CSP连铸工艺设备
8-武钢CSP连铸结晶器液面波动控制实践
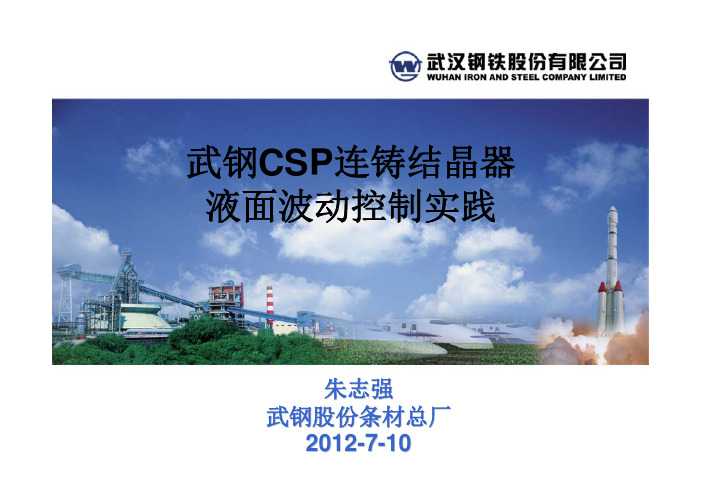
武钢CSP连铸结晶器液面波动控制实践朱志强武钢股份条材总厂2012-7-10主要内容工艺装备与背景概述典型液面波动的特点及原因 控制液面波动的措施结论一、背景与工艺装备1. 背景薄板坯连铸机由于结晶器厚度薄,容积小,其流动强度是传统厚板坯铸机的3-4倍,高拉速下容易产生液面波动,极易发生卷渣,恶化保护渣的熔化、润滑与传热,导致薄板坯出现裂纹、凹陷、夹杂等质量缺陷,严重时还将导致漏钢事故。
2.武钢CSP连铸机主要设备工艺参数3250mm弯曲半径10305mm 冶金长度18185mm 铸机长度5段7个冷却区,17个冷却回路扇形段数自动(Co60放射源)结晶器液面控制1100mm 结晶器长度漏斗型冷坯宽度:900—1600mm 结晶器类型72mm结晶器:70—50mm (液芯压下后)92mm结晶器:90—70mm (液芯压下后)浇铸厚度(扇形段5出口):72/92mm 浇铸厚度(结晶器出口)900—1600mm 浇铸宽度(标称或冷宽度)2.8—6.0m/min 拉速33t 中包容量170t 钢包容量技术参数项目二、结晶器液面波动的特点及原因分析实际生产中,拉速、过钢量的变化对液面波动的影响是显著的,但除此之外,浇注过程中仍出现了一些异常情况导致的结晶器液面波动,这些异常导致的结晶器液面波动现象的特征也是不一样的。
根据这些结晶器液面异常波动的特点,结晶器液面波动可分为:·包晶反应与鼓肚现象·共振现象·液位检测与控制系统故障·结晶器流场异常1.包晶反应与鼓肚现象鼓肚现象是连铸过程中的常见现象,常见于高拉速、大断面铸坯尺寸的钢种连铸生产条件下,主要原因是冷却不足、坯壳强度不足以抵抗钢水静压力,导致铸坯在两排辊子之间产生鼓肚,鼓肚时产生泵吸效应,导致结晶器液面下降,随着拉坯的进行,鼓肚区域在同一排辊子之间被挤压,液相穴内钢水又回流到结晶器内,导致结晶器内钢水又迅速上涨,如此反复,结晶器内液面呈有节奏的锯齿状的波动。
华菱涟钢CSP生产线情况介绍-4
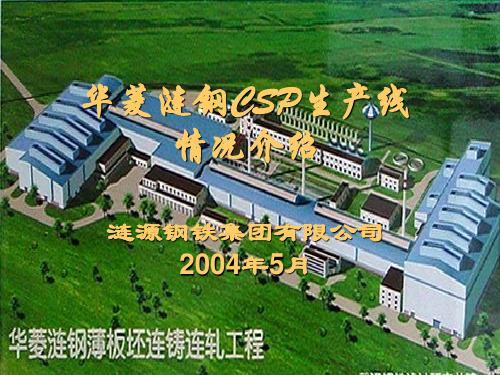
4月主要技术指标
平均连浇炉数: 9.6 连铸钢水收得率: 93.5% 钢材成材率: 97.5% 板卷合格率: 99.35% 板卷产量(吨):78000
主要试轧产品
试生产钢种包括Q345B、Q345D,Q235B、 Q195等,厚度从1.66~12.7mm,宽度为 1000~1550mm;连浇炉数最高为24炉,3 月平均为5.06炉,4月平均连浇炉数达9.6 炉。
采用的主要技术和效果
液芯压下正常,为生产薄规格产品提供可能。 2月热调试期间即开始进行液芯压下的功能测 试,4月6日连铸开浇,铸坯过顶弯辊即开始液 芯压下,将铸坯70mm压到55mm,连续进行 四 炉 , 坯 宽 1500mm , 铸 坯 入 剪 机 拉 速 4.8m/min,至此完成了从70mm压到55mm的 所有测试,没有一次因液芯压下而引起的漏钢。 4月13日,已生产厚度为1.66mm的Q345D薄板。
产品大纲
双流产量220万吨,带卷宽:900~ 1600mm,带钢厚度:0.8~12.7mm[其中 厚度小于3mm的带钢占80%],钢卷内径: 762mm,钢种为普通碳素结构钢、优质碳 素结构钢、低合金高强度结构钢、汽车 结构钢、高耐候结构钢。另外设备考虑 将来能够生产低碳钢和超低碳钢。
工程管理
质量情况钢包精炼炉钢水的成分—C含 量
钢水进出LF炉碳含量
30
碳含量
20 10 0
1 8 15 22 29 36 43 50
炉数
进LF炉碳含量 出LF炉碳含量
57 64 71 78
钢包精炼炉钢水的成分—C含量
统计3月生产的83炉Q235B,钢水进LF炉 的C:0.08~0.16%,钢水出LF炉的C: 0.17~0.20%。3月生产Q235B出站C控制 比 2 月 稳 定 , 2 月 的 钢 水 出 LF 炉 的 C : 0.15~0.23%。
CSP的设备特点和工艺特点
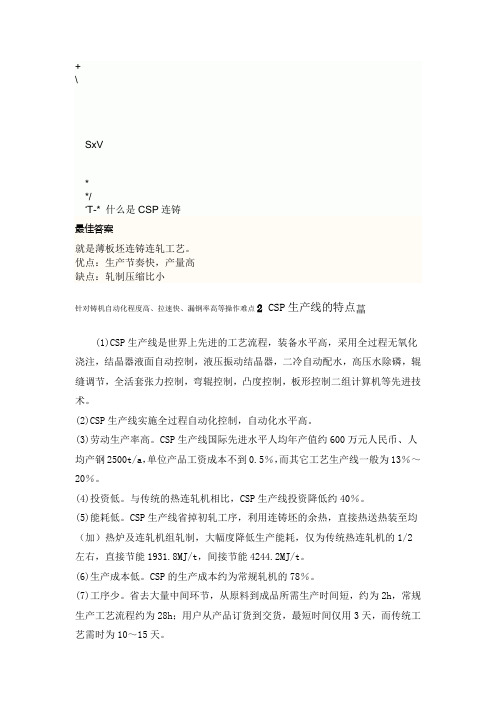
+\SxV**/‘T-* 什么是CSP连铸最佳答案就是薄板坯连铸连轧工艺。
优点:生产节奏快,产量高缺点:轧制压缩比小针对铸机自动化程度高、拉速快、漏钢率高等操作难点2 CSP生产线的特点(1)CSP生产线是世界上先进的工艺流程,装备水平高,采用全过程无氧化浇注,结晶器液面自动控制,液压振动结晶器,二冷自动配水,高压水除磷,辊缝调节,全活套张力控制,弯辊控制,凸度控制,板形控制二组计算机等先进技术。
(2)CSP生产线实施全过程自动化控制,自动化水平高。
(3)劳动生产率高。
CSP生产线国际先进水平人均年产值约600万元人民币、人均产钢2500t/a,单位产品工资成本不到0.5%,而其它工艺生产线一般为13%~20%。
(4)投资低。
与传统的热连轧机相比,CSP生产线投资降低约40%。
(5)能耗低。
CSP生产线省掉初轧工序,利用连铸坯的余热,直接热送热装至均(加)热炉及连轧机组轧制,大幅度降低生产能耗,仅为传统热连轧机的1/2左右,直接节能1931.8MJ/t,间接节能4244.2MJ/t。
(6)生产成本低。
CSP的生产成本约为常规轧机的78%。
(7)工序少。
省去大量中间环节,从原料到成品所需生产时间短,约为2h,常规生产工艺流程约为28h;用户从产品订货到交货,最短时间仅用3天,而传统工艺需时为10~15天。
(8)占地面积少。
CSP生产工艺线流程短,布局紧凑,比传统生产工艺占地面积少。
(9)污染少。
(10)成材率比常规轧机高1.8%。
(11)维修费用约为常规轧机的39%。
1结晶器的种类及主要特点薄板坯和中薄板坯连铸设备的核心是结晶器。
设计要求结晶器弯月面区域必须有足够的空间,以插入浸入式水口,且满足水口壁与结晶器壁之间无凝固桥形成,钢液温度分布均匀,有利于保护渣熔化;弯月面区钢液流动平稳,防止过大紊流而卷渣;结晶器几何形状应满足拉坯时坯壳承受的应力最小。
CSP工艺设备技术特点及采用的新技术1 CSP连铸工艺设备技术特点及采用的新技术1)连铸部分工艺介绍连铸部分工艺如图2所示。
1.CSP连铸连轧的轧制工艺控制
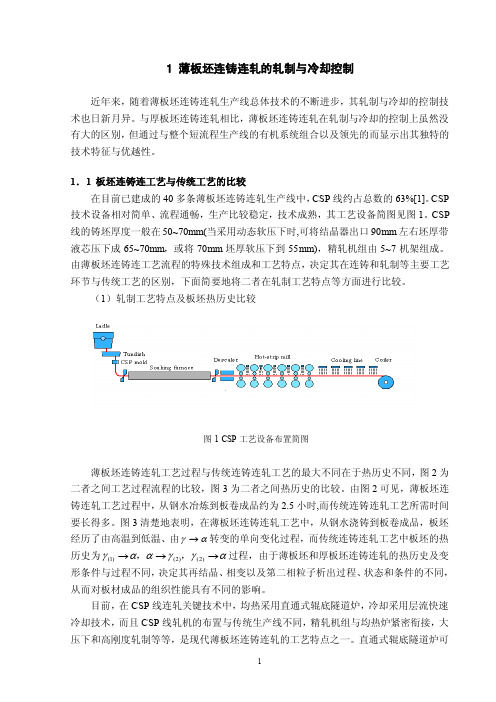
1 薄板坯连铸连轧的轧制与冷却控制近年来,随着薄板坯连铸连轧生产线总体技术的不断进步,其轧制与冷却的控制技术也日新月异。
与厚板坯连铸连轧相比,薄板坯连铸连轧在轧制与冷却的控制上虽然没有大的区别,但通过与整个短流程生产线的有机系统组合以及领先的而显示出其独特的技术特征与优越性。
1.1 板坯连铸连工艺与传统工艺的比较在目前已建成的40多条薄板坯连铸连轧生产线中,CSP 线约占总数的63%[1]。
CSP 技术设备相对简单、流程通畅,生产比较稳定,技术成熟,其工艺设备简图见图1。
CSP 线的铸坯厚度一般在50~70mm(当采用动态软压下时,可将结晶器出口90mm 左右坯厚带液芯压下成65~70mm ,或将70mm 坯厚软压下到55mm),精轧机组由5~7机架组成。
由薄板坯连铸连工艺流程的特殊技术组成和工艺特点,决定其在连铸和轧制等主要工艺环节与传统工艺的区别,下面简要地将二者在轧制工艺特点等方面进行比较。
(1)轧制工艺特点及板坯热历史比较薄板坯连铸连轧工艺过程与传统连铸连轧工艺的最大不同在于热历史不同,图2为二者之间工艺过程流程的比较,图3为二者之间热历史的比较。
由图2可见,薄板坯连铸连轧工艺过程中,从钢水冶炼到板卷成品约为2.5小时,而传统连铸连轧工艺所需时间要长得多。
图3清楚地表明,在薄板坯连铸连轧工艺中,从钢水浇铸到板卷成品,板坯经历了由高温到低温、由αγ→转变的单向变化过程,而传统连铸连轧工艺中板坯的热历史为αγγααγ→→→)2()2()1(,,过程,由于薄板坯和厚板坯连铸连轧的热历史及变形条件与过程不同,决定其再结晶、相变以及第二相粒子析出过程、状态和条件的不同,从而对板材成品的组织性能具有不同的影响。
目前,在CSP 线连轧关键技术中,均热采用直通式辊底隧道炉,冷却采用层流快速冷却技术,而且CSP 线轧机的布置与传统生产线不同,精轧机组与均热炉紧密衔接,大压下和高刚度轧制等等,是现代薄板坯连铸连轧的工艺特点之一。
华菱涟钢CSP生产线情况介绍-4
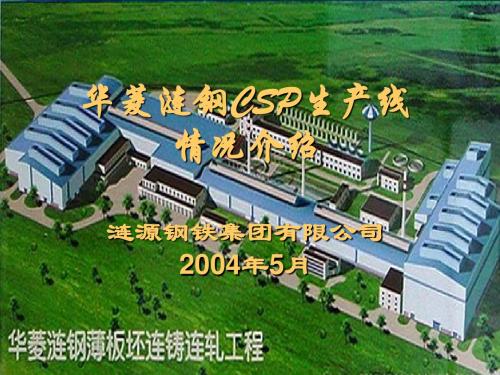
项目目标:建一流薄板,创一流团队 工 期:国内同类项目最短工期 投 资:比概算投资低5-10% 质 量:冶金工程优质奖 达产达效:半年内达设计产量,一年达 到各项设计技术指标
工程管理
科学管理 (1)、制度建设 (2)、建立工程管理系统,信息沟通通畅 (3)、加强计划管理,采用统一的工程软件 (4)、工程目标制 (5)、工作日志 (6)、工程量清单结算
钢包精炼炉三座,采 用双工位回转台形式。变压器容量 18000kvA,电极心圆直径为700mm,最 大升温度速度为4.5℃/min。平均精炼时 间40min(不包括软吹Ar时间),三座 LF炉可满足两台CSP连铸机最大生产能 力的需要。
薄板坯连铸机
两台立弯式连铸机,弧半径3250mm,流间距 26m。铸坯导向段长度为9705mm。中间包升 降行程为600mm,回转台钢包升降行程 1000mm。中间包容量为36t,液面高为 1050mm。结晶器长度1100mm,漏斗长度 850mm,漏斗宽度为190mm、180mm两种, 即大漏斗和小漏斗。出结晶器坯厚70mm,经 液芯压下,可压到55mm,预留压到45mm。 最高拉速6.0m/min,机械设备预留的最高拉速 为8.0m/min,最低质量保证拉速为2.6m/min。
4月主要技术指标
平均连浇炉数: 9.6 连铸钢水收得率: 93.5% 钢材成材率: 97.5% 板卷合格率: 99.35% 板卷产量(吨):78000
主要试轧产品
试生产钢种包括Q345B、Q345D,Q235B、 Q195等,厚度从1.66~12.7mm,宽度为 1000~1550mm;连浇炉数最高为24炉,3 月平均为5.06炉,4月平均连浇炉数达9.6 炉。
CSP生产线投产前的准备
薄板坯连铸连—包钢CSP
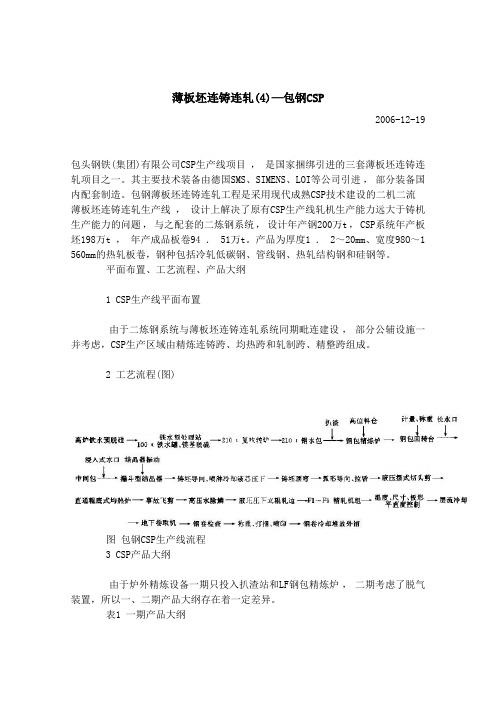
薄板坯连铸连轧(4)—包钢CSP2006-12-19包头钢铁(集团)有限公司CSP生产线项目,是国家捆绑引进的三套薄板坯连铸连轧项目之一。
其主要技术装备由德国SMS、SIMENS、LOI等公司引进,部分装备国内配套制造。
包钢薄板坯连铸连轧工程是采用现代成熟CSP技术建设的二机二流薄板坯连铸连轧生产线,设计上解决了原有CSP生产线轧机生产能力远大于铸机生产能力的问题,与之配套的二炼钢系统,设计年产钢200万t,CSP系统年产板坯198万t,年产成品板卷94.51万t。
产品为厚度1.2~20mm、宽度98O~1 560mm的热轧板卷,钢种包括冷轧低碳钢、管线钢、热轧结构钢和硅钢等。
平面布置、工艺流程、产品大纲1 CSP生产线平面布置由于二炼钢系统与薄板坯连铸连轧系统同期毗连建设,部分公辅设施一并考虑,CSP生产区域由精炼连铸跨、均热跨和轧制跨、精整跨组成。
2 工艺流程(图)图包钢CSP生产线流程3 CSP产品大纲由于炉外精炼设备一期只投入扒渣站和LF钢包精炼炉,二期考虑了脱气装置,所以一、二期产品大纲存在着一定差异。
表1 一期产品大纲表2 二期产品大纲主要设备特点1 冶炼部分在转炉炼钢车间内布置一座210 t顶底复吹转炉,在精炼连铸跨内布置一座钢水扒渣站,一座200 t LF钢包精练炉以及两流薄板坏连铸机,分别预留了2号转炉和脱气装置的位置。
转炉采用首钢1997年购买的美国加州钢厂设备,具有顶底复吹工艺,装有副枪操作设备,可实现气动挡渣功能和溅渣护炉技术,冶炼过程可以实现动态计算机控制,抬炼和精炼部分配有专门的除尘装置,以保护环境。
两机两流的立弯式薄板坯连铸机由SMS公司提供,采用漏斗式结晶器,结晶器长度为1.1m;铸机冶金长度为7.14m,弯曲半径为3.25 m,采用了60t大容量双流中间罐。
结晶器可实现在线调宽和液面自动控制,浇铸过程还采用了保护浇铸、自动称量及液芯压下技术,通过流芯压下,可以把结晶器出口65 mm的铸坯厚度压至50 mm,以保证某些产品在质量方面的需求。
CSP生产线统计

表1世界薄板坯连铸连轧生产线CSP工艺也称紧凑式热带生产线,由德国施罗曼-西马克(SMS)公司于1982年开发的,后移植美国纽柯公司克劳福维尔厂,并于1989年经技术改造建成第一台CSP连铸连轧短流程。
CSP工艺流程:转炉或电炉→钢包精炼炉→薄板坯连铸机→均热炉保温→热连轧机→层流冷却→地下卷取。
CONROLL(ASP) 是由奥钢联工程技术公司开发的一种以生产不同钢种的新工艺。
其主要设备配置为∶薄板坯连铸机-步进梁式加热炉-粗轧机-精轧机组-层流冷却-地下卷取机。
它的特点是采用步进梁式加热炉,且板坯厚度在75~125毫米之间(现在已发展到100~150毫米之间) ,较其它短流程技术的板坯偏厚,这与奥钢联认为较厚的板坯对板卷质量有益的设计理论有关。
生产实践证明,它生产的带卷质量较好,可达欧洲“05”标准。
该生产线与常规热连轧机最为接近,瑞典Avesta采用了CONROLL(ASP) 工艺,鞍钢ASP连铸连轧生产工艺的连铸机借鉴了该工艺的精华部分。
TSP(Tipping—Strip Process) 即薄板坯连铸机加炉卷轧机工艺,由美国蒂平斯公司研究开发的。
其主要设备配置为∶薄板坯连铸机-步进梁式加热炉-单机架炉卷轧机-层流冷却-地下卷取机。
它的特点是在投资很低的情况下,可进行带材生产,比较适合于中小钢厂。
炉卷轧机是带有炉内卷取机的可逆式热轧带钢轧机。
QSP(Quality Strip Production) 工艺是日本住友金属公司开发出的技术,在设备布置上与fTSR工艺类似,不同之处是此工艺采用热卷箱。
且其铸坯厚度为90~100毫米。
它的主要设备布置为∶薄板坯连铸机-隧道式加热炉-粗轧机-双工位热卷箱-飞剪-热连轧机-层流冷却-地下卷取机。
美国北极星厂采用了该工艺。
ESP是意大利阿维迪公司的ESP技术在德马克的ISP技术基础上开发的,生产线中连铸机采用平行板式直--弧形结晶器,铸坯导向采用铸轧结构,经液芯压下铸坯直接进入粗轧机轧制成中厚板,而后经剪切可下线出售,不下线的板坯进入五机架精轧机轧制成簿带钢,经冷切后卷曲成带卷。
CSP连铸结晶器的技术特点

定高度 , 并提供足够大的空问放置浸入式水 口。漏 斗区 以 晶器在形状上满 足了浸入式水 口插入 、 护渣熔化 和板坯厚 保
外的两侧壁依然平行 , 侧壁问距离即为板坯厚 度。漏斗 型结 度的要求 , 在多条生产线上使用并收到 良好 的效果 。
3 3 C P结 晶器 的 工艺特 性 . S
一
() 8考虑结 晶器 钢 板材 质 , 传导 率 不能 太 大。从 C P 热 S 工艺 多年生产实践 , 实漏斗 型结 晶器 是非 常成熟 的技 术 , 证 漏斗型设计完全可以避免内部裂 纹的产生 。
() 晶器内腔曲面形状 的优化设计 是确 保薄 板坯 连铸 9结
高拉速和铸坯质量的关键 。钢铁研究 总院通 过结 晶器 内腔 形状的优化设 计 , 在漏斗形 结 晶器设 计方 面形成 自有技 术 , 开发 出两种不 同类 型的薄板坯连铸用漏斗形结 晶器 , 称之 为
拉坯过程 中, 根据沿 横截面钢 液流 量相等 的原 则 , 斗 漏
型结晶器钢液 向下流动 的速度沿 横截面 的各个部 位的差 别
较大 , 因而易造成紊 流 , 出现 表面 夹渣现 象 , 速越 高 , 种 拉 这
图 1 漏 斗型 结晶 器 示 意
现象越 明显。 3 3 3 结晶器的传热 ..
臻 孵
维普资讯
l 6
甘
肃
冶
金
第2 8卷
3 1 漏 斗型结 晶器 的形状 .
图1 S 是 MS公司 C P工 艺采用的漏斗型结 晶器 。它的 S 上 口宽边 两侧各 有一段平行 段 , 然后 与一 圆弧连接 , 宽面 在 板之 间形成一个垂 直方向带锥 度的漏斗 区, 斗形状保 持在 漏
珠钢CSP生产线工艺与设备情况简介
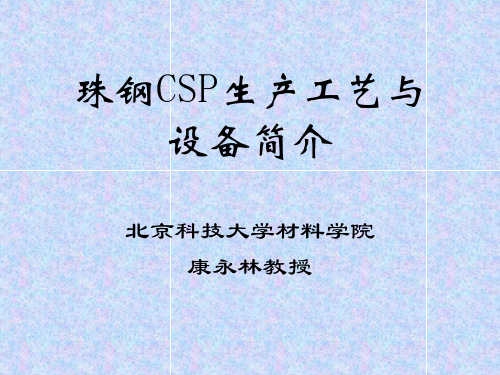
珠钢生产工艺简图
钢包
中间包
CSP 结晶器 均热炉 除鳞机
热连轧机组
冷却线
卷取机
2300mm
191800mm 5500mm×5
48000mm 73825 mm 卷取温度: 550-650 ℃
拉速:2.8-6 m/min 连铸坯厚度:50 mm
开轧温度: 1050-1100 ℃
终轧温度: 850-900 ℃
珠钢CSP生产工艺与 设备简介
北京科技大学材料学院 康永林教授
珠钢CSP建设进度简介
• • • • • • 1997年8月:开始土建工作 1998年11月13日:安装第一座轧机牌坊 1999年7月15日:电炉和CSP连铸机热调试 1999年8月3日:CSP精轧机热调试 1999年8月7日:全线(电炉—CSP)联动热调试 1999年8月26日:投产仪式
CSP 轧机
电弧炉
竖式电弧炉为德国的 FUCHS公司供货,交流,OBT 出钢,装有水冷手指以预热废钢,主要技术参数为: •容量(t):180 •出钢量(t):150 •变压器(MVA):120 •电极直径(mm):610 •碳氧枪O2流量(Nm3/h):4800 •氧油烧嘴(MW):6×7 •废钢预热:100% •留钢量(t):30 •电耗(KWH/t):310
珠钢CSP主要设备
• 电弧炉:德国FUCHS公司产品;容量为180吨; 出钢量为150吨;出钢周期为58分钟(平均)。 • LF炉:150吨;升温速率4℃/min;精炼时间一般 为45min;电耗为0.46kwh/t.℃。 • 连铸机:中间包容量为28t;最大拉速为6m/min; 铸坯厚度为50mm;宽度范围为1000~1350mm; 结晶器为漏斗型+垂直型。 • 加热炉:长度为191.8m;燃料为轻柴油;缓冲时 间大约为20min。
武钢CSP工艺和设备特点
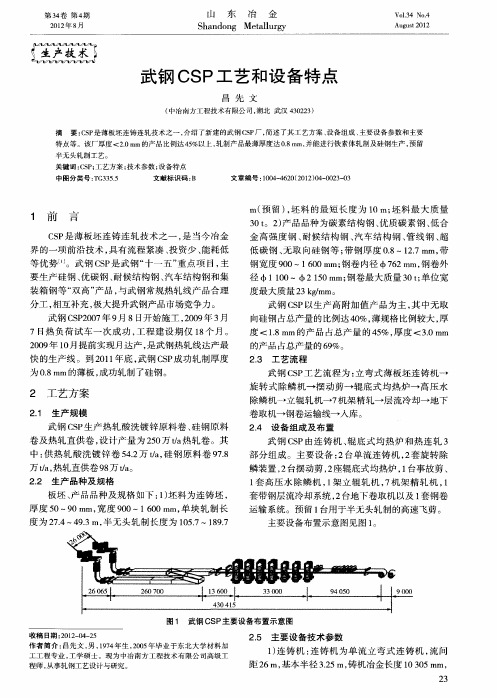
为 2 07m和 2 59r, 动段 长 度 5 缓 冲 时 间 6. 4. n摆 3m; 1 4 n 薄板 坯入 炉温度 8 5~115℃ , 2~ 0 mi; 1 0 出炉 温
的产 品 占总产 量 的 6 %。 9
23 工艺流 程 .
武 钢 C P工艺 流 程为 : S 立弯 式 薄板 坯 连铸 机一 旋 转 式 除 鳞 机一 摆 动 剪 辊底 式 均热 炉 一 高 压水
除鳞机 一 立辊 轧机一 7 机架 精轧一 层 流冷 却一 地 下 卷 取机一 钢卷 运输线一 入库 。 24 设 备组成 及布置 .
武 钢 C P系 紧凑式 短 流程 热 轧带 钢生 产线 , S 轧 制产 品最 薄 厚 度 08 . mm, 能进 行 铁 素体 轧 制 , 并 预
留半无 头轧制 工艺 。主要工艺 和设备 特点如下 :
约 了能源 , 提 高 金 属收 得 率 ( 践 证 明成 材 率 提 还 实
高2 , %) 而且 易于 实现 低温 加热 和 高温 卷取 。所 以 C P 有生产 硅钢 的天 然优势 。 S具 3 连 铸 坯最 大 厚度 增 加 到 9 m, 高 了带 钢 ) 0m 提 的总压缩 比 , 可提 高产品 的性 能质量 。 4 连 铸机 采用 漏 斗形结 晶器 , ) 扩大 了浸 入式 水 口的操 作空 间 , 长 了水 口寿命 , 高 了薄板 坯 连 延 提 铸 机 连 浇 炉 数 。 可 提 高 生 产 率 , 少 耐 火 材 料 消 减 耗, 降低生 产成本 。 5 采用 了液 芯软 压下 技术 , 活满 足 轧钢 品种 ) 灵
武钢 C P工艺和设备特点 S
世界薄板坯连铸连轧技术设备发展综述

世界薄板坯连铸连轧技术设备发展综述世界薄板坯连铸连轧技术设备发展综述1989年美国纽柯公司采用德国西马克公司开发的紧凑型带钢生产(CSP)作业线,在全球率先开展了工业化生产,之后德国、中国、日本、意大利、俄罗斯、加拿大、埃及、印度、奥地利等国的钢铁公司也相继安装,并对其工艺进行进一步设计和开发,获得了一批颇具影响、独具特色的科研成果,使CSP发展成为20年来全球钢铁业一项具有重要意义的创新技术。
西马克的紧凑型带钢生产技术1985年,德国西马克公司在实验工厂成功地铸造出来第一块50毫米的薄板坯后,又创造设计了紧凑型带钢生产技术。
在生产实践中,CSP工艺不仅降低了能量需求,而且,由于其独特的工艺条件,还提高了带钢质量。
与厚板坯相比,薄板坯凝固速度更快,对生产高质量的钢种如微合金钢和硅钢十分有利。
与传统工艺相比,CSP生产的非取向电工钢的变形损失显著减少。
另外,由于温度均匀,薄板坯在宽度、厚度和长度上都达到了严格的标准,“冷边”问题不再出现,粗大晶粒的现象也消失了。
CSP生产线保证了轧制工艺的高效稳定,确保了带钢的宽度、厚度都被控制在理想的公差范围内。
紧凑型带钢生产技术的优势引起了中国珠钢、邯钢、马钢、唐钢、涟钢、酒钢的高度关注。
邯钢、马钢通过从西马克公司引入传统生产线,提高了他们的热轧生产能力,并开发了一批特色产品。
涟钢利用半无头轧制技术,铸造出270米超长扁坯和0.78毫米超薄产品。
武钢于2009年2月建成新的CSP生产线,专门生产非取向电工钢。
达涅利加强表面质量控制意大利达涅利研制开发了独特的薄板坯连铸技术,目的是克服第一代连铸机在产品质量和设备生产能力方面受到的限制。
这项新技术已借助于灵活的薄板坯连铸机概念而变为现实,到目前为止,达涅利薄板坯连铸机已经能够浇铸用于板带生产的所有钢种。
达涅利开发的新一代薄板坯连铸机,充分利用了漏斗形结晶器设计的优点,使最早凝固的初生坯壳沿出坯方向从漏斗形逐渐过渡到较为平坦的形状,从而解决了铸坯表面质量问题。
华菱涟钢CSP生产线情况介绍-4概要

钢包精炼炉
公称容量为100t的钢包精炼炉三座,采 用双工位回转台形式。变压器容量 18000kvA,电极心圆直径为700mm,最 大升温度速度为4.5℃/min。平均精炼时 间40min(不包括软吹Ar时间),三座 LF炉可满足两台CSP连铸机最大生产能 力的需要。
薄板mm,流间距 26m。铸坯导向段长度为9705mm。中间包升 降行程为600mm,回转台钢包升降行程 1000mm。中间包容量为36t,液面高为 1050mm。结晶器长度1100mm,漏斗长度 850mm,漏斗宽度为190mm、180mm两种, 即大漏斗和小漏斗。出结晶器坯厚70mm,经 液芯压下,可压到55mm,预留压到45mm。 最高拉速6.0m/min,机械设备预留的最高拉速 为8.0m/min,最低质量保证拉速为2.6m/min。
采用的主要技术和效果
液芯压下正常,为生产薄规格产品提供可能。 2 月热调试期间即开始进行液芯压下的功能测 试,4月6日连铸开浇,铸坯过顶弯辊即开始液 芯压下,将铸坯 70mm 压到 55mm ,连续进行 四 炉 , 坯 宽 1500mm , 铸 坯 入 剪 机 拉 速 4.8m/min ,至此完成了从 70mm 压到 55mm 的 所有测试,没有一次因液芯压下而引起的漏钢。 4月 13日,已生产厚度为 1.66mm的 Q345D薄板。
产品大纲
双流产量220万吨,带卷宽:900~ 1600mm,带钢厚度:0.8~12.7mm[其中 厚度小于3mm的带钢占80%],钢卷内径: 762mm,钢种为普通碳素结构钢、优质碳 素结构钢、低合金高强度结构钢、汽车 结构钢、高耐候结构钢。另外设备考虑 将来能够生产低碳钢和超低碳钢。
工程管理
均热炉
A线炉子长度约291.0米, A线(1区到5区)主体 长度约194.7米,摆动段49.2米,出坯段47.1米。 B线炉子主体长约294.3米,包括密封室和烟道, 摆动段长 49.2 米。炉膛宽 2.080 米 , 里面耐火材料 在轧制线上方 ,约1.800米高。最短坯长6.000米, 半无头轧制时坯的最大长度 200 米, B 线的坯最 长不超过44.9米。燃气为混合煤气。 铸坯在炉内通过的速度范围为2.0-60.0m/min,不 同 速 度 驱 动 最 大 加 速 度 , 从 2.0m/min 到 60.0m/min 为 3 秒。铸坯出坯时温度为 1150℃+/10℃。
CSP工艺介绍
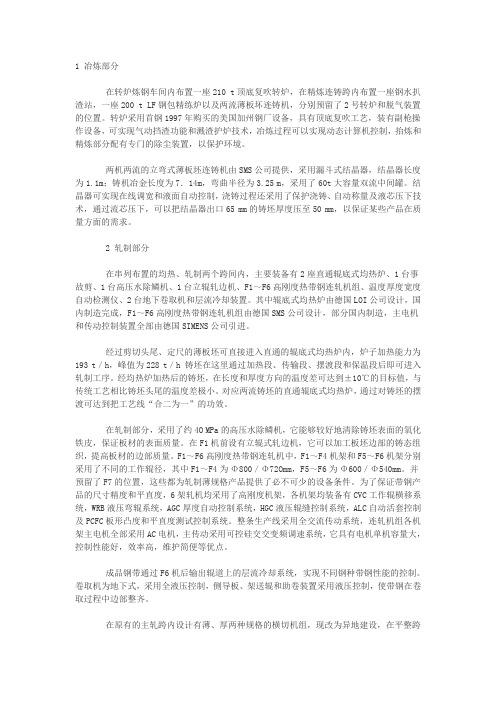
1 冶炼部分在转炉炼钢车间内布置一座210 t顶底复吹转炉,在精炼连铸跨内布置一座钢水扒渣站,一座200 t LF钢包精练炉以及两流薄板坏连铸机,分别预留了2号转炉和脱气装置的位置。
转炉采用首钢1997年购买的美国加州钢厂设备,具有顶底复吹工艺,装有副枪操作设备,可实现气动挡渣功能和溅渣护炉技术,冶炼过程可以实现动态计算机控制,抬炼和精炼部分配有专门的除尘装置,以保护环境。
两机两流的立弯式薄板坯连铸机由SMS公司提供,采用漏斗式结晶器,结晶器长度为1.1m;铸机冶金长度为7.14m,弯曲半径为3.25 m,采用了60t大容量双流中间罐。
结晶器可实现在线调宽和液面自动控制,浇铸过程还采用了保护浇铸、自动称量及液芯压下技术,通过流芯压下,可以把结晶器出口65 mm的铸坯厚度压至50 mm,以保证某些产品在质量方面的需求。
2 轧制部分在串列布置的均热、轧制两个跨间内,主要装备有2座直通辊底式均热炉、1台事故剪、1台高压水除鳞机、1台立辊轧边机、F1~F6高刚度热带钢连轧机组、温度厚度宽度自动检测仪、2台地下卷取机和层流冷却装置。
其中辊底式均热炉由德国LOI公司设计,国内制造完成,F1~F6高刚度热带钢连轧机组由德国SMS公司设计,部分国内制造,主电机和传动控制装置全部由德国SIMENS公司引进。
经过剪切头尾、定尺的薄板坯可直接进入直通的辊底式均热炉内,炉子加热能力为193 t/h,峰值为228 t/h 铸坯在这里通过加热段、传输段、摆渡段和保温段后即可进入轧制工序。
经均热炉加热后的铸坯,在长度和厚度方向的温度差可达到±10℃的目标值,与传统工艺相比铸坯头尾的温度差极小。
对应两流铸坯的直通辊底式均热炉,通过对铸坯的摆渡可达到把工艺线“合二为一”的功效。
在轧制部分,采用了约4O MPa的高压水除鳞机,它能够较好地清除铸坯表面的氧化铁皮,保证板材的表面质量。
在F1机前设有立辊式轧边机,它可以加工板坯边部的铸态组织,提高板材的边部质量。
武钢CSP概况4Word 文档
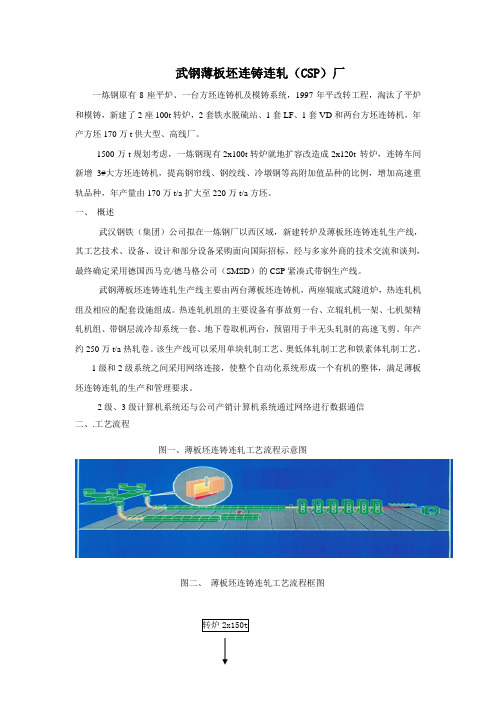
武钢薄板坯连铸连轧(CSP)厂一炼钢原有8座平炉、一台方坯连铸机及模铸系统,1997年平改转工程,淘汰了平炉和模铸,新建了2座100t转炉,2套铁水脱硫站、1套LF、1套VD和两台方坯连铸机,年产方坯170万t供大型、高线厂。
1500万t规划考虑,一炼钢现有2x100t转炉就地扩容改造成2x120t 转炉,连铸车间新增3#大方坯连铸机,提高钢帘线、钢绞线、冷墩钢等高附加值品种的比例,增加高速重轨品种,年产量由170万t/a扩大至220万t/a方坯。
一、概述武汉钢铁(集团)公司拟在一炼钢厂以西区域,新建转炉及薄板坯连铸连轧生产线,其工艺技术、设备、设计和部分设备采购面向国际招标,经与多家外商的技术交流和谈判,最终确定采用德国西马克/德马格公司(SMSD)的CSP紧凑式带钢生产线。
武钢薄板坯连铸连轧生产线主要由两台薄板坯连铸机,两座辊底式隧道炉,热连轧机组及相应的配套设施组成。
热连轧机组的主要设备有事故剪一台、立辊轧机一架、七机架精轧机组、带钢层流冷却系统一套、地下卷取机两台,预留用于半无头轧制的高速飞剪。
年产约250万t/a热轧卷。
该生产线可以采用单块轧制工艺、奥低体轧制工艺和铁素体轧制工艺。
1级和2级系统之间采用网络连接,使整个自动化系统形成一个有机的整体,满足薄板坯连铸连轧的生产和管理要求。
2级、3级计算机系统还与公司产销计算机系统通过网络进行数据通信二、.工艺流程图一、薄板坯连铸连轧工艺流程示意图图二、薄板坯连铸连轧工艺流程框图转炉2x150t三、板坯规格板坯宽度900~1600mm板坯厚度50~90mm板坯长度单块轧制:27.4m~49.3m半无头轧制:105.7~189.7m(预留)板坯最小长度:10m板坯厚度公差:≤ 1% ×板坯中心厚度板坯楔形:≤ 0.8% ×板坯厚度板坯长度公差:0~30mm板坯宽度公差:0~8mm四、钢卷规格带钢厚度:0.8~12.7mm带钢宽度:900~1600mm钢卷内径:762mm钢卷外径:2150mm(max.)钢卷质量:30t(max.)单位卷重:23kg/mm(max.)五、钢种及产量生产的钢种为碳素结构钢、优碳钢、低合金高强度钢、耐候结构钢、汽车结构钢、管线钢、超低碳钢、无取向硅钢。
某企业CSP介绍

GB4171 GB/T14164
注:1. 热轧产品的 70~80%作为冷轧原料 2. 表 2 中超低碳钢的标准为马钢企业标准。
三、原料及金属平衡
钢水供应
转炉座数:
转炉平均出钢量
3(其中2#、3#转炉主要为CSP提高钢水)
1#炉 2#、3#炉 平均100t,最大110t 平均120t,最大130t
转炉平均冶炼周期 LF钢包精炼炉
(5)板坯在炉内的运行速度 正常的速度范围 最大速度 (6)板坯入炉温度 2.0-60 m/min 65 m/min 800~1085 ℃
辊底式均热炉
(7)板坯的出炉速度(进F1轧机) 两块板坯之间的时间间隔(两卷) (8)板坯出炉温度 (9)燃料 12-15.6 m/min 15s 980-1150 ℃ 混合煤气
辊缝润滑 工作辊弯辊和CVC系统
事故剪
液压AGC系统
热连轧机
(2)高压水除鳞装置
除鳞喷咀水压
入口侧24MPa(max)
出口侧38MPa(max)
除鳞水量
390m3/h(max) φ750/700 mm 约800~1750 mm
(3)立辊机
量
液压压下
2500kN 约40 mm (两边总和)
产品方案 带钢厚度: 带钢宽度: 钢卷内径: 钢卷外径: 钢卷重量: 1.0(0.8)~8.0mm 900~1600mm 762mm 1000~1950mm 28.8 t (max.)
单位卷重:
18kg/mm (max.)
产品宽度、厚度规格产量分配见表1
表 1 不同宽度、厚度的产量分配表
mm
单位:t/a
钢包升降行程 钢包升降速度
1000mm 1.8m/min
- 1、下载文档前请自行甄别文档内容的完整性,平台不提供额外的编辑、内容补充、找答案等附加服务。
- 2、"仅部分预览"的文档,不可在线预览部分如存在完整性等问题,可反馈申请退款(可完整预览的文档不适用该条件!)。
- 3、如文档侵犯您的权益,请联系客服反馈,我们会尽快为您处理(人工客服工作时间:9:00-18:30)。
CSP 连铸理论培训教材
一、csp连铸总体描述
连续铸钢技术的发展趋势是近终型连铸技术的开发应用,上下连铸与轧钢工序的无缝连接,实现紧凑的生产工艺流程,最大限度的节能和减少环境污染,提高金属收得率,缩短从钢水到成材的生产周期。
csp连铸机为立弯式,于2004年2月5日一次热试车成功,生产第一块连铸坯,创造了达产达效世界第一的世界记录。
铸机主要设备为蝶式钢包回转台、中间包车、漏斗型结晶器、液压振动台、扇形1、2、3、4段,带刚性引锭杆的顶弯夹送装置、拉矫装置、以及摆动剪,其核心设备是漏斗型结晶器。
在钢包回转台的两侧各有一个中包车和和中包预热站,车上配有浸入式水口预热烧嘴。
每台中包车都配备有称重系统,以称量中间包钢水重量。
每个中间包在正常工作情况下,容量为26-28吨,溢渣情况下为30-32吨。
中间包钢水液位可采用自动和手动进行控制,钢水从中间包注入结晶器采用塞棒伺服机构控制,它和Co60放射源、闪烁记数器和PLC装置一起组成结晶器液位控制系统。
塞棒是整体式的,而塞棒机构采用压缩空气冷却。
结晶器液位控制系统可实现连铸机的自动开浇,即当液位控制系统检测到钢水液位的10%时,铸机振动台开始振动,夹送辊开始拉坯。
钢水从中间包注入结晶器,是通过一个扁平式的整体式浸入式水口,它的出钢口是专门设计的,以适应结晶器形状结构要求。
结晶器是一个直的漏斗式结晶器,上大下小,在宽边铜板上部中心有一个宽的垂直、锥形的漏斗区域,以保证浸入式水口有足够的空间。
漏斗区域为从铜板上部向下大约850mm,以下便是结晶器下部平行出口部分。
下部结晶器模壁是平行的,从而形成最后铸坯的断面尺寸。
结晶器振动装置是一个短杆式的液压振动系统,可以产生正弦和非正弦振动,目前涟钢采用的是非正弦振动。
而结晶器下面则为铸坯导向的扇形1、2、3、4段。
打开结晶器后,可以允许刚性引锭杆的插入,也可以清除漏钢后形成的坯壳。
漏钢后通常影响到结晶器和扇形1段,他可以很容易的作为一个整体用吊车吊出更换。
结晶器的宽度和锥度可以远程调整,借助于主控室内驱动PLC方式进行预设定,在浇注期间,主控操作人员可以根据生产计划或轧制规格要求
进行在线调宽,通常情况下还可以通过调锥来进行结晶器热流的控制,以稳定浇注状态,确保铸坯坯壳的均匀冷却。
通常涟钢二次冷却有3条冷却曲线,根据不同钢种,选择不同的冷却曲线,随着拉速的增加,水量不断增大。
铸坯出扇形段后,进入夹送辊顶弯装置,依靠液压,顶弯辊将铸坯与引锭杆分离,铸坯进入3.25m半径的弧形段,再通过拉矫机进行一点矫直。
夹送辊顶弯装置及拉矫装置的冷却均为内冷。
然后铸坯进入摆动剪,在摆动剪处进行铸坯切头和定尺铸坯的剪切,在主控室HMI画面可进行铸坯长度的设定。
通常铸坯在摆剪处的温度为950-1050℃,主要由于不同拉速所致。
二、技术参数
机型立弯式
流数2流
流间距26000mm
浇铸平台标高15165mm
冶金长度9705mm
顶弯半径3250mm
浇注断面:900~1600mm×70~55mm(冷尺寸)
回转台参数:
回转台承载能力2×200t
回转半径5500mm
回转速度 1.0rpm(电机驱动)
0.5rpm(事故驱动)
回转臂升降行程1000mm
回转臂升降速度30mm/s
包盖升降行程850mm
包盖旋转角度65°
包盖升降速度50mm/s
中间包容量:
工作液位27t(液位深度1050mm)
溢流液位30t(液位深度1150mm)
中间包车参数:
中间包车承载能力65t
行走速度 1.5/15m/min
中间包升降行程600mm
中间包升降速度60mm/s
中包横移距离±40mm
位置精度±1mm
结晶器:
材质宽面:Cu-Ag;窄面:Cu-Ni-Be
高度1100mm
出口宽度900~1600mm×72mm
结晶器漏斗上口宽度×长度×高度180/190mm×880/1100mm×850mm
结晶器振动:
振幅±2mm~±5mm 基本设定±3mm
频率0~600cpm
EMBr:
最大线圈电流460A
变压器功率160kV A
塞棒:
行程100mm(±50mm)
驱动方式机电驱动
引锭杆形式:刚性下装式
拉矫辊对数4对(其中2~4上辊为驱动辊)
铸坯清洗装置:
喷咀数2×13(上下各13个)
喷咀压力6~10bar
摆动剪:
剪切力12400kN
马达功率450kW
最快剪切速度8块/分钟。