各种常见无损探伤方法简介与比较
无损探伤的常用方法介绍

无损探伤的常用方法介绍资料整理:无损检测资源网五大常规方法是指射线探伤法、超声波探伤法、磁粉探伤法、涡流探伤法和渗透探伤法。
1、射线探伤方法射线探伤是利用射线的穿透性和直线性来探伤的方法。
这些射线虽然不会像可见光那样凭肉眼就能直接察知,但它可使照相底片感光,也可用特殊的接收器来接收。
常用于探伤的射线有x光和同位素发出的γ射线,分别称为x光探伤和γ射线探伤。
当这些射线穿过(照射)物质时,该物质的密度越大,射线强度减弱得越多,即射线能穿透过该物质的强度就越小。
此时,若用照相底片接收,则底片的感光量就小;若用仪器来接收,获得的信号就弱。
因此,用射线来照射待探伤的零部件时,若其内部有气孔、夹渣等缺陷,射线穿过有缺陷的路径比没有缺陷的路径所透过的物质密度要小得多,其强度就减弱得少些,即透过的强度就大些,若用底片接收,则感光量就大些,就可以从底片上反映出缺陷垂直于射线方向的平面投影;若用其它接收器也同样可以用仪表来反映缺陷垂直于射线方向的平面投影和射线的透过量。
由此可见,一般情况下,射线探伤是不易发现裂纹的,或者说,射线探伤对裂纹是不敏感的。
因此,射线探伤对气孔、夹渣、未焊透等体积型缺陷最敏感。
即射线探伤适宜用于体积型缺陷探伤,而不适宜面积型缺陷探伤。
2、超声波探伤方法 人们的耳朵能直接接收到的声波的频率范围通常是20Hz到20kHz,即音(声)频。
频率低于20 Hz的称为次声波,高于20 kHz的称为超声波。
工业上常用数兆赫兹超声波来探伤。
超声波频率高,则传播的直线性强,又易于在固体中传播,并且遇到两种不同介质形成的界面时易于反射,这样就可以用它来探伤。
通常用超声波探头与待探工件表面良好的接触,探头则可有效地向工件发射超声波,并能接收(缺陷)界面反射来的超声波,同时转换成电信号,再传输给仪器进行处理。
根据超声波在介质中传播的速度(常称声速)和传播的时间,就可知道缺陷的位置。
当缺陷越大,反射面则越大,其反射的能量也就越大,故可根据反射能量的大小来查知各缺陷(当量)的大小。
五大常规探伤方法概述
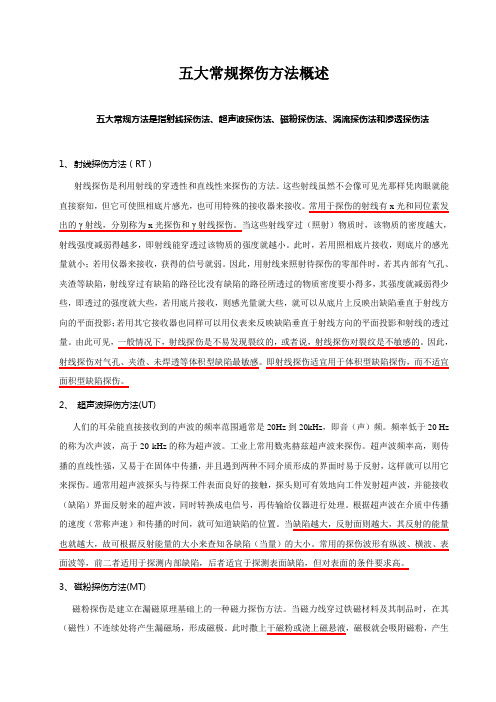
五大常规探伤方法概述五大常规方法是指射线探伤法、超声波探伤法、磁粉探伤法、涡流探伤法和渗透探伤法1、射线探伤方法(RT)射线探伤是利用射线的穿透性和直线性来探伤的方法。
这些射线虽然不会像可见光那样凭肉眼就能直接察知,但它可使照相底片感光,也可用特殊的接收器来接收。
常用于探伤的射线有x光和同位素发出的γ射线,分别称为x光探伤和γ射线探伤。
当这些射线穿过(照射)物质时,该物质的密度越大,射线强度减弱得越多,即射线能穿透过该物质的强度就越小。
此时,若用照相底片接收,则底片的感光量就小;若用仪器来接收,获得的信号就弱。
因此,用射线来照射待探伤的零部件时,若其内部有气孔、夹渣等缺陷,射线穿过有缺陷的路径比没有缺陷的路径所透过的物质密度要小得多,其强度就减弱得少些,即透过的强度就大些,若用底片接收,则感光量就大些,就可以从底片上反映出缺陷垂直于射线方向的平面投影;若用其它接收器也同样可以用仪表来反映缺陷垂直于射线方向的平面投影和射线的透过量。
由此可见,一般情况下,射线探伤是不易发现裂纹的,或者说,射线探伤对裂纹是不敏感的。
因此,射线探伤对气孔、夹渣、未焊透等体积型缺陷最敏感。
即射线探伤适宜用于体积型缺陷探伤,而不适宜面积型缺陷探伤。
2、超声波探伤方法(UT)人们的耳朵能直接接收到的声波的频率范围通常是20Hz到20kHz,即音(声)频。
频率低于20 Hz 的称为次声波,高于20 kHz的称为超声波。
工业上常用数兆赫兹超声波来探伤。
超声波频率高,则传播的直线性强,又易于在固体中传播,并且遇到两种不同介质形成的界面时易于反射,这样就可以用它来探伤。
通常用超声波探头与待探工件表面良好的接触,探头则可有效地向工件发射超声波,并能接收(缺陷)界面反射来的超声波,同时转换成电信号,再传输给仪器进行处理。
根据超声波在介质中传播的速度(常称声速)和传播的时间,就可知道缺陷的位置。
当缺陷越大,反射面则越大,其反射的能量也就越大,故可根据反射能量的大小来查知各缺陷(当量)的大小。
无损探伤方法

无损探伤方法无损探伤是一种在不破坏被检测物体的情况下,通过一定的物理方法和检测设备,对被检测物体进行内部和表面的缺陷、结构和性能的检测和评价的技术手段。
无损探伤方法在工业生产中起着至关重要的作用,它可以帮助我们及时发现和排除各种缺陷,确保产品的质量和安全。
本文将介绍几种常见的无损探伤方法。
首先,我们来介绍超声波无损探伤方法。
超声波无损探伤是利用超声波在材料中传播的特性来检测材料内部的缺陷和异物的方法。
它可以检测金属、非金属、复合材料等各种材料的内部缺陷,如裂纹、夹杂、气孔等。
超声波无损探伤具有检测速度快、响应灵敏、成像清晰等优点,被广泛应用于航空航天、汽车制造、钢铁冶炼等行业。
其次,磁粉无损探伤是一种利用磁粉检测材料表面和近表面缺陷的方法。
它通过在被检测物体表面喷洒磁粉,再通过磁场的作用,磁粉会聚集在缺陷处,形成磁粉痕迹,从而可以直观地观察到缺陷的位置和形状。
磁粉无损探伤适用于检测各种金属材料的表面裂纹、疲劳裂纹、焊接缺陷等,具有操作简便、效果明显等特点。
另外,涡流无损探伤是一种利用涡流原理检测导电材料表面和近表面缺陷的方法。
它通过在被检测物体表面引入交变磁场,产生涡流,当涡流遇到缺陷时,会产生涡流密度变化,从而可以检测到缺陷的存在。
涡流无损探伤适用于检测金属材料的表面裂纹、疲劳裂纹、焊接缺陷等,具有高灵敏度、高分辨率等优点。
最后,热波无损探伤是一种利用热波原理检测材料内部缺陷的方法。
它通过在被检测物体表面加热,再通过红外热像仪等设备观察被检测物体表面的温度分布,从而可以检测到内部缺陷。
热波无损探伤适用于检测复合材料、陶瓷材料等非金属材料的内部缺陷,具有检测范围广、适用性强等特点。
综上所述,无损探伤方法是一种非常重要的技术手段,它在工业生产中发挥着不可替代的作用。
各种无损探伤方法各有特点,可以根据不同的需求和材料特性选择合适的方法进行检测。
希望本文介绍的无损探伤方法能够对大家有所帮助,谢谢阅读!。
五大常规无损检测

五大常规无损检测PT=渗透探伤MT=磁粉探伤UT=超声波探伤RT=射线探伤ET=涡流探伤五大常规无损检测:渗透探伤、磁粉探伤、超声波探伤、射线探伤、涡流探伤,1.射线探伤也就是X光拍片简称RT,2.超声波检查简称UT,射线探伤和超声波探伤一般适用于主甲板,外板,横舱壁,内底板,上下边柜斜板等对接的焊缝。
施工者对要求射线探伤的焊缝及热影响区域进行打磨处理,消除焊缝表面的凹凸不平对底片影像显示的影响,确保无油污、无油漆、无飞溅。
射线探伤有一定的杀伤性,船方及各施工部门在X光射线探伤时段、不得靠近X光射线探伤位置半径三十米范围的警示区域,防止射线伤害人员。
3.磁粉探伤又称MT或者MPT(Magnetic Particle Testing),一般适用于对接焊缝,角焊缝,尾轴及锻钢件,铸钢等磁性材料的表面附近进行探伤的检测方法。
利用铁受磁石吸引的原理进行检查。
在进行磁粉探伤检测时,使被测物收到磁力的作用,将磁粉(磁性微型粉末)散布在其表面。
然后,缺陷的部分表面所泄漏出来泄露磁力会将磁粉吸住,形成图案。
指示图案比实际缺陷要大数十倍,因此很容易便能找出缺陷。
磁粉探伤检测一般按照前处理→磁化→喷淋磁粉→观察→后处理的步骤进行4.渗透探伤简称PT,着色一般适用于船体对接焊缝,角焊缝等,螺旋桨叶根部,锻钢件、铸钢件表面。
当机械零部件需磁粉探伤或着色探伤时,则要将被探物件表面的油污清洁干净并摆放整齐,如果焊缝做磁粉探伤或着色探伤时,则需将焊道清洁干净,要求无油污、无油漆、无飞溅。
5.涡流检测(ET)的英文名称是:Eddy Current Testing工业上无损检测的方法之一。
给一个线圈通入交流电,在一定条件下通过的电流是不变的。
如果把线圈靠近被测工件,像船在水中那样,工件内会感应出涡流,受涡流影响,线圈电流会发生变化。
由于涡流的大小随工件内有没有缺陷而不同,所以线圈电流变化的大小能反映有无缺陷。
适用于导电材料..由于导体自身各种因素(如电导率,磁导率,形状,尺寸和缺陷等)的变化,会导致感应电流的变化,利用这种现象而判知导体性质,状态的检测方法叫做涡流检测方法.属于表面探伤法,适用于钢铁、有色金属、石墨等导电体工件,因为并不需要接触工件,所以检测速度很快,但设备昂贵。
工业无损探伤的方法

工业无损探伤的方法很多,目前国内外最常用的探伤方法有五种,即人们常称的五大常规探伤方法。
本文将首先介绍五大常规探伤方法及其特点,并结合汽车维修中的特定条件和需求,选出更适合于汽车维修的探伤方法。
一、五大常规探伤方法概述五大常规方法是指射线探伤法RT、超声波探伤法UT、磁粉探伤法MT、涡流探伤法ET和渗透探伤法PT。
1、射线探伤方法射线探伤是利用射线的穿透性和直线性来探伤的方法。
这些射线虽然不会像可见光那样凭肉眼就能直接察知,但它可使照相底片感光,也可用特殊的接收器来接收。
常用于探伤的射线有x光和同位素发出的γ射线,分别称为x光探伤和γ射线探伤。
当这些射线穿过(照射)物质时,该物质的密度越大,射线强度减弱得越多,即射线能穿透过该物质的强度就越小。
此时,若用照相底片接收,则底片的感光量就小;若用仪器来接收,获得的信号就弱。
因此,用射线来照射待探伤的零部件时,若其内部有气孔、夹渣等缺陷,射线穿过有缺陷的路径比没有缺陷的路径所透过的物质密度要小得多,其强度就减弱得少些,即透过的强度就大些,若用底片接收,则感光量就大些,就可以从底片上反映出缺陷垂直于射线方向的平面投影;若用其它接收器也同样可以用仪表来反映缺陷垂直于射线方向的平面投影和射线的透过量。
由此可见,一般情况下,射线探伤是不易发现裂纹的,或者说,射线探伤对裂纹是不敏感的。
因此,射线探伤对气孔、夹渣、未焊透等体积型缺陷最敏感。
即射线探伤适宜用于体积型缺陷探伤,而不适宜面积型缺陷探伤。
2、超声波探伤方法人们的耳朵能直接接收到的声波的频率范围通常是20Hz到20kHz,即音(声)频。
频率低于20 Hz的称为次声波,高于20 kHz的称为超声波。
工业上常用数兆赫兹超声波来探伤。
超声波频率高,则传播的直线性强,又易于在固体中传播,并且遇到两种不同介质形成的界面时易于反射,这样就可以用它来探伤。
通常用超声波探头与待探工件表面良好的接触,探头则可有效地向工件发射超声波,并能接收(缺陷)界面反射来的超声波,同时转换成电信号,再传输给仪器进行处理。
五大常规探伤方法概述及其特点
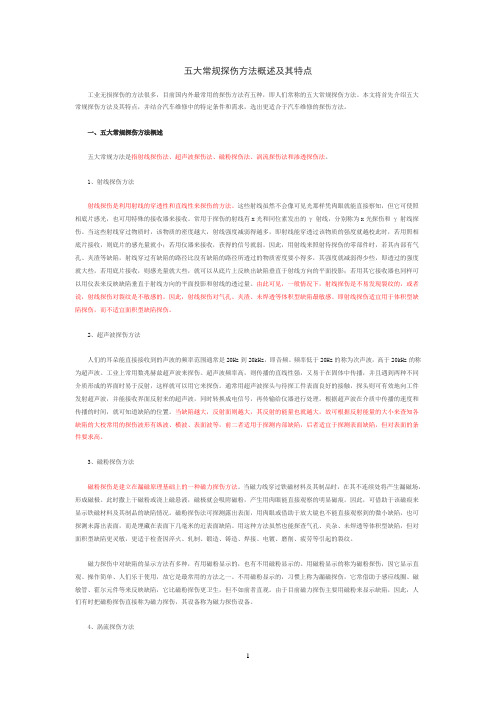
五大常规探伤方法概述及其特点工业无损探伤的方法很多,目前国内外最常用的探伤方法有五种,即人们常称的五大常规探伤方法。
本文将首先介绍五大常规探伤方法及其特点,并结合汽车维修中的特定条件和需求,选出更适合于汽车维修的探伤方法。
一、五大常规探伤方法概述五大常规方法是指射线探伤法、超声波探伤法、磁粉探伤法、涡流探伤法和渗透探伤法。
1、射线探伤方法射线探伤是利用射线的穿透性和直线性来探伤的方法。
这些射线虽然不会像可见光那样凭肉眼就能直接察知,但它可使照相底片感光,也可用特殊的接收器来接收。
常用于探伤的射线有x光和同位素发出的γ射线,分别称为x光探伤和γ射线探伤。
当这些射线穿过物质时,该物质的密度越大,射线强度减弱得越多,即射线能穿透过该物质的强度就越校此时,若用照相底片接收,则底片的感光量就小;若用仪器来接收,获得的信号就弱。
因此,用射线来照射待探伤的零部件时,若其内部有气孔、夹渣等缺陷,射线穿过有缺陷的路径比没有缺陷的路径所透过的物质密度要小得多,其强度就减弱得少些,即透过的强度就大些,若用底片接收,则感光量就大些,就可以从底片上反映出缺陷垂直于射线方向的平面投影;若用其它接收器也同样可以用仪表来反映缺陷垂直于射线方向的平面投影和射线的透过量。
由此可见,一般情况下,射线探伤是不易发现裂纹的,或者说,射线探伤对裂纹是不敏感的。
因此,射线探伤对气孔、夹渣、未焊透等体积型缺陷最敏感。
即射线探伤适宜用于体积型缺陷探伤,而不适宜面积型缺陷探伤。
2、超声波探伤方法人们的耳朵能直接接收到的声波的频率范围通常是20Hz到20kHz,即音频。
频率低于20Hz的称为次声波,高于20kHz的称为超声波。
工业上常用数兆赫兹超声波来探伤。
超声波频率高,则传播的直线性强,又易于在固体中传播,并且遇到两种不同介质形成的界面时易于反射,这样就可以用它来探伤。
通常用超声波探头与待探工件表面良好的接触,探头则可有效地向工件发射超声波,并能接收界面反射来的超声波,同时转换成电信号,再传输给仪器进行处理。
无损探伤方案

无损探伤方案无损探伤是一种非破坏性检测方法,通过使用物理学的原理和科学的仪器设备来检测物体的内部或表面缺陷、杂质、裂纹等。
它广泛应用于航空、航天、核能、军工、建筑、交通等领域。
本文将介绍无损探伤方案的几种常见方法。
一、磁粉探伤法磁粉探伤法是一种适用于铁、钢等金属表面、近表面缺陷的无损探伤方法。
其原理是在被检测物体表面均匀涂有铁磁性粉末,利用外加磁场引导粉末在裂纹、缺陷处留下磁纹,从而发现该处的缺陷。
磁粉探伤法灵敏度高、速度快、成本低,但只适用于铁、钢等铁磁性材料。
二、涡流探伤法涡流探伤法是一种适用于金属、导体等导电材料表面或近表面缺陷的无损探伤方法。
其原理是将交流电源通入探测器,电流在待检测金属或导体中产生涡流,从而形成磁场,利用磁场对探测器产生的信号进行检测,可以发现缺陷。
涡流探伤法灵敏度高、速度快、适用于各种导电材料。
三、超声波探伤法超声波探伤法是一种适用于大多数材料内部缺陷的无损探伤方法。
其原理是利用超声波在材料内部的传播和反射来检测材料内部缺陷。
可以通过探头的不同位置、不同方向进行检测,对材料内部的缺陷、尺寸、定位等都可以进行准确的检测。
超声波探伤法灵敏度高、适用范围广,但在检测厚度较大、表面不平整、材料吸音性较强时可能存在一定的局限性。
四、射线探伤法射线探伤法是一种适用于金属、非金属等大多数材料内部缺陷的无损探伤方法。
其原理是利用电磁波的作用直接透射材料,得到材料内部组织、缺陷等信息来实现无损检测。
射线探伤法灵敏度高、适用范围广,但需要射线源,且辐射可能对人体和环境造成危害,需要进行详细的安全措施。
五、热波探伤法热波探伤法是一种利用材料吸收热能散热规律来检测缺陷的无损探伤方法。
其原理是利用探测器对材料表面施加热源,通过测量热能的传播和分布情况来检测材料内部的缺陷。
热波探伤法适用范围广,可以检测小到几毫米的缺陷,但需要加热、冷却,操作比较繁琐。
综上所述,无损探伤方案是通过选择不同的探测方法和仪器设备,根据被检材料的不同特性来进行无损检测。
无损探伤方法

无损探伤方法无损探伤方法是一种非破坏性的检测技术,它可以在不损伤被测物体的情况下,通过各种物理学原理和技术手段,对被测物体进行内部和表面的缺陷、异物、组织结构等进行检测和评定的一种方法。
无损探伤方法在工业生产、航空航天、军事装备、建筑结构等领域有着广泛的应用。
本文将介绍几种常见的无损探伤方法及其应用。
首先,我们来介绍超声波无损探伤方法。
超声波无损探伤是利用超声波在材料中传播的特性,通过对超声波的发射和接收,来检测被测物体内部的缺陷和异物。
超声波无损探伤方法具有检测灵敏度高、分辨率高、适用范围广等优点,在航空航天、汽车制造、铁路运输等领域得到了广泛的应用。
其次,磁粉无损探伤方法也是一种常见的无损探伤技术。
磁粉无损探伤是利用磁场和磁粉的作用,通过观察磁粉在被测物体表面的分布和聚集情况,来检测被测物体的表面缺陷。
磁粉无损探伤方法适用于对铁磁性材料的缺陷检测,如焊接接头、铸件、锻件等的表面裂纹、气孔、夹杂等缺陷的检测。
此外,涡流无损探伤方法也是一种常用的无损探伤技术。
涡流无损探伤是利用涡流的感应作用,通过对被测物体表面感应涡流信号的变化,来检测被测物体的表面和近表面的缺陷。
涡流无损探伤方法适用于对导电材料的缺陷检测,如金属材料的裂纹、疲劳损伤、腐蚀等缺陷的检测。
最后,X射线无损探伤方法也是一种常见的无损探伤技术。
X射线无损探伤是利用X射线的穿透能力,通过对被测物体的X射线透射图像进行观察和分析,来检测被测物体的内部缺陷和异物。
X射线无损探伤方法适用于对金属、合金、陶瓷、塑料等材料的内部缺陷检测,如气孔、夹杂、异物、焊接缺陷等的检测。
综上所述,无损探伤方法是一种非破坏性的检测技术,它在工业生产和科学研究中有着广泛的应用。
不同的无损探伤方法各有特点,可以根据被测物体的材料、形状、尺寸、缺陷类型等特点,选择合适的无损探伤方法进行检测。
随着科学技术的不断进步,无损探伤方法也在不断发展和完善,将会为各个领域的质量检测和安全保障提供更加可靠的技木支持。
五种探伤介绍
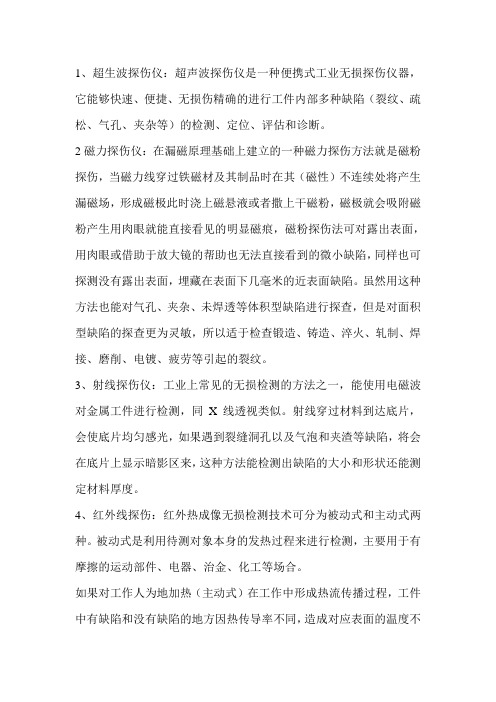
1、超生波探伤仪:超声波探伤仪是一种便携式工业无损探伤仪器,它能够快速、便捷、无损伤精确的进行工件内部多种缺陷(裂纹、疏松、气孔、夹杂等)的检测、定位、评估和诊断。
2磁力探伤仪:在漏磁原理基础上建立的一种磁力探伤方法就是磁粉探伤,当磁力线穿过铁磁材及其制品时在其(磁性)不连续处将产生漏磁场,形成磁极此时浇上磁悬液或者撒上干磁粉,磁极就会吸附磁粉产生用肉眼就能直接看见的明显磁痕,磁粉探伤法可对露出表面,用肉眼或借助于放大镜的帮助也无法直接看到的微小缺陷,同样也可探测没有露出表面,埋藏在表面下几毫米的近表面缺陷。
虽然用这种方法也能对气孔、夹杂、未焊透等体积型缺陷进行探查,但是对面积型缺陷的探查更为灵敏,所以适于检查锻造、铸造、淬火、轧制、焊接、磨削、电镀、疲劳等引起的裂纹。
3、射线探伤仪:工业上常见的无损检测的方法之一,能使用电磁波对金属工件进行检测,同X线透视类似。
射线穿过材料到达底片,会使底片均匀感光,如果遇到裂缝洞孔以及气泡和夹渣等缺陷,将会在底片上显示暗影区来,这种方法能检测出缺陷的大小和形状还能测定材料厚度。
4、红外线探伤:红外热成像无损检测技术可分为被动式和主动式两种。
被动式是利用待测对象本身的发热过程来进行检测,主要用于有摩擦的运动部件、电器、治金、化工等场合。
如果对工作人为地加热(主动式)在工作中形成热流传播过程,工件中有缺陷和没有缺陷的地方因热传导率不同,造成对应表面的温度不同,使对应的红外辐射强度也不同,我们只要采用红外热像仪记录工件表五的温度场分布(红外热图像)就可以检测出工件中是否有裂纹、剥离、夹层等缺陷。
5、渗透探伤:(1)工作原理简单,对操作者的技术要求不高。
(2)应用面广,可用于多种材料的表面检测而且基本上不受工件形状和尺寸的限制。
(3)显示不受缺陷方向的限制,一次检测可同时探测不同方向的表面缺陷。
(4)检测用设备简单、成本低廉、使用方便。
(5)渗透检测对各材料的开口式缺陷(如裂纹、气孔、分层、夹杂物、折叠、熔合不良、池漏等都能进行检查。
无损探伤的五种检测方式

无损探伤的五种检测方式无损检测就是利用声、光、磁和电等特性,在不损害或不影响被检对象使用性能的前提下,检测被检对象中是否存在缺陷或不均匀性,给出缺陷的大小、位置、性质和数量等信息,进而判定被检对象所处技术状态(如合格与否、剩余寿命等)的所有技术手段的总称无损检测是指对材料或工件实施一种不损害或不影响其未来使用性能或用途的检测手段。
无损探伤的五种检测方式:超声检测Ultrasonic Testing(缩写UT);射线检测Radiographic Testing(缩写RT);磁粉检测Magnetic particle Testing(缩写MT);渗透检测Penetrant Testing (缩写PT);涡流检测Eddy Current Testing (缩写ET);无损检测检测产品:压力管道:工业压力管道、油气长输管道、工业金属热力管道、工业金属燃气管道压力容器(含气瓶):电力工业锅炉压力容器、固定式压力容器、移动式压力容器钢结构工程:建筑工程用钢结构、路桥钢结构、水利工程钢结构、电力工程钢结构锅炉:蒸汽锅炉、热水锅炉、有机热载体锅炉起重机械:桥式起重机、门式起重机、塔式起重机、流动式起重机、铁路起重机、门座起重机、桅杆起重机、悬臂式起重机、缆索起重机、轻小型起重机客运索道、大型游乐设施船舶及船用产品:动力装置、舱室设备、甲板机械海上设施水面以上钢结构铸件、钢锻件、紧固件螺栓、螺钉、螺柱和螺母相关无损检测标准GB/T 5616-2014无损检测应用导则GB/T 7704-2017无损检测X射线应力测定GB/T 11343-2008无损检测接触式超声斜射检测GB/T 11344-2008无损检测接触式超声脉冲回波法测厚GB/T 11345-2013焊缝无损检测超声检测技术、检测等级和评定GB/T 12604.1-2005无损检测术语超声检测GB/T 12604.2-2005无损检测术语射线照相检测。
无损探伤技术的主要三种方法的操作
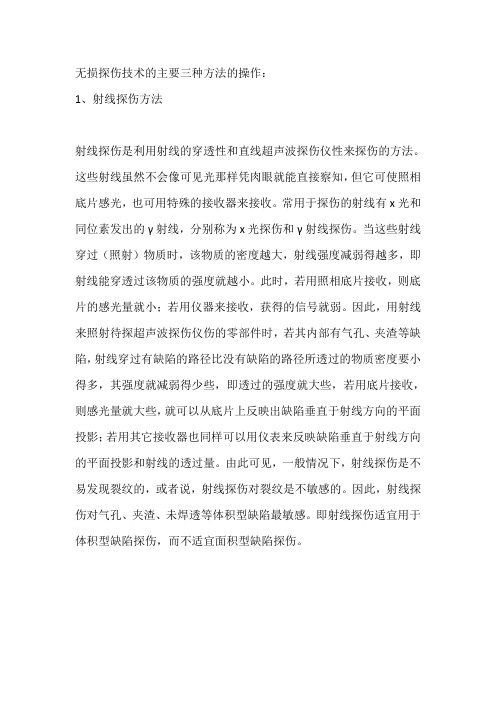
无损探伤技术的主要三种方法的操作:1、射线探伤方法射线探伤是利用射线的穿透性和直线超声波探伤仪性来探伤的方法。
这些射线虽然不会像可见光那样凭肉眼就能直接察知,但它可使照相底片感光,也可用特殊的接收器来接收。
常用于探伤的射线有x光和同位素发出的γ射线,分别称为x光探伤和γ射线探伤。
当这些射线穿过(照射)物质时,该物质的密度越大,射线强度减弱得越多,即射线能穿透过该物质的强度就越小。
此时,若用照相底片接收,则底片的感光量就小;若用仪器来接收,获得的信号就弱。
因此,用射线来照射待探超声波探伤仪伤的零部件时,若其内部有气孔、夹渣等缺陷,射线穿过有缺陷的路径比没有缺陷的路径所透过的物质密度要小得多,其强度就减弱得少些,即透过的强度就大些,若用底片接收,则感光量就大些,就可以从底片上反映出缺陷垂直于射线方向的平面投影;若用其它接收器也同样可以用仪表来反映缺陷垂直于射线方向的平面投影和射线的透过量。
由此可见,一般情况下,射线探伤是不易发现裂纹的,或者说,射线探伤对裂纹是不敏感的。
因此,射线探伤对气孔、夹渣、未焊透等体积型缺陷最敏感。
即射线探伤适宜用于体积型缺陷探伤,而不适宜面积型缺陷探伤。
2、超声波探伤方法人们的耳朵能直接接收到的声波的频率范围通常是20Hz到20kHz,即音(声)频。
频率低于20 Hz的称为次声波,高于20kHz的称为超声波。
工业上常用数兆赫兹超声波来探伤。
超声波频率高,则传播的直线性强,又易于在固体中传播,并且遇到两种不同介质形成的界面时易于反射,这样就可以用它来探伤。
通常用超声波探头与待探工件表面良好的接触,探头则可有效地向工件发射超声波,并能接收(缺陷)界面反射来的超声波,同时转换成电信号,再传输给仪器进行处理超声波探伤仪。
根据超声波在介质中传播的速度(常称声速)和传播的时间,就可知道缺陷的位置。
当缺陷越大,反射面则越大,其反射的能量也就越大,故可根据反射能量的大小来查知各缺陷(当量)的大小。
无损探伤的方法
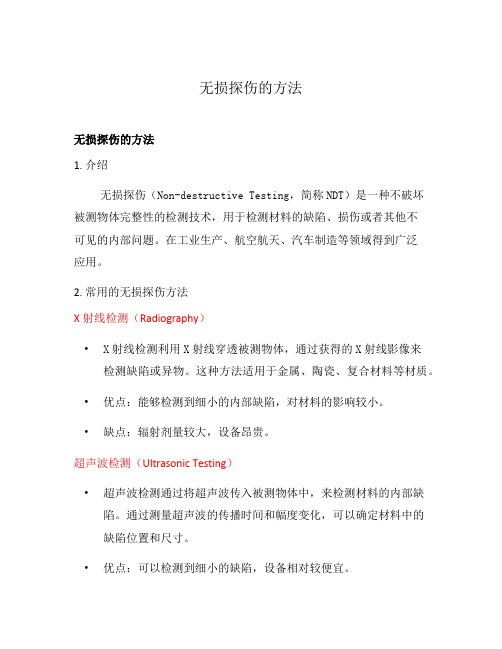
无损探伤的方法无损探伤的方法1. 介绍无损探伤(Non-destructive Testing,简称NDT)是一种不破坏被测物体完整性的检测技术,用于检测材料的缺陷、损伤或者其他不可见的内部问题。
在工业生产、航空航天、汽车制造等领域得到广泛应用。
2. 常用的无损探伤方法X射线检测(Radiography)•X射线检测利用X射线穿透被测物体,通过获得的X射线影像来检测缺陷或异物。
这种方法适用于金属、陶瓷、复合材料等材质。
•优点:能够检测到细小的内部缺陷,对材料的影响较小。
•缺点:辐射剂量较大,设备昂贵。
超声波检测(Ultrasonic Testing)•超声波检测通过将超声波传入被测物体中,来检测材料的内部缺陷。
通过测量超声波的传播时间和幅度变化,可以确定材料中的缺陷位置和尺寸。
•优点:可以检测到细小的缺陷,设备相对较便宜。
•缺点:对材料的表面粗糙程度、材料的声速等因素要求较高。
磁粉检测(Magnetic Particle Testing)•磁粉检测通过在被测物体表面施加磁场,并在表面涂覆磁性颗粒,通过观察磁颗粒在表面的分布状态来检测出材料中的缺陷。
•优点:适用于导电材料,对检测结果的观察直观。
•缺点:只能检测到表面缺陷,无法检测到深层缺陷。
热红外检测(Thermography)•热红外检测利用红外辐射设备来检测被测物体的温度变化,从而找出温度异常区域,进而检测出材料中的缺陷。
•优点:能够检测到与温度相关的缺陷,不需要接触被测物体。
•缺点:对环境的要求较高,不能在高温或阳光直射下进行。
液体渗透检测(Liquid Penetrant Testing)•液体渗透检测通过涂覆可渗透液体(通常为颜色鲜艳的液体)在被测物体表面,待其渗入材料表面缺陷后再经过清洗,利用渗透液体残留在缺陷处的方法来检测材料中的缺陷。
•优点:适用于不同材质,对于小缺陷有较高的检测灵敏度。
•缺点:需要事先清洗被测物体表面,不适用于粗糙表面。
无损探伤知识常欢
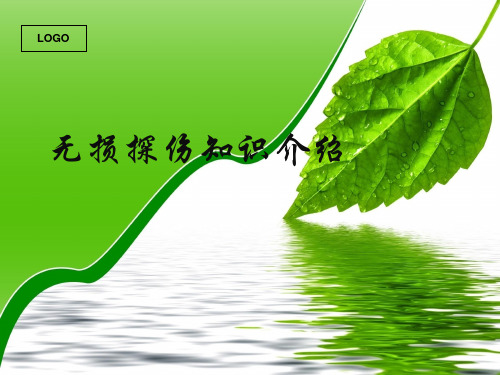
2 过热和过 烧
若焊接规范使用不当,热影响区长时间在高温下停留,会使晶粒 变得粗大,即出现过热组织。若温度进一步升高,停留时间加长, 可能使晶界发生氧化或局部熔化,出现过烧组织。过热可通过热 处理来消除,而过烧是不可逆转的缺陷。
3 白点
在焊缝金属的拉断面上出现的象鱼目状的白色斑,即为白点,白 点是由于氢聚集而造成的危害极大。
4.使用中的常见缺陷
疲劳裂纹、应力腐蚀裂纹、氢损伤、晶间腐蚀、摩擦腐蚀
LOGO
常见检测方法原理及特点
一、射线检测(RT)
射线照相法原理 X射线是从X射线管中产生的,X射线管是一种两极电子管。 将阴极灯丝通电,使之白炽,电子就在从阴极移向阳极的方 向加速飞行,获得很大的动能,当这些电子撞击阳极时,与 阳极金属原子的核外库仑场作用,发出轫致辐射而放出X射 线。射线还有一个性质就是能使胶片感光,能使胶片乳剂层 中的卤化银产生潜象中心,经过显影和定影后就会黑化。
危害
1、咬边减少了 母材的有效截 面积,降低结 构的承载能力。 2、造成应力集 中,发展为裂 纹源。
防止措施
矫正操作姿势,选 用合理的规范,采 用良好的运条方式 都会有利于消除咬 边。
备 注
LOGO
LOGO
LOGO
序
缺陷 名称
定义
产生原因
危害
防止措施
备注
2
焊瘤
焊缝中的液 态金属流到 加热不足未 熔化的母材 上或从焊缝 根部溢出, 冷却后形成 的未与母材 熔合的金属 瘤即为焊瘤
LOGO
表面探伤需注意的几个问题 A.探伤时机的选择:需要提供探伤报告的表面探伤都应 该在最后一道加工工序完成后进行;表面探伤合格后重 新进行机械加工,砂轮打磨时,原探伤结果失效. B.用于奥氏体钢或钛钢的渗透剂要控制卤族元素如氟 和氯离子的含量;用于高温条件下的镍基合金钢要控制 所用渗透剂中的硫离子含量; C.有延迟裂纹倾向的材料,至少应在焊后24小时后再进 行无损检测.
常用无损检测方法介绍

3.2磁粉检测灵敏度及试片
磁粉检测的灵敏度用标准灵敏度试片验证。 灵敏度试片有多种,常用A型灵敏度试片,其分15/100, 30/100, 60/100三种规格。试片厚度为100μm,槽深分别为15、30、60μm,灵敏度依次降低。其中30/100为最常用的试片。
3.3磁粉检测工艺
由原是可知,磁粉检测只能检测出表面和近表面缺陷。 为防止漏检,每一检测部位应进行两次接近相互垂直的磁化检测。不然会有一个方向的缺陷漏检。 为了提高灵敏度,可以采用反差增强剂提高工件表面与磁粉之间的色差,易于观察磁痕。 要求更高灵敏度时,可采用荧光磁粉检测。
4.渗透检测
4.1渗透检测原理 4.2渗透检测灵敏度试片
1.1射线检测原理
将透过工件的射线用胶片进行记录,经暗室处理后形成底片,其底片黑度不均匀程度与工件内部组织状况和异物的吸收系数密切相关。 如焊缝中存在气孔、夹渣、未焊透、未熔合、裂纹、内凹、咬边等在底片上呈黑色。焊瘤、焊缝余高过高等在底片上呈较白的影像。夹钨缺陷由于其吸收系数比钢材大的多,其在底片上的影像呈亮的白点。
1.1射线检测原理
射线能穿透物质,并能使胶片感光,射线强度越大,感光的胶片冲洗后黑度越大,反之则黑度小。射线透照布置见图1. 射线在穿透物质时呈指数规律被吸收衰减,当物质内存在异物或表面不均匀时,在异物或不均匀表面所在的部位会形成对射线衰减的不均衡,其不均衡的程度与所透过物质的厚度差成正比。 将透过工件的射线用胶片进行记录,经暗室处理后形成底片,其底片黑度不均匀程度与工件内部组织状况和异物的吸收系数密切相关。
5.1TOFD检测原理
发射探头
接收探头
横向波
LW
上端点
下端点
内壁反射波
常用无损探伤方法的种类

常用无损探伤方法的种类
生产中通过无损检测可以改进制造工艺;降低制造成本;提高产品的可能性;保证设备的安全运行。
常用的无损探伤方法有以下几种:X光射线探伤、超声波探伤、磁粉探伤、渗透探伤、涡流探伤、γ射线探伤、荧光探伤、着色探伤等方法。
射线探伤的基本原理是利用X射线或γ射线在穿透被检物各部分时强度衰减的不同,检测被检物中缺陷的一种无损检测方法。
X射线是在高真空状态下用高速电子冲击阳极靶而产生的。
γ射线是放射性同位素在原子蜕变过程中放射出来的。
两者都是具有高穿透力、波长很短的电磁波。
不同厚度的物体需要用不同能量的射线来穿透,因此要分别采用不同的射线源。
超声波探伤的基本原理是利用超声能透入金属材料的深处,并由一截面进入另一截面时,在界面边缘发生反射的特点来检查零件缺陷的一种方法,当超声波束自零件表面由探头通
至金属内部,遇到缺陷与零件底面时就分别发生反射波来,在萤光屏上形成脉冲波形,根据这些脉冲波形来判断缺陷位置和大小。
磁粉探伤的基本原理是:当工件磁化时,若工件表面有缺陷存在,由于缺陷处的磁阻增大而产生漏磁,形成局部磁场,磁粉便在此处显示缺陷的形状和位置,从而判断缺陷的存在。
着色(渗透)探伤的基本原理是利用毛细现象使渗透液渗入缺陷,经清洗使表面渗透液支除,而缺陷中的渗透残瘤,再利用显像剂的毛细管作用吸附出缺陷中残瘤渗透液而达到检验缺陷的目的。
涡流探伤的基本原理是利用电磁感应原理,使导电的容器元件内产生涡流,当涡流碰到裂纹或缺陷时会迂回通过,从而造成涡流分布紊乱,通过测量涡流的变化量进行检测。
荧光探伤应属于液体渗透探伤的基本原理是利用荧光物质在紫外丝照射下发光的性质,将荧光物质涂在零件表面上,借助荧光检验零件表面缺陷。
四种常用探伤方法特点及区别

四种常规无损检测方法的比较无损检测就是利用声、光、磁和电等特性,在不损害或不影响被检对象使用性能的前提下,检测被检对象中是否存在缺陷或不均匀性,给出缺陷的大小、位置、性质和数量等信息,进而判定被检对象所处技术状态(如合格与否、剩余寿命等)的所有技术手段的总称。
常用的无损检测方法:超声检测(UT)、磁粉检测(MT)、液体渗透检测(PT)及X射线检测(RT).超声波检测(UT)1、超声波检测的定义:通过超声波与试件相互作用,就反射、透射和散射的波进行研究,对试件进行宏观缺陷检测、几何特性测量、组织结构和力学性能变化的检测和表征,并进而对其特定应用性进行评价的技术.2、超声波工作的原理:主要是基于超声波在试件中的传播特性。
声源产生超声波,采用一定的方式使超声波进入试件;超声波在试件中传播并与试件材料以及其中的缺陷相互作用,使其传播方向或特征被改变;改变后的超声波通过检测设备被接收,并可对其进行处理和分析;根据接收的超声波的特征,评估试件本身及其内部是否存在缺陷及缺陷的特性.3、超声波检测的优点:a。
适用于所有金属、非金属和复合材料等多种制件的无损检测;b。
穿透能力强,可对较大厚度范围内的试件内部缺陷进行检测.如对金属材料,可检测厚度为1~2mm的薄壁管材和板材,也可检测几米长的钢锻件;c.缺陷定位较准确;d。
对面积型缺陷的检出率较高;e。
灵敏度高,可检测试件内部尺寸很小的缺陷;f.检测成本低、速度快,设备轻便,对人体及环境无害,使用较方便。
4、超声波检测的局限性a。
对试件中的缺陷进行精确的定性、定量仍须作深入研究;b。
对具有复杂形状或不规则外形的试件进行超声检测有困难;c.缺陷的位置、取向和形状对检测结果有一定影响;d.材质、晶粒度等对检测有较大影响;e。
以常用的手工A型脉冲反射法检测时结果显示不直观,且检测结果无直接见证记录。
5、超声检测的适用范围a.从检测对象的材料来说,可用于金属、非金属和复合材料;b。
五种常规无损探伤方法比较

涡流
1.适于自动化检测(可直接以电信号输出)
2.非接触式检测,无需耦合剂且速度快
3.适用范围较广(既可检测缺陷也可检测材质、形状与尺寸变化等)
1.只限用于导电材料
2.对形状复杂试件及表面下较深部位的缺陷检测有困难,检测结果尚不直观,判断缺陷性质、大小及形状尚难
渗透
1.设备简单,操作简便,投资小
2.效率高(对复杂试件也只需一次检验)
3.适用范围广(对表面缺陷,一般不受试件材料种类及其外形轮廓限制)
1.只能检测开口于表面的缺陷,且不能显示缺陷深度及缺陷内部的形状和尺寸
2.无法或难以检查多孔的材料,检测结果受试件表面粗糙度影响
3.难于定量控制检验操作程序,多凭检验人员经验、认真程度和视力的敏锐程度
表1-1 五种常规无损探伤方法比较
探伤
方法
优点
缺点
适用范围
射线
1.适用于几乎所有材料
2.探伤结果(底片)显示直观、便于分析
3.探伤结果可以长期保存
4.探伤技术和检验工作质量可以检测
1.检验成本较高
2.对裂纹类缺陷有方向性限制
3.需考虑安全防护问题(如X,γ射线的传播)
检测铸件及焊接件等构件内部缺陷,特别是体积型缺陷(即具有一定空间分布的缺陷)
磁粉
1.直观显示缺陷的形状、位置、大小
2.灵敏度高,可检缺陷最小宽度约为1μm
3.几乎不受试件大小和形状的限制
4.检测速度快、工艺简单、费用低廉
5.操作简便、仪器便于携带
1.只能用于铁磁性材料
2.只能发现表面和近表面缺陷
焊缝无损探伤的方法有哪些及区别在哪里

焊缝无损探伤的方法有哪些及区别在哪里无损检测就是利用声、光、磁和电等特性,在不损害或不影响被检对象使用性能的前提下,检测被检对象中是否存在缺陷或不均匀性,给出缺陷的大小、位置、性质和数量等信息,进而判定被检对象所处技术状态(如合格与否、剩余寿命等)的所有技术手段的总称。
常用的无损检测方法:超声检测(UT)、磁粉检测(MT)、液体渗透检测(PT)及X射线检测(RT)。
超声检测UT (Ultrasonic Testing)工业上无损检测的方法之一。
超声波进入物体遇到缺陷时,一部分声波会产生反射,发射和接收器可对反射波进行分析,就能异常精确地测出缺陷来.并且能显示内部缺陷的位置和大小,测定材料厚度等。
超声检测优点:1、穿透能力较大,例如在钢中的有效探测深度可达1米以上;2、对平面型缺陷如裂纹、夹层等,探伤灵敏度较高,并可测定缺陷的深度和相对大小;3、设备轻便,操作安全,易于实现自动化检验。
缺点:不易检查形状复杂的工件,要求被检查表面有一定的光洁度,并需有耦合剂充填满探头和被检查表面之间的空隙,以保证充分的声耦合。
磁粉检测首先来了解一下,磁粉检测的原理。
铁磁性材料和工件被磁化后,由于不连续性的存在,工件表面和近表面的磁力线发生局部畸变,而产生漏磁场,吸附施加在工件表面的磁粉,形成在合适光照下目视可见的磁痕,从而显示出不连续性的位置、形状和大小。
磁粉检测的适用性和局限性有:1、磁粉探伤适用于检测铁磁性材料表面和近表面尺寸很小、间隙极窄目视难以看出的不连续性。
2、磁粉检测可对多种情况下的零部件检测,还可多种型件进行检测。
3、可发现裂纹、夹杂、发纹、白点、折叠、冷隔和疏松等缺陷。
4、磁粉检测不能检测奥氏体不锈钢材料和用奥氏体不锈钢焊条焊接的焊缝,也不能检测铜铝镁钛等非磁性材料。
对于表面浅划伤、埋藏较深洞和与工件表面夹角小于20°的分层和折叠很难发现。
液体渗透检测液体渗透检测的基本原理,零件表面被施涂含有荧光染料或着色染料后,在一段时间的毛细管作用下,渗透液可以渗透进表面开缺陷中;经去除零件表面多余的渗透液后,再在零件表面施涂显像剂。
- 1、下载文档前请自行甄别文档内容的完整性,平台不提供额外的编辑、内容补充、找答案等附加服务。
- 2、"仅部分预览"的文档,不可在线预览部分如存在完整性等问题,可反馈申请退款(可完整预览的文档不适用该条件!)。
- 3、如文档侵犯您的权益,请联系客服反馈,我们会尽快为您处理(人工客服工作时间:9:00-18:30)。
各种常见无损探伤方法简介与比较
三种常规无损检测方法的比较
无损检测就是利用声、光、磁和电等特性,在不损害或不影响被检对象使用性能的前提下,检测被检对象中是否存在缺陷或不均匀性,给出缺陷的大小、位置、性质和数量等信息,进而判定被检对象所处技术状态(如合格与否、剩余寿命等)的所有技术手段的总称。
常用的无损检测方法:超声检测(UT)、磁粉检测(MT)和液体渗透检测(PT)。
超声波检测(UT)
1、超声波检测的定义:
通过超声波与试件相互作用,就反射、透射和散射的波进行研究,对试件进行宏观缺陷检测、几何特性测量、组织结构和力学性能变化的检测和表征,并进而对其特定应用性进行评价的技术。
2、超声波工作的原理:
主要是基于超声波在试件中的传播特性。
声源产生超声波,采用一定的方式使超声波进入试件;超声波在试件中传播并与试件材料以及其中的缺陷相互作用,使其传播方向或特征被改变;改变后的超声波通过检测设备被接收,并可对其进行处理和分析;根据接收的超声波的特征,评估试件本身及其内部是否存在缺陷及缺陷的特性。
3、超声波检测的优点:
a.适用于金属、非金属和复合材料等多种制件的无损检测;
b.穿透能力强,可对较大厚度范围内的试件内部缺陷进行检测。
如对金属材料,可检测厚度为1~2mm的薄壁管材和板材,也可检测几米长的钢锻件;
c.缺陷定位较准确;
d.对面积型缺陷的检出率较高;
e.灵敏度高,可检测试件内部尺寸很小的缺陷;
f.检测成本低、速度快,设备轻便,对人体及环境无害,使用较方便。
4、超声波检测的局限性
a.对试件中的缺陷进行精确的定性、定量仍须作深入研究;
b.对具有复杂形状或不规则外形的试件进行超声检测有困难;
c.缺陷的位置、取向和形状对检测结果有一定影响;
d.材质、晶粒度等对检测有较大影响;
e.以常用的手工A型脉冲反射法检测时结果显示不直观,且检测结果无直接见证记录。
5、超声检测的适用范围
a.从检测对象的材料来说,可用于金属、非金属和复合材料;
b.从检测对象的制造工艺来说,可用于锻件、铸件、焊接件、胶结件等;
c.从检测对象的形状来说,可用于板材、棒材、管材等;
d.从检测对象的尺寸来说,厚度可小至1mm,也可大至几米;
e.从缺陷部位来说,既可以是表面缺陷,也可以是内部缺陷。
锻件是金属被施加压力,通过塑性变形塑造要求的形状或合适的压缩力的物件。
这种力量典型的通过使用铁锤或压力来实现。
铸件过程建造了精致的颗粒结构,并改进了金属的物理属性。
在零部件的现实使用中,一个正确的设计能使颗粒流在主压力的方向。
磁粉检测(MT)
1. 磁粉检测的原理:
铁磁性材料和工件被磁化后,由于不连续性的存在,使工件表面和近表面的磁力线发生局部畸变而产生漏磁场,吸附施加在工件表面的磁粉,形成在合适光照下目视可见的磁痕,从而显示出不连续性的位置、形状和大小
2. 磁粉检测的适用性和局限性:
a.磁粉探伤适用于检测铁磁性材料表面和近表面尺寸很小、间隙极窄(如可检测出长0.1mm、宽为微米级的裂纹),目视难以看出的不连续性。
b.磁粉检测可对原材料、半成品、成品工件和在役的零部件检测,还可对板材、型材、管材、棒材、焊接件、铸钢件及锻钢件进行检测。
c.可发现裂纹、夹杂、发纹、白点、折叠、冷隔和疏松等缺陷。
d.磁粉检测不能检测奥氏体不锈钢材料和用奥氏体不锈钢焊条焊接的焊缝,也不能检测铜、铝、镁、钛等非磁性材料。
对于表面浅的划伤、埋藏较深的孔洞和与工件表面夹角小于20°的分层和折叠难以发现。
渗透检测(PT)
1.液体渗透检测的基本原理:
零件表面被施涂含有荧光染料或着色染料的渗透剂后,在毛细管作用下,经过一段时间,渗透液可以渗透进表面开口缺陷中;经去除零件表面多余的渗透液后,再在零件表面施涂显像剂,同样,在毛细管的作用下,显像剂将吸引缺陷中保留的渗透液,渗透液回渗到显像剂中,在一定的光源下(紫外线光或白光),缺陷处的渗透液痕迹被现实,(黄绿色荧光或鲜艳红色),从而探测出缺陷的形貌及分布状态。
2.渗透检测的优点:
a.可检测各种材料;金属、非金属材料;磁性、非磁性材料;焊接、锻造、轧制等加工方式;
b.具有较高的灵敏度(可发现0.1μm宽缺陷)
c.显示直观、操作方便、检测费用低。
3.渗透检测的缺点及局限性:
a.它只能检出表面开口的缺陷;
b.不适于检查多孔性疏松材料制成的工件和表面粗糙的工件;
c.渗透检测只能检出缺陷的表面分布,难以确定缺陷的实际深度,因而很难对缺陷做出定量评价。
检出结果受操作者的影响也较大。
由于各种检测方法都具有一定的特点,为提高检测结果可靠性,应根据设备材质、制造方法、工作介质、使用条件和失效模式,预计可能产生的缺陷种类、形状、部位和取向,选择最适当无损检测方法。
任何一种无损检测方法都不是万能的,每种方法都有自己的优点和缺点。
应尽可能多用几种检测方法,互相取长补短,以保障承压设备安全运行。