AnlexVC++2
阿西克斯 IM 标准2形C双联接电路(2CO 联接电路)信号电继说明书
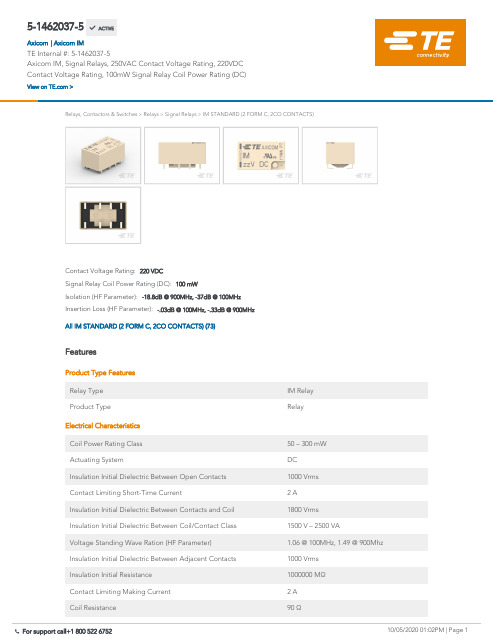
5-1462037-5Axicom IM, Signal Relays, 250VAC Contact Voltage Rating, 220VDC Contact Voltage Rating, 100mW Signal Relay Coil Power Rating (DC)10/05/2020 01:02PM | Page 1For support call+1 800 522 6752Relays, Contactors & Switches > Relays > Signal Relays >IM STANDARD (2 FORM C, 2CO CONTACTS)Insertion Loss (HF Parameter):-.03dB @ 100MHz, -.33dB @ 900MHzIsolation (HF Parameter):-18.8dB @ 900MHz, -37dB @ 100MHzSignal Relay Coil Power Rating (DC):100 mWContact Voltage Rating:220 VDCAll IM STANDARD (2 FORM C, 2CO CONTACTS) (73)FeaturesProduct Type Features Relay Type IM Relay Product TypeRelayElectrical Characteristics Coil Power Rating Class 50 – 300 mW Actuating SystemDC Insulation Initial Dielectric Between Open Contacts 1000 Vrms Contact Limiting Short-Time Current2 A Insulation Initial Dielectric Between Contacts and Coil 1800 Vrms Insulation Initial Dielectric Between Coil/Contact Class 1500 V – 2500 VAVoltage Standing Wave Ration (HF Parameter) 1.06 @ 100MHz, 1.49 @ 900Mhz Insulation Initial Dielectric Between Adjacent Contacts 1000 Vrms Insulation Initial Resistance 1000000 MΩContact Limiting Making Current 2 A Coil Resistance90 ΩContact Limiting Continuous Current2 A5-1462037-5 ACTIVEAxicom TE Internal #:5-1462037-5Axicom IM, Signal Relays, 250VAC Contact Voltage Rating, 220VDC Contact Voltage Rating, 100mW Signal Relay Coil Power Rating (DC)View on >Axicom IM|Contact Limiting Continuous Current 2 ACoil Type BistableContact Limiting Breaking Current 2 AContact Switching Load (Min).1mA @ .0001VContact Voltage Rating220 VDCSignal Relay Coil Power Rating (DC)100 mWSignal Relay Coil Voltage Rating 3 VDCSignal Relay Contact Switching Voltage (Max)220 VDCSignal Relay Coil Magnetic System Bistable, 1 CoilSignal CharacteristicsIsolation (HF Parameter)-18.8dB @ 900MHz, -37dB @ 100MHzInsertion Loss (HF Parameter)-.03dB @ 100MHz, -.33dB @ 900MHzBody FeaturesInsulation Special Features2500V Initial Surge Withstand Voltagebetween Contacts & CoilWeight.75 g[.026 oz]Contact FeaturesContact Plating Material GoldContact Current Class0 – 2 AContact Special Features Bifurcated/Twin ContactsSignal Relay Terminal Type PCB-SMTSignal Relay Contact Current Rating 2 ASignal Relay Contact Arrangement 2 Form C (2 CO)Contact Material PdRu+AuContact Number of Poles2Termination FeaturesTermination Type Surface MountMechanical AttachmentSignal Relay Mounting Type Printed Circuit BoardDimensionsWidth Class (Mechanical)0 – 6 mmWidth 6 mm[.222 in]Height 5.65 mm[.221 in]10/05/2020 01:02PM | Page 2 For support call+1 800 522 6752Height 5.65 mm[.221 in]Length Class (Mechanical)0 – 10 mmLength10 mm[.393 in]Height Class (Mechanical)0 – 6 mmDimensions (L x W x H) (Approximate)10 x 6 x 5.65 mm[.393 x .236 x .222 in]Usage ConditionsEnvironmental Ambient Temperature (Max)85 °C[185 °F]Environmental Ambient Temperature Class70 – 85°CEnvironmental Category of Protection RTVOperating Temperature Range-40 – 85 °C, -40 – 85 °COperation/ApplicationPerformance Type StandardPackaging FeaturesPackaging Method ReelOtherAdditional Features J LegProduct ComplianceFor compliance documentation, visit the product page on >EU RoHS Directive 2011/65/EU CompliantEU ELV Directive 2000/53/EC CompliantChina RoHS 2 Directive MIIT Order No 32, 2016No Restricted Materials Above ThresholdEU REACH Regulation (EC) No. 1907/2006Current ECHA Candidate List: JUN 2020(209)Candidate List Declared Against: JUL 2019(201)Does not contain REACH SVHCHalogen Content Low Bromine/Chlorine - Br and Cl < 900ppm per homogenous material. Also BFR/CFR/PVC FreeSolder Process Capability Reflow solder capable to 260°CProduct Compliance DisclaimerThis information is provided based on reasonable inquiry of our suppliers and represents our current actual knowledgebased on the information they provided. This information is subject to change. The part numbers that TE has identified asEU RoHS compliant have a maximum concentration of 0.1% by weight in homogenous materials for lead, hexavalentchromium, mercury, PBB, PBDE, DBP, BBP, DEHP, DIBP, and 0.01% for cadmium, or qualify for an exemption to theselimits as defined in the Annexes of Directive 2011/65/EU (RoHS2). Finished electrical and electronic equipment products10/05/2020 01:02PM | Page 3 For support call+1 800 522 675210/05/2020 01:02PM | Page 4For support call+1 800 522 6752limits as defined in the Annexes of Directive 2011/65/EU (RoHS2). Finished electrical and electronic equipment products will be CE marked as required by Directive 2011/65/EU. Components may not be CE marked. Additionally, the part numbers that TE has identified as EU ELV compliant have a maximum concentration of 0.1% by weight in homogenous materials for lead, hexavalent chromium, and mercury, and 0.01% for cadmium, or qualify for an exemption to these limits as defined in the Annexes of Directive 2000/53/EC (ELV). Regarding the REACH Regulation, the information TE provides on SVHC in articles for this part number is based on the latest European Chemicals Agency (ECHA) ‘Guidance on requirements for substances in articles’ posted at this URL: https://echa.europa.eu/guidance-documents/guidance-on-reachTE Model / Part #2267072-2PMS9P1B10M6RETE Model / Part #2176325-6CRGP 0402 27R 1%TE Model / Part #1447009-7SPRING FINGERSTE Model / Part #20000980-00MS5840-02BA LOW PROFILE PRESSURE SENSORSignal Relays(122)RJ45 Connectors(2) TE Model / Part #CAT-AX41-IM11B IM STANDARD (2 FORM C, 2CO CONTACTS)Compatible PartsAlso in the Series Axicom IMCustomers Also Bought10/05/2020 01:02PM | Page 5For support call+1 800 522 6752TE Model / Part #2-1825010-2ASE42RL04=4PDT AUTOSLIDETE Model / Part #1367710-1assy guide frame x2 cast metal type 2TE Model / Part #103240-816 MODII HDR DRST B/A .100CLTE Model / Part #5-2176309-1RP 1E 0.1W 33R2 0.1% 25PPM 1K RLTE Model / Part #1-1879623-4H4 500K 0.1% 25PPMTE Model / Part #3-1825059-7ADF08S04=DIP SWT,FLUSH,SMT-GWDocumentsProduct DrawingsIM41JR=IM RELAY 100 MW 3 V BISEnglishIM41JR=IM RELAY 100 MW 3 V BISEnglish CAD Files3D PDF3DCustomer View ModelENG_CVM_CVM_1462037-3_A.2d_dxf.zipEnglishCustomer View ModelENG_CVM_CVM_1462037-3_A.3d_igs.zipEnglishCustomer View ModelENG_CVM_CVM_1462037-3_A.3d_stp.zipEnglishBy downloading the CAD file I accept and agree to the of use.Terms and Conditions Datasheets & Catalog PagesAxicom Signal and High Frequency Relays (RF Switches) APPLICATION NOTE #2EnglishLighting Relays GuideEnglishIM Relay DatasheetEnglishIndustrial Relays Quick Reference GuideEnglishIndustrial Relays Quick Reference GuideEnglishProduct SpecificationsDefinitions RelaysEnglish10/05/2020 01:02PM | Page 6 For support call+1 800 522 6752。
Lorex LNC226X系列无线高清网络摄像头说明书
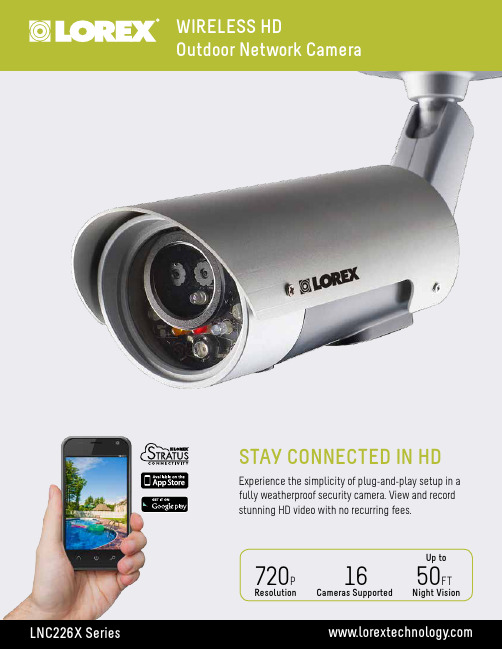
FEATURES:• View, record & playback in real-time HD• Weatherproof indoor/outdoor camera (IP66 rated) • Cold climate capability (operates to -4°F/ -20°C)• Record to smartphone, tablet, PC, Mac or NASFEATURES:• iOS, Android, PC and Mac compatible*• Real-Time (30fps) HD 1280x800 Mega-pixel resolution • Wi-Fi & wired internet connectivity• 5 Second pre-recording on SD cardLNC226X SpecificationsMode: Day & NightPower: 20V, 0.6AProcessors: RISC CPU, hardware video processing andcompressionNetwork interface: Ethernet 10BaseT/100BaseTX, Auto-MDIX, RJ-45 Wireless interface: IEEE 802.11b/g/nImage sensor: HD up to 1280x800 resolution1/4” Megapixel Color CMOSSeparate sensors for day and night with automaticgain, white balance, exposure and brightness control Light sensitivity: 0.2 Lux (IR LED off)0 Lux (with 9 meters IR LED on)Automatically turn on the IR LED in low lightenvironmentLens: 4.2mm, F2.4, viewing angle: 62°, fixed irisDay and night separate lensButtons: One reset button, to factory default settingsOne WPS button for automatic WiFi setup Indicators: One LED for Internet connection status indicationOne LED for Ethernet connection indicationOne LED for SD card recording indicationVideo compression: H.264Video streaming: Separate frame rate/resolution/bandwidth settingsfor PC and mobileResolution: 1280x800, 1024x768, VGA (640x480), QVGA(320x240)Bandwidth: 64Kbps ~ 3MbpsFrame rate: 1~30fpsAudio: Built-in microphone for audio monitoringVideo management software: L-View software for viewing and archiving up to 16cameras (PC/Mac)Lorex Ping app for viewing cameras on mobile(iOS/Android™)Security: Web management username/password protectionVideo display ID/password protectionWiFi WEP and WPA/WPA2 security mode Installation, management and maintenance:Plug & play by ID/passwordFirmware upgrades by FTPL-View SW upgrade Push Notification Users: Up to 20 simultaneous users (depends on videosettings and Internet bandwidth)Alarm and event management: Events triggered by motion and sound detectionE-mail/FTP alarm messagePush notification on supported mobile devices Approvals: EMC — CE, FCC Part 15 Subpart B Class B, IC Class BWireless RF — CE, FCC Part 15 Subpart C Indoor / Outdoor: Both (IP66 rated)*Operating conditions: -20 – 50°CHumditiy 20–80% RH (non-condensing) Dimensions (W x D x H): 58 x 230 x 52mm / 2.3 x 9.1 x 2.1”Weight: 0.37kg / 0.81lbs (including camera bracket)LNC204 SpecificationsMode: Day & NightPower: 5V (USB) - 12V, 1AProcessors: RISC CPU, hardware video processing andcompression.Network interface: Ethernet 10BaseT/100BaseTX, Auto-MDIX, RJ-45 Wireless interface: IEEE 802.11b / g / nImage sensor: HD up to 1280x800 resolution1/4" Megapixel Color CMOSSeparate sensors for day and night with automaticgain, white balance, exposure and brightnesscontrolPIR sensor: Effective distance – 7 metersLight sensitivity: 0.2 Lux ( IR LED off )0 Lux (with 9 meters IR LED on)Automatically turn on the IR LED on low lightenvironment.Infrared thermometer: Infrared Range: -40 ~ 115 °C, accuracy:+-0.5°C Lens: 4.2 mm, F2.4, viewing angle: 66°, fixed iris.Day and night separate lensButtons: One reset button, to factory default settingsOne WPS button for automatic WiFi setup Indicators: One LED for Internet connection status indicationOne LED for Ethernet connection indicationOne LED for SD card recording indicationVideo compression: H.264, baseline profile level 3.1Video streaming: Separate frame rate/resolution/bandwidth settingsfor PC and mobile.Resolution: 1280x800, 1024x768, VGA(640x480),QVGA(320x240)Bandwidth: 64Kbps ~ 3MbpsFrame rate: 1~30 fpsAudio: Built-in 0.5W speaker for alarm and half-duplextwo-way audio.Speaker jack for external speakerVideo management software: L-View software for viewing and recording up to 4cameras (PC/Mac)Lorex Ping app for viewing cameras on mobile (iOS/Android™)Security: Web management username/password protectionVideo display ID/password protectionWiFi WEP and WPA/WPA2 security mode Installation, management and maintenance:Plug & play by ID/password.Firmware upgrades via FTPL-View SW upgrade Push NotificationUsers Up to 20 simultaneous users (depends on videosettings and internet bandwidth)Alarm and event management: Events triggered by PIR and sound detectionEmail/ftp alarm messageTemperature alarm for low/high room temperaturePush notification on supported mobile devices. Dimensions: 68 x 25 x 95mm/2.8 x 1.0 x 3.7" (W x D x H) Weight: 0.28kg/0.62lbs (including camera bracket) Approvals: EMC - CE, FCC Part 15 Subpart B Class B, IC Class BWireless RF - CE, FCC Part 15 Subpart C, RSS210Power supply: CE, FCC, UL, EN 60950 Operating conditions 0-50 °CHumidity 20 – 80% RH (non-condensing)© 2015 Lorex CorporationAs our product is subject to continuous improvement, Lorex Corporation & subsidiaries reserve the right to modify product design, specifications &Lorex Corporation250 Royal Crest Court Markham, Ontario,901 Elkridge Landing Road, Suite Product InformationLNC226X Wireless HD Outdoor Network Camera UPC7-78597-00226-3Package Weight:0.8 kg / 1.8 lbsPackage Dimensions:(W x D x H)280 x 89 x 191mm / 11 x 3.5 x 7.5”Package Cube:0.0048 CBM x 0.168 CBFContents:Indoor/outdoor camera, Ethernet cable, Power adapter, Quick Setup Guide, CD (user manual included on CD)1. Not intended for submersion in water. Installation in a sheltered location recommended.2. Requires a high speed Internet connection and a wired connection to arouter (not included). An upload speed of 1Mbps is recommended for optimal video performance. Up to 3 devices may connect to the system at the same time. For the latest compatibility list check /support as new models become available in the market.3. Compatible with WPS enabled routers (not included).4. Stated IR illumination ranges are based on ideal conditions in total darkness and typical outdoor night time ambient lighting. Actual range and image clarity depends on installation location, viewing area and light reflection / absorption.5. microSD card not included (supports up to 32GB).6. Connection speed may vary depending Internet bandwidth.7. Additional cameras sold separately.LNC226X DisclaimersLNC226X Dimensions129mm/5.1"92mm/3.6"210/8.3"LNC226XPK2B Wireless HD Outdoor Network Camera, 2 Pack UPC6-95529-00217-0Package Weight: 2.1 kg / 4.8 lbsPackage Dimensions:(W x D x H)304 x 254x 190mm / 12 x 10 x 7.5”Package Cube:0.014 CBM x 0.52 CBFContents:2 x Indoor/outdoor cameras, 2 x Ethernet cables, 2 x Power adapters, Quick Setup Guide, CD (user manual included on CD)1. Compatible with WPS enabled routers (not included).2. Infrared illumination range under ideal conditions. Actual range and clarity may vary depending on scene/object reflection and camera application.3. microSD Card not included (supports up to 32GB).4. Connection speed may vary depending on internet bandwidth.5. Up to 4 simultaneous camera views available on PC, Mac and tablets. Selectable single camera viewing on smartphones.LNC204 DisclaimersLNC204 Dimensions75mm/3.0"35mm/1.4"128mm/5.1"LNC226PK22B Wireless HD Outdoor/Indoor Network Camera, 2 Pack UPC6-95529-00257-6Package Weight: 2.2 kg / 5 lbsPackage Dimensions:(W x D x H)304 x 228 x 228mm / 12 x 9 x 9”Package Cube:0.01 CBM x 0.56 CBFContents:1 x Indoor camera, 1 x Outdoor camera,2 x Ethernet cables, 2 x Power adapters, Quick Setup Guide, CD (user manual included on CD)。
Audio-Technica ATR2100x-USB卡诺伊动态USB XLR麦克风用户手册说明书

User ManualContentsIntroduction & features 2 Setting up your microphone with pivot mount & desk stand 3Preliminary setup with MacOS Mojave 4Advanced setup with MacOS Mojave 7Preliminary setup with Windows 10 9Advanced setup with Windows 10 11Using headphones 15Selecting software 15Setting your software levels 15Positioning your microphone 15XLR 0peration 15Protecting your microphone 15Specifications 16Warranty 17Compliance with FCC rules (USA only)This device complies with Part 15 of the FCC rules. Operation is subject to the following two conditions:(1) this device may not cause harmful interference, and (2) this device must accept any interference received,including interference that may cause undesired operation.FCC WARNINGYou are cautioned that any changes or modifications not expressly approved in this manual could void yourauthority to operate this equipment.Canada onlyThis Class B digital apparatus complies with Canadian ICES-003.Cet appareil numérique de la classe B est conforme á la norme NMB -003 du Canada.Thank you for buying the Audio-Technica ATR2100x-USB cardioid dynamic USB/XLR microphone. Equipped with both USB-C and XLR outputs, this digital/analog mic is designed both for live performance and digitally capturing music or any acoustic audio source using your favorite recording software.The ATR2100x-USB offers high-quality articulation and intelligibility perfect for home studio recording, field recording, podcasting, voice over, and on-stage use. Its cardioid polar pattern reduces pickup of sounds from the sides and rear, improving isolation of desired sound source.The microphone also features a built-in headphone jack with volume control that allows you to directly monitor your microphone’s output during recording. The microphone’s focused pickup pattern delivers excellent off-axis rejection, while its A/D converter with up to 24-bit, 192 kHz sampling rate ensures clear, articulate sound reproduction.Audio-Technica’s state-of-the-art design and manufacturing techniques ensure that the microphone complies with the company’s renowned consistency and reliability standards.Features• Handheld dynamic microphone with USB digital output and XLR analog output• USB output connects to your computer for digital recording, while the XLR output connects with your sound system’s conventional microphone input for use in live performance• Smooth, extended frequency response ideally suited for podcasting, home studio recording, field recording, voice over, and on-stage use• Built-in headphone jack allows you to directly monitor your microphone’s output without audible delay• Adjust headphone volume with easy-to-use controls on the bottom of the microphone• High-quality A/D converter with up to 24-bit, 192 KHz sampling rate• Compatible with Windows and Mac• Low-mass diaphragm provides excellent frequency response• Cardioid polar pattern reduces pickup of sounds from the sides and rear, improving isolation of desired sound source• Tripod desk stand with folding legs for secure, easily portable tabletop use• Pivoting, threaded stand mount attaches securely to the supplied tripod or to a conventional microphone stand • USB-C to USB-A, USB-C to USB-C and XLR cables included• Durable metal construction for long-lasting performance• On/off switch functions for both USB and analog operation23ATR2100x-USB SetupStand clampScrew the microphone stand clamp onto the threaded portion of the desk stand. The front of the microphone should be facing the A-T logo on the desk stand.Install the microphone into the stand clamp, w ith ON/OFF switch facing up.Extend the tripod legs to provide a wide, securebase, and place the tripod desk stand on a flat e a screwdriver or coin to loosen/tighten the pivot screws for angle adjustment.For digital use, plug one of the provided USBcables into the base of the microphone thenconnect the other end of the cable to your digitalrecording device.When connecting the microphone to a USB-C port,you must use a USB On-The-Go (USB OTG) cable like the one included.For analog use, plug the provided XLR cable intothe base of the microphone then connect the otherend o f the cable to your analog audio device.When using with equipment that includes abuilt-in mic, consult that device’s user guide forinstructions on disabling its mic.Optional headphone monitoring: Connectheadphones with 3.5 mm (⅛") plug into base ofmicrophone. Use the dial to control volume.1234564NOTICE Regarding MacOS CatalinaWith the release of MacOS Catalina, Apple has introduced restrictions on using non-Apple software. Unless the recording application is officially supported to run under MacOS Catalina, you will not be able to access the microphone even if it shows up as a sound input device!If you are using an older version of MacOS, your computer will automatically recognize the USB deviceand install the appropriate driver.If you are using MacOS Mojave, you must enable software access to the microphone, using the security and privacy settings.1. Connect the ATR2100x-USB microphone to an open USB port on the Mac (Type A or Type C).Open the system preferences by clicking the Apple logo in the upper left corner of the menu bar and selecting System Preferences. Alternatively, you can click on the gear icon in the dock. Click the Loudspeaker icon to open the sound preferences.2. By default the Mac selects the internal microphone as the sound input device. When the ATR2100x-USB is plugged in, the Mac assumes that it is the desired input device and automatically selects it.Verify that the ATR2100x-USB is highlighted.The input volume for the microphone can be adjusted by moving the input slider and watching the level meter while speaking into the microphone. Setting the level too low will not provide enough input signal to yourrecording application. Setting it too high can overload the input to the recording application resulting in clipping or distortion.Note: The output volume slider controls the Mac’s speaker or headphone jack output and does not affect the input sound level. This slider replicates the volume control associated with the small speaker icon in the menu bar and the volume controls on the keyboard.Preliminary setup with MacOS MojaveClick the Apple Logo and select System PreferencesClick the Loudspeaker icon to open thesound preferencesPreliminary setup with MacOS Mojave(continued)3. Because the ATR2100x-USB Microphone has a built-in headphone output, the Mac selects it as the output device. Should you desire to use the internal speakers for playback audio, click the Output tab and choose the desiredoutput device.The balance control sets the left to right balance in the output device.The Output volume controls the playback level from the Mac. It is the same as clicking on the small speaker icon inthe menu bar and adjusting volume or using the keyboard controls.With recent updates to MacOS Mojave and the latest MacOS Catalina, Apple implemented a privacy setting allowing you to control which apps have access to the microphone.If you are using MacOS Mojave, you must enable software access to the microphone, using the security and privacy settings.1. In order to use the ATR2100x-USB microphone with certain applications you need to verify that the apps areenabled to have access to the microphone.Open the system preferences and click on the Security and Privacy icon.562. To make changes, you will need to unlock the padlock on the Security and Privacy window by entering your user name and password.Scroll down to make certain the apps you want to use the microphone with are enabled. If not, use the switch slider associated with the App to turn it on.3. Click the microphone icon and verify that a check mark appears next to the applications that need access to the microphone.Make certain to click the lock to lock it after making the changes.Preliminary setup with MacOS Mojave(continued)7Advanced Sound Settings1. At this point the Mac is set up to use the ATR2100x-USB microphone as the input device and your selection as the output device. The sample rate is set for the default value (44.1 KHz CD Quality). However, additional settings are available that enable you to change the audio sampling rate and individually adjust left and right input signal levels if you desire.To access these settings, open a new finder window and navigate to “Applications—Utilities” and double-click the Audio MIDI Setup application.Advanced setup with MacOS MojaveAudio MIDI Setup2. A list of audio devices appears on the left side and the adjustable settings for the selected device appear on the right.The ATR2100x-USB appears as two separate devices. One is an input device (2 ins / 0 outs) while the other represents its output (0 ins / 2 outs).Clicking the input device (2 ins / 0 outs) shows the current settings.The Format section contains the sample rate settings.The Master Stream section allows you to individually adjust the microphone signal levels for theleft and right audio inputs.Select input version ATR2100x-USB with 2 ins / 0 outsAdvanced setup with MacOS Mojave(continued)3.The ATR2100x-USB is capable of very high-quality recording and supports sample rates of up to 192 KHz. In somesituations higher sample rates can provide better results. However, as the sample rate increases, the file sizebecomes much larger.If you are recording voice-overs for video or music that will be synchronized with video, the default sample rateneeds to be changed from 44.1 KHz to 48 KHz.To change the sample rate, click the drop-down arrows next to the Format box. A sub window opens listingavailable sample rates. Click on the desired one to choose it and close the sub-window.Remember that the selected sample rate must match the value set in your recording application or you will hearpops and clicks in the recorded audio.89If you are using an older version of Windows, your computer will automatically recognize the USB deviceand install the appropriate driver.The first time you plug the microphone in, you may see a message that new hardware has been found, or you may see a driver software installed notice. After the first time, you will not see any of these as the computer has already installed the necessary drivers for a USB microphone.When the ATR2100x-USB microphone is connected, Windows 10 will automatically select it as the input and output device.1. To verify or make changes click the Start window and click settings (the gear).2. When the settings window opens, Click “System.”Preliminary setup with Windows 1010Preliminary setup with Windows 10 (continued)4. The Sound tab opens showing the active input and output device which should be the USB microphone. To use the computer speakers as your output device, click “Choose your output device” and in the drop-downmenu choose the desired item.3. When the System window opens, in the left column, click “Sound.”At this point, your computer is set up to use the ATR2100x-USB microphone as the audio input device and whatever you chose as the audio output device. However, in the recent versions of Windows 10, Microsoft has instituted some additional privacy settings, allowing users to control which apps and programs have access to the microphone. Refer to the section on privacy for more information.There are additional settings available for the microphone, allowing you to set the input level, change the sampling rate and manage other aspects of the audio. Refer to the next section for more details.At this point Windows 10 is set up to use the ATR2100x-USB microphone as the input and output device. The sample rate is set for the Windows default (44.1 KHz CD Quality). However, additional settings are available, including input level and sampling rate.1. To access these settings, click “Sound Control Panel.”2. When the Sound Control Panel opens, select the “Recording” tab and select the ATR2100x-USB microphone.3. Click “Properties.”4. Click the Levels tab and move the slider to the right or left to set the input gain for the microphone. Setting it too low will not provide enough signal to your recording application. Setting it too high can cause the recording application to distort.Note that this level setting is different from the volume control slider on the main sound settings window.Advanced setup with Windows 105. The ATR2100x-USB is capable of very high-quality recording and supports sample rates of up to 192 KHz. In some situations higher sample rates can provide better results. However, as the sample rate increases, the file size becomes much larger.If you are recording voice-overs for video or music that will be synchronized with video, the default sample rate needs to be changed from 44.1 KHz to 48 KHz.To change the sample rate, click the Advanced tab. The default sample rate (44100 Hz CD Quality) is shown in the drop-down box. Click the drop-down and choose the desired sample rate.6. Leaving the “Exclusive Mode” boxes checked allows the recording application to take control of the microphone. This will set the sample rate correctly based on the recording project settings.When the sample rate is changed, a “Device in use” warning dialog box appears letting you know that a change has been made that may affect other applications (non-exclusive) that might be using the microphone.Click “Yes” to continue and use the new sample rate.Advanced setup with Windows 10 (continued)With recent updates to Windows 10, Microsoft has included a privacy setting allowing you to control which apps have access to the microphone.In order to use the ATR2100x-USB microphone with certain applications you need to verify that the apps are enabled to have access to the microphone.1. In the main Sound setup window, click the “Microphone privacy settings.”2. The Privacy settings window for the microphone opens. Verify that the “Allow apps to access your microphone” switch is set to “On.”Advanced setup with Windows 10(continued)3. Scroll down to make certain the apps you want to use the microphone with are enabled. If not use the switch slider associated with the app to turn it on.4. Scroll down to the section ”Allow desktop apps to access your microphone” and verify that the switch is turned on. This allows applications such as Audacity to have access to the microphone (or other chosen audio source).Advanced setup with Windows 10(continued)Additional InformationUsing headphonesThe 1/8" (3.5 mm) headphone jack on the bottom of the microphone allows you to directly monitor your recording with a pair of headphones. When your preliminary setup is completed, and your USB microphone is connected to your computer’s USB port (the microphone’s blue LED is illuminated), plug your headphones into the headphone jack on the bottom of the microphone. While talking into the microphone, you should hear yourself in the headphones. Adjust the volume up or down by rotating the Up/ Down dial on the bottom of the microphone. Note: The Up/ Down dial only adjusts the volume of the mic’s headphone output; it does not adjust the microphone level.Selecting softwareYou have many choices in recording software. Audacity, available for free online at /, is a widely used software program that provides basic recording software.Setting your software levelsCorrect adjustment of microphone level is important for optimum performance. Ideally, the microphone level should be as high as possible without overloading the input of your computer. If you hear distortion, or if your recording program shows levels that are consistently overloaded (at peak levels), turn the microphone volume (or level) down, either through your control panel (or system preferences) settings, or through your recording software. If your recording program shows insufficient level, you can increase the microphone gain either from the control panel (or system preferences) settings or through your recording program.No further microphone level adjustments should be needed, as long as the acoustic input does notchange significantly.Positioning your microphoneIt is important to position the microphone directly in line (on axis) with the person speaking/singing or instrument (or other sound source) to achieve the best frequency response of the microphone.For use in speaking/singing applications, the ideal placement for the microphone is directly in front of the person speaking/singing. The same placement is optimal when miking an instrument such as an acoustic guitar, drums or piano. Experiment with different mic placements to find the best sound for your particular setup.XLR operationFor live-sound applications, connect the XLRF connector of the included XLR cable to the XLRM output on the bottom of the microphone; connect the cable’s XLRM connector to a standard XLRF microphone input on your mixer. Turn the microphone’s ON/OFF switch to the “ON” position. Set the microphone’s level by following the instructions included with your mixer. Note: The ON/OFF switch does not affect the LED.Protecting your microphoneTake care to keep foreign particles from entering the windscreen. An accumulation of iron or steel filings on the diaphragm, and/or foreign material in the windscreen’s mesh surface, can degrade performance.Element: DynamicPolar Pattern: CardioidFrequency Response: 50 – 15,000 HzPower Requirements: USB Power (5V DC)Bit Depth: Up to 24 bitSample Rate: 44.1 kHz/48 kHz/96 kHz/192 kHzControls: On/off switch; headphone volume controlWeight: 268 g (9.5 oz)Dimensions: 183.0 mm (7.20") long, 51.0 mm (2.01") maximum body diameterOutput Connector: USB-C/XLRHeadphone Output Power: 10 mW @ 16 ohmsHeadphone Jack: 3.5 mm TRS (stereo)Accessories Included: Stand clamp for ⅝"-27 threaded stands, tripod desk stand, 2 m (6.6') USB-C to USB-C cable (USB On-The-Go Compliant), 2 m (6.6') USB-C to USB-A cable, 3 m (9.8') XLRF to XLRM cableSystem Requirements: Macintosh: Mac OS X; USB 1.0 or 2.0; 64 MB RAM (minimum)Windows: Windows 7/8/10; USB 1.0 or 2.0; 64 MB RAM (minimum)†In the interest of standards development, A.T.U.S. offers full details on its test methods to other industry professionals on request.Specifications are subject to change without notice.ATR2100x-USB Specifications †R e s p o n s e i n d B LEGEND 200 Hz 1 kHz 5 kHz 8 kHz SCALE IS 5 DECIBELS PER DIVISION240˚180˚210˚270˚300˚330˚0˚150˚120˚90˚30˚60˚Frequency ResponsePolar PatternATR2100x-USB U.S. Lifetime Limited WarrantyThis product is warranted in the U.S.A. by Audio-Technica U.S., Inc. (A.T.U.S.) for the lifetime of the original purchaser. During the warranty period, A.T.U.S. will repair or replace these products, provided they are sent prepaid to the address below, with proof of original purchase and $15.00 for handling and return to a U.S. address. Check or money order required; no cash or stamps. A.T.U.S. reserves the right to replace any product with one of equal value.Except to the extent precluded by applicable state law, A.T.U.S. will have no liability for any consequential, incidental, or special damages; any warranty of merchantability or fitness for particular purpose expires when this warranty expires. This warranty gives you specific legal rights, and you may have other rights which vary from state to state. Outside the U.S.A., please contact your local dealer for warranty details.Register your product at Audio-Technica U.S., Inc.1221 Commerce Drive, Stow, Ohio 44224 USAAudio-Technica Corporation (Headquarters)2-46-1 Nishi-naruse, Machida, Tokyo, 194-8666, JapanAudio-Technica U.S., Inc.1221 Commerce Drive, Stow, Ohio, 44224, USA© 2019 Audio-Technica Corporation P52830。
陕西亚成微电子股份有限公司 RM9026A B 双电压高压线性恒流芯片说明书

产品概述:RM9026A/B是一款高压线性全电压LED 高压驱动芯片,可以根据输入电压的高低切换灯珠的串并联方式,兼容120Vin和230Vin 两种工作模式,主要应用于球泡灯,吸顶灯等LED光源模组。
高PF或者无频闪应用,内置600V集成MOS。
RM9026A恒功率,线电压补偿模块可以有效的抑制电压波动时候输入功率的变化,线电压在一定的范围里波动时,芯片可以保持一定的恒功率的功能。
RM9026B支持PWM调光/模拟调光功能。
应用领域:⏹LED日光灯管T5/T8/T10…⏹LED灯丝灯/球泡灯/蜡烛灯…⏹其它小功率的LED电光源典型特点:⏹灯串串并联方式芯片控制自动转换⏹内置500V高压MOS,最大输出电流2*100mA⏹RM9026A具备功率补偿功能⏹RM9026B具备数字模拟调光功能⏹芯片具有过温保护功能⏹芯片应用无EMI问题⏹应用于球泡灯、投光灯、筒灯等管脚定义:RM9026A RM9026B 管脚说明:管脚名称管脚描述OUT1内部集成高压MOS漏端VCC供电端口VSP线电压检测端口CS1电流检测端口CS2电流检测端口CP功率补偿端口DIM模拟/数字调光端口SPC串并联控制端口OUT2内部集成高压MOS漏端GND芯片地典型应用:产品型号说明:产品型号具体说明RM9026A双压恒功率OTP140℃RM9026B双压DIM调光OTP140℃极限参数:符号参数参数范围CS电流采样输入电压-0.3V to7VTJ工作结温范围-40℃to150℃Tc工作温度-40℃to100℃TSTG储存温度范围-55℃to150℃注:极限值是指超出该工作范围,芯片有可能损坏。
推荐工作范围是指在该范围内,器件功能正常,但并不完全保证满足个别性能指标。
电气参数定义了器件在工作范围内并且在保证特定性能指标的测试条件下的直流和交流电参数规范。
对于未给定上下限值的参数,该规范不予保证其精度,但其典型值合理反映了器件性能。
电气参数:(无特别说明情况下,TA=25℃)符号参数测试条件最小典型最大单位VCC_ONVCC启动电压V CC=10V,DIM/CP悬空141uA V CS1/V CS2CS参考电压600mVI OUT输出电流驱动能力V OUT=30V5100mAV OUT集成MOS漏端耐压V OUT=30V500VF DIM PWM调光频率范围2001000HzV DIM模拟调光输入范围输出功率0%~100%0 1.2V I_DIM调光脚输出电流30uAICP 流入CP端口电流有效控制VCS电流范围0500uAOTP过温调节RM9026A&RM9026B140℃OTP过温调节RM9026AB&RM9026BB125℃订购信息:订购型号封装形式包装方式卷盘尺寸编带RM9026A ESOP-84000只/盘13寸RM9026B ESOP-84000只/盘13寸。
莫克A V2201系列极小型x86嵌入式计算机产品说明书
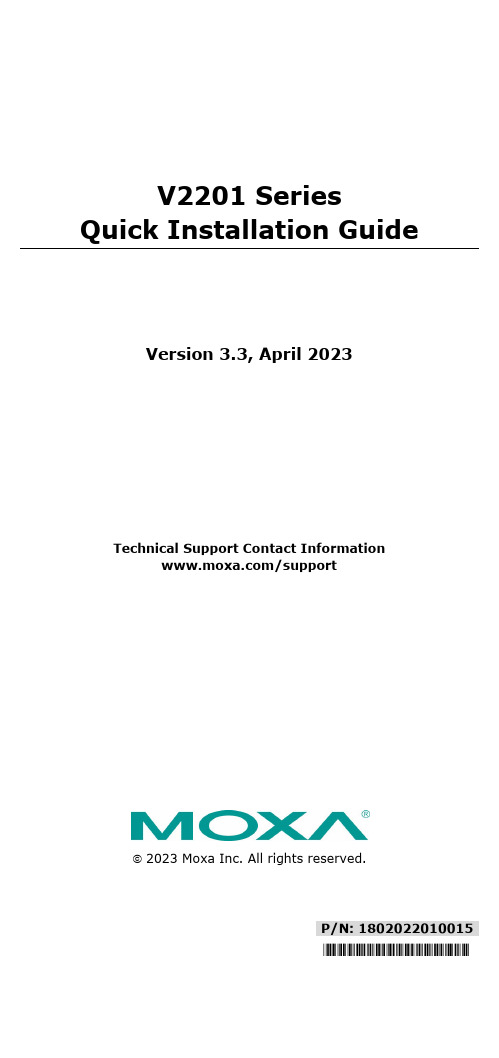
P/N: 1802022010015 *1802022010015*V2201 SeriesQuick Installation GuideVersion 3.3, April 2023Technical Support Contact Information/support2023 Moxa Inc. All rights reserved.OverviewThe Moxa V2201 Series ultra-compact x86 embedded computer is based on the Intel® Atom™ E3800 Series processor, features the most reliable I/O design to maximize connectivity, and supports dual wireless modules, making it suitable for a diverse range of communication applications. The computer’s thermal design ensures reliable system operation in temperatures ranging from -40 to 85°C, and wireless operation in temperatures ranging from -40 to 70°C with a special purpose Moxa wireless module installed. The V2201 Series supports Proactive Monitoring function for device I/O status monitoring and alerts, system temperature monitoring and alerts, and system power management. Closely monitoring the system status makes it easier to recover from errors and provides the most reliable platform for your applications.Package ChecklistBefore installing the V2201, verify that the package contains the following items:•V2201 embedded computer•Terminal block to power jack converter•Wall mounting kit•Quick installation guide (printed)•Warranty cardNOTE Notify your sales representative if any of the above items are missing or damaged.V2201 Panel LayoutThe following figures show the panel layouts of the V2201-W models. In the “non -W” models, the five antenna connectors will not be installed during production.Front PanelRight PanelLeft PanelLED IndicatorsThe following table describes the LED indicators located on the front panel of the V2201.LED Name Status Function Power Green Power is on and computer is functioning normally.Off Power is offUser Defined Red Event has occurred Off No alert mSATA Yellow Blinking: Data is being transmittedOff Not connected / No data transmissionSD Card Yellow Blinking: Data is being transmittedOff Not connected / No data transmissionWireless 1 Green Steady On: Link is OnBlinking: Data is being transmittedOff Not connectedWireless 2 Green Steady On: Link is OnBlinking: Data is being transmittedOff Not connectedLAN 1 Yellow Steady On: 1000 Mbps Ethernet linkBlinking: Data is being transmittedGreen Steady On: 100 Mbps Ethernet linkBlinking: Data is being transmittedLED Name Status FunctionOff 10 Mbps Ethernet link or LAN is not connectedLAN 2 Yellow Steady On: 1000 Mbps Ethernet linkBlinking: Data is being transmittedGreen Steady On: 100 Mbps Ethernet linkBlinking: Data is being transmittedOff10 Mbps Ethernet link or LAN is not connectedTx 1 Green Blinking: Data is being transmittedOff Not connectedTx 2 Green Blinking: Data is being transmittedOff Not connectedRx 1 Yellow Blinking: Data is being transmittedOff Not connectedRx 2 Yellow Blinking: Data is being transmittedOff Not connectedNOTE The Mini PCIe card’s LED behavior depends on the moduleInstalling the Wireless ModulesThe V2201 has two Mini PCIe sockets on the rear panel. One socket only supports USB signals using the MC9090, MC7354, or MC7354 Mini PCIe cards. The other socket supports standard USB and PCIe signals.STEP1: Loosen the four screws located at the middle of the rear panel and open the cover.STEP 2: Insert the wireless module card at an angle.STEP 3: Push the wireless module card down and fasten it with the two screws included with the product.The V2201 has the following two Mini PCIe sockets.Socket 1: USB signal, for 3G/LTE Mini PCIe card (Sierra Wireless MC9090, MC7304, or MC7354). NOTE: The cellular card heat sink is installed in socket 1. Socket 2: Standard USB + PCIe signals, for Wi-Fi Mini PCIe card (SparkLAN WPEA-252NI).STEP 4: Connect the corresponding wireless module cards to connectors of the Mini PCIe sockets.The following five connectors are available:No. 1 & No. 3:For the Wi-Fi Mini PCIe card No. 2 & No. 4:For the 3G/LTE Mini PCIe card No. 5:For the GPS moduleSTEP 5: Replace the rear cover.You can also purchase and install external antennas from Moxa. Contact a Moxa sales representative for information.After installing the wireless modules and wireless external antennas, the computer should appear as follows:Installing the V2201DIN-rail MountingThe DK-DC50131 die-cast metal kit (shipped only with V2201-E4-W-T-LX; to be purchased separately for all other models), enables easy and robust installation of the V2201. Use the six M4*6L FMS screwsincluded to attach the DIN-rail mounting kit to the side panel of theV2201.Installation:STEP 1:Insert the upper lip of the DIN rail intothe DIN-rail mounting kit.STEP 2:Press the V2201 towards the DIN railuntil it snaps into place.Removal:STEP 1:Pull down the latch on themounting kit with a screwdriver.STEP 2 & 3:Use the screwdriver to pry theV2201 slightly forward away fromthe DIN rail, and then lift theV2201 upwards to remove it fromthe DIN rail.STEP 4:Press the recessed button on the spring-loaded bracket to lock it into position untilthe next time you need to install theV2201 on to a DIN rail.Wall or Cabinet MountingThe V2201 computers (with the exclusion of the V2201-E4-W-T-LX model) come with two metal brackets for attaching to a wall or the inside of a cabinet. Four screws (Phillips truss headed, M3*6L, and nickel plated with Nylok®) are included in the kit.Step 1:Use two screws for eachbracket and attach the bracketto the rear of the V2201.Step 2:Use two screws on each side toattach the V2201 to a wall orcabinet.The product package does notinclude the four screws requiredfor attaching the wall-mountingkit to the wall or cabinet; theyneed to be purchasedseparately. We recommendusing standard M3*5L screws.Connector DescriptionPower ConnectorConnect the 9 to 36 VDC LPS or Class 2 power line to the V2201’s terminal block. If the power is supplied properly, the Power LED will light up. The OS is ready when the Ready LED glows a solid green.Grounding the V2201Grounding and wire routing help limit the effects of noise due to electromagnetic interference (EMI). Run the ground connection from the grounding screw (M4) to the grounding surface prior to connecting the power.SG:The Shielded Ground (sometimes calledProtected Ground) contact is the right most oneon the 3-pin power terminal block connector when viewed from the angle shown here.Connect the SG wire to an appropriate grounded metal surface.HDMI OutputsThe V2201 comes with a type A HDMI female connector on the front panel to connect an HDMI monitor.The screw hole above the HDMI connector is used to attach a custom lock to the HDMI connector; a custom lock is needed since the shape of different HDMI connectors are not the same. Please contact a Moxa sales representative for details. Before Attaching the LockAfter Attaching the LockEthernet PortsThe 10/100/1000 Mbps Ethernet ports use RJ45 connectors.Pin 10/100 Mbps 1000 Mbps1 ETx+ TRD(0)+2 ETx- TRD(0)-3 ERx+ TRD(1)+4 – TRD(2)+5 – TRD(2)-6 ERx- TRD(1)-7 – TRD(3)+8 – TRD(3)-Serial PortsThe serial ports use DB9 connectors. Each port can be configured by software for RS-232, RS-422, or RS-485. The pin assignments for the ports are shown in the following table:Pin RS-232 RS-422 RS-485(4-wire)RS-485(2-wire)1 DCD TxDA(-) TxDA(-) –2 RxD TxDB(+) TxDB(+) –3 TxD RxDB(+) RxDB(+) DataB(+)4 DTR RxDA(-) RxDA(-) DataA(-)5 GND GND GND GND6 DSR – – –7 RTS – – –8 CTS – – –SD SlotThe V2201 has an SD slot for storage expansion. The SD slot allows users to plug in an SD 3.0 standard SD card. To install an SD card, gently remove the outer cover from the left, and then insert the SD card into the slot.Mini SIM SlotThe V2201 has a Mini SIM slot for 3G/LTE wireless Internet connections. To install a Mini SIM card, gently remove the outer cover from the left, and insert the card into the slot.USB HostsThe V2201 has 1 USB 3.0 and 2 USB 2.0 Type-A connectors. 2 USB 2.0 ports are located on the front panel, and 1 USB 3.0 port is on the right panel. The port supports keyboard and mouse and can also be used to connect a Flash drive for storing additional data.Audio InterfaceThe audio output of the V2201 is combined with the HDMI connector.DI/DOThe V2201 comes with four digital inputs and four digital outputs on a 2 x 5 terminal block.Reset ButtonPress the “Reset Button” on the left side panel of the V2201 to reboot the system automatically. Real-time ClockThe V2201’s real-time clock is powered by a lithium battery. Westrongly recommend that you do not replace the lithium battery without help from a qualified Moxa support engineer. If you need to change the battery, contact the Moxa RMA service team.Powering on the V2201To power on the V2201, connect the “terminal block to power jack converter” to the V2201’s DC terminal block (located on the sidepanel), and then connect the 9 to 36 VDC power adapter. The computer is automatically switched on once the power adapter is plugged in. If it does not, press the Power Button to turn on the computer. Note that the Shielded Ground wire should be connected to the top pin of the terminal block. It takes about 30 seconds for the system to boot up. Once the system is ready, the Power LED will light up.Connecting the V2201 to a PCPower on the V2201 computer after connecting a monitor, keyboard, and mouse, and verifying that the power source is ready. Once the operating system boots up, the first step is to configure the Ethernet interface. The factory default settings for the V2201’s LANs are shown below (W7E uses DHCP):Default IP AddressNetmaskLAN 1 192.168.3.127 255.255.255.0 LAN 2 192.168.4.127255.255.255.0- 11 - Configuring the Ethernet Interface Linux OSIf you use the console cable to configure network settings for the first time, use the following commands to edit the interfaces file:#ifdown –a //Disable LAN1~LAN2 interface first, before you reconfigure the LAN settings. LAN1 = eth0, LAN2 = eth1// #vi /etc/network/interfaces //check the LAN interface first//After the boot setting of the LAN interface has been modified, use the following commands to immediately activate the LAN settings: #sync; ifup –a W7E OSSTEP 1: Go to Start → Control Panel → Network and Internet → Viewnetwork status and tasks → Change adapter setting.STEP 2: In the Local Area Connection Properties screen, click InternetProtocol (TCP/IP) and then select Properties. Select InternetProtocol Version 4, and then click Properties.STEP 3: Click OK after inputting the proper IP address and netmask.NOTERefer to the V2201 user’s manuals for additional configuration information.。
DS-2XC6646G0 P-IZH(R)S 4 MP ANPR IR Varifocal Bull

DS-2XC6646G0/P-IZH(R)S4 MP ANPR IR Varifocal Bullet Network Camera⏹High quality imaging with 4 MP resolution⏹Excellent low-light performance via DarkFighter technology⏹Clear imaging against strong back light due to 120 dB WDR technology⏹License Plate Recognition⏹Efficient H.265+ compression technology to save bandwidth and storage⏹ 5 streams to meet a wide variety of applications⏹Water and dust resistant (IP67)⏹316L stainless steel enclosure, protecting cameras to be used in corrosive environments, providing reliability andlongevity compared to standard cameras⏹ A built-in wiper(-R) removes water and dust on the screen and ensures clear images when the camera is used in dustyor damp environmentsSpecificationCameraImage Sensor 1/1.8" Progressive Scan CMOSMax. Resolution 2688 × 1520Min. Illumination Color: 0.0005 Lux @ (F1.2, AGC ON), B/W: 0.0001 Lux @ (F1.2, AGC ON), 0 Lux with IR Shutter Time 1 s to 1/100,000 sDay & Night IR cut filterBlue glass module to reduce ghost phenomenonLensFocal Length & FOV 2.8 to 12 mm, horizontal FOV 100.8° to 40.2°, vertical FOV 53.3° to 22.5°, diagnol FOV 122.3° to 46.2°8 to 32 mm, horizontal FOV 40.7° to 14.6°, vertical FOV 22.3° to 8.3°, diagnol FOV 47.4°to 16.7°Focus Auto, semi-auto, manualAperture 2.8 to 12 mm: F1.38 to F2.5 8 to 32 mm: F1.7DORIDORI Wide:2.8 to 12 mm: D: 60 m, O: 23.8 m, R: 12 m, I: 6 m8 to 32 mm: D: 150.3 m, O: 59.7 m, R: 30.1 m, I: 15 m Tele:2.8 to 12 mm: D: 149 m, O: 59.1 m, R: 29.8 m, I: 14.9 m 8 to 32 mm: D: 400 m, O: 158.7 m, R: 80 m, I: 40 mIlluminatorSupplement Light Type IRSupplement Light Range 2.8 to 12 mm: 60 m 8 to 32 mm: 100 mSmart Supplement Light YesIR Wavelength 850 nm VideoMain Stream 50 Hz: 25 fps (2688 × 1520, 2560 × 1440, 1920 × 1080, 1280 × 720) 60 Hz: 30 fps (2688 × 1520, 2560 × 1440, 1920 × 1080, 1280 × 720)Sub-Stream 50 Hz: 25 fps (704 × 576, 640 × 480) 60 Hz: 30 fps (704 × 480, 640 × 480)Third Stream 50 Hz: 25 fps (1920 × 1080, 1280 × 720, 704 × 576, 640 × 480) 60 Hz: 30 fps (1920 × 1080, 1280 × 720, 704 × 480, 640 × 480)Fourth Stream 50 Hz: 25 fps (704 × 576, 640 × 480) 60 Hz: 30 fps (704 × 480, 640 × 480)Fifth Stream 50 Hz: 25 fps (704 × 576, 640 × 480) 60 Hz: 30 fps (704 × 480, 640 × 480)Video Compression Main stream: H.265+/H.265/H.264+/H.264Sub-stream/Fourth stream/Fifth stream: H.265/H.264/MJPEG Third stream: H.265/H.264Video Bit Rate 32 Kbps to 8 MbpsH.264 Type Baseline Profile/Main Profile/High Profile H.265 Type Main ProfileBit Rate Control CBR/VBRScalable Video Coding (SVC) H.265 and H.264 encodingRegion of Interest (ROI) 5 fixed regions for each streamTarget Cropping YesAudioAudio Type Mono soundAudio Compression G.711/G.722.1/G.726/MP2L2/PCM/AAC-LC/MP3Audio Bit Rate 64 Kbps (G.711)/16 Kbps (G.722.1)/16 Kbps (G.726)/32 to 192 Kbps (MP2L2)/16 to 64 Kbps (AAC-LC)/8 to 320 Kbps (MP3)Audio Sampling Rate 8 kHz/16 kHz/32 kHz/44.1 kHZ/48 kHz Environment Noise Filtering YesNetworkProtocols TCP/IP, ICMP, HTTP, HTTPS, FTP, SFTP, SRTP, DHCP, DNS, DDNS, RTP, RTSP, RTCP, PPPoE, NTP,UPnP, SMTP, SNMP, IGMP, 802.1X, QoS, IPv6, UDP, Bonjour, SSL/TLS, WebSocket, WebSocketsSimultaneous Live View Up to 20 channelsAPI Open Network Video Interface (Profile S, Profile G, Profile T), ISAPI, SDK, ISUP User/Host Up to 32 users. 3 user levels: administrator, operator and userSecurity Password protection, complicated password, HTTPS encryption, 802.1X authentication (EAP-TLS, EAP-LEAP, EAP-MD5), watermark, IP address filter, basic and digest authentication for HTTP/HTTPS, WSSE and digest authentication for Open Network Video Interface, RTP/RTSP OVER HTTPS, Control Timeout Settings, Security Audit Log, TLS 1.2Network Storage NAS (NFS, SMB/CIFS), auto network replenishment (ANR)Together with high-end Hikvision memory card, memory card encryption and health detection are supported.Client iVMS-4200, Hik-Connect, Hik-CentralWeb Browser Plug-in required live view: IE10, IE11Plug-in free live view: Chrome 57.0+, Firefox 52.0+, Safari12+ Local service: Chrome 57.0+, Firefox 52.0+ImageImage Parameters Switch YesImage Settings Rotate mode, saturation, brightness, contrast, sharpness, gain, white balance adjustable by client software or web browserDay/Night Switch Day, Night, Auto, Schedule, Alarm Trigger, Video TriggerWide Dynamic Range (WDR) 120 dBSNR ≥ 52 dBImage Enhancement BLC, HLC, Defog, 3D DNRPicture Overlay LOGO picture can be overlaid on video with 128 × 128 24bit bmp formatImage Stabilization EISInterfaceEthernet Interface 1 RJ45 10 M/100 M/1000 M self-adaptive Ethernet portOn-Board Storage Built-in memory card slot, support microSD/microSDHC/microSDXC card, up to 256 GBAudio 1 input (line in), two-core terminal block, max. input amplitude: 3.3 Vpp, input impedance: 4.7 KΩ, interface type: non-equilibrium; 1 output (line out), two-core terminal block, max. output amplitude: 3.3 Vpp, output impedance: 100 Ω, interface type: non-equilibriumAlarm 1 input, 1 output (max. 24 VDC, 1 A or max. 110 VAC, 500 mA)RS-485 Without -R: 1 RS-485 (half duplex, HIKVISION, Pelco-P, Pelco-D, self-adaptive) -R: does not supportReset Key YesWiegand /P: 1 Wiegand (CardID 26bit, SHA-1 26bit, Hik 34bit, NEWG 72bit) EventBasic Event Motion detection, video tampering alarm, exception (network disconnected, IP address conflict, illegal login, abnormal reboot, HDD full, HDD error), video quality diagnosis, vibration detectionSmart Event Line crossing detection, intrusion detection, region entrance detection, region exiting detection (support alarm triggered by specified target types (human and vehicle)) Scene change detection, audio exception detection, defocus detectionLinkage Upload to FTP/NAS/memory card, notify surveillance center, send email, trigger alarm output, trigger recording, trigger capture, audible warningDeep Learning FunctionRoad Traffic and Vehicle Detection Blocklist and allowlist: up to 10,000 recordsCaptures vehicle that has no license plateSupport license plate recognition of motorcycles (only in checkpoint scenario) Support vehicle attribute detection, including vehicle type, color, brand, etc. (City Street mode is recommended.)Metadata Metadata of road traffic is supported. GeneralPower 12 VDC ± 20%, 1.8 A, max. 22 W, three-core terminal blockPoE: 802.3at, Type 2, Class 4, 42.5 V to 57 V), 0.5 A to 0. 4 A, max. 22 WMaterial 316L and anti-corrosion coatingDimension With -R: 240.8 mm × 145 mm × 166.6 mm (9.5" × 5.7" × 6.6") Without -R: 224 mm × 145 mm × 143.5 mm (8.8" × 5.7" × 5.6")Package Dimension 477 mm × 235 mm × 302 mm (18.7" × 9.3" × 11.9")Weight With -R: approx. 4265 g (9.4 lb.) Without -R: approx. 3710 g (8.2 lb.)With Package Weight With -R: approx. 5115 g (11.3 lb.) WIthout -R: approx. 4560 g (10.1 lb.)Storage Conditions -40 °C to 60 °C (-40 °F to 140 °F). Humidity 95% or less (non-condensing) Startup and OperatingConditions-40 °C to 60 °C (-40 °F to 140 °F). Humidity 95% or less (non-condensing)Language 33 languages: English, Russian, Estonian, Bulgarian, Hungarian, Greek, German, Italian, Czech, Slovak, French, Polish, Dutch, Portuguese, Spanish, Romanian, Danish, Swedish, Norwegian, Finnish, Croatian, Slovenian, Serbian, Turkish, Korean, Traditional Chinese, Thai, Vietnamese, Japanese, Latvian, Lithuanian, Portuguese (Brazil), UkrainianGeneral Function Anti-banding, 5 streams, heartbeat, mirror, privacy mask, flash log, password reset via email, pixel counterHeater YesWiper -R: Yes ApprovalEMC FCC: 47 CFR Part 15, Subpart BCE-EMC: EN 55032: 2015, EN 61000-3-2:2019, EEN 61000-3-3:2013+A1:2019, EN 50130-4: 2011 +A1: 2014RCM: AS/NZS CISPR 32: 2015IC: ICES-003: Issue 7KC: KN 32: 2015, KN 35: 2015Safety UL: UL 62368-1CB: IEC 62368-1:2014+A11CE-LVD: EN 62368-1:2014/A11:2017BIS: IS 13252(Part 1):2010/ IEC 60950-1 : 2005 LOA: IEC/EN 60950-1Environment CE-RoHS: 2011/65/EUWEEE: 2012/19/EUReach: Regulation (EC) No 1907/2006Protection IP67: IEC 60529-2013IK10: IEC 62262: 2002 (without -R)Anti-Corrosion Protection NEMA 4X: NEMA 250-2018C5-M: 720H neutral salt spray, 480H water condensation;Exterior environments: industrial areas with high humidity and aggressive atmosphere and coastal areas with high salinity;Interior environments: buildings or areas with almost permanent condensation and with high pollution.⏹FunctionRoad Traffic and Vehicle DetectionWith embedded deep learning based license plate capture and recognition algorithms, the camera alone can achieve plate capture and recognition. The algorithm enjoys the high recognition accuracy of common plates and complex-structured plates, which is a great step forward comparing to traditional algorithms. Blocklist and allowlist are available for plate categorization and separate alarm triggering.⏹Typical ApplicationHikvision products are classified into three levels according to their anti-corrosion performance. Refer to the following description to choose for your using environment.This model has TOP-LEVEL PROTECTION.Level DescriptionTop-level protection Hikvision products at this level are equipped for use in areas where professionalanti-corrosion protection is a must. Typical application scenarios include coastlines, docks,chemical plants, and more.Moderate protection Hikvision products at this level are equipped for use in areas with moderate anti-corrosiondemands. Typical application scenarios include coastal areas about 2 kilometers (1.24miles) away from coastlines, as well as areas affected by acid rain.No specific protection Hikvision products at this level are equipped for use in areas where no specificanti-corrosion protection is needed.050704020220921⏹ Dimension⏹ Accessory⏹Optional DS-1704ZJ-Y-AC(OS)Wall Mount⏹ Available ModelDS-2XC6646G0/P-IZHS (2.8 to 12 mm, 8 to 32 mm) DS-2XC6646G0/P-IZHRS (2.8 to 12 mm, 8 to 32 mm)。
Matrox Meteor-II Camera Link相机接口应用指南说明书

JAI CV-M4CL March 26, 2002Basics about thecameraCamera Descriptions§Effective resolution: 1280 × 1024 × 10-bit @ 24 fps (Full resolution). §Camera Link BASE interface (single channel).§Progressive scan.§Internal or external sync.§Internal or external exposure control.§40.49 MHz pixel clock rate.Mode of operations as per Matrox Imaging (in parentheses as per camera manufacturer)Interface Mode §Continuous§Asynchronous resetBasics about theinterface modesCamera Interface BriefsMode 1: Continuous§1280 × 1024 × 10-bit @ 24 fps (Full resolution).§Camera Link BASE interface (single channel).§Progressive scan.§Matrox Meteor-II/Camera Link receiving LEN, FEN, Pclk and video data fromcamera.§ DCF used:CVM4CLC.DCFMode 2: Asynchronous reset (Pulse width control trigger)§1280 × 1024 × 10-bit.§Camera Link BASE interface (single channel).§Progressive scan.§Matrox Meteor-II/Camera Link receiving external trigger signal.§Matrox Meteor-II/Camera Link sending EXPOSURE1 (CC1) signal to camerato initiate and control exposure time.§Matrox Meteor-II/Camera Link receiving LEN, FEN, Pclk and video data fromcamera.§ DCF used:CVM4CLA.DCFJAI CV-M4CL March 26, 2002 Specifics about theCamera Interface Detailsinterface modesMode 1: Continuous§Frame Rate: Matrox Meteor-II/Camera Link receives the continuousvideo from the camera at 24 frames per second (Full resolution).§Exposure time: Exposure time is determined by the shutter setting.Refer to the camera manual for more information.§Camera switch settings: Refer to the camera manual for additionalinformation. Internal and external switches should be set as follows:External Switches Internal Switches (SW50)Shutter 1 OFF 1 OFFShutter 2 OFF 2 ONShutter 3 OFF 3 OFFShutter 4 OFF 4 OFFExt. Trigger 5 OFFExt. Trigger 6 OFFScan 7 OFFScan 8 OFFSmear-less 9 OFFControl 10 OFFMode 2: Asynchronous reset (Pulse width control trigger)§Frame Rate: The frame rate is determined by the frequency of theexternal trigger signal and the exposure time period.§Exposure time: The width (falling edge to rising edge) of theEXPOSURE1 (CC1) signal is the exposure time. The exposure time canbe modified in the DCF using Matrox Intellicam, with the MILMdigControl() function. Consult the respective manual for moreinformation.§Camera switch settings: Refer to the camera manual for additionalinformation. Internal and external switches should be set as follows:External Switches Internal Switches (SW50)Shutter 1 OFF 1 OFFShutter 2 OFF 2 ONShutter 3 OFF 3 OFFShutter 4 OFF 4 OFFExt. Trigger 5 ONExt. Trigger 6 OFFScan 7 OFFScan 8 OFFSmear-less 9 OFFControl 10 OFFMatrox Meteor-II/Camera Link Camera Interface Application NoteJAI CV-M4CL March 26, 2002 Cabling details for theCabling Requirementsinterface modesMode 1: ContinuousCable and Connection: Standard Camera Link cable.Mode 2: Asynchronous reset (Pulse width control)Cable and Connection: Standard Camera Link.External trigger: External trigger should be connected to the OPTOTRIG input of the DB9 connector (pins 7 and 2) on the Expanded I/Oadapter bracket.EXPANDED I/O BRACKET(DB9 connector) External Trigger SourceOPTOTRIG + 07 ←SIGNAL --OPTOTRIG - 02 ←GROUND --The DCF(s) mentioned in this application note can be found on our FTP site (/pub/imaging/).The information furnished by Matrox Electronics System, Ltd. is believed to be accurate and reliable. Please verify all interface connections with camera documentation or manual. Contact your local sales representative or Matrox Sales office or Matrox Imaging Applications at 514-822-6061 for assistance.Matrox Electronic Systems Ltd.1055 St. Regis Blvd.Dorval, Quebec H9P 2T4CanadaTel: (514) 685-2630Fax: (514) 822-6273。
Microsemi IGLOO2 FPGA 评估板说明书

IGLOO2 FPGA Evaluation KitQuickstart CardKit Contents—M2GL-EVAL-KITQuantity Description1IGLOO2 FPGA 12K LE M2GL010T-1FGG484 Evaluation Board 112 V, 2 A AC power adapter1FlashPro4 JTAG programmer1USB 2.0 A-Male to Mini-B cable1Quickstart cardOverviewThe Microsemi IGLOO®2 FPGA Evaluation Kit makes it easier to develop embedded applications that involve motor control, system management, industrial automation, and high-speed serial I/O applications such as PCIe, SGMII, and user-customizable serial interfaces. The kit offers best-in-class feature integration coupled with the lowest power, proven security, and exceptional reliability. The board is also small form-factor PCIe-compliant, which allows quick prototyping and evaluation using any desktop PC or laptop with a PCIe slot.The kit enables you to:• Develop and test PCI Express Gen2 x1 lane designs• Test signal quality of the FPGA transceiver using the full-duplex SerDes SMA pairs• Measure the low power consumption of the IGLOO2 FPGA• Quickly create a working PCIe link with the included PCIe Control Plane DemoHardware Features• 12K LE IGLOO2 FPGA in the FGG484 package (M2GL010T-1FGG484)• 64 Mb SPI flash memory• 512 Mb LPDDR• PCI Express Gen2 x1 interface• Four SMA connectors for testing the full-duplex SerDes channel • RJ45 interface for 10/100/1000 Ethernet • JTAG/SPI programming interface• Headers for I2C, SPI, and GPIOs• Push-button switches and LEDs for demo purposes• Current measurement test pointsRunning the DemoThe IGLOO2 FPGA Evaluation Kit is shipped with the PCI Express Control Plane demo preloaded. Instructions on running the demo design are available in the IGLOO2 FPGA Evaluation Kit PCIe Control Plane Demo user guide. See the Documentation Resources section for more information. ProgrammingThe IGLOO2 FPGA Evaluation Kit comes with a FlashPro4 programmer. Embedded programming with the IGLOO2 FPGA Evaluation Kit is also available, and it is supported by the Libero SoC v11.4 SP1 or later.Jumper SettingsJumper Development Kit Function Pins Factory DefaultJ23Selects switch-side MUX inputsof A or B to the line side 1–2 (input A to the line side) thatis on board 125 MHz differentialclock oscillator output will berouted to line sideClosed2–3 (input B to the line side)that is external clock requiredto source through SMAconnectors to the line sideOpenJ22Selects the output enablecontrol for the line side outputs 1–2 (line-side output enabled)Closed 2–3 (line-side output disabled)OpenJ24Provides the VBUS supply toUSB when using in Host mode OpenJ8Selects between RVI headeror FP4 header for applicationdebug1–2 FP4 for SoftConsole/FlashPro Closed2–3 RVI for Keil ULINK/IARJ-Link Open2–4 for toggling JTAG_SELsignal remotely using the GPIOcapability of the FT4232 chipOpenJ3Selects either the SW2 inputor the ENABLE_FT4232 signalfrom the FT4232H chip1–2 for manual power switchingusing the SW7 switch Closed2–3 for remote power switchusing the GPIO capability of theFT4232 chipOpenJ31Selects between FTDI JTAGprogramming and FTDI slaveprogramming1–2 for FlashPro FTDI JTAGprogramming Closed2–3 for SPI slave programming OpenJ32Selects between FTDI SPI andSC_SCI header 1–2 for programming throughFTDI SPI Closed 2–3 for programming throughSC_SPI header OpenJ35Selects between FP4 headerand FTDI JTAG 1–2 for programming throughFP4 header Closed 2–3 for programming throughFTDI JTAG Open©2016–2017 Microsemi Corporation. All rights reserved. Microsemi and the Microsemi logo are registered trademarks of Microsemi Corporation. Microsemi Corporate Headquarters One Enterprise, Aliso Viejo, CA 92656 USA Within the USA: +1 (800) 713-4113 Outside the USA: +1 (949) 380-6100 Fax: +1 (949) 215-4996Email:***************************Microsemi makes no warranty, representation, or guarantee regarding the information contained herein or the suitability of its products and services for any particular purpose, nor does Microsemi assume any liability whatsoever arising out of the application or use of any product or circuit. The products sold hereunder and any other products sold by Microsemi have been subject to limited testing and should not be used in conjunction with mission-critical equipment or applications. Any performance specifications are believed to be reliable but are not verified, and Buyer must conduct and complete all performance and other testing of the products, alone and together with, or installed in, any end-products. Buyer shall not rely on any data and performance specifications or parameters provided by Microsemi. It is the Buyer’s responsibility to independently determine suitability of any products and to test and verify the same. The information provided by Microsemi hereunder is provided “as is, where is” and with all faults, and the entire risk associated with such information is entirely with the Buyer. Microsemi does not grant, explicitly or implicitly, to any party any patent rights, licenses, or any other IP rights, whether with regard to such information itself Software and LicensingLibero ® SoC Design Suite offers high productivity with its comprehensive, easy-to-learn, easy-to-adopt development tools for designing with Microsemi’s low power Flash FPGAs and SoC. The suite integrates industry standard Synopsys Synplify Pro ® synthesis and Mentor Graphics ModelSim ® simulation with best-in-class constraints management and debug capabilities.Download the latest Libero SoC release/products/fpga-soc/design-resources/design-software/libero-soc#downloads Generate a Libero Silver license for your kit/products/fpga-soc/design-resources/licensingDocumentation ResourcesFor more information about the IGLOO2 FPGA Evaluation Kit, including user’s guides, tutorials, and design examples, see the documentation at /products/fpga-soc/design-resources/dev-kits/igloo2/igloo2-evaluation-kit#documentation .SupportTechnical support is available online at /soc/support and by email at **********************Microsemi sales offices, including representatives and distributors, are located worldwide. To find your local representative, go to /salescontacts。
维泰克2客户信-clsi折点性能参数补充说明书

VITEK 2客户信编号: CSN 4757-2尊敬的生物梅里埃用户:2020年7月, 生物梅里埃发布了客户信CSN-4757通知VITEK®2用户梅里埃已经完成了气单胞菌和弧菌多个抗生素CLSI折点的验证工作。
如果您在2020年7月收到通知后已经更新了折点, 我们抱歉地通知您当时发布的客户信表2性能参数部分存在笔误。
此次客户信的表2已经进行了更新,为便于识别,更新部分用黄色高亮显示。
该客户信其它部分同此前版本保持一致。
该评估使终端用户可以在VITEK® 2软件中应用CLSI折点。
表1中的CLSI折点都已经成功验证,均满足可接受标准,可用于患者或其它菌株测试,某些情况下需要增加一些限制信息.为了应用这些折点,需要在AES中创建自定义参数。
请参考VITEK® 2软件用户手册(修改折点部分)中的详细信息。
这些折点会被整合进未来新版本VITEK® 2软件Global CLSI-based参数集。
表2提供了应用CLSI折点下这些抗菌药物的性能参数信息。
之前出版的VITEK® 2文档尚未公布这些性能参数信息。
假如您选择实施这些CLSI折点,请留存该客户信。
附录1:举例如何创建高级报告工具(BIOART)规则,用于管理该客户信5-8页中的局限。
做为我们持续改善项目的一部分,梅里埃致力于提升产品质量,功能和易用性。
感谢您选择使用VITEK® 2系统,如果您有任何问题,请随时联系您当地的生物梅里埃代表。
此致敬礼梅里埃诊断产品(上海)有限公司2022年5月10日bioMérieux (Shanghai) Company Limited/梅里埃诊断产品(上海)有限公司表1:使用更新后的CLSI折点,表格中抗菌药物性能满足要求bioMérieux (Shanghai) Company Limited/梅里埃诊断产品(上海)有限公司*以下抗生素/细菌组合的结果存在局限,需要屏蔽报告。
AnlexVC++4
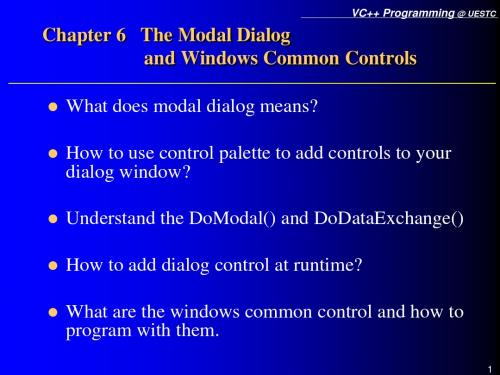
2
VC++ Programming @ UESTC
Chapter 6 The Modal Dialog and Windows Common Controls
A dialog window almost always tied to a Windows resource that identifies the dialog’s elements and specifies their layout. The elements on the dialog are called dialog controls, which include edit control, buttons, list boxes, combo boxes, labels, tree views, progress indicators, sliders and so forth. Windows manages these controls using special grouping and tabbing logic. The dialog controls can be referenced by the CWnd pointer or by an index number.
4
3.
4.
VC++ Programming @ UESTC
Chapter 6 The Modal Dialog and Windows Common Controls
5
VC++ Programming @ UESTC
Chapter 6 The Modal Dialog and Windows Common Controls
三星品牌钽电容说明书

�
Domestic Distributors
KORCHIP INC #219 - 8 Gasan - dong, Gumchun - gu, Seoul, Korea Te l: +82 - 2 - 838 - 5588 E-mail:hjh0064@ CHUNG HAN #16-96 Hangang - lo 3, Youngsan - Gu, Seoul, Korea Te l: +82 - 2 - 718 - 3322 E-mail:james - kim@ichunghan.co.kr SAMTEK #154-16 Samsung- dong Kangnam- Gu, Seoul, Korea Te l: +82- 2- 3458- 9340 E-mail:sinsog1@samtek.co.kr CHUNGMAC #53-5 Wonhyolo3 Youngsan- gu, Seoul, Korea Te l: +82- 2- 716 - 6428~9 E-mail:any@anycam.co.kr APEXINT #1258 Gulo - dong Gulo-Gu, Seoul, Korea Te l: +82- 2- 6679- 5116, 5118 E-mail:djlee@apexint.co.kr
�
Manufacturing Site
Suwon Plant 314, Maetan 3- dong, Youngtong- gu, Suwon, Kyonggi Province 442- 743, Korea Te l: +82- 31- 218- 2063 E-mail:sh386.kim@ Pusan Plant 1623-2, Songjong-dong, Kangso - gu, Pusan 618 - 270, Korea Te l: +82- 51- 970 - 7741 E-mail:absyong.kim@ Tianjin Plant 27, Heiniu, Cheng - Road, Tianjin, China 300210 Te l: +86 - 22 - 2830 - 3333(3450) E-mail:gk.ryu@ Philippines Plant Calamba Premiere International Park, Batino, Calamba, Laguna, manila Te l: +63 - 2 - 809 - 2873 E-mail:ksj1445@
SMT专用术语缩写

uBGA VMI
Checklist
FIFO LCD VF WI BOM ECR ECN DFT line KanBan IPK TQCI RIP 钢网
回流曲线
IC贴片机
屏蔽盖贴片机 自动光学检查
喂料器 工夹具
生产线设计 试产批量生产 温湿敏元件
回流炉 X光检查 CIP
Acceptability of Printed Circuit’s. An IPC publication.
Surface Mount Device Surface Mount Technology表面贴装技术
Micro-Pitch Ball Grid Array Visual-Mechanical Inspection 肉眼检查 生产线文件工位对照单 First in first out先进先出 Liquid crystal display液晶显示器 Virtual factory虚拟工厂 Work instruction操作指示 bill of material物料清单 Engineering change report Engineering change note 按需求流动技术生产线Demand Flow Technology 看板 In process Kanban流程看板 Total quality control inspection 全面质量控制检查 Raw in process在线物料 Stencil Reflow Profile Feeder Tool & fixture Line design Pilot run & bulk run Moisture sensitive component 湿度Humidity
ANSI/IPC-A-610 Acceptability of Electronic Assemblies. An IPC publication.
QSAN XEVO 2.2 软件手册说明书

XEVO 2.2 软件手册2023年四月公告版权©版权所有2023 QSAN广盛科技保留所有权利。
未经QSAN广盛科技书面许可,不得复制或传播本文档的任何部分。
QSAN认为本出版物在发布之日内容准确无误。
信息如有更改,恕不另行通知。
商标▪QSAN、QSAN标志、、XCubeFAS、XCubeSAN、XCubeNXT、XCubeNAS、XCubeDAS、XEVO、SANOS是QSAN广盛科技的商标或注册商标。
▪Microsoft、Windows、Windows Server和Hyper-V是Microsoft Corporation在美国和 / 或其他国家/地区的商标或注册商标。
▪Linux是Linus Torvalds在美国和 / 或其他国家 / 地区的商标。
▪UNIX是The Open Group在美国和其他国家 / 地区的注册商标。
▪Mac和OS X是Apple Inc. 在美国和其他国家 / 地区的注册商标。
▪Java和所有基于Java的商标和标志是Oracle和 / 或其附属公司的商标或注册商标。
▪VMware、ESXi和vSphere是VMware, Inc. 在美国和 / 或其他国家 / 地区的注册商标或商标。
▪Citrix和Xen是Citrix Systems, Inc. 在美国和 / 或其他国家 / 地区的注册商标或商标。
▪本文件中用于宣称拥有商标和名称的实体或其产品的其他商标和商品名称均为其各自所有者的财产。
目录公告 (i)注意 (viii)前言......................................................................................................................................... i x 关于本手册 (ix)相关文档 (ix)技术支持 (ix)信息、提示和注意事项 (x)约定 (xi)1.开始 (12)1.1. 寻找存储系统 (12)1.2. 初始设置 (13)2.XEVO 用户界面 (14)2.1. XEVO网页用户界面概述 (14)2.2. 访问管理USB LCM (16)3.仪表板选项 (18)3.1. 仪表板概述 (18)4.存储选项 (24)4.1. 存储信息 (24)4.2. 配置存储池 (27)4.3. 热备用硬盘 (38)4.4. 硬盘漫游 (38)4.5. SSD缓存 (39)4.6. 自动分层 (40)5.主机选项 (41)5.1. 配置主机组 (41)6.保护选项 (48)6.1. 保护功能 (48)6.2. 配置保护组 (50)7.分析选项 (63)7.1. 分析功能 (63)7.2. 阵列分析 (63)8.系统选项 (65)8.1. 阵列信息 (65)8.2. 配置系统设置 (67)8.3. 配置数据端口设置 (71)8.4. 维护 (74)8.5. 数据加密 (82)9.消息选项 (83)9.1. 日志中心 (83)9.2. 配置通知设置 (84)10.支持和其他资源 (88)10.1. 获得技术支持 (88)10.2. 文档反馈 (89)附录90最终用户许可协议 (EULA) (90)图表图表2-1 XEVO 仪表板 (14)图表 2-2 便携式USB LCM (16)图表2-3 USB LCM屏幕 (16)图表3-1 XEVO仪表板 (18)图表3-2 仪表板中的性能图表 (21)图表3-3 右上角图标 (22)图表4-1 精简资源调配存储池详细信息 (28)图表4-2 列出硬盘组 (31)图表4-3 列出存储卷 (34)图表5-1 iSCSI主机组详细信息 (42)图表5-2 光纤通道主机组详细信息 (42)图表5-3 列出主机配置文件 (44)图表5-4 列出连接的存储卷 (45)图表6-1 保护组 (50)图表6-2 具有快照计划的保护组 (52)图表6-3 列出快照任务 (52)图表6-4 快照中心 (54)图表6-5 本地复制计划保护组 (58)图表6-6 列出复制任务 (58)图表6-7 远程复制计划保护组 (60)图表6-8 列出复制任务 (61)图表7-1 性能图 (64)表格表格3-1 硬件警报窗格说明 (19)表格 4-1 一般存储参数 (24)表格4-2 厚配置存储池参数 (24)表格4-3 精简配置和自动分层存储池参数 (25)表格4-4 SSD缓存参数 (26)表格4-5 存储卷参数 (26)注意文档中包含的信息已经过审核以确保准确性。
Anton Bauer VCLX 2 充电器手册说明书
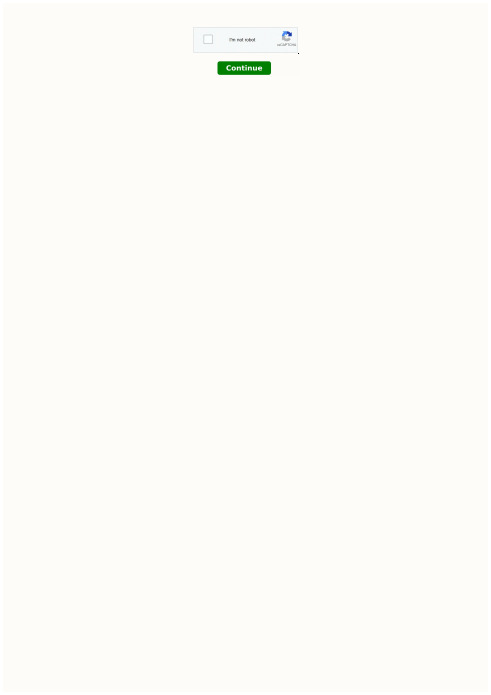
Anton bauer vclx.
4Visions Spólka z ograniczona odpowiedzialnoscia Sp. K. Contact A. F. Marcotec Warszawa Sp zo.o. Contact AM Tecnologia SA de CV Contact AVC Group Slovenia Contact AbelCine New York Contact Amperel Electronica Industrial, S.A Contact Aret Engineering SRL Contact Ariston Broadcast & Telecom Solutions Sa Contact AVC Group Macedonia Contact Audio Video Consulting d.o.o. Sarajevo Contact B&H Photo Video Pro Audio Contact BLK - Broadcast & Prof. Equipment Contact BPM Broadcast & Professional Media GmbH Buy now Band Pro Film & Digital, Inc. Contact Barbizon Electric Co., Inc HQ Contact Broadcast Technology Ltd. (BTL HK) Contact CVP Group - London Contact D & P Multimedia Products Ltd Contact ES Broadcast & Media Cont
科瑞爱特 CT22200KVVAA 系列单相工频电力专用 UPS 电源 用户手册说明书
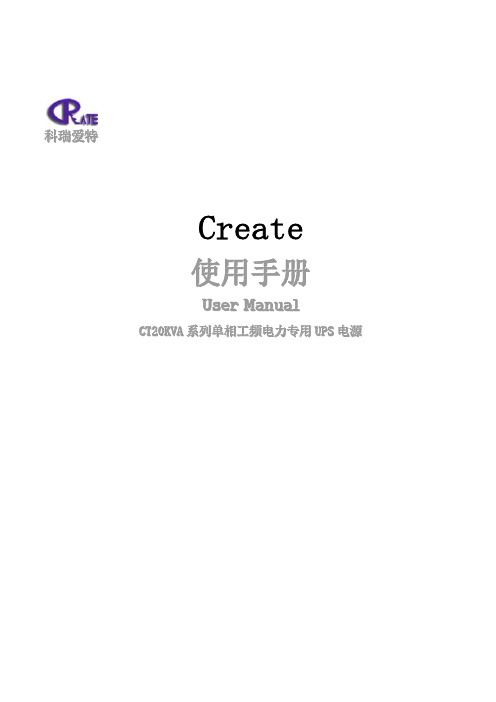
科瑞爱特CreateU s e r M a n u a lC T20K V A系列单相工频电力专用U P S电源声明本资料著作权属科瑞爱特科技开发有限公司所有。
未经著作权人书面许可,任何单位或个人不得以任何方式摘录、复制或翻译。
侵权必究。
是科瑞爱特科技开发有限公司的注册商标。
科瑞爱特产品的名称和标志是科瑞爱特的专有标志或注册商标。
在未经科瑞爱特或第三方商标或商名所有者事先书面同意的情况下,本手册不以任何方式授予阅读者任何使用本手册上出现的任何标记的许可或权利。
本产品符合关于环境保护和人身安全方面的设计要求,产品的存放、使用和弃置应遵照产品手册、相关合同或相关国家法律、法规的要求进行。
由于产品和技术的不断更新、完善,本资料中的内容可能与实际产品不完全相符,敬请谅解。
如需查询产品的更新情况,请联系那个地办事处。
若需了解最新的资料信息,请访问网站:感谢您选择单相工频电力专用UPS电源!尊敬的用户:首先感谢您选用我们的产品,从现在开始我们将成为朋友!我们非常高兴向您提供这一系列电源产品,希望它在未来的岁月里为您提供方便、可靠的服务,保证您的设备安全运作。
为了您的安全和更好的使用该系列电源,请您在安装使用前务必仔细阅读此使用手册!如果您对本手册的内容有疑问或不明确之处,请您在使用逆变电源产品前与我们联系。
警告:不要拆卸电力U P S电源上的任何外壳或器件。
设备内部零件带有致命性的电压或存有高能量的危险!目录第一章 序言 (5)1.1 注意事项 (5)1.2 开箱检查 (6)1.3 储存环境 (6)1.4 搬运 (6)第二章 产品简介 (7)2.1 产品外观 (7)2.2 工作原理 (9)2.3 主要技术参数 (10)2.4 保护功能 (11)2.5 工作环境 (11)第三章 安装运行 (12)3.1 安装准备 (12)3.2 安装位置 (12)3.3 安装接线 (12)3.4 前面板操作和显示示意图及说明 (13)3.5 UPS电源试运行 (14)3.6 UPS电源的正常启动、关闭操作步骤 (15)第四章 显示异常信息和报警信号 (15)4.1 常见故障的原因及处理方法 (15)第五章 维护保养和售后服务 (16)5.1 维护保养 (16)5.2 售后服务 (16)第一章 序言单相工频电力专用UPS电源是为了电力保障,专为电力、通信系统设计,是一种将市电及电池的电能转化为净化的交流电能的变换装置,用以给计算机和其他电气设备提供可使用的连续交流电源,以备市电的不稳定及断电。
安科电器XFC XRC 系列2型流量计 远程控制器使用指南说明书

Introduction:This startup guide is to assist in the startup of any flow computer or remote controller of the XFC (flow computer) or XRC (remote controller) series. It is however, primarily intended for gas orifice applications. It is hoped that this guide in conjunction with other drawings and documentation that accompanies your order will result in a smooth installation. If for some reason, you have questions that are not answered in this guide or your other documentation, call your local Totalflow representative or call the number listed on the back page of this guide.Installation & Start-Up SequenceHINT: Step 1 thru 22 is a recommended start-up sequence and some of the steps do not go into any great detail. Some steps because detail is not needed and some because more information is available later in the Start-Up Guide. For example there are later topics for installing and wiring the RTD, installing the main battery, solar panel Installation plus other information. So, scan through the guide to see what information is available before you begin the installation.Physical mounting and piping:1. Unpack2. Inspect for damage and missing or incorrect components.3. Determine where to mount the unit.4. Install bracing for unit; (pipe saddle, direct mount, pipe driven inground). Attach U-bolts to 2” pipe using silicone spray or Teflon tape to prevent galling. (See Figures 1 & 2)5. Mount manifold to bottom of unit; Right port of unit is NORMALLYhigh pressure (upstream side). Check the AMU model number to see if it is designed for flow from left to right (4CYC) or right to left (4AYC). You can also look on the transducer for (H or +) for high side and (L or –) for low side. For direct mount manifolds, the direction is very important. (See Figure 3 for a typical manifold configuration)6. Connect stainless steel tubing from manifold to orifice tap valves.With the manifold equalized to avoid damaging the transducer, apply pressure to the manifold and check for leaks. For best measurement, use large bore, short, equal length gage lines with a downward slope to taps (at least 1" per 3 feet).23PipeRun"U" M BoltFigure 1 (Saddle Mount)Figure 3 (Typical Manifold Mount)Figure 2 (Pipe Mount)Install RTD Probe:7. Install RTD and connect wiring to connector block J7 on the XFCboard. The XRC board does not have RTD inputs. (See Figure 5)Install Battery(s):8. Verify that Memory Backup is Enabled. This is J13 on the XFC andJ1 on the XRC. (See Figures 5 & 6)9. Mount and connect a fully charged battery to J1 on the XFC board orJ16 on the XRC board. The connectors are located in the same position on both boards. (See Page 7 & Figures 5 & 6)10. The display should go quickly through the startup routine then startscrolling through the default display items. (If not, see Tip on Page19) This typically insures that the components and wiring are good.Refer to "Standard Displays" on page 15 for typical default displays.Refer to "Visual Alarm & Status Codes" on page 16 for location, symbols, and descriptions. You should see a L C code in the A7 (upper right) annunciator since the charging source has not been connected. This is the typical annunciator for the I/O Subsystem but could possibly vary on different systems.Install Solar Panel:11. Assemble, mount, and connect solar panel or AC charger.NEVER CONNECT CHARGER WITH THE MAIN BATTERY PACK DISCONNECTED. (See pages 8 & 9) The L C code should go away after the charging source is connected. Solar powered units will naturally depend on available sunlight.Setup:12. Connect FS/2 or laptop running PCCU32 to the unit. To use an FS/2,system must have been ordered from factory as single tube application and with FS/2 support. PCCU32 must have software Version 4.3 or higher and FS/2 must be 2018583-007 or higher.13. Set date/time, ID, location and AGA setup using Entry Mode inPCCU32 or an FS/2.14. In Calibration Mode, verify registers for Static pressure, Differentialpressure and Temperature. (PCCU32 Only)15. In Calibration Mode, select RTD Installed, un-check Use Fixed TF,and adjust RTD Bias if a temperature standard is used.16. In Calibration Mode, perform as found calibration checks.417. If calibration is needed, calibrate static pressure first, then differentialpressure, using a deadweight tester or acceptable standard. Insure that both orifice taps are closed and bypass valves are open during AP calibration to avoid a false DP. Make sure there are no leaks in the manifold or test equipment.18. Perform as left calibration checks as needed.19. Place unit on line: To avoid inducing toggle and/or a calibration shift,close vent valve, open both bypass valves, then open orifice tap valves SLOWLY (high pressure side first). Once both orifice tap valves are fully opened, the bypass valves can be closed.20. Verify that the unit is calculating volume correctly. Watch the displayor look at the Current Values in the Entry Mode of PCCU32.21. Collect data and review the event and characteristic files to insure allparameters are set properly.22. Optional: When you are reasonably sure that all setup andcalibration is complete and the unit is on line calculating volume, it is recommended that a Reset Volume command be sent using PCCU.This allows the unit to have what might be considered as an official starting point for good live data. The Reset Volume will be recorded in the Events file to mark the date and time.56 Installing and Wiring RTD and ProbeThe RTD measures flowing gas temperature. Procedures presented in this section enable the user to install the RTD into the meter run and wire leads to the main electronics board. This procedure is for the XFC; the XRC does not have RTD inputs.Totalflow Materials Supplied♦ RTD Probe with 10’ of cable. Optional lengths 15’, 25’, 30’, 40’,and 50’.♦ One (1) thermowell with ¾" NPT threads. Optional threads are½" and 1".♦ Nylon tie wraps Customer Materials Supplied• Customer must specify or provide Thermowell "U" length. • Teflon tape1. Install thermowell into meter run.2. Using snap ring pliers, adjust probe lengthso that it is spring loaded against bottom of thermowell.3. Remove one of the hole plugs and installcord connector. Remove nut, sealing ring and rubber grommet from cord connector. Slide nut, sealing ring and grommet overRTD cable and insert cable through body of cord connector. Allow enough cable to extend into unit for connecting wires to RTD termination block J7. 4. Secure the cable with the grommet, sealing ring and nut.Note: Charging source and Power should be removed from unitbefore performing any field wiring. 5. Connect RTD probe to the XFC’s RTD connector as follows: Beforemaking connections to terminal block, remove spade lugs if attached and trim wire ends back 1/4". Remove J7 terminal block from the XFC main electronics board. (See Figure 5) 6. Loosen terminal block securing screws, insert wire and thenretighten. Reinstall terminal block with wires attached.7Battery Installation1. To extend the life of the battery pack, fully charge the battery prior toinstallation. A system using solar panels may not fully charge the battery. Also a fast charge, which the solar panel can’t provide, improves the life of the battery. (See tip below) 2. Remove the unit’s battery cover plate and insert battery pack intobattery compartment. Insert battery pack with its long dimension facing outward. When cover plate is reinstalled, it will fit snugly against some battery packs. The screws can be loosened to accommodate large batteries.3. Connect battery pack connector to main electronics board Batteryconnector J1 on XFCs or J16 on XRCs, located in upper right corner of Board. 4. Observe LCD, the display should power up displaying Warm Startinformation and begin scrolling through the default display items. 5. Caution: Do not connect solar panel power cable to the unit unlessthe main battery pack is connected. TIP: To recharge a battery, a quick charge will remove the buildup in thebattery much more effectively than a "trickle charge". A battery slowly drained by low light conditions on a solar charged system or setting in storage for instance, will be less likely to recover than a battery pack that was quickly discharged from a short for instance. Store batteries in a cool environment for less drainage.Lithium Battery1. Verify that the Memory Backup is Enabled with a jumper on theupper two pins of J13 on the XFC or J1 on the XRC. 2. Verify that the L L (low lithium alarm) is not being displayed on the A7annunciator (default). This alarm indicates the Lithium battery is below 2.5 volts and should be replaced.AMUBracketBattery CommunicationsEnclosureAMUBracketBatterySolar Panel InstallationTotalflow Materials Supplied •One Solar Panel and Cable•Two U-Bolts and fastening hardware •One Solar Panel BracketCustomer Materials Supplied • Cable Ties•One 9-inch or greater extension of 2-inch pipe •One 2-inch collarProcedure:Note: Step 1 and 2 are not required if pipe is tall enough without the extension.1. Attach 2-inch pipe collar to top end of XFC or XRC mounting pipe.Securely tighten. (See Figure 4)2. Install a 2-inch pipe extension into collar and securely tighten.3. Install Solar Panel on mounting bracket with provided hardware.4. Attach Solar Panel mounting plate to top end of 2-inch pipe with U-bolts and associated mounting hardware. Do not tighten U-bolts until Solar Panel has been correctly oriented.5. If needed, connect Solar Panel power cable to Solar Panel connectoron back of unit. DO NOT connect the other end of the cable to the unit until all steps are complete AND main battery pack has been connected.6. Position Solar Panel to face south in the northern hemisphere andnorth in the southern hemisphere. Tighten U-bolts securely to avoid movement by wind or vibration.7. Check solar panel polarity using digital voltmeter to insure (+) and (-)wires are properly identified.8. The Solar Panel power cable connects to XFC terminal block J5 orXRC terminal block J17 Charger Input terminals. Refer to Figure 5 or 6 for terminal locations. Remove one of the hole plugs and install cord connector. Remove nut, sealing ring and rubber grommet from cord connector. Slide nut, sealing ring and grommet over cable and insert cable through body of cord connector. Allow enough cable to extend into the unit for connection to Charger Input +/- terminals.9. Secure Solar Panel cable using grommet, sealing ring and nut.TIP: To prevent moisture from entering the unit, allow cable to "dip"below, and then rise to access hole. This will provide a path forrainwater away from the access hole.8Figure 4 (Solar Panel Mounting)9Figure 5 (XFC Layout)NOTE: Refer to Wiring Interconnect drawing 2015225-WI for more information on communications wiring.10Figure 6 (XRC Layout)NOTE: Refer to Wiring Interconnect drawing 2015225-WI for more information on communications wiring.11Remote CommunicationsThe following discussion deals primarily with the unit communicating with the Host (typically WinCCU).To communicate with the Host, the XFC or XRC has remote communication’s ports that can function as RS232, RS485 or RS422. Depending on the customer’s order, most units are shipped with the appropriate wiring in place for the specified communication’s equipment. After installation of the unit and with the communications path complete, the user needs to enter the appropriate communication’s parameters. The unit was most likely shipped with Comm 1 set up for Totalflow Remote protocol. If not, select the Protocol using the Entry mode of PCCU32 as shown below. The protocol must be selected first for the appropriate communications parameters to be displayed. A blinking telephone pole symbol "Comm 1 port is active.The data bits, stop bits and all required communications parameters can be modified with PCCU32. Units will typically be shipped with correct default comm port settings but may need fine tuning for optimum operation.Warning: As opposed to the XRC, the XFC has only one Switched V-Batt/Operate line; if it is needed, Enable it only on one Comm Port even though both ports may require its use. The V-Batt/Operate line will switch on/off at the Listen Cycle timing of the port that enabled it.Figure 7 (PCCU32 Entry Mode)12Communications TroubleshootingA new radio or modem system that doesn’t communicate is difficult to troubleshoot because proper operation has never been proven, and all the initial hardware and software settings are suspect. More than one problem can be present, causing component replacement to be an inadequate trouble shooting technique. Use the following checklist as an aid.•Does the "" flash (Totalflow Remote Protocol only) with the Listen Cycle time in the A8 display (default position)? If no,1) The Protocol needs to be selected in the Entry Mode usingPCCU32.2) The communication’s module in Comm 1 or Comm 2 is missingor bad or the module is the wrong type (RS232 or RS485).Note: Comm 1 and Comm 2 are in opposite locations whencompared to the previous electronics board (2015333).3) Inadequate 12 VDC battery voltage.•Insure base radio is working for other locations.•Verify Station ID and Device ID matches with WinCCU and is the only Totalflow device with that ID.•Verify Baud rate, Stop Bits, Security Code, and Link Establishment time are same as CCU.•Verify WinCCU is using Packet Protocol. X Series devices support only DB2 Packet Protocol.•Verify wiring to antenna, to UCI, UCI to Radio for RS485 installation or to Radio/Modem for RS232 installation.TIP: To check for wiring shorts or opens with two or more wire connections, use a multimeter set on continuity (resistance).Check two wires at a time from one unit to another. If black and white wires are to be tested, disconnect both wires at both ends, set one probe on black, the other on white. The meter should read OL or OFL (over range) if no shorts. Jumper the two wires at the other end. The meter should read a low resistance if no opens.This method requires only one end of wiring to be tested, no matter how far the units are apart.13•If a radio is used, verify directional antenna with correct frequency range is pointed toward base (±6°). The antenna should be mounted vertically, with the vanes perpendicular to the ground.Verify radio is good, with the same frequencies used.•If a modem is used, verify dial tone on line at the telephone company’s termination box by checking Tip and Ring. Check wiring from phone company’s box to dial-up modem. If cellular, also check for proper Tip & Ring voltage. Insure that the phone number is correct in the unit and WinCCU.NOTE: Telephone companies in the United States typically use a 48 volt power supply so the on-hook voltage between the Tipand Ring wires should be something less than 48 volts.Measuring another way, Tip to ground is approx. zero voltsand Ring to ground is approx. –48 volts.In the off-hook condition; Tip to ground will be approx. –20volts while Ring to ground will be approx. –28 volts orapprox. 8 volts between Tip and Ring.Users in other countries will need to consult with their localtelephone company.WiringSpecific wiring drawings are sent with each unit, based on the options ordered. Most wiring diagrams, including communications are available on the web at /totalflow. Select “Continuing Customer Service and Support”, and then select “Wiring Instructions”. Communications pin-outs of the XFC and XRC are shown on pages 10 and 11 of this guide.14Standard DisplaysItems that appear on the unit’s display are programmable by the user,however based on the measurement application; units will be shippedwith some default display items. The following table is a typical set ofdefault displays for an AGA-3 application. Engineering units may varyfrom those shown if the unit supports the “Selectable Units” feature.Description StandardDisplayCurrent Date and Time 24 hour clock DATE/TIMEMM/DD/YY HH:MM:SSYesterday’s Percent DP Low Limit Percent time below DP Low Set Point Yest DP LowNNPERCENTYesterday’s Percent DP High Limit Percent time above DP High Set Point Yest DP HighNNPERCENTCurrent Flow RateProgrammable SCF, MCF or MMCF Flow RateNNNNNN.NSCF/HRTotal Accumulated Volume Programmable SCF, MCF or MMCF Total Accum. VolumeNNNNNN.NNMCFBattery Voltage Displayed in Volts Battery VoltageNN.NVOLTSStation IDID of the box.Station IDDifferential Pressure Inches H2O Diff. PressureNNN.N IN. H2OStatic Pressure Absolute PSIA Static PressureNNN.NPSIAFlowing Temperature °F TemperatureNN.N DEG. FYesterday’s Volume Programmable SCF, MCF or MMCF Yesterday’s VolumeNNNN.NMCFPrevious Calculation Period Volume Last Calc. VolumeNNNN.NSCF Device IDIndividual application IDDevice IDCharger Voltage ChargerNN.NVOLTS The duration that each parameter is displayed can vary from 1 to 255 seconds (default is 4 seconds); a setting of 0 seconds will turn that display item off.1516 Visual Alarm & Status CodesAfter the unit completes recording of Log Period flow and operational records, the LCD will show any alarm conditions that have occurred. Also, the date, hour and type of alarm conditions are stored in the device’s memory. Status codes are also displayed when the conditions exist. An alarm or status code can be a character, letter or symbol. The alarm and status codes shown in Table 1 will appear on the right side of the LCD screen; see illustration below. Descriptions of each code are described in Table 1.Figure 8 (Annunciator Locations)Note: Applications in X Series devices can be assigned to any annunciator. To verify the current assignments, see Annunciators under Display in PCCU32’s Entry Mode. (See Figure 9)Figure 9 (Annunciator Assignments)Table 1 Alarm & Status - Codes and Description17M MODBUS ASCII: Modbus ASCII protocol is selected for this port.m MODBUS RTU: Modbus RTU protocol is selected for this port.L Local Protocol: Displayed when PCCU32 port is active and running Totalflow Local Protocol.¥ Packet Protocol: Totalflow Packet Protocol is active on this port.R LevelMaster Protocol: LevelMaster protocol is selected for this port.Valve ControlV Valve Control: Displayed when the Valve Control option is installed and no other Valve Control symbols are valid.= Valve Control: Valve Control option installed. Process Value (PV) is within the user set dead band. No control actionrequired.⎡Valve Control: Valve Control option installed. Valve is in full open position.⎦Valve Control: Valve Control option installed. Valve is in full closed position.↑Valve Control: Valve Control option installed. Valve is opening (open signal is being sent to valve actuator).↓Valve Control: Valve Control option installed. Valve is closing.(Close signal is being sent to valve actuator).ÖValve Control: Valve Control option installed. Valve controller override conditions met (DP/SP override set point or LowBattery).L L Valve Control: Valve Control option installed. Local Lock-out is initiated.18Measurement ApplicationsB F Back Flow Condition: Visible only when DP variable displayed.Z Zero Flow Condition: Visible only when Flow Rate displayed.H Hold: Displayed when PCCU32 is in Calibration Mode andhas a measurement application in Hold mode.A Alarm Condition: Need to view alarm. You may need tocompare application limits to current values to determinewhere the alarm condition is present.A D A to D Failure: Displayed if A to D Converter’s Differential Pressure, Absolute Static Pressure or temperature readings exceed maximum counts or are less than minimum counts.The Display Does Not Scroll As ExpectedWhen power is first applied, the unit should quickly go through startup and begin cycling through the pre-programmed display items. If the display does not scroll after startup and/or looks similar to the following: (Part numbers are for example only)2100204 Boot/Loader PROM2100809-002 (COPYRIGHT)Disconnect the main power and then re-connect it. You should see something similar to:Verifying FlashXXXXX Checksum = XXXX Verify Passed orCOLD BOOTFlash 2100826-003X Series Flow Computer2100826-003 (COPYRIGHT)If the display still doesn’t scroll, try disconnecting the power and re-connecting it again. If still no success, do the following:With PCCU32, connect to the unit and establish communications such as Connect To Totalflow, Entry Mode, etc. Go into Terminal Mode and type “0.0.0=COLD” (Do not enter quotes). The unit should go through a Cold Start procedure and begin scrolling. If this does not succeed, call the number on the back of this guide and talk to a customer service representative.19ABB Inc.Totalflow Products7051 Industrial Blvd.Bartlesville, Oklahoma 74006Tel: USA (800) 442-3097International 001-918-338-4880。
LinkSwitch-II产品系列应用指南说明书
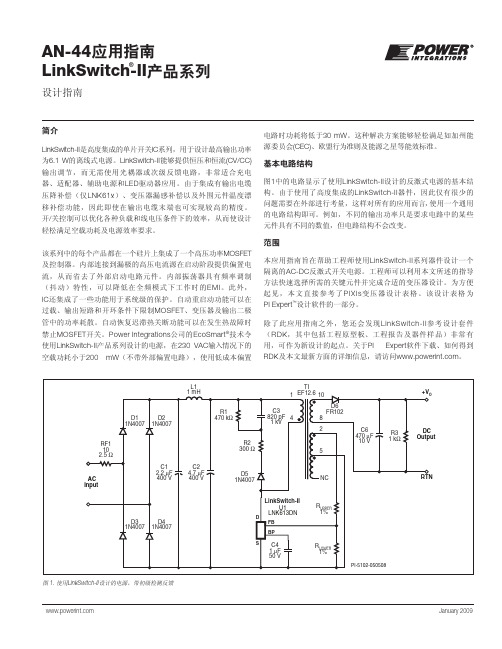
AN-44应用指南LinkSwitch-II 产品系列 January 2009设计指南®简介LinkSwitch-II 是高度集成的单片开关IC 系列,用于设计最高输出功率 为6.1 W 的离线式电源。
LinkSwitch-II 能够提供恒压和恒流(CV/CC) 输出调节,而无需使用光耦器或次级反馈电路,非常适合充电器、适配器、辅助电源和LED 驱动器应用。
由于集成有输出电缆压降补偿(仅LNK61x )、变压器漏感补偿以及外围元件温度漂移补偿功能,因此即使在输出电缆末端也可实现较高的精度。
开/关控制可以优化各种负载和线电压条件下的效率,从而使设计轻松满足空载功耗及电源效率要求。
该系列中的每个产品都在一个硅片上集成了一个高压功率MOSFET 及控制器。
内部连接到漏极的高压电流源在启动阶段提供偏置电流,从而省去了外部启动电路元件。
内部振荡器具有频率调制 (抖动)特性,可以降低在全频模式下工作时的EMI 。
此外,IC 还集成了一些功能用于系统级的保护。
自动重启动功能可以在过载、输出短路和开环条件下限制MOSFET 、变压器及输出二极管中的功率耗散。
自动恢复迟滞热关断功能可以在发生热故障时禁止MOSFET 开关。
Power Integrations 公司的EcoSmart ®技术令使用LinkSwitch-II 产品系列设计的电源,在230 VAC 输入情况下的空载功耗小于200 mW (不带外部偏置电路),使用低成本偏置电路时功耗将低于30 mW 。
这种解决方案能够轻松满足如加州能源委员会(CEC)、欧盟行为准则及能源之星等能效标准。
基本电路结构图1中的电路显示了使用LinkSwitch-II 设计的反激式电源的基本结构。
由于使用了高度集成的LinkSwitch-II 器件,因此仅有很少的问题需要在外部进行考量,这样对所有的应用而言,使用一个通用的电路结构即可。
例如,不同的输出功率只是要求电路中的某些元件具有不同的数值,但电路结构不会改变。
爱丽丝电子 ELC-GP02 图形面板系列操作指南说明书

ELC-GP02GRAPHIC PANEL SERIESInstruction SheetWARNING• DANGER - DC input power must be disconnected before any maintenance. Do not connect ordisconnect wires and connectors while power is applied to the circuit. Maintenance must be performed by qualified technicians.•DANGER - The ELC-GP02 requires 24VDC input power. The 24VDC input power should not be connected to the RS-485 communication port. The unit may be destroyed or can’t be repaired if the input power is improperly applied. Please always check the correctly input power wiring before apply power.• DANGER - An electrical charge will remain on the DC-link capacitors for 1 minute after power has been removed. Do not conduct any wiring or investigation on the ELC-GP02 until 1 minute after power has been removed. Do NOT touch terminals when power on.• CAUTION - Always ground the ELC-GP02 by using the grounding terminal. Not only this acts as a safety, but also filter out electrical noise. The ground method must comply with the laws of the country where the unit is to be installed.• CAUTION - ELC-GP02 may be damaged if the fixed support (shipped with the pack) is adjusted too tight.• Please carefully read this instruction before using the ELC-GP02.• The ELC-GP02 display panel is waterproof. But please prevent grease, corrosive liquids and sharp objects from contacting the ELC-GP02.• Do not disconnect while circuit is live unless area is known to be non-hazardous.• This equipment is suitable for use in Class I, Division 2, Groups A, B, C, D or Non-Hazardous Locations only.• Explosion Hazard – Substitution of components may impair suitability for class I, Division 2. • Explosion Hazard – Do not disconnect equipment unless power has been switched off or the area is known to be Non – Hazardous.•Power, input and output (I/O) wiring must all be in accordance with Class I, Division 2 wiring methods, Article 501-4 (b) of the National Electrical Code, NEPA 70,or as specified in Section 18-152 of the Canadian Electrical Code for units installed within Canada, and in accordance with that location’s authority.1INTRODUCTION1.1 Model ExplanationThank you for choosing Eaton Logic Controler (ELC) GP series products. The features of ELC-GP02 are: resolution is 160*32, display 10*2 Chinese characters max. and Multilanguage support. Built-in two communication ports (RS-232 and RS-485/RS-422, can be used simultaneously).Communication and alarm indication LEDs. Extension slot for ELC-GPXFERMOD to copy settings and programs rapidly and save download time. Built-in variety objects to meet your requirements. 1.2 Outline1.3 Panel Function ExplanationPANEL COMPONENTEXPLANATIONAlarm Indication LED Status 1: When power is on, the LED will flash three times slowly.Status 2: When there is an abnormal situation, the LED will flash quickly along with an alarm sound.RS-232 Indication LED (Yellow)It will be flashing when transmitting program and communicating by using RS-232.RS-485 Indication LED (Green)It will be flashing when communicating by using RS-485. LCM display Area Liquid Crystal Module display area used to display current program state. Esc Escape/Exit)Used to cancel an incorrect input, or to Exit a programming step. Arrow KeysUP/Pg Up : Used to increase the value or move up one page.Pg Dn/DOWN : Used to decrease the value or move down one page. Left: Left direction key. (move curser to left) Right : Right direction key. (move cursor to right)Enter Key Used to input a value or accept a programming command.Function KeysF0/0: It is used to be constant 0 and user can define the function of F0. F1/1: It is used to be constant 1 and user can define the function of F1. F2/2: It is used to be constant 2 and user can define the function of F2. F3/3: It is used to be constant 3 and user can define the function of F3. F4/4: It is used to be constant 4 and user can define the function of F4.F5/5: It is used to be constant 5 and user can define the function of F5. F6/6: It is used to be constant 6 and user can define the function of F6. F7/7: It is used to be constant 7 and user can define the function of F7. F8/8: It is used to be constant 8 and user can define the function of F8. F9/9: It is used to be constant 9 and user can define the function of F9.1.4 BackPanel5-PIN terminals:Wire gauge: 12-24 AWG Torque: 4.5 lb.-inch1.5 DimensionFront panel (unit: mm [inch])Right side diagram (unit: mm [inch])Vertical view (Unit: mm)1.6 InstallationMounting ELC-GP02 into the opening is done by carefully fitting the unit into the opening and pressing firmly on all four corners. You could fix it by using the fixed support packaged withELC-GP02. You should infix the fixed support in the back cover and turn the screw in to fix. Warning: If you turn the screw exceeds torque: 4-5(kg-cm), ELC-GP02 may be damaged. (Note :the flat surface shoud be a Type 4 “Indoor Use Only” enclosure or equivalent.) Please leave sufficient space (more than 50mm) around the unit for heat dissipation.Thickness:50mm50mmMounting dimension (unit: mm [inch])2.2 Function SpecificationITEMELC-GP02D i s p l a y S c r e e nScreen STN-LCDColor MonochromaticBack-lightThe back-light automatic turn off time is 1~99 minutes(0 = do not to turn off)(back-light life is about 50 thousand hours at 25℃)Resolution 160X32 dots■ ELC-GP02 may connect to ELC using cable ELC-CBPCELC36COMMUNICATION CONNECTION■ELC-GP02 may connect to a PC by using cable ELC-CBPCGP3ELC-CBPCGP39 PIN D-SUBON PC (RS-232)ON ELC-GP02/049 PIN D-SUBRS-232:ITEMELC-GP02 Display Range 72 mm (W) X 22 mm (H) Contrast Adjustment 15-step contrast adjustmentLanguage Font ASCII: characters Other: user define Font Size (ASCII) 5 X 8, 8 X 8, 8 X 12, 8 X 16ALARM Indication LED 1. Power on indication (Flash three times) 2. Flash for communication error or other alarm 3. Special Indication by user programming RS-232 Indication LED Flashing when communicating by using RS-232. RS-485 Indication LED It will be flashing when communicating by using RS-485.Program Memory256KB flash memoryE x t e r n a l I n t e r f a c eSerial Communication Port RS-232 (COM1) RS-232Data length: 7 or 8 bitsStop bits: 1or 2 bits Parity: None/Odd/EvenTransmission speed: 4800bps~115200bpsRS-232: 9 PIN D-SUB maleExtension Communication PortRS-485 (COM2)RS-485Data length: 7 or 8 bitsStop bits: 1 or 2 bits Parity: None/Odd/EvenTransmission speed: 4800bps~115200bpsRS-485: 5-Pin Removal TerminalExtension SlotThe slot for program copy card 5-Pin Removal TerminalThere are DC 24V input and RS-485 input3TRANSFER MODULEThe function of program copy card that ELC-GP02 provides to copy user program, system function and passwords is different from the copy program. It is used to copy the whole HMI environment settings and application programs to another HMI rapidly. It can save much time and manpower. The operation is in the following.Definition: ELC-GPXFERMOD = XMOD, GP Series = GPStep GP ÆXMODXMOD ÆGP1 Turn the switch on the XMOD to GP ÆXMOD Turn the switch on the XMOD to XMOD ÆGP2 Insert the XMOD into the extension slot of GP Insert the XMOD into the extension slot of GP3 Input the power to GPInput the power to GP4It will display “remove XMOD” on the screen and power on againIt will display “remove XMOD” on the screen and power on againHMI display messageCopy HMI program to XMOD (GP ÆXMOD) Copy XMOD program to HMI (XMOD ÆGP) If the model type of GP does not correspond with the model type of program of XMOD, GP will display “GP series and XMOD is different. Press Enter to Confirm GP series ÆXMOD. Press Esc to Exit”.If there is no program in XMOD, GP will display “The XMOD is Empty. XMOD ÆGP series is illegal”.GP will display “GP ÆXMOD series Please wait!” during transmission.GP will display “GP ÆXMOD series Please wait!” during transmission.GP will display “Please Remove the XMOD and Reboot” when completing transmitting.GP will display “Please Remove the XMOD and Reboot” when completing transmitting.4PASSWORD FUNCTION1 If the password is forgotten, the password may be cleared using the following code: 8888. Thisuniversal code will clear the password and all internal programs of ELC-GP02. The ELC-GP02 will be re-set to the factory settings.2 Users may use 0~9 and A~Z as characters for the password. Users must use the function keysF0~F4 to input the password characters.F0: scrolls in a loop as follows 0 Æ A Æ B Æ C Æ D Æ E Æ F Æ 0F1: scrolls in a loop as follows 1 Æ G Æ H Æ I Æ J Æ K Æ 1 F2: scrolls in a loop as follows 2 Æ L Æ M Æ N Æ O Æ P Æ 2 F3: scrolls in a loop as follows 3 Æ Q Æ R Æ S Æ T Æ U Æ V Æ3 F4: scrolls in a loop as follows 4 Æ W Æ X ÆY Æ Z Æ 4 F5: it just can be used to be constant 5. F6: it just can be used to be constant 6. F7: it just can be used to be constant 7. F8: it just can be used to be constant 8. F9: it just can be used to be constant 9.5HARDWARE OPERATIONThe steps to Startup the ELC-GP02:1 Apply 24V DC power,2 Enter into the startup display,3 Enter the user-designed program,4 Press Esc key and hold on for5 seconds to return to system menu. There are five selections in the system menu and are described below.SELECTIONSEXPLANATIONDownload ProgramUse the connection cable (ELC-CBPCTP3) to connect the serial communication port RS-232 of ELC-GP02 to a PC. Then use the ELCSoftGP software to download an application program to the ELC-GP02.Upload Program Use the connection cable (ELC-CBPCTP3) to connect the serial communication port RS-232of ELC-GP02 to a PC. Then use the ELCSoftGP software to upload an application programfrom the ELC-GP02.Copy ProgramTransfer a program between two ELC-GP02 units. 1: transmit programs2: receive programsWhen transmitting programs and data between two ELC-GP02 unit. Set one ELC-GP02 to “Receive Program” mode and the other ELC-GP02 to “Transmit Program” mode. Please usetwisted pair wires to connect the two units via the RS-485 ports.GP02 SettingsUsed to modify the ELC-GP02 system settings. There are 8 items that may be modified. 1.Communication protocol: Set the address of ELC-GP02 and the communication string for either RS-232 or RS-485.2. Contrast: Adjust the contrast of LCM display screen.3.Back-light: adjust the automatic turn off time of LCM. Setting range is 00~99 seconds. If set to 00, the LCM Back-light will not turn off.4. Buzzer: Used to set the buzzer sound, normal mode or quiet mode.5.Language Setting: Used to set the displayed language. English, Traditional Chinese, simplified Chinese or user defined language.6. Password setting: Used to set, enable, and disable the password function. If the password function is enabled, it will require the user to input a password before the system menu may be accessed. The factory password is 1234.7. Startup display: Used to select the ELC-GP02 startup display.8.Comm. Indicator : Used to select the communication Indicator enable or disable.ELC ConnectionThere are two methods to connect to ELC:1. Use the connection cable (ELC-CBPCELC3) to connect program communication I/ORS-232C of ELC to serial communication port (COM1) RS-232 of ELC-GP02. 2. Use twisted cable to connect RS-485 of ELC to extension communication port (COM2)RS-485.ExecutionExecute the internal program that download from ELCSoftGP or transmitted from otherELC-GP02 units. When entering execution program, you can return to system menu by pressing Escape/Exit (Esc) key for 5 seconds.■ The Pin definition of 9 PIN D-SUB。
- 1、下载文档前请自行甄别文档内容的完整性,平台不提供额外的编辑、内容补充、找答案等附加服务。
- 2、"仅部分预览"的文档,不可在线预览部分如存在完整性等问题,可反馈申请退款(可完整预览的文档不适用该条件!)。
- 3、如文档侵犯您的权益,请联系客服反馈,我们会尽快为您处理(人工客服工作时间:9:00-18:30)。
BEGIN_MESSAGE_MAP(CMyView, Cview)
ON_WM_LBUTTONDOWN() END_MESSAGE_MAP()
17
VC++ Programming @ UESTC
Chapter 4 Basic Event Handling, Mapping Modes and a Scrolling View
At this point, we simply need to know that there’re predefined windows message and user defined message which will respond to different events. Visual C++ provides a tool ClassWizard to help us make this job easier.
4
VC++ Programming @ UESTC
Chapter 3 Getting Started with AppWizard
Project Type MFC AppWizard (exe)
Application Type Single document Files Generated ex03aView.cpp and ex03aView.h Compile and link Test the application Browse the application Source Browser
Automatic switch stores compiler output in a database file. /Yc, used only with stdAfx.cpp causes the creation of the precompiled (PCH) file. /Yu , used with all other source file , causes use of the existing PCH file.
12
VC++ Programming @ UESTC
Chapter 3 Getting Started with AppWizard
13
VC++ Programming @ UESTC
Chapter 4 Basic Event Handling, Mapping Modes and a Scrolling View
Chapter 5
The Graphics Device Interface, Colors and Fonts
Chapter 6 The Modal Dialog and Windows Common Controls
1
VC++ Programming @ UESTC
Part II
MFC View Class
A Message ID defines a message for the specific event. In class header .h file , you must have prototype
afx_msg void OnLButtonDown(UINT nFlags, Cpoint point); DECLARE_MESSAGE_MAP() SECTION
10
VC++ Programming @ UESTC
Chapter 3 Getting Started with AppWizard
Debug Target vs. Release Target
What is the purpose of using debug build option? Executable size difference between the two options Path to locate the target Other related settings Debug Enables the Diagnostic Macros Use Tracer utility
8
VC++ Programming @ UESTC
Chapter 3 Getting Started with AppWizard
Contents of the Resource File ( ex03a.rc)
Accelerator Dialog Icon Menu String Table Toolbar Version
Use ClassView to add the OnDraw function
Add codes inside OnDraw() to do something
6
VC++ Programming @ UESTC
Chapter 3 Getting Started with AppWizard
3
VC++ Programming @ UESTC
Chapter 3 Getting Started with AppWizard
What’s a View?
From a user’s standpoint, a view is a window where the user can play with a mouse and keyboard; From a programmer’s perspective, a view is a C++ object of a class derived from a CView class. We’ll make a single document application (SDI) to show the details.
11
VC++ Programming @ UESTC
Chapter 3 Getting Started with AppWizard
“StdAfx.h” file contains the MFC header files used in this project. switch setting and precompiled headers Automatic precompiled headers /Yx vs. Manual precompiled headers /Yc /Yu
5
VC++ Programming @ UESTC
Chapter 3 Getting Started with AppWizard
Simply Drawing inside the View Window
Window Reaction Mechanism Window Changes Invalidate() OnDraw()
16
VC++ Programming @ UESTC
Chapter 4 Basic Event Handling, Mapping Modes and a Scrolling View
In class source code file (.cpp file), you must have member function OnLButtonDown(UINT nFlags, Cpoint point);
2
VC++ Programming @ UESTC
Chapter 3 Getting Started with AppWizard
This hands-on chapter shows you how to build a MFC library application working with only the view element.
Chapter 7 The Modeless Dialog and Windows Common Dialogs Chapter 8 Using ActiveX Controls Chapter 9 Win32 Memory Management Chapter 10 Bitmaps Chapter 11 Windows Message Processing and Multithreaded Programming
How to use Graphics Device Interface (GDI) How to use Resource Editor Debug Target vs. Release Target Understand Diagnostic Macros Understand the Precompiled Headers
what about the menu, toolbar event?
15
VC++ Programming @ UESTC
Chapter 4 Basic Event Handling, Mapping Modes and a Scrolling View
Event Handling Mechanism
9
VC++ Programming @ UESTC
Chapter 3 Getting Started with AppWizard
Statements inside ex03a.rc to be reexamined
#include “afxres.h” #include “afxrec.rc” ---contains MFC library resource common to all application #include “resource.h” --- contains special resource in this project