不同促进剂对天然橡胶性能影响
活性氧化锌和传统氧化锌对天然橡胶胶料性能的影响

3 结论
在生胶和添加剂不变的情况下,硫化胶中分别加 入同等份数的活性氧化锌和传统氧化锌。结果表明加 入活性氧化锌的胶料邵氏硬度、定伸应力、拉伸撕裂 强度都得到提高,交联密度增大,硫化时间缩短,门 尼黏度提升。总之加入活性氧化锌的胶料各项性能均 优于加入传统氧化锌的胶料,而且活性氧化锌的生产 成本远低于传统氧化锌。综上,活性氧化锌可以代替 传统氧化锌在橡胶生产工艺中的应用。
入活性氧化锌后胶料的黏度有所提升,是因为活性氧 化锌相对与传统氧化锌体积较小,能够在炼胶的过程 中更加完整的接触到其他配合剂的表面,使胶料反应 更佳充分,从而加速了分子的生成,使胶料的黏度有 所提升。
对比 t10、t50、t90 可以发现加入活性氧化锌的胶料 比传统氧化锌的胶料硫化时间有所缩短。这是由于活 性氧化锌较大的表面结构可以增强橡胶大分子链的物 理吸附和化学吸附,从而加速促进剂的反应,缩短了 硫化时间。Fmax-FL 的数值可以反应分子的交联密度 [6], 对 比 Fmax-FL 的 数 值 可 以 发 现, 加 入 活 性 氧 化 锌 的数值偏高。活性氧化锌具有极强的表面能,它的添 加能够起到促进硫化反应的作用,随着表面能的增大 会使自由基产生的速度变快,使自由基与胶料分子快 速结合,交联密度增大。最终导致胶料的硫化特性整 体提高。
2.2 门尼黏度和硫化特性
活性氧化锌和传统氧化锌对天然橡胶门尼黏度和 硫化特性的影响如下表 3、表 4 所示。
对比表 3 和表 4 可知,加入活性氧化锌的胶料比 加入传统氧化锌的胶料它的门尼黏度升高 2 个单位, 变化不显著。门尼黏度是反映橡胶加工性能的好坏和 分 子 量 高 低 及 分 布 范 围 宽 窄 的 一 种 指 标[5]。 氧 化 锌 一 般是作为活化剂加入,所以对黏度影响不明显。但加
橡胶件实验报告

一、实验目的本次实验旨在通过实际操作,了解橡胶件的制备过程,掌握橡胶的基本性能测试方法,并分析不同橡胶配方对橡胶件性能的影响。
二、实验原理橡胶是一种具有高弹性、耐磨性、耐腐蚀性等特性的高分子材料,广泛应用于汽车、机械、电子、建筑等领域。
橡胶件的制备过程主要包括混炼、成型、硫化等步骤。
通过调整橡胶配方和工艺参数,可以改变橡胶件的性能。
三、实验材料与设备材料:1. 天然橡胶2. 硫磺3. 促进剂4. 填料(如炭黑)5. 油脂设备:1. 混炼机2. 压缩机3. 硫化罐4. 万能力学试验机5. 摩擦系数试验机四、实验步骤1. 混炼:将天然橡胶、硫磺、促进剂、填料和油脂等材料按照一定比例投入混炼机中,进行充分混炼。
2. 成型:将混炼好的橡胶料投入压缩机中,进行压制成型,制成所需形状的橡胶件。
3. 硫化:将成型后的橡胶件放入硫化罐中,在特定温度和压力下进行硫化,使橡胶分子结构交联,提高橡胶件的性能。
4. 性能测试:- 拉伸强度测试:将硫化后的橡胶件放置在万能力学试验机上,按照规定速度拉伸至断裂,记录最大拉伸强度。
- 压缩永久变形测试:将硫化后的橡胶件放置在压缩试验机上,在一定压力下压缩一定时间,记录压缩后的变形量。
- 摩擦系数测试:将硫化后的橡胶件放置在摩擦系数试验机上,测试其与不同材质表面的摩擦系数。
五、实验结果与分析1. 拉伸强度:实验结果显示,不同配方的橡胶件拉伸强度存在差异。
增加填料含量可以提高橡胶件的拉伸强度,但过高的填料含量会导致拉伸强度下降。
2. 压缩永久变形:实验结果显示,增加硫磺和促进剂的含量可以提高橡胶件的压缩永久变形性能,但过高的含量会导致变形性能下降。
3. 摩擦系数:实验结果显示,增加炭黑含量可以提高橡胶件的摩擦系数,提高其耐磨性能。
六、结论通过本次实验,我们掌握了橡胶件的制备过程和性能测试方法。
不同配方的橡胶件具有不同的性能,通过调整配方和工艺参数,可以满足不同应用场景的需求。
七、实验建议1. 在进行橡胶件制备时,应注意控制温度、压力和时间等工艺参数,以保证橡胶件的性能。
助交联剂HVA-2对天然橡胶性能的影响

1 . 2 基本 配方
品) 按G B/ T 1 6 8 8 -2 0 0 8 ( ( 硫化 橡胶 伸张疲 劳的测 定》 测试 伸 张疲劳性 能 , 应变 为 1 0 0 %, 固定 伸 张 1 0
万次。
NR 1 0 0 , 炭黑N2 2 0 4 0 , 氧 化锌
( 1 ) 硫化 特 性 。采 用MR — C3 型无 转子 硫化 仪
( 北京环 峰化工机械 实验厂产 品) 测试硫 化特性 。 ( 2 ) 物 理 性 能 。 采 用 微 控 电子 万 能 试 验 机 ( 深 圳 市新 三 思材 料检 测 有 限公 司产 品) 按GB / T
5 2 8 -2 0 0 9 《 硫 化橡 胶 或 热 塑性 橡 胶 拉伸 应 力 应
3 . 5 , 硬 脂
( 3 ) 耐 热 氧 老化 性 能 。采 用GT 一 7 0 1 固体 石 蜡 2 , 硫黄
2 , 防 老剂 R D 1 , 防 老剂 4 0 2 0
空气老 化箱 ( 高铁 检 测仪 器有 限公 司 产 品) 按GB / T 3 5 1 2 —2 0 1 4 《 硫 化橡 胶或 热 塑性橡 胶 热 空气 加 速 老化 和耐热试 验 》 测 试耐 热氧老 化性 能 , 老 化温
1 0 0 0 2 9 ; 3 . 北 京化 工 大 学 北 京市 先 进 弹性 体 工程 技 术 研究 中心 , 北 京 1 0 0 0 2 9 )
摘要 : 研 究 助 交 联剂 HV A一 2 在硫 黄 硫 化 体 系 下 对 天然 橡 胶 ( NR ) 性 能 的影 响 。 结果 表 明 : 加 入 助 交 联 剂HV A一 2 后,
不同硫化体系对天然橡胶动静态性能的影响

不同硫化体系对天然橡胶动静态性能的影响天然橡胶是一种广泛应用于橡胶制品中的重要原材料,其性能的表现与硫化体系密切相关。
硫化体系是指硫化剂与橡胶中的其他成分(如促进剂、防老剂等)之间的相互作用关系。
不同硫化体系对天然橡胶的动静态性能会产生明显影响,下面将从几个方面进行详细介绍。
首先,硫化体系对天然橡胶的硫化速度和硫化程度具有重要影响。
硫化速度是指硫化剂与橡胶中的双键发生反应的速度,而硫化程度则是指橡胶中的双键被硫化剂反应后形成交联结构的程度。
不同硫化体系对硫化速度和硫化程度的影响不同,从而影响天然橡胶的硬度、拉伸强度和断裂伸长率等物理性能。
例如,采用过氧化物硫化体系可以实现较快的硫化速度和较高的硫化程度,使得天然橡胶的硬度增加、拉伸强度和断裂伸长率下降。
其次,不同硫化体系对天然橡胶的热老化性能具有显著影响。
热老化是指橡胶在高温环境下发生的化学变化和物理性能的变化。
硫化体系中的防老剂可以降低天然橡胶的热老化速度,提高其抗热老化性能。
例如,添加亚磺酰胺类、腈酮类和脂肪酰胺类防老剂的硫化体系可以有效降低天然橡胶的热老化速度,提高其热稳定性和抗老化性能。
此外,不同硫化体系还会对天然橡胶的动态性能产生影响。
动态性能主要包括橡胶的弹性模量、损耗因子和耐疲劳性能等。
硫化体系中的促进剂对天然橡胶的动态性能具有关键影响。
例如,采用低温快速硫化体系可以提高天然橡胶的动态弹性模量和耐疲劳性能。
动态性能的改善对于橡胶制品的耐用性和舒适性具有重要意义。
综上所述,硫化体系对天然橡胶的动静态性能有着显著影响。
硫化体系的选择可以通过调节硫化速度、硫化程度、抗热老化性能和动态性能等方面的参数,来实现对天然橡胶性能的调控。
因此,在橡胶制品的开发和应用过程中,合理选择硫化体系具有重要意义,可以使得天然橡胶在不同应用场景下更好地发挥其性能优势。
橡胶促进剂的分类

橡胶促进剂的分类硫化促进剂简称为促进剂。
凡能加快硫化反应速度,缩短硫化时间,降低硫化反应温度,减少硫化剂用量产能提高或改善硫胶有物理机械性能的配合剂,称为硫化促进剂。
应用促进剂可以提高橡胶制品的生产效率,降低产品成本,可以提高的改善制品的物理机械性能,使厚制品质量均匀,并改善制品的外观质量并使色泽鲜艳。
目前橡胶工业采用的促进剂种类很多,按其性质和化学组成可以分为两大类:无机促进剂、有机促进剂。
无机促进剂使用最早,但因促进效果小,硫化胶性能差,除在外别情况仍少量使用以外,绝大多数场合已为有机促进剂所取代。
有机促进剂促进效果大,硫化特性好,硫化胶有物理机械性能优良,因而发展迅速。
随着合成橡胶品种和用途有不断发展,现有促进剂名目日益繁杂,但目前最常用的亦不过数十种。
促进剂按其化学结构、促进效果大小、以及与硫化氯反应所呈现和酸碱性分类。
根据化学结构的不同,促进剂分可以为噻唑类、秋兰姆类、次磺酰胺类、胍类、二硫代氨基甲酸盐类、醛胺类、黄原酸盐类和硫脲类等八大类。
一、噻唑类这是有机促进剂中较早的品种。
属于酸性促进剂。
其特点是具有较高的硫化活性,能赋予硫化胶良好的耐老化性能和耐疲劳性能。
所以在橡胶工业中应用比较广泛,耗用量较大。
主要品种有如下两种。
(1)2硫醇基苯并噻唑商品名称为促进剂M。
本品为淡黄色粉末,味极苦,无毒,贮藏稳定。
为通用型促进剂,对天然橡胶及二烯类通用合成橡胶具有快速促进作用,硫化平坦性较好,硫化临界温度为125℃,混炼时有脑炎烧的可能。
在橡胶中容易分散,不污染,但不适于食品用橡胶制品。
用作第一促进剂的用量为1~2份,作第二促进剂的用量为0.2~0.5份。
还可用于天然橡胶的塑解剂。
(2)二硫化二苯并噻唑商品名称为促进剂DM。
本品为淡黄色粉末,味苦,无毒,贮藏时稳定。
其特性和用途与M相似,但硫化临界温度为130℃。
140℃以上活性增大,有较好的后效性,硫化操作安全。
常与其它促进剂并用以提高其活性。
新型促进剂STU对天然橡胶性能的影响

中 图分 类 号 : T Q3 3 0 . 3 8 5 ; T Q3 3 2
文 献 标 志码 : A
文章编号: 1 0 0 0 — 8 9 0 X( 2 0 1 3 ) 0 4 — 0 2 1 6 - 0 5
促进剂品 种— T — — — —
基 金 项 目: 国家 自然 科 学 基 金 资 助 项 目 ( 5 0 6 0 8 0 3 4 和
— —
5 0 8 7 3 0 3 6 ) ; 华 南 理 工 大学 中央 高 校 基 本 科 研 业 务 费 专 项 资 金 资
助项 目 ( 2 0 0 9 Z M0 3 O 6 ) ; 广 东 省 大 学 生创 新 性 实 验 计 划 项 目
( S 1 0 1 0 5 6 1 0 4 2 )
作者简介: 杨树颜( 1 9 8 4 一) , 男, 广东茂名人 , 博士, 现 在 东 莞
理工学院工作, 主要 从 事 固 体 聚合 物 电解 质 的 制备 及 其 性 能 的应
用研究。
*通 信 联 系人
第 4期
杨树 颜 等 . 新型促进剂 S T U 对 天 然橡 胶性 能 的影 响
2 1 6
橡
胶
工
业
2 0 1 3 年第 6 O卷
新型 促 进 剂 S T U对 天 然橡 胶 性 能 的影 响
杨树 颜 , 刘 岚 , 罗远 芳 , 贾德 民, 刘亚蓝 , 林 晓 萍
( 华 南 理 工 大 学 材 料 科 学 与工 程 学 院 , 广 东 广 州 5 1 0 6 4 0 )
恒粘剂2-巯基苯并噻唑对天然橡胶性能的影响

5 7 1 7 3 7 1 2 . 海 南大 学 应用 科 技学 院 , 海南 儋州
5 7 1 7 3 7 ; 3 . 海 南 大 学 材 料 与 化 工 学 院
摘要: 采用 恒 粘 剂 2 一 巯基苯并噻唑( MT) 制备 恒粘天然 橡胶 ( C VNR) , 研究其性 能 , 并 与 传 统 的 恒 粘 剂 盐 酸 羟 胺
备C VNR, 研究 其 性 能 , 并 与传 统 的 恒 粘 剂 盐 酸
羟胺 ( HH) 进行对 比。
在贮 存 过程 中, 分子 间 的醛基发 生 缩合 反应 , 也 可
能 2个 醛基 与 1个 氨 基 酸 的 氨 基缩 合 而 交 联 , 导
1 实 验
致橡 胶 的粘 度增 大 。其后 研究 者们 相继 提 出 了其
第 5 期 ห้องสมุดไป่ตู้
段 志松 等 . 恒粘剂 2 一 巯 基 苯 并 噻 唑 对 天 然 橡 胶 性 能 的影 响
2 7 9
恒粘剂 2 m 巯 基 苯 并 噻 唑对 天 然 橡胶 性 能 的影 响
段 志松 , 廖 建和孙 , 廖禄 生 , 陈永平。 , 从琴 琴 , 廖 巧 干。
( 1 . 海南 大 学 农学 院 , 海南 儋州
毒 的恒 粘剂 尤为 重要 。 本 工作采 用 恒粘剂 2 一 巯 基 苯并 噻 唑 ( MT) 制
化后 的 NR在 贮 存 和 运 输 过 程 中 门尼 粘 度 不 稳
定, 会增大塑炼、 混 炼 和挤 出工 艺难 度 , 延 长 混 炼
时间, 从而导致产 品出现质量缺陷、 生 产 效 率 降 低、 生 产成 本增 加 、 经济 效益 降低 。我 国 NR在很
活性氧化锌对天然橡胶顺丁橡胶丁苯橡胶胶料性能的影响

活性氧化锌 /氧化锌并用比
0 /5 2 /3 2. 5 /2. 5 3 /2 4 /1
16. 8 12. 0 15. 0 15. 0 14. 0
6. 1 5. 0 5. 0 5. 0 5. 0
51
50
49
47 47
8. 80 6. 93 6. 71 6. 67 6. 64
20. 14 19. 23 18. 39 18. 12 18. 36
表 3 为活 性氧化 锌 /氧 化锌 并用 比对 NR / BR / SBR并用胶硫化特性和物理性能的影响 。
表 3 活性氧化锌 /氧化锌并用比对 NR / BR / SBR 并用胶硫化特性和物理性能的影响
项 目
t90 /m in t10 /m in 邵尔 A 型硬度 /度 300%定伸应力 /MPa 拉伸强度 /MPa 拉断伸长率 / % 拉断永久变形 / % 撕裂强度 / ( kN ·m - 1 )
活性氧化锌 /氧化锌并用比 0 /5 2 /3 2. 5 /2. 5 3 /2 4 /1
6. 4 6. 1 6. 1 6. 1 6. 1
3. 6 3. 5 3. 5 3. 6 3. 6
65
61
63
63 63
9. 06 9. 92 10. 01 10. 29 10. 46
200 240 220 220 240
1 实验 1. 1 原材料
天然橡胶 (NR ) SCR5,海南省八一橡胶厂产 品 ;顺丁橡胶 (BR ) ,北京燕化石油化工股份有限 公司产品 ;丁苯橡胶 ( SBR ) ,中国石油兰州石化公 司产品 ;活性氧化锌均由广东南海林岳橡胶厂提 供 ;其它配合剂均为橡胶工业常用配合剂 。 1. 2 配方
NR /BR并用胶配方 : NR 70 , BR 30,防老 剂 RD 1 ,促进剂 NOB S 0. 9 ,防老剂 4010NA 115,促进剂 TM TD 2. 4,氧化锌 4 ,高耐磨炭黑 35,通用炭黑 10,硬脂酸 2. 5,硫黄 0. 9。
橡胶助剂实用手册

橡胶助剂实用手册摘要:一、橡胶助剂的概述二、橡胶助剂的分类三、橡胶助剂的选用原则四、橡胶助剂的应用实例五、橡胶助剂的发展趋势正文:一、橡胶助剂的概述橡胶助剂,顾名思义,是指在橡胶制品生产过程中,为了改善橡胶的性能、加工性、耐久性等,而加入的一种或多种物质。
橡胶助剂在橡胶制品中的应用,不仅能够提高橡胶制品的性能,同时还能够降低生产成本,提高生产效率。
二、橡胶助剂的分类橡胶助剂按照其功能和作用,主要可以分为以下几类:硫化橡胶助剂、促进剂、加速剂、填充剂、增塑剂、防老剂、耐磨剂、颜料等。
1.硫化橡胶助剂:主要用于提高橡胶的硫化程度,改善硫化橡胶的性能。
2.促进剂和加速剂:主要用于加快橡胶的硫化速度,提高生产效率。
3.填充剂:主要用于增加橡胶的体积,改善橡胶的加工性能。
4.增塑剂:主要用于提高橡胶的柔韧性和弹性。
5.防老剂:主要用于延缓橡胶的老化,提高橡胶的使用寿命。
6.耐磨剂:主要用于提高橡胶的耐磨性能。
7.颜料:主要用于改变橡胶的颜色,提高橡胶的美观性。
三、橡胶助剂的选用原则在选用橡胶助剂时,需要根据橡胶制品的性能要求、加工工艺和使用环境等因素进行综合考虑。
具体原则如下:1.满足橡胶制品的性能要求:根据橡胶制品的使用环境和性能要求,选择能够满足这些要求的橡胶助剂。
2.考虑橡胶助剂的相容性:选择与橡胶相容性好的橡胶助剂,以保证橡胶制品的稳定性和使用寿命。
3.考虑橡胶助剂的加工性能:选择易于加工和分散的橡胶助剂,以提高生产效率。
4.考虑橡胶助剂的环保性:选择环保的橡胶助剂,以减少对环境和人体的危害。
四、橡胶助剂的应用实例以轮胎为例,轮胎的主要原料是天然橡胶和合成橡胶,为了提高轮胎的性能,通常需要加入硫化橡胶助剂、促进剂、加速剂、填充剂、增塑剂、防老剂、耐磨剂等橡胶助剂。
五、橡胶助剂的发展趋势随着科技的发展和环保的要求,橡胶助剂的发展趋势主要表现在以下几个方面:1.环保型橡胶助剂:随着对环境保护的重视,环保型橡胶助剂的需求将会越来越大。
硫黄与促进剂的比例对天然橡胶交联结构、返原和强度的影响

9
硫 黄 与促 进 剂 的 比例 对 天 然橡 胶 交联 结构 、 返 原 和 强 度 的 影 响
李 亚 平 编译
通 过在 橡胶 分 子链之 间形 成硫 键 而发生硫 黄 硫 化 。通 常 ,网络 由单 硫 、双 硫 和 多 硫 键 混 合 形 成 ,它 们 的相对 分 布 主要 取 决 于 胶 料 中使 用 的硫 黄 与促 进剂 的 比例 (S/A)、促 进剂 类 型 、硫 化 温度 和硫化 时 间 。在硫 化 早 期 阶 段 ,形 成 了 长 的多 硫 键 。在 硫 化过 程 中有 两 个 过 程 :初 始 多硫 键 的脱 硫 和热 降解 。在 脱 硫 过 程 产 生更 多交 联 键 ,从 而 生成较 短 的硫键 ,而 交联 键 的减 少 是 由于 主链 改 性 的热 降解 引起 的 。一旦 开始 破坏 的交 联键 比形 成 的多 ,净 交联键 减少 ,这 被称 为硫化 返 原 。已经 进 行 了大量 的研究 来 评估 天然 橡胶 (NR)配方 、交 联 结构 和不 同硫 化胶 最终性 能 之 间的关 系 。提 出 了 键 解 离 能 是 不 同 硫 化 胶 性 能 变 化 的 根 本 原 因 , 因为键 解 离能 随着 交 联键 内硫原 子数 量 的增加 而 降低 。一般 来 说 ,当采 用 高 S/A 比例 (常 规 硫 化 体 系 ,CV)时得 到 的硫 化胶 多硫 键 比例 高 ,更容 易 产 生热 老化 。总 之 ,由于多 硫键 的键 能较 低 ,与那 些 具有 高单 硫或 双 硫 键 比例 的硫 化 胶 相 比 ,这 些 由高 S/A 比例得 到 的硫 化 胶 的 硫 化返 原 程 度 高 得 多 ,而且其 老化 性能 的保 留率 比较 差 。同时 ,相 对 较弱 ,在应 变下 更容 易断 裂 ,以及能 生成 多硫 键 的能力 使得硫 化胶 具有 较 高 的机 械强 度 。该过 程 可 以 降低 应 力集 中 (否 则 可 能会 引 发破 坏 ),并 形 成 更均 匀 的应力分 布 。使用 低含 量 的硫 黄和相 应 的高含量 的促 进剂 (有 效硫 化体 系 ,EV)成功 获 得 了单硫键 和双硫 键 比例 高 的硫 化 胶 ,具 有 较 高 的 热 稳定性 ,但 是 以牺牲 机械 强度 为代 价 。
橡胶促进剂的分类
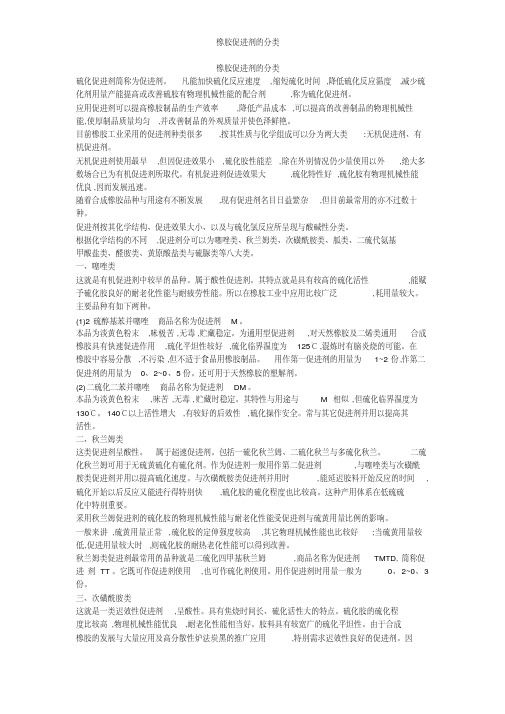
橡胶促进剂的分类硫化促进剂简称为促进剂。
凡能加快硫化反应速度,缩短硫化时间,降低硫化反应温度,减少硫化剂用量产能提高或改善硫胶有物理机械性能的配合剂,称为硫化促进剂。
应用促进剂可以提高橡胶制品的生产效率,降低产品成本,可以提高的改善制品的物理机械性能,使厚制品质量均匀,并改善制品的外观质量并使色泽鲜艳。
目前橡胶工业采用的促进剂种类很多,按其性质与化学组成可以分为两大类:无机促进剂、有机促进剂。
无机促进剂使用最早,但因促进效果小,硫化胶性能差,除在外别情况仍少量使用以外,绝大多数场合已为有机促进剂所取代。
有机促进剂促进效果大,硫化特性好,硫化胶有物理机械性能优良,因而发展迅速。
随着合成橡胶品种与用途有不断发展,现有促进剂名目日益繁杂,但目前最常用的亦不过数十种。
促进剂按其化学结构、促进效果大小、以及与硫化氯反应所呈现与酸碱性分类。
根据化学结构的不同,促进剂分可以为噻唑类、秋兰姆类、次磺酰胺类、胍类、二硫代氨基甲酸盐类、醛胺类、黄原酸盐类与硫脲类等八大类。
一、噻唑类这就是有机促进剂中较早的品种。
属于酸性促进剂。
其特点就是具有较高的硫化活性,能赋予硫化胶良好的耐老化性能与耐疲劳性能。
所以在橡胶工业中应用比较广泛,耗用量较大。
主要品种有如下两种。
(1)2硫醇基苯并噻唑商品名称为促进剂M。
本品为淡黄色粉末,味极苦,无毒,贮藏稳定。
为通用型促进剂,对天然橡胶及二烯类通用合成橡胶具有快速促进作用,硫化平坦性较好,硫化临界温度为125℃,混炼时有脑炎烧的可能。
在橡胶中容易分散,不污染,但不适于食品用橡胶制品。
用作第一促进剂的用量为1~2份,作第二促进剂的用量为0、2~0、5份。
还可用于天然橡胶的塑解剂。
(2)二硫化二苯并噻唑商品名称为促进剂DM。
本品为淡黄色粉末,味苦,无毒,贮藏时稳定。
其特性与用途与M相似,但硫化临界温度为130℃。
140℃以上活性增大,有较好的后效性,硫化操作安全。
常与其它促进剂并用以提高其活性。
促进剂DPG在白炭黑填充天然橡胶胶料混炼中加料顺序对胶料性能的影响
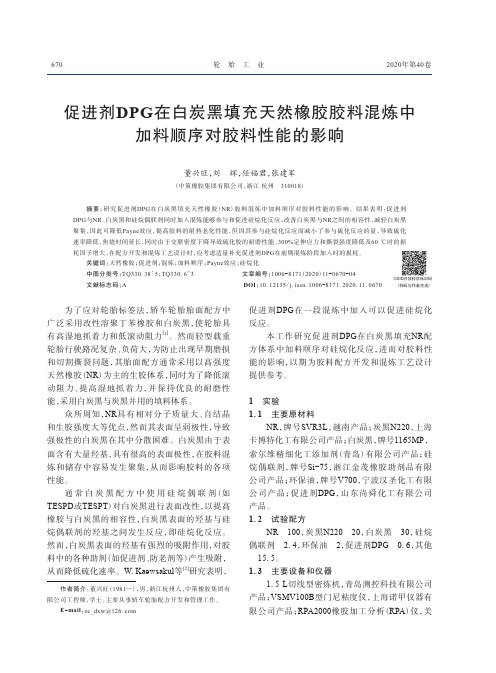
促进剂DPG在白炭黑填充天然橡胶胶料混炼中加料顺序对胶料性能的影响董兴旺,刘 辉,任福君,张建军(中策橡胶集团有限公司,浙江杭州 310018)摘要:研究促进剂DPG在白炭黑填充天然橡胶(NR)胶料混炼中加料顺序对胶料性能的影响。
结果表明:促进剂DPG与NR、白炭黑和硅烷偶联剂同时加入混炼能够参与和促进硅烷化反应,改善白炭黑与NR之间的相容性,减轻白炭黑聚集,因此可降低Payne效应,提高胶料的耐热老化性能,但因其参与硅烷化反应而减小了参与硫化反应的量,导致硫化速率降低,焦烧时间延长,同时由于交联密度下降导致硫化胶的耐磨性能、300%定伸应力和撕裂强度降低及60 ℃时的损耗因子增大,在配方开发和混炼工艺设计时,应考虑适量补充促进剂DPG在前期混炼阶段加入时的损耗。
关键词:天然橡胶;促进剂;混炼;加料顺序;Payne效应;硅烷化中图分类号:TQ330.38+5;TQ330.6+3 文章编号:1006-8171(2020)11-0670-04文献标志码:A DOI:10.12135/j.issn.1006-8171.2020.11.0670为了应对轮胎标签法,轿车轮胎胎面配方中广泛采用改性溶聚丁苯橡胶和白炭黑,使轮胎具有高湿地抓着力和低滚动阻力[1]。
然而轻型载重轮胎行驶路况复杂、负荷大,为防止出现早期磨损和切割撕裂问题,其胎面配方通常采用以高强度天然橡胶(NR)为主的生胶体系,同时为了降低滚动阻力、提高湿地抓着力,并保持优良的耐磨性能,采用白炭黑与炭黑并用的填料体系。
众所周知,NR具有相对分子质量大、自结晶和生胶强度大等优点,然而其表面呈弱极性,导致强极性的白炭黑在其中分散困难。
白炭黑由于表面含有大量羟基,具有很高的表面极性,在胶料混炼和储存中容易发生聚集,从而影响胶料的各项性能。
通常白炭黑配方中使用硅烷偶联剂(如TESPD或TESPT)对白炭黑进行表面改性,以提高橡胶与白炭黑的相容性,白炭黑表面的羟基与硅烷偶联剂的羟基之间发生反应,即硅烷化反应。
促进剂TBzTD对白炭黑补强天然橡胶

第 7 期谢诚坚等.促进剂TBzTD对白炭黑补强天然橡胶/溶聚丁苯橡胶并用胶性能的影响415促进剂TBzTD对白炭黑补强天然橡胶/溶聚丁苯橡胶并用胶性能的影响谢诚坚,高 超,熊 能,王 超,刘 辉,董兴旺,王丹灵(中策橡胶集团股份有限公司,浙江杭州310018)摘要:研究促进剂TBzTD对白炭黑补强天然橡胶(NR)/溶聚丁苯橡胶(SSBR)并用胶性能的影响。
结果表明:在白炭黑补强NR/SSBR并用体系中,随着促进剂TBzTD用量的增大,胶料的门尼焦烧时间缩短,硫化速率增大,硫化胶的300%定伸应力和拉伸强度增大,拉断伸长率减小,撕裂强度先增大后减小,耐磨性能和抗湿滑性能提高,滚动阻力降低;促进剂TBzTD用量为0.5份时,胶料的耐老化性能最佳。
关键词:促进剂;白炭黑;天然橡胶;溶聚丁苯橡胶;耐磨性能;动态力学性能;滚动阻力中图分类号:TQ330.38+5 文章编号:1006-8171(2023)07-0415-03文献标志码:A DOI:10.12135/j.issn.1006-8171.2023.07.0415自2012年欧盟实施标签法规以来,消费者越来越重视轮胎的滚动阻力和抗湿滑性能。
轮胎配方工程师采用诸多方法改善胶料的滞后损失,如采用溶聚丁苯橡胶(SSBR)、白炭黑、树脂、硅烷偶联剂、分散剂等来增大胶料在0 ℃时的损耗因子(tanδ),减小胶料在60 ℃时的tanδ,以期提高轮胎的抗湿滑性能,降低轮胎的滚动阻力[1-7]。
有专利[8]介绍,采用有机硫给予体可以提高胶料的抗硫化返原性,增大胶料模量,减小压缩永久变形,降低压缩温升。
促进剂TBzTD为二硫化四苄基秋兰姆,是一种绿色、安全、环保、高效的硫化促进剂[9-10]。
本工作研究促进剂TBzTD对白炭黑补强天然橡胶(NR)/SSBR并用胶性能的影响。
1 实验1.1 主要原材料NR,SVR3L,越南产品;SSBR,牌号E581,日本旭化成公司产品;炭黑N234,上海卡博特化工有限公司产品;白炭黑,牌号1165MP,索尔维精细化工添加剂(青岛)有限公司产品;偶联剂Si69,浙江金茂橡胶助剂品有限公司产品;硫黄,无锡华盛橡胶新材料科技股份有限公司产品;促进剂TBzTD,江苏连连化学股份有限公司产品;促进剂CBS,科迈化工股份有限公司产品。
不同胶粘剂对天然橡胶粘接性能的影响

响
作者: 作者单位: 刊名: 英文刊名: 年,卷(期): 孟宪印, 张会莲, 胡雅婷 青岛海力威新材料科技股份有限公司,山东青岛,266113 世界橡胶工业 World Rubber Industry 2014,41(2)
本文链接:/Periodical_sjxjgy201402008.aspx
表I胶粘剂种类
工艺过程为涂底胶,干燥,涂面胶,干燥, 24工艺过程为涂胶,干燥,
包装。
单涂层工艺与双涂层工艺的干燥温度和 时间均以各胶粘剂的要求工艺执行。 1.5测试标准 拉伸法硫化橡胶与金属粘合强度试验按 GB/T11211.2009测试;90。剥离法硫化橡胶 与金属粘合强度试验按GB/T7760.2003测试。
万方数据
世界 股份有限公司:
橡胶T业
2014
1.4金属骨架表面涂胶工艺 底涂Chemlok 205、面涂Chemlok 和底涂Thixon
包装。
cilbond P一1 252x
1.EF、面涂Megum 538的
闭
3结果与讨论
在橡胶与金属骨架的粘合作用中,胶粘 剂是影响粘合性能的主要原材料。本次共实 验3种胶粘剂(见表1),以粘合强度和附胶 率作为其主要评判参数.
图3不同胶粘剂拉伸强度研究
中提高生产效率,降低生产成本。
参考文献: [1]高守超,张康助,郭平军.橡胶与金属的硫化粘接[J].化学与粘合,2003,(4):176—178. [2]马兴法,吴崇光,王仲平,金衍芬,文香莲.金属与天然橡胶的热硫化粘接[J].中国胶粘剂,1993(2):4042
【责任编辑:朱胤】
2粘接原理
2.1双涂层胶粘剂粘接原理 双涂层胶粘剂,一般来说其底涂c,对金 属的粘接性能要优于面涂c的,同时面涂c对 橡胶的粘接性能优于底涂c,的,这样,在实际 作用时依靠面涂c来提高橡胶R和底涂c.的粘 接强度,同时依靠底涂C.来提高金属M和面涂 c的粘接强度,达到橡胶R和金属M粘接的目
硫磺硫化中促进剂在橡胶中的反应机理
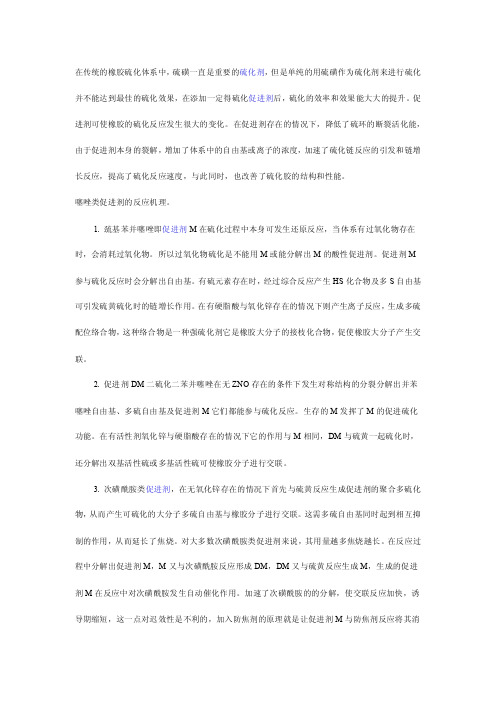
在传统的橡胶硫化体系中,硫磺一直是重要的硫化剂,但是单纯的用硫磺作为硫化剂来进行硫化并不能达到最佳的硫化效果,在添加一定得硫化促进剂后,硫化的效率和效果能大大的提升。
促进剂可使橡胶的硫化反应发生很大的变化。
在促进剂存在的情况下,降低了硫环的断裂活化能,由于促进剂本身的裂解,增加了体系中的自由基或离子的浓度,加速了硫化链反应的引发和链增长反应,提高了硫化反应速度,与此同时,也改善了硫化胶的结构和性能。
噻唑类促进剂的反应机理。
1. 巯基苯并噻唑即促进剂M在硫化过程中本身可发生还原反应,当体系有过氧化物存在时,会消耗过氧化物。
所以过氧化物硫化是不能用M或能分解出M的酸性促进剂。
促进剂M 参与硫化反应时会分解出自由基。
有硫元素存在时,经过综合反应产生HS化合物及多S自由基可引发硫黄硫化时的链增长作用。
在有硬脂酸与氧化锌存在的情况下则产生离子反应,生成多硫配位络合物,这种络合物是一种强硫化剂它是橡胶大分子的接枝化合物,促使橡胶大分子产生交联。
2. 促进剂DM二硫化二苯并噻唑在无ZNO存在的条件下发生对称结构的分裂分解出并苯噻唑自由基、多硫自由基及促进剂M它们都能参与硫化反应。
生存的M发挥了M的促进硫化功能。
在有活性剂氧化锌与硬脂酸存在的情况下它的作用与M相同,DM与硫黄一起硫化时,还分解出双基活性硫或多基活性硫可使橡胶分子进行交联。
3. 次磺酰胺类促进剂,在无氧化锌存在的情况下首先与硫黄反应生成促进剂的聚合多硫化物,从而产生可硫化的大分子多硫自由基与橡胶分子进行交联。
这需多硫自由基同时起到相互抑制的作用,从而延长了焦烧。
对大多数次磺酰胺类促进剂来说,其用量越多焦烧越长。
在反应过程中分解出促进剂M,M又与次磺酰胺反应形成DM,DM又与硫黄反应生成M,生成的促进剂M在反应中对次磺酰胺发生自动催化作用。
加速了次磺酰胺的的分解,使交联反应加快,诱导期缩短,这一点对迟效性是不利的,加入防焦剂的原理就是让促进剂M与防焦剂反应将其消耗一部份,来延长焦烧时间。
橡胶各类促进剂的特点及主要品种总结

橡胶各类促进剂的特点及主要品种总结
1、噻唑类
噻唑类(酸性)促进剂硫化速度快,硫化曲线平坦,硫化胶综合性能好,有良好的耐老化性能,应用范围广泛,适合于天然橡胶和各种合成胶,宜和酸性炭黑配合,与炉法炭黑配合须注意焦烧的危险性。
主要品种:促进剂M、DM、MZ
2、次磺酰胺类
次磺酰胺类促进剂与噻唑类相同地方是促进基相同,但又比噻唑类多了一个防焦基和活化基。
促进基是酸性的,活化基呈碱性,因此次磺酰胺类促进剂是一种酸碱自我并用型的促进剂,它兼有噻唑类促进剂的优点,又克服了焦烧时间短的缺点。
其特点
(1)诱导期长,硫化速度快,硫化曲线平坦,硫化胶综合性能好;
(2)宜与炉法炭黑配合,有充分安全性,利于压出、压延及压模胶料的充分流动性;
(3)适用于高温快速硫化和厚制品硫化;
(4)与酸性促进剂并用,形成一个活化的次磺酰胺硫化体系。
主要品种:促进剂CZ、NOBS、NS(TBBS)、DZ
3、秋兰姆类
秋兰姆类促进剂含有二个活性基和二个促进基所组成,因此硫化速度快,焦烧时间短,是一种超速级的酸性促进剂。
应用时应特别注意焦烧倾向。
主要品种:促进剂TMTD、TMTM、TRA
4、二硫代氨基甲酸盐类
二硫代氨基甲酸盐类促进剂比秋兰姆促进剂的硫化速度更快,是一种超超速级的酸性促进剂。
它诱导期极短,用于室温硫化及胶乳制品的硫化,也用于丁基橡胶、三元乙丙橡胶的硫化,它赋予硫化胶优良的耐老化性能。
主要品种:促进剂PX、ZDC、ZDMC
5、胍类
胍类促进剂是有活性基,没有促进基和其他官能团,因此硫化起步较慢,操作安全性好,硫化速度较慢。
适用于厚制品硫化,提高海绵的定伸应力。
胍类促。
促进剂dm对橡胶的作用

促进剂dm对橡胶的作用
促进剂DM在橡胶中主要起促使硫化剂活化的作用,通过加速硫化剂与橡
胶分子间的交联反应,达到缩短硫化时间、降低硫化温度、增加产量、降低生产成本的实用效果。
此外,促进剂DM是合成橡胶、天然橡胶和再生橡胶的通用促进剂,其性
能和用途与促进剂M基本相似,但固化温度较高,后效显着,无需早期固化,操作安全。
另外,在氯丁胶中加入促进剂DM会有增塑作用,可用作氯丁胶的粘合剂,特别是G型氯丁胶的防焦剂。
使用该产品的硫化橡胶具有极好的耐老化性,可用于制造轮胎、橡胶带、橡胶软管、橡胶鞋和一般工业产品。
以上信息仅供参考,如需了解更多信息,建议查阅化学专业书籍或咨询化学专家。
促进剂dpg 硫化临界温度

促进剂dpg 硫化临界温度以促进剂DPG硫化临界温度为标题,本文将介绍DPG促进剂的硫化临界温度以及其对橡胶硫化性能的影响。
一、DPG促进剂概述DPG(二苯基胺)是一种常用的橡胶促进剂,它可以促进橡胶的硫化反应。
硫化是橡胶加工过程中的重要步骤,通过在橡胶中加入硫化剂和促进剂,可以使橡胶分子之间形成交联结构,增强橡胶的力学性能和耐热性能。
二、DPG促进剂的硫化临界温度硫化临界温度是指橡胶在一定温度下开始进行硫化反应的最低温度。
对于DPG促进剂而言,其硫化临界温度是指在何种温度下,DPG 能够起到促进橡胶硫化的作用。
实验研究表明,DPG促进剂的硫化临界温度与橡胶种类、硫化剂的种类和用量、DPG的用量等因素有关。
不同类型的橡胶对DPG的硫化临界温度有不同的要求。
例如,对于天然橡胶而言,其硫化临界温度通常在140-150摄氏度之间;而对于丁苯橡胶而言,其硫化临界温度通常在110-120摄氏度之间。
硫化剂的种类和用量也会影响DPG的硫化临界温度。
一般来说,硫化剂的用量越大,DPG的硫化临界温度越低。
这是因为硫化剂可以提供足够的硫原子,促进橡胶的硫化反应,降低了DPG的起始硫化温度。
三、DPG对橡胶硫化性能的影响DPG作为一种促进剂,可以提高橡胶的硫化速度和硫化程度,从而改善橡胶的力学性能和耐热性能。
具体来说,DPG可以加快硫化反应的速率,减少硫化时间,提高硫化效率。
同时,DPG还可以增强橡胶的耐热性能和耐老化性能。
然而,过量使用DPG促进剂可能会导致一些问题。
首先,过量的DPG会降低橡胶的强度和耐磨性能;其次,过量的DPG还会对橡胶的电性能产生负面影响;此外,DPG还可能引起橡胶制品的变色等问题。
因此,在使用DPG促进剂时,需要根据橡胶种类和具体要求来确定合适的用量。
总结:DPG促进剂的硫化临界温度是指DPG起到促进橡胶硫化作用的最低温度。
硫化临界温度受到橡胶种类、硫化剂的种类和用量、DPG 的用量等因素的影响。
- 1、下载文档前请自行甄别文档内容的完整性,平台不提供额外的编辑、内容补充、找答案等附加服务。
- 2、"仅部分预览"的文档,不可在线预览部分如存在完整性等问题,可反馈申请退款(可完整预览的文档不适用该条件!)。
- 3、如文档侵犯您的权益,请联系客服反馈,我们会尽快为您处理(人工客服工作时间:9:00-18:30)。
研究不同促进剂对天然橡胶/白炭黑复合材料的制备
与性能的影响
课程设计报告
学院:启新学院
专业班级: 08材化生实验班
姓名:俞峰
学号: Q08120139
指导教师:杜明亮
完成日期: 2011年12月26日
浙江理工大学
不同促进剂对天然橡胶硫化的性能影响
摘要:通过设计配方,对于不同促进剂对天然橡胶在硫化时间,拉伸性能与撕裂性能上的分析对比,得出促进剂TT比DM无论在硫化速度还是交联程度上都更为有效快速,拉伸和撕裂性能也更好。
关键字:促进剂TT、DM 硫化时间拉伸撕裂交联
引言:橡胶和其他线型高分子材料一样都属于热塑性材料,当温度升高到它的流动温度时,便成为粘稠的液体,在外力(或自重)的作用下,产生不可逆的流动;在适当的溶剂中发生溶胀和溶解。
橡胶的这种性质不适合用于许多实际使用要求。
线型聚合物在化学的或物理的作用下,通过化学键的连接,成为空间网状结构的化学变化过程称为硫化(或交联)。
天然橡胶通常都必须经过硫化才具有实际用途。
为了缩短硫化时间,提高交联效率,改善硫化胶的性能,橡胶的硫化过程需要一个硫化系统,为硫化机,促进剂,活化剂,助交联剂,防老化剂等。
有机促进剂的使用是橡胶工业技术的重大进步。
它不仅仅可大大缩短硫化时间、减少硫化用量、降低硫化温度,而且对橡胶的工艺性能和物理机械性能也有大量改善。
随着对有机促进剂结构、有机促进剂与橡胶的反应机理以及对硫化胶结构和性能的研究,使得有可能在一定程度上视使用需要来选择适宜的有机促进剂以及适宜的促进剂和硫化用量的比例,以期得到符合性能要求的硫化胶结构。
所以,在此就TT和DM两种促进剂对天然橡胶硫化的性能影响做以下分析。
一、实验部分
1.1 原料
天然橡胶,硫磺,促进剂TT,促进剂DM,氧化锌,硬脂酸钠,白炭黑,防老化剂(4010Na)。
1.2 主要仪器设备
1.3试验配方
1.4 试样制备
制备工艺流程:配料→塑炼→混炼→硫化特性测定→试样硫化→性能测试。
在开炼机上完成塑炼,辊距0.5~1 mm,辊温50~60℃,采用一段薄通法,薄通次数为5次。
塑炼后直接混炼,混炼也在开炼机上进行。
按下表表1的配方加入配合剂,其顺序为促进剂→氧化锌→硬脂酸→白炭黑→硫磺。
未加硫磺之前的混炼胶,按辊距为1.5mm左右和辊温为50~℃60℃,薄通打三角包混炼5次。
待全部配合剂加入后,按规定次数(6次)打卷、薄通打三角包(8个),增大辊距(2 mm左右)下片,混炼胶停放一段时间。
硫化特性测定是用GT-M2000-A型无转子硫化仪按国标测定胶料的硫化时间,测定的温度143℃。
在硫化机上试片进行硫化,硫化条件为143℃×10MPa 。
1.5性能测试
硫化过程曲线: 混炼胶在GT-M2000-A硫化仪上进行硫化的同时测定其硫化过程中弹性扭矩曲线。
拉伸性能按GB528—1998标准进行测试,试样形状为哑铃型,拉伸速率为500mm/min;撕裂性能按GB529—1999标准进行测试,试样形状为直角型,拉伸速率为500mm/min;硬度(邵氏A)按GB527—1998标准进行测试。
二、结果与讨论
2.1两组配方硫化时间的比较
图1-1
促进剂可以大大缩短硫化时间、减少硫磺用量,降低硫化温度,而且对橡胶的工艺性能和物理机械性能也有较大改善。
不同促进剂对硫化的效率明显不同。
从图1-1中看出,加入促进剂TT的橡胶硫化时间比促进剂DM的短,并且交联程度也更好。
2.2两组配方拉伸强度的比较
图1-2
从图1-2可知,加促进剂TT的组分拉伸强度明显大于加DM的组分的配方,主要是由于加入TT可很好的让橡胶进行交联,拉伸模量大,拉伸强度大。
2.3两组配方撕裂强度的比较
图1-3
从图1-3的撕裂强度图,可看出加入促进剂TT的撕裂强度明显高于加入促进剂DM的撕裂强度。
这是由于促进剂TT具有非常高的交联效率;促进剂DM,交联效率低,因而在撕裂时容易被撕裂开,从而致使其撕裂强度不高。
三、结论
(1)塑炼的目的一方面是为了切断天然橡胶大分子链,减小弹性,提高可塑性;另一方面是为了降低粘度,提高流动性,改善橡胶的加工性能
(2)促进剂TT在硫化速度上比促进剂DM快,因而硫化时间短。
(3)促进剂TT可更大程度的提高天然橡胶的交联程度,因此其橡胶在拉伸强度和撕裂强度上都比加促进剂DM的橡胶的性能要好。
参考文献
[1]沈新元主编.高分子材料加工原理(第2版).北京:中国纺织出版社,2009.3
[2]王贵恒主编.高分子材料成型加工原理.北京:化学工业出版社,2004.
[3]张萍,张合伟,赵树高.通用橡胶/硫磺/DM体系硫化中的交联网络演变.高分子材料与工程第27卷第5期.。