年产200吨YG类硬质合金的烧结车间设计文献综述
毕业设计_年产200万吨钢的转炉炼钢车间设计——钢包设计

攀枝花学院本科毕业设计(论文)摘要攀枝花学院本科毕业设计(论文)年产200万吨钢的转炉炼钢车间设计——钢包设计攀枝花学院本科毕业设计(论文)摘要摘要根据年产200万吨钢转炉车间设计的要求和国家相关政策的规定,确定转炉的大小为220吨,进一步得到了符合实际生产的与之匹配的钢包容量大小为250吨,通过计算确定钢包上部内径和高度均为4289mm,生产过程中所需要的钢包的数量为11个。
对钢包用耐火材料进行了设计,分为2套钢包即浇注钢包和砌筑钢包。
分别对其进行分析确定了他们的绝热层和工作层的设计方法,对于浇注钢包采用整体浇注和或剥皮浇注,对砌筑钢包采用综合砌筑的方案;通过对钢包透气砖和滑动水口系统耐火材料的外形设计,确定了透气砖系统耐火材料的尺寸和滑动水口系统耐火材料的尺寸;最后根据钢包用耐火材料的使用要求,针对不同钢种和不同部位的不同要求以及耐火材料的理化性能指标,对钢包所用的耐火材料进行了优化选择。
关键词炼钢,钢包,砌筑,浇注,耐火材料攀枝花学院本科毕业设计(论文)ABSTRACTABSTRACTAccording to the annual output of 2 million tons of steel converter workshop design requirements and relevant national policies and regulations, determine the size of the converter is 220 tons, has been further conform to the actual production of matching the ladle size capacity of 250 tons, through the calculate and determine the ladle upper inner diameter and height is 4289 mm, the production process required the number of ladles for 11. Ladle refractory materials used for the design, divided into 2 sets of ladle pouring ladle and laying the ladle. Respectively to analyze it to determine their thermal barrier and layer, the design method of the work for adopts the integral casting and or peeling pouring ladle cover in casting, for the composite masonry methods in laying the ladle; Through the vent brick of ladle refractory and slide gate system design, determine the size of the system of gas supply brick and refractory materials and refractory materials the size of the slide gate system; Finally according to the requirements of the ladle refractory material used, according to different steel grade and the different requirements of different parts and the rational index of the refractory, the ladle refractory material used in the optimized choice.Key words steelmaking, ladle, laying, casting, refractory material攀枝花学院本科毕业设计(论文)目录目录摘要 (II)ABSTRACT (III)1 绪论 (1)2 转炉的座数、公称容量及生产能力的确定 (2)2.1 转炉的容量和座数的确定 (2)2.2 计算年出钢炉数 (2)2.3 车间的年产钢量的计算 (3)3 钢包尺寸及数量的确定 (4)3.1 钢包尺寸的计算 (4)3.2 钢包质量的计算 (7)3.3 钢包重心计算 (8)3.4钢包数量的计算 (9)4 钢包用耐火材料的设计 (10)4.1浇注钢包的设计方法 (10)4.1.1包壁绝热层的设计方法 (10)4.1.2钢包工作层的设计方法 (10)4.1.2.1普通不精炼钢包 (10)4.1.2.2简单炉后处理的精炼钢包 (12)4.1.3钢包浇注的工作方案 (12)4.1.3.1整体浇注钢包的方法 (12)4.1.3.2采用剥皮套浇的浇注钢包施工方法 (13)4.2砖砌钢包的设计 (14)4.2.1砖砌钢包的结构设计 (14)4.2.1.1绝热层的设计 (14)4.2.1.2永久层的设计 (14)4.2.1.3工作层的设计 (14)4.3钢包透气砖和滑动水口系统耐火材料的外形设计 (14)4.3.1透气砖系统耐火材料的尺寸设计 (14)4.3.2滑动水口系统耐火材料的尺寸设计 (16)5 钢包用耐火材料的选择 (19)攀枝花学院本科毕业设计(论文)目录5.1钢包用耐火材料的要求 (19)5.2钢包耐火材料的选用 (21)5.2.1钢包隔热层和永久层 (21)5.2.2钢包工作层 (21)5.2.3滑动水口用耐火材料 (22)结论 (23)参考文献 (24)致谢 (1)攀枝花学院本科毕业设计(论文) 1 绪论1 绪论钢包是连接转炉和连铸中间的容器,而且几乎所有钢水的炉外精炼过程都是在钢包中进行;钢包的工作状态好坏不仅影响炼钢过程钢液质量、生产节奏、炉衬寿命;也会影响后序精炼和连铸过程中的包衬寿命、钢水质量和生产节奏,特别是影响最终的钢铁产品的制造成本和内在质量。
年产200万吨钢的转炉炼钢车间设计——钢包设计设计0000

年产200万吨钢的转炉炼钢车间设计——钢包设计设计0000攀枝花学院本科毕业设计(论文)年产200万吨钢的转炉炼钢车间设计——钢包设计学生姓名:蒲维学生学号: 200911103045院(系):资源与环境工程学院年级专业: 2009级冶金工程1班指导教师:芶淑云教授二〇一三年五月攀枝花学院本科毕业设计(论文)摘要摘要根据年产200万吨钢转炉车间设计的要求和国家相关政策的规定,确定转炉的大小为220吨,进一步得到了符合实际生产的与之匹配的钢包容量大小为250吨,通过计算确定钢包上部内径和高度均为4289mm,生产过程中所需要的钢包的数量为11个。
对钢包用耐火材料进行了设计,分为2套钢包即浇注钢包和砌筑钢包。
分别对其进行分析确定了他们的绝热层和工作层的设计方法,对于浇注钢包采用整体浇注和或剥皮浇注,对砌筑钢包采用综合砌筑的方案;通过对钢包透气砖和滑动水口系统耐火材料的外形设计,确定了透气砖系统耐火材料的尺寸和滑动水口系统耐火材料的尺寸;最后根据钢包用耐火材料的使用要求,针对不同钢种和不同部位的不同要求以及耐火材料的理化性能指标,对钢包所用的耐火材料进行了优化选择。
关键词炼钢,钢包,砌筑,浇注,耐火材料ABSTRACTAccording to the annual output of 2 million tons of steel converter workshop design requirements and relevant national policies and regulations, determine the size of the converter is 220 tons, has been further conform to the actual production of matching the ladle size capacity of 250 tons, through the calculate and determine the ladle upper inner diameter and height is 4289 mm, the production process required the number of ladles for 11. Ladle refractory materials used for the design, divided into 2 sets of ladle pouring ladle and laying the ladle. Respectively to analyze it to determine their thermal barrier and layer, the design method of the work for adopts the integral casting and or peeling pouring ladle cover in casting, for the composite masonry methods in laying the ladle; Through the vent brick of ladle refractory and slide gate system design, determine the size of the system of gas supply brick and refractory materials and refractory materials the size of the slide gate system; Finally according to the requirements of the ladle refractory material used, according to different steel grade and the different requirements of different parts and the rational index of the refractory, the ladle refractory material used in the optimized choice.Key words steelmaking, ladle, laying, casting, refractory material目录摘要 (I)ABSTRACT (II)1 绪论 (1)2 转炉的座数、公称容量及生产能力的确定 (3)2.1 转炉的容量和座数的确定 (3)2.2 计算年出钢炉数 (3)2.3 车间的年产钢量的计算 (4)3 钢包尺寸及数量的确定 (5)3.1 钢包尺寸的计算 (5)3.2 钢包质量的计算 (8)3.3 钢包重心计算 (9)3.4钢包数量的计算 (11)4 钢包用耐火材料的设计 (12)4.1浇注钢包的设计方法 (12)4.1.1包壁绝热层的设计方法 (12)4.1.2钢包工作层的设计方法 (12)4.1.2.1普通不精炼钢包 (12)4.1.2.2简单炉后处理的精炼钢包144.1.3钢包浇注的工作方案 (16)4.1.3.1整体浇注钢包的方法 (16)4.1.3.2采用剥皮套浇的浇注钢包施工方法 (16)4.2砖砌钢包的设计 (17)4.2.1砖砌钢包的结构设计 (17)4.2.1.1绝热层的设计 (17)4.2.1.2永久层的设计 (17)4.2.1.3工作层的设计 (17)4.3钢包透气砖和滑动水口系统耐火材料的外形设计 (18)4.3.1透气砖系统耐火材料的尺寸设计184.3.2滑动水口系统耐火材料的尺寸设计 (19)5 钢包用耐火材料的选择 (23)5.1钢包用耐火材料的要求 (23)5.2钢包耐火材料的选用 (25)5.2.1钢包隔热层和永久层 (25)5.2.2钢包工作层 (25)5.2.3滑动水口用耐火材料 (26)结论 (28)参考文献 (29)致谢 (30)1 绪论钢包是连接转炉和连铸中间的容器,而且几乎所有钢水的炉外精炼过程都是在钢包中进行;钢包的工作状态好坏不仅影响炼钢过程钢液质量、生产节奏、炉衬寿命;也会影响后序精炼和连铸过程中的包衬寿命、钢水质量和生产节奏,特别是影响最终的钢铁产品的制造成本和内在质量。
年产200吨YG类硬质合金的烧结车间设计说明书

四川理工学院课程设计年产200吨YG类硬质合金的烧结车间设计学生:学号:专业:材料科学与工程班级:指导老师:四川理工学院材料与化学工程学院二O一一年六月摘要本文进行了年产200吨YG类硬质合金烧结车间的设计,介绍了WC-Co硬质合金的力学性能、应用、发展前景和常规制备方法等。
根据设计任务书的要求和相关粉末冶金车间设计规则制定了WC-Co硬质合金的工艺流程。
另外,主要针对球磨、压制和烧结三大工序进行了物料衡算,查阅资料对当前国内的相关设备进行了搜集整理,根据物料衡算和设备参数对球磨机、成型压力机、真空烧结炉等基本设备进行了选型和台数的合理选取,并进行了工作制度的合理性制定、设备的合理化布置及车间平面和厂区平面的布置。
最后,根据国家相关制图标准绘制了WC-Co硬质合金生产的工艺流程图、厂区平面布置图、烧结车间平面布置图和烧结车间的剖面图。
关键词:WC-Co硬质合金;物料衡算;设备选型;车间设计;烧结AbstractThe sintering workshop in where WC-Co hard alloys are produced for 200 tons per year has been designed in this paper.The mechanical properties of WC-Co hard alloy’s, its applications and prospects for development and the conventional preparation method were introduced. According to the design assignment and the correlative powder metallurgy workshop design practice, the WC-Co hard alloy technical process was developed. In addition,mainly for ball milling, pressing and sintering processes three primary working procedures were calculated material balance. Accessing to information on the current domestic related equipment were collected more, the ball mill, molding presses, vacuum sintering furnace and other basic equipment for the selection of a reasonable selection and number of units were carried out. The rationality of the working system formulated, equipments rationalization arrangement and workshop plane and factory plane layout were also carried out. Finally, the author has drawn the chart of the WC-Co hard alloy production flow, the floor-plans of the factory area and the sintering workshop, and the Sintering workshop sectional drawing according to the interrelated national charting standard.Key words: WC-Co hard alloy; material balance; equipment selection; workshop design; Sintering目录摘要 (I)Abstract (II)第一章绪论 (1)第二章概述 (3)2.1 设计依据 (3)2.2 设计原则 (3)2.3 设计范围 (3)2.4 原料及组成 (3)第三章WC—Co硬质合金生产的工艺过程 (4)3.1混合料的制备 (4)3.2干燥、筛分 (4)3.3掺胶制粒 (4)3.4成形 (5)3.5烧结 (5)3.5.1 烧结过程 (5)3.5.2 真空烧结 (6)第四章工厂工艺计算 (7)4.1工艺流程 (7)4.2物料衡算 (7)4.2.1 物料平衡计算的方法和步骤 (7)4.2.2 物料平衡的计算 (8)4.3工艺设备选型和计算 (11)4.3.1 生产车间及设备简述 (11)4.3.2 球磨机 (12)4.3.3 振动过筛机 (14)4.3.4 干燥柜 (14)4.3.5 掺胶混合机 (15)4.3.6 成型压力机 (16)4.3.7 真空烧结炉 (17)4.3.8喷砂机 (19)第五章环境保护 (20)5.1粉尘污染 (20)5.2噪声污染 (21)第六章总结 (22)参考文献 (23)致谢 (24)附录 (24)第一章绪论硬质合金(Cemented carbide)是以难熔金属碳化物(WC、TiC等)为基体,铁族金属(Co、Fe、Ni等)作粘结剂,用粉末冶金方法制造的一种多相组合材料。
硬质合金烧结方法的新进展
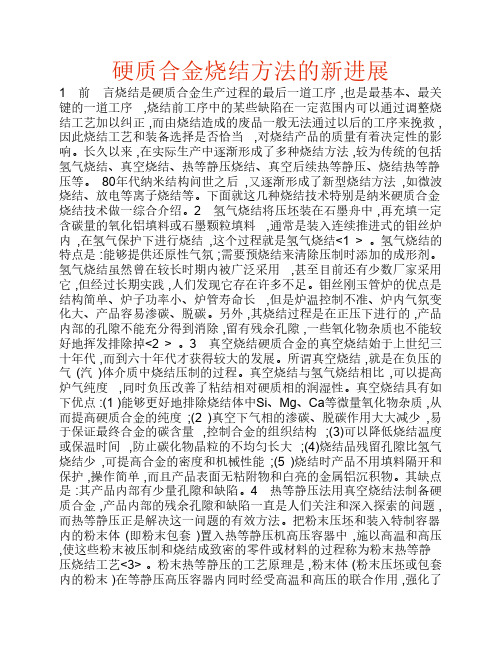
硬质合金烧结方法的新进展1 前 言烧结是硬质合金生产过程的最后一道工序 ,也是最基本、最关键的一道工序,烧结前工序中的某些缺陷在一定范围内可以通过调整烧结工艺加以纠正 ,而由烧结造成的废品一般无法通过以后的工序来挽救 ,因此烧结工艺和装备选择是否恰当,对烧结产品的质量有着决定性的影响。
长久以来 ,在实际生产中逐渐形成了多种烧结方法 ,较为传统的包括氢气烧结、真空烧结、热等静压烧结、真空后续热等静压、烧结热等静压等。
80年代纳米结构问世之后,又逐渐形成了新型烧结方法,如微波烧结、放电等离子烧结等。
下面就这几种烧结技术特别是纳米硬质合金烧结技术做一综合介绍。
2 氢气烧结将压坯装在石墨舟中 ,再充填一定含碳量的氧化铝填料或石墨颗粒填料,通常是装入连续推进式的钼丝炉内,在氢气保护下进行烧结,这个过程就是氢气烧结<1 > 。
氢气烧结的特点是 :能够提供还原性气氛 ;需要预烧结来清除压制时添加的成形剂。
氢气烧结虽然曾在较长时期内被广泛采用,甚至目前还有少数厂家采用它 ,但经过长期实践 ,人们发现它存在许多不足。
钼丝刚玉管炉的优点是结构简单、炉子功率小、炉管寿命长,但是炉温控制不准、炉内气氛变化大、产品容易渗碳、脱碳。
另外 ,其烧结过程是在正压下进行的 ,产品内部的孔隙不能充分得到消除 ,留有残余孔隙 ,一些氧化物杂质也不能较好地挥发排除掉<2 > 。
3 真空烧结硬质合金的真空烧结始于上世纪三十年代 ,而到六十年代才获得较大的发展。
所谓真空烧结 ,就是在负压的气(汽)体介质中烧结压制的过程。
真空烧结与氢气烧结相比,可以提高炉气纯度,同时负压改善了粘结相对硬质相的润湿性。
真空烧结具有如下优点 :(1 )能够更好地排除烧结体中Si、Mg、Ca等微量氧化物杂质 ,从而提高硬质合金的纯度;(2 )真空下气相的渗碳、脱碳作用大大减少,易于保证最终合金的碳含量,控制合金的组织结构;(3)可以降低烧结温度或保温时间,防止碳化物晶粒的不均匀长大;(4)烧结品残留孔隙比氢气烧结少,可提高合金的密度和机械性能;(5 )烧结时产品不用填料隔开和保护 ,操作简单 ,而且产品表面无粘附物和白亮的金属铝沉积物。
硬质合金真空烧结

硬质合金真空烧结硬质合金的烧结为液相烧结,即再黏结相呈液相的条件下进行。
将压坯在真空炉中加热到1350℃—1600℃。
烧结时压坯的线收缩率约为18%,体积收缩在50%左右,收缩量的准确值取决于粉末的粒度和合金的成分。
硬质合金的烧结是一个复杂的物理化学过程,株洲三鑫硬质合金生产有限公司友情出品。
这一过程包括增塑剂脱除、脱气、固相烧结、液相烧结、合金化、致密化、溶解析出等过程。
压坯在特定烧结条件下形成具有一定化学成分、组织结构、性能和形状尺寸的制品。
这些工艺条件依不同的烧结装置具有较大的差异。
硬质合金真空烧结是在低于1atm(1atm=101325Pa)下进行烧结的工艺过程。
在真空条件下烧结,大大降低了粉末表面吸附气体和封闭孔隙内气体对致密化的阻碍作用,有利于扩散过程和致密化的进行,避免了烧结过程中金属与气氛中某些元素的反应,可显著改善液体黏结相与硬质相的湿润性,但真空烧结要注意防止钴的蒸发损失。
真空烧结一般可以分为四个阶段,即增塑剂脱除阶段、预烧阶段、高温烧结阶段、冷却阶段。
增塑剂脱除阶段是从室温开始升温到200℃左右,压坯中粉末颗粒表面吸附的气体在热的作用下脱离颗粒表面,不断从压坯中逃逸出来。
压坯中的增塑剂受热化逸出压坯。
保持较高的真空度有利于气体的解除和逸出。
不同种类增塑剂受热变化的性能不尽相同,制定增塑剂脱除工艺要根据具体情况进行试验确定。
一般增塑剂的气化温度在550℃以下。
预烧阶段是指高温烧结前进行预烧结,使粉末颗粒中的化合氧与碳发生还原反应,生成一氧化碳气体离开压坯,如果这种气体在液相出现时不能排除,将成为封闭孔隙残留在合金中,即使加压烧结,也难以消除。
另一方面,氧化存在会严重影响液相对硬质相的湿润性,最终影响硬质合金的致密化过程。
在液相出现前,应充分得脱气,并采用尽可能高得真空度。
高温烧结阶段是硬质合金压坯发生致密化得关键阶段,而烧结温度及烧结时间是压坯实现致密化、形成均匀得组织结构、获得所要求性能的重要工艺参数。
《硬质合金的烧结》课件
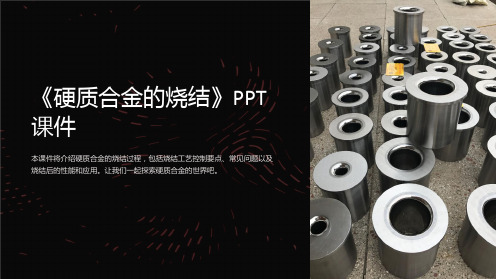
本课件将介绍硬质合金的烧结过程,包括烧结工艺控制要点、常见问题以及 烧结后的性能和应用。让我们一起探索硬质合金的世界吧。
硬质合金
1 什么是硬质合金?
硬质合金,又称硬质合金钎焊,是一种由金属粉末和结合剂经过高温烧结而成的高硬度 材料。
2 硬质合金的特点
具有高硬度、耐磨损、高强度、耐腐蚀等优良特性,广泛应用于切削、钻石工具、矿山 钻石等领域。
硬质合金制成的齿轮具有高 强度和耐磨损性,适用于高 负荷的工业应用。
总结和展望
1 总结
硬质合金的烧结是一个关键的生产工序,影响着最终产品的性能和质量。
2 展望
随着科技的进步,烧结工艺将不断改进,使得硬质合金能够实现更广泛的应用和发展。
3 硬质合金的组成
硬质合金由主要成分的金属粉末和结合剂组成,结合剂常用的有钴、镍等金属。
硬质合金的烧结过程
1
模具制备
2
将原料放入预先设计的模具中,并
施加压力,使其形成所需形状。
3
冷却和处理
4
将烧结后的硬质合金材料进行冷却, 并进行后续的处理工序,以提高其
性能。
原料制备
将金属粉末和结合剂按一定比例混 合,形成硬质合金的原料。
烧结
将模具中的硬质合金原料放入高温 炉中进行加热,使金属粉末与结合 剂烧结成坚固的材料。
烧结工艺控制要点
热处理时间
控制加热时间,保证硬质合金材料具有 一定的密度和强度。
烧结温度
选择适当的烧结温度,保证金属粉末和结 合剂能够充分烧结。
烧结环境
烧结温度
烧结温度的升高可以促进金属粉末的烧结, 但过高的温度会导致材料变形和开裂。
烧结压力
年产200万吨宽厚板轧钢车间设计毕业论文

二战后,对中厚板需求量和质量提出了更高的要求。因此,50年代发达国家除完成大量技术改造外,还新建了一批4060mm以下高刚度轧机,实现了控制轧制,提高了中厚板质量。60年代发展了以4700mm为主大刚度的双机架轧机,并掌握了中厚板生产的计算机控制,提高了控制精度。70年代发展到5500mm为主的特宽型的单机架轧机,以满足石油和天然气等长距离输送所需大直径管线用板。60年代由于中厚板使用部门的萧条,中厚板产量下降,西欧、日本和美国都淘汰了一批低档次中厚板轧机。虽然套数少了,但轧机的素质和生产技术却提高了。我国现在大规格、高质量中厚板需求量的增加,但数量过剩,也迫使加快落后工艺设备的中厚板轧机的淘汰,同时,也有现代化大型中厚板厂的兴建。
11.5.1厂房跨度布置79
11.5.2厂房跨度大小80
11.5.3柱距尺寸80
11.5.4吊车轨面标高80
结论81
参考文献82
致谢83
引 言
随着我国基础建设事业的发展,我国继美国与日本之后掀起了世界第三次中厚板生产线的建设高潮,目前我国已成为了全球中厚板生产线发展最快、数量最多的国家。纵观我国中厚板轧机的发展历史,2005以后我国新建的中厚板轧机对设备配置和工艺的完善更加重视:单位辊面宽轧制力都达到了2t/mm以上,轧制力矩达到1.5KN.m/mm,轧制功率达到4KW/mm,轧机刚度达到了10MN/mm以实现低温大压下控制轧制;同时采用了世界先进的厚度AGC和宽度AWC以及轧辊连续可变凸度控制技术(CVC),精整环节配备了超声波探伤装置,以保做证钢板的部质量,热处理环节配备了辊底式热处理炉,以保证产品的组织性能,此外还配备了淬火机与抛丸机能更好的保证产品的质量性能。
硬质合金低压烧结工艺的探索

硬质合金低压烧结工艺的探索背景介绍硬质合金是一种具有优异性能的材料,广泛应用于切削工具、磨料工具、钻头等领域。
然而,传统的硬质合金烧结工艺存在一些问题,如高温烧结过程中易产生裂纹、粉末不易压实等。
为了解决这些问题,近年来,低压烧结工艺被引入硬质合金的生产中,取得了良好的效果。
本文将对硬质合金低压烧结工艺进行探索。
低压烧结工艺的原理低压烧结工艺是在传统的高温烧结工艺基础上进行的改进。
该工艺是在相对较低的温度和压力下进行的,能够有效降低硬质合金烧结过程中的应力,减少裂纹的产生。
具体工艺流程如下:1.硬质合金粉末的制备:首先,根据所需的产品要求,将合适的金属粉末混合,并加入适量的粘结剂和稳定剂,经过混合、湿法粉碎、干燥等工序得到合适的硬质合金粉末。
2.模具填充与压实:将制备好的硬质合金粉末填充至模具中,然后施加一定的压力进行初步压实。
这一步骤旨在保证硬质合金粉末的均匀分布和初步的固结。
3.低压烧结过程:将填充好硬质合金粉末的模具放入低压烧结炉中,根据设计要求,控制合适的温度和压力进行烧结过程。
相对于传统高温烧结工艺,低压烧结的温度和压力要求更低,从而减少了产生裂纹的可能性。
4.冷却与脱模:低压烧结过程结束后,将烧结好的硬质合金模具从炉中取出,进行冷却。
待冷却后,使用合适的方法将硬质合金产品从模具中取出,完成脱模操作。
优势与挑战低压烧结工艺相比传统高温烧结工艺具有以下优势:1.减少裂纹的产生:传统高温烧结工艺中,由于温度和压力较高,易导致硬质合金产生内应力,从而产生裂纹。
低压烧结工艺通过降低温度和压力,减小了硬质合金内应力的产生,有效减少了裂纹的发生。
2.增加硬质合金的致密度:低压烧结工艺在初步压实的基础上,通过烧结过程进一步压实硬质合金粉末,提高了硬质合金的致密度,从而提高了其力学性能和耐磨性。
3.环保节能:相对于高温烧结工艺,低压烧结工艺不需要经过高温环境,减少了能源的消耗,同时也减少了对环境的污染。
硬质合金烧结变形及控制方法

硬质合金烧结变形及控制方法摘要:硬质合金烧结变形及其控制方法是硬质合金制造领域的一个重要研究方向。
本文通过对硬质合金材料的组成和制备工艺进行综述,分析了烧结变形的成因和影响因素。
在此基础上,提出了一系列控制方法,包括优化烧结工艺参数、改进烧结模具设计、合理选择烧结添加剂等。
同时,本文通过实际案例分析,验证了这些控制方法的有效性。
研究结果表明,通过合理控制烧结过程中的变形,可以显著提高硬质合金材料的性能和质量,为硬质合金制造提供了理论依据和技术支持。
关键词:硬质合金、烧结变形、控制方法、制备工艺、烧结工艺参数引言:硬质合金是一种重要的工程材料,在机械、航空航天、石油化工等领域具有广泛的应用。
硬质合金的制备过程中,烧结是一个关键的工艺步骤,它决定了硬质合金材料的性能和质量。
然而,烧结过程中常常会出现各种变形问题,如开裂、弯曲等,严重影响了硬质合金的制造效率和质量稳定性。
因此,研究硬质合金烧结变形及其控制方法具有重要的理论意义和实际价值。
一、硬质合金的组成和制备工艺1.1 硬质合金的组成硬质合金通常由两个主要组分组成:金属碳化物和粘结相。
金属碳化物主要是钨碳化物(WC),它具有高硬度、高熔点和良好的耐磨性。
粘结相通常是钴(Co)或镍(Ni),它的作用是将金属碳化物颗粒牢固地粘结在一起,并提供一定的韧性和冲击强度。
此外,硬质合金还可能含有其他元素或添加剂,如钛(Ti)、铌(Nb)、钼(Mo)等,以进一步改善其性能。
1.2 硬质合金的制备工艺硬质合金的制备工艺通常包括粉末混合、成型和烧结三个主要步骤。
首先,将金属碳化物粉末和粘结相粉末按照一定的配比进行混合,通常使用球磨或干法混合的方法,以确保两种粉末均匀混合。
然后,将混合粉末通过成型工艺,如压制、注射成型等,制备成所需的形状,如板材、棒材、刀片等。
最后,成型体经过烧结工艺,即在高温下进行加热处理,以使金属碳化物颗粒结合成整体。
烧结过程中,首先进行预烧结,将成型体加热至金属碳化物颗粒开始颗粒间结合的温度。
冶金工厂设计文献综述

冶金工厂设计文献综述摘要:一、引言二、冶金工厂设计的重要性三、冶金工厂设计的基本原则1.安全可靠性2.经济合理性3.环保可持续性4.操作便利性四、冶金工厂设计的主要内容1.工厂布局设计2.设备选型与配置3.工艺流程设计4.自动化控制系统设计五、冶金工厂设计的现状与发展趋势1.我国冶金工厂设计的现状2.国际冶金工厂设计的发展趋势3.我国冶金工厂设计的发展方向六、结论正文:一、引言冶金工业是国民经济的重要支柱产业,冶金工厂设计对于提高生产效率、保障产品质量、降低生产成本具有重要意义。
本文旨在综述冶金工厂设计的相关文献,探讨冶金工厂设计的基本原则、主要内容、现状与发展趋势。
二、冶金工厂设计的重要性冶金工厂设计关系到企业的核心竞争力。
优良的设计可以提高生产效率、降低能耗、减少污染排放、延长设备使用寿命,从而为企业创造良好的经济效益和社会效益。
三、冶金工厂设计的基本原则1.安全可靠性:设计应充分考虑生产过程中的安全风险,确保设备和人员安全。
2.经济合理性:设计应追求最佳的投入产出比,降低成本,提高经济效益。
3.环保可持续性:设计应遵循国家环保法规,减少污染物排放,保护环境。
4.操作便利性:设计应便于生产操作、设备维护和管理,提高生产效率。
四、冶金工厂设计的主要内容1.工厂布局设计:合理划分生产区域、办公区域和生活区域,优化人流、物流、信息流。
2.设备选型与配置:根据生产工艺要求,选择高效、节能、可靠的设备,合理配置设备数量。
3.工艺流程设计:优化生产工艺,确保产品质量,提高生产效率。
4.自动化控制系统设计:实现生产过程的自动化、信息化、智能化,提高企业管理水平。
五、冶金工厂设计的现状与发展趋势1.我国冶金工厂设计的现状:总体水平不断提高,部分企业已达到国际先进水平,但仍存在一定的差距。
2.国际冶金工厂设计的发展趋势:绿色制造、智能制造、数字化设计、模块化建设。
3.我国冶金工厂设计的发展方向:加大科技创新力度,提高设计水平,推动产业结构调整,实现可持续发展。
文献综述烧结

碱性溶剂对固体燃料燃烧性能的影响二i概述所谓烧结,即是将各种粉状含铁原料。
按要求配入一定数t的燃料和熔剂,均匀混合侧拉后布到烧结设备上点火烧结;在樵料撼烧产生高沮和一系列物理化学反应的作用下,混合料中部分易熔物质发生软化、熔化,产生一定数t的掖相,液相物质润湿其他未熔化的矿石硕粒。
随着温度的降低,液相物质将矿粉绷粒粘结成块。
这个过程称为烧结。
所得的块矿叫烧结矿。
目前,生产入造富矿的方法主要有烧结法和焙烧球团法。
由于烧结矿和球团矿都是经过高温制成的。
因此又统称为熟料。
.1.1烧结的目的和惫义离炉炼铁冶炼过程中。
为了保证料柱的透气性良好.要求护料粒度均匀,粉末少,机械强度(冷强度和热强度)高。
为了降低高炉焦比,要求炉料含铁品位高、有害杂质少,且具有自熔性和良好的还原性能二采用烧结方法后,上述要求几乎能全部达到。
贫矿经过选矿后所得到的细粒精矿.夭然富矿在开采过程中和破碎分级过程中所产生的粉矿,都必须经过烧结成块才能进入高炉。
含碳酸盐和结晶水较多的矿石。
经过破碎进行烧结,可以除去挥发分而使铁富集。
某些难还原的矿石,或还原期间容易破碎或休积肆胀的矿石,经过烧结可以变成还原性良好和热稳定性商的沪料。
铁矿石中的某些有害元家甲如硫、氛、钾、钠、铅、锌、砷等,都可以在烧绪过程中大部分去除或回收利用。
通过烧结过程,可以利用工业生产中的副产品。
如离护沪尘、转炉护尘、轧钢皮、硫酸渣等。
使其变废为宝,合理利用资想,扩大原料来晾,降低生产成本,并可净化环境。
生产实践证明,高护使用烧结矿和球团矿之后,高护冶炼可以达到高产、优质、低耗、长寿的目的口1*1.}烧结技术的发展及现状烧结生产起源于英国和德国:大约在1870年.这些国家就开始使用烧结锅,用来处理矿山开采、冶金工厂一化工厂等的废弃物}. 1$}2年美国也出现了烧结锅。
世界钢轶工业第一台带式烧结机于1910年在美国投人生产.:这台烧结机的面积为8.325郝} l . 07 m义7 .7$ m}。
硬质合金烧结技术的发展

硬质合金烧结技术的发展发布时间:2022-06-22T07:52:03.829Z 来源:《科技新时代》2022年6期作者:秦发雄, 陈勇[导读] 文中介绍了硬质合金工业生产中烧结技术的发展,对比了不同烧结方式优缺点,同时对当前研究热门的几种新型烧结方法的原理和特点进行了阐述,展望了目前硬质合金行业烧结方面需要研究努力的方向。
秦发雄, 陈勇(自贡硬质合金有限责任公司成都分公司,四川成都610100)摘要:文中介绍了硬质合金工业生产中烧结技术的发展,对比了不同烧结方式优缺点,同时对当前研究热门的几种新型烧结方法的原理和特点进行了阐述,展望了目前硬质合金行业烧结方面需要研究努力的方向。
关键词:烧结,真空烧结,热等静压烧结,微波烧结1引言钨钴硬质合金因具有优异的硬度、耐磨性、强度和断裂韧性等综合性能被广泛应用。
硬质合金生产工序繁多,烧结是最后一道关键工序,烧结工艺及装备先进与否,对产品质量有着决定性的影响[1]。
长期以来, 各国科研工作者在实际生产中逐渐形成了多种烧结方法, 工业生产所使用的包括真空烧结、真空后热等静压、烧结热等静压等,80年代以来,发展了一些新型烧结方法,如微波烧结、选择性激光烧结、放电等离子烧结等。
这些新型的烧结技术具有样品同时受热、加热速度快、选择性加热以及非热效应等传统加热方式所不具有的特点[2],但由于同样存在缺点,目前仍不能广泛用于工业化生产,本文将对这些烧结方式使用情况做一个介绍。
2工业生产硬质合金烧结方法2.1 真空烧结真空烧结始于上世纪三十年代,是硬质合金烧结较为普遍采用的一种方法,所谓真空烧结, 就是在负压的气体介质中烧结压制的过程。
真空烧结能提高炉气纯度,同时负压改善了粘结相对硬质相的润湿性。
由于真空烧结能提高冶金质量,特别对含钛钽复式碳化物的合金更为明显[3],因此,60年代初期以来,国外大多数厂家纷纷放弃氢气烧结而采用真空烧结,各种各样的真空烧结炉不断涌现,并随着时间的推移不断改进和发展。
硬质合金示范生产线设计方案
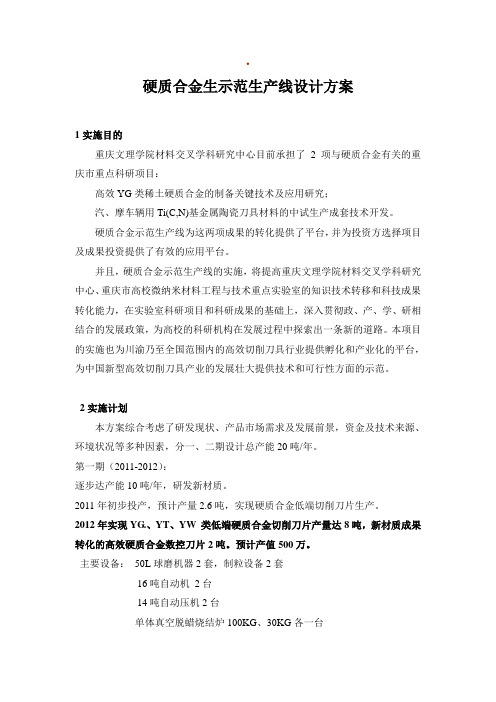
.硬质合金生示范生产线设计方案1实施目的重庆文理学院材料交叉学科研究中心目前承担了2项与硬质合金有关的重庆市重点科研项目:高效YG类稀土硬质合金的制备关键技术及应用研究;汽、摩车辆用Ti(C,N)基金属陶瓷刀具材料的中试生产成套技术开发。
硬质合金示范生产线为这两项成果的转化提供了平台,并为投资方选择项目及成果投资提供了有效的应用平台。
并且,硬质合金示范生产线的实施,将提高重庆文理学院材料交叉学科研究中心、重庆市高校微纳米材料工程与技术重点实验室的知识技术转移和科技成果转化能力,在实验室科研项目和科研成果的基础上,深入贯彻政、产、学、研相结合的发展政策,为高校的科研机构在发展过程中探索出一条新的道路。
本项目的实施也为川渝乃至全国范围内的高效切削刀具行业提供孵化和产业化的平台,为中国新型高效切削刀具产业的发展壮大提供技术和可行性方面的示范。
2实施计划本方案综合考虑了研发现状、产品市场需求及发展前景,资金及技术来源、环境状况等多种因素,分一、二期设计总产能20吨/年。
第一期(2011-2012):逐步达产能10吨/年,研发新材质。
2011年初步投产,预计产量2.6吨,实现硬质合金低端切削刀片生产。
2012年实现YG.、YT、YW 类低端硬质合金切削刀片产量达8吨,新材质成果转化的高效硬质合金数控刀片2吨。
预计产值500万。
主要设备:50L球磨机器2套,制粒设备2套16吨自动机2台14吨自动压机2台单体真空脱蜡烧结炉100KG、30KG各一台第二期(2013-2015):纳米及陶瓷新材质应用,实现高端数控刀片生产,逐步替代低端产品,产品共计达产20吨/年。
其中低端硬质合金切削刀片产量5吨/年,中端数控刀片8吨/年,高端纳米及金属陶瓷硬质合金刀片在2015年实现7吨/年,在2015年实现产值2000万/年。
主要设备:低压真空烧结炉子精磨设备3 工艺路线3.1 工艺流程简图WC-Co、WC-TiC-Co、WC-Ti(Ta\Nb)C-Co滚动球磨擦篩制粒模压成型真空烧结精磨涂层激光打标检验包装3.2 工艺路线3.2.1 原辅材料主料采用国内外优质的碳化钨(WC)、钴粉(Co)、复式碳化物(CK);辅料为:石蜡或SD增塑剂、酒精湿磨介质。
- 1、下载文档前请自行甄别文档内容的完整性,平台不提供额外的编辑、内容补充、找答案等附加服务。
- 2、"仅部分预览"的文档,不可在线预览部分如存在完整性等问题,可反馈申请退款(可完整预览的文档不适用该条件!)。
- 3、如文档侵犯您的权益,请联系客服反馈,我们会尽快为您处理(人工客服工作时间:9:00-18:30)。
年产200吨YG类硬质合金的烧结车间设计文献综述学生:学号:专业:材料科学与工程班级:指导老师:四川理工学院材料与化学工程学院二O一一年三月前言硬质合金(Cemented carbide)是以难熔金属碳化物(WC、TIC等)为基体,铁族金属(Co、Fe、Ni等)作粘结剂,用粉末冶金方法制造的一种多相组合材料。
硬质合金具有很高的硬度、耐磨性、抗压强度和弹性模量,并具有一定的抗冲击性和小的热膨胀系数,其良好的耐腐蚀性、导热导电性是区别非金属硬质材料的显著特征。
世界上人工制成的第一种硬质合金诞生于1923年,德国人施勒特尔[1]往碳化钨粉末中加进10%~20%的钴做粘结剂,发明了硬度仅次于金刚石的碳化钨和钴的新合金,即是硬质合金,并很快将这种新技术运用到刀具的生产中。
随后的1929年美国人施瓦茨科夫在原有成分中加进了一定量的碳化钨和碳化钛的复式碳化物,改善了刀具切削钢材的性能,这是硬质合金发展史上的又一成就。
从此,硬质合金开始在工业的各个领域中得到广泛的应用。
硬质合金经过70多年的发展,经历了普通合金、亚微细晶粒合金、超细及纳米晶粒合金3大发展阶段,到如今已经取得了惊人的进步:它由小规模的生产发展为一个完整的独立的工业体系,它的触角几乎伸到所有的工业和技术部门,己成为现代工业部门和新技术领域不可缺少的工具材料和结构材料。
到目前为止,以WC和Co粘结剂为基的硬质合金仍然是此类产品的主要潮流。
硬质合金有着工业的“牙齿”[2]的美称,就在于它有着很高的硬度。
纯WC 的硬度相当高,其洛式硬度达到了94,纯度高的Co特别的软,但它有一个特点:纯Co对碳化物有很好的润湿性。
将WC与Co结合起来制成的WC-Co硬质合金在受力的情况下,由碳化物颗粒形成的骨架可以承受很大的压力,显示出很高的硬度,而作为粘结相的钴,则通过形变吸收产生机械变形的能量,抑制裂纹的延伸,呈现出较好的韧性和耐磨性[3],同时,WC在Co中的溶解度较低,所以Co 粘结的WC基硬质合金强度最高,硬质合金的这些优良的性能,使它成为工业上不可缺少的工具材料和结构材料。
硬质合金具有以下的主要特点:l)具有很高的硬度和耐磨性,尤其可贵的是在较高的温度下仍有很高的硬度;2)具有很高的抗压强度,可高达6000MPa;3)具有很高的弹性模量,在常温下刚性好;4)具有较稳定的化学性,耐腐蚀性和抗氧化性好,耐酸,耐碱,600-800℃时不发生明显氧化;5)冲击韧性较低,且导热系数及导电系数与铁及其合金接近。
由于硬质合金具有很高的硬度,常温下可达89~93HRA,而且可以在800℃以上的高温下进行工作,使其切削效率比高速钢高很多,它的诞生引起了金属切削加工工业的技术革命,它被看作是工具材料发展中,继碳素工具刚和高速钢之后的第三个阶段的标志。
与高速钢刀具相比,硬质合金较脆,可加工性差,过去仅限于用在车刀与面铣刀,但近年已扩展到整体与镶齿钻头、铰刀、立铣刀、正面刃铣刀和螺纹、齿轮刀具等,因为硬质合金与工具钢、高速钢相比,有自身的优点[4];(1)很大程度上提高了工具寿命,如切削工具寿命提高了5-80倍,量具寿命提高了20-150倍,模具寿命提高了50-100倍;(2)使金属切削速度和地壳钻进速度提高了几倍,甚至几十倍,从而提高了劳动效率;(3)提高了工件的精度和光洁度;(4)某些难加工材料的切削加工得以实现;(5)能够制成某些耐高温或抗腐蚀的耐磨零件,从而提高了在特殊恶劣条件下的零件的寿命。
随着科学技术和工业的发展,人们对硬质合金的要求日益提高,越来越多国家对硬质合金基础理论、生产工艺、工艺装备、使用技术等展开了大量的卓有成效的研究,使其生产工艺日趋成熟、工艺装备日臻完善、应用技术日益提高,从而推动了硬质合金生产不断发展,新技术不断涌现,质量不断提高,品种不断扩大,市场不断开拓。
1硬质合金工业的发展现代硬质合金作为一种新型工具材料,自1926年由德国克虏伯公司开始工业生产以来,迄今已有80多年的发展历史,其间主要经历了四个发展阶段[5]。
第一阶段(1927一1936)—世界硬质合金的形成阶段1926年德国的克虏伯公司将K.施律特尔制得的具有高强度、硬度的硬质合金投放入市场,随后美国、奥地利、英国、苏联、日本等国相继研究成功并生产硬质合金。
同时为了解决钢材加工问题,一些国家开始研究通过在WC-Co硬质合金中添加其它难熔化合物来改善其性能[6]。
第二阶段(1937一1949)—世界硬质合金工业的发展阶段第二次世界大战刺激了硬质合金工业的大发展,在这一阶段,为了满足军工生产的需要,硬质合金品种不断扩大,质量不断升高,不仅在生产中广泛应用含铌的硬质合金,而且开发了无钨合金以解决缺钨的问题。
第三阶段(1950-1969)—硬质合金工业的成熟阶段战后经济的恢复和发展,硬质合金工业进入了新的发展阶段,其应用领域也迅速扩大。
随着硬质合金生产和应用的扩大,对硬质合金提出了更高的要求。
具体体现在以下几个方面[7]:(l)完善硬质合金生产工艺,研制并推广一些新型工艺设备;(2)在硬质合金材质方面,用WC- TaC(NbC)-Co和WC-TiC-TaC(NbC)-Co 硬质合金来代替WC-Co和WC-TiC-Co合金;(3)在硬质合金刀具形状方面,采用可转位刀片。
第四阶段(1970年到现在卜世界硬质合金工业的产品精密化阶段进入到七、八十年代以后,世界硬质合金工业无论在生产技术和工艺装备方面,还是在材质和品种方面都取得了一些新的进展,采用了一些新技术和新设备,从而进一步推动了硬质合金工业的发展。
在生产技术领域中主要是进一步完善和推广七十年代出现的新工艺和新设备,诸如喷雾干燥、搅拌球磨、各种成形方法,热等静压、真空烧结等工艺与设备,并开发成功一些新工艺,诸如钨钴复合氧化物直接碳化衬取WC-Co化学混合料的工艺,毫微相WC-Co混合料的化学生产工艺、流化床制粒工艺、烧结—热等静压工艺,以及各种硬质合金后续处理技术等。
这些工艺和改进和新工艺的推广应用,大大地提高了硬质合金质量,扩大了硬质台金的应用领域。
在产品开发方面,研制并推广一些新型硬质合金,诸如新型超细硬质台金、碳氮化钛基硬质合金、低钨少担硬质合金、新型钢结硬质合金、新型粘结剂硬质合金、新型间隙硬质合金、新型多元硼化物基硬质合金、WC-Ni-Fe高比重合金为基础添加硼化物制取的新型无钴非传统硬质合金、二硼化钛基金属陶瓷硬质合金等。
这些新型硬质合金的开发,不仅对于满足工业发展的需要,特别是满足新技术领域的某些特殊需要起了重要的作用,而且也扩大了硬质合金的品种,开拓了新的应用领域。
与此同时,硬质合金产品结构也发生了一些明显的变化,切削工具和地质矿山工具的硬质合金用量有下降的趋势,而模具和耐磨零件的硬质合金用量则呈增长的倾向。
其间硬质合金的发展有三个突出的特点[8]:(l)涂层硬质合金发展迅速,其产量大幅度增加,应用领域不断扩大,已成功地应用于铣削等重加工工序;(2)研制成功并迅速普及了低压热等静压技术;(3)硬质合金制品向精密化、小型化的方向发展,己出现微型麻花钻头、点阵打印针、精密工模具等高新产品。
2国外硬质合金的研究进展近10多年来,世界硬质合金的研究与发展取得了举世瞩目的成绩。
新结构、新晶粒尺寸范围、新概念、新涂层硬质合金,新结构硬质合金刀具,硬质合金新材料,硬质合金生产新技术、新设备(如微波烧结设备、放电等离子体快速烧结设备)不断涌现。
美国的Nanodyne公司采用喷雾转化系列专利技术,己能大规模工业生产WC-Co纳米复合粉,目前已达到了年产500吨的生产水平;瑞典的Sandvik于1999年5月10日在新闻发布会上隆重推出了晶粒度为0.2um的新型纳米硬质合金PN90,从而在国际上开创了工业规模生产0.2um超细硬质合金的先河;德国的Konrad Fried richs KG硬质合金工厂(世界最著名的硬质合金挤压棒生产企业)也推出了牌号为KFK55SFspecial晶粒度为0.2um的超细硬质合金,用这种合金可以制造直径为0.1mm的PCB微钻,而且此公司还采用先进的硬质合金挤压技术,已能工业规模生产直径达38毫米的带或不带精确螺旋冷却孔的棒材,而目前我国只能生产直径小于20毫米的棒材;美国Kennametal公司开发出一种铣削高速钢用的多层涂层硬质合金刀片(KC792M),这种涂层刀片可进行平稳切削,并可使用较尖的刀头,降低功率消耗,延长使用寿命[9]。
3我国硬质合金的研究进展我国硬质合金工业的发展始于本世纪五十年代初期。
1958年,苏联援建的我国第一家硬质合金厂—株洲硬质合金厂(当时称株洲六O一厂)的建成投产,开创了我国硬质合金工业发展的新篇章。
随着国民经济发展以及国内有关技术人才队伍的成长壮大,我国第二个硬质合金厂—南昌硬质合金厂相继投产。
1965年,我国自行设计的第二大硬质合金厂—自贡硬质合金厂破土动工,尽管时值文革,但在党和政府的关怀及株洲硬质合金厂的大力支持下,于1970年正式试车投产。
从此,我国硬质合金工业步入了一个大的发展阶段。
经过50多年的风风雨雨,我国硬质合金工业大致经历了五个阶段,即雏形期(1958年以前)、发展壮大期(1958~1980年)、技改期(1980~1990年)、繁荣期(1990~2000年)、战略重组与竞争期(2000年以来)。
从上世纪70年代中期,我国就开始起步研究超细硬质合金,但由于技术基础和工艺装备水平起点较低等原因,与国外先进水平的差距逐渐拉开。
80-90年代,国内的株洲硬质合金集团有限公司和自贡硬质合金有限责任公司都对亚微米和超细硬质合金的研究投入了大量的人力、物力。
“九五”期间,在国际纳米材料发展热潮的推动下,国家“863计划”立项支持武汉理工大学、株洲硬质合金集团有限公司、北京科技大学、清华大学联合开发“超细晶粒WC基硬质合金的工业化制备技术”,试图在创新性的超细硬质合金材料制备技术方面缩短与国际先进水平的差距。
经过5年时间的努力,可以制备出了细小、均匀的纳米复合WC-Co原料粉末。
“十五”期间国家“863计划”继续支持复合粉工艺的完善和工程化“火炬计划”和“国家重点新产品计划”则支持优化传统的混合粉工艺制备超细硬质合金。
在超细粉末原料方面,厦门金鹭特种合金有限公司、株洲硬质合金集团有限公司、自贡硬质合金有限责任公司等单位都己掌握了制备BET粒度约为0.1-0.2um级别纳米WC粉末的技术、武汉理工大学采用流化床技术可获得50nm左右的WC-Co复合纳米粉末。
通过“七五”、“八五”、“九五”和“十五”期间的建设、技术引进与改造,以及科技攻关,国内硬质合金工业已形成了覆盖大半个中国(从广东至黑龙江、从上海至四川陕西均有硬质合金生产企业)的合理格局,工艺技术与装备水平不断提高,有的设备已能自主设计与制造,与国外同行的差距正在逐渐缩小。