直接还原铁的品质与用途
2024年直接还原铁市场需求分析

2024年直接还原铁市场需求分析引言直接还原铁是一种重要的铁合金材料,广泛应用于钢铁冶炼和其他相关工业领域。
对直接还原铁市场需求进行分析,有助于了解市场趋势和预测未来发展方向。
本文将对直接还原铁市场需求进行详细分析。
1. 直接还原铁市场概述1.1 市场定义直接还原铁是一种通过化学反应将铁矿石还原为含有高铁含量的铁合金。
它可以直接作为原材料用于钢铁冶炼,具有高效、节能、环保等特点。
1.2 市场规模直接还原铁市场规模受到国内外钢铁产量和消费需求的影响。
近年来,随着全球钢铁行业的发展,直接还原铁市场呈现出稳步增长的趋势。
2. 直接还原铁市场需求因素分析2.1 钢铁产量增长推动市场需求钢铁产量是直接还原铁市场需求的主要驱动因素。
随着国内外工业化进程的加速推进,全球钢铁产量持续增长,导致对直接还原铁的需求也在不断上升。
2.2 环保政策推动市场需求直接还原铁具有高效、低排放等环保特性,符合国家和地区环保政策的要求。
环保政策的推动使得直接还原铁的需求增加,特别是在环保压力较大的地区。
2.3 价格因素影响市场需求直接还原铁的价格与供需关系密切相关。
需求增加或供应减少都可能导致价格上涨,从而影响市场需求。
同时,市场需求的变化也会对价格产生反馈作用。
2.4 新技术应用改变市场需求随着科技的进步和创新,新的直接还原铁生产技术不断涌现,改变了市场需求。
新技术的应用可以提高生产效率、降低成本,推动市场需求增加。
3. 直接还原铁市场需求预测3.1 国内市场需求预测随着中国钢铁产量的增长,国内直接还原铁市场需求有望继续增加。
同时,环保政策的加强也将推动直接还原铁市场需求的增长。
3.2 国际市场需求预测全球钢铁需求持续增长,加上环保政策的影响,国际直接还原铁市场需求有望呈现出增长态势。
中国等发展中国家的钢铁产量增加将成为国际市场需求增长的关键因素。
结论直接还原铁市场需求受到钢铁产量、环保政策、价格因素和新技术应用等因素的影响。
铁矿石还原技术在钢铁冶炼中的应用
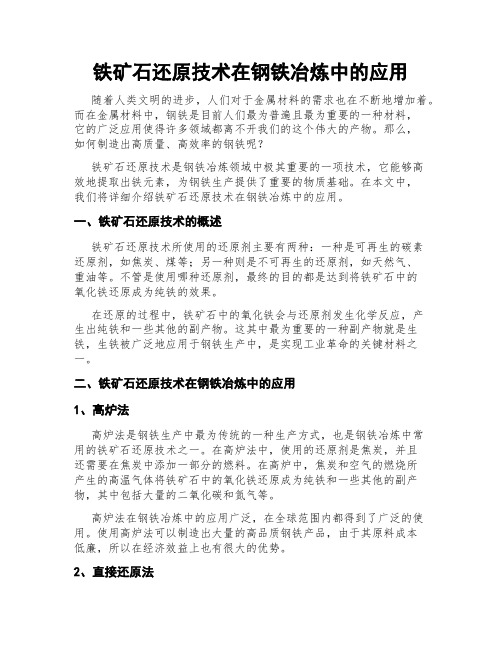
铁矿石还原技术在钢铁冶炼中的应用随着人类文明的进步,人们对于金属材料的需求也在不断地增加着。
而在金属材料中,钢铁是目前人们最为普遍且最为重要的一种材料,它的广泛应用使得许多领域都离不开我们的这个伟大的产物。
那么,如何制造出高质量、高效率的钢铁呢?铁矿石还原技术是钢铁冶炼领域中极其重要的一项技术,它能够高效地提取出铁元素,为钢铁生产提供了重要的物质基础。
在本文中,我们将详细介绍铁矿石还原技术在钢铁冶炼中的应用。
一、铁矿石还原技术的概述铁矿石还原技术所使用的还原剂主要有两种:一种是可再生的碳素还原剂,如焦炭、煤等;另一种则是不可再生的还原剂,如天然气、重油等。
不管是使用哪种还原剂,最终的目的都是达到将铁矿石中的氧化铁还原成为纯铁的效果。
在还原的过程中,铁矿石中的氧化铁会与还原剂发生化学反应,产生出纯铁和一些其他的副产物。
这其中最为重要的一种副产物就是生铁,生铁被广泛地应用于钢铁生产中,是实现工业革命的关键材料之一。
二、铁矿石还原技术在钢铁冶炼中的应用1、高炉法高炉法是钢铁生产中最为传统的一种生产方式,也是钢铁冶炼中常用的铁矿石还原技术之一。
在高炉法中,使用的还原剂是焦炭,并且还需要在焦炭中添加一部分的燃料。
在高炉中,焦炭和空气的燃烧所产生的高温气体将铁矿石中的氧化铁还原成为纯铁和一些其他的副产物,其中包括大量的二氧化碳和氮气等。
高炉法在钢铁冶炼中的应用广泛,在全球范围内都得到了广泛的使用。
使用高炉法可以制造出大量的高品质钢铁产品,由于其原料成本低廉,所以在经济效益上也有很大的优势。
2、直接还原法直接还原法是一种新型的铁矿石还原技术,在这种技术中,铁矿石经过还原反应之后,可以直接转化成为高品质的钢铁材料。
直接还原法使用的还原剂通常是少量的天然气或其他的低碳还原剂,而且现代钢铁冶炼技术的发展已经可以使得直接还原法的应用范围越来越广泛。
在直接还原法中,利用的是自然气体的能量,将铁矿石直接还原成为钢铁材料,这样一来死生产的能耗相对较低,而且还可以将铁矿石中的一些杂质直接去除掉,使得钢铁材料的品质得到了进一步的提高。
直接还原用耐火材料的特点与应用
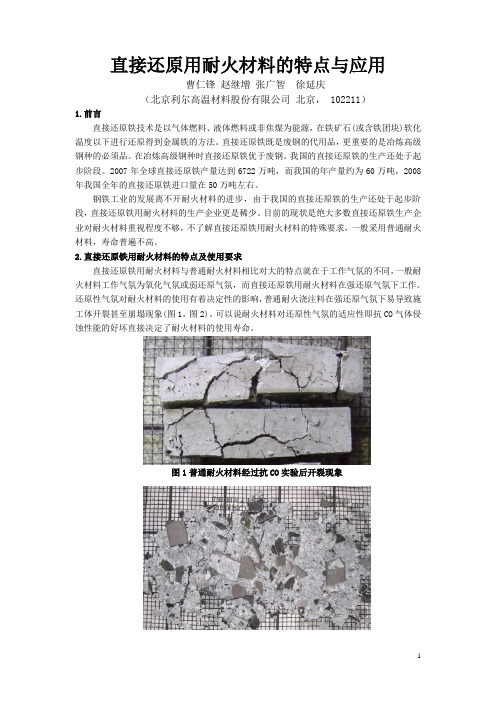
直接还原用耐火材料的特点与应用曹仁锋赵继增张广智徐延庆(北京利尔高温材料股份有限公司北京, 102211)1.前言直接还原铁技术是以气体燃料、液体燃料或非焦煤为能源,在铁矿石(或含铁团块)软化温度以下进行还原得到金属铁的方法。
直接还原铁既是废钢的代用品,更重要的是冶炼高级钢种的必须品。
在冶炼高级钢种时直接还原铁优于废钢。
我国的直接还原铁的生产还处于起步阶段。
2007年全球直接还原铁产量达到6722万吨,而我国的年产量约为60万吨,2008年我国全年的直接还原铁进口量在50万吨左右。
钢铁工业的发展离不开耐火材料的进步,由于我国的直接还原铁的生产还处于起步阶段,直接还原铁用耐火材料的生产企业更是稀少。
目前的现状是绝大多数直接还原铁生产企业对耐火材料重视程度不够,不了解直接还原铁用耐火材料的特殊要求,一般采用普通耐火材料,寿命普遍不高。
2.直接还原铁用耐火材料的特点及使用要求直接还原铁用耐火材料与普通耐火材料相比对大的特点就在于工作气氛的不同,一般耐火材料工作气氛为氧化气氛或弱还原气氛,而直接还原铁用耐火材料在强还原气氛下工作。
还原性气氛对耐火材料的使用有着决定性的影响,普通耐火浇注料在强还原气氛下易导致施工体开裂甚至崩塌现象(图1,图2)。
可以说耐火材料对还原性气氛的适应性即抗CO气体侵蚀性能的好坏直接决定了耐火材料的使用寿命。
图1普通耐火材料经过抗CO实验后开裂现象图2普通耐火材料经过抗CO实验后崩塌现象除了必须具备优良的抗CO气体侵蚀性能,直接还原铁用耐火材料在使用过程中还应具备以下性能:1)高强度:以保证浇注料能经受炉壳的弯曲。
2)高耐磨性:以保证耐火材料能抵抗物料在上面移动时的磨蚀作用。
3)高的化学稳定性:以保证材料能抵抗由铁矿、脱硫剂和媒组成的炉料接触时形成的液体的作用。
4)高的耐热震稳定性:以保证耐火材料在温度发生冷热变化时不被破坏。
3.还原气氛下耐火材料的损毁机理直接还原铁的基本原理是还原剂还原Fe203成金属Fe。
直接还原铁作为废钢替代品在电弧炉中的应用

摘 要 :为了满足用户对优质钢和纯净钢的要求 ,直接还原铁作为废钢的替代品用 于电弧炉炼钢应是一种可行的选择 。概述了直接还原铁的特点 ,指出高比例使用 DRI 可以得到 N、Cu、Cr 、Ni 、As、Sn 等含量低的钢 ,直接还原铁可认为是一种较好的电弧炉炼 钢原料 。
关键词 :直接还原铁 ; w (N) ;电弧炉 ;泡沫渣 中图分类号 :TF741. 8 文献标识码 :A 文章编号 :1001 - 1447 (2004) 05 - 0053 - 05
Keywords :DRI ; w (N) ; EAF ;foamed slag
1 前 言
电弧炉短流程炼钢工艺投资省 ,见效快 ,因此 发展很快 。但随炉容量的逐渐扩大 ,作为电弧炉 炼钢的主要炉料 ———废钢越来越少 。而废钢经过 多次循环利用 ,残余元素及有害元素 (铬 、铜 、锡 、 铝等) 急剧增加 ,不利于提高产品质量 ,难以生产 出优质的清洁钢 。20 世纪 60 年代以后 ,直接还 原技术进入工业化阶段 ,为缺少废钢地区提供了 发展电弧炉炼钢的可能性 。而直接还原铁具有其 自身的优点 ,残余元素及有害元素含量低 。实践 证明 ,在提高产品的质量方面 ,直接还原铁是比较 理想的废钢替代料 。在使用轻质的废钢时 ,可配 加 DRI ,减轻废钢中的残存元素及有害元素的影 响 ,既能生产出质量比较高的钢 ,又可以合理地利 用废钢资源 。因此在废钢资源越来越少的情况
烧结直接还原铁概述

烧结直接还原铁概述
直接还原铁品质洁净、杂质少,有害元素相当少,是生产优质钢、合金钢、低合金钢和微合金钢不可替代的高品质原料,它不仅是炼钢的重要原料,而且是电炉冶炼中添加不同比例的直接还原铁,控制和稀释电炉钢中有害元素的重要手段。
海绵铁是直接还原铁的俗称,是铁精粉作高炉直接还原铁的产物,直接还原铁是世界冶金两个前沿技术之一。
其最大特点:不用焦碳炼铁,是优质废钢的替代品,与高炉相比,它具有能耗低、投资小、效益高、污染低等重大优越性。
直接还原铁品质洁净、杂质少,有害元素相当少,是生产优质钢、合金钢、低合金钢和微合金钢不可替代的高品质原料,它不仅是炼钢的重要原料,而且是电炉冶炼中添加不同比例的直接还原铁,控制和稀释电炉钢中有害元素的重要手段,否则有再好的电炉冶炼技术装备也是达不到指标的。
随着冶金行业钢铁产量的日益增长,高品质的钢材在市场的竞争能力,加上废钢材的成份复杂,冶炼难度大,优质废钢材的短缺等因素,生产直接还原铁正好是优质废钢的替代品,它不仅提高钢材品质,降低钢材的生产成本,更增强了企业的竞争能力,由于工业产品不断提高,还原铁产品应用的领域越来越宽,需求量越来越大,市场前景非常看好。
直接还原炼铁

一 直接还原炼铁简介
7、世界直接还原铁生产概况 2012年,全球直接还原铁产量达到7402万吨,其中
印度位居第一,2005万吨。伊朗第二,1158万吨。
全球主要直接还原铁生产大国/MT
国家
印度
伊朗
墨西 哥 委内 瑞拉 中国
2004 9.37 6.41 6.54
7.83 0.43
2005 2006 2007 2008 2009 2010 2011 2012 12.04 14.74 19.06 21.20 22.03 23.42 21.97 20.05 6.85 6.85 7.44 7.46 8.20 9.53 10.37 11.58 5.98 6.17 6.26 6.01 4.15 5.37 5.85 5.59
2.4 Fastmet转底炉法工艺
2.5 CODIR煤基回转窑法工艺
➢该工艺原料可为球团矿、块矿,也可为粉矿,还原剂采用挥 发分较小的高活性煤 ,脱硫剂用石灰石或白云石。炉料、还 原煤和脱硫剂从回转窑尾部进入窑内后在与炉气逆向运动 过程中将矿石还原为海绵铁。
➢CODIR 回转窑工艺流程中约占总量 70 %的还原煤由窑头 用压缩空气喷入 ,因此较好地抑制了再氧化和结圈现象。冷 却筒采用间接和直接水冷相结合的方式 ,提高了设备的作业 率 ,有利于回转窑的连续、 稳定生产 ,在多种回转窑工艺中 具有较突出的优势。
目前投入工业应用的直接还原工艺主要有Midrex工艺、HYLIII工艺、Finmet工艺、SL/RN工艺等。2012年全球DRI产量达 到7402万吨,Midrex工艺和HYL-III工艺生产的DRIDRI所占比 例达到76.3%。
2.1 Midrex(米德兰)法工艺
➢ Midrex 法具有工艺成熟、操作简单、生产率高、热耗低、 产品质量高等优点, 因此在直接还原工艺中占统治地位。
非高炉炼铁-直接还原

5
直接还原技术概况
直接还原炼铁工艺分为气基和煤基直接还原两大类,其 产品是固态海绵铁,主要供电炉炼钢用。
气基直接还原是用天然气经裂化产出的H2和CO作为还 原剂在竖炉、固定床罐式炉或流化床内将铁矿石中的氧化 铁还原成海绵铁。主要有Midrex法和HYL法。
煤基直接还原是用煤作还原剂在回转窑或转底炉内将矿 石中的氧化铁还原。
生产块矿矿山 Aguas Claras
Alegria Bailadila Bellary Hospet Brumadinho
Caue Cerro Bolivar
Conceica Corumba CVRD
El Pao Esperanza
Ferteco Feijao
表10 Midrex工厂曾使用的商品块矿石
15
MIDREX工艺过程
16
MIDREX流程图
17
18
2 Midrex直接还原工艺的原燃料
2.1 Midrex用燃料与还原剂
Midrex属于气基直接还原流程,还原气使用天然气经催化 裂化制取,裂化剂采用炉顶煤气。炉顶煤气含CO与H2约70%。 经洗涤后,约60%~70%加压送入混合室与当量天然气混合 均匀。混合气首先进入一个换热器进行预热。换热器热源是 转化炉尾气。预热后的混合气送入转化炉中的镍质催化反应 管组,进行催化裂化反应,转化成还原气。还原气含 (CO+H2)95%左右,温度为850~900℃。
>2500
小于500N/个/wt%
<5.0
<2.0
23
对于Midrex工艺直接还原来说,含铁原料的高温特性,如还原 速率、还原粉化性能、粘结趋势和高温还原强度等,对整个竖炉 生产的顺行以及技术经济指标都非常关键。表8列出了Midrex工 艺对球团矿和块矿高温冶金性能的要求。
直接还原炼铁

炉内压力: 250KPa左右 天然气能耗:
10.2~11t/GJ 炉料在整个炉内停 留时间:10h左右
还原区温度: 850℃左右
金属化率:>92%
H 2 C O 1
C4 H 1/22 O催 化 剂 CO 2H 2
C4 H C2 O 催 化 剂 2CO 2H A2
12
2.2 HYL-III(Energiron)法工艺
A
13
2.2 HYL-III(Energiron)法工艺
C4 H H 2 O 催 化 3剂 2H CO
炉内压力:600KPa 天然气能耗:
10~11.3t/GJ 炉料在整个炉内停留
时间:大于10h 还原区温度:
900~960℃ 金属化率:>91%
H 2 C> O 2
A
14
2.3 HYL-ZR法工艺
直接还原炼铁
A
1
一 直接还原炼铁简介
1 、定义 直接还原炼铁(Direct Reduction Iron)是一种采用
天然气、煤气、非焦煤粉作燃料和还原剂, 使用球团矿、 块矿、粉矿在在软化温度以下直接还原生产固体直接还原 铁( DRI /HBI) 的炼铁工艺技术。
2 、优点 ① 使用非焦煤,取消了炼焦和烧结等高能耗高污染工序 ② DRI/HBI 中P、S和和有色杂质(Cu、Ni、Cr、Mo、Sn等)
➢ HYL-ZR是在原HYL工艺系列上发展起来的一种新型气基自 重整直接还原工艺,HYL-ZR技术可在其工艺和设备无任何改 动情况下使用焦炉煤气、Corex熔融还原炉产生的煤气或者 合成气 ,而其他技术大都需要对其基本配置进行重大改动 。目前开始在我国和印度等地区应用。
➢在竖炉内通过对还原气进行控制而产生合乎要求的还原气 体 ,其还原气体经过不完全燃烧 ,以及在还原反应器内经 过金属铁的催化作用在现场重整而生成 ,从而对铁矿石进 行还原;而传统HYL-Ⅲ 工艺是在添加蒸汽条件下使天然气 在催化重整装置中裂解。
直接还原铁的用途

直接还原铁的用途直接还原铁是精铁粉在炉内经低温还原形式的低碳多孔状物质,其化学成分稳定,杂质含量少,主要用作电炉炼钢的原料,也可作为转炉炼钢的冷却剂,如果经二次还原还可供粉末冶金用。
近年来由于钢铁产品朝小型轻量化、功能高级化、复合化方向发展,故钢材中非金属材料和有色金属使用比例增加,致使废钢质量不断下降。
废钢作为电炉钢原料,由于其来源不同,化学成分波动很大,而且很难掌握、控制,这给电炉炼钢作业带来了极大的困难。
如果用一定比例的直接还原铁(30-50%)作为稀释剂与废钢搭配不仅可增加钢材的均匀性,还可以改善和提高钢的物理性质,从而达到生产优质钢的目的。
因此,直接还原铁不仅仅是优质废钢的替代物,还是生产优质钢材必不可少的高级原料(天津无缝钢管公司国外设计中就明确要求必须配50%的直接还原铁)。
根据国外报导,高功率电炉冶炼时,炉料搭配30—50%直接还原铁,生产率提高10-25%,作业率提高25-30%。
1996年2月26日我们在鹿泉市轧钢厂三吨电炉上试验表明,在炉料中搭配30—50%直接还原铁,每吨炉料平均节约电能27%,节约炼钢时间28%,耗氧量降低22%,钢材物理性能明显提高。
就此,在电炉钢炉料中搭配一定量直接还原铁不仅可以提高电炉的生产能力,而且还能降低电耗和生产成本。
根据国家统计局公布的数字显示,我国九七年的钢产量已突破亿吨大关,成为世界第一产钢大国,但能源的消耗也是惊人的,吨钢能耗比日本和西方国家高出很多,除技术上的原因外,与我国不同工艺流程的比例有很大的关系。
截止目前,我国电炉钢产量只占总产量的25%,大大低于西方国家的平均值45%。
提高电炉钢的产量必须在电力供应和原料保证上做文章。
实践证明,纯净合格的直接还原铁,是电炉的理想原料,这在西方发达国家普遍得到了认可。
“九五”期间,冶金工业调整——优化钢材结构,由注重规模与产量转变为注重质量和效益,要提高钢的质量,如果原料仍以废钢为主,将是很困难的。
直接还原铁

直接还原铁直按还原铁和熔融还原铁的生产直接还原铁和熔融还原铁的冶炼统称为非高炉法炼铁。
(一)直接还原法生产生铁直接还原法是指在低于熔化温度之下将铁矿石还原成海绵铁的炼铁生产过程,其产品为直接还原铁(即DRI),也称海绵铁。
该产品未经熔化,仍保持矿石外形,由于还原失氧形成大量气孔,在显微镜下观察团形似海绵而得名。
海绵铁的特点是含碳低(<1%),并保存了矿石中的脉石。
这些特性使其不宜大规模用于转炉炼钢,只适于代替废钢作为电炉炼钢的原料。
直接还原法分气基法和煤基法两大类。
前者是用天然气经裂化产出H2和CO气体,作为还原剂,在竖炉、罐式炉或流化床内将铁矿石中的氧化铁还原成海绵铁。
主要有Midrex法、HYL Ⅲ法、FIOR法等。
后者是用煤作还原剂,在回转窑、隧道窑等设备内将铁矿石中的氧化铁还原。
主要有FASMET法等。
直接还原法的优点有:(1)流程短,直接还原铁加电炉炼钢;(2)不用焦炭,不受炼焦煤短缺的影响;(3)污染少,取消了焦炉、烧结等工序;(4)海绵铁中硫、磷等有害杂质与有色金属含量低,有利于电炉冶炼优质钢种。
直接还原法的缺点有:(1)对原料要求较高:气基要有天然气;煤基要用灰熔点高、反应性好的煤;(2)海绵铁的价格一般比废钢要高。
直接还原法已有上百年的发展历史,但直到20世纪60年代才获得较大突破。
进入20世纪90年代,其生产工艺日臻成熟并获得长足发展。
其主要原因是:(1)天然气的大量开发利用,特别是高效率天然气转化法的采用,提供了适用的还原煤气,使直接还原法获得了来源丰富、价格相对便宜的新能源。
(2)电炉炼钢迅速发展以及冶炼多种优质钢的需要,大大扩展了对海绵铁的需求。
(3)选矿技术提高,可提供大量高品位精矿,矿石中的脉石量降低到还原冶炼过程中不需加以脱除的程度,从而简化了直接还原技术。
当前世界上直接还原铁量的90%以上是采用气基法生产的。
我国天然气主要供应化工和民用,不可能大量用于钢铁工业。
直接还原铁在钢铁制造流程中的应用价值

直接还原铁在钢铁制造流程中的应用价值(1)直接还原铁在钢铁制造流程的应用直接还原铁(Direct ReducedIron,DRI)是通过直接还原固态铁矿石或其它含铁原料生产的,使用还原剂(煤或煤气)去除铁矿石中的氧,在低于其熔化温度下进行还原生产球团或块状的高度金属化的含铁产品(取决于铁矿石原料,球团矿或块状矿石的类型)。
由此产生的DRI产品本质上是非常多孔的,因此也叫海绵铁,主要分为冷态DRI、热压块DRI、热态DRI(表1)。
目前,全球DRI的产量接近有8700万吨(表2),主要集中在印度、伊朗、墨西哥、俄罗斯等国家:热压块DRI的生产商主要是俄罗斯,委内瑞拉,美国,马来西亚,利比亚和伊朗。
冷态DRI的供应商非常少,基本上只有直接还原短流程电炉厂的富余产量,例如在伊朗,还有一些来自巴林。
另外,纽柯的特立尼达工厂生产的大量冷DRI运送到其美国的其他钢铁厂。
印度生产的海绵铁主要用于国内消费,仅有少量出口到周边市场。
表2 全球直接还原铁产量近两年,中国国内的钢铁市场运行较为稳健,各个企业生产成本低,利润空间大,钢材市场价格不断走高。
近期,部分企业采购的优质废钢的市场价格在2800元/吨,炼钢生铁均价达到3200元/吨,铸造生铁达到3700元/吨,而当前生产的优质炼钢直接还原铁的生产成本不到1700元/吨,无论是与废钢还是生铁的价格相比,直接还原铁都具有明显的成本优势,使得还原铁在钢铁生产流程中的高炉、转炉、电炉各工序的应用成为了可能并有很大的应用前景。
1 直接还原铁在高炉工序的应用价值直接还原铁的选用给高炉生产带来了较大的灵活性,尤其是在需要扩大高炉生产能力的时候。
直接还原铁相比废钢更适合用于高炉的原料系统,长期使用可以有效解决高炉产能不足的问题,提高铁水产量,短期使用可以调节高炉定修带来的铁水不足的问题,另外也解决了铁块或焦炭的短缺或价格偏高增加了生产成本的问题。
高炉使用直接还原铁的比例一般不超过入炉料的40%,这主要是由于高炉冶炼时炉身中上部需要一定的高温煤气量来预热入炉料,否则,高炉炉况就会失常。
直接还原铁的过去
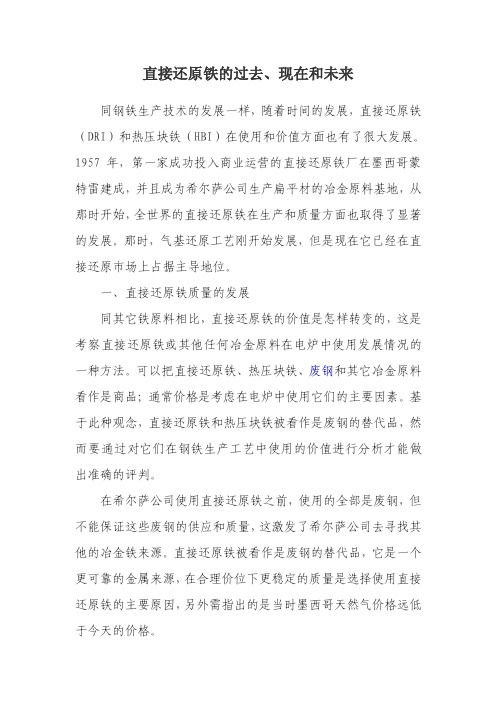
直接还原铁的过去、现在和未来同钢铁生产技术的发展一样,随着时间的发展,直接还原铁(DRI)和热压块铁(HBI)在使用和价值方面也有了很大发展。
1957年,第一家成功投入商业运营的直接还原铁厂在墨西哥蒙特雷建成,并且成为希尔萨公司生产扁平材的冶金原料基地,从那时开始,全世界的直接还原铁在生产和质量方面也取得了显著的发展。
那时,气基还原工艺刚开始发展,但是现在它已经在直接还原市场上占据主导地位。
一、直接还原铁质量的发展同其它铁原料相比,直接还原铁的价值是怎样转变的,这是考察直接还原铁或其他任何冶金原料在电炉中使用发展情况的一种方法。
可以把直接还原铁、热压块铁、废钢和其它冶金原料看作是商品;通常价格是考虑在电炉中使用它们的主要因素。
基于此种观念,直接还原铁和热压块铁被看作是废钢的替代品,然而要通过对它们在钢铁生产工艺中使用的价值进行分析才能做出准确的评判。
在希尔萨公司使用直接还原铁之前,使用的全部是废钢,但不能保证这些废钢的供应和质量,这激发了希尔萨公司去寻找其他的冶金铁来源。
直接还原铁被看作是废钢的替代品,它是一个更可靠的金属来源,在合理价位下更稳定的质量是选择使用直接还原铁的主要原因,另外需指出的是当时墨西哥天然气价格远低于今天的价格。
当时直接还原铁是以低金属化率为特点的,其金属化率大约为86%~88%,由于当时电炉没有使用吹氧操作工艺,所以没有考虑碳的含量,直接还原铁中碳的含量大约为1.8%,只用来还原残余氧化铁。
直接还原铁的价值足够高于增加的能量消耗和生产损失。
直接还原铁附加带来的好处很快就被认识到。
例如给扁平材生产带来好处的低残留量。
最初直接还原铁像废钢一样向电炉分批给料。
尽管直接还原铁比废钢有较高的散装密度,这种工艺也没有使直接还原铁提高电炉的生率。
随着直接还原铁在电炉应用方面认识的不断深入,其更多的优点被发现。
随着在直接还原工艺中使用球团矿替代块矿变得越来越普遍,直接还原铁向电炉连续给料在不久之后就开始发展起来,并且在很短时间内就成了标准操作工艺。
直接还原铁技术

直接还原铁技术直接还原铁是铁矿在固态条件下直接还原为铁,可以用来作为冶炼优质钢、特殊钢的纯净原料,也可作为铸造、铁合金、粉末冶金等工艺的含铁原料。
这种工艺是不用焦碳炼铁,原料也是使用冷压球团不用烧结矿,所以是一种优质、低耗、低污染的炼铁新工艺,也是全世界钢铁冶金的前沿技术之一。
直接还原炼铁工艺有气基法和煤基法两种,按主体设备可分为竖炉法、回转窑法、转底炉法、反应罐法、罐式炉法和流化床法等。
目前,世界上90%以上的直接还原铁产量是用气基法生产出来的。
但是天然气资源有限、价高,使生产量增长不快。
用煤作还原剂在技术上也已过关,可以用块矿,球团矿或粉矿作铁原料(如竖炉、流化床、转底炉和回转窑等)。
但是,因为要求原燃料条件高(矿石品位要大于66%,含SiO2+Al2O3杂质要小于3%,煤中灰分要低等),规模小,设备寿命低,生产成本高和某些技术问题等原因,致使直接还原铁生产在全世界没有得到迅速发展。
因此,高炉炼铁生产工艺将在较长时间内仍将占有主导地位。
1.直接还原铁的质量要求直接还原铁是电炉冶炼优质钢种的好原料,所以要求的质量要高(包括化学成份和物理性能),且希望其产品质量要均匀、稳定。
1.1 化学成份直接还原铁的含铁量应大于90%,金属化率要>90%。
含SiO2每升高1%,要多加2%的石灰,渣量增加30Kg/t,电炉多耗电18.5kwh。
所以,要求直接还原铁所用原料含铁品位要高:赤铁矿应>66.5%,磁铁矿>67.5%,脉石(SiO2+Al2O3)量<3%~5%。
直接还原铁的金属化率每提高1%,可以节约能耗8~10度电/t。
直接还原铁含C<0.3%,P<0. 03%,S<0.03%,Pb、Sn、As、Sb、Bi等有害元素是微量。
1.2 物理性能回转窑、竖炉、旋转床等工艺生产的直接还原铁是以球团矿为原料,要求粒度在5~30mm。
隧道窑工艺生产的还原铁大多数是瓦片状或棒状,长度为250~380mm,堆密度在1.7~2. 0t/m³。
铁的直接还原度
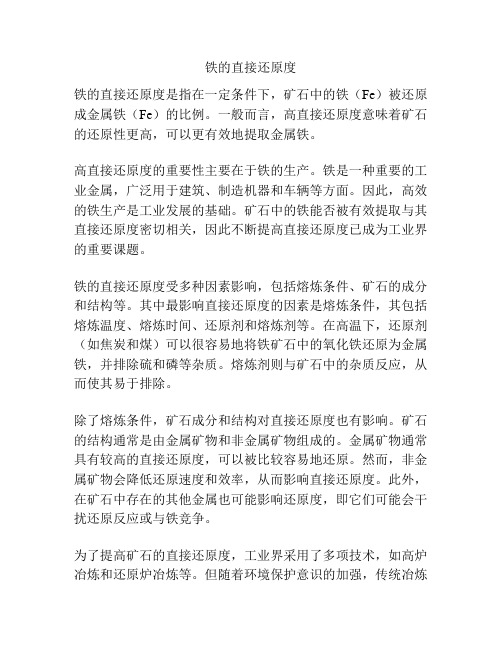
铁的直接还原度铁的直接还原度是指在一定条件下,矿石中的铁(Fe)被还原成金属铁(Fe)的比例。
一般而言,高直接还原度意味着矿石的还原性更高,可以更有效地提取金属铁。
高直接还原度的重要性主要在于铁的生产。
铁是一种重要的工业金属,广泛用于建筑、制造机器和车辆等方面。
因此,高效的铁生产是工业发展的基础。
矿石中的铁能否被有效提取与其直接还原度密切相关,因此不断提高直接还原度已成为工业界的重要课题。
铁的直接还原度受多种因素影响,包括熔炼条件、矿石的成分和结构等。
其中最影响直接还原度的因素是熔炼条件,其包括熔炼温度、熔炼时间、还原剂和熔炼剂等。
在高温下,还原剂(如焦炭和煤)可以很容易地将铁矿石中的氧化铁还原为金属铁,并排除硫和磷等杂质。
熔炼剂则与矿石中的杂质反应,从而使其易于排除。
除了熔炼条件,矿石成分和结构对直接还原度也有影响。
矿石的结构通常是由金属矿物和非金属矿物组成的。
金属矿物通常具有较高的直接还原度,可以被比较容易地还原。
然而,非金属矿物会降低还原速度和效率,从而影响直接还原度。
此外,在矿石中存在的其他金属也可能影响还原度,即它们可能会干扰还原反应或与铁竞争。
为了提高矿石的直接还原度,工业界采用了多项技术,如高炉冶炼和还原炉冶炼等。
但随着环境保护意识的加强,传统冶炼技术面临着许多问题,如废气污染等。
因此,新的技术也正在发展中,如氢气还原和电解还原等。
这些新技术在直接还原度方面有着更好的效果,同时也具有更好的环保性能。
总之,铁的直接还原度是影响工业铁生产的重要因素。
虽然处理直接还原度的技术已经非常成熟,但还有许多机会来提高这项技术。
未来,更加环保的技术将更受青睐,而这些技术也可能有助于提高铁的直接还原度。
直接还原炼铁

直接还原炼铁在低于矿石熔化温度下,通过固态还原,把铁矿石炼制成铁的工艺过程。
这种铁保留了失氧时形成的大量微气孔,在显微镜下观察形似海绵,所以也称为海绵铁;用球团矿制成的海绵铁也称为金属化球团。
直接还原铁的特点是碳、硅含量低,成分类似钢,实际上也代替废钢使用于炼钢。
习惯上把铁矿石在高炉中先还原冶炼成含碳高的生铁。
而后在炼钢炉内氧化,降低含碳量并精炼成钢,这项传统工艺,称作间接炼钢方法;而把炼制海绵铁的工艺称作直接还原法,或称直接炼铁(钢)法。
直接还原原理与早期的炼铁法(见块炼铁)基本相同。
高炉法取代原始炼铁法后,生产效率大幅度提高,是钢铁冶金技术的重大进步。
但随着钢铁工业大规模发展,适合高炉使用的冶金焦的供应日趋紧张。
为了摆脱冶金焦的羁绊,18世纪末提出了直接还原法的设想。
20世纪60年代,直接还原法得到发展,其原因是:①50~70年代,石油及天然气大量开发,为发展直接还原法提供了方便的能源。
②电炉炼钢迅速发展,海绵铁能代替供应紧缺的优质废钢,用作电炉原料,开辟了海绵铁的广阔市场。
③选矿技术提高,能提供高品位精矿,使脉石含量可以降得很低,简化了直接还原工艺。
1980年全世界直接还原炼铁生产量为713万吨,占全世界生铁产量的1.4%。
最大的直接还原工厂规模达到年产百万吨,在钢铁工业中已占有一定的位置。
海绵铁中能氧化发热的元素如硅、碳、锰的含量很少,不能用于转炉炼钢,但适用于电弧炉炼钢。
这样就形成一个直接还原炉-电炉的钢铁生产新流程。
经过电炉内的简单熔化过程,从海绵铁中分离出少量脉石,就炼成了钢,免除了氧化、精炼及脱氧操作,使新流程具有作业程序少和能耗低的优点。
其缺点是:①成熟的直接还原法需用天然气作能源,而用煤炭作能源的直接还原法尚不完善,70年代后期,石油供应不足,天然气短缺,都限制了直接还原法的发展。
②直接还原炉-电炉炼钢流程,生产一吨钢的电耗不少于600千瓦·时,不适于电力短缺地区使用。
炼钢中的直接还原技术及其应用

炼钢中的直接还原技术及其应用随着钢铁行业的发展,炼钢技术也在不断的变革与创新。
直接还原技术作为一种新型炼钢技术,已经开始得到广泛的应用。
本文将从直接还原技术的基础和应用方面进行阐述,以期为读者提供更深入的了解。
一、直接还原技术的基础直接还原技术是使用还原剂将炉料中的氧化铁还原为金属铁的炼钢技术。
与传统的高炉技术相比,在直接还原技术中,直接使用还原剂还原炉料中的氧化铁,不需要通过高温和高压使其发生氧化还原反应。
这种技术具有明显的优点,主要表现在以下几个方面:1.制造成本低:由于直接还原技术不需要高压和高温,所需能源也更少,因此生产成本低于传统的高炉技术。
2.环保节能:使用直接还原技术炼钢可以减少CO2和NOx等大气污染物的排放,一定程度地保护了环境。
另外,由于直接还原技术对能源的需求更小,也有利于节能减排。
3.操作简便:在直接还原技术中,制造过程更加简单直接,操作也更加方便,更容易实现自动化和智能化。
以上3个方面是直接还原技术的主要优点。
相比于传统的高炉技术,直接还原技术在生产成本、环保和操作方便等方面都有更多的优势。
二、直接还原技术的应用1.直接还原工艺的应用直接还原技术的应用范围很广,从小型加工厂到大型钢铁制造企业都在使用该技术。
其中,直接还原工艺是一种常见的应用方式。
直接还原工艺主要包括三部分:还原反应、冶金物理化学过程和钢水净化过程。
还原反应过程是指在以还原剂为主体的还原反应中,将冶金炉中的氧化铁还原为冶金铁的化学反应过程。
冶金物理化学过程是指冶金炉内金属铁的脱硫、脱锰、脱孔及相应物理化学反应。
钢水净化过程是指将冶金炉内钢水经过捞渣、渣加剂、精炼等工艺处理后实现除杂,使钢水纯净。
直接还原工艺是炼钢企业中最常用的炼钢技术之一,它主要的应用优势在于高效、短周期、节能、环保等方面。
2.直接冶炼的应用直接冶炼是指将原料中的氧化铁直接还原至金属铁进行炼制的技术。
在直接冶炼过程中,仅使用还原剂,不需要其它辅助材料。
直接还原铁在一重炼钢生产中的应用

!"#$%& 冷轧辊是现阶段国内冷轧机组使用最
多的零部件 " 而冷轧行业的发展趋势需要冷轧辊 具备三个方面的要求 & 一是抗失效能力 ( 即抗裂 纹 $ 抗剥落性能 / # 二是辊身工作层的耐磨性 ( 包 括耐粗糙性 / # 三是辊身工作层的淬硬层深度 % 由 于冷轧辊的抗失效能力对钢的组织和性能不均匀 性十分敏感 " 并且这种能力在生产 $ 使用中经济 性指标较高 " 因此有必要对与之相关的材料 $ 锻 造 $ 热处理等问题进行一定的探讨 " 以便改进工 艺措施 %
678
4,/$13+ ,-,4, 4,/$143 ,-,,+ 4,/$134 ,-,4, 4,/$142 ,-,+/ 4,/$131 ,-,41 4,/$1/3 ,-,,.
总计 平均值
"#!! 直接还原铁对产品化学成分的影响
抚顺特钢和哈尔滨东方海绵铁厂所生产的直 接还原铁化学成分列于表3 & +!
表 "! 熔清后磷含量 !
! 678
金 属 化 率
,-.. 抚顺 ,-,1+ 特钢 ,-42 ,-/0
哈尔滨 东方
21-0, 25-4+ 21-., 25-05
,-,0
,-,,0 11-,,
表 $! 直接还原铁杂质元素含量 !
"9 ": ;< => =? ",-,+ ,-,3 ,-,,+ / @*
678
=A
",-,,0 ",-,,+ ",-,,0 ,-,,3
# )& $
!""! 年第 " 期 ! 总 #$% 期 "
铁的直接还原度名词解释
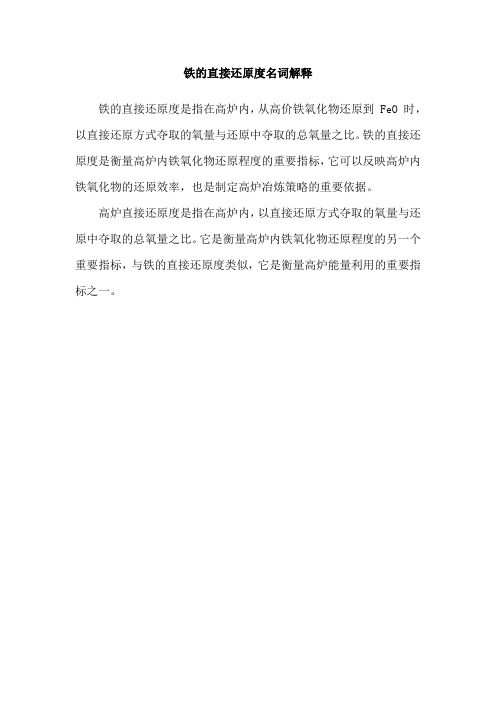
铁的直接还原度名词解释
铁的直接还原度是指在高炉内,从高价铁氧化物还原到 FeO 时,以直接还原方式夺取的氧量与还原中夺取的总氧量之比。
铁的直接还原度是衡量高炉内铁氧化物还原程度的重要指标,它可以反映高炉内铁氧化物的还原效率,也是制定高炉冶炼策略的重要依据。
高炉直接还原度是指在高炉内,以直接还原方式夺取的氧量与还原中夺取的总氧量之比。
它是衡量高炉内铁氧化物还原程度的另一个重要指标,与铁的直接还原度类似,它是衡量高炉能量利用的重要指标之一。
- 1、下载文档前请自行甄别文档内容的完整性,平台不提供额外的编辑、内容补充、找答案等附加服务。
- 2、"仅部分预览"的文档,不可在线预览部分如存在完整性等问题,可反馈申请退款(可完整预览的文档不适用该条件!)。
- 3、如文档侵犯您的权益,请联系客服反馈,我们会尽快为您处理(人工客服工作时间:9:00-18:30)。
直接还原铁的品质与用途
直接还原铁即粉末冶金还原铁粉生产中的海绵铁。
炼钢中的海绵铁的品质要求与粉末冶金用海绵铁的品质要求不同,其含铁量在90%以上,但要控制S,P,Pb,Zn,Bi,As等有害元素的含量。
用于生产还原铁粉的直接还原铁其技术条件为:TFe=97.5%~98.0%、金属化率≥95%、C=0.3%~0.4%、S、P≤0.020%、Si≤0.10%。
用于炼钢的直接还原铁其技术条件为:TFe≥91%、金属化率≥85%、S、P≤0.020%、Si≤0.20%。
直接还原铁除了作为电弧炉冶炼原料以外,直接还原铁还是氧气转炉的优质冷却剂和炉料,对转炉的冷却效果是废钢的112~2倍。
应用直接还原铁后转炉冶炼可获得多种效果,如稀释铁水中的S、P、Bi、Pb、Zn、As等有害杂质元素含量,消除废钢对炉衬的机械损耗作用,改善自动加料和终点控制,提高计算机自控水平,提高生产率等。
所以将钢厂的含铁氧化物为原料建立直接还原铁生产线,投产后其产品在钢铁企业的用途是广泛的、有益的。
基本特点:
1、化学成分稳定,有效稀释钢中残余和夹杂金属元素含量,改善钢的质量;
2、P、S有害元素含量低,可缩短精炼时间;
3、减少装料次数、减少停电作业和热损失,熔化速度快、电耗低、可提高效率、降低成本;
4、熔化期中,供电作业稳定,允许大功率供电、口音低、烟尘少、工作环境好;
5、使用成本低廉,经济效益高。
编辑本段生产工艺:在工业上应用较多的有铁磷还原法,铁精矿粉还原法等,即将轧钢氧化铁磷或精矿粉经还原铁压块机压制成块后,装入焙烧管进窑焙烧,生产出了优质还原铁。
直接还原铁经粗破(将直接还原铁锭破成块状)中破(将块状直接还原铁破碎成0~15mm的颗粒状)后,再经过磁选,去除SiO2、、CaS和游离碳等杂质。
用户可再次使用还原铁压块机压制直接还原铁颗粒,使直接还原铁颗粒成型并达到一定的堆比重g/cm3要求。
直接还原铁破碎颗粒直接影响压块物理特性(压缩性、成型性、堆比重g/cm3)对特钢生产起到至关重要的作用。
1. 铁磷还原法:轧钢氧化铁磷是钢材在加热炉中加热后在轧制过程中,其表面氧化层自行脱落而产生的。
还原海绵铁可采用热轧沸腾钢氧化铁磷作原料,因为沸腾钢氧化铁磷中的TFe、C、S、P化学成分含量,能满足还原海绵铁生产的技术要求,在还原海绵铁中最好不要以高碳钢或合金钢氧化铁磷为原料。
2. 铁精矿粉还原法:磁铁矿的主要成分是Fe3O4经采用湿式球磨、湿式磁选、联合选矿工艺后产出的普通精矿粉,是生产还原海绵铁的优选原料。
3. 隧道窑工艺即固态碳还原工艺。
碳是通过与耐火罐中的氧在高温下形成一氧化碳以气相还原的,见下式:C+O2→CO2 CO2+C→2CO Fe3O4+CO→3FeO+CO2 FeO+CO→Fe+CO2 为了脱除固态还原剂中的硫配入石灰石粉通过炉中的化学反应吸收还原剂中挥发的H2S以免渗入海绵铁中,见下列反应式:CaCO3→CaO+CO2 CaO+H2S+C→CaS+H2+CO 氧化铁在隧道窑中加热被固体碳还原的过程是比较复杂的过程。
炉料以预热到还原、冷却将产生一系列物理化学变化,隧道结构和性能是影响海绵铁产量、质量的重要因素。
但控制和调节有关工艺参数使炉内整个系统达到平衡,从而达到还原目的。
又是决定产品产量、质量的关键。
编辑本段工艺流程:直接还原铁的生产工艺流程可分为如下五个工序:一.原料准备及其烘干破碎工序:将脱硫剂、还原剂两种物料装入定量料斗,定量料斗按两种物料的重量比,通过输送机将物料送到烘干室内对两物料进行烘干、混合。
烘干后的物料含水量小于3%,烘干后的物料,通过输送机送到还原剂破碎机内进行粉碎,粉碎粒度为1.5mm以下。
破碎后的
物料,经输送机提升到高位料仓,然后再由输送机送到储存料仓。
精矿粉由输送机直接送入烘干机组进行烘干,烘干后含水量小于3%,烘干后的精矿粉由输送机送入高位料仓,然后再由输送机送至储存料仓。
二.自动装料工序:本工艺根据需要可生产桶状、柱状或瓦片状直接还原铁。
装料系统由料仓、定量管和装料头三部分组成,精矿粉和还原剂,经过储存料仓,将料卸到布料仓内,再由装料头装入每个还原坩埚,实现向坩埚布料。
三.还原焙烧工序:此工序在快速还原炉内完成。
适宜稳定的炉温和还原时间是决定直接还原铁质量的关键,此工序包括预热、还原、冷却三个阶段。
首先,载车经过传动机构,将载车送入快速还原炉内的预热段,在此间,物料中的水分完全蒸发,脱硫剂分解,温度升至还原温度,进入高温还原段,在此间,氧化铁被充分还原,形成单质铁,然后进入冷却段进行冷却,冷却到200℃以下后出炉。
四.自动卸料工序:物料出炉后在常温中降到100℃~50℃后进入卸料系统进行卸料。
粉灰通过风力吸走,直接还原铁通过抓钳,从坩埚中取走,实现自动卸料。
五.产品处理工序:由该工序完成直接还原铁磁选、破碎及钝化处理----压块。
卸完料的载车进入装料系统装料。
直接还原铁经过卸料装置进入中间料仓。
中间料仓的直接还原铁经过输送机输送至直接还原铁破碎机进行破碎,破碎后的直接还原铁经干磁选机进行磁选,磁选后的直接还原铁粉由输送机输送到HDYJ还原铁压块机组进行压块成形,通过传动机构入库。
冷压块的实现有效地改善了直接还原铁的抗氧化性能。
降低了直接还原铁的吸水性,缩小了体积,有利于直接还原铁的长期存储和长途运输,同时使用时也提高了钢水的收得率,因此倍受炼钢企业的欢迎,在市场竞争中具有很强的生命力和竞争力。