粉末冶金技术基础与新技术(第四章)
粉末冶金培训资料

粉末冶金培训资料粉末冶金是一种先进的加工技术,其特点是利用粉末材料直接制造成零件或制品。
由于其制造过程不需要熔化和冷凝,因此可以实现高纯度和均匀性的材料制备,从而提高材料的性能和品质。
粉末冶金的应用领域包括汽车、航空航天、电子、机械等多个行业,具有广阔的市场前景。
为了能够更好地掌握粉末冶金技术,培训资料的准备至关重要。
首先,了解粉末冶金的基本概念和原理是非常必要的。
粉末冶金是一种通过粉末材料的压制和烧结来制造零件或制品的方法。
其核心原理是将金属或非金属粉末按一定比例混合,并通过冷压或热压的方式将其压制成形,然后在高温下进行烧结,使粉末颗粒间发生结合,最终形成致密的零件或制品。
在整个过程中,粉末冶金不需要熔化金属,因此可以保持材料的高纯度。
其次,对于粉末冶金材料的性能和特点进行深入了解也是必不可少的。
粉末冶金制造的零件或制品具有高纯度、均匀性好、尺寸复杂等特点。
与传统的金属加工方法相比,粉末冶金可以制造出更复杂的形状,同时还可以用于制备高性能的金属材料,如高温合金、硬质合金等。
此外,由于粉末冶金不需要进行熔融处理,所以可以节约能源和原材料,有利于环境保护。
对于粉末冶金加工过程的基本流程和设备,需要详细了解。
粉末冶金加工过程主要包括粉末制备、粉末混合、成型和烧结等几个环节。
首先是粉末制备,根据材料的要求选择合适的方法进行制备,如球磨法、气相法、电化学法等。
然后是粉末混合,将不同的粉末按照一定的比例混合均匀,通常采用干法或湿法进行。
接下来是成型,通过冷压或热压的方式将粉末压制成形,常用的成型方法有压铸、注射成形、压制等。
最后是烧结,将压制成形的粉末在高温下进行加热处理,使粉末颗粒结合成致密的零件或制品。
在粉末冶金过程中,需要注意一些关键因素和技术细节。
首先是粉末的选择和处理,不同的粉末材料有不同的性质和特点,因此需要根据零件或制品的要求选择合适的粉末,并对其进行必要的处理,如除杂、粒度控制等。
其次是成型的工艺参数控制,这包括压力、温度、保压时间等方面,对于不同的粉末材料和形状复杂度,需要进行合理的参数选择和控制。
粉末冶金材料及制备技术第四章
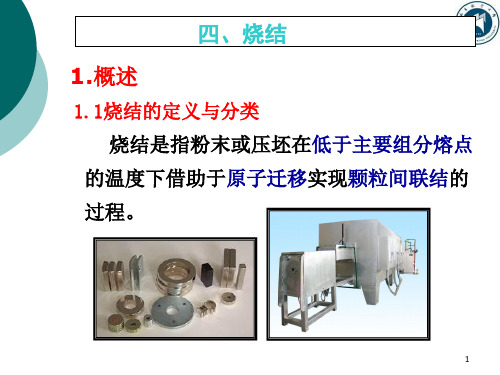
四、烧结
烧结机构的研究方法与步骤
建立简单的几何模型,如烧结球模型;
选定表征烧结过程的可测的几何参数,如烧结颈尺寸, 中心距;
假定某一物质迁移方式,建立物质流的微分方程;
38
四、烧结
Efo—无应力时生成一个空位所需的能量 在烧结颈部因受到拉应力的作用 空位形成能降低 产生过剩空位浓度 大于平衡空位浓度
39
四、烧结
应力作用时其值发生改变 压缩应力 Ef= Efo +σΩ 拉伸应力 Ef= Efo –σΩ σΩ—应力对空位所作的功
40
1 粉末冶金工艺两个基本加工步骤之一 磁粉芯和粘结磁性材料例外
2 决定了P/M制品的性能
3 烧结废品很难补救,如铁基部件的 脱渗碳和严重的烧结变形 4 热处理,过程能耗大→降低烧结温度是 有意义(降低能耗和提高烧结炉寿命) 5 纳米块体材料的获得必须依赖烧结过程的 控制
9
四、烧结
1.2 烧结理论的研究范畴和目的
33
四、烧结
34
四、烧结
(2)中期
孔隙网络形成,烧结颈长大。有效烧 结应力Ps为 Ps =Pv-γ/ρ(Pv为烧结气氛的 压力,若在真空中,为0)
35
四、烧结
(3)后期
孔隙网络坍塌,形成孤立孔隙 →封闭的孔隙中的气氛压力随孔隙半径r收缩而 增大。 由气态方程Pv.Vp=nRT 气氛压力Pv=6nRT/(πD3) 此时的烧结驱动力σ=-4γ/D 令Ps=0,即封闭在孔隙中的气氛压力与烧结 应力达到平衡 孔隙收缩停止 最小孔径为Dmin=(Po/4γ)1/2.Do3/2
《粉末冶金新技术》课件

4 等离子热惯性成形法
利用高速等离子体热传导原理,实现金属粉 末的瞬时烧结成形。
粉末成型技术
1
注射成型法
基于金属、合金或陶瓷粉末制成的糊状物通过注射成型机构,进而制得密实件。
2
热压成型法
将金属或陶瓷粉末放入橡胶模具中,在高温高压条件下进行成型。
3
热等静压成型法
将金属或陶瓷粉末放入模具中,在高温高压条件下进行成型。
2 粉末冶金的未来发展
随着科技的不断进步,粉末冶金技术将继续创新,为各个领域提供更加先进和优质的材 料。
3 粉末冶金的应用前景
粉末冶金材料的应用领域将会进一步拓展,为人类的生活和工业发展带来更多的便利和 创新。
粉末冶金的发展现状
当前,粉末冶金技术已经取得了许多突破,应用范围不断扩大。
粉末制备技术
1 机械合金化法
通过高能球磨等方法,将金属粉末与化合物金属离子,制备溶胶,再通过凝胶 化和烧结得到陶瓷制品。
3 沸腾床法
通过控制气体流动,在高温高压环境下制备 金属和陶瓷的纳米粉末。
《粉末冶金新技术》PPT 课件
粉末冶金新技术是一门前沿的材料学科,通过粉末制备与成型技术,实现材 料的精细化、多功能化和资源节约型制备,在航空、汽车、医疗和化学等领 域有广泛应用。
简介
粉末冶金概述
粉末冶金是一种通过将金属或陶瓷粉末加工、压实、烧结制得密实体材料的方法。
粉末冶金的历史
粉末冶金技术在古代文明中已有应用,如古埃及制造金属器具。
粉末冶金新发展趋势
新材料及制备技术
研发新材料和制备技术,如纳米 材料、复合材料等,推动粉末冶 金技术的发展。
资源节约型粉末冶金技术
开发更加环保、节约资源的粉末 冶金技术,实现可持续发展。
粉末冶金行业新技术管理知识

粉末冶金行业新技术管理知识简介粉末冶金是一种常见的制造工艺,它使用金属或非金属粉末作为原材料,经过一系列的工艺步骤进行成型和烧结,最终得到所需产品。
粉末冶金技术具有高效、节能、材料利用率高等优势,被广泛应用于汽车、电子、航空航天等行业。
随着科技的不断进步,粉末冶金行业也不断涌现出新的技术,这些新技术的管理知识对于提高企业竞争力和市场占有率至关重要。
1. 新技术的引入和评估引入新技术是提高企业创新能力和竞争力的重要手段。
在引入新技术之前,企业需要对新技术进行评估,包括技术可行性评估、市场需求评估和经济效益评估等。
技术可行性评估技术可行性评估是指评估新技术在现有生产工艺中的可行性。
要考虑新技术是否能够与现有设备和工艺相适应,是否能够满足产品的质量要求等。
市场需求评估市场需求评估是指评估新技术在市场上的需求情况。
要了解市场上是否存在对该技术的需求,以及该技术是否能够满足市场需求。
经济效益评估经济效益评估是指评估新技术引入后的经济效益。
要考虑新技术引入后是否能够提高生产效率、降低成本、增加销售额等。
2. 新技术的培训和推广在引入新技术后,企业需要对员工进行培训,以提高员工对新技术的理解和运用能力。
培训内容可以包括新技术的原理、操作方法、常见故障处理等。
培训计划企业需要制定培训计划,明确培训的时间、地点、培训内容等。
同时,要根据不同岗位的需求,制定相应的培训方案。
培训方式培训方式可以采用面对面培训、在线培训、视频教学等方式。
根据不同人群的学习特点和需求,选择适合的培训方式。
推广和应用培训结束后,企业需要积极推广新技术的应用。
可以通过内部宣传、外部推广和技术交流等方式,提高新技术的认知度和应用率。
3. 新技术的优化和改进随着新技术的应用,企业应不断地进行新技术的优化和改进,以提高技术的可靠性和稳定性。
技术优化技术优化可以包括工艺参数的优化、设备的优化以及材料的优化等。
通过优化技术,可以提高产品的质量和性能。
粉末冶金新的技术
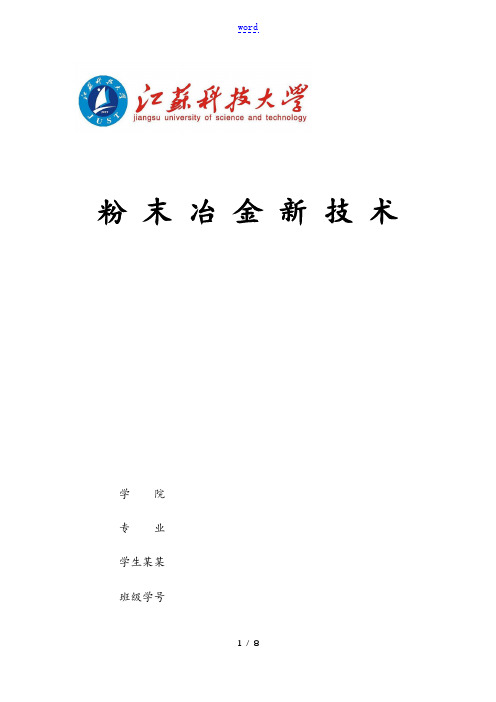
粉末冶金新技术学院专业学生某某班级学号指导教师二〇一六年十二月粉末冶金新技术(某某科技大学冶材院213)摘要:本文简要介绍粉末冶金的根本工艺原理和方法,重点介绍近年来粉末冶金新技术和新工艺的开展和应用状况。
关键词:粉末冶金;新技术粉末冶金(P/M)技术是一门重要的材料制备与成形技术,被称为是解决高科技、新材料问题的钥匙…。
高性能、低本钱、净近成形一直以来是粉末冶金工作者重要研究课题之一。
粉末冶金法能实现工件的少切削、无切削加工,是一种高效、优质、精细、低耗节能制造零件的先进技术。
它是制取金属粉末或用金属粉末(或金属粉末与非金属粉末的混合物)作为原料,经过成形和烧结,制造金属材料、复合材料以与各种类型制品的工艺技术)3。
粉末冶金工艺的第一步是制取原料粉末,第二步是将原料粉末通过成形、烧结以与烧结后处理制得成品。
进入20世纪80年代许多行业,特别是汽车工业比以往任何时候更加依赖于粉末冶金技术,尽可能多地采用粉末冶金高性能的零部件是提高汽车尤其是轿车在市场中的竞争能力的一种有力手段1。
高密度的P/M产品是保证其具有优异的力学性能的关键因素。
因此,为扩大粉末冶金P/M零部件的应用X围,必须提高其密度以获得力学性能优异的粉末冶金零部件。
性。
故,为了提高材料的性能,降低生产本钱,冶金技术的开展无疑具有重要的科学意义和实用价值。
1 几种冶金新技术20世纪80年代末,Hoeganaes公司的Musella等人为提高零件密度,在扩散粘结铁粉制备工艺的研究根底上,将粉末和模具加热到一定温度进展压制,开发出一种所谓温压的新工艺,即ANCORDENSE工艺。
温压工艺就是采用特制的粉末加温、粉末输送和模具加热系统,将混有特殊聚合物润滑剂的金属粉末和模具加热至130~150℃,然后按传统粉末压制工艺进展压制和烧结以提高压坯密度的新方法据资料分析,虽然温压工艺比常规的一次压制烧结工艺的相对本钱提高了20%,但比渗铜工艺、复压烧结工艺、粉末热锻工艺分别降低了20%、30%和80%的本钱,开拓了粉末冶金应用的潜力。
粉末冶金新工艺4
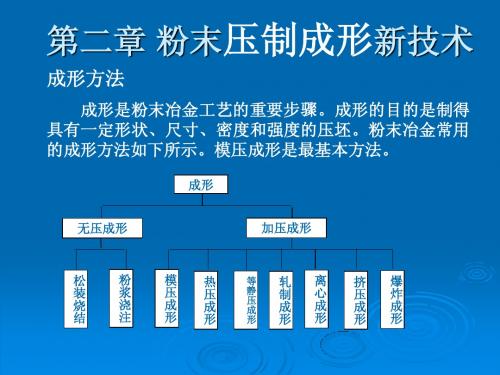
昆明理工大学材料与冶金学院 胡劲
第二章 粉末冶金成型新技术
2.高速压制 与传统压制相比, 高速压制的优点是: 压制件密度提高,提高幅度在0.3g/cm3左右;
压制件抗拉强度可提高20%~25%;
昆明理工大学材料与冶金学院 胡劲
第二章 粉末冶金成型新技术
2.高速压制 瑞典开发出粉末冶金用高速压制法。这可能是
粉末冶金工业的又一次重大技术突破。高速压制采
用液压冲击机,它与传统压制有许多相似之处,但关 键是压制速度比传统快500~1000倍,其压头速度高 达2~30m/s,因而适用于大批量生产。液压驱动的 重锤(5~1200kg)可产生强烈冲击波,0.02s内将压
昆明理工大学材料与冶金学院 胡劲
第二章 粉末冶金成型新技术
1.动磁压制技术 许多合金钢粉用动磁压制做过实验,粉末中不 添加任何润滑剂,生坯密度均在95%以上。动磁压 制件可以在常规烧结条件下进行烧结,其力学性能
高于传统压制件。动磁压制适用于制造柱形对称
的近终形件、薄壁管、纵横比高的零件和内部形
状复杂的零件。
昆明理工大学材料与冶金学院 胡劲
第二章 粉末冶金成型新技术
3.温压成型技术
特点 : (2)生坯强度高 常规工艺的生坯强度约为10~20MPa,温压压坯的强度则为 25~30MPa,提高了1.25-2倍。生坯强度的提高可以大大降 低产品在转移过程中出现的掉边、掉角等缺陷,有利于制备 形状复杂的零件;同时,还有望对生坯直接进行机加工,免 去烧结后的机加工工序,降低了生产成本。这一点在温压烧结连杆制备中表现得尤为明显。
昆明理工大学材料与冶金学院 胡劲
粉末冶金成形
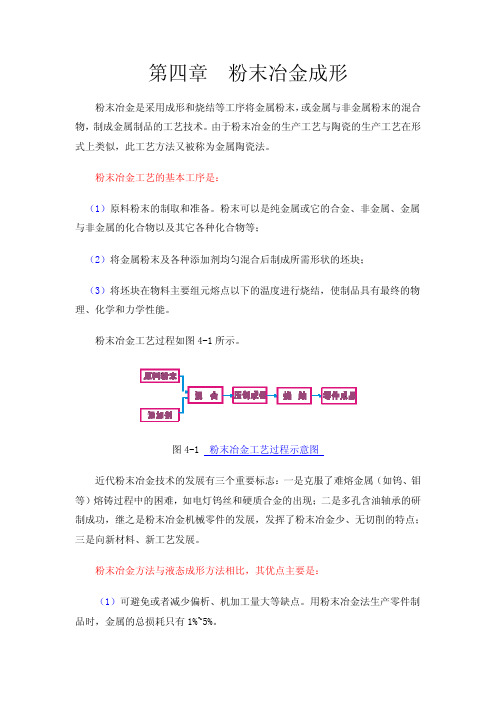
粉末冶金是采用成形和烧结等工序将金属粉末,或金属与非金属粉末的混合 物,制成金属制品的工艺技术。由于粉末冶金的生产工艺与陶瓷的生产工艺在形 式上类似,此工艺方法又被称为金属陶瓷法。
粉末冶金工艺的基本工序是: (1)原料粉末的制取和准备。粉末可以是纯金属或它的合金、非金属、金属 与非金属的化合物以及其它各种化合物等; (2)将金属粉末及各种添加剂均匀混合后制成所需形状的坯块; (3)将坯块在物料主要组元熔点以下的温度进行烧结,使制品具有最终的物 理、化学和力学性能。
1.机械粉碎法 机械粉碎是靠压碎、击碎和磨削等作用,将块状金属、合 金或化合物机械地粉碎成粉末。依据物料粉碎的最终程度,可以分为粗碎和细碎 两类。以压碎为主要作用的有碾碎、辊轧以及鄂式破碎等;以击碎为主的有锤磨; 属于击碎和磨削等多方面作用的机械粉碎有球磨、棒磨等。实践表明,机械研磨 比较适用于脆性材料,塑性金属或合金制取粉末多采用涡旋研磨、冷气流粉碎等 方法。
冷却了的颗粒粉碎。气流压力愈大,制得的粉末粒度愈细。冷气流冲击方法适用 于粉碎硬质的、以及比较昂贵的材料,可迅速将 6 目或更小的颗粒原料变成微米 级的颗粒。该方法工艺简单、生产费用低、作业温度低(可防止氧化和自燃)、 能保持高纯度以及控制被粉碎材料的粒度。
2.雾化法 各种雾化高质量粉末与新的致密技术相结合,出现了许多粉末 冶金新产品,其性能往往优于相应的铸锻产品。
(1)机械研磨法 包括减小粉末粒度;合金化;固态混料;改善、转变或 改变材料的性能等。研磨后的金属粉末会有加工硬化、形状不规则、出现流动性 变坏和团块等特征。
(2)机械合金化 是一种高能球磨法。用这种方法可制造具有可控细显微 组织的复合金属粉末。它是在高速搅拌球磨的条件下,利用金属粉末混合物的重 复冷焊和断裂,进行机械合金化的。也可以在金属粉末中加入非金属粉末来实现 机械合金化。用机械合金化制造的材料,其内部的均一性与原材料粉末的粒度无 关。因此,用较粗的原材料粉末(50~100μm)可制成超细弥散体(颗粒间距小 于 1μm)。制造机械合金化弥散强化高温合金的原材料,是工业上广泛采用的 纯金属粉末,粒度约为 1~200μm。
粉末冶金新技术
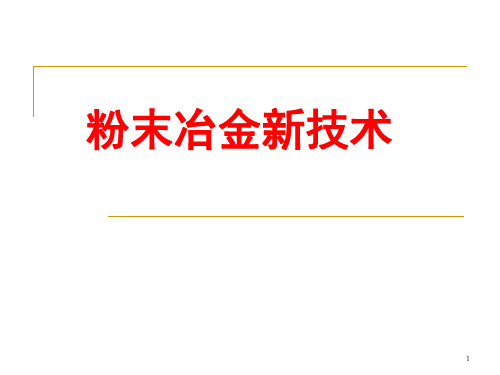
3.燃烧火焰--化学气相法生产纳米粉末
采用燃烧火焰-化学气相法生产纳米粉末。在 此法中,稳定的平头火焰是由低压燃料/氧气混合气 的燃烧产生的。化学母体与燃料一起导入燃烧室, 在火焰的热区进行快速热分解。由于燃烧室表面温 度分布良好,气相逗留时间短以及化学母体浓度均 匀,并在很窄的热区进行热分解,因而能生产出粒 度分布集中的高质量的纳米粉。
成型新技术 34
温压技术主要适合生产铁基合金零件。同时人 们正在尝试用这种技术制备铜基合金等多种材料 零件。由于温压零件的密度得到了较好的提高, 从而大大提高了铁基等粉末冶金制品的可靠性, 因此温压技术在汽车制造 机械制造、武器制造等 领域存在着广阔的应用前景。
成型新技术 35
4.流动温压技术 德国Fraunbofer应用材料研究所研发出来的新技术 流动温压技术以温压技术为基础,并结合了金
制粉新技术 7
磁粉芯是由铁磁性粉粒与绝缘介质混合压制而 成的一种软磁材料。由于铁磁性颗粒很小(高 频下使用的为0.5~5 微米),又被非磁性电 绝缘膜物质隔开,因此,一方面可以隔绝涡流, 材料适用于较高频率;另一方面由于颗粒之间 的间隙效应,导致材料具有低导磁率及恒导磁 特性;又由于颗粒尺寸小,基本上不发生集肤 现象,磁导率随频率的变化也就较为稳定。主 要用于高频电感。磁粉芯的磁电性能主要取决 于粉粒材料的导磁率、粉粒的大小和形状、它 们的填充系数、绝缘介质的含量、成型压力及 热处理工艺等。 常用的磁粉芯有铁粉芯、坡 莫合金粉芯及铁硅铝粉芯三种。
成型新技术 28
2.高速压制
High velocity compaction,HVC
瑞典开发出粉末冶金用高速压制法。这可能是 粉末冶金工业的又一次重大技术突破。高速压制采 用液压冲击机,它与传统压制有许多相似之处,但关 键是压制速度比传统快500~1000倍,其压头速度高 达2~30m/s,因而适用于大批量生产。液压驱动的重 锤(5~1200kg)可产生强烈冲击波,0.02s内将压制能 量通过压模传给粉末进行致密化。重锤的质量与冲 击时的速度决定压制能量与致密化程度。
电子教案与课件:现代粉末冶金技术课件-化工 第四章喷射沉积技术及应用

• 喷射沉积实际上是一个统计过程,金属颗粒的尺寸分 布以及热交换行为受很多因素的影响,沉积物的凝固 状态非常复杂。以上分析的第一种和第二种状态是不 希望发生的,理想的情况是处于后两种状态。对于第 三种状态,由于喷射速度较快,在下一排金属颗粒到 达之前,已达到沉积层表面的溅射物尚未完全凝固, 这样在沉积层表面形成液体薄层,其厚度非常小,为 此后的雾化沉积提供了一个坚固的表面,溅射过程将 继续下去。液体薄层的厚度应足够小,以防止横向流 动,抑制宏观范围内的成分偏析。此外,借助于雾化 沉积时的机械作用,还可将部分凝固的沉积层内部的 细小枝晶打碎,获得无原始边界的等轴细晶组织。由 于颗粒处于半固态,并且有液体薄层的存在,沉积层 中的孔隙率将会非常小。
• 在高的喷射密度下,在前一批溅射物完全凝固之前, 也就是在先前溅射物的顶部尚保持一层液态金属薄膜 时,下一批溅射物已到达该处。在这种情况下,两个 液体表面相遇,新到达的熔滴立即扩散,两个液体混 合,因此消除了引起孔隙度的任何空隙,并消除了溅 射边界。而且在许多情况下,前一批溅射物中的晶体 已经形核,并随着新到达的溅射物继续长大。这样, 就可以看到有柱状晶或其它形状的晶体穿过溅射边界 而长大。高喷射密度的优点是沉积物孔隙度低、无溅 射边界、产量高、喷射沉积后续热加工没有内部氧化 危险,缺点是沉积物冷却速度较低。如果通过气体和 辐射带走热量不充分,并且沉积层的顶部液体层较厚 时,就会恶化成为一般铸造状态。
此外喷射沉积还是一种适用性广的成形工艺改变水冷基底的形状和机械运动方式等参数可以生产出不同形状的毛坯如盘环由于在喷射沉积过程中金属液流可以通过水冷基体传导和高速气流的对流辐射等方式来传导热量因而与铸造工艺相比具有较高的冷却速度10102ks并且能够获得晶粒细小无宏观偏析的微晶组织
粉末冶金新技术

粉末冶金新技术近年来,为了满足对粉末的各种要求,粉末冶金技术得到飞速发展,出现了各种各样生产粉末的新方法,如机械合金化、粉末注射成形、温压成形、喷射成形、微波烧结、放电等离子烧结、自蔓延高温合成、使得粉末冶金材料和技术等。
粉末冶金不仅是一种材料制造技术,而且其本身包含着材料的加工和处理,它以少无切削的特点越来越受到重视,并逐步形成了自身的材料制备工艺理论和材料性能理论的完整体系。
现代粉末冶金技术不仅保持和大大发展了其原有的传统特点(如少无切削、少无偏析、均匀细晶、低耗、节能、节材、金属-非金属及金属高分子复合等),而且已发展成为制取各种高性能结构材料、特种功能材料和极限条件下工作材料、各种形状复杂的异型件的有效途径。
粉末冶金新技术得到了各国的普遍重视,其应用也越来越广泛,本文主要具体介绍了粉末冶金的一些新技术。
1.快速原形制备技术(RP)[1]快速原型制造技术,又称快速成型技术,简称RP 技术。
快速成型(RP) 技术是20世纪80年代后期发展起来的一项先进制造技术,它可以在无需准备任何模具、刀具和工装卡具的情况下,直接根据产品设计(CAD) 数据,快速制造出新产品的样件、模具或模型,与传统的铸、锻、轧、焊、车、铣、刨、磨等一系列加工过程相比,原型制造的加工过程大大缩短了加工周期并降低了产品研制的成本,对促进企业产品创新、提高产品竞争力有积极的推动作用。
美国、欧洲及日本等发达国家已将快速成型技术应用于电子信息、汽车、通讯、机械交通、轻工家电、航天航空、医疗器械、塑料、模具、建筑模型等众多行业。
但目前国内外对金属快速成型还在起步阶段,成功的示例并不多,主要集中在碳钢和其他几种特殊的金属以及它们的合金上面。
快速原型技术是在现代CAD/CAM 技术、激光技术、计算机数控技术、精密伺服驱动技术以及新材料等技术的基础上集成发展起来的,是多学科交叉技术综合的结晶。
RP 的基本原理是首先将三维实体模型数据(STL文件) 按一定方向分层为层片模型数据(CLI文件) ,快速原型成型机再根据这些数据,利用特定的材料,形成一系列具有一个微小厚度的片状实体,再采用熔结、聚合、粘结等手段使其逐层堆积成一体,便可以制造出所设计的新产品样件、模型或模具,直至完成整个实体的创建。
粉末冶金新技术的研究详解共72页
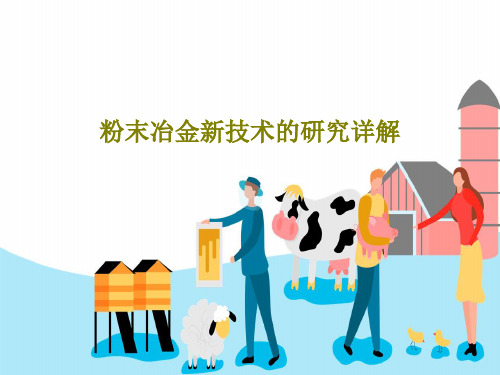
12、法律是无私的,对谁都一视同仁。在每件事上,她都不徇私情。—— 托马斯
13、公正的法律限制不了好的自由,因为好人不会去做法律不允许的事 情。——弗劳德
14、法律是为了保护无辜而制定的。——爱略特 15、像房子一样,法律和法律都是相互依存的。——伯克
21、要知道对好事的称颂过于夸大,也会招来人们的反感轻蔑和嫉妒。——培根 22、业精于勤,荒于嬉;行成于思,毁于随。——韩愈
23、一切节省,归根到底都归结为时间的节省。——马克思 24、意志命运往往背道而驰,决心到最后会全部推倒。——莎士比亚
粉末冶金
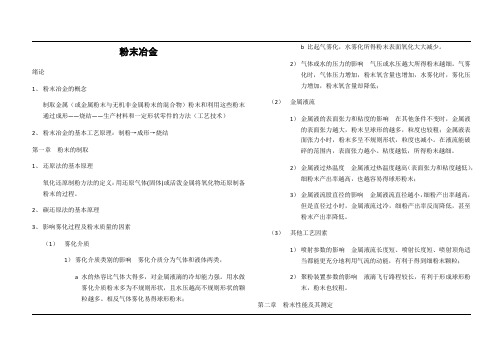
粉末冶金绪论1、粉末冶金的概念制取金属(或金属粉末与无机非金属粉末的混合物)粉末和利用这些粉末通过成形——烧结——生产材料和一定形状零件的方法(工艺技术)2、粉末冶金的基本工艺原理:制粉→成形→烧结第一章粉末的制取1、还原法的基本原理氧化还原制粉方法的定义:用还原气体(固体)或活泼金属将氧化物还原制备粉末的过程。
2、碳还原法的基本原理3、影响雾化过程及粉末质量的因素(1)雾化介质1)雾化介质类别的影响雾化介质分为气体和液体两类,a 水的热容比气体大得多,对金属液滴的冷却能力强。
用水做雾化介质粉末多为不规则形状,且水压越高不规则形状的颗粒越多。
相反气体雾化易得球形粉末;b 比起气雾化,水雾化所得粉末表面氧化大大减少。
2)气体或水的压力的影响气压或水压越大所得粉末越细。
气雾化时,气体压力增加,粉末氧含量也增加,水雾化时,雾化压力增加,粉末氧含量却降低;(2)金属液流1)金属液的表面张力和粘度的影响在其他条件不变时,金属液的表面张力越大,粉末呈球形的越多,粒度也较粗;金属液表面张力小时,粉末多呈不规则形状,粒度也减小。
在液流能破碎的范围内,表面张力越小。
粘度越低,所得粉末越细。
2)金属液过热温度金属液过热温度越高(表面张力和粘度越低),细粉末产出率越高,也越容易得球形粉末;3)金属液流股直径的影响金属液流直径越小,细粉产出率越高,但是直径过小时,金属液流过冷,细粉产出率反而降低,甚至粉末产出率降低。
(3)其他工艺因素1)喷射参数的影响金属液流长度短、喷射长度短、喷射顶角适当都能更充分地利用气流的动能,有利于得到细粉末颗粒;2)聚粉装置参数的影响液滴飞行路程较长,有利于形成球形粉末,粉末也较粗。
第二章粉末性能及其测定1、粉末的表征(1)化学成分粉末的化学成分应包括主要金属的含量和杂质的含量。
杂质主要指:1)与主要金属结合,形成固溶体或化合物的金属或非金属成分;2)从原料和从粉末生产过程中带进的机械夹杂;3)粉末表面吸附的氧、水汽和其他气体。
- 1、下载文档前请自行甄别文档内容的完整性,平台不提供额外的编辑、内容补充、找答案等附加服务。
- 2、"仅部分预览"的文档,不可在线预览部分如存在完整性等问题,可反馈申请退款(可完整预览的文档不适用该条件!)。
- 3、如文档侵犯您的权益,请联系客服反馈,我们会尽快为您处理(人工客服工作时间:9:00-18:30)。
加水量:聚合法和颗粒法所需水量不同
–聚合法:在控制水解的条件下,使水解产物及部 分未水解的醇盐分子之间继续聚合而形成,加水 量少,对于Al(OR)3, r在0.5~1之间 –颗粒法:在加入大量水,使醇盐充分水解的条件 下形成粒子溶胶,对于Al(OR)3, r在100以上 –聚合物溶胶与粒子溶胶热力学属性不同,前者属 于大分子溶液(化学溶胶),体系内无固液界面, 是热力学稳定系统;后者存在固、液界面的二相 体系(物理溶胶),在热力学上不稳定,必须加 胶溶剂。
溶胶制备 要求:溶胶中聚合物分子或胶体粒子具 有能满足产品性能要求或加工工艺要求 的结构和尺度,分布均匀,溶胶外观澄 清透明,无浑浊或沉淀,能够稳定存放 足够长的时间,并具有适宜的流变性和 其它理化性质;
M(OR) n + xH 2 O → M(OH) x (OR) n − x + xROH
金属卤化物与醇或碱金属醇盐反应
MCln + nROH → M (OR) n + nHCl ↑
M为B、Si或P;当M为Si、Ti、Zr、Hf、Nb、Ge、 Fe、V、Ce、U、Ta、Sb、Th等时通常需加NH3做 催化剂 用醇钠代替醇与金属卤化物反应也可得到金属 醇盐
MCln + nNaOR → M (OR) n + nNaCl ↓
–加聚反应:由不饱和的或环状单体分子相互 加成的反应,反应后不析出小分子副产物。
» 如由两种或两种以上单体所进行的加聚反应又称 为共聚反应。
–缩聚反应:Condensation,单分子相互进行 聚合反应的同时还析出小分子(水、醇)副 产物的反应。
S-G法常用测试方法
前驱体-金属醇盐-水解程度
–如:单金属醇盐:乙醇钠,NaOE –双金属醇盐:异丙醇铌钾,KNb(OPri)6 –Me、Et、Pri、But、Bu、Amt分别表示甲基、 已基、异丙基、叔丁基、正丁基、叔戊基
金属醇盐的合成 金属与醇直接反应
M + nROH → M (OR) n + n / 2 H 2 ↑
活泼金属:Li、Na、K、Ca、Sr、Ba等可 直接与醇反应;活性较差的金属:Be、 Mg、Al、Y等需有I2、HgCl2等做催化剂
Pc = 1/(f − 1 )
其中f是某单体的功能团数,Pc是形成无限大 分子所可能生成的全部键中已成键的部分键分 数,前提是单体聚合生长过程中不生成封闭圈 环结构
穿透理论 (percolation theory) :不排 除在凝胶化时生 成封闭圈环结构 的凝胶体 。
–每个方格结点是 任意的单体,当 相邻的两个结点 均为单体所占据 时,它们之间就 形成键,这个过 程称为结点的穿 透。
溶 胶
(涂层、成纤、成 型)
湿凝 胶
干燥
干凝胶
热处 理
成 品
均相溶液制备 溶剂:一般用醇,由于醇既与醇盐互溶,又与 水互溶 醇的加入量不能太少,否则可能落入三元互溶 区,也不能太多,因为醇是醇盐水解产物,对 水解反应有抑制作用 水/醇比(r)是关键参数。水本身是反应物。对 于一些水解活性高的醇盐,如钛醇盐,往往需 控制加水速度,否则极易生成沉淀 催化剂的添加对整个过程都有影响。酸催化剂: HCl,碱催化剂:NH4OH 为了保证溶液的均相性,通常需强烈搅拌
金属氢氧化物或氧化物与醇反应
M (OH ) n + nROH ⇔ M (OR) n + nH 2O MOn + nROH ⇔ M (OR) n + n H 2O 2 2
M为Na、Th、B、Si、Ge、Sn、Pb、As、 Se、V、Hg等
醇解法制备醇盐
M (OR) n + R ' OH ⇔ M (OR) n − m (OR' ) m + mROH
凝胶的陈化
–在陈化过程中,凝 胶粒子也可能熟化 (溶解再沉淀), 小颗粒消失,大颗 粒长大,同时凝胶 变硬,强度增大; 在不同介质中陈化 时,得到的凝胶干 缩结构不同。
a:酸性介质 b:碱性介质 c:高溶解度条件 d:低溶解度条件
凝胶的干燥
–凝胶干燥时,包裹在胶粒中的大量液体要排 出,凝胶同时收缩,在干凝胶中留下大量的 开口和闭口气孔,在凝胶干燥过程中表现出 收缩、硬固,同时产生应力,并可能使凝胶 开裂。为防止凝胶干燥过程中粉体团聚,开 发了多种干燥技术,如共沸蒸馏、溶剂置换 法、冷冻干燥、超临界干燥等。
凝胶:Gห้องสมุดไป่ตู้l,亦称冻胶,是溶胶失去流动性后, 一种富含液体的半固态物体,其中液体含量有 时高达99.5%,固体粒子则呈连续的网络体。
– 溶胶向凝胶转变过程主要是溶胶粒子聚集成键的聚 合过程 – 凝胶又分为弹性凝胶和脆性凝胶。
名词解释
胶凝时间:Gel Point,在完成凝胶的大分子 聚合过程中最后键合的时间 单体:Monomer, 一种简单的化合物,它的分 子量通过功能团起聚合反应得到分子量较高的 化合物(聚合物)
溶胶、凝胶粒子的结构
–单体聚合度(胶粒中分子由几个单体所组成)和聚 合物的性质,低聚合物分子用气相色谱配以质谱分 析,高聚物分子可用凝胶色谱测定分子量分布
M-O键的聚合结构状态
–核磁共振谱
基本原理
发展概况 1846年,J J Ebelmen用SiCl4 与乙醇混合后, 发现在湿空气中发生水解并形成了凝胶; 20世纪30年代,W Geffcken证实用这种方法可 制备氧化物薄膜; 1971德国H Dislich通过金属醇盐水解,制备 了SiO2-B2O-Al2O3-Na2O-K2O多组分玻璃 1975年制备了整块陶瓷材料和多孔氧化铝 80年代以后,S-G技术成为无机合成中的重要 方法
不可电离原料: 金属醇盐的水解:直至生成M(OH)n M(OR) + xH O → M(OH) (OR) 硅醇盐水解:
n 2 x n−x
+ xROH
水中的氧原子与硅原子作亲核结合 Si-OR+H18OH↔ Si-18OH+ROH
此外,硅、铝、磷、硼以及许多过 渡族金属元素的醇盐(或无机盐) 在水解同时均会发生聚合反应,例 如失水、失醇缩聚等
催化剂和溶液pH值 催化剂种类不同,机理不同,形成的产物也不 同:
–Si(OCH3)4, 酸催化时,醇盐水解系由H3O+的亲电机 理(与羟基反应)引起,水解速度快,易形成低交 联度的缩聚物;碱催化时,水解系由OH-的亲核取 代(与金属原子结合)引起,水解速度慢,易形成 高交联度产物 –pH值影响溶胶的稳定性,在粒子溶胶中加入酸或碱 往往也是使粒子均匀分散形成胶体体系的胶溶剂, 粒子表面因吸附H+或OH-荷电而形成稳定的溶胶
S-G方法的优点 制品均匀度高,尤其多组分制品均匀度可达分 子或原子尺度 制品纯度高 烧结温度低
–比传统方法低400~500°C。凝胶比表面积大,活性 高;
反应过程易控制,大幅减少支反应、分相并可 避免结晶等; 制品灵活性高。改变工艺过程,可获得不同的 制品,如纤维、粉末或薄膜等。
S-G工艺过程影响参数
均相溶液制备:溶剂种类、水/醇比 溶胶制备:加水量、催化剂和溶液pH值、 醇盐种类及浓度、水解温度、溶剂种类 等 陈化:粘度、稳定剂 凝胶干燥:干燥条件、添加剂 干凝胶热处理:温度、时间、升温速度 等
S-G工艺过程
金属盐 、溶剂 、水、 催化剂
水解缩 聚 陈化
利用金属醇盐与醇的反应特性,可由 “低级”醇盐合成“高级”醇盐
电化学合成法制备金属醇盐 以惰性元素电极——铂电极或石墨电极 为阴极,以欲制备的金属醇盐的金属为 牺牲阳极,在醇溶液中添加少量电解质 载体,通电使阴极和阳极间发生电解反 应以制备预定金属元素的醇盐。 具有醇盐纯度高、产率高、作业环境好、 污染少、后处理工作易做等优点
S-G主要原料——金属醇盐
S-G原料: 金属醇盐、醋酸盐、已酰丙酮盐、硝酸 盐、氯化物等 金属醇盐优点:容易用蒸馏、重结晶技 术提纯、可溶于普通有机溶剂、易水解 等 2/3以上元素能够形成醇盐
结构: M(OR)n,(M:价态为n的金属, R:烃基或芳香基)分子结构中至少有一 个M-O-C单元 分类:可根据其分子中所含不同金属原 子的数目或不同有机基团分:
为防止在液相反应时发生团聚,常用化学表面改性的方法, 如加有机螯合剂、表面活性剂及其它有机添加剂改性,降 低粉末表面能,增加胶粒间静电排斥,或产生空间位阻作 用而使胶体稳定。
凝胶化过程 凝胶化是指溶胶化的粒子由于化学键合的作用 而聚集长大为具有三维结构的较大分子的过程。 凝胶化现象两种理论解释 : 经典的Flory和Stockmeyer理论 :形成凝胶的 临界条件是,
–(C2H5O)4Si是硅乙醇盐,与一般金属有机化 合物的差别在于金属醇盐以M-O-C键的形式 结合,金属有机化合物则是M-C键结合
溶胶:Sol,又称胶体溶液,是在分散体系中保 持固体物质不沉淀的胶体,这里的分散介质主 要是液体。
– 溶胶中的固体粒子大小常在1~5nm,也就是胶体粒子 的最小尺寸,因此比表面积十分大。
S-G方法的特点: 原料:液体化学试剂(或将粉状试剂溶于溶剂) 或溶胶,而不是传统的粉状物体; 反应过程:在液相下均匀混合并进行反应; 反应产物:稳定的溶胶体系,不发生沉淀,放 置一定时间后转变为凝胶 脱水:凝胶中含有大量液相,需借助蒸发除去, 而不是机械脱水; 成型:在溶胶或凝胶状态下即可成型为所需制 品,再在低于传统烧成温度下烧结
–单体一般是不饱和的或含有两个或更多功能团的小 分子化合物,如Si(OH)4
聚合物:Polymer,从至少含两个功能团的单 体经聚合反应成为很大分子的化合物。