冲压件复合模设计
落料冲孔复合模设计方案实例

落料冲孔复合模设计方案实例一、引言随着工业制造技术的不断发展,冲压工艺在各个领域得到广泛应用。
而在冲压过程中,落料冲孔操作是一个非常重要的环节。
为了提高生产效率和产品质量,设计和制造一套高效可靠的落料冲孔复合模非常关键。
本文将以某企业生产的金属工件为例,介绍一种落料冲孔复合模设计方案。
二、设计目标在设计落料冲孔复合模时,需实现以下目标:1. 提高生产效率:减少生产过程中的冲孔次数和时间。
2. 保证产品质量:减少冲压产生的变形和裂纹,提高工件尺寸和形状的一致性。
3. 提高模具使用寿命:减少因冲压而导致的模具磨损和损坏。
三、设计要素1. 材料选择:选用高硬度和高耐磨性的冷作工具钢作为模具材料,以确保模具的使用寿命和稳定性。
2. 设计结构:根据金属工件的形状和尺寸要求,合理设计落料冲孔复合模的结构和布局。
模具的结构应有利于材料的流动和排气,并能够减小冲压时的变形和应力集中。
3. 润滑系统:在模具设计中,考虑设置润滑系统来减少摩擦和热量的产生,以延长模具寿命。
4. 加工工艺:考虑使用先进的数控加工设备和软件,进行精确的模具制造和调试,以确保模具的准确度和稳定性。
四、具体方案基于以上设计要素,我们提出以下具体方案:1. 模具结构设计:采用分层式复合模设计,将落料和冲孔的功能集成在同一个模具内。
同时,在模具底部设计合适的排气孔和排渣槽,以确保材料的流动性和排气性。
2. 润滑系统设计:在模具的摩擦面和冲孔孔径处设置润滑油槽和喷油装置,以减少热量的产生和模具磨损。
同时,结合自动化控制系统,实现润滑油的定量供给和循环利用,提高润滑效果。
3. 加工工艺设计:采用数控加工设备进行模具的制造和加工,结合CAD和CAM软件进行模具的设计和调试。
优化加工工艺参数,确保模具的精度和稳定性。
五、验证和改进在设计完成后,进行模具的试制和测试。
通过实际生产的验证,对设计方案进行评估和改进。
调整模具的结构和加工工艺参数,优化模具的性能和稳定性,以实现更好的生产效果和质量要求。
垫片复合冲压模具的设计

垫片复合冲压模具的设计垫片是一种常见的密封元件,广泛应用于机械设备、汽车、航空航天和化工等领域。
垫片的作用是填充两个相互连接部件的间隙,防止介质泄漏。
垫片的形状多样,常见的有方形、圆形、椭圆形和不规则形状等。
为了生产高质量的垫片,可以采用复合冲压模具进行制造。
下面将介绍垫片复合冲压模具的设计过程和注意事项。
一、垫片复合冲压模具的设计过程1.确定垫片的形状和尺寸。
首先需要根据产品要求和使用环境确定垫片的形状和尺寸,例如内径、外径、厚度等。
可以根据实际需要选择合适的材料来制作垫片。
2.设计冲压模具的结构。
冲压模具通常由上模具、下模具和导向机构组成。
上模具用于固定和引导被加工材料,下模具用于对材料进行冲压成形。
导向机构用于确保上下模具的准确对位。
可以采用三合一的结构来设计垫片复合冲压模具,即上模、下模和导向机构集成在一个模具中。
3.设计冲压模具的工作原理。
在设计冲压模具时,需要考虑垫片材料的弹性变形和变形量,确定适当的压力和冲床速度。
同时,还需考虑垫片的形状和尺寸,以及冲压模具的结构和材料选择,确保冲压过程中垫片的质量和精度。
4.选择合适的冲床设备。
根据垫片的尺寸和生产需求,选择合适的冲床设备。
冲床设备通常根据最大冲床力和行程来选取。
同时,还需考虑冲床的速度和精度,以及冲床与冲压模具的配合性,确保冲压过程中的稳定性和可靠性。
5.设计冲压模具的加工工艺。
在设计冲压模具时,需要考虑其加工工艺。
例如,选择合适的模具材料、加工方法和工艺参数,确保冲压模具的加工效率和质量。
二、垫片复合冲压模具设计的注意事项1.选择合适的模具材料。
冲压模具的材料需要具备高强度、耐磨性和耐腐蚀性,以满足冲压加工的要求。
常用的模具材料有优质合金工具钢和硬质合金等。
根据垫片的材料和形状,选择合适的模具材料。
2.注意冲压模具的使用寿命。
冲压模具在使用过程中会受到磨损和疲劳的影响,因此需要进行定期的维护和保养。
可以采用表面涂层和热处理等方式来延长冲压模具的使用寿命。
方形垫圈冲压复合模具设计

方形垫圈冲压复合模具设计
设计一个方形垫圈冲压复合模具需要考虑以下几个方面:模具结构设计、材料选择、工艺流程和模具加工。
1.模具结构设计:
上模由切割机构、冲头和定位销组成。
切割机构用于切割板材成为合
适的尺寸,冲头用于将板材冲击成为方形形状,定位销用于确保上模位于
恰当的位置。
下模由定位销、导向柱和冲头组成。
定位销用于将下模固定在机床上,导向柱用于保证上模和下模的准确对位,冲头用于将板材冲击成为带有孔
的方形形状。
背模由切割机构、冲头和导向柱组成。
切割机构用于将垫圈从板材中
切割出来,冲头用于将垫圈从板材上弹出,导向柱用于保持背模和上下模
的准确对位。
2.材料选择:
考虑到垫圈需要具有一定的弹性和耐用性,一般选择具有良好塑性和
高强度的金属材料,如不锈钢、铜等。
3.工艺流程:
在制造方形垫圈的过程中,首先需要将适当尺寸的板材切割成相应的
形状,然后使用上模和下模将板材冲压成为带有孔的方形形状。
最后,使
用背模将垫圈从板材上切割出来。
4.模具加工:
根据设计需求和材料选择,可以采用车削、铣削、线切割、磨削等工艺进行模具的加工。
同时,需要考虑加工精度和模具的寿命,以确保模具的可靠性和稳定性。
在设计方形垫圈冲压复合模具时,还需要考虑到其使用环境和应用要求,例如垫圈的尺寸、材料厚度、产量要求等。
通过综合考虑以上因素,可以设计出适合生产方形垫圈的冲压复合模具。
冲压模具设计说明书复合模

工件名称:传动片 工件见图:如图(1) 生产批量:大批量 材料:A3 厚度:2mm1. 此工件只有落料和冲孔两个工序。
材料为Q235—A 钢,具有良好的冲压性能,适合冲裁。
抗剪强度为310~380 t/MPa ,抗拉强度为380~470 бb /MPa ,屈服强度为240 бb /MPa 。
工件结构相对简单,有2个Φ10的孔,孔与孔,孔与边缘之间的距离也满足要求,最小壁厚为7MM ,工件除了12 0-0.11 为IT11级外,其余都是IT14级。
尺寸精度较低,普通冲裁完全能满足要求。
2. 冲裁工艺方案的确定该工件包括落料、冲孔两个基本工序,可有以下三种工艺方案:方案一:先落料,后冲孔。
采用单工序模生产。
方案二:落料—冲孔复合冲模。
采用复合模生产。
方案三:冲孔—落料级进冲模。
采用级进模生产。
方案一结构简单,但需要两道工序两副模具,成本高生产效率低,难以满足大批量生产的要求。
方案二只需要一副模具,工件精度及生产效率都教高,工件最小壁厚为7MM 模具强度较好。
方案三也只需要一副模具,生产效率高,操作方便,但是制造精度不如复合模。
通过对上述三种方案的分析比较,该件的冲压声场采用方案二为佳,即复合模。
3. 主要设计计算(1) 排样方式的确定及其计算传动片的形状为左右对称,下端水平,采用直对排效率较高。
如图(2)所示的排样方法。
查(《冲压工艺与模具设计》表 2.5.2 )所得,工件间a1=2MM ,沿边a2=2.2MM ,条料宽度为70MM ,步距S=32MM ,一个步距的材料利用率为56%。
计算部分见表(1)。
图(2)(2)冲压力的计算图(1)该模具采用复合模,拟选用弹性卸料,结构采用倒装式复合模。
冲压力的相关计算见表(1)表(1)。
项目分类项目公式结果排样冲裁件面积A A=37/360×π30²+(14.5+32.5)×24-2×π5²1253.6条料宽度B B=65+2x2.2+0.6 70 步距S 32 一个步距的材料利用率ηη=A/BSx100%=1253.6/(70x32)x100%56%冲压力冲裁力F F=KLtτb=1.3x(37/360x2π30+65+2x14.5+ 2x24+2π5x2)x2x350203512.4 卸料力Fx Fx=KxF=0.05x203512.4 10180.17 顶件力FD FD=KDF=0.06203512.4 12210.74 冲压工艺总力FZFZ= F+ Fx +FD=203512.4+10180.17+12210.74225902公称压力:250KN发生公称压力时滑块离下极点距离:6MM滑块周边行程80MM调节行程10MM标准行程均数:100次/MIN最大闭合高度最低360MM,最高160MM闭合高度调节是70MM滑块中心到机身距离190MM工作台左右尺寸560MM前后尺寸300MM工作台孔尺寸左右260 M M(3)压力中心工件为几何对称形状,则复合模的压力中心定位工件的几何中心。
冲压复合模毕业设计

密级:学号:109202030104本科生毕业论文(设计)盖板的冷冲压模设计学院:江西科技学院专业:机械设计制造及其自动化班级: 09级机设本(2)班学生姓名:陈亮指导老师:李刚龙完成日期: 2013年5月15日江西科技学院本科生毕业论文(设计)学士学位论文原创性申明本人郑重申明:所呈交的论文和设计是本人在指导老师的指导下独立进行研究,所取得的研究成果。
除了文中特别加以标注引用的内容外,本论文和设计不包含任何其他个人或集体已经发表或撰写的成果作品。
对本文的研究做出重要贡献的个人和集体,均已在文中以明确方式表明。
本人完全意识到本申明的法律后果由本人承担。
学位论文作者签名(手写):签字日期:年月日学位论文版权使用授权书本学位论文作者完全了解学校有关保留、使用学位论文的规定,同意学校保留并向国家有关部门或机构送交论文的复印件和电子版,允许论文被查询阅和借阅。
本人现授权江西科技学院可以将本论文的全部或部分内容编入有关数据库进行检索,可以采用缩印、影印或扫描等复制手段保存和汇编本学位论文。
(请在以上相应方框内打“√”)学位论文作者签名(手写):指导老师签名(手写):签字日期:年月日签字日期:年月日2摘要在日常生产和制造业中,特别是钣金加工方面冷冲压已经占据了主导地位,它具有生产快、市场投放能力强、加工精度较高等特点而被广泛使用。
本篇文章叙述了盖板零件的设计,其中主要包括了模具的选择、模具内部标准件的选择、凸模的设计计算、凹模的设计计算、加工时各个作用力的大小、压力机的选择。
简述了零件的制造过程、冲压模的结构设计、零件的公差分析、对该类型的模具前景浅谈。
关键词:冲压模具、冲裁、弯曲ABSTRACTStamping production by the mould and press finish machining process, compared with other processing method of its stable quality, good interchangeability.Machining surface quality is high, the shape of complex parts.High efficiency, saving material.So the stamping die in the actual industrial production can be used widely.Blanking, punching, bending structure design and working process of compound die were introduced, through the analysis of the technology, uses blanking bending, punching through, the top pieces, pressing force, stripping force, bending strength calculation, determine the type mold. The posterior mold using derivative-scale, blanking die with insert structure, waste discharged from the slot die.Key words :Pressing mold、Cutting、Bending目录第1章绪论 (2)1.1 概述 (2)1.3 模具发展史 (2)第2章盖板工艺分析 (4)2.1 零件的工艺特点 (4)2.2 盖板工艺方案分析及确定 (5)2.3 盖板排样设计 (6)第3章盖板冲裁模设计 (8)3.1 盖板主要工艺参数计算 (8)3.2 冲压机的选择 (10)3.3 主要工作部分尺寸计算 (11)3.4 模具主要零件及结构设计 (12)第4章模具标准件选择 (14)4.1 模架及主要零件选择 (14)4.2 其余零件选择 (18)第5章结论及展望 (20)参考文献 (21)致谢 (22)第一章绪论1.1 概述熟练的掌握徒手绘制各类图纸的能力和AutoCAD的运用能力,并能够熟练的通过查找各类参考文献,设计手册,国家标准及规范等,能独立的完成设计的能力。
一模多件冲压复合模具设计

收稿日期:2017-04-06作者简介:张田荣(1978—),男,副教授。
文章编号:1001-4934(2017)06-0019-03一模多件冲压复合模具设计张田荣(甘肃机电职业技术学院 机械工程系,甘肃 天水 741001)摘 要:通过对变电器开关压圈、大垫圈和小垫圈零件的冲压工艺分析,优化了模具结构设计,在一次成形过程中,使得冲孔、落料、拉深3个工序复合,在1套模具中可生产出3种不同类型的零件。
生产实践表明,模具结构合理,模具工作过程可靠且操作简便。
3种不同类型零件的冲压复合设计,满足了现代工业生产高精度、低成本、高效率的要求。
关键词:冲孔;落料;拉深;工序复合中图分类号:TG 386文献标识码:BCompound die design for multi-workpiece stampingZHANG Tian-rongAbstract:Through the analysis of the stamping process of the switch,the large washer andthe small washer workpiece,the die structure design is optimized.In the process of form-ing,the punching,blanking and drawing process are compounded in one set of die,whichcan produce 3different types of workpieces.Production practice shows that the die struc-ture is reasonable,the die work reliably and easy to operate.The stamping composite designof 3different types of workpiece meet the high precision,low cost,high efficiency require-ments of modern production.Keywords:punching;blanking;deep drawing;procedure compound1 零件分析图1所示为一变电器开关压圈,材料为Q235,料厚为1mm,属于规则形状回转体拉深件。
第六章 复合模

校核:凸 凹 Z max Z min
0.02mm 0.02mm 0.04mm 0.06mm
证明了所取的凸与凹是合适的。
对于孔1800。021 IT 7级精度, 则取模具的凸、凹模的制造公差为IT5级,查书
末附录E3得δ凸=δ凹=0.008mm,则:
d凸
d
x
凸模的圆角半径与零件的弯曲半径相同,R凸=2.5mm。
凹模的圆角半径由表3-7查得,R凹=5mm。
凸、凹模单面间隙值Z/2=0.9t=2.7mm。
对于工件尺寸
86
0 0.87
(4)推件力 F推=nK推F冲 式中K推—推件力因数,其值由表2-15查
得K推=0.045。 冲孔凹模刃口直壁高度h=6mm,则: n 6mm 2 3mm P推=2×0.045×91.11kN ≈8.2kN
(5)弯曲力计算
按近似压弯力公式计算: F1
0.7KBt 2 b
Rt
式中: F1—自由弯曲力(N); B—弯曲件的宽度,B=40mm;
四、复合模设计要点
从设计本质与单工序
模无区别,但根据实际经验,需注意以下几个问题:
1、曲柄压力机的许用压力曲线与复合 模压力曲线的关系
对于单工序冲压加工,冲压力曲线不能超 过曲柄压力机许用压力曲线,否则设备会因超 载而损坏。对复合模加工也应满足这一要求。
但由于复合冲压时所用压力机的行程中有 更大比例的工作行程,这样就容易造成超载。 尤其是对落料、拉深复合模,落料在先,拉深 在后,落料力一般较大,拉深力较小,而设备 压力曲线的变化趋势则相反,所以极易产生超 载,如右图。因此在选择设备时要特别注意。
则: F落=(1.3×257.28×310)N≈311.05kN
冲压模具设计方案研究以垫片落料冲孔复合模为例

SolidWorks软件概述
SolidWorks是一款由达索系统开发的三维CAD软件,它适用于各种机械设计 领域,包括模具设计。SolidWorks具有强大的图形绘制功能,支持零件建模、装 配体设计、工程图制作等。此外,软件还提供了丰富的材料库、标准件库和渲染 工具,方便设计师进行产品建模、性能分析和效果图制作。
3、设计模具结构:根据工艺分析结果,设计模具的结构,包括垫片的定位、 落料口的尺寸和位置、冲孔的形状和深度等。
4、选用材料和标准件:根据模具的结构和设计要求,选用合适的材料和标 准件,如模架、弹簧、螺栓等。
5、完成细节设计:对模具的细节部分进行设计,如斜楔、导柱、加热元件 等。
6、绘制模具图:完成模具结构设计后,绘制模具装配图和零件图,标注技 术要求和加工信息。
制造质量和生产效率。经过实际生产验证,该模具的定位准确、运行稳定, 能够高效地生产出合格的刹车片产品。与传统的冲压工艺相比,垫片落料冲孔复 合模的使用简化了生产流程,提高了生产效率,降低了生产成本和劳动强度。
因此,垫片落料冲孔复合模在汽车刹车片的生产中取得了良好的应用效果和 经济效果。
结论
本次演示对垫片落料冲孔复合模的设计方案进行了研究,重点探讨了模具的 结构设计、制造工艺和关键技术点。通过案例分析,阐述了垫片落料冲孔复合模 在工业生产中的应用及实际效果。结果表明,合理的模具设计方案对于提高模具 的制造质量和生
冲压工艺与冲压模具设计在制造业中具有重要地位,特别是在汽车、机械制 造等领域。本次演示将从冲压工艺和冲压模具设计的基本概念入手,深入探讨其 原理、特点和未来发展趋势。
一、冲压工艺基本原理及分类
冲压工艺是一种利用压力机将金属板料变形或分离,以获得一定形状、尺寸 和性能的零件的制造方法。冲压工艺按照工艺特点可分为分离工序和成形工序两 大类。分离工序是指将金属板料分割成若干个小部分,如冲裁、剪切等;成形工 序则是指将金属
冲压模具设计-落料拉深复合模
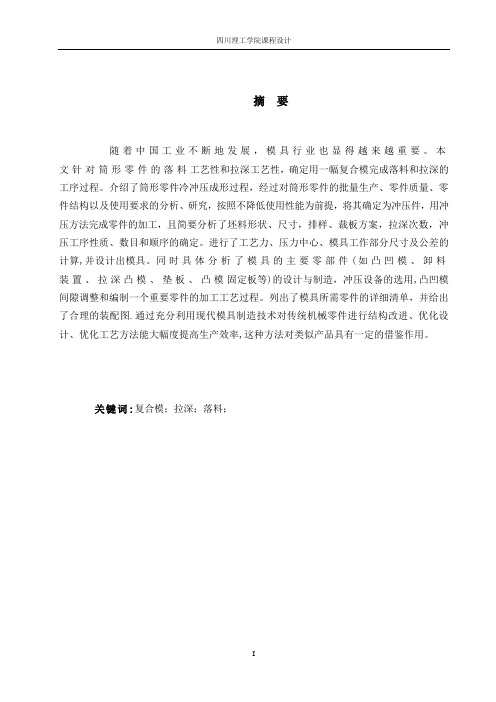
产品零件图是分析和制定冲压工艺方案的重要依据,设计冲压工艺过程要从分析产品的零件图人手。分析零件图包括技术和经济两个方面:
1.2.1
冲压加工方法是一种先进的工艺方法,因其生产率高,材料利用率高,操作简单等一系列优点而广泛使用.由于模具费用高,生产批量的大小对冲压加工的经济性起着决定性作用,批量越大,冲压加工的单件成本就越低,批量小时,冲压加工的优越性就不明显,这时采用其他方法制作该零件可能有更好的经济效果.例如在零件上加工孔,批量小时采用钻孔比冲孔要经济;有些旋转体零件,采用旋压比拉深会有更好的经济效果。所以,要根据冲压件的生产纲领,分析产品成本,阐明采用冲压生产可以取得的经济效益。
方案一:落料、拉深、修边,共三道工序。
方案二:落料+拉深复合、修边,共两道工序。
综合各方面因素,显然方案二更加合理。
2。3 主要工艺参数的计算
2。3.1 确定排样、裁板方案
考虑到操作方便,排样采用单排。
1)搭边值:查【1】表2。5.2
条料两边a = 1.0 mm,
进距方向a1= 0。8mm
进距s = D + a1= 72。8 + 0。8= 73.6 mm
冲模的零部件
通常模具由两类零件组成,一类是公益零件,这类零件直接参与工艺过程的完成并和坯料有直接接触,包括工作零件、定位零件、卸料与压料零件等;另一类是结构零件,这类零件不直接参与完成工艺过程,也不和坯料直接接触,只对模具完成工艺过程起保证作用,或对模具功能起完善作用,包括导向零件、紧固零件、标准件及其他零件等。
在综合方析,研究零件成形性的基础上,以材料的极限变形参数,各种变形性质的复合程度及趋向性,当前的生产条件和零件的产量质量要求为依据,提出各种可能的零件成形总体工艺方案.根据技术上可靠,经济上合理的原则对各种方案进行对比,分析,从而选出最佳工艺方案(包括成形工序和各辅助工序的性质,内容,复合程度,工序顺序等),并尽可能进行优化。
模具毕业设计8冲裁冲孔复合模设计说明书

冲裁冲孔复合模学校:班级:组别:学号:姓名:指导老师:冲压工艺设计复合模具如图1所示零件:钢板生产批量:中小批量材料:08F 料厚t=1.2mm公差按IT14级制造本零件为落料冲孔模设计该零件的冲压工艺与模具。
图1 钢板设计该零件的冲压工艺与模具(一)冲压工艺分析设计冲裁件的工艺性是指从冲压工艺方面来衡量设计是否合理。
一般的讲,在满足工件使用要求的条件下,能以最简单最经济的方法将工件冲制出来,就说明该件的冲压工艺性好,否则,该件的工艺性就差。
当然工艺性的好坏是相对的,它直接受到工厂的冲压技术水平和设备条件等因素的影响。
以上要求是确定冲压件的结构,形状,尺寸等对冲裁件工艺的实应性的主要因素。
根据这一要求对该零件进行工艺分析。
零件尺寸部分公差已经给出,其余未标注公差,属自由尺寸,可按IT14级确定工件尺寸的公差,经查公差表,各尺寸公差为:500-0.62、24.70-0.52、70-0.36、6.50-0.36、10±0.18、150+0.43以根据图纸要求进行设计并画图,利用普通冲裁方式可达到图样要求。
材料为08F钢板是优质碳素结构钢,具有良好的可冲压性能。
材料的厚度为1.2mm。
由于该件外形简单,形状规则,适于落料冲孔加工。
(二)确定工艺方案及模具结构形式确定方案就是确定冲压件的工艺路线,主要包括冲压工序数,工序的组合和顺序等。
确定合理的冲裁工艺方案应在不同的工艺分析进行全面的分析与研究,比较其综合的经济技术效果,选择一个合理的冲压工艺方案。
经分析,该零件属于中小批量生产,工艺性较好,冲压件尺寸精度不高,形状简单。
根据现有冲模制造条件与冲压设备,采用冲裁冲孔复合模,模具制造周期短,价格低廉,工人操作安全,方便可靠。
(三)模具设计计算1.排样因为矩形边长L=50mm 查表1可知两工件间按矩形取搭边值a=1.8,工件与边缘搭边值a1=1.5.条料宽度按相应的公式计算:B=(D+2a+δ)-δ查表2 ⊿=0.5 C=0.2B=(50+2×2+0.5)0-0.5B=54.50-0.5 mm表1 搭边值和侧边值的数值材料厚度t (mm)圆件及r>2t圆角矩形边长l≤50 矩形边长l>50或圆角r≤2 工件间a1 侧边a 工件间a 侧边a1 工件间a1侧边a0.25以下 1.8 2.0 2.2 2.5 2.8 3.0 0.25~0.5 1.2 1.5 1.8 2.0 2.2 2.5 0.5~0.8 1.0 1.2 1.5 1.8 1.8 2.00.8~1.2 0.8 1.0 1.2 1.5 1.5 1.81.2~1.5 1.0 1.2 1.5 1.8 1.92.0 1.6~2.0 1.2 1.5 2.0 2.2 2.0 2.2表2 剪裁下的下偏差△(mm)条料宽度b(mm)条料厚度t(mm)≤50>50~100 >100~200 >200 ≤10.5 0.5 0.7 1.0 >1~30.5 1.0 1.0 1.0 >3~4 1.0 1.0 1.0 1.5 >4~6 1.0 1.0 1.0 2.0根据上述数据可知图形搭边值和条料宽度,如图2可示:图2 排样图2.计算冲裁力若采用平刃冲裁模,其冲裁力P p按下式计算:P—冲裁力;L—冲裁周边长度;t—材料厚度;τ—材料抗剪强度;K—系数;系数K是考虑到实际生产中,模具间隙值的波动和不均匀,刃口磨损、板料力学性能和厚度波动等原因的影响而给出修正系数,一般取K=1.3。
连接扣冲压模具设计复合
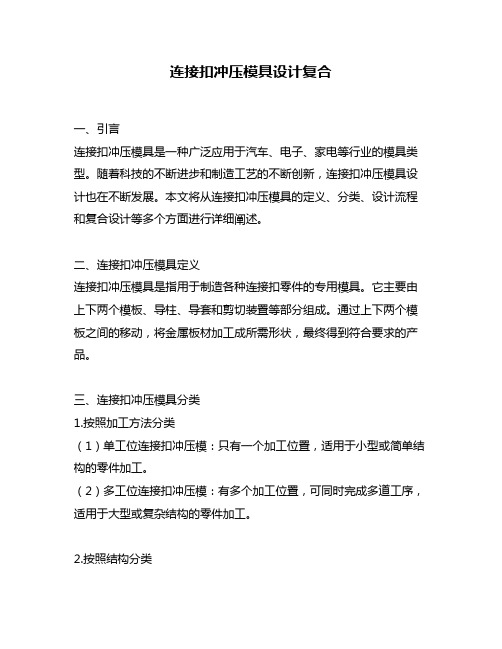
连接扣冲压模具设计复合一、引言连接扣冲压模具是一种广泛应用于汽车、电子、家电等行业的模具类型。
随着科技的不断进步和制造工艺的不断创新,连接扣冲压模具设计也在不断发展。
本文将从连接扣冲压模具的定义、分类、设计流程和复合设计等多个方面进行详细阐述。
二、连接扣冲压模具定义连接扣冲压模具是指用于制造各种连接扣零件的专用模具。
它主要由上下两个模板、导柱、导套和剪切装置等部分组成。
通过上下两个模板之间的移动,将金属板材加工成所需形状,最终得到符合要求的产品。
三、连接扣冲压模具分类1.按照加工方法分类(1)单工位连接扣冲压模:只有一个加工位置,适用于小型或简单结构的零件加工。
(2)多工位连接扣冲压模:有多个加工位置,可同时完成多道工序,适用于大型或复杂结构的零件加工。
2.按照结构分类(1)平面式连接扣冲压模:上下两个模板平行移动,适用于平面或简单曲面的零件加工。
(2)立体式连接扣冲压模:上下两个模板垂直移动,适用于复杂曲面的零件加工。
四、连接扣冲压模具设计流程1.确定产品要求:包括产品形状、尺寸、材料等要求。
2.分析产品结构:根据产品结构特点,确定模具加工方法和结构类型。
3.制定设计方案:根据产品要求和结构特点,制定合理的设计方案,并进行初步设计。
4.优化设计方案:通过仿真等手段对初步设计方案进行优化,提高模具加工效率和加工精度。
5.制作图纸:根据最终的设计方案,制作出详细的图纸,并进行审查和修改。
6.制作模具:按照图纸要求进行模具制作,并进行试模和调试。
五、连接扣冲压模具复合设计1.概念连接扣冲压模具复合设计是指将多种不同类型的连接扣冲压模具组合在一起,形成一套可实现多种不同功能的复合型连接扣冲压模具。
2.优点(1)可实现多种不同类型零件加工;(2)节约生产成本;(3)提高生产效率和加工精度。
3.设计要点(1)确定复合模具的功能需求;(2)根据功能需求选取不同类型的连接扣冲压模具,并进行组合设计;(3)进行仿真分析,优化设计方案;(4)制作图纸,制作模具。
第二章第6节冲压模具设计——复合模和连续模
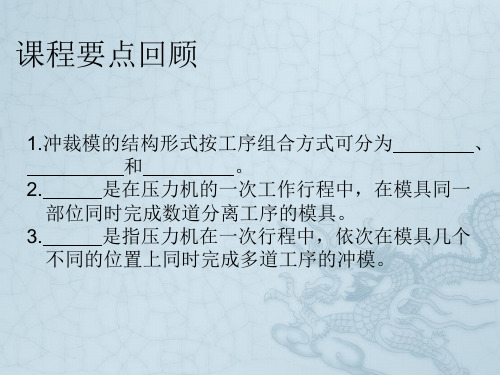
2
2.连续模的排样设计
2.1 连续模设计步骤
连续模设计与普通冲模有很大的不同,要求也要高的多。
2.8 载体设计
载体:多工位冲压时条料上连接工序件,并使工序 件在模具上稳定送进的部分材料。载体与工序件之 间的连接段称为搭接头。
载体的形式:单侧载体、双侧载体、中间载体、无 载体和边料载体。
单侧载体
双侧载体
中间载体
无载体
边料载体
工序排样过程
带局部成形时的工序排样
2.9连续模结构设计
课程要点回顾
1.冲裁模的结构形式按工序组合方式可分为
、
和
。
2.
是在压力机的一次工作行程中,在模具同一
部位同时完成数道分离工序的模具。
3.
是指压力机在一次行程中,依次在模具几个
不同的位置上同时完成多道工序的冲模。
课程要点回顾
1.冲裁模的结构形式按工序组合方式可分为 单工序 模 、 复合模 和 连续模 。
4.5模架
若采用中间导柱模架,则导柱对称分布, 受力平衡,滑动平稳,拔模方便,但只能一个方 向送料。若采用对焦导柱模架,则受力平衡,滑 动平稳,可纵向或横向送料。若采用后侧导柱模 架,则可三方向送料,操作者视线不被阻挡,结 构比较紧凑,但模具受力不平衡,滑动不平稳。
本设计决定采用中间导柱模架。
4.6计算模具刃口尺寸
在倒装复合模中,如果在上模内采用弹性装置, 也可保证冲件有较高的平直度。所以,倒装模比正 装模应用更广泛。
冲大小垫圈复合模具设计

冲大小垫圈复合模具设计冲压件是一类常见的制造工艺,常用于汽车制造、家电制造、电子设备制造等行业。
而冲压模具是冲压成形过程中必不可少的工具,它的设计质量直接关系到冲压件的质量和生产效率。
在冲压模具中,大小垫圈复合模具是一种常见的冲压模具,其设计涉及到多个方面的问题。
首先,大小垫圈复合模具的设计需要考虑冲压件的形状和尺寸。
冲压件形状的复杂程度直接影响着模具的设计难度和加工工艺。
在设计过程中,需要对冲压件进行全面的分析和理解,确定其外形、内部结构和尺寸要求,以便为模具的设计提供依据。
其次,大小垫圈复合模具的设计需要考虑冲压件在冲压过程中的变形和应力分布情况。
冲压过程中,受力和变形的分析是模具设计的核心问题之一、通过有限元分析等方法,可以模拟和分析冲压件在冲压过程中的变形情况,以及模具在受力时的应力分布情况。
在此基础上,可以优化模具的结构设计,提高其刚度和抗变形能力。
再次,大小垫圈复合模具的设计需要考虑模具的结构和工艺。
模具的结构设计主要包括冲头、模座、导向结构、定位结构等,这些结构需要根据冲压件的形状和尺寸要求进行设计。
而模具的工艺设计主要包括模具的装卸、夹紧、冲裁、冲压等工艺步骤的设计。
在模具设计过程中,需要综合考虑冲压件的复杂程度、生产效率和加工成本等因素,进行合理的结构和工艺设计。
最后,大小垫圈复合模具的设计需要考虑模具材料的选择和热处理工艺。
模具材料的选择直接影响到模具的使用寿命和加工质量。
常见的模具材料有高速钢、合金工具钢、硬质合金等,不同材料具有不同的硬度、强度和耐磨性能,选择合适的材料是保障模具寿命的重要因素之一、此外,模具在使用过程中还需要进行热处理,以提高其硬度和耐磨性能。
综上所述,大小垫圈复合模具的设计需要综合考虑冲压件的形状和尺寸、变形和应力分布情况、模具的结构和工艺、模具材料的选择和热处理工艺等多个方面的问题。
只有对这些问题进行全面的分析和研究,才能设计出合理、可靠的大小垫圈复合模具。
冲压正装复合模课程设计

冲压正装复合模课程设计一、课程目标知识目标:1. 学生能理解冲压正装复合模的基本概念,掌握其工作原理及结构组成。
2. 学生能掌握冲压正装复合模的设计步骤和关键参数,具备初步的模具设计能力。
3. 学生了解冲压正装复合模在制造业中的应用,熟悉相关行业标准和规范。
技能目标:1. 学生能运用所学知识,独立完成冲压正装复合模的设计方案,具备一定的创新设计能力。
2. 学生能运用CAD/CAM软件进行冲压正装复合模的参数化设计和模拟分析,提高实际操作技能。
3. 学生具备一定的团队协作能力,能在项目中进行有效沟通和分工合作。
情感态度价值观目标:1. 学生培养对模具设计专业的热爱,增强职业认同感和责任感。
2. 学生通过学习,认识到冲压正装复合模在制造业中的重要性,激发对先进制造技术的探究兴趣。
3. 学生在学习过程中,养成严谨、认真、细致的工作态度,培养良好的职业道德。
本课程针对高年级模具设计与制造专业学生,结合课程性质、学生特点和教学要求,明确以上课程目标,旨在培养学生具备扎实的专业知识、熟练的操作技能和良好的职业素养。
通过分解目标为具体学习成果,为后续教学设计和评估提供依据。
二、教学内容1. 冲压正装复合模基本概念:介绍冲压正装复合模的定义、分类及特点,使学生了解模具的广泛应用和重要性。
教学内容涉及教材第1章“冲压模具概述”。
2. 冲压正装复合模工作原理及结构组成:讲解模具的工作原理,分析正装复合模的结构组成及各部分功能。
教学内容涉及教材第2章“冲压模具结构与设计原理”。
3. 冲压正装复合模设计步骤及关键参数:详细介绍模具设计的基本步骤,解析关键参数的确定方法。
教学内容涉及教材第3章“冲压模具设计方法”。
4. 冲压正装复合模应用案例分析:通过实际案例,使学生了解模具在制造业中的应用,提高实际操作能力。
教学内容涉及教材第4章“冲压模具应用实例”。
5. CAD/CAM软件在冲压正装复合模设计中的应用:教授学生运用CAD/CAM 软件进行模具设计、模拟分析及优化。
冲压倒装复合模的结构设计

摘要本次设计了一套冲孔、落料的模具。
经过查阅资料,首先要对零件进行工艺性分析,经过工艺分析和对比,采用冲孔落料工序,通过冲裁力、顶件力、卸料力等计算,确定压力机的型号。
再分析对冲压件加工的模具适用类型选择所需设计的模具。
得出将设计的模具类型后将磨具的各工作零部件设计工程表达出来。
在设计第一部分,主要叙述了冲压模具的发展状况,说明了冲压模具的重要性与本次设计的意义,接着是对冲压件的工艺性分析,完成工艺方案的确定。
第二部分,对零件排样图的设计,完成了材料利用率的计算。
再进行冲裁工艺力的计算和冲裁模工作部分的设计计算,对选择冲压设备提供依据。
最后对主要零部件的设计和标准件的选择,为本次设计模具的绘制和模具的成型提供依据,以及为装配图个尺寸提供依据。
通过前面的设计方案画出模具各零件图和装配图。
本次设计阐述了冲压倒装复合模的结构设计及工作过程。
本模具性能可靠,运行平稳,提高了产品质量和生产效率,降低劳动强度和生产成本。
关键词: 冲压;落料冲孔;复合模;模具结构ABSTRACTThis design carries on blanking, the piercing progressive dies design. The article has briefly outlined the press die at present development condition and the tendency. It has carries on the detailed craft analysis and the craft plan detemination to the product. According to general step which the press die designs, calculated and has designed on this set of mold main spare part, forexample: The punch, the matrix, the punch plate, the backing strip, the standard mould bases, has selected the appropriate press equipment. In the design has carries on the essential examination computation to the working elements and the press specification. In addition, this die employs the finger stop pin and the hook shapes stop pin. The mold piercing and blanking punch are fixed with the different plates separately in order to coordinate the gap cenveniently; The piercing matrix and blanking matrix are fixed by the overall plate.Fdll in the blanking punch is loaded by pilot, guarante the relative position of the hole and the contour, increase the processing precision. This structure may guarantee the die move reliably and the request of mass production.Key words: Progeressive dies; Press mold; Standard die sets; Press equipment; Examination; Piercing;Blanking目录第一章绪论 (1)1.1冲压加工的概念 (1)1.2冲压加工的特点及应用 (1)1.3冲压模具发展历史和技术水平状况 (2)1.4模具工业在国民经济中的地位 (2)1.5现代模具制造技术的发展趋势 (3)第二章模具设计计算 (5)2.1工件的工艺分析 (5)2.2确定工艺方案 (5)2.3排样 (6)2.4材料利用率 (7)2.5冲压力的计算 (7)2.6压力机的选择 (9)2.7确定压力中心 (9)2.8计算凸、凹模刃口尺寸 (9)2.9零件尺寸的设计 (11)第三章模具零件设计及选择 (14)3.1模架结构的设计 (14)3.2凸模固定板、垫板的设计 (15)3.3定位零件的选择 (16)3.4卸料装置与推件装置的选择 (17)3.5卸料弹簧的选取 (18)3.6模柄的选择 (18)3.7闭合高度的计算 (19)3.8导柱、导套的选择 (19)第四章模具装配图 (21)总结 (23)谢辞 (24)参考文献 (25)第一章绪论1.1冲压加工的概念冲压加工是借助于常规或专用冲压设备的动力,使板料在模具里直接受到变形力并进行变形,从而获得一定形状,尺寸和性能的产品零件的生产技术。
冲压模具复合模的工作过程
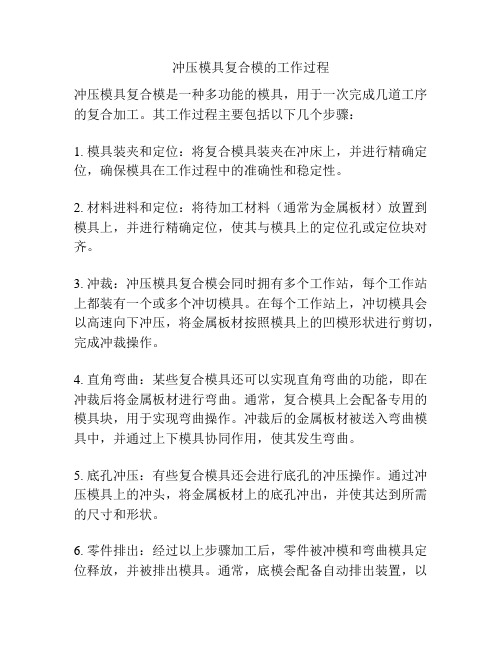
冲压模具复合模的工作过程
冲压模具复合模是一种多功能的模具,用于一次完成几道工序的复合加工。
其工作过程主要包括以下几个步骤:
1. 模具装夹和定位:将复合模具装夹在冲床上,并进行精确定位,确保模具在工作过程中的准确性和稳定性。
2. 材料进料和定位:将待加工材料(通常为金属板材)放置到模具上,并进行精确定位,使其与模具上的定位孔或定位块对齐。
3. 冲裁:冲压模具复合模会同时拥有多个工作站,每个工作站上都装有一个或多个冲切模具。
在每个工作站上,冲切模具会以高速向下冲压,将金属板材按照模具上的凹模形状进行剪切,完成冲裁操作。
4. 直角弯曲:某些复合模具还可以实现直角弯曲的功能,即在冲裁后将金属板材进行弯曲。
通常,复合模具上会配备专用的模具块,用于实现弯曲操作。
冲裁后的金属板材被送入弯曲模具中,并通过上下模具协同作用,使其发生弯曲。
5. 底孔冲压:有些复合模具还会进行底孔的冲压操作。
通过冲压模具上的冲头,将金属板材上的底孔冲出,并使其达到所需的尺寸和形状。
6. 零件排出:经过以上步骤加工后,零件被冲模和弯曲模具定位释放,并被排出模具。
通常,底模会配备自动排出装置,以
便收集和分拣成品零件。
以上就是冲压模具复合模的工作过程。
在整个过程中,模具的装夹和材料的定位是非常重要的环节,直接影响加工精度和成品质量。
另外,操作人员还需密切关注冲压模具的磨损情况,并定期进行维护和更换,以保证模具的正常工作和使用寿命。
- 1、下载文档前请自行甄别文档内容的完整性,平台不提供额外的编辑、内容补充、找答案等附加服务。
- 2、"仅部分预览"的文档,不可在线预览部分如存在完整性等问题,可反馈申请退款(可完整预览的文档不适用该条件!)。
- 3、如文档侵犯您的权益,请联系客服反馈,我们会尽快为您处理(人工客服工作时间:9:00-18:30)。
U 形弯曲件模具设计(一)零件工艺性分析工件图为图15所示活接叉弯曲件,材料45钢,料厚3mm 。
其工艺性分析内容如下:1.材料分析45钢为优质碳素结构钢,具有良好的弯曲成形性能。
2.结构分析零件结构简单,左右对称,对弯曲成形较为有利。
可查得此材料所允许的最小弯曲半径mm 5.15.0min ==t r ,而零件弯曲半径mm 5.1mm 2>=r ,故不会弯裂。
另外,零件上的孔位于弯曲变形区之外,所以弯曲时孔不会变形,可以先冲孔后弯曲。
计算零件相对弯曲半径567.0/<=t r ,卸载后弯曲件圆角半径的变化可以不予考虑,而弯曲中心角发生了变化,采用校正弯曲来控制角度回弹。
3.精度分析零件上只有1个尺寸有公差要求,由公差表查得其公差要求属于IT14,其余未注公差尺寸也均按IT14选取,所以普通弯曲和冲裁即可满足零件的精度要求。
4.结论:由以上分析可知,该零件冲压工艺性良好,可以冲裁和弯曲。
(二)工艺方案的确定零件为U 形弯曲件,该零件的生产包括落料、冲孔和弯曲三个基本工序,可有以下三种工艺方案:方案一:先落料,后冲孔,再弯曲。
采用三套单工序模生产。
方案二:落料—冲孔复合冲压,再弯曲。
采用复合模和单工序弯曲模生产。
方案三:冲孔—落料连续冲压,再弯曲。
采用连续模和单工序弯曲模生产。
方案一模具结构简单,但需三道工序三副模具,生产效率较低。
方案二需两副模具,且用复合模生产的冲压件形位精度和尺寸精度易保证,生产效率较高。
但由于该零件的孔边距为4.75mm ,小于凸凹模允许的最小壁厚6.7mm ,故不宜采用复合冲压工序。
方案三也需两副模具,生产效率也很高,但零件的冲压精度稍差。
欲保证冲压件的形位精度,需在模具上设置导正销导正,故其模具制造、安装较复合模略复杂。
通过对上述三种方案的综合分析比较,该件的冲压生产采用方案三为佳。
图15 弯曲工件图(三)零件工艺计算 1.弯曲工艺计算 (1)毛坯尺寸计算对于t r 5.0>有圆角半径的弯曲件,由于变薄不严重,按中性层展开的原理,坯料总长度应等于弯曲件直线部分和圆弧部分长度之和,可查得中性层位移系数28.0=x ,所以坯料展开长度为64mm 63.9)]328.02(18090[2)1025(2)5916(Z ≈=⨯+⨯⨯+-+⨯-+=πL由于零件宽度尺寸为18mm ,故毛坯尺寸应为64mm×18mm 。
弯曲件平面展开图见图16,两孔中心距为46mm 。
(2)弯曲力计算弯曲力是设计弯曲模和选择压力机的重要依据。
该零件是校正弯曲,校正弯曲时的弯曲力校F 和顶件力D F 为kN 541201825=⨯⨯==Ap F 校kN5325503183.17.03.07.03.0)8.0~3.0(2b2D =+⨯⨯⨯⨯⨯=+⨯==tr KBt F F σ自对于校正弯曲,由于校正弯曲力比顶件力大得多,故一般D F 可以忽略,即压力机F ≥校F生产中为安全,取压力机F ≥kN 2.97548.18.1=⨯=校F ,根据压弯力大小,初选设备为JH23—25。
2.冲孔落料连续模工艺计算 (1)刃口尺寸计算由图3-2可知,该零件属于一般冲孔、落料件。
根据零件形状特点,冲裁模的凸、凹模采用分开加工方法制造。
尺寸18mm 、R9mm 由落料获得,2×φ8.5mm 和46±0.31mm 由冲孔同时获得。
查得凸、凹模最小间隙mm 48.0min =Z ,最大间隙mm 66.0max =Z ,所以mm 18.048.066.0min max =-=-Z Z 。
图16 坯料展开图按照模具制造精度高于冲裁件精度3~4级的原则,设凸、凹模按IT8制造,落料尺寸mm 18043.0-,凸、凹模制造公差mm 027.0A T ==δδ,磨损系数X 取0.75。
冲孔尺寸mm 5.836.00+φ,凸、凹模制造公差mm 022.0A T ==δδ,磨损系数X 取0.5。
根据冲裁凸、凹模刃口尺寸计算公式进行如下计算:落料尺寸mm 18043.0-,校核不等式A T δδ+≤min max Z Z -,代入数据得18.0054.0027.0027.0<=+。
说明所取的T δ与A δ合适,考虑零件要求和模具制造情况,可适当放大制造公差为: mm 072.0mm 18.04.0T =⨯=δ, mm 108.0mm 18.06.0A =⨯=δ。
将已知和查表的数据代入公式得mm 678.17mm 0.43)0.75-18()(027.000.02700max A A +++=⨯=-=δ∆X L Lmm 198.17mm 0.48)-678.17()(0027.000.027-0min A T T --==-=δZ L L故落料凸模和凹模最终刃口尺寸为:mm 678.17108.00A +=L ,mm 198.170072.0T -=L 。
落料R9mm ,属于半边磨损尺寸。
由于是圆弧曲线,应该与落料尺寸18mm 相切,所以其凸、凹模刃口尺寸取为mm 8.839mm 678.17210.05402/108.00A ++=⨯=Rmm 599.8mm 198.17210036.002/072.0T --=⨯=R冲孔:mm 5.836.00+φ校核min max A T Z Z -≤+δδ,代入数据得:18.0044.0022.0022.0<=+。
说明所取的T δ与A δ合适,考虑零件要求和模具制造情况,可适当放大制造公差为:mm 072.0mm 18.04.0T =⨯=δ, mm 108.0mm 18.06.0A =⨯=δ。
将已知和查表的数据代入公式得mm 68.8mm )36.05.05.8()(0022.00022.00min T T ---=⨯+=+=δ∆X d d mm 16.9mm )48.068.8()(022.00022.000min T A A +++=+=+=δZ d d故冲孔凸模和凹模最终刃口尺寸为:mm 68.80072.0T -=d ,mm 16.9108.00A +=d 。
孔心距46±0.31mm因为两个孔同时冲出,所以凹模型孔中心距为mm 078.0468/62.0468/'A ±=±=±=∆L L(2)排样计算分析零件形状应采用单直排的排样方式,零件可能的排样方式有如图17所示两种。
比较方案a 和方案b ,方案a 是少废料排样,显然材料利用率高,但因条料本身的剪板公差以及条料的定位误差影响,工件精度不易保证,且模具寿命低,操作不便,排样不适合连续模,所以选择方案b 。
同时,考虑凹模刃口强度,其中间还需留一空工位。
现选用规格为3mm ×1000mm ×1500mm 的钢板,则需计算采用不同的裁剪方式时,每张板料能出的零件总个数。
经查得零件之间的搭边值mm 2.31=a ,零件与条料侧边之间的搭边值mm 5.3=a ,条料与导料板之间的间隙值mm 5.0=C ,则条料宽度为mm 5.71mm )5.05.3264()2(08.008.00max ---=+⨯+=++=∆C a D B步距 mm 2.212.3181=+=+=a D S由于弯曲件裁板时应考虑纤维方向,所以只能采用横裁。
即裁成宽71.5mm 、长1000mm 的条料,则一张板材能出的零件总个数为个94047202.212.310005.711500=⨯=⎥⎦⎤⎢⎣⎡-⨯⎥⎦⎤⎢⎣⎡=n图17 可能的排样方式计算每个零件的面积222mm 9.9685.8421846184=⨯⨯-⨯+⨯=ππS ,则材料利用率为%7.60%100100015009.968940%100b b =⨯⨯⨯=⨯⨯⨯=B L S n η。
排样图如图18所示。
3.冲裁力计算此例中零件的落料周长为148.52mm ,冲孔周长为26.69mm ,材料厚度3mm ,45钢的抗剪强度取500MPa ,冲裁力基本计算公式τKLt F =。
则冲裁该零件所需落料力kN 6.289N 289614500352.1483.11≈=⨯⨯⨯=F冲孔力 kN 1.104N 104091500369.263.122≈=⨯⨯⨯⨯=F模具结构采用刚性卸料和下出件方式,所以所需推件力T F 为kN 53kN )1.1046.289(045.039)(21T T ≈+⨯⨯=+=F F NK F 计算零件所需总冲力kN 7.446kN )531.1046.289(T 21=++=++=F F F F 总 初选设备为JC23—63。
4.压力中心计算零件为一对称件,所以压力中心就是冲裁轮廓图形的几何中心,但由于采用级进模设计,因此需计算模具的压力中心。
排样时零件前后对称,所以只需计算压力中心横坐标,如图19所示建立图18 零件的排样图图19 压力中心的计算坐标系。
设模具压力中心横坐标为0x (计算时取代数值),则有0201)4.42(x F x F ⋅=- 即 001.104)4.42(6.289x x ⋅=-⨯, 解得 mm 2.310=x所以模具压力中心坐标点为(-31.2 , 0)。
(四)冲压设备的选用 1. 冲孔落料连续模设备的选用根据冲压力的大小,选取开式双柱可倾台压力机JC23—63,其主要技术参数如下:公称压力:630kN 滑块行程:120mm 最大闭合高度:360 mm 闭合高度调节量:80 mm 滑块中心线到床身距离:260mm 工作台尺寸:480 mm ×710 mm 工作台孔尺寸:φ250mm 模柄孔尺寸:φ50 mm ×80 mm 垫板厚度:90 mm 2.弯曲模设备的选用根据弯曲力的大小,选取开式双柱可倾台压力机JH23—25,其主要技术参数如下:公称压力:250kN 滑块行程:75mm 最大闭合高度:260 mm 闭合高度调节量:55mm 滑块中心线到床身距离:200mm 工作台尺寸:370 mm ×560mm 工作台孔尺寸:φ260mm 模柄孔尺寸:φ40 mm ×60mm 垫板厚度:50 mm(五)模具零部件结构的确定 1.冲孔落料连续模零部件设计图20 凸模结构图(1)标准模架的选用标准模架的选用依据为凹模的外形尺寸,所以应首先计算凹模周界的大小。
根据凹模高度和壁厚的计算公式得凹模高度 mm 25mm 6435.0≈⨯==Kb H 凹模壁厚 mm 46mm 258.1)2~5.1(≈⨯==H C所以,凹模的总长mm 14846256=⨯+=L ,为了保证凹模结构对称并有足够的强度,将其长度增大到163mm 。
凹模的宽度mm 15646264=⨯+=B 。