IE工业工程改善手法(中文)
IE工业工程七大手法的改善方案

IE七大手法之四 — 五五法
1.手法名称: 5 * 5W 1H法;又称5 * 5何法;又称质疑创意法;简称五五 法。
2.目的: 学习本手法的目的在于:
熟悉有系统的质问的技巧,以协助我们发掘 出问题的真正根源所在以及可能的创造改 善途经。
3.1 基本观念:
头脑就像降落伞,○○○只有在开放的情 況下才工作○○○。
工作改善最大的阻碍并不在于技术不足, 而是在于一个人的想法~当他觉得是以最 好的方法在工作着,并且以为满足。
当你认为工作已无法改善了,那就代表你 已落伍了,虽然你是专家,拥有高深的学识.
一个虽然沒有多大学识的人,只要他认为 工作仍有改善的可能,那么他就比您更适 合这工作。
3.2 何处最需要改善 您的時間非常宝贵,应妥善运用;挑最重要的事情
手掌的张 度
三
肘
+前臂
前臂的张 度
四
五
肩
身躯
+上臂
+肩
上臂的张 上臂+身躯
度
弯曲
速度
1
2
3
4
5
体力消耗 最少
少
中
多
最多
动作力量 最弱
弱
中
强
最强
疲劳度
最小
小
中
大
时间(以 25mm为准)
0.0016分
0.0017分
0.0018分
0.0026分
最大
原則5: 物体的“动量”尽可能利用;但如 需用肌力制止时,则应将减至最小度。
1.手法名称 又称动作改善法,简称为“动改法”,是: * 省力动作原則 * 省时动作原則 * 动作舒适原則 * 动作简化原則 此原則以最少的劳力到达最大的工作效果,其原为吉而博斯
IE工业工程改善七大手法

IE工业工程改善七大手法概述IE工业工程是指以科学方法为基础,运用系统工程理论和方法,在生产过程中对人、机、料、法、环境进行综合优化的一门工程学科。
IE工业工程改善七大手法是指在IE工业工程领域中常用的七种改善方法,本文将详细介绍这七大手法。
1. 横向流程优化横向流程优化是指通过对生产过程中不同环节进行分析,找出其中存在的瓶颈和浪费,并采取相应的措施来优化流程。
这种方法可以提高生产效率,减少物料和资源浪费,同时还能提升产品质量。
横向流程优化通常包括以下几个步骤: - 流程分析:对生产流程进行细致的分析,了解每个环节的具体操作和所需资源。
- 瓶颈分析:找出流程中的瓶颈环节,即造成生产效率降低和浪费的主要原因。
- 流程改善:通过重新设计流程或引入新的技术和设备,解决瓶颈环节问题,从而提升整体流程效率。
2. 垂直流程优化垂直流程优化是指在生产过程中,对整个生产线上下游环节进行优化,以实现生产过程的高效协同。
垂直流程优化的关键是实现信息的及时传递和合理协调,以确保每个环节对上下游环节的要求和交接点的协调。
垂直流程优化通常包括以下几个方面: - 信息流优化:通过引入信息化系统或升级现有系统,实现信息的实时传递和共享,从而提高生产过程中的响应速度和准确性。
- 协调改善:通过改善沟通和协作机制,减少生产过程中的延误和误解,提高协同效率。
- 质量管理:在生产过程中引入全面质量管理的理念和方法,强调各个环节的质量控制和持续改进。
3. 设备改善设备改善是指通过技术改进和设备优化来提高生产效率和产品质量。
设备改善可以通过以下方式实现: - 技术创新:引入新的生产技术和设备,提高生产过程中的效率和自动化程度。
- 设备维护:建立定期维护和保养计划,保证设备的正常运行和延长使用寿命。
- 能源节约:优化设备的能源使用,减少能源消耗和环境污染。
4. 物料管理物料管理是指对生产过程中的原材料和半成品进行有效的控制和管理,以确保生产过程的顺利进行。
生产干部必备的IE改善手法

生产干部必备的IE改善手法1. 引言IE(Industrial Engineering)是指工业工程,它是通过优化工业生产过程,提高生产效率的一种方法。
对于生产干部来说,掌握IE改善手法是提升生产效率、降低成本的关键。
本文将介绍一些生产干部必备的IE改善手法,帮助他们更好地管理生产过程。
2. 价值流分析价值流分析是一种用于分析和改善生产过程的工具。
通过价值流分析,生产干部可以了解整个生产过程中的每个环节,找出其中的瓶颈和浪费,进而进行改进。
在进行价值流分析时,以下几个步骤是必不可少的:•绘制当前状态的价值流地图:绘制出从原材料采购到产品出货的整个生产过程地图,标注出每个环节的信息流和物流。
•识别瓶颈环节:通过分析各个环节的生产能力,找出生产过程中的瓶颈环节,即制约整个生产过程的关键环节。
•消除浪费:通过分析每个环节中的浪费,采取相应的措施来消除这些浪费,提高生产效率。
3. 连续流水线连续流水线是一种用于大批量生产的工业生产方式。
它将产品在生产过程中分成多个环节,并将每个环节的工作分配给不同的工人或机器。
通过优化流水线上各个环节的工作效率,可以提高生产效率,降低成本。
在建立连续流水线时,以下几个因素需要考虑:•流程平衡:各个环节的工作时间应该平衡,以避免某个环节成为瓶颈。
•工位布局:合理的工位布局可以减少操作员之间的移动距离,提高工作效率。
•节拍时间:合理的节拍时间可以保证连续流水线的稳定运行。
4. 作业分析作业分析是通过评估工作任务的性质和要求,确定完成任务所需的资源和时间的过程。
通过作业分析,生产干部可以更好地了解每个工作岗位的任务和要求,为员工提供相应的培训和指导,提高工作效率。
在进行作业分析时,以下几个步骤是必要的:•观察和记录:观察员工在工作岗位上的表现,并记录下每个工作任务的具体内容。
•任务分解:将每个工作任务分解成更小的子任务,确定每个子任务所需的时间和资源。
•评估和改进:评估每个工作任务的效率和质量,并根据评估结果进行改进,提高工作效率。
2020年(IE工业工程)改善(IE)七大手法
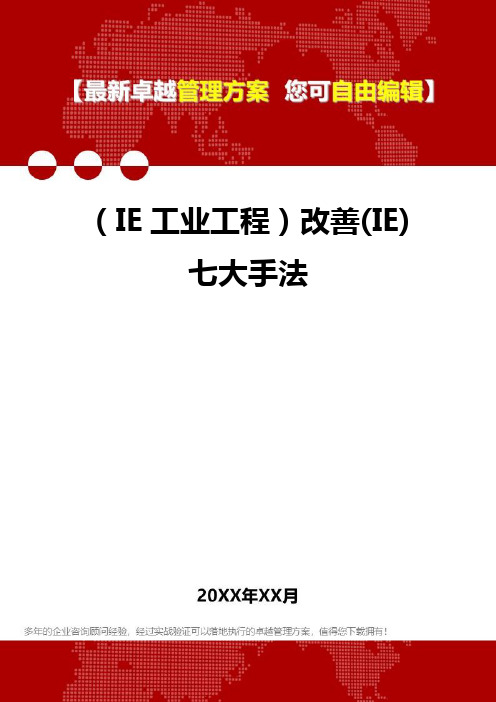
(IE工业工程)改善(IE)七大手法改善(IE)七大手法人機法1.手法名稱人機配合法(Man-MachineChart),簡稱為”人機法”。
2.目的學習如何記錄人與機器配合工作時之過程。
3.意義以圖表的方式,記錄操作者與一部機器或多部機器之操作關係,並藉此記錄來做進一步之分析與改善。
4.應用範圍(1)1人操作1部機器或多部機器。
(2)數人操作1部機器或多部機器。
(3)數人操作一共同之工作。
5.功用(1)了解在現況下,操作者之時間與機器之時間是否妥善應用。
(2)依上述之記錄加以質疑,尋求改善之地方。
(3)用以比較改善前及改善後之差異情形。
6.填表說明:(1)編號:自行設定編號系統,填入此次研究之代號。
例:MM-8601(2)工作名稱:填寫此研究之名稱。
(3)現況/改善方法:依此次研究係以現況或抑以改善為記載之記錄在適用者前面之方格內打““。
(4)研究者:填寫做此項研究者之姓名。
(5)日期:填寫做此項研究之日期。
(6)總結:將此項研究所獲得”人”及”機器”之各項時間及百分比之總結資料整理於此欄內。
(7)位置簡圖:繪製有關此項研究”人”與”機器”之相關位置簡圖,視必要時再繪製。
(8)製品簡圖:繪製此項工作之製品之製品之簡圖,視必要時再繪製。
(9)時間刻度:以刻度之長短來代表”人”或”機器”之動作時間之長短,刻度單位可以自行設定每一小格為一分鐘,或任何其他之適當時間之單位。
(10)類別:依照動作之類別,即”共同作業”,”單獨作業”,或“等待”以其代表之方格類別配合動作之起迄時刻範圍,繪製出來。
(11)人之動作:記錄有關”人”之動作過程。
(12)機器之動作:記錄有關”機器”之動作過程,注意此欄可以靈活運用,如果是探討二個人其同工作之情形時,此時機器之動作,可改為另一個人之動作,如果是探討有關1人與2人部機器之配合問題之研究時,則可以再增加一頁紙張,利用右邊之”機器之動作欄”再記錄其他機器之動作。
7.1案例:老王家裏庭院內有棵大樹,枝葉長得很茂盛,其中有一支大樹枝長得太靠近窗口的室外電線。
IE(工业工程)基本内容及技法

载支持。
IE基本内容及技法1.简介:IE英文为(industrial engineering),中文翻译为工业工程.发展历程为:起源于19世纪美国人泰勒,他最先提出了动作研究,被后人称为工业工程之父.成功应用于福特汽车公司,使福特汽车公司迅速崛起.在七十年代流行于欧美日等发达国家.IE是一门集技术与管理于一体的边缘科学.IE定义:是对人员,物料,设备,能源及信息所组成的集成系统,进行设计、改善和设置的一门学科.它综合运用数学、物理学和社会科学方面的专门知识以及工程分析和设计的原理和方法,对该系统所取得的成果进行确定、预测和评价.简而言之, 就是运用人,机,料做最有效的组合, 以达到最有效的产出(OUT PUT)IE目标:是设计一个生产系统及该系统的控制方法.使之成本最低,具有特定的质量水平,并且这种生产必须是在保证工人和最终用户的健康和安全的条件下进行.IE的特点:(1)以人为中心进行设计,注重人的因素.(2)面向微观管理:关注减少浪费,降低成本.2.基础IE:IE专业入门课.基础IE主要内容分为三部分:动作研究,时间测定及现场管理优化.基础IE的全过程为:利用程序分析、操作分析、动作分析研究获得最佳程序和方法,然后再利用作业测定将所有作业制定出标准时间.整個制造程序分析-操作程序圖Operation Process Chart產品或材料之流動--流程程序圖Flow Process Chart程序分析Process Analysis布置与路徑分析--線圖Flow Diagram人--机程序圖Man-Machines閉系統能量分析-聯合程序圖Process Chart多動作程序圖工作時兩手之移動-操作人程序圖Multiple-Activity ChartOperator Process Chart操作分析Operation Analysis方法研究Method Study目視動作研究Cursory Analysis微速度動作分析Memo-motion Study動作研究影片分析細微動作研究Motion Study Micro-motion Study動作軌跡影片Cycle-graphic工作研究Operation 動作經濟原則Reserch Principles of Motion Economy標准應用設備選定標准操作員馬表時間研究實施時間研究決定基本操作時間Stop-watch Study計算時間資料賦予評比(Rating)決定標准時值賦予寬放(Allowance)作業測定預定動作時間研究Work Pre-determined Motion Time StudyMeasurement工作抽查Work Sampling標准動作說明工作指導單Instruction Sheet對動圖(Simo-chart)設定工作標准(Standardizing )1.方法2.材料3.工具与設備微細動作指導第一篇方法研究从操作、运输、贮存、检验、等待这五个方面来进行分析.例如检验经常考虑以下问题:能否取消或与其它操作合并;能否同时使用多种量具或多用途量具;增加亮度或改善灯光布置是否可减少检验的时间;检验物与检验者眼睛的距离是否合适;检验物的数量是否足够采用电动自动检验.一.程序分析:程序分析:完成任何工作所需经过的路线和手续即为程序.常用程序图,线路图.程序图以工作内容为主,线路图以料件从投入到产出的路线为主.二.操作分析:研究分析以人为主体的工序.依据人与机器的关系分为人机操作分析、联合操作分析、双手操作分析三种.三.动作研究:研究分析人在进行各种操作时的身体动作.人体的生产动作基本可以分为十七个动素.台湾一个教授将动素分为四个同心圆.由里向外依次为1.(核心动素)使用,装配,拆卸.2.(常用动素,需要改善)伸手,运送,抓取,放下.3.(辅助性动素,生产中越少越好)检查,寻找,选择,定位,预定位,持住.4.(消耗性动素,尽可能予以取消)延迟,故延,思考,休息.IE七大手法1>.防错法(也叫防呆法或愚巧法FOOL-PROOF):第一次就把事情做好.2>.动作改善:改善人体动作方式,减少疲劳.使工作更舒适,更有效率3>.流程法: 研究探讨涉及几个不同工站或地点之流动关系,藉以发掘改善之处.4>.六何分析法即5W1H提问技术:when,who,where,what,why,how.式.5>.人机配合法.6>.经济动作(双手法)7>.抽查法:通过抽查统计能了解问题真象.四.ECRS四大原则.1>.删除─所研究之工作,首先考虑取消之可能性,如不必要的作业,不必要的搬运,不必要的检验,不必要的停滞.2>.合并──通过对生产线平衡的分析,对不平衡之环节重新整合.3>.重组──改变工作程序,使前后顺序,重新的组合,以达到改善之目的.4>.简化──在经过删除,合并.重组之后,再对每一项工作作深入分析,昼量简化动作,使新的方法能产生更高之效率.五.PDCA循环:与ISO9000中的质量环相同.方法研究步骤1.选择问题运用IE手法发现3U(不合理, 不平衡, 不节省)2.掌握现状运用IE手法调查,研究, 分析3.改良方法设计运用现场布置法或搬运布置法加予研究改良4.改良方法试行依照改良的新方法试行, 并加以统计.5.比较新旧方法之结果依新方法试行结果与原方法在效率,成本方面进行比较6.做成结论改良的新方法是接受或经修改后重新回到步骤47.标准化经接受的新方法是做成新的工作标准通过方法研究,目的是建立标准化,及找出问题所在,进行改善.第二篇作业测定定义:运用各种技术来确定合格工人按规定的作业标准,完成某项工作所需的间.在成本预算中,人工成本占有很大的比例.而且在相同的环境下,人工成本的高低反映了企业经营管理的水平.所以,作业测定的真实性、准确性至关重要.标准工时的测定应该建立在作业标准化的基础上,否则将失去应有的意义.标准工时:是指在适宜的操作条件下,用最合适的操作方法,以普通熟练工人的正常速度完成标准作业所需的劳动时间.作业测定常用的方法:一.经验判断法:即估工.根据图纸,样品等来估计所需的工时.如冲床,生产效率以冲床的开动率为主.多任务序模产能可以定为300件/小时,连续模可定为600件/小时.二.历史纪录法:即统计分析法.根据以往的生产纪录或同类型产品的纪录.三.秒表法:在一段时间内,连续观测,纪录下来给予一个评比值,再加上宽放值,最后确定出该项作业的时间标准.秒表法是目前常用的方法,但误差很大.因为国内没有专门的训练机构,所以时间测定员不同,所得的时间也会有差别.秒表法所测的标准时间=平均操作时间*评比系数+宽放时间.宽放率=宽放时间/稼动时间*100%一般宽放包括:作业宽放(物), 需要宽放(人), 疲劳宽放(人)评比因素分为1.熟练度2.努力度3.工作环境4.一致性(及操作者生产多个料件所用的时间是否一致.)四.工作抽样法:在较长时间内,以随机方式,分散观测.利用分散抽样来研究工时的利用效率.它主要应用于以下两个方面:1.工作改善,调查操作者或机器的利用率. 2.制定标准时间.它的计算公式为标准时间=总观测时间*工作比率*平均绩效指针/观测期间的总产量+宽放.五.MOD法:不需观测,可以客观地确定出标准时间.MOD法所有人力操作时的动作,均包含在一些基本的动作里.可以归纳为21种;不同人做相同的动作所需的时间值基本相同.1MOD=0.129s(实际值) 0.142s(宽放后的值).例如,手指动作=M1,手腕动作=M2,小臂动作=M3,大臂动作=M4,伸直的臂=M5,坐下~站起=S30,弯曲~站起=B17,用眼=E2,判断=D3,走步=W5等.(数字即为MOD值,共有0、1、2、3、4、5、17、30八个值)六.标准资料法:综合以上测定所得,进行分门别类,建立动作、操作、程序的标准时间.第三篇现场管理优化现场是一个系统,IE要求从人,机,物,料,环五个方面进行综合考察.1.5S2.定置管理.是5S的深化.3.目视管理.现场只存在两种劳动,一种创造价值,一种不创造价值,IE的使命就是减少甚至消除不创造价值的劳动,即消除浪费.现场工作改善常用的IE手法有关”物”的方面1.工程分析法2.现场布置法3.搬运布置法4.稼动分析法5.工作简化法6.生产平衡法生产平衡分析的步骤A.确定工序B.确定各工序人数C.计算各工序之平均时间D.最高工序之时间划线E.计算不平衡损失时间不平衡损失时间=(最高DM*总人数) – (各工序时间合计)F.计算不平衡损失率不平衡损失率= 各工序时间合计/(最高DM*人数)生产线工时平衡实例分析分析手法/技巧在工序工时平衡中运用举例核准审核制作工作中心***** 线点时间13秒生产时间8小时x y z制品名称**** 料号********* 生产数量2000PCS不良率2%工程名称1234567合计工作人数11111117实际时间12(秒)101391181275工序工时平衡率:75/改善着眼点:第三工程工时降低,第四,六工程重排工序工时不平衡率损失:17.58%备注:不平衡率在15%内可接受,10%为良好.7.时间研究8.标准时间有关”人”的方面动作分析法动作经济原则1.双手应同时对称,谐调(最好反向)完成动作.除规定的休息时间外,双手不应同时空闲.例如,方法一为在拉钉机上装拉钉,左手拿取拉钉,右手一次一个将拉钉插入拉钉孔中.方法二为双手同时做拿取拉钉和插入拉钉的动作.很明显,双手同时动作较单手操作节省时间,并且不易疲劳.2.人体的动作应以最低的等级而能得到满意的结果.人体的动作可以分位五级:第一级为手指动作(食指最灵活,迅速) 第二级为手指、手腕的动作. 第三级为手指、手腕及小臂的动作. 第四级为手指、手腕及大臂的动作.第五级为大臂及身体的动作.应该尽可能选择级次最低的动作,使工作距离缩短,材料、工具、零件尽可能靠近工作地.例如组装在线的电批及气动拉钉枪,可以悬挂在夹具上,用一根弹簧来使其复位.在需要使用时,用手一拉就可以将电动工具拉下来就位,用完之后一松手电动工具就回复到上面.夹具做成可移动式,花费并不大.3.动作尽可能运用轻快的自然节奏,因为节奏能使动作流利及自发;连续的曲线运动,比方向突变的直线运动为佳.例如,冲压部擦拭冲压件油污,按正常情况,应先根据制件的表面情况,规定擦拭方法.如先擦何处,再擦何处,擦几下,如何擦.决无到处乱擦,反复寻找的浪费动作,有节奏,工作效率自可提高.4.工具、物料及装置应放置在固定的地方,最好在操作者的前面近处;工具物料应依最佳的工作顺序排列.5.零件、物料的供给,应利用其重量坠送至工作者的手边,坠落尽量依靠重力自然下滑.6.应有适当的照明,使视觉舒适;工作台及座椅的高度,应保证工作者坐立适宜.7.尽量解除手的动作,以夹具或脚踏工具代替.8.可能时,应该将两种工具合并使用.9.工具、物料尽可能预放在工作位置上.10.设计夹具、手柄时,尽可能增大与手的接触面.IE其余内容有运筹学,工效学,技术经济分析,工程师质量管理,激励学,生产管理,现代制造技术,现代生产方式等,不一一介绍了.IE的发展新时代的工业工程师赵耀东着天下文化出版新时代的工业工程师应培养世界观的气质,切忌划地自限,坐井观天,如此才能打破国内有限资源及狭小市场的瓶颈,寻求更佳的生产及贸易机会。
【2022年管理】IE工业工程的改善手法

改善案
現狀
改善案
單獨自動
0.2(2)
0.2(3)
2.0(24)
2.0(33)
2.5(30)
2.5(41)
必需徒手做的作業
8.0(98)
6.0(97)
3.0(37)
3.0(48)
5.0(61)
3.0(48)
等待、賦閑
0(0)
0(0)
3.2(39)
1.2(19)
0.7(9)
0.7(11)
合計
8.2(100)
作業者─機械分析改善的著眼點
分析結果
著眼點
作業者在“等待”的場合
自動運轉時間的縮短,高速化、以及機械的改善等。自己動手的時間之改善,找找看,有沒有在自動運轉中,能夠從事的作業。
機械在賦閒的場合
縮短作業者單獨作業的時間改善必需動手做的作業,以及徒手作業的自動化
作業者、機械都在賦閒的場合
重新編制作業次序考慮到1及2項的著眼點
3.0
37
5.0
61
等待、賦閒
0
0
3.2
39
0.7
9
合計
8.2
100
8.2
100
8.2
100
做成改善案
參考次頁的“作業者─機械分析”改善的著眼點,舉行檢討並製成改善案。從本例來看,作業甲很忙,根本沒時間休息,但機械A及B都賦閒,尤其是B的更換工程階段時間太長。此外注意到A、B更換工程階段時間有差異,進一步檢討此種差異何以會發生,提出改善。次頁為各項改善狀況的比較。
分析一周期作業
恰如實施作業者工程分析一樣,對於作業者及機械,各自要針對一週期的作業內容,製作一份工程流動圖。以本例繪成流動圖,如次頁所附。
IE工业工程的改善手法
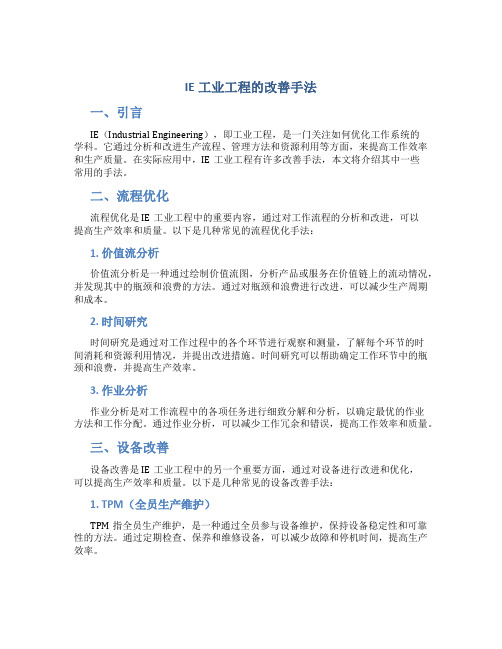
IE工业工程的改善手法一、引言IE(Industrial Engineering),即工业工程,是一门关注如何优化工作系统的学科。
它通过分析和改进生产流程、管理方法和资源利用等方面,来提高工作效率和生产质量。
在实际应用中,IE工业工程有许多改善手法,本文将介绍其中一些常用的手法。
二、流程优化流程优化是IE工业工程中的重要内容,通过对工作流程的分析和改进,可以提高生产效率和质量。
以下是几种常见的流程优化手法:1. 价值流分析价值流分析是一种通过绘制价值流图,分析产品或服务在价值链上的流动情况,并发现其中的瓶颈和浪费的方法。
通过对瓶颈和浪费进行改进,可以减少生产周期和成本。
2. 时间研究时间研究是通过对工作过程中的各个环节进行观察和测量,了解每个环节的时间消耗和资源利用情况,并提出改进措施。
时间研究可以帮助确定工作环节中的瓶颈和浪费,并提高生产效率。
3. 作业分析作业分析是对工作流程中的各项任务进行细致分解和分析,以确定最优的作业方法和工作分配。
通过作业分析,可以减少工作冗余和错误,提高工作效率和质量。
三、设备改善设备改善是IE工业工程中的另一个重要方面,通过对设备进行改进和优化,可以提高生产效率和质量。
以下是几种常见的设备改善手法:1. TPM(全员生产维护)TPM指全员生产维护,是一种通过全员参与设备维护,保持设备稳定性和可靠性的方法。
通过定期检查、保养和维修设备,可以减少故障和停机时间,提高生产效率。
2. SMED(单分钟交换模具)SMED是一种通过改进模具更换过程来减少生产停机时间的方法。
通过优化模具的设计和更换过程,可以缩短模具更换时间,提高生产效率和灵活性。
3. 设备自动化设备自动化是一种通过引入自动化设备和系统,自动完成生产过程的方法。
通过减少人工操作和提高生产速度,可以提高生产效率和精度。
四、人力资源管理人力资源管理是IE工业工程中一个重要的方面,通过合理管理和配置人力资源,可以提高工作效率和质量。
ie工业工程现场改善手法

录 目
Training Within Industry
课程一 课程二 课程三 课程四 课程五 课程六 课程七 课程八
管理基础与职责认识 有效人际沟通 部下培养与有效激励 现场质量管理 现场设备管理 现场成本管理 现场改善手法 高效率工作方法
Training Within Industry
目录
练习1 羊年造牛 练习2 空中画葫芦 练习3 石头记 练习4 钎焊的烦恼
问题 发现
原因 分析
设计 实验
确定 对策
Training Within Industry
实验设计
有目的、计划地在某种条件下进行实 验,从而获得能预测某种现象的统计资料, 并通过分析实验结果,从该现象中归纳出 普遍性及再现性规律的改善方法。
Training Within Industry
实验设计
原因
0、业务的两种基本类型
Training Within Industry
富有魅力 的质量
理所当然 的质量
问题解决型 业务
(消除浪费)
现状课题
目标实现型 业务
(创造价值)
面向未来 的课题
1、改善过程全貌
动态 管理
严格 遵守
标准 化
变化
事故
NG OK 改善
确认
Training Within Industry
标准化 巩固措施 今后打算
分层法 调查表 排列图 因果图 直方图 控制图 散布图
●
●
●
●
●
●
●
●
●
●
●
●
●
●
●
●
●
●
●
●
●
●
IE工业工程现场改善:5防错法

工业工程现场改善:第五章防錯法(愚巧法、防呆法)第一節防錯法概述防錯法日文稱POKA-YOKE,又稱愚巧法、防呆法。
意即在過程失誤發生之前即加以防止。
是一種在作業過程中采用自動作用、報警、標識、分類等手段,使作業人員不特別注意也不會失誤的方法。
一. 防錯法的作用在作業過程中,作業者不時會因疏漏或遺忘而發生作業失誤,由此所致的品質缺陷所占的比例很大,如果能夠用防錯法防止此類失誤的發生,則品質水平和作業效率必會大幅提高。
1. 防錯法意味著“第一次把事情做好”因為防錯法采用一系列方法或工具防止失誤的發生,其結果即為第一次即將事情做好。
2. 提升産品品質,減少由於檢查而導致的浪費防錯法意味著“第一次即把事情做好”,直接結果就是産品品質的提高,與靠檢查來保證品質相比,防錯法是從預防角度出發所采取的預防措施。
而檢查不能防止缺陷的産生,檢查發現的缺陷只能去糾正。
這是一種浪費,防錯法消除了這種浪費。
3. 消除返工及其引起的浪費防錯法會提升産品品質,消除缺陷,這會導致返工次數的削減,由於返工所致的時間和資源浪費便得以消除。
二. 基本原則1. 輕松原則—使作業的動作輕松難以辨認﹑難拿﹑難動等作業即變得難做﹐使作業員疲勞而發生失誤。
可以這樣進行改善﹕(1)用不同顏色區分﹐放大標識—容易辨認例﹕SMT機台指示燈不同顏色代表不同的運行狀況。
(2)加上把手—容易拿例﹕較大型的治具為了減少搬動的動作﹐可考慮加上把手﹐降低動作等級。
(3)使用搬運器具—動作輕松例﹕各種手推車﹐烏龜車等。
2. 簡單原則—使作業不需要技能和直覺需要高度技能與直覺的作業﹐容易發生人為失誤﹐考慮用治具或工具進行機械化﹐使新進人員或支援人員也不容易出錯。
3. 安全原則—使作業不會有危險有不安全或不安定因素時﹐加以改善﹐使其不會有危險﹔馬虎作業或勉強作業有危險時﹐設法安裝無法馬虎或無法勉強作業的裝置。
4. 自動化原則—使作業不依賴感官(1)依賴像眼睛﹑耳朵等感官進行作業時﹐容易發生失誤﹐制作治具使之機械化﹐減少用人的感官來判斷作業。
IE工业工程工作改善方法
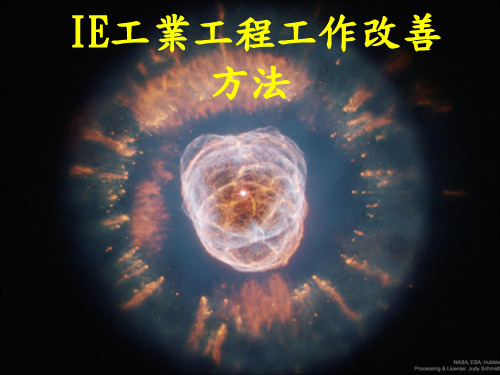
第一章、 防錯法
三、意 義: 防錯法又稱防愚法,其義即是防止愚笨的人做錯事。
亦即,連愚笨的人也不會做錯事的設計方法。 狹義:如何設計一個東西,使錯誤絕不會發生。 廣義:如何設計一個東西,而使錯誤發生的機會減至最低
的程度。 因此,更具體的說“防錯法”是:
3.1具有即使有人爲疏忽也不會發生錯誤的構造——不需要 注意力。
例:抽水馬桶之水箱內設計有浮球,水升至某一高度時, 浮球推動拉捍,切斷水源。 (二)以“重量”控制的方式來完成
例:電梯超越時,門關不上,電梯不能上下,警告鍾也 鳴起。 (三)以“光線”控制的方式來完成
例:自動照相機,光線若不足時,則快門按不下去。
第二章、防错法應用原理介绍
(四)以“時間”控制的方式來完成例:洗手間內的“烘手 機”, 按一次只有“一分鐘”,時間一到自動停止。
第一章、 防錯法
七、進行步驟 防錯法進行方法的基本步驟如下:
[步驟1]發現人爲疏忽 无论發生何種之人爲疏忽,收集資料進行調
查,重估自己的工作找出疏忽所在。 [步驟2]設定目標,制訂實施計划。
計划要明确5W1H。 [步驟3]調查人爲疏忽的原因
盡可能廣泛的收集情報或資料,設法找出真 正的原因。
第一章 、 防錯法
第二章、防错法應用原理介绍
5順序原理 避免工作之順序或流程前後倒置,可依編號順序排列,
工业工程七大手法(IE)的七大手法与合理化改善

是可以降低其損害的程度. EXL: 1.雞蛋之隔層裝運盒減少搬運途中的損傷.(緩和原理) 2.設立多層之檢查方法,考試后檢查一次看看,有沒有犯錯的地方.(保險原理) 3.自動消防洒水系統,火災發生了開始自動洒水滅火.(警告原理) 4.汽車之安全帶,騎機車戴安全帽.(保險原理) 5.加保利龍或紙板以減少產品在搬運中之碰傷.(緩和原理) 6.原子筆放在桌上老是給別人不經意中拿走,怎麼辦呢?貼上姓名條或加條繩子固
* 持續的進步是企業及個人長久生存的根基.
* 改善就是進步的原動力,沒有改善就沒有進步.—學如逆水行舟,不進則退.
* 改善是永無止境的,必須長久持續去進行.
2020/1/16
3
IE簡介
4
4.IE的主要範圍?
* 工程分析 * 價值分析(V.A) * 動作研究 * 工作標準
* 時間研究 * 時間標準
* 工廠布置 * 運搬設計
原則1: 兩手同時開始及完成動作
原則2: 除休息時間外,兩手不應同時空閒
原則3: 兩臂之動作應反射同時對稱.
原則4: 盡可能以最低級動作工作
說明: 欲使動作迅速而輕易,唯有從動作距離之縮短,以及動作所耗體力減少上著手.欲達到此目的,
其實際對策則為選取級次最低之動作,使動作範圍縮小.並使物料及工具盡可能靠近手之動作範圍 內.工作時,人體之動作可分為下列五級:
18
3.2 何處最需要改善 ※ 您的時間非常富貴,應妥善運用;挑最重要的事情優先做!
瓶頸的地方是最值得改善的,順利的地方留待以后有時間再去研究. 耗時多的地方往往是改善的好機會. 緊急情況由於材料、工具設備或公文制度造成時間及人力的浪費~是極需改善的地方. 浪費須要改善的事物,往往不是顯而易見的,除非您小心的觀察,否則日過一日在浪費的情況下而
(IE工业工程)IE七大手法介绍

壹、IE七大手法介绍一、什么是IEIE就是指Industrial工业,Engineering工程,是由二个英文字母的前缀结合。
“IE”是应用科学及社会学的知识,以合理化、舒适化的途径来改善我们工作的品质及效率,以达到提高生产力,增进公司之利润,进而使公司能长期的生存发展,个人的前途也有寄托之所在。
因此,简单地说“IE”就是代表“合理化及改善”的意义,为了顾及记忆的方便,我们就以中文“改善”来代表“IE”的含义。
二、改善(IE)七大手法1. 手法名称简称(1)防止呆子法(Fool-Proof) 防呆法(2)动作改善法(动作经济原则) 动改法(3)流程程序法流程法(4)5X5WIH(5X5何法) 五五法(5)人机配合法(多动作法) 人机法(6)双手操作法双手法(7)工作抽查法抽查法三、七大手法的用途名称用途(1)防呆法如何避免做错事情,使工作第一次就做好的精神能够具体实现。
(2)动改法改善人体动作的方式,减少疲劳使工作更为舒适、更有效率,不要蛮干。
(3)流程法研究探讨牵涉到几个不同工作站或地点之流动关系,藉以发掘出可资改善的地方。
(4)五五法借着质问的技巧来发掘出改善的构想。
(5)人机法研究探讨操作人员与机器工作的过程,藉以掘出可资改善的地方。
(6)双手法研究人体双手在工作时的过程,藉以发掘出可资改善的地方。
(7)抽查法借着抽样观察的方法能很迅速有效地了解问题的真象。
四、改善(IE)七大手法与品管(QC)七大手法之差别“品管(QC)七手法”较着重于对问题的分析与重点的选择,但对如何加以改善则较少可应用。
“改善(IE)七手法”较着重于客观详尽了解问题之现象,以及改善方法的应用,以期达到改善的目标。
有了“改善(IE)七手法”正可弥补品管(QC)手法的缺陷而达到相辅相成之效果,使得改善的效果更为落实也更容易实现。
同时最重要的是改善(IE)七手法亦可单独使用,因其本身具有分析、发掘问题的技巧之故。
贰、防呆法(Fool-Proof)一、目的认识“防呆法”的意义,及学习如何应用“防呆法”的原理于我们的工作上,以避免工作错误的发生,进而达到“第一次就把工作做对”之境界。
(IE工业工程)IE改善七手法
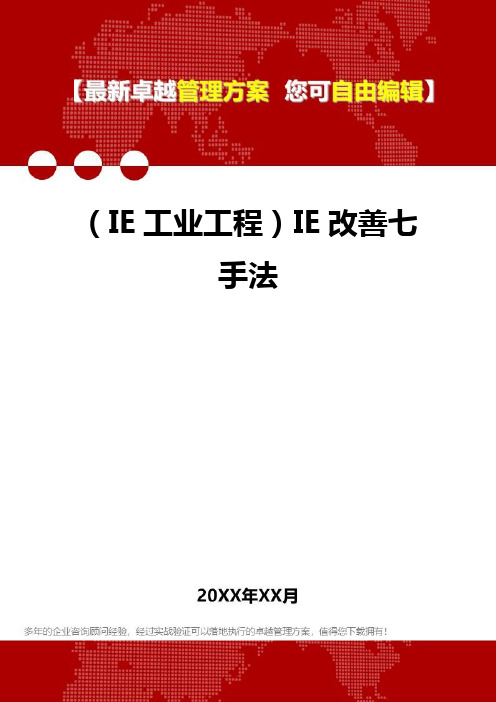
协助我们进一步的认清事实的状况,以及建立其改善的基础及启发点。
(3)五五法、防错法、动改法
协助我们对己知的问题,质问探寻改善的具体方法,以实现改善的目标。
10.改善(IE)七大手法与品管(QC)七大手法之差别
“品管(QC)七手法”较着重于对问题的分析与重点的选择,但对如何加以改善则较少可应用。
“改善(IE)七手法”较着重于客观详尽了解问题之现象,以及改善方法的应用,以期达到改善目标。
有了“改善(IE)七手法”正可弥补品管(QC)七手法的缺陷而达到相辅相成之效果,使得改善的效果更为落实,也更容易实现。同时,最重要的是改善(IE)七手法亦可单独使用,因其本身具有分析、发掘问题的技巧之故。
七手法有时亦称为七工具。
4.为什么要有IE
持续的进步是企业及个人长久生存的根基。
改善是进步的原动力,没有改善就没有进步,学习如逆水行舟,不进则退。
改善是永无止境的,必须长久持续地进行。
5.为什么要有改善(IE)七大手法
以不教而战,谓之杀。
徒然要求改善而不讲求方法、技巧,于事无补。
给人一条鱼,不如教他捕鱼的技术。
要求捕更多的鱼,首先必须讲求捕鱼技术的传授与使用。
(8)以“压力”控制的方式来完成
例:厨房内之快锅内压力过大时,则“泄压阀”就开启,使锅内之压力外泄,以免造成爆炸之危机。
(9)以“计数”控制的方式来完成
例:防止忘记换基片
改良前:
因基片磨损而必须换基片,但因忘记换基片而使基片尖端发生不合标准情形,此时即成为不合于块金(NUGGET)直径之标准。
难于观察、难拿、难动等作业变得难做,变得易疲劳而发生失误。区分颜色使得容易看,或放大标识,或加上把手使得容易拿,或使用搬运器具使动作轻松。
IE工业工程实战改善技法

6)动作要素改善检查
针对每一个动作要素,检查时都必须考虑如下几个问题: • 这个动作是否必要,有没有可能剔除? • 两个或更多的动作是否可以合并? • 顺序是否可以改变? • 有没有改善作业环境的方法来降低作业难度,缩短作业时间?
IE工业工程实战改善技法 之
人机配合法
目的
主要在分析人工或机器之闲置,以谋消除浪费增进效率 ——“人”的工作时间以及”机器”的工作时间所占之比例有多少. ——一个”人”最多可操作几部机器?? 学习如何记录人与机器配合工作时之过程
1)观察分析表第三类动作的比例,寻找消除或减少的方法 2)观察双手的动作是否保持平衡 3)尽量不使用眼力
双手可同时进行动作表
右手 伸出 搬运 使用 抓住 装配 分解 放开 用力
左手
伸出 A
A
A
B
B
B
A
B
搬运 A
A
A
B
B
B
A
B
使用 A
A
A
B
B
B
A
B
抓住 B
B
B
B
C
C
A
C
装配 B
B
B
C
B
C
A
C
分解 B
(5) 对“工作顺序”(When)的质问
质问的目的:寻求可能的“合并”,“重组/变更”的改善方向 变更时间的顺序 将操作发生时刻、时期,耗费时间予以变更,是否可以掌握些改善 的头绪? 为此,宜进行以下之质问: 在何时做的? 为何要在当时做? 改在别的时候做是否更有利? 在何时做最好?何时要完成?需要几天才算合理? 何时最合适?将来有何转变?
(6) 对地点(Where)的质疑
工业工程(IE)现场改善方法_图文(精)

广东德美精细化工股份有限公司工业工程(IE现场改善方法一线班组长管理技能培训内训策划案讲师简介马老师,资深职业讲师,曾长期任职于某著名合资企业精益生产推进项目负责人,从事过生产现场管理、工业工程等多项管理的负责人,长期的企业实战经历使他对企业的生产方式运作有深入了解,丰富的实际工作经验和培训经验,使得他在讲授生产课程方面倍具说服力。
他思路清晰、逻辑严密、善于运用通俗易懂的语言对课程内容进行讲授,并且案例详实、融会贯通。
其课程互动性强,课堂生动有趣。
马老师培训及咨询服务过的企业有:中国航天、中石油、宝钢集团、海南航空、一汽集团、上汽集团、东风汽车、东南汽车、宇通客车、重庆长安铃木、万家乐集团、成飞集团、沈飞集团、建龙钢铁、中铁轨道、武汉铁路局、浙江移动、甘肃移动、四川长虹、夏新股份、美的集团、联合电子、法雷奥、盖茨优霓塔、锦湖轮胎、韩泰轮胎、蒂森克虏伯、浙江钱潮集团、福臻模具、罗比照明、ABB、埃梯梯、无锡唐纳森、东方通信、虹信集团、广北电、杰普智能卡、金斯顿、西蒙电器、赛尔康电子、升德升电子、东莞科泰电子、柏瑞安电子、安费诺电子、华联电子、华科光电、株州电力机车、北京博维航空设施、斯奈克玛航空发动机、斯必克制冷、远东控股、睿固精密件、波尔亚太、金洲刀具、库尔兹烫印、成都印钞、宜宾纸业、渤海能克、上海金泰、辽宁电力、中山电力、盘山发电、蒙牛集团、伊利集团、光明乳业、辉山乳业、顶新集团、汇源果汁、中烟集团、三得利啤酒、百威啤酒、泰山啤酒、北京空港配餐、青岛康地恩、天士力药业、九芝堂药业、双鹤药业、敖东制药、吉斯特药业、永康制药、诺康医药、英科制药、京博农化、海科化工、拉法基水泥、秋水伊人服装、云南阿舍冶炼等。
目录01诠释工业工程(IE02五五法03流程法与设施布置04人机法07标准时间与生产线平衡分析08标准操作(SOP目录06动改法05双手法5什么是工业工程?工业工程是对有关人员、物料、设备、能源和信息等组成的整体系统进行规划、设计、改进和实施的一门科学,它利用数学、物理和社会学的专门知识与技术,同时使用工程分析和设计的原理与方法,对上述整体系统所能得到的成果予以说明、预测和评价。
- 1、下载文档前请自行甄别文档内容的完整性,平台不提供额外的编辑、内容补充、找答案等附加服务。
- 2、"仅部分预览"的文档,不可在线预览部分如存在完整性等问题,可反馈申请退款(可完整预览的文档不适用该条件!)。
- 3、如文档侵犯您的权益,请联系客服反馈,我们会尽快为您处理(人工客服工作时间:9:00-18:30)。
Measure 现状的把握和阻害要因的、 IE或QC、活用MI手法定量的对現状进行把握、
抽出提出要因
抽出阻害要因。
ቤተ መጻሕፍቲ ባይዱ
Analyze 阻害要因的验证
要因的验证要基于客観的数据进行实施 实施期待効果的验证
Improve 确认改善策的实施和効果 将验证結果作为基础实施有効的改善策 能够确认効果。
Control 防止恢复原始状态的构筑和 为了使改善効果持久、管理方法要
确认效果
明确、实施有効的构筑并确认其効果。
東芝テック海外IE教育教材
東芝テック海外IE教育教材
東芝テック海外IE教育教材
「MI步骤和IE手法」
2011.2.21 東芝テック(株) 生産本部TP/IE教育事務局
東芝テック海外IE教育教材
通过IE工具来提炼车间的课题和确定改善的顺序
设定目标、选定对象产品 对象职场 Define
概况调查、找出课题 (测定、调查、分析) Measure
课题的深入和详细分析 (查明真正原因) Analyze
动作经济的原则、TOC、生产线均衡、VE、 ECRS、其他的改善手法、CFT等
※改善策略是智慧的凝结。
标准作业、标准时间、教育训练、效果 可视化等
※必须确认经济效果
東芝テック海外IE教育教材
MI步骤和应有的身姿
Define
MI步骤
设定目标、选定对象产品, 对象职场
各步骤应有的状态
在明确和部门的课题相关连的部分的同时、 也要明确目标值的设定依据
改善方案的确立和实施 Improve
预想、确认效果、构筑防止 反复体系 Control
公司或职场的目标(BCM、DDT等) 选定对象产品或对象职场、PQ分析
产品工序分析、动作路径分析、搬运分 析、作业抽样调查、生产线平衡分析、 时间分析、QC分析、特性要素图等
作业人员工序分析、连续运转分析、复 式作业分析、时间分析、双手作业分析 等