22.Reliability_Module_V1.0
HV320WX2-262 Product Specification For Other Customer Rev O(1)

1.4 General Specification
< Table 1. General Specifications > Parameter Active area Number of pixels Pixel pitch Pixel arrangement Display colors Display mode Open Cell Transmittance(ACC Off) Weight Power Consumption Surface Treatment Specification 697.685(H) × 392.256(V) 1366(H) × 768(V) 170.25(H) × RGB× 510.75(V) Pixels RGB Vertical stripe 16.7M(8bits-true) Transmission mode, Normally Black colors Unit mm pixels ㎛ Remark
6.6 (typ.)
1180 (typ.) 4.0 (typ.) Haze 10%, 3H, Semi-glare or Antiglare treatment (Front Polarizer) Clear (Bottom Polarizer)
%
gram Watt
At center point with BOE BLU
Wu Xingji
SPEC. NUMBER S8-64-8A-034/O
SPEC. TITLE HV320WX2-262 Product Specification
PAGE 2 of 24 A4(210 X 297)
B2010-8002-O (2/3)
PRODUCT GROUP TFT LCD Contents
Battery Charger Technical Manual

BATTERY CHARGER TECHNICAL MANUALM O D E L:U Y900-H M6010-1V E R S I O N:V1.0Contents1.Revised History ...................................................................................................................................... 12.Warning ................................................................................................................................................... 13.Notes........................................................................................................................................................ 14.Product Number System....................................................................................................................... 25.Product Weight And Appearance ........................................................................................................ 26.Indicator LEDs........................................................................................................................................ 37.Electronic Characteristics ..................................................................................................................... 38.Protect Characteristics.......................................................................................................................... 48.1Output Over V oltage Protection ................................................................................................... 48.2Output Over Current Protection .................................................................................................. 48.3Short Circuit Protection ............................................................................................................... 48.4Reverse Polarity Protection ......................................................................................................... 48.5Over-Temperature protection ....................................................................................................... 49.Environmental......................................................................................................................................... 49.1Working Conditions ..................................................................................................................... 49.2Storage Conditions ...................................................................................................................... 410.Reliability............................................................................................................................................... 511.Safety .................................................................................................................................................... 511.1Insulation Characteristics ............................................................................................................ 511.2Leakage Current .......................................................................................................................... 511.3Standard specifies ........................................................................................................................ 511.4Electromagnetic Interference ....................................................................................................... 511.5Electromagnetic Immunity .......................................................................................................... 51. Revised HistoryTable 1. Revised HistoryVersion Detail DateV1.0 The initial version 03/25/2014Remark: This table will be updated for product upgrade. Users can download the latest version of the product technical manual at .2. WarningPlease use the charger in accordance with the parameters and connections in the manual, and do not disassemble it. Or we will not be liable for the resulting loss.3. Notes(1) High voltage inside the case, may cause harm to the human body. If the charger fails, please contact us. Users and non-professional maintenance staff is forbidden to open the charger.(2) Charger should not be used where in damp, water, direct sunlight or near heat sources.(3) Charger should be used where clean and well ventilated. Don’t sheltered inlet or outlet during charging, and make sure that both inlet and outlet have air space of at least 10cm.(4) Charger should be used to prevent children closer and touch.(5) Is prohibited that the charger used or stored near flammable, explosive goods.(6) While cleaning the charger please do not wash with water, we recommend using a clean rag dipped a small amount of alcohol.4. Product Number SystemUY900 H M 60 10 - 1VersionMax charge currentNominal voltage of battery packBattery Type. F: 3.65V/cell. M: 4.2V/cell. A: For lead acid battery.Input voltage range. W: 100~240Vac. H: 200~240Vac. L: 100~120Vac,UY900 series charger 5. Product Weight And AppearanceUY900 series charger is about 3kg without input AC wire. Charger appearance as figure 1 below.Size: 220mm×135mm×70mmFigure 1. Appearance6. Indicator LEDsGreen: Charge complete, standbyRed: Charging7. Electronic CharacteristicsTable 3. Electronic characteristicsNo. Item Unit Min. Typ. Max. Remark01 Input voltage Vac 200 220 26002 Input power W - - 86903 Constant chargevoltageVdc 71.1 71.4 71.704 Float voltage(forlead acid batteryonly)Vdc - - -05 Constant chargecurrentA 9.7 10 10.306 Charge completecurrentA 0.65 0.8 0.9507 Ripple voltage - - - Constant charge voltage*1%08 Efficiency % 85 - - Full load Charge Curve8. Protect Characteristics8.1 Output Over Voltage ProtectionWhen the charger output voltage exceeds the maximum charging voltage, the charger enters the standby state protection. Troubleshooting can be automatically restored to normal working condition.8.2 Output Over Current ProtectionWhen the charger output current exceeds the maximum charging current, the charger enters the over current protection status. Troubleshooting automatically restored to normal working condition.8.3 Short Circuit ProtectionWhen the charger has short circuit at output, the charger enters short-circuit protection status. Troubleshooting automatically return to normal working condition.8.4 Reverse Polarity ProtectionWhen the charger output positive negative pole and battery pack are connected in reverse, the internal relay of the charger is not sucked and there is no voltage current at the output terminal of the charger. After the correct connection, the charger can be charged normally.8.5 Over-Temperature protectionWhen charger internal temperature exceed 75℃, it will be Into the over-temperature protection state and the cuts off output .When the temperature returns to 65℃, the charge is restored again.9. Environmental9.1 Working ConditionsAmbient temperature: -5℃~+40℃;RH: 5% ~95%;Max. altitude: 2000 meter;Cooling: UY series chargers use of forced air cooling system. Under dustless and ventilated conditions, the full load temperature rise not exceeding 40℃.9.2 Storage ConditionsAmbient temperature: -40℃~+70℃;RH: 0% ~95%;Max. altitude: 20000 meter.10. ReliabilityTable 4. ReliabilityNo. Item Description Remark01 MTBF average operating life ≥ 30000h25℃02 Anti-vibration 5mm/50Hz/600s vibration test PASS 11. Safety11.1 Insulation CharacteristicsTable 5. Insulation characteristicsInsulation resistant Input to output DC500V 50MΩmin (25℃, Humidity≤70%) Input to case DC500V 50MΩmin (25℃, Humidity≤70%) Output to case DC500V 50MΩmin (25℃, Humidity≤70%)Hi-Pot Input to output 1500Vac 50Hz 1minute ≤10mA Input to case 1500Vac 50Hz 1minute ≤10mA Output to case 500Vac 50Hz 1minute ≤10mA11.2 Leakage CurrentWith max input and full load, the leakage current < 0.75m A, meet to Class II.11.3 Standard specifiesEN 55022:2006+A1:2007EN 61000-3-2:2006+A1:2009+A2::2009EN 61000-3-3:2008EN 55024:1998+A1:2001+A2:200311.4 Electromagnetic InterferenceConducted interference: EN55011.13.14-1.15.22.FCC part 15&18.VCCI;Radiated interference: EN55011.13.22.FCCpart 15&18.VCCI/EN55013.EN55014-1.11.5 Electromagnetic ImmunityAnti-static: IEC/EN61000-4-2 8KV;Pulse group: IEC/EN61000-4-4 2KV;Lightning surge: IEC/EN61000-4-5 1.5KV;Harmonic: IEC/EN61000-3-2 <25%.。
JUMO safetyM STB STW 安全温度限制器和安全温度监测器说明书

Page 1/14JUMO safetyM STB/STW Safety Temperature Limiter,Safety Temperature Monitor According to DIN EN 14597Brief descriptionThe safety temperature limiter JUMO safety M STB and the safety temperature monitor JUMO safety M STW are used to reliably detect and avert hazards that could cause injuries to people,that could be harmful to the environment, or that could cause destruction of production plants and produced goods at an early stage.Its primary task is to reliably monitor thermal processes and switch the systems to an opera-tional safe status in the event of malfunctions.The measured value at the analog input can be recorded by various probes or standard sig-nals. The exceedance of the limit value is indicated by the installed LEDs K1 and K2 (red) for each channel, and the safety relevant relay output alarm (terminal 14 and 16) switches the system to an operational safe status (alarm range).The high standards of DIN EN 61508 and DIN EN ISO 13849 are met by a device concept that has a 1oo2D structure (2-channel structure with diagnostic channel) which ensures reliable de-tection of errors. This device concept can also be used for applications that correspond to the new machinery directive 2006/42/EC.Block diagramData Sheet 701150Type 701150/ …Special featuresk 1oo2D structure for a high degree of pro-cess safety and reliability k LCD display with background lightingand plain text display for more comfortable operation k Setup program for configuration and archiving via USB interface k Digital input filter with adjustable filter time constantk Pre-alarm absolute, adjustable as a margin from the limit value or window function k Wide voltage supply rangefrom AC 110 to 240V +10%/-15% or AC/DC 20to 30V k Can be configured as STB or STW k 12 linearizations can be setk Internal and external unlocking possible k Approvals for DIN EN 14597, SIL, PL (Per-formance Level), Gl and UL k Two relay outputs can be used as pre-alarm or limit value alarmApprovals/approval marks (see "Technical Data")Data Sheet 701150Page2/14Technical dataAnalog inputsRTD temperature probe ThermocouplesDirect current Analog outputDesignationMeasuring range Accuracy2/3-wire circuit 1Ambient temperature error Pt100 DIN IEC 60751:2008-200to +850°C 0.5%/0.1%50ppm/K Pt1000 DIN IEC 60751:2008-200to +850°C 0.5%/0.1%50ppm/KConnection type Maximum lead wire resistance 2-wire circuit 15 Ω, 3-wire circuit 30 ΩSampling rate 210 msError tolerance time ≤ 5s: time taken into account for all diagnostic testsInput filter Digital filter, 2nd order; filter constant can be set from 0 to 100 s Special featuresSingle probe Pt100 2-wire,display can also be programmed in °FDesignationMeasuring range Accuracy 1Ambient temperature influence Fe-CuNi “L” DIN 43710: 1985-12-200to +900°C 0.4%100ppm/K Fe-CuNi “J” DIN EN 60584-1:1996-10-200to +1200°C 0.4%100ppm/K Cu-CuNi “U” DIN 43710:1985-12-200to +600°C 0.4%100ppm/K Cu-CuNi “T” DIN EN 60584-1:1996-10-200to +400°C 0.4%100ppm/K NiCr-Ni “K” DIN EN 60584-1:1996-10-200to +1372°C 0.4%100ppm/K Pt10Rh-Pt “S” DIN EN 60584-1:1996-10-50to +1768°C 0.4%100ppm/K Pt13Rh-Pt "R" DIN EN 60584-1:1996-10-50to +1768°C 0.4%100ppm/K Pt30Rh-Pt6Rh “B” DIN EN 60584-1:1996-100to 1820°C 0.4%2100ppm/K NiCrSi-NiSi …N“ DIN EN 60584-1:1996-10-100to +1300°C 0.4%2100ppm/K W3Re-W25Re “D”ASTM E1751M-09 (bis 2315 °C): 20090to 2495°C0.4%100ppm/K W5Re-W26Re …C“ ASTM E230M-11: 20110to 2315 °C 0,4%100 ppm/KCold junctionPt100 internal Cold junction accuracy ±1K Sampling rate 210 msError tolerance time ≤5s: time taken into account for all diagnostic testsInput filterDigital filter, 2nd order; filter constant can be set from 0to 100s1. The accuracy refers to the maximum extent of the measuring range.2.The accuracy is garanteed above 300° C Measuring rangeAccuracy Ambient temperature influence 4to 20mA, voltage drop < 2 V 0.2%150 ppm/KScaling Can be freely programmed within the limits Sampling rate 210 msError tolerance time ≤ 5s: time taken into account for all diagnostic testsInput filter Digital filter, 2nd order; filter constant can be set from 0to 100s Special featuresSingle probe 4 to 20mASignal typeAccuracy Residual ripple Load influence Temperature influence Load resistance Current 4 to 20 mA ≤ 0.5 %± 0.5 % at 300 Ω± 0.05 mA/100Ω150 ppm/K≤ 500 Ω0 to 20 mA Voltage2 to 10V ≤ 0.5 %± 0.5 %± 15 mV150 ppm/K÷ 500 Ω0 to 10VData Sheet 701150Page3/14Binary inputRelay outputsMeasuring circuit monitoringVoltage supplyTest voltages according to EN 60730, part 1Electrical safetyConnection Function1 floating contactUnlocking, key inhibit, level inhibit can be configuredRelay output KVRelay (changeover contact) without contact protection30000 switching operations at a switching capacity of 250 V , 3 A, 50 Hz (resistive load)or up to DC 30 V , 3 A. Minimum current DC 12 V, 100 mA.Relay output alarmRelay (changeover contact)Contact protection circuit: fuse cut-out 3.15 AT, installed in the N/O contact arm30000 switching actions at a switching capacity of 230 V , 3 A, 50 Hz (resistive load)or up to DC 30 V , 3 A. Minimum current DC 12 V, 100 mA.RTD temperature probe in 3-wire circuit and double thermocouplesThermocouples Current 4 to 20 mAOverrangeand underrange Is detectedLED K1, K2, KD, and KV are lit;">>>>“ flashes in the display for overrange, "<<<<“ for underrange.Probe/cable breakIs detectedLED K1, K2, KD, and KV are lit">>>>“ flashes in the display; relay output alarm is inactive LED K1, K2, KD, and KV are lit;">>>>“ flashes in the display; relay output alarm is inactive Probe short circuitIs detectedLED K1, K2, KD, and KV are lit "<<<<“ flashes in the display;relay output alarm is inactiveIs detected by difference monitor-ing of the analog inputs LED K1, K2, KD, and KV are lit;"<<<<“ flashes in the display;relay output alarm is inactiveVoltage supplyAC/DC 20 to 30V , 48 to 63Hz AC 110to 240V +10% /-15%, 48 to 63Hz Power consumption, Power lossmax. 12Wmax. 12W Power consumption, Power lossfor the following mode:Analog output 10mA; background lighting Display off; Re-lay output "Alarm" on;Relay output pre-alarm off; Sensor: 2xPt1005W 5WInput and output against voltage supply- At voltage supply AC 110to 240V +10% /-15% 3.7kV/50Hz - At voltage supply AC/DC 20to 30V , 48to 63Hz3.7kV/50HzClearances / creepage distancesMains voltage to electronic compo-nents and probes≥ 6 mm / ≥ 8 mm Mains voltage to the relay ≥ 6 mm / ≥ 8 mmRelay to electronic components and probes ≥ 6 mm / ≥ 8 mmElectrical safety According to DIN EN 14597 (DIN EN 60730-2-9)Overvoltage category III, pollution degree 2Protection rating IWith internal separation to SELV electrical circuitsData Sheet 701150Page4/14Environmental influencesCaseApprovals/approval marksAmbient temperature range 0to +55°C Storage temperature range -30to +70°CTemperature influence ≤ ± 0.005% / K dev. from 23×C 1 for RTD temperature probe ≤ ± 0.01% / K dev. from 23×C 1 for thermocouple, currentTerminal temperature RangeIf the temperature range of -10 °C to +80 °C is exceeded or undercut, the device shows the error message “Terminal temperature Range“.The output changes to a safe state (quiescent current principle).The message can only be acknowledged, if the temperature is back again in the valid range.Resistance to climatic conditions 85% rel. humidity without condensation(3K3 with extended temperature range according to DIN EN 60721-3-3)EMCAccording to DIN EN 14597 and standards from the standard series DIN EN 61326Interference emission Class BInterference immunityEvaluation criteria FS according to DIN EN 14597, regulation and control devices (RS)1.All specifications refer to the measuring range end valueMaterialPolycarbonate Flammability class UL 94 V0Electrical connection On the front via screw terminals up to 2.5 mm 2Installation On 35mm DIN rail acc. to EN 60715Installation position vertical Weight Approx. 230 g Protection typeIP 20 acc. to EN 60529Approval marks Testing agency Certificates/certification numbersInspection basis Valid forDIN DIN CERTCOSTB/STW1223DIN EN 14597All device versions:SIL2, SIL3TÜV Nord (German Techni-cal Inspection Agency)SEBS-A.102606/16-2 V1.0DIN EN 61508All device versions:PL e DIN EN ISO 13849-1All device versions:c UL us Underwriters Laboratories E325456-20120611UL 60730-2-9 submittedAll device versions:GLGermanischer Lloyd36 790-11HHAll device versions:Pressure Equipment Di-rective TÜV Süd (German Techni-cal Inspection Agency)07 202 1045 Z 0031/14/D0046Pressure Equipment Di-rective 97/23/EGAll device versions:Data Sheet 701150Page5/14Display and control elementsElectrical isolationLegend:Comment3LCD displayBlack/white with background lighting 96 x 64 pixels6LED KV (yellow)Is lit if the pre-alarm is triggered.7LED KD (yellow)Is lit if the diagnostic processor has performed a switch-off 8Keys(can only be operated when the transparent hood is folded upward)Increase value, Decrease valueProgramming RESET12Setup interface13LED K2 (red)aIs always simultaneously lid with K1 when errors occuron analog input 1 or 2 or in the event of limit value exceedance a.The exceedance of the limit value is indicated by the installed LEDs K1 and K2 (red) for each channel, andthe safety relevant relay output alarm (terminal 14 and 16) switches the system to an operational safe status (alarm range).14LED K1 (red)aIs always simultaneously lid with K2 when errors occuron analog input 1 or 2 or in the event of limit value exceedance 15LED OKGreen: Good range Off: Error occurred(1) Analog inputs(3) Binary input (5) Setup interface (6) Display (7) Analog output(8) Voltage supply(2) Relay output alarm(4) Relay output pre-alarmPage 6/14Data Sheet 701150Switching behavior of the relay output pre-alarmAbsolute value or Limit val. dist. directAbsolute value or Limit val. dist. inverseWindow direct (it is irrelevant if Min-Alarm or Max-Alarm is set)Window inverse (it is irrelevant if Min-Alarm or Max-Alarm is set)Data Sheet 701150Page7/14Switching behavior min. alarmData Sheet 701150Page8/14Connection diagramThe connection diagram in the data sheet provides preliminary information about the connection possibilities. For the electrical connection only use the installation instructions or the operating manual. The knowledge and the correct technical execution of the safety information/instruc-tions contained in these documents are mandatory for installation, electrical connection, and startup as well as for safety during operation.The connection occurs via screw terminals.Lead Admissible cross section 1 wire ≤ 2.5 mm 2Fine-strand,with ferrule≤ 1.5 mm 2Tightening torque of the screws:max. 0.5 NmData Sheet 701150Page9/14DimensionsType 701150/...Internal circuitrySPPage 10/14Data Sheet 701150Probes for the operating-medium airProbes for operating medium water and oilNote: Because of the high response accuracy, the use of thermowell s (pockets) is not admi ss ible .Actual type de s ignationOld type de s ignationProbe typeTemperature rangeNom. length mmP roce ss connectionRTD temperature probe Data S heet 90.2006902006/65-228-1003-1-15-500-668/000- 1 x Pt100-170 ... +700°C500902006/65-228-1003-1-15-710-668/000-710902006/65-228-1003-1-15-1000-668/000-1000902006/55-228-1003-1-15-500-254/000- 1 x Pt100-170 ... +700°C500902006/55-228-1003-1-15-710-254/000-710902006/55-228-1003-1-15-1000-254/000-1000902006/65-228-2003-1-15-500-668/00090.271-F01 2 x Pt100-170 ... +700°C500Stop flange,movable902006/65-228-2003-1-15-710-668/00090.272-F01710902006/65-228-2003-1-15-1000-668/00090.273-F011000902006/55-228-2003-1-15-500-254/000- 2 x Pt100-170 ... +700°C500movableG1/2 compression clamp 902006/55-228-2003-1-15-710-254/000-710902006/55-228-2003-1-15-1000-254/000-1000Thermocouple s Data S heet 90.1006901006/65-547-2043-15-500-668/00090.019-F01 2 x NiCr-Ni, Typ E …K“-35 ... +800°C500Stop flange,movable901006/65-547-2043-15-710-668/00090.020-F01710901006/65-547-2043-15-1000-668/00090.021-F011000901006/65-546-2042-15-500-668/00090.019-F11 2 x Fe-CuNi, Typ E …L“-35 ... +700°C500901006/65-546-2042-15-710-668/00090.020-F11710901006/65-546-2042-15-1000-668/00090.021-F111000901006/66-550-2043-6-500-668/00090.023-F01 2 x NiCr-Ni, Typ E …K“-35 ... +1000°C500901006/66-550-2043-6-355-668/00090.023-F023********/66-550-2043-6-250-668/00090.023-F03250901006/66-880-1044-6-250-668/00090.021 1 x PT10Rh-PT, Typ E …S“0 ... 1300°C250901006/66-880-1044-6-355-668/00090.022*********/66-880-1044-6-500-668/00090.023*********/66-880-2044-6-250-668/00090-D-021 2 x PT10Rh-PT, Typ E …S“0 ... 1300°C250Stop flange,movable 901006/66-880-2044-6-355-668/00090-D-022*********/66-880-2044-6-500-668/00090-D-023500901006/66-953-1046-6-250-668/00090.027 1 x PT30Rh-PT6Rh, Typ E …B“600 ... 1500°C 250901006/66-953-1046-6-355-668/00090.028*********/66-953-1046-6-500-668/00090.029500901006/66-953-2046-6-250-668/00090-D-027 2 x PT30Rh-PT6Rh, Typ E …B“600 ... 1500°C 250901006/66-953-2046-6-355-668/00090-D-028*********/66-953-2046-6-500-668/00090-D-029500Note: Because of the high response accuracy, the use of thermowell s (pockets) is not admi ss ible .Actual type de s ignationOld type de s ignationProbe typeTemperature rangeNom. length mmP roce ss connectionRTD temperature probe Data S heet 90.200690.2006/10-402-1003-1-9-100-104/000 1 x Pt100-40 ... +400°C100G1/2 screw connection90.2006/10-402-2003-1-9-100-104/000 2 x Pt100100902006/54-227-2003-1-15-710-254/00090.272-F02 2 x Pt100-170 ... 550°C 65...670movableG1/2 compression clamp 902006/54-227-1003-1-15-710-254/00090.272-F03 1 x Pt10065...670902006/10-226-1003-1-9-250-104/00090.239 1 x Pt100-170 ... 480°C 250G1/2 screw connection 902006/10-226-2003-1-9-250-104/00090-D-2392 x Pt100250Thermocouple s Data S heet 90.1006901006/54-544-2043-15-710-254/00090.020-F02 2 x NiCr-Ni, Type …K“-35 ... 550°C65...670movableG1/2 compression clamp901006/54-544-1043-15-710-254/00090.020-F03 1 x NiCr-Ni, Type …K“65...670901006/54-544-2042-15-710-254/00090.020-F12 2 x FeCuNi, Type …L“65...670901006/54-544-1042-15-710-254/00090.020-F131 x FeCuNi, Type …L“65 (670)Page 11/14Data Sheet 701150Probes for operating medium water and oilProbes for the operating medium air, water, and oilSafety control and regulating devicesSafety temperature monitor STW 1The safety temperature monitor is a device that is automatically reset when activated once the sensor temperature has fallen below or risen above the set limit value by an amount equal to the switching differential. Possible settings: monitoring for limit value overrange or underrange.Mode of operations:Minimum requirements: 2B, 2K, 2P Additional requirements: 2N, 2DSafety temperature limiter STB 1The safety temperature limiter is a device that is permanently locked after responding.Manual reset using the RESET key is possible once the probe temperature has fallen below / has exceeded the limit value by the amount of the switching differential. Possible settings: monitoring for overrange or underrange.Mode of operations:Minimum requirements: 2B, 2J, 2V , 2K, 2P and adjustable with special tools Additional requirements: 2N, 2F , 2D1. For more detailed explanation, see DIN EN 14 597.Note:The probes described in data sheets 901006 and 902006 are also certified for the Pressure Equipment DirectiveNote: Because of the high response accuracy, only u s e thermowell s (pockets) that are included in the s cope of delivery .Actual type de s ignationOld type de s ignationProbe typeTemperature rangeNom. length mmP roce ss connectionRTD temperature probe Data S heet 90.2006902006/53-505-2003-1-12-190-815/00090D239-F03 2 x Pt100-40 ... +400 °C 190902006/53-507-2003-1-12-100-815/00090.239-F02 2 x Pt100(arranged one below the other in protection tube)-40 ... +480 °C100902006/53-507-2003-1-12-160-815/00090.239-F12160902006/53-507-2003-1-12-190-815/000190902006/53-507-2003-1-12-220-815/00090.239-F22220902006/53-507-1003-1-12-100-815/00090.239-F01 1 x Pt100-40 ... +480 °C100weld-in sleeve902006/53-507-1003-1-12-160-815/00090.239-F11160902006/53-507-1003-1-12-220-815/00090.239-F21220902006/53-505-1003-1-12-190-815/00090.239-F03 1 x Pt100-40 ... +400 °C 190902006/53-505-3003-1-12-100-815/00090.239-F07 3 x Pt100-40 ... +400 °C100902006/53-505-3003-1-12-160-815/00090.239-F17160902006/53-505-3003-1-12-220-815/00090.239-F27220902006/40-226-1003-1-12-220-815/00090.280-F30 1 x Pt100-170 ... +480°C220weld-in sleeve 902006/40-226-1003-1-12-160-815/00090.280-F31160902006/40-226-1003-1-12-100-815/00090.280-F32100Thermocouple s Data S heet 90.1006901006/53-543-1042-12-220-815/00090.111-F01 1 x Fe-CuNi Type …L“-35 ... 480°C220weld-in sleeve901006/53-543-2042-12-220-815/00090.111-F022 x Fe-CuNi Type …L“220Note: Because of the high response accuracy, the use of thermowell s (pockets) is not admi ss ible .Actual type de s ignationOld type de s ignationProbe typeTemperature rangeIn s tall. length mmP roce ss connectionRTD temperature probe Data S heet 90.200690.2006/10-390-1003-1-8-250-104/00090.210-F951 x Pt100max. 300°C250Thermocouple s Data S heet 90.1006901006/45-551-2043-2-xxxx-11-xxxx2 x NiCr-Ni, Typ E …K“max. 1 50°C50 (2000)Page 12/14Data Sheet 701150Connection possibilities of the sensors (SIL)The JUMO safety M STB/STW 701150 evaluation device structure is basically identical. Various possibilities to connect the sensors are available. These possibilities are listed in the following table along with the achievable SIL level:Note:Variants 1 to 4 were evaluated with JUMO probes according to data sheets 901006 and 902006. For variant 5 no sensor system was taken into account. In this case, the user selects the sensor system. For this reason, the user is responsible for evaluating the achievable SIL.If the used SIL-capable sensor consists of hardware and software (e.g. transmitter), the maximum SIL that can be achieved —irrespective of the architecture—is the one according to which the sensor software was developed (so, for example, if the sensor software has SIL 2, the max. achievable SIL is 2).The possibility to connect passive sensors such as double thermocouples, Pt100, or Pt1000 sensors means that the sensors do not necessarily require a SIL qualification. In this case, the specification of the failure rates for the passive sensors is sufficient for the SIL qualification of the overall system. The user of the system must always determine the PFD avg and/or PFH value of the overall safety circuit to evaluate the achieved SIL.Failure rates and SFF for 70.1150...23 (AC 240 V)Failure rates and SFF for 70.1150...25 (AC/DC 24 V)Note:Variants 1 to 4 were evaluated with JUMO probes according to data sheets 901006 and 902006.For variant 5 no sensor system was taken into account. In this case, the user selects the sensor system.The PFH and PFD avg values were calculated assuming that the time to restore the system is 8 h (MTTR = 72 h). Furthermore, the calculation was based on a lifetime of 10 years (T 1 = 10 y). The Common Cause Factor was determined according to the tables of DIN EN 61508 for sensor systems and logic.Variant Connected sensorsArchitectureAchievable SILSensor systemLogics 1 1 × Pt100 in 2-wire circuit individual sensor1oo11oo2D 21a 2x Pt100/1000 2-wire circuit 1oo21oo2D 322x Pt100/1000 3-wire circuit 1oo21oo2D 332x thermocouple 1oo21oo2D 341x Pt100/10002-wire and 3-wire circuit 1x thermocouple1oo21oo2D35STB/STW 70.1150 without sensor system 1oo2D archi-tectureno probe or use 4 to 20 mA (means that the sensor is not taken into account for the cal-culation).Sensors connected by the system user Architecture acc. to connection 1oo1 or 1oo21oo2D SIL of the used sen-sor (HW only)The systematic ca-pability (SC) of the used sensor Max. achievable SIL of the system with1oo1 sensor sys-tem architecture Max. achievable SILof the system with 1oo2 sensor system architecture 11111212222223233333Variant λs[Fit]λdd[Fit]λdd[Fit]SFF PFH (1/h)PFD avg 1865.21306.2432.3196% 4.56 e -9 2.02 e -41a 865.21306.2432.3196% 1.05 e -9 4.57 e -52868.17303.2832.3196% 1.05 e -9 4.57 e -53881.62326.7833.6296% 1.03 e -9 4.49 e -54887.68343.8235.5296% 1.22 e -9 5.30 e -55881.02313.4335.5796%1.04 e -94.48 e -5Variant λs[Fit]λdd[Fit]λdd[Fit]SFF PFH (1/h)PFD avg 1799.3306.3233.6196% 6.59 e -9 2.91 e -41a 799.3306.3233.6196% 3.07 e -9 1.35 e -42802.26303.3633.6196% 3.07 e -9 1.35 e -43827.25324.7137.9196% 3.13 e -9 1.37 e -44833.31341.7539.8196% 3.23 e -9 1.41 e -45818.96323.0736.2696%3.05 e -91.33 e -4Page 13/14Data Sheet 701150Calculations DIN EN ISO 13849-1 Performance Level - low voltage 230 VCalculations DIN EN ISO 13849-1 Performance Level - extra low voltage (ELV) 24 V3.The MTTF d value of a partial system must be limited to 100 years according to the DIN EN ISO 13849-1 requirements.Variant MTTF dDC avg CCF PL 1100 years 3 (337 years)90%80PLd 1a 100 years3 (337 years)90%80PLe 2100 years 3 (340 years)90%80PLe 3100 years 3 (317 years)91%80PLe 4100 years 3 (313 years)91%80PLe5100 years3 (327 years)91%80See "Connection possibilities of the sensors" tableVariant MTTF dDC avg CCF PL 1100 years 3 (336 years)90%80PLd 1a 100 years3 (336 years)90%80PLe 2100 years 3 (339 years)90%80PLe 3100 years 3 (315 years)90%80PLe 4100 years 3 (311 years)90%80PLe5100 years3 (318 years)90%80See "Connection possibilities of the sensors" tableScope of delivery1 JUMO safety M STB/STW in ordered version 1 operating manualPage 14/14Data Sheet 701150Order details Array AccessoriesArticle Part no.Setup program, multilingual00548742USB cable00506252External unlocking button RT97097865。
第四章 防火墙访问控制列表v1

第四章防火墙访问控制列表v1.0 幻灯片 1包过滤指在网络层对每一个数据包进行检查,根据配置的安全策略来转发或拒绝数据包。
包过滤防火墙的基本原理是:通过配置ACL(Access Control List,访问控制列表)实施数据包的过滤。
实施过滤主要是基于数据包中的源/目的IP 地址、源/目的端口号、IP 标识和报文传递的方向等信息。
访问控制列表定义的数据流在防火墙上的处理规则,防火墙根据规则对数据流进行处理。
因此,访问控制列表的核心作用是:根据定义的规则对经过防火墙的流量进行筛选,由关键字确定筛选出的流量如何进行下一步操作。
在防火墙应用中,访问控制列表是对经过防火墙的数据流进行网络安全访问的基本手段,决定了后续的应用数据流是否被处理。
访问控制列表根据通过报文的源地址、目的地址、端口号、上层协议等信息组合定义网络中的数据流。
ACL 能够通过报文的源地址、目的地址、端口号、上层协议等信息组合定义网络中的数据流,是包过滤、NAT、IPSec、QoS、策略路由等应用的基础。
访问控制列表的使用:1、访问控制列表可以用于防火墙2、访问控制列表可以用于Qos(Quality of Service),对数据流量进行控制3、在DCC中,访问控制列表还可用来规定触发拨号的条件4、访问控制列表还可以用于地址转换5、在配置路由策略时,可以利用访问控制列表来作路由信息的过滤包过滤包过滤作为一种网络安全保护机制,用于控制在两个不同安全级别的网络之间流入和流出网络的数据。
在防火墙转发数据包时,先检查包头信息(例如包的源地址/目的地址、源端口/目的端口和上层协议等),然后与设定的规则进行比较,根据比较的结果决定对该数据包进行转发还是丢弃处理。
地址转换NAT(Network Address Translation)是将数据报报头中的IP地址转换为另一个IP地址的过程,主要用于实现内部网络(私有IP地址)访问外部网络(公有IP地址)的功能。
M150XN07_07中文资料
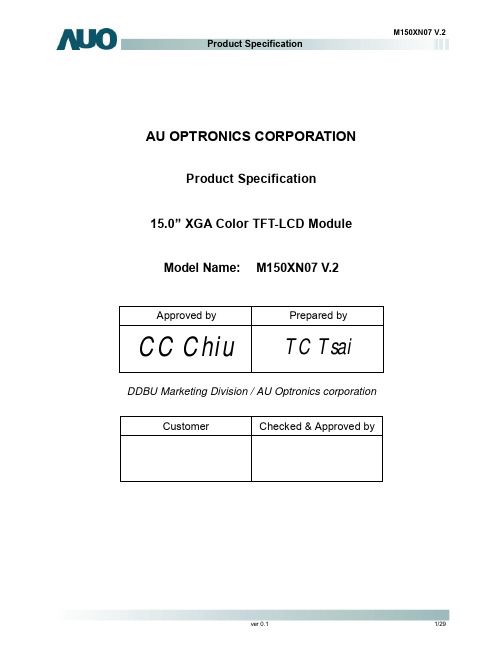
M150XN07 V.2Product SpecificationAU OPTRONICS CORPORATIONProduct Specification15.0” XGA Color TFT-LCD ModuleModel Name: M150XN07 V.2Approved by Prepared byCC Chiu TC TsaiDDBU Marketing Division / AU Optronics corporationCustomer Checked & Approved byProduct Specification15.0” XGA Color TFT-LCD ModuleModel Name: M150XN07V.2 (u) Preliminary Specifications( ) Final Specifications Note: This Specification is subject to change without notice.Contents1.0 Handling Precautions (5)2.0 General Description (6)2.1 Display Characteristics (6)2.2 Optical Characteristics (7)3.0 Functional Block Diagram (12)4.0 Absolute Maximum Ratings (13)4.1 TFT LCD Module (13)4.2 Backlight Unit (13)4.3 Absolute Ratings of Environment (13)5.0 Electrical characteristics (14)5.1 TFT LCD Module (14)5.1.1 Power Specification (14)5.1.2 Signal Electrical Characteristics (15)5.2 Backlight Unit (16)6.0 Signal Characteristic (17)6.1 Pixel Format Image (17)6.2 The input data format (18)6.3 Signal Description (19)6.4 Interface Timing (20)6.4.1 Timing Characteristics (20)6.4.2 Timing diagram (21)6.5 Power ON/OFF Sequence (22)7.0 Connector & Pin Assignment (23)7.1 TFT LCD Module (23)7.2 Backlight Unit (24)7.3 Signal for Lamp connector (24)8.0 Reliability (25)9.0 Safety (26)9.1 Sharp Edge Requirements (26)9.2 Materials (26)9.2.1 Toxicity (26)9.2.2 Flammability (26)9.3 Capacitors (26)10.0 Other requirement (26)10.1 National Test Lab Requirement (26)10.2 Label (26)11.0 Mechanical Characteristics (27)Record of RevisionVersion and Date Page Old description New Description Remark 0.1 2005/02/14 All First Edition for Customer1.0 Handling Precautions1) Since front polarizer is easily damaged, pay attention not to scratch it.2) Be sure to turn off power supply when inserting or disconnecting from input connector.3) Wipe off water drop immediately. Long contact with water may cause discoloration or spots.4) When the panel surface is soiled, wipe it with absorbent cotton or other soft cloth.5) Since the panel is made of glass, it may break or crack if dropped or bumped on hard surface.6) Since CMOS LSI is used in this module, take care of static electricity and insure human earth whenhandling.7) Do not open nor modify the Module Assembly.8) Do not press or pat the panel surface by fingers,hand or tooling.9) Do not press the reflector sheet at the back of the module to any directions.10) In case if a module has to be put back into the packing container slot after once it was taken out from thecontainer, do not press the center of the CCFL reflector edge. Instead, press at the far ends of the CCFL reflector edge softly. Otherwise the TFT module may be damaged.11) At the insertion or removal of the Signal Interface Connector, be sure not to rotate nor tilt the InterfaceConnector of the TFT module.12) After installation of the TFT module into an enclosure (Desktop monitor Bezel, for example), do not twistnor bend the TFT Module even momentary. At designing the enclosure, it should be taken into consideration that no bending/twisting forces are applied to the TFT module from outside. Otherwise the TFT module may be damaged.2.0 General DescriptionThis specification applies to the 15.0 inch Color TFT/LCD Module M150XN07 V2.This module is designed for a display unit of personal computer.The display supports the XGA (1024 (H) x 768(V)) screen format and 16.2M colors (RGB 6-bits + FRC data). All input signals are 1 Channel LVDS interface compatible.This module does not contain an inverter card for backlight.2.1 Display CharacteristicsThe following items are characteristics summary on the table under 25 ℃condition:ITEMS Unit SPECIFICATIONSScreen Diagonal [mm] 381 (15”)Active Area [mm] 304.128 (H) x 228.096Pixels H x V 1024(x3) x 768Pixel Pitch [mm] 0.297 (per one triad) x 0.297Pixel Arrangement R.G.B. Vertical StripeDisplay Mode TN mode, Normally WhiteWhite Luminance [cd/m2] 250 (Typ) @ 8mAContrast Ratio 500 : 1 (Typ)Optical Rise Time/Fall Time [msec] 12 (Typ) (Note 1) Color Saturation 65% NTSCNominal Input Voltage VDD [Volt] +3.3 VPower Consumption(VDD line + CCFL line)[Watt] 13.3 W (Typ.) @8mA (All Black Pattern)Weight [Grams] 1100 (Typ)Min. Typ. Max.Horizatal(H) 326.0 326.5 327.0Vertical(V) 253.0 253.5 254.0Physical Size [mm]Depth(D) - - 12.0Electrical Interface 1 Channel LVDSSupport Color 16.2M colors (RGB 6-bit + FRC data)Temperature RangeOperating Storage (Shipping) [o C][o C]0 to +50-20 to +60Surface Treatment Hard-coating (3H), anti-glare treatment Note 1 :System should warm up for at least one hourmeasuring distance2.2 Optical CharacteristicsThe optical characteristics are measured under stable conditions at 25℃ (Room Temperature):Item Unit Conditions Min. Typ. Max.Note Horizontal (Right) CR = 10 (Left) TBD6565- Vertical (Up) CR = 10 (Down) TBD65 55keep total 120(Mayb e 60,60)Horizontal (Right) CR = 5 (Left) TBD TBD Viewing Angle [degree]Vertical (Up) CR = 5 (Down)TBD TBD Contrast ratioNormal Direction TBD 500 -Rising Time - TBD TBD Falling Time - TBD TBD Response Time[msec]Rising + Falling - 12 Note 1Red x 0.61 0.64 0.67 Red y0.30 0.33 0.36 Green x 0.27 0.30 0.33 Green y 0.56 0.59 0.62 Blue x 0.12 0.15 0.18 Color / Chromaticity Coordinates (CIE)Blue y0.07 0.10 0.13 White x 0.28 0.31 0.34 Color Coordinates(CIE)WhiteWhite y 0.30 0.33 0.36 White Luminance @ CCFL 8mA (center)[cd/m 2] 200 250 - Luminance Uniformity [%] 75 80 Note 2 Crosstalk (in 75Hz) [%] 1.2 1.5 Note 3 FlickerdB-20Note 4 Equipment Pattern Generator, Power Supply, Digital Voltmeter, Luminance meter (PR 880, BM-5A ,BM 7 ,CS-1000, CA210, SR_3 & EZ Contrast(ELDIM)* )Aperture1∘with 50cm viewing distanceTest Point Center (VESA point 9) Environment < 1 lux*’ EZ Contrast is different measurement tool with very close viewing distance.Note 1: Definition of Response timeThe output signals of photo detector are measured when the input signals are changed from “Black” to “White”(rising time), and from “White” to “Black ”(falling time), respectively. The response time is interval between the 10% and 90% of amplitudes.Note 2: Brightness uniformity of these 9 points is defined as below50 %90 % 90 % 50 %10 %10 %Note 3: Crosstalk is defined as below :Unit: percentage of dimension of display areal L A -L A ’ l / L A x 100%= 1.5% max., L A and L Bl L B -L B ’ l / L B x 100%= 1.5% max., L A ’ and L B ’ are brightness at location A ’ and B ’Note 4: Test Paterm: Subchecker Pattern at 127 gray levelR G B R G BR G B R G B R G B R G B1/2 1/21/61/61/2 1/21/61/6 2/3 1/3 1/3 2/3Gray Level = L127Gray Level = L0Time3.0 Functional Block DiagramThe following diagram shows the functional block of the 15.0 inches wide Color TFT/LCD Module:CWY20G – A0G16 / MSB240420 JST-BHR-03VS-1Mating Type : HRS DF14-20S-1.25C SM02(8.0)B-BHS-1-TB4.0 Absolute Maximum RatingsAbsolute maximum ratings of the module is as following:4.1 TFT LCD ModuleItem Symbol Min Max Unit Conditions Logic/LCD Drive VDD 0.3 +3.6 [Volt] Note 1,24.2 Backlight UnitItem Symbol Min Max Unit Conditions CCFL Current IRCFL - 8.5 [mA] rms Note 1,24.3 Absolute Ratings of EnvironmentItem Symbol Min Max Unit Conditions Operating Temperature TOP 0 +50 [o C] Note 3 Operating Humidity HOP 8 90 [%RH] Note 3 Storage Temperature TST -20 +60 [o C] Note 3 Storage Humidity HST 8 90 [%RH] Note 3Note 1: With in Ta (25℃)Note 2: Permanent damage to the device may occur if exceed maximum valuesNote 3:For quality perfermance, please refer to AUO IIS(Incoming Inspection Standard). Please refer the graph below for the corresponding of temperature and humidity."5.0 Electrical characteristics5.1 TFT LCD Module 5.1.1 Power SpecificationInput power specifications are as follows;Symbol Parameter Min Typ Max Units ConditionVDD Logic/LCD Drive Voltage 3.0 3.3 3.6 [Volt] ±10%IDD VDD current - 600 700 [mA] Vin=3.3V , Gray Bar Pattern, at 60HzIrush LCD Inrush Current - - 3 [A] NotePDD VDD Power 2.0 2.3 [Watt] Vin=3.3V , Gray Bar Pattern, at 60HzVDDrpAllowableLogic/LCD Drive Ripple Voltage100[mV] p-pVin=3.3V , All Black Pattern, at 75HzNote: Measurement conditions:SWVin rising time0V3.3V5.1.2 Signal Electrical CharacteristicsInput signals shall be low or Hi-Z state when Vin is offIt is recommended to refer the specifications of SN75LVDS82DGG (Texas Instruments) in detail.Each signal characteristics are as follows;Symbol Parameter Min Typ Max Units ConditionVTH Differential Input High Threshold - - 100 [mV] VICM = 1.2V NoteVTL Differential Input Low Threshold -100 -- [mV] VICM = 1.2V Note │VID │ Input DifferentialVoltage100 400 600 [mV] Note VICMDifferential Input Common ModeVoltage1.1-1.45[V]VTH/VTL = ± 100mV NoteNote: LVDS Signal Waveform5.2 Backlight UnitParameter guideline for CCFL InverterSymbol Parameter Min.Typ.Max.Unit ConditionIRCFL CCFL operation range 2.5 8 8.5 [mA]rms(Ta=25o C)Note 4ICFL CCFL Inrush current - - 20 [mA]FCFL CCFL Frequency 40 55 80 [KHz] (Ta=25o C) Note 1ViCFL(0o C) (reference) CCFL Ignition Voltage1450 - -[Volt]rms(T a=0o C) Note 3ViCF (25o C) (reference) CCFL Ignition Voltage1100 - -[Volt]rms(Ta=25o C) Note 3VCFL CCFL Discharge Voltage-620(@8mA)710(@2.5mA)[Volt]rms(Ta=25o C) Note 2PCFL CCFL Power consumption@8mA(excluding inverter)- 10 11 [Watt] (Ta=25o C) Note 2Note 1: CCFL frequency should be carefully determined to avoid interference between inverter and TFT LCD.Note 2: Calculator value for reference (IRCFLxVCFLx2=PCFL).Note 3: CCFL inverter should be able to give output a voltage more than 1450 volt. Lamp units need 1450 volt minimum for ignition.Note 4: CCFL life time is 30,000hr at 8.0mA, it’s defined as when the brightness is reduced by half. It’s recommended not to exceed 8.0mA for CCFL life time concern and it’s prohibited to exceed 8.5mA for safety concern.6.0 Signal Characteristic6.1 Pixel Format ImageFollowing figure shows the relationship of the input signals and LCD pixel format.6.2 The input data formatDE VS HS OG0OR5OR4OR3OR2OR1OR0OB0OG3OG4OG1OG2OB1OG5OB5OB3OB4OB2OR7OB7OR6OB6OG7OG6CLKIN+RIN0 +/-CLKIN-Rsvd Current CycleRIN1 +/-RIN2 +/-RIN3 +/-Note1: Please follow PSWG. Note2: 8-bit inNote3: R/G/B data 7:MSB, R/G/B data 0:LSB6.3 Signal DescriptionThe module using a pair of LVDS receiver SN75LVDS82(Texas Instruments) or compatible. LVDS is a differential signal technology for LCD interface and high speed data transfer device. Transmitter shall be SN75LVDS83(negative edge sampling) or compatible. The first LVDS port(RxOxxx) transmits odd pixels while the second LVDSport(RxExxx) transmits even pixels.CWY20G-A0D1T (PTWO) or MSB240420 (STM)Pin No. Symbol Description1 VDD Power Supply, 3.3V (typical)2 VDD Power Supply, 3.3V (typical)3 VSS Ground4 VSS Ground5 Rin0-- LVDS differential data input (R0-R5, G0)6 Rin0++ LVDS differential data input (R0-R5, G0)7 VSS Ground8 Rin1-- LVDS differential data input (G1-G5, B0-B1)9 Rin1++ LVDS differential data input (G1-G5, B0-B1)10 VSS Ground11 Rin2-- LVDS differential data input (B2-B5, HS, VS, DE)12 Rin2++ LVDS differential data input (B2-B5, HS, VS, DE)13 VSS Ground14 ClkIN-- LVDS differential clock input15 ClkIN++ LVDS differential clock input16 VSS Ground17 Rin3-- LVDS differential data input (R6-R7, G6-G7,B6-B7)18 Rin3+- LVDS differential data input (R6-R7, G6-G7,B6-B7)19 VSS Ground20 VSS GroundNote: Please follow PSWG.6.4 Interface Timing6.4.1 Timing CharacteristicsBasically, interface timings described here is not actual input timing of LCD module but output timing of SN75LVDS82DGG (Texas Instruments) or equivalent.Signal Parameter Symbol MIN TYP MAX Unit Clock Timing Clock frequency clk 50 65 81 MHz Hsync TimingHorizontal active Thd 1024 1024 1024 TclkHorizontal blanking Thbl 40 320 400 TclkHorizontal period Th 1064 1344 1424 Tck Vsync TimingVertical active Tvd 768 768 768 ThVertical blanking Tvbl 8 38 75 ThVertical period Tv 776 806 843 ThNote:DE mode onlyNote: Typical value refer to VESA STANDARD6.4.2 Timing diagram6.5 Power ON/OFF SequenceVin power and lamp on/off sequence is as follows. Interface signals are also shown in the chart. Signals from any system shall be Hi-Z state or low level when Vin is off.On7.0 Connector & Pin AssignmentPhysical interface is described as for the connector on module.These connectors are capable of accommodating the following signals and will be following components.7.1 TFT LCD ModuleConnector Name / Designation Interface Connector / Interface card Manufacturer P-TWO or compatibleType Part Number CWY20G – A0G16 / MSB240420Mating Housing Part Number HRS DF14-20S-1.25CPin#Signal Name Pin#Signal Name1 VDD2 VDD3 VSS4 VSS5 Rin0-6 Rin0+7 VSS8 Rin1-9 Rin1+10 VSS11 Rin2-12 Rin2+13 VSS14 ClkIN-15 ClkIN+16 VSS17 Rin3-18 Rin3+19 VSS20 VSS7.2 Backlight UnitConnector Name / Designation For Lamp ConnectorManufacturer JST or compatibleType / Part Number BHR-03VS-1Mating Type / Part Number SM02(8.0)B-BHS-1-TB 7.3 Signal for Lamp connectorPin Symbol Description1 HV Lamp High Voltage2 NC No connection3 LV Groundu Cable length: 140 +- 5 mmu Connector-output position: right side (front view)u Lamp assembly design shall be easy for replacement and repair.8.0 ReliabilityReliability test conditionNo Test Item Test Condition1 Temperature Humidity Bias (THB) 50℃, 80%, 300hours2 High Temperature Operation (HTO) 50℃, 300hours3 Low Temperature Operation (LTO) 0℃, 300hours4 High Temperature Storage (HTS) 60℃, 300hours5 Low Temperature Storage (LTS) -20℃, 300hours6 Thermal Shock Test (TST) -20℃/30min, 60℃/30min, 100 cycles7 On/Off Test On/10sec, Off/10sec, 30,000 cycles8 Shock Test (Non-Operating) 50G, 20ms, Half-sine wave (+ X, +Y, +Z)9 Vibration Test (Non-Operating) 1.5G(10~200Hz P- P), 30 Minutes each Axis (X, Y, Z)10 ESD (ElectroStatic Discharge) Contact Discharge: ± 8KV, 150pF(330Ω ) 1sec, 8 points, 25 times/ pointAir Discharge: ± 15KV, 150pF(330Ω ) 1sec, 8 points, 25 times/ point11 Altitude Test Operation:10,000 ftNon-Operation:30,000 ft12 Drop Test The drop height is 60cm9.0 Safety9.1 Sharp Edge RequirementsThere will be no sharp edges or comers on the display assembly that could cause injury.9.2 Materials9.2.1 ToxicityThere will be no carcinogenic materials used anywhere in the display module. If toxic materialsare used, they will be reviewed and approved by the responsible AUO Toxicologist.9.2.2 FlammabilityAll components including electrical components that do not meet the flammability gradeUL94-V1 in the module will complete the flammability rating exception approval process.The printed circuit board will be made from material rated 94-V1 or better. The actual ULflammability rating will be printed on the printed circuit board.9.3 CapacitorsIf any polarized capacitors are used in the display assembly, provisions will be made to keepthem from being inserted backwards.10.0 Other requirement10.1 National Test Lab RequirementThe display module will satisfy all requirements for compliance toUL 1950, First Edition U.S.A. Information Technology EquipmentCSA C22.2 No.950-M89 Canada, Information Technology EquipmentEEC 950 International, Information Technology EquipmentEN 60 950 International, Information Processing Equipment(European Norm for IEC950)10.2 LabelThe label is on the panel as shown below:。
1XN 光开关 使用说明书

中文&English1XN光开关使用说明书(N≤16)四川莱特索斯光电科技有限公司NOTICE本手册所有提及之商标与名称皆属莱特索斯公司所有。
本手册解释权归属于莱特索斯公司。
目录安全须知 (3)一、产品简介 (4)二、光开关模块外形图 (5)三、管脚定义 (6)四、光开关模块切换图 (7)五、光开关模块联机示意图 (7)六、控制使用说明 (8)七、其他 (10)保修须知 (18)安全须知在使用光模块前,为了避免任何对光模块造成损害的可能性,请先阅读以下的细则:∙光模块光纤输入输出连接器端头应避免与硬物、赃物接触。
∙使用前请用脱脂棉球(蘸95%以上高纯度无水乙醇)清洁连接器的光纤端面,不工作时盖好防尘保护盖,防止灰尘或其它赃物污染或损坏光纤端面。
∙本器件属精密光器件,可靠性好,不得擅自拆卸,以免损坏。
光模块使用时注意事项:∙确保连线的正确,控制接口的详细的管脚定义、典型联机图参考表1、图4两部分。
在确定联机无误后,再加电操作。
∙当光模块有光输入时,请勿直视光纤端面。
因为激光辐射不可见,但会对人眼造成伤害。
∙本器件要防火、防冲击。
避免在过度潮湿的环境中储存、工作。
∙严禁拉扯、折和扭曲光纤,以防光纤损坏。
∙当需要修改外部电路时,请先关掉电源,再断开模块的控制线。
对控制线应禁止带电热插拔。
∙通信接口:TTL+RS232。
一、产品简介1×N微机械型光开关是一种具有切换光路作用的功能器件,可做单模,多模,保偏等多种类型。
其的主要用途:∙远程多路光监控系统∙组建光纤自愈网络∙光测试系统多路测试∙光纤子系统集成产品特性:∙低插入损耗∙多种并行接口控制∙模块化设计∙使用寿命长∙切换速度快∙极高可靠性产品性能:∙工作波长:850nm、1310nm、1550nm或根据用户需求订制∙插入损耗:≤1.0dB∙串扰:≤-70dB∙切换时间:≤2ms(任意通道切换)∙重复性:≤0.05dB∙工作温度:-10℃~65℃∙储藏温度:-20℃~85℃∙回波损耗:≥55dB(单模光纤)∙寿命:108次∙电源要求:5V DC电源,200mA电流。
赛米控丹佛斯 SEMITRANS 全碳化硅功率模块 SKM260MB170SCH17 数据表
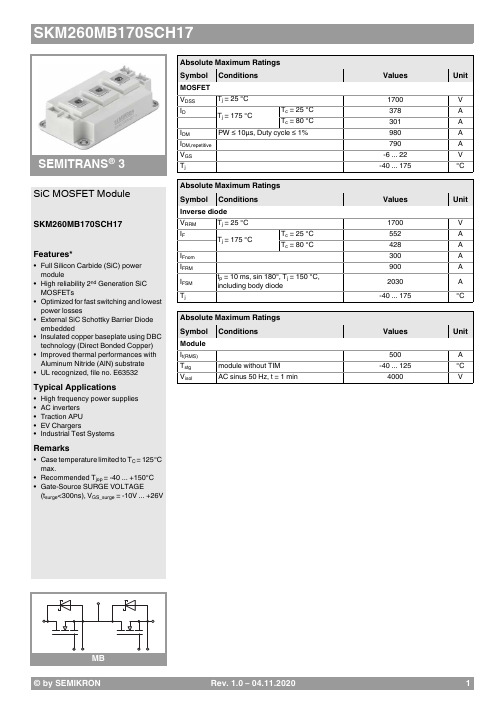
© by SEMIKRONRev. 1.0–04.11.20201SEMITRANS ®3SiC MOSFET ModuleSKM260MB170SCH17Features*•Full Silicon Carbide (SiC) power module•High reliability 2nd Generation SiC MOSFETs•Optimized for fast switching and lowest power losses•External SiC Schottky Barrier Diode embedded•Insulated copper baseplate using DBC technology (Direct Bonded Copper)•Improved thermal performances with Aluminum Nitride (AlN) substrate •UL recognized, file no. E63532Typical Applications•High frequency power supplies •AC inverters •Traction APU •EV Chargers•Industrial Test SystemsRemarks•Case temperature limited to T C = 125°C max.•Recommended T jop = -40 ... +150°C •Gate-Source SURGE VOLTAGE(t surge <300ns), V GS_surge = -10V ... +26VAbsolute Maximum Ratings SymbolConditions Values UnitMOSFET V DSS T j =25°C 1700VI D T j =175°CT c =25°C 378 A T c =80°C301 A I DMPW ≤ 10µs, Duty cycle ≤ 1%980A I DM,repetitive790A V GS -6...22V T j-40 (175)°CAbsolute Maximum Ratings SymbolConditionsValuesUnitInverse diodeV RRM T j =25°C 1700V I F T j =175°CT c =25°C 552A T c =80°C428A I Fnom 300A I FRM 900A I FSM t p =10ms, sin 180°, T j =150°C, including body diode2030A T j-40 (175)°CAbsolute Maximum Ratings SymbolConditions Values UnitModule I t(RMS)500A T stg module without TIM -40...125°C V isolAC sinus 50 Hz, t =1min4000V2Rev. 1.0–04.11.2020© by SEMIKRONSEMITRANS ®3SiC MOSFET ModuleSKM260MB170SCH17Features*•Full Silicon Carbide (SiC) power module•High reliability 2nd Generation SiC MOSFETs•Optimized for fast switching and lowest power losses•External SiC Schottky Barrier Diode embedded•Insulated copper baseplate using DBC technology (Direct Bonded Copper)•Improved thermal performances with Aluminum Nitride (AlN) substrate •UL recognized, file no. E63532Typical Applications•High frequency power supplies •AC inverters •Traction APU •EV Chargers•Industrial Test SystemsRemarks•Case temperature limited to T C = 125°C max.•Recommended T jop = -40 ... +150°C •Gate-Source SURGE VOLTAGE(t surge <300ns), V GS_surge = -10V ... +26VMOSFET V (BR)DSS V GS =0V,I D =1mA, T j =25°C 1700V V GS(th)V DS =V GS , I D =57.75mA1.62.84V I DSS V GS =0V,V DS =1700V, T j =25°C 1.8mA I GSS V GS =22V,V DS =0V 700nA R DS(on)V GS =18V I D =161AchiplevelT j =25°C 8.110m ΩT j =150°C 14m ΩC iss V GS =0V V DS =800Vf =1MHzT j =25°C 27nF C oss T j =25°C 0.88nF C rss T j =25°C0.105nF R Gint T j =25°C2.1ΩQ G V DD =1000V, V GS =-5 ... 20V, I D =300A 1470nC t d(on)V DD =900V I D =300A V GS =-5 / +20VR Gon =0.7ΩR Goff =0.7Ωdi/dt on =12kA/µs di/dt off =9.5kA/µsdv/dt off =22kV/µs T j =150°C 64ns t r T j =150°C 60ns t d(off)T j =150°C162ns t f T j =150°C 32ns E on T j =150°C 7.59mJ E off T j =150°C6.21mJ R th(j-c)per MOSFET0.065K/W R th(c-s)per MOSFET (λgrease =0.81 W/(m*K))0.03K/WCharacteristics SymbolConditionsmin.typ.max.UnitInverse diodeV F = V SD I F =300A chiplevel T j =25°C 1.65 1.95V T j =150°C 2.51 2.86V V F0chiplevel T j =25°C 1.00 1.10V T j =150°C 0.860.96V r F chiplevelT j =25°C2.2 2.8m ΩT j =150°C5.56.3m ΩC j parallel to C oss , f =1MHz, V R =1700V, T j =25°C1.026nF Q c V R =800V, di/dt off =500A/µs, T j =25°C 0.95µCR th(j-c)per diode0.056K/W R th(c-s)per diode (λgrease =0.81 W/(m*K))0.027K/W© by SEMIKRONRev. 1.0–04.11.20203SEMITRANS ®3SiC MOSFET ModuleSKM260MB170SCH17Features*•Full Silicon Carbide (SiC) power module•High reliability 2nd Generation SiC MOSFETs•Optimized for fast switching and lowest power losses•External SiC Schottky Barrier Diode embedded•Insulated copper baseplate using DBC technology (Direct Bonded Copper)•Improved thermal performances with Aluminum Nitride (AlN) substrate •UL recognized, file no. E63532Typical Applications•High frequency power supplies •AC inverters •Traction APU •EV Chargers•Industrial Test SystemsRemarks•Case temperature limited to T C = 125°C max.•Recommended T jop = -40 ... +150°C •Gate-Source SURGE VOLTAGE(t surge <300ns), V GS_surge = -10V ... +26VModule L DS 15nH R DD'+SS'measured per switchT C =25°C0.55m ΩT C =125°C0.85m ΩR th(c-s)1calculated without thermal coupling (λgrease =0.81 W/(m*K))0.008K/W R th(c-s)2including thermal coupling, T s underneath module (λgrease =0.81 W/(m*K))0.013K/W M s to heat sink M635Nm M tto terminals M62.55Nm Nmw325g4Rev. 1.0–04.11.2020© by SEMIKRON© by SEMIKRON Rev. 1.0–04.11.202056Rev. 1.0–04.11.2020© by SEMIKRON© by SEMIKRON Rev. 1.0–04.11.20207This is an electrostatic discharge sensitive device (ESDS) due to international standard IEC 61340.*IMPORTANT INFORMATION AND WARNINGSThe specifications of SEMIKRON products may not be considered as guarantee or assurance of product characteristics ("Beschaffenheitsgarantie"). The specifications of SEMIKRON products describe only the usual characteristics of products to be expected in typical applications, which may still vary depending on the specific application. Therefore, products must be tested for the respective application in advance. Application adjustments may be necessary. The user of SEMIKRON products is responsible for the safety of their applications embedding SEMIKRON products and must take adequate safety measures to prevent the applications from causing a physical injury, fire or other problem if any of SEMIKRON products become faulty. The user is responsible to make sure that the application design is compliant with all applicable laws, regulations, norms and standards. Except as otherwise explicitly approved by SEMIKRON in a written document signed by authorized representatives of SEMIKRON, SEMIKRON products may not be used in any applications where a failure of the product or any consequences of the use thereof can reasonably be expected to result in personal injury. No representation or warranty is given and no liability is assumed with respect to the accuracy, completeness and/or use of any information herein, including without limitation, warranties of non-infringement of intellectual property rights of any third party. SEMIKRON does not assume any liability arising out of the applications or use of any product; neither does it convey any license under its patent rights, copyrights, trade secrets or other intellectual property rights, nor the rights of others. SEMIKRON makes no representation or warranty of non-infringement or alleged non-infringement of intellectual property rights of any third party which may arise from applications. Due to technical requirements our products may contain dangerous substances. For information on the types in question please contact the nearest SEMIKRON sales office. This document supersedes and replaces all information previously supplied and may be superseded by updates. SEMIKRON reserves the right to make changes.8。
SIWAREX WP351 weighing module 商品说明说明书

2Weighing ElectronicsSIWAREX weighing electronics for SIMATIC Dosing/filling/bagging and checking scales■Overview The SIWAREX WP351 is a compact, precise weighing module in the SIMATIC ET 200SP format.With a width of just 20 mm it is one of the slimmest weighing modules on the market, yet its firmware includes the functional-ities of an automatic totalizing weighing instrument, check weigher, bagging and filling scale.All operating modes are part of the firmware and certified ac-cording to OIML R-51, R-61, R-76 and R-107. This means the WP351 can be used in both scales requiring official calibration and those that do not, where demands are high regarding speed and accuracy.■Benefits•Low space requirements with only 20mm module width •Seamless integration into SIMATIC ET 200SP •1000Hz sampling rate und processing time•Installation of legal-for-trade multi-interval/multi-range scales with up to 3×6000d•Operation with SIMATIC S7-300, S7-400, S7-1200 and S7-1500 controllers•Operation in Ethernet IP or Modbus TCP-based systems using ET 200SP multi-field bus IM•Three digital inputs and outputs each ex works•High degree of scalability in connection with all available SIMATIC standard components•Open SIWAREX concept – all settings and parameters acces-sible, no encapsulated black box in the field•Unrestricted access to all scale parameters and functions from the SIMATIC S7 Controller / HMI•Internal, legal-for-trade protocol memory for up to 1000000 entries•Commissioning and maintenance from HMI or module-internal web server•Legal-for-trade main display integrated in the SIMATIC HMI■ApplicationSIWAREX WP351 offers a compact and extremely versatile solu-tion for automatic and non-automatic scale applications with high requirements for accuracy and performance.Typical areas of application include:•Silo, hopper and platform scales, requiring official calibration/not requiring official calibration•Totalizing automatic weighing instruments, requiring official calibration/not requiring official calibration•Filling scales, requiring official calibration/not requiring official calibration•Static check weighers, requiring official calibration/not requiring official calibration•Automatic dynamic check weighers, not requiring official calibration•Recipe-controlled batch/mixing scales■DesignThe SIWAREX WP351 is a technology module of the SIMATIC ET 200SP distributed I/O system.Installation is on a type U0 BaseUnit. The load cells, serialRS 485 interface and digital inputs/outputs are wired directly on the BaseUnit with user-friendly push-in terminals. This makes is quick and easy to replace modules without any wiring effort. The web server is addressed via an Ethernet interface in the module. Should more interfaces and I/O be required, they can be added with the ET 200SP system components.■FunctionThe weighing module controls automatic proportioning, check-ing and loading processes completely autonomously. The intel-ligence required is contained in the module firmware, thus rep-resenting a standard. Dosing signals can be controlled directly via the three digital outputs – typically coarse flow/fine flow and emptying. Internal control algorithms and signal filters continu-ally optimize and adjust the weighing process.The controller only transfers the desired setpoint, as well as other material-specific parameters, to the module via the WP351 func-tion block. A start command initiates the dosing process, which is executed by the weighing module independently of the cycle time of the main controller with maximum accuracy. Finally the WP351 carries out a tolerance check and signals the result to the controller. In addition, the result is included in the statistics cal-culated in the background, which can be called up at any time from the controller. Depending on the operating mode, a log is generated in the internal protocol memory, either automatically or initiated by the user. If the scales are calibrated, the log con-forms to the requirements of the Weights and Measures Act.The open and standardized SIWAREX concept means that theplant operator can service the scales themselves if necessary.2Weighing ElectronicsSIWAREX weighing electronics for SIMATICDosing/filling/bagging and checking scales■Technical specifications*At a height of more than 2000 meters above sea level, a derating of theambient temperature of -1°C / 100 m has to be adhered to. The maximumpermissible height is 5000 meters above sea level. At over 0.6A totalcurrent of the digital outputs DQ, a derating of the ambient temperature of-1°C per 100mA has to be adhered to. The max. permissible total currentis 1.5A.SIWAREX WP351Firmware version V1.0•FW update possible YesUsable BaseUnits BU type U0ReliabilityMean time between failures (MTBF)62 years @ TA=40°CProduct functionI&M data Yes, I&M0 to I&M3Engineering with•STEP 7 TIA Portal can be configured/integratedConfigurable as of V15 usingHSP0281•PROFIBUS as of GSD version/GSDrevisionGSD V04.02.41•PROFINET as of GSD version/GSDrevisionGSDML V2.34Supply voltageLoad voltage L+•Rated value (DC)24V•Permissible range, low limit,static (DC)19.2V•Permissible range, high limit,static (DC)28.8V•Permissible range, low limit,dynamic (DC)18.5V•Permissible range, high limit,dynamic (DC)30.2V•Reverse polarity protection Yes•Non-periodic overvoltages35V DC for 500ms with a recoverytime of 50sInput currentCurrent consumption, max.Max. 140mA @ 24V DC +[DQ3×0.5A]Power lossTypical power loss 1.7WAddress rangeAssigned address range•Inputs32 bytes•Outputs32 bytesPower supply from SIMATIC S7backplane busCurrent consumption from ET 200SPbackplane busMax. 27mA @ 3.5V (SBK4)Analog load cell interfaceconnectionError limit according to DIN1319-1 at20°C (-4°F) +/-10KRelative accuracy(absolute accuracy can only beachieved with local calibration usingcalibration standards)≤0.002%v.E.Measuring accuracy in accordancewith OIML R76-1:2006/EN45501:2015•Class III•Resolution (d=e) 3 x 6000d•Error percentage pi0.4•Step voltage0.4µV/eAccuracy delivery stateThe accuracy is relevant for moduleexchange or theoretical adjustmentTyp. 0.1% v.E.Sampling rate 1.024msInput signal resolution±20000000Measuring ranges0...±1mV/V0...±2mV/V0...±4mV/VCommon mode voltage range+2.8…7.7VStrain gauge supply(constant voltage)10V DC (+1%/-3%) at the EXCterminalsShort-circuit and overload protection YesConnection6-wire or 4-wire (parameterizable)Sensor voltage monitoring Typ. ≤5.0VMin. strain gauge input resistance perchannel•Without SIWAREX IS Ex-i interface56ΩLower impedance by means of exter-nal supply possible•With SIWAREX IS Ex-i interface87Ω @ type 7MH4710-5BA180Ω @ type 7MH4710-5CAMax. DMS resistance4100ΩTemperature coefficient range≤±5ppm/KTemperature coefficient zero point≤±0.015μV/KLinearity error≤0.0025%Measured value filtering Low-pass and average value filterconfigurable (DR3)Galvanic isolation500V AC50Hz/ 60Hz noise suppressionCMRR>80dBInput resistance•Signal line Typ. 8*106Ω•Sense line Typ. 300*106ΩCable length•When using SIWAREX cable7MH4702-8AGMax. 500mAmbient conditionsAmbient temperature in operation•Horizontal mounting position *Min. -30°CMax. +60°C•Vertical mounting position *Min. -30°CMax. +50°CStorage and transport temperature-40...+70°C (-40...+158°F)SIWAREX WP3512Weighing ElectronicsSIWAREX weighing electronics for SIMATIC Dosing/filling/bagging and checking scales■Selection and ordering dataArticle No.Article No.TM SIWAREX WP351 weighing moduleSIMATIC ET 200SP ,TM SIWAREX WP351HF , legal-for-trade weighing module for automatic dosing and filling scales, check weighers and totalizing weighing instruments 7MH4138-6BA00-0CU0SIWAREX WP351 Equipment ManualAvailable in a range of languages Free download on the Internet at:/weighing/documentation SIWAREX WP351 "Getting Started" sample projectSample software shows beginners how to program the scales in TIA Por-tal V15.1Free download on the Internet at:/weighing/documentation SIWAREX WP351legal-for-trade verification set For verification of up to 3 scales consisting of3x labeling film for descriptive plate, 1x protection film,3x unlocking device,6x screw.Attention: For legal trade applications please follow the local laws applying in the country of verification.ET 200SP BaseUnit type U0•For constructing a new potential group (white)6ES7193-6BP00-0DU0•For continuing an existing potential group (gray)6ES7193-6BP00-0BU0Shield connection for ET 200SP Includes 5 shield connections 6ES7193-6SC00-1AM0SIWAREX JB junction box, aluminum housingFor connecting up to 4 load cells in parallel, and for connecting multiple junction boxes.7MH5001-0AA20SIWAREX JB junction box, stainless steel housingFor connecting up to 4 load cells in parallel.7MH5001-0AA00SIWAREX JB junction box, stainless steel housing (ATEX)For parallel connection of up to 4 load cells (for zone allocation, see manual or type-examination certificate).7MH5001-0AA01SIWAREX IS Ex interfaceFor intrinsically-safe connection of load cells. With ATEX approval (not UL/FM). Suitable for SIWAREX elec-tronic weighing systems. Compatibil-ity of load cells must be checked separately.•With short-circuit current <199mA DC7MH4710-5BA •With short-circuit current <137mA DC7MH4710-5CA Cable (optional)Cable Li2Y 1x 2x 0.75ST +2x (2x 0.34ST)–CYFor connecting SIWAREX electronic weighing systems to junction box (JB), extension box (EB) and Ex inter-face or between two EBs. For perma-nent installation. Occasional bending is possible.External diameter:approx. 10.8mm (0.43inch)Permissible ambient temperature -40...+80°C (-40...+176°F) Sold by the meter.•Sheath color: orange7MH4702-8AG •For hazardous atmospheres. Sheath color: blue.7MH4702-8AFCommissioningCommissioning charge for one static scale with SIWAREX module (Flat charge for travel and setup must be ordered separately)9LA1110-8SN50-0AA0Scope:•Recording of data•Checking of mechanical installation of the scale•Checking of electrical wiring and function•Static adjustment of the scale Requirements:•Mechanical design functional •Modules electrically wired and tested•Calibration weights available •Free access to scaleFlat charge for travel and setup in Germany9LA1110-8RA10-0AA0。
P120ZDG-BF3 Spec.V 1.0_20190604 Summary 公版(1)
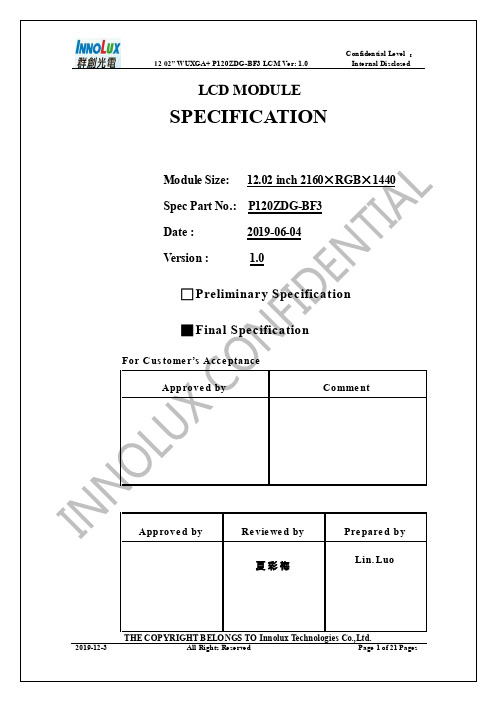
2019-12-3
THE COPYRIGHT B ELONGS TO Innolux Technologies Co.,Ltd.
All Rights Reserved
Page 3 of 21 Pages
12 02” WUXGA+ P120ZDG-BF3 LCM Ver: 1.0
1 General Specification
1.1 LCM Features
-- TFT-LCD Panel wi th IPS type -- 2160RGBx1440 Resolution --Interface eDP 1.3 --NTSC 69.2% --One backlight with 54 pcs LED -- Landscape LCD
0.0392(W)*0. 1176(H)
14 Pixel Pitch
0.1176(W)× 0.1176(H)
15 Pixe l Aspect Ratio
1:1
16 Driver IC
Pre pare d by Lin. Luo
2019-12-3
THE COPYRIGHT B ELONGS TO Innolux Technologies Co.,Ltd.
All Rights Reserved
Page 1 of 21 Pages
12 02” WUXGA+ P120ZDG-BF3 LCM Ver: 1.0
3 Pin Assignments...................................................................................................................................7 3.1 Display Interface ....................................................................................................................7
LC550EGE-FHM1_V1.0_151030 (1)

Ver 1.0
2 /35
LC550EGE
Product Specification
1. General Description
The LC550EGE is a Color Active Matrix Liquid Crystal Display with an integral Light Emitting Diode (LED) b ac k l i g ht s ys t em . T he m a t r i x em p l o ys a - S i T h i n F i lm T r an s is t or a s t he a c t i v e e l em en t . It is a transmissive display type which is operating in the normally black mode. It has a 54.64 inch diagonally measured active display area with QWUXGA resolution (2160 vertical by 3840 horizontal pixel array). Each pixel is divided into Red, Green, Blue and White sub-pixels or dots which are arrayed in vertical stripes. Gray scale or the luminance of the sub-pixel color is determined with a 10-bit gray scale signal for each dot. Therefore, it can present a palette of more than 1.07Bilion colors. It has been designed to apply the 10-bit 8 Lane V by One interface. It is intended to support LCD TV, PCTV where high brightness, super wide viewing angle, high color gamut, high color depth and fast response time are important.
HGT_20573-2012分散型控制系统工程设计规范

HGT.20573-2012分散型控制系统工程设计规范前言 (v)1 范围 (1)2规范性引用文件 (1)3术语定义和缩略语 (1)1.1术语定义 (1)1.2缩略 (4)4DCS总体要求4.1基本技术要求 (5)4.2应用要求 (6)4.3硬件配置要求 (7)5DCS工程设计原则与职责分工 (7)5.1设计原则 (7)5.2职责分工 (7)6控制站(过程控制站) (8)6.1控制站功能 (8)6.2控制站构成 (9)6. 3控制站技术要求 (9)7操作员站 (10)7.1操作员站功能 (10)7.2操作员站构成 (10)7.3操作站员技术要求 (11)8工程师操作站 (12)8.1工程师操作站功能 (12)8.2工程师操作站构成 (12)10.3软件组态文件 (14)10. 4 软件组态 (14)11DCS工程设计程序 (15)11.1基础工程设计.................................................................1511.2详细工程设计 (15)12DCS控制室设计 (16)13DCS供电、接地、防雷系统设计 (16)13.1供电系统设计 (16)13.2接地系统设计 (16)13.3防雷系统设计 (16)14DCS验收测试、安装、联调与投运 (16)14.1DCS验收测试 (16)14.2DCS 安装 (17)14.3DCS联调与投运 (17)附录A DCS技术规格书编制要求 (18)A. 1 概述 (18)A.2买卖双方职责及供货范围 (18)A. 3 DCS硬件配置及功能要求 (18)A.4 DCS技术要求 (19)A.5 DCS软件要求 (19)A.6控制室设计要求 (19)A.7供电、接地、防雷系统设计要求 (19)A. 8端子柜及安全栅/隔离器柜 (20)A.9备品备件及专用工具 (20)A. 10文件资料 (20)A. 11 工程管理 (20)A. 12 验收测试 (20)A. 13 培训 (21)A. 14初步的I/O清单...............................................................21本规范用词说明 (22)附:条文说明 (23)分散型控制系统工程设计规范1总则1.0.1本规范规定了 DCS的技术要求、DCS工程设计程序与任务,以及DCS技术规格书编制要求。
ORT可靠性试验规范与控制指导培训

在线可靠性试验规范(Ongoing Reliability Testing)拟制:___________________日期:__________ 审核:___________________日期:__________ _______________________________________________ 规范化审查:_________________日期:__________ 批准:___________________日期:__________更改信息登记表规范名称: 在线可靠性试验(Ongoing Reliability Testing)规范规范编码:目录1.目的 (4)2.适用范围 (4)3.引用/参考标准或资料 (4)4.定义 (4)5.规范内容 (4)5.1 在线可靠性试验程序 (4)5.2 失效分析 (7)附录一:在线可靠性试验周报表................................ 错误!未定义书签。
附录二:可靠性计算报表 ...................................... 错误!未定义书签。
1.目的本文规定了在生产中实施在线可靠性试验的基本程序和方法,以规范在线可靠性试验的开展。
本试验可以快速评估产品初期的可靠性,能及时发现在来料、加工等过程中引起产品批量缺陷的问题,促进及时地控制生产质量。
2.适用范围适用于公司S1、S2、S3、S4、S5、S6、S7等硬件产品,不适用于软件产品。
3.引用/参考标准或资料NPS50154-500 S tandard Range PCB Mountable DC-DC ConvertersMIL-HDBK-338B 《Electronic Reliability Design Handbook》,1998.104.定义3.1 【在线可靠性试验】Ongoing Reliability Testing (ORT),也叫做Early Life Testing (ELT),是在生产过程中控制生产质量的一种可靠性试验手段。
锐捷RG-RAP1201 接入点硬件安装和参考指南说明书

Ruijie Reyee RG-RAP1201 Access PointDocument Version: V1.0Date: 2023-07-28CopyrightCopyright © 2023 Ruijie NetworksAll rights are reserved in this document and this statement.Any reproduction, excerption, backup, modification, transmission, translation orcommercial use of this document or any portion of this document, in any form or by any means, without the prior written consent of Ruijie Networks is prohibited.Trademarks including , , areowned by Ruijie Networks.All other trademarks or registered trademarks mentioned in this document are owned by their respective owners.DisclaimerThe products, services, or features you purchase are subject to commercial contracts and terms. Some or all of the products, services or features described in this document may not be within the scope of your purchase or use. Unless otherwise agreed in the contract, Ruijie Networks does not make any express or implied statement or guarantee for thecontent of this document.Due to product version upgrades or other reasons, the content of this document will be updated from time to time. Ruijie Networks reserves the right to modify the content of the document without any notice or prompt.This manual is for reference only. Ruijie Networks endeavors to ensure content accuracy and will not shoulder any responsibility for losses and damages caused due to content omissions, inaccuracies or errors.PrefaceAudienceThis document is intended for:● Network engineers● Technical support and servicing engineers ● Network administratorsTechnical Support● Official website of Ruijie Reyee: https:///products/reyee ● Technical support website: https:///support ● Case portal: https:// ● Community: https:// ● Technical support email: *****************************Conventions1. GUI Symbols2. SignsThe signs used in this document are described as follows:WarningAn alert that calls attention to important rules and information that if not understood or followed can result in data loss or equipment damage.CautionAn alert that calls attention to essential information that if not understood or followed can result in function failure or performance degradation.NoteAn alert that contains additional or supplementary information that if not understood or followed will not lead to serious consequences.SpecificationAn alert that contains a description of product or version support.3.NoteThis document provides the installation steps, troubleshooting, technical specifications, as well as the specifications and use guidelines of cables and connectors. It is intended for users who want to understand the above contents, and are familiar with the installation and maintenance of networking hardware.ContentsPreface (I)1 Product Overview (1)1.1 Package Contents (1)1.2 Product Appearance (2)1.2.1 Front Panel (2)1.2.2 Rear Panel (3)1.3 Technical Specifications (4)1.4 Power Module Technical Specifications (6)1.5 Cooling (6)2 Preparing for Installation (7)2.1 Safety Precautions (7)2.2 Installation Environment Requirements (7)2.2.1 Temperature/Humidity (7)2.2.2 Cleanliness (8)2.2.3 ESD Protection (9)2.2.4 Anti-interference (9)2.2.5 Mounting Workbench (10)2.3 Tools (10)3 Installing the AP (11)3.1 Before You Begin (11)3.2 Safety Precautions (11)3.3 Installing the AP (12)3.4 Bundling Cables (13)3.5 Verifying Installation (13)4 Verifying the Operating Status (15)4.1 Setting up the Environment (15)4.2 Powering on the AP (15)4.2.1 Checking Before Power-On (15)4.2.2 Checking After Power-on (15)4.3 Troubleshooting Power Failures (15)5 Monitoring and Maintenance (16)5.1 Monitoring (16)5.2 Hardware Maintenance (16)6 Troubleshooting (17)6.1 Troubleshooting Flowchart (17)6.2 Common Faults (17)6.2.1 The LED Is Off After the Device is Powered On (17)6.2.2 Ethernet Port Is Not Working After the Ethernet Cable Is Plugged In (17)6.2.3 A STA Cannot Discover the AP (18)7 Appendix (19)7.1 Connectors and Media (19)7.2 List of Hazardous Substances (10 Years) (20)1 Product Overview1.1 Package ContentsTable 1-1Package ContentsNoteThe package contents above are intended to provide a general overview, and are subject to the terms of the order contract. Please check your goods carefully against the package contents or order contract. If you have any questions, please contact the distributor.1.2 Product Appearance 1.2.1 Front PanelFigure 1-1Front PanelTable 1-2LEDsTable 1-3Ports and Buttons on the Front PanelStick the pin to the Reset hole: Restart the access point.Press and hold the pin to the Reset hole for more than 5seconds: Restore the access point to factory settings. 1.2.2 Rear PanelFigure 1-2Rear PanelTable 1-4Ports on the Rear Panel1.3 Technical SpecificationsTable 1-5SpecificationsThe peak gain mentioned above refers to the gain of aThe transmitted power may vary based on local laws and1.4 Power Module Technical SpecificationsThe RG-RAP1201 wall-plate wireless access point is compatible with PoE (Power overEthernet) standards 802.3at and 802.3bt. To power this access point using PoE, makesure that the PSE supports IEEE 802.3af power supply. This ensures that the access point can operate at its full performance potential.1.5 CoolingThis access point features a fanless design, and can be mounted in an 86 mm junction box on the wall.2 Preparing for Installation2.1 Safety PrecautionsNote●To avoid personal injury and device damage, carefully read the safety precautionsbefore you install the device.●The following safety precautions may not cover all possible dangers.The RG-RAP1201 wall plate wireless access point plays a vital role in connectingnetworks, and its proper functioning is crucial for ensuring the normal operation of all interconnected sub-networks.The following safety precautions must be followed during installation and use.●Do not place the device in a damp or wet place, and keep the device away from anykind of liquid.●Install the device in a position far away from any heat sources.●Wear an ESD wrist strap during installation and maintenance.●Do not wear loose clothing and tighten your belt, scarf, and sleeves to prevent themfrom getting caught on the device.●Keep tools and accessories away from walking areas.●Use an uninterruptible power source (UPS) to avoid power failures and disturbance.2.2 Installation Environment RequirementsThe RG-RAP1201 wall plate wireless access point must be installed indoors to ensure its normal operation and prolonged service life. The installation site must meet thefollowing requirements.2.2.1 Temperature/HumidityYou are advised to maintain an appropriate temperature and humidity at the installation site to ensure normal operation and prolonged service life of the device. High humidity can lead to poor insulation and electrical performance issues such as leakage. On theother hand, low humidity can cause shrinkage of insulation gaskets and looseness offastening screws, which can generate static electricity and pose a risk to internal circuits, especially in dry climate environments. High temperature can significantly impact thereliability and service life of the device by accelerating the aging process of insulationmaterials. See the following table for temperature and humidity requirements.Table 2-1Temperature/Humidity Requirements2.2.2 CleanlinessDust poses a significant risk to the operational safety of the device. When indoor dustaccumulates on the device, it can lead to electrostatic adsorption and result in poorcontact. This not only affects the lifespan of the device, but also increases the likelihood of communication failures. The risk of electrostatic adsorption increases when the indoor relative humidity is low.The following table describes the requirements for the dust content and granularity.Table 2-2Requirements for DustIn addition to dust, the device also has specific requirements on the presence of harmful gases such as hydrochloric acid sulfides in the air at the installation site. These gases can cause accelerated corrosion of metals and aging of certain components. The table below displays the specific limits for harmful gases including SO2, H2S, NO2, NH3, and Cl2 at the installation site.Table 2-3Requirements for Gases2.2.3 ESD ProtectionThe RG-RAP1201 wall plate wireless access point has been designed with rigorous anti-static procedures during circuit design. However, excessive static electricity can stillcause damage to its circuit board. Static electricity in the communication networkconnected to the access point mainly originates from two sources:●Outdoor high-voltage transmission lines, lightning and other external electric fields;and●Internal systems such as indoor flooring materials and overall structure of the accesspoint.To prevent damage caused by static electricity, please pay attention to the following:●Keep the indoor installation environment clean and free of dust.●Maintain appropriate temperature and humidity.2.2.4 Anti-interferenceAnti-interference measures primarily target electromagnetic and current interferences.The following requirements should be considered to ensure effective mitigation ofinterference:●Take interference prevention measures for the power supply system.●Keep the device away from the grounding facility or lightning and grounding facility ofthe power device as much as possible.●Keep the device far away from high-frequency current devices such as high-powerradio transmitting stations and radar launchers.2.2.5 Mounting WorkbenchWhen installing the device on a wall, the following conditions must be met:●The wall surface must be smooth and clean.●The network cables must be in good condition.2.3 ToolsTable 2-4ToolsNoteThe RG-RAP1201 is not shipped with a tool kit. You need to prepare a tool kit by yourself.3 Installing the APCautionBefore installing the AP, make sure that you have carefully read the requirementsdescribed in Chapter 2.3.1 Before You BeginCarefully plan and arrange the installation location, networking mode, power supply, and cabling before installation. Confirm the following requirements before installation:●The installation location should meet the temperature and humidity requirements ofthe device.●The installation location should meet the voltage and current requirements of thedevice.●The selected power supply should meet the system power requirements of the device.●The installation location should meet the network cable requirements of the device.●The installation location should meet the installation site requirements of the device.●Ensure that all the specific requirements of the intended users are met if this device isdesigned for special purpose.3.2 Safety PrecautionsTo ensure the normal operation and prolonged service life of the device, the followingsafety precautions must be followed:●Do not power on the device during installation.●Place the device in a well-ventilated environment.●Do not expose the device to high temperature.●Keep the device away from high-voltage power cables.●Install the device indoors.●Do not expose the device in a thunderstorm or strong electric field.●Keep the device clean and dust-free.●Cut off the power before cleaning the device.●Do not wipe the device with a damp cloth.●Do not wash the device with liquid.●Do not open the enclosure when the device is working.●Fasten the device tightly.3.3 Installing the AP(1) Remove the protective cover of an 86 mm junction box.(2) Insert the network cable into the WAN/PoE port on the rear of the device.(3) Place the device in the 86 mm junction box, and tighten it with Philips head screws.(4) Install the protective cover on the device. The installation process is complete.3.4 Bundling CablesPrecautions●Bundle the cables in a visually pleasing way.●Bend twisted pairs naturally or to a large radius close to the connector.●Do not over tighten twisted pair bundle as it may reduce the cable life andperformance.Bundling Procedure(1) Bundle the hanging part of the twisted pairs using cable ties, and route themconveniently to the WAN/PoE port of the device.(2) Fasten the twisted pair cables to the cable trough of the mounting bracket.(3) Extend the twisted pair cables under the device and route them in a straight line.3.5 Verifying Installation●Verify that the device is firmly and reliably secured.Hardware Installation and Reference Guide Installing the AP●Verify that the twisted pair cable matches the port type.●Verify that cables are properly bundled.●Verify that the PSE device is 802.3af-compliant.Hardware Installation and Reference Guide Verifying the Operating Status 4 Verifying the Operating Status4.1 Setting up the EnvironmentWhen powering the device through PoE (Power over Ethernet), ensure that the powercord is properly connected and meets safety requirements.4.2 Powering on the AP4.2.1 Checking Before Power-OnVerify that the PSE device connected to the WAN/PoE port of the device is 802.3af-compliant.4.2.2 Checking After Power-on●Verify that the LED status is normal.●After the device is powered on, verify that the SSID can be successfully connected toby a mobile phone or any other wireless device.4.3 Troubleshooting Power FailuresThe working status of the LED on the device indicates whether the device power systemis malfunctioning or not. See LEDs for the LED statuses. Perform the following checks inthe case of any abnormality:●Verify that the AP is properly powered.●Verify that the network cable of the device is connected correctly.NoteIf the AP still cannot be powered on after the preceding check, please contact your localdistributor or technical support.Hardware Installation and Reference Guide Monitoring and Maintenance 5 Monitoring and Maintenance5.1 MonitoringYou can monitor the device in operation by observing its LED.5.2 Hardware MaintenanceIf the hardware is faulty, please contact Ruijie Networks technical support.6 Troubleshooting6.1 Troubleshooting Flowchart6.2 Common Faults6.2.1 The LED Is Off After the Device is Powered OnCheck whether the PSE connected to the WAN/ PoE port is 802.3af-compliant, andwhether the Ethernet cable is connected properly.6.2.2 Ethernet Port Is Not Working After the Ethernet Cable IsPlugged InCheck whether the PSE connected to the WAN/ PoE port is working properly, andwhether the Ethernet cable is capable of providing the required data rate and is properly connected.6.2.3 A STA Cannot Discover the AP(1) Verify that the AP is properly powered.(2) Verify that the Ethernet port is correctly connected.(3) Verify that the AP is correctly configured.(4) Move the client closer to the AP.7 Appendix7.1 Connectors and Media1000BASE-T/100BASE-TX/10BASE-T portThe 1000BASE-T/100BASE-TX/10BASE-T is a 10/100/1000 Mbps auto-negotiation port that supports auto MDI/MDIX Crossover.Compliant with IEEE 802.3ab, 1000BASE-T requires Category 5e 100-ohm UTP or STP(recommended) with a maximum distance of 100 meters (328 feet).The 1000BASE-T port requires all four pairs of wires to be connected for datatransmission. The following figure shows the four pairs of wires for the 1000BASE-T port.Figure 7-11000BASE-T Twisted Pair Connections100BASE-TX/10BASE-T can be interconnected using cables of the precedingspecifications. For 10 Mbps, the 100BASE-TX/10BASE-T port can be connected using 100-ohm Category 3, Category 4, and Category 5 cables; for 100 Mbps, the 100BASE-TX/10BASE-T port can be connected using 100-ohm Category 5 cables with a maximum distance of 100 meters (328 feet). The following table shows 100BASE-TX/10BASE-T pin assignments.Table 7-1100BASE-TX/10BASE-T Pin AssignmentsThe following figure shows feasible connections of the straight-through and crossover twisted pairs for a 100BASE-TX/10BASE-T port.Figure 7-2100BASE-TX/10BASE-T Twisted Pair Connections7.2 List of Hazardous Substances (10 Years)Table 7-2Name and Content of Hazardous Substances in the Product1. This table is prepared in accordance with SJ/T 11364.○: Indicates that the content of this hazardous substance in all homogeneous materials of the component is below the limit specified in GB/T 26572.×: Indicates that the content of this hazardous substance at least in a certain homogeneous material of the component exceeds the limit specified in GB/T 26572.2. This table shows the components, in which hazardous substances are found in Ruijie products. Depending on the model, products may not contain all of the above components. The actual model you purchased shall prevail.3. Unless otherwise marked on the product, the “environmentally friendly service life” of all attached products and their components is indicated by the symbol displayed here. This environmentally friendly service life only applies to the usage conditions specified in the product manual.。
迪文科技 DMG80480C050_03WTR 5.0英寸触摸屏数据手册说明书

DMG80480C050_03WTR基于T5L ASIC的5.0英寸800×480像素点阵、16.7M色、TN屏、电阻触摸屏、标准指令集(TA)/DGUSⅡ系统Based on T5L ASIC5.0Inch,800xRGBx480,16.7M Colors, TN,RTP,Standard instruction set(TA)/DGUSⅡsystem修订记录Record of Revision版本Rev日期Revise Date描述Content编辑人Editor 002019-03-28首次发布First edition质控部012019-08-22修改串口模式Modify interface质控部022019-11-26修改串口模式说明Modify interfacedescription质控部032021-01-14修改Nor Flash Modify Nor Flash李精精042021-03-15更新实物图、存储温度、支持外设、CAD图Update figure,storage temperature,peripheral,CAD drawing李精精●参数Item数据Parameter说明Description 颜色Color16.7M(16777216)colors24bit color8R8G8B显示尺寸(A.A)Active Area(A.A)108.0mm(W)×64.8mm(H)800x480像素点阵视域尺寸(V.A)View Area(V.A)110.6mm(W)×66.9mm(H)800x480像素点阵分辨率Resolution800x480可以设置成0°/90°/180°/270°显示模式Support0°/90°/180°/270°rotated display背光模式Backlight LED 不低于10000H(以最高亮度连续工作,亮度减半时间)≥10000H(Continuous working with maximum brightness,time of brightness halves)亮度Brightness200nit TA模式:可进行64级亮度调节;DGUSⅡ模式:可进行100级亮度调节(当亮度调节至最高亮度的1%~30%时,可能出现闪烁现象,不建议在此范围使用)。
重载列车智能化操控系统项目-系统结构设计规范

项目编号:400-008重载列车智能化操控系统系统结构设计规范版本记录版本号日期修改章节修改内容及说明编制者V0.1 2013.04.12 全部新建郝一凡编制:2013-04-12 审核:2013-04-12 批准:2013-04-12目录1.简介 (7)1.1.系统简介 (7)1.2.文档目的 (7)1.3.文档范围 (7)1.4.与其它开发任务/文档的关系 (7)1.5.术语和缩写词 (8)2.参考文档 (9)3.系统设计原理 (10)3.1.系统软硬件结构概述 (11)3.2.软件结构和功能 (12)3.3.硬件结构设计 (14)4.接口设计 (15)4.1.外部接口 (15)4.2.内部接口 (15)5.机械结构 (16)0.1图 3-1 智能化操控系统结构示意图 (10)图 3-2 智能化操控系统总体架构图 (11)图 3-3 智能化操控系统软件架构图 (12)图 3-4 软件组件功能 (13)图 3-5 组件协作示例 (13)图 3-6 智能化操控系统硬件架构图 (14)图 5-1 机械结构 (16)0.1表 1-1术语解释表 (8)表 2-1 参考文档列表 (9)0.11.简介1.1.系统简介重载铁路智能化操控系统(以下简称“智能化操控系统”)适用于重载铁路货运领域。
智能化操控系统结合重载列车动力分布无线重联控制技术、列车编组、调度命令下达等运输组织模式以及结合重载铁路大轴重、长编组、复杂的线路状况、动力分布无线重联控制系统等特点,构建重载列车智能化操控技术体系和指标,实现列车智能操控,提供列车辅助自动控制等功能,保证列车运输安全,优化运行效率,提升线路运输能力的车载系统。
1.2.文档目的本文档定义智能化操控系统的结构并使其能够满足系统需求和系统安全需求。
本文档为系统整体设计方案,后续子系统和模块的具体设计必须遵循本设计方案。
1.3.文档范围本文档描述了智能化操控系统的结构和接口设计,适用于智能化操控系统开发生命周期的设计开发阶段。
泰科电子 GPS 模块 A1082-A 用户手册说明书

GPS Receivers A1082-AA description of Tyco Electronics’GPS module A1082-AUser’s ManualVersion 1.0Hardware Revision 01This page was intentionally left blank.Revision HistoryRevision HistoryRev. Date Description1.0 25-10-07 Initial Draft.mm-dd-yyV1.0 - 10/07 User’s Manual Page 3 of 27DisclaimerDisclaimerTHIS DOCUMENT CONTAINS PROPRIETARY INFORMATION OF TYCO ELEC-TRONICS CORPORATION/POWER SYSTEMS (TYCO ELECTRONICS). IT MAY NOT BE COPIED OR TRANSMITTED BY ANY MEANS, PASSED TO OTHERS, OR STORED IN ANY RETRIEVAL SYSTEM OR MEDIA, WITHOUT PRIOR CONSENT OF TYCO ELECTRONICS OR ITS AUTHORIZED AGENTS.THE INFORMATION IN THIS DOCUMENT IS, TO THE BEST OF OUR KNOWLEDGE, ENTIRELY CORRECT. HOWEVER, TYCO ELECTRONICS CAN NEITHER ACCEPT LIABILITY FOR ANY INACCURACIES, OR THE CONSEQUENCES THEREOF, NOR FOR ANY LIABILITY ARISING FROM THE USE OR APPLICATION OF ANY CIRCUIT, PRODUCT, OR EXAMPLE SHOWN IN THE DOCUMENT.THE PRODUCT (HARD- AND SOFTWARE) DESCRIBED IN THIS DOCUMEN-TATION IS NOT AUTHORIZED FOR USE IN LIFE SUPPORT DEVICES OR SYSTEMS WITHOUT THE EXPRESS WRITTEN APPROVAL OF TYCO ELEC-TRONICS.THIS DOCUMENT MAY PROVIDE LINKS TO OTHER WORLD WIDE WEB SITES OR RESOURCES. BECAUSE TYCO ELECTRONICS HAS NO CONTROL OVER SUCH SITES AND RESOURCES, TYCO ELECTRONICS SHALL NOT BE RESPONSIBLE FOR THE AVAILABILITY OF SUCH EXTERNAL SITES OR RESOURCES, AND DOES NOT ENDORSE AND IS NOT RESPONSIBLE OR LIABLE FOR ANY CONTENT, ADVERTISING, PRODUCTS, OR OTHER MATERIALS ON OR AVAILABLE FROM SUCH SITES OR RESOURCES. TYCO ELECTRONICS SHALL NOT BE RESPONSIBLE OR LIABLE, DIRECTLY OR INDIRECTLY, FOR ANY DAMAGE OR LOSS CAUSED OR ALLEGED TO BE CAUSED BY OR IN CONNECTION WITH USE OF OR RELIANCE ON ANY SUCH CONTENT, GOODS OR SERVICES AVAILABLE ON OR THROUGH ANY SUCH SITE OR RESOURCE.TYCO ELECTRONICS RESERVES THE RIGHT TO CHANGE, MODIFY, OR IMPROVE THIS DOCUMENT OR THE PRODUCT DESCRIBED HEREIN, AS SEEN FIT BY TYCO ELECTRONICS WITHOUT FURTHER NOTICE.Page 4 of 27 User’s Manual V1.0 - 10/07Table of ContentTable of Contents1 Introduction (7)1.1 Label (7)1.2 Characteristics (8)1.2.1 GPS Characteristics (8)1.2.2 Mechanical Characteristics (8)1.3 Handling Precautions (8)2 Ordering Information (9)2.1 GPS Receiver A1082-A (9)2.2 Packing (9)2.2.1 Packaging of the A1082-A (9)2.3 Additional Equipment (10)3 Quick Start (11)3.1 Minimum Configuration (11)3.2 Antenna (13)3.3 Serial Port Settings (13)3.4 Improved TTFF (13)4 Mechanical Outline (14)4.1 Details Component Side A1082-A (14)4.2 Details Solder Side A1082-A (15)5 Pin-out Information (16)5.1 Layout A1082-A (16)5.2 Description A1082-A Signals (16)5.3 General Comments (17)6 Electrical Characteristics (18)6.1 Operating Conditions (18)6.2 Typical Operating Conditions (18)6.3 Absolute maximum ratings (19)7 Mounting (20)7.1 Proposed Footprint for Soldering (20)7.2 Recommended Profile for Reflow Soldering (20)8 Use of Antenna (21)8.1 Connection of RF Signal (21)9 Quality and Reliability (22)9.1 Environmental Conditions (22)9.2 Product Qualification (22)9.3 Production Test (22)Demonstration Kits (23)9.4 Evaluation Kit A1082-A (23)10 Application and Hints (24)V1.0 - 10/07 User’s Manual Page 5 of 27Table of contentPage 6 of 27 User’s Manual V1.0 - 10/0710.1 Enable PIN (P1.6) (24)10.2 1PPS PIN (24)10.3 Standby PIN (P1.5) (24)10.4 FDOUT PIN (24)11 Related Information (25)11.1 Contact (25)11.2 Related Documents (25)12 List of Tables (27)13 List of Figures (27)GPS receiver A1082-A1 IntroductionTyco Electronics’ GPS module A1082-A is a highly integrated GPS receiver module that can be used as an SMT component. It is capable to receive signals from up to 12 GPS satellites and transferring them into position and timing information that can be read over a serial port. This new generation of GPS module combines small size and high-end GPS functionality at lowest power consumption:•Operable at 1.8V / 65mW (typ.) @ trickle power mode•Small form factor of 13.97 x 11.43 mm (0.55” x 0.45”)•Cost-effective antenna input• Single-sided SMD-BGA component, for reflow soldering•Tape & reel packagingThe A1082-A GPS receivers are available as off-the-shelf component, 100% tested and shipped in standard tape-and-reel package.1.1 LabelThe A1082-A label holds the following information:Figure 1: A1082-A labelV1.0 - 10/07 User’s Manual Page 7 of 27GPS receiver A1082-A1.2 CharacteristicsThe modules are characterized by the following parameters.1.2.1 GPS CharacteristicsChannels12, parallel tracking Correlators20.000 FrequencyL1 (= 1575 MHz) Tracking Sensitivity-157dBm Horizontal Position Accuracy Stand alone (5)< 2,5m CEP (SA off) Obscuration recovery (1)0.1s Hot start (2)< 1s Warm (3)< 35s Time To First Fix – TTFF (theoretical minimum values; values in real world may differ) Cold (4)< 37sTable 1: A1082 GPS characteristics(1) The calibrated clock of the receiver has not stopped, thus it knows precise time (to the µs level).(2) The receiver has estimates of time/date/position and valid almanac and ephemeris data.(3) The receiver has estimates of time/date/position and recent almanac.(4) The receiver has no estimate of time/date/position, and no recent almanac.(5) CEP 50% 24 hours static1.2.2 Mechanical CharacteristicsA1082-A Mechanical dimen-sionsLength Width Height 13.97mm, 0.55” 11.43mm, 0.45” 2.4mm, 0.095” A1082-A Weight1g, < 0.05ozTable 2: A1082-A dimensions and weight1.3 Handling PrecautionsThe GPS receiver module A1082-A is sensitive to electrostatic discharge (ESD). Please handle with appropriate care.Page 8 of 27 User’s Manual V1.0 - 10/07GPS receiver A1082-A2 Ordering Information2.1 GPS Receiver A1082-AThe order number is built as follows:•V23993A1082AV23993 stands for Tyco Electronics wireless and communication products, A1082A for the A1082-A module.2.2 Packing2.2.1 Packaging of the A1082-AThe A1080-A GPS module comes in a tape and reel package suitable for pick and place machines.Figure 2: A1082-A tape specifications (1)V1.0 - 10/07 User’s Manual Page 9 of 27GPS receiver A1082-AFigure 3: A1082-A tape specifications (2)2.3 Additional EquipmentV23993EVA1082A Evaluation Kit (including one module V23993A1082A)Table 3: Additional equipmentA detailed description of the additional kit can be found in the according manuals. Page 10 of 27 User’s Manual V1.0 - 10/073 Quick StartIn order to allow an easy and quick start with the modules A1082-A, this chapter provides a short overview on the most important steps to receive NMEA messages with position information on a serial port.3.1 Minimum ConfigurationThe following picture shows a recommended minimum configuration for NMEA out-put and commands sent and received via an RS232 interface based on the GPS module A1082-A.3.2 AntennaThe A1082-A GPS module is optimized for active antennas.3.3 Serial Port SettingsThe default configuration within the standard GPS firmware is:•Serial 0 (NMEA) 4,800 baud, 8 data bits, no parity, 1 stop bit, no flow control3.4 Improved TTFFIn order to improve the TTFF (Time To First Fix), it is recommend to keep the Vcc & VCC_CPU all the time and use Enable PIN (see chapter 10.1 Enable Pin) or soft-ware standby function.Please see Firmware User manual for details.4.2 Details Solder Side A1082-A1.27.27PIN1 PIN2 PIN3 PIN4 PIN5 PIN6 PIN7PIN8 PIN16 PIN15 PIN14 PIN13 PIN12PIN11 PIN10PIN9Solder pad size: Ø 0.6mm All dimensions in [mm]Figure 6: Mechanical outline solder side A1082-ATable 4: Pin description A1082-A5.3 General CommentsThe following comments should be considered for a design with and use of the module:•Standard configuration of serial port (standard GPS software): Serial 0 (NMEA) 4,800 baud, 8 data bits, no parity, 1 stop bit, no flow control •Antenna (Antenna connected to Antenna Pin)Use ground pins (PIN6, PIN8) close to the antenna input for RF ground.6 Electrical Characteristics6.1 Operating ConditionsPin Description Min Typical Max Vcc1.75V 1.8V 1.85V Peak Acquisition Current (1) 110mA 120mA Tracking Current (2)50mA 60mA Tracking Current, trickle mode (3) 35mA 50mA 7 Standby Current (4)30 µATable 5: A1082 electrical characteristics(1) Peak acquisition current is characterized by millisecond bursts above average acquisition cur-rent(2) Tracking current typically includes tracking and the post acquisition portion of TTFF (3) Tracking current with activated trickle power mode (standard configuration) (4) During standby state: RTC block and core powered on and clock off.6.2 Typical Operating Conditions12345Figure 8: typical operating condition A1082-A1Acquiring first satellite (cold start only)2Acquiring all satellites which are necessary to calculate a fix (cold start only) 3Ephemeris download from all visible satellitesTrickle power mode4Hot start after resetting the module56.3 Absolute maximum ratingsSymbol Parameter Min Max Unit V CC Power Supply GSCi500x -0.3 +1.85VV CC_CPU Power Supply host processor -0.3 +1.85VV in Voltage to any input pin -0.3 +2.0 VI out Input current on any pin -10 +10 mA I tdv Absolute sum of all input currents during overload condition 200 mATable 6: Absolute maximum ratingsStresses beyond those listed under “Absolute Maximum Ratings” may cause per-manent damage to the device. This is a stress rating only. Functional operation of the device at these or any other conditions beyond those indicated in the opera-tional sections of this specification is not implied. Exposure to absolute maximum rating conditions for extended periods may affect device reliability.7 MountingThis chapter covers the mounting of the A1082-A.7.1 Proposed Footprint for SolderingThe following proposal of a footprint for soldering is assuming a stencil thickness of 150µm. ³ marks the center of the through holes.TBDFigure 9: Soldering footprint proposal A1082-APlease note that copper and solder paste footprint are identical. The final footprint has to be evaluated and qualified by the manufacturer according to the specific processes.7.2 Recommended Profile for Reflow SolderingTypical values for reflow soldering of the module in convection or IR/convection ov-ens are as follows:Peak temperature (RoHS compliant process) 245°CAverage ramp up rate to Peak (183°C to Peak) 3°C / second max.Preheat temperature 125 (±25°C) 120 seconds max. Temperature maintained above 183°C 60 … 150 secondsTime within 5°C of actual peak temperature 10 … 20 secondsRamp Down rate 6°C / second max.Time 25°C to peak temperature 6 minutes max.Table 7: Reflow soldering profile A1082-AAs results of soldering may vary among different soldering systems and types of solder and depend on additional factors like density and types of components on board, the values above should be considered as a starting point for further optimi-zation.GPS receiver A1082-A8 Use of Antenna8.1 Connection of RF SignalThe ANT pin is used to connect the receiver with the GPS antenna. The design of the antenna connection has to be done strictly according to RF design rules. A 50Ω PCB strip line is required. The following drawings shall explain the guidelines. A major rule is to keep the strip line as short as possible. Additionally, antenna ground (GNDANT) should be routed to the ground plane of the PCB (the ground plane is on a lower PCB layer) by via as demonstrated in the drawing.Motherboard GND layerMotherboard top layerFigure 10: Antenna connector strip line A1082-AIn order to gain the impedance of 50Ω, the width of the strip line needs to be calcu-lated. It depends on the thickness or height of the PCB layer (both parameters are shown in following drawing). For the calculation, it is assumed that the PCB mate-rial is FR4.Figure 81: Strip line parameters A1082-AIn this case, the width should be about 1.8 times the height of the PCB:W = 1.8 x HIn the example, one would get a width of W = 1.8 x 0.8mm = 1.44mm.Vias to Top Layer Vias to GND LayerBGA Solder padsGPS receiver A1082-A9 Quality and Reliability9.1 Environmental ConditionsOperating temperature -40 … +85°COperating humidity Max. 85% r. H., non-condensing, at 85°C3MSL JEDEC(Moisture Sensitivity Level)Storage 6 months in original package.Table 8: Environmental conditions9.2 Product QualificationPrior to product qualification the GPS receiver is preconditioned according to EIA/JEDEC standard JESD22-A113-B / Level 3.Basic qualification tests:•MSL Classification according to J-STD-020C (MSL3 @ 245°C)•MSL Rework Compatibility according to J-STD-020C•Temperature Cycling –40°C … +85°C•Temperature Humidity Bias 70°C / 85% RH•High / Low Temperature Operating –40° / +85°C•High Temperature Operating Life +85°C•Vibration Variable Frequency• Mechanical ShockPlease contact Tyco Electronics for detailed information.9.3 Production TestEach module is electrically tested prior to packing and shipping to ensure state of the art GPS receiver performance and accuracy.GPS receiver A1082-ADemonstration Kits9.4 Evaluation Kit A1082-AFor demonstration and easy evaluation of GPS performance Tyco Electronics offers a Demonstration Kit (including one GPS A1082-A module). It contains a USB inter-face with according drivers to connect easily to a PC. The USB interface is an ex-tension of the serial port 0, therefore sending NMEA sentences and accepting commands. At the same time it provides power to the module. Accompanied by an antenna it offers a ready-to-go set.For the development of new software and applications the Evaluation Kit also pro-vides NMEA messages on C-MOS level via a terminal plug.For further information please contact Tyco Electronics.GPS receiver A1082-A10 Application and Hints10.1 Enable PIN (P1.6)The Enable PIN is an input PIN and low active.The module will immediately switch to standby mode by pulling the Enable PIN to “low”. The RTC keeps running and the internal SRAM will be back upped. This keeps the Ephemeris and Almanac stored. Pulling the Enable PIN back to “high” within 2 hours will end in hot start situation.10.2 1PPS PINThe 1PPS pin is an output pin.In addition to precise positioning, GPS also allows for accurate timing due to the synchronized atomic clocks in the GPS satellites. While the current date and time is transmitted in NMEA sentences, an exact and accurate timing signal is provided via the 1PPS pin of the A1082-A modules.10.3 Standby PIN (P1.5)The Standby pin is an input pin and high active.Pulling Standby pin to high will activate trickle power mode with factory preset vari-ables. Please see Firmware manual A1082-A.10.4 FDOUT PINFDOUT Pin is an output pin.FDOUT indicates active low power modes (trickle, standby). Typical application to use this pin is to deactivate external LNA or active antenna to reduce power consumption to mini-mum.GPS receiver A1082-A11 Related Information11.1 ContactThis manual was created with due diligence. We hope that it will be helpful to the user to get the most out of the GPS module.Anyway, inputs about errors or mistakable verbalizations and comments or propos-als to TYCO Electronics, Power Systems in Munich, Germany, for further improve-ments are highly appreciated.Tyco ElectronicsPower SystemsFinsinger Feld 185521 Ottobrunn, GermanyTel.: +49 89 6089 838Fax: +49 89 6089 835mailto:***********************./gps.Further contact addresses:Info.mailto:***********************.support.mailto:***********************.sales.mailto:***********************.11.2 Related Documents•Manual: Instant GPS IC Interface Control Drawing manual (SiRF)GPS receiver A1082-AThis page was intentionally left blank.List of tables and figures12 List of TablesTable 1: A1082 GPS characteristics (8)Table 2: A1082-A dimensions and weight (8)Table 3: Additional equipment (10)Table 4: Pin description A1082-A (16)Table 5: A1082 electrical characteristics (18)Table 6: Absolute maximum ratings (19)Table 7: Reflow soldering profile A1082-A (20)Table 8: Environmental conditions (22)13 List of FiguresFigure 1: A1082-A label (7)Figure 2: A1082-A tape specifications (1) (9)Figure 3: A1082-A tape specifications (2) (10)Figure 4: Recommended minimum configuration A1082-A (12)Figure 5: Mechanical outline component side A1082-A (14)Figure 6: Mechanical outline solder side A1082-A (15)Figure 7: Pin-out information A1082-A (16)Figure 8: typical operating condition A1082-A (18)Figure 9: Soldering footprint proposal A1082-A (20)Figure 10: Antenna connector strip line A1082-A (21)Figure 81: Strip line parameters A1082-A (21)。
AMOLED模块说明书 PV017802T45C

SPECIFICATION 产品说明书Revision: 1.0 版本: 1.0PV017802T45CThis module uses ROHS material模块用环保材料``PRODUCT 产品名称 : AMOLED MODULEMODEL NO .模块型号 : PV017802T45C SUPPLIER 供应商 : Kingtech Group Co.,Ltd.DATE 日期 : 2021-06-17REVISION RECORD 修改记录REV NO. 版本号REV DATE修改日期CONTENTS内容REMARKS注释1.0 2021-06-17Firstrelease PrimaryCONTENTS 内容GENERAL INFORMATION主要特征描述EXTERNAL DIMENSIONS外形尺寸ABSOLUTE MAXIMUM RATINGS极限参数ELECTRICAL CHARACTERISTICS模块电气特性ELECTRO-OPTICAL CHARACTERISTICS光电参数INTERFACE DESCRIPTION接口定义描述REFERENCE APPLICATION CIRCUIT参考应用电路RELIABILITY TEST CONDITIONS可靠性试验条件INSPECTION CRITERION检查标准PRECAUTIONS FOR USING LCM MODULES 使用注意事项PACKING SPECIFICATION包装规格书PRIOR CONSULT MATTER提前商议事项WRITTEN BY制作CHECKED BY检查APPROVED BY核准XUKAIXUAN DAIZHENMING DAIZHENMINGGENERAL INFORMATION主要特征描述Item ContentsUnit Display Mode AMOLED /LTPS Glass Outline (W×H) 30.60×37.99 mm Module Outline 30.60×37.19mmActive area 34.90×28.7 mmNumber of Dots 368(RGB)×448 /Diagonal Inch 1.78 inchPixel pitch (W×H) 0.078×0.078 mmModule Thickness 0.784 mm外形尺寸ABSOLUTE MAXIMUM RATINGS 极限参数Parameter Symbol Min Max UnitSupply voltage (Display)VCC -0.3 5.5 V IOVCC -0.3 5.5 VELVDD 0.0 6.5 V ELVSS -6.5 0.0 V Supply voltage (TP)TSP_VCC -0.5 6 VTSP_IOVCC -0.5 6 VOperating temperature T OP -20 70 °C Storage temperature T ST -30 80 °CHumidity RH - 90 %RHNote: Absolute maximum ratings means the product can withstand short-term, NOT more than 120 hours. If the product is a long time to withstand these conditions, the life time would be shorter.ELECTRICAL CHARACTERISTICS 模块电气特性DC CHARACTERISTICS 直流特性ParameterSymbol ConditionMinTypMax UnitSupply voltage (Display)VCC 3.2 3.33.4 V IOVCC 3.2 3.3 3.4 VELVDD 4.55 4.6 4.65 VELVSS -2.25 -2.2 -2.15 VSupply voltage (TP)TSP_VCC 3.2 3.3 3.4 VTSP_IOVCC 3.2 3.3 3.4 V Input voltage'L' level VIL IOVCC=1.65V~3.3V GND - 0.2*IOVCC V 'H' level VIH 0.8*IOVCC-IOVCCVOutput voltage'L' levelVOL I(OH)=-1mA I(OL)=+1mAGND - 0.2*IOVCC V 'H' level VOH0.8*IOVCC-IOVCCVCurrent (Display)Sleep outmodeI VCCFull white display - 1 2 mA I IOVCC 1.2 2.4 mA Ielvdd - 30.1 46 mAIelvss 30.1 46 mA Sleep in mode I VCC0.59 1.2 uAI IOVCC 74 150 uA Deep Standby ModeI V A VDD- - 1 uAI IOVCC - - 1 uAFrame Frequencyf FRM - 30 - HzELECTRO-OPTICAL CHARACTERISTICS 光电参数Item Symbol Condition Min Type Max Unit NoteSurface Luminance Lv θ=0°∅=0° Ta=25℃500 550 - cd/m2 Note1Luminance uniformity δWHITE 80 - - % Note2Contrast Ratio Cr 60000- - - Note3 Viewing Angle θUp/Down/Right/LeftCr ≥20070 80 - deg Note4 Color Coordinate of CIE1931Red xθ=0° ∅=0° Ta=25℃.0.64310.68310.7231 - Note 5Red y 0.27650.31650.3565 - Green x 0.18250.22250.2825 - Green y 0.69280.73280.7728 -Blue x 0.10710.13710.1671 - Blue y 0.02440.05440.0844 - White x 0.28 0.300.32 - White y0.29 0.310.33 -NTSC ratio - - 90 100 - % CIE1931Gamma - θ=0° ∅=0° Ta=25℃V(Gray)=44,68,100,132,164,196,228,252,2552.0 2.2 2.4 -Lifetime T95 25℃240 hNote1. Surface Luminance• Measurement equipment: CS2000 or similar equipment. • Measuring surroundings: Dark room. • Measuring temperature: Ta=25℃.• The data are measured after OLEDs are lighted on for more than 5 minutes and all pixels are fully white.• The Surface Luminance is the average value of 5 measured spots (Fig-1):Lv = Average Luminance with all white pixels (P1, P2, P3, P4, P5) Note2. Luminance Uniformity• Measurement equipment: CS2000 or similar equipment. • Measuring surroundings: Dark room. • Measuring temperature: Ta=25℃.• The data are measured after OLEDs are lighted on for more than 5 minutes and all pixels are fully white.• The Luminance Uniformity is calculated by using following formula: δ WHITE = Lp (Min.) / Lp (Max.)×100 (%) Lp (Min.) = Minimum Luminance with all white pixels (P1, P2, P3, P4, P5)Lp (Max.) = Maximum Luminance with all white pixels (P1, P2, P3, P4, P5)Note3. Contrast Ratio• Measurement equipment: CS2000 or similar equipment.• Measuring surroundings: Dark room.• Measuring temperature: Ta=25℃.• The data are measured after OLEDs are lighted on for more than 5 minutes.• The Contrast Ratio is calculated by using following formula:Contrast Ratio(Cr) = Lw / LbLw = Average Luminance with all white pixels (P1, P2, P3, P4, P5)Lb = Average Luminance with all black pixels (P1, P2, P3, P4, P5)Fig-1Note4. Viewing Angle• Measurement equipment: DMS803 or similar equipment.• Measuring surroundings: Dark room.• Measuring temperature: Ta=25℃.• The Viewing Angle is the angle at which the contrast ratio is greater than 10. The angles are determined for the horizontal or x axis and the vertical or y axis with respect to the z axis which is normal to the display surface.Fig-2Note5. Color Coordinate of CIE1931• Measurement equipment: CS2000 or similar equipment.• Measuring surroundings: Dark room.• Measuring temperature: Ta=25℃.• The x, y value of Color Coordinate is determined by measuring at center position of the display panel.INTERFACE DESCRIPTION 接口定义描述Interfa ce NO. Symbol I/O or Connected to DescriptionWhen not in use 1MTP_PWRPowerMTP programming power supply pin.Left open or connected to GND2 GNDConnectedto GND Ground. / 3 NC - - / 4 NC--/5 GNDConnectedto GND Ground. / 6 NC - - / 7 NC--/8 GNDConnectedto GND Ground. 9 NC - - / 10 NC - -/11 GND Connected to GNDGround.12IM0IInterface type selection pin./13 IM114 GND Connected to GND Ground. / 15 TSP_SDA I/O Touch I2C data / 16 TSP_SCL I Touch I2C clock 17 TSP_RESET I TSP Reset signal. Active low. / 18 TSP_INT I Touch State change interrupt19TSP_VCCPowerTP Power Supply / 20 TSP_IOVCC Power TP Power Supply 21D[1]I/O 4-bit data bus for Q-SPI .OPEN 22 D[0]23 GND Connectedto GNDGround. /24 CSX I Chip select input pin (“Low” enable) in SPI I/F.Connecte ToIOVCC25 WRX_SCL I SCL: A synchronous clock signal in SPI I/F.Connecte TOGND26 DCX I Display data / command selection in 4-wireSPII/F. DCX = ”0” : Command DCX = ”1” :Display data or ParameterConnecte TOGND27SDI_RDX I/O SDI: Serial inputs signal in SPI I/F. The data isinput on the rising edge of the SCL signal.OPEN28SDOOSerial outputs signal in SPI I/F. The data is output on the rising/falling edge of the SCLsignal. If the host places the SDI line into high-impedance state during the read interval, the SDI and SDO can be tied together.OPEN 29 RESETI This signal will reset the device and must beapplied to properly initialize the chip. Signal is active low./30 TEO Tearing effect output pin to synchronize MCU to frame writing, activated by S/W command.When this pin is not activated, this pin is outputlow.If not used, please open this pin. OPEN 31 NC --/32 SWIREO Swire protocol setting pin (Note: “H” = VDDIlevel, “L” = VSSI level.)/33 GND Connectedto GND Ground. /34VCCPowerInput Voltage for analog power supply/ 35 IOVCC Power Input voltage for logic/interface power supply /36 GND Connected to GNDGround. /37 ELVDDPower Power supply for pixel circuit. / 38 ELVDD / 39 ELVDD /40 GND Connected to GND Ground. /41 ELVSS PowerPower supply for pixel circuit./ 42 ELVSS / 43 ELVSS/44 GND Connected to GND Ground. / 45 GNDConnectedto GND Ground. /REFERENCE APPLICATION CIRCUIT参考应用电路Please consult our technical department for detail information. 详细信息请联系我们的技术部RELIABILITY TEST CONDITIONS 可靠性试验条件No. Test ItemTest ConditionQtyInspection after test1 High Temperature Storage 80℃±2℃/240 hours 5 Inspection after 2 hours storage at room temperature, the sample shall be free from defects:1. Remarkable deterioration of No clearly visible defects or display quality. However, any polarizer's deteriorations by the high temperature/ High humidity Storage test and the High temperature/ High humidity Operation test are permitted.2. No function-related abnormalities.3. Optical criteria : .White △u'v' ≤0.024. No visible defects .(optical / mechanical) .5. No function-related abnormalities2 Low Temperature Storage -30℃±2℃/240 hours 53 High Temperature Operating 70℃±2℃/120 hours 54 Low Temperature Operating -20℃±2℃/120 hours5 5 Temperature Cycle storage-30℃±2℃~80℃±2℃×100cycles(30min.) (5min.) (30min.) 56 ESD testV oltage:±4KV R: 330Ω C:150pFAir discharge, 10time57 Vibration Test Frequency :10Hz~55Hz~10Hz Amplitude :1.5mm,X ,Y ,Z direction for total 3hours (Packing condition)58 Dropping test Drop to the ground from 1m height, one time,every side of carton. (Packing condition)5Remark:1.The test samples should be applied to only one test item.2.For Damp Proof Test, Pure water(Resistance >10M Ω) should be used.3.In case of malfunction defect caused by ESD damage, if it would be recovered to normal state after resetting, it would be judged as a good part.4.Failure Judgment Criterion: Basic Specification, Electrical Characteristic, Mechanical Characteristic, Optical Characteristic.INSPECTION CRITERION检查标准1.0抽样计划按照抽样方案GB/T2828.1-2003/ISO 2859-1:1999 和 ANSI/ASQC Z1.4-1993 Level Ⅱ划分样品可以接受或拒绝的等级如下:重缺陷:AQL 0.65轻缺陷:AQL 1.52.0 检查条件检查样品时,外观检查的观察距离距检查者眼睛30cm ,在20~40W日光灯的光照环境下(外观检查亮度 1000±200 LUX;功能检查亮度 100-300 LUX; ),保持检查样品应在垂直方向45度以内. (正常温度和湿度分别为20~25℃,60±15%RH )3.0 检查区域定义:屏幕显示区域定义:区域 A: 符号或数字显示区域区域 B: 视区(除A区)(A区+B区=最小视区,相对于模块确认的V A区范围)区域 C: 视区外围(模块确认图的V A区外,客户机装机后看不到此区域)如上图:LCD的检查区域定义注意:在区域C中看得见的缺陷,但不影响产品质量以及客户组装,允许出货。
Pain Interference Scoring Manual

PAIN INTERFERENCE SCORING MANUALA brief guide to scoring the PROMIS © Pain Interference instruments: ADULT ADULT CANCER PEDIATRIC PARENT PROXYPROMIS Item Bank v1.1 – Pain Interference PROMIS Item Bank v1.1 – Pain Interference (recommended) PROMIS Item Bank v1.1 – Pain Interference (screen-to-CAT) PROMIS Short Form v1.1 – Pain Interference 4a PROMIS Short Form v1.1 – Pain Interference 6a PROMIS Short Form v1.1 – Pain Interference 6b PROMIS Short Form v1.1 – Pain Interference 8a PROMIS Item Bank v1.0 – Pain Interference* PROMIS Short Form v1.0 – Pain Interference 4a* PROMIS Short Form v1.0 – Pain Interference 6a* PROMIS Short Form v1.0 – Pain Interference 6b* PROMIS Short Form v1.0 – Pain Interference 8a* PROMIS-Ca Bank v1.1 – Pain Interference PROMIS-Ca Bank v1.0 – Pain Interference* PROMIS Pediatric Bank GenPop v3.0 – Pain Interference PROMIS Pediatric Bank GenPop v3.0 – Pain Interference (screen-to-CAT) PROMIS Pediatric Short Form GenPop v3.0 – Pain Interference 8a PROMIS Pediatric Item Bank v2.0 – Pain Interference* PROMIS Pediatric Item Bank v2.0 – Pain Interference (recommended)* PROMIS Pediatric Item Bank v2.0 – Pain Interference (screen-to-CAT)* PROMIS Pediatric Short Form v2.0 – Pain Interference 8a* PROMIS Pediatric Item Bank v1.0 – Pain Interference* PROMIS Pediatric Short Form v1.0 – Pain Interference 8a* PROMIS Parent Proxy Bank GenPop v3.0 – Pain Interference PROMIS Parent Proxy Bank GenPop v3.0 – Pain Interference (screen-to-CAT) PROMIS Parent Proxy Short Form GenPop v3.0 – Pain Interference 8a PROMIS Parent Proxy Item Bank v2.0 – Pain Interference* PROMIS Parent Proxy Item Bank v2.0 – Pain Interference (recommended)* PROMIS Parent Proxy Item Bank v2.0 – Pain Interference (screen-to-CAT)* PROMIS Parent Proxy Short Form v2.0 – Pain Interference 8a* PROMIS Parent Proxy Item Bank v1.0 – Pain Interference* PROMIS Parent Proxy Short Form v1.0 – Pain Interference 8a* *Retired MeasureCOMPARING SCORES ACROSS VERSIONSSome PROMIS domains have multiple versions of instruments (i.e., v1.0, v1.1, v2.0, v3.0). Generally, it is recommended that you use the most recent version available which can be identified as the instrument with the highest version number. In most cases, an instrument that has a decimal increase (v1.0 to v1.1) retains the same item-level parameters as well as instrument reliability and validity. In cases where a version number increases by a whole number (e.g., v1.0 to v2.0), the changes to the instrument are more substantial.• For Adult Pain Interference, scores from the v1.0 and v1.1 measures can be compared with each other. • For Pediatric and Parent Proxy Pain Interference, the calibrations between v1.0 and v2.0 are identical, as is the item content on short forms. Consequently, T-scores from v1.0 can be compared to T-scores from v2.0.• Scores from Pediatric and Parent Proxy GenPop v3.0 Pain Interference measures are NOT comparable with v1.0 or v2.0 measure scores. Transforming Scores between Versions: To transform T-scores from Pediatric/Parent Proxy v1.0/v2.0 Pain Interference measures to the Pediatric/Parent Proxy GenPop v3.0 metric, rescore v1.0/v2.0 measures using the HealthMeasures Scoring Service or Assessment Center API. This is the preferred strategy as it produces precise scores.1.Download the v3.0 measure from Search & View Measures on .2.Revise your dataset as needed to match the v3.0 item IDs and response scores:o No items were revised between the v2.0 and GenPop v3.0 Pain Interference measures.3.Follow the instructions for using the HealthMeasures Scoring Service. Contact*********************** if using the Assessment Center API for rescoring.The crosswalk tables in Appendix 3 may also be used as a reference to guide understanding of how scores have shifted from the older v1.0, v1.1, and v2.0 measures to the v3.0 measures. If these tables are used to convert older T-scores to GenPop v3.0, please note that the resulting T-scores are not as precise as those generated by using HealthMeasures Scoring Service or Assessment Center API.WHICH CALIBRATION SAMPLE SHOULD I USE?Some PROMIS Parent Proxy v1.0, v1.1, and v2.0 measures (Anxiety, Depressive Symptoms, Fatigue, Mobility, Pain Interference, Peer Relationships) had two calibration samples – “Parent Proxy” and “Parent Proxy Without Local Dependence.” The former (Parent Proxy) included calibrations for all items. This was the default calibration sample. The Parent Proxy Without Local Dependence did not include calibrations for some items. The items without calibrations are enemy items. That is, a dyad or triad of items was identified in which there are psychometric reasons to only administer one of those items to a given respondent. For example, itemPf2anxiety5 and Pf2anxiety4 are enemy items. A participant should only see one of these items in a CAT. Thev3.0 GenPop measure have a single calibration sample and no enemy items.SCORING THE INSTRUMENTShort Forms: PROMIS instruments are scored using item-level calibrations. This means that the most accurate way to score a PROMIS instrument is to use the HealthMeasures Scoring Service(https:///ac_scoringservice) or a data collection tool that automatically calculates scores (e.g., REDCap auto-score). This method of scoring uses responses to each item for each participant. We refer to this as “response pattern scoring.” Because response pattern scoring is more accurate than the use of raw score/scale score look up tables included in this manual, it is preferred. Response pattern scoring is especially useful when there is missing data (i.e., a respondent skipped an item), different groups of participants responded to different items, or you have created a new questionnaire using a subset of questions from a PROMIS item bank.Instructions for the HealthMeasures Scoring Service1.Download the Input Template from the HealthMeasures Scoring Service home page.2.Add your data (all respondents’ individual answers to questions) for one PROMIS measure to thetemplate (multiple timepoints are okay).3.Determine how much data is missing. In order to produce a precise score, a respondent must answer atleast 4 items in measures that include 4 or more items. If a precise score is required, removerespondents who answered less than 4 items from the input template and do not calculate a T-score.4.Upload your spreadsheet to the HealthMeasures Scoring Service. If this is your first time, register as anew user.5.Access your email to receive a spreadsheet with calculated scores.Instructions for Using Raw Sum Score to T-score Conversion TablesEach question usually has five response options ranging in value from one to five. To find the total raw score for a short form with all questions answered, sum the values of the response to each question. For example, for the adult 6-item form, the lowest possible raw score is 6; the highest possible raw score is 30 (see all short form scoring tables in Appendix 1). All questions must be answered in order to produce a valid score using the scoring tables. If a participant has skipped a question, use the HealthMeasures Scoring Service(https:///ac_scoringservice) to generate a final score.Locate the applicable score conversion table in Appendix 1 and use the appropriate table to translate the total summed raw score i nto a T-score for each participant. The T-score rescales the raw score into a standardized score with a mean of 50 and a standard deviation (SD) of 10. Therefore, a person with a T-score of 40 is one SD below the mean.For the adult PROMIS Pain Interference 6b short form, a raw score of 10 converts to a T-score of 53.8 with a standard error (SE) of 1.8 (see scoring table for the 6b short form in Appendix 1).CAT: A minimum number of items (e.g., 4) must be answered in order to receive a score for the Pain Interference CAT. The response to the first item will guide the system’s choice of the next item for the participant. The participant’s response to the second item will dictate the selection of the following question, and so on. As additional items are administered, the potential for error is reduced and confidence in the respondent’s score increases. The CAT will continue until either the standard error drops below a specified level (e.g., on the T-score metric 3.0), or the participant has answered the maximum number of questions (e.g., 12), whichever occurs first. For some CATs, specifically “recommended” and “screen-to-CAT” there are additional stopping rules. These include stopping when the standard error isn’t improving much or if a respondent is asymptomatic. For details on the exact stopping rules for Pain Interference CATs, view the Measure Differences summary.SCORESFor most PROMIS instruments, a score of 50 is the average for the United States general population with a standard deviation of 10 because calibration testing was performed on a large sample of the general population. For the pediatric and parent proxy Pain Interference measures, a score of 50 is the mean for a general population + clinical sample. You can read more about the calibration and centering samples on (/score-and-interpret/interpret-scores/promis). The T-score is provided with an error term (Standard Error or SE). The Standard Error is a statistical measure of variance and represents the “margin of error” for the T-score.Important:A higher PROMIS T-score represents more of the concept being measured. For negatively-worded concepts like pain interference, a T-score of 60 is one SD worse than average. That is, a person has more problems with pain hindering activities. By comparison, a pain interference T-score of 40 is one SD better than average.Standard Error (SE): A PROMIS score includes a T-score and a standard error (SE). The standard error is a measure of the variability for a given T-score across hypothetical repeated measurements. The standard error can be used to construct confidence intervals around a T-score. A 95% confidence interval is common. A 95% confidence interval means there is a 95% probability that the true T-score is within this range. The formula for a 95% confidence interval is (T-score + (1.96*SE). For example, if T=52 and SE=2, the lower boundary of the confidence interval is (52 – (1.96*2) = 48 and the upper boundary is (52 + (1.96*2) = 56.FREQUENTLY ASKED QUESTIONS (FAQs)Q: I am interested in learning more. Where can I do that?Review the HealthMeasures website at w .Q: How do I handle multiple responses when administering a short form on paper?Guidelines on how to deal with multiple responses have been established. Resolution depends on the responses noted by the research participant.•If two or more responses are marked by the respondent, and they are next to one another, then a data entry specialist will be responsible for randomly selecting one of them to be entered and willwrite down on the form which answer was selected. Note: To randomly select one of two responses,the data entry specialist will flip a coin (heads - higher number will be entered; tails – lower numberwill be entered).To randomly select one of three (or more) responses, a table of random numbersshould be used with a statistician’s assistance.•If two or more responses are marked, and they are NOT all next to one another, the response will be considered missing.Q: What is the minimum change on a PROMIS instrument that represents a clinically meaningful difference? To learn more about research on the meaning of a change in scores, we suggest conducting a literature review to identify the most current information. The HealthMeasures website (/score-and-interpret/interpret-scores/promis) has additional information on interpreting scores.APPENDIX 1 – SCORING TABLES*SE = Standard Error on T-Score metric PROMIS Adult v1.0 and v1.1 – Pain Interference 4a Short Form Conversion Table Raw Summed Score T-Score SE* 4 41.6 6.1 5 49.6 2.5 6 52.0 2.0 7 53.9 1.9 8 55.6 1.9 9 57.1 1.9 10 58.5 1.8 11 59.9 1.8 12 61.2 1.8 13 62.5 1.8 14 63.8 1.8 15 65.2 1.8 16 66.6 1.8 17 68.0 1.8 18 69.7 1.9 19 71.6 2.1 20 75.6 3.7PROMIS Adult v1.0 and v1.1 – Pain Interference 6a Short Form Conversion TableRaw Summed Score T-Score SE*6 41.1 6.07 48.6 2.48 50.7 1.89 52.2 1.610 53.4 1.611 54.5 1.612 55.6 1.513 56.6 1.514 57.6 1.515 58.6 1.516 59.5 1.517 60.4 1.418 61.2 1.419 62.1 1.420 63.0 1.521 63.8 1.522 64.8 1.523 65.7 1.524 66.7 1.525 67.6 1.526 68.7 1.527 69.8 1.528 71.0 1.629 72.6 2.030 76.3 3.6*SE = Standard Error on T-Score metricPROMIS Adult v1.0 and v1.1 – Pain Interference 6b Short Form Conversion TableRaw Summed Score T-Score SE*6 41.0 6.07 48.5 2.68 50.8 2.19 52.5 1.910 53.8 1.811 55.0 1.712 56.1 1.713 57.1 1.714 58.1 1.715 59.1 1.616 60.0 1.617 60.9 1.618 61.8 1.619 62.7 1.620 63.6 1.621 64.5 1.622 65.5 1.623 66.4 1.624 67.4 1.725 68.5 1.726 69.6 1.827 70.9 1.928 72.4 2.129 74.4 2.430 78.3 3.7*SE = Standard Error of T-Score metricPROMIS Adult v1.0 and v1.1 –Pain Interference 8aShort Form Conversion Table Raw SummedScore T-Score SE*8 40.7 5.99 47.9 2.410 49.9 1.811 51.2 1.512 52.3 1.413 53.2 1.414 54.1 1.415 55 1.416 55.8 1.417 56.6 1.418 57.4 1.319 58.1 1.320 58.8 1.321 59.5 1.322 60.2 1.323 60.8 1.324 61.5 1.325 62.1 1.326 62.8 1.327 63.5 1.328 64.1 1.329 64.8 1.330 65.5 1.331 66.2 1.332 66.9 1.333 67.7 1.334 68.4 1.335 69.2 1.336 70.1 1.437 71 1.438 72.1 1.639 73.5 1.940 77 3.4 *SE = Standard Error on T-Score metricPROMIS Pediatric GenPop v3.0 – PainInterference 8aShort Form Conversion Table Raw SummedScore T-score SE*8 43.8 7.19 52.1 4.210 53.9 4.111 56.2 3.512 57.6 3.313 59.0 2.814 60.1 2.615 61.2 2.516 62.1 2.417 62.9 2.318 63.7 2.319 64.5 2.220 65.3 2.221 66.0 2.222 66.7 2.223 67.4 2.224 68.1 2.225 68.8 2.226 69.6 2.227 70.3 2.228 71.0 2.229 71.7 2.230 72.4 2.231 73.2 2.232 74.0 2.233 74.8 2.334 75.6 2.335 76.5 2.436 77.5 2.537 78.5 2.538 79.8 2.739 81.2 2.840 83.5 3.0 *SE = Standard Error on T-score metricPROMIS Parent Proxy GenPop v3.0 –Pain Interference 8aShort Form Conversion Table Raw SummedScore T-score SE*8 45.4 7.59 55.2 4.010 57.6 3.711 59.8 3.012 61.3 2.813 62.7 2.514 63.8 2.315 64.8 2.316 65.8 2.217 66.7 2.218 67.6 2.219 68.4 2.220 69.3 2.221 70.1 2.222 71.0 2.223 71.8 2.224 72.6 2.225 73.4 2.226 74.3 2.227 75.1 2.228 75.9 2.229 76.7 2.130 77.5 2.131 78.4 2.132 79.2 2.133 80.0 2.134 80.9 2.135 81.8 2.236 82.8 2.237 83.8 2.338 84.9 2.339 85.9 2.240 87.1 1.9 *SE = Standard Error on T-score metricAPPENDIX 2 – SCORING TABLES FOR RETIRED MEASURES*SE = Standard Error on T-Score metric PROMIS Pediatric v1.0 – Pain Interference 8a Short Form Conversion Table Raw Summed Score T-Score SE* 0 34.0 5.6 1 38.7 4.4 2 40.6 4.2 3 42.7 3.8 4 44.3 3.7 5 45.8 3.4 6 47.1 3.3 7 48.4 3.2 8 49.5 3.2 9 50.6 3.1 10 51.7 3.1 11 52.7 3.1 12 53.7 3.0 13 54.7 3.0 14 55.7 3.0 15 56.6 3.0 16 57.6 3.0 17 58.5 3.0 18 59.5 3.0 19 60.4 3.0 20 61.4 3.0 21 62.4 3.0 22 63.4 3.0 23 64.4 3.0 24 65.4 3.1 25 66.5 3.1 26 67.6 3.2 27 68.8 3.2 28 70.1 3.3 29 71.5 3.4 30 73.2 3.7 31 75.0 3.8 32 78.0 4.3PROMIS Parent Proxy v1.0 – Pain Interference 8a Short Form Conv e rsion TableRaw Summed Score T-Score SE*0 38.0 6.01 44.0 3.02 46.0 3.03 48.0 3.04 49.0 2.05 50.0 2.06 51.0 2.07 52.0 2.08 53.0 2.09 54.0 2.010 55.0 2.011 56.0 2.012 57.0 2.013 58.0 2.014 58.0 2.015 59.0 2.016 60.0 2.017 61.0 2.018 62.0 2.019 62.0 2.020 63.0 2.021 64.0 2.022 65.0 2.023 66.0 2.024 67.0 2.025 67.0 2.026 68.0 2.027 69.0 2.028 70.0 2.029 71.0 3.030 73.0 3.031 74.03.032 78.04.0*SE = Standard Error on T-Score metricPROMIS Pediatric v2.0 –Pain Interference 8aShort Form Conversion Table RawT-Score SE* SummedScore8 34.0 5.69 38.7 4.410 40.6 4.211 42.7 3.812 44.3 3.713 45.8 3.414 47.1 3.315 48.4 3.216 49.5 3.217 50.6 3.118 51.7 3.119 52.7 3.120 53.7 3.021 54.7 3.022 55.7 3.023 56.6 3.024 57.6 3.025 58.5 3.026 59.5 3.027 60.4 3.028 61.4 3.029 62.4 3.030 63.4 3.031 64.4 3.032 65.4 3.133 66.5 3.134 67.6 3.235 68.8 3.236 70.1 3.337 71.5 3.438 73.2 3.739 75.0 3.840 78.0 4.3 *SE = Standard Error on T-Score metricPROMIS Parent Proxy v2.0 –Pain Interference 8aShort Form Conv e rsion TableRawT-Score SE*SummedScore8 38.0 6.09 44.0 3.010 46.0 3.011 48.0 3.012 49.0 2.013 50.0 2.014 51.0 2.015 52.0 2.016 53.0 2.017 54.0 2.018 55.0 2.019 56.0 2.020 57.0 2.021 58.0 2.022 58.0 2.023 59.0 2.024 60.0 2.025 61.0 2.026 62.0 2.027 62.0 2.028 63.0 2.029 64.0 2.030 65.0 2.031 66.0 2.032 67.0 2.033 67.0 2.034 68.0 2.035 69.0 2.036 70.0 2.037 71.0 3.038 73.0 3.039 74.0 3.040 78.0 4.0*SE = Standard Error on T-Score metric.All scoring tables based on default Parent Proxy calibrations.APPENDIX 3 – CROSSWALK BETWEEN PEDIATRIC AND PARENT PROXY V2.0 T-SCORES AND PEDIATRIC AND PARENT PROXY GENPOP V3.0 T-SCORES Table 1. PROMIS Pediatric Pain Interference: Crosswalk between v2.0 T-scores and GenPop v3.0 T-scoresPROMIS Pediatric Pain Interference T-Score PROMIS Pediatric Pain Interference T-Scorev2.0 v3.0 GenPop v2.0 v3.0 GenPop33 43.0 71 79.534 48.9 72 80.035 48.9 73 81.536 49.5 74 83.037 51.1 75 85.538 52.2 76 85.539 53.3 77 85.540 54.6 78 85.541 55.8 79 85.542 56.9 80 85.543 57.9 81 85.544 59.1 82 85.545 60.0 83 88.046 60.547 61.148 62.149 63.550 64.451 64.752 65.253 65.854 66.555 67.756 68.557 69.158 69.959 70.960 71.861 72.562 73.063 73.364 73.565 74.566 75.267 75.568 76.569 78.070 79.0Table 2. PROMIS Parent Proxy Pain Interference: Crosswalk between v2.0 T-scores and GenPop v3.0 T-scoresPROMIS Parent Proxy Pain Interference T-Score PROMIS Parent Proxy Pain Interference T-Scorev2.0 v3.0 GenPop v2.0 v3.0 GenPop37 45.0 75 87.038 50.5 76 87.039 50.5 77 87.040 50.5 78 87.041 51.0 79 87.042 53.6 80 87.043 54.6 81 89.044 56.045 57.046 58.547 59.448 60.449 61.750 62.851 64.052 64.853 65.654 66.955 67.756 68.857 69.758 70.859 71.860 72.861 73.862 75.063 75.864 76.565 77.566 79.067 79.068 80.569 83.070 83.071 83.072 85.073 87.074 87.0。
新伦克电容器系列 AGM 铅酸电池说明书

Page <1>V1.019/06/20AGM Lead Acid Batteries/exclusive-brands /exclusive-brands /exclusive-brandsPart Number Model Voltage Capacity Dimensions W × H × DWeight Terminal PEL01428ES6-3.26V 3.2Ah 61 × 67 × 35mm 68g T1PEL01429ES6-46V 4Ah 101 × 107 × 47mm 67g T1PEL01430ES6-56V 5Ah 101 × 107 × 47mm 82g T1PEL01431ES6-76V 7Ah 94 × 100 × 34mm 105g T1PEL01432ES6-126V 12Ah 94 × 100 × 50mm 170g T1/ T2PEL01433ES12-1.212V 1.2Ah 52 × 58 × 43mm 55g T1PEL01434ES12-2.312V 2.3Ah 61 × 67 × 35mm 95g T1PEL01435ES12-3.212V 3.2Ah 61 × 67 × 67mm 130g T1PEL01436ES12-712V 7Ah 95 × 101 × 65mm 205g T1/T2PEL01437ES12-1212V 12Ah 95 × 101 × 98mm 345g T1/T2PEL01438ES12-1812V18Ah167 × 167 × 77mm512gT3/T8Features• Design Life: 5 years @20°C/68°F • Stable Quality & High Reliability • Sealed Construction • Environmentally friendly• Maintenance-Free Operation • Low Pressure Venting System • Heavy Duty Grid •Low Self DischargeApplicationsAlarm Systems Cable TelevisionCommunications Equipment Control Equipment ComutersElectronic Cash Registers Electric Test EquipmentElectric Powered Bicycle and Wheel chair Emergency lighting Systems Fire & SecurityGeophysical EquipmentImportant Notice : This data sheet and its contents (the “Information”) belong to the members of the AVNET group of companies (the “Group”) or are licensed to it. No licence is granted for the use of it other than for information purposes in connection with the products to which it relates. No licence of any intellectual property rights is granted. The Information is subject to change without notice and replaces all data sheets previously supplied. The Information supplied is believed to be accurate but the Group assumes no responsibility for its accuracy or completeness, any error in or omission from it or for any use made of it. Users of this data sheet should check for themselves the Information and the suitability of the products for their purpose and not make any assumptions based on information included or omitted. Liability for loss or damage resulting from any reliance on the Information or use of it (including liability resulting from negligence or where the Group was aware of the possibility of such loss or damage arising) is excluded. This will not operate to limit or restrict the Group’s liability for death or personal injury resulting from itsnegligence. pro- ELEC is the registered trademark of Premier Farnell Limited 2019.DescriptionValve regulated lead acid battery designed with AGM(Absorbent Glass Mat) technology and for general application purposes such as UPS, emergency lighting and electrical utilities. Complies with popular international standards; such as IEC60896-21/22, VDS2344:2005-12(06), BS6290-4 and Eurobat Guide.Marine Equipment Medical EquipmentMicro Processor Based Office MachinesPortable Cine & Video Lights Power ToolsSolar Powered SystemsTelecommunications Systems Television & Video Recorders ToysUninterruptible Power Supplies Vending Machines。
- 1、下载文档前请自行甄别文档内容的完整性,平台不提供额外的编辑、内容补充、找答案等附加服务。
- 2、"仅部分预览"的文档,不可在线预览部分如存在完整性等问题,可反馈申请退款(可完整预览的文档不适用该条件!)。
- 3、如文档侵犯您的权益,请联系客服反馈,我们会尽快为您处理(人工客服工作时间:9:00-18:30)。
Constant Failure Rate: Probability Distribution of reliability is an exponential function. Although an individual component may not have an exp reliability distribution, in a complex system with many components the overall reliability may appear as a series of random events and the system will follow an exponential reliability distribution. Space Systems Engineering: Reliability Module
Some expressions you will hear in the aerospace community:
Reliability of 0.9997 No single point failure mode design Single thread design Must not fail Graceful degradation is OK Fully redundant system Critical function redundancy only Faster, better, cheaper
Galileo high-gain antenna example Apollo 13 example
Space Systems Engineering: Reliability Module
9
Ways to Achieve Reliability in Space System
Also known as "Fault Avoidance" Provide ample environmental and design margins, or use appropriate de-rating guidelines. Use high-quality, carefully selected, screened parts where needed.
7
The "Bathtub" Failure Rate Curve
Burn-in or debugging period
Useful life period
Old age period
(or cycles) Because of burn-in failures and/or inadequate quality assurance practices, the failure rate is initially high, but gradually decreases during the infant period. During the useful life period, the failure rate remains constant, reflecting randomly occurring failures. Later, the failure rate begins to increase because of wear-out failures.
Space Systems Engineering: Reliability Module 8
Redundancy
Fault Tolerance Fault tolerance is a system design characteristic associated with the ability of a system to continue operating after a component failure has occurred. It is implemented by having design redundancy and a fault detection response capability. Design redundancy can take several forms: parallel, stand-by, and cross-strapped (see upcoming block diagram slide). Functional Redundancy Functional redundancy is a system design and operations characteristic that allows the system to respond to component failures in a way sufficient to meet mission requirements. This usually involves operational work-arounds and the use of components in ways that were not originally intended.
= -(1/R) dR/dt
= f(t) / (1 - F(t))
R(t)
= ∫t f(λ)d λ
t
∞
= 1 - F(t)
= e(- λt) = e(- t/MTBF)
F(t)
= ∫0 f(λ)d λ
= 1 - R(t)
f(t)
= - dR(t)/dt
= λ(t)R(t)
For systems that must operate continuously, it is common to express their reliability in terms of the Mean Time Between Failure (MTBF), where MTBF = 1/ λ.
Space Systems Engineering: Reliability Module 6
Constant Failure Rate
Source: Blanchard and Fabrycky, Systems Engineering and Analysis, Prentice Hall, 1998
Reliability Module
Space Systems Engineering, version 1.0
Space Systems Engineering: Reliability Module
Module Purpose: Reliability To understand the importance of reliability as a engineering discipline within systems engineering, particularly in the aerospace industry. To understand key reliability concepts, such as constant failure rate, mean-time-between failure, and "bathtub" curve. To introduce different forms of system redundancy, including fault tolerance, functional redundancy, and fault avoidance. Review ways to calculate reliability and the use of block diagrams.
Reliability engineering is a specialty discipline within the systems engineering process. Reflected in key activities:
Design - including design features that ensure the system can perform in the predicted physical environment throughout the mission. Trade studies - reliability as a figure of merit. Often traded with cost. Modeling - reliability prediction models, reflecting environmental considerations and applicable experience from previous projects. Test - making independent predictions of system reliability for test planning/program; sets environmental test requirements and specifications for hardware qualification.
Reliability is an inherent system design characteristic. Reliability plays a key role in determining the system's costeffectiveness. Reference: NASA Systems Engineering Handbook definition (1995 version)
Henry Petroski Design Paradigms Case Histories of Error and Judgment in Engineering
Space Systems Engineering: Reliability Module
Risk Philosophy – A Key Design Driver