多色印刷中色差产生原因分析
浅谈色差产生的原因

浅谈色差产生的原因色差也叫色偏,在印刷中是不可避免的,只是大小的差异,一般要求△E*<3。
在这里主要从客观环境、印刷材料、印刷工艺、印刷设备四个方面分析色差产生的原因。
一、客观环境(一)照明光源。
我们一般说纯白才是标准的照明光源,但事实上并不是所有的照明光源都符合标准要求,或多或少都带有点偏色。
常见光源色偏情况如下表:偏色。
一般来说,光源偏色会导致印刷品往相应色偏色。
若光源偏黄,印刷品偏黄,光源偏蓝,印刷品偏蓝。
(二)环境色的影响。
环境色对人眼判断色彩影响很大。
同一绿色快置于红色环境中,它偏红。
如如将黑色60%置于实地和5%网点的环境中,可以明显的感受到它们的亮度有所差异。
因此辨别色差时必须注意消除环境色的影响。
二、印刷材料印刷材料主要是指纸张和油墨。
(一)纸张:1.纸张的白度,白度不同对印刷品颜色有重要影响,这是因为白度不同的纸张其效果就相当于在油墨中加入了不同程度的灰和黑,所以即使印刷时所用的墨量、色相都没有变化,由于白度也会造成色差。
2.纸张的吸收性,吸收性大的纸张,印迹不能很好地形成墨层,色彩不再鲜艳饱和。
3.纸张的光泽度和平滑度,如果纸张的光泽度和平滑度较高,我们观察到的颜色基本上是透过墨层反射出的颜色,主色光饱和度高。
如果纸张的表面粗糙、光泽度低,就会产生漫反射,就会降低主色光的饱和度,使我们人眼观察印刷品的颜色感觉变淡。
相同的墨量用密度计测量密度值。
平滑度光泽度高的纸张,密度值高。
平滑度光泽度低的纸张,密度值低。
(二)油墨:印刷墨层厚度和粘度不适容易产生印刷色差,印刷时,只有以适度而又均匀的印刷墨层,才能较好地保证印品的墨色质量,并有效防止印刷粘脏故障的产生。
若印刷墨层偏厚其粘度相应就增加,由此容易引起印刷中的纸面掉粉、拉毛现象,进而影响印品墨色均匀。
但若印刷墨层偏薄及油墨粘稠度过小,印品的墨色就显得偏淡,印品的视觉效果也就差。
随着印刷机转动时间的增长以及印刷速度的加快,摩擦系数增大,油墨温度升高,油墨的粘度会有所下降,所以调墨时必须考虑这些因素,以确保同批产品获得相对均衡的印刷墨色。
印刷质量问题总结
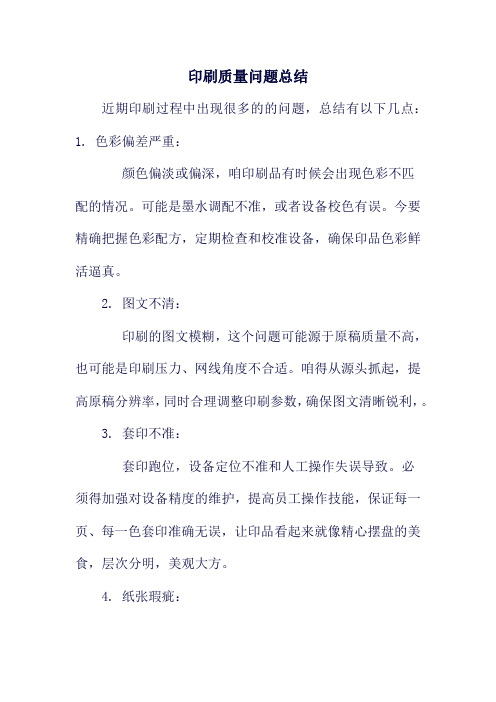
印刷质量问题总结
近期印刷过程中出现很多的的问题,总结有以下几点:1. 色彩偏差严重:
颜色偏淡或偏深,咱印刷品有时候会出现色彩不匹
配的情况。
可能是墨水调配不准,或者设备校色有误。
今要精确把握色彩配方,定期检查和校准设备,确保印品色彩鲜活逼真。
2. 图文不清:
印刷的图文模糊,这个问题可能源于原稿质量不高,也可能是印刷压力、网线角度不合适。
咱得从源头抓起,提高原稿分辨率,同时合理调整印刷参数,确保图文清晰锐利,。
3. 套印不准:
套印跑位,设备定位不准和人工操作失误导致。
必
须得加强对设备精度的维护,提高员工操作技能,保证每一页、每一色套印准确无误,让印品看起来就像精心摆盘的美食,层次分明,美观大方。
4. 纸张瑕疵:
纸张质量差、有污渍或破损必须严格筛选供应商,确保纸张质量过关,同时加强仓储管理,避免纸张受潮变形等问题,让每一张纸都成为印制精品的优质基材。
要想印刷质量过硬,咱就得从选材到工艺,从设备到人员,每个环节都得精细把控让人看了赏心悦目,用了满意放心。
今后必须要得吸取经验教训,不断改进,提升印刷品质,做到精益求精。
标签上有其他颜色字体的压印和色差特别大的原因分析和处理对策

标签上有其他颜色字体的压印和色差特别大的原因分析和处理对策印刷品色差大致分为两种现象,一是指的是:同一批产品的颜色一致,但与样稿的颜色有色差。
二是指的是:同批颜色之中存在色差,有的与样稿一致,但有的与样稿不一致。
智彤印刷厂小编现从以下的几个方面与大家进行探讨和分析。
一、第一种现象(同一批产品的颜色一致,但与样稿的颜色有色差)1、人为因素:与机长的技能水平无关,但与机长的责任心有关,既然同一批产品的颜色能保持一致,说明机长的技能水平还是不低的,但为什么与样稿不一致还敢印下来?首件签样了吗?这完全是机长的责任心问题。
(也不排除签样失误,如果是,这又与签样人的责任心有关)。
2、纸张颜色:白度不同的纸张对印刷墨层的颜色显现有不同的影响。
因为白度不同等于在油墨中加进不同黑、红、兰或黄,所以在印刷中尽管墨量、色相都没有变化,但实际油墨具有一定的透明性,色彩的效果随着纸张的白度不同而显现出来,造成不同的色差。
在开料时,就必须使用同一批号的纸张。
因为克重、规格、尺寸虽然相同,但生产的批号日期不同,纸张的白度就会有一定的差异,从而导致印品的颜色色差。
所以必须使用相同白度的纸张作为同一产品的印刷纸。
3、纸张的光泽度与平滑度:印刷品的光泽度取决于纸张的光泽度与平滑度。
胶印彩色印刷是当光线入射照到纸张表面时,光的反射到人眼的视网膜,通过感色细胞接受的光合作用而看到颜色的。
如果纸张的光泽度和平滑度较高,我们观察到的颜色基本上是透过墨层反射出的颜色,主色光饱和度高。
如果纸张的表面粗糙、光泽度低,就会产生漫反射,就会降低主色光的饱和度,使我们人眼观察印刷品的颜色感觉变淡。
相同的墨量用密度计测量密度值。
平滑度光泽度高的纸张,密度值高。
平滑度光泽度低的纸张,密度值低。
剖析胶印故障之色差

剖析胶印故障之色差色差也称色偏,是印刷过程中典型的质量弊病之一,在生产过程中,时常发生印刷品与打样样张色彩不相符的偏红、偏黄或偏青现象,或者图案画面叠印后混色故障,轻者影响产品质量,严重的会使整批产品报废,引起色偏和混色故障可归纳为以下原因:(1) 制版操作不规范引起的黄、品红、青某一色网点过深或过浅。
这里主要是指印版晒制过程中,晒版光源强度,光谱同印版感光特性不匹配,或曝光时间不当,显影液PH值以及显影时间长短掌握不恰当等,都可能造成印版网点过深或过浅。
(2) 油墨色彩调配不当或三原色油墨不相匹配。
即不是同品牌、同型号的油墨。
(3) 色序安排不合理,主要指多色胶印机的色序安排。
(4) 印刷纸张本身存在较严重的色偏现象。
(5) 由于印版两侧空白处严重挂脏,而引起混色现象(常见于半卫星式胶印机)。
(6)换色时,墨辊洗不干净。
(7)输纸不正常。
(8)换版不及时。
(9)签样者不负责任。
(10)水墨不平衡。
针对以上原因,胶印机操作者必须注意以下几个方面。
(1)在校正墨色时,必须做到墨色基本符合样张,才能开印,片面追求产量,往往墨色离付印样距离较大就开始印刷,这样势必造成前后印刷产品色差较大。
正确的操作应该是:印版校好后用过版纸来校正墨色,试印样张必须基本符合付印样时,方可正常印刷。
(2)一般情况下签样者必须在较短时间内签样完毕,以减少色差发生。
(3)正确掌握水墨平衡,特别注意润湿液的PH值,在同样的墨量情况下,水大水小也会影响颜色的深淡,用水量大小的原则为不挂脏的情况下,采用最小的供液量。
(4)根据纸张质量的情况,决定清洗橡皮布的频率,如纸张质量较差,而又没有及时清洗橡皮布,也会造成色差。
(5)保证输纸正常,每次输纸停顿都会造成张产品偏深。
所以要养成良好的习惯,即每次输纸停顿后再印刷时拿掉6~8张产品,以免混在成品中,造成色差。
(6)长版产品如发现印版花版,应及时更换。
花版对油墨的吸附能力降低,也会造成产品印迹的深淡,形成色差。
印刷色差标准

印刷色差标准印刷色差是指印刷品在印刷过程中出现的颜色偏差,是印刷行业中常见的质量问题。
印刷色差的产生会影响印刷品的质量和美观度,因此对于印刷色差的控制是非常重要的。
本文将就印刷色差标准进行详细介绍,希望能够帮助大家更好地了解和控制印刷色差。
首先,印刷色差的产生原因有很多,主要包括原材料的品质、印刷设备的精度、印刷工艺的控制等方面。
在印刷色差的控制过程中,我们需要从这些方面入手,全面提升印刷品的质量。
在选择原材料时,需要确保颜料的色彩稳定性和质量一致性,以避免色差的产生。
在印刷设备的使用过程中,需要保持设备的清洁和精度,定期进行维护和保养,以确保印刷品的色彩准确度。
此外,印刷工艺的控制也至关重要,需要严格按照标准操作流程进行操作,确保印刷品的色彩一致性。
其次,印刷色差的标准是非常重要的。
印刷色差标准是指在印刷过程中,对于色彩的准确度和一致性所做的规定和要求。
在印刷色差标准中,通常包括了颜色的测量方法、色差的判定标准、色彩的调配要求等内容。
通过严格执行印刷色差标准,可以有效地控制印刷色差的产生,提升印刷品的质量和稳定性。
另外,印刷色差标准的制定需要考虑到印刷品的具体要求和实际情况。
不同的印刷品可能对色彩的要求不同,因此在制定印刷色差标准时,需要根据具体的印刷需求来确定标准的内容和要求。
同时,印刷色差标准也需要考虑到印刷设备和工艺的实际情况,确保标准的执行性和可操作性。
最后,印刷色差标准的执行是非常关键的。
在印刷色差标准的执行过程中,需要严格按照标准要求进行操作,确保印刷品的色彩准确度和一致性。
在执行过程中,需要加强对印刷品的质量控制,及时发现和处理色差问题,确保印刷品的质量达到标准要求。
总之,印刷色差标准对于印刷行业来说是非常重要的。
通过严格执行印刷色差标准,可以有效地控制印刷色差的产生,提升印刷品的质量和稳定性,满足客户的需求和要求。
希望大家能够重视印刷色差标准的制定和执行,共同提升印刷品的质量,推动印刷行业的发展。
浅谈色差产生的原因

浅谈色差产生的原因色差也叫色偏,在印刷中是不可避免的,只是大小的差异,一般要求△E*<3。
在这里主要从客观环境、印刷材料、印刷工艺、印刷设备四个方面分析色差产生的原因。
一、客观环境(一)照明光源。
我们一般说纯白才是标准的照明光源,但事实上并不是所有的照明光源都符合标准要求,或多或少都带有点偏色。
常见光源色偏情况如下表:偏色。
一般来说,光源偏色会导致印刷品往相应色偏色。
若光源偏黄,印刷品偏黄,光源偏蓝,印刷品偏蓝。
(二)环境色的影响。
环境色对人眼判断色彩影响很大。
同一绿色快置于红色环境中,它偏红。
如如将黑色60%置于实地和5%网点的环境中,可以明显的感受到它们的亮度有所差异。
因此辨别色差时必须注意消除环境色的影响。
二、印刷材料印刷材料主要是指纸张和油墨。
(一)纸张:1.纸张的白度,白度不同对印刷品颜色有重要影响,这是因为白度不同的纸张其效果就相当于在油墨中加入了不同程度的灰和黑,所以即使印刷时所用的墨量、色相都没有变化,由于白度也会造成色差。
2.纸张的吸收性,吸收性大的纸张,印迹不能很好地形成墨层,色彩不再鲜艳饱和。
3.纸张的光泽度和平滑度,如果纸张的光泽度和平滑度较高,我们观察到的颜色基本上是透过墨层反射出的颜色,主色光饱和度高。
如果纸张的表面粗糙、光泽度低,就会产生漫反射,就会降低主色光的饱和度,使我们人眼观察印刷品的颜色感觉变淡。
相同的墨量用密度计测量密度值。
平滑度光泽度高的纸张,密度值高。
平滑度光泽度低的纸张,密度值低。
(二)油墨:印刷墨层厚度和粘度不适容易产生印刷色差,印刷时,只有以适度而又均匀的印刷墨层,才能较好地保证印品的墨色质量,并有效防止印刷粘脏故障的产生。
若印刷墨层偏厚其粘度相应就增加,由此容易引起印刷中的纸面掉粉、拉毛现象,进而影响印品墨色均匀。
但若印刷墨层偏薄及油墨粘稠度过小,印品的墨色就显得偏淡,印品的视觉效果也就差。
随着印刷机转动时间的增长以及印刷速度的加快,摩擦系数增大,油墨温度升高,油墨的粘度会有所下降,所以调墨时必须考虑这些因素,以确保同批产品获得相对均衡的印刷墨色。
印刷过程中颜色不稳定的原因
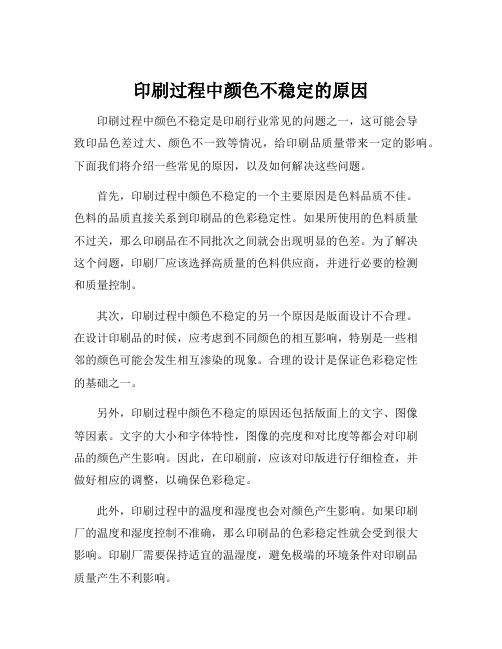
印刷过程中颜色不稳定的原因印刷过程中颜色不稳定是印刷行业常见的问题之一,这可能会导致印品色差过大、颜色不一致等情况,给印刷品质量带来一定的影响。
下面我们将介绍一些常见的原因,以及如何解决这些问题。
首先,印刷过程中颜色不稳定的一个主要原因是色料品质不佳。
色料的品质直接关系到印刷品的色彩稳定性。
如果所使用的色料质量不过关,那么印刷品在不同批次之间就会出现明显的色差。
为了解决这个问题,印刷厂应该选择高质量的色料供应商,并进行必要的检测和质量控制。
其次,印刷过程中颜色不稳定的另一个原因是版面设计不合理。
在设计印刷品的时候,应考虑到不同颜色的相互影响,特别是一些相邻的颜色可能会发生相互渗染的现象。
合理的设计是保证色彩稳定性的基础之一。
另外,印刷过程中颜色不稳定的原因还包括版面上的文字、图像等因素。
文字的大小和字体特性,图像的亮度和对比度等都会对印刷品的颜色产生影响。
因此,在印刷前,应该对印版进行仔细检查,并做好相应的调整,以确保色彩稳定。
此外,印刷过程中的温度和湿度也会对颜色产生影响。
如果印刷厂的温度和湿度控制不准确,那么印刷品的色彩稳定性就会受到很大影响。
印刷厂需要保持适宜的温湿度,避免极端的环境条件对印刷品质量产生不利影响。
最后,对于印刷过程中颜色不稳定的解决方法,我们可以通过加强色号管理来进行控制。
印刷厂可以建立完善的色号管理系统,记录各个印刷作业所使用的色彩配置信息,保证每次印刷都能够重现相同的色彩效果。
总之,印刷过程中颜色不稳定是一个印刷行业常见的问题,影响着印刷品的质量。
要解决这个问题,我们需要从色料品质、版面设计、文字、图像、温湿度以及色号管理等多个方面进行控制,并保持持续的检测和调整。
相信通过这些努力,印刷品的色彩稳定性将得到大幅提升。
印刷色差定义
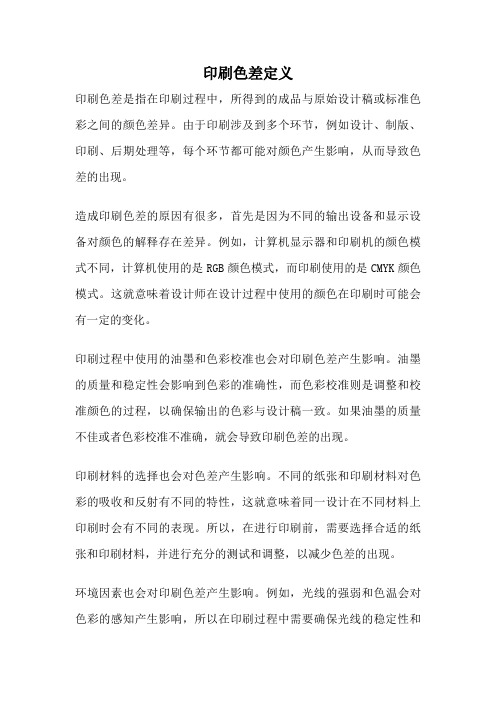
印刷色差定义印刷色差是指在印刷过程中,所得到的成品与原始设计稿或标准色彩之间的颜色差异。
由于印刷涉及到多个环节,例如设计、制版、印刷、后期处理等,每个环节都可能对颜色产生影响,从而导致色差的出现。
造成印刷色差的原因有很多,首先是因为不同的输出设备和显示设备对颜色的解释存在差异。
例如,计算机显示器和印刷机的颜色模式不同,计算机使用的是RGB颜色模式,而印刷使用的是CMYK颜色模式。
这就意味着设计师在设计过程中使用的颜色在印刷时可能会有一定的变化。
印刷过程中使用的油墨和色彩校准也会对印刷色差产生影响。
油墨的质量和稳定性会影响到色彩的准确性,而色彩校准则是调整和校准颜色的过程,以确保输出的色彩与设计稿一致。
如果油墨的质量不佳或者色彩校准不准确,就会导致印刷色差的出现。
印刷材料的选择也会对色差产生影响。
不同的纸张和印刷材料对色彩的吸收和反射有不同的特性,这就意味着同一设计在不同材料上印刷时会有不同的表现。
所以,在进行印刷前,需要选择合适的纸张和印刷材料,并进行充分的测试和调整,以减少色差的出现。
环境因素也会对印刷色差产生影响。
例如,光线的强弱和色温会对色彩的感知产生影响,所以在印刷过程中需要确保光线的稳定性和合适性,以减少色差的出现。
针对印刷色差的问题,可以采取一些措施来进行调整和修正。
首先,设计师可以在设计时使用专门的色彩模式,以便更好地适应印刷的要求。
其次,印刷厂可以加强对油墨和色彩校准的管理,确保印刷成品的颜色准确性。
此外,对于特殊的印刷需求,可以进行样张测试和颜色校正,以确保最终的印刷效果符合要求。
总的来说,印刷色差是印刷过程中常见的问题,但可以通过正确的操作和管理来减少其发生。
通过合理的设计和选择合适的印刷材料,可以使印刷成品的色彩更加准确和稳定,从而提高印刷品质。
同时,印刷厂和设计师之间的紧密合作也是解决印刷色差问题的关键,只有共同努力,才能实现印刷品的高质量和一致性。
在印刷过程中引起专色油墨色差的因素分析

在印刷过程中引起专色油墨色差的因素分析在印刷过程中,导致专色油墨生产色差的因素很多,下面对这些因素分别进行探讨。
1.纸张对颜色的影响纸张对墨层颜色的影响主要体现在3个方面。
(1)纸张白度:白度不同(或带有一定颜色)的纸张,对印刷墨层的颜色显现有不同的影响。
对同一种白板纸而言,白度不同,印刷墨层的颜色差异主要体现在专色墨中黑墨成分的多少,尤其是对明度在70以上的颜色,影响特别明显,造成专色墨的配比差别很大。
因此,在实际生产中应尽量选用白度相同的纸张印刷,以减小纸张白度对印刷颜色的影响。
(2)吸收性:同一种油墨在相同条件下印刷到吸收性不同的纸张上时,会有不同的印刷光泽。
纸张的结构决定了纸张表面存在着由植物纤维形成的凹凸和孔隙,为了使纸面获得良好的均匀性和平滑度,一般要在纸张表面涂布不同厚度的涂料。
涂料的性质和厚度决定了纸张表面对油墨的吸收能力。
吸收能力不同,必然要使印刷墨层的颜色产生差异。
非涂料纸与涂料纸相比,黑色墨层会显得灰暗、无光泽,并且彩色墨层会产生漂移,由青色墨和品红色墨调配出的颜色表现最明显。
(3)光泽度与平滑度:印刷品的光泽度取决于纸张的光泽度与平滑度。
印刷用纸的表面属于半光泽表面,尤其是涂料纸。
在彩色印刷品上,当光线以45°入射角照射到纸张表面时,约有4%的光会被反射掉,这就是首层表面反射光。
而其余入射光穿过油墨层,经过油墨的选择性吸收后,再透过墨层反射出来,进入人眼,被人眼所感知,这就是我们观察到的颜色。
若纸张的光泽度和平滑度较高,则首层表面反射光是做镜面反射,不易进入人眼,此时观察到的颜色基本就是透过墨层反射出的颜色。
若纸张表面粗糙,光泽度低,则首层表面反射光将发生漫反射,此时我们看到的颜色是主色光和首层表面反射光产生的混合色。
由于这里面含有白光成分,因此降低了主色光的饱和度,所以人们观察印品时感觉颜色变浅,用密度计测量时密度值降低,明度上升。
2.表面处理对颜色的影响包装类产品的表面处理方式主要有覆膜(亮光膜、亚光膜)、上光(罩亮光油、亚光油、UV光油)等。
印刷套色偏差分析报告
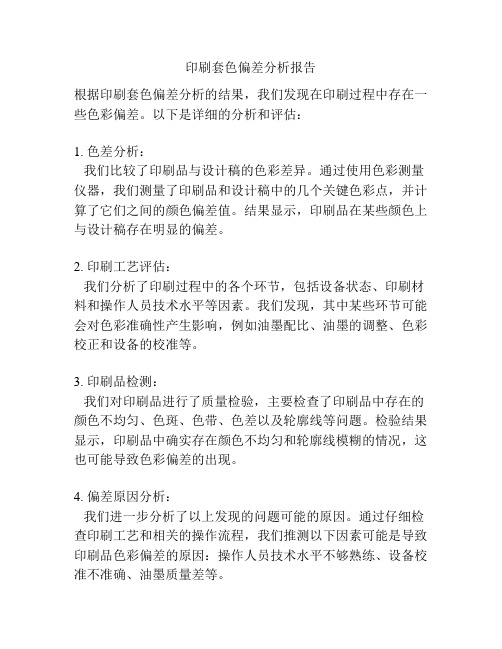
印刷套色偏差分析报告根据印刷套色偏差分析的结果,我们发现在印刷过程中存在一些色彩偏差。
以下是详细的分析和评估:1. 色差分析:我们比较了印刷品与设计稿的色彩差异。
通过使用色彩测量仪器,我们测量了印刷品和设计稿中的几个关键色彩点,并计算了它们之间的颜色偏差值。
结果显示,印刷品在某些颜色上与设计稿存在明显的偏差。
2. 印刷工艺评估:我们分析了印刷过程中的各个环节,包括设备状态、印刷材料和操作人员技术水平等因素。
我们发现,其中某些环节可能会对色彩准确性产生影响,例如油墨配比、油墨的调整、色彩校正和设备的校准等。
3. 印刷品检测:我们对印刷品进行了质量检验,主要检查了印刷品中存在的颜色不均匀、色斑、色带、色差以及轮廓线等问题。
检验结果显示,印刷品中确实存在颜色不均匀和轮廓线模糊的情况,这也可能导致色彩偏差的出现。
4. 偏差原因分析:我们进一步分析了以上发现的问题可能的原因。
通过仔细检查印刷工艺和相关的操作流程,我们推测以下因素可能是导致印刷品色彩偏差的原因:操作人员技术水平不够熟练、设备校准不准确、油墨质量差等。
5. 改进建议:结合以上的分析结果,我们提出以下改进建议,以减少或解决印刷套色偏差的问题:- 对操作人员进行培训,提高其技术水平和对色彩准确性的敏感度;- 定期校准和维护印刷设备,确保其准确度和一致性;- 选择质量稳定的印刷材料和油墨,并进行充分的测试和调整;- 加强对印刷过程中各个环节的监控和质量控制;- 定期对印刷品进行质量检验和评估,及时发现并解决问题。
通过以上的改进措施,我们相信可以显著减少印刷套色偏差的发生,提高印刷品的色彩准确性和稳定性。
印刷色差标准

印刷色差标准印刷色差是印刷行业中常见的问题,它指的是在印刷过程中,由于各种原因导致的印刷品与设计稿或者标准色样之间的色彩差异。
色差严重影响了印刷品的质量,因此对印刷色差的控制和管理是非常重要的。
首先,印刷色差的原因有很多,主要包括原材料的差异、印刷设备的差异、印刷环境的差异等。
其中,原材料的差异包括纸张、油墨、版材等,它们的质量和特性不同都会对印刷色彩产生影响。
印刷设备的差异主要指的是不同印刷机的性能和调整能力不同,会对色彩的还原产生影响。
印刷环境的差异包括温度、湿度等因素,也会对印刷色彩产生影响。
因此,要控制印刷色差,首先要从这些方面入手,对原材料、设备和环境进行有效的管理和控制。
其次,针对不同的印刷品,有不同的色差标准。
比如,对于彩页印刷品,一般采用的是国际通用的CMYK四色印刷标准,色差一般控制在3ΔE以内。
而对于专色印刷品,一般采用的是Pantone等专色标准,色差一般控制在2ΔE以内。
此外,对于不同的印刷品种,比如书籍、包装、广告等,也有不同的色差标准。
因此,印刷色差的控制需要根据具体情况有针对性地制定相应的标准。
另外,印刷色差的控制还需要依靠一些专业的仪器和设备,比如色差仪、印刷品检测仪等。
这些仪器可以帮助印刷厂对印刷品的色差进行准确的测量和分析,从而找出问题所在,采取相应的措施进行调整和改进。
最后,印刷色差的控制是一个系统工程,需要印刷厂从原材料采购到印刷生产再到最终的质量检验都要进行全面的管理和控制。
只有这样,才能够保证印刷品的色彩质量达到客户的要求,提高印刷企业的竞争力。
综上所述,印刷色差的控制是印刷行业中非常重要的一个环节,需要印刷企业高度重视。
只有通过科学的管理和有效的控制,才能够生产出高质量的印刷品,满足客户的需求,赢得市场的认可。
希望各位印刷从业者都能够重视印刷色差的控制,不断提升自身的印刷技术水平和管理水平,为印刷行业的发展做出更大的贡献。
印刷色差产生的原因
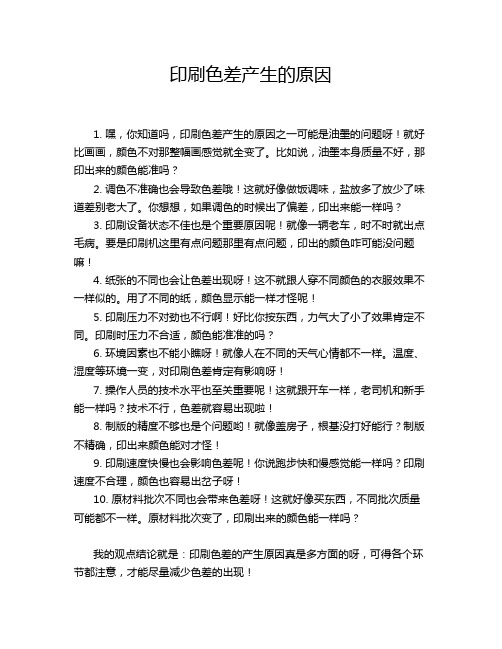
印刷色差产生的原因
1. 嘿,你知道吗,印刷色差产生的原因之一可能是油墨的问题呀!就好比画画,颜色不对那整幅画感觉就全变了。
比如说,油墨本身质量不好,那印出来的颜色能准吗?
2. 调色不准确也会导致色差哦!这就好像做饭调味,盐放多了放少了味道差别老大了。
你想想,如果调色的时候出了偏差,印出来能一样吗?
3. 印刷设备状态不佳也是个重要原因呢!就像一辆老车,时不时就出点毛病。
要是印刷机这里有点问题那里有点问题,印出的颜色咋可能没问题嘛!
4. 纸张的不同也会让色差出现呀!这不就跟人穿不同颜色的衣服效果不一样似的。
用了不同的纸,颜色显示能一样才怪呢!
5. 印刷压力不对劲也不行啊!好比你按东西,力气大了小了效果肯定不同。
印刷时压力不合适,颜色能准准的吗?
6. 环境因素也不能小瞧呀!就像人在不同的天气心情都不一样。
温度、湿度等环境一变,对印刷色差肯定有影响呀!
7. 操作人员的技术水平也至关重要呢!这就跟开车一样,老司机和新手能一样吗?技术不行,色差就容易出现啦!
8. 制版的精度不够也是个问题哟!就像盖房子,根基没打好能行?制版不精确,印出来颜色能对才怪!
9. 印刷速度快慢也会影响色差呢!你说跑步快和慢感觉能一样吗?印刷速度不合理,颜色也容易出岔子呀!
10. 原材料批次不同也会带来色差呀!这就好像买东西,不同批次质量可能都不一样。
原材料批次变了,印刷出来的颜色能一样吗?
我的观点结论就是:印刷色差的产生原因真是多方面的呀,可得各个环节都注意,才能尽量减少色差的出现!。
印刷色差8d报告完整版范文
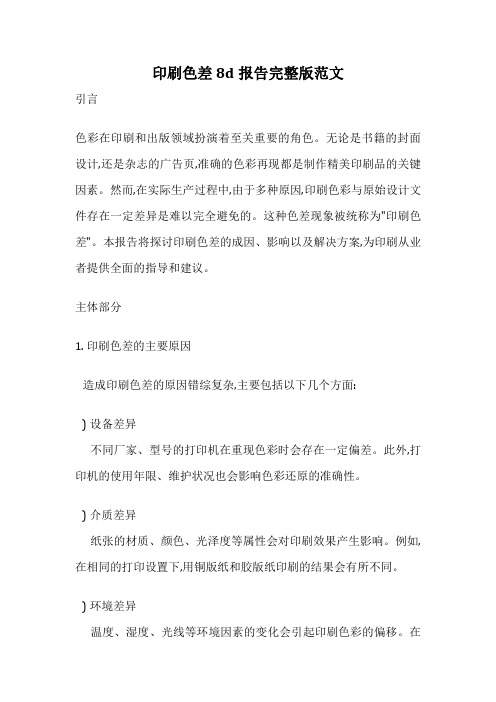
印刷色差8d报告完整版范文引言色彩在印刷和出版领域扮演着至关重要的角色。
无论是书籍的封面设计,还是杂志的广告页,准确的色彩再现都是制作精美印刷品的关键因素。
然而,在实际生产过程中,由于多种原因,印刷色彩与原始设计文件存在一定差异是难以完全避免的。
这种色差现象被统称为"印刷色差"。
本报告将探讨印刷色差的成因、影响以及解决方案,为印刷从业者提供全面的指导和建议。
主体部分1. 印刷色差的主要原因造成印刷色差的原因错综复杂,主要包括以下几个方面:) 设备差异不同厂家、型号的打印机在重现色彩时会存在一定偏差。
此外,打印机的使用年限、维护状况也会影响色彩还原的准确性。
) 介质差异纸张的材质、颜色、光泽度等属性会对印刷效果产生影响。
例如,在相同的打印设置下,用铜版纸和胶版纸印刷的结果会有所不同。
) 环境差异温度、湿度、光线等环境因素的变化会引起印刷色彩的偏移。
在不同的生产车间,色差现象会更加明显。
) 人为操作差异印刷工人对机器的设置、调试以及后期的人工修饰等操作,都可能导致印刷色差的发生。
2. 印刷色差的影响印刷色差不仅会影响最终成品的视觉效果,还可能对企业的品牌形象、营销策略等造成负面影响。
具体来说:) 视觉体验受损色彩失真会破坏设计师原先的构思,降低印刷品的美学价值和观赏性。
) 信息传达受阻在包装印刷中,色差会干扰产品的识别度,影响营销信息的有效传播。
) 品牌形象遭损对于重视(视觉识别)系统的企业而言,色差会削弱品牌在视觉层面的统一性和专业性。
3. 解决印刷色差的策略为了尽量减小印刷色差,行业内通常采取以下对策:) 标准化色彩管理通过建立统一的色彩工作流程,并使用行业标准的(国际色彩联盟)色彩配置文件,在设计源文件和打印输出之间建立"色彩桥梁"。
) 定期校准设备对打印机、显示器等设备进行定期校准和维护,确保色彩再现的一致性。
) 控制环境变量在印刷车间内安装恒温恒湿设备,并使用标准光源,将环境因素对色彩的影响降至最低。
印刷色差的不良因素
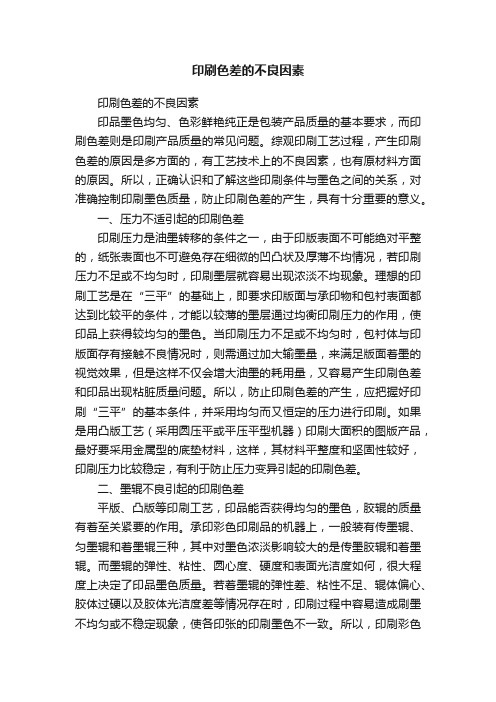
印刷色差的不良因素印刷色差的不良因素印品墨色均匀、色彩鲜艳纯正是包装产品质量的基本要求,而印刷色差则是印刷产品质量的常见问题。
综观印刷工艺过程,产生印刷色差的原因是多方面的,有工艺技术上的不良因素,也有原材料方面的原因。
所以,正确认识和了解这些印刷条件与墨色之间的关系,对准确控制印刷墨色质量,防止印刷色差的产生,具有十分重要的意义。
一、压力不适引起的印刷色差印刷压力是油墨转移的条件之一,由于印版表面不可能绝对平整的,纸张表面也不可避免存在细微的凹凸状及厚薄不均情况,若印刷压力不足或不均匀时,印刷墨层就容易出现浓淡不均现象。
理想的印刷工艺是在“三平”的基础上,即要求印版面与承印物和包衬表面都达到比较平的条件,才能以较薄的墨层通过均衡印刷压力的作用,使印品上获得较均匀的墨色。
当印刷压力不足或不均匀时,包衬体与印版面存有接触不良情况时,则需通过加大输墨量,来满足版面着墨的视觉效果,但是这样不仅会增大油墨的耗用量,又容易产生印刷色差和印品出现粘脏质量问题。
所以,防止印刷色差的产生,应把握好印刷“三平”的基本条件,并采用均匀而又恒定的压力进行印刷。
如果是用凸版工艺(采用圆压平或平压平型机器)印刷大面积的图版产品,最好要采用金属型的底垫材料,这样,其材料平整度和坚固性较好,印刷压力比较稳定,有利于防止压力变异引起的印刷色差。
二、墨辊不良引起的印刷色差平版、凸版等印刷工艺,印品能否获得均匀的墨色,胶辊的质量有着至关紧要的作用。
承印彩色印刷品的机器上,一般装有传墨辊、匀墨辊和着墨辊三种,其中对墨色浓淡影响较大的是传墨胶辊和着墨辊。
而墨辊的弹性、粘性、圆心度、硬度和表面光洁度如何,很大程度上决定了印品墨色质量。
若着墨辊的弹性差、粘性不足、辊体偏心、胶体过硬以及胶体光洁度差等情况存在时,印刷过程中容易造成刷墨不均匀或不稳定现象,使各印张的印刷墨色不一致。
所以,印刷彩色产品应采用质量较好的胶辊,才能确保每一印刷周期涂布于版面上的油墨保持基本一致。
专色印刷:导致产生色差的五个因素
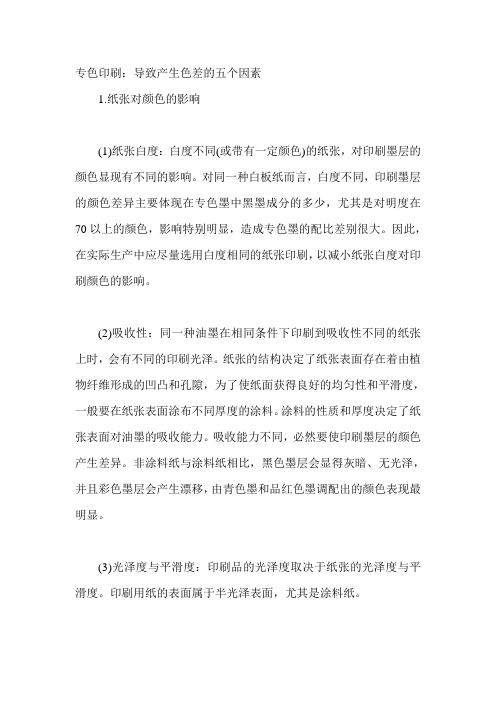
专色印刷:导致产生色差的五个因素1.纸张对颜色的影响(1)纸张白度:白度不同(或带有一定颜色)的纸张,对印刷墨层的颜色显现有不同的影响。
对同一种白板纸而言,白度不同,印刷墨层的颜色差异主要体现在专色墨中黑墨成分的多少,尤其是对明度在70以上的颜色,影响特别明显,造成专色墨的配比差别很大。
因此,在实际生产中应尽量选用白度相同的纸张印刷,以减小纸张白度对印刷颜色的影响。
(2)吸收性:同一种油墨在相同条件下印刷到吸收性不同的纸张上时,会有不同的印刷光泽。
纸张的结构决定了纸张表面存在着由植物纤维形成的凹凸和孔隙,为了使纸面获得良好的均匀性和平滑度,一般要在纸张表面涂布不同厚度的涂料。
涂料的性质和厚度决定了纸张表面对油墨的吸收能力。
吸收能力不同,必然要使印刷墨层的颜色产生差异。
非涂料纸与涂料纸相比,黑色墨层会显得灰暗、无光泽,并且彩色墨层会产生漂移,由青色墨和品红色墨调配出的颜色表现最明显。
(3)光泽度与平滑度:印刷品的光泽度取决于纸张的光泽度与平滑度。
印刷用纸的表面属于半光泽表面,尤其是涂料纸。
在彩色印刷品上,当光线以45°入射角照射到纸张表面时,约有4%的光会被反射掉,这就是首层表面反射光。
而其余入射光穿过油墨层,经过油墨的选择性吸收后,再透过墨层反射出来,进入人眼,被人眼所感知,这就是我们观察到的颜色。
若纸张的光泽度和平滑度较高,则首层表面反射光是做镜面反射,不易进入人眼,此时观察到的颜色基本就是透过墨层反射出的颜色。
若纸张表面粗糙,光泽度低,则首层表面反射光将发生漫反射,此时我们看到的颜色是主色光和首层表面反射光产生的混合色。
由于这里面含有白光成分,因此降低了主色光的饱和度,所以人们观察印品时感觉颜色变浅,用密度计测量时密度值降低,明度上升。
2.表面处理对颜色的影响包装类产品的表面处理方式主要有覆膜(亮光膜、亚光膜)、上光(罩亮光油、亚光油、UV光油)等。
印品经过这些表面处理后,会有不同程度的色相变化和色密度变化。
印刷色偏原因分析及解决方法
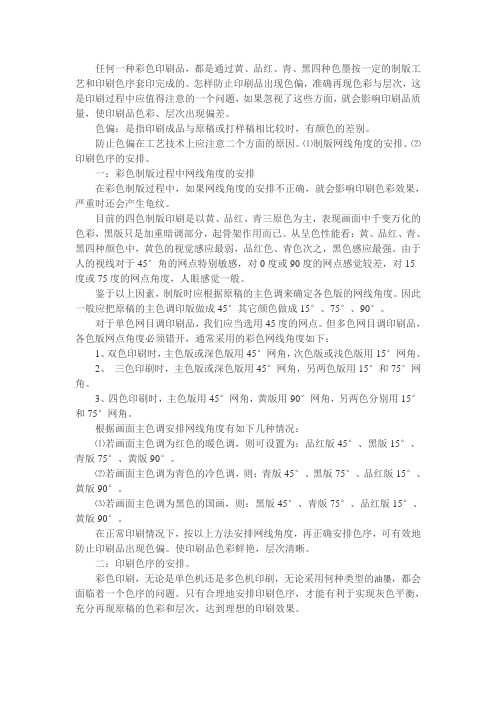
任何一种彩色印刷品,都是通过黄、品红、青、黑四种色墨按一定的制版工艺和印刷色序套印完成的。
怎样防止印刷品出现色偏,准确再现色彩与层次,这是印刷过程中应值得注意的一个问题,如果忽视了这些方面,就会影响印刷品质量,使印刷品色彩、层次出现偏差。
色偏:是指印刷成品与原稿或打样稿相比较时,有颜色的差别。
防止色偏在工艺技术上应注意二个方面的原因。
⑴制版网线角度的安排。
⑵印刷色序的安排。
一:彩色制版过程中网线角度的安排在彩色制版过程中,如果网线角度的安排不正确,就会影响印刷色彩效果,严重时还会产生龟纹。
目前的四色制版印刷是以黄、品红、青三原色为主,表现画面中千变万化的色彩,黑版只是加重暗调部分,起骨架作用而已。
从呈色性能看:黄、品红、青、黑四种颜色中,黄色的视觉感应最弱,品红色、青色次之,黑色感应最强。
由于人的视线对于45°角的网点特别敏感,对0度或90度的网点感觉较差,对15度或75度的网点角度,人眼感觉一般。
鉴于以上因素,制版时应根据原稿的主色调来确定各色版的网线角度。
因此一般应把原稿的主色调印版做成45°其它颜色做成15°、75°、90°。
对于单色网目调印刷品,我们应当选用45度的网点。
但多色网目调印刷品,各色版网点角度必须错开,通常采用的彩色网线角度如下:1、双色印刷时,主色版或深色版用45°网角,次色版或浅色版用15°网角。
2、三色印刷时,主色版或深色版用45°网角,另两色版用15°和75°网角。
3、四色印刷时,主色版用45°网角,黄版用90°网角,另两色分别用15°和75°网角。
根据画面主色调安排网线角度有如下几种情况:⑴若画面主色调为红色的暖色调,则可设置为:品红版45°、黑版15°、青版75°、黄版90°。
⑵若画面主色调为青色的冷色调,则:青版45°、黑版75°、品红版15°、黄版90°。
印刷色差临时措施

印刷色差临时措施报告一、引言在印刷行业中,色差问题一直是困扰企业和客户的一大难题。
由于设备、材料、环境等多种因素的影响,印刷品在实际生产过程中往往难以完全达到预期的色彩效果。
这不仅影响了印刷品的美观度和品质,还可能给企业带来经济损失和声誉损害。
因此,制定一套有效的临时措施来应对印刷色差问题显得尤为重要。
二、问题分析在解决印刷色差问题之前,我们首先需要对其产生的原因进行深入分析。
一般来说,印刷色差可能由以下几个方面导致:1. 设备因素:印刷设备的精度、稳定性以及维护状况都会影响印刷品的色彩效果。
例如,印刷机的压力、速度、温度等参数设置不当,都可能导致色差问题。
2. 材料因素:印刷材料的质量也是影响印刷品色彩的重要因素。
不同批次的油墨、纸张等原材料可能存在色差,从而影响最终产品的色彩一致性。
3. 环境因素:印刷环境的温度、湿度、光照等条件都会对印刷品的色彩产生影响。
例如,湿度过高可能导致油墨干燥不彻底,从而影响色彩效果。
4. 操作因素:操作人员的技能水平和操作习惯也会对印刷品的色彩产生影响。
例如,调色不准确、印刷压力过大等都可能导致色差问题。
三、临时措施制定针对以上分析的原因,我们制定以下临时措施来应对印刷色差问题:1. 设备调整与优化:对印刷设备进行全面的检查和维护,确保设备处于良好状态。
同时,根据印刷品的要求调整设备的各项参数,如压力、速度、温度等,以达到最佳的印刷效果。
2. 材料控制:加强原材料的采购和检验工作,确保油墨、纸张等原材料的质量稳定且符合生产要求。
对于不同批次的原材料,要进行严格的色差检测和控制,避免因原材料色差导致的印刷品色差问题。
3. 环境控制:对印刷环境进行严格的监控和调整,确保温度、湿度、光照等条件符合生产要求。
在必要时,可以采取加湿、除湿、恒温等措施来改善环境条件。
4. 操作规范:加强对操作人员的培训和监督,提高其技能水平和操作规范性。
制定详细的操作规程和调色标准,确保操作人员在调色、印刷等关键环节能够准确、稳定地控制色彩效果。
印刷过程中颜色不稳定的原因
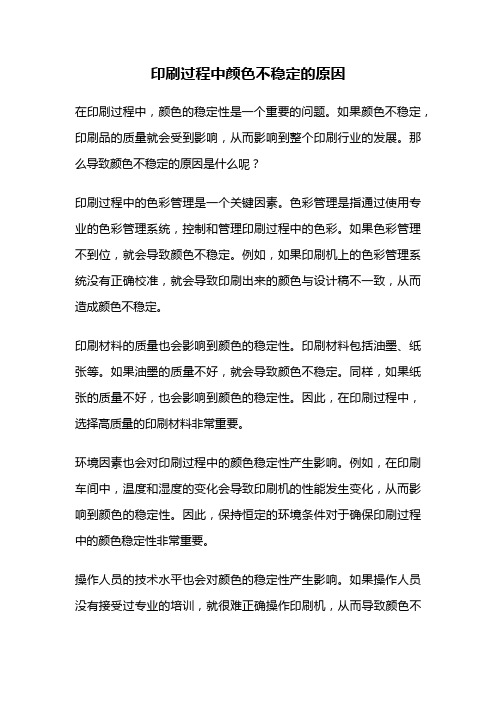
印刷过程中颜色不稳定的原因在印刷过程中,颜色的稳定性是一个重要的问题。
如果颜色不稳定,印刷品的质量就会受到影响,从而影响到整个印刷行业的发展。
那么导致颜色不稳定的原因是什么呢?印刷过程中的色彩管理是一个关键因素。
色彩管理是指通过使用专业的色彩管理系统,控制和管理印刷过程中的色彩。
如果色彩管理不到位,就会导致颜色不稳定。
例如,如果印刷机上的色彩管理系统没有正确校准,就会导致印刷出来的颜色与设计稿不一致,从而造成颜色不稳定。
印刷材料的质量也会影响到颜色的稳定性。
印刷材料包括油墨、纸张等。
如果油墨的质量不好,就会导致颜色不稳定。
同样,如果纸张的质量不好,也会影响到颜色的稳定性。
因此,在印刷过程中,选择高质量的印刷材料非常重要。
环境因素也会对印刷过程中的颜色稳定性产生影响。
例如,在印刷车间中,温度和湿度的变化会导致印刷机的性能发生变化,从而影响到颜色的稳定性。
因此,保持恒定的环境条件对于确保印刷过程中的颜色稳定性非常重要。
操作人员的技术水平也会对颜色的稳定性产生影响。
如果操作人员没有接受过专业的培训,就很难正确操作印刷机,从而导致颜色不稳定。
因此,提高操作人员的技术水平,加强培训非常重要。
设计稿的质量也会影响到颜色的稳定性。
如果设计稿中的颜色不准确,就很难在印刷过程中获得稳定的颜色。
因此,在设计稿制作的过程中,要注意颜色的准确性。
印刷过程中颜色不稳定的原因有很多,包括色彩管理不到位、印刷材料质量不好、环境因素的变化、操作人员技术水平不高以及设计稿质量不佳等。
为了解决这些问题,印刷企业需要加强对色彩管理的重视,选择高质量的印刷材料,确保恒定的环境条件,提高操作人员的技术水平,并加强对设计稿的审核和校对工作。
只有这样,才能够确保印刷过程中颜色的稳定性,提高印刷品的质量,推动印刷行业的健康发展。
浅析胶印印刷品色差产生原因分析与控制方法

浅析胶印印刷品色差产生原因分析与控制方法经过分析,大部分包装印刷品还是采用胶印的方式进行,利用这种方式,能具有丰富的色彩、质感比较强烈,图案层次性比较好,更能符合实际的需求。
所以,在现代胶印机设备情况下,能够实现多色一次成型具有较高效率。
但是,相比于其他印刷方式来说,这种胶印的印刷品往往具有色差比较大的问题。
为了进一步从工艺的角度考虑上述问题,分析其色差产生的原因,主要涉及到人员、机器、方法等方面的内容。
这里结合自身的工作经验进行分析如下:1人员第一,在进行墨色换的过程中,没有彻底清洗,其中残墨存留在磨辊、墨斗中,如果为深色墨换成浅色墨的过程中,这种影响更为明显,则具有更大的色相偏差;同时,如果存在时间比较长的深色墨印情况,则应该清洗相关的水斗、水辊等[1]。
比如,某六色胶印机的第二组具有长时间的蓝条印刷情况,在进行黄色条的过程中,则要进行多次的洗车处理,否则则会造成黄墨越来越黑的情况。
第二,在进行墨色的调配比例中存在一定问题,存在着各个批色间的差异。
比如,由于不重视这方面的内容,容易造成机盒墨色和封样的不一致问题。
所以,在进行专用墨的调配过程中,一定要从细节入手,重视相应的精确化称量工作,否则则会造成色相改变,出现色差问题。
第三,如果校墨色时间比较短,这样还没有实现均匀化的墨色情况,这往往是会形成局部色差的重要原因。
第四,对于不均匀的墨色来说,特别是存在局部色差情况,人为出现手动拍墨以及没有合理化进行收紧磨牙等问题,在这样不断加剧的过程中,存在着不稳定的情况,有效方式则是多走坏片,实现墨的均匀。
第五,考虑脏点、毛绒、墨皮等方面的影响,会实现停机频繁的问题出现,也会造成同批色差的影响,在这样影响下,肯定会使得水墨平衡受到影响。
所以,刚开机的过程中,应该实现坏片的多加的要求,能实现跑匀墨色,保证墨色一致性要求。
第六,如果存在着比较长的印刷时间的影响,也会造成水墨失去平衡,出现油墨乳化问题,造成颜色的暗淡,所以,切记盲目增加墨量,而应该保证能及时洗车,进行重新上墨处理。