液压系统安装手册pdf
旭阳液压站安装和维护使用手册R1
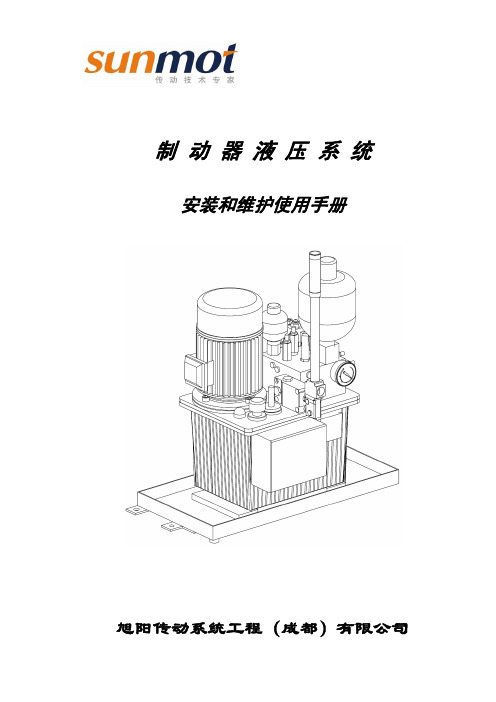
闪点 (开杯口)
倾点℃
159/160 -42
151/242 -42
152/244 -39
153/246 -39
152/252 -36
152/260 -30
如果相关数据和以上情况都不一样请按照以下表格选择液压油:
环境温度
平均油液温度
油液类型
-10℃/ +30℃
-10℃/+50℃
ISO-VG-46
-20℃/ +20℃
* 主轴输出压力:通过调整减压阀(16)调整主轴输出压力,顺时针调高,反时针调低。 压力值通过测压装置(辅件)在检测口(17)检测(换向阀 14 得电)。
4.7 手动操作
4.7.1 手动泵操作:可使用手动泵(25)为系统增压,将手动杆取下(油箱背部),插入手 柄内,摇动手柄即可。
4.7.2 主轴处 2 位 3 通电磁阀(14)、偏航在偏航时 2 位 2 通电磁阀(24)和,偏航零压 时回油 2 位 2 通电磁阀(23),均可利用手动操作实现电磁阀得电功能。
第 1 页 共 17 页
制动器液压系统安装和维护使用手册
1 简介
1.1 概述 本系统由电机(2)、泵(4)、溢流阀(9)、换向阀(14、20、23、24)、减压阀(16)、 背压阀(21)、蓄能器(13、19)以及检测元件等构成。工作时,由电机(2)带动泵(4) 顺时针方向旋转,由溢流阀(9)调定工作压力,经换向阀(14)输出到主轴制动器进行 主轴制动;压力经换向阀(20)输出到偏航制动器进行偏航制动,压力经换向阀(24)、 背压阀(21)输出到偏航进行偏航阻尼制动。由压力表(12)和压力传感器(11)检测系 统工作压力,液位继电器(7)检测油箱液位。油站电机处于间隙工作状态,电机不工作 时,系统压力由蓄能器(13)保持。序号(25)为手动泵,序号(18)为主轴压力输出压 力开关,序号(17、22)为输出压力检测口。
使用手册(液压部分)
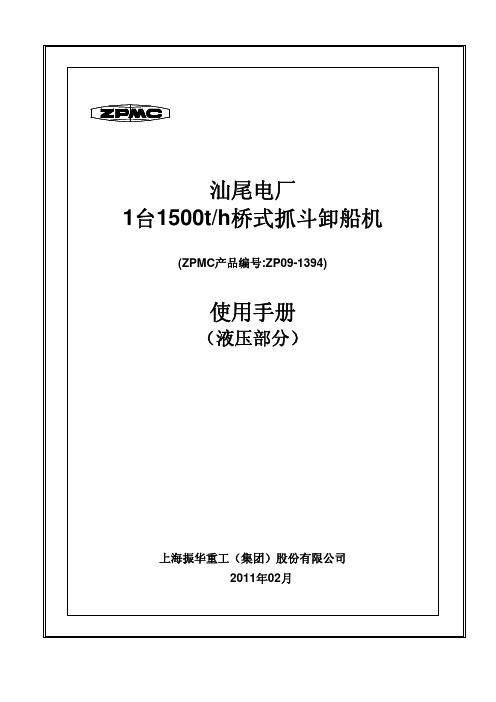
19 SLWC-M60-1-B250NC-01-01-1-T70NC-PG11 低油位报警器 20 FSA127 1.1/T12 21 22 KXT-040-16NM 23 TECFLY-40-NBR-LS 24 CI43-6 ST2P1A11X700S 25 125/70-700 注: 液压油用壳牌46#液压油 液位计 油箱 柔性接头 蝶阀 位移传感器 油缸
1 ABB.SH 1 1 REXROTH 1 HYDAC 1 HYDAC 4 REXROTH 8 HYDAC 1 REXROTH 1 ZPMC 1 BARKSDALE 1 FUKA 3 WIKA.SH 3 FUKA 4 HYDAC 1 HYDAC 1 HYDAC 3 HYDAC 1 HYDAC 1 STAUFF 1 HYDAC 1 ZPMC 1 ZPMC 4 HYDAC 6 ZPMC 6 ZPMC
2.工况: 概述: 桥吊开机时,电动机M即自动启动,油泵向蓄能器充油。当压力继电器高位发讯 时,电动机停止,液压系统进入准备“松轮”状态。当司机按“松轮”按钮后,电动 机M、电磁阀S得电,直到海陆侧(各9只)行程开关T1~T9闭合发讯且压力继电器高位 发讯,电动机M才可以停止,进入自动保压状态。 系统处于自动保压状态时,如果在一分钟之内电机M启动超过三次,则系统将报 “油泵启动频繁”故障,且电机停转。 2.1 按“松轮”按钮→松轮→允许大车行走→自动保压→若大车行走连续停止5分 钟,则自动进入夹轮状态。 按"松轮"按钮或大车行走操作手 柄离开零位后,S得电,M得电,蓄 能器和油泵同时向夹轮器和夹轨 器输入压力油,开始松轮。 压力继 ⎯⎯⎯→ 续上升 待压力≥130bar 时,压力继电器高 位发讯,M失电。 进入保压 ⎯⎯⎯⎯→ 状态 当系统压力≤110bar时, 压力继电器低位发讯,M重新启动, 当压力≥130bar时,压力继电器高 位发讯后,M失电。完成自动补油动 作。 自动夹轮(大车行走 ⎯⎯⎯⎯⎯⎯⎯⎯→ 连续停止5分钟后) 松轮 ⎯⎯→ 绿灯亮,表示已处于松轮状态,大 车允许行走。
ZDYZ-Z液压支架电液控制系统用户手册

ZDYZ-Z液压支架电液控制系统用户手册中国·凡尔机械集团有限公司目录前言........................................................................................................................................................ - 1 -一、概述.................................................................................................................................................. - 2 -1.主要用途........................................................................................................................................ - 2 -2.适用范围........................................................................................................................................ - 2 -3.主要特点........................................................................................................................................ - 2 -二、系统配置和连接 .............................................................................................................................. - 3 -三、系统工作原理 ................................................................................................................................ - 10 -四、系统主要设备介绍 ........................................................................................................................ - 11 -1.液压支架控制器.......................................................................................................................... - 11 -2.KDW127/12矿用隔爆兼本安型直流稳压电源 ........................................................................... - 11 -3.隔离耦合器.................................................................................................................................. - 12 -4.压力传感器.................................................................................................................................. - 12 -5.行程传感器.................................................................................................................................. - 12 -6.红外检测器.................................................................................................................................. - 13 -五、系统主要功能介绍 ........................................................................................................................ - 13 -1.单个支架的本架控制 .................................................................................................................. - 14 -2.单个支架的邻架控制 .................................................................................................................. - 14 -3.多个支架的成组控制 .................................................................................................................. - 17 -4.自动补液功能.............................................................................................................................. - 19 -5.自动反冲洗功能.......................................................................................................................... - 20 -6.闭锁和紧急停止功能 .................................................................................................................. - 20 -7.工作面所有支架的编号功能 ...................................................................................................... - 21 -8.软件程序升级功能...................................................................................................................... - 22 -9.参数设置和修改功能 .................................................................................................................. - 22 -10.信息功能.................................................................................................................................... - 23 -六、控制器硬件配置 ............................................................................................................................ - 24 -七、控制器按键功能 ............................................................................................................................ - 25 -八、控制器菜单显示功能 .................................................................................................................... - 28 -1.默认显示画面.............................................................................................................................. - 29 -2.菜单项的调动方法...................................................................................................................... - 29 -3.菜单结构...................................................................................................................................... - 29 -九、维护与故障分析 ............................................................................................................................ - 35 -1.维护.............................................................................................................................................. - 35 -2.常见故障及排除方法 .................................................................................................................. - 35 -十、注意事项........................................................................................................................................ - 38 -前言感谢您选购本产品,为了保证安全,安装使用前请详细阅读本使用说明书,并妥善保管,以备今后参考。
电气液压手册_液压系统
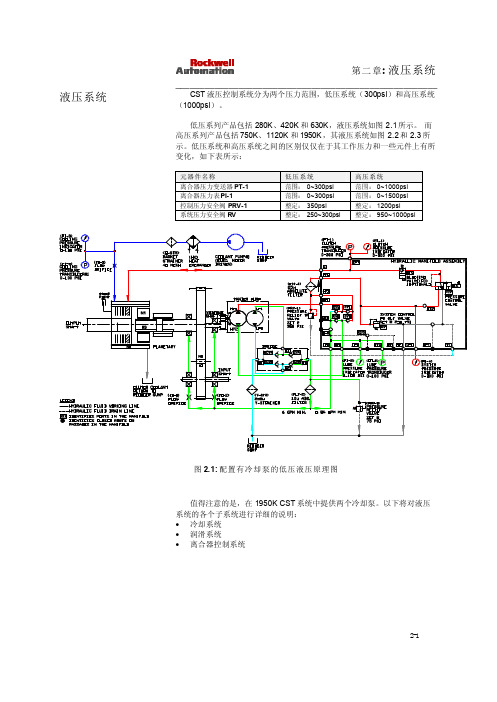
______________________________________________________CST 液压控制系统分为两个压力范围,低压系统(300psi )和高压系统(1000psi )。
低压系列产品包括280K 、420K 和630K ,液压系统如图2.1所示。
而高压系列产品包括750K 、1120K 和1950K ,其液压系统如图2.2和2.3所示。
低压系统和高压系统之间的区别仅仅在于其工作压力和一些元件上有所变化,如下表所示:元器件名称低压系统 高压系统 离合器压力变送器PT-1范围: 0~300psi 范围: 0~1000psi 离合器压力表PI-1范围: 0~300psi 范围: 0~1500psi 控制压力安全阀 PRV-1整定: 350psi 整定: 1200psi 系统压力安全阀RV 整定: 250~300psi 整定: 950~1000psi值得注意的是,在1950K CST 系统中提供两个冷却泵。
以下将对液压系统的各个子系统进行详细的说明:• 冷却系统• 润滑系统• 离合器控制系统液压系统图2.1: 配置有冷却泵的低压液压原理图______________________________________________________图2. 2: 配置单冷却泵的高压液压原理图图2.3: 配置双冷却泵的高压液压原理图______________________________________________________图2.4中描述了冷却系统的组成部分,包括:冷却系统•冷却泵 + 电机(1950K系统中需要两台泵)•热交换器(HX)•篮式过滤器(B-STR)•冷却压力表(PI-3)•冷却压力变送器(PT-3)•进口单向阀(CV-6/CV-7,1950K CST系统)•节流孔( FO-3/FO-5)电机驱动冷却泵将热油从CST油箱里抽出,并经过油/空气热交换器、一个40目的篮式过滤器、离合器摩擦盘后返回到油箱。
液压系统设计简明手册

液压系统设计简明手册本书是由机械电子工业部教材编辑室与全国机械制造专业教学指导委员会和教材编审委员会联合组织编写的系列机械制造简明手册中的一本。
本书着重介绍液压系统的计算和结构设计,通过具体实例叙述了液压系统设计的全过程,对液压缸、油路板、集成块和液压站的设计方法也作了详细说明,并提供实际图样作参考。
同时也收集了常用的液压元件和辅助元件的产品和安装尺寸,以便读者在设计时选用。
"第一章液压系统的设计与实例一、液压系统的设计步骤和内容二、组合机床液压系统设计实例第二章液压缸的设计一、液压缸主要尺寸的确定二、液压缸的结构设计三、液压缸的典型结构第三章集成油路的设计一、液压油路板的结构与设计二、液压集成块结构与设计三、叠加阀装置设计第四章液压站的设计一、液压油箱的设计二、液压站的结构设计第五章常用液压元件一、液压泵和液压马达二、液压阀(GE系列)第六章辅助元件一、管道二、管接头三、密封件四、滤油器五、蓄能器六、空气滤清器七、液位计附录附录A 工作介质的种类、性能和应用(摘自)附录B 常用液压与气动元件图形符号(摘自)制钉机的液压系统设计作者:广东五邑大学尹学军刘海刚摘要:本文介绍了自动制钉机液压系统的设计,采用了较先进的集成油路板式结构。
关键词:制钉机;液压系统原理图;集成油路板式结构1前言射钉枪由于其效率高,使钉受力均匀、一致,使用方便等优点而广泛用于包装、广告装饰及家具制造、制鞋业等方面。
而作为其“子弹”的排钉,也就有了大量的需求。
笔者曾在珠江三角洲地区的制钉厂调查,发现这种钉子不仅在本地区,而且在内地和港澳、东南亚等地,都有相当的需要,经济效益可观。
排钉的制造过程为:(1)压线——将一定直径、一定强度的铁丝在压辊机上压扁;(2)排线——将若干条(一般为80~150条)压扁的铁线拉直并排在一起;(3)并线——将排好的线用粘合剂粘合在一起并烘干,成为板料;(4)制钉——将板料送到制钉机上成型。
力士乐液压安装要求和验收实用手册(中英文) 01

baffle
隔板
穩固的底架 Stiff frame for power units
動力單元的最佳設計:適用於小型動力單元 optimal design for all power units: for small power units possible
安裝底架 mounting base
使用L或U型鋼材以增加穩固性 L- or U-beams for frame stiffness
新液壓油 2 33,121 5 7,820 10 5,010 15 2,440 ISO 4406 - 22/20/18 ( NAS 12 )
新液壓系本身的污染物 2 79,854 5 21,070 10 12,320 15 8,228 ISO 4406 - 23/22/20 ( > NAS 12 )
Contamination level comparison – 污 染 度 的 對 比
按裝有基本液壓過濾的系统 2 5 10 15 9,870 2.400 1,800 540 ISO 4406 - 20/18/16 ( NAS 9 )
按 裝 有 過 濾 B x > 200 的 液 壓 系 统 2 5 10 15 80 41 20 12 ISO 4406 - 14/13/11 ( NAS 4 )
Content 內 容
1. Precautions for oil tanks & suction lines 油箱與吸油管按裝的預防措施 2. Contamination control and filtration fundamentals 油污染控制與過濾的基本原理 3. Piping installations & flushing 管路按裝與沖洗
四方SFYB90A-FD7077液压偏航制动器安装维护说明书
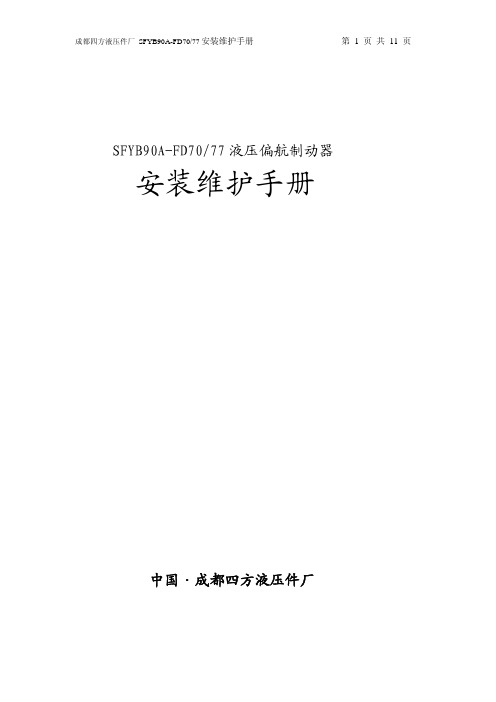
SFYB90A-FD70/77液压偏航制动器 安装维护手册中国·成都四方液压件厂目 录页数 一:制动器的特性和参数 3 二:制动片的特性和参数 4 三:制动盘和支撑座 4 四:制动器的安装 5 五:制动器的运行 7 六:更换摩擦片 7 七:周期性维护 9 八:备件清单 10 附件一: 油管接头安装技术要求 11※注意:本手册中带★处为重点内容一:制动器的特性和参数特性:液压力制动介质:矿物油工作压力:160 bar最大压力:200 bar液压油供应体积:100 cm3制动过程中所需油体积:新摩擦片10 cm3旧摩擦片320 cm3安装孔数量和直径:8*28mm压力油孔螺纹:M14*1.5泄油孔螺纹:M14*1.5制动力:170000N (160bar)制动盘线性速度:≤ 5 m/s工作温度:-30℃-+60℃生存温度:-45℃-+60℃相对湿度:≤85%质 量:34Kg二:制动片的特性和参数材料:复合材料摩擦片颜色:灰色供应领域:重型装备及汽车盘式制动器制动片类型:盘式制动器摩擦片最高允许温度:300℃平均摩擦系数:0.38静摩擦系数:0.45平均磨损率:V=10ˉ7×0.13三:制动盘和支撑座制动盘:厚度30±0.2 ,配置足够强度的支撑座制动器安装表面及其支撑座表面不能刷油漆,并且仔细清除油脂。
建议安装表面涂乐泰胶 Loctite510 或518 按照安装图给出的相对位置要求安装(尺寸、公差、技术要求…) 见图2★更换摩擦片而无需折下相邻制动器之端头挡块的最小尺寸要求安装结束后清洁制动盘四:制动器的安装出厂的状态:两个半套制动器;摩擦片已安装并调整完毕;压力油孔由堵头密封。
安装:拆下堵头,将活塞推至活塞缸内。
清洁安装制动器的支撑座表面, 并建议安装面涂乐泰胶 Loctite510 或518用两条M10螺栓标准预紧力矩将半套制动器固定在支撑座上, 再用8 条10.9 级M27 螺栓加垫片将另半套制 动器固定在支撑座上,在支撑座上螺纹深度不小于20mm。
海天液压系统综合维护手册

液压系统 综合维护手册
3. 变量叶片泵的调整如图: 3.1 此泵的压力调整泵顶端有压力调节杆通过调节杆螺 钉,顺时针方向旋转压力上升,反时针旋转压力下降。 调好后把锁紧螺母紧固。一般出厂压力后压力已确定用 户不必过多调整,只需微调调至要求压力。 3.2 流量调整没有特殊情况下泵的流量调整螺钉,用户 不要改动出厂前已调好。 3.3 噪音调整:叶片变量泵关于噪音调整不允许用户调 整,出厂已经调试完毕。如叶片泵在运行一段时间后, 噪音稍微变大属正常现象,可与供应商联系处理或远程 指导处理,变量叶片泵噪音标准:测量距离一米位置测 得噪音低于 75 分贝属合格产品。
沈阳东大伟业液压气动装备有限责任公司
液压系统 综合维护手册
螺母顺时针方向旋转流量减少、反之旋转流量增大。此 螺钉控制罗盘角度从而改变泵的流量。一般用户不必调 整,出厂前已由制造厂商调整完毕。 2.3 变量泵在开始试车时必须在注油口处加满液压油确 定正反转后点动启动。
沈阳东大伟业液压气动装备有限责任公司
2. 减压阀的用法与调整方法 2.1 减压的目的是减低主回油路的压力使二次压力出口 可控制,减压阀的压力调整手柄或调节螺钉顺时针旋转 出口压力变大,反时针旋转出口压力减小。如液压卡盘、
沈阳东大伟业液压气动装备有限责任公司
液压系统 综合维护手册
液压尾座等系统支路低于系统压力均采用减压阀。 3. 压力继电器的用法与调整方法
3.1 液压系统使用压力继电器的目的是系统压力的检 测,或压力信号的发讯是液压力转换成电信号、通信号 发出使油路卸压换向等,执行元件实现各种动作,在机 床液压系统中广泛应用。 3.2 压力继电器的调整比较简单,我司选择的基本是柱 塞式克服弹簧反力,当压力达到设定值时通过开关发出 控制信号。旋转调压旋钮改变设定压力。顺时针旋转压 力上升,反之下降。美国百纳压力继电器在调整时请把 顶端插头取下,用内六角扳手旋转顺时针方向转压力上 升,反方向则压力下降。调整完毕把插头装上固定好。 4. 平衡阀的用法与调整方法 4.1 此阀是减压阀、溢流阀的组合,主要用于控制平衡 油缸负载均衡,平衡油路的三通阀即 PAT。P 为系统压 力 A 为平衡压力 T 为外泄回油。平衡油缸的平衡力对应 的平衡压力 A 由平衡阀的手柄调节打开锁紧螺母,顺时 针方向转为平衡压力上升、反之下降。 4.2 叠加式的平衡阀调整时打开锁紧螺母顺时针方向转 平衡阀压力上升、反之下降(参看平衡压力表的显示)。 5. 流量阀的用法与调整方法 5.1 流量阀主要用于控制油缸运行速度,采用流量控制
自卸车液压系统安装手册
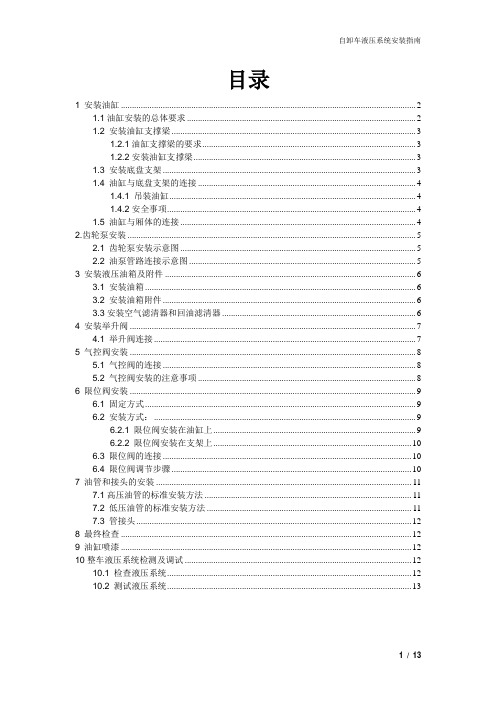
目录1 安装油缸 (2)1.1油缸安装的总体要求 (2)1.2 安装油缸支撑梁 (3)1.2.1油缸支撑梁的要求 (3)1.2.2安装油缸支撑梁 (3)1.3 安装底盘支架 (3)1.4 油缸与底盘支架的连接 (4)1.4.1 吊装油缸 (4)1.4.2安全事项 (4)1.5 油缸与厢体的连接 (4)2.齿轮泵安装 (5)2.1 齿轮泵安装示意图 (5)2.2 油泵管路连接示意图 (5)3 安装液压油箱及附件 (6)3.1 安装油箱 (6)3.2 安装油箱附件 (6)3.3安装空气滤清器和回油滤清器 (6)4 安装举升阀 (7)4.1 举升阀连接 (7)5 气控阀安装 (8)5.1 气控阀的连接 (8)5.2 气控阀安装的注意事项 (8)6 限位阀安装 (9)6.1 固定方式 (9)6.2 安装方式: (9)6.2.1 限位阀安装在油缸上 (9)6.2.2 限位阀安装在支架上 (10)6.3 限位阀的连接 (10)6.4 限位阀调节步骤 (10)7 油管和接头的安装 (11)7.1高压油管的标准安装方法 (11)7.2 低压油管的标准安装方法 (11)7.3 管接头 (12)8 最终检查 (12)9 油缸喷漆 (12)10整车液压系统检测及调试 (12)10.1 检查液压系统 (12)10.2 测试液压系统 (13)自卸车液压系统的安装1 安装油缸1.1油缸安装的总体要求●油缸的安装位置取决于实际应用条件或车辆的安全和额定载荷。
● 油缸的应用要求(举升能力和举升角度)取决于车辆的轴荷分配和厢体的外形(如后悬、厢体长度、厢体高度、旋转点等)。
● 车辆的轴荷分配取决于当地法规或汽车制造商提供的技术参数。
● 额定举升重量=厢体容积(长×宽×高)×货物比重+厢体自重+5%超载重量。
● 其他可能影响安装位置的因素如图1所示:①驾驶室间隙——确保油缸与驾驶室间留有足够空间,以便于驾驶室的翻转、举升过程中厢体的运动及安装区域内可接触到其它部件。
ZY9000-23-45D型掩护式液压支架操作说明书
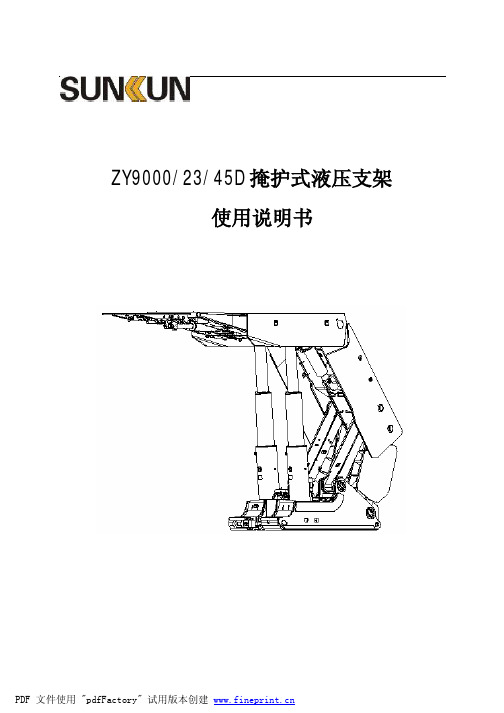
PDF 文件使用 "pdfFactory" 试用版本创建
目录
支架电控…………………………………………………… 83
液压操作介质……………………………………………… 83 7.联系方式…………………………………………………84 我们的服务……………………………………………………85
液压系统的操作……………………………………………37
液压系统的组成…………………………………………… 38 反冲洗过滤器的操作……………………………………… 41 电控模块面板的操作及功能……………………………… 46
维护……………………………………………………………47 问题分析………………………………………………………49
后果是:严重的伤害甚至死亡。
小心!
在本书由此标记的地方是提醒您对有伤害的地方引起注
意。可能造成的后果有:对液压支架造成破坏或者是对邻近
的地方产生破坏。
注意!
这些符号是让您对一些危险处引起注意。可能造成的后
果是:轻度或中度程度的伤害以及造成支架设备的损坏。
重要提示!
在本书中有此标记的的地方提供了一些对您工作有用的
目录
支架井下运输……………………………………………… 17
4.安装…………………………………………………… 20 下井前地面联调试运转……………………………………21 井下安装…………………………………………………… 22
5.操作及维护………………………………………………25 基本要求………………………………………………………26
7
PDF 文件使用 "pdfFactory" 试用版本创建
液压系统技术手册
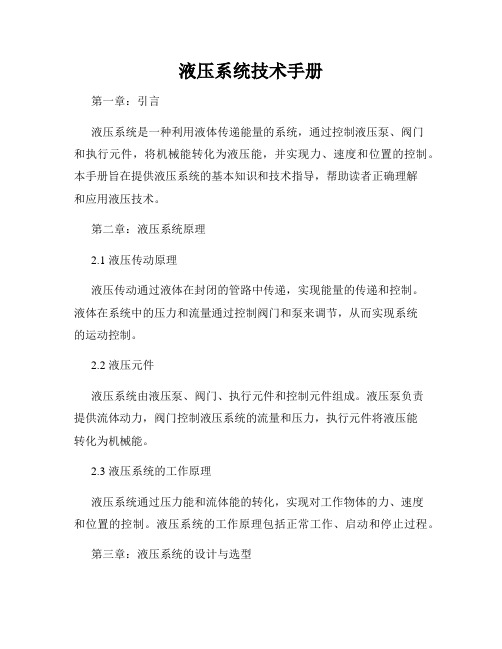
液压系统技术手册第一章:引言液压系统是一种利用液体传递能量的系统,通过控制液压泵、阀门和执行元件,将机械能转化为液压能,并实现力、速度和位置的控制。
本手册旨在提供液压系统的基本知识和技术指导,帮助读者正确理解和应用液压技术。
第二章:液压系统原理2.1 液压传动原理液压传动通过液体在封闭的管路中传递,实现能量的传递和控制。
液体在系统中的压力和流量通过控制阀门和泵来调节,从而实现系统的运动控制。
2.2 液压元件液压系统由液压泵、阀门、执行元件和控制元件组成。
液压泵负责提供流体动力,阀门控制液压系统的流量和压力,执行元件将液压能转化为机械能。
2.3 液压系统的工作原理液压系统通过压力能和流体能的转化,实现对工作物体的力、速度和位置的控制。
液压系统的工作原理包括正常工作、启动和停止过程。
第三章:液压系统的设计与选型3.1 液压系统设计的基本原则液压系统的设计应根据工作需求、系统参数和安全性要求进行合理选型。
设计时需要考虑系统的压力、流量、温度和安全因素,并选择合适的泵、阀和执行元件。
3.2 液压元件的选型和应用液压泵、阀门和执行元件的选型应考虑系统的工作压力和流量要求,同时还需要考虑其稳定性、寿命和价格因素。
液压元件的正确选型和合理应用对于系统的性能和可靠性至关重要。
3.3 液压系统的布置和安装液压系统的布置和安装应根据实际情况进行设计,确保液压元件的安全可靠运行。
布置时应考虑管路的长度、弯头的数量和角度、支撑和固定装置,以及对液压元件的冷却和降噪措施。
第四章:液压系统的维护和故障排除4.1 液压系统的日常维护液压系统的日常维护包括定期检查液压元件的工作状态、清洗管路和过滤器、添加液压油和更换密封件等。
正确的维护措施能够延长液压系统的使用寿命,并提高系统的可靠性和性能。
4.2 液压系统的故障排除液压系统故障的排除是液压技术中重要的一环。
故障排除需要借助故障诊断仪器和经验,通过逐步排查系统的各个部分,分析可能的原因并进行修复。
麦克西马多系列气动液压泵安装与维护手册说明书

Installation and Maintenance ManualMAXIMATORSERIESPUMPSModel #Serial #Order #Mfg. DateWhen ordering spare parts please specify model, serial and order numbers. INTRODUCTIONThe Maximator pump described in this manual is a pneumatically operated, gate valve controlled piston pump similar in style to a double-acting pneumatic cylinder.The pump model number indicates the ratio of areas between the pneumatic piston and the hydraulic plunger. For example, the S60 pump has an area ratio of 60:1 between the pneumatic piston and hydraulic plunger.This relates to a maximum hydraulic output pressure that is 60 times greater than the pneumatic drive pressure. e.g. With 100psi air, the outlet would be 6,000psi.INSTALLATIONThe pump can, in principle, be installed in any position but maximum service life of the seals is achieved in a vertical installation.There are two 3/8"-16 taps in bottom of body for use in mounting the pump.Printed in USA Page 1COMPRESSED AIR SUPPLYDo not use an air lubricator because the pump was lubricated with a silicon free grease when built. (Kluber Lube)A compressed air filter is required and if the air is not dry, a water separator must be used.Air control packages including a filter, regulator, gauge and shut-off valve are available as an option.The air pressure connection is a 1/2" FNPT and is located at the spool valve housing.HYDRAULIC SECTIONAttention! Never loosen the cap nut in the hydraulic seal area of the pump to orient the pump for installation. This nut must always be tight to assure proper operation of the high pressure seals.The suction and discharge piping must be at least the same size or larger, as the pump connections and properly rated for the pump being used.A suction filter with a maximum of 100 mesh should be installed in the suction line.The discharge and suction connections are in the sides of the pump head.INITIAL SET-UPThe liquid pressure can be precisely selected by adjusting the air pressure according to the pressure ratio of the pump being used.The pump will stop and maintain pressure for an indefinite period of time, at about 100% to 110% of the ratio, assuming no air or hydraulic leaks.For example, an S60 pump with an air drive pressure of 100psi, will operate at a pressure of 6,000psi and completely stop at about 6,600psi.Operate the pump slowly until it is completely primed.Page 2MAINTENANCEUSE ONLY ORIGINAL MAXIMATOR SPARE PARTSThe air drives of all liquid pumps are factory pre-treated with silicon free grease (Kluber Lube) and require no further lubrication except during routine maintenance.Pumps can be repaired at your local authorized service center or returned directly toyour distributor for quick turn-around service.Pumps returned for repair should be accompanied with the pump s model, serial and order numbers as well as mfg. date and description of the problem / symptom.DESCRIPTION OF OPERATIONThe automatically operated pump is controlled by a floating slide valve which alternately applies air pressure to the piston and subsequently vents the air again. The control system as such is operated with out springs and arresting fixtures as pressure is alternately supplied to and vented from the front surfaces of the pneumatically operated floating slide valve.The main parts in the hydraulic section are the pump body, plunger, seals with thrust rings and inlet and outlet check valves. The check valves are rated for full flow with dynamic sealing. TROUBLESHOOTING - PNEUMATIC SECTIONSymptom: Pump cannot be operated at low air pressure.Cause: Excessive friction of O-rings on spool valveRemedy: Relubricate or replace the O-ringsSymptom: Pump can only be actuated at high air pressure.Cause: Air escapes through the piston guide in the top air cap.Remedy: Replace O-ring on the piston extension.Symptom: Pump runs slowly or not at all.Cause: Exhaust or spool valve is icy.Remedy: Stop pump for a short while and, if necessary, clear air line and supply of moisture. Symptom: Pump will not run and air escapes through the exhaust muffler.Cause: Pilot valve tappet is not sealing in top cap.Remedy: Clean and grease tappet, check for wear and replace if necessary.Page 3Symptom:Pump will not run and air escapes through small holes in the spool valve housing. Cause: Spool valve fails.Remedy: Clean spool valve and sleeve, check O-rings and sleeve, lubricate and/or replace. Symptom: Pump will not run and escapes through the small holes in the bottom cap.Cause: Pilot valve tappet is not sealing in the bottom cap.Remedy: Clean and grease tappet, check for wear and re[lace if necessary.Symptom: Pump operates at a high frequency and short strokes.Cause: Pilot valve defective.Remedy: Clean, check and lubricate pilot valve parts or replace if necessary.TROUBLESHOOTING - HYDRAULIC SECTIONSymptom: Pump does not have flow, operates irregularly or does not maintain pressure. Cause: 1. Air in the hydralulic system.2. Suction line of excess length.3. Suction pipe size to small.4. Failure of one of the chack valves.5. Suction filter is blocked.6. High pressure seal is worn excessively.Remedy: 1.1 Check suction line and pipe joints for leaks.1.2 Check seals between air and high pressure sections.2. Shorten line as much as possible.3. Increase suction pipe size.4. Check both valve assemblies and clean or replace if necessary.5. Clean suction filter6. Replace seal.Symptom: Fluid escapes through the air exhaust.Cause. Worn high pressure seal.Remedy: Clean fluid from air section, relubricate and replace seal.SERVICEFor factory authorized service, contact your local Distributor.Page 4。
液压自动爬升模板SKE100安装操作手册-完整版
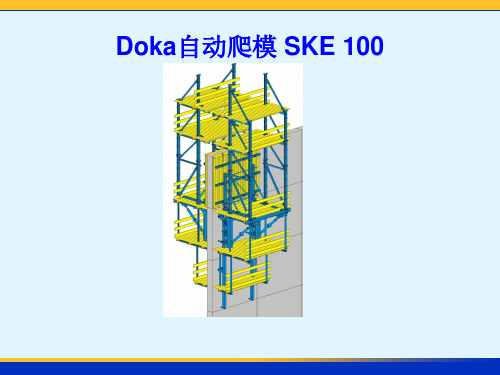
3.首次液压爬升
• • • • • 拆模 清理模板 安装上部悬挂靴 吊车提升爬升导轨就位 液压爬升整个爬架及模板
爬升阶段 SKE 100 „起始阶段“
1.浇注第一节段砼 2.浇注第二节段砼
3.首次液压爬升
4. 浇注第三节段砼
• • • • • • 安装-2层悬挂平台 立一侧模板 安装定位锥体 绑扎钢筋 合模 浇注第三节段砼.
爬升阶段 SKE 100 „起始阶段“
1.浇注第一节段砼 2. 浇注第二节段砼
• • • • • • • 安装悬挂靴 将爬架(包括-1层悬挂平台)悬挂在悬挂靴上 将模板与爬架相连 安装定位锥体 绑扎钢筋 支设模板 浇注第二节段砼
爬升阶段 SKE 100 „起始阶段“
1.浇注第一节段砼 2.浇注第二节段砼
典型操作阶段简要说明 SKE 100 – „爬升导轨“
• • • • • • 在下一个节段上安装悬挂靴 将上下提升机构的手柄推至 „Profile“ 位置 提升爬升导轨约2个行程 取出悬挂楔铁 继续提升爬升导轨,直至悬挂靴位置 将爬升导轨逐个滑入悬挂靴
典型操作阶段简要说明 SKE 100 – „爬升导轨“
典型操作阶段简要说明 SKE 100 – „爬升导轨“
• 在下一个节段上安装悬挂靴
典型操作阶段简要说明 SKE 100 – „爬升导轨“
• • 在下一个节段上安装悬挂靴 将上下提升机构的手柄推至 „Profile“ 位置
典型操作阶段简要说明 SKE 100 – „爬升导轨“
• • • • • 在下一个节段上安装悬挂靴 将上下提升机构的手柄推至 „Profile“ 位置 提升爬升导轨约2个行程 取出悬挂楔铁 继续提升爬升导轨,直至悬挂靴位置
爬升阶段 SK • • 拆模 清理模板和平台 安装上部悬挂靴 液压提升爬升导轨 拆除底部悬挂靴 液压 爬升爬架及模板
EHU组合液压系统使用说明书

警告 z 如在油箱无油时运转,会使油泵部分损坏烧毁。 z 在机器的初始运转时,由于需向机器侧的液压回路供油,应注意油箱内油位在减少。 z 由于机器侧的液压回路作用,使油箱内的油面变动很大,应注意油箱内的油有时会溢出,有时
(1) 应通过端子盒的配线口配置电线。
配线口应采用符合 IP54 以上要求的配线电线管,电缆
夹紧件等。
[ 推荐电缆夹紧件:RAPPU 公司产品 ST16]
[ 螺钉尺寸
:PG16]
※电源线应使用 245IEC/H05RR-F 的电线。
(2)接地线应接在端子板的地线连接处。
(3)电源线应接在电源端子板 (L1、 L2、 L3)上 (无极 性)。
会不足。
11
电气配线 应按照端子盒盖里面的配线图 (下图),正确而可靠地连接电气配线。
危险 z 为了防止电路过电流如短路等和防止控制部件过载,请在主电源电路配备根据欧共体EN60204-
1 规定的无熔丝热继电器或漏电断路器等安全装置。 (各机型的电流容量,请参照下表。) z 为了泄放变频回路泄漏的电流,接地端子必须使用第三接地等级以上的接地方式。 (必须不通过断路器等保护装置,直接接地) z 必须在主机安装好以后再进行配线作业。 z 进行配线作业之前,必须切断总电源侧的断路器,并确认电源已切断。 z 电源线绝对不能与报警端子和控制信号端子连接。 z 不能使用超过液压装置规定电压的电源。
重量表 (但是,不包含工质油)
危险 z 如不安装防振橡胶保护衬垫,起吊时会使防振橡胶磨损、滑脱,设备会有掉下、翻倒的危险。 z 勾住吊环螺栓以外 (泵配管)等,的构件起吊时有掉下、翻倒的危险。 z 应确认液压设备的重量,在起重吊具额定承重内吊装。
HYCOM作手册中文译本 HT2000-E revB May2011 (1)

中 文 手 册
型号 HT2000HT2000-E
2011
年 5 月版本 B
本中文手册只作参考用途,一切以英语版本为准
HT2000E 液压车指引手册 目录
1. 1.1 1.2 1.3 1.4 1.5 1.6 1.7 1.8 1.9 1.10 1.11 1.12 1.13 1.14 1.15 1.16 2.
此图示表示须要相关的行为-
配 戴保护手套 配 戴保护眼罩
此图示表示须要相关的行为-
此图示表示须要相关的行为-穿着保护衣物
操作及维护工作只可由熟练的及熟读相关操作及维护手册的人员进行及实现 有关本液压测试车的相关责任,只有在极度关 注下使用才得到 保证。 如 有任 何 疑 问 ,请联系制造单位 提出 询问。 因 不适当使用而引 致 的一 切 损坏,制造 单位将 不 会承担任 何责任 如有需要,一切现行 来用于防止意外发生的国家规条、用于工作时的防护守规等, 即使这些 条文不是专用于本测试车,操作人员都必须关注 危险物品 的泄漏及 处理,必须 在不危害 个人及环境 下实现。相关的法规必须关注 于液压测试车上作任 何工序时,供电电鑬及马达不可连接电源
所有于高压力下的液体都可能引致身体损伤及死亡,工作于含有高 压液体的环境下,所有的安全守规都必须要绝对遵守
日常性 日常 性 的安全预防
1.7
本中文手册只作参考用途,一切以英语版本为准
1.8
人员的培训
只有经过培训及受 命的人员才 可于液压测试车工作 应清楚地指定每名 人员的工作 权限 于培训中 的人员只可在富有经验的人员指导下才可操作液压测试车
首次启动
3) 在首次启动前,必须 加注液压油到液压 泵泵体内,这可于泵体 顶部的回油 接头来实现(如图示) 。
G771 G772 G773电动液压工业伺服阀安装、操作和故障排除手册

G77X/77X Series Installationand Operation Instruction ELECTROHYDRAULIC VALVE CUT -AWA YUpper Polepiece Flexure Sleeve Lower Polepiece Flapper Magnet (not shown)Coil Figure 1 Moog Series G77X/77X3.HYDRAULIC SYSTEM PREPARATIONT o prolong servovalve operational life and to reduce hydraulic system maintenance,it is recommended that the hydraulic fluid be kept at a cleanliness level of ISO DIS 4406 Code 16/13 maximum,14/11 recommended.The most effective filtration scheme incorporates the use of a kidney loop or “off-line”filtration as one of the major filtration components.The filter for the “off-line”filtration scheme should be a ß3≥75 filter for maximum effectiveness. Upon system startup and prior to mounting the servovalve,the entire hydraulic system should be purged of built-in contaminating particles by an adequate flushing.The servovalve should be replaced by a flushing manifold and the hydraulic circuit powered up under conditions of fluid temperature and fluid velocity,reasonably simulating normal operating conditions.New system filters are installed during the flushing process whenever the pressure drop across the filter element becomes excessive.The flushing processes should turn over the fluid in the reservoir between fifty to one hundred times.T o maintain a clean hydraulic system,the filters must be replaced on a periodic basis.It is best to monitor the pressure drop across the filter assembly and replace the filter element when the pressure drop becomes excessive.In addition to other filters that are installed in the hydraulic circuit,it is recommended that a large capacity,low pressure ß3≥75 filter be installed in the return line.This filter will increase the interval between filter element replacements and greatly reduce the system contamination level.4.INSTALLATIONThe Moog G77X/77X Series Industrial Servovalve may be mounted in any position,provided the servovalve pressure,piston and return ports match respective manifold ports.The mounting pattern,port location and mounting bolts of the servovalve are shown on Figure 4.Apply a light film of oil to the screw threads and torque to 57 inch-pounds.Wire mating connector for desired coil configuration and polarity. Thread connector to valve.5.MECHANICAL NULL ADJUSTMENTIt is often desirable to adjust the flow null of a servovalve independent of other system parameters.The “mechanical null adjustment” on the MoogG77X/77X Series servovalve allows at least ±20% adjustment of flow null.The “mechanical null adjustor” is an eccentric bushing retainer pin located above the port designation on the valve body (see Figure 2) which,when rotated,provides control of the bushing position.Mechanical feedback elements position the spool relative to the valve body for a given input signal.Therefore,a movement of the bushing relative to the body changes the flow null.Adjustment ProcedureUsing a 3/8inch offset box wrench,loosen the self-locking fitting until the null adjustor pin can be rotated.(This should usually be less than 1/2 turn). DO NOT remove self-locking fitting.Insert a 3/32inch Allen wrench in null adjustor e the 3/32Allen wrench to rotate the mechanical null adjustor pin to obtain desired flow null.T orque self-locking fitting to 57 inch lbs.Note:Clockwise rotation of null adjustor pin produces open loop flow from port B to port A.6.GENERAL SERVICING RECOMMENDATIONSa.Disconnect electrical lead to servovalve.b.Relieve hydraulic system of residual pressure.c.Remove servovalve.Figure 2Mechanical Null AdjustmentFILTER ASSEMBL Y REPLACEMENTRemove four socket head cap screws and lockwashers using a 3/16inch End capEnd Cap O-RingsFigure 3FilterInlet Orifice O-Rings (two at each end cap)G77X/77X SERIES INSTALLATION AND OPERATION INSTRUCTIONMoog Inc.,East Aurora,NY 14052-0018 T elephone:+1-716-652-2000Fax:+1-716-687-7910T oll Free:+1-800-272-MOOG /industrial©2007 Moog Inc.All changes are reserved.NOTESTYPICAL WIRING SCHEMATIC3Figure 447.81.5744.5MAX47.81.34335.364.7726.2P3.0OR[28.4] 1.751.275.8441.06MAX PIN C 1.00 2.122.182.8117.04.0141.68834.111.561.88PIN D1.88.12.007(OPTION)21.4425.426.91.3939.61.12 MAX 1.03MTG HGTPIN B.67153.855.471.4PIN A32.392.55042.88ELECTRICAL CONNECTORLOCATING PINØ.062EXTERNAL NULL ADJUST 3/32 IN. HEX SOCKET4X Ø.221(5.61) THRU (G771 AND G772)4X Ø.265(6.73) THRU (G773)YX TBA PF2F3F4F1T GThe products described herein are subject to change at any time without notice, including, but not limited to, product features, specifications, and designs.4 6CDS6674 REV C 500-380 807。
- 1、下载文档前请自行甄别文档内容的完整性,平台不提供额外的编辑、内容补充、找答案等附加服务。
- 2、"仅部分预览"的文档,不可在线预览部分如存在完整性等问题,可反馈申请退款(可完整预览的文档不适用该条件!)。
- 3、如文档侵犯您的权益,请联系客服反馈,我们会尽快为您处理(人工客服工作时间:9:00-18:30)。
液压系统的安装液压系统的安装液压系统安装质量的好坏是关系到液压系统能否可靠工作的关键。
必须科学、正常、合理地完成安装过程中的每个环节,才能使液压系统能够正常运行;充分发挥其效能。
2.1 安装前的准备工作1)明确安装现场施工程序及施工进度方案。
2)熟悉安装图样,掌握设备分布及设备基础情况。
3)落实好安装所需人员、机械、物资材料的准备工作。
4)做好液压设备的现场交货验收工作,根据设备清单进行验收。
通过验收掌握设备名称、数量、随机备件、外观质量等情况,发现问题及时处理。
5)根据设计图纸对设备基础和预埋件进行曲检查,对液压设备地脚尺寸进行复核,对不符合要求的地方进行处理,防止影响施工进度。
2.2 液压设备的就位1)液压设备应根据平面布置图对号吊装就位,大型成套液压设备,应由里向外依次进行吊装。
2)根据平面布置图测量调整设备安装中心线及标高点,可通过调整安装螺栓旁的垫板达到将设备调平找正,达到图纸要求。
3)由于设备基础相关尺寸存在误差,需在设备就位后进行微调,保证泵吸油管处于水平、正直对接状态,4)油箱放油口及各装置集油盘放污口应在设备微调时给予考虑,应是设备水平状态时的最低点。
5)应对安装好的设备做适当防护,防止现场脏物污染系统。
6)设备就位调整完成后,一般需对设备底座下面进行混凝土浇灌,即二次灌浆。
2.3 液压配管(1)管材选择应根据系统压力及使用场合来选择管材。
必须注意管子的强度是否足够,管径和壁厚是否符合图纸要求,所选用的无缝钢管内壁必须光洁、无锈蚀、无氧化皮、无夹皮等缺陷。
若发现下列情况不能使用:管子内外壁已严重锈蚀。
管体划痕深度为壁厚的10%以上;管体表面凹入达管径的20%以上;管断面壁厚不均、椭圆度比较明显等。
中、高压系统配管一般采用无缝钢管,因其具有强度高、价格低、易于实现无泄漏连接等优点,在液压系统中被广泛使用。
普通液压系统常采用冷拔低碳钢10、15、20号无缝管,此钢号配管时能可靠地与各种标准管件焊接。
液压伺服系统及航空液压系统常采用普通不锈钢管,具有耐腐蚀,内、外表面光洁,尺寸精确,但价格较高。
低压系统也可采用紫铜管、铝管、尼龙管等管材,因其易弯曲给配管带来了方便,也被一部分低压系统所采用。
(2)管子加工管子的加工包括切割、打坡口、弯管等内容。
管子的加工好坏对管道系统参数影响较大,并关系到液压系统能否可靠运行。
因此,必须采用科学、合理的加工方法,才能保证加工质量。
1)管子的切割 管子的切割原则上采用机械方法切割,如切割机、据床或专用机床等,严禁用手工电焊、氧气切割方法,无条件时允许用手工锯切割。
切割后的管子端面与轴向中心线应尽量保持垂直,误差控制在90°±0.5°。
切割后需将锐边倒钝,并清除铁屑。
2)管子的弯曲 管子的弯曲加工最好在机械或液压弯管机上进行。
用弯管机在冷状态下弯管,可避免产生氧化皮而影响管子质量。
如无冷弯设备时也可采用热弯曲方法,热弯时容易产生变形、管壁减薄及产生氧化皮等现象。
热弯前需将管内注实干燥河砂,用木塞封闭管口,用气焊或高频感应加热法对需弯曲部位加热,加热长度取决于管径和弯曲角度。
直径为28mm的管子弯成30°、45°、60°和90°时,加热长度分别为60mm、100mm、120mm、和160mm;弯曲直径为34mm、42mm的管子,加热长度需比上述尺寸分别增加25~35mm。
热弯后的管子需进行清砂并采用化学酸洗方法处理,清除氧化皮。
弯曲管子应考虑弯曲半径。
当弯曲半径过小时,会导致管路应力集中,降低管路强度。
表1给出钢管最小弯曲半径。
表1 钢管最小弯曲半径(mm)钢管外径14 18 22 28 34 42 50 63 76 89 102D最小冷弯 70 100 135 150 200 250 300 360 450 540 700弯曲半径热弯 35 50 65 75 100 130 150 180 230 270 350R(3)管路的敷设管路敷设前,应认真熟悉配管图,明确各管路排列顺序、间距与走向,在现场对照配管图,确定阀门、接头、法兰及管夹的位置并划线、定位、管夹一般固定在预埋件上,管夹之间距离应适当,过小会造成浪费,过大将发生振动。
推荐的管夹距离见表2。
表2 推荐管夹间距离(mm)管子外径D 14 18 22 28 34 42 50 63管夹间最大距450 500 600 700 800 850 900 1000 离L管路敷设一般遵循的原则:① 大口径的管子或靠近配管支架里侧的管子,应考虑优先敷设。
② 管子尽量成水平或垂直两种排列,注意整齐一致,避免管路交叉。
③ 管路敷设位置或管件安装位置应便于管子的连接和检修,管路应靠近设备,便于固定管夹。
④ 敷设一组管线时,在转弯处一般采用90°及45°两种方式。
⑤ 两条平行或交叉管的管壁之间,必须保持一定距离。
当管径≤φ42mm时最小管距离应≥35mm;当管径≤φ75mm时,最小管壁距离应≥45mm;当管径≤φ127mm时,最小管壁距离应≥55mm。
⑥ 管子规格不允许小于图纸要求。
⑦ 整个管线要求尽量短,转弯处少,平滑过渡,减少上下弯曲,保证管路的伸缩变形,管路的长度应能保证接头及辅件的自由拆装,又不影响其它管路。
⑧ 管路不允许在有弧度部分内连接或安装法兰。
法兰及接头焊接时,须与管子中心线垂直。
⑨ 管路应在最高点设置排气装置。
⑩ 管路敷设后,不应对支承及固定部件产生除重力之外的力。
(4)管路的焊接管路的焊接一般分三步进行。
①管道在焊接前,必须对管子端部开坡口,当焊缝坡口过小时,会引起管壁未焊透,造成管路焊接强度不够;当坡口过大时,又会引起裂缝、夹渣及焊缝不齐等缺陷。
坡口角度应根据国标要求中最利于焊接的种类执行。
坡口的加工最好采用坡口机,采用机械切削方法加工坡口既经济,效率又高,操作又简单,还能保证加工质量。
②焊接方法的选择是关系到管路施工质量最关键的一环,必须引起高度重视。
目前广泛使用氧气-乙炔焰焊接,手工电弧焊接、氩气保护电弧焊接三种,其中最适合液压管路焊接的方法是氩弧焊接,它具有焊口质量好,焊缝表面光滑、美观,没有焊渣,焊口不氧化,焊接效率高等优点。
另两种焊接方法易造成焊渣进入管内,或在焊口内壁产生大量氧化铁皮,难以清除。
实践证明:一旦造成上述后果,无论如何处理,也很难达到系统清洁度指标。
所以不要轻易采用。
如遇工期短、氩弧焊工少时,可考虑采用氩弧焊焊第一层(打底),第二层开始用电焊的方法,这样既保证了质量,又可提高施工效率。
③管路焊接后要进行焊缝质量检查。
检查项目包括:焊缝周围有无裂纹、夹杂物、气孔及过大咬肉、飞溅等现象;焊道是否整齐、有无错位、内外表面是否突起、外表面在加工过程中有无损伤或削弱管壁强度的部位等。
对高压或超高压管路,可对焊缝采用射线检查或超声波检查,提高管路焊接检查的可靠性。
2.4 管道的处理管路安装完成后要对管道进行酸洗处理。
酸洗的目的是通过化学作用将金属管内表面的氧化物及油污去除,使金属表面光滑。
保证管道内壁的清洁。
酸洗管道是保证液压系统可靠性的一个关键环节,必须加以重视。
2.4.1管道酸洗管道酸洗方法目前在施工中均采用槽式酸洗法和管内循环酸洗法两种。
槽式酸洗法:就是将安装好的管路拆下来,分解后放入酸洗槽内浸泡,处理合格后再将其进行二次安装。
此方法较适合管径较大的短管、直管、容易拆卸、管路施工量小的场合,如泵站、阀站等液压装置内的配管及现场配管量小的液压系统,均可采用槽式酸洗法。
管内循环酸洗法:在安装好的液压管路中将液压元器件断开或拆除,用软管、接管、冲洗盖板联接,构成冲洗回路。
用酸泵将酸液打入回路中进行循环酸洗。
该酸洗方法是近年来较为先进的施工技术,具有酸洗速度快、效果好、工序简单、操作方便,减少了对人体及环境的污染,降低了劳动强度,缩短了管路安装工期,解决了长管路及复杂管路酸洗难的问题,对槽式酸洗易发生装配时的二次污染问题,从根本上得到了解决。
已在大型液压系统管路施工中得到广泛应用。
2.4.2 管道酸洗工艺有无科学、合理的工艺流程、酸洗配方和严格的操作规程,是管道酸洗效果好坏的关键,目前国内外酸洗工艺较多,必须慎重选择、高度重视。
管道酸洗配方及工艺不合理会造成管内壁氧化物不能彻底除净、管壁过腐蚀、管道内壁再次锈蚀及管内残留化学反应沉积物等现象的发生。
为便于使用,现将实践中筛选出的一组酸洗效果较好的管道酸洗工艺介绍如下:槽式酸洗工艺流程及配方(1)脱脂脱脂液配方为:ω(NaOH)=9%~10%;ω(Na 3PO 4)=3%;ω(NaHCO 3)=1.3%;ω(Na 2SO 3)=2%;其余为水操作工艺要求为:温度70~80℃,浸泡4h。
(2)水冲压力为0.8MPa 的洁净水冲干净。
(3)酸洗酸洗液配方为:ω(HCl)=13%~14%;ω[(CH 2)6N 4]=1%;其余为水。
操作工艺要求为:常温浸泡1.5h~2h。
(4)水冲用压力为0.8MPa的洁净水冲干净。
(5)二次酸洗酸洗液配方同上。
操作工艺要求为:常温浸泡5min。
(6)中和中和液配方为:OH稀释至pH值在10~11的溶液。
操作工艺要求为:常NH4温浸泡2min。
(7)钝化钝化液配方为:)=8%~10%;ω(NaN2OH)=2%;ω(NH4其余为水。
操作工艺要求为:常温浸泡5min。
(8)水冲用压力为0.8MPa的净化水冲净为止。
(9)快速干燥用蒸汽、过热蒸汽或热风吹干(10)封管口用塑料管堵或多层塑料布捆扎牢固。
如按以上方法处理的管子,管内清洁、管壁光亮,可保持二个月左右不锈蚀;若保存好,还可以延长时间。
循环酸洗工艺流程及配方(1)试漏用压力为1MPa压缩空气充入试漏。
(2)脱脂脱脂液配方与槽式酸洗工艺中脱脂液配方相同。
操作工艺要求为:温度40~50℃连续循环3h。
(3)气顶用压力为0.8MPa压缩空气将脱脂液顶出。
(4)水冲用压力为0.8MPa的洁净水冲出残液。
(5)酸洗酸洗液配方为:ω(HCl)=9%~11%;ω[(CH2)6N4]=1%;其余为水。
操作工艺要求为:常温断续循环50min。
(6)中和中和液配方为:NH4OH稀释至pH值在9~10的溶液。
操作工艺要求为:常温连续循环25min。
图1 循环酸洗示意图(7)钝化钝化液配方为:ω(NaNO)=10%~14%;2其余为水。
操作工艺要求为:常温断续循环30min。
(8)水冲用压力为0.8MPa,温度为60℃的净化水连续冲洗10min。
(9)干燥用过热蒸汽吹干。
(10)涂油用液压泵注入液压油。
循环酸洗注意事项:1)使用一台酸泵输送几种介质,因此操作时应特别注意,不能将几种介质混淆(其中包括水),严重时会造成介质浓度降低,甚至造成介质报废。