V23848-C18-C56中文资料
V23826-C18-C363中文资料
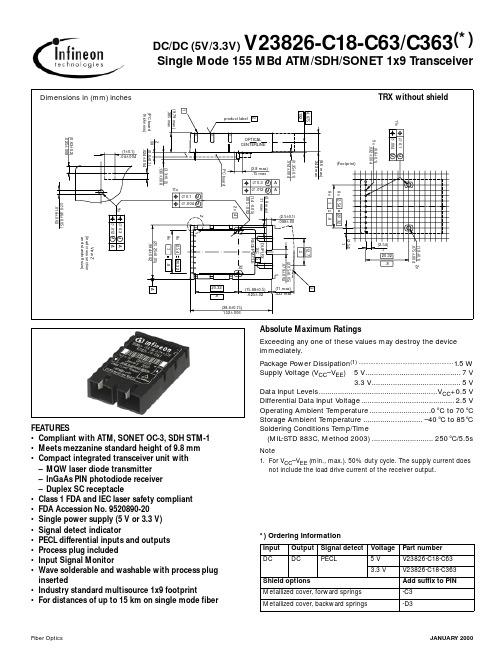
DC/DC (5V/3.3V) V23826-C18-C63/C363(*) Single Mode 155 MBd ATM/SDH/SONET 1x9 T ransceiver•Compliant with ATM, SONET OC-3, SDH STM-1•Meets mezzanine standard height of 9.8 mm •Compact integrated transceiver unit with– MQW laser diode transmitter– InGaAs PIN photodiode receiver– Duplex SC receptacle•Class 1 FDA and IEC laser safety compliant•FDA Accession No. 9520890-20•Single power supply (5 V or 3.3 V)•Signal detect indicator•PECL differential inputs and outputs•Process plug included•Input Signal Monitor•Wave solderable and washable with process plug inserted•Industry standard multisource 1x9 footprint•For distances of up to 15 km on single mode fiber(MIL-STD 883C, Method 2003).............................250°C/5.5s Note1. For V CC–V EE (min., max.). 50% duty cycle. The supply current doesnot include the load drive current of the receiver output.*) Ordering InformationInput Output Signal detect Voltage Part numberDC DC PECL 5 V V23826-C18-C633.3 V V23826-C18-C363 Shield options Add suffix to PIN Metallized cover, forward springs-C3Metallized cover, backward springs-D3DESCRIPTIONThe Infineon single mode ATM transceiver complies with the ATM Forum’s Network Compatible ATM for Local Network Applications document and ANSI’s Broadband ISDN—Cus-tomer Installation Interfaces, Physical Media Dependent Speci-fication, T1.646-1995, Bellcore - SONET OC-3 / IR-1 andITU-T G. 957 STM-1 / S.1.1.ATM was developed to facilitate solutions in multimedia appli-cations and real time transmission. The data rate is scalable, and the ATM protocol is the basis of the broadband public net-works being standardized in the International Telecommunica-tions Union (ITU), the former International Telegraph and Telephone Consultative Committee (CCITT). ATM can also be used in local private applications.The Infineon single mode ATM transceiver is a single unit com-prised of a transmitter, a receiver, and an SC receptacle. This design frees the customer from many alignment and PC board layout concerns. The module is designed for low cost WAN applications. It can be used as the network end device interface in workstations, servers, and storage devices, and in a broad range of network devices such as bridges, routers, and intelli-gent hubs, as well as wide area ATM switches.This transceiver operates at 155.520 Mbit/s from a single power supply (+5 Volt or 3.3 Volt). The differential data inputs and out-puts are PECL compatible.Functional DescriptionThis transceiver is designed to transmit serial data via single mode cable.The receiver component converts the optical serial data into PECL compatible electrical data (RD and RDnot). The Signal Detect (SD, active high) shows whether optical datais present(1).The transmitter converts electrical PECL compatible serial data (TD and TDnot) into optical serial data.This version contains an Input Signal Monitor (ISM), that switches the optical power off if a continuously low level is applied at Data Input.The transmitter contains a laser driver circuit that drives the modulation and bias current of the laser diode. The currents are controlled by a power control circuit to guarantee constant out-put power of the laser over temperature and aging.The power control uses the output of the monitor PIN diode (mechanically built into the laser coupling unit) as a controlling signal, to prevent the laser power from exceeding the operating limits.Single fault condition is ensured by means of an integrated automatic shutdown circuit that disables the laser when it detects transmitter failures. A reset is only possible by turning the power off, and then on again.The transceiver contains a supervisory circuit to control the power supply. This circuit generates an internal reset signal whenever the supply voltage drops below the reset threshold. It keeps the reset signal active for at least 15 milliseconds after the voltage has risen above the reset threshold. During this time the laser is inactive.Note1.We recommend to switch off the transmitter supply (V CC-Tx) if notransmitter input data is applied.TECHNICAL DATAThe electro-optical characteristics described in the following tables are only valid for use under the recommended operating conditions.Recommended Operating ConditionsNote1. For V CC–V EE (min., max.) 50% duty cycle. The supply current doesnot include the load drive current of the receiver output.T ransmitter Electro-Optical CharacteristicsNotes1. Into single mode fiber, 9 µm diameter.2. Laser power is shut down if power supply is below V TH andswitched on if power supply is above V TH after t RES.3. Transmitter meets ANSI T1E1.2, SONET OC-3 and ITU-T G.957 maskpatterns.Receiver Electro-Optical CharacteristicsNotes1. Minimum average optical power at which the BER is less than1x10-10 or lower. Measured with a 223-1 NRZ PRBS as recom-mended by ANSI T1E1.2, SONET OC-3 and ITU-T G.957.2.An increase in optical power of data signal above the specified levelwill cause the SIGNAL DETECT to switch from a Low state to a High state.3.A decrease in optical power of data signal below the specified levelwill cause the SIGNAL DETECT to switch from a High state to a Low state.4. DC/DC, PECL for Signal DetectPECL compatible. Load is 50 Ω into V CC–2 V for data, 500 Ω to V EE for Signal Detect. Measured under DC conditions. For dynamic mea-surements a tolerance of 50 mV should be added. V CC=3.3 V/5 V.T AMB=25°C.Parameter Symbol Min.T yp.Max.Units Ambient Temperature T AMB070°CPower Supply Voltage 3.3 V V CC–V EE 3.1 3.3 3.5V 5 V 4.755 5.25Supply Current(1)3.3 V I CC175230mA 5 V190270T ransmitterData Input High VoltageDC/DCV IH–V CC–1165–880mVData Input Low VoltageDC/DCV IL–V CC–1810–1475Input Data Rise/FallTime 10%–90%t R, t F0.4 1.3ns ReceiverInput Center WavelengthλC12601360nmT ransmitter Symbol Min.T yp.Max.Units Launched Power(Average)(1)P O–15–11–8dBm Center WavelengthλC12601360nm Spectral Width (RMS)σl7.7 Extinction Ratio (Dynamic)ER8.2dB Reset Threshold(2) 3.3 V V TH 2.7V5 V 3.5Reset Time Out(2)t RES152235ms Eye Diagram(3)ED Receiver Symbol Min.T yp.Max.Units Sensitivity(Average Power)(1)P IN–36–31dBmSaturation(Average Power)P SAT–8Signal DetectAssert Level(2)P SDA-37.5–34Signal DetectDeassert Level(3)P SDD–44-40Signal Detect Hysteresis P SDA–P SDD1 2.56dB Signal Detect Assert Time t ASS100µs Signal Detect DeassertTimet DAS350Output Low Voltage(4)V OL-V CC–1950–1620mVOutput High Voltage(4)V OH-V CC–1025–720Output Data Rise/FallTime, 20%–80%t R, t F375psOutput SDRise/Fall Time40nsPin Description Regulatory Compliance EYE SAFETYThis laser based single mode transceiver is a Class 1 product. It complies with IEC 60825-1 and FDA 21 CFR 1040.10 and 1040.11.To meet laser safety requirements the transceiver shall be oper-ated within the Absolute Maximum Ratings.CautionAll adjustments have been made at the factory prior to ship-ment of the devices. No maintenance or alteration to the device is required.T ampering with or modifying the performance of the device will result in voided product warranty.NoteFailure to adhere to the above restrictions could result in a modifica-tion that is considered an act of “manufacturing,” and will require, under law, recertification of the modified product with the U.S. Food and Drug Administration (ref. 21 CFR 1040.10 (i)).Laser DataAPPLICATION NOTEATM transceivers and matching circuits are high frequency components and shall be terminated as recommended in the application notes for proper EMI performance. Electromagnetic emission may be caused by these components.To prevent emissions it is recommended that cutouts for the fiber connectors be designed as small as possible.It is recommended that the Tx plug and the Rx plug be separated with a bar that divides the duplex SC opening.Pin Name Level/Logic Pin#Description RxV EE Rx Ground Power Supply1Negative powersupply, normallygroundRD Rx OutputData PECL Output2Receiver outputdataRDn3Inverted receiveroutput dataSD Rx SignalDetect PECL4 A high level on thisoutput shows thatoptical data is ap-plied to the opticalinput.Rx-V CC Rx 3.3 V/5 V Power Supply5Positive power sup-ply, 3.3 V/5 VTxV CC Tx 3.3 V/5 V6TDn TxInputData PECL Input7Inverted transmit-ter input dataTD8Transmitter inputdataTxV EE Tx Ground Power Supply9Negative powersupply, normallygroundStud Pin Mech. Support S1/2Not connected Feature Standard CommentsElectrostatic Discharge (ESD) to the Electrical Pins MIL-STD 883CMethod 3015.4Class 1 (>1000 V)Immunity: Electrostatic Discharge (ESD) to the Duplex SC Receptacle EN 61000-4-2IEC 61000-4-2Discharges of ±15kV withan air discharge probe onthe receptacle cause nodamage.Immunity: Radio Frequency Electromagnetic Field EN 61000-4-3IEC 61000-4-3With a field strength of10V/m rms, noisefrequency ranges from10MHz to 1GHz. Noeffect on transceiver per-formance between thespecification limits.Emission: Electromagnetic Interference EMI FCC Class BEN 55022 Class BCISPR 22Noise frequency range:30MHz to 6GHz; Marginsdepend on PCB layout andchassis designWavelength1300 nmTotal output power (as defined by IEC: 50mmaperture at 10 cm distance)less than2 mWTotal output power (as defined by FDA: 7 mmaperture at 20 cm distance)less than180 µWBeam divergence4°APPLICATION NOTEThis Application Note assumes Fiber Optic Transceivers using 5 V power supply and SerDes Chips using 3.3 V power supply. It also assumes no self biasing at the receiver data inputs (RD+/ RD-) of the SerDes chip (Refer to the manufacturer data sheet for other applications). 3.3 V-Transceivers can be directly con-nected to SerDes-Chips using standard PECL Termination network.Value of R1...R4 may vary as long as proper 50 Ω termination to V EE or 100 Ω differential is provided. The power supply filtering is required for good EMI performance. Use short tracks from the inductor L1/L2 to the module V CC Rx/V CC Tx. Further applica-tion notes for electrical interfacing are available upon request. Ask for Appnote 82.We strongly recommend a V EE plane under the module for get-ting good EMI performance.The transceiver contains an automatic shutdown circuit. Reset is only possible if the power is turned off, and then on again. (V CC Tx switched below V TH).Application Board available on request.Published by Infineon T echnologies AG© Infineon T echnologies AG 1999All Rights ReservedAttention please!The information herein is given to describe certain components and shall not be considered as warranted characteristics.T erms of delivery and rights to technical change reserved.We hereby disclaim any and all warranties, including but not limited to warranties of non-infringement, regarding circuits, descriptions and charts stated herein. Infineon T echnologies is an approved CECC manufacturer.InformationFor further information on technology, delivery terms and conditions and prices please contact the Infineon Technologies offices or our Infineon T echnologies Representatives worldwide - see our webpage at/fiberoptics WarningsDue to technical requirements components may contain dangerous substances. For information on the types in question please contact your Infineon Technologies offices.Infineon T echnologies Components may only be used in life-support devices or systems with the express written approval of Infineon Technologies, if a failure of such components can reasonably be expected to cause the failure of that life-support device or system, or to affect the safety or effectiveness of that device or system. Life support devices or systems are intended to be implanted in the human body, or to support and/or maintain and sustain and/or protect human life. If they fail, it is reasonable to assume that the health of the user or other persons may be endangered.元器件交易网This datasheet has been download from:Datasheets for electronics components.。
C中文参数
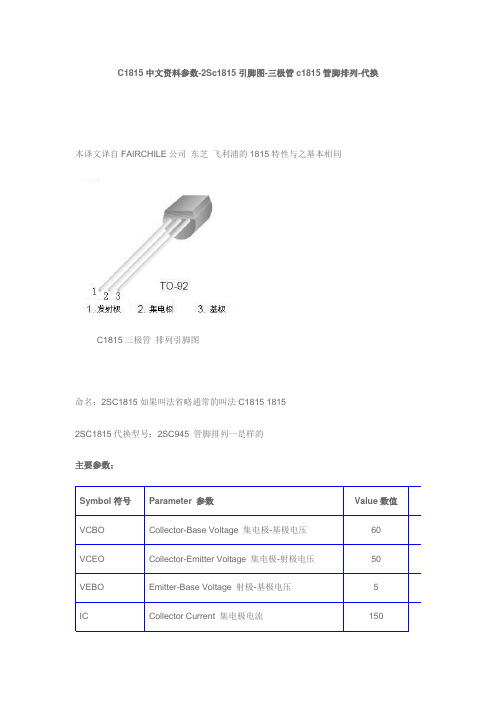
C1815中文资料参数-2Sc1815引脚图-三极管c1815管脚排列-代换
本译文译自FAIRCHILE公司东芝飞利浦的1815特性与之基本相同
C1815三极管排列引脚图
命名:2SC1815如果叫法省略通常的叫法C1815 1815
2SC1815代换型号:2SC945 管脚排列一是样的
主要参数:
Symbol符号Parameter 参数Value数值Un VCBO Collector-Base Voltage 集电极-基极电压60
VCEO Collector-Emitter Voltage 集电极-射极电压50
VEBO Emitter-Base Voltage 射极-基极电压 5
IC Collector Current 集电极电流150
电参数:
放大倍数表示:
后缀符号O Y GR L 放大倍数70-140120-240200-400350-700
C1815特性曲线:
静态特性曲线
传输特性曲线
直流电流增益曲线
基极-发射饱和电压曲线集电极-射极饱和电压曲线
输出电容曲线
电流增益带宽曲线
外形封装图。
2SC5658中文资料
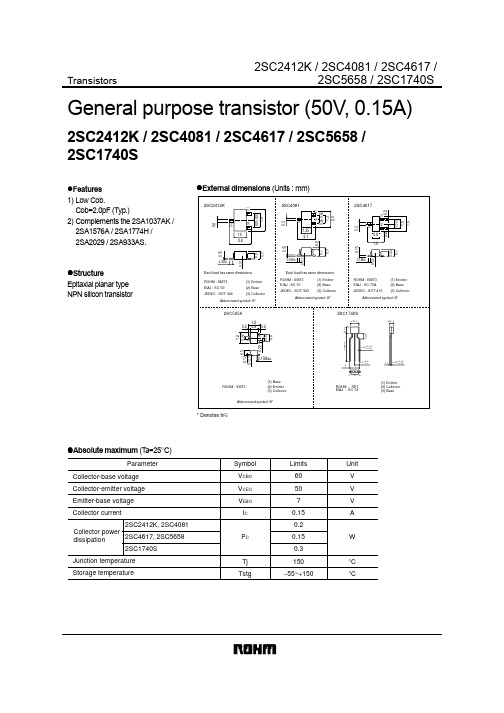
Transistors 2SC5658 / 2SC1740SGeneral purpose transistor (50V, 0.15A)2SC2412K / 2SC4081 / 2SC4617 / 2SC5658 /2SC1740S!Features 1) Low Cob.Cob=2.0pF (Typ.)2) Complements the 2SA1037AK /2SA1576A / 2SA1774H /2SA2029 / 2SA933AS.!StructureEpitaxial planar type NPN silicon transistor!External dimensions (Units : mm)* Denotes h FE!Absolute maximum (T a=25°C)Collector-base voltage Collector-emitter voltage Emitter-base voltage Collector currentCollector powerdissipationJunction temperature Storage temperatureParameterV CBO V CEO V EBO P CTj Tstg60V V V AW °C °C 5070.15I C0.20.150.32SC2412K, 2SC40812SC1740S 2SC4617, 2SC5658150−55~+150Symbol Limits UnitTransistors 2SC5658 / 2SC1740S!Electrical characteristics (T a=25°C)Collector-base breakdown voltage Collector-emitter breakdown voltage Emitter-base breakdown voltage Collector cutoff current Emitter cutoff current DC current transfer ratioCollector-emitter saturation voltage Output capacitanceParameterSymbol BV CBO BV CEO BV EBO I CBO I EBO h FE V CE(sat)f T CobMin.60507−−120−−−−−−−−−−1802−−−0.10.15600.4−3.5V I C =50µA I C =1mA IE =50µA V CB =60V V EB =7VV CE =6V, I C =1mA I C /I B =50mA/5mAV CE =12V, I E =−2mA, f=100MHz V CE =12V, I E =0A, f=1MHzV V µA µA −V MHz pFTyp.Max.Unit ConditionsTransition frequency !Packaging specifications and h FEh FE values are classified as follows :Item Q R S h FE120~270180~390270~560!Electrical characterristic curvesFig.1 Grounded emitter propagationcharacteristics C O L L E C T O R C U R R E N T: I C (m A )BASE TO EMITTER VOLTAGE : V BE (V)Fig.2 Grounded emitter outputcharacteristics ( Ι )C O L L E C T O R C U R R E N T : I C (m A )COLLECTOR TO EMITTER VOLTAGE : V CE (V)C O L L E C T O R C U R R E N T : I C (m A )COLLECTOR TO EMITTER VOLTAGE : V CE (V)Fig.3 Grounded emitter outputcharacteristics ( ΙΙ )Transistors2SC5658 / 2SC1740SFig.4 DC current gain vs.collector current ( Ι )D C C U R RE N T G A I N: h F ECOLLECTOR CURRENT : I C (mA)Fig.5 DC current gain vs.collector current ( ΙΙ )D C C U R R E N T G A I N : h F ECOLLECTOR CURRENT : I C (mA)Fig. 6 Collector-emitter saturationvoltage vs. collector currentC O L L E C T O R S A T U R A T I O N V O L T A G E : V C E (s a t ) (V )COLLECTOR CURRENT : I C (mA)Fig.7 Collector-emitter saturation voltage vs. collector current ( Ι )C O L L E C T O R S A T U R A T I O N V O L T A G E : V C E (s a t ) (V )COLLECTOR CURRENT : I C (mA) Fig.8 Collector-emitter saturationvoltage vs. collector current (ΙΙ)C O L L E C T O R S A T U R A T I O N V O L T A G E : V C E (s a t ) (V )COLLECTOR CURRENT : I C (mA)Fig.9 Gain bandwidth product vs.emitter current−EMITTER CURRENT : I E (mA)T R A N S I T I O N F R E Q U E N C Y : f T (M H z )Fig.10 Collector output capacitance vs.collector-base voltageEmitter input capacitance vs.emitter-base voltageCOLLECTOR TO BASE VOLTAGE : V CB (V)EMITTER TO BASE VOLTAGE : V EB (V)C O L L E C T O R O U T P U T C A P A CI T A N C E : C o b (p F )E M I T T E R I N P U T C A P A C I T A N C E : C i b (p F )Fig.11 Base-collector time constantvs. emitter current− B A S E C O L L E C T O R T I M E C O N S T A N T : C c ·r b b (p s )EMITTER CURRENT : I E (mA)。
93c56芯片参数
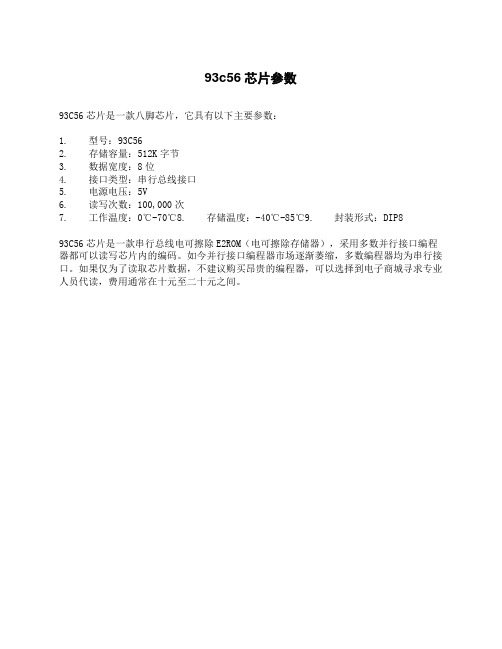
93c56芯片参数
93C56芯片是一款八脚芯片,它具有以下主要参数:
1. 型号:93C56
2. 存储容量:512K字节
3. 数据宽度:8位
4. 接口类型:串行总线接口
5. 电源电压:5V
6. 读写次数:100,000次
7. 工作温度:0℃-70℃8.存储温度:-40℃-85℃9.封装形式:DIP8
93C56芯片是一款串行总线电可擦除E2ROM(电可擦除存储器),采用多数并行接口编程器都可以读写芯片内的编码。
如今并行接口编程器市场逐渐萎缩,多数编程器均为串行接口。
如果仅为了读取芯片数据,不建议购买昂贵的编程器,可以选择到电子商城寻求专业人员代读,费用通常在十元至二十元之间。
TLC386A中文资料
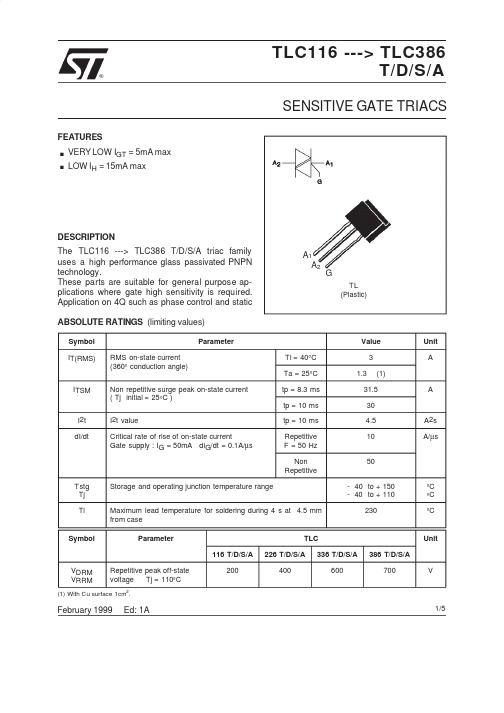
TLC116--->TLC386T/D/S/AFebruary 1999Ed:1ASENSITIVE GATE TRIACS®Symbol ParameterValue Unit I T(RMS)RMS on-state current (360°conduction angle)Tl =40°C 3ATa =25°C 1.3(1)I TSMNon repetitive surge peak on-state current (Tj initial =25°C )tp =8.3ms 31.5Atp =10ms 30I 2t I 2t valuetp =10ms 4.5A 2s dI/dtCritical rate of rise of on-state currentGate supply :I G =50mA di G /dt =0.1A/µsRepetitive F =50Hz 10A/µsNon Repetitive50Tstg Tj Storage and operating junction temperature range-40to +150-40to +110°C °C TlMaximum lead temperature for soldering during 4s at 4.5mm from case230°CTL (Plastic).VERY LOW I GT =5mA max .LOW I H =15mA maxDESCRIPTIONSymbol ParameterTLCUnit116T/D/S/A226T/D/S/A336T/D/S/A386T/D/S/AV DRM V RRMRepetitive peak off-state voltage Tj =110°C200400600700VABSOLUTE RATINGS (limiting values)FEATURESThe TLC116--->TLC386T/D/S/A triac family uses a high performance glass passivated PNPN technology.These parts are suitable for general purpose ap-plications where gate high sensitivity is required.Application on 4Q such as phase control and static (1)With Cu surface 1cm 2.A 1GA 21/5GATE CHARACTERISTICS (maximum values)Symbol ParameterValue Unit Rth (j-a)Junction to ambient on printed circuit with Cu surface 1cm 250°C/W Rth (j-l)DC Junction leads for DC 20°C/W Rth (j-l)ACJunction leads for 360°conduction angle (F=50Hz)15°C/WSymbolTest ConditionsQuadrantSuffix UnitTD S A I GTV D =12V(DC)R L =33ΩTj=25°CI-II-III MAX 551010mA IVMAX 5101025V GT V D =12V(DC)R L =33ΩTj=25°C I-II-III-IV MAX 1.5V V GD V D =V DRM R L =3.3k ΩTj=110°C I-II-III-IV MIN 0.2V tgt V D =V DRM I G =40mA dI G /dt =0.5A/µs Tj=25°C I-II-III-IV TYP 2µs I LIG=1.2I GTTj=25°CI-III-IV MAX15152525mA II15152525I H *I T =100mA gate open Tj=25°C MAX 15152525mA V TM *I TM =4A tp=380µs Tj=25°C MAX 1.85V I DRM I RRM V DRM Rated V RRMRatedTj=25°C MAX 0.01mATj=110°C MAX 0.75dV/dt *Linear slope uptoV D =67%V DRM gate open Tj=110°CTYP10102020V/µs(dV/dt)c *(dI/dt)c =1.3A/msTj=110°C TYP 1155V/µs*For either polarity of electrode A 2voltage with reference to electrode A 1.P G (AV)=0.1WP GM =2W (tp =20µs)I GM =1A (tp =20µs)V GM =16V (tp =20µs).ELECTRICAL CHARACTERISTICSTHERMAL RESISTANCESTLC116T/D/S/A --->TLC386T/D/S/A2/5Package I T(RMS)V DRM/V RRM Sensitivity SpecificationA V T D S A TLC..63200X X X X400X X X X600X X X X700X X X X ORDERING INFORMATIONFig.1:Maximum RMS power dissipation versus RMS on-state current(F=50Hz).(Curves are cut off by(dI/dt)c limitation)Fig.2:Correlation between maximum RMS power dissipation and maximum allowable temperatures(T amb and T lead).Fig.3:RMS on-state current versus case temperature.Fig.4:Thermal transient impedance junction to caseand junction to ambient versus pulse duration.TLC116T/D/S/A--->TLC386T/D/S/A3/5Fig.5:Relative variation of gate trigger current and holding current versus junction temperature.Fig.6:Non Repetitive surge peak on-state current versus number of cycles.Fig.7:Non repetitive surge peak on-state current for a sinusoidal pulse with width:t≤10ms,and corresponding value of I2t.Fig.8:On-state characteristics(maximum values).TLC116T/D/S/A--->TLC386T/D/S/A 4/5PACKAGE MECHANICAL DATA TL PlasticMarking:type number Weight:0.75g REF.DIMENSIONSMillimeters InchesMin.Max.Min.Max. A9.5510.050.3750.396 B7.558.050.2970.317 C12.700.500D 4.25 4.750.1670.187E 1.25 1.750.0490.069F 6.757.250.2660.285G 4.500.177H 2.04 3.040.800.120 I0.750.850.0290.033DEFABCGH HIInformation furnished is believed to be accurate and reliable.However,STMicroelectronics assumes no responsibility for the conse-quences of use of such information nor for any infringement of patents or other rights of third parties which may result from its use.No license is granted by implication or otherwise under any patent or patent rights of STMicroelectronics.Specifications mentioned in this publication are subject to change without notice.This publication supersedes and replaces all information previously supplied. STMicroelectronics products are not authorized for use as critical components in life support devices or systems without express written approval of STMicroelectronics.The ST logo is a registered trademark of STMicroelectronics©1999STMicroelectronics-Printed in Italy-All rights reserved.STMicroelectronics GROUP OF COMPANIESAustralia-Brazil-Canada-China-France-Germany-Italy-Japan-Korea-Malaysia-Malta-Mexico-Mo-rocco-The Netherlands-Singapore-Spain-Sweden-Switzerland-Taiwan-Thailand-United Kingdom-U.S.A.TLC116T/D/S/A--->TLC386T/D/S/A5/5。
CH384DS2
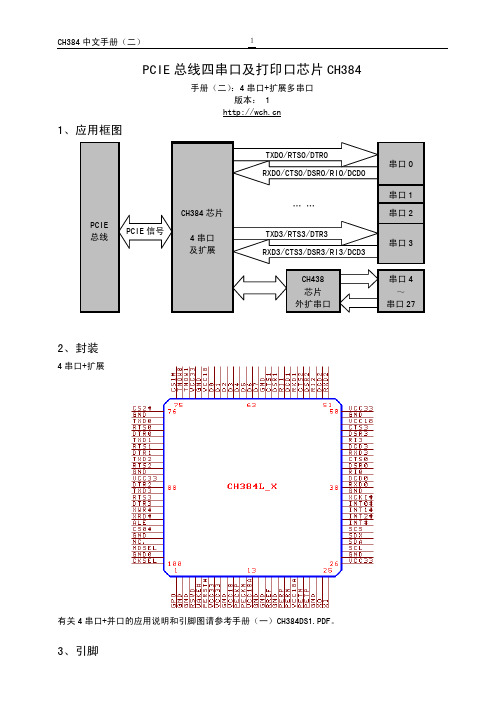
PCIE 总线四串口及打印口芯片CH384手册(二):4串口+扩展多串口版本: 1 1、应用框图2、封装4串口+扩展有关4串口+并口的应用说明和引脚图请参考手册(一)CH384DS1.PDF 。
3、引脚3.1. 电源线引脚号引脚名称类型引脚说明7,8,26,50,72,87 VCC33 电源 3.3V I/O电源10,48,70 VCC18 电源 1.8V内核电源13,20 VCC18A 电源 1.8V传输电源2,3,9,14,15,17,23,27,37,49,61,71,77,86,96,99GND 电源公共接地端97 NC. 空脚禁止连接3.2. PCIE总线信号线引脚号引脚名称类型引脚说明6 PERST# 输入系统复位信号线,低电平有效11,12 PECKP/PECKN 输入系统参考时钟差分输入18,19 PERP/PERN PCIE输入PCIE接收器差分信号输入22,21 PETP/PETN PCIE输出PCIE发送器差分信号输出5 WAKE# 开漏输出总线唤醒输出,低电平有效,未用到则可以不连接3.3. 串口0~串口3信号线引脚号引脚名称类型引脚说明42/60 55/47 CTS0/CTS1CTS2/CTS3输入MODEM信号,清除发送,低电平有效,内置上拉电阻41/59 54/46 DSR0/DSR1DSR2/DSR3输入MODEM信号,数据装置就绪,低电平有效,内置上拉电阻40/58 53/45 RI0/RI1RI2/RI3输入MODEM信号,振铃指示,低电平有效,内置上拉电阻39/57 52/44 DCD0/DCD1DCD2/DCD3输入MODEM信号,载波检测,低电平有效,内置上拉电阻38/56 51/43 RXD0/RXD1RXD2/RXD3输入异步串行数据输入,内置上拉电阻80/83 88/91 DTR0/DTR1DTR2/DTR3输出MODEM信号,数据终端就绪,低电平有效79/82 85/90 RTS0/RTS1RTS2/RTS3输出MODEM信号,请求发送,低电平有效78/81 84/89 TXD0/TXD1TXD2/TXD3输出异步串行数据输出74/73 TNOW0/TNOW1 输出串口正在发送状态输出(半双工收发切换),高电平有效3.4. 扩展CH438信号线引脚号引脚名称类型引脚说明62-69 D7~D0 三态双向8位并行数据输出及输入,内置上拉电阻,接D7~D092 XWR# 输出写选通输出,低电平有效,接WR#93 XRD# 输出读选通输出,低电平有效,接RD#94 ALE 输出复用地址的地址锁存使能输出,高电平有效,接ALE95 CS0# 输出外扩串口片选0输出,接0# CH438的CS#,低电平有效75 CS1# 输出外扩串口片选1输出,接1# CH438的CS#,低电平有效76 CS2# 输出外扩串口片选2输出,接2# CH438的CS#,低电平有效35 INT0# 输入0# CH438的中断状态输入,低电平有效,内置上拉电阻34 INT1# 输入1# CH438的中断状态输入,低电平有效,内置上拉电阻33 INT2# 输入2# CH438的中断状态输入,低电平有效,内置上拉电阻32 INT# 输入备用的中断状态输入,低电平有效,内置上拉电阻3.5. 辅助信号线引脚号引脚名称类型引脚说明16 RREF 输入系统参考电流输入,需要外接12KΩ电阻到GND25 XI 输入可选,晶体振荡的输入端,外接晶体及振荡电容24 XO 输入输出可选,晶体振荡的反相输出端,外接晶体及振荡电容28 SCL 输出通用输出,外部配置芯片的时钟输出,可以外接串行EEPROM配置芯片24CXX的SCL引脚29 SDA 开漏输出及输入通用输出及输入,内置上拉电阻,可以外接串行EEPROM配置芯片24CXX的SDA引脚30 SDX 三态双向通用输出及输入,内置上拉电阻31 SCS 输出通用输出100 CKSEL 输入串口时钟频率选择输入,内置上拉电阻98 MDSEL 输入软件识别模式选择输入,内置上拉电阻36 XCKI# 输入外部输入串口时钟源选择输入,内置上拉电阻1 GPO 输出通用输出4 RSVD 保留保留引脚,禁止连接4、配置CH384芯片具有两种主要硬件功能模式:4串口+并口功能模式,4串口+扩展多串口功能模式。
2SC5845资料
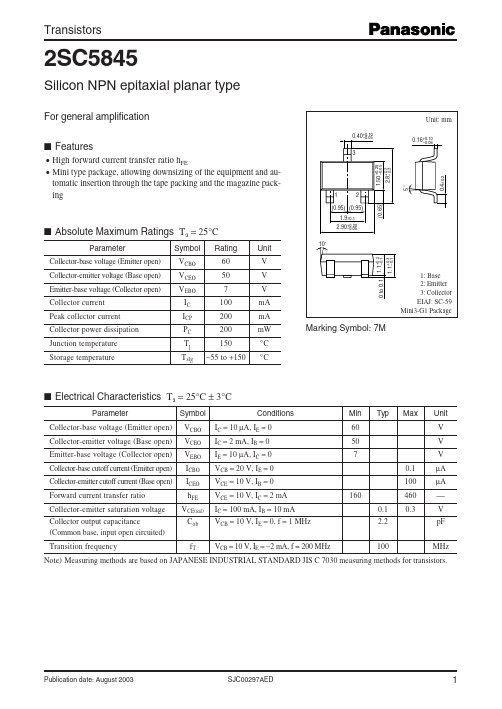
350 300 25°C 250 –25°C 200 150 100 50 0
Forward current transfer ratio hFE
1
10
100
1 000
1
0
8
16
24
32
40
Collector current IC (mA)
Collector-base voltage VCB
SJC00297AED
1
2SC5845
PC Ta
240 50 Ta = 25°C IB = 160 µA 40
IC VCE
140 120 VCE = 10V Ta = 25°C
IC I B
Collector power dissipation PC (mW)
200
Collector current IC (mA)
10˚1.1+0来自2 –0.11.1+0.3 –0.1
1: Base 2: Emitter 3: Collector EIAJ: SC-59 Mini3-G1 Package
Marking Symbol: 7M
■ Electrical Characteristics Ta = 25°C ± 3°C
Parameter Collector-base voltage (Emitter open) Collector-emitter voltage (Base open) Emitter-base voltage (Collector open) Collector-base cutoff current (Emitter open) Collector-emitter cutoff current (Base open) Forward current transfer ratio Collector-emitter saturation voltage Collector output capacitance (Common base, input open circuited) Transition frequency Symbol VCBO VCEO VEBO ICBO ICEO hFE VCE(sat) Cob fT Conditions IC = 10 µΑ, IE = 0 IC = 2 mA, IB = 0 IE = 10 µΑ, IC = 0 VCB = 20 V, IE = 0 VCE = 10 V, IB = 0 VCE = 10 V, IC = 2 mA IC = 100 mA, IB = 10 mA VCB = 10 V, IE = 0, f = 1 MHz VCB = 10 V, IE = −2 mA, f = 200 MHz 160 0.1 2.2 100 Min 60 50 7 0.1 100 460 0.3 Typ Max Unit V V V µA µA V pF MHz
BZX84C56中文资料
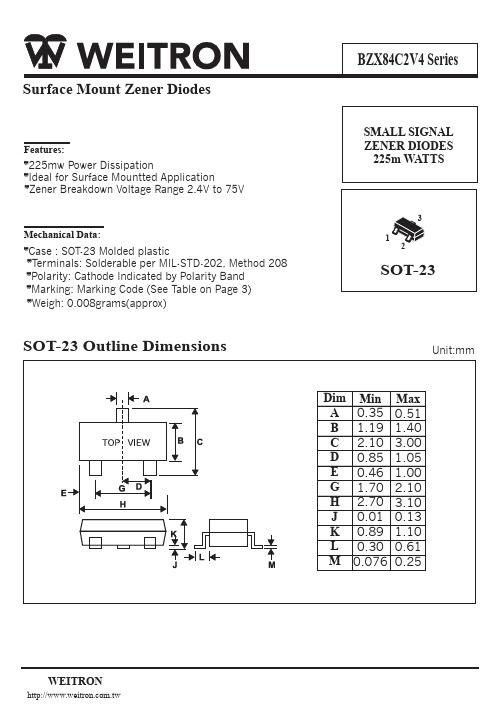
1
2
SOT-23
SOT-23 Outline Dimensions
Dim A B C D E G H J K L M Min 0.35 1.19 2.10 0.85 0.46 1.70 2.70 0.01 0.89 0.30 0.076 Max 0.51 1.40 3.00 1.05 1.00 2.10 3.10 0.13 1.10 0.61 0.25
7 8 8 8 10.5 11.2 12.6 14 15.4 16.8
4.5 5.4 6.0 7.0 9.2 10.4 12.4 14.4 16.4 18.4
VZ
8.0 9.0 10.0 11.0 13.0 14.0 16.0 18.0 20.0 22.0
130 130 130 120 110 105 100 85 85 80
Z ZT 1 B elow @ I ZT 1 = 2mA 80 80 80 90 130 150 170 180 200 215 240 255
V Z2 B elow @ I ZT 2 = 0.1 mA Min 25 27.8 30.8 33.8 36.7 39.7 43.7 47.6 51.5 57.4 63.4 69.4 Max 28.9 32 35 38 41 46 50 54 60 66 72 79
Z ZT 2 B elow @ I ZT 4 = 0.5mA 300 300 325 350 350 375 375 400 425 450 475 500
V Z3 B elow @ I ZT 3 = 10 mA Min 25.2 28.1 31.1 34.1 37.1 40.1 44.1 48.1 52.1 58.2 64.2 70.3 Max 29.3 32.4 35.4 38.4 41.5 46.5 50.5 54.6 60.8 67 73.2 80.2
施耐德Modicon M258可编程控制器产品目录
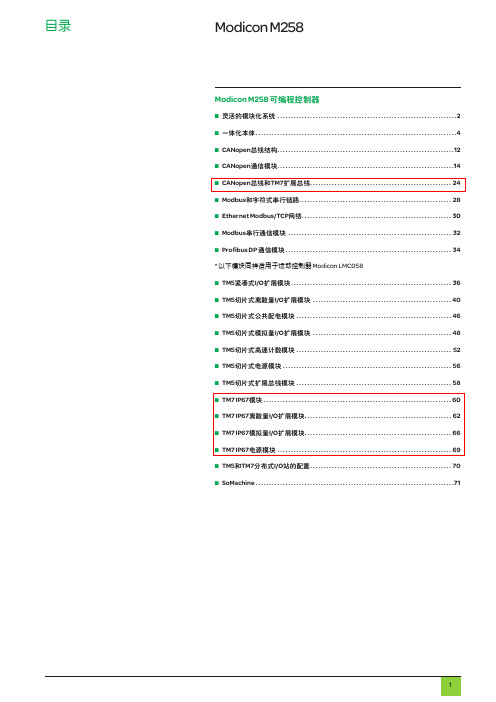
M258 可编程控制器都标配 4 路电压或电流模拟量输入 (12 位分辨率)。
<பைடு நூலகம்温度控制
此外还提供2、4或6通道以及12或16位不同分辨分辨率的扩展模块。 M258可编程控制器性能强大,能够连接多达200个模拟量I/O和/或温度模块,从而减
2
少了对设备需求的限制。
模拟量控制功能
< 速度控制
最多8通道高速 计数
软件组态
所有 M258
置和编程功能旨在降低成本和优化设备性能。
SoMachine 软件支持六种 IEC 61131-3 编程语言: v IL (指令表) v LD (梯形图) v SFC (顺序功能块) v ST (结构文本) v FBD (功能块图) v CFC (连续功能图)
另外还支持 PLCopen 功能块,以管理设备的运动控制和轴控制。
4个控制器状态ledrunmsbatteryapp0app16个内置通信端口状态ledethlaethstethnsusbhostmbscomcansts用于在5对称导轨上安装卸载的锁扣两个用于通信模块的pci闲置插槽带有可插拔接线端子和锁扣显示块和标签插槽的24电源模块io模块每个模块都具有带锁扣的可插拔接线端子显示io状态的显示块和标签夹持器插槽带上锁解锁功能的锁扣的可插拔接线端子在侧面用于连接下一个模块的总线扩展连接器rtc实时时钟电池插槽连接usb存储卡用于传输程序数据或固件更新的usba连接器标记为host用于连接编程计算机的usbb微型连接器标记为pgrport用于连接以太网和或magelisxbtgt图形终端的rj45连接器标记为ethernet用于连接rs232或rs485串行链路的rj45连接器标记为mbs9芯subd公头连接器标记为can0用于连接canopen总线仅限tm258lf42dt4ltm258lf42drtm258lf66dt4l1011
V23848-N305-C56资料
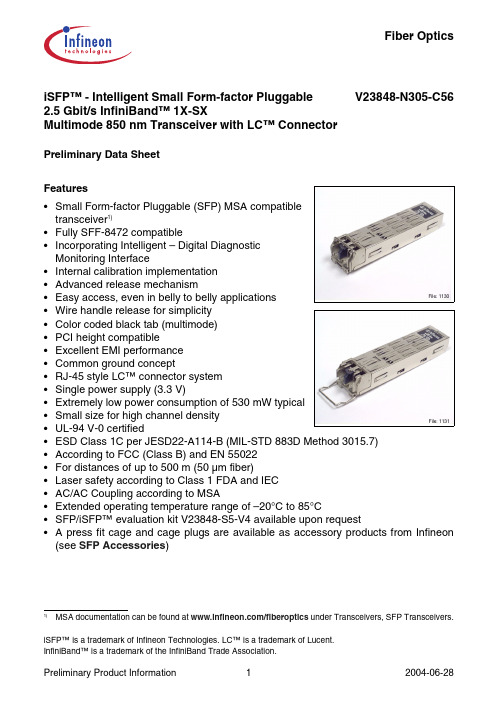
iSFP™ - Intelligent Small Form-factor Pluggable 2.5 Gbit/s InfiniBand™ 1X-SXMultimode 850 nm Transceiver with LC™ ConnectorPreliminary Data Sheet File: 1130File: 1131Fiber OpticsiSFP™ is a trademark of Infineon Technologies. LC™ is a trademark of Lucent.InfiniBand™ is a trademark of the InfiniBand Trade Association.V23848-N305-C56Features•Small Form-factor Pluggable (SFP) MSA compatible transceiver 1)•Fully SFF-8472 compatible•Incorporating Intelligent – Digital Diagnostic Monitoring Interface•Internal calibration implementation •Advanced release mechanism•Easy access, even in belly to belly applications •Wire handle release for simplicity •Color coded black tab (multimode)•PCI height compatible•Excellent EMI performance •Common ground concept•RJ-45 style LC™ connector system •Single power supply (3.3 V)•Extremely low power consumption of 530 mW typical •Small size for high channel density •UL-94 V-0 certified•ESD Class 1C per JESD22-A114-B (MIL-STD 883D Method 3015.7)•According to FCC (Class B) and EN 55022•For distances of up to 500 m (50 µm fiber)•Laser safety according to Class 1 FDA and IEC •AC/AC Coupling according to MSA•Extended operating temperature range of –20°C to 85°C•SFP/iSFP™ evaluation kit V23848-S5-V4 available upon request• A press fit cage and cage plugs are available as accessory products from Infineon (see SFP Accessories )1)MSA documentation can be found at /fiberoptics under Transceivers, SFP Transceivers.Pin ConfigurationFigure1iSFP™ Transceiver Electrical Pad LayoutPin DescriptionPin Logic Level Function1V EE T N/A Transmitter Ground1)2Tx Fault LVTTL Transmitter Fault Indication2)8)3Tx Disable LVTTL Transmitter Disable3)4MOD-DEF(2)LVTTL Module Definition 24)8)5MOD-DEF(1)LVTTL Module Definition 15)8)6MOD-DEF(0)N/A Module Definition 06)8)7Rate Select N/A Not connected8LOS LVTTL Loss Of Signal7)8)9V EE R N/A Receiver Ground1)10V EE R N/A Receiver Ground1)11V EE R N/A Receiver Ground1)12RD–LVPECL Inv. Received Data Out9)13RD+LVPECL Received Data Out9)14V EE R N/A Receiver Ground1)15V CC R N/A Receiver Power16V CC T N/A Transmitter Power17V EE T N/A Transmitter Ground1)18TD+LVPECL Transmit Data In10)19TD–LVPECL Inv. Transmit Data In10)20V EE T N/A Transmitter Ground1)1)Common transmitter and receiver ground within the module.2) A high signal indicates a laser fault of some kind and that laser is switched off.3) A low signal switches the transmitter on. A high signal or when not connected switches the transmitter off.4)MOD-DEF(2) is the data line of two wire serial interface for serial ID.5)MOD-DEF(1) is the clock line of two wire serial interface for serial ID.6)MOD-DEF(0) is grounded by the module to indicate that the module is present.7) A low signal indicates normal operation, light is present at receiver input. A high signal indicates the receivedoptical power is below the worst case receiver sensitivity.8)Should be pulled up on host board to V CC by 4.7 - 10 kΩ.9)AC coupled inside the transceiver. Must be terminated with 100 Ω differential at the user SERDES.10)AC coupled and 100 Ω differential termination inside the transceiver.DescriptionThe Infineon pluggable multimode transceiver – part of Infineon iSFP™ family – is designed for applications with data rates up to 2.5 Gbit/s and compatible to InfiniBand™1X-SX (IB-1X-SX) Release 1.1.The appropriate fiber optic cable is 62.5 µm or 50 µm multimode fiber with LC™connector.The Infineon iSFP™ multimode transceiver is a single unit comprised of a transmitter, a receiver, and an LC™ receptacle.This transceiver supports the LC™ connectorization concept. It is compatible with RJ-45style backpanels for high end datacom and telecom applications while providing the advantages of fiber optic technology.This module is designed for 2.5 Gbit/s and InfiniBand™ applications. It can be used as the network end device interface in mainframes, workstations, servers, and storage devices, and in a broad range of network devices such as bridges, routers, hubs, and local and wide area switches.This transceiver operates at 2.5 Gbit/s from a single power supply (+3.3 V). The 100 Ωdifferential data inputs and outputs are LVPECL and CML compatible.Link Length Fiber TypeReachUnitmin.1)1) A 0 m link length (loop-back connector) is supported.max.2)2)Longer reach possible depending upon link implementation.at 2.5 Gbit/s 50 µm, 500 MHz*km 2250meters50 µm, 2000 MHz*km 250062.5 µm, 200 MHz*km2125Functional Description of iSFP™ TransceiverThis transceiver is designed to transmit serial data via multimode cable.Figure2Functional DiagramThe receiver component converts the optical serial data into CML compatible electrical data (RD+ and RD–). The Loss Of Signal (LOS) shows whether an optical signal is present.The transmitter converts CML compatible electrical serial data (TD+ and TD–) into optical serial data. Data lines are differentially 100 Ω terminated.The transmitter contains a laser driver circuit that drives the modulation and bias current of the laser diode. The currents are controlled by a power control circuit to guarantee constant output power of the laser over temperature and aging. The power control uses the output of the monitor PIN diode (mechanically built into the laser coupling unit) as a controlling signal, to prevent the laser power from exceeding the operating limits. Single fault condition is ensured by means of an integrated automatic shutdown circuit that disables the laser when it detects laser fault to guarantee the laser Eye Safety. The transceiver contains a supervisory circuit to control the power supply. This circuit makes an internal reset signal whenever the supply voltage drops below the reset threshold. It keeps the reset signal active for at least 140 milliseconds after the voltage has risen above the reset threshold. During this time the laser is inactive.A low signal on TxDis enables transmitter. If TxDis is high or not connected the transmitter is disabled.An enhanced Digital Diagnostic Monitoring Interface (Intelligent) has been incorporated into the Infineon Small Form-factor Pluggable (SFP) transceiver. This allows real time access to transceiver operating parameters, based on the SFF-8472.This transceiver features Internal Calibration. Measurements are calibrated over operating temperature and voltage and must be interpreted as defined in SFF-8472. The transceiver generates this diagnostic data by digitization of internal analog signals monitored by a new diagnostic Integrated Circuit (IC).This diagnostic IC has inbuilt sensors to include alarm and warning thresholds. These threshold values are set during device manufacture and therefore allow the user to determine when a particular value is outside of its operating range.Alarm and Warning Flags are given. Alarm Flags indicate conditions likely to be associated with an inoperational link and cause for immediate action. Warning Flags indicate conditions outside the normally guaranteed bounds but not necessarily causes of immediate link failures.These enhanced features are in addition to the existing SFP features provided by the manufacturer i.e. serial number and other vendor specific data.The serial ID interface defines a 256 byte memory map in EEPROM, accessible over a 2 wire, serial interface at the 8 bit address 1010000X (A0h).The Digital Diagnostic Monitoring Interface makes use of the 8 bit address 1010001X (A2h), so the originally defined serial ID memory map remains unchanged and is therefore backward compatible.Digital Diagnostic Monitoring ParametersParameter Accuracy SFF-8472Accuracy Actual Tx Optical Power±3 dB±1 dBRx Optical Power±3 dB±3 dBBias Current±10%±10%Power Supply Voltage±3%±3% Transceiver Temperature±3°C±3°CRegulatory Compliance (EMI)compliance of the concerned product. As a consequence thereof this could void the user’s authority to operate the equipment.Technical DataExceeding any one of these values may permanently destroy the device.Absolute Maximum Ratings Parameter Symbol Limit Values Unit min.max.Data Input VoltageV ID max V CC +0.5V Differential Data Input Voltage Swing V ID pk-pk 5V Storage Ambient Temperature T S –4085°C Operating Case Temperature 1)1)Operating case temperature measured at transceiver reference point (in cage through 2nd centre hole from rear, see Figure 9).T C–2085°C Storage Relative Humidity RH s 595%Operating Relative Humidity RH o585%Supply Voltage V CC max 4V Data Output Current I data50mA Receiver Optical Input PowerRx P max3dBmElectrical Characteristics (V CC = 2.97 V to 3.63 V, T C = –20°C to 85°C) Parameter Symbol Values Unitmin.typ.max. CommonSupply Voltage V CC–V EE 2.97 3.3 3.63VIn-rush Current1)I IR max30mA Power Dissipation P400700mW TransmitterDifferential Data Input Voltage Swing2)VIDpk-pk5003200mVTx Disable Voltage Tx Dis2V CC V Tx Enable Voltage Tx En V EE0.8V Tx Fault High Voltage Tx FH 2.4V CC VTx Fault Low Voltage TxFL VEE0.5VSupply Current3)I Tx100150mA ReceiverDifferential Data Output Voltage Swing4)VODpk-pk5001000mVLOS Active LOS A 2.4V CC VLOS Normal LOS N V EE0.5VRise Time5)t R-Rx100psFall Time5)t F-Rx100ps Contributed Deterministic Jitter6)CDJRx40ps Contributed Total Jitter7)CTJ Rx117ps Jitter (pk-pk)8)J Rx ps Power Supply Noise Rejection9)PSNR100mV pp Supply Current3)10)I Rx8090mA1)Measured with MSA recommended supply filter network (Figure7). Maximum value above that of the steadystate value.2)Internally AC coupled. Typical 100 Ω differential input impedance.3)MSA defines maximum current at 300 mA.4)Internally AC coupled. Load 50Ω to GND or 100Ω differential. For dynamic measurement a tolerance of50mV should be added.5)Measured values are 20% - 80%.6)Deterministic Jitter is that jitter measured by a bathtub scan, using a 27–1 NRZ PRBS, and extrapolating to1BER.7)Total Jitter is that jitter measured by a bathtub scan, using a 27–1 NRZ PRBS, and extrapolating to 1x10–12 BER.8)Jitter (pk-pk) is measured using a 223–1 NRZ PRBS and a Digital Communications Analyzer.9)Measured using a 20 Hz to 1 MHz sinusoidal modulation with the MSA recommended power supply filternetwork (Figure7) in place. A change in sensitivity of less than 1 dB can be typically expected.10)Supply current excluding Rx output load.Optical Characteristics (V CC = 2.97 V to 3.63 V, T C = –20°C to 85°C)Parameter Symbol Values Unitmin.typ.max.TransmitterOptical Modulation Amplitude OMA T196µW Launched Power (Average)1)P O–8.5–6–4dBm Extinction Ratio (Dynamic)ER914.5dB830850860nm Center WavelengthλCSpectral Width (rms)σI0.150.85nm Relative Intensity Noise RIN–117dB/Hz Tx Disable Laser Output Power P O-TxDis–50dBm Contributed Deterministic Jitter2)CDJ Tx52ps Contributed Total Jitter3)CTJ Tx122psps Jitter (pk-pk)4)JTxRise Time5)t R-Tx150psFall Time5)t F-Tx150ps Receiver6)50µW Optical Modulation Amplitude OMARSensitivity (Average Power)7)P IN–16dBm Average Received Power P IN-R–1.5dBm LOS Assert Level8)P LOSA–30–28dBm LOS Deassert Level8)P LOSD–25–20dBm LOS Hysteresis8)P LOSA12dB–P LOSDInput Center WavelengthλC770850860nm Optical Return Loss ORL12dB1)Into multimode fiber, 62.5 µm or 50 µm diameter.2)Deterministic Jitter is that jitter measured by a bathtub scan, using a 27–1 NRZ PRBS, and extrapolating to1BER.3)Total Jitter is that jitter measured by a bathtub scan, using a 27–1 NRZ PRBS, and extrapolating to 1x10–12 BER.4)Jitter (pk-pk) is measured using a 223–1 NRZ PRBS and a Digital Communications Analyzer.5)Values are 20% - 80%. Measured at nominal data rate, unfiltered, using an O/E plug-in with a bandwidth of2.85 GHz or higher.6)Receiver characteristics are measured with a worst case reference laser.7)Average optical power at which the BER is 1x10–12. Measured with a 223–1 NRZ PRBS and ER = 9 dB.8)See Figure3.Figure3Timing of Control and Status I/OParameter Symbol Values Unit Conditionmin.max.Tx Disable Assert Time t_off10µs Time from rising edge of TxDisable to when the opticaloutput falls below 10% ofnominalTx Disable Negate Time t_on1ms Time from falling edge of TxDisable to when the modulatedoptical output rises above 90%of nominalTime to Initialize, Including Reset of Tx Fault t_init300ms From power on or negation ofTx Fault using Tx DisableTx Fault AssertTimet_fault100µs Time from fault to Tx Fault onTx Disable to Reset t_reset10µs Time Tx Disable must be heldhigh to reset Tx FaultLOS Assert Time t_loss_on100µs Time from LOS state to RxLOS assertLOS Deassert Time t_loss_off100µs Time from non-LOS state to RxLOS deassertI/O Timing of Soft Control and Status FunctionsParameter Symbol Max.ValueUnit ConditionTx Disable assert time t_off100ms Time from Tx Disable bit set1)until optical output falls below10% of nominalTx Disable deassert time t_on100ms Time from Tx Disable bitcleared until optical outputrises above 90% of nominalTime to initialize, including reset of Tx Fault t_init300ms Time from power on ornegation of Tx Fault usingTx Disable until transmitteroutput is stable2)Tx Fault assert time t_fault100ms Time from fault to Tx Fault bitsetLOS assert time t_loss_on100ms Time from LOS state toRx LOS bit setLOS deassert time t_loss_off100ms Time from non-LOS state toRx LOS bit clearedRate select change time3)t_rate_sel100ms Time from change of state ofRate Select bit1) until receiverbandwidth is in conformancewith appropriate specificationSerial ID clock rate4)f_serial_clock400kHz N/AAnalog parameter data ready t_data1000ms From power on to data ready,bit 0 of byte 110 setSerial bus hardware ready t_serial300ms Time from power on untilmodule is ready for datatransmission1)Measured from falling clock edge after stop bit of write transaction.2)See Gigabit Interface Converter (GBIC). SFF-0053, Rev. 5.5, September 27, 2000.3)Not implemented.4)The maximum clock rate of the serial interface is defined by the I2C bus interface standard.Eye SafetyEye SafetyThis laser based multimode transceiver is a Class 1 product. It complies with IEC 60825-1/A2: 2001 and FDA performance standards for laser products (21 CFR 1040.10and 1040.11) except for deviations pursuant to Laser Notice 50, dated July 26, 2001.CLASS 1 LASER PRODUCTTo meet laser safety requirements the transceiver shall be operated within the Absolute Maximum Ratings.Note:All adjustments have been made at the factory prior to shipment of the devices.No maintenance or alteration to the device is required.Tampering with or modifying the performance of the device will result in voided product warranty.Failure to adhere to the above restrictions could result in a modification that is considered an act of “manufacturing”, and will require, under law, recertification of the modified product with the U.S. Food and Drug Administration (ref. 21 CFR1040.10 (i)).Figure 4Required LabelsFigure 5Laser EmissionLaser Emission Data Wavelength850 nmMaximum total output power(as defined by IEC: 7mm aperture at 14mm distance)709 µW / –1.5 dBm Beam divergence (full angle) / NA (half angle)20° / 0.18 radApplication NotesEMI RecommendationsTo avoid electromagnetic radiation exceeding the required limits set by the standards, please take note of the following recommendations.When Gigabit switching components are found on a PCB (e.g. multiplexer, serializer-deserializer, clock data recovery, etc.), any opening of the chassis may leak radiation; this may also occur at chassis slots other than that of the device itself. Thus every mechanical opening or aperture should be as small as feasible and its length carefully considered.On the board itself, every data connection should be an impedance matched line (e.g. strip line or coplanar strip line). Data (D) and Data-not (Dn) should be routed symmetrically. Vias should be avoided. Where internal termination inside an IC or a transceiver is not present, a line terminating resistor must be provided. The decision of how best to establish a ground depends on many boundary conditions. This decision may turn out to be critical for achieving lowest EMI performance. At RF frequencies the ground plane will always carry some amount of RF noise. Thus the ground and V CC planes are often major radiators inside an enclosure. As a general rule, for small systems such as PCI cards placed inside poorly shielded enclosures, the common ground scheme has often proven to be most effective in reducing RF emissions. In a common ground scheme, the PCI card becomes more equipotential with the chassis ground. As a result, the overall radiation will decrease. In a common ground scheme, it is strongly recommended to provide a proper contact between signal ground and chassis ground at every location where possible. This concept is designed to avoid hotspots which are places of highest radiation, caused when only a few connections between chassis and signal grounds exist. Compensation currents would concentrate at these connections, causing radiation. However, as signal ground may be the main cause for parasitic radiation, connecting chassis ground and signal ground at the wrong place may result in enhanced RF emissions.For example, connecting chassis ground and signal ground at a front panel/bezel/chassis by means of a fiber optic transceiver/cage may result in a large amount of radiation especially where combined with an inadequate number of grounding points between signal ground and chassis ground. Thus the transceiver becomes a single contact point increasing radiation emissions. Even a capacitive coupling between signal ground and chassis ground may be harmful if it is too close to an opening or an aperture. For a number of systems, enforcing a strict separation of signal ground from chassis ground may be advantageous, providing the housing does not present any slots or other discontinuities. This separate ground concept seems to be more suitable in large systems where appropriate shielding measures have also been implemented. The return path of RF current must also be considered. Thus a split ground plane between Tx and Rx paths may result in severe EMI problems.The bezel opening for a transceiver should be sized so that all contact springs of the transceiver cage make good electrical contact with the face plate. Please consider that the PCB may behave like a dielectric waveguide. With a dielectric constant of 4, the wavelength of the harmonics inside the PCB will be half of that in free space. Thus even the smallest PCBs may have unexpected resonances.Large systems can have many openings in the front panel for SFP transceivers. In typical applications, not all of these ports will hold transceivers; some may be intentionally left empty. These empty slots may emit significant amounts of radiation.Thus it is recommended that empty ports be plugged with an EMI plug as shown in Figure 6. Infineon offers an EMI/dust plug, P/N V23818-S5-B1.SFP AccessoriesFigure 6Cage:Infineon TechnologiesPart Number: V23838-S5-N1/V23838-S5-N1-BB Cage EMI/Dust Plug:Infineon TechnologiesPart Number: V23818-S5-B1Host Board Connector:Tyco ElectronicsPart Number: 1367073-1Cage Dust Plug:Infineon TechnologiesPart Number: V23818-S5-B2EEPROM Serial ID Memory Contents (A0h)Addr.Hex ASCII Name/Description Addr.Hex ASCII Name/Description 003Identifier3247G Vendor name104Extended identifier 336D m 207Connector3462b 308Transceiver optical compatibility3548H4003600Reserved 5003700Vendor OUI 600380370039198004056V Vendor part number900413221000423331101Encoding 433881219BR, nominal 443441300Reserved453881400Length (9 µm) - km 462D -1500Length (9 µm)474E N 1619Length (50 µm)48333170C Length (62.5 µm)493001800Length (copper)503551900Reserved 512D -2049I Vendor name 5243C 216E n 533552266f 543662369i 5520246E n 5641A Vendor revision, product status dependent 2565e 57344266F o 5841A 276E n 5939928206003Wavelength 2946F 6152304F O6200Reserved 3120638BCheck sum of bytes 0 - 626400Transceiver signaloptions 9620Vendor specificEEPROM651A9720 6600BR, maximum9820 6700BR, minimum9920 68Vendor serial number10020 6910120 7010220 7110320 7210420 7310520 7410620 7510720 762010820 772010920 782011020 792011120 802011220 812011320 822011420 83201152084Vendor manufacturingdate code 116208511720 8611820 8711920 8812020 8912120 902012220 912012320 9268Diagnostic monitoringtype12420 93B0Enhanced options12520 9401SFF-8472 compliance1262095Low order 8 bits of thesum of the contents ofall the bytes from byte64 to byte 94, inclusive 12720128 -25500Vendor specific.Reserved for futureuseEEPROM Serial ID Memory Contents (A0h) (cont’d)Addr.Hex ASCII Name/Description Addr.Hex ASCII Name/DescriptionDigital Diagnostic Monitoring Interface – IntelligentAlarm and Warning Thresholds (2-Wire Address A2h)Address# Bytes Name Description Value00 - 012Temp High Alarm MSB at low address95°C1)02 - 032Temp Low Alarm MSB at low address–20°C1)04 - 052Temp High Warning MSB at low address90°C1)06 - 072Temp Low Warning MSB at low address–15°C1)08 - 092Voltage High Alarm MSB at low address 3.7 V2)10 - 112Voltage Low Alarm MSB at low address 2.85 V2)12 - 132Voltage High Warning MSB at low address 3.63 V2)14 - 152Voltage Low Warning MSB at low address 2.97 V2)16 - 172Bias High Alarm MSB at low address20 mA18 - 192Bias Low Alarm MSB at low address 3.1 mA20 - 212Bias High Warning MSB at low address14.8 mA22 - 232Bias Low Warning MSB at low address 4.6 mA24 - 252Tx Power High Alarm MSB at low address–3 dBm26 - 272Tx Power Low Alarm MSB at low address–9.5 dBm 28 - 292Tx Power High Warning MSB at low address–4 dBm30 - 312Tx Power Low Warning MSB at low address–8.5 dBm 32 - 332Rx Power High Alarm MSB at low address–3.5 dBm 34 - 352Rx Power Low Alarm MSB at low address–17 dBm36 - 372Rx Power High Warning MSB at low address–4 dBm38 - 392Rx Power Low Warning MSB at low address–15 dBm40 - 5516Reserved Reserved for futuremonitored quantities1) A delta exists between actual transceiver temperature and value shown as measurement is taken internal toan IC located on the underside of the iSFP™ PCB.2)Transceiver voltage measured after input filter with typical 0.1 V voltage drop.Calibration Constants for External Calibration Option (2-Wire Address A2h) Address# Bytes Name Description Value56 - 594Rx_PWR (4)Single precision floating pointcalibration data, Rx optical power.060 - 634Rx_PWR (3)0 64 - 674Rx_PWR (2)0 68 - 714Rx_PWR (1)1 72 - 754Rx_PWR (0)0 76 - 772Tx_I(Slope)Fixed decimal (unsigned)calibration data, laser bias current.178 - 792Tx_I (Offset)Fixed decimal (signed two’scomplement) calibration data,laser bias current.80 - 812Tx_PWR (Slope)Fixed decimal (unsigned)calibration data, transmittercoupled output power.182 - 832Tx_PWR (Offset)Fixed decimal (signed two’scomplement) calibration data,transmitter coupled output power.84 - 852T (Slope)Fixed decimal (unsigned)calibration data, internal moduletemperature.186 - 872T (Offset)Fixed decimal (signed two’scomplement) calibration data,internal module temperature.88 - 892V (Slope)Fixed decimal (unsigned)calibration data, internal modulesupply voltage.190 - 912V (Offset)Fixed decimal (signed two’scomplement) calibration data,internal module supply voltage.92 - 943Reserved Reserved951Check sum Byte 95 contains the low order8bits of the sum of bytes 0 - 94.A/D Values and Status Bits (2-Wire Address A2h)Byte Bit Name DescriptionConverted Analog Values. Calibrated 16 Bit Data.96All Temperature MSB Internally measured moduletemperature1)97All Temperature LSB98All V CC MSB Internally measured supply voltagein transceiver99All V CC LSB100All Tx Bias MSB Internally measured Tx Bias Current 101All Tx Bias LSB102All Tx Power MSB Measured Tx output power103All Tx Power LSB104All Rx Power MSB Measured Rx input power105All Rx Power LSB106All Reserved MSB Reserved for 1st future definition ofdigitized analog input107All Reserved LSB Reserved for 1st future definition ofdigitized analog input108All Reserved MSB Reserved for 2nd future definition ofdigitized analog input109All Reserved LSB Reserved for 2nd future definition ofdigitized analog inputOptional Status/Control Bits1107Tx Disable State2)Digital state of the Tx Disable InputPin1106Soft Tx Disable2)Read/write bit that allows softwaredisable of laser. Writing 1 disableslaser1105Reserved1104Rx Rate Select State2)Digital state of the SFP Rx RateSelect Input Pin1103Soft Rx Rate Select2)Read/write bit that allows softwareRx rate select. Writing 1 selects fullbandwidth operation. Notimplemented.A/D Values and Status Bits (2-Wire Address A2h) (cont’d)Byte Bit Name Description1102Tx Fault Digital state of the Tx Fault OutputPin1101LOS Digital state of the LOS Output Pin 1100Data_Ready_Bar Indicates transceiver has achievedpower up and data is ready1117 - 0Reserved Reserved1)Temperature measurement is performed on an IC located on the underside of the iSFP™ PCB.2)Not implemented.Alarm and Warning Flags (2-Wire Address A2h)Byte Bit Name Description1127Temp High Alarm Set when internal temperatureexceeds high alarm level1126Temp Low Alarm Set when internal temperature isbelow low alarm level1125V CC High Alarm Set when internal supply voltageexceeds high alarm level1124V CC Low Alarm Set when internal supply voltage isbelow low alarm level1123Tx Bias High Alarm Set when Tx Bias current exceedshigh alarm level1122Tx Bias Low Alarm Set when Tx Bias current is belowlow alarm level1121Tx Power High Alarm Set when Tx output power exceedshigh alarm level1120Tx Power Low Alarm Set when Tx output power is belowlow alarm level1137Rx Power High Alarm Set when received power exceedshigh alarm level1136Rx Power Low Alarm Set when received power is belowlow alarm level1135Reserved Alarm1134Reserved Alarm1133Reserved Alarm1132Reserved Alarm1131Reserved Alarm1130Reserved Alarm114All Reserved115All Reserved1167Temp High Warning Set when internal temperatureexceeds high warning level1166Temp Low Warning Set when internal temperature isbelow low warning level1165V CC High Warning Set when internal supply voltageexceeds high warning levelAlarm and Warning Flags (2-Wire Address A2h) (cont’d)Byte Bit Name Description1164V CC Low Warning Set when internal supply voltage isbelow low warning level1163Tx Bias High Warning Set when Tx bias current exceedshigh warning level1162Tx Bias Low Warning Set when Tx bias current is belowlow warning level1161Tx Power High Warning Set when Tx output power exceedshigh warning level1160Tx Power Low Warning Set when Tx output power is belowlow warning level1177Rx Power High Warning Set when received power exceedshigh warning level1176Rx Power Low Warning Set when received power is belowlow warning level1175Reserved Warning1174Reserved Warning1173Reserved Warning1172Reserved Warning1171Reserved Warning1170Reserved Warning118All Reserved119All ReservedVendor Specific Memory Addresses (2-Wire Address A2h)Address# Bytes Name Description120 -1278Vendor Specific Vendor specificUser EEPROM (2-Wire Address A2h)Address# Bytes Name Description128 - 247120User EEPROM User writable EEPROM248 - 2558Vendor Specific Vendor specific control functions。
880 870螺纹钢管诊断仪说明书
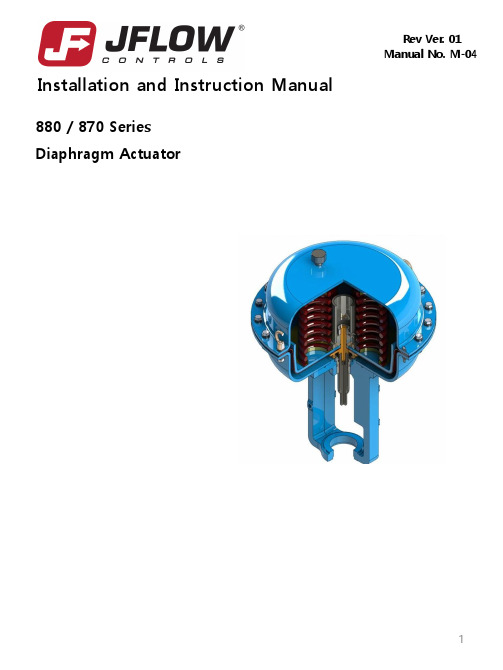
Installation & Instruction Manual
Safety Information
Important – Please Read Before Installation
J Flow Controls 880 / 870 Series Diaphragm Actuator instructions contain Danger, Warning and Caution labels, where necessary, to alert you to safety related or other important information. Read the instructions carefully before installing and maintaining your control valve. Danger and Warning hazards are related to personal injury. Caution hazards involve equipment or property damage. Operation of damaged equipment can, under certain operational conditions, result in degraded process system performance that can read to injury or death. Total compliance with all Danger, Warning and Caution notices is required for safe operation. The safety terms Danger, Warning, Caution and Note have used in these instructions to highlight particular dangers and/or to provide additional information on aspects that may not be readily apparent.
V23816-N1018-C312资料
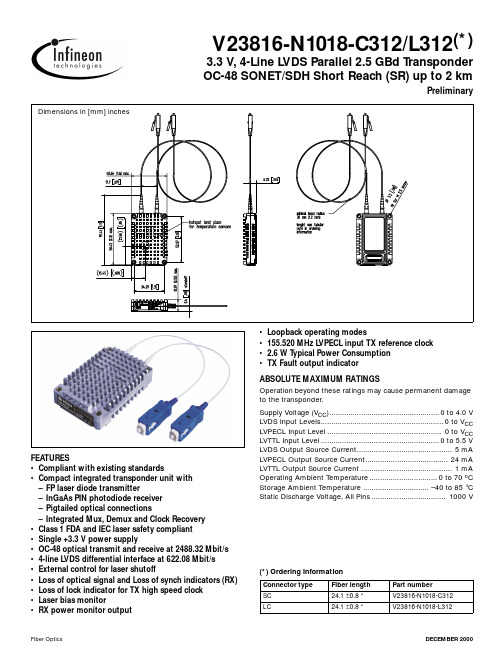
V23816-N1018-C312/L312(*)3.3 V, 4-Line L VDS Parallel 2.5 GBd T ransponderOC-48 SONET/SDH Short Reach (SR) up to 2 kmPreliminaryFEATURES•Compliant with existing standards•Compact integrated transponder unit with– FP laser diode transmitter– InGaAs PIN photodiode receiver– Pigtailed optical connections– Integrated Mux, Demux and Clock Recovery•Class 1 FDA and IEC laser safety compliant•Single +3.3 V power supply•OC-48 optical transmit and receive at 2488.32 Mbit/s•4-line L VDS differential interface at 622.08 Mbit/s•External control for laser shutoff•Loss of optical signal and Loss of synch indicators (RX)•Loss of lock indicator for TX high speed clock•Laser bias monitor•RX power monitor output•Loopback operating modes•155.520 MHz L VPECL input TX reference clock•2.6 W T ypical Power Consumption•TX Fault output indicatorABSOLUTE MAXIMUM RATINGSOperation beyond these ratings may cause permanent damageto the transponder.Supply Voltage (V CC)....................................................0 to 4.0 VLVDS Input Levels..........................................................0 to V CCLVPECL Input Level...................................................... 0 to V CCLVTTL Input Level........................................................0 to 5.5 VLVDS Output Source Current............................................. 5 mALVPECL Output Source Current....................................... 24 mALVTTL Output Source Current........................................... 1 mAOperating Ambient Temperature................................0 to 70 o CStorage Ambient Temperature............................... –40 to 85 °CStatic Discharge Voltage, All Pins................................... 1000 V(*) Ordering InformationConnector type Fiber length Part numberSC24.1 ±0.8 “V23816-N1018-C312LC24.1 ±0.8 “V23816-N1018-L312DESCRIPTIONThe Infineon single mode SONET/SDH transponder is compli-ant with the Bellcore GR-253, ITU-T G.957, and ITU-T G.958 specifications. It is also compliant with the OIF99.102 proposal. The transmitter section consists of a multiplexer (Mux), laser driver, Fabry Perot (FP) laser diode and pigtail single mode fiber with LC/PC or SC/PC 0 ° termination. The receiver section consists of a multimode fiber pigtail with LC/PC or SC/PC termi-nation, a packaged PIN photodiode and preamplifier, postampli-fier, clock and data recovery (CDR), and a demultiplexer (Demux). The Mux and Demux functions are integrated together onto a single Transceiver IC. The 622.08 MHz parallel data interface frees the user from the concerns of pcb layout at 2.5 Gb/s. The pluggable connector blind mates easily to the customer pcb, and allows the transponder to be removed prior to any solder reflow or washing of the users pcb.The transponder operates from a single +3.3 V power supply. The electrical interface is via a 60 pin pluggable connector. The transmit and receive electrical signals each consist of 4 parallel differential LVDS data, and a differential LVDS clock. The trans-mit input data and clock lines, and the receive output data and clock lines, are all internally biased and terminated. All lines are DC coupled to the interface connector.The transponder is designed to transmit and receive serial OC-48 (2488.32 Mb/s) data over standard non-dispersion-shifted single mode fiber at a wavelength of 1310 nm.T ransmitter (Mux Section)Please refer to the transponder block diagram.The transmitter accepts a 4 bit wide parallel input data word, TXDATAP/N[3:0], at a 622.08 Mb/s data rate. The TX input clock, TXCLKP/N, is synchronous with the incoming data, at a fre-quency of 622.08 MHz. This clock is used to load the data into a 4-bit latch. The data is read in on the rising edge of the positive input clock. (See TX Input Timing Diagram).A reference input clock, REFCLKP/N, at 155.52 MHz, is sup-plied as a reference input to the high speed Clock Synthesizer. The high speed output of the clock synthesizer will clock the Timing Generator and the Parallel-to-Serial Converter. The Paral-lel-to-Serial Converter will output the retimed data as a serial bit stream, TSDP/N, at 2488.32 Mb/s data rate. Bit 3 of the TXDATAP/N parallel input word is the MSB, and is transmitted first in the data stream. Bit 0, the LSB, is transmitted last.The output of the high speed Clock Synthesizer, which is inter-nally set to 2488.32 MHz, is tapped off the Timing Generator, and is divided to 622.08 MHz. This output (PCLKP/N) is intended to be used as a reference clock for TX upstream logic. The PHASE_INITP/N input signal is used to realign the internal timing of the Timing Generator by resetting and centering the FIFO in the Transceiver IC. The realignment will occur on the ris-ing edge of PHASE_INITP, which must be held high for at least 10 ns.The PHASE_ERRP/N output will pulse high during each clock cycle when there is a potential set-up & hold timing violation between the internal byte clock and the TXCLKP/N input, indi-cating that PHASE_INITP/N must be strobed.If the Reference Clock input, REFCLKP/N, is derived from and is synchronous with the TX Byte Clock, TXCLKP/N, then there should never be any short setup and hold times between the two timing domains, and the FIFO should never need to be recentered. However, if the REFCLKP/N input is, for instance, produced by a free running oscillator, then such potential viola-tions may exist. When FIFO realignment occurs, up to 10 bytes of data will be lost. Automatic FIFO realignment can be enabled by simply connecting the PHASE_ERRP/N output directly to the PHASEINITP/N input. The user can also take the PHASE_ERRP/ N output, process it and send a signal to the PHASE_INITP/N in such a way that idle bytes are lost during the realignment pro-cess.The TX Clock Synthesizer section provides a lock alarm output signal, TXLOCK, which indicates if the clock synthesizer is prop-erly phase locked.T ransmitter (Electro-Optical Section)The serial data output, TSDP/N, of the Transceiver IC is input to a laser driver IC. The laser driver provides both bias and modula-tion to a laser diode. The laser bias current is controlled by a closed-loop circuit, which regulates the output average power of the laser over conditions of temperature and aging. The Mon-itor PIN diode, which is mechanically built into the laser, pro-vides a feedback signal to the laser driver, and prevents the laser power from exceeding the factory preset operating limits. The laser driver includes an eye safety feature that will automat-ically shut off power to the laser if a fault condition occurs which causes excessively high laser bias current or excessively high average output power. Such a fault will be indicated on the TX_FAULT output. The fault can be cleared by cycling DC power, or by strobing the RESET_L input.The Mux and Laser Driver can be reset with the RESET_L input. During the time that RESET_L is held active, there will be no optical output from the transmitter. The RESET_L input will clear any fault indication that has occurred on the TX_FAULT output.The laser can be switched off at any time with theLASER_DISABLE input.The TX_BIASMON output is provided as an alarm to indicate if the laser bias current is outside of the normal operating range. This output can be used to monitor the aging of the laser.The laser diode is a Fabry-Perot type, which, due to the cavity nature of its design, will emit light at several longitudinal wave-lengths, or modes centered about 1310 nm. This type of laser is suitable for the short reach transmission over single-mode fiber that this transponder is intended for. The laser has a single-mode fiber pigtail, which is terminated in an LC/PC 0 ° optical connector.Receiver (Electro-Optical Section)The input light to the RX is coupled from the transmission fiber into a PIN/Preamp assembly on the transponder. The PIN/ Preamp contains a multi-mode fiber pigtail, which is terminated in an LC/PC or SC/PC 0 ° optical connector. The multi-mode fiber pigtail has a larger core diameter (50 µm) than the single-mode transmission fiber (9 µm). Therefore, all the light from the single-mode fiber is coupled into the larger diameter core of the multi-mode pigtail.The PIN/Preamp contains a PIN photodiode, trans-impedance amplifier and non-limiting post-amplifier in one package. The PIN diode produces a current output, which is directly propor-tional to the intensity of the incoming light. The trans-imped-ance amplifier performs current-to-voltage conversion, and the non-limiting post-amplifier quantizes the signal into a digital out-put.The receiver contains a RX power monitor output, which is a voltage output directly proportional to the average optical input power.The Limiting Post-Amplifier provides additional voltage amplifi-cation, and also provides a Loss Of Signal (RX_LOS) indicator. LOS will occur at a RX input power level less than the specified RX Sensitivity, and is an indication that the RX is taking bit errors.The Clock and Data Recovery (CDR) uses a PLL based approach to recover the high speed clock from the incoming serial data stream. A lock alarm, RX_LOSYNC, indicates if the CDR has lost synchronization. This will occur if the input RX power level is very low (below the LOS threshold level), or if the input data rate is outside the specified frequency tolerance. In these cases, the CDR will phase lock to a Crystal Oscillator so it can produce a valid clock output, with a frequency accuracy of ±20 ppm. In both cases of Loss Of Signal or Loss Of Synchroniza-tion, the Transceiver IC will force all the RX output data bits, RXDATAP/N [3:0] to a constant zero state.Receiver (Demux section)The incoming serial data is latched into the Transceiver IC by the recovered clock. The data and clock are applied to a 4 bit wide Serial-to-Parallel Converter (Demux), which demultiplexes the data into a parallel format. The first bit received, i.e. the MSB which is transmitted first in the serial data stream, is placed into the highest order bit of the parallel output word, i.e. Bit 3 = MSB. The Transceiver IC, however, does not perform a frame alignment function. This means that the parallel output word will contain the bits in the correct order, however, the position of the bits within the parallel output word may be shifted by an arbitrary amount between 0 and 4 bits. It is the function of downstream framer logic to realign the bits.The retimed RX output data, RXDATAP/N[3:0], is output at a 622.08 Mb/s data rate. The output clock, RXCLKP/N, is at 622.08 MHz. The RXDATAP/N[3:0] data is updated on the falling edge of RXCLKP. (See RX Output Timing Diagram).Loopback OperationFour loopback modes of operation are provided.Line Loopback is enabled with the LLEB_L input. In Line Loop-back operation, the RX Serial Data and Clock inputs to the Transceiver IC (RSDP/N and RSCLKP/N) are routed directly to the TX Serial outputs of the IC (TSDP/N and TSCLKP/N). This effectively eliminates the Transceiver IC from the signal path. Diagnostic Loopback is enabled with the DLEB_L input. In Diag-nostic Loopback operation, the TX output Serial Data and Clock of the Transceiver IC (TSDP/N and TSCLKP/N) are routed directly to the RX Serial Data and Clock inputs of the IC (RSDP/ N and RSCLKP/N). This effectively eliminates the optical and electro-optical components from the signal path.Reference Loop Time is enabled with the RLPTIME input. In Reference Loop Time operation, a divide-by-4 version of the POCLKP/N output of the RX is used as the reference clock input to the TX. Serial Loop Time is enabled with the SLPTIME input. In Serial Loop Time operation, the recovered high-speed clock (RSCLKP/ N) from the RX section is used in place of the synthesized transmit clock.JitterThe transponder is specified to meet the Sonet Jitter perfor-mance as outlined in ITU-T G.958 and Bellcore GR-253.Jitter Generation is defined as the amount of jitter that is gener-ated by the transponder. The Jitter Generation specifications are referenced to the optical OC-48 signals. If no or minimum jitter is applied to the electrical inputs of the transmitter, then Jitter Generation can simply be defined as the amount of jitter on the TX Optical output. The Sonet specifications for Jitter Generation are 0.01 UI rms, maximum and 0.1 UI p-p, maxi-mum. Both are measured with a 12 KHz-20 MHz filter in line. A UI is a Unit Interval, which is equivalent to one bit slot. At OC-48, the bit slot is 400 ps, so the Jitter Generation specification translates to 4 ps rms, max. and 40 ps p-p, max.Jitter Tolerance is defined as the amount of jitter applied to the RX Optical input that the receiver will tolerate while producing less than a 1 dB penalty in RX Sensitivity. The minimum Jitter Tolerance levels are normally expressed as a mask of jitter amplitude versus jitter frequency. Measured Jitter Tolerance levels must be greater than the mask limits. The Jitter Toler-ance mask specified in the Bellcore GR-253 document covers jitter frequencies down to 10 Hz. The transponder will be designed to meet this mask.Sonet Jitter T ransfer Mask (ITU-T G.958 & Bellcore GR-253) Sonet Jitter T olerance Mask (Bellcore GR-253)Jitter Transfer is defined as the ratio of output jitter to input jit-ter. Referenced to an optical transponder, it is defined as the ratio of TX Optical Output Jitter to RX Optical Input Jitter. To measure Jitter Transfer, the transponder must be operating in electrical loopback mode, with the RX electrical outputs looped back into the TX electrical inputs. Jitter Transfer is defined to be less than 0.1 dB up to 2 MHz, then dropping at –20 dB decade thereafter, per ITU-T G.958 and Bellcore GR-253. The Jitter Transfer must be less than the following mask limits.Block DiagramFunctional Signal DescriptionT ransmit FunctionsSignal Name Level I/O Pin #DescriptionTXDATAP0 TXDATAN0 TXDATAP1 TXDATAN1 TXDATAP2 TXDATAN2 TXDATAP3 TXDATAN3LVDS I137913151921Transmit Parallel input dataat 622.08 Mb/s, aligned tothe TXCLKP/N parallel inputclock. TXDATAP/N[3] is themost significant bit (MSB),and is the first bit transmit-ted in the outgoing OC-48serial data stream. TX-DATAP/N[3:0] is sampledon the rising edge of TX-CLKP. DC coupled and in-ternally terminated.TXCLKP TXCLKN LVDS I2725Transmit Parallel inputclock, 622.08 MHz, towhich TXDATAP/N[3:0] isaligned. TXCLK transfersthe data on the TXDATAP/N inputs into a 4-bit widelatch in the Transceiver IC.Data is sampled on the ris-ing edge of TXCLKP. DCcoupled and internally ter-minated.REFCLKP REFCLKN LVPECL I3133155.52 MHz Transmit Ref-erence Clock input to thebit clock frequency synthe-sizer of the Transceiver IC.DC coupled and internallybiased.PHASE_INITPPHASE_INITNLVDS I3739Phase Initialization. Risingedge of PHASE_INITP willrealign internal timing. DCcoupled. No internal termi-nation.LASER_DISABLELVTTL I49Laser Disable. Control in-put to disable Transmit la-ser. High = Disable laser.Pulled low through 1 kΩ=resistor.TXLOCK LVTTL O51Loss Of Lock alarm for TXPLL of the Transceiver IC.High = Locked. Asynchro-nous output.PHASE_ERRPPHASE_ERRNLVDS O4543Phase Error. Active high.PHASE_ERRP will pulseshigh during each clock cy-cle for which there is a po-tential set-up and holdtiming violation betweenthe internal byte clock ofthe Transceiver IC and theTXCLK timing domains.DC coupled and internallyterminated.Signal Name Level I/O Pin #DescriptionReceive Functions Loopback Modes DC Power TX_FAULTLVTTLO53Transmit Fault alarm out-put. Indicates that the laser has been automatically shut off due to a fault in the TX laser circuit. High = TX Fault. Fault may be cleared by cycling DC power, or by strobing the RESET_L in-put.TX_BIASMON LVTTL O 59Transmit Bias Monitor alarm output. Indicates that the bias current of the TX laser is currently outside normal operating limits. High = TX Bias outside lim-its.PCLKP PCLKNLVDS O108622.08 MHz Parallel Clock output. Generated by divid-ing the internal high-speed TX clock by 4.RESET_L LVTTL I 56Master Reset input. A Low level resets the TX Mux and Laser Driver. RESET_L must be held low for at least 6 millisec. Pulled high through a 1 k Ω resistor.Signal Name Level I/O Pin #Description RXDATAP0RXDATAN0RXDATAP1RXDATAN1RXDATAP2RXDATAN2RXDATAP3RXDATAN3LVDSO4442343228262220Parallel Output Data at 622.08 Mb/s from the Re-ceiver, aligned to the Parallel Output Clock (RXCLKP/N). RXDATAP/N[3] is the Most Significant Bit, and is the first bit received in the incoming OC-48 serial data stream. RXDATAP/N[3:0] is updated on the falling edge of RX-CLKP. All data outputs are forced to zero level under Loss Of Signal or Loss Of Synchronization conditions. DC coupled outputs. Internal-ly terminated.RXCLKP RXCLKNLVDS O1614Parallel Output Clock from the Receiver at 622.08 MHz. This clock is aligned to the RXDATAP/N[3:0] parallel out-put data. RXDATAP/N[3:0] is updated on the falling edge of RXCLKP. Clock output is continuous under Loss Of Signal or Loss Of Synchroni-zation conditions. DC cou-pled output. Internally terminated.RX_LOS LVTTL O 55Receive Loss Of Signal alarm output. A High output level indicates RX input power is below the sensitivity level of the receiver (high BER condi-tion).Signal Name Level I/O Pin #Description RX_LOSYNCLVTTL O57Receive Loss Of Synchroni-zation alarm output. A High output level indicates that the receive Clock Recovery unit has lost synchronization, due to either very low RX in-put power level, or input data rate outside of frequency tol-erance.RX_MON Analog O 58Receive power monitor output. A voltage output which is directly proportional to the optical RX input power.Signal NameLevelI/O Pin #DescriptionLLEB_L LVTTL I38Line Loopback Enable input. A Low level enables Line Loopback mode. When active, the RX inputs to the Transceiver IC will be routed directly to the TX outputs. Pulled high through a 1 k Ω resistor. DLEB_L LVTTL I 40Diagnostic Loopback Enable input. A Low level enables Diagnostic Loopback mode. When active, the TX outputs of the Transceiver IC are routed directly to the RX in-puts. Pulled high through a 1 k Ω re-sistor.RLP-TIMELVTTL I 4Reference Loop Time Enable in-put. A High level enables Refer-ence Loop Time. When active, a divide-by-4 version of the PO-CLKP/N output of the RX is used as the reference clock input to the TX. Pulled low through a 1 k Ω resistor. SLP-TIMELVTTL I 2Serial Loop Time Enable input. A High level enables Serial Loop Time. When active, the recovered high-speed clock (RSCLKP/N) from the RX section is used in place of the synthesized transmit clock. Pulled low through a 1 k Ω resistor.Signal NameLevelI/O Pin #DescriptionGROUND 0 V DCI5,6,11,12,17,18,23,24,29,30,35,36,BladeGround connection for both signal and chassis ground on the transponder. The blade contact of the 60 pin interface connector is tied to ground in the transponder. Therefore, the blade of the user‘s mating connector should be connected to ground, as well.V CC+3.3 V DC I41,47,46,48,50,52,54DC Power Input. +3.3 V DC, nominal.Signal Name Level I/O Pin #DescriptionFunctional DiagramsTX Input Timing DiagramRX Output Timing DiagramT ECHNICAL DATARecommended Operating ConditionsNote1.T CASE is measured on top of the transponder (see details on page 1,outline dimensions)For T AMBIENT below 50 °C no airflow is required. For T AMBIENT50 °C - 70 °C a minimum airflow of 300 lfm (1.5 m/s) is required.Please note: installation of multiple transponders require the total airflow.DC Electrical CharacteristicsParameter Symbol Min.T yp.Max.Units Operating Case Tempera-ture(1)T C070o CTransponder Total PowerConsumptionP TOT 2.6 2.9W 3.3 V Supply Voltage V CC 3.13 3.3 3.46V3.3 V Supply Current I CC0.790.89AInput Differential Noise, All Pins N DIFF15mV0-pParameter Symbol Min.T yp.Max.UnitsLVDS Input High Volt-ageLVDS V IH 1.1 1.9VLVDS Input Low Volt-ageLVDS V IL0.6 1.5LVDS Input VoltageDifferentialLVDSV INDIFF2001200mVLVDS Input SingleEnded VoltageLVDSV INSING100600LVDS Differential In-put ResistanceLVDS R DIFF80100120ΩLVDS Output HighVoltageLVDS V OH 1.13 1.8VLVDS Output LowVoltageLVDS V OL0.7 1.4LVDS Output Differ-ential VoltageLVDSV OUTDIFF4407401100mVLVDS Output SingleEnded VoltageLVDSV OUTSIN-GLE220370550LVPECL Input LowVoltageLVPECL V IL V CC–1.9V CC–1.4VLVPECL Input HighVoltageLVPECLV IHV CC–1.1V CC–0.55LVPECL Input SingleEnded SwingLVPECLV INSINGLE2001200mVLVPECL Input Differ-ential SwingLVPECLV INDIFF4002400LVPECL Input DCBiasLVPECLV BIASV CC–0.5V CC–0.3VLVTTL Input HighVoltageLVTTL V IH 2.0V CCLVTTL Input LowVoltageLVTTL V IL00.8LVTTL Input HighCurrentLVTTL I IH50µALVTTL OutputCurrentLVTTL I O–500LVTTL Output HighVoltageLVTTL V OH 2.4VLVTTL Output LowVoltageLVTTL V OL0.8AC Electrical CharacteristicsNotes1.T CASE is measured on top of the transponder (see details on page 1, outline dimensions)For T AMBIENT below 50 °C no airflow is required. For T AMBIENT 50 °C - 70 °C a minimum airflow of 300 lfm (1.5 m/s) is required.Please note: installation of multiple transponders require the total airflow.2.Maximum allowable jitter on the reference clock input (REFCLKP/N) such that the transmitter will meet ITU-T G.958 and Bellcore GR-253 Jitter Generation requirements. Measured with a 12 KHz - 20 MHz filter.Parameter Sym-bol Condi-tionsMin.T yp.Max.UnitsT ransmitter TXDATAP/N[3:0] Input Bit Rate 622.08Mb/s TXCLKP/N Input Frequency 622.08MHz TXCLKP/N Input Duty Cycle 4060%TXCLKP/N Input Rise/Fall Time 20-80%100300psTXDATA Setup Time with re-spect to the Ris-ing edge of TXCLKPT ST See TX Timing Dia-gram 200TXDATA Hold Time with re-spect to the Ris-ing edge of TXCLKP T HT See TX Timing Dia-gram200REFCLKP/N In-put Frequency 155.520MHz REFCLKP/N In-put Frequency Tolerance ±20ppmREFCLKP/N In-put Duty Cycle 4555%REFCLKP/N In-put Rise/Fall Time10-90%500psREFCLKP/N In-put Jitter (2)1ps, rms PHASE_INITP/N Input Min. Pulse Width 3.2nsPCLKP/N Out-put Frequency 622.08MHz PCLKP/N Out-put Duty Cycle 4555%Return Loss, All AC Inputs & Out-puts10 MHz - 1 GHz15dBRESET_L Input Min. Pulse Width6msParameter Sym-bol Condi-tionsMin.T yp.Max.UnitsReceiver RXDATAP/N[3:0]Output Bit Rate 622.08Mb/s RXCLKP/N Out-put Frequency 622.08MHz RXCLKP/N Out-put Duty Cycle 4060%RXCLKP/N Out-put Rise/Fall Time20-80%100300psRXDATA Setup Time with re-spect to the Ris-ing edge of RXCLKPT SR See RXTiming Dia-gram 600RXDATA Hold Time with re-spect to the Ris-ing edge of RXCLKP T HR See RX Timing Dia-gram 600Return Loss, all AC Inputs & Out-puts10 MHz - 1 GHz 15dBRXCLKP/N Out-put Frequency Accuracy during LOS or LO-SYNC (1)Over operat-ing Temp Range±20ppmT ransmitter Electro-Optical CharacteristicsNotes1.The laser driver contains a control circuit, which regulates the aver-age optical output power. Nominal output power is factory set to be within the specified range.2.The Eye Diagram is compliant with Bellcore GR-253 and ITU-T G.957Eye Mask specifications.3.Jitter Generation is defined as the amount of jitter on the TX OpticalOutput, when there is no or minimum jitter on the TX electricalinputs. Jitter Generation is compliant with GR-253 and ITU-T G.958 specifications, when measured using a 12 KHz - 20 MHz filter, and with a jitter level on the REFCLKP/N input which is less than the level specified in ”AC Electrical Characteristics - Transmitter”.4.If the +3.3 V power supply drops below the specified level, the laserbias and modulation currents will be held disabled until the supply voltage rises above threshold and after the Power On Delay Time period.5.A fault, such as high laser bias current or high average power, whichlasts longer than the specified Fault Delay time, will cause the trans-mitter to be disabled. The fault can be cleared by cycling of DCpower, or by strobing the RESET_L input.Receiver Electro-Optical CharacteristicsNotes1.Average RX power for a 1x10–10 BER, and using a PRBS pattern of223–1 length with 72 zeros and 72 ones inserted, as per ITU-TG.958.2.Jitter Tolerance is defined as the amount of jitter applied to the RXoptical input that the receiver will tolerate without producing biterrors. The minimum required Jitter Tolerance for a 1 dB power pen-alty is defined to be 15 UI from 10 Hz to 600 Hz, 1.5 UI from 6 KHz to 100 KHz, and 0.15 UI from 1 MHz onwards, per Bellcore GR-253. 3.Jitter Transfer is defined as the ratio of TX Output Jitter to RX InputJitter, when the transponder is operated in electrical loopback mode (RX electrical outputs looped back into TX electrical inputs). Jitter Transfer is specified to be less than 0.1 dB up to 2 MHz, and drop-ping at –20 dB/Decade after that point, per ITU-T G.958 and Bellcore GR-253.4.The RX_LOS output is an active high LVTTL output, which is setHIGH if there is a loss of RX optical signal input (LOS), A decrease in optical input power below the assert level will cause the RX_LOSParameter Symbol Min.T yp.Max.Units Nominal Center Wave-lengthTX λNOM1310nmRange Of Center Wave-lengths TX λMIN-λMAX12601360Spectral Bandwidth TX∆λRMS 5nm,rmsAverage OutputPower(1)TX P AVG–11–4–3dBmExtinction Ratio TX ER8.214dB Output Rise Time20%-80%TX T R100200psOutput Fall Time80%-20%TX T F175250Eye Diagram(2)TX EDTX Jitter Generation, rms(3)TXJ GEN rms0.0070.01UIrmsTX Jitter Generation, p-p(3)TXJ GEN p-p0.0750.1UI p-pReset Threshold forV CC(4)TX V TH 2.2 2.95VPower On Delay forV CC(4)TX T POD20msFault Delay(5)TXT FAULT20TX Bias Monitor switch-ing threshold TX I BIAS60mAParameter Symbol Min.T yp.Max.UnitsNominal CenterWavelengthRX λNOM1310nmSensitivity (AveragePower)(1)RX P SENS–25–18dBmOverload (AveragePower)(1)RX P OL–3Optical Return Loss RX RL27dBRX Jitter Tolerance(2)RX J TOLRX-to-TX Jitter Trans-fer(3)RX-TX J XFROptical Path Penalty RX P PEN 1.0dBClock Recovery Cap-ture FrequencyRange(5)RX F CAPT±200ppmClock Recovery Ac-quisition Lock TimeRX T LOCK32250µsRX_LOS Output As-sert relative To RXOptical Input Power(4)RX_LOS ASSERT–30–25dBmRX_LOSYNC OutputAssert relative to RXinput frequency(5)RX_LOSYNC AS-SERT±450±600±770ppmRX_LOS Output Hys-teresis(4)RX_LOS HYST3dBRX_LOS &RX_LOSYNC OutputAssert Time(4, 5)RXT ASSERT100µsRX_LOS &RX_LOSYNC OutputDeassert Time(4, 5)RXT DEASSERT100RX_MON TransferSlope(6)4.4mV/µWRX_MON Dark OffsetVoltage(6)53mVRX_MON OutputVoltage atP IN = –17 dBm(6)142RX_MON OutputVoltage atP IN = –7 dBm(6)900。
2SC4208A中文资料
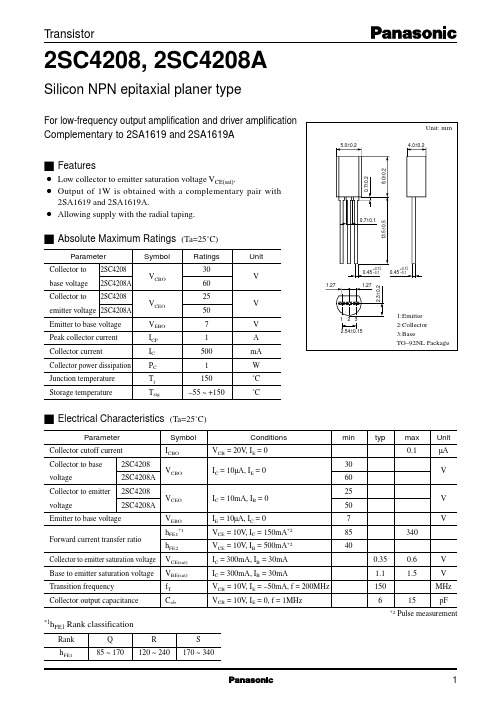
Collector current IC (A)
fT — IE
240 12
Cob — VCB
Collector output capacitance Cob (pF)
Collector to emitter voltage VCER (V)
VCB=10V Ta=25˚C IE=0 f=1MHz Ta=25˚C 120
VCER — RBE
IC=2mA Ta=25˚C 100
Transition frequency fT (MHz)
200
10
160
8
80
120
6
60 2SA4208A 40 2SA4208 20
80
4
40
2
0 –1
0 –3 –10 –30 –100 1 3 10 30 100
0 1 3 10 30 100 300 1000
(Ta=25˚C)
Symbol ICBO VCBO VCEO VEBO hFE1*1 hFE2 VCE(sat) VBE(sat) fT Cob Conditions VCB = 20V, IE = 0 IC = 10µA, IE = 0 IC = 10mA, IB = 0 IE = 10µA, IC = 0 VCE = 10V, IC = 150mA*2 VCE = 10V, IB = 500mA*2 IC = 300mA, IB = 30mA IC = 300mA, IB = 30mA VCB = 10V, IE = –50mA, f = 200MHz VCB = 10V, IE = 0, f = 1MHz 30 60 25 50 7 85 40 0.35 1.1 150 6
VBE(sat) — IC
2SC5858中文资料
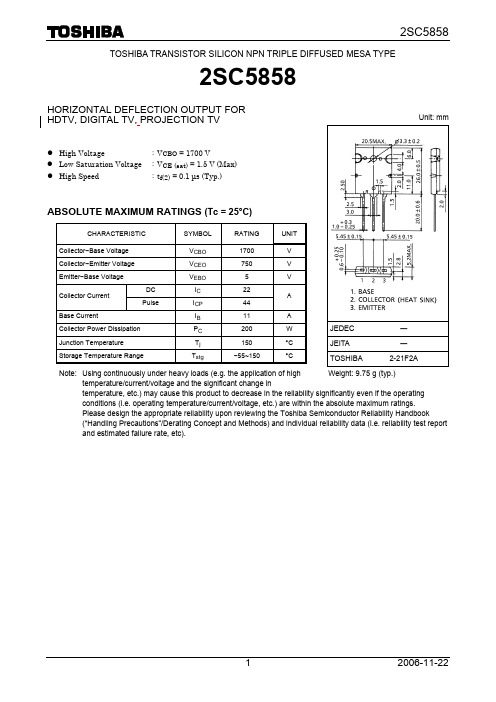
Fall Time Storage Time
Fall Time
ICBO IEBO V (BR) CEO hFE (1) hFE (2) hFE (3) VCE (sat) VBE (sat)
fT Cob tstg(1) tf(1) tstg(2) tf(2)
VCB = 1700 V, IE = 0 VEB = 5 V, IC = 0 IC = 10 mA, IB = 0 VCE = 5 V, IC = 2 A VCE = 5 V, IC = 8 A VCE = 5 V, IC = 17 A IC = 17 A, IB = 4.25 A IC = 17 A, IB = 4.25 A VCE = 10 V, IC = 0.1 A VCB = 10 V, IE = 0, f = 1 MHz
DC Current Gain
Collector−Emitter Saturation Voltage
Base−Emitter Saturation Voltage
Transition Frequency
Collector Output Capacitance
Storage Time
Switching Time
0.1
1
10
100
Collector current IC (A)
20 Common emitter VCE = 5 V
16
IC – VBE
12
Tc = 100°C
−25
8
25 4
0
0
0.2
0.4
0.6
0.8
1.0
1.2
Base−emitter voltage VBE (V)
3
C28新版说明书 (1)
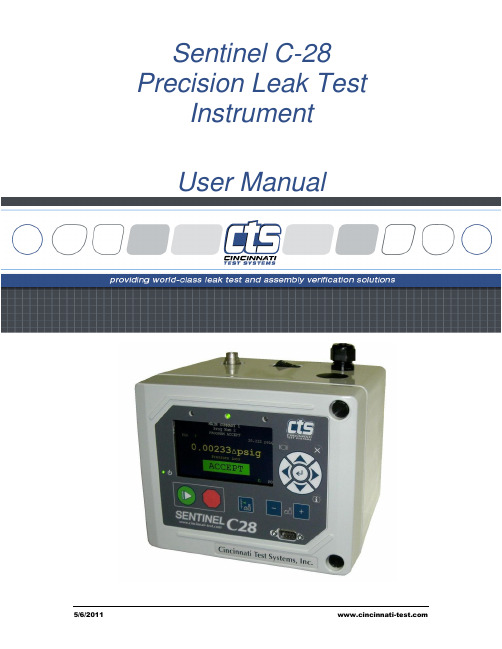
Sentinel C-28 Precision Leak Test InstrumentUser ManualThis page intentionally left blank.IMPORTANT INFORMATIONInformation in this document is subject to change without notice and does not represent a commitment on the part of Cincinnati Test Systems, Inc. No part of the manual and/or software may be reproduced or transmitted in any form or by any means, electronic or mechanical, including photocopying, recording, or information storage and retrieval systems, for any purpose, other than the purchaser’s personal use, without the express permission of Cincinnati Test Systems, Inc.No patent liability is assumed with respect to the use of the information contained herein. While every precaution has been taken in the preparation of this book, Cincinnati Test Systems, Inc. assumes no responsibility for errors or omissions.Because of the variety of uses for this equipment and because of the differences between this solid-state equipment and electromechanical equipment, the user of and those responsible for applying this equipment must satisfy themselves as to the acceptability of each application and use of the equipment. In no event will Cincinnati Test Systems be responsible or liable for indirect or consequential damages resulting from the use or application of this equipment.The illustrations, charts, and layout examples shown in this manual are intended solely to illustrate the text of this manual. Because of the many parameters and requirements associated with any particular installation, Cincinnati Test Systems cannot assume responsibility or liability for actual use based upon the illustrative uses and applications.CAUTION - When you see this warning symbol on the product, refer to the instruction manual for information before proceeding.CAUTION - To avoid personal injury due to electric shock, disconnect all power services before servicing.If this instrument is not used according to the instructions of this manual, the protection provided by this equipment' design may be compromised.This page intentionally left blank.T able of ContentsIntroduction (1)Unpacking (1)Installation (1)Supply Connections (2)User Interface Navigation (5)Menu Structure (7)Setup (9)Selection of Test Types (9)Tooling Control (11)Programming the Inputs and Outputs (11)Channel Configuration (11)Setting the Units of Measure (11)Setting the Leak Standard Values (12)Program Configuration (13)Setting the Pneumatic Regulator (13)Setting the Test Parameters (13)Verifying Setup (13)Security (13)Backup the Instrument Settings (13)Pressure Decay ∆P (15)Timer Parameters (16)Pressure Parameters (17)Test Parameters (18)Pressure Decay ∆P/∆T (19)Timer Parameters (20)Pressure Parameters (21)Test Parameters (22)Pressure Decay Leak Std (23)Auto Setup Sequence (24)Timer Parameters (26)Pressure Parameters (27)Test Parameters (28)Program Calibration (29)Initiating the Program Cal Sequence (29)Calibration Parameters (30)Occlusion Test (31)Timer Parameters (32)Pressure Parameters (32)Test Parameters (32)Tooling Control (33)Inputs and Outputs (35)Input and Output Wiring (36)Inputs (37)Outputs (41)Output Timing Diagram (44)Communication (45)Establishing RS232 Communication (45)Establishing Ethernet (TCP/IP) Communication (46)Understanding the Header Information (47)Test Results via RS232 or Ethernet (TCP/IP) communications (48)Streaming Measured Data (49)Reports (50)Security (51)Features (53)Selecting the Display User Level (53)Setting the Date & Time (53)Changing the Instrument Language (53)Copy & Paste Programs (53)Instrument Backup & Restore (54)Instrument Cloning (54)Open Internal Leak Standard (54)Self Test (54)Update Firmware (55)Changing the Functionality of the Prefill Timer (55)Turning On/Off Pressure Correction (56)Setting the Cal Method and Leak Standard Location (56)Auto Run (57)Calibrating Transducers and Electronic Regulators (59)Calibrating a Transducer (59)Pressure Transducer Cal 1 (Pressure) (59)Verifying a Transducer (60)Calibrating an Electronic Regulator (60)Messages & Error Codes (61)Test Messages & Errors (61)Quik Test (69)How it works (69)Test Parameters (70)Environmental Drift Correction (71)How it works (71)This page intentionally left blank.Chapter 1IntroductionIn this chapter you will be introduced to the basic pneumatic, electricalconnections, and the simple menu structure and navigation of the instrument.hank you for purchasing the Sentinel C-28 precision leak test instrument. The Sentinel C-28 is capable of testing using a variety of pre-packaged test algorithms designed to get you testing as quickly and easily as possible. Let’s get started!UnpackingCarefully remove the instrument from the shipping carton. Locate the quick connect test port fitting located in the test port of the instrument. This can be used to connect the test line to the instrument.InstallationThe leak test instrument is designed to operate in a manufacturing, clean room, or lab environment. To operate trouble-free, it requires:Clean, dry instrument air for test and pilot air (recommend 0.3 and 5.0-micron coalescing filter)Vacuum for vacuum test applicationsSupply power: 24 VDC OR 88-264 VAC 50/60 Hz auto sensing/switching electrical (based on configuration)Because this is a precision instrument, it is preferable to locate this instrument at least 15 feet away fromhigh electromagnetic energy devices (induction heat treat equipment and welders) whenever possible. In addition, plants having poor quality electrical power or ground systems should consider using isolationtransformers on the power drops.When supplying power it is important to check to make sure there is a zero voltage difference between the neutral and ground wires connected to the instrument.TSupply ConnectionsAfter mounting or locating the instrument, connect the inlet air or vacuum supply to the inlet port shown in the pneumatic diagram supplied with your specific instrument, as this will vary depending on instrument configuration. To reduce future maintenance requirements install the recommended 0.3 and 5.0-micron coalescing filters in the air supply connected to the instrument. Be certain to replace the filter elements at least quarterly as preventative maintenance.Front ViewTest Regulator ExhaustRS232Self Test CapTest Line ConnectionTop ViewSide ViewExhaust I/O Connection Power Cable Power Switch Access Hole ExhaustCONNECTION REQUIRED Pneumatic Supply PortsTest Air SupplyPilot Air Supply Test RegulatorSelf Test CapDoor Open View Ethernet USB PortUser Interface NavigationThere are multiple monitoring screens available for the instrument. Selecting the Monitor Icon will give you access to all of these screens.The instrument is designed with a simple graphical icon-based interface. The main menu isactivated by pressing the Main Menu button.The Arrow/Enter Selection buttons are used to navigate through the icons on the screenand select the appropriate menus. The center Enter arrow is also used to select parametersfor editing and saving the edits once they are complete.The Cancel/Back button is used go back to the previous menu. Multiple presses willeventually exit you out of the menu structure entirely and place you on the Monitor Screen.This button is also used to cancel out of any edits before saving.The Information button is used to get a help screen that is associated the parametercorresponding to where the cursor is located.The instrument is capable of storing up to 32 different programs. Switchingbetween these programs is done with the Program Select buttons on the front ofthe instrument. The current program is shown in the lower right hand corner of the screen designated by “P” and then a two digit number corresponding to the current program number.Hint: Holding down the “+” or the “-” button for 2 seconds will prompt a screen to appear in which the value of the program may be entered using the arrow buttons. The up and down arrows will increment and decrement the ones digit. The right and left arrows will increment and decrement the tens digit.Note: The Program may also be changed via Digital I/O (See Chapter 8), RS232 or TCP/IP Communications (See Chapter 9)Menu StructureBelow is an overview of the menu structure for the instrument.Note: Not all of the menus are available for all configurations and Test Types.This page intentionally left blank.Chapter 2SetupIn this chapter you will be asked how you intend for the instrument to function toconduct the test or sequence of tests for the application.Setting up the instrument to meet specific application requirements is most effectively accomplished by answering a few questions. These questions will guide you through the initial stages of the setup and point you to the appropriate chapters that detail specific instructions based on the answers.It is highly recommended that each type of part being tested, whether they differ in volume or construction, have their own set of parameters defined in the instrument via individual Programs. Pressure decay lea k testing is a volume dependent function. In certain cases, it is possible to group “like parts” together to use the same parameters. In this case we recommend you talk to a CTS applications specialist to assure proper functionality.Selection of Test TypesThe first step in setting up the instrument is to select the type of test you would like to conduct via the pre-packaged test sequences. Once you set up one type of test repeating this step under a different program will enable you to configure up to 32 different test configurations. The table below (Table 1 –Test Type Selection Options) includes the different test types available in the instrument, a brief description, and the associated chapter that details the pre-packaged test program. The availability of these test types are based on the configuration of the instrument.Once you determine which test type is appropriate for your application go toProgram 1 (press the + or – buttons until you see a P01 in the lower right handcorner of the screen.Press the Main Menu button to view the Main Menu screen.Select Program Config menu using the Arrow/Enter Selection buttonsSelect Test Type IconSelect the appropriate test type using the Enter button to enable editing and then the up anddown arrows to view the options. When you see the desired selection press the Enter buttonto select.Before we begin setting the parameters of the program we need to determine some of the capabilities and features required for the application.Tooling ControlThe instrument is capable of controlling one tooling or seal action to possibly eliminate the need for a PLC or other computer that would control a cylinder or sealing motion.Question:Are you planning to use the instrument to control a sealing operation?Yes: It is important that you understand the concepts and safety requirements of Tooling Control. Please see Chapter 7 and then come back and continue the setup.No: ProceedProgramming the Inputs and OutputsThe instrument comes with 6 inputs and 3 outputs (24VDC) that are user configurable for each program.Question:Are you planning to use the instrument to control any ancillary devices or communicate with a PLC using discrete I/O?Yes: Please see Chapter 8 and then come back and continue the setup.No: ProceedChannel ConfigurationSetting the Units of MeasureThe instrument has the capability to utilize different units of measure for each configured program. In order to keep things simple and user friendly if you always use the same unit of measure, you can set the units in one place and have them apply instrument wide. This is done in the Channel Configuration menu.Question:Are you planning to use the same units of measure for every program?Yes: Please press the Main Menu button. Select the Channel Config Icon. From the Channel Config menu select the Units Icon. Change the Unit/Prec Define parameter to “Channel”. Set the desired units on that same screen. These units will apply to every program.No: Please press the Main Menu button. Select the Channel Config Icon. From the Channel Config menu select the Units Icon. Change the Unit/Prec Define parameter to “Program”. The Unit Icon will now appear under the Program Config menu. When aprogram is created, the units for the program will use the units under the Channel Config menu as the default settings but now can be changed per program.Note: The units set on the Channel Config screen are also the units used for Self Test and Auto Setup (where applicable).Note: The precision displayed for each unit may also be set on this screen.Setting the Leak Standard ValuesThe instrument has the capability to utilize different leak standards for each configured program that uses a leak standard. In order to keep things simple and user friendly if you always use the same leak standard, you can set the leak standard value and pressure in one place and have it apply instrument wide to any program that uses a leak standard. This is done in the Channel Configuration menu.Question:Are you planning to use the same leak standard for every program that requires a leak standard?Yes: Please press the Main Menu button. Select the Channel Config Icon. From the Channel Config menu select the Leak/Cal Icon. Change the Leak Std/Cal Define parameter to “Channel”. Set the leak standard value and the pressure at which it was calibrated on that same screen. This leak standard value will apply to every program that utilizes a leak standard for calibration.No: Please press the Main Menu button. Select the Channel Config Icon. From the Channel Config menu select the Leak/Cal Icon. Change the Leak Std/Cal Define parameter to “Program”. The leak standard parameters will now appear on the TST:*** screen under the Program Config menu. When a program is created, the units for the program will use the leak standard value under the Channel Config menu as the default settings but now can be changed per program.Note: Every time the leak standard value changes due to a calibration or when a new leak standard is used this value needs to be modified to reflect the new value.Note: The parameter that determines whether the physical leak standard is located either inside the instrument or connected to a port on the outside is also located in the Leak/Cal Menu or the TST menu. However, to view this parameter you must be in the “Advanced”or “Admin” Display User Level. To read how to change the Display User Level go to Chapter 11.Remember: Press the information button with the cursor on that parameter if you want to know the definition of the options.Program ConfigurationNow that you have created a program, configured the tooling and associated I/O, and set the channellevel parameters, it is time to set the regulators to the correct test pressure.Setting the Pneumatic RegulatorQuestion:Does the pressure source you are using for this program have an electronic regulator?Yes: The electronic regulator has been setup and calibrated at the factory and will beready to use. For calibrating the electronic regulator please see Chapter 12.No: Setting the regulator is done via the Channel Config screen under the Set/Spanmenu. In order to set the regulator the test port will need to be blocked which will allow the instrument to hold pressure. This may be done with the test port plug, mounted tothe bottom of the instrument, placed in the test port.Setting the Test ParametersIt is time to set the test parameters to fit your application. Please refer to the chapter associated with thetest type chosen from Table 1 – Test Type Selection Options.Verifying SetupOnce you have everything programmed, run a repeatability study based o n your company’s qualitystandards to assure you are getting the results you desire.SecurityNow that the instrument is setup the way you want, make sure to lock down the parameters that youdon’t want changed until a key or password is used. See Chapter 10Backup the Instrument SettingsThe setup of the instrument for one program is completed. You may now go back and setup multipleprograms. Once you have completed, it is highly recommended that you backup the instrument. This can be done with a USB memory stick. See Instrument Backup & Restore in Chapter 11.This page intentionally left blank.Chapter 3Pressure Decay ∆PIn this chapter you will understand the theory and parameters for conducting apressure decay test measuring a pressure loss over time. The result of this test isthe pressure loss (or gain for a vacuum test) measured over a fixed period of time.The basic principle of operation of a pressure decay leak test instrument is to fill the test part to a specified target test pressure, isolate the test part from the source air and allow the pressure to stabilize, and then measure the pressure loss due to a leak over a defined time.The Charts below give an overview of the parameters used to setup a Pressure Decay ∆P Test. The Tables that follow give detailed descriptions of each parameter and also document the Display User Level associated with each parameter.Note: To read how to change the Display User Level go to Chapter 11.Timer ParametersThe Timers for the program may be viewed and modified by going to the Program Config menu and selecting the Timers Icon.Pressure ParametersThe Pressures for the program may be viewed and modified by going to the Program Config menu and selecting the Pressures Icon.Test ParametersThe Test parameters for the program may be viewed and modified by going to the Program Config menu and selecting the TST:PLO Icon.Chapter 4Pressure Decay ∆P/∆TIn this chapter you will understand the theory and parameters for conducting apressure decay test measuring the rate of change of pressure loss / time. Theresult of this test is the rate of pressure change measured over a selected unit oftime.The basic principle of operation of a pressure decay leak test instrument is to fill the test part to a specified target test pressure, isolate the test part from the source air and allow the pressure to stabilize, and then measure the pressure loss due to a leak over a defined time.The Charts below give an overview of the parameters used to setup a Pressure Decay ∆P/∆T Test. The Tables that follow give detailed descriptions of each parameter and also document the Display User Level associated with each parameter.Note: To read how to change the Display User Level go to Chapter 11.Timer ParametersThe Timers for the program may be viewed and modified by going to the Program Config menu and selecting the Timers Icon.Pressure ParametersThe Pressures for the program may be viewed and modified by going to the Program Config menu and selecting the Pressures Icon.Test ParametersThe Test parameters for the program may be viewed and modified by going to the Program Config menuand selecting the TST:DPT Icon.Chapter 5Pressure Decay Leak StdIn this chapter you will understand the theory and parameters for conducting apressure decay test and correlating the pressure loss to a leak rate using a leakstandard. The result of this test is in the form of a flow rate.The basic principle of operation of a pressure decay leak test instrument is to fill the test part to a specifiedtarget test pressure, isolate the test part from the source air and allow the pressure to stabilize, and then measure the pressure loss due to a leak over a defined time. The leak test instrument translates thepressure loss value measured over the fixed test time to a leak or flow rate.The Charts below give an overview of the parameters used to setup a Pressure Decay Test and correlatingthe results to a flow rate using a leak standard. The Tables that follow give detailed descriptions of each parameter and also document the Display User Level associated with each parameter.Note: To read how to change the Display User Level go to Chapter 11.Auto Setup SequenceThe easiest way to setup the proper timers in the instrument, when using the leak rate test type, is by usingthe Auto Setup routine. The Auto Setup routine resets the Input and Output functions for a program to the default (inactive) values. Therefore, Auto Setup must be performed with the part manually sealed.After completing the Auto Setup routine, the inputs, outputs, and tooling functions for the program will need to be reconfigured.Note: If you want to setup the program parame ters manually or don’t want to have to reconfigure the inputs and outputs proceed to Timer ParametersThe Auto Setup routine is a unique patented process developed by Cincinnati Test Systems for the Sentinel Blackbelt instrument that makes the initial setup of the instrument to a new test part quick, easy and efficient. The process will determine the best time sequence to test a part within the limits of a desired maximum cycle time. If the desired maximum cycle time is set too short, the final test will not produce repeatable results. Any leak test needs a certain amount of cycle time to achieve sufficient resolution and repeatability that are dependent on the part volume, leak rate, test pressure, and part characteristics. The Auto Setup routine will set the best possible test cycle within the maximum cycle time specified for the test.Upon successful completion of the Auto Setup routine there is no need to continue the setup parameters in the rest of this chapter unless you want to adjust parameters.Timer ParametersThe Timers for the program may be viewed and modified by going to the Program Config menu and selecting the Timers Icon.Pressure ParametersThe Pressures for the program may be viewed and modified by going to the Program Config menu and selecting the Pressures Icon.Test ParametersThe Test parameters for the program may be viewed and modified by going to the Program Config menu and selecting the TST:PLR Icon.Program CalibrationIn order to convert the pressure loss measured by the instrument to a leak (flow) rate, the instrument uses a leak standard and needs to run the “Program Cal” procedure. This procedure requires at least one known non-leaking part referred to as a “master part.” This procedure tests a non-leaking master part connected to the instrument using the timers and pressures established for the program. The procedure automatically tests the non-leaking master part twice with the Relax timer delay between tests. Within each program that uses a leak standard, Program Cal can be configured to use one of four methods. See Setting the Cal Method and Leak Standard Location in Chapter 11Remember: The Leak/Cal menu has a parameter called Leak Std/Cal Definethat can be configured for the leak standard information to be used Globally, inwhich case it would be located under the Channel Config menu, or per Program in which case it would be located under the Program menu. Make sure you check which method you have set your instrument. It is critical to make sure the leak standard values are correct for proper use. In order to view the Cal Method parameter you must be in the “Advanced” or “Admin” Display User Level. To read how to change the Display User Level go to Chapter 11.Initiating the Program Cal SequenceTo initiate a Program Cal sequence press the shortcut key on the front of the instrument or goto Main Menu and select the Program Cal Icon. The Program Cal wizard will tell you toconnect a non-leaking master part. Connect the non-leaking master part to the instrument. Push the Start button to initiate the Program Cal sequence. The system will conduct an initial test of the non-leaking master part to measure the pressure loss associated with a non-leaking part. This represents the typical offset associated with testing parts within the environment of the test system. The pressure loss value is saved as the Master Part Loss. The system will conduct a second test on a non-leaking master part with a known calibrated leak standard included in the test. The pressure loss value result for this test is saved as the Master+Leak Loss.Upon the successful completion of the Program Cal routine, the display will show the calculated Performance Factor for the calibration. The Performance Factor is an estimate of the quality of the calibration. It combines the ratio of the Hi Limit Leak result to the non-leaking master part result, the test pressure, and difference between the Hi Lim result and the non-leaking master part result to scale its anticipated performance. This value ranges from 0 to 100. It is generally desirable to have a Performance Factor of 35 to 100. The actual acceptable Performance Factor can vary depending on the desired Gage R&R performance of the test. Generally, longer timer settings will produce higher Performance Factors and improved Gage R&R performance.Note: The instrument will require a Program Cal Sequence if any parameters aremodified that effects the calibration.Several conditions must be met during the Program Calibration procedure for the instrument to accept and store the calibration results. If the procedure does not meet these conditions, error messages are displayed at the completion of tests.If the Program Cal routine is successfully completed, “Program-C al Passed” will be displayed. If there are any problems during the Program Cal sequence an error will be displayed. Please see Chapter 13Calibration ParametersCalibration parameters are values that are measured or calculated as a result of the Program Cal routine for a pressure decay leak rate test. The table below describes the parameters.Chapter 6Occlusion T estIn this chapter you will understand the theory and parameters for conducting anOcclusion Test. The result of this test is the measured back pressure at theexpiration of the Test sequence.The Occlusion Test is a back pressure test. The part is pressurized throughout the test from a fixedpressure regulator setting. At the end of the Test timer the actual test pressure is compared to the Low Limit Pressure and High Limit Pressure settings. Low Limit Pressure indicates high flow or minimumblockage or low back pressure. High Limit Pressure indicates low flow or maximum blockage or high back pressure.The Chart below give an overview of the parameters used to setup an Occlusion Test. The Tables that follow give detailed descriptions of each parameter and also document the Display User Level associated with each parameter.Note: To read how to change the Display User Level go to Chapter 11.Timer ParametersThe Timers for the program may be viewed and modified by going to the Program Config menu and selecting the Timers Icon.Pressure ParametersThe Pressures for the program may be viewed and modified by going to the Program Config menu and selecting the Pressures Icon.Test ParametersThe Test parameters for the program may be viewed and modified by going to the Program Config menu and selecting the TST:OCC Icon.。
Tri LED-56 CAN用户手册说明书

w w w.p r o l i g h t.c o.u kTRI LED-56 CAN USER MANUALOrder code: LEDJ38 - BlackOrder code: LEDJ39 - PolishedWARNINGFOR YOUR OWN SAFETY, PLEASE READ THIS USER MANUAL CAREFULLYBEFORE YOUR INITIAL START-UP!SAFETY INSTRUCTIONSEvery person involved with the installation, operation & maintenance of thisequipment should:- Be competent- Follow the instructions of this manualBefore your initial start-up, please make sure that there is no damage caused during transportation. Should there be any, consult your dealer and do not use theequipment.To maintain the equipment in good working condition and to ensure safe operation, it is necessary for the user to follow the safety instructions and warning notes written in this manual.Please note that damages caused by user modifications to this equipment are notsubject to warranty.IMPORTANT:The manufacturer will not accept liability for any resulting damages causedby the non-observance of this manual or any unauthorised modification to the equipment.• Never let the power-cable come into contact with other cables. Handle the power-cable and all mains voltage connections with particular caution!• Never remove warning or informative labels from the equipment.• Do not open the equipment and do not modify the equipment.• Do not connect this equipment to a dimmer-pack.• Do not switch the equipment on and off in short intervals, as this will reduce thesystem’s life.• Only use the equipment indoors.• Do not expose to flammable sources, liquids or gases.• Always disconnect the power from the mains when equipment is not in use or beforecleaning! Only handle the power-cable by the plug. Never pull out the plug by pulling the power-cable.• Make sure that the available voltage is between 220v/240v.• Make sure that the power-cable is never crimped or damaged. Check the equipment and the power-cable periodically.• If the equipment is dropped or damaged, disconnect the mains power supply immediately.Have a qualified engineer inspect the equipment before operating again.• If the equipment has been exposed to drastic temperature fluctuation (e.g. aftertransportation), do not switch it on immediately. The arising condensation might damage the equipment. Leave the equipment switched off until it has reached room temperature.• If your product fails to function correctly, discontinue use immediately. Pack the unitsecurely (preferably in the original packing material), and return it to your Prolight dealer for service.• Only use fuses of same type and rating.• Repairs, servicing and power connection must only be carried out by a qualifiedtechnician. THIS UNIT CONTAINS NO USER SERVICEABLE PARTS.• WARRANTY; One year from date of purchase.OPERATING DETERMINATIONSIf this equipment is operated in any other way, than those described in this manual,the product may suffer damage and the warranty becomes void.Incorrect operation may lead to danger e.g.: short-circuit, burns, electric shocks,lamp failure etc.Do not endanger your own safety and the safety of others!Incorrect installation or use can cause serious damage to people and property.You should find inside the LEDJ carton the following items :1, Tri LED-56 Can 2, Instruction manualTechnical Specifications:DMX channels: 69 x Ultra Bright 3W Tri-colour LEDs 3-pin XLR in/out sockets 400Hz flicker free Power supply: 240VPower consumption: 41WDimensions: 342 x 249 x 171mm Weight: 2.8KgsOperating modes: 1, Static colour 2, Auto run 3, Colour fade 4, Sound active 5, Master/slave 6, DMX Overview:7, Down button 8, Enter button37Operation:There are 6 different operation modes to choose from:1) Static colour mode 2) Colour change mode 3) Colour fade mode4) Sound active mode 5) DMX mode 6) Slave mode1, Static colour modeMode button - Press the “MODE” button under the LED display, to show “C000”, then press the “ENTER” button to choose one of the static colours using the “UP” and “DOWN” buttons.The “C1” represents Red, “C2” = Green, “C3” = Blue and “CF” = strobe.The two digits after it are the brightness 00 to 99 or in “CF” they are the strobe speed.Examples: If you set C1, C2 and C3 to zero, the Tri LED-56 can will have no LEDs on (blackout).If you set C1 to 99 and C2 and C3 to zero, the Tri Par will be 100% Red.NOTE: For static selection of Red, Green, and Blue, ensure that the unwantedcolours are set to “00”.2, Colour change modeMode button - Press the “MODE’ button until the LED display shows “J000”, then press the “ENTER” button to choose one of the colour changing modes using the “UP” and “DOWN” buttons. The colour change programmes are as follows:1, “J300” = RGB, 2, “J700” = 7 colour, 3, “JF00” = Strobe,Now press the “ENTER” button again and you can then select the colour change speed using the “UP” and “DOWN” buttons.The speed settings are from 00-99 (00 = slow, 99 = fast)3, Colour fade modeMode button - Press the MODE button until the LED display shows “F000”, then press the “ENTER” button to choose one of the colour fading modes using the “UP” and “DOWN” buttons. The colour fade programmes are as follows:1, “F300” = RGB, 2, “F700” = 7 colour, 3, “FF00” = Strobe,Now press the “ENTER” button again and you can then select the colour fade speed using the “UP” and “DOWN” buttons.The speed settings are from 00-99 (00 = slow, 99 = fast)4, Sound activeMode button - Press the “MODE” button until the LED display shows “S000”, then press the “ENTER” button to choose one of the sound active modes using the “UP” and “DOWN” buttons.1, “S300” = RGB, 2, “S700” = 7 colourNow press the “ENTER” button again to set the sensitivity level from 00-99 using the “UP” and “DOWN” buttons.(00 = low, 99 = high)Note: To confirm the setting in any of the above mode always press the “ENTER” button a final time so that the LED display stops flashing.5, DMX Addressing modeTo access the DMX address mode, press the “MODE” button until the LED display shows “A001”, and use the “UP and “DOWN” buttons to select the desired DMX address and press the “ENTER” button to confirm the setting. Then follow the DMX channel assignment and function table below.6. Master/Slave modeLink the units together using a 3-pin DMX cable, then press the “MODE” button to select one of the above modes. On the Slave units press the mode button until the LED display shows “SLAV”. The Slave units will then follow in sequence with the Master unit.6 Channel DMX chartChannel123456Value000-255000-255000-255000-2550-45-8485-169170-2550-255FunctionMaster dimmerRed (0 - 100%)Green (0 - 100%)Blue (0-100%)No functionColour macroColour jumpColour fadeStrobeDMX-512:• DMX (Digital Multiplex) is a universal protocol used as a form of communication between intelligent fixtures and controllers. A DMX controller sends DMX data instructions form thecontroller to the fixture. DMX data is sent as serial data that travels from fixture to fixture via the DATA “IN” and DATA “OUT” XLR terminals located on all DMX fixtures (most controllers only have a data “out” terminal).DMX Linking:• DMX is a language allowing all makes and models of different manufactures to be linked together and operate from a single controller, as long as all fixtures and the controller are DMX compliant. To ensure proper DMX data transmission, when using several DMX fixtures try to use theshortest cable path possible. The order in which fixtures are connected in a DMX line does not influence the DMX addressing. For example; a fixture assigned to a DMX address of 1 may be placed anywhere in a DMX line, at the beginning, at the end, or anywhere in the middle. When a fixture is assigned a DMX address of 1, the DMX controller knows to send DATA assigned to address 1 to that unit, no matter where it is located in the DMX chain.DATA Cable (DMX cable) requirements (for DMX operation):• The Tri LED-56 Can can be controlled via DMX-512 protocol. The DMX address is set on the back of the unit. Your unit and your DMX controller require a standard 3-pin XLR connector for data input/output (figure 1).Figure 1Also remember that DMX cable must be daisy chained and cannot be split.Further DMX cables can be purchased from all good sound and lighting suppliers or Prolight dealers.Please quote: CABL10 – 2M CABL11 – 5M CABL12 – 10MNotice:• Be sure to follow figures 2 & 3 when making your own cables. Do not connect the cable’s shield conductor to the ground lug or allow the shield conductor to come in contact with the XLR’s outer casing. Grounding the shield could cause a short circuit and erratic behaviour.Special Note: Line termination:• When longer runs of cable are used, you may need to use a terminator on the last unit to avoid erratic behaviour.Using a cable terminator (part number CABL90) will decrease the possibilities of erratic behaviour.5-Pin XLR DMX Connectors:• Some manufactures use 5-pin XLR connectors for data transmission in place of 3-pin. 5-Pin XLR fixtures may be implemented in a 3-pin XLR DMX line. When inserting standard 5-pin XLR connectors in to a 3-pin line a cable adaptor must be used. The Chart below details thecorrect cable conversion.Termination reduces signal transmission problems and interferance. it is always advisable to connect a DMX terminal, (resistance 120 Ohm 1/4 W) between pin 2 (DMX-) and pin 3 (DMX+) of the last fixture.。
2SC3928资料
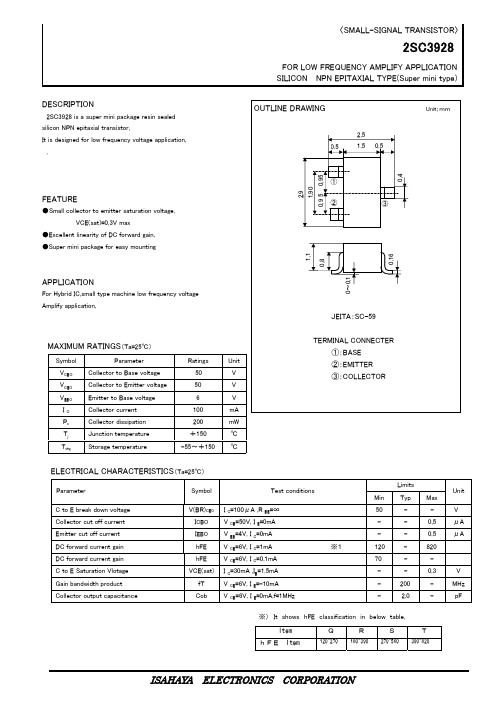
2.9 1.90 0.9 5 0.95
0.4
〈SMALL-SIGNAL TRANSISTOR〉
2SC3928
FOR LOW FREQUENCY AMPLIFY APPLICATION SILICON NPN EPITAXIAL TYPE(Super mini type)
OUTLINE DRAWING
.
FEATURE
●Small collector to emitter saturation voltage. VCE(sat)=0.3V max
●Excellent linearity of DC forward gain. ●Super mini package for easy mounting
Cob
V CB=6V, I E=0mA,f=1MHz
Limits Unit
Min Typ Max
50
-
-
V
-
-
0.5 μA
-
-
0.5 μA
120
-
820
70
-
-
-
-
0.3
V
-
200
-
MHz
-
2.0
-
pF
※) It shows hFE classification in below table.
Item hFE Item
Collector dissipation
200
mW
Tj
Junction temperature
+150
℃
Tstg
Storage temperature
-55~+150 ℃
TERMINAL CONNECTER ①:BASE ②:EMITTER ③:COLLECTOR
2SC2131-2SC2148产品数据表说明书

/2SC2188-datasheet.html
Silicon NPN epitaxial planer type
/2SC2188-datasheet.html
The Japanese Transistor Manual 1981
/2SC2194-datasheet.html
Shortform Data and Cross References (Misc Datasheets)
/2SC2194-datasheet.html
2SC2148
N/A
2SC2148
NEC Electronics
2SC2148
NEC Electronics
2SC2148
NEC Electronics
2SC2148 2SC2149
NEC Electronics N/A
2SC2149
N/A
2SC2149
N/A
2SC2149
N/A
2SC2149
N/A
Semiconductor Selection Guide 1995
/2SC2148-datasheet.html
Semiconductor Selection Guide
/2SC2148-datasheet.html
/2SC2148-datasheet.html
MICROWAVE LOW NOISE AMPLIFIER NPN SILICON EPITAXIAL TRANSISTOR
/2SC2148-datasheet.html
2SC2166 2SC2167
Various Russian Datasheets
N/A
2SC2167
N/A
UC3842充电器原理和维修之欧阳家百创编
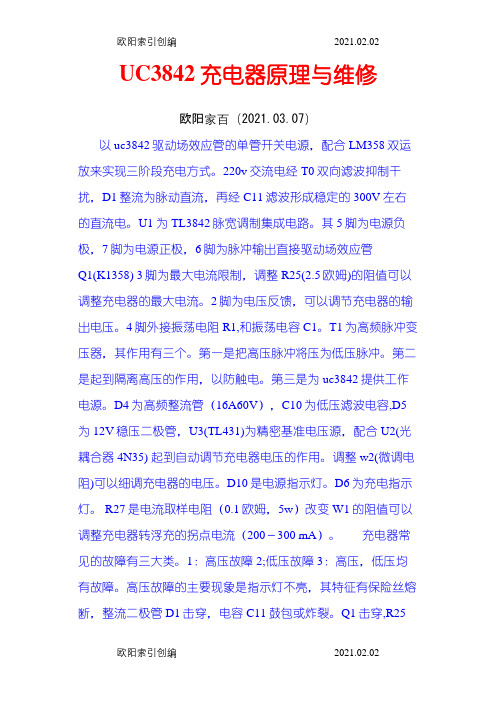
UC3842充电器原理与维修欧阳家百(2021.03.07)以uc3842驱动场效应管的单管开关电源,配合LM358双运放来实现三阶段充电方式。
220v交流电经T0双向滤波抑制干扰,D1整流为脉动直流,再经C11滤波形成稳定的300V左右的直流电。
U1 为TL3842脉宽调制集成电路。
其5脚为电源负极,7脚为电源正极,6脚为脉冲输出直接驱动场效应管Q1(K1358) 3脚为最大电流限制,调整R25(2.5欧姆)的阻值可以调整充电器的最大电流。
2脚为电压反馈,可以调节充电器的输出电压。
4脚外接振荡电阻R1,和振荡电容C1。
T1为高频脉冲变压器,其作用有三个。
第一是把高压脉冲将压为低压脉冲。
第二是起到隔离高压的作用,以防触电。
第三是为uc3842提供工作电源。
D4为高频整流管(16A60V),C10为低压滤波电容,D5为12V稳压二极管,U3(TL431)为精密基准电压源,配合U2(光耦合器4N35) 起到自动调节充电器电压的作用。
调整w2(微调电阻)可以细调充电器的电压。
D10是电源指示灯。
D6为充电指示灯。
R27是电流取样电阻(0.1欧姆,5w)改变W1的阻值可以调整充电器转浮充的拐点电流(200-300 mA)。
充电器常见的故障有三大类。
1:高压故障 2;低压故障 3:高压,低压均有故障。
高压故障的主要现象是指示灯不亮,其特征有保险丝熔断,整流二极管D1击穿,电容C11鼓包或炸裂。
Q1击穿,R25开路。
U1的7脚对地短路。
R5开路,U1无启动电压。
更换以上元件即可修复。
若U1的7脚有11V以上电压,8脚有5V电压,说明U1基本正常。
应重点检测Q1和T1的引脚是否有虚焊。
若连续击穿Q1,且Q1不发烫,一般是D2,C4失效,若是Q1击穿且发烫,一般是低压部分有漏电或短路,过大或UC3842的6脚输出脉冲波形不正常,Q1的开关损耗和发热量大增,导致Q1过热烧毁。
高压故障的其他现象有指示灯闪烁,输出电压偏低且不稳定,一般是T1的引脚有虚焊,或者D3,R12开路,TL3842及其外围电路无工作电源。
- 1、下载文档前请自行甄别文档内容的完整性,平台不提供额外的编辑、内容补充、找答案等附加服务。
- 2、"仅部分预览"的文档,不可在线预览部分如存在完整性等问题,可反馈申请退款(可完整预览的文档不适用该条件!)。
- 3、如文档侵犯您的权益,请联系客服反馈,我们会尽快为您处理(人工客服工作时间:9:00-18:30)。
iSFP™ - Intelligent Small Form-factor PluggableSONET OC-3 IR-1 / SDH STM S-1.1Multirate Applications up to 155 Mbit/sSingle Mode 1310 nm Transceiver with LC™ ConnectorV23848-C18-C56V23848-C19-C56File: 1132File: 1133Fiber OpticsFor ordering information see next page.iSFP™ is a trademark of Infineon Technologies. LC™ is a trademark of Lucent.Features•Small Form-factor Pluggable (SFP) MSA compatible transceiver 1)•Fully SFF-8472 compatible•Incorporating Intelligent – Digital Diagnostic Monitoring Interface•Internal calibration implementation •Advanced release mechanism•Easy access, even in belly to belly applications •Wire handle release for simplicity •Color coded blue tab (single mode)•PCI height compatible•Excellent EMI performance•Separate and common chassis/signal ground module concepts available•RJ-45 style LC™ connector system •Single power supply (3.3 V)•Low power consumption•Small size for high channel density •UL-94 V-0 certified•ESD Class 1C per JESD22-A114-B (MIL-STD 883D Method 3015.7)•According to FCC (Class B) and EN 55022•For distances of up to 21 km (see Supported Link Lengths )•Fabry Perot laser, PIN photo diode•Laser safety according to Class 1 FDA and IEC •AC/AC Coupling according to MSA•Suitable for multirate applications up to 155 Mbit/s •Fast Ethernet (FE) compatible•Extended operating temperature range of –40°C to 85°C •SFP evaluation kit V23848-S5-V4 available upon request• A press fit cage and cage plugs are available as accessory products from Infineon (see SFP Accessories )1)MSA documentation can be found at /fiberoptics under Transceivers, SFP Transceivers.Ordering InformationPart Number Chassis/Signal Grounding Concept V23848-C18-C56CommonV23848-C19-C56SeparatedPin ConfigurationFigure1iSFP™ Transceiver Electrical Pad LayoutPin DescriptionPin Logic Level Function1V EE T N/A Transmitter Ground1)2Tx Fault LVTTL Transmitter Fault Indication2)8)3Tx Disable LVTTL Transmitter Disable3)4MOD-DEF(2)LVTTL Module Definition 24)8)5MOD-DEF(1)LVTTL Module Definition 15)8)6MOD-DEF(0)N/A Module Definition 06)8)7Rate Select N/A Not connected8LOS LVTTL Loss Of Signal7)8)9V EE R N/A Receiver Ground1)10V EE R N/A Receiver Ground1)11V EE R N/A Receiver Ground1)12RD–LVPECL Inv. Received Data Out9)13RD+LVPECL Received Data Out9)14V EE R N/A Receiver Ground1)15V CC R N/A Receiver Power16V CC T N/A Transmitter Power17V EE T N/A Transmitter Ground1)18TD+LVPECL Transmit Data In10)19TD–LVPECL Inv. Transmit Data In10)20V EE T N/A Transmitter Ground1)1)Common transmitter and receiver ground within the module.2) A high signal indicates a laser fault of some kind and that laser is switched off.3) A low signal switches the transmitter on. A high signal or when not connected switches the transmitter off.4)MOD-DEF(2) is the data line of two wire serial interface for serial ID.5)MOD-DEF(1) is the clock line of two wire serial interface for serial ID.6)MOD-DEF(0) is grounded by the module to indicate that the module is present.7) A low signal indicates normal operation, light is present at receiver input. A high signal indicates the receivedoptical power is below the worst case receiver sensitivity.8)Should be pulled up on host board to V CC by 4.7 - 10 kΩ.9)AC coupled inside the transceiver. Must be terminated with 100 Ω differential at the user SERDES.10)AC coupled and 100 Ω differential termination inside the transceiver.DescriptionThe Infineon OC-3 transceiver – part of Infineon iSFP™ family – is compatible to the Physical Medium Depend (PMD) sublayer and baseband medium compatible to SONET OC-3 IR-1 (Telcordia GR-253-CORE) and SDH STM-1 S-1.1 (ITU-T G.957).The appropriate fiber optic cable is 9 µm single mode fiber with LC™ connector.Supported Link LengthsCategory within Standard Reach Unitmin.max.1)SDH STM-1 S-1.1015,000meters SONET OC-3 IR-1021,0001)Maximum reach over fiber type SM-G.652 as defined by ITU-T G.957 and Telcordia GR-253-CORE standards.Longer reach possible depending upon link implementation.The Infineon iSFP™ single mode transceiver is a single unit comprised of a transmitter, a receiver, and an LC™ receptacle.This transceiver supports the LC™ connectorization concept. It is compatible with RJ-45 style backpanels for high end datacom and telecom applications while providing the advantages of fiber optic technology.The Infineon single mode OC-3 transceiver is a single unit comprised of a transmitter, a receiver, and an LC receptacle. This design frees the customer from many alignment and PC board layout concerns. The module is designed for low cost LAN and applications with datarates from 10 to 155 Mbit/s. It can be used as the network end device interface in workstations, servers, and storage devices, and in a broad range of network devices such as bridges, routers, and intelligent hubs, as well as local and wide area ATM switches.This transceiver operates at up to OC-3 datarates from a single power supply (+3.3 V). The 100 Ω differential data inputs and outputs are LVPECL and CML compatible.Functional Description of iSFP™ TransceiverThis transceiver is designed to transmit serial data via single mode cable.Figure2Functional DiagramThe receiver component converts the optical serial data into CML compatible electrical data (RD+ and RD–). The Loss Of Signal (LOS) shows whether an optical signal is present.The transmitter converts CML compatible electrical serial data (TD+ and TD–) into optical serial data. Data lines are differentially 100 Ω terminated.The transmitter contains a laser driver circuit that drives the modulation and bias current of the laser diode. The currents are controlled by a power control circuit to guarantee constant output power of the laser over temperature and aging. The power control uses the output of the monitor PIN diode (mechanically built into the laser coupling unit) as a controlling signal, to prevent the laser power from exceeding the operating limits. Single fault condition is ensured by means of an integrated automatic shutdown circuit that disables the laser when it detects laser fault to guarantee the laser Eye Safety.The transceiver contains a supervisory circuit to control the power supply. This circuit makes an internal reset signal whenever the supply voltage drops below the reset threshold. It keeps the reset signal active for at least 140 milliseconds after the voltage has risen above the reset threshold. During this time the laser is inactive.A low signal on TxDis enables transmitter. If TxDis is high or not connected the transmitter is disabled.An enhanced Digital Diagnostic Monitoring Interface (Intelligent) has been incorporated into the Infineon Small Form-factor Pluggable (SFP) transceiver. This allows real time access to transceiver operating parameters, based on the SFF-8472.This transceiver features Internal Calibration. Measurements are calibrated over operating temperature and voltage and must be interpreted as defined in SFF-8472. The transceiver generates this diagnostic data by digitization of internal analog signals monitored by a new diagnostic Integrated Circuit (IC).This diagnostic IC has inbuilt sensors to include alarm and warning thresholds. These threshold values are set during device manufacture and therefore allow the user to determine when a particular value is outside of its operating range.Alarm and Warning Flags are given. Alarm Flags indicate conditions likely to be associated with an inoperational link and cause for immediate action. Warning Flags indicate conditions outside the normally guaranteed bounds but not necessarily causes of immediate link failures.These enhanced features are in addition to the existing SFP features provided by the manufacturer i.e. serial number and other vendor specific data.The serial ID interface defines a 256 byte memory map in EEPROM, accessible over a 2 wire, serial interface at the 8 bit address 1010000X (A0h).The Digital Diagnostic Monitoring Interface makes use of the 8 bit address 1010001X (A2h), so the originally defined serial ID memory map remains unchanged and is therefore backward compatible.Digital Diagnostic Monitoring ParametersParameter Accuracy SFF-8472Accuracy ActualTx Optical Power±3 dB±2 dBRx Optical Power±3 dB±3 dBBias Current±10%±10%Power Supply Voltage±3%±3%Transceiver Temperature±3°C±3°CRegulatory Compliance (EMI)2)Any kind of modification not expressly approved by Infineon Technologies may affect the regulatorycompliance of the concerned product. As a consequence thereof this could void the user’s authority to operate the equipment.Technical DataExceeding any one of these values may permanently destroy the device.Absolute Maximum Ratings Parameter Symbol Limit Values Unit min.max.Data Input VoltageV ID max V CC +0.5V Differential Data Input Voltage Swing V ID pk-pk 5V Storage Ambient Temperature T S –4085°C Operating Case Temperature 1)1)Operating case temperature measured at transceiver reference point (in cage through 2nd centre hole from rear, see Figure 9).T C–4085°C Storage Relative Humidity RH s 595%Operating Relative Humidity RH o585%Supply Voltage V CC max 4V Data Output Current I data50mA Receiver Optical Input PowerRx P max3dBmElectrical Characteristics (V CC = 2.97 V to 3.63 V, T C = –40°C to 85°C) Parameter Symbol Values Unitmin.typ.max. CommonSupply Voltage V CC–V EE 2.97 3.3 3.63VIn-rush Current1)I IR max30mA Power Dissipation P1W TransmitterDifferential Data Input Voltage Swing2)VIDpk-pk5003200mVTx Disable Voltage Tx Dis2V CC V Tx Enable Voltage Tx En V EE0.8V Tx Fault High Voltage Tx FH 2.4V CC VTx Fault Low Voltage TxFL VEE0.5VSupply Current3)I Tx150mA ReceiverDifferential Data Output Voltage Swing4)VODpk-pk5001000mVLOS Active LOS A 2.4V CC VLOS Normal LOS N V EE0.5VRise Time5)t R-Rx120psFall Time5)t F-Rx120ps Power Supply Noise Rejection6)PSNR100mVpp Supply Current3)7)I Rx130mA1)Measured with MSA recommended supply filter network (Figure7). Maximum value above that of the steadystate value.2)Internally AC coupled. Typical 100 Ω differential input impedance.3)MSA defines maximum current at 300 mA.4)Internally AC coupled. Load 50Ω to GND or 100Ω differential. For dynamic measurement a tolerance of50mV should be added.5)Measured values are 20% - 80%.6)Measured using a 20 Hz to 1 MHz sinusoidal modulation with the MSA recommended power supply filternetwork (Figure7) in place. A change in sensitivity of less than 1 dB can be typically expected.7)Supply current excluding Rx output load.Optical Characteristics (V CC = 2.97 V to 3.63 V, T C = –40°C to 85°C)Parameter SymbolValues Unitmin.typ.max.TransmitterLaunched Power (Average)1)1)Into single mode fiber, 9 µm diameter.P O–15–8dBm Extinction Ratio (Dynamic)ER 8.2dB Center Wavelength λC 12701355nm Spectral Width (rms)σI2.5nm Tx Disable Laser Output Power P O-TxDis–50dBm Optical Eye Mask 2)2)Transmitter eye is according to ITU-T G.957 S-1.1 and SONET OC-3 IR-1. Measured with 10% eye mask margin.According to standardsJitter Generation (pk-pk)3)3)The transceiver is specified to meet the SONET/SDH Jitter performance as outlined in ITU-T G.958 and Telcordia GR-253. Jitter Generation is defined as the amount of jitter that is generated by the transceiver. The Jitter Generation specifications are referenced to the optical OC-3 signals. If no or minimum jitter is applied to the electrical inputs of the transmitter, then Jitter Generation can simply be defined as the amount of jitter on the Tx optical output. The SONET specifications for Jitter Generation are 0.01 UI rms, maximum and 0.1 UI pk-pk, maximum. For SDH, 10 mUI rms, maximum. Both are measured with a 12 kHz - 1.3 MHz filter in line.A UI is a Unit Interval, which is equivalent to one bit slot.J pk-pk Tx 0.0330.045UI Jitter Generation (rms)3)J rms Tx0.0010.0025UI Rise Time 4)4)Values are 20% - 80%, filtered and measured at nominal data rate.t R-Tx 40ps Fall Time 4)t F-Tx 155ps Receiver 5)5)Receiver characteristics are measured with a worst case reference laser.Saturation (Average Power)6)6)At 9 dB Extinction Ratio of the incoming signal.P SAT –8dBm Sensitivity (Average Power)7)@ 155 Mbit/s @ 125 Mbit/s @ 10 Mbit/s 8)P IN–32–32–35–28–28–28dBmLOS Assert Level 9)P LOSA –39dBm LOS Deassert Level 9)P LOSD –30dBm LOS Hysteresis 9)P LOSA –P LOSD0.53dB Input Center WavelengthλC12601580nm7)Minimum average optical power at which the BER is less than 1x10–10. Measured with a 223–1 NRZ PRBS asrecommended by ANSI T1E1.2, SONET, and ITU-T G.957.8)8B/10B, K28.5 and equivalent coding only.9)See Figure3.Figure3Timing of Control and Status I/OParameter Symbol Values Unit Conditionmin.max.Tx Disable Assert Time t_off10µs Time from rising edge of TxDisable to when the opticaloutput falls below 10% ofnominalTx Disable Negate Time t_on1ms Time from falling edge of TxDisable to when the modulatedoptical output rises above 90%of nominalTime to Initialize, Including Reset of Tx Fault t_init300ms From power on or negation ofTx Fault using Tx DisableTx Fault AssertTimet_fault100µs Time from fault to Tx Fault onTx Disable to Reset t_reset10µs Time Tx Disable must be heldhigh to reset Tx FaultLOS Assert Time t_loss_on100µs Time from LOS state to RxLOS assertLOS Deassert Time t_loss_off100µs Time from non-LOS state to RxLOS deassertI/O Timing of Soft Control and Status FunctionsParameter Symbol Max.ValueUnit ConditionTx Disable assert time t_off100ms Time from Tx Disable bit set1)until optical output falls below10% of nominalTx Disable deassert time t_on100ms Time from Tx Disable bitcleared until optical outputrises above 90% of nominalTime to initialize, including reset of Tx Fault t_init300ms Time from power on ornegation of Tx Fault usingTx Disable until transmitteroutput is stable2)Tx Fault assert time t_fault100ms Time from fault to Tx Fault bitsetLOS assert time t_loss_on100ms Time from LOS state toRx LOS bit setLOS deassert time t_loss_off100ms Time from non-LOS state toRx LOS bit clearedRate select change time3)t_rate_sel100ms Time from change of state ofRate Select bit1) until receiverbandwidth is in conformancewith appropriate specificationSerial ID clock rate4)f_serial_clock400kHz N/AAnalog parameter data ready t_data1000ms From power on to data ready,bit 0 of byte 110 setSerial bus hardware ready t_serial300ms Time from power on untilmodule is ready for datatransmission1)Measured from falling clock edge after stop bit of write transaction.2)See Gigabit Interface Converter (GBIC). SFF-0053, Rev. 5.5, September 27, 2000.3)Not implemented.4)The maximum clock rate of the serial interface is defined by the I2C bus interface standard.Eye SafetyEye SafetyThis laser based single mode transceiver is a Class 1 product. It complies with IEC 60825-1/A2: 2001 and FDA performance standards for laser products (21 CFR 1040.10and 1040.11) except for deviations pursuant to Laser Notice 50, dated July 26, 2001.CLASS 1 LASER PRODUCTTo meet laser safety requirements the transceiver shall be operated within the Absolute Maximum Ratings.Note:All adjustments have been made at the factory prior to shipment of the devices.No maintenance or alteration to the device is required.Tampering with or modifying the performance of the device will result in voided product warranty.Failure to adhere to the above restrictions could result in a modification that is considered an act of “manufacturing”, and will require, under law, recertification ofthe modified product with the U.S. Food and Drug Administration (ref. 21 CFR 1040.10 (i)).Figure 4Required LabelsFigure 5Laser EmissionLaser Emission Data Wavelength1310 nmMaximum total output power(as defined by IEC: 7mm aperture at 14mm distance)15.6 mW / 11.9 dBm Beam divergence (full angle) / NA (half angle)11° / 0.1 radApplication NotesEMI RecommendationsTo avoid electromagnetic radiation exceeding the required limits set by the standards, please take note of the following recommendations.When Gigabit switching components are found on a PCB (e.g. multiplexer, serializer-deserializer, clock data recovery, etc.), any opening of the chassis may leak radiation; this may also occur at chassis slots other than that of the device itself. Thus every mechanical opening or aperture should be as small as feasible and its length carefully considered.On the board itself, every data connection should be an impedance matched line (e.g. strip line or coplanar strip line). Data (D) and Data-not (Dn) should be routed symmetrically. Vias should be avoided. Where internal termination inside an IC or a transceiver is not present, a line terminating resistor must be provided. The decision of how best to establish a ground depends on many boundary conditions. This decision may turn out to be critical for achieving lowest EMI performance. At RF frequencies the ground plane will always carry some amount of RF noise. Thus the ground and V CC planes are often major radiators inside an enclosure. As a general rule, for small systems such as PCI cards placed inside poorly shielded enclosures, the common ground scheme has often proven to be most effective in reducing RF emissions. In a common ground scheme, the PCI card becomes more equipotential with the chassis ground. As a result, the overall radiation will decrease. In a common ground scheme, it is strongly recommended to provide a proper contact between signal ground and chassis ground at every location where possible. This concept is designed to avoid hotspots which are places of highest radiation, caused when only a few connections between chassis and signal grounds exist. Compensation currents would concentrate at these connections, causing radiation. However, as signal ground may be the main cause for parasitic radiation, connecting chassis ground and signal ground at the wrong place may result in enhanced RF emissions.For example, connecting chassis ground and signal ground at a front panel/bezel/chassis by means of a fiber optic transceiver/cage may result in a large amount of radiation especially where combined with an inadequate number of grounding points between signal ground and chassis ground. Thus the transceiver becomes a single contact point increasing radiation emissions. Even a capacitive coupling between signal ground and chassis ground may be harmful if it is too close to an opening or an aperture. For a number of systems, enforcing a strict separation of signal ground from chassis ground may be advantageous, providing the housing does not present any slots or other discontinuities. This separate ground concept seems to be more suitable in large systems where appropriate shielding measures have also been implemented.In many situations the question on which ground concept to implement in the design cannot be easily decided prior to the receipt of first EMI measurement results. Infineon thus offers both module versions; V23848-Xx8-Xxx for common ground and V23848-Xx9-Xxx for separate ground concept.The return path of RF current must also be considered. Thus a split ground plane between Tx and Rx paths may result in severe EMI problems irrespective of which module ground concept has been applied.The bezel opening for a transceiver should be sized so that all contact springs of the transceiver cage make good electrical contact with the face plate. Please consider that the PCB may behave like a dielectric waveguide. With a dielectric constant of 4, the wavelength of the harmonics inside the PCB will be half of that in free space. Thus even the smallest PCBs may have unexpected resonances.Large systems can have many openings in the front panel for SFP transceivers. In typical applications, not all of these ports will hold transceivers; some may be intentionally left empty. These empty slots may emit significant amounts of radiation. Thus it is recommended that empty ports be plugged with an EMI plug as shown in Figure6. Infineon offers an EMI/dust plug, P/N V23818-S5-B1.SFP AccessoriesFigure 6Cage:Infineon TechnologiesPart Number: V23838-S5-N1/V23838-S5-N1-BB Cage EMI/Dust Plug:Infineon TechnologiesPart Number: V23818-S5-B1Host Board Connector:Tyco ElectronicsPart Number: 1367073-1Cage Dust Plug:Infineon TechnologiesPart Number: V23818-S5-B2EEPROM Serial ID Memory Contents (A0h), V23848-C18-C56Addr.Hex ASCII Name/Description Addr.Hex ASCII Name/Description 003Identifier3247G Vendor name104Extended identifier 336D m 207Connector3462b 300Transceiver optical compatibility3548H4103600Reserved 5023700Vendor OUI 600380370039198004056V Vendor part number900413221000423331105Encoding 433881202BR, nominal 443441300Reserved45388140F Length (9 µm) - km 462D -1596Length (9 µm)4743C 1600Length (50 µm)483111700Length (62.5 µm)493881800Length (copper)502D -1900Reserved 5143C 2049I Vendor name 52355216E n 533662266f 54202369i 5520246E n 5646F Vendor revision, product status dependent 2565e 57333266F o 5841A 276E n 5939928206005Wavelength 2946F 611E 304F O6200Reserved 312063BACheck sum of bytes 0 - 626400Transceiver signaloptions 9620Vendor specificEEPROM651A9720 6600BR, maximum9820 675E BR, minimum9920 68Vendor serial number10020 6910120 7010220 7110320 7210420 7310520 7410620 7510720 762010820 772010920 782011020 792011120 802011220 812011320 822011420 83201152084Vendor manufacturingdate code 116208511720 8611820 8711920 8812020 8912120 902012220 912012320 9268Diagnostic monitoringtype12420 93B0Enhanced options12520 9401SFF-8472 compliance1262095Low order 8 bits of thesum of the contents ofall the bytes from byte64 to byte 94, inclusive 12720128 -25500Vendor specific.Reserved for futureuseEEPROM Serial ID Memory Contents (A0h), V23848-C18-C56 (cont’d)Addr.Hex ASCII Name/Description Addr.Hex ASCII Name/DescriptionEEPROM Serial ID Memory Contents (A0h), V23848-C19-C56Addr.Hex ASCII Name/Description Addr.Hex ASCII Name/Description 003Identifier3247G Vendor name104Extended identifier 336D m 207Connector3462b 300Transceiver optical compatibility3548H4103600Reserved 5023700Vendor OUI 600380370039198004056V Vendor part number900413221000423331105Encoding 433881202BR, nominal 443441300Reserved45388140F Length (9 µm) - km 462D -1596Length (9 µm)4743C 1600Length (50 µm)483111700Length (62.5 µm)493991800Length (copper)502D -1900Reserved 5143C 2049I Vendor name 52355216E n 533662266f 54202369i 5520246E n 5646F Vendor revision, product status dependent 2565e 57333266F o 5841A 276E n 5939928206005Wavelength 2946F 611E 304F O6200Reserved 312063BBCheck sum of bytes 0 - 626400Transceiver signaloptions 9620Vendor specificEEPROM651A9720 6600BR, maximum9820 675E BR, minimum9920 68Vendor serial number10020 6910120 7010220 7110320 7210420 7310520 7410620 7510720 762010820 772010920 782011020 792011120 802011220 812011320 822011420 83201152084Vendor manufacturingdate code 116208511720 8611820 8711920 8812020 8912120 902012220 912012320 9268Diagnostic monitoringtype12420 93B0Enhanced options12520 9401SFF-8472 compliance1262095Low order 8 bits of thesum of the contents ofall the bytes from byte64 to byte 94, inclusive 12720128 -25500Vendor specific.Reserved for futureuseEEPROM Serial ID Memory Contents (A0h), V23848-C19-C56 (cont’d)Addr.Hex ASCII Name/Description Addr.Hex ASCII Name/DescriptionDigital Diagnostic Monitoring Interface – IntelligentAlarm and Warning Thresholds (2-Wire Address A2h)Address# Bytes Name Description Value00 - 012Temp High Alarm MSB at low address95°C1)02 - 032Temp Low Alarm MSB at low address–40°C1)04 - 052Temp High Warning MSB at low address90°C1)06 - 072Temp Low Warning MSB at low address–35°C1)08 - 092Voltage High Alarm MSB at low address 3.7 V2)10 - 112Voltage Low Alarm MSB at low address 2.85 V2)12 - 132Voltage High Warning MSB at low address 3.63 V2)14 - 152Voltage Low Warning MSB at low address 2.97 V2)16 - 172Bias High Alarm MSB at low address70 mA18 - 192Bias Low Alarm MSB at low address 4 mA20 - 212Bias High Warning MSB at low address60 mA22 - 232Bias Low Warning MSB at low address 5 mA24 - 252Tx Power High Alarm MSB at low address–7 dBm26 - 272Tx Power Low Alarm MSB at low address–16 dBm28 - 292Tx Power High Warning MSB at low address–8 dBm30 - 312Tx Power Low Warning MSB at low address–15 dBm32 - 332Rx Power High Alarm MSB at low address–7 dBm34 - 352Rx Power Low Alarm MSB at low address–32 dBm36 - 372Rx Power High Warning MSB at low address–8 dBm38 - 392Rx Power Low Warning MSB at low address–28 dBm40 - 5516Reserved Reserved for futuremonitored quantities1) A delta exists between actual transceiver temperature and value shown as measurement is taken internal toan IC located on the underside of the iSFP™ PCB.2)Transceiver voltage measured after input filter with typical 0.1 V voltage drop.Calibration Constants for External Calibration Option (2-Wire Address A2h) Address# Bytes Name Description Value56 - 594Rx_PWR (4)Single precision floating pointcalibration data, Rx optical power.060 - 634Rx_PWR (3)0 64 - 674Rx_PWR (2)0 68 - 714Rx_PWR (1)1 72 - 754Rx_PWR (0)0 76 - 772Tx_I (Slope)Fixed decimal (unsigned)calibration data, laser bias current.178 - 792Tx_I (Offset)Fixed decimal (signed two’scomplement) calibration data,laser bias current.80 - 812Tx_PWR (Slope)Fixed decimal (unsigned)calibration data, transmittercoupled output power.182 - 832Tx_PWR (Offset)Fixed decimal (signed two’scomplement) calibration data,transmitter coupled output power.84 - 852T (Slope)Fixed decimal (unsigned)calibration data, internal moduletemperature.186 - 872T (Offset)Fixed decimal (signed two’scomplement) calibration data,internal module temperature.88 - 892V (Slope)Fixed decimal (unsigned)calibration data, internal modulesupply voltage.190 - 912V (Offset)Fixed decimal (signed two’scomplement) calibration data,internal module supply voltage.92 - 943Reserved Reserved951Check sum Byte 95 contains the low order8bits of the sum of bytes 0 - 94.A/D Values and Status Bits (2-Wire Address A2h)Byte Bit Name DescriptionConverted Analog Values. Calibrated 16 Bit Data.96All Temperature MSB Internally measured moduletemperature1)97All Temperature LSB98All V CC MSB Internally measured supply voltagein transceiver99All V CC LSB100All Tx Bias MSB Internally measured Tx Bias Current 101All Tx Bias LSB102All Tx Power MSB Measured Tx output power103All Tx Power LSB104All Rx Power MSB Measured Rx input power105All Rx Power LSB106All Reserved MSB Reserved for 1st future definition ofdigitized analog input107All Reserved LSB Reserved for 1st future definition ofdigitized analog input108All Reserved MSB Reserved for 2nd future definition ofdigitized analog input109All Reserved LSB Reserved for 2nd future definition ofdigitized analog inputOptional Status/Control Bits1107Tx Disable State2)Digital state of the Tx Disable InputPin1106Soft Tx Disable2)Read/write bit that allows softwaredisable of laser. Writing 1 disableslaser1105Reserved1104Rx Rate Select State2)Digital state of the SFP Rx RateSelect Input Pin1103Soft Rx Rate Select2)Read/write bit that allows softwareRx rate select. Writing 1 selects fullbandwidth operation. Notimplemented.。