超声波清洗气体保护焊丝表面质量分析
超声波清洗技术在焊丝生产中的应用

405 ) 50 2 (郑州机械研究所
摘
要
介绍超声波清洗污垢的原理。超声波清洗应 用于焊 丝镀前处理 , 可减轻 电解碱洗 的负担 , 高化镀速度 。 提
清洗时超声波频率为 1 — 0 H , 5 3 z声强 l 2 c 。水做清洗液时温度控制 在 6 左 右 ; k 一 m , W/ 0c c 在焊丝生产 线使被 淹没 的焊丝高于振予表面 10 m 超声 波清洗 宦在 敞 口容器 中进行 。 0 , m 关键词 超声波清洗 ; 焊丝生 产; 脱脂
me tb fr lt gc n l he h u d n o e t lssak l ce n u ,r ies e d o h mia — l t g h ' u n y n eo e pa i a g tn t e b r e fe cr y i l ai la o t as p e f e c l n i l o c Cu p ai .T e f q e c n i e o l a o i s 1 fu t s n c i r 5—3 Hza d s u d i tn i s1—2 W / m a la ig. t r e e au e i c n r l d a b u 0℃ . 0k n o n ne s y i t e sce n n wae mp r t r s o tol t o t t e a 6 T e w r s i ae r b v h i r tr b u h i n w tra e a o e t e vb ao s a o t1 0 mm n wed n ie p o u t n l e U ta o i ce n u ss i b e t e 0 i l i g w r r d c i i . l s n c la o ti u t l o o n r a
气体保护焊检验及评价

气体保护焊检验及评价刘 朋 材料技术科-金属组质保部材料技术科 Quality Assurance - Material Lab供应商专项技术交流系列-焊接Special Technique Communication Series for Suppliers主要内容:气体保护焊及应用 气体保护焊检验流程 气体保护焊检验标准质保部材料技术科 Quality Assurance-Material Lab供应商专项技术交流系列-焊接Special Technique Communication Series for Suppliers气体保护焊类型1.钨极惰性气体保护焊 TIG2.熔化极气体保护焊 MAG & MIG质保部材料技术科 Quality Assurance-Material Lab供应商专项技术交流系列-焊接Special Technique Communication Series for Suppliers气体保护焊类型MAG-熔化极活性气体保护焊CO2气体保护焊—目前最常见类型 车身件、座椅等MIG-熔化极惰性气体保护焊熔化极氩弧焊—某些不锈钢零件的焊接TIG-钨极氩弧焊钨极氩弧焊—某些铝合金零件的焊接质保部材料技术科 Quality Assurance-Material Lab供应商专项技术交流系列-焊接Special Technique Communication Series for Suppliers典型汽车零件焊接应用副车架支架 消音器 保险杠支架质保部材料技术科 Quality Assurance-Material Lab供应商专项技术交流系列-焊接Special Technique Communication Series for Suppliers气体保护焊检验流程图纸特殊要求焊缝尺寸特殊要求? (排气、消音) 剖切位置特殊要求(副车架)无特殊要求按流程检验质保部材料技术科 Quality Assurance-Material Lab供应商专项技术交流系列-焊接Special Technique Communication Series for Suppliers尺寸特殊要求质保部材料技术科 Quality Assurance-Material Lab供应商专项技术交流系列-焊接Special Technique Communication Series for Suppliers尺寸特殊要求质保部材料技术科 Quality Assurance-Material Lab供应商专项技术交流系列-焊接Special Technique Communication Series for Suppliers位置特殊要求质保部材料技术科 Quality Assurance-Material Lab供应商专项技术交流系列-焊接Special Technique Communication Series for Suppliers剖切检验流程1.先进行外观检验、对焊缝拍照留记录 2.焊接剖切、记录剖切位置并拍照留记录 3.剖切样块、记录制样日期、批次等信息OK 剖切位置要求 记录以备查4.磨样检验、结合VW01106识别接头类型、测量焊缝尺寸 5.缺陷评价、结合ISO5817识别缺陷并评价磨样检验需要6.最终评价、对整个结构综合评价、结果附照片的报告质保部材料技术科 Quality Assurance-Material Lab供应商专项技术交流系列-焊接Special Technique Communication Series for Suppliers气体保护焊检验标准VW01106-1 2004-07 钢类零件焊接* 注意:以后以最新版为准VW01106-3 2007-07 铝合金焊接 ISO5817 焊接缺陷质保部材料技术科 Quality Assurance-Material Lab供应商专项技术交流系列-焊接Special Technique Communication Series for SuppliersVW01106-1 适用范围结构承受动态载荷 无涂层/有涂层钢板 高合金钢&优质钢 厚度:0.5-6mm 质量等级要求:ISO 5817 B质量等级 其他特殊说明应该在图纸中指出和说明质保部材料技术科 Quality Assurance-Material Lab供应商专项技术交流系列-焊接Special Technique Communication Series for Suppliers材料相关—可焊接的材料超低碳钢: DC01-04 焊接性好 热轧钢:S235等 焊接性较好 微合金化高屈服强度钢: ZStE260 - ZStE420 磷化钢:H220PD至H300PD 不锈钢:奥氏体X5CrNi18-10 1.4301 铁素体X2CrTi12 1.4512质保部材料技术科 Quality Assurance-Material Lab供应商专项技术交流系列-焊接Special Technique Communication Series for Suppliers接头类型对接接头 端接接头 搭接接头 T型接头 角接接头 多重接头质保部材料技术科 Quality Assurance-Material Lab供应商专项技术交流系列-焊接Special Technique Communication Series for Suppliers焊缝类型填充焊 对焊和卷边焊 搭接焊 端焊 塞焊质保部材料技术科 Quality Assurance-Material Lab供应商专项技术交流系列-焊接Special Technique Communication Series for Suppliers焊缝尺寸计算焊缝厚度 a=0.7tmin 填充焊 实际焊缝厚度S>a 最小公用焊缝厚度 SN 代替S SN:最短有效焊缝厚度 多余金属不能算 实际焊缝长度一般>图纸长度,因为动态载荷质保部材料技术科 Quality Assurance-Material Lab供应商专项技术交流系列-焊接Special Technique Communication Series for Suppliers焊接质量保证DINEN729-1 DINEN729-2 熔深 一般>0.2mm 一些断面100%熔化 如果熔深<0.2mm,需要在图纸中说明,并进行动载试 验和金相检验 对于因为“焊接工艺窗口”较窄,导致熔深<0.2 mm,监 控时间间隔缩短或者剖切间隔长度缩短。
超声波无损探伤检测钢结构焊接质量分析

超声波无损探伤检测钢结构焊接质量分析超聲波探伤技术在钢结构焊接中的逐渐应用,给我国的工业发展带来很大的便利。
超声波探伤工作对探伤人员及超声波探伤仪的要求较为严格,探伤人员需要有过硬的专业知识及技术,对不同的钢结构焊缝需要选择不同的扫查方式、探头种类和检测面等。
通过加强对各方面的要求,以提高钢结构焊缝的质量,尽可能减少焊缝问题的出现。
鉴于此,本文对超声波无损探伤检测钢结构焊接质量进行了分析探讨。
标签:焊接质量;超声波探伤;无损检测一、钢结构焊接和检测要求根据GB50205-2001《钢结构工程及验收规范》的规定,要求对全焊透的一级焊缝进行100%超声波探伤检测,二级焊缝进行20%超声波探伤检测。
特别是对按焊缝百分比探伤的长度应不小于200mm,当长度不足200mm时应对整条焊缝进行探伤。
于不小于30mm的钢板,在钢梁和支撑梁连接部分处的焊接需求进行超声波补充探测,同时要声超波探测焊缝附近的金属,防止焊接层裂的出现。
钢结构中的钢构件拼接焊接要求采用埋弧自动焊,而对箱型柱和箱型支撑钢板的连接采用二氧化碳气体保护焊打底埋弧自动焊盖面的焊接形式。
二、国内钢结构焊接中出现的问题及原因1、夹渣、气孔出现夹渣主要是因为在进行钢结构焊接时未将焊缝内的熔渣或者其他杂质清理干净,这些夹渣形状各异,主要有点状和条状夹渣之分。
点状夹渣在某种意义上与点状气孔类似,在进行超声波探伤时反射出来的信号相差不大。
条状夹渣的回波信号表现明显,通过超声波探伤仪可看出其形状与呈锯齿状类似,由于夹渣声阻抗较大,所以夹渣的反射波幅较低,且随超声波探测仪探头位置的改变而改变,波形一般表现为树枝状。
气孔是在钢结构焊接时由于温度过高,焊缝中融入大量气体,在焊缝冷凝时气体没有得到完全排除,从而随着焊缝的凝固而在焊缝中形成形状大小各不相同的孔穴。
这些孔穴的形状以球形为主,按照气孔的密集程度可以分为单个与密集气孔。
在检测过程中,因为气孔内含气体声阻抗较小,故反射回拨较高,单个气孔与密集气孔的波高、波形均会有所不同。
超声波焊接质量分析

超声波焊接质量分析
一.切断或焊不牢
1.焊接压力不合适
2.振幅不合适
3.焊接方式不合适
4.下限位不合适
5.焊头和下声极网纹不合适
6.焊头和下声极网纹磨损严重
二.工件粘在焊头和下声极上
1.焊头或下声极网纹磨损
2.焊头或下声极表面污染
3.压力过大
4.焊头网纹或下声极表面有毛刺
三.焊接强度低,焊不牢
1.焊接方式不正确
2.焊头尺寸不正确
3.工件表面有油污或氧化膜
4.焊头下压行程不够
5.焊头网纹磨损严重
6.焊接能量没有完全传输至焊点(检查连接螺丝或换能器)。
钢结构无损检测中超声探伤的应用

钢结构无损检测中超声探伤的应用摘要:随着我国城镇化水平的不断提高,建筑业取得了长足的进步,而钢结构在这个过程中发挥着骨干支撑的重要作用,决定着我国社会主义发展的质量。
对钢结构工程质量进行必要的检查,及时发现问题,解决问题,尽可能减少损失,具有重要意义。
本文详细分析了超声波探伤在钢结构无损检测中的应用。
关键词:钢结构;无损检测技术;超声探伤;应用一、超声波探伤技术介绍及原理超声波探伤技术,顾名思义,就是利用超声波检测钢结构的缺陷。
它是一种重要的无损检测方法,应用范围很广。
超声波探伤设备结构简单,操作条件不是特别苛刻,安全性能好。
由于超声波穿透能力强,检测结果比较准确可靠,具有广阔的发展前景。
超声探伤主要构成有超声波探伤仪、耦合剂、探头、标准试块等部分。
根据设备运行所产生的波形不同,机械波可分为纵波、横波、板波和表面波,其中常用的波形为纵波和横波。
超声波探伤技术的应用主要是检测钢结构中是否存在气泡、缩孔、夹渣、、焊接裂纹以及不同部位的熔接,还可以确定铸件的厚度。
主要原理如下:超声波的频率在20000Hz以上,穿透能力强,设备产生超声波并通过探头发射,声波会在被检部位以一定的速度传播,当存在夹渣等异面介质时,部分超声波会被反射回来,通过接收机的处理,可以将缺陷的回波显示在示波器屏幕上,然后通过相关计算得到缺陷的深度和大小。
二、超声波探伤法在实际工作中的应用在进行探伤之前,我们需要了解图纸对焊接质量的技术要求。
目前,钢结构验收标准按照《钢结构工程施工质量验收规范》(GB50205-2001)执行。
标准规定:图纸要求焊缝焊接质量等级为一级,评定等级为一级时,规范要求100%超声波探伤;要求焊缝焊接质量等级为二级的图纸,评价等级为二级,按照现行规范,要求进行20%的超声波探伤;对于要求焊接质量等级 3 级的图纸,不进行超声波内部缺陷检查。
这里值得注意的是,超声波探伤用于全熔透焊缝,探伤率以每条焊缝长度的百分比计算,且不小于200mm。
超声波无损探伤检测焊接质量分析
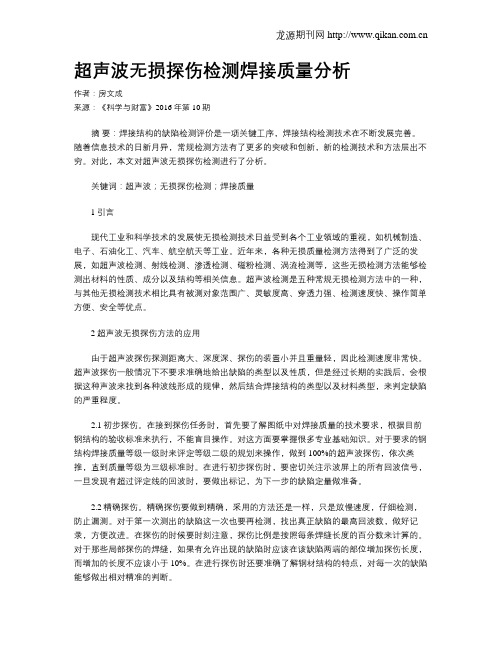
超声波无损探伤检测焊接质量分析作者:房文成来源:《科学与财富》2016年第10期摘要:焊接结构的缺陷检测评价是一项关键工序,焊接结构检测技术在不断发展完善。
随着信息技术的日新月异,常规检测方法有了更多的突破和创新,新的检测技术和方法层出不穷。
对此,本文对超声波无损探伤检测进行了分析。
关键词:超声波;无损探伤检测;焊接质量1引言现代工业和科学技术的发展使无损检测技术日益受到各个工业领域的重视,如机械制造、电子、石油化工、汽车、航空航天等工业。
近年来,各种无损质量检测方法得到了广泛的发展,如超声波检测、射线检测、渗透检测、磁粉检测、涡流检测等,这些无损检测方法能够检测出材料的性质、成分以及结构等相关信息。
超声波检测是五种常规无损检测方法中的一种,与其他无损检测技术相比具有被测对象范围广、灵敏度高、穿透力强、检测速度快、操作简单方便、安全等优点。
2超声波无损探伤方法的应用由于超声波探伤探测距离大、深度深、探伤的装置小并且重量轻,因此检测速度非常快。
超声波探伤一般情况下不要求准确地给出缺陷的类型以及性质,但是经过长期的实践后,会根据这种声波来找到各种波线形成的规律,然后结合焊接结构的类型以及材料类型,来判定缺陷的严重程度。
2.1初步探伤。
在接到探伤任务时,首先要了解图纸中对焊接质量的技术要求,根据目前钢结构的验收标准来执行,不能盲目操作。
对这方面要掌握很多专业基础知识。
对于要求的钢结构焊接质量等级一级时来评定等级二级的规划来操作,做到100%的超声波探伤,依次类推,直到质量等级为三级标准时。
在进行初步探伤时,要密切关注示波屏上的所有回波信号,一旦发现有超过评定线的回波时,要做出标记,为下一步的缺陷定量做准备。
2.2精确探伤。
精确探伤要做到精确,采用的方法还是一样,只是放慢速度,仔细检测,防止漏测。
对于第一次测出的缺陷这一次也要再检测,找出真正缺陷的最高回波数,做好记录,方便改进。
在探伤的时候要时刻注意,探伤比例是按照每条焊缝长度的百分数来计算的。
气保焊常见的质量缺陷分析与防止措施
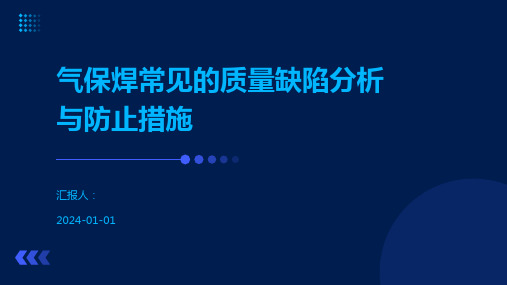
气保焊的应用领域
• 气保焊广泛应用于制造业,特别是汽车、航空、造船和建筑行 业。它能够提供高质量、高效率的焊接,适用于各种金属材料 的连接。
气保焊的优缺点
优点
气保焊具有焊接速度快、焊接质 量高、成本低等优点。它能有效 地连接各种金属材料,且焊接强 度和外观质量均较好。
03
质量缺陷产生的原因分析
气孔产生的原因
01
02
03
保护气体不纯
保护气体中含有过多的水 分或氧气,导致焊接过程 中产生气孔。
焊接速度过快
焊接速度过快,气体在熔 池中停留时间不足,导致 气体无法完全逸出。
焊丝受潮
焊丝受潮或表面有锈迹, 影响气体保护效果。
裂纹产生的原因
热输入过大
焊接过程中热输入过大,导致焊接接 头过热,产生裂纹。
咬边的防止措施
总结词
咬边是由于焊接过程中热输入量过大或操作 不当导致的焊缝边缘被熔化后形成的凹陷。
详细描述
为防止咬边的产生,应控制焊接速度和热输 入量,保持合适的焊丝角度和停留时间。同 时,应选择合适的坡口形式和角度,避免在 焊接过程中出现操作不当的现象。
THANKS
谢谢您的观看
焊缝结构设计不合理
焊缝结构设计不合理,如坡口角度过 小或焊缝太直,易产生应力集中。
焊缝金属组织不良
焊缝金属组织疏松或存在杂质,导致 焊接接头强度下降。
未熔合产生的原因
焊接电流过小
焊接电流过小,导致熔深 不足,造成未熔合。
焊接速度过快
焊接速度过快,导致熔池 停留时间不足,造成未熔 合。
焊丝伸出长度过长
详细描述
超声波焊接质量
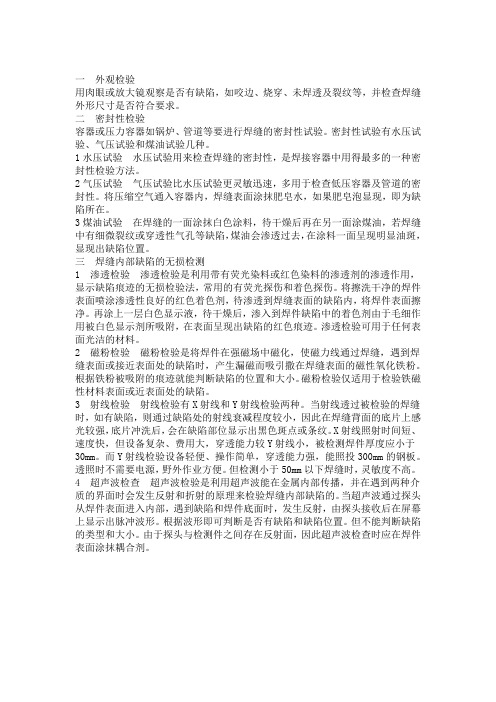
一外观检验用肉眼或放大镜观察是否有缺陷,如咬边、烧穿、未焊透及裂纹等,并检查焊缝外形尺寸是否符合要求。
二密封性检验容器或压力容器如锅炉、管道等要进行焊缝的密封性试验。
密封性试验有水压试验、气压试验和煤油试验几种。
1水压试验水压试验用来检查焊缝的密封性,是焊接容器中用得最多的一种密封性检验方法。
2气压试验气压试验比水压试验更灵敏迅速,多用于检查低压容器及管道的密封性。
将压缩空气通入容器内,焊缝表面涂抹肥皂水,如果肥皂泡显现,即为缺陷所在。
3煤油试验在焊缝的一面涂抹白色涂料,待干燥后再在另一面涂煤油,若焊缝中有细微裂纹或穿透性气孔等缺陷,煤油会渗透过去,在涂料一面呈现明显油斑,显现出缺陷位置。
三焊缝内部缺陷的无损检测1 渗透检验渗透检验是利用带有荧光染料或红色染料的渗透剂的渗透作用,显示缺陷痕迹的无损检验法,常用的有荧光探伤和着色探伤。
将擦洗干净的焊件表面喷涂渗透性良好的红色着色剂,待渗透到焊缝表面的缺陷内,将焊件表面擦净。
再涂上一层白色显示液,待干燥后,渗入到焊件缺陷中的着色剂由于毛细作用被白色显示剂所吸附,在表面呈现出缺陷的红色痕迹。
渗透检验可用于任何表面光洁的材料。
2 磁粉检验磁粉检验是将焊件在强磁场中磁化,使磁力线通过焊缝,遇到焊缝表面或接近表面处的缺陷时,产生漏磁而吸引撒在焊缝表面的磁性氧化铁粉。
根据铁粉被吸附的痕迹就能判断缺陷的位置和大小。
磁粉检验仅适用于检验铁磁性材料表面或近表面处的缺陷。
3 射线检验射线检验有X射线和Y射线检验两种。
当射线透过被检验的焊缝时,如有缺陷,则通过缺陷处的射线衰减程度较小,因此在焊缝背面的底片上感光较强,底片冲洗后,会在缺陷部位显示出黑色斑点或条纹。
X射线照射时间短、速度快,但设备复杂、费用大,穿透能力较Y射线小,被检测焊件厚度应小于30mm。
而Y射线检验设备轻便、操作简单,穿透能力强,能照投300mm的钢板。
透照时不需要电源,野外作业方便。
但检测小于50mm以下焊缝时,灵敏度不高。
焊接质量的超声波探伤无损检测

焊接质量的超声波探伤无损检测摘要:在工程建设项目的运行过程中,需要保证焊接质量等方面的控制措施能够得到有效落实,切实的提高工程建设作业的实施质量,进一步保障了工程项目的安全性。
为此,在开展工程项目作业的过程中,需要采取钢结构焊接的形式,加强工程建设的施工力度,及时地掌握损伤无损检测技术的应用要求,在使用的过程中选用合适的校准仪器,基于超声波损伤无损检测方法,进一步提高了焊接作业的实施质量,为工程项目的稳定性和安全性奠定了良好的基础。
关键词:焊接质量;超声波探伤;无损检测;措施引言:在修理基础附件的过程中,对人员的专业技能和焊接水平提出了较高的要求,需要选用合适的焊接技术,及时地解决在焊接作业实施阶段的质量问题,通过对无损检测技术的灵活使用,保障了检测工序的设施质量。
一、超声探伤检测措施的应用无损耗的超声波控制需要相关应用点的有效支持,注意本程序:热焊线采用超声波故障检测,误差检测速度按每条焊缝的百分比长度计算,长度不小于200mm,重点控制超声波损耗:工作人员在局部焊接过程中发现不合格缺陷,缺陷两端需增加,若发现不合格缺陷,工人必须检查10%的焊缝缺陷,超声波损伤控制的应用点数有效,检测时间确定,如结构钢用煤冷却后必须出口到12小时焊缝温度,低碳钢必须在焊后24小时超声波探伤有效改善。
在进行故障检查之前,必须把握图纸对焊接质量的客观要求。
目前钢铁结构的硬度指标是:根据图纸客观要求,焊接质量等级为一级时,其评价等级为二级,发生10%的超声波探伤。
根据图纸的客观要求,焊接焊缝的质量等级被评定为二级,等级为三级。
按照规定的要求进行20%的超声波探伤。
但是,如果图纸的客观要求包括:焊接品质等级3不需要超声波检查。
上述内容尤其是在全熔透焊接焊缝中进行超声波探伤,根据各焊缝的长度比,探伤误差一般在200mm以下,当误差检测焊缝的局部位置存在问题时,在两端的拉伸位置应延长误差检测长度,其长度应低于焊接长度的10%类似点不应小于200mm,如果存在缺陷,则对该焊缝进行10%的误差检测,并记录误差检测时间。
塑胶件超声波焊接常见缺陷及处理

塑胶件超声波焊接常见缺陷及处理塑胶件超声波焊接是一种常见的塑胶加工技术,它使用超声波振动将两个塑胶件表面加热并压合在一起。
然而,由于焊接过程中的各种因素,常常会出现一些焊接缺陷。
本文将介绍一些常见的塑胶件超声波焊接缺陷,并讨论它们的处理方法。
1. 出现漏焊漏焊是指塑胶件焊接过程中出现的焊缝不完全封闭,造成塑胶件连接不牢固的问题。
产生漏焊的原因有很多,可能是焊接参数设置不合理,例如超声波功率、焊接时间和焊接压力等;也可能是塑胶材料的选择不当,例如塑胶材料的熔点过高或过低都会影响焊缝的形成。
处理漏焊的方法一般是调整焊接参数、更换合适的塑胶材料或采取其他补救措施,例如使用热熔胶进行补焊。
2. 出现气泡气泡是指塑胶件焊接过程中,在焊缝中形成的气体囊泡。
气泡的形成可能是由于塑胶材料中的水分、气体或其他杂质没有完全排除导致的。
处理气泡的方法通常包括增加超声波震动时间,更换低含水量的塑胶材料或进行预干燥处理,以消除杂质。
3. 出现焊缝不均匀焊缝不均匀是指塑胶件焊接过程中焊缝的宽度、深度或形状不一致。
这可能是由于超声波振动均匀性差、焊具设计不合理或超声波能量传递不均匀等原因导致的。
处理焊缝不均匀的方法可以是调整焊接机的参数、优化焊具设计或采用其他工艺改进方法。
4. 出现熔崩熔崩是指塑胶件焊接过程中塑胶材料出现熔化破裂或溢出的现象。
这可能是由于焊接参数设置不当,例如超声波功率过高或焊接时间过长导致的。
处理熔崩的方法一般是调整焊接参数,降低超声波功率或缩短焊接时间,以避免过热导致塑胶材料熔化破裂。
5. 出现焊接接头强度不足焊接接头强度不足是指塑胶件焊接完毕后,焊缝的强度不够,容易出现开裂或断裂的现象。
减少焊接接头强度不足的方法包括增加焊接压力、增加超声波能量传递效率或更换更适合的焊接表面。
总之,塑胶件超声波焊接在实际应用中常常会出现一些焊接缺陷,这些缺陷可能是由于焊接参数、塑胶材料选择不当,甚至是焊接设备或工艺的设计问题所致。
基于超声清洗的CMT焊缝质量分析

上海工程技术大学学报JOURNAL OF SHANGHAI UNIVERSITY OF ENGINEERING SCIENCE Vol34No3 Sept2020第34卷第3期2020年9月文章编号:1009-444X(2020)03-0284-06基于超声清洗的CMT焊缝质量分析杨帅!邢彦锋!刘文杰(上海工程技术大学机械与汽车工程学院%上海201620)摘要:以6Q61铝合金为研究材料,使用超声工艺对焊接材料进行5和9min的清洗,研究超声清洗工艺对板件的冷金属过渡(CMT)搭接焊的影响.通过扫描电子显微镜(SEM)测试可知,改变清洗溶液的成分和清洗时间可以清洁铝合金表面并破碎铝合金表面氧化膜,提高焊接质量.分别采用超声水洗和超声盐酸清洗工艺,研究不同超声时间下焊缝的质量,并与无清洗铝合金焊缝质量进行对比.结果表明:在保证焊接拉伸质量的前提下,使用超声清洗可以有效优化焊接熔深,使其达到母材的Q.25;与超声水洗相比,超声盐酸清洗效果更好;清洗板材焊缝成型系数均值比非盐酸清洗的均值大67.8%.对焊缝的纵向切割分析表明,超声清洗还可以优化焊缝熔深的均匀性,减小气孔的尺寸和数量.关键词:冷金属过渡;铝合金;超声清洗;焊接气孔中图分类号:TG457文献标志码:AAnalysis of CMT Weld Quality Based on Ultrasonic CleaningYANG Shuai%XINGYanfng%LIU Wenjie(School of Mechanical and Automotive Engineering%Shanghai Universty of Engineering Science%Shanghai201620,China)Abstract:Using6061aluminum a l oyastheresearch material%ultrasonic cleaning process was used to cleanthewelding materialfor5and9mintostudytheinfluenceofultrasoniccleaningprocessonthe cold metaltransition(CMT)lapweldingoftheplates Scanningelectron microscope(SEM)testshows that changing the composition and cleaning time of the cleaning solution could clean the surface of aluminum a l oy and break the surface oxide film of aluminum a l oy%thus improving the weldingquality Ultrasonic washing and ultrasonic hydrochloric acid cleaning processes were used respectively to study the weldquality under di f erent cleaning times%and compared with that of non-cleaned aluminum a l oy Theresultsshowedthatunderthepremiseofensuringthe weldingtensilequality%ultrasoniccleaning could effectively optimize the welding depth,making it reach Q.25of the base pared with ultrasonicwashing%ultrasonichydrochloricacidhasbe t ercleaninge f ect%andtheaveragecoe f icientof weldformation ofcleaned plateis678%higherthan that of non-hydrochloric acid cleaning The longitudinalcu t inganalysisofweldshowsthatultrasoniccleaningcanalsooptimizetheuniformityof weldpenetrationdepthandreducethesizeandnumberofporesKey words:cold metal transition(CMT);aluminum;ultrasonic cleaning;welding pore收稿日期:2019-11-22作者简介:杨帅(1996-),男,在读硕士,研究方向为复杂薄板连接与装配制造.E-mail:yssues@通信作者:邢彦锋(1978-),男,教授,博士,研究方向为复杂薄板连接技术与装备.E-mail:smsmsues@第 3 期杨 帅,等:基于超声清洗的CMT 焊缝质量分析・285・铝合金作为一种轻型结构材料具有自重轻、耐 腐蚀和易加工等优异性能'-2(,广泛应用于汽车制造、航空航天、船舶和化工等领域.冷金属过渡 (Cold Metal Transition,CMT )技术由于具有电弧稳定、焊接过程中热输入量小、起弧无飞溅、弧长控 制精确等优点,在各种行业中应用的越来越广泛.在车身铝合金焊接过程中,氧化膜的存在会影响焊 接性能,如何处理表面氧化膜,提升铝合金的焊接性能变得至关重要.目前,涉及CMT 焊接焊缝中铝合金表面氧化膜的研究相对较少•有关研究中,李艳等「3 - 4(使用X 线衍射法和金相法,对1420合金板材在氩弧焊中的气孔来源进行研究,发现接头处的氧化膜是焊 缝中形成气孔的主要原因•李俐群等页使用激光自 熔焊研究不同焊接速度和送丝方式对焊接气孔的影响,发现在低速焊接和后送丝方式的焊缝中会存 在大量气孔.Yonekura 等页对超声波辅助无铅焊料与玻璃钎焊的机理进行了研究,发现运用超声波辅助钎焊时钎料在玻璃表面具有很好的润湿性,但如果超声波没有参与到焊接过程中,熔化的钎料则 不能很好的粘附于玻璃表面.Zhu 等「7(通过导电原子力显微镜(CAFM )技术明确了氯化物钎焊熔剂 中各组分在去除氧化膜过程中的作用,展示了氧化膜去除的机理,发现F 离子渗透进入到AI 2O3晶 格的间隙位置会引起晶格畸变,导致氧化膜与基底铝之间的局部裂解;Zn 离子在膜下产生Zn 沉淀,破坏了氧化膜与铝基板之间的结合;证明了氯化物钎焊活性剂中对去除氧化膜起作用的主要是F 离 子和Zn 离子.Yu 等「8(使用Sn-Ag-Ti 钎料通过超声波振动辅助铝和石墨的焊接,产生了稳定焊接接 头,并证明了超声波振动辅助焊接可以去除金属和钎料本身的表面氧化膜,改善液态钎料的润湿性和 延展性.Farzia 等⑼将光纤传感器和直流电化学方 式相结合,在阳极氧化的过程中实时监测氧化膜厚度,为测试氧化膜提供了新的方向•王力锋等「10(根 据气孔率分析焊缝气孔产生的原因,并研究激光一电弧复合焊接中熔池流动对焊接气孔的影响,最终 发现气孔率与焊接能量有直接联系,适当控制焊接能量可以减小焊接气孔关于焊接中铝合金表面氧化膜的研究,目前主要集中在小型钎焊和传统弧焊的领域,而对使用超声清洗处理再进行CMT 焊接的研究较少.为提高CMT 焊接质量,本文对铝合金薄板件使用超声水洗和超声盐酸清洗两种工艺进行处理,并对清洗工 艺进行了研究.1超声清洗及焊接试验试验材料为汽车车身所用的铝合金板件,型号 为 AA 6061-T 6,尺寸为 150 mm — 150 mm —2 mm,焊接布置方式为搭接焊.试验所用焊机为 Fronius 4000,超声清洗机为DK-3610D ,如图1所示•焊丝材料为4043铝硅,焊丝直径为1. 2 mm , 采用CMT 焊接方法,焊接参数见表1.每组焊接试验前,分别用超声波+盐酸/超声波+自来水的方 式对含有氧化膜的铝板在50〜60 \温度下进行清 洗,研究超声盐酸清洗法对焊缝质量的影响•焊接采用平焊的焊接方式图1超声清洗及焊接设备Fig. 1 Ultrasonic cleaning and weldingequipment・286・上海工程技术大学学报第34卷表1焊接参数Table1Welding parameters电流强度/A电弧电压/V电流种类焊接速度/(mm・s厂&)10022直流正接5无清洗板件表面含有油污、颗粒等不可控因素,所以对无清洗板件进行4组焊接试验,不同工艺超声清洗后的板件分别进行2组焊接试验,具体参数和样品编号见表2.对焊后样本进行切割、镶嵌、抛光处理,使用凯勒试剂对焊接截面进行腐蚀,最后使用徕卡金相显微镜DM4M对熔深、熔宽进行分析•根据国家标准+B/T228.1—2010制定静拉伸试样,在型号为MJDW-200B的万能试验机上进行拉伸试验,拉伸试样如图2所示.表2试验方案Table2Experimental scheme试验样品编号清洗时间/min盐酸浓度/(g*L-&) U-100U-200U-300U-400W9-190W9-290A5-155A5-255A9-195A9-295图2试样尺寸示意图Fig.2Sample size diagramt1205.;-------------------'-----___丿-------------------65'---------------------单位:mm2超声清洗焊接结果与分析2.1超声清洗效果分析使用扫描电子显微镜(SEM)对试验样品进行观察,发现超声盐酸清洗使铝合金表面形貌发生了变化•不同处理状态的试样表面微观形貌如图3所示.从图3(a)可以看出,没有清洗的铝合金表面存在划痕和污渍.不同处理方式的表面形貌如图3(b)所示,从图3(b)可以看出无清洗板件的表面存在油污且颜色暗黄,使用盐酸对板件表面进行腐蚀,盐酸腐蚀后的表面出现白色颗粒状的物质,颜色较暗且粗糙度也更大,使用凯勒试剂对铝合金板件进行腐蚀,表面出现气泡,酒精冲洗后表面出现白色的膜状物质,且膜状物质基本覆盖了整个试件•经过超声盐酸清洗处理后表面较为洁净,表面同时出现泛白的膜状物质,并出现更白的雪花状花纹,这表明稀释盐酸与超声空化效应相结合共同对表面处理发挥了作用.(a)未清洗的微观形貌(b)不同处理方式的表面形貌024681012keV图3不同处理方式试样的表面状态Fig.3Surface#tate#of#ample#treatedindiferentway#质量分数/%原子分数/% 054.2567.30 Mg0.410.33 Al10.6429.89 Si0.320.23 Cl 3.57 2.00 Cu0.810.25总量100.00100.00(c)超声盐酸清洗后表面元素分布在500倍显微镜下,发现未清洗的铝合金氧化膜表面存在大量的划痕及凹陷,如图3(a)所示,这是由于试验原材料的表面工艺导致表面缺陷.放大10000倍后,可以在铝合金氧化膜表面观察到长约50'm大小的杂质颗粒,这种缺陷有可能影响焊接熔滴的润湿性,进而改变焊接熔深和熔宽经过超声清洗之后,板件表面存在微量的氯(C1)元素,如图3(c)所示,这表明盐酸的反应可以在超声处理中正常发生.由于稀释盐酸酸性较弱,第 3 期杨 帅,等:基于超声清洗的CMT 焊缝质量分析・287・与铝合金表面氧化膜和铝基质反应效果较差,铝合金表面氧化膜轻微破裂,通过超声加热清洗的辅助 作用可以使表面氧化膜破裂程度提高并清洗表面杂质,反应式为A12O 3 +6HCl = 2AlCl 3 +3H 2O (1)2.2焊缝成型及拉伸力学性能分析熔深和清洗效果如图4所示.焊缝熔深效果较 为理想,均可以达到母材厚度的0.25.由焊缝成型系数# = !/#(#为熔深为熔宽)可知,超声盐酸清洗的焊材#值比非盐酸清洗工艺下的#值大, 计算超声盐酸清洗两种工艺下的#均值和非盐酸清洗两种工艺下的#均值可知,超声盐酸清洗的均值比非盐酸清洗的均值大67. 8%.超声盐酸清洗9 min 时#值最大,熔融焊材在母材表面的流动性提高,焊缝成型最好,且熔深、熔宽也较好.由此可知超声盐酸清洗可以优化焊缝成型质量■3.709 mm(p =4.706广O(a)无清洗(P =8.921(d)超声盐酸清洗9 min4.365 mm0=5.780(c)超声盐酸清洗5 min4.327 mm(p =4.053(b)超声水洗9 min图4焊接熔深Fig.4 Weldingpenetration在相同试验条件下分别对4种焊接试样进行 拉伸试验,试验结果对比如图5所示.由试验结果可知,焊接后熔合的焊缝材料为金属混合物,具有 非线性材料的特性 对比超声水洗和无清洗的试验数据 可 知 , 超 声 盐 酸 清 洗 5 min 对 焊 接 拉 伸 性 能 影 响较小,载荷为6. 827 kN.超声水洗9 min 所承受的载荷为5. 388 kN,为所有试验条件中的最小值.由此可知超声盐酸清洗可以在一定程度上优化焊接拉伸性能2.3焊接熔深和气孔分析位移/ mm由于焊缝的不均匀性,单一测点的截面熔深很 难体现焊缝不同位置的熔深情况[11 - 12(.为评估焊图5试样拉伸力学分析Fig.5 Tensileanalysisofsamples缝总体熔深,沿着焊缝中间位置进行纵向剖切,如 图6所示.随机选取间距为10 mm 的13个测点,测量各个测点处的熔深7 5.859654320235----超声水洗9 min ....超声盐酸洗5 min ----超声盐酸洗9 min -一无清洗'3%6.612 6.:827 -•I- -i無不同清洗时间纵向测点熔深对比如图7所示.图中出现熔深为0的测点,是由于切割位置误差 导致•相对横向切割测得的熔深,在纵向不同测点・288・上海工程技术大学学报第34卷图6多测点清洗效果Fig.6Multi-point cleaning effect 处熔深波动较大,一定程度上证明了焊缝的不均匀性.无清洗的样品纵向测点的熔深主要集中在0.3〜11mm;超声水洗9min样品的纵向测点熔深差距较大,主要分布在0.5〜1.0mm;超声盐酸清洗5min样品纵向测点熔深主要集中在0.6〜0.8mm;超声盐酸清洗9min样品纵向测点熔深主要集中在0.4〜0.7mm;超声盐酸清洗5和 9min后样品纵向测点熔深有明显改善,测点之间的熔深波动较小,焊缝均匀性较好.2日、嶷鉴砸W(C)超声盐酸清洗5min (d)超声盐酸清洗9min图7纵向测点熔深对比Fig.7Penetration comparison of longitudinal measuring points不同清洗条件下测得的气孔数量和气孔尺寸对比如图8和图9所示.由图可见,无清洗处理的试样焊接后气孔较多,气孔尺寸较大.由孔径变化可知,超声清洗处理后的气孔数目和大小均有所改善.长为15cm的无清洗焊接试样,焊接后的气孔数在5〜9个,平均每条焊缝中的气孔数为7个.超声水洗9min的样品,气孔数量相比未清洗试样明显减少,平均气孔数为2.5个,超声盐酸清洗5和9min的样品气孔数量差异不太明显,平均气孔数也维持在2.5个,但超声盐酸清洗5min时出现气孔数为0的情况,这是因为铝合金由于其金属活泼性,容易产生氧化膜,经过超声盐酸清洗后的焊接试样,虽然气孔数量有所减少,但产生的气孔数量仍会有一定的波动.O□无清洗□超声水洗9min实验样品编号图*气孔数量对比图Fig.8Comparison of poresnumber第 3 期杨 帅,等:基于超声清洗的CMT 焊缝质量分析・289・分析气孔尺寸中位数(图9中黑色虚线)可知, 超声清洗可以降低焊缝中气孔尺寸的大小,无清洗的焊接试样中气孔较大,最大尺寸为2.67 mm,最 小为0. 361 mm,严重影响了焊接质量.超声盐酸清洗5和9 min 的样品气孔尺寸变化较小.2.6701.988L 1-4700.882- 0.6040.361 0.610u 无清洗超声水洗9 min;二二超声盐酸清洗5 min 二二超声盐酸詹注9 min4 1 件 0.977」10.530'、、、0.948甲生:…:㈡”[」、、阴62\叮芯4。
焊接检验习题册答案

焊接检验习题册答案绪论一、填空题1.焊接产品整体结构与性能2.质量3.拉伸试验,硬度试验,弯曲试验,冲击试验4.水压试验,气压实验5.射线探伤,超声探伤,磁粉探伤,渗透探伤6.铁磁性材料7.金属不连续,不致密,连接不良8.种类,大小,数量,形态,分布9.尖锐的缺口,长宽比大10.垂直,平行11.密集气孔,条虫状气孔,针状气孔二、简答题1.答:焊接检验应贯穿于产品的全过程,从全面质量管理出发,除做好质量教育工作、标准化工作、计量工作、质量情报工作及质量责任制工作外,还必须树立以下三个基本观点:(1)下道工序是用户、工作对象是用户,用户第一,要求把对用户高度负责的精神渗透到生产的全过程,把各工序之间、各部门之间和各工作对象之间都看作下道工序,形成一个上道工序保下道工序、道道工序保成品、一切为用户的局面。
(2)预防为主、防检结合,焊接结构的优良质量主要依靠设计和制造,而不是依靠检验。
因此,应在产品的设计和制造阶段采取措施来保证其质量。
(3)检验是企业每个员工的本职工作,产品质量是由企业每个员工的工作质量来决定的,因此要求每个职工都要有根据、有程序、有效率地工作并达到工作质量标准,以良好的工作质量来保证产品的高质量。
2.答:焊接缺陷是指在焊接过程中,在焊接接头中发生的金属不连续、不致密或者连接不良的现象。
焊接结构中一般都存在缺陷,缺陷的存在将影响焊接接头的质量,例如:气孔会影响致密性、减小焊缝的有效面积、降低焊缝的强度和韧性;裂纹的危害比气孔更为严重,裂纹两端的缺口效应会造成严重的应力集中,容易引起扩展而形成宏观裂纹或整体断裂。
焊接缺陷的种类很多,各类缺陷的形态不同,对接头质量的影响也不相同。
任务1 焊接结构备件及焊缝外观缺陷一、填空题1.焊条,焊丝,焊剂,保护气体2.夹持焊条,传导电流3.预热4.600,30°,低倍放大镜5.主尺,高度尺二、简答题1.答:1.防护面罩;2.焊钳;3.焊接电缆2.答:焊接环境对焊接质量有较大影响,根据GB150.4-2011《压力容器第4部分:制造、检验和验收》中规定,当施焊环境中出现以下任一情况,且无有效防护措施时,禁止施焊:1)雨、雪环境2)相对湿度大于90%3)焊条电弧焊时风速大于10m/s4)气体保护焊时风速大于2m/s5)焊件温度低于-20℃任务2 焊接结构几何尺寸和耐压能力检验一、填空题1.致密性2.强度,致密性3.水压4.空气5.排气口二、简答题1.答:水压试验是最常用的压力试验方法,水的压缩性很小,容器一旦因缺陷扩展而发生泄露,水压便立即下降,不会引起爆炸。
超声波焊接工艺问题及解决

超声波焊接工艺问题及解决
超声波焊接是一种高效、无污染、无需补充材料、无烟尘的焊接方法,广泛应用于汽车、电子、塑料等行业。
然而,在使用超声波焊接时,也会出现一些问题,下面我们就来看看这些问题及其解决方法。
1. 焊点质量不稳定的问题
造成焊点质量不稳定的原因有很多,比如工件表面有油污、污渍、氧化物等,超声波振动系统不稳定,焊接时间不足等。
解决方法是要保证工件表面清洁,定期清洗设备;检查超声波振动系统是否正常,及时维护;控制好焊接时间,确保焊点的稳定性。
2. 焊接强度低的问题
焊接强度低的原因可能是焊接温度不足、压力不够、超声波振动系统不稳定等。
解决方法是增加焊接时间和温度,加大焊接压力,检查并维护超声波振动系统。
3. 焊接出现气泡的问题
焊接时出现气泡可能是由于工件表面不干净、焊接时间不足、焊接压力不够等原因造成的。
解决方法是保证工件表面清洁,焊接时间要足够长,加大焊接压力,确保焊接时工件表面无气泡。
4. 焊接出现裂纹的问题
焊接时出现裂纹可能是由于焊接温度过高、焊接时间过长、焊接压力过大等原因造成的。
解决方法是控制好焊接的温度、时间和压力,避免造成工件变形或者损坏。
总之,超声波焊接的技术越来越成熟,但是在使用过程中还是需
要注意一些常见问题,及时进行维护和处理,确保焊接质量和效率。
气体保护焊焊丝中杂质对焊接质量的影响
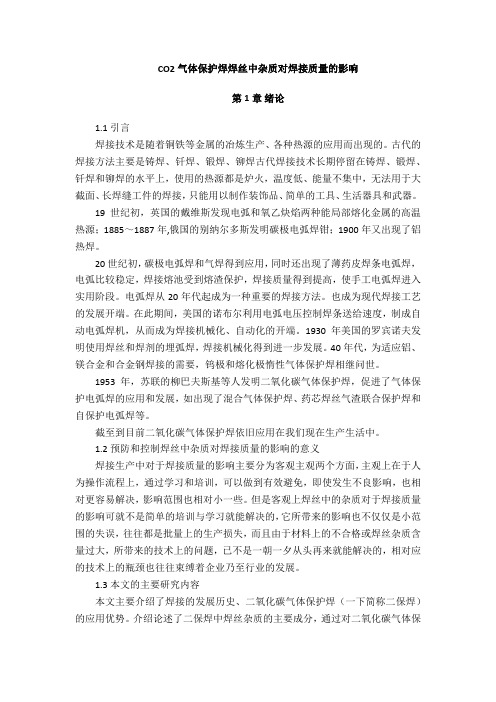
CO2气体保护焊焊丝中杂质对焊接质量的影响第1章绪论1.1 引言焊接技术是随着铜铁等金属的冶炼生产、各种热源的应用而出现的。
古代的焊接方法主要是铸焊、钎焊、锻焊、铆焊古代焊接技术长期停留在铸焊、锻焊、钎焊和铆焊的水平上,使用的热源都是炉火,温度低、能量不集中,无法用于大截面、长焊缝工件的焊接,只能用以制作装饰品、简单的工具、生活器具和武器。
19世纪初,英国的戴维斯发现电弧和氧乙炔焰两种能局部熔化金属的高温热源;1885~1887年,俄国的别纳尔多斯发明碳极电弧焊钳;1900年又出现了铝热焊。
20世纪初,碳极电弧焊和气焊得到应用,同时还出现了薄药皮焊条电弧焊,电弧比较稳定,焊接熔池受到熔渣保护,焊接质量得到提高,使手工电弧焊进入实用阶段。
电弧焊从20年代起成为一种重要的焊接方法。
也成为现代焊接工艺的发展开端。
在此期间,美国的诺布尔利用电弧电压控制焊条送给速度,制成自动电弧焊机,从而成为焊接机械化、自动化的开端。
1930年美国的罗宾诺夫发明使用焊丝和焊剂的埋弧焊,焊接机械化得到进一步发展。
40年代,为适应铝、镁合金和合金钢焊接的需要,钨极和熔化极惰性气体保护焊相继问世。
1953年,苏联的柳巴夫斯基等人发明二氧化碳气体保护焊,促进了气体保护电弧焊的应用和发展,如出现了混合气体保护焊、药芯焊丝气渣联合保护焊和自保护电弧焊等。
截至到目前二氧化碳气体保护焊依旧应用在我们现在生产生活中。
1.2 预防和控制焊丝中杂质对焊接质量的影响的意义焊接生产中对于焊接质量的影响主要分为客观主观两个方面,主观上在于人为操作流程上,通过学习和培训,可以做到有效避免,即使发生不良影响,也相对更容易解决,影响范围也相对小一些。
但是客观上焊丝中的杂质对于焊接质量的影响可就不是简单的培训与学习就能解决的,它所带来的影响也不仅仅是小范围的失误,往往都是批量上的生产损失,而且由于材料上的不合格或焊丝杂质含量过大,所带来的技术上的问题,已不是一朝一夕从头再来就能解决的,相对应的技术上的瓶颈也往往束缚着企业乃至行业的发展。
二氧化碳气体保护电弧焊焊接接头的超声波检测及缺陷分析

二氧化碳气体保护电弧焊焊接接头的超声波检测及缺陷分析摘要:二氧化碳气体保护电弧焊的特点:易产生未熔合、气孔、裂纹等缺陷。
对缺陷产生的成因做一定的了解,在超声波检测过程中,会有事半功倍的效果。
关键词:二氧化碳气体保护电弧焊;超声波检测;缺陷;反射波二氧化碳气体保护电弧焊采用co2 作为保护气体,与其他方法相比,虽飞溅较大,但这种焊接方法具有很多特点,如焊接效率高;在相同电流下,熔深比焊条电弧焊大;焊接速度快、变形小;焊缝金属含氢量低等优点,二氧化碳气体保护电弧焊广泛用于钢结构桥梁的焊接。
1. 缺陷统计根据我公司对2006年—2011年间12座钢结构桥梁的焊接接头无损检测发现的缺陷粗略统计,发现二氧化碳气体保护焊的各种缺陷的近似比例,气孔占50%左右、未溶合占30%左右、未焊透占5%左右、裂纹占5%左右,其它缺陷占10%左右。
从各种缺陷所占缺陷总数的百分比来看,除气孔外,未熔合缺陷占的比重最大,也是除裂纹外最严重的缺陷。
缺陷比例示意图2.典型缺陷产生原因及缺陷回波的特征二氧化碳气体保护电弧焊焊接过程中,根据该焊接方法的特点,该焊接方法易产生未熔合、气孔、裂纹等缺陷。
对缺陷产生的成因做一定的了解,在超声波检测过程中,会有事半功倍的效果。
2.1气孔气孔是指在焊接过程中,熔池金属中的气体在金属冷却以前未能来得及逸出,而在焊缝金属中(内部或表面)所形成的孔穴。
焊接区的保护气体二氧化碳易受外来气流的破坏而失去保护作用,保护气体的主要作用是防止空气的有害作用,实现对焊缝和近焊缝区的保护在现场施焊时,为防止上述情况的发生,必须在焊接区周围加挡风屏障;另外液态co2中含水较高,在焊接过程中一起进入焊接区,易产生气孔等缺陷,为防止上述情况的发生,必须提高焊接用co2的纯度,采取适当的减少水分的措施。
气孔产生的回波在显示屏上显示出一个尖锐的回波,当探头前后、左右扫查时,其幅度平滑地由零上升到最大值,然后又平滑地下降到零,这是缺陷尺寸小于超声波探头在缺陷位置处声束直径的信号特征。
超声波焊接质量评价
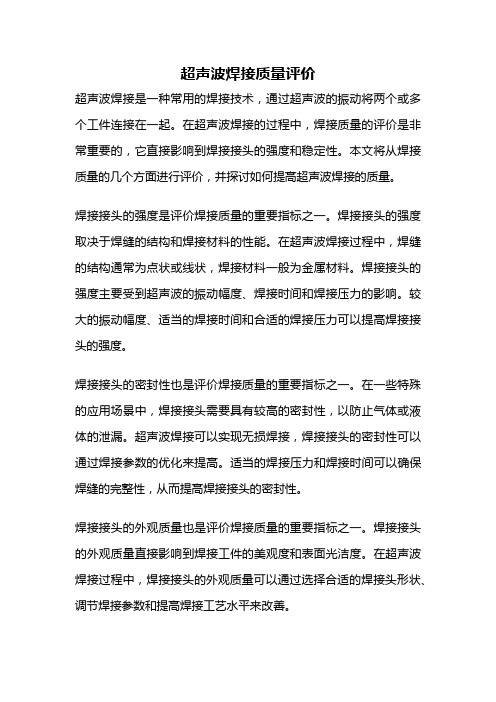
超声波焊接质量评价超声波焊接是一种常用的焊接技术,通过超声波的振动将两个或多个工件连接在一起。
在超声波焊接的过程中,焊接质量的评价是非常重要的,它直接影响到焊接接头的强度和稳定性。
本文将从焊接质量的几个方面进行评价,并探讨如何提高超声波焊接的质量。
焊接接头的强度是评价焊接质量的重要指标之一。
焊接接头的强度取决于焊缝的结构和焊接材料的性能。
在超声波焊接过程中,焊缝的结构通常为点状或线状,焊接材料一般为金属材料。
焊接接头的强度主要受到超声波的振动幅度、焊接时间和焊接压力的影响。
较大的振动幅度、适当的焊接时间和合适的焊接压力可以提高焊接接头的强度。
焊接接头的密封性也是评价焊接质量的重要指标之一。
在一些特殊的应用场景中,焊接接头需要具有较高的密封性,以防止气体或液体的泄漏。
超声波焊接可以实现无损焊接,焊接接头的密封性可以通过焊接参数的优化来提高。
适当的焊接压力和焊接时间可以确保焊缝的完整性,从而提高焊接接头的密封性。
焊接接头的外观质量也是评价焊接质量的重要指标之一。
焊接接头的外观质量直接影响到焊接工件的美观度和表面光洁度。
在超声波焊接过程中,焊接接头的外观质量可以通过选择合适的焊接头形状、调节焊接参数和提高焊接工艺水平来改善。
焊接接头的稳定性也是评价焊接质量的重要指标之一。
焊接接头的稳定性取决于焊接过程中的温度变化和焊接材料的熔化程度。
超声波焊接的特点是焊接过程中温度升高较快,熔化程度较高,可以实现快速、稳定的焊接。
然而,焊接接头的稳定性还需要通过合理选择焊接参数和控制焊接过程中的温度变化来保证。
超声波焊接质量评价是焊接技术中的重要内容。
通过评价焊接接头的强度、密封性、外观质量和稳定性,可以判断焊接质量的优劣,并采取相应的措施来提高焊接质量。
为了获得更好的焊接质量,需要合理选择焊接参数、优化焊接工艺和提高人员技术水平。
超声波焊接作为一种高效、环保的焊接技术,在汽车制造、电子设备、医疗器械等领域有着广泛的应用前景。
二氧化碳气体保护焊焊丝中杂质对焊接质量的影响
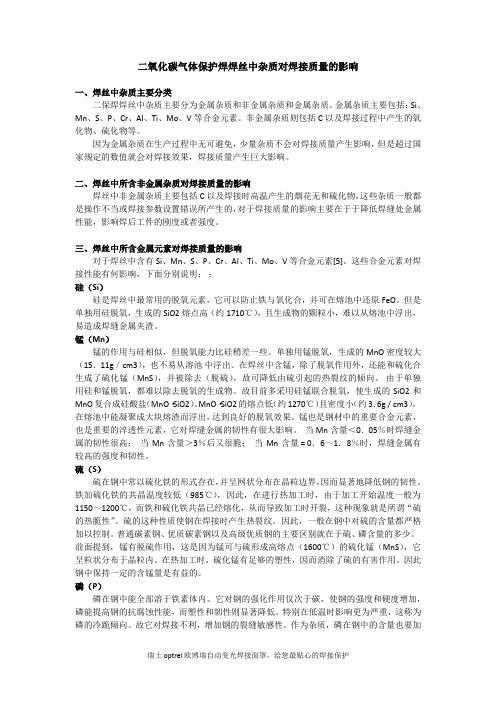
二氧化碳气体保护焊焊丝中杂质对焊接质量的影响一、焊丝中杂质主要分类二保焊焊丝中杂质主要分为金属杂质和非金属杂质和金属杂质。
金属杂质主要包括:Si、Mn、S、P、Cr、AI、Ti、Mo、V等合金元素。
非金属杂质则包括C以及焊接过程中产生的氧化物、硫化物等。
因为金属杂质在生产过程中无可避免,少量杂质不会对焊接质量产生影响,但是超过国家规定的数值就会对焊接效果,焊接质量产生巨大影响。
二、焊丝中所含非金属杂质对焊接质量的影响焊丝中非金属杂质主要包括C以及焊接时高温产生的烟花无和硫化物,这些杂质一般都是操作不当或焊接参数设置错误所产生的,对于焊接质量的影响主要在于于降低焊缝处金属性能,影响焊后工件的刚度或者强度。
三、焊丝中所含金属元素对焊接质量的影响对于焊丝中含有Si、Mn、S、P、Cr、AI、Ti、Mo、V等合金元素[5]。
这些合金元素对焊接性能有何影响,下面分别说明;:硅(Si)硅是焊丝中最常用的脱氧元素,它可以防止铁与氧化合,并可在熔池中还原FeO。
但是单独用硅脱氧,生成的SiO2熔点高(约1710℃),且生成物的颗粒小,难以从熔池中浮出,易造成焊缝金属夹渣。
锰(Mn)锰的作用与硅相似,但脱氧能力比硅稍差一些。
单独用锰脱氧,生成的MnO密度较大(15.11g/cm3),也不易从溶池中浮出。
在焊丝中含锰,除了脱氧作用外,还能和硫化合生成了硫化锰(MnS),并被除去(脱硫),故可降低由硫引起的热裂纹的倾向。
由于单独用硅和锰脱氧,都难以除去脱氧的生成物。
故目前多采用硅锰联合脱氧,使生成的SiO2和MnO复合成硅酸盐(MnO·SiO2)。
MnO·SiO2的熔点低(约1270℃)且密度小(约3.6g / cm3),在熔池中能凝聚成大块熔渣而浮出,达到良好的脱氧效果。
锰也是钢材中的重要合金元素,也是重要的淬透性元素,它对焊缝金属的韧性有很大影响。
当Mn含量<0.05%时焊缝金属的韧性很高;当Mn含量>3%后又很脆;当Mn含量 = 0.6~1.8%时,焊缝金属有较高的强度和韧性。
- 1、下载文档前请自行甄别文档内容的完整性,平台不提供额外的编辑、内容补充、找答案等附加服务。
- 2、"仅部分预览"的文档,不可在线预览部分如存在完整性等问题,可反馈申请退款(可完整预览的文档不适用该条件!)。
- 3、如文档侵犯您的权益,请联系客服反馈,我们会尽快为您处理(人工客服工作时间:9:00-18:30)。
超 声 波 清 洗 气 体 保 护 焊 丝 表 面质 量分 析
赵 振 海
( 天津冶金集团中兴盛达钢业有 限公司 , 天津 3 0 1 6 1 6 )
摘要 : 焊丝拉拔后表面残 留物不易清洗 , 影 响后续镀铜质量 。在分析造成焊丝镀铜缺 陷的基础上 , 从 焊丝镀铜前 的
清洗人手 , 通过实验对比不同清洗方法对焊丝镀铜质量的影响。结果表明, 焊丝拉 a i ( 死0 , n Me t a l l u r g y G r o u p F l o u r i s h S t e e l I n d u s t r i a l C o . , L t d . ,T i a n i f n 3 0 1 6 1 6 ,C h i n a )
,
w e l d i n g w i r e c o p p e r p l a t i n g ,c o n t r a s t t h e i n l f u e n c e o f d i f f e r e n t wa s h i n g me t h o d s o n w e l d i n g w i r e c o p p e r p l a t i n g q u li a t y
s u r f a c e q u a l i t y .Ba s e d o n t h e a n ly a s i s t h a t c a u s i n g we l d i n g wi r e c o p p e r p l a t i n g d e f e c t s b e g i n n i n g f r o m t h e wa s h i n g b e f o r e
中 图分 类 号 : 0 6 4 6 文 献标 识 码 : A
Su r f a c e q ua l i t y a na l y s i s o f ul t r a s o ni c c l e a ni ng g a s s h i e l de d we l di ng wi r e
第4 1 卷
Vo L4 1
第3 期
N o . 3
金
属 制 品
P r o d u c t s
2 0 1 5年 6月
J u n e 2 0 1 5
Me t a l
d o i : 1 0 . 3 9 6 9 / j . i s s n . 1 0 0 3— 4 2 2 6 . 2 0 1 5 . 0 3 . 0 1 0
Abs t r ac t : We l di n g wi r e s uI f a e e r e s i d u a l i s n o t e a s y t o c l e a n a f t e r d r a wi n g, S O i t wi l l i n lue f n c e s u b s e q u e n t c o pp e r pl a t i n g
s o n i c w a s h i n g i s g o o d,a n d h a s h i g h e f f i c i e n c y a n d f a s t s p e e d .
Ke y wor d s: g a s s h i e l de d we l di n g wi r e; c o pp e r p l a t i ng;l u br ic a n t ;pi c k l i n g; a l ka li wa s h i ng;ul t r a s o n i c wa s h i ng
的焊 丝表 面污染 , 是降低焊丝镀 铜层 质量的主要原 因 ; 酸洗 、 碱涝 、 清洗液只能部 分清除焊 丝表面残 留的润滑剂 , 但
不能彻底清除 , 而超声 波清洗效 果好 , 效率高 , 速度快 。 关键词 : 气体保护焊丝 ; 镀铜 ; 润 滑剂 ; 酸洗 ; 碱洗 ; 超 声波清洗
w e l d i n g wi r e d r a w i n g i s t h e ma i n r e a s o n t o r e d u c e we l d i n g w i r e c o p p e r p l a t i n g q u a l i t y; p i c k l i n g a l ka li wa s hi n g s o l u t i o n c a n
,
o n l y e l i mi n a t e p a r t i a l r e s i d u l a l u b r i c a n t o f we l d i n g wi r e s u r f a c e ,b u t c a n n o t e l i mi n a t e c o mp l e t e l y ,a n d t h e e f f e c t o f u l t r a —
t h r o u g h e x p e r i m e n t .T h e r e s u l t s h o w s : w e l d i n g w i r e s u r f a c e p o l l u t i o n c a u s e d b y w a t e r - i n s o l u b l e l u b r i c nt a i n t h e p r o c e s s o f