浅谈粉末冶金材料的热处理工艺的分析与研究
材料加工中的热处理工艺研究
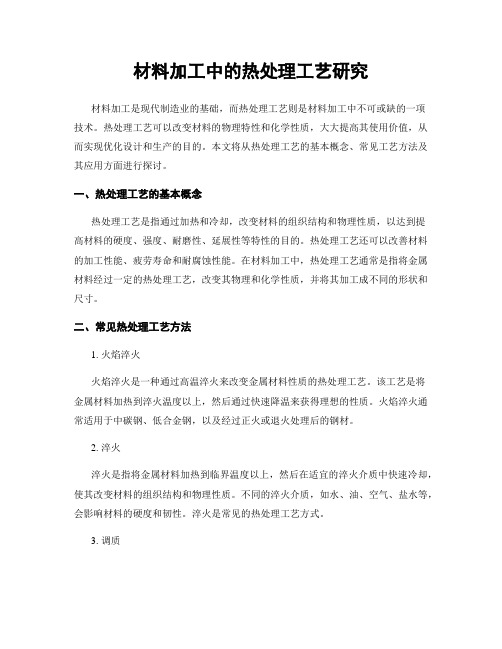
材料加工中的热处理工艺研究材料加工是现代制造业的基础,而热处理工艺则是材料加工中不可或缺的一项技术。
热处理工艺可以改变材料的物理特性和化学性质,大大提高其使用价值,从而实现优化设计和生产的目的。
本文将从热处理工艺的基本概念、常见工艺方法及其应用方面进行探讨。
一、热处理工艺的基本概念热处理工艺是指通过加热和冷却,改变材料的组织结构和物理性质,以达到提高材料的硬度、强度、耐磨性、延展性等特性的目的。
热处理工艺还可以改善材料的加工性能、疲劳寿命和耐腐蚀性能。
在材料加工中,热处理工艺通常是指将金属材料经过一定的热处理工艺,改变其物理和化学性质,并将其加工成不同的形状和尺寸。
二、常见热处理工艺方法1. 火焰淬火火焰淬火是一种通过高温淬火来改变金属材料性质的热处理工艺。
该工艺是将金属材料加热到淬火温度以上,然后通过快速降温来获得理想的性质。
火焰淬火通常适用于中碳钢、低合金钢,以及经过正火或退火处理后的钢材。
2. 淬火淬火是指将金属材料加热到临界温度以上,然后在适宜的淬火介质中快速冷却,使其改变材料的组织结构和物理性质。
不同的淬火介质,如水、油、空气、盐水等,会影响材料的硬度和韧性。
淬火是常见的热处理工艺方式。
3. 调质调质是指在经过淬火处理后的金属材料中,通过加热再冷却的处理过程,使其达到一定的硬度和韧性,以增加其使用寿命和稳定性。
调质可以改变材料的化学性质和晶粒结构。
常见的调质工艺包括低温回火和高温回火等。
4. 回火回火是在淬火处理过后,通过加热材料至一定温度然后以适当速度冷却的过程,以消除淬火过程中残留的应力,达到降低硬度,提高韧性的目的。
回火通常适用于高碳钢、合金钢等具有较高硬度的金属材料。
三、热处理工艺的应用1. 工具钢加工工具钢是一种高硬度、高韧性和高温稳定性材料,广泛应用于机床加工、模具制造等领域。
常见的工具钢热处理工艺包括硬化淬火、正火、调质和表面处理等。
热处理工艺可以提高工具钢的硬度和韧性,延长其使用寿命,提高加工效率和工作稳定性。
粉末冶金材料及冶金技术发展探讨

粉末冶金材料及冶金技术发展探讨摘要:我国拥有悠久的金属冶炼历史,生铁冶金技术是最早的冶金技术。
随着我国工业技术的发展和经济基础的进步,粉末冶金技术已经被广泛应用于各个领域。
和传统的冶金技术相比,粉末冶金技术具有明显的节能、高效、环保等优点。
本文针对粉末冶金技术的特点、发展历史以及该技术的发展趋势进行探讨,以期能够促进我国冶金行业的进步。
关键词:粉末冶金材料;冶金技术;发展一、冶金材料分类(一)传统冶金材料分类传统冶金材料一般分为铁基粉末冶金材料、钢基粉末冶金材料、难溶性冶金材料、电子冶金材料等几种。
其中最常见也是应用最多的冶金材料之一便是铁基粉末冶金材料,一般被应用于机械制造行业中。
钢基粉末冶金材料多用于现代电器生产制造中,主要是因其独特的性能特征,不同于其它冶金材料,钢基粉末金属的材料构成以及配比度具有较大的差异。
例如黄铜材料具有较强的塑性和耐磨性,铜合金具有优良的导电和导热性。
难溶性技术冶金材料具有很高的熔点,一般熔点在1700℃以上,又因其优异的硬度和强度表现,多用于航空制造业和军事制造业。
电子冶金材料具有极强的耐磨性,主要被应用于通信产品生产中,目前也在逐渐渗透到其它各领域。
(二)现代冶金材料分类现代冶金材料一般是用于现代信息行业以及生物材料制造、新能源研究及高端军事制造领域中。
用于信息行业中的冶金材料主要分为金属类材料以及铁氧材料,目前铁氧材料中的铁氧体磁性材料只能通过现代化的粉末冶金技术制得,生产成本偏高,如磷铁、硅钢等。
在新能源研究领域,现代冶金材料满足了我国大力倡导的节能政策的落实需求,现代冶金材料中的储能式材料与新能源材料的研发推动了我国低碳环保、经济节能理念的传承。
在生物材料制造行业中,现代冶金最明显和最有价值的体现便是应用于医疗领域中,如人造机械骨骼的医学研究成果,不仅降低了人体免疫排斥反应,延长人类寿命,同时降低了医疗成本。
在军事制造以及航天制造领域中,粉末冶金材料的防辐射以及耐高温特性具有重要价值。
粉末冶金力学性能和增强机理研究
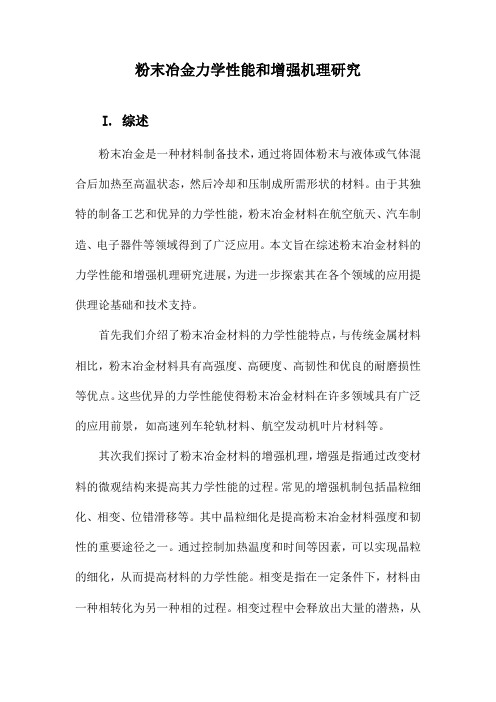
粉末冶金力学性能和增强机理研究I. 综述粉末冶金是一种材料制备技术,通过将固体粉末与液体或气体混合后加热至高温状态,然后冷却和压制成所需形状的材料。
由于其独特的制备工艺和优异的力学性能,粉末冶金材料在航空航天、汽车制造、电子器件等领域得到了广泛应用。
本文旨在综述粉末冶金材料的力学性能和增强机理研究进展,为进一步探索其在各个领域的应用提供理论基础和技术支持。
首先我们介绍了粉末冶金材料的力学性能特点,与传统金属材料相比,粉末冶金材料具有高强度、高硬度、高韧性和优良的耐磨损性等优点。
这些优异的力学性能使得粉末冶金材料在许多领域具有广泛的应用前景,如高速列车轮轨材料、航空发动机叶片材料等。
其次我们探讨了粉末冶金材料的增强机理,增强是指通过改变材料的微观结构来提高其力学性能的过程。
常见的增强机制包括晶粒细化、相变、位错滑移等。
其中晶粒细化是提高粉末冶金材料强度和韧性的重要途径之一。
通过控制加热温度和时间等因素,可以实现晶粒的细化,从而提高材料的力学性能。
相变是指在一定条件下,材料由一种相转化为另一种相的过程。
相变过程中会释放出大量的潜热,从而提高材料的强度和硬度。
位错滑移是指晶体中原子或分子沿晶格方向发生移动的现象,通过合理设计合金元素含量和分布等方式,可以有效地调控位错滑移行为,从而改善材料的力学性能。
我们总结了当前国内外关于粉末冶金力学性能和增强机理的研究现状和发展趋势。
随着科学技术的不断进步和人们对高性能材料的不断追求,粉末冶金材料的研究将会越来越深入和广泛。
未来研究方向主要包括:优化粉末冶金制备工艺以提高材料性能;探索新的增强机制以拓展材料的适用范围;开发新型粉末冶金材料以满足不同领域的需求等。
粉末冶金技术的发展历程和应用领域粉末冶金(Powder Metallurgy,PM)是一种将金属粉末与有机或无机载体相结合,通过加热、压制、烧结等工艺过程制备出具有特殊性能的材料的方法。
自19世纪末期发明以来,粉末冶金技术经历了一个漫长的发展过程,从最初的简单粉末混合到现代的多相材料制备,其应用领域也不断拓展,涵盖了航空航天、汽车、电子、能源等多个重要领域。
铁基粉末冶金零件热处理
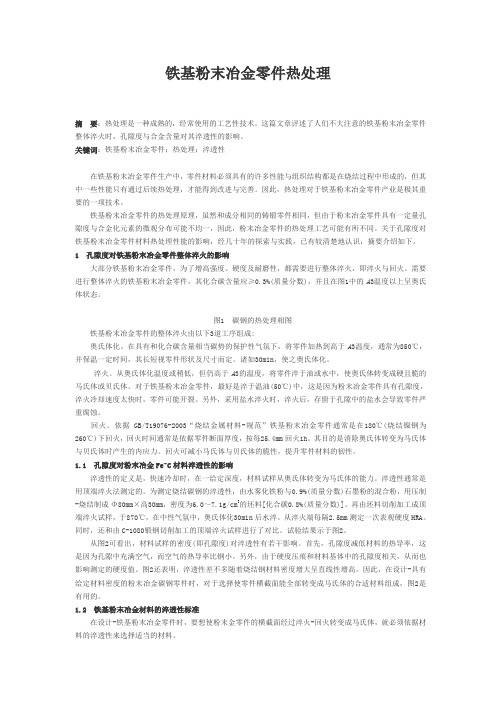
铁基粉末冶金零件热处理摘要:热处理是一种成熟的,经常使用的工艺性技术。
这篇文章评述了人们不大注意的铁基粉末冶金零件整体淬火时,孔隙度与合金含量对其淬透性的影响。
关键词:铁基粉末冶金零件;热处理;淬透性在铁基粉末冶金零件生产中,零件材料必须具有的许多性能与组织结构都是在烧结过程中形成的,但其中一些性能只有通过后续热处理,才能得到改进与完善。
因此,热处理对于铁基粉末冶金零件产业是极其重要的一项技术。
铁基粉末冶金零件的热处理原理,虽然和成分相同的铸锻零件相同,但由于粉末冶金零件具有一定量孔隙度与合金化元素的微观分布可能不均一,因此,粉末冶金零件的热处理工艺可能有所不同。
关于孔隙度对铁基粉末冶金零件材料热处理性能的影响,经几十年的探索与实践,已有较清楚地认识,摘要介绍如下。
1 孔隙度对铁基粉末冶金零件整体淬火的影响大部分铁基粉末冶金零件,为了增高强度、硬度及耐磨性,都需要进行整体淬火,即淬火与回火。
需要进行整体淬火的铁基粉末冶金零件,其化合碳含量应≥0.3%(质量分数),并且在图1中的A3温度以上呈奥氏体状态。
图1 碳钢的热处理相图铁基粉末冶金零件的整体淬火由以下3道工序组成:奥氏体化。
在具有和化合碳含量相当碳势的保护性气氛下,将零件加热到高于A3温度,通常为850℃,并保温一定时间,其长短视零件形状及尺寸而定。
诸如30min,使之奥氏体化。
淬火。
从奥氏体化温度或稍低,但仍高于A3的温度,将零件淬于油或水中,使奥氏体转变成硬且脆的马氏体或贝氏体。
对于铁基粉末冶金零件,最好是淬于温油(50℃)中,这是因为粉末冶金零件具有孔隙度,淬火冷却速度太快时,零件可能开裂。
另外,采用盐水淬火时,淬火后,存留于孔隙中的盐水会导致零件严重腐蚀。
回火。
依据GB/T19076-2003“烧结金属材料-规范”铁基粉末冶金零件通常是在180℃(烧结镍钢为260℃)下回火,回火时间通常是依据零件断面厚度,按每25.4mm回火1h。
粉末冶金材料的热处理工艺
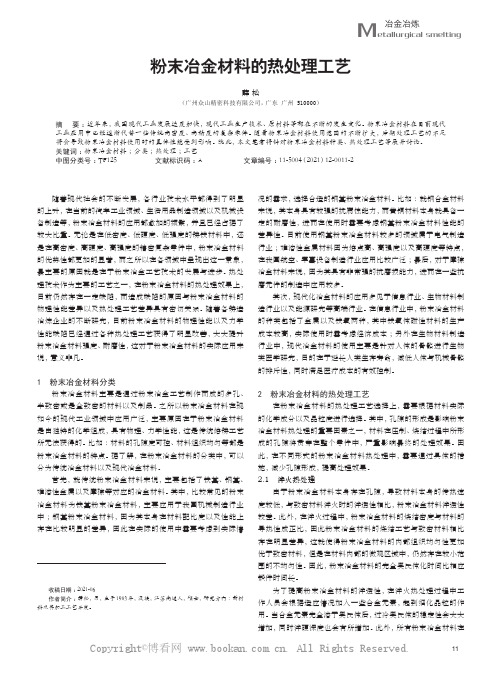
11Metallurgical smelting冶金冶炼粉末冶金材料的热处理工艺薛 松(广州众山精密科技有限公司,广东 广州 510000)摘 要:近年来,我国现代工业发展速度加快,现代工业生产技术、原材料等都在不断的发生变化。
粉末冶金材料在目前现代工业应用中已经逐渐代替一些传统高密度、高精度的复杂零件。
随着粉末冶金材料使用范围的不断扩大,后期处理工艺的不足将会导致粉末冶金材料使用时的具体性能受到影响。
就此,本文笔者将针对粉末冶金材料种类、热处理工艺等展开讨论。
关键词:粉末冶金材料;分类;热处理;工艺中图分类号:TF125 文献标识码:A 文章编号:11-5004(2021)12-0011-2收稿日期:2021-06作者简介:薛松,男,生于1983年,汉族,江苏南通人,硕士,研究方向:新材料及其加工工艺开发。
随着现代社会的不断发展,各行业技术水平都得到了明显的上升,在当前的汽车工业领域、生活用品制造领域以及机械设备制造等,粉末冶金材料的应用都愈加的频繁,并且已经占据了较大比重。
无论是在低密度、低硬度、低强度的铸铁材料中,还是在高密度、高硬度、高强度的精密复杂零件中,粉末冶金材料的优势性都更加的显著,而之所以在各领域中呈现出这一景象,最主要的原因就是在于粉末冶金工艺技术的发展与进步。
热处理技术作为主要的工艺之一,在粉末冶金材料的热处理效果上,目前仍然存在一定缺陷,而造成缺陷的原因与粉末冶金材料的物理性能差异以及热处理工艺差异具有密切关系。
随着各铸造冶炼企业的不断研究,目前粉末冶金材料的物理性能以及力学性能缺陷已经通过各种热处理工艺获得了明显改善,大大提升粉末冶金材料强度、耐磨性,这对于粉末冶金材料的实际应用来说,意义非凡。
1 粉末冶金材料分类粉末冶金材料主要是通过粉末冶金工艺制作而成的多孔、半致密或是全致密的材料以及制品。
之所以粉末冶金材料在现如今的现代工业领域中应用广泛,主要原因在于粉末冶金材料是由独特的化学组成,具有物理、力学性能,这是传统熔铸工艺所无法获得的。
粉末冶金材料的热处理工艺

粉末冶金材料的热处理工艺粉末冶金材料在现代工业中的应用越来越广泛,特别是汽车工业、生活用品、机械设备等的应用中,粉末冶金材料已经占有很大的比重。
它们在取代低密度、低硬度和强度的铸铁材料方面已经具有明显优势,在高硬度、高精度和强度的精密复杂零件的应用中也在逐渐推广,这要归功于粉末冶金技术的快速发展。
全致密钢的热处理工艺已经取得了成功,但是粉末冶金材料的热处理,由于粉末冶金材料的物理性能差异和热处理工艺的差异,还存在着一些缺陷。
各铸造冶炼企业在粉末冶金材料的技术研究中,热锻、粉末注射成型、热等静压、液相烧结、组合烧结等热处理和后续处理工艺,在粉末冶金材料的物理性能与力学性能缺陷的改善中,取得了一定效果,提高了粉末冶金材料的强度和耐磨性,将大大扩展粉末冶金的应用范围。
粉末冶金材料的热处理工艺粉末冶金材料的热处理要根据其化学成分和晶粒度确定,其中的孔隙存在是一个重要因素,粉末冶金材料在压制和烧结过程中,形成的孔隙贯穿整个零件中,孔隙的存在影响热处理的方式和效果。
粉末冶金材料的热处理有淬火、化学热处理、蒸汽处理和特殊热处理几种形式:1、淬火热处理工艺粉末冶金材料由于孔隙的存在,在传热速度方面要低于致密材料,因此在淬火时,淬透性相对较差。
另外淬火时,粉末材料的烧结密度和材料的导热性是成正比关系的;粉末冶金材料因为烧结工艺与致密材料的差异,内部组织均匀性要优于致密材料,但存在较小的微观区域的不均匀性,所以,完全奥氏体化时间比相应锻件长50%,在添加合金元素时,完全奥氏体化温度会更高、时间会更长。
在粉末冶金材料的热处理中,为了提高淬透性,通常加入一些合金元素如:镍、钼、锰、铬、钒等,它们的作用跟在致密材料中的作用机理相同,可明显细化晶粒,当其溶于奥氏体后会增加过冷奥氏体的稳定性,保证淬火时的奥氏体转变,使淬火后材料的表面硬度增加,淬硬深度也增加。
另外,粉末冶金材料淬火后都要进行回火处理,回火处理的温度控制对粉末冶金材料的的性能影响较大,因此要根据不同材料的特性确定回火温度,降低回火脆性的影响,一般的材料可在175-250℃下空气或油中回火0.5-1.0h。
粉末冶金热作模具材料的热处理工艺
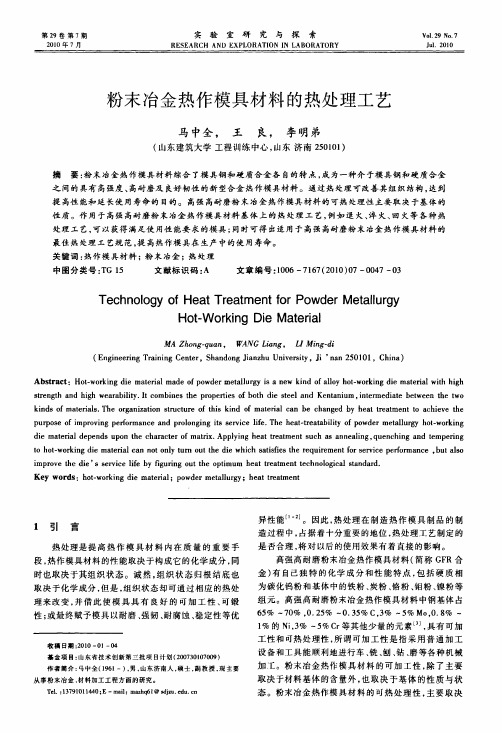
异性能¨‘2 ·。因此,热处理在制造热作模具制品的制 造过程中,占据着十分重要的地位,热处理工艺制定的 是否合理,将对以后的使用效果有着直接的影响。
高强高耐磨粉末冶金热作模具材料( 简称GFR合 金) 有自已独特的化学成分和性能特 点,包括硬质相 为碳化钨 粉和基体中的 铁粉、炭粉、 铬粉、钼粉、 镍粉等 组元。高强高耐磨粉末冶金热作模具材料中钢基体占
65%一70%,0.25%一0.35%C,3%一5%Mo,0.8%~
l %的Ni ,3%~5%Cr 等其他少量的元素”1,具有可加 工性和可热处理性,所谓可加工性是指采用普通加工 设备和工 具能顺利地进 行车、铣、刨 、钻、磨等各 种机械 加工。粉末冶金热作模具材料的可加工性,除了主要 取决于材料基体的含量外,也取决于基体的性质与状 态。粉末冶金热作模具材料的可热处理性,主要取决
Abst r a ct :Hot - - wor ki ng di e ma t er i a l mad e of powder met al l ur gy i s a new ki nd of al l oy hot ·- wor ki ng di e ma t e r i a l wi t h hi gh st r e ngt h a nd hi gh wear abi l i t y. I t combi nes t h e pr ope r t i e s of bot h di e s t eel and Kent ani um,i nt e rme di a t e bet ween t h e t wo ki nds of ma t e r i al s .Th e or ga ni zat i o n st r uc t ur e of t hi s ki nd of ma t e r i a l can be changed by heat t r e a t ment t o a chi e ve t h e purpos e of i mpr ovi ng pe rf or ma nc e and pr ol ongi ng i t s se r v i ce l i f e. The heat —t r eat abi l i t y of powder met a l l ur gy hot - worki ng di e ma t e r i a l depends upon t h e c ha r a ct er of mat r i x. Appl yi ng heat t r e at me nt s uc h as a nne a l i ng, que nc hi ng and t emper i ng
铁基粉末冶金零件蒸汽处理的工艺分析及质量控制
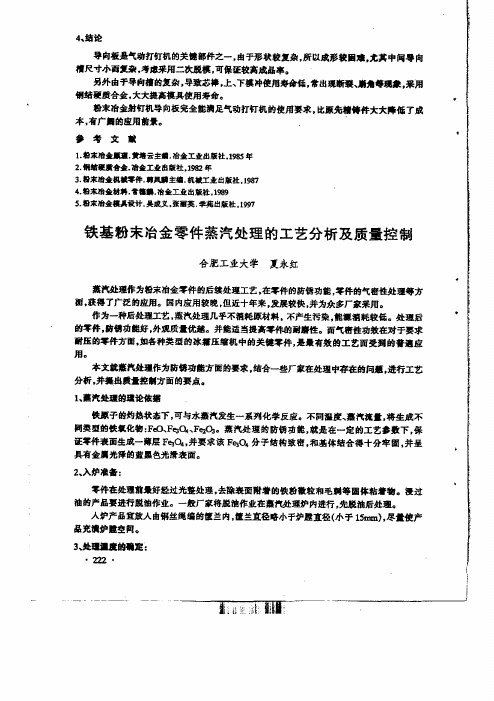
零件在处理前量好经过光整处理,去豫袭面附着的铁耪截粒和毛捌簪同律粘着物。爱过 油的产品要进行脱油作业。一般厂家将脱油作业在燕^处理炉内进行.先脱油后处理。
人炉产品宜放人由钢丝绳编的筐兰内.筐兰直径略小于妒腔直径(小于15nm),辱量使产
品充糠炉建空闽。
3、处曩■童黼定:
·Z12·
掇据圈l中。不同汪崖、水蒸汽和氢气生成旧、
亦■一台蒸汽处理炉内。产品散量不宜过步。有些厂采新上蒸汽处理工艺,由于工艺不藏岙。
往往采用小样试验.鄄在一台∞l嗨左右装柏炉内,仅技敷公斤产品.甚至只放敦十件样晶来摸
童工艺参敦。嫱暴匿为炉内产晶太少,●C化反应生戚的琏量太少.蒸汽藏量又来降下来,根容
量使平囊常数K值增得很大。而促进反应(4)的进行。使处理失败.屎因就在遣里。
台肥工业大学 夏永红
蒸汽处理作为粉末精金零件的后续处理工艺,在零件的防镭功能.零件的气密性处理等方 面。获得了广泛的应用。国内应用较晚.但近十年来.发晨较快.并为众多厂家采用。
作为一种后处理工芑。蒸汽处理几乎不清耗原材料,不产生枵染,靛彝涓耗较氍。处理岳 的零件,骑锈曲麓好.外观质量优越。并姥适当提高零件的耐磨性。面气密性琦效在对于要求 耐压的零件方面,如各种类型的冰霜压缩机中的关健零件,是量有效的工艺面受翻的蕾追应
兰熏色,但量罨粗糙不光滑,元金属光泽等块陷。逮种 情况。在一些工厂中是经常可l;l看刭的。
4、蒸汽蕾■的■定
蒸^流量应控翻在一个合适的范砸内,不可过大,
也不蕾过小。选一点慧泣有引起厂索的足够t视。
曩据圈2中FeO,Fe304、及F∞.的生成与早奢常
数K■盈汪虞的关系中可以看出,巳生成的F耐0.在永
蒸汽量过大时.(更圈中上半部分曲续),亦■承蒸汽和
粉末冶金材料的热处理工艺

粉末冶金材料的热处理工艺Final revision by standardization team on December 10, 2020.粉末冶金材料的热处理工艺【摘要】粉末冶金材料在现代工业中的应用越来越广,在取代锻钢件的高密度和高精度的复杂零件的应用中,随着粉末冶金技术的不断进步也取得了快速发展。
但是由于后续处理工艺的差异,其物理性能和力学性能还存在着一些缺陷,本文就针对粉末冶金材料的热处理工艺进行简要阐述分析,并分析其影响因素,提出改善工艺的策略。
【关键词】粉末冶金材料热处理密度强度淬透性碳氮共渗一. 前言粉末冶金材料在现代工业中的应用越来越广泛,特别是汽车工业、生活用品、机械设备等的应用中,粉末冶金材料已经占有很大的比重。
它们在取代低密度、低硬度和强度的铸铁材料方面已经具有明显优势,在高硬度、高精度和强度的精密复杂零件的应用中也在逐渐推广,这要归功于粉末冶金技术的快速发展。
全致密钢的热处理工艺已经取得了成功,但是粉末冶金材料的热处理,由于粉末冶金材料的物理性能差异和热处理工艺的差异,还存在着一些缺陷。
各铸造冶炼企业在粉末冶金材料的技术研究中,热锻、粉末注射成型、热等静压、液相烧结、组合烧结等热处理和后续处理工艺,在粉末冶金材料的物理性能与力学性能缺陷的改善中,取得了一定效果,提高了粉末冶金材料的强度和耐磨性,将大大扩展粉末冶金的应用范围。
二. 粉末冶金材料的热处理工艺粉末冶金材料的热处理要根据其化学成分和晶粒度确定,其中的孔隙存在是一个重要因素,粉末冶金材料在压制和烧结过程中,形成的孔隙贯穿整个零件中,孔隙的存在影响热处理的方式和效果。
粉末冶金材料的热处理有淬火、化学热处理、蒸汽处理和特殊热处理几种形式:1.淬火热处理工艺粉末冶金材料由于孔隙的存在,在传热速度方面要低于致密材料,因此在淬火时,淬透性相对较差。
另外淬火时,粉末材料的烧结密度和材料的导热性是成正比关系的;粉末冶金材料因为烧结工艺与致密材料的差异,内部组织均匀性要优于致密材料,但存在较小的微观区域的不均匀性,所以,完全奥氏体化时间比相应锻件长50%,在添加合金元素时,完全奥氏体化温度会更高、时间会更长。
粉末冶金材料论文
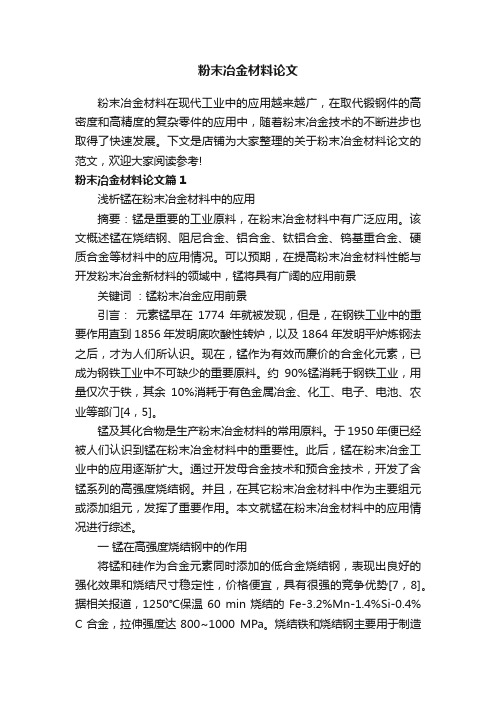
粉末冶金材料论文粉末冶金材料在现代工业中的应用越来越广,在取代锻钢件的高密度和高精度的复杂零件的应用中,随着粉末冶金技术的不断进步也取得了快速发展。
下文是店铺为大家整理的关于粉末冶金材料论文的范文,欢迎大家阅读参考!粉末冶金材料论文篇1浅析锰在粉末冶金材料中的应用摘要:锰是重要的工业原料,在粉末冶金材料中有广泛应用。
该文概述锰在烧结钢、阻尼合金、铝合金、钛铝合金、钨基重合金、硬质合金等材料中的应用情况。
可以预期,在提高粉末冶金材料性能与开发粉末冶金新材料的领域中,锰将具有广阔的应用前景关键词:锰粉末冶金应用前景引言:元素锰早在1774年就被发现,但是,在钢铁工业中的重要作用直到1856年发明底吹酸性转炉,以及1864年发明平炉炼钢法之后,才为人们所认识。
现在,锰作为有效而廉价的合金化元素,已成为钢铁工业中不可缺少的重要原料。
约90%锰消耗于钢铁工业,用量仅次于铁,其余10%消耗于有色金属冶金、化工、电子、电池、农业等部门[4,5]。
锰及其化合物是生产粉末冶金材料的常用原料。
于1950年便已经被人们认识到锰在粉末冶金材料中的重要性。
此后,锰在粉末冶金工业中的应用逐渐扩大。
通过开发母合金技术和预合金技术,开发了含锰系列的高强度烧结钢。
并且,在其它粉末冶金材料中作为主要组元或添加组元,发挥了重要作用。
本文就锰在粉末冶金材料中的应用情况进行综述。
一锰在高强度烧结钢中的作用将锰和硅作为合金元素同时添加的低合金烧结钢,表现出良好的强化效果和烧结尺寸稳定性,价格便宜,具有很强的竞争优势[7,8]。
据相关报道,1250℃保温60 min烧结的Fe-3.2%Mn-1.4%Si-0.4% C合金,拉伸强度达800~1000 MPa。
烧结铁和烧结钢主要用于制造机械零件,在选择合金元素时,必须注意到其对尺寸稳定性的影响。
在一般情况下,加入硅会引起压坯在烧结时收缩,而加入锰则会引起压坯膨胀。
同时加入锰和硅,能够较好控制烧结体的外观形状和尺寸[9]。
粉末冶金工艺简介及问题点展示PPT课件
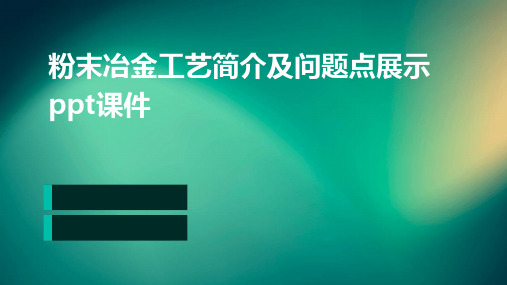
粉末冶金工艺能够生产传统熔铸工艺无法生产的具有特殊结 构和性能的材料和制品,如多孔、半致密或全致密材料和制 品,具有节材、省能、性能优异、产品精度高且稳定性好等 一系列优点。
粉末冶金工艺流程简介
制粉
将原料制成所需粉末,制粉方法包括 机械法(如球磨法)和物理化学法 (如还原法、雾化法、电解法)。
包括力学性能、物理性能、化学性能等,确保产品各项性能指标符 合标准要求。
检测方法
采用先进的检测设备和方法,如光谱分析、金相检验、力学性能测 试等,确保检测结果的准确性和可靠性。
评价标准
根据国家和行业标准,结合产品实际应用情况,制定合理的性能评价 标准,为产品质量判定提供依据。
06 问题点展示与解决方案探 讨
注射成型技术特点及应用范围
注射成型技术特点
将金属粉末与粘结剂混合后制成喂料 ,通过注射机将喂料注入模具型腔中 成型,具有成型精度高、生产效率高 、可成型复杂形状等优点。
应用范围
注射成型技术广泛应用于汽车、电子 、医疗器械等领域,如制造发动机零 件、齿轮、轴承、结构件等。
其他成型方法概述
轧制成型
将金属粉末通过轧辊压制成连续带材或板 材的方法,适用于制造薄板、带材等。
烧结过程中组织性能变化规律
致密化过程
随着烧结温度的升高和时间的延 长,粉末颗粒之间逐渐靠近、结 合,孔隙率逐渐降低,材料逐渐
致密化。
晶粒长大
在烧结过程中,粉末颗粒之间的 界面逐渐消失,晶粒逐渐长大。 过高的烧结温度或过长的烧结时 间会导致晶粒异常长大,影响材
料的力学性能。
相变与化学反应
在烧结过程中,可能会发生相变 或化学反应,如固溶、脱溶、氧 化、还原等。这些反应会改变材
粉末冶金压制成形理论与工艺综述
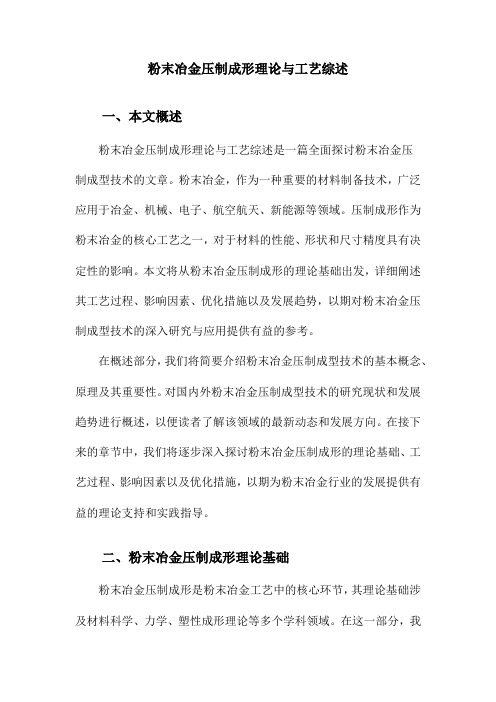
粉末冶金压制成形理论与工艺综述一、本文概述粉末冶金压制成形理论与工艺综述是一篇全面探讨粉末冶金压制成型技术的文章。
粉末冶金,作为一种重要的材料制备技术,广泛应用于冶金、机械、电子、航空航天、新能源等领域。
压制成形作为粉末冶金的核心工艺之一,对于材料的性能、形状和尺寸精度具有决定性的影响。
本文将从粉末冶金压制成形的理论基础出发,详细阐述其工艺过程、影响因素、优化措施以及发展趋势,以期对粉末冶金压制成型技术的深入研究与应用提供有益的参考。
在概述部分,我们将简要介绍粉末冶金压制成型技术的基本概念、原理及其重要性。
对国内外粉末冶金压制成型技术的研究现状和发展趋势进行概述,以便读者了解该领域的最新动态和发展方向。
在接下来的章节中,我们将逐步深入探讨粉末冶金压制成形的理论基础、工艺过程、影响因素以及优化措施,以期为粉末冶金行业的发展提供有益的理论支持和实践指导。
二、粉末冶金压制成形理论基础粉末冶金压制成形是粉末冶金工艺中的核心环节,其理论基础涉及材料科学、力学、塑性成形理论等多个学科领域。
在这一部分,我们将详细讨论粉末冶金压制成形的基本原理、影响因素以及优化方法。
粉末冶金压制成形的基本原理是通过对粉末颗粒施加压力,使其在模具中发生塑性变形,从而得到所需形状和尺寸的压坯。
这一过程中,粉末颗粒之间的摩擦、粘结和重排等行为对压坯的质量和性能具有重要影响。
粉末冶金压制成形受到多种因素的影响,包括粉末特性、模具设计、压制工艺参数等。
粉末特性如颗粒大小、形状、表面能等直接影响压坯的成形质量和性能。
模具设计则决定了压坯的形状、尺寸和精度。
压制工艺参数如压制压力、压制速度、保压时间等也对压坯的成形效果产生显著影响。
为了优化粉末冶金压制成形过程,研究者们提出了多种方法。
例如,通过改进粉末制备工艺,提高粉末的流动性和压缩性;优化模具设计,减少压坯内部的应力集中和缺陷;调整压制工艺参数,实现压坯的均匀致密化等。
随着数值模拟技术的发展,越来越多的研究者开始利用有限元分析等数值模拟方法对粉末冶金压制成形过程进行仿真研究,以进一步揭示其成形机理和优化方法。
粉末冶金的烧结技术(2篇)
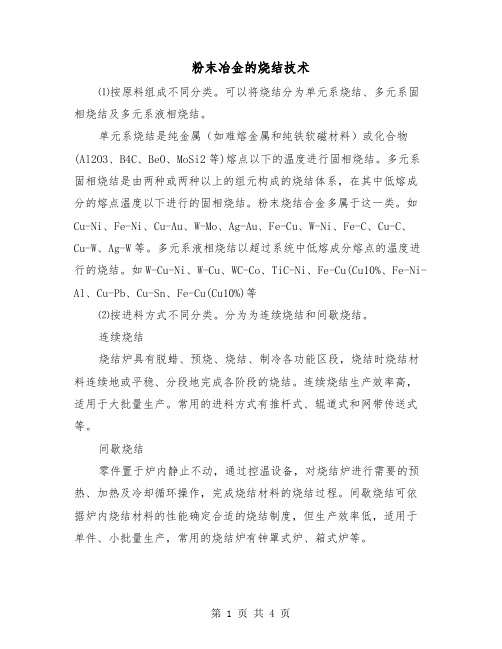
粉末冶金的烧结技术⑴按原料组成不同分类。
可以将烧结分为单元系烧结、多元系固相烧结及多元系液相烧结。
单元系烧结是纯金属(如难熔金属和纯铁软磁材料)或化合物(Al2O3、B4C、BeO、MoSi2等)熔点以下的温度进行固相烧结。
多元系固相烧结是由两种或两种以上的组元构成的烧结体系,在其中低熔成分的熔点温度以下进行的固相烧结。
粉末烧结合金多属于这一类。
如Cu-Ni、Fe-Ni、Cu-Au、W-Mo、Ag-Au、Fe-Cu、W-Ni、Fe-C、Cu-C、Cu-W、Ag-W等。
多元系液相烧结以超过系统中低熔成分熔点的温度进行的烧结。
如W-Cu-Ni、W-Cu、WC-Co、TiC-Ni、Fe-Cu(Cu10%、Fe-Ni-Al、Cu-Pb、Cu-Sn、Fe-Cu(Cu10%)等⑵按进料方式不同分类。
分为为连续烧结和间歇烧结。
连续烧结烧结炉具有脱蜡、预烧、烧结、制冷各功能区段,烧结时烧结材料连续地或平稳、分段地完成各阶段的烧结。
连续烧结生产效率高,适用于大批量生产。
常用的进料方式有推杆式、辊道式和网带传送式等。
间歇烧结零件置于炉内静止不动,通过控温设备,对烧结炉进行需要的预热、加热及冷却循环操作,完成烧结材料的烧结过程。
间歇烧结可依据炉内烧结材料的性能确定合适的烧结制度,但生产效率低,适用于单件、小批量生产,常用的烧结炉有钟罩式炉、箱式炉等。
除上述分类方法外。
按烧结温度下是否有液相分为固相烧结和液相烧结;按烧结温度分为中温烧结和高温烧结(1100~1700℃),按烧结气氛的不同分为空气烧结,氢气保护烧结(如钼丝炉、不锈钢管和氢气炉等)和真空烧结。
另外还有超高压烧结、活化热压烧结等新的烧结技术。
2.影响粉末制品烧结质量的因素影响烧结体性能的因素很多,主要是粉末体的性状、成形条件和烧结的条件。
烧结条件的因素包括加热速度、烧结温度和时间、冷却速度、烧结气氛及烧结加压状况等。
⑴烧结温度和时间烧结温度的高低和时间的长短影响到烧结体的孔隙率、致密度、强度和硬度等。
粉末冶金钼管热挤压工艺基础研究
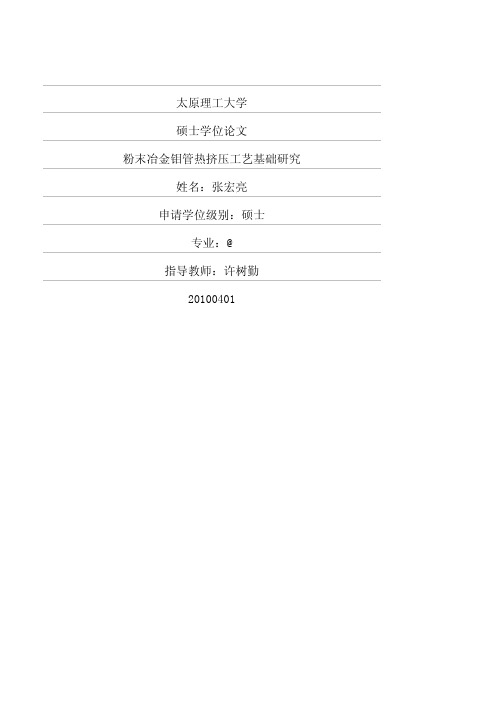
太原理工大学硕士研究生学位论文Βιβλιοθήκη 粉末冶金钼管热挤压工艺基础研究
摘 要
液晶显示器制造工艺中的降低反射层、透明电极、发射极与阴极等均 由溅射方法形成。而溅射靶材多以金属纯钼板材为主。近年来随着液晶屏 幕尺寸的不断增大,与之对应的溅射板形钼靶也随之增大了其自身的面积。 若采用旋转的钼筒作靶材,则屏幕的长度由钼管长度决定,屏幕的宽度则 不受限制。为了提高溅射层的均匀性,要求溅射靶材具有较高的致密度(在 99.7%以上)。然而最常用的成形钼制品工艺(粉末冶金)达不到靶材的致密 度要求,所以必须再加一道热加工工艺来提高其制品的致密度——本文采 用热挤压工艺。 针对使用粉末冶金坯料挤压成形圆筒(管)形钼靶材并提高其制品致密 度的问题,本文采用高温单向压缩试验与有限元数值模拟相结合的方法对 粉末冶金钼管热挤压工艺进行了基础研究。其中包括研究粉末冶金钼坯的 高温塑性变形行为、钼管材热挤压过程和挤压模具结构的优化。 通过 Gleeble-3800 热模拟试验机,分别在变形温度为 1100℃、1150℃、 1200℃、1250℃,变形应变速率为 11.5 s-1、17.3 s-1 和 23s-1 下对φ8×12 粉末 冶金钼圆柱体试样进行了单向压缩实验。根据实验数据建立了粉末冶金钼 坯的高温稳态流变应力本构方程,并研究了粉末冶金钼坯的高温塑性变形 时流变力学行为的特点。 研究结果表明:粉冶钼在高温变形时明显表现出动态回复与再结晶特 征;金属钼是正应变速率敏感性材料,即流变应力随着变形速率的增加而
I
太原理工大学硕士研究生学位论文
增大。粉末冶金钼坯高温塑性变形过程是受位错运动控制的热激活过程, 且其高温变形过程可以用包含 Arrhenius 项的 Zener-Hollomon 参数来描述。 通过悬重法测量热变形后粉末冶金钼坯致密度的变化情况。结果表明: 通过变形量为 70%的变形后,粉末冶金坯料可以达到靶材所要求的致密度。 通过光学显微镜观察其热变形后的微观组织结构,并探讨了热变形后 不同热处理温度(750℃、850℃和 950℃)对其组织结构的影响。金相组织分 析表明, 粉末冶金坯料在 70%的相对应变量下, 热处理以退火温度为 850℃ 并在此温度下保温 60min 最佳,此时大多晶粒相互交错搭接并伴随有细小 等轴亚晶的生成,即大部分的带状组织任然保留并消除了热加工造成的残 余应力,故性能最好。 为了优化粉冶坯钼管材挤压模具结构, 应用 DEFORM 有限元软件对挤 压工艺进行模拟。挤压工艺方案为:挤压温度为 1250℃,挤压速度为 225mm/s, 平模长度分别为 8%D、 10%D、 11%D 和 12%D, 模角分别为 55°、 60°、65°、70°。 为了定量比较不同挤压工艺方案的优劣,定义了以挤压力、管材成材 率、总费用节省率和坯料所承受的应力应变情况为综合评判函数,得出平 锥模的平模长度为 10%D,模角为 65°时模具结构最优。
粉末冶金材料的热处理工艺

粉末冶金材料的热处理工艺热处理是粉末冶金材料制备过程中的关键步骤之一,通过控制材料的温度和时间,在一定的环境条件下改变材料的组织结构和性能,从而达到提高材料性能的目的。
本文将介绍粉末冶金材料的热处理工艺及其影响因素。
一、热处理的基本原理热处理是通过加热和冷却来改变材料的组织结构和性能。
具体来说,热处理可以改变材料的晶粒尺寸、晶界分布、相组成和相形态等。
通过调控这些因素,可以改善材料的硬度、强度、耐磨性、耐腐蚀性等性能。
二、热处理的基本步骤粉末冶金材料的热处理通常包括加热、保温和冷却三个步骤。
1. 加热:将粉末冶金材料置于炉中,通过加热设备提供的热能使材料升温。
加热温度应根据材料的成分和热处理要求进行选择,一般可以分为预热、保温和回火等几个阶段。
2. 保温:在达到所需的加热温度后,将材料保持在一定温度下一段时间,以使材料内部发生相应的组织变化。
保温时间的长短应根据材料的性质和要求来确定。
3. 冷却:在保温结束后,需要将材料迅速冷却至室温。
冷却速度的选择对于材料性能的改善至关重要,过快或过慢的冷却速度都可能导致材料性能不理想。
三、影响热处理效果的因素1. 温度:热处理温度是影响材料组织和性能的重要因素。
过高的温度可能导致材料过度烧结或晶粒长大,而过低的温度则可能使材料的相变不完全。
2. 时间:保温时间的长短对于材料的组织结构和性能有着重要影响。
过短的保温时间可能无法完全实现相变,而过长的保温时间则可能导致材料的晶粒长大。
3. 冷却速度:冷却速度的选择对于材料性能的改善至关重要。
过快的冷却速度可能导致材料的内部应力过大,而过慢的冷却速度则可能使材料的相变不完全。
4. 环境气氛:热处理过程中的气氛对于材料的表面质量和性能有着重要影响。
不同的气氛条件下,材料的表面可能会发生氧化、碳化等现象,从而影响材料的性能。
四、热处理工艺的应用粉末冶金材料的热处理工艺广泛应用于汽车、航空航天、电子、机械等行业。
例如,在汽车制造中,通过热处理可以提高发动机零部件的耐磨性和耐高温性能;在航空航天领域,热处理可以提高飞机结构材料的强度和耐腐蚀性能。
粉末冶金高速钢的特性、热处理工艺及应用

$%!&’ 为代表的新型淬火介质逐渐被推广应用,它不仅 具有良好的冷却特性,而且与油相比还具有安全可靠、 无火灾隐患的特点,所以受到众多企业的欢迎。 在应用的初期, $%!&’ 反映出的效果非常良好,但 随着时间的推移,这种水溶性淬火介质的缺点也开始暴 露出来,那就是它的老化问题。因水溶性淬火介质老化 引发的质量问题曾频繁出现,造成了许多无法挽回的损 失。某机车厂 !""& 年因淬火介质老化造成的材料毛坯 损失就在 &" 万元以上,中频淬火也出现大量表面淬火 裂纹。
几个国家的粉末冶金高速钢牌号、成分及热处理工艺
表 " 三代粉末冶金高速钢的制备技术与性能
类别 普通高速钢 项目 制备技术 特性 冶炼铸锭锻轧 第一代粉末冶金高速钢 ;4<=> .1 )-制粉热等静压烧结 第二代粉末冶金高速钢 ?-) .1 )-电渣加热法 ?-) 技术 第三代粉末冶金高速钢 @A<BCD;1.1 )-在 ?-) 技术基础上作数 项改进形成 @A<BCD;1法
物颗粒细小而均匀,一般为 % ( )! 最大尺寸不超过 & ( ,这就大大提高了钢的强度和韧性。 #! &) #" 粉末冶金高速钢的性能和特点 粉末冶金的特殊冶炼方法与普通高速钢相比,具有 更优异的性能和特点 ( 见表 %) 。
表 ! 粉末冶金高速钢与普通高速钢的性能对比
钢种 普通高速钢 项目 特性 碳 化 物 颗 粒 粗 大, 最大 直 径 尺 寸 可 达 *" &, 分 布 不 匀 有 ! 堆集 碳化物颗粒细 小, 一 般 为 % ( ) &,最 大 直 径 尺 ! 寸小 于 # &, 且 分 ! 布十分均匀 消除了共晶碳化 物的不均匀性 无偏析 可提高合金元素 含量,不 会 引 起 碳 化物颗粒粗化和成 分 偏 析, +、 ,-、 ./、 0、 .- 等 主 要 合金元素含量可高 达 *"’ 左右,碳化 钒 含 量 可 高 达 %*’ ,含 碳 量 最 高 !2*1’ 合金元素和碳化 物含 量 增 加,提 高 钢的 硬 度 和 耐 磨 性,不 影 响 钢 的 加 工性,其 车 削 和 磨 削性 好,无 需 锻 轧 加工 各 向 同 性,具 有 高 强 度、 高 硬 度、 高 耐 磨 性、 高 韧 性,适 用 于 高 冲 击 性、大 切 削 量 和 断 续切削加工 ## ( $!34. 粉末冶金高速钢
粉末冶金工艺
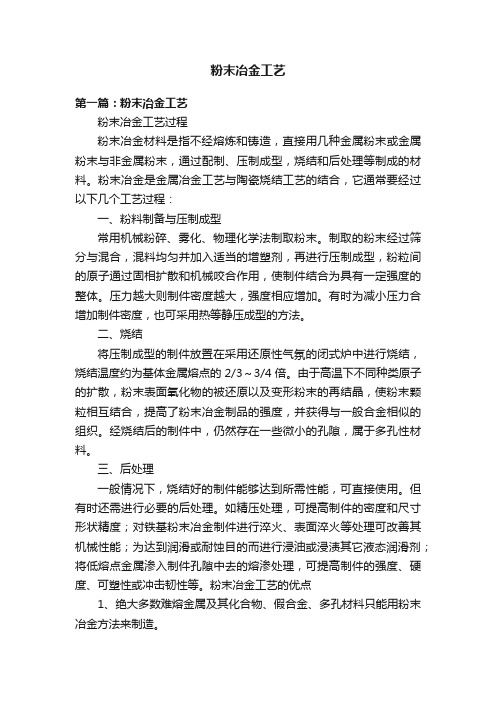
粉末冶金工艺第一篇:粉末冶金工艺粉末冶金工艺过程粉末冶金材料是指不经熔炼和铸造,直接用几种金属粉末或金属粉末与非金属粉末,通过配制、压制成型,烧结和后处理等制成的材料。
粉末冶金是金属冶金工艺与陶瓷烧结工艺的结合,它通常要经过以下几个工艺过程:一、粉料制备与压制成型常用机械粉碎、雾化、物理化学法制取粉末。
制取的粉末经过筛分与混合,混料均匀并加入适当的增塑剂,再进行压制成型,粉粒间的原子通过固相扩散和机械咬合作用,使制件结合为具有一定强度的整体。
压力越大则制件密度越大,强度相应增加。
有时为减小压力合增加制件密度,也可采用热等静压成型的方法。
二、烧结将压制成型的制件放置在采用还原性气氛的闭式炉中进行烧结,烧结温度约为基体金属熔点的2/3~3/4倍。
由于高温下不同种类原子的扩散,粉末表面氧化物的被还原以及变形粉末的再结晶,使粉末颗粒相互结合,提高了粉末冶金制品的强度,并获得与一般合金相似的组织。
经烧结后的制件中,仍然存在一些微小的孔隙,属于多孔性材料。
三、后处理一般情况下,烧结好的制件能够达到所需性能,可直接使用。
但有时还需进行必要的后处理。
如精压处理,可提高制件的密度和尺寸形状精度;对铁基粉末冶金制件进行淬火、表面淬火等处理可改善其机械性能;为达到润滑或耐蚀目的而进行浸油或浸渍其它液态润滑剂;将低熔点金属渗入制件孔隙中去的熔渗处理,可提高制件的强度、硬度、可塑性或冲击韧性等。
粉末冶金工艺的优点1、绝大多数难熔金属及其化合物、假合金、多孔材料只能用粉末冶金方法来制造。
2、由于粉末冶金方法能压制成最终尺寸的压坯,而不需要或很少需要随后的机械加工,故能大大节约金属,降低产品成本。
用粉末冶金方法制造产品时,金属的损耗只有1-5%,而用一般熔铸方法生产时,金属的损耗可能会达到80%。
3、由于粉末冶金工艺在材料生产过程中并不熔化材料,也就不怕混入由坩埚和脱氧剂等带来的杂质,而烧结一般在真空和还原气氛中进行,不怕氧化,也不会给材料任何污染,故有可能制取高纯度的材料。
硬度在HRC50以上的粉末材料的开发与烧结热处理工艺的研究

硬度在HRC50以上的粉末材料的开发与烧结热处理工艺的研究摘要:本文研究了一种高硬度铁基粉末冶金材料及其生产工艺。
通过选用不同的粉末材质并在不同工艺条件下做各项对比实验得到的性能数据,开发出了一种硬度在HRC50以上的高性价比的粉末冶金材料和烧结热处理工艺。
关键字:粉末冶金、预合金、表面硬度、烧结硬化、渗铜、热处理一、前言现代粉末冶金工业,除了通常所讲的生产铁粉、铜粉等金属粉末和生产铁基、铜基粉末冶金制品等产业外,广义地讲,还应包括用粉末冶金技术制造的所有产品门类的产业。
本文主要介绍铁基粉末冶金材料及其生产工艺。
铁基金属粉末是粉末冶金生产的基本原料,为满足铁基粉末冶金制品生产对金属粉末的各种性能要求,又研究了各种各样的铁粉的生产方法、不同的压制成型工艺、烧结工艺及热处理方法。
文中开发了一种硬度在HRC50以上的铁基粉末冶金产品。
常规条件下,需要将粉末冶金产品的表面硬度达到HRC50以上是有一定难度的。
为满足粉末冶金产品表面的高硬度,整个过程必须非常谨慎严格。
铁粉分为普通纯铁粉和添加合金元素的预合金化铁粉,从原料铁粉的选用上我们需要选取添加一定合金成分的预合金化铁粉,文中各种铁粉均由山东鲁银新材料科技有限公司提供;压制、烧结、热处理等工艺均在禹城粉末冶金制品有限公司进行。
二、实验的方法和过程(一)实验的原料粉末和材料配比:选用5种铁粉作为基粉加入适量的石墨粉、铜粉和润滑剂,润滑剂的含量为0.7%,将粉末压制成形。
5种实验粉末的材料配比分别如下,1#粉:LAP100.29+1.0%C+1.8%Cu+0.7%润滑剂,LAP100.29为水雾化纯铁粉,粉末600MPa压缩性能为7.18g/cm3;2#粉:LAP100.29Mo2+0.6%C+0.7%润滑剂,LAP100.29Mo2为水雾化预合金化钼元素铁粉,Mo含量为0.80—1.00%;3#粉:LAP100.29Mo3+0.6%C+0.7%润滑剂,LAP100.29Mo3为水雾化预合金化钼元素铁粉,Mo含量为1.40—1.60%;4#粉:LAP100.29A4+0.6%C+0.7%润滑剂,LAP100.29A4为水雾化预合金化镍和钼元素铁粉,Mo含量1.30%,Ni含量为1.45%;5#粉:LAP100.29A5+0.6%C+0.7%润滑剂,LAP100.29A4为水雾化预合金化低镍和低钼元素铁粉,Mo含量0.90%,Ni含量为0.50%。
粉末冶金热处理

粉末冶金热处理一、前言粉末冶金热处理是一种重要的金属材料加工方法,它能够通过高温处理改善材料的性能,提高其机械性能、耐腐蚀性和耐磨损性等。
本文将从粉末冶金的基础知识开始,详细介绍粉末冶金热处理的原理、方法和应用。
二、粉末冶金基础知识1. 粉末冶金定义粉末冶金是一种制造零件的技术,它通过将金属或非金属材料制成微小颗粒,再利用压缩、烧结等工艺将这些颗粒化为块体或形成复合材料。
2. 粉末制备方法常用的粉末制备方法有机械法、化学法和物理法等。
其中机械法是最常用的方法之一,包括球磨法、振荡球磨法和高能球磨法等。
3. 粉末冶金加工工艺主要包括压制、烧结和后处理等过程。
其中压制是将粉末填充到模具中进行压缩成形;烧结则是将压制好的坯体进行高温处理,使其颗粒结合成为固体材料;后处理则是对烧结好的材料进行加工和表面处理。
三、粉末冶金热处理原理1. 热处理定义热处理是指通过加热和冷却等方式改变材料的组织结构和性能,以达到提高其机械性能、耐腐蚀性和耐磨损性等目的的过程。
2. 粉末冶金热处理原理粉末冶金材料在制备过程中由于颗粒之间存在空隙,因此其密度较低。
而经过高温热处理后,这些空隙会被填充,颗粒之间的结合力也会增强,从而提高了材料的密度和强度。
此外,热处理还可以改善材料的晶体结构和组织状态,增强其机械性能、耐腐蚀性和耐磨损性等。
四、粉末冶金热处理方法1. 真空烧结法真空烧结法是一种在真空环境下进行高温加工的方法。
由于真空环境下不存在氧化反应,因此可以避免材料表面被氧化和污染。
此外,真空烧结法还可以控制材料的晶体结构和组织状态,从而提高其机械性能和耐腐蚀性能。
2. 气氛烧结法气氛烧结法是一种在特定气氛下进行高温加工的方法。
常用的气氛有惰性气体、还原性气体和氧化性气体等。
这种方法可以控制材料的晶体结构和组织状态,从而改善其性能。
3. 热等静压法热等静压法是一种将粉末填充到模具中后,在高温高压下进行加工的方法。
这种方法可以使材料颗粒之间更加紧密地结合,从而提高其密度和强度。
- 1、下载文档前请自行甄别文档内容的完整性,平台不提供额外的编辑、内容补充、找答案等附加服务。
- 2、"仅部分预览"的文档,不可在线预览部分如存在完整性等问题,可反馈申请退款(可完整预览的文档不适用该条件!)。
- 3、如文档侵犯您的权益,请联系客服反馈,我们会尽快为您处理(人工客服工作时间:9:00-18:30)。
浅谈粉末冶金材料的热处理工艺的分析与研究
发表时间:2019-04-30T14:04:43.727Z 来源:《基层建设》2019年第5期作者:罗艳归[导读] 摘要:粉末冶金材料在现代工业中的应用越来越广泛,特别是汽车工业、生活用品、机械设备等的应用中,粉末冶金材料已经占有很大的比重。
国家知识产权局专利局专利审查协作广东中心摘要:粉末冶金材料在现代工业中的应用越来越广泛,特别是汽车工业、生活用品、机械设备等的应用中,粉末冶金材料已经占有很大的比重。
它们在取代低密度、低硬度和强度的铸铁材料方面已经具有明显优势,在高硬度、高精度和强度的精密复杂零件的应用中也在逐渐推广,这要归功于粉末冶金技术的快速发展。
全致密钢的热处理工艺已经取得了成功,但是粉末冶金材料的热处理,由于粉末冶金材
料的物理性能差异和热处理工艺的差异,还存在着一些缺陷。
各铸造冶炼企业在粉末冶金材料的技术研究中,热锻、粉末注射成型、热等静压、液相烧结、组合烧结等热处理和后续处理工艺,在粉末冶金材料的物理性能与力学性能缺陷的改善中,取得了一定效果,提高了粉末冶金材料的强度和耐磨性,将大大扩展粉末冶金的应用范围。
粉末冶金材料在现代工业中的应用越来越广,在取代锻钢件的高密度和高精度的复杂零件的应用中,随着粉末冶金技术的不断进步也取得了快速发展。
但是由于后续处理工艺的差异,其物理性能和力学性能还存在着一些缺陷,本文就针对粉末冶金材料的热处理工艺进行简要阐述分析,并分析其影响因素,提出改善工艺的策略。
关键词:粉末冶金材料;热处理;密度;强度;淬透性;碳氮共渗
一.前言
粉末冶金材料在现代工业中的应用越来越广泛,特别是汽车工业、生活用品、机械设备等的应用中,粉末冶金材料已经占有很大的比重。
它们在取代低密度、低硬度和强度的铸铁材料方面已经具有明显优势,在高硬度、高精度和强度的精密复杂零件的应用中也在逐渐推广,这要归功于粉末冶金技术的快速发展。
全致密钢的热处理工艺已经取得了成功,但是粉末冶金材料的热处理,由于粉末冶金材料的物理性能差异和热处理工艺的差异,还存在着一些缺陷。
各铸造冶炼企业在粉末冶金材料的技术研究中,热锻、粉末注射成型、热等静压、液相烧结、组合烧结等热处理和后续处理工艺,在粉末冶金材料的物理性能与力学性能缺陷的改善中,取得了一定效果,提高了粉末冶金材料的强度和耐磨性,将大大扩展粉末冶金的应用范围。
二.粉末冶金材料的热处理工艺
粉末冶金材料的热处理要根据其化学成分和晶粒度确定,其中的孔隙存在是一个重要因素,粉末冶金材料在压制和烧结过程中,形成的孔隙贯穿整个零件中,孔隙的存在影响热处理的方式和效果。
粉末冶金材料的热处理有淬火、化学热处理、蒸汽处理和特殊热处理几种形式:
1.淬火热处理工艺
粉末冶金材料由于孔隙的存在,在传热速度方面要低于致密材料,因此在淬火时,淬透性相对较差。
另外淬火时,粉末材料的烧结密度和材料的导热性是成正比关系的;粉末冶金材料因为烧结工艺与致密材料的差异,内部组织均匀性要优于致密材料,但存在较小的微观区域的不均匀性,所以,完全奥氏体化时间比相应锻件长50%,在添加合金元素时,完全奥氏体化温度会更高、时间会更长。
比如,以不同化合碳含量的烧结碳钢为例,淬火温度如表1所示,在粉末冶金材料的热处理中,为了提高淬透性,通常加入一些合金元素如:镍、钼、锰、铬、钒等,它们的作用跟在致密材料中的作用机理相同,可明显细化晶粒,当其溶于奥氏体后会增加过冷奥氏体的稳定性,保证淬火时的奥氏体转变,使淬火后材料的表面硬度增加,淬硬深度也增加。
另外,粉末冶金材料淬火后都要进行回火处理,回火处理的温度控制对粉末冶金材料的的性能影响较大,因此要根据不同材料的特性确定回火温度,降低回火脆性的影响,一般的材料可在175-250℃下空气或油中回火0.5-1.0h。
2.化学热处理工艺
化学热处理一般都包括分解、吸收、扩散三个基本过程,比如,渗碳热处理的反应如下: 2CO≒[C]+CO2(放热反应) CH4≒[C]+2H2(吸热反应)碳分解出后被金属表面吸收并逐渐向内部扩散,在材料的表面获得足够的碳浓度后再进行淬火和回火处理,会提高粉末冶金材料的表面硬度和淬硬深度。
由于粉末冶金材料的孔隙存在,使得活性炭原子从表面渗入内部,完成化学热处理的过程。
但是,材料密度越高,孔隙效应就越弱,化学热处理的效果就越不明显,因此,要采用碳势较高的还原性气氛保护。
根据粉末冶金材料的孔隙特点,其加热和冷却速度要低于致密材料,所以加热时要延长保温时间,提高加热温度。
粉末冶金材料的化学热处理包括渗碳、渗氮、渗硫和多元共渗等几种形式,在化学热处理中,淬硬深度主要与材料的密度有关。
因此,可以在热处理工艺上采取相应措施,比如:渗碳时,在材料密度大于7g/cm3时适当延长时间。
通过化学热处理可提高材料的耐磨性,粉末冶金材料的不均匀奥氏体渗碳工艺,使处理后的材料渗层表面的含碳量可达2%以上,碳化物均匀分布于渗层表面,能够很好地提高硬度和耐磨性能。
3.蒸汽处理
蒸汽处理是把材料通过加热蒸汽使其表面氧化,在材料表层形成氧化膜,从而改善粉末冶金材料的性能。
特别是对于粉末冶金材料的表面的防腐,其有效期比发蓝处理效果明显,处理后的材料硬度和耐磨性明显增加。
4.特殊热处理工艺
特殊热处理工艺是近些年来科技发展的产物,包括感应加热淬火、激光表面硬化等。
感应加热淬火是在高频电磁感应涡流的影响下,加热温度提升快,对于表面硬度的增加有显著效果,但是容易出现软点,一般可以采取间断加热法延长奥氏体化时间;激光表面硬化工艺是以激光为热源使金属表面快速升温和冷却,使奥氏体晶粒内部的亚结构来不及回复再结晶而获得超细结构。
三.粉末冶金材料热处理的影响因素分析
粉末冶金材料在烧结过程中生成的孔隙是其固有特点,也给热处理带来了很大影响,特别是孔隙率的变化与热处理的关系,为了改善致密性和晶粒度,加入的合金元素也对热处理有一定影响: 1.孔隙对热处理过程的影响
粉末冶金材料在热处理时,通过快速冷却抑制奥氏体扩散转变成其他组织,从而获得马氏体,而孔隙的存在对材料的散热性影响较大。
通过导热率公式:
导热率=金属理论导热率×(1-2×孔隙率)/100
可以看出,淬透性随着孔隙率的增加而下降。
另一方面,孔隙还影响材料的密度,对材料热处理后表面硬度和淬硬深度的效果又因密度影响而有关联,降低了材料表面硬度。
而且,因为孔隙的存在,淬火时不能用盐水作为介质,以免因盐分残留造成腐蚀,所以,一般热处理是在真空或气体介质中进行的。
2.孔隙率对热处理时表面淬硬深度的影响
粉末冶金材料的热处理效果与材料的密度、渗(淬)透性、导热性和电阻性有关,孔隙率是造成这些因素的最大原因,孔隙率超过8%时,气体就会通过空隙迅速渗透,在进行渗碳硬化时,增加渗碳深度,表面硬化的效果就会降低。
而且,如果渗碳气体渗入速度过快,在淬火中会产生软点,降低表面硬度,使材料脆变和变形。
3.合金含量和类型对粉末冶金热处理的影响
合金元素中常见的是铜和镍,它们的含量与类型都会对热处理效果产生影响。
热处理硬化深度随铜含量、碳含量的增加而逐渐增高达到一定含量时又逐渐降低;镍合金的刚度要大于铜合金,但是镍含量的不均匀性会导致奥氏体组织不均匀;
4.高温烧结的影响
高温烧结虽然可以获得最佳的合金化效果和促进致密化,但是,烧结温度的不同,特别是温度较低时,会导致热处理的敏感性下降(固溶体中的合金减少)和机械性能下降。
因此,采用高温烧结,辅助以充分的还原气氛,可以获得较好的热处理效果。
四、结语
粉末冶金材料的热处理工艺是一个复杂的过程,它与孔隙率、合金类型、合金元素含量、烧结温度有关系,同致密材料相比,内部的均匀性较差,要想获得较高的淬透性,要提高完全奥氏体化温度并延长时间,不均匀奥氏体渗碳可得到不受奥氏体饱和碳浓度限制的高碳浓度。
另外,加入合金元素也可提高淬透性。
蒸汽处理可显著提高其防腐性能和表面硬度。
参考文献:
[1]曹放,粉末冶金材料的热处理工艺试验,粉末冶金技术,2017,11
[2]刘传习,周作平,解子章等,粉末冶金工艺学,科学普及出版社,2017,27
[3]董盼,合金化对粉末冶金铁基合金的组织结构与性能的影响,合肥工业大学材料学院2001届硕士论文。