电炉熔炼技术操作条件电极
熔炼电炉操作规程
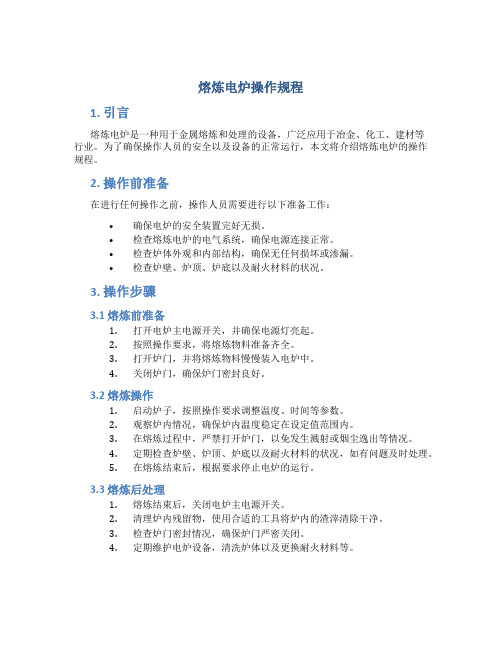
熔炼电炉操作规程1. 引言熔炼电炉是一种用于金属熔炼和处理的设备,广泛应用于冶金、化工、建材等行业。
为了确保操作人员的安全以及设备的正常运行,本文将介绍熔炼电炉的操作规程。
2. 操作前准备在进行任何操作之前,操作人员需要进行以下准备工作:•确保电炉的安全装置完好无损。
•检查熔炼电炉的电气系统,确保电源连接正常。
•检查炉体外观和内部结构,确保无任何损坏或渗漏。
•检查炉壁、炉顶、炉底以及耐火材料的状况。
3. 操作步骤3.1 熔炼前准备1.打开电炉主电源开关,并确保电源灯亮起。
2.按照操作要求,将熔炼物料准备齐全。
3.打开炉门,并将熔炼物料慢慢装入电炉中。
4.关闭炉门,确保炉门密封良好。
3.2 熔炼操作1.启动炉子,按照操作要求调整温度、时间等参数。
2.观察炉内情况,确保炉内温度稳定在设定值范围内。
3.在熔炼过程中,严禁打开炉门,以免发生溅射或烟尘逸出等情况。
4.定期检查炉壁、炉顶、炉底以及耐火材料的状况,如有问题及时处理。
5.在熔炼结束后,根据要求停止电炉的运行。
3.3 熔炼后处理1.熔炼结束后,关闭电炉主电源开关。
2.清理炉内残留物,使用合适的工具将炉内的渣滓清除干净。
3.检查炉门密封情况,确保炉门严密关闭。
4.定期维护电炉设备,清洗炉体以及更换耐火材料等。
4. 安全注意事项•操作人员必须穿戴符合要求的个人防护装备。
•在操作过程中严禁单人操作,必须实行双人联锁操作。
•在电炉运行过程中,严禁触摸电炉内部以及高温部件,以免烫伤。
•在电炉运行过程中,如发现异常情况,应立即停止操作,并及时报告相关人员。
•在操作电炉过程中,应严格按照操作要求进行,禁止随意更改操作参数。
5. 总结熔炼电炉是一种重要的冶金设备,对于操作人员来说,掌握正确的操作规程至关重要。
通过本文的介绍,我们了解了熔炼电炉的操作步骤和安全注意事项,希望能够保障操作人员的安全,确保电炉的正常运行。
在实际操作中,操作人员应严格按照规程进行操作,并不断更新知识,提高自身技能水平,以避免意外事件的发生。
电炉熔炼操作规程(一)

电炉熔炼操作规程(一)引言:电炉熔炼是常见的金属冶炼工艺之一,广泛应用于各种金属材料的加工和制备过程。
为了确保电炉熔炼操作的规范性和安全性,本文将详细介绍电炉熔炼操作规程的相关内容。
正文:一、电炉熔炼前的准备工作1. 清洁电炉炉腔和炉屋,确保工作环境整洁,以防杂质污染。
2. 检查电炉的电力供应和控制系统,确保其正常运行并进行必要的维护。
3. 准备合适的炉膛钢材或陶瓷容器,确保其耐高温和耐腐蚀性能。
二、电炉熔炼操作的步骤1. 将待熔炼的金属材料按照工艺要求放入炉腔,注意避免混合使用不相容的金属材料。
2. 设置电炉的加热温度和时间,并启动电炉的加热系统,使炉腔温度逐渐升高。
3. 监控电炉的温度变化,确保炉腔温度达到熔点并保持稳定。
4. 若有必要,添加熔剂或助熔剂,以提高熔化速度和熔化效果。
5. 在炉腔温度达到预设温度后,停止加热并进行冷却,待熔炼物材料冷却后取出。
三、电炉熔炼中的安全注意事项1. 佩戴适当的防护装备,如耐高温手套、护目镜和防火服,确保人员的安全。
2. 注意金属材料在高温下的熔融性质,避免烫伤和其它意外伤害。
3. 谨慎操作电炉的控制系统和电源开关,避免电击和其他电气安全事故。
4. 在炉腔温度达到熔点时,注意避免喷溅和溅出物的伤害,确保操作环境的安全。
5. 停止加热后,等待熔炼物材料冷却后再取出,避免烫伤和其他安全隐患。
四、电炉熔炼后的处理工作1. 将冷却后的熔炼物材料取出,并进行外观检查,确保其质量符合要求。
2. 清理电炉炉腔和炉屋,清除残留物和杂质,保持电炉的卫生与干净。
3. 对电炉的加热系统和控制系统进行维护和保养,确保其正常运行和延长使用寿命。
4. 在必要的情况下,对炉膛钢材或陶瓷容器进行清洗和维护,以保证其再次使用的可靠性。
5. 撰写熔炼操作记录,标注熔炼物材料、温度曲线和操作要点等重要信息,为后续工序提供参考。
总结:本文详细介绍了电炉熔炼操作规程的相关内容,包括熔炼前的准备工作、熔炼操作的步骤、安全注意事项、熔炼后的处理工作等。
电炉炼铁的原理和方法
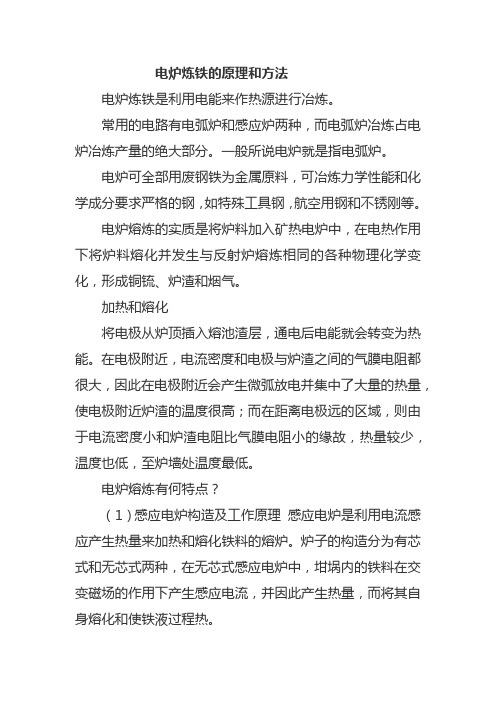
电炉炼铁的原理和方法电炉炼铁是利用电能来作热源进行冶炼。
常用的电路有电弧炉和感应炉两种,而电弧炉冶炼占电炉冶炼产量的绝大部分。
一般所说电炉就是指电弧炉。
电炉可全部用废钢铁为金属原料,可冶炼力学性能和化学成分要求严格的钢,如特殊工具钢,航空用钢和不锈刚等。
电炉熔炼的实质是将炉料加入矿热电炉中,在电热作用下将炉料熔化并发生与反射炉熔炼相同的各种物理化学变化,形成铜锍、炉渣和烟气。
加热和熔化将电极从炉顶插入熔池渣层,通电后电能就会转变为热能。
在电极附近,电流密度和电极与炉渣之间的气膜电阻都很大,因此在电极附近会产生微弧放电并集中了大量的热量,使电极附近炉渣的温度很高;而在距离电极远的区域,则由于电流密度小和炉渣电阻比气膜电阻小的缘故,热量较少,温度也低,至炉墙处温度最低。
电炉熔炼有何特点?(1)感应电炉构造及工作原理感应电炉是利用电流感应产生热量来加热和熔化铁料的熔炉。
炉子的构造分为有芯式和无芯式两种,在无芯式感应电炉中,坩埚内的铁料在交变磁场的作用下产生感应电流,并因此产生热量,而将其自身熔化和使铁液过程热。
在有芯式感应电炉中,需要加入用其它熔炉(如冲天炉)熔化的铁液,在环形铁芯内产生的交变磁场使沟槽内的铁液过程,并利用沟槽中铁液与其上面熔池中的铁液循环作用而加热全部铁液。
无芯式感应电炉具有熔化固体炉料的能力,而有芯感应电炉只能过热已熔化的铁液,但在过热铁液的电能消耗方面,则以有芯感应电炉更为节省。
(2)感应电炉熔炼的优缺点及其应用与冲天炉熔炼相比,感应电炉熔炼的优点是熔炼过程中不会有增碳和增硫现象,而且熔炼过程可以造渣覆盖铁液,在一定程度上能防止铁液中硅、锰及合金元素的氧化,并减少铁液从炉气中吸收气体,从而使铁液比较纯净。
这种熔炼方法的缺点是电能耗费大。
感应电炉适用于熔炼高质量灰铸铁、合金铸铁、球墨铸铁及蠕墨铸铁等。
无芯感应电炉能够直接熔化固体炉料,而且开炉及停炉比较方便,适合于间断性生产条件。
有芯感应电炉开炉及停炉不便,适合于连续性生产。
中频感应电炉熔炼操作规程
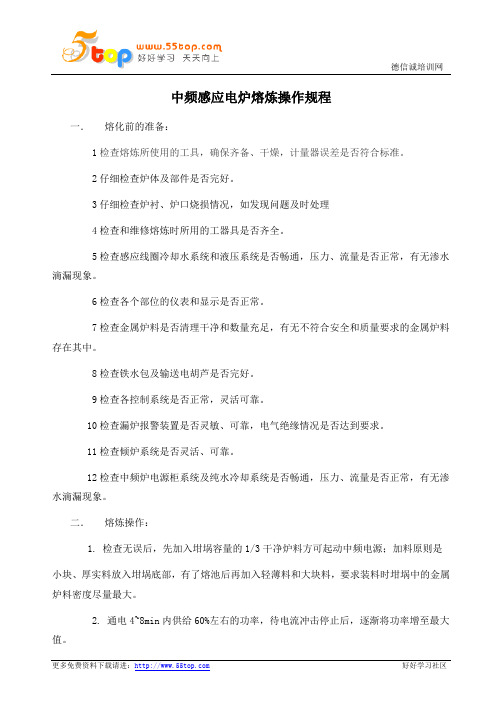
中频感应电炉熔炼操作规程一.熔化前的准备:1检查熔炼所使用的工具,确保齐备、干燥,计量器误差是否符合标准。
2仔细检查炉体及部件是否完好。
3仔细检查炉衬、炉口烧损情况,如发现问题及时处理4检查和维修熔炼时所用的工器具是否齐全。
5检查感应线圈冷却水系统和液压系统是否畅通,压力、流量是否正常,有无渗水滴漏现象。
6检查各个部位的仪表和显示是否正常。
7检查金属炉料是否清理干净和数量充足,有无不符合安全和质量要求的金属炉料存在其中。
8检查铁水包及输送电胡芦是否完好。
9检查各控制系统是否正常,灵活可靠。
10检查漏炉报警装置是否灵敏、可靠,电气绝缘情况是否达到要求。
11检查倾炉系统是否灵活、可靠。
12检查中频炉电源柜系统及纯水冷却系统是否畅通,压力、流量是否正常,有无渗水滴漏现象。
二.熔炼操作:1.检查无误后,先加入坩埚容量的1/3干净炉料方可起动中频电源;加料原则是小块、厚实料放入坩埚底部,有了熔池后再加入轻薄料和大块料,要求装料时坩埚中的金属炉料密度尽量最大。
2. 通电4~8min内供给60%左右的功率,待电流冲击停止后,逐渐将功率增至最大值。
3. 熔炼过程中要经常检查炉衬的烧损情况、中频电源柜上各种仪表、冷却水循环状况;炉膛里不准有炉料架空棚料现象,如有此现象,随时注意捣料,防止“搭桥”。
4. 95%的炉料熔毕时,取钢样进行成分分析,并将其余5%的炉料加入炉内继续熔化。
5.全部炉料溶毕后,降低功率至40%~60%,倾炉扒渣;为防止铁水溢出,铁水液面与炉沿保持50mm的距离。
6. 往铁水液面上加脱氧剂(质量比为:石灰粉:铝粉=2:1)进行扩散脱氧;脱氧过程中可用石灰粉和氟石粉调整炉渣的粘度,使炉渣具有良好的流动性。
7.根据化学分析结果,调整钢液化学成分,其中含硅量应在出钢前10min以内进行调整。
8. 测温,做圆杯试样:测量钢液温度,并作圆杯试样,检查钢液脱氧情况。
9. 钢液温度达到1630~1650°C(高锰钢1520~1560℃),圆杯试样收缩良好时,扒除一半炉渣后,加硅锰各0.15%,镇静一分钟,每吨钢液插铝0.15-0.25%终脱氧,插铝后2~3min以内停电倾炉出钢。
高真空电弧熔炼炉规范操作步骤及注意事项

真空电弧熔炼炉操作步骤与规范开机准备1、打开循环水阀门,出水口有持续的水流出。
检查水路,电路,机械泵油以及分子泵是否正常。
检查V6、V4、V2、V7、G1、G2、DF1、DF2是否处于关闭状态。
检查氩气储量以及减压阀的气体流量调节是否正常。
2、开启总电闸(控制箱中的开关)。
开启熔炼炉电源(右侧墙壁上配电箱电闸和空开)。
开启控制箱中的总电源。
3、开启V6,观察气压表直至一个大气压。
升熔炼室门到适当高度,清洗炉底和样品室,装样品,旋转将电极提高并置海绵钛正上方,降熔炼室门,关闭V6。
【注意事项】开启熔炼室门前,炉内气压必须为一个大气压强。
抽气前必须关闭所有气阀。
在未使用氩气时关闭总阀门。
关闭熔炼室门的时候注意对齐、对正,以及橡胶垫圈处的清洁。
放入的样品不得多于坩埚高度的2/3,不得少于1/3.(粉末或者颗粒可以适当放多一些)。
易氧化的样品需要打磨后立刻放入熔炼室抽真空处理。
抽真空、洗气1、检查所有气阀是否关闭,打开机械泵(机械泵开关同为电磁阀DF1的开关)。
待声音平稳后缓慢开启V7,声音发生改变暂停开启,待声音平稳后继续开启V7直至完全开启。
2、观察真空计到达-0.1Pa两分钟后,开复合真空计电源(电弧炉)。
3、复合真空计显示小于10 Pa时,打开G1和前级阀DF2,此时复合真空计示数变大。
,待示数恢复10Pa以内后,打开分子泵电源,LED消零后,打开start,马上关闭V7。
观察分子泵LED显示400且复合真空计显示1.0E-1Pa后,则认为工作正常。
4、当复合真空计达到5.5E-3Pa时, 先关闭G1,然后按分子泵控制台stop,同时关闭前级阀DF2防止因气压上升引起的机械泵油的反扩散,半分钟后断开分子泵电源。
待分子泵由于惯性泵叶轮转子逐渐停止转动后(大概6分钟,且有一声长鸣),可以认为分子泵已经停止工作。
5、关复合真空计电源。
开氩气(0.05Pa)充氩气到一个大气压(0或-0.05Pa)时,关V2,关氩气。
矿热炉熔炼技术要求与技术操作规程
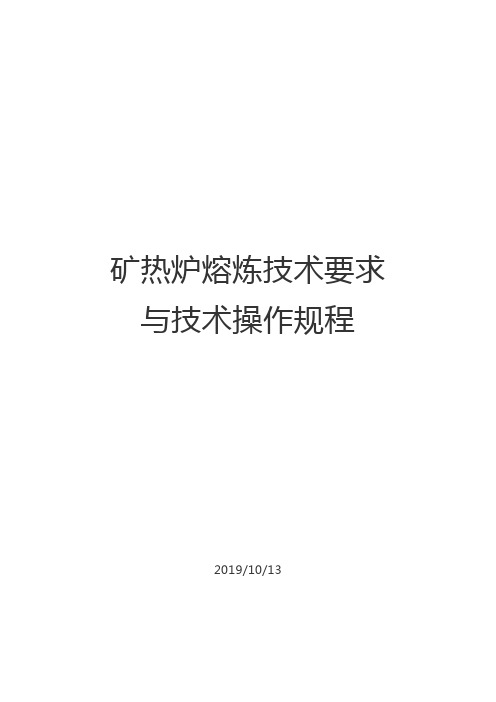
矿热炉熔炼技术要求与技术操作规程2019/10/13目录01、矿热炉熔炼技术要求 (3)正常炉况的要求 (3)料面的维护 (4)配电 (4)处理异常 (5)干烧 (6)出炉精炼 (7)02、冶炼工技术操作规程 (8)03、出炉工技术操作规程 (9)04、配电工技术操作规程 (10)05、炉外吹氧精炼技术操作规程 (11)06、矿热炉生产包装操作规程 (12)07、配料工、上料工技术操作规程 (12)01、矿热炉熔炼技术要求正常炉况的要求1.1电极埋入深度要合适,正常时电极电弧声音小,无局部刺火现象。
1.2料面呈半圆形,冒火均匀,火焰呈淡黄色,料面距炉台的高度不得超过300厘米。
1.3电流平稳,三相负荷均衡,正常情况下电压为130±3V,电流为145A,炉料下降均匀,电极逐渐有所下降。
1.4产量均衡,成分稳定,炉眼畅通,硅水温度高,流动性好。
1.5极心圆直径保持在1850~1900mm之间,以达到炉心料面正常下沉。
1.6机械、电气设备运转正常,各部循环水畅通。
捣炉2.1接班时根据炉况使用捣炉机彻底捣炉一次(特殊情况如刺火等应立即处理),捣炉杆不得碰电极、铜瓦等部位,捣炉后先推熟料后加生料,加料要均匀,捣完炉后应将捣杆立即收回。
2.2料面局部发死的地方,应及时用捣炉机或木杆扎眼松动,必要时应将挑出的粘料块拉出,并适当加轻料。
2.3根据所用原料的特点和炉况,应尽量少使用捣炉机。
料面的维护3.1按正常炉况的要求按(1)(3)两条执行。
3.2拌料要均匀,不准偏加料,发现料过轻或过重,应及时通知车间或炉长调整,如大调时应请示主管工艺总工批准。
3.3发现塌料后应将未塌料部位用大铲捣开并及时推入熟料后加生料。
配电4.1接班时必须认真检查各种仪表指示灯、变压器运行情况,发现异常及时报告班长。
4.2一次电流不超过145A,电压为130±3V,调级时必须征得技术人员同意,并报告车间主任。
4.3停送电必须听从班长亲自指挥。
真空电弧熔炼炉操作步骤精选全文

可编辑修改精选全文完整版真空电弧熔炼炉操作步骤与规范抽真空1、开闸刀总开关(控制箱中的开关)2、开电源(墙壁上配电箱中的开关)、冷却水3、开总控电源(机器上的开关)4、放气至一个大气压(V6)5、开照明,升降机(升),清洗炉底和样品室,装样品,旋转将电极提高并置海绵钛正上方,升降机(降),关V6,关照明。
6、开机械泵(预热大约20分钟左右,有利于机器和抽低真空)7、缓慢打开V7抽气(打开快会把油气抽入管道损坏机械泵)8、当气压表达到-0.1 Pa两分钟后,开复合真空计电源(电弧炉)9、复合真空计显示10 Pa时,关V7,开前级阀门,开分子泵(On-Start), 开炉体与分子泵之间的旋钮10、复合真空计达到5.5×10-3次方Pa时, 关旋钮,关分子泵(先按Stop, 半分钟后按分子泵Off),关前级阀11、关复合真空计电源。
开氩气充氩气到一个大气压(0或-0.05)时,关V2,关氩气。
12、重复抽真空洗气,充氩气2—3次(7—11步)13、最后一次充氩气后就可以开始以下熔炼操作熔炼(I=100 A)1、开照明,将电极放在起弧电极上方2毫米左右2、开电焊机(启动),开高频电源3、启动,引弧后迅速顺时针旋转把手以稍提起电极一段高度,并且同时保证电极移到海绵钛上方4、熔炼海绵钛1-3分钟(吸氧),然后可以最大提高电极并快速移动(*特别注意这点以防止电弧火花熔到海绵钛坩埚周围的很易熔穿的焊接部分)到样品逐个熔炼。
操作过程把持好电极高度小心触底毁坏电极,电极在样品熔炼停留一般20-30秒(太长有害坩埚和形成黑烟沉淀影响熔炼),然后提高电极迅速转移(以防熔坏铜坩埚托盘)到下一个样品熔炼。
熔完每一遍的最后一个样后,先提高电极,然后关引弧前的启动,然后把电极提高并移置海绵钛中心正上方。
5、翻样,然后熔第二遍。
,一般需要翻样2-3次即熔炼3-4次,以求样品熔炼均匀6、最后一遍熔完,关“启动”,并最大提高摆电极与海绵钛正上方,关高频电源,关电焊机7、带样品和腔体、电极冷却(10-15分钟)后,放气(开V6)到一个大气压(气压表0),升升降机(升),取样8、清洗样品室,降升降机,抽低真空(关V6,缓慢开V7,达到-0.1 Pa后,关V7),关机械泵,关电源(总控电源、电源、闸刀开关),1小时后,关冷却水。
电弧炉熔炼工安全操作规程
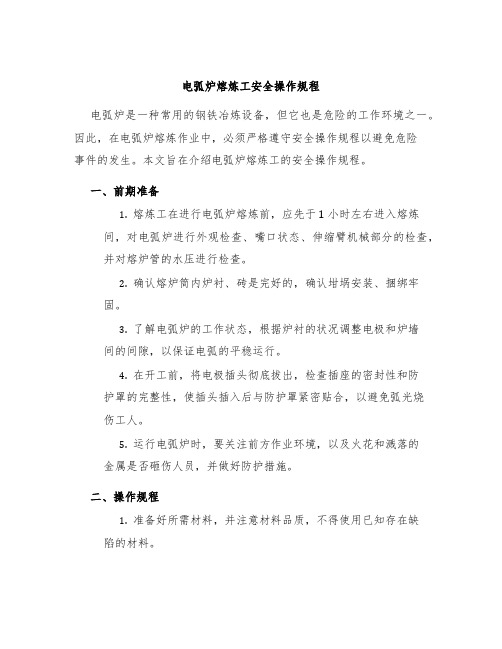
电弧炉熔炼工安全操作规程电弧炉是一种常用的钢铁冶炼设备,但它也是危险的工作环境之一。
因此,在电弧炉熔炼作业中,必须严格遵守安全操作规程以避免危险事件的发生。
本文旨在介绍电弧炉熔炼工的安全操作规程。
一、前期准备1.熔炼工在进行电弧炉熔炼前,应先于 1 小时左右进入熔炼间,对电弧炉进行外观检查、嘴口状态、伸缩臂机械部分的检查,并对熔炉管的水压进行检查。
2.确认熔炉筒内炉衬、砖是完好的,确认坩埚安装、捆绑牢固。
3.了解电弧炉的工作状态,根据炉衬的状况调整电极和炉墙间的间隙,以保证电弧的平稳运行。
4.在开工前,将电极插头彻底拔出,检查插座的密封性和防护罩的完整性,使插头插入后与防护罩紧密贴合,以避免弧光烧伤工人。
5.运行电弧炉时,要关注前方作业环境,以及火花和溅落的金属是否砸伤人员,并做好防护措施。
二、操作规程1.准备好所需材料,并注意材料品质,不得使用已知存在缺陷的材料。
2.操作过程中,熔炼工人必须穿戴适宜的劳动防护用品,包括头盔、手套、防护服、安全带等。
3.在熔化钢水时,要掌握钢液温度、化学成分和炼钢工艺的参数等,以确保钢水质量。
4.在进行操作时,要严格按照规定操作,禁止违章操作和操作失误。
如需更改操作方法,必须报经班组长同意后方可进行。
5.在电弧炉熔炼操作过程中,要及时调整炉衬和电极之间的间隙,保持电弧熔化钢水的稳定,避免冷却堵塞和产生爆炸。
6.熔炼工在操作过程中不得在电弧炉周围晃动,以免引燃周围易燃物,保证周围环境的安全。
7.如果发现电弧炉有异常情况,如出现炉内压力异常增大、有异味或声响,需要立即向负责人报告,停止操作,迅速撤离现场并进行必要的警示措施。
三、结束操作1.在电弧炉关闭前,熔炼工应检查操作是否符合规程,关闭所有管道和开关。
2.关闭电源之前,熔炼工人应对电弧炉进行全面的检查,并清除炉内残留物、护套等余渣。
3.拆卸电极时,工作人员必须停止电弧熔炼过程,并保持熔炼间内散热,以避免烧伤和出现其他危险情况。
电炉熔炼操作规程(二)

电炉熔炼操作规程(二)引言:电炉熔炼是一种常见的金属冶炼方法,在工业生产中被广泛应用。
本文将介绍电炉熔炼操作规程的相关内容,以便操作人员正确进行电炉熔炼工作。
正文:一、设备准备1.选择适当的电炉进行熔炼,并对其进行检查和维护。
2.调整电炉的温度和加热时间,保证炉内温度达到所需的熔点。
二、原料准备1.选择优质的原料,并根据需要进行筛选和混合。
2.确定所需的原料配比,并计算出相应的投料量。
三、操作步骤1.将原料按照配比依次投放到电炉中。
2.启动电炉并设定适当的加热温度和时间。
3.观察炉内的熔化情况,根据需要进行搅拌和调整加热参数。
4.待炉内的物料完全熔化后,停止加热并进行炉内温度的保持。
5.将熔融的物料从炉内倒出,并进行后续的处理和冷却。
四、安全措施1.操作人员要戴好个人防护用品,如防护眼镜、手套等。
2.严禁在炉内投放易燃、易爆等危险物品。
3.定期检查电炉的电线和设备,如发现异常及时修复或更换。
五、操作注意事项1.操作人员应熟悉电炉的使用说明书并按照说明进行操作。
2.注意炉内温度的控制,避免过高或过低导致物料熔炼不彻底或烧结。
3.物料的投放要均匀,避免堆积过高或不均匀导致熔炼不均。
4.搅拌物料时要轻柔,避免过度搅拌导致波动和溅出。
5.操作人员要密切观察炉内的变化,并根据需要及时调整操作参数。
总结:电炉熔炼操作规程是保证熔炼质量和工作安全的重要指南。
通过设备准备、原料准备、操作步骤、安全措施和操作注意事项的合理安排,可以有效地提高电炉熔炼工作的效率和精确度,确保生产过程顺利进行。
电炉熔炼技术操作条件电极
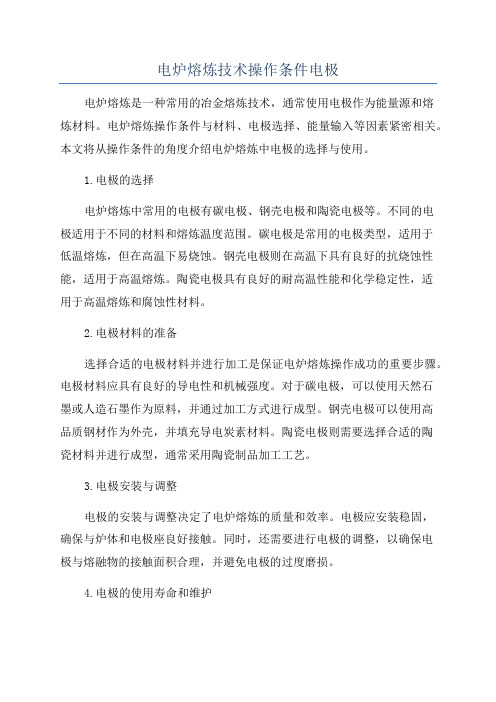
电炉熔炼技术操作条件电极电炉熔炼是一种常用的冶金熔炼技术,通常使用电极作为能量源和熔炼材料。
电炉熔炼操作条件与材料、电极选择、能量输入等因素紧密相关。
本文将从操作条件的角度介绍电炉熔炼中电极的选择与使用。
1.电极的选择电炉熔炼中常用的电极有碳电极、钢壳电极和陶瓷电极等。
不同的电极适用于不同的材料和熔炼温度范围。
碳电极是常用的电极类型,适用于低温熔炼,但在高温下易烧蚀。
钢壳电极则在高温下具有良好的抗烧蚀性能,适用于高温熔炼。
陶瓷电极具有良好的耐高温性能和化学稳定性,适用于高温熔炼和腐蚀性材料。
2.电极材料的准备选择合适的电极材料并进行加工是保证电炉熔炼操作成功的重要步骤。
电极材料应具有良好的导电性和机械强度。
对于碳电极,可以使用天然石墨或人造石墨作为原料,并通过加工方式进行成型。
钢壳电极可以使用高品质钢材作为外壳,并填充导电炭素材料。
陶瓷电极则需要选择合适的陶瓷材料并进行成型,通常采用陶瓷制品加工工艺。
3.电极安装与调整电极的安装与调整决定了电炉熔炼的质量和效率。
电极应安装稳固,确保与炉体和电极座良好接触。
同时,还需要进行电极的调整,以确保电极与熔融物的接触面积合理,并避免电极的过度磨损。
4.电极的使用寿命和维护电极使用过程中的寿命和维护也是重要的操作条件。
碳电极的寿命受到燃烧和烧蚀的影响,需要定期检查和更换。
钢壳电极在高温下也会受到烧蚀的影响,需要定期进行维护和更换。
陶瓷电极的寿命通常较长,但需要注意避免碰撞和破损。
5.能量输入与控制电炉熔炼需要通过供电系统提供电力能量来加热电极和熔融材料。
电炉熔炼中常用的供电方式有直流供电和交流供电。
对于不同的材料和熔炼温度,需要选择合适的供电方式和参数,并通过实时监测和控制来维持适当的温度和能量输入。
总结起来,电炉熔炼中电极的选择与使用是关键的操作条件之一、正确选择合适的电极类型和材料,进行合理的电极安装与调整,并进行定期的维护和更换,以及控制适当的能量输入和温度,可以提高电炉熔炼的质量和效率。
电炉熔炼技术操作条件铜锍、炉渣的放出
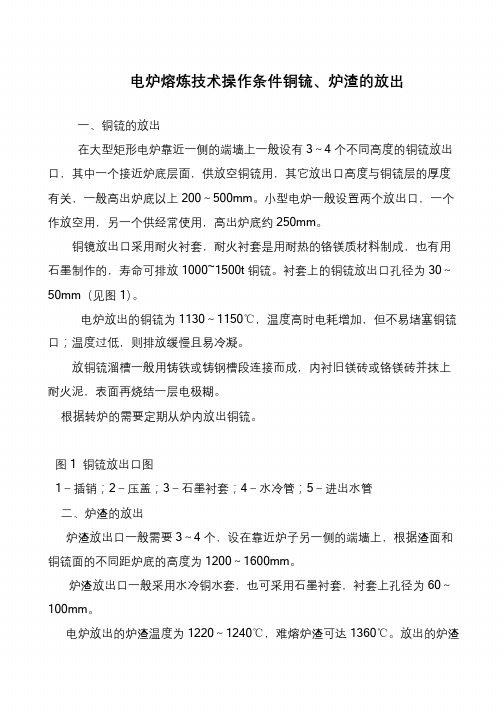
书山有路勤为径,学海无涯苦作舟
电炉熔炼技术操作条件铜锍、炉渣的放出
一、铜锍的放出
在大型矩形电炉靠近一侧的端墙上一般设有3~4 个不同高度的铜锍放出口,其中一个接近炉底层面,供放空铜锍用,其它放出口高度与铜锍层的厚度有关,一般高出炉底以上200~500mm。
小型电炉一般设置两个放出口,一个作放空用,另一个供经常使用,高出炉底约250mm。
铜镜放出口采用耐火衬套,耐火衬套是用耐热的铬镁质材料制成,也有用石墨制作的,寿命可排放1000~1500t 铜锍。
衬套上的铜锍放出口孔径为30~50mm(见图1)。
电炉放出的铜锍为1130~1150℃,温度高时电耗增加,但不易堵塞铜锍口;温度过低,则排放缓慢且易冷凝。
放铜锍溜槽一般用铸铁或铸钢槽段连接而成,内衬旧镁砖或铬镁砖并抹上耐火泥,表面再烧结一层电极糊。
根据转炉的需要定期从炉内放出铜锍。
图1 铜锍放出口图
1-插销;2-压盖;3-石墨衬套;4-水冷管;5-进出水管
二、炉渣的放出
炉渣放出口一般需要3~4 个,设在靠近炉子另一侧的端墙上,根据渣面和铜锍面的不同距炉底的高度为1200~1600mm。
炉渣放出口一般采用水冷铜水套,也可采用石墨衬套,衬套上孔径为60~100mm。
电炉放出的炉渣温度为1220~1240℃,难熔炉渣可达1360℃。
放出的炉渣。
中频电炉熔炼工序操作工艺守则
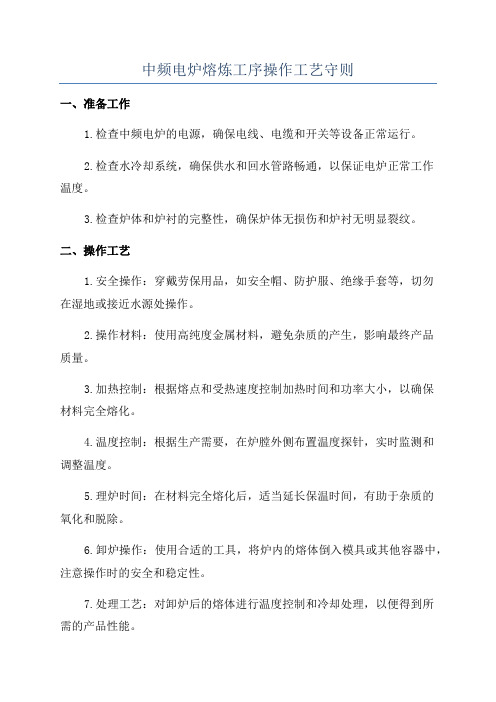
中频电炉熔炼工序操作工艺守则一、准备工作1.检查中频电炉的电源,确保电线、电缆和开关等设备正常运行。
2.检查水冷却系统,确保供水和回水管路畅通,以保证电炉正常工作温度。
3.检查炉体和炉衬的完整性,确保炉体无损伤和炉衬无明显裂纹。
二、操作工艺1.安全操作:穿戴劳保用品,如安全帽、防护服、绝缘手套等,切勿在湿地或接近水源处操作。
2.操作材料:使用高纯度金属材料,避免杂质的产生,影响最终产品质量。
3.加热控制:根据熔点和受热速度控制加热时间和功率大小,以确保材料完全熔化。
4.温度控制:根据生产需要,在炉膛外侧布置温度探针,实时监测和调整温度。
5.理炉时间:在材料完全熔化后,适当延长保温时间,有助于杂质的氧化和脱除。
6.卸炉操作:使用合适的工具,将炉内的熔体倒入模具或其他容器中,注意操作时的安全和稳定性。
7.处理工艺:对卸炉后的熔体进行温度控制和冷却处理,以便得到所需的产品性能。
三、异常处理1.电炉故障:一旦发生电炉故障,首先切断电源,并通知电炉维修人员进行检修。
2.材料异常:如果出现材料污染、气体生成或其他异常情况,应立即停止生产,安全处理,并向上级报告。
3.温度异常:如果出现温度突然上升或下降,应立即停炉检查炉体和温度控制系统,确保问题得到解决后再重新启动。
四、清洁与维护1.每次使用结束后,应清理炉体内部和周围的杂物和残留物,保持工作环境整洁。
2.定期对中频电炉进行维护,清洗,更换炉衬和其他部件,以提高电炉的使用寿命和稳定性。
3.对于出现故障或老化的设备,及时更换或修理,确保设备的正常运行。
总之,中频电炉熔炼工序操作工艺守则是确保生产过程安全、高效、产品质量稳定的重要规范。
在操作过程中,必须保持高度的警惕性和细致的仔细性,严格按照规定的程序和标准进行操作,不仅能够保障人身安全,还能提高生产效率和产品的质量,并确保设备的正常运行。
电炉熔炼操作规程

1 目的为获得优质铁水,保证电炉熔炼过程正常进行,特制定本操作规程。
2 适用范围适用于铸铁铸造车间电炉熔炼过程。
3 内容要求3.1 熔化前的准备操作者在工作前穿戴齐全劳保用品,检查所用的工具、设备、器具是否齐全、合格;浇包、炉衬、炉口、包嘴是否光滑顺畅,并备好合格炉料。
3.2 烘炉大修后的炉衬应在开炉前预热烘烤,先将炉内放少须铁屑,再放入废铁件,要小心轻放,不要碰炉壁,烘烤通常用“空炉低功率慢升温”的方法,先小电流≤300A工作半小时,再缓慢升温至废件发红(约1000度),保温1小时,然后升高电流600A至铁水熔化满以后(铁水温度1450℃)烧结炉衬1小时,以使炉衬结壳。
3.3 熔炼3.3.1按工艺部出具的《熔炼配料通知单》要求的比例称重加料。
3.3.2各炉料的块度和长度要符合要求:a.生铁块度一般在2Kg-10Kg,10Kg以上及2Kg以下块度含量不超过5%;b.废钢单件外形尺寸不大于炉口直径2/3(具体如下表),单件重量不大于13kg ;c.硅、锰铁的块度不大于70×70mm;d.回炉料、废铸件外形尺寸不大于炉口直径2/3,具体如下表严禁加入密封管件及其它有害杂物。
3.3.4 炉料加料顺序铁屑---增碳剂---生铁---废钢---回炉铁---铁合金3.3.5 炉料加入后,即可通小电流(≤500A)预热,然后再改用大电流(>600A)送电,以使炉料自下而上慢慢预热和熔化;熔炼中发现有棚料现象时,应把电炉倾斜至一定角度,用铁水融开炉料。
3.3.6 待炉料完全熔化后,加入铁合金或所需金属,升温至约1400℃,用取样小勺伸入铁液表面下100~300mm取样,通过铁水成分快速分析仪示值确定调整碳硅量,时间一般为3~5分钟,同时加温至要求的出铁温度。
3.3.7 用快速热电偶测量铁水温度;出铁温度一般控制在:灰铁1450~1500℃,球铁1530~1560℃;轻薄小件取上限,厚重大件取下限。
铁水烫包回炉后温度升至规定要求方可出炉。
全电极熔炉操作方法
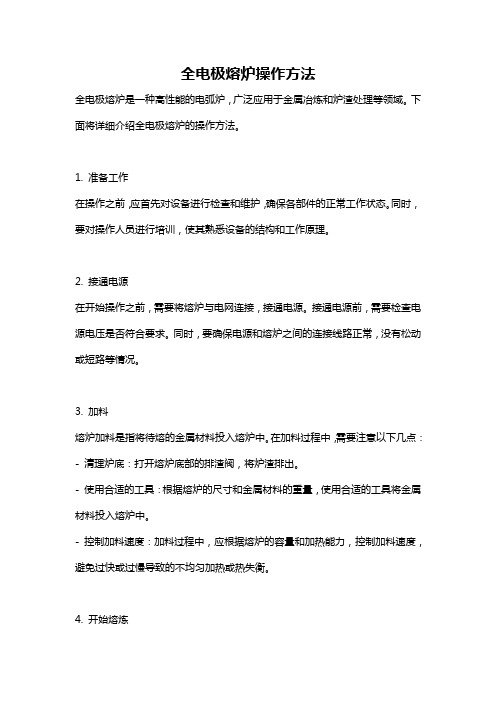
全电极熔炉操作方法全电极熔炉是一种高性能的电弧炉,广泛应用于金属冶炼和炉渣处理等领域。
下面将详细介绍全电极熔炉的操作方法。
1. 准备工作在操作之前,应首先对设备进行检查和维护,确保各部件的正常工作状态。
同时,要对操作人员进行培训,使其熟悉设备的结构和工作原理。
2. 接通电源在开始操作之前,需要将熔炉与电网连接,接通电源。
接通电源前,需要检查电源电压是否符合要求。
同时,要确保电源和熔炉之间的连接线路正常,没有松动或短路等情况。
3. 加料熔炉加料是指将待熔的金属材料投入熔炉中。
在加料过程中,需要注意以下几点:- 清理炉底:打开熔炉底部的排渣阀,将炉渣排出。
- 使用合适的工具:根据熔炉的尺寸和金属材料的重量,使用合适的工具将金属材料投入熔炉中。
- 控制加料速度:加料过程中,应根据熔炉的容量和加热能力,控制加料速度,避免过快或过慢导致的不均匀加热或热失衡。
4. 开始熔炼在完成加料后,可以开始进行熔炼操作。
具体步骤如下:- 关闭熔炉门:在加料完成后,关闭熔炉门,确保熔融金属不会有溅出的风险。
- 启动电弧:通过控制系统,启动电弧,使电极与金属材料产生弧光放电。
在启动电弧时,可以选择使用点火枪或手动点火的方式。
- 控制加热时间和功率:通过调整电流、电压和电弧的稳定性等参数,控制熔炉的加热时间和功率。
根据金属材料的熔点和冶炼过程的要求,合理调整加热参数,确保金属材料完全熔融。
- 炉渣处理:在熔炉操作过程中,会产生炉渣。
根据熔炉的设计,可以选择使用底吹除渣或侧吹除渣等方法进行炉渣处理。
5. 结束熔炼在熔炼完成后,需要采取以下措施进行收尾工作:- 停止加热:关闭电弧和供电系统,停止熔炼过程。
同时,要确保电流和电压恢复到安全值,避免意外事故的发生。
- 倒出熔融金属:打开熔炉底部的出渣阀,将熔融金属倒出。
- 清洁炉体:清理熔炉内部的残渣和炉渣,保持炉体的清洁和整洁。
总之,全电极熔炉的操作方法涉及准备工作、加料、熔炼和结束熔炼等多个环节。
电炉熔炼操作规程
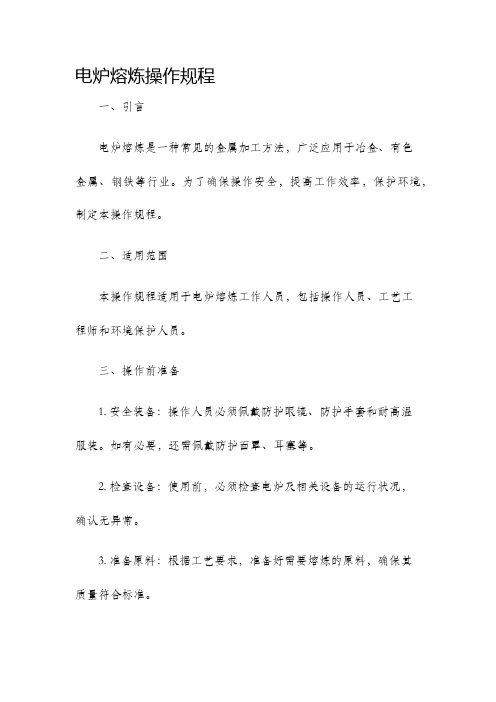
电炉熔炼操作规程一、引言电炉熔炼是一种常见的金属加工方法,广泛应用于冶金、有色金属、钢铁等行业。
为了确保操作安全,提高工作效率,保护环境,制定本操作规程。
二、适用范围本操作规程适用于电炉熔炼工作人员,包括操作人员、工艺工程师和环境保护人员。
三、操作前准备1. 安全装备:操作人员必须佩戴防护眼镜、防护手套和耐高温服装。
如有必要,还需佩戴防护面罩、耳塞等。
2. 检查设备:使用前,必须检查电炉及相关设备的运行状况,确认无异常。
3. 准备原料:根据工艺要求,准备好需要熔炼的原料,确保其质量符合标准。
4. 准备工具:准备好必要的熔炼工具,如熔化碗、长钳、砂轮等。
四、操作步骤1. 打开电源:按照操作顺序,打开电炉电源,确保供电正常。
2. 加入原料:将准备好的原料定量加入熔炼碗中,注意不要超过炉子容量限制。
3. 封闭炉门:将炉门关闭,并确保密封良好,以防止热量散失。
4. 启动加热设备:根据工艺要求,启动电炉加热设备,设定适当的熔炼温度。
5. 观察熔炼过程:通过炉窗观察熔炼过程,注意观察温度、熔化情况等。
6. 搅拌原料:熔炼过程中,定期使用长钳或类似工具搅拌原料,均匀加热。
7. 控制温度:根据工艺要求,调节电炉加热设备,控制熔炼温度稳定在设定值。
8. 熔炼结束:根据工艺要求,确定熔炼时间,待熔炼结束后,关闭电炉加热设备。
9. 关闭电源:熔炼结束后,切断电炉电源,做好安全措施。
五、操作注意事项1. 安全第一:操作人员要严格按照安全操作规程进行操作,确保人身安全。
2. 环保要求:严格按照环保要求进行操作,注意废气、废水等的处理。
3. 温度控制:加热温度要控制在设定值范围,避免过热或过低。
4. 注意观察:熔炼过程中,要时刻观察炉内情况,防止温度异常、溢流等情况发生。
5. 熔炼时间:熔炼时间根据工艺要求确定,不可随意更改。
六、事故应急处理1. 发生炉体温度异常时,立即切断电源,并及时通知相关人员进行排除故障。
2. 如发生溢流、喷溅等情况,应迅速切断电源,并使用安全工具进行处理。
中频电炉熔炼操作工艺规程
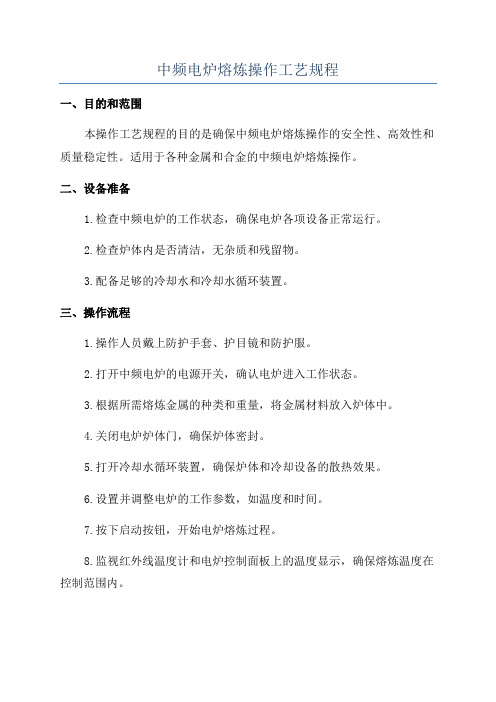
中频电炉熔炼操作工艺规程一、目的和范围本操作工艺规程的目的是确保中频电炉熔炼操作的安全性、高效性和质量稳定性。
适用于各种金属和合金的中频电炉熔炼操作。
二、设备准备1.检查中频电炉的工作状态,确保电炉各项设备正常运行。
2.检查炉体内是否清洁,无杂质和残留物。
3.配备足够的冷却水和冷却水循环装置。
三、操作流程1.操作人员戴上防护手套、护目镜和防护服。
2.打开中频电炉的电源开关,确认电炉进入工作状态。
3.根据所需熔炼金属的种类和重量,将金属材料放入炉体中。
4.关闭电炉炉体门,确保炉体密封。
5.打开冷却水循环装置,确保炉体和冷却设备的散热效果。
6.设置并调整电炉的工作参数,如温度和时间。
7.按下启动按钮,开始电炉熔炼过程。
8.监视红外线温度计和电炉控制面板上的温度显示,确保熔炼温度在控制范围内。
9.当金属材料完全熔化并达到需要的温度时,按下停止按钮,关闭电炉。
10.打开电炉炉体门,倾倒熔炼好的金属在预先准备好的容器中。
11.关闭电炉炉体门,停止冷却水循环装置。
四、安全注意事项1.操作人员必须穿戴好个人防护装备,包括防护手套、护目镜和防护服。
2.只有经过培训和授权的人员才能操作中频电炉。
3.在熔炼过程中,严禁将手或其他物体伸入电炉内。
4.在电炉工作过程中,严禁擅自更改电炉的工作参数和设定值。
5.在熔炼操作结束后,应及时关闭电炉和冷却水循环装置,并将残留的金属材料和废渣清理干净。
6.在操作过程中,如发现电炉有异常情况或故障,请立即停止操作,并向上级报告和寻求维修。
五、质量控制1.在熔炼前,应检查金属材料的质量和净度,确保其符合要求。
2.监控和记录熔炼过程中的温度和时间,以确保熔炼温度和时间控制在合理范围内。
3.熔炼后,对熔炼好的金属进行质量检测,包括化学成分、物理性能等指标。
4.对于不合格品,应及时调整熔炼参数或更换原材料,以确保产品质量符合要求。
六、操作记录1.每次熔炼过程都应有详细的操作记录,包括熔炼时间、熔炼温度、原材料种类和重量等。
镍电炉熔炼操作及常见故障处理
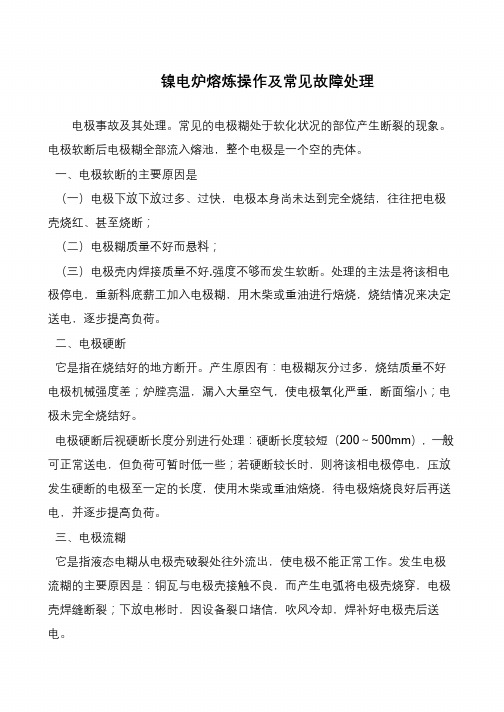
书山有路勤为径,学海无涯苦作舟
镍电炉熔炼操作及常见故障处理
电极事故及其处理。
常见的电极糊处于软化状况的部位产生断裂的现象。
电极软断后电极糊全部流入熔池,整个电极是一个空的壳体。
一、电极软断的主要原因是
(一)电极下放下放过多、过快,电极本身尚未达到完全烧结,往往把电极壳烧红、甚至烧断;
(二)电极糊质量不好而悬料;
(三)电极壳内焊接质量不好,强度不够而发生软断。
处理的主法是将该相电极停电,重新料底薪工加入电极糊,用木柴或重油进行焙烧,烧结情况来决定送电,逐步提高负荷。
二、电极硬断
它是指在烧结好的地方断开。
产生原因有:电极糊灰分过多,烧结质量不好电极机械强度差;炉膛亮温,漏入大量空气,使电极氧化严重,断面缩小;电极未完全烧结好。
电极硬断后视硬断长度分别进行处理:硬断长度较短(200~500mm),一般可正常送电,但负荷可暂时低一些;若硬断较长时,则将该相电极停电,压放发生硬断的电极至一定的长度,使用木柴或重油焙烧,待电极焙烧良好后再送电,并逐步提高负荷。
三、电极流糊
它是指液态电糊从电极壳破裂处往外流出,使电极不能正常工作。
发生电极流糊的主要原因是:铜瓦与电极壳接触不良,而产生电弧将电极壳烧穿,电极壳焊缝断裂;下放电彬时,因设备裂口堵信,吹风冷却,焊补好电极壳后送电。
高真空电弧熔炼炉规范操作步骤及注意事项

真空电弧熔炼炉操作步骤与规范开机准备1、打开循环水阀门,出水口有持续的水流出。
检查水路,电路,机械泵油以及分子泵是否正常。
检查V6、V4、V2、V7、G1、G2、DF1、DF2是否处于关闭状态。
检查氩气储量以及减压阀的气体流量调节是否正常。
2、开启总电闸(控制箱中的开关)。
开启熔炼炉电源(右侧墙壁上配电箱电闸和空开)。
开启控制箱中的总电源。
3、开启V6,观察气压表直至一个大气压。
升熔炼室门到适当高度,清洗炉底和样品室,装样品,旋转将电极提高并置海绵钛正上方,降熔炼室门,关闭V6。
【注意事项】开启熔炼室门前,炉内气压必须为一个大气压强。
抽气前必须关闭所有气阀。
在未使用氩气时关闭总阀门。
关闭熔炼室门的时候注意对齐、对正,以及橡胶垫圈处的清洁。
放入的样品不得多于坩埚高度的2/3,不得少于1/3.(粉末或者颗粒可以适当放多一些)。
易氧化的样品需要打磨后立刻放入熔炼室抽真空处理。
抽真空、洗气1、检查所有气阀是否关闭,打开机械泵(机械泵开关同为电磁阀DF1的开关)。
待声音平稳后缓慢开启V7,声音发生改变暂停开启,待声音平稳后继续开启V7直至完全开启。
2、观察真空计到达-0.1Pa两分钟后,开复合真空计电源(电弧炉)。
3、复合真空计显示小于10 Pa时,打开G1和前级阀DF2,此时复合真空计示数变大。
,待示数恢复10Pa以内后,打开分子泵电源,LED消零后,打开start,马上关闭V7。
观察分子泵LED显示400且复合真空计显示1.0E-1Pa后,则认为工作正常。
4、当复合真空计达到5.5E-3Pa时, 先关闭G1,然后按分子泵控制台stop,同时关闭前级阀DF2防止因气压上升引起的机械泵油的反扩散,半分钟后断开分子泵电源。
待分子泵由于惯性泵叶轮转子逐渐停止转动后(大概6分钟,且有一声长鸣),可以认为分子泵已经停止工作。
5、关复合真空计电源。
开氩气(0.05Pa)充氩气到一个大气压(0或-0.05Pa)时,关V2,关氩气。
- 1、下载文档前请自行甄别文档内容的完整性,平台不提供额外的编辑、内容补充、找答案等附加服务。
- 2、"仅部分预览"的文档,不可在线预览部分如存在完整性等问题,可反馈申请退款(可完整预览的文档不适用该条件!)。
- 3、如文档侵犯您的权益,请联系客服反馈,我们会尽快为您处理(人工客服工作时间:9:00-18:30)。
电炉熔炼技术操作条件电极
大型电炉一般采用自焙电极,低于500kVA小型电炉也可以采用炭素电极或石墨电极。
一、电极壳
自焙电极的外壳用薄钢板焊接或轧制件铆接而成,外壳上钻有直径3~5mm的小孔以排除壳内挥发物(如用标准电极糊,可设一定数量排气孔;用密闭糊,则可不必开孔)。
内设筋片若干片。
自焙电极壳的有关尺寸见表1。
自焙电极的筋片形式见图1。
表1 自焙电极壳尺寸,mm
图1 自焙电极的筋片形式图
云冶电极壳规格为:
(一)材料规格
钢板型号:P-3F普通钢板
化学成分,%:C-0.18;Si-0.2;Mn-0.41;P-0.025;S-0.033。
物理规格:2000×1000×1.5mm
(二)电极壳制作规格(mm)
为加强电极的抗拉强度,在电极壳中心焊接两根直径18的螺纹钢。
自焙电机外壳用钢的耗量,一般为电极糊耗量的5%。
二、电极糊
电极糊用无烟煤、焦炭、煤焦油和沥青制成。
块状电极糊每块重约25~30kg,经破碎后装入电极壳内。
其块度以能在相邻两筋片间自由落下为准,一般为20~40mm。
国外有的工厂采用颚式破碎机破碎电极糊。
生产操作时,电极糊面高度即铜瓦上电极糊装料高度一般为0.5~1.5m。
电极糊要保持清洁,防止泥沙等杂物混入。
不同厂的电极糊要分别堆存。
目前国内几家工厂产电极糊物理化学性质列于表2。
表2 国产电极糊物理化学性质数据表(一)
续表2 国产电极糊物理化学性质数据表(二)
在工作过程中,电极上部焙烧的部分逐渐下降,当接近高温带时,逐渐烧结。
图2为前苏联北方镍公司矿热电炉的电极内电极糊在不同高度下的温度变化。
图2 自焙电极糊沿电极高度的温度变化
在区间Ⅰ内,温度为50~70℃,电极糊软化并与原先加入的电极糊表面牢固地粘结起来;
在区间Ⅱ内,即在铜瓦区,电极糊的温度从70℃升到300℃,电极糊粘结剂中的挥发物开始挥发;
在区间Ⅲ内,电极烧结,大量挥发物在400~540℃时挥发出来。
在730℃时,电极糊内的挥发物全部挥发,烧结过程完结;
在区间Ⅳ内,电极以完成了进入工作状态的准备,其温度超过900℃。
不同温度下自焙电极,电极糊的物理性质列于表3。
表3 不同温度下自焙电极、电极糊的物理性质
三、电极钢带
云冶采用UR―63型炭素冷轧钢带和20号钢带。
其规格如下:
(一)元素含量,按部颁标准(%): C-0.2~0.3;Si-0.17~ 0.37;P-0.04 ;S-0.04;Cr-0.25;Ni-0.25。
(二)抗拉强度:20号钢带为550~800MPa,伸长率小于2%。
(三)物理规格:3000×300×1.5mm。
四、电极的升降
中小型电炉电极升降采用卷扬驱动,大型电炉电极升降采用液压装置。
一般直径为1100~1200mm的自焙电极重量达18~20t,需用35t卷扬机。
电极升降速度可按表4选取。
表4 自焙电极的升降速度
电极下降速度一般比提升速度慢20~25%,以免电极下降时电流发生过大的波动。
如果发生故障时能较快的提升电极。
大型电炉每次下放电极的长度不超过150~200mm,下放相隔时间一般不少于炉子全负荷工作6h,故每天的下放长度一般不超过400~600mm。
下放操作时带电进行的,但一般要降低负荷40~60%,以免烧坏电极壳。
下放完毕后10~
30min内逐渐恢复正常负荷。
云冶每次下放不大于150mm,连续下放不超过400mm,下放时,每相电流不超过50A,降低负荷为原来的50%。
五、电极密封
电炉电炉熔炼时大量冷空气电极四周空隙漏入炉内,致使烟气量增大,烟气中S0
浓度降低。
目前熔矿电炉电极密封方式较多,常用的有:
2
(一)采用靠近炉子侧壁的循环气体密电极。
该法系利用从炉子排出的气体通过支管将气体通入电极周围的喷嘴,把溢出的气体压人炉中。
图3为循环气体密封示意图。
图3 循环气体密封示意图
(二)折叠式密封装置该装置由三个直径递增的钢制上、中、下部密封圈组成,其相对间隙为30~50mm。
每段密封圈高度为350mm左右,三段总长为1050mm,略大于或等于电极行程。
整个密封圈用三根吊链沿周边成120°角固定于夹紧圆环上,它随电极上升而上升,随电极摆动而摆动。
始终将电极与炉顶接触处的间隙密封。
折叠式电极密封装置见图4。
图4 折叠式电极密封装置结构示意图
1-下吊环;2-下密封圈;3-中密封圈;4-上密封圈;5-上部吊环;
6-密封填料;7-吊链;8-炉顶;9-电极;10-夹紧圆环;
11-电极夹持器
(三)采用在电极周围用填料圈密封,或采用水冷密封圈密封电极孔。
图5为固定式水套密封装置结构图。
通过弹簧和油缸的作用使锥形环上升时,锥形环的斜面就对颚板产生足够的压力以保持与电极紧密接触。
在锥形环上部用法兰和螺丝将密封材料(耐火砖)和玻璃丝布压紧,而密封水套和密封圈则固定在电炉炉顶上。
当电极上下动作时,靠密封材料与密封水套及密封圈内表面的摩擦而保持良好密封。
为了防止产生涡流而增加电能的损失,全部密封件都用不锈钢制作。
图5 固定式水套冷却电极密封装置
1-电极;2-导电颚板;3-压紧颚板的锥形环;4-密封材料;5-玻璃丝布;
6-密封水套;7-密封圈。