热处理工艺3-加热
钢的五种热处理工艺

钢的五种热处理工艺热处理工艺——表面淬火、退火、正火、回火、调质工艺:1、把金属材料加热到相变温度(700度)以下,保温一段时间后再在空气中冷却叫回火。
2、把金属材料加热到相变温度(800度)以上,保温一段时间后再在炉中缓慢冷却叫退火。
3、把金属材料加热到相变温度(800度)以上,保温一段时间后再在特定介质中(水或油)快速冷却叫淬火。
◆表面淬火•钢的表面淬火有些零件在工件时在受扭转和弯曲等交变负荷、冲击负荷的作用下,它的表面层承受着比心部更高的应力。
在受摩擦的场合,表面层还不断地被磨损,因此对一些零件表面层提出高强度、高硬度、高耐磨性和高疲劳极限等要求,只有表面强化才能满足上述要求。
由于表面淬火具有变形小、生产率高等优点,因此在生产中应用极为广泛。
根据供热方式不同,表面淬火主要有感应加热表面淬火、火焰加热表面淬火、电接触加热表面淬火等。
感应表面淬火后的性能:1.表面硬度:经高、中频感应加热表面淬火的工件,其表面硬度往往比普通淬火高2~3单位(HRC)。
2.耐磨性:高频淬火后的工件耐磨性比普通淬火要高。
这主要是由于淬硬层马氏体晶粒细小,碳化物弥散度高,以及硬度比较高,表面的高的压应力等综合的结果。
3.疲劳强度:高、中频表面淬火使疲劳强度大为提高,缺口敏感性下降。
对同样材料的工件,硬化层深度在一定范围内,随硬化层深度增加而疲劳强度增加,但硬化层深度过深时表层是压应力,因而硬化层深度增打疲劳强度反而下降,并使工件脆性增加。
一般硬化层深δ=(10~20)%D。
较为合适,其中D。
为工件的有效直径。
◆退火工艺退火是将金属和合金加热到适当温度,保持一定时间,然后缓慢冷却的热处理工艺。
退火后组织亚共析钢是铁素体加片状珠光体;共析钢或过共析钢则是粒状珠光体。
总之退火组织是接近平衡状态的组织。
•退火的目的①降低钢的硬度,提高塑性,以利于切削加工及冷变形加工。
②细化晶粒,消除因铸、锻、焊引起的组织缺陷,均匀钢的组织和成分,改善钢的性能或为以后的热处理作组织准备。
焊后热处理的加热方式

焊后热处理是对焊接接头进行热加工,以改善焊缝和母材的性能,减轻残余应力,并提高焊接接头的强度和韧性。
以下是几种常见的焊后热处理加热方式:
1.炉加热:将焊接接头放入特定的热处理炉中进行加热。
这种方法适用于大型工件或需要
进行长时间均匀加热的情况。
可以根据具体要求设定加热温度和保持时间。
2.电阻加热:使用电流通过工件的导电性材料产生热量,将焊接接头进行加热。
这种方法
适用于较小尺寸的工件或需要局部加热的情况。
可以通过调整电流强度和加热时间来控制加热效果。
3.感应加热:利用感应加热原理,在焊接接头周围产生交变磁场,使其自身发热。
这种方
法适用于需要快速且局部加热的情况,对于大型工件,也可以组合多个感应加热装置进行加热。
4.火焰加热:使用火焰或火炬对焊接接头进行加热。
这种方法适用于简单的焊后热处理,
可以通过调整火焰大小和距离来控制加热温度。
在选择加热方式时,需要考虑工件尺寸、材料特性、加热速度要求以及所需的温度控制精度等因素。
加热过程中还需要注意避免温度过高或过低,以免引起不均匀加热、脆性相形成或工件变形等问题。
热处理升温工艺
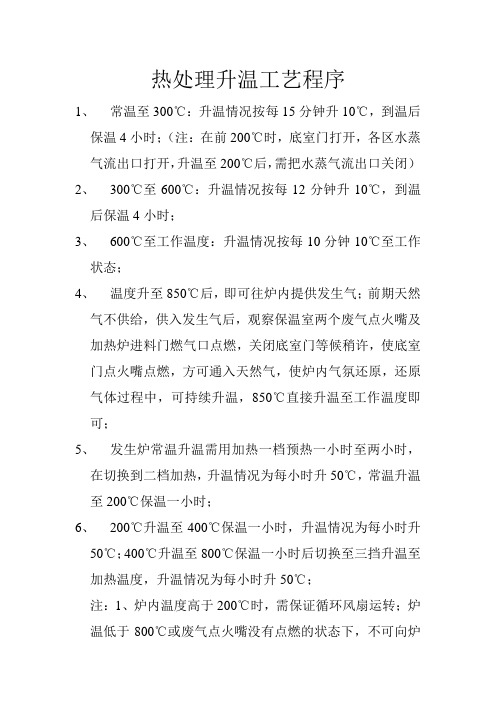
热处理升温工艺程序1、常温至300℃:升温情况按每15分钟升10℃,到温后保温4小时;(注:在前200℃时,底室门打开,各区水蒸气流出口打开,升温至200℃后,需把水蒸气流出口关闭)2、300℃至600℃:升温情况按每12分钟升10℃,到温后保温4小时;3、600℃至工作温度:升温情况按每10分钟10℃至工作状态;4、温度升至850℃后,即可往炉内提供发生气;前期天然气不供给,供入发生气后,观察保温室两个废气点火嘴及加热炉进料门燃气口点燃,关闭底室门等候稍许,使底室门点火嘴点燃,方可通入天然气,使炉内气氛还原,还原气体过程中,可持续升温,850℃直接升温至工作温度即可;5、发生炉常温升温需用加热一档预热一小时至两小时,在切换到二档加热,升温情况为每小时升50℃,常温升温至200℃保温一小时;6、200℃升温至400℃保温一小时,升温情况为每小时升50℃;400℃升温至800℃保温一小时后切换至三挡升温至加热温度,升温情况为每小时升50℃;注:1、炉内温度高于200℃时,需保证循环风扇运转;炉温低于800℃或废气点火嘴没有点燃的状态下,不可向炉内送入天然气;各区送入天然气后才可将碳控仪表由手动改为自动(“Man”为手动自动切换);2、起炉前,碳控仪差值需归零,碳势升至设定值保持1~2个小时由技术员进行定碳分析,并根据定碳结果对碳控仪显示值进行修正,碳势测定标准详见《JB/T 10312-2011 钢箔称重法》3、连续炉各区碳势设定值如下:a、强渗一区设定值为1.08;b、强渗二区设定值为1.09;c、扩散三区设定值为0.85;d、预冷四区设定值为0.8;e、保温室设定值为0.77;4、低温回火炉升温可在产品进满预冷炉后进行,升温前需启动风扇;5、废气排放系统可在设备运行前启动;6、设备正常运行前需确认各基本位置是否在规定位置上,各行程开关及限位块都在规定位置上,如不满足,需调整到指定位置上;。
热处理

任何一种热处理的工艺过程,都包括下列三个步骤
1.加热。加热是以一定速度把工件加热到规 定的温度范围;这个温度范围根据不同的 金属材料、不同的热处理要求而定; 2.保温。保温是在要求的加热温度下把工件 保温,使工件表面及内部温度一致; 3.冷却。冷却是以某种速度把工件冷却下来, 这个冷却速度根据不同的金属材料、不同 的热处理要求而定。
5.表面热处理 有些零件使用时希望它的心部保持一定 的强度和韧性,又要求表面层具有耐磨性、 抗腐蚀性、抗疲劳性。这些性能可通过表 面热处理来得到。表面热处理按处理工艺 特点可分为表面淬火和表面化学热处理两 大类。
(1)表面淬火 表面淬火是将零件表面层迅速加热到淬 火温度,然后快速冷却下来的热处理工艺。 由于通过快速加热,使零件表面层快速达 到淬火温度,在热量来不及传到心部时, 就立即冷却,实现了局部淬火。通常零件 在表面淬火前均进行正火或调质处理,表 面淬火后应进行低温回火。这样,不仅可 以保证其表面的高硬度和高耐磨性,而且 可以保证心部的强度和韧性。 根据加热方法,表面淬火可分为火焰加 热表面淬火和感应加热表面淬火
(1)低温回火 将淬火工件加热到150~250 ℃的回火。 低温回火可以部分消除淬火造成的内应力, 适当地降低工件的脆性,提高工件的韧性, 同时使工件仍保持很高的硬度。工具、量 具、滚动轴承多采用低温回火。
(2)中温回火 将淬火工件加热到300~450 ℃的回火。 淬火工件经中温回火后,可消除大部分内 应力,获得一定的弹性和韧性,具有中等 硬度。中温回火一般用于热锻模、弹簧等。
(3)高温回火 将淬火工件加热到500~650 ℃的回火。 高温回火可以完全消除内应力,使零件具 有高强度和高韧性等综合机械性能。淬火 后再经高温回火,这一相结合的工艺,也 成为调制处理。一般要求具有较高综合机 械性能的重要结构零件,都要进行调制处 理。调制处理广泛应用于中碳优质结构钢 和中碳合金结构钢的重要零件,如车床主 轴、齿轮、连杆、曲轴等。用于调制处理 的钢成为调制钢。
热处理工艺过程三个阶段

热处理工艺过程三个阶段热处理是一种将金属部件加热到一定温度并进行一定时间的加工过程,其主要目的是改变材料的组织结构从而提高其力学性能。
热处理过程主要分为三个阶段:加热、保温和冷却。
一、加热阶段加热阶段是指将金属部件加热到所需的温度。
加热的目的是为了使材料遵循相图发生相变并从而改变其性质。
加热的温度、保温时间和冷却方式都是根据材料的性质和需要调整的。
加热的类型包括常温加热、高温加热、均匀加热和局部加热。
常温加热适用于低温热处理,它具有温度变化缓慢的优点;高温加热适用于高温热处理,其具有晶界扩散快的优点;均匀加热适用于保证加热均匀,防止温差过大;局部加热适用于改善部位性能,避免金属件的整体加热所造成的不必要浪费。
二、保温阶段保温阶段是指将加热至所需温度的金属部件,固定在适当的温度下保持一段时间,以使其达到到放热、相变、扩散的平衡状态。
保温时间与加热温度成正比例,可以根据材料的特性和工艺的需要进行调整。
在保温过程中,金属件的温度要控制得相当精确,以确保材料状态达到所需要的水平。
三、冷却阶段冷却阶段是指将处于保温温度下的金属部件迅速降温至室温以下的过程,以使材料在所需时间内固化。
冷却方式的选择对于零件性能的形成和稳定具有重要影响。
冷却方式主要包括自然冷却和强制冷却,其中自然冷却是在室温下自然降温,强制冷却则是通过多种方式对零件进行冷却,包括沿水平或垂直方向喷水冷却、在冷却槽中冷却、强制通风降温等。
总之,在进行热处理过程中,每个阶段都十分重要,在加热、保温和冷却过程中,各环节的温度、时间和冷却方式都会影响最终金属材料的结构和性质,因此需要有专业的技术人员进行操作和控制,确保所得到的材料性能满足需求。
热处理工艺
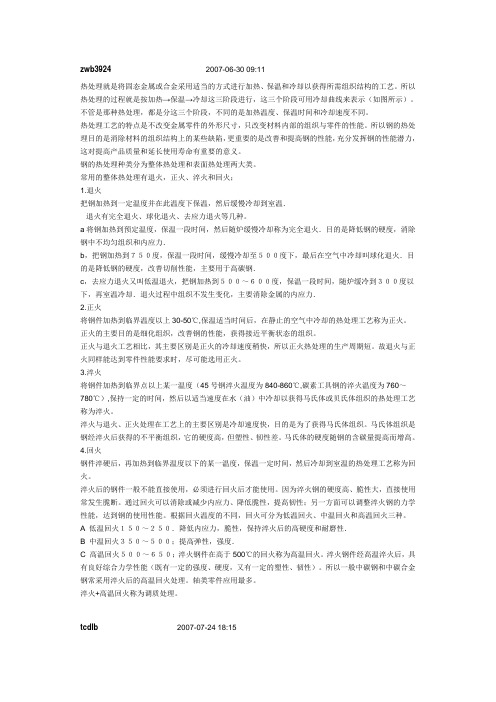
zwb39242007-06-30 09:11热处理就是将固态金属或合金采用适当的方式进行加热、保温和冷却以获得所需组织结构的工艺。
所以热处理的过程就是按加热→保温→冷却这三阶段进行,这三个阶段可用冷却曲线来表示(如图所示)。
不管是那种热处理,都是分这三个阶段,不同的是加热温度、保温时间和冷却速度不同。
热处理工艺的特点是不改变金属零件的外形尺寸,只改变材料内部的组织与零件的性能。
所以钢的热处理目的是消除材料的组织结构上的某些缺陷,更重要的是改善和提高钢的性能,充分发挥钢的性能潜力,这对提高产品质量和延长使用寿命有重要的意义。
钢的热处理种类分为整体热处理和表面热处理两大类。
常用的整体热处理有退火,正火、淬火和回火;1.退火把钢加热到一定温度并在此温度下保温,然后缓慢冷却到室温.退火有完全退火、球化退火、去应力退火等几种。
a将钢加热到预定温度,保温一段时间,然后随炉缓慢冷却称为完全退火.目的是降低钢的硬度,消除钢中不均匀组织和内应力.b,把钢加热到750度,保温一段时间,缓慢冷却至500度下,最后在空气中冷却叫球化退火.目的是降低钢的硬度,改善切削性能,主要用于高碳钢.c,去应力退火又叫低温退火,把钢加热到500~600度,保温一段时间,随炉缓冷到300度以下,再室温冷却.退火过程中组织不发生变化,主要消除金属的内应力.2.正火将钢件加热到临界温度以上30-50℃,保温适当时间后,在静止的空气中冷却的热处理工艺称为正火。
正火的主要目的是细化组织,改善钢的性能,获得接近平衡状态的组织。
正火与退火工艺相比,其主要区别是正火的冷却速度稍快,所以正火热处理的生产周期短。
故退火与正火同样能达到零件性能要求时,尽可能选用正火。
3.淬火将钢件加热到临界点以上某一温度(45号钢淬火温度为840-860℃,碳素工具钢的淬火温度为760~780℃),保持一定的时间,然后以适当速度在水(油)中冷却以获得马氏体或贝氏体组织的热处理工艺称为淬火。
常用的热处理工艺及目的
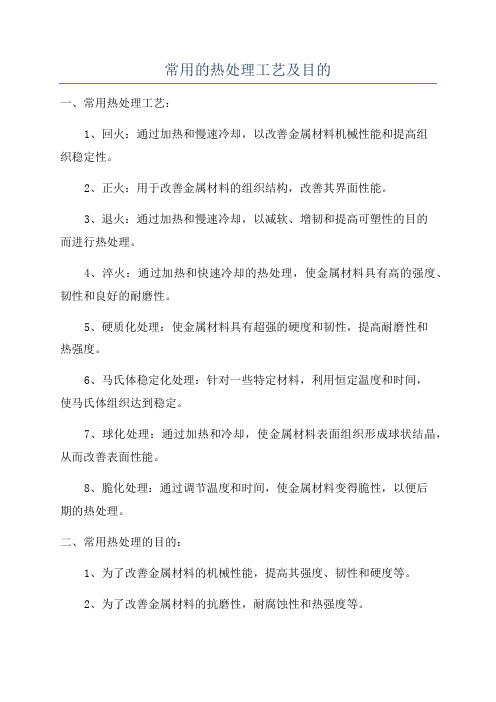
常用的热处理工艺及目的
一、常用热处理工艺:
1、回火:通过加热和慢速冷却,以改善金属材料机械性能和提高组
织稳定性。
2、正火:用于改善金属材料的组织结构,改善其界面性能。
3、退火:通过加热和慢速冷却,以减软、增韧和提高可塑性的目的
而进行热处理。
4、淬火:通过加热和快速冷却的热处理,使金属材料具有高的强度、韧性和良好的耐磨性。
5、硬质化处理:使金属材料具有超强的硬度和韧性,提高耐磨性和
热强度。
6、马氏体稳定化处理:针对一些特定材料,利用恒定温度和时间,
使马氏体组织达到稳定。
7、球化处理:通过加热和冷却,使金属材料表面组织形成球状结晶,从而改善表面性能。
8、脆化处理:通过调节温度和时间,使金属材料变得脆性,以便后
期的热处理。
二、常用热处理的目的:
1、为了改善金属材料的机械性能,提高其强度、韧性和硬度等。
2、为了改善金属材料的抗磨性,耐腐蚀性和热强度等。
3、为了改变材料组织结构,改善显微组织形貌,改变金属材料的晶粒大小。
4、为了改善金属材料的界面性能,使其变为球状结晶,从而改善了其可塑性和抗锈腐性。
热处理工艺
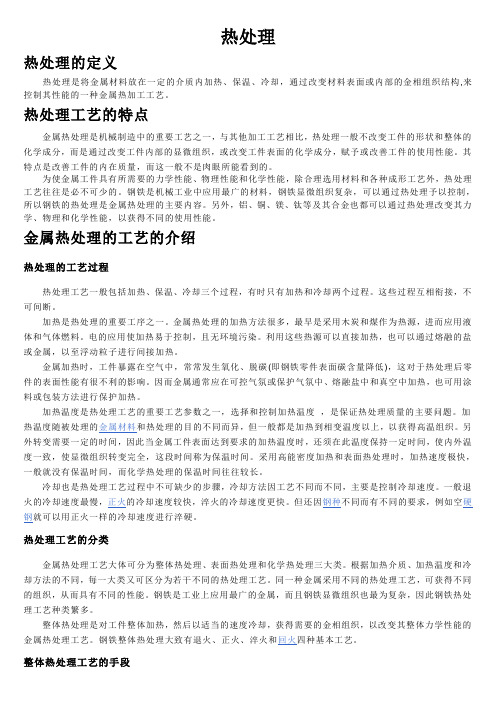
热处理热处理的定义热处理是将金属材料放在一定的介质内加热、保温、冷却,通过改变材料表面或内部的金相组织结构,来控制其性能的一种金属热加工工艺。
热处理工艺的特点金属热处理是机械制造中的重要工艺之一,与其他加工工艺相比,热处理一般不改变工件的形状和整体的化学成分,而是通过改变工件内部的显微组织,或改变工件表面的化学成分,赋予或改善工件的使用性能。
其特点是改善工件的内在质量,而这一般不是肉眼所能看到的。
为使金属工件具有所需要的力学性能、物理性能和化学性能,除合理选用材料和各种成形工艺外,热处理工艺往往是必不可少的。
钢铁是机械工业中应用最广的材料,钢铁显微组织复杂,可以通过热处理予以控制,所以钢铁的热处理是金属热处理的主要内容。
另外,铝、铜、镁、钛等及其合金也都可以通过热处理改变其力学、物理和化学性能,以获得不同的使用性能。
金属热处理的工艺的介绍热处理的工艺过程热处理工艺一般包括加热、保温、冷却三个过程,有时只有加热和冷却两个过程。
这些过程互相衔接,不可间断。
加热是热处理的重要工序之一。
金属热处理的加热方法很多,最早是采用木炭和煤作为热源,进而应用液体和气体燃料。
电的应用使加热易于控制,且无环境污染。
利用这些热源可以直接加热,也可以通过熔融的盐或金属,以至浮动粒子进行间接加热。
金属加热时,工件暴露在空气中,常常发生氧化、脱碳(即钢铁零件表面碳含量降低),这对于热处理后零件的表面性能有很不利的影响。
因而金属通常应在可控气氛或保护气氛中、熔融盐中和真空中加热,也可用涂料或包装方法进行保护加热。
加热温度是热处理工艺的重要工艺参数之一,选择和控制加热温度,是保证热处理质量的主要问题。
加热温度随被处理的金属材料和热处理的目的不同而异,但一般都是加热到相变温度以上,以获得高温组织。
另外转变需要一定的时间,因此当金属工件表面达到要求的加热温度时,还须在此温度保持一定时间,使内外温度一致,使显微组织转变完全,这段时间称为保温时间。
金属材料热处理工艺(详细工序及操作手法)
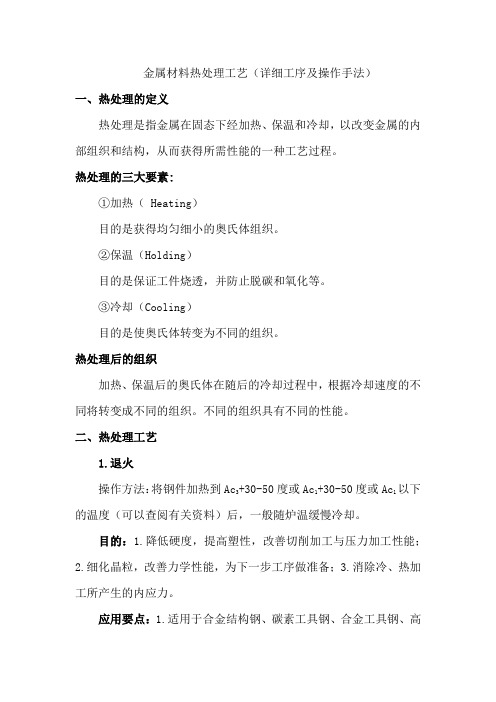
金属材料热处理工艺(详细工序及操作手法)一、热处理的定义热处理是指金属在固态下经加热、保温和冷却,以改变金属的内部组织和结构,从而获得所需性能的一种工艺过程。
热处理的三大要素:①加热( Heating)目的是获得均匀细小的奥氏体组织。
②保温(Holding)目的是保证工件烧透,并防止脱碳和氧化等。
③冷却(Cooling)目的是使奥氏体转变为不同的组织。
热处理后的组织加热、保温后的奥氏体在随后的冷却过程中,根据冷却速度的不同将转变成不同的组织。
不同的组织具有不同的性能。
二、热处理工艺1.退火操作方法:将钢件加热到Ac3+30-50度或Ac1+30-50度或Ac1以下的温度(可以查阅有关资料)后,一般随炉温缓慢冷却。
目的:1.降低硬度,提高塑性,改善切削加工与压力加工性能;2.细化晶粒,改善力学性能,为下一步工序做准备;3.消除冷、热加工所产生的内应力。
应用要点:1.适用于合金结构钢、碳素工具钢、合金工具钢、高速钢的锻件、焊接件以及供应状态不合格的原材料;2.一般在毛坯状态进行退火。
2.正火操作方法:将钢件加热到Ac3或Acm 以上30-50度,保温后以稍大于退火的冷却速度冷却。
目的:1.降低硬度,提高塑性,改善切削加工与压力加工性能;2.细化晶粒,改善力学性能,为下一步工序做准备;3.消除冷、热加工所产生的内应力。
应用要点:正火通常作为锻件、焊接件以及渗碳零件的预先热处理工序。
对于性能要求不高的低碳的和中碳的碳素结构钢及低合金钢件,也可作为最后热处理。
对于一般中、高合金钢,空冷可导致完全或局部淬火,因此不能作为最后热处理工序。
3.淬火操作方法:将钢件加热到相变温度Ac3或Ac1以上,保温一段时间,然后在水、硝盐、油、或空气中快速冷却。
目的:淬火一般是为了得到高硬度的马氏体组织,有时对某些高合金钢(如不锈钢、耐磨钢)淬火时,则是为了得到单一均匀的奥氏体组织,以提高耐磨性和耐蚀性。
应用要点:1.一般用于含碳量大于百分之零点三的碳钢和合金钢;2.淬火能充分发挥钢的强度和耐磨性潜力,但同时会造成很大的内应力,降低钢的塑性和冲击韧度,故要进行回火以得到较好的综合力学性能。
316l不锈钢固溶热处理工艺
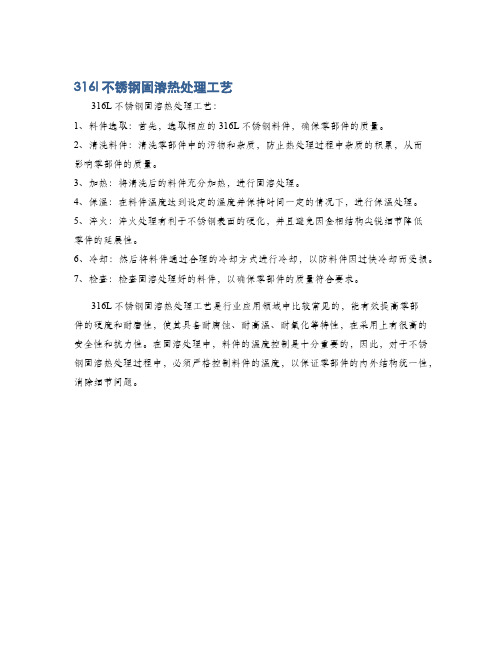
316l不锈钢固溶热处理工艺
316L不锈钢固溶热处理工艺:
1、料件选取:首先,选取相应的316L不锈钢料件,确保零部件的质量。
2、清洗料件:清洗零部件中的污物和杂质,防止热处理过程中杂质的积累,从而
影响零部件的质量。
3、加热:将清洗后的料件充分加热,进行固溶处理。
4、保温:在料件温度达到设定的温度并保持时间一定的情况下,进行保温处理。
5、淬火:淬火处理有利于不锈钢表面的硬化,并且避免因金相结构尖锐细节降低
零件的延展性。
6、冷却:然后将料件通过合理的冷却方式进行冷却,以防料件因过快冷却而受损。
7、检查:检查固溶处理好的料件,以确保零部件的质量符合要求。
316L不锈钢固溶热处理工艺是行业应用领域中比较常见的,能有效提高零部
件的硬度和耐磨性,使其具备耐腐蚀、耐高温、耐氧化等特性,在采用上有很高的安全性和抗力性。
在固溶处理中,料件的温度控制是十分重要的,因此,对于不锈钢固溶热处理过程中,必须严格控制料件的温度,以保证零部件的内外结构统一性,消除细节问题。
热处理工艺介绍

置循环风扇,保证气体向钢件表面的对流。
渗碳的基本过程
3. 活性碳原子向钢件表面迁移
4. 钢件表面吸收碳 首先要求钢件表面洁净,另外要控制渗碳剂的分解和钢件表面对碳的吸
• 正火是将钢材或钢件加热到临界温度以上,保温后空冷的 热处理工艺。
• 正火(退火)的目的: 1 、降低硬度,便于切削加工。 2 、提高钢的塑性和韧性,以便于冷变形加工。 3 、消除锻件的组织缺陷。 4 、细化晶粒,改善组织,为最终热处理做准备。 5 、消除应力,防止畸变和开裂。
正火工艺简介
• 正火工艺的特点 • 加热温度一般在 AC3 以上 • 保温时间足够长
碳势 Cp=(W2-W1)/ W2 X100%+Co
W2: 钢箔渗碳后的重量 碳量
W1: 钢箔渗碳前的重量
Co: 钢箔的原始含
渗碳剂介绍
1 、井式气体渗碳炉所用介质是煤油,煤油是分子中含有 11~17 个碳原 子的多种烃类的混合物。 850℃ 以下裂解不充分,低分子烃较多,易 产生碳黑和结焦。由于成分不固定,不能作为自动控制的介质使用。
钢材简介
通常所指的钢铁材料是钢和铸铁的总称,指所有的铁碳合金。 • 碳素钢(简称碳钢)是含碳量大于 0.0218% 而小于 2.11% 的铁碳合金。 • 合金钢是在碳钢的基础上,添加某些合金元素,用以保证一定的生产和
加工工艺以及所要求的组织与性能的铁基合金。 • 按钢材的化学成分可分为碳素钢和合金钢两大类。 • 碳素钢(简称碳钢)是含碳量大于 0.0218% 而小于 2.11% 的铁碳合金。
根据毛坯的大小和炉子的加热能力来制订保温时间 • 冷却速度一般较慢
热处理的三个过程
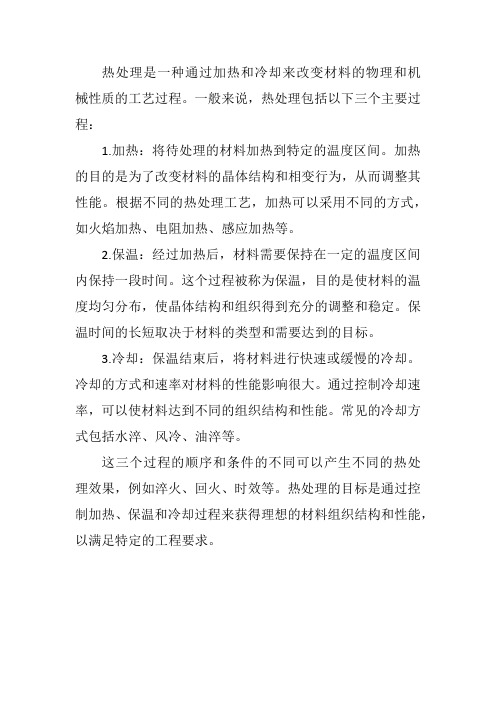
热处理是一种通过加热和冷却来改变材料的物理和机械性质的工艺过程。
一般来说,热处理包括以下三个主要过程:
1.加热:将待处理的材料加热到特定的温度区间。
加热的目的是为了改变材料的晶体结构和相变行为,从而调整其性能。
根据不同的热处理工艺,加热可以采用不同的方式,如火焰加热、电阻加热、感应加热等。
2.保温:经过加热后,材料需要保持在一定的温度区间内保持一段时间。
这个过程被称为保温,目的是使材料的温度均匀分布,使晶体结构和组织得到充分的调整和稳定。
保温时间的长短取决于材料的类型和需要达到的目标。
3.冷却:保温结束后,将材料进行快速或缓慢的冷却。
冷却的方式和速率对材料的性能影响很大。
通过控制冷却速率,可以使材料达到不同的组织结构和性能。
常见的冷却方式包括水淬、风冷、油淬等。
这三个过程的顺序和条件的不同可以产生不同的热处理效果,例如淬火、回火、时效等。
热处理的目标是通过控制加热、保温和冷却过程来获得理想的材料组织结构和性能,以满足特定的工程要求。
热处理工艺规范

编号:PKJS0628-2103 文件名称:热处理工艺规程编号:PKJS0628-2103一、热处理工艺规范1.1正火(1)定义:正火是把钢加热到Ac3(亚共析钢)或Acm(过共析钢)以上适当温度,保温后在空气中冷却的热处理方法。
(2)范围:A、作为低碳钢和某些低合金结构铸钢及锻件消除应力、细化组织、改善切削加工性能和淬火前的预备热处理。
B、消除网状碳化物,为球化退火作准备。
C、用于某些碳素钢、低合金钢工件在淬火返修时,消除内应力和细化组织,以防重新淬火时产生开裂和变形。
D、作为普通结构件的最终热处理。
一些受力不大,只需一定的综合力学性能的的结构件,采用正火就能满足其使用性能要求。
(3)工艺:A、加热温度。
亚共析钢的加热温度为Ac3+30~50℃,过共析钢的加热温度为Acm+30~50℃。
B、保温时间。
保温时间与工件有效厚度有关,以工件截面温度均匀为原则(保温时间的计算可参考淬火)。
C、冷却。
正火工件的冷却一般为空冷,大型工件根据截面尺寸的大小,可采用风冷或喷雾冷却,以获得预期的组织和性能。
1.2淬火(1)定义:淬火是把钢加热到Ac3或Ac1以上温度,保温一定时间,然后以适当方式冷却,以获得马氏体或(和)贝氏体组织的热处理工艺。
工件经淬火和回火处理后,其组织与淬火前相比发生了很大的变化,力学性能有很大的提高,可以充分地发挥材料的潜力,使工件具有良好的使用性能。
(2)目的:A、提高工件的力学性能,如硬度、强度、耐磨性、弹性极限等。
B、改善某些特殊钢种的物理性能或化学性能,如耐蚀性、磁性、导电性等。
(3)工艺:淬火温度主要取决于钢的化学成分,再结合具体工艺因素综合考虑决定,如工件的尺寸、形状、钢的奥氏体晶粒长大倾向、加热方式及冷却介质等。
1)淬火温度A、亚共析钢淬火温度为Ac3+ 30~50℃。
亚共析钢加热到这一温度范围时,钢中的铁素体完全溶于奥氏体中,成为细晶粒奥氏体,淬火后便得到晶粒细小的马氏体。
热处理工艺
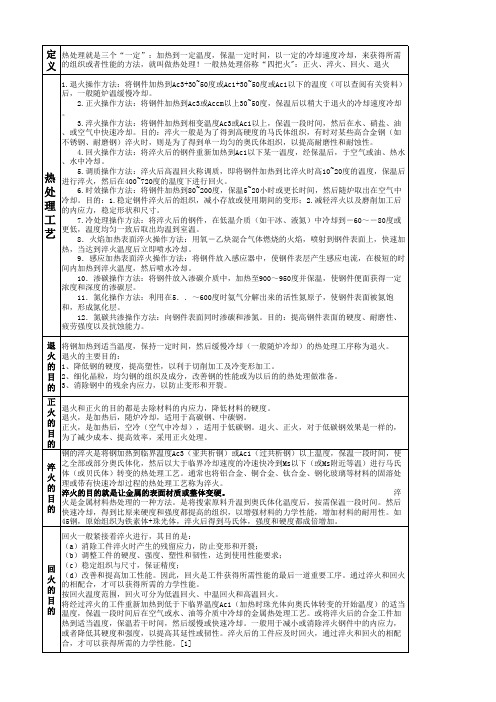
4.回火操作方法:将淬火后的钢件重新加热到Ac1以下某一温度,经保温后,于空气或油、热水
、水中冷却。
热
5.调质操作方法:淬火后高温回火称调质,即将钢件加热到比淬火时高10~20度的温度,保温后 进行淬火,然后在400~720度的温度下进行回火。
处 6.时效操作方法:将钢件加热到80~200度,保温5~20小时或更长时间,然后随炉取出在空气中
淬 之全部或部分奥氏体化,然后以大于临界冷却速度的冷速快冷到Ms以下(或Ms附近等温)进行马氏
火 的 目
体(或贝氏体)转变的热处理工艺。通常也将铝合金、铜合金、钛合金、钢化玻璃等材料的固溶处
理或带有快速冷却过程的热处理工艺称为淬火。
淬火的目的就是让金属的表面材质或整体变硬。
淬
火是金属材料热处理的一种方法。是将搜索原料升温到奥氏体化温度后,按需保温一段时间。然后
和,形成氮化层。
12.氮碳共渗操作方法:向钢件表面同时渗碳和渗氮。目的:提高钢件表面的硬度、耐磨性、
疲劳强度以及抗蚀能力。
退 将钢加热到适当温度,保持一定时间,然后缓慢冷却(一般随炉冷却)的热处理工序称为退火。 火 退火的主要目的:
的 1、降低钢的硬度,提高塑性,以利于切削加工及冷变形加工。
目 2、细化晶粒,均匀钢的组织及成分,改善钢的性能或为以后的的热处理做准备。 的 3、消除钢中的残余内应力,以防止变形和开裂。
定 热处理就是三个“一定”:加热到一定温度,保温一定时间,以一定的冷却速度冷却,来获得所需 义 的组织或者性能的方法,就叫做热处理!一般热处理俗称“四把火":正火、淬火、回火、退火
1.退火操作方法:将钢件加热到Ac3+30~50度或Ac1+30~50度或Ac1以下的温度(可以查阅有关资料)
热处理加热方式有哪些?

热处理加热方式有哪些?什么是热处理?常用的热处理 ... 有哪些热处理:金属材料在固态下,通过加热、保温、冷却的手段,改变金属材料内部的组织状态,从而获得所需性能的一种热加工工艺。
常用的 ... 有:1、退火:有完全退火、不完全退火、等温退火、球化退火、去应力退火、再结晶退火、均匀化退火、去氢退火、扩散退火等等。
2、正火3、淬火:有单介质淬火、双介质淬火、分级淬火、等温淬火、局部淬火等等。
4、回火:有低温回火、中温回火、高温回火、稳定化回火、附加回火等等5、化学热处理:有渗碳、渗氮、离子氮化、碳氮共渗、渗金属等等6、表面热处理:有火焰加热、中频加热、高频加热、超音频加热、激光热处理等等常用的热处理 ... 有哪几种?各有什么特点?1.退火操作 ... :将钢件加热到Ac3+30~50度或Ac1+30~50度或Ac1以下的温度(可以查阅有关资料)后,一般随炉温缓慢冷却。
目的:1.降低硬度,提高塑性,改善切削加工与压力加工性能;2.细化晶粒,改善力学性能,为下一步工序做准备;3.消除冷、热加工所产生的内应力。
应用要点:1.适用于合金结构钢、碳素工具钢、合金工具钢、高速钢的锻件、焊接件以及供应状态不合格的原材料;2.一般在毛坯状态进行退火。
2.正火操作 ... :将钢件加热到Ac3或Accm 以上30~50度,保温后以稍大于退火的冷却速度冷却。
目的:1.降低硬度,提高塑性,改善切削加工与压力加工性能;2.细化晶粒,改善力学性能,为下一步工序做准备;3.消除冷、热加工所产生的内应力。
应用要点:正火通常作为锻件、焊接件以及渗碳零件的预先热处理工序。
对于性能要求不高的低碳的和中碳的碳素结构钢及低合金钢件,也可作为最后热处理。
对于一般中、高合金钢,空冷可导致完全或局部淬火,因此不能作为最后热处理工序。
3.淬火操作 ... :将钢件加热到相变温度Ac3或Ac1以上,保温一段时间,然后在水、硝盐、油、或空气中快速冷却。
热处理工艺过程三个步骤

热处理工艺过程三个步骤
热处理工艺过程是材料加工中的重要环节,它直接影响材料的物理、机械和化学性能。
热处理主要分为三个步骤:加热、保温和冷却。
加热是热处理的起始步骤,其目的是使材料达到所需的温度。
温度的高低和加热速度的快慢,直接影响材料内部的物理和化学变化。
加热过程中,金属内部的原子或分子的运动速度会增加,为后续的相变做好准备。
保温的目的是保持材料在所需温度下充分发生所需的相变。
不同的材料和工艺所需的保温时间不同,如果保温时间不足,可能会导致相变不充分,影响处理效果;而如果保温时间过长,则可能会引起材料的氧化或过热,同样影响处理效果。
冷却步骤是热处理的收尾步骤。
冷却方式对最终的热处理效果有着至关重要的影响。
常见的冷却方式有自然冷却、风冷、水冷等。
不同的材料和工艺需要不同的冷却方式,选择合适的冷却方式可以有效地提高材料的性能。
在热处理过程中,精确控制每个步骤的参数是至关重要的。
这需要丰富的实践经验和专业知识,以及对材料的深入了解。
通过合理的热处理,我们可以提高材料的硬度、韧性、强度等性能,以满足各种不同的需求。
热处理工艺过程虽然复杂,但只要掌握了其基本原理和操作方法,就可以根据具体需求进行合理的调整,实现对材料性能的有效控制。
随着科技的不断进步,热处理技术也在不断发展,未来我们有望看到更加高效、环保的热处理方法。
热处理工艺过程有那三个阶段组成

热处理工艺过程有那三个阶段组成:加热、保温和冷却。
影响铸铁石墨化的因素:(1)化学成分(2)冷却速度
?浇注位置的选择原则:①铸件的重要加工面应朝下或位于侧面:②铸件宽大平面应朝下:③面积较大的薄壁部分应置于铸型下部或垂直:④易形成缩孔的铸件,较厚部分置于上部或侧面:⑤应尽量减少型蕊的数量:⑥要便于安放型蕊、固定和排气:
冒口和冷铁的作用:冒口的作用主要是在铸件凝固期间进行补偿,还可用于调节铸件各部分的冷却速度。
冷铁的作用可以减少冒口的数量和尺寸,提高金属利用率;在铸件难以设置冒口的厚实部位,设置冷铁同样可防止产生缩孔和缩松;在铸件的适当部位安放冷铁可控制铸件的凝固顺序,增加冒口的有效补缩距离;使用冷铁可消除局部热应力,防止裂纹的产生。
可锻性常用金属的塑性和变形抗力来综合衡量。
自由锻增加余块的目的:简化外形,较为合理。
?
模锻件结构工艺性:(1)必须保证模锻件能从模膛中取出(2)模锻件形状应力求简单(3)零件上只有与其他机件配合的表面才需要进行机械加工,其他表面应设计为非加工表面(4)在零件结构允许的情况下,应尽量避免设计有深孔或多孔的结构(5)采用组合工艺。
板料冲压的基本工序可分为分离工序和成形工序两大类。
焊接接头由焊缝区、熔合区、热影响区构成。
防止和减少焊接变形的措施:(1)机构设计方面(2)焊接工艺方面A 反变形法B刚性固定法C合理安排焊接次序D焊前预热和焊后缓冷E焊后热处理(3)焊后矫形处理A机械矫形B火焰矫形
埋弧焊适合于平焊位置、长直焊缝和大直径环缝。
常用的电阻焊有电焊、缝焊和对焊。
电阻对焊和闪光对焊焊接过程特点。
热处理工艺
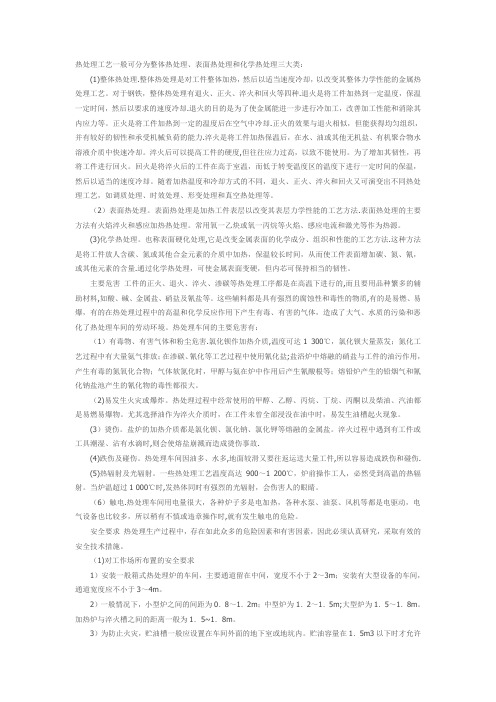
热处理工艺一般可分为整体热处理、表面热处理和化学热处理三大类:(1)整体热处理.整体热处理是对工件整体加热,然后以适当速度冷却,以改变其整体力学性能的金属热处理工艺。
对于钢铁,整体热处理有退火、正火、淬火和回火等四种.退火是将工件加热到一定温度,保温一定时间,然后以要求的速度冷却.退火的目的是为了使金属能进一步进行冷加工,改善加工性能和消除其内应力等。
正火是将工件加热到一定的温度后在空气中冷却.正火的效果与退火相似,但能获得均匀组织,并有较好的韧性和承受机械负荷的能力.淬火是将工件加热保温后,在水、油或其他无机盐、有机聚合物水溶液介质中快速冷却。
淬火后可以提高工件的硬度,但往往应力过高,以致不能使用。
为了增加其韧性,再将工件进行回火。
回火是将淬火后的工件在高于室温,而低于转变温度区的温度下进行一定时间的保温,然后以适当的速度冷却。
随着加热温度和冷却方式的不同,退火、正火、淬火和回火又可演变出不同热处理工艺,如调质处理、时效处理、形变处理和真空热处理等。
(2)表面热处理。
表面热处理是加热工件表层以改变其表层力学性能的工艺方法.表面热处理的主要方法有火焰淬火和感应加热热处理。
常用氧一乙炔或氧一丙烷等火焰、感应电流和激光等作为热源。
(3)化学热处理。
也称表面硬化处理,它是改变金属表面的化学成分、组织和性能的工艺方法.这种方法是将工件放人含碳、氮或其他合金元素的介质中加热,保温较长时间,从而使工件表面增加碳、氮、氰,或其他元素的含量.通过化学热处理,可使金属表面变硬,但内芯可保持相当的韧性。
主要危害工件的正火、退火、淬火、渗碳等热处理工序都是在高温下进行的,而且要用品种繁多的辅助材料,如酸、碱、金属盐、硝盐及氰盐等。
这些辅料都是具有强烈的腐蚀性和毒性的物质,有的是易燃、易爆,有的在热处理过程中的高温和化学反应作用下产生有毒、有害的气体,造成了大气、水质的污染和恶化了热处理车间的劳动环境。
热处理车间的主要危害有:(1)有毒物、有害气体和粉尘危害.氯化钡作加热介质,温度可达1 300℃,氯化钡大量蒸发;氮化工艺过程中有大量氨气排放;在渗碳、氰化等工艺过程中使用氰化盐;盐浴炉中熔融的硝盐与工件的油污作用,产生有毒的氮氧化合物;气体软氮化时,甲醇与氨在炉中作用后产生氰酸根等;熔铅炉产生的铅烟气和氰化钠盐池产生的氰化物的毒性都很大。
热处理的工艺曲线

热处理的工艺曲线热处理是一种通过加热和冷却来改变材料性质的工艺。
在热处理过程中,材料的性质会发生变化,这些变化可以通过工艺曲线来描述。
工艺曲线是描述热处理过程中温度和时间的变化的图表。
它可以帮助工程师和技术人员了解材料的性质如何随着温度和时间的变化而变化。
在热处理过程中,工艺曲线可以用来确定最佳的加热和冷却速率,以及最佳的温度和时间组合。
在热处理过程中,有三个主要的工艺曲线:加热曲线、保温曲线和冷却曲线。
加热曲线描述了材料在加热过程中的温度变化。
保温曲线描述了材料在保温过程中的温度变化。
冷却曲线描述了材料在冷却过程中的温度变化。
加热曲线通常是一个斜率较大的曲线,因为在加热过程中,材料的温度需要快速升高。
加热曲线的斜率取决于材料的类型和厚度。
对于某些材料,加热曲线可能需要更缓慢的斜率,以避免材料的变形或破裂。
保温曲线通常是一个水平的曲线,因为在保温过程中,材料的温度需要保持稳定。
保温曲线的时间取决于材料的类型和厚度。
对于某些材料,保温曲线可能需要更长的时间,以确保材料的性质得到充分改变。
冷却曲线通常是一个斜率较大的曲线,因为在冷却过程中,材料的温度需要快速降低。
冷却曲线的斜率取决于材料的类型和厚度。
对于某些材料,冷却曲线可能需要更缓慢的斜率,以避免材料的变形或破裂。
在热处理过程中,工艺曲线的设计非常重要。
如果工艺曲线设计不当,可能会导致材料的性质不符合要求。
因此,工程师和技术人员需要仔细地设计工艺曲线,以确保材料的性质得到充分改变。
总之,热处理的工艺曲线是描述热处理过程中温度和时间的变化的图表。
它可以帮助工程师和技术人员了解材料的性质如何随着温度和时间的变化而变化。
在热处理过程中,工艺曲线的设计非常重要,需要仔细地设计,以确保材料的性质得到充分改变。
- 1、下载文档前请自行甄别文档内容的完整性,平台不提供额外的编辑、内容补充、找答案等附加服务。
- 2、"仅部分预览"的文档,不可在线预览部分如存在完整性等问题,可反馈申请退款(可完整预览的文档不适用该条件!)。
- 3、如文档侵犯您的权益,请联系客服反馈,我们会尽快为您处理(人工客服工作时间:9:00-18:30)。
2. 3.
•
选择依据:一般依据热处理所需要的加热温度及金属和 液体介质的化学性质,即金属与液体介质不能发生化学 反应。例如,铝合金采用硝酸钠和硝酸钾混合盐,在 550℃以下使用。工具钢淬火加热采用氯化钾和氯化钠等 的混合盐或单盐,在650~1350℃使用。等温淬火一般用 硝盐或苛性碱。低温回火则用油类。
感应加热
金属加热
直接加热 热源
电阻 电磁波 低能粒子 真空
电 阻 加 热 电 接 触 加 热 电 解 液 加 热 红 外 线 加 热 感 应 加 热 激 光 加 热 电 子 束 加 热 等 离 子 体 加 热 低 压 充 气 的 高 纯 度 的 金 属 传 导
间接加热 热源 介质
固体
固 态 颗 粒 流 动 粒 子
– 加热设备的影响 为了正确的选定与执行加热规范,必须要考虑设备条件。因为 加热设备的介质状况;设备的输出功率大小;炉膛内有效加热 区范围及温度均匀性等均影响加热工艺的制订和实施。加热介 质直接影响工件的加热速度和表面质量,设备的输出功率决定 了工件的装炉量以及生产率,对加热速度及可达到的加热温度 也有重要影响。 有效加热区:在炉膛内能够保证由给定热处理加热工艺所要求的 加热温度的装料区域。加热炉内温度一般是不均匀的,只有在 炉膛内有效加热区中装料作业才能达到预定的控温经度及均匀 度要求。
0~1300
0~1600 -40~900
0~1600
0~1800
0~1600 ±1.5
0~1600 ±4
高温抗氧化性好, 不适于还原气氛
高温抗氧化性好, 不适于还原气氛
-40~1100 在氧化、中性、 40~1200 真空中使用 ±2.5 -40~400 40~350 ±1.5 在氧化、中性、 真空中使用
– 传感器(热电偶) – 传输线路(补偿导线) – 显示仪表(指针式、数字式)
• 当检测系统某一部分出现故障或者更换某 个部分后,容易出现显示温度与实际温度 之间产生偏差:温度显示偏低则过热,显 示偏高则欠热。
如何使测温准确
• 热电偶 • 热电偶的工作原理是:两种不 同成份的导体,一端焊接在一 起,另一端接显示仪表,形成 回路,直接测量端叫工作端 (热端),接线端子端叫冷端, 当热端和冷端存在温差时,就 会在回路里产生热电流,接上 显示仪表,仪表上就会指示所 产生的热电动势的对应温度值, 电动势随温度升高而增长。 • 热电动势的大小只和热电偶的 材质以及两端的温度有关,和 热电偶的长短粗细无关。
– 控制炉内气氛的成分 – 真空中加热 – 盐浴或流态床中加热 – 防护涂层
2.5.1加热时的组织缺陷
• 加热时的组织缺陷有欠热、过热、过烧。 1、欠热:也叫加热不足,是由于加热温度过低或
加热时间太短,未充分进行奥氏体化而引起的组
织缺陷。例如钢在淬火后出现软点和硬度不均的
现象,在退火或限于100mm以下;
• • • • • • • •
综合计算方法: t=C1C2C3C4D (8-4) t——加热时间,min; C1——加热介质系数; C2——材料系数; C3——工件形状系数; C4——工件间隔系数; D——工件有效厚度,mm.
表2-1 加热炉的介质系数(C1)
D>h
>h
2.4.3加热速度与加热制度 • 希望快速加热 根据等温动力学曲线可知,快速加热时: 速度快,相变温度高 晶粒细——性能好 表面氧化、脱碳少,表面质量好 • 问题: 内应力> 弹性极限——变形、扭曲 内应力> 强度极限——开裂 合金钢、高合金钢导热性差,所以要分段加热。 各种加热方式如下图所示。
化学成分 临界点 热处理工艺要求 加热温度的确定 对成分与结构的 要求及控制 对晶粒度的控制 小批试验 性能鉴定,转变 产物形态与性能 最优的加热温度规范 原材料成分、组织、加工状态 热处理应力与变形开裂的控制
图2-2
加热温度优选的程序图
加热温度的确定
• ①据 Fe--C 相图, • ② 查有关热处理手册(常用), • ③ 通过实践试验。
T
+ -
-40~350
思考:更高温度、低温、还原性气氛下,使用何种热电偶?
热电偶使用注意事项
• 使用前必须经过实验室检定,确定出不同 温度下的误差值。(如何检定?) • 现场安装与校准由专职人员进行,不允许 擅自移位和移动。 • 必须安装在炉温有代表性的部位,不能与 炉门和加热元件太近 • 多支热电偶测温时,插入炉膛的深度必须 一致。 • 铠装热电偶每次使用前要检查保护套管的 完整性。
液体
金 盐 油 属 浴 浴 浴
气体
空 保 护 气 气 氛 可 控 气 氛 高 温 火 烟
图2-1
工业上金属加热的方式
2.2 间接加热的加热介质种类
2.2.1气体介质加热 • 这种加热方法的特点是被加热金属周围的介质为气体。是 热处理工艺中应用最广泛的加热方法。
• 气体介质中加热时,由燃料燃烧或加热体产生的热量是通 过对流和辐射传递给被加热的金属。
3、过烧 • 由于加热温度过高,已经接近固相线,使得奥氏体晶界 发生了局部熔化,使奥氏体晶界严重氧化,这种现象称 为过烧。 • 产生了过烧的工件无法挽回,只能报费。
组织缺陷产生的途径
• • • • 原因肯定是温度过低或过高了。 设计的工艺温度错了?(制定工艺) 操作人员不按测温仪表指示操作?(管理) 温度测量显示系统出现错误——误差
2.4.2加热时间的确定 零件加热时的温度与时间关系如图2-3。
– 加热时间概念:热处理加热过程的时间(t加)是 工件升温时间(t升)、透热时间(t透)、与保温 时间(t保)的总和。
t加= t升+ t透+ t保
(8-1)
图2-3 工件加热时的温度与时间关系
图2-4 在盐浴炉中1000 ℃加热钢棒的时间-温度曲线 实线——表面温度,虚线——中心温度
除冶炼及热加工过程中存在的偏析、粗大自由铁
素体、魏氏组织、网状碳化物等,致使最终性能 不能满足要求。
2、过热 • 热处理生产中应严格控制奥氏体晶粒度, 由于热处理操作不当或者其他原因,加热 时使晶粒度超过规定的大小,称为过热。 • 一般规律:加热温度>预定奥氏体化温度 +150℃.碳钢及合金钢>950 ℃ ;工具钢及 高碳铬轴承钢>1000 ℃ 。 • 过热在淬火组织中,表现为马氏体组织粗 大,引起变形和开裂; • 在正火组织中,容易形成魏氏组织; • 均使钢的性能变化,特别是使韧性严重下 降。 • 过热的工件必须重新返修。
热处理生产常用的热电偶
热电 偶名 称 分 热电极材料 度 号 极性 化学成分/% 使用温度范围 误差(≤)主要 特点 /℃ 长期 短期
铂铑 10-铂
铂铑铂铑 镍铬镍硅 铜-康 铜
S
B K
+
+ + -
Pt90-Rh10
Pt Pt70-Rh30 Pt94-Rh6 Cr10Si0.4Ni9 Si3.0-Ni97 Cu100 Cu55-Ni45
– 在600~700℃以下时,对流传热是主要的传热方式,为了使炉内 温度均匀,当炉子体积较大时需要对气体进行强制循环。 – 在700~800℃以上时,辐射是主要的传热方式,此时气体介质的 扰动对加热速度实际没什么影响,不需要强制循环。
• 气体的种类:根据被加热金属的种类和外在质量要求,可 分别采用氧化性的空气、惰性的保护气氛、可控制的还原 性气氛和真空。
工件比炉膛长不超过1/3
工件与炉膛长度刚好相等
炉 内 温 度
工件比炉膛长不超过1/3
炉膛长度
• 作业2:
– 1.查找有关“有效加热区”的标准,以便更好 地理解“有效加热区”的概念。 – 2.查找有关“晶粒度分级”的标准。
2.4.1加热温度的确定 确定加热温度时,金属及合金的相变临界点、再结晶温度 等是基本的理论依据,但还不能就凭此来确定各种不同热 处理工艺的加热温度,而应当根据具体零件热处理的目的 来决定,因此,选择加热温度是一个较复杂的问题。
图2-8 高温入炉温度时间曲线
• 阶梯加热:预热可以缩短高温加热时间,减少热应力, 常用于大型及高合金钢工件的退火、正火、淬火等。
图2-9 阶梯加热时间-温度曲线
2.5加热缺陷及防护措施
• 加热缺陷
– 欠热、过热、过烧 – 变形、开裂 – 氧化、脱碳、增碳 – 吸气(氧、氢、氮)(有色金属)
• 防护措施
第二章 热处理加热及加热设备
• 金属热处理工艺一般是由加热、保温和冷却过程组成 的,加热是各种热处理工艺作业中的第一道工序。通 过加热:
– 可以改变金属材料的热力学状态、晶体结构、组织形态、物 理化学性质及化学成分分布等,从而实现预期的组织结构以 致化学成分的改变,获得所需要的性能。即直接影响其内在 质量。 – 同时,由于金属在一定的环境介质中加热时表面与介质之间 发生一系列化学反应,会造成金属表面的某些缺陷(氧化、 脱碳、腐蚀等),所以加热也会影响金属的外部质量。 – 在产品生产中,在保证质量的前提下,如何降低成本永远是 要特别考虑的问题。热处理的成本中60~80%是加热时的能源 消耗,所以加热时如何降低能耗,提高效率是热处理生产企 业提高竞争力的根本所在。
加热炉类型 箱式炉 炉温 介质系数 800 1 盐浴炉 800 0.5 盐浴炉 1200 0.125
表2-2 不同钢种的材料系数(C2) 钢种 材料系 数 低碳钢 1 中碳钢 1.2 高碳钢 1.4 一般合 金钢 1.5 高合金 钢 2
工件形状系数(C3)
工件间隔系数(C4)
有效厚度的确定原则与计算(D)
2.1 加热方式 • 金属加热的方式分为直接加热和间接加热两类。
• 直接加热是利用金属内部的电能-热能转换, 电磁-热能转换,低能粒子轰击的能量-热能转 换,不需要通过加热介质向被加热金属传递热 量。