IE工业工程与QC七大手法7.doc
QC七大手法(精简版)

0
6 0 0 0 11 2 0 1 0 0
12、其他
合 计
1
14 7 0
1
21
16
如何设计点检表
• 步骤1.明确点检项目
–明确工作步骤 –就各步骤分别检讨4M1E(人Man、机Machine、料 Material、法Method、环Environment)所需条件 –针对影响工作结果较大的条件(要因)设定为点检 项目
一般型-分类项目有原因別、设备別、不良 项目別、人员別、缺点別..等。
• 调查异常(不良)原因用查检表 • 点检用查检表
14
如何设计查检表
• 步骤1.明确目的-了解问题?证明假设?要因解析? 数据收集的 对象范围,以利解析及解释。 • 步骤2.决定层别的角度 • 步骤3.决定查检项目:非执行不可的作业, 非检查不可的事项等 • 步骤4.决定查检表的格式 • 步骤5.决定数据记录方式 • 步骤6.决定数据收集方式-用5W1H明确下列事项: (when时间/where地点/what事件/who人/why原因/how方法) (a)收集人员 (b)测定、检查判定方法 (c)收集数据之期间、周期、时间 (d)检查方式:抽验或全检 (e)如何抽样及样本个数
• 步骤2.决定点检顺序 • 步骤3.决定点检周期 • 步骤4.决定点检表格格式
17
点检表范例
每日下班生产线点检表
项目 11月1日 √ √ √ × 11月2日 √ √ × √ 11月3日 √ √ √ √
电源开关是否 关闭
窗户是否关妥 现场是否打扫 工具是否归位 …… ……
18
一.查检表
1.召集所有相关人员,运用脑力激荡法制作特 性要因图,以列出要因项目。 2.将所列出的要因项目层别后,并填入检核表 中。 3.操作人员运用简单的记号,将检核结果纪录 于表中。 4.利用所得之数据,整理分析,以便了解管制 情况或采取必要措施。
工业工程七大手法培训教材
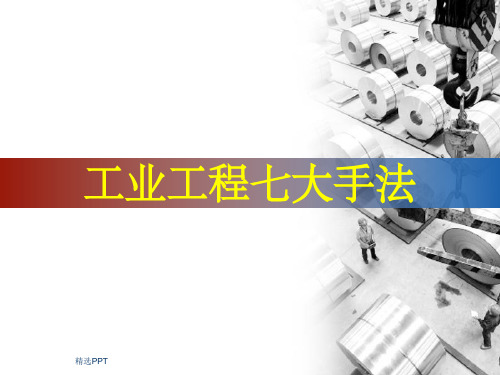
IE七大手法——五五法
精选PPT
16
IE七大手法——五五法
精选PPT
17
IE七大手法——五五法
精选PPT
18
IE七大手法——五五法
精选PPT
19
IE七大手法——五五法
精选PPT
20
IE七大手法——五五法
精选PPT
21
IE七大手法——五五法
精选PPT
22
IE七大手法——五五法
精选PPT
(1) 抽查法: 首先协助我们去认清问题的所在以及问题的事实真象。
(2) 双手法、人机法、流程法: 协助我们进一步的认清事实的状况,以及建立其改善基
础的启发点。 (3) 五五法、防错法、动改法:
协助我们对己知的问题,探寻改善的具体方法,以实现 改善的目标。
7
四、IE七大手法与QC七大手法的差别
(1)"品管(QC)七手法"较着重于对问题的分析与重点的 选择,但对如何加以改善则较少可应用。 (2)“改善(IE)七手法”较着重于客观详尽地了解问题的现 象.以及改善方法的应用,以期达到改善目标. (3)有了"改善(IE)七手法"正可弥补品管(QC)手法的 缺陷,从而达到相辅相成的效果,使得改善的效果更为实际 也更容易实现,同时最重要是改善(IE)七手法也可单独使 用,因为其本身就具有分析和发掘问题的技巧,七手法有时 亦称为七工具。
工业工程七大手法
精选PPT
1
主要内容
01
IE七大手法整体介绍
目
02
录
03
五五法 流程法
04
人机法
2
主要内容
05
双手法
目
06
录
07
动改法 防错法
IE工业工程改善七大手法

IE工业工程改善七大手法概述IE工业工程是指以科学方法为基础,运用系统工程理论和方法,在生产过程中对人、机、料、法、环境进行综合优化的一门工程学科。
IE工业工程改善七大手法是指在IE工业工程领域中常用的七种改善方法,本文将详细介绍这七大手法。
1. 横向流程优化横向流程优化是指通过对生产过程中不同环节进行分析,找出其中存在的瓶颈和浪费,并采取相应的措施来优化流程。
这种方法可以提高生产效率,减少物料和资源浪费,同时还能提升产品质量。
横向流程优化通常包括以下几个步骤: - 流程分析:对生产流程进行细致的分析,了解每个环节的具体操作和所需资源。
- 瓶颈分析:找出流程中的瓶颈环节,即造成生产效率降低和浪费的主要原因。
- 流程改善:通过重新设计流程或引入新的技术和设备,解决瓶颈环节问题,从而提升整体流程效率。
2. 垂直流程优化垂直流程优化是指在生产过程中,对整个生产线上下游环节进行优化,以实现生产过程的高效协同。
垂直流程优化的关键是实现信息的及时传递和合理协调,以确保每个环节对上下游环节的要求和交接点的协调。
垂直流程优化通常包括以下几个方面: - 信息流优化:通过引入信息化系统或升级现有系统,实现信息的实时传递和共享,从而提高生产过程中的响应速度和准确性。
- 协调改善:通过改善沟通和协作机制,减少生产过程中的延误和误解,提高协同效率。
- 质量管理:在生产过程中引入全面质量管理的理念和方法,强调各个环节的质量控制和持续改进。
3. 设备改善设备改善是指通过技术改进和设备优化来提高生产效率和产品质量。
设备改善可以通过以下方式实现: - 技术创新:引入新的生产技术和设备,提高生产过程中的效率和自动化程度。
- 设备维护:建立定期维护和保养计划,保证设备的正常运行和延长使用寿命。
- 能源节约:优化设备的能源使用,减少能源消耗和环境污染。
4. 物料管理物料管理是指对生产过程中的原材料和半成品进行有效的控制和管理,以确保生产过程的顺利进行。
工业工程的定义及七大手法
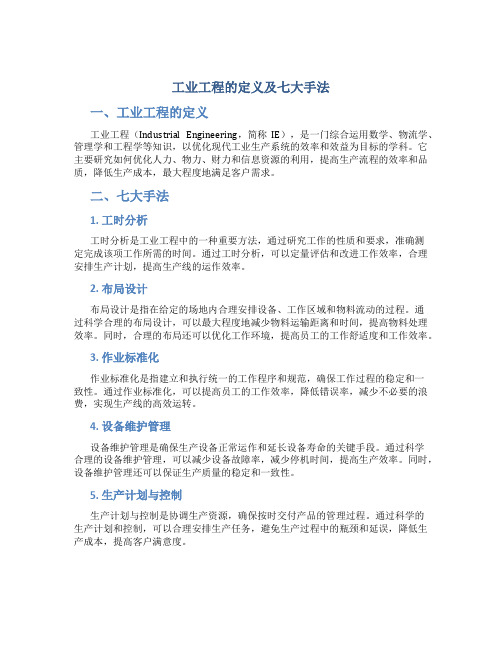
工业工程的定义及七大手法一、工业工程的定义工业工程(Industrial Engineering,简称IE),是一门综合运用数学、物流学、管理学和工程学等知识,以优化现代工业生产系统的效率和效益为目标的学科。
它主要研究如何优化人力、物力、财力和信息资源的利用,提高生产流程的效率和品质,降低生产成本,最大程度地满足客户需求。
二、七大手法1. 工时分析工时分析是工业工程中的一种重要方法,通过研究工作的性质和要求,准确测定完成该项工作所需的时间。
通过工时分析,可以定量评估和改进工作效率,合理安排生产计划,提高生产线的运作效率。
2. 布局设计布局设计是指在给定的场地内合理安排设备、工作区域和物料流动的过程。
通过科学合理的布局设计,可以最大程度地减少物料运输距离和时间,提高物料处理效率。
同时,合理的布局还可以优化工作环境,提高员工的工作舒适度和工作效率。
3. 作业标准化作业标准化是指建立和执行统一的工作程序和规范,确保工作过程的稳定和一致性。
通过作业标准化,可以提高员工的工作效率,降低错误率,减少不必要的浪费,实现生产线的高效运转。
4. 设备维护管理设备维护管理是确保生产设备正常运作和延长设备寿命的关键手段。
通过科学合理的设备维护管理,可以减少设备故障率,减少停机时间,提高生产效率。
同时,设备维护管理还可以保证生产质量的稳定和一致性。
5. 生产计划与控制生产计划与控制是协调生产资源,确保按时交付产品的管理过程。
通过科学的生产计划和控制,可以合理安排生产任务,避免生产过程中的瓶颈和延误,降低生产成本,提高客户满意度。
6. 管理信息系统管理信息系统是指采用计算机和通信设备等技术手段,对企业内部和外部的信息进行收集、整理、存储、处理和传递的系统。
通过建立有效的管理信息系统,可以及时获得准确的信息,提高管理决策的科学性和准确性,实现生产活动的高效管理。
7. 质量管理质量管理是通过采用一系列的管理方法和工具来保证产品和服务的质量。
QC七大手法,有图有案例,太实用了!

QC七大手法,有图有案例,太实用了!导读作为质量人,对QC七大手法肯定不陌生。
但对于有些人来说,又是知其然,不知其所以然。
今天将QC手法的这些信息,一网打尽!Part 1QC七大手法QC七大手法又称为QC七大工具,一般指旧QC七大手法,即层别法、检查表、柏拉图、因果图、管制图、散布图和直方图,是质量管理及改善运用的有效工具。
Part 2适用范围QC手法的用途非常广泛,可以用于企业管理的方方面面。
包括计划管控、员工思想意识行为管理、质量管控、成本管控、交期管控、士气管理、环境管理、安全管理、效率管理、绩效考核、日常管理等等,但主要用于品质管理及改善。
Part 3七大手法口诀因果追原因检查集数据柏拉抓重点直方显分布散布看相关管制找异常层别作解析QC七大手法Part 4因果图(特性要因图、石川图、鱼骨图)【定义】当一个问题的特性(结果)受到一些要因(原因)影响时,将这些要因加以整理,成为有相互关系且有条理的图形,这个图形就称为特性要因图,又叫鱼骨图(Fish-Bone Diagram)。
【用途说明】1.整理问题。
2.追查真正的原因。
3.寻找对策。
【制作步骤】1. 决定问题或品质的特性——特性的选择不能使用看起来很抽象或含混不清的主题。
2. 决定大要因——须是简单的完整句,且具有某些程度或是方向性。
3. 决定中小要因。
4. 决定影响问题点的主要原因。
5. 填上制作目的、日期及制作者等资料。
【注意事项】1.脑力激荡。
2.以事实为依据。
3.无因果关系者,予以剔除,不予分类。
4.多加利用过去收集的资料。
5.重点放在解决问题上,并依结果提出对策,依5W2H原则执行。
· WHY——为什么?为什么要这么做?理由何在?原因是什么?· WHAT——是什么?目的是什么?做什么工作?· WHERE——何处?在哪里做?从哪里入手?· WHEN——何时?什么时间完成?什么时机最适宜?· WHO——谁?由谁来承担?谁来完成?谁负责?· HOW ——怎么做?如何提高效率?如何实施?方法怎样?· HOW MUCH——多少?做到什么程度?数量如何?质量水平如何?费用产出如何?6.依据特性别,分别制作不同的特性要因图。
工业工程(IE)七大手法(完整版)
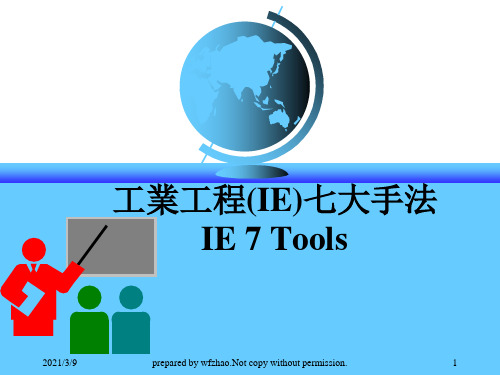
險或錯誤的現象發生.隔離原理亦稱保護原理. 7>. 復制原理: 同一件工作,如需做二次以上,最好采用“復制”方式來達成,
省時又不錯誤. 8>. 層別原理: 為避免將不同工作做錯,而設法加以區別出來.
IE七大手法之一 — 防呆法
2.應用範圍
任何工作無論是在機械操作、產品使用上,以及文書處理等皆可應用到.
IE七大手法之一 — 防呆法
3.基本原則 在進行”防呆法”時,有以下四原則可供參考:
1>. 使作業的動作輕鬆 2>. 使作業不要技能與直覺 3>. 使作業不會有危險 4>. 使作業不依賴感官 EXL: 在連續幾個測試站間加檔板,防止未測品流至下一站. 4.應用原理 1>. 斷根原理: 將會造成錯誤的原因從根本上排除掉,使絕不發生錯誤. 2>. 保險原理: 采用二個以上的動作必需共同或依序執行才能完成工作.
的主要工作.
大綱
IE 简介 IE 七大手法简介 IE 七大手法之一 防 呆 法 IE 七大手法之二 動 改 法 IE 七大手法之三 流 程 法 IE 七大手法之四 五 五 法 IE 七大手法之五 人 機 法 IE 七大手法之六 雙 手 法 IE 七大手法之七 抽 查 法 IE 手法之改善步骤
IE簡介
這里归纳为三大类/十大原則:
1>. 关于人体的运用; 2>. 关于工作地的布置; 3>. 关于工具设备
第一条原则:双手的动作应同时而对称 。
第二条原则:人体的动作应以尽量应用最低级而能得到满意结果为妥。
。級 別
一
二
三
四
IE-QC七大手法
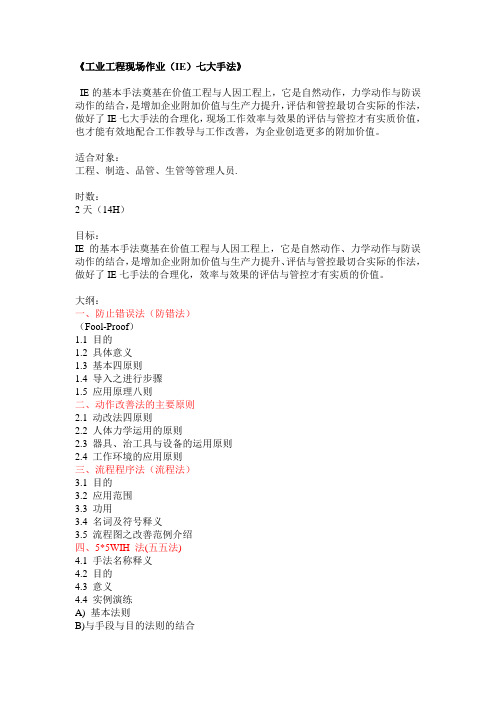
《工业工程现场作业(IE)七大手法》IE的基本手法奠基在价值工程与人因工程上,它是自然动作,力学动作与防误动作的结合,是增加企业附加价值与生产力提升,评估和管控最切合实际的作法,做好了IE七大手法的合理化,现场工作效率与效果的评估与管控才有实质价值,也才能有效地配合工作教导与工作改善,为企业创造更多的附加价值。
适合对象:工程、制造、品管、生管等管理人员.时数:2天(14H)目标:IE的基本手法奠基在价值工程与人因工程上,它是自然动作、力学动作与防误动作的结合,是增加企业附加价值与生产力提升、评估与管控最切合实际的作法,做好了IE七手法的合理化,效率与效果的评估与管控才有实质的价值。
大纲:一、防止错误法(防错法)(Fool-Proof)1.1 目的1.2 具体意义1.3 基本四原则1.4 导入之进行步骤1.5 应用原理八则二、动作改善法的主要原则2.1 动改法四原则2.2 人体力学运用的原则2.3 器具、治工具与设备的运用原则2.4 工作环境的应用原则三、流程程序法(流程法)3.1 目的3.2 应用范围3.3 功用3.4 名词及符号释义3.5 流程图之改善范例介绍四、5*5WIH 法(五五法)4.1 手法名称释义4.2 目的4.3 意义4.4 实例演练A) 基本法则B)与手段与目的法则的结合五、人机法5.1 手法名称5.2 目的5.3 意义5.4 应用范围5.5 功用5.6 名词释义5.7 人机配合图表介绍5.8 举例说明5.9 间除能量分析说明三则六、双手操作法6.1 目的6.2 意义6.3 应用范围6.4 功用6.5 名词及符号释义6.6 范例介绍6.7 绘图注意之点七、工作抽查法7.1 意义7.2 工作抽查之实验7.3 工作抽查之应用7.4 工作抽查之好处7.5 工作抽查之技巧7.6 工作抽查之要点7.7 以不同的对象进行层别与分类7.8 应用例子(工作绩效衡量)《SPC--统计制程管制》课程背景:实践是验证真理的唯一标准,统计制程管制便是验证事实的工具,通常,统计制程管制的使用很普及,但是多半流于形式,错用之处很多,诸如,方法选错,数据收集有问题,分析及情报提供没有彻底,没有数量化,高阶管理者不太相信这些数据,SPC 的应用经常停滞不前或失败,所以,SPC必须重新学起,端正使用技巧,初学者更是不可错过学习真功夫的机会.适合对象:工程、研发、品保、品管人员,以及6σ绿带、黑带时数:1 天课程目标:1. 了解统计手法的真正特性与限制,避免误用SPC手法而不自知2. SPC手法可以灵活使用,或多或少,或浅或深,皆应学习如何收放自如3. SPC必需与KPI结合,也必需与目标管理结合,才能收到20%/80%的功效4. SPC还需与CTQ(关键品质)与CTP(关键制程)结合,才能立竿见影地收到实效课程大纲:1.持续改进及统计过程控制概述:1.1 预防与检测;1.2 过程控制系统;1.3 变差;1.4 局部措施和对系统采取措施;1.5 过程控制和过程能力1.6 过程改进循环及过程控制;2.计量型数据控制图:2.1 均值和极差图(X bar-R Chart);2.2 计量型数据控制图过程能力解释和分析;2.2.1 Ca;Cp2.2.2 Cpk;Ppk2.2.3 由Z1及Z2求算p1及p22.2.4 改善制程能力2.3 其它控制图及控制图的层别与分类,分组的合理应用3.计数型数据控制图:3.1 不合格品率的p Chart;3.2 不合格品数的np Chart;3.3 不合格数的C Chart;3.4 其它管制图;4.其它品质手法的应用:4.1简易品质手法之应用4.2 综合应用;4.3 各种品管手法的条件限制与误用的说明;5.控制图的重点控制项目与控制方法的应用;6. SPC的实务应用与改善--八则;6.1以平均值與全距管制圖來解析製程能力6.2不良率管制圖(關鍵性要項)6.3原始数据分析6.4品質改善的三種措施6.5实例分析6.6傳統不良率與統計品管之比較6.7莖葉點繪法--簡易直方圖與管制圖6.8管制圖在實施上常見的疏失授课方式:1. 讲授2. 课堂练习3. 讨论4. Q&A意见交流5. 测验6. 课后服务,免费指导企业SPC的困境工业工程管理(IE七大手法)时间分析、动作研究流程分析、价值分析品质管理(品管七大手法、TQM、QCC)全面质量管理(TQM)品管统计技术(SPC)品管部门职责和架构(QA、QC)品管圈的运作实务技术(QCC)5S——卓越管理的基础区域颜色管理、标签管理组织设计和运作管理业务流程重组(BPR)全面设备管理和维护(TPM)现场工作改善技巧(4M1E)QC7大手法(1)第二章数据一.何谓数据? 就是根据测量所得到的数值和资料等事实.因此形成数据最重要的基本观念就是:数据=事实二.运用数据应注意的重点:1.收集正确的数据2.避免主观的判断3.要把握事实真相三.数据的种类A.定量数据:长度.时间.重量等测量所得数据,也称计量值;(特点连续不间断)以缺点数,不良品数来作为计算标准的数值称为计数值.(特点离散性数据)B.定性数据:以人的感觉判断出来的数据,例如:水果的甜度或衣服的美感.四.整理数据应注意的事项1.问题发生要采取对策之前,一定要有数据作为依据.2.要清楚使用的目的.3.数据的整理,改善前与改善后所具备条件要一致.4.数据收集完成之后,一定要马上使用.第二章查检表一.何谓查检表?为了便于收集数据,使用简单记号填记并予统计整理,以作进一步分析或作为核对、检查之用而设计的一种表格或图表。
QC七种工具以及IE七大手法

三
层別法(Stratification)
作业条件的层別 时间的层別 原材料的层別
测量的层別
检查的层別 环境、天候的层別
地区的层別
制品的层別 其 他
三 层别法
层化意味着根据关键特征将数据分组(层) 关键特征是指数据的某些方面,即你认为能够帮助你 解释问题存在的时间,地点及原因的一些方面。 数据分组是用来探寻能使问题局部化的样式,或者说 用来解释为什么频率或影响会随时间,地点或条件变 化。
几何失真 白平衡 不良
敲閃
無畫面 畫面傾斜
其他
四 柏拉图
-步驟 6:繪累計比率。
不 合 格 數
170 153 136 119 102 85 68 51 34 17 0 收斂
图表的种类 依使用目的分
• 分析用图表 • 管理用图表 • 计划用图表 • 统计用图表 • 计算用图表 • 说明用图表
第一章 QC统计手法概述-数据与图表
图表制作要領 图 名(Title) 图形的大小(Chart Proportions)
坐标轴(Coordinate)
刻 度(Scale) 零基准(Zero Base)
第一章 QC统计手法概述-数据与图表
依来源可分为 • 原物料及产品市场数 • 过程数据 • 检验数据 依时间先后可分为 • 过去数据 • 日常数据 • 新数据
第一章 QC统计手法概述-数据与图表
应用数据注意的重点 收集正确可用的数据 避免个人主观的判断 掌握真实的真相 有一定的量 整理数据的方法 机器整理法 人工整理法
凡事物不能完全单独用平均数来考虑,应了解事物都有变差存在 ,須从平均数与变异性来考虑——直方图(Histogram)、控制图 (Control Chart)。
工业工程(IE)七大手法(完整版)课件

03
逐渐发展成为一个独立的工程学
工业工程在制造业中应用广泛 ,涉及生产计划、生产线设计
、质量控制等方面。
物流业
工业工程在物流业中的应用包 括运输规划、仓储管理、配送 优化等。
服务行业
工业工程在服务行业中的应用 包括业务流程优化、服务系统 设计等。
公共部门
工业工程在公共部门中的应用 包括城市规划、交通管理、卫
在实际应用中,企业可以根据具体问题和需求选择合适的手法进行改进和优化,以达到最佳效果。
03
七大手法详解
5W1H法
总结词
5W1H法是一种常用的思考方法,用于分析问题的根本原因和提出解决方案。
详细描述
5W1H法的五个W包括“What(什么)”、“Why(为什么)”、“When(何时)”、“Where(在哪里) ”、“Who(谁)”,一个H是“How(如何)”。通过这六个方面对问题进行深入分析,有助于全面了解问题 并找到解决方案。
的竞争力和盈利能力。
时间研究
要点一
总结词
时间研究是一种测量和改进工作时间的方法,通过合理安 排工作时间,提高工作效率。
要点二
详细描述
时间研究通过对工作时间进行测量和分析,找出时间浪费 的环节,进而制定合理的作业计划和时间表,以提高工作 效率。这种方法广泛应用于企业管理和生产过程中,有助 于提高企业的生产效率和盈利能力。
ECRS分析法
总结词
ECRS分析法是一种改进生产流程的方法,通过消除(Eliminate)、合并( Combine)、重排(Rearrange)、简化(Simplify)四个步骤来提高生产效 率和降低成本。
详细描述
ECRS分析法的四个步骤分别针对生产流程中的冗余、重复、不必要的环节进行 优化,通过消除、合并、重排、简化来提高生产效率和降低成本,提升企业的 竞争力。
IE工业工程与QC七大手法7.doc
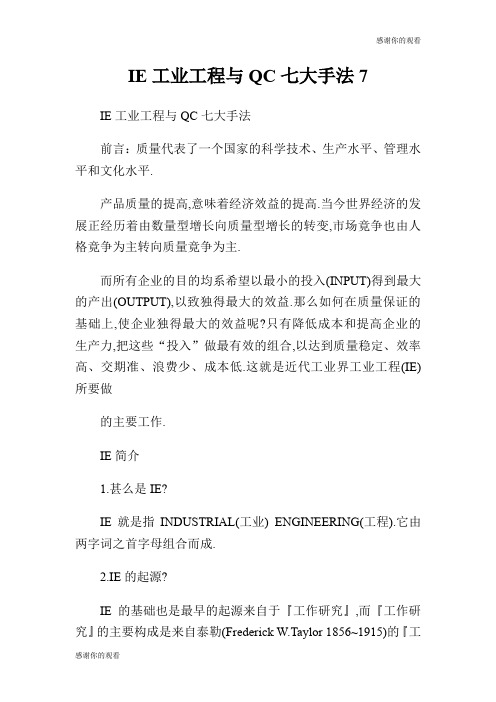
IE工业工程与QC七大手法7 IE工业工程与QC七大手法前言:质量代表了一个国家的科学技术、生产水平、管理水平和文化水平.产品质量的提高,意味着经济效益的提高.当今世界经济的发展正经历着由数量型增长向质量型增长的转变,市场竟争也由人格竟争为主转向质量竟争为主.而所有企业的目的均系希望以最小的投入(INPUT)得到最大的产出(OUTPUT),以致独得最大的效益.那么如何在质量保证的基础上,使企业独得最大的效益呢?只有降低成本和提高企业的生产力,把这些“投入”做最有效的组合,以达到质量稳定、效率高、交期准、浪费少、成本低.这就是近代工业界工业工程(IE)所要做的主要工作.IE简介1.甚么是IE?IE就是指INDUSTRIAL(工业) ENGINEERING(工程).它由两字词之首字母组合而成.2.IE的起源?IE的基础也是最早的起源来自于『工作研究』,而『工作研究』的主要构成是来自泰勒(Frederick W.Taylor 1856~1915)的『工作研究』与吉尔布雷斯(Frank B Gilbreth 1868~1924)的『动作研究』二者所构成.3.IE的目的?应用科学及社会学的知识,以合理化、舒适化的途径来改善我们工作的质量及效率以达到提高生产力增进公司之利润进而使公司能长期的生存发展下去,个人的前途也有寄托之所在.因此,简单地说,IE的目的就是充分利用工厂的人力、设备、材料,以最经济有效的工作方法,使企业独得最大的效益.4.为甚么要有IE?*持续的进步是企业及个人长久生存的根基.*改善就是进步的原动力,没有改善就没有进步.—学如逆水行舟,不进则退.*改善是永无止境的,必须长久持续去进行.4.IE的主要范围?*工程分析*价值分析(V.A) *动作研究*工作标准*时间研究*时间标准*工厂布置*搬运设计5.为甚么要有改善(IE)七大手法?*以不教而战,谓之杀.*徒然要求改善而不讲求方法、技巧,于事无补.*给人一条鱼吃,不如教他捕鱼的技术.*要求捕更多的鱼,首先必须讲求捕鱼技术的传授与使用.*改善七大手法(IE 7 TOOLS)就是协助我们改善我们工作的技术.IE七大手法简介改善(IE)七大手法有哪些?名称目的1.动改法改善人体动作的方式,减少疲劳使工作更为舒适、更有效率,不要蛮干.2.防错法如何避免做错事情,使工作第一次就做好的,精神能够具体实现.3.五五法借着质问的技巧来发掘出改善的构想.4.双手法研究人体双手在工作时的过程,藉以发掘出可资改善之地方.5.人机法研究探讨操作人员与机器工作的过程,藉以发掘出可资改善的地方.6.流程法研究探讨牵涉到几个不同工作站或地点之流动关系,藉以发掘出可资改善的地方.7.抽查法借着抽样观察的方法能很迅速有效地了解问题的真象.IE手法—工作简化的循环有效的实施「工作简化」机构—增加生产机构—提高工作实际降低成本管理上情绪利益个人—工时缩短收获个人—聪明才智收益增加有发展机会提高工作效率IE七大手法之一—-------- 防错法1.意义::防错法又称防愚法,其义为防止愚笨的人做错事.也就是说,连愚笨的人也不会做错事的设计方法. 狭义: 如何设计一个东西(一套方法),使错误绝不会发生.广义: 如何设计一个东西(一套方法),而使错误发生的机会减至最低的程度.因此,更具体的说”防错法”是:1>. 具有即使有人为疏忽也不会发生错误的构造—不需要注意力.2>. 具有外行人来做也不会做错的构造—不需要经验与直觉.3>.具有不管是谁或在何时工作能不出差错的构造—不需要专门知识与高度的技能.2.功用1>. 积极: 使任何的错误,绝不会发生.2>. 消极: 使错误发生的机会减至最低程度.3.应用范围任何工作无论是在机械操作、产品使用上,以及文书处理等皆可应用到.4.基本原则在进行”防错法”时,有以下四原则可供参考:1>. 使作业的动作轻松2>. 使作业不要技能与直觉3>. 使作业不会有危险4>. 使作业不依赖感官EXL:在连续几个测试站间加档板,防止未测品流至下一站.5.基本原理1>. 排除化: 剔除会造成错误的原因.2>. 替代化: 利用更确实的方法来代替.3>. 容易化: 使作业变得更容易、更合适、更独特,或共同性以减低失败.适合化、共同化、集中化、特殊/个别化.4>. 异常检出: 虽然已经有不良或错误现象,但在下一制程中,能将之检出,以减少或剔除其危害性.5>. 缓和影响: 作业失败的影响在其波及的过程中,用方法使其缓和或吸收.6.应用原理1>. 断根原理: 将会造成错误的原因从根本上排除掉,使绝不发生错误.2>. 保险原理: 采用二个以上的动作必需共同或依序执行才能完成工作.3>. 自动原理: 以各种光学、电学、力学、机构学、化学等原理来限制某些动作的执行或不执行,以避免错误之发生.目前这些自动开关非常普遍,非常简易的“自动化”之应用.4>. 相符原理: 藉用检核是否相符合的动作,来防止错误的发生.5>. 顺序原理: 避免工作之顺序或流程前后倒置,可依编号顺序排列,可以减少或避免错误的发生.6>. 隔离原理: 藉分隔不同区域的方式,来达到保护某些地区,使不能造成危险或错误的现象发生.隔离原理亦称保护原理.7>. 复制原理: 同一件工作,如需做二次以上,最好采用“复制”方式来达成,省时又不错误.8>. 层别原理: 为避免将不同工作做错,而设法加以区别出来.9>. 警告原理: 如有不正常的现象发生,能以声光或其它方式显示出各种“警告”的讯号,以避免错误即将发生.10>. 缓和原理: 以藉各种方法来减少错误发生后所造成的损害,虽然不能完全排除错误的发生,但是可以降低其损害的程度.EXL:1.鸡蛋之隔层装运盒减少搬运途中的损伤.(缓和原理)2.设立多层之检查方法,考试后检查一次看看,有没有犯错的地方.(保险原理)3.自动消防洒水系统,火灾发生了开始自动洒水灭火.(警告原理)4.汽车之安全带,骑机车戴安全帽.(保险原理)5.加保利龙或纸板以减少产品在搬运中之碰伤.(缓和原理)6.原子笔放在桌上老是给别人不经意中拿走,怎么办呢?贴上姓名条或加条绳子固定在桌上.(隔离原理、警告原理、缓和原理)IE七大手法之二—动改法1.手法名称又称动作改善法,简称为“动改法”,是:*省力动作原则*省时动作原则*动作舒适原则*动作简化原则此原则以最少的劳力达到最大的工作效果,其原为吉尔博斯(Gibreth)最先提出,后经研究整理增删.其中以巴恩斯(Ralph M.Barnes)将之补充完成.2.动作改善原则可分为三大类二十项.3.三大分类为:1>. 有关于人体动用方面之原则,共包含8项.2>. 有关于工作场所之布置与环境之原则,共包含6项.3>. 有关于工具和设备之设计原则.共包含6项.详细之20项原则将在后面详加介绍.4.有关人体动用原则(动作经济原则)原则1: 两手同时开始及完成动作原则2: 除休息时间外,两手不应同时空闲原则3: 两臂之动作应反射同时对称.原则4: 尽可能以最低级动作工作说明:欲使动作迅速而轻易,唯有从动作距离之缩短,以及动作所耗体力减少上着手.欲达到此目的,其实际对策则为选取级次最低之动作,使动作范围缩小.并使物料及工具尽可能靠近手之动作范围内.工作时,人体之动作可分为下列五级:原则5: 物体之”动量”尽可能利用;但如需用肌力制止时,则应将其减至最小度.原则6: 连续曲线运动较方向突变直线运动为佳.原则7: 弹道式运动较轻快.原则8: 动作宜轻松有节奏.原则9: 眼睛的视点应尽少变动并尽量接近.原则10: 适当之照明;应有适当之照明设备,使视觉满意舒适.所谓合适的照明,其意义应包括:1>.必须有合适其工作的充足光度. 2>.必须有合适颜色的光线,且应避免闪光.3>.必须有合适的投射方向.原则11: 工作抬椅高度适当舒适原则12: 尽量以足踏/夹具替代手之工作.原则13: 尽可能将二种工具合并.EXL: 将两种功能不同的印章,修改成具有两种功能的单独印章.原则14: 工具物料预放在工作位置.原则15: 依手指负荷能力分配工作.原则16: 手柄接触面尽可能加大原则17: 操作杆应尽可能少变更姿势.IE七大手法之三—流程法现场作业改善方法:现场作业改善方法:。
QC七手法(DOC 8页)
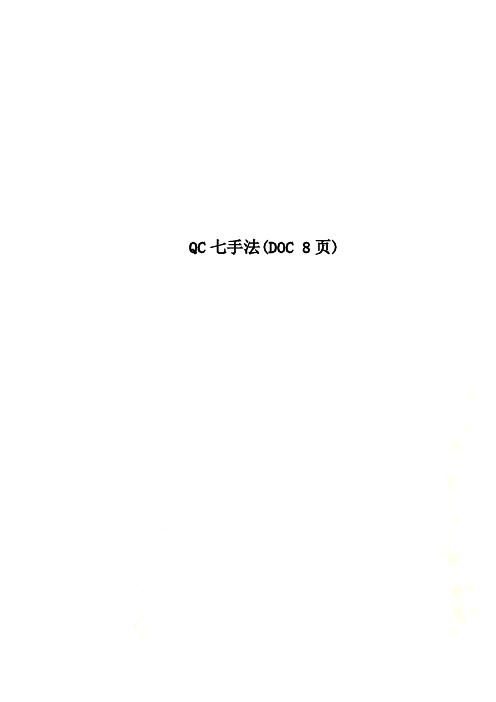
QC七手法(DOC 8页)壹、概论品质是企业的生命,当产品日益精致时,品质管理使成为影响企业存绩的重要关键。
品管是以其统计的数据来管理「过程」,而从过程中去改善才是其目的。
品质管制是根据消费者导向之思想,利用公司固有技术能力,使该要求能便宜、适时、安全而具体实现。
因此,公司里每一个份子在自己岗位上,应具备问题意识,自主意识,改善意识及价值意识,寻求本身工作方法或推展方法之缺失,谋求因应之道,全员协力之下达成顾客之需求与社会之要求,其手段(管理方法)即是应用统计手法与观念。
采用「根据数据、事实表达」的统计方法来管理,除了可客观判断事实外,亦具有相当合理的说服力。
QC活动中所采用之统计手法极为简单,一般称为「QC七大手法」。
七大手法之使用情形可归纳如下:1.根据事实,数据表达−图表(G r ap h)、查检表(C h ec k S h ee t),散布图(S ca tt e r Di ag r am)。
2.整理原因与结果之关系,以探讨潜在性之问题−特性要因图(C ha r ac te r is ti c D i ag r am)。
3.凡事物不能完全单用平均值来考虑,应了解事物均有变异存在,须从平均值与变异性来考虑−直方图(H is to g ra m)、管制图(C on t ro l C ha rt)。
4.所有数据不可仅止于平均,须根据数据之履历,考虑适当分层区别−层别法(Stratification)。
5.并非对所有原因采取处置,而是先就其中影响较大的2~3项采取措施,亦即为重点管理−柏拉图(P ar e to D i ag ra m)。
简单来说,这些手法是要「以现实合理之眼光,来观察产生不良情形之现场的现物」,以达到做好所谓的「三现主义」之异常处理与管制。
全员改善常用工具─QC七大手法一、查检表1.定义以简单的数据用容易了解的方式,作成图形或表格,只要记上检查记号,并加以统计整理,作为进一步分析或核对检查用。
IE与QC七大手法
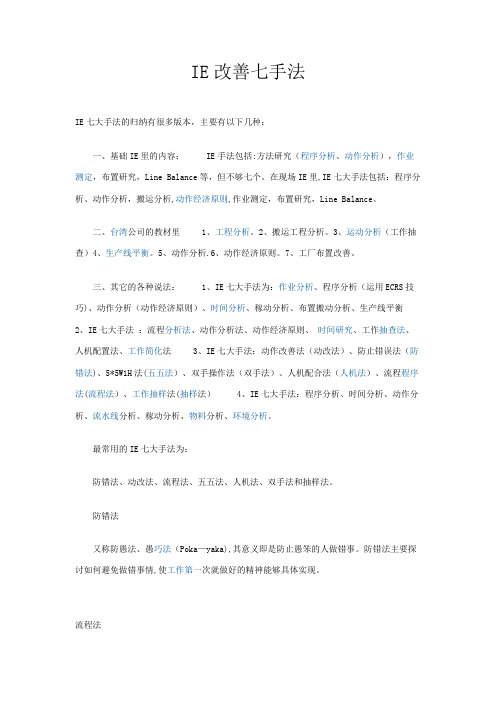
IE改善七手法IE七大手法的归纳有很多版本,主要有以下几种:一、基础IE里的内容:IE手法包括:方法研究(程序分析、动作分析),作业测定,布置研究,Line Balance等,但不够七个。
在现场IE里,IE七大手法包括:程序分析、动作分析,搬运分析,动作经济原则,作业测定,布置研究,Line Balance。
二、台湾公司的教材里1、工程分析。
2、搬运工程分析。
3、运动分析(工作抽查)4、生产线平衡。
5、动作分析.6、动作经济原则。
7、工厂布置改善。
三、其它的各种说法:1、IE七大手法为:作业分析、程序分析(运用ECRS技巧)、动作分析(动作经济原则)、时间分析、稼动分析、布置搬动分析、生产线平衡2、IE七大手法:流程分析法、动作分析法、动作经济原则、时间研究、工作抽查法、人机配置法、工作简化法3、IE七大手法:动作改善法(动改法)、防止错误法(防错法)、5*5W1H法(五五法)、双手操作法(双手法)、人机配合法(人机法)、流程程序法(流程法)、工作抽样法(抽样法)4、IE七大手法:程序分析、时间分析、动作分析、流水线分析、稼动分析、物料分析、环境分析。
最常用的IE七大手法为:防错法、动改法、流程法、五五法、人机法、双手法和抽样法。
防错法又称防愚法、愚巧法(Poka—yaka),其意义即是防止愚笨的人做错事。
防错法主要探讨如何避免做错事情,使工作第一次就做好的精神能够具体实现。
流程法研究探讨牵涉几个不同工作站或地点之流动关系,藉以发掘出可资改善的地方。
五五法借着质问的技巧来发掘出改善的构想.在改善时可以借用5W1H来进行质问.改善的前提是发现问题,而发现问题则全在于怀疑的态度。
然而怀疑并非仅是笼统的抽象思维,应是有系统的、循序渐进的,而且是有具体的方向.如果没有采用系统化的技巧,往往疏漏了某些值得去改善的地方。
5WIH是一种找寻问题之根源及寻找系统化的质问技巧.依照5WIH的方法进行质问,那么,改善工作所需要的数据,将从这些质问的答案中获得。
QC七大手法,有图有案例,太实用了!

QC七大手法,有图有案例,太实用了!作为质量人,对QC七大手法肯定不陌生。
但对于有些人来说,又是知其然,不知其所以然。
今天将QC手法的这些信息,一网打尽!1.QC七大手法QC七大手法又称为QC七大工具,一般指旧QC七大手法,即层别法、检查表、柏拉图、因果图、管制图、散布图和直方图,是质量管理及改善运用的有效工具。
2.适用范围QC手法的用途非常广泛,可以用于企业管理的方方面面(包括计划管控、员工思想意识行为管理、质量管控、成本管控、交期管控、士气管理、环境管理、安全管理、效率管理、绩效考核、日常管理等等),但主要用于品质管理及改善。
3.七大手法口诀因果追原因检查集数据柏拉抓重点直方显分布散布看相关管制找异常层别作解析QC七大手法4.因果图(特性要因图、石川图、鱼骨图)【定义】当一个问题的特性(结果)受到一些要因(原因)影响时,将这些要因加以整理,成为有相互关系且有条理的图形,这个图形就称为特性要因图,又叫鱼骨图(Fish-Bone Diagram)。
【用途说明】1.整理问题。
2.追查真正的原因。
3.寻找对策。
【制作步骤】1. 决定问题或品质的特性——特性的选择不能使用看起来很抽象或含混不清的主题。
2. 决定大要因——须是简单的完整句,且具有某些程度或是方向性。
3. 决定中小要因。
4. 决定影响问题点的主要原因。
5. 填上制作目的、日期及制作者等资料。
【注意事项】1.脑力激荡。
2.以事实为依据。
3.无因果关系者,予以剔除,不予分类。
4.多加利用过去收集的资料。
5.重点放在解决问题上,并依结果提出对策,依5W2H原则执行。
•WHY——为什么?为什么要这么做?理由何在?原因是什么?•WHAT——是什么?目的是什么?做什么工作?•WHERE——何处?在哪里做?从哪里入手?•WHEN——何时?什么时间完成?什么时机最适宜?•WHO——谁?由谁来承担?谁来完成?谁负责?•HOW ——怎么做?如何提高效率?如何实施?方法怎样?•HOW MUCH——多少?做到什么程度?数量如何?质量水平如何?费用产出如何?6.依据特性别,分别制作不同的特性要因图。
- 1、下载文档前请自行甄别文档内容的完整性,平台不提供额外的编辑、内容补充、找答案等附加服务。
- 2、"仅部分预览"的文档,不可在线预览部分如存在完整性等问题,可反馈申请退款(可完整预览的文档不适用该条件!)。
- 3、如文档侵犯您的权益,请联系客服反馈,我们会尽快为您处理(人工客服工作时间:9:00-18:30)。
IE工业工程与QC七大手法7 IE工业工程与QC七大手法前言:质量代表了一个国家的科学技术、生产水平、管理水平和文化水平.产品质量的提高,意味着经济效益的提高.当今世界经济的发展正经历着由数量型增长向质量型增长的转变,市场竟争也由人格竟争为主转向质量竟争为主.而所有企业的目的均系希望以最小的投入(INPUT)得到最大的产出(OUTPUT),以致独得最大的效益.那么如何在质量保证的基础上,使企业独得最大的效益呢?只有降低成本和提高企业的生产力,把这些“投入”做最有效的组合,以达到质量稳定、效率高、交期准、浪费少、成本低.这就是近代工业界工业工程(IE)所要做的主要工作.IE简介1.甚么是IE?IE就是指INDUSTRIAL(工业) ENGINEERING(工程).它由两字词之首字母组合而成.2.IE的起源?IE的基础也是最早的起源来自于『工作研究』,而『工作研究』的主要构成是来自泰勒(Frederick W.Taylor 1856~1915)的『工作研究』与吉尔布雷斯(Frank B Gilbreth 1868~1924)的『动作研究』二者所构成.3.IE的目的?应用科学及社会学的知识,以合理化、舒适化的途径来改善我们工作的质量及效率以达到提高生产力增进公司之利润进而使公司能长期的生存发展下去,个人的前途也有寄托之所在.因此,简单地说,IE的目的就是充分利用工厂的人力、设备、材料,以最经济有效的工作方法,使企业独得最大的效益.4.为甚么要有IE?*持续的进步是企业及个人长久生存的根基.*改善就是进步的原动力,没有改善就没有进步.—学如逆水行舟,不进则退.*改善是永无止境的,必须长久持续去进行.4.IE的主要范围?*工程分析*价值分析(V.A) *动作研究*工作标准*时间研究*时间标准*工厂布置*搬运设计5.为甚么要有改善(IE)七大手法?*以不教而战,谓之杀.*徒然要求改善而不讲求方法、技巧,于事无补.*给人一条鱼吃,不如教他捕鱼的技术.*要求捕更多的鱼,首先必须讲求捕鱼技术的传授与使用.*改善七大手法(IE 7 TOOLS)就是协助我们改善我们工作的技术.IE七大手法简介改善(IE)七大手法有哪些?名称目的1.动改法改善人体动作的方式,减少疲劳使工作更为舒适、更有效率,不要蛮干.2.防错法如何避免做错事情,使工作第一次就做好的,精神能够具体实现.3.五五法借着质问的技巧来发掘出改善的构想.4.双手法研究人体双手在工作时的过程,藉以发掘出可资改善之地方.5.人机法研究探讨操作人员与机器工作的过程,藉以发掘出可资改善的地方.6.流程法研究探讨牵涉到几个不同工作站或地点之流动关系,藉以发掘出可资改善的地方.7.抽查法借着抽样观察的方法能很迅速有效地了解问题的真象.IE手法—工作简化的循环有效的实施「工作简化」机构—增加生产机构—提高工作实际降低成本管理上情绪利益个人—工时缩短收获个人—聪明才智收益增加有发展机会提高工作效率IE七大手法之一—-------- 防错法1.意义::防错法又称防愚法,其义为防止愚笨的人做错事.也就是说,连愚笨的人也不会做错事的设计方法. 狭义: 如何设计一个东西(一套方法),使错误绝不会发生.广义: 如何设计一个东西(一套方法),而使错误发生的机会减至最低的程度.因此,更具体的说”防错法”是:1>. 具有即使有人为疏忽也不会发生错误的构造—不需要注意力.2>. 具有外行人来做也不会做错的构造—不需要经验与直觉.3>.具有不管是谁或在何时工作能不出差错的构造—不需要专门知识与高度的技能.2.功用1>. 积极: 使任何的错误,绝不会发生.2>. 消极: 使错误发生的机会减至最低程度.3.应用范围任何工作无论是在机械操作、产品使用上,以及文书处理等皆可应用到.4.基本原则在进行”防错法”时,有以下四原则可供参考:1>. 使作业的动作轻松2>. 使作业不要技能与直觉3>. 使作业不会有危险4>. 使作业不依赖感官EXL:在连续几个测试站间加档板,防止未测品流至下一站.5.基本原理1>. 排除化: 剔除会造成错误的原因.2>. 替代化: 利用更确实的方法来代替.3>. 容易化: 使作业变得更容易、更合适、更独特,或共同性以减低失败.适合化、共同化、集中化、特殊/个别化.4>. 异常检出: 虽然已经有不良或错误现象,但在下一制程中,能将之检出,以减少或剔除其危害性.5>. 缓和影响: 作业失败的影响在其波及的过程中,用方法使其缓和或吸收.6.应用原理1>. 断根原理: 将会造成错误的原因从根本上排除掉,使绝不发生错误.2>. 保险原理: 采用二个以上的动作必需共同或依序执行才能完成工作.3>. 自动原理: 以各种光学、电学、力学、机构学、化学等原理来限制某些动作的执行或不执行,以避免错误之发生.目前这些自动开关非常普遍,非常简易的“自动化”之应用.4>. 相符原理: 藉用检核是否相符合的动作,来防止错误的发生.5>. 顺序原理: 避免工作之顺序或流程前后倒置,可依编号顺序排列,可以减少或避免错误的发生.6>. 隔离原理: 藉分隔不同区域的方式,来达到保护某些地区,使不能造成危险或错误的现象发生.隔离原理亦称保护原理.7>. 复制原理: 同一件工作,如需做二次以上,最好采用“复制”方式来达成,省时又不错误.8>. 层别原理: 为避免将不同工作做错,而设法加以区别出来.9>. 警告原理: 如有不正常的现象发生,能以声光或其它方式显示出各种“警告”的讯号,以避免错误即将发生.10>. 缓和原理: 以藉各种方法来减少错误发生后所造成的损害,虽然不能完全排除错误的发生,但是可以降低其损害的程度.EXL:1.鸡蛋之隔层装运盒减少搬运途中的损伤.(缓和原理)2.设立多层之检查方法,考试后检查一次看看,有没有犯错的地方.(保险原理)3.自动消防洒水系统,火灾发生了开始自动洒水灭火.(警告原理)4.汽车之安全带,骑机车戴安全帽.(保险原理)5.加保利龙或纸板以减少产品在搬运中之碰伤.(缓和原理)6.原子笔放在桌上老是给别人不经意中拿走,怎么办呢?贴上姓名条或加条绳子固定在桌上.(隔离原理、警告原理、缓和原理)IE七大手法之二—动改法1.手法名称又称动作改善法,简称为“动改法”,是:*省力动作原则*省时动作原则*动作舒适原则*动作简化原则此原则以最少的劳力达到最大的工作效果,其原为吉尔博斯(Gibreth)最先提出,后经研究整理增删.其中以巴恩斯(Ralph M.Barnes)将之补充完成.2.动作改善原则可分为三大类二十项.3.三大分类为:1>. 有关于人体动用方面之原则,共包含8项.2>. 有关于工作场所之布置与环境之原则,共包含6项.3>. 有关于工具和设备之设计原则.共包含6项.详细之20项原则将在后面详加介绍.4.有关人体动用原则(动作经济原则)原则1: 两手同时开始及完成动作原则2: 除休息时间外,两手不应同时空闲原则3: 两臂之动作应反射同时对称.原则4: 尽可能以最低级动作工作说明:欲使动作迅速而轻易,唯有从动作距离之缩短,以及动作所耗体力减少上着手.欲达到此目的,其实际对策则为选取级次最低之动作,使动作范围缩小.并使物料及工具尽可能靠近手之动作范围内.工作时,人体之动作可分为下列五级:原则5: 物体之”动量”尽可能利用;但如需用肌力制止时,则应将其减至最小度.原则6: 连续曲线运动较方向突变直线运动为佳.原则7: 弹道式运动较轻快.原则8: 动作宜轻松有节奏.原则9: 眼睛的视点应尽少变动并尽量接近.原则10: 适当之照明;应有适当之照明设备,使视觉满意舒适.所谓合适的照明,其意义应包括:1>.必须有合适其工作的充足光度. 2>.必须有合适颜色的光线,且应避免闪光.3>.必须有合适的投射方向.原则11: 工作抬椅高度适当舒适原则12: 尽量以足踏/夹具替代手之工作.原则13: 尽可能将二种工具合并.EXL: 将两种功能不同的印章,修改成具有两种功能的单独印章.原则14: 工具物料预放在工作位置.原则15: 依手指负荷能力分配工作.原则16: 手柄接触面尽可能加大原则17: 操作杆应尽可能少变更姿势.IE七大手法之三—流程法现场作业改善方法:现场作业改善方法:IE工业工程与生产效率改善1 IE工业工程与生产效率改善主办:上海普瑞思管理咨询有限公司时间:2010年8月13-14日课程价格:¥2600/人(特(包括授课费、资料费、会务费、证书、午餐等)课程地点:上海【课程目标】伴随人类社会工业化的进程,工业工程走过了百年历史。
工业工程(IE)是一门旨在提高生产效率和经济效益的工程技术,其任务是研究生产经营及管理系统的设计、改善和实施;其方法是综合运用自然科学、社会科学和工程技术知识,进行科学的规划、设计、实施、评价和创新,把各种生产要素(人员、物料、设备、能源、场地和信息等)组成更富有生产力和有效运行的整体系统,从而不断降低成本、确保质量、提高生产率。
是一门把技术与管理有机地结合起来学科通过本课程培训,使学员实现从传统的生产管理,工程技术支持向现代的工业工程技术支持,精益生产管理模式的转变,帮助学员通过工艺及流程程序分析、操作分析、动作分析,改善工艺流程,提高人机协作效率,提高动作的经济性并使动作更加符合人因工程学,从而提高生产效率,并保护操作员工的身体健康;通过工厂布局及路径分析提高作业场地的利用率,减少无价值增值的移动。
通过时间研究,工作抽样,预定动作时间标准来科学地制定标准工时及工作定额。
通过生产线平衡来消除流水线作业中的瓶颈,缩短制程时间。
【参加人员】IE工程师,精益制造工程师,工艺工程师,生产主管,生产经理,工程经理等。
【课程大纲】一、第一单元:工业工程概论-- 工程的定义-- 工业工程的作用和应用-- 工业工程的发展-- 工业工程的内容-- 工业工程的意识二、第二单元:方法研究---程序分析-- 工作研究的内容和步骤-- 程序分析1. 工艺程序分析a)工艺程序分析介绍b)案例:产品生产工艺程序分析实例c)练习:用工艺程序分析的方法画出你所熟悉的工艺生产流程2. 流程程序分析a)流程程序分析介绍b)案例:某产品生产流程分析实例-- 人型-- 物料型c)练习:用流程程序分析的方法画出你所熟悉的工艺生产流程3. 布置与路径程序分析a)布置与路径分析的意义b)几种Layout 布局类型-- 基于流程的布局-- 基于产品的布局-- 固定式布局-大型设备的生产-- 细胞式生产布局-- 柔性制造生产布局-- 混线式生产布局c)案例:路径与布置分析d)练习:用路径与布置程序分析的方法画出你所熟悉的产品生产流程布局4. 生产布局Video-- 程序分析改善1)程序改善的原则2)程序分析技巧3)程序改善的步骤三、第三单元:方法研究---操作分析-- 操作分析的定义-- 操作分析1. 人机配合操作1)人机配合操作分析图2)案例: 某产品测试的人机配合图3)练习:用人机配合操作分析的方法画出你所熟悉的产品生产人机配合图并分析人员与设备的利用效率及如何改善的方法2. 联合操作1)联合操作分析的意义2)联合操作分析图3. 双手操作分析1)双手操作分析的符合2)双手操作分析图四、第四单元:方法研究---动作分析-- 动作分析的意义-- 动作分析1. 细微动作分析1)动作分析沙布利克符号2)沙布利克动作分析案例2. 动作经济性原则1)动作经济原则2)动作经济原则的制约因素3)动作改善的基本原则案例: 用A VIX软件进行动作分析五、第五单元:工作测量-- 时间研究1. 时间研究的方法1)马表测时法2)速度评比法3)宽放时间-- 工作抽样-- 预定动作时间标准(PTS)2. 预定动作时间标准的方法1)模特排时法(MOD)2)方法时间衡量(MTM)3)工作因素(WF)-- 标准工时的制定六、第六单元:生产率改善与生产线平衡-- 生产率改善1. IE 的追求-ABCDEF2. IE 改善的基础-3S3. IE 改善四原则4. IE 现场改善步骤-- 生产线平衡1. 生产线平衡的目的2. 生产线平衡的几个因素1)节拍时间---TAKT Time2)网络活动图---AOV3)生产周期时间---CT4)理论工位数3. 生产线平衡改善实例1)消除生产流程中的瓶颈2)在线作业转化为离线作业-- 工业工程与精益生产的关系4. 丰田生产模式Video七、第七单元:应用IE与6 Sigma 的方法进行产能改进的成功实例:本案例是某企业成功应用IE及6 Sigma 进行改进的典型案例。