五轴数控机床旋转轴位置测定与加工设置22
五轴数控机床的运动精度检测

五轴数控机床的精度检测方法分析摘要:本文首先对五轴数控机床的精度检测技术做了一个简要概括,然后介绍数控机床精度检测的必要性,指出数控机床常见的精度要求及传统检测方法,并介绍先进检测方法和检测仪器、工具,以及各个检测方法的特点。
关键词:五轴数控机床;精度检测Precision analysis of detection method of five axis CNC machine toolsAbstract: Firstly,this paper introduces the precision detection technology of five axis NC machine tools, and then introduces the necessity of CNC machine tool accuracy detection accuracy requirements of CNC machine tools, points out the common and the traditional detection method, and introduce advanced detection method and detection instruments, tools, and the characteristics of each detection method.Key words: Five axis NC machine tool;Precision detection1 引言五轴联动数控机床目前已大量用于航空制造等高端制造领域。
由于机床复杂的机械结构及控制系统,五轴联动机床加工精度检测及优化一直是机械制造行业内研究的热点和难点,成为影响产品加工质量及效率的关键。
对企业来说,购买数控机床是一笔相当大的投资,特别是购买大型机床。
实践表明,大多数大型数控机床解体发运给用户安装时,必须在现场调试才能符合其技术指标,因此,在新机床检收时,要进行严格的检定,使机床一开始安装就能保证达到其枝术指标预期使用性能和生产效率。
五轴设定
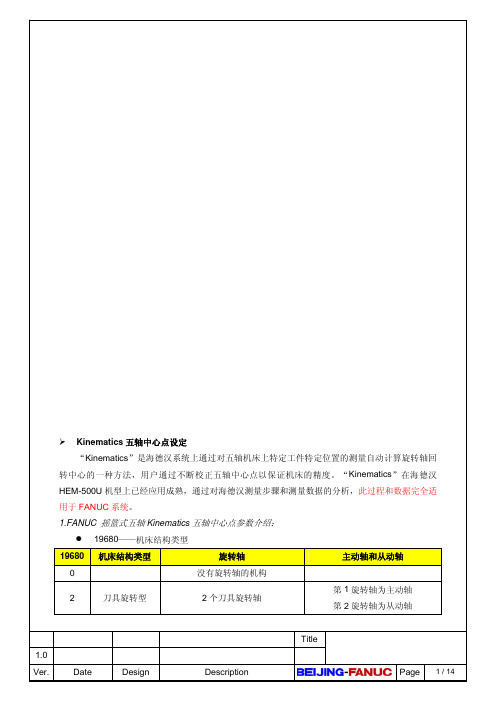
图2:控制轴号与伺服轴号的区别 19682——第1旋转轴轴方向
图3:旋转轴轴方向设定旋转轴旋转方向
图6:工作台第1旋转轴到工作台第2旋转轴交叉矢量
图7:五轴中心点测量STEP-1
工作台旋转轴上A 、B 点选取
轴旋转轴线上一点,B 点为C 轴旋转轴线上一点,为方便测量和计算,选取轴轴线上Y 位置相等,选取B 点为C 轴旋转轴线上工作台面位置。
图8:五轴中心点测量STEP-2
STEP-3 ZP1、ZB1、XB1坐标值测量
,测量B 点在Z 向的坐标ZP1(Z-)、工件上表面Z 向的坐标ZB1((X-)。
L L
Y+
Z+
A B
B 轴旋转中心线
C 轴旋转中心线
Y+
矢量AB 可以分成X 向和Z 向的分量,
Y 向重合。
ZP1(Z-)ZB1(Z-)
XB1(X-)
图9:五轴中心点测量STEP-3
YC2坐标值测量
度,测量工件Y+向侧面坐标YC1(Y+);
YC2(Y-)
YC1(Y+)
10:五轴中心点测量STEP-4
向侧面坐标XC2(X+)。
XC2(X+)
11:五轴中心点测量STEP-5
坐标值测量
向侧面坐标XB2(X+);
ZB2(Z-)
XB2(X+)
12:五轴中心点测量STEP-6 五轴中心点计算介绍:
B(X0->C
图15:旋转轴输出角度判定过程 以BC类型工具轴Z轴机床加以说明:
图17::1221#4=0时 G53.1执行前后两个旋转轴的旋转位置图18::1221#4=1时 G53.1执行前后两个旋转轴的旋转位置。
【海德汉】干货集锦 - 旋转轴定位精度五轴加工的关键(上)
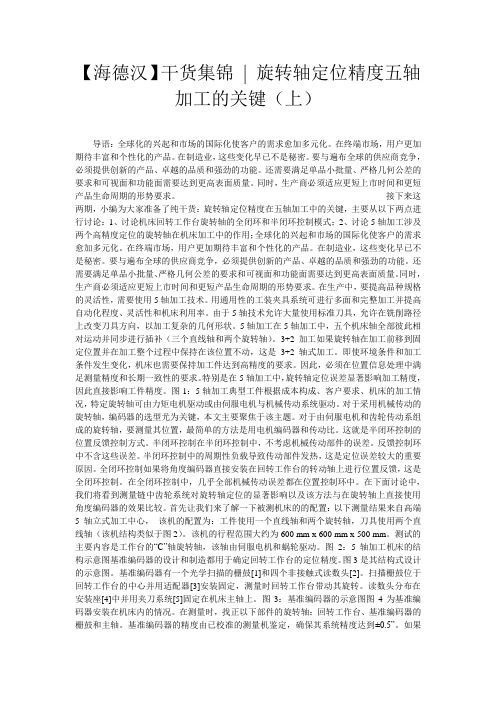
【海德汉】干货集锦| 旋转轴定位精度五轴加工的关键(上)导语:全球化的兴起和市场的国际化使客户的需求愈加多元化。
在终端市场,用户更加期待丰富和个性化的产品。
在制造业,这些变化早已不是秘密。
要与遍布全球的供应商竞争,必须提供创新的产品、卓越的品质和强劲的功能。
还需要满足单品小批量、严格几何公差的要求和可视面和功能面需要达到更高表面质量。
同时,生产商必须适应更短上市时间和更短产品生命周期的形势要求。
接下来这两期,小编为大家准备了纯干货:旋转轴定位精度在五轴加工中的关键,主要从以下两点进行讨论:1、讨论机床回转工作台旋转轴的全闭环和半闭环控制模式;2、讨论5轴加工涉及两个高精度定位的旋转轴在机床加工中的作用;全球化的兴起和市场的国际化使客户的需求愈加多元化。
在终端市场,用户更加期待丰富和个性化的产品。
在制造业,这些变化早已不是秘密。
要与遍布全球的供应商竞争,必须提供创新的产品、卓越的品质和强劲的功能。
还需要满足单品小批量、严格几何公差的要求和可视面和功能面需要达到更高表面质量。
同时,生产商必须适应更短上市时间和更短产品生命周期的形势要求。
在生产中,要提高品种规格的灵活性,需要使用5轴加工技术。
用通用性的工装夹具系统可进行多面和完整加工并提高自动化程度、灵活性和机床利用率。
由于5轴技术允许大量使用标准刀具,允许在铣削路径上改变刀具方向,以加工复杂的几何形状。
5轴加工在5轴加工中,五个机床轴全部彼此相对运动并同步进行插补(三个直线轴和两个旋转轴)。
3+2加工如果旋转轴在加工前移到固定位置并在加工整个过程中保持在该位置不动,这是3+2轴式加工。
即使环境条件和加工条件发生变化,机床也需要保持加工件达到高精度的要求。
因此,必须在位置信息处理中满足测量精度和长期一致性的要求。
特别是在5轴加工中,旋转轴定位误差显著影响加工精度,因此直接影响工件精度。
图1:5轴加工典型工件根据成本构成、客户要求、机床的加工情况,特定旋转轴可由力矩电机驱动或由伺服电机与机械传动系统驱动。
五轴联动数控加工中旋转角度的选取与优化_吴宝利

48 2013 / 9
轴 的 极 限 角 速 度 相 等 ,不 考 虑 线 性 轴 ,假 设 A、C 都 以
极限速度进行插补,A、C 中变化较大的轴的插补时间,
即为整个过程的插补时间。 最优化目标是使两个坐标
点 之 间 ,效 率 最 高 ,故 取 A、C 变 化 较 大 的 作 为 优 化 的
轴的最小极限值和最大极限值。 角度选取的流程如图
3 所示。
3 角度的优化
读取一组刀位点
刀具的中心 轨迹是依照工件 的轮廓形状而生 成的, 在五轴加 工的零件中,常常 会碰到自由曲面 形状复杂的案例。 在这些零件的某 些高曲率的地方, 会出现刀位点间 的法向矢量的变 化幅度和变化频 率比较大的情况。 这样会大大降低 零件的加工精度, 尤其是五轴侧刃 铣,很容易产生较 大的过切。 刀位 点间的法向矢量 变化幅度和变化
刀位点间的法向矢量变化幅度和变化读取一组刀位点计算得到ac角度基值约束条件是否存在ac可能取值读一组可能ac值计算目标函数值将其存入数组ac可能值读取完毕选取得到使目标函数值最小的ac值刀位文件结束结束无解报警处理nynynyijk图3角度选取流程图制造材料制造材料auiijkc图2刀具从初始点绕xz轴的逆时针方向到达目的点48机械制造51卷第589期20139频率较大反映到nc加工代码中就是旋转角度变化较大
* 广州市科技计划项目(编号:2009Z2-D351) 收稿日期:2013 年 3 月
NC 代 码 进 行 插 值 处 理 ,以 提 高 零 件 的 加 工 精 度 ,并 通 过 VERICUT 仿真软件进行仿真和实际加工实验,验证 角度选取与优化的合理性。
五坐标数控机床旋转轴定位精度的校正方法

2019年 第5期图1 绕X 轴坐标的转动图中,C -P 1这一段以C 为中心绕X 坐标旋转了一个角度a ,这样C -P 1的末端从P 1移到了P 2。
当把这种概念用于机床时(可以认为C 点是转动主轴头的中心,P 1是刀具的中心),可以看到转动一个坐标的结果是使刀具中心在XYZ 坐标系中产生位移。
如果有RTCP 功能,数控系统将使刀具中心始终保持在一个固图2 无RTCP图3 有RTCP5.影响RTCP 精度的因素RT C P 精度是一个综合的空间精度,从RTCP 的运行状态,可以看到,RTCP 精度的好与差受到多种因素的影响。
这些因素包括机床的几何精度(如C 轴画圆精度等)、定位精度和重复定位精度、RTCP 的中心点长度、RTCP 机械偏心的补偿及回转坐标的绝对零点位置等。
图 4由于线性轴在RTCP 角度旋转时,如果角度旋转不大,如5 º,则移动距离只有40m m ,而机床的线性轴定位精度一般可以达到0.015mm/2 000mm ,所以线性轴的定位精度误差在旋转角度较小时对RTCP 精度的影响可以忽略不计(见图5)。
图 5在微小角度条件下,弧可以认为是垂直于一条边,并是一直线,由此我们可以得到:tan α=y /x α=arctan y /x由此,由于X (旋转轴旋转中心到刀具中心的距离)一般在700m m 以上,而Y (RT C P 精度值)一般很小,在0.1m m 以下,经计算,可以得到如果RTCP 变化2019年冷加工图 6图 7图 8图 9图 10图 11图 12成大先.机械设计手册[M]. 6版.北京:化学工业出版社,2016.(截稿日期:20190301)。
五轴数控机床的RTCP精度调整方法
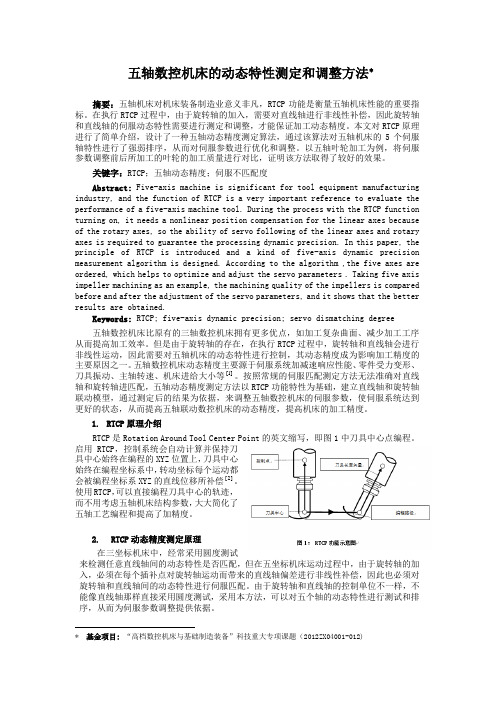
五轴数控机床的动态特性测定和调整方法 摘要:五轴机床对机床装备制造业意义非凡,RTCP功能是衡量五轴机床性能的重要指标。
在执行RTCP过程中,由于旋转轴的加入,需要对直线轴进行非线性补偿,因此旋转轴和直线轴的伺服动态特性需要进行测定和调整,才能保证加工动态精度。
本文对RTCP原理进行了简单介绍,设计了一种五轴动态精度测定算法,通过该算法对五轴机床的5个伺服轴特性进行了强弱排序,从而对伺服参数进行优化和调整。
以五轴叶轮加工为例,将伺服参数调整前后所加工的叶轮的加工质量进行对比,证明该方法取得了较好的效果。
关键字:RTCP;五轴动态精度;伺服不匹配度Abstract: Five-axis machine is significant for tool equipment manufacturing industry, and the function of RTCP is a very important reference to evaluate the performance of a five-axis machine tool. During the process with the RTCP function turning on, it needs a nonlinear position compensation for the linear axes because of the rotary axes, so the ability of servo following of the linear axes and rotary axes is required to guarantee the processing dynamic precision. In this paper, the principle of RTCP is introduced and a kind of five-axis dynamic precision measurement algorithm is designed. According to the algorithm ,the five axes are ordered, which helps to optimize and adjust the servo parameters . Taking five axis impeller machining as an example, the machining quality of the impellers is compared before and after the adjustment of the servo parameters, and it shows that the better results are obtained.Keywords: RTCP; five-axis dynamic precision; servo dismatching degree五轴数控机床比原有的三轴数控机床拥有更多优点,如加工复杂曲面、减少加工工序从而提高加工效率。
五轴数控机床的检测与标定技术

五轴数控机床的检测与标定技术国家数控系统技术工程研究中心五轴数控机床的检测与标定技术摘要长期以来,一个普遍存在的问题一直困扰着使用大型机床进行生产、加工的企业,即企业所购买的价格不菲的高精度大型机床在生产加工过程中总会产生大大小小的误差,使其加工出的产品达不到精度要求。
数控机床的检测与标定技术就是为了解决这一难题,现在已成为提高机床加工精度和加工效率的关键技术之一。
本文介绍了检测和标定方法与原理,详细介绍了空间误差补偿技术。
关键词:机床误差,检测技术,标定技术,空间误差补偿技术国家数控系统技术工程研究中心1. 前言随着全球市场经济的一体化,市场竞争越来越激烈,市场向着个性化、小批量、高质量、交货周期短的方向发展。
现在,我国数控厂家多,但是产量都不大。
产量低的原因有很多,其中重要的一条是在机电联调过程中,要对机床的精度进行评价,测定机床的精度是否满足要求,同时对机床误差进行补偿。
提高机床的精度,原有的方法效率低、价格高、使用环境要求高,同时对操作者的要求也较高[1]。
提高数控机床的精度是保证加工件质量的重要途径。
数控机床精度的提高主要是通过误差补偿来实现。
现代制造业已经发展成为融合信息技术、数控技术、系统控制工程而生成的先进制造系统。
其发展趋势可归结为两个方向:一是以提高效率为目的的自动化,即将信息技术贯穿与整个制造过程,提高制造信息处理和控制的自动化程度,以此来提高效率,缩短生产周期;二是以提高加工精度为目的的精密化,通过先进的检测手段来实现超精密加工及检测,以控制产品质量。
采用先进的制造和检测技术来迅速的提高装备制造业的水平,是当前一个重要的发展方向,研究和发展现代检测技术有着广阔的市场前景。
2. 研究现状2.1. 机床误差产生原因普遍认为数控机床的误差有以下几方面的起因[2]:1.机床的原始制造误差。
它是指由组成机床各部件工作表面的几何形状、表面质量、相互之间的位置误差所引起的机床运动误差,是数控机床几何误差产生的主要原因。
五轴机床回转轴精度检测

五轴机床回转轴精度检测摘要:与三轴机床相比,五轴机床能加工复杂曲面,具有加工效率高、装夹方便等优点。
然而,五轴机床的结构更复杂,两个回转轴会引入额外的几何误差,从而极大地影响了机床精度。
关键词:五轴机床;误差;检测五轴数控机床是现代制造技术的关键设备,用于加工高精度、复杂的曲面零件,其精度和技术水平在一定程度上决定了当前的工业水准。
五轴数控机床以其加工精度高、可靠性高、柔性好等优点,在航空航天、航海、医疗设备、军事等先进现代制造领域取得了巨大成就,得到了广大用户的认可,为制造企业的进一步研究做好了铺垫。
一、五轴数控机床发展概况五轴加工中心是一种专门用于加工机翼、叶轮、叶片、重型发电机转子等具有复杂空间曲面零件的高科技含量、高精密度的现代数控加工中心。
其优点为:①能加工一般三轴联动机床不能加工或无法一次装夹加工完成的自由曲面,节省装夹次数和时间。
②可提髙空间曲面加工精度、效率、质量。
一直以来,国内五轴数控机床相对于国外整体水平还较低,主要原因在于机床关键功能还未实现自主研发,与国外同类产品相比,国产机床稳定性、精度等指标较差,同时,在高精度技术含量精密机床方面,国外对我国实行技术封闭和进口限制,目前国内市场上的五轴机床仍以进口机床为主。
但国家十分重视机床行业的发展,2009年初启动了“高档数控机床与基础制造装备”国家科技重大专项,重点支持高档数控机床、基础制造装备、数控系统、功能部件、工具、关键部件、共性技术等方面的研发,且在各高校及相关企业的共同努力下,我国五轴数控机床技术也得到了飞速发展,已逐渐形成为较成熟的产品。
国内著名的五轴数控机床生产厂家有沈机集团、大连机床厂、济南二机床、昆明机床厂、普什宁江机床厂等。
随着经济的发展和国防建设的需要,用户对设备需求正向柔性、生产效率、功能多样和高性能等个性化需求方向转移,由此也促进了数控机床向高速高效化、模块化、高精度和复合加工等方向发展,对带动和提升我国机床工业水平具有重要战略意义。
五轴设定
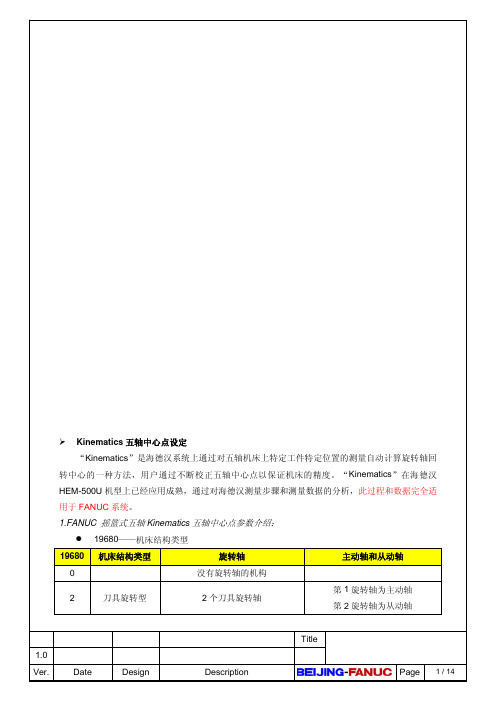
图2:控制轴号与伺服轴号的区别 19682——第1旋转轴轴方向
图3:旋转轴轴方向设定旋转轴旋转方向
图6:工作台第1旋转轴到工作台第2旋转轴交叉矢量
图7:五轴中心点测量STEP-1
工作台旋转轴上A 、B 点选取
轴旋转轴线上一点,B 点为C 轴旋转轴线上一点,为方便测量和计算,选取轴轴线上Y 位置相等,选取B 点为C 轴旋转轴线上工作台面位置。
图8:五轴中心点测量STEP-2
STEP-3 ZP1、ZB1、XB1坐标值测量
,测量B 点在Z 向的坐标ZP1(Z-)、工件上表面Z 向的坐标ZB1((X-)。
L L
Y+
Z+
A B
B 轴旋转中心线
C 轴旋转中心线
Y+
矢量AB 可以分成X 向和Z 向的分量,
Y 向重合。
ZP1(Z-)ZB1(Z-)
XB1(X-)
图9:五轴中心点测量STEP-3
YC2坐标值测量
度,测量工件Y+向侧面坐标YC1(Y+);
YC2(Y-)
YC1(Y+)
10:五轴中心点测量STEP-4
向侧面坐标XC2(X+)。
XC2(X+)
11:五轴中心点测量STEP-5
坐标值测量
向侧面坐标XB2(X+);
ZB2(Z-)
XB2(X+)
12:五轴中心点测量STEP-6 五轴中心点计算介绍:
B(X0->C
图15:旋转轴输出角度判定过程 以BC类型工具轴Z轴机床加以说明:
图17::1221#4=0时 G53.1执行前后两个旋转轴的旋转位置图18::1221#4=1时 G53.1执行前后两个旋转轴的旋转位置。
五轴联动加工中心的精度检测方法
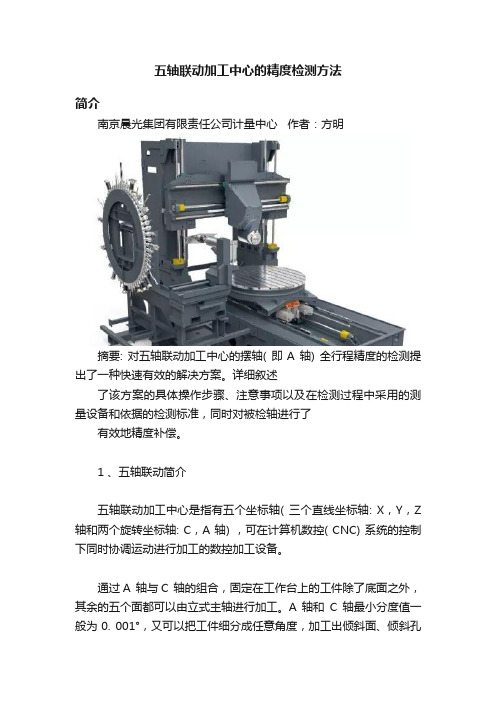
五轴联动加工中心的精度检测方法简介南京晨光集团有限责任公司计量中心作者:方明摘要: 对五轴联动加工中心的摆轴( 即A 轴) 全行程精度的检测提出了一种快速有效的解决方案。
详细叙述了该方案的具体操作步骤、注意事项以及在检测过程中采用的测量设备和依据的检测标准,同时对被检轴进行了有效地精度补偿。
1 、五轴联动简介五轴联动加工中心是指有五个坐标轴( 三个直线坐标轴: X,Y,Z 轴和两个旋转坐标轴: C,A 轴) ,可在计算机数控( CNC) 系统的控制下同时协调运动进行加工的数控加工设备。
通过A 轴与C 轴的组合,固定在工作台上的工件除了底面之外,其余的五个面都可以由立式主轴进行加工。
A 轴和C 轴最小分度值一般为0. 001°,又可以把工件细分成任意角度,加工出倾斜面、倾斜孔等。
A 轴和C 轴如与XYZ 三个直线轴实现联动,依靠先进的数控系统、伺服系统以及软件的支持可加工出复杂的空间曲面。
常见的立式五轴联动加工中心有两个回转轴,如图1 所示,一个是工作台回转轴,以X 轴方向为轴心线,± 90°来回摆动,定义为摆轴,也称A 轴; 一个就是设置工作台的中间的回转台,在图示的位置上环绕Z 轴方向360°回转,定义为C 轴。
图1 常见的立式五轴联动加工中心示意图加工中心XYZ 以及C 轴的精度检测,技术手段现在已经很成熟。
XYZ 三个直线轴一般是采用双频激光干涉仪作为标准进行检测,回转C 轴用双频激光干涉仪以及配套的回转分度器检测,或者用传统的正多面棱体配上自准直仪进行角分度检测,这里不再详述。
而对于A 轴,同样是角分度检测,也可用双频激光干涉仪回转分度器或者是正多面棱体和自准直仪作为标准进行检测。
但是如果是照搬全套C 轴的检测方法,将无法在全行程内完成测量,因为随着A 轴的转动,工作台将遮挡测量光路,无法继续检测,只能检测到部分角度,也就不能判断A 轴整个行程范围的精度。
探讨数控机床五轴精度快速校准方法

探讨数控机床五轴精度快速校准方法
Q253=1000;(预定位进给速度)
Q380=0;(参考角)
Q411=-90;(A轴起始角,为第一次测量时的角度)
Q412=+110;(A轴终止角,为最后一次测量时的角度)Q413=0;(A轴仰角,为测量其他旋转轴时的角度)
Q414=3;(A轴探测测量点数,值为0时不测量该轴)Q415=-90;(B轴起始角,为第一次测量时的角度)
Q416=+90;(B轴终止角,为最后一次测量时的角度)Q417=0;(B轴仰角,为测量其他旋转轴时的角度)Q418=0;(B轴探测测量点数,值为0时不测量该轴)
Q419=-210;(C轴起始角,为第一次测量时的角度)
Q420=+220;(C轴终止角,为最后一次测量时的角度)Q421=0;(C轴仰角,为测量其他旋转轴时的角度)
Q422=2;(C轴探测测量点数,值为0时不测量该轴)
Q423=4;(TNC用一个平面的4点还是3点测量基准球)Q432=1;(预设点)
图4KinematicsOpt功能
机床执行以上测量循环Cycle451,全自动地测量旋转轴A、C,计算测量值并将结果自动保存在机床相应运动特性表中,快速调整和优化数控机床五轴精度。
3.结语
使用iTNC530控制系统的KinematicsOpt功能,测量过程只需要一个接触式探头和校准
球,操作人员只需执行一个测量循环,就能在机床上校准五轴头精度,而不再必须由专门的技术人员来完成,给使用用户带来极大方便,同时大大提高了生产效率和加工精度。
旋转轴中心测量方法和5轴功能参数设定
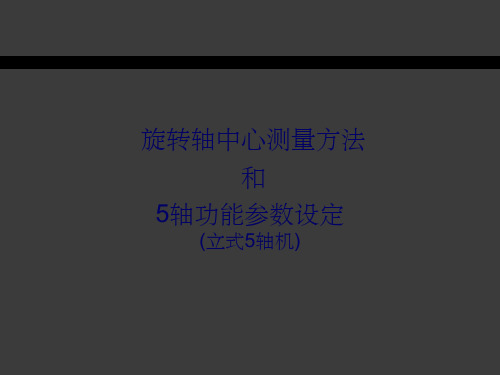
β
B90°
Z2 计算
(Z2; C轴中心的Z 机械坐标值 (B90°)) 测量 ”δ”, 再计算 Z2
Z2 = Z1-δ-γ
Z1 Z2
δ γ
B90°
如何计算B轴中心位置
B 轴中心位置通过使用三角函数可以很方便的计算.
B0°
(X1、 Z1)
45deg
B90°
(X2、Z 2)
B 轴中心
NO.19701 B轴中心的Y机械坐标值
NO.19702 B轴中心的Z机械坐标值
NO.19703 X方向上B轴与C轴的中心距
NO.19704 Y方向上B轴与C轴的中心距
(V33-5XB、V22-5XB:setting value=0)
NO.19705 B轴中心到卡盘顶端的距离
C axis
B axis
2.哪些位置需要测量?
卡盘顶部
Z1 Z2
h a
X2 h a X1
B 轴中心
Y
测量位置
1.当B轴为0°时C轴中心位置. →(X1,Y,Z1) 2.当B轴为90°时C轴中心位置 →(X2,Z2)
Ⅱ.哪些位置需要测量?
卡盘顶端
Z1 Z2
h a
Y
X2 h a X1
B 轴中心
测量位置(工作坐标系值)
X1 :C轴中心 (B0°) X2 :卡盘顶部(B90°) Z1 :卡盘顶部 (B0°) Z2 :C轴中心(B90°) Y :C 轴中心
旋转角度轴坐标位置设定与计算功能 更改5轴功能 NC 参数后O9798需要编辑.
O9798 #141=-90 #146=2 #142=-175.0094 #143=-485.0569 #144=-149.994 #145=-485.0673 M99
五轴联动数控机床旋转轴中心坐标的自动测量程序设计

量次数 n < 10, 否则停止测量, 给出错误报警。流程图
如图 4所示。
( 下转第 79页 )
2010年第 4期
片的轮廓。调用 sobel算子: [ g, t] = edge( ,f sobe l ) 其 中 f 为输入的刀具图像, g 为输出的逻辑类图像, 它在检 测到的边缘时显示为 1其它位置为 0。 t 为系统自动返 回的阈值。这个阈值为初始值。得到单张照片的刀具 轮廓如图 3所示。
收稿日期: 2009- 10 - 26 作者简介: 李光友 ( 1978 ), 男, 山东定陶人, 大连大森数控技术发展中心有限公司, 5轴项目担当, 硕士, ( E- m ail) liguangyou201@ s ina. com。
! 75!
! 控制与检测 !
组合机床与自动化加工技术
P2: 测量方向向量, 比如, 如果测量方向为 Z 轴负 方向, 则使用 ( 0, 0, - 1)。
( 上接第 76页 )
图 4 所有照片叠加后得到的刀具实际轮廓
[参考文 献 ] [ 1] 杨勇生. 数控加工编程中刀具干涉的研究现状及存 在问题
[ J]. 计算机辅助工程, 1999( 4): 41- 47. [ 2] 李 壮, 汪 文 彬, 李 应 勇. 基 于 M ATLA B 的 图 像 压 缩 处 理
由于测量头距离 B 轴旋转中心有一个固定长度的 旋转半径 R, 所以要实现自动测量必须对 B 轴由于旋转 而造成的测量头偏移进行补偿, 测量分如下 2个过程:
( 1)初步计算出 B 轴的旋转中心和旋转半径。 如图所示, B 轴旋转一个小角度, 由旋转造成的偏 差也比较小, 利用这个特点, 对 B 轴在 B = 0∃, B = 1∃, B = 2∃分别进行 测量, 使用 宏指令 P rbSphere 可以测 出 P 0, P 1, P 2三点坐标矢量。根据宏指令 GetCentO ri( P0 P1 P2 R Pbd) 计算出 B 轴旋转中心坐标矢量 Pb、旋转 半径 R 和旋转轴心方向矢量 P bd。 ( 2)逐 步对 B 轴的 旋转 中心和 旋转半 径进行 校 正。 根据步骤 1中的 B 轴旋转中心坐标矢量 P b 和旋 转半径 R, 对 X 轴和 Z 轴进行补偿移动 ( Y 轴偏移量很 小, 不用补偿 ), 补偿公式如下:
五轴说明书(编程部分)
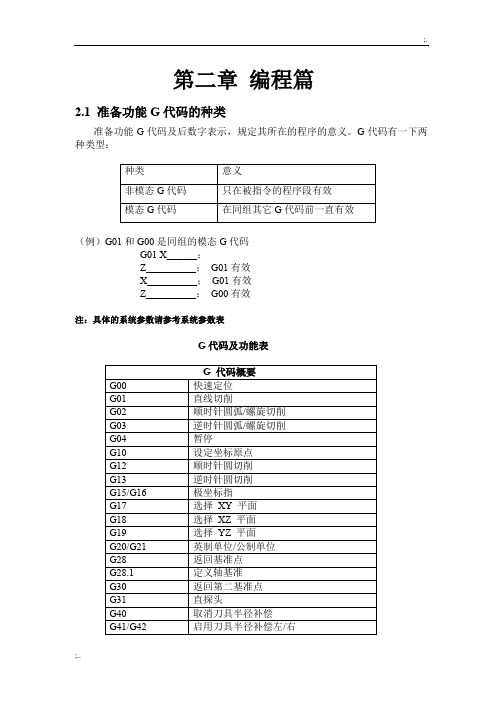
第二章编程篇2.1 准备功能G代码的种类准备功能G代码及后数字表示,规定其所在的程序的意义。
G代码有一下两种类型:(例)G01和G00是同组的模态G代码G01 X______;Z__________;G01有效X__________;G01有效Z__________;G00有效注:具体的系统参数请参考系统参数表G代码及功能表U、V、W分别和A、B、C 同义,同时使用A 和U 或B 和V 等会产生错误(也就是一行中用了两次A)。
在U、V、W 代码的描述中没有指定它们在同一程序行使用的次数,但A、B、C 代码的描述决定了他们只能使用一次。
2.1.1快速直线移动- G00(1)对于快速直线移动,程序G00 X__ Y__ Z__ A__ C__ 中的所有功能字,除了至少选用其中的一个外其它都为可选,如果当前移动模式为G00那么G00也是可选的,刀具可以以协调线性移动的方式以最大进给到达目的点,执行G00命令不会有切削动作发生。
(2)如果执行了G16命令设置了极坐标原点,在极坐标中使用半径和角度表示目的地,也可以使用G00 X__ Y__控制快速直线移动,X__是目的地相对于极坐标原点的半径,Y__则是目的地与极坐标原点连线与3点钟方向逆时针方向的夹角(也就是通常用的四象限标准)。
执行G16 时的当前点坐标就是极坐标原点。
如果在程序中省略了所有的轴功能字将会产生错误。
如果启用了刀具半径补偿,刀具的移动将与上面所描述的不同(见刀具补偿)。
如果程序在同一行有G53 命令,刀具的移动也同与上述不同(见绝对坐标系)。
2.1.2 以进给直线切削– G01(1)对于以进给直线切削来说,程序G01 X__ Y__ Z__ A__ C__中的所有功能字,除了必须至少使用的之外其它的轴功能字都为可选。
如果当前移动模式为G01,那么G01也是可选的,刀具将以协调线形移动的方式以当前进给移动到目的地。
(2)如果执行了G16命令设置了极坐标原点,在极坐标中使用半径和角度表示目的地,也可以使用G00 X__ Y__控制快速直线移动,X__是目的地相对于极坐标原点的半径,Y__则是目的地与极坐标原点连线与3点钟方向逆时针方向的夹角(也就是通常用的四象限标准)。
五轴数控机床精度检测以及标定技术应用分析

五轴数控机床精度检测以及标定技术应用分析五轴数控机床是现代制造技术一种很关键的设备,在高精尖的现代制造行业得到了广泛的应用,但是,一些通过机床进行生产或者加工的企业一直受到购买的高精度机床经常会出现各种各样的误差的困扰,加工或者生产出来的产品不能满足精度要求。
而精度检测以及标定技术为解决这个问题提供了一个很好的思路,目前,已经成为了加工精度以及提高加工效率的技术之一。
标签:五轴数控机床;精度检测;标定技术数控机床精度的提高保证了加工质量,而提高机床精度的主要途径就是进行误差补偿。
目前,现代制造业的加工越来越精密化,使用先进检测的手段来完成超精密的加工以及精度检测,确保产品的质量可以得到控制。
1 五轴数控机床引起误差的原因通常情况下,引起五轴数控机床误差的因素有:(1)五轴数控机床原始的制造误差数控机床原始的制造误差就是指由于部件工作表面的形状、质量以及部件间位置的误差而引起的运动误差,这种误差是产生数控机床的几何误差最主要的原因[1]。
(2)五轴数控机床由于热变形引起的误差数控机床热变形引起误差的主要原因是数控机床内部热源以及环境热的扰动而导致机床结构产生热变形,进而导致误差产生。
(3)由于切削负荷导致的工艺系统误差工艺系统的误差主要包括:机床变形导致的误差、刀具变形导致的误差、加工件变形导致的误差以及夹具变形导致的误差等。
通常情况下,人们把这种误差也称作为让刀。
这种误差可以导致加工件形状产生畸变,在薄壁工件的加工时这种误差特别明显和严重[2]。
(4)五軸数控机床振动导致的误差数控机床在进行切削加工时,因为工艺柔性以及多变的工序,数控机床的运行状态可能进入到不稳定的区域,激起了强烈颤振,致使加工件表面的粗糙度不能满足要求,甚至还会导致几何形状误差的出现。
(5)五轴数控机床的检测系统测试误差检测系统的测试误差主要包括:因为测量传感器制造误差以及其安装误差而引起的反馈系统自身的误差;因为机床零件以及机构的误差,或者在使用过程中的产生变形而致使测量传感器产生的误差。
五轴机床检测方法

五轴铣床检测方法五轴铣床一般是比三轴铣床多两个旋转轴。
首先,要对三个直线轴进行检测;其次,是针对两个旋转轴的检测;最后,要对五轴联动性能进行检测。
一三个直线轴的检测方法和三轴铣床一样,所以这里不做叙述。
二两个旋转轴的检测因为旋转轴的各项精度对五轴加工精度的影响远远大于三个直线轴精度的影响,所以对五轴铣床的检测重点是两个旋转轴的精度。
旋转轴的精度包括两个方面:一方面是旋转轴运动的精度,主要要检测每个旋转轴的重复定位精度;另一方面是两个旋转轴相互之间的关系,主要检测两个旋转轴轴线和主轴轴线之间空间几何关系是否正确。
(一)测量旋转轴的重复定位精度方法和直线轴测量方法类似:对于转台类型的旋转轴,在转台上固定一个方块,用千分表接触方块的表面,旋转转台一定角度,再反向旋转转台同样多角度,回到原位,观察两次表针接触方块表面时的表读数是否一致,误差多少(如图1);对于摆头类型的旋转轴,在主轴上装上检测用芯棒,用千分表指针接触芯棒来检测(如图2)。
图1 测量转台的重复定位精度图2 测量摆头的重复定位精度(二) 测定两个旋转轴和主轴之间的空间几何关系这项需要按照五轴铣床的类型分为三种情况:1 双转台结构的五轴铣床图3为一个双转台结构的示意图,在图中标出了两个旋转轴的轴线,这两根轴线应该如图中那样相交于一点。
如果这两个旋转轴的轴线不相交,则要测定出两个轴线的偏心距离。
图3 双转台结构示意图测定方法如下:先将C 轴转台校正,使C 轴转台平行于XY 平面(方法略);再如图4所示,分别旋转B 轴+90°和-90°,测量两个方位下B 轴转台侧面最高点的高度差。
如果高差为零,则双转台的空间几何关系符合理想情况,如果高差不为零,则B 、C 轴的偏心量为此高差的二分之一。
C 轴轴线 B 轴轴线转台最高点转台最高点图4 双转台轴线偏心量测定3 转台和单摆头结构的五轴铣床图5为单摆头结构的示意图,图中标出了B轴的轴线和主轴的轴线,这两个轴线应该相交于一点,如果它们不相交,需要测定出它们的距离,即主轴和摆动轴B轴的偏心量。
五轴数控机床旋转轴位置测定与加工设置22

五轴加工数控机床根据旋转部件的运动方式不同,可归纳为双转台、双摆头和一转台一摆头三种形式。
双转台五轴联动机床的运动坐标包括三个直线坐标轴X、Y、Z和两个旋转坐B(A)、C,其结构如图1所示。
该种结构是中、小A 型五轴加工机床采用较多的一种结构形式,其优点是旋转坐标有足够的行程范围,工艺性好,适合中小型体零件的五面粗、精铣削加工,机床能在加工时减少装夹次数,达到高效率、高精度、高可靠性的要求。
1 五轴加工设置内容介绍零件在进行五轴加工时主要设置的内容有:编程方式选择及转台旋转中心到摆动中心位置偏置设置、编程零点到c轴中心位置偏置设置、加工工件坐标系的位置偏置设置、刀具长度补偿设置、机床五轴RTCPJJIJ工设置及。
下面以广数GSK 25i五轴数控系统、CAXA制造工程师201 1软件五轴后置处理为例,介绍双转台式五轴数控加工中心的加工设置与机床精度的测量、调整方法。
2 旋转轴与直线轴的位置偏置(1)旋转中心到摆动中心偏置距离测量如图2所示,具体操作方法如下:第1步:通过旋转B轴,采用打表方式校平、校正C轴,使c轴平面与z轴垂直,然后在C轴上安装一圆棒,旋转C轴铣出圆棒直径为D,最后对圆棒进行分中,找出XYZ车由的坐标系零点位置坐标C,使C轴旋转轴轴线与Z轴轴线重合,在机床坐标相对坐标系中将X、B轴坐标清零。
第2步:手动旋转摆动轴B轴至90°位置,采用打表方式校正B轴使C轴平面与Z轴轴线平行,然后移动X轴,用百分表或分中棒对C轴平面进行多次校准取平均值,使z轴轴线位于旋转轴C轴平面上,aOz轴轴线到旋转轴C 轴平面的距离为0,所移动的距离为L(z’+x’),最后移动z、y轴,采用打表方式,测出圆柱旋转后(B轴相对坐标90°位置)其侧面至旋转前(B轴相对坐标0度位置)的高度值日。
依据以上步骤得出c轴旋转中,GNB轴摆动中心的偏置值:X轴方向为:X'=(H+D/2-L)/2Z轴方向为:z'=(H+D/2+L)/2另外,上述偏置坐标中均采用已测得的绝对值进行计算。
五轴数控机床旋转轴位置测定与加工设置

五轴数控机床旋转轴位置测定与加工设置
郎永兵
【期刊名称】《金属加工:冷加工》
【年(卷),期】2013(000)014
【摘要】五轴数控加工是在三个基本直线坐标轴(X、Y、Z)上增加了两个旋转轴(A、B、C轴的任意组合)的一种多轴数控加工方式。
五轴机床的三个直线轴与两个旋转轴的联动加工方式,被称为五轴联动加工;两个旋转轴进行旋转定位,使刀具呈现一定的姿态角度不变,三个直线轴作联动,这种加工方式被称为五轴定向加工。
【总页数】3页(P60-62)
【作者】郎永兵
【作者单位】广东省工商高级技工学校乐昌512200
【正文语种】中文
【相关文献】
1.双转台五轴数控机床设置与加工仿真
2.五轴数控机床旋转轴安装误差测量辨识方法
3.五轴数控机床旋转轴误差辨识方法研究进展
4.摇篮式五轴数控机床转台设置与加工调试研究
5.五轴数控机床旋转轴误差辨识及补偿
因版权原因,仅展示原文概要,查看原文内容请购买。
- 1、下载文档前请自行甄别文档内容的完整性,平台不提供额外的编辑、内容补充、找答案等附加服务。
- 2、"仅部分预览"的文档,不可在线预览部分如存在完整性等问题,可反馈申请退款(可完整预览的文档不适用该条件!)。
- 3、如文档侵犯您的权益,请联系客服反馈,我们会尽快为您处理(人工客服工作时间:9:00-18:30)。
五轴加工数控机床根据旋转部件的运动方式不同,可归纳为双转台、双摆头和一转台一摆头三种形式。
双转台五轴联动机床的运动坐标包括三个直线坐标轴X、Y、Z和两个旋转坐B(A)、C,其结构如图1所示。
该种结构是中、小A 型五轴加工机床采用较多的一种结构形式,其优点是旋转坐标有足够的行程范围,工艺性好,适合中小型体零件的五面粗、精铣削加工,机床能在加工时减少装夹次数,达到高效率、高精度、高可靠性的要求。
1 五轴加工设置内容介绍
零件在进行五轴加工时主要设置的内容有:编程方式选择及转台旋转中心到摆动中心位置偏置设置、编程零点到c轴中心位置偏置设置、加工工件坐标系的位置偏置设置、刀具长度补偿设置、机床五轴RTCPJJIJ工设置及。
下面以广数GSK 25i五轴数控系统、CAXA制造工程师201 1软件五轴后置处理为例,介绍双转台式五轴数控加工中心的加工设置与机床精度的测量、调整方法。
2 旋转轴与直线轴的位置偏置
(1)旋转中心到摆动中心偏置距离测量如图2所示,具体操作方法如下:
第1步:通过旋转B轴,采用打表方式校平、校正C轴,使c轴平面与z轴垂直,然后在C轴上安装一圆棒,旋转C轴铣出圆棒直径为D,最后对圆棒进行分中,找出XYZ车由的坐标系零点位置坐标C,使C轴旋转轴轴线与Z轴轴线重合,在机床坐标相对坐标系中将X、B轴坐标清零。
第2步:手动旋转摆动轴B轴至90°位置,采用打表方式校正B轴使C轴平面与Z轴轴线平行,然后移动X轴,用百分表或分中棒对C轴平面进行多次校准取平均值,使z轴轴线位于旋转轴C轴平面上,aOz轴轴线到旋转轴C 轴平面的距离为0,所移动的距离为L(z’+x’),最后移动z、y轴,采用打表方式,测出圆柱旋转后(B轴相对坐标90°位置)其侧面至旋转前(B轴相对坐标0度位置)的高度值日。
依据以上步骤得出c轴旋转中,GNB轴摆动中心的偏置值:
X轴方向为:X'=(H+D/2-L)/2
Z轴方向为:z'=(H+D/2+L)/2
另外,上述偏置坐标中均采用已测得的绝对值进行计算。
当x方向测得值为一L时,偏置值为X’,X方向测得值为L时,偏置值为一x’;当z方向测得值为H时,偏置值为Z',Z方向测得值为H时,z轴方向偏置值为-Z'。
(2)零件编程零点到C轴中心偏置距离测量如图3所示,具体操作方法如下:
第1步:通过旋转B轴,采用打表方式校平、校正C轴,使C轴平面与z轴垂直、c轴轴线与z轴轴线重合,记录机床的机械坐标(X、Y、B、C)或将该坐标输入不常使用的六号工件坐标系(G59)中。
第2步:安装、校正夹具。
夹具校正时x方向可采用转动c轴的方式进行。
装夹加工工件,采用试切法或分中棒对刀并设置工件坐标系。
以1号工件坐标系(G54)为例:在MDI方式下运行“G90G54 G0 X0 Y0 B0 C0”一在机床相对坐标系中将各坐标轴清零一手动移动机床坐标至第1步操作中记录机床的机床坐标(X、Y、B、C)或MDI方式下运行“G90 G59 GO X0 Y0 B0 C0”。
此时,机床坐标相对坐标系中的坐标X、Y就是零件编程零点到c轴中心的偏置(X'、Y')。
第3步:Z向坐标偏置测量,采用打表方式移动Z轴使百分表位于工件坐标系零平面记录百分表表针位置,在机床相对坐标系中将z轴坐标清零,移动Z轴使位于C轴平面表针位置与前面相同。
此时,机床坐标相对坐标系中的坐僦是零件编程坐标系D中的编程零点到c轴中心的偏置z’。
3 五轴加工功能刀具中心点控制(RTCP)
特征编程的操作和设置方法
(1)使用CAM软件后置处理旋转轴位置偏置功能进行补偿时的编程设置
①进入CAXA制造工程师软件后置设置,选择广州数控B C轴双工作台五轴后置配置文件GSK 5X TB/TC,进入【多轴】界面,根据机床结构型式与转轴参数设置如图4所示。
②进入CAXA制造工程师软件后置设置,选择广州数控B—C轴双工作台五轴后置配置文件GSK-5X-TB/TC,【多轴2】界面如图5所示,旋转中心摆动中心偏置距离表示以机床旋转轴中心为参考的坐标系中摆动中心的位置坐标(X'、
Z') (见图2)。
编程零点到C轴中心偏置距离表示以加工工件的输出坐标系O为参考机床c轴中心的位置坐标(X'、Y'、Z'),如图3所示。
③在非数控系统五轴功能模式下后置程序时除上述设置外,需要删除后置处理程序中的五轴功能G43.4H_等,若需多把刀具进行加工、换刀时只可单独使用刀具长度补偿。
(2)使用数控系统五轴加工功能编程时旋转轴位置偏置的设置广州数控GSK25i数控系统在五轴加工中用于设置转轴位置的参数主要有转台中心位置参数8020和工作台第一旋转轴和工作台第二旋转轴的偏置矢量参数8021,如图6所示。
转台中心位置设置(参数8020):转台中心位置是指装夹工件的第二旋转轴(C轴)的轴心处“机床坐标值”。
以BC 双图6转台为例,此处为C转台的轴心位置。
当对刀方式不同时,“机床机械坐标值”会不同,在设置时必须要保持和工件坐标系同样的对刀方式。
当工件坐标系设置是用主轴端面对刀时,此处的“转台中心位置”也必须是用主轴端面降到旋转轴心处时的“机床机械坐标值”。
用刀尖对刀时,此处的“转台中心位置”也必须是该刀具降到旋转轴心处时的“机床机械坐标值”。
当换刀时,如果使用刀具补偿,而不是重新设定工件坐标系,此参数不需要修改,否则必须重新设定坐标系。
另外,在测量时,必须首先将旋转工作台放置在水平位置。
第一旋转轴到第二旋转轴的偏置矢量设置(参数8021):以Bc双转台为例,在数控系统中第一旋转轴为B轴,第二旋转轴为C轴。
该参数是一个矢量,矢量起点为主动轴轴心,终点为从动轴轴心,参照为机床坐标系。
如果C转台在B转台之上,此参数为正;如果C转台在B转台之下,此参数为负。
即表示以机床摆动中心为参考的坐标系中旋转轴中心的位置坐标。
第一旋转轴B轴到第二旋转轴c轴的偏置距离测量同图2中旋转中心到摆动中心偏置距离测量,其矢量方向相反坐标参考轴为B轴。
使用五轴加工功能程序后处理:当使用五轴加工功能刀具中心点控制(RTCP)、特征编程(倾斜面Diem)功能时,不需要在后处理程序提供机床类型和结构方面的参数,只要旋转轴类型相同,可以通用于双转台,摆头转台和双摆头机床。
以BC双转台为例,构建后处理器时选择双摆头方式。
旋转轴设置为Bc方式,机床坐标轴偏置参数设置为0。
这样经过后处理的坐标值就和特定的机床参数没有关系了。
然后手工添加刀具中心点控制G43.4_心点控制取ING49,程序就可在机床运行、加工。
4 结语
文章较为全面地介绍了五轴双转台式机床加工设置方法及其五轴加工程序后置设置等方面的内容,并详细说明了五轴机床参数设置时旋转轴、摆动轴的位置偏置与坐标值的测量方法、技巧。
同时,也为其他形式多轴数控机床的加工设置提供了参考。