第三章热浸镀技术 ppt课件
热浸镀锌技术
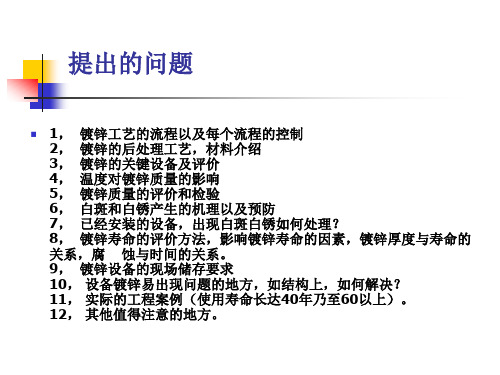
1-18 铬酸盐钝化后处理(日本大阪) 铬酸盐钝化后处理(日本大阪)
1-19 铬酸盐钝化后处理(宁波永丰) 铬酸盐钝化后处理(宁波永丰)
1-20 铬酸盐钝化的替代物 -
有机物方面:植酸、羟乙叉基二膦酸、 有机物方面:植酸、羟乙叉基二膦酸、单宁酸 、 及其衍生物、 二氨基三氮杂茂 (BAT4)及其衍生物、苯骈三氮唑 及其衍生物 )、季铵盐 (BTA)、季铵盐、硅烷等 )、季铵盐、 无机盐方面:磷酸盐、钼酸盐、钨酸盐、 无机盐方面:磷酸盐、钼酸盐、钨酸盐、硅酸盐 含硅溶胶)、锆盐、钴盐、 )、锆盐 (含硅溶胶)、锆盐、钴盐、稀土盐等 无机盐+有机物方面:水溶性丙烯酸树脂 硅溶胶 硅溶胶、 无机盐 有机物方面:水溶性丙烯酸树脂+硅溶胶、 有机物方面 硅烷+钼酸盐 钼酸盐、 钨酸盐等。 硅烷 钼酸盐、BTA+钨酸盐等。 钨酸盐等 复合涂层 : 一步法 ,两步法
1-17
常规铬酸盐钝化
机理:由三价铬和六价铬形成的 机理 由三价铬和六价铬形成的Cr/金属混合物钝化膜 由三价铬和六价铬形成的 金属混合物钝化膜 组成,其中三价铬作为骨架,而六价铬(铬酸盐离子) 组成,其中三价铬作为骨架,而六价铬(铬酸盐离子) 很容易从钝化膜中渗出来作为缓蚀剂,使膜层具有 使膜层具有“ 很容易从钝化膜中渗出来作为缓蚀剂 使膜层具有“自 能力。 愈”能力。 特点:隔绝、自愈、 特点:隔绝、自愈、结合力好 优点:使用浓度低(批量热镀锌用 )、成 优点:使用浓度低(批量热镀锌用0.1~0.2%)、成 ~ )、 本低、耐白锈效果好。 本低、耐白锈效果好。 缺点:六价铬盐毒性高且致癌。 缺点:六价铬盐毒性高且致癌。部分铬酸盐钝化电气 产品已在欧洲禁用。 产品已在欧洲禁用。
1-8 溶剂处理设备(上海聚丰) 溶剂处理设备(上海聚丰)
输变电工程钢构件热浸镀锌铝镁稀土合金镀层技术条件

输变电工程钢构件热浸镀锌铝镁稀土合金镀层技术条件你知道吗,钢铁的生命其实比我们想象的还要脆弱,尤其是在输变电工程这样的环境里。
那些铁骨铮铮的钢构件,天天都得和风霜雨雪打交道,不被腐蚀那才怪!这时候,热浸镀锌铝镁稀土合金镀层就成了钢铁的“护身符”。
咱们俗话说,“千里之堤毁于蚁穴”,一丁点的腐蚀都可能让这坚固的钢构件提前退休。
所以,镀层可得搞得像个铁饭碗一样,保护好这些钢铁勇士。
说到热浸镀锌铝镁稀土合金镀层,可能有点绕口,不过简单说就是一种把钢铁“包裹”上防护层的技术。
这个“包裹”可不只是拿个塑料袋随便套套,而是通过一系列高温工艺,把锌、铝、镁等金属融化,浸入钢铁表面形成一层坚固的合金保护层。
这层镀层就像钢铁的“铠甲”,无论是面对风吹雨打,还是海风盐雾,它都能抵挡得住。
所以,你可以想象,钢铁就穿上了一件高科技战斗服,既轻便又防护力十足。
这技术的好处可大了去了。
镀层能够大大增强钢材的耐腐蚀性,尤其在那些潮湿、多雨或者盐雾较重的环境下,钢铁表面如果没有这层保护,早晚会“中招”生锈腐蚀。
你看那些海边的铁轨、铁塔,没几年就锈得发红,严重影响使用寿命。
而镀锌铝镁稀土合金镀层就像是一把防腐的“定海神针”,能让钢材在严酷环境中坚持得更久。
要是你住在海边或者经常去海边旅游,应该对这种技术有些理解了吧,毕竟海风咸湿、空气湿度大,什么金属都怕这种环境。
不过,镀层的好坏可不是只看外表就能决定的哦。
可得考察它的厚度、附着力、耐磨性、抗氧化性等等。
厚度是关键,太薄了可能不够强韧,太厚了又怕增加重量,反而不好。
还得看附着力,镀层跟钢铁的结合必须牢牢地“粘”在一起,不能随便掉皮或者脱落。
那样的话,钢材又得裸奔了。
耐磨性也是一大亮点,镀层不但要防腐,还得经得住摩擦,能保护钢材不被擦伤,维持长期的防护效果。
有些人可能会觉得,镀层做得好不好其实都差不多,反正有个保护就行。
错了!这是个技术活,做得不好,钢铁还会被腐蚀,而且镀层的质量不好,可能还会影响钢材本身的性能。
热浸镀
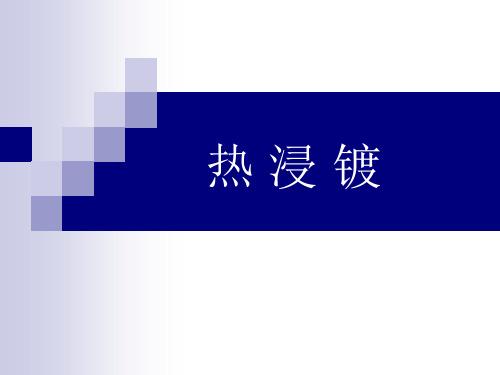
单张钢板热镀锡装置
1.熔剂,2.镀锡原板,3加锡口,4。加热盘管,5.导板,6.刮锡 扳;7.镀锡辊;8.空气冷却装置,9.提升机;10,11.烟道
钢丝热镀锡工艺
工件→酸洗→水洗→溶剂处理→热浸镀锡→浸油处 理→空冷→脱油→分选→成品。
工艺与单张板同,但要注意如下几点。
1)溶剂处理 溶剂为在氧化锌中加10%氯化铵的混 合水溶液。溶剂槽温度480~220℃。溶剂槽中因 加水生成盐酸,可再次对钢丝表面氧化物清洗。
热浸镀
一、热浸镀原理
将经过表面处理的金属工件,放入远比工件熔点低
的熔融金属中,以获得金属镀层的过程,这个过程称热
浸镀(熔融镀、热镀)。
热浸镀层金属一般为锡(熔点231.9℃)、锌(熔点
419.5℃)、铝(熔点658.7℃)、铅(熔点327.4℃)。
基体材料一般是钢铁,有时也用铜。浸镀前工件需进行
表面预处理,清除表面的油污和氧化皮。热浸镀后还要 进行化学处理、涂油或必要的整形。
热镀锡原理
热镀锡原理
在300℃时,铁与锡相互反应生成FeSn2。例如,在热镀 锡时,经过前处理的钢板进人含有氯化按及氯化锌的熔剂 层,形成铁锡合金。 ZnCl2+2H2O—Zn(OH)2十2HCl FeO十2HCl——FeCl2十H2O Fe十2HCl—FeCl2十H2 生成的氯化亚铁(FeCl2)与炼锡(Sn)反应,生成SnC12及 FeSn2 3Sn十FeCl2——SnC12十FeSn2 生成的化合物FeSn2一部分附在钢板上。另一部分进入锡 槽形成锡渣。附着FeSn2层的钢板再进入炼锡中浸镀锡。
2)热浸镀锡 锡液温度为260~290℃之间。 3)浸油处理 棕榈油温度为230~240℃之间。
热浸镀锡钢板性能
热浸镀工艺与应用

热浸镀工艺与应用1 前言热浸镀简称热镀,是将被镀金属材料浸于熔点较低的其它液态金属或合金中形成镀层的方法。
热浸镀锌是当今世界上应用最广泛的钢材防腐方法之一;热浸镀铝工艺难度较大,但是也实现了工业化生产;热浸镀铝锌合金是近年来发展迅速的新型镀层之一。
热浸镀具有工艺简便、性能可靠、成本低廉、生产效率高、便于机械化生产、能迅速施加镀层等优点;热浸镀镀层美观,耐蚀性好。
因此热浸镀在钢材防腐方面得到广泛应用。
如钢板(管),型材,桥梁,铁塔,海洋栈桥,钻井平台和井架,民用建筑等。
2 热浸镀工艺的特点前处理:将镀件表面的油污(碱洗或高温除油)、氧化物(酸洗)等清除干净;热浸镀:镀件洁净的基体表面浸入熔融金属液体中形成镀层;后处理:对制品进行化学处理(如钝化)和物理处理(如涂油防护整形等)。
根据热浸镀的前处理方法不同,热浸镀工艺可以分为熔剂法和保护气体还原法:(1)熔剂法是利用熔剂的化学作用对己经除油、除锈的钢材在浸入镀液前保护其表面不再氧化并对其进一步活化,保证镀液与洁净的钢基体表面浸润,并通过化学反应和扩散,形成合金层。
该法设备简单、成本低、操作简便易学、生产灵活,可进行批量生产也可进行单件浸镀,可根据产品批量随时调控连续浸镀或间断浸镀,且浸镀产品范围广,适应多种品种规格的产品,因此,在我国极具推广价值,有必要进行深入研究。
(2)保护气体还原法又称森吉米尔法,是现代带钢连续热浸镀采用的最普遍和最广泛的一种工艺。
该法生产速度快、效率高、镀层结合力好、无污染等优点,另外,还原型生产线高温辐射加热的温度高,退火时间长,可以生产加工良好的产品;但设备比较复杂,投资大,技术难度大,适合单一产品的批量生产。
由于我国多数热浸镀厂家资金相对薄弱,工艺水平达不到该法的要求,因而极大地限制保护气体还原法在我国的发展。
3热浸镀层的种类因为热浸镀层金属的熔点要求比基体材料低得多,所以热浸镀常常限于采用低熔点金属及其合余,如锡、锌、铝、铅及其合金,其中应用最为广泛的镀层金属是锌,近年来为了提高镀层的耐蚀性能或机械性能,以适应不同的应用场合,开发了多种锌基合金镀层。
热浸镀工艺流程-概述说明以及解释

热浸镀工艺流程-概述说明以及解释1.引言1.1 概述热浸镀工艺是一种常见的表面处理技术,通过将金属材料浸入熔融的金属溶液中,使其表面形成均匀、致密、耐腐蚀的镀层。
热浸镀工艺具有广泛的应用领域,包括汽车工业、建筑领域、电子设备制造等。
热浸镀工艺的流程包括表面准备、预处理、浸镀、冷却、清洗等多个步骤。
首先,需要对待镀物的表面进行清洗和脱脂处理,以去除表面的污垢和油脂。
接下来,将待镀物浸入预处理液中,进行除锈、除氧和活化处理,以提高镀层与基材之间的结合力。
在预处理完成后,将待镀物浸入熔融的金属溶液中,如锌、镍、铝等。
待镀物在金属溶液中浸泡一段时间后,金属溶液中的金属元素会在其表面析出,形成均匀且致密的镀层。
浸镀后的待镀物需要经过冷却过程,以确保镀层的稳定性和良好的表面质量。
最后,浸镀完成的待镀物需要进行清洗,以去除残留的金属溶液和其他污染物。
清洗过程通常采用酸碱中和、水冲洗等方法,以确保镀层的纯净度和质量。
热浸镀工艺流程具有工艺简单、成本较低、镀层质量优良等优点。
它不仅能够提高金属制品的耐腐蚀性能,还能增加其外观美观度和使用寿命。
随着工艺技术的不断发展,热浸镀工艺在各个领域的应用前景非常广阔。
1.2 文章结构文章结构部分的内容应该是对整篇文章的框架进行介绍和解释。
在这个部分,可以提供以下信息:文章结构部分介绍了整篇文章的组织和框架。
它主要包括以下几个方面:1. 引言部分(Introduction):主要概述了热浸镀工艺流程的背景和重要性。
这一部分会介绍热浸镀工艺流程的一般概念和应用领域。
2. 正文部分(Main Body):包括了热浸镀工艺流程的详细说明。
其中,2.1节将概述热浸镀工艺流程的一般步骤,2.2节将详细描述每个步骤的具体操作流程和要点。
通过这一部分,读者将能够了解热浸镀工艺流程的整个过程。
3. 结论部分(Conclusion):总结了热浸镀工艺流程的特点和应用前景。
3.1节对热浸镀工艺流程进行了简要总结,指出了其优点和局限性。
第三章 电镀工艺(8学时)PPT课件
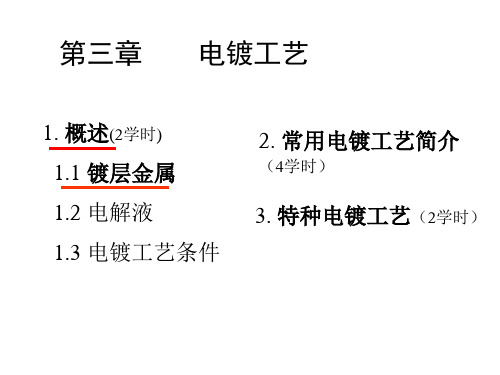
耐蚀 镀层
封闭镍是一个典型的例子 含铝粉10 %(wt)的复合锌镀层,耐蚀性提高6.2倍
第三章 电镀工艺
1. 概述 1.1 镀层金属 1.2 电解液 1.3 电镀工艺条件
主盐有如下几种
单盐电解液
被镀金属以简 单离子形式存 在于电解液中
• 硫酸盐,如ZnSO4溶液镀锌 • 氯化物,如ZnCl2溶液镀锌 • 氟硼酸盐,如Ni(BF4)2溶液镀镍 • 氨基磺酸盐,如Ni(NH2SO3)2溶液镀镍 • 氟硅酸盐,如PbSiF6溶液镀铅
----提高阴极电流密度。因为升高温度可以增大 id ,就可以 使用更大的阴极电流密度,从而增大阴极极化。
锌-镍(13%)
(5m)
(未钝化) (未钝化) (彩色钝化) (彩色钝化)
出白锈时间(hr)
3
5
96
672
出红锈时间(hr) 280
1300
960
>2300
镍 合金
镍铁合金
含铁在 40% 以下,耐蚀性和光亮镍层相当,硬度高于镍镀层,
韧性比光亮镍镀层好,用于代替镀镍,以降低成本。
镍钴合金
含钴 15% 以下的主要用于装饰,如手表零件; 含钴在30% 以上的为磁性镀层。
• 装饰性 铬镀层---镜面光泽的银白色,非常悦目。温度
镀
不超过500℃,能长久保持其光泽外观。
铬层
性
• 防护性 铬是负电性金属,Cr/Cr3+ 的标准电位为 -0.74 V;
但铬具有强烈钝化能力,生成稳定致密的钝化膜。
能 • 耐磨性 铬镀层硬度高,其硬度超过淬火钢。同时铬镀
层摩擦系数低,利于提高工件表面的耐磨性能。
添加剂的作用
• 光亮剂
热浸镀

2)良好的耐磨性能: 3)良好的粘附性能:
2.4热镀锌钢材性能及应用 2.4.2 热镀锌钢材应用:
(1)热镀锌板、带
交通运输业:高速公路护栏、汽车车体、运输机械面板、底 板; 机械制造业:仪表箱、开关箱壳体;各种机器、家用电器、 通风机壳体; 建筑业:各种内外壁材料、屋顶板、百叶窗、排水道等; 器具:各种水桶、烟囱、槽、箱子、柜子等。
它是把退火工艺和热镀锌工艺联合起来, 因此,森吉米尔法产量高、镀锌质量较好,此法曾得到广 泛应用。
2.2 热浸镀锌生产工艺
(2)线内退火 美国钢铁公司法:
冷轧→碱性电解脱脂→水洗→烘干 →还原炉(有保护气体)→退火→冷 却到镀锌温度→镀锌→冷却→矫直
2.2 热浸镀锌生产工艺
优:这种方法因
带钢不经过氧化炉加 热,所以表面的氧化 膜较薄,可适当降低 还原炉中保护气体的 氢含量。这样对炉安 全和降低生产成本有 利
温度: 对于待定工件,在规定的镀锌温度范围内(一般为430— 490℃),锌液温度↑→锌液流动性↑→锌层表面质量↑、镀层 厚度↓
时间: 一定温度下,浸镀时间↑,镀层中间金属相得到快速生长→锌 层厚度↑。
2.3 影响热浸镀锌的因素
(2) 钢结构和成分 碳对镀层结构的影响:
C↑→Fe-Zn 反应越剧烈,铁损越高,Fe-Zn合金层越厚→镀层 性能越坏。
就是热轧或冷轧钢板进入热镀锌作业线之前, 首先在抽底式退火炉或罩式退火炉中进行再结晶退 火,这样在镀锌线内就不存在退火工序了。
溶剂不烘干→湿法热镀锌 溶剂烘干 →干法热镀锌
2.2 热浸镀锌生产工艺
(1)线外退火:
• 湿法热镀锌:该方法已基本被淘汰。 • 干法热镀锌:这种方法生产的热镀锌板比湿法镀锌成品质 量有显著提高,只对小规模生产有一定价值。 • 惠林法热镀锌:这种方法生产工艺复杂,生产成本高,更 为主要的是此方法生产的产品常常带有溶剂缺陷,影响镀 层的耐蚀性。因而此方法虽然已问世近三十年,但在世界 热镀锌行业中并未得到发展。
热浸镀
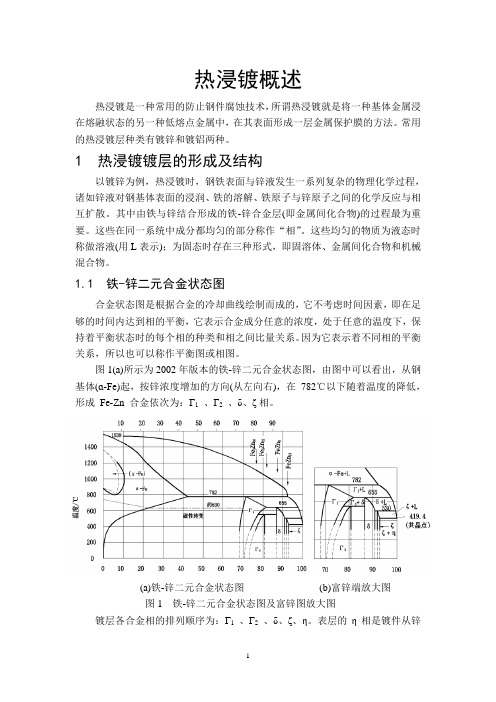
热浸镀概述热浸镀是一种常用的防止钢件腐蚀技术,所谓热浸镀就是将一种基体金属浸在熔融状态的另一种低熔点金属中,在其表面形成一层金属保护膜的方法。
常用的热浸镀层种类有镀锌和镀铝两种。
1 热浸镀镀层的形成及结构以镀锌为例,热浸镀时,钢铁表面与锌液发生一系列复杂的物理化学过程,诸如锌液对钢基体表面的浸润、铁的溶解、铁原子与锌原子之间的化学反应与相互扩散。
其中由铁与锌结合形成的铁-锌合金层(即金属间化合物)的过程最为重要。
这些在同一系统中成分都均匀的部分称作“相”。
这些均匀的物质为液态时称做溶液(用L表示);为固态时存在三种形式,即固溶体、金属间化合物和机械混合物。
1.1 铁-锌二元合金状态图合金状态图是根据合金的冷却曲线绘制而成的,它不考虑时间因素,即在足够的时间内达到相的平衡,它表示合金成分任意的浓度,处于任意的温度下,保持着平衡状态时的每个相的种类和相之间比量关系。
因为它表示着不同相的平衡关系,所以也可以称作平衡图或相图。
图1(a)所示为2002年版本的铁-锌二元合金状态图,由图中可以看出,从钢基体(ɑ-Fe)起,按锌浓度增加的方向(从左向右),在782℃以下随着温度的降低,形成Fe-Zn 合金依次为:Г1、Г2、δ、ζ相。
(a)铁-锌二元合金状态图(b)富锌端放大图图1 铁-锌二元合金状态图及富锌图放大图镀层各合金相的排列顺序为:Г1、Г2、δ、ζ、η。
表层的η相是镀件从锌液中提出时,附着在ζ 相上的纯锌层(含Fe量极微的固溶体)。
传统理论认为(Г1 +Г2)是一个薄层相,当浸镀时间较短时通常不会形成Г相。
δ相呈柱状形态,是垂直于基体或Г相界面,成栅栏状,故又称栅栏层。
ζ相位于δ相与纯锌层η相之间,它呈柱状或针束状,但没有δ相那么致密,在热浸镀锌过程中,随着时间的延长ζ结晶会部分地从合金层上脱落下来,并漂于锌液中,故被称为漂移层;在液态锌中这些ζ晶粒由于密度大于纯锌(液态锌)而沉于锌锅底部,称为底渣,漂浮于锌液中的称为浮渣,统称为锌渣。
热浸镀
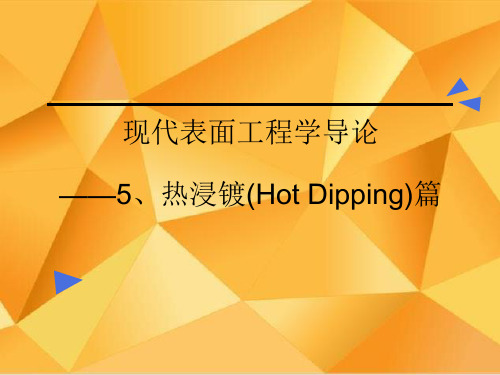
2.2 影响镀层成长的因素
1) 锌液的温度 • 镀层成长速率一般与镀液的 温度成比例。但是在 500℃ 时锌与铁会产生异常快速的 反应。 2) 浸镀时间
• 锌镀层通常是随着锌与铁之
间的扩散机制基材的厚度所影响。太薄的基材上无法析镀出 厚的镀层。因此欲析镀出厚的镀层需考虑基材的厚度。
• 热浸镀的金属层一般较厚,因此能在某些腐蚀环境中长期使 用(镀锌与镀锡等 ),或作为抗特种介质腐蚀的防蚀镀层 (如镀 锡与镀铅—组合金制品等)。
第二节 热浸镀原理 (Principle of Hot dipping)
• 1、热浸镀基本过程(图-2):
• (1)介质中发生化学反应,以提供界面反应所需要的反 应物
• 4.3.3镀铝钢材的用途
• 1、镀铝钢板
heat durability
1.2 热浸镀工艺与制品的发展 • 古罗马时代就有把金属容器浸入
熔融锡中进行热镀的方法
• 13 世纪后半期到 16 世纪中叶用
热镀法在薄铁板上制成镀锡板
• 1742 年由法国化学家把熔融锌
镀在钢铁制品上
• 1837 年英国人 Grawford 取得熔 融法专利
1937年在美国建成第一条带钢连续热镀锌生产线
c 必须保持一定的温度,使原子具有一定的扩散动力
d 生成的活性原子的化学反应必须满足一定的热力学条件
第三节 热浸镀锌 (Hot-dip zincing)
1. 工艺过程(Technical process)
工业上的热浸镀锌可分两种:分
批浸镀制程与连续浸镀工艺过程
1.1 1)
分批浸镀工艺过程
应用 Applition
1.3 热浸镀工艺的分类 1.3.1 热浸镀的工艺 预镀件 前处理 热浸镀 后处理 制品 Work fore-treatment dipping after-treatment product 1.3.2 热浸镀分类 根据前处理不同分: 1)熔剂法 Method of flux 2)保护气体还原法 Method of protective gas reduction
热浸镀原理 工艺及应用
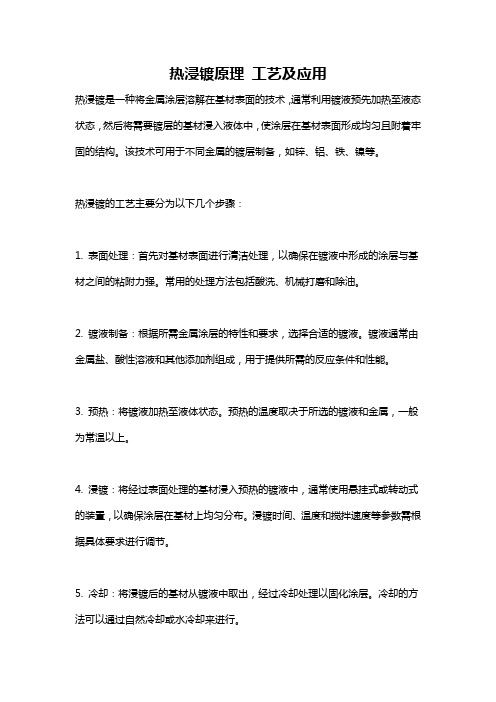
热浸镀原理工艺及应用热浸镀是一种将金属涂层溶解在基材表面的技术,通常利用镀液预先加热至液态状态,然后将需要镀层的基材浸入液体中,使涂层在基材表面形成均匀且附着牢固的结构。
该技术可用于不同金属的镀层制备,如锌、铝、铁、镍等。
热浸镀的工艺主要分为以下几个步骤:1. 表面处理:首先对基材表面进行清洁处理,以确保在镀液中形成的涂层与基材之间的粘附力强。
常用的处理方法包括酸洗、机械打磨和除油。
2. 镀液制备:根据所需金属涂层的特性和要求,选择合适的镀液。
镀液通常由金属盐、酸性溶液和其他添加剂组成,用于提供所需的反应条件和性能。
3. 预热:将镀液加热至液体状态。
预热的温度取决于所选的镀液和金属,一般为常温以上。
4. 浸镀:将经过表面处理的基材浸入预热的镀液中,通常使用悬挂式或转动式的装置,以确保涂层在基材上均匀分布。
浸镀时间、温度和搅拌速度等参数需根据具体要求进行调节。
5. 冷却:将浸镀后的基材从镀液中取出,经过冷却处理以固化涂层。
冷却的方法可以通过自然冷却或水冷却来进行。
热浸镀技术在许多不同领域有着广泛的应用。
以下是几个常见的应用领域:1. 防腐蚀:热浸镀锌是常用的防腐方法之一。
通过在钢铁表面形成一层锌涂层,能够有效防止钢铁与环境氧化物发生反应,从而延长其使用寿命。
2. 电子电器:热浸镀在电子电器领域中也有广泛的应用。
例如,铁氧体材料常常需要通过热浸镀方法来提高其导电性和抗腐蚀性能。
3. 汽车工业:在汽车制造过程中,热浸镀可用于制作防锈、防腐蚀的零部件。
例如,发动机零件、底盘零件和排气管等。
4. 金属制品:热浸镀可以在金属制品上创建美观的表面涂层,提高其外观和耐用性。
例如,热浸锌常用于金属护栏、门窗和金属家具等制作中。
总之,热浸镀是一种常用的金属涂层技术,通过在基材表面形成金属涂层,提供了防腐、美观和耐用等优良性能。
它在防腐、电子电器、汽车工业和金属制品等多个领域都有广泛的应用。
电镀基础知识

一、电镀层的基本要求
目录 要点 上一页 下一页 退出
1、与基本金属结合牢固,附着力好。 2、镀层完整、结晶细致紧密、孔隙率小。 3、具有良好的物理、化学及机械性能。 4、具有符合标准规定的镀层厚度,而且镀 层分布要均匀。
⑧、烘干老化:钝化膜经烘干后才具有好抗蚀性。
⑨、除氢处理:零件在酸洗阴极电解除油及电镀过 程中都可能在镀层和基体金属的晶格中渗氢,造成晶格 扭歪,内应力增大产生脆性(称为氢脆)。除氢通常镀 好4 h内放入烘箱温度为200℃-250℃,时间2-3h。
⑩、目前我司还有黑色钝化和军绿色钝化等新工艺。
目录 返回 上一页 下一页 退出
目录 返回 上一页 下一页 退出
四、浸药
1、开机工作时要将药桶内温度调到25—30℃,粘 度在55-85秒要搅拌均匀,产品浸泡时间在10—20秒, 因在生产中会有少量的砂粒带入桶中,所以,浸药桶内 药液需每周过滤一次,做螺帽时则须多过滤,以防砂粒 沉积在牙纹当中,生产过程中要随时测量药液的温度、 粘度。
钝化膜的封闭:在钝化后经清洗再在含铬酸酐0.20.3 g/l的热水中浸渍(80℃-100℃),可提高盐 雾。
钝化液的老化:钝化液在使用后锌含量不断提高, 当含量达到15 g/l时,就达到容许的极限需冲淡或 重新更换。
目录 要点 上一页 下一页 退出
⑦、硝酸活化:硝酸起化学抛光作用。含量高加速 镀层的溶解,含量低则光亮度差。
目录 返回 上一页 下一页 退出
1、氧化锌 (电流效率); 2、氢氧化钠(络合导电作用); 3、DE.DPE添加剂。
钢管的镀锌和热浸镀锌技术
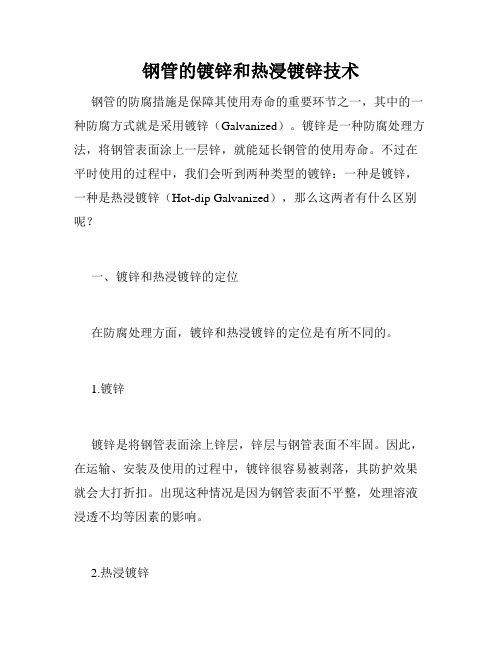
钢管的镀锌和热浸镀锌技术钢管的防腐措施是保障其使用寿命的重要环节之一,其中的一种防腐方式就是采用镀锌(Galvanized)。
镀锌是一种防腐处理方法,将钢管表面涂上一层锌,就能延长钢管的使用寿命。
不过在平时使用的过程中,我们会听到两种类型的镀锌:一种是镀锌,一种是热浸镀锌(Hot-dip Galvanized),那么这两者有什么区别呢?一、镀锌和热浸镀锌的定位在防腐处理方面,镀锌和热浸镀锌的定位是有所不同的。
1.镀锌镀锌是将钢管表面涂上锌层,锌层与钢管表面不牢固。
因此,在运输、安装及使用的过程中,镀锌很容易被剥落,其防护效果就会大打折扣。
出现这种情况是因为钢管表面不平整,处理溶液浸透不均等因素的影响。
2.热浸镀锌热浸镀锌将钢管浸泡于高温的锌溶液中,使钢管表面及内外壁均匀地附上一层厚厚的锌层,不易被剥落。
这与其采用较为复杂的工艺有关。
钢管先进行酸洗,除去表面污染,然后通过氯化铵水溶液或氯化铵粉末与有机溶液混合的脱脂池清洗表面并除去氧化铁,然后进出水洗净,最后放入热镀锌槽中进行反应镀锌,达到防腐的效果。
二、镀锌和热浸镀锌的对比1.防腐性能在对镀锌和热浸镀锌的对比中,最主要的区别在于两者的防腐性能有着明显的差异。
虽然理论上,两种处理方式都是将钢管表面涂上锌,不过由于镀锌的处理方式是将锌溶液喷涂在钢管表面,因此,镀锌的防腐蚀性能相对较差,因其表面不平整、处理在溶液中的时间不一致、锌层的均匀性等原因,很容易剥落,从而在使用过程中出现磨损,降低了其使用寿命。
而热浸镀锌却不同,其由于是将钢管放入锌溶液中热浸镀,涂层厚度均匀,牢度强,具有极高的耐腐蚀性。
通过实际应用情况来看,采用热浸锌处理的钢管传统的使用寿命会长出许多,生命周期增加了。
2.外观质量常规镀锌管透过肉眼能够明显看到与钢管表面不紧密的开裂、气泡、垫片和棉絮等缺陷。
这些缺陷会降低钢管的外观质量,严重影响其美观度和可感度。
热浸镀锌钢管的表面光洁度一般很高,质量更为均匀。
玻璃热浸技术PPT课件
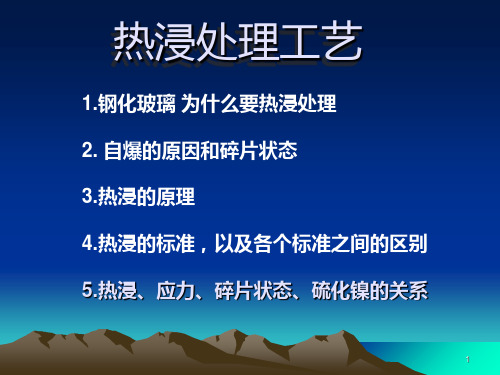
10
采用EN14179-1,需要记 录的测试参数:
T1,第一个玻璃表面测温点 到达280℃时的时间;
Tc1,时间内控温元件的温 度;
Tcmax,到达最高温度点 Tcmax的时间;
T2,最后一个玻璃表面测温 点到达280℃时的时间;
Tc,任意一个控温元件的温 度;
Tglass,任意时刻热电偶测 到的玻璃表面温度;
玻璃摆放间距、所用的分隔 材料、形状;
玻璃摆放形式。
11
EN14179-1 21个热电偶离边距离大于25mm
12
EN14179-1 21个热电偶离边距离大于25mm
13
EN14179-1 21个热电偶离边距离大于25mm,8种摆放方式。 DIN18516/PNAP106/PNAP239均没此项的规定。
8
EN、DIN、PNAP标准均提到了钢化玻璃需要热浸处理,解决玻璃 本体中存在的硫化镍可能造成的自爆。严格按照EN14179-1热浸后, 每1万平方米玻璃,在1年之内再发生1例自爆的概率小于1% 。同 时,不同的标准也涉及不同的恒温时间和热浸成本。 EN14179-1:2005是对钢化玻璃热浸处理进行规范,并明确提出温度控制 范围、恒温时间、不同摆放形式的玻璃表面的测温方法和位置。通过对热 电偶测温点定位,对炉子的热风循环系统要求严格。 DIN18516规定了钢化玻璃热浸处理的各个阶段的温度范围和恒温阶段的 时间长度。 PNAP106规定了热浸过程恒温温度范围以及恒温时间。 PNAP239规定了热浸过程恒温温度范围以及恒温时间。
但是,经过热浸的玻璃也不是就完全根除了自爆。 热浸后的玻璃 自爆,主要的原因是热浸炉内的温差大,温差超过30度,那么就会出 现这样的情况,因为在280下热浸NiS的相变速率是250下热浸的100 倍。
热镀锌专业技能培训(ppt28张)
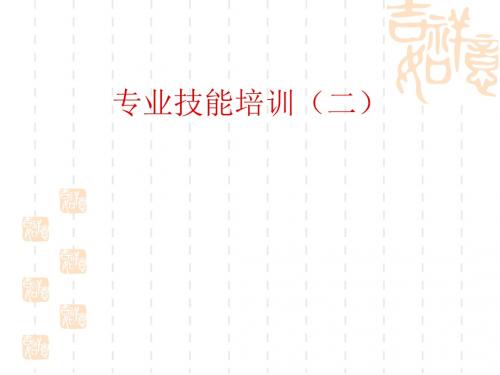
十八、露点发生突然变化的原因
(1)仪表本身失常。 (2)炉子漏气,有漏点的缘故。 (3)生产保护气体的脱水系统失常, 造成保护气体中的水分突然升高。
十九、为何炉内正压还是会因为炉子 漏气而渗入空气
(1)因炉内、炉外存在着极大的氧气浓度 差,这是造成渗入氧气的主要动力。 (2)因漏点往往是不规则的,使保护气体 从炉内渗出时受到很大的阻力,渗出流速 大大减慢,这也是造成氧气渗入炉内的有 利条件。
五、带钢带正电脱脂和带负电脱脂各 有什么特点
带钢带正电脱脂时,表面析出的是氧气, 分子体积大、气泡大、数量少、面积小, 所以除油和乳化作用较弱,脱脂效果较带 负电时差,但较大的气泡能带走带钢表面 的铁粉和粉尘。 带钢带负电脱脂时,表面析出的是氢气, 分子体积小、气泡小、数量多、面积大, 所以除油和乳化作用较强。但会因造成带 钢渗氢,带来氢脆缺陷。
四、电解脱脂段的清洗原理
1. 带钢在经过盛有碱性电解液的电解清洗槽时,两侧的电栅因 通以低电压、高电流的直流电而极化。带钢的两面分别作为 阴极和阳极发生电化学反应,带钢表面析出氢气或氧气的小 气泡。在电极极化和气体的机械撕裂综合作用下,带钢表面 的残留油脂被进一步除去,从而达到了清洗的目的。 2. 电解脱脂的过程中,气体的析出过程实质是电解水的过程 3. 当带钢作阳极时,其表面上进行的是氧化反应,并析出氧 气: 4. 4OH--4e→O2↑+2H2O 5. 当带钢作阴极时,其表面上进行的是还原反应,并析出氢 气: 6. 4H2O+4e→2H2↑+4HO-
六、影响预脱脂和电解脱脂清洗效果 的因素(二)
太过高温的液体会导致刷毛加速老化,致使刷毛断裂,断 毛在循环过程中,返回来堵塞喷淋管口,严重影响到带钢 的表面清洗质量,另外,在机械搅拌下,温度升高,泡沫 增多,造成脱脂液回流不及,从侧面溢出,增加成本消耗。 电解清洗的电解液,温度控制在70℃±5℃,电解液温 度升高,增加电解液电导率及除油效果。但是,过高的温 度,热能消耗大,溶液大量蒸发,还会恶化工作环境。 (3)清洗时间对清洗效果的影响 清洗时间对带钢的清洗质量影响很大。如果机组速度 慢,皂化脱脂、乳化脱脂和电解脱脂的时间增加,对带钢 清洗质量有积极的影响,但如果清洗时间过长,会影响到 机组的产能发挥,增加消耗。
- 1、下载文档前请自行甄别文档内容的完整性,平台不提供额外的编辑、内容补充、找答案等附加服务。
- 2、"仅部分预览"的文档,不可在线预览部分如存在完整性等问题,可反馈申请退款(可完整预览的文档不适用该条件!)。
- 3、如文档侵犯您的权益,请联系客服反馈,我们会尽快为您处理(人工客服工作时间:9:00-18:30)。
洗与溶剂处理等一系列操作步骤,将钢材连续 退火与热浸镀连在同一生产线上,适合连续化 生产,主要用于钢板、钢带的连续热浸镀。
3.2 热浸镀锌
3.2.1 热镀锌层的形成
(1)Fe—Zn二元系状态图及镀锌层相结构
在钢材热镀锌时,锌液与钢材之间发 生一系列的复杂的物理化学过程,在钢 材表面便形成了由铁与锌结合的Fe-Zn合 金层。图3-1为Fe—Zn二元系状态图。
(2) 铁与熔融铝的反应及镀铝层的形成
图3-46
3.3.2 影响热镀铝层的因素[5]
(1) 钢基体化学成分的影响 (a) 碳的影响 (b) 镍的影响 (c) 锰的影响(图3-49) (d) 硅的影响(图3-48) 综上所述,缩小γ相区的元素,均 能增大镀层厚度 ,反之,减小厚度。
(2)铝液化学成分的影响 (a) 硅的影响 (e) 铁的影响 (b) 铜的影响 (f) 锰和镍的影响 (c) 铍的影响 (g) 镁的影响 (d) 锌的影响 (h) 稀土金属的影响
第三章 热浸镀技术[2,5,6]
3.1 概述 3.2 热镀锌 3.3 热镀铝 3.4 热镀锌铝合金
3.1 概述
热浸镀简称热镀,是将被镀金属材 料浸于熔点较低的其它液态金属或合金 中进行镀层的方法。该方法的基本特征 是在基体金属与镀层金属之间有合金形 成,因此,热浸镀层是由合金金属和镀 层金属构成的。被镀金属材料一般为钢、 铸铁及不锈钢等。用于热镀的低熔点金 属有锌、铝、铅、锡及其合金等[5]。
Zn-5%Al-RE合金镀层具有典型的共 晶组织的层状结构。
3.4.2 热镀锌铝合金镀层钢板的性能与用途
(1)55%Al-Zn合金镀层钢板的性能与用途 (2)Zn-5%Al-RE合金镀层钢板的性能与用
途
图3-1 Fe-Zn二元系状态图
图3-2 镀层相结构示意图
热浸镀工艺方法:
热浸镀工艺基本过程分为前处理、热浸镀、 后处理。根据浸镀前的预处理方法不同,其工 艺可分为溶剂法和保护气体还原法两大类。
(1)溶剂法
溶剂法是最常用的热浸镀方法。在热浸镀 之前,在清洁的金属表面涂一层助镀剂,防止 钢铁腐蚀。浸入镀液后,助镀层能迅速分解, 并起到清除基体金属表面的氧化物、降低熔融 金属表面张力的作用,提高镀层质量。溶剂法 主要用于钢管、钢丝和零件的热浸镀。
当热镀纯锌时,从钢基体起,按锌 浓度增大方向,形成的Fe—Zn合金相依 次为Γ、δ1、ζ、η 四个相,如图3-2所示[5]。
(2) 镀锌层的形成过程[6,5]
热镀锌层的形成过程大致可分成以下三 个步骤:
(a) 铁基表面被锌液溶解形成铁锌合金相层。 (b) 合金层中的锌原子进一步向基体扩散,
形成锌铁互溶层。 (c) 合金表面包络着一薄层锌。
3.2.3 镀锌钢板的用途
3.3 热浸镀铝
钢材的热镀铝一般指热镀纯铝和热镀铝 硅两种镀层[5]。
3.3.1 热镀铝层的形成 (1) 铁铝和铁铝硅状态图及镀层的结构
当固态铁与熔融铝接触时,在铁表 面发生铁、铝原子的相互扩散,并在两 种金属中形成扩散层。
由图3-43可知,在一般热镀铝温度 710~730℃内,有可能存在三个金属间化 合物,即:FeAl2(ζ相)、Fe2Al5(η相) 和 FeAl3 (θ相)。
(b) 硅的影响:钢中的硅对热镀锌层的影响最 为突出。
ⅰ) 硅对铁在锌液中的溶解速度的影响 图3-8、图3-9
ⅱ) 硅对镀锌层厚度的影响 图3-10、图3-11
ⅲ) 硅对镀层结构的影响[5](见P182) 0.04%; 0.05-0.12%; 0.13-0.25%; 0.26-0.45%
(3) 锌液成分的影响[5、6] 铝、铅、铁、镉、锡、铜 图3-12、图3-13
结构是由α-Al和ß-Zn构成的双相结构。
(2)镀层成分及第三组分 耐蚀性 漏铁点
(图3-69) (图3-70)
(3) 镀层显微结构
55%Al-Zn镀层具有成核的枝晶状显 微结构。它由80%(体积)的富铝枝晶 臂和约20%(体积)的富锌枝晶间物质 构成。此镀层的耐蚀性比厚度相同的普 通热镀锌层有很大提高。
(3)热镀铝工艺参数的影响 (a) 镀铝温度和时间的影响 (b) 提升速度和铝液黏度的影响Biblioteka 3.3.3 镀铝钢材的应用
3.4 热镀锌铝合金[5]
近年来,已经商品化并投入大量生产的两 种Zn-Al合金镀层钢板是55%Al-Zn镀层钢板和Zn5%Al-RE镀层钢板。
3.4.1 Zn-Al 合金镀层成分及镀层结构 (1) Zn-Al二元系状态图(图3-68) 由此状态图看出,Zn-Al合金在室温下的平衡
(2)保护气体还原法
典型的生产工艺是森吉米耳(Sendzimir)法。 它是将待镀的钢材先通过煤气或天然气直接加 热的微氧化炉,将钢材表面残余的油污、乳化 液等烧掉,同时钢材表面被氧化,生成蓝色的 氧化薄膜。然后进入通有保护气的还原炉,把 钢材表面的氧化皮还原为适合热浸镀的活性海 绵状铁,并使钢材继续加热,完成再结晶退火 的目的。接着在保护气氛中,钢材被冷却到适 当温度后,进入镀锅。
3.2.2 热镀锌层厚度、相结构 和性能的影响因素[5,6]
(1)锌液温度和浸镀时间的影响[5]
(图3-3、图3-4、图3-5、图3-6)
(2)钢基体化学成分的影响[5]
在钢的五大元素中,以碳和硅的影响最为 突出,锰、磷、硫的影响最小。 (a) 碳的影响: 一般地说,钢中碳含量愈高,
Fe-Zn反应愈强烈,铁损愈大, 合金层也厚。其中的ζ、δ1 相的生长更快,使镀层变脆, 塑性下降。