密,头部气泡小,中间基本没有,该类缺陷严重影响到了棒材的质量,需亟待解决。
王凤春[1]将2A14铝合金挤压棒材气泡分为夹杂气泡、挤压分层气泡和气体通透性气泡三类,且认为夹杂气泡占大多数。
刘俊生[2]等人通过试验发现2024棒材表面气泡属于通透性气泡,通过降低铸锭氢含量、保证热处理时气氛干燥能有效避免气泡的产生。
彭自业[3]等人认为7075棒材后续固溶处理不当会促使表面成层缺陷处产生气泡。
刘建生[4]等研究发现6×××系铝合金挤压棒材气泡内部成分含有C、O 元素,认为气泡是由石墨、油污、含碳有机物等分解所产生的。
本文从铸锭熔铸、模具结构、挤压生产工艺以及固溶处理这4个方面分析了产生表面气泡的影响因素,提出减少和避免2014铝合金挤压棒材产品表面气泡的措施,以期减少报废,降低生产成本。
1实验材料及方法图1为我公司正向1800t 挤压机挤压的2014铝合金ϕ38mm 挤压棒材。
从图中可以看出固溶处理后表面出现气泡并沿挤压方向不连续分布,尾部分布多,且直径大。
从棒材横截面可以发现气泡为皮下隆起的空腔。
图1棒材表面气泡(箭头为挤压方向)对影响表面气泡形成的四大因素的分析按单因素分别进行,即采用不同氢含量、表面有及无油污铸棒分析铸锭因素;采用是否对铸锭剥皮、不同镦粗压力、不同压余厚度来分析挤压工艺因素;采用不同的导流孔来分析模具因素;采用不同固溶温度、是否烘炉来分析固溶因素。
采用光学显微镜和扫描电镜观察棒材显微组织,采用能谱仪检测气泡处微区成分。
2实验结果与分析2.1棒材的低倍组织与金相显微组织棒材的低倍组织和金相显微组织见图2。
从图中可以看出,棒材横截面晶粒细小,表层有个别粗大晶粒,并未连续形成粗晶环,故排除因粗晶环层破裂产生裂纹引起气泡缺陷。
减少铝合金棒材表面气泡的方法与设计方案

本技术属于铝合金热处理技术领域,涉及一种减少铝合金棒材表面气泡的方法,挤压工序中将均匀化后的铝合金铸锭置于挤压机进行挤压墩粗,其中主剪刀与模具座间隙为20μm~40μm,主剪刀的上部开设有夹角为90~135°的L型缺口,铝合金铸锭棒径与挤压筒内径差值为6mm~8mm,铝合金铸锭长度与挤压筒长度比值为0.8,挤压筒的挤压比为10~25,铝合金铸锭头尾部温度为450±10℃,中间铸锭加热温度为500±10℃,挤压墩粗次数为2次,首次墩粗压力设定为40%×F突破压力,二次墩粗压力设定为65%×F突破压力,挤压机为18MN~75MN单动正向挤压机,解决了现有工艺制备的多孔铝合金棒材表面气泡占比高,导致废品率高,人力物力成本高的问题。
技术要求1.一种减少铝合金棒材表面气泡的方法,其特征在于,包括以下步骤:A、配料:将制备铝合金棒材的原料按照重量百分比进行配料,即Si:0.2~1.3%、Fe:≤0.3%,Cu:≤0.10%,Mn:0.30%~1.0%,Mg:0.45%~1.2%,Zn:≤0.20%,Ti:≤0.02%、单个杂质≤0.05%,合计≤0.15%,余量为Al;B、熔铸:将配制好的铝合金原料加入到熔炼炉中均匀混合后熔炼为液态铝合金,经过搅拌、扒渣、除气除渣、细化工序后,将液态铝合金熔铸为铝合金铸锭;C、均匀化:将铝合金铸锭在均质炉中进行均匀化热处理;D、挤压墩粗:将均匀化后的铝合金铸锭置于挤压机进行挤压墩粗,其中主剪刀与模具座间隙为20μm~40μm,主剪刀的上部开设有夹角为90~135°的L型缺口,铝合金铸锭棒径与挤压筒内径差值为6mm~8mm,铝合金铸锭长度与挤压筒长度比值为0.8,挤压筒的挤压比为10~25,铝合金铸锭头尾部温度为450±10℃,中间铸锭加热温度为500±10℃,挤压墩粗次数为2次,首次墩粗压力设定为40%×F突破压力,二次墩粗压力设定为65%×F突破压力,挤压机为18MN~75MN单动正向挤压机;E、固溶:将挤压后的铝合金棒材进行固溶淬火处理;F、预拉伸:将固溶后的铝合金棒材置于拉伸矫直机进行拉伸矫直;G、时效:将拉伸后的铝合金棒材进行时效热处理;H、将时效后铝合金棒材进行表面质量、尺寸低倍、高倍组织、力学性能检验,对满足客户要求的产品进行包装。
7075铝合金厚板表面气泡原因的分析
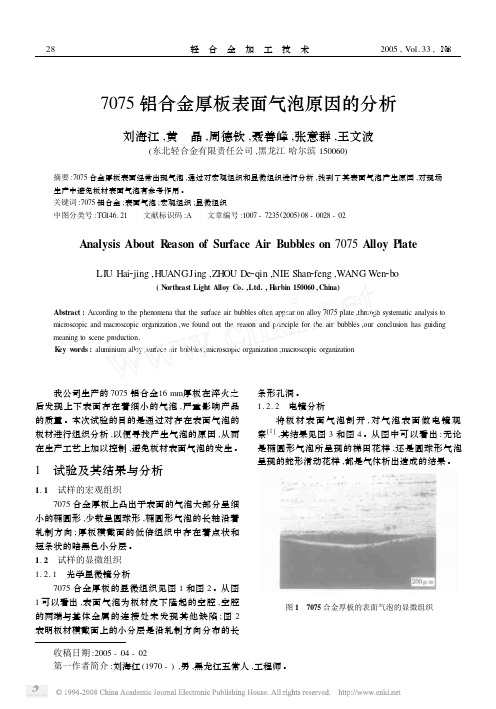
收稿日期:2005-04-02 第一作者简介:刘海江(1970-),男,黑龙江五常人,工程师。
7075铝合金厚板表面气泡原因的分析刘海江,黄 晶,周德钦,聂善峰,张意群,王文波(东北轻合金有限责任公司,黑龙江哈尔滨150060)摘要:7075合金厚板表面经常出现气泡,通过对宏观组织和显微组织进行分析,找到了其表面气泡产生原因,对现场生产中避免板材表面气泡有参考作用。
关键词:7075铝合金;表面气泡;宏观组织;显微组织中图分类号:TG 146.21 文献标识码:A 文章编号:1007-7235(2005)08-0028-02Analysis About R eason of Surface Air Bubbles on 7075Alloy PlateLI U Hai 2jing ,HUANGJing ,ZHOU De 2qin ,NIE Shan 2feng ,WANG Wen 2bo(N ortheast Light Alloy Co.,Ltd.,H arbin 150060,China)Abstract :According to the phenomena that the surface air bubbles often appear on alloy 7075plate ,through systematic analysis to microscopic and macroscopic organization ,we found out the reas on and principle for the air bubbles ,our conclusion has guiding meaning to scene production.Key w ords :aluminium alloy ;surface air bubbles ;microscopic organization ;macroscopic organization 我公司生产的7075铝合金16mm 厚板在淬火之后发现上下表面存在着细小的气泡,严重影响产品的质量。
挤压铝型材表面起泡起皮原因及处理方法

挤压铝型材表面起泡起皮原因及处理方法
气泡或起皮:在制品表面出现凸形的泡,常见于头、尾部,完整的叫气泡,已破裂的叫起皮。
一.挤压产品气泡、起皮产生的原因:
1.挤压筒、挤压垫磨损超差,挤压筒和挤压垫尺寸配合不当,同时使用的两个垫片之直径差超过允许值;
2.挤压筒和挤压垫太脏,粘有油污、水分、石墨等;
3.润滑油中含有水;
4.铸锭表面铲槽太多,过深,或铸锭表面有气孔、砂眼,组织疏松、有油污等;
5.更换合金时,筒内未清理干净;
6.挤压筒温度和挤压铸锭温度过高;
7.铸锭温度、尺寸超过允许负偏差;
8.铸锭过长,填充太快,铸锭温度不均,引起非鼓形填充,因而筒内排气不完全,或操作不当,未执行排气工序;
9.模孔设计不合理,或切残料不当,分流孔和导流孔中的残料被部分带出,挤压时空隙中的气体进入表面。
二.消除方法:
1.合理设计挤压筒和挤压垫片的配合尺寸,经常检查工具尺寸,保证符合要求,挤压筒出现大肚要及时修理,挤压垫不能超差;
2.工具、铸锭表面保持清洁、光滑和干燥;
3.更换合金时,彻底清筒;
4.经常检查设备和仪器,防止温度过高、速度过快;
5.严格执行工艺规程和各项制度;
6.合理设计、制造工模具,导流孔和分流孔设计成1度过~3度内斜度;
7.严格操作,正确剪切残料和完全排气。
压铸铝合金铸件的一般缺陷和产生成因

压铸铝合金铸件的一般缺陷和产生成因?铝合金压铸件的一般缺陷和产生成因?A:拉伤,沿开模方向铸件表面呈现条状的拉伤痕迹,有一定的深度,严重时为一面状伤痕。
另一种是金属液与模具产生焊合,粘附而拉伤。
以致铸件表面多肉或缺肉。
产生原因:型腔表面有损伤,出模方向斜度太小或倒斜,顶出进偏斜,浇注温度过高,模温过高导致合金液产生粘附。
脱模剂使用效果不好,铁含量低于0。
6%等B气泡:铝合金压铸件表面有米粒大小的隆起也有皮下形成的空洞。
产生原因,合金液在压室充满度过低,易产生卷气,压射速度过高,模具排气不良,熔液未除气,熔炼温度过高,模温过高,金属凝固时间不够,强度不够,而过早开模顶出铸件,受压气体膨胀起来,脱模剂太多。
C:冷隔,压铸件表面有明显的,不规则的、下陷线性纹路(有穿透与不穿透两种)形状细小而狭长,有时交接边缘光滑,在外力作用下有发展的可能。
产生原因:两股金属流相互对接,但未完全熔合而又无夹杂存在其间,两股金属结合力奶薄弱。
浇注温茺或压铸模温度偏低,选择合金不当,流动性差,浇道位置不对或流路过长,真充速度低,压射比压低。
D:变色、斑点:铸件表面上呈现出不同于基体金属颜色。
产生原因:不合适的脱模剂,脱模剂使用量过多、过勤,含有石墨的润滑剂中的石墨落入铸件表面。
锌合金铸造过程中主要缺陷的产诺基亚n70手机qq2010生和成因?A;气孔:是在金属液凝固过程中由于气体串入而导致锌合金压铸件的表面或内部产生的孔洞,这类气泡大多是圆形的。
细少的气孔不影响铸件的机械性能,但大颗粒的气泡会大大地降低铸件的抗冲性能,铸件表面气孔在表面处理时会装入水分,喷漆或电镀之后,因孔内的水气澎胀至气泡。
B:收缩孔:是液体在凝固过程中由于体积的缩小而导致在铸件表面或内部产生的孔洞。
收缩孔在形状上往往都带有棱角而且外表呈树枝状,铸件表面上或靠近表面内的收缩孔会给后续加工带来问题。
同气孔一样,收缩孔会在表面处理时串入液体,喷漆或电镀时产生气泡。
- 1、下载文档前请自行甄别文档内容的完整性,平台不提供额外的编辑、内容补充、找答案等附加服务。
- 2、"仅部分预览"的文档,不可在线预览部分如存在完整性等问题,可反馈申请退款(可完整预览的文档不适用该条件!)。
- 3、如文档侵犯您的权益,请联系客服反馈,我们会尽快为您处理(人工客服工作时间:9:00-18:30)。
维普资讯
第2 8卷第 4期 20 年 1 06 2月
中图分类号 :G 9 T 22 文献标识码 : A
An l sst h b l r d o u f c fAl mi i m ay i o t e Bu b e Fo me n S ra e o u n u I g tDu i g Ho g n z to n a i g n o rn mo e ia i n An e l n
甘
肃Байду номын сангаас
冶
金
Vo . 8 No 4 1: 2 . D q ,06 e .2 0
G ANS ME A L RGY U T L U
文章编号 :624 6 (0 6 0 -0 1 3 17 -4 1 20 )40 2 - 0
浅 析 铝 合 金 铸 锭 均 匀 化 退 火表 面起 泡 原 因
4 5 o 、 4 —4 5 o 5 C 4 0 4 C。
() 验结果 。在前 5个 温度 区间 条件 均 匀化后 的试 片 2 试 上 , 出现不 同程 度的气泡 , 都 在最 后 1个 温度 区间 条 件下 均 匀化后 的试片上无气泡 。从 在前 5个 温度 区 间条 件下 均 匀
安 锦 如
( 兰州铝业股份有 限公 司, 甘肃 摘 兰州 7 06 ) 30 0
要: 本文通过考察铸锭均匀化退火起泡与生产条件 、 均匀化退 火和环境气氛等的关系 。 初步分析 了铸锭均 火起泡 的实质 。 J 成
规律 、 理等。 机
关键词 : 匀化退火 ; 均 气泡 ; 铝合金铸锭
() 1 试验情况 。本试验 在箱式电阻炉 中进 行 , 样为 正常 试
米 粒大 小 、 并多半沿锯 痕或车痕分布的气泡 。气泡外观近 似
于 半球 形 , 纵剖开后 内表面呈现金属光泽 。这种均匀化退 火 后 的气 泡多出现在 L I 、Yl Y 2 L 1和 L 2合金的小规格铸锭 上 Y ( 空心 ( 7/ 0 m、 2 0 10 m 实 心 12 mm 及 以 I 0 16 m q 7/ 4 m, ) 2 b 9 下 ) 有 时也出现在 L 4 L 7和 L 1 , C 、D D 0的小规格合金铸锭 上。 但在高镁合金的任何规格 的铸 锭上 , 都从来没有发 现过 这种 性 质的气 泡 。另外在大规格铸锭 上 , 即使在有严重疏松 缺陷 存在的大规格铸锭上 , 也没有发现这种性 质的气泡 。 这种气泡到底是什 么 , 是怎样形成 的 , 与哪些因素有 关?
略地考察 了这些 问题 。这里所 要介 绍 的就是铸 锭均匀 化退
2 2 均匀化起泡与均匀化保温 时间的关系 .
( 试验情况。本试验 的均匀 化退 火 炉及 试样 均 与上 述 1 ) 试验相 同 , 均匀化 4 0— 9 , 8 40 试验 共进行 了 7个; 同的均 匀化保温 时问 , 些保温时 间( ) 这 h 分别是 :6 1 、 、 10 5 1 、2 8 、 、. 。 () 验结果 。在经 过 以上 7个不 同保温 时 间均 匀化 后 2 试 的试 片上都 出现不 同程 度的气 泡。从经 过 以 上 7爪 不 同保
化后的试片上的出泡情 况来 看 , 当其它 条 件一 定时 , 泡 严 气 重程度与均匀化温度成幂指 数关系 , 图 1 见 。泡 的严 重程 度 级别单位为气泡个数/m , 为 1 e 其余类 推。 c 一级 个/m ,
在前几年 比较长的一 段时 间里 , 通过一 些生 产实践 , 粗 比较
生 产的 L 1 — 合金  ̄ 7/0 m 规格试片 , t2h试 Y2 1 20 16m 保温 , 1
验共进行 了 6个不 同的 温度 区 间 , 些 温度 区间 是 :9 这 4 0~
4 5 ℃ 、 8 ~4 5 C 、 7 — 4 5 C 、 6 ~ 4 5 【 、 5 ~ 9 40 8 40 7 o 4 0 6 c: 4 0
AN Jn n i — l
( a zo lmnu o , . azo 3 0 0 Ch a L nhuAu iim C .1d ,Lnhu7 0 6 , i ) t n
Ab t a t y s u yn e r lt n h p b t e u b e fr d o e au n u i g ts r c n r d c in c n i o t sr c :B t d i g t ea i s i ewe n b b l ome n t l mi im n o u a e a d p o u t o d t r,a h o h f o i b sc a ay i t u be i gv n i e mso s n t r a i n s o b b l s ie n tr fi au e.r a o s a d r ls l s t e s n n ue . Ke r s:h mo e ia in a n a ig;b b l ;a u n u i g t y wo d o g nz t n e l o n u b e l mi i m n o
火起泡与铸锭生产条件 、 均匀化退火 和环境气 氛关系的试验
考察情况 。并在这 些试验考察结果的基础上 , 初步分析铸锭 均火起泡 的实质 , 形成规律 、 机理 , 以及我们认识它的形成规
律和机理后在 生产上的指导意义 。
l 刖 昂
验 。在每个试验 中, 除了所 考察 的因 素为 变量 外 , 它条 件 j
都是相 同的 。
在铝加 工生 产的过程当中 , 正常均匀化退火后 的半 经过
连续生产 的铸锭加 工 ( 锯切 和车 皮 ) 面上 , 时发现 有像 表 有
21 均 匀化 起泡 与均 匀化 温 度 的关 系 .