塑料注射成型机基础知识.doc
第二章-注塑成型机基本知识
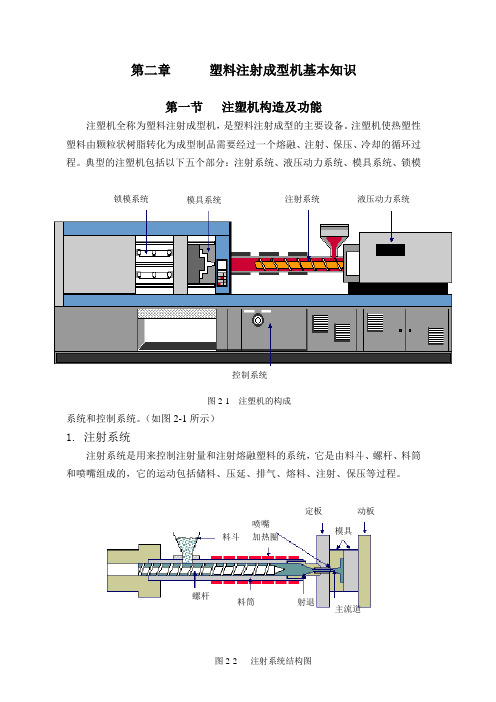
喷嘴是连接料筒和模具浇口套的部分,在料筒和模具之间起连接密封作用。喷嘴的温度一般设为材料的熔融温度或低于熔融温度,可参考材料供应商的推荐温度。当注射开始时,料筒运动到行程末端,喷嘴球型直径正好配合浇口套凹槽以保证密封;清洗料筒时,料筒退后一段距离,使熔料可以对空注射,这就是喷嘴的两个注射位置(如图2-4所示)。
3.15 设置保压时间
确定最小的保压时间值的最简便的方法是首先调节一个较长的保压时间,然后逐渐减少保压时间直到缩痕最小。
3.16 设置冷却时间
冷却时间的确定可以通过不断减少冷却时间直到制品表面的温度达到材料的转化温度,材料的转化温度可以由材料供应商提供。
第四节 我司注塑设备简介
模具公司现有HTF180、WG760、HTF450、HTW1080、HTF1800五种型号的注塑机。其中HTF180、HTF450、HTW1080、HTF1800是宁波海天系列注塑机,WG760是无锡格兰系列注塑机。注塑机是按照设备锁模力进行划分的,下面分别介绍各注塑机的技术规格。
3.4 设置螺杆旋转速率
理想的螺杆旋转速率是指在注塑循环最后阶段塑化完全而且不延长成型周期时的速率。
3.5 设置背压
背压推荐值为5-10MPa,背压过低容易导致制品不稳定,增加背压会提高摩擦力对于塑化的影响,减少塑化时间。
3.6 设置最大注射压力
注射压力是熔料在螺杆前端的压力,注射压力应尽量低,以减少制品的内应力。在注塑机中,压力设定值为最大注塑压力,以保证注塑压力不限制注塑速率。
模具的长宽尺寸需与注塑机模板尺寸和拉杆间距相适应,保证模具能通过拉杆间距顺利安装到模板上。定位时应考虑到:模具的主流道中心与料筒喷嘴的中心线相重合;模具上的定位环尺寸要与注塑机定模板上的定位孔尺寸相一致且采用间隙配合;注塑机喷嘴的球面半径应与相接触的模具主流道始端的球面半径相吻合;模具前后模的模脚尺寸应与注塑机动定模上的螺纹孔排列相匹配。
塑料第三章 塑料注射成型机

1.通用型注射成型机的主要组成(见图3-1)
图3-1 注射成型机的结构组成 1—料斗 2—机筒 3—分流梭 4—柱塞 5—液压缸
1.通用型注射成型机的主要组成(见图3-1)
(1)注射成型系统 它使塑料均匀地塑化成熔融状态,并以足够的速率和压 力将一定量的熔料注射入模腔内。它主要由料斗、料筒、喷嘴、螺杆、螺 杆传动装置、注射成型座移动液压缸、注射液压缸和计量装置等组成。 (2)合模系统(亦称锁模装置) 其主要作用是保证成型模具的可靠闭合,实 现模具的开、合动作以及顶出制品。它通常由合模机构、拉杆、模板、安 全门、制品顶出装置、调模装置等组成。 (3)液压与电气控制系统 保证注射成型机按工艺过程预定的要求和动作程 序准确有效地工作,液压系统主要由各种阀件、管路、动力液压泵及其他 附属装置组成;电气系统主要由各种电器仪表等组成。
三、注塑机结构
注塑机的结构组成形式比较多,但不管是哪种组成形式的注塑机,要想全 部完成塑料制品的注射成型工作,它就必须具备有原料的塑化、注射、成 型模具合模、保压、降温冷却固化和制件的脱模等功能动作。 1.原料塑化注射装置结构 2.注射成型机的塑化装置 2.螺杆类型A为突变、B为渐变。 3.注塑成型机的合模装置系统 4.注塑成型机的合模装置系统的分类
图3-6 卧式注射成型机 1—合模装置 2—注射装置 3—机身
3)角式注射成型机。
注射成型装置与合模装置的轴线相互垂直排列,注射时,熔料从模具分型面 进入型腔,如图3-7所示。该类注射成型机适用于成型中心不允许留有浇口 痕迹的制品。
图3-7 直角式注射成型机 1—合模装置 2—注射装置 3—机身
4)多模注射成型机。
三、注塑机结构
图3-12中所示注塑机是目前国内应用比较普遍的,数量最多的一种普通卧式 注塑机的立体外观。从图中可以看到,注塑机主要组成部件有塑化注射部分、 合模成型制品部分、液压传动部分、电控加热冷却系统、润滑和安全保护及 监控测试等。
塑料注射成型机

21
卧式注射机
2021/9/24
22
2021/9/24
卧式注射机
23
立 式 注 射 机
2021/9/24
24
2021/9/24
立 式 注 射 机
25
2021/9/24
角 式 注 射 机
26
2 按机器加工能力分类
类型 超小型
合模力kN 注射量cm3 <200~400 <30
小型
400~2000 60~500
2021/9/24
29
一塑料在有机筒内塑化 熔融物理模型 1 塑化过程主要包括两个阶段 – 第一阶段可看作是短暂的挤出过程 – 第二阶段螺杆静止 2 影响塑化质量的主要因素及其调整 a 树脂性能 b 加工条件 c 螺杆形状及要素
2021/9/24
30
二 熔料的充模与成型
熔料充模与成型是指熔料在模内发生的全部 行为 塑料在模内的状态可用Spencer—Gilmore 状 态方程表示
2) 注射成型机的主要组成
– 注射装置
– 合模装置
– 液压传动和电气控制系统
2021/9/24
19
合模装置
注射装置
2021/9/24
电气控制系统
液压传动系统
20
三 注射成型机的分类
1 按排列形式分类 – 立式注射成型机 – 卧式注射成型机 – 角式注射成型机(L型) – 多模注射成型机
2021/9/24
14
2021/9/24
15
2021/9/24
16
2021/9/24
17
2021/9/24
18
二 注射成型机的组成
1) 由单元操作分析可知注射机应具备的功能
注塑机基础知识

1 塑料注射成型机生产简介注射成型机(简称注射机或注塑机)是将热塑性塑料或热固性料利用塑料成型模具制成各种形状的塑料制品的主要成型设备。
注射成型是通过注塑机和模具来实现的。
尽管注塑机的类型很多,但是无论那种注塑机,其基本功能有两个:(1)、加热塑料,使其达到熔化状态;(2)、对熔融塑料施加高压,使其射出而充满模具型腔。
2 注塑机的结构及功能注塑过程是将已熔融的热塑性塑料用压力将它从一个已加热的料筒注入闭合着的模具内,经过一段时间冷却后,将模具分开,取出制成的制品。
模具再闭合与塑料注入进行配合,形成有次序的操作过程,并不断重复进行。
注塑机通常由注射系统、合模系统、液压传达动系统、电气控制系统、润滑系统、加热及冷却系统、安全监测系统等组成。
(1)注塑系统注射系统的作用:注射系统是注塑机最主要的组成部分之一,一般有柱塞式、螺杆式、螺杆预塑柱塞注射式3种主要形式。
目前应用最广泛的是螺杆式。
其作用是,在注塑料机的一个循环中,能在规定的时间内将一定数量的塑料加热塑化后,在一定的压力和速度下,通过螺杆将熔融塑料注入模具型腔中。
注射结束后,对注射到模腔中的熔料保持定型。
注射系统的组成:注射系统由塑化装置和动力传递装置组成。
螺杆式注塑机塑化装置主要由加料装置、料筒、螺杆、射咀部分组成。
动力传递装置包括注射油缸、注射座移动油缸以及螺杆驱动装置(熔胶马达)。
(2)合模系统合模系统的作用:合模系统的作用是保证模具闭合、开启及顶出制品。
同时,在模具闭合后,供给予模具足够的锁模力,以抵抗熔融塑料进入模腔产生的模腔压力,防止模具开缝,造成制品的不良现状。
合模系统的组成:合模系统主要由合模装置、调模机构、顶出机构、前后固定模板、移动模板、合模油缸和安全保护机构组成。
(3)液压系统液压传动系统的作用是实现注塑机按工艺过程所要求的各种动作提供动力,并满足注塑机各部分所需压力、速度、温度等的要求。
它主要由各自种液压元件和液压辅助元件所组成,其中油泵和电机是注塑机的动力来源。
注塑机知识
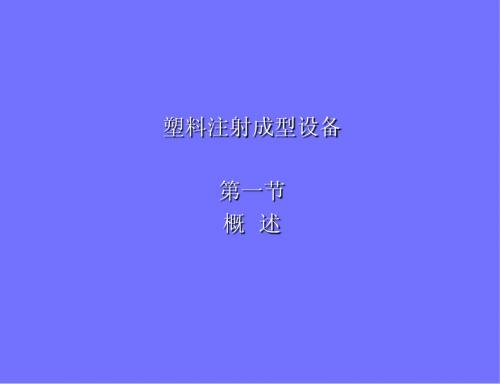
完成注塑成型需要经过三个过阶段:塑化、注射和定型。完成一 次注塑循环周期需要经过三个动作程序:合模、注射 保压、 冷却定型 制品脱模、预塑。 (1)塑化阶段--塑料原料从料斗落入料筒,被转动的螺杆 塑化阶段--塑料原料从料斗落入料筒,被转动的螺杆 向前输送。塑料一是接收料筒外部的加热升温,另一方面因螺槽 容积的减小而被压实,同时由于螺杆旋转产生强列的搅拌和剪切 作用,导致塑料之间及塑料与料筒和螺杆之间发生强列的摩擦, 塑料在前进时塑化成熔融态。螺杆后退行程由一次成型制品所需 的注射料量决定。 (2)注射阶段--当螺杆停止旋转和后退时,合模部分使模 注射阶段--当螺杆停止旋转和后退时,合模部分使模 具闭合,继而注射装置前移,使喷嘴与模具浇道口贴合,注射油 缸活塞推动螺杆迅速前移,按成型工艺所要求的注射压力和速度 把熔融塑料注入模具腔内。为防止熔料回流及补充收缩所需的熔 料,仍需一定的压力,即所谓的保压,直到浇口处的熔料冷却。 (3)定型阶段--模腔内的熔料经冷却,由粘流态恢复到玻 定型阶段--模腔内的熔料经冷却,由粘流态恢复到玻 璃态。制品完全冷却后,合模机构开启模具,顶出机构将制品脱 出,完成注塑制品成型的全程。
其主要组成部分:前后固定模板、移动模板、拉杆、合模 油缸、移动油缸、连杆机构、调模机构、制品顶出机构。 3.液压控制系统 3.液压控制系统 液压控制系统的作用是保证注塑机按预定的工艺条件(压 力、速度、温度和时间)及动作程序(合模、注射、保压、预 塑、冷却、开模、顶出制品)准确有效地工作。 其主要组成部分:各种液压元件、回路和液压辅助元件。 4.电气控制系统 4.电气控制系统 电气控制系统的作用是与液压系统相配合,控制注塑机准 机准 确无误地实现预定的工艺过程要求,并为注塑机实现各种程序 动作提供动力。 其主要组成部分:各种电气、电子元件、仪表、加热器、传 感器。 5.加热冷却系统 5.加热冷却系统 加热系统是用来加热料筒和注射喷嘴的;注塑机料筒一般采 用电阻加热圈,套在料筒的外部,并用热电偶分段检测;热量 能过筒壁导热为塑料塑化提供热源。
注塑机基本知识

第一章注塑机的基础知识第一节注塑机的分类1.按排列形式分类主要根据注塑螺杆的轴线与模板运动的导轨的排列关系进行分类,平行且水平放置为卧式,平行且垂直放置为立式,相互垂直为角式。
1.1 卧式注塑机具有以下优点:机身低机器重心较低,运行平稳:有利于操纵和维修:成型的制品可以利用自身的重量自动下落,容易实现全自动操作,应此应用广泛。
对大,中,小型机都适用,是目前国内外注塑机采用的最基本形式。
经过多年的技术发展,卧式注塑机细分为曲式,直压式,全自动式三大系列。
根据塑制品成型精度的高低,又可分为普通型和精密型两种类别。
1.2 立式注塑机具有以下优点:占地面积小:模具拆装方便;成型制品的嵌件容易安装。
其缺点是:制品顶出后往往要用手或其他方法将制品取出,不易实现自动化操作,机身较高稳定性差,加料及维修不便。
目前主要用在注塑量在60G以下的小型机上。
1.3 角式注塑机其优缺点介于卧,立两机之间,制品成型时容料经分型面进入模腔,它特别适合成型中心不允许留有浇口痕迹的制品。
如果用卧式或立式注塑机,模具必须设计成多型腔或偏置一边,会经常受到机器模板尺寸的限制。
2 按机器加工能力分类一般用来表示注塑机加工能力的参数的机器的型号规格里标出,有合模力和注塑质量,而多数是合模力表示,过去也有用合模力和注塑质量同时表示的。
例如1 海太牌HTL2000-F5(F6)注塑机,HT表示海太品牌,L表示系列,2000表示机器的和模力为2000吨或2000*10千牛(KN);F5(F6)表示配置等级。
例如2 海太牌HTE160-F5(F6,7)注塑机,HT表示海太品牌,L表示系列,160表示机器的和模力为160吨或160*10千牛(KN);F5(F6,7)表示配置等级。
例如3 ZS980/122注塑机,ZS表示卧式注塑机, 980表示机器的和模力为980千牛;122表示机器标准螺杆(B)的注塑质量为122克。
欧洲有些厂商还采用“合模力”和“注射能量”同时表示的方法,如:DH100—430注塑机,DH表示制造商的品牌。
成型机基础知识

一、成型机基础知识1、结构组成:注射成型机的三个基本职能:塑化、注射、成型,主要由两部分组成,合模装置与注射装置(完成塑化与注射两个基本职能)⑴.结构组成注射装置:主要作用是将塑料均匀的塑化,并以足够的压力和速度将一定量的熔料注射到模具的型腔中。
主要由塑化部件、料斗、计量装置、传动装置、注射和移动油缸等组成。
塑化部件----由螺杆、料筒和喷嘴所组成。
⑵.合模装置:其作用是实现模具的开、合,在射出时保证成型模具可以紧密地合紧,以及脱出制品。
主要由固定模板、移动模板、连接固定模板的拉杆、合模油缸,移模油缸、连杆机构、调模装置以及制品顶出装置等组成。
⑶.液压系统和电气控制系统:其作用是保证机器按工艺过程预定要求(压力、速度、温度、时间)和动作程序准确有效地工作。
2、分类:⑴.按外型:立式、卧式、角式、多模式⑵.按传动方式:液压式和机械式⑶.按塑化和注射方式:柱塞式、螺杆式、螺杆塑化柱塞注射式3、成型机的基本参数:⑴.公称注射量:在对空注射条件下,注射螺杆或柱塞作一次最大注射行程时,注射装置所能达到的最大注射量,注射量的单位为:g/cm 立方⑵.注射压力:其大小与流动阻力、制品的形状、塑料性能、塑化方式、温度和模温及对制品精度要求等因素有关。
⑶.注射速率:指注射时间、速度⑷.塑化能力:单位时间内所能塑化的物料量。
⑸.锁模力:注射机的合模机构对模具所能施加的最大夹紧力。
锁模力F≥KPA(公斤或吨) K-----压力损失的拆算系数0.4----0.7P -----注射压力 A ------制品在模具分型面上的投影面积(cm 平方)⑹.合模装置的基本尺寸:模板尺寸、拉杆空间、模板间最大开距、动模板行程、模具最大厚度与最小厚度。
⑺.开合模速度:料嘴或动模以某个速度运动到与下模或定模相吻合。
⑻.空循环时间:在没有塑化、注射保压、冷却、射出制品动作的情况下完成一次循环所需的时间,它由合模注射、座升、降、开模以及动作间切换时间组成。
塑料注射成型机
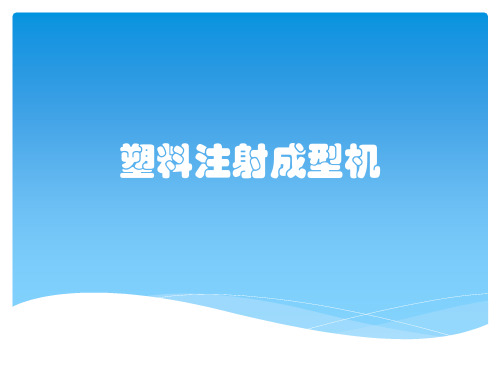
材料成形设备
14
2018/4/17
一、常用注射装置
第二节 注射装置
1. 柱塞式注射装置的组成和工作原理
组成:定量加料装置、塑化部件、注射液压缸、注射座移动液压缸等。 工作原理:粒料从料斗6落入加料装置5的计量室7中,当注射
液压缸中的活塞10前进时,推动柱塞8前移,与之相连的传动 臂9带动计量室7同时前移,从而将一定量的粒料推入料筒的 加料口。当柱塞后退时,加料口的粒料进入料筒,同时料斗 中的第二份粒料又落入计量室7中。注射动作反复进行,粒料 在料筒中不断前移,在前移的过程中,依靠料筒加热器3加热 塑化,使粒料逐渐变为粘流态,通过分流梭2与料筒内壁间的 窄缝,使熔料温度均匀,流动性进一步提高。最后,在柱塞 的推动下,熔料通过喷嘴1注射到模腔中成型。
塑料注射成型机
内容
塑料注射成型过程 注射装置 合模装置 注射机的控制系统 注射机的技术参数与使用维护 新型专用注射机
材料成形设备
2 2018/4/17
第一节 塑料注射成型过程
塑料注射成型机是将热塑性塑料 或热固性塑料利用塑料成型模具制成 塑料制件的主要成型设备。注射成型 能一次成型出形状复杂、尺寸精确和 带有嵌件的塑料制品,生产率高,易 于实现自动化。所以塑料注射成型机 是目前塑料成型设备中增长最快、产 量最多、应用最广的塑料成型设备。
第一节 塑料注射成型过程
3.角式注射成型机 注射装置与合模装置的轴线相互垂直排列。 优缺点介于立、卧式两种注射成型机之间。 适合于成型制品中心不允许留有浇口痕迹的制件。
5-1-6 角式注射机示意图1 5-1-6 角式注射机示意图2 5-1-6 角式注射机示意图3
材料成形设备
11 2018/4/17
注塑模具入门基础知识
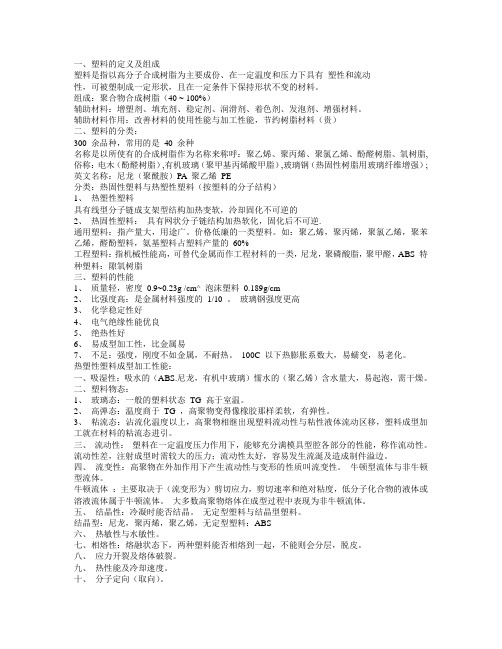
分开模具能取出塑件的面,称作分型面,其它的面称作分离面或称分模面,注射模只有一个分 型面。 分型面的方向尽量采用与注塑机开模是垂直方向,形状有平面,斜面,曲面。 选择分型面的位置时 〈1〉 分型面一般不取在装饰外表面或带圆弧的转角处 〈2〉 使塑件留在动模一边,利于脱模 〈3〉 将同心度要求高的同心部分放于分型面的同一侧,以保征同心度 〈4〉 轴芯机构要考虑轴芯距离 〈5〉 分型面作为主要排气面时,分型面设于料流的末端。 一般在分型面凹模一侧开设一条深 0.025 ~ 0.1mm 宽 1.5~6 mm 的排气槽。亦可以利用顶杆,型腔,型芯镶块排气 二、 浇注系统 浇注系统是指模具中从注射机喷嘴接触处到型腔为止的塑料熔体的流动通道。 作用: 〈1〉输送流体 〈2〉传递压力 〈一〉 浇注系统的组成及设计原则 1、 组成:由主流道,分流道,内浇口,冷料穴等结构组成。 2、 浇注系统的设计原则: 〈1〉 考虑塑料的流动性,保征流体流动顺利,快,不紊乱。 〈2〉 避免熔体正面冲出小直径型芯或脆弱的金属镶件。 〈3〉 一模多腔时,防止大小相差悬殊的制件放一模内。 〈4〉 进料口的位置和形状要结合塑件的形状和技术要求确定。 〈5〉 流道的进程要短,以减少成型周期及减少废料。 〈二〉 主流道设计 指喷嘴口起折分流道入口处止的一段,与喷嘴在一轴线上,料流方向不改变。 (1) 便于流道凝料从主流道衬套中拔出,主流道设计成圆锥形 。 7-15 锥角 =2°~ 4°粗糙 度 Ra≤0.63 与喷嘴对接处设计成半球形凹坑,球半径略大于喷嘴头半经。 (2) 主流道要求耐高温和摩擦,要求设计成可拆卸的衬套,以便选 用优质材料单独加工和热 处理。 (3) 衬套大端高出定模端面 5~10mm ,并与注射机定模板的定位孔成间隙配合,起定位隙作 用。 (4) 主流道衬套与塑料接触面较大时,由于腔体内反压力的作用使衬套易从模具中退出,可 设计定住 。 (5) 直角式注射机中,主流道设计在分型面上,不需沿轴线上拔出凝料可设计成粗的圆柱形。 〈三〉 分流道设计 指塑料熔体从主流道进入多腔模各个型腔的通道,对熔体流动起分流转向作用,要求熔体压力 和热量在分流道中损失小。 (1)分流道的截面形式: a、 图形断面:比表面积小(流道表面积与其体积之比) h/D = 2/3 ~ 4/5 边斜度 5~15° c、 u 形:加工方便,h/R=5/4 d、 半圆形:h/R=0.9 (2) 分流道的断面尺寸要视塑件的大小, 品种注射速度及分流道的长度而定。 一般分流道直经在 5~6mm 以下时,对流动性影响较大, 当直经大于 8mm 时,对流动性影响较小。 (3) 多腔模中,分流道的排布: a、 平衡式和非平衡式: 平衡式:分流道的形状尺寸一致。 非平衡式: a、靠近主流道浇口尺寸设计得大于远离主流道的浇口尺寸。 b、分流道不能太细长,太细长,温度,压加体大会使离主流道较远的型腔难以充满。
《塑料注射成型》教学课件—第二章塑料注射成型机第一节概述

液压传动主要由各种液压元件、液压基本回路和其它附属 装置所组成。电气控制主要由各种电器元件、仪表、电控系 统(加热、测量)、微机控制系统等组成。
按照习惯,我们把一个注射成型周期称为注射机的工作循 环。根据上述动作,按时间先后程序可绘制成注射机的工作过 程循环框图。
注射成型过程循环图
注射成型机的结构组成 一台通用型注塑机主要由注塑系统、合模系统、液压传
动与电气控制系统等所组成。
1—合模系统 2—安全门 3—控制电脑 4—注塑系统 5—电控箱 6—液压系统
注射成型过程
注射成型过程是热塑性塑料或热固性塑料在加热机筒中经 过加热、剪切、压缩、混合及输送作用,使之均匀塑化,塑 化好的熔融物料在喷嘴的阻挡作用下,积聚在机筒的前端, 然后借助于螺杆或柱塞施加的推力,经喷嘴与模具的浇注系 统进入闭合好的低温模腔中。充满模腔的熔料在受压作用下, 经冷却(热塑性塑料)或加热(热固性塑料)固化成形,开 启模具取出制品,在操作上即完成了一个成型周期,以后是 不断重复上述周期的生产过程。各种注射机完成注射成型的 动作程序可能不完全一致,但所要完成的工艺内容即基本过 程还是相同的。现以螺杆式注射机为例予以说明。
注射成型系统
➢ 注射系统的主要作用
注射系统的主要作用是“吃进”物料,使之均匀地加热塑 化和熔融,并以足够的压力和速度将一定量的熔料注入模具 型腔中。
➢ 注射系统结构组成 注射系统主要由塑化装置(螺杆或柱塞、机筒、喷嘴、加
热器等)、料斗、计量装置、螺杆传动装置、注射油缸、注 射座整体移动油缸等组成。
➢ 注射座后退
螺杆预塑化计量结束后,为了不使喷嘴长时间与冷的模具 接触形成冷料,而影响下一次注射和制品的质量,有些塑料 制品需要将喷嘴离开模具,即注塑座后退。在试模时也经常 使用这一动作。此动作进行与否或先后次序,根据所加工物 料的工艺条件而定,机器均可进行选择。
注塑机基本知识2

(4) 對工作程式及工藝條件設定與控制的功能。
爲此,注塑機主要由下列部件組成:
20
注射裝置:主要作用是使塑膠均勻地塑化成熔融狀態,並以足夠的壓力
和速度將一定量的熔料注射到模腔內。因此,注射裝置應具有塑化良好, 計量精確的性能,並且在注射時對熔料能夠提供足夠的壓力和速度。注 射裝置一般由塑化部件(機筒、螺杆、射嘴等)、料斗、計量裝置、螺 杆傳動裝置(熔膠馬達)、注射和移動油缸等。
鎖模裝置:主要是爲了保證成型模具可靠的閉合和實現模具啓閉動作,
即成型製品的工作部件。由於在注射時,進入模腔的熔料還具有一定的 壓力,這就要求合模裝置給予模具足夠的合模力,以防止在熔料的壓力 下模具被打開,從而導致製品溢邊或使製品精度下降。鎖模裝置主要包 括:模板、哥林柱、機鉸、頂針、安全門等。
液壓裝置:提供機器各部件運行所需的動力油的裝置﹐包括:電馬達(
4﹑制品冷卻和預塑化 當保壓進行到模腔內的熔料失去從澆口回流可能性時(即澆口封 閉),注射油缸內的保壓壓力即可卸去﹐使製件在模內自然冷卻定 型。為縮短機器成型周期﹐此時﹐螺杆在油馬達(或電機)驅動下 轉動﹐將來自料斗的粒狀塑膠向前輸送﹐並使其塑化熔融。進入 螺杆頭部的熔料﹐在正常操作條件下﹐其壓力低於熔料從噴咀流 出的阻力﹐並高於油缸內工作油的回泄阻力﹐故螺杆在熔料壓力 作用下﹐邊轉動邊後退。螺杆在塑化時的後移量﹐即表示了螺杆 頭部熔料所積存的量。當螺回退到計量值時﹐螺杆即停止轉動(由 行程開關或位移傳感器進行位置控制)﹐准備下一次注射。製品冷 卻與螺杆塑化在時間上是同時進行的﹐在一般情況下﹐要求螺杆 塑化計量時間要少於製品冷卻時間。 5﹑注射裝置後退和開模頂出製品 螺杆塑化計量完畢後﹐為了使噴嘴口不致於因長時間和冷模接觸 而形成冷料等緣故﹐經常需要將噴嘴撤離模具﹐即注射裝置後退。 此動作進行與否或先後的程式﹐機器均可供選擇。模腔內的熔料 經冷卻定型後﹐合模裝置即行開模﹐並自動頂落製品。
注塑机及工艺基础知识第一
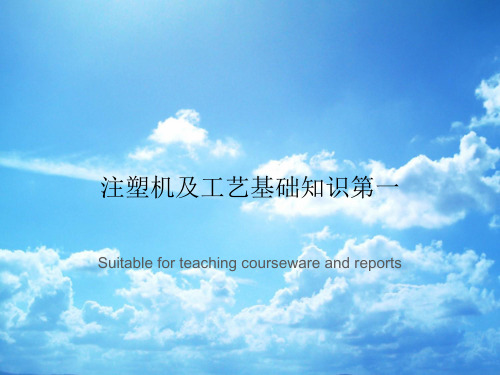
2.注塑机分类:非金属
a.按塑化方式分类:往复螺杆式和柱塞式
b.按合模方式分类:液压式、全电式、
卧式
油电混合式、机械式、液压-机械式
c.按外形特征分裂:卧式、立式、角式
常用的形式:我司使用设备
卧式、液压、往复螺杆式
3.液压式与全电式的优劣:
液压式:液体本身产生的压强大可以用来生
立式
角式
产精度一般而且很大的部品但精密度及稳定
210℃后降温 呈 180℃操作
200~220
500~1500
PP PA6 PA6/6 DELRIN PC
塑料种类
PS ABS PMMA PC 变性PPO 硬质PVC
200~270
210~280
225~280
240~280
260~280
270~310
180~200
190~220
260~270
260~280
b.保压速度、保压压力、保压时间:每段保压由一组保压速度、保压压力、 保压时间组成用来表示该阶段螺杆旋转的速度、施加的压力以及持续的 时间
5.冷却与脱模
冷却指为保证产品顺利脱模产品在模具中停留一段时间直至开模的过程 脱模指模具开模后通过顶杆、顶快、抓手或者气动装置使产品脱离模具的过程 涉及的工艺参数:
模具的锁紧力 它很大程度上反映了注塑机加工制品能力的大小所以 也把它作为表征注塑机规格的参数
3.注射
注射指螺杆旋转产生推进物料的动力把物流射入模具中的环节 涉及的工艺参数:
a.注射位置、注射速度、注塑压力:一般情况均采用分段注射每一段注塑 位置均会有一组注射速度和注射压力用来表示该阶段螺杆旋转的速度和 施加的压力
3.背压
a.增加背压可增加螺杆对熔融树脂所做的功、消除未熔的 塑料颗粒、增加料管内原料密度及其均匀程度、减少射 出收压和翘曲等问题
塑料注射成型机介绍-专业文档资料

三位四通换向阀
二位三通换向阀
电液阀
单向阀
2、液压 电液比例阀(流量、压力) 溢流阀 液控阀 节流阀
油路图示例
3、电气部件 机器的电气控制是发展是很快的,以
前由继电器进行控制,然后是采用PLC控 制,发展到现在的专用电脑控制器控制。 主要由以下器件组成: 自动空气开关 接触器 断电器 接线板 按钮开关
塑化分部件
射嘴、前体、螺杆头、混炼头、止回环、 止回垫、熔胶筒、螺杆。
射移油缸分部件
射移油缸盖、射移活塞杆、射移油缸、射 移活塞、射移活塞螺母。
注射缸分部件
注射缸前盖、活塞螺母、活塞、注射油缸、 注射座、注射活塞杆、调整螺母、注射缸 后盖、压板。
传动分部件
半环、端盖、传动座、传动轴、油马达法 兰。
(3)机架部件
合模机架分部件 图示
注射机架分部件 图示 以上内容主要包括有: 油箱、糟钢、角钢、工字钢、封板、 电箱
2、液压
由注射板、移模阀板、比例阀板、中 子阀板、顶针阀板等,以及外购件:油管 (一般以管径作为规格,重量为单位)、 管接头、管夹、压力表、油泵、电机、油 马达、阀类。
阀类主要用到以下的名称:
一、概述
注射成型机是将热塑性或热固性塑料制成 各种塑料制件的主要设备。
制品的形式(由模具决定)。
生产工作的过程。
合模 注射 储料(予塑) 抽胶 开模 顶出 顶针退 再循环
冷却
பைடு நூலகம்
1、注射成型机的型式
外形分 (1)卧式注射成型机 (2)立式注射成型机 (3)角式注射成型机 合模结构分 (1)机械式 (2)油压式 (3)二板式 控制形式分(机械、电动)
2、注射成型机的能力(大小)
类别 超小型 小型 中型 大型 超大型
塑料注射成型机.
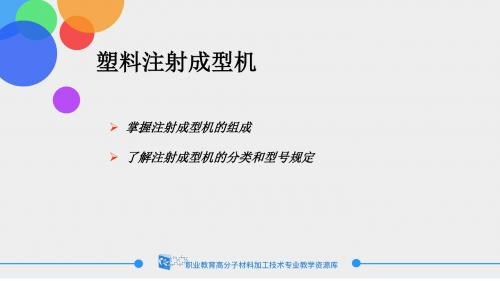
② 合模装置(锁模装置):
主要作用: 保证成型模具可靠的闭合和实现模具
启闭动作,即制成品。
结构组成: 模板、拉杆、合模机构、制品顶出装
置、安全门系统……;
③ 液压传动和电气控制系统:
主要作用: 保证注射机按工艺过程预定的要求(压力、
速度、温度、时间)和动作程序,准确无误地 进行工作。
结构组成: 液压部分——液压泵、液压马达、方向阀、
塑料注射成型机
掌握注射成型机的组成 了解注射成型机的分类和型号规定
原理:将热塑性塑料或热固性塑料利用塑 料成型模具制成塑料制件。
特点:能一次成型出外形复杂、尺寸精确 或带有嵌件塑料制件。生产率高及易于实现自 动化。
应用:国防工业、机械、电子、航空、交 通运输、建筑、农业、文教、卫生及人民生活 等各个成型机组成
1、合模装置 2、注射装置 3、液压传动系统 4、电器控制系统
① 注射装置:
主要作用: 使塑料的均匀塑化熔融,以足够压力和
速度将一定量的熔料注射到模腔内。
结构组成: 塑化部件(机筒、螺杆、喷嘴……)、
料斗、计量装置、螺杆传动装置、注射和移 动油缸……
流量阀、压力阀、控制阀…… 电气部分——动力、动作程序和加热等控
制部件……
- 1、下载文档前请自行甄别文档内容的完整性,平台不提供额外的编辑、内容补充、找答案等附加服务。
- 2、"仅部分预览"的文档,不可在线预览部分如存在完整性等问题,可反馈申请退款(可完整预览的文档不适用该条件!)。
- 3、如文档侵犯您的权益,请联系客服反馈,我们会尽快为您处理(人工客服工作时间:9:00-18:30)。
塑料注射成型机基础知识注塑机具有能一次成型外型复杂、尺寸精确或带有金属嵌件的质地密致的型料制品,被广泛应用于国防、机电、汽车、交通运输、建材、包装、农业、文教卫生及人们日常生活各个领域。
注射成型工艺对各种型料的加工具有良好的适应性,生产能力较高,并易于实现自动化。
在塑料工业诅速发展的今天,注塑机不论在数发上或品种上都占有重要地位,从而成为目前架料机械中增长最快,生产数量最多的机种之一。
我国规•料加工企业星罗其布,遍布全国各地,设备的技术水平参差不齐,大多数加工企业的设备都需要技术改造。
这几年来,我国槊机行业的技术进步十分显著,尤其是注塑机的技术水平与国外名牌产品的差距大大缩小,在控制水平、产品内部质量和外观造型等方面均取得显著改观。
选择国产设备,以较小的投入,同样也能生产出与进口设备质量相当的产品。
这些为企业的技术改造创造了条件。
要有好的制品,必须要有好的设备。
设备的磨损和腐蚀是一种自然规律,人们掌握了这种规律,就可以预防或减少设备的磨损和腐蚀,延长设备的使用周期,保证设备的完好率。
为加强塑料机械的使用、维护和管理工作,我国有关部门己制订了有关标准和实施细则, 要求各设备管理部门和生产企业对设备的管理和使用做到“科学管理、正确使用、合理润滑、精心维护、定期保养、计划检修,提高设备完好率,使设备经常处于良好状态。
槊料注射成型技术是根据压铸原理从十九世纪末二十世纪初发展起来的,是目前塑料加工中最•普遍采JIJ的方法之一。
该法适用于全部热型性塑料和部分热固性塑料(约占卿料总量的1/3)o1.1隹塑成型机的工作原理注塑机的工作原理与打针用的注射器相似,它是借助螺杆(或柱塞)的推力,将己槊化好的熔融状态(即粘流态)的型料注射入闭合好的模腔内,经固化定型后取得制品的工艺过程。
注射成型是一个循环的过程,每一周期主要包括:定量加料一熔融塑化一施压注射一充模冷却一启模取件。
取出塑件后又再闭模,进行下一个循环。
1.2注塑机的结构注塑机根据塑化方式分为柱塞式注塑机和螺杆式注塑机;按机器的传动方式又可分为液压式、机械式和液压一机械(连杆)式;按操作方式分为自动、半自动、手动注型机。
(1)卧式注州机:这是最常见的类型。
其合模部分和注射部分处于同一水平中心线上,且模具是沿水平方向打开的。
其特点是:机身矮,易于操作和维修;机器重心低,安装较平稳; 制品顶出后可利用重力作用自动落下,易于实现全自动操作。
目前,市场上的注可机用采用此神型式。
(2)立式注塑机:其合模部分和注射部分处于同一垂直中心线上,且模具是沿垂直方向打开的。
因此,其占地面积较小,容易安放嵌件,装卸模具较方便,自料斗落入的物料能较均匀地进行型化。
但制品顶出后不易自动落下,必须用手取下,不易实现自动操作。
立式注•塑机宜用于小型注塑机,一般是在60克以下的注塑机采用较多,大、中型机不宜采用。
(3)角式注塑机:其注射方向和模具分界面在同一个面上,它特别适合于加工中心部分不允许留有浇口痕迹的平面制品。
它占地面积比卧式注型.机小,但放入模具内的嵌件容易倾斜落下。
这种型式的注型机宜用于小机。
(4)多模转盘式注槊机:它是一种多工位操作的特殊注塑机,其特点是合模装置采用了转描式结构,模具围绕转轴转动。
这种型式的注具机充分发挥了注射装置的塑化能力,可以缩短生产周期,提高机器的生产能力,因而特别适合于冷却定型时间长或因安放嵌件而需要较多辅助时间的大批量塑制品的生产,但因合模系统庞大、复杂,合模装置的合模力往往较小, 故这种注塑机在鲫•胶鞋底等制品生产中应用较多。
一般洼塑机包括注射装置、合模装置、液压系统和电气控制系统等部分。
注射成型的基本要求是塑化、注射和成型。
塑化是实现和保证成型制品质量的前提,而为满足成型的要求,注射必须保证有足够的压力和速度。
同时,由于注射压力很高,相应地在模腔中产生很高的压力(模腔内的平均压力一般在20〜45MPa之间,见表1),因此必须有足够大的合模力。
由此可见,注射装置和合模装置是注阳机的关键部件。
1.4注塑机的操作1.4.1注塑机的动作程序喷嘴前进一注射一保压一预塑一倒缩一喷嘴后退一冷却一开模-顶出一退针一开门一关门一合模一喷啪前进。
142注型机操作项目:注塑机操作项目包括控制键盘操作、电器控制柜操作和液压系统操作三个方面。
分别进行注射过程动作、加料动作、注射压力、注射速度、顶出型式的选择, 料筒各段温度及电流、电压的监控,注射压力和背压压力的调节等。
1.4.2.1注射过程动作选择:一般注•塑机既可手动操作,也可以半白动和全日动操作。
手动操作是在一个生产周期中,每一个动作都是由操作者拨动操作开关而实现的。
一•般在试机调模时才选用。
半自动操作时机器可以自动完成一个工作周期的动作,但每一个生产周期完毕后操作者必须拉开安全门,取下工件,再关上安全门,机器方可以继续下一个周期的生产。
全自动操作时注塑机在完成一个工作周期的动作后,可日动进入下一个工作周期。
在正常的连续工作过程中无须停机进行控制和调整。
但须注意,如需要全自动工作,则(1)中途不要打开安全门,否则全自动操作中断;(2)要及时加料;(3)若选用电眼感应,应注意不要遮闭了电眼。
实际上,在全自动操作中通常也是需要中途临时停机的,如给机器模具喷射脱模剂等。
正常生产时,一般选用半自动或全自动操作。
操作开始时,应根据生产需要选择操作方式(手动、半自动或全自动),并相应拨动手动、半自动或全自动开关。
半自动及全自动的工作程序已由线路本身确定好,操作人员只需在电柜面上更改速度和压力的大小、时间的长短、顶针的次数等等,不会因操作者调错键钮而使工作程序出现混乱。
当一个周期中各个动作未调整妥当之前,应先选择手动操作,确认每个动作正常之后,再选择半自动或全自动操作O1.4.2.2预塑动作选择根据预塑加料前后注座是否后退,即喷嘴是否离开模具,注塑机一般设有三种选择。
(1)固定加料:预翊前和预卿后喷嘴都始终贴进模具,注座也不移动。
(2)前加料:喷嘴顶着模具进行预型加料,预塑完毕,注座后退,喷嘴离开模具。
选择这种方式的目的是:预塑时利用模具注射孔抵助喷嘴,避免熔料在背压较高时从喷瞄流出,预槊后可以避免喷嘴和模具长时间接触而产生热量传递,影响它们各自温度的相对稳定。
(3)后加料:注射完成后,注座后退,喷嘴离开模具然后预模,预型完再注座前进。
该动作适用于加工成型温度特别窄的塑料,由于喷嘴与模具接触时间短,避免了热量的流失,也避免了熔料在喷嘴孔内的凝固。
注射结束、冷却计时器计时完毕后,预槊动作开始。
螺杆旋转将塑料熔融并挤送到螺杆头前面。
由于螺杆前端的止退环所起的单向阀的作用,焰融皇料积存在机筒的前端,将螺杆向后迫退。
当螺杆退到预定的位置时(此位置由行程开关确定,控制螺杆后退的距离,实现定量加料),预塑停止,螺杆停止转动。
紧接着是倒缩动作,倒缩即螺杆作微量的轴向后退, 此动作可使聚集在喷嘴处的熔料的压力得以解除,克服由于机筒内外压力的不平衡而引起的“留涎”现象。
若不需要倒缩,则应把倒缩停|上开关调到适当位置,让预槊停止•开关被压上的同一时刻,倒缩停止开关也被压上。
当蝶杆作倒缩动作后退到压上停止开关时,倒缩停止。
接着注座开始后退。
当注座后退至压上停止开关时,注座停止后退。
若采用固定加料方式, 则应注意调整好行程开关的位置。
一般生产多采用固定加料方式以节省注座进退操作时间,加快生产周期。
1.4.2.3注射压力选择注塑机的注射压力由调压阀进行调节,在调定压力的情况下,通过高压和低压油路的通断,控制前后期注射压力的高低。
普通中型以上的注塑机设置有三种压力选择,即高压、低压和先高压后低压。
高压注射是由注射汕缸通入高压压力汕来实现。
由于压力高,塑料从一开始就在高压、高速状态下进入模腔。
高压注射时卿•料入模迅速,注射油缸压力表读数上升很快。
低压注射是由注射油缶工通入低压压力油来实现的,注射过程压力表读数上升缓慢,划料在低压、低速下进入模腔。
先高压后低压是根据塑料种类和模具的实际要求从时间上来控制通入油缸的压力油的压力高低来实现的。
为了满足不同塑料要求有不同的注射压力,也可以采用更换不同直径的螺杆或柱塞的方法,这样既满足了注射压力,乂充分发挥了机器的生产能力。
在大型注塑机中往往具有多段注射压力和多级注射速度控制功能,这样更能保证制品的质量和精度。
1.4.2.4注射速度的选择一般注塑机控制板上都有快速一慢速旋钮用来满足注射速度的要求。
在液压系统中设有一个大流量汕泉和一个小流量泉同时运行供汕。
当汕路接通大流量时,注塑机实现快速开合模、快速注射等,当液压油路只提供小流量时,注塑机各种动作就缓慢进行。
1.4.2.5顶出形式的选择注塑机顶出形式有机械顶出和液压顶出二种,有的还配有气动顶出系统,顶出次数设有单次和多次二种。
顶出动作可以是手动,也可以是自动。
顶出动作是由开模停止限位开关来启动的。
操作者可根据需要,通过调节控制柜上的顶出时间按钮来达到。
顶出的速度和压力亦可通过控制柜面上的开关来控制,顶针运动的前后距离由行程开关确定。
1.4.2.6温度控制以测温热电偶为测温元件,配以测温亳伏计成为控温装置,指挥料筒和模具电热圈电流的通断,有选择地固定料筒各段温度和模具温度。
表5列出了一些槊料的成型加工温度范围,可供参考。
料筒电热圈一般分为二段、三段或四段控制。
电器柜上的电流表分别显示各段电热圈电流的大小。
电流表的读数是比较固定的,如果在运行中发现电流表读数比较长时间的偏低, 则可能电热圈发生了故障,或导线接触不良,或电热丝氧化变细,或某个电热圈烧毁,这些都将使电路并联的电阻阻值增大而使电流下降。
在电流表有一定读数时也可以简单地用槊料条逐个在电热圈外壁上抹划,看料条焰融与否来判断某个电热圈是否通电或烧毁。
1.4.2.7合模控制合模是以巨大的机械推力将模具合紧,以抵挡注塑过程熔融槊料的高压注射及填充模具而令模具发生的巨大张开力。
关妥安全门,各行程开关均给出信号,合模动作立即开始。
首先是动模板以慢速启动,前进一小短距离以后,原来压住慢速开关的控制杆压块脱离,活动板转以快速向前推进。
在前进至靠近合模终点时,控制杆的另一端压杆又压上慢速开关,此时活动板又转以慢速且以低压前进。
在低压合模过程中,如果模具之间没有任何障碍,则可以顺利合拢至压上高压开关,转高压是为了伸直机钗从而完成合模动作。
这段距离极短,一般只有0.3〜1.0mm,刚转高压旋即就触及合模终止限位开关,这时动作停止,合模过程结束。
迳塑机的合模结构有全液压式和机械连杆式。
不管是那一种结构形式,最后都是由连杆完全伸直来实施合模力的。
连杆的伸直过程是活动板和尾板撑开的过程,也是四根拉杆受力被拉伸的过程。
合模力的大小,可以从合紧模的瞬间油压表升起之最高值得知,合模力大则油压表的最高值便高,反之则低。