一些常用刀具使用参数的参考值
雕刻刀具参数表

刀具工艺参数表——黄铜的加工参数下图为计算刀具路径时的“设定切削用量”对话框,根据当前所用刀具正确查取刀具工艺表格,对应图中的“吃刀深度”即最大单边切深度、“开槽深度”即一次开槽深度、“路径间距”即侧向进给,分别输入加工参数值。
最大单边切削深一次开槽深度侧向进给表一:20○系列刀具开粗加工黄铜材料的工艺参数表表二:20○系列刀具修边加工黄铜材料的工艺参数表表三:20○系列刀具清角加工黄铜材料的工艺参数表表四:10○系列刀具开粗加工黄铜材料的工艺参数表表五:10○系列刀具修边加工黄铜材料的工艺参数表表六:10○系列刀具清角加工黄铜材料的工艺参数表表七:30○系列刀具修边加工黄铜材料的工艺参数表表八:30○系列刀具清角加工黄铜材料的工艺参数表表九:使用螺纹铣刀开粗加工黄铜时的工艺参数表使用螺纹铣刀开粗是充分利用螺纹铣刀的侧向切削能力强的优势,从实际加工的现象来看是:吃刀深度大,侧向进给量小,进给速度大,整体的材料去除量大,加工效率大幅度提高,这种加工方式称为:“大吃深,少吃料,快进给”。
螺纹铣刀不但加工效率高,而且刀具比较耐用,加工的底面效果好,尺寸精度容易保证。
紫铜的加工参数表一:20○系列刀具开粗加工紫铜材料的工艺参数表表二:20○系列刀具修边加工紫铜材料的工艺参数表表三:20○系列刀具清角加工紫铜材料的工艺参数表表四:30○系列刀具修边加工紫铜材料的工艺参数表表五:30○系列刀具清角加工紫铜材料的工艺参数表表六:使用螺纹铣刀进行紫铜开粗加工时的工艺参数铬钢的加工参数表一:20○系列刀具开粗加工铬钢材料的工艺参数表表二:20系列刀具修边加工铬钢材料的工艺参数表表三:20○系列刀具清角加工铬钢材料的工艺参数表表四:30○系列刀具修边加工铬钢材料的工艺参数表表五:30○系列刀具清角加工铬钢材料的工艺参数表表六:使用螺纹铣刀进行铬钢开粗加工时的工艺参数切削线速度切削线速度计算公式: V=πDN其中N是主轴转速,D是刀具直径。
常用刀具的切削参数
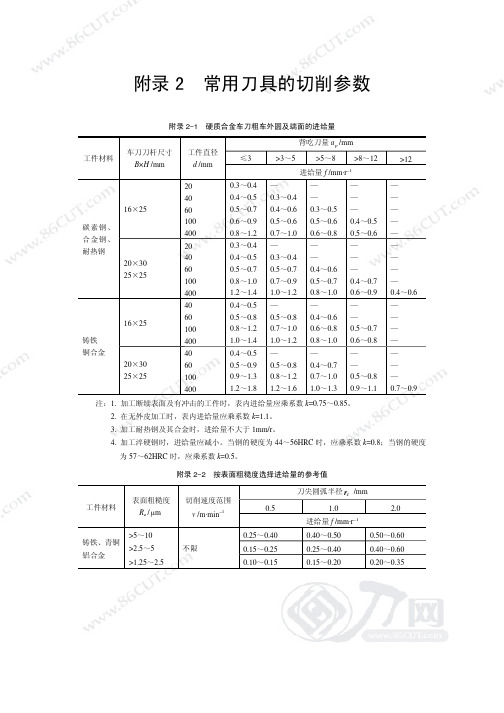
附录2 常用刀具的切削参数附录2-1 硬质合金车刀粗车外圆及端面的进给量背吃刀量p a /mm≤3 >3~5 >5~8 >8~12>12工件材料车刀刀杆尺寸 B ×H /mm工件直径 d /mm 进给量f /mm·r –116×2520 4060 100 400 0.3~0.4 0.4~0.5 0.5~0.7 0.6~0.9 0.8~1.2 — 0.3~0.4 0.4~0.6 0.5~0.6 0.7~1.0 — — 0.3~0.5 0.5~0.6 0.6~0.8 — — — 0.4~0.5 0.5~0.6 — — — — — 碳素钢、合金钢、耐热钢20×30 25×2520 40 60 100 400 0.3~0.4 0.4~0.5 0.5~0.7 0.8~1.0 1.2~1.4 — 0.3~0.4 0.5~0.7 0.7~0.9 1.0~1.2 — — 0.4~0.6 0.5~0.7 0.8~1.0 — — — 0.4~0.7 0.6~0.9 — — — — 0.4~0.6 16×254060 100 400 0.4~0.5 0.5~0.8 0.8~1.2 1.0~1.4 — 0.5~0.8 0.7~1.0 1.0~1.2 — 0.4~0.6 0.6~0.8 0.8~1.0 — — 0.5~0.7 0.6~0.8 — — — — 铸铁 铜合金20×30 25×2540 60 100 4000.4~0.5 0.5~0.9 0.9~1.3 1.2~1.8— 0.5~0.8 0.8~1.2 1.2~1.6— 0.4~0.7 0.7~1.0 1.0~1.3— — 0.5~0.8 0.9~1.1— — — 0.7~0.9 注:1. 加工断续表面及有冲击的工件时,表内进给量应乘系数k =0.75~0.85。
切削参数和计算公式参考
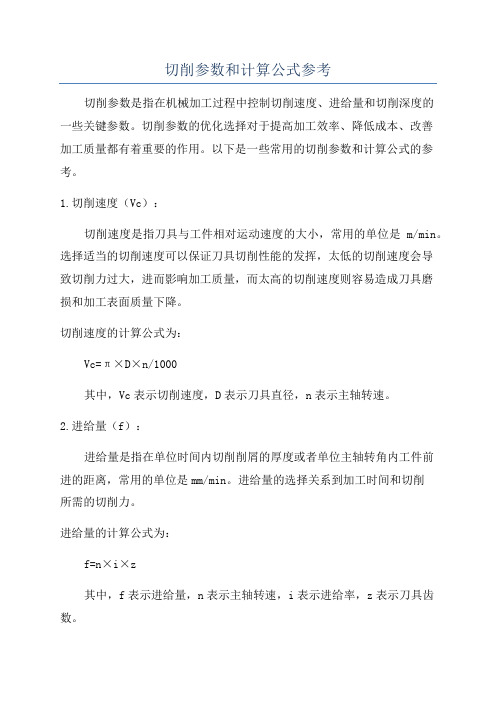
切削参数和计算公式参考切削参数是指在机械加工过程中控制切削速度、进给量和切削深度的一些关键参数。
切削参数的优化选择对于提高加工效率、降低成本、改善加工质量都有着重要的作用。
以下是一些常用的切削参数和计算公式的参考。
1.切削速度(Vc):切削速度是指刀具与工件相对运动速度的大小,常用的单位是m/min。
选择适当的切削速度可以保证刀具切削性能的发挥,太低的切削速度会导致切削力过大,进而影响加工质量,而太高的切削速度则容易造成刀具磨损和加工表面质量下降。
切削速度的计算公式为:Vc=π×D×n/1000其中,Vc表示切削速度,D表示刀具直径,n表示主轴转速。
2.进给量(f):进给量是指在单位时间内切削削屑的厚度或者单位主轴转角内工件前进的距离,常用的单位是mm/min。
进给量的选择关系到加工时间和切削所需的切削力。
进给量的计算公式为:f=n×i×z其中,f表示进给量,n表示主轴转速,i表示进给率,z表示刀具齿数。
3. 切削深度(ap):切削深度是指切削层厚度的大小,即刀具和工件之间的垂直距离。
切削深度的选择应根据工件材料和刀具性能来进行合理的安排。
4.切削力(Fc,Fr):切削力是指刀具对工件施加的力,也是切削参数的重要指标之一、切削力的大小与切削材料的性质、切削速度、进给量和切削深度等因素有关。
切削力的计算公式为:Fc = k × ap × f其中,Fc表示切削力,k表示切削力系数。
5.切削功率(P):切削功率是指切削过程中单位时间内切削所需要的能量,常用单位为W。
切削功率的计算可以帮助选取合适的切削参数,保证切削过程的稳定性和高效性。
切削功率的计算公式为:P=Fc×Vc/6000其中,P表示切削功率,Fc表示切削力,Vc表示切削速度。
综上所述,切削参数的选择是一项复杂的任务,需要结合实际加工情况、刀具性能和工件要求等多方面因素进行综合考虑。
各材料常用刀具转速进给参数对照表

各材料常用刀具转速进给参数对照表在机械加工领域,刀具的转速和进给参数对于加工质量、效率和成本都有着至关重要的影响。
不同的材料具有不同的物理和机械性能,因此需要根据材料的特性来选择合适的刀具转速和进给参数。
下面是一份常见材料的刀具转速进给参数对照表,希望能为您的加工工作提供一些参考。
一、铝合金铝合金是一种广泛应用于航空航天、汽车制造和电子工业等领域的轻质材料。
由于其良好的导热性和较低的强度,加工时需要较高的转速和较快的进给速度。
1、粗加工刀具:硬质合金立铣刀转速:3000 5000 rpm进给速度:800 1500 mm/min切削深度:2 5 mm切削宽度:刀具直径的 70% 80%2、半精加工刀具:硬质合金立铣刀转速:5000 8000 rpm进给速度:500 1000 mm/min切削深度:05 15 mm切削宽度:刀具直径的 50% 60%3、精加工刀具:硬质合金球头铣刀转速:8000 12000 rpm进给速度:200 500 mm/min切削深度:01 03 mm切削宽度:刀具半径的 20% 30%二、钢材钢材是机械加工中最常见的材料之一,其种类繁多,性能各异。
以下是常见钢材的加工参数。
1、低碳钢粗加工刀具:硬质合金涂层立铣刀转速:1500 2500 rpm进给速度:300 600 mm/min切削深度:3 6 mm切削宽度:刀具直径的 60% 70%半精加工刀具:硬质合金涂层立铣刀转速:2500 4000 rpm进给速度:200 400 mm/min切削深度:1 2 mm切削宽度:刀具直径的 40% 50%精加工刀具:硬质合金涂层球头铣刀转速:4000 6000 rpm进给速度:100 200 mm/min切削深度:01 02 mm切削宽度:刀具半径的 15% 20% 2、中碳钢粗加工刀具:硬质合金涂层立铣刀转速:1000 1800 rpm进给速度:200 400 mm/min切削深度:2 4 mm切削宽度:刀具直径的 50% 60%半精加工刀具:硬质合金涂层立铣刀转速:1800 3000 rpm进给速度:150 300 mm/min切削深度:05 10 mm切削宽度:刀具直径的 30% 40%精加工刀具:硬质合金涂层球头铣刀转速:3000 5000 rpm进给速度:80 150 mm/min切削深度:005 015 mm切削宽度:刀具半径的 10% 15% 3、高碳钢粗加工刀具:硬质合金涂层立铣刀转速:800 1200 rpm进给速度:100 200 mm/min切削深度:1 3 mm切削宽度:刀具直径的 40% 50%半精加工刀具:硬质合金涂层立铣刀转速:1200 2000 rpm进给速度:80 150 mm/min切削深度:03 08 mm切削宽度:刀具直径的 20% 30%精加工刀具:硬质合金涂层球头铣刀转速:2000 3500 rpm进给速度:50 100 mm/min切削深度:003 008 mm切削宽度:刀具半径的 8% 12%三、不锈钢不锈钢具有良好的耐腐蚀性和耐磨性,但加工难度较大,需要较低的转速和较慢的进给速度。
常用加工刀具参数(仅供参考)
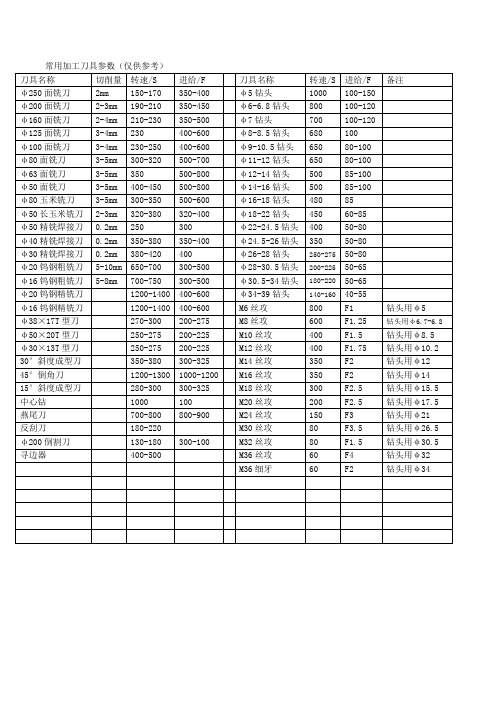
250
300
φ22-24.5钻头
400
50-80
φ40精铣焊接刀
0.2mm
350-380
350-400
φ24.5-26钻头
350
50-80
φ30精铣焊接刀
0.2mm
380-420
400
φБайду номын сангаас6-28钻头
250-275
50-80
φ20钨钢粗铣刀
5-10mm
650-700
300-500
φ28-30.5钻头
200-225
50-65
φ16钨钢粗铣刀
5-8mm
700-750
300-500
φ30.5-34钻头
180-220
50-65
φ20钨钢精铣刀
1200-1400
400-600
φ34-39钻头
140-160
40-55
φ16钨钢精铣刀
1200-1400
400-600
M6丝攻
800
F1
钻头用φ5
φ38×17T型刀
φ7钻头
700
100-120
φ125面铣刀
3-4mm
230
400-600
φ8-8.5钻头
680
100
φ100面铣刀
3-4mm
230-250
400-600
φ9-10.5钻头
650
80-100
φ80面铣刀
3-5mm
300-320
500-700
φ11-12钻头
650
80-100
φ63面铣刀
3-5mm
350
常用加工刀具参数(仅供参考)
常用刀具的切削参数

常用刀具的切削参数刀具切削参数是指在切削过程中,对刀具进行设置和调整的一系列参数。
这些参数包括切削速度、进给速度、切削深度、切削角度等,它们的选择和调整直接影响到切削效果和刀具寿命。
下面是常用刀具的切削参数的一些介绍:1. 切削速度(Cutting Speed):切削速度是指刀具在切削过程中移动的速度,一般用单位时间内刀具切削的长度来表示。
切削速度的选择取决于工件材料的硬度和切削材料的种类。
一般来说,硬度较高的材料需要较低的切削速度,而硬度较低的材料则可以使用较高的切削速度。
2. 进给速度(Feed Rate):进给速度是指刀具在切削过程中每分钟进给到工件上的距离。
进给速度的选择取决于工件的材料和切削操作的要求。
较低的进给速度可以获得更好的切削质量,而较高的进给速度可以提高生产效率。
3. 切削深度(Depth of Cut):切削深度是指刀具切削时每次切削进入工件的深度。
切削深度的选择需要考虑工件材料的硬度和切削工具的强度。
一般来说,较硬的材料需要较小的切削深度,而较软的材料则可以选择较大的切削深度。
4. 切削角度(Cutting Angle):切削角度是指刀具切削刃与工件表面之间的夹角。
切削角度的选择取决于工件材料的硬度和切削操作的要求。
一般来说,较硬的材料需要较大的切削角度,而较软的材料则可以选择较小的切削角度。
5. 切削液(Cutting Fluid):切削液是在切削过程中起冷却、润滑和清洁作用的液体。
切削液的选择取决于切削材料的种类和切削条件的要求。
常见的切削液有切削油、切削液和切削蜡等。
6. 切削力(Cutting Force):切削力是指切削过程中刀具对工件施加的力。
切削力的大小受到切削参数的影响,包括切削速度、进给速度、切削深度和切削角度等。
合理选择切削参数可以降低切削力,提高切削效率和刀具寿命。
7. 切削温度(Cutting Temperature):切削温度是指刀具和工件在切削过程中产生的热量。
常用加工刀具参数(仅供参考)

85-100
φ50面铣刀
3-5mm
400-450
500-800
φ14-16钻头
500
85-100
φ80玉米铣刀
3-5mm
300-350
500-600
φ16-18钻头
480
85
φ50长玉米铣刀
2-3mm
320-380
320-400
φ18-22钻头
450
60-85
φ50精铣焊接刀
250
300
φ钻头
400
50-80
φ40精铣焊接刀
350-380
350-400
φ钻头
350
50-80
φ30精铣焊接刀
380-420
400
φ26-28钻头
250-275
50-80
φ20钨钢粗铣刀
5-10mm
650-700
300-500
φ钻头
200-225
50-65
φ16钨钢粗铣刀
5-8mm
700-750
300-500
φ钻头
常用加工刀具参数(仅供参考)
刀具名称
切削量
转速/S
进给/F
刀具名称
转速/S
进给/F
备注
φ250面铣刀
2mm
150-170
350-400
φ5钻头
1000
100-150
φ200面铣刀
2-3mm
190-210
350-450
φ钻头
800
100-120
φ160面铣刀
2-4mm
210-230
350-500
φ7钻头
180-220
不同材质刀具切削参数

不同材质刀具切削参数在机械加工中,刀具的选择和切削参数的设置对于生产效率和产品质量具有重要影响。
不同的材料对切削条件有不同的需求,因此了解各种材料的特性并相应地调整切削参数是至关重要的。
本文将探讨几种常见金属材料的刀具切削参数。
一、不锈钢不锈钢具有良好的强度和耐腐蚀性,但相对较硬,切削时需要较高的切削力和适当的冷却。
一般建议使用硬度较高(如高速钢)的刀具,以避免过度磨损。
切削速度应保持在较低水平,进给量也应适当控制。
为了确保良好的冷却效果,通常会使用水基或油基切削液。
二、铝合金铝合金轻便且易于加工,但其易脆性和敏感性使得切削过程需要特别注意。
推荐使用硬质合金或涂层刀具,因为它们能够抵抗铝的氧化作用。
切削速度应控制在中等范围,进给量也需适度降低。
为防止粘刀现象,可以使用乳化油或极压切削油。
三、碳钢碳钢是常用的结构材料,其质地均匀、韧性好。
对于碳钢的切削,可以选择钨钻类刀具,由于其高硬度和高温性能良好,可以有效地进行切削。
切削速度可在中等偏高的范围内,进给量和背吃力矩应适中。
推荐使用润滑性能好的乳化油。
四、钛合金钛合金具有优异的抗腐蚀性和高强度,但也因此而变得异常敏感和脆弱。
钛合金的切削要求非常精确的控制,包括缓慢的切削速度、小直径的切入和切出路径以及充分冷却等。
通常建议使用金刚石涂层的高速钢刀具或者超细颗粒硬质合金涂层刀具,这样可以更好地适应钛合金的高温高压环境。
此外,还需根据实际情况选择合适的冷却剂来减少热变形和提高加工质量。
五、铜合金铜合金具有良好的导电性和导热性,适合于制造电气元件和其他相关产品。
然而,由于其软性,需要更小的切削力和更大的容屑空间。
一般来说,高速钢或硬质合金刀具都能满足这种材料的切割需求。
切削速度应在低速范围内,进给量也要适当减小。
同时,为了防止过热和粘刀现象,我们推荐使用水溶性切削液。
六、高强度钢高强度钢具有较高的硬度和强度,因此需要更高的切削力和更大的切削深度。
推荐使用硬度较高(如超细颗粒硬质合金)的刀具,并适当提高切削速度和进给量。
常用车床参数

8940-8949
初始画面标题字符代码1-9
5
可以编辑()
7
0: 报警通过“CAN” + “RESET”操作来清除。
12255 往后是防止错误操作相 关的参数
伺服电机的最大速度
伺服电机的最大加速度
伺服电机的最大加速度
7105设 1 时
第1台手轮的 X 地址
12351
手轮进给m n的倍率
看说明书
0
设置为1 时显示SV1067 FSSB配置错误(软件)
3701
3701
2
1
外部操作信息履历画面显示
键盘上显示的请看参数资料
0
是否对当前位置显示
1
是否显示待走量显示
屏保时间 分钟
当前显示的轴名称 绝对坐标 当前显示的轴名称 相对对坐标
本参数设定为0时,使用参数(NO.1020)的设定值
0 是否对程序8000-8999的编辑
0不禁止 1禁止
4 是否对程序9000-9000的编辑
M,S,T,B 的选通脉冲信号和结束 信号之间的
0 G4.3 1 使用高速信号(关机重启M功能无效)
0
进给,快速移动倍率信号0:使用负逻辑 1:使用正逻辑
1
互锁信号无效,G8.0
1
各轴互锁信号无效,G130
1
不同轴向的互锁信号无效,G132,G134
回参考点时 0信号在0时减速
1信号在1时减速
程序段开始互锁
对9000后程序编辑设置口令
对9001后程序编辑口令输入解码后才能改3202#4
0
8000-8999的程序显示
1
9000-9999的程序显示
7
C系列 储存器保护信号,参数可 写设定
刀具角度选择
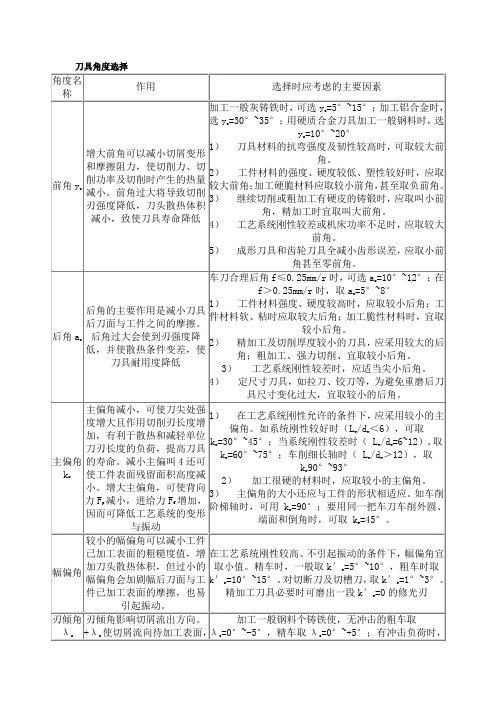
后角的主要作用是减小刀具后刀面与工件之间的摩擦。后角过大会使到刃强度降低,并使散热条件变差,使刀具耐用度降低
车刀合理后角f≤0.25mm/r时,可选ao=10°~12°;在f>0.25mm/r时,取ao=5°~8°
1) 工件材料强度、硬度较高时,应取较小后角;工件材料软、粘时应取较大后角;加工脆性材料时,宜取较小后角。
1)前刀面Ay—切下的切屑沿其流出的表面。
2)主后刀面Aa—与工件上过渡表面相对的表面。
3)副后刀面A'a—与工件上已加工表面相对的的表面。
4)主切削刀S—前刀面与主后刀面的交线,它承担主要切削工作。
5)副切削刃S'—前刀面与副后刀面的交线,它协同主切削刃完成切削工作,并最终形成已加工表面。
6)刀尖—主切削刃与副切削刃连接处的那部分切削刃。
刀具角度选择
角度名称
作用
选择时应考虑的主要因素
前角yo
增大前角可以减小切屑变形和摩擦阻力,使切削力、切削功率及切削时产生的热量减小。前角过大将导致切削刃强度降低,刀头散热体积减小,致使刀具寿命降低
加工一般灰铸铁时,可选yo=5°~15°;加工铝合金时,选yo=30°~35°;用硬质合金刀具加工一般钢料时,选yo=10°~20°
2) 精加工及切削厚度较小的刀具,应采用较大的后角;粗加工、强力切削、宜取较小后角。
3) 工艺系统刚性较差时,应适当尖小后角。
4) 定尺寸刀具,如拉刀、铰刀等,为避免重磨后刀具尺寸变化过大,宜取较小的后角。
主偏角kr
主偏角减小,可使刀尖处强度增大且作用切削刃长度增加,有利于散热和减轻单位刀刃长度的负荷,提高刀具的寿命。减小主偏叫4还可使工件表面残留面积高度减小。增大主偏角,可使背向力Fp减小,进给力Ff增加,因而可降低工艺系统的变形与振动
数控加工常用刀具及参数选择

数控加工常用刀具及加工参数刀具的选择和刀具参数的设置是数控加工工艺中的重要内容,合理地选用刀具和设置刀具参数不仅可以影响数控机床的加工效率,而且可以直接影响加工质量。
1.数控铣削加工常用刀具铣削用刀具通常称为铣刀,普通铣床上的刀具可以用于数控铣床和加工中心上。
一般立式数控加工用铣刀的种类可以有很多种划分方法,既可以从刀具的材料上划分,也可以从刀具的外形上划分,还可以从刀具的用途等方面来划分。
依刀具的外形,数控加工常用的刀具有平刀、圆鼻刀(飞刀)、球刀三种。
(1)平刀平刀底面是平面,平刀是一种以侧刃切削的刀具,所以使用平刀加工时应尽量避免切入底面的工件表面,一般平刀用作开粗和加工平面。
常用平刀大小有D1、D2、D4、D6、D8、D10、D12、D16、D20。
(2)圆鼻刀(飞刀)圆鼻刀底面是平面,每刃都带有圆角,因为底面是平面,所以加工时也应尽量避免切入底面的工件表面,一般圆鼻刀用作开粗,圆鼻刀开粗效果比平刀好。
常用圆鼻刀(飞刀)大小有D25R5、D3OR5。
(3)球刀球刀的切削刃有180°,所以球刀一般用作精加工,球刀切削时较稳定,但球刀不能用作开粗。
常用球刀大小有R1、R2、R3、R4、R5、R6、R8。
2.加工参数的选择随着模具制造技术的高速发展,刀具的加工参数的设置对加工的效率和加工质量的影响越来越大。
熟练掌握刀具加工参数的设置有利于提高加工的效率和加工质量。
刀具加工参数包括切削速度、进给量、背吃刀量(切削深度)和切削宽度。
(1)切削速度v切削速度是指铣刀刀齿切削处的线速度。
v=πDn/1000式中v—切削速度(m/min);D—铣刀直径(mm),周铣时为圆柱铣刀外圆直径;n—主轴转速(rmin)(2)进给量a,f铣削进给量有三种形式:铣刀每转过一个刀齿相对工件移动的距离称为每齿进给量a,其大小决定着一个刀齿的负载,a越大,切削力越大,刀齿的负载也越大。
铣刀每转相对工件移动的距离称为每转进给量f。
《机械制造基础》——刀具几何参数的选择

(二)、主偏角的选择原则
1、根据工艺系统刚性选择 工艺系统刚性足够时,选较小的主偏角,使切削厚度减 少,切削宽度增加,从而使单位长度切削刃所承受的载荷 减轻,散热条件改善,可使刀具使用寿命提高。 工艺系统刚性不足时,应选较大的主偏角,以减小径向 力。 一般取kr=60°~75°,车细长轴时,常取kr≥90°
若减小前角,可以增大切屑的变形,使之易于脆化断裂。
(二)、 前角的选择原则
在选择刀具前角时首先应保证刀刃锋利,同时 也要兼顾刀刃的强度与耐用度。 刀具前角的合理选择,主要由刀具材料和工件材 料的种类与性质以及加工要求决定。
1、工件材料 加工钢件等塑性材料时,切屑沿前刀面流出时和前 刀面接触长度长,压力与摩擦较大,为减小变形和摩擦, 一般采用选择大的前角。
精加工时,宜取较大的前角,以减小工件变形与表
面粗糙度。 总之,前角选择方法为(课后作业):
(1)材料强度、硬度较低时,γo宜大;塑性材料γo 宜大;脆性材料γo宜小; (2)刀具强度和韧性好时γo宜大; (3)粗加工、断续切削、加工铸锻件,γo宜小。
硬质合金车刀合理前角参考值
合理前角(度)
工件材料
获得较小的表面粗糙度值。 修光刃主要用于精加工,用 带有修光刃的车刀切削时, 背向力很大,因此要求工艺
系统要有较好的刚性。
五、刃倾角的选择
(一)刃倾角的功用
1、控制切屑的流向(作业) 切屑向床头方向流出, 影响工人操作;
切屑向尾座方向流出, 影响已加工表面;
切屑沿垂直切削刃的方向流出。
39
2、控制切削刃切入时,首先与工件接触的位臵;
问
题 ?
1、强度和韧性大的刀具材料选择大的还是小的前角, 而脆性大的刀具又如何选择? 强度和韧性大的刀具材料可以选择大的前角,而 脆性大的刀具选择较小的前角甚至取负的前角。 2、加工塑性材料时,一般选择大的还是小的前角? 加工钢件等塑性材料时,一般采用选择大的前角。 3、加工脆性材料时,刀具前角相对塑性材料如何选 择? 加工脆性材料时,因此刀具前角相对塑性材料取 得小些或取负值,以提高刀刃的强度。 4、粗加工和精加工时刀具的前角有何区别? 粗加工时,一般取较小的前角;精加工时,宜取 较大的前角,以减小工件变形与表面粗糙度。
不锈钢的车削参数

不锈钢的车削参数不锈钢是一种耐腐蚀、耐高温的金属材料,常用于制造机械零件、压力容器、航空航天器械等领域。
在进行车削加工时,需要根据不锈钢的特性和要求选择合适的车削参数,以达到理想的加工效果。
一、切削速度(vc)切削速度是车刀在工件表面移动的速度,也是车削过程中最基本的参数。
不锈钢的切削速度较低,一般在30-60m/min之间。
过高的切削速度会导致刀具过热、磨损加剧,影响切削质量和加工效率;过低的切削速度则会造成切削力增大,刀具负荷过大,甚至造成刀具断裂。
二、进给速度(f)进给速度是指车刀在单位时间内向工件进给的量。
在车削不锈钢时,进给速度一般在0.05-0.15mm/r之间。
进给速度过高会造成刀具磨损加剧、表面质量下降;进给速度过低则会导致车削效率低下。
需要根据具体材料硬度和刀具的质量要求来确定合适的进给速度。
三、切削深度(ap)切削深度是指车刀在一次切削过程中,刀尖与工件表面的距离。
不锈钢的切削深度一般在0.5-4mm之间,具体取决于工件的硬度和刀具的强度。
切削深度过大会增加切削力,容易造成刀具断裂;切削深度过小则会导致车削效率低下。
四、切削角度(γ)切削角度是指车刀主切削刃与工件表面的切削角。
在车削不锈钢时,一般选择切削角较小的刀具,如30度左右。
切削角较小的刀具可以减小切削力,提高刀具的切削性能和寿命。
五、冷却液由于不锈钢的切削过程会产生较高的温度,因此在车削不锈钢时需要使用冷却液进行冷却和润滑。
冷却液的选择应根据不锈钢的材质和车削过程的具体要求来确定,以保证切削效果和刀具的使用寿命。
六、切削工具选择不锈钢的切削难度较大,对切削工具的要求也比较高。
一般采用硬质合金或散热钨钢制成的切削工具。
此外,还可以通过涂覆刀具和刀具几何形状的优化来提高不锈钢的切削效果。
总结起来,车削不锈钢需要根据不锈钢的特性和要求选择适当的车削参数,包括切削速度、进给速度、切削深度、切削角度等。
同时还需要选择合适的切削工具和冷却液,以保证切削效果和刀具的使用寿命。
常用刀具的切削参数

附录2 常用刀具的切削参数附录2-1 硬质合金车刀粗车外圆及端面的进给量背吃刀量p a /mm≤3 >3~5 >5~8 >8~12>12工件材料车刀刀杆尺寸 B ×H /mm工件直径 d /mm 进给量f /mm·r –116×2520 4060 100 400 0.3~0.4 0.4~0.5 0.5~0.7 0.6~0.9 0.8~1.2 — 0.3~0.4 0.4~0.6 0.5~0.6 0.7~1.0 — — 0.3~0.5 0.5~0.6 0.6~0.8 — — — 0.4~0.5 0.5~0.6 — — — — — 碳素钢、合金钢、耐热钢20×30 25×2520 40 60 100 400 0.3~0.4 0.4~0.5 0.5~0.7 0.8~1.0 1.2~1.4 — 0.3~0.4 0.5~0.7 0.7~0.9 1.0~1.2 — — 0.4~0.6 0.5~0.7 0.8~1.0 — — — 0.4~0.7 0.6~0.9 — — — — 0.4~0.6 16×254060 100 400 0.4~0.5 0.5~0.8 0.8~1.2 1.0~1.4 — 0.5~0.8 0.7~1.0 1.0~1.2 — 0.4~0.6 0.6~0.8 0.8~1.0 — — 0.5~0.7 0.6~0.8 — — — — 铸铁 铜合金20×30 25×2540 60 100 4000.4~0.5 0.5~0.9 0.9~1.3 1.2~1.8— 0.5~0.8 0.8~1.2 1.2~1.6— 0.4~0.7 0.7~1.0 1.0~1.3— — 0.5~0.8 0.9~1.1— — — 0.7~0.9 注:1. 加工断续表面及有冲击的工件时,表内进给量应乘系数k =0.75~0.85。
铰刀的切削参数参考

铰刀的切削参数参考铰刀是一种常用的切削工具,用于铰削工件的外轮廓或孔的内腔。
切削参数是指在铰削过程中,对铰刀进行切削的工作参数的设定,包括铰刀直径、进给速度、切削速度和铰削深度等。
正确的切削参数的选择和设定,可以确保铰削质量和铰削工艺的稳定性。
下面将介绍铰刀的切削参数参考。
1.铰刀直径:铰刀直径是选择铰刀的重要参数,一般要根据工件的孔径和铰削的要求来确定。
当工件孔径较大,要求铰削精度较低时,可以选择较大直径的铰刀。
而当工件孔径较小,要求铰削精度较高时,则可以选择较小直径的铰刀。
2.进给速度:进给速度是指铰刀在单位时间内对工件的进给量。
进给速度的选择要结合铰削材料、刀具材料和切削深度等因素来确定。
进给速度过高会导致切削过程中的切削力增大,引起振动和刀具损耗;而进给速度过低则容易造成刀具表面磨损。
3.切削速度:切削速度是指铰刀切削工件时刀具的相对运动速度。
切削速度的选择要综合考虑材料的切削性和刀具的耐用性。
一般来说,切削速度过高会引起刀具表面温度升高,磨损加剧;切削速度过低则导致铰削效率低下。
4.铰削深度:铰削深度是指每次切削时铰刀切削的深度。
铰刀的铰削深度要尽量合理控制,一般不宜过大过小。
铰削深度过大易导致切削力增大,振动加剧,降低铰削质量和刀具寿命;而铰削深度过小则会浪费加工时间。
5.刀具材料:刀具材料的选择是决定切削参数的重要因素之一、一般铰削常见材料时,可选择刚度高且刃口坚硬的合金刀具,以提高切削效率和工具寿命。
而对于切削硬材料时,可以选择刚性好、耐高温的PVD或CVD涂层刀具。
6.刀具涂层:刀具涂层是为了提高刀具的耐磨性和切削性能而进行的表面处理。
铰削过程中,刀具涂层能够减少切削温度,降低切削力,延长刀具寿命。
常见的刀具涂层有TiN、TiCN、TiAlN等。
综上所述,铰刀的切削参数参考包括铰刀直径、进给速度、切削速度、铰削深度、刀具材料和刀具涂层等。
正确设定这些切削参数,可以提高铰削质量,延长刀具寿命,并保证铰削过程的稳定性。
白钢铣刀切削参数

白钢铣刀切削参数白钢铣刀是一种常用的切削工具,广泛应用于机械加工领域。
针对白钢铣刀的切削参数,我们需要考虑切削速度、进给速度、切削深度、切削力等多个方面的因素。
以下是关于白钢铣刀切削参数的详细介绍。
一、切削速度切削速度是指刀具在切削过程中在工件上移动的速度,通常以单位时间内切削长度来表示。
对于白钢铣刀而言,切削速度是一个关键的切削参数。
切削速度的选择需要考虑到工件材料的硬度、刀具材料、刀具形状等因素。
一般情况下,白钢铣刀的切削速度可以在50-300米/分钟之间。
二、进给速度进给速度是指刀具在切削过程中对工件的进给速度,是切削参数中非常重要的一个因素。
进给速度的选择需要根据切削速度、刀具的刀尖半径、切削深度等因素进行综合考虑。
白钢铣刀的进给速度通常在0.1-0.5毫米/刀齿之间。
三、切削深度切削深度是指每次刀具对工件切削的深度。
刀具的切削深度选择要考虑到工件材料、刀具材料、刀尖半径等因素。
对于白钢铣刀而言,一般的切削深度可以在0.5-5毫米之间。
四、切削力切削力是切削参数中的一个重要指标,它直接影响到刀具的使用寿命和加工质量。
切削力的大小与切削速度、进给速度、切削深度、刀具的刃口半径等因素有关。
合理控制切削力,可以提高刀具的寿命,同时还能减小加工中的振动和噪音。
五、切屑处理在使用白钢铣刀进行切削加工时,要及时处理好切屑,避免切屑堆积在刀具和工件之间,影响切削质量和加工效率。
采取适当的冷却润滑方式,保持切屑的及时排出,对于提高加工质量和刀具寿命具有重要意义。
关于白钢铣刀切削参数的选择,需要根据具体的加工要求、工件材料、刀具情况等因素进行综合考虑。
合理选择切削参数可以有效提高加工效率、延长刀具寿命,同时还可以保证加工质量。
在进行白钢铣刀切削加工时,需要在实践中不断总结经验,以便更好地制定切削参数。