SYNC 5100 Operating instructions
5100 Enterprise Mainstream SATA SSD 产品指南说明书

5100 Enterprise Mainstream SATA SSDsProduct Guide (withdrawn product)The 5100 Enterprise Mainstream SATA solid-state drives (SSDs) use Micron NAND flash memory technology with a SATA 6Gbps interface. They provide an affordable solution for mixed read/write applications such as excellent choice as cache in transactional application and high-speed storage for enterprise databases.The 5100 Enterprise Mainstream SATA SSD is shown in the following figure.Figure 1. 5100 Enterprise Mainstream SATA SSDDid you know?The 5100 Series of SATA SSDs is available from Lenovo in two levels of endurance. The Enterprise Mainstream SSDs covered in this product guide offer drive write endurance of between 2.5 and 5.0 total drive writes per day (DWPD) whereas the Enterprise Entry SSDs are more for read-intensive workloads and offer write endurance of under 1.0 DWPD.Rigorous testing of the 5100 Series SSDs by Lenovo through the ServerProven program assures a high degree of storage subsystem compatibility and reliability. Providing additional peace of mind, these drives are covered under Lenovo warranty.Click here to check for updatesPart number informationWithdrawn: All 5100 Mainstream drives are now withdrawn from marketingThe following table lists the ThinkSystem part numbers.Table 1. ThinkSystem ordering informationPart number Feature Description2.5-inch hot-swap drives - ThinkSystem7SD7A05765B10W ThinkSystem 2.5" 5100 240GB Mainstream SATA 6Gb Hot Swap SSD7SD7A05764B10X ThinkSystem 2.5" 5100 480GB Mainstream SATA 6Gb Hot Swap SSD7SD7A05763B10Y ThinkSystem 2.5" 5100 960GB Mainstream SATA 6Gb Hot Swap SSD7SD7A05762B10Z ThinkSystem 2.5" 5100 1.92TB Mainstream SATA 6Gb Hot Swap SSD7SD7A05761B110ThinkSystem 2.5" 5100 3.84TB Mainstream SATA 6Gb Hot Swap SSD3.5-inch hot-swap drives - ThinkSystem7SD7A05760B111ThinkSystem 3.5" 5100 240GB Mainstream SATA 6Gb Hot Swap SSD7SD7A05759B112ThinkSystem 3.5" 5100 480GB Mainstream SATA 6Gb Hot Swap SSD7SD7A05758B113ThinkSystem 3.5" 5100 960GB Mainstream SATA 6Gb Hot Swap SSD7SD7A05757B114ThinkSystem 3.5" 5100 1.92TB Mainstream SATA 6Gb Hot Swap SSD7SD7A05756B115ThinkSystem 3.5" 5100 3.84TB Mainstream SATA 6Gb Hot Swap SSDThe following table lists the System x part numbers and feature codes. These part numbers are also for NeXtScale and Flex System servers.Table 2. System x ordering informationPart number Feature Description2.5-inch hot-swap drives - System x01GV843AXFV5100 240GB Enterprise Mainstream SATA G3HS 2.5" SSD01GV848AXFW5100 480GB Enterprise Mainstream SATA G3HS 2.5" SSD01GV853AXFX5100 960GB Enterprise Mainstream SATA G3HS 2.5" SSD01GV858AXFY5100 1.92TB Enterprise Mainstream SATA G3HS 2.5" SSD01GV863AXFZ5100 3.84TB Enterprise Mainstream SATA G3HS 2.5" SSD3.5-inch hot-swap drives - System x01GV868AXG05100 240GB Enterprise Mainstream SATA HS 3.5" SSD01GV873AXG15100 480GB Enterprise Mainstream SATA HS 3.5" SSD01GV878AXG25100 960GB Enterprise Mainstream SATA HS 3.5" SSD01GV883AXG35100 1.92TB Enterprise Mainstream SATA HS 3.5" SSD01GV090AXG45100 3.84TB Enterprise Mainstream SATA HS 3.5" SSD2.5-inch non-hot-swap drives for NeXtScale01GV888AXHE5100 240GB Enterprise Mainstream SATA 2.5" SSD for NeXtScale01GV893AXHF5100 480GB Enterprise Mainstream SATA 2.5" SSD for NeXtScale01GV898AXHG5100 960GB Enterprise Mainstream SATA 2.5" SSD for NeXtScale01GV903AXHH5100 1.92TB Enterprise Mainstream SATA 2.5" SSD for NeXtScalePart number Feature Description01GV095AXHJ5100 3.84TB Enterprise Mainstream SATA 2.5" SSD for NeXtScaleThe following table lists the ThinkServer part numbers.Table 3. ThinkServer ordering informationPart number Description2.5-inch hot-swap drives - ThinkServer4XB0K12416LTS Gen 5 2.5" 240GB 5100 Enterprise Mainstream SATA 6Gbps Hot Swap SSD4XB0K12417LTS Gen 5 2.5" 480GB 5100 Enterprise Mainstream SATA 6Gbps Hot Swap SSD4XB0K12418LTS Gen 5 2.5" 960GB 5100 Enterprise Mainstream SATA 6Gbps Hot Swap SSD4XB0K12419LTS Gen 5 2.5" 1.92TB 5100 Enterprise Mainstream SATA 6Gbps Hot Swap SSD4XB0K12420LTS Gen 5 2.5" 3.84TB 5100 Enterprise Mainstream SATA 6Gbps Hot Swap SSD3.5-inch hot-swap drives - ThinkServer4XB0K12421LTS Gen 5 3.5" 240GB 5100 Enterprise Mainstream SATA 6Gbps Hot Swap SSD4XB0K12423LTS Gen 5 3.5" 480GB 5100 Enterprise Mainstream SATA 6Gbps Hot Swap SSD4XB0K12425LTS Gen 5 3.5" 960GB 5100 Enterprise Mainstream SATA 6Gbps Hot Swap SSD4XB0K12427LTS Gen 5 3.5" 1.92TB 5100 Enterprise Mainstream SATA 6Gbps Hot Swap SSD4XB0K12428LTS Gen 5 3.5" 3.84TB 5100 Enterprise Mainstream SATA 6Gbps Hot Swap SSD3.5-inch non-hot-swap drives for TS1504XB0K12422LTS TS150 2.5" 240GB 5100 Enterprise Mainstream SATA 6Gbps SSD with 3.5" Tray4XB0K12424LTS TS150 2.5" 480GB 5100 Enterprise Mainstream SATA 6Gbps SSD with 3.5" Tray4XB0K12426LTS TS150 2.5" 960GB 5100 Enterprise Mainstream SATA 6Gbps SSD with 3.5" Tray2.5-inch and3.5-inch non-hot-swap drives for RS1604XB0K12429LTS 2.5" 240GB 5100 Enterprise Mainstream SATA 6Gbps SSD for RS-Series4XB0K12430LTS 2.5" 480GB 5100 Enterprise Mainstream SATA 6Gbps SSD for RS-Series4XB0K12431LTS 2.5" 960GB 5100 Enterprise Mainstream SATA 6Gbps SSD for RS-Series4XB0K12432LTS 2.5" 240GB 5100 Enterprise Mainstream SATA 6Gbps SSD with 3.5" Tray for RS-Series 4XB0K12433LTS 2.5" 480GB 5100 Enterprise Mainstream SATA 6Gbps SSD with 3.5" Tray for RS-Series 4XB0K12434LTS 2.5" 960GB 5100 Enterprise Mainstream SATA 6Gbps SSD with 3.5" Tray for RS-SeriesFeaturesTechnical specificationsThe following table presents technical specifications for the 5100 Enterprise Entry SATA SSDs.Tip : Drives listed in this product guide with the exception of the 480 GB drive are the Lenovo versions of the Micron 5100 PRO family of SSDs. The 480 GB drive is the Lenovo version of the Micron 5100 MAX SSD with higher drive endurance.Table 4. Technical specificationsFeature 240 GB drive 480 GB drive 960 GB drive 1.92 TB drive 3.84 TB drive Interface 6 Gbps SATA 6 Gbps SATA 6 Gbps SATA 6 Gbps SATA 6 Gbps SATA Capacity 240 GB 480 GB 960 GB 1.92 TB 3.84 TB Endurance (drive writes per day) 3.4 DWPD 5.0 DWPD 2.5 DWPD 2.5 DWPD 2.5 DWPD Endurance(total bytes written)1500 TB 4400 TB 4400 TB 8800 TB 17,600 TB Data reliability < 1 in 10bits read < 1 in 10bits read < 1 in 10bits read < 1 in 10bits read < 1 in 10bits read MTBF2,000,000hours 2,000,000hours 2,000,000hours 2,000,000hours 2,000,000hours IOPS reads (4 KB blocks)78,00093,00093,00093,00093,000IOPS writes (4 KB blocks)26,00074,00037,00037,00030,000Sequential read rate (128 KB blocks)540 MBps 540 MBps 540 MBps 540 MBps 540 MBps Sequential write rate (128 KB blocks)250 MBps 460 MBps 520 MBps 520 MBps 520 MBps Read latency (seq)500 µs 500 µs 500 µs 500 µs 500 µs Write latency (seq)500 µs 500 µs 500 µs 500 µs 500 µs Shock, non-operating 1,500 G (Max)at 0.5 ms 1,500 G (Max)at 0.5 ms 1,500 G (Max)at 0.5 ms 1,500 G (Max)at 0.5 ms 1,500 G (Max)at 0.5 ms Vibration,non-operating 3.13 G (5-800 Hz) 3.13 G (5-800 Hz) 3.13 G (5-800 Hz) 3.13 G (5-800 Hz) 3.13 G (5-800 Hz)Typical power4.5 W4.5 W5 W5.5 W6 WServer support - ThinkSystem1717171717RMS RMS RMS RMS RMSServer support - ThinkSystemThe following table lists the ThinkSystem servers that are compatible. Table 5. ThinkSystem server supportDescription and part number E1S Intel2S Intel AMD4S IntelDense/Blade2.5-inch hot-swap drives - ThinkSystem2.5" 5100 240GB Mainstream SATA6Gb Hot Swap SSD, 7SD7A05765N N N N N Y Y Y Y Y Y Y N N N Y N Y Y Y N Y Y2.5" 5100 480GB Mainstream SATA6Gb Hot Swap SSD, 7SD7A05764N N N N N Y Y Y Y Y Y Y N N N Y N Y Y Y N Y Y2.5" 5100 960GB Mainstream SATA6Gb Hot Swap SSD, 7SD7A05763N N N N N Y Y Y Y Y Y Y N N N Y N Y Y Y N Y Y2.5" 5100 1.92TB Mainstream SATA6Gb Hot Swap SSD, 7SD7A05762N N N N N Y Y Y Y Y Y Y N N N Y N Y Y Y N Y Y2.5" 51003.84TB Mainstream SATA6Gb Hot Swap SSD, 7SD7A05761N N N N N Y Y Y Y Y Y Y N N N Y N Y Y Y N Y Y 3.5-inch hot-swap drives - ThinkSystem3.5" 5100 240GB Mainstream SATA6Gb Hot Swap SSD, 7SD7A05760N N N N N Y Y Y Y Y Y Y N N N N N N N N N N N3.5" 5100 480GB Mainstream SATA6Gb Hot Swap SSD, 7SD7A05759N N N N N Y Y Y Y Y Y Y N N N N N N N N N N N3.5" 5100 960GB Mainstream SATA6Gb Hot Swap SSD, 7SD7A05758N N N N N Y Y Y Y Y Y Y N N N N N N N N N N N3.5" 5100 1.92TB Mainstream SATA6Gb Hot Swap SSD, 7SD7A05757N N N N N Y Y Y Y Y Y Y N N N N N N N N N N N3.5" 5100 3.84TB Mainstream SATA 6Gb Hot Swap SSD, 7SD7A05756N N N N N Y Y Y Y Y Y Y N N N N N N N N N N N SE35(7Z46/7D1X)ST5(7Y48/7Y5)ST25(7Y45/7Y46)SR15(7Y54)SR25(7Y51/7Y52)ST55(7X9/7X1)SR53(7X7/7X8)SR55(7X3/7X4)SR57(7Y2/7Y3)SR59(7X98/7X99)SR63(7X1/7X2)SR65(7X5/7X6)SR67(7Y36/7Y37/7Y38)SR635(7Y98/7Y99)SR655(7Y/7Z1)SR85(7X18/7X19)SR85P(7D2F/2D2G)SR86(7X69/7X7)SR95(7X11/12/13)SD53(7X21)SD65(7X58)SN55(7X16)SN85(7X15)Server support - System xThe following tables list the System x servers that are compatible.Support for System x and dense servers with Xeon E5/E7 v4 and E3 v5 processors Table 6. Support for System x and dense servers with Xeon E5/E7 v4 and E3 v5 processorsPart numberDescription01GV8435100 240GB Enterprise Mainstream SATA G3HS 2.5" SSD Y Y Y Y Y Y Y N 01GV8485100 480GB Enterprise Mainstream SATA G3HS 2.5" SSD Y Y Y Y Y Y Y N 01GV8535100 960GB Enterprise Mainstream SATA G3HS 2.5" SSD Y Y Y Y Y Y Y N 01GV8585100 1.92TB Enterprise Mainstream SATA G3HS 2.5" SSD Y Y Y Y Y Y Y N 01GV8635100 3.84TB Enterprise Mainstream SATA G3HS 2.5" SSD Y Y Y Y Y Y Y N 01GV8685100 240GB Enterprise Mainstream SATA HS 3.5" SSD Y Y Y Y N N N N 01GV8735100 480GB Enterprise Mainstream SATA HS 3.5" SSD Y Y Y Y N N N N 01GV8785100 960GB Enterprise Mainstream SATA HS 3.5" SSD Y Y Y Y N N N N 01GV8835100 1.92TB Enterprise Mainstream SATA HS 3.5" SSD Y Y Y Y N N N N 01GV0905100 3.84TB Enterprise Mainstream SATA HS 3.5" SSD Y Y Y Y N N N N 01GV8885100 240GB Enterprise Mainstream SATA 2.5" SSD forNeXtScale N N N N N Y N Y 01GV8935100 480GB Enterprise Mainstream SATA 2.5" SSD forNeXtScale N N N N N Y N Y 01GV8985100 960GB Enterprise Mainstream SATA 2.5" SSD forNeXtScale N N N N N Y N Y 01GV9035100 1.92TB Enterprise Mainstream SATA 2.5" SSD forNeXtScale N N N N N Y N Y 01GV0955100 3.84TB Enterprise Mainstream SATA 2.5" SSD forNeXtScaleNNNNNYNY Server support - ThinkServerThe following tables list the ThinkServer systems that are compatible.Support for sd350: The drives supported with the sd350 are listed in Table 4.The following tables list the ThinkServer systems that are compatible.x 3250 M 6 (3943)x 3250 M 6 (3633)x 3550 M 5 (8869)x 3650 M 5 (8871)x 3850 X 6/x 3950 X 6 (6241, E 7 v 4)n x 360 M 5 (5465, E 5 v 4)s d 350 (5493)n x 360 M 5 W C T (5467, E 5 v 4Support for ThinkServer Gen 5 servers with E5 v4 or E3 v5 processorsTable 7. Support for ThinkServer Generation 5 servers with E5 v4 or E3 v5 processorsPart number Description4XB0K12416LTS Gen 5 2.5" 240GB 5100 Enterprise Mainstream SATA 6GbpsHot Swap SSDN Y Y N N Y Y Y Y4XB0K12417LTS Gen 5 2.5" 480GB 5100 Enterprise Mainstream SATA 6GbpsHot Swap SSDN Y Y N N Y Y Y Y4XB0K12418LTS Gen 5 2.5" 960GB 5100 Enterprise Mainstream SATA 6GbpsHot Swap SSDN Y Y N N Y Y Y Y4XB0K12419LTS Gen 5 2.5" 1.92TB 5100 Enterprise Mainstream SATA 6GbpsHot Swap SSDN N N N N Y Y Y Y4XB0K12420LTS Gen 5 2.5" 3.84TB 5100 Enterprise Mainstream SATA 6GbpsHot Swap SSDN N N N N Y Y Y Y4XB0K12421LTS Gen 5 3.5" 240GB 5100 Enterprise Mainstream SATA 6GbpsHot Swap SSDN Y Y N N Y Y Y Y4XB0K12423LTS Gen 5 3.5" 480GB 5100 Enterprise Mainstream SATA 6GbpsHot Swap SSDN Y Y N N Y Y Y Y4XB0K12425LTS Gen 5 3.5" 960GB 5100 Enterprise Mainstream SATA 6GbpsHot Swap SSDN Y Y N N Y Y Y Y4XB0K12427LTS Gen 5 3.5" 1.92TB 5100 Enterprise Mainstream SATA 6GbpsHot Swap SSDN N N N N Y Y Y Y4XB0K12428LTS Gen 5 3.5" 3.84TB 5100 Enterprise Mainstream SATA 6GbpsHot Swap SSDN N N N N Y Y Y Y4XB0K12422LTS TS150 2.5" 240GB 5100 Enterprise Mainstream SATA 6GbpsSSD with 3.5" TrayY N N N N N N N N4XB0K12424LTS TS150 2.5" 480GB 5100 Enterprise Mainstream SATA 6GbpsSSD with 3.5" TrayY N N N N N N N N4XB0K12426LTS TS150 2.5" 960GB 5100 Enterprise Mainstream SATA 6GbpsSSD with 3.5" TrayY N N N N N N N N4XB0K12429LTS 2.5" 240GB 5100 Enterprise Mainstream SATA 6Gbps SSD forRS-SeriesN N N Y N N N N N4XB0K12430LTS 2.5" 480GB 5100 Enterprise Mainstream SATA 6Gbps SSD forRS-SeriesN N N Y N N N N N4XB0K12431LTS 2.5" 960GB 5100 Enterprise Mainstream SATA 6Gbps SSD forRS-SeriesN N N Y N N N N N4XB0K12432LTS 2.5" 240GB 5100 Enterprise Mainstream SATA 6Gbps SSDwith 3.5" Tray for RS-SeriesN N N Y N N N N N4XB0K12433LTS 2.5" 480GB 5100 Enterprise Mainstream SATA 6Gbps SSDwith 3.5" Tray for RS-SeriesN N N Y N N N N N4XB0K12434LTS 2.5" 960GB 5100 Enterprise Mainstream SATA 6Gbps SSD with 3.5" Tray for RS-Series N N N Y N N N N N TS15(E3v5)TS45(E3v5)TS46(E3v5)RS16(E3v5)TD35(E5v4)RD35(E5v4)RD45(E5v4)RD55(E5v4)RD65(E5v4)Support for ThinkServer Gen 5 servers with E5 v3 processorsTable 8. Support for ThinkServer Generation 5 servers with E5 v3 processorsPart number Description4XB0K12416LTS Gen 5 2.5" 240GB 5100 Enterprise Mainstream SATA 6Gbps Hot SwapSSD N N N N N N 4XB0K12417LTS Gen 5 2.5" 480GB 5100 Enterprise Mainstream SATA 6Gbps Hot SwapSSD N N N N N N 4XB0K12418LTS Gen 5 2.5" 960GB 5100 Enterprise Mainstream SATA 6Gbps Hot SwapSSD N N N N N N 4XB0K12419LTS Gen 5 2.5" 1.92TB 5100 Enterprise Mainstream SATA 6Gbps Hot SwapSSD N N N N N N 4XB0K12420LTS Gen 5 2.5" 3.84TB 5100 Enterprise Mainstream SATA 6Gbps Hot SwapSSD N N N N N N 4XB0K12421LTS Gen 5 3.5" 240GB 5100 Enterprise Mainstream SATA 6Gbps Hot SwapSSD N N N N N N 4XB0K12423LTS Gen 5 3.5" 480GB 5100 Enterprise Mainstream SATA 6Gbps Hot SwapSSD N N N N N N 4XB0K12425LTS Gen 5 3.5" 960GB 5100 Enterprise Mainstream SATA 6Gbps Hot SwapSSD N N N N N N 4XB0K12427LTS Gen 5 3.5" 1.92TB 5100 Enterprise Mainstream SATA 6Gbps Hot SwapSSD N N N N N N 4XB0K12428LTS Gen 5 3.5" 3.84TB 5100 Enterprise Mainstream SATA 6Gbps Hot SwapSSD N N N N N N 4XB0K12422LTS TS150 2.5" 240GB 5100 Enterprise Mainstream SATA 6Gbps SSD with3.5" Tray N N N N N N 4XB0K12424LTS TS150 2.5" 480GB 5100 Enterprise Mainstream SATA 6Gbps SSD with3.5" Tray N N N N N N 4XB0K12426LTS TS150 2.5" 960GB 5100 Enterprise Mainstream SATA 6Gbps SSD with3.5" TrayN N N N N N4XB0K12429LTS 2.5" 240GB 5100 Enterprise Mainstream SATA 6Gbps SSD for RS-Series N N N N N N 4XB0K12430LTS 2.5" 480GB 5100 Enterprise Mainstream SATA 6Gbps SSD for RS-Series N N N N N N 4XB0K12431LTS 2.5" 960GB 5100 Enterprise Mainstream SATA 6Gbps SSD for RS-Series N N N N N N 4XB0K12432LTS 2.5" 240GB 5100 Enterprise Mainstream SATA 6Gbps SSD with 3.5" Tray for RS-Series N N N N N N4XB0K12433LTS 2.5" 480GB 5100 Enterprise Mainstream SATA 6Gbps SSD with 3.5" Tray for RS-Series N N N N N N4XB0K12434LTS 2.5" 960GB 5100 Enterprise Mainstream SATA 6Gbps SSD with 3.5" Tray for RS-SeriesN N N N N NServer support - Flex SystemT D 350 (E 5 v 3)R D 350 (E 5 v 3)R D 450 (E 5 v 3)R D 550 (E 5 v 3)R D 650 (E 5 v 3)R Q 750 (E 5 v 3)TrademarksLenovo and the Lenovo logo are trademarks or registered trademarks of Lenovo in the United States, other countries, or both. A current list of Lenovo trademarks is available on the Web athttps:///us/en/legal/copytrade/.The following terms are trademarks of Lenovo in the United States, other countries, or both:Lenovo®Flex SystemNeXtScaleServeRAIDServerProven®System x®ThinkServer®ThinkSystem®The following terms are trademarks of other companies:Intel® and Xeon® are trademarks of Intel Corporation or its subsidiaries.Other company, product, or service names may be trademarks or service marks of others.。
SITRANS F 产品系列操作指南说明书

Electromagnetic flowmeter, types 3100 / 3100HT / 3100P / 5100WMAG 3100 / 3100HT / 3100P / 5100WFor more information see the operating instructions on the enclosed CD-ROM. SITRANS F2Quick Start MAG 3100 / 3100HT / 3100P / 5100WBefore installing, including in hazardous areas, refer to the operating instructions on the enclosed CD-ROM.It contains detailed safety regulations, information and specifications which must be observed when installing. Changes can occur. Documentations and approvals can be found on the Internet at /flowdocumentation.Caution!Correct, reliable operation of the product requires proper transport, storage, positioning and assembly as well as careful operation and maintenance. Only qualified personnel should install or operate this instrument.General instructionsCHFor safety reasons it is important that the following points are read and understood before the installation of the equipment:•Installation, connection, commissioning and service must be carried out by personnel qualified and authorized to do so.•It is the responsibility of the customer that the instructions and directions provided in the Quick Start and in the operating instructions on the enclosed CD-ROM are read, understood and followed by the relevant personnel before installing the equipment.•It is the responsibility of the customer to instruct and authorize personnel to operate the equipment.•It is the responsibility of the customer to ensure that the measuring system is connected correctly and is in accordance with the connection diagram.•Equipment used in hazardous areas must be Ex-approved and marked for Europe, FM for USA and CSA for Canada. It is required that the special conditions for safe use provided in the manual and in the Ex certificate are followed!•Installation of the equipment must comply with national regulations. For example EN 60079-14 for the European Community.•Repair and service must be carried out by approved Siemens Flow Instruments personnel only.Safety instructionsCHCHFlow conditionsThe pipe must be completely filled with liquid!CHMAG 3100/3100HT/3100P or MAG 5100W with Ebonite liner - Max. torqueMAG 3100/3100HT/3100P or MAG 5100W with Ebonite liner -PN40PN63PN100F/Lbs Nm F/Lbs Nm7/flowdocumentationCHStep 4Mount the connection plate in the terminal box. The SENSORPROM unit Step 5Fit the supply and output cables respectively and tighten the cable glands to CHStep 1Remove and discard the terminal box lid of the sensor. Fit the cable glands for the Step 3Connect earth wire on connection board to bottom of connection box.Connect the 2 pin connector and 3 pin connector as shown.345/flowdocumentation9Quick Start MAG 3100 / 3100HT / 3100P / 5100W 10Potting kit for IP 68 application.Quick Start MAG 3100 / 3100HT / 3100P / 5100W 12/flowdocumentation13Quick Start MAG 3100 / 3100HT / 3100P / 5100W 14SITRANS “Product name”We have reviewed the contents of this publication to ensure consistency with the hardware and software described. Since variance can-not be precluded entirely, we cannot guarantee full consistency. However, the information in this publication is reviewed regularly and any necessary corrections are included in subsequent editions. Responsibility for suitability and intended use of this instrument rests solely with the user.Copyright © Siemens AG 03.2009 All Rights Reserved. Technical data subject to change without prior notice.CHSiemens Flow Instruments A/S 6430 NORDBORGDENMARK/flowdocumentationOrder no.: A5E02451851-01Literature no.: SFIDK.PQ.027.F2.2P A5E02451851-0115Quick Start MAG 3100 / 3100HT / 3100P / 5100W。
布隆光电频率系统RFS 2.1操作指南说明书

1Case2lithium button cellLi-Mn CR2450(560mAh,3V) 3Display4USB socket5Sync in6Sync out7"test"key8Base plate(only with receiver kit)9"set"key(to set lamp channel and studio channel)10Keys"☐","❑"(to regulate the flash energy and for adjustment of the lamp channel and studio address)11Sync cable for flash unit mini to mini(only with receiver kit) 12Sync cable for camerascOpe OF delivery34567891011121 213Rechargeable battery pack for receiver operation(incl.rechargable batteries)14Power supply device (only with receiver kit)15Charge cable (for use in car)(only with receiver kit)16USB cable (only with receiver kit)13151614BRONCOLOR RADIO FREQUENCY SYSTEM2.1 before useWe are very pleased you have chosen a broncolor Radio Frequency System RFS2.1unit,which is a high-quality product in every respect.If used properly, it will render you many years of good service.Please read the information contained in these operating instructions carefully.They contain important details on the use,safety and maintenance of the device.Keep these opera-ting instructions in a safe place and pass them on to further users if neces-sary.They are also available online at .With the broncolor RFS2.1you can trigger and operate by remote control broncolor units,which are equipped with an integrated RFS2or RFS2.1in-terface.1.OperatiOn as transmitter Or receiverThe transceiver can be operated in two modes.The unit is always in trans-mitting mode when used in battery operation.The transceiver functions as transmitter.If the transceiver is supplied with energy through the provided power supply unit via the USB-port,the device switches over automatically to receiving mode.The transceiver functions as receiver.It is not necessary to switch modes manually.2.radiO Frequency system 2.1(rFs 2.1)The radio frequency system broncolor RFS 2.1consists of the following ele-ments:>RFS 2.1as transmitter on the camera>RFS 2.1as receiver at the power packs /monolights without internal RFS 2or RFS 2.1radio frequency system>RFS 2or RFS 2.1as internal radio frequency system integrated in the power packs /monolights2.1rFs 2transceiver as transmitterThe RFS 2.1transceiver is used to remote-control one or more broncolor power packs or monolights equipped with RFS 2or RFS 2.1interface using radio signals to trigger flashes.Power packs or monolights without integra-ted RFS 2or RFS 2.1interfaces can be operated by connecting an RFS 2.1transceiver (as receiver)to them (see chapter 1).RFS 2or RFS 2.1RFS 2or RFS 2.1RFS 2orRFS 2.1RFS 2orRFS 2.1To enable several RFS2or RFS2.1devices to communicate with each other, they must all be set at the same studio address.RFS2and RFS2.1devices with the same studio address can be simultaneously remote controlled.Thus, thanks to the various studio addresses,several RFS2and RFS2.1groups of units can be independently remote controlled without interfering with each other.Flash triggering is synchronized either via the central contact of the hot shoe or the sync jack of the camera.Outdoors,the remote control range is up to 50m;indoors,it is up to30m.The transceiver is powered by a lithium button cell(Li-Mn CR2450).To minimise energy consumption,the transceiver is set to an energy-saving mode after eight hours have elapsed.If a flash triggering action occurs through the camera whilst the RFS2or RFS2.1transceiver is in energy-saving mode,a slight delay of the synchronization with the camera shutter release can take place.The RFS2or RFS2.1transceiver quits the energy-saving mode after this flash release.attention:although this radio system allows the selection of up to99stu-dio addresses,the number of actually available channels depends on the connected rFs2or rFs2.1flash unit.For detailed instructions,please consult the manual of the respective flash unit.2.2rFs2.1transceiver as receiverThe device can be used as an external receiver for broncolor power packs, monolights,and third-party units that are not equipped to receive RFS2or RFS2.1data.When using the device as a receiver,use the respective power supply unit and plug it into the USB socket on the side of the device.The device will automatically switch to the receiver mode.Connect the sync cable with the"out"jack of the RFS2.1transceiver and the sync jack on the flash unit.2.3Operation>KeysThe device has four keys:"test","set","☐"and"❑".Depending on the current mode of the device,they have different functions.The functions depend on how long the keys are pressed.>Key press durationA short key press is shorter than a second,a longer actuation is longer thana second.3.set studiO addressThe transceiver must have the same studio address as the flash units or re-ceivers that are to be used.To set the studio address,please proceed as follows:(the RFS2.1transceiver must be in"ST"mode.Should"LP"mode be selected, change to mode"ST"by pressing"set"for longer)1.)Press the"set"key briefly until the display blinks"ST"and shows thestudio number.2.)Set the studio address with keys"☐"and"❑".3.)Save the setting by pressing the"set"key briefly.The unit synchroniseswith the flash units and"ST"is shown in the display(not blinking).Overview of key assignment:Key Operation Function executedtest Press key briefly Triggers a test flashtest Press key for longer Switches modelling light on or off test+set Press keys for longer than4s Resets the unitset Press key for longer Toggles between studio selectionand lamp selectionset Press key briefly Enters menu"☐"Press key briefly>adjusts power selection upwards>adjusts studio channel upwards>adjusts lamp channel upwards "❑"Press key briefly>adjusts power selectiondownwards>adjusts studio channeldownwards>adjusts lamp channedownwardscomments(If the display does not illuminate,the unit must first be woken up by pressing"set"briefly.)If there is no action within3s,menu is exited again.(If the display does not illuminate,the unit must first be woken up by pressing"set"briefly.) Depending on status of unitDepending on status of unit4.setting the lamp channelWith the RFS2.1Transceiver you can define and adjust the individual lamp outlets on the flash units as you wish.To make the adjustments,please fol-low the procedure given in the operating instructions for the flash unit con-cerned.To set the lamp address,proceed as follows:(the RFS2.1Transceiver must be in"LP"mode.Should the"ST"mode be selected,please change to mode"LP"by pressing"set"for longer)1.)Press the"set"key briefly until the display blinks"LP"and shows thelamp number.2.)Use the"☐"and"❑"keys to set the lamp address.3.)Save the setting by pressing the"set"key briefly."LP"will now be displayed(without blinking).5.energy cOntrOlThe RFS2.1transceiver allows you to change the power outlet of all RFS2 or RFS2.1flash units that are set to the same studio address(in"ST"mode), and to change the output of individual lamp channels(in"LP"mode).The output can be adjusted in1/10and whole f-stops.mode"st"Briefly press the key"☐":all the RFS2or RFS2.1units increase the total energy by1/10f-stopBriefly press the key"❑":all the RFS2or RFS2.1units reduce the total energy by1/10f-stopLong press of the key"☐":all the RFS2or RFS2.1units increase the total energy by1f-stopLong press of the key"❑":all the RFS2or RFS2.1units reduce the total energy by1f-stopmode"lp"Briefly press the key"☐":The lamp channel indicated increases its total output by1/10f-stopBriefly press the key"❑":The lamp channel indicated reduces its total output by1/10f-stopLong press of the key"☐":The lamp channel indicated increases its total output by1f-stopLong press of the key"❑":The lamp channel indicated reduces its total output by1f-stop>Resetting the deviceTo reset the device to factory settings,first press and hold the"test"key and then press the"set"key for longer than four seconds.This resets the device.system compatible with commentsRFS2.1RFS2.1RFS2On units with RFS2,individual lamp and modelling light settings are not possibleRFS2RFS2RFS2.1Only RFS2functions are available (individual lamp and modelling light settings are not possible)RFS RFS No compatibility with RFS2or RFS2.1.Also no flash triggering.patibilitytransceiver technical dataStudio address setting range1–99Lamp address setting range1–40Radio frequency channels(automatically regulated)40 Frequency 2.4GHz Transmission time(transmitter to receiver)0.425ms Diaphragm shutter speed up to1/1500s Focal-plane shutter speed up to1/320s Flash triggering possible via:>Integrated hot shoe on central contact>Lateral3.5-mm sync jack in or outRange outdoors up to50m Range indoors up to30m Range up to200m Integrated antennaDimensions(LxBxH)68x38.5x33mm/2.7x1.5x1inch Weight46g/35oz(including battery)in the event of problems and undefined communication malfunctions bet-ween rFs 2.1devices,the cause may be strong frequency interference.in such cases,make sure the devices are not within the range of baby phones,video bridges,microwave ovens,cordless dect telephones,Wlan routers or bluetooth devices,or use a different studio channel.Subject to change in the interest of technical progress.This device complies with Part 15of the FCC Rules.Operation is subject to the following two conditions:(1)this device may not cause harmful interference,and (2)this device must accept any interference received,including interference that may cause undesired operation.Changes or modifications not expressly approved by the party responsible for compliance could void the user's authority to operate the equipment.Releases per second 100Button cell battery in transceiver Li-Mn CR2450(560mAh,3V)Automatic switchover to energy-saving mode after 8hoursTypical battery life approx.8–12monthsor 100,000flashesSync voltage 3V。
Kinetix 5100 I O 终端扩展模块安装指南说明书

Installation InstructionsOriginal InstructionsKinetix 5100 I/O Terminal Expansion BlockCatalog Number 2198-TBIOThe I/O terminal expansion block lets you wire I/O directly to the Kinetix® 5100 drive without the use of an extension cable and a separate terminal block. The I/O terminal expansion block securely mounts to the drive with its own mounting screws and simplifies I/O wiring. This publication provides installation and wiring instructions for the Kinetix 5100 I/O terminal expansion block. For further installation instructions on the Kinetix 5100 drive, refer to the Kinetix 5100 Single-axis EtherNet/IP Servo Drive User Manual, publication 2198-UM004.Before You BeginThe I/O terminal expansion block is attached to the I/O terminal on the front of the drive. When used the expansion block requires additional cabinet height and width.Front view of Kinetix 5100 drive.2198-E1004-ERS Kinetix 5100 drive is shown.Partial top view of Kinetix 5100 drive show additional clearance required for I/O terminal expansion block.PadDimensions are in mm (in.).2Rockwell Automation Publication 2198-IN020A-EN-P - August 2019Kinetix 5100 I/O Terminal Expansion BlockInstall the I/O Terminal Expansion BlockFollow these steps to install your I/O terminal expansion block.1.Wire the I/O terminal expansion block, by using the pinout table on page 3. The terminal block accepts the following.2.T o obtain a high-frequency bond between the cable shield and the expansion block and for stress relief, firmly attach the cable to the expansion block by using a tie wrap (you supply).3.Attach expansion block to the I/O connector on the front of the Kinetix 5100 drive by using a screwdriver and torque to 0.2 N•m (1.77 lb•in).Attribute 2198-TBIOWire gauge 1.5…0.05 mm 2 (16…30 AWG)Strip length 6…7 mm (0.24…0.27 in.)Torque value20 N•cm (1.77 lb•in)Tie WrapExposed copper pad is under cable shield.Route wires such that it limits stress on cable.Rockwell Automation Publication 2198-IN020A-EN-P - August 20193Kinetix 5100 I/O Terminal Expansion BlockWire the I/O Terminal Expansion BlockUse the following pinout table to wire the I/O from your system.I/O Terminal Expansion Block PinoutIOD PinDescriptionSignal1Digital output 4+OUTPUT4+2Digital output 3-OUTPUT3-3Digital output 3+OUTPUT3+4Digital output 2-OUTPUT2-5Digital output 2+OUTPUT2+6Digital output 1-OUTPUT1-7Digital output1+OUTPUT1+8Digital input 4INPUT49Digital input 1INPUT110Digital input 2INPUT211Common for digital inputs, connected to +24 or 0V DC DCOM 12Analog input signal ground AGND 13Analog input signal ground AGND 14Reserved (1)(1)The reserved pins are not present on I/O terminal expansion block.—15Analog monitor output 2AOUT216Analog monitor output 1AOUT117Reserved (1)—18Analog torque input COMMAND119Analog input signal ground AGND 20Reserved (1)—21Buffered encoder output Ch A+AMOUT+22Buffered encoder output Ch A-AMOUT-23Buffered encoder output Ch B-BMOUT-24Buffered encoder output Ch Z-ZMOUT-25Buffered encoder output Ch B+BMOUT+Allen-Bradley, Kinetix, Rockwell Automation, and Rockwell Software are trademarks of Rockwell Automation, Inc.Trademarks not belonging to Rockwell Automation are property of their respective companies.Rockwell Otomasyon Ticaret A.Ş., Kar Plaza İş Merkezi E Blok Kat:6 34752 İçerenköy, İstanbul, T el: +90 (216) 5698400Rockwell Automation maintains current product environmental information on its website at/rockwellautomation/about-us/sustainability-ethics/product-environmental-compliance.page .Publication 2198-IN020A-EN-P - August 2019Copyright © 2019 Rockwell Automation, Inc. All rights reserved. Printed in the U.S.A.Additional ResourcesThese documents contain additional information concerning related products from Rockwell Automation.Y ou can view or download publications at /global/literature-library/overview.page .Rockwell Automation SupportFor technical support, visit /support/overview.page .ResourceDescriptionKinetix Servo Drives Specifications Technical Data, publication KNX-TD003Product specifications for Kinetix Integrated Motion over the EtherNet/IP network, Integrated Motion over Sercos interface, EtherNet/IP networking, and component servo drive families.Kinetix 5100 Single-axis EtherNet/IP Servo Drive User Manual, publication 2198-UM004.Provides information on how to install, configure, start up, and troubleshoot your Kinetix 5100 servo drive system.Industrial Automation Wiring and Grounding Guidelines, publication 1770-4.1Provides general guidelines for installing a Rockwell Automation industrial system.Product Certifications website: rok.auto/certificationsProvides declarations of conformity, certificates, and other certification details.。
OperatingInstructionsMULTIchargerLN-5014

U L T I c h a r g e r L N -5014 # M 92523 (06-05/R E V 1)Operating Instructions MULTIcharger LN-5014! These operating instructions are an integral part of this product containing important information and safety notes. They should be kept in a safe place and available for reference.1. SpecificationInput voltage11 – 15 VCell count, Battery type 1 – 14 cells NiCd 1 – 14 cells NiMH1 – 5 cells Li-Po or Li-Io1 – 6 cells lead-acid Charge current 0.1 A – 5 A Discharge current 0.01 A – 1 A Trickle charge current0 – 250 mACharge termination methodDelta-Peak for NiCd and NiMHConstant current / constant voltage forLi-Po and Li-IoBattery Cycling max. 5 cycles, ending charged ordischargedLCD 2 lines, 16 characters, illuminated2. CE- Conformity DeclarationMULTIPLEX Modellsport GmbH & Co. KG declares that the MULTIcharger LN-5014 conforms with the following harmonised EU directives: EN 50081, EN 50082, EN 55014, EN 550223. Safety notes! Read the instructions before using the charger for the first time ! Do not open the case, and do not modify the unit in any way! Use the charger to recharge Li-Ion / Li-Polymer, Pb, NiCd or NiMH batteries ! Observe the battery manufacturer’s charging instructions for all battery types! Use the charger only to recharge packs consisting of cells of the same type and capacity ! Do not attempt to charge two battery packs simultaneously! Do not recharge packs which are hot to the touch; allow them to cool down to ambient temperature first ! Do not connect charger and battery with reverse polarity ! Do not leave the charger operating unsupervised! The charger may become hot when operating - take care when touching the unit ⇒ Do not cover the charger; provide adequate cooling⇒ Do not subject the chargers LCD display screen to direct sunshine! Keep the charger, battery and cables well away from flammable or temperature-sensitive objects ! Protect the charger from moisture4. FeaturesØ Automatic charge / discharge cycles Ø Lightweight, compact, easy to transport Ø Strong aluminium caseØ Error messages for out-of-range input voltage,incorrect connection or reversed polarity at input or output, poor battery state and internal errors5. Button functionsBATTERY TYPE buttonWhen you press this button, the currently set battery type - NiCd, NiMH, Li-Po / Li-Io or Pb (lead-acid) - starts to flash.While the battery type is flashing, further pressing of the BATTERY TYPE button will switch to the next battery type in the following sequence (NiCD è NiMH è Li-Io / Li-Po è Pb è NiCd è ...).If you press another button (or no button), the battery type ceases to flash after about five seconds. Holding this button pressed in, the current charge settings are displayed for about three seconds. ENTER / START buttonIf you press this button briefly, the variable value in the current menu starts flashing.Press the ENTER button again, the next variable value starts to flash. If you press no button for about three seconds, the value ceases flashing.Holding this button pressed in starts the charge process or if charging is occurring, stops the charge process.INC/DEC buttonsWith these buttons the flashing values can be increased or decreased, or charging/discharging modes are selected as per the flow charts.U L T I c h a r g e r L N -5014 # M 92523 (06-05/R E V 1)Refer to the flow chart diagrams for step by step directionson what button to press for each function.For discharging or cycling batteries, please note the Discharge Current capabilities chart in this manual. This function is only practical for lower voltage and lower capacity packs such as used for Tx and Rx power.6. Programming for NiCd mode or NIMH modeSelect Battery typeSelect the type of battery, NiCD or NiMH with the battery type button. Charge currentIn this menu the charge current can be set within the range 0.1 A to 5 A in increments of 50mA using the INC and DEC buttons. Discharge current (Note Discharge Current capabilities chart in this manual)In this menu the discharge current can be set within the range 0.1A to 1A using the INC and DEC buttons. Final discharge voltageIn this menu the termination voltage for the discharge process can be set within the range 0.1 V to 16.8 V. Charge / Discharge cycles (Cycle)In this menu you can set the values and method of the charging / discharging cycles. C->D charge to discharge = ending with discharged battery D->C discharge to charge = ending with fully charged battery Number of cycles: 1 to 5Press and hold down the ENTER button to start the charging/discharging or cycling process.7. Programming for LiPo and LiIo modeYou can use the unit to charge a maximum of five Lithium cells. The combined charge method of constant current and constant voltage ensures that your Lithium-Ion and Lithium-Polymer batteries are fully charged every time. The unit starts by charging at aconstant current. As soon as the pack reaches a cell voltage of about 4 V the charger switches over to constant voltage. The constant voltage charge process is terminated when the charge current falls below 100 mA. This ensures that the battery is fully charged at the end of the charge process. Battery typeIn this menu the battery type Li-Po or Li-Io can be selected using the INC and DEC buttons. NOTE: take care to select the correct battery type!The maximum voltage for Lithium batteries is as follows: 4.1 V per cell for Lithium-Ion (Li-Io) batteries, 4.2 V per cell for Lithium-Polymer (Li-Po) batteries. The difference in voltage makes it extremely important to select the correct battery type (Li-Po or Li-Ion) with great care, and to check the setup before starting the charge process. If you select the wrong battery type, the pack may be damaged or ruined, and could even explode. Battery capacityIn this menu the capacity of the battery to be charged can be set within the range 100 mAh to 5000 mAh in increments of 50 mAh using the INC and DEC buttons.Voltage for Lithium Ion batteries (Li-Io)In this menu the nominal voltage of the battery to be connected for charging and discharging can be set using the INC and DEC buttons. Possible values are 3.6 V, 7.2 V, 10.8 V, 14.4 V and 18.0 V. Voltage for Lithium-Polymer batteries (Li-Io)In this menu the nominal voltage of the battery to be connected for charging and discharging can be set using the INC and DEC buttons. Possible values are 3.7 V, 7.4 V, 11.1 V, 14.8 V and 18.5 V.Discharge current (Note Discharge Current capabilities chart in this manual)In this menu the desired discharge current can be set within the range 0.1 A to 1 A using the INC and DEC buttons. Charge currentFor safety reasons the charger always uses the 1 C value as the charge current for Lithium cells (Li-Po or Li-Io). The current is calculated from the battery capacity you have entered.Example for a Li-Po cell of 1500 mAh capacity: 1 C = 1500 mAh, charge current = 1.5 APress and hold down the ENTER button to start the charging/discharging or cycling process8. Programming for Lead-Acid battery modeCharge currentIn this menu the charge current can be set within the range 0.1A to 5A in increments of 100mA using the INC and DEC buttons. Battery VoltageIn this menu the voltage of the battery to be charged can be set within the range of 2V through 12V in increments of 2V using the INC and DEC buttons.Discharge current (Note Discharge Current capabilities chart in this manual)In this menu the discharge current can be set within the range of 0.01A to 1A using the INC and DEC buttons.Press and hold down the ENTER button to start the charging or discharging process.U L T I c h a r g e r L N -5014 # M 92523 (06-05/R E V 1)9. Screen displaysDisplays during charging or discharging Display after charge terminationEND 030:00 00000 NC 100mA 10.75VPressing the ENTER button while this message is displayed returns you to the main menu.Display of current valuesThis information is available for the last battery charged if you hold the BATTERY TYPE button pressed in for longer than three seconds, after a charge or discharge process.You can switch between the three windows using the INC and DEC buttons. If you do not press any button for longer than about three seconds, the screen reverts to the normal display.10. E rror messagesINPUT BATTERY VOLTAGE ERROR Input voltage below 11.0 V or above 15.0 VOUTPUT BATTERY REVERSE POLARITY Battery connected to the charger with reversed polarity CHECK THE BATT. OPEN CIRCUIT Break in charge circuitNO BATTERYNo battery connected to the charger’s output OUTPUT CIRCUIT PROBLEMInternal error in chargerProgramming flow charts for MULTIcharger LN-5014Note: Flow chart for the Pb or Lead acid battery appears first due to space constraints in this manualŒ PBMenus MULTIcharger LN-5014U L T I c h a r g e r L N -5014 # M 92523 (06-05/R E V 1)• NiCd and NiMH (Screen Menu for NiMH will show NiMH)Ž LiPo & LiIo。
Ophir RF 5100F RF 功率放大器说明书
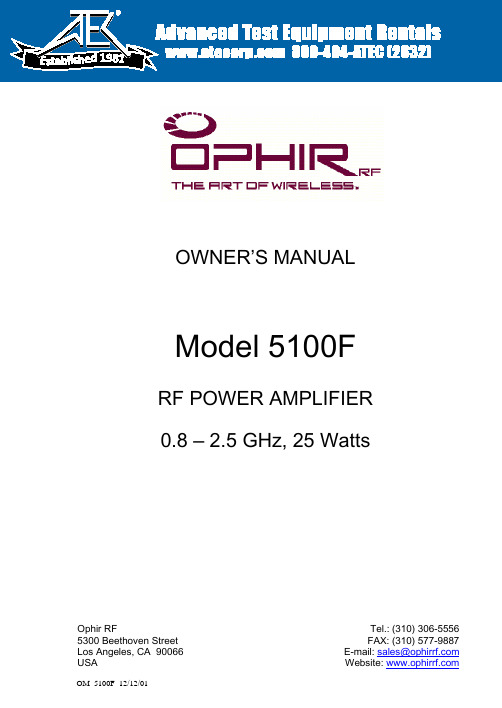
OWNER’S MANUALModel 5100F RF POWER AMPLIFIER 0.8 – 2.5 GHz, 25 WattsOphir RF5300 Beethoven Street Los Angeles, CA 90066 USATel.: (310) 306-5556FAX: (310) 577-9887 E-mail: ***************** Website: OM_5100F 12/12/011981___________________________________________________ CertificationOphir RF certifies that this product met its published specifications at the time of shipment from the factory._____________________________________________________________________ WarrantyThis Ophir RF product is warranted against defects in material and workmanship for a period of two (2) years from date of receipt. During the warranty period, Ophir RF, will,at its option, either repair or replace products that prove to be defective. For warranty service or repair, this product must be returned to a service facility designated by Ophir RF.Limitation of WarrantyThe foregoing warranty shall not apply to defects resulting from improper orinadequate maintenance by Buyer, Buyer-supplied software or interfacing,unauthorized modification or misuse, operation outside of the environmentalspecifications for the product, or improper site preparation or maintenance.NO OTHER WARRANTY IS EXPRESSED OR IMPLIED. OPHIR RF SPECIFICALLY DISCLAIMS THE IMPLIED WARRANTIES OF MERCHANTABILITY AND FITNESS FOR A PARTICULAR PURPOSE.Exclusive RemediesTHE REMEDIES PROVIDED HEREIN ARE BUYER’S SOLE AND EXCLUSIVEREMEDIES. OPHIR RF SHALL NOT BE LIABLE FOR ANY DIRECT,INDIRECT, SPECIAL, INCIDENTAL, OR CONSEQUENTIAL DAMAGES, WHETHER BASED ON CONTRACT, TORT, OR ANY OTHER LEGAL THEORY._____________________________________________________________________ AssistanceFor any assistance, contact your Ophir RF Sales and Service Office.OM_5100F 12/12/01 Page 1 of 14_____________________________________________________________________ Safety InformationThe following safety notes and symbol are used in this manual and on the equipment. Familiarize yourself with each and its meaning before operating this equipment.Caution Caution denotes a hazard. It calls attention to a procedure that, if not correctly performed or adhered to, would result in damage to, ordestruction of, the equipment. Do not proceed beyond a caution noteuntil the indicated conditions are fully understood and met._____________________________________________________________________ Warning Warning denotes a hazard. It calls attention to a procedure which, if not correctly performed or adhered to, could result in injury or lossof life. Do not proceed beyond a warning note until the indicatedconditions are fully understood and met._____________________________________________________________________The instruction documentation symbol. The product is marked with thissymbol when it is necessary for the user to refer to the instructions in thedocumentation._____________________________________________________________________ General Safety ConsiderationsWarning This is a safety Class I product provided with a protective earthing ground incorporated in the AC power cord. The AC power cordshall only be inserted in a socket outlet provided with a protectiveearth contact. Any interruption of the protective conductor, insideor outside of the equipment, is likely to make the equipmentdangerous. Intentional interruption is prohibited._____________________________________________________________________ Warning No operator serviceable parts inside. Refer servicing to qualified personnel. To prevent electrical shock, do not remove covers._____________________________________________________________________ Warning If this equipment is used in a manner not specified by Ophir RF, the protection provided by the equipment may be impaired._____________________________________________________________________ Caution Before switching on this equipment, make sure that the line voltage is correct and that an External Load has been applied. (Refer to 2.2.3)OM_5100F 12/12/01 Page 2 of 14ContentsSection PageInformation 5I GeneralDeclaration of Conformity 5Scope 5Description 5Equipment Specifications 6II Installation 7Incoming Inspection 7Preparation for Use 7Power Requirements 7Earthing 7Load Requirements 7Connections 7CableIII Operation 8Introduction 8AgainstUnspecified Use 8StatementControls, Indicators, and Connectors 8Basic Operating Procedures 8Before Turn On 8Turn On 9Operation 9Turn Off 9IV Maintenance 1010IntroductionTest 10PerformanceProcedures 10AdjustmentProcedures 10TroubleshootingImproper Power Distribution 10Low or No RF Output Power 10Cleaning 10Service 11V CustomerServicing 11Return11(RMA)MaterialAuthorizationShipment11forRepackaging12FormRequestRMAOM_5100F 12/12/01 Page 3 of 14Figuresdiagram 131 BlockFigureFigure 2 System View 14Tables6TableSpecifications1 EquipmentOM_5100F 12/12/01 Page 4 of 14SECTION IGeneral Information1.1 Declaration Of ConformityDECLARATION OF CE CONFORMITYOphir RF Inc., 5300 Beethoven Street, Los Angeles, CA 90066, declares under sole responsibility that the RF Power Amplifier, Model 5100F, to which this declaration relates, meets essential health and safety requirements and is in conformity with ISO 3864. The CE marking has been applied according to the relevant Safety and CE Directives listed below using the relevant section of the following EC standards and other normative documents:EU EMC DIRECTIVE 89/366/EEC - Essential health and safety requirements relating to electromagnetic compatibilityENEN55022 Class BEN50082-1 EC generic immunity requirements, Category A & BIEC801-2, IEC801-3, IEC801-4EC Low Voltage Directive 72/23/EEC Essential health and safety requirements relating to electrical equipment designed for use within certain violate limits.EN61010-1 Safety requirements of Test Measurement and LaboratoryEquipment.1.2 ScopeThis owner’s manual contains operating instructions for a model 5100F amplifier.1.3 DescriptionThe power amplifier operates in the RF frequency. The input to the power amplifier is rated at 0 dBm nominal CW signal between the 0.8 – 2.5 GHz frequency range. The output of the power amplifier is specified at 25 Watts CW RF signal. Detailed specifications for the power amplifier are given in table 1-1. OM_5100F 12/12/01 Page 5 of 14Equipment SpecificationsTable 1-1. Specifications @ 25º COperation:A/ABofClass2.5GHz–Range:Frequency0.8Output Power @ Saturation: 25 Watts CW TypicalOutput Power @ 1 dB Compression: 20 Watts CW minimumdB+45minimumGain:SmallSignalSmall Signal Gain Flatness: ± 2.0 dB maximumnominalohmsInput/OutputImpedance:50Input VSWR: 2:1 maximumdBmInput +10RFMax.Operating Temperature Range: 0º C to 50º COperating Humidity Range: 95%, Non-condensingTemp. Protection: Shut down @ 80º C minimumAirForcedCoolingsystem:InternalAC Input: 100 - 240 VAC, 50/60 Hz, 1¯Wattsmaximum200ACPower:InputDimensions: 19" W x 3.5" H x 18" DmaximumPoundsWeight: 30Option(s) included:-Type-N Connectors on Front Panel.*NOTE – Specifications subject to change without noticeOM_5100F 12/12/01 Page 6 of 14SECTION IIInstallationInspection2.1 IncomingWARNING!Do not apply power until you have read Sections II and III and you have performed all specified procedures. If you fail to observe this warning, damage to the equipment and/or bodily injury may result.The power amplifier has been mechanically and electrically inspected prior to shipment. If the equipment has been damaged or if electrical performance is not within specification, notify the carrier and OPHIR RF immediately.2.2 Preparation For Use2.2.1 Power RequirementsThe power amplifier requires a power source of 100 – 240 VAC, 50/60Hz capable of delivering 200 Watts. Turn off the front panel ‘ON/OFF’switch before connecting the AC power source.2.2.2 EarthingEarthing is achieved simultaneously with connection of the AC powercords to a properly grounded power source.2.2.3 Load RequirementsThe power amplifier requires a load, antenna, or dummy load with a 50-Ohm nominal impedance.CAUTION!Make this external load connection before applying any power to theequipment.2.2.4 Cable ConnectionsThe AC power cable connection is made at the rear of the poweramplifier via the receptacle connector. RF connections for Input andOutput are made at the front via Type-N connectors. (Refer to Figure 2) OM_5100F 12/12/01 Page 7 of 14SECTION IIIOperation3.1 IntroductionThis section describes the operating controls and procedures of the power amplifier.3.2 Statement Against Unspecified UseThis amplifier must be used as specified by the manufacturer. Use of this equipment in any way not specified by the manufacturer may result in bodily injury and/or damage to the equipment.3.3 Controls, Indicators, and ConnectorsWhen set to ‘ON’, the ON/OFF switch will light indicating that AC power is present. The RF INPUT and OUTPUT connections are located on the front of the power amplifier. Refer to figure 2 and the following discussion for the location and functional description of all controls, indicators, and connectors.3.4 Basic Operating ProceduresNOTE!The operation of the power amplifier is passive; that is, after an External Load and Input power have been applied, no procedures other than turn off are required.3.5 Before Turn OnCAUTION!Do not obstruct the airflow at the front and rear of the power amplifier. If you do not verify that this equipment has an unobstructed airflow, you may cause this equipment to overheat or otherwise impair its operation.Perform the following preliminary procedures before energizing the equipment:a. Check that the ON/OFF switch is set to the ‘OFF’ position.b. At the rear of the RF power amplifier, verify that the AC cord is properlyinserted into the receptacle connector.c. Verify that 50 ohm loads are connected to the RF Input and Output ports.3.6. Turn OnPerform the following procedures to energize the equipment:a. Set the ON/OFF switch to the ‘ON’ position. Verify that the green switchlamp is lit.b. Apply RF power.OM_5100F 12/12/01 Page 8 of 14CAUTION!To maintain specified performance and retain certain operating characteristics, RF input power should not exceed +10 dBm.3.7. Operation3.7.1 ON/OFF SwitchIn the ‘ON’ position, AC power is supplied to the power amplifier.3.7.2 ON/OFF Switch LampLights to indicate the distribution of AC power throughout the poweramplifier.3.7.3 TEMP. FAULT IndicatorLights at an internal temperature exceeding 80º C with the amplifierturning off DC bias voltage to the main amplifiers’ modules. DC biasvoltage will automatically return at temperatures below 75º C.Off.3.8 TurnWARNING!In the event of ANY power failure, whenever possible and practical, it is advisable to reset the ON/OFF switch on the front panel to the “OFF”position before y ou reconnect AC power to the power amplifier. This is to prevent any possible electrical damage to the amplifier, due to the initial power surge, once power is restored.Turn off the RF power amplifier by first lowering or removing the RF Input drive level and then placing the ON/OFF switch in the ‘OFF’ position.OM_5100F 12/12/01 Page 9 of 14Maintenance4.1 IntroductionThis section describes the performance tests, adjustments and troubleshooting procedures for the power amplifier.4.2 Performance TestThe performance test is identical to the operating procedure described in Section III.4.3 Adjustment ProcedureThere are no operator adjustments applicable for the power amplifier.4.4 Troubleshooting ProcedureNOTE!Troubleshooting beyond the level described in this procedure must be performed at an authorized service facility or the warranty may be voided.The following troubleshooting procedure is to be used as a guide to help ascertain whether the equipment is malfunctioning.4.4.1 Improper Power DistributionWhenever there appears to be improper power distributed throughout theamplifier, perform the following steps:a. Verify the ‘ON/OFF’ switch lamp is illuminated on the front panel.b. Verify that the internal fans are operating.c. If neither step A or B above appear to be working, verify the presenceof AC power at the source and also at rear panel connection.4.4.2 Low or No RF Output PowerWhenever the RF output power of the amplifier and/or the current drawnfrom the power supply is low, or the operating temperature has exceeded80°C, the system may have triggered the thermal protection function.Perform the following procedure:a. Verify that the drive level is correct.b. Check that the ‘TEMP. FAULT’ indicator is not illuminated.If the above conditions are verified and there is still low or no RF outputpower, then contact your nearest authorized Ophir RF Service Center. 4.5. CLEANINGUse a rag with isopropyl alcohol to clean exterior surfaces. Use a vacuum to remove dust from the screens on the front and rear of the equipment.Customer Service5.1 ServicingAll servicing and repair must be done by an authorized repair and servicing facility.5.2 Return Material Authorization (RMA)In the unlikely event you experience equipment difficulties that can not be resolved without opening up the equipment, you will need to obtain authorization and an RMA number prior to returning the equipment.NOTE!It is Ophir RF’s policy not to accept any returned equipment without an authorized RMA number!5.3 Repackaging for Shipment.WARNING!It is always recommended that two people carry this system due to its weight.Use the original shipping container and packing materials if possible. If these have been discarded or are not in good condition for reuse, use a heavy-duty carton capable of providing adequate protection. Whenever the amplifier is being returned to the manufacturer, attach an identifying tag, indicating the RMA number, on the outside of the container.Wrap the equipment in heavy paper or plastic, and use enough shock-absorbing material (3 to 4-inch layers) around all sides to provide a firm cushion and to prevent movement within the container. Protect the front and rear panels with cardboard or foam blocks. Seal the shipping container securely and mark the container "FRAGILE".To receive your RMA number, contact our customer service department.Customer ServicePhone: 310-306-5556Fax: 310-577-9887Email: ***************************You will be required to complete a simple questionnaire prior to receiving your RMA number. Once you have your RMA number, you are authorized to return your equipment.To help you expedite this process, we have included a copy of the form you will be required to complete prior to receiving your RMA number.5300 Beethoven Street, Los Angeles, CA 90066Tel: (310) 306-5556 • FAX (310) 577-9887 •e-mail:***************************RMA REQUEST FORMRMA NUMBER:NAME:CUSTOMERRECEIVEDROM RESS:F ADD(STREET ADDRESS – INCLUDING SUITE OR M/S NUMBER)(CITY – STATE – ZIP OR COUNTRY CODE) (COUNTRY)RETURN TOADDRESS:(STREET ADDRESS – INCLUDING SUITE OR M/S NUMBER)(CITY – STATE – ZIP OR COUNTRY CODE) (COUNTRY)CONTACT PERSON:(FIRST AND LAST NAME) (TITLE/RANK)(TELEPHONE) (FAX)(E-MAIL)MODEL NUMBER SERIAL NUMBERREASON FOR RMA:PLEASE FAX THIS FORM TO OPHIR RF, INC.AT (310) 577-9887 ATTN: CUSTOMER SERVICETHERE IS A $500 MINIMUM EVALUATION CHARGE FOR ALL NON-WARRANTY REPAIRS. PURCHASE ORDER TO BE PRESENTED PRIOR TO COMMENCEMENT OF REPAIRS. FOLLOWING EVALUATION, THE COST OF REPAIRS WILL BE SUBMITTED FOR YOUR APPROVAL AND PURCHASE ORDER AMENDMENT.DO NOT SHIP AMPLIFIERS C.O.D. – OPHIR RF WILL NOT ACCEPT ANY C.O.D. SHIPMENTS. PLEASE CALL US WITH ANY SHIPPING QUESTIONS.。
稳压二极管的作用

稳压二极管的作用2007-09-06 08:44稳压二极管(又叫齐纳二极管)它的电路符号是:此二极管是一种直到临界反向击穿电压前都具有很高电阻的半导体器件.在这临界击穿点上,反向电阻降低到一个很少的数值,在这个低阻区中电流增加而电压则保持恒定,稳压二极管是根据击穿电压来分档的,因为这种特性,稳压管主要被作为稳压器或电压基准元件使用.其伏安特性见图1,稳压二极管可以串联起来以便在较高的电压上使用,通过串联就可获得更多的稳定电压.稳压管的应用:1、浪涌保护电路(如图2):稳压管在准确的电压下击穿,这就使得它可作为限制或保护之元件来使用,因为各种电压的稳压二极管都可以得到,故对于这种应用特别适宜.图中的稳压二极管D是作为过压保护器件.只要电源电压VS超过二极管的稳压值D就导通,使继电器J吸合负载RL就与电源分开.2、电视机里的过压保护电路(如图3):EC是电视机主供电压,当EC电压过高时,D 导通,三极管BG导通,其集电极电位将由原来的高电平(5V)变为低电平,通过待机控制线的控制使电视机进入待机保护状态.3、电弧抑制电路如图4:在电感线圈上并联接入一只合适的稳压二极管(也可接入一只普通二极管原理一样)的话,当线圈在导通状态切断时,由于其电磁能释放所产生的高压就被二极管所吸收,所以当开关断开时,开关的电弧也就被消除了.这个应用电路在工业上用得比较多,如一些较大功率的电磁吸控制电路就用到它.4、串联型稳压电路(如图5):在此电路中,串联稳压管BG的基极被稳压二极管D 钳定在13V,那么其发射极就输出恒定的12V电压了.这个电路在很多场合下都有应用常用二极管的参数-1N系列2007-09-06 12:27型号反向工作峰值电压额定正向整流电流正向不重复浪涌峰值电流正向压降反向电流工作频率外形封装U RM/V I F/A I FSM/A U F/V I R/uA f/KHZ1N4000 1N4001 1N4002 1N4003 1N4004 1N4005 1N4006 1N4007255010020040060080010001 30 ≤1<5 3 DO-411N5100 1N5101501001.5 75 ≤1<5 3 DO-151N5103 1N5104 1N5105 1N5106 1N5107 1N5108300 400 500 600 800 10001N5200 1N5201 1N5202 1N5203 1N5204 1N5205 1N5206 1N5207 1N52085010020030040050060080010002 100 ≤1<10 31N5400 1N5401 1N5402 1N5403 1N5404 1N5405 1N5406 1N5407501002003004005006008003 150多媒体协处理器SM501在嵌入式系统中的应用 ---从网上下载的PXA170的PROTEL99原理图中有SM5012007-09-11 10:47多媒体协处理器SM501在嵌入式系统中的应用无锡商业职业技术学院王立凤引言近年来,从手持消费电子到工业控制系统,嵌入式处理器的应用已经深入到人们工作和生活的方方面面,在某些应用领域,系统需要提供如1280×1024这类高分辨率的显示界面,而多数嵌入式处理器不能支持,或者在高分辨率下提供的显示效果不好。
西玛德舵手 TP10、TP20 和 TP30 维修手册说明书

TILLERPILOT TP10, TP20 & TP30 SERVICE MANUALIssue 4.0 17/09/03SIMRADSimrad Margate LtdStar Lane, Margate, Kent CT9 4NP,UKTelephone +44 (0) 1843 290290Facsimile +44 (0) 1843 290471E-Mail:********************************CONTENTS1 INTRODUCTIONPCBs1.1 ElectronicComponents1.2 Mechanical2 OPERATIONINSTRUCTIONS3 ASSEMBLY4 MECHANICAL ASSEMBLY DRAWINGSDESCRIPTIONS5 CIRCUIT6 CIRCUITDIAGRAMSSchematics6.1 Circuit6.2 Component Lists and Layouts7 PROGRAMMING AND CONFIGURATIONFINDING8 FAULT8.1 Common User Faults8.2 Common Technical Faults9SPARE PARTS DETAIL9.1 SparesAids9.2 Service9.3 AccessoriesNOTES10 TECHNICAL© 2003 Simrad Margate LtdThe technical data, information and illustrations contained in this publication were to the best of our knowledge correct at the time of going to print. We reserve the right to change specifications, equipment, installation and maintenance instructions without notice as part of our policy of continuous development and improvement. No part of this publication may be reproduced, stored in a retrieval system or transmitted in any form, electronic or otherwise without prior permission from Simrad Margate Ltd. No liability can be accepted for any inaccuracies or omissions in the publication, although every care has been taken to make it as complete and accurate as possible.Tiller Pilot TP10, TP20 & TP30Section 1IntroductionIssue 4.0 17/09/03SIMRAD 1INTRODUCTION TO THE TP10, TP20 AND TP30 TILLERPILOTThe TP10, TP20 and TP30 Tillerpilots combine highly sophisticated electronics with advanced software and powerful mechanical drive to provide accurate and reliable steering performance under a variety of different conditions with minimal current consumption.TP10 – is suitable for tiller steered sailing yachts up to 10M (34 Ft) in length.TP20 – offers the same facilities as the TP10 and is fully compatible with the Navico Corus instrument system to provide a complete navigation system. Options offered include connection to an external compass, wind sensor or navigational receiver together with additional remote control facilities.TP30 – offers the same facilities as the TP20 with an improved re-circulating ball screw drive andis suitable for tiller steered sailing yachts up to 12.8M (42 Ft) in length.The main components of the Tiller Pilot are listed below:Electronics PCBsEarly versionsTP10 PCB (TP10 only)TP30 PCB (TP 20 & TP30)Current Versions. The same PCB is used for all products. The wiringloom carrying the NMEA data is left disconnected in the TP10.TP10 / 20 / 30 Re-engineered PCB (Common to all)Mechanical ComponentsGeneral Assy : TP10General Assy : TP20General Assy : TP30Tiller Pilot TP10, TP20 & TP30Section 2OperationIssue 4.0 17/09/03SIMRAD 2OPERATING SIMRADThis Service Manual only contains operating instructions for those features of the Simrad Tiller Pilot range that are not normally available to the end user. For details of normal operation please refer to the appropriate Simrad Instruction Manual.Tiller Pilot TP10, TP20 & TP30Section 3 Assembly Instructions3ASSEMBLY INSTRUCTIONSGeneral Assembly : TP10Motor and Drive Assembly. The Bottom Case Assembly is supplied fitted with appropriate cables. Refer to detail in Drawing Number E03504 and insert the Push Rod Seal E00747, which has a taper inner bore, into the case with the larger bore of the seal facing outwards. Fit “O” Ring 190026, spacer E02870 and End Cap E02495 and push home. Fit Retainer E03084 and secure with 2 screws 200002 to hold the end cap, ensuring it is pushed fully in when the two screws are tightened. Using a small brush, grease the ‘trough’ area and the bore which houses the seal, “O”ring and spacer. Insert the Drive Assembly E03264 ensuring that the bearing slots into the bearing housing and the drive belt 280027 is fitted around the pulley. Insert the Motor Assembly E02788 fitted with front and rear Motor Mounts E02502 and E02503 ensuring that the blue wire is uppermost, the motor sits snugly into the bottom of the retaining slot and the drive belt is engaged over the motor drive pulley. Check that the motor, belt and drive screw assembly move freely. Fit Bearing Clamp E02497 on two Nylon Spacers 200115, one on each screw 200137, into the case bottom and secure the bearing with the two screws. Refer to the sketch below and check that the belt tension is within +/- 3mm.Fit the Tiller Connector E02607 into the end of the Push Rod E02522 and screw in, finger tight.Hall Effect PCB. Fit the Hall effect PCB onto the 2 pillars using 2 nylon washers 200037 as spacers between the pillars and the PCB, and 2 screws 200139. Ensure that the separation distance between the Magnets (E03208), seated in the 71 Tooth Pulley (E02505), and the Hall Effect Devices (140010) does not exceed 1mm.Main PCB. Feed the power, motor and feedback leads through the 2 grommets 190036 and the appropriate grommet in the PCB Assembly cover and solder the connections to the PCB. Refer to drawing and push PCB Assembly firmly onto the four bosses in the PCB Cover E02680. Clip the compass Assembly E02637 into the Drilled PCB Cover E02680, it can only be fitted one way round, ensuring that the lugs on the compass assembly line up with the 2 holes in the PCB cover and push in. Refer to drawing E03504 and ensuring that the wires from the compass to the connector lay over the PCB, insert plug into the socket on the PCB. Ensure all wires are clear of, and not fouling the PCB cover seal, and position the PCB Cover complete with the PCB and compass into the Case Top Assembly E02612. Screw down the PCB cover with 6 screws 200139 and fully tighten. Position the two grommets into case top, and push home into the two slots. Wrap the ‘Wits” fixing 200196 around the cable loom, and using a screw 200139 fix into the top cover.Main Seal. Fit the pivot pin into the square section at the rear of the prepared bottom case ensuring that the pin hangs out of the case with the notch on the pivot facing towards the operating rod of the tillerpilot. Fold the metal pin into its recess in the lower case. Position the Case Seal E02498 onto the case bottom ensuring it is pushed fully into the grooved housing. Carefully lift the case seal from around the area of the pivot pin and using a cotton bud apply Dow Corning 1205 Primer 260029 to the case. Fill a small hypodermic syringe with Dow Corning 3140 Silicone sealant 260001 and run a small bead of sealant completely around the case seal in the area of the square as shown below.Refit the seal onto the case.Final Assembly. Carefully position the case top onto the bottom ensuring that the case seal is correctly located all round, squeeze the top and bottom halves of the case together, and fit the 10 screws 200088. Tighten down evenly all round in the sequence shown below:Post Assembly Test. Remove the Tiller Connector E02607 and push the Tillerpilot Test Syringe Part No. TP-SRY over the end of the Push Rod E02522. Depress the syringe piston and release, the piston should return to its original position indicating that the integrity of the case seal has not been compromised during fitting. Remove the Test Syringe and refit the Tiller Connector. General Assembly : TP20Refer to Drawing No. E03505. Assembly is identical to the TP10 with the following exceptions:Case Bottom. The case bottom includes a third wiring (communications) loom to carry NMEA and CANBUS data.PCB Cover E02681. The PCB Cover is drilled with a third access point and grommet to accept the NMEA and CANBUS data leads.Issue 4.0 17/09/03SIMRAD General Assembly : TP30Refer to Drawing No. E03506. Assembly is identical to the TP20 with the following exception:Drive Assembly E02618. The Drive Assembly employs a re-circulating ball screw. The assembly is held in place by the metal mounting plate sitting in the mounting slots in both top and bottom cases and drive belt tension is adjusted by the inclusion of spacing shims E02754 as required.Tiller Pilot TP10, TP20 & TP30Section 4Mechanical Assembly DrawingsIssue 4.0 17/09/03SIMRAD4MECHANICAL ASSEMBLY DRAWINGSGeneral Assembly : TP10E03504General Assembly : TP20E03505General Assembly : TP30E03506Tiller Pilot TP10, TP20 & TP30Section 5Circuit Descriptions5CIRCUIT DESCRIPTIONSTillerpilot Common PCB AssemblyIntroduction. The PCB Assembly is a common item to all Wheelpilots and Tillerpilots. However, when the PCB is used in the TP10 or WP10 those components concerned with NMEA and CANBUS data are present but not in use, these components are highlighted in Red on the Circuit Diagram Drawing No. E03372.Supply and Regulation. The Tiller Pilots are designed to work from a 12 V source. Protection against incorrect polarity is provided by D1 and D4. Capacitors C1and C3 are used as reservoirs to hold up the supply voltage and reduce any supply dips. Protection against over-voltage spikes is provided by Resistor R2 and Zener Diode ZD1 and Regulator REG1 provides a 5V regulated supply. Transient Voltage Suppresser TVS1 protects the MOSFET drive transistors, TR10 to TR13, from voltage spikes greater than +16V.Microprocessor. Light Emitting Diodes LED1 to LED4 are driven from the microprocessor IC2 Ports P0.0 and P0.2 to P0.4 and turn OFF when the line goes HIGH via the transistor switches TR2 to TR5. When the transistors are off, resistors R32, R34, R36 and R38 provide a low current path for the LEDs to provide low level night illumination. The Audio Resonator AR1 is self resonating and switches ON when Port P0.5 goes HIGH via the transistor switch TR1 and resistors R59 and R60. The control key lines on Ports P4.0 to P4.4, normally pulled to +5V via resistors R7 to R11, are “scanned” by the microprocessor to detect if any of the switches have been operated and pulled the line LOW.NMEA Data In. NMEA data is optically isolated by IC5 and then fed into Port P2.4 of the microprocessor. Transistors TR6, TR7 and TR8 and components D6, D7, D8, R17, R18 and R19 form a switch, protected from high voltages, driven from Port P0.1 of the microprocessor. The switch is used to apply the synchronisation pulse (HR200_SYNC) to the NMEA line for products employing a Hand (Remote) Controller.CANBUS Data. CANBUS data in and out is driven by IC3 directly to and from Ports P2.1 and P2.0 respectively.NB. Components shown in RED on the circuit diagram, Drawing No. E03372, are not in circuit when the PCB is used with WP10 or TP10. The cable loom to connect them is absent from these products.Configuration Links. The Links, L1, L2 and L3, are used to configure the Microprocessor to either Wheelpilot or Tillerpilot operation and to model versions 10, 20 or 30 in accordance with the table below:1 Model Link 1Link 2Link 3TP 10N / C N / C N / CWP 10N / O N /C N / CTP 20N / C N / C N / OTP 30N / C N / O N / OWP 30N / O N / O N / OLEGEND N / C Normally Closed (soldered)N / O Normally Open (unsoldered)Microprocessor Reset. Integrated Circuit IC6 is an integrated reset generator for the microprocessor which produces a reset LOW pulse of approximately 50mS duration at switch on and whenever a 5v supply failure occurs. In addition to the reset provided by IC6, the microprocessor has a built in watchdog timer which will create a reset if a software crash occurs for any reason.Non-Volatile Memory (NVM). Integrated Circuit IC3 provides 1Kbit of E2 memory for the retention of important data after power down.Fluxgate (Compass). Two anti-phase signals are provided from microprocessor Ports P1.7 andP1.6. These signals are buffered by TR15 and TR16 to provide a higher current drive to the excitation coil of the fluxgate. A reference voltage level of +2 volts is provided by R46 and R53 decoupled by C53. The 2 coils, mounted at right angles, provide output signals proportional to the sine and cosine of the Earth’s magnetic field. These signals are fed via the electronic switch IC9,to 2 dual slope integrating analogue to digital converters IC7 and IC 8 plus associated components. The outputs of the comparator IC7 are fed to the microprocessor Ports P1.4 andP1.5 which provide input capture facilities. Accurate timing of the conversion is kept by the microprocessor to provide simultaneous precision analogue to digital conversion of both sine and cosine signals to avoid errors created by multiplexing the inputs.Motor Drive. The motor drive signals (MDRIVE_A and MDRIVE_B) are generated from the microprocessor at Ports P0.7 and P0.6, these lines being LOW when there is no drive and HIGH to drive. The drive outputs control IC10 and IC11 which are comparators set at threshold levels of+4V and +1V produced by the resistor network R71, R72 and R73. The comparators invert the signals and provide the current to switch the MOSFETs in stages which prevents both P and N channel MOSFETs on the same side of the “H-bridge” configuration, (i.e. TR10 and TR11 or TR12 and TR13), being partially switched on at the same time. When there is no drive, both N-channel MOSFETs TR11 and TR13 are switched on giving a direct short across the motor to the 0V linethus providing active brakingEMC. Capacitors with values of 100pF, 100nF and 1nF are extensively used to decouple noise from switched data lines. Two A.C. coupled connections labelled “CHASSIS” , routed via capacitors C63 and C64, were provided for interconnection to the internal metalwork for EMC purposes. Tests have confirmed that connection is not required.Hall Effect PCB.Introduction. The Hall Effect PCB is a generic item which can be used for both Tillerpilots TP10, TP20 and TP30 and Wheelpilots WP10 and WP30. For Tillerpilots, the Hall Effect devices are mounted vertically into the PCB and horizontally for Wheelpilots. The circuit diagram for the Hall Effect PCB is given in Drawing No. E03182.Feedback.Two Hall Effect sensors HE1 and HE2 are mounted on the Hall Effect PCB and sense the rotation of 2 small bar magnets mounted 1800 apart in the pulley wheel. This produces a quadrature feedback output, at logic levels, FB1 and FB2. The PCB is powered from the host unit+5V regulated supply, the line being filtered by C1, and signals FB1 and FB2 are fed back to the microprocessor via pull-up resistors on the host unit PCB.Tiller Pilot TP10, TP20 & TP30Section 6Circuit DiagramsIssue 4.0 17/09/03SIMRAD 6 CIRCUIT DIAGRAMSCircuit SchematicsCommon PCB Circuit Diagram E03372Hall Effect PCB Circuit Diagram E03182Component Lists and LayoutsCommon PCB Assembly Detail E03178Hall Effect PCB Assembly Detail E03184Early Version WP10 / TP10 Assembly Detail E03181Early Version WP30 / TP20/30 Assembly Detail E03178 (Pre Iss. 6)22Tiller Pilot TP10, TP20 & TP30Section 7 Programming and ConfigurationIssue 4.0 19/09/03SIMRAD 7PROGRAMMING AND CONFIGURATIONThis Service Manual only contains programming and configuration information for those features of the autopilot which are not normally available to the end user. For details of normal programming and configuration please refer to the appropriate user manual.Tiller Pilot TP10, TP20 & TP30Section 8Fault FindingIssue 4.0 19/09/03SIMRAD8FAULT FINDINGCommon User Faults. Common user faults are included in the Diagnostics Guide included in the user manual.Common Technical Faults. None yet identified.Tiller Pilot TP10, TP20 & TP30Section 9Spare Parts Detail9SPARE PARTS DETAILSpares PacksTPPK1TP10 / 20 MECHANICAL ASSEMBLY TPPK2TP10 TOP CASETPPK3TP20/30 BOTTOM CASETPPK4TP10 PCB CASETPPK5WITHDRAWNTPPK6FLUXGATE ASSEMBLYTPPK7MOUNTING PIN, CUP AND CONNECTOR TPPK8MOTOR ASSEMBLYTPPK9FEEDBACK KITTPPK10DRIVE BELTTPPK11CASE SCREW PACKTPPK12PUSH ROD SEAL PACKTPPK13CASE SEAL PACKTPPK14TP100 TOP CASETPPK15GREY BOTTOM CASETPPK16TP20 TOP CASETPPK1 7TP20/30 PCB CASETPPK18WITHDRAWNTPPK19WITHDRAWNTPPK20TP30 TOP CASETPPK21COMMON PCB ASSEMBLYTPPK22TP30 MECHANICAL ASSEMBLYTPPK23TP300CX TOP CASETPPK24TP200CX TOP CASETPPK25TP10 BOTTOM CASE9.2AccessoriesTB30TILLER BRACKET 30mmTB60TILLER BRACKET 60mmTB90TILLER BRACKET 90mmTB120TILLER BRACKET 120mmPB30PEDESTAL BRACKET 30mmPB60PEDESTAL BRACKET 60mmPB90PEDESTAL BRACKET 90mmCB1CANTILEVER BRACKETPRE30PUSH ROD EXTENSION 30mmPRE60PUSH ROD EXTENSION 60mmPRE90PUSH ROD EXTENSION 90mmPRE120PUSH ROD EXTENSION 120mmPRE150PUSH ROD EXTENSION 150mmPRE300PUSH ROD EXTENSION 300mm9.3Service AidsTP-SRY TILLERPILOT TEST SYRINGETiller Pilot TP10, TP20 & TP30Section 10 Technical Notes10TECHNICAL NOTESPS 139Identification of Tillerpilot variantsPS 140Improved bonding of drive pulley to motor drive shaft PS 173Positioning of Feedback PCBPS 174Re-engineered Main PCBTechnical NoteFOR THE ATTENTION OF THE SERVICE MANAGER139NUMBER :PSPRODUCT :Tillerpilot – TP100 / TP200CX /TP300C / TP300CX / TP10 / TP20 /TP30SUBJECT:Identification of VariantsDATE: 1 October 1999There are a number of variants of Tillerpilots currently in use which, though similar in appearance, are built and operate differently. Positive identification is therefore essential when ordering spare parts to ensure that the correct item is dispatched.The main aids to identification are:ck of a Hall Effect PCB indicates Back emf, earliest, version.2.Hall Effect PCB with microprocessor mounted in socket indicatesintermediate version.3.Hall Effect PCB with surface mount microprocessor indicateslatest version.A table of variants identified by serial number and drawings, General Assembly, PCB Assembly and Circuit Diagram, to aid identification of the different PCBs, is given below:Issue 4.0 19/09/03 SIMRAD 36TILLERPILOT VARIANTS. The Tillerpilot variants can be conveniently divided into 3 groups:1. Feedback produced from the motor back emf.2. Feedback produced from a Hall Effect PCB.3. Introduction of Surface Mount microprocessor (SMu)TP100Back emf TP200CX Back emf TP300C Back emf TP300CX Back emf TP100Hall Effect TP200CX Hall Effect TP300CX Hall Effect TP200CX SM u TP300CXSM uu No.E02517E02520E02520E02520E03190E03189E03189E03398E03398Man from Start Start Start MK3143PE8818PB1484OD6415Not Yet In Production SerNo.to PE8818PB1483MI2954OD6414Continue Continue ContinueGen Assy E02587Not Issued E02616E02616E03299E03262E03300PCB Assy E02515E02518E02518E02518E03181E03178E03178Cct Diag E02549E02550E02550E02550E03179E03176E03176TP10SM u TP20SM u TP30SM uu No.E03398E03398E03398Man from OL7635OL1384OL7190SerNo.to Continue Continue ContinueGen Assy E03504E03505E03506PCB Assy E03181E03178E03178Cct Diag E03371E03372E03372Issue 4.0 19/09/03SIMRADTechnical NoteFOR THE ATTENTION OF THE SERVICE MANAGER140NUMBER :PSPRODUCT :Tillerpilot – TP100 / TP200CX /TP300C / TP300CX / TP10 / TP20 /TP30SUBJECT:Improved bonding of drive pulleyto motor drive shaft.DATE: 1 October 1999The 20 Toothed Pulley Part No. E02839 is a push fit onto the motor drive shaft, see sketch below, and the bonding is enhanced with Loctite 270 Part No. 260025. Instances have occurred where the bonding has weakened resulting in reduced drive efficiency or operational failure. An improved bonding adhesive Loctite 638 Part No. 260063 has been identified and approved for use. All Tillerpilot repairs should be carried out using the new adhesive.The new bonding agent has been used in the manufacture of all Tillerpilots with the alphabetic prefix PC, 1 March 1999, and subsequent serial numbers. The Product Support Department should be informed of any units found to be slipping post production date 1 March 1999.Issue 4.0 22/09/03SIMRAD。
黑白视频摄像头模块G XC-ES50 EI50 CE和XC-ES30 EI30 CE的产品特性说明书

B/W VIDEO CAMERA MODULE
XC-ES50/ES30 XC-ES50CE/ES30CE XC-EI50/EI30 XC-EI50CE/EI30CE
OUTLINE
The XC-ES50/50CE and XC-ES30/30CE are compact, light-weight one-piece black and white camera modules incorporating the latest 1/2" Interline (IT) CCD which produces new levels of picture detail. With dimensions of 29mm x 29mm x 32mm, these units can easily be installed in places where installation was previously difficult for other larger cameras. Similar to the XC-ES50/ES30 cameras, the XC-EI50/50CE and XC-EI30/30CE cameras also have near-infrared sensitivity. When used with an IR LED illuminator, these cameras can capture clear images in very low light environments. All four models have identical dimensions and controls, making it easy to interchange them. A variety of settings are available for differing subject and lighting conditions. All camera control switches are accessible from the outside of the camera. Excellent vibration and shock characteristics make these cameras ideal for demanding machine vision applications.
UC-5100系列嵌入式计算机商品说明书

P/N: 1802051001010 *1802051001010*UC-5100 SeriesQuick Installation GuideEdition 1.0, May 2018Technical Support Contact Information/supportMoxa Americas:Toll-free: 1-888-669-2872 Tel: 1-714-528-6777 Fax: 1-714-528-6778 Moxa China (Shanghai office): Toll-free: 800-820-5036 Tel: +86-21-5258-9955 Fax: +86-21-5258-5505 Moxa Europe:Tel: +49-89-3 70 03 99-0 Fax: +49-89-3 70 03 99-99 Moxa Asia-Pacific:Tel: +886-2-8919-1230 Fax: +886-2-8919-1231 Moxa India:Tel: +91-80-4172-9088 Fax: +91-80-4132-10452018 Moxa Inc. All rights reserved.OverviewThe UC-5100 Series embedded computers are designed for industrial automation applications. The computers feature 4 RS-232/422/485 full-signal serial ports with adjustable pull-up and pull-down resistors, dual CAN ports, dual LANs, 4 digital input channels, 4 digital output channels, a SD socket, and a mini PCIe socket for wireless module in a compact housing with convenient front-end access to all these communication interfaces.Model Names and Package ChecklistThe UC-5100 Series includes the following models:UC-5101-LX: Industrial computing platform with 4 serial ports, 2 Ethernet ports, SD socket, 4 DI, 4 DO, -10 to 60°C operating temperature rangeUC-5102-LX: Industrial computing platform with 4 serial ports, 2 Ethernet ports, SD socket, mini PCIe socket, 4 DI, 4 DO, -10 to 60°C operating temperature rangeUC-5111-LX: Industrial computing platform with 4 serial ports, 2 Ethernet ports, SD socket, 2 CAN ports, 4 DI, 4 DO,-10 to 60°C operating temperature rangeUC-5112-LX: Industrial computing platform with 4 serial ports, 2 Ethernet ports, SD socket, mini PCIe socket, 2 CAN ports, 4 DI, 4 DO, -10 to 60°C operating temperature rangeUC-5101-T-LX: Industrial computing platform with 4 serial ports, 2 Ethernet ports, SD socket, 4 DI, 4 DO, -40 to 85°C operating temperature rangeUC-5102-T-LX: Industrial computing platform with 4 serial ports, 2 Ethernet ports, SD socket, mini PCIe socket, 4 DI, 4 DO, -40 to 85°C operating temperature rangeUC-5111-T-LX: Industrial computing platform with 4 serial ports, 2 Ethernet ports, SD socket, 2 CAN ports, 4 DI, 4 DO, -40 to 85°C operating temperature rangeUC-5112-T-LX: Industrial computing platform with 4 serial ports, 2 Ethernet ports, SD socket, 2 CAN ports, mini PCIe socket, 4 DI, 4 DO, -40 to 85°C operating temperature rangeNOTE The operating temperature range of the wide temperature models is:-40 to 70°C with an LTE accessory installed-10 to 70°C with a Wi-Fi accessory installedBefore installing a UC-5100 computer, verify that the package contains the following items:•UC-5100 Series computer•Console cable•Power jack•Quick Installation Guide (printed)•Warranty cardNotify your sales representative if any of the above items are missing or damaged.NOTE The console cable and power jack can be found beneath the molded pulp cushioning inside the product box.AppearanceUC-5101UC-5102UC-5111UC-5112LED IndicatorsThe function of each LED is described in the table below:LED Name Status FunctionPowerGreen Power is on and the device isfunctioning normally Off Power is off ReadyYellow OS has been successfully enabledand the device is readyEthernet Green Steady On: 10 Mbps Ethernet linkBlinking: Data transmission is in progressYellow Steady On: 100 Mbps EthernetlinkBlinking: Data transmission is inprogressOff Transmission speed below 10Mbps or the cable is not connectedLED Name Status FunctionSerial (Tx) Green Serial port is transmitting data Off Serial port is not transmittingdataSerial (Rx)Yellow Serial port is receiving data Off Serial port is not receiving data L1/L2/L3 (UC-5102/5112) YellowThe number of glowing LEDs indicates the signal strength. All LEDs: Excellent L1 & L2 LEDs : Good L1 LED : PoorOffNo wireless module detected L1/L2/L3 (UC-5101/5111)Yellow/OffProgrammable LEDs defined by usersReset ButtonThe UC-5100 computer is provided with a Reset button, which is located on the front panel of the computer. To reboot the computer, press the reset button for 1 second.Reset to Default ButtonThe UC-5100 is also provided with a Reset to Default button which can be used to reset the operating system back to the factory default status. Press and hold the Reset to Default button between 7 to 9seconds to reset the computer to the factory default settings. When the reset button is held down, the Ready LED will blink once every second. The Ready LED will become steady when you hold the buttoncontinuously for 7 to 9 seconds. Release the button within this period to load the factory default settings.Installing the ComputerDIN-Rail MountingThe aluminum DIN-rail attachment plate comes attached to the product casing. To mount the UC-5100 on to a DIN rail, make sure that the stiff metal spring is facing upwards and follow these steps.Step 1Insert the top of the DIN rail into the slot just below the stiff metal spring in the upper hook of the DIN-rail mounting kit. Step 2Push the UC-5100 towards the DIN rail until the DIN-railattachment bracket snaps into place.Wiring RequirementsBe sure to read and follow these common safety precautions before proceeding with the installation of any electronic device:• Use separate paths to route wiring for power and devices. If powerwiring and device wiring paths must cross, make sure the wires are perpendicular at the intersection point. NOTE Do not run signal or communication wiring and power wiring in the same wire conduit. To avoid interference, wires with different signal characteristics should be routed separately.•Use the type of signal transmitted through a wire to determine which wires should be kept separate. The rule of thumb is that wiring that shares similar electrical characteristics can be bundled together.• Keep input wiring and output wiring separate.•It is strongly advised that you label wiring to all devices for easyConnecting the PowerConnect the 9 to 48 VDC power line to the terminal block, which is connector to the UC-5100 Series computer. If the power is supplied properly, the Power LED will glow a solid green light. The power input location and pin definition are shown in the adjacent diagram.SG: The Shielded Ground (sometimes called Protected Ground) contact is the contact at the bottom of the 3-pin power terminal blockconnector when viewed from the angle shown here. Connect the wire to an appropriate grounded metal surface or to the grounding screw on top of the device.NOTE The input rating of UC-5100 Series is 9-48 VDC, 0.95-0.23 A.Grounding the UnitGrounding and wire routing help limit the effects of noise due toelectromagnetic interference (EMI). Run the ground connection from the terminal block connector to the grounding surface prior toconnecting the power. Note that this product is intended to be mounted on a well-grounded mounting surface, such as a metal panel.Connecting to the Console PortThe UC-5100’s console port is an RJ45-based RS-232 port located on the front panel. It is designed for connecting to serial console terminals, which are useful for viewing boot up messages, or for debugging system boot up issues.PIN Signal1 -2 -3 GND4 TxD5 RxD6 -7 - 8-Connecting to the NetworkThe Ethernet ports are located on the front panel of the UC-5100. The pin assignments for the Ethernet port are shown in the following figure. If you are using your own cable, make sure that the pin assignments on the Ethernet cable connector match the pin assignments on the Ethernet port.PinSignal 1 Tx+ 2 Tx- 3 Rx+ 4 – 5 – 6 Rx- 7 – 8–Connecting to a Serial DeviceThe serial ports are located on the front panel of the UC-5100 computer. Use a serial cable to connect your serial device to thecomputer’s serial port. These serial ports have RJ45 connectors and can be configured for RS-232, RS-422, or RS-485 communication. The pin location and assignments are shown in the table below.Pin RS-232 RS-422 RS-4851 DSR - -2 RTS TxD+ -3 GND GND GND4 TxD TxD- -5 RxD RxD+ Data+6 DCD RxD-Data-7 CTS - -8 DTR - - Connecting to DI/DO DevicesThe UC-5100 computer comes with4 digital inputs and 4 digitaloutputs. The DI/DO connectors arelocated on the top panel of thecomputer. Refer to the adjacentdiagram for the pin definitions.The DI/DO wiring diagram is given below:Connecting to a CAN DeviceThe UC-5111 and UC-5112 are provided with 2 CAN ports, allowing users to connect to a CAN device. The pin location and assignments are shown in the following table:PIN Signal1 CAN_H2 CAN_L3 CAN_GND4 -5 -6 -7 CAN_GND8 -Connecting the Cellular/Wi-Fi Module and AntennaThe UC-5102 and UC-5112computers come with oneMini PCIe socket forinstalling a cellular or Wi-Fimodule. Unfasten the twoscrews on the right panel toremove the cover and findthe location of the socket.The cellular module package includes 1 cellular module, and 2 screws. The cellular antennas should be purchased separately to fit your installation requirements.Follow these steps to install the cellular module.1.Set the antenna cables asidefor convenience of installationand clear the wireless modulesocket as shown in the figure.2. Insert the cellular moduleinto the socket and fasten two screws (included in the package) on to the top of the module.We recommended using a tweezer when installing or removing the module.3. Connect the free ends of thetwo antenna cables next to the screws as shown in the image.4. Replace the cover and secureit using two screws.5. Connect the cellular antennasto the connectors.Antenna connectors arelocated on the front panel of the computer.The Wi-Fi module package includes 1 Wi-Fi module, and 2 screws. The antenna adapters and Wi-Fi antennas should be purchased separately to fit your installation requirements.Follow these steps to install a Wi-Fi module. 1. Set the antenna cablesaside for convenience of installation and clear the wireless module socket as shown in the figure.2. Insert the cellular moduleinto the socket and fastentwo screws (included in thepackage) on to the top of themodule.We recommended using atweezer when installing orremoving the module.3. Connect the free ends of thetwo antenna cables next tothe screws as shown in theimage.4. Replace the cover and secureit with two screws.5. Connect the antennaadapters to the connectors onthe front panel of thecomputer.6. Connect the Wi-Fi antennasto the antenna adapters.Installing Micro SIM CardsYou will need to install a Micro SIM card on your UC-5100 computer. Follow these steps to install the Micro SIM card.1. Remove the screw on the coverlocated on the front panel of theUC-5100.2. Insert the Micro SIM card into thesocket. Make sure you place thecard in the right direction.To remove the Micro SIM card,simply push the Micro SIM card andrelease it.Note: There are two Micro SIM cardsockets allowing users to install twoMicro SIM cards simultaneously.However, only one Micro SIM card can be enabled for use.Installing the SD CardThe UC-5100 Series computers come with a socket for storage expansion that allows users to install an SD card.Follow these steps to install the SD card:1. Unfasten the screw and removethe panel cover.The SD socket is located on thefront panel of the computer.2. Insert the SD card into thesocket. Ensure that the card isinserted in the right direction.3. Replace the cover and fasten thescrew on the cover to secure thecover.To remove the SD card, simply pushthe card in and release it.Adjusting the CAN DIP SwitchThe UC-5111 and UC-5112 computers come with one CAN DIP switch for users to adjust the CAN termination resistor parameters. To set up the DIP switch, do the following:1. Find the DIP switch location on thetop panel of the computer2. Adjust the setting as required. TheON value is 120Ω, and the defaultvalue is OFF.Adjusting the Serial Port DIP SwitchThe UC-5100 computers come with a DIP switch for users to adjust the pull-up/pull-down resistors for the serial port parameters. The serial port DIP switch is located on the bottom panel of the computer.Adjust the setting as required. The ON setting corresponds to 1KΩ and the OFF setting corresponds to 150KΩ. The default setting is OFF.Each port consists of 4 pins; you must switch all 4 pins of a portsimultaneously to adjust the value of the port.。
5301系列负载筒操作手册说明书

5301 Series Load PinsOperating ManualSafety noteUse for intended purposeThe force transducers in model series F5301 are intended for the measurement of static and dynamic tensile or compressive force.These devices have been constructed and tested in accordance with the safety regulations for electronic measuring equipment.Any other usage is deemed to be incorrect. The transducers can only be guaranteed to operate correctly and safely if the information in the operating instructions is complied with. The legal and safety regulations that apply to the respective application must also be observed during use (e.g. VDE 0100). This also applies to the use of accessories.The transducer is not intended to be used a safety element.The correct and safe operation of this transducer depends on correct transportation and proper storage, installation and assembly and careful operation and maintenance.General dangers if the safety instructions are not followedForce transducers made by NOSHOK are manufactured in accordance with the latest state of technology and are safe during operation.However, the transducers can be the source of residual danger if they are used or operated improperly.Any person who is entrusted to install, start up, maintain or repair a force transducer must have read and understood the operating instructions, particularly the technical safety instructions.Residual dangersThe performance and scope of delivery of the transducer only cover a sub-area of force measuring technology. The technical safety aspects of force measuring technology must also be planned and implemented by the system planner / equipper / operator in such a way that residual dangers are minimised. The existing regulations must be complied with. Residual dangers associated with force measuring technology must be pointed out.2NOSHOK, Inc. • 1010 West Bagley Road, Berea, OH 44017 • Ph: 440.243.0888 • Fax 440.243.3472 • 3MaintenanceThe force transducers in the F5301 model series are maintenance-free.During welding work the transducer must be bypassed with a copperwire (min. 50 mm 2) so that welding current does not flow through the transducer and weld the force introduction points.NOSHOK, Inc. • 1010 West Bagley Road, Berea, OH 44017 • Ph: 440.243.0888 • Fax 440.243.3472 • Ambient temperatureThe temperature range of -20°C to +80°C that is specified in the data sheet applies with regard to deployment. The specified error limits are not guaranteed outside this temperature range.Moisture and corrosion protectionTropical climates and condensation are not a problem because the transducers comply with protection class IP 67 in accordance with EN 60529:1991+A1:2000 / IEC 529.DepositsDust, dirt and other object must not be allowed to form deposits in such a way that they create a force short-circuit to the measuring spring, which would falsify the measuring signal.Precautions to take during assembly• Force measuring equipment is extremely sensitive and must be handled carefully.• Attention must be paid to the installation position and therefore the load direction when the force transducers are being installed.• The transverse loads and side forces also include the relevant components of the measured variables, which may be introduced at an incline.• Care must therefore be taken to keep the transducer free of lateral loads and torsion during assembly (e.g. when tightening the lock nuts).• Overloading must be prevented at all times.• The output signal (c=1-2mV/V, 4...20mA, 0…20mA, 0...10V) is noted on the name plate (Fig. 1). The connection assignments are also noted on the name plate and can also be found in the section entitled “Electrical connection”. The polarity must be correct at all times. SEE NEXT PAGE FOR NAME PLATE DIAGRAM.4TypeModel OutputPower Supply S# Serial NumberUB+ Pin assignment – power supply + 0V/S- Pin assignment – power supply - / output - S+ Pin assignment – output +TensionCompressionFig. 1 Name plateNOSHOK, Inc. • 1010 West Bagley Road, Berea, OH 44017 • Ph: 440.243.0888 • Fax 440.243.3472 • General Installation Guidelines•The loads acting upon the force transducer must be as exact aspossible in the load direction.•Torsion and lateral force must be avoided. The transverse loads and side forces also include the relevant components of the measured variables, which may be introduced at an incline.•Torsional moments, off-centre loads and lateral loads or side forcescause measuring errors and can permanently damage the transducers.•The axle bracket grooves also serve as a reference for aligning the measuring axle.•The DIN 15 058 axle bracket must be attached in such a way that the measuring axle is prevented from twisting in the bearing and doesnot have any axial play.•The measuring axle may only be subjected to load if the correct type of bearing has been used. Loads occurring in other equipment may change the zero signal and result in permanent damage.•The introduction of force in the centre must not wander and must beinstalled in such a way that axial shifts are prevented. However, force by-passing may not occur.Fig. 2 Installation situation of a load pin5NOSHOK, Inc. • 1010 West Bagley Road, Berea, OH 44017 • Ph: 440.243.0888 • Fax 440.243.3472 • 6Please note the following: • Always use shielded, low-capacity measuring cables(all NOSHOK cables meet these requirements, see chapter 10.1). • Do not route the measuring cable parallel to high-voltage current andcontrol cables. • Avoid leakage fields from transformers, motors and contactors.•The transducer, the amplifier and the display unit must not have multiple grounds. Attach all equipment to the same protective conductor.SIL-3 ElektronicAmplifier-Electronics 4...20mA or 0 (10V)for SIL-3 applications with 2-channel PC control NOSHOK, Inc. • 1010 West Bagley Road, Berea, OH 44017 • Ph: 440.243.0888 • Fax 440.243.3472 • This well proven design has been amended by an additional resistor R7 in order to monitor the condition of the amplifier unit and signal path. This resistor is connected as a shunt to resistor R5 by a relay contact (a) as soon as an excitation voltage U r appears at relay A.UrU0The connection of resistor R7 will always result in a defined unbalancing of the zero point (diagonal voltage) of the Wheatstone Bridge.An external independent control unit activates relay A which changes the output by a certain value. Because of security reasons the control unit has to be a 2-channel one. When the expected change of the output signal is detected it can be assumed that the whole signal path (Wheatstone Bridge – amplifier – output) works well. If it does not appear it can be concluded that there is a defect in the signal path.The standard adjustment of force transducers with current output for overload control is e.g.:7With activating the check relay a fixed signal jump of 8 mA will exceed the overload limit in every working condition. The measurement’s upper limit of 20 mA however will never be reached. This makes the checking of the signal jump possible.3,821 cable break short circuit [mA] (125% nominal load) NOSHOK, Inc. • 1010 West Bagley Road, Berea, OH 44017 • Ph: 440.243.0888 • Fax 440.243.3472 • Round connector M12x1, 4-pin940E01SIL-3Round connector M12x1, 4-pin940E04SIL-3Mini-Hirschmann connector G4a1MMT940E02Cable output940E03Mini-Hirschmann connector G4a1MMT940E05Cable output940E06NOSHOK, Inc. • 1010 West Bagley Road, Berea, OH 44017 • Ph: 440.243.0888 • Fax 440.243.3472 • 89Round connector M12x1, 5-poligNOSHOK, Inc. • 1010 West Bagley Road, Berea, OH 44017 • Ph: 440.243.0888 • Fax 440.243.3472 • 10Technical data)3-L I S (1035l e d o M Nominal force F nom5 / 10 / 20 / 30 / 50 / 100 / 200 kN5 / 10 / 20 / 30 / 50 kNForce limit 150 % F nom Breaking limit > 300 % F nom Accuracy < 2 % of F.S. and < 0,5 % of F.S. < 0,5 % of F.S. Relative backlash width (Hysteresis) < 0,5 % of F.S. and <0,2 % of F.S.< 0,5 % of F.S.Creeping, 30 min. at F nom0,1 % of F.S. Nominal temperature range -4 ... 176 °F (-20 … 80 °C) Storage temperature -40 ... 212 °F (-40 … 100 °C) Temperature influence - Meas.range - Null signal 0,1 % / 10K 0,1 % / 10K Transverse force action(signal at 100% nominal load under 90°)< 5 %Vibration resistance 20g, 100h, 50...150Hz acc. to DIN EN 60068-2-6 925 C E I / 925 06 N E o t .c c a 76 P I s s a l c n o i t c e t o r P Interfering emission acc. to EN 61326 Interference immunity acc. to 61326Electrical protection class Reverse polarity, overvoltage and short circuit protectionAnalogue outputsOutput signal 4 … 20 mA – 2-wire or 0 … 10 VDC – 3-wire 4 … 16 mA - 2-L 0 … 7 V - 3-L Power consumption Current output: 4 … 20 mA: Signal current Voltage output:: ca. 8 mAAuxiliary power 10 ... 30 VDC for output 4...20 mA 14 ... 30 VDC for output 0 ... 10 VBurden≤ (UB–10 V)/0,02 A for output 4...20 mA > 10 kOhm for output 0 ... 10 V).S .F f o % 09 o t p u % 01 n i h t i w ( s m 1 ≤e m i t g n i t s u j d A Electrical connectionRound connector M12x1, 4-pin 5-pinNOSHOK, Inc. • 1010 West Bagley Road, Berea, OH 44017 • Ph: 440.243.0888 • Fax 440.243.3472 • 1035 CANOpen Output signal CANopen protocol in acc.with CiA DS-301V.402, Device profile DS-404 V. 1.2 Reproducibility ≤ ± 0.05 % of setting Stability per year ≤ ± 0.2 % of setting under reference conditions Electrical connection Round connector M12 x 1 - 5-pin. Auxiliary power 10 ... 30 VDC )W 7.0< n o i t a r a p e s c i n a v l a g h t i w ( W 5.0 < n o i t p m u s n o c r e w o PCommunication services LSS (CiA DSP 305, Version 1.1.1) ServicesConfiguration of device address and baud rateSync/Async, Node/Lifeguarding, Heartbeat FiltersIndividually programmable filters for specificremoval of resonance frequencies, for example AdjustmentZero point and measuring range ±10% bymaking entries in object directory Adjustment time1.5 ms (baud rate ≥ 125K) within10 % up to 90 % of setting.Measuring frequency Internal 1000 Hz (adjustable up to approx. 4 Hz) Measuring element made from stainless steelLoad pin, dimensionsFor two-sided measuring axle mounting the following applies:Bolt/Hole Mating Tolerances: H9/f9** Other bolt dia meters available on request, drill hole tolerance H9Axle bracket in acc.with DIN 15 058(not included in scope of delivery)Plug M12x1 Version up to 10 kN Version from 20 kN Operating manual 5301 Series Load PinCORPORATE HEADQUARTERS1010 West Bagley Road · Berea, Ohio 44017P 440.243.0888 · F 440.243.3472E-mail:*****************Web: NK095301TM-*** Case diameter 40 mm。
Canon 相机兼容性表说明书

Compatibility ChartE O S R 6E O S RE O S 1D x M a r k I IE O S 1D xE O S 1D s M a r k I I IE O S 1D s M a r k I IE O S 1D sE O S 1D M a r k I VE O S 1D M a r k I I IE O S 1DE O S 1D M a r k I I (N )E O S 1D M a r k I IE O S 5D s R -E O S 5D s -E O S 5D M a r k I V -E O S 5D M a r k I I IE O S 5D M a r k I IE O S 5DE O S 6D M a r k I IE O S 6DE O S 7D M a r k I IE O S 7DE O S 90D -E O S 80DE O S 70DE O S 60DE O S 50DE O S 40DE O S 30DE O S 20DE O S 10DE O S 77D (9000D ) (R e b e l T 7i ) -E O S 760D (8000D ) (R e b e l T 6s )E O S 750D (K i s s X 8i ) (R e b e l T 6i ) -E O S 700D (K i s s X 7i ) (R e b e l T 5i )E O S 100D (K i s s X 7) (R e b e l S L 1)E O S 650D (K i s s X 6i ) (R e b e l T 4i )E O S 600D (K i s s X 5) (R e b e l T 3i )E O S 550D (K i s s X 4) (R e b e l T 2i )E O S 500D (K i s s X 3) (R e b e l T 1i )E O S 450D (K i s s X 2) (R e b e l X S i )E O S 400D (K i s s D i g i t a l X ) (R e b e l X T i )E O S 350D (K i s s D i g i t a l N ) (R e b e l X T )E O S 300D (K i s s D i g i t a l ) (R e b e l X )E O S 3000DE O S 1500D (K i s s X 90) (R e b e l T 7)E O S 1200D (K i s s X 70) (R e b e l T 5)E O S 1100D (K i s s X 50) (R e b e l T )E O S 1000D (K i s sF ) (R e b e l X S )P o w e r S h o t G 1X M a r k I IP o w e r S h o t G 1XP o w e r S h o t G 11P o w e r S h o t G 7XP o w e r S h o t G 7 / G 9 / G 10P o w e r S h o t G 5XP o w e r S h o t G 3XP o w e r S h o t S 5 I SP o w e r S h o t S X 1 I SP o w e r S h o t S X 10 I SP o w e r S h o t S X 20 I SE O S M 5E O S M 3E O S MNissin Model MG80 Pro New ●●●●---●●-----●●●-●●●●-●●●●●---●●●●●●●●●●---●●●●●○○○○○○○○○○○○○○Air 10s Commander -●●●---●●-----●●●-●●●●-●●●●●---●●●●●●●●●●---●●●●●○○○○○○○○○○○○○○Air 1 Commander -●●*2*3●*2●●○●●○●*1●●*2●*2●*2*3●●●*1●●●*2●-●*3●●●●●*1●*1●*1●●●●●●●●●●●*1●*1●*1●●●●●○○○○○○○○○○○○○○Di700 A ●●●*3●●●○●●○●*1●●●●*3●●●*1●*3●●●-●*3●●●●●*1●*1●*1●●●●●●●●●●●*1●*1●*1●●●●●●*5*8○○●*5*8○●*5*8○○○○○○○○i60A ●●●●--○●●○●*1-●●●●●●*1●●●●●●●●●●●*1●*1●*1●●●●●●●●●●●*1●*1●*1●●●●●-○○-○--○○○○●*5●*5●*5i600-●●●--○●●○●*1-●●●●●●*1●●●●-●●●●●●*1●*1●*1●●●●●●●●●●●*1●*1●*1●●●●●-○○-○--○○○○●*5●*5●*5i40●●●*3●--○●●○●*1●●●●*3●●●*1●*3 *9●●*4●-●*3●●●●●*1●*1●*1●●*4●●●●●●●●●*1●*1●*1●●●●●●*5*8●*5*8●*5*8●*5*8●*5*8●*5*8●*5*8●*5*8●*5*8●*5*8●*5*8●*5●*5●*5i400-●●*3●--○●●○●*1●●●●*3●●●*1●*3 *9●●*4●-●*3●●●●●*1●*1●*1●●*4●●●●●●●●●*1●*1●*1●●●●●●*5*8●*5*8●*5*8●*5*8●*5*8●*5*8●*5*8●*5*8●*5*8●*5*8●*5*8●*5●*5●*5MF18-●○●●●●●●●●●---●●●○●●●●○●●●●●●●○●○●●●●●●●●●●●●●●●○○○○○○○○○○○○○○MG8000 Extreme (discontinued)○○○●○○○○●○●●●●○●●●○●●*4●○○●●●●●●●○●*4○●●●●●●●●●●○○●●●○○○○○○○○○○○○○○Di866 Mark II (discontinued)○○○●●●○●●○●●○●○●●●○●●*4●○○●●●●●●●○●*4○●●●●●●●●●●○○●●●○○○○○○○○○○○○○○Di700 (discontinued)○○○●○○○●●○●○○○○●●●*1○●●*4●○○●●●●●*1●*1●*1○●○●●●●●●●●*1●*1●*1○○●●●○○○○○○○○○○○○○○Di600 (fade out model)○○●*3●*7○○○●●○●●●●●*3●*7●●●*9●*7●●○●*3●●●●●●●○●○●●●*6*7●●●●●●●○○●●●○○○○●*5*8○○●*5*8○●*5*8○○○○●Compatible Model ○incompatible Model-No information available. To be confirmed.*1HSS High speed sync. and second-curtain sync not supported.*2For using with those Canon camera models, before Binding setting, please set Commander Air 1 to "Mode 2". At the same time, the second curtain sync can not be selected. For details, please refer to Air 1's user manual page8 - Appendix1.*3When using the the first 4 product's serial numbers digits smaller-than the following value : Di600: 6803020001~ Di700A:6720100001~ Air 1:C67217001~ i40:67281609001~ an error message would appear on camera display when changing "external flash function setting", but the setting is reflected normally. AF assist lamp function on the flash will not work *4Wireless Slave mode does not support the camera built-in flash as the master function.*5Since those camera built-in flash have not the master function, they should use a optional master remote unit (e.g. Canon ST-E2) to control wirelessly any slave flash eqipped optical slave recevier.*6Zoom head operation not supported.*7The flash charging lamp in the camera viewfinder will not go out.*8Limited by the camera system function, Flash TTL function will be disabled when camera set to M manual exposure mode.*9When shooting in continuous mode, flash exposure of TTL mode may become unstable.i 40 C a n o nD i 466 C a n o nD i 622 C a n o nD i 622 M a r k I I C a n o nD i 600 C a n o nD i 700 C a n o nD i 866 M a r k I I C a n o nM G 8000 C a n o n220E X270E X I I320E X430E X430E X I I430E X I I I -R T550 E X580 E X580 E X I I600 E X R T600 E X I I - R T●●●●●●●●●●●●●●●●●●●● Compatible ModelGN Mode. 25-49GN Mode. 50-65Canon FlashesNissin Flashes Air R Receiver Canon Last update: Jan 2021Compatibility ChartNikon CamerasZ 7Z 6 I IZ 6D 5 -D 4sD 4D 3xD 3sD 3D 2X sD 2H sD 2HD 1D fD 850 -D 810D 800ED 800D 780D 750D 700D 610D 600D 500 -D 300sD 300D 200D 100D 7500 -D 7200D 7100D 7000D 5600 -D 5500D 5300D 5200D 5100D 5000D 3400 -D 3300D 3200D 3100D 3000D 90D 80D 70 / D 70sD 60D 50D 40 / D 40XC o o l p i x AC o o l p i x P 7700C o o l p i x P 5100C o o l p i x P 5000Nissin Model MG80 Pro New ●●●●●●●●●○○○○●●●●●○●●●●●●●●○-●●●●●●●●●-●●●●●-----○○○○Air 10s Commander ●●●●●●●●●○○○○●●●●●●●●●●●●●●○-●●●●●●●●●-●●●●●-----○○○○Air 1 Commander ○○○●*1●*2●*2●●●○○○○●●*5●●●○●●●●●●●●○●●●●-●●●●●●●●●●●○○○○○○○○○Di700 A ●●●●●●●●●○○○○●●●●●●●●●●●●●●○-●●●-●●●●●○●●●●●●●●●●○○○○i60A ●●●●●●●●●○○○○●●●●●●●●●●●●●●○●●●●●●●●●●●●●●●●●●●●●●*4●*4○○i600●●●●●●●●●○○○○●●●●●●●●●●●●●●○-●●●●●●●●●●●●●●●●●●●●●*4●*4○○i40●●●●●●●●●○○○○●●●●●●●●●●●●●●○●●●●●●●●●●●●●●●●●●●●●●*4●*4●*4●*4i400●●●●●●●●●○○○○●●●●●●●●●●●●●●○-●●●●●●●●●●●●●●●●●●●●●*4●*4●*4●*4MF18○○○●●●●●●○○○○●●●●●○●●●●●●●●○●●●●●●●●●●●●●●●●●●●●●○○○○MG8000 Extreme (discontinued)○○○●●●●●●○○○○●○●●●●●●●●●●●●○●○●●○●●●●●●●●●●●●●●●●○○○○Di866 Mark II (discontinued)○○○●*3●●●●●●○○○●○●●●○●●●●●●●●○●●●●○●●●●●●●●●●●●●●●●○○○○Di700 (discontinued)○○○○●●●●●○○○○●○●●●○●●●●○●●●○○○●●○●●●●●○●●●●●●●●●●○○○○Di600 (fade out model)○○○○●●●●●●○○○●○●●●○●●●●○●●●○○○●●○●●●●●●●●●●●●●●●●○○○○●○- No information available. To be confirmed.*1 Extremely underexposure (about -2EV) appear when Air 1 mounted on D5 to control wirelessly the slave flash and the flash light does not hit the subject directly, such as bouncing or diffusing,*2 In D4 · D4s, when manual flash is set, when you shoot continuously and rapidly manually in the Q mode · 1 sheet shooting mode, emission may be missing. Please understand that it is based on specifications.*3 At the time of FP flash, it may be underexposed by about 1 stage compared with the genuine strobe *4 SD Mode not supported*5 Commander / Flash unit may be freeze when camera turn on the electronic shutter mode with mirror up mode. If Commander / Flash unit freezes, remove and re-insert the battery. Turn off the in-compatible function of camera then power on Commander / Flash unit again.*6A firmware update may required in the future.i 40 N i k o nD i 466 N i k o nD i 600 N i k o nD i 622 M a r k I I N i k o nD i 700 N i k o nD i 866 N i k o nD i 866 M a r k I I N i k o nM G 8000 N i k o nS B -500S B -600S B -700S B -800S B -900S B -910S B -5000●●●●*5●●●●●●●●●●●●Compatible ModelAir R's GN Mode. 25-49Air R's GN Mode. 50-65*5 FP/HSS high speed sync function not supportedIncompatible ModelCompatible Model Air R Receiver Nikon Nikon FlashesNissin FlashesLast update: Jan 2021Compatibility ChartSony Camerasα9 -α7S M a r k I Iα7Sα7R M a r k I V -α7R M a r k I I Iα7R M a r k I Iα7R -α7 M a r k I I I -α7 M a r k I Iα7α6500 -α6400 -α6300α6000α3000N E X -7N E X -6α99 M a r k I I -α99α77 M a r k I Iα77α65α58α57α55Vα33α900α850α700α580α560α550α500α450α390α380α350α330α300α290α230α200α100R X 1R M a r k I I -R X 1R X 10R X 10 M a r k I IR X 10 M a r k I I I -R X 10 M a r k I V -R X 100 M a r k I IH X 400V - H X 60VNissin Model MG80 Pro New --●●●●-●●●-●●●○--●*4●●-●*1-●*1○○●*1●*1○○-○○○-○○○-○○○○-●●-●●○-●Air 10s Commander ●-●●●●-●●●-●●●○--●*4●●-●*1-●*1○○●*1●*1○○-○○○-○○○-○○○○-●●-●●○-●Air 1 Commander ●*4●*4●○●*4●*4●●*4●*4●●*4-●●○●*1●●*4●●*4●*1●*1●●*1○○●*1●*1○○○○○○○○○○○○○○○●●●●●●○-●Di700 A ●●●●●●●●●●●-●●●●*1●●●●●*1●*1●●*1●*1●*1●*1●*1●*1●*1○●*1●*1●*1○●*1●*1●*1○●*1●*1●*1●*1●●●●●●●●●i60A ●●●●●●●●●●●●●●●●*1●●●●●*1●*1●●*1●*1●*1●*1●*1●*1●*1○●*1●*1●*1○●*1●*1●*1○●*1●*1●*1●*1●*2●●-●●●●●i600●●●●●●●●●●●-●●●●*1●●●●●*1●*1●●*1●*1●*1●*1●*1●*1●*1○●*1●*1●*1○●*1●*1●*1○●*1●*1●*1●*1●*2●●-●●●●●i40●●●●●●●●●●●-●●●●*1●●●●●*1●*1●●*1●*1●*1●*1●*1●*1●*1○●*1●*1●*1○●*1●*1●*1○●*1●*1●*1●*1●*2●●●●●●●●i400●●●●●●●●●●●-●●●●*1●●●●●*1●*1●●*1●*1●*1●*1●*1●*1●*1○●*1●*1●*1○●*1●*1●*1○●*1●*1●*1●*1●*2●●●●●●●●MF18--●●●●-●●●--●●●*3●*1●-●●●*1●*1●●*1●*1 *3●*1 *3●*1●*1○○○○○○○○○○○○○○○●*2●●●●●○●●●Compatible Model ○incompatible Model-No information available. To be confirmed.*1Use the Sony Shoe Adaptor (ADP-AMA)*2It slightly interferes (contacts) with the EVF. Since you can not use EVF, it can not be used because diopter correction does not work by interfering.*3Optical wireless function are not available.*4For using with those Sony camera models, not support the Air R's HSS High-speed sync function :: α9, α7R Mark III, α7R Mark II, α7S Mark II, α7 Mark III, α7 Mark II , α99 Mark II , α6500i 40 S o n yD i 622 M a k I I S o n yD i 866 M a k I I S o n yH V L -F 32MH V L -F 42A MH V L -F 43MH V L -F 58A MH V L -F 60MAir R Receiver Sony *3●●*2●*2●●*2●●*2●● Compatible ModelGN Mode. 25-49GN Mode. 50-65*1Use the Sony Shoe Adaptor (ADP-AMA)*2Use the Sony Shoe Adaptor (ADP-MAA).Due to the design of the ADP-MAA adapter, bad contact may always occur when using ADP-MAA.Depends on the situtaion of use, the operation may be unstable.*3For using with those Sony camera models, the HSS High-speed sync function of the flash inserted on Air R can not be used, α9, α7R Mark III, α7R Mark II, α7S Mark II, α7 Mark III, α7 Mark II , α99 Mark II , α6500Sony FlashesNissin Flashes Last update: Jan 2021Compatibility ChartFujifilm CamerasG F X 50sX -H 1X -T 4X -T 3X -T 2X -T 1 / X -T 1 G SX -T 20X -T 10X -P r o 2X -P r o 1X -E 3X -E 2SX -E 2X -E 1X -M 1X -A 5X -A 3X -A 2X -A 1X 100FX 100TX 100SX 100X 70X 30X 20X 10X -S 1H S 50E X RH S 30E X RH S 20E X RNissin Model Air 10s Commander -●●●●*1●*1●●●*1●●●●●●●●●●●●●●●●●●●●●-Air 1 Commander ●*1 *2●●●●*1●*1●●●*1●●●●●●○●●●●●●●●●●●●●●○Di700 A ●*1 *2●●●●*1●*1●●●*1●●●●●●●●●●●●●●●●●●●●●○i60A ●*1 *2●●●●*1●*1●●●*1●●●●●●●●●●●●●●●●●●●●●○i600●*1 *2●●●●*1●*1●●●*1●●●●●●●●●●●●●●●●●●●●●○i40●*1 *2●●●●*1●*1●●●*1●●●●●●○○●●●●●●●●●●●●●○i400●*1 *2●●●●*1●*1●●●*1●●●●●●○○●●●●●●●●●●●●●○●Compatible Model ○Incompatible ModelThis camera supports HSS/FP High speed synchronize function.*1The Fujifilm camera is supporting of High speed synchronize function after camera firmware updated*2Flash can be insert on the hot shoe of main body or that of EVF. When inserted a flash on the EVF shoe, do not tilt-up EVF since this may make the EVF damage.Last update: June2018Last update: Jan 2021Compatibility ChartOlympus Micro Four Thirds / Four Thirds CamerasE-M1MarkII(OMD)E-M1(OMD)E-M5MarkII(OMD)E-M5(OMD)E-M1MarkIII(OMD)E-M1MarkII(OMD)E-M1(OMD)PEN-FE-P5E-P3E-P2E-P1E-PL8NewE-PL7E-PL6E-PL5E-PL3E-PL2E-PL1E-PM2E-PM1E-62E-52E-5E-41E-30 Nissin Model●●●●●-●-●●●●●-●●-●●●●-----●●●●○●●●*1●●●●●●●●●●●●●●●●●●●●●*3●○●●●*1●●●●●●●●●●●●●●*2●*2●*2●*2●*2●●●*1●○●●●*1●●●●●●●●●●●●●●*2●*2●*2●*2●*2●●●*1●○●●●*1●●●●●●●●●●●●●●*2●*2●*2●*2●*2●*1●●*1●●*4●●●*1●●●●●●●●●●●●●●*2●*2●*2●*2●*2●*1●●*1●●*4●●●*1●●●●●●●●●●●●●●*2●*2●*2●*2●*2-●○●-○●○●●●●-○●●●●●●●●●●●●●Compatible Model○Incompatible Model-No information available. To be confirmed.*1Unstable operation may appear when turn on the S-OVF Function ( Optical view finder simulation ) of EVF and shoot with EVF.*2Flash's optical slave wireless mode is incompatible with camera's wireless flash system.*3Di700A for FT version will be supporting Olympus E-M5 Mark II after flash firmware updated.*4Compatibility ChartPanasonic Micro Four Thirds Cameras *4GH5GH4GH3GH2GH1GX8GX7GX7MarkII/GX85/GX8GX1G1G9G8/G8/G85G7/G7G6G5G3G2G1GF2GF1LX1LX7LX5LX3FZ20 Nissin Model●-●-●-●---●--●--●●●●-●●●●●●●●●●●●●●●●●●●●●●●●●●●●●●●●●●●●●●●●●●●●●●●●●●●●●●●-●●●●●●●●●●●●●●●●●●●●●●●●-●●●●●●●●●●●●●●●●●●●●●●●●●●●●●●●●●●●●●●●●●●●●●●●●●●●●●●●●●●●●●●●●●●●●●●●●●-●●●●○●○●●--○●●●●●●●●●●●●●Compatible Model○Incompatible Model-No information available. To be confirmed.*4According to the specifications of Panasonic Lumix series, the continuous shooting function cannot be used when an external flash is installed on the hot shoe.Di466(Four Thirds ver.)Air 1 Commander(Four Thirds ver.)Di700 A(Four Thirds ver.)i60A(Four Thirds ver.)i40(Four Thirds ver.)Di466(Four Thirds ver.)i40(Four Thirds ver.)i400(Four Thirds ver.)Hardware compatible on or above the following Serial Number: i40: 8A18XXXXXXX~ i400:8927XXXXXXX~Di700 A(Four Thirds ver.)i60A(Four Thirds ver.)Air 1 Commander(Four Thirds ver.)Air 10s Commander New(Four Thirds ver.)Air 10s Commander New(Four Thirds ver.)i600(Four Thirds ver.)i400(Four Thirds ver.)i600(Four Thirds ver.)Last update: Jan 2021Last update: Jan 2021。
飞利浦 105S5 彩色显示器 说明书

SAFETY PRECAUTIONS AND MAINTENANCEDisconnect the monitor from the mains supply if the monitor is not to be used for extended period of time.Do not attempt to remove the back cover, as you will be exposed to shock hazard. The back cover should only be removed by qualified services personnel.Do not place objects on top of the monitor cabinet, which could fall into vents or which could cover them and prevent proper cooling of the monitor’s electronic devices.Do not expose the monitor to rain or excessive moisture to avoid the risk of shock or permanent damage to the set.Avoid exposing the monitor to direct sunlight, stoves or any other heat sources.To prevent overheating, make sure that the ventilation openings of the monitor are not covered. Keep moisture and dust away.Keep away from any magnetic objects, such as speakers, electric motors, transformers,…etc. When positioning this monitor, make sure that the mains plug and socket are easily accessible. Do not use alcohol or ammonia based liquid to clean the monitor. If necessary, clean with a slightly damp cloth. Disconnect the monitor from the mains supply before cleaning.Consult a service technician if the monitor does not operate normally when operating instructions of this manual are followed.1INTRODUCTIONWe would like to thank you for your purchase of this Philips color monitor 105S5. This monitor set can be used with IBM PC and PS/2 computers or compatibles with analog RGB output. It also supports timings of graphics adapters including:-VGA, SVGA, XGA, 1024X768Please read this user’s guide carefully to obtain the best performance from your Monitor, and keep this user’s guide for future reference.FEATURESAutomatically scan horizontal and vertical frequencies.Analog input signal provides the capability of unlimited display colors.Horizontal size/position, vertical size/position and pincushion controls are adjustable to adapt to a variety of graphics cards.Fine phosphor pitch provides greater image clarity.On-Screen-Display and Digital Control features provide user-friendliness and easy-to-use when operating the monitor.ENERGY STAR® is a U.S. registered mark.As an ENERGY STAR® Partner, we have determined that this product meets theENERGY STAR® guidelines for energy efficiency.IBM, IBM PC and IBM PS/2 are registered trademarks of International Business Machines Corporation.Windows is a registered trademark of Microsoft Corporation.VESA is a registered trademark of the Video Electronics Standards Association.DDC are trademarks of VESA.23INSTALLATION INSTRUCTIONSCAUTION:Be sure to turn off the AC Power to the monitor before making connections1. Assemble the tilt/swivel base as shown below.2. Connect the power cord.3. Connect the end of the signal cable to the display connector of the computer and tightenthe screws.CONTROLS AND OPERATIONTILT/SWIVEL BASETurn the monitor for comfortable viewing angle within 180° horizontally and 20° vertically. (please refer to installation instructions.)SIGNAL CABLE CONNECTOR (15-pin mini D-SUB)Connect to the display adapter output of a computer having analog video output.AC INPUT CONNECTOR (Appliance coupler)Connect to AC outlet with supplied power cord.POWER SWITCH AND INDICATORPress this switch to turn on the monitor and the indicator will light up.To turn off the monitor, press it again.USER ADJUSTMENT BUTTONSTo Display OSD main menu.Push again to exit from main menu.To entry the adjustment function.4OSD MENUBASIC CONTRASTBRIGHTNESSFACTORY RESETZOOMH-POSITIONH-SIZEV-POSITIONV-SIZEGEOMETRY PINCUSHIONPIN BALANCETRAPEZOIDPARALLELCOLOR 9300o K/6500 o KUSERLANGUAGE ENGLISHFRENCHSPANISHCHINESE(simple font)CHINESE(complex font)OTHER H.MOIREV.MOIREOSD H-POSITIONOSD V-POSITIONINPUT LEVEL POWER MANAGEMENT5THIS MONITOR CAN SUPPORT EPA AND NUTEK POWER MANAGEMENT SYSTEMS, INDICATED BY THE LED ON THE FRONT PANEL:The monitor remains in the power-saving state until you press a key on the keyboard or move the mouse (if available).INPUT PIN ASSIGNMENTSTATE LED COLOR OSD INDICATIONPOWERCONSUMPTIONON GREEN -------------- 75W ACTIVE OFF AMBER POWER SAVING < 8WPinSIGNALNo1 Red Video2 Green Video3 Blue Video4 Digital Ground or No Pin5 Digital Ground or No Pin6 Red Video Return7 Green Video Return8 Blue Video Return9 Digital Ground or No Pin10 Digital Ground or No Pin11 Digital Ground or No Pin12 SDA (DDC1/2B Data)13 Horizontal Sync14 Vertical Sync15 SCL (DDC1/2B Clock) SPECIFICATIONS78TROUBLE SHOOTING GUIDEMODEL105S5SIZE15” DIAGONAL (14” VIEWABLE)DEFLECTION ANGLE90 DEGREES CRTPHOSPHOR PITCH0.28MM RESOLUTION (MAX)1024X768 VIDEO BANDWIDTH75MHz HORIZONTAL30~54KHz SYNCHRONI-ZATIONVERTICAL 50~120HzVIDEORGB ANALOG 0.7 Vp-p, 1Vp-p/75 Ohms POSITIVEINPUT SIGNALSYNCTTL SEPARATE/COMPOSITE (+/-)DISPLAY COLORSUNLIMITEDDISPLAY AREA (HXV)270mmX202mm(RECOMMENDED)Problem Possible Cause RemedyNo pictureIs the power Cord Connected?Is the power switch on?Is the signal cable properlyconnected?Is the monitor in the powersave mode? Connect power cord.Turn on power switch. Connect signal cable properly. Check connector for bent pins. Press any key on the keyboard or move the mouse.Picture is unstable Is the signal cable properlyconnected?Is the scanning frequencyoutside the acceptable range?Are the pin arrangements ofthe signal connector correct?Connect signal cable properly.Check for bent or missing pins.Reconfigure the graphics board.within the range of the monitor.Use correct signal cable.The color of image on screen is abnormal. Is there magnetic object nearby?Are the pin arrangements of thesignal connector correct?Move the object away.Use correct signal cable.* Due to continuous product improvement, the specifications in this manual are subject to change without notice.Your International GuaranteeDear Customer,9Thank you for purchasing this Philips product which has been designed and manufactured to the highest quality standards.If, unfortunately, something should go wrong with this product Philips guarantees free of charge labor and replacement parts irrespective of the country where it is repaired during a period of 12 months from date of purchase. This international Philips guarantee complements the existing national guarantee obligations to you of dealers and Philips in the country of purchase and does not affect your statutory rights as a customer.The Philips guarantee applies provided the product is handled properly for its intended use, in accordance with its operating instructions and upon presentation of the original invoice or cash receipt, indicating the date of purchase, dealer's name and model and production number of the product.The Philips guarantee may not apply if:• the documents have been altered in any way or made illegible;• the model or production number on the product has been altered, deleted, removed or made illegible;• repairs or product modifications and alterations have been executed by unauthorized service organizations or persons;• damage is caused by accidents including but not limited to lightning, water or fire, misuse or neglect.Please note that the product is not defective under this guarantee in the case where modifications become necessary in order for the product to comply with local or national technical standards which apply in countries for which the product was not originally designed and/or manufactured. Therefore always check whether a product can be used in a specific country.In case your Philips product is not working correctly or is defective, please contact your Philips dealer. In the event you require service whilst in another country a dealer address can be given to you by the Philips Consumer Help Desk in that country, the telephone and fax number of which can be found in the relevant part of this booklet.In order to avoid unnecessary inconvenience, we advise you to read the operating instructions carefully before contacting your dealer. If you have questions which your dealer cannot answer or any related question please contact the Philips Consumer Information Centers or via:Website: 使用及安全須知:10若顯示器長久不用請與主機斷開連接。
青岛喜客咖啡 Saeco 魔术豪华咖啡机OPERATING INSTRUCTIONS 说明书

Saeco 魔术豪华咖啡机Automatic espresso coffee machine SAECO MAGIC COMFORTOPERATING INSTRUCTIONS 说 明 书青岛喜客咖啡有限公司目录索引一、安全预防............................................................2 二、前言..................................................................3 三、机器参数............................................................3 四、基本介绍............................................................4 五、安装..................................................................6 六、使用..................................................................7 七、菜单与设置......................................................10 八、调节与设定......................................................14 九、清理与保养......................................................15 十、故障处理.........................................................20 十一、保证书 (21)青岛喜客咖啡有限公司一、 安全预防1、 本机不能在户外使用,不要靠近热源。
Elcometer 5100 Payne 渗透杯 操作说明书
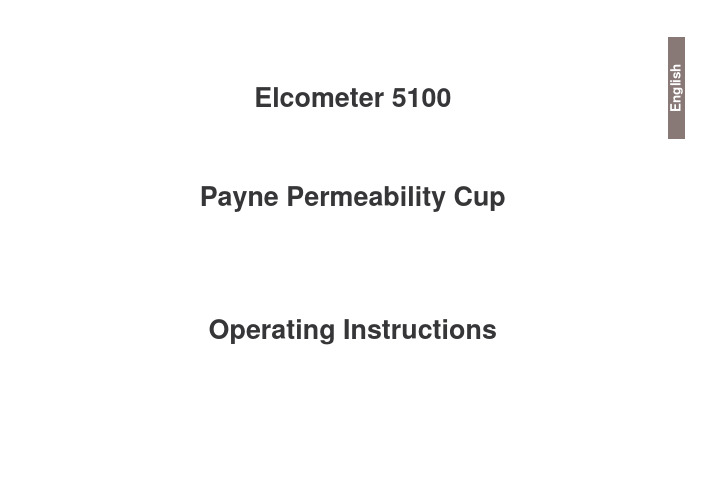
Elcometer 5100 Payne Permeability Cup Operating InstructionsAll other trademarks acknowledged.© Copyright Elcometer Limited. 2008.All rights reserved. No part of this Document may be reproduced, transmitted, transcribed, stored (in a retrieval system or otherwise) or translated into any language, in any form or by any means (electronic, mechanical, magnetic, optical, manual or otherwise) without the prior written permission of Elcometer Limited.A copy of this Instruction Manual is available for download on our Websitevia /downloads.Doc.No. TMA-0340 Issue 03Text with Cover No: 19611CONTENTSSection Page 1About this instrument. . . . . . . . . . . . . . . . . . . . . . . . . . . . . . . . . . . . . . . . . . . . . . . . . . . . . . . . . . . . . 2 2Taking a measurement. . . . . . . . . . . . . . . . . . . . . . . . . . . . . . . . . . . . . . . . . . . . . . . . . . . . . . . . . . . . 3 3Spare parts & Accessories. . . . . . . . . . . . . . . . . . . . . . . . . . . . . . . . . . . . . . . . . . . . . . . . . . . . . . . . . 5 4The Elcometer 5100 range . . . . . . . . . . . . . . . . . . . . . . . . . . . . . . . . . . . . . . . . . . . . . . . . . . . . . . . . . 6 5Related equipment . . . . . . . . . . . . . . . . . . . . . . . . . . . . . . . . . . . . . . . . . . . . . . . . . . . . . . . . . . . . . . . 61Thank you for your purchase of this Elcometer 5100 Payne Permeability Cup. Welcome to Elcometer. Elcometer are world leaders in the design, manufacture and supply of inspection equipment for coatings and concrete. Our products cover all aspects of coating inspection, from development, through application to post application inspection.This Elcometer 5100 Payne Permeability Cup is a world beating product. With the purchase of this product you now have access to the worldwide service and support network of Elcometer. For more information visit our website at 1 ABOUT THIS INSTRUMENTThe Elcometer 5100 Payne Permeability Cup is a simple instrument which is used to determine the vapour transmission rate of unsupported films of paint, varnish, plastic, paper, etc.The Payne cup is filled with a suitable liquid or dry desiccant and then the film being tested is clamped and sealed across the open end of the cup.The assembly is weighed at the start of the test and again at the end. Any difference between the two weights will be due to water-vapour which has permeated through the film in a given time.The instrument is simple to use and is available in three sizes to suit the requirements of the film being tested. The instrument is manufactured from anodised aluminium.1.1 STANDARDSYour Elcometer 5100 Payne Permeability Cup can be used in accordance with the following National and International Standards:ASTM D1653; ASTM E96; ISO 7783 supersedes NF T30-018.231.2 WHAT THE BOX CONTAINS•Elcometer 5100 Payne Permeability Cup •Storage case •Operating instructionsThe Elcometer 5100 Payne Permeability Cup is packed in acardboard and foam package. Please ensure that thispackaging is disposed of in an environmentally sensitivemanner. Consult your local Environmental Authority for furtherguidance.To maximise the benefits of your new Elcometer 5100please take some time to read these Operating Instructions. Do not hesitate to contact Elcometer or your Elcometer supplier if you have any questions.2 TAKING A MEASUREMENT2.1 TEST PROCEDURE1.Prepare the film to be tested.Figure 1. Elcometer 5100 Payne Permeability Cups4The coating has to be applied a onto a substrate (eg Leneta RP-1K) which allows the film to be removed after it has dried. Silicone coated paper is suitable for many types of coating, however the user of the cup should determine the most suitable substrate for their application.2.Fill the Payne cup with specified liquid or dry desiccant.3.Place the film carefully over the top of the cup ensuring that the film covers the flange of the cup.4.Place the rubber gasket and the sealing ring on the film and secure using the clamps provided.5.Weigh the assembly and record the result in grams (m 1).6.Leave the cup undisturbed for the period of time stated in the standard conditions.7.At regular intervals re-weigh the assembly and record the result in grams (m 2) until linear.8.Calculate the water-vapour transmission rate of the film in grams per sq. metre per day (g/(m 2.d)):P = 240 x ∆m / AWhere ∆m = rate of change in mass in mg/h, and A = area in square centimetres of test piece taken from the following table:a.Elcometer supplies a wide range of manual and motorised film applicators. See “Related equipment” on page 6 for more information.CupArea Elcometer 5100/110 cm²Elcometer 5100/230cm²Elcometer 5100/330cm²52.2 AFTER THE TESTClean the cup and lid.After cleaning, ensure that all materials are removed and that the instrument is dry.3 SPARE PARTS & ACCESSORIESYour Elcometer 5100 Payne Permeability Cup is complete with all the items required to start taking measurements. Over the life of the instrument, replacement rubber gaskets may be required:Rubber gasketPart number Elcometer 5100/1KT005100P001Elcometer 5100/2KT005100P002Elcometer 5100/3KT005100P003Leneta Chart RP-1K (250 pcs)K0004695M112Do not use wire brushes, metal scrapers,metal files or other metallic tools forcleaning.Clean the cup, rubber gasket and sealing ring using a suitable solvent.4 THE ELCOMETER 5100 RANGEModel Volume Area Part Number(cm3)(cm²)(sq. inch)5100/11510 1.55K0005100M2015100/25030 4.65K0005100M2025100/37530 4.65K0005100M2035 RELATED EQUIPMENTIn addition to the Elcometer 5100 Payne Permeability Cup, Elcometer produces a wide range of other coating testing equipment. Users of the Elcometer 5100 Payne Permeability Cup may also benefit from the following Elcometer products:•Elcometer Laboratory Scales•Elcometer Film Applicators•Elcometer Motorised Film ApplicatorsFor further information contact Elcometer or your local supplier.Details of Elcometer offices around the world are given on the outside cover of these operating instructions. Alternatively visit the Elcometer website, 6。
美的空调使用说明书

IMPORTANT NOTE:Read this manual carefully before installing or operating your new air conditioning unit. Make sure to save this manual for future reference.SPLIT-TYPE ROOM AIR CONDITIONEROwner’s ManualSYSPLIT WALL FLEXI SeriesSafety Precautions (04)Table of Contents 0Care and Maintenance ......................................................................................1214Troubleshooting................................................................................................. . (3)4European Disposal Guidelines185Safety PrecautionsRead Safety Precautions Before InstallationIncorrect installation due to ignoring instructions can cause serious damage or injury. The seriousness of potential damage or injuries is classified as either a WARNING or CAUTION.WARNING This symbol indicates that ignoring instructions may cause death or serious injury.This symbol indicates that ignoring instructions may cause moderate injury to your person, or damage to your appliance or other property.CAUTION③ Page 4 ④③ Page 5 ④Unit Speci cations and Features1 Unit Parts)③ Page 6 ④③ Page 7 ④To further optimize the performance of your unit, do the following:• Keep doors and windows closed.• Limit energy usage by using TIMER ON and TIMER OFF functions.• Do not block air inlets or outlets.• Regularly inspect and clean air lters.FOR UNITS WITH AUXILARY ELECTRIC HEATERAchieving Optimal PerformanceOptimal performance for the COOL, HEAT, and DRY modes can be achieved in the following temperature ranges. When your air conditioner is used outside of these ranges, certain safety protection features will activate and cause the unit to perform less than optimally.Inverter Split TypeFixed-speed TypeWhen outsidetemperature is below 0°C (32°F ), we strongly recommend keeping the unit plugged in at all timers to ensure smooth ongoing performance.For a detailed explanation of each function, refer to the Remote Control Manual.Other Features• Auto-RestartIf the unit loses power, it will automatically restart with the prior settings once power has been restored.• Anti-mildew (some units)When turning o the unit from COOL, AUTO (COOL), or DRY modes, the air conditioner will continue operate at very low power to dry up condensed water and prevent mildew growth.• Wi-Fi Control (some units)Wi-Fi control allows you to control your air conditioner using your mobile phone and a Wi-Fi connection.• Louver Angle Memory(some units)When turning on your unit, the louver will automatically resume its former angle.• Refrigerant Leakage Detection (some units)The indoor unit will automatically display “EC” when it detects refrigerant leakage.For a detailed explanation of your unit’sadvanced functionality (such as TURBO mode and its self-cleaning functions), refer to the Remote Control Manual.③ Page 8 ④Setting vertical angle of air owWhile the unit is on, use the SWING /DIRECT button to set the direction (vertical angle) ofairflow.1. Press the SWING /DIRECT button once toactivate the louver. Each time you pressthe button, it will adjust the louver by 6°.Press the button until the direction youprefer is reached.2. To make the louver swing up and downcontinuously, press and hold the SWING/DIRECT button for 3 seconds. Press itagain to stop the automatic function.The horizontal angle of the air ow must be set manually. Grip the de ector rod (See Fig.2.3)and manually adjust it to your preferred direction. For some units, the horizontal angle of the air ow can be set by remote control. please refer to theRemote Control Manual.When using COOL or DRY mode, do not set louver at too vertical an angle for long periodsof time. This can cause water to condense on the louver blade, which will drop on your floor or furnishings. (See Fig. 2.2)When using COOL or HEAT mode, setting the louver at too vertical an angle can reduce the performance of the unit due to restricted airflow.Do not move louver by hand. This will cause the louver to become out of sync. If this occurs, turn o the unit and unplug it for a few seconds, then restart the unit. This will reset the louver.Fig. 2.2 Fig. 2.3Setting Angle of Air FlowSetting horizontal angle of air ow•Deflectorrod③ Page 9 ④③ Page 10 ④The SLEEP function is used to decrease energy use while you sleep (and don’t need the same temperature settings to stay comfortable). This function can only be activated via remote control.Press the SLEEP button when you are ready to go to sleep. When in COOL mode, the unit will increase the temperature by 1°C (2°F) after 1 hour, and will increase an additional 1°C (2°F) after another hour. When in HEAT mode, the unit will decrease the temperature by 1°C (2°F) after 1 hour, and will decrease an additional 1°C (2°F) after another hour.It will hold the new temperature for 7 hours, then the unit will turn o automatically.Note: The SLEEP function is not available in FAN or DRY mode.Sleep OperationFig. 3.1•③ Page 11 ④How to operate your unit without the remote controlIn the event that your remote control fails to work, your unit can be operated manually with the MANUAL CONTROL button located on the indoor unit. Note that manual operation is not a long-term solution, and that operating the unit with your remote control is strongly recommended.Manual Operation (Without Remote)2Manual control buttonBEFORE MANUAL OPERATION Unit must be turned o before manual operation.To operate your unit manually:1. Open the front panel of the indoor unit.2. Locate the MANUAL CONTROL button on the right-hand side of the unit.3. Press the MANUAL CONTROL button one time to activate FORCED AUTO mode.4. Press the MANUAL CONTROL again to activate FORCED COOLING mode.5. Press the MANUAL CONTROL button a third time to turn the unit o .6. Close the front panel.③ Page 12 ④Cleaning Your Indoor UnitCleaning Your Air FilterA clogged air conditioner can reduce the cooling efficiency of your unit, and can also be bad for your health. Make sure to clean the filter once every two weeks.1. Lift the front panel of the indoor unit.2. Grip the tab on the end of the lter, push it up slightly, then pull it a little towards yourself.3. Now pull down to extract the lter.4. If your lter has a small air freshening lter, unclip it from the larger lter. Clean this air freshening lter with a hand-held vacuum.5. Clean the large air lter with warm, soapy water. Be sure to use a mild detergent.Care and Maintenance36. Rinse the lter with fresh water, then shake o excess water.7. Dry it in a cool, dry place, and refrain from exposing it to direct sunlight.8. When dry, re-clip the air freshening lter to the larger lter, then slide it back into the indoor unit.9.Close the front panel of the indoor unit.Care and Maintenancerevert to its previous display.To reset the reminder, press the LED buttonon your remote control 4 times, or press the MANUAL CONTROL button 3 times. If you don’tTurn o the unit anddisconnect the powerRemove batteriesfrom remote control Maintenance –Pre-Season Inspection③ Page 14 ④Common IssuesThe following problems are not a malfunction and in most situations will not require repairs.Troubleshooting4Troubleshooting③ Page 15④TroubleshootingWhen troubles occur, please check the following points before contacting a repair company.Troubleshooting③ Page 16④③ Page 17④NOTE: If your problem persists after performing the checks and diagnostics above, turn o yourunit immediately and contact an authorized service center.European Disposal Guidelines 5 This appliance contains refrigerant and other potentially hazardous materials. When disposing ofthis appliance, the law requires special collection and treatment. Do not dispose of this product as household waste or unsorted municipal waste.When disposing of this appliance, you have the following options:•Dispose of the appliance at designated municipal electronic waste collection facility.•When buying a new appliance, the retailer will take back the old appliance free of charge.•The manufacturer will take back the old appliance free of charge.•Sell the appliance to certi edscrap metal dealers.③ Page 18 ④CS369U-11M 16122000002414 20150825The design and speci cations are subject to change without prior notice forproduct improvement. Consult with the sales agency or manufacturer for details.。
施密特+施密特 messko zt-f2.1 变压器温度传感器 操作说明书 operating

BA2526030/03ZH-ENMESSKO® ZT-F2.1变压器温度传感器TRANSFORMER TEMPERATURE TRANSMITTER 操作说明书/ Operating Instructions目录1 安全.................................101.1 安全说明 ..............................101.2 指定应用 ..............................101.3 关于运行设备运转的重要提示.............10 2 产品规格 ..............................103 安装条件和试验........................114 表盘式温度计..........................115 组装 .................................115.1 组装 ZT-F2.1 变压器温度传感器 ............115.2安装表盘式温度计的感温包 (11)6 电气连接 ..............................126.1 连接电流互感器........................126.2 Pt100 测量电阻 .........................126.3 可选项:模拟输出端 4...20 mA ............127 设置热点梯度 .........................127.1 2 A CT 标称电流的设置 ...................12 7.2 CT 标准电流 ≠ 2 A 的设置................138 检查显示屏 ............................149 服务.................................1410 维护.................................1411 过电压保护装置 1412 技术数据 (1413)附录 (16)13.1 尺寸.................................1613.2 2 A CT 标称电流的热点梯度表 .............1713.3 更换传感器 (20)请妥善保存本手册以备将来参考!Contents1 Safety . . . . . . . . . . . . . . . . . . . . . . . . . . . . . . . . . . . .101 .1 Safety instructions . . . . . . . . . . . . . . . . . . . . . . . . .101 .2 Specified application . . . . . . . . . . . . . . . . . . . . . . . .101 .3 Important notes on equipment operation . . . . . . .10 2 Product specification . . . . . . . . . . . . . . . . . . . . . . . .103 Installation conditions and testing . . . . . . . . . . . .114 Dial-type thermometer . . . . . . . . . . . . . . . . . . . . . .115 Assembly . . . . . . . . . . . . . . . . . . . . . . . . . . . . . . . . .115 .1 Assembling the ZT-F2 .1 transformer temperaturetransmitter . . . . . . . . . . . . . . . . . . . . . . . . . . . . . . . .115 .2Installing the temperature bulb of the dial-type . . . thermometer . . . . . . . . . . . . . . . . . . . . . . . . . . . . . .116 Electrical connection . . . . . . . . . . . . . . . . . . . . . . . .126 .1 Connecting the current transformer . . . . . . . . . . .126 .2 Pt100 measuring resistor . . . . . . . . . . . . . . . . . . . .126 .3 Option: Analog output 4 . . .20 mA . . . . . . . . . . . . . .127 Setting the hot-spot gradient . . . . . . . . . . . . . . . .127 .1 Setting for 2 A CT nominal current . . . . . . . . . . . .12 7 .2 Setting for CT nominal current ≠ 2 A . . . . . . . . . .13 8Checking the display . . . . . . . . . . . . . . . . . . . . . . . .149 Service . . . . . . . . . . . . . . . . . . . . . . . . . . . . . . . . . . .1410 Maintenance . . . . . . . . . . . . . . . . . . . . . . . . . . . . . .1411 Overvoltage protection . . . . . . . . . . . . . . . . . . . . . .1412Technical data . . . . . . . . . . . . . . . . . . . . . . . . . . . . .1413 Appendix . . . . . . . . . . . . . . . . . . . . . . . . . . . . . . . .1613 .1 Dimensions . . . . . . . . . . . . . . . . . . . . . . . . . . . . . . .1613 .2 Hot-spot gradient table for 2 A CT nominalcurrent . . . . . . . . . . . . . . . . . . . . . . . . . . . . . . . . . . .1713 .3 Replacement sensor . . . . . . . . . . . . . . . . . . . . . . . .20Please keep this manual for future reference!1 安全1.1 安全说明参与本运行设备的安装、调试、运行或维护的所有人员都必须:- 具备相应的专业资格并- 严格遵守本操作说明书。
Bosch 肉筋机 MUZ5FW1.GB 使用手册说明书

29,7% aus poolAB142% aus Poolen Safety81 SafetyObserve the following safety instructions.1.1 General information¡Read this instruction manual carefully.¡Observe the instructions for the base unit.1.2 Intended useOnly use the accessories:¡with a kitchen machine from the same series MUM5.¡With genuine parts and accessories.¡For cutting up raw or cooked food, e.g. meat, fish and veget-ables.¡For additional applications described in these instructions.1.3 Safety instructionsWARNING ‒ Risk of injury!Rotating drives, tools or accessory parts may cause injury.▶Do not reach into the filling shaft.▶Only use the pusher to push down ingredients.Improper use may cause injuries.▶Never assemble the accessories on the base unit.▶Only attach and remove accessories once the drive has stopped and the appliance has been unplugged.▶Only use the accessories once fully assembled.▶The accessories should only be used in the intended operating position.Avoiding material damage en92 Avoiding material dam-ageATTENTION!Improper use may cause material damage.▶Do not process food that contains hard components, e.g. bones.▶Do not insert objects into the filling shaft or housing, e.g. wooden spoons.▶Before use, check the filling shaft and housing for foreign objects.3 Unpacking and check-ingFind out here what you need to note when unpacking the appliance.3.1 Unpacking the accessor-ies and parts1.Take the accessories out of thepackaging.2.Take all other parts and the ac-companying documents out of the packaging and place them to hand.3.Remove any packaging material.4.Remove any stickers or film.3.2 Contents of packageAfter unpacking all parts, check for any damage in transit and complete-ness of the delivery.→ Fig. 13.3 Cleaning the accessoriesbefore using for the first time1.Clean all parts that come into con-tact with food before using for the first time.→ "Cleaning and servicing",Page 122.Put the cleaned and dried parts out ready for use.4 Familiarising yourself with the accessories4.1 ComponentsYou can find an overview of the parts of your accessories here.→ Fig. 2en Before using the appliance104.2 Special accessoryYou can find an overview of the spe-cial accessories and how to use them here.Perforated discsThe fine and the coarse perforated disc are suitable for additional pro-cessing functions.Juicer attachmentThe juicer attachment is suitable for squeezing soft fruit and vegetables,e.g. berries, tomatoes, apples, pears,rose hips.Notes¡Do not press fruit whose pips are similar in diameter to the hole dia-meter in the strainer insert, e.g.raspberries.¡Cook hard food before squeezing to make it soft enough, e.g. rose hips.Viennese whirl attachmentThe Viennese whirl attachment is suit-able for shaping biscuit dough or shortcrust pastry.Grater attachmentThe grater attachment is suitable for grating hard foods, e.g. almonds,nuts, chocolate, hard cheese or dry bread rolls.Note: Only process dry nuts and al-monds in small quantities.4.3 Overload protectionThe overload protection system pre-vents the motor and other compon-ents from being damaged through being overloaded.If the meat mincer is overloaded or blocked, the agitator paddle on the worm gear will break at the predeter-mined breaking point.Note: Spare parts with a predeter-mined breaking point are not covered by our warranty obligations. A new agitator paddle is available from cus-tomer service under order number 00418076.Replacing the agitator paddle1.Release the fastening screw in the agitator paddle using a suitable screwdriver and remove.2.Remove the faulty agitator paddle.3.Insert a new agitator paddle and screw tight.5 Before using the appli-ancePrepare the base unit and the ac-cessories for use.Before using the appliance en5.1 Preparing the base unit Note: The food processor shown in the pictures may differ from your model in terms of shape and fea-tures.1.Set up the base unit as describedin the main operating instructions.2.Press the release button and movethe swivel arm down until it en-gages in the vertical position.→ Fig. 3a The swivel arm is fixed in posi-tion 3.3.Rotate the base unit to the operat-ing position.→ Fig. 45.2 Inserting the seal▶Insert the seal into the housing and press in firmly.→ Fig. 5The recesses must match up ex-actly.5.3 Assembling the attach-mentsNote: To use the special accessory, you need the parts of the meat min-cer, except for the knife and perfor-ated disc.Assembling the meat mincer1.Fit the worm gear into the housingwith the agitator paddle at thefront.→ Fig. 62.Fit the knife onto the worm gearwith the square projection at thefront.→ Fig. 73.Insert the required perforated discinto the housing.→ Fig. 8Observe the recess on the perfor-ated disc.4.Fit the threaded ring and tightenclockwise slightly.→ Fig. 9Assembling the juicer attachment1 Follow the illustrated instructions.→ Fig. 10 - 14Assembling the Viennese whirl attachment1Follow the illustrated instructions.→ Fig. 15 - 18Assembling the grater attachment1Follow the illustrated instructions.→ Fig. 19 - 225.4 Fitting the attachment1.Open the locking lever.→ Fig. 232.Hold the prepared attachment hori-zontally and match up the ends of the agitator paddle with the drive.→ Fig. 243.Push the attachment fully onto thedrive.4.Rotate the attachment anticlock-wise as far as possible.→ Fig. 255.Close the locking lever.→ Fig. 266.Tighten the threaded ring clock-wise.7.Attach the filling tray.→ Fig. 278.Place a suitable container underthe attachment.→ Fig. 28en Basic operation6 Basic operation6.1 Recommended speeds Observe the recommended speeds for optimum results.Note: Your model is equipped with a 4- or 7-level rotary switch depending on the features of the appliance. The recommended speeds for the 4-level rotary switch are always shown in brackets in these instructions for use. Setting Use7 (4)Meat mincer7 (4)Juicer attachment4-5(2-3)Viennese whirl attachment3-4(2-3)Shredding attachment6.2 Processing food1.Prepare your food.Cut large items of food into pieces so they fit into the filling shaft.2.Insert the mains plug.3.Set the rotary switch to the recom-mended speed.→ Fig. 294.Insert the food into the filling shaftand press down with the pusher,applying light pressure.→ Fig. 305.Set the rotary switch to .→ Fig. 31Wait until the appliance stops.6.Unplug the mains plug.Processing food with the juicer attachment1Note: When working with the juicer attachment, note the following special features.1.Place two containers under the rel-evant openings.2.Before starting processing, turn thesetting screw anticlockwise andopen.→ Fig. 323.During processing use the settingscrew to select the desired con-sistency of the fruit purée andpulp.6.3 Removing the attachment1.Remove the filling tray and pusherand open the locking lever.→ Fig. 332.Rotate the attachment and removefrom the base unit.→ Fig. 34Tip: Clean all parts immediately after use so that residues do not dry on.7 Cleaning and servicing 7.1 Cleaning productsFind out here what cleaning agents are suitable for your accessories. ATTENTION!Using unsuitable cleaning agents or incorrect cleaning may damage the accessories.▶Do not use cleaning agents con-taining alcohol or spirits.▶Do not use sharp, pointed or metal objects.Cleaning and servicing en ▶Do not use abrasive cloths orcleaning agents.▶Only clean the control panel andthe display using a damp mi-crofibre cloth.7.2 Cleaning the individualparts1.Dismantle the attachment used.To do so, proceed in reverse orderas described for assembly.→ "Assembling the attachments",Page 112.Clean all individual parts with de-tergent solution and a soft cloth orsponge.3.Dry metal parts. Dry the otherparts.Note: Rub the cleaned metal partswith a little cooking oil to protectthem from rust.7.3 Overview of cleaningHere you will find a overview of thebest way to clean the individual com-ponents.→ Fig. 35ms Keselamatan1 KeselamatanPerhatikan panduan keselamatan berikut.1.1 Maklumat umum¡Baca panduan ini dengan teliti.¡Ikuti arahan untuk peranti asas.1.2 Pengendalian mengikut peraturanGunakan aksesori hanya:¡dengan mesin dapur siri ini MUM5.¡dengan alat ganti dan aksesori tulen.¡Untuk mencincang makanan yang mentah dan yang telah dimasak contoh daging, ikan dan sayur-sayuran.¡untuk aplikasi tambahan yang dijelaskan dalam manual ini.1.3 Arahan keselamatanAMARAN ‒ Risiko kecederaan!Pemacu, alat atau bahagian aksesori yang berputar boleh menyebabkan kecederaan.▶Jangan pegang di dalam bahagian suapan.▶Hanya gunakan penghentak untuk menambahkan bahan. Penggunaan yang tidak betul boleh menyebabkan kecederaan.▶Jangan sesekali pasang aksesori pada unit asas.▶Hanya pasang dan tanggalkan aksesori semasa pemacu berhenti dan peranti tidak terpasang.▶Gunakan aksesori hanya apabila dipasang sepenuhnya.▶Hanya gunakan aksesori pada kedudukan kerja yang dimaksudkan.Elakkan kerosakan harta benda ms2 Elakkan kerosakanharta bendaPERHATIAN!Penggunaan yang tidak betul boleh menyebabkan kerosakan harta benda.▶Jangan proses makanan yang mengandungi komponen keras,contohnya tulang.▶Jangan masukkan objek ke dalam bahagian suapan atau perumah,contohnya sudu kayu.▶Periksa benda asing di bahagian suapan dan perumah sebelumdigunakan.3 Buka pembungkusan dan periksaAnda ketahui di sini perkara yang perlu diperhatikan semasa membuka pembungkusan.3.1 Buka pembungkusanaksesori dan komponen1.Keluarkan aksesori daripadabungkusan.2.Keluarkan semua komponen laindan dokumen yang disertakan dari bungkusan dan sediakan.3.Tanggalkan bahan pembungkusanyang sedia ada.4.Tanggalkan pelekat dan kerajangyang sedia ada.3.2 Skop penghantaran Periksa kerosakan semasa penghantaran pada semua komponen dan kelengkapan penghantaran selepas membuka pembungkusan.→ Raj. 13.3 Sebelum penggunaanpertama basuh semuabahagian aksesoridengan teliti dankeringkan.1.Bersihkan semua komponen yangbersentuhan dengan makanansebelum penggunaan pertama.→ "Pembersihan dan penjagaan",Halaman 192.Sediakan komponen yangdibersihkan dan dikeringkan untuk digunakan.4 Pengenalan aksesori 4.1 KomponenDi sini, terdapat gambaran keseluruhan komponen aksesori anda.→ Raj. 21Aksesori pilihanms Pengenalan aksesori1Aksesori pilihan4.2 Aksesori pilihanDi sini, terdapat gambaran keseluruhan tentang aksesori pilihan dan penggunaannya.Cakera berlubangCakera berlubang halus dan besar sesuai untuk kemungkinan pemprosesan tambahan.Alat tambah pemerahAlat tambah pemerah sesuai untuk memerah buah-buahan atau sayur-sayuran yang lembut, contohnya beri, tomato, epal, pear dan rose hip.Nota¡Jangan perah buah-buahan yang mempunyai diameter teras yangsama dengan diameter lubangsisipan penapis, contohnyaraspberi.¡Rebus makanan keras hingga cukup lembut sebelum memerah, contohnya rose hip.Alat tambah biskut kek rapuhAlat tambah biskut kek rapuh sesuai untuk membentuk adunan biskut atau pastri rapuh.Alat tambah pemarutAlat tambah pemarut sesuai untuk memarut makanan keras, contohnya badam, kekacang, coklat, keju keras atau roti kering.Nota: Hanya proses kekacang dan badam secara kering dan dalam jumlah yang sedikit.4.3 Pelindung bebanberlebihanPelindung beban lebih menghalang motor dan komponen lain daripada rosak akibat beban berlebihan. Sekiranya penggiling daging berlebihan atau tersumbat, pemacu skru pecah pada titik pemecahan yang telah ditentukan.Nota: Bahagian alat ganti dengan titik pecah yang telah ditentukan adalah bukan sebahagian daripada kewajipan waranti kami. Pemacu baharu boleh didapati daripada perkhidmatan pelanggan dengan menggunakan nombor pesanan 00418076.Ganti pemacu1.Longgarkan dan tanggalkan skrupengikat pada pemacu denganpemutar skru yang sesuai.Sebelum penggunaan ms2.Tanggalkan pemacu yang rosak.3.Masukkan dan ketatkan pemacubaharu.5 Sebelum penggunaanSediakan unit asas dan aksesori untuk digunakan.5.1 Sediakan perkakas asas. Nota: Pemproses makanan yang digambarkan mungkin berbeza dalam bentuk dan peralatan dari model anda.1.Siapkan peranti asas seperti yangdijelaskan dalam arahan utama. 2.Tekan butang pelepas dangerakkan pemutar lengan kebawah sehingga terkunci padakedudukan menegak.→ Raj. 3a Lengan putar dipasang padakedudukannya 3.3.Putar perkakas asas kekedudukan kerja.→ Raj. 45.2 Masukkan pengedap▶Letakkan pengedap pada perumah dan tekan dengan kuat.→ Raj. 5Lekuk mesti diselaraskan dengantepat.5.3 Pasang alat tambahNota: Untuk menggunakan aksesori pilihan, anda memerlukan bahagian pengisar, kecuali bilah dan cakera berlubang.Pasang pengisar1.Letakkan dahulu skru denganpemacu pada perumah.→ Raj. 62.Letakkan dahulu bilah denganbonjol segi empat sama padaskru.→ Raj. 73.Letakkan cakera berlubang yangdiinginkan pada perumah.→ Raj. 8Perhatikan lekuk pada cakeraberlubang.4.Pasang cincin skru dan ketatkansedikit mengikut arah jam.→ Raj. 9Pasang alat tambah pemerah1 Ikut panduan bergambar.→ Raj. 10 - 14Pasang alat tambah biskut kek rapuh1Ikut panduan bergambar.→ Raj. 15 - 18Pasang alat tambah pemarut1 Ikut panduan bergambar.→ Raj. 19 - 225.4 Lekatkan alat tambah1.Buka tuil kunci.→ Raj. 232.Pegang alat tambah yangdisediakan secara mendatar dan selaraskan hujung pemacu pada penggerak.→ Raj. 243.Tolak sepenuhnya alat tambahpada penggerak.4.Putar alat tambah mengikut arahlawan jam sehingga ia berhenti.→ Raj. 25ms Operasi asas5.Tutup tuil kunci.→ Raj. 266.Putar sehingga ketat cincin skrumengikut arah jam.7.Pasang mangkuk pengisian.→ Raj. 278.Letakkan bekas yang sesuai dibawah alat tambah.→ Raj. 286 Operasi asas6.1 Cadangan kelajuanIkuti cadangan kelajuan untuk hasil terbaik.Nota: Bergantung pada peralatan, model anda dilengkapi dengan suis putar 4-tahap atau 7-tahap. Dalam arahan operasi ini, kelajuan yang disyorkan untuk suis putar 4 kedudukan diberikan dalam kurungan.TetapanPenggunaan7 (4)Pengisar7 (4)Alat tambah pemerah4-5 (2-3)Alat tambah biskut kek rapuh3-4(2-3)Alat tambah pengikir 6.2 Proses makanan1.Sediakan makanan.Potong makanan besar menjadi kepingan sehingga masuk kedalam tabung makanan.2.Pasangkan palam kuasa.3.Tetapkan suis putar ke kelajuanyang dicadangkan.→ Raj. 294.Letak makanan yang hendakdiproses dalam tiub suapan dantolak dengan perlahan ke bawahdengan penolak.→ Raj. 305.Tetapkan suis putar ke .→ Raj. 31Tunggu perkakas berhenti.6.Tanggalkan plag.Proses makanan dengan alat tambah pemerah1Nota: Apabila anda menggunakan alat tambah pemerah, perhatikan ciri khas yang berikut.1.Letakkan dua bekas di bawahsetiap bukaan.2.Sebelum proses dimulakan, putardan buka skru pelarasan mengikut arah lawan jam.→ Raj. 323.Semasa memproses dengan skrupelarasan, tetapkan hasil puri buah dan hampas buah yang diinginkan.6.3 Tanggalkan alat tambah1.Tanggalkan penghentak danmangkuk pengisian dan buka tuilkunci.→ Raj. 332.Putar alat tambah dan tanggalkandaripada unit asas.→ Raj. 34Petua: Bersihkan semua bahagian sebaik sahaja digunakan sehingga sisa tidak kering.Pembersihan dan penjagaan ms7 Pembersihan danpenjagaan7.1 Agen pembersihKetahui agen pembersih yang sesuai untuk aksesori anda.PERHATIAN!Agen pembersih yang tidak sesuai atau pembersihan yang tidak betul boleh merosakkan aksesori.▶Jangan gunakan agen pembersih yang mengandungi alkohol.▶Jangan gunakan objek tajam, berbucu atau logam.▶Jangan gunakan kain atau agen pembersih yang melelas.▶Bersihkan panel kawalan dan paparan hanya dengan kainmikrofiber yang lembap.7.2 Bersihkan setiapkomponen1.Nyahpasangkan alat tambah yangdigunakan.Teruskan langkah mengikutsusunan terbalik, seperti yangditerangkan untuk pemasangan.→ "Pasang alat tambah",Halaman 172.Bersihkan setiap komponendengan air sabun dan kain lembut atau span.3.Keringkan bahagian logam.Biarkan bahagian lain kering. Nota: Sapu bahagian logam yang telah dibersihkan dengan sedikit minyak masakan untuk melindungi bahagian tersebut daripada berkarat.7.3 Gambaran keseluruhanpembersihanBerikut adalah gambaran keseluruhan mengenai cara terbaik membersihkan komponen masing-masing.→ Raj. 35zh-tw 安全性1 安全性請注意以下的安全須知。
- 1、下载文档前请自行甄别文档内容的完整性,平台不提供额外的编辑、内容补充、找答案等附加服务。
- 2、"仅部分预览"的文档,不可在线预览部分如存在完整性等问题,可反馈申请退款(可完整预览的文档不适用该条件!)。
- 3、如文档侵犯您的权益,请联系客服反馈,我们会尽快为您处理(人工客服工作时间:9:00-18:30)。
We reserve all rights in this document and in the information contained therein. Reproduction, use or disclosure to third parties without express authority is strictly forbidden. ABB Switzerland LtdSYNCHROTACT® 5Operating instructionsSYN 5100Issued Esmaeil Habashi 00.05.03 Operating instructions No of pages5 39 Checked Werner Zimmerli 00.07.25 SYNCHROTACTReleased Werner Zimmerli 00.07.25Document No Art Part Language Revision Page abb ABB Switzerland Ltd 3BHS109760 E01 en B 1Document No Art PartLanguage RevisionpageContent1 GENERAL INFORMATIONS........................................................................................32 FUNCTIONAL PRINCIPLE...........................................................................................53 HARDWARE CONSTRUCTION...................................................................................94 PARAMETERS...........................................................................................................135 ENGINEERING INSTRUCTIONS...............................................................................176 INSTALLATION AND DISPOSAL..............................................................................197 OPERATING INSTRUCTIONS...................................................................................218 COMMISSIONING......................................................................................................23 9MAINTENANCE AND FAULTS (29)10 TECHNICAL DATA.....................................................................................................31 11 SCHEMATIC...............................................................................................................35 12 RECORD AND QUESTIONNAIRE.. (37)abbABB Switzerland Ltd3BHS109760 E01en B 2Document No Art Part Language Revision page1General informations1.1IntroductionThis User Manual is aimed at persons who have a basic knowledge of working with electronic equipment, who understand electrical symbols in schematic diagrams, but who know little or nothing about working with SYNCHROTACT 5 equipment.The User Manual provides the information required in order to install, commission and operate the SYNCHROTACT 5 device of type SYN 5100.1.2 Marking of text sectionsGeneral warningThis symbol placed before the text indicates situations or conditions which can cause a risk of death or serious injury. The text describes the procedure for preventing these risks.Dangerous voltagesThis symbol indicates that, when handling the equipment, dangerous voltages occur which can cause death or serious injury.The sections of text marked with "Caution" contain information on situations which canlead to material damage or equipment failure if the instructions are disregarded. The sections of text marked with "Note" provide additional information. This must be taken into consideration in order to prevent malfunctions.Caution Note1.3 Purpose and use of the SYN 5100The digital synchronizer can be used for the following applications:• As a paralleling monitoring device (synchrocheck) for monitoring automatic or manu-al paralleling sequences including dead bus.1.4 Manufacturer’s addressABB Switzerland LtdSynchronizing devices and voltage regulators CH-5300 Turgi/SwitzerlandPhone: +41 58 589 24 86 Fax: +41 58 589 23 33 Email: pes@Internet: /synchrotact24 h - hot line for urgent service inquiries: +41 844 845 845abbABB Switzerland Ltd3BHS109760 E01en B 3Document No Art Part Language Revision page abb ABB Switzerland Ltd 3BHS109760 E01en B 42 Functional principle2.1 Brief descriptionThe digital synchronizing device SYNCHROTACT 5 is used as Synchrocheck formonitoring of automatic or manual paralleling of generators with lines as well as for theparalleling of already synchronized lines. The device is designed for system frequenciesof either 50/60 Hz or 16 2/3 Hz.The setting values are entered via the keys provided on the front side of the device.2.2 Paralleling functionsThe paralleling process can basically be divided into four function blocks:1. Measuring2. Voltage and frequency matching3. Monitoring of paralleling conditions4. Paralleling command generationThe functions measuring and monitoring of the paralleling conditions are both integratedin the application of the Synchrocheck.S00030Document No Art Part Language Revision page abb ABB Switzerland Ltd 3BHS109760 E01en B 5Document No Art Part Language Revision page2.2.1 MeasuringThe following measured variables are generated from the two single-phase measuring voltages:Voltage U1, U2U1 is the reference voltage e.g. lineU2 sit the adjustable voltage e.g. generator. Frequency f1, f2f1 is the reference frequency f2 is the adjustable frequency. Voltage difference ΔU ΔU = IU1I – IU2IΔU > 0 Adjustable voltage is lower ΔU < 0 Adjustable voltage is higher Slip s%100*21fnf f s −=s > 0 Adjustable frequency is less (e.g. generator is sub-synchronous) s < 0Adjustable frequency is greater (e.g. generator is oversynchronous)Phase-angle difference α 21ϕϕα−= α > 0 Adjustable frequency is lagging α < 0 Adjustable frequency is leadingVoltage measurementThe two input voltages U1 and U2 are passed through high-impedance input resistors and differential amplifiers. The signal for the amplitude value is formed from this by conversion and filtering . For zero-passage detection, the signal is filtered and passed through a comparator. The signals prepared in this way are passed to the processor via the A/D converter.S00023abbABB Switzerland Ltd3BHS109760 E01en B 62.2.2 Monitoring of paralleling conditionsThe monitoring of the paralleling conditions can be divided into these parallel-functioningblocks:•voltage-carrying lines•no-voltage linesParalleling of two voltage-carrying linesThe monitoring of the paralleling conditions enables a paralleling command (CHKRELEASE) if the following conditions are fulfilled simultaneously:•the phase-angle difference is within the tolerance band•the slip is within the tolerance band•the voltage difference is within the tolerance bandParalleling of no-voltage lines (dead bus)A special case for the monitoring is the paralleling of no-voltage lines. A parallelingcommand release is only issued if the external release signal is active.The monitoring issues the paralleling command if the following conditions are fulfilledsimultaneously:•the releasing signal for dead bus (digital input) is issued•the zero voltage(s) does not exceed the set threshold U0max2.3 Sequences of the synchronization processThe software is initialised after switching on the auxiliary voltage and immediatelyafterwards the synchronizing process is started. The device begins issuing theparalleling command release as soon as, and as long as the paralleling conditions arefulfilled.The synchronizing process can be interrupted by disconnecting the auxiliary voltage.Since the device has only a monitoring function as a Synchrocheck, the synchronizingprocess can remain in operation.2.4 Self-monitoring of the synchronizerExtensive monitoring includes the following functions:2.4.1 Hardware monitoringAuxiliary voltage: The internally stabilised (reference) voltages are monitored. In theevent of inadmissible deviations, the device is immediately blocked.Paralleling command circuit: Contact monitoring is provided by means of forciblyguided contacts (normally closed = NC) on the command releasing relay. The deviceshould be controlled in such a way that the switching on the auxiliary voltage as well asthe command issuing circuit is only possible by closed NC contacts.Document No Art Part Language Revision page abb ABB Switzerland Ltd 3BHS109760 E01en B 72.4.2 Software monitoringThe program sequence is interrupted and reset by the internal watchdog, if an erroroccurs. After reset, it is again started automatically. This starting procedure is carried outthree times, afterwards the device is totally blocked.2.5 Stored dataThe parameter values are permanently stored in a non-volatile memory, and are notaffected by ageing or failure of the auxiliary voltage. The parameter settings can only bechanged by means of write commands.Document No Art Part Language Revision page abb ABB Switzerland Ltd 3BHS109760 E01en B 8Document No Art Part Language Revision page3Hardware construction3.1Type code for devices2: internal code Communication B: Ethernet & Modbus C: Ethernet & Profibus D: Ethernet & Lon-Bus 0: none 1: Ethernet 2: Modbus 3. Profibus 4: Lon-BusNumber of parameter sets1: 1 Parameter set 7: 7 Parameter setsAuxiliary voltage / System frequency 1: 24...48 VDC; 50/60 Hz2: 100...125 VAC/ VDC; 50/60 Hz 3: 220...250 VDC; 50/60 HzSynchronization mode 02: Dual channel device Construction size 1: Small size 2: Middle size 3: Large size SYNCHROTACT SYN = SYNCHROTACT 5: fifth generationOptionsTypeS0001000: Synchrocheck01: Single channel device 235: 100...125 VAC/VDC; 16 / Hz 236: 220...250 VDC; 16 / Hz 4: 24...48 VDC; 16 / Hz23abbABB Switzerland Ltd3BHS109760 E01en B 9Document No Art Part Language Revision page3.2 Front panelOn the front panel of the SYN 5100 there is a status display (LED’s). The built-in control unit consisting of six keys and the display is located on the front side of the device.Status displays (LED)Designation FunctionΔU < ΔUmax s < smax α < αmax U1/U2 = 0(colour: yellow)Indicate if ΔU, α and s are within the tolerance band or at least one measuring voltage is lacking.Control unitThe parameter settings can be viewed or modified by means of the control panel. The keypad consists of 6 keys with the following functions: abbABB Switzerland Ltd3BHS109760 E01en B10An LED-display is used to display parameter values.The electrical connections are fixed with screwable connectors and spring clamps on the top and bottom of the front side.3.3 Rear of unitAt the rear side there is the snap-profile for mounting a horizontal top-hat rail.Document No Art Part Language Revision page abb ABB Switzerland Ltd 3BHS109760 E01en B 11Document No Art Part Language Revision page abb ABB Switzerland Ltd 3BHS109760 E01en B 12Document No Art Part Language Revision page4Parameters4.1Parameter tableParametersNo. Parameter name SymbolRange/resolution Unit Default setting 1. Slip limit smax 0.1 to 2.0 % 0.5 2. Angle limit αmax 5 to 40/5 DEG 15 3. Maximumvoltage differenceΔUmax 5 to 40/5 % 5 4. Maximum zero voltage U0max 0 to 50/5 % 50 5. Nominal voltageUn50 to 130/5VAC1104.2 Parameter settingsNominal voltage UnThe nominal voltage is set in volts. The nominal voltage is plant-dependent. It is typically 58 (100/3); 64 (110/3); 100; 110 VAC, but can also have a different value. Slip limit smaxThe setting value is based on different criteria, depending on the application: a) normal synchronizationb) paralleling of synchronous lines c) paralleling of asynchronous linesa) Normal synchronizationThe slip limit values set in practice are far from placing a serious load on the machine, even in large machines. Usual setting values in synchrocheck operation for monitoring of a manual paralleling: 0.1 to 0.3 %. For monitoring of automatic paralleling: larger than the limiting value of the automatic device. Default setting: 0.5 %The following are a number of points which can influence the setting value: • Smaller slip limits should be chosen for large and modern generators. • Gas turbines are more sensitive than hydrogenerators.• Lower values should be selected if fine synchronization has priority and highervalues if fast synchronization is to take place.• Lower slip values are usually selected where settings are made for synchrocheckoperation to monitor manual synchronizing. b) Paralleling of synchronous linesIf only synchronous sources are paralleled, the slip limits do not need to be setabbABB Switzerland Ltd3BHS109760 E01en B 13Document No Art Part Language Revision pagec) Paralleling of asynchronous lines:If two lines do not form a ring connection, the slip limits are restricted by the current limit permitted after paralleling. If the flow of power in a particular direction is to be avoided, the corresponding slip limit must be set to zero .Angle limit αmaxThe permissible angle limit is based on different criteria, depending on the application: a) paralleling of asynchronous sources. b) paralleling of synchronous sources.a) Paralleling of asynchronous sources:If 3,6*fn *smax *t+3 > 10 DEG (t = closing time of the circuit breaker), the value should be rounded up to whole degrees. Setting values above 15 DEG are not usual. If the calculation produces such a result, it should be checked whether the maximum slip can be reduced. For monitoring of automatic paralleling: larger than the limiting value of the automatic device.b) Paralleling of synchronous sources:The coupling reactance x K in ring mains lines and the balancing current I K flowing through these cause a phase shift between the two voltages U1 and U2.Line 2 (L.V. line)S00014abbABB Switzerland Ltd3BHS109760 E01en B 14Document No Art Part Language Revision pageThe maximum phase shift αmax permitted for paralleling is calculated from the greatest phase shift which occurs plus a reserve. αmax is limited by the current i T = f(U1, U2, x T ) flowing after paralleling.Maximum voltage difference ΔUmaxMaximum permitted amplitude difference between the two voltages. Line 1 (H.V. line)Line 2 (L.V. line)S00015• usual values for generators: 1 to 5 %• usual values for synchronous lines 3 to 10 %For monitoring of automatic paralleling: larger than the limiting value of the automatic device.Recommended setting: default settingMaximum zero voltage U0maxMaximum voltage at which the SYNCHROTACT 5 still recognises the measuring voltages as zero voltage. A different value should only be set if necessary.abbABB Switzerland Ltd3BHS109760 E01en B 15Document No Art Part Language Revision page abb ABB Switzerland Ltd 3BHS109760 E01en B 16Document No Art Part Language Revision page5Engineering instructions5.1 General advice 5.1.1Cable connectionsCables or wires with cross sections of 0.4 mm 2 to 2.5 mm 2 can be connected to all the connection terminals. It is recommended that 1 mm 2 should be used for control circuits and power supply connections; at least 1,5 mm 2 should be used for measuring circuits. Connection of more than one cable to a terminal is not permitted.The casing must be connected with the earth potential via the connection provided for this purpose.In order to prevent polarity errors, marked cables should be used for all voltage transformers (measuring circuits).5.1.2 Recommended measures for long distancesFor distances >50 m, the following measures are recommended:• The cables for the actual value measurement should have a cross section ≥ 2.5 mm 2and should be twisted or shielded.• The control circuits should be operated with a nominal voltage of ≥125 VDC in orderto prevent inductive interference.• All cables must be laid separately from high-voltage and high-current cables.5.2 Sequences of the synchronizing processSwitching on the paralleling point: measuring voltage, auxiliary voltage and command circuit are all switched-on on the device.The normally closed contact of the paralleling command release relay is provided toavoid the switching on, if the command release issuing contact (normally open) is in a closed status as a result of pre-occurred error (see also the schematic diagram).Caution abbABB Switzerland Ltd3BHS109760 E01en B 17Document No Art Part Language Revision page abb ABB Switzerland Ltd 3BHS109760 E01en B 18Document No Art Part Language Revision page6 Installation and disposalSYNCHROTACT 5 devices operate with in some cases dangerous voltages (>50 V), e.g. measuring inputs up to 170 VAC and relay outputs up to 250 VAC/VDC. Manipulations carried out on these parts can cause death or injury to the persons involved or damage to surrounding objects. If handled correctly and in the proper environment, as described in these instructions, there is no risk.All relevant regulations must be observed during installation. It is essential that these safety regulations are read before starting any work on the SYNCHROTACT 5 equipment.The safe operation of the device requires appropriate transport and proper storage,erection and installation.The equipment should be unpacked with the usual degree of care, without the use of force and using suitable tools.The device should be checked visually for any damage caused during transport. Any complaints of defects caused by improper transport should be addressed immediately to the receiving station or the last carrier.Only interior rooms which are dry and dust-free and which contain no gases, acid fumes or similar are suitable as sites for installation.Caution 6.1 Diagram of dimensionsS00024abbABB Switzerland Ltd3BHS109760 E01en B 19Document No Art Part Language Revision page6.2 FixingSnap on the device on a top-hat rail. Check for the correct fitting.6.3 Earthing and wiringThe casing must be connected with the earth potential via the connection provided for this purpose.The use of shielded cables is not necessary. If shielded cables are nonetheless used for protection against high-frequency interference, it is recommended that the shielding be connected to the earth potential at both ends over as wide an area as possible. If it is not possible to earth the cables at both ends, one of the following procedures can be taken:• Earthing of the shielding via a capacitor. The shielding is earthed directly at one endand via a capacitor at the other end.• Use of a double shielded cable: one of the two shields is earthed at one end, theother at the other end.6.4 DisposalThe inappropriate disposal of electrical equipment can lead to an environmental hazard. It is therefore important that electrical equipment be disposed of by qualified personnel. The metallic casing, cover and front frame do not present any environmental risk and can be recycled.The circuit boards must be removed and should be disposed by a licensed disposal company. Environmentally harmful elements such as capacitors must be separated from the circuit boards.The SYNCHROTACT 5 devices are environmentally friendly designed. The circuit boards are easy to remove.abbABB Switzerland Ltd3BHS109760 E01en B 207 Operating instructions7.1 Operation for commissioning and maintenance purposes7.1.1 CommandsThe following commands can be carried out using the keypad.7.1.2 DisplayAfter switching on the auxiliary voltage, all the elements light up for short time. The pointat the bottom right blinks. As soon as, one of the pre-selction key is pressed, itscorresponding setting value is displayed. The display is cleared 1 minute after the lastkey press.7.2 Operational control7.2.1 Starting and stopping the synchronizing processThe software is initialised after switching on the auxiliary voltage and immediatelyafterwards the synchronizing process is started. The device begins issuing theparalleling command releases as soon as, and as long as the paralleling conditions arefulfilled.The synchronizing process can be interrupted by disconnecting the auxiliary voltage.Since the device has only a monitoring function as a Synchrocheck, the synchronizingprocess can remain in operation.7.2.2 Use of the built-in control panelThe service controls are not normally required with commissioned devices. However, ifone wishes to use these, in order to read out setting values, this can be done bypressing the keys as shown in the table in section 7.1.1. The commands don’t changethe functionality of the SYNCHROTACT 5, as long as, the save command is not issuedwithin 30 s after modification of the setting value.Document No Art Part Language Revision page abb ABB Switzerland Ltd 3BHS109760 E01en B 21Document No Art Part Language Revision page abb ABB Switzerland Ltd 3BHS109760 E01en B 22Document No Art Part Language Revision page8Commissioning8.1Warnings and instructionsSYNCHROTACT 5 devices operate with in some cases dangerous voltages (>50 V), e.g. voltage transformer inputs up to 170 VAC and relay outputs up to 250 VAC/VDC. Manipulations carried out on these parts can cause death or injury to the persons involved or damage to surrounding objects. If handled correctly and in the proper environment, as described in these instructions, there is no risk.All relevant regulations must be observed during commissioning. It is essential that these safety regulations are read before starting any work on the SYNCHROTACT 5 equipment.After the device has been switched off, it must be ensured, by measuring, that no measuring voltages or control voltages >50 V are present at the terminals before anything is done to the device itself, e.g. unplugging the connector to replace the device. In order to prevent open voltage circuits being accidentally closed by third parties, the circuits in question should be marked at the disconnection point (e.g. with a warning sign).If work is being carried out in the environment of the SYNCHROTACT 5, e.g. on the relay controls, electronics power supply, synchronizing instruments, all voltages greater than 50 V which are connected to the system must be switched off.Before switching on, always check whether all connectors are plugged in .The device may only be opened by qualified personnel. It is essential that ESDregulations are complied with.Caution Caution 8.2 Work carried out with the machine at a standstill 8.2.1Wiring checkThe casing must be connected with the earth potential via the connection provided for this purpose. All electrical connections must be checked against the system schematic (connection point and cross section).8.2.2 First power-upInterrupt paralleling circuit(s): Bring the machine circuit breaker or circuit breaker to Test position, draw out the carriage or pull command relay.Switch on auxiliary voltage. All the elements light up on the LED-display. The the point at the bottom right blinks.abbABB Switzerland Ltd3BHS109760 E01en B 23Document No Art Part Language Revision page8.2.3Pre-setting of parametersInstructions on the correct use of the service control panel can be found in section 7 Operating instructions. Advice on the parameter settings can be found in section 4.2 Parameter settings.NoteSome parameter settings can already be determined and set while the machine is at a standstill: Un, smax, αmax, ΔUmax, U0max.Each single parameter setting after its modification must be confirmed within 30 s. If thisrule is not complied with, the old value remains in the memory.Caution 8.2.4 Comparison of measuring points and switching pointsIf there are several paralleling points, it is essential to check whether the parallelingcommand and the measuring circuits (both) go to the same circuit breaker.8.2.5 Test of the phase sequence and tuning of the measuring voltagesabbABB Switzerland Ltd3BHS109760 E01en B 24The following tasks are the most important ones during the entire commissioning.They don't concern the synchronization device itself, but their right connections at the measuring voltages. In case of ignorance, damages may be caused to the plant! It is a prerequisite for the following work and for the correct functioning of thesynchronization that the nominal voltage Un is set.When disconnecting high voltage cables, it is essential that the corresponding regulations on working on high voltage installations are complied with.Bring the circuit breaker to operating position so that it can be operated manually.Caution CautionDocument No Art Part Language Revision pageClosing the CB:• Isolate one voltage source: open either isolator on generator side or star pointisolator or isolator on busbar side• The other voltage source must be connected The three LED’s ΔU < ΔUmax, s < smax, α < αmax must light up now, in particular thelast one. Otherwise, either the measuring cables are incorrectly connected (in terms of polarity) or there is a phase shift. Incorrect polarity cannot be detected by the synchronizer. Paralleling with incorrect polarity can lead to serious damage.The synchronizing instruments (double voltmeter, double frequency meter andsynchroscope) if present, must be checked. The synchronoscope must stand at “twelve o‘clock”!If this is not the case, the measuring circuits must be checked.If the synchronoscope stands at “six o‘clock”, one voltage has been incorrectly connected. In other positions, either measuring is being carried out on incorrect phases or a phase shift caused by the connection group of a step-up transformer has not been compensated.The circuit breaker should be opened again (or brought into test position) and the paralleling circuit interrupted.If it is not possible to test the phase sequence as described above, it is still essential toCaution CautionCaution NoteabbABB Switzerland Ltd3BHS109760 E01en B 25Caution test the measuring circuits. For example, the phase positions can be tested using high voltage measuring sensors.Document No Art Part Language Revision page8.3 Work carried out while the machine is running 8.3.1Function testsChecking the parallelingAt the end of commissioning, “blind“ synchronization should be carried out several times (circuit breaker in Test position). The differential voltage and the paralleling command should thereby be recorded using a transient recorder. At the same time, the synchronizing process should be observed using the synchronizing instruments in the plant.Bring circuit breaker to operating position, adjust voltage and frequency and carry out “live“ synchronization. Record the synchronizing process.Example of a correct paralleling dU = Voltage difference u1 – u2 S1 = Manual paralleling command S2 = Paralleling command releaseby SYN 5100abbABB Switzerland Ltd3BHS109760 E01en B 26Document No Art Part Language Revision pageAngle error(switches too early) Possible causes:• α-measuring incorrect (phaseerror) • Manual paralleling switchclosed to early or automatic synchronizing device wrongly setAngle error(switches too late) Possible causes:• α- measuring incorrect (phaseerror) • Manual paralleling switchclosed to late or automatic synchronizing device wrongly setSlip too big/angle error Possible causes: • smax set too highVoltage difference Possible causes:• ΔUmax set too high • Measuring errorabbABB Switzerland Ltd3BHS109760 E01en B 278.3.2 Keeping recordsIf parameter settings are carried out, these should be entered in the settings record atthe end of this operating manual.Document No Art Part Language Revision page abb ABB Switzerland Ltd 3BHS109760 E01en B 28。