造成生料不稳定的原因及维护生料措施稳定的.doc
生产运作过程中的问题与解决方案

生产运作过程中的问题与解决方案引言在任何生产过程中,都会遇到各种问题。
这些问题可能导致生产效率下降,产品质量下降,甚至会给公司带来经济损失。
因此,及时发现问题并采取有效的解决方案非常重要。
本文将讨论一些常见的生产运作问题,并提供相应的解决方案。
问题一:生产工艺不稳定生产工艺不稳定是造成产品质量不稳定的主要原因之一。
工艺不稳定可能导致产品变异,无法达到规定的质量要求。
此外,工艺不稳定还会导致生产效率下降,浪费资源和时间。
解决方案要解决生产工艺不稳定的问题,可以采取以下措施:1.定期对生产工艺进行评估和优化,找出可能存在的问题并加以改进。
2.提供员工培训,确保他们熟悉并正确执行生产工艺。
3.使用先进的监测和控制设备,实时监测生产过程,并进行必要的调整。
4.建立有效的反馈机制,及时获取生产数据和产品质量信息,以便及时发现问题并采取措施。
问题二:设备故障设备故障是生产过程中常见的问题之一。
设备故障可能导致生产停工,增加维修成本,并且会给客户带来延误。
解决方案解决设备故障问题的关键在于预防和维修。
以下是一些解决方案:1.建立定期维护计划,对设备进行定期检查和保养,及时更换老化和磨损的零部件。
2.合理使用设备,避免过度使用和超负荷运行。
3.建立设备故障记录,并进行分析,找出故障的原因,并采取措施防止再次发生。
4.培训员工,使他们能够正确操作设备,并能够在设备故障时采取正确的应急措施。
问题三:供应链问题供应链问题可能包括供应商延误、物料短缺等。
这些问题会直接影响到生产计划和交货期。
解决方案解决供应链问题的关键在于合理规划和管理。
以下是一些建议:1.与供应商建立良好的合作关系,确保及时获取有关物料供应的信息。
2.预测需求并制定合理的采购计划,避免物料短缺。
3.建立备用供应商,以防止主要供应商的延误或破产。
4.使用供应链管理软件,实时跟踪物料供应情况,并进行及时调整。
问题四:人力资源问题人力资源问题可能包括员工流动率高、技术空缺等。
三元材料指标产异常原因及措施

1、排除设备、操作手法的问题,并进 行复测,跟踪复测结果; 2、若复测结果仍不合格,及时通知技 术、品质等相关部门,决定如何处理 (返工/报废/让步接收);
1、出炉料残碱偏低,证明生料Li%低, 说明物料缺Li%,会降低材料的电性能及 充放电效率,影响电池性能; 2、物料残碱高,会增加物料制浆时粘 度,导致物料无法正常使用。
1、人员操作不熟练 2、检测设备未校准 3、物料存在问题 4、未按照作业指导书进行操作 5、环境影响 6、测试偏差
1、人员操作不熟练 2、检测设备未校准 3、物料存在问题 4、未按照作业指导书进行操作 5、环境影响 6、测试偏差
1、Ni:提高容量,过高与Li离子混排使循环下降; 2、Co:降低混排,稳定层状架构,降低阻抗,提高电导率。过 高,导致晶胞参数a和c减小且c/a增大,导致容量降低; 3、Mn:降低成本和改善材料的结构稳定性和安全性。过高,降 低材料克容量,并且容易产生尖晶石相而破坏材料的层状结构。
1、人员操作不熟练 2、检测设备未校准 3、物料存在问题 4、未按照作业指导书进行操作 5、测试偏差
1、人员操作不熟练 2、检测设备未校准 3、物料存在问题 4、未按照作业指导书进行操作 5、测试偏差
异常后果
措施
1、水分过高会导致前驱体中有效物质含量不足; 2、影响一次配料生料均匀性。
1、排除设备、操作手法、环境的问题, 并进行复测,跟踪复测结果; 2、若复测结果仍不合格,及时通知技 术、品质等相关部门,决定如何处理 (退换货/让步接收);
1、人员操作不熟练 2、检测设备未校准 3、物料存在问题 4、未按照作业指导书进行操作 5、环境影响 6、测试偏差
1、人员操作不熟练 2、检测设备未校准 3、物料存在问题 4、未按照作业指导书进行操作 5、环境影响 6、测试偏差
浅谈提高混匀料稳定性的几点措施
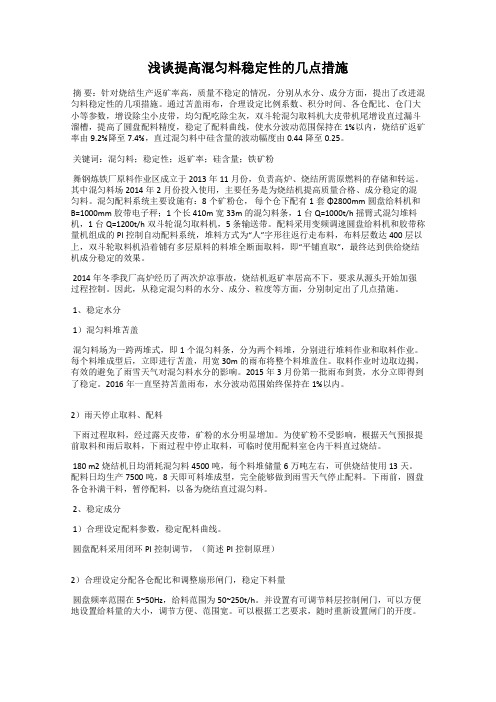
浅谈提高混匀料稳定性的几点措施摘要:针对烧结生产返矿率高,质量不稳定的情况,分别从水分、成分方面,提出了改进混匀料稳定性的几项措施。
通过苫盖雨布,合理设定比例系数、积分时间、各仓配比、仓门大小等参数,增设除尘小皮带,均匀配吃除尘灰,双斗轮混匀取料机大皮带机尾增设直过漏斗溜槽,提高了圆盘配料精度,稳定了配料曲线,使水分波动范围保持在1%以内,烧结矿返矿率由9.2%降至7.4%,直过混匀料中硅含量的波动幅度由0.44降至0.25。
关键词:混匀料;稳定性;返矿率;硅含量;铁矿粉舞钢炼铁厂原料作业区成立于2013年11月份,负责高炉、烧结所需原燃料的存储和转运。
其中混匀料场2014年2月份投入使用,主要任务是为烧结机提高质量合格、成分稳定的混匀料。
混匀配料系统主要设施有:8个矿粉仓,每个仓下配有1套Φ2800mm圆盘给料机和B=1000mm胶带电子秤;1个长410m宽33m的混匀料条,1台Q=1000t/h摇臂式混匀堆料机,1台Q=1200t/h双斗轮混匀取料机,5条输送带。
配料采用变频调速圆盘给料机和胶带称量机组成的PI控制自动配料系统,堆料方式为“人”字形往返行走布料,布料层数达400层以上,双斗轮取料机沿着铺有多层原料的料堆全断面取料,即“平铺直取”,最终达到供给烧结机成分稳定的效果。
2014年冬季我厂高炉经历了两次炉凉事故,烧结机返矿率居高不下,要求从源头开始加强过程控制。
因此,从稳定混匀料的水分、成分、粒度等方面,分别制定出了几点措施。
1、稳定水分1)混匀料堆苫盖混匀料场为一跨两堆式,即1个混匀料条,分为两个料堆,分别进行堆料作业和取料作业。
每个料堆成型后,立即进行苫盖,用宽30m的雨布将整个料堆盖住。
取料作业时边取边揭,有效的避免了雨雪天气对混匀料水分的影响。
2015年3月份第一批雨布到货,水分立即得到了稳定。
2016年一直坚持苫盖雨布,水分波动范围始终保持在1%以内。
2)雨天停止取料、配料下雨过程取料,经过露天皮带,矿粉的水分明显增加。
提高生料成分稳定性的技术措施

[ 1 0 ] 沈威 . 水泥工艺学( 重排版) [ M] . 武汉 :武汉理工 大学 出版
社 1 9 9 1 : 1 4 4 — 1 5 2 .
【 1 1 ] 张永龙, 王美园, 王学敏. 国产大型辊 压机及粉磨 系统工 艺方案[ J 】 . 中国水泥 , 2 0 0 6 ( 4 ) : 5 0 — 5 5 .
—
[ 8 ] 唐兴 国. 中国水泥助磨剂行业现状及发展趋势『 J 1 . 中国水
泥 2 0 1 0 ( 1 0 ) : 3 0 — 3 2 .
1 0 4.
( 收稿 日期 :2 0 1 3 — 3 — 1 2 )
【 9 ] 朱建 民. 环氧 乙烷产业的发展[ J 1 . 日用化学品科学, 2 0 0 9 ,
我 厂 拥 有 三 条 预 分 解 窑 水 泥 熟 料 生 产 线 ,采 用 石灰 石 、砂 岩 、钢 渣 、炉渣 四组分 配料 。为 了充
塞 ~
:
≥
≥- 4 @
— 耋
3 2 ( 1 1 1 : 9 — 1 1 .
_
量
~
靠性 与 产 品有效 性 的持续 改进 ,提 升企 业技 术 服务 水 平和 产 品创新 能力 ,这 样才 能在 激烈 的竞 争 和市 场 变革 中获 得长 足发 展 。
—
f 6 1 史伟 , 王冬 2 0 0 9 年 ̄ 1 2 0 5 0 年 中国国水 泥产量预N[ c ] / / 中
国水泥技术年会暨第十一届全 国水泥技术交流 大会论文 集, 重庆: 建筑材料工业技术情报研究所, 2 0 0 9 : 9 - 2 6 .
2 0 1 水泥工业大气污染物排放标准( 征求 意见稿) [ s 】 .
PTA成品料仓下料波动原因及对策

P T A装置 由于 设备故 障率 高 , 工艺介 质 流动性 差
造成 系统 经常 出现 不平稳 现象 , 这 直接影 响最终产 品
的各项 指标 。例如 : 旋转真空过滤机 B M 7 0 2滤饼厚 , 溢 流侧 因为设计 原 因经常容 易积料使 得溢 流量减小 , 造 成溢流管线容易堵塞使得浆 料漫入干燥机 最终造成 含
料不 畅或不下料 。 ・
精制 2个单元 , 共有 5个料仓 , 其 中 2个半 成品料仓 , 2 个班料 仓 一 个 成 品料仓 。其 中成 品料 仓设 计 容 量 1
5 0 0 t , 正 常情况 下存料不能超过 1 0 0 0 t 。 其 中精制单元 主要是在钯炭催化剂作 用下通过加
1 概述
洛阳石化 P T A装置采用美 国 B P - A MO C O工艺 , 日
加热效果差 , 干燥机出 口温度低含湿量 高 ; 结 晶器管线
频 繁堵塞 , 在 处理过 程 中造成 液位时高 时低使结 晶器
压 力也上 下波动 造成产 品粒径分 布不稳 , 偶尔会 造成 小粒径 增多 的现象 。以上几 种 情 况都 曾 在装 置发 生
第3 0卷第 4期
2 01 7- 0 7
聚 酯 工 业
P o l y e s t e r I n d u s t r y
Vo 1 . 3 0 No. 4
J u 1 . 01 2 7
d o i : 1 0 . 3 9 6 9 / j . i s s n . 1 0 0 8 - 8 2 6 1 . 2 0 1 7 . 0 4 . 0 1 1
2 措 施及 注意事项
2 . 1 措 施
从 上 述原 因分 析 可 以看 出 , 产 品 品质 的好坏 是
影响维生素预混料稳定性的因素及保护措施

实践Practice文 ⊙ 王方园 青岛莱西市畜牧兽医局预混料中维生素活性受多方面因素的影响,在生产和贮存过程中保持维生素预混料效价的稳定具有十分重要的意义,本文综述了影响维生素预混料稳定性的因素及保护措施以供参考。
影响维生素预混料稳定性的因素及保护措施在现代配合饲料生产中,复合预混料的应用极大地简化了生产过程,节省了大量设备投资,在平衡畜禽配合饲料营养方面发挥了重要的作用,从而得到普遍应用。
预混料提供的营养物质种类多,配方和生产过程中技术含量高,所含的组分一般占全价料的1%~5%。
预混料一般含有维生素、矿物质等。
其中,维生素在动物体内以辅酶和催化剂的形式参与几乎所有的新陈代谢反应,对维持细胞功能和各种酶的活性,调节三大物质代谢有不可替代的功能。
但维生素因富含不饱和的碳原子、双键、羟基等对化学反应极敏感的结构部分,极易被氧化还原,使其活性降低甚至全部丧失,是预混料中最不稳定的成分。
维生素活性损失后,会引起全价料营养价值降低,轻则影响畜禽的生长性能,重则引起某些营养缺乏症的出现。
因此,预混料中维生素活性的稳定对饲料品质、动物生长与健康有重大的影响,在贮存和加工过程保持其稳定至关重要。
1 影响维生素预混料稳定性的主要因素1.1 水分水分被认为是影响维生素稳定的首要因素,在加工和贮存过程中环境湿度过高或载体与原料含水量过高,均会破坏维生素的稳定性。
这是由于高水分会造成维生素微粒基质软化,氧气在基质表面的渗透性增加,加速了维生素的氧化变性及氯化胆碱、微量元素和其他化学反应对维生素的破坏作用。
据报道,VB 1、VB 2、烟酸、VE、VC等在低水分条件下储存1年后,仍会有很高的存留率;而高水分条件下贮存21d后,VB 1仅剩48%,VC几乎全部损失,贮存3个月后,VB 2含量低于50%。
为维持维生素良好的稳定性,预混料水分含量不应超过7%。
1.2 温度温度越高维生素预混料损失越大。
有研究表明,当温度低于10℃时,维生素损失较少;15~25℃(室温)时,一些较不稳定维生素会损失;当高于30℃时,大部分维生素都会受到破坏。
饲料品质波动的原因分析及其解决策略

CP
Lys
SAA
Thr
基于赢创德固赛2009年为客户分析的样品
| Page | 23
Feed Additives – amino acids and more.
如何确定原料中氨基酸成分?
参照营养成分表,如Amino Dat 3.0。 测定粗蛋白,用氨基酸与粗蛋白比例关系(氨基酸
组成比例)预测。
粕
粉
中国原料的必须氨基酸平均变异
30% 25% 20%
CV %
15% 10% 5% 0%
玉米 膨化 米糠 鱼粉 棉粕 麦麸 D DG S 羽毛 次粉 肉粉 菜粕 小麦 肉骨 玉米
原料
10.4%
葵花
大豆
豆粕
玉米 小麦 次粉 麦麸 米糠 DDGS 玉米蛋 膨化 白粉 980 大豆 407
蛋白 粉
样品数 1098 187 151 485 795 296 *校正到标准DM,植物类为88%,动物类91% *根据Degussa 帮助中国客户分析的样品数据统计
Page | 26
印度 (N=20) 均值 88 46.3 1.28 2.68 6.03 3.83 1.32 7.46 4.42 7.49 4.61 CV % 4.4 4.4 4.7 2.5 2.1 2.0 3.5 3.0 2.3 2.8
CV % 3.9 5.2 4.3 2.6 2.9 2.5 2.6 2.9 1.6 3.0
48 47
1996-2000 2001-2005
粗蛋白质,%
46 45 44 43 42
阿根廷
巴西
印度
美国
来源: 赢创德固赛氨基酸数据库AminoDat 2.0 and 3.0
|
Page | 20
聚丙烯挤压造粒机造粒质量不稳定原因及改进探究
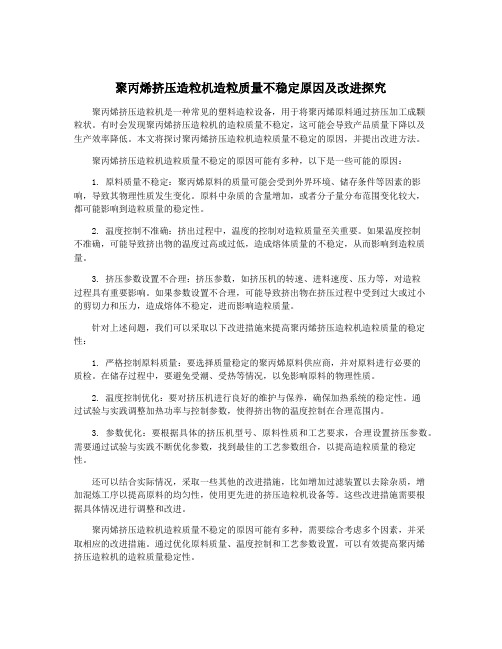
聚丙烯挤压造粒机造粒质量不稳定原因及改进探究聚丙烯挤压造粒机是一种常见的塑料造粒设备,用于将聚丙烯原料通过挤压加工成颗粒状。
有时会发现聚丙烯挤压造粒机的造粒质量不稳定,这可能会导致产品质量下降以及生产效率降低。
本文将探讨聚丙烯挤压造粒机造粒质量不稳定的原因,并提出改进方法。
聚丙烯挤压造粒机造粒质量不稳定的原因可能有多种,以下是一些可能的原因:1. 原料质量不稳定:聚丙烯原料的质量可能会受到外界环境、储存条件等因素的影响,导致其物理性质发生变化。
原料中杂质的含量增加,或者分子量分布范围变化较大,都可能影响到造粒质量的稳定性。
2. 温度控制不准确:挤出过程中,温度的控制对造粒质量至关重要。
如果温度控制不准确,可能导致挤出物的温度过高或过低,造成熔体质量的不稳定,从而影响到造粒质量。
3. 挤压参数设置不合理:挤压参数,如挤压机的转速、进料速度、压力等,对造粒过程具有重要影响。
如果参数设置不合理,可能导致挤出物在挤压过程中受到过大或过小的剪切力和压力,造成熔体不稳定,进而影响造粒质量。
针对上述问题,我们可以采取以下改进措施来提高聚丙烯挤压造粒机造粒质量的稳定性:1. 严格控制原料质量:要选择质量稳定的聚丙烯原料供应商,并对原料进行必要的质检。
在储存过程中,要避免受潮、受热等情况,以免影响原料的物理性质。
2. 温度控制优化:要对挤压机进行良好的维护与保养,确保加热系统的稳定性。
通过试验与实践调整加热功率与控制参数,使得挤出物的温度控制在合理范围内。
3. 参数优化:要根据具体的挤压机型号、原料性质和工艺要求,合理设置挤压参数。
需要通过试验与实践不断优化参数,找到最佳的工艺参数组合,以提高造粒质量的稳定性。
还可以结合实际情况,采取一些其他的改进措施,比如增加过滤装置以去除杂质,增加混炼工序以提高原料的均匀性,使用更先进的挤压造粒机设备等。
这些改进措施需要根据具体情况进行调整和改进。
聚丙烯挤压造粒机造粒质量不稳定的原因可能有多种,需要综合考虑多个因素,并采取相应的改进措施。
出磨生料质量影响因素分析及改进

出磨生料质量影响因素分析及改进2007.No.7水渗f一35一出磨生料质量影响因素分析及改进许玉真,陈中飞(曙光强兴水泥有限公司,河北唐山063708)中图分类号:TQ172.614.1文献标识码:B文章编号:1002—9877(2007)07-0035-03 新型干法水泥生产线普遍采用生料均化库以提高均化效果,但受料位,均化设施等的影响,生料均化效果并不十分理想,因此提高出磨生料质量合格率仍是稳定熟料质量的关键.现结合我公司生产过程质量控制情况,对影响出磨生料质量合格率的因素及工艺条件进行分析,针对出磨生料质量控制中常见的问题,谈一下自己的看法.l生产工艺流程及主机设备简介我公司是一条2500ffd的新型干法水泥熟料生产线,生料质量控制采用QCX生料配料自动控制系统,利用荧光分析仪对出磨生料进行快速检测,通过调整生料的三率值来实现对出磨生料质量的控制.主要工艺设备规格能力见表1.表1主要工艺设备参数设备名称规格型号设计能力实际能力石灰石预均化堆场2—250mx60m2.5万t2.5万t煤预均化堆场2—169m~25m3000t3000t生料均化库l8mx43.5m90oot9000t生料磨qb4.6mx(10+3.5)Inl90t,h205t,h煤磨qb2.8rex(5.75+2.25)In22t/h2Ot,h回转窑中4.2m~60m2500t/d2750t/d篦冷机BL2500水平推动式25oGd275O洲2原材料及生,熟料质量控制情况2.1原材料及主要化学成分我公司采用四组分配料:石灰石,砂岩,铝矾土和钢渣,均是当地资源.其中石灰石有两种:一种是碱石尾矿,CaO含量51%,MgO含量2.0%左右,这种石灰石结构疏松,易磨性好;另一种石灰石CaO含量在48%左右,其矿物成分以方解石为主,其次是O/一石英,质地较硬.在生产中两种石灰石按2:1搭配使用. 砂岩SiO含量较高,烧失量小,主要物相为结晶良好的一石英晶体,晶粒粗大完整,杂质很少,易磨性较差.铝矾土主要物相为O/一石英晶体,且含有较多反应活性较好的黏土类矿物,各矿物晶体粒度细小,结构疏松,反应活性以及易磨性较好;钢渣则是附近钢厂的副产品,经除铁处理后的颗粒状物料,其易磨及易烧性相对较好.原材料的主要化学成分见表2.表2原材料主要化学成分分析%名称LossSiO2Al203F0203Ca0MgO0Na20SO3∑石灰石40.794.10l-390.4949.742-350.400.060.0299.34 砂岩1.0593.642.561.050.100.560.4l0.0999.37铝矾土l3.7440.5733.8210.56O.19O.12O.230.0799-3O 钢渣-0.9416.284.5325.4540.4010.550.040.0496-35 2.2生,熟料主要化学成分及指标入窑生料中,由于掺入了饱和比较高的收尘灰,使得入窑生料比出磨生料的三率值有一定的变化. 生,熟料主要化学成分及指标见表3.表3生,熟料主要化学成分及指标化学成分/%率值物料名称80lXm筛余/%水分/%LossSiO2Al203F0203Ca0MgO∑KHsMlM出磨生料36.o3l3.7l2.841.8642.652.3299.4l0.972.921.5315.O1.O 人窑生料35.95l3.552.901.8343.002.1299350.992.871.58l5.01.0 熟料O.O321.565.063-3865.1303.4l98.44O.922.551.5O3影响出磨生料质量因素的分析及改进自2005年11月投产以来,在生产中曾出现过如下几方面的问题,通过不断的分析和摸索,采取相应的措施,使问题得到了较好地解决.3.1配料库下频繁堵料当砂岩和铝矾土水分大时,常常会发生配料库下堵料现象,尤其在7,8月份的雨季时,堵料更加频繁,有时因为砂岩堵料而被迫停磨处理,至少每班一次,生料质量根本无法控制.靠人工捅堵料来保证入磨物料的连续性,往往比较被动,既浪费了人力,又影响了一36一t'E,41~IT产量.我们分析,这2种物料在库内容易"结拱","架桥",致使库内有料而下不来,或者是结大块,卡死下料口,主要原因有二:1)配料库是为2条生产线设计的(目前二线还未建设),所以配料库直径较大,并且入料口与下料口不在库的几何中轴上,属于偏库下料,物料在库内的流动性差是导致堵料的一个原因.2)物料本身(特别是物料中粒度较小的粉状料)的黏滞性和含水分大,是造成堵料的根本原因.针对这些现象,我们采取了以下措施:1)从供货上控制砂岩,铝矾土中粉状料的比例,尽量选块状物料进厂,但粒度控制在30ram以下,否则也容易卡住下料口,划破皮带秤.2)控制物料进厂(保证进厂尽可能是干的,尽量安排在晴天进),并且在天气好时,在堆场对物料加以晾晒.3)在这2个配料库锥部增设了方便操作的捅料孔,以提高工作效率,减少劳动强度.另外,定期清库,防止物料结拱堆积,架死.通过以上工艺条件的改善,以及对进厂原料水分,粒度的控制,目前堵料的状况已经大有缓解.3.2配料库内物料的离析现象我公司使用的4种原材料中,铝矾土和钢渣的用量较少,况且钢渣的粒度细小均匀,均在10ram以下,基本没有离析现象.石灰石和砂岩的用量大,在库内的离析作用也比较明显,所以对出磨生料质量的稳定起着决定性作用.被均化过的石灰石进入配料库后,不同粒径的石灰石会产生离析,中间粉料多,边缘块料多,造成人磨物料粒度,成分呈周期性变化,波动较大,出磨生料质量控制困难.由于石灰石采用连续倒库的方式,在一个生产班中仅用一半的时间就能把石灰石配料库人满.入料的不连续,使得入磨石灰石粒度的波动具有较强的跳跃性.当粒度较大的石灰石入磨时,不仅使成分发生了明显的变化,而且其粒度大,在磨内停留时间较长,容易引起生料磨饱磨,磨况不稳定,也给出磨生料成分带来很大的影响.对于砂岩,因偏库下料,也有类似的离析现象.通过试验分析,块状砂岩的SiO含量在98%左右,而粉状的只有88%左右,两者的差别较大,从而使得出磨生料SiO的变化跳跃性较强.从配料计算公式KH=(CaO一1.65A12O3—0.35Fe203)/(2.8SiO2)中可以明显看出,SiO2 的变化远大于CaO的变化对KH带来的影响.因此.当入磨砂岩粒度发生变化时,配料操作员难以作出准确判断,从而给出磨生料质量带来波动.针对以上两种物料在库内的离析现象,我们主要2007.No.7从以下两个方面加以改善:1)把石灰石取料机速度降下来,保证石灰石倒库的连续性,大大减小了石灰石在库内的离析;2)从进厂砂岩的粒度上加以控制,缓解了其在库内的离析.经过上述措施的实施,出磨生料的质量有了明显改善,生料磨的台时产量也有了提高.3.3校正原料质量的波动除石灰石有均化设施外,其它3种校正原料因堆场场地有限,没有设计预均化堆场.由于同一种校正料的供货商不一,主要成分差别较大.尤其是铝矾土, 两家供货,一家Al0含量33%左右,而另一家却只有26%,若两者搭配不匀入磨,使得出磨生料的Al0 含量时高时低,波动较大,配料操作员无法准确的调整入磨物料配比,直接影响到t/,,P合格率.为此,我们严格按厂家堆放,并且坚持"先检验,后使用"的原则, 在堆场搭配混匀后入库.这样,入磨物料成分稳定了, 出磨生料t/,,P的合格率比以前大有好转.3.4原材料易磨性不同的影响在生产中经过多次观察发现,在原材料配比不变的情况下,在开磨最初的一两个小时内,出磨生料成分随着时间的延长呈一定的规律性变化:SiO的含量逐渐增大.进而我们还发现,增加石灰石的配比同时减少砂岩的配比,与减少石灰石的配比同时增加砂岩的配比,当其变化幅度一样时,KH的变化速度却是不同的(中控其他操作参数不变).增加石灰石,同时减少相同份额的砂岩,出磨生料KH上升的速度慢;而减少石灰石,同时增加相同份额的砂岩,出磨生料KH下降的速度快.这主要是由于原材料易磨性的差别所至.原材料的易磨性受原料的粒度,原料中SiO总量,游离SiO:含量,胶结物料性质,结晶形态,风化程度和自然水分等因素的影响.在这些因素中,SiO总量(游离的和结合的)及方解石,石英的颗粒尺寸和非均齐性等结构特征,是控制石灰石,砂岩易磨性的主要因素.在入磨原料中,我公司石灰石以质地相对较软的碱石尾矿为主,而砂岩中矿物又以OL一石英为主,相对易磨性系数砂岩小于石灰石,这必然导致同时入磨的原料中石灰石成分总要比砂岩成分早一个时间段到达取样点.了解了这一规律,配料员就可以根据具体情况,适当的进行配比调节.同样,铝矾土和钢渣也有类似的特点.3.5磨机工况的影响生料磨台时产量的变化,循环负荷的变化,空饱磨,选粉机以及风量的调节等都将直接影响到出磨生料的质量.磨况的稳定与否,在很大程度上与操作员的手法,原材料的性能及设备运行情况密切相关.不2007.No.7许玉真,等:出磨生料质量影响因素分析及改进一37一同操作员在操作过程中控制产量,风量,差压,出磨生料细度及风温等操作参数不尽相同,其操作手法的不一致,多少会影响到磨机的工况.3.5.1台时产量变化的影响由于我公司生料磨系统初始未进行循环风设计,系统拉风不足,导致出磨生料粉温度偏高,选粉机选粉效率差,造成出磨斗提电流偏高,曾一度严重制约了生料磨的台时产量,也影响了生料的质量.2006年8月份技改后,对生料磨系统增设了磨头,磨尾以及选粉机的循环风管道,选粉效率得到了提高,生料磨的台时产量由原来的170t/h提高至205t/h,出磨生料质量也比以前稳定了许多.稳定磨机的台时产量,不仅可以稳定磨机的负荷,提高粉磨效率,也可以提高出磨生料的均匀性和稳定性.3.5.2循环负荷的影响循环负荷的变化是由于出磨粉,粗粉和精粉三者中的一个或一个以上筛余量发生变化而引起的.其中粗粉量的变化必然引起磨头,磨尾喂料量的变化,从而引起生料CaO,SiO:含量的波动.因此,稳定循环负荷是稳定生料质量必不可少的工艺措施.生料磨的循环用风自技改后,循环负荷有了相对的稳定性.3.5_3饱磨的影响入磨物料水分,粒度的变化,将直接影响到粉磨状况.当物料水分变大时,磨内气体湿含量增大,若不及时排出,细物料易黏附在钢球和衬板上形成"物料垫",使粉磨效率下降,严重时堵塞隔仓板和篦板,出现饱磨现象;当物料粒度增大时,粉磨时间延长,磨内物料量失去平衡,也容易引起饱磨.饱磨时,磨内物料积存较多,由于砂岩易磨性较差,积存物料中砂岩比例较大,因而出磨砂岩较少,此时生料KH偏高.饱磨发生后要及时停止喂料使磨机空转,严重时一般需要15min磨音才能正常.磨内所存砂岩随着磨机空转逐渐流出,此时出磨KH将偏低.3.6预均化堆场石灰石堆头,堆尾成分波动大预均化堆场的石灰石取料换堆时,石灰石的粒度,成分有较大波动,使得出磨生料的质量难以控制, 严重时常常要影响到两个班的生料质量.这是因为石灰石布料时,料堆两头由于离析作用不可避免地聚集了大颗粒物料.尤其当两种石灰石布料搭配比例不稳定,品位差别较大时,影响更加突出.对这一问题,我们采取了以下措施:加强对进厂石灰石的管理,严格按照厂家,品位堆放,控制好进厂的数量及品位,杜绝未经检验直接使用,增加布料石灰石取样频次,提高取样代表性,尽量减少堆与堆之间的成分差异.这样一来,石灰石的堆头,堆尾成分的波动相对有了一定程度的缓解.3.7入磨物料配比的调整入磨物料的配比调整也是影响出磨生料质量的一大因素.配料操作员应依据出磨生料成分的分析结果,倒推计算应调节的配料比例,有依据地调节原料配比.但要注意粉磨系统滞后时间长的特点,一般情况下,配料比例的变化,在25min后才会引起出磨生料成分的变化(经过多次观察,发现开磨时出磨斗提电流至少在20rain以后才开始有变化),待出磨生料成分稳定地与配料比例相对应,所需的时间在45min 以上(选粉机的选粉效率比较低,仅50%左右,回粉多又加重了出磨生料的滞后).原料配比的调节应灵活运用,当原材料,磨机工况较稳时,配比调节应在稳中求变,采取少调,微调的方式;当原材料,磨机工况波动较大时,比如在石灰石均化堆场换堆,生料磨研磨体发生变化,窑系统开机与停机时,配比调节要大胆,果断,调节可频繁,幅度适当大一些,必要时可以增加分析出磨生料的瞬时样,以便及时改变原料配比.总之,在完善工艺条件的同时,实际生产中配料操作员还要多观察,勤动脑,善积累,综合考虑各个方面的影响因素,尽可能掌握更全面的信息,消除由于人为调节失误而对出磨生料带来的质量波动.4效果随着我公司生产工艺与生产设备的不断磨合,工艺条件的逐步完善,生料磨操作员与配料操作员在实践中的探索积累,工作经验的丰富,出磨生料质量合格率大致呈逐月上升趋势.表4是我公司投产一年多来部分月份的生料率值合格率.表4出磨生料率值格率%月份KHSMfM2006-0143.055.164.22006-0251.865.879.0——2oo6-0365.766.487.42006-0571-289.995.42006-0769.069.087.72Oo6-0972.187.497.12006-1074.887-297.42006-1178.185.698.42006—1273.881.495.92007-0179.687.697.82007—0280.589.998-3一38一.渗砸T处理"黄心料''的体会李涛(泉山水泥有限公司,山东苍山277700)中图分类号:TQ172.622.26文献标识码:B文章编号:1002-9877(2007)07-0038—02 我公司中4.0mx60m回转窑自2006年4月份投产以来,设备运转正常,在很短时间内达标达产.但随着生产的不断深入,一些质量问题逐渐地暴露出来,熟料经常出现"黄心料",fCaO含量偏高,熟料28d抗压强度偏低,严重影响熟料质量的提高.为此,公司采取相应技术措施,成功地解决了"黄心料"的问题.本文将处理"黄心料"的体会做一介绍.1"黄心料"形成的原因1.1原燃材料及生,熟料中有害成分过高进厂原材料化学成分见表1,煤工业分析见表2,生,熟料化学成分及率值见表3.2007.No.7名称LossSiO2Al203Fe2O3CaOMg0K20Na20SO3Cl一∑石灰石41.134.080.860.4550.112.040.190.1l0.0220.o03199.o0粉煤灰5.4061.6722.453.852.560.96O.26O.15O.950.003598.25砂岩0.539O.102.402.1l1.650.800.6o0.44O.0190.o05298.65铁矿石3.9559.884.0223.432.202.100.350.212.210.005898.36尾矿煤灰52.8418.2117.793.260.890.670.245.260.o03199.16表2煤的工业分析lM.a,%A,%,%℃,%lQ/(kJ/k曲llIo.8625.0428.3745.73l238621l表3生,熟料化学成分,率值及矿物组成化学成分,%率值矿物组成,%项目LossSiO2Al203Fe203CaOMgOK20Na20SO3CI一佗aOKHKHsMIMC3SC2sCC止AF生料35.5412.983.021.9543.322.040.25O.150.460.o081.O52.611.54_熟料0.4821.624.942.7864.513.010.36O.240.710.o0922.080.9150.8812.8O1.7852.8322.15 8.388.45从表1~表3可以看出,铁矿石尾矿和煤灰中SO,含量偏高,导致熟料中硫碱比过高(so/(o.85K20+1.29Na20)=1.15),部分硫在窑尾循环富集,造成窑尾烟室结皮.若处理不及时,影响窑内通风,煤粉燃烧不完全,产生还原气氛,导致熟料出现"黄心料".1.2二次风温过低为防止熟料在篦冷机上"堆雪人",料层厚度一般控制在250~300mm,这样造成入窑二次风温偏低(在900~1000~C),直接影响煤粉中固定碳的燃烧速度,使煤粉后燃,高温带后移,液相提前出现,导致窑尾结圈和烟室结皮,影响窑内通风,煤粉不完全燃烧,形成还原气氛,熟料出现"黄心料".1.3三次风闸板开度过大三次风闸板受热变形及磨损,使闸板实际开度比设定开度大(设定闸板开度为50%,实际上达到65%),导致窑内风量减少,从而降低煤粉燃烧速度,使煤粉后燃,发生不完全燃烧,还原气氛下Fe元素的价态发生变化,产生"黄心料".1,4窑速偏低由于出现窑尾结皮,结圈,使烧成带温度偏低和出窑熟料煅烧不完全等现象,中控操作员误认为是窑速过快所致,故采取降低窑速的措施.这样导致窑内物料填充率上升,窑内通风不畅,窑头煤粉燃烧状况差,火点温度提不上去,窑尾温度升高,窑头加不上5结束语根据出磨生料成分的分析结果,调节配料比例,不论是采用人工方法,还是自动控制,都应尽量消除其它引起出磨生料成分波动的干扰因素,才能取得好的调节效果.提高出磨生料成分的均匀性,稳定性,只靠配料控制技术是不够的,还应尽量完善与之相关的各个环节.比如要正确标定电子秤,稳定磨机工况等,以消除其对出磨生料成分稳定性的干扰.参考文献:…1黄忠祥,周卓鑫.出磨生料CaO波动规律的分析及应用[J].水泥, 2004,(6):38—39.【2】林彬.利用配料自动控制技术提高出磨生料质量【J].云南建材, 1999,(1):15-16.(编辑王新频)。
饲料品质稳定性控制

3. 检查是否有漏料的现象发生,是否及时处理。
4. 检查是否及时调整低料位的高度或风机风门的大小, 达到理想料温。
5. 检查是否在停机不生产后把冷却器内的物料排空清 理干净。
6. 检查是否在开机前振动分级筛应换合适的筛网,在 保证产品质量的基础上提高效率。
液体
手工添加 进桶仓正确 报告系统
流量准确检查
手工添加原料的准备,称 量准确 标上标签
每批手工添加原料的准备
粉碎粒度
粉碎是饲料加工中能耗最高的工段之一, 也是后续其它工段能实现其加工目标的前提 条件。粉碎粒度的大小,直接影响到动物的 消化吸收、粉碎成本、后续加工工序和产品 质量。控制好物料的粉碎粒度是饲料生产的 一个关键环节。
合适的粉碎粒度对饲料营养价值和其它品质的贡献主要表现 在:
①增加了动物肠道消化酶或微生物作用的机会,提高了饲料的 消化利用率,减少了动物粪便排泄量和营养物质流失及对环 境的污染。
②使得各种原料组分能混合均匀,能生产质地均匀的饲料。
③可提高饲料调质效率和熟化程度,改善制粒和挤压膨化效果。
不同的动物品种,不同的饲养阶段,不同的原料组成,不 同的调质熟化和成型方式对饲料粉碎粒度的要求不同,应根 据生产不同品种的饲料,及时更换筛片,对物料的细度进行 不同要求的调整。
• (注意:玉米中90%的霉菌毒素在粉尘中)
幼畜用膨化玉米 127摄氏度,淀粉糊化度90%以上
油糠
• 灰份及CF • 挤压加工后的米糠SDF含量增加了7.26%;米糠蛋白降解,
蛋白质分子量整体降低;淀粉含量减少,部分淀粉降解为糊 精,糊化度大幅度增大,直链淀粉含量增加;在240d的时间里 FFA值仅增加了0.6%,很好地解决了米糠稳定化问题;
物料供应失控的原因及对策管理分析

物料供应失控的原因及对策管理分析一、物料供应失控的原因生产物料供应失控的原因可能很复杂,如多种少量、交货期紧、订购物料不清楚等。
要改善,还是要从内部管控上下功夫,缺乏管控是物料供应失控的真正原因。
Q)订单中订单不良,紧急订单多。
紧急订单多,付款周期短,导致生产设备供应不及,计划粗糙,投产仓促,导致物料供应混乱。
(2)产品技术变更频繁。
产品设计和工艺更改频繁,图纸不完整或一直在更改,生产制造无所适从,导致物料供应失控,生产延期。
(3)物料计划不良。
用料计划差,供应不及时,停工待料,在制品转移不顺,导致物料供应延迟。
(4)制程品质控制不良。
不良品多,成品低,影响物料数量。
(5)设备维护不足。
设备故障多,工夹具管理不当,造成物料消耗过多。
(6)升轿呈不佳。
排程不合理或产品漏排,导致生产低效或该用的物料没有使用。
(7)能力和负荷失调。
产能不足,外协排产不当,或外协厂商选择不当,作业分配不正确等,导致物料供应不足。
(8)其他。
没有生产管理或生产管理不得力,生产和物料控制差,部门沟通差,内部管理制度不规范,不健全,都会导致物料供应失控。
二、改善物料供应1.改善原则Q)加强产销合作①建立产销衔接管理制度,明确生产和销售的权责;②确定紧急订单的处理原则;③生管与制造的密切配合。
(2)完善设计/技术变更规范:减少或消除临时性、随机性变更。
⑶合理的制程安排:①产能管理和维护;②建立异常管理机制。
⑷改善物料控制:①合理的物料计划;②做好采购管理和供应商管理;③加强仓储控制,料账一致。
(5)完善质量管理体系:①不合格品的管理和控制;②外协品的质量管理。
(6)生产绩效管理体系的建立和实施:①人员出勤和绩效有效性的评价分析;②提高设备完好率和使用率;③简化生产准备,缩短准备时间。
事实上,从销售、设计开发、采购到生产部门,其部门运作和部门之间的协调都会影响物料供应。
只有建立科学合理的生产管理体系,形成系统化、规范化的操作,才能从根本上杜绝物料供应失控,这是最根本的对策。
生料和熟料质量控制

生料和熟料质量控制一、生料质量控制1、生料均化链:矿山搭配开采一工厂内原料预均化一磨内粉磨过程均化一生料均化库均化2、控制项目①生料化学成份及三个率值干法线生产,生料控制一般采用CaO快速测定和X-荧光分析按一定频次(通常1H/次)进行,在原料中Si02和A1203含量比较稳定的前提下,才能只控制CaO和Fe203,一般应同时控制以上四个氧化物含量。
目前新型干法窑生产线,原料均有大型的均化堆场,采用堆场堆取物料,使物料的均匀得到进一步加强,通过磨头的计量秤对各比例进行适当调整后,出磨生料相对比较稳定。
为保证入窑生料的化学成份均齐稳定,生料应在均化库内进行均化后入窑使用。
生产控制中一般应按一定频次(通常2H/次)检测入窑生料X-荧光分析,供质量控制中的调整参考。
②细度:细度对煨烧影响大,细度越细比面积越大,反应快,但要求过细会影响磨机产能且使电耗增加。
③水份:水份小生料流动性良好,确保均化效果。
入窑生料的细度、水份与熟料的煨烧密切相关,细度偏粗或水份偏高将对熟料煨烧制度、熟料质量稳定有较大影响,应控制好生料细度与水份在一定范围内。
3、生料成份波动的原因及防范措施。
原因:a、原燃材料成份波动b、各种物料配比的波动工艺设备不能满足配料要求:①粒度不均齐,或粒度过大;②计量设备精度差,计量不准确;③磨头仓容量小,造成断料及物料压力难以稳定,影响下料量准确,均匀;④物料水份波动。
c、磨机工况影响d、生料化学分析不正确,误导配料,取样代表性差措施:①稳定原材料质量;②运用可靠计量准确的配料设备;③采用几何形状合理磨头仓,保持仓内物料压力稳定即控制好仓料位或入磨物料粒度;④严格控制入磨物料水份;⑤加强岗位操作人员责任心,提高操作水平;⑥通过抽查对比等措施确保检验数据准确。
4、生料均化目前各新建基地生料均化库均为CF库,其特点是多点进料多点出料,理论上,是相当先进的一种均化库,实际使用,如各方面满足要求,其均化效果较好。
生物药在生产过程中的稳定性问题及解决方案

生物药在生产过程中的稳定性问题及解决方案摘要:生物药是一类以生物技术为基础制备的药物,因其具有高效、高选择性、低副作用等优点而被广泛应用于临床治疗。
近几年来,以单克隆抗体为主的生物工程药物已逐步占据了主导地位。
然而,蛋白生物药物通常具有结构复杂、不稳定等特点,特别是在制备过程中,由于各种不稳定因素的影响,导致药物的降解或失活。
生物药物的生产过程十分复杂,通常要经过生物合成、原液提纯与精制和制剂过程等过程,才能完成药物的生产与储存运输过程。
如何克服这一不稳定现象,是其能否顺利走向临床的重要环节。
本文总结了在工业生产中出现的一些问题,并给出了一些解决办法。
关键词:高效;临床治疗;不稳定前言在生物药的生产过程中,需要考虑多个因素,如细胞培养条件、分离纯化技术、质量控制和稳定性等。
其中,细胞培养是制备生物药的关键步骤之一,需要保证细胞的生长和代谢状态,同时避免细胞的感染和污染。
分离纯化技术则是提取和纯化生物药的重要步骤,需要采用适当的技术和方法来获得高纯度的生物药。
在质量控制方面,需要对生产过程中的每个步骤进行严格的监控和检查。
稳定性则是生物药生产中需要解决的另一个重要问题。
为了解决生物药生产过程中的各种问题,研究人员和生产企业需要不断地进行技术创新和优化。
通过不断地探索和实践,相信生物药的生产技术和质量水平将会得到进一步提高,为临床治疗提供更为可靠的支持。
1生物药物制备中存在的稳定性问题生物药物的复杂多变是影响其稳定性的重要因素。
生物药物的结构与功能十分复杂,与温度、pH值、氧气、光照等环境因子密切相关。
而在实际生产中,由于缺乏有效的控制,使其在使用中的稳定性较差。
另外,在制备过程中,由于受到污染,搅拌,振动等多种因素的干扰,会对制剂的稳定性造成一定的影响。
在药物制备中,药物的稳定性一直是药物研发与生产中亟待解决的难题。
在此基础上,对其进行深入研究,以期进一步提高其在体内的稳定性,为其在临床上的应用提供更加可靠的依据。
磨机操作和工况对生料成分稳定性的影响及采取的相应措施

磨机操作和工况对生料成分稳定性的影响及采取的相应措施【摘要】本文分析和讨论了生料粉磨过程中,磨机操作和工况等非原料化学成分因素所造成生料成分波动的原因,通过实际生产数据比较了这些因素对立磨和闭路球磨影响的大小,并提出了在粉磨过程中减少生料成分波动的措施。
【关键词】操作;工况;生料成分;影响引言生料成分的稳定是水泥窑系统稳产、优质高产的基础和前提条件,为此新型干法窑生产中,通过原料预均化、生料配料控制、生料均化等一系列工艺环节来保证生料的化学成分符合设计需要,并维持其稳定。
在实际生产过程中,大部分工厂的生料质量由化验室进行控制,而生料产量由生产车间完成。
生产车间的人员在操作中往往只关注磨机产量,根据磨机工作状况频繁大幅度加减产量,磨机工况时常变化,甚至出现饱磨等非正常工况,认为生料成分的波动全是由于原料成分变化或原料配比调整失误造成,忽视了粉磨过程对生料成分的影响,给化验室的生料质量控制带来很大困难。
以下分析和讨论了生料粉磨过程中,磨机操作和工况等非原料化学成分因素所造成生料成分波动的原因,通过实际生产数据比较了这些因素对立磨和闭路球磨影响的大小,并提出了在粉磨过程中减少生料成分波动的措施。
1、磨机操作和工况对生料成分稳定性的影响1.1开停磨对生料成分稳定性的影响生料的粉磨过程包括了各种原料(石灰石、页岩和硫酸渣等)的配料、磨细以及混合均匀的过程。
由于各种原料的化学成分和易磨性不一致,在磨内完成破碎、磨细直至达到生料细度要求所需的时间也不一样,所以生料成分从开始喂料至达到稳定需要一定时间。
以石灰石、页岩和硫酸渣三组分配料为例,硫酸渣和页岩的易磨性好,在磨机内粉磨很短时间便可达到细度要求出磨,而石灰石易磨性相对较差,粉磨时间较长。
因此空磨刚开始喂料时,先出磨的生料中Fe2O3、Si02、Al2O3含量高,而Ca0含量低,并且出磨的生料量也很小,随着继续喂料和粉磨,越来越多的石灰石磨细并出磨,生料中Ca0含量逐渐升高,并最终达到稳定,磨机进入平衡状态。
出磨生料成分波动原因分析

出磨生料成分波动原因分析目前,公司熟料库与水泥库基本处于低库位运行,生产压力大,为稳定生料配料,提高出磨生料合格率,确保窑系统稳定运行,就近期出磨生料成份波动原因进行了梳理,并制定相应措施如下:一、原因分析1、原材料影响我公司生料制备主要原材料有石灰石、自采高低硅砂岩、钢渣、少量铁尾渣和铁矿尾渣,其中高硅砂岩采自3#山头,SiO2含量在78~83%之间,低硅砂岩采自520平台砂岩夹层,SiO2含量在67~72%之间,因公司配料中砂岩的掺量较少,砂岩成分小范围的波动对配料的影响相对较小,钢渣中Fe2O3含量22%左右,且含量比较稳定,铁尾渣和铁矿尾渣中Fe2O3含量在26%和35%左右,因其量少,一般作应急备用。
目前对配料影响最大的是石灰石,因公司石灰石堆场为长形堆场,均化效果相对圆形堆场要好,但那只是在同样的出矿点预搭配条件下,如果一味地放宽下山石灰石品质的波动范围,再好的均化设施也发挥不了好的均化效果,我公司石灰石破碎台产按每小时1000吨计算,每车石灰石按40吨计算,相当于每小时破碎25车,约每2.5分钟破碎一车,堆场堆料机行走一个区域约20秒钟时间,堆头堆尾时间约60秒钟,走完整个料堆约5分钟时间,即2车石灰石,意味着每破碎一车石灰石,只能堆半个料堆区域,现下山石灰石每小时取样检测,每次取样时间10分钟,样品基本包涵了各平台的物料,近一个月来,矿山对下山石灰石搭配采取先下低品位,再进行纯石补堆方式,入堆石灰石单点CaO最低只有32.13%,最高达51.53%,虽然堆平均基本上达到了46%以上,但是由于入堆石灰石的品质波动范围太宽,在堆料的过程中会出现石灰石高低品位单向迭加,导致局部区域石灰石品位偏高或偏低较多,加上料堆堆头堆尾物料的离析,另外石灰石在堆料过程中还存在延堆,堆头取料未取完而又增加堆头等现象,同时石灰石料堆小,换堆频繁,配料过程中严重影响了出磨生料成分,原材料每波动一次,影响配料三个小时,石灰石堆头堆尾影响配料四个小时,如中间再出现数次波动,出磨生料合格率就大幅度降低了。
- 1、下载文档前请自行甄别文档内容的完整性,平台不提供额外的编辑、内容补充、找答案等附加服务。
- 2、"仅部分预览"的文档,不可在线预览部分如存在完整性等问题,可反馈申请退款(可完整预览的文档不适用该条件!)。
- 3、如文档侵犯您的权益,请联系客服反馈,我们会尽快为您处理(人工客服工作时间:9:00-18:30)。
造成生料质量不稳定的因素
1)物料不稳定的影响,生料配料时原料未经烘干,水分波动较大,对于粘滞性物料。
下料不稳畅,料层不稳有卡料现象,在现场断料或下料不够的情况下(大块的物料卡住下料口)荧光分析配料曲线往往显示十分正常,影响物料的实际流量,缺乏及时有效的监控措施。
2)生料取样点的影响,出磨生料代表性差,误导控制。
生料取样是由螺旋输送连续取样机取样,取样位置在成品空气斜槽和均化库之间,成品生料经空气斜槽流经连续取样器,取样螺旋输送机在工作时还有部分是收尘的料,在生产中一直存在出磨生料和入窑生料细度相差较大的问题,两者饱和也有所差距,综合以上因素,由于除尘和回灰和取样点气压的不稳,干扰取样工作,进一步影响到检测结果对生产的指导。
3)要考虑X荧光分析曲线是否有漂移而影响结果准确性的问题,另外取样是否有代表性的问题(如样品在原料磨停的前后所取,其代表性必然受到影响)、制样的方法的正确性等。
4)各种物料配比的波动,工艺设备不能满足配料的要求,由于破碎工艺的不完备,使物料的粒度不均齐,或粒度过大,喂料及计量设备精度差,不能有效控制各种物料的流量,磨头仓容量过小,造成断料或料仓中的压力难以稳定,影响下料的准确和均匀性。
5)配比调节不当,对于成份波动大的生料,判断不准却,缺乏良好的预见性,配比分配不合理,促使生料成份的波动。
磨机的不稳定操作及物料易磨性的改变,对生料的成份影响很大。
特别当生料磨空转时,一般的经验是物料的饱和显著提高,CaO高于平时的水平。
6)均化后生料质量不易判定。
均化后生料成分与出磨生料平均成分、细度存在着较大的差别,这种相关性差的现象除了受出磨生料代表性影响外,也受均化效果的影响。
均化气路不畅通,均化过程
7)原材料成份波动大,石灰石成份的波动主要表现在CaO和MgO含量及其夹带杂质的变化,当石灰石中的CaO含量降低(或升高)时,没及时调整配比。
粘土成份的波动主要表现在SiO2和Al2O3上,砂岩成份的波动主要是SiO2的含量上,特别是SiO2变化较大时,对生料饱和比的影响很显著。
稳定回转窑生料的方法
<1、中控生料磨操作人员,要严格遵守操作规程,磨机加减台时,不要大起大落,加减料的幅度不要过大,以防对出磨生料质量带来波动。
要严禁空磨运转,空磨运转时间不得超过10分钟。
<2、稳定出磨取样点气压。
加强取样器的状态检查,尽量减少由于压力给取样带来的误差,通过压力调节保证正常取样。
<3、加强对配料站的现场管理。
对配料过程要求保证物料的连续性和料层的稳定,当几组分物料有一路出现故障时,其他几组分物料要同时止料,超过10分钟不能恢复正常下料时,要立即停磨。
<4、配料岗位操作人员要加强责任心,努力提高业务操作水平。
做到勤抽查、勤观察、勤调整。
分析配比及生料成分的相关性,以此判断出磨生料质量及计量设备的可靠性。
<5、统计分析确定出磨、入窑生料成分的对照关系。
根据荧光分析的结果,确定出磨、入窑生料成分的相关性,从而对出磨生料的控制目标做出正确的判断。
对于均化效果的判断,也利用统计的方法,确定均化后生料质量是否符合要求。
<6、确定原材料矿点,加强均化。
定期考察原材料矿点,掌握原材料的质量情况,严把进厂关,缩小进厂原才物料品位的波动范围。
石灰石矿山采用工程机械进行搭配和均化作业。
严格控制控石灰石的品位及粒度,要求保证石灰石均化库有一定库位。