210tRH精炼炉脱氢工艺研究与应用
首钢第二炼钢厂210t CAS—OB炉外精炼的工艺实践

为进 一步 提 高品种 钢 等高 附加 值产 品生 产 和开 发
炉渣隔离 ,也使钢液与大气隔离,从而减少合金
损 失 ,稳 定合 金 收得率 。C SO A . B法 是在 C S法 A 的基 础 上 发展起 来 的 ,是在 浸渍 罩 内增设 氧 枪 吹 氧 ,用 铝或 硅 铁合金 与氧反应 所 放 出 的热量 对 钢 水 加 热 ,起 到补 偿 C S法 工 序 温 降 ,为 中 间包 A
C SO 操作实践 A -B 实施 效果
炼工艺生产的高附加值 品种 钢产 品的质量较好且稳定 。
关键词
The Pr c s a tc fSe o da y Re n ng o 1 o e sPr cie o c n r f i f2 0 t i
CAS OB n S o g n . tem a i g Pln - i h u a g No 2 S e l k n a t
首 钢第 二 炼 钢 厂 ( 称 第 二 炼 钢 厂 ) 原 只 简 有 1台 L F钢包 精 炼炉 ,而 后道 工序 有 多 台 品种 钢 连铸机 , 由于 品种 钢对 钢水 洁净 度 的要 求 ,吹 氩 站 的功 能 不 能 满 足 品 种 钢 生 产 需 要 ,且 1台
L F炉生 产 能力远 低 于 品种 钢连 铸 机 的设 计 能 力 。
维普资讯
基 础上 进 行 改 造 而 成 。其 利 旧设 备 包 括 原 料 系 统 、各层 平 台基 础 、除 尘 系统 和 底 吹氩 系统 等 , 同时充分 兼顾 现场 空 间结构 。该 C SO A — B装 置有
以下特点 :
Q = 2. 3× 2 4×
包 内喷吹 惰 性 气 体 均 匀 钢 水 成 分 和 温 度 的功 能
涟钢210tRH炉生产超低碳钢的工艺优化

涟钢 20R 炉因 到站温度 普遍较 低 , H 1tH R
图 2 原 工 艺 对 应 R 炉 出 站 碳 H
炉顶枪使用 率高 , 吹氧量 大 , 用循环 2~ rn 采 6i a
后下枪吹氧 , 枪位 、 不变 的吹氧模 式 , 流量 钢水 吹氧时喷溅 严重 , 弯管顶部 高温摄 像头经 常 热
一
R 炉处理 前通 过 布料 器 将铝 渣 球 均 匀 的 撒 H 在 钢渣 表 面 , 对钢 渣 的表面 进行脱 氧 。
钢 水通过 了真 空槽 的流 量最 大合金 混匀 时 问 最 短 。通 过优 化 环 流控 制 缩 短 了 2 0R 炉 1 tH 的脱碳 时 间 、 金混匀 时 间以及纯 脱气 时 问 , 合 相对 以前工 艺处 理时 间缩短 5— mi。 8 n 4 2 吹氧参 数 、 . 吹氧升 温操作 以及 真 空泵 控
氧后期保证喷溅较小 的前提下枪 位不变提高吹 氧流量缩短吹氧时间 , 吹氧工艺优化后 , 喷溅得 到明显控制 ( 见图 6 。吹 氧升温操 作过程尽量 )
冷态抽气 时间; i a rn
在吹氧前期加入铝 丸, 将钢水温度弁到 目标 温 度 ; 钢 温度 低 时 , 来 需要 吹 氧 升 温 操 作 , 吹
氧 时真 空泵 保 持 在 四级 泵 , 空 槽 压力 7— 真
80 90 l( 0) o 6 7
8P , 氧结束 后 点击 H 画 面 自动启 动 真 k a吹 MI
水 碳 含量 如 图 2平 均值 2 pm。 , 8p
化, 优化后工 艺的吹 氧枪位提 高到 50 m 吹 50 m,
氧时机为真空主阀打开后 l i mn下枪吹氧 , 前期
4 R H工艺优化与效果
210t转炉厂钢包全程加盖装置的应用

环境恶劣 , 温 降较大; 还有一部分采用不揭 盖热 修, 这样 不利 于观 察耐材 侵蚀 , 钢包 内情 况无 法 掌
握 。我厂采 用 半开 盖 方式 解 决 以上 各利, 问题 , 仳
得其他钢厂借鉴。
2 设备操作工艺
涟钢 2 1 0转 炉 厂 钢 包 加 揭 盖 布 置 如 图 1所
盖系统进行 加 盖保温 , 揭 盖工作 。只有 在遇 到 长达几个 小时 的钢包 等待或 大修 钢包 , 钢包 才
需 要 烘烤 预热 。
失效 , 且本身不便 于安装对环境敏感的电气控制 部件 和传感 器 , 不 能精 确制 动 , 通过 在轨 道两 侧 布
设非 接触 式 的红外 线 发 射 器实 现 钢 包 车 的 定位 , 提 高加揭 盖定位 的 准确性 。 c .半 开 盖 热 修 维 护方 式 确 保 钢 包 维 护 。 内热修钢 包 时部分 采 用 卷 扬 全 打 开盖 维 修 , 这 样
热辐 射 速度 非 常快 , 尤 其 是 空包 状 态 下 。在 生 产
后, 对 钢包 口积渣 厚度 要实行 较严 格管 理 , 每次进 行钢 包水 口清理 作_ q k H  ̄ , 顺便 清 理包 口积渣 , 确保
包 口积渣 厚度 不能高 于 2 0 0 m m。
因改造过 程 中条 件 限制 , 使得该套设备有 一
挂 钩式 。该种 方 式通 过 液 压缸 驱 动设 备 横 移 、 升
降 实现加 揭盖 功能 , 系统运 行更平 稳 。
b .钢包 车 红外 线 定 位 指 示 。挂 钩 式 加 揭 盖 方 式对 钢包 车停 车位 置要 求 较 严格 , 而钢 包 车 长 期 工作 在高 温 、 红 渣 的恶 劣环 境下 , 制 动部 件 极易
210t高效VD精炼炉的研制与优化
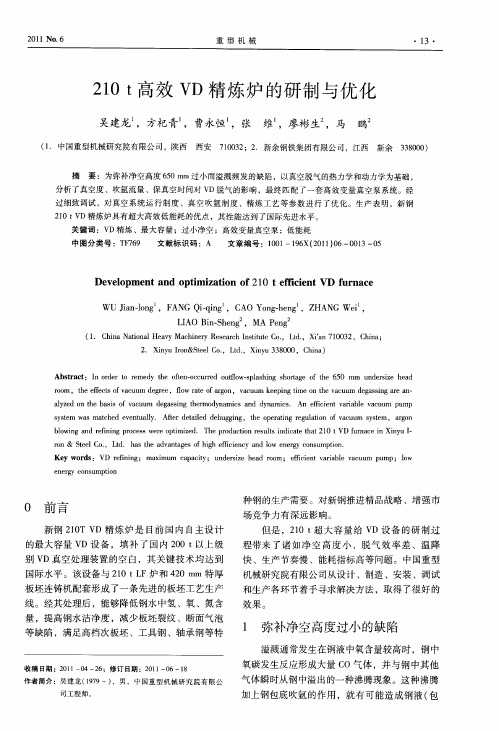
( . C i ai a H ay Mahn r ee rh Is tt C . t . i n7 0 3 ,C ia 1 hn N t n l e v c ie R sac tue o,L d,X ’ 1 0 2 hn ; a o y n i a
r o , te ef cso a u om h fe t fv c um e r e, fo rt fag n, v c m e n i n te v c u de a snga e a — d ge l w aeo r o a uu ke pig tme o h a u m g s i r n
2 XnuI n Sel o,Ld,Xn u3 80 . i r & t . t. iy 3 00,C ia y o eC h ) n
Absr c : I r e o r me y t e o e — c u rd o t o s ls i g s ot g f t e 6 0 t a t n o d r t e d h f n o c re u f w—p a hn h r e o h 5 mm n esz e d t l a u d ri h a e
De eo m e ta ptm ia i n o f c e tVD ur a e v lp n nd o i z to f2 te 1 0 i in f n c
WU J n1 g ,F N i ig ,C O Y n .e g ,Z N i, i . n A G Q — n A oghn HA G We a o q
效果 。
新 钢 20 D精 炼 炉 是 目前 国 内 自主 设 计 1TV
的最 大 容量 V D设 备 ,填 补 了 国 内 2 0 t 0 以上 级
浅谈影响RH浸渍管使用寿命的因素

浅谈影响RH浸渍管使用寿命的因素摘要:首先介绍济钢210TRH炉设备情况及生产能力,通过日常对济钢210tRH精炼炉浸渍管使用过程中出现的各种问题,分析出影响浸渍管使用寿命的因素,最后总结出从生产组织、工艺优化等方面采取措施延长浸渍管的使用寿命,保障RH稳定生产。
关键词:RH精炼炉、浸渍管、寿命1 前言RH精炼装置是重要的炉外精炼设备,是调整品种结构、生产高附加值产品的重要保障。
因此RH设备广泛用于各大钢铁企业。
济南钢铁股份公司结合自身实际在提出建设国际竞争力钢铁强企的目标下在2010年建成投产一座210T精炼炉,济钢210tRH炉主要生产济钢 210t RH 精炼炉主要以生产高级船板钢、管线钢、锅炉压力容器钢、高强结构钢、桥梁钢等。
浸渍管位于真空槽的最底部,在钢水冶炼时直接与高温钢水接触,不生产时直接暴露于大气;工作条件非常恶劣,是影响RH正常生产的关键部位。
济钢210RH在投产初期浸渍管使用寿命低、下线频繁,严重影响生产节奏,降低了生产率。
通过日常对浸渍管使用过程中出现的各种问题,结合现场实际进行观察和分析、以及对参考其他兄弟钢厂经验,分析出影响浸渍管使用寿命的因素,最后总结出从生产组织、工艺优化等方面采取措施延长浸渍管的使用寿命,保障RH稳定生产。
2 RH工作原理及基本功能整个RH处理过程是由一套完整的真空系统正常工作下完成,主要由吸入和排出钢水的浸渍管和真空槽以及真空排气装置所组成。
真空槽的下部是两个带耐火衬的浸渍管,一个为上升管,一个为下降管。
处理钢水时,先将两个浸渍管浸入到钢包,使钢包和真空室形成密闭系统。
然后,真空排气系统启动,使真空室形成真空。
这时,从一个浸渍管吹入气体(氩气或氮气)。
根据气泡泵原理,钢水被吹入真空槽内并飞溅。
钢水在真空室内脱气后,因钢水自重从另一侧的浸渍管流回到钢包内。
这样,钢水不断地从钢包进入真空室,然后又从真空室返回到钢包内,形成连续不断地环流,直到真空室内的真空状态被破坏,回到一个大气压为止。
首钢RH精炼炉长寿高效国内领先
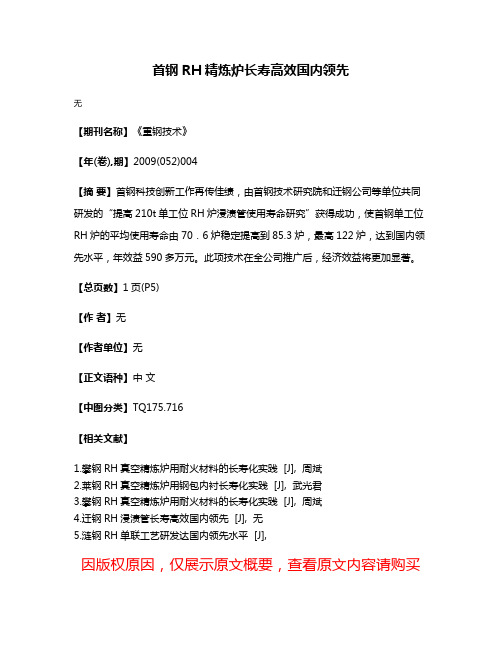
首钢RH精炼炉长寿高效国内领先
无
【期刊名称】《重钢技术》
【年(卷),期】2009(052)004
【摘要】首钢科技创新工作再传佳绩,由首钢技术研究院和迁钢公司等单位共同研发的“提高210t单工位RH炉浸渍管使用寿命研究”获得成功,使首钢单工位RH炉的平均使用寿命由70.6炉稳定提高到85.3炉,最高122炉,达到国内领先水平,年效益590多万元。
此项技术在全公司推广后,经济效益将更加显著。
【总页数】1页(P5)
【作者】无
【作者单位】无
【正文语种】中文
【中图分类】TQ175.716
【相关文献】
1.攀钢RH真空精炼炉用耐火材料的长寿化实践 [J], 周斌
2.莱钢RH真空精炼炉用钢包内衬长寿化实践 [J], 武光君
3.攀钢RH真空精炼炉用耐火材料的长寿化实践 [J], 周斌
4.迁钢RH浸渍管长寿高效国内领先 [J], 无
5.涟钢RH单联工艺研发达国内领先水平 [J],
因版权原因,仅展示原文概要,查看原文内容请购买。
深冲钢RH精炼渣的配比研究与应用

- 43 -工 业 技 术0 前言冷轧产品对强度、延伸率、表面质量都有较高的要求,特别是用于汽车、家电等行业产品,这也对热轧产品的生产提出了更高的要求。
2007年日照钢铁冲压用钢SPHC 开发成功,获得了明显经济效益,也加快了对深冲钢SPHD 开发的脚步。
2011年6月开始试生产,日照钢炼钢厂生产冷轧料过程中克服水口结瘤、夹杂物影响铸坯质量等问题,通过优化渣系组分和碱度,提高吸收率,改善了钢水质量。
1 生产现状日钢炼钢工序有120t 转炉、120tRH 真空精炼炉、1×1板坯连铸机断面(1050mm~2040mm)×210,以及配套的热连轧设备。
目前工艺路线是:高炉铁水→铁水预处理→转炉→RH 炉→LF 炉→板坯连铸机→轧钢,工艺生产过程中出现水口结瘤、夹杂物影响铸坯质量等的问题。
根据对SPHD 钢种加工性能的要求,日照钢铁SPHD 钢种成分见表1。
表1 SPHD 钢种成分序号钢种C(%)Si(%)Mn(%)P(%)S(%)Al(%)1SPHD≤0.03≤0.030.15 ̄0.30≤0.020≤0.0250.020 ̄0.060冷轧料属于低碳铝镇静,w (Alt)一般为0.02%~0.055%,太高易生成Al 2O 3夹杂物,影响连铸生产造成结瘤和夹杂物过多,使产品质量得不到保证。
为提高钢水的纯净度,应在精炼过程中尽可能除去钢水中的夹杂物,确保造渣效果,满足最终产品使用性能的要求。
通过取样化验分析,深入了解RH 处理过程超低碳铝镇静钢中夹杂物变化,优化RH 钢中顶渣成分,确定精炼渣系CaO-SiO 2-Al 2O 3,以及渣中各组分的含量。
2 RH精炼渣组分优化2.1 渣系确定对所取的试样采用化学常规分析,确定各类夹杂物的类型和对应的数量,同时进行定量分析,明确影响深冲钢生产和产品质量的夹杂物类型,以及其成分的演变过程,寻找优化改进的目标。
夹杂物主要是B 类夹杂物,成分主要是Al 2O 3,因此采用精炼渣系为CaO-SiO 2-Al 2O 3的三元渣系,进一步分析不同配比条件下精炼渣的脱氧、脱硫效果,以及不同碱度的影响。
RH精炼炉

RH精炼炉1 RH的历史与发展RH精炼全称为RH真空循环脱气精炼法。
于1959年由德国人发明,其中RH为当时德国采用RH精炼技术的两个厂家的第一个字母。
真空技术在炼钢上开始应用起始于1952年,当时人们在生产含硅量在2%左右的硅钢时在浇注过程中经常出现冒渣现象,经过各种试验,终于发现钢水中的氢和氮是产生冒渣无法浇注或轧制后产生废品的主要原因,随之各种真空精炼技术开始出现,如真空铸锭法、钢包滴流脱气法、钢包脱气法等,从而开创了工业规模的钢水真空处理方法,特别是蒸汽喷射泵的出现,更是加速了真空炼钢技术的发展。
随着真空炼钢技术的开发与发展,最终RH和VD因为处理时间短、成本低、可以大量处理钢水等优点而成为真空炼钢技术的主流,70年代开始随着全连铸车间的出现,RH因为采用钢水在真空槽环流的技术从而达到处理时间短、效率高、能够与转炉连铸匹配的优点而被转炉工序大量采用。
RH从开始出现到现在40多年来,有多项关键性技术的出现,从而加速了RH精炼技术的发展。
表1为40多年来RH技术的发展情况。
2RH系统概述RH系统设备是一种用于生产优质钢的钢水二次精炼工艺装备。
整个钢水冶金反应是在砌有耐火衬的真空槽内进行的。
真空槽的下部是两个带耐火衬的浸渍管,上部装有热弯管。
被抽气体由热弯管经气体冷却器至真空泵系统排到厂房外。
钢水处理前,先将浸渍管浸入待处理的钢包钢水中。
当真空槽抽真空时,钢水表面的大气压力迫使钢水从浸渍管流入真空槽内(真空槽内大约0.67mbar时可使钢水上升1.48m高度)。
与真空槽连通的两个浸渍管,一个为上升管,一个为下降管。
由于上升管不断向钢液吹入氩气,相对没有吹氩的下降管产生了一个较高的静压差,使钢水从上升管进入并通过真空槽下部流向下降管,如此不断循环反复。
在真空状态下,流经真空槽钢水中的氩气、氢气、一氧化碳等气体在钢液循环过程中被抽走。
同时,进入真空槽内的钢水还进行一系列的冶金反应,比如碳氧反应等;如此循环脱气精炼使钢液得到净化。
RH炉精炼过程中钢水吸氮过程研究

[ ] 的计算公式 为 : N。
式中
’
N , () 1
[ = .4 N] 0O4
精炼因其在均匀钢水、脱气和脱碳等方面具有广 泛优势而被多数新建厂选用。R H炉精炼虽脱氢 和脱 氧 等能力 较 强 ,但 脱 氮能力 一般 ,尤 其 是在
钢 水氮 含量 较 低 情 况下 ,主要 表 现 为 钢 水 吸氮 。 本 文探讨 造成 R 炉 在 真 空 情 况 下 吸氮 的规 律 , H 以期 为生产 更低 氮含 量 的超低碳 钢 提供 帮助 。
R 炉精 炼 过 程 中钢 水 吸氮 过 程研 究 H
单庆林 陈玉鑫 王朝斌 黄财德 庞在 刚
( 首钢京唐钢铁联合有限责任公司)
摘 要 分析 了 R 炉精炼过程中钢水氮含量变化过程及 钢水 吸氮 和脱 氮现 象 ,指 出 R H H炉真空槽 构造决 定 了 R 炉存 在漏气现象 ,导致 钢水在精炼 过程 中吸氮 ,尤 其 当漏气 部位 在钢 液面 以下 时钢水 吸氮 明显 。 H 另外 ,冷钢和合金也会使钢水氮含 量增加 1×1 ~ ~1 0 0×1 0~。生产 实践表 明,当精炼 前钢水 氮含 量大 于 3 0×1 I 时 ,R 炉脱氮能力较强 ,而当精炼前钢水氮含量小于 3 1 I 时 ,R 06 H 0× 0 6 H炉主要表现为钢水 吸氮 。
RH精炼深脱硫实践
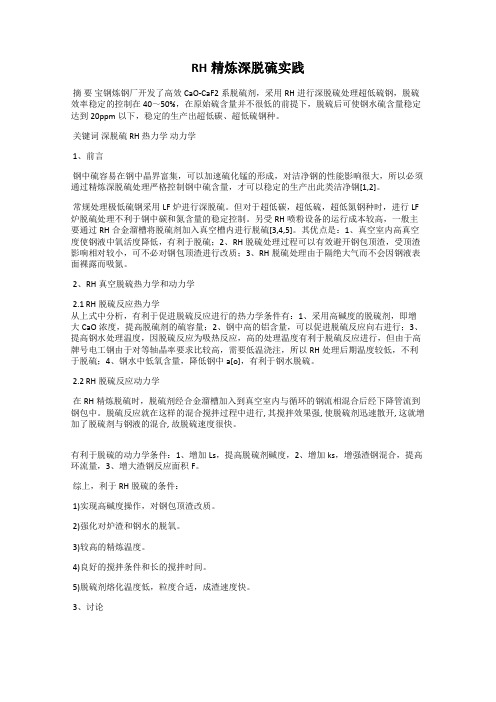
RH精炼深脱硫实践摘要宝钢炼钢厂开发了高效CaO-CaF2系脱硫剂,采用RH进行深脱硫处理超低硫钢,脱硫效率稳定的控制在40~50%,在原始硫含量并不很低的前提下,脱硫后可使钢水硫含量稳定达到20ppm以下,稳定的生产出超低碳、超低硫钢种。
关键词深脱硫 RH 热力学动力学1、前言钢中硫容易在钢中晶界富集,可以加速硫化锰的形成,对洁净钢的性能影响很大,所以必须通过精炼深脱硫处理严格控制钢中硫含量,才可以稳定的生产出此类洁净钢[1,2]。
常规处理极低硫钢采用LF炉进行深脱硫。
但对于超低碳,超低硫,超低氮钢种时,进行LF 炉脱硫处理不利于钢中碳和氮含量的稳定控制。
另受RH喷粉设备的运行成本较高,一般主要通过RH合金溜槽将脱硫剂加入真空槽内进行脱硫[3,4,5]。
其优点是:1、真空室内高真空度使钢液中氧活度降低,有利于脱硫;2、RH脱硫处理过程可以有效避开钢包顶渣,受顶渣影响相对较小,可不必对钢包顶渣进行改质;3、RH脱硫处理由于隔绝大气而不会因钢液表面裸露而吸氮。
2、RH真空脱硫热力学和动力学2.1 RH脱硫反应热力学从上式中分析,有利于促进脱硫反应进行的热力学条件有:1、采用高碱度的脱硫剂,即增大CaO浓度,提高脱硫剂的硫容量;2、钢中高的铝含量,可以促进脱硫反应向右进行;3、提高钢水处理温度,因脱硫反应为吸热反应,高的处理温度有利于脱硫反应进行,但由于高牌号电工钢由于对等轴晶率要求比较高,需要低温浇注,所以RH处理后期温度较低,不利于脱硫;4、钢水中低氧含量,降低钢中a[o],有利于钢水脱硫。
2.2 RH脱硫反应动力学在RH精炼脱硫时,脱硫剂经合金溜槽加入到真空室内与循环的钢流相混合后经下降管流到钢包中。
脱硫反应就在这样的混合搅拌过程中进行, 其搅拌效果强, 使脱硫剂迅速散开, 这就增加了脱硫剂与钢液的混合, 故脱硫速度很快。
有利于脱硫的动力学条件:1、增加Ls,提高脱硫剂碱度,2、增加ks,增强渣钢混合,提高环流量,3、增大渣钢反应面积F。
210T—LF钢包精炼炉的设计

210T—LF钢包精炼炉的设计作者:习德兵来源:《科技传播》2015年第23期摘要主要介绍湖南华菱涟钢2台双工位210T钢包精炼炉的主要设备的设计,包括铜钢导电横臂,水冷炉盖及液压系统。
关键词铜钢导电横臂;水冷炉盖;液压系统中图分类号 TK22 文献标识码 A 文章编号 1674-6708(2015)152-0158-02随着我国钢产量的提高,用户对钢材质量提出了越来越高的要求,各钢厂都纷纷采用新技术新工艺来提高产品的竞争力。
LF钢包精炼炉作为一种成熟的精炼技术,已经在钢厂得到广泛的应用。
它取代初炼炉进行还原期操作,同时对钢液进行升温、脱氧、脱硫、脱气、合金化、吹氩搅拌,提高钢液质量,喂丝改变夹杂物形态,去除夹杂,作为转炉、板坯连铸合浇之间的缓冲器。
2008年~2009年,由西安桃园冶金设备公司设计并制造的2座双工位电极旋转式210T-LF炉在华菱涟钢顺利投产达效,大大提高了连铸机的生产效率。
1 总体布置及主要设备参数LF钢包精炼炉与转炉采用离线-横轨布置,采用双加热工位,双水冷炉盖,共用一套供电系统,采用双处理工位电极旋转方式,两工位共用一套电极横臂升降和电极旋转系统,并建有+6.3m操作台,在平台上可以进行测温取样等操作。
钢包公称容量200t,最小/最大容量140t/230t,耳轴中心距/钢包上口外径5 300mm/Φ4 288mm,自由空间高度400mm,钢水罐置于钢包车上罐口标高+5.3m。
采用铜钢复合导电横臂。
2 导电横臂2.1 导电横臂设备简图2.2 设备构造中空的菱形电极升降立柱为焊接构件,立柱前后焊有导轨(16Mn),焊后整体退火,立柱内部装有电极升降的液压缸,立柱上部的水冷托架通过绝缘装置与导电横臂相联。
导电横臂为钢铜复合板的矩形梁结构件,内部通水冷却,中间为无缝钢管的芯管,导电横臂采用修正三角形布置。
电极夹放机构依靠弹簧的恢复力将石墨电极夹紧,依靠油缸压缩碟簧完成电极的放松。
科技成果——RH精炼功能提升关键技术

科技成果——RH精炼功能提升关键技术技术开发单位北京科技大学所属领域钢铁冶金成果简介钢铁工业是我国国民经济的重要基础产业和实现工业化的支柱产业。
钢的高效化、洁净化、稳定化和智能化生产是钢铁企业生存和发展的方向。
钢铁生产过程中,根据钢种的不同,所采用的精炼工艺和设备也不同。
其中,RH真空精炼工艺具有高效、高洁净的生产特点,广泛应用于IF钢和硅钢为代表的冷轧钢种、管线钢为代表的热轧钢种、以及轴承钢为代表的特殊钢种的生产。
因此,提升RH真空精炼的效率和能力能够一方面缩短各高品质钢种的精炼时间,更好地与高拉速连铸相匹配,提升生产效率,另一方面能够更好地脱碳和去除夹杂物,提升产品质量,这两方面都能够给钢铁企业带来很好的效益。
根据几何相似和动力学相似建立了对应实际RH模型比例为1:5的RH物理模型。
利用PIV技术测量流场,示踪粒子选用空心SiO2微球,获得了RH水模型钢包和真空室内中心纵截面上的速度矢量分布,并根据速度场分布计算出对应的湍动能及其耗散率的分布;在RH水模型钢包内布置监测点,在加入示踪粒子(饱和NaCl溶液)的同时开始测量监测点处电导率的变化,获得电导率变化曲线后,将电导率变化在±5%之内的时间为混匀时间,密集布置监测点并多次重复测量,得到整个钢包中心纵截面上的混匀时间分布。
根据上述方法分别研究吹气流量、真空室压力、吹气孔数对RH内部流场特性及混匀状态的影响。
图1 项目技术方案在原物理模型基础上改变浸渍管的形状,分别设计两浸渍管均为椭圆管RH、两浸渍管中上升管为圆管下降管为椭圆管RH以及标准圆管对比RH水模型,研究浸渍管形状对流场特性及混匀状态的影响。
两浸渍管均为椭圆管时,能够增大液体的循环流量,降低钢包整体的混匀时间;当只改变下降管形状,选用椭圆管作为下降管时,能够起到增大钢水涌入真空室的速度同时降低钢水对钢包底部的冲击的效果。
通过工业实验,对某超低碳钢RH全精炼过程进行密集取样,分别取圆管和椭圆管RH冶炼的钢样分析,检测钢中碳含量。
提高RH真空处理过程热能利用率的生产实践
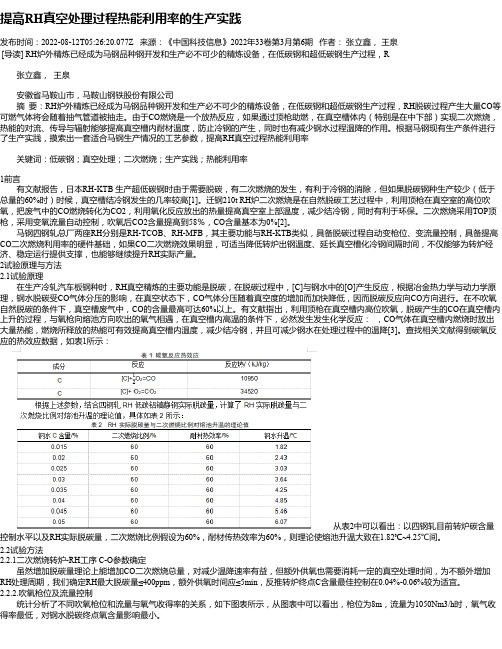
提高RH真空处理过程热能利用率的生产实践发布时间:2022-08-12T05:26:20.077Z 来源:《中国科技信息》2022年33卷第3月第6期作者:张立鑫,王泉[导读] RH炉外精炼已经成为马钢品种钢开发和生产必不可少的精炼设备,在低碳钢和超低碳钢生产过程,R 张立鑫,王泉安徽省马鞍山市,马鞍山钢铁股份有限公司摘要:RH炉外精炼已经成为马钢品种钢开发和生产必不可少的精炼设备,在低碳钢和超低碳钢生产过程,RH脱碳过程产生大量CO等可燃气体将会随着抽气管道被抽走。
由于CO燃烧是一个放热反应,如果通过顶枪助燃,在真空槽体内(特别是在中下部)实现二次燃烧,热能的对流、传导与辐射能够提高真空槽内耐材温度,防止冷钢的产生,同时也有减少钢水过程温降的作用。
根据马钢现有生产条件进行了生产实践,摸索出一套适合马钢生产情况的工艺参数,提高RH真空过程热能利用率关键词:低碳钢;真空处理;二次燃烧;生产实践;热能利用率1前言有文献报告,日本RH-KTB 生产超低碳钢时由于需要脱碳,有二次燃烧的发生,有利于冷钢的消除,但如果脱碳钢种生产较少(低于总量的60%时)时候,真空槽结冷钢发生的几率较高[1]。
迁钢210t RH炉二次燃烧是在自然脱碳工艺过程中,利用顶枪在真空室的高位吹氧,把废气中的CO燃烧转化为CO2,利用氧化反应放出的热量提高真空室上部温度,减少结冷钢,同时有利于环保。
二次燃烧采用TOP顶枪,采用变氧流量自动控制,吹氧后CO2含量提高到58%,CO含量基本为0%[2]。
马钢四钢轧总厂两座RH分别是RH-TCOB、RH-MFB,其主要功能与RH-KTB类似,具备脱碳过程自动变枪位、变流量控制,具备提高CO二次燃烧利用率的硬件基础,如果CO二次燃烧效果明显,可适当降低转炉出钢温度、延长真空槽化冷钢间隔时间,不仅能够为转炉经济、稳定运行提供支撑,也能够继续提升RH实际产量。
2试验原理与方法2.1试验原理在生产冷轧汽车板钢种时,RH真空精炼的主要功能是脱碳,在脱碳过程中,[C]与钢水中的[O]产生反应,根据冶金热力学与动力学原理,钢水脱碳受CO气体分压的影响,在真空状态下,CO气体分压随着真空度的增加而加快降低,因而脱碳反应向CO方向进行。
包钢薄板厂新建210t RH精炼炉设计特点
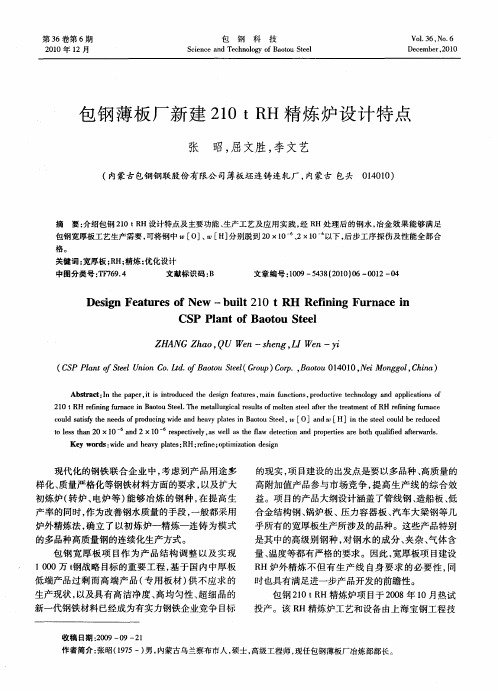
( 内蒙古包钢钢联股份有限公 司薄板坯连铸连轧厂, 内蒙古 包头 04 1 ) 100
摘
要 : 绍包 钢 20t H设 计 特 点 及 主 要功 能 、 工 艺 及 应 用 实 践 , R 处 理 后 的 钢 水 , 金 效 果 能 够 满 足 介 1 R 生产 经 H 冶
Ab ta t I h a e , s i t d c d t e d sg e tr s man f n t n , r d cie t c n lg n p l ain f sr c :n t e p p r i i nr u e h e i n f au e , i u ci s p o u t e h oo y a d a p i t s o t o o v c o 2 0t 1 RH e n n r a e i a tu S e 1 T e meal r ia e u t o l n s e f r h r ame t f rf i gf n c B oo te . h tl gc l s l f i u n u r s mot t l t ete t n e e aet o RH e nn r a e rf ig f n c i u
包钢宽厚板工艺生产需要 , 可将钢 中 W[ 、 H] 0] W[ 分别脱 到 2 0×1 I 、 1 “以下, 0 ¨ 2× 0 后步工序探伤 及性能全部合
格。
关键词 : 宽厚板 ; H; R 精炼 ; 优化设计
中图分类号 :F 6 . T 7 94 文献标识码 : B 文章 编号 : 0 5 3 (0 0 0 0 1 0 1 9— 4 8 2 1 )6— 0 2— 4 0
Ke r s: i e a d h a y p ae ; H ;e n ; p i z t n d sg y wo d w d n e v l ts R r f e o t ai e in i mi o
RH脱氢能力分析
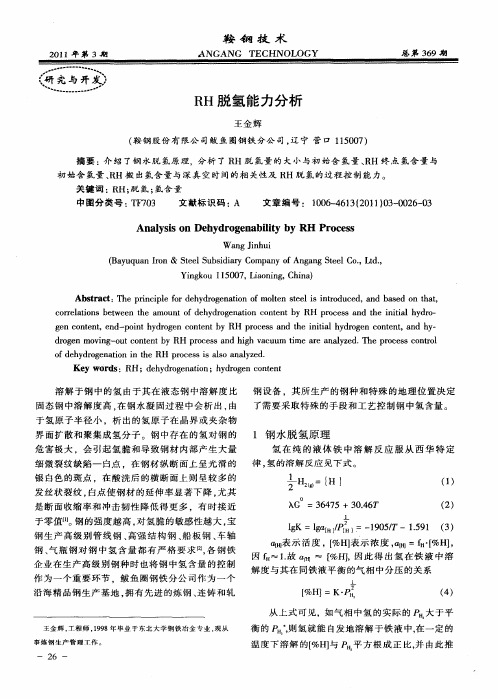
I g gl] 1 一95 K=I H% l 10/ . 1 () a / _ T一1 9 3 5
q 表 示 活 度 , H】 示 浓度 ,呻 =f・ H , 表 口 H 】 因 f 1故 a 一 [ I H . 删 %H ,因此 得 出氢 在 铁 液 中 溶
解度 与其 在 同铁 液平衡 的气 相 中分压 的关 系
持在 01k a以 内 . 升气 体 流量 基本 维 持在 最 大 . P 提
设 计 流 量 10m3 .脱 气 时 间 基 本 保 持 在 2 n 6 / h 0mi
酾 疆
初 始 氢含 量 范 围/ 1 0
内 。为保 证 R H脱氢 能力 , 求在 R 处理 时采 用 要 H 深真 空模 式 . 保证 一 定 的循 环时 间 , 保证 钢 中氢 含 量小 于 2 1  ̄ x 0 。可 以说 , R 该 H装 置 的设 备 能力 基 本发 挥 到 最 大处 理 水 平 。 为 进一 步 有 效 提 升 R H
温 度 下 溶 解 的 【 ] P . 方 根 成 正 比 , 由 此 推 %H 与 H 平 并
简析钢渣处理的优化工艺
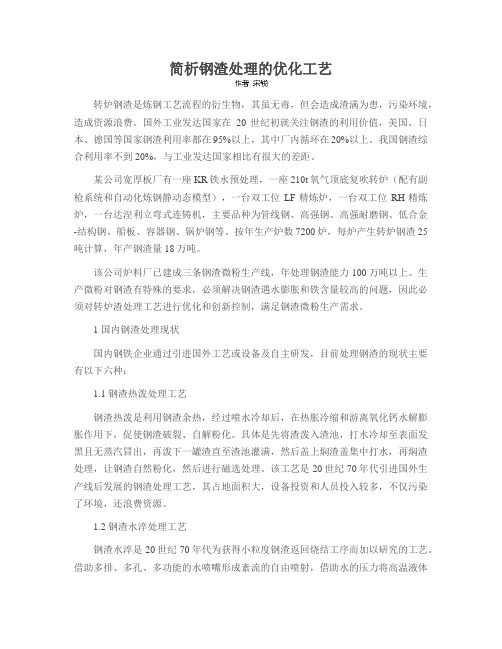
简析钢渣处理的优化工艺转炉钢渣是炼钢工艺流程的衍生物,其虽无毒,但会造成渣满为患,污染环境,造成资源浪费。
国外工业发达国家在20世纪初就关注钢渣的利用价值,美国、日本、德国等国家钢渣利用率都在95%以上,其中厂内循环在20%以上。
我国钢渣综合利用率不到20%,与工业发达国家相比有很大的差距。
某公司宽厚板厂有一座KR铁水预处理,一座210t氧气顶底复吹转炉(配有副枪系统和自动化炼钢静动态模型),一台双工位LF精炼炉,一台双工位RH精炼炉,一台达涅利立弯式连铸机,主要品种为管线钢、高强钢、高强耐磨钢、低合金-结构钢、船板、容器钢、锅炉钢等。
按年生产炉数7200炉,每炉产生转炉钢渣25吨计算,年产钢渣量18万吨。
该公司炉料厂已建成三条钢渣微粉生产线,年处理钢渣能力100万吨以上。
生产微粉对钢渣有特殊的要求,必须解决钢渣遇水膨胀和铁含量较高的问题,因此必须对转炉渣处理工艺进行优化和创新控制,满足钢渣微粉生产需求。
1 国内钢渣处理现状国内钢铁企业通过引进国外工艺或设备及自主研发,目前处理钢渣的现状主要有以下六种:1.1 钢渣热泼处理工艺钢渣热泼是利用钢渣余热,经过喷水冷却后,在热胀冷缩和游离氧化钙水解膨胀作用下,促使钢渣破裂、自解粉化。
具体是先将渣泼入渣池,打水冷却至表面发黑且无蒸汽冒出,再泼下一罐渣直至渣池灌满,然后盖上焖渣盖集中打水,再焖渣处理,让钢渣自然粉化,然后进行磁选处理。
该工艺是20世纪70年代引进国外生产线后发展的钢渣处理工艺,其占地面积大,设备投资和人员投入较多,不仅污染了环境,还浪费资源。
1.2 钢渣水淬处理工艺钢渣水淬是20世纪70年代为获得小粒度钢渣返回烧结工序而加以研究的工艺。
借助多排、多孔、多功能的水喷嘴形成紊流的自由喷射,借助水的压力将高温液体抛流熔渣,在瞬间内击散、粒化、冷凝成小固体颗粒钢渣的过程。
水淬的优点是排渣迅速,有利于发挥炼钢转炉等设备的潜力,减轻了人工清渣的繁重工序,人工费用降低。
RH炉模式炼钢在涟钢210转炉厂的应用

涟钢210转炉厂RH炉平均炉产量210T,由真空系统、液压钢包提升系统、钢包车走行系统、顶枪及预热枪系统、加料系统、环流系统、冷却水系统组成。控制系统由西门子S7-400系列PLC组成基础自动化控制系统,原控制系统由宝信软件基于step7 v5.3和Win图为轻处理模式参数,操作人员冶炼之前可以通过此画面熟悉此模式的功能。
3.3下图为深脱碳处理模式参数,操作人员冶炼之前可以通过此画面熟悉此模式的功能。
3.4下图为本处理模式参数,操作人员冶炼之前可以通过此画面熟悉此模式的功能。
后期为了更高效的节约蒸汽消耗,又增加了深脱碳处理退泵模式,并可选择退B3和4A+4B。
参考文献:
1.《西门子S7-300/400PLC工程应用技术》(机械工业出版社)
2、孔祥东,王益群.控制工程基础[M].北京:机械工业出版社.2011年
RH炉模式炼钢在涟钢210转炉厂的应用
摘要:推行模式炼钢实现了RH炉操作标准化,在减轻了操作人员劳力强度的情况下,大大提高了钢水的冶炼质量,减少了蒸汽消耗,规范了操作习惯,给涟钢210转炉厂RH炉品种钢冶炼提供了可靠的设备保证。
关键词PLC、环流、真空系统模式炼钢、轻处理模式、本处理模式、深脱碳模式、深脱碳退泵模式
4结束语
通过大量、细致的调试、试运行和优化工作,我厂逐步将五种模式炼钢在RH炉冶炼中推广应用,至2016年底,我厂已实现RH炉100%模式炼钢,真正实现了RH炉真空系统和环流系统一键操作,实现了RH炉操作标准化,在减轻了操作人员劳力强度的情况下,大大提高了钢水的冶炼质量,减少了蒸汽消耗,规范了操作习惯,杜绝了人为因素对钢水质量的影响,通过合金化后由退泵至三级泵调整到四级泵的工艺固化,实现了无人工干预,每年可降低蒸汽消耗成本120余万元,给我厂RH炉品种钢冶炼提供了可靠的保证。
硅钢RH炉设计的创新与应用

硅钢RH炉设计的创新与应用陆斌;华国龙【期刊名称】《金属世界》【年(卷),期】2015(000)005【总页数】3页(P65-67)【作者】陆斌;华国龙【作者单位】内蒙古包钢钢联股份有限公司薄板坯连铸连轧厂,内蒙古包头014010;内蒙古包钢钢联股份有限公司薄板坯连铸连轧厂,内蒙古包头 014010【正文语种】中文随着竞争日益激烈,各钢铁企业都通过提高质量、结构调整、优化工艺等手段降本增效,提高钢铁产品的盈利能力。
包钢薄板坯连铸连轧厂CSP生产线加大力度,改变了仅有转炉-LF精炼炉-CSP工艺的现状。
同时为开发新产品,提升产品档次,优化产品结构,于2013年建设了2#RH真空精炼炉,并月2014年7月热试投产。
该套RH精炼炉形成了设备设计、三电设计、设备制造、安装调试一体化的成套集成技术,采用了机械真空泵、快速硅铁料斗等多项创新设计,投产后效果显著,实现了调整产品结构、优化工艺水平的目的。
RH精炼炉主要技术参数,详见表1。
RH设备组成部分2#RH钢液真空精炼装备主要由以下部分组成:1) 钢包台车系统。
钢包台车系统共2套,主要由钢包台车、钢包升降装置、钢包升降液压站、手动测温取样定氧装置、保温剂投入装置、喂丝装置、浸渍管维修台车、吹氩装置等组成。
2) 钢包升降和升降液压装置。
钢包升降装置共2套,每个处理位下方的顶升坑内设1套。
钢包升降装置通过液压缸带动升降框架可将钢包顶升,使真空槽浸渍管插入到钢包中进行处理。
本RH装置为双工位,液压系统共用1套。
3) 浸渍管维修台车。
浸渍管维修台车轨道与钢包台车轨道垂直。
车上带1套浸渍管除渣装置和1套喷补机,可在处理的间歇,在线对浸渍管外表面进行除渣和内、外表面喷补。
4) 过渡车。
利用过渡车将1台浸渍管维修台车在2套钢包车轨道上实现平移过渡。
车上设轨道与钢包台车轨道对接。
5) 真空室、热弯管及真空式运输系统。
真空室、热弯管是连接处理钢液与真空系统的关键设备,分体的真空室可以整体吊装, 热弯管与真空室可以实现液压顶升分离,真空室安装真空槽运输车上, 提高了更换真空室时的运输效率, 更好地保证生产节奏。
- 1、下载文档前请自行甄别文档内容的完整性,平台不提供额外的编辑、内容补充、找答案等附加服务。
- 2、"仅部分预览"的文档,不可在线预览部分如存在完整性等问题,可反馈申请退款(可完整预览的文档不适用该条件!)。
- 3、如文档侵犯您的权益,请联系客服反馈,我们会尽快为您处理(人工客服工作时间:9:00-18:30)。
钢中 W[ ] H 高时 , 会形成白点 , 这对一些应用条
件苛 刻 的钢材 来说 是致 命 的 , 管线 钢 、 些高 强度 如 一 的结 构钢 等 。在宽 厚板 生产 线 中采用 的脱 氢工 艺有 钢水 脱氢 和连 铸坯 或成 品钢 板脱 氢 2种 J 。通 常为
了去 除钢 中 的氢 , 用对 钢水 进行 真空 处理 , 采 通过 降 低氢 分压 来 降低钢 液 中 的氢 , 用 的钢 水真 空 处 理 常 设备 有 R V 文 章 主要 研究 的是包 钢 二炼 钢供 宽 H、 D,
12 合 金等 添加 料要 保持 干燥 .
保证人炉合金干燥 , 在合金存 放、 运输 过程要注意 采取 防潮措施 , 时进行合 金烘 烤 ; 它炉料要进 必要 对其 行科学 的管理 , 能长 时间存放 , 如 白灰 , 不 例 保证使 用 新鲜 的白灰 , 能缩短炉料存放时间 , 尽可 防止吸潮。
陆 斌 , 宏盛 , 王 王建 林
( 内蒙古包钢钢联股份有 限公 司薄板坯连铸连轧厂 , 内蒙古 包头 04 1 ) 100
摘
要 : 章分析 了钢水增氢原 因以及影响 R 文 H精炼脱氢效果 的因素 , 出在 目前状况下真空处理时间超过 2 i 指 0m n
对脱氢效果不 明显 , 真空下部槽减薄后对 R H脱氢效果较明显 ,H精炼的平均脱氢效率为 7 %。 R 6
的饱 和溶 解 度 , 在实 际处理 过程 中 , 了快 速达 到极 为
限真空 度 , 通常 采用 预抽 真空 方 式 来 尽 可 能 缩短 抽
真空 时 间 。
表 1 不 同氢分 压下 [ 的饱和 溶解 度 H]
氢分压/ P ka
1 O
图3
[ ] H 的饱和溶解度/× 0 6 1I
}/ O6 f ×l一 1
处理时间的延长, 钢液中的的 [ ] H 在逐渐降低。
图 l 钢水初 始 [ 分布 H]
2 影 响 R 脱 氢 效果 的 因素 H
2 1 真 空度 .
真空 度对 R H精炼炉 脱氢 的影 响 主要 体 现在 两
方 面 , 方 面 真 空 度 的高 低 决 定 着 氢 分 压 , 究 表 一 研 明 , 真空 度 在 0 2k a . P 以下 时 , 氢 的速 度 才会 很 脱 明显 。在 真 空 度 大 于 0 2k a时 , 氢 比较 缓 慢 。 . P 脱 表 1 钢水 温度 在 183K时不 同氢分 压 下 , [ 是 7 ∞ H]
Abt c: epprtecue r H] fiuds e ic ae n e at sn unig f c f e yr e — sr tI t ae, ass ow[ o l i elnr sdadt c r i ec et o dhdo n a nh h f q t e h f o f l ne s g
l 2 i 后钢水中的W[ ] 6~ 0rn a H 分布状况 , 终点W H [] 都小 于 2×1 。平 均为 1 5×1 0‘, ’ . 0一。
浸 渍管 内径 为 60m 0 m;
处理 周 期为 3 i。 5m n
包钢 二炼钢 经 R H精炼供 宽厚 板铸机 的钢 水 , 有 2种处理模式 , 一种 模式 是高 真空 度下 ( .7ka ≤O2 P ) 的本处 理模式 , 要求 R H处理结束 后钢 水 中的 [ H] < 2×1 ~, 一 种 是 轻 处 理 模 式 , 空 度 在 8— 0 另 真
7 8 .O
[ 随真 空 处理 时 间的变化 H]
表 2是 利 用 H re sMut—l y r eau l a H di 线 测 i b s在
5
1
5 5 .0 2 5 .O
17 . 0 O 7 . 8
定不同处理时间时钢水中的氢含量然后计算其对应 时 间脱 氢率 得 到 的结 果 , 果 发 现 真 空处 理 时 间为 结
蘸 = _ ■.1 . _ {
擘 i 焉
8
从脱 氢动 力 学分 析 , R 精 炼 真 空 度 保 持稳 在 H 定 的情 况 下 , 空 处 理 时 间是 影 响 R 处 理 后 钢水 真 H
中氢 含量 的重要 因素 , 图 3中可 以看 出 , 从 随着真 空
仞 始
第 1 期
20t H精炼 炉脱氢工艺研究与应用 1 R
表 2 不 同 真 空 处 理 时 间 的脱 氢 率
1 3
响脱氢的速度和效率 ;1 R 20t H精炼的在 目前工况 下 , 到极 限真空 度后 , 均脱 氢 率 为 7 % , 达 平 6 真空 处
理 时间超 过 2 i 对脱氢 率不 明显 。 0mn后
第3 第 1 8卷 期 21 0 2年 2月
包
钢
科
技
Vo . 8, 1 3 No. 1 F br r 201 e uay, 2
S in e a d T c n lg fB oo t e c e c n e h oo y o a t u S e l
20t H精 炼 炉脱 氢 工 艺 研究 与应 用 1 R
2 n和 2 n的脱氢 率 很接 近 , 0mi 4mi 其平 均 脱 氢率 为 7 %左 右 , 明 20t H 精 炼 在 目前 的工 况 下 , 6 说 1 R 在 真空 处理 时 间达到 2 i 0mn时脱 氢 达到 了平 衡 , 延 再
长 时间脱 氢效 果不 明显 。
O. 5 0 1 .
炉 数
下 一炉 真空 处理 时未 完 全 排 出 的水分 就会 进入 钢液 中引起增 氢 , 运用 H resMut—lbH di在 线 测 eau l a yr i s 定 对 比发现 , 初始 [ 相 同 、×/}处理 工艺参 数 在 H] 真空 一
。 Biblioteka 图 4 真 空槽 底部 减 薄脱 氢效果 对 比 ( ) 空 下 部 槽 减 薄 后 脱 氢 效 果 明显 , 工 艺 2真 在
a o r R rf i g ae a ay e . ro e . sp i td o tt a h f cs o e y r g n t n a e n to v o s w e h i o f n f H e n n r lz d Mo e v r i i o ne u h tt e e e t fd h d o e ai r o b i u h n t e i n t o t a u m r ame ti v r2 n i o v c u te t n so e 0 mi .wi r s n i ai n d t e r b iu f rt e lw r p r o e v  ̄ u l me f t p e ts u t s a h y ae o vo s at h o e a t ft a? n h e t o n e h u tn hn ela h v r g f ce c fd h d o e ain frRH f ig i 7 % . a k t i sa w l s t e a e a e e in y o e y r g n t s i o o e n ri n s 6 Ke r s: H ; e y o e ain; e r e o a u m y wo d R dhd gnt r o d ge f c u v
收 稿 日期 :0 1 2—1 2 1 —1 6
包 钢 2 0t H 主要设 计工艺 参数 如下 : 1 R 真 空 泵 抽 气 能 力 为 90 k/ 2 9 空 气 , 0 gh( 0C干
作者简介 : 陆
斌 ( 9 7一)男 , 17 , 山西省大 同市人 , 工程师 , 现从事钢铁 冶金研究工作 。
L i WA n U B n, NG Ho g—s e g, NG Ja h n WA in一屁 n
( S ln o t lU i o Ld o B oo t l Gop C r. B oo 1 0 0 N i n g lC i ) C P Pa tfSe no C . t. atuSe ( ru ) o , a t 0 4 1 , e Mog o , hn e n f e p u a
2 3 真 空槽 及浸 渍 管 . 真空 槽 及 浸 渍 管对 脱 氢 有 重要 影 响 , 渍 管 与 浸 钢水 直接 接触 , 使 用 初 期 , 进 行 完 全 烘烤 , 在 要 确保 浸 渍 管干燥 ; 浸渍 管 进行 喷 补 维护后 , 及 时进行 对 要
烘烤 , 如果 喷补 后 的耐 火材 料 没有 完 全干燥 , 进行 在
相 同时 , 补后 未充 分 进 行 烘 烤 就 立 即 生产 比正 常 喷 生 产终点 氢 大约 高 ( . 0 4 0 3~ . )×1 ~。 0 另外 试 验 了真空 槽底 部 减 薄 10nn后 的脱 氢 0 q / 效果 , 因槽 底 减 薄后 增加 真 空槽 内钢水 提升 高度 , 使 进入 真空 槽 内 的钢 液 增 多 。图 4是 真空槽 底部 减 薄
真 空槽 内径 为 22 0m 0 m;
流 量有关 系 , H 真 空 槽 内 的真 空 度 在 达 到 2 P R 0ka 左 右时 , 钢水才 能 很 好 的在 真 空 槽 里 循 环 。 图 2是 在 驱动 气 体 气 流量 为 180N mn时 , 空 处 理 0 m / i 真
1 2
包钢科技
第3 8卷
6 a ) 7P 时 ;
裁
4 2 O 8
另一 方 面 , 空 度 高 低 与 R 精 炼 钢 水 的循 环 真 H
6 4 2 0
抽 真空 时 间为 ≤4rn 从大气 压 降到 6 a不 i( a 7P , 预 抽真 空 ) ; 钢水 循 环最 大速 度为 18tmn 7 i; / 循环 气 体最 大 流量为 10N h m/ ; 8
水分 解 产 生 的 氢 溶 解 在 钢 中 , 另外 如 转 炉罩 裙 、 F L