换热器各种管束支撑的结构与传热性能
(完整)管壳式换热器强化传热技术概述

管壳式换热器强化传热技术概述马越中国矿业大学化工学院,江苏徐州,221116摘要:总结了近年来国内外新型管壳式换热器的研究进展,从管程、壳程、管束三方面介绍了管壳式换热器的发展历程、结构改进及强化传热机理,并与普通弓形折流板换热器进行对比,概括了各式换热器的强化传热特点。
最后指出了换热器的研究方向。
关键词:管壳式换热器;强化传热;研究方向Overview of the Shell and Tube Heat Exchangers about Heat TransferEnhancement TechnologyMA YueCUMT,Xuzhou,jiangsu,221116Abstract:Abstract : The research progress of shell and tube heat exchanger were summarized. The development structural improvement and heat transfer enhancement of the heat exchangers were introduced through three aspects e. g. tube pass shell pass and the whole tub bundle etc. Compared with the traditional segmental bame heat exchanger various types of heat exchangers'characteristics about heat transfer enhancement were epitomized。
At last,the studying directions of heat exchangers were pointed out.Key words:shell and tube heat exchanger;heat transfer enhancement;studying direction1引言《“十二五”节能减排综合性工作方案》明确提出,到2015年,全国万元国内生产总值能耗下降到0。
几种换热管强化传热性能实验分析与比较
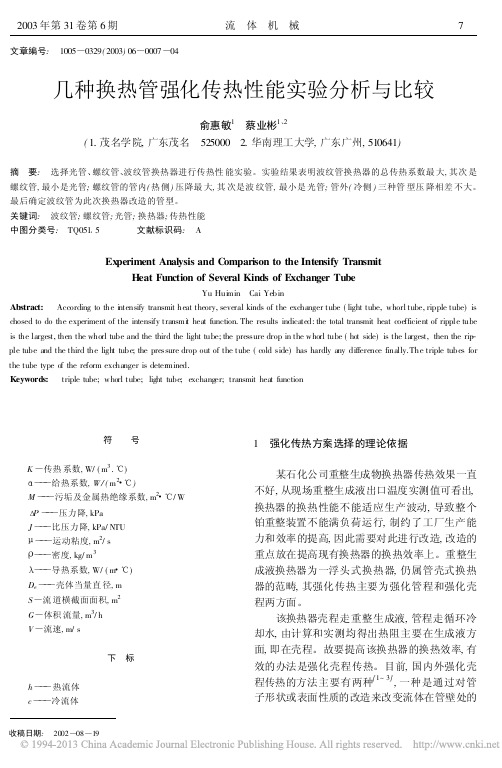
文章编号:1005)0329(2003)06)0007)04几种换热管强化传热性能实验分析与比较俞惠敏1蔡业彬1、2(1.茂名学院,广东茂名5250002.华南理工大学,广东广州,510641)摘要:选择光管、螺纹管、波纹管换热器进行传热性能实验。
实验结果表明波纹管换热器的总传热系数最大,其次是螺纹管,最小是光管;螺纹管的管内(热侧)压降最大,其次是波纹管,最小是光管;管外(冷侧)三种管型压降相差不大。
最后确定波纹管为此次换热器改造的管型。
关键词:波纹管;螺纹管;光管;换热器;传热性能中图分类号:TQ05115文献标识码:AExperiment Analysis and C omparison to the Intensify TransmitHeat Function of Several Kinds of Exchanger TubeYu Hui min Cai YebinAbstract:According to the i ntensify transmit heat theory,several kinds of the exchanger tube(light tube,whorl tube,ripple tube)is chosed to do the experiment of the intensify transmi t heat function.The results indicated:the total transmit heat coefficient of ripple tube is the largest,then the whorl tube and the third the light tube;the pressure drop in the whorl tube(hot side)is the largest,then the rip-ple tube and the third the ligh t tube;the pressure drop out of the tube(cold side)has hardly any difference finally.The triple tubes for the tube type of the reform exchanger is determined.Keywords:triple tube;whorl tube;light tube;exchanger;transmit heat function符号K)传热系数,W/(m3.e)A)))给热系数,W/(m2#e)M)))污垢及金属热绝缘系数,m2#e/W $P)))压力降,kPaJ)))比压力降,kPa/NTUL)))运动粘度,m2/sQ)))密度,kg/m3K)))导热系数,W/(m#e)D e)))壳体当量直径,mS)流道横截面面积,m2G)体积流量,m3/hV)流速,m/s下标h)))热流体c)))冷流体1强化传热方案选择的理论依据某石化公司重整生成物换热器传热效果一直不好,从现场重整生成液出口温度实测值可看出,换热器的换热性能不能适应生产波动,导致整个铂重整装置不能满负荷运行,制约了工厂生产能力和效率的提高,因此需要对此进行改造,改造的重点放在提高现有换热器的换热效率上。
十三种类型换热器结构原理及特点(图文并茂)

十三种类型换热器结构原理及特点(图文并茂)一、板式换热器的构造原理、特点:板式换热器由高效传热波纹板片及框架组成。
板片由螺栓夹紧在固定压紧板及活动压紧板之间,在换热器内部就构成了许多流道,板与板之间用橡胶密封。
压紧板上有本设备与外部连接的接管。
板片用优质耐腐蚀金属薄板压制而成,四角冲有供介质进出的角孔,上下有挂孔。
人字形波纹能增加对流体的扰动,使流体在低速下能达到湍流状态,获得高的传热效果。
并采用特殊结构,保证两种流体介质不会串漏。
板式换热器结构图二、螺旋板式换热器的构造原理、特点:螺旋板式换热器是一种高效换热器设备,适用汽-汽、汽-液、液-液,对液传热。
它适用于化学、石油、溶剂、医药、食品、轻工、纺织、冶金、轧钢、焦化等行业。
结构形式可分为不可拆式(Ⅰ型)螺旋板式及可拆式(Ⅱ型、Ⅲ型)螺旋板式换热器。
螺旋板式换热器结构图三、列管式换热器的构造原理、特点:列管式换热器(又名列管式冷凝器),按材质分为碳钢列管式换热器,不锈钢列管式换热器和碳钢与不锈钢混合列管式换热器三种,按形式分为固定管板式、浮头式、U型管式换热器,按结构分为单管程、双管程和多管程,传热面积1~500m2,可根据用户需要定制。
列管式换热器结构图四、管壳式换热器的构造原理、特点:管壳式换热器是进行热交换操作的通用工艺设备。
广泛应用于化工、石油、石油化工、电力、轻工、冶金、原子能、造船、航空、供热等工业部门中。
特别是在石油炼制和化学加工装置中,占有极其重要的地位。
换热器的型式。
管壳式换热器结构图五、容积式换热器的构造原理、特点:钢衬铜热交换器比不锈钢热交换器经济,并且技术上有保证。
它利用了钢的强度和铜的耐腐蚀性,即保证热交换器能承受一定工作压力,又使热交换器出水质量好。
钢壳内衬铜的厚度一般为1.0mm。
钢衬铜热交换器必须防止在罐内形成部分真空,因此产品出厂时均设有防真空阀。
此阀除非定期检修是绝对不能取消的。
部分真空的形成原因可能是排出不当,低水位时从热交换器,或者排水系统不良。
管壳式换热器结构介绍

3、管壳程流体的确定
主要根据流体的操作压力和温度、可以利用的压力降、结构和腐蚀 特性,以及所需设备材料的选择等方面,考虑流体适宜走哪一程。下面 的因素可供选择时考虑:
适于走管程的流体有水和水蒸气或强腐蚀性流体;有毒性流体;容易 结构的流体;高温或高压操作的流体等。
1、管壳式换热器结构介绍
管壳式换热器:是以封闭在壳体中管束的壁面作为传热面的间 壁式换热器,这种换热器结构较简单、操作可靠,可用各种结构材 料(主要是金属材料)制造,能在高温、高压下使用,是目前应用 最广的类型。(设计制造遵循标准:国外 TEMA ASME 国内 GB151、GB150)
换热器封头选取原则
换热器折流板
单弓形折流板:优点是可以达到最大的错流,缺点是压降较高,且窗口 的管束容易发生振动;设计要点是折流板圆缺率在17%-35%之间,折流 板间距在0.2-1.0倍的壳径。此种类型折流板适用于大部分场合。
NITW:该折流板窗口不布管,管少,需要的壳体直径大。设计要点:15%的 折流板圆缺率。适合的场合是气体振动和压降受限。
谢谢!
K型壳体:主要用于管程热介质,壳侧蒸发的工况,在废热回收条件下使 用。
X型壳体:冷热流体属于错流流动,其优点是压降非常小,当采用其他壳 体发生振动,且通过调整换热器参数无法消除该振动时可以使用此壳体 形式,其不足之处是流体分布不均匀,X型壳体并不经常使用。
在化工工艺手册中,I型壳体类型可EDR软件中的不是同一种壳体, 其形式见I1,它的使用方式仅有一种搭配,就是BIU,U型管换热器。
螺纹管性能特点
在管子类型中,螺纹管属于管外扩展表面的类型,在普通换热管外 壁轧制成螺纹状的低翅片,用以增加外侧的传热面积。螺纹管表面积比 光管可扩展1.6-2.7倍,与光管相比,当管外流速一样时,壳程传热热阻 可以缩小相应的倍数,而管内流体因管径的减小,则压力降会略有增大。 螺纹管比较适宜于壳程传热系数相当于管程传热系数1/3-3/5的工况。
管束排列及管间距对换热器传热性能的影响分析

1 换热器传热性能数值模拟方法1.1 换热器传热性能数值模拟实验装置在化工设备领域,圆形翅片管换热器各个参数对换热器传热性能的影响,是研究者长期以来关注的重要内容[1]。
根据圆形翅片管换热器参数问题的研究现状,一些前沿化的研究成果多集中于翅片间距、翅片厚度、翅片半径、翅片数目和换热条件等多方面内容。
在笔者看来,根据换热器翅片管的结构,雷诺数、纵向管间距及管束排列方式等内容对换热器性能的影响,也是换热器传热性能研究过程中所不可忽视的内容。
在分析上述因素对换热器传热性能的银杏是,人们可以借助碳钢板材质的内插翅片管矩形通风管道,调整换热器的管束排列与管间距。
根据一些试验人员在在相关实验中所采取的经验,矩形通风管道的管道长度可以控制为2000mm、宽度可以控制为350mm ;高度可以控制为360mm,管道之中可以安插9排差翅片管;翅片管的直径为16mm 或32mm ;厚度为1mm,翅片之间的间距可以控制为6mm。
1.2 物理模型与计算方法转换器传热性能数值的物理模型建立在碳钢板材质的矩形通风管道的基础之上。
与之相关的简化模型应用有三维双精度解法器。
在边界条件设定过程中,研究人员可以将物理模型管壁看作是常温壁,管壁厚度对换热器导热的影响和翅片与管壁之间的接触热阻可以忽略不计。
在物理模型建构完成以后,流动过程与传热过程的支配因素主要涉及到了以下内容:一是连续性方程;二是动量方程;三是能量方程。
前文所述的实验设备的速度入口与压力出口可以被看作是模型的进出口,为避免试验模型出口处出现的回流现象,研究人员可以对出口处的计算区域进行延长处理。
在换热器近壁面区域温度变化较为激烈的情况下,研究者需要对近壁面区域进行网格加密处理,与之相关的湍流模型为RMG k-ε模型。
速度和压力耦合的计算方法为SIMPLE 算法,压力离散为Standard。
为保证实验过程的精确性,动量、湍动能和动量离散等内容需要采用二阶迎风格式,能量残差需要控制在10-9以下;其余物理量的残差需要控制在10-6以下。
换热器管束级别
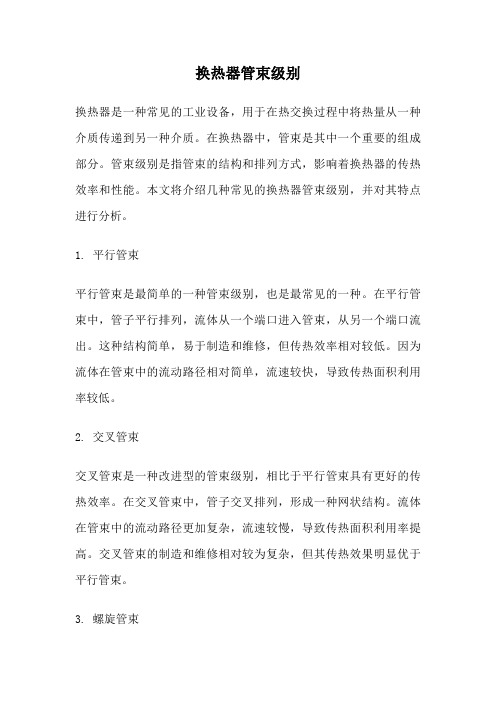
换热器管束级别换热器是一种常见的工业设备,用于在热交换过程中将热量从一种介质传递到另一种介质。
在换热器中,管束是其中一个重要的组成部分。
管束级别是指管束的结构和排列方式,影响着换热器的传热效率和性能。
本文将介绍几种常见的换热器管束级别,并对其特点进行分析。
1. 平行管束平行管束是最简单的一种管束级别,也是最常见的一种。
在平行管束中,管子平行排列,流体从一个端口进入管束,从另一个端口流出。
这种结构简单,易于制造和维修,但传热效率相对较低。
因为流体在管束中的流动路径相对简单,流速较快,导致传热面积利用率较低。
2. 交叉管束交叉管束是一种改进型的管束级别,相比于平行管束具有更好的传热效率。
在交叉管束中,管子交叉排列,形成一种网状结构。
流体在管束中的流动路径更加复杂,流速较慢,导致传热面积利用率提高。
交叉管束的制造和维修相对较为复杂,但其传热效果明显优于平行管束。
3. 螺旋管束螺旋管束是一种较为特殊的管束级别,适用于一些对流体流动有特殊要求的情况。
在螺旋管束中,管子呈螺旋状排列,形成一种螺旋流动路径。
这种结构可以增加流体与管壁之间的摩擦,提高传热效率。
螺旋管束的制造和维修相对较为复杂,但在某些特定的工艺条件下,其传热效果明显优于其他管束级别。
4. 管板管束管板管束是一种常用的管束级别,适用于一些对流体流动有特殊要求的情况。
在管板管束中,管子与管板相连,形成一种管板与管束交替的结构。
这种结构可以增加流体与管壁之间的接触面积,提高传热效率。
管板管束的制造和维修相对较为复杂,但在某些特定的工艺条件下,其传热效果明显优于其他管束级别。
5. 多级管束多级管束是一种将多个管束级别组合在一起的换热器结构。
通过多级管束的设计,可以进一步提高换热器的传热效率和性能。
多级管束的制造和维修相对较为复杂,但其传热效果明显优于单一管束级别。
换热器管束级别是影响换热器传热效率和性能的重要因素。
不同的管束级别具有不同的特点和适用范围,工程师在设计换热器时应根据具体工艺条件选择适合的管束级别。
螺旋折流板换热器传热和流动性能分析

94在化工装置中管壳式换热器型式众多,当壳侧流体流量大且压降限制严格时,通常会采用双弓形折流板形式。
但是双弓形折流板在支撑结构和流动方式上存在诸多缺陷:壳侧流动存在冲刷不充分的流动死区、死区内局部换热系数低,壳侧整体换热不均匀,同时死区容易结垢,威胁换热设备的安全运行[1]。
为了提高壳侧单位压降下传热和避免壳侧由于沉积污垢造成的腐蚀泄漏,工业应用中越来越多的采用螺旋折流板代替壳侧弓形折流板,使壳侧在螺旋折流板引导下形成复杂的螺旋流形态,提高管束间的流速、实现壳体横向截面流体充分混合同时壳侧压降不增加,从而达到强化传热的目的[2]。
工程应用中最多采用的为四片式螺旋折流板结构,见图1,螺旋折流板一个螺旋节距的长度上是由四片式扇形板片按一定的安装倾角上、下、左、右交错排列而成,再用定距管将其定位,使其形成螺旋状[3]。
但是四片式螺旋折流板结构为非连续螺旋折流,中间相邻板片间会出现三角形的漏流区,严重削弱了传热能力[4]。
针对四片式螺旋折流板三角区短路漏流的缺点,中国石化工程建设公司联合抚顺化工机械设备制造有限公司和辽宁石油大学提出了一种新型的六片式螺旋折流板换热器型式,并获得专利授权[5]。
图1 四片式螺旋折流板 图2 六片式螺旋折流板1 模型设置1.1 几何模型三维数值模拟用SolidWorks分别建立尺寸180x1200mm下六片式螺旋折流板、四片式螺旋折流板和双弓折流板结构,设备型式BEM,水平安装,10mm换热管,正方形布管,换热管间距13mm,布108根换热管,换热器所有材质均采用碳钢。
双弓折流板结构采用16块折流板,间距60mm。
六片式螺旋折流板和四片式螺旋折流板都采用10度螺旋角,搭接度42%[6]。
由于管束元件较多,内部结构复杂,本文对换热器的结构进行适当简化如下:(1)认为换热管与折流板、筒体与折流板和管束与壳体都为紧密切合,忽略流体通过缝隙渗螺旋折流板换热器传热和流动性能分析宁静 中国石化工程建设有限公司 北京 100101 摘要:利用CFD分析软件FLUENT,研究10度螺旋角条件下,六片式螺旋折流板换热器和常见四片式螺旋折流板换热器传热和流动特性,并与双弓形折流板换热器进行对比。
常见一般换热器结构、优缺点及适用范围

一般常见换热器结构、优缺点及适用范围浮头换热器结构:两端管板中只有一端与壳体固定,另一端可相对壳体自由移动,称为浮头。
浮头由浮头管板,钩圈和浮头盖组成,是可拆连接,管束可从壳体中抽出。
管束与壳体的热变形互不约束,不会产生热应力。
优点:可抽式管束,当换热管为正方形或转角正方形排列时,管束可抽出进行机械清洗,适用于易结垢及堵塞的工况。
一端可自由浮动,无需考虑温差应力,可用于大温差场合。
缺点:结构复杂,造价高,设备笨重,材料消耗大。
浮头端结构复杂影响排管数。
浮头密封面在操作时,易产生内漏。
适用范围:适用于壳体和管束之间壁温差较大或壳程介质易结垢的场合。
浮头换热器在炼油行业或乙烯行业中应用较多,由于内浮头结构限制了使用压力和温度一般情况Pmax≤6.4MPa,Tmax≤400℃。
固定管板换热器结构:管束连接在管板上,管板与壳体相焊。
优点:结构简单紧促,能承受较高压力,造价低,管程清洗方便,管子损坏时方便堵管或更换。
排管数比U 形管换热器多。
缺点:管束与壳体的壁温或材料的线胀系数相差较大时,壳体和管束中将产生较大热应力,为此应需要设置柔性元件(如膨胀节)。
不能抽芯无法进行机械清洗。
不能更换管束,维修成本较高。
适用范围:壳程侧介质清洁不易结垢,不能进行清洗,管程与壳程两侧温差不大或温差较大但壳侧压力不高的场合。
管壳式换热器的管子是换热器的基本构件,它为在管内流过一种流体和穿越管外的另一种流体之间提供传热面。
根据两侧流体的性质决定管子材料,将具有腐蚀性,水质差的海水放在管内流动,水质较好的除盐水放在管子外壳侧,这样管子只需采用耐海水腐蚀的钛管,同时清洗污垢较为方便,管径从传热流体力学角度考虑,在给定壳体内使用小直径管子,可以得到更大的表面密度但大多数流体会在管子表面上沉积污垢层,尤其管内冷却水水质较差,泥沙和污物及海生物的存在,都可能会在管壁上形成沉积物,将传热恶化并使定期的清洗工作成为必要,管子清洗限制管径最小约为20 mm,钛管一般采Φ25 mm,对给定的流体,污垢形成主要受管壁温度和流速的影响,为得到合理的维修周期,管内侧水的流速应在2 m/s左右(视允许压降的要求)。
换热器的操作及传热系数的测定实验报告

换热器的操作及传热系数的测定实验报告换热器是一种用于传递热量的设备,常用于工业生产中的加热、冷却和废热利用等方面。
换热器的基本结构包括热交换管路、壳体、传热管束、挂板、密封装置、支撑装置、进出口法兰等部分。
换热器的工作原理是通过将两种流体分别在管束和壳体中流动,使它们在壳体内接触并交换热量,从而达到加热或冷却的目的。
其中一种流体在管束内流动,称为管束流体;另一种流体在壳体内流动,称为壳体流体。
管束流体和壳体流体之间的热量传递是通过管壁进行的。
2.换热器传热系数的测量方法和计算公式换热器传热系数是评价换热器传热性能的重要指标,它是指单位面积换热器传递的热量与传热面积和传热温差的比值。
传热系数的测量方法主要有实测法、计算法和综合法,其中实测法是最常用的一种方法。
实测法的基本思路是通过实验来测定换热器的传热系数。
具体测量步骤如下:(1)将待测流体进入传热侧管束,另一侧进入冷却水,调节流量和温度,使达到稳定状态;(2)测量进出口流量和温度,根据能量守恒原理计算出管束流体的热量传递量;(3)根据壳侧冷却水的温升和流量,计算出壳侧的热量传递量;(4)根据了解的流体物理性质和实验数据,计算出传热系数。
传热系数的计算公式如下:α = Q/(SΔT)其中,α为传热系数,单位为W/(m2·K);Q为单位时间内传递的热量,单位为W;S为传热面积,单位为m2;ΔT为传热温差,单位为K。
三、实验设备和材料1.换热器2.温度计3.流量计4.水泵5.电源6.水槽7.热交换介质8.计算机四、实验步骤1.准备工作(1)检查实验设备是否完好无损,如有损坏应及时修理;(2)检查实验室环境是否符合实验要求;(3)将实验设备接通电源并进行预热。
2.操作换热器(1)将加热介质进入传热侧管束,另一侧进入冷却水;(2)打开水泵,调节流量和温度,使达到稳定状态;(3)测量进出口流量和温度。
3.传热系数的测量和计算(1)根据实验数据计算出传热系数。
换热器的结构与性能特点
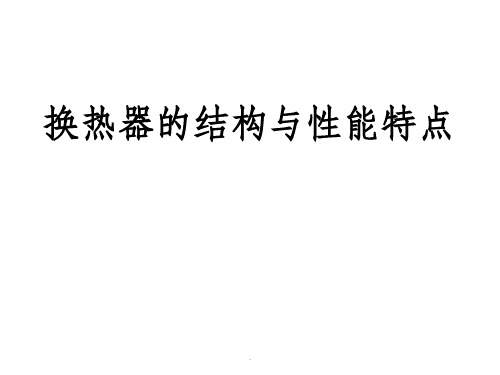
(1)沉浸式蛇管换热器
多以金属管弯绕而成,制成适应容器的形状,沉浸在容器内的液体中。两种 流体分别在管内、管外进行换热。
.
蛇管的形状主要取决于容器的形 状和生产队要求。如化工生产中 的反应器内的加热或冷却管,多 做成圆盘形或螺旋形的;氨冷的 冷冻盐水槽中的换热管,则多用 长的蛇形管构成。实际上,蛇管 可以制成任意需要的形状。如图 所示。 蛇管可以由钢管,铜管,银管或 其它有色金属和非金属材料如玻 璃,陶瓷,石墨和塑料等制成。
.
一、夹套式换热器
夹套式换热器是最简单的板式换热器, 它是在容器外壁安装夹套制成,夹套 与容器之间形成的空间为加热介质或 冷却介质的通路。这种换热器主要用 于反应过程的加热或冷却。在用蒸汽 进行加热时,蒸汽由上部接管进入夹 套,冷凝水由下部接管流出。作为冷 却器时,冷却介质(如冷却水)由夹 套下部接管进入,由上部接管流出。 特点:
几种常用的蛇管形状
沉浸式蛇管换热器的优点:结构简单、价格低廉、便于防腐蚀、能承受高压。 缺点:由于容器的体积较蛇管的体积大得多,管外流体的传热膜系数较小, 故常需加搅拌装置,以提高其传热效率. 。 多应用于小型容器内的液体换热。
(2)喷淋式蛇管换热器
喷淋式换热器也为蛇管式换热器,多用作冷却 器。这种换热器是将蛇管成行地固定在钢架上, 热流体在管内流动,自最下管进入,由最上管 流出。冷水由最上面的淋水管流下,均匀地分 布在蛇管上,并沿其两侧逐排流经下面的管子 表面,最后流入水槽而排出,冷水在各排管表 面上流过时,与管内流体进行热交换。这种换 热器的管外形成一层湍动程度较高的液膜,因 而管外对流传热系数较大。另外,喷淋式换热 器常放置在室外空气流通处,冷却水在空气中 汽化时也带走一部分热量,提高了冷却效果。
多股流绕管式换热器的管束排布及传热计算

2019年第38卷增刊1 CHEMICAL INDUSTRY AND ENGINEERING PROGRESS收稿日期:2019–05–13;修改稿日期:2019–05–20。
第一作者:欧阳新萍(1964—),男,硕士,教授,研究方向为换热器及强化传热。
E-mail :xpoy@ 。
通信作者:秦洁,硕士研究生,研究方向为换热器及强化传热。
E-mail :qinjie1996@ 。
引用本文:欧阳新萍, 秦洁, 薛林锋. 多股流绕管式换热器的管束排布及传热计算[J]. 化工进展, 2019, 38(s1): 39–45.Citation: OUYANG Xinping, QIN Jie, XUE Linfeng. Tube bundle arrangements and heat transfer calculations of multi-stream spiral-wound heat exchanger[J]. Chemical Industry and Engineering Progress, 2019, 38(s1): 39–45.·39·化 工 进展DOI :10.16085/j.issn.1000–6613.2019–0774多股流绕管式换热器的管束排布及传热计算欧阳新萍1,秦洁1,薛林锋2,白桦1,夏荣鑫1,赵加普1,李思思1(1上海理工大学制冷与低温工程研究所,上海 200093;2江阴金童石化装备有限公司,江苏 无锡214400) 摘要:多股流绕管式换热器的结构复杂,传热计算的难度较大。
常见的计算方法是根据一些假定条件建立计算模型、进行数值求解,这种计算方法较复杂,不适合工程计算。
而一些能用于工程计算的简便解析计算方法则存在迭代计算复杂、应用范围受限的缺点。
本文列举了几种典型的多股流绕管式换热器的管束排列结构,分析了各自的结构特点;给出了多股流换热器的管板结构及相应的流体进出口接管方式,分析了各自的优缺点及应用场合。
各种换热器的原理特点及适用范围介绍

各种换热器的原理特点及适用范围介绍一、T 型翅片管一、原理及特点1、原理T型翅片管是由光管经过滚轧加工成型的一种高效换热管。
其结构特点是在管外表面形成一系列螺旋环状T型隧道。
管外介质受热时在隧道中形成一系列的气泡核,由于在隧道腔内处于四周受热状态,气泡核迅速膨大充满内腔,持续受热使气泡内压力快速增大,促使气泡从管表面细缝中急速喷出。
气泡喷出时带有较大的冲刷力量,并产生一定的局部负压,使周围较低温度液体涌入T型隧道,形成持续不断的沸腾。
这种沸腾方式在单位时间内,单位表面积上带走的热量远远大于光管,因而这种管型具有较高的沸腾传热能力。
2、特点⑴传热效果好。
在R113工质中T管的沸腾给热系数比光管高1.6-3.3倍。
⑵常规的光管换热器,只有当热介质的温度高于冷介质的沸点或泡点12℃-15℃时,冷介质才会起泡沸腾。
而T型翅片管换热器只需2℃-4℃的温差,冷介质就可沸腾,且鼓泡细密、连续、快速,形成了与光管相比的独特优势。
⑶以氟利昂11为介质的单管实验表明,T型管沸腾给热系数可达光管的10倍;以液氨为介质的小管束实验结果,总传热系数为光管的2.2倍;C3、C4烃类分离塔的再沸器工业标定表明,低负荷时,T 型管总传热系数比光滑管高50%,大负荷时高99%。
⑷较铝多孔表面传热管的价格便宜。
⑸由于隧道内部的气液扰动非常激烈以及气体沿T缝高速喷出,因而无论是T型槽内部还是管外表面,都不易结垢,这一点保证了设备能长期使用而传热效果不会受到结垢的影响。
二、应用场合只要壳侧介质比较干净、无固体颗粒、无胶质,均可采用T型翅片管作换热元件,形成T型翅片管式高效换热器,以提高壳侧沸腾传热效果。
二、低螺纹翅片管一、原理及特点1、原理低螺纹翅片管是普通换热管经轧制在其外表面形成螺纹翅片的一种高效换热管型,其结构如图所示:这种管型的强化作用是在管外。
对介质的强化作用一方面体现在螺纹翅片增加了换热面积;另一方面是由于壳程介质流经螺纹管表面时,表面螺纹翅片对层流边层产生分割作用,减薄了边界层的厚度。
板翅式换热器的结构与传热机理简述

板翅式换热器的结构与传热机理简述板翅式换热器(Plate fin heat exchanger)是一种高效的换热设备,常用于工业生产过程中的热交换。
它的特点是具有大的换热面积、紧凑的结构和高效的传热性能。
本文将简述板翅式换热器的结构和传热机理。
1.结构板翅式换热器包括主要的三个部分:热交换芯片、翅片和壳体。
热交换芯片是由多层薄板叠压而成,通过焊接或胶合等方法固定。
在热交换芯片的表面上,通过铝合金或不锈钢等材料制作的翅片固定,增加了换热的表面积。
壳体用于包容热交换芯片和翅片,同时起到支撑和固定的作用。
换热介质通过壳体的进出口与热交换芯片进行传热。
2.传热机理对流换热是指当热介质在板翅式换热器内部流动时,通过对流传热,将热量从一个介质传递到另一个介质。
对流传热是由流体在换热器内的速度和温度差驱动的。
通过铝合金或不锈钢制成的翅片可以增加传热的表面积,增加了对流传热的效果。
传导换热是指热量通过固体传导而进行的传热过程。
在板翅式换热器中,热介质通过热交换芯片流动,热交换芯片由多层薄板堆叠而成,薄板之间通过焊接或胶合固定。
通过热交换芯片的传导,将热量从一个介质传递到另一个介质。
辐射换热是指热量通过辐射传递而进行的传热过程。
板翅式换热器中的翅片由金属材料制成,金属具有良好的导热性能,通过翅片的辐射作用,将热量从一个介质辐射到另一个介质。
总结:板翅式换热器具有大的换热面积、紧凑的结构和高效的传热性能,适用于需要高效换热的工业生产过程。
其结构主要包括热交换芯片、翅片和壳体,通过对流、传导和辐射的综合作用,实现高效的传热。
在实际应用中,可以根据具体的换热需求选择不同的材料和结构,以实现更好的换热效果。
石墨换热器结构
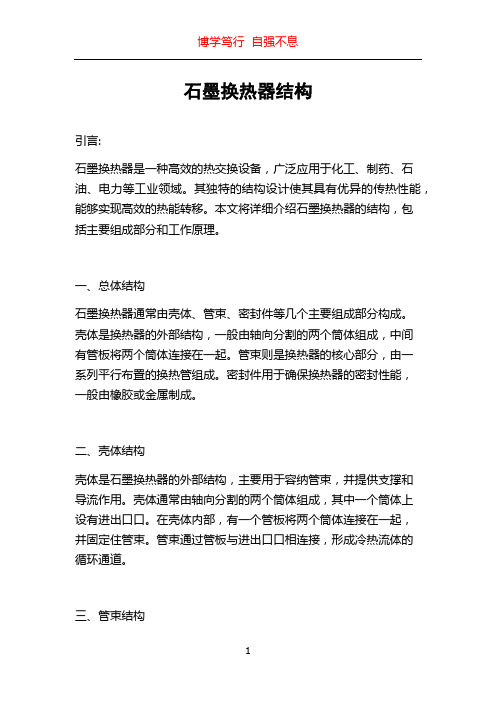
石墨换热器结构引言:石墨换热器是一种高效的热交换设备,广泛应用于化工、制药、石油、电力等工业领域。
其独特的结构设计使其具有优异的传热性能,能够实现高效的热能转移。
本文将详细介绍石墨换热器的结构,包括主要组成部分和工作原理。
一、总体结构石墨换热器通常由壳体、管束、密封件等几个主要组成部分构成。
壳体是换热器的外部结构,一般由轴向分割的两个筒体组成,中间有管板将两个筒体连接在一起。
管束则是换热器的核心部分,由一系列平行布置的换热管组成。
密封件用于确保换热器的密封性能,一般由橡胶或金属制成。
二、壳体结构壳体是石墨换热器的外部结构,主要用于容纳管束,并提供支撑和导流作用。
壳体通常由轴向分割的两个筒体组成,其中一个筒体上设有进出口口。
在壳体内部,有一个管板将两个筒体连接在一起,并固定住管束。
管束通过管板与进出口口相连接,形成冷热流体的循环通道。
三、管束结构管束是石墨换热器的核心部分,是实现热能转移的关键组件。
管束由一系列平行布置的换热管组成,管束的数量和布局根据具体的工艺需求而定。
换热管通常由石墨材料制成,具有良好的导热性能和耐腐蚀性能。
换热管的内外壁经过特殊处理,以增加其表面积和换热效率。
管束两端通过管板与进出口口相连接,形成冷热流体的循环通道。
四、密封件结构密封件用于确保石墨换热器的密封性能,防止流体泄漏。
密封件一般由橡胶或金属制成,具有较好的弹性和密封性能。
在石墨换热器的壳体和管束连接部分,安装有密封件以确保其密封性能。
同时,在进出口口等位置也会安装密封件以避免泄漏。
五、工作原理石墨换热器通过壳体将流体分成冷热两侧,冷热流体分别通过管束的内外壁进行传热。
当冷热流体分别从管束的两端进入时,它们会在管束内部的换热管上交替流动,实现传热。
此时,冷热流体在换热管的内外壁之间发生传热,达到冷热流体之间热能转移的目的。
结论:石墨换热器是一种高效的热交换设备,其结构设计非常重要。
壳体、管束和密封件是石墨换热器的主要组成部分,各自承担着不同的功能。
换热器结构介绍
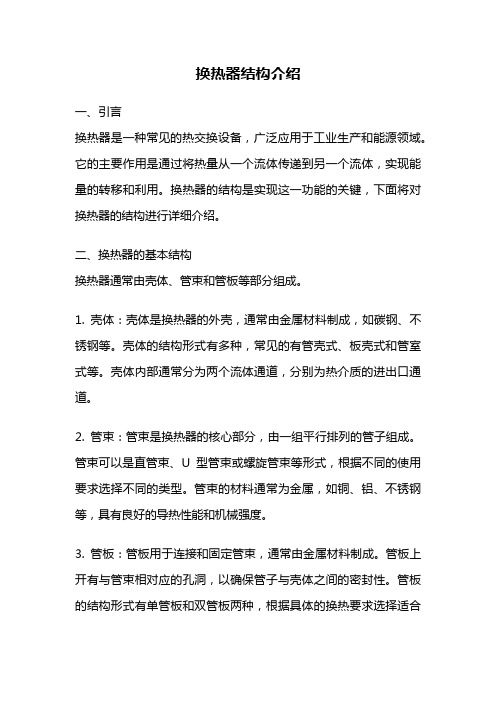
换热器结构介绍一、引言换热器是一种常见的热交换设备,广泛应用于工业生产和能源领域。
它的主要作用是通过将热量从一个流体传递到另一个流体,实现能量的转移和利用。
换热器的结构是实现这一功能的关键,下面将对换热器的结构进行详细介绍。
二、换热器的基本结构换热器通常由壳体、管束和管板等部分组成。
1. 壳体:壳体是换热器的外壳,通常由金属材料制成,如碳钢、不锈钢等。
壳体的结构形式有多种,常见的有管壳式、板壳式和管室式等。
壳体内部通常分为两个流体通道,分别为热介质的进出口通道。
2. 管束:管束是换热器的核心部分,由一组平行排列的管子组成。
管束可以是直管束、U型管束或螺旋管束等形式,根据不同的使用要求选择不同的类型。
管束的材料通常为金属,如铜、铝、不锈钢等,具有良好的导热性能和机械强度。
3. 管板:管板用于连接和固定管束,通常由金属材料制成。
管板上开有与管束相对应的孔洞,以确保管子与壳体之间的密封性。
管板的结构形式有单管板和双管板两种,根据具体的换热要求选择适合的结构。
三、换热器的工作原理换热器的工作原理是通过壳体内外两个流体之间的传热来实现能量的转移。
其中,一个流体在管束内流动,称为管侧流体;另一个流体在壳体内流动,称为壳侧流体。
在换热过程中,壳侧流体和管侧流体的热量通过管壁传递,实现热量的交换。
壳侧流体流经壳体,将热量传递给管侧流体,使管侧流体的温度升高,壳侧流体的温度降低。
换热器的工作过程可以分为对流传热和传导传热两个过程。
对流传热是指流体通过壳体和管束时产生的传热,而传导传热是指热量在管壁内部传递的过程。
四、换热器的应用领域换热器广泛应用于各个行业,包括化工、石油、电力、制药、冶金等领域。
具体应用包括以下几个方面:1. 工业生产:在化工、石油和制药等行业,换热器用于热媒的加热、冷却和回收利用,提高能源利用效率。
2. 电力行业:在发电厂中,换热器用于锅炉的燃烧热量回收、蒸汽凝结和冷却水循环等工艺。
3. 食品加工:在食品加工工业中,换热器常用于蒸汽蒸煮、热水加热和冷却等过程。
各种换热器工作原理和特点,值得收藏
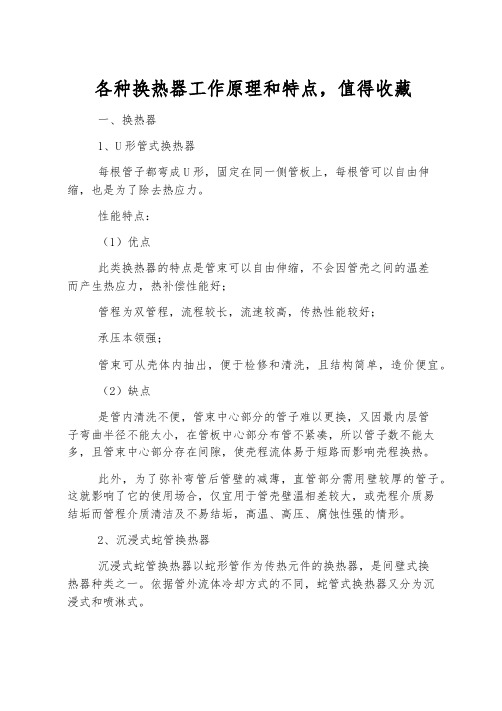
各种换热器工作原理和特点,值得收藏一、换热器1、U形管式换热器每根管子都弯成U形,固定在同一侧管板上,每根管可以自由伸缩,也是为了除去热应力。
性能特点:(1)优点此类换热器的特点是管束可以自由伸缩,不会因管壳之间的温差而产生热应力,热补偿性能好;管程为双管程,流程较长,流速较高,传热性能较好;承压本领强;管束可从壳体内抽出,便于检修和清洗,且结构简单,造价便宜。
(2)缺点是管内清洗不便,管束中心部分的管子难以更换,又因最内层管子弯曲半径不能太小,在管板中心部分布管不紧凑,所以管子数不能太多,且管束中心部分存在间隙,使壳程流体易于短路而影响壳程换热。
此外,为了弥补弯管后管壁的减薄,直管部分需用壁较厚的管子。
这就影响了它的使用场合,仅宜用于管壳壁温相差较大,或壳程介质易结垢而管程介质清洁及不易结垢,高温、高压、腐蚀性强的情形。
2、沉浸式蛇管换热器沉浸式蛇管换热器以蛇形管作为传热元件的换热器,是间壁式换热器种类之一。
依据管外流体冷却方式的不同,蛇管式换热器又分为沉浸式和喷淋式。
(1)优点这是一种古老的换热设备。
它结构简单,制造、安装、清洗和维护和修理便利,便于防腐,能承受高压,价格低廉,又特别适用于高压流体的冷却、冷凝,所以现代仍得到广泛应用。
(2)缺点由于容器体积比管子的体积大得多、笨重、单位传热面积金属耗量多,因此管外流体的表面传热系数较小。
为提高传热系数,容器内可安装搅拌器。
3、列管式换热器冷流体走管内,热流体经折流板走管外,冷、热流体通过间壁换热。
性能特点:列管式换热器的结构比较简单、紧凑、造价便宜,但管外不能机械清洗。
此种换热器管束连接在管板上,管板分别焊在外壳两端,并在其上连接有顶盖,顶盖和壳体装有流体进出口接管。
通常在管外装置一系列垂直于管束的挡板。
同时管子和管板与外壳的连接都是刚性的,而管内管外是两种不同温度的流体。
因此,当管壁与壳壁温差较大时,由于两者的热膨胀不同,产生了很大的温差应力,以至管子扭弯或使管子从管板上松脱,甚至毁坏换热器。
换热器管束的排列方式
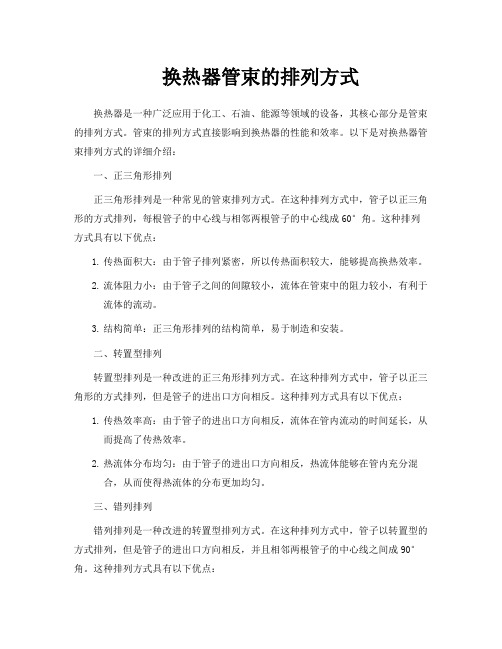
换热器管束的排列方式换热器是一种广泛应用于化工、石油、能源等领域的设备,其核心部分是管束的排列方式。
管束的排列方式直接影响到换热器的性能和效率。
以下是对换热器管束排列方式的详细介绍:一、正三角形排列正三角形排列是一种常见的管束排列方式。
在这种排列方式中,管子以正三角形的方式排列,每根管子的中心线与相邻两根管子的中心线成60°角。
这种排列方式具有以下优点:1.传热面积大:由于管子排列紧密,所以传热面积较大,能够提高换热效率。
2.流体阻力小:由于管子之间的间隙较小,流体在管束中的阻力较小,有利于流体的流动。
3.结构简单:正三角形排列的结构简单,易于制造和安装。
二、转置型排列转置型排列是一种改进的正三角形排列方式。
在这种排列方式中,管子以正三角形的方式排列,但是管子的进出口方向相反。
这种排列方式具有以下优点:1.传热效率高:由于管子的进出口方向相反,流体在管内流动的时间延长,从而提高了传热效率。
2.热流体分布均匀:由于管子的进出口方向相反,热流体能够在管内充分混合,从而使得热流体的分布更加均匀。
三、错列排列错列排列是一种改进的转置型排列方式。
在这种排列方式中,管子以转置型的方式排列,但是管子的进出口方向相反,并且相邻两根管子的中心线之间成90°角。
这种排列方式具有以下优点:1.传热效率高:由于管子的进出口方向相反,流体在管内流动的时间延长,从而提高了传热效率。
2.流体阻力小:由于相邻两根管子的中心线之间成90°角,流体在管束中的阻力较小,有利于流体的流动。
3.结构紧凑:错列排列的结构紧凑,能够减小换热器的体积和重量。
四、双排错列排列双排错列排列是一种更为复杂的管束排列方式。
在这种排列方式中,管子以转置型的方式排列成两排,并且相邻两根管子的中心线之间成90°角。
这种排列方式具有以下优点:1.传热效率高:由于管子排列紧密,并且进出口方向相反,流体在管内流动的时间延长,从而提高了传热效率。
不同翅片形式管翅式换热器流动换热性能比较

不同翅片形式管翅式换热器流动换热性能比较摘要:随着制冷空调行业的发展,人们已经把注意力集中在高效、节能节材的紧凑式换热器的开发上,而翅片管式换热器正是制冷、空调领域中所广泛采用的一种换热器形式。
对于它的研究不仅有利于提高换热器的换热效率及其整体性能,而且对改进翅片换热器的设计型式,推出更加节能、节材的紧凑式换热器有着重要的指导意义。
由于翅片管式换热器在翅片结构形式和几何尺寸的不同,造成其换热性能和阻力性能上的极大差异。
本文概述目前国内外空调制冷行业中的普遍采用的几种不同翅片类型(平直翅片、波纹翅片、开缝翅片、百叶窗形翅片)的换热及压降实验关联式及其影响因素,对不同翅片形式的管翅式换热器的换热及压降特性的实验关联式进行总结,并对不同翅片的流动换热性能进行了比较。
正确地选用实验关联式及性能指标,将对翅片管式换热器的优化设计及其制造提供可靠的依据。
关键词:翅片形式;管翅式;换热器;关联式;流动换热性能Study on heat transfer and flow characteristics of fin-and-tube heat exchangers with various fin typesAbstract:With the development of refrigeration and air conditioning, high efficiency, energy saving and material saving compact type of heat exchanger is development, as one kind of compact heat exchanger, fin-and-tube heat exchanger has a wide application in future. It is necessary to develop compact heat exchanger which is more energy saving and material saving to improve the heat exchanger thermal efficiency and the overall performance of heat transfer.This paper summaries the heat transfer and pressure drop correlations of different fin surfaces, and the corresponding influencing factors. The heat transfer and friction characteristic of these kinds of fin types are compared, and the results show the difference of these fin types. The appropriate correlation and evaluation criterion will provide reliable foundation to the design and optimization of compact heat exchangers.Key words:Fin-and-tube heat exchanger; Heat transfer and flow characteristics; Experimental correlations; Comparison目录1 绪论 (2)1.1课题背景及研究意义 (3)1.2管翅式换热器简介 (3)1.3管翅式换热器的特点 (4)1.4 管翅式换热器的换热过程 (4)1.5研究现状 (5)1.5.1国外实验及模拟研究进展 (5)1.5.2国内研究现状和数值模拟 (6)1.5.3管翅式换热器及发展趋势 (8)1.6 管翅式换热器的不同形式的翅片研究现状 (9)2影响翅片换热和压降性能的主要结构因素 (11)2.1翅片间距对换热特性和压降特性的影响 (12)2.2管排数对换热特性和压降特性的影响 (12)2.3管径对换热特性和压降特性的影响 (13)2.4管间距对换热特性和压降特性的影响 (13)3.不同翅片经验关系式总结及比较 (14)3.1 平直翅片经验关系式的总结 (14)3.2 波纹翅片经验关系式的总结 (18)3.3 百叶窗翅片经验关系式的总结 (23)3.4 开缝翅片经验关系式的总结 (26)4.四种翅片经验关系式比较 (31)结论 (38)参考文献 (40)致谢 (44)1绪论1.1课题背景及研究意义换热器是国民生产中的重要设备,其应用遍及动力、冶金、化工、炼油、建筑、机械制造、食品、医药及航空等各工业部门。
各种换热器工作原理
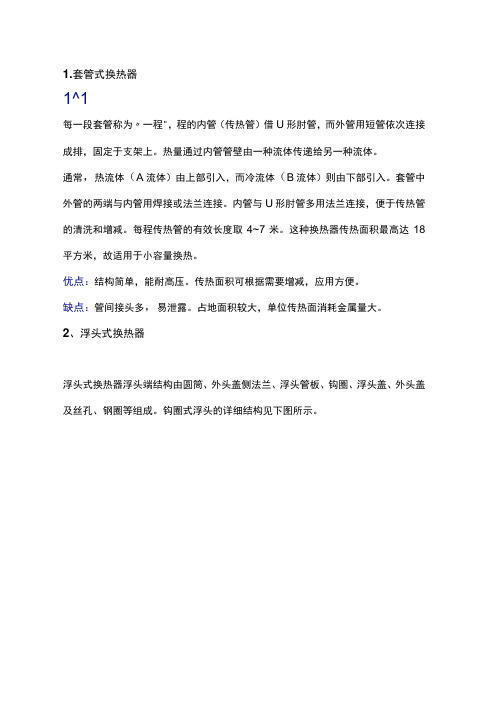
1.套管式换热器1^1每一段套管称为〃一程",程的内管(传热管)借U形肘管,而外管用短管依次连接成排,固定于支架上。
热量通过内管管壁由一种流体传递给另一种流体。
通常,热流体(A流体)由上部引入,而冷流体(B流体)则由下部引入。
套管中外管的两端与内管用焊接或法兰连接。
内管与U形肘管多用法兰连接,便于传热管的清洗和增减。
每程传热管的有效长度取4~7米。
这种换热器传热面积最高达18平方米,故适用于小容量换热。
优点:结构简单,能耐高压。
传热面积可根据需要增减,应用方便。
缺点:管间接头多,易泄露。
占地面积较大,单位传热面消耗金属量大。
2、浮头式换热器浮头式换热器浮头端结构由圆筒、外头盖侧法兰、浮头管板、钩圈、浮头盖、外头盖及丝孔、钢圈等组成。
钩圈式浮头的详细结构见下图所示。
盖娜去兰外头盖法兰B型钩圈浮头盖法兰优点:当换热管与壳体有温差存在,壳体或换热管膨胀时,互不约束,不会产生温差应力。
管束可从壳体内抽出,便于管内和管间的清洗。
缺点:结构较复杂,用材量大,造价高。
浮头盖与浮动管板之间若密封不严,发生内漏,造成两种介质的混合。
3、沉浸蛇管换热这种换热器是将金属管弯绕成各种与容器相适应的形状,并沉浸在容器内的液体中。
优点:结构简单,能承受高压,可用耐腐蚀材料制造。
缺点:容器内液体湍动程度低,管外换热系数小为提高传热系数,容器内可安装搅拌器。
板式换热器是液一液、液一汽进行热交换的理想设备。
它是由具有一定波纹形状的一系列金属片叠装而成的一种新型高效换热器。
板式换热器的结构原理:可拆卸板式换热器是由许多冲压有波纹薄板按一定间隔,四周通过垫片密封,并用框架和压紧螺旋重叠压紧而成,板片和垫片的四个角孔形成了流体的分配管和汇集管,同时又合理地将冷热流体分开,使其分别在每块板片两侧的流道中流动,通过板片进行热交换。
5、具有补偿圈的换热器由挡板、补偿圈和放热嘴构成的换热器。
当流体为高温换热时,由于壳体与管束因温度相差太大,引起不同的热膨胀率,补偿圈就是为了消除这种热应力。
管壳式换热器传热系数
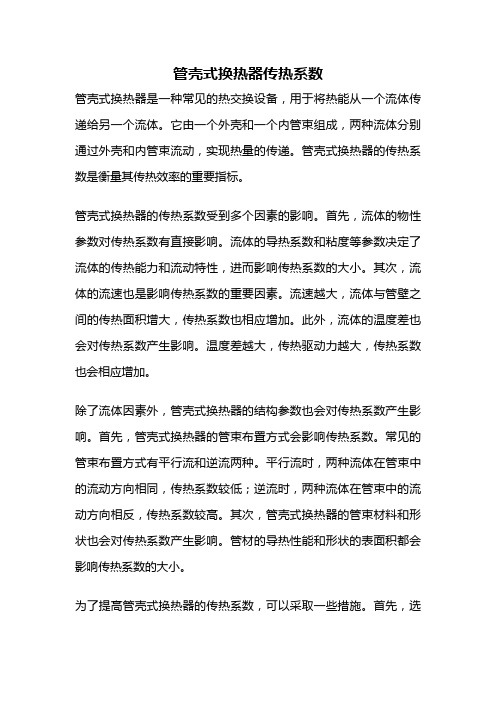
管壳式换热器传热系数管壳式换热器是一种常见的热交换设备,用于将热能从一个流体传递给另一个流体。
它由一个外壳和一个内管束组成,两种流体分别通过外壳和内管束流动,实现热量的传递。
管壳式换热器的传热系数是衡量其传热效率的重要指标。
管壳式换热器的传热系数受到多个因素的影响。
首先,流体的物性参数对传热系数有直接影响。
流体的导热系数和粘度等参数决定了流体的传热能力和流动特性,进而影响传热系数的大小。
其次,流体的流速也是影响传热系数的重要因素。
流速越大,流体与管壁之间的传热面积增大,传热系数也相应增加。
此外,流体的温度差也会对传热系数产生影响。
温度差越大,传热驱动力越大,传热系数也会相应增加。
除了流体因素外,管壳式换热器的结构参数也会对传热系数产生影响。
首先,管壳式换热器的管束布置方式会影响传热系数。
常见的管束布置方式有平行流和逆流两种。
平行流时,两种流体在管束中的流动方向相同,传热系数较低;逆流时,两种流体在管束中的流动方向相反,传热系数较高。
其次,管壳式换热器的管束材料和形状也会对传热系数产生影响。
管材的导热性能和形状的表面积都会影响传热系数的大小。
为了提高管壳式换热器的传热系数,可以采取一些措施。
首先,选择导热性能好的流体作为工质,可以提高传热系数。
其次,合理设计管壳式换热器的结构参数,如管束布置方式、管壁材料和形状等,可以优化传热效果。
此外,还可以通过增大流体的流速和温度差来提高传热系数。
在工程应用中,需要根据具体的工艺要求和经济效益来选择合适的管壳式换热器。
传热系数是一个重要的性能指标,但不是唯一的评价指标。
除了传热系数外,还需要考虑换热器的压降、材料成本、维护成本等因素,综合评价换热器的性能。
管壳式换热器的传热系数是衡量其传热效率的重要指标。
传热系数受到多个因素的影响,包括流体的物性参数、流速、温度差以及换热器的结构参数等。
为了提高传热系数,可以选择合适的流体、优化换热器的结构设计,并增大流速和温度差。
- 1、下载文档前请自行甄别文档内容的完整性,平台不提供额外的编辑、内容补充、找答案等附加服务。
- 2、"仅部分预览"的文档,不可在线预览部分如存在完整性等问题,可反馈申请退款(可完整预览的文档不适用该条件!)。
- 3、如文档侵犯您的权益,请联系客服反馈,我们会尽快为您处理(人工客服工作时间:9:00-18:30)。
换热器各种管束支撑的结构与传热性能换热器各种管束支撑的结构与传热性能李安军邢桂菊周丽雯(辽宁科技大学材料科学与工程学院鞍山市114051) 摘要:管束支撑是管壳式换热器的重要元件,改变管束支撑的的形状和结构是强化传热的重要手段,文中详细描述和分析了弓形折流板、整圆形折流板、折流杆、螺旋隔板、空心圆环、管子自支撑结构、抗振折流杆和旋流片的结构特点和传热特性,并对各种管束支撑的传热性能比较。
每一种管束支撑都有自己的特点和工作环境,其优缺点是相对的,但总的发展趋势是管束支撑物的结构加工工艺趋于简单化,传热强化和抗振功能明显提高。
关键词:管束支撑; 传热性能; 换热器中图分类号:TQ051文献标识码:A文章编号:1009 3281(2008)02 0028 0420世纪80年代以来,强化传热技术被誉为第二代传热技术[1],并得到了充分的发展。
它是能够显著改善传热性能的节能技术,其主要内容是强化传热元件和改变换热器壳程的支撑结构,用以提高换热效率,达到生产的最优化。
管束支撑是管壳式换热器的重要原件,主要起到支撑管束、减小管束振动和引导壳程流体的流向的作用,一种好的管束支撑,能够强化壳程热交换,节约投资和运营成本,因此,开发优良的管束支撑结构是非常必要的。
工程上已应用的管束支撑主要有:弓形折流板、整圆形折流板、折流杆、螺旋隔板、空心圆环、抗振折流杆、旋流片和管子自支撑结构等,这些管束支撑各有优缺点。
1 各种管束支撑1.1 弓形折流板弓形折流板包括单弓形折流板和双弓形折流板。
单弓形折流板是化工企业用得最多的一种,其结构见图1a,但是这种折流板具有流阻大,易结垢,易引发流体诱导振动等缺点[2]。
双弓形折流板由双弓形隔板和中心隔板组成,结构见图1b。
两种隔板沿管束方向交替排列,引导流体波浪式前进。
双弓形隔板换热器与间距和缺口相同的单弓型隔板换热器相比,虽然其压降为后者的0.3~0.5,传热系数为后者的0.6~0.8,但总体的传热性能是提高的[3]。
弓形折流板换热器可以用于单相、沸腾和冷凝的各种工况中,适用的介质也比较多,如水、汽、原油、轻质油等。
1.2 整圆形折流板已开发出的整圆形折流板有五种结构,如图2。
大管孔整圆形折流板出现得较早,板上有比管径大的圆孔,圆心与管轴共线,既让管子穿过,又可以让管间流体通过,这种纵流式结构可以减小传热管的振动,但缺乏对管子的支撑作用。
后来开发出带小圆孔的整圆形折流板,折流板上除钻有等于管外径的管孔外,管孔之间再钻小圆孔,让管间流体由小圆孔流过折流板,可以克服大管孔整圆折流板的缺点。
为进一步提高性能,又开发出了矩形孔、梅花孔整圆形折流板,既能支撑管子,又能让管间流体流过折流板。
还有一种网状整圆形折流板,其结构仍按普通折流板划线、钻孔,然后将折流板上的横排孔以4个为一组,将管桥处铣通而成[4]。
整圆形孔板能有效地堵塞壳程中管束与壳体之间的缝隙,从而阻止流体在该缝隙中的无效流动;流体从孔板开孔处穿过,孔板的“节流作用”使流体产生波动和二次流而加剧湍流,有效地提高传热效率[5]。
整圆形折流板结构的换热器壳程介质主要为水和轻质油,可适用于各种工况。
1.3 折流杆结构折流杆纵流式换热器是1970年美国菲利浦石油公司首先提出的,是为了解决传统折流板换热器中管子与折流板的切割破坏和流体诱导振动,这种结构是将管壳式换热器中的折流板改成杆式支承,如图3。
折流杆式换热器压降很低,低于弓形隔板的1/4;传热特性比也高,传热强化达1.3~2.4倍[3]。
在相同设计条件下,双壳程折流杆换热器的壳程流速提高了1倍,壳程的给热系数可提高52%~74%。
另外,折流杆与换热器的接触面积很小,传热面积得到充分利用,消除壳程滞留区,改变了壳程流场的温度分布。
由于折流杆可以有效地避免流体诱导振动,因而流体可以在壳体内高速流动。
折流杆结构壳程适用的介质有水、轻质油和水蒸气,可以用于汽———液和液———液等工况的强化换热。
)1.4 螺旋隔板支撑LutchaJ和NemcanskyJ[6]于1983年提出壳程流体作螺旋运动可以有效地清除污垢死角、增强壳程湍流度、强化换热器壳程传热,其壳侧支撑结构是用一系列的扇形面相间连接,从而在壳侧形成近似的螺旋面,亦称螺旋折流板换热器[3]。
这种换热器折流板形成一种特殊的螺旋形结构,与常规折流板的布置方式不同,它使得壳程的流体做螺旋运动。
通过已知实验研究可以看出,这种换热器的优良性能,对于以压缩空气为工质,在相同的Re下,光滑管螺旋隔板换热器的管外膜传热系数是光滑管弓形隔板换热器的1.25~1.8倍[7];螺旋隔板换热器的传热系数最大可以为弓形隔板换热器的1.39倍,压降随着螺旋角的不同大约可降低26%~60%。
螺旋隔板支撑结构的换热器具有良好的防垢特性,适用于易结垢、高黏的介质(如原油、油渣)的强化传热。
1.5 空心圆环空心圆环支撑结构是采用小直径金属短管以一定间隔布置在换热管束之间,起到支撑传热管和导流作用。
这种结构的特点是:壳程间隙率大,流阻小,流速变化小,流体在空心环处可以充分形成湍流,增强传热;节约钢材,减轻设备重量,钢材的消耗量大大减少,所以,与传统换热器相比,空心圆环换热器在投资费用方面占有很大的竞争力,可节省25%[8]。
空心圆环结构换热器壳程介质主要为低黏度液体,如水、酸、轻质油等。
1.6 管子自支撑结构管子自支撑结构是管束依靠自身的结构相互支撑,而不是通过附加的折流板、折流杆等结构。
节省了钢材,节约了成本,减轻了设备的重量。
这样的结构有变截面管、螺旋椭圆扁管、刺孔膜片和螺旋折流片[9,10]。
1.6.1 螺旋椭圆扁管螺旋椭圆扁管是把圆形光管压成椭圆形,然后扭曲而成,结构如图4b,流体在管内处于螺旋流动状态,因而破坏了管壁附近的层流边界层,提高了传热效率。
这种管束结构的特点是:两个并行排列相邻的管子在椭圆长轴处相互接触、互相支撑,应用这种管的换热器取消了附加的管束支撑物,节约了材料和成本。
研究表明,螺旋椭圆扁管换热器具有较好的强化传热性能,管径大小和螺旋导程对传热和阻力性能均有影响。
从综合性能来看,大管径优于小管径。
对于相同规格的管子,导程增大,传热性能降低,流动阻力减小[11]。
这种结构的换热器与光管换热器相比,热流密度高50%,容积小30%。
螺旋椭圆扁管支撑结构的换热器也可以用于单相、沸腾和冷凝的各种工况中。
1.6.2 螺旋折流片螺旋片传热管是在光管上均匀布置螺旋片,有左旋片管和右旋片管之分。
换热器的换热管布置情况是螺旋片管与光管交错排列,左右两根管是螺旋片管,螺旋方向分别是左旋和右旋,上下两根管是光管,放置在螺旋片上,不需要附加管束支撑。
螺旋片能诱导生成涡旋流体,形成二次流,增强流体的湍流度,强化流体微团混合,使壁面附近的流速梯度增大,从而减薄粘性边界层底层的厚度,有效提高传热系数。
同时螺旋片形成的通道还增加了流体的流动路径,提高了流动速度。
数值模拟结果表明,螺旋片管的传热系数随着螺旋角的增大而平缓增加,流动阻力损失加大,传热性能明显优于光管,传热系数可提高40%~100%[12]。
螺旋折流片管子支撑结构的换热器壳程的工作介质可以是重油等高粘度的流体。
1.7 抗振折流杆下面介绍一种新型抗振折流杆结构,如图5。
这种结构保持了传统折流杆换热器纵流的特征,并且对换热管也起到夹持式支撑作用,能够显著消除流体诱导振动;流体流过波浪型折流杆时使文丘里效应和涡流脱离明显增大,提高了流体的湍动,又使换热器在低雷诺数流动情况下有较好的传热系数。
通过数值模拟对传热量和传热系数的比较,夹持式折流杆换热器都优于传统的折流杆换热器,而且还克服了传统折流杆换热器结构在高雷诺数下换热管间的菱形磨损及低雷诺数下湍流扰动不足、传热效率急剧下降等缺点[13]。
抗振折流杆是折流杆结构的一种,适用的工况和介质也基本相同。
1.8 旋流片旋流片的结构类似扭带,结构如图6[14]。
扭带是一种管的内插件,其主要作用是扰动管内流体,增加湍流度,强化传热,Saha等[15]研究了在管内间隔扭片插入物的流动和换热情况,发现旋流片能以较小的阻力损失为代价显著地提高换热性能。
旋流片支撑结构作为新型的壳程构件,可以减小壳程流体的阻力、改善换热性能,同时也可以起到支撑管束的作用。
当流经旋流片时,流体在螺旋型流道内受迫做螺旋流动,由原来的一股分裂成两个螺旋流。
由于流道面积的减小及曲面的变化,流体得到充分扰动,有效地冲刷壁面,减薄了边界层。
当流体离开旋流片后,流体进入自旋流状态,随着距离的延长,两个螺旋流逐渐合并成一个大的纵向涡。
通过对空心圆环和旋流片支撑结构的比较研究表明[14],旋流片的换热效果优于空心环,但是阻力损失却大于空心环,并且,旋流片的扭率是旋流片阻力损失的主要影响因素,小扭率的旋流片产生的形体阻力较大,流体不易形成湍流。
有旋流片的换热器壳程工作介质可以是汽、液等工作介质,可适用于冷却、冷凝、沸腾等各种工况。
2 各种支撑的性能比较每一种管束支撑都有自己的长处和缺点,不同的工况下,与不同的传热元件组合,传热效果是不同的。
实验研究表明在相同跨距和流量下大管孔孔板折流板的组合,梅花形孔板的传热效果最好,是单弓型孔板的2.8倍,矩形孔板是单弓形孔板的2.5倍[16];横纹槽管束的最佳支撑物是空心圆环或弹性波形薄片支撑,与弓形板支撑相比,传热面积可以减少35%,传热效率可以提高38%,与折流杆支撑相比分别可以提高33%和35%[17]。
综合传热效果纵流式支撑要好于横流式的,但也不是绝对的,需要不同的组合配比。
总之,在选取管束支撑时要考虑到换热器结构、经济成本等综合因素。
3 结论与展望(1)壳程管束支撑物的结构加工工艺发展趋于简单化,管间空隙趋于扩大化,壳程的综合传热性能明显提高;具有很强的抗振功能,能够有效避免流体诱导振动造成的破坏,设备使用寿命更长。
开发新型高效的支撑结构是非常必要的。
(2)纵向流管束支撑结构具有优良的特性,如果纵向流支撑结构与不同型式的强化管组合使用,能够同时实现壳侧与管侧的传热强化,这种为实现不同强化传热技术的优化组合仍需要进一步研究。