新型刀具材料PCD~~1
刀具材料PCD

XX大学2014~2015 学年秋季学期研究生课程考试课程名称:课程编号:论文题目:刀具材料PCD概述研究生:学号:论文评语:成绩:任课教师:评阅日期:刀具材料PCD概述摘要:好的刀具材料是制造出好的刀具的前提,更是加工出好的产品的关键。
随着制造业的快速发展,金刚石刀具的生产和应用正在逐年增加。
天然金刚石价格昂贵,金刚石广泛应用于切削加工的还是PCD。
本文针对刀具材料PCD做了比较系统的论述,主要包括PCD材料的介绍,PCD复合片及刀具的制造技术,PCD 复合片的主要优缺点以及PCD刀具材料的应用。
关键词:PCD;材料;刀具The overview about cutting tool materials of PCDAbstract:Good tool material is a prerequisite to create a good tool, it is also a key processing of making a good product .With the sharp development of making industry, production and application of diamond tools is increasing year by year.Natural diamonds are expensive,PCD is widely used in cutting .This paper makes a systematic introduction of tool material PCD,including the introduction of PCD materials ,the manufacturing techniques of PCD composite sheet and tool, the main advantages and disadvantages of PCD composite sheet materials and the application of PCD tools.Key words:PCD;Materials ; Tool1引言随着人类生活、生产水平的提高,高速钢刀具已不能满足高加工效率和高加工质量的新要求。
什么是PCD
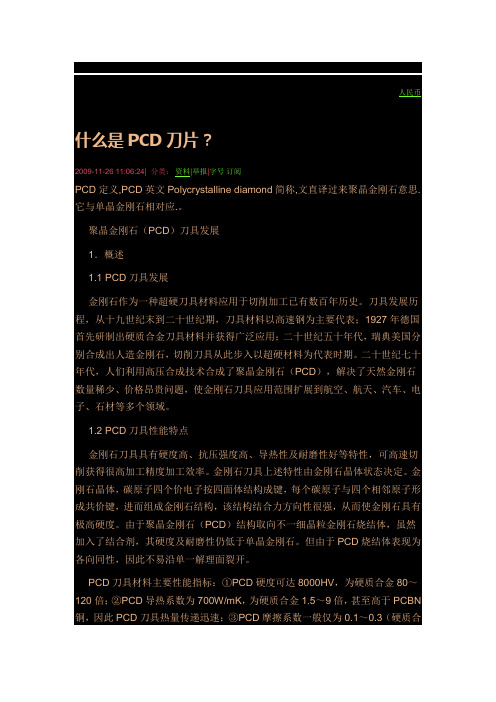
人民币什么是PCD刀片?2009-11-26 11:06:24| 分类:资料|举报|字号订阅PCD定义,PCD英文Polycrystalline diamond简称,文直译过来聚晶金刚石意思.它与单晶金刚石相对应.。
聚晶金刚石(PCD)刀具发展1.概述1.1 PCD刀具发展金刚石作为一种超硬刀具材料应用于切削加工已有数百年历史。
刀具发展历程,从十九世纪末到二十世纪期,刀具材料以高速钢为主要代表;1927年德国首先研制出硬质合金刀具材料并获得广泛应用;二十世纪五十年代,瑞典美国分别合成出人造金刚石,切削刀具从此步入以超硬材料为代表时期。
二十世纪七十年代,人们利用高压合成技术合成了聚晶金刚石(PCD),解决了天然金刚石数量稀少、价格昂贵问题,使金刚石刀具应用范围扩展到航空、航天、汽车、电子、石材等多个领域。
1.2 PCD刀具性能特点金刚石刀具具有硬度高、抗压强度高、导热性及耐磨性好等特性,可高速切削获得很高加工精度加工效率。
金刚石刀具上述特性由金刚石晶体状态决定。
金刚石晶体,碳原子四个价电子按四面体结构成键,每个碳原子与四个相邻原子形成共价键,进而组成金刚石结构,该结构结合力方向性很强,从而使金刚石具有极高硬度。
由于聚晶金刚石(PCD)结构取向不一细晶粒金刚石烧结体,虽然加入了结合剂,其硬度及耐磨性仍低于单晶金刚石。
但由于PCD烧结体表现为各向同性,因此不易沿单一解理面裂开。
PCD刀具材料主要性能指标:①PCD硬度可达8000HV,为硬质合金80~120倍;②PCD导热系数为700W/mK,为硬质合金1.5~9倍,甚至高于PCBN 铜,因此PCD刀具热量传递迅速;③PCD摩擦系数一般仅为0.1~0.3(硬质合金摩擦系数为0.4~1),因此PCD刀具可显著减小切削力;④PCD热膨胀系数仅为0.9×10 -6~1.18×10 -6,仅相当于硬质合金1/5,因此PCD刀具热变形小,加工精度高;⑤PCD刀具与有色金属非金属材料间亲力很小,加工过程切屑不易粘结刀尖上形成积屑瘤。
pcd是什么材料

pcd是什么材料PCD是多晶金刚石(Polycrystalline Diamond)的缩写,是一种由金刚石微粉和金属结合剂通过高温高压烧结而成的超硬材料。
PCD具有极高的硬度、耐磨性和热导性,因而被广泛应用于刀具、磨具、车削刀具、铣刀、钻头等领域。
PCD材料是由金刚石微粉和金属结合剂混合而成的,经过高温高压烧结而成的一种超硬材料。
金刚石微粉作为主要成分,赋予了PCD极高的硬度和耐磨性,而金属结合剂则起到了固化和连接金刚石微粉的作用。
PCD的硬度仅次于天然金刚石,但相对于单晶金刚石而言,PCD更具有韧性和耐磨性,因此在实际应用中更加耐用和稳定。
PCD材料的硬度主要来源于其中的金刚石微粉,金刚石是自然界中最坚硬的物质之一,其摩氏硬度高达10级,是其他材料无法比拟的。
而PCD材料中的金刚石微粉经过高温高压烧结后,其硬度更是得到了进一步的提升,使得PCD具有了出色的耐磨性和切削性能。
因此,PCD被广泛应用于刀具、磨具等领域,用于加工各类硬质材料。
除了硬度和耐磨性之外,PCD材料还具有优异的热导性能。
金刚石是一种优良的热导体,因此PCD材料具有良好的散热性能,可以有效减少加工过程中的热量积聚,提高刀具的使用寿命和加工质量。
这使得PCD材料在高速切削和高效加工领域有着广泛的应用前景。
在实际应用中,PCD材料已经成为了现代制造业中不可或缺的材料之一。
其在航空航天、汽车制造、机械加工等领域都有着重要的应用价值。
例如,PCD刀具可以用于加工铝合金、铜合金、纤维增强复合材料等难加工材料,具有较高的切削效率和表面质量。
此外,PCD磨具也被广泛应用于精密磨削、超精密加工等领域,为工件加工提供了高效、精确的加工解决方案。
总的来说,PCD是一种具有极高硬度、耐磨性和热导性的超硬材料,其在现代制造业中有着广泛的应用前景。
随着制造技术的不断进步和创新,PCD材料在未来将会有更加广阔的发展空间,为工业制造领域带来更多的创新和突破。
加工石墨的刀具选择—PCD刀具

加工石墨的刀具选择—PCD刀具石墨是碳的一种同素异形体,尤其石墨的高磨蚀性、耐高温等性能,广泛应用于模具、坩埚、点击、电池、电刷等领域。
但由于石墨质坚而脆,所以采用车、铣等常规机械加工方法时,旺旺在加工表面会产生崩损现象。
因此车、铣加工石墨模/石墨电极等制品时,切削刀具需具备高的耐磨损性和抗冲击性。
本文就重点介绍一下车、铣加工石墨模具/石墨电极等制品的刀具材质选择,及其加工刀具的规格型号选择。
1、石墨制品的介绍(1)石墨制品之石墨模具的介绍模具作为工业生产中使用极为广泛的基础工艺装备,大到机身外壳,小到一个螺丝,都是根据成型模具,通过冲压、锻压、压铸、挤压、注塑等方式使坯料成为符合产品要求的零件。
模具的形状和加工质量、精度决定着产品的外形和质量。
近年来随着模具行业飞速发展,石墨以其良好的物理和化学性能逐渐成为模具制作的理想选择材料。
现如今许多产业部门,如机电、汽车、家电轻工、电器仪表、通讯、军械等行业的发展均依赖于模具工业的技术提高和发展。
(2)石墨制品之石墨电极的介绍石墨电极是指以石油焦、沥青焦为骨料,煤沥青为黏结剂,经过原料煅烧、破碎磨粉、配料、混捏、成型、焙烧、浸渍、石墨化和机械加工而制成的一种耐高温石墨质导电材料,称为人造石墨电极(简称石墨电极)。
石墨电极的优点是加工较容易,放电加工去除率高,石墨损耗小,因此,部分群基火花机客户放弃了铜电极而改用石墨电极。
目前石墨电极主要用于电弧炼钢炉,矿热电炉,电阻炉等行业,同时石墨电极的毛坯还用于加工成各种坩埚、模具、舟皿和发热体等异型石墨产品。
(3)石墨制品之石墨坩埚的介绍石墨坩埚,又称熔铜包、熔铜等,是指以石墨、粘土、硅石和腊石为原料烧制而成的一类坩埚。
石墨坩埚具有耐高温、导热性能强、热膨胀系数小、抗腐蚀性能好,化学稳定性强,使用寿命长等特点。
被广泛用于合金工具钢冶炼和有色金属(紫铜、黄铜、金、银、锌和铅)及其合金的冶炼。
(4)其他石墨制品介绍除了以上是那种零部件,石墨广泛用于耐火材料、导电材料、耐磨材料、润滑剂、耐高温密封材料、耐腐蚀材料、隔热材料、吸附材料、摩擦材料和防辐射等材料中,这些材料广泛应用于冶金、石油化工、机械工业、电子产业、核工业和国防等。
PCD﹑PCBN刀具材料及刀具涂层
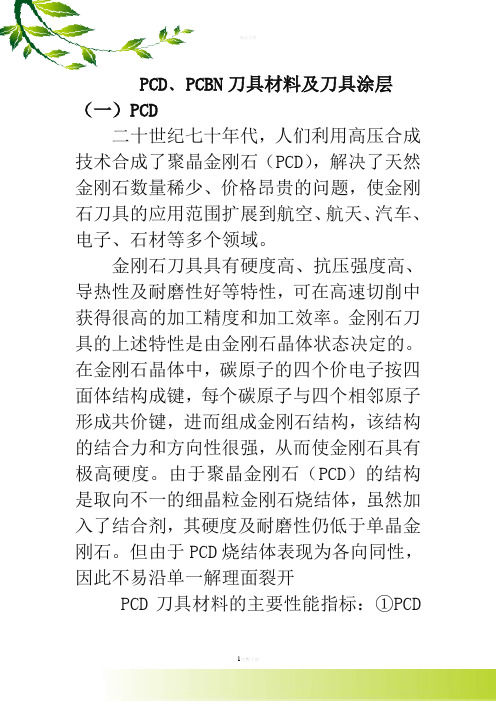
PCD﹑PCBN刀具材料及刀具涂层(一)PCD二十世纪七十年代,人们利用高压合成技术合成了聚晶金刚石(PCD),解决了天然金刚石数量稀少、价格昂贵的问题,使金刚石刀具的应用范围扩展到航空、航天、汽车、电子、石材等多个领域。
金刚石刀具具有硬度高、抗压强度高、导热性及耐磨性好等特性,可在高速切削中获得很高的加工精度和加工效率。
金刚石刀具的上述特性是由金刚石晶体状态决定的。
在金刚石晶体中,碳原子的四个价电子按四面体结构成键,每个碳原子与四个相邻原子形成共价键,进而组成金刚石结构,该结构的结合力和方向性很强,从而使金刚石具有极高硬度。
由于聚晶金刚石(PCD)的结构是取向不一的细晶粒金刚石烧结体,虽然加入了结合剂,其硬度及耐磨性仍低于单晶金刚石。
但由于PCD烧结体表现为各向同性,因此不易沿单一解理面裂开PCD刀具材料的主要性能指标:①PCD的硬度可达8000HV,为硬质合金的80~120倍;②PCD的导热系数为700W/mK,为硬质合金的1.5~9倍,甚至高于PCBN和铜,因此PCD刀具热量传递迅速;③PCD的摩擦系数一般仅为0.1~0.3(硬质合金的摩擦系数为0.4~1),因此PCD刀具可显著减小切削力;④PCD的热膨胀系数仅为0.9×10 -6~1.18×10 -6,仅相当于硬质合金的1/5,因此PCD刀具热变形小,加工精度高;⑤PCD 刀具与有色金属和非金属材料间的亲和力很小,在加工过程中切屑不易粘结在刀尖上形成积屑瘤。
PCD刀具的应用: 工业发达国家对PCD刀具的研究开展较早,其应用已比较成熟。
自1953年在瑞典首次合成人造金刚石以来,对PCD刀具切削性能的研究获得了大量成果,PCD刀具的应用范围及使用量迅速扩大。
目前,国际上著名的人造金刚石复合片生产商主要有英国De Beers公司、美国GE公司、日本住友电工株式会社等。
据报道,1995年一季度仅日本的PCD刀具产量即达10.7万把。
pcd材料

pcd材料PCD (Polycrystalline Diamond) 是一种具有高硬度和优异耐磨性的材料,由多个小晶体颗粒组成。
PCD材料在工业领域具有广泛的应用,尤其是在切削和磨削工具领域,其独特的性能使其成为一种非常受欢迎的选择。
PCD材料的主要成分是人工合成的金刚石微粉和硬质合金基体。
通过高温高压的工艺,在合适的温度和压力条件下,将金刚石微粉和金属粉末进行烧结,最终形成了坚硬且具有优异耐磨性的PCD材料。
PCD材料具有几个显著的特点。
首先,PCD材料具有极高的硬度,比普通刚玉和硬质合金要高。
其硬度可达到5800-10000HV,使得PCD材料具有出色的切削性能,可以用于切割各种高硬度材料,如铸铁、铝合金、镍合金等。
其次,PCD材料具有出色的耐磨性。
其耐磨性能比一般刚玉和硬质合金高5-10倍,可以大大延长刀具的使用寿命。
这使得PCD材料成为高效率切削工具的理想选择,在高速加工和大批量生产中发挥了重要的作用。
此外,PCD材料还具有良好的导热性能和化学稳定性。
它的导热系数很高,能够迅速将切削过程中产生的热量分散,从而减少切削温度,保护切削刀具不易被热疲劳破坏。
同时,PCD 材料对酸、碱和大部分有机溶剂具有较高的耐腐蚀性,适用于多种工作环境。
在实际应用中,PCD材料可用于制造各种切削工具,如刀具、钻头、车刀和铣刀等。
这些工具广泛用于机械加工、汽车制造、航空航天、电子、模具制造等领域。
虽然PCD材料具有众多优点,但也存在一些限制。
首先,由于其高硬度和脆性,PCD材料容易受到冲击和碰撞而破裂。
因此,在使用过程中需要注意避免过大的冲击力。
其次,PCD 材料的制造成本较高,导致其价格相对较高。
这也限制了其在某些领域的应用。
总之,PCD材料以其高硬度、优异耐磨性和良好的导热性能而受到广泛关注。
在工业领域,PCD材料被广泛应用于切削和磨削工具制造中,并发挥了重要的作用。
随着科学技术的不断进步,相信PCD材料将在更多领域发挥其优势,为人们的生产和生活带来更多便利和效益。
关于铝合金材料PCD刀具加工应用的研究

关于铝合金材料PCD刀具加工应用的研究作者:刘源来源:《科教导刊·电子版》2017年第12期摘要铝合金材料被广泛运用于汽车、飞机等装备制造领域,有利于减轻机械动力负荷,实现机械设备的轻型化、小型化发展。
在铝合金材料的运用过程中,PCD切割工具以其硬度高、热膨胀系数低、与铝合金亲合小的特点被广泛运用于铝合金的切削加工领域。
本文对PCD刀具加工应用方法进行了研究,探索了PCD刀具钝化处理的技术,以及钝化处理后对于切削铝合金材料的影响。
关键词 PCD刀具钝化处理铝合金材料目前,PCD(金刚石)刀具已经大规模的运用铝合金等有色金属的切削加工中。
为提高PCD刀具的使用寿命和加工质量,笔者在工作实践的基础上,结合现有的研究成果,进行了PCD刀具钝化和铝合金材料切削实验,对PCD刀具钝化技术和要求,有针对性地进行了优化。
1 PCD刀具的钝化技术的原理PCD刀具的钝化技术是对PCD刀具进行深加工,提高刀具运用水平的重要方法。
笔者在实践中发现,PCD刀具在切削加工铝合金的过程中,使用初期会表现出加工质量不高、磨损较快等问题。
随着使用时间的延长,其加工的质量越来越高。
其实现的原理主要是:PCD刀具在刃磨后会出现一些毛刺和微缺口,但是在车削铝合金材料长时间磨损中,刀具刃口出现钝化,毛刺和微缺口被去除,切削刃变得光滑,提高刀具的使用寿命和加工质量。
2 PCD刀具的钝化和铝合金材料车削实验本文进行的实验主要由两个部分组成:一是PCD刀具的钝化实验;一是钝化PCD刀具对铝合金材料的切削实验。
2.1关于的PCD刀具的钝化实验在实验中,笔者采用了小型可转位刀片刃口钝化机,通过刀具与钝化机磨刷之间的磨损运动,对PCD刀具进行刃口钝化观察。
为了观察不同的磨刷与PCD刀具钝化的关系,笔者在试验中分别选用含400目、800目、1000目、1200目金刚石磨料的磨料刷,转速800r/min,切削刃和磨料刷接触长度为2mm进行实验。
聚晶金刚石( PCD )和聚晶金刚石复合片( PDC )

聚晶金刚石(PCD)和聚晶金刚石复合片(PDC)与大单晶金刚石相比,作为刀具材料的聚晶金刚石(PCD)以及聚晶金刚石复合刀片(PDC)具有以下优点:①晶粒呈无序排列,各向同性,无解理面,因此它不像大单晶金刚石那样在不同晶面上的强度、硬度以及耐磨性有较大区分,以及因解理面的存在而呈现脆性。
②具有较高的强度,特别是PDC材料由于有硬质合金基体的支撑而有较高的抗冲击强度,在冲击较大时只会产生小晶粒碎裂,而不会像单晶金刚石那样大块崩缺,因而PCD或PDC刀具不仅可以用来进行精紧密削加工和一般半精密加工,还可用作较大切削量的粗加工和断续加工(如铣削等),这大大扩充了金刚石刀具材料的使用范围。
③可以制备大块PDC金刚石复合片刀具坯料,充足大型加工刀具如铣刀的需要。
④可以制成特定形状以适合于不同加工的需要。
由于PDC刀具大型化和加工技术如电火花和激光切割技术的提高,三角形、人字形以及其他异形刀坯均可加工成形。
为适应特别切削刀具的需要还可设计成包裹式、夹心式与花卷式PDC刀具坯料。
⑤可以设计或推测产品的性能,给与产品必要的特点以适应它的特定用途。
比如选择细粒度的PDC刀具材料可使刀具的刃口的质量提高,粗粒度的PDC刀具材料能够提高刀具的耐用度,等等。
总之,随着PCD、PDC金刚石复合片刀具材料的讨论进展,其应用已经快速扩展到很多制造工业领域,广泛应用于有色金属(铝、铝合金、铜、铜合金、镁合金、锌合金等)、硬质合金、陶瓷、非金属材料(塑料、硬质橡胶、碳棒、木材、水泥制品等)、复合材料(纤维加强塑料、金属基复合材料MMCs等)的切削加工,尤其在木材和汽车加工业,已经成为传统硬质合金的高性能替代产品。
切削刀具用PDC、PCD材料要求:①金刚石颗粒间能广泛地形成D—D自身结合,残余粘结金属和石墨尽量少,其中粘结金属不能以聚结态或呈叶脉状分布,以保证刀具具有较高的耐磨性和较长的使用寿命。
②溶媒金属残留量少。
最好是在烧结过程中能起溶媒作用,而在烧结过程完成后将以不起溶媒作用的合金形式充填于烧结金刚石晶粒间隙中,或烧结后残留的溶媒性金属被隔离,避开溶媒金属与金刚石表面直接接触,以提高PCD的抗氧化本领,从而保证刀具具有充足的耐热温度。
pcd木工刀片简介

1 引言随着现代科学技术的高速发展,由聚晶金刚石(PCD)、聚晶立方氮化硼(PCBN)等超硬材料制成的刀具品种越来越丰富,其性能也得到不断发展和提高。
刀片磨料粒径从数十微米、几微米到纳米级;金刚石、立方氮化硼的含量分为低含量、中等含量和高含量;结合剂既有金属、非金属也有混合材料;PCD层厚度从毫米级到微米级;PCD层与硬质合金衬底的结合方式有平面、波纹面;PCD层有高耐磨、高韧性、高耐热等不同特性。
目前PCD、PCBN刀具的应用范围扩大到汽车、航天航空、精密机械、家电、木材、电子电气等行业,用于制作车刀、镗刀、铣刀和钻头、铰刀、锪刀、锯刀、镂刀、剃刀等。
尽管PCD、PCBN刀具发展如此之快,但因其高硬度导致的刀具刃磨困难一直困扰着大多数用户,刀片的重磨也主要由原刀具生产厂家来完成。
不仅刀具价格高,交货期长,而且占用企业流动资金。
因此,很有必要认真研究PCD的磨削特点及PCD刀具的刃磨技术。
2 PCD刀具的制造工艺PCD切削刀具的生产工艺流程一般包括抛光、切割、固接、刃磨、质检等。
PCD超硬材料毛坯直径通常有1/2、1、2、3、4英寸,其表面一般较粗糙(Ra2~10μm),不能直接用于制作刀具,需经研磨抛光使其表面达到镜面(Ra≤0.01μm),然后通过激光切割或电火花线切割加工成一定几何形状和尺寸要求的刀片,再进一步对刀片和基体待固接面进行机械和化学处理,然后采用银基硬钎焊将刀片固接于基体上,最后经金刚石砂轮刃磨。
PCD切削刀具制造技术的关键之一是切削刃的刃磨质量。
优质刀头材料缺乏理想的刃磨工艺和技术将会造成资源浪费,采用好的刃磨工艺则会提升刀具的产品质量,降低刀具使用成本。
3 PCD材料的磨削加工特点PCD是由特殊处理的金刚石与少量粘结剂在高温超高压下烧结而成。
无序排列的金刚石晶粒使PCD具有均匀的、极高的硬度和耐磨性。
PCD可用于切削刀具、砂轮修整、地质钻探、量具测头、拉丝摸具、喷砂摸具等。
pcd是什么材料
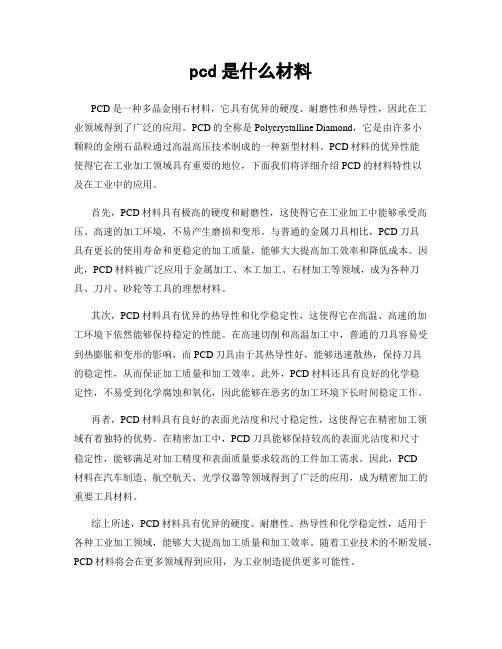
pcd是什么材料PCD是一种多晶金刚石材料,它具有优异的硬度、耐磨性和热导性,因此在工业领域得到了广泛的应用。
PCD的全称是Polycrystalline Diamond,它是由许多小颗粒的金刚石晶粒通过高温高压技术制成的一种新型材料。
PCD材料的优异性能使得它在工业加工领域具有重要的地位,下面我们将详细介绍PCD的材料特性以及在工业中的应用。
首先,PCD材料具有极高的硬度和耐磨性,这使得它在工业加工中能够承受高压、高速的加工环境,不易产生磨损和变形。
与普通的金属刀具相比,PCD刀具具有更长的使用寿命和更稳定的加工质量,能够大大提高加工效率和降低成本。
因此,PCD材料被广泛应用于金属加工、木工加工、石材加工等领域,成为各种刀具、刀片、砂轮等工具的理想材料。
其次,PCD材料具有优异的热导性和化学稳定性,这使得它在高温、高速的加工环境下依然能够保持稳定的性能。
在高速切削和高温加工中,普通的刀具容易受到热膨胀和变形的影响,而PCD刀具由于其热导性好,能够迅速散热,保持刀具的稳定性,从而保证加工质量和加工效率。
此外,PCD材料还具有良好的化学稳定性,不易受到化学腐蚀和氧化,因此能够在恶劣的加工环境下长时间稳定工作。
再者,PCD材料具有良好的表面光洁度和尺寸稳定性,这使得它在精密加工领域有着独特的优势。
在精密加工中,PCD刀具能够保持较高的表面光洁度和尺寸稳定性,能够满足对加工精度和表面质量要求较高的工件加工需求。
因此,PCD材料在汽车制造、航空航天、光学仪器等领域得到了广泛的应用,成为精密加工的重要工具材料。
综上所述,PCD材料具有优异的硬度、耐磨性、热导性和化学稳定性,适用于各种工业加工领域,能够大大提高加工质量和加工效率。
随着工业技术的不断发展,PCD材料将会在更多领域得到应用,为工业制造提供更多可能性。
PCD(金刚石)刀片

ø85 19
ø70 ø85
■ 切削数据
• 活塞 • Vc = 1000m/min • ap = 2.0mm (Only spree d=5mm) • f = 0.25mm/rev • 湿式 • CNMM120408M
AC8A
Spree 凹面部
60
(加工长度)
75
超微颗粒
KPD001
10,000 个/刃
■ 应用
被加工材料
切削范围 JIS(日本工业规格)分类
精加工 N01
KPD001
PCD
KPD025 KPD010
KPD002
非铁材料 (铝/非铁金属)
N10
N20
粗加工 N30
精加工 S01
KPD001 KPD025
KPD010 KPD002
难于加工材料 (钛合金/镍合金)
S10
S20
粗加工 S30
• 湿式
• 铜焊圆形刀柄
(刀尖半径 = 0.5mm)
超微颗粒
KPD001
1,350 个/刃
传统PCD H
500 ~ 1,060 个/刃
•由于切屑控制情况差而发生崩损。KPD001加工时无崩损
与毛边,工具寿命得到改善。
烧结金属(Cu)
• 连杆 • Vc = 350m/min • ap = 0.08 ~ 0.1mm • f = 0.07mm/rev • 湿式 • TPGN160304SE
90 切削部件
烧结金属(Cu)
超微颗粒
KPD001
300 个/刃
其他公司的PCD G (超微颗粒聚晶PCD)
•间断加工。
(烧结金属存在微小的间隙)
•耐磨损性较其他公司的G更佳。
PCD聚晶金刚石刀具特性及其适合加工的材料简介

PCD 聚晶金刚石刀具特性及其适合加工的材料简介图1努氏硬度图2断裂韧性图3导热性制备工艺PCD是由大量随机定向的金刚石颗粒在极困难的条件下进行人工合成得到的。
它通过在高压高温下烧结精选的金刚石颗粒进行制备。
烧结过程在金刚石稳定区内被严格地控制,于是生产出一种极硬且耐磨的结构。
特性PCD是由大量随机定向的金刚石颗粒在极困难的条件下进行人工合成得到的。
它通过在高压高温下烧结精选的金刚石颗粒进行制备。
烧结过程在金刚石稳定区内被严格地控制,于是生产出一种极硬且耐磨的结构。
特性以聚晶形态组成的金刚石提供了一种强大的切削刀具,它提供极好的硬度及由此得到的耐磨性,并与聚晶结构所带来的极佳韧性相结合。
此外,金刚石拥有所有刀具材料中最高的导热性,使得热量迅速从切削刃传递出来。
除PCD与铁的高亲合力以外,PCD不会与工件材料粘结,在正确的切削参数下,积屑瘤是最小化的。
所有的SecomaxPCD刀具都拥有镜面抛光的前刀面,提供最低的摩擦系数和光滑的切削刃。
适合加工的工件材料铝合金铝合金已成为交通工业需求的致力于减轻重量的理想材料。
尽管铝合金的生产在能量消耗上具有更大的初始需求,但在长期运作中证明有更多的益处,这些合金的性能将超过其它与其竞争的材料。
纯铝的硬度低、耐腐蚀。
举例讲,添加铜或镁等合金元素将使该材料具有更高的强度。
巿场上有很多种铝合金,最著名的莫过于分别用于汽车与航空航天行业的2000及6000系列。
锻造和铸造铝合金之间有明显的分界线,各有几种不同的材质等级,而且有各式各样的硬化处理性能。
对于硅(Si)含量低到中等的硅合金来说,PCD在铣削应用与粗加工中提供了最好的耐磨性,见下表。
所遭遇到的最常见的问题应该是积屑瘤。
即使是很高的切削速度,加工低硅铝合金时也会发生这种情况。
切削刃的几何角度和质量必须要被小心地应用。
采用这样的参数,当与工件的接触时间越久,产生的热量上升,其直接的影响就是刀具寿命的缩短。
对于加工高硅铝合金,PCD的耐磨性被完全地利用。
超硬刀具金刚石刀具介绍

超硬刀具金刚石刀具介绍PCD聚晶金刚石刀具;CVD金刚石膜刀具(物理涂层)PVD物理涂层金刚石刀具PCBN聚晶立方氮化硼刀具;一、概述超硬刀具材料是指比陶瓷材料更硬的刀具材料。
包括:单晶金刚石、聚晶金刚石(PCD)、聚晶立方氮化硼(PCBN)和CVD金刚石等。
超硬刀具主要是以金刚石和立方氮化硼为材料制作的刀具,其中以人造金刚石复合片(PCD)刀具及立方氮化硼复合片(PCBN)刀具占主导地位。
许多切削加工概念,如绿色加工、以车代磨、以铣代磨、硬态加工、高速切削、干式切削等都因超硬刀具的应用而起,故超硬刀具已成为切削加工中不可缺少的重要手段。
随着科技的进步,制造业的高速发展,CNC 加工技术的迅猛发展以及数控机床的普遍使用,超硬刀具的生产及应用也越来越广泛。
PCD和PCBN刀具已广泛应用于机械加工的各个行业,如汽车零部件的切削加工,强化木地板的加工等,极大地促进了切削加工及先进制造技术的飞速发展。
二、切削材料及超硬材料发展史3、金刚石、超硬材料的特性与作用众所周知,金刚石材料的成分是碳,金刚石与铁系有亲和力,切削过程中,金刚石的导热性优越,散热快,但是要注意切削热不宜高于700度,否则会发生石墨化现象,工具会很快磨损。
因为金刚石在高温下和W、Ta、Ti、Zr、Fe、Ni、Co、Mn、Cr、Pt等会发生反应,与黑色金属(铁碳合金)在加工中会发生化学磨损,所以,金刚石不能用于加工黑色金属只能用在有色金属和非金属材料上,而CBN即使在1000oC的高温下,切削黑色金属也完全能胜任。
已成为未来难加工材料的主要切削工具材料。
一般超硬材料指的是人造金刚石、人造CBN。
这两种材料的同时存在,起到了互补的作用、可以覆盖当前与今后发展的各种新型材料的加工,对整个切削加工领域极为有利。
1.PCD金刚石烧结体(PCD)的出现,在许多方面代替了天然单晶金刚石。
PCD与天然金刚石比较,价格便宜,且刃磨远比天然金刚石方便,所以其应用、推广特别迅速。
PCD刀具和PCBN刀具的性能优势及应用行业
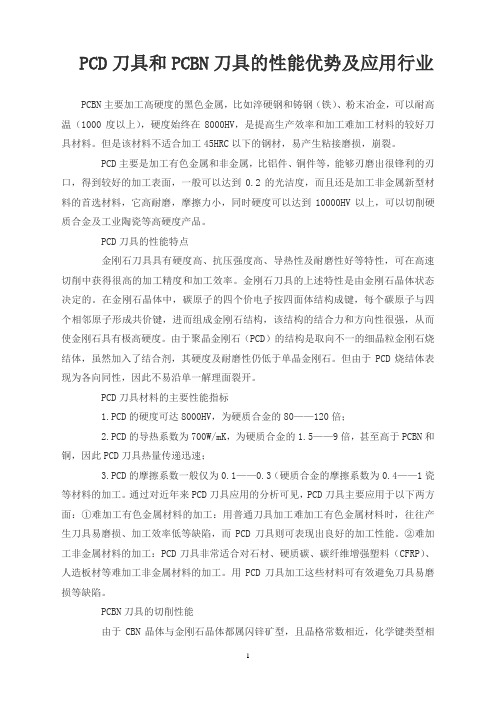
PCD刀具和PCBN刀具的性能优势及应用行业PCBN主要加工高硬度的黑色金属,比如淬硬钢和铸钢(铁)、粉末冶金,可以耐高温(1000度以上),硬度始终在8000HV,是提高生产效率和加工难加工材料的较好刀具材料。
但是该材料不适合加工45HRC以下的钢材,易产生粘接磨损,崩裂。
PCD主要是加工有色金属和非金属,比铝件、铜件等,能够刃磨出很锋利的刃口,得到较好的加工表面,一般可以达到0.2的光洁度,而且还是加工非金属新型材料的首选材料,它高耐磨,摩擦力小,同时硬度可以达到10000HV以上,可以切削硬质合金及工业陶瓷等高硬度产品。
PCD刀具的性能特点金刚石刀具具有硬度高、抗压强度高、导热性及耐磨性好等特性,可在高速切削中获得很高的加工精度和加工效率。
金刚石刀具的上述特性是由金刚石晶体状态决定的。
在金刚石晶体中,碳原子的四个价电子按四面体结构成键,每个碳原子与四个相邻原子形成共价键,进而组成金刚石结构,该结构的结合力和方向性很强,从而使金刚石具有极高硬度。
由于聚晶金刚石(PCD)的结构是取向不一的细晶粒金刚石烧结体,虽然加入了结合剂,其硬度及耐磨性仍低于单晶金刚石。
但由于PCD烧结体表现为各向同性,因此不易沿单一解理面裂开。
PCD刀具材料的主要性能指标1.PCD的硬度可达8000HV,为硬质合金的80——120倍;2.PCD的导热系数为700W/mK,为硬质合金的1.5——9倍,甚至高于PCBN和铜,因此PCD刀具热量传递迅速;3.PCD的摩擦系数一般仅为0.1——0.3(硬质合金的摩擦系数为0.4——1瓷等材料的加工。
通过对近年来PCD刀具应用的分析可见,PCD刀具主要应用于以下两方面:①难加工有色金属材料的加工:用普通刀具加工难加工有色金属材料时,往往产生刀具易磨损、加工效率低等缺陷,而PCD刀具则可表现出良好的加工性能。
②难加工非金属材料的加工:PCD刀具非常适合对石材、硬质碳、碳纤维增强塑料(CFRP)、人造板材等难加工非金属材料的加工。
PCD﹑PCBN刀具材料及刀具涂层

PCD﹑PCBN刀具材料及刀具涂层(一)PCD二十世纪七十年代,人们利用高压合成技术合成了聚晶金刚石(PCD),解决了天然金刚石数量稀少、价格昂贵的问题,使金刚石刀具的应用范围扩展到航空、航天、汽车、电子、石材等多个领域。
金刚石刀具具有硬度高、抗压强度高、导热性及耐磨性好等特性,可在高速切削中获得很高的加工精度和加工效率.金刚石刀具的上述特性是由金刚石晶体状态决定的。
在金刚石晶体中,碳原子的四个价电子按四面体结构成键,每个碳原子与四个相邻原子形成共价键,进而组成金刚石结构,该结构的结合力和方向性很强,从而使金刚石具有极高硬度。
由于聚晶金刚石(PCD)的结构是取向不一的细晶粒金刚石烧结体,虽然加入了结合剂,其硬度及耐磨性仍低于单晶金刚石.但由于PCD烧结体表现为各向同性,因此不易沿单一解理面裂开PCD刀具材料的主要性能指标:①PCD的硬度可达8000HV,为硬质合金的80~120倍;②PCD的导热系数为700W/mK,为硬质合金的1.5~9倍,甚至高于PCBN和铜,因此PCD刀具热量传递迅速;③PCD的摩擦系数一般仅为0。
1~0.3(硬质合金的摩擦系数为0.4~1),因此PCD刀具可显著减小切削力;④PCD的热膨胀系数仅为0.9×10 —6~1。
18×10 —6,仅相当于硬质合金的1/5,因此PCD刀具热变形小,加工精度高;⑤PCD刀具与有色金属和非金属材料间的亲和力很小,在加工过程中切屑不易粘结在刀尖上形成积屑瘤。
PCD 刀具的应用:工业发达国家对PCD刀具的研究开展较早,其应用已比较成熟。
自1953年在瑞典首次合成人造金刚石以来,对PCD刀具切削性能的研究获得了大量成果,PCD刀具的应用范围及使用量迅速扩大。
目前,国际上著名的人造金刚石复合片生产商主要有英国De Beers公司、美国GE公司、日本住友电工株式会社等。
据报道,1995年一季度仅日本的PCD刀具产量即达10。
7万把。
pcd是什么材料

pcd是什么材料PCD是多晶金刚石(Polycrystalline Diamond)的缩写,是一种由金刚石微粉和金属结合而成的超硬材料。
PCD因其硬度高、耐磨性强、热稳定性好等特点,被广泛应用于切削加工、磨削加工、研磨加工等领域。
下面将从PCD的结构、特性、应用领域等方面进行详细介绍。
首先,PCD的结构是由金刚石微粉和金属结合而成的复合材料。
金刚石微粉是PCD的主要成分,而金属则起到了固定和支撑的作用。
这种结构使得PCD具有了金刚石的硬度和金属的韧性,使其成为一种理想的超硬材料。
其次,PCD具有许多优良的特性。
首先是其硬度高,仅次于天然金刚石,因此具有极强的耐磨性,能够在高速切削中保持较长的使用寿命。
其次是其热稳定性好,即使在高温高速切削的环境下,PCD也能保持较好的切削性能。
此外,PCD还具有良好的化学稳定性和导热性,使得其在切削加工、磨削加工等领域得到了广泛的应用。
PCD在切削加工领域有着广泛的应用。
它可以用于加工铝合金、铜合金、铸铁、玻璃纤维增强塑料等难加工材料,具有很好的切屑控制和表面质量。
在汽车、航空航天、机械制造等行业,PCD刀具被广泛应用于车削、铣削、钻削等加工工艺中。
此外,PCD还可以用于加工非金属材料,如陶瓷、石英、玻璃等,在这些材料的加工中,PCD具有良好的耐磨性和切削性能。
除了切削加工领域,PCD还在磨削加工领域有着重要的应用。
PCD砂轮具有高效、精密的磨削性能,可以用于加工硬质合金、陶瓷、玻璃等材料,具有较长的使用寿命和高的加工精度。
在模具、工具、轴承等行业,PCD砂轮被广泛应用于精密磨削加工中。
总的来说,PCD作为一种超硬材料,具有硬度高、耐磨性强、热稳定性好等优良特性,被广泛应用于切削加工、磨削加工、研磨加工等领域。
它在汽车、航空航天、机械制造、模具、工具等行业发挥着重要的作用,为材料加工提供了高效、精密的加工工具和技术支持。
随着科技的不断进步,PCD的应用领域还将不断拓展,为工业生产和社会发展带来更多的创新和进步。
pcd刀片切削参数

pcd刀片切削参数PCD刀片切削参数PCD刀片是一种具有超硬度和高热稳定性的切削工具,广泛应用于高效精密切削加工中。
为了获得最佳的切削效果,合理选择和控制PCD刀片的切削参数至关重要。
本文将从切削速度、进给速度、切削深度和切削角度四个方面介绍PCD刀片的切削参数。
一、切削速度切削速度是指PCD刀片在单位时间内切削边缘通过的距离。
切削速度的选择应根据被加工材料的硬度、切削方式和刀具磨损情况等因素进行综合考虑。
一般来说,对于高硬度材料,切削速度应较低;对于低硬度材料,切削速度可以适当提高。
在选择切削速度时,还需考虑刀具的耐用性和切削表面质量。
二、进给速度进给速度是指PCD刀片在单位时间内切削边缘与被加工材料之间的相对运动速度。
进给速度的选择应根据被加工材料的硬度、切削方式和刀具磨损情况等因素进行综合考虑。
一般来说,对于高硬度材料,进给速度应较低;对于低硬度材料,进给速度可以适当提高。
进给速度过高会导致切削力过大,影响刀具寿命;进给速度过低则会降低生产效率。
三、切削深度切削深度是指PCD刀片切削时刀具与被加工材料间的垂直距离。
切削深度的选择应根据被加工材料的硬度、切削方式和刀具磨损情况等因素进行综合考虑。
一般来说,对于高硬度材料,切削深度应较小;对于低硬度材料,切削深度可以适当增大。
切削深度过大会导致刀具受力过大,容易断裂;切削深度过小则会降低切削效率。
四、切削角度切削角度是指PCD刀片切削边缘与被加工材料表面之间的夹角。
切削角度的选择应根据被加工材料的硬度、切削方式和刀具磨损情况等因素进行综合考虑。
一般来说,对于高硬度材料,切削角度应较小;对于低硬度材料,切削角度可以适当增大。
切削角度过小会导致刀具受力集中,容易产生刀具磨损和断裂;切削角度过大则会增加切削力和摩擦,影响切削表面质量。
PCD刀片的切削参数包括切削速度、进给速度、切削深度和切削角度。
合理选择和控制这些切削参数可以提高切削效率、延长刀具寿命和提高加工质量。
- 1、下载文档前请自行甄别文档内容的完整性,平台不提供额外的编辑、内容补充、找答案等附加服务。
- 2、"仅部分预览"的文档,不可在线预览部分如存在完整性等问题,可反馈申请退款(可完整预览的文档不适用该条件!)。
- 3、如文档侵犯您的权益,请联系客服反馈,我们会尽快为您处理(人工客服工作时间:9:00-18:30)。
论文题目
新型刀具材料:聚晶金刚石
所在学院:机电工程学院专业:机械电子
年级:10级
学生姓名:袁荣章
学号:102261013008 2011年11月11日
摘要:金刚石作为一种超硬刀具材料应用于切削加工已有数百年历史。
在刀具发展历程中,从十九世纪末到二十世纪中期,刀具材料以高速钢为主要代表;1927年德国首先研制出硬质合金刀具材料并获得广泛应用;二十世纪五十年代,瑞典和美国分别合成出人造金刚石,切削刀具从此步入以超硬材料为代表的时期。
二十世纪七十年代,人们利用高压合成技术合成了聚晶金刚石(PCD),解决了天然金刚石数量稀少、价格昂贵的问题,使金刚石刀具的应用范围扩展到航空、航天、汽车、电子、石材等多个领域。
关键词:刀具、材料、PCD
金刚石刀具具有硬度高、抗压强度高、导热性及耐磨性好等特性,可在高速切削中获得很高的加工精度和加工效率。
金刚石刀具的上述特性是由金刚石晶体状态决定的。
在金刚石晶体中,碳原子的四个价电子按四面体结构成键,每个碳原子与四个相邻原子形成共价键,进而组成金刚石结构,该结构的结合力和方向性很强,从而使金刚石具有极高硬度。
由于聚晶金刚石(PCD)的结构是取向不一的细晶粒金刚石烧结体,虽然加入了结合剂,其硬度及耐磨性仍低于单晶金刚石。
但由于PCD烧结体表现为各向同性,因此不易沿单一解理面裂开。
1.PCD刀具的性能特点:金刚石刀具具有硬度高、抗压强度高、导热性及耐磨性好等特性,可在高速切削中获得很高的加工精度和加工效率。
金刚石刀具的上述特性是由金刚石晶体状态决定的。
在金刚石晶体中,碳原子的四个价电子按四面体结构成键,每个碳原子与四
个相邻原子形成共价键,进而组成金刚石结构,该结构的结合力和方向性很强,从而使金刚石具有极高硬度。
由于聚晶金刚石(PCD)的结构是取向不一的细晶粒金刚石烧结体,虽然加入了结合剂,其硬度及耐磨性仍低于单晶金刚石。
但由于PCD烧结体表现为各向同性,因此不易沿单一解理面裂开。
2.PCD刀具材料的主要性能指标:①PCD的硬度可达8000HV,为硬质合金的80~120倍;②PCD的导热系数为700W/mK,为硬质合金的1.5~9倍,甚至高于PCBN和铜,因此PCD刀具热量传递迅速;③PCD的摩擦系数一般仅为0.1~0.3(硬质合金的摩擦系数为0.4~1),因此PCD刀具可显著减小切削力;④PCD的热膨胀系数仅为0.9×10^-6~1.18×10^-6,仅相当于硬质合金的1/5,因此PCD刀具热变形小,加工精度高;⑤PCD刀具与有色金属和非金属材料间的亲和力很小,在加工过程中切屑不易粘结在刀尖上形成积屑瘤。
3.PCD刀具的应用:工业发达国家对PCD刀具的研究开展较早,其应用已比较成熟。
自1953年在瑞典首次合成人造金刚石以来,对PCD刀具切削性能的研究获得了大量成果,PCD刀具的应用范围及使用量迅速扩大。
目前,国际上著名的人造金刚石复合片生产商主要有英国DeBeers公司、美国GE公司、日本住友电工株式会社等。
据报道,1995年一季度仅日本的PCD刀具产量即达10.7万把。
PCD 刀具的应用范围已由初期的车削加工向钻削、铣削加工扩展。
由日本一家组织进行的关于超硬刀具的调查表明:人们选用PCD刀具的主
要考虑因素是基于PCD刀具加工后的表面精度、尺寸精度及刀具寿命等优势。
金刚石复合片合成技术也得到了较大发展,DeBeers公司已推出了直径74mm、层厚0.3mm的聚晶金刚石复合片。
国内PCD刀具市场随着刀具技术水平的发展也不断扩大。
目前中国第一汽车集团已有一百多个PCD车刀使用点,许多人造板企业也采用PCD刀具进行木制品加工。
PCD刀具的应用也进一步推动了对其设计与制造技术的研究。
国内的清华大学、大连理工大学、华中理工大学、吉林工业大学、哈尔滨工业大学等均在积极开展这方面的研究。
国内从事PCD刀具研发、生产的有上海舒伯哈特、郑州新亚、南京蓝帜、深圳润祥、成都工具研究所等几十家单位。
目前,PCD刀具的加工范围已从传统的金属切削加工扩展到石材加工、木材加工、金属基复合材料、玻璃、工程陶瓷等材料的加工。
通过对近年来PCD 刀具应用的分析可见,PCD刀具主要应用于以下两方面:①难加工有色金属材料的加工:用普通刀具加工难加工有色金属材料时,往往产生刀具易磨损、加工效率低等缺陷,而PCD刀具则可表现出良好的加工性能。
如用PCD刀具可有效加工新型发动机活塞材料——过共晶硅铝合金(对该材料加工机理的研究已取得突破)。
②难加工非金属材料的加工:PCD刀具非常适合对石材、硬质碳、碳纤维增强塑料(CFRP)、人造板材等难加工非金属材料的加工。
如华中理工大学1990年实现了用PCD刀具加工玻璃;目前强化复合地板及其它木基板材(如MDF)的应用日趋广泛,用PCD刀具加工这些材料可有效避免刀具易磨损等缺陷。
4.结语:PCD刀具因其良好的加工质量和加工经济性在非金属材料、有色金属及其合金材料、金属基复合材料等切削加工领域显示出其它刀具难以比拟的优势。
随着PCD刀具的理论研究日益深入及其应用技术的进一步推广,PCD刀具在超硬刀具领域的地位将日益重要,其应用范围也将进一步拓展。
参考文献:
1.中国数控机床网:/
2.百度:/view/70197.htm#1。