全自动焊接实用工艺
全自动焊接工艺
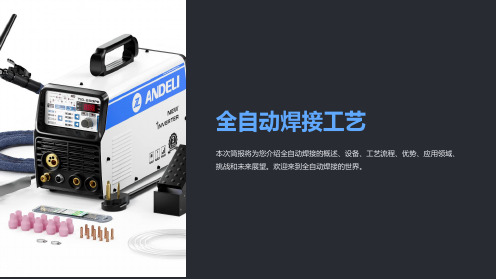
• 同一个项目中可能需 要多种焊接工艺。
焊接操作步骤
• 根据所选工艺进行具 体操作。
• 严格按照操作指南完 成区域排除和焊接工 具维护。
全自动焊接工艺的优势
1 提高生产效率
全自动焊接可以在更短的时间内进 行更多的焊接,从而提高整体生产 效率。
全自动焊接将受益于新材料和新工艺的不断 发展,其中许多具有更好的可焊性、更轻、
更耐高温等优势。
全自动焊接工艺的挑战和解决方案
复杂焊接结构的处 理
在生产中,复杂的焊接结构 可能无法被标准全自动化机 器所处理。因此,需要考虑 自适应机器人技术的应用, 提升设备和系统的适应性。
材料选择和适应性
不同的材料需要不同的材料 处理方式。许多传统的焊接 设备难以处理新型材料,例 如复合材料和纳米材料。因 此,需采用先进的焊接设备 和技术。
线
应用
改进
全自动焊接技术广泛应用于汽车制造业,某 汽车制造公司采用了全自动化的焊接生产线
术也在航空航天工业中大显身 手。某航空航天公司采用了全自动化的焊接
生产线,提高了生产效率和焊接质量。
某电子制造企业的焊接过程中问题频发,他 们采取全自动化的焊接产线改进,显著提高
全自动焊接工艺
本次简报将为您介绍全自动焊接的概述、设备、工艺流程、优势、应用领域、 挑战和未来展望。欢迎来到全自动焊接的世界。
焊接工艺概述
定义和作用
焊接是指将两个或以上零部件拼接在一 起,使其坚固无动摇。全自动焊接工艺 可以提高焊接的得当性和效率。
全自动焊接的定义和特点
全自动焊接是指使用计算机控制的操作 机器来完成焊接过程。它提供更加整齐 熟练的焊接,且不受人力影响。
大型压力容器全方位自动焊接施工工法(2)
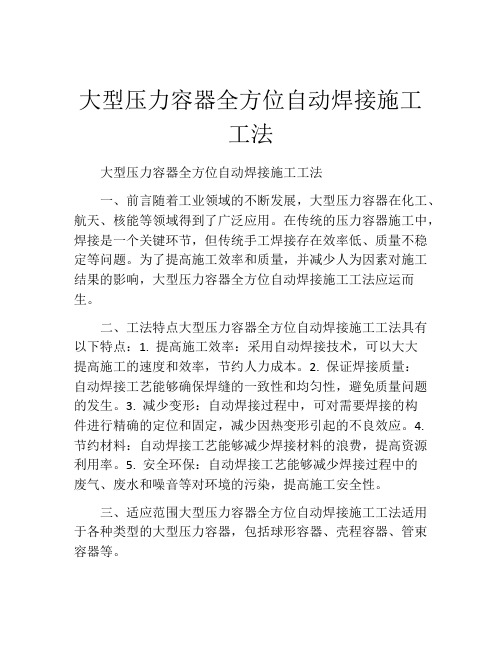
大型压力容器全方位自动焊接施工工法大型压力容器全方位自动焊接施工工法一、前言随着工业领域的不断发展,大型压力容器在化工、航天、核能等领域得到了广泛应用。
在传统的压力容器施工中,焊接是一个关键环节,但传统手工焊接存在效率低、质量不稳定等问题。
为了提高施工效率和质量,并减少人为因素对施工结果的影响,大型压力容器全方位自动焊接施工工法应运而生。
二、工法特点大型压力容器全方位自动焊接施工工法具有以下特点:1. 提高施工效率:采用自动焊接技术,可以大大提高施工的速度和效率,节约人力成本。
2. 保证焊接质量:自动焊接工艺能够确保焊缝的一致性和均匀性,避免质量问题的发生。
3. 减少变形:自动焊接过程中,可对需要焊接的构件进行精确的定位和固定,减少因热变形引起的不良效应。
4. 节约材料:自动焊接工艺能够减少焊接材料的浪费,提高资源利用率。
5. 安全环保:自动焊接工艺能够减少焊接过程中的废气、废水和噪音等对环境的污染,提高施工安全性。
三、适应范围大型压力容器全方位自动焊接施工工法适用于各种类型的大型压力容器,包括球形容器、壳程容器、管束容器等。
四、工艺原理大型压力容器全方位自动焊接施工工法的工艺原理主要包括施工工法与实际工程之间的联系和采取的技术措施。
通过精确的工艺参数调控和设备操作,实现焊缝的全方位自动焊接。
工法通过提前对焊接路径进行设计和规划,然后根据工艺要求进行焊接设备和材料的选择。
通过对焊接路径进行全方位的控制,确保焊接过程的稳定性和焊接质量的可靠性。
五、施工工艺大型压力容器全方位自动焊接施工工法的施工工艺主要分为以下几个阶段:1. 准备阶段:包括焊接工艺参数的确定、设备和材料的准备就绪。
2. 定位固定阶段:确保工件的准确定位和固定,以保证焊接过程的稳定。
3. 焊接阶段:按照事先设计和规划的焊接路径进行自动焊接,采用适当的焊接方法和技术措施。
4. 检测与修磨阶段:对焊接后的焊缝进行检测,并进行必要的修磨处理,以保证焊缝的质量和外观。
自动焊工艺技术

自动焊工艺技术自动焊工艺技术是一种应用于工业生产中的现代焊接技术。
它利用计算机控制系统来控制焊接参数和焊接过程,使焊接质量得到保障并提高工作效率。
以下将介绍自动焊工艺技术的相关知识。
自动焊工艺技术主要包括焊接设备的结构和组成,焊接参数的选择与控制,以及焊接质量的检测与评定。
首先,焊接设备的结构和组成是实现自动化焊接的基础,它主要包括焊接机器人、焊接电源、传感器和控制系统等组成部分。
焊接机器人是自动焊的核心设备,它能够根据预设的程序自动完成焊接工作。
焊接电源是提供焊接电流和电压的设备,通过对电流和电压的控制,可以实现焊接参数的调节。
传感器可以对焊接过程中的温度、压力等参数进行检测,从而实时监控焊接质量。
控制系统是整个自动焊系统的大脑,它负责接收传感器的信号,并根据预设的程序自动调节焊接参数和控制焊接机器人的动作。
其次,焊接参数的选择与控制是实现自动焊的关键。
焊接参数包括焊接电流、电压、速度、间隙等,不同的焊接材料和焊接方式对焊接参数有不同的要求。
在自动焊过程中,通过对焊接参数的选择和控制,可以达到最佳的焊接效果和焊接质量。
例如,在焊接薄板材料时,可以选择较小的焊接电流和速度,以免过热导致变形;在焊接厚板时,可以选择较大的焊接电流和速度,以确保焊缝的充实度。
最后,焊接质量的检测与评定是保证焊接质量的重要环节。
自动焊工艺技术可以通过传感器对焊接过程中的焊接温度、电压、电流等参数进行实时监测,并将监测数据传输给控制系统进行分析和处理。
通过对焊接质量的检测,可以及时发现焊接中的问题,并采取相应的措施进行修正。
此外,还可以通过对焊缝的形貌和颜色进行评定,从而检测焊接质量是否达到要求。
综上所述,自动焊工艺技术是一种高效、准确的焊接技术。
它通过计算机控制系统来控制焊接参数和焊接过程,实现了焊接质量的保障和工作效率的提高。
随着科技的不断发展,自动焊工艺技术将在各个领域得到更广泛的应用,为工业生产带来更大的便利和效益。
e-PSP钢塑复合管全自动智能电磁热熔焊接施工工法

e-PSP钢塑复合管全自动智能电磁热熔焊接施工工法e-PSP钢塑复合管全自动智能电磁热熔焊接施工工法一、前言e-PSP钢塑复合管全自动智能电磁热熔焊接施工工法是一种先进的管道施工技术,通过采用电磁热熔焊接方法,实现了管道连接的高效、自动化和智能化。
本文将详细介绍该工法的特点、适应范围、工艺原理、施工工艺、劳动组织、机具设备、质量控制、安全措施、经济技术分析和工程实例,以期提供参考和指导。
二、工法特点e-PSP钢塑复合管全自动智能电磁热熔焊接施工工法具有以下特点:1. 高效自动化:采用全自动化电磁热熔焊接设备,实现了管道连接的高效率、高精度和高质量。
2. 智能化管理:通过智能化设备控制和质量管理系统,实现了施工过程的监控、数据采集和分析,提高了施工效率和质量。
3. 工期短、成本低:相比传统的手工焊接方法,该工法具有施工周期短、人力成本低、材料费用低等优势,能够大幅度降低工程总成本。
4. 安装牢固可靠:通过电磁热熔焊接技术,实现了管道连接的牢固、密封和耐久性,降低了管道漏水和破损的风险。
5. 环保节能:该工法采用无火焰、无焊渣的电磁热焊接方式,不产生有害气体和固体废料,符合环保要求。
三、适应范围e-PSP钢塑复合管全自动智能电磁热熔焊接施工工法适用于各种建筑、工程和市政管道的施工,包括给水、排水、暖通、燃气等。
特别适用于高层建筑、大型工程和复杂地形条件下的管道施工,能够满足各种需求和规格的管道连接要求。
四、工艺原理e-PSP钢塑复合管全自动智能电磁热熔焊接施工工法基于电磁感应原理,使用电磁感应线圈将焊接区域加热到适当温度,然后施加压力使管道连接。
该工法采取了以下技术措施:1. 选用专用电磁感应线圈和智能控制系统,实现精准、稳定的焊接温度控制,并能实时监测施工质量。
2. 采用特殊工艺和焊接剂,增强焊接接头的密封性和强度,确保管道连接的可靠性和稳定性。
3. 设计合理的焊接工艺和参数,根据实际情况选择合适的工艺方案,确保施工过程的规范和连续性。
X80管线钢全自动下向焊焊接工艺
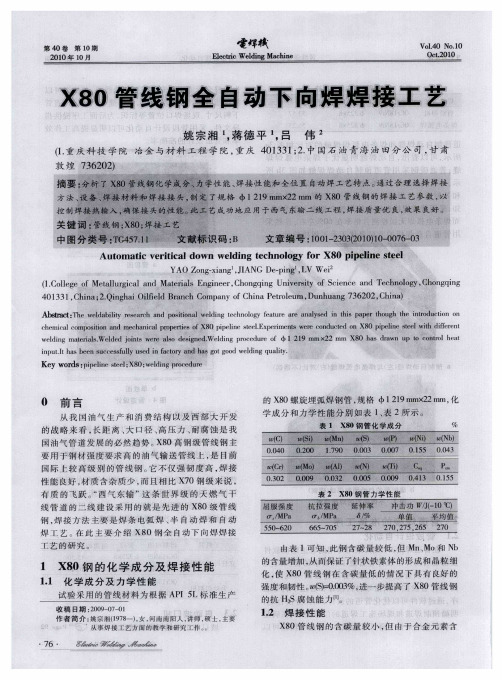
工艺 的研究 。
屈 服强 度 o /P -M a
c e c l o o io n c a ia r p r e fX8 i ei e se 1 x e i ns w r o d ce n X8 ie i e s e i i e e t h mia c mp st n a d me h n c lp o et s o 0 p p l te . p r i i n E me t ee c n u td o 0 pp l t lw t d f r n n e h f
YAO Z n —in JAN Depn L W e o gxa g ,I G —ig , V i
(.o eeo t lria a dMaei sE gn e, h n qn nv r t o ce c n eh ooy C o g ig 1 l g f C l Mea ug l n t a n ierC og ig U i s y fS inea d T c n l , h n qn l c rl e i g
wedn tr l. le onsw r s ein dWedn rc d r f中12 9 mmx 2mm X8 a rw p t c nrlh a lig maei s a Wed d jit e a od sg e . lig po e ue o e l 1 2 0 h sd a n u O o t e l o
55 62 0~ 0
表 2 X8 0钢 管 力 学 性 能
全自动焊接工艺
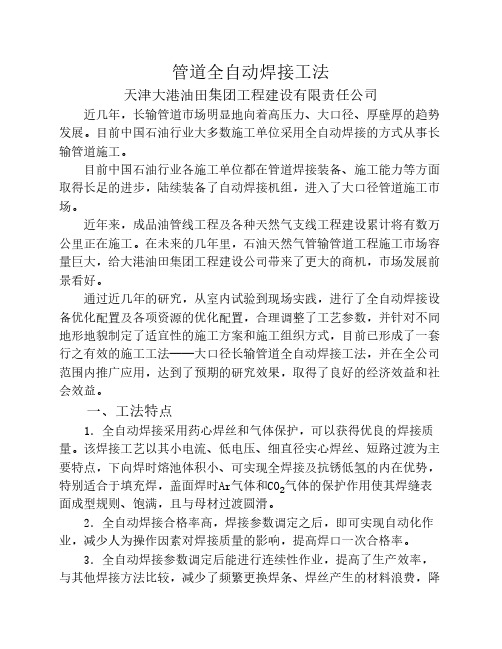
管道全自动焊接工法天津大港油田集团工程建设有限责任公司近几年,长输管道市场明显地向着高压力、大口径、厚壁厚的趋势发展。
目前中国石油行业大多数施工单位采用全自动焊接的方式从事长输管道施工。
目前中国石油行业各施工单位都在管道焊接装备、施工能力等方面取得长足的进步,陆续装备了自动焊接机组,进入了大口径管道施工市场。
近年来,成品油管线工程及各种天然气支线工程建设累计将有数万公里正在施工。
在未来的几年里,石油天然气管输管道工程施工市场容量巨大,给大港油田集团工程建设公司带来了更大的商机,市场发展前景看好。
通过近几年的研究,从室内试验到现场实践,进行了全自动焊接设备优化配置及各项资源的优化配置,合理调整了工艺参数,并针对不同地形地貌制定了适宜性的施工方案和施工组织方式,目前已形成了一套行之有效的施工工法——大口径长输管道全自动焊接工法,并在全公司范围内推广应用,达到了预期的研究效果,取得了良好的经济效益和社会效益。
一、工法特点1.全自动焊接采用药心焊丝和气体保护,可以获得优良的焊接质量。
该焊接工艺以其小电流、低电压、细直径实心焊丝、短路过渡为主要特点,下向焊时熔池体积小、可实现全焊接及抗锈低氢的内在优势,特别适合于填充焊,盖面焊时Ar气体和CO2气体的保护作用使其焊缝表面成型规则、饱满,且与母材过渡圆滑。
2.全自动焊接合格率高,焊接参数调定之后,即可实现自动化作业,减少人为操作因素对焊接质量的影响,提高焊口一次合格率。
3.全自动焊接参数调定后能进行连续性作业,提高了生产效率,与其他焊接方法比较,减少了频繁更换焊条、焊丝产生的材料浪费,降低施工成本。
同时全自动化焊接作业也降低了工人的劳动强度,但对工人的自身素质和操作能力有更高的要求。
4.全自动焊接工艺对管道组对坡口质量和坡口型式要求严格,需要配套的坡口整形机等设备。
5.全自动焊接的保护气体为Ar气体和CO2气体,因此与其他焊接方法比较,施工环境更为苛刻,现场施工时要求环境风速小于2m/s。
焊接工艺的自动焊接技术要点

焊接工艺的自动焊接技术要点焊接工艺的自动焊接技术在工业生产中扮演着重要角色。
随着科技的不断发展和进步,自动焊接技术不仅提高了焊接工艺的效率和质量,还减少了人为因素对焊接过程的影响。
本文将介绍焊接工艺的自动焊接技术的要点。
一、自动焊接技术的分类自动焊接技术可以分为以下几类:点焊、脉冲焊、气保焊、激光焊和电弧焊等。
每种技术都有其适用的场景和特点,下面将逐一介绍。
1. 点焊技术点焊技术是将两个焊接材料通过电流加热并压紧在一起,形成有强强度的焊接方式。
该技术通常用于焊接薄板、网格、铸造件等。
2. 脉冲焊技术脉冲焊技术是在焊接过程中通过间歇加热和冷却的方式实现焊接。
这种技术可以有效避免焊接过程中的热变形和残余应力。
3. 气保焊技术气保焊技术是通过在焊缝周围引入保护气体,以防止未焊接金属部分接触空气而产生氧化的现象。
气保焊技术通常适用于对焊接质量要求较高的情况。
4. 激光焊技术激光焊技术是通过高能激光束对焊接材料进行加热和熔融,从而实现焊接的。
该技术具有焊接速度快、变形小等特点。
5. 电弧焊技术电弧焊技术是利用电能形成的电弧进行焊接。
这种技术适用于各种金属材料的焊接,应用广泛。
二、自动焊接技术的优势自动焊接技术相比传统手工焊接技术具有许多优势。
1. 提高效率:自动焊接技术可以实现连续、高效的焊接过程,大大提高了焊接的效率。
2. 降低人为因素:自动焊接技术减少了人为因素对焊接过程的影响,提高了焊接质量的稳定性和一致性。
3. 减少工作量:自动焊接技术可以减少工人的劳动强度,降低了工作成本和安全风险。
4. 提高焊接质量:自动焊接技术可以精确控制焊接参数,确保焊接质量的稳定和一致。
5. 适应各种环境:自动焊接技术可以适应各种恶劣环境,如高温、低温、高海拔等,提高了焊接的适应性和稳定性。
三、自动焊接技术的注意事项在使用自动焊接技术时,需要注意以下几个方面。
1. 焊接设备的选择:根据不同的焊接需求,选择合适的自动焊接设备,包括焊接机器人、焊接电源等。
全自动管道焊接操作方法

全自动管道焊接操作方法
全自动管道焊接是一种高效、精准的焊接方法,可以提高焊接质量和生产效率。
以下是全自动管道焊接的一般操作方法:
1. 准备工作:根据焊接要求选择合适的设备、工具和焊接材料。
检查设备和工具的状态,确保其正常运行。
2. 准备管道:清洁管道表面,去除任何污垢、油脂和氧化物。
确保管道端部平整、无毛刺。
检查管道的尺寸和焊缝线,确保其符合要求。
3. 安装焊接设备:根据焊接要求,安装好自动焊接设备,包括自动焊机、电源和控制系统。
调整设备参数,使其适应具体焊接工艺。
4. 设置焊接参数:根据管道材料、厚度和焊接要求,设置合适的焊接参数,包括焊接电流、电压、速度和电弧稳定性等。
确保参数的合理性和稳定性。
5. 开始焊接:根据焊接程序和机器人的编程,启动焊接过程。
焊接机器人自动识别焊缝位置,自动对焊接速度进行控制,实现全自动焊接。
6. 检查焊接质量:焊接完成后,对焊缝进行质量检查。
检查焊缝的外观、尺寸和无损检测结果,确保其符合要求。
7. 收尾工作:清理焊接现场,将焊接设备和工具进行维护和保养。
整理焊接记录和报告,做好焊接质量的记录和归档工作。
总结起来,全自动管道焊接的操作方法主要包括准备工作、设备安装、参数设置、起焊、质检和收尾工作等环节。
通过合理操作和严格管理,可以实现高质量、高效率的全自动管道焊接。
全自动焊接工艺
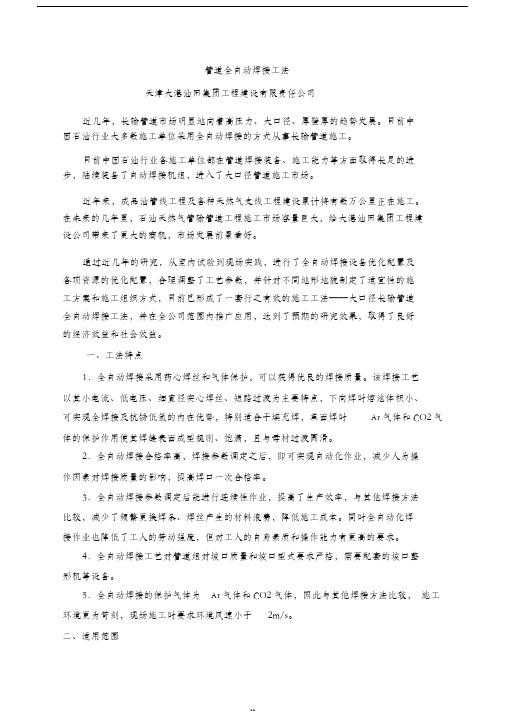
管道全自动焊接工法天津大港油田集团工程建设有限责任公司近几年,长输管道市场明显地向着高压力、大口径、厚壁厚的趋势发展。
目前中国石油行业大多数施工单位采用全自动焊接的方式从事长输管道施工。
目前中国石油行业各施工单位都在管道焊接装备、施工能力等方面取得长足的进步,陆续装备了自动焊接机组,进入了大口径管道施工市场。
近年来,成品油管线工程及各种天然气支线工程建设累计将有数万公里正在施工。
在未来的几年里,石油天然气管输管道工程施工市场容量巨大,给大港油田集团工程建设公司带来了更大的商机,市场发展前景看好。
通过近几年的研究,从室内试验到现场实践,进行了全自动焊接设备优化配置及各项资源的优化配置,合理调整了工艺参数,并针对不同地形地貌制定了适宜性的施工方案和施工组织方式,目前已形成了一套行之有效的施工工法——大口径长输管道全自动焊接工法,并在全公司范围内推广应用,达到了预期的研究效果,取得了良好的经济效益和社会效益。
一、工法特点1.全自动焊接采用药心焊丝和气体保护,可以获得优良的焊接质量。
该焊接工艺以其小电流、低电压、细直径实心焊丝、短路过渡为主要特点,下向焊时熔池体积小、可实现全焊接及抗锈低氢的内在优势,特别适合于填充焊,盖面焊时Ar 气体和 CO2气体的保护作用使其焊缝表面成型规则、饱满,且与母材过渡圆滑。
2.全自动焊接合格率高,焊接参数调定之后,即可实现自动化作业,减少人为操作因素对焊接质量的影响,提高焊口一次合格率。
3.全自动焊接参数调定后能进行连续性作业,提高了生产效率,与其他焊接方法比较,减少了频繁更换焊条、焊丝产生的材料浪费,降低施工成本。
同时全自动化焊接作业也降低了工人的劳动强度,但对工人的自身素质和操作能力有更高的要求。
4.全自动焊接工艺对管道组对坡口质量和坡口型式要求严格,需要配套的坡口整形机等设备。
5.全自动焊接的保护气体为Ar 气体和 CO2气体,因此与其他焊接方法比较,施工环境更为苛刻,现场施工时要求环境风速小于2m/s。
管道全自动焊接技术及工艺研究
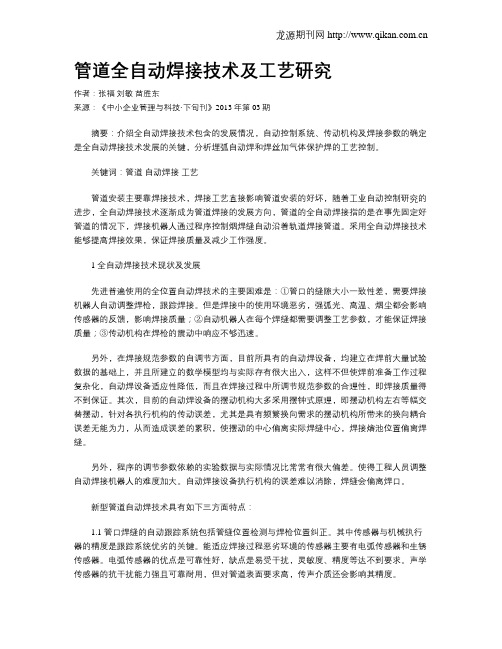
管道全自动焊接技术及工艺研究作者:张福刘敏苗胜东来源:《中小企业管理与科技·下旬刊》2013年第03期摘要:介绍全自动焊接技术包含的发展情况,自动控制系统、传动机构及焊接参数的确定是全自动焊接技术发展的关键,分析埋弧自动焊和焊丝加气体保护焊的工艺控制。
关键词:管道自动焊接工艺管道安装主要靠焊接技术,焊接工艺直接影响管道安装的好坏,随着工业自动控制研究的进步,全自动焊接技术逐渐成为管道焊接的发展方向,管道的全自动焊接指的是在事先固定好管道的情况下,焊接机器人通过程序控制烟焊缝自动沿着轨道焊接管道。
采用全自动焊接技术能够提高焊接效果,保证焊接质量及减少工作强度。
1 全自动焊接技术现状及发展先进普遍使用的全位置自动焊技术的主要困难是:①管口的缝隙大小一致性差,需要焊接机器人自动调整焊枪,跟踪焊接。
但是焊接中的使用环境恶劣,强弧光、高温、烟尘都会影响传感器的反馈,影响焊接质量;②自动机器人在每个焊缝都需要调整工艺参数,才能保证焊接质量;③传动机构在焊枪的震动中响应不够迅速。
另外,在焊接规范参数的自调节方面,目前所具有的自动焊设备,均建立在焊前大量试验数据的基础上,并且所建立的数学模型均与实际存有很大出入,这样不但使焊前准备工作过程复杂化,自动焊设备适应性降低,而且在焊接过程中所调节规范参数的合理性,即焊接质量得不到保证。
其次,目前的自动焊设备的摆动机构大多采用摆钟式原理,即摆动机构左右等幅交替摆动,针对各执行机构的传动误差,尤其是具有频繁换向需求的摆动机构所带来的换向耦合误差无能为力,从而造成误差的累积,使摆动的中心偏离实际焊缝中心,焊接熔池位置偏离焊缝。
另外,程序的调节参数依赖的实验数据与实际情况比常常有很大偏差。
使得工程人员调整自动焊接机器人的难度加大。
自动焊接设备执行机构的误差难以消除,焊缝会偏离焊口。
新型管道自动焊技术具有如下三方面特点:1.1 管口焊缝的自动跟踪系统包括管缝位置检测与焊枪位置纠正。
机器人全自动双丝焊接工艺技术
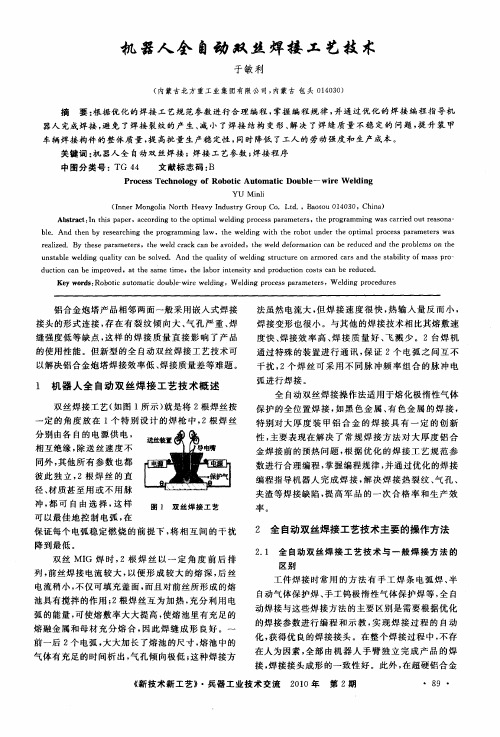
以解 决铝合 金炮 塔焊接 效率低 、 焊接 质量 差等难 题 。
1 机 器 人 全 自动双 丝焊 接 工 艺 技 术概 述
双丝焊 接工艺 ( 图 1 如 所示 ) 就是将 2 焊丝 按 根
一
全 自动 双丝 焊接操 作法适 用于熔 化极 惰性气 体
保 护 的全位 置焊 接 , 黑 色金 属 、 色金 属 的 焊 接 , 如 有 特 别对 大厚 度 装 甲铝 合 金 的焊 接 具 有 一 定 的创 新 性, 主要 表现 在解决 了常 规焊 接 方 法对 大厚 度 铝合
u s a l l i g q a i a e s l e . An h u l y o l i g sr c u e o r r d c r n h t b l y o s r — n t b e wed n u l y c n b o v d t d t e q ai fwed n t u t r n a mo e a sa d t e s a i t fma s p o t i
金 焊接前 的预热 问 题 , 据优 化 的焊 接工 艺 规 范参 根
定 的 角度 放 在 1 特 别 设计 的焊枪 中 , 个 2根焊 丝
分别 由各 自的电 源供 电 ,
相 互 绝 缘 , 送 丝 速 度 不 除
机 器人 全 自动 双 丝 焊 接 工 艺 技 术
于敏ห้องสมุดไป่ตู้利
( 内蒙 古 北 方 重 工 业 集 团 有 限 公 司 , 内蒙 古 包 头 0 4 3 ) 10 0
摘
要: 根据 优化 的焊接 工 艺规 范参数 进行 合理 编程 , 掌握 编程 规律 , 并通过 优 化 的焊接 编程 指 导机
器人 完成 焊接 , 免 了焊接 裂纹的产 生、 小 了焊接 结构 变形 、 决 了焊 缝质 量 不稳 定 的 问题 , 避 减 解 提升 装 甲 车辆 焊接 构件 的整 体质 量 , 高批 量 生产稳 定性 , 提 同时降低 了工人 的劳动 强度和 生产成 本 。
核岛主设备稳压器加热器全自动焊接工艺

0 前 言
在核 电站核 岛主设 备 中 , 压器 作 为核 I 设 稳 级 备 , 主要 作用 是稳 定 和调 节一 回路 主 系统 冷却 剂 其
1 焊 接 结 构 工 艺 性 分 析
加 热 器 与 加 热 器 套 管 材 料 均 为 Z C D1. N , 2 N 81 S 2
该 材料 为法 国牌 号 , 于含 Mo元 素控 氮 型奥 氏体 属 不 锈钢 , 似 于 3 6 , 货 状 态 为 固溶 处 理 , 处 类 1L 供 热 理 温度 1 5 0℃~ 5 。 0 110o 控氮 型奥 氏体 不锈钢与 一 C
Ke o d : u l r o e ; i al u e a tm t e i ;a k p n t t ; o y es i dg s y w r s n c a w rt nw l tb ;uo ai w l n b c e e a t p he a e p h c d g re w t l
间腐蚀 和 晶间应 力 腐蚀 性 能优 良的特点 , 泛运 用 广
于 核 电 站 核 岛 主 设 备 , 学 成 分 如 表 2所 示 。 化
表 1 Z CND 1 .2 2 81 NS 力 学 性 能
加 热器 套管焊 接 又是其 焊接 制造 的难 点之 一 。 在该 项 目的一 期合 同 中 , 接程 序 和操 作都 是 由外 方负 焊 责 , 没 有 实现 真 正 的 国产 化 , 了打 破 国 外公 司 并 为 的垄 断 , 成稳 压 器 国产化 制 造 的 目标 , 方 锅炉 完 东 股 份公 司技术 人员 经 过反 复调 试 和摸 索 , 功 地调 成 试 出 了一套合 适 的焊接 程 序 和操作 技 术 , 并成 功运
p n t t .rc d r t t n e t eut h w t t on t e w l n t i , e ige up n , r e t e g sw li rga e e a po e u e e d t s l s o h i y , ed g ma r lw l n q ime tpo c v a , e n p orm, re sa sr aj t p i ea d t i d g
简述塞焊的工艺过程
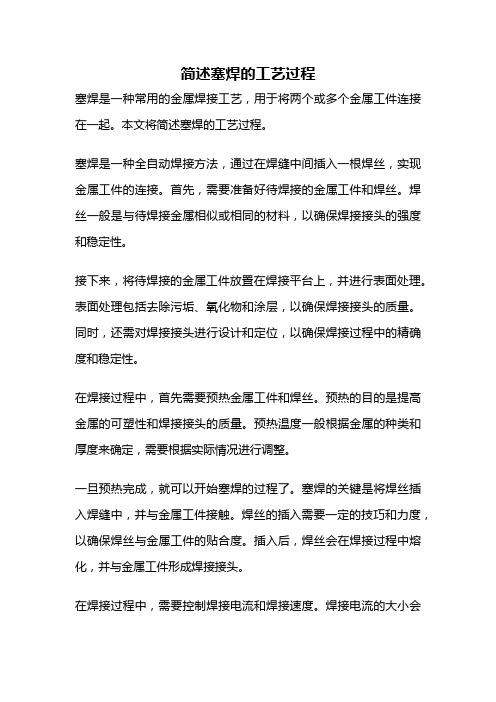
简述塞焊的工艺过程塞焊是一种常用的金属焊接工艺,用于将两个或多个金属工件连接在一起。
本文将简述塞焊的工艺过程。
塞焊是一种全自动焊接方法,通过在焊缝中间插入一根焊丝,实现金属工件的连接。
首先,需要准备好待焊接的金属工件和焊丝。
焊丝一般是与待焊接金属相似或相同的材料,以确保焊接接头的强度和稳定性。
接下来,将待焊接的金属工件放置在焊接平台上,并进行表面处理。
表面处理包括去除污垢、氧化物和涂层,以确保焊接接头的质量。
同时,还需对焊接接头进行设计和定位,以确保焊接过程中的精确度和稳定性。
在焊接过程中,首先需要预热金属工件和焊丝。
预热的目的是提高金属的可塑性和焊接接头的质量。
预热温度一般根据金属的种类和厚度来确定,需要根据实际情况进行调整。
一旦预热完成,就可以开始塞焊的过程了。
塞焊的关键是将焊丝插入焊缝中,并与金属工件接触。
焊丝的插入需要一定的技巧和力度,以确保焊丝与金属工件的贴合度。
插入后,焊丝会在焊接过程中熔化,并与金属工件形成焊接接头。
在焊接过程中,需要控制焊接电流和焊接速度。
焊接电流的大小会影响焊接接头的质量和强度,而焊接速度的快慢会影响焊接接头的均匀性和外观。
因此,需要根据金属的种类和厚度,调整焊接电流和焊接速度,以达到最佳的焊接效果。
焊接完成后,需要对焊接接头进行冷却和清理。
冷却的目的是使焊接接头固化和稳定,而清理则是为了去除焊接过程中产生的残留物和氧化物。
冷却和清理后,焊接接头就可以进行进一步的加工和使用了。
总的来说,塞焊是一种常用的金属焊接工艺,通过插入焊丝实现金属工件的连接。
塞焊的工艺过程包括准备金属工件和焊丝、表面处理、预热、焊接、冷却和清理等步骤。
通过控制焊接电流和焊接速度,可以实现高质量的焊接接头。
塞焊具有操作简便、效率高和焊接质量好等优点,被广泛应用于各个领域的金属焊接中。
管道全自动焊接技术及工艺控制
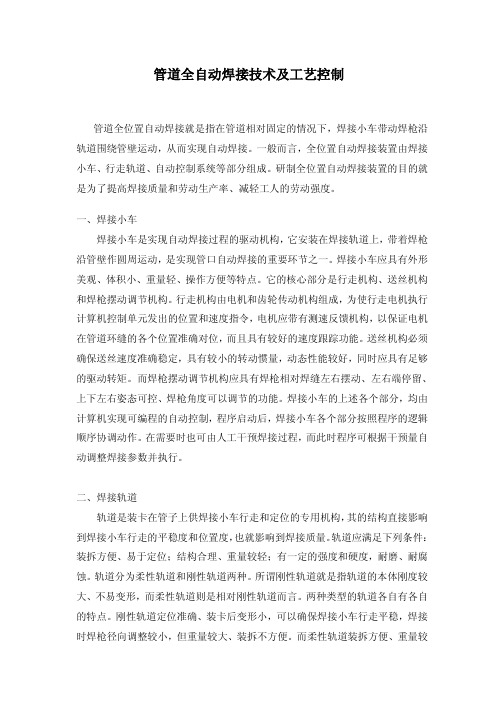
管道全自动焊接技术及工艺控制管道全位置自动焊接就是指在管道相对固定的情况下,焊接小车带动焊枪沿轨道围绕管壁运动,从而实现自动焊接。
一般而言,全位置自动焊接装置由焊接小车、行走轨道、自动控制系统等部分组成。
研制全位置自动焊接装置的目的就是为了提高焊接质量和劳动生产率、减轻工人的劳动强度。
一、焊接小车焊接小车是实现自动焊接过程的驱动机构,它安装在焊接轨道上,带着焊枪沿管壁作圆周运动,是实现管口自动焊接的重要环节之一。
焊接小车应具有外形美观、体积小、重量轻、操作方便等特点。
它的核心部分是行走机构、送丝机构和焊枪摆动调节机构。
行走机构由电机和齿轮传动机构组成,为使行走电机执行计算机控制单元发出的位置和速度指令,电机应带有测速反馈机构,以保证电机在管道环缝的各个位置准确对位,而且具有较好的速度跟踪功能。
送丝机构必须确保送丝速度准确稳定,具有较小的转动惯量,动态性能较好,同时应具有足够的驱动转矩。
而焊枪摆动调节机构应具有焊枪相对焊缝左右摆动、左右端停留、上下左右姿态可控、焊枪角度可以调节的功能。
焊接小车的上述各个部分,均由计算机实现可编程的自动控制,程序启动后,焊接小车各个部分按照程序的逻辑顺序协调动作。
在需要时也可由人工干预焊接过程,而此时程序可根据干预量自动调整焊接参数并执行。
二、焊接轨道轨道是装卡在管子上供焊接小车行走和定位的专用机构,其的结构直接影响到焊接小车行走的平稳度和位置度,也就影响到焊接质量。
轨道应满足下列条件:装拆方便、易于定位;结构合理、重量较轻;有一定的强度和硬度,耐磨、耐腐蚀。
轨道分为柔性轨道和刚性轨道两种。
所谓刚性轨道就是指轨道的本体刚度较大、不易变形,而柔性轨道则是相对刚性轨道而言。
两种类型的轨道各自有各自的特点。
刚性轨道定位准确、装卡后变形小,可以确保焊接小车行走平稳,焊接时焊枪径向调整较小,但重量较大、装拆不方便。
而柔性轨道装拆方便、重量较轻,精度没有刚性轨道高。
三、送丝方式送丝的平稳程度直接影响焊接质量。
核电模块GMAW全自动焊焊接工艺

(6) 应对熔入焊缝的定位焊焊缝及去除定位焊 缝的坡口进行外观和 PT 渗透检验。 1.4 焊接与切割气体
焊接与切割用气体应满足相应标准要求, 双相不 锈钢焊接保护气体混合比采用 φ(Ar)98%+φ(CO2)2%。
Welding Technology Vol.48 No.5 May 2019
1.5 焊接工艺
(1) 定制柔性金属导轨, 采用磁力式固定, 并 调整导轨与焊件的距离。
(2) 安装 GMAW 半自动焊机头, 调整焊枪角度 与距离。 接通电源, 在导轨上来回运动, 验证导轨 是否安装到位。
(3) 接通气源, 安装焊丝盘, 调整焊枪位置。 (4) 在模拟现场高空拼装时, 柔性金属导轨布 置必须考虑整体框架刚性固定或卡块固定以及周围 脚手架等障碍物的影响。 1.2 施工环境 (1) 焊 接 区 域 1 m 范 围 内 的 环 境 空 气 相 对 湿 度<90%。 (2) 焊接时应采取措施保护焊接工作不受污染, 以及雨、 雪、 风的影响。 (3) 不允许在潮湿的表 面 或 雨 雪 环 境 中 施 焊 , 露天场地组装必须搭设防护棚。 (4) 气体保护焊风速≤2 m/s, 环境温度≥0 ℃。 1.3 组对及焊前检查 (1) 焊件组对前应仔细检查坡口面以及距坡口 边缘 20~50 mm 范围内的内外侧表面, 采用酒精、 丙 酮及其他经批准的材料对待焊表面存在的油污等杂 质进行清理, 直至焊接坡口及两侧露出金属光泽, 保证该区域内无油、 漆、 垢、 毛刺、 锈迹等杂物, 且不得有任何影响焊接质量的缺陷存在。 对接接头 及角接接头坡口形式设计如图 2 所示。 (2) 试件组装时可通过调整组装间隙来控制定 位焊时的焊接收缩变形, 并用工装卡具, 定位焊或 临时性附件在应有的位置上进行装配、 对中和定位。 设计的工装卡具如图 3 所示。 (3) 错 边 量≤所 连 接 的 较 薄 部 件 厚 度 的 10% , 且≤1 mm, 定位焊完成以后必须重新检查定位的尺 寸是否改变。 (4) 不锈钢母材坡口表面的清理要用专用的不 锈钢清理工具, 如不锈钢钢丝刷、 不锈钢专用砂轮
T91钢小径管全自动TIG焊接工艺
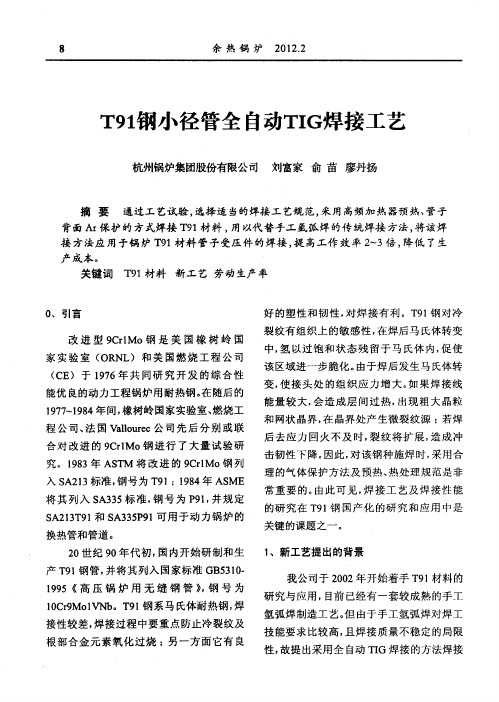
后 去 应 力 回 火 不 及 时 , 纹 将 扩 展 , 成 冲 裂 造
击 韧 性 下 降 。 此 , 该钢 种施 焊 时 , 用合 因 对 采 理 的气 体保 护 方 法 及 预热 、 处理 规 范 是非 热 常重要的。 由此 可 见 , 接 工 艺 及 焊 接 性 能 焊 的研 究在 T 1 国产 化 的研 究 和 应 用 中是 9钢 关 键 的课题 之一 。
关键 词
T1 9 材料 新工 艺 劳动 生产率
0 、引言 改 进 型 9 rMo钢 是 美 国 橡 树 岭 国 Cl 家 实 验 室 ( RN O L) 和 美 国燃 烧 工 程 公 司
( E)于 1 7 C 9 6年 共 同 研 究 开 发 的 综 合 性 能优 良的 动 力工 程 锅 炉用 耐 热 钢 。 随后 的 在
送 丝
I / 广
・ ‘
一
广 l 一一 I :
— 3 一 1 I 1 l 【1 t 4
I
0 cI l
z
焊 丝检 测
’ ● ‘ —‘。 。。。。。— —
t
热 丝电 流
/
/
t9
一
I
\
/ n \
/ r—一
一 ———] \
好 的塑 性 和 韧 性 , 焊 接 有 利性 , 在焊 后 马 氏体转 变 中 , 以过饱 和 状 态 残 留于 马 氏体 内 , 使 氢 促
该 区域进 一 步 脆化 。 由于 焊后 发 生 马 氏体 转 变 , 接 头 处 的组 织 应 力 增 大 。 果 焊 接 线 使 如
8
余 热 锅 炉 2 l . 0 22
T9 钢小 径管全 自动T G焊接 工艺 1 I
钢结构自动焊接方法

钢结构自动焊接方法钢结构是现代建筑中常见的一种结构形式,其特点是重量轻、强度高、抗震性好等。
在钢结构制作过程中,焊接是一项非常重要的工艺,决定着钢结构的质量和稳定性。
为了提高焊接效率和质量,钢结构自动焊接方法应运而生。
钢结构自动焊接是指利用自动化设备和技术,实现钢结构焊接过程的自动化和智能化。
与传统手工焊接相比,自动焊接具有以下优势:1. 提高生产效率:自动焊接设备可以实现连续作业,无需人工干预,大大提高了焊接速度和效率。
2. 保证焊接质量:自动焊接设备可以精确控制焊接参数,确保焊缝的质量和一致性。
3. 降低劳动强度:自动焊接设备可以取代人工焊接,减少了工人的劳动强度和作业风险。
4. 减少焊接变形:自动焊接设备可以通过合理的焊接顺序和工艺,减少焊接变形的发生。
5. 节约材料:自动焊接设备可以准确控制焊接参数,避免材料的浪费和损耗。
钢结构自动焊接方法主要包括以下几种:1. 点焊法:点焊法是指在钢结构的连接部位,采用电阻焊接的方法进行焊接。
该方法适用于连接较小的部件,焊接速度快,焊缝质量高。
2. 熔焊法:熔焊法是指通过加热钢材使其熔化,然后冷却固化,实现钢材之间的连接。
常用的熔焊方法有电弧焊、气体保护焊和等离子焊等。
3. 摩擦焊接法:摩擦焊接法是指通过摩擦热将钢材加热至一定温度,然后施加一定的力使其连接。
该方法适用于连接较大的构件,可以实现高效、高质量的焊接。
4. 激光焊接法:激光焊接法是利用激光束对钢材进行加热和熔化,然后冷却固化,实现焊接连接。
激光焊接具有高能量密度、焊接速度快等特点,适用于焊接细小和复杂的部件。
5. 电阻焊接法:电阻焊接法是指利用电流通过焊接部位的电阻产生热量,使钢材熔化并连接在一起。
该方法适用于连接较大和厚度较大的构件,焊缝质量高。
钢结构自动焊接方法的选择应根据具体的焊接任务和要求来确定。
在实际应用中,还应注意以下几点:1. 合理选择焊接材料和焊接参数,确保焊接质量和强度满足设计要求。
薄壁不锈钢管全自动氩弧焊工艺方法
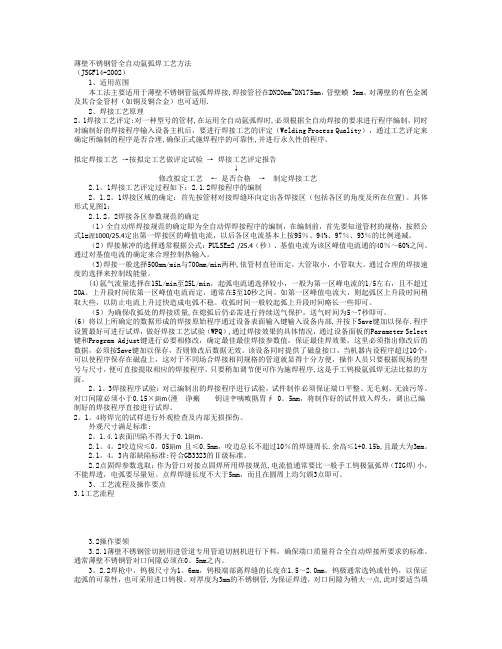
薄壁不锈钢管全自动氩弧焊工艺方法(JSGF14-2002)1、适用范围本工法主要适用于薄壁不锈钢管氩弧焊焊接,焊接管径在DN20mm~DN175mm,管壁蟆 3mm。
对薄壁的有色金属及其合金管材(如铜及铜合金)也可适用.2、焊接工艺原理2。
1焊接工艺评定:对一种型号的管材,在运用全自动氩弧焊时,必须根据全自动焊接的要求进行程序编制,同时对编制好的焊接程序输入设备主机后,要进行焊接工艺的评定(Welding Process Quality),通过工艺评定来确定所编制的程序是否合理,确保正式施焊程序的可靠性,并进行永久性的程序。
拟定焊接工艺→按拟定工艺做评定试验→焊接工艺评定报告↓修改拟定工艺←是否合格→制定焊接工艺2.1。
1焊接工艺评定过程如下:2.1.2焊接程序的编制2。
1.2。
1焊接区域的确定:首先按管材对接焊缝环向定出各焊接区(包括各区的角度及所在位置)。
具体形式见图1:2.1.2。
2焊接各区参数规范的确定(1)全自动焊焊接规范的确定即为全自动焊焊接程序的编制,在编制前,首先要知道管材的规格,按照公式1=渥1000/25.4定出第一焊接区的峰值电流,以后各区电流基本上按95%、94%、97%、93%的比例递减。
(2)焊接脉冲的选择通常根据公式:PULSE=2/25.4(秒)、基值电流为该区峰值电流通的40%~60%之间。
通过对基值电流的确定来合理控制热输入。
(3)焊接一般选择500mm/min与700mm/min两种,依管材直径而定,大管取小,小管取大。
通过合理的焊接速度的选择来控制线能量。
(4)氩气流量选择在15L/min至25L/min,起弧电流通选择较小,一般为第一区峰电流的1/5左右,且不超过20A。
上升段时间依第一区峰值电流而定,通常在5至10秒之间。
如第一区峰值电流大,则起弧区上升段时间稍取大些,以防止电流上升过快造成电弧不稳。
收弧时间一般较起弧上升段时间略长一些即可。
(5)为确保收弧处的焊接质量,在熄弧后仍必需进行持续送气保护,送气时间为5~7秒即可。
自动焊接方案
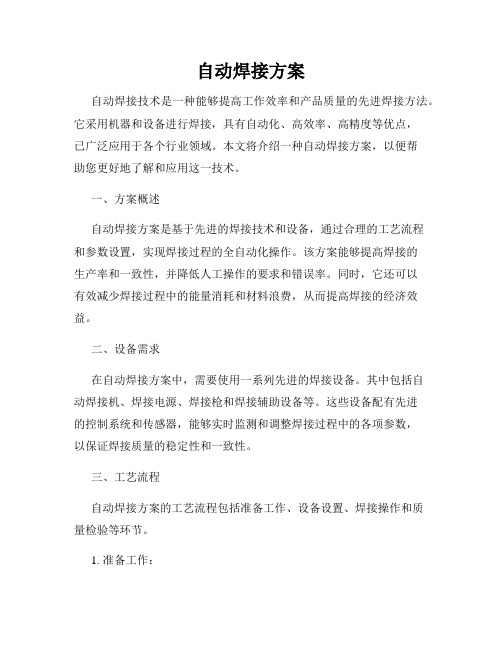
自动焊接方案自动焊接技术是一种能够提高工作效率和产品质量的先进焊接方法。
它采用机器和设备进行焊接,具有自动化、高效率、高精度等优点,已广泛应用于各个行业领域。
本文将介绍一种自动焊接方案,以便帮助您更好地了解和应用这一技术。
一、方案概述自动焊接方案是基于先进的焊接技术和设备,通过合理的工艺流程和参数设置,实现焊接过程的全自动化操作。
该方案能够提高焊接的生产率和一致性,并降低人工操作的要求和错误率。
同时,它还可以有效减少焊接过程中的能量消耗和材料浪费,从而提高焊接的经济效益。
二、设备需求在自动焊接方案中,需要使用一系列先进的焊接设备。
其中包括自动焊接机、焊接电源、焊接枪和焊接辅助设备等。
这些设备配有先进的控制系统和传感器,能够实时监测和调整焊接过程中的各项参数,以保证焊接质量的稳定性和一致性。
三、工艺流程自动焊接方案的工艺流程包括准备工作、设备设置、焊接操作和质量检验等环节。
1. 准备工作:在进行自动焊接之前,需要对焊接工件进行准备。
这包括清洁工件表面、确保焊接接头的准确配对以及检查焊接材料的质量等。
只有在工件准备充分的情况下,才能保证焊接的质量和稳定性。
2. 设备设置:根据焊接工艺要求和工件特点,对焊接设备进行合理的设置。
这包括选择合适的焊接电流、焊接速度和焊接时间等参数,并调整设备的工作模式和操作参数。
通过合理的设备设置,可以确保焊接过程中的温度和能量分布达到理想状态。
3. 焊接操作:根据设备设置,进行焊接操作。
自动焊接机根据预设的程序和参数,自动进行焊接操作,并实时监测和调整焊接过程中的各项参数。
焊接工人只需进行简单的操作和监控,无需进行繁琐的焊接操作。
4. 质量检验:焊接完成后,进行质量检验。
这包括外观检查、尺寸测量和焊缝检测等项目。
只有通过质量检验,才能确认焊接的质量是否符合要求,并对不合格品进行修复或返工。
四、应用范围自动焊接方案广泛应用于各个行业领域。
它在汽车制造、航空航天、电子设备、船舶制造、建筑结构等领域中具有重要作用。
- 1、下载文档前请自行甄别文档内容的完整性,平台不提供额外的编辑、内容补充、找答案等附加服务。
- 2、"仅部分预览"的文档,不可在线预览部分如存在完整性等问题,可反馈申请退款(可完整预览的文档不适用该条件!)。
- 3、如文档侵犯您的权益,请联系客服反馈,我们会尽快为您处理(人工客服工作时间:9:00-18:30)。
管道全自动焊接工法天津大港油田集团工程建设有限责任公司近几年,长输管道市场明显地向着高压力、大口径、厚壁厚的趋势发展。
目前中国石油行业大多数施工单位采用全自动焊接的方式从事长输管道施工。
目前中国石油行业各施工单位都在管道焊接装备、施工能力等方面取得长足的进步,陆续装备了自动焊接机组,进入了大口径管道施工市场。
近年来,成品油管线工程及各种天然气支线工程建设累计将有数万公里正在施工。
在未来的几年里,石油天然气管输管道工程施工市场容量巨大,给大港油田集团工程建设公司带来了更大的商机,市场发展前景看好。
通过近几年的研究,从室内试验到现场实践,进行了全自动焊接设备优化配置及各项资源的优化配置,合理调整了工艺参数,并针对不同地形地貌制定了适宜性的施工方案和施工组织方式,目前已形成了一套行之有效的施工工法——大口径长输管道全自动焊接工法,并在全公司范围内推广应用,达到了预期的研究效果,取得了良好的经济效益和社会效益。
一、工法特点1.全自动焊接采用药心焊丝和气体保护,可以获得优良的焊接质量。
该焊接工艺以其小电流、低电压、细直径实心焊丝、短路过渡为主要特点,下向焊时熔池体积小、可实现全焊接及抗锈低氢的内在优势,特别适合于填充焊,盖面焊时Ar气体和CO2气体的保护作用使其焊缝表面成型规则、饱满,且与母材过渡圆滑。
2.全自动焊接合格率高,焊接参数调定之后,即可实现自动化作业,减少人为操作因素对焊接质量的影响,提高焊口一次合格率。
3.全自动焊接参数调定后能进行连续性作业,提高了生产效率,与其他焊接方法比较,减少了频繁更换焊条、焊丝产生的材料浪费,降低施工成本。
同时全自动化焊接作业也降低了工人的劳动强度,但对工人的自身素质和操作能力有更高的要求。
4.全自动焊接工艺对管道组对坡口质量和坡口型式要求严格,需要配套的坡口整形机等设备。
5.全自动焊接的保护气体为Ar气体和CO2气体,因此与其他焊接方法比较,施工环境更为苛刻,现场施工时要求环境风速小于2m/s。
二、适用范围1.本工法适用于管径DN700以上、壁厚11mm以上的油气长距离输送管道水平固定对接的全位置下向焊焊接施工。
2.本工法需要良好的工程施工环境,适于在地势平坦开阔的地段。
三、工艺原理管道全自动气体保护下向焊接工艺使用可熔化的焊丝与主要焊金属之间的电弧为热焊来溶化焊丝和钢管,在焊接时向焊接区域输送保护气体以隔离空气的有害作用,通过连续送丝完成焊接。
管道全自动焊接其整个焊接过程是一个从平焊状态到立焊状态再到仰焊状态的平滑过度过程。
管道全自动焊机的焊接速度、送丝速度、摆动宽度、摆动速度、焊接电压和焊接电流都要随着状态的变化而变化。
圆周各点参数均由计算机程序自动控制完成,实现焊接工艺参数的连续变化。
本工法采用STT半自动根焊+自动外焊机填充、盖面。
根焊设备为林肯STT-Ⅱ型焊接电源+相匹配的送丝机,填充焊、盖面焊设备为PAW2000型自动外焊机。
保护气体采用Ar气体和CO2气体。
四、施工工艺流程及操作要点(一)施工工艺流程图1 工艺流程图(二)操作要点大港油田工程建设公司在西气东输—陕京二线联络线工程第8标段中采用了全自动气体保护下向焊焊接方法,根据该工法在工程中的实际运用,概括总结出以下几点操作要点。
1.管口清理组装前使用专用清管工具清除管内的所有杂物;使用棉纱和钢丝刷等工具将管口两端100mm范围内的尘土、油污、铁锈等清理干净,露出金属光泽,螺纹管端口焊缝处需把余高打磨平滑,严禁使用砂轮机打磨坡口以外的管材表面,然后由管工用对口器进行管口组对,用间隙板定间隙。
并检查管口是否存在压痕、裂纹等缺陷,如果发现要及时按要求修复,不符合要求的管子不得组装。
2.管口修整与组对全自动焊接对坡口要求严格,必要时用坡口整形机对管口进行整形。
管道全自动焊接管口组对尺寸如下图:图2 管口组对管组对接头的坡口形式应为V型,管道坡口角度应为22.5°±0.5°,钝边 1.2~2.0mm,间隙2.0~3.0mm,组对错边量按10%管壁厚控制。
对口采用内对口器(连头碰死口及其它不能使用时内对口器时采用外对口器)施工时,应在根焊一遍后,方可卸除内对口器。
使用外对口器时,必须在焊口整个圆周上均匀分布4~6处定位焊,每一处定位焊长度不应小于100mm,且在卸下外对口器前,定位焊的累计长度不得少于管周长的50%。
两相邻管的螺旋焊缝在对口处应错开不小于100 mm的距离。
3.安装焊接轨道自动焊接小车行走在焊接轨道上,轨道与管道的同心度和与管口的平行度直接影响着焊接的质量,应采用专用工具安装轨道,轨道专用安装工具可以测量和调整轨道边缘与管道坡口之间的距离,调整轨道的松紧度。
轨道安装专用工具的锤面硬度应稍低于焊接轨道的硬度,过硬易造成轨道的损伤。
轨道安装后,应保证轨道与管道表面的距离小于3mm,轨道与管口端面的距离小于2mm。
4.输入焊接参数轨道安装完毕后,将焊机安装在轨道上,按焊接指导书的要求调整焊机的焊枪位置和角度。
通过焊接参数输入器,将焊接参数输入到计算机中。
表1 根焊焊接工艺参数注:① D C+表示焊丝接正。
②根焊电压为参考值,填充、盖面焊电流为参考值。
③ (75-90)%Ar+(25-10)%CO2表2 填充焊、盖面焊焊接工艺参数注:①极性为焊丝接正。
②填充、盖面焊电流为参考值5.焊接根据焊接工艺规程的要求,管线焊前需预热管口,预热温度≥100℃且小于150℃,预热宽度为坡口两侧不小于75mm的范围内,预热方法应保障在预热范围内温度均匀,可用非接触式温度计在距管口50mm处测量,预热结束温度高于但不超过规定温度50℃,预热源撤离后1~2分钟后,开始焊接,以保证温度均匀。
预热源为液化气,配备专用的中环型火焰加热器加热。
火焰要远离防腐层,严禁用气焊和其它高温火源。
6.外观检查外观:宽度为坡口两侧外表面0.5~2.0mm;余高为0~2.0mm,局部不得大于3mm,余高大于2mm且小于3mm部分的长度不得大于50mm;焊缝外表面都不得低于母材表面,咬边深度不得大于0.5mm,咬边深度在0.3~0.5mm的单个长度不得超过30mm,累计长度不得大于焊缝周长的15%;接口错边量小于2mm。
焊缝及附近表面上不得有裂纹、未熔合、气孔、夹渣、凹陷、引弧痕迹、有害的焊瘤、夹具焊点、溶合性飞溅等,外观成形均匀一致。
自检合格后,写焊工号(不准打钢印) 做自检记录,如此流水作业进行组对焊接。
7.探伤检验焊完的焊缝先检查外观合格后再进行无损探伤。
管道焊缝100%进行环向焊缝的X 射线照相,执行《石油天然气钢质管道对接焊缝射线照相及质量分级》标准Ⅱ级为合格。
将检测结果及时确认核实后,对不合格的焊口安排专人进行返修。
8.不合格焊口返修组织专门返修小组对不合格焊缝进行返修,焊口返修采用手工焊接返修。
二次返修不合格的焊口需割口重新焊接、拍片检查至合格。
五、材料、设备及劳动力组织(一)工程材料该工法在西气东输—陕京二线联络线工程第8标段运用时采用地工程材料有:1.钢管钢管标准:API Spec 5L(GB/T 9711.2)钢级:X70(L485)直径:Φ1016mm 壁厚:17.5mm其化学成分和机械性能见表3。
表3 钢管的化学成分和机械性能表2.焊接材料表4 焊接材料表3.保护气体本工法用到的保护气体为Ar气体和CO2气体。
其中Ar气体纯度:≥99.96%,CO2气体纯度:≥99.5%,CO2气体含水量:≥0.005%。
(二)机具设备本工法使用的主要机械设备见表5。
表5 主要机械设备表(三)劳动力组织本工法人员组织见表6。
表6 劳动力组织表六、质量控制1.制定长输管道全自动焊接施工项目管理质量方针、目标。
成立施工质量管理项目组,明确项目部岗位质量管理职责。
2.施工前,检查验收管子的长度、钢管厚度、防腐层厚度、防腐质量、管口质量(直径、椭圆度、管口垂直度、管子直度)等。
对螺旋焊缝管,检查测量管口周长、直径,以使匹配对口,做到使两相邻管口直径误差<1mm,周长误差≤4mm。
对检查出的不合格的管子应标识隔离。
3.清理管口,采用专用清理工具将管口的坡口、钝边修好;机制坡口的内卷边要清除掉,螺旋管、直缝管管端内外焊道高出管壁10mm范围内要用砂轮机抹平且平缓过渡;管端内外20mm内的锈迹要清除,直至见到金属本色。
管组对接头的坡口形式应为V型,管道坡口角度应为22.5°±0.5°,钝边1.2~2.0mm,间隙2.0~3.0mm,组对错边量按10%管壁厚控制。
4.对口时,起吊管子的吊具不得损坏防腐层。
组对时应控制错边量、螺旋焊缝或直焊缝错开量以及对口间隙,使其符合焊接规范要求。
5.焊接施工前对所有参加施工的人员进行交底,明确各项质量指标及要求,同时明确各岗位人员的质量职责,严格按规范及设计要求进行施工。
6.参加施焊的焊工必须是经过培训取得专业资格证书,同时通过针对当前施工管线焊接要求考试的合格者。
7.管口根焊没有完成时,不得撤出内对口器。
在根焊过程中,不得活动管子或碰撞管子。
根焊必须熔透,背面成形良好。
根焊完成后,焊工应仔细自查是否有裂纹、夹渣、气孔等缺陷,如有,应消除后重焊。
8.焊缝接头点,应略加打磨,相邻两层的接头点不得重叠,应错开20mm以上每遍焊完后焊工应认真清根,除去表层气孔、夹渣等缺陷,砂轮粉末也应清除。
9.焊接过程中,应注意控制层间温度,当层间温度低于规定要求时,应重新加热。
10.使用的焊接极性、电流、电压、焊接速度等应符合焊接工艺规程要求11.焊道表面应成型良好,管口和焊道表面应无飞溅、裂纹、焊疤、气孔和夹渣等缺陷,焊道外观检验执行《油气长输管道工程施工及验收规范》GB50369-2006的规定12.所用焊机须是完好设备,设备性能满足焊接工艺的要求。
13.所用焊材与设计要求相符,且通过焊接工艺评定,满足设计要求。
14.在下列任何一种环境中,如未采取有效防护措施不得进行焊接:1)雨、浓雾天气;2)大气相对湿度超过90%;3)风速大于2米/秒,应采取有效的措施(如防风棚等);4)环境温度低于5℃,应采取有效措施(如石棉被等进行层间或焊后保温),防止焊缝冷速过快。
15.严把好各工序的施工质量,质检人员施工期间不离场,随时检查施工质量。
七、安全措施1.建立安全保证体系,确定安全生产责任人。
2.对所有参加施工人员进行HSE安全教育,对施工中容易出现的安全隐患提前预防。
做好各工序安全教育和安全技术交底。
3. 定期召开安全生产例会,定期组织进行安全检查工作,例行安全检查每周一次,安全员及相关人员对施工全过程进行全方位、全过程监督检查。
4.施工机械操作处要有规范的操作规程,特殊工种及专业施工人员要持证上岗,严格执行岗位责任制,做到自我安全保护“三不伤害”。